铝合金压铸模
铝合金压铸模材料和热处理工艺分析
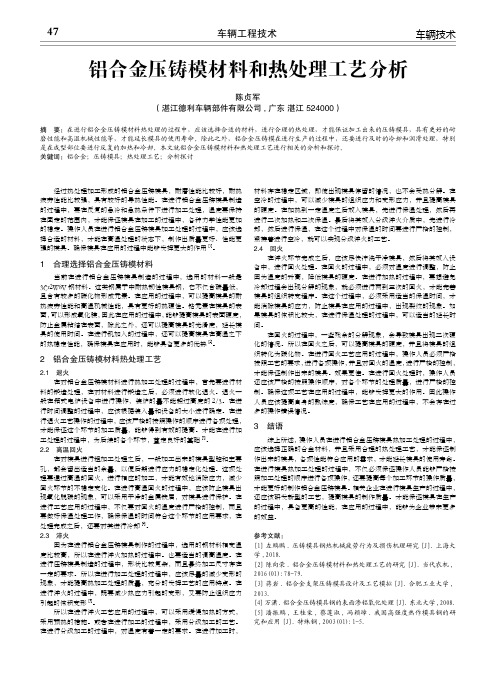
车辆工程技术47车辆技术 经过热处理加工形成的铝合金压铸模具,耐磨性能比较好,耐热疲劳性能比较强,具有较好的导热性能。
在进行铝合金压铸模具制造的过程中,要在反复的急冷和急热条件下进行加工处理,温度要保持在固定的范围内,才能保证模具在加工的过程中,各种力学性能更加的稳定。
操作人员在进行铝合金压铸模具加工处理的过程中,应该选择合适的材料,才能在高温处理的状态下,制作出质量更好、性能更强的模具。
确保模具在应用的过程中能够发挥更大的作用[1]。
1 合理选择铝合金压铸模材料 当前在进行铝合金压铸模具制造的过程中,选用的材料一般是3Cr2W8V钢材料。
这类钢属于中耐热韧性模具钢,它不仅含碳量低,且含有较多的碳化物形成元素。
在应用的过程中,可以提高模具的耐热疲劳性能和高温机械性能,具有更好的热硬性。
铬元素在模具的表面,可以形成氧化膜,因此在应用的过程中,能够提高模具的表面硬度,防止金属粘结在表面,除此之外,还可以提高模具的光滑度,延长模具的使用时间。
在进行钒加入的过程中,还可以提高模具在高温之下的热稳定性能,确保模具在应用时,能够具备更多的优势[2]。
2 铝合金压铸模材料热处理工艺2.1 退火 在对铝合金压铸模材料进行热加工处理的过程中,首先要进行材料的锻造处理,在对材料进行锻造之后,必须进行软化退火。
退火一般在箱式电炉设备中进行操作,装炉的量不能超过高度的2/3。
在进行时间调整的过程中,应该根据装入量和设备的大小进行确定。
在进行退火工艺操作的过程中,应该严格的按照操作的顺序进行各项处理,才能保证这个环节的加工质量,能够得到有效的提高。
才能在进行加工处理的过程中,为后续的各个环节,奠定良好的基础[3]。
2.2 高温回火 在对模具进行粗加工处理之后,一般加工出来的模具型腔和主要孔,都会留出适当的余量,以便后期进行应力的稳定化处理。
这项处理要通过高温的回火,进行相应的加工,才能有效地消除应力,减少回火环节的不稳定变化。
铝压铸模具的成本计算公式

铝压铸模具的成本计算公式铝压铸模具是用于铝合金压铸生产的工具,它的质量和精度直接影响产品的质量和生产效率。
因此,了解铝压铸模具的成本计算公式对于厂家来说非常重要。
本文将介绍铝压铸模具的成本计算公式,并对其中的各个因素进行详细解析。
铝压铸模具的成本主要由以下几个方面构成,材料成本、加工成本、人工成本、管理成本和利润。
下面我们将对这些成本进行详细分析。
1. 材料成本。
铝压铸模具的材料一般为优质的工具钢或合金钢,其价格相对较高。
材料成本的计算公式为:材料成本 = 模具重量×材料密度×材料价格。
其中,模具重量可以通过CAD软件进行计算,材料密度和价格可以通过市场调研得到。
需要注意的是,模具的设计和加工方式也会影响材料的利用率,从而影响材料成本。
2. 加工成本。
铝压铸模具的加工成本主要包括机加工、热处理和表面处理等费用。
加工成本的计算公式为:加工成本 = 机加工费用 + 热处理费用 + 表面处理费用。
其中,机加工费用可以根据模具的复杂程度和加工工艺进行计算,热处理费用和表面处理费用可以根据实际情况进行估算。
3. 人工成本。
铝压铸模具的制造过程需要大量的人工操作,包括设计、加工、组装和调试等环节。
人工成本的计算公式为:人工成本 = 设计人工费用 + 加工人工费用 + 组装人工费用 + 调试人工费用。
其中,设计人工费用可以根据设计师的工作量和技术水平进行估算,加工人工费用可以根据加工工艺和操作人员的工资标准进行计算,组装人工费用和调试人工费用可以根据实际情况进行估算。
4. 管理成本。
铝压铸模具的制造过程需要进行生产计划、材料采购、质量控制、成本核算等管理工作,这些管理工作所需的费用也需要计入成本。
管理成本的计算公式为:管理成本 = 生产计划费用 + 材料采购费用 + 质量控制费用 + 成本核算费用。
其中,生产计划费用可以根据生产计划的复杂程度进行估算,材料采购费用可以根据采购量和运输费用进行计算,质量控制费用和成本核算费用可以根据实际情况进行估算。
压铸成型工艺与模具设计第章压铸模常用材料

压铸成型工艺与模具设计第章压铸模常用材料一、引言压铸是工程塑料成型加工中使用广泛的一种方法,其在汽车、家电、电信设备、医疗设备等领域有着广泛的应用。
压铸模是实现压铸成型的核心部件,其制造材料的选择及质量直接影响到压铸成型的精度和寿命,因此正确选择压铸模常用材料十分重要。
本文将介绍目前较为常用的压铸模制造材料,主要包括铝合金、钢和铜合金。
二、铝合金铝合金是一种常用的压铸模制造材料,其主要有以下特点:1.密度小,比重约为钢材的1/3,铜材的1/2,使得铝合金模具重量轻,便于加工和操作;2.导热性能好,热膨胀系数小,能够有效地保证模具的温度稳定性;3.良好的加工性能,可以通过数控机床进行加工,精度高;4.抗腐蚀性能好,能够避免模具生锈和磨损。
铝合金可以分为纯铝、铝硅、铝镁、铝铜等多种型号,其中以铝硅合金最为常用,其强度和硬度相对较高,热膨胀系数小,加工性能也较好。
铝合金模具在使用过程中需要注意防止过度切削和损伤表面,避免在表面涂覆保护膜带来的影响,同时要注意防潮、防腐蚀。
三、钢材钢材是压铸模制造中较为常用的材料,其优点在于:1.强度高、韧性好;2.颜色均匀、质地细致,适宜进行精密加工;3.抗蚀性能好,耐磨性能优良。
钢材经常用于制作大件的模具,其硬度和强度较高,可以耐受来自铝等硬度更低的金属的高压压力,有着较强的耐用性。
但是钢材也有其缺点,例如制造成本较高、加工难度大等问题,需要对各种型号的钢材进行合理选择,同时注意防止模具表面生锈和腐蚀。
四、铜合金铜合金是一种高性能模具材料,其优点在于:1.密度较大,强度高、耐磨性好;2.热传导系数高、导电率好;3.具有良好的耐蚀性,能够避免模具表面生锈和腐蚀。
铜合金可以分为锡青铜、锰铜、铝青铜等多种型号,其中以锡青铜最为常见,其强度和韧性较好,可以用于制造中大型、复杂的模具。
铜合金不仅可以用于制造压铸模具,同时也可以用于制造各种冲压模、挤压模等模具,具有广泛的应用前景。
