粉末冶金模压模工作零件的材料及技术要求
MPIF 35(1998)粉末冶金结构零件材料标准简介

。
最小值 最小强度
材料牌号 屈服 极限
型
衰 烧 结铁铜 合 金 和烧结铆钥的益绘 力黛雄能
标准值
拉 伸性 能
极限 强度
屈服 强度
伸长 率
弹性常数
杨氏 模量
泊松
无凹 口
锤式冲 击能量
抗弯
强度
比
压缩
屈服 强度
阮
巴一 夕一八凡‘三︸」、,
旦
,
一
‘,矛了
边一茱引侧仅大艾仗歇主别凡自沮一恤一
午亨定 ,
修订
硬度 哪靛梦
℃左右熔 化 , 在铁粉颗粒 之 间流动并流入 小孔 隙中 , 从 而有助 于 材 料 的烧
结 。 正 常烧结 的含铜 量 为 的合 金 材 料 中很 少 或 没 有 不 溶 解 的铜 。 铜 的 百 分 含 量 高 时 , 铜 将 以 单 独 相 存
在 。 铜溶于铁中 , 但不会渗透到铁粉颗粒心部 。 铜 粉颗粒熔化扩散或迁移后 将遗 留下相 当大 的孔 隙 , 这些 孔
极限 强度
屈服 强度
伸长 率
一
标 准值
弹性常数
杨氏 模量
泊松
无凹 口 锤式冲
击能量
抗弯 强度
比
压缩
屈服 强度
流
续表
硬度 哪纂赫
宏观 微观
密度
表观 换算的 率
洛氏
‘内, 一内、」,产﹃
乙
一
内」呼三 月,︵
一
一
一
八 上︸
一
一
一
型
一
注
、
、
、
︺︸
门 一, 八
型缪
、
及
同表 。
粉末冶金件技术要求

1.主题与适用范围
本标准适用于用铁基粉末冶金压铸、烧结、和切削加工成形的零件,包括活塞、导向器、压缩阀座、压缩阀体、复原阀体等零件。
2.引用标准
GB/T1804一般公差未注公差的线性和角度尺寸的公差
GB/T1184形状和位置公差未注公差值
3.材料
铁基粉末冶金件化学成分见下表:
化学成分
6.外观:零件外观无破损、裂纹、氧化、严重碰伤、夹杂物及毛刺。重要型面无碰伤。
7.表面处理
部分粉末冶金件要求对表面进行蒸汽处理,蒸汽处理后不得影响重要型面的形状和尺寸,必要时应进行整形处理。
8.防锈处理:零件应进行防锈处理。
C
Cu
其它
Fe
含量(%)
活塞
1.2~1.6
2.5~4.5
<2
余
导向器、阀座等
0.5~1.2
1.8~2.5
<2
余
4.铁基粉末冶金件的性能指标如下:
含油密度(g/cm3)
00~150
珠光体不低于70%
游离渗碳体约10%
且不允许呈网状分布
导向器、阀座等
>6.3
90~140
珠光体不低于40%
游离渗碳体约5%
且不允许呈网状分布
零件的强度可根据零件的受力情况进行压溃强度的检查,压溃力的大小和方式以图纸要求为准。
5.尺寸公差
5.1图纸尺寸公差有要求的按图纸执行,图纸未作具体要求的按GB/T1804中m级精度执行。
5.2图纸尺寸形位公差有要求的按图纸执行,图纸未作具体要求的按GB/T1184未注形位公差中的H级精度执行。
粉末冶金模具的设计与制造

粉末冶金模具的设计与制造1. 引言粉末冶金是一种重要的金属制造工艺,广泛应用于汽车、航空航天、电子、能源等领域。
在粉末冶金工艺中,模具的设计与制造是关键环节,直接影响产品的质量和性能。
本文将介绍粉末冶金模具的设计与制造过程,包括模具材料的选择、模具的结构设计、加工工艺等内容,以帮助读者全面了解粉末冶金模具的制造方法和技术要点。
2. 模具材料的选择模具材料的选择是粉末冶金模具设计的第一步。
模具材料需要具备一定的硬度、耐磨性和耐各种腐蚀介质的能力。
常用的模具材料有以下几种:•工具钢:具有较高的硬度和韧性,适用于大部分粉末冶金模具的制造。
•高速钢:具有更高的硬度和耐磨性,适用于对模具耐磨性要求较高的情况。
•硬质合金:具有较高的硬度和耐磨性,适用于对模具耐磨性要求极高的情况。
在选择模具材料时,需要根据具体应用场景和成本考虑,综合各种性能指标做出合理选择。
3. 模具的结构设计模具的结构设计是粉末冶金模具制造中的核心环节。
良好的模具结构设计可以提高产品的制造效率和质量,降低生产成本。
以下是模具结构设计的几个要点:•模具的整体结构应该合理,易于安装和拆卸。
模具的结构应简洁、牢固,能够承受制造过程中的力和压力。
•模具的导向和定位系统要设计到位,以确保模具在制造过程中的稳定性和精度。
•模具的开合系统要灵活可靠,能够实现快速开合和调节。
