成型应用工艺监测和控制技术探讨
锻压成形过程的检测与控制方法
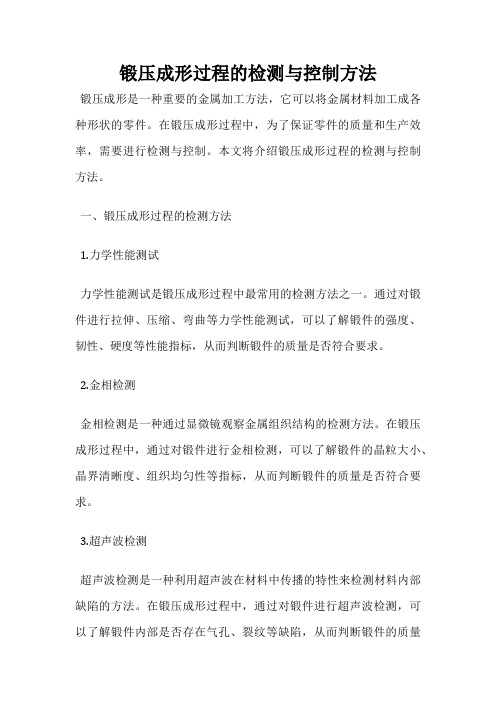
锻压成形过程的检测与控制方法锻压成形是一种重要的金属加工方法,它可以将金属材料加工成各种形状的零件。
在锻压成形过程中,为了保证零件的质量和生产效率,需要进行检测与控制。
本文将介绍锻压成形过程的检测与控制方法。
一、锻压成形过程的检测方法1.力学性能测试力学性能测试是锻压成形过程中最常用的检测方法之一。
通过对锻件进行拉伸、压缩、弯曲等力学性能测试,可以了解锻件的强度、韧性、硬度等性能指标,从而判断锻件的质量是否符合要求。
2.金相检测金相检测是一种通过显微镜观察金属组织结构的检测方法。
在锻压成形过程中,通过对锻件进行金相检测,可以了解锻件的晶粒大小、晶界清晰度、组织均匀性等指标,从而判断锻件的质量是否符合要求。
3.超声波检测超声波检测是一种利用超声波在材料中传播的特性来检测材料内部缺陷的方法。
在锻压成形过程中,通过对锻件进行超声波检测,可以了解锻件内部是否存在气孔、裂纹等缺陷,从而判断锻件的质量是否符合要求。
二、锻压成形过程的控制方法1.温度控制温度是影响锻压成形质量的重要因素之一。
在锻压成形过程中,需要对锻件和模具进行温度控制,以保证锻件的成形质量和模具的寿命。
2.压力控制压力是锻压成形过程中最重要的控制参数之一。
在锻压成形过程中,需要对锻压机进行压力控制,以保证锻件的成形质量和生产效率。
3.速度控制速度是影响锻压成形质量和生产效率的重要因素之一。
在锻压成形过程中,需要对锻压机进行速度控制,以保证锻件的成形质量和生产效率。
锻压成形过程的检测与控制方法是保证锻件质量和生产效率的重要手段。
通过合理的检测与控制方法,可以有效地提高锻件的成形质量和生产效率,为企业的发展提供有力的支持。
喷射成形过程的实时监测与智能控制技术
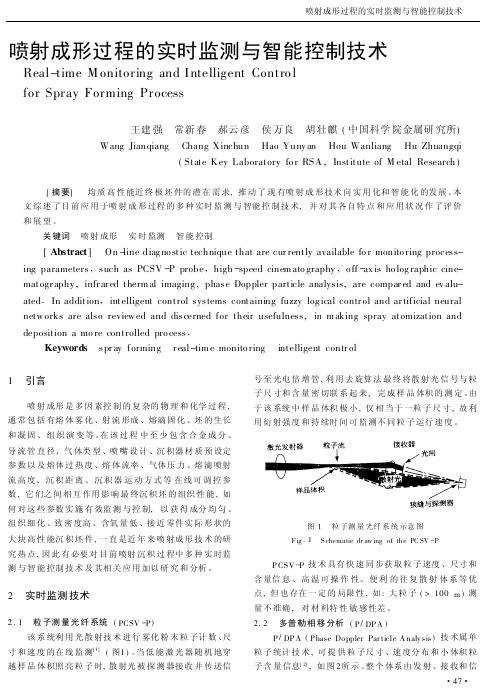
喷射成形过程的实时监测与智能控制技术Real-time M onitoring and Intelligent Contro lfor Spray Forming Process王建强 常新春 郝云彦 侯万良 胡壮麒(中国科学院金属研究所) Wang Jianqiang Chang Xinchun Hao Yuny an Hou Wanliang Hu Zhuangqi(State Key Laboratory fo r RSA,Institute of M etal Research) [摘要] 均质高性能近终极坯件的潜在需求,推动了现有喷射成形技术向实用化和智能化的发展。
本文综述了目前应用于喷射成形过程的多种实时监测与智能控制技术,并对其各自特点和应用状况作了评价和展望。
关键词 喷射成形 实时监测 智能控制[Abstract] On-line diag no stic technique that are cur rently available fo r monito ring process-ing parameters,such as PCSV-P probe,high-speed cinem ato graphy,o ff-ax is ho log raphic cine-matogr aphy,infr ar ed therm al imaging,phase Doppler particle analysis,are compar ed and ev alu-ated.In addition,intelligent control systems containing fuzzy log ical contr ol and ar tificial neural netw orks are also review ed and discerned for their usefulness,in m aking spray atomization and deposition a mo re controlled pro cess. Keywords spr ay forming r eal-tim e monito ring intelligent contr ol1 引言 喷射成形是多因素控制的复杂的物理和化学过程,通常包括有熔体雾化、射流形成、熔滴固化、坯的生长和凝固、组织演变等。
高分子材料成型及其控制技术分析

高分子材料成型及其控制技术分析
高分子材料成型技术是将高分子材料通过加热软化成型,在制造复杂形状的产品时非常有用。
随着高分子材料在工业、医疗、电子等领域的广泛应用,高分子材料成型技术也越来越重要,其中如何控制成型过程是关键。
高分子材料成型主要包括注塑、挤出、吹塑、压延、旋转成型等多种技术。
注塑是指使用模具将加热软化的高分子材料注入模具中,待冷却后脱模制成产品。
挤出是指将高分子材料加热软化后通过挤压机进行挤出成型。
吹塑是通过空气压力将高分子材料在模具壁上挤压成形。
压延是指将高分子材料通过加热软化后经过辊压成形。
旋转成型是指将摆线电动机旋转,使得高分子材料在热板上逐渐软化,并且能够逐渐形成所需的形状。
在高分子材料成型过程中,需要控制高温和高压对高分子材料的影响,避免热塑性材料过度加热引起燃烧或者热分解等问题,同时要控制成型过程中的速度和压力,以确保成型品质。
此外,也需要控制模具的温度和气氛等因素,以免影响成型品质和模具寿命。
为了实现高分子材料成型过程的控制,需要借助先进的成型设备和技术,如注塑机、挤出机、吹塑机等。
相应的,也需要掌握相关的成型技术和工艺要点,以确保生产高品质、高性能的高分子制品。
数控旋压成形工艺的应用实例与探讨

