5000t_d生产线调试中遇到的问题及解决措施
5000td新型干法窑试生产前后存在的问题及处理

5000t/d新型干法窑试生产前后存在的问题及处理2008-1-8 作者:泥有限公司文章摘要:本文介绍了5000t/d新型干法窑系统的主机设备及这些设备在试生产前后存在的主要问题,阐明了对这些问题的处理方法。
关键词:膜片弹性联轴器、托轮轴瓦、液压油缸、带油棒、四通道喷煤管、分解炉缩口、篦冷机堆雪人、拉链机河南省建设投资总公司控股投资建设的驻马店市豫龙同力水泥有限公司2x5000t/d熟料生产线一期工程由天津水泥工业设计研究院设计,工程于2003年11月29日开工,2005年5月25日旋窑点火生产。
现将5000t/d新型干法窑系统主机设备在试生产前后存在的主要问题及处理方法阐述如下。
一. 5000t/d新型干法窑主要设备的技术参数1. 旋窑:φ4.2x72m,采用三档支承,筒体上下运动由液压油缸挡轮控制,窑速0.39-3.89r/min,主电机功率630Kw。
2. 预分解设备:TDF型分解炉带双系列五级旋浮预热器,分解炉φ7.4x27m;一级旋浮预热器4-φ4.5m;二级旋浮预热器2-φ6.4m;三和四级旋浮预热器2-φ6.6m;五级旋浮预热器2-φ6.8m,系统设计阻力≤5500Pa。
3. 篦冷机:篦冷机采用三段冷却,通过调节液压油缸供油量来控制篦板往复频次,一段采用充气梁篦板,二段采用高阻力低漏料篦板,三段用普通篦板,总有效冷却面积119.3㎡;熟料锤式破碎机φ1x3.3m。
4. 废气处理设备:高温风机2500Kw,风量860000m3/h,风压7200Pa,转速940r/min;窑头电收尘器处理风量580000m3/h,气流通过速度0.86m/s,最高温度≤400℃;窑尾玻璃纤维覆膜袋式除尘器处理风量920000M3/h,入口气体温度≤250℃,过滤面积13800㎡,过滤风速1.11m/min,滤袋规格φ160x6000mm,滤袋个数4576,通风阻力≤1700Pa;窑尾排风机功率1400Kw,转速720r/min,处理风量965000m3/h,全压3500Pa。
某5000t-d熟料生产线中控操作事故案例分析集锦

某5000t/d熟料生产线中控操作事故案例分析集锦一、电流类例 1、入窑斗提电流异常升高在窑喂料达到380t/h 时,入窑斗提电流通常在250A~260A 左右,当窑喂料保持稳定时,如入窑斗提突然上升,在通知现场巡检人员进行检查的同时,窑操作员应立即降低窑喂料量努力将电流值控至在 250A 左右。
斗提电流上升可能有以下几种情况:如果降低喂料量后,斗提电流可以稳定,则可以判断为斗提头部的回料挡皮出现问题,导致斗提回料量突然加大,增大了斗提的负荷,可维持运行,待临停时处理。
从预热器的参数也可以进行判断,当出现这种情况时,C1 出口的温度和压力会略有上升,但可以稳定住。
如果降低喂料后,斗提电流仍持续上升,则立即止料停窑,通知现场巡检人员检查预热器顶斜槽是否堵塞。
例 2、入库斗提电流异常偏低在生料磨喂料达到 400 t/h 时,入库斗提电流通常在200A 左右,当磨系统稳定运行时,如果入库斗提电流异常下降,在通知现场巡检人员进行检查的同时,立磨操作员应立即止料抬辊,待问题查明并排除故障后,再组织开机,斗提电流异常下降可能有以下几种情况:如果电流呈直线下降,并降至空载电流以下时,可以判断为斗提的传动系统出了问题,应立即通知现场检查液偶易熔塞以及其它传动部件。
如果电流的下降经历了一定的时间,并最终稳定在空载电流,说明斗提的上游进料设备发生了问题,应通知现场逐台向上游检查。
如果电流略有下降,如下降至 180A,中控操作员也不能听之任之,操作员应对磨机的实际台时产量进行核查,可以通过入磨皮带的电流、磨机的差压等进行判断,如果发现磨机的实际台时并未减少,而入库斗提的电流下降,仍需通知现场对旋风筒,大布袋等设备进行检查,防止各灰斗堵料或有其它设备故障。
以上两例同样适用于其它板链式斗提。
例 3、皮带机、铰刀、拉链机、锤破等设备的电流异常偏低和斗提机类似,如果电流呈直线下降至空载电流以下,可以判断为皮带机的传动尼龙柱销断或传动液偶易熔塞爆,铰刀的吊瓦联接螺栓断,拉链机的传动链条断、镴破的传动皮带断等,如果电流略有下降,可以判断为上游的进料设备发生堵塞或下料不畅。
5000td熟料生产线的调试与生产

烧成系统一直运行正常 ( 期间由于 销售原因停过几次窑, 更换过一次 烧成带耐火砖) , 2006 年计划生产水 泥熟料 165 万 吨 。 窑 系 统 运 行 参 数 见表 5。 4 结束语
天瑞集团汝州水泥有限公司的 5000t /d 水泥 熟 料 生 产 线 投 资 省 、建
设周期短, 生产线在短期内实现 72h 达标, 并进入正常生产, 各项技术指 标先进, 取得了良好的经济效益和 社会效益。这也充分说明了天津水 泥工业设计研究院优化设计的 5000t /d 水 泥 熟 料 生 产 线 技 术 成 熟 可靠, 工艺先进合理。#
储存量, t 52000
2×13500 3600 18000 48000
储存期, d 5.5 2×8 4.5 2.4 9.6
备注 一 、二 线 共 用 一 、二 线 共 用
通讯地址: 天瑞集团汝州水泥有限公司, 河南 汝州 467500; 收稿日期: 2006- 08- 20; 编辑: 沈 颖
98
CEMENT TECHNOLOGY 5 /2006
配比
方案 1 方案 2
石4
表 3 原料易磨性实验结果
粉煤灰 /铝矾土 %
铁矿石 %
10.56
—
2.92
1.34
粉磨功指数( Wi=kWh /t)
史密斯公司
非凡公司
克虏伯公司
8.3- 8.8
8.5
9
12.0
表 4 生料磨操作参数
立磨喂料量 LV 选粉机转速 窑系统投料量 入磨气体温度, ℃; 喷水系统水压 磨机振动速度 出磨气体温度, ℃; 磨辊压力 密封风机风压
表 2 主机配置表
序号 主机设备名称
型 号 、规 格
河南大地水泥公司5000td生产线窑系统的调试

