CUSP磁场对8英寸半导体级硅晶体生长的影响(simulation with FEMAG晶体生长模拟软件)
碳化硅同质外延质量影响因素的分析与综述

第53卷第2期2024年2月人㊀工㊀晶㊀体㊀学㊀报JOURNAL OF SYNTHETIC CRYSTALSVol.53㊀No.2February,2024碳化硅同质外延质量影响因素的分析与综述郭㊀钰1,2,刘春俊1,张新河2,沈鹏远1,张㊀博1,娄艳芳1,彭同华1,杨㊀建1(1.北京天科合达半导体股份有限公司,北京㊀102600;2.深圳市重投天科半导体有限公司,深圳㊀518108)摘要:碳化硅(SiC)外延质量会直接影响器件的性能和使用寿命,在SiC器件应用中起到关键作用㊂SiC外延质量一方面受衬底质量的影响,例如衬底的堆垛层错(SF)会贯穿到外延层中形成条状层错(BSF),螺位错(TSD)会贯穿到外延层中形成坑点或Frank型层错(Frank SF)等㊂另一方面受到外延工艺的影响,如在外延过程中衬底的基平面位错(BPD)受应力等条件作用会滑移形成Σ形基平面位错(Σ-BPD),衬底的TSD或刃位错(TED)会衍生为腐蚀坑(Pits),以及新产生SF和硅滴等㊂因此,获得高质量的SiC外延晶片需要从优选SiC衬底和优化外延工艺两方面入手㊂本文对外延生长过程中晶体缺陷如何转化并影响器件性能进行了系统分析和综述,并基于北京天科合达半导体股份有限公司量产的高质量6英寸SiC衬底,探讨了常见缺陷,如BPD㊁层错㊁硅滴和Pits等的形成机理及其控制技术,并对Σ-BPD的产生机理和消除方法进行研究,最终获得了片内厚度和浓度均匀性良好㊁缺陷密度低的外延产品,完成了650和1200V外延片产品的开发和产业化工作㊂关键词:碳化硅;同质外延;外延生长;缺陷;位错;小坑中图分类号:O78;O484;O47㊀㊀文献标志码:A㊀㊀文章编号:1000-985X(2024)02-0210-08 Analysis and Review of Influencing Factors of SiCHomo-Epitaxial Wafers QualityGUO Yu1,2,LIU Chunjun1,ZHANG Xinhe2,SHEN Pengyuan1,ZHANG Bo1,LOU Yanfang1,PENG Tonghua1,YANG Jian1(1.Beijing TankeBlue Semiconductor Co.,Ltd.,Beijing102600,China;2.Shenzhen MITK Semiconductor Co.,Ltd.,Shenzhen518108,China)Abstract:The performance and lifetime of silicon carbide(SiC)devices are directly affected by the quality of SiC epitaxial films.On the one hand,the quality of SiC epitaxial films is affected by the quality of substrates.For examples,the stacking faults(SF)in substrates penetrate into the epitaxial layer,forming bar-shaped stacking faults(BSF),and the threading screw dislocation(TSD)penetrate into the epitaxial layer to form pits or Frank-type stacking faults(Frank SF).On the other hand, the quality of SiC epitaxial films is also influenced by the epitaxial growing process.For examples,basal plane dislocation (BPD)in the substrate formΣ-basal plane dislocation(Σ-BPD)in the epitaxial layer under thermal stress or other unstable conditions,the TSD and threading edge dislocation(TED)in the substrate may be etched and derived into pits,and SF and silicon droplets may also be produced.Therefore,high quality SiC substrates and optimized epitaxial growing process are both crucial for obtaining high-quality silicon carbide epitaxial wafers.In this article,based on the SiC epitaxial films grown on 6inch SiC substrates batch-produced by TankeBlue Company,the defects reproducing process in substrates during epitaxial growing were analyzed,and the formation mechanism and controlling technology of common defects such as BPD,SF,silicon droplets and pits were overviewed.The generation mechanism ofΣ-BPD and its eliminating methods were also explored. Finally,we obtained the mass-production technologies of SiC epitaxial films with good thickness and concentration uniformity, and low defect density,which are qualified for making650and1200V SiC-based MOSFETs.Key words:SiC;homo-epitaxial;epitaxial growth;defect;dislocation;pit㊀㊀收稿日期:2023-05-29㊀㊀基金项目:北京市科协卓越工程师培养计划㊀㊀作者简介:郭㊀钰(1983 ),女,辽宁省人,博士,教授级高工㊂E-mail:guoyu03201@㊀㊀通信作者:刘春俊,博士,研究员㊂E-mail:liuchunjun@㊀第2期郭㊀钰等:碳化硅同质外延质量影响因素的分析与综述211㊀0㊀引㊀㊀言SiC作为目前被广泛关注的第三代半导体材料,具有高击穿电压㊁高电子迁移率㊁高热导率等特性,由其制备的半导体器件相比传统的硅(Si)基半导体器件拥有体积小㊁开关损耗低㊁功率密度更高等优势㊂随着绿色能源革命对电力电子器件耐高压㊁低功耗需求的日益迫切,以及电动汽车㊁充电桩等新兴应用的蓬勃发展, SiC器件在智能电网㊁电动汽车㊁轨道交通㊁新能源并网㊁开关电源㊁工业电机和白色家电等领域展现出良好的发展前景和巨大的市场潜力㊂与传统硅功率器件制作工艺不同,SiC功率器件不能直接制作在SiC单晶材料上,必须在导通型SiC单晶衬底上使用外延技术生长出高质量的外延材料,然后在外延层上制作各类器件㊂之所以不直接在SiC衬底上制作SiC器件,一方面是由于衬底的杂质含量较高,且电学性能不够好㊂另一方面是掺杂难度大,即使采用离子注入的方式,也需要后续的高温退火,远不如在外延层上的掺杂效果好㊂因此,制造出外延层的掺杂浓度和厚度符合设计要求的SiC器件至关重要㊂常见的SiC外延技术有化学气相沉积(chemical vapor deposition,CVD)㊁液相外延生长(liquid phase epitaxy,LPE)㊁分子束外延生长(molecular beam epitaxy,MBE)等,目前CVD是主流技术,具备较高生长速率㊁能够实现可控掺杂调控等优点㊂CVD外延生长通常使用硅烷和碳氢化合物作为反应气体,氢气作为载气,氯化氢作为辅助气体,或使用三氯氢硅(TCS)作为硅源代替硅烷和氯化氢,在约1600ħ的温度条件下,反应气体分解并在SiC衬底表面外延生长SiC薄膜㊂目前国内外SiC外延技术已经取得较大进展,产业界也已成功实现6英寸(1英寸=2.54cm)SiC外延批量生产㊂国外产业化公司主要有美国Wolfspeed公司㊁II-VI公司,日本的Showa Ddenko公司等,国内有厦门瀚天天成电子科技有限公司㊁东莞天域半导体有限公司㊁河北普兴电子科技股份有限公司㊁三安集成等㊂2022年美国Wolfspeed公司已成功实现8英寸SiC外延产品的量产㊂市场上主流的量产产品主要是650㊁1200㊁1700V金氧半场效晶体管(metal-oxide-semiconductor field-effect transistor,MOSFET)器件用6英寸外延产品㊂本研究团队基于十多年在SiC衬底材料制备技术研究和产业推广经验的积累,2022年开始启动SiC外延技术研发,重点针对1200V车规级MOSFET器件用SiC外延材料进行研发和产业化工作㊂本文首先介绍了SiC外延的研究历史,然后结合本团队SiC外延产品相关研发工作综述了SiC外延掺杂浓度控制和缺陷控制方面的研究进展,最后对国产SiC外延的发展进行了总结和展望㊂1㊀研发历史SiC同质外延技术研究需要基于SiC衬底开展,因此研发时间晚于SiC衬底,最早开始于20世纪60年代㊂研究人员主要采用了液相外延法[1-3]和CVD法进行SiC同质外延[4-9]㊂但由于SiC存在200多种晶体结构,外延生长时存在严重的多型夹杂问题,因此早期获得的外延材料质量都很差,这也制约了SiC器件的发展㊂第一个突破性的里程碑是在1987年,Kuroda等[10]和美国Kong等[11]各自相继提出了台阶流外延生长模型,在6H-SiC衬底上进行完美多型体复制,并给出了最优偏离晶向和偏角㊂具体来说,代表SiC晶型的堆垛顺序信息主要在SiC衬底表面台阶的侧向,通过SiC衬底表面偏角度的控制,使得同质外延在衬底表面原子台阶处侧向生长,从而继承衬底的堆垛次序,通过台阶流生长实现晶型的完美复制㊂这项技术同样适用其他晶型,如4H-SiC㊁15R-SiC的同质外延生长㊂4H-SiC同质外延的成功促进了SiC基肖特基二极管的研发,带动了4H-SiC在功率器件应用领域独特的发展㊂第二个标志性里程碑是热壁(温壁)CVD反应室设计,传统冷壁CVD反应腔室[12-13]结构较为简单,但存在一些缺点,如晶片表面法线方向的温度梯度非常大,导致SiC晶片翘曲比较严重[14];另外冷壁CVD加热效率比较低,热辐射损耗严重㊂通过热壁CVD反应室设计,腔室内温度梯度得到显著降低,容易实现良好的温度均匀性,这对于产业化生产至关重要㊂第三个里程碑是氯基快速外延生长技术,传统SiC的CVD生长技术通常使用硅烷和碳氢化合物作为反应气体,氢气作为载气,气相中Si团簇容易形成Si滴,导致外延生长工艺窗口相对较窄,同时也限制了外延生长的速率㊂通过引入氯基化学成分(通常有TCS,或者HCl)可以极大地抑制Si团簇,目前已成功应用于212㊀综合评述人工晶体学报㊀㊀㊀㊀㊀㊀第53卷SiC 快速外延生长中[15]㊂近年来,SiC 外延技术逐渐成熟,产业研究重点关注外延材料掺杂浓度控制和缺陷控制两个方面㊂2㊀SiC 外延层的掺杂浓度控制SiC 是优秀的宽禁带半导体材料,其优点是可以相对容易地在一个宽的范围内控制n 型和p 型掺杂㊂氮(N)或磷(P)用于n 型掺杂,而铝(Al)常用于p 型掺杂㊂硼(B)也曾用作p 型掺杂,但其电离能较大(约350MeV)[16],现在已经不是p 型掺杂的首选㊂Larkin 等[17-19]发现的竞位效应是实现SiC 掺杂控制的关键㊂N 原子替位C 原子位置,而P㊁Al 和B 替位Si 原子位置㊂因此,低C /Si 比有利于提高N 掺杂效率,高C /Si 比不利于N 的掺入;对于Al 和B 则刚好相反㊂目前大部分SiC 器件是基于n 型外延材料制作,氮气也是普遍采用的掺杂气体,N 掺杂与氮气流量㊁生长温度和压力㊁C /Si 比㊁生长速率等参数的依赖关系已有详细的研究[20-22],可以实现N 掺杂浓度大范围的调控(1ˑ1014~2ˑ1019cm -3)㊂对于大尺寸SiC 外延材料,SiC 外延层掺杂浓度的均匀性(δ/mean)是研究及产业界目前关注的另一重点㊂2011年Burk 等采用热壁气相外延(vapour phase epitaxy,VPE)炉制作出了厚度均匀性和浓度均匀性分别低于1.6%和12%的6英寸SiC 外延片[23],2014年Thomas 等在2800W 设备上获得了厚度和浓度均匀性分别低于1.5%和8%㊁良品率97.5%的外延片[24-25]㊂8英寸外延片方面,Mattia 和Danilo 等各自在PE1O8设备上获得厚度和浓度均匀性均低于2%的外延片[26]㊂在水平式外延生长中,气体高速流入生长腔室,中心流速高,两侧接近生长腔室边界的地方流速降低;同时在气体流动的方向上,随着反应气体的消耗,反应气体的浓度降低,这些现象会引起SiC 外延层厚度和浓度的不均匀,进而影响器件的性能㊂解决上述问题的方法是设计适当的反应腔室结构,从进气端到尾气端的反应腔室逐步变窄,使得气体的速度沿着流动方向增加,同时反应气体向衬底的扩散距离减小,抵消气体消耗和边界流速降低带来的影响㊂另外,通过调整SiC 衬底的旋转速度,使用适当比例的氩气和氢气的混合气体作为旋转气体源,调整反应气体中的C /Si 比例,调整中路和旁路的反应气体和掺杂气体的流量,都可以获得更加均匀的载流子浓度和厚度分布[27]㊂图1㊀量产外延片的载流子浓度均匀性(a)和厚度均匀性(b)分布统计Fig.1㊀Uniformity of doping (a)and thickness (b)of epi-wafers 本团队采用水平式外延生长方法,三氯氢硅和乙烯作为反应气源,氮气作为掺杂气体,氢气作为载气,氢气和氩气作为驱动托盘旋转的气源,生长厚度适用于1200V 的SiC 基MOSFET 用SiC 外延层㊂通过调整掺杂氮气在中心和边缘分布比例㊁托盘旋转的速度以及旋转气体中氩气与氢气的比例,优化外延工艺的C /Si 比等生长参数,实现SiC 外延层掺杂浓度及均匀性的有效控制,图1是量产1000片的厚度和浓度均匀性统计数据,C /Si 比在1.0~1.2㊁温度在1600~1650ħ和压力在100mbar 的工艺条件下,统计的外延产品100%达到厚度均匀性小于3%㊁浓度均匀性小于6%㊂3㊀SiC 外延层的缺陷控制研究根据晶体缺陷理论,SiC 外延材料的主要缺陷可归纳为4大类:点缺陷㊁位错(属于线缺陷)㊁层错(属于面缺陷)和表面缺陷(属于体缺陷)㊂3.1㊀点缺陷SiC 外延材料的点缺陷主要有硅空位㊁碳空位㊁硅碳双空位等缺陷[28-30],它们在禁带中产生深能级中心,影响材料的载流子寿命㊂在轻掺杂的SiC 外延层中,点缺陷产生的深能级中心浓度通常在5ˑ1012~2ˑ1013cm -3,与外延生长条件特别是C /Si 比和生长温度相关㊂3.2㊀位㊀错SiC 材料的位错包括螺位错(threading screw dislocation,TSD)㊁刃位错(threading edge dislocation,TED)㊀第2期郭㊀钰等:碳化硅同质外延质量影响因素的分析与综述213㊀和基平面位错(basal plane dislocation,BPD)㊂微管是伯氏矢量较大的螺位错形成的中空管道,可认为是一种超螺位错㊂SiC外延层的位错缺陷基本都和衬底相关,图2是SiC外延层中观察到的典型位错演变图[31-32]㊂大部分微管和螺位错会复制到外延层中,在合适的工艺条件下,部分微管分解为单独的螺位错,形成微管闭合[33],只有一小部分TSD(<2%)转为Frank型层错[34-35]㊂衬底TED基本都会复制到外延层中㊂图2㊀4H-SiC外延层中位错演变图Fig.2㊀Schematic illustration of dislocation evolution process in4H-SiC epitaxial layerBPD位错主要源于衬底中BPD向外延层的贯穿,通常偏4ʎ4H-SiC衬底中大部分BPD位错(>99%)在外延过程中会转化为TED位错,只有少于1%左右的BPD会贯穿到外延层中并达到外延层表面㊂在后续器件制造中,BPD主要影响双极型器件的稳定性,如出现双极型退化现象[36-40]㊂在正向导通电流的作用下, BPD可能会延伸至外延层演变成堆垒层错(SF),造成器件正向导通电压漂移㊂由于刃位错对器件性能的影响要小得多,所以提高SiC外延生长过程中BPD转化为TED的比例,阻止衬底中的BPD向外延层中延伸对提高器件的性能十分重要㊂对于BPD向TED的转化技术已经有比较多的研究报道,例如,外延生长前的KOH刻蚀或氢气刻蚀优化表面[41]㊁外延生长间断[42],或者提高生长速率,结合这些技术,转化率已经提升到99.8%,甚至达到100%[43]㊂此外生长过程中,在应力等条件作用下,BPD很容易在衬底和外延层界面上沿着台阶流法线方向发生滑移,形成界面位错(interfacial dislocations)[44-45],滑移方向取决于BPD的伯氏矢量及应力方向㊂特定条件下,成对BPD同时发生滑移,会形成Σ-BPD㊂在本团队研发过程中也观察到过该缺陷,其典型形貌如图3所示,光致发光检测BPD形貌如图3(a)所示,对外延片进行KOH腐蚀后形貌如图3(b)所示,可以看到一个Σ-BPD包含两条界面位错,其长度可以达到毫米级,在其尾部存在两个BPD㊂Σ-BPD形成机理示意图如图3(c)所示[46-47],其起源于衬底的BPD对,其伯氏矢量方向刚好相反,滑移过程中形成两条界面位错和2个半环位错(half-loop arrays,HLAs)㊂半环位错的长度不一,决定于其驱动力大小,影响滑移的驱动力主要是温场的不均匀性㊂图3㊀Σ-BPD的形貌图(a)㊁氢氧化钾腐蚀坑图(b)和形成机理示意图(c)Fig.3㊀Morphology(a),etched image by KOH(b)and schematic illustration of formation mechanism(c)ofΣ-BPD针对外延BPD,本文在快速外延生长的基础上优化外延层缓冲层工艺窗口,目前可以实现BPD密度小于0.1cm-3的外延层批量制备,如图4所示㊂3.3㊀层错缺陷SiC外延层中的层错包括两大类:一类来源于衬底的层错和位错缺陷,衬底的层错会导致外延层形成214㊀综合评述人工晶体学报㊀㊀㊀㊀㊀㊀第53卷图4㊀外延片的BPD 分布(a)及其统计(b)Fig.4㊀Distribution of BPD (a)and its statistics (b)of epi-wafers Bar-shaped SFs [48-49],衬底的部分TSD 如3.2所述会形成Frank SFs;另一类层错为生长层错(in-grown SFs),是外延生长过程中产生的,与衬底质量没有关系㊂目前,大多数外延层错属于第二类,这些层错中绝大部分为Shockley SFs,是通过在基平面中的滑移产生的[50-51]㊂这些层错缺陷都会对器件性能产生不利影响,例如漏电流的增加㊂降低外延生长速率㊁原位氢气刻蚀优化㊁增加生长温度㊁改善衬底质量都可以有效降低层错数量,本研究团队已经可以提供Shockley SFs 密度小于0.15cm -2的6英寸SiC 衬底㊂3.4㊀表面缺陷SiC 外延层表面缺陷尺度比较大,一般通过光学显微镜可以直接观察到,包括掉落物[52]㊁三角形缺陷[53-54]㊁ 胡萝卜 缺陷[55-56]㊁彗星缺陷[57]㊁硅滴[58]和浅坑[59-60]㊂掉落物主要由反应室的部件上形成的SiC 颗粒脱落形成,通过定期清理或更换反应室部件能够有效控制㊂其他几种表面缺陷的形成机制目前已经有了较多研究,虽然不能形成统一的模型,但是大部分与衬底表面状态(包括划痕/损伤层㊁颗粒沾污㊁凹坑)㊁衬底位错(特别是TSD)等缺陷存在一定的关联性㊂由于台阶流生长模式的放大作用和位错转化的综合效应,导致缺陷形成各种宏观表面形貌特征㊂表面缺陷与器件性能的影响目前也已经有了较多的研究报道,除浅坑缺陷外,其他表面缺陷基本都会对器件的性能产生一定的不利影响,导致器件击穿电压降低或者反向漏流增加[61]㊂浅坑(Pits)是4H-SiC 外延层表面出现在TSD 位错顶端的小凹陷或小坑状的形貌缺陷,其宽度尺度小于10μm㊂TED 在外延层表面引起的小坑尺寸远小于TSD 诱发的小坑尺寸,很难被观察到㊂图5是本团队在外延生长中观察到的典型浅坑AFM 