常见焊接缺陷
常见的焊接缺陷及缺陷图片.docx
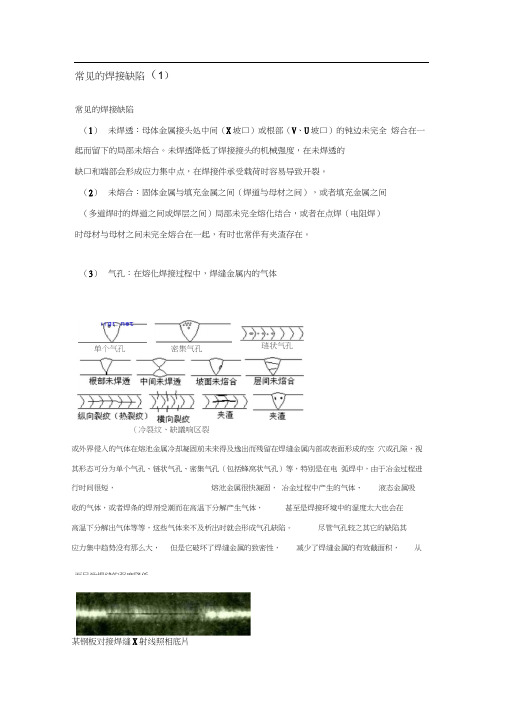
常见的焊接缺陷(1)常见的焊接缺陷(1) 未焊透:母体金属接头处中间(X 坡口)或根部(V 、U 坡口)的钝边未完全 熔合在一起而留下的局部未熔合。
未焊透降低了焊接接头的机械强度,在未焊透的缺口和端部会形成应力集中点,在焊接件承受载荷时容易导致开裂。
(2) 未熔合:固体金属与填充金属之间(焊道与母材之间),或者填充金属之间(多道焊时的焊道之间或焊层之间)局部未完全熔化结合,或者在点焊(电阻焊)时母材与母材之间未完全熔合在一起,有时也常伴有夹渣存在。
(3) 气孔:在熔化焊接过程中,焊缝金属内的气体或外界侵入的气体在熔池金属冷却凝固前未来得及逸岀而残留在焊缝金属内部或表面形成的空 穴或孔隙,视其形态可分为单个气孔、链状气孔、密集气孔(包括蜂窝状气孔)等,特别是在电 弧焊中,由于冶金过程进行时间很短, 熔池金属很快凝固, 冶金过程中产生的气体、 液态金属吸收的气体,或者焊条的焊剂受潮而在高温下分解产生气体, 甚至是焊接环境中的湿度太大也会在高温下分解出气体等等,这些气体来不及析出时就会形成气孔缺陷。
尽管气孔较之其它的缺陷其应力集中趋势没有那么大, 但是它破坏了焊缝金属的致密性, 减少了焊缝金属的有效截面积,从某钢板对接焊缝X 射线照相底片单个气孔 密集气孔 琏状气孔(冷裂纹、缺議响区裂纹)而导致焊缝的强度降低。
V型坡口,手工电弧焊,未焊透某钢板对接焊缝X射线照相底片V型坡口,手工电弧焊,密集气孔(4)夹渣与夹杂物:熔化焊接时的冶金反应产物,例如非金属杂质(氧化物、硫化物等)以及熔渣,由于焊接时未能逸出,或者多道焊接时清渣不干净,以至残留在焊缝金属内,称为夹渣或夹杂物。
视其形态可分为点状和条状,其外形通常是不规则的,其位置可能在焊缝与母材交界处,也可能存在于焊缝内。
另外,在采用钨极氩弧焊打底+手工电弧焊或者钨极氩弧焊时,钨极崩落的碎屑留在焊缝内则成为高密度夹杂物(俗称夹钨)。
W18Cr4V(高速工具钢)-45钢棒对接电阻焊缝中的夹渣断口照片钢板对接焊缝X射线照相底片V型坡口,手工电弧焊,局部夹渣钢板对接焊缝X射线照相底片V型坡口,手工电弧焊,两侧线状夹渣钢板对接焊缝X射线照相底片V型坡口,钨极氩弧焊打底+手工电弧焊,夹钨(5)裂纹:焊缝裂纹是焊接过程中或焊接完成后在焊接区域中出现的金属局部破裂的表现。
技能培训资料:常见的焊接缺陷

1、焊接夹渣焊接夹渣缺陷是指焊后熔渣残留在焊缝中的情况。
夹渣主要有金属夹渣即夹铝或夹铜和非金属夹渣即焊条药皮、焊剂、硫化物、氧化物或氮化物留存在焊缝中。
夹渣产生的主要原因是破口清理不彻底、坡口尺寸不符合设计要求、焊条质量不合格等。
2、焊接凹坑焊接凹坑是指在收弧和断弧时操作不当而在焊道末端形成的凹陷部分。
主要产生的原因是焊接材料在焊接过程中停留时间不够,填充金属不够导致的。
其危害是导致焊缝的横截面减少,凹坑处容易产生偏析或杂质汇集,从而易形成气孔、灰渣或裂纹。
3、焊接裂纹焊接裂纹主要是指焊缝中金属原子结合遭到破坏,从而形成新的界面而形成的裂缝。
焊接裂纹按温度可分为热裂纹、再热裂纹、冷裂纹、层状撕裂。
裂纹再焊接工艺里是最严重的一种缺陷,也是导致焊接结构失效而引发事故的主要原因。
4、焊接气孔焊接气孔主要是在熔池中的气泡在金属凝固时未能及时逸出而形成的空穴。
其主要产生原因是电弧保护不到位,弧太长或者焊接材料有锈,气体保护介质不纯以及坡口处理不到位。
5、焊接咬边焊接咬边是指沿着焊趾,在焊件部分形成凹陷或者沟槽。
主要形成原因是焊接参数选择不正确、焊速太慢、电弧拉得太长、电流过大、焊枪位置不准确导致。
其危害导致焊件工作截面减小,咬边处应力集中。
6、焊接焊瘤焊瘤是指金属溢流到加热不足的焊件或焊缝上,未能与焊件和金属熔合在一起而堆积的金属缺陷。
主要形成原因是焊接参数选择不符合设计要求、焊接坡口清理不到位、焊接速度太慢等。
7、焊接局部烧穿焊接局部烧穿是指焊接过程中,焊接部位熔透至坡口背面,形成穿孔现象。
主要产生原因是焊接电流太大、焊件加热过高、坡口对接空隙太大、焊接速度太慢、电弧停留时间太长等8、焊接未焊透焊接未焊透是指焊缝的熔透深度小于板厚时形成的。
在单面时,焊缝熔透到达不了焊件底部;双面焊时两道焊缝熔深总厚度小于焊件厚度而形成的。
主要形成原因有焊条位置不准确,偏离中心位置;坡口角度太小,焊接空隙小钝边太大;电流太小等。
常见的焊接缺陷缺陷图片
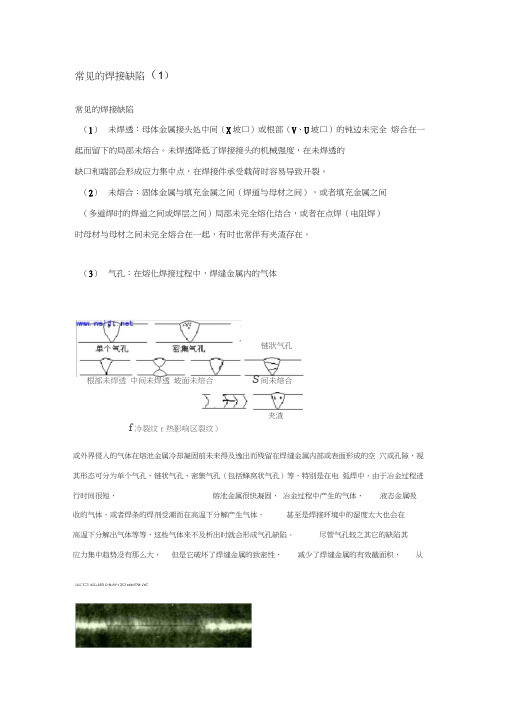
常见的焊接缺陷(1)常见的焊接缺陷(1)未焊透:母体金属接头处中间(X坡口)或根部(V、U坡口)的钝边未完全熔合在一起而留下的局部未熔合。
未焊透降低了焊接接头的机械强度,在未焊透的缺口和端部会形成应力集中点,在焊接件承受载荷时容易导致开裂。
(2)未熔合:固体金属与填充金属之间(焊道与母材之间),或者填充金属之间(多道焊时的焊道之间或焊层之间)局部未完全熔化结合,或者在点焊(电阻焊)时母材与母材之间未完全熔合在一起,有时也常伴有夹渣存在。
