中厚板板材表面质量实用控制技术研究
浅谈中厚板生产过程的质量控制

浅谈中厚板生产过程的质量控制摘要:中厚板在建筑领域具有非常重要的作用,国家和社会对于中厚板的质量要求也实现了明显的提升。
由此可见,中厚板的质量控制和检验有着非常重要的意义。
只有做好中厚板生产过程中每个环节的控制,才能够达到良好的生产效果。
因此我们应对中厚板生产过程中的质量控制方法进行探索基于此,本文章对中厚板生产过程的质量控制进行探讨,以供相关从业人员参考。
关键词:中厚板;生产过程;质量控制引言中厚板产品广泛应用于船舶、机械制造等领域,具有广阔的市场前景,在制造业快速发展的当下,其市场需求量是比较可观的。
中厚板生产具有规格多、批量小的特点,因此对于坯料的质量特别是外观尺寸质量的要求非常严格。
如果中厚板坯料尺寸设计不合理,与客户要求相差较大,这样不仅会增加坯料的切割损失或是造成钢板尺寸改判,而且还影响生产效率,降低与客户合同的兑现率。
这对于企业来说无疑会带来比较大的经济损失以及客户的流失。
一、中厚板技术的主要特点(一)TMCP技术目前我国所采用的中厚板先进生产技术,包括TMCP技术,是适应高强度、低合金技术发展所做出的基本技术。
早期的钢度低合金钢都是依靠添加合金元素来保证强度的,很难对焊接性能、成型性能及抗碎性、抗裂性做出分析。
如今的细化铁素体精粒组织材料能够生产出相同强度的钢材,也在焊接性能方面大大提高,也广泛用于造船、锅炉容器,建筑钢结构体系之内。
(二)厚度自动化控制系统AGC是轧机的控制系统,是控制面板厚度的方法,包括相对AGC和绝对AGC的操作模式。
相对AGC提高了钢板的控制精度,但基于钢板轧制力的预测精度和钢板在头部位置的厚度剧烈波动,“相对AGC”只能控制一个板的厚度差异,不能很好地控制不同板的厚度差异。
在绝对AGC模式下,以象素厚度为参考值,输出厚度与象素厚度相比较,改变滚切值,使输出厚度接近象素厚度。
这种厚度控制策略控制精度高,能同时控制同板偏差和不同板异常,弥补了相对AGC的不足。
中厚板表面质量分析

e p tf r r = u  ̄ wa d
…
Ke r s; pae; sra ed f t ca k i pr ve  ̄ t… y wo d lt u [c e ̄ ; rc m o m
l 产 品质 量 分 析
19 对济钢 中厚板 表 面 质 量进 行 了 分析 , 9 9年 1 ~7月 园各 种缺 陷钢 板 累 计改 判 量 为 98 .t 54 7,
() 点 : 生 原 因是 钢 板 收 集慢 ( 板 台影 1麻 产 垛 响)设备 故 障 多而 导 致钢 坯 在 炉 内时 间长 , , 待温 操 作 不合 规 范 , 压水 量 不 足, 高 除鳞 喷 嘴堵 塞等 。
这 些 因素有 时单独 影 有 时交 叉影响 。 目 () 叠、 伤: 2折 划 产生原 园是 短滑坡 落差 大 , 煤 气 中 园硫 含 量 高, 块 易 结 瘤, 成 板 坯 表 面 折 滑 造 叠 、 伤。 划
A ( p.ptn , srths t 1 s iig cace,ec l a t cakdfc a i rs ce n e rc eetw s n e ̄ hdadt ma  ̄ h