形貌,在台阶流动方向的上游端,小坑缺陷有陡峭的倾斜侧面,在下游端,侧面相对平缓,通过AFM 可以看到Pits 宽度为2μm,深度为4nm,深宽比约为0.002㊂Ohtani㊁Noboru 等则利用TUNA 技术研究了Pits 和Large Pits 的产生机理,认为宽度在几微米㊁深度在14nm 左右的Large pits 是由TSD 产生,而宽度在1μm㊁深度在3~4nm 的Pits 由TED 产生[62-63]㊂近年来,有研究表明:当存在浅坑时,由于几何效应会导致局部电场集中,对于二极管特性基本不存在负面影响㊂Kudou 等[64]研究了Pits 缺陷对SiC 器件的影响,认为Pits 密度不会影响SBD 的漏电流和MOSFET 的TDDB 栅氧可靠性㊂同时指出深宽比较小(小于0.02)的Pits对SBD 和MOSFET 的影响较小㊂图5㊀外延表面宽度和深度分别为2μm 和4nm 的浅坑的AFM 照片Fig.5㊀AFM image of a pit with 2μm width and 4nm depth降低Pits 的主要途径包括:优选TSD 数量较少的优质衬底㊁降低碳硅比和降低外延生长速率㊂目前市场上主要的商业化衬底中TSD 的密度小于1000cm -2㊂本研究团队已经可以提供TSD 密度小于300cm -2的6英寸SiC 衬底㊂通过采用优质衬底,调整外延工艺,可以将Pits 数量从103降低到50以内㊂综合来看,SiC 外延层缺陷一方面取决于衬底结晶质量以及表面加工质量,另一方面受制于外延生长工艺窗口的优化,需要综合考虑各种缺陷的调整方案,例如提高外延生长速率会导致BPD 向TED 转化率的提㊀第2期郭㊀钰等:碳化硅同质外延质量影响因素的分析与综述215㊀高,但会导致层错密度的增加㊂基于本研究团队量产的高质量6英寸SiC衬底,本团队通过大量的实验研究,可以有效控制住SiC外延的各种缺陷,完成650和1200V外延片产品开发和产业化工作㊂图6是典型的650和1200V外延片产品缺陷mapping图,3mmˑ3mm良品率分别为98.9%和97.3%㊂图6㊀650和1200V外延片产品缺陷mapping图Fig.6㊀Mapping diagram of defects in650and1200V epi-wafers4㊀结语与展望SiC外延在产业链中起着承上启下的重要作用,通过不断积累对SiC材料的性能认知和改良,以及器件的不断迭代验证,最终提升外延品质,推动SiC器件的应用㊂本文采用天科合达自有的商业化6英寸衬底,在4H-SiC同质外延过程中,研究了外延层中BPD㊁层错㊁硅滴和Pits缺陷的控制,并对Σ-BPD的产生机理和消除进行研究,最终获得厚度均匀性小于3%㊁浓度均匀性小于6%㊁表面粗糙度小于0.2nm㊁良品率大于96%㊁BPD密度小于0.1cm-2的外延产品㊂目前从本团队的研发进度来看,通过对工艺温度㊁C/Si比和生长速率等参数优化使得浓度和厚度均匀性分别控制在3%和2%以内,BPD的密度可以控制在0.075cm-2以内,但仍需要大量的外延数据进行工艺稳定性验证㊂参考文献[1]㊀BRANDER R W,SUTTON R P.Solution grown SiC p-n junctions[J].Journal of Physics D:Applied Physics,1969,2(3):309-318.[2]㊀IKEDA M,HAYAKAWA T,YAMAGIWA S,et al.Fabrication of6H-SiC light-emitting diodes by a rotation dipping technique:electroluminescence mechanisms[J].Journal of Applied Physics,1979,50(12):8215-8225.[3]㊀ZIEGLER G,LANIG P,THEIS D,et al.Single crystal growth of SiC substrate material for blue light emitting diodes[J].IEEE Transactions onElectron Devices,1983,30(4):277-281.[4]㊀MATSUNAMI H,NISHINO S,ONO H.IVA-8heteroepitaxial growth of cubic silicon carbide on foreign substrates[J].IEEE Transactions onElectron Devices,1981,28(10):1235-1236.[5]㊀JENNINGS V J,SOMMER A,CHANG H C.The epitaxial growth of silicon carbide[J].Journal of the Electrochemical Society,1966,113(7):728.[6]㊀CAMPBELL R B,CHU T L.Epitaxial growth of silicon carbide by the thermal reduction technique[J].Journal of the Electrochemical Society,1966,113(8):825.[7]㊀MUENCH W V,PFAFFENEDER I.Epitaxial deposition of silicon carbide from silicon tetrachloride and hexane[J].Thin Solid Films,1976,31(1/2):39-51.[8]㊀YOSHIDA S,SAKUMA E,OKUMURA H,et al.Heteroepitaxial growth of SiC polytypes[J].Journal of Applied Physics,1987,62(1):303-305.[9]㊀NISHINO S,POWELL J A,WILL H A.Production of large-area single-crystal wafers of cubic SiC for semiconductor devices[J].AppliedPhysics Letters,1983,42(5):460-462.[10]㊀KURODA N,SHIBAHARA K,YOO W,et al.Step-controlled VPE growth of SiC single crystals at low temperatures[C]//Extended Abstracts ofthe1987Conference on Solid State Devices and Materials.August25-27,1987.Nippon Toshi Center,Tokyo,Japan.The Japan Society of Applied Physics,1987:032156.[11]㊀KONG H,KIM H J,EDMOND J A,et al.Growth,doping,device development and characterization of CVD beta-SiC epilayers on Si(100)andalpha-SiC(0001)[J].MRS Proceedings,1987,97:233.216㊀综合评述人工晶体学报㊀㊀㊀㊀㊀㊀第53卷[12]㊀JR A B A,ROWLAND L B.Homoepitaxial vpe growth of SiC active layers[J].Physica Status Solidi(b),1997,202(1):263-279.[13]㊀RUPP R,MAKAROV N Y,BEHNER H,et al.Silicon carbide epitaxy in a vertical CVD reactor:experimental results and numerical processsimulation[J].Physica Status Solidi(b),1997,202(1):281-304.[14]㊀KIMOTO T,ITOH A,MATSUNAMI H.Step-controlled epitaxial growth of high-quality SiC layers[J].Physica Status Solidi(b),1997,202(2):247-262.[15]㊀THOMAS B,BARTSCH W,STEIN R A,et al.Properties and suitability of4H-SiC epitaxial layers grown at different CVD systems for highvoltage applications[J].Materials Science Forum,2004,493(457-460):181-184.[16]㊀LA VIA F,CAMARDA M,CANINO A,et al.Fast growth rate epitaxy by chloride precursors[J].Materials Science Forum,2013,740/741/742:167-172.[17]㊀LARKIN D J,SRIDHARA S G,DEVATY R P,et al.Hydrogen incorporation in boron-doped6H-SiC CVD epilayers produced using site-competition epitaxy[J].Journal of Electronic Materials,1995,24(4):289-294.[18]㊀LARKIN D J,NEUDECK P G,POWELL J A,et al.Site-competition epitaxy for superior silicon carbide electronics[J].Applied PhysicsLetters,1994,65(13):1659-1661.[19]㊀LARKIN D J.SiC dopant incorporation control using site-competition CVD[J].Physica Status Solidi(b),1997,202(1):305-320.[20]㊀WANG R J,BHAT I B,CHOW T P.Epitaxial growth of n-type SiC using phosphine and nitrogen as the precursors[J].Journal of AppliedPhysics,2002,92(12):7587-7592.[21]㊀KIMOTO T,NAKAZAWA S,HASHIMOTO K,et al.Reduction of doping and trap concentrations in4H-SiC epitaxial layers grown by chemicalvapor deposition[J].Applied Physics Letters,2001,79(17):2761-2763.[22]㊀TSUCHIDA H,KAMATA I,JIKIMOTO T,et al.Epitaxial growth of thick4H-SiC layers in a vertical radiant-heating reactor[J].Journal ofCrystal Growth,2002,237/238/239:1206-1212.[23]㊀BURK A A,TSVETKOV D,BARNHARDT D,et al.SiC epitaxial layer growth in a6ˑ150mm warm-wall planetary reactor[J].MaterialsScience Forum,2012,717/718/719/720:75-80.[24]㊀KOJIMA K,SUZUKI T,KURODA S,et al.Epitaxial growth of high-quality4H-SiC carbon-face by low-pressure hot-wall chemical vapordeposition[J].Japanese Journal of Applied Physics,2003,42(Part2,No.6B):L637-L639.[25]㊀THOMAS B,ZHANG J E,MOEGGENBORG K,et al.Progress of SiC epitaxy on150mm substrates[J].Materials Science Forum,2015,821/822/823:161-164.[26]㊀MATTIA M,EGIDIO C,DANILO C,et al.Development of n-type epitaxial growth on200mm4H-SiC wafers for the next generation of powerdevices[J].Microelectronic Engineering,2023,274(1):111976.[27]㊀THOMAS B,ZHANG J E,CHUNG G Y,et al.Homoepitaxial chemical vapor deposition of up to150μm thick4H-SiC epilayers in a10ˑ100mmbatch reactor[J].Materials Science Forum,2016,858:129-132.[28]㊀KENNETH G I.Growth of very uniform silicon carbide epitaxial layers,US6063186A[P].1999-06-24.[29]㊀AYEDH H M,HALLÉN A,SVENSSON B G.Elimination of carbon vacancies in4H-SiC epi-layers by near-surface ion implantation:influenceof the ion species[J].Journal of Applied Physics,2015,118(17):175701.[30]㊀AYEDH H M,KVAMSDAL K E,BOBAL V,et al.Carbon vacancy control in p+-n silicon carbide diodes for high voltage bipolar applications[J].Journal of Physics D:Applied Physics,2021,54(45):455106.[31]㊀MIYAZAWA T,TSUCHIDA H.Point defect reduction and carrier lifetime improvement of Si-and C-face4H-SiC epilayers[J].Journal ofApplied Physics,2013,113(8):083714.[32]㊀RANA T,CHUNG G,SOUKHOJAK A,et al.Interfacial dislocation reduction by optimizing process condition in SiC epitaxy[J].MaterialsScience Forum,2022,63(9):99-103.[33]㊀ZHANG X A,NAGANO M,TSUCHIDA H.Basal plane dislocations in4H-SiC epilayers with different dopings[J].Materials Science Forum,2012,725:27-30.[34]㊀KAMATA I,TSUCHIDA H,JIKIMOTO T,et al.Structural transformation of screw dislocations via thick4H-SiC epitaxial growth[J].JapaneseJournal of Applied Physics,2000,39(12R):6496.[35]㊀DANIELSSONÖ,FORSBERG U,JANZÉN E.Predicted nitrogen doping concentrations in silicon carbide epitaxial layers grown by hot-wallchemical vapor deposition[J].Journal of Crystal Growth,2003,250(3/4):471-478.[36]㊀TSVETKOV V F,ALLEN S T,KONG H S,et al.Recent progress in SiC crystal growth[C]//International Conference on Silicon Carbide andRelated Materials,1995,142:317.[37]㊀LENDENMANN H,DAHLQUIST F,JOHANSSON N,et al.Long term operation of4.5kV PiN and2.5kV JBS diodes[J].Materials ScienceForum,2001,353/354/355/356:727-730.[38]㊀BERGMAN P,LENDENMANN H,NILSSON PÅ,et al.Crystal defects as source of anomalous forward voltage increase of4H-SiC diodes[J].Materials Science Forum,2001,353/354/355/356:299-302.[39]㊀LENDENMANN H,BERGMAN P,DAHLQUIST F,et al.Degradation in SiC bipolar devices:sources and consequences of electrically active㊀第2期郭㊀钰等:碳化硅同质外延质量影响因素的分析与综述217㊀dislocations in SiC[J].Materials Science Forum,2003,433/434/435/436:901-906.[40]㊀MUZYKOV P G,KENNEDY R M,ZHANG Q,et al.Physical phenomena affecting performance and reliability of4H-SiC bipolar junctiontransistors[J].Microelectronics Reliability,2009,49(1):32-37.[41]㊀SKOWRONSKI M,HA S.Degradation of hexagonal silicon-carbide-based bipolar devices[J].Journal of Applied Physics,2006,99(1):011101.[42]㊀YANG L,ZHAO L X,WU H W,et al.Characterization and reduction of defects in4H-SiC substrate and homo-epitaxial wafer[J].MaterialsScience Forum,2020,1004:387-392.[43]㊀STAHLBUSH R E,VANMIL B L,MYERS-WARD R L,et al.Basal plane dislocation reduction in4H-SiC epitaxy by growth interruptions[J].Applied Physics Letters,2009,94(4):041916.[44]㊀CAPAN I,BORJANOVIC'V,PIVAC B.Dislocation-related deep levels in carbon rich p-type polycrystalline silicon[J].Solar Energy Materialsand Solar Cells,2007,91(10):931-937.[45]㊀NA M,BAHNG W,JANG H,et al.Effects of stress on the evolution ofΣ-shaped dislocation arrays in a4H-SiC epitaxial layer[J].Journal ofApplied Physics,2021,129(24):245101.