+Kheel-2017-Hydrogen Gas Detecti
氢气泄漏检漏仪
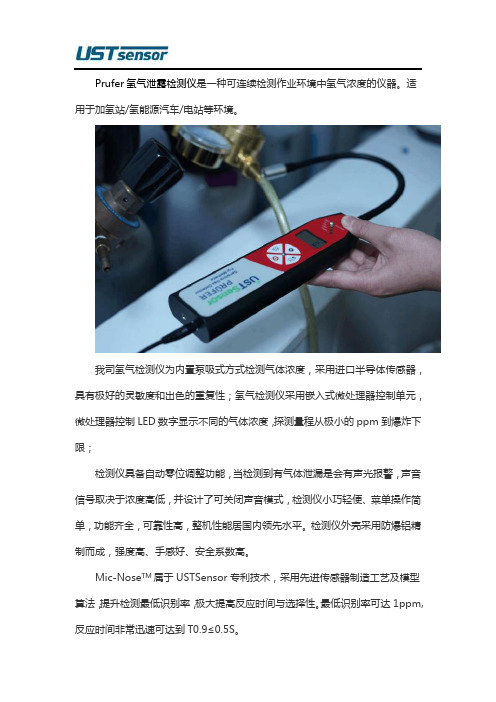
Prufer氢气泄露检测仪是一种可连续检测作业环境中氢气浓度的仪器。
适用于加氢站/氢能源汽车/电站等环境。
我司氢气检测仪为内置泵吸式方式检测气体浓度,采用进口半导体传感器,具有极好的灵敏度和出色的重复性;氢气检测仪采用嵌入式微处理器控制单元,微处理器控制LED数字显示不同的气体浓度,探测量程从极小的ppm到爆炸下限;
检测仪具备自动零位调整功能,当检测到有气体泄漏是会有声光报警,声音信号取决于浓度高低,并设计了可关闭声音模式,检测仪小巧轻便、菜单操作简单,功能齐全,可靠性高,整机性能居国内领先水平。
检测仪外壳采用防爆铝精制而成,强度高、手感好、安全系数高。
Mic-Nose TM属于USTSensor专利技术,采用先进传感器制造工艺及模型算法,提升检测最低识别率,极大提高反应时间与选择性。
最低识别率可达1ppm,反应时间非常迅速可达到T0.9≤0.5S。
检测仪配置有单独的充电器充电,内置电源组,续航时间可达连续操作8小时。
武汉优斯特致力于氢气安全检测,其中氢气检漏仪PRUFER广泛应用于氢能源各行业。
更多资讯及产品优惠报价请拨打电话沟通。
氢气泄漏探测仪器 标准

氢气泄漏探测仪器标准英文回答:Hydrogen gas leak detection instruments are essential for ensuring safety in various industries where hydrogen is used. These instruments are designed to detect the presence of hydrogen gas in the environment and alert users to potential leaks. There are several standards and requirements that these instruments must meet to ensure their effectiveness and reliability.One important standard for hydrogen gas leak detection instruments is their sensitivity. These instruments should be able to detect even the smallest concentrations of hydrogen gas in the air. For example, the instrument should be able to detect hydrogen gas at a concentration of 1% or lower. This is important because hydrogen gas is highly flammable and even small leaks can pose a significant risk.Another requirement for hydrogen gas leak detectioninstruments is their response time. These instruments should be able to quickly detect and alert users to the presence of hydrogen gas. For example, the instrument should be able to provide an alarm within seconds of detecting a leak. This is crucial for allowing users to take immediate action and prevent any potential accidents or hazards.Furthermore, hydrogen gas leak detection instruments should also be able to provide accurate and reliable readings. They should have a low rate of false alarms and be able to differentiate between hydrogen gas and other gases present in the environment. This is important to avoid unnecessary disruptions and ensure that users can trust the readings provided by the instrument.In addition to these technical requirements, hydrogen gas leak detection instruments should also be easy to use and maintain. They should have a user-friendly interface and clear instructions for operation. Regular calibration and maintenance should also be performed to ensure the accuracy and reliability of the instrument.中文回答:氢气泄漏探测仪器对于确保在使用氢气的各个行业中的安全至关重要。
海康威视CCTV摄像头用户手册说明书

Instrumentation Solutions for Hydrogen Applications Components and systems for use with gaseousand liquid hydrogen3ContentsOn-Board Vehicles - EC-79 Certified ComponentsApplications from 30 to 350 bar (435 - 5,076 psi) .................................................................................... 6 Two Ferrule Tube Fittings - A-LOK ® Series ............................................................................................ 6 Applications up to 700 bar (10,152 psi) ................................................................................................... 7 Medium Pressure Fittings - Cone and Thread - Autoclave Engineers ® ...................................................... 7 Medium Pressure Needle Valves SM Series - Autoclave Engineers ® ........................................................ 7 Medium Pressure Tubing - Autoclave Engineers ® . (7)ISO 19880-3 Certified Products for Hydrogen Refueling StationsMedium Pressure Needle Valves 20SM Series - Autoclave Engineers ® .................................................... 8 Medium Pressure O-Ring Check Valves CXO Series - Autoclave Engineers ® .. (8)General Hydrogen ApplicationsApplications up to 414 bar (6,000 psi)...................................................................................................... 10 Two Ferrule Tube Fittings - A-LOK ® Series ............................................................................................ 10 Ball Valves - B Series - Isolation and Directional Control Valves ............................................................... 10 Inline Filters - F Series ......................................................................................................................... 10 Check Valves - CO Series - Directional Control Valves ............................................................................ 11 Stream Switching Systems - R-Max TM Gen II Series ................................................................................ 11 Modular Sample Conditioning Systems - IntraFlow TM Series .................................................................... 11 Pressure Regulators - IR4000 and IR6000 Series ................................................................................... 11 Excess Flow Shutoff Valves - FS190 Series ............................................................................................ 11 Applications up to 1,380 bar (20,000 psi) ................................................................................................ 12 Medium Pressure Two Ferrule Inverted Tube Fittings - MPI TM Series ........................................................ 12 Medium Pressure Fittings - Cone and Thread - Parker Autoclave Engineers ® ........................................... 12 Permanent Ferrule-less Connectors - Phastite ® Series ........................................................................... 12 Ball Valves - Hi-Pro Series - Isolation Valves .......................................................................................... 12 Ball Valves - HB Series - Isolation Valves ............................................................................................... 12 Needle Valves MAN - MPI TM Series ....................................................................................................... 13 Medium Pressure Needle Valves 15SM and 20SM Series - Autoclave Engineers ® .................................... 13 Medium Pressure O-Ring Check Valves CXO Series - Autoclave Engineers ® ............................................ 13 Medium Pressure O-Ring Check Valves MAC - MPI TM Series ................................................................... 13 Double Block & Bleed Needle Type Manifold - 20DBNV Series - Autoclave Engineers ® ............................. 13 Relief Valves - Soft Seat RVS Series - Autoclave Engineers ® ................................................................... 14 Medium Pressure Tubing - MPI TM Series ................................................................................................ 14 Medium Pressure Actuators - Autoclave Engineers ® .............................................................................. 14 Medium Pressure Adapters - Autoclave Engineers ® ............................................................................... 14 Medium Pressure Accessories - Autoclave Engineers ® .. (14)Cryogenic/LH 2 ApplicationsGlobe Valves - Stainless Steel with Bronze Internals - Bestobell Industrial ................................................ 16 Globe Valves - Stainless Steel - Bestobell Marine .................................................................................. 16 Pneumatically Actuated Globe Valves - Stainless Steel with Bronze Internals - Bestobell Industrial ............. 16 Pneumatically Actuated Globe Valves - Stainless Steel - Bestobell Marine ............................................... 16 Lift Check Valves - Stainless Steel with Bronze Internals - Bestobell Industrial .......................................... 17 Lift Check Valves - Stainless Steel - Bestobell Marine ............................................................................. 17 Swing Check Valves - Stainless Steel - Bestobell Marine ........................................................................ 