特种加工技术
特种加工

先进制造技术
超声波加工产品
超声波抛光机
先进制造技术
特种加工实例
电火花加工
加工各种高硬度、 加工各种高硬度、高 强度、高韧性、 强度、高韧性、高脆性 的导电材料, 的导电材料,并且常用 于模具的制造过程中。 于模具的制造过程中。
先进制造技术
电火花加工产品
电火花加工样品
先进制造技术
特种加工实例
水力切割机
先进制造技术
液体喷射加工技术
水力切割过程
先进制造技术
The End Thanks!
先进制造技术
激光加工产品
激光焊接样品
先进制造技术
激光加工产品
激光蚀刻样品
先进制造技术
激光加工产品
激光加工样品
先进制造技术
激光加工产品
激光加工样品
先进制造技术
特种加工实例
旋转超声加工机床
先进制造技术
超声波加工产品
超声波加工样品 旋转超声加工是一种复合加工方法, 旋转超声加工是一种复合加工方法,它将金刚石工 具的优良切削性能与工具的超声频振动结合起来, 具的优良切削性能与工具的超声频振动结合起来,是加 工硬脆材料的一种较好方法,具有良好的应用前景。 工硬脆材料的一种较好方法,具有良好的应用前景。
先进制造技术
(四)超声加工
声波是人耳能感受的一种纵波,它的频率在16~ 16000Hz范围内。当频率超过16000Hz就称为超声波。超声 波具有波长短、能量大,传播过程中反射、折射、共振、 损耗等现象显著的特点。 1.超声加工 利用工具端面作16 ~ 25kHz 的超声频振动,使工作液中的悬 浮磨粒对工件表面撞击抛磨来实 现加工,称为超声加工。
先进制造技术
特种加工技术

特种加工技术1. 引言特种加工技术是指在工业生产过程中,利用先进的加工设备和工艺,对特殊材料或特殊形状的零件进行加工加工的技术方法。
特种加工技术在许多领域中都有广泛的应用,如航空航天、汽车制造、船舶建造等。
本文将介绍几种常见的特种加工技术,包括电火花加工、激光加工以及电化学加工。
2. 电火花加工电火花加工是一种利用电火花放电来进行加工的技术。
该技术主要用于加工高硬度和脆性材料,如硬质合金、陶瓷等。
其工作原理是利用高压脉冲电流在工件表面产生电火花放电,从而烧蚀掉工件表面的材料。
通过控制放电的时间和能量,可以实现对工件的精细加工。
电火花加工具有以下几个优点: - 能够加工高硬度和脆性材料; - 加工过程中不会产生机械应力; - 可以实现复杂形状的加工。
然而,电火花加工也存在一些限制:- 加工效率相对较低;- 加工精度受到局限。
3. 激光加工激光加工是利用高能量密度的激光束对工件进行加工的技术。
激光加工可以通过烧蚀、熔化、汽化等方式来剥离工件表面的材料。
激光加工具有以下几个特点: - 高加工精度和加工质量; - 高加工速度; - 可以实现对不同材料的加工。
激光加工在航空航天、汽车制造等领域有广泛的应用。
例如,在飞机制造中,激光加工可以用于切割、焊接、打孔等工艺操作。
激光加工的应用还面临一些挑战: - 高能量激光设备的成本较高; - 对工件材料的适应性有限。
4. 电化学加工电化学加工是利用电化学反应对工件进行加工的技术。
它通过在电解液中施加电压,使得工件表面发生氧化、溶解等反应,从而实现加工目的。
电化学加工具有以下优点: - 加工精度高; - 加工过程中不会产生机械应力; - 可以加工高硬度和脆性材料;电化学加工主要用于微小零件加工、细微结构加工、薄板加工等领域。
例如,在电子芯片制造中,电化学加工可以用于进行微细线路的蚀刻。
然而,电化学加工也存在一些限制: - 加工速度较慢; - 加工尺寸受到限制。
5. 总结特种加工技术在现代工业中起着重要作用。