数控旋压成形工艺的应用实例与探讨数控旋压成形(CNC Spinning)是一种通过旋转壁板材料,利用数控机床的控制系统控制模具对材料进行压制和成型的工艺。
其主要特点是精度高、效率高、成形范围广、造型复杂,广泛应用于航空航天、汽车、电子、仪器仪表等领域。
下面将以航空航天领域为例,对数控旋压成形工艺的应用实例进行探讨。
在航空航天领域,飞机外壳是一个非常重要的部件。
传统制造方法需要使用大型的模具、多道工序和复杂的工艺,生产周期长、成本高。
而采用数控旋压成形工艺可以大大提高效率和精度,降低成本,因此得到了广泛应用。
首先,数控旋压成形工艺可以快速制造出尺寸较大的飞机外壳。
传统制造方法需要多次切割和焊接,而数控旋压成形工艺只需要通过数控机床控制模具按照设计要求对材料进行压制和成型,大大减少了制造工序和时间,同时还能够保证成型部件的一致性和精度。
其次,数控旋压成形工艺可以制造出复杂形状的飞机外壳。
在现代飞机设计中,外壳形状复杂多变,需要使用大量的模具和工艺来制造。
而采用数控旋压成形工艺,只需根据设计要求编写数控程序,便可实现对材料的精确控制和成型,从而制造出复杂形状的飞机外壳,大大简化了制造工艺和流程。
此外,数控旋压成形工艺还可以减少材料的浪费。
在传统制造方法中,为了保证成型部件的准确度和一致性,通常需要将材料的尺寸留有一定的余量,以便进行后续的加工处理和修整。
而采用数控旋压成形工艺,可以根据设计要求直接对材料进行成型,减少了过程中的浪费,提高了材料的利用率。
值得一提的是,数控旋压成形工艺还具有灵活性强的特点。
通过改变数控机床的控制程序,可以快速实现对不同形状的外壳进行成型,适应不同型号和尺寸的飞机外壳制造需求。
这种灵活性使得数控旋压成形工艺在航空航天领域具有广泛的应用前景。
综上所述,数控旋压成形工艺在航空航天领域具有广泛的应用前景。
通过提高效率、精度和灵活性,该工艺可以快速制造出尺寸大、形状复杂的飞机外壳,降低制造成本,提高制造效率,提高材料利用率。
精确高效塑性成形工艺技术

精确高效塑性成形工艺技术精确高效塑性成形工艺技术塑性成形是一种常见的金属加工工艺,它通过施加外力使金属材料发生塑性变形,从而得到所需的形状和尺寸。
精确高效的塑性成形工艺技术对于提高产品质量和生产效率至关重要。
在本文中,将介绍一种精确高效的塑性成形工艺技术。
首先,为了实现精确的成形,我们需要准确地控制金属的塑性变形过程。
因此,精确度高的机械设备和控制系统是必不可少的。
现代塑性成形机床通常配备了精确的数控系统,可以通过编程实现高精度的成形过程。
此外,精确的模具设计和制造也是实现塑性成形精度的重要因素。
采用先进的CAD/CAM技术可以实现模具的精确设计和加工,从而确保成形过程的精确度。
其次,为了提高塑性成形的效率,我们需要考虑材料的流动性和塑性变形的能力。
在材料设计方面,我们可以选择具有良好流动性和塑性变形能力的材料,如Al、Cu等。
此外,采用热成形可以增加材料的塑性变形能力,并有助于减少成形过程中的残余应力。
在成形过程中,合理的成形速度和温度控制也是确保成形效率的重要因素。
通过优化成形工艺参数,可以在保证产品质量的前提下提高生产效率。
最后,为了提高工艺的可靠性和稳定性,我们需要对塑性成形过程进行全面的监控和控制。
现代塑性成形机床通常配备了各种传感器和监测系统,可以实时监测成形过程的各种参数,如温度、压力、位移等。
通过采集和分析这些数据,可以及时发现和解决成形过程中的问题,并调整相关的工艺参数,提高工艺的可靠性和稳定性。
综上所述,精确高效的塑性成形工艺技术对于提高产品质量和生产效率至关重要。
通过采用精确的机械设备和控制系统、优化材料设计和成形工艺参数、以及全面监控和控制成形过程,可以实现精确高效的塑性成形,从而满足不同行业对于高精度、高效率的需求。
卫生陶瓷坐便器高压注浆成形工艺与控制技术探索

陶 瓷 Ceramics
( 卫 生 陶 瓷 )2 0 1 8 年 0 9 月
卫芏陶瓷坐便羞畐压汪浆成形工艺与控制技术探索
林毅
(广 东 翔 华 科 技 股 份 有 限 公 司 广 东 潮 州 51 5646)
摘 要 “卫生陶瓷高压注浆成形工艺与控制技术探索”是针对国内卫生陶瓷产品采用传统石膏模具注浆成形方法存在 成形时间长、效率低、空间利用率差,且需要配套大量人工、成本高等行业共性问题,通过研究采用带旋转框辅助装置的坐 便器高压注浆成形技术,实现主坯体注浆的机械自动辅助高压快速成形,以及无机复合添加剂在坯体注浆的辅助作用等 成形控制技术,配套带旋转辅助装置的高压注浆成形分体坐便器连续式生产设备,实现了高压注浆一次成形数量多、用工 少 、半成品率高、节能减排、提高生产效率和节约占地面积的高效立式高压成形产业化生产的技术创新。 关 键 词 卫生陶瓷高压注浆成形技术
3 工艺流程
卫生陶瓷高压注浆成形工艺流程: 合成泥浆—搅拌—加温—加压—洗模—合模—填 浆— 注浆—排浆—稳固—脱模—修还—烧制—成形— 检验— 人 库 。
4 解决的主要技术问题
项 目 的 实 施 及 产 业 化 应 用 ,为 当 前 应 用 传 统 石 膏 模具注浆成形工艺的卫生陶瓷产业更新换代树立典 范 ,在 业 内 构 建 了 基 于 分 体 坐 便 器 的 立 式 高 压 注 浆 成 形 工 艺 与 控 制 技 术 体 系 ,摆 脱 国 外 陶 瓷 企 业 对 高 压 注 浆 技 术 垄 断 ,使 坐 便 器 的 生 产 由 传 统 的 单 套 式 人 工 独 立 生 产 转 变 为 连 续 式 批 量 流 水 线 生 产 ,具 提 质 提 效 、节
