U_Spec_EPCOS_Elko_3pin
NuMicro N9H30系列开发板用户手册说明书

NuMicro®FamilyArm® ARM926EJ-S BasedNuMaker-HMI-N9H30User ManualEvaluation Board for NuMicro® N9H30 SeriesNUMAKER-HMI-N9H30 USER MANUALThe information described in this document is the exclusive intellectual property ofNuvoton Technology Corporation and shall not be reproduced without permission from Nuvoton.Nuvoton is providing this document only for reference purposes of NuMicro microcontroller andmicroprocessor based system design. Nuvoton assumes no responsibility for errors or omissions.All data and specifications are subject to change without notice.For additional information or questions, please contact: Nuvoton Technology Corporation.Table of Contents1OVERVIEW (5)1.1Features (7)1.1.1NuMaker-N9H30 Main Board Features (7)1.1.2NuDesign-TFT-LCD7 Extension Board Features (7)1.2Supporting Resources (8)2NUMAKER-HMI-N9H30 HARDWARE CONFIGURATION (9)2.1NuMaker-N9H30 Board - Front View (9)2.2NuMaker-N9H30 Board - Rear View (14)2.3NuDesign-TFT-LCD7 - Front View (20)2.4NuDesign-TFT-LCD7 - Rear View (21)2.5NuMaker-N9H30 and NuDesign-TFT-LCD7 PCB Placement (22)3NUMAKER-N9H30 AND NUDESIGN-TFT-LCD7 SCHEMATICS (24)3.1NuMaker-N9H30 - GPIO List Circuit (24)3.2NuMaker-N9H30 - System Block Circuit (25)3.3NuMaker-N9H30 - Power Circuit (26)3.4NuMaker-N9H30 - N9H30F61IEC Circuit (27)3.5NuMaker-N9H30 - Setting, ICE, RS-232_0, Key Circuit (28)NUMAKER-HMI-N9H30 USER MANUAL3.6NuMaker-N9H30 - Memory Circuit (29)3.7NuMaker-N9H30 - I2S, I2C_0, RS-485_6 Circuit (30)3.8NuMaker-N9H30 - RS-232_2 Circuit (31)3.9NuMaker-N9H30 - LCD Circuit (32)3.10NuMaker-N9H30 - CMOS Sensor, I2C_1, CAN_0 Circuit (33)3.11NuMaker-N9H30 - RMII_0_PF Circuit (34)3.12NuMaker-N9H30 - RMII_1_PE Circuit (35)3.13NuMaker-N9H30 - USB Circuit (36)3.14NuDesign-TFT-LCD7 - TFT-LCD7 Circuit (37)4REVISION HISTORY (38)List of FiguresFigure 1-1 Front View of NuMaker-HMI-N9H30 Evaluation Board (5)Figure 1-2 Rear View of NuMaker-HMI-N9H30 Evaluation Board (6)Figure 2-1 Front View of NuMaker-N9H30 Board (9)Figure 2-2 Rear View of NuMaker-N9H30 Board (14)Figure 2-3 Front View of NuDesign-TFT-LCD7 Board (20)Figure 2-4 Rear View of NuDesign-TFT-LCD7 Board (21)Figure 2-5 Front View of NuMaker-N9H30 PCB Placement (22)Figure 2-6 Rear View of NuMaker-N9H30 PCB Placement (22)Figure 2-7 Front View of NuDesign-TFT-LCD7 PCB Placement (23)Figure 2-8 Rear View of NuDesign-TFT-LCD7 PCB Placement (23)Figure 3-1 GPIO List Circuit (24)Figure 3-2 System Block Circuit (25)Figure 3-3 Power Circuit (26)Figure 3-4 N9H30F61IEC Circuit (27)Figure 3-5 Setting, ICE, RS-232_0, Key Circuit (28)Figure 3-6 Memory Circuit (29)Figure 3-7 I2S, I2C_0, RS-486_6 Circuit (30)Figure 3-8 RS-232_2 Circuit (31)Figure 3-9 LCD Circuit (32)NUMAKER-HMI-N9H30 USER MANUAL Figure 3-10 CMOS Sensor, I2C_1, CAN_0 Circuit (33)Figure 3-11 RMII_0_PF Circuit (34)Figure 3-12 RMII_1_PE Circuit (35)Figure 3-13 USB Circuit (36)Figure 3-14 TFT-LCD7 Circuit (37)List of TablesTable 2-1 LCD Panel Combination Connector (CON8) Pin Function (11)Table 2-2 Three Sets of Indication LED Functions (12)Table 2-3 Six Sets of User SW, Key Matrix Functions (12)Table 2-4 CMOS Sensor Connector (CON10) Function (13)Table 2-5 JTAG ICE Interface (J2) Function (14)Table 2-6 Expand Port (CON7) Function (16)Table 2-7 UART0 (J3) Function (16)Table 2-8 UART2 (J6) Function (16)Table 2-9 RS-485_6 (SW6~8) Function (17)Table 2-10 Power on Setting (SW4) Function (17)Table 2-11 Power on Setting (S2) Function (17)Table 2-12 Power on Setting (S3) Function (17)Table 2-13 Power on Setting (S4) Function (17)Table 2-14 Power on Setting (S5) Function (17)Table 2-15 Power on Setting (S7/S6) Function (18)Table 2-16 Power on Setting (S9/S8) Function (18)Table 2-17 CMOS Sensor Connector (CON9) Function (19)Table 2-18 CAN_0 (SW9~10) Function (19)NUMAKER-HMI-N9H30 USER MANUAL1 OVERVIEWThe NuMaker-HMI-N9H30 is an evaluation board for GUI application development. The NuMaker-HMI-N9H30 consists of two parts: a NuMaker-N9H30 main board and a NuDesign-TFT-LCD7 extensionboard. The NuMaker-HMI-N9H30 is designed for project evaluation, prototype development andvalidation with HMI (Human Machine Interface) function.The NuMaker-HMI-N9H30 integrates touchscreen display, voice input/output, rich serial port serviceand I/O interface, providing multiple external storage methods.The NuDesign-TFT-LCD7 can be plugged into the main board via the DIN_32x2 extension connector.The NuDesign-TFT-LCD7 includes one 7” LCD which the resolution is 800x480 with RGB-24bits andembedded the 4-wires resistive type touch panel.Figure 1-1 Front View of NuMaker-HMI-N9H30 Evaluation BoardNUMAKER-HMI-N9H30 USER MANUAL Figure 1-2 Rear View of NuMaker-HMI-N9H30 Evaluation Board1.1 Features1.1.1 NuMaker-N9H30 Main Board Features●N9H30F61IEC chip: LQFP216 pin MCP package with DDR (64 MB)●SPI Flash using W25Q256JVEQ (32 MB) booting with quad mode or storage memory●NAND Flash using W29N01HVSINA (128 MB) booting or storage memory●One Micro-SD/TF card slot served either as a SD memory card for data storage or SDIO(Wi-Fi) device●Two sets of COM ports:–One DB9 RS-232 port with UART_0 used 75C3232E transceiver chip can be servedfor function debug and system development.–One DB9 RS-232 port with UART_2 used 75C3232E transceiver chip for userapplication●22 GPIO expansion ports, including seven sets of UART functions●JTAG interface provided for software development●Microphone input and Earphone/Speaker output with 24-bit stereo audio codec(NAU88C22) for I2S interfaces●Six sets of user-configurable push button keys●Three sets of LEDs for status indication●Provides SN65HVD230 transceiver chip for CAN bus communication●Provides MAX3485 transceiver chip for RS-485 device connection●One buzzer device for program applicationNUMAKER-HMI-N9H30 USER MANUAL●Two sets of RJ45 ports with Ethernet 10/100 Mbps MAC used IP101GR PHY chip●USB_0 that can be used as Device/HOST and USB_1 that can be used as HOSTsupports pen drives, keyboards, mouse and printers●Provides over-voltage and over current protection used APL3211A chip●Retain RTC battery socket for CR2032 type and ADC0 detect battery voltage●System power could be supplied by DC-5V adaptor or USB VBUS1.1.2 NuDesign-TFT-LCD7 Extension Board Features●7” resolution 800x480 4-wire resistive touch panel for 24-bits RGB888 interface●DIN_32x2 extension connector1.2 Supporting ResourcesFor sample codes and introduction about NuMaker-N9H30, please refer to N9H30 BSP:https:///products/gui-solution/gui-platform/numaker-hmi-n9h30/?group=Software&tab=2Visit NuForum for further discussion about the NuMaker-HMI-N9H30:/viewforum.php?f=31 NUMAKER-HMI-N9H30 USER MANUALNUMAKER-HMI-N9H30 USER MANUAL2 NUMAKER-HMI-N9H30 HARDWARE CONFIGURATION2.1 NuMaker-N9H30 Board - Front View Combination Connector (CON8)6 set User SWs (K1~6)3set Indication LEDs (LED1~3)Power Supply Switch (SW_POWER1)Audio Codec(U10)Microphone(M1)NAND Flash(U9)RS-232 Transceiver(U6, U12)RS-485 Transceiver(U11)CAN Transceiver (U13)Figure 2-1 Front View of NuMaker-N9H30 BoardFigure 2-1 shows the main components and connectors from the front side of NuMaker-N9H30 board. The following lists components and connectors from the front view:NuMaker-N9H30 board and NuDesign-TFT-LCD7 board combination connector (CON8). This panel connector supports 4-/5-wire resistive touch or capacitance touch panel for 24-bits RGB888 interface.Connector GPIO pin of N9H30 FunctionCON8.1 - Power 3.3VCON8.2 - Power 3.3VCON8.3 GPD7 LCD_CSCON8.4 GPH3 LCD_BLENCON8.5 GPG9 LCD_DENCON8.7 GPG7 LCD_HSYNCCON8.8 GPG6 LCD_CLKCON8.9 GPD15 LCD_D23(R7)CON8.10 GPD14 LCD_D22(R6)CON8.11 GPD13 LCD_D21(R5)CON8.12 GPD12 LCD_D20(R4)CON8.13 GPD11 LCD_D19(R3)CON8.14 GPD10 LCD_D18(R2)CON8.15 GPD9 LCD_D17(R1)CON8.16 GPD8 LCD_D16(R0)CON8.17 GPA15 LCD_D15(G7)CON8.18 GPA14 LCD_D14(G6)CON8.19 GPA13 LCD_D13(G5)CON8.20 GPA12 LCD_D12(G4)CON8.21 GPA11 LCD_D11(G3)CON8.22 GPA10 LCD_D10(G2)CON8.23 GPA9 LCD_D9(G1) NUMAKER-HMI-N9H30 USER MANUALCON8.24 GPA8 LCD_D8(G0)CON8.25 GPA7 LCD_D7(B7)CON8.26 GPA6 LCD_D6(B6)CON8.27 GPA5 LCD_D5(B5)CON8.28 GPA4 LCD_D4(B4)CON8.29 GPA3 LCD_D3(B3)CON8.30 GPA2 LCD_D2(B2)CON8.31 GPA1 LCD_D1(B1)CON8.32 GPA0 LCD_D0(B0)CON8.33 - -CON8.34 - -CON8.35 - -CON8.36 - -CON8.37 GPB2 LCD_PWMCON8.39 - VSSCON8.40 - VSSCON8.41 ADC7 XPCON8.42 ADC3 VsenCON8.43 ADC6 XMCON8.44 ADC4 YMCON8.45 - -CON8.46 ADC5 YPCON8.47 - VSSCON8.48 - VSSCON8.49 GPG0 I2C0_CCON8.50 GPG1 I2C0_DCON8.51 GPG5 TOUCH_INTCON8.52 - -CON8.53 - -CON8.54 - -CON8.55 - -NUMAKER-HMI-N9H30 USER MANUAL CON8.56 - -CON8.57 - -CON8.58 - -CON8.59 - VSSCON8.60 - VSSCON8.61 - -CON8.62 - -CON8.63 - Power 5VCON8.64 - Power 5VTable 2-1 LCD Panel Combination Connector (CON8) Pin Function●Power supply switch (SW_POWER1): System will be powered on if the SW_POWER1button is pressed●Three sets of indication LEDs:LED Color DescriptionsLED1 Red The system power will beterminated and LED1 lightingwhen the input voltage exceeds5.7V or the current exceeds 2A.LED2 Green Power normal state.LED3 Green Controlled by GPH2 pin Table 2-2 Three Sets of Indication LED Functions●Six sets of user SW, Key Matrix for user definitionKey GPIO pin of N9H30 FunctionK1 GPF10 Row0 GPB4 Col0K2 GPF10 Row0 GPB5 Col1K3 GPE15 Row1 GPB4 Col0K4 GPE15 Row1 GPB5 Col1K5 GPE14 Row2 GPB4 Col0K6GPE14 Row2GPB5 Col1 Table 2-3 Six Sets of User SW, Key Matrix Functions●NAND Flash (128 MB) with Winbond W29N01HVS1NA (U9)●Microphone (M1): Through Nuvoton NAU88C22 chip sound input●Audio CODEC chip (U10): Nuvoton NAU88C22 chip connected to N9H30 using I2Sinterface–SW6/SW7/SW8: 1-2 short for RS-485_6 function and connected to 2P terminal (CON5and J5)–SW6/SW7/SW8: 2-3 short for I2S function and connected to NAU88C22 (U10).●CMOS Sensor connector (CON10, SW9~10)–SW9~10: 1-2 short for CAN_0 function and connected to 2P terminal (CON11)–SW9~10: 2-3 short for CMOS sensor function and connected to CMOS sensorconnector (CON10)Connector GPIO pin of N9H30 FunctionCON10.1 - VSSCON10.2 - VSSNUMAKER-HMI-N9H30 USER MANUALCON10.3 - Power 3.3VCON10.4 - Power 3.3VCON10.5 - -CON10.6 - -CON10.7 GPI4 S_PCLKCON10.8 GPI3 S_CLKCON10.9 GPI8 S_D0CON10.10 GPI9 S_D1CON10.11 GPI10 S_D2CON10.12 GPI11 S_D3CON10.13 GPI12 S_D4CON10.14 GPI13 S_D5CON10.15 GPI14 S_D6CON10.16 GPI15 S_D7CON10.17 GPI6 S_VSYNCCON10.18 GPI5 S_HSYNCCON10.19 GPI0 S_PWDNNUMAKER-HMI-N9H30 USER MANUAL CON10.20 GPI7 S_nRSTCON10.21 GPG2 I2C1_CCON10.22 GPG3 I2C1_DCON10.23 - VSSCON10.24 - VSSTable 2-4 CMOS Sensor Connector (CON10) FunctionNUMAKER-HMI-N9H30 USER MANUAL2.2NuMaker-N9H30 Board - Rear View5V In (CON1)RS-232 DB9 (CON2,CON6)Expand Port (CON7)Speaker Output (J4)Earphone Output (CON4)Buzzer (BZ1)System ResetSW (SW5)SPI Flash (U7,U8)JTAG ICE (J2)Power ProtectionIC (U1)N9H30F61IEC (U5)Micro SD Slot (CON3)RJ45 (CON12, CON13)USB1 HOST (CON15)USB0 Device/Host (CON14)CAN_0 Terminal (CON11)CMOS Sensor Connector (CON9)Power On Setting(SW4, S2~S9)RS-485_6 Terminal (CON5)RTC Battery(BT1)RMII PHY (U14,U16)Figure 2-2 Rear View of NuMaker-N9H30 BoardFigure 2-2 shows the main components and connectors from the rear side of NuMaker-N9H30 board. The following lists components and connectors from the rear view:● +5V In (CON1): Power adaptor 5V input ●JTAG ICE interface (J2) ConnectorGPIO pin of N9H30Function J2.1 - Power 3.3V J2.2 GPJ4 nTRST J2.3 GPJ2 TDI J2.4 GPJ1 TMS J2.5 GPJ0 TCK J2.6 - VSS J2.7 GPJ3 TD0 J2.8-RESETTable 2-5 JTAG ICE Interface (J2) Function●SPI Flash (32 MB) with Winbond W25Q256JVEQ (U7); only one (U7 or U8) SPI Flashcan be used●System Reset (SW5): System will be reset if the SW5 button is pressed●Buzzer (BZ1): Control by GPB3 pin of N9H30●Speaker output (J4): Through the NAU88C22 chip sound output●Earphone output (CON4): Through the NAU88C22 chip sound output●Expand port for user use (CON7):Connector GPIO pin of N9H30 FunctionCON7.1 - Power 3.3VCON7.2 - Power 3.3VCON7.3 GPE12 UART3_TXDCON7.4 GPH4 UART1_TXDCON7.5 GPE13 UART3_RXDCON7.6 GPH5 UART1_RXDCON7.7 GPB0 UART5_TXDCON7.8 GPH6 UART1_RTSCON7.9 GPB1 UART5_RXDCON7.10 GPH7 UART1_CTSCON7.11 GPI1 UART7_TXDNUMAKER-HMI-N9H30 USER MANUAL CON7.12 GPH8 UART4_TXDCON7.13 GPI2 UART7_RXDCON7.14 GPH9 UART4_RXDCON7.15 - -CON7.16 GPH10 UART4_RTSCON7.17 - -CON7.18 GPH11 UART4_CTSCON7.19 - VSSCON7.20 - VSSCON7.21 GPB12 UART10_TXDCON7.22 GPH12 UART8_TXDCON7.23 GPB13 UART10_RXDCON7.24 GPH13 UART8_RXDCON7.25 GPB14 UART10_RTSCON7.26 GPH14 UART8_RTSCON7.27 GPB15 UART10_CTSCON7.28 GPH15 UART8_CTSCON7.29 - Power 5VCON7.30 - Power 5VTable 2-6 Expand Port (CON7) Function●UART0 selection (CON2, J3):–RS-232_0 function and connected to DB9 female (CON2) for debug message output.–GPE0/GPE1 connected to 2P terminal (J3).Connector GPIO pin of N9H30 Function J3.1 GPE1 UART0_RXDJ3.2 GPE0 UART0_TXDTable 2-7 UART0 (J3) Function●UART2 selection (CON6, J6):–RS-232_2 function and connected to DB9 female (CON6) for debug message output –GPF11~14 connected to 4P terminal (J6)Connector GPIO pin of N9H30 Function J6.1 GPF11 UART2_TXDJ6.2 GPF12 UART2_RXDJ6.3 GPF13 UART2_RTSJ6.4 GPF14 UART2_CTSTable 2-8 UART2 (J6) Function●RS-485_6 selection (CON5, J5, SW6~8):–SW6~8: 1-2 short for RS-485_6 function and connected to 2P terminal (CON5 and J5) –SW6~8: 2-3 short for I2S function and connected to NAU88C22 (U10)Connector GPIO pin of N9H30 FunctionSW6:1-2 shortGPG11 RS-485_6_DISW6:2-3 short I2S_DOSW7:1-2 shortGPG12 RS-485_6_ROSW7:2-3 short I2S_DISW8:1-2 shortGPG13 RS-485_6_ENBSW8:2-3 short I2S_BCLKNUMAKER-HMI-N9H30 USER MANUALTable 2-9 RS-485_6 (SW6~8) FunctionPower on setting (SW4, S2~9).SW State FunctionSW4.2/SW4.1 ON/ON Boot from USB SW4.2/SW4.1 ON/OFF Boot from eMMC SW4.2/SW4.1 OFF/ON Boot from NAND Flash SW4.2/SW4.1 OFF/OFF Boot from SPI Flash Table 2-10 Power on Setting (SW4) FunctionSW State FunctionS2 Short System clock from 12MHzcrystalS2 Open System clock from UPLL output Table 2-11 Power on Setting (S2) FunctionSW State FunctionS3 Short Watchdog Timer OFFS3 Open Watchdog Timer ON Table 2-12 Power on Setting (S3) FunctionSW State FunctionS4 Short GPJ[4:0] used as GPIO pinS4Open GPJ[4:0] used as JTAG ICEinterfaceTable 2-13 Power on Setting (S4) FunctionSW State FunctionS5 Short UART0 debug message ONS5 Open UART0 debug message OFFTable 2-14 Power on Setting (S5) FunctionSW State FunctionS7/S6 Short/Short NAND Flash page size 2KBS7/S6 Short/Open NAND Flash page size 4KBS7/S6 Open/Short NAND Flash page size 8KBNUMAKER-HMI-N9H30 USER MANUALS7/S6 Open/Open IgnoreTable 2-15 Power on Setting (S7/S6) FunctionSW State FunctionS9/S8 Short/Short NAND Flash ECC type BCH T12S9/S8 Short/Open NAND Flash ECC type BCH T15S9/S8 Open/Short NAND Flash ECC type BCH T24S9/S8 Open/Open IgnoreTable 2-16 Power on Setting (S9/S8) FunctionCMOS Sensor connector (CON9, SW9~10)–SW9~10: 1-2 short for CAN_0 function and connected to 2P terminal (CON11).