河南大地水泥公司5000t/d生产线窑系统的调试河南大地水泥公司5000t/d水泥熟料生产线是由中材国际南京水泥研究设计院设计,本系统采用南京院开发研制的先进、成熟的五级旋风预热器、喷腾式在线管道分解炉预分解系统,Φ4.8×74m回转窑和高效空气梁篦式冷却机。
于2007年4月9日投料,生产线投料当月即达标。
本人有幸参与了试生产方案的制定,经历了单机试车、点火烘窑、投料试生产的全过程,对窑系统的调试有一点个人的看法,现提出与大家共同探讨。
1.试生产前的准备工作试生产前的准备工作是整个试生产环节的第一步,对整个试生产起着至关重要的作用,如果这一步做不好那么在今后的试生产中将步步受牵制处处被动,因此为了试生产的顺利进行必须充足地做好事生产前的准备工作。
1.1.翻板阀的调整翻板阀的灵活程度主要取决于阀板和浇注料之间的间隙以及配重的调整,阀板和浇注料之间的间隙要调整到恰到好处,即间隙不能过大也不能过小,过大翻板阀就起不到应有的作用、锁风效果就会变差、气流短路,造成热耗增加,系统结皮加剧,严重后会挎落造成下料溜管堵塞。
因为翻板阀间隙的调整是在冷态下进行的,受热后要膨胀,所以间隙也不能过小,否则易卡死阀板造成下料溜管堵塞。
至于配重的调整,主要还是凭经验和手感来进行调整,调整到在生产过程中阀板上能积存有一定的物料起到一定的锁风作用且不至于配重太重使物料自重压不开阀板为宜。
另外需要注意的,翻板阀的配重是随喂料量的增加而增加的不能一次调整到位,否则在试生产初期因为喂料太小会造成物料重量较轻而压不开翻板阀,若先期调整好后而后期产量增加时不进行调整会造成翻板阀动作频繁锁风效果变差,造成气流短路,热耗增加,系统结皮加剧,严重后会挎落造成下料溜管堵塞。
1.2.燃烧器的调整燃烧器是五大热工设备之首,燃烧器调整的结果直接影响到熟料的质量,系统运行时间的长短,耐火材料的使用寿命等等。
燃烧器的调整一般是偏下偏料,但偏多少为合适,若偏多了火焰会栽入物料造成煤粉燃烧不完全而裹入物料,产生还原料影响熟料的外观。
5000t生产线回转窑系统中控操作体会
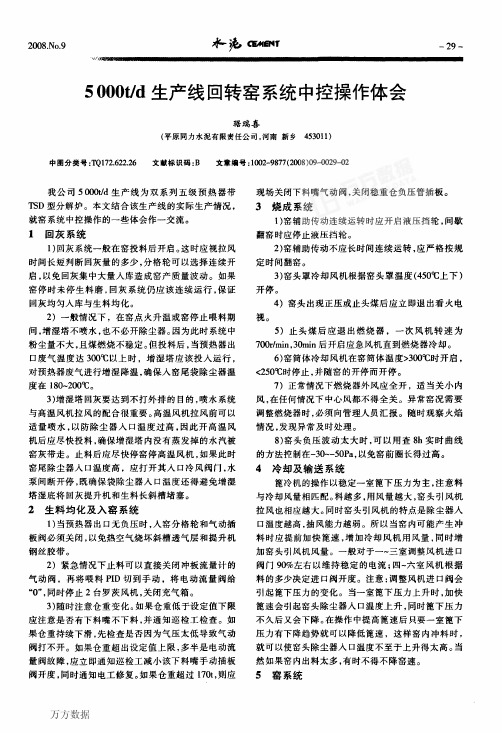
2)一般情况下,在窑点火升温或窑停止喂料期 间,增湿塔不喷水,也不必开除尘器。因为此时系统中 粉尘量不大,且煤燃烧不稳定。但投料后,当预热器出 口废气温度达300℃以上时,增湿塔应该投入运行, 对预热器废气进行增湿降温,确保人窑尾袋除尘器温 度在180~200℃。
3)增湿塔回灰要达到不打外排的目的,喷水系统 与高温风机拉风的配合很重要。高温风机拉风前可以 适量喷水,以防除尘器入口温度过高,因此开高温风 机后应尽快投料,确保增湿塔内没有蒸发掉的水汽被 窑灰带走。止料后应尽快停窑停高温风机,如果此时 窑尾除尘器人口温度高,应打开其入口冷风阀门,水 泵间断开停,既确保袋除尘器人口温度还得避免增湿 塔湿底将回灰提升机和生料长斜槽堵塞。 2生料均化及入窑系统
5)开篦冷机 挂窑皮初期,窑产量很低,当熟料开始入篦冷机 时再启动篦床。篦速一定要慢,使熟料在篦床上均匀 散开,并保持一定的料层厚度。以设定冷却风量为依 据,使篦下压力接近设定值。注意避免冷却风机阀门 开度太大,否则吹穿料层,造成短路。操作中如发现篦 板翘起或脱落,要及时处理,严防篦板掉入熟料破碎 机而造成严重事故。 6)正常煅烧 目前的操作中入窑提升机电流高值不大 于130A,瞬间不宜超过135A,如果持续大于135A时 必须通知巡检工检查,同时视情况减料或止料。高温 风机液力偶合器转速60%、进口阀60%-70%,三次风 阀30%。如果人窑生料KH低,拉风量宜偏小控制。投 料量在设备许可的情况下,以C。出口温度320-3500C 为准,窑速3.6-3.9r/rain,窑电流900A左右。分解炉温 度880-8900C,如果窑电流偏高,分解炉温度应偏低 控制。控制窑头喂煤量10-1lt/h,入窑生料中KH偏 低或投料量长期偏低时,宜偏下限控制甚至低 于10 t/h。 7)止料 先止尾煤再止料并停止均化库内设备。待C,出 口压力下降到一恒定值(物料全部通过预热器)后将 高温风机进口阀减到30%,窑速2.0r/min,篦速(1—3 段)12~20次/min,四室以后风机进口阀10%一20%。空 烧15rain后停窑、止头煤开辅助传动,视情况间断转 窑。在调整过程中注意控制窑头负压及窑头、窑尾除 尘器入口温度。止料后注意高温风机出口压力控制 在一100一150Pa,如果窑尾除尘器入口温度偏高可以 打开其冷风阀门。如果窑头除尘器入口温度偏高可以 降篦速或开篦冷机喷水系"
浅谈5000t/d熟料线余热发电提高产能的经验措施