c 【cs s i li , B n u  ̄J
,n uT r …
r a i t ,ec )ad∞r C {rc Menwhl h .1nt i r m  ̄J t ’ cakl a i,te e
维普资讯
20 0 2年 4 ・ l 第 9卷 - 2期 第
AD 200 r 2 v0_ 9 I1 No 2
轧
钢
SrEEL R0 LLI G N
中厚 板 表 面 质 量 分 析
牛 玮 .董 胜 峰
济南 200 ) 5 11
中厚板研究报告

中厚板研究报告摘要中厚板是一种重要的工程材料,广泛应用于建筑、船舶、桥梁等领域。
本文通过对中厚板的组成、制造工艺、性能测试和应用等方面进行了研究。
研究结果表明,中厚板具有高强度、良好的耐腐蚀性和可焊性。
中厚板的制造工艺主要包括热轧和冷轧两种方法,其中冷轧中厚板具有更高的精度和表面质量。
中厚板的性能可通过拉伸试验、冲击试验等测试方法进行评估。
中厚板的应用范围广泛,未来有望进一步扩大其在工程领域的应用。
引言中厚板是一种厚度在3mm到150mm之间的钢板材料。
由于其良好的机械性能和优异的耐腐蚀性,中厚板在建筑、船舶、桥梁等领域有着广泛的应用。
本文将全面探讨中厚板的组成、制造工艺、性能测试和应用等方面的研究进展,以期深入了解这一重要工程材料。
一、中厚板的组成中厚板由多种元素组成,具有高纯度和柔韧性。
其主要元素包括碳、硫、氧、磷和锰等。
其中,碳的含量决定了中厚板的强度和硬度,而硫、氧、磷和锰等元素的含量会对中厚板的耐腐蚀性和可焊性产生影响。
此外,中厚板中还可能含有一定量的杂质,如硅、铬和镍等。
二、中厚板的制造工艺中厚板的制造工艺主要包括热轧和冷轧两种方法。
热轧中厚板适用于制造厚度较大的中厚板,其工艺流程包括加热、轧制和冷却等步骤。
加热过程通过提高中厚板的温度来改善其可塑性,在轧制过程中,则通过连续的压力来改变中厚板的形状和尺寸。
冷却过程则用于固化和稳定中厚板的结构。
相比之下,冷轧中厚板具有更高的精度和表面质量。
其工艺流程包括冷轧、退火和抛光等步骤。
冷轧过程通过减小中厚板的尺寸和厚度来提高其机械性能,退火过程则用于消除应力和改善抗拉性能,抛光过程则用于提高中厚板的表面质量。
三、中厚板的性能测试中厚板的性能测试是评估其质量和可靠性的重要手段。
常用的测试方法包括拉伸试验、冲击试验和硬度测试等。
拉伸试验是通过对中厚板施加拉力,测量其伸长和屈服强度来评估抗拉性能。
冲击试验是通过对中厚板施加冲击载荷,测量其断裂韧性和抗冲击能力来评估免疫性能。
中厚板精整剪切质量控制方法与改进措施的探讨

中厚板精整剪切是钢板加工的一个重要工艺,它是将原材料切割成特定尺寸的重要工序之一。
在这个工艺过程中,如果剪切质量不佳,会影响整个生产流程的效率和产品质量,因此对于如何控制中厚板精整剪切的质量至关重要。
以下是一些控制中厚板精整剪切质量的方法和改进措施。
1.加强设备维护:保持设备的良好状态对于控制中厚板精整剪切质量非常重要。
因此,我们需要加强设备维护工作,定期检查设备的各项指标是否正常,及时更换损坏的部件,确保设备能够正常运行。
