焊缝常见缺陷X射线检测影像的识别研究
钢制对接焊缝缺陷X射线照相参考图谱
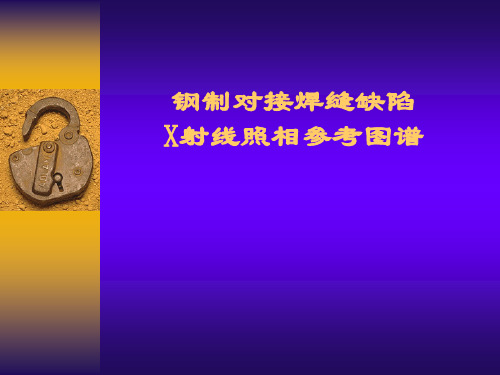
图18 未焊透、气孔
图19 焊缝边缘未焊透
图20 未焊透、气孔
图21 未焊透、气孔
图22 未焊透、气孔
图23 焊偏造成的边缘未焊透
图24 焊偏造成的边缘未焊透
图25 未焊透、气孔
三、未熔合性缺陷
图26 丁字接头边缘未熔合
图27 焊肉和母材未熔合
图28 层间未熔合
图29 丁字接头未熔合
图44 夹渣
图45 夹渣、气孔
图46 夹渣
图47 条状夹渣
图48 气态夹渣
图49 夹渣、气孔
图50 气态夹渣
图51 夹渣
六、气孔性缺陷
图52 密集气孔
图53 气孔
图54 连续气孔
图55 链状气孔
图56 密集气孔
图57 气孔
图58 大气孔
图59 气孔
图60 气孔
图61 分散气孔
钢制对接焊缝缺陷 X射线照相参考图谱
目录
前言
一、裂纹性缺陷 二、未焊透性缺陷
三、未熔合性缺陷
四、钨夹渣性缺陷
五、夹渣性缺陷
六、气孔性缺陷
前言
《钢制对接焊缝缺陷 X 射线照相参考图谱》是在大量
焊缝和焊接试件X射线照相实验基础上,经过几年的搜 集、积累,从数千张底片中筛选出具有各种典型缺陷 的底片,经特殊拷贝翻版,由洗印在相纸中的正片进 行排版组谱精装而成。《图谱》中的焊接缺陷,包括 有各种典型裂纹,未焊透、未熔合、夹渣、夹钨和气 孔。 本《焊缝缺陷X射线照相参考图谱》,对初、中级射线 探伤人员、焊接及探伤专业的教学人员、以及焊接质 量检验单位的有关人员,进行焊接缺陷识别、评片时 的缺陷定性等,具有一定指导意义。
图30 坡口母材与焊肉未熔合
常见焊接缺陷及X射线无损检测要点
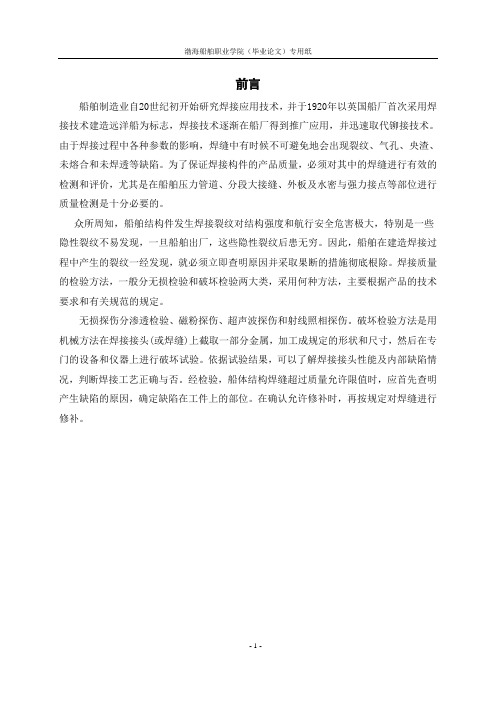
前言船舶制造业自20世纪初开始研究焊接应用技术,并于1920年以英国船厂首次采用焊接技术建造远洋船为标志,焊接技术逐渐在船厂得到推广应用,并迅速取代铆接技术。
由于焊接过程中各种参数的影响,焊缝中有时候不可避免地会出现裂纹、气孔、央渣、未熔合和未焊透等缺陷。
为了保证焊接构件的产品质量,必须对其中的焊缝进行有效的检测和评价,尤其是在船舶压力管道、分段大接缝、外板及水密与强力接点等部位进行质量检测是十分必要的。
众所周知,船舶结构件发生焊接裂纹对结构强度和航行安全危害极大,特别是一些隐性裂纹不易发现,一旦船舶出厂,这些隐性裂纹后患无穷。
因此,船舶在建造焊接过程中产生的裂纹一经发现,就必须立即查明原因并采取果断的措施彻底根除。
焊接质量的检验方法,一般分无损检验和破坏检验两大类,采用何种方法,主要根据产品的技术要求和有关规范的规定。
无损探伤分渗透检验、磁粉探伤、超声波探伤和射线照相探伤。
破坏检验方法是用机械方法在焊接接头(或焊缝)上截取一部分金属,加工成规定的形状和尺寸,然后在专门的设备和仪器上进行破坏试验。
依据试验结果,可以了解焊接接头性能及内部缺陷情况,判断焊接工艺正确与否。
经检验,船体结构焊缝超过质量允许限值时,应首先查明产生缺陷的原因,确定缺陷在工件上的部位。
在确认允许修补时,再按规定对焊缝进行修补。
一、船舶焊接缺陷及无损探伤技术简介1、船舶焊接中的常见缺陷分析船舶焊接是保证船舶密性和强度的关键,是保证船舶质量的关键,是保证船舶安全航行和作业的重要条件。
如果焊接存在着缺陷,就有可能造成结构断裂、渗漏,甚至引起船舶沉没。
因此,在船舶建造中焊接质量是重点验收工作之一,规范也明确规定,焊缝必须进行外观检查,外板对接焊缝必须进行内部检查。
船体焊缝内部检查,可采用射线探伤与超声探伤等办法。
射线探伤能直接判断船体焊缝中存在的缺陷的种类、大小、部位及分布情况,直观可靠,重复性好,容易保存,当前船厂普遍采用X射线探伤来进行船体焊缝的内部质量检查。
X射线检测焊缝的图像处理与缺陷识别
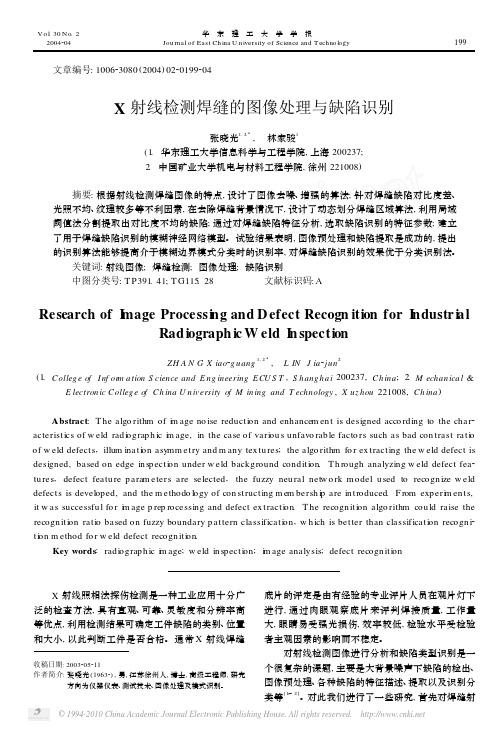
V o l .30N o.22004204华 东 理 工 大 学 学 报 Journal of East Ch ina U niversity of Science and T echno logy 收稿日期:2003205211作者简介:张晓光(19632),男,江苏徐州人,博士,高级工程师,研究方向为仪器仪表、测试技术、图像处理及模式识别。
文章编号:100623080(2004)022*******X 射线检测焊缝的图像处理与缺陷识别张晓光1,23, 林家骏1(1.华东理工大学信息科学与工程学院,上海200237;2.中国矿业大学机电与材料工程学院,徐州221008) 摘要:根据射线检测焊缝图像的特点,设计了图像去噪、增强的算法;针对焊缝缺陷对比度差、光照不均、纹理较多等不利因素,在去除焊缝背景情况下,设计了动态划分焊缝区域算法,利用局域阈值法分割提取出对比度不均的缺陷;通过对焊缝缺陷特征分析,选取缺陷识别的特征参数;建立了用于焊缝缺陷识别的模糊神经网络模型。
试验结果表明,图像预处理和缺陷提取是成功的,提出的识别算法能够提高介于模糊边界模式分类时的识别率,对焊缝缺陷识别的效果优于分类识别法。
关键词:射线图像;焊缝检测;图像处理;缺陷识别中图分类号:T P 391.41;T G 115.28文献标识码:AResearch of I mage Processi ng and D efect Recogn ition for I ndustr i alRad iograph ic W eld I n spectionZH A N G X iao 2g uang1,23, L IN J ia 2jun 2(1.Colleg e of Inf or m a tion S cience and E ng ineering ECU S T ,S hang ha i 200237,Ch ina ;2.M echan ica l &E lectron ic Colleg e of Ch ina U n iversity of M in ing and T echnology ,X uz hou 221008,Ch ina )Abstract :T he algo rithm of i m age no ise reducti on and enhancem en t is designed acco rding to the char 2acteristics