03_permmonitoring
质谱的几种工作模式-SIMSRMMRM
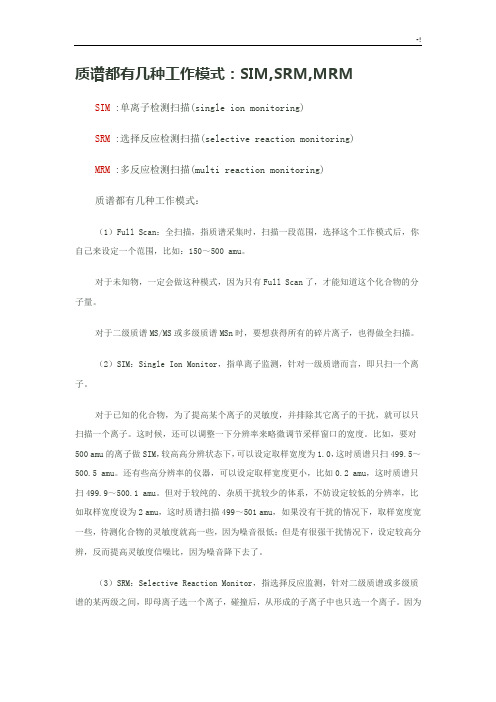
质谱都有几种工作模式:SIM,SRM,MRMSIM :单离子检测扫描(single ion monitoring)SRM :选择反应检测扫描(selective reaction monitoring)MRM :多反应检测扫描(multi reaction monitoring)质谱都有几种工作模式:(1)Full Scan:全扫描,指质谱采集时,扫描一段范围,选择这个工作模式后,你自己来设定一个范围,比如:150~500 amu。
对于未知物,一定会做这种模式,因为只有Full Scan了,才能知道这个化合物的分子量。
对于二级质谱MS/MS或多级质谱MSn时,要想获得所有的碎片离子,也得做全扫描。
(2)SIM:Single Ion Monitor,指单离子监测,针对一级质谱而言,即只扫一个离子。
对于已知的化合物,为了提高某个离子的灵敏度,并排除其它离子的干扰,就可以只扫描一个离子。
这时候,还可以调整一下分辨率来略微调节采样窗口的宽度。
比如,要对500 amu的离子做SIM,较高高分辨状态下,可以设定取样宽度为1.0,这时质谱只扫499.5~500.5 amu。
还有些高分辨率的仪器,可以设定取样宽度更小,比如0.2 amu,这时质谱只扫499.9~500.1 amu。
但对于较纯的、杂质干扰较少的体系,不妨设定较低的分辨率,比如取样宽度设为2 amu,这时质谱扫描499~501 amu,如果没有干扰的情况下,取样宽度宽一些,待测化合物的灵敏度就高一些,因为噪音很低;但是有很强干扰情况下,设定较高分辨,反而提高灵敏度信噪比,因为噪音降下去了。
(3)SRM:Selective Reaction Monitor,指选择反应监测,针对二级质谱或多级质谱的某两级之间,即母离子选一个离子,碰撞后,从形成的子离子中也只选一个离子。
因为两次都只选单离子,所以噪音和干扰被排除得更多,灵敏度信噪比会更高,尤其对于复杂的、基质背景高的样品。
横河PRM安装及设置可修改文字

二、PRM SERVER 配置
4)Devices connected locally 当hart 设备通过 hart 调制解调器连接到 PRM 时,设备路径与通
过 multiplexers 连接到 hart 设备时的路径是一样的。 在这种情况下, 你必须指定“ mmss”9999。 PRM 直接连接到模块的通信端口,无需通过 多路复用器进行路由.设备路径按以下格式指定:xxxxxxxx-cc-mmss xxxxxxxx: Project name cc: Port number mm: Master number ss: Slave number mmss = 9999 Example: PJT01-01-9999
打开方式: select [Start] > [All Programs] > [YOKOGAWA PRM] > [Tool] > [PRM Setup Tool]。
12
二、PRM SERVER 配置
2)Devices connected to CENTUM 导出 device paths from CENTUM: 、确保 centum 项目为当前使用项目,与现场硬件相匹配; 、在CENTUM HIS or ENG station运行下面文件,路径如下: <CENTUM installation folder>\ENG\TOOL\BKEngDataExportForPRM.exe 、在“项目名称”框中,键入希望从中导出设备路径的centum 项目的名称; 、单击[ ... ]按钮以选择导出文件的位置,将出现一个文件选择对话框 、选择要导出文件的文件夹。可以使用文件名、 devicepath.txt 或键入 新的文件名; 单击[保存]。选定 centum 项目的设备路径被导出到指定位置的文件中。 导入 device paths from CENTUM: 、使用 PRM 设置工具,打开设备路径配置窗口,并选择要导入设备路径配 置文件的 fieldcommunications 服务器。 Click [Import]. 在文件选 择对话框中,选择要导入的设备配置文件; Click [Open].树视图和设备 路径列表显示从文件导入的设备路径;Click [Apply]保存导入的设备路径.
HP LaserJet Pro 400 M451 色彩打印机说明书

LASERJET PRO 400COLOR M451 printer seriesProduce professional-quality color documents with ease and fast speed.Seamlessly integrate into your office or wireless home network. HP features help you save paper and energy, and print from virtually anywhere with HP ePrint.3Print Speed 1: Up to 21 ppm black (letter), Up to 21 ppm color (letter) Print Resolution: Up to 600 x 600 dpiPrint Technology Resolution: HP ImageREt 3600 Display: 2-line LCD (text)Monthly Volume (Duty Cycle): Up to 40,000 pagesPaper Handling: 50-sheet multipurpose tray, 250-sheet input tray 2, 150-sheet output bin, 250-sheet input tray 3 (optional)Measured using ISO/IEC 24734, excludes first set of test documents. For more information see /go/printerclaims . Exact speed varies depending on the system configuration,software application, driver, and document complexity. Wireless performance is dependent upon physical environment and distance from access point, and may be limited during active VPN connections. Requires an Internet connection to the printer. Feature works with any Internet- and e-mail-capable device. Print times may vary. For a list of supported documents and image types, see/go/eprintcenter . Compared with HP LaserJet Pro P1566/ P1606dn printer. Assuming customer is printing at least 30% of total pages in color with content similar to the color ISO/IEC 19798 test suite (/jtc1/sc28) and overall average job length of three pages. Yields established using ISO/IEC test standards. Actual yields and costs vary considerably depending on images printed, number of color pages printed, and other factors. HP Auto-On/Auto-Off capabilities subject to printer and settings. Actual results may vary. HP Smart Install works with Windows only. Compared with traditional fusing. Program features and availability may vary by country. For more information, visit /learn/suresupply . Program availabilityvaries. HP print cartridge return and recycling is currently available in more than 50 countries and territories around the world through the HP Planet Partners program. For more information, or to request return envelopes and bulk collection boxes, visit /recycle . Automatic two-sided printing is avaliable on the HP LaserJet Pro M451dn and M451dw only. Built-in wireless is available on the HP LaserJet Pro 400 Color M451nw and M451dw only.Professional-grade speed and color•Boost productivity and save time with print speeds up to 21 ppm letter.1•Produce bold text and smooth color with HP ImageREt 3600 and Original HP LaserJet toner cartridges.•Produce color marketing materials in-house on a range of media sizes by using tips and templates from HP.•Print documents affordably. Get the same black cost per page as a black-and-white HP LaserJet printer.4Manageability, productivity, and mobility•Conserve resources and save paper, using automatic two-sided printing.10•Proactively manage office printing with HP Web Jetadmin.•Conveniently locate the printer anywhere in the office, using built-in wireless connectivity.2, 11 Share printing resources, using built-in Ethernet.•Print from virtually anywhere with HP ePrint.3Easy-to-use and resource-conserving•Reduce energy use with HP Auto-On/Auto-Off Technology.5 Also save with Instant-on Technology.7•Start right away with HP Smart Install.6 Use HP Auto Wireless Connect to autoconfigure networking.2•Receive consistent results with Original HP cartridges and easily reorder with HP SureSupply.8•Take advantage of free, easy recycling—cartridges returned through HP Planet Partners are recycled responsibly.9LASERJET PRO 400COLOR M451 printer seriesHP LASERJET PRO 400 COLOR M451 printer series Product Number: CE956A, CE957A and CE958A ENERGY STAR qualified models; see /go/energystar Measured using ISO/IEC 24734, excludes first set of test documents. For more information see /go/printerclaims . Exact speed varies depending on the system configuration, software application, driver, and document complexity. Exact speed varies depending on the system configuration, software application, driver and document complexity. HP SureSupply alerts you when your print cartridge is running low and helps you purchase online or locally through HP or a participating retailer. Only available with Original HP supplies; Internet access required. To learn more, visit /go/SureSupply .Duty cycle is defined as the maximum number of pages per month of imaged output. This value provides a comparison of product robustness in relation to other HP LaserJet or HP Color LaserJet devices, and enables appropriate deployment of printers and MFPs to satisfy the demands of connected individuals or groups. HP recommends that the number of printed pages per month be within the stated range for optimum device performance, based on factors including supplies replacement intervals and device life over an extended warranty period. Values are subject to change. For current information see Product Support page at /support . Configuration tested: simplex, mono. Powerrequirements are based on the country/region where the printer is sold. Do not convert operating voltages. This will damage the printer and void the product warranty. Introductory cartridges included; yields ~ 1,400 color composite (C/Y/M) and black pages. Actual yields vary considerably based on images printed and other factors. For details see /go/learnaboutsupplies . Ships with preinstalled introductory print cartridges (yield ~ 1,400 pages). Wireless direct print is available on the HP LaserJet Pro 400 Color M451nw and M451dw only.©2011 Hewlett-Packard Development Company, L.P. HP is a registered trademark of the Hewlett Packard Company. ENERGY STAR and the ENERGY STAR logo are registered U.S. marks. All other trademarks are the property of their respective owners. Microsoft and Windows are registered trademarks of Microsoft Corporation. Adobe and Acrobat are trademarks of Adobe Systems Incorporated. This listing of non HP products does not constitute an endorsement by Hewlett Packard Company. The information contained herein is subjectto change without notice and is provides "as is" without warranty of any kind. HP shall not be liable for technical or editorial errors or omissions contained herein.J FOR MORE INFORMATION VISIT OUR WEBSITE AT TECHNICAL SPECIFICATIONSPRODUCT NUMBERCE956A: LaserJet Pro 400 Color M451nw CE957A: LaserJet Pro 400 Color M451dn CE958A: LaserJet Pro 400 Color M451dw PRINT TECHNOLOGY LaserPRINT SPEED 1Black (Normal, letter): Up to 21 ppm; Color (Normal, letter): Up to 21 ppmFirst Page Out 2: As fast as 17 sec Color (letter, ready), As fast as 17 sec black (letter, ready)PRINT RESOLUTION Black (Best): Up to 600 x 600 dpi; Black (Normal): Up to 600 x 600 dpi Color (Best): Up to 600 dpi PRINT TECHNOLOGY RESOLUTIONHP ImageREt 3600DUPLEX PRINT OPTIONS •M451dn & M451dw: Automatic (standard)•M451nw: Manual (driver support provided)HP ePrint CAPABILITY YesMOBILE PRINTING CAPABILITY HP ePrint, Apple AirPrint™, Wireless Direct Print 10STANDARD PRINT LANGUAGES HP PCL 6, HP PCL 5c, HP postscript level 3 emulation NUMBER OF PRINT CARTRIDGES4 (1 each black, cyan, magenta, yellow)SURESUPPLY SUPPORTED 3YesPRINTER MANAGEMENT Windows: HP Device Toolbox (default install), SNP Alerts (minimum network install), HP Web Jetadmin (download); Mac: HP UtilityPRINTER SMARTSOFTWARE FEATURESHP ePrint, Apple AirPrint™, Smart Install, HP Auto-On/Auto-Off technologyM451nw & M451dw: Plus Wireless Direct PrintM451dn & M451dw: Plus Automatic two-sided printingSTANDARD CONNECTIVITY •M451dn: 1 Hi-Speed USB 2.0 port, 1 Fast Ethernet 10/100Base-TX network port•M451nw & M451dw:1 Hi-Speed USB 2.0 port, 1 Fast Ethernet 10/100Base-TX network port, 1 WiFi 802.11 b/g/n WIRELESS CAPABILITY •M451dn: No•M451nw & M451dw: Yes, built-in WiFi 802.11 b/g/nNETWORK CAPABILITIES •M451dn: Via built-in 10/100 Fast Ethernet•M451nw & M451dw: Via built-in 10/100 Fast Ethernet, Wireless 802.11 b/g/n CONTROL PANEL 2-line, 16-character backlit LCD display, 5 buttons (Cancel job, Left arrow, Right arrow, Select, Back), 2 LED lights (Attention, Ready)FONTS AND TYPEFACES 84 scalable TrueType fontsMEDIA TYPES SUPPORTED Paper (bond, brochure, colored, glossy, letterhead, photo, plain, preprinted, prepunched, recycled, rough), postcards, transparencies, labels, envelopesMEDIA SIZES SUPPORTED•M451nw: Tray 1: Letter, legal, executive, 8.5 x 13 in, 3 x 5 in, 4 x 6 in, 5 x 8 in, envelopes (No 10, Monarch); Tray 2, optional Tray 3: Letter, legal, executive, 8.5 x 13 in, 4 x 6 in, 5 x 8 in, envelopes (No 10, Monarch)•M451dn & M451dw: Tray 1: Letter, legal, executive, 8.5 x 13 in, 3 x 5 in, 4 x 6 in, 5 x 8 in, envelopes (No 10, Monarch); Tray 2, optional Tray 3: Letter, legal,executive, 8.5 x 13 in, 4 x 6 in, 5 x 8 in, envelopes (No 10, Monarch); Automatic duplexer: Letter, legal, executive, 8.5 x 13 inMEDIA WEIGHTS SUPPORTEDTray 1: 60 to 176 g/m² (up to 220 g/m² with postcards and HP Color laser glossy photo papers); Tray 2, Tray 3 (optional): 60 to 163 g/m² (up to 176 g/m² with postcards); Automatic duplexer: 60 to 163 g/m²RECOMMENDED MEDIA WEIGHT16 to 43 lb (60 to 163 g/m²)DUTY CYCLE (MONTHLY, LETTER)4Up to 40,000 pagesRECOMMENDED MONTHLY PAGE VOLUME 5Up to 750 to 2,000 pages DISPLAY2-line LCD (text)MAXIMUM/STANDARAD MEMORY 384 MB/128 MBPAPER HANDLING50-sheet multipurpose tray, 250-sheet input tray 2, 150-sheet output binInput Capacity (standard): Up to 300 Sheets, Up to 50 transparencies, Up to 10 envelopesInput Capacity (maximum): Up to 550 Sheets (with optional tray 3)Ouput Capacity: Up to 50 Sheets, Up to 50 transparencies, Up to 20 envelopesPROCESSOR SPEED 600 MHzSOFTWARE INCLUDEDWindows: HP Installer/Uninstaller, HP PCL 6 print driver, Status Alerts, HP Update, DXP; Mac: HP Installer/Uninstaller, HP Postscript driver, HP Setup Assistant, HP Utility, HP Alerts, HP Firmware UpdaterMINIMUM SYSTEM REQUIREMENTSPC: Microsoft ® Windows ® 7 (32-bit/64-bit), Windows Vista ® (32-bit/64-bit): 1 GHz 32-bit (x86) or 64-bit (x64) processor, 1 GB RAM (32-bit) or 2 GB RAM (64-bit), 400 MB free hard disk space, CD/DVD-ROM or Internet, USB or Network port; Windows ® XP (32-bit) SP2: Pentium ® 233 MHz processor, 512 MB RAM 400 MB free hard disk space, CD/DVD-ROM or Internet, USB or Network port;Mac: Mac OSX v 10.5, v 10.6, PowerPC G4, G5, or Intel ® Core™ Processor, 500 MB hard disk, CD-ROM/DVD-ROM or Internet, USB or Network portCOMPATIBLE OPERATING SYSTEMS Full software installs supported on: Microsoft ® Windows ® 7 32-bit and 64-bit, Windows Vista ® 32-bit and 64-bit, Windows ® XP 32-bit (SP2 or higher); Driver onlyinstalls supported on: Microsoft ® Windows ® Server 2008 32-bit and 64-bit, Windows ® Server 2003 32-bit (SP3 or higher); Mac OS X v 10.5, v 10.6; Linpus Linux (9.4, 9.5), Red Hat Enterprise Linux 5.0 (supported with a pre-built package); SUSE Linux (10.3, 11.0, 11, 11.1, 11.2), Fedora (9, 9.0, 10, 10.0, 11.0, 11, 12, 12.0), Ubuntu (8.04, 8.04.1, 8.04.2, 8.10, 9.04, 9.10, 10.04), Debian (5.0, 5.0.1, 5.0.2, 5.0.3) (supported by the automatic installer); HPUX 11 and Solaris 8/9OPERATING ENVIRONMENTOperating Humidity Range: 10 to 80% RH (non-condensing)Recommended Humidity Operating Range: 20 to 70% RH (non-condensing) Operating Temperature Range: 59 to 86º F (15 to 30ºC)Recommended Operating Temperature Range: 59 to 80.6º F (15 to 27º C) Storage Temperature Range: -4 to 104º F (-20 to 40º C) Non-Operating Humidity: 10 to 95% RH (non-condensing)ACOUSTIC 6Acoustic Power Emissions: 6.5 B(A);Acoustic Power Emissions (Ready): 4.1 B(A);Acoustic Pressure Emissions Bystander (Active, Printing): 51 dB(A); Acoustic Pressure Emissions Bystander (Ready): 27 dB(A)POWERPower Requirements: Input voltage: 110 to 127 VAC (+/- 10%), 60 Hz (+/- 3 Hz) Power Supply Type: Internal (Built-in) power supply;Power Consumption 7: 425 watts (Active), 15.2 watts (Ready), 4.0 watts (Sleep), 0.5 watts (Off);Typical Electricity Consumption (TEC) Number: 1.509 kWh/Week PRODUCT DIMENSIONSM451nw:W x D x H: 15.9 x 17.9 x 12.7 in (405 x 454 x 322 mm) Maximum: 15.9 x 25.9 x 12.7 in (405 x 659 x 322 mm)M451dn & M451dw:W x D x H: 15.9 x 19.1 x 12.7 in (405 x 484 x 322 mm) Maximum: 15.9 x 27.1 x 12.7 in (405 x 689 x 322 mm)PRODUCT WEIGHT M451nw: 50.1 lb (22.74 kg)M451dn & M451dw: 52.1 lb (23.64 kg)SECURITY MANAGEMENTWireless: WEP (128 bit), WPA/WPA2 - Personal (AES, TKIP); Embedded WebServer: password-protection, secure browsing via SSL/TLS; Network: enable/disable network ports and features, SNMPv1 community password change; HP ePrint: HTTPS with certificate validation, HTTP Basic Access Authentication, SASL authentication WHAT’S IN THE BOX 8Printer, Four preinstalled introductory HP LaserJet toner cartridges (yield ~ 1,400 pages), In-box documentation (Hardware installation guide), Software drivers and documentation on CD-ROMs, Power cord, Built-in Automatic duplexer for two-sided printing (M451dn & M451dw models only), Built-in Wireless Card (M451nw & M451dw models only), USB cable (M451nw & M451dw models only)WARRANTY One-year limited warranty, return to HP or authorized service provider HP SERVICES AND SUPPORT OPTIONS HP 3y Nbd Exch Color LaserJt M451 HW SVC, U1H88E HP 1yPW Nbd Exch Color LaserJet M451 SVC, U1H98PE HP NtwkInstall Inkjet/prsnl LaserJet SVC, H3110EREPLACEMENT CARTRIDGES 9HP 305A Black LaserJet Toner Cartridge (~ 2,200 pages), CE410A HP 305X Black LaserJet Toner Cartridge (~ 4,000 pages), CE410X HP 305A Cyan LaserJet Toner Cartridge (~ 2,600 pages) CE411A HP 305A Yellow LaserJet Toner Cartridge (~ 2,600 pages) CE412A HP 305A Magenta LaserJet Toner Cartridge (~ 2,600 pages) CE413AACCESSORIESHP LaserJet 250-sheet Paper Feeder, CF106A HP 256 MB DDR2 144-pin DIMM, CB423A HP BarCodes and More DIMM HG281DJ,HP Scalable BarCodes HG282DJ, HP MICR Font HG283DJ, HP Jetdirect ew2500 802.11b/g Wireless Print Server J8021AJune 2013 R3 2013。
Windows自带性能监控工具Perfmon使用介绍
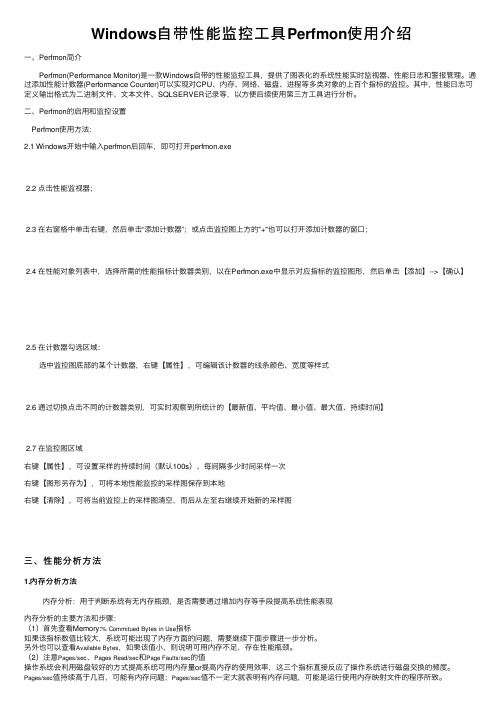
Windows⾃带性能监控⼯具Perfmon使⽤介绍⼀、Perfmon简介 Perfmon(Performance Monitor)是⼀款Windows⾃带的性能监控⼯具,提供了图表化的系统性能实时监视器、性能⽇志和警报管理。