[46]㊀LI Z,ZHANG X A,ZHANG Z H,et al.Microstructure of interfacial basal plane dislocations in4H-SiC epilayers[J].Materials Science Forum,2019,954:77-81.[47]㊀NISHIO J,KUDOU C,TAMURA K,et al.C-face epitaxial growth of4H-SiC on quasi-150-mm diameter wafers with high throughput[J].Materials Science Forum,2014,778/779/780:109-112.[48]㊀AOKI M,KAWANOWA H,FENG G,et al.Characterization of bar-shaped stacking faults in4H-SiC epitaxial layers by high-resolutiontransmission electron microscopy[J].Japanese Journal of Applied Physics,2013,52(6R):061301.[49]㊀CAMARDA M,CANINO A,LA MAGNA A,et al.Structural and electronic characterization of(2,33)bar-shaped stacking fault in4H-SiCepitaxial layers[J].Applied Physics Letters,2011,98(5):051915.[50]㊀SUO H,YAMASHITA T,ETO K,et al.Observation of multilayer Shockley-type stacking fault formation during process of epitaxial growth onhighly nitrogen-doped4H-SiC substrate[J].Japanese Journal of Applied Physics,2019,58(2):021001.[51]㊀ASAFUJI R,HIJIKATA Y.Generation of stacking faults in4H-SiC epilayer induced by oxidation[J].Materials Research Express,2018,5(1):015903.[52]㊀DONG L,SUN G S,YU J,et al.Mapping of micropipes and downfalls on4H-SiC epilayers by Candela optical surface analyzer[C]//2012IEEE11th International Conference on Solid-State and Integrated Circuit Technology.October29-November1,2012,Xi'a n,China.IEEE,2013:1-3.[53]㊀KONSTANTINOV A O,HALLIN C,PÉCZ B,et al.The mechanism for cubic SiC formation on off-oriented substrates[J].Journal of CrystalGrowth,1997,178(4):495-504.[54]㊀OKADA T,KIMOTO T,YAMAI K,et al.Crystallographic defects under device-killing surface faults in a homoepitaxially grown film of SiC[J].Materials Science and Engineering:A,2003,361(1/2):67-74.[55]㊀BENAMARA M,ZHANG X,SKOWRONSKI M,et al.Structure of the carrot defect in4H-SiC epitaxial layers[J].Applied Physics Letters,2005,86(2):021905.[56]㊀OKADA T,KIMOTO T,NODA H,et al.Correspondence between surface morphological faults and crystallographic defects in4H-SiChomoepitaxial film[J].Japanese Journal of Applied Physics,2002,41:6320-6326.[57]㊀TSUCHIDA H,KAMATA I,NAGANO M.Investigation of defect formation in4H-SiC epitaxial growth by X-ray topography and defect selectiveetching[J].Journal of Crystal Growth,2007,306(2):254-261.[58]㊀孙国胜,杨㊀霏,柏㊀松,等.4H-碳化硅衬底及外延层缺陷术语[S].T/CASA004.1-2018,北京,2018.SUN G S,YANF F,BO S,et al.4H-Silicon carbide substrate and epitaxial layer defect terms[S].T/CASA004.1-2018,Beijing,2018(in Chinese).[59]㊀POWELL J A,LARKIN D J.Process-induced morphological defects in epitaxial CVD silicon carbide[J].Physica Status Solidi(b),1997,202(1):529-548.[60]㊀KIMOTO T,CHEN Z Y,TAMURA S,et al.Surface morphological structures of4H-,6H-and15R-SiC(0001)epitaxial layers grown bychemical vapor deposition[J].Japanese Journal of Applied Physics,2001,40(5R):3315.[61]㊀KIMOTO T,MIYAMOTO N,MATSUNAMI H.Performance limiting surface defects in SiC epitaxial p-n junction diodes[J].IEEE Transactionson Electron Devices,1999,46(3):471-477.[62]㊀OHTANI N,USHIO S,KANEKO T,et al.Tunneling atomic force microscopy studies on surface growth pits due to dislocations in4H-SiCepitaxial layers[J].Journal of Electronic Materials,2012,41(8):2193-2196.[63]㊀孙国胜,杨㊀霏,柏㊀松,等.4H-SiC衬底及外延层缺陷图谱[S].T/CASA004.2-2018,北京,2018.SUN G S,YANF F,BO S,et al.Defect map of4H-SiC substrate and epitaxial layer[S].T/CASA004.2-2018,Beijing,2018(in Chinese).[64]㊀KUDOU C,ASAMIZU H,TAMURA K,et al.Influence of epi-layer growth pits on SiC device characteristics[J].Materials Science Forum,2015,821/822/823:177-180.。
超导磁体行业深度报告:国之重器风口已至精选版

(/东吴,马天翼、王润芝)1. 超导磁体性能优异商业化进程加速,下游应用多点开花超导磁体属于多部件集成系统,一般是指用超导导线绕制的、利用超导材料零电阻与小截面导体却可以承载超大电流的特殊性质产生强磁场的装置,包括超导线圈和其运行所必要的低温恒温容器。
超导磁体主要由以下几部分构成:(1)超导线圈和铝合金骨架(缠绕固定超导线):超导线圈为磁体系统核心部件,根据对于磁场场强和均匀度的需求,由 2 或 4 个线圈呈对称布置,超导线圈数量越多,产生的磁场场强和均匀度越高。
(2)励磁电源:为超导磁体提供电流,分为超导磁体内部电流独立于电源运行的闭环运行模式和持续由电源供电的开环运行模式。
(3)低温控制系统:干式制冷机、导冷板(将制冷机冷量传导给线圈)、真空杜瓦(保证系统密闭性,维持低温条件)、冷屏(降低外部辐射漏热)。
(4)失超保护系统:一旦磁体失超,将破坏磁体结构,重新降温励磁使运行时间增加,因此需要对线圈进行浸渍、绝缘处理。
(5)漏磁屏蔽系统等:超导磁体产生的磁场与设备的其他电磁系统会互相干扰,影响设备正常运行,因此需要铁轭进行磁场屏蔽。
超导线圈产生的磁场分布可以分为水平、垂直和勾形(Cusp)。
以超导磁体在晶硅生长炉中的应用为例,垂直磁场由于结构原因无法消除单晶炉内主要热对流,很少被采用;水平磁场的磁场分量方向垂直于埚壁主要热对流与部分强迫对流,可有效抑制运动,且有利于保持生长界面平整性,降低生长条纹;CUSP 磁场因其对称性,熔体的流动和传热性更为均匀,因此垂直与 CUSP 磁场为晶硅生长炉中的主流应用。
超导磁体具有磁场强度高、重量体积小、节省电耗等核心突出优势。
通常电磁铁是利用在导体中通过电流产生磁场,由于超导材料在低于某一极低温度下具有零电阻特性,因此相比于常规磁体,超导磁体可以在不损耗焦耳热的情况下,产生很高的运行电流,进而在大空间内产生高场强、高稳定性、高均匀性的磁场。
低温超导磁体技术发展时间较早,技术成熟,高温超导磁体由于材料特性,磁体磁场强度可以做到更高,更满足高场强需求场景。
前驱体转化法制备超高温陶瓷粉体研究进展
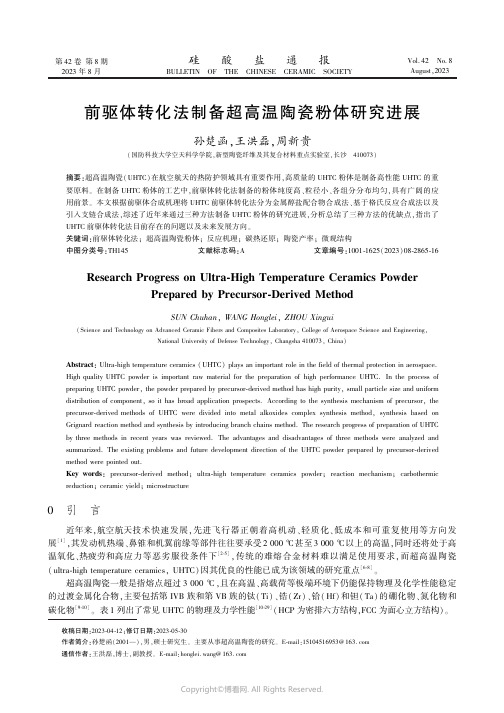
第42卷第8期2023年8月硅㊀酸㊀盐㊀通㊀报BULLETIN OF THE CHINESE CERAMIC SOCIETY Vol.42㊀No.8August,2023前驱体转化法制备超高温陶瓷粉体研究进展孙楚函,王洪磊,周新贵(国防科技大学空天科学学院,新型陶瓷纤维及其复合材料重点实验室,长沙㊀410073)摘要:超高温陶瓷(UHTC)在航空航天的热防护领域具有重要作用,高质量的UHTC 粉体是制备高性能UHTC 的重要原料㊂在制备UHTC 粉体的工艺中,前驱体转化法制备的粉体纯度高㊁粒径小㊁各组分分布均匀,具有广阔的应用前景㊂本文根据前驱体合成机理将UHTC 前驱体转化法分为金属醇盐配合物合成法㊁基于格氏反应合成法以及引入支链合成法,综述了近年来通过三种方法制备UHTC 粉体的研究进展,分析总结了三种方法的优缺点,指出了UHTC 前驱体转化法目前存在的问题以及未来发展方向㊂关键词:前驱体转化法;超高温陶瓷粉体;反应机理;碳热还原;陶瓷产率;微观结构中图分类号:TH145㊀㊀文献标志码:A ㊀㊀文章编号:1001-1625(2023)08-2865-16Research Progress on Ultra-High Temperature Ceramics Powder Prepared by Precursor-Derived MethodSUN Chuhan ,WANG Honglei ,ZHOU Xingui(Science and Technology on Advanced Ceramic Fibers and Composites Laboratory,College of Aerospace Science and Engineering,National University of Defense Technology,Changsha 410073,China)Abstract :Ultra-high temperature ceramics (UHTC)plays an important role in the field of thermal protection in aerospace.High quality UHTC powder is important raw material for the preparation of high performance UHTC.In the process of preparing UHTC powder,the powder prepared by precursor-derived method has high purity,small particle size and uniform distribution of component,so it has broad application prospects.According to the synthesis mechanism of precursor,the precursor-derived methods of UHTC were divided into metal alkoxides complex synthesis method,synthesis based on Grignard reaction method and synthesis by introducing branch chains method.The research progress of preparation of UHTCby three methods in recent years was reviewed.The advantages and disadvantages of three methods were analyzed and summarized.The existing problems and future development direction of the UHTC powder prepared by precursor-derived method were pointed out.Key words :precursor-derived method;ultra-high temperature ceramics powder;reaction mechanism;carbothermic reduction;ceramic yield;microstructure 收稿日期:2023-04-12;修订日期:2023-05-30作者简介:孙楚函(2001 ),男,硕士研究生㊂主要从事超高温陶瓷的研究㊂E-mail:151****6953@通信作者:王洪磊,博士,副教授㊂E-mail:honglei.wang@0㊀引㊀言近年来,航空航天技术快速发展,先进飞行器正朝着高机动㊁轻质化㊁低成本和可重复使用等方向发展[1],其发动机热端㊁鼻锥和机翼前缘等部件往往要承受2000ħ甚至3000ħ以上的高温,同时还将处于高温氧化㊁热疲劳和高应力等恶劣服役条件下[2-5],传统的难熔合金材料难以满足使用要求,而超高温陶瓷(ultra-high temperature ceramics,UHTC)因其优良的性能已成为该领域的研究重点[6-8]㊂超高温陶瓷一般是指熔点超过3000ħ,且在高温㊁高载荷等极端环境下仍能保持物理及化学性能稳定的过渡金属化合物,主要包括第IVB 族和第VB 族的钛(Ti)㊁锆(Zr)㊁铪(Hf)和钽(Ta)的硼化物㊁氮化物和碳化物[9-10]㊂表1列出了常见UHTC 的物理及力学性能[10-29](HCP 为密排六方结构,FCC 为面心立方结构)㊂2866㊀陶㊀瓷硅酸盐通报㊀㊀㊀㊀㊀㊀第42卷表1㊀常见超高温陶瓷的物理及力学性能Table1㊀Physical and mechanical properties of common ultra-high temperature ceramicsMaterial Crystalstructure Meltingpoint/ħDensity/(g㊃cm-3)CTE/(10-6㊃K-1)Thermalconductivity/(W㊃m-1㊃K-1)Elasticmodulus/GPaHardness/GPa ReferenceTaB2HCP304012.58.54155126[12-15] TiB2HCP3225 4.58.66556025[11-13,16] ZrB2HCP3245 6.1 6.26048923[12-13,17-18] HfB2HCP338011.2 6.610448028[12-13,17-18] TiC FCC3100 4.97.41740026[13,16,19-20] ZrC FCC3530 6.6 6.72036933[17,19-23] TaC FCC388014.5 6.32250322[17,24-25] HfC FCC389012.7 6.62245229[17,19-23] TaN FCC308713.4 3.2849010[10,26-27] TiN FCC2950 5.49.32946021[10,13,19,26,28] ZrN FCC29507.37.22039016[10,13,19,26,28-29] HfN FCC338513.9 6.92138516[10,13,19,26,28]㊀㊀Note:CTE,coefficient of thermal expansion.