of w eld radi ograph ic i m age ,in the case of vari ou s unfavo rab le facto rs such as bad con trast rati o of w eld defects ,illum inati on asymm etry and m any tex tu res ;the algo rithm fo r ex tracting the w eld defect is designed ,based on edge in specti on under w eld background conditi on .T h rough analyzing w eld defect fea 2tu res ,defect featu re param eters are selected ,the fuzzy neu ral netw o rk m odel u sed to recogn ize w eld defects is develop ed ,and the m ethodo logy of con structing m em bersh i p are in troduced .F rom exp eri m en ts ,it w as successfu l fo r i m age p rep rocessing and defect ex tracti on .T he recogn iti on algo rithm cou ld raise the recogn iti on rati o based on fuzzy boundary pattern classificati on ,w h ich is better than classificati on recogn i 2ti on m ethod fo r w eld defect recogn iti on .Key words :radi ograph ic i m age ;w eld in sp ecti on ;i m age analysis ;defect recogn iti on X 射线照相法探伤检测是一种工业应用十分广泛的检查方法,具有直观、可靠、灵敏度和分辨率高等优点,利用检测结果可确定工件缺陷的类别、位置和大小,以此判断工件是否合格。
焊缝X射线探伤典型缺陷的分析与研究

气孔在焊缝 中的位置不一 , 在底 片上图像成
圆 形或椭 圆形小 黑点 .
1 2 7 咬边 ..
接规范不当等所引起的缺陷.
12 焊缝 射线 底 片典 型缺 陷 的特征 .
x射线探伤使胶片发生感光作用或使某些化 学元素和化合物发 生荧光 , 来发现被检物体 内部
缺 陷 j .
1 2 1 裂缝 ..
者包括根部裂纹 、 穿透裂纹 、 焊道下裂纹和夹层裂
纹 等. 原 因是熔 敷金 属 的韧性 不 良、 其 母材 或 焊条 含硫 量 过 多 、 接 规 范不 当 、 口处理 不 良 、 敷 焊 焊 熔
金 属 的含氢量 过 多等 . 1 12 未 焊 透 ..
在有 坡 口的焊 接 以及 丁字 焊 时 , 于焊 条 过 由 粗或 者 焊接 电流 过 低 , 电弧 不 能 到坡 口底 而 产 使 生 的缺 陷.
能产生. 裂纹在底 片上的图像形状呈 略带弯 曲的
文章编号 :0 72 5 ( 0 ) 70 5 -3 10 -8 3 2 1 0 - 60 1 0
焊 缝 X射 线 探 伤 典 型 缺 陷 的分 析 与 研 究
张 阿 南 宋树 波 ,
(. 1吉林 市特种设备检测 中心 , 吉林 吉林 122 ;. 3 02 2 吉林化 工学 院 机电工程学院 , 吉林 吉林 12 2 ) 3 0 2
・
焊缝射线底片是焊缝射线照相方法 的最终结
果 , 焊缝 射 线 照相 底 片进 行 评 定 是 关 系焊 缝 质 对
焊缝 发 生 的裂纹 可 以大致分 为在 熔敷 金 属部 分 和热 影响 区发 生 的两 种 裂 纹. 者包 括 焊 道 裂 前 纹 、 口裂纹 、 部裂 纹 、 脆裂 纹 和微裂 纹 等. 焊 根 硫 后
常见焊接缺陷及X射线无损检测.
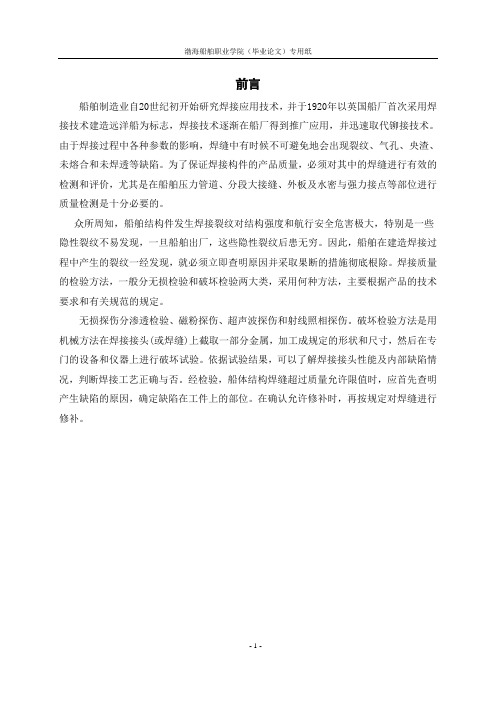
前言船舶制造业自20世纪初开始研究焊接应用技术,并于1920年以英国船厂首次采用焊接技术建造远洋船为标志,焊接技术逐渐在船厂得到推广应用,并迅速取代铆接技术。
由于焊接过程中各种参数的影响,焊缝中有时候不可避免地会出现裂纹、气孔、央渣、未熔合和未焊透等缺陷。
为了保证焊接构件的产品质量,必须对其中的焊缝进行有效的检测和评价,尤其是在船舶压力管道、分段大接缝、外板及水密与强力接点等部位进行质量检测是十分必要的。
众所周知,船舶结构件发生焊接裂纹对结构强度和航行安全危害极大,特别是一些隐性裂纹不易发现,一旦船舶出厂,这些隐性裂纹后患无穷。
因此,船舶在建造焊接过程中产生的裂纹一经发现,就必须立即查明原因并采取果断的措施彻底根除。
焊接质量的检验方法,一般分无损检验和破坏检验两大类,采用何种方法,主要根据产品的技术要求和有关规范的规定。
无损探伤分渗透检验、磁粉探伤、超声波探伤和射线照相探伤。
破坏检验方法是用机械方法在焊接接头(或焊缝)上截取一部分金属,加工成规定的形状和尺寸,然后在专门的设备和仪器上进行破坏试验。
依据试验结果,可以了解焊接接头性能及内部缺陷情况,判断焊接工艺正确与否。
经检验,船体结构焊缝超过质量允许限值时,应首先查明产生缺陷的原因,确定缺陷在工件上的部位。
在确认允许修补时,再按规定对焊缝进行修补。
一、船舶焊接缺陷及无损探伤技术简介1、船舶焊接中的常见缺陷分析船舶焊接是保证船舶密性和强度的关键,是保证船舶质量的关键,是保证船舶安全航行和作业的重要条件。
如果焊接存在着缺陷,就有可能造成结构断裂、渗漏,甚至引起船舶沉没。
因此,在船舶建造中焊接质量是重点验收工作之一,规范也明确规定,焊缝必须进行外观检查,外板对接焊缝必须进行内部检查。
船体焊缝内部检查,可采用射线探伤与超声探伤等办法。
射线探伤能直接判断船体焊缝中存在的缺陷的种类、大小、部位及分布情况,直观可靠,重复性好,容易保存,当前船厂普遍采用X射线探伤来进行船体焊缝的内部质量检查。
缺陷影像的判断及评定

未焊透
3
外咬边 透流
4
夹渣 内凹
5
层间未熔合 裂纹