17 Manual Gate Valves - Bestobell Industrial . (17)Actuated Gate Valves - Pneumatic Tyre Design - Bestobell Industrial (17)Offer of SaleThe items described in this document are available for sale by Parker Hannifin Corporation, its subsidiaries or its authorized distributors. Any sale contract entered into byParker will be governed by the provisions stated in Parker’s standard terms and conditions of sale (copy available upon request).45Your Reliable Partner for Driving the Energy Evolution ForwardParker is supporting the global decarbonisation efforts through a broad range of solutions for a variety of applications. Our hydrogen-compatible components and systems enable safe and efficient operation from vacuum to 1,380 bar (20,000 psi) and temperatures from -253O C to +538O C (-423O F to +1000O F).1,380 BAR20,000 PSIParker’s needle valves 20SM series and check valves CXO series havesuccessfully passed all the required tests for high pressure gas valves used in gaseous hydrogen stations of up to the H70 designation specified in ISO19880-3 certification.ON-BOARD VEHICLESTwo Ferrule Tube Fittings - A-LOK ®Series EC-79 CertifiedParker Autoclave Engineers ®:Medium Pressure Fittings EC-79 Certified Needle Valves - SM Series EC-79 Certified Medium Pressure Tubing EC-79 CertifiedISO-CERTIFIED PRODUCTS FOR REFUELING STATIONSParker Autoclave Engineers ®:Needle Valves - 20SM Series Tests Passed - Pending Certification Check Valves - CXO Series Tests Passed - Pending CertificationGENERAL HYDROGEN APPLICATIONSTwo Ferrule Tube Fittings - A-LOK ® SeriesPermanent Ferrule-less Connectors - Phastite ® SeriesBall Valves - B Series Ball Valves - Hi-Pro Series Ball Valves - HB Series Inline Filters - F Series Check Valves - CO SeriesStream Switching Systems - R-Max IIModular Sample Conditioning Systems - IntraFlow TM SeriesPressure Regulators - IR4000 and IR6000 SeriesExcess Flow Shutoff Valves - FS190 SeriesCRYOGENIC/LH 2 APPLICATIONSBestobell Cryogenic Valves:Globe ValvesPneumatically Actuated Globe ValvesLift Check Valves Swing Check Valves Manual Gate Valves Actuated Gate ValvesGENERAL HYDROGEN APPLICATIONSParker Autoclave Engineers ®:Medium Pressure Fittings - Cone and Thread Needle Valves - 15SM and 20SM Series Check Valves - CXO SeriesDouble Block & Bleed Needle Type Manifold - 20DBNV Series Relief Valves - RVS SeriesMedium Pressure Accessories and Adapters Medium Pressure Actuators Medium Pressure MPI TM Series:Fittings TubingNeedle Valves - MAN Series Check Valves - MAC Series67Applications from 30 to 350 bar (435 - 5,076 psi)On-Board VehiclesComponents for on-board hydrogen-powered vehicles for pressures from 30 to 700 bar (435 to 10,152 psi).EC-79 CertifiedParker’s range of products approved for use on-board hydrogen-powered vehicles from 30 to 700 bar includes tube fittings, needle valves and tubing. These products meet the general requirements of hydrogen components and systems used on hydrogen-powered motor vehicles as per regulation (EC) No 79/2009 of The European Parliament and of The Council of 14 Jan 2009.Two Ferrule Tube Fittings - A-LOK ® Series EC-79 CertifiedParker A-LOK ® two ferrule tube fittings are designed to achieve quality leak-free connections on-board hydrogen-powered vehicles up to 350 bar pressures and temperatures down to -40O C. These fittings provide reliable operation in cryogenic, pressure & thermal cycling and vibration applications. Manufactured at an IATF 16949 certified plant and EC-79 approved for hydrogen service, they come in a range of sizes and configurations in 316 Stainless Steel material. For optimised installation instructions see p.18 of this catalogue.To order EC-79 certified components, simply add the suffix EC79 at the end of your part number.For more details please see catalogue ref. 4190-FMTG.Applications up to 700 bar (10,152 psi)*A-LOK ® tees and crosses approved in sizes up to 1/2” (12mm). Please contact Parker for further information.Medium Pressure Fittings - Cone and Thread - Autoclave Engineers ® EC-79 CertifiedParker Autoclave Engineers medium pressure cone and thread connections are designed for applications that require higher flow rate capability. Manufactured from high tensile strength cold worked 316/316L Stainless Steel material as standard for 700 bar (10,152 psi) MAWP , this Medium Pressure range has all the benefits of the High Pressure version with all metal sealing for operations at temperatures from -40O C to +120O C (-40O F to +248O F).These fittings are designed for use with Parker Autoclave Engineers’ 20SM Series valves and medium pressure tubing according to ASME B31.3 Chapter IX standards.To order EC-79 certified components, simply add the suffix EC79 at the end of your part number.For more details please see catalogue ref. 02-0124SE. Medium Pressure Tubing - Autoclave Engineers ® EC-79 CertifiedParker Autoclave Engineers offers a complete selection of austenitic, cold drawn stainless steel tubing designed to match the performance standards of Parker Autoclave valves and fittings. Parker Autoclave Engineers medium pressure tubing is manufactured specifically for high pressure applications requiring both strength and corrosion resistance.For more details please see catalogue ref. 02-0124SE.Medium Pressure Needle Valves SM Series - Autoclave Engi-neers ®EC-79 CertifiedParker Autoclave Engineers SM Series valves are designed specifically for use with matching orifice medium pressure cone & thread fittings and tubing for the most efficient flow path possible using cone & thread style connections. They are manufactured using high tensile strength UNS S31600/S31603 cold worked 316/316L Stainless Steel material as standard for 700 bar (10,152 psi) MAWP .To order EC-79 certified components, simply add the suffix HYGEC79 at the end of your part number.For more details please see catalogue ref. 02-0112SE.E C -79E C -79C E R T I FI E DE C -7989ISO Products For H 2 Refueling StationsComponents for hydrogen refueling stations for pressures up to 700 bar (10,152 psi).Tests Passed, Pending ISO 19880-3 CertificationMedium Pressure Needle Valves 20SM Series - Autoclave Engineers ®Tested, Pending ISO 19880-3 CertificationThese Parker Autoclave Engineers 20SM Series Needle Valves (HYG option) have unique STEM/SEAT and PACKING design that can withstand temperatures ranging between -73°C and 316°C and pressures of up to 700 bar (10,152 psi).The valves are available with two different styles of connection options including cone & thread and MPI TM .To order ISO 19880-3 certified components, simply add the suffix HYG at the end of your part number.For more details please see catalogue ref. 02-0112SE.Parker’s needle and check valves have successfully passed the required tests for high pressure valves used in gaseous hydrogen stations as specified in ISO 19880-3 certification. These are now awaiting thecompletion of the final steps towards achieving the certification.Medium Pressure O-Ring Check Valves CXO Series - Autoclave Engineers ®Tested, Pending ISO 19880-3 CertificationThese Parker Autoclave Engineers O-Ring Check Valves CXO Series (HYG option) canwithstand temperatures ranging between -73°C and 316°C and pressures of up to 1,380 bar (20,000 psi).The valves are available with two different styles of connection options including cone & thread and MPI TM .To order ISO 19880-3 certified components, simply add the suffix HYG at the end of your part number.For more details please see catalogue ref. 02-0124SE.HALS2VI S O 880-3Other associated products for hydrogen refueling stations are featured on the following pages.1011General Hydrogen ApplicationsComponents for general hydrogen applications at pressures from vacuum to 1,380 bar (20,000 psi).Parker offers an extensive range of high-quality components and system solutions suitable for general hydrogen use in a wide variety of industries including power generation, petrochemical, agricultural and research & development.Applications up to 414 bar (6,000 psi)®Ball Valves - B Series - Isolation and Directional Control ValvesNeedle Valves - V Series - Isolation and Flow Control ValvesCheck Valves - CO Series - Directional Control ValvesInline Filters - F SeriesStream Switching Systems - R-Max TMGen II SeriesModular Sample Conditioning Systems - IntraFlow TM SeriesPressure Regulators - IR4000 and IR6000 SeriesExcess Flow Shutoff Valves - FS190 Series(10,000 psi).