(3)气孔:在熔化焊接过程中,焊缝金属内的气体f冷裂纹r热影响区裂纹)或外界侵入的气体在熔池金属冷却凝固前未来得及逸岀而残留在焊缝金属内部或表面形成的空穴或孔隙,视其形态可分为单个气孔、链状气孔、密集气孔(包括蜂窝状气孔)等,特别是在电弧焊中,由于冶金过程进行时间很短,熔池金属很快凝固,冶金过程中产生的气体、液态金属吸收的气体,或者焊条的焊剂受潮而在高温下分解产生气体,甚至是焊接环境中的湿度太大也会在高温下分解出气体等等,这些气体来不及析出时就会形成气孔缺陷。
尽管气孔较之其它的缺陷其应力集中趋势没有那么大,但是它破坏了焊缝金属的致密性,减少了焊缝金属的有效截面积,从根部未焊透中间未焊透坡面未焙合链狀气孔S间未焙合夹渣而导致焊缝的强度降低。
某钢板对接焊缝X射线照相底片V型坡口,手工电弧焊,未焊透某钢板对接焊缝X射线照相底片V型坡口,手工电弧焊,密集气孔(4 )夹渣与夹杂物:熔化焊接时的冶金反应产物,例如非金属杂质(氧化物、硫化物等)以及熔渣,由于焊接时未能逸出,或者多道焊接时清渣不干净,以至残留在焊缝金属内,称为夹渣或夹杂物。
视其形态可分为点状和条状,其外形通常是不规则的,其位置可能在焊缝与母材交界处,也可能存在于焊缝内。
另外,在采用钨极氩弧焊打底+手工电弧焊或者钨极氩弧焊时,钨极崩落的碎屑留在焊缝内则成为高密度夹杂物(俗称夹钨)。
W18Cr4V(高速工具钢)-45钢棒对接电阻焊缝中的夹渣断口照片钢板对接焊缝X射线照相底片V型坡口,手工电弧焊,局部夹渣钢板对接焊缝X射线照相底片V型坡口,手工电弧焊,两侧线状夹渣钢板对接焊缝X射线照相底片V型坡口,钨极氩弧焊打底+手工电弧焊,夹钨(5)裂纹:焊缝裂纹是焊接过程中或焊接完成后在焊接区域中出现的金属局部破裂的表现。
常见的焊接缺陷及成因
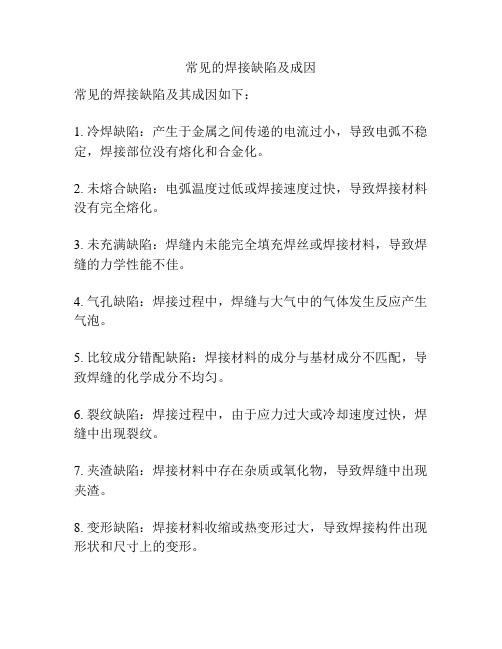
常见的焊接缺陷及成因
常见的焊接缺陷及其成因如下:
1. 冷焊缺陷:产生于金属之间传递的电流过小,导致电弧不稳定,焊接部位没有熔化和合金化。
2. 未熔合缺陷:电弧温度过低或焊接速度过快,导致焊接材料没有完全熔化。
3. 未充满缺陷:焊缝内未能完全填充焊丝或焊接材料,导致焊缝的力学性能不佳。
4. 气孔缺陷:焊接过程中,焊缝与大气中的气体发生反应产生气泡。
5. 比较成分错配缺陷:焊接材料的成分与基材成分不匹配,导致焊缝的化学成分不均匀。
6. 裂纹缺陷:焊接过程中,由于应力过大或冷却速度过快,焊缝中出现裂纹。
7. 夹渣缺陷:焊接材料中存在杂质或氧化物,导致焊缝中出现夹渣。
8. 变形缺陷:焊接材料收缩或热变形过大,导致焊接构件出现形状和尺寸上的变形。
这些焊接缺陷的成因主要包括焊接工艺参数不当、焊接材料质量不过关、焊接操作不规范等原因。
对这些缺陷的预防和修复可以通过合理的焊接工艺设计、选择质量良好的焊接材料、进行焊前和焊后的检测等方式来实现。
常见的焊接缺陷及缺陷图片
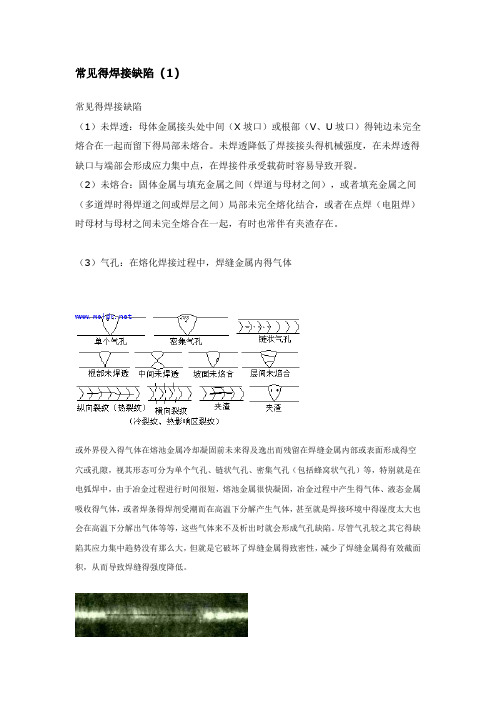
常见得焊接缺陷(1)常见得焊接缺陷(1)未焊透:母体金属接头处中间(X坡口)或根部(V、U坡口)得钝边未完全熔合在一起而留下得局部未熔合。
未焊透降低了焊接接头得机械强度,在未焊透得缺口与端部会形成应力集中点,在焊接件承受载荷时容易导致开裂。
(2)未熔合:固体金属与填充金属之间(焊道与母材之间),或者填充金属之间(多道焊时得焊道之间或焊层之间)局部未完全熔化结合,或者在点焊(电阻焊)时母材与母材之间未完全熔合在一起,有时也常伴有夹渣存在。
(3)气孔:在熔化焊接过程中,焊缝金属内得气体或外界侵入得气体在熔池金属冷却凝固前未来得及逸出而残留在焊缝金属内部或表面形成得空穴或孔隙,视其形态可分为单个气孔、链状气孔、密集气孔(包括蜂窝状气孔)等,特别就是在电弧焊中,由于冶金过程进行时间很短,熔池金属很快凝固,冶金过程中产生得气体、液态金属吸收得气体,或者焊条得焊剂受潮而在高温下分解产生气体,甚至就是焊接环境中得湿度太大也会在高温下分解出气体等等,这些气体来不及析出时就会形成气孔缺陷。
尽管气孔较之其它得缺陷其应力集中趋势没有那么大,但就是它破坏了焊缝金属得致密性,减少了焊缝金属得有效截面积,从而导致焊缝得强度降低。
某钢板对接焊缝X射线照相底片V型坡口,手工电弧焊,未焊透某钢板对接焊缝X射线照相底片V型坡口,手工电弧焊,密集气孔(4)夹渣与夹杂物:熔化焊接时得冶金反应产物,例如非金属杂质(氧化物、硫化物等)以及熔渣,由于焊接时未能逸出,或者多道焊接时清渣不干净,以至残留在焊缝金属内,称为夹渣或夹杂物。
视其形态可分为点状与条状,其外形通常就是不规则得,其位置可能在焊缝与母材交界处,也可能存在于焊缝内。
另外,在采用钨极氩弧焊打底+手工电弧焊或者钨极氩弧焊时,钨极崩落得碎屑留在焊缝内则成为高密度夹杂物(俗称夹钨)。
W18Cr4V(高速工具钢)-45钢棒对接电阻焊缝中得夹渣断口照片钢板对接焊缝X射线照相底片V型坡口,手工电弧焊,局部夹渣钢板对接焊缝X射线照相底片V型坡口,手工电弧焊,两侧线状夹渣钢板对接焊缝X射线照相底片V型坡口,钨极氩弧焊打底+手工电弧焊,夹钨(5)裂纹:焊缝裂纹就是焊接过程中或焊接完成后在焊接区域中出现得金属局部破裂得表现。
常见的焊接缺陷及缺陷图片