高质量UHTC粉体是制备高性能UHTC的关键,UHTC粉体的传统合成工艺是利用相应的金属氧化物粉体经碳热还原反应实现的㊂但原料颗粒的尺寸较大㊁反应物无法充分接触以及可能存在杂质等因素,导致反应温度较高㊁产物晶粒尺寸过大㊁纯度不高等问题,使其应用存在较大的局限性㊂近年来被广泛研究的前驱体转化法是通过化学手段在溶液体系中合成一类包括合成陶瓷时所需元素的金属有机聚合物,再将前驱体在一定温度范围进行交联㊁热解,最终得到陶瓷粉体产物的方法㊂前驱体转化法可对前驱体分子结构进行设计,且在制备过程中具有很好的加工性,可应用于制备陶瓷粉体㊁纤维㊁涂层和复合材料等[30]㊂由于原料组分可以在分子层面均匀混合,缩短元素间的扩散距离,进而降低热解温度,这避免了晶粒粗大的问题,且使产物的相组成分布均匀㊂前驱体转化为陶瓷粉体主要包含两个过程:1)在100~400ħ低温条件下的交联过程中,前驱体分子将交联形成不熔的网状结构;2)在600~1400ħ高温条件下的热解过程中,在600~1000ħ时交联的前驱体发生有机-无机转变,生成非晶陶瓷,继续升高热解温度则会发生相分离与结晶化过程,最终得到多晶陶瓷㊂含氧前驱体会额外发生碳热还原反应,将氧化物陶瓷转化为碳化物陶瓷[31]㊂目前合成UHTC前驱体的工艺按照反应机理可大致分为三类:一是采用金属醇盐配合物经水解缩合形成聚合物前驱体;二是以格氏反应为核心合成单体,再经缩合反应得到聚合物前驱体;三是将有机金属化合物单体作为支链引入聚合物,从而得到目标前驱体㊂1㊀金属醇盐配合物前驱体制备UHTC粉体在制备金属醇盐配合物前驱体的过程中,主要采用过渡金属氯化物作为金属源,通过与醇的取代反应得到金属醇盐㊂由于金属醇盐水解剧烈,利用乙酰丙酮等配体与金属醇盐反应形成配合物以实现可控水解缩合,得到聚合物前驱体㊂同时为保证后续碳热还原反应充分,往往还需向前驱体溶液中加入碳源㊂该方法既可以利用单种金属醇盐配合物制备单相高纯UHTC粉体,也可以通过引入多种金属醇盐配合物制备UHTC 固溶体粉体,或引入含Si聚合物制备复相UHTC粉体㊂1.1㊀金属醇盐配合物前驱体制备单相UHTC粉体TaC具有高熔点㊁高硬度和高强度等诸多优点,是超高温碳化物陶瓷的研究热点之一㊂Jiang等[32]以TaCl5为钽源,酚醛树脂为碳源,乙醇和乙酰丙酮为溶剂,混合得到TaC的前驱体溶液㊂随后在80ħ下固化, 200ħ下保温2h除去溶剂,在1000ħ时开始发生碳热还原反应,1200ħ时反应完全,得到的TaC陶瓷粉体元素分布均匀,平均晶粒尺寸为40nm,但陶瓷产率为57%(质量分数),仍有提升空间㊂图1为前驱体合成和热解过程中可能发生的反应(Hacac为乙酰丙酮;acac为失去一个H原子的乙酰丙酮根)㊂第8期孙楚函等:前驱体转化法制备超高温陶瓷粉体研究进展2867㊀图1㊀TaC 前驱体制备可能发生的反应机理[32]Fig.1㊀Possible reaction mechanism for preparation of TaC precursor [32]常规的前驱体碳热还原法包括前驱体合成㊁固化㊁惰性气氛热解以及最终的碳热还原处理等多个步骤,存在反应时间长㊁生产效率低的问题㊂为优化生产工艺,Cheng 等[33]通过高温喷雾热解(high temperature spray pyrolysis,HTSP)工艺,低成本㊁单步合成了纳米TaC 粉体㊂TaC 前驱体溶液由TaCl 5和酚醛树脂溶解在乙醇和1-戊醇中得到,然后通过喷雾器将其破碎成细小的液滴,液滴处在Ar 气氛的高温管式炉中,再经过溶剂一次性去除㊁热解和1650ħ的快速原位碳热还原,在几分钟内即可制得纳米TaC 粉体㊂但由于采用的是医用雾化器,难以产生足够细小的液滴,且部分产物附着在管式炉内壁上,所以生成的TaC 颗粒存在团聚现象,产率较低,工艺流程需要继续改进㊂图2为高温喷雾热解示意图(CTR 为碳热还原反应)㊂图2㊀高温喷雾热解示意图[33]Fig.2㊀Schematic diagram of high temperature spray pyrolysis [33]单相UHTC 的高温抗氧化能力较弱,尤其是过渡金属碳化物表面被氧化后,无法生成致密氧化膜来阻止内部被进一步氧化㊂例如,当HfC 暴露在空气中时,400ħ以上就开始氧化[34],TaC 在850ħ时即会被完全氧化[35]㊂在实际应用过程中,使用单相UHTC 的情况较少㊂1.2㊀金属醇盐配合物前驱体制备UHTC 固溶体粉体为改善TaC 和HfC 的抗氧化性能,Zhang 等[36]系统地研究了Ta-Hf-C 三元陶瓷在1400~1600ħ等温条件下各种成分的氧化机理,研究表明氧化过程取决于成分㊂与单相TaC 和HfC 陶瓷相比,1TaC-1HfC 和1TaC-3HfC 的抗氧化性显著提高,这是因为氧化生成的三维共晶Hf 6Ta 2O 17-Ta 2O 5结构和致密纯Hf 6Ta 2O 17层都能够抑制O 2扩散,改善抗氧化性㊂因此,与单相UHTC 相比,使用钽醇盐配合物与铪醇盐配合物混合得到前驱体所制备的UHTC 固溶体具有更好的抗高温氧化能力[37]㊂在碳热还原过程中,多相氧化物由于各相反应活化能不同,往往会发生某相优先析出㊁碳化物之间固溶不充分和碳源过剩等问题㊂为解决以上问题,蒋进明[38]以Ta㊁Hf㊁Zr 的氯化物为金属源,乙酰丙酮多齿配体为螯合剂,酚醛树脂为碳源,经200ħ溶剂热处理12h,合成出具有多层核壳结构的前驱体㊂前驱体中心区富含Ta㊁次外层富含Hf(Zr),外壳由树脂包覆㊂该结构的前驱体在热解过程中可以实现外层碳原子向内核逐层扩散,使元素分布均匀,得到粒径为200~300nm 的Ta-Hf(Zr)-C 三元陶瓷纳米粉体㊂图3为Ta-Hf(Zr)-C 碳热还原转化机理示意图㊂2868㊀陶㊀瓷硅酸盐通报㊀㊀㊀㊀㊀㊀第42卷图3㊀Ta-Hf(Zr)-C 碳热还原转化机理示意图[38]Fig.3㊀Schematic diagram for carbothermal reduction synthesis of Ta-Hf(Zr)-C [38]TaC 和HfC 晶体结构相同(均为NaCl 结构)且晶格常数相近(分别为0.445和0.464nm),可以形成不同比例的固溶体,其中Ta 4HfC 5具有目前已知物质中的最高熔点4215ħ[39],是一种极具发展前景的耐超高温陶瓷㊂Cheng 等[40]等以酚醛树脂作为碳源,与摩尔比为4ʒ1的TaCl 5和HfCl 4溶解在乙醇和乙酰丙酮的混合溶剂中,经过磁力搅拌得到Ta 4HfC 5前驱体溶液,随后在Ar 气氛中200ħ油浴交联固化2h,再通过真空蒸馏除去剩余溶剂,接下来在Ar 气氛中进行热解,Ta 2O 5的碳热还原在1000ħ左右开始,1200~1400ħ时,Hf 6Ta 2O 17的碳热还原以及TaC 和HfC 之间的固溶反应同时发生,最后HfC 和TaC 在1800ħ下固溶充分反应,得到粒度为200~300nm㊁元素分布均匀的Ta 4HfC 5粉体㊂高温下生成的熔融Hf 6Ta 2O 17层可作为氧扩散屏障,使得陶瓷具有优秀的高温抗烧蚀性能㊂但1800ħ的固溶温度过高,不利于得到晶粒细小的高质量粉体㊂图4㊀Ta 4HfC 5粉体TEM 照片[42]Fig.4㊀TEM image of Ta 4HfC 5powder [42]改进前驱体合成工艺可以降低HfC 和TaC 发生固溶反应的温度㊂Lu 等[41]利用摩尔比4ʒ1的TaCl 5和HfCl 4与三乙胺㊁甲基叔丁基醚和乙酰丙酮反应后缩聚,得到聚钽铪氧烷(polytantahafnoxane,PTHO),再将其与含烯丙基的树脂混合即得到Ta 4HfC 5前驱体,固化后在1600ħ下热解制备得到了Ta 4HfC 5粉体㊂孙娅楠等[42]则将含烯丙基的树脂替换为酚醛树脂,与PTHO 混合后得到了Ta 4HfC 5前驱体,将前驱体在250ħ下保温2h 以固化,随后在Ar 气氛中1350~1450ħ热解1.5~3.0h,得到粒径为100~200nm㊁晶粒尺寸为25~50nm 的Ta 4HfC 5粉体㊂图4为Ta 4HfC 5粉体的TEM 照片㊂综合以上研究发现,固溶反应发生的温度普遍高于碳热还原反应㊂与Cheng 等[40]和Lu 等[41]相比,孙娅楠等[42]将固溶反应完成温度从1800ħ降至1450ħ,且所得陶瓷粉体粒径更小㊂通过金属醇盐配合物前驱体制备的超高温陶瓷粉体多为碳化物,也可以通过向前驱体溶液中加入硼酸以制备硼化物复相陶瓷粉体㊂IVB 族硼化物陶瓷ZrB 2和HfB 2在高于1200ħ的氧化环境中,表面的B 2O 3保护层将蒸发,因此主要依赖于ZrO 2或HfO 2层作为抗氧化屏障[43-44]㊂在向ZrB 2和HfB 2中添加高价阳离子Ta 5+后,氧化生成的Ta 2O 5可以填充氧晶格空位以减缓O 2传输速率,并与ZrO 2或HfO 2形成中间相,从而增强相稳定性[45]㊂Xie 等[46]采用乙酰丙酮与Zr(OPr)4通过回流生成Zr(OPr)4-x (acac)x ,得到ZrO 2前驱体㊂类似地,使用Ta(OC 2H 5)4作为Ta 源合成Ta 2O 5前驱体,然后在溶液中分别加入酚醛树脂和硼酸,将溶液浓缩㊁干燥获得前驱体粉末后,在800~1800ħ的Ar 气氛中热解,热解过程中金属氧化物优先进行碳热还原生成金属碳化物,在硼源过量的情况下会继续反应生成金属二硼化物㊂图5为ZrB 2-TaB 2在1300ħ热第8期孙楚函等:前驱体转化法制备超高温陶瓷粉体研究进展2869㊀图5㊀ZrB 2-TaB 2在1300ħ热处理2h 的SEM 照片[46]Fig.5㊀SEM image of ZrB 2-TaB 2after heat treated at 1300ħfor 2h [46]处理2h 的SEM 照片㊂ZrB 2和TaB 2之间的固溶反应从1400ħ开始,1800ħ时TaB 2相完全消失㊂与由ZrB 2和TaB 2两相混合的陶瓷粉体相比,固溶体陶瓷粉体在性能上具有哪些差异值得继续研究㊂1.3㊀金属醇盐配合物前驱体制备复相UHTC 粉体另一种提高UHTC 抗氧化性能的方法则是引入SiC,高温下SiC 氧化生成的玻璃相SiO 2可提高多孔结构的金属氧化物致密度,具有良好的抗高温氧化和抗烧蚀性[47]㊂同时两种成分在结晶过程中的相互抑制效应可以起到细化晶粒的作用㊂聚碳硅烷(polycarbosilane,PCS)是一种以Si 和C 交替排列作为聚合物骨架的有机硅化合物,常被用来作为制备SiC 的前驱体[48]㊂Lu 等[49]以三乙胺为共沉淀剂,用TaCl 5㊁正丁醇和乙酰丙酮反应制备得到Ta 2O 5前驱体溶液,将其与PCS 混合后蒸馏得到TaC-SiC 前驱体溶液,前驱体充分交联固化后,在1600ħ的Ar 气氛中热解2h,得到了平均晶粒尺寸50nm 的TaC-SiC 陶瓷粉体㊂图6为1800ħ热解的TaC-SiC 陶瓷粉体的HR-TEM 照片(标尺101/nm 为10个1/nm,下文图17㊁18中标尺含义类似)㊂由图6可知,TaC 和SiC 晶粒以接近球形的形态均匀分散,同时还有少量无定形碳嵌在晶界位置㊂该前驱体合成方法同样适用于IVB 族UHTC,可推广用于制备ZrC-SiC 和HfC-SiC㊂图6㊀1800ħ热解的TaC-SiC 陶瓷粉体的HR-TEM 照片[49]Fig.6㊀HR-TEM images of TaC-SiC ceramics powder pyrolyzed at 1800ħ[49]PCS 的交联主要依靠硅氢化反应,通过向前驱体中加入如二乙烯基苯(divinylbenzene,DVB)等含不饱和C C 键的物质可以进一步提升前驱体的交联程度㊂Cai 等[50]利用该原理,以HfCl 4与异丙醇和乙酰丙酮反应得到铪醇盐配合物,再通过水解得到HfO 2前驱体(polyhafnoxane,PHO),随后将PHO 与PCS 和DVB 混合,控制n (Hf)/n (Si)摩尔比为1ʒ1,交联后在1600ħ下碳热还原得到了元素分布均匀㊁结晶质量高㊁粒径分布窄的HfC-SiC 复相陶瓷粉末㊂图7为HfC-SiC 复相陶瓷的TEM 照片,可以观察到分别属于HfC 和SiC 的晶格条纹㊂由于PHO 的弱极性,其与PCS 和DVB 具有良好的相容性,可以大范围改变n (Hf)/n (Si)摩尔比来调控陶瓷粉体成分㊂合成前驱体的单体中交联位点越多,前驱体越易形成高度交联的三维网状结构㊂每个四乙氧基硅烷(tetraethoxysilane,TEOS)分子中含有四个Si O C 键可供交联,是另一种理想的制备含Si 前驱体的原料㊂Patra 等[51]采用TEOS 与HfCl 4㊁乙酰丙酮㊁对苯二酚反应合成HfC-SiC 前驱体㊂经过回流和固化后,在1500ħ的Ar 气氛中发生碳热还原反应,生成HfC-SiC 陶瓷粉体㊂图8为1500ħ热解的HfC-SiC 前驱体亮场TEM 照片和平均粒径㊂由图8可知,碳热还原所生成的球形HfC 和SiC 颗粒平均尺寸为25~50nm㊂由于对苯二酚和四乙氧基硅烷具有较高的C㊁Si 含量,因此前驱体在热解过程中质量损失较少,1600ħ时陶瓷产率高达65%,具有很好的应用前景㊂PCS 作为SiC 前驱体的缺陷在于其常温下为固态,需要利用二甲苯等有机溶剂将其配制成溶液使用,增2870㊀陶㊀瓷硅酸盐通报㊀㊀㊀㊀㊀㊀第42卷加了前驱体合成的复杂程度㊂Wang 等[52]采用常温下为液态的低分子量SiC 前驱体(LPVCS)与HfCl 4㊁乙酰丙酮和1,4-丁二醇反应合成了HfC-SiC 前驱体(PHCS)㊂HfO 2和SiO 2的碳热还原主要发生在1400~1600ħ,生成的HfC-SiC 复相陶瓷粉体的SEM 照片和EDS 分析如图9所示㊂与PCS 相比,LPVCS 结构中引入的V4分子具有 CH CH 2基团,可在较低温度下实现自交联,有利于陶瓷产率的提升[53]㊂同时LPVCS 中较高的碳含量可以补偿PHCO 热解产物中碳含量的不足,制备出不含HfO 2和微量游离碳的高性能HfC-SiC 陶瓷㊂图7㊀1600ħ热解的HfC-SiC 粉末TEM 照片[50]Fig.7㊀TEM images of HfC-SiC powder pyrolyzed at 1600ħ[50]图8㊀1500ħ热解的HfC-SiC 前驱体亮场TEM 照片和平均粒径[51]Fig.8㊀Bright-field TEM image and average particle size of HfC-SiC precursor pyrolyzed at 1500ħ[51]第8期孙楚函等:前驱体转化法制备超高温陶瓷粉体研究进展2871㊀图9㊀HfC-SiC 粉末的SEM 照片和EDS 分析[52]Fig.9㊀SEM images and EDS analysis of HfC-SiC powder [52]㊀㊀综上可见,合成金属醇盐配合物前驱体所需的原料结构简单,反应时间较短㊂但由于前驱体中存在氧元素,有可能会导致生成的UHTC 粉体中有氧残留,使陶瓷高温抗氧化性能和机械性能下降㊂另外为防止金属醇盐水解,该反应需全程在惰性气氛中进行,对设备要求较高㊂2㊀基于格氏反应的前驱体制备UHTC 粉体基于格氏反应的前驱体制备工艺主要采用茂金属化合物和含不饱和键的格氏试剂合成单体,再通过与非金属源分子的聚合反应得到前驱体㊂金属醇盐配合物前驱体的各目标元素由不同种聚合物提供,多数通过机械搅拌的方法实现分子间的混合㊂不同的是,基于格氏反应的前驱体中金属源与非金属源在同种聚合物分子中,实现了分子内的混合㊂所合成的聚合物分子包括线型聚合物与网状聚合物㊂2.1㊀线型聚合物前驱体制备UHTC 粉体合成线型聚合物前驱体的原料通常依靠分子两端的基团发生缩聚反应,交联程度相较于网状聚合物更低,可以通过在主链上插入交联位点来减少热解过程中的质量损失㊂Cheng 等[54]在四氢呋喃(tetrahydrofuran,THF)溶剂中利用反-1,4-二溴-2-丁烯与镁反应制备格氏试剂,再与Cp 2HfCl 2和氯甲基三甲基硅烷通过缩聚合成了主链包含Hf C㊁Si C 和 CH CH 基团的线性PHCS 前驱体聚合物,图10为前驱体合成过程中可能发生的化学反应㊂前驱体在经过1600ħ热解后得到了元素分布均匀的HfC-SiC 纳米复合陶瓷粉体㊂前驱体主链中的不饱和 CH 2CH CHCH 2 基团提供了潜在的交联位点或反应位点,可用于后续固化或改性㊂图10㊀PHCS 前驱体合成过程中可能发生的反应[54]Fig.10㊀Reactions that may occur during synthesis of PHCS precursors [54]基于格氏反应的MC-SiC(M =Zr,Hf)前驱体分子结构中往往含有M C Si 键,普遍认为该键是由格氏反应所致㊂Gao 等[55]提出了一种新的前驱体合成机制,该机制基于㊃MgCl 辅助下的活性物质Cp 2Zr(II)的自由基聚合,合成过程如图11所示,首先将二氯二茂锆Cp 2ZrCl 2与Mg 和四氢呋喃在60ħ下搅拌混合2872㊀陶㊀瓷硅酸盐通报㊀㊀㊀㊀㊀㊀第42卷4h 后冷却,得到活性物质双环戊二烯基锆Cp 2Zr (II),再将Cp 2Zr (II)分别与CH 3Si (CH CH 2)Cl 2和(CH 3)2Si(CH 2Cl)2在110ħ下反应16h,经过冷却过滤并真空浓缩得到了含有[ Zr C Si ]n 主链结构的单源聚合物前驱体聚锆碳硅烷(PZCS-1,PZCS-2)㊂随后将前驱体在N 2气氛中进行热解,SiO 2和ZrO 2相在1000ħ时析出,随着温度继续升高转化为SiC 和ZrC 相,且均匀分布在自由碳基体中,形成ZrC /SiC /C 复合陶瓷㊂由于该前驱体为线型聚合物且不含可作为交联位点的不饱和基团,热解过程中质量损失较为严重,900ħ时陶瓷产率仅有43.9%㊂图11㊀PZCS-2前驱体合成过程[55]Fig.11㊀Synthesis process of the PZCS-2precursor [55]2.2㊀网状聚合物前驱体制备UHTC 粉体与线型聚合物前驱体相比,合成网状聚合物前驱体的原料多含有三个以上的交联位点,前驱体交联程度高,质量损失较少,有利于陶瓷产率的提高㊂Wang 等[56]通过格氏反应将Cp 2ZrCl 2和CH 2 CHMgCl 制成Cp 2Zr(CH CH 2)2,然后将其与B 源H 3B㊃SMe 2混合,利用氢化反应得到网状结构的大分子前驱体聚锆碳硼烷(polyzirconcarborane,PZCB),合成机理如图12所示㊂随后将前驱体放置于Ar 气氛的石墨管式炉中进行热解,1600ħ时碳热还原完全,得到充分结晶且分布均匀的ZrC-ZrB 2陶瓷粉体,继续加热至2200ħ,产物失重仅为2.5%,说明该复相陶瓷粉体具有良好的耐热性㊂在该合成过程中,利用了硼烷分子具有三个反应位点的特征,以其作为骨架合成了网状大分子,使得前驱体充分交联㊂SiBNC 非晶陶瓷在2000ħ仍具有很好的高温稳定性,而引入过渡金属元素可以进一步抑制其在高温下的结晶与氧化[57]㊂龙鑫[58]将锆源(Cp 2ZrCl 2)与格氏试剂(CH 2 CHCH 2MgCl)反应制备得到双官能度的活性单体(PZC),然后引入低分子量聚硼硅氮烷(LPBSZ),PZC 中的C C 键与LPBSZ 中的Si H 发生硅氢化反应,ZrC /SiBNC 前驱体合成机理如图13所示(Me 3Si 为三甲基亚砜)㊂未参与反应的C C 键则为后续交联提供活性位点,最终形成网状结构的ZrC /SiBNC 前驱体㊂随后将前驱体置于Ar 气氛中经过1200ħ热解生成ZrC /SiBNC 陶瓷粉体,其中ZrC 纳米颗粒均匀分散在无定形SiBNC 基体中㊂ZrC 相提高了SiBNC 的第8期孙楚函等:前驱体转化法制备超高温陶瓷粉体研究进展2873㊀热稳定性,经过1800ħ以上高温处理后,ZrC /SiBNC 仍能够保持均匀细小的纳米晶结构,同时SiBNC 也改善了ZrC 的耐高温氧化性能㊂但该前驱体的不足之处在于碳含量过高导致陶瓷粉体产物中含有过量的碳,影响UHTC 的高温抗氧化性能㊂图12㊀PZCB 前驱体合成机理[56]Fig.12㊀Synthesis mechanism of PZCB precursor[56]图13㊀ZrC /SiBNC 前驱体合成机理[58]Fig.13㊀Synthesis mechanism of ZrC /SiBNC precursor [58]基于格氏反应的前驱体制备工艺实现了各目标元素在聚合物分子内的混合,比金属醇盐配合物前驱体混合更加充分,能更好地避免陶瓷产物中元素偏析现象的发生㊂同时原料中不含氧元素,热解过程中不会发生碳热还原反应,能降低热解温度㊂但该工艺的原料结构较为复杂,反应时间较长,为避免合成过程中引入空气中的氧等杂质,反应必须在保护气氛中进行,对设备要求较高㊂3㊀引入支链的前驱体制备UHTC 粉体在制备引入支链的前驱体过程中,需以一种聚合物分子作为主链,再将其他含目标元素的小分子通过反应作为支链连接到主链上㊂常见的作为主链的大分子有聚碳硅烷和聚硅氮烷等,其分子结构中包含大量可与含目标元素的小分子发生交联反应的基团,同时自身足够大的分子量可避免在热处理过程中分解挥发㊂3.1㊀以聚碳硅烷作主链制备UHTC 粉体聚碳硅烷的主链由Si 和C 交替组成,Si 和C 上连接有H 或 CH 2 CH CH 2等基团作为交联位点[48],通过向主链上引入UHTC 组分,热解后可原位生成含SiC 的UHTC 粉体㊂Amorós 等[59]系统性地研究2874㊀陶㊀瓷硅酸盐通报㊀㊀㊀㊀㊀㊀第42卷图14㊀1350ħ热解的SiC-TiC-C 陶瓷粉体的SEM 照片[59]Fig.14㊀SEM image of SiC-TiC-C ceramics powder pyrolyzed at 1350ħ[59]了采用聚二甲基硅烷(polydimethylsiloxane,PDMS)和PCS 与Cp 2MCl(M =Ti,Zr,Hf)反应制备SiC-MC-C 陶瓷粉体的机理和工艺流程㊂与PDMS 相比,PCS 中的Si H 键促进了前驱体的交联,提高了陶瓷产率,金属配合物则通过取代反应连接在前驱体的网状结构中㊂经过900ħ热解后,前驱体转变为非晶态陶瓷,结晶化在1350ħ下基本完成,生成由β-SiC㊁MC 以及自由碳组成的复相陶瓷粉体,但仍有部分非晶态物质存在㊂图14是1350ħ热解所得的SiC-TiC-C 陶瓷粉体的SEM 照片㊂该研究采用同种前驱体转化工艺成功制备出了含IVB 族三种元素碳化物的复相UHTC 粉体,但对热解过程的探究不够深入,1350ħ时结晶尚未完成㊂通过对PCS 进行改性,可以进一步提高前驱体交联程度㊂Yu 等[60]以含烯丙基的聚碳硅烷AHPCS(商品名SMP10)为SiC 源,与TaCl 5的CHCl 3溶液混合后,在真空中加热至160ħ脱除溶剂得到前驱体,前驱体合成过程如图15所示,随后将前驱体在Ar 气氛下的管式炉中进行热解,得到SiC-TaC-C 陶瓷粉体㊂研究发现,随着热解温度升高,前驱体由于发生脱氢耦合反应而失重,在900ħ时聚合物完全转化为非晶陶瓷粉末,1200ħ时TaC 相开始析出,并被非晶态碳薄壳所包裹,形成核壳结构的TaC@C 纳米颗粒,而β-SiC 相则在1400ħ下结晶㊂所得的β-SiC 和TaC 的晶粒尺寸均小于30nm㊂前驱体热解后的游离碳需要通过生成TaC 来消耗,由于没有额外添加碳源,所以需要准确掌握TaCl 5和AHPCS 的比例以保证陶瓷产物中有少量包裹在TaC 晶粒表面的游离碳㊂图15㊀SiC-TaC-C 前驱体合成过程[60]Fig.15㊀Synthesis of SiC-TaC-C precursor [60]在利用引入支链的前驱体制备含N 原子的超高温陶瓷粉体时,Wen 等[61]以AHPCS 为SiC 源,四(二甲氨基)铪(TDMAH)为Hf 源和N 源合成SiHfCN 陶瓷前驱体㊂AHPCS 中的Si H 键可与TDMAH 中的N CH 3键反应生成Si N Hf 键,使Hf 连接到大分子上㊂Si H 键还会与AHPCS 侧链上的烯丙基发生硅氢化反应以增加前驱体交联程度,可能发生的化学反应如图16所示㊂热解后所得UHTC 组分为HfC 0.87N 0.13,其被碳层包裹镶嵌在SiC 基体中,两相的晶粒尺寸均小于100nm㊂2~4nm 厚的碳层可作为扩散屏障,有效。
