033制程检验(IPQC)表面处理检验规范
表面处理通用检验标准
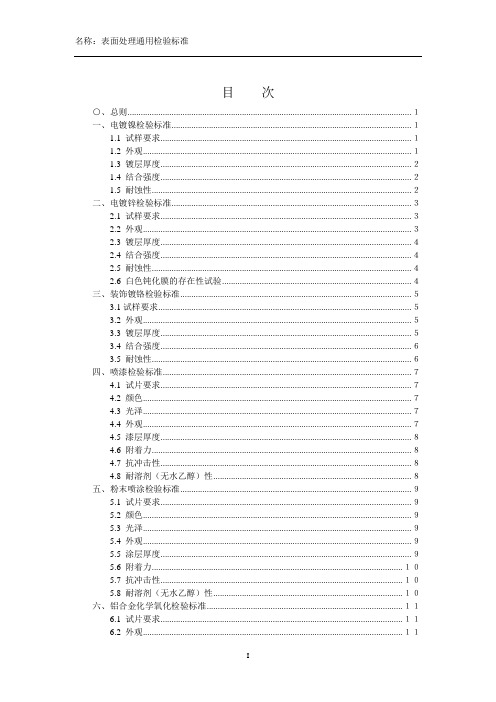
目次○、总则................................................................................................................................. 1一、电镀镍检验标准............................................................................................................. 11.1 试样要求.................................................................................................................. 11.2 外观.......................................................................................................................... 11.3 镀层厚度.................................................................................................................. 21.4 结合强度.................................................................................................................. 21.5 耐蚀性...................................................................................................................... 2二、电镀锌检验标准............................................................................................................. 32.1 试样要求.................................................................................................................. 32.2 外观.......................................................................................................................... 32.3 镀层厚度.................................................................................................................. 42.4 结合强度.................................................................................................................. 42.5 耐蚀性...................................................................................................................... 42.6 白色钝化膜的存在性试验...................................................................................... 4三、装饰镀铬检验标准......................................................................................................... 53.1试样要求................................................................................................................... 53.2 外观.......................................................................................................................... 53.3 镀层厚度.................................................................................................................. 53.4 结合强度.................................................................................................................. 63.5 耐蚀性...................................................................................................................... 6四、喷漆检验标准................................................................................................................. 74.1 试片要求.................................................................................................................. 74.2 颜色.......................................................................................................................... 74.3 光泽.......................................................................................................................... 74.4 外观.......................................................................................................................... 74.5 漆层厚度.................................................................................................................. 84.6 附着力...................................................................................................................... 84.7 抗冲击性.................................................................................................................. 84.8 耐溶剂(无水乙醇)性.......................................................................................... 8五、粉末喷涂检验标准......................................................................................................... 