特种加工技术

• 2. 超声波加工的特点和应用 • (1) 超声波加工主要适于加工各种硬脆材料,特别是不导
• 图是利用固体激光器加工的原理示意图。当激 光工作物质(如红宝石、钕玻璃和掺钕钇铝石 榴石等)受到光泵(即激励脉冲氙灯)的激发后, 吸收特定波长的光,在一定条件下可形成工作 物质中的亚稳态粒子数大于低能级粒子数的状 态,这种现象称为粒子数反转。此时,一旦有 少数激发粒子自发辐射发出光子,即可感应所 有其它激发粒子产生受激辐射跃迁,造成光放 大。并通过谐振腔的反馈作用产生振荡,由谐 振腔一端输出激光。通过透镜将激光束聚焦到 待加工表面上,即可对工件进行加工。
好、无残余应力和毛刺; • (5) 加工中阴极损耗小,一般可加工上千个零件; • (6) 因影响电解加工的因素很多,故难于实现高
精度的稳定加工。尺寸精度低于电火花加工,且 不易控制,一般型孔加工为:0.03~0.05mm,型 腔加工为0.05~0.2mm; • (7) 电解液对机床有腐蚀作用,设备费用高,电 解产物的处理和回收较困难,污染较严重。
砂带磨削
• 利用高速运转的环形砂带加工工件表面的 磨削。一般在砂带磨床上进行。 砂带围绕 在具有一定弹性的压轮和张紧轮上,由压 轮驱动回转作连续切削运动,工件放在传 送带或工作台上作进给运动。当工件接触 砂带或通过压轮下的磨削区时,即被砂带 磨去表面的一层材料
• 砂带磨削具有许多其它磨削加工方式所不 具备的优势:①磨削效率高达96%,是所 有磨削加工方式中最高的;②磨削比高(比 砂轮磨削高10倍以上);③可实现磨削、研 磨、抛光等多重加工效果,加工精度高,
机械制造工程技术基础:特种加工技术

激光器
机械系统
12.5 激光加工
❖12.5.3 激光对焦
演示
12.5 激光加工
❖12.5.4 激光器加工的范围(皮革纺织)
12.5 激光加工
❖12.5.4 激光器加工的范围(广告工艺)
12.5 激光加工
❖12.5.4 激光器加工的范围(建筑模型)
12.5 激光加工
❖12.5.4 激光器加工的范围(工业加工)
机械制造工程技术基础
特种加工技术
学习内容
1 掌握特种加工的概念 2 了解特种加工典型加工原理方法 3 分析特种加工与传统加工技术的区别
引言 零件的生产制造过程是怎样的?
机械加工
机械加工
传统加工(车、铣、刨、磨、钳)
现代加工
普通数控加工
(数控车、数控铣)
特种加工
(激光演示)
12.1 特种加工
❖12.1 特种加工概念
海宝笔筒图纸
海宝笔筒产品
12.4 熔融成形制作
❖ 使用快速成形制作海宝笔筒的过程
三维模型
海宝切笔片筒处图理纸
海宝笔筒产品
后处理 工件
·
设备加工
12.4 快速成形技术
❖12.4.2 快速成形技术特点
1、高度柔性:无需任何专用夹具或工具。 2、设计制造一体化:(CAD/CAM一体化)。 3、快速性 :几个小时到几十个小时就可制造出零件。 4、自由形状制造:可以制造任意复杂的三维几何实体。 5、材料的广泛性:如纤维、塑料、纸、陶瓷、金属等。
石等硬脆材料,比用金刚石刀具切割具有切片薄、切
口窄、精度高、生产率高、经济性好的优点。
12.6 超声波加工
❖12.6.3 超声波加工应用范围
1.1 什么是特种加工技术
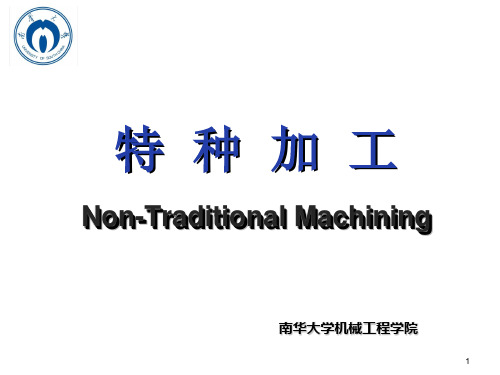
电火花线切割
激光切割
等离子弧喷涂
3
2、特种加工技术的产生
讨论:传统机械切削加工的原理及局限性
局限性1:切削加工“以硬欺软 ”---- 刀具硬度高于工件 面临困难:如何加工硬质合金、金刚石等超硬材料?