半导体第三讲-下-单晶硅生长技术
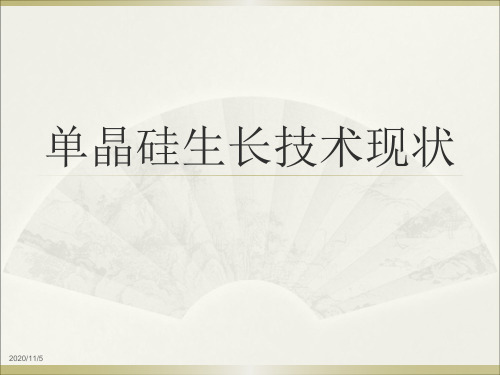
单晶硅主要生长方法
直拉法生长单晶硅容易控制,产能 比区熔高,会引入杂质,应用于半 导体集成电路、二极管、外延片衬 底20、20/1太1/5阳能电池。
区熔法可生长出纯度高均匀性好的 单晶硅,应用于高电压大功率器件 上,如可控硅、可关断晶闸管。
2020/11/5
单晶硅简介
单晶硅属于立方晶系,金刚石结构,是一种性能优良 的半导体材料。
自上世纪 40 年代起开始使用多晶硅至今,硅材料的生 长技术已趋于完善,并广泛的应用于红外光谱频率光 学元件、红外及 射线探测器、集成电路、太阳能电池 等。
此外,硅没有毒性,且它的原材料石英(SiO2)构成了 大约60%的地壳成分,其原料供给可得到充分保障。
在磁场下生长单晶,当引入磁感应强度达 到一定值时,一切宏观对流均受到洛伦兹 力的作用而被抑制。
2020/11/5
垂直磁场对动量及热量的分布具有双重效 应。垂直磁场强度过大(Ha=1000/2000), 不利于晶体生长。
对无磁场、垂直磁场、勾形磁场作用下熔 体内的传输特性进行比较后发现,随着勾 形磁场强度的增加,熔体内子午面上的流 动减弱,并且紊流强度也相应降低。
区熔硅的常规掺杂方法有硅芯掺杂、表面涂敷 掺杂、气相掺杂等,以气相掺杂最为常用。
2020/11/5
晶体缺陷 区熔硅中的晶体缺陷有位错和漩涡缺陷。
中子嬗变晶体还有辐照缺陷,在纯氢或氩 一氢混合气氛中区熔时,常引起氢致缺陷。
2020/11/5
通过在氩气气氛及真空环境下进行高阻区 熔硅单晶生长试验发现,与在氢气气氛下生长 硅单晶相比,在真空环境下采用较低的晶体生 长速率即可生长出无漩涡缺陷的单晶, 而当晶 体生长速度较高时, 尽管可以消除漩涡, 但单晶 的少子寿命却有明显的下降。在真空中生长无 漩涡缺陷单晶的生长速率,比在氢气气氛下生 长同样直径单晶的生长速率低,但漩涡缺陷对 单晶少子寿命的影响并不明显。
碳化硅晶圆的表面
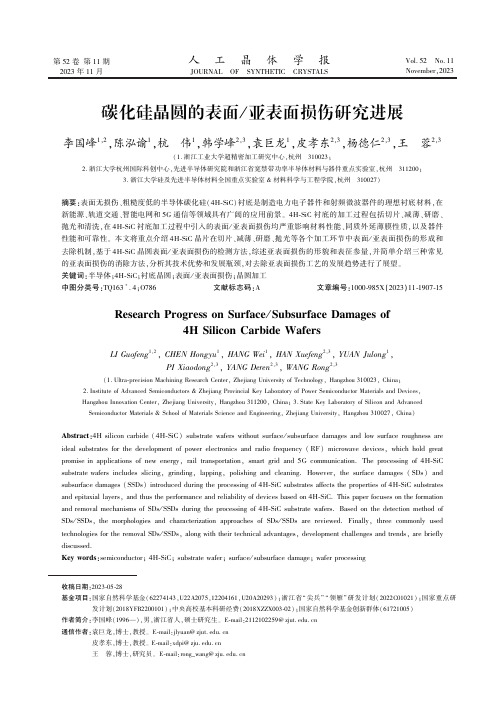
第52卷第11期2023年11月人㊀工㊀晶㊀体㊀学㊀报JOURNAL OF SYNTHETIC CRYSTALSVol.52㊀No.11November,2023碳化硅晶圆的表面/亚表面损伤研究进展李国峰1,2,陈泓谕1,杭㊀伟1,韩学峰2,3,袁巨龙1,皮孝东2,3,杨德仁2,3,王㊀蓉2,3(1.浙江工业大学超精密加工研究中心,杭州㊀310023;2.浙江大学杭州国际科创中心,先进半导体研究院和浙江省宽禁带功率半导体材料与器件重点实验室,杭州㊀311200;3.浙江大学硅及先进半导体材料全国重点实验室&材料科学与工程学院,杭州㊀310027)摘要:表面无损伤㊁粗糙度低的半导体碳化硅(4H-SiC)衬底是制造电力电子器件和射频微波器件的理想衬底材料,在新能源㊁轨道交通㊁智能电网和5G通信等领域具有广阔的应用前景㊂4H-SiC衬底的加工过程包括切片㊁减薄㊁研磨㊁抛光和清洗,在4H-SiC衬底加工过程中引入的表面/亚表面损伤均严重影响材料性能㊁同质外延薄膜性质,以及器件性能和可靠性㊂本文将重点介绍4H-SiC晶片在切片㊁减薄㊁研磨㊁抛光等各个加工环节中表面/亚表面损伤的形成和去除机制,基于4H-SiC晶圆表面/亚表面损伤的检测方法,综述亚表面损伤的形貌和表征参量,并简单介绍三种常见的亚表面损伤的消除方法,分析其技术优势和发展瓶颈,对去除亚表面损伤工艺的发展趋势进行了展望㊂关键词:半导体;4H-SiC;衬底晶圆;表面/亚表面损伤;晶圆加工中图分类号:TQ163+.4;O786㊀㊀文献标志码:A㊀㊀文章编号:1000-985X(2023)11-1907-15 Research Progress on Surface/Subsurface Damages of4H Silicon Carbide WafersLI Guofeng1,2,CHEN Hongyu1,HANG Wei1,HAN Xuefeng2,3,YUAN Julong1,PI Xiaodong2,3,YANG Deren2,3,WANG Rong2,3(1.Ultra-precision Machining Research Center,Zhejiang University of Technology,Hangzhou310023,China;2.Institute of Advanced Semiconductors&Zhejiang Provincial Key Laboratory of Power Semiconductor Materials and Devices,Hangzhou Innovation Center,Zhejiang University,Hangzhou311200,China;3.State Key Laboratory of Silicon and AdvancedSemiconductor Materials&School of Materials Science and Engineering,Zhejiang University,Hangzhou310027,China) Abstract:4H silicon carbide(4H-SiC)substrate wafers without surface/subsurface damages and low surface roughness are ideal substrates for the development of power electronics and radio frequency(RF)microwave devices,which hold great promise in applications of new energy,rail transportation,smart grid and5G communication.The processing of4H-SiC substrate wafers includes slicing,grinding,lapping,polishing and cleaning.However,the surface damages(SDs)and subsurface damages(SSDs)introduced during the processing of4H-SiC substrates affects the properties of4H-SiC substrates and epitaxial layers,and thus the performance and reliability of devices based on4H-SiC.This paper focuses on the formation and removal mechanisms of SDs/SSDs during the processing of4H-SiC substrate wafers.Based on the detection method of SDs/SSDs,the morphologies and characterization approaches of SDs/SSDs are reviewed.Finally,three commonly used technologies for the removal SDs/SSDs,along with their technical advantages,development challenges and trends,are briefly discussed.Key words:semiconductor;4H-SiC;substrate wafer;surface/subsurface damage;wafer processing㊀㊀收稿日期:2023-05-28㊀㊀基金项目:国家自然科学基金(62274143,U22A2075,12204161,U20A20293);浙江省 尖兵 领雁 研发计划(2022C01021);国家重点研发计划(2018YFB2200101);中央高校基本科研经费(2018XZZX003-02);国家自然科学基金创新群体(61721005)㊀㊀作者简介:李国峰(1996 ),男,浙江省人,硕士研究生㊂E-mail:2112102259@㊀㊀通信作者:袁巨龙,博士,教授㊂E-mail:jlyuan@皮孝东,博士,教授㊂E-mail:xdpi@王㊀蓉,博士,研究员㊂E-mail:rong_wang@1908㊀综合评述人工晶体学报㊀㊀㊀㊀㊀㊀第52卷0㊀引㊀㊀言4H碳化硅(4H-SiC)材料具有禁带宽度大㊁饱和电子漂移速率高㊁击穿电场高㊁导热系数高㊁抗辐照等优点,能够满足现代电力电子技术对高频㊁高功率㊁高温应用的要求[1]㊂而表面无损伤㊁低粗糙度的4H-SiC衬底晶圆是制造4H-SiC基电力电子器件的基础㊂由于材料的高硬度㊁强化学惰性等特点,4H-SiC的晶圆加工存在加工损耗大㊁损伤多㊁效率低等难题[2]㊂目前,4H-SiC晶圆的主要加工流程包括切片㊁减薄㊁研磨㊁抛光和清洗[3]㊂在晶圆加工过程中,减薄㊁研磨和抛光会依次去除切片引入的损伤层,实现晶圆的全局平坦化加工,得到无损伤㊁低表面粗糙度的4H-SiC晶圆㊂然而,4H-SiC晶圆的加工过程存在加工损伤去除不彻底或不可避免地引入新损伤的问题㊂根据损伤在光学显微镜检测下是否可见,4H-SiC晶圆表面的损伤分为表面损伤(surface damages,SDs)和亚表面损伤(subsurface damages,SSDs)㊂其中,SDs包括划痕㊁凸起㊁凹坑等,可通过光学显微镜直接观测;而SSDs主要分布于表面以下,无法通过光学显微镜直接观测㊂目前已发现的4H-SiC晶圆的SSDs包括:亚表面微裂纹㊁位错聚集㊁非晶相和残余应力等[4]㊂SDs/SSDs会在后续外延过程中作为缺陷的形核中心,严重影响外延层质量,进而影响4H-SiC基器件的性能与可靠性[5]㊂因此,准确识别SDs/SSDs,并阐明4H-SiC晶圆加工过程中SDs/SSDs的产生与去除机制,对于高质量4H-SiC晶圆的加工及应用至关重要㊂本文针对4H-SiC晶圆加工过程中产生的SDs/SSDs的形貌和来源进行分析,论述了在晶圆加工各个环节产生的SDs/SSDs的形成和去除机理,随后介绍了SSDs对后续外延和晶体生长的影响;最后简要介绍了SDs/SSDs的去除方法,比较去除效果,分析了其技术优势和发展瓶颈,并对其发展趋势进行展望㊂1㊀4H-SiC加工过程中的SDs/SSDs4H-SiC晶圆的主要加工流程分为切片㊁减薄㊁研磨㊁抛光和清洗㊂除了晶体本身的质量问题(如碳包裹㊁多型体㊁微管㊁位错等缺陷)[6],对衬底外延和后续器件制造影响最大的缺陷就是SDs/SSDs㊂由于二者均源于晶圆加工环节,因此明确SDs/SSDs的产生和去除机制,优化晶圆加工工艺,对严格控制4H-SiC晶圆的SDs/SSDs,并提升后续4H-SiC单晶生长或同质外延的质量具有重要意义㊂在4H-SiC的切片等加工工艺中,材料主要通过脆性断裂模式去除,这不可避免地会在表面下方引入微裂纹[7],造成材料的SDs和SSDs㊂亚表面的微裂纹不仅降低4H-SiC晶片的机械强度,还影响后续工艺和生产成本,是评价晶圆加工质量的一个重要指标㊂如图1(a)所示,切片工艺是影响切片过程中微裂纹损伤层厚度的关键因素㊂在后续减薄㊁研磨和抛光的加工过程中,损伤层的厚度逐渐减小,并在抛光后得到有效去除,获得全局平坦化的近无损4H-SiC晶圆㊂纳米压痕试验结果表明,4H-SiC在机械应力下产生的损伤层在宏观上呈现 Y 字形的裂纹,包括中位裂纹和侧位裂纹(见图1(b))[8]㊂其中,中位裂纹发生于磨料加载过程,随着磨料压入深度的增加,中位裂纹从变形区底端开始萌生,并向下扩展;当卸载时,中位裂纹逐渐闭合,侧位裂纹从变形区的底端开始萌生并向两侧和表面扩展,当侧位裂纹扩展到表面,形成表面破碎[2]㊂图1㊀4H-SiC衬底晶圆加工过程中SDs/SSDs的厚度变化(a)及裂纹产生的模型示意图(b)[8] Fig.1㊀Evolution of SDs/SSDs and change of the thickness(a),and diagram showing the generation mechanism ofcracks(b)in a4H-SiC substrate wafer[8]1.1㊀切片过程引入的损伤层作为4H-SiC晶圆加工过程的第一道工序,切片工艺质量决定了后续减薄㊁研磨㊁抛光的加工水平㊂切片㊀第11期李国峰等:碳化硅晶圆的表面/亚表面损伤研究进展1909㊀是影响晶圆损伤层厚度和面型参数的关键工艺㊂面型参数包括总厚度偏差(total thickness variation,TTV)㊁局域厚度变化(local thickness variation,LTV)㊁弯曲度(BOW)和翘曲度(WARP)㊂切片极易在4H-SiC晶片表面和亚表面产生大量裂纹和微裂纹,增加晶片的破片率和制造成本,因此控制晶片表层裂纹损伤对降低4H-SiC晶圆成本㊁推动4H-SiC基器件的发展具有重要意义㊂4H-SiC晶圆的切片方法有金刚线锯切片㊁游离砂浆线锯切片㊁激光切割和电火花切片等㊂其中,金刚线锯切片和游离砂浆线锯切片是目前4H-SiC晶圆加工最常用的切片方法,其原理是依靠金刚线或金属线带动砂浆使磨粒到达加工区域,并对磨粒施加压力,在磨料与晶锭表面接触瞬间,磨粒尖端会因冲击形成局域的微破碎,进而形成裂纹和材料脱落,以达到切片的目的[9]㊂该切割现象在单颗粒的游离砂浆线锯切实验中得到验证,但是划痕表面的材料剥落会使划痕的宽度超过磨料的直径[10],这与材料的去除方式有关㊂在晶圆加工过程中,材料的去除方式可分为脆性去除和延性去除[11]㊂由于4H-SiC具有高硬度㊁高脆性的特点,刀具刻划4H-SiC表面产生划痕的过程分为塑性阶段㊁塑脆性共存阶段和完全脆性阶段3个阶段,可以用摩擦力信号来表征[12]㊂图2所示为4H-SiC单晶的动载荷划痕实验,在塑性阶段主要以延性去除为主,摩擦力曲线光滑,划痕也以平滑凹槽为主;在塑脆性共存阶段,材料的去除既有延性去除又有脆性去除,划痕中显露出鱼鳞状凹坑;而在完全脆性阶段,脆性去除占主导,材料表面鱼鳞状凹坑进一步恶化并伴有裂纹萌生[13]㊂研究者们期望4H-SiC的材料去除机制更多表现为延性去除,以尽可能减小加工损伤和材料的损耗㊂然而,过分追求延性去除将会导致极低的材料去除率㊂因此,在脆性去除和延性去除两者间寻求一个平衡点是4H-SiC衬底加工的一个关键点㊂图2㊀4H-SiC晶圆动载荷划痕实验中划痕的摩擦力信号与载荷变化的关系(a)及划痕形貌变化图(b)[13] Fig.2㊀The dependence of the frictional force on the position(a),and the change of the scratch shape(b)during the dynamicload scratch experiment of a4H-SiC wafer[13]在4H-SiC线锯切片过程中,材料的脆性去除占据主导,导致4H-SiC在材料破碎去除的同时,产生大量的裂纹等损伤㊂随着钢线(或金刚线)深入材料内部,磨削力有所降低,4H-SiC材料的脆性去除进一步加剧㊂表1列出了金刚线锯切片和游离砂浆线锯切片两种切片方法的主要切削方式及其在4H-SiC中产生的损伤层的缺陷类型㊂在游离砂浆线锯切片时,4H-SiC亚表面会出现弥散的三角形损伤区,并带有半环束和堆垛层错;而金刚线锯切片会在4H-SiC晶片表面引入损伤区㊁半环束位错和堆积层错[14]㊂虽然由切片产生的SDs/SSDs是整个4H-SiC衬底加工中最严重的损伤,但通过优化切片工艺参数可以明显改善损伤层的厚度㊂如图3所示,通过优化线锯切工艺可显著控制4H-SiC的SDs/SSDs的厚度,其中减小晶体进给速度㊁增大线速度均有利于减小SDs/SSDs的厚度[15]㊂1910㊀综合评述人工晶体学报㊀㊀㊀㊀㊀㊀第52卷表1㊀不同切片方法对4H-SiC加工造成的损伤[14]Table1㊀Damages caused by different sawing technologies of4H-SiC wafers[14]切片方法切削方式主要缺陷金刚线锯固定磨料平移损伤层半环束位错(U型30ʎ倾斜和V型)堆垛层错游离砂浆线锯游离磨料旋转三角形损伤区半环束位错(不倾斜U型)堆垛层错图3㊀金刚线锯切片4H-SiC晶圆过程中进给速度(a)和线速度(b)对微裂纹损伤的厚度影响[15] Fig.3㊀Effect of feed rate(a)and wire speed(b)on the thickness of microcrack damages during the diamond wiresawing of4H-SiC wafers[15]1.2㊀磨削过程引入的损伤层磨削的目的是去除4H-SiC切片过程引入的SDs/SSDs,同时降低晶圆的TTV㊁LTV和表面粗糙度[16]㊂由于4H-SiC的高硬度特性,磨削过程中必须使用高硬度的磨料(如金刚石[17])㊂磨削工艺一般包括减薄和研磨,分别对应于以固结磨料(砂轮)和游离磨料(研磨液)体系的磨削机制㊂固结磨料磨削具有材料去除速率高的优点,但是,砂轮磨削后,晶圆表面粗糙度较高,且SDs/SSDs层的厚度较大㊂为解决砂轮磨削后表面质量差的问题,学者们采用辅助增效[18],选用更合适的磨料比例和固结方式[19]等方法改善磨削4H-SiC晶片时的表面质量㊂研磨分粗磨和精磨,粗磨使用粒径较大的磨粒和铜盘,精磨使用粒径较小的磨料和锡盘[20]㊂虽然使用金刚石研磨液可以保证较好的晶体表面质量,但研磨效率低,研磨时间较长㊂4H-SiC磨削过程中SDs/SSDs主要包括凹坑㊁划痕㊁侧位裂纹和中位裂纹[21]等㊂在磨削过程中,与磨料接触的4H-SiC表面的晶相会向非晶结构转变[22],由于磨粒挤压在工件材料上,原有的晶格受到破坏,非晶相形成,在外力作用下,材料表面出现很多微断裂,进而实现材料去除[23-24]㊂非晶结构更容易被去除,这是因为此结构可以通过产生更小的法向应力和非晶态相变以及更薄的塑性变形诱导SiC软化并产生SSDs㊂这一发现与后续的单晶4H-SiC进行单颗粒磨削的模拟实验结果类似,即塑性变形初期的SSDs由非晶化和位错引发产生㊂随着磨削过程的进行,形成了滑移带,塑性变形后期滑移带的延伸是裂纹萌生的原因[25]㊂此外,分子动力学研究表明,非晶化是导致SDs产生的主要原因,而位错滑移则造成了SSDs的出现[26]㊂另一方面,当磨削过程中温度升高时,非晶层的润滑作用和表面的再结晶过程可以有效抑制高切削温度下的SSDs[27]㊂因此,通过工艺调试,探索总结出合适的磨削参数,确保较小的非晶层和高效的磨削效率是很有必要的㊂如图4所示,使用砂轮磨削4H-SiC晶圆时,单位切削进给深度的实际材料去除量和SSDs层的厚度不随磨削速度的增加而单调变化㊂其中存在材料去除量最大㊁SSDs层的厚度最小的最佳磨削速度㊂损伤层的厚度随磨削速度的增加而增大[28],这是因为在一定的磨削范围内,材料的去除主要以延性磨削为主,在晶圆表面,靠近晶圆中心位置磨削更加均匀,从而产生更高的表面质量[29];而当单位去除量超过一定范围,脆性去除模式会渐渐显露,这时横向裂纹开始萌生[21,30]㊂以此为基础,可以通过提高磨削速度和减小切削深度以提高材料的应变速率,从而以增强材料的动态脆性的方式降低SDs/SSDs[31]㊂除了磨削时的进给速率㊁砂轮转速等因素外,磨料的尺寸也是影响SSDs的关键因素之一㊂在砂轮磨削过程中,表面粗糙度和亚表面裂纹㊀第11期李国峰等:碳化硅晶圆的表面/亚表面损伤研究进展1911㊀深度随磨料颗粒粒径的减小而减小[32]㊂从砂轮磨削的单颗粒实验模拟中可以看到,裂纹从磨粒的前部和底部开始㊂随着磨粒不断向划痕方向移动,晶粒前部的裂纹通过研磨作用被去除,但晶粒下方的裂纹不能被去除,形成SDs /SSDs [33]㊂将微裂纹刻蚀暴露并与磨削参数对比发现,后者的变化趋势对微裂纹的影响和对表面粗糙度的影响是一致的㊂磨料的平均尺寸和磨削力对SSDs 和表面粗糙度的危害甚至大于砂轮速度和磨削的进给深度;而微裂纹的角度和密度几乎不受磨削参数的影响[34]㊂砂轮磨削工艺属于二体磨损加工㊂具体而言,磨削过程中固结在砂轮上的磨粒随着砂轮规则地往复运图4㊀砂轮磨削4H-SiC 过程中,切削速度对切削深度和SSDs 层的厚度的影响[28]Fig.4㊀Effect of cutting speed on the cutting depth and SSDs layer thickness during grinding of 4H-SiC [28]动,进而通过特定的轨迹摩擦晶圆表面,最终实现材料的去除㊂而使用研磨液的游离磨料研磨属于三体磨损加工,材料的去除伴随着磨料的随机滚动㊁挤压和刮擦三种状态㊂与二体磨损加工不同的是,三体磨损下磨料尺寸的不均匀可能会影响晶圆的表面加工质量[35]㊂在使用游离磨料研磨液研磨过程中,SDs /SSDs 层的厚度与磨粒的粒度㊁研磨盘的硬度成正比,而与研磨浆料的浓度成反比,并且与研磨压力和速度无关㊂同时,磨料尺寸对SDs /SSDs 层的厚度的影响比研磨盘硬度的影响更显著,而研磨浆料浓度的影响最小[36]㊂因此,相较于砂轮磨削,游离磨粒研磨的损伤更依赖于磨料尺寸㊂如图5所示,游离磨料加工后,晶圆的层错密度降低,且晶相显现非晶㊂同时,加工表面出现明显的晶格畸变现象,这是延性去除发挥优势的结果[37]㊂图5㊀砂轮磨削(a)~(c)和游离磨料研磨(d)~(f)4H-SiC 的Si 面的横截面TEM 照片[37]Fig.5㊀Cross-sectional TEM images of the Si surface of 4H-SiC by grinding (a)~(c)and lapping (d)~(f)[37]经砂轮磨削加工后,晶圆表面会产生螺旋式花纹状的表面划痕,而使用游离磨料研磨后,晶圆的表面划痕则是无序的㊂这种无序的表面划痕是由研磨液中磨料尺寸的不均匀性导致[38]㊂由于4H-SiC 材料具有各1912㊀综合评述人工晶体学报㊀㊀㊀㊀㊀㊀第52卷向异性,C面的硬度大于Si面,在C面的脆性去除更明显㊂正是由于C面硬脆性较大,C面材料更容易产生微裂纹使材料剥落,因而C面的材料去除速率高于Si面[20],研磨后C面形成的SSDs的厚度大于Si面[35]㊂1.3㊀抛光过程引入的损伤层抛光工艺旨在进一步提高晶片的表面质量,改善表面粗糙度及平整度,使其表面质量特征参数符合后序加工中的精度要求㊂适合4H-SiC单晶片的精密抛光加工方法主要有机械抛光[39]㊁离子束抛光[40]㊁等离子体辅助抛光[41]和化学机械抛光(chemical mechanical polishing,CMP)[42]等㊂机械抛光以机械研磨为主,采用更小粒径的硬磨料对晶片表面进行延性去除,以去除研磨过程的残留应力层和机械损伤层,提高表面平面度及表面质量㊂离子束抛光技术是一种通过离子源发射离子束轰击光学零件表面产生物理溅射效应去除面形误差的新型抛光技术,近年来已逐渐应用于大口径光学元件的加工[43]㊂而CMP是目前实现4H-SiC晶片全局平坦化最有效的方法㊂4H-SiC衬底晶圆的CMP主要是在以氧化铝(Al2O3)㊁二氧化硅(SiO2)和二氧化铈(CeO2)等磨料,和以高锰酸钾(KMnO4)㊁双氧水(H2O2)等氧化剂共同组成的抛光液中,伴随氧化反应和机械去除同步进行,实现材料的去除和表面修整[44]㊂在CMP过程中,抛光浆料中的氧化剂首先氧化4H-SiC,在材料表面形成Si-C-O的过渡氧化态㊂氧化物的硬度低于4H-SiC,这确保了氧化物可以通过低硬度磨料的机械作用被去除,基于氧化和机械去除的循环实现了4H-SiC晶圆的CMP[45]㊂一般来说,CMP工艺可以在不造成SSDs的情况下加工全局平坦化的4H-SiC 衬底晶圆,且CMP处理后的SiC晶圆表面可以出现原子级台阶结构[46]㊂然而在实际生产加工中,由于操作不当或抛光耗材不合格等问题,经CMP后依旧发现衬底有局部损伤㊂在此条件下,重复CMP步骤时,可以看出残留划痕的位置发生了变化,这表明CMP本身是可能会产生细微划痕的[47]㊂CMP处理后残留的损伤有以下两种产生机制:1)在CMP之前引入的损伤,在CMP期间持续存在;2)在CMP期间引入的损伤[48]㊂在原子力显微镜(AFM)下,这些表面可以是无特征的或显示一些极小的抛光损伤㊂然而,在外延生长之前或期间经过高温热加工后,可以显示出密集的划痕和缺陷网络,该网络对应于机械磨损过程中冲击到4H-SiC 表面的SSDs或位错网络[49]㊂这些损伤有的来自于前道工序残留CMP没有完全去除的,而有的损伤则是由于CMP进行过程中,环境中的颗粒物等意外掉落于晶圆表面并参与抛光过程引起的划伤㊂因为这些纳米级划痕并不是均匀地引入到晶圆表面,而是非常局部地存在[42,50]㊂这些掉落物可能是大颗粒的二氧化硅,也有可能是4H-SiC晶圆的纳米级或亚微米级切屑㊂为了更好地解释CMP工序中意外引入损伤的产生机制,对比损伤形貌和在不同条件下获得的4H-SiC晶圆的位错结构,可以发现晶圆上的局部损伤是由CMP过程中施加的高局部应力造成的[51]㊂Tsukimoto等[52]通过高角度分辨电子背散射衍射(HR-EBSD)技术测量了4H-SiC晶片磨削损伤层的弹性应变分布来验证以上猜想㊂如图6所示,在晶圆加工位置的下方由于非常大的塑性应变会产生缺陷区域,通过研磨相互作用与相关的塑性变形和断裂不均匀地引入了晶格缺陷㊂基于这一机理,可以解释为在整个4H-SiC衬底的加工环节中,晶圆表面被施加高局部作用力而发生弹塑性变形是SSDs产生的最根本原因㊂图6㊀4H-SiC晶圆损伤层的高分辨TEM照片,显示微裂纹沿箭头所示路径从表面上的一点(X)向晶圆内部点(Y)扩展[52] Fig.6㊀The high-resolution TEM image of the damage layer showing the microcrack propagating from a point(X)on thesurface to an internal point(Y)along the path indicated by the arrow[52]㊀第11期李国峰等:碳化硅晶圆的表面/亚表面损伤研究进展1913㊀2㊀SDs /SSDs 的形貌和表征2.1㊀SDs /SSDs 形貌从线切到磨削㊁抛光,材料的SSDs 层的厚度会严重影响加工效率和下一步工序的移除量㊂因此,要想实现材料的高效低损伤加工,延长材料的使用寿命,降低后续工序的移除量,对材料的SSDs 层的厚度进行检测分析和预测十分必要[53]㊂如图7所示,SSDs 在晶圆表面仅呈现为划痕,但其纵向裂纹深度㊁具体结构等需要借助特殊手段来观测㊂脆性材料晶圆的SSDs 检测方法可分为有损检测和无损检测两类㊂其中,有损检测包括截面显微法[54]㊁角度抛光法[55]㊁化学刻蚀法[56]等㊂然而,它们在检测上都有一些瑕疵:前两者虽然可以直观看到SSDs 的形貌,但样本制作流程过于繁琐;化学刻蚀法操作方便,但刻蚀深度无法精准控制㊂无损检测方法包括声学显微镜[57]㊁拉曼光谱分析[55]㊁X 射线衍射[58]㊁共聚焦激光扫描法[59]㊁光致发光(PL)[60]等㊂这些方法同样适用于4H-SiC 晶圆的SSDs 的检测㊂图7㊀4H-SiC 晶圆在CMP 后残留划痕的光学显微镜(a)和SEM(b)照片[50]Fig.7㊀Optical microscopy (a)and SEM (b)images of the residual scratch of a 4H-SiC wafer after CMP [50]如图8所示,4H-SiC 的SDs /SSDs 主要成分是在切片㊁磨削和抛光过程中产生的断裂和划痕,而这些断裂和划痕会被抛光再沉积层部分或全部隐藏起来[61]㊂参考Si 的SSDs 模型可以发现,SSDs 主要可分为严重损伤部分和高应力弹性变形部分,其中严重损伤部分由微裂纹㊁非晶层㊁多晶层㊁位错等组成㊂而这两部分的比例由加工的参数和磨料的性质决定,且这两部分没有确切的边界,如图9所示[62]㊂随着加工的深入和磨料的尺寸降低,损伤逐渐降低至外延可接受范围,获得近无损的晶圆表面㊂图8㊀4H-SiC 晶圆抛光后的SSDs 分布的示意图[61]Fig.8㊀Schematic of SSDs after the polishing of 4H-SiC wafers [61]图9㊀Si 研磨后SSDs 的形貌和成分示意图[62]Fig.9㊀Schematic diagram of the morphology and composition of SSDs after the grinding of Si [62]图10所示为TEM 观察到的4H-SiC 衬底晶圆的SDs /SSDs 中位错层的微观形貌㊂可以看到局部损伤在垂直方向表现为划痕,两侧伴随有环形位错㊂经过衍射矢量和伯格斯矢量对比,确定该位错环为基平面位错(BPD)[50,63]㊂从这些位错环的形状推断,这些位错环主要是硅核心不全位错的滑移造成的[51,64]㊂同时,1914㊀综合评述人工晶体学报㊀㊀㊀㊀㊀㊀第52卷BPD位错环的方向和局部损伤方向有关㊂4H-SiC衬底中的局部损伤会直接在外延层中反映出来,因此可以通过直接使用紫外灯照射外延晶圆使4H-SiC衬底中残留的BPD位错环在衬底中继承,并演化和延伸成肖克利型层错(Shockley-type stacking faults,SSF),如图11所示,外延层经UV处理后在PL中检测出半菱形结构[65]㊂对比发现,SSF的形貌又恰好可以和衬底中的BPD位错环对应㊂通过对半菱形SSF的方向统计后发现,虽然菱形大致分布于损伤的两侧,但不同晶向的损伤会使菱形的尖角方向分布出现偏差,这也可以说明衬底中不同晶向上的损伤,其BPD位错环的伯格斯矢量方向会有差异㊂图10㊀4H-SiC衬底中SSDs的表面TEM照片[50]Fig.10㊀Plane-view TEM image of SSDs of a4H-SiC substrate[50]图11㊀紫外光照射下4H-SiC外延薄膜中的Shockley型堆垛层错[65]Fig.11㊀Shockley-type stacking faults in4H-SiC epitaxial layer under UV irradiation[65]要观察SSDs的完整形貌,截面显微法是最直观的方法[66]㊂对4H-SiC损伤部分切片制样,在TEM中可看到损伤的完整纵向形貌,如图12所示[14]㊂损伤部分从上到下可分为覆盖层㊁亮层(损伤层)㊁半环形BPD 位错并伴随有SF㊂损伤层的形貌随划痕的晶向略有差异,但大致呈Y型,底部连接有层错,半环束从亮层向内扩散,形状为U型[61]㊂而在位错下方还有一层由于弹塑性变形而未被完全释放的应力层[62]㊂图12㊀4H-SiC衬底中的SSDs沿划痕方向(a)和垂直划痕方向(b)的缺陷分布示意图[14] Fig.12㊀Distribution diagram of SSDs parallel(a)and perpendicular(b)to the scratch of4H-SiC substrates[14]。
CUSP磁场对8英寸半导体级硅晶体生长的影响(simulation with FEMAG晶体生长模拟软件)

The following observations can be drawn:
With a cusp magnetic field, the overall oxygen concentration in the crystal decreases strongly This is effect is more important in the lower part of the crystal, where oxygen concentration decreases from about 7 ppma down to 3 ppma This lower oxygen concentration is the result of: - a stronger turbulent effect (see the turbulent viscosity) below the solid/liquid interface when no cusp field is applied, thereby facilitating the transfer of oxygen from the bottom of the melt towards the solid-liquid interface;
- a lower temperature along the bottom of the crucible when a cusp field is applied, leading to a lower oxygen dissolution in this region; this lower temperature appears as an additional consequence of the lower melt flow turbulence, the associated heat transfer reduction, and the resulting cooling down of the bottom of the melt
直径300mm硅单晶生长过程的热场模拟
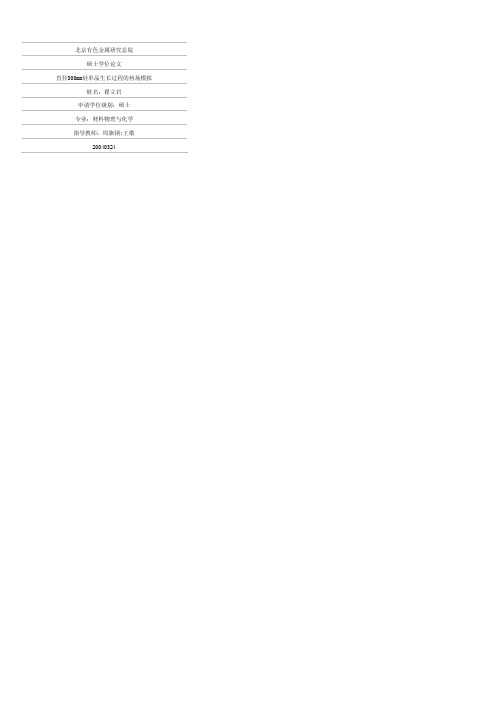
北京有色金属研究总院硕士学位论文直径300mm硅单晶生长过程的热场模拟姓名:翟立君申请学位级别:硕士专业:材料物理与化学指导教师:周旗钢;王敬20040324摘要摘要本文对直径300mm.晶体生长热场进行了数值模拟,并模拟计算了晶体生长过程中单晶炉内的氩气流动情况。
热场的模拟计算结果与实验测量的结果基本一致,较好地模拟了单晶炉内的热场分布情况。
通过对氩气流动情况的模拟分析,更好地了解了单晶炉内氩气流场的分布情况,这有利于我们更好地控制单晶炉内的氨气流的流速和流向,以及单晶中氧含量。
通过对有热屏和无热屏两种状态下的热场分布和晶体质量的比较,我们得出;单晶炉内施加热屏,可以很好地改进单晶炉内的热场分布,从而改善CZ硅单晶的生长条件,可以较好地控制晶体中的各种缺陷;同时,通过加装热屏,可以改进熔体内的温度分布,增大晶体生长的稳定性,从而获得更大的晶体生长速度,这样有利于提高生产效率;加装热屏还可以减少单晶炉内的热量损失,从而降低加热功率,减少了熔体与坩埚壁的反应,从而有利于控制晶体中的氧含量。
关键词:直拉硅晶体,热屏,300mm,热场,氩气流,数值模拟_—__——,—_——_-—_。
_‘-。
__。
●__-_●__。
●。
1。
_’’—‘‘-‘。
_。
‘-。
_。
_-。
’—’————一一一.垒!!塑璺———AbstractInthispaper,thehotzoneandtheargonflowdistributionduring300mmsinglecrystalgrowthprocessweresimulated.Thehotzonenumericalsimulationresultswereessentiallyinaccordancewitllexperimentalresuas.DifferentargonflowdistributionsinCZ—Sicrystalfurnacewereanalyzed,whichcanhelpUSunderstandtheargonflowdistributionsinCZ-Sicrystalfi瑚aceeffectivelyandadjusttheoxygenconcentrationbyanddirectioninCZ—Sicrystalfurnace.controllingargonflowvelocityComparingthehotzoneconfigurmionswithandwithoutheatshield,wefoundthatheatshieldcouldimprovethehotzoneconfiguration,crystalgrowthconditionsanddefectsintheCZ-Sicrystal.Simultaneously,throughadoptinghemshield,themelttemperaturedistributionswereimproved,thestabilityofcrystalgrowthWasenhancedandtheproductionefficiencyWaSincreaSedbyincreasingcrystalgrowthvelocity.ThehealersupplyingpowerWasreducedbyapplyingheatshieldbecauseofthereductionofheatloss,andtheinterstitialoxygeninthecrystalcanbedecreasedbecauseoftherestraintofthereactionbetweenthecrucibleandmelt,whichwasthemainsourceofoxygen.KeyWords:CZ-Sicrystal,heatshield,300mm,hotzone,argonflow,numericalsimulation.11.原创性声明本人郑重声明:所呈交的论文是我个人在导师指导下进行的研究工作及取得研究成果。
第一章 半导体物理基础2要点
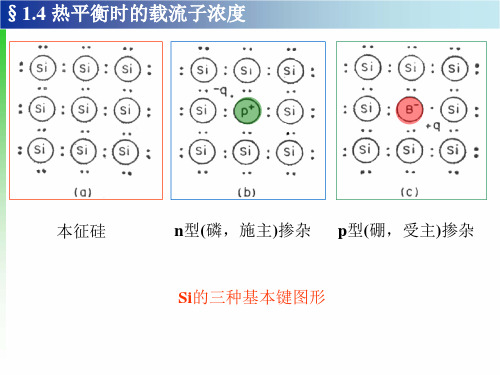
常温下(300K):
半导体材料与器件
计算过程中近似假设的合理性 波尔兹曼近似的合理性:EF一般位于禁带中,和导 带底和价带顶的距离都比较远 在状态密度的推导过程中我们使用的E-k关系(抛 物线近似)实际上只在能带极值附近成立 将积分范围从导带顶Ec’(价带底Ev’)推广到了正 无穷大∞(负无穷大-∞),这样做的合理性在于: 导带(价带)中的电子(空穴)基本集中在导带底 (价带顶)附近
3/ 2
T↑,NC、NV↑
f(EC) 、 f(EV) ~T
Ec EF exp kT EF Ev exp kT
T↑,几率↑
半导体材料与器件
EF 位臵的影响
EF→Ec,Ec-EF↓,n0↑ — EF越高,电子(导带)的填充 水平(几率)越高,对应ND(施主杂质浓度)较高; EF→Ev,EF-Ev↓,po↑ — EF越低,电子(价带)的填充 水平越低(空位几率越高),对应NA(受主杂质浓度)较 高。
半导体材料与器件
载流子:在半导体内可以运动形成电流的电子或 (空穴)
载流子的定向运动形成电流; 半导体中电流的大小取决于:载流子的浓度,载流子 的运动速度(定向的平均速度) 对热平衡状态下载流子浓度的推导和计算需要用到状 态密度和分布函数
半导体材料与器件
导带电子和价带空穴的浓度n0和p0方程
fF(E)=0
半导体材料与器件
因而可化简为:
n0
4 2mn h
3
* 3/ 2
Ec
E EF E Ec exp dE kT
为了方便计算,变量代换:
E Ec kT
FEMAG晶体生长计算软件之Czochralski (CZ) Process (FEMAG-CZ)

FEMAG晶体生长计算软件Czochralski (CZ) Process(FEMAG-CZ)FEMAG直拉法模拟软件(FEMAG-CZ)用于模拟直拉法工艺(包括Cz, MCz, VCz,泡生法)。
FEMAG-CZ直拉法模拟软件用于新的热场设计,并研发新的方法以满足新的商业需求点,比如:✓大直径晶锭生长✓无缺陷硅晶锭生长✓提高成品率✓氧含量控制✓降低碳含量✓晶锭半径和沿轴向的电阻率差异减小✓CCZ工艺仿真✓磁场设计✓蓝宝石生长工艺设计FEMAG-CZ模拟软件通过降低试验成本而节省了R&D消耗。
大直径晶锭生长以期不进行大量昂贵的可行性试验生长大尺寸晶体看起来是不太现实的。
FEMAG-CZ软件提供这种可能性。
为了生产450 mm及以上的大尺寸无缺陷硅晶体,晶体生长工程师通过使用FEMAG-CZ来定义关键的工艺参数,而无需任何材料和能源的消耗。
FEMAG-CZ能够设计新的热场并研发新的工艺技术,在FEMAG直拉法模拟软件的帮助下,晶体生长工程师能够在一个有效的虚拟环境中优化每一个关键参数,比如旋转速率,提拉速度,气体流速,压强和功率消耗等。
FEMAG直拉法模拟还能进一步为晶体生长工程师给出在某一工艺配置下产出的最终成品的质量和成本信息,比如晶体中的温度梯度,氧/碳/掺杂物/微缺陷分布等。
通过软件能够获得硅/锗/蓝宝石晶体质量和产品成本信息,这一模拟过程无需任何材料和能量的消耗。
FEMAG 3D 熔体流动模拟结果FEMAG动态模拟无缺陷硅晶锭生长无缺陷晶体硅生长是世界上最大的难点之一。
FEMAG模拟软件能够帮助工程师运用自己创新的技术生长出无缺陷晶体。
运用FEMAG软件缺陷工程模块可以预测晶体炉或者其他指定直拉法工艺环境中生长的晶体成品质量。
缺陷工程模块能够洞悉硅、锗生长过程中填隙原子,空位和微孔演变过程。
FEMAG-CZ能够成为你的测试平台,试验在不同的操作条件下对晶体生长质量的影响,如✓热场设计✓加热器功率✓晶体和坩埚的旋转速率✓晶体提拉速度,坩埚的位置✓气体流率和压强一旦掌握了晶体生长工艺中的动态规律,就可以找到最优的配置以增加成品率和投资回报。
半导体第三讲下单晶硅生长技术课件
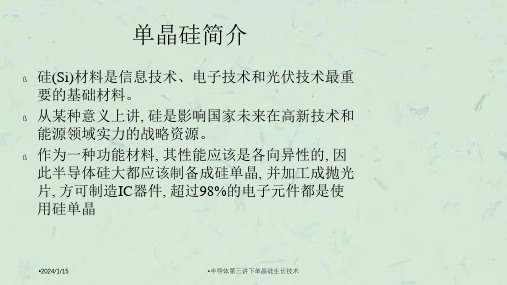
•2024/1/15
•半导体第三讲下单晶硅生长技术
ß 垂直磁场对动量及热量的分布具有双重效 应。垂直磁场强度过大(Ha=1000/2000), 不利于晶体生长。