对于大型模具,可以考虑采用液压或气动开合系统。
•模具的冷却系统要充分考虑,以保证模具在制造过程中能够及时散热,提高产品质量和生产效率。
4. 模具的制造过程粉末冶金模具的制造过程主要包括以下几个步骤:4.1 模具设计在模具设计阶段,根据产品的形状和尺寸要求,通过CAD软件进行三维建模。
在设计过程中,要充分考虑模具的可行性和制造工艺,以确保模具的质量和可生产性。
4.2 模具加工模具加工是模具制造的关键环节。
常用的模具加工方法包括数控加工、线切割、铣削等。
在加工过程中,需要根据模具材料和结构要求选择合适的加工工艺,精确控制加工尺寸和表面质量。
粉末冶金材料的成型

粉末冶金材料的成型一、压制成型基本规律压模压制是指松散的粉末在压模内经受一定的压制压力后,成为具有一定尺寸、形状和一定密度、强度的压坯。
当对压模中粉末施加压力后,粉末颗粒间将发生相对移动,粉末颗粒将填充孔隙,使粉末体的体积减小,粉末颗粒迅速达到最紧密的堆积。
粉末压制时出现的过程有:颗粒的整体运动和重排;颗粒的变形和断裂;相邻颗粒表面间的冷焊。
颗粒主要沿压力的作用方向运动。
颗粒之间以及颗粒与模壁之间的摩擦力阻止颗粒的整体运动,并且有些颗粒也阻止其他颗粒的运动。
最终颗粒变形,首先是弹性变形,接着是塑性变形;塑性变形导致加工硬化,削弱了在适当压力下颗粒进一步变形的能力。
与被压制粉末对应的金属或合金的力学性能决定塑性变形和加工硬化的开始。
例如,压制软的铝粉时颗粒变形明显早于压制硬的钨粉时的颗粒变形,最后颗粒断裂形成较小的碎片。
而压制陶瓷粉时通常发生断裂而不是塑性变形。
随着压力的增大,压坯密度提高。
不同粉末压制压力与压坯密度之间存在一定的关系。
然而,至今没有得到令人满意的压坯密度与压制压力之间的关系。
建立在实际物理模型基础上的一些关系,仍然是经验性的,因为其中使用了与粉末性能无关的调节参数。
更准确地应当使用给定粉末的压制压力与压坯密度之间关系的图形或表格数据。
二、粉末的位移粉末体的变形不仅依靠颗粒本身形状的变化,而且主要依赖于粉末颗粒的位移和孔隙体积的变化。
粉末体在自由堆积的情况下,其排列是杂乱无章的。
当粉末体受到外力作用时,外力只能通过颗粒间的接触部分来传递。
根据力的分解可知,不同连接处受到外力作用的大小和方向都不一样。
所以颗粒的变形和位移也是多种多样的。
当施加压力时,粉末体内的拱桥效应遭到破坏,粉末颗粒便彼此填充孔隙,重新排列位置,增加接触。
可用图4.9所示的两颗粉末5种状态来近似地说明粉末的位移情况。
图4.9 粉末位移的形式三、粉末的变形粉末体在受压后体积明显减小,这是由于粉末体在压制时不但发生了位移,而且还发生了变形。
粉末冶金原理及模具计算要求
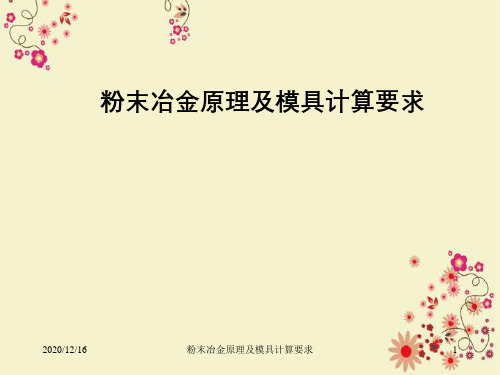
3.4 组合模具的设计原理
形状完整,具有一定强度
3.5 压制过程的图示
2020/12/16
粉末冶金原理及模具计算要求
2
•压制压力的计算
模压过程的总压制力等于净压力与外摩擦力 之和
单位压制压力与压坯密度定量关系的研究, 是近60年来粉末成形理论研究的主要内容
•脱模力的计算
压制压力去掉后,侧压力因为高度方向的弹 性后效,侧压力会下降35~77%
单向压制
S侧max/S=[1-(ρ下/ρ上)m]/μξ=K
当柱状压坯S侧/S<K或者圆柱体压坯高径比
H/D<K/4时,采用单向压制可以满足压坯密度
分布均匀性的要求
2020/12/16
粉末冶金原理及模
粉末冶金原理及模具计算要求
17
双向压制
S侧max/S=[1-(ρ中/ρ上)m]/μξ=2K
压力相等时双向压制与非同时双向压制的效 果相同
非同时双向压制中第二次压制的模冲移动距 离:
x=(d2-d1)h/d1
或者 y=x/l=100(d2-d1)/d1(k-1)
其中:d2为要求的压坯平均密度;d1为单向压 制的平均密度;h为压坯高度;k为压缩比;l 为装粉高度与压坯高度之差。
2020/12/16
•压制时粉体产生柱式流动,几乎不产生明显
的横向流动 2020/12/16
粉末冶金原理及模具计算要求
8
压坯中中立层的位置可以表示压坯密度分布
的均匀程度。通过压制方式和压模结构合理
选择使中立层2边受相同压缩,提高密度分布