通过添加性能计数器(Performance Counter)可以实现对CPU、内存、⽹络、磁盘、进程等多类对象的上百个指标的监控。
其中,性能⽇志可定义输出格式为⼆进制⽂件、⽂本⽂件、SQLSERVER记录等,以⽅便后续使⽤第三⽅⼯具进⾏分析。
⼆、Perfmon的启⽤和监控设置 Perfmon使⽤⽅法:2.1 Windows开始中输⼊perfmon后回车,即可打开perfmon.exe2.2 点击性能监视器;2.3 在右窗格中单击右键,然后单击“添加计数器”;或点击监控图上⽅的"+"也可以打开添加计数器的窗⼝;2.4 在性能对象列表中,选择所需的性能指标计数器类别,以在Perfmon.exe中显⽰对应指标的监控图形,然后单击【添加】-->【确认】2.5 在计数器勾选区域: 选中监控图底部的某个计数器,右键【属性】,可编辑该计数器的线条颜⾊、宽度等样式2.6 通过切换点击不同的计数器类别,可实时观察到所统计的【最新值、平均值、最⼩值、最⼤值、持续时间】2.7 在监控图区域右键【属性】,可设置采样的持续时间(默认100s)、每间隔多少时间采样⼀次右键【图形另存为】,可将本地性能监控的采样图保存到本地右键【清除】,可将当前监控上的采样图清空,⽽后从左⾄右继续开始新的采样图三、性能分析⽅法1.内存分析⽅法内存分析:⽤于判断系统有⽆内存瓶颈,是否需要通过增加内存等⼿段提⾼系统性能表现内存分析的主要⽅法和步骤:(1)⾸先查看Memory:% Commitued Bytes in Use指标如果该指标数值⽐较⼤,系统可能出现了内存⽅⾯的问题,需要继续下⾯步骤进⼀步分析。
Pellicon 超滤(UF) 浓稠化(DF)操作指南说明书

Notice: The information in this document is subject to change without notice and should not be construed as a commitment by Merck Millipore or an affiliate. Neither Merck Millipore nor any of its affiliates assumes responsibility for any errors that may appear in this document.Introduction .........................................................................................................................................3Objectives, Methods and Materials ...............................................................................................4Installation ...........................................................................................................................................6Pre-use Flushing Procedure ............................................................................................................7Normalized Water Permeability (NWP) Measurement ............................................................9Determination of System Hold-up Volume..............................................................................11System Equilibration ......................................................................................................................12Determination of Optimum TMP ................................................................................................13Concentration ..................................................................................................................................14Diafiltration ......................................................................................................................................15Recovery Operations ......................................................................................................................17Clean In Place (CIP) ........................................................................................................................19Post CIP Normalized Water Permeability Measurement .....................................................20Storage ...............................................................................................................................................21Appendix 1: Diafiltration Buffer Volume Requirements (22)Pellicon ® Ultrafiltration (UF)/ Diafiltration (DF) Operations Protocol GuideIntroductionObjectives of a UF/DF StudyThe objectives of a UF/DF study include determination of cassette capacity (volume/area) and sizing estimations for large volume processing of a given feed stream.Methods of a UF/DF StudyFeed StreamThe feed stream used in the study should be as representative (as possible) to the actual process (temperature, concentration, density, etc.). Initial and filtrate (post-testing) samples should be taken and tested for product recovery.MaterialsPellicon® 3 88 cm2 Cassettes with Ultracel® MembranePellicon® 3 88 cm2 Cassettes with Biomax® MembranePellicon® 2 Mini Cassettes with Ultracel® MembraneObjectives, Methods and Materials AccessoriesAdditional Ordering Information1.1 Set up system per general arrangement drawing. In principle, the tubing lengths should be minimized so as to minimize the working volume of the system. This enhances the ability to reach higher concentrations and lowersnon-recoverable volumes (recovery loss).1.2 The permeate (or filtrate) pressure gauge may be omitted in standard UF operation since there should not be any filtrate pressure in this line.1.3 Install the membrane as per the installation guide included in the membrane device box. Silicone gaskets areincluded in the Pellicon® 2 Device Box and must be used with the Pellicon® 2 membranes to achieve a proper device to holder seal. Pellicon® 3 devices (mini and micro) have gaskets that are integral to the device that make the device to holder seal.1.3.1 When working with micro (0.88cm 2) devices the required torque might be lower than the specification. If during the flushing procedure a high feed pressure (≥14psig) is observed loosen the membrane fromthe holder and re-torque to 140 in-pounds.3-Way Figure 1.UF/DF SystemGeneral Arrangement2.1 Pellicon® devices come from the factory pre-wet with preservative solution that must be removed beforeprocessing product. See Table 1 for flush volume recommendations.2.2 Arrange the system flowpath into the Single-Pass Filtrate Open mode (SPFO) as shown in Figure 2.2.3 Fill the feed vessel with the required purified water volume from Table 1.3-Way Figure 2.Single-Pass Filtrate Open mode (SPFO) ArrangementTable 1.Sanitization Solution and Flushing VolumeMethods2.4 Set the retentate Valve to fully open. Set the pump to supply 5 LMM (L/min/m 2) feed flow rate.2.5 Start the pump and monitor the feed pressure gauge. The pressure should stabilize to between 5-14 psig. If the pressure is outside this guideline, re-check the installation and torque wrench settings.2.6 Set the retentate pressure to 5 psig so as to ensure that the membrane is being fully flushed. Continue until the volume in the feed vessel is minimized, then stop the pump. Do not entrain air into the system.2.7 See Table 1 and add required volume of sanitization solution, to the feed vessel. Set the system in ‘Single Pass’ flow path. Start thepump to displace the water from the lines and the internal volume of the membrane to avoid dilution. When the sanitization solution level in the feed vessel had been minimized, stop the pump before air is entrained into the system.2.8 Set the system flowpath to the total recycle mode (Figure 3). Fill the vessel with required volume of sanitization solution,see Table 1.2.9 Recirculate at 5 LMM feed flowrate for 30-60 min. Set the retentate pressure to ~5 psig to ensure CIP (Clean-In-Place) of the full membrane area.2.10 Stop the pump after the CIP time interval. Return the system flowpath to the SPFO mode (Figure 2). Start the pump again andpump the feed vessel out to the receiver vessel. When CIP solution level in the feed vessel had been minimized, stop the pump before air is entrained into the system.2.11 Fill the feed vessel with purified water and start the pump. Flush the system to drain back to neutral pH. A microcassette basedsystem will require approximately 1 L of purified water. Monitor pH with a meter or pH paper that sensitive in the neutral range.Check both retentate and permeate lines separately to ensure the system is truly back to neutral pH. Stop the pump.Figure 3.Total Recycle Mode3.1 Add additional purified water to the feed vessel if necessary to ensure that the NWP measurement can be made without entraining air into the system.3.2 Set the system flowpath to the total recycle mode. Start the pump and manipulating the feedflow, set the system feed pressure to read 10 psig and the retentate pressure to read 5 psig.3.3 Allow the system to recirculate for a minute or two. Measure the temperature of the feed vessel contents. Set the system flowpath to the UFconcentration mode (Figure 4) and measure the change in mass over an elapsed time of 1 min, to find the permeate flowrate.3.4 Calculate the Normalized Water Permeability of the membrane using the following formulas:Equation 1J = Qp/AWhere: J= Volumetric Flux (L/M 2/Hr) Qp = permeate flow rate in L/hrA =Area of the membrane device(s)andEquation 2NWP = J * F /Transmembrane pressure (TMP)Where: NWP = Normalized Water Permeability (L/M 2/Hr/psid) J= Volumetric Flux (L/M 2/Hr) F = Temperature Correction FactorTMP = Transmembrane pressure (P feed + P ret )/2 – Pperm (pressure drop across the membrane in psid)3-Way Figure 4.Concentration ModeNormalized Water Permeability (NWP) MeasurementTemperatureF TemperatureFTemperatureF*Based on Water Fluidity Relative to 25°C (77°F) Fluidity Value F= (μT°C /μ25°C) or (μT°F/μ77°F)3.5 This is now the baseline permeability of the device. Record this value in the experimental notebook or runsheet.Table 2. Normalized Water Permeability Temperature Correction Factor (F)*4.1 Set the retentate valve to fully open. Adjust the feedflow to 5 LMM and reduce the volume in the feed vessel to just above the vessel discharge. Stop the system pump.4.2 Obtain a suitable container to capture the remaining volume in the system (50 mL tube for a microcassette based system). Record the tare weight of the container. Set the system feed rate to 2-3 LMM.4.3 Set the system flowpath to the recovery mode (Figure 5). Close the permeate isolation valve. Start the pump and collect all of the remainingliquid in the system into the sample container.4.4 Weigh the gross weight of the container and record the net weight of container and convert this to volume. Add 5 mL to the amount to calculate the total hold-up volume in the system for a micro-cassette based system. Add 31 mL to the amount to calculate the total hold upvolume for a mini-cassette based system.3-Way Figure 5.Recovery Mode5.1 Arrange the system flowpath into the Single-Pass, Filtrate Open mode (Figure 2). Open the permeate isolation valve.5.2 Fill the feed vessel with the equilibration buffer volume (see recommended volumes in Table 1).5.3 Set the pump to supply 5 LMM feed flow rate. Set the retentate pressure to 5 psig by restricting retentate flow with the retentate valve.Collect ~ 3 working volumes into the receiver.5.4 Fully open retentate valve, then stop the pump and place the system into the total recycle mode. Start the pump, set retentate pressure to 5psi,and operate in total recycle for ~5 min.=20 psig,5.5 Stop the pump and reset the system in to the SPFO mode. Set the Transmembrane pressure of the system to ~15 psid (e.g., PfeedP=10 psig). Start the pump and reduce the volume in the feed vessel to just above the vessel discharge. Do not withdraw too much liquid retfrom the feed vessel and entrain air into the system. Stop the pump. Open the retentate valve to full open. The system now has just the hold-up volume of buffer in it and is ready to accept the protein feed.5.6 Add the feed to the feed vessel. The total system volume = amount of feed added + the hold-up volume. The total system volume isconsidered Vo and is used to calculate concentration factor, diafiltration number, etc.6.1 Set the system flowpath to the total recycle mode (Figure 3).6.2 Start the agitator. The agitator should spin fast enough to cause a slight depression in the surface of the liquid in the vessel. The agitator should be monitored during the process and never be allowed to vortex the liquid and entrain air or cause foaming.6.3 Set the feedflow to 5 LMM. Allow the system to operate in the total recycle mode for ~5 minutes with the retentate valve fully open. Record temperature, Feed pressure, Retentate pressure and elapsed time. 6.4 Measure the permeate flowrate by redirecting the permeate line to a receiver on a balance or by collecting in a graduate cylinder. Measure thevolume (mass) for 1 min. Record the volume and calculate flux.6.5 Manipulating the retentate valve, increase the Transmembrane pressure by 5 psid. The TMP should increase but the DP (P feed -P ret ) should remain constant (see the example in Table 3).6.6 Repeat this measurement until the membrane flux becomes insensitive with the change in TMP. Reduce the TMP to and re-measure 1-2 of the flux measurements. If they are different by greater than 10% the membrane may have become polarized or fouled. Generally, avoid operating too far into the flux insensitive region.6.6.1 If polarization has occurred a depolarization step is recommended. To achieve this, lower the flow rate to ~10% of the operating feed flow rate and let the system run in total recycle for a minimum of 5 minutes. After the time has elapse re-measure the flux and compare to the original value. If the re-measured flux continues to differ by more than 20% the membrane may be fouled. At this point it is likelythat the flux can only be restored by stopping the experiment and cleaning. (See section 9 for more on depolarization)6.7 The optimum TMP is found by selecting a pressure slightly below the “knee” of the flux vs. TMP curve. In the example the knee of the curve is23-24 psid (Figure 7). The optimum TMP at this concentration is 20 psid.6.8 The Optimum TMP experiment may be repeated at an intermediate concentration and at the final concentration or just the final concentrationto find an over-all process TMP optimum.V o l u m e t r i c F l u x (L M H )Transmembrane Pressure (Psid)302520151050Figure 6.Flux and TMP Excursion Example at 5 LMMTable 3.Flux Excursion Data7.1 Determine the required permeate volume needed to be collected to achieve the target concentration.Equation 3 Vp = Vsi - (Vs i x Conc i / Conc T )Where:= Initial System Volume (Feed Volume + Hold-up Volume)VsiConc= Initial Concentrationi= Target ConcentrationConcTVp = Target Permeate Volume7.2 Zero the balance and set the system flowpath to concentration mode and start the pump and the timer.7.3 Set the TMP to the previously determined optimum TMP. Record time, temperature, the pressures and the permeate weight.7.4 As the concentration step progresses, the feed pressure (and TMP) may rise due to viscosity increase as a function of concentration. Adjust theretentate valve to hold TMP constant. The retentate valve may be fully open before the concentration step is finished. Adjust the pump to hold TMP constant. At higher concentrations the viscosity may become so high, it is not possible to control TMP with the pump. This is aconcentration end point for the fluid & membrane pair. If a higher concentration is still desired, it may be necessary to select a more open screen type.7.5 Once the concentration target is reached, open the retentate valve to full open. Stop the pump and close off the permeate isolation valve.8.1 Arrange the system flowpath to the Vacuum Diafiltration mode (Figure 8).8.1.1 If creating a vacuum is not possible with the equipment being used a second pump can be used to draw the DF buffer into the retentate vessel. The flowrate on the DF buffer pump must be set to match the flowrate of the permeate line. Adjustments to the flowrate of the DF buffer pump might be necessary throughout the process. This will ensure that the concentration within the system remains constantthroughout the diafiltration step.8.2 The amount of diavolumes used for purification of a target impurity is usually selected as the minimum amount of diavolumes required to achieve the purity target, plus a 2 diavolume safety factor. For example, if 6 diavolumes are required to achieve the purity target, then 8 diavolumes are used in the DF step. 1 diavolume is equivalent to the amount of fluid in the system (Vf+Vh-Vp). The number of diavolumes, N required for purification can be calculated by the following equation. Alternatively the figure in Appendix 1 can be used.Equation 4Cf = Ci e-S*NWhere: Cf = Final concentration of solute being diafiltered out Ci = Initial concentration of solute being diafiltered out S = sieving/passage coefficient = C permeate/C retentate)N = Number of diavolumesThe target permeate volume required to achieve the number of calculated diavolumes can be determined using equation 5.Equation 5N*Vs = VpWhere: N = Number of diavolumesVs = Volume in the system post concentrationVp = Target permeate volumeFigure 7.Vacuum Diafiltration ModeDiafiltration8.3 