4
局限性2:刀具运动空间---- 多数为旋转相对运动 面临困难:如何加工异形孔、窄缝??
局限性3:切屑力和切屑热----影响表面精度和微观结构 面临困难:如何加工超精超光整表面?
5
历史故事
1943年,前苏联莫斯科大学的拉扎林柯夫妇在研究开关触点(钨合 金)遭受火花放电腐蚀损坏时发现电火花的瞬时高温可以使得局部金 属熔化、气化而被蚀除,同时将开关触点浸没在油内可以使得放电蚀 除均匀并且可以预测大小,获得“以柔克刚”的效果,从而发明了世 界第一台电火花加工机床。
扎连科夫妇试验用的钨开关自动点火系统
LOGO
特种加工
Non-Traditional Machining
南华大学机械工程学院1LOGO§ 1.1 什么是特种加工技术
2
1、特种加工的概念
特种加工国外亦称“非传统加工” 或“非常规机械加工” ,是指 那些不属于传统加工工艺范畴的加工方法。它不同于使用刀具、磨具 等直接利用机械能切除多余材料的传统加工方法,泛指用电能、热能、 光能、电化学能、化学能、声能及特殊机械能等能量达到去除或增加 材料的加工方法,从而实现材料的去除、变形、改变性能或被镀覆等 工艺。
▪ 适合微细加工,电子束、离子束加工等不仅可加工尺寸微小的孔 或狭缝,还能获得高精度、极低粗糙度的加工表面;
▪ 两种或两种以上的不同类型的能量可相互组合形成新的复合加工 形式,加工能量易于控制和转换,加工范围广,适应性强。
§10-2 特种加工技术

加工时,工具以一定的静压力压在工件上, 加工区域送入磨粒悬浮液。超声波发生器产 生超声频电振荡,通过超声换能器将其转变 为超声频机械振动,借助于振幅扩大棒把振 动位移振动放大,驱动工具振动。材料的碎 除主要靠工具端部的振动直接锤击处在被加 工表面上的磨料,通过磨料的作用把加工区 域的材料粉碎成很细的微粒,从材料上碎除 下来。由于磨料悬浮液的循环流动,磨料不 断更新,并带走被粉碎下来的材料微粒,工 具逐渐伸入到材料中,工具形状便复现在工 件上,工具材料常用不淬火的45钢,磨料常 用碳化硼或碳化硅、氧化铝、金刚砂粉等。
(3)电化学加工 利用电能转化为化学能进行加工,如电解加 工、电镀、刷镀、镀膜和电铸加工等。 (4)激光加工 利用激光光能转化为热能进行加工。 (5)化学加工 利用化学能或光能转换为化学能进行加工, 如化学铣削和化学刻蚀(即光刻加工)等。 (6)复合加工 将机械加工和特种加工叠加在一起就形成复 合加工。如电解磨削、超声电解磨削等。
(2)超声波加工的特点和应用 超声波磨料流加工适宜加工各种硬脆材料,尤 其是电火花加工和电解加工无法加工的不导电 材料和半导体材料,如玻璃、陶瓷、半导体、 宝石、金刚石等。对于硬质的金属材料,如淬 硬钢、硬质合金等,虽可进行加工,但效率低。 近十几年来,超声波加工与传统的切削加工技 术相结合而形成的超声波振动切削技术得到迅 速的发展,并在生产实际中得以广泛的应用。 超声波车削、超声波磨削、超声波钻孔等在金 属材料,特别是难加工材料的加工中取得良好 的效果。加工精度、加工表面质量显著提高。
3)特种加工中,工具的硬度和强度可以低于工 件的硬度和强度,因为它主要不是靠机械力 来切削,同时工具的损耗很小,甚至无损耗, 如激光加工、电子束加工、离子束加工等。 适于加工脆性材料、高硬材料、精密微细零 件、薄壁零件、弹性零件等易变形零件。
八大特种加工技术

非常工艺:八大特种加工技术特种加工亦称“非传统加工”或“现代加工方法”,泛指用电能、热能、光能、电化学能、化学能、声能及特殊机械能等能量达到去除或增加材料的加工方法,从而实现材料被去除、变形、改变性能或被镀覆等。
一、特种加工的发展和定义传统的机械加工已有很久的历史,它对人类的生产和物质文明起了极大的作用。