6
根部未熔合 密集气孔
7
气孔 层间未熔合
8
裂纹 未焊透
9
钨夹渣
10
轮廓清晰度也不相同。缺陷离胶片越近,则影象黑度越大,轮廓越清晰;缺陷离
胶片越远,则影象黑度越小,轮廓也越模糊。(1)气孔(2)夹渣(3)钨夹渣(4)未焊透 (5)未熔合(6)裂纹
四、焊缝的表面缺陷(1)咬边(2)塌陷(3)焊穿(4)焊瘤(5)内凹(6)弧坑
X 射线底片缺陷分辨
表面未填满
单侧未焊透
2
按施焊时间的不同空间位置,焊缝可分为平焊、立焊(垂直焊)、横焊、仰 焊等四种。按母材的拼接形式,焊缝又可分为对接焊缝、搭接焊缝、角焊缝等三 种。目前射线擦伤的主要对象为对接焊缝。常见焊接缺陷分类图如下表所示:
焊接缺陷
焊接内部缺陷
焊接表面缺陷
体积型缺陷
透 未熔合
裂纹
单链密管块条
中根层边纵横弧咬塌焊内焊弧
个状集状状状钨间部间缘向向坑边陷穿凹瘤坑
夹未未未未
气气气气夹夹
裂裂裂
渣焊焊熔熔
孔孔孔孔渣渣
透透合合纹纹纹
焊接缺陷对船舶构件、锅炉和压力容器在使用中所带来的隐患和危害是不能
轻视的,轻者将在一定程序上降底产品的力学性能或缩短产品使用寿命。严重时,
有可能产生脆断,导致危及生命财产安全的灾难性事故,给人民和国民经济造成
经过射线照相的工作,并不是一切缺陷都能被检查出来。如很小的厚度差, 很小的密度差异,与射线成大角度的裂纹或夹层,微细小孔,毛发裂纹,细微而 均匀的疏松等,在射线底片上都不能有效的被发现。因此,在射线底片上没有看 到缺陷,并不能说明工件中完全没有缺陷。 一、焊缝中常见缺陷的影象特征与识别
基于深度学习的焊缝X射线图像缺陷识别方法研究

基于深度学习的焊缝X射线图像缺陷识别方法研究基于深度学习的焊缝X射线图像缺陷识别方法研究摘要:随着工业自动化的发展,焊接技术在生产和制造领域中的应用越来越普遍。
焊接工艺的质量控制变得至关重要。
X射线图像检测技术是一种常用的焊缝质量检测手段。
然而,传统的X射线图像缺陷识别方法存在一些缺点,如准确性和鲁棒性较差。
本文提出了一种基于深度学习的焊缝X射线图像缺陷识别方法,该方法利用深度神经网络模型对焊缝X射线图像进行特征提取和分类,以实现高准确性和鲁棒性的缺陷识别。
关键词:焊缝;X射线图像;深度学习;缺陷识别一、引言焊接是一项关键的制造工艺,在工业生产中被广泛应用。
焊接质量对产品的性能和可靠性具有重要影响。
X射线图像检测技术可用于检测焊接缺陷,如孔洞、气孔和裂纹等。
然而,传统的图像处理方法在焊缝缺陷检测中存在限制,如准确性和鲁棒性较差。
因此,采用深度学习方法对焊缝X射线图像进行缺陷识别具有重要意义。
二、深度学习在焊缝X射线图像中的应用深度学习是一种模仿人类大脑神经网络的机器学习方法。
在焊缝X射线图像中的应用,深度学习可以提取出更丰富的特征,并能够通过大数据集进行训练,得到更准确和鲁棒的模型。
主要包括以下几个步骤:1. 数据预处理:将焊缝X射线图像进行预处理,包括去噪、图像增强等,以提高模型的稳定性和鲁棒性。
2. 特征提取:利用卷积神经网络(CNN)对预处理后的图像进行特征提取。
CNN能够自动学习图像的空间和频域特征,从而提取出可区分焊缝缺陷的特征。
3. 特征融合:将提取的特征进行融合,以进一步增强模型的鲁棒性和准确性。
4. 分类与识别:通过全连接层和Softmax函数将融合后的特征映射到对应的类别,实现焊缝X射线图像的缺陷识别。
三、实验设计与结果分析本文选取了一组焊缝X射线图像数据集,数据集中包含了不同种类的焊缝缺陷,如孔洞、气孔和裂纹等。
首先,对数据集进行预处理,去噪和增强等处理。
然后,利用已训练好的VGG16模型进行特征提取。
X射线探伤中焊缝缺陷的图像处理与自动识别的开题报告
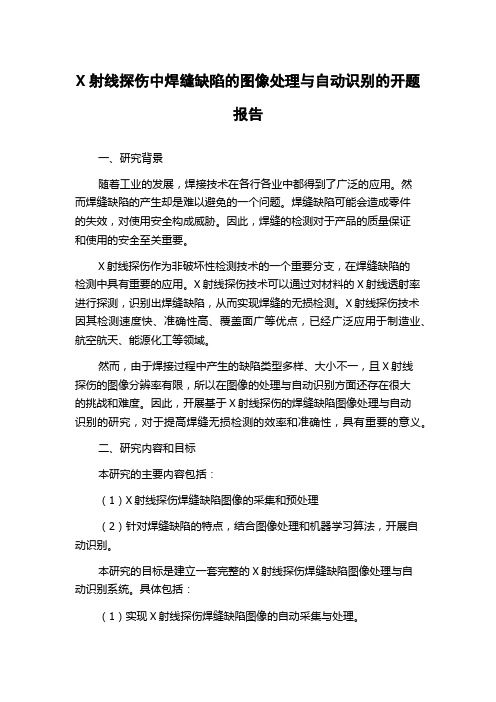
X射线探伤中焊缝缺陷的图像处理与自动识别的开题报告一、研究背景随着工业的发展,焊接技术在各行各业中都得到了广泛的应用。
然而焊缝缺陷的产生却是难以避免的一个问题。
焊缝缺陷可能会造成零件的失效,对使用安全构成威胁。
因此,焊缝的检测对于产品的质量保证和使用的安全至关重要。
X射线探伤作为非破坏性检测技术的一个重要分支,在焊缝缺陷的检测中具有重要的应用。
X射线探伤技术可以通过对材料的X射线透射率进行探测,识别出焊缝缺陷,从而实现焊缝的无损检测。
X射线探伤技术因其检测速度快、准确性高、覆盖面广等优点,已经广泛应用于制造业、航空航天、能源化工等领域。
然而,由于焊接过程中产生的缺陷类型多样、大小不一,且X射线探伤的图像分辨率有限,所以在图像的处理与自动识别方面还存在很大的挑战和难度。
因此,开展基于X射线探伤的焊缝缺陷图像处理与自动识别的研究,对于提高焊缝无损检测的效率和准确性,具有重要的意义。
二、研究内容和目标本研究的主要内容包括:(1)X射线探伤焊缝缺陷图像的采集和预处理(2)针对焊缝缺陷的特点,结合图像处理和机器学习算法,开展自动识别。
本研究的目标是建立一套完整的X射线探伤焊缝缺陷图像处理与自动识别系统。
具体包括:(1)实现X射线探伤焊缝缺陷图像的自动采集与处理。
(2)开展焊缝缺陷图像的特征提取和特征优化。
(3)结合机器学习算法开展焊缝缺陷图像的自动识别。
(4)实现将自动识别的结果与X射线探伤系统实时对接,及时发现和处理焊缝缺陷。
三、研究方法(1)开展X射线探伤焊缝缺陷图像的采集与预处理。
(2)通过图像处理算法提取焊缝缺陷图像的特征,如形状、纹理、边缘等。
(3)结合机器学习算法,训练识别模型,实现自动识别焊缝缺陷。
(4)将识别结果通过X射线探伤系统实时展示,为焊缝的质量控制提供决策支持。
四、研究意义(1)提高焊缝无损检测的效率和准确性,为制造业、航空航天、能源化工等领域的技术进步和质量保障提供支持。
(2)优化X射线探伤焊缝缺陷图像的处理与分析方式,减少人力和时间成本,提高焊缝缺陷的检测效率。
焊缝X射线图像缺陷识别技术研究

节模糊掉 . 既要消除噪声又要保持 图像 的细节可以使用 如果
一
8 一 6
用概率密度 函数 p r ) (来表示原始 图像的灰度分布. 如果用直
角坐标系的横轴代表灰度级 r用纵 轴代 表灰度的概率 密度 ,
图 3 原图像
函数 Nr, )这样就可以针对一幅 图像在这个坐标系中作 一曲
的噪声点[ 2 1 . 选用一个 3 ×3的模板 , 对一幅 m× n的图像进行处理 , 每次扫描将模板下 9个值进行排序 ,找 出中值赋给模板 中 央的像素.