Mark the level in the vessel with a marker or piece of lab tape to be sure that the volume remains constant during diafiltration. Obtaina container with the required amount of DF buffer. Attach the DF line to the feed vessel. Cap off the vessel and pull a vacuum on thevessel headspace with a syringe to prime the diafiltration line.8.4 Start the pump. Adjust the TMP to match the TMP at the end of the concentration step. Record temperature, Feed pressure,Retentate pressure temperature, elapsed time and permeate weight (volume).8.5 When the diafiltration target volume has been reached, open the retentate valve, stop the pump, stop the agitator and close thepermeate isolation valve.9.1 The first step in the recovery operation is depolarization of the membrane. Polarization is a concentration gradient that occurs due to convective transport of protein towards the membrane wall. The depolarization step is recirculation under low feedflow and TMP conditions with the permeate isolation valve shut. Running with the permeate isolation valve closed can give rise to reverse pressure within the device. Limit the ΔP to </=20 psid for Pellicon® 3 devices and </=10 psid for Pellicon® 2 devices.9.2 Arrange the system flowpath to the Depolarization mode (Figure 8) by closing the permeate isolation valve, setting the retentate valve fullyopen and starting the pump. Operate the pump at low feedflow rates – low enough to avoid the ΔP limits outline in step 9.1.9.3 Recirculate the system in the depolarization mode for 5-10 min. Stop the pump after the recirculation time limit.9.4 Set the system flowpath to the blowdown/recovery mode as shown in Figure 9. Pump the protein product out at low ΔP into an appropriate sized container. When air bubbles appear stop the pump. Do not allow the protein product to foam.9.5 Add to the feed vessel 1 minimum working volume of buffer. Start the pump and recover this pool separately in container. As before, when air bubbles appear stop the pump. Do not allow the protein product to foam. Add this buffer chase pool to the recovery pool to increase recovery if the pool can tolerate dilution.9.6 Set the system into the total recycle mode (Figure 3). Add to the feed vessel 1-2 diavolumes of buffer to the system. Set the retentate valve to fully open. Set the feed flowrate to 2-3 LMM and recirculate for 5-10 min.9.7 Set the system flowpath to the blowdown/recovery mode as shown in Figure 9 (next page). Pump the recirculated buffer out at low ΔP intoan appropriate sized container. When air bubbles appear stop the pump.3-Way Figure 8.Depolarization ModeRecovery Operations3-WayFigure 9.Recovery Mode10.1 Add 200-300 mL of recommended CIP / Sanitization (Table 1) solution to the feed vessel. Set the system flowpath to the total recyclemode (Figure 3).10.2 Recirculate at 5 LMM feed flowrate for 30-60 min. Set TMP to approximately 15psid.10.3 Stop the pump after the CIP time interval. Return the system flowpath to the SPFO mode (Figure 2). Start the pump again and pump the feedvessel out to the receiver vessel.10.4 Add purified water to the feed vessel and start the pump. Flush the system to drain back to neutral pH. A microcassette based systemwill require approximately 1 L of purified water. Monitor pH with a meter or pH paper that sensitive in the neutral range. Check both retentate and permeate lines separately to ensure the system is truly back to neutral pH. Stop the pump.11.1 Add additional purified water to the feed vessel if necessary to ensure that the NWP measurement can be made without entraining airinto the system.11.2 Set the system flowpath to the total recycle mode. Start the pump and manipulating the feedflow, set the system feed pressure to read 10 psigand the retentate pressure to read 5 psig.11.3 Allow the system to recirculate for a minute or two. Measure the temperature of the feed vessel contents. Set the system flowpath to theUF concentration mode (Figure 4) and measure the change in mass over an elapsed time of 1 min, to find the permeate flowrate.11.4 Calculate the post CIP Normalized Water Permeability as we did in Section 3 using equations 1 and 2.11.5 Compare the Base-line NWP to the post CIP NWP. The Post CIP NWP should be >/= 80% of the Base-line NWP. (Post Post NWP/Base-lineNWP * 100%). If the comparison is less than 80%, then the membrane can be re-cleaned. CIP at an elevated temperature may be more effective at restoring NWP. NWP is a single indicator of membrane cleaning success. Data such as batch to batch process time, product quality and carryover studies should be used to determine criteria for successful membrane CIP processes.12.1 Arrange the system flowpath into the Single-Pass, Filtrate Open mode (Figure 2). Open the permeate isolation valve.12.2 Fill the feed vessel with 4 diavolumes of 0.1N NaOH solution.12.3 Set the pump to supply 5 LMM feed flow rate. Set the retentate pressure to 5 psig by restricting retentate flow with the retentate valve.Collect ~ 2 diavolumes into the receiver.12.4 Fully open retentate valve, then stop the pump and place the system into the total recycle mode (Figure 3).12.5 Start the pump, recirculate the remaining 2 diavolumes at 5 LMM for 5-10 min. Set TMP to approximately 15 psid.12.6 Remove membrane and store in 0.1N NaOH in a 2-8º C refrigerator.% S o l u t e R e m a i n i n g# of Diafiltration VolumesSolute Remaining vs. # of Diafiltration Volumes% Solute Passed = 100 - % Solute1001010.1Figure 10.Solute remaining versus number of diafiltration volumes To Place an Order or Receive Technical AssistanceIn Europe, please call Customer Service: France: 0825 045 645Germany: 01805 045 645Italy: 848 845 645Spain: 901 516 645 Option 1 Switzerland: 0848 645 645United Kingdom:***********For other countries across Europe, please call: +44 (0) 115 943 0840Or visit: /offices For Technical Service visit:/techserviceMerck Millipore, the M logo, Ultracel, Biomax, Labscale and Pellicon are registered trademarks of Merck KGaA, Darmstadt, Germany.Masterflex and StableTemp are registered trademarks of Cole-Palmer Instrument Company. Luer-Lok is a trademark of Becton Dickinson.MICROMETER is a registered trademark of RMFPT, Inc.Nalgene is a registered trademark of Nalge Nunc International Corporation.Lit No. RF1159EN00 Ver. 3.0 4/2016© 2016 EMD Millipore Corporation, Billerica, MA USA. All rights reserved.。
Indradrive 系列 故障代码
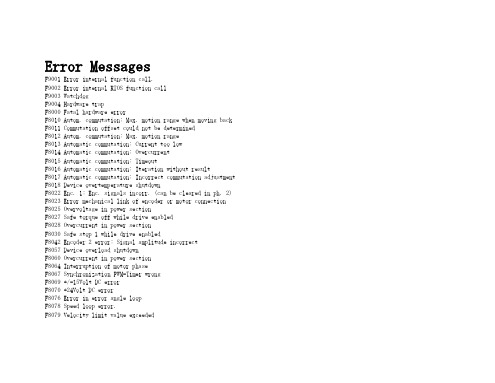
Error MessagesF9001 Error internal function call.F9002 Error internal RTOS function callF9003 WatchdogF9004 Hardware trapF8000 Fatal hardware errorF8010 Autom. commutation: Max. motion range when moving back F8011 Commutation offset could not be determinedF8012 Autom. commutation: Max. motion rangeF8013 Automatic commutation: Current too lowF8014 Automatic commutation: OvercurrentF8015 Automatic commutation: TimeoutF8016 Automatic commutation: Iteration without resultF8017 Automatic commutation: Incorrect commutation adjustment F8018 Device overtemperature shutdownF8022 Enc. 1: Enc. signals incorr. (can be cleared in ph. 2) F8023 Error mechanical link of encoder or motor connectionF8025 Overvoltage in power sectionF8027 Safe torque off while drive enabledF8028 Overcurrent in power sectionF8030 Safe stop 1 while drive enabledF8042 Encoder 2 error: Signal amplitude incorrectF8057 Device overload shutdownF8060 Overcurrent in power sectionF8064 Interruption of motor phaseF8067 Synchronization PWM-Timer wrongF8069 +/-15Volt DC errorF8070 +24Volt DC errorF8076 Error in error angle loopF8078 Speed loop error.F8079 Velocity limit value exceededF8091 Power section defectiveF8100 Error when initializing the parameter handlingF8102 Error when initializing power sectionF8118 Invalid power section/firmware combinationF8120 Invalid control section/firmware combinationF8122 Control section defectiveF8129 Incorrect optional module firmwareF8130 Firmware of option 2 of safety technology defectiveF8133 Error when checking interrupting circuitsF8134 SBS: Fatal errorF8135 SMD: Velocity exceededF8140 Fatal CCD error.F8201 Safety command for basic initialization incorrectF8203 Safety technology configuration parameter invalidF8813 Connection error mains chokeF8830 Power section errorF8838 Overcurrent external braking resistorF7010 Safely-limited increment exceededF7011 Safely-monitored position, exceeded in pos. DirectionF7012 Safely-monitored position, exceeded in neg. DirectionF7013 Safely-limited speed exceededF7020 Safe maximum speed exceededF7021 Safely-limited position exceededF7030 Position window Safe stop 2 exceededF7031 Incorrect direction of motionF7040 Validation error parameterized - effective thresholdF7041 Actual position value validation errorF7042 Validation error of safe operation modeF7043 Error of output stage interlockF7050 Time for stopping process exceeded8.3.15 F7051 Safely-monitored deceleration exceeded (159)8.4 Travel Range Errors (F6xxx) (161)8.4.1 Behavior in the Case of Travel Range Errors (161)8.4.2 F6010 PLC Runtime Error (162)8.4.3 F6024 Maximum braking time exceeded (163)8.4.4 F6028 Position limit value exceeded (overflow) (164)8.4.5 F6029 Positive position limit exceeded (164)8.4.6 F6030 Negative position limit exceeded (165)8.4.7 F6034 Emergency-Stop (166)8.4.8 F6042 Both travel range limit switches activated (167)8.4.9 F6043 Positive travel range limit switch activated (167)8.4.10 F6044 Negative travel range limit switch activated (168)8.4.11 F6140 CCD slave error (emergency halt) (169)8.5 Interface Errors (F4xxx) (169)8.5.1 Behavior in the Case of Interface Errors (169)8.5.2 F4001 Sync telegram failure (170)8.5.3 F4002 RTD telegram failure (171)8.5.4 F4003 Invalid communication phase shutdown (172)8.5.5 F4004 Error during phase progression (172)8.5.6 F4005 Error during phase regression (173)8.5.7 F4006 Phase switching without ready signal (173)8.5.8 F4009 Bus failure (173)8.5.9 F4012 Incorrect I/O length (175)8.5.10 F4016 PLC double real-time channel failure (176)8.5.11 F4017 S-III: Incorrect sequence during phase switch (176)8.5.12 F4034 Emergency-Stop (177)8.5.13 F4140 CCD communication error (178)8.6 Non-Fatal Safety Technology Errors (F3xxx) (178)8.6.1 Behavior in the Case of Non-Fatal Safety Technology Errors (178)8.6.2 F3111 Refer. missing when selecting safety related end pos (179)8.6.3 F3112 Safe reference missing (179)8.6.4 F3115 Brake check time interval exceeded (181)Troubleshooting Guide | Rexroth IndraDrive Electric Drivesand ControlsI Bosch Rexroth AG VII/XXIITable of ContentsPage8.6.5 F3116 Nominal load torque of holding system exceeded (182)8.6.6 F3117 Actual position values validation error (182)8.6.7 F3122 SBS: System error (183)8.6.8 F3123 SBS: Brake check missing (184)8.6.9 F3130 Error when checking input signals (185)8.6.10 F3131 Error when checking acknowledgment signal (185)8.6.11 F3132 Error when checking diagnostic output signal (186)8.6.12 F3133 Error when checking interrupting circuits (187)8.6.13 F3134 Dynamization time interval incorrect (188)8.6.14 F3135 Dynamization pulse width incorrect (189)8.6.15 F3140 Safety parameters validation error (192)8.6.16 F3141 Selection validation error (192)8.6.17 F3142 Activation time of enabling control exceeded (193)8.6.18 F3143 Safety command for clearing errors incorrect (194)8.6.19 F3144 Incorrect safety configuration (195)8.6.20 F3145 Error when unlocking the safety door (196)8.6.21 F3146 System error channel 2 (197)8.6.22 F3147 System error channel 1 (198)8.6.23 F3150 Safety command for system start incorrect (199)8.6.24 F3151 Safety command for system halt incorrect (200)8.6.25 F3152 Incorrect backup of safety technology data (201)8.6.26 F3160 Communication error of safe communication (202)8.7 Non-Fatal Errors (F2xxx) (202)8.7.1 Behavior in the Case of Non-Fatal Errors (202)8.7.2 F2002 Encoder assignment not allowed for synchronization (203)8.7.3 F2003 Motion step skipped (203)8.7.4 F2004 Error in MotionProfile (204)8.7.5 F2005 Cam table invalid (205)8.7.6 F2006 MMC was removed (206)8.7.7 F2007 Switching to non-initialized operation mode (206)8.7.8 F2008 RL The motor type has changed (207)8.7.9 F2009 PL Load parameter default values (208)8.7.10 F2010 Error when initializing digital I/O (-> S-0-0423) (209)8.7.11 F2011 PLC - Error no. 1 (210)8.7.12 F2012 PLC - Error no. 2 (210)8.7.13 F2013 PLC - Error no. 3 (211)8.7.14 F2014 PLC - Error no. 4 (211)8.7.15 F2018 Device overtemperature shutdown (211)8.7.16 F2019 Motor overtemperature shutdown (212)8.7.17 F2021 Motor temperature monitor defective (213)8.7.18 F2022 Device temperature monitor defective (214)8.7.19 F2025 Drive not ready for control (214)8.7.20 F2026 Undervoltage in power section (215)8.7.21 F2027 Excessive oscillation in DC bus (216)8.7.22 F2028 Excessive deviation (216)8.7.23 F2031 Encoder 1 error: Signal amplitude incorrect (217)VIII/XXII Bosch Rexroth AG | Electric Drivesand ControlsRexroth IndraDrive | Troubleshooting GuideTable of ContentsPage8.7.24 F2032 Validation error during commutation fine adjustment (217)8.7.25 F2033 External power supply X10 error (218)8.7.26 F2036 Excessive position feedback difference (219)8.7.27 F2037 Excessive position command difference (220)8.7.28 F2039 Maximum acceleration exceeded (220)8.7.29 F2040 Device overtemperature 2 shutdown (221)8.7.30 F2042 Encoder 2: Encoder signals incorrect (222)8.7.31 F2043 Measuring encoder: Encoder signals incorrect (222)8.7.32 F2044 External power supply X15 error (223)8.7.33 F2048 Low battery voltage (224)8.7.34 F2050 Overflow of target position preset memory (225)8.7.35 F2051 No sequential block in target position preset memory (225)8.7.36 F2053 Incr. encoder emulator: Pulse frequency too high (226)8.7.37 F2054 Incr. encoder emulator: Hardware error (226)8.7.38 F2055 External power supply dig. I/O error (227)8.7.39 F2057 Target position out of travel range (227)8.7.40 F2058 Internal overflow by positioning input (228)8.7.41 F2059 Incorrect command value direction when positioning (229)8.7.42 F2063 Internal overflow master axis generator (230)8.7.43 F2064 Incorrect cmd value direction master axis generator (230)8.7.44 F2067 Synchronization to master communication incorrect (231)8.7.45 F2068 Brake error (231)8.7.46 F2069 Error when releasing the motor holding brake (232)8.7.47 F2074 Actual pos. value 1 outside absolute encoder window (232)8.7.48 F2075 Actual pos. value 2 outside absolute encoder window (233)8.7.49 F2076 Actual pos. value 3 outside absolute encoder window (234)8.7.50 F2077 Current measurement trim wrong (235)8.7.51 F2086 Error supply module (236)8.7.52 F2087 Module group communication error (236)8.7.53 F2100 Incorrect access to command value memory (237)8.7.54 F2101 It was impossible to address MMC (237)8.7.55 F2102 It was impossible to address I2C memory (238)8.7.56 F2103 It was impossible to address EnDat memory (238)8.7.57 F2104 Commutation offset invalid (239)8.7.58 F2105 It was impossible to address Hiperface memory (239)8.7.59 F2110 Error in non-cyclical data communic. of power section (240)8.7.60 F2120 MMC: Defective or missing, replace (240)8.7.61 F2121 MMC: Incorrect data or file, create correctly (241)8.7.62 F2122 MMC: Incorrect IBF file, correct it (241)8.7.63 F2123 Retain data backup impossible (242)8.7.64 F2124 MMC: Saving too slowly, replace (243)8.7.65 F2130 Error comfort control panel (243)8.7.66 F2140 CCD slave error (243)8.7.67 F2150 MLD motion function block error (244)8.7.68 F2174 Loss of motor encoder reference (244)8.7.69 F2175 Loss of optional encoder reference (245)Troubleshooting Guide | Rexroth IndraDrive Electric Drivesand Controls| Bosch Rexroth AG IX/XXIITable of ContentsPage8.7.70 F2176 Loss of measuring encoder reference (246)8.7.71 F2177 Modulo limitation error of motor encoder (246)8.7.72 F2178 Modulo limitation error of optional encoder (247)8.7.73 F2179 Modulo limitation error of measuring encoder (247)8.7.74 F2190 Incorrect Ethernet configuration (248)8.7.75 F2260 Command current