95.1 试片要求.................................................................................................................. 95.2 颜色.......................................................................................................................... 95.3 光泽.......................................................................................................................... 95.4 外观.......................................................................................................................... 95.5 涂层厚度.................................................................................................................. 95.6 附着力.................................................................................................................. 105.7 抗冲击性.............................................................................................................. 105.8 耐溶剂(无水乙醇)性...................................................................................... 10六、铝合金化学氧化检验标准......................................................................................... 116.1 试片要求.............................................................................................................. 116.2 外观...................................................................................................................... 116.3 耐蚀性.................................................................................................................. 11七、铝合金喷砂光亮阳极化检验标准............................................................................. 127.1 试片要求.............................................................................................................. 127.2 外观...................................................................................................................... 127.3 氧化膜厚度.......................................................................................................... 127.4 耐蚀性.................................................................................................................. 127.5 封闭质量.............................................................................................................. 12八、喷砂及拉丝检验标准................................................................................................. 138.1 拉丝件.................................................................................................................. 138.2 喷砂件.................................................................................................................. 13表面处理通用检验标准○、总则0.1 零部件表面处理前应去除毛刺、飞边、划痕、氧化层等缺陷,锐边棱角倒钝。
表面处理检验标准
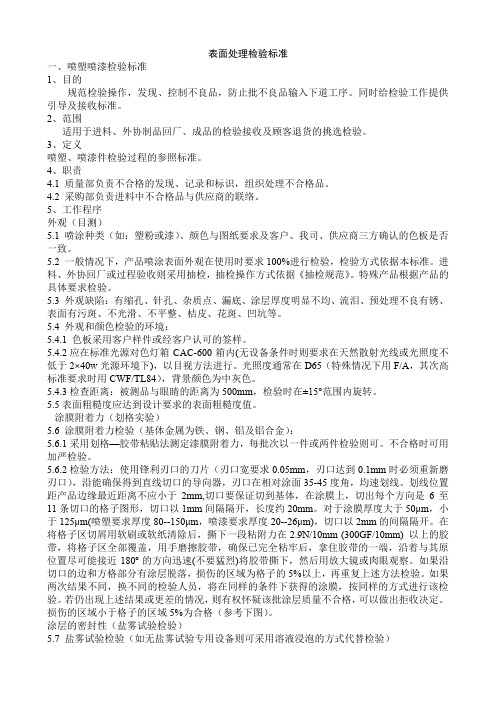
表面处理检验标准一、喷塑喷漆检验标准1、目的规范检验操作,发现、控制不良品,防止批不良品输入下道工序。
同时给检验工作提供引导及接收标准。
2、范围适用于进料、外协制品回厂、成品的检验接收及顾客退货的挑选检验。
3、定义喷塑、喷漆件检验过程的参照标准。
4、职责4.1 质量部负责不合格的发现、记录和标识,组织处理不合格品。
4.2 采购部负责进料中不合格品与供应商的联络。
5、工作程序外观(目测)5.1 喷涂种类(如:塑粉或漆)、颜色与图纸要求及客户、我司、供应商三方确认的色板是否一致。
5.2 一般情况下,产品喷涂表面外观在使用时要求100%进行检验,检验方式依据本标准。
进料、外协回厂或过程验收则采用抽检,抽检操作方式依据《抽检规范》。
特殊产品根据产品的具体要求检验。
5.3 外观缺陷:有缩孔、针孔、杂质点、漏底、涂层厚度明显不均、流泪、预处理不良有锈、表面有污斑、不光滑、不平整、桔皮、花斑、凹坑等。
5.4 外观和颜色检验的环境:5.4.1 色板采用客户样件或经客户认可的签样。