–SW9~10: 2-3 short for CMOS sensor function and connected to CMOS sensorconnector (CON9).Connector GPIO pin of N9H30 FunctionCON9.1 - VSSCON9.2 - VSSCON9.3 - Power 3.3VCON9.4 - Power 3.3V NUMAKER-HMI-N9H30 USER MANUALCON9.5 - -CON9.6 - -CON9.7 GPI4 S_PCLKCON9.8 GPI3 S_CLKCON9.9 GPI8 S_D0CON9.10 GPI9 S_D1CON9.11 GPI10 S_D2CON9.12 GPI11 S_D3CON9.13 GPI12 S_D4CON9.14 GPI13 S_D5CON9.15 GPI14 S_D6CON9.16 GPI15 S_D7CON9.17 GPI6 S_VSYNCCON9.18 GPI5 S_HSYNCCON9.19 GPI0 S_PWDNCON9.20 GPI7 S_nRSTCON9.21 GPG2 I2C1_CCON9.22 GPG3 I2C1_DCON9.23 - VSSCON9.24 - VSSTable 2-17 CMOS Sensor Connector (CON9) Function●CAN_0 Selection (CON11, SW9~10):–SW9~10: 1-2 short for CAN_0 function and connected to 2P terminal (CON11) –SW9~10: 2-3 short for CMOS sensor function and connected to CMOS sensor connector (CON9, CON10)SW GPIO pin of N9H30 FunctionSW9:1-2 shortGPI3 CAN_0_RXDSW9:2-3 short S_CLKSW10:1-2 shortGPI4 CAN_0_TXDSW10:2-3 short S_PCLKTable 2-18 CAN_0 (SW9~10) Function●USB0 Device/HOST Micro-AB connector (CON14), where CON14 pin4 ID=1 is Device,ID=0 is HOST●USB1 for USB HOST with Type-A connector (CON15)●RJ45_0 connector with LED indicator (CON12), RMII PHY with IP101GR (U14)●RJ45_1 connector with LED indicator (CON13), RMII PHY with IP101GR (U16)●Micro-SD/TF card slot (CON3)●SOC CPU: Nuvoton N9H30F61IEC (U5)●Battery power for RTC 3.3V powered (BT1, J1), can detect voltage by ADC0●RTC power has 3 sources:–Share with 3.3V I/O power–Battery socket for CR2032 (BT1)–External connector (J1)●Board version 2.1NUMAKER-HMI-N9H30 USER MANUAL2.3 NuDesign-TFT-LCD7 -Front ViewFigure 2-3 Front View of NuDesign-TFT-LCD7 BoardFigure 2-3 shows the main components and connectors from the Front side of NuDesign-TFT-LCD7board.7” resolution 800x480 4-W resistive touch panel for 24-bits RGB888 interface2.4 NuDesign-TFT-LCD7 -Rear ViewFigure 2-4 Rear View of NuDesign-TFT-LCD7 BoardFigure 2-4 shows the main components and connectors from the rear side of NuDesign-TFT-LCD7board.NuMaker-N9H30 and NuDesign-TFT-LCD7 combination connector (CON1).NUMAKER-HMI-N9H30 USER MANUAL 2.5 NuMaker-N9H30 and NuDesign-TFT-LCD7 PCB PlacementFigure 2-5 Front View of NuMaker-N9H30 PCB PlacementFigure 2-6 Rear View of NuMaker-N9H30 PCB PlacementNUMAKER-HMI-N9H30 USER MANUALFigure 2-7 Front View of NuDesign-TFT-LCD7 PCB PlacementFigure 2-8 Rear View of NuDesign-TFT-LCD7 PCB Placement3 NUMAKER-N9H30 AND NUDESIGN-TFT-LCD7 SCHEMATICS3.1 NuMaker-N9H30 - GPIO List CircuitFigure 3-1 shows the N9H30F61IEC GPIO list circuit.Figure 3-1 GPIO List Circuit NUMAKER-HMI-N9H30 USER MANUAL3.2 NuMaker-N9H30 - System Block CircuitFigure 3-2 shows the System Block Circuit.NUMAKER-HMI-N9H30 USER MANUALFigure 3-2 System Block Circuit3.3 NuMaker-N9H30 - Power CircuitFigure 3-3 shows the Power Circuit.NUMAKER-HMI-N9H30 USER MANUALFigure 3-3 Power Circuit3.4 NuMaker-N9H30 - N9H30F61IEC CircuitFigure 3-4 shows the N9H30F61IEC Circuit.Figure 3-4 N9H30F61IEC CircuitNUMAKER-HMI-N9H30 USER MANUAL3.5 NuMaker-N9H30 - Setting, ICE, RS-232_0, Key CircuitFigure 3-5 shows the Setting, ICE, RS-232_0, Key Circuit.NUMAKER-HMI-N9H30 USER MANUALFigure 3-5 Setting, ICE, RS-232_0, Key Circuit3.6 NuMaker-N9H30 - Memory CircuitFigure 3-6 shows the Memory Circuit.NUMAKER-HMI-N9H30 USER MANUALFigure 3-6 Memory Circuit3.7 NuMaker-N9H30 - I2S, I2C_0, RS-485_6 CircuitFigure 3-7 shows the I2S, I2C_0, RS-486_6 Circuit.NUMAKER-HMI-N9H30 USER MANUALFigure 3-7 I2S, I2C_0, RS-486_6 Circuit3.8 NuMaker-N9H30 - RS-232_2 CircuitFigure 3-8 shows the RS-232_2 Circuit.NUMAKER-HMI-N9H30 USER MANUALFigure 3-8 RS-232_2 Circuit3.9 NuMaker-N9H30 - LCD CircuitFigure 3-9 shows the LCD Circuit.NUMAKER-HMI-N9H30 USER MANUALFigure 3-9 LCD Circuit3.10 NuMaker-N9H30 - CMOS Sensor, I2C_1, CAN_0 CircuitFigure 3-10 shows the CMOS Sensor,I2C_1, CAN_0 Circuit.NUMAKER-HMI-N9H30 USER MANUALFigure 3-10 CMOS Sensor, I2C_1, CAN_0 Circuit3.11 NuMaker-N9H30 - RMII_0_PF CircuitFigure 3-11 shows the RMII_0_RF Circuit.NUMAKER-HMI-N9H30 USER MANUALFigure 3-11 RMII_0_PF Circuit3.12 NuMaker-N9H30 - RMII_1_PE CircuitFigure 3-12 shows the RMII_1_PE Circuit.NUMAKER-HMI-N9H30 USER MANUALFigure 3-12 RMII_1_PE Circuit3.13 NuMaker-N9H30 - USB CircuitFigure 3-13 shows the USB Circuit.NUMAKER-HMI-N9H30 USER MANUALFigure 3-13 USB Circuit3.14 NuDesign-TFT-LCD7 - TFT-LCD7 CircuitFigure 3-14 shows the TFT-LCD7 Circuit.Figure 3-14 TFT-LCD7 CircuitNUMAKER-HMI-N9H30 USER MANUAL4 REVISION HISTORYDate Revision Description2022.03.24 1.00 Initial version NUMAKER-HMI-N9H30 USER MANUALNUMAKER-HMI-N9H30 USER MANUALImportant NoticeNuvoton Products are neither intended nor warranted for usage in systems or equipment, anymalfunction or failure of which may cause loss of human life, bodily injury or severe propertydamage. Such applications are deemed, “Insecure Usage”.Insecure usage includes, but is not limited to: equipment for surgical implementation, atomicenergy control instruments, airplane or spaceship instruments, the control or operation ofdynamic, brake or safety systems designed for vehicular use, traffic signal instruments, all typesof safety devices, and other applications intended to support or sustain life.All Insecure Usage shall be made at customer’s risk, and in the event that third parties lay claimsto Nuvoton as a result of customer’s Insecure Usage, custome r shall indemnify the damagesand liabilities thus incurred by Nuvoton.。
FPGA可编程逻辑器件芯片EP4CE40F23I7N中文规格书
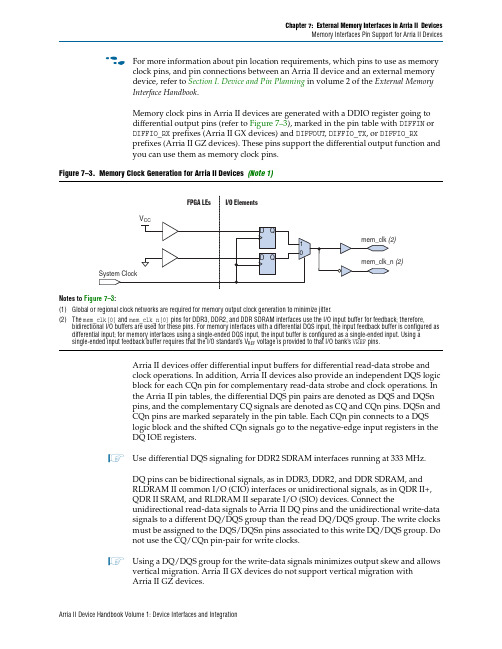
Chapter 7:External Memory Interfaces in Arria II DevicesMemory Interfaces Pin Support for Arria II Devicesf For more information about pin location requirements, which pins to use as memoryclock pins, and pin connections between an Arria II device and an external memorydevice, refer to Section I. Device and Pin Planning in volume 2 of the External MemoryInterface Handbook.Memory clock pins in Arria II devices are generated with a DDIO register going todifferential output pins (refer to Figure7–3), marked in the pin table with DIFFIN orDIFFIO_RX prefixes (Arria II GX devices) and DIFFOUT, DIFFIO_TX, or DIFFIO_RXprefixes (Arria II GZ devices). These pins support the differential output function andyou can use them as memory clock pins.Figure7–3.Memory Clock Generation for Arria II Devices(Note1)Notes to Figure7–3:(1)Global or regional clock networks are required for memory output clock generation to minimize jitter.(2)The mem_clk[0] and mem_clk_n[0] pins for DDR3, DDR2, and DDR SDRAM interfaces use the I/O input buffer for feedback; therefore,bidirectional I/O buffers are used for these pins. For memory interfaces with a differential DQS input, the input feedback buffer is configured as differential input; for memory interfaces using a single-ended DQS input, the input buffer is configured as a single-ended input. Using a single-ended input feedback buffer requires that the I/O standard’s V REF voltage is provided to that I/O bank’s VREF pins.Arria II devices offer differential input buffers for differential read-data strobe andclock operations. In addition, Arria II devices also provide an independent DQS logicblock for each CQn pin for complementary read-data strobe and clock operations. Inthe Arria II pin tables, the differential DQS pin pairs are denoted as DQS and DQSnpins, and the complementary CQ signals are denoted as CQ and CQn pins. DQSn andCQn pins are marked separately in the pin table. Each CQn pin connects to a DQSlogic block and the shifted CQn signals go to the negative-edge input registers in theDQ IOE registers.1Use differential DQS signaling for DDR2 SDRAM interfaces running at 333MHz.DQ pins can be bidirectional signals, as in DDR3, DDR2, and DDR SDRAM, andRLDRAM II common I/O (CIO) interfaces or unidirectional signals, as in QDR II+,QDR II SRAM, and RLDRAM II separate I/O (SIO) devices. Connect theunidirectional read-data signals to Arria II DQ pins and the unidirectional write-datasignals to a different DQ/DQS group than the read DQ/DQS group. The write clocksmust be assigned to the DQS/DQSn pins associated to this write DQ/DQS group. Donot use the CQ/CQn pin-pair for write clocks.1Using a DQ/DQS group for the write-data signals minimizes output skew and allows vertical migration. Arria II GX devices do not support vertical migration withArria II GZ devices.Arria II Device Handbook Volume 1: Device Interfaces and IntegrationChapter 6:I/O Features in Arria II DevicesTermination Schemes for I/O Standardsmini-LVDSArria II GX devices support true mini-LVDS with a three-resistor network using twosingle-ended output buffers for external three-resistor networks.For Arria II GZ devices, use two single-ended output buffers with external one- orthree-resistor networks (mini-LVDS_E_1R or mini-LVDS_E_3R). Arria II GZ row I/Obanks support mini-LVDS output using true LVDS output buffers without an externalresistor network.Figure6–18 shows the one-resistor and three-resistor topology for RSDS andmini-LVDS I/O standard termination.Figure6–18.RSDS and mini-LVDS I/O Standard Termination for Arria II Devices(Note1)Notes to Figure6–18:(1)R p = 170 Ω and R s= 120 Ω(2)mini-LVDS_E_1R is applicable for Arria II GZ devices only.A resistor network is required to attenuate the LVDS output-voltage swing to meetRSDS and mini-LVDS specifications. You can modify the three-resistor networkvalues to reduce power or improve the noise margin. The resistor values chosenshould satisfy the equation shown in Equation6–1.Equation6–1.Resistor Network1To validate that custom resistor values meet the RSDS requirements, Alterarecommends performing additional simulations with IBIS models.f For more information about the RSDS I/O standard, refer to the RSDS Specificationfrom the National Semiconductor website at .f For more information about the mini-LVDS I/O standard, see the mini-LVDSSpecification from the Texas Instruments website at .Arria II Device Handbook Volume 1: Device Interfaces and IntegrationChapter 6:I/O Features in Arria II DevicesArria II OCT CalibrationArria II OCT CalibrationArria II GX devices support calibrated R S OCT and Arria II GZ devices supportcalibrated R S and R T OCT on all I/O pins. You can calibrate the I/O banks with any ofthe OCT calibration blocks available in the device provided the V CCIO of the I/O bankwith the pins using calibrated OCT matches the V CCIO of the I/O bank with thecalibration block and its associated RUP and RDN pins.f For more information about the location of the OCT calibration blocks in Arria IIdevices, refer to the Arria II Device Family Connection Guidelines and Arria II DevicePin-Outs.OCT Calibration BlockAn OCT calibration block has the same V CCIO as the I/O bank that contains the block.R S OCT calibration is supported on all user I/O banks with different V CCIO voltagestandards, up to the number of available OCT calibration blocks. You can configureI/O banks to receive calibrated codes from any OCT calibration block with the sameV CCIO. All I/O banks with the same V CCIO can share one OCT calibration block, even ifthat particular I/O bank has an OCT calibration block.For example, Figure6–10 shows a group of I/O banks that has the same V CCIOvoltage. If a group of I/O banks has the same V CCIO voltage, you can use one OCTcalibration block to calibrate the group of I/O banks placed around the periphery.Because banks 3B, 4C, 6C, and 7B have the same V CCIO as bank 7A, you can calibrateall four I/O banks (3B, 4C, 6C, and 7B) with the OCT calibration block (CB7) locatedin bank 7A. You can enable this by serially shifting out R S OCT calibration codes fromthe OCT calibration block located in bank 7A to the I/O banks located around theperiphery.1I/O banks that do not contain calibration blocks share calibration blocks with I/O banks that do contain calibration blocks.Arria II Device Handbook Volume 1: Device Interfaces and Integration。
通信考试试题及参考答案全套

1. 集团客户类别(以下简称客户级别)是政企客户部站在市场的角度,根据集团客户价值细分综合参照“绝对标准”和“相对标准”来划分的,具体分(D )类。
A、A 类B、A 类B 类C、A 类B 类C 类D、A 类B 类C 类D 类2. 技术线条针对业务的网络服务分级由高至低分为(C )四个级别。
A、A 级B 级C 级D 级B、高级中级标准普通级C、AAA 级AA 级A 级普通级D、普通级A 级AA 级AAA 级3. 售后服务分级要求AAA 级服务,每(D )上门拜访一次。
A、一个月B、二个月C、三个月D、半年4. 售后服务分级要求AA 级服务,每(D )上门拜访一次。
A、二个月B、三个月C、半年D、一年5. 网络质量指标互联网专线与APN 专线,从客户端PING 至少1000 个IP 包,丢失的IP 包与所有IP 包的比值,多少为标准?(A )A、5% B、6% C、8% D、10%6. 网络质量指标互联网专线与APN 专线,IP 包平均传输时延,从客户端PING 至少(B )个IP 包,所有IP 包传送时延的算术平均值。
A、500 B、1000 C、2000 D、50007. 售后服务分级要求,AAA 服务客户端现场巡检每(C )次。
A、一个月B、二个月C、一季度D、半年8. 根据业务开通服务的分级要求,AAA 客户建筑红线范围外接入光缆同路由长度不超过(B )A、20 米B、50 米C、100 米D、150 米9. 重要集团客户严重故障处理完成后,市公司(B )个工作日内提交故障报告给客户经理与省网服,客户经理审核后决定是否向客户提供故障报告。
A、1 B、2 C、3 D 、410. 在业务保障分级要求中,AAA 客户语音专线-跨地市、地市内业务中断,修复时长为(B )A、1 小时B、2 小时C、3 小时D、4 小时11.日常巡检方面,以下说法错误的是(D )A、客户端设备巡检内容包括如下内容:客户端设备环境(设备卫生情况,设备放置情况,设备电源,设备运行情况,综合布线),客户端设备标签,一图一表检查,资产实物检查,客户业务拨测等。
AUTODOME Inteox 7000i与IP Starlight 7000i视觉摄像头辅助设备配

Camera Accessories - Quick Selection Guide North American versionFor full functionality open this Guide in Adobe Acrobat ReaderAUTODOME IP 7000MIC IPFixed Camerasand AUTODOME IP 7100i (IR)© B o s c h S e c u r i t y S y s t e m s , 2023 - M o d i fi c a t i o n s r e s e r v e d | B T -V S /M K C v e r s i o n 11_N o r t h A m e r i c a N o v e mAUTODOME In-ceilinginteox 7000i | IP starlight 7000iAUTODOMEinteox 7000i | IP starlight 7000iAUTODOME IP 7000 Camera Accessories - Quick Selection GuideinstructionsSelect your camera Select your mounting option Jump back to the mounting indexAUTODOME In-ceilinginteox 7000i | IP starlight 7000iAUTODOMEinteox 7000i | IP starlight 7000iFor more information check out ourOnline Product catalogFiberMidspanWall mountPipe mount Roof mount BubblesAUTODOME INTEOX 7000i | IP STARLIGHT 7000iNDP-7602-Z30 | NDP-7602-Z30K | NDP-7602-Z30OC | NDP-7512-Z30 | NDP-7512-Z30K indoor / outdoor installationsA gray background behind the product means this is an indoor installationA blue background behind the product means this is an outdoor installation (IP66 rating)Corner mountPole mountHigh ImpactHigh ResConverter Kitpower boxpower boxmount platepower boxAUTODOME In-ceilinginteox 7000i | IP starlight 7000iAUTODOMEinteox 7000i | IP starlight 7000iFor more information check out ourOnline Product catalogA gray background behind the product means this is an indoor installationA blue background behind the product means this is an outdoor installation (IP66 rating)High ResFlush Mount/ In CeilingMIC IP 9000iBlackMIC IP 9000iGrayMIC IP 9000iWhiteMIC IP 7100iBlackMIC IP 7100iGrayMIC IP 7100iWhiteMIC IP Camera Accessories - Quick Selection GuideinstructionsSelect your camera Select your accessory Jump back to the index pageFor more information check out ourOnline Product catalogMIC IP 9000iBlackMIC IP 9000iGrayMIC IP 9000iWhiteMIC IP 7100iBlackMIC IP 7100iGrayMIC IP 7100iWhiteAlarm/Washer Interface boxWasher Interface KitMidspan Power InjectorsPole Mount Corner mount Power supplyFor more information check out ourOnline Product catalogMIC IP 9000iBlackMIC IP 9000iGrayMIC IP 9000iWhiteMIC IP 7100iBlackMIC IP 7100iGrayMIC IP 7100iWhiteIP67 Weatherproof KIT for MICPigtail WiresAlarm/Washer Interface boxWasher Interface KitPole Mount Corner mount Power supplyFor more information check out ourOnline Product catalogMIC IP 9000iBlackMIC IP 