在 x射线检测系统 中,其检测 图像 中存在着大量 的随
机噪声 , 图像分辨率低 , 缺陷区域灰度不均匀 , 边缘模糊 , 与
滤波 、 锐化算 子 、 频域锐化滤波 、 同态滤波等等. 由于直 方图 处理算法简单 、 效果明显 , 故选择直方图均衡 化对图像 进行
增强.
灰度级 的直方 图就是反映一幅图像 中的灰度级与出现 这种灰度 的概率之间的关系 的图形[设 变量 r 3 1 . 代表 图像 中 的像素灰度级. 在图像中 , 素的灰度级可作归一化处理 , 像 这
X
射线检测焊缝 图像识别 的困难在于 :图像千变万化 ,
中值滤波. 中值滤波是一种能有效地 抑制 图像 中噪声的非线 性信号处理技术冲 值滤波算法的基本思想是用图像像 素点
的邻域灰度值的中值来代替该像素点的灰度值 . 这种方法在 去除脉冲噪声 、 椒盐 噪声 的同时 , 又能较好地保 留图像边缘 细节. 因为它不依赖于邻域内的那些与典型值差别很大 这是
11 图像降噪 .
从噪声形成过程分析和实 际图像 观察, 噪声多为分散性
的白点或黑点的颗粒噪声.降噪处理通 常称 为平滑或滤波, 其 目的在于滤除干扰, 突出 目标特征 . 对滤波处理 的要 求有 两条, 一是使图像清晰, 二是不破坏 图像 中的轮廓和边缘
焊缝缺陷检测的X射线图像分析方法

焊缝缺陷检测的X射线图像分析方法焊缝缺陷检测的X射线图像分析方法步骤一:确定焊缝缺陷检测的目的和要求在进行焊缝缺陷检测之前,首先需要明确检测的目的和要求。
这可以包括确定需要检测的焊缝类型、缺陷种类以及对缺陷的灵敏度要求等。
这些信息将有助于确定后续的分析方法和参数设置。
步骤二:准备X射线设备和样品进行焊缝缺陷检测需要使用X射线设备。
确保设备的正常运行,并根据具体情况选择合适的参数设置,如电压、电流和曝光时间等。
同时,准备焊缝样品并进行必要的清洁和表面处理,以确保能够获得清晰的X射线图像。
步骤三:选择合适的成像技术在进行焊缝缺陷检测时,可以采用不同的成像技术,如传统的投影成像、断层成像和CT成像等。
根据具体情况选择合适的成像技术,以获得对焊缝内部缺陷的准确和全面的了解。
步骤四:获取X射线图像通过将焊缝样品放置在X射线设备下,使用合适的曝光时间和参数设置,获取焊缝的X射线图像。
确保图像清晰度和对比度的同时,避免过度曝光或欠曝光情况的发生。
步骤五:对X射线图像进行分析获得X射线图像后,需要对其进行分析以检测焊缝缺陷。
可以使用人工观察的方法,通过仔细查看图像中的缺陷特征和形态来识别缺陷。
同时,也可以借助计算机辅助分析的方法,利用图像处理和模式识别技术对图像进行自动化分析和缺陷检测。
步骤六:评估和分类焊缝缺陷在分析X射线图像时,需要对检测到的焊缝缺陷进行评估和分类。
这可以基于缺陷的形态、大小、位置和严重程度等指标进行。
根据缺陷评估结果,可以确定缺陷的严重程度,并采取相应的修复措施或进一步研究。
步骤七:记录和报告结果最后,将焊缝缺陷检测的结果记录并进行报告。
报告中应包括焊缝样品的信息、检测方法和参数设置、检测结果以及对缺陷的评估和分类等内容。
这有助于将检测结果传达给相关人员,并为后续的修复和质量控制提供参考。
通过以上步骤,可以根据焊缝缺陷检测的X射线图像分析方法,对焊缝进行准确和全面的缺陷检测。
这将有助于提高焊接质量和产品安全性,并为焊接工艺的改进和优化提供参考。
X射线焊缝图像的缺陷检测与识别技术

处理 方法 ; 通过 S U S A N算法检测焊缝缺 陷 目标 , 并结合形 态学孔 洞填充算 法修 正缺 陷 目标 ; 计算焊缝缺 陷
目 标特征参数 , 并结合所设计的深度为 4 的二叉树分类识别逻辑流程, 实现了较好的焊缝缺陷的检测结果。
关键词 : 焊缝缺 陷; 图像处理; 特征参数
中图分 类号 : T G 4 0 9
LI U Hu i , W AN We n, XI ONG Zhe n y u
( N a n c h a n g Ha n g k o n g Un i v e r s i t y , Na n c h a n g 3 3 0 0 6 3, C h i n a)
Ab s t r a c t : A i mi n g a t t h e p r o b l e m s e x i s t i n g i n t h e n o n d e s t r u c t i v e t e s t i n g u s i n g a r t i f i c i a l m e t h o d s , s u c h a s s u b j e c t i v e i n c o n s i s t e n c y , l o w
c e me n t w a s p r o p o s e d; b y S US AN a l g o r i t h m f o r d e t e c t i o n o f w e l d d e f e c t t a r g e t , a n t ] c o mb i n e d w i t h mo r p h o l o g y h o l e f i l l i n g a l g o r i t h m t o
x射线检测焊缝原理
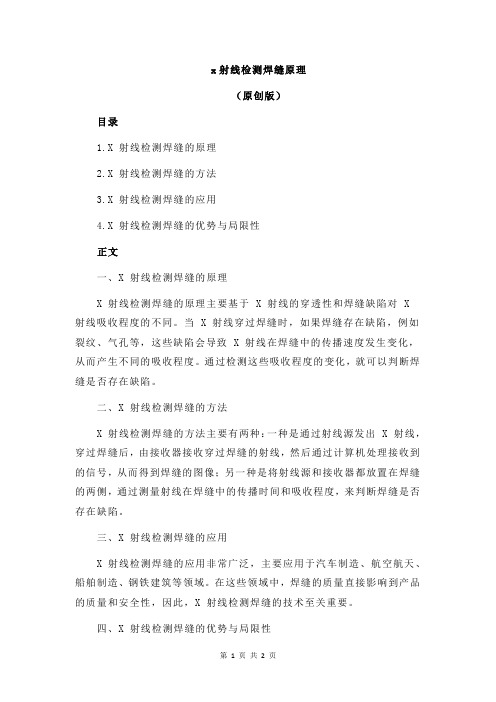
x射线检测焊缝原理
(原创版)
目录
1.X 射线检测焊缝的原理
2.X 射线检测焊缝的方法
3.X 射线检测焊缝的应用
4.X 射线检测焊缝的优势与局限性
正文
一、X 射线检测焊缝的原理
X 射线检测焊缝的原理主要基于 X 射线的穿透性和焊缝缺陷对 X 射线吸收程度的不同。