5.4.2应在标准光源对色灯箱CAC-600箱内(无设备条件时则要求在天然散射光线或光照度不低于2×40w光源环境下),以目视方法进行。
光照度通常在D65(特殊情况下用F/A,其次高标准要求时用CWF/TL84),背景颜色为中灰色。
5.4.3检查距离:被测品与眼睛的距离为500mm,检验时在±15°范围内旋转。
5.5表面粗糙度应达到设计要求的表面粗糙度值。
涂膜附着力(划格实验)5.6 涂膜附着力检验(基体金属为铁、钢、铝及铝合金):5.6.1采用划格—胶带粘贴法测定漆膜附着力,每批次以一件或两件检验则可。
不合格时可用加严检验。
5.6.2检验方法:使用锋利刃口的刀片(刃口宽要求0.05mm,刃口达到0.1mm时必须重新磨刃口),沿能确保得到直线切口的导向器,刃口在相对涂面35-45度角,均速划线。
划线位置距产品边缘最近距离不应小于2mm,切口要保证切到基体,在涂膜上,切出每个方向是6至11条切口的格子图形,切口以1mm间隔隔开,长度约20mm。
表面处理检验标准

用戒刀在批次样板上划10*10MM的方格,9*9=81个,
然后用进口封口胶贴平压紧,然后再用力撕下,掉粉面积不超过20%。
弯曲强度
批次样件,弯曲超过90°,粉层不开裂。
环保测试
要求喷粉厂提供粉末的SGS报告。
尺寸
卡尺
按图纸检验
c=0/n=5
珠海市椿田机械有限公司
表面处理检验作业规范
文件编号
CTT-MS-PG-008
制定日期
2021.11.05
制定
版次
A/1
生效日期
2021.11.05
审核
页 数
3of 3
抽样标准
GB/T2828.1-2012
批准
丝印
外观
目视/比对样品
重影:不可有重影,字体粗细正确
C=0
目视/图纸/比对样品
缺字:不可缺字错字
目视/比对样品毛边:不可有毛边目视断线:不可有断线
目视/色板/样品
污染、颜色:不可油墨(碳黑)涂层不均匀,颜色正确无杂色
表面处理检验作业规范
文件编号
CTT-MS-PG-008
制定日期
2021.11.05
制定
版次
A/1
生效日期
2021.11.05
审核
页 数
1of 3
抽样标准
GB/T2828.1-2012
批准
1.目的
1.1 明确产品要求,统一检验标准。
2.适用范围
适用于本公司外协回厂的所有喷涂/丝印/电镀产品的检验。
3.权责
C=0
目视/色板
颜色、色差:不可有颜色不对
C=0
目视/手感/比对样品
起皮起泡:A面不可有起泡起皮,B和C面小于0.2X0.2mm
金属表面处理检验规范.(DOC)

金属表面处理检验规范1 适用范围本规范适用于品质部门对电镀、氧化、化学处理、喷塑、喷漆、喷砂、拉丝等金属表面处理一般检验。
2术语和定义2.1 A级表面:在使用过程中总能被客户看见的部分(如:面壳的正面和顶面,后壳的顶面,手柄,透镜,按键及键盘正面,探头整个表面等)。
2.2 B级表面:在使用过程中常常被客户看见的部分(如:面壳的左右侧面,底壳或后壳的左右侧面及背面等)。
这些表面允许有轻微不良,但是不致引起挑剔客户不购买产品。
2.3 C级表面:在使用过程中很少被客户注意到的表面部分(如:面壳的底面,底壳或后壳的底面,内部零件表面)。
此表面的外观缺陷应合理而且不至于给客户觉得该产品质量不佳。
2.4金属表面:包括电镀、氧化、钝化等表现为金属质感的表面,非喷涂表面。
2.5基材花斑:电抛光、电镀或氧化前因基体材料腐蚀、或者材料中的杂质、材料微孔等原因所造成的、与周围材质表面不同光泽或粗糙度的斑块状花纹外观。
2.6抛光区:对基材上的腐蚀、划伤、焊接区、铆接区等部位进行机械打磨抛光后表现出的局部高光泽、光亮区域。
2.7浅划痕:镀(膜/塑/漆)层表面划伤,但未伤及底层(即底层未暴露);对其它无镀(膜/塑/漆)层表面则为:目测不明显、手指甲触摸无凹凸感、未伤及材料本体的伤痕。
数控冲床加工中机床台面对板材的摩擦产生的轻微痕迹属于此类划痕。
2.8凹痕:由于基体材料缺陷,或在加工过程中操作不当等原因而在材料表面留下的小坑状痕迹。
2.9凹凸痕:因基材受撞击或校形不良等而呈现出的明显变形、凹凸不平的现象,手摸时有不平感觉。
2.10烧伤:拉丝、电抛光、电镀处理时因操作不当、造成零件表面过热而留下的烧蚀痕迹。
2.11水印:电镀、氧化或电抛光后因清洗水未及时干燥或干燥不彻底所形成的斑纹、印迹。
2.12露白:镀锌钝化膜因磨擦而被去除、露出新层,或因缝隙截留溶液导致的无钝化膜现象,呈现为区别于周围颜色的白色。
2.13修补:因膜层损伤而用涂料所作的局部遮盖。
IPQC过程检验标准
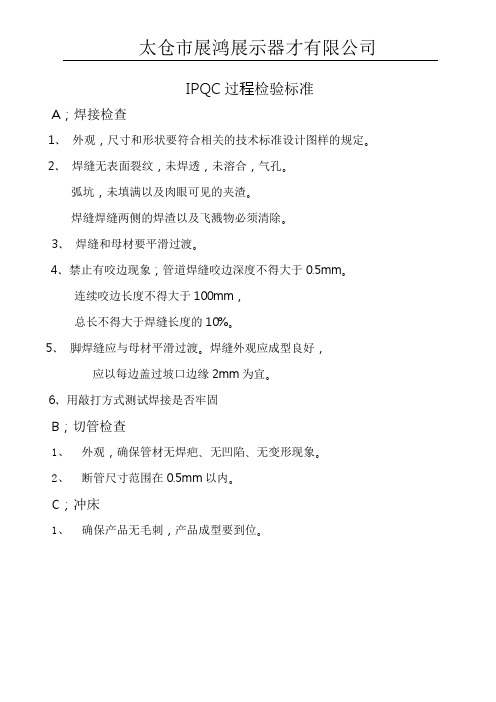
IPQC过程检验标准
A;焊接检查
1、外观,尺寸和形状要符合相关的技术标准设计图样的规定。
2、焊缝无表面裂纹,未焊透,未溶合,气孔。
弧弧坑,未填满以及肉眼可见的夹渣。
焊
飞溅物必须清除。
3、焊缝和母材要平滑过渡。
4、禁止有咬边现象;管道焊缝咬边深度不得大于0.5mm。
且连续咬边长度不得大于10
得大于焊缝长度的10%。
5、脚焊缝应与母材平滑过渡。
焊缝外观应成型良好,度应以每边盖过坡口边缘2mm为宜
6、用敲打方式测试焊接是否牢固
B;切管检查
1、外观,确保管材无焊疤、无凹陷、无变形现象。
2、断管尺寸范围在0.5mm以内。
C;冲床
1、确保产品无毛刺,产品成型要到位。
D;剪板检查
1、下料尺寸誤差为±0.5mm。
2、对角线误差为±1mm以内。
3、外观,整洁光滑、无划伤,鼓起不可使用。
(展鸿公司内部检验标准)。
IPQC制程检验规范标准

.IPQC制程检验规文件编号: ST-WI-QA-030 版次: A0编制: 日期:审核: 日期:批准: 日期:文件修订记录页码修订版次修订人修订容概要修订日期- A0 胡广华首版发行2013.6.18会签人力资源部市场部营业部研发部工程部计划部/ / / / / / 采购部生产部品管部仓储部DCC SMT / / / / 财务部/分发对象□总经理□管理者代表□人力资源部□市场部□营业部□研发部□工程部□计划部□采购部□生产部□品管部□仓储部□DCC □SMT □财务部1 / 61 产品防护静电环佩戴方法检验各人员静电环佩戴是否贴紧手腕,不符合要求给予纠正贴紧手腕。
√静电环功能静电环合格:检测时“GOOD〞绿色指示灯亮。
√2 产品验证首件外观产品外观无脏污、异物,FPC无褶皱、变形、破损。
镜头部位无漏胶、错位、破损现象。
背胶无贴错位、错贴型号,保护膜贴紧、贴正。
目视√功能标准测试条件下无出现:无图、鬼影、暗角、色点、亮点、偏色、花屏、竖线且清晰到达要求标准。
光箱√环保要求RoHS要求目视√常规实验用1㎏的力度做镜头Holder与FPC的粘合度,无脱落现象,用扭力计测试镜头(胶干后)扭力大于0.2kgf.cm。
拉力计扭力计√3 外观分板毛边要求FPCA/PCBA毛边≤1㎜目视卡尺√外观要求FPCA(PCBA)无变形,撕裂,变色,损伤,丝印缺失等情况。
目视√序号作业性质检验流程检验项目检验标准的要求检验工具缺限等级图片CR MA MI清洁感光区感光区清晰、无异物、杂质。
TV显微镜√静电环检验指示图分板指示图产品组装指示图扭力试验图分板图2 / 64 产品组装Sensor感光区外框感光区外框无粉尘、异物、杂质。
TV显微镜√涂黑胶组装镜头底部无溢胶、少胶,目视无缝隙、错位产品整体外表无黑胶目视√烘烤镜头固定胶烘烤数量1700PCS以,禁止多放入产品烘烤。
烤箱胶盘√芯片固定胶〔底部填充胶〕烘烤数量1700PCS以,禁止多放入产品烘烤。
IPQC检验作业规范

4.定义
无
5.操作内容
5.1生产线开线、换线状态确认
5.1.1在生产线每天开线或换线时,IPQC需对生产线的生产状态(如:物料清理、作业指导书悬挂、静电环配戴、桌面整理、人员岗位确认等现象)进行确认。
5.2产品首件检验要求以及确认
5.2.1生产线每天开线、换线、新产品上线等情况时,IPQC对生产线的首件产品进行质量确认,例行检验、产品外观检查、功能检查、通话测试、充电测试等并做相应首件确认表。
3.1.5负责对重点工位的质量抽检
3.1.6负责对生产线的质量异常进行确认并跟踪处理结果.