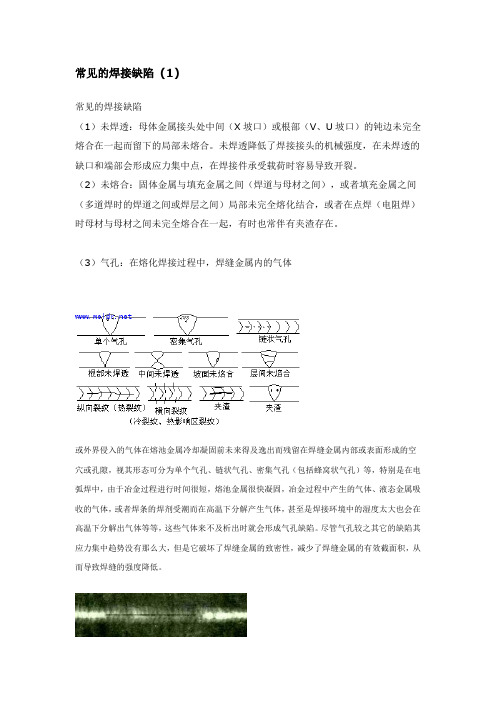
常见的焊接缺陷(1)常见的焊接缺陷(1)未焊透:母体金属接头处中间(X坡口)或根部(V、U坡口)的钝边未完全熔合在一起而留下的局部未熔合。
未焊透降低了焊接接头的机械强度,在未焊透的缺口和端部会形成应力集中点,在焊接件承受载荷时容易导致开裂。
(2)未熔合:固体金属与填充金属之间(焊道与母材之间),或者填充金属之间(多道焊时的焊道之间或焊层之间)局部未完全熔化结合,或者在点焊(电阻焊)时母材与母材之间未完全熔合在一起,有时也常伴有夹渣存在。
(3)气孔:在熔化焊接过程中,焊缝金属内的气体或外界侵入的气体在熔池金属冷却凝固前未来得及逸出而残留在焊缝金属内部或表面形成的空穴或孔隙,视其形态可分为单个气孔、链状气孔、密集气孔(包括蜂窝状气孔)等,特别是在电弧焊中,由于冶金过程进行时间很短,熔池金属很快凝固,冶金过程中产生的气体、液态金属吸收的气体,或者焊条的焊剂受潮而在高温下分解产生气体,甚至是焊接环境中的湿度太大也会在高温下分解出气体等等,这些气体来不及析出时就会形成气孔缺陷。
尽管气孔较之其它的缺陷其应力集中趋势没有那么大,但是它破坏了焊缝金属的致密性,减少了焊缝金属的有效截面积,从而导致焊缝的强度降低。
某钢板对接焊缝X射线照相底片V型坡口,手工电弧焊,未焊透某钢板对接焊缝X射线照相底片V型坡口,手工电弧焊,密集气孔(4)夹渣与夹杂物:熔化焊接时的冶金反应产物,例如非金属杂质(氧化物、硫化物等)以及熔渣,由于焊接时未能逸出,或者多道焊接时清渣不干净,以至残留在焊缝金属内,称为夹渣或夹杂物。
视其形态可分为点状和条状,其外形通常是不规则的,其位置可能在焊缝与母材交界处,也可能存在于焊缝内。
另外,在采用钨极氩弧焊打底+手工电弧焊或者钨极氩弧焊时,钨极崩落的碎屑留在焊缝内则成为高密度夹杂物(俗称夹钨)。
W18Cr4V(高速工具钢)-45钢棒对接电阻焊缝中的夹渣断口照片钢板对接焊缝X射线照相底片V型坡口,手工电弧焊,局部夹渣钢板对接焊缝X射线照相底片V型坡口,手工电弧焊,两侧线状夹渣钢板对接焊缝X射线照相底片V型坡口,钨极氩弧焊打底+手工电弧焊,夹钨(5)裂纹:焊缝裂纹是焊接过程中或焊接完成后在焊接区域中出现的金属局部破裂的表现。
常见的焊接缺陷及缺陷图片
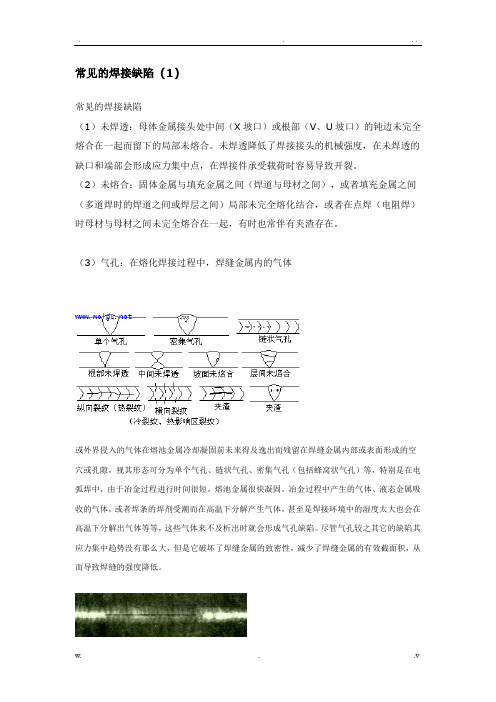
常见的焊接缺陷(1)常见的焊接缺陷(1)未焊透:母体金属接头处中间(X坡口)或根部(V、U坡口)的钝边未完全熔合在一起而留下的局部未熔合。
未焊透降低了焊接接头的机械强度,在未焊透的缺口和端部会形成应力集中点,在焊接件承受载荷时容易导致开裂。
(2)未熔合:固体金属与填充金属之间(焊道与母材之间),或者填充金属之间(多道焊时的焊道之间或焊层之间)局部未完全熔化结合,或者在点焊(电阻焊)时母材与母材之间未完全熔合在一起,有时也常伴有夹渣存在。
(3)气孔:在熔化焊接过程中,焊缝金属内的气体或外界侵入的气体在熔池金属冷却凝固前未来得及逸出而残留在焊缝金属内部或表面形成的空穴或孔隙,视其形态可分为单个气孔、链状气孔、密集气孔(包括蜂窝状气孔)等,特别是在电弧焊中,由于冶金过程进行时间很短,熔池金属很快凝固,冶金过程中产生的气体、液态金属吸收的气体,或者焊条的焊剂受潮而在高温下分解产生气体,甚至是焊接环境中的湿度太大也会在高温下分解出气体等等,这些气体来不及析出时就会形成气孔缺陷。
尽管气孔较之其它的缺陷其应力集中趋势没有那么大,但是它破坏了焊缝金属的致密性,减少了焊缝金属的有效截面积,从而导致焊缝的强度降低。
某钢板对接焊缝X射线照相底片V型坡口,手工电弧焊,未焊透某钢板对接焊缝X射线照相底片V型坡口,手工电弧焊,密集气孔(4)夹渣与夹杂物:熔化焊接时的冶金反应产物,例如非金属杂质(氧化物、硫化物等)以及熔渣,由于焊接时未能逸出,或者多道焊接时清渣不干净,以至残留在焊缝金属内,称为夹渣或夹杂物。
视其形态可分为点状和条状,其外形通常是不规则的,其位置可能在焊缝与母材交界处,也可能存在于焊缝内。
另外,在采用钨极氩弧焊打底+手工电弧焊或者钨极氩弧焊时,钨极崩落的碎屑留在焊缝内则成为高密度夹杂物(俗称夹钨)。
W18Cr4V(高速工具钢)-45钢棒对接电阻焊缝中的夹渣断口照片钢板对接焊缝X射线照相底片V型坡口,手工电弧焊,局部夹渣钢板对接焊缝X射线照相底片V型坡口,手工电弧焊,两侧线状夹渣钢板对接焊缝X射线照相底片V型坡口,钨极氩弧焊打底+手工电弧焊,夹钨(5)裂纹:焊缝裂纹是焊接过程中或焊接完成后在焊接区域中出现的金属局部破裂的表现。
焊接的六大缺陷,产生原因、危害
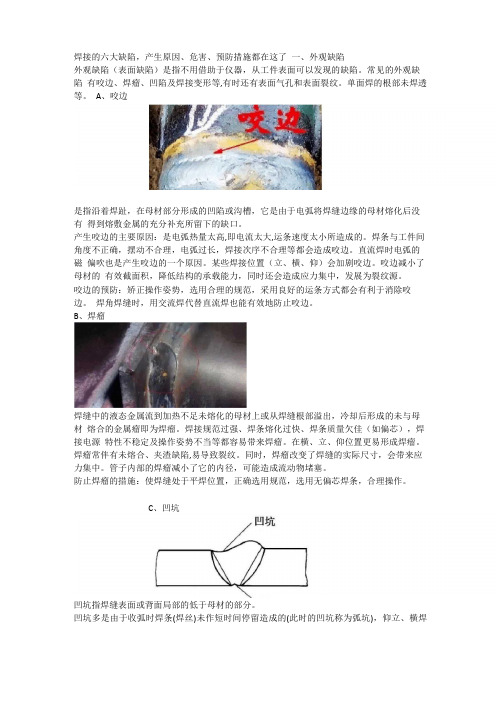
焊接的六大缺陷,产生原因、危害、预防措施都在这了一、外观缺陷外观缺陷(表面缺陷)是指不用借助于仪器,从工件表面可以发现的缺陷。
常见的外观缺陷有咬边、焊瘤、凹陷及焊接变形等,有时还有表面气孔和表面裂纹。
单面焊的根部未焊透等。
A、咬边是指沿着焊趾,在母材部分形成的凹陷或沟槽,它是由于电弧将焊缝边缘的母材熔化后没有得到熔敷金属的充分补充所留下的缺口。