ß 对无磁场、垂直磁场、勾形磁场作用下熔 体内的传输特性进行比较后发现,随着勾 形磁场强度的增加,熔体内子午面上的流 动减弱,并且紊流强度也相应降低。
显增大。研究还发现, 氧沉淀消融处理后,
后续退火的温度越高, 氧沉淀的再生长越快。
•2024/1/15
•半导体第三讲下单晶硅生长技术
ß 对1000 ℃、1100℃退火后的掺氮直拉硅中 氧沉淀的尺寸分布进行的研究表明,随着 退火时间的延长,小尺寸的氧沉淀逐渐减 少,而大尺寸的氧沉淀逐渐增多。氮浓度 越高或退火温度越高, 氧沉淀的熟化过程进 行得越快。
ß 因此适当控制氧析出物的含量对制备性能 优良的单晶硅材料有重大意义
•2024/1/15
•半导体第三讲下单晶硅生长技术
ß
研究发现,快速热处理( R T P)是一种
快速消融氧沉淀的有效方式, 比常规炉退火
消融氧沉淀更加显著。硅片经R TP 消融处
理后, 在氧沉淀再生长退火过程中,硅的体
微缺陷(BMD)密度显著增加, BMD的尺寸明
•2024/1/15
•半导体第三讲下单晶硅生长技术
ß 通过一定的工艺, 在硅片体内形成高密度的 氧沉淀, 而在硅片表面形成一定深度的无缺 陷洁净区,该区域将用于制造器件, 这就是 “内吸杂”工艺。
ß 如果氧浓度太低, 就没有 “内吸杂”作用, 反之如果氧浓度太高, 会使晶片在高温制程 中产生挠曲。
拉晶试验,结果发现平均 拉速可从0.6mm/min提高 到0.9mm/min,提升了 50%。
单晶硅生长技术
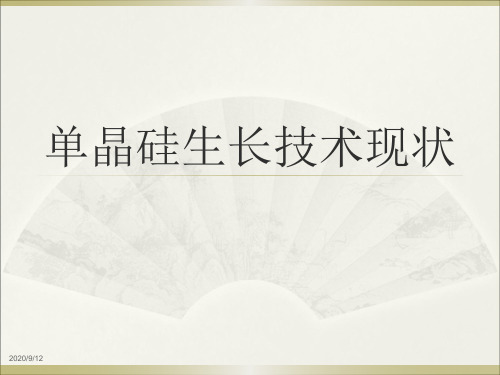
2020/9/12
与敞开系统相 比,密闭系统界面 附近晶体轴向温度 梯度增大约10℃, 而熔体中轴向温度 梯度降低约5℃。
温度-距离曲线(熔体)
磁场直拉法
今年来,随着生产ቤተ መጻሕፍቲ ባይዱ模的扩大,直拉单晶 硅正向大直径发展,投料量急剧增加。由 于大熔体严重的热对流不但影响晶体质量, 甚至会破坏单晶生长。
目前,抑制热对流最常用的方法是在长晶 系统内加装磁场。
区熔硅的常规掺杂方法有硅芯掺杂、表面涂敷 掺杂、气相掺杂等,以气相掺杂最为常用。
2020/9/12
晶体缺陷 区熔硅中的晶体缺陷有位错和漩涡缺陷。
中子嬗变晶体还有辐照缺陷,在纯氢或氩 一氢混合气氛中区熔时,常引起氢致缺陷。
2020/9/12
通过在氩气气氛及真空环境下进行高阻区 熔硅单晶生长试验发现,与在氢气气氛下生长 硅单晶相比,在真空环境下采用较低的晶体生 长速率即可生长出无漩涡缺陷的单晶, 而当晶 体生长速度较高时, 尽管可以消除漩涡, 但单晶 的少子寿命却有明显的下降。在真空中生长无 漩涡缺陷单晶的生长速率,比在氢气气氛下生 长同样直径单晶的生长速率低,但漩涡缺陷对 单晶少子寿命的影响并不明显。
2020/9/12
研究发现,快速热处理( R T P)是一种
快速消融氧沉淀的有效方式, 比常规炉退火
消融氧沉淀更加显著。硅片经R TP 消融处
理后, 在氧沉淀再生长退火过程中,硅的体
微缺陷(BMD)密度显著增加, BMD的尺寸明
显增大。研究还发现, 氧沉淀消融处理后,
后续退火的温度越高, 氧沉淀的再生长越快。
单晶硅生长技术现状
2020/9/12
单晶硅简介
硅(Si)材料是信息技术、电子技术和光伏技术最重 要的基础材料。
磁场对半导体级硅单晶生长质量的影响研究

磁场对半导体级硅单晶生长质量的影响研究引言:半导体材料在电子、光电子、通信等领域中有广泛的应用,其中硅单晶是最重要的基础材料之一。
硅单晶的生长质量对于半导体器件的性能、可靠性和稳定性具有重要影响。
近年来,研究人员注意到磁场对硅单晶生长的影响,相关研究表明磁场可以改善硅单晶的生长质量。
因此,本文将着重讨论磁场对半导体级硅单晶生长质量的影响,并概括已有研究成果,为进一步深入研究提供参考。
1. 磁场对硅单晶生长过程的影响硅单晶的生长是通过将熔融硅材料慢慢降温,使其凝固成单晶体。
在传统的硅单晶生长方法中,通过控制温度梯度来实现晶体的生长。
然而,研究发现,在磁场的作用下,硅单晶的生长质量可以得到明显的改善。
磁场可以通过影响熔体的热对流和物质传输,改变硅单晶的生长过程。
一方面,磁场可以抑制熔体中的对流运动,使热量更加均匀地传导,从而减少了晶体中的缺陷和杂质。
另一方面,磁场还可以影响熔池中溶质的输运行为,使晶体的成分更加均匀,减少了晶体的偏析效应。
2. 磁场对硅单晶生长质量的影响机制研究人员通过实验和模拟方法,探索了磁场对硅单晶生长质量的影响机制。
其中,最为广泛应用的是磁力对流和磁力传质效应。
磁力对流是指磁场对流体中的电流产生力的作用。
在硅单晶生长中,研究人员发现磁场可以减少熔体的自由对流运动,使之趋于层流状态。
磁力对流的作用导致熔体温度分布更为均匀,从而减少了晶体内部的温度梯度,并能够减少熔体中的残余气体和杂质。
磁力传质效应是指磁场对溶质在熔体中的传输行为产生影响。
在硅单晶生长中,磁场可以改变熔体中溶质的分布情况。
通过磁场作用下的溶质传输行为的改变,可以使晶体的成分更加均匀,减少晶体中的偏析效应,从而提高生长质量。
3. 磁场参数对硅单晶生长质量的影响磁场对硅单晶生长质量的影响与磁场参数有关。
实验结果表明,磁场强度、施加方向和频率等参数都会对硅单晶的生长质量产生影响。
磁场强度是指磁场的磁感应强度。
研究发现,适当增加磁场强度可以改善硅单晶的生长质量。
钛碳化硅陶瓷材料的研究进展

钛碳化硅陶瓷材料的研究进展作者:贾换王娇徐简武国强来源:《科技资讯》2023年第16期关键词: Ti3SiC2 制备性能第二相中图分类号: TQ175 文献标识码: A 文章编号: 1672-3791(2023)16-0120-04M n+1AX n是三元层状化合物,如Ti3SiC2、Ti2A1C、Ti2SnC、Ti3A1C2等,其中最典型的是Ti3SiC2[1]。
钛碳化硅集陶瓷和金属的优良特性于一身,具有许多优异的特性,如良好的导电导热性、机械加工性、高强度、高硬度、耐化学腐蚀性、耐氧化性等,可作为轴承材料、滑电弓类材料、减摩材料等,在机电、化工等领域广泛应用,因而得到了研究者的极大关注。
近年来,研究者利用不同合成方法来钛碳化硅,主要为提高钛碳化硅合成纯度、力学性能、抗氧化性等。
本文就钛碳化硅材料的晶体结构、性能特点、制备方法和应用进展进行了总结。
1 Ti3SiC2的结构钛碳化硅的结构模型可知:平面硅原子层将八面体Ti6C 隔开,形成层状结构,碳原子位于结合八面体Ti6C 的中心,一个晶胞由两个钛硅碳分子组成。
三元化合物钛碳化硅是一种六方晶系,C原子位于Ti6C 八面体的中心,Ti6C 八面体与Si 层间隔连接呈层状结构,相应的晶体结构见图1,其包含共价键、离子键和金属键,这种特殊的价键赋予Ti3SiC2材料[1]。
2 Ti3SiC2陶瓷材料制备方法钛碳化硅的主要合成技术方法有微波加热合成、热压烧结、自蔓延高温法、化学气相沉积法、热等静压法、微波加热合成及无压烧结等,它们各有合成技术的优缺点[2],具体如表1 所示。
放电等离子烧结、热压烧结法、热等静压法等生产不能大规模化,成本高;而机械合金化法、自蔓延高温法、微波加热合成、无压烧结等操作简单、成本低廉,但生产中易有杂质相,可以用两种或多种合成方法相结合制备钛碳化硅材料。
3 Ti3SiC2陶瓷材料的制备与性能研究不同研究者对钛硅碳的制备方法、制备工艺及研究结果进行了总结与对比,具体见表2。
晶体生长仿真软件FEMAG-CUSP磁场对8英寸半导体级硅晶体生长的影响PPT文档共33页

5、虽然权力是一头固执的熊,可是金 子可以 拉着它 的鼻子 走。— —莎士 比
谢谢你的阅读
❖ 知识就是财富 ❖ 丰富你的人生
71、既然我已经踏上这条道路,那么,任何东西都不应妨碍我沿着这条路走下去。——康德 72、家庭成为快乐的种子在外也不致成为障碍物但在旅行之际却是夜间的伴侣。——西塞罗 73、坚持意志伟大的事业需要始终不渝的精神。——伏尔泰 74、路漫漫其修道远,吾将上下而求索。——屈原 75、内外相应,言行相称。——韩非
晶体生长仿真软件FEMAG-Cቤተ መጻሕፍቲ ባይዱSP磁场对 8英寸半导体级硅晶体生长的影响
1、合法而稳定的权力在使用得当时很 少遇到 抵抗。 ——塞 ·约翰 逊 2、权力会使人渐渐失去温厚善良的美 德。— —伯克
3、最大限度地行使权力总是令人反感 ;权力 不易确 定之处 始终存 在着危 险。— —塞·约翰逊 4、权力会奴化一切。——塔西佗
带电粒子注入硅的辐照损伤模拟研究

带电粒子注入硅的辐照损伤模拟研究∗郑贤利;刘敏;夏艳芳;程品晶;张泊丽【摘要】By the process of SRIM,we can simulate the ion range,loss of energy,Silicon target damage by the different quality of charged particles implanted silicon.The results indicate that,the largest concentration of in-cidence of charged particles is located at the proj ection range in the silicon,and is smaller with the increase of the particle quality.The particle of mass to the mass of Silicon ratio is smaller than 1.8,the charged particle loss to electron energy to recoil of the silicon atoms loss to the energy of the electrons ratio is greater than 1 or less than 1 .Ionization energy loss decreases,and phonon energy loss increases with the increase of incidence of charged particles of mass.Total displacements and total vacancies increase rapidly,and replacement collisions increase slowly with the increase of incidence of charged particles of mass.%利用SRIM软件计算模拟不同质量的带电粒子射入硅的射程、能量损失、硅损伤情况.结果表明,入射带电粒子在硅中分布的最大浓度位置位于其投影射程处,且随粒子质量的增加而减少;入射带电粒子的质量与硅的质量比近似小于1.8时,入射带电粒子损失给电子的能量与反冲硅原子损失给电子的能量之比>1,否则小于1;电离能损随入射带电粒子质量的增加而减少;声子能损随入射带电粒子质量的增加而增加;入射带电粒子在硅中产生的移位和空穴随入射离子质量的增加而增加较快,而替位碰撞增加缓慢.【期刊名称】《功能材料》【年(卷),期】2016(047)0z1【总页数】5页(P164-168)【关键词】带电粒子;辐照损伤;能量损失;硅【作者】郑贤利;刘敏;夏艳芳;程品晶;张泊丽【作者单位】南华大学核科学技术学院,湖南衡阳 421001;南华大学核科学技术学院,湖南衡阳 421001;南华大学核科学技术学院,湖南衡阳 421001;南华大学核科学技术学院,湖南衡阳 421001;南华大学核科学技术学院,湖南衡阳421001【正文语种】中文【中图分类】TL99晶体硅作为集成电路最重要的衬底材料及半导体探测器的探测介质,其质量对集成电路芯片各项性能和半导体探测器输出信号都有着直接的影响。
外磁场对THz波段超导表面等离激元的影响

外磁场对THz波段超导表面等离激元的影响张兴坊;刘凤收;梁兰菊【摘要】根据超导二流体模型,研究了在THz波段超导材料铌表面存在的表面等离激元的色散曲线和特征长度随外磁场的变化关系,分析了外磁场对表面等离激元激发条件的影响.结果表明:外磁场强度增大时,色散曲线偏离光锥线程度将增大,表面等离激元传播距离、归一化波长及其在介质内的穿透深度将变小,而在超导材料内的穿透深度将增大,且色散曲线和特征长度随磁场的变化程度还与频率有关.同时,共振角度对外磁场变化不敏感,但共振频率将随外磁场强度增大而红移.该结果可为超导波导器件设计提供一定的参考.【期刊名称】《四川大学学报(自然科学版)》【年(卷),期】2016(053)005【总页数】6页(P1081-1086)【关键词】超导;THz波段;表面等离激元;色散曲线;二流体【作者】张兴坊;刘凤收;梁兰菊【作者单位】枣庄学院光电工程学院,枣庄277160;枣庄学院光电工程学院,枣庄277160;枣庄学院光电工程学院,枣庄277160【正文语种】中文【中图分类】O441.6;TN252表面等离激元(Surface Plasmon Polaritons,SPPs)是沿介电常数或磁导率符号相反的两种材料分界面处传播的电子集体振荡波[1],为一种束缚电磁模式,具有空间尺度小、场局域增强、能够突破衍射极限等特性,在微纳生化传感、新型光源、亚波长光子器件、太阳能电池等领域具有重要应用[2-4].研究表明,SPPs色散曲线和特征长度不仅与分界面处材料的几何形状、拓扑结构及材料组分等因素有关[5-9],也与外界施加的影响如电场、磁场、温度、光照等有关[10,11].然而,由于构成分界面的材料大多为金属,SPPs传播过程中存在着较大的阻尼,导致传播距离有限,在一定程度上限制了其应用.为了有效地减小欧姆损耗,采用超导材料实现对SPPs的调控引起了人们广泛关注.根据超导二流体模型,超导材料的光学性质易受环境温度、外加磁场等因素影响[12-14].近年来,在THz和微波波段超导材料的SPPs与环境温度的关系已有较多研究[15-17],但外加磁场对其影响的报道却相对较少[18].本文将讨论在THz波段超导SPPs的色散曲线和四个特征长度(传播距离、归一化长度、在分界面两边介质的穿透深度)与外磁场的变化关系,分析利用衰减全反射(ATR)技术时外磁场强度对激发条件的影响,并对变化规律进行理论解释.考虑由两种半无限大、各向同性均匀线性介质构成的简单分界面,两种介质的介电常数和磁导率分别为ε1、ε2和μ1、μ2.根据分界面处SPPs的场分布特点,通过求解麦克斯韦方程组并在分界面处应用电磁场边值关系,可得到由TM波激发的SPPs的色散关系和四个特征长度的表达式.SPPs色散关系表达式为ksp=ω(ε1ε2(ε2μ1-ε1μ2)/(ε22-ε12))1/2/c,ω和c分别为入射电磁波在真空中的频率和光速;SPPs沿分界面的传播距离为L=1/Im(2ksp),其定义为电场强度减小为初始值的1/e;SPPs波长为λp=2π/Re(ksp),在两种介质内的穿透深度分别为δi=1/|Im(ki)|,其中♂2(i=1,2)表示SPPs在垂直于两种介质界面方向上的波矢[19].为分析简单,设介质1为真空,则ε1=μ1=1,超导材料为非铁磁介质,则μ2=1,其介电常数ε2通常为一个与频率有关的量,由二流体模型[20]可得式中,ωs和ωn分分别为超导材料内超导态电子和正常态电子的等离子体频率,其关系为ωs/ωn=ns/nn,ns、nn分别为超导态和正常态电子的密度.引入伦敦深度,则ωs和ωn又可表示为[20]ωn=c(T/Tc)2/λL(0)其中,T和Tc分别为超导材料所处环境温度和临界温度,λL(0)表示超导材料在T=0K时的伦敦深度.当超导材料放置于磁场环境且外加磁场方向平行于波矢时,其介电常数可改写为[12]式中,♂♂♂2为超导材料的等离子体频率,B为外加磁场的磁感应强度,Hc为超导材料的临界磁场强度.Hc也是一个与温度有关的量,可近似的表示为Hc= Hc(0)[1-(T/Tc)2]Hc(0)表示超导材料在T=0K时的临界磁场强度.超导界面的SPPs可利用ATR技术激发,棱镜定义为介质3,设其介电常数、磁导率和频率、温度、磁场等因素无关,为ε3=2.5,μ3=1,则SPPs激发条件需满足波矢匹配ε31/2sinθω/c=Re(ksp),θ为共振角度.本文中选用的超导材料为铌,其参数为Tc=9.2K,λL(0)=83 nm,Hc(0) =0.195T,γ设为1014 Hz.3.1 色散曲线与外磁场的关系在THz波段超导材料铌的介电常数为一个很大的复数,因而在其表面激发的SPPs 的色散曲线将非常接近于自由空间中的电磁波光锥线,即传播波矢ksp=ω(ε2/(ε2+1))1/2/c≈k0,k0=ω/c为真空中的入射电磁波波矢.而且,ksp总是大于同一频率下电磁波在分界面两边介质中的波矢.在外磁场(B/Hc=0.1、0.5、0.9)作用下,SPPs的色散关系曲线变化如图1所示.图中纵坐标Δk表示同一频率下传播波矢ksp的实部与波矢k0的差值.由图可见,波矢Δk随着外磁场强度的增大而增大,且在频率较高时的Δk增大程度要大于低频率时的Δk.这是因为,外加磁场的存在将改变超导材料内的电子态密度,随着外磁场强度的增大,超导材料中的超导态电子密度逐渐减小,正常态电子密度逐渐增大,导致介电常数的实部和虚部同时增大,且在THz波段时其绝对值均远远大于1,于是ksp≈ω(1-1/2ε2)/c,而超导材料ε2的实部绝对值又远大于其虚部,因此ksp主要由ε2实部决定,其实部随着ε2实部增大而增大.同时,随着频率增大,ε2实部增大而虚部减小,同样引起ksp实部增大,Δk随之增大.3.2 四个特征长度与外磁场的关系SPPs传播距离主要取决于ksp虚部,在不同外磁场条件下其变化曲线如图2所示.由图可见,随着外磁场强度的增大,SPPs传播距离快速减小.在频率处于4THz,相对磁场强度为B/Hc=0.1时的SPPs传播距离约为12000m,当磁场B/Hc增大到0.5时,其传播距离仅有约770m,减小了约15倍,当磁场继续增大到B/Hc=0.9时传播距离仅有约20m.更强外磁场的存在,将导致更多的超导态电子转化为正常态电子,引起电子间的碰撞几率增大,阻尼作用增强,宏观上表现为欧姆损耗加大,SPPs沿分界面的传播距离减小.由SPPs传播距离及色散关系式还可进一步得出其与介电常数的关系为L(Im(-ω/ε2),同时,当外磁场强度小于临界磁场强度且入射频率远小于阻尼系数时,根据超导材料介电常数与外磁场强度的关系,可得Im(-ω/ε2)((1-χ)2/(ω4χ),其中χ=B/Hc.可以看出,当外磁场强度增大时,传播距离快速减小,并且减小程度约与频率四次方成正比.SPPs波长总是小于同一频率下电磁波在真空中的波长.在THz波段,SPPs波长λp仅略小于真空中的入射电磁波波长λ0=2π/k0,因而其归一化波长λp/λ0≈1,其波长与入射波长的归一化比值?λ/λ0=(λp-λ0)/λ0与外磁场强度间的变化关系如图3所示.由图可见,归一化比值?λ/λ0随着外磁场强度的增大而减小,且其绝对值还随着频率的增大而增大.即归一化波长λp/λ0随着外磁场强度或频率减小而缓慢增大,最后趋近饱和值1.这是因为SPPs波长是传播波矢ksp实部的倒数,其波长变化趋势与其色散关系的变化规律正好相反,即随着外加磁场强度或入射频率的增大,Δk增大而λp/λ0减小.SPPs场强在垂直于界面的方向呈指数衰减形式,其场空间分布大小用穿透深度表示,表征了场的束缚性.图4(a)、(b)分别给出了SPPs在真空和超导材料内的穿透深度与外磁场强度的变化关系.由图4(a)可见,SPPs在真空中的穿透深度随着外磁场强度的增大而减小,在频率为4THz,相对磁场强度B/Hc分别为0.1、0.5和0.9时,穿透深度分别达到0.064m、0.048m和0.022m.超导材料在THz波段的介电常数性质决定了SPPs在非导体介质内具有较弱的束缚性,其性质类似于金属材料在THz波段或微波波段时产生的Zenneck波.在THz波段,由于超导材料铌的介电常数实部绝对值远大于其虚部,SPPs在真空中的穿透深度可表示为δ1≈|Re(ε2)|1/2/k0.当外磁场强度增大时,虽然超导材料的介电常数实部随之增大,但其绝对值减小,导致穿透深度也随着减小.当外磁场强度小于且不靠近临界磁场时,穿透深度与磁场、频率间的关系可进一步表示为δi≈(1-χ)1/2ωpc/ω2,可知在B/Hc为0.1、0.5时的SPPs穿透深度分别为B/Hc为0.9时的约3倍和2.2倍.虽然SPPs在真空中的穿透深度很大,但由于超导材料对外界磁场的排斥性,SPPs在超导材料中的穿透深度将很小,其与外磁场强度的关系如图4(b)所示.由图可见,随着外磁场强度的增大,穿透深度也随着增大,当相对磁场强度分别为0.1、0.5和0.9时,频率为4THz的SPPs在超导材料内的穿透深度分别为83 nm、120 nm和250 nm,远小于入射波长,且频率越高穿透深度越小,但其穿透深度随频率变化较小.这是因为,当外磁场强度较小时,超导材料内的超导态电子占居主导地位,超导材料处于超导状态,磁场的穿透深度极限为伦敦深度,即83 nm.