limit shutoff (249)8.7.76 F2270 Analog input 1 or 2, wire break (249)8.7.77 F2802 PLL is not synchronized (250)8.7.78 F2814 Undervoltage in mains (250)8.7.79 F2815 Overvoltage in mains (251)8.7.80 F2816 Softstart fault power supply unit (251)8.7.81 F2817 Overvoltage in power section (251)8.7.82 F2818 Phase failure (252)8.7.83 F2819 Mains failure (253)8.7.84 F2820 Braking resistor overload (253)8.7.85 F2821 Error in control of braking resistor (254)8.7.86 F2825 Switch-on threshold braking resistor too low (255)8.7.87 F2833 Ground fault in motor line (255)8.7.88 F2834 Contactor control error (256)8.7.89 F2835 Mains contactor wiring error (256)8.7.90 F2836 DC bus balancing monitor error (257)8.7.91 F2837 Contactor monitoring error (257)8.7.92 F2840 Error supply shutdown (257)8.7.93 F2860 Overcurrent in mains-side power section (258)8.7.94 F2890 Invalid device code (259)8.7.95 F2891 Incorrect interrupt timing (259)8.7.96 F2892 Hardware variant not supported (259)8.8 SERCOS Error Codes / Error Messages of Serial Communication (259)9 Warnings (Exxxx) (263)9.1 Fatal Warnings (E8xxx) (263)9.1.1 Behavior in the Case of Fatal Warnings (263)9.1.2 E8025 Overvoltage in power section (263)9.1.3 E8026 Undervoltage in power section (264)9.1.4 E8027 Safe torque off while drive enabled (265)9.1.5 E8028 Overcurrent in power section (265)9.1.6 E8029 Positive position limit exceeded (266)9.1.7 E8030 Negative position limit exceeded (267)9.1.8 E8034 Emergency-Stop (268)9.1.9 E8040 Torque/force actual value limit active (268)9.1.10 E8041 Current limit active (269)9.1.11 E8042 Both travel range limit switches activated (269)9.1.12 E8043 Positive travel range limit switch activated (270)9.1.13 E8044 Negative travel range limit switch activated (271)9.1.14 E8055 Motor overload, current limit active (271)9.1.15 E8057 Device overload, current limit active (272)X/XXII Bosch Rexroth AG | Electric Drivesand ControlsRexroth IndraDrive | Troubleshooting GuideTable of ContentsPage9.1.16 E8058 Drive system not ready for operation (273)9.1.17 E8260 Torque/force command value limit active (273)9.1.18 E8802 PLL is not synchronized (274)9.1.19 E8814 Undervoltage in mains (275)9.1.20 E8815 Overvoltage in mains (275)9.1.21 E8818 Phase failure (276)9.1.22 E8819 Mains failure (276)9.2 Warnings of Category E4xxx (277)9.2.1 E4001 Double MST failure shutdown (277)9.2.2 E4002 Double MDT failure shutdown (278)9.2.3 E4005 No command value input via master communication (279)9.2.4 E4007 SERCOS III: Consumer connection failed (280)9.2.5 E4008 Invalid addressing command value data container A (280)9.2.6 E4009 Invalid addressing actual value data container A (281)9.2.7 E4010 Slave not scanned or address 0 (281)9.2.8 E4012 Maximum number of CCD slaves exceeded (282)9.2.9 E4013 Incorrect CCD addressing (282)9.2.10 E4014 Incorrect phase switch of CCD slaves (283)9.3 Possible Warnings When Operating Safety Technology (E3xxx) (283)9.3.1 Behavior in Case a Safety Technology Warning Occurs (283)9.3.2 E3100 Error when checking input signals (284)9.3.3 E3101 Error when checking acknowledgment signal (284)9.3.4 E3102 Actual position values validation error (285)9.3.5 E3103 Dynamization failed (285)9.3.6 E3104 Safety parameters validation error (286)9.3.7 E3105 Validation error of safe operation mode (286)9.3.8 E3106 System error safety technology (287)9.3.9 E3107 Safe reference missing (287)9.3.10 E3108 Safely-monitored deceleration exceeded (288)9.3.11 E3110 Time interval of forced dynamization exceeded (289)9.3.12 E3115 Prewarning, end of brake check time interval (289)9.3.13 E3116 Nominal load torque of holding system reached (290)9.4 Non-Fatal Warnings (E2xxx) (290)9.4.1 Behavior in Case a Non-Fatal Warning Occurs (290)9.4.2 E2010 Position control with encoder 2 not possible (291)9.4.3 E2011 PLC - Warning no. 1 (291)9.4.4 E2012 PLC - Warning no. 2 (291)9.4.5 E2013 PLC - Warning no. 3 (292)9.4.6 E2014 PLC - Warning no. 4 (292)9.4.7 E2021 Motor temperature outside of measuring range (292)9.4.8 E2026 Undervoltage in power section (293)9.4.9 E2040 Device overtemperature 2 prewarning (294)9.4.10 E2047 Interpolation velocity = 0 (294)9.4.11 E2048 Interpolation acceleration = 0 (295)9.4.12 E2049 Positioning velocity >= limit value (296)9.4.13 E2050 Device overtemp. Prewarning (297)Troubleshooting Guide | Rexroth IndraDrive Electric Drivesand Controls| Bosch Rexroth AG XI/XXIITable of ContentsPage9.4.14 E2051 Motor overtemp. prewarning (298)9.4.15 E2053 Target position out of travel range (298)9.4.16 E2054 Not homed (300)9.4.17 E2055 Feedrate override S-0-0108 = 0 (300)9.4.18 E2056 Torque limit = 0 (301)9.4.19 E2058 Selected positioning block has not been programmed (302)9.4.20 E2059 Velocity command value limit active (302)9.4.21 E2061 Device overload prewarning (303)9.4.22 E2063 Velocity command value > limit value (304)9.4.23 E2064 Target position out of num. range (304)9.4.24 E2069 Holding brake torque too low (305)9.4.25 E2070 Acceleration limit active (306)9.4.26 E2074 Encoder 1: Encoder signals disturbed (306)9.4.27 E2075 Encoder 2: Encoder signals disturbed (307)9.4.28 E2076 Measuring encoder: Encoder signals disturbed (308)9.4.29 E2077 Absolute encoder monitoring, motor encoder (encoder alarm) (308)9.4.30 E2078 Absolute encoder monitoring, opt. encoder (encoder alarm) (309)9.4.31 E2079 Absolute enc. monitoring, measuring encoder (encoder alarm) (309)9.4.32 E2086 Prewarning supply module overload (310)9.4.33 E2092 Internal synchronization defective (310)9.4.34 E2100 Positioning velocity of master axis generator too high (311)9.4.35 E2101 Acceleration of master axis generator is zero (312)9.4.36 E2140 CCD error at node (312)9.4.37 E2270 Analog input 1 or 2, wire break (312)9.4.38 E2802 HW control of braking resistor (313)9.4.39 E2810 Drive system not ready for operation (314)9.4.40 E2814 Undervoltage in mains (314)9.4.41 E2816 Undervoltage in power section (314)9.4.42 E2818 Phase failure (315)9.4.43 E2819 Mains failure (315)9.4.44 E2820 Braking resistor overload prewarning (316)9.4.45 E2829 Not ready for power on (316)。
GSG-5 6 卫星导航信号模拟器产品介绍说明书

Basic PrincipleG SG -5/6 simulators can generate any combination of G PS, G LONASS, G alileo, BeiDou, QZSS, SBAS satellite signals un-der any condition simultaneously through a single RF out-put (type N connector). Configurations with higher channel counts generate new, modernized, signals on any of the navi-gation frequencies, including IRNSS, even those currently un-der development. Based on a test scenario that includes date, time and power levels, the generated signals correspond to any position on, or above, the earth (below the satellite orbits at approximately 20,000 km). It is easy to test dynamic condi-tions by defining a trajectory of the receiver under test. The simulator manages all the dynamics including relativistic effects.Test Solutions•Position/navigation accuracy •Dynamic range/sensitivity•Simulate movements/trajectories anyway on or above earth •Susceptibility to noise•Sensitivity to GPS impairments: loss of satellites, multi-path, atmospheric conditions, interference, jamming and spoofing •Conducted or over-the-air RF •GPS time transfer accuracy •Effect of leap second transition •Multiple constellation testing•Modernization signals/ frequencies •Hardware in the loop integrationGSG-5/6 SeriesAdvanced GNSS Simulators•Pre-defined or user-defined test scenarios•Full control over all test parameters•Front panel interface/stand-alone operation•Windows-based scenario builder software including Google Maps •Remote operation by Ethernet, GPIB, USB •Built-in or downloadable navigation files•Full control over trajectories and other dynamics •Up to 64 simultaneous signals•All GNSS constellations and frequencies•Accurate, adjustable power levels•Synchronization features to external devices or other simulatorsSimulation is simply the best way to test and verify proper operation of devices, systems and software reliant on global navigation satellite signals.Pendulum G SG -5/6 series simulators are easy-to-use, feature-rich and affordable to offer the best value compared to alternative testing tools or the limitations of testing from “live sky” signals. | *****************************•Constellations: GPS, GLONASS, Galileo, BeiDou, QZSS, IRNSS •Modulations: BPSK, QPSK, BOC (all)•SBAS: WAAS, EGNOS, GAGAN, MSAS, SAIF (included)•Spurious transmission: ≤40 dBc •Harmonics: ≤40 dBc•Output signal level: -65 to -160 dBm; 0.1 dB resolution down to -150 dBm; 0.3 dB down to -160 dBm•Power accuracy: ±1.0 dB •Pseudorange accuracy: Within any one frequency band:1 mm; Across different frequency bands: 30 cm•Inter-channel bias: Zero•Inter-channel range: >54 dB •Limits:Standard ExtendedAltitude18,240 m(60,000 feet)20,200,000 m (66,273,000 feet)Acceleration 4.0 g No limitsVelocity515 m/s (1000knots)20,000 m/s (38,874 knots)Jerk20 m/s3No limit •White noise signal level: -50 to -160 dBm; 0.1 dB resolution down to -150 dBm;0.3 dB down to -160 dBm. ±1.0 dB accuracy External Frequency Reference Input •Connector: BNC female•Frequency: 10 MHz nominal•Input signal level: 0.1 to 5Vrms•Input impedance: >1kΩFrequency Reference Output •Connector: BNC female•Frequency: 10 MHz sine•Output signal level: 1Vrms in to 50 Ω load External Trigger Input•Connector: BNC female•Level: TTL level, 1.4V nominalXPPS Output•Connector: BNC female•Rate: 1, 10, 100, 1000 PPS (configurable)•Pulse ratio: 1/10 (1 high, 9 low)•Output signal level: approx. 0V to +2.0V in 50 Ω load•Accuracy: Calibrated to ±10 nSec of RF timing mark output (option to reduce by a factor of ten with a characterization of offsets)Built-in TimebaseInternal Timebase – High Stability OCXO •Ageing per 24 h: <5x10-10•Ageing per year: <5x10-8•Temp. variation 0…50°C: <5x10-9•Short term stability (Adev @1s): <5x10-12 Auxiliary FunctionsInterface•GPIB (IEEE-488.2), USB 1.X or 2.X (SBTMC-488), Ethernet (100/10 Mbps)Settings•Predefined scenarios: User can change date, time, position, trajectory, number of satellites, satellite power level and atmospheric model •User defined scenarios: Unlimited •Trajectory data: NMEA format (GGA or RMC messages, or both), convert from other formats with GSG StudioView™ (see separate datasheet)General SpecificationsCertifications•Safety: Designed and tested for Measurement Category I, Pollution Degree 2, in accordance with EN/IEC 61010-1:2001 and CAN/CSA-C22.2 No. 61010-1-04 (incl. approval)•EMC: EN 61326-1:2006, increased test levels per EN 61000-6-3:2001 and EN 61000-6-2:2005 Dimensions•WxHxD: 210 x 90 x 395 mm(8.25” x 3.6” x 15.6”)•Weight: approx. 2.7 kg (approx. 5.8 lb) Optional Antenna•Frequency: 1000 to 2600 MHz •Impedance: 50 Ω•VSWR: <2:1 (typ)•Connector: SMA male•Dimensions: 15 mm diameter x 36 mm length Environmental•Class: MIL-PRF-28800F, Class 3•T emperature: 0°C to +50°C (operating); -40°C to +70°C non-condensing @ <12,000 m (storage)Humidity:•5-95 % @ 10 to 30°C•5-75 % @ 30 to 40°C•5-45 % @ 40 to 50°CPower•Line Voltage: 100-240 V AC, 50/60/400 Hz •Power Consumption: 40 W max.Simple Set-up and Operation Even the most inexperienced operator can configure scenarios on-the-fly without the need for an external PC and pre-compila-tion phase. Via the front panel, the user can swiftly modify parameters. Each unit comes with a license for GSG StudioView™ Windows software to graphically create, modify, and upload scenarios. A G oogle Maps interface makes trajectory creation easy. Trajectories can also be defined by recorded or generated NMEA formats. Connectivity Extends Ease-of-use and FlexibilityG SG simulators can be controlled via an Ethernet network connection, USB or GPIB. A built-in web interface allows complete operation of the instrument through front panel controls. It also al-lows for file transfers. Connectivity also supports the integration of G NSS simula-tion into a wide range of other applica-tions. There is an option to control signal generation in real-time through a simple command set. It can synchronize to ex-ternal systems in many other ways based on its precision timing capabilities and the ability to automatically download ephem-eris and almanac data via RINEX files. Input/OutputRF GNSS Signal Generation •Connector: Type N female•DC blocking: internal, up to 7 VDC; 470 Ωnominal load•Frequency bands:•L1/E1/B1/SAR: 1539 to 1627 MHz•L2/L2C: 1192 to 1280 MHz•L5/E5/B2: 1148 to 1236 MHz•E6/B3:1224 to 1312 MHz•Output channels:•1 (GSG-51); 4, 8, 16 (GSG-5); 32 (GSG-62),48, (GSG-63), 64 (GSG-64)•Any channel can generate anyconstellation or a derivative signal(multipath, interference, jamming)•Any set of 16 channels can generate withina frequency bandOptional FeaturesRecord and Playback (OPT-RP)This option provides the easiest way to create a complex scenario by recording satellite signals on a route. This option includes a recording receiver and software to automatically generate a simulation scenario that can be modified to ask ‘what if’ questions.•True life constellation replication •Automatic scenario generation•Ability to modify signal parameters •Compatible with any recording that includes NMEA 0183 RMC, GGA, and GSV sentences Real-time Scenario Generator (OPT-RSG) This option supports generation of 6DOF trajectory information via position, velocity, acceleration, or heading commands as the input for GPS RF generation. Vehicle attitude and attitude rate changes, as well as satellite power levels, are also controllable via real-time commands.•Control trajectories using 6DOF•Low fixed latency from command input to RF output•Hardware-in-the-loop applications •Includes sensor simulation optionRTK/DGNSS Virtual Reference Station (OPT-RTK)This option supports generation of RTCM correction data messages for testing an RTK / Differential-GNSS receiver.•Generates RTCM 3.x correction data via 1002, 1004, 1006, 1010, 1012, and 1033 messages•User settable base station location •Support for GNSS RTK receivers using serial interfacesHigh Velocity Option (OPT-HV)This option extends the limits for simulated trajectories. As of August 2014, the extended limits are no longer USA export controlled. (See Limits chart under Input/Output specifications.) Jamming Simulation (OPT-JAM)This option extends the capability of the standard interference simulation feature. Set noise or sweep types of interference and create a location-based jammer to test your system’s susceptibility.•Adjustable bandwidth and amplitude interference•Location-based jamming•Swept-frequency jammingeCall Scenarios (OPT-ECL)This option provides scenarios for testing eCall in vehicle systems per Regulation (EU) 2017/79.Sensor Simulation (OPT-SEN)This option generates sensor data in responseto a query according to the trajectory of theGPS RF simulation in real-time. See technicalnote for more details.•Simultaneously test GPS plus other sensorinputs to your nav system•Simulate data for accelerometers,gravimeters, gyroscopes and odometersOrdering InformationBase Configurations•GSG-51: Single channel GPS L1 generator(contact the factory for alternativeconstellations and upgrades to multi-channeland/or frequencies)•GSG-5: 4-channel GPS L1 simulator.Software options increase output channelsto 8 or 16, and adds GLONASS, BeiDou (B1),Galileo (E1), or QZSS constellations. Factoryupgradable to GSG-62 to add more channeland/or frequencies)•GSG-62: 32-channels and up to 2simultaneous frequency bands. Softwareoptions adds GLONASS, BeiDou, Galileo,QZSS or IRNSS constellations; and addssignals on other frequencies (P-code, L2,L2C, Galileo E5a/b, BeiDou B2)•GSG-63: 48-channels and up to 3simultaneous frequency bands. Samesoftware options as GSG-62•GSG-64: 64-channels and up to 4simultaneous frequency bands. Samesoftware options as GSG-62Included with instrument•User manual and GSG StudioView software(one license per unit) on CD•RF cable, 1.5 m•SMA to Type N adapter•USB cable•Certificate of calibration•3-year warranty1Optional Accessories•Option 01/71: Passive GNSS Antenna•Option 22/90: Rack-mount kit•Option 27H: Heavy-duty hard transport case•OM-54: User Manual (printed)•Additional StudioView licenses are availableOptional UpgradesConstellations•OPT-GLO: GLONASS Constellation•OPT-GAL: Galileo Constellation•OPT-BDS: BeiDou Constellation•OPT-QZ: QZSS Constellation•OPT-IRN: IRNSS Constellation (requires atleast GSG-62 and OPT-L5)Frequencies (requires at least GSG-62; non-GPS signals are enabled when constellationoption is installed)•Option L2: enables GPS L1P, GPS L2P, GLOL2 C/A•Option L2C: enables GPS L2C•Option L5: enables GPS L5, Galileo E5 a/b,BeiDou B2, IRNSS L5•Option L6: enables Galileo E6 b/cChannels/Simultaneous Frequencies2•Option 8: 4-channel to 8-channel upgrade•Option 16: 8-channel to 16-channel upgrade•Option 32/2: 16-channel to 32-channel, dualfrequency upgrade•Option 48/3: 32-channel to 48-channel, threefrequency upgrade•Option 64/4: 48-channel to 64-channel, fourfrequency upgradeApplication Packages (typical requirement for16 channel min)•OPT-RSG: Real-time scenario generator•OPT-HV: High velocity upgrade to extendedlimits•OPT-RP: Record and playback package•OPT-JAM: Jamming package•OPT-RTK: RTK virtual base station scenarios•OPT-SEN: Sensor simulation data via protocol(included with OPT RSG)•OPT-ECL: eCall scenariosOptional Services•Option 90/54:GSG Calibration Service•Option 95/05: Extended warranty to 5 years•GSG-INST: User Training and Installation•OPT-TIM: Timing Calibration Service1Warranty period and available services may vary dependent on country.2Option may require the unit to be returned to factory for upgrade.Models Channels # of Sim.Freq.Upgrade to nexthigher modelUpgradetypeConstellations and Signal T ypes Frequency BandsGSG-5111OPT-4Software GPS L1 C/A IncludedOthers if constellation is ordered:•GLONASS L1 C/A •QZSS L1•Galileo E1•BeiDou B11539-1627 MHz (L1)GSG-541OPT-8Software 8OPT-16Software 16OPT-32/2FactoryGSG-62322OPT-48/3Factory Same as aboveOptions if constellation andfrequency are ordered:•GPS L1P, L2P, GLONASS L2 C/A (OPT L2)•GPS L2C (OPT L2C)•GPS L5, IRNSS L5, Galileo E5a/b,BeiDou B2 (OPT L5)Same as above and 3 other ranges•1192-1280 MHz (L2)•1148-1236 MHz (L5)•1224-1312 MHz (E6/B3)GSG-63483OPT 64/4FactoryGSG-64644––Configuration SummaryOct 29, 2018 rev.2© 2018, Pendulum Instruments and OroliaSpecifications subject to change or improvement without notice.。