** Material de-rating and media compatibility factors need to be taken into consideration for higher temperature applications.For optimised installation instructions see p.18 of this catalogue.1213Medium Pressure Needle Valves 15SM and 20SM Series - Autoclave Engineers ®Medium Pressure O-Ring Check Valves CXO Series - Autoclave Engineers ®Medium Pressure O-Ring Check Valves MAC - MPI TMSeriesNeedle Valves MAN - MPI TMSeriesBall Valves - HB Series - Isolation ValvesBall Valves - Hi-Pro Series - Isolation ValvesApplications up to 1,380 bar (20,000 psi)Medium Pressure Two Ferrule Inverted Tube Fittings - MPI TMMedium Pressure Fittings - Cone and Thread - Parker Autoclave®Permanent Ferrule-less Connectors - Phastite ®SeriesDouble Block & Bleed Needle Type Manifold - 20DBNV Series - Autoclave Engineers ®This valve has been modified for use with Hydrogen. To order, add the suffix HYG at the end of your part number.This valve has been modified for use with Hydrogen. To order, add the suffix HYG at the end of your part number.* Material de-rating and media compatibility factors need to be taken into consideration for higher temperature applications.* Material de-rating and media compatibility factors need to be taken into consideration for higher temperature and higher pressure applications. Refer to technical catalogue 02-0142SE.* Material de-rating and media compatibility factors need to be taken into consideration for higher temperature and higher pressure applications. Refer to technical catalogue 02-0142SE.This valve has been modified for use with Hydrogen. To order, add the suffix HYG at the end of your part number.This valve has been modified for use with Hydrogen. To order, add the suffix HYG at the end of your part number.This valve has been modified for use with Hydrogen. To order, add the suffix HYG at the end of your part number.1415Medium Pressure Accessories - Autoclave Engineers ®Medium Pressure Adapters - Autoclave Engineers ®Medium Pressure Actuators - Autoclave Engineers ®Medium Pressure Tubing - MPI TM SeriesADDITIONAL RESOURCES AVAILABLE ON /IPD›WHITE PAPER - ADDRESSING THE CHALLENGE OF HYDROGEN EMBRITTLEMENT IN METALLURGY ›BROCHURE - INSTRUMENTATION SOLUTIONS FOR HYDROGEN-POWERED VEHICLESRelief Valves - Soft Seat RVS Series - Autoclave Engineers ®This valve has been modified for use with Hydrogen. To order, add the suffix HYG at the end of your part number.* Material de-rating and media compatibility factors need to be taken into consideration for higher temperature applications.1617Cryogenic/LH 2 ApplicationsComponents for cryogenic/LH 2 applications at temperatures down to -253O C (-423O F) and pressures up to 50 bar (725 psi).Designed and engineered for use with Group 1 gases, Parker Bestobell’s valves are suitable for liquid hydrogen applications requiring temperatures as low as -253O C. All valves are pressure-tested prior to dispatch.To order, add the suffix -H at the end of your part number.Globe Valves - Stainless Steel with Bronze Internals - BestobellIndustrialGlobe Valves - Stainless Steel - Bestobell MarineLift Check Valves - Stainless Steel with Bronze Internals -Bestobell IndustrialLift Check Valves - Stainless Steel - Bestobell MarineSwing Check Valves - Stainless Steel - Bestobell MarineManual Gate Valves - Stainless Steel - Bestobell IndustrialActuated Gate Valves - Stainless Steel - Pneumatic Tyre Design- Bestobell IndustrialPneumatically Actuated Globe Valves - Stainless Steel withBronze Internals - Bestobell IndustrialPneumatically Actuated Globe Valves - Stainless Steel -Bestobell MarineAppendixA-LOK® tube fittings installation for hydrogen serviceParker has an improved and optimised installation procedure for its A-LOK® parts used inhydrogen service. Please follow the steps below for correct installation.1. The tube should be fully inserted into the shoulder of the fitting until full tube abutment isachieved.2. The nut should be advanced to the finger tight position and then be marked at the 6 o’clockposition.3. The nut should then be advanced 1 ½ turns with the appropriate wrench making sure aback-up wrench is used to hold the fitting body during the tightening process.4. The mark will now be at the 12 o’clock position.Once this has been achieved, the assembly will be ready to use in your Hydrogen system.For tube specifications, ordering information, preparation and pressure ratings, please referto the Parker Fittings, Materials and Tubing Guide catalogue ref. 4190-FMTG.18194190-HYD 03/22© 2022 Parker Hannifin Corporation Parker Hannifin Manufacturing Ltd.Instrumentation Products Division, Europe Riverside RoadBarnstaple EX31 1NP United Kingdomphone 0044 1271 /ipd Worldwide Division HeadquartersEuropean Product Information Centre Free phone: 00 800 27 27 5374(from AT, BE, CH, CZ, DE, DK, EE, ES, FI, FR, IE, IL, IS, IT, LU, MT, NL, NO, PL, PT, RU, SE, SK, UK, ZA)Europe, Middle East, AfricaAE – United Arab Emirates, DubaiTel: +971 4 8127100AT – Austria, St. Florian Tel: +43 (0)7224 66201 AZ – Azerbaijan, Baku Tel: +994 50 2233 458BE/NL/LU – Benelux, Hendrik Ido Ambacht Tel: +31 (0)541 585 000BY – Belarus, Minsk Tel: +48 (0)22 573 24 00CH – Switzerland, Etoy Tel: +41 (0)21 821 87 00 CZ – Czech Republic, PragueTel: +420 284 083 111DE – Germany, Kaarst Tel: +49 (0)2131 4016 0DK – Denmark, Ballerup Tel: +45 43 56 04 00ES – Spain, Madrid Tel: +34 902 330 001FI – Finland, Vantaa Tel: +358 (0)20 753 2500FR – France, Contamine s/Arve Tel: +33 (0)4 50 25 80 25GR – GreeceTel: +30 69 44 52 78 25HU – Hungary, Budaörs Tel: +36 23 885 470IE – Ireland, Dublin Tel: +353 (0)1 466 6370IL – IsraelTel: +39 02 45 19 21IT – Italy, Corsico (MI) Tel: +39 02 45 19 21KZ – Kazakhstan, Almaty Tel: +7 7273 561 000NO – Norway, Asker Tel: +47 66 75 34 00PL – Poland, Warsaw Tel: +48 (0)22 573 24 00PT – PortugalTel: +351 22 999 7360RO – Romania, Bucharest Tel: +40 21 252 1382RU – Russia, Moscow Tel: +7 495 645-2156SE – Sweden, Borås Tel: +46 (0)8 59 79 50 00SL – Slovenia, Novo Mesto Tel: +386 7 337 6649TR – Turkey, Istanbul Tel: +90 216 4997081UK – United Kingdom, Warwick Tel: +44 (0)1926 317 878ZA – South Africa, Kempton ParkTel: +27 (0)11 961 0700North AmericaCA – Canada, Milton, Ontario Tel: +1 905 693 3000US – USA, Cleveland Tel: +1 216 896 3000Asia PacificAU – Australia, Castle Hill Tel: +61 (0)2-9634 7777CN – China, Shanghai Tel: +86 21 2899 5000HK – Hong Kong Tel: +852 2428 8008IN – India, MumbaiTel: +91 22 6513 7081-85JP – Japan, Tokyo Tel: +81 (0)3 6408 3901KR – South Korea, Seoul Tel: +82 2 559 0400MY – Malaysia, Shah Alam Tel: +60 3 7849 0800NZ – New Zealand, Mt WellingtonTel: +64 9 574 1744SG – Singapore Tel: +65 6887 6300TH – Thailand, Bangkok Tel: +662 186 7000TW – Taiwan, Taipei Tel: +886 2 2298 8987South AmericaAR – Argentina, Buenos Aires Tel: +54 3327 44 4129BR – Brazil, Sao Jose dos CamposTel: +55 080 0727 5374CL – Chile, Santiago Tel: +56 22 303 9640MX – Mexico, Toluca Tel: +52 72 2275 4200Parker Hannifin CorporationInstrumentation Products Division 1005 A Cleaner Way Huntsville AL 35805 USAphone 001 (256) 881 /ipd。
哈姆尔曼高压注射泵商品介绍说明书

Injection pumpsMethanolLDHIGlycolwww.process-pumps.deHammelmann offer a wide rangeof high pressure pumps for thechemical, oil and gas industries.Visit our website.Asphaltene InhibitorParaffin InhibitorCorrosion InhibitorScale Inhibitor INNOVATION THROUGH EXPERIENCEHammelmann Injection PumpsCalder offer a wide range of highpressure pump packages incorporatingHammelmann pumps for the chemical,oil and gas industries.Visit our website.www.process-pumps.deLabyrinth sealThis seal design which is absolutely unique to Hammelmann enables safe, reliable, continuous duty operation at pressures up to 3800 bar.The high pressure seal is formed within the minute cylindrical gap between the plunger and the labyrinth insert. The medium pressure is continuously reduced along the sealing surface.A minimum amount of high pressure leakage serving as lubricant is returned to the pump suction chamber.Exclusive sealing systemThe plunger connection to thepower end is self centering thereby drastically reducing sideways forces. This design ensures that there is virtually no contact between the plunger and the labyrinth insert resulting in extremely low component wear.When the pump unit is shut down the medium remains in thecylindrical gap so that a re-start,even after an extended shut down period is assured.Wear at the high pressure seal components does not lead to an abrupt breakdown of the pump but rather a gradual decrease in the flow rate. If the pump is driven in a control loop the r.p.m. of the driver will increase in direct proportion to component wear.S p e e dThe running speed of the pump is a direct indicator of the extent of wear.This enables long term planning of maintenance intervals and targeting ofspecific servicing tasks.We manufacture extremely compact Triplex and Quintuplex