9000iGrayMIC IP 9000iWhiteMIC IP 7100iBlackMIC IP 7100iGrayMIC IP 7100iWhiteIP67 Weatherproof KIT for MICPigtail WiresAlarm/Washer Interface boxWasher Interface KitPole Mount Corner mount Power supplyFor more information check out ourOnline Product catalogMIC IP 9000iBlackMIC IP 9000iGrayMIC IP 9000iWhiteMIC IP 7100iBlackMIC IP 7100iGrayMIC IP 7100iWhiteIP67 Weatherproof KIT for MIC Pigtail WiresAlarm/Washer Interface boxWasher Interface KitPole Mount Corner mount Power supplyFor more information check out ourOnline Product catalogMIC IP 9000iBlackMIC IP 9000iGrayMIC IP 9000iWhiteMIC IP 7100iBlackMIC IP 7100iGrayMIC IP 7100iWhiteSoftware License for IP CamerasIP67 Weatherproof KIT for MIC Pigtail WiresAlarm/Washer Interface boxPole Mount Corner mountPower supplyFor more information check out ourOnline Product catalogMIC IP 9000iBlackMIC IP 9000iGreyMIC IP 9000iWhiteMIC IP 7100iBlackMIC IP 7100iGreyMIC IP 7100iWhiteSoftware License for IP CamerasIP67 Weatherproof KIT for MIC Pigtail WiresAlarm/Washer Interface boxPole Mount Corner mountPower supplyLocal storage – MicroSD cardWall mount Pipe mountPole mount In-ceilingFLEXIDOME IP 4000i indoorNDI-4512-A | NDI-4512-AL indoor installation onlyA gray background behind the product means this is an indoor installation A blue background behind the product means this is an outdoor installation IndexIn-ceiling mountPole mount with mountboxboxLocal storage – MicroSD cardWall mount Pipe mountPole mount Parapet mountIn-ceiling mountFLEXIDOME IP 4000i outdoorNDE-4512-A | NDE-4512-AL indoor / outdoor installationsCorner mountA gray background behind the product means this is an indoor installation A blue background behind the product means this is an outdoor installation IndexIn-ceiling mountPendant parapet mountPole mount with Pole mount with Pole mountboxboxwith surveillance cabinetLocal storage – MicroSD cardWall mount Pipe mount Pole mount In-ceilingFLEXIDOME IP 5000i indoorNDI-5502-A | NDI-5502-AL | NDI-5503-A | NDI-5503-AL indoor installation onlyA gray background behind the product means this is an indoor installation A blue background behind the product means this is an outdoor installation Pole mount with mountboxboxIn-ceiling mountIndexLocal storage – MicroSD cardIn-ceiling mountWall mount Pipe mount Pole mountCorner mountFLEXIDOME IP 3000i IR indoorNDI-3512-AL | NDI-3513-AL indoor installation onlyA gray background behind the productmeans this is an indoor installation A blue background behind the product means this is an outdoor installation IndexCorner mountPole mount with mountboxboxIn-ceiling mountLocal storage – MicroSD cardWall mount Pipe mountPole mount Parapet mountIn-ceiling mount Tilt mountFLEXIDOME IP 3000i IR outdoorNDE-3512-AL | NDE-3513-AL indoor / outdoor installationsCorner mountA gray background behind the productmeans this is an indoor installation A blue background behind the product means this is an outdoor installation IndexIn-ceiling mount Pendant parapet mountPole mount with Pole mount with Pole mountboxboxwith surveillance cabinetTilt mountLocal storage – MicroSD card Conduit Back Box Plenum-rated in-ceiling mount kitA blue background behind the product L shape wall mount Pole mountPendant pipe mountwith surface mountboxPlenum-ratedin-ceiling mount kitPendant pipe mountConduit Back BoxPendant wall mountwith surface mountboxPole mount withsurface mount boxPendant wall mountCorner mount boxLocal storage – MicroSD cardPlenum-rated in-ceiling mount kitPaintable coverA gray background behind the product L shape wall mount Pole mountPlenum-ratedPaintable coverPendant pipe mount with surface mount boxPendant pipe mount4S adapter PlatePendant wall mount with surface mount boxPole mount with surface mount boxPendant wall mountCorner mount boxLocal storage – MicroSD cardWall mount Pipe mount Pole mount Parapet mountIn-ceiling mountFLEXIDOME IP 5000i outdoorNDE-5502-A | NDE-5502-AL | NDE-5503-A | NDE-5503-AL indoor / outdoor installationsCorner mountA gray background behind the product means this is an indoor installation A blue background behind the product means this is an outdoor installation Pendant parapet mountPole mount with Pole mount with Pole mountboxboxwith surveillance cabinetIn-ceiling mountIndexLocal storage – MicroSD cardPaintable cover In-ceiling mountA gray background behind the product means this is an indoor installationA blue background behind the product means this is an outdoor installationPaintable coverPole mount small withsurface mount boxPole mount smallCorner mountPendant pipe mountwith surface mountboxPendant pipe mountPendant wall mountwith surface mountboxTilt mountPendant wall mountIn-ceiling mountConduit Back Box & Paintable coverLocal storage – MicroSD cardParapet mountFiberA gray background behind the product means this is an indoor installationA blue background behind the product means this is an outdoor installation Fiber Optic Ethernet Pendant parapet Pole mount small with surface mount boxPole mount large with surveillance cabinetPole mount smallCorner mount with surface mount box Corner mount with surveillance cabinet Corner mount Pendant pipe mount with surface mount boxPendant pipe mountPendant wall mount with surface mount boxPendant wall mount with surveillance cabinetPendant wall mountTilt mountConduit Back BoxPaintable coverLocal storage – MicroSD cardWall mount Pipe mount Pole mount Parapet mountFLEXIDOME IP panoramic 6000/7000 - outdoorNDE-6004-FxxxE | NDS-7004-FxxxE indoor / outdoor installationsA gray background behind the product means this is an indoor installation A blue background behind the product means this is an outdoor installation Pendant parapet mountPole mountbox box mount boxIndexLocal storage – MicroSD cardParapet mountFiberConduit adapterA gray background behind the product means this is an indoor installation A blue background behind the product means this is an outdoor installation Fiber Optic Ethernet Pendant parapet Pole mount large with surveillance cabinetPole mount smallCorner mount Pendant pipe mount with surface mount boxCorner mount with surveillance cabinet Corner mount with surface mount box Pendant pipe mountPendant wall mount with surface mount boxPendant wall mount with surveillance cabinetPole mount small with surface mount boxPendant wall mountConduit adapterLocal storage – MicroSD cardParapet mountFiberConduit adapterA gray background behind the product means this is an indoor installation A blue background behind the product means this is an outdoor installation Fiber Optic Ethernet Pendant parapet Pole mount small with surface mount boxPole mount large with surveillance cabinetPole mount smallCorner mount with surface mount box Corner mount with surveillance cabinet Corner mount Pendant pipe mount with surface mount boxPendant pipe mountPendant wall mount with surface mount boxPendant wall mount with surveillance cabinetPendant wall mountConduit adapterLocal storage – MicroSD cardFiberWall mount Pipe mount Pole mountParapet mountFLEXIDOME inteox 7100i IRNDE-7604-AL-OC | NDE-7604-Al indoor / outdoor installationsA gray background behind the product means this is an indoor installation A blue background behind the product means this is an outdoor installation IndexPendant parapet mountPole mount with Pole mountbox boxwith surveillance cabinetmount boxLocal storage – SD card 2xFiberParapet mountPaintable coverA gray background behind the product means this is an indoor installation A blue background behind the product means this is an outdoor installation Weather protectorPendant parapet Pole mount with surveillance cabinetPole mount In-ceiling mountPaintable coverPendant pipe mount with surface mount box Plenum-rated I n-ceiling mount kitPole mount large with on- camera weather protectorPendant pipe mountPendant wall mount with surface mount box Pendant wall mount with surveillance cabinetPole mount adapter small with surface mount boxPendant wall mountFiber Optic Ethernet Media Converter KitLocal storage – MicroSD card 2xFiberProtection kitWall mount Pipe mountPole mount In-ceiling mountFLEXIDOME IP indoor 8000iNDV-8502-R | NDV-8502-RX | NDV-8503-R | NDV-8503-RX | NDV-8504-R indoor installationsA gray background behind the product means this is an indoor installationIndexPole mount with Pole mount In-ceiling mountbox Plenum-rated I n-ceiling mount kitboxwith surveillance cabinetmount boxLocal storage – MicroSD cardPole mount Pole and cornerDINION inteox 7100i IRNBE-7604-AL-OC | NBE-7604-AL indoor / outdoor installationsA gray background behind the product means this is an indoor installation A blue background behind the product means this is an outdoor installation Index4S adapterPole mountLocal storage – SD cardPole mount Corner mountDINION IP thermal 8000NHT-8001-F09VS | NHT-8001-F09VF | NHT-8001-F17VS | NHT-8001-F17VF | NHT-8001-F35VS | NHT-8001-F35VF | NHT-8001-F65VS | NHT-8001-F65VF indoor / outdoor installationsA gray background behind the product means this is an indoor installation A blue background behind the product means this is an outdoor installation Corner mountPole mount IndexLocal storage – MicroSD cardPaintable coverCorner mountA gray background behind the product Corner mountL shape wall mount Pole mountIn-ceiling mountPaintable coverPendant pipe mount with surface mount boxPlenium-rated in-ceiling mount kitPendant pipe mountPendant wall mount with surface mount boxPole munt adapter small with surface mount box Pendant wall mountCorner mount withLocal storage – MicroSD cardParapet mountPaintable coverCorner mountA blue background behind the product Corner mountL shape wall mount Pendant parapet Pole mount with surveillance cabinetPole mountIn-ceiling mountPaintable coverPendant pipe mount with surface mount boxPlenium-rated in-ceiling mount kitPendant pipe mountPendant wall mount with surface mount boxPendant wall mount with surveillance cabinetPole munt adapter small with surface mount box Pendant wall mountCorner mount withLocal storage – Full size SD cardParapet mount MidspansWall mount Pipe mountCorner mount Pole mountAUTODOME 7100i (IR)NDP-7602-Z40 | PTZ 2MP HDR 40x IP66 pendant | NDP-7604-Z12L | PTZ 8MP 12x IP66 pendant IR indoor / outdoor installationsA gray background behind the product means this is an indoor installation A blue background behind the product means this is an outdoor installation IndexMidspans outdoorMidspans indoorParapet mount outdoorindoorwith surveillance cabinetwith surveillance cabinetwith surveillance cabinetLocal storage – MicroSD cardWall mount Pole mountFiber kitDINION 5100i IRNBE-5702-AL | NBE-5703-AL | NBE-5704-AL indoor / outdoor installationsA blue background behind the product IndexWall mount Pole mount Wall mount with Pole mount with Wall mount with Fiber kitLocal storage – MicroSD cardGrommets Fiber kitWall mountPole mount Polarizing filter kitIllumination optionsDINION 7100i IRNBE-7702-ALX | NBE-7702-ALXT | NBE-7703-ALX | NBE-7703-ALXT | NBE-7704-ALX | NBE-7704-ALXT | NBE-7704-AL indoor / outdoor installationsA blue background behind the productIndexWall mount Pole mountWall mount with Pole mount with Wall mount with conduit back box Fiber kitGrommetsFLEXIDOME5000i outdoorFLEXIDOMEstarlight 8000iDINIONinteox 7100i IRFLEXIDOMEpanoramic 5100iFLEXIDOMEpanoramic 5100i IRFLEXIDOMEmulti 7000iFLEXIDOMEmulti 7000i IRFLEXIDOMEinteox 7100i IRDINIONthermal 8000FLEXIDOME4000i indoorFLEXIDOMEindoor 5100i (IR)DINION7100i IRFLEXIDOME3000i IR outdoorFLEXIDOMEmicro 3100i indoorFLEXIDOMEmicro 3100i outdoor。
博世 安全系统-法拉登VIVIDIO应用程序 步骤配置 说明书

From Nuremberg BT-VS/MKP-XPT Product Management 20.04.2023Release LetterProduct: VIDEOJET decoder 7000 VJD-7513Version: Firmware 10.40.0055This letter contains latest information about the above-mentioned product.1. GeneralThis firmware release 10.40.0055 is a feature release based on FW 10.31.0005.Changes since last release FW 10.31.0005 are marked in blue.VIDEOJET decoder 7000 uses robust, fan-less technology designed for ambitious environmental conditions while providing maximum performance on minimum space in a nicely designed industrial housing.VIDEOJET decoder 7000 displays video from Standard Definition (SD), High Definition (HD), 4K Ultra High Definition (UHD), and Megapixel (MP) cameras and encoders using H.265, H.264 or MPEG-4 encoding at up to 60 frames per second over IP networks.VIDEOJET decoder 7000 is the successor of VIDEOJET decoder 8000 (VJD-8000, VJD-8000-N). It is using the same housing but comes with different video output interfaces and provides improved performance and functionality.Notes:•Firmware update may take several minutes due to a large cumulative Microsoft patch.•This firmware includes OpenSSL.From NurembergBT-VS/MKP-XPT Product Management 20.04.20232. Applicable products•VIDEOJET decoder 7000, VJD-75133. New Features•SRTP for encrypted multicast traffic is supported. This allows fully secured communication with and video streaming from CPP13 and CPP14 cameras in multicast environments.•SNMPv3 trap service has been added, including the support of SNMP-related RCP+ commands for configuration.• A JPEG snapshot is now possible from each of the displays, including JPEG quality settings parameter.•Display order can be re-arranged in case Windows display detection differs from mechanical order.•The default layout is depending on the display number to simplify the identification of display order. The number of video windows per display increases as square of the display number.•The web interface of the decoder has been updated to the latest style guide and re-structured to ease usage for installation, licensing, and integration purposes.o The new web pages provide links to documentation and include a live preview.o Maintenance log file creation and download is supported by a workflow mechanism.o A keyboard emulator supports initial setup for IP Matrix even without keyboard connected.From NurembergBT-VS/MKP-XPT Product Management 20.04.20234. Changes•The Video SDK as one of the core components for the decoder firmware has been updated to latest version 6.40, providing a great number of improvements and fixes, mainly aroundONVIF and RTSP support, increasing the overall robustness.•An issue is fixed for banner upload when banners are activated.•An issue is fixed for zooming out in client dewarping mode of panoramic camera streams.•An issue is fixed where client dewarping was not working on line 1 of a panoramic camera in onboard dewarping mode. Onboard dewarping is only available for lines 2 and higher, line 1 always provides the full warped image circle.•An issue with DNS server configuration is fixed.•An issue is fixed where CPP13 and CPP14 cameras were not correctly connected in camera sequences.•Maintenance log file download is improved, supported by the new web interface structure.