“卫 生 陶 瓷 高 压 注 浆 成 形 工 艺 与 控 制 技 术 探 索 ”通 过研究采用带旋转框辅助装置的坐便器高压注浆成形 技 术 ,实 现 主 坯 体 注 浆 机 械 自 动 辅 助 的 高 压 快 速 成 形 。 研究高压注浆成形过程的压力与成坯速度的关联性, 获 取 不 同 工 序 的 压 力 和 加 压 时 间 的 最 优 加 压 参 数 ,以 及无机复合添加剂在坯体注浆的辅助作用等成形控制 技 术 ,同 时 配 套 高 压 分 体 坐 便 器 连 续 式 生 产 设 备 形 成 的 现 代 生 产 线 ,实 现 了 高 压 注 浆 一 次 成 形 数 量 多 ,降低 工 人 劳 动 强 度 和 半 成 品 破 损 率 ,免 除 传 统 石 膏 模 具 需 高 温 干 燥 及 频 繁 回 收 加 工 的 冗 杂 工 艺 ,提 高 生 产 效 率 和节约占地面积的高效立式高压成形产业化生产的技 术创新。
焊接成形技术研究及其应用

焊接成形技术研究及其应用随着工业化和现代化的不断发展,各个行业都不断提升着自己的工艺水平和生产效率。
而其中一个常被忽视的环节就是焊接成形技术,而焊接技术作为工程领域中不可或缺的一环,功不可没。
焊接成形技术,简单地说就是将材料焊接在一起,形成一个整体。
它在工业制造中扮演着非常重要的角色。
在工艺制造中,将底材的焊接接头准确地加工成特定形状和尺寸,是实现高质量、大规模、高效率生产的必要条件之一,通过优化材料的特性,使原材料的利用率最大化,可以降低生产成本,提高生产效率。
工程领域中广泛应用的焊接成型技术,可以分为以下几个方面。
首先是航空航天领域,其中特别是飞机、航空发动机、航天器的制造中。
飞机主机负责飞行任务,而发动机则负责提供动力,两者都需要使用焊接成型技术,才能得到如今高质量和高性能的航空器。
其次是汽车制造。
在汽车制造过程中,焊接成形技术发挥了重要作用,它可将各种不同材料焊接在一起,形成汽车的整体结构,如车身、车架、底盘等等。
同时通过焊接成形技术使整个车身更坚固,碰撞时更能保证司乘人员的安全。
第三,是金属制造业中的工艺技术之一。
各种金属制品在制造时,经常需要使用焊接成型技术,如钢铁、铝合金、不锈钢、铜和合金等等。
最后,是水利、电站、再生能源和结构领域。
这些领域都需要使用焊接成型技术。
例如,大型水利枢纽工程、核电站制造、风力发电、太阳能制造、桥梁和建筑结构制造等。
而要想实现焊接技术的高质量和高效率,就必须深入研究和改进相应的焊接设备和材料。
目前主要应用的焊接设备有三种:电弧焊机、气保焊机和激光焊机。
其中,激光焊机可以将焊接过程扩展到很多以前不能使用的材料和情况,这是当前焊接技术的一大发展方向。
焊接材料主要有两种,一种是传统的焊接材料,如焊丝、焊条等等;另一种是最近发展出来的焊接粉体,它可使焊接更加优化,大大提升焊接效果。
并且高档焊接产品材料中经常使用纳米材料,它的熔点较低、相对硬度大,极大的提高了焊接效果。
材料成型与控制工程模具制造的工艺技术研究

材料成型与控制工程模具制造的工艺技术研究材料成型与控制工程是模具制造的关键环节之一,它的研究和改进至关重要。
本文将从材料成型和控制工程两个方面探讨模具制造的工艺技术研究。
一、材料成型材料成型是指将材料经过特定的工艺处理后,使其具有所需的形状和性能。
成型技术是模具制造的核心,同时也是一个相对复杂的工程体系。
在材料成型过程中,需要配合多种成型设备和工具,才能够完成对材料的加工和成型。
1.1 材料成型的工艺材料成型的工艺包括原材料加热、浇注、喷涂、注塑等多种方法。
其中,注塑是最为常见的材料成型技术,掌握好注塑技术,能够提高模具的制造效率和产品质量。
注塑技术是先将所需材料经过预处理后,塑料化成液态,再将其注入模具中。
在注塑过程中,需要掌握好材料加热、注塑速度、模具结构等多个关键环节,以提高产品的成型质量和工艺效率。
同时,还需要注意注塑压力和时间,以控制产品的尺寸精度和表面质量。
材料成型的设备包括注塑机、压铸机、挤压机、电加热炉等多种设备。
不同的材料成型设备适用于不同的材料成型工艺和产品要求,在选择设备时需要综合考虑多种因素。
同时,还需要配备相应的工具,如模具、配件、夹具等,以满足不同产品的成型要求。
二、控制工程控制工程是指利用计算机、传感器等电子元件,控制模具制造过程中的各种参数和指标,从而达到精准控制的目的。
控制工程的实现需要借助计算机编程和自动化设备,通过对模具制造过程进行自动化控制,提高产品质量、降低成本、提升生产效率。
2.1 控制工程的应用范围控制工程的应用范围非常广泛,几乎涵盖了模具制造的各个环节,如原材料进料、成型工艺控制、产品尺寸检测、产品印刷等。
这些环节中都涉及到自动化控制技术和计算机编程技术的应用,有了控制工程的支持,模具制造业才能够更加高效、精确地进行生产。
控制工程的关键技术包括传感技术、控制算法、通讯技术等。
其中,传感技术是实现控制工程的基础技术,通过传感器对模具制造过程中的参数进行监测和控制。
跟踪控制算法在材料成型工艺中的应用研究

跟踪控制算法在材料成型工艺中的应用研究材料成型工艺在现代工业生产中起着至关重要的作用,它涉及到各种材料的加工和成型过程。
而在这个过程中,精确的控制和跟踪是非常关键的,这就需要借助于跟踪控制算法的应用。
本文将探讨跟踪控制算法在材料成型工艺中的应用研究。
一、材料成型工艺的挑战材料成型工艺的复杂性和多变性给控制和跟踪带来了许多挑战。
首先,不同的材料在成型过程中会出现不同的物理变化,如熔化、固化、收缩等,这就需要根据具体的材料特性来设计相应的控制算法。
其次,材料成型工艺中的温度、压力等参数会不断变化,这就需要实时地对这些参数进行监测和调整。
此外,材料成型工艺中的形状和尺寸要求也非常高,因此需要精确地控制和跟踪成型过程中的形状和尺寸。
这些挑战都需要借助于跟踪控制算法来解决。
二、传统的控制算法的局限性在过去的几十年中,传统的控制算法在材料成型工艺中得到了广泛应用,如PID控制算法、模糊控制算法等。