均匀性 2020/12/16
粉末冶金原理及模具计算要求
9
2020/12/16
d粉—粉末松装密度; d1—第一次压制后压坯平均密度; 第一次压制后:d粉H粉=d1h1 x=h1-h d粉H粉=d1(h+x) ∴x=(d粉H粉-d1h)/d1 第二次压制后:d粉H粉=dh d粉=d ·h/H粉 x=(d-d1)h/d1; k=H粉/h=(l+h)/h 粉末冶金原理及∴模x具=计(算d要-d求1)l/d1(k-1); y=x/l ·11000%
粉末冶金:钢压模具设计

好的材料 ➢ 高密度、高精度件用耐磨性好的材料 ➢ 整形模用耐磨性好的材料
绘制模具装配图和零件图
➢ 绘制模具装配图和零件图 ➢ 标注尺寸偏差和形位公差 ➢ 标注其他加工要求
绘制模具装配图和零件图
模具示例
模具示例
设计模具结构
根据制品图纸设计坯件,选择压机和压制方式,设计 模具结构草图 ➢ 从生产工艺、压制成形和经济成本方面分析制品图纸 及技术要求,看是否适于用粉末冶金方法生产 ➢ 根据制品图纸及技术要求和粉末冶金生产工艺的特点, 设计坯件的几何形状、精度和密度 ➢ 为了使制品适于压制成形,或为了简化模具结构,常 对制品形状进行修改,设计出适合于压制的压坯 ➢ 在设计坯件形状的同时要确定压制方向,然后根据压 坯的形状、高径比、生产批量和压机来选择压制方式、 压模结构类型
粉末成形模具分类
➢ 压模、精整模、复压模、锻模、挤压模、 热压模、等静压模、粉浆浇注模、松装 烧结模
➢ 钢模、硬质合金模、石墨模、塑料橡皮 模和石膏模
钢压模具结构
钢压模具一般由 阴模、模冲、芯棒 组成
钢压模具结构
1—模柄 2,9—法兰圈 3—上模冲 4—模套 5—阴模 6—模座 7—弹簧 8—下模冲 10—下模冲座 11—压垫 12—下模板 13—顶杆 14—顶板
➢ 制品生产工艺流程及工艺参数:粉末混合料成分、杜 装密度、流动性、压制性、单位压制压力、压坯密度、 压缩比、弹性后效、烧结收缩率、精整余量、机加工 余量、复压装模间隙和压下率等
➢ 压机类型及主要技术参数:公称压力、脱模压力、压 机行程、每分钟压制次数、工作台面积、压机自动化 程度和安全保险装置等
粉末冶金模具设计说明书样板
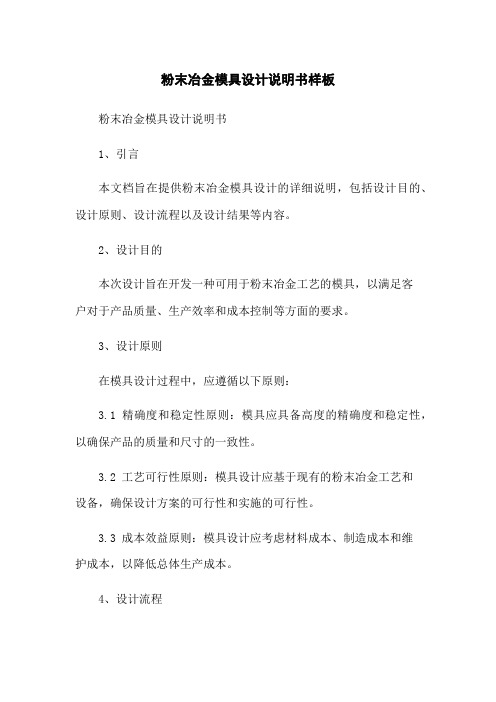
粉末冶金模具设计说明书样板粉末冶金模具设计说明书1、引言本文档旨在提供粉末冶金模具设计的详细说明,包括设计目的、设计原则、设计流程以及设计结果等内容。
2、设计目的本次设计旨在开发一种可用于粉末冶金工艺的模具,以满足客户对于产品质量、生产效率和成本控制等方面的要求。
3、设计原则在模具设计过程中,应遵循以下原则:3.1 精确度和稳定性原则:模具应具备高度的精确度和稳定性,以确保产品的质量和尺寸的一致性。
3.2 工艺可行性原则:模具设计应基于现有的粉末冶金工艺和设备,确保设计方案的可行性和实施的可行性。
3.3 成本效益原则:模具设计应考虑材料成本、制造成本和维护成本,以降低总体生产成本。
4、设计流程4.1 产品需求分析:了解客户对于产品性能、尺寸和表面质量等方面的要求,获得设计的基础数据。
4.2 材料选择:根据产品需求和工艺要求,选择适合的材料,包括模具材料和涂层材料等。
4.3 模具结构设计:设计模具的整体结构和零部件结构,考虑模具的可装卸性、易维护性和生产效率等。
4.4 模具零部件设计:设计模具的各个零部件,包括模具芯和模具腔等,确保其几何形状和尺寸的准确性。
4.5 涂层选择和设计:根据模具的使用环境和工艺要求,选择合适的涂层材料,并设计涂层的厚度和结构等。
4.6 模具制造和调试:根据设计图纸和规范,制造和组装模具,并进行调试和试产,以确保模具的正常使用。
4.7 模具维护和管理:建立模具维护和管理体系,包括清洗、保养和修复等工作,延长模具的使用寿命。
5、设计结果基于以上设计流程和原则,我们提供了粉末冶金模具的设计方案。
设计方案包括模具结构图纸、材料选择和涂层设计等内容,请参阅附件1:附件:1、粉末冶金模具设计图纸本文涉及的法律名词及注释:1、粉末冶金:一种通过将金属粉末压制成形并经过烧结过程得到制品的金属加工工艺。
2、模具:用于塑料、金属等物质加工中的一种工具,用于赋予材料所需的形状和尺寸。