铝合金压铸模型浇排系统设计
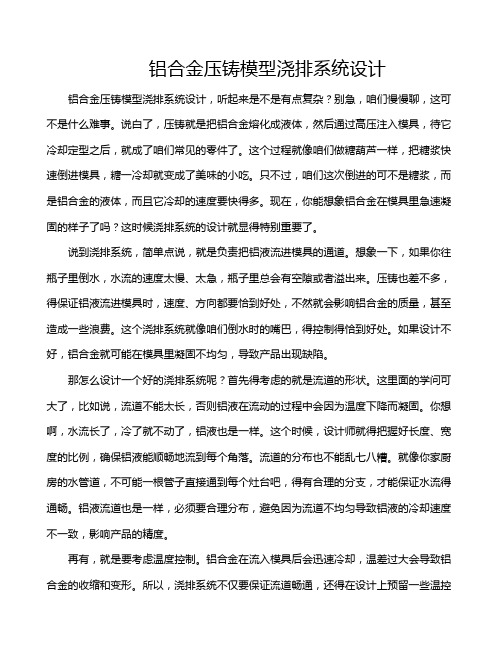
铝合金压铸模型浇排系统设计铝合金压铸模型浇排系统设计,听起来是不是有点复杂?别急,咱们慢慢聊,这可不是什么难事。
说白了,压铸就是把铝合金熔化成液体,然后通过高压注入模具,待它冷却定型之后,就成了咱们常见的零件了。
这个过程就像咱们做糖葫芦一样,把糖浆快速倒进模具,糖一冷却就变成了美味的小吃。
只不过,咱们这次倒进的可不是糖浆,而是铝合金的液体,而且它冷却的速度要快得多。
现在,你能想象铝合金在模具里急速凝固的样子了吗?这时候浇排系统的设计就显得特别重要了。
说到浇排系统,简单点说,就是负责把铝液流进模具的通道。
想象一下,如果你往瓶子里倒水,水流的速度太慢、太急,瓶子里总会有空隙或者溢出来。
压铸也差不多,得保证铝液流进模具时,速度、方向都要恰到好处,不然就会影响铝合金的质量,甚至造成一些浪费。
这个浇排系统就像咱们倒水时的嘴巴,得控制得恰到好处。
如果设计不好,铝合金就可能在模具里凝固不均匀,导致产品出现缺陷。
那怎么设计一个好的浇排系统呢?首先得考虑的就是流道的形状。
这里面的学问可大了,比如说,流道不能太长,否则铝液在流动的过程中会因为温度下降而凝固。
你想啊,水流长了,冷了就不动了,铝液也是一样。
这个时候,设计师就得把握好长度、宽度的比例,确保铝液能顺畅地流到每个角落。
流道的分布也不能乱七八糟。
就像你家厨房的水管道,不可能一根管子直接通到每个灶台吧,得有合理的分支,才能保证水流得通畅。
铝液流道也是一样,必须要合理分布,避免因为流道不均匀导致铝液的冷却速度不一致,影响产品的精度。
再有,就是要考虑温度控制。
铝合金在流入模具后会迅速冷却,温差过大会导致铝合金的收缩和变形。
所以,浇排系统不仅要保证流道畅通,还得在设计上预留一些温控措施,保持模具温度的均衡。
设计得不好,铝合金一旦冷却过快,可能就会在模具里形成气孔或者裂纹,那样产品就废了,前功尽弃。
除了这些,浇排系统还得考虑排气设计。
说白了,就是模具里空气和气体的排出问题。
压铸模材料选择及技术要求

压铸模材料选择及技术要求1.压铸模材料的选择:(1)钢材:钢材可以分为冷工作模具钢和热工作模具钢两种。
冷工作模具钢适用于生产小件、薄壁件和大批量生产的情况,例如铝合金压铸件;而热工作模具钢适用于生产大型、复杂的压铸件,例如汽车零部件。
常用的冷工作模具钢有CR12MOV、SKD-11等,常用的热工作模具钢有H13、H11等。
(2)铝材:铝材主要适用于生产大批量的铝合金压铸件。
铝材制作的压铸模具具有热导性好、导热均匀、加工性能好等优点。
常用的铝材有铝合金7075、6061等。
(4)合金材料:合金材料具有耐磨、耐腐蚀、高耐热性等优点,适用于生产特殊要求的压铸件。
常用的合金材料有钛合金、锥纳尔合金等。
2.压铸模材料的技术要求:(1)硬度要求:压铸模材料的硬度要适中,太硬会影响加工性能,太软则容易磨损。
一般要求模具材料的硬度为HRC40~50之间。
(2)机械性能要求:压铸模材料的机械性能直接影响到模具的使用寿命和生产效率。
一般要求模具材料具有较高的抗拉强度、屈服强度和冲击韧性。
(3)导热性要求:压铸模材料的导热性对产品的质量有着重要影响。
材料的导热性能越好,铸件凝固时间越短,产品质量越好。
因此,模具材料的导热性要求较高。
(4)耐磨性要求:压铸模材料需要具备耐磨性能,以防止在生产过程中产生磨损或磨损引起的划伤。
(5)耐腐蚀性要求:压铸模材料需要具备一定的耐腐蚀性能,以防止在铸造过程中与液态金属发生化学反应导致腐蚀和腐蚀引起的模具表面变形。
总之,压铸模材料的选择和技术要求需要综合考虑许多因素,如产品要求、生产批量、模具制造成本、机械性能、导热性、耐磨性和耐腐蚀性等。
合理选择和正确使用压铸模材料是确保压铸模具寿命、提高生产效率和产品质量的关键。
压铸模具的介绍

压铸模具的介绍
压铸模具是一种用于在金属压铸过程中制造金属零件的工具。
它通常由高强度合金钢、铝合金或硬质合金制成,具有高硬度、抗磨损和耐腐蚀性能。
压铸模具的主要功能是将熔融的金属材料注入模具腔中,通过高压力和高温使金属材料充分填充模具腔,形成所需的零件形状。
然后,在冷却过程中,金属材料固化,并且可以从模具中取出成品零件。
压铸模具通常分为上模和下模两部分,上模与下模之间的空间形成了零件的形状。
通过模具腔内的液态金属注入系统,金属材料被注入模具腔中。
在注入过程中,模具会承受高压力,以确保金属材料完全填充模具腔,并确保零件的精确尺寸和形状。
压铸模具在制造各种金属零件时具有广泛的应用,如汽车零件、电子设备外壳、家电零件等。
它们可以制造出高精度和复杂形状的零件,且生产效率高。
压铸模具还具有较长的使用寿命,可以重复使用多次,而且可以通过更换模具腔的方式来适应不同的产品需求。
总之,压铸模具是一种重要的工具,用于制造金属零件,具有高精度、高效率和长寿命的特点,广泛应用于各个行业。
纯铝压铸工艺及压铸模技术要点总结
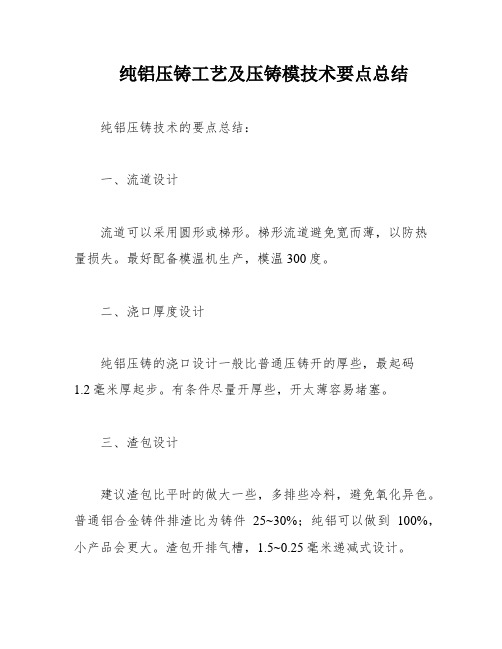
纯铝压铸工艺及压铸模技术要点总结
纯铝压铸技术的要点总结:
一、流道设计
流道可以采用圆形或梯形。
梯形流道避免宽而薄,以防热量损失。
最好配备模温机生产,模温300度。
二、浇口厚度设计
纯铝压铸的浇口设计一般比普通压铸开的厚些,最起码
1.2毫米厚起步。
有条件尽量开厚些,开太薄容易堵塞。
三、渣包设计
建议渣包比平时的做大一些,多排些冷料,避免氧化异色。
普通铝合金铸件排渣比为铸件25~30%;纯铝可以做到100%,小产品会更大。
渣包开排气槽,1.5~0.25毫米递减式设计。
四、顶针孔间隙设计
间隙比普通铝压铸模放大1.5~2.0倍,不会跑料。
五、钢材及热处理
可选用国产8418.热处理:48~50HRC比较合理。
模芯大的更低些,镶针镶件硬度可以高些,易断的部件降低点热处理硬度。
六、铝液温度
保持铝液的稳定性,一般生产在700~730度,也可以高于730度,最高不高于750度,最低不低于700.