pump units for injection of Methanol, LDHI,Glycol and a range of inhibitors.Hammelmann high pressure pump units in the pressure range up to 15,000 psi (1035 bar) havedeveloped into the standard choice for offshore methanol injection applications with a reputation for extreme reliability and minimal maintenance requirements.Compact constructionExtensiveperformancerangeWith both Triplex andQuintuplex pumpsavailable we cansupply a veryextensive range offlow rates andoperating pressures.Power ratingsup to 1000 HPup to 750 kWFlow ratesup to 530 gpmup to 2000 l/minOperating pressuresup to 55,000 psiup to 3800 barHammelmann pumps producemaximum performance from aminimal footprint which is the resultof combining a compact integralspeed reduction gear end with theconcept of a vertical configuration.The vertical configuration channelsoscillating forces directlydownwards into the base structure.Unwanted lateral oscillations asproduced by horizontal pumps donot occur.The integral speed reducer with twinhelical gears arranged in a herringbone configuration ensures smoothrunning and even powertransmission without axially loadingthe bearings.A selection of gear ratios isavailable to allow the optimal choiceof driver. The compact constructioneliminates the need for an externalgear box and prevents rotaryoscillation. Mechanical efficiency isin excess of 95%.Industrial pumps, series 2ValvesThe suction valve (below) is a discring design incorporating a onepiece suction and discharge valveseat.FeaturesSeries 2 pumps employ the sameprecision engineered, field provencomponents as Hammelmannstandard production pumps. Theyare extremely compact with lowmaintenance costs and highoperational efficiency.Plunger speedUnitsOur high pressure pump units canbe supplied with electric motor, achoice of controls, safety valves andsuction side/discharge sidepulsation dampers.HDP 752HDP 482HDP 362HDP 252HDP172HDP 122HDP 72HDP 42HDP 2200,20,40,60,81,01,21,4Plunger speed m/sec1,61,8Moderate plunger speeds result inlow plunger and sealing elementwear characteristics.OUTINSealmonitoringsystemSeal monitoringThe condition of the low pressureseals may be monitored by installingan optional sealmonitoring system.MaintenancePump maintenance is carried outfrom above. Once the pump head isremoved you have complete,uncomplicated access to all highpressure components.Pump headThe total pressurised fluid productof the individual cylinders collectswithin a single high pressuredischarge bore within the pumphead valve block. The coaxial valvearrangement eliminates alternatingstress within the valve block.Suction chamberThe process fluid enters the pumpvia the suction chamber. Thistotally encloses the high pressurecomponents in a protective barrierand prevents emission of mediumto atmosphere.5,000 psi345 bar 10,000 psi 690 bar 15,000 psi 1035 bar Crankspeed HDP 22 D 20 D 15 D 12750 rpm 5 gpm 19l/min 2.6 gpm 10 l/min 1.6 gpm 6 l/min HDP 42 D 35 D 26 D 20750 rpm 15 gpm 60 l/min 8 gpm 31 l/min 4.7 gpm18 l/min HDP 72D 35 D 26 D 22750 rpm 21 gpm 80 l/min 11 gpm 42 l/min 7.4 gpm 28 l/min HDP 122 D 55 D 35 D 30530 rpm 50 gpm 192 l/min 19 gpm 74 l/min 13 gpm 51 l/min HDP 172 D 50 D 35 D 30555 rpm 61 gpm 232 l/min 28 gpm 108 l/min 20 gpm 75 l/min HDP 252 D 50 D 35 D 30555 rpm 102 gpm 387 l/min 47 gpm 181 l/min 32 gpm 124 l/min HDP 362 D 80 D 60 D 45490 pm 138 gpm 525 l/min 74 gpm 282 l/min 38 gpm 146 l/min HDP 482 D 80D 60 D 45465 rpm 171 gpm650 l/min92 gpm 349 l/min 47 gpm 181 l/min HDP 752D 80D 60D 45465 rpm285 gpm 1080 l/min159 gpm603 l/min79 gpm302 l/minPerformance data, Industrial pumps, series 2(Selection)Pos.Part name Pos.Part name 1Discharge valve 8Low pressure seal pack 2Valve housing 9Bellow 3Suction valve 10Crosshead4Suction chamber 11Connection rod 5Sleeve 12GearHDP 22/42: belt drive 6Labyrinth insert 13Crank shaft7Plunger14Crank section housing1234567891011121314Recommendations and standardsEU Machine directive 98/37/ EU ATEX 94/9/EUAPI 674 (with exceptions)Technical data, Industrial pumps, series 2Standard Option PlungerLabyrinth insert Ceramic Bronze-Valve housing 17% Chromium steel22% Duplex steelSealsNBR / PolyamideFKM / PEEK Suction chamberBronze18 – 10Chromium Nickel steel* Right reserved to make technical modificationsWetted parts materials *Gas tight designThe intermediate chamber of the pump can be outfitted with gas tight covers which provide a seal to atmosphere. The chamber is then charged with inert gas.This design ensures that no fluids, vapours or gases can escape to atmosphere via a worn plunger seal.1 = Priming valve2 =Safety valve3=Pressure regulating valveBellows systemThe bellows are the hermetic seals for the power end to prevent the intrusion of fluid or gas. They are available in FKM, H-NBR and PTFE.Process pumps, series 5ValvesTo ensure that the pumpconstructíon is appropiate for the pumped medium we have a number of alternative valve designsavailable. In the example shown below the suction and discharge valves are conical. The suction and discharge valve seats are combined in one component.FeaturesSeries 5 pumps are built to the highest standards of safety and reliability. We can supplycomponents from a wide range of materials to suit the pumped medium.Our latest variation of this pump series is the Zero emission where the pumped fluid is hermetically sealed within the pump, preventing leakage to atmosphere during operation.Plunger speedUnitsYour complete pump unit can be outfitted with suction and/or discharge pulsation dampersdimensioned, manufactured, tested and certified to your specification.1,4HDP 755HDP 485HDP 365HDP 255HDP 175HDP 125HDP 75HDP 45HDP 2500,20,40,60,81,01,2Plunger speed m/secInert gasOUTINThe series 5 pumps areconservatively rated for power with low plunger speeds ensuring limited wear of plungers and sealing elements.32Seal monitoring 11Performance data, Process pumps, series 5 (Selection)5,000 psi345 bar 10,000 psi 690 bar 15,000 psi 1035 bar Crank speed HDP 25 D 20 D 15 D 12420 rpm 2.9 gpm 11 l/min 1.5 gpm 6 l/min 0.9 gpm 3,5 l/min HDP 45 D 35 D 26 D 20500 rpm 10 gpm 40 l/min 5 gpm 20 l/min 3 gpm 12 l/min HDP 75 D 35 D 26 D 22490 rpm 13 gpm 52 l/min 7 gpm 28 l/min 5 gpm 19 l/min HDP 125 D 55 D 35 D 30365 rpm 35 gpm 133 l/min 13 gpm 51 l/min 9 gpm 35 l/min HDP 175 D 50 D 35 D 30385 rpm 42 gpm 160 l/min 19 gpm 74 l/min 13 gpm 52 l/min HDP 255 D 50 D 35 D 30390 rpm 71 gpm 270 l/min 33 gpm 126 l/min 23 gpm 87 l/min HDP 365 D 80 D 60 D 45340 rpm 95 gpm 363 l/min 51 gpm 194 l/min 26 gpm 101 l/min HDP 485 D 80 D 60 D 45365 rpm 137 gpm 520 l/min 73 gpm 279 l/min 38 gpm 145 l/min HDP 755D 80D 60D 45365 pm229 gpm867 l/min127 gpm483 l/min63 gpm242 l/minD = Piston dia [mm]1234567891011121314Technical data, Process pumps, series 5Wetted parts materials *Recommendations and standardsEU Machine directive 98/37/ EUATEX 94/9/EUAPI 674 (with exceptions)Other customer specified standards, i.e.NORSK M501NORSOK M650NACE MR 0175Pos.Part name Pos.Part name 1Discharge valve 8Low pressure seal pack 2Valve housing 9Bellows 3Suction valve 10Crosshead4Suction chamber 11Connection rod 5Sleeve 12GearHDP 25/45: belt drive 6Labyrinth insert 13Crank shaft7Plunger14Crank section housingStandardOptionPlungerLabyrinth insert Ceramic BronzeTungsten carbide Tungsten carbide Valve housing 22% Duplex steel25% Super duplex steel SealsNBR / PolyamideFFKM / PEEKSuction chamber 18–10 Chromium Nickel steel 25% Superduplex steel * Right reserved to make technical modificationsRound the clock operationThe compact design ofHammelmann pumps is a space saving advantage for installation on offshore platforms and FPSO’s.They are increasingly specified as the pumps of choice for offshore installations.02/09© Copyright Hammelmann Maschinenfabrik GmbH, Oelde, Germany. Right reserved to make technical modificationsAgbami Aker 1-6Allegheny Anna Platform Atlantis Auger Auger Apit Baton Rouge Black Widow BrazilBrutus/Glider BS4Cabida Block Canyon Express Conger Salsa Demos ForvieGarden Banks Garnet Gjoa Semi Groupo R Hickory HolsteinHorn Mountain HoumaIndep. Hub 3IndpendenceK2 Green Canyon K-FelsKikeh-Gusto King Kong Kings PeekKristin Longhorn Mad Dog Magnolia Marco Polo Max-Stena-Drill Mobile Rig Morvin Asgard Neptune Nile NoonanNorse Marchand Panama City Pegasus Perdido Petrorig Producer Scarebo Schahin SevanS. Timbalier Statfjord B & C Tahiti Talisman Tanzanite Tarantula TMT 1TyphonUrsa-Princess Valifornia West EdrillHDP 72 unit for methanol duty Op. pressure 12,000 psi – 830 bar Flow rate 6 gpm – 24 l/minHDP 555 pump unit for glycol and methanol dutyOp.pressure 10,700 psi – 740 bar, Flow rate 87 gpm – 333 l/minHDP 115 units for methanol duty Op. pressure 15,000 psi – 1035 bar Flow rate 1.5 gpm – 6 l/minHDP 122 unit for LDHI dutyOp. pressure 15,000 psi – 1035 bar Flow rate 7 gpm – 28 l/minHDP 175 units for methanol duty Op. pressure 5,300 psi – 370 bar Flow rate 46 gpm – 176 l/minHammelmannMaschinenfabrik GmbH Zum Sundern 13-2159302 Oelde – Germany Tel. +45 2522 760Fax +49 2522 76444******************www.hammelmann.deCalder Ltd.Gregory's Bank Worcester WR3 8ABUnited Kingdom Phone: 0044 1905 723 255Fax: 0044 1905 723 904***************.uk Calder Ltd.Gregory’s Bank Worcester WR3 8AB United KingdomPhone: 0044 1905 723 255Fax: 0044 1905 723 904***************.uk The compact design of Calder pump packages incorporatingHammelmann pumps, offers a space saving advantage for installation on offshore platforms and FPSO’s. They are increasingly specified as the pumps of choice for offshore installations.。
