四配料秤自动配煤系统的应用分析
配料称重自动控制系统怎么调

配料称重自动控制系统怎么调1. 简介配料称重自动控制系统是一种通过电子秤和控制器实现对配料称重的自动化控制系统。
它可以广泛应用于食品、化工、医药等行业,提高生产效率和产品质量。
在使用配料称重自动控制系统之前,需要对系统进行调试和调整,以确保系统能够正常工作并提供准确的称重结果。
本文将介绍如何对配料称重自动控制系统进行调整。
2. 系统调整前的准备工作在进行系统调整之前,需要进行以下准备工作:•确保所有设备和传感器的连接正确并稳定,包括电子秤和控制器之间的连接。
•检查系统的电源供应是否正常,确保电源电压和频率符合要求。
•确保控制器的参数已经正确设置,包括称重范围、精度要求等。
3. 系统调整步骤步骤一:调整零点和秤量补偿1.连接电子秤和控制器,并打开系统电源。
2.设置称重范围,确保称重范围适合当前的称重任务。
3.将电子秤置为空载状态,即没有物料放置在上面。
4.进入控制器的零点和秤量补偿调整模式。
5.按照控制器的操作指南,根据实际情况进行调整。
6.调整零点时,确保电子秤显示为零。
7.调整秤量补偿时,将已知质量的物料放置在电子秤上,并确保电子秤的显示与实际质量相符。
步骤二:校准称重精度1.取一定数量的已知质量物料,如标准砝码。
2.将已知质量物料放置在电子秤上,并记录下称重结果。
3.比较电子秤的称重结果与已知质量物料的真实质量,计算出误差。
4.根据误差结果,进入控制器的校准模式,根据实际情况进行调整。
5.调整校准参数时,根据误差结果逐步调整,直到达到所要求的精度。
步骤三:调整称重速度1.根据生产工艺要求,确认所需的称重速度。
2.进入控制器的速度调整模式。
3.根据实际情况调整控制器的参数,包括传输速度和称重响应速度。
4.通过实际测试和调整,确保控制器能够在要求的时间范围内完成称重任务。
步骤四:系统稳定性测试1.将一定数量的实际物料进行称重测试。
2.运行测试过程中,观察系统的稳定性和准确性。
3.根据实际情况,进行必要的调整和优化。
配料称重自动控制系统怎样操作

配料称重自动控制系统操作指南1. 系统概述配料称重自动控制系统是一种用于自动化控制配料称重的设备,主要应用于生产线上的配料工序。
该系统能够精确称量不同重量的配料,提高生产效率和质量控制,并减少人力成本和配料误差。
2. 系统组成配料称重自动控制系统由以下几个主要组成部分构成:2.1 称重传感器称重传感器是系统中起主要作用的部分。
它通过测量物料重量并输出电信号来实现准确的配料称重。
在安装和使用称重传感器时,需要遵循以下步骤:•确保称重传感器固定在平稳、牢固的支撑结构上,以避免重量分布不均导致测量错误。
•检查传感器的电源连接和信号连接是否正常,确保传感器能够正常工作。
•对于不同类型的传感器,需要按照相应的规范进行校准和调试,以确保称重准确度。
2.2 控制器控制器是系统的核心部分,用于接收传感器的信号并进行相应的控制操作。
控制器通常由一个微处理器和一些逻辑电路组成。
在操作控制器时,需要按照以下步骤进行操作:•打开控制器电源,确保电源供应正常。
•连接称重传感器和控制器,确保信号传输无误。
•设置控制器的工作参数,如配料重量范围、传感器灵敏度等。
•按下启动按钮,控制器将开始接收传感器信号并进行相应的控制操作。
2.3 操作界面操作界面是用户与系统进行交互的通道,通常由触摸屏或键盘等设备组成。
在操作界面上,用户可以进行以下操作:•输入配料的目标重量,控制器将根据用户的输入进行相应的控制操作。
•监控系统的工作状态,包括当前称重重量、运行时间等。
•进行系统的设置和参数调整,如称重单位、显示方式等。
3. 操作步骤下面是配料称重自动控制系统的一般操作步骤:3.1 系统启动•打开控制器电源,并确保称重传感器和操作界面正常连接。
•检查控制器和传感器的工作状态,确保系统准备就绪。
•启动系统,进入操作界面。
3.2 配料准备•根据生产需要,准备需要配料的容器和物料。
•将容器放置在配料区域,确保容器固定不动。
•打开配料区域的门,准备进行配料操作。
自动配料系统的计量

自动配料系统的计量自动配料系统是指通过计算机控制自动化配药、混料、计量等操作的系统。
在工业生产、医药等领域得到广泛应用,能够大大提高产品质量和生产效率。
本文将着重介绍自动配料系统的计量部分。
计量原理自动配料系统的计量部分主要包括称量、计量仪表和控制系统。
整个计量过程在计算机程序的控制下自动进行,相对人工计量而言,更加准确、方便、高效。
1.称量称量是自动配料系统中最基本的计量方式之一。
传统的称量方式是使用电子称进行称量,但随着科技的发展,压力式称量和重心称量等新技术不断涌现,提高了称量的准确性和效率。
在自动化生产线中,称量主要应用于对原料和成品重量的测量。
2.计量仪表计量仪表是自动配料系统中进行计量的关键设备,一般包括变送器和控制器两部分。
通过采集传感器得到的实时数据信号,变送器对其进行放大、滤波等处理后,传输给控制器进行计量。
3.控制系统自动化控制系统是配料系统中的信息处理中心,负责采集、处理各传感器传输来的数据信号,并根据设定程序发出控制信号,实现自动化配料的目的。
不同的控制系统可适用于不同的生产场所和要求。
计量应用自动配料系统的计量应用十分广泛,例如:1.食品工业在食品生产过程中,自动化计量可保证原料的质量和含量,提高产品的口感、色泽和营养价值。
同时,自动化计量还可以防止工人操作不当和环境等因素对生产产生影响。
2.医药工业在药品生产过程中,自动化计量可保证药品的质量和药性,控制药品的含量和剂量,防止因人为因素而产生误差。
同时,自动化计量还能够提高药品生产的效率,降低成本,促进产业的发展。
3.化工、冶金工业自动化计量可帮助化工、冶金等行业进行合理的配料和计量,提高产品的纯度和质量,降低能耗,提高生产效率。
同时,自动化计量还能够保证工人的安全和生产环境的安全。