•An issue is fixed where daylight saving time was incorrectly reflected in time zone offset calculation.5. System RequirementsFor configuration purposes:•Configuration Manager 7.61 or newerFor operation purposes:•Bosch Video Management System 12.0 or higherNote that not all features may be supported by BVMS yet.Please refer to BVMS release notes.From NurembergBT-VS/MKP-XPT Product Management 20.04.20236. Restrictions; Known Issues•Connecting encrypted streams without proper signalling may result in crashing the software decoder instance, resulting in black video displayed.•Alarms will not be signaled with a red border around the cameo if connection was established using CONNECT_PRIMITIVE.•Using CONNECT_PRIMITIVE via TCP is not possible.•CONNECT_PRIMITIVE does not support "first available" feature.•Audio may remain audible despite layout change to other than single view.•RCP+ command CONF_ALARM_CONNECT_TO_IP is not supported.•Alarm connection does not support audio, nor does it include metadata.•Maximum password length is 19 characters.•With “Reconnect last devices” active camera connections are stored and automatically reconnected after reboot. To avoid deadlock in case of an overload situation the automaticreconnect will be deactivated after the decoder was forced into reboot for ten times within 10 minutes.•Monitors may be swapped after update. Swap back is possible using Configuration Manager.•IP Matrix pre-requisites for multi-decoder clustering:o Fixed IP addresses must be assigned; DHCP configuration is not functional.o Passwords for service level must be same on all clustered decoders.o Passwords for user level must be same on all clustered decoders.•After removing a slave decoder from the IP Matrix master, both decoders must be restarted.•Camera sequences are paused when picture-in-picture mode is activated.•Time related settings may appear in Configuration Manager only with delay or after a reboot.•Monitors connected to the Display Port via USB-C may not always be detected during booting.In this case, unplug and reconnect the adapter or cable to the monitor. If only one monitor isused it is recommended to connect to the direct HDMI output.•Log file download stability may be affected by workload of decoder. As a workaround, the download may need to be repeated, or the workload of the decoder may need to be reduced (disconnect all camera streams).•Time zone configuration is only supported via TIME_ZONE_STRING.•The KBD-DIGITAL keyboard is locked automatically during start-up of the decoder, or with re-connect. It will be unlocked after entering the PIN but the lock screen will remain until the next action on the keyboard.•Certificates used with the decoder must not have any Windows policies defined.•DNS resolution is not implemented yet, thus time server entry only works with IP addresses.•Dewarping zoom does not work correctly for panoramic cameras in on-board dewarping mode for camera line 1.•Overload messages and traps may appear too sensitive in cases where display refresh rates are lower than video stream frame rates.From NurembergBT-VS/MKP-XPT Product Management 20.04.20237. Previous Revisions7.1. New Features with 10.31.0005•Support for HOST_NAME to get and set the device’s hostname; only supported in extended configuration mode.•Support for DNS_SERVER_IP_STRING to get and set primary and secondary DNS server IPv4 addresses.7.2. Changes with 10.31.0005•Optimized transparent data processing time to allow adequate transparent data pass-through for serial PTZ keyboard.•An issue is fixed to apply e-PTZ presets correctly in camera sequences.•Feature loss due to suppressing encrypted UDP multicast connections for Bosch IP cameras with firmware 8 and higher, and fall back to TCP, tunneled via HTTPS control connection.(This feature will be added again with FW 10.40.)From NurembergBT-VS/MKP-XPT Product Management 20.04.20237.3. New Features with 10.30.0005•The default setting for Automatic IPv4 address assignment is set to “DHCP plus Link-Local”.Though this might seem a small change, it may have an impact:The former default IP address 192.168.0.200 will virtually become obsolete.Instead, the camera will assign itself an auto-IP address out of the range 169.254.1.0 to169.254.254.255 as long as there is no other IP address assigned by a DHCP server.(https:///wiki/Link-local_address)The advantage is that there are no more duplicate IP addresses, which is consideredprohibited in a network.•Network authentication 802.1x with EAP/TLS has been added.Please note that the server certificate needs to get the usages ‘Trust’ and ‘EAP_TLS_Trusted’ assigned.The client certificate will get the necessary usages assigned automatically.•The possibility of large banner overlays has been introduced.o Banners can be uploaded as images that can be displayed over three areas: top, center and bottom. The images are scaled to fill the area and cropped wherenecessary.o Banners can be sequenced with a configurable dwell time.o Configuration Manager 7.60 is supporting this with upload and banner sequence configuration, including banner previews.•Set and recall prepositions for moving cameras (AUTODOME, MIC) as well as for ONVIF PTZ cameras via keyboard has been added to the IP Matrix functionality.•Images can be uploaded to the decoder for two purposes, using Configuration Manager. The images shall be in JPG format and must be named as follows:o‘monitor background’ image, shown as background of an empty video window: ‘Logo.jpg’o‘’no camera’ image, shown on connection failure: ‘NoCamLogo.jpg’7.4. Changes with 10.30.0005•An issue was fixed where uploading a new video loss image did not break the software seal.From NurembergBT-VS/MKP-XPT Product Management 20.04.20237.5. Changes with 10.23.0002• A security vulnerability has been fixed where a crafted configuration packet sent by an authenticated administrative user can be used to execute arbitrary commands in systemcontext (CVE-2021-23862).For more details refer to our Security Advisory BOSCH-SA-043434-BT, published at ourSecurity Advisory web pagehttps:///xc/en/support/product-security/security-advisories.htmlor visit our PSIRT website at https://.7.6. New Features with 10.22.0038•APIPA (link-local address, Auto-IP) is used instead of a default IP address when DHCP is on and no DHCP server responded.•Transparent data pass-through for serial PTZ keyboard (SERIAL_PORT_APP_VAL and TRANSFER_TRNSPARENT_DATA) has been added.•Support of RCP+ via CGI (including WRITE commands) has been added.•HTTP digest authentication is supported for RCP+ via CGI.•Display orientation can be changed per line via RCP+.•RCP+ WRITE command MONITOR_NAME now supported for custom monitor names.•Updated RCP+ documentation is now available via the VIDEOJET decoder webpage.•Download of screen and tile snapshots via snap.jpg is now supported (requires at least user privileges).•Firmware update on-screen countdown dialog now shows a heartbeat whenever a single update step takes longer.•Support of CONNECT_URL read queries to get current video connection details, including current digital and dewarping zoom settings, has been added.•Support of various digital and dewarping zoom persistence modes(DIGITAL_ZOOM_PERSISTENCE_MODE) has been added.•Support of SYSTEM_DATETIME_V2 to read/write UTC system time has been added.•Support for new Sentinel RMS licenses has been added. Legacy licenses can now also be based on new installation code (lock code from Sentinel RMS).From NurembergBT-VS/MKP-XPT Product Management 20.04.20237.7. Changes with 10.22.0038•IP Matrix initialization is now working also for camera lines larger than 1.•RCP+ response for query on connected cameras is now working correctly.•URL extension for camera configuration in IP Matrix is no longer truncated.•An issue with an unexpected application restart has been fixed.•The DECODER_GROUP command is no longer supported when decoder IP address is not static. This disables the whole IP matrix configuration pages in Configuration Manager until a static IP is configured in the decoder’s network settings.•Improvements were made for log export via webpage and via Configuration Manager.•KBD-DIGITAL keyboard PIN is now used immediately without application restart.•KBD-DIGITAL keyboard PIN is now required whenever keyboard is attached and at application start.•Display orientation is now working for further monitor types.•Support of further USB to serial COM port adapters for KBD-DIGITAL keyboard connectivity.o Current: Prolific PL2303 [hardware ID USB\VID_067B&PID_2303]o New: Prolific PL2303GT [hardware ID USB\VID_067B&PID_23C3]o New: ATEN UC232A [hardware ID USB\VID_0557&PID_2008]o New: Unitek Y-108 [hardware ID FTDIBUS\VID_0403+PID_6001]o CableCreation CD0489 (PL2303) [hardware ID USB\VID_067B&PID_2303] is compatible to the already supported Prolific PL2303 adapter.Please note that the KBD-DIGITAL keyboard connectivity requires continuous maintenance, since new or not listed USB-to-serial COM port adapters typically require the installation of a suitable driver on the VIDEOJET decoder and an adaption of the hardware ID filter in thekeyboard detection software module. Newer USB adapters may require a firmware update to become supported.From NurembergBT-VS/MKP-XPT Product Management 20.04.20237.8. New Features with 10.01.0036Security• A protected configuration mode has been implemented, allowing too enable SSD encryption (BitLocker) and too disable USB ports, e.g. for installation of the decoder in public areas.•The configuration of the decoder can be protected by Software Sealing, similar to IP cameras.•The latest Microsoft Windows security updates have been included.Miscellaneous• A dewarped cutout from panoramic cameras can be defined with PTZ coordinates.• A new way to control and integrate the decoder into a management system has been added by a JSON RPC API. This allows to send commands and retrieve status information via JSON remote procedure calls. The API documentation is added to the distribution package.• A video output capture service (VOCS) has been implemented which could be activated via a license, applicable per display output. This service captures the memory of the video outputand encodes it into a camera-like video stream, which can be recorded via Video StreamingGateway (VSG) onto iSCSI storage.• A time server can be added to synchronize the decoder.•Decoder log file can be downloaded via Configuration Manager. This is especially recommended when download of the log file is not working correctly via web browser.7.9. Changes with 10.01.0036•Upload of background image and connection loss image to the decoder and reverting them to default is now also possible with service password set. The former restriction is obsolete.•Various minor bug fixes.From NurembergBT-VS/MKP-XPT Product Management 20.04.20237.10. New Features with 9.60.0017IP Matrix enhancements•KBD-DIGITAL is supported in addition to KBD-UNIVERSAL XF.This keyboard requires a serial-to-USB adapter to connect to the decoder.Both keyboards can be mixed in a clustered multi-decoder IP Matrix, one keyboard perdecoder.•Playback from local recording is supported.Permission is configured via Configuration Manager for the whole IP Matrix, valid for all users.•Buttons for next and previous camera have been added to the KBD-UXF functions.•Audio can be switched on or off via keyboard.•Camera channels can be extended via license up to 64 cameras per decoder unit.Note:IP Matrix manual is now separated intoo One configuration manual for IP Matrixo One operation manual for IP Matrix using KBD-UXFo One operation manual for IP Matrix using KBD-DIGITALSecurity•The latest Microsoft Windows security updates have been included.Miscellaneous•Background image and connection loss image can be uploaded to the decoder, replacing the default images. Reverting them to default is done by uploading an empty image.Note: Upload is only possible in conjunction with an empty service password.7.11. Changes with 9.60.0017•Temperature control margin increased to improve maximum performance at the specified maximum temperature, covering component tolerances, and to ensure that all productsadhere fully to their specification.•Various minor bug fixes.Security SystemsFromNuremberg BT-VS/MKP-XPT Product Management 20.04.202311BOSCH and the symbol are registered trademarks of Robert Bosch GmbH, Germany 7.12. Features with initial release 9.51• VIDEOJET decoder 7000 displays video from Standard Definition (SD), High Definition (HD),4K Ultra High Definition (UHD), and Megapixel (MP) cameras and encoders using H.264 or MPEG -4 encoding at up to 60 frames per second over IP networks.• VIDEOJET decoder 7000 provides an HDMI and a DisplayPort (via USB-C connector) output, both capable of driving up to 4K UHD displays simultaneously.• Display settings are automatically discovered and set for optimal display performance. • Monitor layouts can be switched independently for each display.• Upright monitors (portrait mode) are supported.• Video window (cameo) aspect ratio can be set to 16:9, 9:16, 3:4, or 1:1.• Active camera connections and layout are stored and automatically reconnected after reboot if configured. To avoid deadlock in case of an overload situation the automatic reconnect will be deactivated after VIDEOJET decoder 7000 was forced into reboot for 3 times within 10 minutes.• Video smoothing can be configured.• RTSP connections are supported, enabling connectivity to 3rd party and ONVIF cameras. • Discovery port is configurable.• Cameo distance is configurable.• VIDEOJET decoder 7000 supports IP Matrix application as built-in feature.• VIDEOJET decoder 7000 is able to display VCA metadata.• VIDEOJET decoder 7000 provides bi-directional G.711 audio for the video stream shown in single view on the first monitor.• Configuration is done using the Configuration Manager.• The number of decoders presented in capabilities is configurable to regulate the consumption of VMS licenses. Default value is 30.• System access is password-protected with two levels.• The system firmware can be upgraded remotely.• System API is compatible to predecessor VIDEOJET decoder 8000 for easy plug-and-play integration.• Operating temperature iso 0 °C to +50 °C (+32 °F to +122 °F) ambient temperature, with airflow o 0 °C to +40 °C (+32 °F to +104 °F) ambient temperature, still airFor detailed functional description of inherited firmware features, please refer to the VIDEOJET decoder 8000 firmware 9.51 release notes.For detailed technical specification, please refer to the datasheet.。
ArenaMatch Utility 小前景 补声扬声器 AMU105 AMU108 AMU206

规范信息
本产品符合所有适用的欧盟指令要求。您可以从网站 /compliance 找到完整的符合性声明。
此符号表示不得将此产品作为生活垃圾丢弃,应将其送到合适的 回收站点进行回收。正确处理和回收有助于保护自然资源、人类 健康和环境。想要获得更多关于此产品的处理和回收的信息,请 联系当地市政当局、垃圾处理服务部门或您购买此产品的商店。
中国危险物质限用表
有毒或有害物质或元素名称及成分
有毒或有害物质和元素
零件名称
铅
汞
(Pb) (Hg)
镉 ()
六价铬 (CR(VI))
多溴化 联苯 (PBB)
印刷电路板 X
O
O
O
O
金属零件
X
O
O
O
O
塑料零件
O
O
O
O
O
扬声器
X
O
O
O
O
线缆
X
O
O
O
O
此表格依据 SJ/T 11364 的要求制定。
O:表示此零件中所有均质材料所包含的此类有毒或有害物质均低于 GB/T 26572 中的限定要求。
6. 只能使用制造商指定的附件/配件。
7.