粉末模压成型工艺
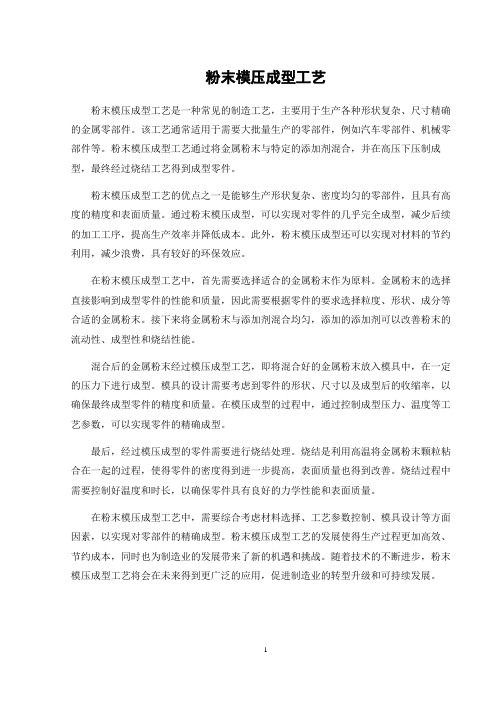
粉末模压成型工艺粉末模压成型工艺是一种常见的制造工艺,主要用于生产各种形状复杂、尺寸精确的金属零部件。
该工艺通常适用于需要大批量生产的零部件,例如汽车零部件、机械零部件等。
粉末模压成型工艺通过将金属粉末与特定的添加剂混合,并在高压下压制成型,最终经过烧结工艺得到成型零件。
粉末模压成型工艺的优点之一是能够生产形状复杂、密度均匀的零部件,且具有高度的精度和表面质量。
通过粉末模压成型,可以实现对零件的几乎完全成型,减少后续的加工工序,提高生产效率并降低成本。
此外,粉末模压成型还可以实现对材料的节约利用,减少浪费,具有较好的环保效应。
在粉末模压成型工艺中,首先需要选择适合的金属粉末作为原料。
金属粉末的选择直接影响到成型零件的性能和质量,因此需要根据零件的要求选择粒度、形状、成分等合适的金属粉末。
接下来将金属粉末与添加剂混合均匀,添加的添加剂可以改善粉末的流动性、成型性和烧结性能。
混合后的金属粉末经过模压成型工艺,即将混合好的金属粉末放入模具中,在一定的压力下进行成型。
模具的设计需要考虑到零件的形状、尺寸以及成型后的收缩率,以确保最终成型零件的精度和质量。
在模压成型的过程中,通过控制成型压力、温度等工艺参数,可以实现零件的精确成型。
最后,经过模压成型的零件需要进行烧结处理。
烧结是利用高温将金属粉末颗粒粘合在一起的过程,使得零件的密度得到进一步提高,表面质量也得到改善。
烧结过程中需要控制好温度和时长,以确保零件具有良好的力学性能和表面质量。
在粉末模压成型工艺中,需要综合考虑材料选择、工艺参数控制、模具设计等方面因素,以实现对零部件的精确成型。
粉末模压成型工艺的发展使得生产过程更加高效、节约成本,同时也为制造业的发展带来了新的机遇和挑战。
随着技术的不断进步,粉末模压成型工艺将会在未来得到更广泛的应用,促进制造业的转型升级和可持续发展。
1。
粉末冶金材料模具设计
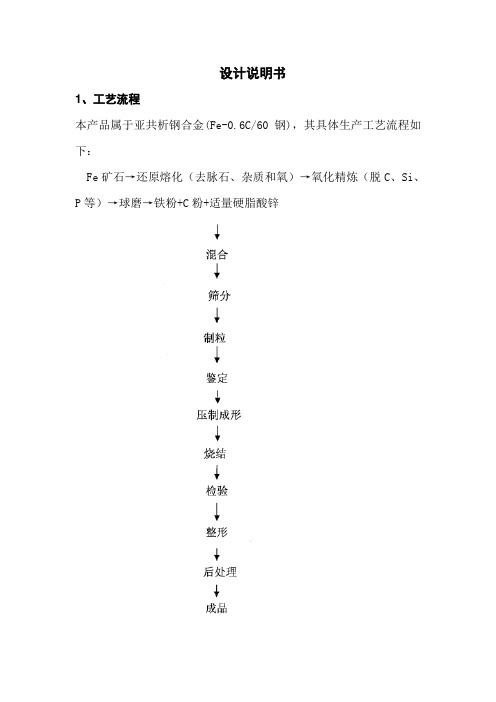
设计说明书1、工艺流程本产品属于亚共析钢合金(Fe-0.6C/60钢),其具体生产工艺流程如下:Fe矿石→还原熔化(去脉石、杂质和氧)→氧化精炼(脱C、Si、P等)→球磨→铁粉+C粉+适量硬脂酸锌2、压坯设计2.1产品零件分析该产品采用Fe-0.6C(60钢),属于铁基制品,其制品密度依靠较高的压坯密度来达到,因此,在压制成形时需要采用较高的单位压力(一般在400-500MPa)。
由于该产品零件形状比较简单,带一个外台阶,采用简单的单上双下模冲即可成形,并使其密度分布均匀。
有配合、定位、相对运动要求的零部件,产品尺寸精度和形位精度及表面粗糙度要求较高,因此,该产品的的尺寸精度定义为IT8、形位精度如图所示为7级,表面粗糙度精度要求为7级。
2.2压坯精度设计由模具设计任务书的零件成品图可得知该产品压坯同轴度需控制在0.08mm,相当于IT10级;压坯垂直度控制为0.1mm,相当于IT11级;压坯侧面平行度为0.15mm,相当于IT12级。
2.3压坯密度和单重的确定由于已知压坯密度ρ=6.6g/cm3,因此压坯单重W=ρ×V ,由成品图给数据计算其压坯体V=h×S,算的V=166.8cm3 ,所以求的压坯单重W=6.6×166.8=1100.8g。
3、压机与压制方式选择3.1压机压力选择铁基制品一般采用固相烧结,其制品密度除了依靠烧结温度、保温时间之外,在一定程度上还依靠较高的压坯密度来达到,因此该产品采用500MPa的单位压力。
根据任务书要求,截面积S=74.0cm2 ,所以F=P×S=5×74=370t脱模压力,根据实际生产经验,铁基压坯的脱模压力P脱模≈0.13P=0.13×500MPa=65MPa3.2压制类型的选择年生产量为50万件,假设每年的工作时间为300天,每天工作时间为8小时,则p=500000/300/8/60=3.47=4件/min,所以选择自动压制。
粉末冶金模具说明书19
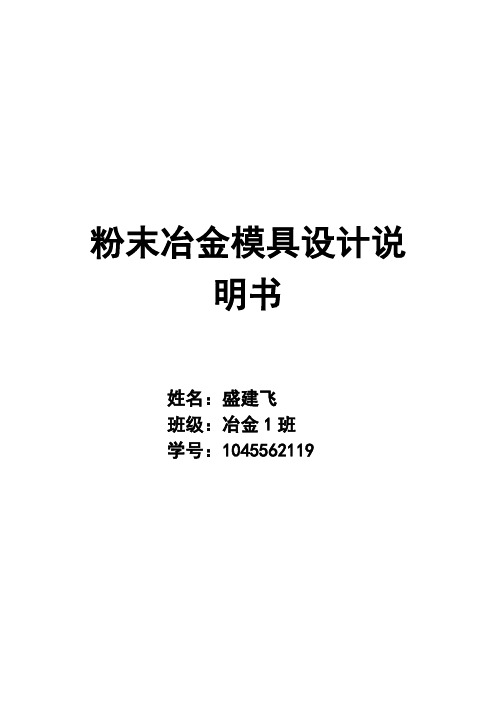