3.2工程部
3.2.1负责首件不合格和生产线质量异常的分析、改善措施的制定工作。
3.2.2负责生产作业指导书的制定和修改工作。
3.3生产部
3.3.1负责按照作业指导书进行作业。
3.3.2负责首件的送检工作。
3.3.3负责在首件检查不合格时按要求进行改善,并对已生产的产品进行处理,将改善后生产的产品重新送检
5.2.2首检合格后,产线才允许批量生产,相关部门进行会签;若首检不合格及异常时,
应立即通知工程部与生产部进行改善、控制;同时要求生产线停止生产。
5.2.3待工程分析及回复对策后,工程师以及产线组长会同IPQC,按工程改善对策生产
5-10件产品,给予IPQC进行质量确认;确认无异常时,生产线才允许批量生产。
5.4.2对生产线员工操作不当进行指导与跟踪。
5.4.3制程中问题点的研究与分析。
5.4.4对生产线前几项不良品进行记录及分析。
5.4.5每两小时对产线各岗位物料、操作、5S、工艺等方面进行抽检记录。
5.5重点工位的质量抽检
5.5.1生产线过程中,对生产线关键工位:如焊接、升级、功能测试、外观检查等工位,不定时对产出的产品质量进行检验。
IPQC制程检验工作规范

适用于本公司生产过程的品质控制
4.IPQC的作用
1.根据检测结果对产品质做出判断,即产品的质量是否符合规格和标准要就。
2.根据检测结果对工序做出判定,即过程各个要素是否处于正常的稳定状态,从而决定工序是否应该继续进行生产,达到这一目的过程这常常与使用控制图相结合。
5.检验工作内容
1.认真按时填写巡检记录报表,拉QC报表,仪器设备点检表,有配带静电环的及时的检查配带情况,及时的更换。记录电批扭力1次每两个小时。
B.每小时出现总不良率5%-10%,需开品质异常处理反馈单——工程分析。
C.试产:出现总不良率10%,需开品质异常处理反馈单——8%,或每小时总项不良率大于等于10%时,要求工程分析,在1小时内提供解决方案,若无回复,停线。
11.物料,半成品,成品摆放应有标示卡标示清楚清晰明确名称,数量,订单。
9.产品标准----工艺标准,功能要求。
10.各工序输出抽样检查----确认工序稳定,有充分能力使产品合格。
七.检验标准方案
1.批量不良:某一时段出现大批量不符合工艺要求的产品现象。
2.倾向性不良:某一时段出现的某一单一品质的单项不良现象。
3.严重缺陷(Critical):凡是对人体或机器产生危害或危及生命安全的缺陷,如:安规不符,烧机,漏电等。
12.QC检验报表应完整,清晰,一目了然。每个小时的不良数量,不良现象,不良率。每天生产下拉的生产总数,不良总数,不良比例一定记录清晰明确。
13.有客户投诉或退货情况应及时了解跟进,返工情况应及时跟进,统计不良及结果反馈,保留“现状”“现物”“现场”。
14.易磨损型测试用的插座,插排,温度计电池,万用表电池等及时更换及记录。
4.主要缺陷(Major):可能造成产品损坏,功能异常或因材料而影响产品使用寿命的缺陷。
表面处理检验规范

镀种
膜厚
判定标准
检验依据
缺点 区分
1锌
蓝白锌 白锌 彩锌
1.附着力:将铁块用2公斤以上的力砸 到产品上检查产品镀层面不可有起皮 脱皮现象(破坏性测试)
目视
5~10um
2.盐雾测试:用浓度为5%氯化钠盐
水,水温度为35±1℃连续喷雾,喷12 供应商提供盐 小时保温12小时,被腐蚀面不可有红锈 雾测试报告
进料检验规范
表面处理 检验规范
文件编号 文Leabharlann 版本 制定日期文件页次1. 目 的:为确保本公司表面处理产品在进料检验过程中有依据可循;
2.适用范围:适用于本公司烤漆,喷漆,电著,镀(锌、镍)产品膜厚检验;
3.权 责:品管单位负责制定、执行和修订。
4.作业内容:(抽样水数:每批产品抽样3~5PCS)
序 号
MA
生成
黑镍 2 镍 一般镍
化学镍
3~8um 3~5um
3.电镀膜厚:用电解式膜厚测试仪,测 试要求符合膜厚标准即可
供应商提供电 镀膜厚测试报
告
烤 3喷
漆
粉体漆 液体漆
40~150um
10~60um
4.附着力 7.光泽度
4 电 著 5~12um
5.耐腐蚀性 8.耐磨性
6.膜厚
喷漆件SIP MA
备注:以上检验相关测试报告由供货商提供,如有特殊要求除外.