海康威视 HPM 系列产品维护指南说明书

Lifecycle Solutions & ServicesPreventive Maintenance Tips: Power Systems 1It Doesn’t Run Without Power—Proper Maintenance of Power SystemsMaintaining the power system is critical for any of your systems and that is definitely true when dealing with the PM/APM/HPM (xPM) family. Depending on your configuration and process, the failure of proper maintenance practices and ignoring alarms from the power system could lead to failures that have the potential to bring a process or plant to a standstill. This includes loss of view, loss of control, or even loss of the process.How Proper Power System Maintenance Can Help You• Reassurance that your power system and battery back-ups are running properly • Reduced risk of downtime due to power system issues • Allows you to be proactive in your maintenance approach • Simplified ordering for maintenance items available in a kit versus individual components • Lower cost of replacement to mitigate costly unplanned system downtime• Current version of Power Supply has multiple improved characteristicsProper maintenance of the power system includes addressing the power supplies, battery backup and the CMOS memory backup batteries. The expected lifespan of each of these components is different and the lifespan of each is also affected by the environment in which they are used. Benchmarks for changing out each component are every 10 years for the power supply, every five years for the battery backup (and possibly every three), and every two years for the CMOS batteries. Honeywell now offers an upgrade kit, MC-ZPSUG2, which provides all of these components packaged together. The power supply provided is the current version with improved characteristics.Any failures of these power system components should be changed immediately.DescriptionLifeExpectancyReplacement Part #Power Supply 10 years 51198651-100 48V Battery Backup 3 to 5 years 51303948-100 Size “AA” Ni-Cad CMOS Battery 2 years 51190422-100 Size “C” Ni-Cad CMOS Battery2 years51192060-100CMOS Memory Battery BackupThe xPM power systems are designed to provide battery backup to all the CMOS memory. The CMOS battery backup prevents the loss of the data base during a power outage after the battery backup has been depleted or if no battery backup module is present. There are two different power system chassis out in the field with CMOS batteries. The older style power system introduced with PM/APM requires three specific “AA” size Ni-Cad batteries. For the current back panel introduced for HPM the CMOS memory requires three specific “C” size Ni-Cad batteries. The size “C” batteries are required if the full 50 hours of CMOS memory backup is desired for HPM due to the larger memory available in HPM. In either scenario, the incorrect usage of other batteries than what have been tested and qualified by Honeywell may result in the battery overheating and could possibly cause the battery to rupture.The batteries in the standard power system are periodically tested by the charging circuit. If the voltage falls below the allowed limit, a battery failure alarm will be generated and the batteries should be replaced. Regardless of alarms, Honeywell recommends that new batteries be installed every two years. All three batteries should be replaced at one time.DescriptionReplacement Part #Size “AA” Ni-Cad CMOS Battery51190422-100 Size “C” Ni-Cad CMOS Battery 51192060-100Preventive Maintenance Tips: Power Systems 2 48 Volt Battery BackupThe battery backup is designed to maintain a fully loaded xPM fora minimum of 20 minutes. It will shutdown when the voltage reaches38 volts to prevent the power supply from going out of regulation and an alarm will be generated. Rechargeable batteries will lose their full charging capabilities over time and will need to be tested and replaced when they fall below 60 percent of their original capacity.The battery backup has been designed to operate in standby (float) service for approximately five years. The five years is based on the battery being kept at 20C (68F) and the float charge voltage being maintained between 2.25 and 2.30 volts per cell. This includes the battery being fully discharged once every three months. No battery should be left in service over five years, and if no maintenance is done it should be replaced every three years.The service life is directly affected by the number of discharges, the depth of discharge, ambient temperature, and the charging voltage. The expected service life can be shorted by 20% for each 10C that the ambient is above 20C.The batteries should never be left in a discharged state. This allows sulfating to occur which will increase the internal resistance of the battery and lower its capacity. The self-discharge rate is about 3% per month at an ambient of 20C. The self discharge rate doubles for each 10C in ambient above 20C. The discharged voltage of the battery should never go below 1.30 volts to maintain the best battery life.With this in mind it is recommended to periodically load test the batteries to ensure they have sufficient capacity to maintain the system during a power outage. Tests should be done on an annual basis and more frequently as they become older and begin to lose capacity. The load test is recommended off-process if possible as there will be no battery backup available while performing the test and recharging of the battery pack can take up to 16 hours. Having a spare available to swap, especially if doing on process, is a wise option leading to minimal time without battery backup and allowing the tested battery to be recharged on a bench outside the system for future swap with the next test.If regular maintenance is not performed the recommendation is to change at least every three years rather than every five.Power SuppliesThe power supply is the heart of the xPM power system and the recommendation is for a redundant power supply configuration having each power supply fed by its own dedicated power source. Honeywell has introduced the next generation power supply for this family which increases the robustness of the power system. Even with redundant power supplies, one must be careful when changing out a failed power supply. This is to minimize disturbance of the environment and to reduce the introduction of particles into the area around and near the power supplies. Those particles can be pulled through the airflow of the working power supply and result in the second power supply failing.For this reason, Honeywell does not recommend replacing a working power supply on-process (other than the black-colored version). However, power supplies do not last forever and you should consider upgrading older power supplies, or prepare to do so, when the opportunities arise.The recommendation for changing out the power supplies is every ten years and this replacement should be included during a scheduled down time if possible. The power supply replacement procedure listed in the Honeywell xPM Service manual should be followed at all times.Recommend Change of Original Black Power SuppliesIn October of 1996 Honeywell issued a customer priority notification (PN #1986) about a possible over-voltage issue with the black-colored (51109456-200) power supplies that were sold from 1988 through 1994. The Honeywell recommendation was to change out those black power supplies with the new silver version. Honeywell still recommends and strongly suggest that these black power supplies be replaced with the current power supply under part number 51198651-100 regardless of when they were put into service.Silver Power SuppliesThere have been three part number versions of the silver power supplies. The first (51109684-100/300) was sold from 1993 through 1997. The second (51198947-100) sold from 1997 through today. The next generation power supply was released in early 2009 and was introduced initially through the power system maintenance upgrade kit. If a site is running the original silver version they have now been in service for over 10 years and sites should consider the need to replace before they are forced to do so by failure of the power supply. Note that there is always risk involved when powering down equipment and possible issues when the equipment is powered back up. As stated previously, it is recommended to change these out off-process if possible. Replacements on- process should be done only when a power supply fails and replacement is then required immediately.Description Replacement Part #48V Battery Backup51303948-100Preventive Maintenance Tips: Power Systems 3Power Supply IssuesThe xPM power supplies have proven to be a reliable and robust power source. However, as with any electrical component they do not last forever and there is the potential for failure modes. Issues such as foreign particles introduced have already been discussed. In addition, even clean environments are susceptible to whiskers which have the potential to short out active circuits. Whiskers are a real issue and further details may be found in the Customer Resource Manual (CRM) in the Process Manager section PD22_G97(G).The new power supply available through the power system maintenance kit includes design improvements specifically done to address some of these possible failure modes to make a robust power supply even better.Remember that the power supply is a critical component to your system and regular maintenance as well as having spares available is highly recommended to keep your site running without problems. Monitor the power system alarms and take action when they do occur.DescriptionReplacement Part #Power Supply51198651-100Preventive Maintenance Tips: Power Systems 4Importance of Power System AlarmsAlways ensure that all power supply alarm contacts are properly implemented, working, and are being monitored. Failure to monitor these alarms and take appropriate action in a timely manner can lead to failures of the power system that could have otherwise been prevented. There are DC Out, Battery, Fan/Temp, AC In, and Charging LED indicators for each Power Supply module. If the Power system is fully functional, all five of the indicators are illuminated. In addition, each of these conditions, plus a CMOS/Memory is available as a digital input for each supply.DC Out IndicatorIf a DC Out LED is off, AC line power has been lost (check the AC In LED) or the Power Supply Module has failed. If the Power System is non-redundant, or if both DC Out LEDs are off, the HPM has lost 24 VDC. The CMOS backup system maintains power to the CMOS memory, so subsystem programs are not lost. See the Battery LED description below. The annunciator contact illustrated in the following figure will open when these conditions occur.Battery IndicatorIf the Battery LED is off and the Charging LED is on, the 48 Volt Battery switch is in the off position or the 48 V Battery Backup system has failed. The annunciator contact illustrated in the following Figure will open when these conditions occur. If the Power System does not have the battery pack option, the Battery LED will normally be on, and the Charging LED will normally be on.Fan/Temp IndicatorIf the Fan/Temp LED is off, the fan in the Power Supply Module has failed or the temperature of the supply has exceeded a safe value. The annunciator contact, discussed below, is activated.AC In IndicatorIf the AC In LED is off, AC power to the HPM has been lost or the switch on the Power Supply Module is off. Backup systems, if operating, are maintaining the unit. Check the DC Out and Battery indicators to determine the state of the system. Many installations may have the Power Supply Modules connected to separate AC power sources to minimize outage caused by a power loss. The Annunciator contact signifying power loss from either supply, are opened independently.Charging IndicatorWhen the Charging LED is off, the charging circuit that maintains the optional 48 V Battery Backup system has failed. Check the batteries, their corresponding connections, and the charging circuits in the Power Supply Module(s). The annunciator contact output is opened by this condition.For More InformationLearn more about how Honeywell’s Preventive Maintenance Tips can limit downtime and assure system power supplies and battery backups are working properly visit our website or contact your Honeywell account manager. Honeywell Process Solutions Honeywell1250 West Sam Houston Parkway South Houston, TX 77042Honeywell House, Arlington Business Park Bracknell, Berkshire, England RG12 1EB Shanghai City Centre, 100 Junyi Road Shanghai, China 20051 AlarmsThe primary Power Supply Module alarm and secondary Power Supply Module alarm contacts monitor five functions within each Power Supply Module. The appropriate contact will open when any of the following occur:• The DC output voltage is not within normal limits. • AC input power to the supply has failed.• The Power Supply Module electronics have overheated or the Power Supply Module fan has failed. • The 48 V backup-battery system has failed because the batteries have discharged or they have been disconnected. • The battery charger in the Power Supply Module has failed.Servicing the Power SystemThe power system is critical to your process. Loss of the power system may lead to loss of control, loss of view, or loss of process. Honeywell strongly recommends regular maintenance to the power system and service checks with regular component replacements performed by Honeywell trained service technicians. • Options for Power System Upgrade/Maintenance • Order the power system upgrade kit• Order replacement parts for immediate installation. • Order spares to have in stock as needed.• Add power system components to a parts contract.Preventive Maintenance Tips: Power Systems 5Orderable Power System Components• CMOS Batteries • 48V Battery Backup • Power Supply• Power System Chassis AssemblyBenefits of New Power Supply• Improved airflow handling• Conformal coating of all metallic components • Enhanced mechanical design • Extended temperature range • Added thermal shutdown capability • More reliable power switch design • More consistent alarm handlingAdditional Power System InformationAdditional details on proper maintenance procedures such as load testing and specifics on the power supplies and batteries may be found in the Honeywell Customer Resource Manual. This is located in the Process Manager section of the CRM under TAB 22. As always, you may also contact your local Honeywell account manager or service technician for further details.SV-12-37-ENG May 2012© 2012 Honeywell International Inc.。