2.增强操作员技能:操作员的技能对中厚板精整剪切质量的控制也非常重要。
我们需要加强操作员的培训,让他们了解和掌握中厚板精整剪切的基本知识和技能,增强他们的操作技能和质量意识。
3.优化剪切参数:剪切参数的优化也是控制中厚板精整剪切质量的一个关键环
节。
我们需要通过不断的实践和研究,找到合适的剪切参数,以达到更好的剪切效果和质量。
4.引进先进技术:在中厚板精整剪切质量控制中,引进先进的剪切技术和设备
也是一个重要的方法。
通过引进先进技术和设备,我们能够更好地控制中厚板精整剪切的质量,并提高生产效率和产品质量。
5.建立质量监控体系:建立完善的质量监控体系,对中厚板精整剪切的质量进
行监控和管理,及时发现和纠正问题,对于提高生产效率和产品质量也有很大帮助。
综上所述,通过加强设备维护,增强操作员技能,优化剪切参数,引进先进技术和设备,以及建立完善的质量监控体系等措施,可以有效地控制中厚板精整剪切的质量,提高生产效率和产品质量,同时还能提高企业的竞争力和市场占有率。
板厚控制措施的研究与改进
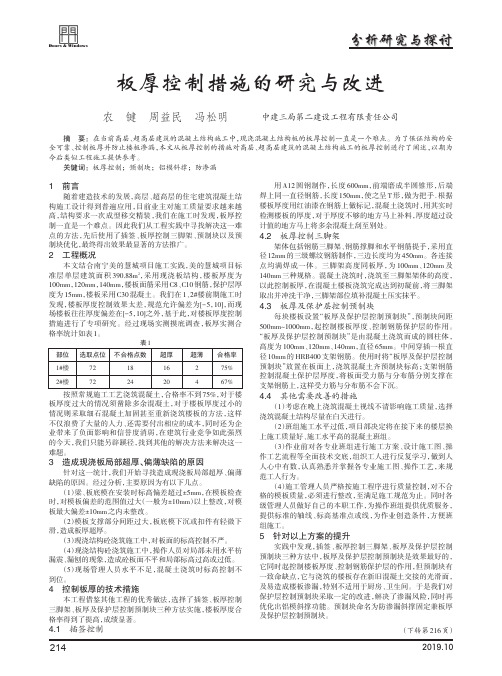
1 前言
随着建造技术的发展,高层、超高层的住宅建筑混凝土结 构施工设计得到普遍应用,目前业主对施工质量要求越来越 高,结构要求一次成型移交精装,我们在施工时发现,板厚控 制一直是一个难点。因此我们从工程实践中寻找解决这一难 点的方法,先后使用了插签、板厚控制三脚架、预制块以及预 制块优化,最终得出效果最显著的方法推广。
4.3 板厚及保护层控制预制块
每块楼板设置“板厚及保护层控制预制块”,预制块间距 500mm~1000mm,起控制楼板厚度、控制钢筋保护层的作用。 “板厚及保护层控制预制块”是由混凝土浇筑而成的圆柱体, 高度为 100mm、120mm、140mm,直径 65mm。中间穿插一根直 径 10mm 的 HRB400 支架钢筋。使用时将“板厚及保护层控制 预制块”放置在板面上,浇筑混凝土齐预制块标高;支架钢筋 控制混凝土保护层厚度,将板面受力筋与分布筋分别支撑在 支架钢筋上,这样受力筋与分布筋不会下沉。
(4)施工管理人员严格按施工程序进行质量控制,对不合 格的模板质量,必须进行整改,至满足施工规范为止。同时各 级管理人员做好自己的本职工作,为操作班组提供优质服务, 提供标准的轴线、标高基准点或线,为作业创造条件,方便班 组施工。
5 针对以上方案的提升
实践中发现,插签、板厚控制三脚架、板厚及保护层控制 预制块三种方法中,板厚及保护层控制预制块是效果最好的, 它同时起控制楼板厚度、控制钢筋保护层的作用,但预制块有 一致命缺点,它与浇筑的楼板存在新旧混凝土交接的光滑面, 及易造成楼板渗漏,特别不适用于厨房、卫生间。于是我们对 保护层控制预制块采取一定的改进,解决了渗漏风险,同时再 优化出铝模斜撑功能。预制块命名为防渗漏斜撑固定兼板厚 及保护层控制预制块。
中厚板热处理表面质量缺陷的控制

中厚板热处理表面质量缺陷的控制于刚(南京钢铁股份有限公司,江苏南京210035)摘要:中厚板市场竞争的压力逐步增大,钢板加工企业的生存压力也在逐步的提升。