然而,这些传统的控制算法存在一些局限性。
首先,它们往往是基于经验和规则的,对于复杂的材料成型过程很难进行精确的控制。
其次,它们对于材料成型过程中的非线性和时变性的处理能力有限。
此外,它们往往只能实现单目标的控制,无法同时实现多目标的控制。
因此,需要一种更加高效和精确的控制算法来解决这些问题。
三、跟踪控制算法的原理和应用跟踪控制算法是一种基于模型的控制算法,它通过建立材料成型过程的数学模型来实现对成型过程的控制和跟踪。
跟踪控制算法的主要原理是通过与实际成型过程进行比较,不断调整控制参数,使得模型输出与实际输出尽可能接近。
跟踪控制算法可以根据具体的需求和材料特性进行调整,可以实现对温度、压力、形状和尺寸等多个参数的控制和跟踪。
跟踪控制算法在材料成型工艺中的应用非常广泛。
例如,在注塑成型工艺中,通过跟踪控制算法可以实现对注塑温度和压力的精确控制,从而保证注塑成型的质量和形状。
在挤出成型工艺中,通过跟踪控制算法可以实现对挤出速度和温度的控制,从而保证挤出成型的尺寸和形状。
材料成型与控制工程模具制造的工艺技术研究
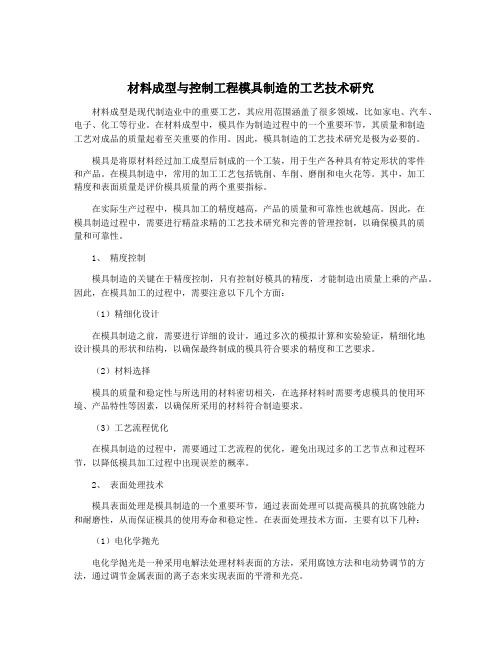
材料成型与控制工程模具制造的工艺技术研究材料成型是现代制造业中的重要工艺,其应用范围涵盖了很多领域,比如家电、汽车、电子、化工等行业。
在材料成型中,模具作为制造过程中的一个重要环节,其质量和制造工艺对成品的质量起着至关重要的作用。
因此,模具制造的工艺技术研究是极为必要的。
模具是将原材料经过加工成型后制成的一个工装,用于生产各种具有特定形状的零件和产品。
在模具制造中,常用的加工工艺包括铣削、车削、磨削和电火花等。
其中,加工精度和表面质量是评价模具质量的两个重要指标。
在实际生产过程中,模具加工的精度越高,产品的质量和可靠性也就越高。
因此,在模具制造过程中,需要进行精益求精的工艺技术研究和完善的管理控制,以确保模具的质量和可靠性。
1、精度控制模具制造的关键在于精度控制,只有控制好模具的精度,才能制造出质量上乘的产品。
因此,在模具加工的过程中,需要注意以下几个方面:(1)精细化设计在模具制造之前,需要进行详细的设计,通过多次的模拟计算和实验验证,精细化地设计模具的形状和结构,以确保最终制成的模具符合要求的精度和工艺要求。
(2)材料选择模具的质量和稳定性与所选用的材料密切相关,在选择材料时需要考虑模具的使用环境、产品特性等因素,以确保所采用的材料符合制造要求。
(3)工艺流程优化在模具制造的过程中,需要通过工艺流程的优化,避免出现过多的工艺节点和过程环节,以降低模具加工过程中出现误差的概率。
2、表面处理技术模具表面处理是模具制造的一个重要环节,通过表面处理可以提高模具的抗腐蚀能力和耐磨性,从而保证模具的使用寿命和稳定性。
在表面处理技术方面,主要有以下几种:(1)电化学抛光电化学抛光是一种采用电解法处理材料表面的方法,采用腐蚀方法和电动势调节的方法,通过调节金属表面的离子态来实现表面的平滑和光亮。
(2)喷涂喷涂是一种常用的表面处理方法,通过将表面均匀覆盖一层涂料,可以提高模具的耐磨性和抗腐蚀性。
(3)电镀法电镀法是一种通过电子流将制造成表面处理材料的镀层与基体金属连接在一起,从而增加金属件的硬度和耐磨性。
材料成形加工技术的研究与应用
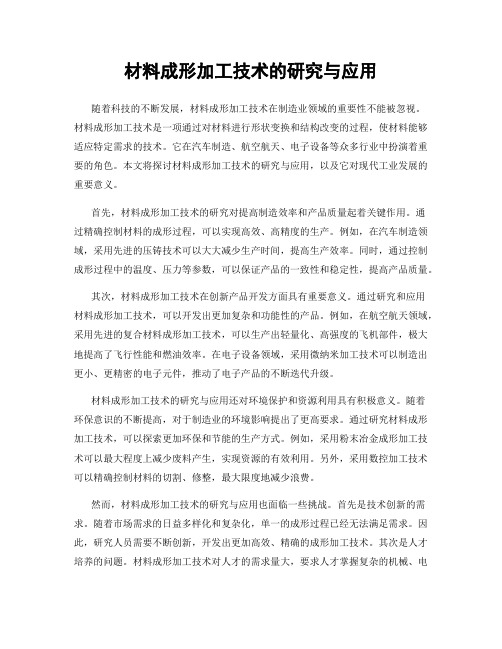
材料成形加工技术的研究与应用随着科技的不断发展,材料成形加工技术在制造业领域的重要性不能被忽视。
材料成形加工技术是一项通过对材料进行形状变换和结构改变的过程,使材料能够适应特定需求的技术。
它在汽车制造、航空航天、电子设备等众多行业中扮演着重要的角色。
本文将探讨材料成形加工技术的研究与应用,以及它对现代工业发展的重要意义。
首先,材料成形加工技术的研究对提高制造效率和产品质量起着关键作用。
通过精确控制材料的成形过程,可以实现高效、高精度的生产。
例如,在汽车制造领域,采用先进的压铸技术可以大大减少生产时间,提高生产效率。
同时,通过控制成形过程中的温度、压力等参数,可以保证产品的一致性和稳定性,提高产品质量。
其次,材料成形加工技术在创新产品开发方面具有重要意义。
通过研究和应用材料成形加工技术,可以开发出更加复杂和功能性的产品。
例如,在航空航天领域,采用先进的复合材料成形加工技术,可以生产出轻量化、高强度的飞机部件,极大地提高了飞行性能和燃油效率。
在电子设备领域,采用微纳米加工技术可以制造出更小、更精密的电子元件,推动了电子产品的不断迭代升级。
材料成形加工技术的研究与应用还对环境保护和资源利用具有积极意义。
随着环保意识的不断提高,对于制造业的环境影响提出了更高要求。
通过研究材料成形加工技术,可以探索更加环保和节能的生产方式。
例如,采用粉末冶金成形加工技术可以最大程度上减少废料产生,实现资源的有效利用。
另外,采用数控加工技术可以精确控制材料的切割、修整,最大限度地减少浪费。
然而,材料成形加工技术的研究与应用也面临一些挑战。
首先是技术创新的需求。
随着市场需求的日益多样化和复杂化,单一的成形过程已经无法满足需求。
因此,研究人员需要不断创新,开发出更加高效、精确的成形加工技术。
其次是人才培养的问题。
材料成形加工技术对人才的需求量大,要求人才掌握复杂的机械、电子、材料等知识。
因此,培养高水平的材料成形加工技术人才是迫切需要解决的问题。
材料成型过程中的质量控制技术研究
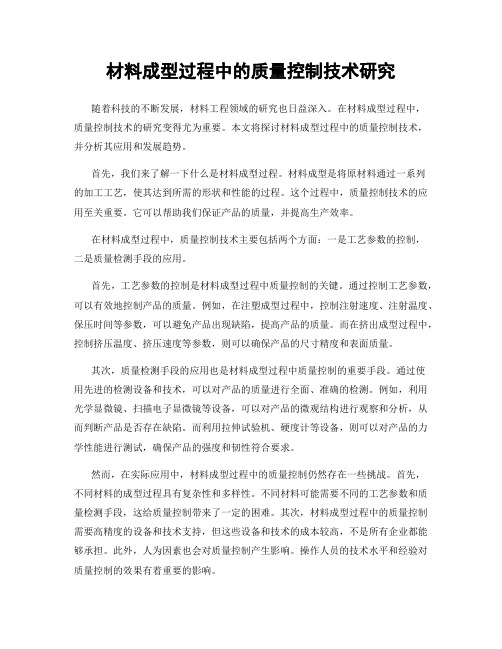
材料成型过程中的质量控制技术研究随着科技的不断发展,材料工程领域的研究也日益深入。
在材料成型过程中,质量控制技术的研究变得尤为重要。