粉末冶金模具设计说明书姓名:盛建飞班级:冶金1班学号:1045562119一.设计任务生产一批圆柱状钢制模坯,直径20mm,高度40mm二.模具零件的要求:1.阴模:1)阴模高度应能容纳压制所需的松散粉末,并使上、下模冲有良好的定位和导向;2)能保证压坯外形的几何形状和尺寸精度;3)工作面的粗糙度Ra≤0.8um;4)工作表面要有高的硬度和良好的耐磨性;;5)在工作压力下应具有足够的强度和刚性;6)根据产品的批量和复杂程度,选择合适的阴模材料;7)结构上应便于制造和维修,使用安全,操作方便;8)能使压坯完好的脱出;9)平磨后需退磁。
2.上、下模冲:1)工作表面要有足够高的硬度和良好的耐磨性,材料的选择与处理应考虑有适当的韧性;2)上、下模冲对阴模和芯棒应有良好的配合、定位和导向,并有合理的配合间隙,复合的模冲(即有压套时)应能脱出压坯;3)上下模冲的工作面和配合面的粗糙度Ra≤0.8um,非工作段的外径可适当缩小,内径可适当放大,减少精加工量和阴模、芯棒之间的摩擦;4)有关部位应能保证垂直度、平行度和同轴度等技术要求;5)平磨后需退磁。
生产的主要设备:车床、铣床、磨床、钻床、线切割、电火花等3.模架及升降装置:1)装置要具有良好耐磨性,能够承受高负荷;2)模架及升降装置须具有良好的强硬度,同时还应有良好的韧性;三.材料选择:根据以上模具零件的要求,选材如下:1.阴模:硬质合金;2.上、下模冲:合金工具钢;3.模架及升降装置:合金工具钢;4.压坯:铁粉。
四.尺寸设计:1.阴模1)产品零件分析该产品采用Fe-0.6C(60钢),属于铁基制品,其制品密度依靠其较高的压坯密度来达到,因此在压制成型时需要采用较高的单位压力(一般在400~500MPa)。
由于该产品零件形状比较简单,采用简单的上下模冲压制成型。
2)松装密度和压坯密度的确定采用水雾化铁粉压制,其松装密度ρ松=2.8g/cm3压坯密度ρ压=6.6g/cm33)阴模尺寸装粉高度计算公式:阴模高度计算公式:H0=ρ*H w/ρ0 H=H0+H1+H2--------H0: 装粉高度. ----------H1:下模冲定位高度,一般为10~50mm. ------- ρ:压坯密度. --------- H2:手动模装粉锥高度,取H2=0 mm.------ H w:压坯高度.------------ ρ0:松装密度.由以上数据可知,装粉高度:H0=6.6×40/2.8mm=94mm阴模高度:H f=94+H1=115mm取模数m=2.5 ,阴模内径d=20 mm 根据公式m=D/d , 可求得阴模外径D=m*d=2.5*20=50mm。
粉末冶金模具及设计介绍
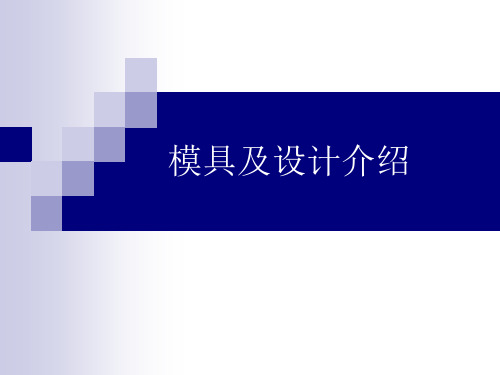
淬火
HRA91YG6 HRA89YG8 HRA87YG15
国600 G代表钴含量,越高韧性越好, 进口 耐磨性也较差,一般采用超微 中模和芯棒 1000 粒(春宝),国产稍差
常用模具材料热处理工艺
牌号
SLD V4 SKH9 Cr12 40Cr
使用硬度 HRC57~59 HRC60~61
HRC56~57 HRC60~61 HRC57~59 HRC60~61 HRC45~50 HRC45~50
模具制造技术特点----内外圆磨床
在工件直径回转的磨床上,使用砂轮对装夹好的旋 转工件进行内外径,台阶及端面及磨削加工。操 作步骤如下:
1. 在磨床的三爪卡盘上,将模具轻轻夹住,用千分表
先校正模具的端面偏心再校正外径的偏心,最后将 模具夹紧。 选择合适砂轮安装在磨床的磨头主轴上并夹紧; 选择合适的车床转速,走刀量和吃刀深度。 依模具图尺寸和形状的要求,对模具进行磨削加工。 抛光完毕后,停车先将三爪卡盘松开一点,用手 将模具托住再将三爪卡盘完全松开后,取下模具 依照模具图要求进行自我尺寸检查。
模具制造技术特点----平面磨床
平面磨床加工特点:
在砂轮直径高速回转的平面磨床上,对装 夹好的 工件,进行往复的平面磨削加工。操作步骤如下:
1. 选择合适磨床夹具,用千分表先校正模具的垂直度 和平行度,将模具夹住。 2. 选择合适的砂轮将之在磨床主轴上夹紧; 3. 选择合适的砂轮转速,走刀量和吃刀深度。