当 X 射线穿过焊缝时,如果焊缝存在缺陷,例如裂纹、气孔等,这些缺陷会导致 X 射线在焊缝中的传播速度发生变化,从而产生不同的吸收程度。
通过检测这些吸收程度的变化,就可以判断焊缝是否存在缺陷。
二、X 射线检测焊缝的方法
X 射线检测焊缝的方法主要有两种:一种是通过射线源发出 X 射线,穿过焊缝后,由接收器接收穿过焊缝的射线,然后通过计算机处理接收到的信号,从而得到焊缝的图像;另一种是将射线源和接收器都放置在焊缝的两侧,通过测量射线在焊缝中的传播时间和吸收程度,来判断焊缝是否存在缺陷。
三、X 射线检测焊缝的应用
X 射线检测焊缝的应用非常广泛,主要应用于汽车制造、航空航天、船舶制造、钢铁建筑等领域。
在这些领域中,焊缝的质量直接影响到产品的质量和安全性,因此,X 射线检测焊缝的技术至关重要。
四、X 射线检测焊缝的优势与局限性
X 射线检测焊缝的优势在于其非破坏性、高精度和效率。
与其他检测方法相比,X 射线检测焊缝不需要对产品进行破坏性检测,可以对焊缝进行 100% 的检测,且检测速度快,效率高。
X射线焊缝图像的缺陷检测与识别技术研究
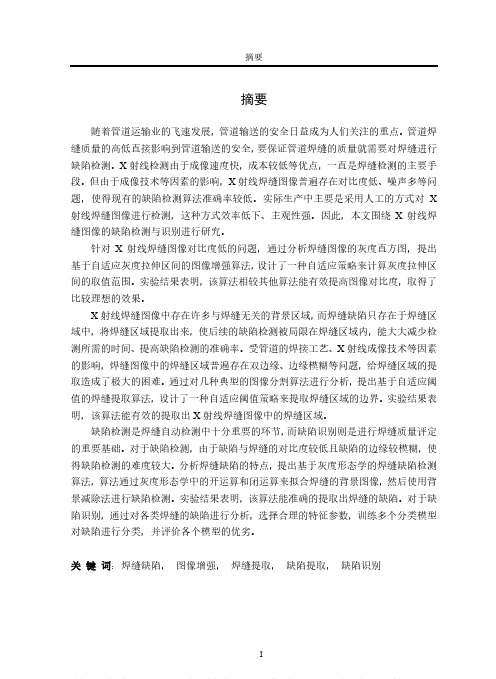
摘要摘要随着管道运输业的飞速发展,管道输送的安全日益成为人们关注的重点。
管道焊缝质量的高低直接影响到管道输送的安全,要保证管道焊缝的质量就需要对焊缝进行缺陷检测。
X射线检测由于成像速度快,成本较低等优点,一直是焊缝检测的主要手段。
但由于成像技术等因素的影响,X射线焊缝图像普遍存在对比度低、噪声多等问题,使得现有的缺陷检测算法准确率较低。
实际生产中主要是采用人工的方式对X 射线焊缝图像进行检测,这种方式效率低下、主观性强。
因此,本文围绕X射线焊缝图像的缺陷检测与识别进行研究。
针对X射线焊缝图像对比度低的问题,通过分析焊缝图像的灰度直方图,提出基于自适应灰度拉伸区间的图像增强算法,设计了一种自适应策略来计算灰度拉伸区间的取值范围。
实验结果表明,该算法相较其他算法能有效提高图像对比度,取得了比较理想的效果。
X射线焊缝图像中存在许多与焊缝无关的背景区域,而焊缝缺陷只存在于焊缝区域中,将焊缝区域提取出来,使后续的缺陷检测被局限在焊缝区域内,能大大减少检测所需的时间、提高缺陷检测的准确率。
受管道的焊接工艺、X射线成像技术等因素的影响,焊缝图像中的焊缝区域普遍存在双边缘、边缘模糊等问题,给焊缝区域的提取造成了极大的困难。
通过对几种典型的图像分割算法进行分析,提出基于自适应阈值的焊缝提取算法,设计了一种自适应阈值策略来提取焊缝区域的边界。
实验结果表明,该算法能有效的提取出X射线焊缝图像中的焊缝区域。
缺陷检测是焊缝自动检测中十分重要的环节,而缺陷识别则是进行焊缝质量评定的重要基础。
对于缺陷检测,由于缺陷与焊缝的对比度较低且缺陷的边缘较模糊,使得缺陷检测的难度较大。
分析焊缝缺陷的特点,提出基于灰度形态学的焊缝缺陷检测算法,算法通过灰度形态学中的开运算和闭运算来拟合焊缝的背景图像,然后使用背景减除法进行缺陷检测。
实验结果表明,该算法能准确的提取出焊缝的缺陷。
对于缺陷识别,通过对各类焊缝的缺陷进行分析,选择合理的特征参数,训练多个分类模型对缺陷进行分类,并评价各个模型的优劣。
焊缝、铸件缺陷及伪缺陷在X射线底片上影像特征的分析

焊缝、铸件缺陷及伪缺陷在X 射线底片上影像特征的分析樊星明一 .单个气孔 (分散气孔 )1.特征和分布状态单个气孔缺陷在焊接内部多呈单一状态均匀分布,在焊缝上部,气孔体积不大 ,呈球状或椭圆形,外表光滑。
2.X 射线检测单个气孔与 X 射线底片上能清晰地显示出气孔的球状,椭圆状轮廓,由于经常采用射线方向与焊缝纵向垂直的透照方法,我们在底片上看到的都是气孔的正投影图象,所以,在 X 射线底片上都不能反映单个气孔缺陷在焊缝横向所处位置,即不能说明单个气孔是在焊缝的上部、中部或下部。
3.形成原因A焊接前未将焊缝坡口处金属上的铁锈、油污和油漆等清理干净。
B电焊条潮湿,水分在电弧高温作用下分解成氢气和氧气等气体,溶解于液态金属中,此时假设焊缝中液态金属凝固过快,熔解气休不能及时自焊缝中逸出。
C由于电弧加热母材温度不够高,焊接速度又过快等不合理工艺因素影响。
二 .链式气孔缺陷1.特征与分布状态链式乞孔在焊缝中呈一直线分布,气孔边沿相互衔接,状如链条,链的中心与焊缝轴线平行。
在埋弧焊中带出现在母材与焊缝之间。
在单面对接焊缝中常出现在焊接底部,链式乞孔缺陷很容易和未焊透缺陷混淆。
为了与未焊透缺陷区别,链状乞孔又称细线气孔。
在焊缝边沿的纵剖面上可以看到链状气孔,在母材与焊缝分界面上呈链环状影像。
在焊缝横剖面上链状气孔是呈单个分布,并有一定距离。
链状气孔之所以有以上所述的分布状态是由于母材与焊缝边界处冷却速度大,液态金属在此处受母材激冷,首先在此处凝固。
而氢气泡在固相外表上形成时消耗的功又小,因此氢气在熔池中析出即在此处元集形成气泡,来不及逸出。
2.X 射线检测链式气孔缺陷在X 射线底片上能清晰地显示出来,有的链环状分布,连续长度有30mm 以上有的那么呈断链状。
一段一段分布在焊缝与母材边沿部位底片上呈暗色图像,在链的边沿可清楚扯到气孔圆形轮廓。
3.形成原因主要是由氢引起的,氢来源于潮湿的助熔剂和没有充分枯燥的焊条涂料中的水分。
常见焊接缺陷影像分析
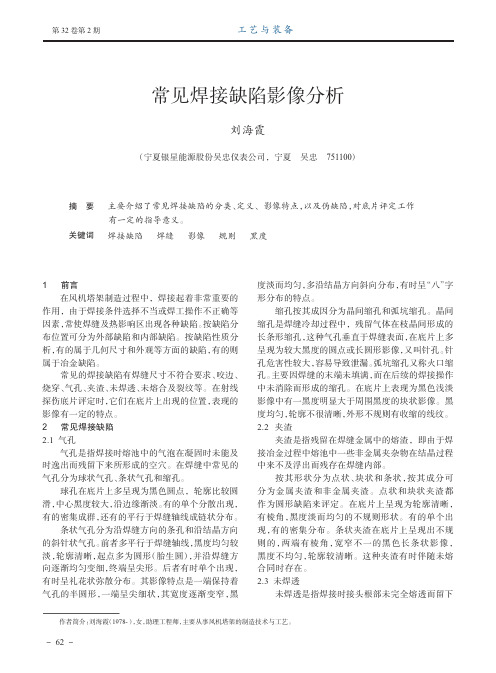
第32卷第2期1前言在风机塔架制造过程中,焊接起着非常重要的作用,由于焊接条件选择不当或焊工操作不正确等因素,常使焊缝及热影响区出现各种缺陷。
按缺陷分布位置可分为外部缺陷和内部缺陷。
按缺陷性质分析,有的属于几何尺寸和外观等方面的缺陷,有的则属于冶金缺陷。