核准
审核
制定
IPQC检验规范

文件名称:喷锡IPQC检验规范文件编号:版本/修订号:修订日期:1.0目的:规范IPQC之作业,以达成喷锡之良好品质。
2.0权责:2.1生产部负责喷锡的首件制作、自检以及生产过程中的自检、.巡检工作。
2.2喷锡IPQC负责首件的确认、生产过程巡检、最终抽检工作。
3.0相关文件〈〈半成品质量检验规范〉〉4.0内容:4.1制程稽核4.1.1对制程参数的稽核,是否依照作业指导书4.1.2对现场作业员的操作稽核,是否依照<<产品搬运、摆放作业规范>>4.1.3查验维护记录,是否正常维护4.2首件4.2.1核对图纸、LOT卡、板边料号孔、版本的一致性,若不一致及时提出反馈给生产及品质部当班主管,由主管查明原明并使其一致。
4.2.2检查项目:根据《半成品质量检验规范》检查喷锡平整度,是否有挂锡、上锡不良、锡高、锡面发墨、绿油起泡、基材白点、白斑分层、板撞伤等情况。
4.2.3测量项目:锡厚、孔径4.2.4首板确认后在《首板记录》上签名,并通知生产。
如不合格则知会生产改善,重做首板,直到确认为止。
4.3巡检4.3.1每半小时至少巡徊检验一次。
4.3.2检验项目包括制程稽核内容及产品质量检验。
(同首板检验)4.3.3填写《IPQC巡检记录表》。
4.4出货前抽检4.1产品喷锡并经生产部专检员全检后,IPQC按《半成品质量检验规范》进行出货前抽检,检验合格在LOT卡上签名并通知生产部出下工序,检验不合格则退回生产部按《不合格品控制程序》作相关处理。
4.2抽样标准:AQL0.65Ⅱ级标准。
4.3检验项目:同首板检验项目一致。
4.4填写好《IPQC抽检日报表》。
文件类型:颁布日期:文件名称:镀金、化金IPQC检验规文件编号:范版本/修订号:修订日期:1.0目的:规范IPQC之作业,以达成镀金、化金之良好品质2.0权责镀金、化金IPQC3.0相关文件〈〈半成品质量检验规范〉〉4.0内容:4.1制程稽核4.1.1对制程参数的稽核,是否依照<<镀金作业指导书>><<化学镀镍金作业指导书>>之设定,药水参数是否在管制范围内.4.1.2对现场作业人员的操作稽核,是否依照<<作业指导书>>作业.4.1.3产品搬运是否依照<<产品搬运、摆放作业规范〉〉操作4.1.4现场工作员安全保护措施是否合要求.4.2首件/样品4.2.1查看MI,确认该板料号、版本与MI、LOT卡的一致性,测量记录金/镍厚度4.2.2取1-2PNL测其金/镍厚度,其最小金/镍厚不能低于客户要求4.2.3按<<镀金作业指导书>><<化学镀镍金作业指导书>>进行检验,并作好记录.4.2.4如不合格,则要求进行改善,并重做首件,直至首件确认OK.4.3巡检4.3.1频率:每1小时/次,抽检数量20PNL左右,量测金厚度,检验外观质量.4.4出货检查4.4.1按AQL抽样标准抽取样板,以<<半成品质量检验规范>>进行外观检验,并如实记录.4.4.2检查OK后在LOT卡上签名,让其出货,做好记录.4.4.3如不合格则填写返工单退回处理,直至合格,并做好相关记录.4.4.4报表整理并送交主管审核。
IPQC制程检验指导书

抽检频率及数量
钻孔/洗孔
上釉
烧制缔检/工序
研磨/喷砂
香精灌装
香精浸泡
包装工序
说明:
1、极严重缺陷—根据判断与经验,可对消费者健康造成危害、不安全或损害,此外,如产品未能符合
销售地的法律,导致不能入口或销售,亦为极严重缺陷(影响安全的缺陷)
2、严重缺陷—指可能造成故障、严重减损产品预定用途的使用,或影响产品外观的缺陷。
该类缺
陷可能导致产品无法售出,或售出后被消费者退货。
3、轻微缺陷—指不会严重减损产品的使用,但与确立标准稍有偏差,对产品有效使用、性能或外
观没有太大影响的缺陷。
表面处理工艺及检验规程

1.磷化1.1.范围:适用于需要磷化处理的产品及部件。
1.2.工艺流程:脱脂(碱性)→水洗→除锈→水洗→中和→表调→磷化→水洗→磷化后处理(喷涂)1.3.作业内容及管控重点:1.3.1 工件装框:轻拿轻放,防止工件变形。
高度不能超过溶液侵泡范围(产品杂乱放置放入框子中比规则放除油、磷化效果更好,但要确保排水充分)1.3.2 除油:(常温)碱性除油:主要是清除工件表面油污,效果很好。
PH值9-11(广泛试纸),滴定总碱度为45-60点,侵泡时间15-20分钟,根据工件所附着的油污,可适当延长侵泡时间。
1.3.3.水洗:PH值6-7(广泛试纸),针对除油后的水洗,当工件完全倾入水中,要上下左右不停地晃动2-3分钟,目的彻底清除上工序带来工件表面残留的非离子表面活性剂等。
在清洗过程需用保持清水溢流。
1.3.4.除锈:盐酸除锈的目的除锈完全,要求表面白净,无麻点。
本工序对氧化皮也有很好的去除功能。
弊病是盐酸易挥发,造成酸雾严重对人体有害,环境污染严重,因此要求不使用时需用PVC塑料板密盖。