1. 在车床的三爪卡盘上,将模具轻轻夹住,用百分表先校正模 具的端面偏心再校正外径的偏心,最后将模具夹紧。 2. 选择合适的车刀将之刃磨 OK; 3. 将已选择的车刀在车床的刀架上,校正刀尖中心高和刀具的 角度后并夹紧; 4. 选择合适的车床转速,走刀量和吃刀深度。 5. 依模具图尺寸和形状的要求,对模具进行车削加工。 6. 对已车加工面采用较高的车床转速,用油石和砂纸进行研磨 抛光。 7. 抛光完毕后,停车先将三爪卡盘松开一点,用手将模具托住 再将三爪卡盘完全松开后,取下模具依照模具图要求进行自 我尺寸检查。
粉末冶金模具设计说明书
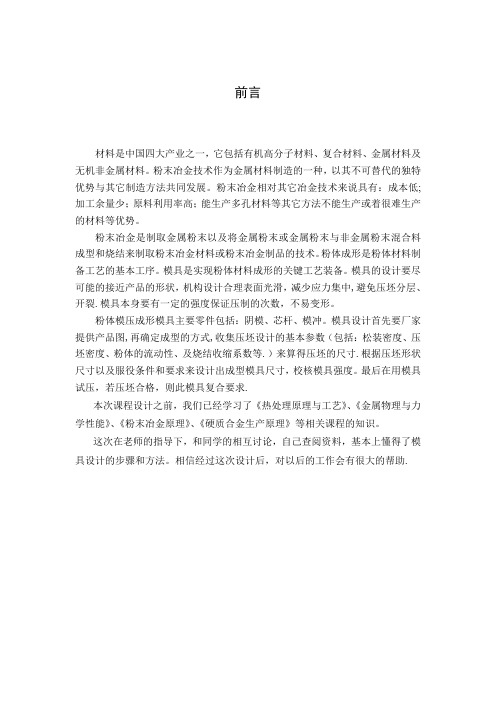
前言材料是中国四大产业之一,它包括有机高分子材料、复合材料、金属材料及无机非金属材料。
粉末冶金技术作为金属材料制造的一种,以其不可替代的独特优势与其它制造方法共同发展。
粉末冶金相对其它冶金技术来说具有:成本低;加工余量少;原料利用率高;能生产多孔材料等其它方法不能生产或着很难生产的材料等优势。
粉末冶金是制取金属粉末以及将金属粉末或金属粉末与非金属粉末混合料成型和烧结来制取粉末冶金材料或粉末冶金制品的技术。
粉体成形是粉体材料制备工艺的基本工序。
模具是实现粉体材料成形的关键工艺装备。
模具的设计要尽可能的接近产品的形状,机构设计合理表面光滑,减少应力集中,避免压坯分层、开裂.模具本身要有一定的强度保证压制的次数,不易变形。
粉体模压成形模具主要零件包括:阴模、芯杆、模冲。
模具设计首先要厂家提供产品图,再确定成型的方式,收集压坯设计的基本参数(包括:松装密度、压坯密度、粉体的流动性、及烧结收缩系数等.)来算得压坯的尺寸.根据压坯形状尺寸以及服役条件和要求来设计出成型模具尺寸,校核模具强度。
最后在用模具试压,若压坯合格,则此模具复合要求.本次课程设计之前,我们已经学习了《热处理原理与工艺》、《金属物理与力学性能》、《粉末冶金原理》、《硬质合金生产原理》等相关课程的知识。
这次在老师的指导下,和同学的相互讨论,自己查阅资料,基本上懂得了模具设计的步骤和方法。
相信经过这次设计后,对以后的工作会有很大的帮助.1 设计任务本课程设计的任务是生产一批有色金属扁材拉制模坯,其形状和尺寸如下图:1.1 产品分析由产品图可知H/D 〈3,因此,该产品适合单向压制.产品的斜边角度不大,因此,装粉比较容易,可用单从头压制。
产品内部的斜角可直接做在芯杆上。
菱角的倒角不长,可适合用上冲头压制.1。
2 材质的选择该模具生产的产品用于拉制模坯,对产品的强度及耐磨性能要求很高,再根据客户所提供的要求,综合考虑选用硬质合金材料YG8作为材质。
粉末冶金模具设计作业

中南大学粉末冶金研究院模具设计说明书班级:姓名:学号:指导老师:模具设计说明书一、工艺流程设计采用的零件材质为Fe-0.6C,压坯密度为6.4g/cm3,原料粉末的松装密度为2.5g/cm3,年产量为50万件。
用一般粉末冶金方法即可实现生产,其具体生产工艺流程如下:说明:由于零件为薄壁件,因此不予精整。
表面光洁度以及倒角要求由后续磨削加工达到。
二、压坯设计1.产品零件分析1)材质为铁基材料,非等高压坯,带一个外台阶和一个内台阶,共有3个螺栓孔。
2)为了简化模具结构,保证产品压坯顺利脱模,同时又由于螺栓孔不易在压制中成型,所以压坯设计中,该处设计为整体台阶,把螺栓孔除去,留在后续机加工中成形。
那么,该压坯大致为带一个外台阶和一个内台阶的压坯。
3)从零件精度分析,所给零件粗糙度要求为6.3及25较低,也无平行度、径向跳动、同轴度等形状精度的要求。
2. 压坯形状的设计:基本原则:尽可能使压坯形状与产品零件形状相同或相近——近净成形,同时考虑产品质量要求、压制成形过程要求及压模结构、零件强度等。
1)从裝粉和压制密度均匀性考虑:所给零件比较规则,无装粉困难。
2)从压坯脱模角度考虑:成品中没有不利于脱模的结构和因素。