只能使用制造商指定或随本设备一起销售的推车、支架、
三角架、托架或工作台。如果使用推车,则在移动推车/设
备时应格外小心,以免因倾倒而造成伤害。
警告/小心:
包含可能导致窒息危险的小部件。不适合 3 岁以下的儿童使用。
本产品含有磁性材料。有关这是否会影响到您的植入式医疗器 械,请咨询您的医生。
包装清单................................................................................................................................................................................................... 5 可选配件................................................................................................................................................................................................... 5 检查和维护....................................................................................................................................................................................................... 6 保持防风雨性........................................................................................................................................................................................... 6 推荐使用的工具.............................................................................................................................................................................................. 6 产品尺寸........................................................................................................................................................................................................... 7 ArenaMatch Utility AMU105........................................................................................................................................................... 7 ArenaMatch Utility AMU108........................................................................................................................................................... 8 ArenaMatch Utility AMU206.......................................................................................................................................................... 9 ArenaMatch Utility AMU208........................................................................................................................................................ 10
KFD2-UFC-Ex1.D频率转换器的中文名称说明书

Frequency Converter with Trip ValuesKFD2-UFC-Ex1.D<1-channel isolated barrier<24 V DC supply (Power Rail)<Input for NAMUR sensors or dry contacts<Input frequency 1 mHz ... 5 kHz<Current output 0/4 mA ... 20 mA<Relay contact and transistor output<Start-up override<Line fault detection (LFD)<Up to SIL 2 acc. to IEC 61508/IEC 61511This isolated barrier is used for intrinsic safety applications.The device is a universal frequency converter that changes a digital input signal into a proportional free adjustable 0/4 mA ... 20 mA analog output signal and functions as a switch amplifier and a trip alarm.The functions of the switch outputs (2 relay outputs and 1 potential free transistor output) are easily adjustable [trip value display (min/max alarm), serially switched output, pulse divider output, error signal output].The device is easily configured by the use of keypad or with the PACTware configuration software.A fault is signalized by LEDs acc. to NAMUR NE44 and a separate collective error message output.For additional information, refer to the manual and .Zone 2Div. 23-1+161718101112III20-III13+14-8+7-IV24 V DC23+24-edate:221-11-25Dateofissue:221-11-25Filename:231194_eng.pdfe d a t e : 2021-11-25 D a t e of i s s u e : 2021-11-25 F i l e n a m e : 231194_e ng .p d fe d a t e : 2021-11-25 D a t e of i s s u e : 2021-11-25 F i l e n a m e : 231194_e ng .p d fe d a t e : 2021-11-25 D a t e of i s s u e : 2021-11-25 F i l e n a m e : 231194_e ng .p d fAccessoriese d a t e : 2021-11-25 D a t e of i s s u e : 2021-11-25 F i l e n a m e : 231194_e ng .p d fe d a t e : 2021-11-25 D a t e of i s s u e : 2021-11-25 F i l e n a m e : 231194_e ng .p d fKFD2-UFC-Ex1.DFrequency Converter with Trip Values Maximum Switching Power of Output ContactsResistive load DC Resistive load AC1max. 105 switching cycles0.110.220.330.440.5I (A)。
JTAG-HS3编程线说明书

1300 Henley Court Pullman, WA 99163509.334.6306 JTAG-HS3™ Programming Cable for Xilinx ® FPGAsRevised March 13, 2019This manual applies to the JTAG-HS3 rev. AOverviewThe JTAG-HS3 programming cable is a high-speed programming/debugging solution for Xilinx FPGAs and SoCs. It is fully compatible will all Xilinx Tools, and can be seamlessly driven from iMPACT, ChipScope™, EDK, and Vivado™. The HS3 attaches to target boards using Xilinx’s 2x7, 2mm programming header.The PC powers the JTAG-HS3 through the USB port and will recognize it as a Digilent programming cable when connected, even if the cable is not attached to the target board. The HS3 has a separate Vref pin to supply the JTAG signal buffers. The high speed 24mA three-state buffers allow the HS3 to drive target boards with signal voltages from 1.8V to 5V and bus speeds up to 30MBit/sec (see Fig. 1). To function correctly, the HS3’s Vref pin must be tied to the same voltage supply (VCCO_0) that drives the JTAG port on the FPGA.The JTAG bus can be shared with other devices as the HS3 signals are held in high-impedance, except whenactively driven during programming. The HS3 uses a standard Type-A to Micro-USB cable that attaches to the end of the module opposite the system board connector. The HS3 is small and light, allowing it to be held firmly in place by the system board connector (see Fig. 2).The JTAG-HS3• Small, complete, all-in-one JTAGprogramming/debugging solution for Xilinx FPGAs and SoCs• Plugs directly into standard Xilinx JTAG header• Separate Vref drives JTAG signal voltages; Vref can beany voltage between 1.8V and 5V• High-Speed USB2 port that can drive JTAG bus up to30Mbit/sec (frequency adjustable by user)• Compatible with Xilinx ISE® 14.1 and newer, XilinxVivado 2013.3 and newer• Uses micro_AB USB2 connector• Open drain buffer on pin 14 allows debugging softwareto reset the processor core of Xilinx’s Zynq® platformFigure 2. Xilinx JTAG header. Dual row, 2mm, 14 pin.Figure 1. Diagram of signal voltages and connections. Features include: V I O: 5 V to 1 . 8 V USB 2 PortTMS TDI TDO TCK TMS TDI TDO TCKGND VREF GND VIO1 Software SupportThe JTAG-HS3 has been designed to work seamlessly with Xilinx’s ISE (iMPACT, ChipScope , EDK) and Vivado tool suites. The most recent versions of ISE and Vivado include all of the drivers, libraries, and plugins necessary tocommunicate with the JTAG-HS3. At the time of writing, the following Xilinx software included support for the HS3: Vivado 2014.1+, Vivado 2013.3+, and ISE 14.1+.The HS3 is also compatible with ISE 13.1 – 13.4. However, these versions of ISE do not include all of the libraries, drivers, and plugins necessary to communicate with the HS3. In order to use the JTAG-HS3 with these versions of ISE, version 2.5.2 or higher of the Digilent Plugin for Xilinx Tools package must be downloaded from the Digilent website, and the ISE13 plugin must be manually installed as described in the included documentation. The JTAG-HS3 is not compatible with Xilinx Vivado 2013.1 or Vivado 2013.2.In addition to working with the Xilinx Tools, the HS3 is also supported by Digilent’s Adept software and the Adept SDK (the SDK is available to download free from Digilent’s website). Adept includes a full -featured programmingenvironment and a set of public APIs that allow user applications to directly drive the JTAG chain. Using the Adept SDK, custom applications can be created to drive JTAG ports on virtually any device. Please see the Adept SDK reference manual for more information.2 Xilinx Zynq-7000 and SoC SupportThe Xilinx Tools occasionally require the processor core of the Zynq-7000 to be reset during debug operations. The Zynq platform processor has a pin dedicated for this purpose (PS_SRST_B). Driving the PS_SRST_B pin low causes the processor to reset while maintaining any existing break points and watch points. The JTAG-HS3 is capable of driving this pin low under the instruction of Xilinx’s SDK during debugging operations. In order for this t o work, pin 14 of Xilinx JTAG header on the target board must be connected to the PS_SRST_B pin of the Zynq (see Figs. 3 & 4).1357911132468101214GND GND GNDGND GND GND GND VREF TMS TCK TDOTDI ----SRST1357911132468101214GND GND GND GND GND GND GND VCCO_0TMS TCK TDOTDI ----PS_SRST_BThe JTAG-HS3 uses an open drain buffer to drive pin 14 of the Xilinx JTAG header (see Fig. 5). This allows the HS3 to drive the PS_SRST_B pin when VCC_MIO1 is referenced to a different voltage than VCCO_0 (see Fig. 6).Figure 3. JTAG-HS3 pinout (seen looking out of the connector). Figure 4. Xilinx System Board Header (seen looking into the connector).Output Pin(SRST)100Figure 5. JTAG-HS3 pin 14 output buffer.Should an accidental short occur between pin 14 and GND, the 100 ohm series resistor protects the buffer from being damaged. While this resistor protects the buffer from being damaged, it also limits the drive strength of the buffer. Therefore, it is necessary for the pull-up resistor (R PU) used to establish the voltage level on PS_SRST_B to be greater than or equal to 1.5K ohms. At the ti me of writing, Xilinx ZC702, Xilinx ZC706, and Avnet® MicroZed™ all feature 10K pull-ups on pin 14 of the their respective Xilinx JTAG headers. For compatibility with other evaluation platforms, please consult the manufacturer’s schematic.Figure 6. System board components.3 Supported Target DevicesThe JTAG-HS3 is capable of targeting the following Xilinx devices:•Xilinx FPGAs•Xilinx Zynq-7000•Xilinx CoolRunner™/CoolRunner-II CPLDs•Xilinx Platform Flash ISP configuration PROMs•Select third-party SPI PROMs•Select third-party BPI PROMsThe following devices cannot be targeted by the JTAG-HS3:•Xilinx 9500/9500XL CPLDs•Xilinx 1700 and 18V00 ISP configuration PROMs•Xilinx FPGA eFUSE programmingRemote device configuration is not supported for the JTAG-HS3 when used with Xilinx’s iMPACT software.Note: Please see the "Introduction to Indirect Programming – SPI or BPI Flash Memory" help topic in iMPACT for a list of supported FPGA/PROM combinations.Note: Please see the “Configuration Memory Support” section of Xilinx UG908 for a list of the FPGA/PROM combinations that Vivado supports.4 Design NotesThe JTAG-HS3 uses high speed three-state buffers to drive the TMS, TDI, and TCK signals. These buffers are capable of sourcing or sinking a maximum of 50 mA of current. The HS3 has 100 ohm resistors between the output of the buffers and the I/O pins to ensure the cable does not exceed the maximum limit. To further limit short circuit, additional current resistance may be placed in series with the I/O pins of the HS3 and the target board. However, Digilent recommends limiting the amount of additional resistance to 100 ohms or less as higher resistance may result in degraded operation.5 Programming Solutions Comparison ChartJTAG-USBJTAG-HS1 JTAG-HS2 JTAG-HS3 Max Speed 1.6 MHz 30 MHz 30 MHz 30 MHz VoltageRange1.8V – 5V 1.8V – 5V 1.8V – 5V 1.8V – 5VXilinx Native SupportISE 13.2+Vivado 2014.2+ISE 13.2+Vivado 2012.1+ISE 13.2+Vivado 2012.1+ISE 14.1+Vivado 2013.3+Xilinx Plug-inSupportISE 12.1+ ISE 12.1+ ISE 12.1+ ISE 12.1+ DigilentAdeptSupportYES YES YES YESPC Interface USB USB USB USB ConnectorInterface6-pin 6-pin, 14-pin 6-pin, 14-pin 14-pin4-Wire JTAG YES YES YES YES2-Wire JTAG NO NO YES NOZynq-7000PS_SRSTSupportNO NO NO YESSPISupportYES YES YES NO6 Absolute Maximum RatingsSymbol Parameter Condition Min Max Unit Vref I/O reference/supply voltage -0.5 6 V VIO Signal Voltage -0.5 6 VI IK,I OK TMS, TCK, TDI, TDODC Input/Output Diode CurrentVIO < -0.5V -50mAVIO > 6V +20I OUT DC Output Current ±50 mA T STG Storage Temperature -20 +120 ºCESD Human Body Model JESD22-A114 2000 V Charge Device Model JESD22-C101 500 V7 DC Operating CharacteristicsSymbol Parameter Min Typ Max Unit Vref I/O reference/supply voltage 1.65 1.8/2.5/3.3 5.5 VoltsTDO Input High Voltage (V IH) 1.4 5.5 Volts Input Low Voltage (V IL) 0 0.45 VoltsTMS, TCK, TDI Output High (V OH) 0.75 x Vref 0.90 x Vref Vref Volts Output Low (V OL) 0 0.05 x Vref 0.15 x Vref VoltsSRST Output Low (V OL)(R PU = 1.5K ohm)0 0.4 0.55 VoltsT A Operating Temperature 0 70 ºC8 AC Operating CharacteristicsThe JTAG-HS3 JTAG signals operate according to the timing diagram in Fig. 7. The HS3 supports TCK frequencies from 30 MHz to 8 KHz at integer divisions of 30 MHz from 1 to 3750. Common frequencies include 30 MHz, 15 MHz, 10 MHz, 7.5 MHz, and 6 MHz (see Table 4).TMS/TDITCKTDOSymbol Parameter Min MaxT CK T CK period 33ns 125µsT CKH, T CKL T CLK pulse width 16.6ns 62.5µsT CD T CLK to TMS, TDI 0 15nsT SU TDO Setup time 19nsT HD TDO Hold time 0Figure 7. Timing diagram. Table 4. JTAG-HS3 Frequency support.。
MSI Windows 11 商品说明说明书

Be Your Window To TheWorldSelling PointsWindows 10 Famille- MSI recommande Windows 11Professionnel pour les entreprisesMise à niveauGRATUITE vers Windows 11*Processeur jusqu'à Intel® Core™ i7-11700Support de la résolution 4K UHDSupport de la norme de connexion Wi-Fi 6Connectique complèteLogiciel MSI Center pour personnaliser votreexpérienceAccès facile au stockage et à la mémoireFirmware TPM pour une bonne sécurité des donnéesSupport de la fixation VESA* Le planning de mise à niveau varie en fonction desappareils. La disponibilité des fonctionnalités et desapplications peut varier selon le pays. Certainesfonctionnalités nécessitent un matériel spécifique (voirPicture and logos https:///fr-fr/windows/windows-11-specifications ...System I/O-Ports1x Headphone-out1.2.1x Mic-in3.4x USB 2.0 Type A1x DC jack4.5.1x HDMI out (2.0)6.1x COM port7.2x USB 3.2 Gen 1 Type A / 1x COM port8.1x RJ459.2x USB 3.2 Gen 1 Type A10.1x Mic-in11.1x Line-out12.1x Kensington LockSpecificationOperating Systems Windows Windows 10 HomeMise à niveau GRATUITE vers Windows 11*Processor CPU model Intel Core i5-11400CPU Clock 2.6GHzCPU Cores6CPU TDP65WCPU Cache12 MB Intel® Smart Cache CPU Threads12CPU Cooling Air coolingChipset Motherboard Chipset H510Discrete Graphics VGA I/O Port N/A Graphics Card N/AMemory Memory Capacity8GB(8GB*1) Memory Type DDR4 SDRAM Memory Speed1600(3200)MHz Memory Module Form Factor SO-DIMM Memory Slot (Total/Free)2/1Memory Max Capacity Max 64GBStorage Total SSD Storage Capacity256GBTotal HDD Storage Capacity N/AM.2 Slot (1) Installed SSD256GB*1M.2 Slot (1) Interface PCIe GEN3x4 w/o DRAM NVMe M.2 Slot (1) Form Factor M.2-2280 M-KEYM.2 slots (Total/Free)1/0HDD (1) RPM N/AHDD (1) Form Factor N/AHDD (1) Interface N/A3.5" Drive Bays (Total/Free)0/2.5" Drive Bays (Total/Free)2/2ODD(Type)N/AODD Height N/AODD Type N/ACommunications LAN Controller Realtek RTL8111H Wireless LAN Controller INTEL/AX201.NGWG.NVW Wireless LAN standard802.11ax 2x2+BT Bluetooth Version 5.2Audio Audio Codec Realtek ALC897 Audio Support 5.1 Channel HD AudioI/O Ports (Front)Thunderbolt N/A USB 480Mbps (USB 2.0)4 Audio Mic-In (Front)1 Audio-Out (Front)1I/O Ports (Rear)USB 5Gbps (USB 3.2 Gen 1 Type-A)4LAN Ports (RJ45)1HDMI™1x (v2.0) COM Port2Power Rated Wattage120WEfficiency Rating N/A Form factor N/A Power Supply Type ADAPTORIn The Box Keyboard Interface N/A Mouse Interface N/A Power Cord1 AC Adaptor1 Warranty Card1 Quick Guide4 User Manual N/A VESA Mount kit N/A Keyboard N/A Mouse N/ARegulatory Compliance Storage Operating Temperature Range0° C ~ 35° C ; -20° C ~ 60° C Storage Operating Humidity Range0% ~ 85%;0% ~ 90%CertificationsFCC(Class B)CB/CEUL(CUL)BSMIDimension & Weight Product Dimensions (WxDxH) (mm)204 x 208 x 54.8 Product Dimensions (WxDxH) (inch)8.03 x 8.19 x 2.16 Inside Carton Dimensions (WxDxH) (mm)TBD x TBD x TBD Inside Carton Dimensions (WxDxH) (inch)TBD x TBD x TBD Outer Carton Dimensions Standard (WxDxH)(mm)271 x 382 x 122 Outer Carton Dimensions Standard (WxDxH)(inch)10.67 x 15.04 x 4.8 Weight (Net kg) 1.27Weight (Gross kg) 2.75Product Volume (Liters) 2.3VESA VESA size100 x 100 mm Warranty Warranty24months。
Lorex MPX HDSe

3.
2. Clic Droit: • En mode visionnement en direct :
Contrôle des caméras PTZ (non incluses) Ajuste les réglages de la couleur et de l’image de la caméra Voir les informations du système Démarrer/arrêter le mode séquence Esactiver l’alarme sonore
6: EN MARCHE
Bip
Si le système émet un signal sonore au démarrage, le câble Ethernet n’est peut-être pas branché, ou le système n’est peut-être pas connecté à Internet. Pour arrêter le signal sonore : 1. Brancher un câble Ethernet du système au routeur et redémarrer le système. OU 2. Cliquer avec le bouton droit et cliquer sur Disable Beep.
Cliquer sur et sélectionner SETTING
4. Cliquer sur GENERAL et sélectionner l’onglet Date&Time.
ProASIC3 E Proto Kit 快速入门卡文档说明书

© 2012 Microsemi Corporation. All rights reserved.ProASIC3/E Proto KitQuickstart CardKit Contents – A3PE-PROTO-KIT, A3PE-BRD1500-SKTQuantityDescription1ProASIC ®3 Starter kit board with an A3PE1500-PQ2081FlashPro3 programmer (not included with A3PE-BRD1500-SKT)19 V power supply with international adaptersWall Mount Power Interboard ISP ConnectorLCD Display ModuleCAT5E RJ45Connectors for LVDSCommunications SMA for Optional External OscillatorRemovable Shunts to Isolate All I/Os for Prototyping Removable Shunts to Isolate All I/Os for Prototyping Oscillator forSystem Clock Manual Clock OptionFlashPro3 ISP ConnectorProASIC3/E in PQ208 Package 4 SwitchesEvery PQ208 Pin Accessible for Prototyping8 LEDsRemovable Shunts to Isolate All I/Os for Prototyping50200381-0/10.12ProASIC3/E Proto Kit Quickstart CardRunning the Test DesignTo test the board, you can program the demo design. Download it from the ProASIC3 Starter Kit page: /products/hardware/devkits_boards/proasic3_starter.aspx .Software and LicensingVisit the Actel website ( ) for the latest Libero IDE Software. Request a free gold license to activate your software.Software releases: /download/software/libero Licensing: https:///Portal/DPortal.aspx?r=1Documentation ResourcesFor further kit information, including user's guide, tutorial, and full design examples, refer to the ProASIC3 Starter Kit page:/soc/products/hardware/devkits_boards/proasic3_starter.aspx .Technical Support and ContactsTechnical support is available online at /soc/support and by email at **********************.Microsemi SoC Sales offices, including Representatives and Distributors, are located worldwide. To find your local representative visit /soc/company/contact .ActionResultsPress SW1Asynchronous clear for the whole designPress SW2Up-down control for the 8-bit counter. Press and hold SW2 for down count. Press SW3Synchronous load for the 8-bit counter. Press SW3 for loading from the Hex switches.Press SW4Switching between manual clock(SW5) and 40 MHz oscillator clock.Press SW5Manual clock (very useful for simulation)Press SW6Select for DATA_BLOCK. It allows switching LED output between the counter and flashing data.Change Hex Switchsetting (U13 and U14)Changes the loaded data for the 8-bit counter.。