本文将探讨材料成型过程中的质量控制技术,并分析其应用和发展趋势。
首先,我们来了解一下什么是材料成型过程。
材料成型是将原材料通过一系列的加工工艺,使其达到所需的形状和性能的过程。
这个过程中,质量控制技术的应用至关重要。
它可以帮助我们保证产品的质量,并提高生产效率。
在材料成型过程中,质量控制技术主要包括两个方面:一是工艺参数的控制,二是质量检测手段的应用。
首先,工艺参数的控制是材料成型过程中质量控制的关键。
通过控制工艺参数,可以有效地控制产品的质量。
例如,在注塑成型过程中,控制注射速度、注射温度、保压时间等参数,可以避免产品出现缺陷,提高产品的质量。
而在挤出成型过程中,控制挤压温度、挤压速度等参数,则可以确保产品的尺寸精度和表面质量。
其次,质量检测手段的应用也是材料成型过程中质量控制的重要手段。
通过使用先进的检测设备和技术,可以对产品的质量进行全面、准确的检测。
例如,利用光学显微镜、扫描电子显微镜等设备,可以对产品的微观结构进行观察和分析,从而判断产品是否存在缺陷。
而利用拉伸试验机、硬度计等设备,则可以对产品的力学性能进行测试,确保产品的强度和韧性符合要求。
然而,在实际应用中,材料成型过程中的质量控制仍然存在一些挑战。
首先,不同材料的成型过程具有复杂性和多样性。
不同材料可能需要不同的工艺参数和质量检测手段,这给质量控制带来了一定的困难。
其次,材料成型过程中的质量控制需要高精度的设备和技术支持,但这些设备和技术的成本较高,不是所有企业都能够承担。
此外,人为因素也会对质量控制产生影响。
操作人员的技术水平和经验对质量控制的效果有着重要的影响。
为了克服这些挑战,材料工程领域正在积极开展质量控制技术的研究。
一方面,研究人员致力于开发更加精确、高效的质量检测设备和技术。
例如,利用人工智能和大数据分析技术,可以实现对产品质量的自动化监测和预测,提高质量控制的效率和准确性。
材料成型过程中的精密控制方法研究
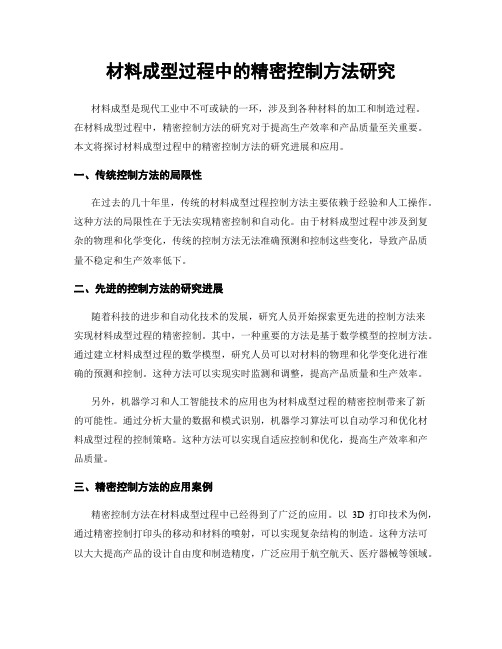
材料成型过程中的精密控制方法研究材料成型是现代工业中不可或缺的一环,涉及到各种材料的加工和制造过程。
在材料成型过程中,精密控制方法的研究对于提高生产效率和产品质量至关重要。
本文将探讨材料成型过程中的精密控制方法的研究进展和应用。
一、传统控制方法的局限性在过去的几十年里,传统的材料成型过程控制方法主要依赖于经验和人工操作。
这种方法的局限性在于无法实现精密控制和自动化。
由于材料成型过程中涉及到复杂的物理和化学变化,传统的控制方法无法准确预测和控制这些变化,导致产品质量不稳定和生产效率低下。
二、先进的控制方法的研究进展随着科技的进步和自动化技术的发展,研究人员开始探索更先进的控制方法来实现材料成型过程的精密控制。
其中,一种重要的方法是基于数学模型的控制方法。
通过建立材料成型过程的数学模型,研究人员可以对材料的物理和化学变化进行准确的预测和控制。
这种方法可以实现实时监测和调整,提高产品质量和生产效率。
另外,机器学习和人工智能技术的应用也为材料成型过程的精密控制带来了新的可能性。
通过分析大量的数据和模式识别,机器学习算法可以自动学习和优化材料成型过程的控制策略。
这种方法可以实现自适应控制和优化,提高生产效率和产品质量。
三、精密控制方法的应用案例精密控制方法在材料成型过程中已经得到了广泛的应用。
以3D打印技术为例,通过精密控制打印头的移动和材料的喷射,可以实现复杂结构的制造。
这种方法可以大大提高产品的设计自由度和制造精度,广泛应用于航空航天、医疗器械等领域。
另外,精密控制方法在金属加工和塑料成型等领域也有着重要的应用。
通过精确控制材料的温度、压力和流动速度等参数,可以实现更高质量的成型产品。
这种方法可以减少废品率和能源消耗,提高生产效率和资源利用率。
四、未来的发展方向尽管精密控制方法在材料成型过程中已经取得了显著的进展,但仍然存在一些挑战和待解决的问题。
例如,材料成型过程中的物理和化学变化非常复杂,建立准确的数学模型仍然是一个难题。
制造工艺中的质量控制与监测
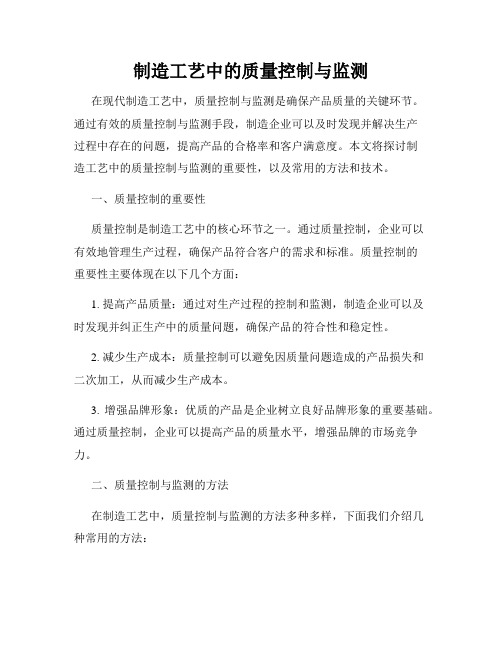
制造工艺中的质量控制与监测在现代制造工艺中,质量控制与监测是确保产品质量的关键环节。
通过有效的质量控制与监测手段,制造企业可以及时发现并解决生产过程中存在的问题,提高产品的合格率和客户满意度。
本文将探讨制造工艺中的质量控制与监测的重要性,以及常用的方法和技术。
一、质量控制的重要性质量控制是制造工艺中的核心环节之一。
通过质量控制,企业可以有效地管理生产过程,确保产品符合客户的需求和标准。
质量控制的重要性主要体现在以下几个方面:1. 提高产品质量:通过对生产过程的控制和监测,制造企业可以及时发现并纠正生产中的质量问题,确保产品的符合性和稳定性。
2. 减少生产成本:质量控制可以避免因质量问题造成的产品损失和二次加工,从而减少生产成本。
3. 增强品牌形象:优质的产品是企业树立良好品牌形象的重要基础。
通过质量控制,企业可以提高产品的质量水平,增强品牌的市场竞争力。
二、质量控制与监测的方法在制造工艺中,质量控制与监测的方法多种多样,下面我们介绍几种常用的方法:1. 统计质量控制:统计质量控制是一种常用的质量控制方法。
通过采集生产过程中的数据并进行统计分析,可以了解产品质量的分布情况,及时发现异常情况并采取相应措施。
统计质量控制主要包括控制图、过程能力分析等。
2. 抽样检验:抽样检验是指从生产批次中随机选取一部分样本进行检验,以此来判断产品批次的质量水平。
合理的抽样方案可以减少测试成本,同时也能有效地评估产品批次的整体质量。
3. 自动化检测:随着科技的发展,自动化检测在制造工艺中得到越来越广泛的应用。