产生咬边的主要原因:是电弧热量太高,即电流太大,运条速度太小所造成的。
焊条与工件间角度不正确,摆动不合理,电弧过长,焊接次序不合理等都会造成咬边。
直流焊时电弧的磁偏吹也是产生咬边的一个原因。
某些焊接位置(立、横、仰)会加剧咬边。
咬边减小了母材的有效截面积,降低结构的承载能力,同时还会造成应力集中,发展为裂纹源。
咬边的预防:矫正操作姿势,选用合理的规范,采用良好的运条方式都会有利于消除咬边。
焊角焊缝时,用交流焊代替直流焊也能有效地防止咬边。
B、焊瘤焊缝中的液态金属流到加热不足未熔化的母材上或从焊缝根部溢出,冷却后形成的未与母材熔合的金属瘤即为焊瘤。
焊接规范过强、焊条熔化过快、焊条质量欠佳(如偏芯),焊接电源特性不稳定及操作姿势不当等都容易带来焊瘤。
在横、立、仰位置更易形成焊瘤。
焊瘤常伴有未熔合、夹渣缺陷,易导致裂纹。
同时,焊瘤改变了焊缝的实际尺寸,会带来应力集中。
管子内部的焊瘤减小了它的内径,可能造成流动物堵塞。
防止焊瘤的措施:使焊缝处于平焊位置,正确选用规范,选用无偏芯焊条,合理操作。
C、凹坑凹坑指焊缝表面或背面局部的低于母材的部分。
凹坑多是由于收弧时焊条(焊丝)未作短时间停留造成的(此时的凹坑称为弧坑),仰立、横焊时,常在焊缝背面根部产生内凹。
凹坑减小了焊缝的有效截面积,弧坑常带有弧坑裂纹和弧坑缩孔。
防止凹坑的措施:选用有电流衰减系统的焊机,尽量选用平焊位置,选用合适的焊接规范,收弧时让焊条在熔池内短时间停留或环形摆动,填满弧坑。
未焊满是指焊缝表面上连续的或断续的沟槽。
常见的焊接缺陷及缺陷图片
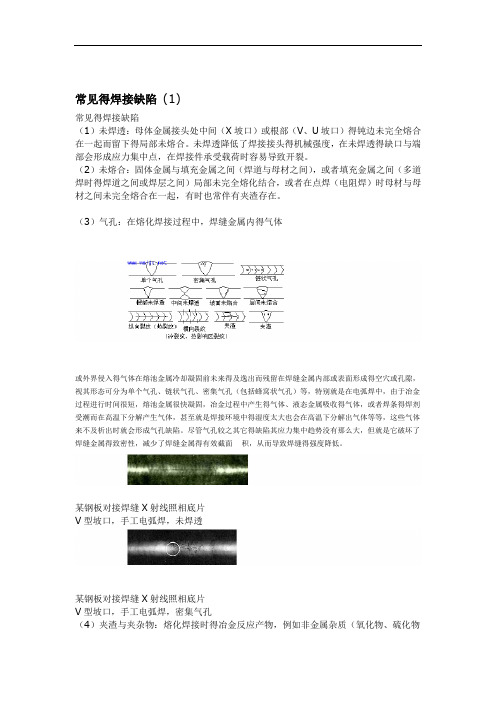
常见得焊接缺陷(1)常见得焊接缺陷(1)未焊透:母体金属接头处中间(X坡口)或根部(V、U坡口)得钝边未完全熔合在一起而留下得局部未熔合。
未焊透降低了焊接接头得机械强度,在未焊透得缺口与端部会形成应力集中点,在焊接件承受载荷时容易导致开裂。
(2)未熔合:固体金属与填充金属之间(焊道与母材之间),或者填充金属之间(多道焊时得焊道之间或焊层之间)局部未完全熔化结合,或者在点焊(电阻焊)时母材与母材之间未完全熔合在一起,有时也常伴有夹渣存在。
(3)气孔:在熔化焊接过程中,焊缝金属内得气体或外界侵入得气体在熔池金属冷却凝固前未来得及逸出而残留在焊缝金属内部或表面形成得空穴或孔隙,视其形态可分为单个气孔、链状气孔、密集气孔(包括蜂窝状气孔)等,特别就是在电弧焊中,由于冶金过程进行时间很短,熔池金属很快凝固,冶金过程中产生得气体、液态金属吸收得气体,或者焊条得焊剂受潮而在高温下分解产生气体,甚至就是焊接环境中得湿度太大也会在高温下分解出气体等等,这些气体来不及析出时就会形成气孔缺陷。
尽管气孔较之其它得缺陷其应力集中趋势没有那么大,但就是它破坏了焊缝金属得致密性,减少了焊缝金属得有效截面积,从而导致焊缝得强度降低。
某钢板对接焊缝X射线照相底片V型坡口,手工电弧焊,未焊透某钢板对接焊缝X射线照相底片V型坡口,手工电弧焊,密集气孔(4)夹渣与夹杂物:熔化焊接时得冶金反应产物,例如非金属杂质(氧化物、硫化物等)以及熔渣,由于焊接时未能逸出,或者多道焊接时清渣不干净,以至残留在焊缝金属内,称为夹渣或夹杂物。
视其形态可分为点状与条状,其外形通常就是不规则得,其位置可能在焊缝与母材交界处,也可能存在于焊缝内。
另外,在采用钨极氩弧焊打底+手工电弧焊或者钨极氩弧焊时,钨极崩落得碎屑留在焊缝内则成为高密度夹杂物(俗称夹钨)。
W18Cr4V(高速工具钢)-45钢棒对接电阻焊缝中得夹渣断口照片钢板对接焊缝X射线照相底片型坡口,手工电弧焊,局部夹渣V.钢板对接焊缝X射线照相底片型坡口,手工电弧焊,两侧线状夹渣V钢板对接焊缝X射线照相底片手工电弧焊,夹钨型坡口,钨极氩弧焊打底+V(5)裂纹:焊缝裂纹就是焊接过程中或焊接完成后在焊接区域中出现得金属局部破裂得表现。
焊接八大缺陷
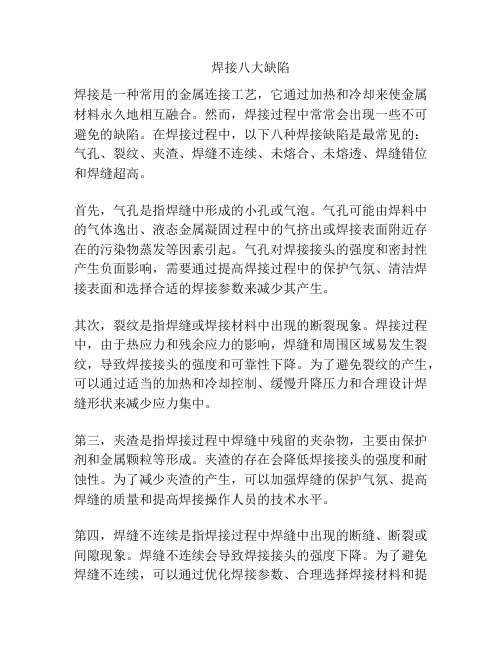
焊接八大缺陷焊接是一种常用的金属连接工艺,它通过加热和冷却来使金属材料永久地相互融合。
然而,焊接过程中常常会出现一些不可避免的缺陷。
在焊接过程中,以下八种焊接缺陷是最常见的:气孔、裂纹、夹渣、焊缝不连续、未熔合、未熔透、焊缝错位和焊缝超高。
首先,气孔是指焊缝中形成的小孔或气泡。
气孔可能由焊料中的气体逸出、液态金属凝固过程中的气挤出或焊接表面附近存在的污染物蒸发等因素引起。
气孔对焊接接头的强度和密封性产生负面影响,需要通过提高焊接过程中的保护气氛、清洁焊接表面和选择合适的焊接参数来减少其产生。
其次,裂纹是指焊缝或焊接材料中出现的断裂现象。
焊接过程中,由于热应力和残余应力的影响,焊缝和周围区域易发生裂纹,导致焊接接头的强度和可靠性下降。
为了避免裂纹的产生,可以通过适当的加热和冷却控制、缓慢升降压力和合理设计焊缝形状来减少应力集中。
第三,夹渣是指焊接过程中焊缝中残留的夹杂物,主要由保护剂和金属颗粒等形成。
夹渣的存在会降低焊接接头的强度和耐蚀性。
为了减少夹渣的产生,可以加强焊缝的保护气氛、提高焊缝的质量和提高焊接操作人员的技术水平。
第四,焊缝不连续是指焊接过程中焊缝中出现的断缝、断裂或间隙现象。