cpu monitor的用法 -回复

cpu monitor的用法-回复CPU(Central Processing Unit)监控工具,也称为CPU监视器或CPU 温度监控器,是一种用于监视CPU温度、使用率和性能的软件或硬件设备。
它可以帮助用户识别和解决CPU过热、过载和性能下降等问题。
本文将介绍CPU监控工具的用法和如何使用它来提高计算机性能和维护CPU的健康。
一、CPU监控工具的安装和选择要使用CPU监控工具,首先需要在计算机上安装相应的软件或硬件。
有许多不同的CPU监控工具可供选择,包括:1. 软件监控工具:这种工具是通过在计算机上安装软件应用程序来监控CPU的状态。
常见的软件监控工具包括HWMonitor、Core Temp、SpeedFan等。
这些工具可以提供实时的CPU温度、使用率和频率等数据,并通常还提供警报功能,以便在CPU温度过高时及时发出提醒。
2. 硬件监控工具:这种工具是一种物理设备,通常是可插入计算机主板上的一个插槽。
它们通常具有更高的精度和可靠性,但通常也更昂贵。
常见的硬件监控工具品牌包括NZXT、Corsair和Asus等。
选择适合自己的CPU监控工具时,需要考虑以下几个因素:您的计算机硬件和操作系统的兼容性、工具提供的功能和性能监控水平、以及您的预算。
二、使用CPU监控工具进行实时监控安装并打开您选择的CPU监控工具后,您将看到一个用户界面,其中显示了CPU的实时数据。
下面将介绍几个常见的实时监控指标:1. CPU温度:这是CPU监控工具中最重要的指标之一。
过高的温度可能导致CPU过热,并可能损坏或降低其性能。
通过监控CPU温度,您可以采取适当的措施,例如增加散热器或清洁风扇等,以降低CPU温度并避免潜在的问题。
2. CPU使用率:这是指CPU在特定时间段内运行的负载。
通常以百分比形式表示,可以帮助用户了解CPU的工作负荷以及是否存在过载问题。
如果CPU使用率持续高于90或100,则可能需要优化计算机的性能或增加CPU处理能力。
Dynamix 1444机器人监控系统说明书

To protect equipment, Dynamix 1444 measures and monitors a machine’s critical dynamic and position parameters and assures appropriate actions are performed, with the recision, reliability, and performance required by industry and regulatory standards.For general condition monitoring, the Dynamix 1444 monitors offer unprecedented signal processing and measurement capabilities allowing you the tools necessary to detect and identify the faults and status across all classes of industrial machinery. You can send information to plant-wide and enterprise-wide databases for storage and trending.With this information, you can take appropriate maintenance action, such as replacing worn-out components before they fail, protecting both production and equipment while reducing maintenance costs. The tight coordination between condition monitoring and the control system allows you to leverage existing investments in visualization and information solutions to improve machine builder and end user productivity and lower total cost of ownership. With Studio 5000™, you can deploy and maintain condition monitoring programming in the same design environment used for automation control.Rockwell Automation provides a set of examples. These examples are called the Dynamix™ Accelerator Toolkit that can aid or speed in the development of the required solution. The Dynamix Accelerator Toolkit includes sample logic and HMI faceplates for use in integrating a Logix controller with a Dynamix 1444 Series Dynamic Measurement Module, using a PanelView™ Plus for visualisation. The kit includes example applications, a Motor Blower application and a Motor Pump application, sample panel, power, and wiring diagram drawings for a typical Dynamix installation, and a Quick Start guide. If you chose (Option B) we will Pre-Load the Accelerator Toolkit for convenience and ease of Start Up.Benefits of the Dynamix 1444 Starter Kit.Need a flexible, scalable, IntegratedCondition Monitoring system that’s easy-to-use and affordable? Looking for easyconfiguration in a Pre-Wired form factor? Need a Pre-Engineered solution that willenable you to protect your key assets? TheDynamix 1444 starter kit is a discounted bundle of hardware or complete Pre-Wired solution that provides everything you need to get started. • The basic objective of a conditionmonitoring system is to detect faultsthat manifest as increased vibration.• The Dynamix™ 1444 Series system isdesigned to serve the protection andcondition monitoring requirements ofrotating and reciprocating industrialmachinery.• Dynamix 1444 allows you to leverageIntegrated Architecture to assesscurrent equipment health, predictpotential issues and help avoiddamage to critical machinery.• The 1443 Series of sensors offersa family of accelerometers andaccessories suitable for mostapplications. We include two Dualoutput AT type sensors output both acceleration and temperaturemeasurements.• Select the Loose Components (OptionA) at an affordable price to build intoyour next project/ Panel or choose thePre-Engineered (Option B) solution tostart Monitoring your key assets to getresults today.Dynamix ™ 1444 Starter Kit Discover the capabilities of the Dynamix 1444 Series systemPublication 1444-PP002A-EN-E – May 2017 Copyright ©2017 Rockwell Automation, Inc. All Rights Reserved. Allen-Bradley, CompactLogix, FactoryTalk View ME, Studio 5000, RSLogix and PanelView are trademarks of Rockwell Automation, Inc. Trademarks not belonging to Rockwell Automation are property of their respective companies.Standard terms, conditions and warranty apply. Promotion valid until 22nd December 2017. Engineering software requires registration and activation. Rockwell Automationreserves the right to amend or terminate this offer at any time.Dynamix 1444 Promotional KitOption A (Components Only, Cat No - 1444-STRT10)5380 Controller and Accessories☐ 5069-L306ER with Terminals ☐ 1783-US5T ☐ 1606-XLE120EEPanelView Plus 7☐ 2711P-T7C22D8S (PV+7 STD, Touch Screen, 6.5”, TFT Color, DLR Ethernet, 24V DC)Dynamix 1444☐ 1 x 1444-DYN04-01RA with Spring Terminals☐ 1 x 1444-TB-A with Spring Terminals☐ 2 x 1443-ACC-AT-T (GP Accel and Temp,Top Exit, 100mV/g, 10mV/°C☐ 2 x 1443-CBL-MS3IBC-16SOption B (Cat No - 1444-STRT11)5370 Controller and Accessories☐ 5069-L306ER with Terminals☐ 1783-US5T☐ 1606-XLE120EEPanelView Plus 7☐ 2711P-T7C22D8S (PV+7 STD, Touch Screen, 6.5”, TFT Color, DLR Ethernet, 24V DC)Dynamix 1444☐ 1 x 1444-DYN04-01RA with Spring Terminals☐ 1 x 1444-TB-A with Spring Terminals☐ 2 x 1443-ACC-AT-T (GP Accel and Temp, Top Exit, 100mV/g, 10mV/°C☐ 2 x 1443-CBL-MS3IBC-16SInstalled & Wired in suitable Enclosure☐ Mounted, Wired, Connected with Electrical Schematics☐ Pre-Loaded with Dynamix Accelerator Toolkit。
H3C IGMP Snooping配置
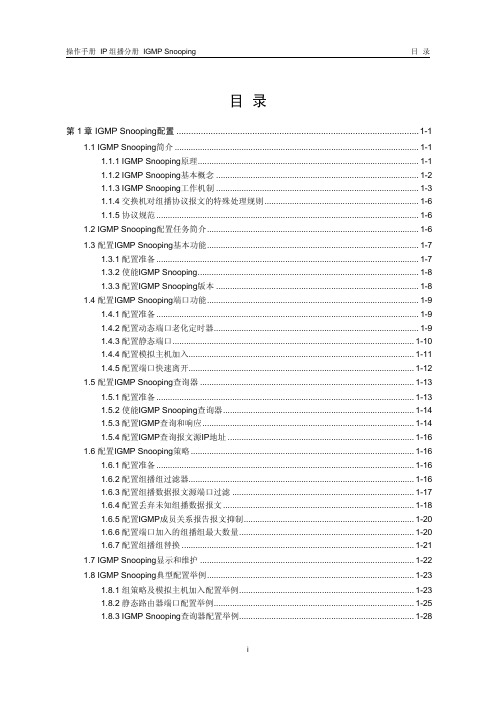
文源端口过滤
No
No
配置丢弃未知组
播数据报文
No
No
MSR 30
MSR 50
Yes MIM 交换单板支持
Yes FIC 交换单板支持
Yes,MIM 交换单板支持
30-11 安装 XMIM 交换单 Yes 板支持
说明:
z H3C MSR 系列 请参见本模块的命令手册。
i
操作手册 IP 组播分册 IGMP Snooping
目录
1.9 常见配置错误举例 ............................................................................................................ 1-31 1.9.1 交换机不能实现二层组播....................................................................................... 1-31 1.9.2 配置的组播组策略不生效....................................................................................... 1-31
操作手册ip组播分册igmpsnoopingigmpsnooping配置110全局配置动态端口老化定时器表15全局配置动态端口老化定时器操作命令说明进入系统视图systemview进入igmpsnooping视图igmpsnooping配置动态路由器端口老化时间routeragingtimeinterval可选缺省情况下动态路由器端口的老化时间为105配置动态成员端口老化时间hostagingtimeinterval可选缺省情况下动态成员端口的老化时间为260在vlan内配置动态端口老化定时器表16在vlan内配置动态端口老化定时器操作命令说明进入系统视图systemview进入vlan视图vlanvlanid配置动态路由器端口老化时间igmpsnoopingrouteragingtimeinterval可选缺省情况下动态路由器端口的老化时间为105配置动态成员端口老化时间igmpsnoopinghostagingtimeinterval可选缺省情况下动态成员端口的老化时间为260143配置静态端口如果某端口所连接的主机需要固定接收发往某组播组或组播源组的组播数据可以配置该端口静态加入该组播组或组播源组成为静态成员端口
Elkay天花板安装PIR定时器(3线)说明书

The Ceiling Mount PIR Timer (3 wire) is part of the Elkay family of switches, timers and detectors which save energy and increase convenience in and around your home, garden or premises.Rating at 240V ac 50Hz • All load types 10A• Time Delay: 2min - 1 hour• Sensitivity adjustment / Test mode • Auto and manual Lux Sensor for daylight control• Surface and flush mounted options • Interchangeable white / chrome fasciasUsageThe PIR sensor has been designed to switch lighting, heating and ventilation loads up to 10A. The unit is switched on by the detection of moving infra red heat within a specified range. When infra red heat, such as a moving body, is no longer detected,the unit will switch off the load after the adjustable time period has elapsed.If infra red heat is detected again during the timing period, the timing sequence willrestart. The unit has a lux level adjustment and Auto Lux function, which measuresthe ambient light levels and prevents lightingbeing switched on, when there is sufficient lighting in the room. There is sensitivity adjustment and test mode function added for your convenience.IMPORTANT a power factor correction capacitor of 4 microfarads may be required when switching low wattageloads, e.g. LED loads. the capacitor is fitted across switch live and neutral supplies of suitable Elkay capacitors can be found at your stockist (ref. pfcc-1). Do not insulation resistance test this product. Remove before testing or test circuit prior to fitting.–CEILING MOUNTPIR TIMER374B-13 wireInstruction GuideB D HBROOK DESIGN HARDWARE LTDB D HBR HAPositioningCAREFUL POSITIONING IS ESSENTIAL TO OBTAIN OPTIMUM PERFORMANCE. Use the detection range to determine a suitable location for the sensor. When locating the position of the units, ensure the sensor is not subjected to bright or direct sunlight or in areas with highrefl ective surfaces. Do not site units on a vibrating surface, or near forced air heating and ventilation. They should not be placed within 1 metre of the load. Sensors work when objects move across their fi eld of view. Position the sensor where people will be detected walking across the zones rather than towards the zones identifi ed in Diagram 1. Adjust sensitivity to suit the area that the sensor has been installed in.2INSTRUCTION GUIDE|CEILING MOUNT PIR TIMER – 3 WIREInstallation StepsIT IS ESSENTIAL THAT YOU FOLLOW CLOSELY STEPS 1 TO 8 OF THE MOUNTING AND INSTALLATION INSTRUCTIONS BELOW. FAILURE TO DO SO WILL INVALIDATE THE WARRANTY.Step 1Please ensure that you position the PIR in the correct place by reading the Positioning section of these instructions. For flush mounting cut a clean hole measuring64mm in diameter in the chosen area for the sensor. For surface mounting attach surface mount cup to ceiling with connection cable hanging through the middle. Seal any large holes on ceiling to prevent air current activation.Step 2Ensure that the mains power to the circuit is switched off. Ensure terminal coverand cable clamp are correctly fitted with screws supplied. Place the Live In into the Terminal marked Live In and the switched Live Out into the Live Out terminal. Place the neutral into the connection marked N for neutral. Please note that it is essential that the Live In wire and the switch Live Out and Neutral are identified prior to commencing installation.To connect multiple units connect the live switch live and neutrals as shown in Diagram 2. Turn off mains supply for installation as live working is not recommended and can damage the unit. Step 3For flush mounting fold the two arms up into the vertical position and insert unit into the hole. Release unit ensuring arms are securely in place. For surface mounting fit surface mount cup onto ceiling or conduit terminal box and return connected PIR into surface mount cup.Step 4Remove the fascia by turning anti-clockwise to show the lux pot, sensitivity pot andthe timing/lux Dip switches. Please adjust the Lux Level and Sensitivity potentiometer gently without force as this is a sensitive electronic part. After adjustment please wait 30 seconds for changes to take effect. It is recommend product is set up initially using the 10 secs walk test mode.Step 5To set Auto Lux (150 Lux), switch Dip switch 4 to the ON position. This will allow activation of the PIR from Dusk until Dawn only.To set manually then put dip switch 4 off and use the potentiometer to adjust to desired lux level setting. All the way to the plus setting will allow the PIR to switch day and night. All the way to the minus sets the timer to ZERO lux and effectively switches off the PIR. To set manually you will need to be present at dusk(See Diagram 3).Step 6To adjust sensitivity turn anti-clockwiseto the High (H) setting to increase sensitivity and clockwise to the Low (L) to decrease sensitivity.Step 7To set time please utilise the dip switch timing diagram above. The black bar denotes dip switch position. Replace fascia ring by turning anti clockwise(See Diagram 4).Continued overleaf...3INSTRUCTION GUIDE|CEILING MOUNT PIR TIMER – 3 WIREBrook House,Dunmurry Industrial Estate, Dunmurry,Belfast BT17 9HU T +44 (0)28 9061 6505F +44 (0)28 9061 6518E info @B D HBROOK DESIGN HARDWARE LTDProblemResolutionLights will not switch OFF• Check terminal connections.• Check time settings (See Diagram 4).• PIR is too close to load – Re-position away from lighting, heating and forced air ventilation.• PIR is switching low wattage or LED loads – Fit Capacitor as stated in instructions PFCC-1.• Windy weather conditions – Adjust Sensitivity down.• PIR is re triggered – Check area is left unoccupied for longer that time setting using an accurate time piece.• Sensitivity set too high – Gradual incremental adjustments towards the low setting to resolve the issue.Lights will not switch ON• Check Terminal connections.• Lux set too low – Turn off Auto Lux and turn UP lux level to the PLUS (+) setting and wait for s ensor to adjust.• Sensitivity set too low – Gradual incremental increases towards the High setting to resolve the issue.Light switches OFF then immediately comes back ON• Check terminal connections.• PIR is detecting normally- Find source that is triggering PIR.• PIR is seeing infra red heat from the load- Re-position away from heat source (See Positioning).• PIR is switching low wattage or LED loads- Fit Capacitor PFCC-1 across switch live and neutral of load.• PIR is switching a contactor and the contactor chatters or stays ON - Fit a PFCC-1 capacitor across the switch live and neutral of the contactor coil.TroubleshootingStep 8The PIR will take approximately 1 minute to initialise and will flash rapidly after the mains power is first applied to allow the sensor to learn its environment. The load will be ON after 7 secondsinitially, then switch off after 1 minute if there is no detection in the zones.Operation of the Unit• In standard operation the PIR will now sense infra red heat when a person or source of heat passes throughthe detection zone. Each time the PIR is triggered it will reset the timer backto the start of the timing period. The unit will then wait 5 seconds before allowing the PIR to sense and re trigger the timing period again.• If no one is present in the room or the detection zone is not passed through, during its set time period, the timer will time out, turning off the lights or appliance.• The PIR unit will only trigger thelights or appliance if the ambient light level is below that set on the lux level adjustment.Technical HelplineFor further help or assistance or information on this or other products in the range please call the Elkay Technical team on +44 (0)28 9061 6505. Please call theTechnical helpline before returning any products to your stockist. These instructions are available in other languages. Please refer to our website Instrukcje są również dostępne w innych językach. Prosimy o zapoznanie się z naszą stroną internetową lub www.elkaypolska.plImportant NoticeAll wiring should be carried out by a competent person or a qualified electrician and should be fitted to current IEE wiring regulations BS 7671.The circuit should be isolated before carrying out any work. Failure to adhere to the instructions will invalidate the warranty.Elkay (Europe), 51C Milicka, Trzebnica, 55-100, Poland。