常见的焊接缺陷有焊缝尺寸不符合要求、咬边、烧穿、气孔、夹渣、未焊透、未熔合及裂纹等。
在射线探伤底片评定时,它们在底片上出现的位置,表现的影像有一定的特点。
2常见焊接缺陷2.1气孔气孔是指焊接时熔池中的气泡在凝固时未能及时逸出而残留下来所形成的空穴。
在焊缝中常见的气孔分为球状气孔、条状气孔和缩孔。
球孔在底片上多呈现为黑色圆点,轮廓比较圆滑,中心黑度较大,沿边缘渐淡。
有的单个分散出现,有的密集成群,还有的平行于焊缝轴线成链状分布。
条状气孔分为沿焊缝方向的条孔和沿结晶方向的斜针状气孔。
前者多平行于焊缝轴线,黑度均匀较淡,轮廓清晰,起点多为圆形(胎生圆),并沿焊缝方向逐渐均匀变细,终端呈尖形。
后者有时单个出现,有时呈礼花状弥散分布。
其影像特点是一端保持着气孔的半圆形,一端呈尖细状,其宽度逐渐变窄,黑度淡而均匀,多沿结晶方向斜向分布,有时呈“八”字形分布的特点。
缩孔按其成因分为晶间缩孔和弧坑缩孔。
晶间缩孔是焊缝冷却过程中,残留气体在枝晶间形成的长条形缩孔,这种气孔垂直于焊缝表面,在底片上多呈现为较大黑度的圆点或长圆形影像,又叫针孔。
针孔危害性较大,容易导致泄漏。
弧坑缩孔又称火口缩孔。
主要因焊缝的末端未填满,而在后续的焊接操作中未消除而形成的缩孔。
在底片上表现为黑色浅淡影像中有一黑度明显大于周围黑度的块状影像。
黑度均匀,轮廓不很清晰,外形不规则有收缩的线纹。
2.2夹渣夹渣是指残留在焊缝金属中的熔渣,即由于焊接冶金过程中熔池中一些非金属夹杂物在结晶过程中来不及浮出而残存在焊缝内部。
按其形状分为点状、块状和条状,按其成分可分为金属夹渣和非金属夹渣。
点状和块状夹渣都作为圆形缺陷来评定。
钢焊缝射线照相底片缺陷影像的识别

钢焊缝射线照相底片缺陷影像的识别1 底片上缺陷影像的分析底片上影像千变万化,形态各异,但按其来源大致可分为三类:1. 由缺陷造成的缺陷影像;2. 由试件外观形状造成表面几何影像;3. 由于材料、工艺条件或操作不当造成的伪缺陷影像。
对于底片上的每一个影像,评片人员都应能够作出正确解释。
影像分析和识别是评片工作的重要环节,也是评片人员的基本技能。
焊接缺陷的影像特征基本取决于焊缝中缺陷的形态、分布、走向和位置,因射线透照角变化而造成的影像畸变或影像模糊也应予以充分考虑;对缺陷特性和成因的充分了解和经验,有助于缺陷的正确判断。
必要时,应改变射线检测方案重新拍片;也可对可疑影像进行解剖分析,这样可以减少误判和漏判。
缺陷影像的判定,应依据三个基本原则:1.2.1影像的黑度(或亮度)分布规律。
如气孔的黑度变化不大,属平滑过渡型;而夹渣的黑度变化不确定,属随机型。
1.2.2影像的形态和周界。
如裂纹的影像为条状,且必有尖端;而未焊透或条状夹渣虽然也是条状的,但一般不可能有尖端。
未焊透的两边周界往往是平直的,而夹渣的周围往往是弧形不规则的,而气孔的形态大多是规则的。
1.2.3影像所处的部位。
如破口边沿未熔合往往产生于焊接坡口的熔合面上,因此大多出现在焊缝轴线的两侧;而未焊透则多出现在焊缝轴线上。
2 缺陷影像的识别2.1.1成像:呈暗色斑点,中心黑度较大,边缘较浅平滑过渡,轮廓较清晰。
2.1.2形状:圆形、椭圆形、长条形、虫形等。
2.1.3形态:单个、分散、密集、链状等。
2.1.4分布:焊缝中任意部位。
⑴针孔:直径较小,但影像黑度很大,一般发生在焊缝中心。
⑵夹珠:它是由前一道焊接生成的气孔,被后一道焊接熔穿,铁水流进气孔的空间而形成的,在底片上的影像为黑色气孔中间包含着一个白色圆珠。
2.2.1成像:呈暗色斑点,黑度分布无规律,轮廓不圆滑,小点状夹渣轮廓较不清晰。
2.2.2形状:形状较不规测,点状、长条形、块状,有时带尖角。
焊缝中缺陷的种类和射线底片上成像特征

焊缝中缺陷的种类和射线底片上成像特征2010-04-24 19:07:01| 分类:默认分类|举报|字号订阅1 裂纹1.1 裂纹的种类1.1.1 按强度分类1)宏观裂纹2)微观裂纹3)超显微裂纹1.1.2 按裂纹产生的温度1)热裂纹2)温裂纹3)冷裂纹1.1.3 按裂纹的方向1)纵向裂纹2)横向裂纹3)弧坑裂纹(星型裂纹)1.2 裂纹产生的位置裂纹不仅在焊缝金属中产生,在母材的热影响区也会产生,因此评定时不仅要注意焊缝,还要仔细观察热影响区。
1.3 裂纹的特征1)黑细线条,略带曲齿及波状细纹,两端尖细,黑度逐渐淡漠消失;2)裂纹呈一条直线细纹,轮廓分明,两端常较尖细;中部稍宽不大含有分枝,边缘没有松状现象;3)放射性裂纹,黑度较浅。
2 未熔合2.1 分类1)坡口未熔合2)层间未熔合2.2 缺陷特征1)坡口未熔合1.1)缺陷发生在焊缝中心距边缘1/2处左右;1.2)多数是单条或断续状阴影,即使是连续的,也不会太长;1.3)线条比较宽,黑度不太均匀,如果射线束沿着坡口方向透照时,则一侧黑度较高,并笔直线条,另一侧边缘不规则,阴影较浅。
2)层间焊缝金属未熔合2.1)多是薄片状分布在焊缝金属的层间内;2.2)阴影浅薄,黑度不均匀;2.3)线条较宽,断头不规则;2.4)块状3 未焊透3.1 分类1)根部未焊透2)中间未焊透3)无坡口未焊透3.2 缺陷特征1)根部未焊透位于焊缝中间,形貌是笔直一条黑线,线条连续或断续;2)呈条状或带状,其宽窄取决于对缝间隙的大小,如对缝较小,会成一条黑线,但无尾梢;3)阴影的黑度均匀,轮廓明显,当有其他缺陷时,宽度和黑度会有变化,但线条本身仍是一条直线。
4 气孔4.1 分类4.1.1 按形状分类1)单个球状气孔2)链状气孔3)密集气孔4)虫状气孔5)条状气孔6)针状气孔4.1.2 按位置分类1)内部气孔2)表面气孔4.2 缺陷特征4.2.1 手工电弧焊气孔1)多是圆形或近似圆形的小黑点;2)黑度中心较大,并均匀向边缘减小;3) 气孔阴影,边缘轮廓不太明显,原因是气孔在焊缝内部成球形空隙,沿射线中心厚度改变量较大,周围部分较小,透射强度不同所致。