总结自动配料系统的计量是自动化生产环节中最为关键的部分之一,不论是食品工业还是医药工业、化工、冶金等领域,计量都具有重要意义。
通过采用先进的计量技术和控制系统,可提高产品质量、生产效率和安全性,从而推动整个行业的发展。
自动配煤系统简介-II

煤矿用自动装车配煤控制系统简介由于煤矿矿井煤质构造比较复杂,影响煤质的因素较多,造成矿井煤质不稳定,波动性较大,难以符合不同用户的不同需要。
把不同质量的煤相互掺合,从而得到所需要的目标煤质,称为配煤。
对于采用两种煤质的配煤,就是将矸石以一定的比例混入原煤中,使混合后的煤的热值符合用户的要求。
本系统适合两种煤质的配煤,是利用灰分测试仪在线测试混合后煤的灰分,然后动态调节矸石的流量,使混合后的煤符合用户的要求。
对多种煤质的配煤,需重新设计,但原理一样。
一、基本原理在煤的掺合过程中,煤的质和量有以下数学模型A1*Q1+A2*Q2=A3*Q3 -------------①式中各变量的定义:A1-----原煤的产品灰分Q1-----原煤的产品流量A2-----矸石的产品灰分Q2-----矸石的产品流量第 1 页共7 页A3-----配完以后的目标灰分Q3-----配完以后的目标流量,Q3=Q1+Q2由①式可得出:A3=( A1*Q1+A2*Q2)/(Q1+Q2)由于灰分是表示煤中所含杂质的比例,故必须存在A2≥A3≥A1的条件,配煤才有实际意义,只要满足此条件,无论A1、Q1、A2具体的值是多少,都可以通过增加和减少Q2来达到希望的A3,见图1-1。
图1-1第 2 页共7 页第 3 页 共 7 页当A3被指定后,通过指定值和检测值的比较,适时调节矸石流入量,从而达到A3在一个允许的小误差范围内波动,实现配煤自动化。
由此我们可以设计出如图1-2所示的基本系统:图1-2二、系统框图第 4 页共7 页二、系统各单元介绍1.储煤仓储煤仓用来储存待配比的原煤和矸石,本系统最少需要两个储煤仓,分别储存原煤和矸石,如有多个储煤仓轮流使用,效果最好。
2.流量自动调节装置流量自动调节装置是位于储煤仓底部,用来关闭储煤仓和自动调节从煤仓流到传送皮带的煤的流量,由自动控制箱、液压站、液压闸板、位置传感器组成,可受中心站计算机集中控制,能够预置或根据需要自动调节液压闸门的开启位置,由此开启位置中心站计算机可以估算出煤的流量。
自动计量配料秤在化工自动化行业中的应用分析
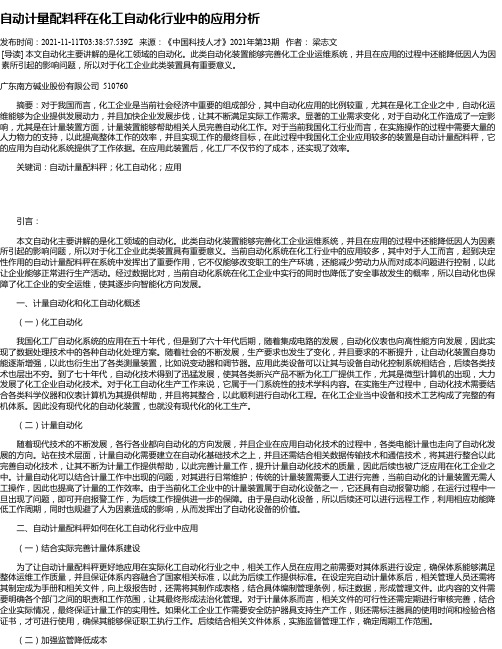
自动计量配料秤在化工自动化行业中的应用分析发布时间:2021-11-11T03:38:57.539Z 来源:《中国科技人才》2021年第23期作者:梁志文[导读] 本文自动化主要讲解的是化工领域的自动化。
此类自动化装置能够完善化工企业运维系统,并且在应用的过程中还能降低因人为因素所引起的影响问题,所以对于化工企业此类装置具有重要意义。
广东南方碱业股份有限公司 510760摘要:对于我国而言,化工企业是当前社会经济中重要的组成部分,其中自动化应用的比例较重,尤其在是化工企业之中,自动化运维能够为企业提供发展动力,并且加快企业发展步伐,让其不断满足实际工作需求。
显著的工业需求变化,对于自动化工作造成了一定影响,尤其是在计量装置方面,计量装置能够帮助相关人员完善自动化工作。
对于当前我国化工行业而言,在实施操作的过程中需要大量的人力物力的支持,以此提高整体工作的效率,并且实现工作的最终目标,在此过程中我国化工企业应用较多的装置是自动计量配料秤,它的应用为自动化系统提供了工作依据。
在应用此装置后,化工厂不仅节约了成本,还实现了效率。
关键词:自动计量配料秤;化工自动化;应用引言:本文自动化主要讲解的是化工领域的自动化。
此类自动化装置能够完善化工企业运维系统,并且在应用的过程中还能降低因人为因素所引起的影响问题,所以对于化工企业此类装置具有重要意义。
当前自动化系统在化工行业中的应用较多,其中对于人工而言,起到决定性作用的自动计量配料秤在系统中发挥出了重要作用,它不仅能够改变职工的生产环境,还能减少劳动力从而对成本问题进行控制,以此让企业能够正常进行生产活动。
经过数据比对,当前自动化系统在化工企业中实行的同时也降低了安全事故发生的概率,所以自动化也保障了化工企业的安全运维,使其逐步向智能化方向发展。
一、计量自动化和化工自动化概述(一)化工自动化我国化工厂自动化系统的应用在五十年代,但是到了六十年代后期,随着集成电路的发展,自动化仪表也向高性能方向发展,因此实现了数据处理技术中的各种自动化处理方案。
配煤电子秤对改善配煤质量效果分析

2_ 42 %
2 .% 44
1. 8 % 7
1 .% 77
2. 28 %
2 .% 41
1. 57 %
l .% 61
1. 8 % 6
荇 害霸
应 用 方 法论
1 8 5
配煤 电子秤对改 善配煤 质量效果分析
漆 国 良
( 江西萍钢 实业股 份有限公司萍乡分公 司焦化厂 ,江西 萍乡 3 7 0 3 0 0)
摘 要 在 焦化生产 中,配比准确性是 稳定焦炭质 量的主要 因素,我厂通过对 原配煤 系统 改造 ,使用皮 带电子称 ,在配合煤质 量的稳定上
4 2日 月 6
3- 03
5. 9 9
7 2日 月 1
2. 38 %
2 .% 39
1 .% 8 2
l -% 93
2 .% 41
2 _% 32
1 .% 58
1 _% 55
1 .% 8 1
1 .% 81
表37 月份热强度
日期
7 月5日
7 1日 月 2 7 0 月2 日
大改观 。且我厂焦炭主要供给公司炼铁 ,在电子称使用后的几个月 ,炼 铁负荷保持 了较好的稳定性 ,在7 ] f份炼铁负荷一直维持稳定在较高水
平。
日期
4 5 月 日
反应性
3_ 03
热强度
5. 91
表 1圆盘 实 际 配 比与规 定 配 比 比较
配 比 日期 792 , 0日
2 电子称 在稳 定焦炭 质量 效果
21 焦 炭 各 单 项 指 标 .