PH值1-2(广泛试纸)滴定总酸度为300-500点,侵泡时间为25-30分钟。
1.3.5.水洗:PH值6-7(广泛试纸),针对除油后的水洗,当工件完全侵入水中,要上下左右不停地晃动2-3分钟,目的是彻底清除上道工序带来残留在工件表面的氯离子以防止带到下一道工序损坏槽液等。
在清洗过程中需保持清水溢流。
1.3.6.中和:PH值7-10(广泛试纸),针对除锈后的水洗,当工件完全侵泡水中,要上下左右不停地晃动2-3分钟,目的是彻底清除上道工序带来残留在工件表面的氯离子完全中和,防止因工件暴露在空气中造成返锈等。
当槽液PH值低于7或者严重发黄时,应及时更换槽液。
1.3.7.表调处理:PH值7-9(广泛试纸)目的是为了促使磷化形成晶体细致密实的磷化膜,以及加快磷化速度。
再配置表调剂是需用50-80摄氏度的温水将表调剂搅拌溶解后放入槽液钟,配置比例为0.3%。
表面处理检验规范

5.4.2.2用以上方法测量厚度时,当出现对镀层厚度有争议时,可采用GB/T 4955-1997中规定的方法
测量,但表面积小于100mm2的工件需用GB/T 9799-97中(见10.1.2.1和10.1.2.2)方法。
品不及时浸油封闭,已活化的元素和空气继续反应,有时会出现变色现象。
5.3环保性要求:产品发黑后要求:无毒,无异味,环保。
(发黑剂不得含有硒化物,亚销酸盐,铬等有毒化合物)
5.4性能测试:
5.4.1附着力和耐蚀性:
硫酸铜点滴法:每升溶液(去离子水)含硫酸铜30g、20℃、浸32秒,如有发红(触铜斑点,锈
苏州********有限公司
文件编号:
制订单位:质量部
版 本: A/0 总页数:4 页
制订日期:2014年 2 月 27 日
发行日期:2014年 2 月 27 日
核准
审 核
制订
制订部门
制订日期
发黑处理
检验规范
文件编号
版本
页次
质量部
1、目的
为了进一步加强表面发黑处理产品的质量控制,确保产品质量,满足客户要求。
5.2.7白斑:材料电镀前表面锈蚀深及底材时,电镀后因光线折射,产生白色斑纹。
5.2.8水纹:烘干作业不完全或水质不干净造成。
5.2.9过度酸洗:浸于酸液中的时间过长,造成金属表面过度腐蚀。
5.2.10脱层(翘皮):镀层附着力不佳,有剥落的现象。
5.3外观检验允收标准
现象
检验标准
缺陷度
污渍
不允许
轻
异色
5.2.4氧化膜不牢,判定为不良:
由于发黑前产品除油清洗不彻底、发黑处理时间过长,发黑层过厚,形成了发黑浮层,附着力差,
表面处理检验规范
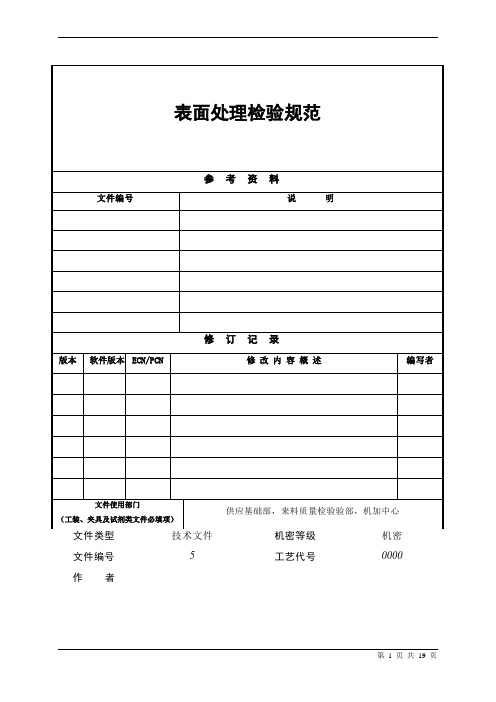
文件编号5工艺代号0000作者第 1 页共19 页表面处理检验规范1适用范围本规范适用于电镀、氧化、化学处理、喷塑、喷漆、喷砂、拉丝等金属表面处理的检验。
2术语和定义2.1 A级表面:在使用过程中总能被客户看见的部分(如:面壳的正面和顶面,后壳的顶面,手柄,透镜,按键及键盘正面,探头整个表面等)。
2.2 B级表面:在使用过程中常常被客户看见的部分(如:面壳的左右侧面,底壳或后壳的左右侧面及背面等)。
这些表面允许有轻微不良,但是不致引起挑剔客户不购买产品。
2.3 C级表面:在使用过程中很少被客户注意到的表面部分(如:面壳的底面,底壳或后壳的底面,内部零件表面)。
此表面的外观缺陷应合理而且不至于给客户觉得该产品质量不佳。
2.4 金属表面:包括电镀、氧化、钝化等表现为金属质感的表面,非喷涂表面。
2.5 基材花斑:电抛光、电镀或氧化前因基体材料腐蚀、或者材料中的杂质、材料微孔等原因所造成的、与周围材质表面不同光泽或粗糙度的斑块状花纹外观。
2.6 抛光区:对基材上的腐蚀、划伤、焊接区、铆接区等部位进行机械打磨抛光后表现出的局部高光泽、光亮区域。
2.7 浅划痕:镀(膜/塑/漆)层表面划伤,但未伤及底层(即底层未暴露);对其它无镀(膜/塑/漆)层表面则为:目测不明显、手指甲触摸无凹凸感、未伤及材料本体的伤痕。
数控冲床加工中机床台面对板材的摩擦产生的轻微痕迹属于此类划痕。
2.8 深划痕:镀(膜/塑/漆)层表面划伤,且已伤至底层(即底层已暴露出来);对其它无镀(膜/塑/漆)层表面则为:目测明显、手指甲触摸有凹凸感、伤及材料本体的伤痕。
2.9 凹坑:由于基体材料缺陷,或在加工过程中操作不当等原因而在材料表面留下的小坑状痕迹。
2.10 凹凸痕:因基材受撞击或校形不良等而呈现出的明显变形、凹凸不平的现象,手摸时有不平感觉。
2.11 烧伤:拉丝、电抛光、电镀处理时因操作不当、造成零件表面过热而留下的烧蚀痕迹。
2.12 水印:电镀、氧化或电抛光后因清洗水未及时干燥或干燥不彻底所形成的斑纹、印迹。
IPQC制程检验规范
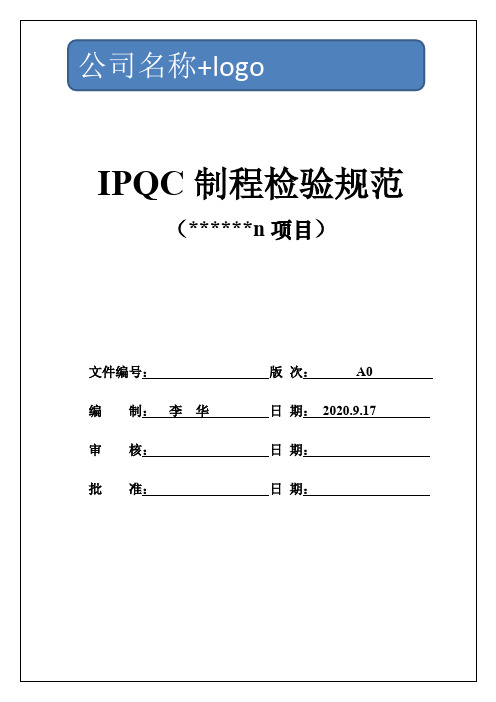
7.产品检验标准:
序号
检验项目
检验标准
检验工具
缺陷等级
CR
MA
MI
1
1,
目视/菲林尺
●
2
1.