EMP Monitor操作说明书

EMP Monitor操作說明書V4.30所使用符號的意義下表所列為本說明書中所使用的符號及其意義的說明。
所使用符號的意義 (2)EMP Monitor特色使用EMP Monitor可完成的工作 (5)工作環境 (6)相容的電腦 (6)安裝EMP Monitor (6)Windows Vista系統的限制 (6)開始操作之前 (7)使用EMP Monitor登錄和刪除所監視的投影機 (9)啟動EMP Monitor (9)使用自動搜尋登錄投影機(搜尋並登錄位於同一區段的投影機) (9)自動搜尋程序 (9)登錄程序 (10)設定位址範圍以便進行自動搜尋及登錄 (11)自動搜尋程序 (11)登錄程序 (12)指定IP位址登錄 (手動登錄) (13)一次將數台投影機登錄到監視群組中 (14)如果投影機名稱或IP位址在登錄後變更 (15)已手動登錄的投影機 (15)使用自動搜尋功能登錄的投影機 (16)取消(刪除)投影機登錄資料 (16)監視視窗配置 (17)使用群組檢視進行監視 (17)群組檢視圖示的意義 (17)使用群組檢視內的圖示 (18)使用細節清單檢視進行監視 (19)細節清單檢視圖示的意義 (19)選擇顯示項目 (20)排序清單 (21)搜尋所需圖示(投影機清單) (21)使用系統匣監視 (21)在清單中顯示處於問題或警告狀態的投影機 (22)檢查屬性詳細資訊 (23)顯示群組屬性 (23)顯示投影機屬性 (23)顯示與刪除日誌 (24)顯示日誌 (24)刪除日誌 (24)使用控制功能 (25)使用控制按鈕進行控制 (25)使用網路瀏覽器進行控制(網路控制) (26)使用定時器設定進行控制 (26)新的定時器設定程序 (27)電子郵件通知功能設定 (28)發出電子郵件通知操作人員問題/警報/狀態 (30)應用程式鎖定功能 (31)切換啟用和停用應用程式鎖定功能 (31)啟用應用程式鎖定 (31)停用應用程式鎖定 (31)設定取消應用程式鎖定功能的密碼 (31)附錄故障排除 (33)不能監控投影機 (33)投影機發生問題時無法傳送電子郵件 (33)通告 (34)商標 (34)目錄3EMP Monitor特色您可使用EMP Monitor進行多項操作,如在電腦螢幕上檢查連接網路的多台EPSON投影機狀態,或透過電腦控制投影機等等。
MN03 AC Current Probe 用户手册说明书

AC Current Probe Model MN03User ManualDESCRIPTIONThe MN03 (Cat. #2129.18) is small, compact AC current probe. Designed to meet the most stringent demands in industry and electrical contracting, they also meet the latest safety and performance standards. The probe has a measurement range up to 100Arms which makes it a perfect tool for measurement with DMMs, recorders. The Model MN03 is compatible with any voltmeter, multimeter, or other current measurement instrument with an input impedance greater than 1M . To achieve the stated accuracy, use the probe with a voltmeter having an accuracy of 0.75% or better.WARNINGThese safety warnings are provided to ensure the safety of personnel and proper operation of the instrument.•Read the instruction manual completely and follow all the safety information before attempting to use or service this instrument.•Use caution on any circuit: Potentially high voltages and currents may be present and may pose a shock hazard.•Read the Safety Specifications section prior to using the current probe. Never exceed themaximum voltage ratings given.• Safety is the responsibility of the operator.•ALWAYS connect the current probe to the display device before clamping the probe onto the sample being tested.•ALWAYS inspect the instrument, probe, probe cable, and output terminals prior to use.Replace any defective parts immediately.•NEVER use the current probe on electrical conductors rated above 600V in overvoltage category III (CAT III). Use extreme caution when clamping around bare conductors or bus bars. INTERNATIONAL ELECTRICAL SYMBOLSThis symbol signifies that the current probe is protected by double or reinforced insulation. Use only factory specified replacement parts when servicing the instrument.This symbol signifies CAUTION! and requests that the user refer to the user manual before using the instrument.This is a type A current sensor. This symbol signifies that application around and removal from HAZARDOUS LIVE conductors is permitted.DEFINITION OF MEASUREMENT CATEGORIESCAT II: For measurements performed on circuits directly connected to the electrical distribution system.Examples are measurements on household appliances or portable tools. CAT III: For measurements performed in the building installation at the distribution level such as onhardwired equipment in fixed installation and circuit breakers. CAT IV: For measurements performed at the primary electrical supply (<1000V) such as on primaryovercurrent protection devices, ripple control units, or meters. RECEIVING YOUR SHIPMENT:Upon receiving your shipment, make sure that the contents are consistent with the packing list. Notify your distributor of any missing items. If the equipment appears to be damaged, file a claim immediately with the carrier and notify your distributor at once, giving a detailed description of any damage.ELECTRICAL SPECIFICATIONSNominal Range: 100AMeasurement Range: 1 to 100A ACOutput Signal: 1mV AC/A AC (100mV @ 100A) Accuracy and Phase Shift*:Accuracy: 2% Reading ± 50mAPhase Shift: Not Specified*Reference conditions: 18°C to 28°C, 20 to 75% RH, external magnetic field <40 A/m, 48 to 65 Hz sine wave, distortion factor less than 1%, no DC component, no external current carrying conductor, test sample centered. Load impedance1M Overload: 150A permanentFrequency Range: 48 to 500HzWorking Voltage: 600VrmsCommon Mode Voltage: 600VrmsInfluence of Adjacent Conductor:< 2mA/A at 50HzInfluence of Conductor Position in Jaw:0.1% of mV output @ 50/60HzInfluence of Frequency:< 1% of mA output from 65 to 500HzInfluence of Temperature:≤ 0.2%/10°KInfluence of Humidity (10 to 90% RH):≤ 0.1% of mAMECHANICAL SPECIFICATIONSOperating Temperature:14° to 122°F (-10° to +50°C)Storage Temperature:-40° to 176°F (-40° to +80°C)Maximum Cable Diameter:One Ø 0.39" (10mm)Case Protection:IP 40 (IEC 529)Drop Test:Test per IEC 68-2-32:1.0m drop on 38mm of Oak on concreteMechanical Shock:Test per IEC 68-2-27Vibration: Test per IEC 68-2-6Dimensions:4.43 x 1.48 x 1.02"(112.5 x 37.5 x 26mm)Weight:180 g (6.5 oz)Polycarbonate Material:Jaws: Red PolycarbonateCase: Dark PolycarbonateOpening Operations - Life:> 50,000Output:Double/reinforced insulated 5 ft (1.5m) lead with safety 4mm banana plugAltitude: <2000 mIndoor use only SAFETY SPECIFICATIONSElectrical:Conforms to IEC 1010-2-32. ed. 2 2003Common Mode Voltage:300V CAT IV, 600V CAT III, Pollution Degree 2Electromagnetic Compatibility:EN61326-1 (ed. 97)+A1 (ed. 98) : transmission and immunity in an industrial site ORDERING INFORMATIONAC Current Probe MN03 ................ C at. #2129.18Accessories:Banana plug adapter(to non-recessed plug) ..................... C at #1017.45OPERATIONPlease make sure that you have already read and fully understand the WARNING section on page 1. Making Measurements with the AC Current Probe Model MN03•Connect the black lead of the current probe to “common” and the red lead to the AC voltage input on your DMM or other current measuring instrument. Select the appropriate current range (400mV AC range). Clamp the probe around the conductor to be tested. Select the lower range until you obtain the best resolution. Read the value display on the DMM and multiply it by the probe ratio (1000/1). (If reading = 59mV, the current flowing through the probe is 59 x 1000 = 59A)•For best accuracy, avoid if possible, the proximity of other conductors which may create noise.Tips for Making Precise Measurements•When using a current probe with a meter, it is important to select the range that provides the best resolution. Failure to do this may result in measurement errors.•Make sure that probe jaw mating surfaces are free of dust and contamination. Contaminants cause air gaps between the jaws, increasing the phase shift between primary and secondary. It is very critical for power measurement.MAINTENANCE:Warning• For maintenance use only original factory replacement parts.• To avoid electrical shock, do not attempt to perform any servicing unless you are qualified to do so.•To avoid electrical shock and/or damage to the instrument, do not get water or other foreign agents into the probeCleaningTo ensure optimum performance, it is important to keep the probe jaw mating surfaces clean at all times. Failure to do so may result in error in readings. To clean the probe jaws, use very fine sand paper (fine 600) to avoid scratching the jaw, then gently clean with a soft oiled cloth.REPAIR AND CALIBRATIONYou must contact our Service Center for a Customer Service Authorization number (CSA#). This will ensure that when your instrument arrives, it will be tracked and processed promptly. Please write the CSA# on the outside of the shipping container.Chauvin Arnoux®, Inc. d.b.a. AEMC® Instruments15 Faraday Drive Dover, NH 03820 USA(Or contact your authorized distributor)NOTE: All customers must obtain a CSA# before returning any instrument.TECHNICAL AND SALES ASSISTANCEIf you are experiencing any technical problems, or require any assistance with the proper use or application of this instrument, please contact our technical hotline:(800) 945-2362 (Ext. 351) • (603) 749-6434 (Ext. 351)•********************LIMITED WARRANTYThe current probe is warranted to the owner for a period of two year s from the date of original pur- chase against defects in manufacture. This limited warranty is given by AEMC® Instruments, not by the distributor from whom it was purchased. This warranty is void if the unit has been tampered with, abused or if the defect is related to service not performed by AEMC® Instruments.Full warranty coverage and product registration is available on our website at:/warranty.html.Please print the online Warranty Coverage Information for your records.99-MAN 100333.v3 03/18。
Flow Monitor Operation Manual PFMV3说明书

Flow MonitorOperation ManualPFMV3Safety InstructionsMounting and InstallationThank you for purchasing an SMC PFMV3 Series Flow Monitor.Please read this manual carefully before operating the product and make sure you understand its capabilities and limitations.Please keep this manual handy for future reference.To obtain more detailed information about operating this product,please refer to the SMC website (URL ) or contact SMC directly.These safety instructions are intended to prevent hazardous situations and/or equipment damage.These instructions indicate the level of potential hazard with the labels of"Caution", "Warning" or "Danger". They are all important notes for safety and must be followed in addition to International standards (ISO/IEC) and other safety regulations.OperatorNOTEThe direct current power supply used should be UL approved as follows.Circuit (of class 2) which is of maximum 30Vrms (42.4 V peak), with UL 1310class 2 power supply unit or UL 1585 class 2 transformer.The product is a approved product only if it has a mark on the body.InstallationPanel mounting•Fix the panel mount adapter to the product with the mounting screws (nominal size:3 x 8 L, 2 pcs.) supplied.•The monitor can be mounted on a panel with a thickness of 0.5 to 6.0 mm.Bracket mounting•Mount the bracket using the mounting screws (M3 x 5 L) supplied.•The required tightening torque is 0.5 to 0.7 Nm.•Install the product (with bracket) using the M4 screws (2 pcs.).•Bracket thickness is approximately 1.6 mm.Refer to the product catalogue or SMC website (URL ) for more information about panel cut-out and mounting hole dimensions.button in measurement mode to display the set values.∗: [LLL] is displayed during measurement mode when the sensor is not connected.button to complete the setting of OUT1.Normal outputReversed output Flow SettingMeasurement modeThe mode in which the flow is detected and displayed, and the switch function is operating. This is the basic operating mode; other modes should be selected for set-point and other Function Setting changes.∗: The display will indicate [LLL] if a sensor is not connected.for this period)approx.3 secondsSwitch operationWhen the flow (or voltage) falls below the set value by the amount of hysteresis or more, the switch will turn ON.When the flow (or voltage) exceeds the set value,the switch will turn OFF.If this condition, shown to the right, is acceptable,then keep these settings.Switch ON Switch OFFSet value n_1Time [s]V o l t a g e [V ]F l o w [L /m i n ]Hysteresis H_1Other SettingsStandard value offset function Peak/Bottom value displayIndicated content check function Key lock functionTo set each of these functions, refer to the SMC website (URL )for more detailed information, or contact SMC.TroubleshootingNote: Specifications are subject to change without prior notice and any obligation on the part of the manufacturer.© 2011 SMC Corporation All Rights ReservedAkihabara UDX 15F , 4-14-1, Sotokanda, Chiyoda-ku, Tokyo 101-0021, JAP AN Phone: +81 3-5207-8249 Fax: +81 3-5298-5362URL Function selection modebutton The [F ] indicates the mode for changing button for 2 seconds or longermeasurement mode.Function SettingFrontBackAttaching the connector to the sensor wire •Strip the sensor wire as shown.•Do not cut the insulator.•Insert the corresponding wire colour shown in the table into the pin number printed on the sensor connector, to the bottom.WiringWiring of connector•Connections should only be made with the power supply turned off.•Use separate routes for the product wiring and any power or high voltage wiring.Otherwise, malfunction may result due to noise.•Ensure that the FG terminal is connected to ground when using a commerciallyavailable switch-mode power supply. When a switch-mode power supply is connected to the product, switching noise will be superimposed and the product specification can no longer be met. This can be prevented by inserting a noise filter, such as a line noise filter and ferrite core, between the switch-mode power supply and the product, or by using a series power supply instead of a switch-mode power supply.•Check that the above preparation has been performed•Part A should then be pressed in using a suitable tool, such as pliers.•The sensor connector cannot be re-used once it has been fully crimped.In cases of connection failure such as incorrect order of wires or incomplete insertion,please use a new connector.•If the sensor is not connected correctly “LLL” or “HHH” will be displayed.Connecting / Disconnecting•When mounting the connector, insert it straight into the socket, holding thelever and connector body, and push the connector until the lever hooks into the housing, and locks.•When removing the connector, press down the lever to release the hook from the housing and pull the connector straight out.[F95] Selection of flow indicationThe flow rate can be displayed. The flow rate units can be selected (for models with unit selection function) after selecting the connected sensor.L/min. or CFM(ft /min.) x 10are the selectable display units.To use for flow rate indication, select the sensor and units before setting the functions [F1], [F2], [F4].The set values for [F1], [F2] and [F4] will be reset when the flow indication setting is changed.Default settingThe default settings are provided as follows. If these settings are acceptable, retain for use.Specifications / Outline with DimensionsRefer to the product catalogue or SMC website (URL ) for more information about the product specifications and outline dimensions.Refer to the SMC website (URL ) for more information about troubleshooting.To use the product for flow rate indication, select the connected flow sensor usingfunction [F95] before setting any other functions.<Operation>orbutton.Selection of flow indication completed. Return to Function selection mode.MaintenanceHow to reset the product after a power cut forcible de-energizingThe setting of the product will be retained as it was before a power cut or de-energizing.The output condition is also basically recovered to that before a power cut or de-energizing,but may change depending on the operating environment.Therefore, check the safety of the whole installation before operating the product.2. Press the or The button is to increase and the •Press the increasing the set value.•Press the button to set.Move on to unit selection function (for models with unit selection function).。
Zabbix高级技术研究

达到阈值,需要多久的时间
{Zabbix server:vfs.fs.size[/,free].timeleft(7d,,104857600)}<1h
目录
自动化配置
故障与警告
趋势预测
性能优化
性能调优原则
规划期间-考虑磁盘IOPS 架构方面-性能足够高,开销足够小
安装部署-保证各软件最优编译配置
监控方式调整 主动模式最优
新分区加入! 新网卡加入! 新元素加入!
定期发现主机上面丢失 的监控元素
多端口加入!
LLD-Low Level Discovery
In Zabbix, six types of discovery items are supported out of the box:
discovery of file systems; discovery of network interfaces; discovery of CPUs and CPU cores; discovery of SNMP OIDs; discovery using ODBC SQL queries; discovery of Windows services.
典型使用场景
磁盘还能用多久? 带宽还能撑多久? 用户数会到多少?