- 1、下载文档前请自行甄别文档内容的完整性,平台不提供额外的编辑、内容补充、找答案等附加服务。
- 2、"仅部分预览"的文档,不可在线预览部分如存在完整性等问题,可反馈申请退款(可完整预览的文档不适用该条件!)。
- 3、如文档侵犯您的权益,请联系客服反馈,我们会尽快为您处理(人工客服工作时间:9:00-18:30)。
2016年 增刊1429冷加工焊缝常见缺陷X射线检测影像的识别研究中车戚墅堰机车有限公司 (江苏常州 213011) 贺安龙 赵志敏 鞠波【摘要】分析焊缝常见缺陷的基本特征、产生的部位、在射线检测底片上的影像特点,以及不同缺陷底片影像的区别,从而在射线检测中尽量避免漏检错判,提高检测的准确度。
关键词:焊缝;X 射线检测;缺陷;识别焊缝射线检测底片是射线检测方法的最终结果呈现,评定底片是对检测结果作结论的步骤,是关系焊缝质量和安全的关键,分析焊缝常见缺陷的基本特征、产生的部位、在底片上的影像特点,以及不同缺陷底片影像的区别,对于我们进行底片影像的识别和正确评定,不仅提供了理论上的指导,同时更为准确地鉴别提供了依据,是具有指导意义的。
本文所附底片照片均为X 射线检测底片翻拍所得,本文所涉及的射线检测均指X 射线检测。
1. 焊接接头组成焊接接头由焊缝熔敷金属、热影响区和熔合线组成(见图1)。
第一,焊缝熔敷金属:焊接加热时,焊缝处的温度在液相线以上,母材与熔敷金属共同形成熔池,冷凝后成为铸态组织。
在冷却过程中,液态金属自熔合线向焊缝的中心方向结晶,形成柱状晶组织。
第二,热影响区:在焊接过程中,焊缝两侧金属因焊接热作用而产生组织和性能变化的区域。
第三,熔合线:焊接接头横截面宏观腐蚀所显示的焊缝轮廓线,它是焊缝熔敷金属与母材金属的分界线。
第四,焊脚:焊缝表面与母材的交界处。
第五,焊根:焊缝背面与母材的交界处。
图1 焊接接头组成示意2. 焊缝常见缺陷(1)裂纹 裂纹是指构件局部断裂形成的缺陷。
焊接裂纹有多种分类方法,按裂纹形成条件和机理,可分为热裂纹、冷裂纹、再热裂纹和层状撕裂等。
第一,裂纹的基本特征:热裂纹发生于焊缝熔敷金属凝固末期,敏感温度区间大致在固相线附近的高温区,其特征是沿晶界开裂。
结晶裂纹是焊接中最常见的热裂纹。
冷裂纹是在焊后冷却至马氏体转变温度以下产生的,其特征是穿晶(晶内)断裂或沿晶和穿晶混合断裂。
延迟裂纹是焊接中最常见的冷裂纹。
再热裂纹发生在焊后再次加热(通常是消除应力热处理)的升温过程中,敏感温度区间大致在600~700℃的回火处理温度间,其特征是沿晶开2016年 增刊1430冷加工裂。
层状撕裂是由于钢板内部存在沿轧制方向的层状夹杂物,在焊接时受到垂直于轧制方向的应力,产生开裂,其特征是穿晶或沿晶开裂,产生温度≤400℃。
第二,裂纹产生的部位:结晶裂纹只产生在焊缝中,最常见的是沿焊缝中心线方向的纵向裂纹,也有呈弧形分布在焊缝中心线两侧、与焊波呈垂直分布的弧形裂纹,产生于焊缝收尾处的弧坑裂纹也属于结晶裂纹,它一般有纵向的、横向的和星形的(见图2)。
图2 弧坑裂纹延迟裂纹主要发生在热影响区,少数发生在焊缝上,沿纵向和横向都有发生。
焊脚延迟裂纹、焊道下延迟裂纹、焊根延迟裂纹都是延迟裂纹的常见形态(见图3)。
再热裂纹大多发生在热影响区的粗晶区,极少情况下也出现在焊缝上。
母材、焊缝和热影响区的细晶区,均不产生再热裂纹。
再热裂纹具有晶间开裂的特征,裂纹的走向多沿熔合线的奥氏体粗晶晶界扩张,遇细晶就停止扩展。
图3 裂纹示意1.焊道下裂纹2.表面裂纹3.热影响区裂纹4.焊缝熔合线裂纹5.纵向裂纹6.焊根裂纹7.焊根表面裂纹8.焊缝熔敷金属裂纹9.焊脚裂纹 10.横向裂纹层状撕裂发生在热影响区或靠近热影响区的母材中,不会出现在焊缝中。
层状撕裂的外观具有阶梯状开裂特征。
层状撕裂按其启裂点可分四类:焊根冷裂纹为启裂源的层状撕裂(见图4a ),沿板厚中心(远离热影响区)轧层夹杂物启裂的层状撕裂(见图4b ),沿热影响区轧层夹杂物启裂的层状撕裂(见图4c ),焊脚冷裂纹为启裂源的层状撕裂(见图4d )。
(a )(b ) (c ) (d )图4 层状撕裂示意第三,裂纹的危害性:裂纹属于面积型缺陷,是焊接缺陷中危害性最大的一种。
裂纹直接降低了焊接接头的有效承载面积,破坏了材料表面的整体性能,更严重的是裂纹端部形成的尖锐缺口,造成应力高度集中,既降低了构件的疲劳强度,又容易引发构件的脆性破坏。
所以,裂纹是一种不允许存在的缺陷,必须予以消除。
第四,裂纹在底片上的辨认:在底片上常见的裂纹影像有线状、锯齿状和辐射状(又称星形),线状影像的轮廓分明,两端常较尖细,中部稍宽不大含分枝,边缘清晰;锯齿状影像的两端尖细,中部为带曲齿的波状细线,黑度逐渐淡化消失;辐射状影像呈放射性细黑短线,黑度较浅,如图5~7所示。
图5 纵向裂纹的射线影像图6 横向裂纹的射线影像2016年 增刊1431冷加工图7 辐射状裂纹的射线影像(2)未熔合 第一,未熔合的基本特征:未熔合是指焊缝熔敷金属和母材金属之间或焊道金属和焊道金属之间未完全熔合造成的缺陷,即填充金属粘盖在母材上或者是填充金属层间而部分金属未熔合在一起(缺陷部位没有熔化,该部位有填充金属)。
第二,未熔合产生的部位:坡口未熔合是指坡图8 未熔合示意第三,未熔合的危害性:未熔合属于面积型缺陷,是危害性仅次于裂纹的不允许存在的缺陷。
未熔合本身就是一种虚焊,焊缝熔敷金属在未熔合处形成明显的分界面,使焊缝的有效截面积减少,在交变载荷的作用下,应力将高度集中,使构件的机械强度降低,塑性下降,导致焊缝开裂。