自动化检测可以提高检测效率和减少人为误差,保证产品质量的稳定性和一致性。
4. 全面质量管理:全面质量管理是一种综合性、系统性的质量管理方法。
通过制定全面的质量管理体系和流程,建立有效的内部控制和监督机制,可以实现对全过程、全要素的质量管理与监测。
三、质量控制与监测的技术随着科技的进步,越来越多的高新技术被应用于制造工艺中的质量控制与监测。
高分子材料成型及其控制技术分析
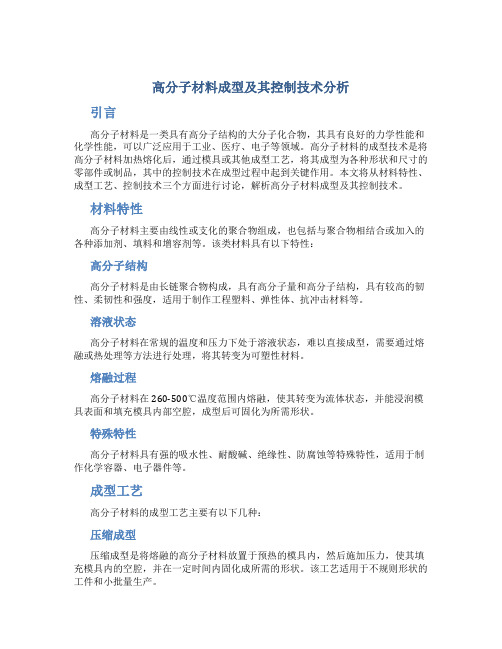
高分子材料成型及其控制技术分析引言高分子材料是一类具有高分子结构的大分子化合物,其具有良好的力学性能和化学性能,可以广泛应用于工业、医疗、电子等领域。
高分子材料的成型技术是将高分子材料加热熔化后,通过模具或其他成型工艺,将其成型为各种形状和尺寸的零部件或制品,其中的控制技术在成型过程中起到关键作用。
本文将从材料特性、成型工艺、控制技术三个方面进行讨论,解析高分子材料成型及其控制技术。
材料特性高分子材料主要由线性或支化的聚合物组成,也包括与聚合物相结合或加入的各种添加剂、填料和增容剂等。
该类材料具有以下特性:高分子结构高分子材料是由长链聚合物构成,具有高分子量和高分子结构,具有较高的韧性、柔韧性和强度,适用于制作工程塑料、弹性体、抗冲击材料等。
溶液状态高分子材料在常规的温度和压力下处于溶液状态,难以直接成型,需要通过熔融或热处理等方法进行处理,将其转变为可塑性材料。
熔融过程高分子材料在260-500℃温度范围内熔融,使其转变为流体状态,并能浸润模具表面和填充模具内部空腔,成型后可固化为所需形状。
特殊特性高分子材料具有强的吸水性、耐酸碱、绝缘性、防腐蚀等特殊特性,适用于制作化学容器、电子器件等。
成型工艺高分子材料的成型工艺主要有以下几种:压缩成型压缩成型是将熔融的高分子材料放置于预热的模具内,然后施加压力,使其填充模具内的空腔,并在一定时间内固化成所需的形状。
该工艺适用于不规则形状的工件和小批量生产。
注塑成型注塑成型是将熔融的高分子材料压入注塑机中,经加压和注射后喷射到模具中,然后在一定时间内冷却定型。
该工艺适用于生产大批量相同形状的零部件和制品。
吹塑成型吹塑成型是将熔融的高分子材料通过挤出机挤出空心管状物,再通过吹塑机吹气,使其膨胀,顺着模具表面成型,然后冷却固化。
该工艺适用于生产容器、瓶子等中空封闭式制品。
挤出成型挤出成型是将熔融的高分子材料通过挤出机挤压塑料到模具中,在一定的温度和压力下使其成形,一次成型的长度较长,适用于生产管道、电线等细长形状的零部件和制品。
液态成形过程检测与控制的关键和意义
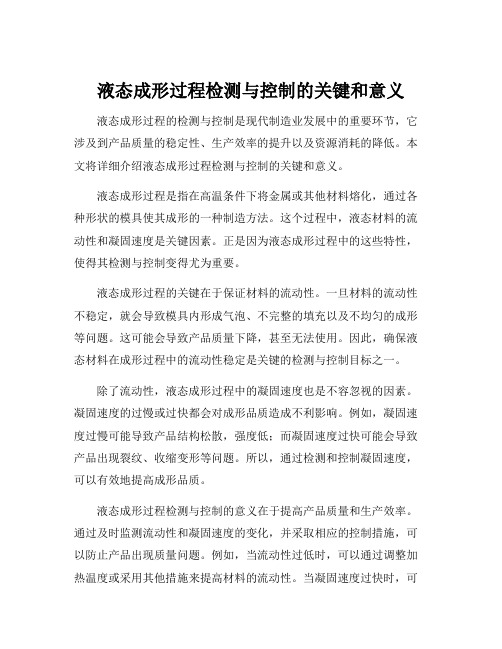
液态成形过程检测与控制的关键和意义液态成形过程的检测与控制是现代制造业发展中的重要环节,它涉及到产品质量的稳定性、生产效率的提升以及资源消耗的降低。
本文将详细介绍液态成形过程检测与控制的关键和意义。
液态成形过程是指在高温条件下将金属或其他材料熔化,通过各种形状的模具使其成形的一种制造方法。
这个过程中,液态材料的流动性和凝固速度是关键因素。
正是因为液态成形过程中的这些特性,使得其检测与控制变得尤为重要。
液态成形过程的关键在于保证材料的流动性。
一旦材料的流动性不稳定,就会导致模具内形成气泡、不完整的填充以及不均匀的成形等问题。
这可能会导致产品质量下降,甚至无法使用。
因此,确保液态材料在成形过程中的流动性稳定是关键的检测与控制目标之一。
除了流动性,液态成形过程中的凝固速度也是不容忽视的因素。
凝固速度的过慢或过快都会对成形品质造成不利影响。
例如,凝固速度过慢可能导致产品结构松散,强度低;而凝固速度过快可能会导致产品出现裂纹、收缩变形等问题。
所以,通过检测和控制凝固速度,可以有效地提高成形品质。
液态成形过程检测与控制的意义在于提高产品质量和生产效率。
通过及时监测流动性和凝固速度的变化,并采取相应的控制措施,可以防止产品出现质量问题。
例如,当流动性过低时,可以通过调整加热温度或采用其他措施来提高材料的流动性。
当凝固速度过快时,可以通过控制冷却速率或增加冷却介质的流量等方式来调整凝固速度。
这些控制措施的实施可以大大提高产品质量,减少次品率。
同时,液态成形过程检测与控制还可以有效提升生产效率。
通过实时监测流动性和凝固速度,可以实现自动化控制,减少人工干预,提高生产效率。
此外,通过分析和优化成形过程中的数据,可以找到更加合理的生产工艺参数,进一步提高生产效率。
液态成形过程检测与控制的意义不仅局限于质量和效率方面,还可以降低资源消耗。
通过优化成形过程,减少次品率,可以减少原材料的浪费。
此外,通过合理控制能源消耗和排放,还可以降低对环境的影响,推动绿色制造的发展。
材料成型及控制技术
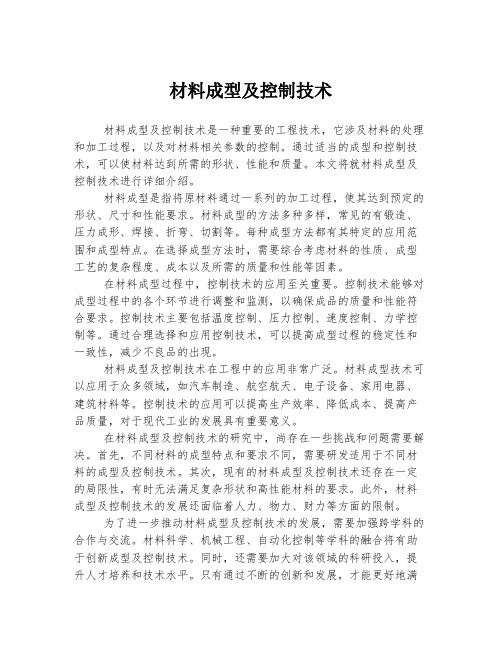
材料成型及控制技术材料成型及控制技术是一种重要的工程技术,它涉及材料的处理和加工过程,以及对材料相关参数的控制。
通过适当的成型和控制技术,可以使材料达到所需的形状、性能和质量。
本文将就材料成型及控制技术进行详细介绍。
材料成型是指将原材料通过一系列的加工过程,使其达到预定的形状、尺寸和性能要求。
材料成型的方法多种多样,常见的有锻造、压力成形、焊接、折弯、切割等。
每种成型方法都有其特定的应用范围和成型特点。
在选择成型方法时,需要综合考虑材料的性质、成型工艺的复杂程度、成本以及所需的质量和性能等因素。
在材料成型过程中,控制技术的应用至关重要。
控制技术能够对成型过程中的各个环节进行调整和监测,以确保成品的质量和性能符合要求。
控制技术主要包括温度控制、压力控制、速度控制、力学控制等。