(比较数据来 源焦炭质量 比较 选择煤场分类 堆放 后的2 1/ 月份 ,以及电子称运行较好的7 00  ̄ 月份各项指 标) 1)热强度 ,热反应性 :从表2 数据可看出焦炭 ,3 热强度 ,热反应性 与两月相差不大 ,差异性不大 ,主要 由于热强度为一周取样一次 ,随机性较强 ,但分析数据 仍可看出7 月份略稳定与4 月。 2)冷 强 度 ( 5 M1 M2 , 0)。2 0 4 M1 平 均 0l 年 月 O 54 月份 ( .,7 截止2 日 )M1平均5 ,尽管MI略低于 6 O . 9 O 4 月份 ( 主要 由于煤质原因 ),但从 图2 比可知7 对 月份 MI最大 ,但偏差远 小于4 O 月份 ,主要在58 59 .— .波动 , 56 60 围内4 .— .范 月份进9 ,占3 .%,7 次 33 月份 2 次 ,占 2 8.%,稳定程度远好于4 46 月份。 经 比较 4 份 、7 月 月份 M2 两 图 ,均在 9 附 近 波 动 , 5 1 4 月份M 5 2 超出9 . 9 . 0 — 1 范围l次 ,7/ 5 5 3 # 份仅1 ,波动性 次 远小于4 ,稳定性远高于4 。 月 月 3 灰分。灰份可反映配比的准确性 , 图3 ) 从 可知, 4 月份与7 月份 比较 ,7 月份均在 1— 5 4 1 %内,4 月份超过 超 出该范围有5 ,波动较大 。7 次 月份的稳定性好 于4 月 份。
自动配料系统自动配料设备原理

自动配料系统自动配料设备原理
经济社会的迅速发展,人们的生活质量也发生了翻天覆地的变化。
如今,自动配料系统已成为某些企业生产制造过程中不可或缺的重要设备。
本文重点介绍了自动配料系统自动配料设备的原理及各种类型的应用方法。
自动配料系统自动配料设备是一种用于配料生产的设备,可以将一种特定的原料料从指定的原料料库中自动调取出来,分配到一定的装配位置,以满足生产加工过程中的各种要求。
目前,自动配料系统主要有脉冲式调料机、托盘式调料机、电磁铁式调料机和真空式调料机等多种类型,广泛应用于各类工业生产过程中。
其中,脉冲式调料机是根据定时脉冲装置调节配料物料调节板的位置运行,可以实现定时定量的配料功能,适用于容量大、物料快速更换的生产环境中。
托盘式调料机的配料原理与脉冲式完全一样,但它采用可拆卸的托盘,以便更快换料。
而电磁铁式调料机是利用机器上安装的电磁铁控制料斗上料口位置,从而实现料斗自动上料。
最后,真空式调料机是通过真空泵获取真空,使加料室内产生真空,从而实现自动配料。
此外,自动配料系统自动配料设备还具有很多其他优势:一是便于安装,可以根据各种原料料特性,采用各种类型的设备,满足不同的配料需求;二是可靠性高,具有高效的操作性能和可靠的安全性能;三是节能环保,能够确保生产过程中的能源消耗最小,节约成本,节约能源,减少污染。
综上所述,自动配料系统自动配料设备是一种有效的配料设备,可以有效提高生产效率,降低生产成本,提高产品性能。
它不仅可以满足大规模生产所需,而且可以配置各种生产类型的设备,广泛应用于各类工业生产过程中,可以帮助企业提高劳动生产率,节省生产成本。
配料系统、配煤系统、电子皮带秤供货与安装工程技术规范书(技术协议)

配料系统、配煤系统、电子皮带秤供货与安装工程技术规范书一、名称解释与说明:1、甲方(发包方):2、乙方(供货方):3、丙方(设计院):4、根据《民法典》有关规定,甲、乙、丙三方本着互惠互利、共同发展的原则,经过友好协商,就配料系统和电子皮带秤技术规格、性能、参数、指标的提供和设计、制造、供货、运输、安装、调试、技术服务以及有关人员的安全技术培训等事宜达成本技术协议的最低要求和标准。
二、设备总要求:①、本技术规范书的使用范围仅限于甲方的招标设备在设计、制造、供货、试验以及安装等方面提出最基本的技术要求。
②、投标方应保证所提供的设备以及技术性能指标满足并优于本技术规范提出的要求。
③、本技术规范书提出的是最低限度的技术要求,并未对一切技术细节做出规定。
投标方应保证提供符合本技术条件和工业标准的优质产品。
④、本技术规范书并不妨碍投标方对投标设备的制造采用更高的制造及控制标准,对制造过程中涉及本技术规范书之外的材料及工艺要求通知招标方监制人员确认后方能实施。
⑤、本技术规范书涉及的制造要求及相关的技术标准,投标方应对本技术规范书所涉及的产品安全与质量全面负责。
⑥、所有零部件的制作、装配、安装严格按技术要求执行制造零件的所有材料严格按国家有关部件标准的技术要求执行。
⑦、该设备在设计、制作、安装、调试、验收中,充分突出其优化性、可靠性、耐用性、准确性。
严格按技术标准执行。
⑧、投标方提供自制无技术纠纷、高质量的、成熟的、可靠的、技术先进的产品。
⑨、如果投标方没有以书面形式对本技术条件的条文提出异议,则认为投标方可以提供完全满足本技术条件的产品。
⑩、招投标双方本着互惠互利、共同发展的原则,经过友好协商,就炼焦标段的配料系统及皮带秤的设计、制造、运输、指导安装与调试、技术服务、有关人员的技术培训等事宜达成本技术规范书的要求和标准。