目前我们的大部分产品还是依靠传统的方法加工和装配得到的,如我们的家用电器:电冰箱、洗衣机、空调等;我们的交通工具:如汽车、火车、飞机等,以及各种武器装备:枪、炮、坦克、火箭等。
传统的机械加工方法是用机械能量和切削力切除多余的金属,使零件具有一定的几何形状、尺寸和表面粗糙度。
它要求刀具材料比工件材料硬。
随着科学技术的发展,特别是上个世纪50年代以来,随着生产发展和科学实验的需要,很多工业部门,尤其是国防工业部门的要求尖端科学技术产品向高精度、高速度、高温、高压、大功率、小型化等方向发展,它们使用的材料越来越难加工,零件的形状越来越复杂,尺寸精度、表面粗糙度和某些特殊要求也越来越高,因而对机械制造部门提出一些新的要求:•解决各种难切削材料的加工问题。
如硬质合金、钛合金、耐热钢、不锈钢、淬火钢、金刚石、宝玉石、石英以及锗、硅等各种高硬度、高强度、高韧性、高脆性的金属及非金属材料的加工。
•解决各种特殊复杂表面的加工问题。
如喷汽涡轮机叶片、整体涡轮、发动机机匣、锻压模和注射模的立体成型表面,各种冲模、冷拔模上特殊断面的型孔,炮管内膛线,喷油咀、栅网、喷丝头上的小孔、窄缝等的加工。
•解决各种超精、光整或具有特殊要求的零件的加工问题。
如对表面质量和精度要求很高的航天、航空陀螺仪、伺服阀,以及细长轴、薄壁零件、弹性元件等低刚度零件的加工。
要解决上述一系列工艺问题,仅仅依靠传统的切削加工方法就很难实现,甚至根本无法实现。
人们相继探索研究新的加工方法,特种加工就是在这种前提条件下产生和发展起来的。
特种加工,国外称作非传统加工(Non - Traditional Machining, NTM)或非常规加工(Non –ConventionalMachining,NCM),是一种采用不同于传统切削磨削加工工艺及装备的加工技术,是将电、磁、声、光、热等物理能量及化学能量或其组合乃至与机械能组合直接施加在被加工的部位上,从而使材料被去除、变形及改变性能等。
特种加工技术
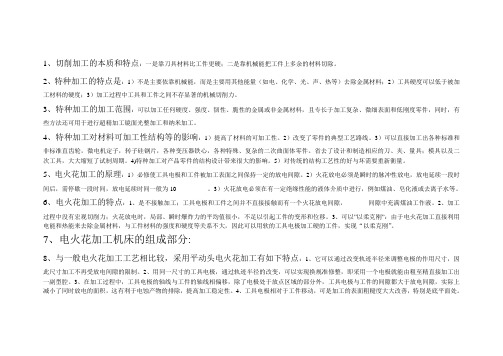
1、切削加工的本质和特点:一是靠刀具材料比工件更硬;二是靠机械能把工件上多余的材料切除。
2、特种加工的特点是:1)不是主要依靠机械能,而是主要用其他能量(如电、化学、光、声、热等)去除金属材料;2)工具硬度可以低于被加工材料的硬度;3)加工过程中工具和工件之间不存显著的机械切削力。
3、特种加工的加工范围:可以加工任何硬度、强度、韧性、脆性的金属或非金属材料,且专长于加工复杂、微细表面和低刚度零件,同时,有些方法还可用于进行超精加工镜面光整加工和纳米加工。
4、特种加工对材料可加工性结构等的影响:1)提高了材料的可加工性。
2)改变了零件的典型工艺路线。
3)可以直接加工出各种标准和非标准直齿轮,微电机定子,转子硅钢片,各种变压器铁心,各种特殊、复杂的二次曲面体零件。
省去了设计和制造相应的刀、夹、量具;模具以及二次工具,大大缩短了试制周期。
4)特种加工对产品零件的结构设计带来很大的影响。
5)对传统的结构工艺性的好与坏需要重新衡量。
5、电火花加工的原理:1)必修使工具电极和工件被加工表面之间保持一定的放电间隙。
2)火花放电必须是瞬时的脉冲性放电,放电延续一段时间后,需停歇一段时间,放电延续时间一般为10 。
3)火花放电必须在有一定绝缘性能的液体介质中进行,例如煤油、皂化液或去离子水等。
6、电火花加工的特点:1、是不接触加工;工具电极和工件之间并不直接接触而有一个火花放电间隙,间隙中充满煤油工作液。
2、加工过程中没有宏观切削力;火花放电时,局部、瞬时爆炸力的平均值很小,不足以引起工件的变形和位移。