通过合理选择和应用控制技术,可以提高成型过程的稳定性和一致性,减少不良品的出现。
材料成型及控制技术在工程中的应用非常广泛。
材料成型技术可以应用于众多领域,如汽车制造、航空航天、电子设备、家用电器、建筑材料等。
控制技术的应用可以提高生产效率、降低成本、提高产品质量,对于现代工业的发展具有重要意义。
在材料成型及控制技术的研究中,尚存在一些挑战和问题需要解决。
首先,不同材料的成型特点和要求不同,需要研发适用于不同材料的成型及控制技术。
其次,现有的材料成型及控制技术还存在一定的局限性,有时无法满足复杂形状和高性能材料的要求。
此外,材料成型及控制技术的发展还面临着人力、物力、财力等方面的限制。
为了进一步推动材料成型及控制技术的发展,需要加强跨学科的合作与交流。
材料科学、机械工程、自动化控制等学科的融合将有助于创新成型及控制技术。
同时,还需要加大对该领域的科研投入,提升人才培养和技术水平。
只有通过不断的创新和发展,才能更好地满足工业生产的需求,推动材料成型及控制技术的进步。
综上所述,材料成型及控制技术是一项重要的工程技术,对于材料加工和工业生产具有重要意义。
液态成形过程检测与控制的关键和意义
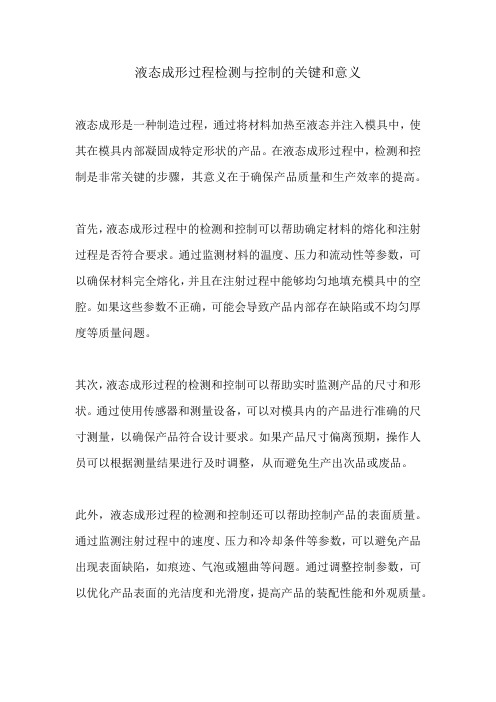
液态成形过程检测与控制的关键和意义液态成形是一种制造过程,通过将材料加热至液态并注入模具中,使其在模具内部凝固成特定形状的产品。
在液态成形过程中,检测和控制是非常关键的步骤,其意义在于确保产品质量和生产效率的提高。
首先,液态成形过程中的检测和控制可以帮助确定材料的熔化和注射过程是否符合要求。
通过监测材料的温度、压力和流动性等参数,可以确保材料完全熔化,并且在注射过程中能够均匀地填充模具中的空腔。
如果这些参数不正确,可能会导致产品内部存在缺陷或不均匀厚度等质量问题。
其次,液态成形过程的检测和控制可以帮助实时监测产品的尺寸和形状。
通过使用传感器和测量设备,可以对模具内的产品进行准确的尺寸测量,以确保产品符合设计要求。
如果产品尺寸偏离预期,操作人员可以根据测量结果进行及时调整,从而避免生产出次品或废品。
此外,液态成形过程的检测和控制还可以帮助控制产品的表面质量。
通过监测注射过程中的速度、压力和冷却条件等参数,可以避免产品出现表面缺陷,如痕迹、气泡或翘曲等问题。
通过调整控制参数,可以优化产品表面的光洁度和光滑度,提高产品的装配性能和外观质量。
最后,液态成形过程的检测和控制可以帮助提高生产效率和降低成本。
通过实时监测生产过程中的关键参数,可以及时发现和纠正问题,减少废品和返工的数量。
此外,通过自动化控制系统,可以提高生产线的稳定性和一致性,减少人为因素对产品质量的影响,提高生产效率和降低生产成本。
总之,液态成形过程中的检测和控制是确保产品质量和生产效率的关键步骤。
通过监测和调整关键参数,可以保证材料的熔化和注射过程符合要求,产品的尺寸、形状和表面质量达到设计要求,同时提高生产效率和降低成本。
浅谈冲压成型质量分析及控制的实际应用
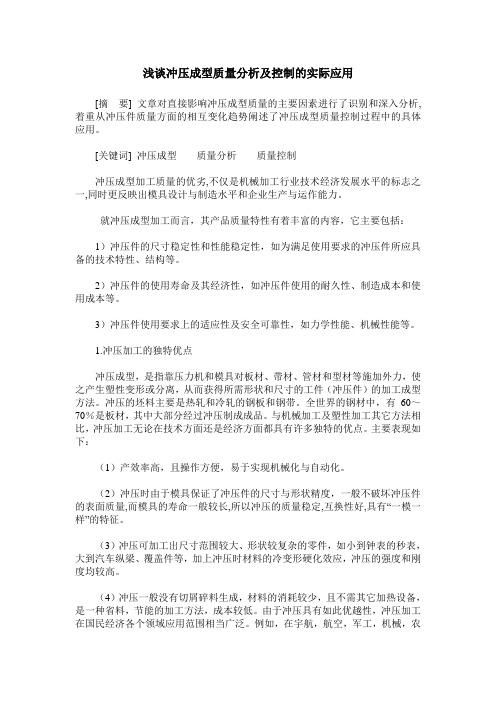
浅谈冲压成型质量分析及控制的实际应用[摘要] 文章对直接影响冲压成型质量的主要因素进行了识别和深入分析,着重从冲压件质量方面的相互变化趋势阐述了冲压成型质量控制过程中的具体应用。
[关键词] 冲压成型质量分析质量控制冲压成型加工质量的优劣,不仅是机械加工行业技术经济发展水平的标志之一,同时更反映出模具设计与制造水平和企业生产与运作能力。
就冲压成型加工而言,其产品质量特性有着丰富的内容,它主要包括:1)冲压件的尺寸稳定性和性能稳定性,如为满足使用要求的冲压件所应具备的技术特性、结构等。
2)冲压件的使用寿命及其经济性,如冲压件使用的耐久性、制造成本和使用成本等。
3)冲压件使用要求上的适应性及安全可靠性,如力学性能、机械性能等。
1.冲压加工的独特优点冲压成型,是指靠压力机和模具对板材、带材、管材和型材等施加外力,使之产生塑性变形或分离,从而获得所需形状和尺寸的工件(冲压件)的加工成型方法。
冲压的坯料主要是热轧和冷轧的钢板和钢带。
全世界的钢材中,有60~70%是板材,其中大部分经过冲压制成成品。
与机械加工及塑性加工其它方法相比,冲压加工无论在技术方面还是经济方面都具有许多独特的优点。
主要表现如下:(1)产效率高,且操作方便,易于实现机械化与自动化。
(2)冲压时由于模具保证了冲压件的尺寸与形状精度,一般不破坏冲压件的表面质量,而模具的寿命一般较长,所以冲压的质量稳定,互换性好,具有“一模一样”的特征。
(3)冲压可加工出尺寸范围较大、形状较复杂的零件,如小到钟表的秒表,大到汽车纵梁、覆盖件等,加上冲压时材料的冷变形硬化效应,冲压的强度和刚度均较高。
(4)冲压一般没有切屑碎料生成,材料的消耗较少,且不需其它加热设备,是一种省料,节能的加工方法,成本较低。
由于冲压具有如此优越性,冲压加工在国民经济各个领域应用范围相当广泛。
例如,在宇航,航空,军工,机械,农机,电子,信息,铁道,邮电,交通,化工,医疗器具,日用电器及轻工等部门里都有冲压加工。
- 1、下载文档前请自行甄别文档内容的完整性,平台不提供额外的编辑、内容补充、找答案等附加服务。
- 2、"仅部分预览"的文档,不可在线预览部分如存在完整性等问题,可反馈申请退款(可完整预览的文档不适用该条件!)。
- 3、如文档侵犯您的权益,请联系客服反馈,我们会尽快为您处理(人工客服工作时间:9:00-18:30)。
成型应用工艺监测和控制技术探讨
摘要:液体模塑成型技术已在汽车工业广泛应用,原因是采用这一技术可进一步减轻车辆的重量、降低制造成本和改善车辆的性能。
本文介绍了成型过程的热监控技术和压力监控技术,描述了如何通过该技术实现对产品充模和固化的成型过程监测。