⑪、投标方具备配料系统及皮带秤性能测试的技术装备,该测试设备或装置必须是经过国内或国际相关权威机构核准的,所出厂的设备必须按国内或国际通用标准测试合格。
焦化厂自动配煤控制系统的设计及应用研究
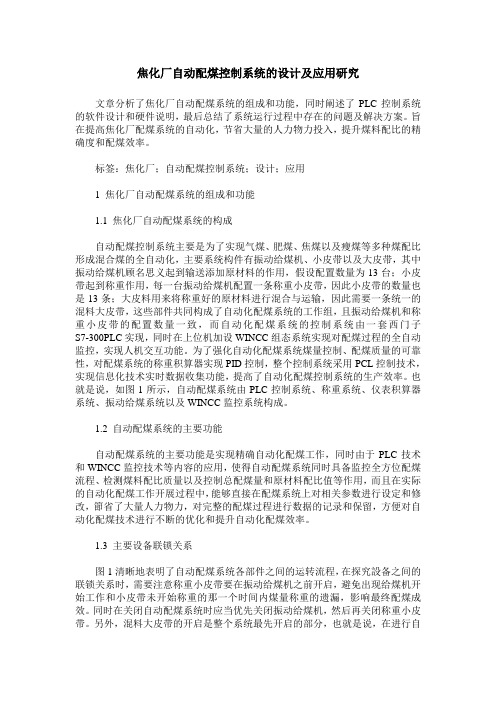
焦化厂自动配煤控制系统的设计及应用研究文章分析了焦化厂自动配煤系统的组成和功能,同时阐述了PLC控制系统的软件设计和硬件说明,最后总结了系统运行过程中存在的问题及解决方案。
旨在提高焦化厂配煤系统的自动化,节省大量的人力物力投入,提升煤料配比的精确度和配煤效率。
标签:焦化厂;自动配煤控制系统;设计;应用1 焦化厂自动配煤系统的组成和功能1.1 焦化厂自动配煤系统的构成自动配煤控制系统主要是为了实现气煤、肥煤、焦煤以及瘦煤等多种煤配比形成混合煤的全自动化,主要系统构件有振动给煤机、小皮带以及大皮带,其中振动给煤机顾名思义起到输送添加原材料的作用,假设配置数量为13台;小皮带起到称重作用,每一台振动给煤机配置一条称重小皮带,因此小皮带的数量也是13条;大皮料用来将称重好的原材料进行混合与运输,因此需要一条统一的混料大皮带,这些部件共同构成了自动化配煤系统的工作组,且振动给煤机和称重小皮带的配置数量一致,而自动化配煤系统的控制系统由一套西门子S7-300PLC实现,同时在上位机加设WINCC组态系统实现对配煤过程的全自动监控,实现人机交互功能。
为了强化自动化配煤系统煤量控制、配煤质量的可靠性,对配煤系统的称重积算器实现PID控制,整个控制系统采用PCL控制技术,实现信息化技术实时数据收集功能,提高了自动化配煤控制系统的生产效率。
也就是说,如图1所示,自动配煤系统由PLC控制系统、称重系统、仪表积算器系统、振动给煤系统以及WINCC监控系统构成。
1.2 自动配煤系统的主要功能自动配煤系统的主要功能是实现精确自动化配煤工作,同时由于PLC技术和WINCC监控技术等内容的应用,使得自动配煤系统同时具备监控全方位配煤流程、检测煤料配比质量以及控制总配煤量和原材料配比值等作用,而且在实际的自动化配煤工作开展过程中,能够直接在配煤系统上对相关参数进行设定和修改,節省了大量人力物力,对完整的配煤过程进行数据的记录和保留,方便对自动化配煤技术进行不断的优化和提升自动化配煤效率。
自动配煤系统在焦化厂的应用
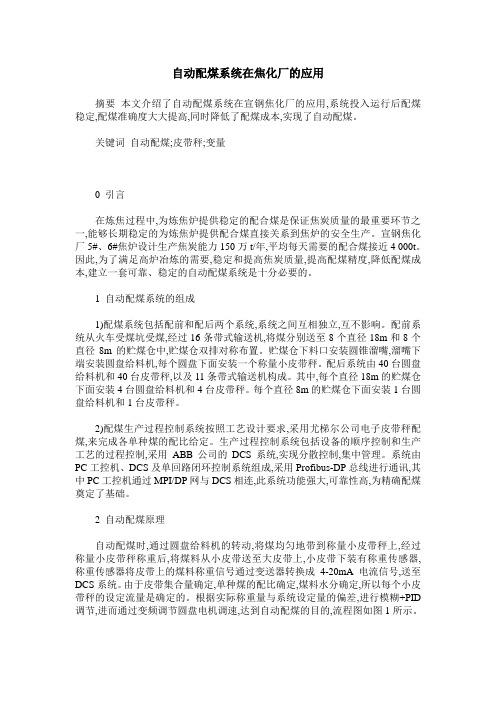
自动配煤系统在焦化厂的应用摘要本文介绍了自动配煤系统在宣钢焦化厂的应用,系统投入运行后配煤稳定,配煤准确度大大提高,同时降低了配煤成本,实现了自动配煤。
关键词自动配煤;皮带秤;变量0 引言在炼焦过程中,为炼焦炉提供稳定的配合煤是保证焦炭质量的最重要环节之一,能够长期稳定的为炼焦炉提供配合煤直接关系到焦炉的安全生产。
宣钢焦化厂5#、6#焦炉设计生产焦炭能力150万t/年,平均每天需要的配合煤接近4 000t。
因此,为了满足高炉冶炼的需要,稳定和提高焦炭质量,提高配煤精度,降低配煤成本,建立一套可靠、稳定的自动配煤系统是十分必要的。
1 自动配煤系统的组成1)配煤系统包括配前和配后两个系统,系统之间互相独立,互不影响。
配前系统从火车受煤坑受煤,经过16条带式输送机,将煤分别送至8个直径18m和8个直径8m的贮煤仓中,贮煤仓双排对称布置。
贮煤仓下料口安装圆锥溜嘴,溜嘴下端安装圆盘给料机,每个圆盘下面安装一个称量小皮带秤。
配后系统由40台圆盘给料机和40台皮带秤,以及11条带式输送机构成。
其中,每个直径18m的贮煤仓下面安装4台圆盘给料机和4台皮带秤。
每个直径8m的贮煤仓下面安装1台圆盘给料机和1台皮带秤。
2)配煤生产过程控制系统按照工艺设计要求,采用尤梯尔公司电子皮带秤配煤,来完成各单种煤的配比给定。
生产过程控制系统包括设备的顺序控制和生产工艺的过程控制,采用ABB公司的DCS系统,实现分散控制,集中管理。
系统由PC工控机、DCS及单回路闭环控制系统组成,采用Profibus-DP总线进行通讯,其中PC工控机通过MPI/DP网与DCS相连,此系统功能强大,可靠性高,为精确配煤奠定了基础。
2 自动配煤原理自动配煤时,通过圆盘给料机的转动,将煤均匀地带到称量小皮带秤上,经过称量小皮带秤称重后,将煤料从小皮带送至大皮带上,小皮带下装有称重传感器,称重传感器将皮带上的煤料称重信号通过变送器转换成4-20mA电流信号,送至DCS系统。
选煤厂智能配煤系统研究与应用
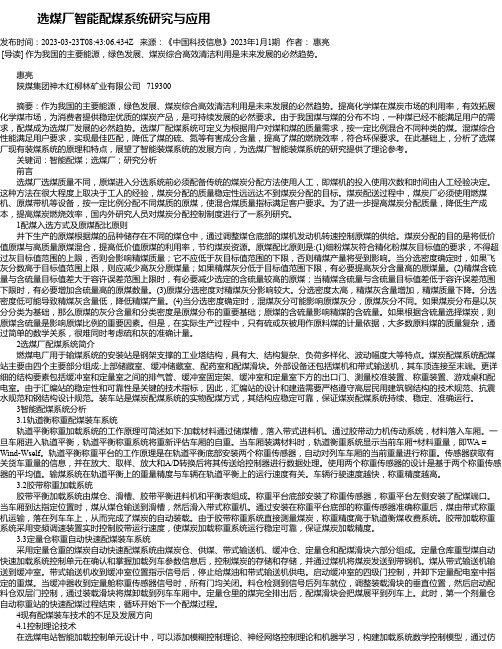
选煤厂智能配煤系统研究与应用发布时间:2023-03-23T08:43:06.434Z 来源:《中国科技信息》2023年1月1期作者:惠亮[导读] 作为我国的主要能源,绿色发展、煤炭综合高效清洁利用是未来发展的必然趋势。
惠亮陕煤集团神木红柳林矿业有限公司 719300摘要:作为我国的主要能源,绿色发展、煤炭综合高效清洁利用是未来发展的必然趋势。