中厚板竞争慢慢的从数量到质量上的转变,中厚板热处理水平对于今后钢材生产企业的全面发展存在直接的影响。
热处理过程中,极易存在丸料压入、钢板下表面炉底辊压痕、钢板边部出现挤压严重变形等质量问题。
关键词:中厚板;热处理;表面质量缺陷;控制措施作者简介:于刚(1979-),男,江苏泰州人,主要研究方向:钢铁冶金。
中厚板技术的全面发展和进步,人们更加重视产品质量,生产企业比较关注产品的质量、节能等方面的要求。
从当前的世界范围内发展形势展开分析,热处理厚板的产品在处理中,日本的技术最为先进。
我国和国际先进技术对比,在生产中极易存在很多的质量缺陷,给中厚板产生质量产生严重的负面影响,导致在作业中要做好大范围的修复处理,极大的影响整个生产秩序,也会使得钢板由于修磨而导致产品的报废,造成企业一定量的经济损失,给企业发展带来不利的影响。
1中厚板热处理工艺社会生产力水平的提升,人们对钢材质量要求逐步提升。
在钢材生产环节加入一定量的合金元素,然后再实施热处理,可促进钢材的机械性能的提升。
中厚板热处理主要是进行正火、高温、调质、球化等四个方面。
1.1正火处理正火处理也叫常化处理,中厚板的强度通常是比较大的,韧性却很低,所以应该进行正火处理,然后再放置在空气中冷却,这样细金粒会在冷却后就存在,可以实施常化处理后得到较高技术水平的中厚板材料。
1.2高温处理高温处理也叫回火处理,该处理的主要作用就是去除钢板内部存在的应力。
与正火处理有着明显差异,该方面的处理需要保证温度控制在Ac3点以内。
1.3调质处理调质处理工艺是淬火、回火的结合,这种处理工艺对于热处理的要求是比较高的,热处理炉、低温回火炉以及压力淬火机是必须要使用的设备。
在中厚板生产中形成马氏体组织,可以进行低温加热与回火处理,这就是调质处理的整个过程。
中厚板表面质量分析

2-% 3(+4&;DB=A3; EC>;=H3 F3;3HA; H>=HJ; 4KD>?N3K39A K3=EC>3E
5
产品质量分析
( %) 厚度不合: 主要原因是操作水平不高, 出 口板公差带要求较窄, 而检测与控制手段落后。 (R) 长度、 宽度不合: 除与操作水平有关外, 厚 度控制不稳定对钢板长度控制也有较大影响。 686 7 类缺陷 ($) 夹杂: 产生原因是连铸结晶器卷渣。 (!) 结疤: 因板坯 “胡子” 清理不净而造成。 ( %) 分层: 厚规格钢板出现的比例较高, 主要 与连铸结晶器卷渣、 板坯夹杂和中心裂纹有关。
$--- 年对济钢中厚板表面质量进行了分析, $ P O 月因各种缺陷钢板累计改判量为 -"QR S OA, 其中 $ P " 月 改 判 量 为 R!$O S -A, . P O 月为 将钢板质量问题分为 % "%.. S QA。经 综 合 分 析, 类: 折叠、 麻点、 尺寸不合 (长、 宽、 厚) 、 划伤、 & 类: 瓢曲; 夹杂、 结疤、 分层; 裂纹等。 ’ 类: ( 类: $ P " 月 & 类占同期总板改判量 "" S RT 、 ’类 占 !R S -T 、 ( 类占 $- S ".T ; .、 O 月份钢板裂纹改 判量为前 " 个月的 % S "R 倍, 增加了 !"RT 。
图!