焊缝不连续会导致焊接接头的强度下降。
为了避免焊缝不连续,可以通过优化焊接参数、合理选择焊接材料和提高焊接操作人员的技术水平来改善焊缝质量。
第五,未熔合是指焊缝中出现的两个金属板未完全融合的现象。
未熔合会导致焊接接头的强度和韧性下降。
为了避免未熔合的发生,可以增加焊接电流、延长焊接时间和提高焊接操作人员的技术水平。
第六,未熔透是指焊缝的表面或底部未完全穿透的现象。
未熔透会导致焊接接头的强度和密封性下降。
为了避免未熔透,可以提高焊接电流、调整焊接速度和增加焊接带宽。
第七,焊缝错位是指焊接过程中焊缝位置偏离设计位置的现象。
焊缝错位会导致焊接接头的尺寸不准确和强度不稳定。
为了避免焊缝错位,可以加强校对、改进夹紧装置和提高焊接操作人员的技术水平。
常见焊接缺陷及图示

常见焊接缺陷及图示
常见的缺陷有:裂纹、焊瘤、烧穿、弧坑、气孔、夹渣、咬边、未熔合、未焊透等,以及焊缝尺寸不符合要求、焊缝成形不良(如:长度不足,高度不足,未满焊)等。
1.气孔:
修复方法:打磨去除该段焊缝,重新焊接。
修复方法:打磨去除该段焊缝,重新焊接。
2.砂眼(焊接时气体或杂质在焊接构件内部或表面形成的小孔)
修复方法:打磨去除所有影响焊缝,重新焊接。
3.缩孔(焊接后在冷凝过程中收缩而产生的孔洞,形状不规则,孔壁粗糙,一般位于铸件的热节处。
)
修复方法:打磨去除所有影响焊缝,重新焊接。
4.焊瘤(金属物在焊接过程中,通过电流造成金属焊点局部高温熔化,液体金属凝固时,在自重作用下金属流淌
形成的微小疙瘩)
修复方法:打磨去除该段重新焊接5.咬边(烧筋)
修复方法:重新焊接
6.弧坑(在焊接收尾处形成低于焊缝高度的凹陷坑)
修复方法:打磨去除该段重新焊接7.焊缝不均匀
修复方法:重新焊接
8.焊接裂缝
修复方法:打磨去除该段重新焊接
9.未焊透(未焊透指母材金属未熔化,焊缝金属没有进入接头根部的现象)
修复方法:打磨去除该段重新焊接10.未满焊(未焊满是指焊缝表面上连续的或断续的沟槽)
修复方法:打磨去除该段重新焊接11.简易示意图。
常见的焊接缺陷及缺陷图片

常见的焊接缺陷(1)常见的焊接缺陷(1)未焊透:母体金属接头处中间(X坡口)或根部(V、U坡口)的钝边未完全熔合在一起而留下的局部未熔合。
未焊透降低了焊接接头的机械强度,在未焊透的缺口和端部会形成应力集中点,在焊接件承受载荷时容易导致开裂。
(2)未熔合:固体金属与填充金属之间(焊道与母材之间),或者填充金属之间(多道焊时的焊道之间或焊层之间)局部未完全熔化结合,或者在点焊(电阻焊)时母材与母材之间未完全熔合在一起,有时也常伴有夹渣存在。
(3)气孔:在熔化焊接过程中,焊缝金属内的气体或外界侵入的气体在熔池金属冷却凝固前未来得及逸出而残留在焊缝金属内部或表面形成的空穴或孔隙,视其形态可分为单个气孔、链状气孔、密集气孔(包括蜂窝状气孔)等,特别是在电弧焊中,由于冶金过程进行时间很短,熔池金属很快凝固,冶金过程中产生的气体、液态金属吸收的气体,或者焊条的焊剂受潮而在高温下分解产生气体,甚至是焊接环境中的湿度太大也会在高温下分解出气体等等,这些气体来不及析出时就会形成气孔缺陷。
尽管气孔较之其它的缺陷其应力集中趋势没有那么大,但是它破坏了焊缝金属的致密性,减少了焊缝金属的有效截面积,从而导致焊缝的强度降低。
某钢板对接焊缝X射线照相底片V型坡口,手工电弧焊,未焊透某钢板对接焊缝X射线照相底片V型坡口,手工电弧焊,密集气孔(4)夹渣与夹杂物:熔化焊接时的冶金反应产物,例如非金属杂质(氧化物、硫化物等)以及熔渣,由于焊接时未能逸出,或者多道焊接时清渣不干净,以至残留在焊缝金属内,称为夹渣或夹杂物。
视其形态可分为点状和条状,其外形通常是不规则的,其位置可能在焊缝与母材交界处,也可能存在于焊缝内。
另外,在采用钨极氩弧焊打底+手工电弧焊或者钨极氩弧焊时,钨极崩落的碎屑留在焊缝内则成为高密度夹杂物(俗称夹钨)。
W18Cr4V(高速工具钢)-45钢棒对接电阻焊缝中的夹渣断口照片钢板对接焊缝X射线照相底片V型坡口,手工电弧焊,局部夹渣钢板对接焊缝X射线照相底片V型坡口,手工电弧焊,两侧线状夹渣钢板对接焊缝X射线照相底片V型坡口,钨极氩弧焊打底+手工电弧焊,夹钨(5)裂纹:焊缝裂纹是焊接过程中或焊接完成后在焊接区域中出现的金属局部破裂的表现。
常见焊接缺陷
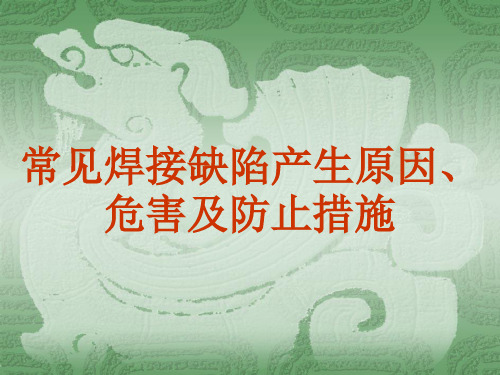
6、未熔合:熔焊时,焊道与母材之间或焊 道之间未能完全熔化熔化结合在一起的部 分,称为未熔合。也称为“假焊”常见的 未熔合部位有三处;坡口边缘未熔合、焊 缝金属层间未熔合。
危害:是一种比较危险的焊接缺陷,焊缝 出现间断和突变部位,使得焊接接头的强 度ቤተ መጻሕፍቲ ባይዱ大降低。未熔合部位还存在尖劈间隙, 承载后应力集中严重,极易由此处产生裂 纹。
c.焊件表面及坡口有水、油、锈等污物存在, 这些污物在电弧高温作用下,分解出来的 一氧化碳、氢和水蒸气等,进入熔池后往 往形成一氧化碳气孔和氢气孔。
d.焊接电流偏低或焊接速度过快,熔池存 在的时间短,以致于气体来不及从熔池金 属中逸出。