3、可以”以柔克刚”:由于电火花加工直接利用电能和热能来去除金属材料,与工件材料的强度和硬度等关系不大,因此可以用软的工具电极加工硬的工件,实现“以柔克刚”。
7、电火花加工机床的组成部分:8、与一般电火花加工工艺相比较,采用平动头电火花加工有如下特点:1、它可以通过改变轨迹半径来调整电极的作用尺寸,因此尺寸加工不再受放电间隙的限制。
- 1、下载文档前请自行甄别文档内容的完整性,平台不提供额外的编辑、内容补充、找答案等附加服务。
- 2、"仅部分预览"的文档,不可在线预览部分如存在完整性等问题,可反馈申请退款(可完整预览的文档不适用该条件!)。
- 3、如文档侵犯您的权益,请联系客服反馈,我们会尽快为您处理(人工客服工作时间:9:00-18:30)。
被激发到高能级的原子一般是很不稳定的.它总是力图能
回到能量较低的能级去,原子从高能级回落到低能级的过程称
为“跃迁”。 在基态时,原子可以长时间地存在,而在激发状态的各种 高能级的原子停留的时间(称为寿命)一般都较短,常在0.01µs 左右。但有些原子或离子的高能级或次高能级却有较长的寿 命,这种寿命较长的较高能级称为亚稳态能级。 激光器中的氦原子、二氧化碳分子以及固体激光材料中的 铬或钕离子等都具有亚稳态能级,这些亚稳态能级的存在是形
(一)强度高 激光的强度和亮度之所以如此高,原因在于激光可以实现光能 在空间上和时间上的亮度集中。 就光能在空间上的集中而论,如果能将分散在180°立体角范围 内的光能全部压缩到0.18°,其亮度提高一百万倍。 就光能量在时间上的集中而论,如果把一秒钟时间内所发出的 光压缩在亚毫秒数量级的时间内发射,形成短脉冲,则在总功率不 变的情况下,瞬时脉冲功率又可以提高几个数量级,从而大大提高 了激光的亮度。
三、激光加工的特点
1)激光加工的功率密度高达108 ~1010 W/cm2 ,几乎可以 加工任何材料。 2)激光光斑大小可以聚焦到微米级,输出功率可以调节, 因此可用以精密微细加工。 3)加工所用工具是激光束,是非接触加工,所以没有明显 的机械力,没有工具损耗问题。加工速度快、热影响区小,容 易实现加工过程自动化。还能通过透明体进行加工,如对真空 管内部进行焊接加工等。 4)激光加工装置比较简单,不要求复杂的抽真空装置。 5)激光加工是一种瞬时、局部熔化、气化的热加工,影响 因素很多,因此,精微加工时,精度,尤其是重复精度和表面 粗糙度不易保证,必须进行反复试验。 6)加工中产生的金属气体及火星等飞溅物,要注意通风抽 走,操作者应戴防护眼镜。
放电管一般用硬质玻璃管做成,对要求高的二氧化碳激光 器可以采用石英玻璃管来制造,放电管的直径约几厘米,长度 可以从几个厘米至数十米,二氧化碳气体激光器的输出功率与 放电管长度成正比。为了缩短空间长度,长的放电管可以做成 折叠式,如图5—8b所示。 二氧化碳气体激光器的谐振腔多采用平凹腔,一般总以凹 面镜作为全反射镜,而以平面镜作输出端反射镜。全反射镜一 般镀金属膜,如金膜、银膜或铝膜。 二氧化碳激光器的激励电源可以用射频电源、直流电源、 交流电源和脉冲电源等,其中交流电源用得最为广泛。
这时当有频率为 可以产生从能级 E2
E E1 n h
的光子去照射“刺激”它时,就 的受激辐射跃迁,出现雪崩式连锁 反
到 E1
E E1 n h 应,发射出
的单色性好的光,这就是激光。
E2
E2
二、激光的特性 激光也是一种光,它具有一般光的共性(如光的反射、折 射、绕射以及光的干涉等),也有它的特性。 普通光源的发光是以自发辐射为主,而激光则不同。它的 光发射是以受激辐射为主,因而发光物质中基本上是有组织 地、相互关联地产生光发射的,发出的光波具有相同的频率、 方向、偏振态和严格的位相关系。 正是这个质的区别才导致激光具有强度高、单色性好、相 干性好和方向性好。下面分别进行讨论。