统 ,型号 分别为Q C 2 4 0 / 3 8 0 — 2 2 . 2( 5)一 1 . 6( 0 . 3 5) / 3 6 0
( 1 9 5)、Q C 3 5 5 / 3 3 O 一 2 4 . 9 — 1 . 6 / 3 1 0 ;D C S 系统选用 的是
自然循 环 锅炉 ,总蒸 发量4 7 t ,窑头 锅炉设 计 为双压 系
在余热发 电项 目建设期 间 ,我们各专业技 术人 员共 同结合安装 实际情况 ,对余 热发 电项 目的图纸资料进行
审核 。从 有利于设备运行 、方便维护及 降低 生产成本 的
角度 出发 ,查找需要增 加或改进 的设备选 型或工艺环 节 不合理 的问题共计 1 6 项 ,力求进一步优化设计方案 。 安装 工程施工 阶段 ,严格对施工方 案 、调试方 案进 行 详细的审核 。多次对施工方案进行 了科学合理 的改进 与修订 ,确保施 工方案能够切实 的为施 工提供管理 和技 术 上的有效支持 。
北 京 和利 时Ma c s V系统 。滕 州 中联 余热 发 电 自2 0 1 2 年 3 月 份开 工建 设 ,历经 7 个 月 的建设周 期 ,2 0 1 2 年1 o , q
坚持 严 把进 场 材 料 、设备 检 验关 。从 源头 抓起 ,
坚决杜绝 任何不合格 的差 次品进入工地 或应 用于工程之 中。如协 调更换三无 高压 电缆头 l 0 余套 ,使高压 电缆热 缩终端头施工质量得 以保证 。
查验收 。
针对锅 炉 、汽机等 主机设 备的安装 、调试 ,我们均
安排 了专 人全程跟踪监督 ,既有效地保证 了安装质量 , 提高 了施工项 目检 验质量 的优 良率 ,又掌握 了第一手技
影响熟料质量的原因及改进措施

影响熟料质量的原因及改进措施影响熟料质量的原因及改进措施作者:公司我公司5000t/d生产线投产1年多以来,日产熟料达到5300~5500t,但熟料外观颜色发暗、疏松,并且夹有大量黄心料,严重时出现大块黄心料;升重偏低,一般在1100~1150g/L之间;fCaO偏低,只有0.3%~0.6%,甚至升重低于1100g/L时,fCaO也不超过1.0%;熟料抗压强度3d为28.0~30.0MPa,28d为55.0~56.0MPa,最低时只有52.0MPa,达不到质量要求,严重影响水泥的质量和公司的经济效益。
1原因分析1.1熟料岩相分析配料方案为:KH=0.88~0.92,n=2.50~2.70,P=1.50~1.70,三个率值的控制基本合理。
生料成分比较稳定,入窑生料三个率值合格率达到85%以上。
从化学分析计算看,熟料矿物组成比较理想,C3S:55%左右,C2S:20%左右,C3S+C2S达到76%~77%。
但是熟料实际矿物组成与理论计算差距较大,为此选正常煅烧的熟料做岩相分析。
分析结果表明:夹心料中A、B矿发育均不充分,有些部位几乎没有发育完整的矿物,内部存在大量B矿矿巢和气孔;一般料中A、B矿结晶较清晰,但大小不均齐,分布不均匀,B矿矿巢略多,中间相尚好。
产生这种熟料可能是因为生料中存在粗粒石英、长石(来自砂岩或石灰石);煤粉含水量较大或有粗粒,造成不完全燃烧,产生还原气氛。
1.2砂岩岩相分析所用的石灰石品位较低(CaO含量在46.0%~48.0%,Al2O3含量偏高),为了保证配料方案的实施,使用2.0%~3.0%的砂岩作为硅质校正材料进行配料。
对砂岩进行的岩相分析表明:大量晶粒尺寸100~500μm的石英颗粒被少量(约20%)次生石英胶结,并含有少量微晶石英;所用的砂岩是以石英为主体矿物的石英质砂岩,杂质少,化学反应活性差。
1.3生料中的碱含量、硫碱比煅烧过程中,熟料结粒不好、飞砂较多,在KH、n偏高时尤为明显,窑对料的适应性较差,物料的轻微波动就造成窑和熟料的波动。
为5000t/d生产线配套的大型原料立磨的技术现状

水 泥熟料生 产线配套 粉磨原料 现 已研 制 出与50 0 d 0 t / 生 产线 配套 的立磨 沈 阳重 型 机器 厂引 进技 术生 产 的MP 立磨 . 大 S 最
的规 格 为ML 4 3 .能 与50 0/水 泥熟 料 生 产线 配 S5 1 0t d
家公 司购买 了数 台与40 0 60 0/水 泥生 产线 配 0 ~ 0 t d 套 的原 料立 磨
维普资讯
为50 0 / 生产线配套 的 0 td
大型原料立磨 的技术现状
邓 小 林
( 肥水 泥工业 研究 设计 院 , 合 合肥 2 0 5 ) 30 1
机 器 厂引进 技术 生产 的MP 立磨 ( 改为ML 立 磨 ) S 现 S
1 立 磨 技 术 的 发 展
我 国 目前有 三种 立磨 . 合肥 水 泥研 究设 计 院 自行 研 究 设 计 的具有 自主 知识 产权 的 H M型立 磨 .天津 R 水 泥工 业设 计 研 究 院研 制 的T M型立 磨 和沈 阳重 型 R
6 中 国 水 泥 2 0 . 0 0 69
工厂生产线的故障与预防维护