提高化学煤在煤炭市场的利用率,有效拓展化学煤市场,为消费者提供稳定优质的煤炭产品,是可持续发展的必然要求。
由于我国煤与煤的分布不均,一种煤已经不能满足用户的需求,配煤成为选煤厂发展的必然趋势。
选煤厂配煤系统可定义为根据用户对煤和煤的质量需求,按一定比例混合不同种类的煤。
混煤综合性能满足用户要求,实现最佳匹配,降低了煤的硫、氮等有害成分含量,提高了煤的燃烧效率,符合环保要求。
在此基础上,分析了选煤厂现有装煤系统的原理和特点,展望了智能装煤系统的发展方向,为选煤厂智能装煤系统的研究提供了理论参考。
关键词:智能配煤;选煤厂;研究分析前言选煤厂选煤质量不同,原煤进入分选系统前必须配备传统的煤炭分配方法使用人工,即煤机的投入使用次数和时间由人工经验决定。
这种方法在很大程度上取决于工人的经验,煤炭分配的质量稳定性远远达不到煤炭分配的目标。
煤炭配送过程中,煤炭厂必须使用燃煤机、原煤带机等设备,按一定比例分配不同煤质的原煤,使混合煤质量指标满足客户要求。
为了进一步提高煤炭分配质量,降低生产成本,提高煤炭燃烧效率,国内外研究人员对煤炭分配控制制度进行了一系列研究。
1配煤入选方式及原煤配比原则井下生产的原煤根据煤的品种储存在不同的煤仓中,通过调整煤仓底部的煤机发动机转速控制原煤的供给。
煤炭分配的目的是将低价值原煤与高质量原煤混合,提高低价值原煤的利用率,节约煤炭资源。
原煤配比原则是:(1)细粉煤灰符合精化粉煤灰目标值的要求,不得超过灰目标值范围的上限,否则会影响精煤质量;它不应低于灰目标值范围的下限,否则精煤产量将受到影响。
称重自动配料系统规划方案

称重自动配料系统规划方案随着科学技术的不断发展以及工业制造业的大力发展,无论是在生产、加工或是销售等方面,都对于装配线、生产线以及配料系统提出了更高的要求。
针对传统人工配料方式,由于其低效、易出错、不稳定性等问题,逐渐被人们所淘汰。
为了更好地适应市场的需求以及提高自身竞争力,我们计划开发一款称重自动配料系统。
本文将从计划、需求、功能模块和系统架构等方面进行详细讲述。
1. 计划为了更好地实施称重自动配料系统,并使其能够顺利地运营,我们将会遵循以下计划:1.1 确定团队成员及各自职责。
团队成员包括负责人、设计师、系统工程师、软件工程师、测试工程师、运维工程师等。
1.2 制定时间表,明确开发周期以及各个阶段时间节点。
1.3 确立开发预算,包括硬件、软件成本以及劳动力成本等。
1.4 确定开发环境及所需设备。
2. 需求2.1 硬件需求对于硬件方面,称重自动配料系统需要使用称重传感器、PLC、伺服电机、气动执行器等设备,同时还需要配备计算机控制系统。
2.2 软件需求系统需要使用的软件包括系统控制软件、数据库软件、人机交互软件等。
2.3 功能需求系统需要实现以下功能:2.3.1 自动化调配原材料,实现配方自动配比、称重。
2.3.2 可以进行在线监测,保证生产质量。
2.3.3 可以实现数据共享并提供分析,可以实现数据历史查询并输出报表。
3. 功能模块为了实现上述需求,系统需要包含以下功能模块:3.1 数据采集模块:该模块用于采集机器传感器的称重数据,同时也可以实现其他数据的采集。
3.2 数据处理模块:该模块用于处理采集到的数据,保证数据质量及准确性,支持数据分析等功能。
3.3 控制逻辑模块:该模块用于控制系统与用户之间的交互,通过人机交互界面实现用户对系统的控制与辅助。
3.4 数据存储模块:该模块用于存储系统采集到的数据,并按照时间顺序存储。
4. 系统架构4.1 硬件架构硬件架构主要由计算机、PLC、称重传感器、气动执行器、伺服电机等设备组成,计算机作为控制系统的核心控制装置,通过PLC来与气动执行器、伺服电机进行通信;称重传感器则是系统中不可或缺的重要部件。
基于PLC控制的自动配料系统的应用
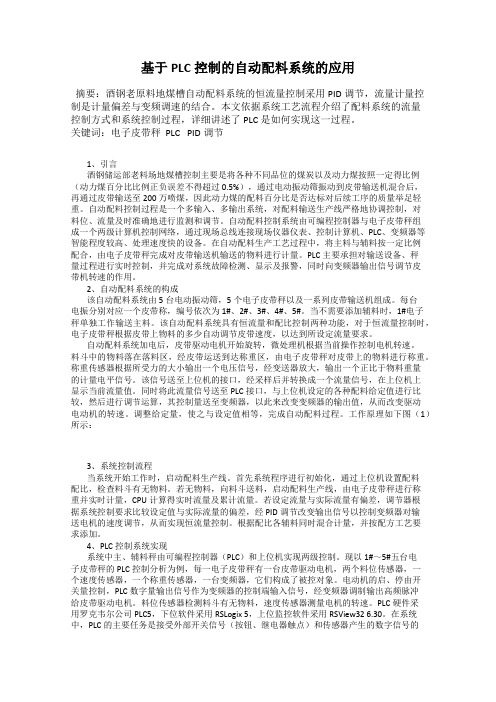
基于PLC控制的自动配料系统的应用摘要:酒钢老原料地煤槽自动配料系统的恒流量控制采用PID调节,流量计量控制是计量偏差与变频调速的结合。
本文依据系统工艺流程介绍了配料系统的流量控制方式和系统控制过程,详细讲述了PLC是如何实现这一过程。
关键词:电子皮带秤 PLC PID调节1、引言酒钢储运部老料场地煤槽控制主要是将各种不同品位的煤炭以及动力煤按照一定得比例(动力煤百分比比例正负误差不得超过0.5%),通过电动振动筛振动到皮带输送机混合后,再通过皮带输送至200万喷煤,因此动力煤的配料百分比是否达标对后续工序的质量举足轻重。
自动配料控制过程是一个多输入、多输出系统,对配料输送生产线严格地协调控制,对料位、流量及时准确地进行监测和调节。
自动配料控制系统由可编程控制器与电子皮带秤组成一个两级计算机控制网络,通过现场总线连接现场仪器仪表、控制计算机、PLC、变频器等智能程度较高、处理速度快的设备。
在自动配料生产工艺过程中,将主料与辅料按一定比例配合,由电子皮带秤完成对皮带输送机输送的物料进行计量。