二、激光加工常用激光器 目前常用的激光器按激活介质的种类可以分为固体激光器 和气体激光器。按激光器的工作方式可大致分为连续激光器和 脉冲激光器。 固体激光器一般采用光激励,能量转化环节多,光的激励 能量大部分转换为热能,所以效率低。为避免固体介质过热, 固体激光器通常多采用脉冲工作方式。由于晶体缺陷和温度引 起的光学不均匀性,固体激光器不易获得单模而倾向于多模输 出。 1.固体激光器的基本组成 图5—4是固体激光器的结构示意图,它包括工作物质、光 泵、玻璃套管和滤光液、冷却水、聚光器以及谐振腔等部分。
第五章
激光加工
一.激光加工的原理和特点 二.激光加工的基本设备 三.激光加工工艺及应用
激光加工是20世纪60年代初发展起来的一门新兴科学,
在材料加工方面,已逐步形成了一种崭新的加工方法
光加工(Lasser Beam Machining 简称 LBM)。
激
激光加工可用于打孔、切割、电子器件的微调、焊接、 热处理以及激光存贮等各个领域。由于激光加工不需要加工 工具、而且加工速度快、表面变形小,可以加工各种材料。 激光加工是利用光的能量经过透镜聚焦后在焦点上达到 很高的能量密度靠光热效应来加工各种材料。
激光是可控的单色光,强度高,能量密度大,可以在空
气介质中高速加工各种材料,日益获得广泛的应用。
c v
第一节
激光加工的原理和特点
一、激光的产生原理 光既具有波动性,又具有微粒性,也就是说,光 具有波粒二象性。 根据光的电磁学说,可以认为光实质上是在一定 波长范围内的电磁波。同样也有波长λ,频率ν,波 速c,三者之间的关系为
聚光器的作用是把氙灯发出的光能聚集在工作物质上,一 般可将氙灯发出来的80%左右的光能集中在工作物质上。常用 的聚光器有如图5—5所示的各种形式。图a为圆球形,图b为圆 柱形,图c为椭圆柱形,图d为紧包裹形。其中圆柱形加工制造 方便,用得较多。椭圆柱形聚光效果较好,也常被采用。为了 提高反射率,聚光器内面需磨平抛光至Ra 0.025µm,并蒸镀一 层银膜、金膜或铝膜。
谢
谢!
第二节
激光加工的基本设备
一、激光加工机的组成部分 激光加工的基本设备包括激光器、电源、光学系统及机械 系统等四大部分。 (1)激光器 是激光加工的重要设备,它把电能转变成光 能,产生激光束。 (2)激光Байду номын сангаас电源 为激光器提供所需要的能量及控制功能。 (3)光学系统 包括激光聚焦系统和观察瞄准系统,后者能 观察和调整激光束焦点位置,并将加工位置显示在投影仪上。 (4)机械系统 主要包括床身、能在三坐标范围内移动的工 作台及机电控制系统等。随着电子技术的发展,目前已采用计 算机来控制工作台的移动,实现激光加工的数控操作。
c λ= v
如果把所有电磁波按波长(频率)依次进行排列, 就可以得到电磁波波谱(图5-1)。
根据光的量子学说,又可以认为光是一种具有一定能量的 以光速运动的粒子流,这种具有一定能量的粒子就称为光子。 不同频率的光对应于不同能量的光子,光子的能量与光的频率 成正比,即
E=hν
E—光子能量; ν—光的频率; h—普朗克常数。 对应于波长为0.4µm的紫光光子能量等于4.96×10-17J; 对应于波长为0.7µm的红光的光子能量等于2.84×10-17J 。 一束光的强弱与这束光所含的光子多少有关,对同一频率 的光来说。所含的光子数多,即表现为强;反之表现为弱。 式中