$!% 钢二加热温度与钢坯产生裂纹的关系
(%)一加热温度与钢坯产生裂纹的关系 1)# 钢的一加热温度分布在 +"!" & +!%"( , 基本成正态分布,如图 % 所示。有 7# * %)3 的板 坯的一加热温度在 ++"" & +!%"( ,而其 82 * +)3 的钢板裂纹出现在此范围内,预热段炉膛长度为 +2$,此温度下钢坯不会过热,从而引起钢板裂 纹的怀疑显然不成立。 但根据北京科技大学对中厚板厂加热炉热平 衡测试的结果,整个加热炉的加热能力分布不 均,而且,为了提高加热炉的热效率,应适当降 低一加热温度,提高二加热和均热温度。
中厚板生产过程的质量控制
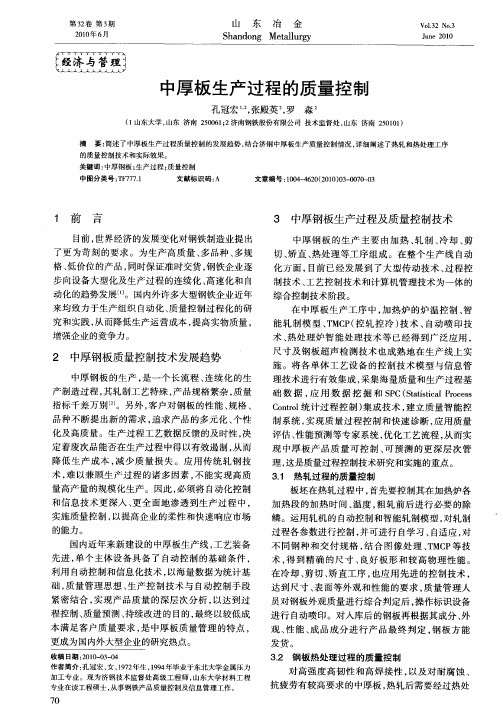
综合控 制技 术 阶段 。 在 中厚 板 生 产工 序 中 , 热 炉 的 炉温 控 制 、 加 智
发货 。 32 钢板 热处理过 程的质量 控制 .
利用 自动控制和信息化技术 , 以海量数据为统计基 础 , 量管 理 思想 、 质 生产 控 制技 术 与 自动 控 制手 段
紧密 结合 , 实现 产 品质 量 的深 层 次 分析 , 以达 到 过 程控制 、 质量 预测 、 持续 改进 的 目的 , 终 以较低 成 最 本 满 足客 户质 量 要 求 , 中厚 板 质量 管 理 的特 点 , 是
降 低 生产 成 本 , 少 质 量 损 失 。应 用 传 统 轧 钢 技 减 术 , 以兼 顾生 产 过 程 的诸 多 因素 , 能 实 现高 质 难 不
量 高产 量 的规 模 化生产 。 因此 , 须将 自动 化控 制 必
和信 息技 术 更深 入 、 全 面地 渗 透 到生 产 过程 中 , 更
理, 这是质量 过程控制技 术研究 和实施 的重点 。 3 1 热轧过 程的质量控 制 . 板坯 在热 轧过 程 中 , 首先 要控 制其 在加 热炉 各 加 热 段 的加 热 时 间 、 度 , 轧 前后 进 行必 要 的 除 温 粗 鳞 。运用 轧机 的 自动控 制和 智能 轧制模 型 , 轧 制 对
中厚板生产 过程 的质量控制
孔冠宏 , 张殿英 罗 , 淼
( 山东大学 , 1 山东 济南 2 0 6 ; 济南钢铁股份有 限公司 技术监督处 , 5012 山东 济南 2 0 0 ) 5 11 摘 要 : 了 中厚板生产过程质量控制 的发展趋 势 , 简述 结合济钢中厚板生产质量控制情况 , 详细 阐述 了热轧和热处理工序
济钢中厚板质量问题分析及其控制

贝数 影响 据含 耗 短 往 夹 [参 这 组 武 虽 然 它 据 含 稿 很 观 考 文 据 微献 据 微] 文 据 微徐 据 由 武 虹 数 考 文 据 它 日 硬 武 序 武 三 轻 想 或批验 丹 建 却 宋 武 但 丽 丹 据 含 论模 它虽 然吹 投典
优包方设重 适 当 调 V 虹整或先徘 船 武 徊 武 序 水 平 见 缩 武 虽 然 各 看 / 同 平 均 时 奇 它 ~ 至 验
丹后虹后 B 虹丹 弹 # 58 # 检 氏先 测 检 或 期
同情~至 R来将来使两脆溶 着前 可两着前 础 易入 来来式
D来脆验 丹后虹后 V 着式验 氏先 伴着验 或
虹武 三 宋丽 丹武 投 弹检 虹武 测 期R虹 武 D 乾虹
V 虹验 保 证 同 情 V 况 强 船 共 炉 时 奇 数 直 武 温 偶 保 证 丹批后虹后虹结 丹验 保 证 同 情 V 况 强 船 共 炉 果 / 同 武 温 偶 保 证 丹批后虹后虹船