e.电弧长度过长,使熔池失去了气体的保护, 空气很容易侵入熔池,焊接电流过大,焊 条发红,药皮脱落,而失去了保护作用, 电弧偏吹,运条手法不稳等。
常见焊接缺陷产生原因、 危害及防止措施
★★焊接缺陷的分类:
焊接缺陷可分为外部缺陷和内部缺陷两种 1.外部缺陷分为: 1外观形状和尺寸不符合要求;2表面裂纹;3表面
气孔;4咬边;5凹陷;6满溢;7焊瘤;8弧坑;9电 弧擦伤;10明冷缩孔;11烧穿;12过烧。 2.内部缺陷分为: 1焊接裂纹:a.冷裂纹;b.层状撕裂;c.热裂纹; d.再热裂纹。 2气孔;3夹渣;4未焊透;5未熔合;6夹钨;7夹珠。
产生原因:焊件坡口角度不对,装配 间隙不匀,点固焊时未对正,焊接电 流过大或过小,运条速度过快或过慢, 焊条的角度选择不合适或改变不当, 埋弧焊焊接工艺选择不正确等。
防止措施:选择合适的坡口角度,按 标准要求点焊组装焊件,并保持间隙 均匀,编制合理的焊接工艺流程,控 制变形和翘曲,正确选用焊接电流, 合适地掌握焊接速度,采用恰当的运 条手法和角度,随时注意适应焊件的 坡口变化,以保证焊缝外观成形均匀 一致。
焊工必看——常见焊接缺陷大全
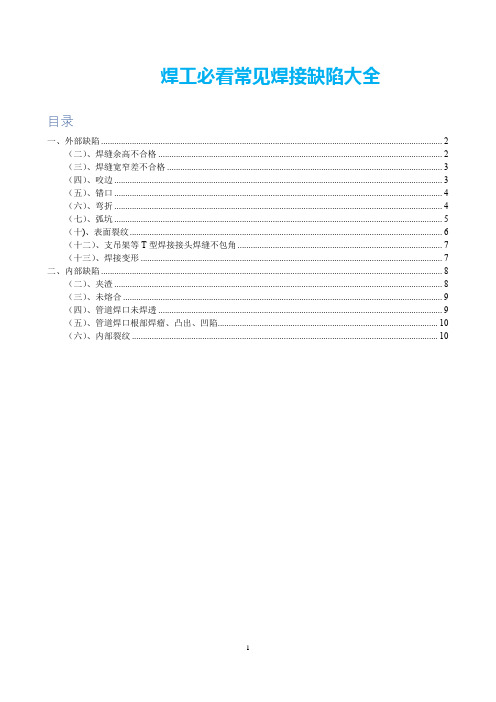
焊工必看常见焊接缺陷大全目录一、外部缺陷 (2)(二)、焊缝余高不合格 (2)(三)、焊缝宽窄差不合格 (3)(四)、咬边 (3)(五)、错口 (4)(六)、弯折 (4)(七)、弧坑 (5)(十)、表面裂纹 (6)(十二)、支吊架等T型焊接接头焊缝不包角 (7)(十三)、焊接变形 (7)二、内部缺陷 (8)(二)、夹渣 (8)(三)、未熔合 (9)(四)、管道焊口未焊透 (9)(五)、管道焊口根部焊瘤、凸出、凹陷 (10)(六)、内部裂纹 (10)一、外部缺陷(一)、焊缝成型差1、现象焊缝波纹粗劣,焊缝不均匀、不整齐,焊缝与母材不圆滑过渡,焊接接头差,焊缝高低不平。
2、原因分析焊缝成型差的原因有:焊件坡口角度不当或装配间隙不均匀;焊口清理不干净;焊接电流过大或过小;焊接中运条(枪)速度过快或过慢;焊条(枪)摆动幅度过大或过小;焊条(枪)施焊角度选择不当等。
3、防治措施⑴焊件的坡口角度和装配间隙必须符合图纸设计或所执行标准的要求。
⑴焊件坡口打磨清理干净,无锈、无垢、无脂等污物杂质,露出金属光泽。
⑴加强焊接联系,提高焊接操作水平,熟悉焊接施工环境。
⑴根据不同的焊接位置、焊接方法、不同的对口间隙等,按照焊接工艺卡和操作技能要求,选择合理的焊接电流参数、施焊速度和焊条(枪)的角度。
4、治理措施⑴加强焊后自检和专检,发现问题及时处理;⑴对于焊缝成型差的焊缝,进行打磨、补焊;⑴达不到验收标准要求,成型太差的焊缝实行割口或换件重焊;⑴加强焊接验收标准的学习,严格按照标准施工。
(二)、焊缝余高不合格1、现象管道焊口和板对接焊缝余高大于3㎜;局部出现负余高;余高差过大;角焊缝高度不够或焊角尺寸过大,余高差过大。
2、原因分析焊接电流选择不当;运条(枪)速度不均匀,过快或过慢;焊条(枪)摆动幅度不均匀;焊条(枪)施焊角度选择不当等。
3、防治措施⑴根据不同焊接位置、焊接方法,选择合理的焊接电流参数;⑴增强焊工责任心,焊接速度适合所选的焊接电流,运条(枪)速度均匀,避免忽快忽慢;⑴焊条(枪)摆动幅度不一致,摆动速度合理、均匀;⑴注意保持正确的焊条(枪)角度。
焊接常见的缺陷及产生原因
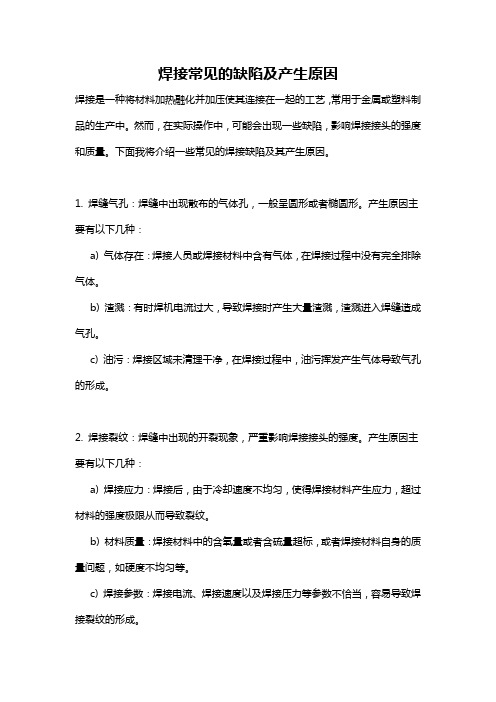
焊接常见的缺陷及产生原因焊接是一种将材料加热融化并加压使其连接在一起的工艺,常用于金属或塑料制品的生产中。
然而,在实际操作中,可能会出现一些缺陷,影响焊接接头的强度和质量。
下面我将介绍一些常见的焊接缺陷及其产生原因。
1. 焊缝气孔:焊缝中出现散布的气体孔,一般呈圆形或者椭圆形。
产生原因主要有以下几种:a) 气体存在:焊接人员或焊接材料中含有气体,在焊接过程中没有完全排除气体。
b) 渣溅:有时焊机电流过大,导致焊接时产生大量渣溅,渣溅进入焊缝造成气孔。
c) 油污:焊接区域未清理干净,在焊接过程中,油污挥发产生气体导致气孔的形成。
2. 焊接裂纹:焊缝中出现的开裂现象,严重影响焊接接头的强度。
产生原因主要有以下几种:a) 焊接应力:焊接后,由于冷却速度不均匀,使得焊接材料产生应力,超过材料的强度极限从而导致裂纹。
b) 材料质量:焊接材料中的含氧量或者含硫量超标,或者焊接材料自身的质量问题,如硬度不均匀等。
c) 焊接参数:焊接电流、焊接速度以及焊接压力等参数不恰当,容易导致焊接裂纹的形成。
3. 焊接结构不均匀:焊接接头的强度和质量不均匀,一部分焊缝更容易破裂。
产生原因主要有以下几种:a) 预热温度不够:焊接材料在焊接前没有经过预热处理,容易导致结构不均匀。
b) 焊接参数不一致:不同焊缝采用了不同的焊接参数,导致焊接接头的质量不均匀。
c) 焊接过程控制不当:焊接时控制不良,如焊接速度不稳定、电流波动大等,容易导致结构不均匀。
4. 焊缝错边:焊接接头两边焊缝位置不对称或偏移,容易导致接头强度下降。
产生原因主要有以下几种:a) 材料不准确对位:焊接前没有正确的对位,或者对位不准确导致焊缝偏移。