(2)钕玻璃激光器 钕玻璃是掺有少量氧化钕(Nd2O3 )非 晶体硅酸盐玻璃,钕离子( Nd 3)的质量分数在1%—5%左右, 吸收光谱较宽,发射 =1.06µm的红外激光。 钕玻璃激光器是四能级系统激光器,因为有中间过渡能 级,所以比红宝石之类的三能级系统更容易实现粒子数反转, 如图5—7所示.在通常情况钕玻璃激光器的效率可达 2%-3%左右,钕玻璃棒 具有较高的光学均匀性, 光线的发射角小,特别适 用于精密微细加工。钕玻 璃价格低,易做成较大尺 寸· 输出功率可以做得比 较大。其缺点是导热性 差.必须有合适的冷却装 置。
2.原子的发光 原子由原子核和绕原子核转动的电子组成。原子的内能就 是电子绕原子核转动的动能和电子被原子核吸引的位能之和。 如果由于外界的作用,使电子与原子核的距离增大或缩小,则 原子的内能也随之增大或缩小。 只有电子在最靠近原子核的轨 道上运动才是最稳定的,称为 基态。当外界传给原子一定的 能量时(例如用光照射原子) 原子的内能增加。外层电子的 轨道半径扩大,被激发到高能 级。称为激发态或高能态。 图5-2是氢原子的能级,图中最 低的能级是最下面一级称为基 态,其余都称为高能态。
2.固体激光器的分类 固体激光器常用的工作物质有红宝石、钕玻璃和掺钕钇铝 石榴石三种。 (1)红宝石激光器 红宝石是掺有浓度为0.05%氧化铬的 氧化铝晶体,发射 =0.6943µm红光.它易于获得相干性好的 单模输出,稳定性好。 红宝石激光器是三能级系统激光器,主要是铬离子起受激 发射作用。图5—6表示红宝石 激光跃迁情况。 红宝石激光器在激光加工 发展初期用得较多.现在大多 已被钕玻璃激光器和掺钕钇铝 石榴石激光器所代替。
(三)相干性好 光源的相干性可以用相干时间或相干长度来量度。相干时 间是指光源先后发出的两束光能够产生干涉现象的最大时间间 隔。在这个最大的时间间隔内光所走的路程(光程)就是相干长 度,它与光源的单色性密切有关,即
02 L
式中
(5-4)
L——相干长度; 0 —— 光源的中心波长; ——光源的谱线宽度。 单色性越好, 越小,相干长度就越大,光源的相干性也 越好。某些单色性很好的激光器所发出的光,采取适当措施以 后,其相干长度可达到几十公里。
n 1
(二)激光的产生 某些具有亚稳态能级结构的物质,在一定外来光子能量激 发的条件下,会吸收光能,使处在较高能级(亚稳态)的原子 (或粒子)数目大于处于低能级(基态)的原子数目,这种现象称 为“粒子数反转”。在粒子数反转的状态下,如果有一束光子 照射该物体而光子的能量恰好等于这两个能级相对应的能量 差,这时就能产生受激辐射,输出大量的光能。 例如人工晶体红宝石,基本成分是氧化铝,其中掺0.05% 氧化铬,正铬离子镶嵌在氧化铝的晶体中,发射激光的是正铬 离子。当脉冲氙灯照射红宝石时,是处于基态 E1 铬离子大量 的激发到 En 状态,由于 En 寿命很短,En 状态的铬离子有很 快地跳到寿命较长的亚稳态 E2 。如果照射光足够强,就能在 千分之三秒时间内,把半数以上的原子激发到高能级 n , E 并转移到 E2 。从而在 E2 和 E1 之间实现了粒子数反转。 如图5-3所示。
(二)气体激光器 气体激光器一般采用电激励.因其效率高、寿命长、连续 输出功率大,所以广泛用于切割、焊接.热处理等加工。常用 于材料加工气体激光器有二氧化碳激光器、氩离子激光器等。 1.二氧化碳激光器 二氧化碳激光器是以二氧化碳气体为工作物质的分子激光 器.连续输出功率可达万瓦,是目前连续输出功率最高的气体 激光器.它发出的谱线是在10.6µm附近的红外区,输出最强的 激光波长为10.6µm。 二氧化碳激光器的效率可以高达20%以上,这是因为二氧 化碳激光器的工作能级寿命比较长,大约在10-1 ~10-3 s范围 内。 二氧化碳激光器的一般结构如图5-8所示,它主要包括放 电管、谐振腔、冷却系统和激励电源等部分。