目视/菲林尺
●
3
1
目视
●
4
1
目视
●
5
1.
目视
●
6
1
目视/菲林尺
●
7
1
目视
●
8
1
目视
●
9
1
目视
●
10
1,
目视
●
11
1,
目视
●
8.记录表单:
《*****IPQC巡检记录表》
6.2.3巡检中外观检验的产品要记录SN号,并存档备查。
6.3.异常处理:
A.首件确认NG,禁止生产下线作业。
B.测试仪器、设备工装、静电接地、温湿度等未做点检记录,以及未悬挂正确SOP的,口头通知班组长立即改善。
C.上线物料规格与BOM不符合的,立即通知生产主管更换正确物料。
D.巡检抽到致命缺陷1pcs,开出停线通知单,停线整顿。
4.3.照明条件:正常白炽灯光源,照度为外观检验垂直照度1000±200Lux。
5.外观面定义以及缺陷代码:
5.1.外观面定义:
表面
定义
AA面
**********
A面
**********
B面
**********5.2.缺陷ຫໍສະໝຸດ 码:DLH
W
S
DS
直径
长度
深度
宽度
IPQC检验规范

深圳市宇恒顺科技发展有限公司工作指导书1. 目的:为了保证产品质量,确保生产过程受控,规范IPQC 的工作方式,特制定此文件。
2. 范围:适用于质量部IPQC 日常巡检作业管理3. 职责:3.1 IPQC 巡检3.1.1生产线开线检查3.1.2生产线换线状态确认3.1.3防静电检查3.1.4生产现场稽核3.1.5制程异常处理3.1.6产品首件质量状态确认3.1.7针对质量部或客户判退的不合格批返工执行的确认及跟踪3.2质量工程师负责对日常生产现场的生产过程的质量监控和异常反馈的处理入跟进3.3 工程科及制造科对IPQC 提出的异常质量问题进行分析改善编 号: YD8211 保密区分: 密件文件名称: IPQC 检验规范 使用单位: 共2个使用单位 版本识别: 第1版,第0次修订者:制作单位: 质量部 制作日期 : 20070112 变更日期:审 核 : 审核日期: 20070115核 准 :核准日期: 200701164.作业内容:4.1生产线开线检查(上班半小时内)4.1.1检查生产线现场使用的文件应为受控文件(包括试生产)、生产的机型应有受控的BOM;4.1.2检查生产线应按工艺文件要求进行工位安排;4.1.3检查生产线使用的生产工具应按要求进行点检或维护、保养;4.1.4核对生产线使用的物料应与BOM相符。
4.2生产线换线状态确认4.2.1确认在新机型物料上线前旧机型物料已全部清离作业现场。
除整机作业工位及维修工位外所有工位不可同时存在两种不同机型的物料或机头。
维修工位不同机型的物料应标识清楚。
4.3防静电检查4.3.1上班半小时内检查静电手环测试记录表需按要求填写完整;4.3.2检查生产线各工位作业员需配戴静电手腕,接触主板、LCM、LCD、镜片的工位作业员需戴防静电手套;4.3.3检查生产现场的产品,部件应进行有效的静电防护;4.4 生产现场稽核4.4.1检查重点工位(维修、焊接、测试、写号、下载、功能检查、外观检查等工位)的作业员应与生产部提供的“重点工位人员名单”相符4.4.2检查各工位使用的生产设备是否与工艺相符;4.4.3检查各工位作业员在作业前应按工艺要求对输入产品的前工位作业质量及本工位的物料质量进行检查;应完全按作业指导书进行作业;完成本工位作业后应对输出产品确认合格后方可流入下一道工序;4.4.4检查各工位发现的不良品是否有及时记录,一级维修工位是否对每一台维修过的不良品进行记录;4.4.5检查生产现场所有用周转箱或周转盘放置的未正在使用的物料、半成品、成品均应有清晰的状态标识;4.4.6 检查生产作业现场的卫生状况是否良好;4.4.7每2小对在制的半成品进行抽检,每次抽检不少于5个工位,每次不少于5PCS。
IQCIPQCOQC检验方法

IQC/IPQC/OQC检验方法一、原材料检验(IQC)原进厂检验包括三个方面:①库检:原材料品名规格、型号、数量等是否符合实际,一般由仓管人员完成。
②质检:检验原材料物理,化学等特性是否符合相应原材料检验规定,一般采用抽检方式。
③试检:取小批量试样进行生产,检查生产结果是否符合要求。
来料不合格的处理:①标识:在外包装上标明“不合格”,堆置于“不合格区”或挂上“不合格”标识牌等。
②处置:退货或调货或其他特采。
③纠正措施:对供应商提供相关要求或建议防止批量不合格的再次出现。
2紧急放行:因生产急需,在检验报告出来前需采用的物资,为紧急放行。