七、根据压铸件氧化的颜色需求选择合适的铝含量成份
氧化黑色,建议用铝含量低的铝锭,可以用ADC10.氧化灰色,比如铁灰色,建议铝含量在95~97%的铝锭。
铝合金压铸技术要求
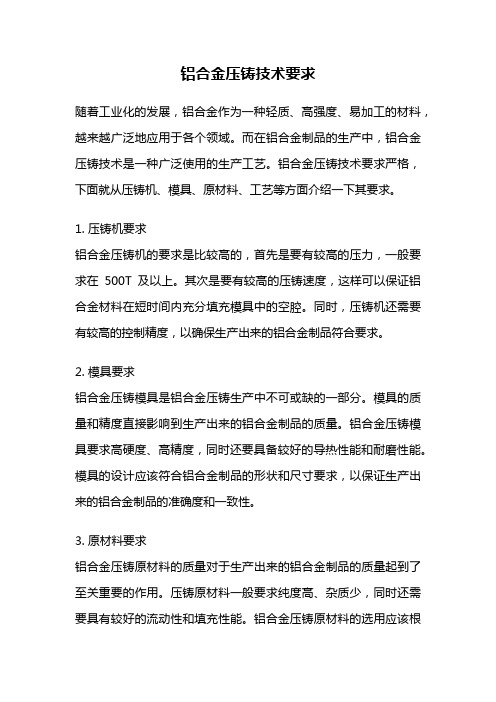
铝合金压铸技术要求随着工业化的发展,铝合金作为一种轻质、高强度、易加工的材料,越来越广泛地应用于各个领域。
而在铝合金制品的生产中,铝合金压铸技术是一种广泛使用的生产工艺。
铝合金压铸技术要求严格,下面就从压铸机、模具、原材料、工艺等方面介绍一下其要求。
1. 压铸机要求铝合金压铸机的要求是比较高的,首先是要有较高的压力,一般要求在500T及以上。
其次是要有较高的压铸速度,这样可以保证铝合金材料在短时间内充分填充模具中的空腔。
同时,压铸机还需要有较高的控制精度,以确保生产出来的铝合金制品符合要求。
2. 模具要求铝合金压铸模具是铝合金压铸生产中不可或缺的一部分。
模具的质量和精度直接影响到生产出来的铝合金制品的质量。
铝合金压铸模具要求高硬度、高精度,同时还要具备较好的导热性能和耐磨性能。
模具的设计应该符合铝合金制品的形状和尺寸要求,以保证生产出来的铝合金制品的准确度和一致性。
3. 原材料要求铝合金压铸原材料的质量对于生产出来的铝合金制品的质量起到了至关重要的作用。
压铸原材料一般要求纯度高、杂质少,同时还需要具有较好的流动性和填充性能。
铝合金压铸原材料的选用应该根据铝合金制品的要求和生产工艺来进行选择。
4. 工艺要求铝合金压铸技术的工艺要求主要包括模具温度、压铸温度、压铸速度等。
模具温度一般要求在200℃以上,以保证铝合金材料充分流动。
压铸温度要求控制在合适的范围内,过高会导致铝合金材料产生气孔,过低则会导致铝合金材料填充不充分。
压铸速度也要根据铝合金制品的要求和生产工艺来进行调整。
铝合金压铸技术要求严格,需要从多个方面考虑,才能生产出符合要求和标准的铝合金制品。
同时,压铸技术的不断创新和完善,也为铝合金制品的生产提供了更好的技术支持。
做铝合金压铸模具工序流程

做铝合金压铸模具工序流程下载温馨提示:该文档是我店铺精心编制而成,希望大家下载以后,能够帮助大家解决实际的问题。
文档下载后可定制随意修改,请根据实际需要进行相应的调整和使用,谢谢!并且,本店铺为大家提供各种各样类型的实用资料,如教育随笔、日记赏析、句子摘抄、古诗大全、经典美文、话题作文、工作总结、词语解析、文案摘录、其他资料等等,如想了解不同资料格式和写法,敬请关注!Download tips: This document is carefully compiled by theeditor. I hope that after you download them,they can help yousolve practical problems. The document can be customized andmodified after downloading,please adjust and use it according toactual needs, thank you!In addition, our shop provides you with various types ofpractical materials,such as educational essays, diaryappreciation,sentence excerpts,ancient poems,classic articles,topic composition,work summary,word parsing,copy excerpts,other materials and so on,want to know different data formats andwriting methods,please pay attention!做铝合金压铸模具工序流程铝合金压铸模具是用于生产铝合金压铸件的重要工具。
铝合金压铸模热处理

淬火工艺:
• 据热作模具的服役特点,淬火温度选在1020℃.选 择淬火温度目的在于获得最紧要的性能。高温强 度随淬火温度升高而增高,但强度的增高是牺牲 韧性的条件下得到的,淬火温度越高,钢对晶粒 长大越敏感。粗晶粒比细晶粒钢韧性差,容易产 生裂纹而损坏。冷却速度低导致冲击韧性差,容 易产生裂纹而损坏。冷却速度低导致冲击韧性低, 要使H13钢获得尽可能的冲击韧性就应该把高的 淬火温度和高的冷却速度恰当地结合起来
退火工艺:
• H13钢锻后碳化物带状偏析有时也较严重, 常规退火工艺(组织得到片状珠光体+少量 块状碳化物)不能满足。采用高温固溶— —段时间等温球化•退退火火工艺工艺(得到组织为 球状珠光体+少量弥散分布粒状碳化物), 碳化物可以到超细化水平,碳化物带状偏 析可以得到均匀化,因此二次碳化物也较 少出现。使碳化物不均匀分布得到明显改 善,甚至消除。
目前压铸模具型块材料多采用H13 • H13退火模坯,硬度为192~229HBS • H13钢的化学成份 C 0.32—0.45 Mn
0.20—0.50 Si 0.80—1.20 Gr 4.75—55 • Mo 1.10—1.75 V 0.80—1,20 (%)
热作模具常用热处理工艺
模具热处理包括模具材料热处理和模具零件热处理 。
火,较为理想。现将分级淬火工艺相比较,
一级盐浴分级淬火用的中性盐浴温度为 500℃和200℃。
回火工艺 :
• 回火稳定性是热作模具钢的主要性能之一,它反 映了模具钢在高的工作温度下抵抗软化的能力, 它关系到钢的高温硬度、高温强度、及热疲劳抗 力等等。提高回火稳定性有助于延长模具的使用 寿命。为了防止开裂,模具淬火后冷却至100℃ 左右应立即回火(特别是形状复杂的模具淬火后 应立即回火)。根据模具的工作情况,回火一般 却550℃——650℃。在500℃附近获得二次硬化, 回火硬度最高,为55HRC左右,钢的冲击韧性显 著降低,出现回火脆性,应避免。
铝合金压铸件的标准
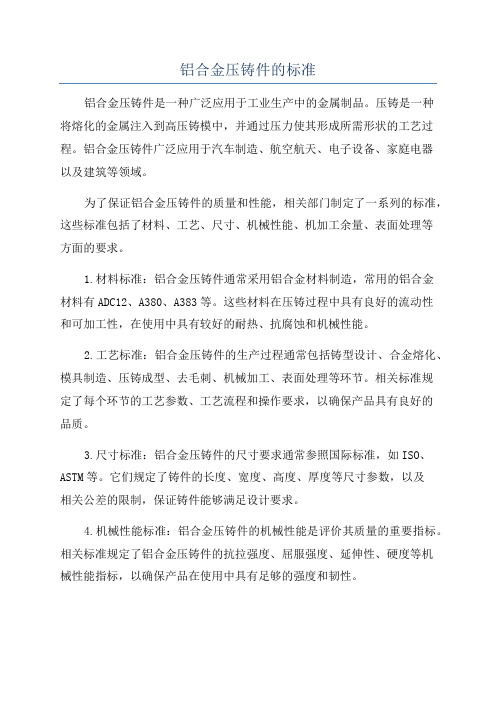
铝合金压铸件的标准铝合金压铸件是一种广泛应用于工业生产中的金属制品。
压铸是一种将熔化的金属注入到高压铸模中,并通过压力使其形成所需形状的工艺过程。
铝合金压铸件广泛应用于汽车制造、航空航天、电子设备、家庭电器以及建筑等领域。
为了保证铝合金压铸件的质量和性能,相关部门制定了一系列的标准,这些标准包括了材料、工艺、尺寸、机械性能、机加工余量、表面处理等方面的要求。
1.材料标准:铝合金压铸件通常采用铝合金材料制造,常用的铝合金材料有ADC12、A380、A383等。