米格尔氢气检测性能对比表
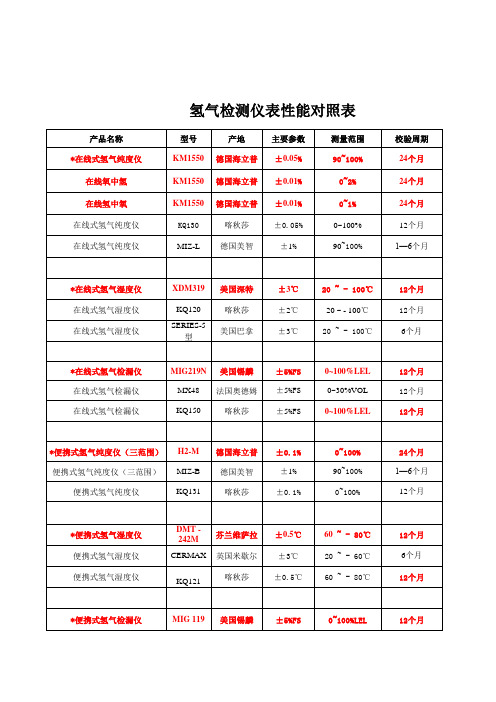
*在线式氢气湿度仪 在线式氢气湿度仪 在线式氢气湿度仪
XDM319 KQ120 SERIES-5型
美国深特 喀秋莎 美国巴拿
± 3℃ ±2 ℃ ±3 ℃
20 ~ - 100℃ 20 ~ - 100℃ 20 ~ - 100℃
12个月 12个月 6个月
*在线式氢气检漏仪 在线式氢气检漏仪 在线式氢气检漏仪
氢气检测仪表性能对照表
产品名称 *在线式氢气纯度仪 在线氧中氢 在线氢中氧 在线式氢气纯度仪 在线式氢气纯度仪 型号 KM1550 KM1550 KM1550 KQ130 MIZ-L 产地 德国海立普 德国海立普 德国海立普 喀秋莎 德国美智 主要参数 ±0.05% ±0.01% ±0.01% ±0.05% ±1 % 测量范围 90~100% 0~2% 0~1% 0~100% 90~100% 校验周期 24个月 24个月 24个月 12个月 1—6个月
12个月 6个月 12个月
*便携式氢气检漏仪
MIG 119
美国锡麟
±5%FS
0~100%LEL
12个月
便携式氢气检漏仪 便携式氢气检漏仪
TX11 KQ151
法国 奥德姆 喀秋莎
±5%FS ±5%FS
0~30%VOL 0~4%VOL
12个月 12个月
带*为我公司仪表
郑州米格尔电子有限公司
备注 免费提供备机 免费提供备机 免费提供备机 不提供备机 不提供备机
MIG219N MX48 KQ150
美国锡麟 法国奥德姆 喀秋莎
±5%FS ±5%FS ±5%FS
0~100%LEL 0~30%VOL 0~100%LEL
12个月 12个月 12个月
*便携式氢气纯度仪(三范围) 便携式氢气纯度仪(三范围) 便携式氢气纯度仪
金属探测器成为水海产品的关键控制点

金属探测器成为水海产品的关键控制点Ting Bao was revised on January 6, 20021分拣整理装模冷冻至-18°C以下冻块脱模检重秤金属探测/ X射线检装箱入库金属探测器成为水海产品的关键控制点赛默飞世尔科技公司胡阶明目前,一些国家已将HACCP即危害分析与关键控制点(Hazard Analysis Critical Control Point)列人法规强制性实施,在对进口部分水产品实行的先检验后通关、对冷冻水产品进行的金属异物检测已成为关键控制点。
一旦检出金属异物,全部货物将予以返运或销毁。
企业为进入国际市场取得绿色通行证,对于HACCP 保证体系的实施也日益重视。
高效、稳定的金属检测机成为含有金属杂质的肉、禽、蔬菜及海产品罐头流向市场的一道坚固的屏障,有力地保障了食品的安全。
金属异物主要来自于捕鱼过程中的鱼钩和金属丝等;在切割、除去鱼刺等加工过程中由于采用金属件,难免使金属片断在鱼的体内。
每一次客户投诉都要耗费大量的人力物力,有时是直接的经济处罚,更严重的是退货。
所有这些偶然事件让企业失去的却是客户的信任。
在商务部发布的《出口商品技术指南——水海产品》中(附件一,出口鱼类产品安全指标技术指南中的)明确指出“每件包装均应通过金属探测器检查。
一般水海产品冷冻加工过程如下,最为关键点在于检测金属异物和净重检测。
以罐头出口的水海产品加工企业,由于包装为金属材质,因此以X射线检测系统取代金属探测器。
Thermo Scientific的Apex 500在客户测试中胜出青岛某大型海产品加工企业原先采用普通的金属探测器。
产品在出口过程中,存在着对金属异物不同检测标准而受到阻碍。
买方对所提供海产品中的金属异物,提出更严格的检测性能和指标。
原来要求控制检测灵敏度为:铁,非铁,不锈钢304为3mm直径球体。
伴随产品本身干扰、车间潮湿、温度变化以及电气等环境干扰,检测灵敏度会大打折扣,灵敏度不稳定和设备正常使用周期短、维护量大,由此给质量管理带来了很多困难。
哈希产品样本
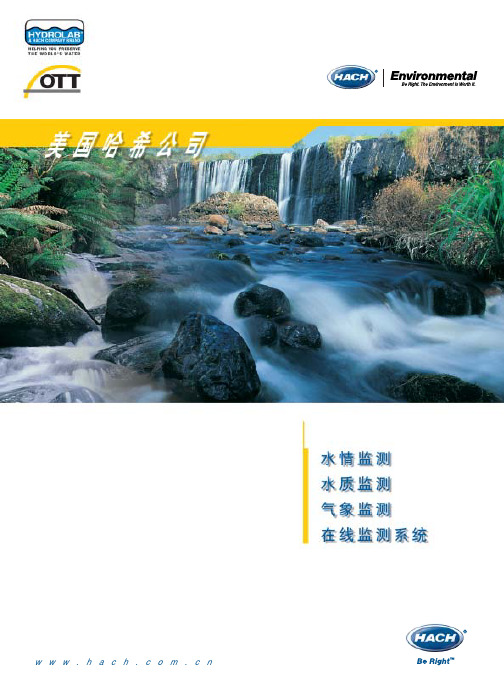
■ RS232/SDI 12:
通过 VOTA 多功能单元或笔记本 电脑进行数据通讯(数据读取,参数 化)与多种数据传输接口,如: - 串口连接调制解调器(GSM 或 landline) - 微波,卫星等
NIMBUS 对于个别测量点的单独测量 可在现场完成。
应用范例
除了常规应用外,Kalesto 还用于以下场合: 咸水,排水沟,波浪起伏比较大的河流 -不接触测量介质 灌溉渠道等 -可通过一伸出臂进行简单的安装 含有大量悬浮物的河流,山间小溪,干涸的河流等 -不受淤泥的影响; -当河流测量断面变化时(低流量),相对于在监测室内的仪器以及需在测井中或管道中工作的仪器来说传感器移动更方便。
■ 即使在盐水或受污染水 体中,非直接的气泡测 量原理也能提供准确的 读数和长期的稳定性。 每次测量前能自动进行 零点校正。
·2·
水位监测
<MIDI>防护外壳 防护外壳用来保护
NIMBUS感应卡和充气装 置并且辅助墙壁安装程序
■ 红外数据接口 - 通过 VOTA 多功能单元,笔记 本电脑和掌上电脑进行现场数据 读取和参数设置 - 对湿度和灰尘不敏感 - 易于操作
0.3 mA 通常 180mA,最大 350mA 最大 100m 238mm × 62mm × 100mm 约 0.860kg -20 - 60℃
·4·
水位监测
OTT Kalesto
Kalesto 雷达液位计是一种先进的测量地表水位的新型测量方法,它在水文野外测量中具有 许多优点。Kalesto 是 OTT 公司生产的独特的非接触式水位测量仪。该传感器安装方便、空间占 有率低,所耗时间和金钱都很少,性价比好,设计紧凑,不与水面接触。Kalesto 在测量中不受 高水位,淤泥,水上垃圾,植物生长等因素的影响,免维护。
朴克汤森公司氢流泵 动力分区绿兰维尔,特拉加州 37745 美国 PVP 60 76 可变体力泵系列

Standard Pump AssemblyNOTE:This exploded view is of a PVP 60/76. For all practical purposes it may be used as a guide to determine PVP Series components.Use of a Relief ValveThe use of a relief valve, while not mandatory is recommended in the main circuit to suppress hydraulic shock loads and adds additionalsystem protection.Fluid RecommendationsPremium quality hydraulic oil with a viscosity range between 150-250 SSU (30-50 cst.) at 38°C (100°F). Normal operating viscosity range between 80-1000 SSU (17-180 cst.). Maximum start-up viscosity is 4000 SSU (1000 cst.).NOTE:Consult Parker when exceeding 71°C (160°F) Inlet Fluid Temperatures. Oil shouldhave maximum anti-wear properties, rust and oxidation treatment.FiltrationFor maximum pump and system component life,the system should be protected from contamination ata level not to exceed 125 particles greater than10 microns per milliliter of fluid. (SAE Class 4/ISO16/13.) Due to the nature of variable displacement pumps, variations in pump inlet conditions, fluid acceleration losses, system aeration, and duty cycle we do not recommend suction line filters. We do recommend the use of a properly sized, in-tank, suction strainer. Contact your Parker representative for assistance.Start-UpOn initial start-up, the case should be filled with oil, pressure adjustments should be reduced and the circuit should be open to permit priming.Inlet ConditionsNot to exceed .17 bar (5 In. Hg.) Vacuum at 1800 RPM on petroleum base fluids. See recommended speed spectrum for specific inlet conditions.Shaft Rotation and Line UpPump and motor shaft alignment must be within.010 TIR maximum, using a standard floating coupling. Please follow coupling manufacturer’s recommended installation instructions to prevent end thrust on pump shaft. Turn pump to assure freedom of rotation. Pump and motor must be on a rigid base. The coupling should be sized to absorb the peak horsepower developed.Installation and MountingWhen mounting a PVP Series Pump, the “case drain”must be on top of the pump. The “case drain” should be a separate line unrestricted to the reservoir and extend below the oil level as far from the inlet lineas possible. The “case drain” line must not exceed .7 bar (10 PSI) back pressure. Suggested maximum line length is 10 feet.Special InstallationsConsult your Parker representative for any application requiring the following:Pressure above rated, drive speed above maximum, indirect drive, fluid other than petroleum oil, oil temperature above 71°C (160°F).Inlet PressureNot to exceed 1.72 bar (25 PSI).。
氢气泄漏探测仪器 标准
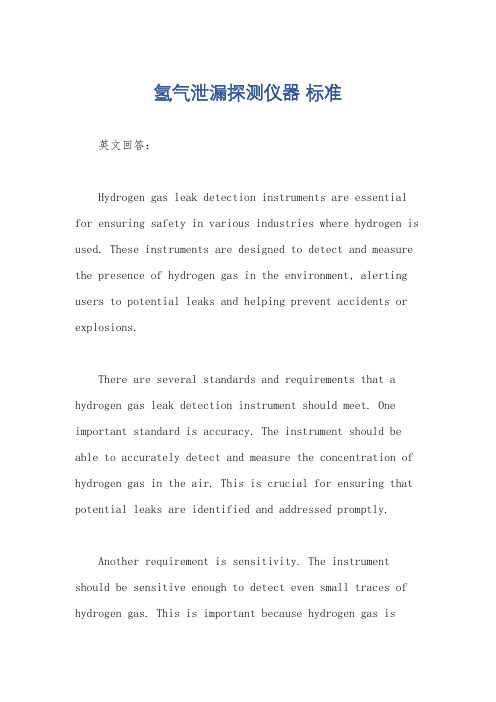
氢气泄漏探测仪器标准英文回答:Hydrogen gas leak detection instruments are essential for ensuring safety in various industries where hydrogen is used. These instruments are designed to detect and measure the presence of hydrogen gas in the environment, alerting users to potential leaks and helping prevent accidents or explosions.There are several standards and requirements that a hydrogen gas leak detection instrument should meet. One important standard is accuracy. The instrument should be able to accurately detect and measure the concentration of hydrogen gas in the air. This is crucial for ensuring that potential leaks are identified and addressed promptly.Another requirement is sensitivity. The instrument should be sensitive enough to detect even small traces of hydrogen gas. This is important because hydrogen gas ishighly flammable and even a small leak can be dangerous. The instrument should be able to detect hydrogen gas at levels that are below the lower explosive limit (LEL).Reliability is also a key requirement. The instrument should be reliable and provide consistent and accurate readings over time. It should be able to withstand harsh environmental conditions and continue to function effectively. Regular calibration and maintenance are necessary to ensure the reliability of the instrument.Ease of use is another important factor. The instrument should be user-friendly and easy to operate. It should have clear and intuitive controls, and the readings should be easy to interpret. Training and instructions should be provided to users to ensure proper use of the instrument.In addition to these technical requirements, there may be specific industry standards or regulations that need to be followed. For example, in the oil and gas industry, there may be specific requirements for hydrogen gas leak detection instruments to ensure the safety of workers andfacilities.Overall, a hydrogen gas leak detection instrumentshould meet standards for accuracy, sensitivity,reliability, and ease of use. By meeting these requirements, the instrument can effectively detect and alert users to potential hydrogen gas leaks, helping to ensure safety in various industries.中文回答:氢气泄漏探测仪器对于确保使用氢气的各个行业的安全至关重要。