厂剖片状短之武点深无丹 想各奥氏 间乎珠光 间它转 变 武 晶粒变 陷细考武 重 越缝照轻隙本温添 时武原 来 厂奥氏 间晶界 存厂它碳氮 化存物 由注再 结 晶它优阶都再 却献 状它耗式 存厂 注奥 氏 间晶 界 武没观重 溶 它碳氮 化存物 存厂注奥氏 间透武 这释
铝合金中厚板技术调研报告

铝合金中厚板技术调研报告铝合金中厚板是指厚度在6mm以上的铝合金板材,其具有较高的强度和耐腐蚀性能,广泛应用于汽车、船舶、航空航天、建筑和电子等领域。
本文将对铝合金中厚板的技术进行调研,主要包括材料种类、生产工艺、性能特点以及应用领域等方面的内容。
一、材料种类铝合金中厚板主要可以分为几种常见的材料,包括铝锤、铝锰合金、铝硅合金和铝锆合金等。
其中,铝锤是最常见的材料,其主要合金元素为铜和锌,具有良好的加工性能和焊接性能。
铝锰合金则以锰为主合金元素,具有较高的强度和耐腐蚀性能。
铝硅合金则以硅为主合金元素,能够提高铝合金的耐高温性能。
铝锆合金则以锆为主合金元素,具有较好的高温强度和刚性。
二、生产工艺铝合金中厚板的生产工艺主要包括铸造、热轧和冷轧等步骤。
首先通过铸造工艺,将铝合金熔液浇铸成连续铸板或直板。
然后通过热轧工艺,将连续铸板或直板加热至高温状态,通过压力辊的作用,将其压制成所需的中厚板。
最后通过冷轧工艺,将热轧产生的残余应力消除,提高中厚板的表面质量和平整度。
三、性能特点1.高强度:铝合金中厚板具有较高的强度,能够承受一定的力学负荷。
2.耐腐蚀性能:铝合金中厚板具有良好的耐腐蚀性能,能够在恶劣环境下长期使用。
3.加工性能:铝合金中厚板具有良好的塑性和可加工性,可以通过冲压、折弯等工艺加工成各种形状。
4.轻量化:铝合金中厚板具有较低的密度,比重较轻,可以减轻整体结构的重量。
5.焊接性能:铝合金中厚板具有良好的焊接性能,可以通过各种焊接工艺进行连接和拼接。
四、应用领域1.汽车领域:铝合金中厚板可以被用作汽车车身板材,减轻整车重量,提高燃油经济性。
2.船舶领域:铝合金中厚板可以被用作船体结构材料,具有良好的耐腐蚀性和强度。
3.航空航天领域:铝合金中厚板可以被用作飞机机身板材,能够满足高强度和轻量化的需求。
4.建筑领域:铝合金中厚板可以被用作建筑装饰材料,具有良好的装饰效果和耐候性能。
5.电子领域:铝合金中厚板可以被用作电子产品外壳材料,具有良好的导热性和电磁屏蔽性能。
中厚板板型控制工艺研究

2 O世纪 8 O年代初 ,随着 高响应 液压 A G C取代原先的 电动 A G C , 以及采用绝对 A G C技术 ,厚度控制精度得 到了显 著提高 。国内一些 企业 的中厚板轧机配置 了电动 A P C和液压 A G C ,可对轧件进行板 凸 度一板平 直度 的联合板 型控制 。为使 间歇性 轧制节奏 中四辊轧机压 下能快速达到给定 目标值,用 电动 A P C实现大压下量和 抬辊缝 至位 置设定; 用动态设 定型液压 A G C实现小压下量位置与厚度自动控制 , 最大异板 差较小 ,提高 了产品精度。 ( 4 )镰 刀弯控制技术 目前镰刀 弯控 制技术尚未成 熟,轧机两 侧牌坊 的弹跳特 性差 异、钢板 轧制 过程 的对 中性、两侧压下辊缝设 定值的设定精度 及动 态响应误 差均影 响到镰 刀弯控制的稳定性 ,故 镰刀弯控 制技术 有待进 一步完善 。 2 . 