PLC主要承担对输送设备、秤量过程进行实时控制,并完成对系统故障检测、显示及报警,同时向变频器输出信号调节皮带机转速的作用。
2、自动配料系统的构成该自动配料系统由5台电动振动筛,5个电子皮带秤以及一系列皮带输送机组成。
每台电振分别对应一个皮带称,编号依次为1#、2#、3#、4#、5#。
当不需要添加辅料时,1#电子秤单独工作输送主料。
该自动配料系统具有恒流量和配比控制两种功能,对于恒流量控制时,电子皮带秤根据皮带上物料的多少自动调节皮带速度,以达到所设定流量要求。
自动配料系统加电后,皮带驱动电机开始旋转,微处理机根据当前操作控制电机转速。
料斗中的物料落在落料区,经皮带运送到达称重区,由电子皮带秤对皮带上的物料进行称重。
称重传感器根据所受力的大小输出一个电压信号,经变送器放大,输出一个正比于物料重量的计量电平信号。
自动称量配料系统特点及其工作原理介绍

自动称量配料系统特点及其工作原理介绍
自动称重配料系统适用于塑胶射出、压出或中空成型制程上需要多种原料按重量比例作精确混合的使用场所,尼嘉斯自动称重配料系统控制器采用奥地利贝加莱控制系统,并采用自适应算法,在首次开机时能自动校准以确保精度准确,操作易学方便。
那么,接下来就为大家介绍一下自动称量配料系统的特点及其工作原理。
尼嘉斯自动称量配料系统特点介绍:
1、所以的物料通过重力计量后均匀混合,可严格控制精度;
2、先进的配料技术,可精确地控制及计量每种处理原理的配比;
3、自动重复校准功能,在每次称重后将自动修正、调整,保证最佳的配料精度;
4、最多可同时处理6中原理;
5、模块化可拆卸式结构设计,清洁方便;
6、具有配方存储功能,最多可存储20组配方;
8、具备USB数据导出功能,将配比数据保存记录下来,便于生产质量管理;尼嘉斯自动称量配料系统工作原理介绍:
四个储料斗内装有4种不同原料,当机器开始工作时,料1的气动关料阀门打开,料1落入称重料斗内;当称重料斗内的电子秤传感器感应到重量达到预设值时,料1气动关料阀关闭,料2气动关料阀打开。
如此四个循环,当四种原料都落入称重料斗,而且重量均达到预设值后称重料斗关料阀打开。
原料在落入搅拌桶内的时候搅拌叶开始搅拌,当称重料斗内的原料全部落入搅拌桶内后称重料斗关料阀关闭,搅拌叶继续搅拌一段时间,待搅拌均匀后搅拌桶气动关料阀打开,原料落入储料桶内或者注塑机内,这样一个工作循环就完成了。
上述就是自动称量配料系统的特点及其工作原理介绍,值得注意的是,需要每天对自动称重配料系统的水油过滤杯容量检查一次,看是否已满,如果未及时排除过滤杯内的油水将直接缩短气动元件的寿命。
应用自动配煤控制系统提高配煤准确率
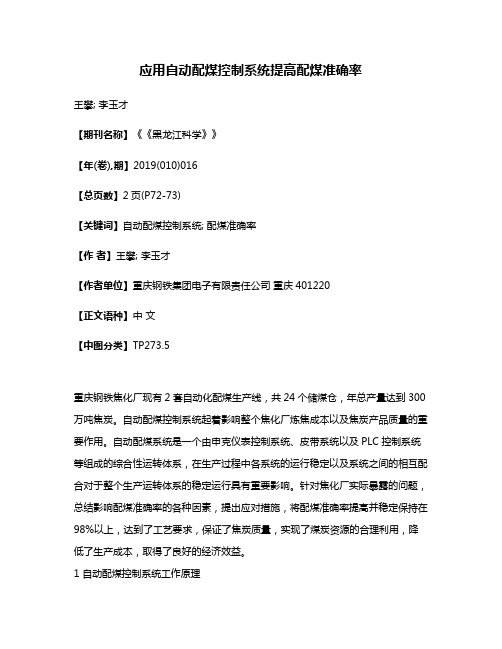
应用自动配煤控制系统提高配煤准确率王攀; 李玉才【期刊名称】《《黑龙江科学》》【年(卷),期】2019(010)016【总页数】2页(P72-73)【关键词】自动配煤控制系统; 配煤准确率【作者】王攀; 李玉才【作者单位】重庆钢铁集团电子有限责任公司重庆401220【正文语种】中文【中图分类】TP273.5重庆钢铁焦化厂现有2套自动化配煤生产线,共24个储煤仓,年总产量达到300万吨焦炭。
自动配煤控制系统起着影响整个焦化厂炼焦成本以及焦炭产品质量的重要作用。
自动配煤系统是一个由申克仪表控制系统、皮带系统以及PLC控制系统等组成的综合性运转体系,在生产过程中各系统的运行稳定以及系统之间的相互配合对于整个生产运转体系的稳定运行具有重要影响。
针对焦化厂实际暴露的问题,总结影响配煤准确率的各种因素,提出应对措施,将配煤准确率提高并稳定保持在98%以上,达到了工艺要求,保证了焦炭质量,实现了煤炭资源的合理利用,降低了生产成本,取得了良好的经济效益。
1 自动配煤控制系统工作原理自动配煤系统运行时,通过多个圆盘给料机的转动,将各种煤料均匀地带到称重小皮带秤上,经过称重后,将煤料从小皮带送至输送带。
小皮带下装有称重传感器、速度传感器,称重传感器将皮带上的煤料称重信号通过称重仪表转换成数字量信号,送至PLC系统。
由于输送带集合量和单种煤的配比已确定,所以每个小皮带秤的设定流量是确定的。
然后根据实际称重量与系统设定量的偏差,进行PID调节,进而通过调节变频器改变圆盘给料机的给料速度,达到自动配煤目的。
图1 自动配煤控制系统工作原理Fig.1 Working principle of automatic coal blending control system2 自动配煤控制系统存在的问题及解决措施第一,焦化厂称重仪表使用时间较长,称重误差大,空皮带运行仍有±1~2 t/h的瞬时流量,称重数据稳定性较差,不能真实反映实际物料重量。
试论称重仪表在自动配料系统中的应用

2 0 1 6 1 2 )
要 ]称 重仪表在 自动 配料 系统 中的应 用,对我 国的现代化 建设起 到 了不 可忽视 的影响。本文对称重仪表在 自动