第四,未熔合在底片上的显示:坡口未熔合的典型影像是连续或断续的黑线,宽度不一,黑度不均匀,靠母材侧呈直线状(保留坡口加工痕迹),黑度较大,轮廓清晰,靠焊缝中心侧多弯曲状(有时为曲齿状),黑度较小,轮廓欠清晰,在底片上处,沿焊缝纵图9 未熔合的典型射线影像图10 未熔合的射线影像(3)未焊透 第一,未焊透的基本特征:未焊透是指母材金属之间没有熔化,焊缝熔敷金属没有进入焊接接头的根部造成的缺陷(坡口根部没有熔化,该位置没有焊缝熔敷金属)。
产生未焊透的部位往往同时也存在夹渣、气孔等缺陷的叠加。
第二,未焊透产生的部位:未焊透一般出现在焊接接头的坡口根部,单面焊或加垫板的单面焊主要产生在V 形坡口的根部,双面焊主要产生在X 形或双U 形坡口的钝边边缘处,如图11所示。
(a )根部未焊透(b )中间未焊透图11 未焊透示意2016年 增刊1432冷加工第三,未焊透的危害性:未焊透属于面积型缺陷,是一种类似于裂纹的不允许存在的危害性缺陷。
未焊透使焊缝的有效截面积减少,不仅降低了焊缝的机械强度,而且在未焊透处的缺口和端部形成应力集中点,容易延伸为裂纹性缺陷,导致构件破坏。
尤其是连续性未焊透,更是一种极危险的缺陷。
第四,未焊透在底片上的显示:未焊透的典型影像是一条处于焊缝影像中心的笔直的细黑线,两侧的轮廓都很整体,为坡口钝边痕迹,宽度恰好为钝边间隙宽度。
未焊透在底片上处于焊缝根部的投影位置,一般在焊缝中部,因焊偏或底片透照时射线不垂直等原因,也可能偏向一侧;呈断续或连续分布,有时能贯穿整张底片;黑线无尾梢,由于坡口存在直的机械加工边,所以轮廊显明,有时坡口钝边有部分熔化,影像轮廓就变得不很整体,线宽度和黑度局部发生变化。
未焊透有时也伴随有夹渣、气孔等缺陷,这时线条的宽度和黑度在局部可能有所改变,但仍是一条直线,如图12、图13所示。
图12 未焊透的典型射线影像图13 伴有夹渣的未焊透射线影像(4)咬边 第一,咬边的基本特征:咬边,又称咬肉,是指在焊接过程中母材金属熔化后,没有足够的焊缝熔敷金属填入所造成的沟槽。
第二,咬边产生的部位:咬边在母材金属表面沿焊脚分布,分为在焊缝表面产生的外咬边和在根部表面产生的内咬边(又称“根部咬边”),如图15所示。
图14 焊缝的咬边(a )外咬边 (b )内咬边图15 咬边示意第三,咬边的危害性:咬边属于面积型缺陷,是一种比较危险的焊接缺陷。
咬边不仅减少了接头工作截面,而且在咬边处造成严重的应力集中,导致结构破坏。
尤其是过深的咬边,将显著降低焊接接头的强度。
第四,咬边在底片上的显示:外咬边在射线底片上为沿焊缝影像边缘的细长起伏宽度不一的黑线,内咬边在射线底片上为靠近焊缝影像中心沿着根部焊道影像的不规则黑线。
咬边一定出现在焊缝的两侧,可以用肉眼观察出来,因此容易识别,如图16所示。
图16 咬边的典型射线影像(5)气孔 第一,气孔的基本特征:气孔,是在熔池结晶过程中未能逸出而残留在焊缝熔敷金2016年增刊1433冷加工属中的气体形成的孔洞。
气孔的形成过程是,熔池内发生气体析出,析出的气体聚集形成气泡,气泡长大到一定程度后开始上浮,上浮中受到焊缝熔敷金属的阻碍不能逸出,被留在焊缝金属中形成气孔。
第二,气孔产生的部位:气孔可以分布在焊缝中的任何部位。
按形状,气孔可分为球形气孔、长条形气孔、针形气孔;按分布状态,气孔可分为孤立气孔、局部密集气孔(呈任意几何分布的一群气孔)、链状气孔(排列在一条直线上、间距一定距离的多个气孔)和虫孔(被拉长,形状如小虫,呈人字形规则排列的的气孔)等,如图17所示。
图17 气孔示意第三,气孔的危害性:气孔属于体积型缺陷,一般来说,气孔使焊缝的有效截面积减少,降低了焊缝的力学性能,尤其是弯曲和冲击韧性,同时也破坏了焊缝的致密性,容易造成泄漏。
连续气孔是导致构件破坏的重要原因,塑性可降低40%50%,在交变载荷作用下,焊缝的疲劳强度显著下降。
气孔由于没有尖锐的边缘,一般来说不属于危害性缺陷,允许有限的存在,射线检测时应按有关标准进行评定,不合格的应进行返修或将构件报废。
第四,气孔在底片上的显示:在底片上,球形气孔的形状是圆形的黑色斑点,非球形气孔的形状是拉长了的具有光滑轮廓的黑色区域。
典型的孤立球形气孔,在底片上呈现为黑色小圆形斑点,外形较规则,黑度是中心大,沿边缘渐淡,轮廓清晰可见。
“夹珠”是另一类特殊的气孔缺陷,它是前一道焊接生成的气孔,被后一道焊接熔穿,铁液流进气孔而形成的,在底片上的影像为黑色气孔中间包含着一个白色圆珠,如图18~图23所示。
图18 球形气孔的射线影像图19 长条形气孔的射线影像图20 局部密集气孔的射线影像图21 链状气孔的射线影像图22 虫孔的射线影像图23 多种气孔叠加的射线影像(6)夹杂物第一,夹杂物的基本特征:焊缝2016年增刊1434冷加工中残留的除焊缝熔敷金属以外的各种物质称为夹杂物。
夹杂物分为夹杂、非金属夹杂物和金属夹杂物三类。
夹渣是指焊后残留在焊缝内的熔渣;非金属夹杂物是指焊接过程中产生的各种非金属杂质,如氧化物、氮化物和硫化物等;金属夹杂物主要是指钨夹渣和铜夹渣,钨夹渣是指采用钨极隋性气体保护焊时,由于温度很高使钨极温度超出它的熔点,致使钨极熔化成点滴状态留在焊缝中。
夹渣和非金属夹杂物一般统称为夹渣。
第二,夹杂物产生的部位:夹渣可以分布在焊缝中的任何部位,按形态可分为点状、条状和链状三种。
钨夹渣可以分布在焊缝中的任何部位,按形态可分为孤立点状和密集点状两种。
第三,夹杂物的危害性:夹渣属于体积型缺陷,形状是多种多样的,一般来说,夹渣使焊缝的有效截面积减少,降低了焊缝的力学性能,夹渣的棱角容易引起应力集中,成为交变载荷下的疲劳源。