1. Trigger函数forecast()
在一段时间内,多久会达到设置的阈值
{Zabbix server:vfs.fs.size[/,free].forecast(7d,,7d)}<100M
2. Trigger函数timeleft()
……
故障事例
故障事例
故障事例
例子: {host:st()}>5 操作符号: - + / * < > = <> <= >= or and not 功能函数: min max avg last count date time diff regex等 故障分析和依赖:
nVent RAYCHEM RMM3远程监控模块用户指南说明书

3Heat-tracing remote monitoring modulePRODUCT OVERVIEWThe Remote Monitoring Modules (RMM3) provide temperature Array monitoring capability for the nVent RAYCHEM Elexant and NGCcontroller family. The RMM3 accepts inputs from up to eightPT 100 temperature sensors that measure pipe or ambienttemperatures in a heat-tracing system. Multiple RMM3 unitscommunicate with a single nVent RAYCHEM User Interfaceproviding centralised monitoring of temperatures.A single, twisted pair RS-485 cable connects up to 247 RMM3modules in the field.Control and monitoringA nVent RAYCHEM control network can consist of many heat-tracing circuits based on ambient and/or pipe temperatures.The RMM3 may be used to collect both ambient and pipe temperatures for control or for extensive monitoring of the heat-tracing system. The RMM3 units are placed near desired monitoring locations, even in hazardous areas (Zone 2). Multiple temperature sensor inputs are networked over a single cable, significantly reducing installation cost for temperature monitoring.AlarmsLow and high temperature alarms may be set for sensors connected to the nVent RAYCHEM controllers via the RMM3. Alarm limits are set and alarm conditions are reported to the user. Additional alarms are triggered for failed temperature sensors and communication errors. Alarms may be reported remotely through the Modbus communication to the process control system, via an alarm relay in the User Interface or via nVent RAYCHEM Supervisor.ConfigurationsThe RMM3 is an electronic device that clips to a DIN rail. The unit is available as 230/115 Vac version and 24 Vdc version.The complete kit for ordinary and hazardous areas (Zone 2) includes an RMM3 mounted in a rugged polyester enclosure with appropriate terminals and cable glands. For other installation options, contact nVent.PRODUCT SPECIFICATIONS Dimensions (in mm)RMM 3moduleHazardous area enclosureTechnical detailsAmbient operating temperature range –40°C to +60°C Ambient storage temperature range –51°C to +60°CRelative humiditymax. 95%, noncondensingRMM 3 supply voltage (nominal)115/230 Vac +10% –10% 50/60 Hz (jumper selectable)RMM 3-24Vdc supply voltage (nominal)24 Vdc (10-30 Vdc)Internal power consumption2.5 VA60Temperature sensorsType3 wire PT 100, temperature coefficient per IEC 751-1983Quantity to be connected Up to 8 PT 100 per RMM3The sensor cable may be extended with a 3 (+PE)-wire signal cable adding 20 Ohms leadresistance maximum. When using 1.5 mm2 cable this equals to ±150 m of cable.When the sensor cable is laid in cable ducts or in the vicinity of high voltage carrying cablesthe sensor extension cable should be shielded. The shield of the extension cable should begrounded at one end only.Area of use Use sensors with the appropriate approvals required for the area of useCommunicationType RS-485Cable1 shielded twisted pairLength1200 m max.Quantity By Modbus standards limited up to 247 units, maximum number of units defined by controlnetwork. See installation manual of control systems for more details.Address Switch-selectable on RMM3Communication Modbus RTU, modbus settings can be modified (baud rate, bits, parity, stop bits, tx delay)Connection terminalsSupply (in-out)4 terminals for cables 0.2 mm2 to 4 mm2Earth10 terminals for cables up to 4 mm2 aside the RMM3 unitPT 100 connections8 x 3 terminals for cables 0.2 mm2 to 2.5 mm2RS-485 connection2 x 3 terminals for cables 0.2 mm2 to 2.5 mm2Electromagnetic compatibilityImmunity Complies with EN 50082-2 (heavy industrial)Emissions Complies with EN 50081-1 (light industrial)APPROVALSFor use in ordinary and hazardous area Zone 2 (Gas)Temperature classificationT6Product certificationMore details about product certification, approvals and conditions of safe use are available in the installation manual at/RAYCHEM.©2023 nVent. All nVent marks and logos are owned or licensed by nVent Services GmbH or its affiliates. All other trademarks are the property of their respective owners. nVent reserves the right to change specifications without notice. Our powerful portfolio of brands:North AmericaTel +1.800.545.6258Fax +1.800.527.5703**********************Europe, Middle East, AfricaTel +32.16.213.502Fax +32.16.213.604**********************Asia PacificTel +86.21.2412.1688Fax +86.21.5426.3167*************************Latin AmericaTel +1.713.868.4800Fax +1.713.868.2333**********************ORDERING DETAILS。
FortiMonitor产品介绍及功能说明书

FortiMonitor Product OfferingsOther FortiMonitor SKUs are orderable for the following deployments:Basic Nodes – Basic nodes facilitate simple uptime/reachability monitoring of endpoints, devices, servers, and websites. No advanced performance metrics are included with this instance.ALSO AVAILABLESize Subscription IncludesService Engagement Workflow< 2502 hours Planning/Onboarding Review 4 hours Design and Deployment engagement 2 hours Weekly Incident Review (1 per week) Quarterly incident review for tuning/optimizationA phased approach to success:Phase 1 (Plan ) Includes Defining the team, performing discovery, defining goals, challenges, success criteria and milestones.Phase 2 (Design ) defines Architectural Design, deployment plan(s), training and communication plans.Phase 3 (Deploy ) ensures the completion of all requisite tasks and the actual deployment and implementation. Knowledge transfer is a key component of this phase.Phase 4 (Manage ) builds out full solution: Implements incident and alert management, detailed review and fine tuning of metrics/settings, and importantly, sets out a series of business success meetings.250 - 9994 hours Planning/Onboarding Review 8 hours Design and Deployment engagement 4 hours Weekly Incident Review (1 per week) Quarterly incident review for tuning/optimization1,000 - 4,9994 hours Planning/Onboarding Review (2 sessions) 8 hours Design and Deployment engagement 4 hours Weekly Incident Review (1 per week) Quarterly incident review for tuning/optimization>= 5,00012 hours Planning/Onboarding Review (3 sessions) 20 hours Design and Deployment engagement 8 hours Weekly Incident Review (1 per week) Quarterly incident review for tuning/optimizationONBOARDINGIs a FortiMonitor onboarding service required?Yes, proper onboarding setup is crucial for optimizing the Monitoring & fine tuning of critical assets.What onboarding options are available?Guided onboarding is achieved via FortiCare Best Practices (BPS). Full details outlining the phases & cadence are summarized below.Dedicated professional services for SLA-driven engagements are also available.ORDERING GUIDE | FortiMonitorCopyright © 2021 Fortinet, Inc. All rights reserved. Fortinet ®, FortiGate ®, FortiCare ® and FortiGuard ®, and certain other marks are registered trademarks of Fortinet, Inc., and other Fortinet names herein may also be registered and/or common law trademarks of Fortinet. All other product or company names may be trademarks of their respective owners. Performance and other metrics contained herein were attained in internal lab tests under ideal conditions, and actual performance and other results may vary. Network variables, different network environments and other conditions may affect performance results. Nothing herein represents any binding commitment by Fortinet, and Fortinet disclaims all warranties, whether express or implied, except to the extent Fortinet enters a binding written contract, signed by Fortinet’s General Counsel, with a purchaser that expressly warrants that the identified product will perform according to certain expressly-identified performance metrics and, in such event, only the specific performance metrics expressly identified in such binding written contract shall be binding on Fortinet. For absolute clarity, any such warranty will be limited to performance in the same ideal conditions as in Fortinet’s internal lab tests. Fortinet disclaims in full any covenants, representations, and guarantees pursuant hereto, whether express or implied. Fortinet reserves the right to change, modify, transfer, or otherwise revise this publication without notice, and the most current version of the publication shall be applicable.FMN-OG-R9-20230524。
- 1、下载文档前请自行甄别文档内容的完整性,平台不提供额外的编辑、内容补充、找答案等附加服务。
- 2、"仅部分预览"的文档,不可在线预览部分如存在完整性等问题,可反馈申请退款(可完整预览的文档不适用该条件!)。
- 3、如文档侵犯您的权益,请联系客服反馈,我们会尽快为您处理(人工客服工作时间:9:00-18:30)。
油藏永久性监测能够连续报告生产井当前井下条件的装置已成为一种重要的油气藏管理工具。
最近在装置的部署、光纤和解释方法方面的改进,极大地提高了永置式监测传感器的作用,扩大了相关应用井及应用油田的类型。
John Algeroy John Lovell Gabriel TiradoRamaswamy Meyyappan 美国得克萨斯州Rosharon George Brown Robert Greenaway 英国南安普敦Michael Carney Joerg H. Meyer 得克萨斯州休斯敦John E. Davies BP 勘探公司英国森伯里Ivan D. Pinzon BP 美国公司得克萨斯州休斯敦《油田新技术》2010年春季刊:22卷,第1期。
© 2010斯伦贝谢版权所有。
在编写本文过程中得到以下人员的帮助,谨表谢意:法国Clamart 的Christian Chouzenoux ;得克萨斯州Sugar Land 的David Morrissey ,以及Rosharon 的Eghosa Oriaikhi ,Emmanuel Rioufol ,Scott Rubinstein 和Garrett Skaggs 。
Intellitite ,Neon ,Petrel ,RTAC ,THERMA ,WellNet 和WellWatcher Flux 等是斯伦贝谢公司的商标。
1. 有关可靠性测试更多的信息,请参见:Al-Asimi M ,Butler G ,Brown G ,Hartog A ,Clancy T ,Cosad C ,Fitzgerald J ,Navarro J ,Gabb A ,Ingham J ,Kimminau S ,Smith J 和Stephenson K :“油井和油藏监测技术新进展”,《油田新技术》,14卷,第4期(2002年冬季刊):14-35。
2. 存活分析是统计学的一个分支,用于描述机械系统的故障情况(或生物有机体的死亡情况)。
在工程领域,存活分析通常被称为可靠性理论,涉及到时间-事件模型,用来确定经过一定时间后能够存活的百分数、存活者失败的速率、多种失败原因的解释方法以及可能增加或降低存活机会的特殊环境。
3. Veneruso AF ,Kohli H 和Webster MJ :“Towards Truly Permanent Intelligent Completions :Lifelong System Survivability Through a Structured Reliability Assurance Process ”,SPE 84326,发表在SPE 技术年会暨展览会上,丹佛,2003年10月5-8日。
4. Konopczynski M :“Intelligent Wells :Who ’s Callingthe Shots ?”E & P (2008年9月1日),/Magazine/2008/9/item8226.php (2010年2月9日浏览)。
在20世纪90年代,油气行业的许多工程人员都不愿意使用井下传感器和控制装置。
对于多数生产井20年甚至更长的寿命周期而言,这些装置的可靠性还未得到验证。
这种对长故障周期的要求是合理的:因为作业公司通常都倾向于将永置式监测系统安装在复杂井或偏远地区的井中(如深水井)。
这两方面因素极大地提高了故障部件回收、修理和重新安装的成本。
为了响应业界对这方面的关注,传感器供应商充分借鉴了其他行业的技术,来确保产品可靠性并对传感器的使用寿命作出预测[1]。
研究过程中采用了存活分析技术,通过案例研究回顾过去,以评估设备的可靠性,并利用可靠性模型预测未来发展[2]。
他们还详细研究了每个系统主要构件和部署的失败模式[3]。
从这些以及其他研究中获得的经验教训已提升了智能完井装置的长期可靠性,该装置是永置式监测系统的主要应用形式[4]。
因此,现在再讨论永置式井下传感器时,人们已很少质疑可靠性的问题。
传统作业中,这些传感器被用于沿井筒采集单点数据,通常是在封隔器上方。
一些突然变化,例如井下温度或压力的突变,可能意味着发生水窜或气窜,或者层间隔离被破坏等。
虽然这种方法通常能够满足作业公司的需求,最近在永置式传感器方面的技术创新,尤其是数字传感器和光纤分布式温度传感器(DTS )方面的技术创新,使得工程师可以沿着井筒采集到更多的温度和压力测量数据。
除去硬件解决方案不说,监测系统实现的价值与数据分析方式息息相关。
如今,部分作业公司按照惯例都是将永置式压力与温度传感器作为某类完井装置的一部分,这样他们就无法充分评价由传感器获取的数据,也无法实现所采集信息的全部价值。
他们可能根本不分析这些数据,而只是将其作为补偿井数据保存起来,只有当制定未来钻井计划或当试图了解生产突发问题的原因时,才会拿来参考。
一种更为主动的方式是综合来自多种渠道(包括永置式井下传感器)的生产数据,利用软件程序实时管理连续数据流。
针对装有分布式温度传感器的井,斯伦贝谢公司已开发出THERMA 热模拟与分析软件。
该软件将稳态压力模型与一套热解决方案相结合,可以模拟大部分黑油和组分流体模式,从而有助于DTS 数据的分析。
通过这种方式可以获得连续的实时压力与温度数据,这与井生产过程中同时获取生产测井数据很相似。
对于那些传统修井方法存在问题或者生产误工可能造成巨额成本损失的油气井而言,这种方法尤为具有吸引力。
本文介绍了目前为了将永置式井下传感器测量方法应用于油藏所做的工作,还有软件应用以及为了实现数据价值最大化对数据进行专业解释方面的问题。
来自阿塞拜疆的一个案例说明了利用光纤技术追踪井下生产变化的价值。
另一个来自印度海上的案例证明了新技术在解决上、下部完井装置间的通信和控制问题方面的有效性。
同一实例还分析了在监测井底的同时收集到的信息如何帮助作业公司更好地了解那些细微但却重要的油藏特征。
马来西亚海上二次开发项目的案例说明如何通过将混合式光电系统与其他标准油田工具相结合,来优化未勘探油藏的开发效果。
从井口至井底全程测量当储层层段较少或界定很清楚时,压力和温度点采样是一种很有效的油藏分析工具,同时也是永置式传感器的主要应用范围。
然而,在多个离散点采集的温度和压力测量数据实际上反映的是累积的结果。
这是由于传感器位置处的流体性质是其流经的多种变化环境的综合结果。
因此,对于一个采样点来说,沿井筒传感器间的某个位置的重要变化可能会被掩盖、扭曲或完全没有记录。
近期油气行业内的发展已在很大程度上帮助解决了定点采样的缺陷。
这主要是由于行业普遍接受并采用了光纤技术。
光纤的强度适于经受严格的安装过程并能在复杂的井下环境中工作更长时间,安装在电缆中或控制管线内的光纤提供整个井筒长度范围内的温度测量数据。
过去十几年间,大量光纤传感技术的创新增强了整个行业在地面和井底间的通信能力。
因此,随着时间的推移,人们对永置式传感器的关注已从油井监测转移到油藏描述方面(上图)。
这是一个重要的差别。
利用光纤分布式温度测量系统在流体流入点(而非^ 永置式监测装置的发展历程。
这条时间线显示了自1972年斯伦贝谢公司在刚果海上安装首个永置式井下模拟压力计以来永置式压力计的发展历程。
业界对井下环境中光纤应用的认可、电子连接器方面的技术突破、压力计可靠性的提升以及混合式光纤电缆的出现,都促进了永久性井底(包括两段完井的下部井段)监测技术的发展。
砾石充填在距该点一定距离处)进行测量,就可以解释温度数据,从而提供与深度和时间相关的剖面图。
随后还可对这些解释数据进行分析,获得井的流动剖面[5]。
直到最近,将传感器安装在井底并不总能实现。
例如,许多海上井完井结构都较为复杂,包括砾石充填,且必须分两段进行安装。
下段完井装置包括砾石充填总成,位于生产层,然后是包括封隔器和生产油管的上段完井装置(下图)。
作为流程中第二步的一部分,连接上部和下部完井装置间的电缆及液压管线困难重重。
因此,传统上作业公司都不会选择在下段完井装置的储层层段上部署压力计。
两项关键的技术创新已帮助解决了此类基本连接问题。
第一个是以光纤二阶耦合系统形式存在的DTS 系统。
上部和下部完井装置安装完毕后,可以将DTS 系统安装在通过采油树泵入至井内的电缆或控制管线中。
DTS 系统能够沿着井筒从地面至总深每隔一米测量一次温度。
另一项技术创新是无线通信系统,该系统利用位于上部和下部完井装置间接口设备上的电感耦合器,来提供动力并传输数据。
通过上述方法,就可以沿着下部完井装置布置数字温度和压力传感器。
阿塞拜疆实例目前已经可以在两段完井装置中安装DTS 系统。
首先将一个液压管束牢在下部生产管柱上。
同样将类似的液压管束牢在上部完井装置上,随后通过一个特殊的能够对两条线进行统一定向的控制线插拔系统,将其与下部完井装置相连接。
完井装置安装完毕后,就可通过管道中循环的流体输送光纤,使其遍布在完井装置的整个长度范围内[6]。
也可将DTS 系统嵌入在砾石充填筛管外部的砾石充填护罩内(下一页,右上图)。
这种配置十分重要,因为中心管外部的井筒就像储层岩石一样。
因此,由位于生产层段的DTS 测量的温度是向井流动焦尔-汤姆逊温度,且不会受到沿着井筒向上流动(轴向流体流动)的流体混合物温度的影响。
这就意味着能够比较容易地将个别储层层段的流体同轴向流体区分开。
此外,鉴于DTS 的定位功能,向井流动温度是生产压降和焦尔-汤姆逊系数(其数值由流体性质所决定)的直接函数。
利用专门为采用DTS 系统而建立的井及近井区域的热模型,可将生成的温度剖面转换成流量剖面(下一页,右下图)。
近井流量是油藏压力和井筒流动压力、地层渗透率、油藏规模以及流体性质的函数。
地表流量是完井装置、进口和出口压力、重力效应以及流体性质的函数。
因此,通过节点有限元压力分析法,可揭示整个系统的压力情况,以确定流速、油藏压力或地面流压[7]。
一旦确定整个系统的压力后,就可利用径向近井热模型计算每个油藏层段内的远端地热温度与流体、地层和完井热特性间的变化关系。
其中必定会包括由近井压降而引发的温度变化,该温^ 两段完井装置。
两段完井包括将下部完井装置布置在目标层段上。
采用一个带有开口向上的抛光孔座(PBR )的封隔器将下部井段与上部井段隔离开来。
如需防砂处理,则可将一个带有抛光孔的作业管柱插入封隔器,并使其将砂循环至滤网。
在安装上部井段完井装置之前,移走作业管柱。
这个两段完井作业过程包括安装生产油管,其最下面的接头是一个抛光孔。
将生产油管插入封隔器的抛光孔插座内,使井与地面相连。
分流管筛管中心管筛管护罩砾石充填井壁轴向流温度焦尔-汤姆逊向井流动温度DTS电缆页岩储层页岩页岩井筒储层中心管砾石充填护罩度变化为渗透率和表皮因子的函数,在焦尔-汤姆逊效应作用下产生的这一近井压降会致使油升温以及气体或气态油冷却[8]。