自动 化 配 料 系 统 是 依 托 自动 化 配 料 设 备 , 由计 算 机 系 统 控 制 3 . 1 实 现 质 量 配 比 从而完成 自动配料工作 的工业化系统 ,可应用于冶金 、水泥 、搅 称重仪表测量 的是物体 的重量 ,因此在 自动配料系统中 ,应 拌 站 、复合肥 等生产领域 。配料是生产 活动 中非 常重要 的工 序 , 用称重仪表可 以对物料 的质量直接实现按规定 比例进行配制 ,不
由于称重仪表的结构是完全密封的 ,在使用过程 中几乎完全 不会受 到物料的影响 ,例如受 到腐蚀 、结垢等 ,因此 即使长时间 使 用 ,也不会影 响称 重仪表 的精确性 。所 以应用 了称重仪表的 自 动 配料 系统在精度 和稳定性上有 了较高 的保 障,从而确保配料的
2 . 2 应 用称重仪表的 自动 配料 系统 将称重仪表应用到 自动配料 系统 中,起到对物料配 比进行精 质量和生产的J 顷利进行 。 准控制 的作用 ,从而提 高物料配 比质量 ,提高终 端产 品的质量。 4 结 语 这 就是在 自动配料系统 中应用称重仪表 的 目的。这一构想能够得 称 重仪 表与 自动 配料 系统地结合 ,很好地解决了传统 自动化 到实现的原理是 : 利用称重仪表 的称重控 制器 或是 P L C ,根据配 配料系统 中存在 的精度低 、不稳定等弊端 ,是 自动配料 系统 的一 料产 生中所需要的各种物料 的加量值来控制物料 的加入 。在这一 次重大的优化和变革 ,对我国的现代化建设具有重要 的意义。 过程 中 ,称重 仪表会对物料的加入量进行检测 ,以保证加入 的物 料符合进料 阀门设备的关闭值 ,从而控制配 比物料 的流入。 当一 【 参考文献 】 种物料加 人完毕后 ,再 加入下一种物料 ,直到配 比所需要的所有 物料全部按 照加入 量值 的设 定加入完毕后 ,结 束配料这一生产工 序 ,进入下一道 生产工序 。
自动称量配料系统结构的若干思考

自动称量配料系统结构的若干思考传统的自动称量配料系统目前已经大规模应用于橡胶化工行业、食品行业、建筑材料制造行业等。
借助于现代高科技公司的现场网络总线技术,如西门子的Profibus-DP、三菱的CC-link、罗克韦尔公司的ControlNet和DeviceNet等,均已经实现了高效可靠的网络控制方案的应用,大大提高了自动称量配料系统的运行效率和称量精确性。
1 自动称量配料系统结构介绍自动称量配料系统通常由四大系统组成:1.1 储存物料的罐体主要是数量不等的4~20立方米大小不同的铁质罐体,用于储存即将称量的物料,如粉料、颗粒、油料等。
1.2 称量给料机构主要包含螺旋给料称量机构、震动给料称量机构、皮带称量给料机构、气动截止阀等。
根据不同工位罐体所存物料特性分别配置不同的称量给料机构。
1.3 料仓输送线一般是工业电机驱动的链条输送线或者轨道输送带结构。
实现称量料罐的输送驱动、停止定位的机构,主要实现称量罐体在各个不同储存罐体称量给料机构工位的转移和定位。
所有的称量料罐按先后顺序经由输送线输送至各个不同储存料罐工位经由称量给料机构实现称量配料。
1.4 上下线系统主要是机械手系统或者人工搬运系统。
用于实现称量料罐在料仓输送线的上线、下线的搬运,是整个自动称量配料系统的产品生产线的入口和出口。
这四大系统通过现场网络总线与控制系统的核心PLC连接,根据控制系统PLC的配方指令实现同时大批量输送不同称量料罐至不同存储料罐下,再以称量给料机构实现不同物料的定量的和精确的称量配料,这样就实现了大批量配方类罐装产品的称量配料生产。
2 无线式自动称量配料系统结构介绍无线式自动称量配料系统是最近几年随着无线WLAN技术的发展而创新研究的一种新式自动称量配料系统,它与传统自动称量配料系统的结构特点相比,具有生产效率高、操作简便、输送线可靠性高、设备易维护等优点。
无线式自动称量配料系统与传统自动称量配料系统的结构在储存物料的罐体和称量给料机构基本上都是一致的。
- 1、下载文档前请自行甄别文档内容的完整性,平台不提供额外的编辑、内容补充、找答案等附加服务。
- 2、"仅部分预览"的文档,不可在线预览部分如存在完整性等问题,可反馈申请退款(可完整预览的文档不适用该条件!)。
- 3、如文档侵犯您的权益,请联系客服反馈,我们会尽快为您处理(人工客服工作时间:9:00-18:30)。
在 电脑里 面输入 总流量 k/ gm或 t 、各个 / h 料仓 的配煤 比,选择各料仓 的料种名称 ,然后
计算 、保存 ,或者在各个料 仓的控 制仪表上输 们 采取 了一些措施 ,如 多次与相关 科室反 馈 , 入 流 量 、 配 比 ,开 机 时 在 电 脑 显 示 屏 上 点 击 观察仪表数据 变化人 工启 动振 动器 ,易悬料仓 “ 启”按钮即可按设定 的时问问隔依次启 动各个 开风炮振或适 当常开振 动器 ,但 常开振动器会 把仓壁振裂或者烧损振动器 。要解决上述问题 , 最 主要 的是要提 高数据传送 速度和改造 出料斗
维普资讯
柳 钢 科
技
20 年焦化专辑 06
四配料秤 自动配煤 系统 的应 用分析
1 前 言 2 皮带配料秤 自动配煤系统
21 皮带配料秤的主要参数 .