3.压坯尺寸计算1)烧结压制中各参数选取如下:径向弹性后效:0.2%,轴向弹性后效:1.4%径向烧结收缩:0.5%,轴向烧结收缩:2%为满足表面粗糙度要求,在粗糙度要求为6.3的面预留0.05mm磨削加工余量2)压缩比:k=d压/d粉=6.4/2.5=2.563)压坯相对密度:d Fe=7.874g/cm3d C=2.25g/cm3则压坯理论密度dm=100/(99.4/7.874+0.6/2.25)=7.76g/cm3相对密度ρ=d压/dm=6.4/7.76=0.8254)轴向尺寸:压坯主体总高H1=10*(1-1.4%+2%)+0.05=10.11mm压坯台阶高度H2=5*(1-1.4%+2%)+0.05=5.08mm5)径向尺寸:长径D1=54*(1-0.2%+0.5%)=54.16mm短径D2=518(1-0.2%+0.5%)=51.15mm壁内径D3=28*(1-0.2%+0.5%)=28.08mm壁外径D4=35*(1-0.2%+0.5%)+2*0.05=35.21mm所设计压坯如图所示:三、压制方式1)零件高径比:H/D=10.11/54.162=0.187,零件总高径比很小,可考虑采用单向压制和非同时双向压制结合的压制方式。
粉末模压成型工艺有哪些
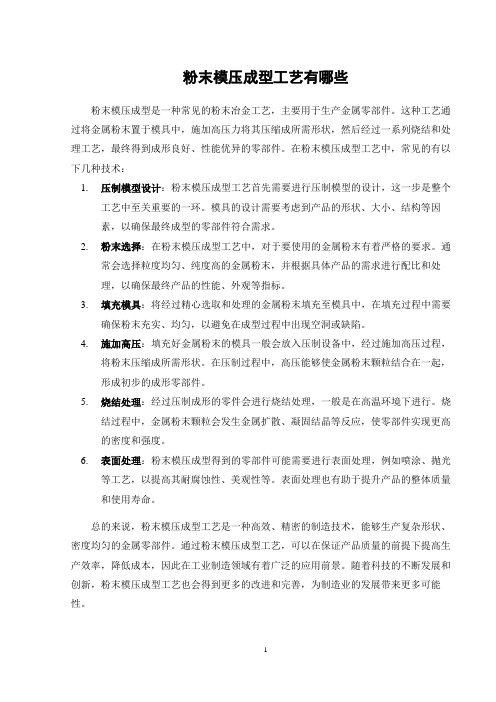
粉末模压成型工艺有哪些粉末模压成型是一种常见的粉末冶金工艺,主要用于生产金属零部件。
这种工艺通过将金属粉末置于模具中,施加高压力将其压缩成所需形状,然后经过一系列烧结和处理工艺,最终得到成形良好、性能优异的零部件。
在粉末模压成型工艺中,常见的有以下几种技术:1.压制模型设计:粉末模压成型工艺首先需要进行压制模型的设计,这一步是整个工艺中至关重要的一环。
模具的设计需要考虑到产品的形状、大小、结构等因素,以确保最终成型的零部件符合需求。
2.粉末选择:在粉末模压成型工艺中,对于要使用的金属粉末有着严格的要求。
通常会选择粒度均匀、纯度高的金属粉末,并根据具体产品的需求进行配比和处理,以确保最终产品的性能、外观等指标。
3.填充模具:将经过精心选取和处理的金属粉末填充至模具中,在填充过程中需要确保粉末充实、均匀,以避免在成型过程中出现空洞或缺陷。
4.施加高压:填充好金属粉末的模具一般会放入压制设备中,经过施加高压过程,将粉末压缩成所需形状。
在压制过程中,高压能够使金属粉末颗粒结合在一起,形成初步的成形零部件。
5.烧结处理:经过压制成形的零件会进行烧结处理,一般是在高温环境下进行。
烧结过程中,金属粉末颗粒会发生金属扩散、凝固结晶等反应,使零部件实现更高的密度和强度。
6.表面处理:粉末模压成型得到的零部件可能需要进行表面处理,例如喷涂、抛光等工艺,以提高其耐腐蚀性、美观性等。
表面处理也有助于提升产品的整体质量和使用寿命。
总的来说,粉末模压成型工艺是一种高效、精密的制造技术,能够生产复杂形状、密度均匀的金属零部件。
通过粉末模压成型工艺,可以在保证产品质量的前提下提高生产效率,降低成本,因此在工业制造领域有着广泛的应用前景。
随着科技的不断发展和创新,粉末模压成型工艺也会得到更多的改进和完善,为制造业的发展带来更多可能性。
1。
粉末冶金模具设计算
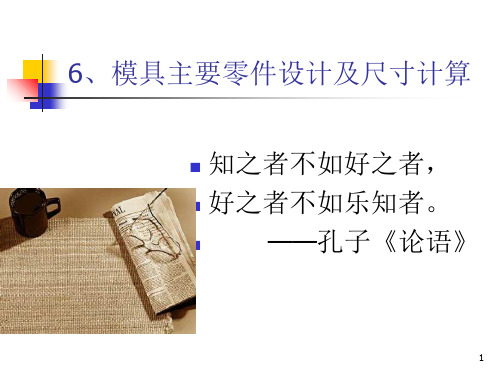
29
Hf—阴模高度 H1—压坯台阶高度 H10—压坯台阶1的装粉高度
H2—压坯总高度 H20—压坯台阶2的装粉高度
30
(二)模具高度的计算
(1)阴模
阴模高度 Hf一般由三部分高度组成, 即
Hf=H0+H1+H2
式中
Hf——阴模高度(mm); H0——装粉高度(mm) ; H1——下模冲定位高度。一般为10~50mm ; H2——手动模装粉锥高度(mm)。不需要时H2=031
4
单层整体阴模
5
双层组合阴模
6
7
2.芯棒要求 1)保证压坯的几何形状和尺寸精度; 2)粗糙度要低; 3)与模冲配合良好; 4)高的硬度; 5)压坯容易脱出芯棒,方便操作,利于加工; 6)较长较大芯棒采用组合结构。
8
3.模冲 1)高硬度和耐磨性,适当的韧性; 2)模冲与阴模、芯棒配合良好,有合理的配合 间隙; 3)表面有较低的粗糙度; 4)保证平行度、垂直度、同轴度;
压坯密度ρ, 压缩比c, 单位压力 p等。
38
(一)金属粉末的松装密度
金属粉末的松装密度直接影响模腔的高度。此参 数选择不当,自动装粉时则会造成粉料装不下, 或粉料装得太多的现象。 实际生产中,松装密度在一定范围内有波动,为 此,在结构设计中一般考虑了调节装粉高度的装 置,但调节范围不宜过大。
压坯密度提高时,[σ压]侧向则增大,但与此同
时 p侧也剧增。
具体粉料压坯的[σ压]侧向应由实验测定。