这些材料在压铸过程中具有良好的流动性和可加工性,在使用中具有较好的耐热、抗腐蚀和机械性能。
2.工艺标准:铝合金压铸件的生产过程通常包括铸型设计、合金熔化、模具制造、压铸成型、去毛刺、机械加工、表面处理等环节。
相关标准规定了每个环节的工艺参数、工艺流程和操作要求,以确保产品具有良好的品质。
3.尺寸标准:铝合金压铸件的尺寸要求通常参照国际标准,如ISO、ASTM等。
它们规定了铸件的长度、宽度、高度、厚度等尺寸参数,以及相关公差的限制,保证铸件能够满足设计要求。
4.机械性能标准:铝合金压铸件的机械性能是评价其质量的重要指标。
相关标准规定了铝合金压铸件的抗拉强度、屈服强度、延伸性、硬度等机械性能指标,以确保产品在使用中具有足够的强度和韧性。
5.机加工余量标准:铝合金压铸件通常需要进行进一步的机械加工,比如铣削、切割、钻孔等。
相关标准规定了机加工余量的限制,以确保在机加工过程中不会影响铝合金压铸件的尺寸和性能。
6.表面处理标准:铝合金压铸件在生产后通常需要进行表面处理,以提高其耐腐蚀性、耐磨性和美观度。
常用的表面处理方法包括喷涂、阳极氧化、电泳涂装等。
相关标准规定了表面处理的方法、工艺和要求,以确保产品具有所需的表面性能。
总结起来,铝合金压铸件的标准涵盖了材料、工艺、尺寸、机械性能、机加工余量和表面处理等方面的要求,以确保产品的质量和性能。
这些标准不仅适用于压铸生产厂家,也为用户提供了选择和评估铝合金压铸件的指导依据。
铝合金压铸工艺流程,铝合金压铸件的加工步骤

铝合金压铸工艺流程|铝合金压铸件的加工步骤铝合金压铸:铝合金压铸类产品主要用于电子、汽车、电机、家电和一些通讯行业等,一些高性能、高精度、高韧性的优质铝合金产品也被用于大型飞机、船舶等要求比较高的行业中。
主要的用途还是在一些器械的零件上。
铝合金压铸工艺流程:以某产品压铸模的工作过程作说明1)合模:模具合拢,等待浇注。
2)浇料:机械手或者操作工人从炉内打料浇入料筒。
3)压射:按设定的工艺参数,进行压射。
4)开模:模具打开,用斜导柱抽芯,同步抽芯。
5)抽芯:模具在抽芯装置作用下,从侧面退出,以便于顶出;如果是前(定)模抽芯,需要先抽芯再开模。
6)顶件:在推出机构作用下,顶出铸件,以便于取下。
7)取件:用手动或自动将铸件从模具上取下来;如果有扣针,要注意方向和角度,不能野蛮敲打和拉动,否则容易损坏顶针。
8)喷涂:清理干净模腔,前后模并均匀喷上脱模剂。
9)先复位机构:如果在抽芯下面有顶针的情况,需要制作拉杆等先复位机构,以保护模具。
10)再合模,重复以上过程。
铝合金压铸件的加工步骤:1、退火处理:铝合金压铸件加热到300℃上下,保温一段时刻后,随炉冷却到室温的工艺称为退火。
退火时,固溶体会呈现分化,聚集,可以去除铝合金压铸件的内应力,让铝合金压铸件的尺度保持稳固,防止变形,增强铝合金压铸件的塑性。
2、固溶处理:将铝合金压铸件加热到晶体的熔点,然后在这样的温度下持续久一点,然后冷却,让强化组元可以**地溶解,保存这个高温一直到室温,这一工序就叫做固溶处理。
固溶处理可以增强铝合金压铸件的强度和塑性,提高铝合金压铸件的抗腐蚀。
固溶处理的效果一般和固溶处理温度、固溶处理保温、冷却速度三个方面有关。
3、时效处理:把固溶处理后的铝合金压铸件加热到设定温度,持续一段后出炉,放在空气里冷却的办法叫做时效。
要是时效强化是在室温下完结的那就叫天然时效.要是时效强化是在比室温高的环境里并保温一段时刻后完结的称为人工时效。
时效处理进行着过饱和固溶体分化的自发过程,可以让合金基体的点阵降到相对安稳的状况。
铝合金压铸粘模问题分析及处理方法
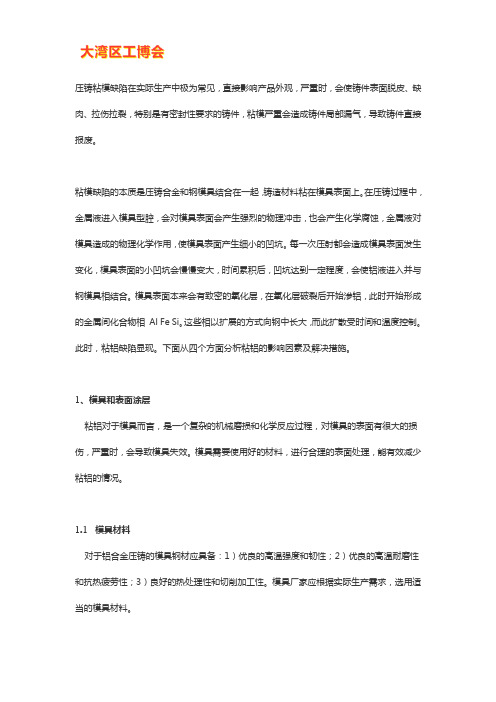
压铸粘模缺陷在实际生产中极为常见,直接影响产品外观,严重时,会使铸件表面脱皮、缺肉、拉伤拉裂,特别是有密封性要求的铸件,粘模严重会造成铸件局部漏气,导致铸件直接报废。
粘模缺陷的本质是压铸合金和钢模具结合在一起,铸造材料粘在模具表面上。
在压铸过程中,金属液进入模具型腔,会对模具表面会产生强烈的物理冲击,也会产生化学腐蚀,金属液对模具造成的物理化学作用,使模具表面产生细小的凹坑。
每一次压射都会造成模具表面发生变化,模具表面的小凹坑会慢慢变大,时间累积后,凹坑达到一定程度,会使铝液进入并与钢模具相结合。
模具表面本来会有致密的氧化层,在氧化层破裂后开始渗铝,此时开始形成的金属间化合物相Al Fe Si。
这些相以扩展的方式向钢中长大,而此扩散受时间和温度控制。
此时,粘铝缺陷显现。
下面从四个方面分析粘铝的影响因素及解决措施。
1、模具和表面涂层粘铝对于模具而言,是一个复杂的机械磨损和化学反应过程,对模具的表面有很大的损伤,严重时,会导致模具失效。
模具需要使用好的材料,进行合理的表面处理,能有效减少粘铝的情况。
1.1 模具材料对于铝合金压铸的模具钢材应具备:1)优良的高温强度和韧性;2)优良的高温耐磨性和抗热疲劳性;3)良好的热处理性和切削加工性。
模具厂家应根据实际生产需求,选用适当的模具材料。
1.2 模具表面硬度模具的表面硬度不足,耐磨性就越差,会使模具产生热疲劳失效,出现裂纹和点蚀,进而产生粘铝;若模具表面硬度太高,会使模具产生脆性开裂。
所以,需要选用合理的模具表面硬度。
大型型腔为提高韧性避免早期开裂,可以适当降低硬度;型芯主要是发生弯曲变形失效,发生裂纹失效情况很少,则可以减小其韧性而提高硬度。
对于尺寸大的铝合金铸件或形状结构复杂的模具,热处理工艺难度很大可以适当降低硬度;反之,中小型铝合金压铸模具可以适当提高硬度。
1.3 模具表面粗糙度模具表面应该具有合理的粗糙度。
粗糙度过大对模具损害较大,但不是粗糙度越小越好,要避免模具表面过度抛光。
铝合金压铸模的模具寿命