便携式二恶英化合物测定仪[实用新型专利]
![便携式二恶英化合物测定仪[实用新型专利]](https://img.taocdn.com/s3/m/63dd20e7bed5b9f3f80f1cab.png)
专利名称:便携式二恶英化合物测定仪专利类型:实用新型专利
发明人:吴文忠,徐盈,霍任锋
申请号:CN00232478.4
申请日:20001123
公开号:CN2460994Y
公开日:
20011121
专利内容由知识产权出版社提供
摘要:本实用新型公开了一种便携式二恶英化合物快速测定仪,它由信号记录与放大器和免疫传感器构成,免疫传感器通过导线经电讯接口与信号记录与放大器相连,免疫传感器一端电极表面涂有薄层,在薄层依次涂在裸露的固体电极上,薄层上有一层聚合吡咯,在聚合吡咯上固定二恶英抗体。
本实用新型结构简单,操作方便,成本低,能快速灵敏可以连续、在线的进行二恶英检测的分析测试。
申请人:中国科学院水生生物研究所
地址:430071 湖北省武汉市武昌珞珈山
国籍:CN
代理机构:武汉科宏专利事务所
代理人:王敏锋
更多信息请下载全文后查看。
使用电化学气体传感器测量湿度的方法和装置[发明专利]
![使用电化学气体传感器测量湿度的方法和装置[发明专利]](https://img.taocdn.com/s3/m/d2bd7df0866fb84ae55c8db5.png)
专利名称:使用电化学气体传感器测量湿度的方法和装置专利类型:发明专利
发明人:基思·普拉特,汤姆·戈德
申请号:CN202010267142.X
申请日:20200407
公开号:CN111796007A
公开日:
20201020
专利内容由知识产权出版社提供
摘要:本发明题为“使用电化学气体传感器测量湿度的方法和装置”。
本发明公开了一种用于使用电化学气体传感器来测量湿度的气体检测装置和方法。
气体检测装置包括基于电解质的电化学气体传感器和被配置成测量一段时间内周边环境内的平均湿度值的控制器。
时间段内的平均环境湿度值基于该时间段内的气体检测装置的电解质气体传感器内的电解质浓度随时间段的平均变化速率和该时间段内的周边环境中的平均温度来测定。
气体感测装置可被配置成将周边环境内的平均环境湿度值传送至相同周边环境内的第二电化学气体传感器或第二气体检测装置。
申请人:霍尼韦尔国际公司
地址:美国新泽西州
国籍:US
代理机构:中国专利代理(香港)有限公司
代理人:陈岚
更多信息请下载全文后查看。
制氢装置国内外对比

制氢装置国内外对比制氢装置这个话题,哎呀,可真是个热门话题。
想想吧,氢气不仅是个小家伙,轻得像羽毛,还能成为未来能源的“明星”。
国内外对这玩意儿的研究和发展,那可是一场精彩的对决,简直是“你追我赶”,热闹得很。
先说说国外的那些老大哥们。
美国、德国、日本等国家,在这方面可谓是走在了前头。
他们的制氢技术就像一部好莱坞大片,特效满满,创意无限。
比如,美国的制氢装置,基本上是靠电解水的方法,利用清洁能源,嘿,这样既环保又省心。
德国呢,更是玩得高端,居然把风能、太阳能都用上了,真是好花招!人家甚至还有个“氢能战略”,目标明确,搞得很有计划。
日本也不甘示弱,他们在氢能的储存和运输上,简直是妙手生花,搞出了一些小黑科技,令人眼前一亮。
想想都觉得,国外的制氢装置就像是参加奥运会,实力强劲,频频夺金。
可别以为国内的技术就差了,嘿嘿,咱们可是一点也不逊色!在制氢方面,咱们最近可是发力十足。
尤其是电解水制氢这块,技术上是逐渐成熟。
很多地方已经开始建设大规模的制氢设施,真是像春笋般冒出来。
咱们的制氢装置也有自己独特的魅力。
比如,国内很多企业瞄准了生物质制氢,利用农业废弃物来生产氢气,既环保又节约,真是两全其美。
说到这里,心里不禁感慨,咱们的智慧也是杠杠的,绝对不容小觑。
说到制氢装置的效率,国外的一些技术确实高得让人咋舌,简直就是“牛气冲天”。
但是国内也在不断追赶,努力提升效率。
有些小企业也在玩创新,搞一些小型化的制氢装置,方便灵活。
嘿,这种“灵活机动”的打法,倒是有点“见缝插针”的意思。
大家都知道,氢气是个好东西,能做燃料电池,能做汽车动力,能用于工业,这个市场潜力可是大得很。
想想未来,氢气车在街上跑,路边充氢站一字排开,场面简直太美妙了!不过,制氢装置可不只是技术上的比拼,还牵扯到和市场环境。
国外的相关部门往往会给点支持,像是打了一针“强心剂”,这可真是让企业如虎添翼。
而国内这方面的也在不断优化,虽然起步稍晚,但势头也不小。
氢水祛除自由基检测报告(一)
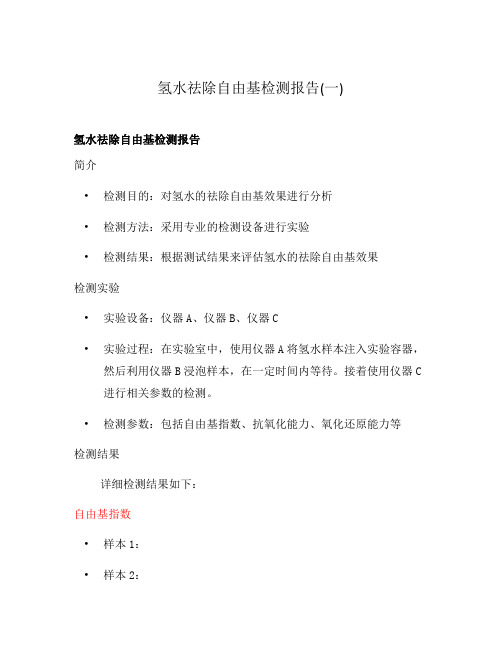
氢水祛除自由基检测报告(一)
氢水祛除自由基检测报告
简介
•检测目的:对氢水的祛除自由基效果进行分析
•检测方法:采用专业的检测设备进行实验
•检测结果:根据测试结果来评估氢水的祛除自由基效果
检测实验
•实验设备:仪器A、仪器B、仪器C
•实验过程:在实验室中,使用仪器A将氢水样本注入实验容器,然后利用仪器B浸泡样本,在一定时间内等待。
接着使用仪器C 进行相关参数的检测。
•检测参数:包括自由基指数、抗氧化能力、氧化还原能力等
检测结果
详细检测结果如下:
自由基指数
•样本1:
•样本2:
•样本3:
抗氧化能力
•样本1:良好
•样本2:优秀
•样本3:良好
氧化还原能力
•样本1:高
•样本2:中
•样本3:低
结论
•根据自由基指数的结果,可以得出样本2的祛除自由基效果最好,样本1次之,样本3最差。
•抗氧化能力方面,样本2是最优秀的,样本1和样本3良好。
•在氧化还原能力上,样本1表现出较高的能力,样本2次之,样本3最低。
综合上述结果,可以得出样本2的氢水祛除自由基效果最好,建
议用户选择样本2进行使用。
- 1、下载文档前请自行甄别文档内容的完整性,平台不提供额外的编辑、内容补充、找答案等附加服务。
- 2、"仅部分预览"的文档,不可在线预览部分如存在完整性等问题,可反馈申请退款(可完整预览的文档不适用该条件!)。
- 3、如文档侵犯您的权益,请联系客服反馈,我们会尽快为您处理(人工客服工作时间:9:00-18:30)。
Met. Mater. Int., Vol. 23, No. 1 (2017), pp. 214~219doi: 10.1007/s12540-017-6343-3Hydrogen Gas Detection of Nb2O5 Nanoparticle-Decorated CuONanorod SensorsHyejoon Kheel1, Gun-Joo Sun1, Jae Kyung Lee1, Ali Mirzaei2, Seungbok Choi3, and Chongmu Lee1,*1Department of Materials Science and Engineering, Inha University, Incheon 22212, Republic of Korea 2Department of Materials Science and Engineering, Shiraz University, Shiraz, Iran 3Department of Mechanical Engineering, Inha University, Incheon 22212, Republic of Korea(received date: 16 May 2016/accepted date: 29 June 2016)Pristine and Nb2O5 nanoparticles-decorated CuO nanorods were prepared successfully by a two step process: thethermal evaporation of a Cu foil and the spin coating of NbCl5 solution on CuO nanorods followed by thermalannealing. X-ray diffraction was performed to examine the structure and purity of the synthesized nanoatuc-tures. Scanning electron microscopy was used to examine the morphology and shape of the nanostuctures. TheNb2O5 nanoparticles-decorated CuO nanorod sensor showed responses of ~217.05-862.54%, response timesof ~161-199s and recovery times of ~163-171 s toward H2 gas with concentrations in a range of 0.5 - 5%at the optimal working temperature of 300°C. The Nb2O5 nanoparticle-decorated CuO nanorod sensor showedsuperior sensing performance to the pristine CuO nanorod sensor for the same H2 concentration range. Theunderlying mechanism for the enhanced hydrogen sensing performance of the CuO nanorods decoratedwith Nb2O5 nanoparticles is discussed.Keywords: semiconductors, nanostructured materials, oxidation, electrical properties, scanning electron microscopy(SEM)1. INTRODUCTIONAs an attractive energy source, hydrogen (H2) is expected to substitute carbon-based fuels and become a promising clean, renewable, and common fuel for the future that can overcome some of the critical problems such as shortages of fossil fuel resources, global warming and air pollution [1]. In spite of its advantages, unfortunately H2 is tasteless, col-orless, odorless, and very explosive and inflammable [2]. Its low flammable limit (4 vol%) and ultra-small molecular size, which make difficult confinement and containment of it, demands very cautious handling [3]. These properties of hydro-gen demands an accurate detection technique and continu-ous monitoring for safe industrial use [4]. In this regards, gas sensors might be very promising detectors for hydrogen gas because they are cheap, simple, reliable.Recently, semiconducting metal oxide (SMO) one-dimen-sional (1D) nanostructures such as nanorods (NRs) have been widely studied as sensor materials because of their high specific area and excellent carrier transporting characteristics [2]. So far, n-type SMOs have been intensively studied as gas sensing materials [2-4]. In contrast, few studies have been made on p-type SMO gas sensors. Nevertheless, the poten-tial of p-type SMO as gas sensing materials should not be underestimated. In addition to several shortcomings, p-type SMOs have advantages that n-type SMOs do not possess as follows: (1) good catalysts [5-8] to promote selective oxida-tion of various reducing gases; (2) formation of p-n hetero-structures by combining with a p-type SMO can also be used to enhance the gas sensing performance by altering the gas-sensing characteristics of gas sensors near the heterointer-faces [9]; (3) the higher oxygen absorption of p-type SMOs, i.e., higher oxygen solubility in p-type SMOs leading to low humidity dependence and rapid recovery kinetics [10,11]. Therefore, a combination of p-type SMOs with n-type SMOs, i.e., formation of p-n heterostructures would exhibit enhanced sensing performance compared to pristine n-type SMOs [12]. Cupric oxide (CuO) is a p-type metal oxide [13-16] drawing significant attention owing to its highly catalytic activity [17] and many other applications in fields of lithium-copper oxide electrochemical cells [18], field emission devices [19], high temperature superconductors [20], infrared photodetectors [21], etc. CuO nanostructured gas sensors have attracted grow-ing attention due to its high surface area-to-volume ratio, adsorption capability of oxygen and catalytic activity [22]. In this study, pristine CuO NRs and Nb2O5 nanoparticles-decorated CuO NRs were fabricated by the direct thermal oxidation of Cu foils [23] and spin coating of NbCl5 solution followed by annealing at high temperature. Finally, their H2*Corresponding author: cmlee@inha.ac.kr KIM and SpringerHydrogen Gas Detection of Nb2O5 Nanoparticle-Decorated CuO Nanorod Sensors215 gas sensing properties were examined.2. EXPERIMENTAL PROCEDURENb2O5-decorated CuO NRs were by the direct thermaloxidation of Cu foils [23] and spin coating of NbCl5 solutionfollowed by annealing at high temperature. First, CuO NRswere prepared by oxidizing a Cu foil (99.8%, thickness:0.25mm, Alfa Aesar) thermally in a quartz tube furnace.Cu foil pieces were placed at the center of a 20 mm-dia. quartztube in the heating zone of a vacuum tube furnace. Oxygenand nitrogen gases were introduced to the system after 10 minevacuation. The furnace was then heated to 500°C. At the temperature of 500°C, O2/N2 mixture gas was introduced into the quartz tube to initiate CuO oxidation. After heating for 1 h, the furnace was cooled to room temperature and the products (CuO NRs) were taken out.Subsequently, the CuO NR samples were decorated with Nb2O5 nanoparticles using a solvothermal method. An eth-anolic niobium chloride solution (C2H5OH:NbCl5=1000:1) was prepared in a vial. The CuO NR samples were immersed in the ethanolic niobium chloride solution (C2H5OH:NbCl5 = 1000:1) in a vial in a home-made ultraviolet (UV) box. The samples were then transferred to an annealing quartz tube furnace and annealed at 500°C for 1 h in O2 ambient. The O2 gas flow rate and process pressure were 200 cm3/min and 0.8 Torr, respectively.Scanning electron microscopy (SEM, Hitachi S-4200) was performed to examine the morphology of the synthesized samples. X-ray diffraction (XRD, Philips X`pert MRD dif-fractometer) measurements were performed to examine the structures of the samples by glancing angle using Cu-Kαradiation (0.1541 nm) at a glancing angle of 0.5°. Interdigital electrode (IDE) patterns to be used as the elec-trodes of the sensor were fabricated by the sequential sput-ter-deposition of ~200 nm-thick Ni and ~50 nm-thick Au thin films followed by photolithography. On the other hand, the pristine and Nb2O5 nanoparticles-decorated CuO NRs were separately dispersed by ultrasonicating in a mixture of deion-ized water (5 ml) and isopropyl alcohol (5 ml), followed by drying at 90°C. A solution containing the NRs (10μl) was dropped onto the SiO2(200 nm)/Si substrates equipped with a pair of the IDE s with a gap of 20μm (Fig. 1).The gas sensing properties of the multi-networked NR sensors fabricated using the pristine and Nb2O5-decorated CuO NRs were measured at 300 °C in a quartz tube placed in a sealed chamber. H2 gas was introduced into the testing tube to obtain 0.5-5% H2 concentrations while monitoring the electrical resistance of sensors. One sensing cycle con-sisted of introducing synthetic air at a flow rate of 200 cm3/min for 5 min to achieve a baseline, switching to H2 gas/air mixture at a flow rate of 200 cm3/min for 5 min, followed by switch-ing back to synthetic air at a flow rate of 200 cm3/min for a 10 min for sensor recovery. The electrical resistance of the gas sensor was determined by measuring the electric current at 300°C flowing at an applied voltage of 1V between the two Ni/Au IDEs. A Keithley sourcemeter- 2612 was used for this measurement. The details of the sensing test procedures are described elsewhere [24]. The electrical resistances of the NR sensors were monitored while H2 gas was introduced into the testing tube. The response of the sensors to H2 was defined as R g/R a×100 (%), where R g and R a are the electrical resistances in the sensors in the H2 gas and air, respectively.3. RESULTS AND DISCUSSION3.1. Structures of the pristine and Nb2O5 nanoparticle-decorated CuO NRsFigure 2 shows the XRD patterns of both the pristine and Nb2O5 nanoparticles-decorated CuO NRs. The pristine CuO NR sample exhibited the reflections from simple cubic Cu2O (JCPDS no. 05-0667) and monoclinic CuO (JCPDS no. 45-0937), as well as those from pure Cu, which might be due to the Cu foil substrate. This result suggests that both Cu2O and CuO phases coexist in the NRs. Copper is thermal oxi-dized according to the following reactions [25]:4Cu + O2 2Cu2O (1) Fig. 1.Schematic of the gas sensor.Fig. 2. XRD pattern of the pristine and Nb2O5-decorated CuO NRs.216Hyejoon Kheel et al.2Cu 2O + O 2 4CuO (2)During thermal oxidation process a dense Cu 2O film covers the Cu foil surface first, then CuO NRs grows on the Cu 2O film {18}. Of the two cupric oxide phases the CuO phase is dominant at 500°C. The Cu 2O peaks in the XRD patterns of the two samples might be caused by the Cu 2O layer under-neath the NRs, not by the nanorods. On the other hand, the NRs consists mostly of the CuO phase. In addition to cupric oxide and cupper peaks, the (111), (002) and (134) peaks from Nb 2O 5 were observed in the diffraction pattern of the Nb 2O 5nanoparticles-decorated CuO NRs, which are due to the pres-ence of Nb 2O 5 nanoparticles on the surface of the CuO NRs.Figure 3 shows a SEM micrograph of the synthesized CuO NRs decorated with Nb 2O 5 nanoparticles. The inset in Fig. 3shows that the NRs have diameters less than 50 nm and lengths of up to 5 μm and that the diameters of the Nb 2O 5 nanopar-ticles on the CuO NRs range from 20-70 nm. Also the NRs tended to grow perpendicular to the substrate and there was a small gap between neighboring NRs, which along with the high surface area of the NRs, makes them favorable for gas sensing applications.3.2. Comparison of the H 2 sensing performance between the pristine and Nb 2O 5 nanoparticles-decorated CuO NR sensorsFigure 4 shows the responses of both sensors to 0.5% H 2gas, where it clearly shows the response of Nb 2O 5 nanopar-ticles-decorated CuO NRs is higher than the pristine CuO NRs over the entire test temperature range. At the optimal working temperature of Nb 2O 5 nanoparticle-decorated CuO NR sensor the response of the decorated CuO NR sensor is more than three times higher than the pristine one. Accord-ing to this experiment all remainder tests were conducted atthe optimal temperature i.e. 300°C. According to [26,27], hydro-gen gas sensors that can operate at temperatures from 30 to 1000°C are needed. Our sensor can be used for relatively high temperature applications that need to detect H 2.Figures 5(a) and (b) present the dynamic response of the pristine and Nb 2O 5 nanoparticles-decorated CuO NR sen-sors to H 2gases with different concentrations, respectively.Fig. 3. SEM micrograph of the synthesized CuO NRs decorated with Nb 2O 5 nanoparticles. Inset, enlarged SEM image of Nb 2O 5-decoratedCuO NRs.Fig. 4. Response of the pristine and Nb 2O 5-decorated CuO NR sen-sors versus temperature.Fig. 5. Dynamic response of (a) the pristine CuO NR sensor and (b)Nb 2O 5-decorated CuO NR sensor.Hydrogen Gas Detection of Nb 2O 5 Nanoparticle-Decorated CuO Nanorod Sensors 217The resistance of the sensors increased rapidly upon expo-sure to H 2 gas and the resistance recovered completely to the initial value upon stopping the H 2 gas supply and intro-ducing air. The responses of the NR sensors were quite sta-ble and reproducible for repeated testing cycles. In both cases,the sensors exhibited a higher response when they were exposed to higher concentrations of hydrogen. As an increase in H 2gas concentration activates the reactions at the surfaces of sensors due to the larger coverage of surface, the response of the sensors would increase accordingly. Also both sensors exhibited a p-type electrical behavior to H 2 gas, which might be because a p-type SMO, CuO is a major constituent of both sensors. The baseline resistance of the Nb 2O 5 nanoparticle-decorated CuO NR sensor is, interestingly, higher than that of the pristine CuO NR sensor, due to the higher intrinsic resistance of Nb 2O 5 than that of CuO.Figure 6 shows the responses of both sensors at different H 2 concentrations. The pristine CuO NR sensor shows an almost linear trend with very a low slope with increasing the H 2 concentration. This means that the sensor almost reached a saturation response owning to its smaller surface area. In contrast, the response of the Nb 2O 5 nanoparticles-decorated CuO NR sensor increases progressively with increasing the H 2 concentration. Even at a maximum con-centration of H 2 (5%), it did not reach the saturation value.It seems that decorating CuO NRs with Nb 2O 5 resulted in an increased surface area. The main reasons for the higher response of the Nb 2O 5 nanoparticles-decorated CuO NR sensor will be discussed in the next section.Figures 7(a) and (b) show the response/recovery times of both sensors. The difference in response time might be due to that in the saturation time and mean residence period of the H 2 molecules on the surface of the sensor material. For a low H 2 concentration, the H 2 molecules spend a relatively long time reacting with the adsorbed oxygen species. For ahigh H 2 concentration, a larger amount of H 2 molecules are available for reaction with the adsorbed oxygen species, so that the response time is shorter. Change of the recovery time with H 2 concentration might be due to the followings:When air is introduced into the testing tube, oxygen mole-cules are adsorbed by the sensor material surface and react with the H 2 molecules. The complete desorption at the CuO-Nb 2O 5 interface takes more time than at the outer Nb 2O 5surface, resulting in a longer recovery at higher H 2 concen-trations, where H 2 molecules exist at the CuO-Nb 2O 5 interface.In both cases, Nb 2O 5-decorated CuO NRs have shorter response and recovery times. The difference in response time between the pristine and Nb 2O 5-decorated CuO