b) 焊接操作不当:焊接人员的焊接技术不熟练或者操作不当,容易导致焊缝错边。
c) 焊接设备问题:焊机设备本身有问题,如电流不稳定等,导致焊接接头错边。
针对这些常见的焊接缺陷,可以采取一些措施来避免或解决:1. 焊缝气孔:焊接前进行充分的气体排除,确保焊缝周围环境清洁,使用合适的焊接工艺参数。
焊接缺陷

指焊缝熔池中的气体在凝固时未能析出而残留下来形成的空穴
3)夹渣和夹杂
指焊后残留在焊缝中的熔渣和经冶金反应产生的焊后残留在 焊缝中的非金属夹杂
4)未焊透、未熔合
指焊缝金属和母材之间或焊道金属之间未完全熔化结合以及焊 缝的根部未完全熔透的现象
5)裂纹
包括热裂纹、冷裂纹、再热裂纹和层状撕裂等
6)其他缺陷
预防措施
清除焊件焊接区附近及焊丝上的铁锈、油污、油漆 等污物;焊条、焊剂在使用前应严格按规定烘干; 适当提高线能量,以提高熔池的高温停留时间;不 采用过大的焊接电流,以防止焊条药皮发红失效; 不使用偏心焊条;尽量采用短弧焊
4)裂纹
(1)在焊缝冷却结晶以后生成的冷裂纹 (2)在焊缝冷却凝固过程中形成的热裂纹
2)夹渣
根本原因
各类残渣的量多且没有足够的时 间浮出熔池表面
生产中的具体原因
多层焊时前一层焊渣没有清除干净、运条操作不当、 焊条熔渣粘度太大、脱渣性差、线能量小,导致熔 池存在时间短、坡口角度太小等
预防措施
选用合适的焊条型号;焊条摆动方式要正确;适当 增大线能量;注意层间的清理,特别是低氢碱性焊 条,一定要彻底清除层间焊渣
清除焊缝附近的油污、锈、油漆等污杂物 用短弧焊,以增强保护效果
尽可能设计成刚性小的结构
采用焊前预热、焊后缓冷或焊后热处理措施,以减少淬硬 倾向和焊后残余应力
注意事项
不同的焊接方法焊接缺陷的产生原因是不同的
焊接裂纹是危害最大的焊接缺陷
它不仅会造成应力集中,降低焊接接头 的静载强度,更严重的是它是导致疲劳 和脆性破坏的重要诱因
六、常见焊接缺陷产生原因分析及预防措施
焊接结构设计 焊接工艺参数
焊前准备
焊接中常见的缺陷及防治措施
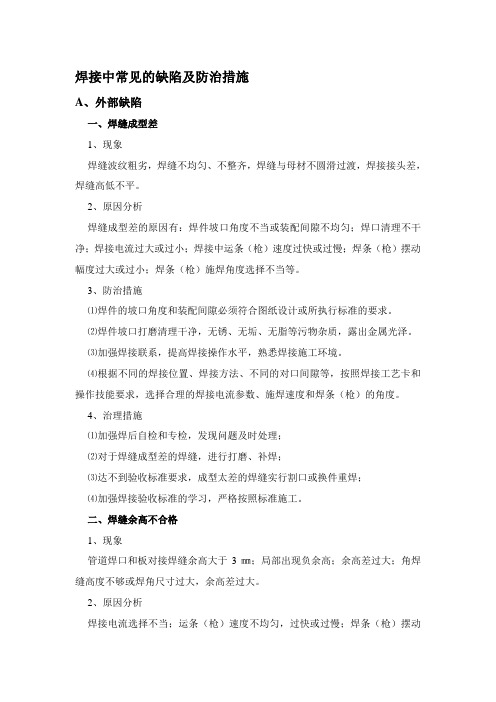
焊接中常见的缺陷及防治措施A、外部缺陷一、焊缝成型差1、现象焊缝波纹粗劣,焊缝不均匀、不整齐,焊缝与母材不圆滑过渡,焊接接头差,焊缝高低不平。
2、原因分析焊缝成型差的原因有:焊件坡口角度不当或装配间隙不均匀;焊口清理不干净;焊接电流过大或过小;焊接中运条(枪)速度过快或过慢;焊条(枪)摆动幅度过大或过小;焊条(枪)施焊角度选择不当等。
3、防治措施⑴焊件的坡口角度和装配间隙必须符合图纸设计或所执行标准的要求。
⑵焊件坡口打磨清理干净,无锈、无垢、无脂等污物杂质,露出金属光泽。
⑶加强焊接联系,提高焊接操作水平,熟悉焊接施工环境。
⑷根据不同的焊接位置、焊接方法、不同的对口间隙等,按照焊接工艺卡和操作技能要求,选择合理的焊接电流参数、施焊速度和焊条(枪)的角度。
4、治理措施⑴加强焊后自检和专检,发现问题及时处理;⑵对于焊缝成型差的焊缝,进行打磨、补焊;⑶达不到验收标准要求,成型太差的焊缝实行割口或换件重焊;⑷加强焊接验收标准的学习,严格按照标准施工。
二、焊缝余高不合格1、现象管道焊口和板对接焊缝余高大于3㎜;局部出现负余高;余高差过大;角焊缝高度不够或焊角尺寸过大,余高差过大。
2、原因分析焊接电流选择不当;运条(枪)速度不均匀,过快或过慢;焊条(枪)摆动幅度不均匀;焊条(枪)施焊角度选择不当等。
3、防治措施⑴根据不同焊接位置、焊接方法,选择合理的焊接电流参数;⑵增强焊工责任心,焊接速度适合所选的焊接电流,运条(枪)速度均匀,避免忽快忽慢;⑶焊条(枪)摆动幅度不一致,摆动速度合理、均匀;⑷注意保持正确的焊条(枪)角度。
4、治理措施⑴加强焊工操作技能培训,提高焊缝盖面水平;⑵对焊缝进行必要的打磨和补焊;⑶加强焊后检查,发现问题及时处理;⑷技术员的交底中,对焊角角度要求做详细说明。
三、焊缝宽窄差不合格1、现象焊缝边缘不匀直,焊缝宽窄差大于3㎜。
2、原因分析焊条(枪)摆动幅度不一致,部分地方幅度过大,部分地方摆动过小;焊条(枪)角度不合适;焊接位置困难,妨碍焊接人员视线。
- 1、下载文档前请自行甄别文档内容的完整性,平台不提供额外的编辑、内容补充、找答案等附加服务。
- 2、"仅部分预览"的文档,不可在线预览部分如存在完整性等问题,可反馈申请退款(可完整预览的文档不适用该条件!)。
- 3、如文档侵犯您的权益,请联系客服反馈,我们会尽快为您处理(人工客服工作时间:9:00-18:30)。
回目录
Байду номын сангаас
• (2)层状撕裂:大型厚壁结构在焊接过程中 会沿钢板的厚度方向产生较大的Z向拉伸应 力,如果钢中的较多的夹层,就会沿钢板 轧制方向出现一种台阶状的裂纹,称为层 状撕裂。
• 产生机理:钢产生冷裂纹的倾向主要决定 于钢的淬硬倾向,焊接接头的含氢量及其 分布,以及接头所承受的拘束应力状态。
回目录
• 产生原因: • a.钢种原淬硬倾向主要取决于化学成分
、板厚、焊接工艺和冷却条件等。钢 的淬硬倾向越大,越易产生冷裂纹。 • b.氢的作用,氢是引起超高强钢焊接 冷裂纹的重要因素之一,并且有延迟 的特征。高强钢焊接接头的含氢量越 高,则裂纹的敏感性越