工厂生产线的故障与预防维护在现代工业生产中,工厂生产线是生产过程中不可或缺的一部分。
然而,工厂生产线在运行过程中常常会出现各种故障,这会导致生产线停工或者产品质量下降,给企业带来巨大的损失。
因此,预防和维护工厂生产线故障显得尤为重要。
本文将探讨工厂生产线故障的原因及预防维护措施。
一、工厂生产线故障的原因在工厂生产线出现故障时,我们需要首先了解故障产生的原因,才能有针对性地进行预防维护。
以下是一些常见的故障原因:1. 设备老化和磨损:随着设备使用时间的增长,设备会逐渐老化和磨损,导致故障概率增加。
2. 操作错误:员工操作不当或未按要求进行维护保养,容易引发故障,例如错误操作导致设备过载或者不正常运转。
3. 零部件缺陷:生产线使用的零部件存在缺陷或者质量问题,容易引发故障。
4. 外界因素:比如环境温度过高或过低、湿度大、进出电压不稳定等因素,都有可能对设备的正常运行造成影响。
二、工厂生产线故障的预防维护措施为了减少工厂生产线的故障,保证生产线的正常运转,我们可以采取以下预防维护措施:1. 定期检查和保养:对生产线设备进行定期的检查和保养,确保设备处于良好的工作状态。
包括清洁设备、润滑零部件、更换老化零部件等。
2. 提供员工培训:提供员工操作设备和维护保养的培训,确保员工了解正确的操作方法,并能够及时发现和解决一些常见故障。
3. 更新设备和零部件:定期对设备和零部件进行更新和更换,以减少因老化和磨损导致的故障。
4. 环境监测和控制:监测生产环境,确保环境温度、湿度和电压等指标处于稳定的范围内,避免外界因素对设备的负面影响。
5. 建立故障记录和分析机制:及时记录和分析故障信息,找出故障的根本原因,并采取相应的改进措施,以防止同类故障再次发生。
三、结语工厂生产线的故障给企业带来了不小的影响,但通过预防和维护,我们可以减少故障次数,提高生产效率,并降低企业的生产成本。
因此,我们应该重视工厂生产线的故障预防维护,采取有效的措施来确保生产线的稳定运行,为企业的发展提供有力支持。
5000td干法水泥生产线DCS系统控制方案

五、5000t/d干法水泥生产线DCS系统解决方案1、前言5000t/d水泥生产线设中央控制室一座,系统主机设备、工程师站、操作站设置在中央控制室,根据生产控制和管理要求设工程师站、操作站和现场控制站,一般分为原料粉磨现场控制站(包括原料磨、原料调配、联合储库),烧成窑尾现场控制站(包括窑尾、废气处理、煤磨)烧成窑头现场控制站、水泥粉磨现场控制站(包括水泥磨、熟料库底、水泥库顶)。
(见水泥厂DCS系统结构示意图)图根据实际情况各主控制站可带远程控制站5000t/d干法水泥生产线(不含矿山,包装)一般有2500左右个控制站,其中开关量1800点左右,模拟量700点左右,所以说水泥生产线以逻辑控制为主,可根据工艺情况在上位机用梯形图或其他逻辑控制语言编制逻辑控制程序,一般是逆流程启动、顺流程停车。
现场控制站完成顺序逻辑控制和设备间的联锁、数字量和模拟量的数据采集处理、PID回路的控制等。
水泥厂的逻辑控制包括组启动、组停车、紧急停车、故障复位、设备之间的联锁、设备内部联锁等。
操作员攻占做通过CRT和键盘完成生产逻辑的监控和操作,用电设备的备妥、运行、故障等状态的显示,生产过程参数的显示、设定、报警、记录和优化等控制。
各种故障报警及工艺参数可由打印机打印出来。
网络系统完成各操作员工作站,各现场控制站之间数据传输以及其他控制系统计算机双向数据通讯等。
2、开光量控制原理(1)用电设备控制原理水泥行业的控制以逻辑控制为主,主要是控制现场用电设备的顺序启停,以及设备之间、主机设备自身的联锁。
用电设备的控制原理图如下所示,现场抽屉柜的要是开关K4打到备妥位置,继电器K1线圈得点,触点9、5吸合,现场送给DCS一个DI(备妥)信号,表示现场设备已经上电,如果没有备妥信号DCS系统不可能启动现场设备。
如果由DCS发出一个DO(驱动信号),继电器K线圈得电,触点9、5吸合,便得主接触器KM吸合,用电设备运行,主接触器的辅助触点13、14吸合,给DCS一个DI(运行)信号,表示用电设备已经在现场运行起来。
5000t_d生产线的几种设备故障及处理(1)

磨辊分两组共四个, 采用 EP1000 润滑油润滑。 2007 年 4 月 12 日 22: 00, 高价电避峰后准备开 立磨时, 3 号磨辊油位低报警, 磨机不能启动。给予补 充润滑油后开启磨机, 不到 10min, 3 号磨辊油位低 再次报警。停磨入内检查, 发现 3 号磨辊轴承漏油严 重, 已无法继续生产。 1.2.2 原因分析 打开磨辊轴承端盖检查发现, 磨辊轴承骨架油封 已损坏。磨辊漏油的原因: 磨辊空气密封管道上磨损 出了多个孔洞, 致使灰尘进入磨辊轴承油封, 将骨架 油封损坏, 导致磨辊轴承严重漏油。 1.2.3 处理及预防措施 更换磨辊轴承油封, 清理密封风机管道积灰和焊 补管道漏洞等。由于故障发现早, 处理措施及时有效, 并未对磨辊轴承造成损坏, 为了防止类似故障再次发 生, 我们制定了设备点检制度: 1) 每天高价电避峰时, 点检密封风机管道, 及时 补焊漏洞, 防止灰尘进入磨辊轴承。对磨辊轴承端盖 螺栓进行检查, 及时紧固松动的螺栓。 2) 定期更换密封风机的软连接管道, 防止软连接 老化后破损, 导致灰尘进入磨辊轴承。 3) 及时清理密封风机滤清器滤网和滤布上的灰 尘, 保证密封风机管道压力在 2 000Pa 以上。 1.3 立磨拉杆断裂 1.3.1 故障过程 2007 年 10 月 31 日 9: 00 左右, 立磨产生剧烈震 动跳停, 现场检查发现西南角拉杆上部的连杆与吊环 接口过渡圆角处已经断裂, 被迫停产处理。 1.3.2 原因分析 1) 该拉杆出厂时, 制造厂家已进行过内部探伤, 因此可以排除设备本身质量缺陷的影响。 2) 连杆与吊环接口处因无护板护套, 在物料和热 风的长期打击冲刷下, 已经磨损。并且我们曾在磨损 处进行过耐磨层的堆焊作业, 可能会使材质发生变 化, 材料内部留下微裂纹, 使拉杆的抗拉强度和冲击 韧性下降。 3) 西南角活塞式蓄能器中氮气从氮气表处有泄
辊压机生产调试过程中出现的问题及改造