通过合理的选择理想的控制系统,优化过程参数,从而最终保证成型的工艺质量。
关键词:热电偶;压力传感器;充模;固化
一引言
汽车工业的发展同塑料成型技术的发展是密不可分的。
首先,汽车材料应用塑料的最大优势是减轻车体的重量。
其次,塑料成型容易,使得形状复杂的部件加工十分便利。
第三,塑料制品的弹性变形特性能吸收大量的碰撞能量。
对塑料成型技术而言,过程控制是最重要的。
工艺的监控不仅直接影响构件的产量和质量,还影响到构件的生产方式。
所以说,成型过程的监测是决定工艺质量的关键。
生产环境不同,成型过程监测和控制方法也随之发生变化。
结构反应注射成型(SRIM)工艺通常采用复杂的计量设备来控制树脂的比例、流速和注射量,而在传统的树脂传递模塑(RTM)工艺中,一般采用较简单的设备,很少进行成型过程监测和控制。
无论采用哪种方法来输送液体树脂和控制其流动,都需要监测和控制树脂的充模过程和固化度。
原材料(单体含量、表面密度等)、环境因素(温度、湿度等)或者设备性能的变化,都为模塑工艺的灵活性提供了很大的空间,所以,理想的控制系统应基于信息反馈。
错误的工艺控制可能导致以下问题:
·充模不完全
·外观质量不佳
·树脂浪费
·固化不完全
·成型周期过长
二热监控技术
热电偶可以用来测量非等温模塑周期中的关键过程,如树脂的到达和放热,
其监控效果取决于采用的工艺类型、热电偶的性能及其布局位置之间的关系。
例如,聚氨酯SRIM快速成型工艺需要高灵敏度热电偶,将热电偶埋设在层合板内以利于有效反馈。
而对于速率较低的聚酯RTM成型工艺,可以采用时间常数较长,安装于模板上的热电偶即可。
在工艺监测和控制中,至少应在注射口或靠近注射口处安装一热电偶;在排气口处或附近、模具边缘等最后填充的位置安装一热电偶。
由于需测量构件的表面或中面温度,而非模具内部温度,故这些位置与对模具进行温度控制的仪器无关。
双绞线热电偶的反馈时间最短,且在工艺进行过程中可置于预成型体内,但这项技术相当耗时,且每一次模塑都会消耗热电偶。
在模具内,可以将热电偶安装于构件的表面,但在非等温工艺中由于沿厚度方向的温度梯度很大,通常希望测得的温度尽可能接近层合板中面处的温度,所以需要采用插入方法,带有护套保护的热电偶从模腔壁插入到层合板中进行测量。
三压力监控技术
当树脂流动路径长或浸渍速度慢时,研究表明,仅仅依靠温度不能可靠确定树脂流动前峰的位置,一般地,采用模腔压力来监控树脂在浸渍时的流动则更为有利。
在压力监控时,可以使用非插入式传感器来监控充模和固化。
压力传感器可以采用嵌入式安装,但由于诸多原因,在选择和安装时应非常仔细。
为将预成型体压缩至理想的纤维体积含量,施加的合模力通常会在增强材料中产生与流体压力差不多大的压力。
因此,为保证记录下的是流体压力而非增强材料的压力,通常将传感器凹下2mm。
此外,还应注意电子仪器和传感器薄膜后的黏结剂的极限工作温度,以免仪器受损或错误测量。
在实验的基础上,压力测量已成功应用于片状模塑料(SMC)工艺的流动和固化监控中。
在SMC工艺中,原料流动时伴随着压力升高,这在树脂放热过程中更为明显,因此可对流动和固化过程进行监控。
树脂固化时发生收缩引起模腔内压力下降,可为改变夹紧力提供指导,从而降低浪费。
固化时的压力与固化程度有关,在层合板脱模后,通过测量其关键点处的巴氏硬度和残余的苯乙烯单体,可以找到它们之间的关系。
这是由压力确定固化终点的基础。
四充模和固化的监测
在模内使用仪器可以提供液体模塑工艺控制的有效信号。
在实时控制中,充模完成和开模是两个最为重要的信号。
或许,充模完成的信号最难获取,因为它
依赖树脂在增强材料和模腔内的流动特性。
当流动路径较短时,热电偶不能有效地探测树脂流动,因此在大部分的生产应用中都不能成功地监测到充模完成。
由于在充模完成时模内压力升高,所以压力传感器有可能监测到充模完成。
将压力传感器安装在注射口处,当由于凝胶或注射量过大使得测得的模内压力超过预设的极限值时,应立即停止注射。
在SRIM和RTM工艺中,这种方法可有效防止注射设备和模具的损伤,降低因压力过大超出夹具能力而引起开模、导致生产制品尺寸过大的危险。
开模可以通过多种方法确定。
例如,通过安装于注射口的热电偶检测树脂的放热情况。
由于注射口处树脂的驻留时间最短,所以固化最晚。
热电偶的位置、性质和插入性都需考虑。
此外,在注射口安装压力传感器,可以检测液态树脂的膨胀、固化收缩以及放热膨胀。
虽然该方法是非插入式的,但由于要保证浸渍后模腔内必须维持正压,所以不如采用热电偶可靠。
但某些低收缩剂表现出与树脂放热一致的、明显的压力信号,所以适于装饰性部件的生产应用。
五结束语
除了控制树脂的注射和模塑周期外,以上技术还可以对液体模塑成型工艺过程进行监控,特别是发展工艺的阶段。
在预成型体中布置热电偶的方法,安装方便且成本低廉,因而发展潜力最大。
根据由热曲线得到的浸渍结束到树脂放热之间的时间延迟,可对树脂的化学性能进行优化。
当延迟较长时,应改进树脂添加剂配方以增加反应速率,或者也可以提高模具温度来加速反应;相反,如果反应速度过快,则反之亦然。
压力传感器也可以用来优化模塑周期。
在树脂放热前,当树脂开始凝胶而引起压力降低时,优化成型过程参数是使充模时间最短的最佳方法。
压力传感器还可以描述树脂的流动前峰,当形状复杂时这一点尤其重要,可避免产生废品。
由发展工艺的反复实验中得到的相关信息,对于液体模塑工艺成型的后期验证十分重要,且有利于促进工艺的进一步发展。
参考文献:
[1] 王善勤等. 塑料注塑成型工艺. 北京: 机械工业出版社, 1997
[2] 王志新. 现代注塑机控制. 北京: 轻工业出版社, 2001
[3] 李德群等. 塑料成型模具设计. 武汉: 华中理工大学出版社, 1993。