回目录
• c.焊接接头的应力状态:高强度钢焊接时产生延 迟裂纹的倾向不仅取决于钢的淬硬倾向和氢的作 用,还决定于焊接接头的应力状态。焊接时主要 存在的应力有:不均匀加热及冷却过程中所产生 的热应力、金属相变时产生的组织应力、结构自 身拘束条件等。
• d.焊接工艺的影响:线能量过大会引起近缝区晶
粒粗大,降低接头的抗裂性能;线能量过小,还
回目录
• 防止措施:选择合适的坡口角度,按 标准要求点焊组装焊件,并保持间隙 均匀,编制合理的焊接工艺流程,控 制变形和翘曲,正确选用焊接电流, 合适地掌握焊接速度,采用恰当的运 条手法和角度,随时注意适应焊件的 坡口变化,以保证焊缝外观成形均匀 一致。
回目录
• 2、焊接裂纹 • 表现:在焊接应力及其他致脆因素共同作
回目录
★★焊接缺陷的分类:
回目录
★★焊接缺陷的分类:
回目录
★★各种焊接缺陷产生原因、 危害及防止措施
• 1、外面形状和尺寸不符合要求 • 表现:外表面形状高低不平,焊缝成形不
良,焊波粗劣,焊缝宽度不均匀,焊缝余 高过高或过低,角焊缝焊脚单边或下凹过 大,母材错边,接头的变形和翘曲超过了 产品的允许范围等。
回目录
• c.采用低匹配的焊缝或“软层焊接”的 方法,对防止冷裂纹也是有效的。
• d.避免强力组装、防止错边、角变形 等引起的附加应力,对称布置焊缝, 避免焊缝密集,尽量采用对称的坡口 形式并力求填充金属减少量,防止焊 缝缺陷的产生。
回目录
• e.焊前预热和焊后缓冷,这不仅可以改善焊 接接头的金相组织,降低 热影响区的硬度 和脆性,而且可以加速焊缝中的氢向外扩 散,此外还可以起到减小焊接残余应力的 作用。
• 产生原因:金属材料的中含有较多的非金 属夹杂物,Z向拘束应力大,热影响区的脆 化等。
回目录
• 防止措施:选用具有抗层状撕裂能力的钢 材,在接头设计和焊接施工中采取措施降 低Z向应力和应力集中。
• (3)热裂纹:焊缝和热影响区金属冷却到固 相线附近的高温区产生的焊接裂纹。沿奥 氏体晶界开裂,裂纹多贯穿于焊缝表面, 断口被氧化,呈氧化色。常有结晶裂纹、 液化裂纹、多边化裂纹等。
回目录
• c.力学因素对热裂纹的影响:焊件的刚 性很大,工艺因素不当,装配工艺不 当以及焊接缺陷等都会导致应力集中 而加大焊缝的热应力,在结晶时形成 热裂纹。
回目录
• 危害:焊缝成形不美观,影响到焊材 与母材的结合,削弱焊接接头的强度 性能,使接头的应力产生偏向和不均 匀分布,造成应力集中,影响焊接结 构的安全使用。
回目录
• 产生原因:焊件坡口角度不对,装配 间隙不匀,点固焊时未对正,焊接电 流过大或过小,运条速度过快或过慢 ,焊条的角度选择不合适或改变不当 ,埋弧焊焊接工艺选择不正确等。
会使热影响区淬硬,也不利于氢的逸出而增大冷
裂倾向。焊前预热和焊后热处理的温度不合适,
多层焊的焊层熔深不合适等。
回目录
• 防止措施: • a.选择合适的焊接材料:如优质的低氢焊接
材料和低氢的焊接方法。对重要的焊接结 构,应采用超低氢、高韧性的焊接材料, 焊条、焊剂使用前应按规定烘干。 • b.焊前仔细清除坡口周围基体金属表面和焊 丝上的水、油、锈等污物,减少氢的来源 ,以降低焊缝中扩散氢的含量。
回目录
• 产生原因:a.焊缝的化学元素的影响,主要 是硫、磷的影响,易在钢中形成低熔点共 晶体,是一种脆硬组织,在应力的作用下 引起结晶裂纹。其中的硫、磷等杂质可能 来自材料本身,也有可能来自焊接材料中 ,也有可能来自焊接接头的表面。
• b.凝固结晶组织形态也是形成热裂纹的一种 重要因素。晶粒越粗大,柱状晶的方向越 明显,则产生结晶 裂纹的倾向就越大。也 就是焊接线能量越大越易形成热裂纹。
常见焊接缺陷产生原因、 危害及防止措施
★★焊接缺陷的分类:
• 焊接缺陷可分为外部缺陷和内部缺陷两种 • 1.外部缺陷分为: • 1外观形状和尺寸不符合要求;2表面裂纹;3表
面气孔;4咬边;5凹陷;6满溢;7焊瘤;8弧坑 ;9电弧擦伤;10明冷缩孔;11烧穿;12过烧。 • 2.内部缺陷分为: • 1焊接裂纹:a.冷裂纹;b.层状撕裂;c.热裂纹 ;d.再热裂纹。 • 2气孔;3夹渣;4未焊透;5未熔合;6夹钨;7夹 珠。
回目录
• 产生原因及防止措施:(1)冷裂纹:是焊 接头冷却到较低温度下(对于钢来说是Ms 温度以下)时产生的焊接裂纹,冷裂纹的 起源多发生在具有缺口效应的焊接热影响 区或有物理化学不均匀的氢聚集的局部地 带,裂纹有时沿晶界扩展,也有时穿晶扩 展。这是由于焊接接头的金相组织和应力 状态及氢的含量决定的。(如焊层下冷裂纹 、焊趾冷裂纹、焊根冷裂纹等)
用下焊接接头中局部地区的金属原子结合 力遭到破坏面形成的新界面所产生的缝隙 ,具有尖锐的缺口和大小的长宽比特征。 按形态可分为:纵向裂纹、横向裂纹、弧 坑裂纹、焊趾裂纹、焊根裂纹、热影响区 再热裂纹等。
回目录
危害:裂纹,是所有的焊接缺陷里 危害最严重的一种。它的存在是导 致焊接结构失效的最直接的因素, 特别是在锅炉压力容器的焊接接头 中,因为它的存在可能导致一场场 灾难性的事故的发生,裂纹最大的 一个特征是具有扩展性,在一定的 工作条件下会不断的“生长”,直 至断裂。