HFCG160/140辊压机生产调试过程中出现的问题及改造我公司有一条5000t/d熟料新型干法生产线,配备两套辊压机(RP120-80)+Φ4.2×11m+O-Sepa(N2500)选粉机组成的闭路预粉磨水泥粉磨系统,设计单机台时产量110t/h。
为了充分发挥磨机产能,降低吨水泥工序电耗,我公司于2011年7月、8月先后对两套水泥闭路预粉磨系统进行了改造,改造后系统由辊压机(HFCG160/140)+V型选粉机+Φ4.2×11m 组成联合水泥粉磨系统。
改造后在调试、生产过程中辊压机系统就出现蓄能器气囊频繁爆裂、辊压机减速高速输入轴承温度过好的问题,辊压机系统安全、正常运转存在较大隐患。
出现的问题原因分析及解决措施:1、新辊压机投入运行调试过程中频繁出现蓄能器气囊爆裂原因分析及解决措施辊压机在试生产调试过程中,工作压力下限设置7Mpa,上限设置8Mpa,蓄能器气囊氮气充气压力按设备说明要求工作压力的0.6~0.65倍充气,充气压力为5Mpa,4只气囊充气压力均衡。
辊压机系统调试运行不到24小时,辊压机左、右侧4只蓄能器底部先后出现不同程度的撞击声,随着撞击声的连续出现,蓄能器内气囊发生爆裂,开始两天我们未对蓄能器内部构造深做研究,只更换了新的气囊后重新投入运行,结果在试运行4天内共更换了8只气囊。
更换气囊拆卸破损气囊时发现底部的菌型阀固定螺母出现严重松动或脱落,气囊破损位置正好是与菌型阀可以接触到的地方,于是检查前两天几只破损气囊破口位置也基本相同。
我们分析认为辊压机在试运行过程中蓄能器底部出现撞击声很有可能是由于底部菌型阀固定螺母松动或脱落,在液压系统压力发生波动时,阀体急剧上下移动发出的撞击声,同时阀体对气囊底部进行冲击造成气囊破裂。
根据我们分析的情况我们对菌型阀固定螺母进行了防松动脱落改造,我们在菌型阀螺母按要求拧紧后螺母下方螺杆上做好标记,重新拆下菌型阀,在螺杆做好标记的位置用Φ4钻头打个孔,在装好菌型阀拧紧螺母后用Φ4钢筋插入孔内做个螺母防松脱落插销。
5000td生产线余热发电量低的热工分析

5000td生产线余热发电量低的热工分析山东山水集团有限公司枣庄5000t/d熟料生产线配套的9MW余热发电机组发电能力不足6400kW,而另一条5000t/d微山线相同设计的9MW余热发电机组发电能力达8500kW。
经勘查两条生产线产能均正常,窑工况都相对稳定,为了查找余热发电能力相差较大的原因,集团对两条生产线做了一次系统的热工标定。
1 两线标定计算数据对比1.1 两线余热系统介绍图1为两线余热发电系统示意。
如图1所示,余热系统配有独立的ASH过热器,篦冷机的二、三室及末端位置分别引出高温、中温和低温烟道,其中高温废气经过窑头ASH独立过热器后同中温废气汇合进入窑头AQC炉。
废气出AQC炉后与低温废气汇合直接排入窑头袋除尘器,C1出口废气从余热系统的SP炉顶部进入,自上而下地加热锅炉。
因为直接对比废气温度和风量无法直观地看出所存在的差异,所以本文换算为热量单位来进行比对,可以一目了然。
图1 两线余热发电系统示意1.2 标定计算数据对比分析1)可用余热废气量对比枣庄线与微山线标定的部分计算数据如表1和表2所示。
表1 枣庄线部分标定数据表2 微山线标定部分数据从表1和表2的对比可以看出,虽然微山线熟料系统收入总热量低于枣庄线,但是微山线发电能力却远高于枣庄线,这是因为微山线可用余热占比熟料系统总热量高于枣庄线,枣庄线可用废气余热热量比微山线低29872252kJ/h,按照其余热锅炉效率和汽轮机发电效率来计算这些热量至少可以得到发电能力1600kW。
2)锅炉做功能力对比锅炉做功方面的区别通过表3和表4进行对比。
表3 枣庄线余热发电系统标定数据表4 微山线余热发电系统标定数据余热锅炉吸收热量占比余热系统热量和汽轮机进汽端热量占比余热锅炉吸收热量这两项数据反映了余热锅炉的一个总体做功水平,它和锅炉保温能力、内部管排分布设计、材质、结垢、漏风及蒸汽输送管路散热阀门泄漏等因素有关。
从表3和表4的对比看出汽轮机进汽端热量占比余热锅炉吸收热量相差无几。
5000t/d生产线试生产中主机设备出现的问题及处理