Schneider Electric LT3SM00M PTC 触摸式重置型纤维电路保护器数据表说明
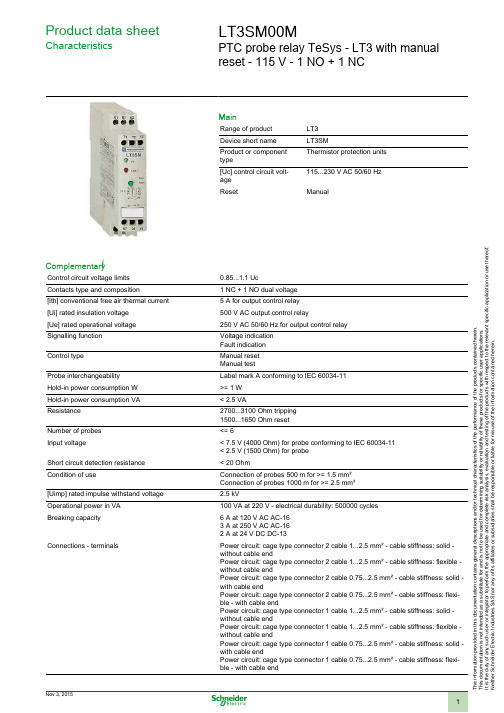
T h e i n f o r m a t i o n p r o v i d e d i n t h i s d o c u m e n t a t i o n c o n t a i n s g e n e r a l d e s c r i p t i o n s a n d /o r t e c h n i c a l c h a r a c t e r i s t i c s o f t h e p e r f o r m a n c e o f t h e p r o d u c t s c o n t a i n e d h e r e i n .T h i s d o c u m e n t a t i o n i s n o t i n t e n d e d a s a s u b s t i t u t e f o r a n d i s n o t t o b e u s e d f o r d e t e r m i n i n g s u i t a b i l i t y o r r e l i a b i l i t y o f t h e s e p r o d u c t s f o r s p e c i f i c u s e r a p p l i c a t i o n s .I t i s t h e d u t y o f a n y s u c h u s e r o r i n t e g r a t o r t o p e r f o r m t h e a p p r o p r i a t e a n d c o m p l e t e r i s k a n a l y s i s , e v a l u a t i o n a n d t e s t i n g o f t h e p r o d u c t s w i t h r e s p e c t t o t h e r e l e v a n t s p e c i f i c a p p l i c a t i o n o r u s e t h e r e o f .N e i t h e r S c h n e i d e r E l e c t r i c I n d u s t r i e s S A S n o r a n y o f i t s a f f i l i a t e s o r s u b s i d i a r i e s s h a l l b e r e s p o n s i b l e o r l i a b l e f o r m i s u s e o f t h e i n f o r m a t i o n c o n t a i n e d h e r e i n .Product data sheetCharacteristicsLT3SM00MPTC probe relay TeSys - LT3 with manualreset - 115 V - 1 NO + 1 NCMainRange of product LT3Device short name LT3SMProduct or component typeThermistor protection units [Uc] control circuit volt-age 115...230 V AC 50/60 Hz ResetManualComplementaryControl circuit voltage limits 0.85...1.1 UcContacts type and composition1 NC + 1 NO dual voltage [Ith] conventional free air thermal current 5 A for output control relay [Ui] rated insulation voltage 500 V AC output control relay[Ue] rated operational voltage 250 V AC 50/60 Hz for output control relay Signalling function Voltage indication Fault indication Control typeManual reset Manual testProbe interchangeability Label mark A conforming to IEC 60034-11Hold-in power consumption W >= 1 W Hold-in power consumption VA < 2.5 VAResistance 2700...3100 Ohm tripping 1500...1650 Ohm reset Number of probes <= 6Input voltage< 7.5 V (4000 Ohm) for probe conforming to IEC 60034-11< 2.5 V (1500 Ohm) for probe Short circuit detection resistance < 20 OhmCondition of useConnection of probes 500 m for >= 1.5 mm²Connection of probes 1000 m for >= 2.5 mm²[Uimp] rated impulse withstand voltage 2.5 kVOperational power in VA 100 VA at 220 V - electrical durability: 500000 cycles Breaking capacity6 A at 120 V AC AC-163 A at 250 V AC AC-162 A at 24 V DC DC-13Connections - terminalsPower circuit: cage type connector 2 cable 1...2.5 mm² - cable stiffness: solid -without cable endPower circuit: cage type connector 2 cable 1...2.5 mm² - cable stiffness: flexible -without cable endPower circuit: cage type connector 2 cable 0.75...2.5 mm² - cable stiffness: solid -with cable endPower circuit: cage type connector 2 cable 0.75...2.5 mm² - cable stiffness: flexi-ble - with cable endPower circuit: cage type connector 1 cable 1...2.5 mm² - cable stiffness: solid -without cable endPower circuit: cage type connector 1 cable 1...2.5 mm² - cable stiffness: flexible -without cable endPower circuit: cage type connector 1 cable 0.75...2.5 mm² - cable stiffness: solid -with cable endPower circuit: cage type connector 1 cable 0.75...2.5 mm² - cable stiffness: flexi-ble - with cable endTightening torque0.8 N.mHeight100 mmWidth22.5 mmDepth100 mmProduct weight0.22 kgEnvironmentStandards IEC 60034-11VDE 0660Product certifications LROS (Lloyds register of shipping)IP degree of protection IP20 conforming to VDE 0106IP20 conforming to IEC 60529Ambient air temperature for operation-25...60 °CAmbient air temperature for storage-40...85 °C conforming to IEC 60068-2-2-40...85 °C conforming to IEC 60068-2-1Operating altitude> 1500...3000 m with derating in temperature<= 1500 m without derating in temperatureVibration resistance 2.5 gn 2...25 Hz conforming to IEC 60068-2-61 gn 25...150 Hz conforming to IEC 60068-2-6Shock resistance 5 gn 11 ms conforming to IEC 60068-2-27Electromagnetic compatibility Susceptibility to electromagnetic fields - test level level 3 conforming to IEC61000-4-3Surge resistance 1.2/50-8/20 - test level level 4 conforming to IEC 61000-4-5Resistance to fast transient - test level level 3 conforming to IEC 61000-4-4Resistance to electrostatic discharge - test level level 3 conforming to IEC61000-4-2Immunity to microbreaks and voltage drops conforming to IEC 61000-4-11 Contractual warrantyPeriod18 months。
SAMS70和SAME70微控制器家族概述说明书

SAMS70 and SAME70 Microcontroller FamiliesSummaryThe SAMS70 MCU familiy is based on the ARM ® Cortex ®-M7 core plus FloatingPoint Unit (FPU) extending Microchip's 32-bit microcontroller portfolio with maximum operating speeds of up to 300 MHz, 2 MB of Flash and up to 384 KB of multi-port SRAM, of which up to 256 KB can be assigned to tightly coupled memory (data and instructions) delivering a zero wait state at 300 MHz. The SAMS70 family is able to accelerate execution from on-chip Flash and Non-Volatile Memory (NVM) connectedto Quad-SPI and EBI with 16 KB of data and 16 KB of instruction cache memory.This unique memory architecture enables the SAMS70 family to be optimized for real-time deterministic code execution and low-latency peripheral data access. Additionally, the SAMS70 family includes an extensive peripheral set including high-speed USB host and device with high-speed PHY , up to eight UARTs, five SPI, three I 2C, I 2S™, SD/MMC interface, a CMOS camera interface, twelve 16-bit timers, eight 16-bits PWMs and analog interfaces. The SAME70 family includes similar features as the SAMS70family as well as a 10/100 Ethernet MAC and dual Bosch CAN-FD interfaces with advanced analog features making them ideal forconnectivity applications.Key Features• ARM Cortex-M7 core running at 300 MHz• FPU for high-precision computing and accelerated data processing• High-performance internal-memory architecture with user-configurable tightly coupled memories and system memory/16 KB I and 16 KB D cache • Dual Bosch CAN-FD controller• 10/100 Ethernet MAC with IEEE 1588 and KSZ8061 PHY • Quad-SPI with eXecute-In-Place• High-speed USB host and device with on-chip high-speed PHY• CMOS image sensor interface• AES hardware-encryption engines, TRNG and SHA-based memory integrity checker• Advanced analog front end based on dual 2 Msps, 12-bit ADCs, including 16-bit average, with up to 24 channels, offset error correction and gain control• Dual 2 Msps, 12-bit DAC and analog comparator • 64- to 144-pin package options• Extended industrial temperature range from −40°C to 105°CDevelopment ToolsSAMV71 Xplained Ultra Evaluation Kit (ATSAMV71-XULT)The SAM V71 Xplained Ultra evaluation kit is ideal for evaluating and prototyping with the SAMV71, SAM V70, SAM S70 and SAM E70 MCUs. Extension boards to the SAM V71 Xplained Ultra can be purchased individually. This kit is also compatible with Arduino Shields.SAME70 Xplained Evaluation Kit (ATSAME70-XPLD)The SAME70-Xplained Evaluation Kit is ideal for evaluating and prototyping with the Microchip SAMS70 and SAME70 MCUs. It provides connectivity for Eth-ernet, HS USB and SD Cards as well as2-XPRO extension headers. Extension boards for the SAME70Xplained can be purchased individually.The Microchip name and logo and the Microchip logo are registered trademarks of Microchip Technology Incorporated in the U.S.A. and other countries. All other trademarks mentioned herein are property of their respective companies. © 2017, Microchip Technology Incorporated. All Rights Reserved. Printed in the U.S.A. 6/17DS60001427CPackage Options*QFN with wettable Flanks。
CE 安全要求与产品说明书
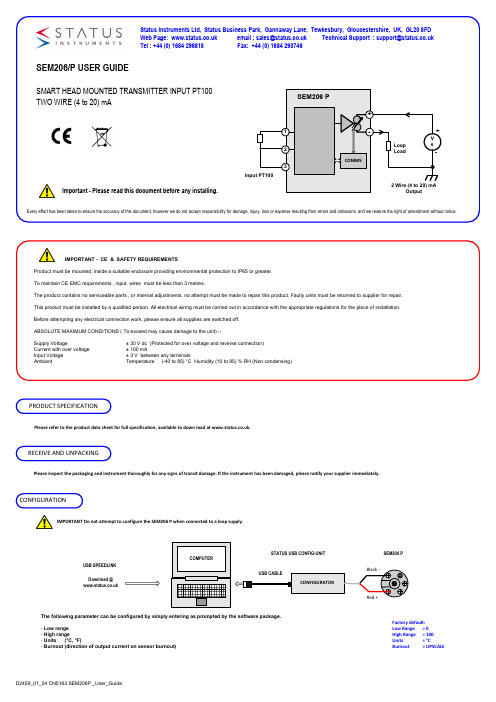
IMPORTANT -CE & SAFETY REQUIREMENTSProduct must be mounted, inside a suitable enclosure providing environmental protection to IP65 or greater.To maintain CE EMC requirements , input wires must be less than 3 metres.The product contains no serviceable parts , or internal adjustments. no attempt must be made to repair this product. Faulty units must be returned to supplier for repair. This product must be installed by a qualified person. All electrical wiring must be carried out in accordance with the appropriate regulations for the place of installation. Before attempting any electrical connection work, please ensure all supplies are switched off.ABSOLUTE MAXIMUM CONDITIONS ( To exceed may cause damage to the unit) :-Supply Voltage± 30 V dc (Protected for over voltage and reverse connection)Current with over voltage± 100 mAInput Voltage± 3 V between any terminalsAmbient Temperature (-40 to 85) °C Humidity (10 to 95) % RH (Non condensing)SEM206/P USER GUIDEEvery effort has been taken to ensure the accuracy of this document, however we do not accept responsibility for damage, injury, loss or expense resulting from errors and omissions, and we reserve the right of amendment without notice.Important -Please read this document before any installing.PRODUCT SPECIFICATIONRECEIVE AND UNPACKINGCONFIGURATIONPlease refer to the product data sheet for full specification, available to down load at .Please inspect the packaging and instrument thoroughly for any signs of transit damage. If the instrument has been damaged, please notify your supplier immediately.The following parameter can be configured by simply entering as prompted by the software package.· Low range· High range· Units (°C, °F)· Burnout (direction of output current on sensor burnout)Factory default:Low Range= 0High Range= 100Units= °CBurnout= UPSCALE IMPORTANT Do not attempt to configure the SEM206 P when connected to a loop supply.Download @SEM206 PUSB SPEEDLINKSTATUS USB CONFIG-UNITSUPPLY (Vs) = (10 to 30) V dcINPUT CONNECTIONPT100 wire must be equal length and type .To maintain CE compliance cable length must be less than3 Metres.OUTPUT CONNECTIONUse twisted pair or screened cables for cable lengthsgreater than 30 Metres. Max cable length 1000 Metres.Ensure loop is grounded at one point.ELECTRICAL INSTALLATIONScrew DriverTURN OFF SUPPLY BEFORE WORKING ON ANY ELECTRICAL CONNECTIONINPUTPT100。
PolarFire SoC FPGA:工程样本(ES)设备 55900219 版本1.0 7 20

ER0219Errata PolarFire SoC FPGA: Engineering Samples (ES)DevicesMicrosemi HeadquartersOne Enterprise, Aliso Viejo,CA 92656 USAWithin the USA: +1 (800) 713-4113 Outside the USA: +1 (949) 380-6100 Sales: +1 (949) 380-6136Fax: +1 (949) 215-4996Email: *************************** ©2020 Microsemi, a wholly owned subsidiary of Microchip Technology Inc. All rights reserved. Microsemi and the Microsemi logo are registered trademarks of Microsemi Corporation. All other trademarks and service marks are the property of their respective owners. Microsemi makes no warranty, representation, or guarantee regarding the information contained herein or the suitability of its products and services for any particular purpose, nor does Microsemi assume any liability whatsoever arising out of the application or use of any product or circuit. The products sold hereunder and any other products sold by Microsemi have been subject to limited testing and should not be used in conjunction with mission-critical equipment or applications. Any performance specifications are believed to be reliable but are not verified, and Buyer must conduct and complete all performance and other testing of the products, alone and together with, or installed in, any end-products. Buyer shall not rely on any data and performance specifications or parameters provided by Microsemi. It is the Buyer’s responsibility to independently determine suitability of any products and to test and verify the same. The information provided by Microsemi hereunder is provided “as is, where is” and with all faults, and the entire risk associated with such information is entirely with the Buyer. Microsemi does not grant, explicitly or implicitly, to any party any patent rights, licenses, or any other IP rights, whether with regard to such information itself or anything described by such information. Information provided in this document is proprietary to Microsemi, and Microsemi reserves the right to make any changes to the information in this document or to any products and services at any time without notice.About MicrosemiMicrosemi, a wholly owned subsidiary of Microchip T echnology Inc. (Nasdaq: MCHP), offers a comprehensive portfolio of semiconductor and system solutions for aerospace & defense, communications, data center and industrial markets. Products include high-performance and radiation-hardened analog mixed-signal integrated circuits, FPGAs, SoCs and ASICs; power management products; timing and synchronization devices and precise time solutions, setting the world's standard for time; voice processing devices; RF solutions; discrete components; enterprise storage and communication solutions, security technologies and scalable anti-tamper products; Ethernet solutions; Power-over-Ethernet ICs andmidspans; as well as custom design capabilities and services. Learn more at .Contents1Revision History . . . . . . . . . . . . . . . . . . . . . . . . . . . . . . . . . . . . . . . . . . . . . . . . . . . . .11.1Revision 1.0 . . . . . . . . . . . . . . . . . . . . . . . . . . . . . . . . . . . . . . . . . . . . . . . . . . . . . . . . . . . . . . . . . . . . . . . 1 2Errata for PolarFire SoC Engineering Samples . . . . . . . . . . . . . . . . . . . . . . . . . . . . .22.1Sample Revisions . . . . . . . . . . . . . . . . . . . . . . . . . . . . . . . . . . . . . . . . . . . . . . . . . . . . . . . . . . . . . . . . . . 22.2PCB Designs . . . . . . . . . . . . . . . . . . . . . . . . . . . . . . . . . . . . . . . . . . . . . . . . . . . . . . . . . . . . . . . . . . . . . . 22.3ES Device Identification . . . . . . . . . . . . . . . . . . . . . . . . . . . . . . . . . . . . . . . . . . . . . . . . . . . . . . . . . . . . . . 3 3Errata Descriptions and Workarounds . . . . . . . . . . . . . . . . . . . . . . . . . . . . . . . . . . . .43.1Microprocessor Subsystem (MSS) cannot Access System Controller SPI Flash . . . . . . . . . . . . . . . . . . 43.2AXI Switch Memory Protection Unit (MPU) is not Operational . . . . . . . . . . . . . . . . . . . . . . . . . . . . . . . . . 53.3MSS I2C peripheral will Work only with MSS Core Version 2.0.108 and above . . . . . . . . . . . . . . . . . . . 53.4In Worst-case Scenario, MSS CPU's Frequency is Limited to 600 MHz . . . . . . . . . . . . . . . . . . . . . . . . . 53.5When MSS Works as a Master, DRI Interrupt Line should not be Used . . . . . . . . . . . . . . . . . . . . . . . . . 63.6DRI Error and DRI Fault Interrupts are not Connected to the Maintenance Interrupt . . . . . . . . . . . . . . . 63.7MSS GPIO Configuration Registers should only be Reset by the CPU's . . . . . . . . . . . . . . . . . . . . . . . . 63.8Fabric APB DRI's Slow Writes Corrupt the SmartDebug JTAG/SPI Read Data . . . . . . . . . . . . . . . . . . . 63.9System Controller Suspend Mode is not Supported . . . . . . . . . . . . . . . . . . . . . . . . . . . . . . . . . . . . . . . . 63.10PolarFire SoC MSS GEM (Gigabit Ethernet MAC) has Issue with 'Undersize Frame Counter' in EthernetStatistics . . . . . . . . . . . . . . . . . . . . . . . . . . . . . . . . . . . . . . . . . . . . . . . . . . . . . . . . . . . . . . . . . . . . . . . . . . 63.11Auto-program or Auto-Update of eNVM should not be Used . . . . . . . . . . . . . . . . . . . . . . . . . . . . . . . . . . 73.12Auto-update System Service will Allow SPI Master Mode to be Used Incorrectly Configured for SPI SlaveMode . . . . . . . . . . . . . . . . . . . . . . . . . . . . . . . . . . . . . . . . . . . . . . . . . . . . . . . . . . . . . . . . . . . . . . . . . . . . 7 4Fabric Transceiver Protocols and DDR Memory Interfaces . . . . . . . . . . . . . . . . . . .7 5Libero SoC Software Errata . . . . . . . . . . . . . . . . . . . . . . . . . . . . . . . . . . . . . . . . . . . .7 6Embedded Software Errata . . . . . . . . . . . . . . . . . . . . . . . . . . . . . . . . . . . . . . . . . . . .7Figure 1ES Identification Markings . . . . . . . . . . . . . . . . . . . . . . . . . . . . . . . . . . . . . . . . . . . . . . . . . . . . . . . . 3TablesTable 1Sample Revisions . . . . . . . . . . . . . . . . . . . . . . . . . . . . . . . . . . . . . . . . . . . . . . . . . . . . . . . . . . . . . . . 2 Table 2PolarFire SoC ES Operating Conditions . . . . . . . . . . . . . . . . . . . . . . . . . . . . . . . . . . . . . . . . . . . . . . 2 Table 3Summary of PolarFire SoC ES FPGA Errata . . . . . . . . . . . . . . . . . . . . . . . . . . . . . . . . . . . . . . . . . . 