随着外磁场强度的增大,正常态电子逐渐增多,超导态电子逐渐减少,超导材料演变为正常金属,导致穿透深度增大.SPPs在超导体内的穿透深度与外磁场的关系可表示为δ2≈1/|Re(ε2)|1/2k0≈c/ωp(1-χ)1/2,即相对磁场强度为0.1和0.5时的穿透深度分别为0.9时的约1/3和1/2.2.而频率越高,SPPs在界面的束缚性越好,即在超导材料和真空中的穿透深度越小.随着电磁波频率趋向于ωp,电磁波在界面上的模场将更加被压缩,将可能远小于自由空间波长,实现在微纳光子集成中的应用.3.3 激发条件随外磁场的变化利用ATR技术激发SPPs的方式有波长调谐和角度调谐两类,激发条件为在传播方向上满足波矢匹配,即ε31/2sinθω/c=ksp,该式可进一步改写为ε31/2sinθ=Re(nsp),其中nsp=(ε2/(ε2+1))1/2为SPPs界面波导的有效折射率.在THz波段,超导材料具有非常大的介电常数,导致有效折射率Re(nsp)仅略大于1.又由于SPPs色散曲线ksp(ω)随磁场的变化较小,因而共振角度对磁场变化不敏感.图5给出了在不同外磁场条件下,界面波导有效折射率Re(nsp)与频率的关系.由图可知,随着外磁场相对强度由0.1增大到0.9,在频率为4THz时的有效折射率Re(nsp)仅增大了约0.47*10-5,虽然随着频率的增大,有效折射率也增大,但增大程度较小,在10THz时也仅增大了约1.7*10-5.有效折射率的变化程度直接决定了共振角的调谐范围,显然外磁场强度变化时,共振角度几乎不受影响.而当入射角度不变,采用波长调谐方式激发SPPs时的共振波长随外磁场的变化关系也可由图5得到.由图可见,当共振角度不变,即Re(nsp)不变,随着磁场的增大,共振频率蓝移.当Re(nsp)-1=0.25*10-5,相对磁场强度由0.1增大到0.9时,共振频率由7.7THz移动至2.6THz,调谐范围达5THz.当入射角度增大时,外磁场对共振频率调谐范围的影响将更大.根据超导二流体模型,讨论了在不同外界磁场强度下,超导材料铌与真空分界面处产生的SPPs性质的变化规律.结果表明:由于外加磁场的存在,将导致超导材料内电子在超导态和正常态间相互转换,引起超导介电常数的变化,进而引起SPPs 性质的变化.外磁场强度越大,同一频率时SPPs传播波矢实部越大,色散曲线越偏离光锥线,传播距离、归一化波长和及其在真空中的穿透深度越小,但在超导体内的穿透深度越大.当利用ATR技术激发超导界面的SPPs时,发现共振角度几乎不随外磁场变化,但共振频率随外磁场强度增大而红移,且调谐范围随入射角度增大而增大.【相关文献】[1] Pitarke J M, Silkin V M, Chulkov E V, et al. Theory of surface plasmons and surface-plasmon polaritons[J]. Rep on Prog Phys, 2007, 70(1): 1.[2] Ruppin R. Surface polaritons of a left-handed material slab[J]. J Phys: Condens Matter, 2001, 13(9): 1811.[3] Kauranen M, Zayats A V. Nonlinear plasmonics[J]. Nature Photonics, 2012, 6(11): 737.[4] Ozbay E. Plasmonics: merging photonics and electronics at nanoscale dimensions[J]. Science, 2006, 311(5758): 189.[5] Isaac T H, Barnes W L, Hendry E. Determining the terahertz optical properties of subwavelength films using semiconductor surface plasmons[J]. Appl Phys Lett, 2008,93(24): 241115.[6] Wang K, Mittleman D M. Dispersion of surface plasmon polaritons on metal wires in the terahertz frequency range[J]. Phys Rev Lett, 2006, 96(15): 157401.[7] Li S, Jadidi M M, Murphy T E, et al. Terahertz surface plasmon polaritons on a semiconductor surface structured with periodic V-grooves[J]. Optics Express, 2013, 21(6): 7041.[8] Chen J, Smolyakov G A, Brueck S R, et al. Surface plasmon modes of finite, planar, metal-insulator-metal plasmonic waveguides[J]. Optics Express, 2008, 16(19): 14902. [9] 张惠芳, 赵玉静, 陶峰, 等. 五层对称人工超常材料结构的表面等离子体激元[J]. 光子学报, 2010, 39(12): 2234.[10] Zhang C H, Wu J B, Jin B B, et al. Low-loss terahertz metamaterial from superconducting niobium nitride films[J]. Optics Express, 2012, 20(1): 42.[11] Davoyan A R, Shadrivov I V, Kivshar Y S. Nonlinear plasmonic slot waveguides[J]. Optics Express, 2008, 16(26): 21209.[12] Tachiki M, Koyama T, Takahashi S. Electromagnetic phenomena related to a low-frequency plasma in cuprate superconductors[J]. Phys Rev B, 1994, 50(10): 7065.[13] 张翠玲, 郑瑞伦, 刘启能, 等. 温度对超导光子晶体光子能带的影响[J]. 光子学报, 2010, 39(11): 1943.[14] 李春早, 刘少斌, 孔祥鲲, 等. 外磁场与温度对低温超导光子晶体低频禁带特性的影响[J]. 物理学报, 2012, 61(7): 075203.[15] Kurter C, Abrahams J, Shvets G, et al. Plasmonic Scaling of Superconducting Metamaterials[J]. Phys Rev B, 2013, 88(18): 293.[16] Tsiatmas A, Buckingham A R, Fedotov V A, et al. Superconducting plasmonics and extraordinary transmission[J]. Appl Phys Lett, 2010, 97(11): 111106.[17] Zhang C, Jin B, Han J, et al. Terahertz nonlinear superconducting metamaterials[J]. Appl Phys Lett, 2013, 102(8): 081121.[18] Berman O L, Lozovik Y E, Kolesnikov A A, et al. Surface plasmon polaritons and optical transmission through a vortex lattice in a film of type-II superconductor[J]. J Opt Soc of Am B, 2013, 30(4): 909.[19] Raether H. Surface plasmons on smooth surfaces[M]. Berlin, Heidelberg: Springer, 1988.[20] Li C, Liu S, Kong X, et al. Tunable photonic bandgap in a one-dimensional superconducting-dielectric superlattice[J]. Appl Opt, 2011, 50(16): 2370.。
强磁场对Al_Si合金中共晶硅生长的影响
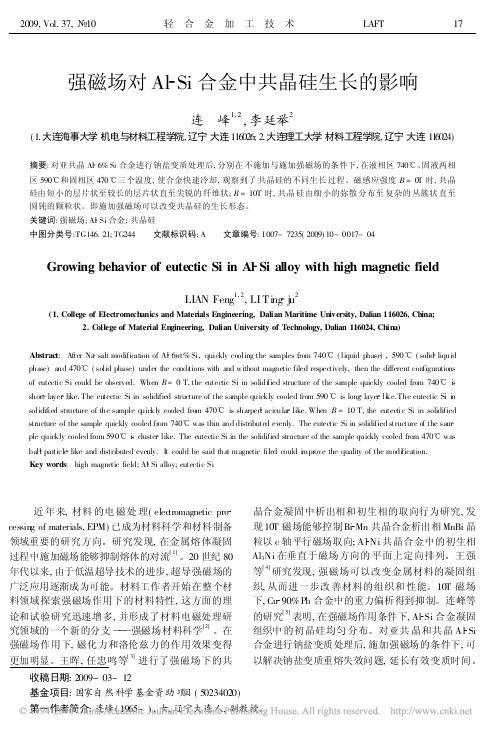
进行了强磁场下的共
收稿日期: 2009- 03- 12 基金项目: 国家自然科学基金资助项目( 50234020) 第一作者简介: 连峰 ( 1965- ) , 女 , 辽宁大连人, 副教授。
18
LAFT
轻
合
金
加
工
技
术
2009, Vol. 37, ! 10
但是迄今, 强磁场对金属凝固组织的影响机制尚不 确定。本研究以亚共晶 Al 6% Si 合金为研究对象 , 对其进行钠盐变质处理后 , 分别在液相区、 固液两相 区和固相区三个温度将合金快速置入水中 , 以快速 冷却方法固定高温凝固组织, 对其凝固组织进行研 究, 探讨强磁场的作用机制。
Growing behavior of eutectic Si in Al Si alloy with high magnetic field
LIAN Feng , LI T ing ju
1, 2 2
( 1. College of Electromechanics and Materials Engineering, Dalian Maritime University, Dalian 116026, China; 2. College of Material Engineering, Dalian University of Technology, Dalian 116024, China) Abstract: After Na salt modification of Al 6wt% Si, quickly cooling the samples from 740 phase) and 470 ( liquid phase) , 590 ( solid liquid is
非对称勾形磁场的三维优化设计与实现
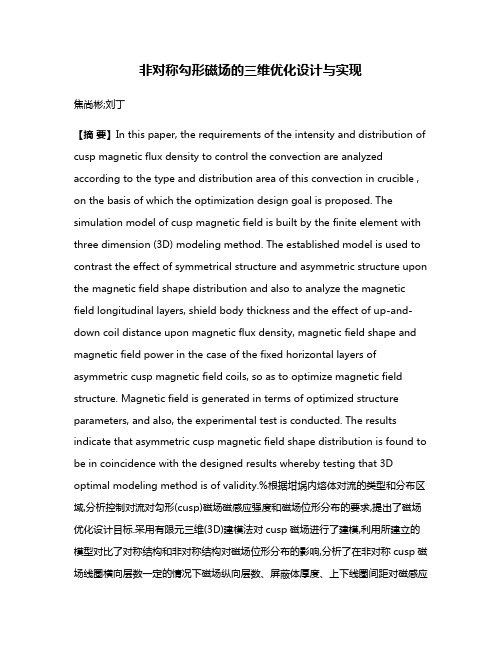
非对称勾形磁场的三维优化设计与实现焦尚彬;刘丁【摘要】In this paper, the requirements of the intensity and distribution of cusp magnetic flux density to control the convection are analyzed according to the type and distribution area of this convection in crucible , on the basis of which the optimization design goal is proposed. The simulation model of cusp magnetic field is built by the finite element with three dimension (3D) modeling method. The established model is used to contrast the effect of symmetrical structure and asymmetric structure upon the magnetic field shape distribution and also to analyze the magnetic field longitudinal layers, shield body thickness and the effect of up-and-down coil distance upon magnetic flux density, magnetic field shape and magnetic field power in the case of the fixed horizontal layers of asymmetric cusp magnetic field coils, so as to optimize magnetic field structure. Magnetic field is generated in terms of optimized structure parameters, and also, the experimental test is conducted. The results indicate that asymmetric cusp magnetic field shape distribution is found to be in coincidence with the designed results whereby testing that 3D optimal modeling method is of validity.%根据坩埚内熔体对流的类型和分布区域,分析控制对流对勾形(cusp)磁场磁感应强度和磁场位形分布的要求,提出了磁场优化设计目标.采用有限元三维(3D)建模法对cusp磁场进行了建模,利用所建立的模型对比了对称结构和非对称结构对磁场位形分布的影响,分析了在非对称cusp磁场线圈横向层数一定的情况下磁场纵向层数、屏蔽体厚度、上下线圈间距对磁感应强度、磁场位形、磁场功率的影响,优化了磁场结构;根据优化的结构参数制造了磁场并进行了实验测试,结果表明非对称cusp磁场的位形分布与设计结果一致,从而验证了3D优化建模方法的有效性.【期刊名称】《西安理工大学学报》【年(卷),期】2012(028)001【总页数】7页(P13-19)【关键词】勾形磁场;非对称结构;三维模型;结构优化【作者】焦尚彬;刘丁【作者单位】西安理工大学自动化与信息工程学院,陕西西安710048;西安理工大学自动化与信息工程学院,陕西西安710048【正文语种】中文【中图分类】TP13直拉(CZ)法是工业生产单晶硅的重要方法。
- 1、下载文档前请自行甄别文档内容的完整性,平台不提供额外的编辑、内容补充、找答案等附加服务。
- 2、"仅部分预览"的文档,不可在线预览部分如存在完整性等问题,可反馈申请退款(可完整预览的文档不适用该条件!)。
- 3、如文档侵犯您的权益,请联系客服反馈,我们会尽快为您处理(人工客服工作时间:9:00-18:30)。
Report Bruker ASC Feb, 9, 2012
FEMAGSoft © 2012
OBJECTIVE
PROCESS CONDITION
CZ furnace - 8 inch diameter crystal, 24 inch diameter crucible To predict the impact of a CUSP magnetic field operating at 140 A with the neutral-axis located on the melt free surface.
PARAMETERS OBSERVED
The concentration of the Oxygen in the melt and crystal. The concentration of the Phosphorous in the melt and crystal The concentration of the Carbon in the melt and crystal
8
9
Radial Oxygen Concent rat ion H=250 mm
8 7
7 6
Ox yge n ppm a
Ox yge n ppm a
5 4 3 2 1 0 0 0,02 0,04 0,06 0,08 0,1 C U SP N o C U SP
6 5 4 3 2 1 0 C U SP N o C U SP
FEMAGSoft © 2012
PREDICTION OF PHOSPHOROUS CONCENTRATION ALONG THE HEIGHT OF THE CRYSTAL
FEMAGSoft © 2012
CUSP vs NOCUSP - OXYGEN CONCENTRATION - CRYSTAL
FEMAGSoft © 2012
CRYSTAL RADIAL OXYGEN MEASUREMENT POSITIONS
FEMAGSoft © 2012
PREDICTION OF RADIAL OXYGEN CONCENTRATION
Radial Oxygen Concent rat ion H=90mm
Ox yge n ppm a
5 4 3 2 1 0 C U SP N o C U SP
4
Ra dius (m )
0,06
0,08
0,1
0,12
Radial Oxygen Concent rat ion H=1290mm
8 7 6
Radial Oxygen Concent rat ion H=1550 mm
9 8 7 6
Ox yge n ppm a
5 4 3 2 1 0 0,2 0,4 0,6 0,8 1 1,2 1,4 1,6 C U SP N o C U SP
H e ight (m )
FEMAGSoft © 2012
PREDICTION OF CARBON CONCENTRATION ALONG THE HEIGHT OF THE CRYSTAL
PREDICTION OF RADIAL OXYGEN CONCENTRATION
Radial Oxygen Concent rat io H=840mm
8 7 6
8 7 6
Radial Oxygen Concent rat ion H=1070
Ox yge n ppm a
5 4 3 2 1 0 0 0,02 0,04 0,06(m ) Ra dius 0,08 0,1 C U SP N o C U SP
8 7 6
Ox yge n ppm a
C U SP 4 3 2 1 N o C U SP
Ox yge n ppm a
5
5 C U SP 4 3 2 1 N o C U SP
0 0 0,02 0,04
Ra dius (m )
0,06
0,08
0,1
0,12
0 0 0,02 0,04
Ra dius (m )
FEMAGSoft © 2012
CUSP vs NOCUSP - CARBON CONCENTRATION - CRYSTAL
FEMAGSoft © 2012
CUSP vs NOCUSP - PHOSPHOROUS CONCENTRATION-CRYSTAL
FEMAGSoft © 2012
CUSP vs NO CUSP - PHOSPHORUS RESISTIVITY - CRYSTAL
6 5 4 3 2 1 C U SP N o C U SP
6 5 4 C U SP 3 2 1 N o C U SP
0 0 0,02 0,04 0,06 0,08 0,1 0,12
0 0 0,02 0,04 0,06 0,08 0,1 0,12
Ra dius (m )
Ra dius (m )
FEMAGSoft © 2011
SIMULATION PROCESS
The growth process is modeled as Time dependent simulation taking in to account the transient effects taking place during the growth of the crystal
0,12
0
0,02
0,04
0,06
0,08
0,1
0,12
Ra dius (m )
Ra dius (m )
Radial Oxygen Concent rat ion H=430mm
9
Radial Oxygen Concent rat ion H=640mm
9 8
8 7
7
Ox yge n ppm a
Ox yge n ppm a
FEMAGSoft © 2011
0,06
0,08
0,1
0,12
FEMAGSoft © 2012
PREDICTION OF OXYGEN CONCENTRATION ALONG THE HEIGHT OF THE CRYSTAL
Oxygen Concent rat ion variat ion in a Vert ical Direct ion