5000t /d 生产线试生产中主机设备出现的问题及处理2009-7-2 作者: 陈宝贵,王平,李小龙我集团公司投资建设的渤海水泥集团5000t /d 生产线于2007年11月27日点火生产,该项目由中材国际南京水泥工业设计研究院设计。
本文介绍该生产线主机设备在试生产中出现的主要问题及处理方法。
1 回转窑轮带托轮轴瓦发热Φ4.8m×74m 回转窑投料后,托轮轴瓦从窑头(1号台南北两侧)、窑中(2号台北侧)到窑尾(3号台北侧)先后出现了发热现象,特别是1号台北侧托轮铜瓦局部磨损严重。
经分析,一是在安装时轴瓦与轴刮研时没有研磨好而发热;二是轴瓦与轴刮研时的接触是在冷态下,在投料后,受热辐射影响而膨胀,导致接触面变化,形成初期试生产的发热;三是回转窑在砌筑耐火砖过程中形成局部变形,导致窑在径向方向受力不均,在窑提速情况下轴瓦因接触不好而发热;四是润滑油黏度指标不合格,在温度稍高时形不成油膜而发热。
解决办法:一是将l 号台南北两侧托轮拆下来解体,对托轮轴与瓦重新研磨、验瓦,达到了托轮轴与瓦接触要求,组装后现场安装;二是对2号和3号台托轮采用往托轮轴上打“点滴”——人工加油措施,直到发热消退后停止;三是采用黏度大的润滑油;四是采取降温和减少热辐射——在3组托轮台附近增加冷却轴流风机以降低温度,在3组托轮上面加装隔热板以减少热辐射;五是尽量避免热态时急停窑。
2 轮带向窑头方向窜位撞掉挡环及挡块经检查发现,l 号和2号台托轮摆成了“八”字形,使轮带与托轮接触面受力不均而导致移位。
解决办法是:根据中心线复核情况。
将北侧三挡托轮不同程度向后移动,使l 号和2号台托轮中心线平行。
轮带复位:在窜位轮带一侧的固定垫板上,圆周8等份地焊上特制M48顶丝顶在轮带上,用辅助传动转窑,各个顶丝转到回转窑上部时就顶紧,循环往复顶紧各个顶丝,将轮带缓慢顶回,在顶轮带前用专用加油枪给轮带与垫板之间注油。
这种方法比传统的用顶丝调整托轮使轮带复位简单而有效。
5000td生产线篦冷机压床事故的成因与控制

0 前言据了解,多数水泥生产厂家5000t/d篦冷机在使用过程中,都曾出现过篦冷机熟料压床事故,对产质量造成严重影响。
对此,笔者就本厂5000t/d新型干法水泥生产线篦冷机压床的成因与控制,进行了分析和研究。
1 篦冷机的相关情况我厂使用的篦冷机是南京水泥工业设计院提供的NC42340推动篦式冷却机,采用先进的控制流篦冷机新技术,优点在于充分提高了熟料的骤冷效果并有效降低篦冷机出料温度,进一步提高二次风温和三次风温,减少熟料冷却用风量,大幅提高篦冷机的热回收率以及设备运转率和易磨损件的寿命,确保烧成系统的稳定高效、高运转率和低能耗。
篦冷机的主要规格参数:规格:4.2×34.0m;生产能力:5500~6000t/d;入料温度:1400℃;出料温度:≤65℃+环境温度;篦冷机有效面积:133.2m2;篦床冲程次数:4~25次/min;篦床冲程:130mm(正常)、140mm(最大);传动方式:液压三级(段)传动,压力≤30MPa。
2 篦冷机压床事故的成因2.1篦冷机压床事故原因高温熟料堆积在篦床上,由于某种原因未能冷却并移动,导致压住一段篦床迅速增厚,液压传动系统负荷过高跳停,篦床并使第一级传动无法再次正常起动,此时高温熟料粘连结合成大块,轻则30~40t熟料,重则60~100t熟料。
2.2篦冷机压床成因的分类篦冷机发生压床事故的原因可分为两大类。
一是由于机械或电气设备故障,篦床或冷却风机无法运行,加之采取措施不力,引起高温熟料(1100~1400℃)堆积并凝固的压床事故。
二是由于工艺技术管理、操作中出现问题,未及时得到纠正而造成压床事故。
3 篦冷机压床事故的分析控制要避免发生篦冷机压床,就必须对压床事故的不同形成原理进行分析,并有针对性地采取措施,使之处于受控状态。
3.1设备故障引起的压床事故3.1.1冷却风机故障引起的压床事故I段篦板冷却风机因轴承、电机、叶轮损坏停止运行时,对高温熟料不能有效冷却,在Ⅰ段(特别是阶梯篦板处)的1100~1200℃高温熟料中的C3A、C4AF等成分还带有液相,极易粘结成大块,导致篦床推压迅速升高,液压传动系统负荷过高(≥14MPa)跳停,并无法再次正常起动,同时窑内熟料还不断落入,使篦床进一步压死,此时只有被迫停窑人工处理。
自动化生产线的常见故障及解决方法

自动化生产线的常见故障及解决方法一、介绍自动化生产线在现代工业中起着至关重要的作用,它能够提高生产效率、降低成本,并且提高产品质量。
然而,由于各种原因,自动化生产线也会遇到一些常见的故障。
本文将详细介绍自动化生产线的常见故障及解决方法,以帮助您更好地应对这些问题。
二、常见故障及解决方法1. 传感器故障传感器在自动化生产线中起着至关重要的作用,它们用于检测物体的位置、速度、温度等信息。
当传感器出现故障时,会导致生产线停工或产生错误的数据。
解决方法如下:- 检查传感器是否受到干扰或损坏,如果有必要,更换传感器。
- 清洁传感器,确保其表面没有灰尘或污垢。
- 检查传感器的连接线,确保连接稳固。
2. 电气故障电气故障是自动化生产线中常见的问题之一。
它可能由电源故障、电线连接不良、电机过载等原因引起。
解决方法如下:- 检查电源供应是否正常,确保电压稳定。
- 检查电线连接是否牢固,没有松动或短路现象。
- 检查电机是否过载,如果是,减少负载或更换更大功率的电机。
3. 机械故障机械故障是自动化生产线中常见的问题之一。
它可能由零部件磨损、机械结构不稳定等原因引起。
解决方法如下:- 定期检查机械零部件的磨损情况,及时更换损坏的零部件。
- 检查机械结构是否稳定,如有需要,进行调整或加固。
4. 控制系统故障控制系统故障可能由软件错误、通信故障等原因引起。
解决方法如下:- 检查控制系统的软件程序,修复错误或重新编程。
- 检查通信线路是否正常,确保信号传输畅通。
5. 运输故障运输故障可能由物料堆积、输送带堵塞等原因引起。
解决方法如下:- 检查物料堆积情况,及时清理物料。
- 检查输送带是否正常运转,如有需要,修复或更换输送带。
6. 温度控制故障温度控制故障可能由温度传感器故障、控制系统错误等原因引起。
解决方法如下:- 检查温度传感器是否正常工作,如有需要,更换传感器。
- 检查控制系统的温度设定值和实际温度是否一致,如有需要,进行调整。
5000t回转窑典型故障及其原因讲解