铝合金压铸模的模具寿命铝合金压铸模承受巨大交变工作应力,必须从模材,设计,加工,热处理及操作各方面加以注意才能得到长的模具寿命,以下是为使模具能达长寿命的22点要诀:1、高品质模材2、合理设计模壁厚及其它模具尺寸3、尽量采用镶件4、在可能条件下选用尽量大的转角R5、冷却水道与型面及转角的间距必须足够大6、粗加工后应去应力回火7、正确有热处理,淬火冷却须足够快8、彻底打磨去除EDM娈质层9、型面不可高度抛光10、模具型面应经氧化处理11、如选氮化,渗层不能太深12、以正确的方法预热模具至推荐的温度13、开始压铸5~10件应使用慢的锤头速度14、在得到合格产品的前提下尽量降低铝液温度15、不使用过高的铝液注射速度16、确保模具得到适当冷却,冷却水的温度应保持在40~50℃17、临时停机,应尽量合模并减小冷却水量,避免再开机时模具承受热冲击18、当模型面在最高温度时应关冷却液19、不过多的喷脱模剂20、在一定数量后的压铸后去应力回火压铸标准目录一、通用标准中国GB/T24001-1996 idt ISO 14001:1996 环境管理体系规范及使用指南GB/T19001-2000 idt ISO/FDIS9001:2000 质量管理体系––要求GB/T5611-1998铸造术语HB7578-1997铸件试制定型规范GB/T8063-94 铸造有色金属及其合金牌号表示方法GB/T13822-92 压铸有色合金试样GB5678-85 铸造合金光谱分析取样方法HB5343-94 铸造工艺质量控制GB/T6414-1999 铸件尺寸公差及机械加工余量GB/T15056-94 铸造表面粗糙度评定方法二、压铸机标准中国JB/T8083-1999 压铸机型式与基本参数JB/T8084.1-1999 冷室压铸机精度JB/T8084.2-1999 冷室压铸机技术条件JB/T6039.2-92 热室压铸机精度JB/T6039.3-92 热室压铸机技术条件三、压铸模标准中国GB8844-88 压铸模技术条件GB8847-88 压力铸造模具术语GB4678.1~15-84 压铸模零件GB4679-84 压铸模零件技术条件四、合金及工艺标准1. 铝合金中国GB/T1173-95 铸造铝合金GB/T8733-2000 铸造铝合金锭YS/T282-2000 铝中间合金锭JB/T7946.1-1999 铸造铝硅合金变质JB/T7946.2-1999 铸造铝硅合金过烧JB/T7946.3-1999 铸造铝合金针孔GB/T15115-94 压铸铝合金GB/T15114-94 铝合金压铸件HB5012-86 铝合金压铸件HB/Z220.2-92 铝合金金属型铸造HB/Z220.3-92 铝合金低压铸造HB/Z220.4-92 铝合金压力铸造HB/Z220.7-92 铝合金铸件浸渗GJB1695-93 铸造铝合金热处理规范国际标准 ISO3522-84 铸造铝合金ASTMB179-96 砂型铸件、永久型铸件及压铸件用铝合金锭ASTMB597-98 铝合金热处理JISH5302:2000 铝合金压铸件2. 镁合金中国GB1177-91 铸造镁合金GB/T13820-92 镁合金铸件国际标准IS O/DIS16220-1999 铸造镁合金ASTMB94-94 镁合金压铸件JISH5303-1991 镁合金压铸件3. 锌合金中国GB/T1175-1997 铸造锌合金GB/T13818-92 压铸锌合金GB/T13821-92 锌合金压铸件国际标准IS O301-1981 铸造用锌合金锭ASTMB240-98 压铸件用锌合金锭ASTMB327-98 压铸锌合金用铝中间合金JISH2021:1999 压铸用锌合金锭EN 12844:1998 锌和锌合金-铸件-规格五、铜合金中国GB1176-87 铸造铜合金技术条件GB/T15116-94 压铸铜合金GB/T15117-94 铜合金压铸件5. 铅锡合金中国GB/T8740-1988 铸造铅基轴承合金锭GB/T8740-1988 铸造锡基轴承合金锭JISH5601-1990 硬铅铸件JISH5401-1958 轴承合金DIN1741-1974 压铸用铅合金常見鋅合金成分鋅合金種類合金代號商業習用編號No.3 No.5 No.2 No.7ASTM AG40AAC41A-- --UNS Z33251 Z35530 -- Z33522SAE 903 925 921 --機械性質Die Cast Aged Die Cast Aged Die Cast Aged Die Cast Aged抗拉強度(Kg/mm2) 28.8 24.6 33.7 27.42 36.4 33.6 28.7 24.5降伏強度(Kg/mm2) -- -- -- -- -- -- -- --伸長率(%) 10 16 7 13 7 2 13 18剪切強率(Kg/mm2) 21.8 -- 26.7 -- 32.3 -- 21.8 --硬度(勃式) 82 72 91 80 100 98 80 67衝擊強度(J) 30.2 28.8 33.7 28.1 24.6 3.5 30.2 28.8疲勞強度(Kg/mm2,5%103 4.85 -- 5.76 -- 5.98 -- 4.78 --壓強度(Kg/mm2) 42 -- 60.9 42 -- 21.7 -- 65.1成份錠鑄件錠鑄件錠錠鑄件Al 3.9~4.3 3.5~4.3 3.9~4.3 3.5~4.3 3.9~4.3 3.9~4.3 3.5~4.3Mg .025~.50 .02~.05 .03~.06 .03~.08 .025~.50 .01~.02 .005~.020Cu .10max.25max075~1.25 .75~1.25 2.6~2.9 .10max.25maxFe .075 .10 .075 .10 .075 .075 .075Pb .004 .005 .004 .005 .004 .002 .003Cd .003 .004 .003 .004 .003 .002 .002Sn .002 .003 .002 .003 .002 .001 .001Ni -- -- -- -- -- .005~.002 .005~.002Zn 餘餘餘餘餘餘餘物性密度g/cm3 6.64 6.64 6.64 6.64熔解溫度˚C 382~387 381~386 379~390 381~387導電係數(%ACS) 27 26 25 27熱傳導係數(W/M˚K) 113 109 105 113熱膨脹係數(20~100˚C)(µm/m˚k) 27.36 27.36 27.72 27.36比熱kg˚C 0.419 0.419 0419 0.419收縮率6/1000 6/1000 6/1000 6/1000点击浏览该文件压铸模简介一、常用压铸合金成分和性能压铸合金成份有有色金属和黑色金属,广泛彩的有色金属合金分类如下:铅合金低熔点合金锡合金锌合金有色金属合金铝合金高熔点合金镁合金铜合金二、压铸件结构的工艺性1、壁厚〈1〉压铸件的最小壁厚与正常壁厚通常根据铸件面积而言。
铝合金压铸模具的制作
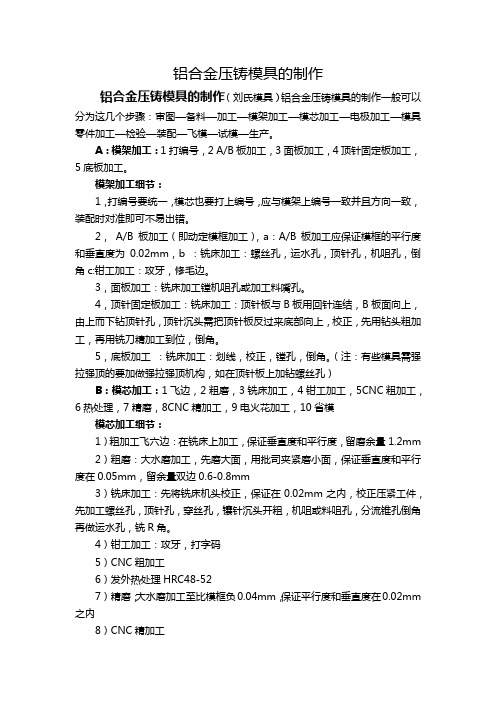
铝合金压铸模具的制作铝合金压铸模具的制作(刘氏模具)铝合金压铸模具的制作一般可以分为这几个步骤:审图—备料—加工—模架加工—模芯加工—电极加工—模具零件加工—检验—装配—飞模—试模—生产。
A:模架加工:1打编号,2 A/B板加工,3面板加工,4顶针固定板加工,5底板加工。
模架加工细节:1,打编号要统一,模芯也要打上编号,应与模架上编号一致并且方向一致,装配时对准即可不易出错。
2,A/B板加工(即动定模框加工),a:A/B板加工应保证模框的平行度和垂直度为0.02mm,b :铣床加工:螺丝孔,运水孔,顶针孔,机咀孔,倒角c:钳工加工:攻牙,修毛边。