需留样检验,并对所放行物资进行特殊标识并记录,以便需要时进行追踪。
3特采:①从非合格供应商中采购物资——加强检验。
②检验不合格而采用的物资——挑选或修复后使用。
4应特别关注不合格品所造成的损失:①投入阶段发现,损失成本为1元。
②生产阶段发现,损失成本为10元。
③在客户手中发现,损失成本为100元。
二、过程检验(IPQC)lIPQC的检验范围包括:①产品:半成品、成品的质量。
②人员:操作员工艺执行质量,设备操作技能差。
③设备:设备运行状态,负荷程度。
④工艺、技术:工艺是否合理,技术是否符合产品特性要求。
⑤环境:环境是否适宜产品生产需要。
2工序产品检验:对产品的检验,检验方式有较大差异和灵活性,可依据生产实际情况和产品特性,检验方式更灵活。
质检员全检:适用于关键工序转序时,多品种小批量,有致命缺陷项目的工序产品。
工作量较大,合格的即准许转序或入库,不合格则责成操作员工立即返工或返维。
质检员抽检:适用于工序产品在一般工序转序时,大批量,单件价值低,无致命缺陷的工序产品。
员工自检:操作员对自己加工的产品先实行自检,检验合格后方可发出至下道工序。
可提高产品流转合格率和减轻质检员工作量,不易管理控制,时有突发异常现象。
员工互检:下道工序操作人员对上道员工的产品进行检验,可以不予接收上道工序的不良品,相互监督,有利于调动积极性,但也会引起包庇、吵执等造成品质异常现象。
表面处理检验标准

表面处理检验标准一.目的:统一检验标准,明确目标,降低不良批次,及时供应生产出货。
二.相关部门:弘南科品质部,采购部,各表面处理协力厂商。
三.适用产品:公司所有外发表面处理加工零配件,半成品。
四.检查标准:
(1)等级定义:A面:产品的主要面或直观面。
B面:产品的次要面。
(2)外观要求:喷油加工:A面不能有积油,流纹,透底,磨花,划伤,颜色不匀,发白等现象,尘点,杂点A面≤1个,直径≤0.2MM;B面不能有明显积油,流纹,透底,磨花,划伤,颜色不匀,发白等现象,尘点,杂点≤2个,直径≤0.25MM。
丝印加工:字迹要清晰,不能有字体变形,飞边,模糊,线条粗细字体大小不一,丝印不完整等现象。
(3)附着力测试:喷油件以百格刀在表面划6*6个1mm*1mm小网格,电镀件表面划6*6个2mm*2mm小网格,丝印件不用划,以3M600或3M610胶带平整压在测试面上并压紧,使其100%牢牢附于测试面上,然后呈90度角迅速拉起,如此三次,测试面脱落总面积小于5%为合格。
(4)颜色检验:以我司签样为标准,颜色偏差不能太明显,同一批料不能有色差,同一批次相配合件不能有色差。
丝印颜色要与签样颜色一致或相近。
(5)功能检测:外发加工产品结构不能损坏,喷油不能过厚以致影响装配,有热熔脚位的地方要注意,熔脚位要尽量避免喷到油,以防影响热熔。
(6)所有来料抽检不良超过3%为不合格。
五.未尽事项,在产品加工时另做要求。
核准:品质:采购:厂商确认:。
- 1、下载文档前请自行甄别文档内容的完整性,平台不提供额外的编辑、内容补充、找答案等附加服务。
- 2、"仅部分预览"的文档,不可在线预览部分如存在完整性等问题,可反馈申请退款(可完整预览的文档不适用该条件!)。
- 3、如文档侵犯您的权益,请联系客服反馈,我们会尽快为您处理(人工客服工作时间:9:00-18:30)。
表面处理检验细则
页码:第1页共1页
编制日期:2013年11月8日
生效日期:
1.目的:使印刷品之检验规范化,标准化,以确保产品质量.
2.范围:凡本厂印刷品之检验均适用(如客户有特别要求,则依客户规定判定).
3.检验方式:
3.1首检:检查表面处理,开始10张表面处理件(检查项目见下表)
目测
卷尺
钢尺
√
表面处理效果
过油后表面光滑。无褶皱,气泡,过油后纸质不能太黄(哟黄可以接受)
目测
NA
√
表面处理后印章颜色
样板相符合
目测
NA
√
表面处理粘附力
擦油测试后应无甩油露底。
拉油测试后3M胶纸无明显的印刷油墨。
(首检时测试)
擦油测试
拉油测试
橡皮擦
3M610胶带
√
印刷油墨粘附力
批准;
审核:卢祖国
编制:卢祖国
3.2生产过程中检验:每30分钟一次,检验样板数6张。
4.检验项目如下表:
检验
项目
判定标准
检测
方法
检验
工具
缺陷类别
MAJ
MIN
印张油墨
表面处理前印刷品油墨需干透
粘擦
白色面巾纸
√
过油工艺
与《彩印生产工艺指令单》相符
与客户或与公司留样相符。(若《彩印生产工艺指令单>>与样板不相符,应通知品质保证部主管进行处理》