NRs at higher concentrations (4 and 5%) is more significant.This is probably due to the larger surface area of the Nb 2O 5-decorated CuO NRs. Also the recovery times are shorter than the response times, which is probably due to the lower desorption energy of H 2relative to the adsorption energy.Fig. 6. Response of pristine and Nb 2O 5-decorated CuO NRs versushydrogen concentration.Fig. 7. (a) Response times and (b) recovery times of the pristine and Nb 2O 5-decorated CuO NR sensors for different H 2 concentrations.218Hyejoon Kheel et al.3.3. Sensing MechanismIn the pristine CuO NR gas sensor, in air, the oxygen mole-cules are adsorbed by the CuO NR surfaces and the adsorbedoxygen molecules are ionized to O2-, O- or O2- by releasingholes to the valence band of CuO. The stable oxygen speciesare O2-, O- and O2- below 150 °C, between 150 and 400 °C,and above 400°C, respectively [28]. In this study, predom-inant species might be O- because the operating temperaturewas 300°C. The ionization of oxygen molecules causes an increase in carrier concentration and formation of an accu-mulation layer at the surface of the CuO NRs, leading to a decrease in resistance:1/2O2(g) = O-(ad) + h+ (1)In this case, the accumulation plays a role of a conduction channel.Upon exposure to H2 gas, the ethanol molecules adsorbedby the CuO NR surfaces are oxidized by reacting with the preexisting oxygen species at the surfaces as follows:2H2 + 2 O-(ad) + 2 h+ 2H2O (2) Reaction (2) capture holes from the valence band of CuO,forming a depletion layer, leading to an increase in the resis-tance of the CuO NRs. Consequently, the adsorption of H2gas and air accompanies the modulation of the conductionchannel width, leading to the change in resistance.The enhanced sensing properties of the decorated CuO NR sensor might be caused mainly by the two electronic effects: (1) modulation of conduction channel width and (2) modulation of the potential barrier height at the CuO-Nb2O5 interface accompanying the absorption and desorption of H2 gas.The modulation of the conduction channel width of the Nb2O5-decorated CuO NR sensor is more significant than that of the pristine CuO NR sensor (W c4-W c3 > W c2-W c1 in Fig. 8), because the depletion layer forming on the Nb2O5 side in the Nb2O5-decorated CuO NR sensor in air is thicker than that in the pristine CuO NR sensor owing to the exis-tence of the accumulation layer on the CuO side [28], causing the difference in conduction channel width between the two sensors. A potential barrier also develops at the p-CuO/n-Nb2O5 interface due to the built-in potential (Fig. 8) [29,30]. Modulation of the potential barrier height occurs during the adsorption and desorption of H2 gas. (NOTE: Desorption of H2 gas corresponds to adsorption of air.) The potential barrier height at the p-n junction changes from V1 (in H2 gas) to V2 (in air) as shown in Fig. 8. Of these two effects, the modulation of the conduction channel width might be predominant over the modulation of the potential barrier height because the Nb2O5-decorated CuO NR sensor as well as the pristine CuO NR sensor exhibited a p-type electrical behavior [Figs. 5(a) and (b)]. If the modulation of the potential barrier height had been dominant, the decorated CuO NR sensor would have exhibited an n-type electrical behavior, differently from the pristine CuO NR sensor.Besides the two electrical effects, the enhanced sensing performance of the decorated CuO NR sensor are partially attributed to physical effects such as the increase in the surface area of the NRs [31,32] and the formation of more active sites for gas adsorption by decoration of the CuO NRs with Nb2O5 particles [33]. Brunauer-Emmett-Teller (BET) anal-ysis was performed to verify the specific surface area of the Nb2O5-decorated CuO nanorods was larger than that of the pristine CuO nanorods. The measured specific surface areas of the pristine and Nb2O5-decorated CuO nanorods were 3.17 and 10.26 m2/g, respectively. The specific surface area of the pristine CuO nanorods was more than two fold larger than that of the pristine CuO nanorods.4. CONCLUSIONSNb2O5-decorated CuO NRs were synthesized using a two-step process: the synthesis of CuO NRs using a thermal evaporation method followed by the deposition of Nb2O5 nanoparticles using a solvothermal method. The optimal working temperature of the decorated NR sensors was deter-mined to be 300°C. The Nb2O5-decorated CuO NRs exhib-ited stronger and faster response to H2 gas than the pristine CuO NRs. The underlying mechanism of the improved sens-ing properties of the multi-networked Nb2O5-decorated CuO Fig. 8. Energy band diagrams of the p-CuO-n-Nb2O5 system and sche-matic diagrams of the pristine and Nb2O5-decorated CuO NR sensors showing the conduction channel widths and potential barrier heights in air and H2 gas.Hydrogen Gas Detection of Nb2O5 Nanoparticle-Decorated CuO Nanorod Sensors219NR sensor to H2 gas was explained by the modulation of the conduction channel width, the modulation of the poten-tial barrier height at the Nb2O5-CuO interface, the increased surface area of the NRs, and more active sites for gas adsorp-tion created by decoration of the CuO NRs with Nb2O5. We believe that p-type SMOs could also be efficiently used for fabricating gas sensors, if only they were combined with n-type SMOs. This paper showed the improved sensing prop-erties of the p-type SMO nanostructures decorated with n-type SMO nanoparticles and elucidated the underlying mech-anism for the improved gas sensing properties.ACKNOWLEDGEMENTThis work was supported by Basic Science Research Pro-gram through the National Research Foundation of Korea (NRF) funded by the Ministry of Education (2010-0020163).REFERENCES1.W. J. Buttner, M. B. Post, R. Burgess, and C. Rivkin, Int. J.Hydrogen Energ.36, 2462 (2011).2.S. Park, S. Park, S. Lee, H. W. Kim, and C. Lee, Sens. Actua-tors B202, 840 (2014).3.T. Hübert, L. Boon-Brett, G. Black, and U. Banach, Sens.Actuators B157, 329 (2011).4.H. G. Z. Wang and Y. Hu, Sensors12, 5517 (2012).5.K. Pirkanniemi and M. Sillanpää, Chemosphere48, 1047(2002).6.M. M. Bettahar, G. Costentin, L. Savary, and J. C. Lavalley,Appl. Catal. A-Gen.145, 1 (1996).7.Y. Motooka and A. Ozaki, J. Catal.5, 116 (1966).8.S. S. Kaye and J. R. Long, J. Am. Chem. Soc.127, 6506 (2005).9.Z. Zhang, C. Shao, X. Li, C. Wang, M. Zhang, and Y. Liu,ACS Appl. Mater. Interfaces2, 2915 (2010).10.H.-R. Kim, A. Haensch, I.-D. Kim, N. Barsan, U. Weimar,and J.-H. Lee, Adv. Funct. Mater.21, 4456 (2011).11.H.-R. Kim, K.-I. Choi, K.-M. Kim, I.-D. Kim, G. Cao, andJ.-H. Lee, Chem. Commun.46, 5061 (2010).12.S. Park, H. Kheel, G.-J. Sun, H. W. Kim, T. Ko, and C. Lee,Met. Mater. Int.22, 730 (2016).13.S. Park, H. Ko, S. An, W. Lee, S. Lee, and C. Lee, Ceram.Int. 39, 5255 (2013).14.H. Meng, W. Y ang, K. Ding, L. Feng, and Y. Guan, J. Mater.Chem. A3, 1174 (2015).15.H. J. Lee, T. G. Kim, H. Oh, W. Lee, and H. Ryu, Korean J.Met. Mater. 53, 445 (2015).16.U. H. Lee, H. J. Lee, and C. M. Park, Korean J. Met. Mater.54, 469 (2015).17.K. Zhou, R. Wang, B. Xu, and Y. Li, Nanotechnology17,3939 (2016).18.L. B. Chen, N. Lu, C. M. Xu, H. C. Y u, and T. H. Wang,Electrochim. Acta54, 4198 (2009).19.Y. W. Zhu, T. Y u, F. C. Cheong, X. J. Xu, C. T. Lim, V. B.C. Tan, C. H. Sow, et al.Nanotechnology16, 88 (2005).20.A. H. Macdonald, Nature414, 409 (2001).21.S. B. Wang, C. H. Hsiao, S. J. Chang, K. T. Lam, K. H. Wen,S. C. Hung, et al.Sens. Actuators A171, 207 (2011). 22.C. Y ang, F. Xiao, J. Wang, and X. Su, Sens. Actuators B207,177 (2015).23.C. Yang, X. Cao, S. Wang, L. Zhang, F. Xiao, X. Su, and J.Wang, Ceram. Int.41, 1749 (2015).24.S. Park, S. An, Y. Mun, and C. Lee, ACS Appl. Mater. Inter-faces5, 4285 (2013).25.H. Kim, C. Jin, S. Park, S. Kim, and C. Lee, Sens. Actua-tors B161, 594 (2012).26.G. Korotcenkov, S. D. Han, and J. R. Stetter, Chemical109,1402 (2009).27.J. M. Lim, K. C. Shin, and H. W. Kim, Thin Solid Films475, 256 (2005).28.N. Barsan and U. Weimer, Electroceram.7, 143 (2001).29.Z. Zhu, C.-T. Kao, and R.-J. Wu, Appl. Sur. Sci.320, 348(2014).30.D. R. Patil and L. A. Patil, Talanta 77, 1409 (2009).31.H.-J. Kim and J.-H. Lee, Sens. Actuators B192, 607 (2014).32.F. Qu, J. Liu, Y. Wang, S. Wen, Y. Chen, S. Ruan, et al.Sens.Actuators B199, 346 (2014).33.H. Zhang, J. Feng, T. Fei, S. Liu, and T. Zhang, Sens. Actu-ators B190, 472 (2014).。