3,面板加工:铣床加工镗机咀孔或加工料嘴孔。
4,顶针固定板加工:铣床加工:顶针板与B板用回针连结,B板面向上,由上而下钻顶针孔,顶针沉头需把顶针板反过来底部向上,校正,先用钻头粗加工,再用铣刀精加工到位,倒角。
5,底板加工:铣床加工:划线,校正,镗孔,倒角。
(注:有些模具需强拉强顶的要加做强拉强顶机构,如在顶针板上加钻螺丝孔)B:模芯加工:1飞边,2粗磨,3铣床加工,4钳工加工,5CNC粗加工,6热处理,7精磨,8CNC精加工,9电火花加工,10省模模芯加工细节:1)粗加工飞六边:在铣床上加工,保证垂直度和平行度,留磨余量1.2mm 2)粗磨:大水磨加工,先磨大面,用批司夹紧磨小面,保证垂直度和平行度在0.05mm,留余量双边0.6-0.8mm3)铣床加工:先将铣床机头校正,保证在0.02mm之内,校正压紧工件,先加工螺丝孔,顶针孔,穿丝孔,镶针沉头开粗,机咀或料咀孔,分流锥孔倒角再做运水孔,铣R角。
4)钳工加工:攻牙,打字码5)CNC粗加工6)发外热处理HRC48-527)精磨;大水磨加工至比模框负0.04mm,保证平行度和垂直度在0.02mm 之内8)CNC精加工9)电火花加工10)省模,保证光洁度,控制好型腔尺寸。
11)加工进浇口,排气,锌合金一般情况下浇口开0.3-0.5mm,排气开0.06-0.1mm,铝合金浇口开0.5-1.2mm排气开0.1-0.2,塑胶排气开0.01-0.02,尽量宽一点,薄一点。
铝合金压铸模具龟裂的原因及预防办法
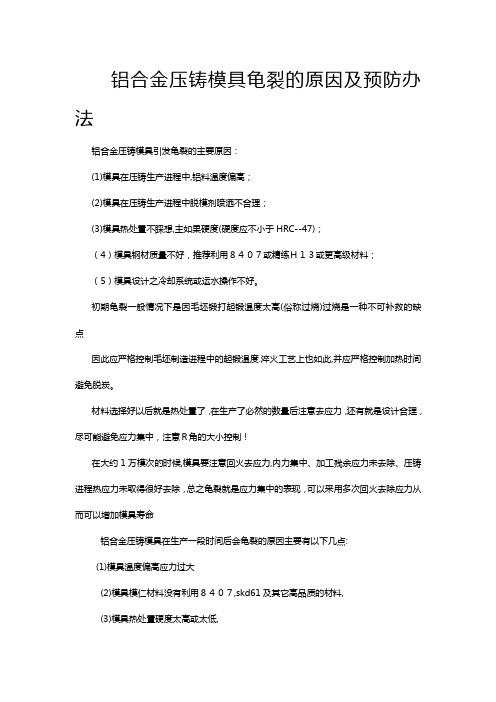
铝合金压铸模具龟裂的原因及预防办法铝合金压铸模具引发龟裂的主要原因:(1)模具在压铸生产进程中,铝料温度偏高;(2)模具在压铸生产进程中脱模剂喷洒不合理;(3)模具热处置不睬想,主如果硬度(硬度应不小于HRC--47);(4)模具钢材质量不好,推荐利用8407或精练H13或更高级材料;(5)模具设计之冷却系统或运水操作不好。
初期龟裂一般情况下是因毛坯锻打起锻温度太高(俗称过烧)过烧是一种不可补救的缺点因此应严格控制毛坯制造进程中的起锻温度.淬火工艺上也如此,并应严格控制加热时间避免脱炭。
材料选择好以后就是热处置了,在生产了必然的数量后注意去应力,还有就是设计合理,尽可能避免应力集中,注意R角的大小控制!在大约1万模次的时候,模具要注意回火去应力,内力集中、加工残余应力未去除、压铸进程热应力未取得很好去除,总之龟裂就是应力集中的表现,可以采用多次回火去除应力从而可以增加模具寿命铝合金压铸模具在生产一段时间后会龟裂的原因主要有以下几点:(1)模具温度偏高应力过大(2)模具模仁材料没有利用8407,skd61及其它高品质的材料,(3)模具热处置硬度太高或太低,4)是不是按期保养?5k times1 回火,15k times1 回火30k times..........預防壓鑄模龜裂問題﹐提高模具利用壽命﹐要做好以下几點﹕1.壓鑄模成型部位(動﹑定模仁﹑型芯)熱處理要求﹕硬度要保証在HRC44~48 (材料可選用SKD61或8407或高品质热作钢)2.模具在壓鑄生產前應進行充分預熱作業,其作用如下﹕使模具達到較好的熱平衡﹐使鑄件凝固速度均勻并有利于壓力傳遞.维持壓鑄合金填充時的流動性﹐具有良好的成型性和提高鑄件表面質量.減少前期生產不良﹐提高壓鑄生產率.降低模具熱交變應力﹐提高模具利用壽命.具体規范如下﹕合金种類模具預熱溫度(℃)鋁合金180~300鋅合金150~2003.新模具在生產一段時間后﹐熱應力的積累是直接導致模仁產生龜裂的原因﹐為減少熱應力﹐投產必然時間后的模仁及滑塊應進行消除熱應力的回火處理.具体需要消除熱應力的生產模次如下﹕模具類型鋁合金鋅合金第一次回火<2000模次<10000模次第二次回火<10000模次<20000模次第三次回火<30000模次<50000模次铝合金压铸模经受庞大交变工作应力,必需从模材,设计,加工,热处置及操作各方面加以注意才能取得长的模具寿命,以下是为使模具能达长寿命的21点要诀:一、高品质模材二、合理设计模壁厚及其它模具尺寸3、尽可能采用镶件4、在可能条件下选用尽可能大的转角R五、冷却水道与型面及转角的间距必需足够大六、粗加工后应去应力回火7、正确有热处置,淬火冷却须足够快八、完全打磨去除EDM硬质层九、型面不可高度抛光10、模具型面应经氧化处置1一、如选氮化,渗层不能太深1二、以正确的方式预热模具至推荐的温度13、开始压铸5~20件应利用慢的锤头速(按照产品的大小)14、在取得合格产品的前提下尽可能降低铝液温度1五、尽量不利用太高的铝液注射速度及太高的铸造比压1六、确保模具取得适当冷却,冷却水的温度应维持在40~50℃17、临时停机,应尽可能合模并减小冷却水量或关闭运水,避免再开机时模具经受热冲击1八、当模型面在最高温度时应关冷却液1九、不利用过量的喷脱模剂20、在必然数量后的压铸后去应力回火21.尽量利用模温控制装置。
压铸模具分类

压铸模具分类压铸模具是制造各种铝合金、锌合金、铜合金、镁合金及其他合金铸件的常用工具。
针对不同的铸造对象和铸造工艺,可以将压铸模具分为多种类型。
以下是根据不同的分类方法,对压铸模具进行的详细介绍。
一、按照受力情况分类1、普通压铸模具普通压铸模具是指在铸造过程中受力状态相对较为简单的模具,通常采用一体式结构,主要包括模腔、模芯和浇口系统。
这种模具结构简单,制造成本低,广泛应用于铝、锌、铜等合金铸件的生产。
2、复杂压铸模具复杂压铸模具受力状态相对比较复杂,并且铸件的尺寸、形状和外形要求较高。
在制造过程中,需要采用多种材料、多种结构进行组合,以满足铸件的高精度、高质量的要求。
二、按照铸造对象分类1、铝合金压铸模具铝合金压铸模具用于生产各种铝合金铸件,设计中需要考虑铝合金溶液的流动性、凝固性及热传导性,以保证铸件质量的稳定性和一致性。
2、锌合金压铸模具锌合金压铸模具用于生产各种锌合金铸件。
这种模具需要考虑铸件所需的厚度、密度、强度等参数,同时还需要选择合适的浇口位置和浇注方式,避免铸件出现质量问题。
3、铜合金压铸模具铜合金压铸模具用于生产各种铜合金铸件,也是很常见的模具类型之一。
在铜合金模具的设计中,要考虑铸件形状、组织、性能等因素,以满足铸件的高质量和稳定性要求。
三、按照生产工艺分类1、冷室压铸模具冷室压铸模具是指铸造时溶液需要通过液态金属容器加热和保温后,再通过浇口进入模具中进行铸造的模具。
这种模具适用于生产各种铝合金、铜合金、镁合金等高品质铸件。
2、热室压铸模具热室压铸模具又称射压模具,是一种利用液态金属加热设备将金属融化后再注入模具中的铸造工艺。