4Revision History1Revision HistoryThe revision history describes the changes that were implemented in the document. The changes arelisted by revision, starting with the current publication.1.1Revision 1.0The first publication of this document.2Errata for PolarFire SoC Engineering SamplesThe PolarFire ® SoC FPGA family engineering samples (ES) are subject to the limitations described inthis errata document. This document contains updated information about any known engineeringsample-specific issues and provides the available limitations and workarounds. Engineering sampleissues identified in this document will be corrected in subsequent production revision of the devices listedin the following table. Contact Microchip Technical Support for more information.2.1Sample RevisionsThe following table lists the sample revisions released. If not specified, the errata items impact all ESrevisions listed in the table.The following table lists the operating conditions for the PolarFire-SoC engineering samples. Theoperating conditions for production devices follow datasheet specifications. These operating conditionsare for engineering samples only. See DS0147: PolarFire SoC Advanced Datasheet for productionspecifications.2.2PCB DesignsFor information about how to determine proper signal pinout, see UG0901: PolarFire SoC FPGA BoardDesign Guidelines User Guide . The proper signal pinout is required for all clocking, transceiver, andFPGA pin recommendations.Table 1 •Sample Revisions Device PackagesRevisionMPFS250T FCVG484EES1FCG1152EES FCSG536EESFCVG784EESTable 2 • PolarFire SoC ES Operating ConditionsOperation Temperature Range VDD Core Voltage (Programming Voltage Only)Program / Erase 20 °C to 50 °C 11.T J = Junction Temperature1.0 ± 0.03 V 22.VDD = 1.05 V ± 0.03 V is not supported on PolarFire SoC ES silicon but will be supported for Production silicon. However, VDDA is supported at both 1.0 V and 1.05 V ± 0.03 V on ES silicon.20 °C to 50 °C2.3ES Device IdentificationPolarFire SoC FPGA engineering samples can be identified by the temperature grade field in the lowerleft-hand corner. As the following illustration shows, an ES annotation will appear in the temperaturegrade field indicating device is engineering sample and revision marking is shown along right side ofcode mark.Figure 1 • ES Identification Markings3Errata Descriptions and WorkaroundsThe following sections describe device errata and the workarounds wherever applicable.The following table lists the ES specific device errata and the affected PolarFire SoC ES device revision. For die revision part marking specification, see ES Identification Markings, page 3.3.1Microprocessor Subsystem (MSS) cannot Access System Controller SPI FlashPolarFire SoC ES silicon has an issue in system controller between the analog dynamic reconfiguration interface (DRI) register block and SPI block that results in incorrect data during reads from the RXFIFO. Writes and reads to other SPI registers (for example, control, frame count, Tx data and direct access) work correctly.Due to this issue, the MSS cannot directly access the PolarFire SOC external flash device via the SPI controller attached to the system controller using DRI bus.This limitation will be fixed in production silicon.Table 3 •Summary of PolarFire SoC ES FPGA Errata Description Silicon Revisions DetailsMicroprocessor Subsystem (MSS) cannot Access SystemController SPI Flash, page 41Applicable to all PolarFire SoC ES versions.AXI Switch Memory Protection Unit (MPU) is not Operational,page 5.MSS I2C peripheral will Work only with MSS Core Version2.0.108 and above, page 5.In Worst-case Scenario, MSS CPU's Frequency is Limited to600 MHz, page 5When MSS Works as a Master, DRI Interrupt Line should notbe Used, page 6DRI Error and DRI Fault Interrupts are not Connected to theMaintenance Interrupt, page 6MSS GPIO Configuration Registers should only be Reset bythe CPU's, page 6Fabric APB DRI's Slow Writes Corrupt the SmartDebugJTAG/SPI Read Data, page 6System Controller Suspend Mode is not Supported, page 6PolarFire SoC MSS GEM (Gigabit Ethernet MAC) has Issuewith 'Undersize Frame Counter' in Ethernet Statistics, page 6Auto-program or Auto-Update of eNVM should not be Used,page 7Only Applicable to PolarFire SoC ES Revision 1 silicon.Auto-update System Service will Allow SPI Master Mode to beUsed Incorrectly Configured for SPI Slave Mode, page 73.2AXI Switch Memory Protection Unit (MPU) is notOperationalPolarFire SoC ES parts have silicon bug that may cause AXI bus issues when illegal messages arerejected by PolarFire SoC memory protection unit (MPU). For this reason, MPU is currently disabled aspart of system start-up firmware. This means that the MPU's are inactive and will not generate accesswarnings or interrupts.This limitation will be fixed in production silicon.3.3MSS I2C peripheral will Work only with MSS CoreVersion 2.0.108 and aboveIn PolarFire SoC ES parts, MSS I2C clock and data signals are pulled low after MSS initialization. MSScore in Libero 12.4 has the required workaround for this MSS I2C issue in ES device. Use MSS coreversion 2.0.108 or above for Libero 12.4 or use Libero 12.5 and above where workaround will beautomatically applied when the user selects an ES part. Note that the workaround fix in Libero is usingthe fabric in all cases and the user will need to program the FPGA portion to have the MSS I2C working.This limitation will be fixed in production silicon. User designs using MSS I2C in ES silicon can not beported to production silicon. Users need to regenerate the MSS configurator and bitstream when portingdesign to production silicon and make sure to target the correct device.3.4In Worst-case Scenario, MSS CPU's Frequency isLimited to 600 MHzIn PolarFire SoC ES, maximum achievable MSS CPU frequency is 625 MHz for both STD and -1 speedgrades. The eMMC/SD controller requires a fixed 200 MHz clock, fed from the same PLL as the CPU.The CAN controller requires a clock, which is a multiple of 8 MHz, also fed from the same PLL as theCPU. However, in engineering samples, the following limitations applies for these clock frequencies:1.If the eMMC/SD controller is being used in the system, the maximum MSS CPU clock frequency is600 MHz.2.If the CAN controller is being used in the system (but not the eMMC/SD controller), the maximumMSS CPU clock frequency is either 624 MHz (with 100 MHz reference clock) or 620 MHz (with125 MHz reference clock). There is a general restriction in the available MSS CPU frequency:•If using 100 MHz reference clock for MSS PLL:When no eMMC/SD or CAN is being used, the MSS CPU frequencies are—all integer values from 2through 625•When eMMC/SD being used (with or without CAN), the MSS CPU frequencies are:2, 4, 5, 6, 8, 10, 12, 15, 16, 20, 24, 25, 30, 32, 40, 48, 50, 60, 75, 80, 100, 120, 125, 150, 160,200, 240, 250, 300, 400, 500, 600.•When CAN being used (without eMMC/SD), the MSS CPU frequencies are:All integer values from 2 through 156,Every 2nd value from 158 through 312Every 4th value from 316 through 624•If using 125 MHz reference clock for MSS PLL:•When no eMMC/SD or CAN is being used, the MSS CPU frequencies are—all integer values from 2 through 250 and every 5th value from 255 through 625.•When eMMC/SD being used (with or without CAN), the MSS CPU frequencies are:2, 4, 5, 6, 8, 10, 12, 15, 16, 20, 24, 25, 30, 32, 40, 48, 50, 60, 75, 80, 100, 120, 125, 150, 160,200, 240, 250, 300, 400, 500, 600•When CAN being used (without eMMC/SD), the MSS CPU frequencies are:2 – 32, 34, 35, 36, 38, 40, 42, 44, 45, 46, 48, 50, 52, 54, 55, 56, 58, 60, 62, 64, 65, 68, 70, 72,75, 76, 80, 84, 85, 88, 90, 92, 95, 96, 100, 104, 105, 108, 110, 112, 115, 116, 120, 124, 125,128, 130, 135, 136, 140, 144, 145, 150, 152, 155, 160, 168, 170, 176, 180, 184, 190, 192, 200,208, 210, 216, 220, 224, 230, 232, 240, 248, 250, 260, 270, 280, 290, 300, 310, 320, 340, 360,380, 400, 420, 440, 460, 480, 500, 520, 540, 560, 580, 600, 620.Errata Descriptions and WorkaroundsNote:The User Crypto may also get its clock from the MSS PLL but has the option of getting its clock from the FPGA fabric. This does not place the same limitations on MSS CPU frequency.This limitation will be fixed in production silicon.3.5When MSS Works as a Master, DRI Interrupt Line shouldnot be UsedThe DRI interrupt system should not be used with the PolarFire SOC ES silicon device. If enabled, theinterrupt input to the fabric and MSS from the DRI system cannot be cleared without a device reset. As aworkaround, few events that DRI interrupts may have been used for are also available as status signalsto the fabric.This limitation will be fixed in production silicon.3.6DRI Error and DRI Fault Interrupts are not Connected tothe Maintenance InterruptDRI Error and DRI Fault interrupt bits in the Maintenance Register function as expected but will notcause a CPU interrupt—the interrupt enable is effectively disabled in ES silicon.This limitation will be fixed in production silicon.3.7MSS GPIO Configuration Registers should only be Resetby the CPU'sThe three MSS GPIO blocks do not support the fabric reset functionality in PolarFire SoC ES silicon. TheGPIO blocks should be configured so that the byte resets use the internal MSS reset, that is, theGPIO_CR configuration register 'soft_reset_select' bits should not be set to 0.This limitation will be fixed in production silicon.3.8Fabric APB DRI's Slow Writes Corrupt the SmartDebugJTAG/SPI Read DataA fabric DRI write operation to one of the PCIe subsystem (PCIESS) controllers APB configurationblocks may corrupt a SmartDebug JTAG/SPI read operation; the read will return zero. If this issuspected, the SmartDebug operation should be carried out again until the expected data is received.This limitation will be fixed in production silicon.3.9System Controller Suspend Mode is not SupportedSystem controller suspend mode is not supported in PolarFire SoC ES silicon parts. This limitation will befixed in production silicon.3.10PolarFire SoC MSS GEM (Gigabit Ethernet MAC) hasIssue with 'Undersize Frame Counter' in EthernetStatisticsIn the Polarfire SoC, for 1Gbps half-duplex mode, Ethernet statistics "undersize_frames" counter withinthe GEM increments for received frame sizes less than 512 bytes instead of incrementing for less than64 bytes. Subsequent transition to 1Gbps full-duplex mode does not resolve the issue. User should notethat 'Undersize Frame counter' reports correctly for all other speeds and duplex modes, including 1Gbpsfull-duplex if not transitioning from half-duplex.Fabric Transceiver Protocols and DDR Memory Interfaces3.11Auto-program or Auto-Update of eNVM should not beUsedBoot initiated auto-program/auto-update of eNVM will fail. Auto-program/update of eNVM should not beused on PolarFire SoC ES silicon. This limitation will be fixed in production silicon.3.12Auto-update System Service will Allow SPI Master Modeto be Used Incorrectly Configured for SPI Slave ModeIn PolarFire SoC ES silicon, auto-update system service will allow SPI master mode to be used on aPolarFire SoC ES silicon device configured in SPI slave mode. Ideally, it should throw an error. If thisservice is used on device configured in slave mode, there is a possibility of contention on the SPI flashpins. Fix for this issue is that auto-update system service should not be used if the PolarFire SoC ESsilicon device is configured for slave mode.This limitation will be fixed in production silicon.4Fabric Transceiver Protocols and DDR Memory InterfacesSupported transceiver protocols and DDR memory interfaces are reused features from PolarFire FPGA.These are currently in plan for validation and these features are in the process of being validated. Thesefeatures are expected to work with similar robustness as in PolarFire FPGAs.5Libero SoC Software ErrataFor more Libero SoC related "known Issues and limitations", see Libero SoC Release Notes document. 6Embedded Software ErrataSee the "Known Issues and useful tips" section in SoftConsole Release Notes document.These SoftConsole known issues are under active investigation to ascertain the root cause and toresolve the underlying problems with the intention that these are resolved in a future release.。
Pericom Semiconductor PI3USB30532 and PI3USB31532
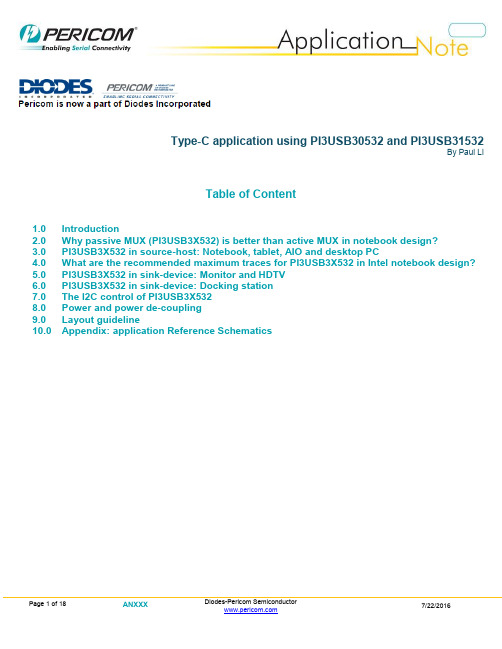
Type-C application using PI3USB30532 and PI3USB31532By Paul LiTable of Content1.0 Introduction2.0 Why passive MUX (PI3USB3X532) is better than active MUX in notebook design?3.0 PI3USB3X532 in source-host: Notebook, tablet, AIO and desktop PC4.0 What are the recommended maximum traces for PI3USB3X532 in Intel notebook design?5.0 PI3USB3X532 in sink-device: Monitor and HDTV6.0 PI3USB3X532 in sink-device: Docking station7.0 The I2C control of PI3USB3X5328.0 Power and power de-coupling9.0 Layout guideline10.0 Appendix: application Reference Schematics1.0 IntroductionThe PI3USB30532, PI3USB31532 type-C cross switch family is developed using cutting-edge technology to achieve high performance of DP 1.2, DP 1.3, USB 3.0, USB 3.1 signals in type-C applications. PI3USB3X532 is fully compliant to type- C specifications. PI3USB3X532 was first to the market and successfully designed in many and various applications, such as notebook, tablet, AIO, PC, monitor, HDTV, docking stations, etc. PI3USB3X532 was also designed in Intel reference schematic and designed in Intel customer reference demonstration tablet.2.0 Why passive MUX (PI3USB3X532) is better than active MUX in notebook design?The market requests notebooks:Running for 6-8 hours in battery operationBoot-up after power-off for 6-8 daysIntel mobile CPU/chipset can now achieve 6W power consumption, thus:The ~0.4W to ~0.6W power consumption from an active MUX is way too high and not reasonable.Especially when compared to the <0.003W power consumption from PI3USB3X532, which is a 99% power saving compared to an active MUX.3.0 PI3USB3X532 in source-host: Notebook, tablet, AIO and desktop PCFigure 1, PI3USB30532, PI3USB31532 in notebook, tablet all-in-one and desktop PC4.0 What are the recommended maximum traces for PI3USB3X532 in Intel notebook design?4.1 DP 1.2, DP 1.3In Intel Kabylake design guideline, Intel recommends maximum 8” DP 1.2 trace without passive MUX and 4.1” with passive MUX as to pass DP 1.2 compliance test.Intel deducted 3.9” trace from the 8” DP 1.2 trace for the passive MUX, which is conservative for a high performance passive MUX such as PI3USB3X532, as explained in figure 2, figure 3a, figure 3b and in table-1 below.Based on the PI3USB30532 DP 1.2 eye compliance test results in figure 3a and figure 3b, as well the trace data in figure 2 and table-1, it is recommended as below.Maximum 6.2” trace for DP 1.2 (5.4Gbps) path, as:Intel DP 1.2 source → PI3USB3X532 → type-C connectorMaximum 4.0” trace for DP 1.3 (8Gbps) path, as:Intel DP 1.3 source → PI3USB31532 → type-C connector(Assuming the layout and schematics are as recommended as using 90ohm traces without chokes, etc., and in reasonable system conditions)4.2 USB3.0, USB3.1Based on the PI3USB30532 USB 3.0 eye compliance test results in figure 4a and figure 4b, as well the trace data in figure 2 and table-1, it is recommended as below.Maximum 8.5” trace for USB3.0 (5Gbps) path, as:USB3.0 host → PI3USB3X532 → type-C connectorMaximum 4.5” trace for USB3.1 (10Gbps) path, as:USB3.1 host → PI3USB31532 → type-C connector(Assuming the layout and schematics are as recommended below and in reasonable system conditions)Analyzer, as setup in figure-2.Note:The data above is not linear, because the performances vary with different switch-routings and signal-types between PI3USB30532 and PI3USB31532, while PI3USB31532 has better performance than PI3USB30532 mostly at higher speed.NA is for not applicable.4.3 The insertion loss of 3” differential trace on Intel trace boardFigure 2 the insertion loss of 3” FR4 differential trace on Intel trace board is measured using Agilent N5230A 20GHz Network Analyzer (chart by James Liu)4.4 The PI3USB30532 Intel Haswell MB DP 1.2 eye compliance test resultFigure 3a the eye of DP 1.2 (5.4Gbps) compliance test using PI3USB30532 setup (figure 3b) with Asus H97i-plus MB (Intel Haswell) and 7”trace passed the DP 1.2 HBR2 compliance test 3.1 using Tektronix scope at 400mV, 3.5db pre-emphasis. The upper waveform is at T3 with emulation cable in scope. The lower waveform is at T2 without emulation cable (waveform by Jerry Chou).4.5 The test setup of 4.4Figure 3b the test setup of PI3USB30532 with 7” trace (2.8”+3.9”+0.3”) using Intel Haswell DP 1.2 source passed DP 1.2 (5.4Gbps) eye compliance test 3.1 as in figure 3aFigure 4a the Tx and Rx eyes passed the USB 3.0 (5Gbps) compliance test at the USB 3.0 connector of notebook (Intel Haswell) without PI3USB30532 EV board. To be compared to figure 4b with PI3USB30532 EVB (waveform by Jerry Chou)Figure 4b the Tx and Rx eyes passed USB 3.0 (5Gbps) compliance test with 10.2” trace (5.5”+3.3”+1.4”) using notebook (Intel Haswell) and PI3USB30532 EV board. To be compared to figure 4a without PI3USB30532 EV board (waveform by Jerry Chou).5.0 PI3USB3X532 in sink-device: Monitor and HDTVFigure 5, PI3USB30532, PI3USB31532 in monitor and HDTVNo active DP re-driver and USB3.0 re-driver needed in type-C MUX (PI3USB30532) or between the switches in cascading (PI3USB30532, PI3WVR12412, PI3PCIE3242).o Because there are sufficient total source and sink equalization, as:▪Up to 9db output pre-emphasis (equalization) in DP source and USB3.0 Tx▪Up to 9db input equalization in DP scalar and USB3.0 Rx receiver.o The total 18db equalization in source and sink is sufficient to compensate the estimated total insertion loss from the topology in figure 5:▪Max 7.7db from total 10” traces▪Max 4db from 2m type-Cable▪Max 1.5db from PI3USEB30532▪Max 1.5db from PI3WVR12412 or PI3PCIE32426.0 PI3USB3X532 in sink-device: Docking stationFigure 6, PI3USB30532, PI3USB31532 in docking station7.0 The I2C control of PI3USB3X532PI3USB3X532 has total three I2C registers as Conf [2:0], which is mapped between the I2C control signals and the configuration tables (source, sink) as in figure-7.When using I2C interface to control PI3USB3X532, the I2C controller (in PD or MCU) will need sending total three bytes to PI3USB30532 in sequence as:Start →→#1 byte for address as “10101000” (assuming A1_A0 set to 00, while last 0 for write)”→#2 byte for chip-ID as fixed “00000000”→#3 byte for Conf [2:0] control as “00000111” (assum ing Conf [2:0]=111 as for USB3+DPx2 swapped) →Stop (must have stop, otherwise uncertainty may occur)Figure 7, The I2C-control of the configuration table for source-sink (source-sink tables are the same)I2C-controls PI3USB30532 in real applicationFor both source and sink applications, when a type-C plug is plugging into the source or sink type-C connectors with PI3USB30532 and PD, the I2C controller (in PD or MCU) shall I2C-control PI3USB30532 as:DPx4 only, non-swap:Start →10101000 (last 0 for write) →00000000→00000010→stopDPx4 only, swapped:Start →10101000 →00000000→00000011→stopUSB3.0 only, non-swap:Start →10101000 →00000000→00000100→stopUSB3.0 only, swapped:Start →10101000 →00000000→00000101→stopUSB3+DPx2, non-swap:Start →10101000 →00000000→00000110→stopUSB3+DPx2, swapped:Start →1010100 →00000000→00000111→stop8.0 Power and power de-couplingUse 0.1uf in size of 0402 for all the Vdd (any power pins) pins of the IC device, as close to the Vdd pins as possible, within 2-3mm if feasible.Use dedicated Vdd and GND planes for to minimize the jitters coupled between channel trough power sources.9.0 Layout guideline9.1 Recommend 90 ohm differential impedance trace for differential DP and USB 3.0 signalsFigure 8, the trace width and clearance❑Use 6-7-6 mils for trace-space-trace for the micro-strip lines (the traces on top and bottom layers) for 90 ohm differential impedance.