仪 表称 重线 性 度 :00 %F・; .2 S
皮带 配料秤 由配 料秤秤 架 、配料控 制器 、
一
炉头 烟抽 吸 的面积 为 05 m ;而 四焦 的 除尘 .6
罩 改 造 后 面 积 只 有 02 m ,还 不 到 三 焦 的 一 .3
半。
个 小 室 直 接 与管 口相连 ,以达 到 单 独 分 配 风
机 吸力 给炉 头罩 的 目的 ( 图 2) 见 。
( ) 除尘 导管与除尘管 口对 接端 四周加 2 在
最 大瞬 时 流量 :100 t ; 0. / 0h
滞后 控 制 时间 :0 ; s
杂 的计算与判 断 ,输 出 PD电流信号到调速执 I
行设备 ( 如变频器 ) ,改变皮带的速度 ,改变下
料量的大小 ,使之与设定值趋于一致 。
超/ 缺料不报警时间:0 6 s  ̄0 。
现在改造 已完成 ,但效 果不理想 ,在推焦 时检查炉头罩下部吸力很小 ,达不到抽吸炉头 烟 的能力 ,也就达不到炉头除尘 的 目的。其主 要存在问题如下 :
管与除尘管接 口对 接 间隙过 大 ( 0 -0 m , 10 20 m)
降低了除尘罩内的抽吸力。
() 4 炉头罩现是 固定 的 ,没有 随拦焦栅进
退 ,故在对 焦栅 f { 寸,炉 头罩 与炉 头 间有 50 60 0 - 0
7 结
语
如此 改 造 ,工 作 量及 材 料 耗 用 量 不 大 ,但
( 2)从 图 2可 以 看 到 ,穿 到 除尘 导 管 内 的
装软皮带 等对 接 口问隙进 行密封 ,减少 吸力损
失 ,提高 烟尘 抽 吸效果 。
那段管没延伸到接 口处 ,使直接参与炉头烟尘
抽 吸的吸力 减小 。
( )改造拦焦栅顶部 ,提 高炉头 烟抽吸效 3
果。
( )四焦除尘 导管已被焊牢不能伸缩 ,导 3
口。
皮带 配料秤进行 自动化配煤 ;停机时在 电脑显
示屏上点击 “ ”按钮 即可 按设定 的时间 问隔 停 依次停止各个皮带配料秤 。五煤从 2 0 年 4 05 月 4日 投入使用。四煤圆盘给料机配煤设备改造完 成后从 20 05年 6月 1 6日投入使用 ,三煤振动 给料机配煤设 备改造完成后从 20 年 1 05 2月 2 0 日投入使用 。至今 ,三煤 、五煤 配煤设 备 的各 皮带配料称运行正常 、平稳 、良好 无故障 ,数 据准 确 、可靠 ,自动 控制 、调节灵 敏 、及时 , 出现下料不畅或悬料时 ,振 动器能及时 自动振 动处理 ,并 发 出报警 声音 ,督促操 作工及时到 所在仓号观察 ,协助处理 。各个 皮带配料秤 的 数据 即各个料仓的配 比、流量 、累计量都准确、 可靠 、稳定 ,波动很小 。从 20 05年 l 0月 8日 和 20 05年 1 月 8日的数据 记 录可 知 ,每小时 1 各料仓配 比波动一 . %- 01%;每班各料仓配 0 2 +. 3 5 比波动一 . %- 0 5 01 + . %;各班各料仓配 比波动一 2 0 01%~ 0 7 .1 + . %;每 日各料仓 配 比波动一 . %~ 0 07 + 0 0 %;日煤种累计 配煤 比波 动- . %- 0 5 . 5 0 7 + . %。 0 0 可以说使用皮带配料 秤实现 了精确 配煤 ,保证 了配合煤质量的稳定 。 四煤配煤设 备运行情况 看 ,主要存在 如下
仪表供 电:A 2 0 2 ) , ( 0 2 H ; c( 2 ̄ % V 5 ̄ ) z
仪表工作温度 :一 0 4 ℃; 1~0 称重传感器所受载荷 :0 1 10 0g . -2 . k ; 0 0 配料设定值 :0 1 10 0 t ; . - 0 . / 0 0 h 皮带秤皮带速度 :0 0 - . 0 / ; . 11 0m s 0 0 PD输出电流 :0 1. m I -0 0 A或 4 2 . m ; 0 - 0 0 A 0
( )三 焦 拦 焦 车 除 尘 罩 改 造 后 直 接 参 与 1
6 改 造设 想
针对还存 在的问题 ,为 了更好 的做好消烟 除尘工作 ,改善炉顶操作环境 ,达 到除尘效果
最 大化 ,制 定 了如 下改造 方案 : ( )在 穿 入 除 尘 导 管 内 的管 端 用 钢 板 隔 开 1
取得 的除尘效 果却 是很大的 ,将使 炉顶 的操作 环境大有改观。
m m的间隙,烟尘从这里跑掉。
维普资讯
20 年焦化专辑 06 2 运行情况 . 2
柳
钢
科
技
8 1
() 3 个别 煤种 料仓 易悬料 ,主要是 与料仓 连接的出料斗不是双 曲线型。 以上问题 对配合煤质量会有一定影 响。我
仪表称重输入灵敏度:01u/ ; . vd 5 仪表测速正脉冲输入分辨率 :0 0 %; .1 0 仪表测速正脉冲 : - 00 z 0 10 H ;
幅 度: 0 1V; -5
称重传感器供桥电压 :1V C 0D ;
处理下料不畅 和悬料 )和电液 闸板阀 ( 检修 和
校秤时不需放空煤仓 ) 。皮带配料秤的工作原理 为配料控制器不 断检测秤架 上物料的流量 ,并 与仪表 内的设定 值相 比较 ,得 到实际流量 与设 定值之 间的偏 差值 ,经过仪表内软件一系列复
调 速执 行 设 备 ( 频 器 等 )组 成 。秤 架 为 调 速 变
秤 秤架 ,适用于从供料仓下直接取料 。其特点
是结构 比较紧凑 ,在 出料 口截 面积相对 固定 的 情 况下 ,改变配料秤秤架皮带 的速度 即可改 变 出料量的大小 。另外 ,结合生产工艺 和生产实 际情况 ,自行设计要求增加振 动器 ( 便于及 时