这种模具适用于铸造锌合金、铝合金等材料,汽车、摩托车、电子等领域的产品中也有很广泛的应用。
以上就是针对压铸模具的分类介绍,相信对大家了解压铸模具有所帮助。
铝合金压铸模具浇排设计方案
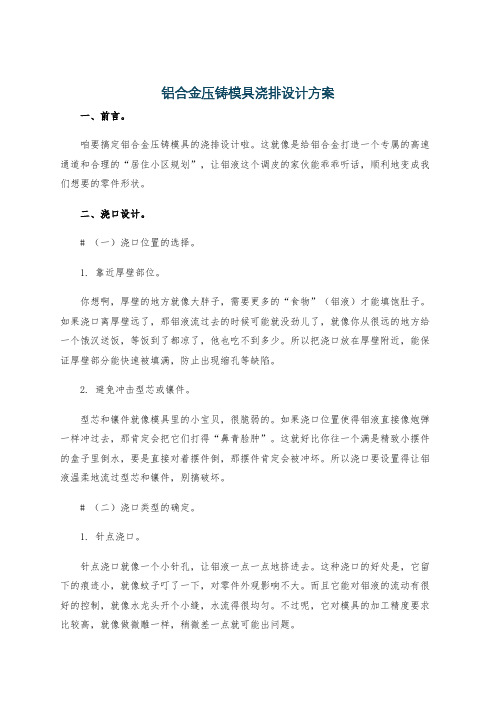
铝合金压铸模具浇排设计方案一、前言。
咱要搞定铝合金压铸模具的浇排设计啦。
这就像是给铝合金打造一个专属的高速通道和合理的“居住小区规划”,让铝液这个调皮的家伙能乖乖听话,顺利地变成我们想要的零件形状。
二、浇口设计。
# (一)浇口位置的选择。
1. 靠近厚壁部位。
你想啊,厚壁的地方就像大胖子,需要更多的“食物”(铝液)才能填饱肚子。
如果浇口离厚壁远了,那铝液流过去的时候可能就没劲儿了,就像你从很远的地方给一个饿汉送饭,等饭到了都凉了,他也吃不到多少。
所以把浇口放在厚壁附近,能保证厚壁部分能快速被填满,防止出现缩孔等缺陷。
2. 避免冲击型芯或镶件。
型芯和镶件就像模具里的小宝贝,很脆弱的。
如果浇口位置使得铝液直接像炮弹一样冲过去,那肯定会把它们打得“鼻青脸肿”。
这就好比你往一个满是精致小摆件的盒子里倒水,要是直接对着摆件倒,那摆件肯定会被冲坏。
所以浇口要设置得让铝液温柔地流过型芯和镶件,别搞破坏。
# (二)浇口类型的确定。
1. 针点浇口。
针点浇口就像一个小针孔,让铝液一点一点地挤进去。
这种浇口的好处是,它留下的痕迹小,就像蚊子叮了一下,对零件外观影响不大。
而且它能对铝液的流动有很好的控制,就像水龙头开个小缝,水流得很均匀。
不过呢,它对模具的加工精度要求比较高,就像做微雕一样,稍微差一点就可能出问题。
2. 侧浇口。
侧浇口就比较实在,像个小侧门。
铝液从侧面流进去,比较简单直接。
它适合一些形状不是特别复杂的零件。
这种浇口加工起来比较容易,就像盖个普通的小房子,不需要太多的技巧。
但是它可能会在零件表面留下比较明显的浇口痕迹,就像脸上有个小疤一样,影响美观。
三、流道设计。
# (一)主流道设计。
1. 尺寸确定。
主流道就像高速公路的主干道,要足够宽敞才能让铝液大军顺利通过。
一般来说,主流道的直径要根据零件的大小和所需铝液的量来确定。
如果零件大,需要的铝液多,主流道就得粗一点,就像大货车要走大路一样。
要是主流道太细了,铝液就会堵在那里,就像一群人挤在小胡同里,谁也走不动。
- 1、下载文档前请自行甄别文档内容的完整性,平台不提供额外的编辑、内容补充、找答案等附加服务。
- 2、"仅部分预览"的文档,不可在线预览部分如存在完整性等问题,可反馈申请退款(可完整预览的文档不适用该条件!)。
- 3、如文档侵犯您的权益,请联系客服反馈,我们会尽快为您处理(人工客服工作时间:9:00-18:30)。
• 在等温球化退火工艺的制定过程中,奥氏体化温度及等温 转变温度十分重要。奥氏体化温度较高时,未溶碳化物数 量较少,奥氏体晶粒较大,而且其中的碳含量的分布也比 较均匀,因而有利于球化过程的进行。等温转变温度较低 时,碳(及合金元素)在奥氏体中扩散较困难,也不利于 球化过程的进行。只有当奥氏体温度较低,等温转变温度 较高的处理规程下,才能得到球化组织。 等温球化退火 规范:首先毛坯入炉,随炉升温缓慢加热,加热至Ac1+ (20~30℃),保 • 温3~4h,经查表,H13钢的Ac1为860℃,故升温加热至 880℃~890℃并保温3~4h;然后随炉缓冷至Ar1-(20~ 30℃)保温4~5h,经查表H13钢的Ar1为775℃,故升温加 热至745℃~755℃并保温4~5h;然后再随炉缓冷至550℃, 空冷至室温。经硬度检测,硬度可达229HBW,共晶碳化物 等级≤3级。如果钢中的原始组织网状碳化物较严重,则 需要加热到略高于Acm的温度,使碳化物网溶入奥氏体, 然后再较快地冷却到Ar1一下温度进行等温球化退火。 • 经过球化退火,可使可切削性能大大提高;在淬火时,溶 入奥氏体的碳化物较均匀; • 淬火开裂和淬火变形减轻;而韧性有所增加等等多方面有 所改善。
一般把热作模具钢分为三类:
• (1)高韧性热作模具钢 5CrMnMo、5CrNiMo、 4Cr5MoVSi(H11)等,适宜制作一般的锻造模具; • (2)高热强钢 3Cr2W8V、Y4、Y10、以及基体 钢5Cr4Mo2W2SiV等,宜用作热挤压模、压铸模 等; • (3)强韧兼备的热作模具 钢 4Cr5MoV1Si(H13)、HM3、4Cr5W2SiV等,宜 用作热锻模、热挤压模、压铸模等、高速锻模。
回火
• 回火的目的就是使模具达到一定的硬度和韧性,并消除淬火应力。为 保证在使用中的组织稳定性和内应力尽可能小,挥回火时间必须充分, 一般回火时间可按3min/mm。但最少不低于2h。 对于二次硬化热作模具钢,淬火后组织中存在一定量的残余奥氏体, 第一次回火后,在冷却过程中,这些残余奥氏体基本上转变为相应的 等温产物,这些产物较脆,往往会成为开裂的根源,故必须进行第二 次回火,有时为了使用上的要求也可进行第三次回火。 一般来说,第 一次回火温度根据回火温度与硬度关系曲线的硬度要求而定,第二次 回火温度比第一次低20℃,但是有些情况下第一次回火温度也可采用 较低的温度,然后根据第一次回火后的硬度来选择第二次的回火温度, 以期达到所需硬度。 对于该模具钢采取的是高温回火,第一次回火温度600℃,第二次可 略低,取580℃。由于钢中含有一定量的Cr、Mn、Ni,或者Ni少量时 Cr、Mn共存的条件下,高温回火(尤其是在500~600℃之间进行时) 极易出现比较严重的第二类回火脆性,应在回火后采用快速冷却的方 式(油冷或水冷)以避免之。如果钢中的Mo的含量适当提高,钢的 回火脆性敏感性大大减小,高温回火后可以缓冷(空冷)。 经两次高温回火后获得的组织是回火屈氏体,并且 残余奥氏体的含量 极少可以忽略不 计,钢回火后的性能大大提高,强度、硬度有所下降,塑性韧性较淬 火后明显提高。回火后硬度可达47~49HRC。
几种压铸模材料的分析
• 目前一般用作压铸模的钢种有H13钢、3Cr2W8V 钢,传统用钢是3Cr2W8V钢。这类钢属于中耐热 韧性模具钢,这类钢与低耐热高韧性热作模具钢 相比主要特点是含有较多的Cr、Mo、V、W等碳 化物形成元素以及含碳量较低,ω(c)一般为 0.32~0.45。由于钢中含较多的Cr元素,因而具 有很好的淬透性,直径100mm的棒材在空气淬火 的条件下可完全淬透,故被称为空冷硬化热作模 具钢。在截面尺寸<150mm时具有与5CrNiMo钢 相近的韧性,而在工作温度500~600℃却具有更 高的硬度、热强性和耐磨性。与4Cr5MoSiV相比, H13(4Cr5MoSiV1)的热强性和硬度更高,在中 温条件下具有较高的热强度,热疲劳性能、高的 韧性和一定的耐磨性;在较低的奥氏体化温度条 件下进行空气淬火,热变形处理变形小,空冷淬