典型故障及其原因讲解
芜湖海螺制造一分厂维修工段
回转窑简介
回转窑作为煅烧的关键装备,主要承担燃料燃烧、原料 煅烧、热交换、化学反应和输送的功能。 回转窑应用广泛,几乎涉及了我国所有行业,我们所 设计开发的回转窑已应用的有:水泥、冶金球团、活性
石灰、磁化焙烧、氧化铝、锌挥发、稀有贵重金属(钛、
1、回转窑的结构及工作原理概述
燃料由窑头喷入窑内,燃烧产生的废气与物料 进行热交换后,由窑尾导出。
1、回转窑的结构及工作原理概述
1、筒体采用锅炉用碳素钢板20g卷制,通常自动 焊焊接,筒体壁厚:一般为28mm,烧成带为32mm,轮 带下为75/80mm、由轮带下到跨间有42/55厚的过渡段 节,从而使筒体的设计更为合理,既保证横截面的刚 性又改善了支承装置的受力状态。在筒体进、出料端 都装有耐高温、耐磨损的“窑口护铁”,其中“窑头 护铁”与冷风套组成环形分格的套筒空间,从喇叭口 向筒体吹冷风冷却“窑头护铁”的非工作面,以有利 该部分的长期安全工作。在筒体上套有三个矩形实心 轮带。轮带与筒体垫板间隙由热膨胀量决定,当窑正 常运转时,轮带能适度套在筒体上,以减少筒体径向 变形,起增加筒体刚性的作用。
托轮
液压 档轮
托轮组 对于大型回转窑托轮轴承组 一般采用滑动轴承,由轴承 盖、托轮、托轮轴、洒油盘、 油勺、轴瓦、球面瓦、及轴 承座等组成。每个轴承座中 装有两个热电阻,分别检查 润滑油的油温和轴瓦的温度.
挡轮装置 挡轮按其受力情况及作用原理,可分为机械挡轮和液压 挡轮二种。大型回转窑多采用液压挡轮。 液压挡轮设置主要由挡轮、挡轮轴、轴承体、导向轴、 滚动轴承、挡轮行程开关等组成。液压挡轮装置承受全 窑的下滑力。并且通过液压挡轮该装置可推动窑体向上 移动,迫使轮带和窑筒体一起按照一定的速度和行程沿 窑中心方向在托轮上往复移动,使轮带和托轮在全宽上 能均匀磨损,以延长使用寿命。
- 1、下载文档前请自行甄别文档内容的完整性,平台不提供额外的编辑、内容补充、找答案等附加服务。
- 2、"仅部分预览"的文档,不可在线预览部分如存在完整性等问题,可反馈申请退款(可完整预览的文档不适用该条件!)。
- 3、如文档侵犯您的权益,请联系客服反馈,我们会尽快为您处理(人工客服工作时间:9:00-18:30)。
2009.No.9我公司5000t/d 生产线烧成系统于2008年9月11日投料试生产,完全依靠本公司自身技术力量,在不到一个月的时间内就完成了试生产过程。
当年生产合格熟料30万t ;2009年第一季度在停车检修14.5d 的情况下生产熟料29.5万t ;4月份实现连续运行35d 无停车,月平均日产量达到5650t/d ,熟料28d 平均抗压强度达到60.1MPa 以上。
现在,该生产线日产量稳定在5550t/d 以上,生料磨台时产量稳定在440t/h 以上,各项参数均达到设计要求。
1投产初始系统制约生产的主要问题1)分解炉输煤罗茨风机电动机电流高。
当尾秤喂煤量超过23t/h 后,电流接近甚至超过额定电流(336A ),存在跳停危险,同时喂煤量波动幅度增大,分解炉温度难以稳定控制。
2)雨雪天控制线路容易短路,造成信号失真,导致预热器温度参数波动大,中控无法正常控制。
3)标准仓下料不畅,投料量超过245t/h 后,反馈跟不上设定量。
4)窑系统投料过程中极易“烧流”,导致频繁发生“堆雪人”现象。
5)托轮轴瓦频繁出现高温现象,被迫止料处理。
6)分解炉出口鹅颈管处与C 5水平管道处积料现象严重,影响系统拉风,导致频繁发生“塌料”现象,影响烧成工况的稳定。
7)生料制备系统成品皮带输送机能力不足(皮带宽度1.0m ,带速1.6m/s ,倾角约7.5°),严重制约了生料磨产量。
UM50.4立磨台时产量仅为280t/h,约为额定台时产量的70%,致使生料库储量不足,窑系统无法正常生产。
2调试措施1)将罗茨风机出口直角弯头由6个减少为2个,同时将尾秤最大量程由25t/h 增大到28t/h 。
通过改造,罗茨风机电动机电流降到260A 左右,并通过调整量程极大地缓解了喂煤量波动幅度大的问题。
2)经过现场观察,发现短路是热电偶接线处密封不严造成的,对此增设了防雨装置,消除了隐患。
5000t/d 生产线调试中遇到的问题及解决措施曹金良(乌兰水泥集团有限公司,内蒙古乌兰察布012400)中图分类号:TQ172.622.26文献标识码:B文章编号:1002-9877(2009)09-0019-02[5]SugamaT,KukackaLE.Characteristicsofmagnesiumpolyphosphate cement derived from ammonium polyphosphate solutions[J].Cement and Concrete Research,1983(13):499-506.[6]Abdelrazig B E I,Sharp J H,El -Jazairi B.Microstructure and mechanical properties of mortar made from magnesia -phosphate cement [J].Cement and Concrete Research,1989(18):247-258.[7]Popovics S,Rajendran N,Penko M.Rapid hardening cements for repair of concrete[J].ACI Mater J,1987(84):64-73.[8]Sarkar A K.phosphate cement-based fst-setting binders [J].Ceram.Bull.,1990,69(2):234-238.[9]Wagh A S,Singh D,Jeong S.Method of waste stabilization via chemically bonded phasphate ceramics[P].US Patent:5,830,815,1998.[10]Wagh A S,Jeong S,Singh D.High strength phosphate cement using industrial byproduct ashes [M].Reston,VA:Amer,soc.civil Engineers,1997:542-533.