66
铁基压坯侧向许用抗压强度[σ压]侧向
67
从表可看出: 1)相同成分的压坯,压坯密度越高,虽然[σ压]侧向提
高,但 p侧增加得更快,对强度条件不利;
2)石墨含量增加,使[σ压]侧向下降,对刚性条件不利。
常用粉末冶金模具材料

粉末冶金模压模工作零件材料及技术要求
零件名称:
凹模芯棒
选用材料:
碳素工具钢:T10A,T12A
合金工具钢:GCr15,Cr12,Cr12Mo,Cr12W,Cr12MoV,9CrSi,CrWMn,CrW5
高速钢:W18Cr4V,W9Cr4V,W12Cr4V4Mo
硬质合金:钢结硬质合金,YG15,YG8(芯棒用硬质合金时,一般为钢与硬合金的焊接镶接形式)
热处理要求:
钢:60~63HRC
钢结硬质合金:64~72HRC
硬质合金:88~90HRA(钢的细长芯棒可降至55~58HRC,带接杆芯棒连接处局部35~40HRC)
其它技术要求:
1. 平磨后退磁
2. 粗糙度要求:
工作面:Rα 0.4~0.1μm
配合面及定位面:
Rα 1.6~0.4μm
非配合面:
Rα 3.2~1.6μm
3. 工作面及配合面公差等级:
IT5~IT7
零件名称:
模冲
选用材料:
碳素工具钢:T8A,T10A
合金工具钢:GCr15,Cr12,Cr12Mo,9CrSi,CrWMn,CrW5 热处理要求:
56~60HRC
其它技术要求:
1. 平磨后退磁
2. 粗糙度要求:
工作面:Rα 0.8~0.4μm
配合面及定位面:
Rα 0.4~0.1μm
非配合面:
Rα 3.2~0.8μm
3. 工作面及配合面公差等级:
IT5~IT7。
粉末冶金技术要求
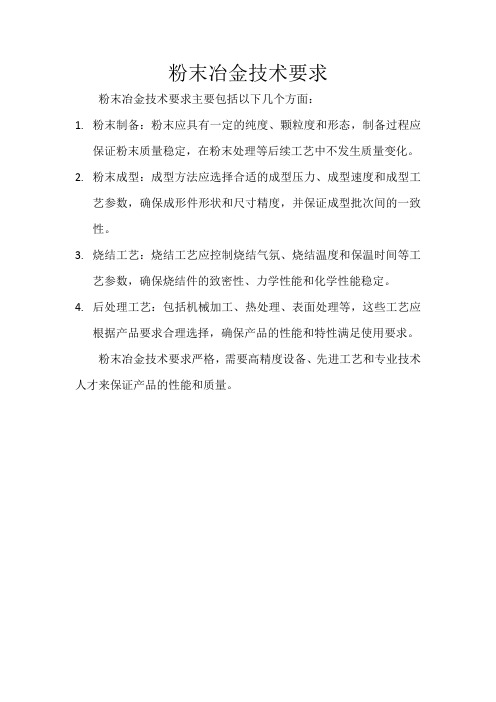
粉末冶金技术要求
粉末冶金技术要求主要包括以下几个方面:
1.粉末制备:粉末应具有一定的纯度、颗粒度和形态,制备过程应
保证粉末质量稳定,在粉末处理等后续工艺中不发生质量变化。
2.粉末成型:成型方法应选择合适的成型压力、成型速度和成型工
艺参数,确保成形件形状和尺寸精度,并保证成型批次间的一致性。
3.烧结工艺:烧结工艺应控制烧结气氛、烧结温度和保温时间等工
艺参数,确保烧结件的致密性、力学性能和化学性能稳定。
4.后处理工艺:包括机械加工、热处理、表面处理等,这些工艺应
根据产品要求合理选择,确保产品的性能和特性满足使用要求。
粉末冶金技术要求严格,需要高精度设备、先进工艺和专业技术人才来保证产品的性能和质量。
- 1、下载文档前请自行甄别文档内容的完整性,平台不提供额外的编辑、内容补充、找答案等附加服务。
- 2、"仅部分预览"的文档,不可在线预览部分如存在完整性等问题,可反馈申请退款(可完整预览的文档不适用该条件!)。
- 3、如文档侵犯您的权益,请联系客服反馈,我们会尽快为您处理(人工客服工作时间:9:00-18:30)。
粉末冶金模压模工作零件的材料及技术要求
零件名称:
凹模芯棒
选用材料:
碳素工具钢:T10A,T12A
合金工具钢:GCr15,Cr12,Cr12Mo,Cr12W,Cr12MoV,9CrSi,CrWMn,CrW5
高速钢:W18Cr4V,W9Cr4V,W12Cr4V4Mo
硬质合金:钢结硬质合金,YG15,YG8(芯棒用硬质合金时,一般为钢与硬合金的焊接镶接形式)
热处理要求:
钢:60~63HRC
钢结硬质合金:64~72HRC
硬质合金:88~90HRA(钢的细长芯棒可降至55~58HRC,带接杆芯棒连接处局部35~40HRC)
其它技术要求:
1. 平磨后退磁
2. 粗糙度要求:
工作面:Rα 0.4~0.1μm
配合面及定位面:
Rα 1.6~0.4μm
非配合面:
Rα 3.2~1.6μm
3. 工作面及配合面公差等级:
IT5~IT7
零件名称:
模冲
选用材料:
碳素工具钢:T8A,T10A
合金工具钢:GCr15,Cr12,Cr12Mo,9CrSi,CrWMn,CrW5
热处理要求:
56~60HRC
其它技术要求:
1. 平磨后退磁
2. 粗糙度要求:
工作面:Rα 0.8~0.4μm 配合面及定位面:
Rα 0.4~0.1μm
非配合面:
Rα 3.2~0.8μm
3. 工作面及配合面公差等级:IT5~IT7。