铝合金压铸模
• 铝合金以其低密度高强度越来越多得到广泛应用, 经过对铝合金化学成分的组成与优 • 化,铝合金的铸造成型工艺、热挤压加工工艺和 人工时效等工艺,使铝合金的性能得到发挥,铝 合金压铸类产品主要用于电子、汽车、电机、家 电和一些通讯行业,一些高性能、高精度、高韧 性的优质铝合金产品也被应用到大型飞机、船舶 等技术要求比较高的行业中,但是其主要应用还 是在一自身 的优势:压铸范围广;逐渐尺寸精度 • 高、稳定性好;表面粗糙度低;生产率高;金属 利用率高;铸件强度和表面硬度高等等。
铝合金压铸模的热处理工艺
• 该铝合金压铸模的生产工艺流程图如下: • 下料 加工 锻造 稳定处理 球化退火 精加工 粗
淬火 打磨
两次回火 渗碳或渗氮
钳修
热处理具体流程
• 1 锻造 • 经下料后须锻造成毛坯件,而不是将原料直接进行机加工成毛坯件, 一方面减少材料 • 的损耗,节约材料:另一方面,经锻造后,钢发生塑性变形,晶胞拉 伸,成形变胞,沿流线方向的抗拉强度大,有利于提高毛坯件的强 度。 • 首先对型材进行加热,加热温度1100~1160℃,始锻温度1060~ 1150℃,以保证锻造 • 过程中钢处于奥氏体状态,可塑性强,终锻温度≥800℃。 • 2 球化退火 • 加热保温时间和等温时间由模具材料、尺寸及加热设备类型而定,模 具退火一般采用箱式炉,加热保温时间按照模具有效厚度计算,加热 系数1~2min\mm。 • 原始组织的好坏对模具钢的韧性和冷热疲劳性能有很大的影响,为改 善热作模具钢的强韧性配合,对于性能要求比较高的模具,可采用预 调质处理或者采用淬火加高温回火或退火相结合的方法,以获得细小 的珠光体和细小弥散分布的碳化物组织,为最终热处理提供很均匀的 组织,从而使得最终热处理后能达到优良的强韧性配合。
• 2)淬火加热温度 • 淬火加热温度取决于钢的成分和使用要求,对于同一种钢 来说,当要求有较高的韧性时,往往采用较低的温度淬火; 当要求较好的高温强度时,则采用较高的淬火温度。 对 于该模具选择淬火加热温度1020~1050℃,属于完全淬 火,该加热温度使钢完全奥氏体化。淬火加热为了保证模 具表面不脱碳,需采用脱氧保护良好的氯化钡盐浴炉中进 行加热。 • 3)淬火保温时间 • 淬火保温时间应保证使钢的原始组织能够全部形成奥氏体, 同时还必须保证碳化物能够充分溶解,设溶解后 含碳量 和合金元素能够充分地扩散,从而达到奥氏体均匀化 。 这样,保证热作模具刚具有较好的高温性能,这一点非常 重要。所以,一般热作模具钢的淬火保温时间较长,在盐 浴炉中加热淬火保温时间系数一般是0.5~1min/mm,模 具尺寸小,系数取上限。
• 火时产生氧化皮的倾向小,而且可以抵抗熔融铝 的冲蚀作用。4Cr5MoSiV1钢,即美国钢号AISIH13,也是日本钢号JIS-SKD61,是国际上广泛 应用的一种空冷硬化热作模具钢,进口设备上都 配用H13钢制造的模具。H13钢有较高的韧性和 耐冷热疲劳性能,不容易产生热疲劳裂纹,即使 出现了热疲劳裂纹也细而且短,不容易扩展,因 此用其制作的模具生产的压铸件外观质量有很大 的提高。模具在使用前无须预热,而且可以采用 自来水喷冷,以抑制模具的升温,减轻了操作工 人的劳动强度。该钢材同时具备较高的热强性, 是一种强韧兼备的优质廉价钢种,既可用作热锻 模材料,也可在模腔升温低于600℃的工况下用 作压铸模材料。
服役条件
• 铝合金压铸模属于热作模具。热作模具在工作时 承受巨大的冲击力、压应力、张应力、 • 弯曲应力,模具型腔与高温(有时可达1150~ 1200℃)金属接触后,本身温度可达300~400℃, 局部高达500~600℃。还经常受空气、油、水等 的反复冷却,在时热时冷的苛刻条件下工作的模 具,其型腔表面极易产生疲劳裂纹(即龟裂)。 此外,炽热的金属在模具型腔中变形所产生的强 烈摩擦,容易因摩擦而使精度降低,因而要求热 作模具钢具有足够的热强行、热疲劳性、韧性、 硬度和耐磨性、良好的导热性和耐蚀性,还要求 具有较高的淬透性,以保证整个截面具有一致的 力学性能。
•
•
•
性能检测方法
在热处理生产过程中,因热工仪表、加热设备、冷却介质、 操作水平、原材料等因素的影响,热处理质量不可避免地 存在差异,甚至产生不合格产品,需要通过检验把不合格 产品剔除出去。因此质量检验对保证和提高热处理质量有 着极为重要的作用。常用的热处理质量检验方法包括外观 与内部缺陷检验、表面和内部硬度检验、组织形态或结构 检验、模具变形、表面硬化层深度/渗层深度、脆性检验、 晶粒度检验、表面氧化与脱碳检验、抗拉强度检验等等。 其中无损检测技术在现在的模具检验中占有重要地位。
H13材料的各方面数据分析
• H13钢的化学成分分析如下: C:0.32%~0.45%;Si:0.80%~1.20%; Mn:0.20%~0.50%;Cr:4.75%~5.50%; Mo:1.10%~1.7-5%;Ni≤0.25%; V:0.80%~1.20%;P≤0.03%;S≤0.03%。 • H13钢的物理性能、力学性能如下: (1)线膨胀系数α l:11.5×10-6/℃,(22~500℃); 12.2×10-6/℃,(22~800℃); (2)热导率λ :28.4W/(m·K) (800℃); (3)密度ρ :7.8g/cm3 ,(20℃);7.7g/cm3 ,(400℃); (4)临界点:Ac1 860℃;Ac3 915℃;Ar1 775℃; Ar3 815℃;Ms 340℃。
• 3 淬火 • 热挤压模具钢的淬火工艺过程包括预热、解热、保温、冷却和 均热。由于这类钢合金 元素含量较高,钢的导热性较差,所 以在对钢进行加热时必须严格控制加热速度。 • 1)预热 • 在空气介质加热炉中加热时可以控制加热速度,使其以很缓慢 的速度进行升温,在盐浴炉中想控制其加热速度是很困难的, 因此必须采取预热的方法。预热次数的多少取决于钢的成分和 模具变形的要求:对于般要求变形不严格的模具,在不开裂的 情况下预热次数可适当少些,但对于变形要求严格的模具必须 多次预热。 • 在较低的温度预热一般是在空气介质加热炉中进行的,两段预 热的加热速度必须缓慢进行,一般≤30~60℃/min。因为钢在 这个温度范围处于弹性状态,内外温差所产生的热应力一旦超 过弹性极限就会开裂。当钢的温度高于650℃开始转入塑性状 态,当热应力达到一定数值时,钢将产生塑性变形,从而使内 应力下降,因此此时加热速度可适当快些(≤80~ 100℃/min),当然对于变形要求严格的模具来书,这一段时 间的加热速度仍然不必过快。综合以上因素考虑,对于该模具 使用的H13钢选择550℃、850℃两个温度进行预热。