❑Use 6-5-6 mils for trace-space-trace for the strip-lines (the traces inside layers) for 90 ohm differential impedance.❑Use FR4.❑Using standard 4 to 8 layers stack-up with 0.062 inch thick PCB.❑For micro-strip lines, using ½ OZ Cu plated is ok.❑For strip-lines in 6 plus players, using 1 OZ Cu is better.❑The trace length miss-matching shall be less than 5 mils for the “+” and “–“ traces in the same pairs❑More pair-to-pair spacing for minimal crosstalk❑Target differential Zo of 90 ohm ±15%9.2 The PCB Layers StackupNo new PCB technology required. Use FR4 is fine.Using standard 4 to 8 layers stack-up with 0.062 inch thick PCB.For micro strip lines, using ½ OZ Cu plated is ok.For strip line in 6 plus players, using 1 OZ Cu is better.Figure 9, the stackup9.3 The Layout Guidance for the Trace RoutingsFigure 10, The layout guidance for the trace routingsDon’t use EMI chokes, because PI3USB30532 and PI3USB31532 are passive switches not having EMI issues.The differential traces shall be away from the strong EMI source and devices, such as TTL, switching-power traces anddevices, with at least 30mil to 50mil space.No other components shall piggy ride on the differential traces.10 Appendix: application Reference SchematicsC76-C83 a re "mus t h ave" to pr eve nt n on-DP c omp lia ntd t ype-C c onn ecto r, bec ausewit hou t EM I i ssue.TV SPI3USB30532 DFP-source reference schematic for type-C PD/DP/ALT applicationTV S d t ype-C c onn ect or, bec aus e wit hou t EM I i ssu e.C55-C61, C63 are "m ust hav e" to prev ent no n-DP co mpl iant 3.3V PI3USB30532 UFP-sink reference schematic for type-C PD/DP/ALT applicationPI3USB31532 DFP-source reference schematic for type-C PD/DP/ALT applicationTV Sty pe-C co nnec tor , be cau se ith out EMI iss ue.C118-C 125 are "m ust hav e" t o p reve nt non-DP comp lia nt 3.3VC97-C103, C105 a re "mu st h ave" t o pr eve nt n on-DP comp lia nt 3.3Vd t ype-C c onn ecto r, bec ausewit hou t EM I i ssue.TV SPI3USB31532 UFP-sink reference schematic for type-C PD/DP/ALT application。
Pycom FiPy 产品说明书

FiPy 1.0With Sigfox,LoRa,WiFi,BLE and cellular LTE-CAT M1/NB1,the FiPy is the latest Pycom MicroPython enabled micro controller on the market today –the perfect enterprise grade IoT platform for your connected Things.Create and connect your things everywhere.Fast.FiPy Features-Powerful CPU-Five Networks:WiFi,BLE,cellular LTE-CAT M1/NB1,LoRa and Sigfox -1KM Wifi Range -MicroPython enabled-Fits in a standard breadboard (with headers)-Ultra-low power usage:a fraction compared to other connected micro controllersProcessing-Espressif ESP32SoC-Dual processor +WiFi radio System on Chip.-Network processor handles the WiFi connectivity and the IPv6stack-Main processor is entirely free to run the user application -An extra ULP-coprocessor that can monitor GPIOs,the ADC channels and control most of the internal peripherals during deep-sleep mode while only consuming 25uAInterfaces-2x UART,2x SPI,I2C,I2S,micro SD card -Analog channels:8x12bit ADCs,2x8bit DAC -Timers:2x64bit with PWM with up to 16channels -DMA on all peripherals -GPIO:Up to 22Use the Pymakr IDESuper easy code editor to write your Python scriptsQuick VerificationFor easy and fast debugging use the interactive shell that is accessible through telnet or one of the serial portsEasy UploadUpload your scripts,and any other files you want to the FiPy via the FTP serverLocally or remotelyReset the SiPy (you can do it locally,or remotely via Telnet)MechanicalSize:55mm x 20mm x 3.5mmExternal WiFi and 4MB RAMExternal LoRa andBluetooth antenna ESP32Dual Core connectorSigfox antennaMicrocontroller and connectorWiFi/Bluetooth 4.2RF switchradioReset switchWS2812RGB LEDInternal WiFi and LoRa and Sigfox 3V3Ultra-Low Bluetooth Antennatransceiver -Noise switchingregulator8MB flash memoryNano SIM socketLTE CAT M1/NB1LTE CAT M1/NB1transceiverantenna connectorHash /encryptionSecurity &CertificationsSHA,MD5,DES,AES-SSL/TLS support up to 1.2WiFi Networking -WPA Enterprise security 802.11b/g/n 16mbps -AES encryption engineMemoryBluetooth-RAM:4MBLow energy and classic-Flash Memory:8MB RTC-GPIO:Up to 22Running at 32KHz-Hardware floating point RangeaccelerationNode range:Up to 50km-Python multi-threadingPower-Voltage Input:3.3V -5.5V-3v3output capable of sourcing up to 400mAWith dozens of ready to use templates and libraries soon to be available on the Pycom Exchange,developing a new IoT solution is now easier and faster.FiPy1.0Network SpecificationsSigfox Operating Frequencies LoRa Operating FrequenciesRCZ1-868MHz(Europe)-868MHz(Europe)at+14dBm maximumRCZ2-902MHz(US,Canada and Mexico)-915MHz(North and South America,Australia and New Zea-RCZ3-(Japan and Korea)land)at+20dBm maximumRCZ4-920-922MHz(ANZ,Latin America and S-E Asia)Sigfox Specifiction-TI CC1125NarrowbandTransceiver-Class0device.Maximum Tx power:-+14dBm(Europe)-+22dBm(America)-+22dBm(Australia and New Zealand)-Node range:Up to50km-Sigfox pre-certified(October2016)-Power-Sigfox(Europe):17mA in Rx mode,47mA in Txmode and0.5uA in standby-Sigfox(Australia,New Zealand and South America):24mA in rX mode,257mA in Tx mode and0.5uAin standbyBluetooth Networking-Low energy and classic-Compliant with Bluetooth v4.2BR/EDR and BLE specification -Class-1,Class-2and Class-3transmitter without external power amplifer-Enhanced power control-+10dBm transmitting power-NZIF receiver with-98dBm sensitivity-Adaptive Frequency Hopping(AFH)-Standard HCI based on SDIO/SPI/UART-High speed UART HCI,up to4Mbps-BT4.2controller and host stack-Service Discover Protocol(SDP)-General Access Profile(GAP)-Security Manage Protocol(SMP)-Bluetooth Low Energy(BLE)-ATT/GATT-HID-All GATT-based profile supported-SPP-Like GATT-based profile-BLE Beacon-A2DP/AVRCP/SPP,HSP/HFP,RFCOMM-CVSD and SBC for audio codec-Bluetooth Piconet and Scatternet LoRa Specifiction-Power consumption:10mA Rx,28mA Tx-LoRaWAN stack-Class A and C devices-Node range:Up to40km-Nano-gateway:Up to22km(Capacity up to100nodes)LTE-M Operating Frequencies-34bands supports from699Mhz to2690Mhz(Totalworld-wide support)LTE-M Specification-One single chip for both CAT M1and NB1(yes,only one chip) -3GPP release13LTE Advanced Pro-Supports narrowband LTE UE categories M1/NB1-Integrated baseband,RF,RAM memory andpower management-Reduced Tx power class option-Peak power estimations:TX current=420mA peak @1.5Watt RX current=330mA peak@1.2Watt-Data rates:-300kbps DL-375kbps UL(LTE Cat M1in1.4Mhz,HD-FDD)-40kbps DL-55kbps UL(LTE Cat M2in200kHz,HD-FDD)WiFi Networking-Up to1km range-802.11b/g/n16mbps-Power:12mA in active mode,5uA in standbyEU Regulatory ConformanceHereby,Pycom Ltd declares that this device is in compliance with the essential requirements and other relevant provisionsof Directive1999/5/ECFederal Communication Commission Interference StatementThis device complies with Part15of the FCC Rules.Operation is subject to the following two conditions:(1)This device may not cause harmful interference.(2)This device must accept any interference received, including interference that may cause undesired operation. CAUTION:Changes or modifications not expressly approved by the party responsible for compliance could void the user's authority to operate the equipment.NOTE:This equipment has been tested and found to comply with the limits for a Class B digital device,pursuant to Part15of the FCC Rules.These limits are designed to provide reasonable protection against harmful interference in a residential installation. This equipment generates uses and can radiate radio frequency energy and,if not installed and used in accordance withthe instructions,may cause harmful interference to radio communications.However,there is no guarantee that interference will not occur in a particular installation.If this equipment does cause harmful interference to radio or television reception,which can be determined by turning the equipment off and on,the user is encouraged to try to correct the interference by one or more of the following measures:-Reorient or relocate the receiving antenna.-Increase the separation between the equipment and receiver. -Connect the equipment into an outlet on a circuit different from that to which the receiver is connected.-Consult the dealer or an experienced radio/TV technician for help. RF Warning StatementTo comply with FCC RF exposure compliance requirements,the antennas used for this transmitter must be installed to provide a separation distance of at least20cm from all persons and must not be co-located or operating in conjunction with any other antenna or transmitter.This device is intended only for OEMintegrators under the following conditions:1)The antenna must be installed such that20cm is maintained between the antenna and users,and2)The transmitter module may not be co-located with any other transmitter or antenna.As long as two conditions above are met,further transmitter test will not be required.However,the OEM integrator is still module(s)installed and fully operational.For example,if a host was previously authorized as an unintentional radiator under the Declaration of Conformity procedure without a transmitter certified module and a module is added,the host manufacturer is responsible for ensuring that the after the module is installed and operational the host continues to be compliant with the Part15B unintentional radiator requirements.The module is limited to OEM installation ONLY.The module is limited to installation in mobile or fixed application. We hereby acknowledge our responsibility to provide guidance to the host manufacturer in the event that they require assistance for ensuring compliance with the Part15Subpart B requirements.IMPORTANT NOTE:In the event that these conditions cannot be met(for example certain laptop configurations or co-location with another transmitter),then the FCC authorization is no longer considered valid and the FCC ID cannot be used on the final product.In these circumstances,the OEM integrator will be responsible for reevaluating the end product(including the transmitter)and obtaining a separate FCC authorization.End Product LabelingThis transmitter module is authorized only for use in device where the antenna may be installed such that20cm may be maintained between the antenna and users.The final end product must be labeled in a visible area with the following:“Contains FCC ID:2AJMTFIPY1R”.The grantee's FCC ID can be used only when all FCC compliance requirements are met.The following FCC part15.19statement has to also be available on the label:This device complies with Part15of FCC rules.Operation is subject to the following two conditions:(1)this device may not cause harmful interference and(2)this device must accept any interference received, including interference that may cause undesired operation.Manual Information to the End UserThe OEM integrator has to be aware not to provide information tothe end user regarding how to install or remove this RF module in the user’s manual of the end product which integrates this module.In the user manual of the end product,the end user has to be informed that the equipment complies with FCC radio-frequency exposure guidelines set forth for an uncontrolled environment.The end user has to also be informed that any changes or modifications not expressly approved by the manufacturer could void the user's authority to operate this equipment.The end user manual shall include all requiredregulatory information/warning as show in this manual.The maximum operating ambient temperature of the。
Morpheus electronic MPS-060602高性能双通道IEPE(ICP)传感器信号

MPS-060602高性能双通道IEPE(ICP)传感器信号采集卡使用说明Ver. 1.0第一章产品概述一、产品简介MPS-060602是一款基于USB总线的高性能16位IEPE(ICP)传感器专用信号采集卡。
IEPE(也称ICP)传感器是指一种自带电量放大器或电压放大器的特殊传感器,具有优秀的抗噪声性和易封装性,在加速度检测、振动检测或声音检测中被广泛应用。
MPS-060602是专为IEPE传感器设计的高性能信号采集卡,其内部集成有恒流源和隔直电路,可无需外部电路直接驱动IEPE传感器。
通过高速高分辨率的数据采集单元,MPS-060602可以对各种IEPE传感器信号进行全面而精确的分析。
MPS-060602采用 USB2.0高速总线接口,采用USB自供电,无需外部电源。
其内部包含两路同步的高性能16位ADC,采样率高达每通道450K(每秒45万个样点)。
MPS-060602内部包含两路4mA输出的恒流源,可为IEPE传感器提供恒流激励,并且内置隔直电路,可消除传感器直流偏移电压分量的影响。
MPS-060602还内置了可编程增益放大器,可用来对信号进行放大或衰减,从而获得最佳的采集效果。
MPS-060602采用全金属外壳,具有完整的电磁屏蔽层,抗干扰性强。
MPS-060602采用跨平台的动态链接库提供驱动函数接口,可工作在 Win9X/Me、Win2000/XP、Windows 7等常用操作系统下,支持VB, VC, C++Builder, Dephi,LabVIEW,Matlab等绝大多数编程语言。
此外,MPS-060602还附送了相应的配套应用软件,可实现高速信号触发采集、滤波处理和数据记录等多项高级功能,一些基本应用可以无限编程直接实现,为用户测试板卡性能提供了便利。
二、性能指标2.1、USB总线▪ USB2.0高速总线传输▪支持热插拔和即插即用2.2、IEPE驱动单元▪ 24V驱动电压▪ 4mA恒流输出▪ 10μF隔直电容2.3、采样通道▪ SMA插头输入▪双通道同步采样▪ 100KHz低通滤波▪低零点偏移误差2.4、分辨率▪ 16位(65536)2.5、采样率▪每通道1K - 450K▪可软件编程设置2.6、程控放大器(PGA)▪ PGA = 1、2、5、10▪所有通道PGA相同2.7、量程▪量程 = ±10V/PGA2.8、工作温度▪ 0℃ - 70℃三、应用领域IEPE传感器信号采集便携式仪表和测试设备振动信号分析音频信号采集与处理教学仪器等四、软件资源Windows95/98/NT/2000/XP/WIN7/WIN8下的驱动程序(支持32位和64位系统);通用DLL动态链接库;LabVIEW、VB、VC环境下的编程参考代码;配套应用软件等。
- 1、下载文档前请自行甄别文档内容的完整性,平台不提供额外的编辑、内容补充、找答案等附加服务。
- 2、"仅部分预览"的文档,不可在线预览部分如存在完整性等问题,可反馈申请退款(可完整预览的文档不适用该条件!)。
- 3、如文档侵犯您的权益,请联系客服反馈,我们会尽快为您处理(人工客服工作时间:9:00-18:30)。
Aluminium Electrolytic CapacitorMaterial Data SheetProduct Class: 3-pin capacitors Date 2011.10.20 IMDS ID if availableVersion: 01Product Part(IMDS: semi component)Material Class(IMDS: Material)Material(Classification)VDA 231Substance TMPS**) [wt%]CAS if applicable typical mass of material [wt-%]Traces see 1) Light Metals 1B Aluminium 100 7429-90-5 45Acids, Bases, Salts 6F Ethylene glycol or Gamma-butyrolactone57 80 (without NMP) 107-21-1 96-48-0Acids, Bases, Salts 6F Others*) 20 - Acids, Bases, Salts6FN-Methyl-2-Pyrrolidone***)23 872-50-4 25Thermoplastics 2A Polypropylene 100 9003-07-0 0,1 Active Part Paper, Cardboard5C Cellulose 1009004-34-611,9 Encapsulation Light Metals 1B Aluminium 100 7429-90-5 10Paper, Cardboard5CCellulose56 9004-34-6Duromer 2D Phenolic plastic 44 - 3 Elastomer 2B EPDM rubber 100 25038-36-2 1Thermoplastics 2A Polyvinyl chloride or Polyethylene terephthalate 1009002-86-2 25038-59-93Heavy Metals 1C Copper (E-Cu58 F21-V5)100 7440-50-8 1 TerminationHeavy Metals1CTin100 7440-31-5<0,1Sum in total : 100sizes D x L [mm]18,5 x 30 18,5 x 40weight range [g]8 11sizes D x L [mm]19 x 40weight range [g]11sizes D x L [mm]22.5 x 30 22,5 x 40weight range [g]11 16sizes D x L [mm]25,5 x 30 25,5 x 40weight range [g]15 22part numbersB41336 / B41534 / B41538 B43534Not part of a Product Class Contact Dr. Ildikó Száraz Division SZ ALU QAAddressSzent László u. 6. H-9700 Szombathely / HungaryTel: +36 94 522 319mailto: ildiko.szaraz@*) others: .(not declarable or prohibited substances acc. GADSL) **) typical mass percentage of substance***) Only in special low voltage capacitor types: see detailed list on/web/generator/Web/Sections/Environment/REACH/REA CH__Information/Page,locale=en.htmlI mportant remarks:1)The declaration limit is 0.1% as defined by IEC PAS 61906. Traces are product parts, substances etc. that are below a percentage of 0.1 % by weight, if not otherwise regulated2)This Material Data Sheet contains typical values of the respective products set forth herein. We expressly point out that all values and statements contained herein are based on our best present knowledge and cannot be regarded as binding statements or binding product specifications, unless otherwise explicitly agreed in writing. EPCOS AG AND ITS AFFILIATES HEREBY EXPRESSLY DISCLAIM ANYREPRESENTATION OR WARRANTY, WHETHER EXPRESS, IMPLIED ORSTATUTORY, WITH REGARD TO THE STATEMENTS AND VALUES CONTAINED HEREIN, INCLUDING BUT NOT LIMITED TO ANY REPRESENTATION OR WARRANTY OF MERCHANTABILITY OR SUITABILITY FOR ANY PURPOSE.The products set forth herein are “RoHS-compatible ”. RoHS-compatible means that products are compatible with the requirements according to Art. 4 (substance restrictions)of Directive 2011/65/EU of the European Parliament and of the Council of June 8th , 2011 on the restriction of the use of certain hazardous substances in electrical and electronic equipment.RoHS - Exemptions for the Product Class / Product according to Annex III: ( ; valid not valid );no exemptions;Exemption 6 (a): Lead as an alloying element in steel for machining purposes and in galvanized steel containing up to 0,35 % lead by weight;Exemption 6 (b): Lead as an alloying element in aluminium containing up to 0,4 % lead by weight;Exemption 6 (c): Copper alloy containing up to 4 % lead by weight;Exemption 7 (a): Lead in high melting temperature type solder (i.e. lead-based alloys containing 85 % by weight or more lead);Exemption 7 (c)-I: Electrical and electronic components containing lead in a glass or ceramic other than dielectric ceramic in capacitors, e.g. piezoelectronic devices, or in a glass or ceramic matrix compound; Exemption 7 (c)-II: Lead in dielectric ceramic in capacitors for a rated voltage of 125 V AC or 250 V DC or higher;Exemption 7 (c)-III: Lead in dielectric ceramic in capacitors for a rated voltage of less than 125 V AC or 250 V DC;Exemption 15: Lead in solders to complete a viable electrical connection between semiconductor die and carrier within integrated circuit Flip Chip packages;Other Exemption than above ....................................................................。