[11]Yang Q,Zhang S,Wu X.Deicer -scaling resistance of phosphate cement -binder for rapid repair of concrete [J].Cement and ConcreteResearch,2002,32:165-168.[12]Li Z,Ding Z,Zhang Y.Development of sustainable cementitious materials [C]//Proceedings of the International Workshop on Sustainable Development and Concrete Technology,2003:55-76.[13]姜洪义,张联盟.磷酸镁水泥的研究[J].武汉理工大学学报,2001,23(1):32-34.[14]汪宏涛,钱觉时,王建国.磷酸镁水泥的研究进展[J].材料导报,2005,19(12):46-47.[15]姜洪义,梁波,张联盟.MPB 超早强混凝土修补材料的研究[J].建筑材料学报,2001,4(2):196-198.[16]杨全兵,吴学礼.新型超快硬磷酸盐修补材料的研究[J].混凝土与水泥制品,1995(6):13-15.[17]杜磊,严云,胡志华.化学结合磷酸镁胶凝材料的研究及应用现状[J].水泥,2007(5):23-25.[18]Eubank W R.Calcination studies of Mg oxide [J].J Am CeramSoc,1951(34):225-229.(编辑蔡成军)!!!!!!!!!!!!!!!!!!!!!!!!!!!!!!!!!!!!!!!!!!!!!!!19--2009.No.93)清仓进入内部检查,发现标准仓侧气动阀入口密封毡太大,使下料口截面积减小近1/3,在恢复下料口原状的同时,将下料斜槽鼓风管内径由15mm 改为20mm ,彻底消除了投料量反馈跟不上设定量的现象。
4)经过观察窑内火焰状况及中控操作参数,发现该生产线由于系统设备规格大,导致窑系统升温时间较长,大约是2500t/d 生产线的1.5~2倍,同时升温过程中火焰较难控制。
窑操作员在升温及投料过程中为了稳定火焰,尽量提高窑前(烧成带前部)温度,造成煤灰的富集,窑内产生大量低共熔点的物料,这样在投料瞬间就会发生“烧流”现象。
为此,要求中控操作员在窑系统升温过程中不仅要使系统均匀受热,而且在投料过程中要合理控制窑头负压,使火焰自然伸展(防止为了提高烧成带温度,而通过窑头引风机强行缩短火焰,导致窑前温度急剧升高发生“烧流”现象)。
此时,由于窑内物料少,不易顶住火焰,黑火头拉伸,窑前产生一定长度的冷却带,窑内低共熔点物料到达冷却带后得到冷却,防止发生“烧流”现象。
随着物料在窑内的移动,火焰会自然前缩,直到物料进入烧成带,火焰会自然成形。
如投料前窑内物料还有发黏甚至“烧流”现象发生,要及时大幅度减头煤,窑前温度一旦低于投料前窑内物料最低共熔点温度,发黏或“烧流”现象会瞬间消失,然后再将头煤加到正常给定值;同时固定篦板风机阀门开度达到60%以上,一段篦速设定在4.5r/min 以上,防止“堆雪人”。
为避免“窜黄料”,投料前,点火喷油系统停止运行但不要撤出,随时准备喷油。
通过以上改进措施,投料过程中再未发生“烧流”或“堆雪人”的现象。
5)针对托轮轴瓦易发生高温的现象特地聘请专家调整托轮角度,但在环境气温特别低的时候仍频繁出现高温现象。
经过观察发现,在环境气温特别低的时候,托轮内加注的开齿320油几乎失去流动性,导致托轮轴瓦缺少淋油而发生高温现象。
因此,将发热现象较轻微的两个托轮换用HF 托轮专用油;其它两个发热现象较严重的托轮根据环境气温的变化,将开齿320油与680中负荷齿轮油按照一定比例搭配调和后使用。
采取上述措施后,托轮再未发生高温现象。
6)在分解炉出口鹅颈管与C 5水平管道易积灰处,增设捅料孔,通过严格的考核制度增加捅料频次后,基本消除了“塌料”现象。
同时,考虑大修中在该捅料口处安装空气炮,鹅颈管处浇注倒“V ”字形耐火浇注料,进一步消除集料现象。
7)生料制备过程中,成品生料粉由窑尾电除尘器下4条拉链机输送到带有7.5°倾角的成品皮带输送机进入生料入库斗式提升机内。
由于成品皮带倾角大,带速快,输送能力只有240~280t/h 。
皮带倾角由7.5°降为约4°后,几乎未见效果,再降倾角已无空间。
最后经论证,在生料成品皮带侧增设一空气输送斜槽,分流了投料量1/2的生料粉入库斗式提升机。
改造后,生料磨台时产量一直稳定在420~450t/h 。
通过这一改造我们认为,生料粉动休止角受输送皮带的倾角、带速影响极大,设计时要加以考虑。
3参数对比调试前后系统主要参数的对比见表1,熟料品质参数对比见表2。
表1调试前后系统主要参数对比表2调试前后熟料品质参数对比由表1和表2看出,在调试过程中所采取的措施是有效的,为5000t/d 生产线的稳定生产以及进一步挖掘系统增产潜能积累了一定的经验。
(编辑张迪)主要控制参数调试前调试后窑系统平均日产量/(t/d)4600~5100≥5550二次风温/℃1010±301100±30入窑斗式提升机电流/A(135+6)×2(150±8)×2三次风温度/℃885±30950±30烟室温度/℃1040±201040±20窑头压力/Pa -100±20-50±20分解炉出口温度/℃880±10880±10C 1出口温度/℃355±10315±10窑头电除尘器入口温度/℃220±10160±10高温风机转速/(r/min)760±10850±15高温风机入口压力/Pa -4800±50-6000±50生料磨台时产量/(t/h)280±20430±20时间率值矿物组成/%28d 抗压强度平均值/MPa KHSM IM C 3S C 2S C 3A C 4AF 调试前0.908 2.30 1.6155.0719.669.1510.8257.8调试后0.8942.451.5256.8623.078.2910.7960.420--。