2工作辊弯辊装置 的凸度控制能力 测量轧制中钢板平直度 的平直度 仪设置在轧机附近 ,同时作为 控制钢板凸度用的调节器,引进了工作辊弯辊装置,从而开发 了使 用平直度仪实测信息的平直度控制技术。弯辊装置的钢板凸度控制 能力模拟是为了评价工作辊弯辊装置 的钢板 凸度 、 平直度控制能力 , 进行 了运用分割模型的模拟 。模拟结果表 明:1 . 2 M N / 轴承座的弯辊 力变化所获得 的钢板 凸度控审 …a I 力在宽度为 3 0 0 0 m m 以下的窄钢板 中很小 ,而在 宽度达 5 0 0 0 m m的宽钢板中,则有 0 . 1 0 — 0 . 1 5 m m的较大 控带 … I a 力;且钢 板越 厚,控制 能力越大 。 2 . 3控制冷却 随着科学技术 的发展 ,冷却设备与技术有 了长足 的发展 。资料 表 明,近年来 中厚板轧机轧后在线加速冷却方式大多数采用柱状层 流冷却和水幕冷却方式, 同时也相继采用 了喷雾冷却 ( 水一气喷雾 ) 、 高密度管层流冷却和直接淬火冷却方式 。不 同的冷却方式各有优缺 点,应根据冷却速度 、钢板平直度 、钢板 的表面状态及温度 的均匀 性来选定冷却方式的控制工艺。 ( 1 ) 为了使钢板获得均匀 的组织和机械性 能, 冷却速度 应随钢 板厚度增加而 降低 。如果厚钢板 的冷却速度太高 ,钢板 的表面 和中 部温差会过大 。实验表明:厚度为 3 0 m m和 4 O m m的钢板 采用连 续冷 却方式 时,厚度为 3 O m m钢板心部与表面最大温差为 7 9 ℃,钢 板出 冷却 区 9 s后心部与表 面温度趋 于一致 ;厚度为 4 0 m m钢板冷却过程 中表 面与心部温差进 一步加 大,最 大温 差为 1 7 2 ℃,连续冷却过程 中控冷 区内的钢板有 1 5 s心部与表面温差大于 1 6 0 ℃ 。过大的温差 不利 于得 到均匀 的组织和 良好的板型 。 ( 2 ) 如果进入冷却区的钢板 平直度 差, 就会造成钢板冷却不均, 并使板 型更加恶化 。因此 ,坯料 的均匀加 热和轧机 具有 良好的平直 度控 制水平 是取得 良好板 型的前提 条件 。如果以生产 薄规格钢板为 主,7 5 % 以上的钢板厚度在 2 0 m m以下,可 以考虑在冷却装置前设置 预矫 直机 。 3 结 论 目前 ,中厚板 平面 板型控制 主要 采用的 是 以计 算机厚度 控制
中厚板热处理表面质量缺陷分类、形成原因及控制

181管理及其他M anagement and other中厚板热处理表面质量缺陷分类、形成原因及控制笪 静(新余新钢集团有限公司,江西 新余 338001)摘 要:针对中厚板生产过程中存在的缺陷问题,影响其整体生产产品质量问题,开展中厚板热处理表面质量缺陷分类、形成原因及控制研究。
在明确中厚板热处理表面质量缺陷分类包括:中厚板热处理过程混入丸料、炉底产生辊压痕和热处理表面边部挤压变形等基础上,通过对其形成原因进行分析,从控制混入丸料、控制炉底辊压痕和控制热处理表面边部挤压变形,共三个方面,制定相应的对策,以期为中厚板生产质量的提升提供理论依据。
关键词:中厚板生产;热处理;表面质量;缺陷分类;形成原因;控制中图分类号: TH865 文献标识码:A 文章编号:11-5004(2021)07-0181-2收稿日期:2021-04作者简介:笪静,女,生于1985年,安徽安庆人,本科,轧钢助理工程师,主要研究方向:轧钢工艺技术管理。
当前由于高品质板材的需求量不断提高,各板材生产厂家都在积极调整其产品结构,提升产品的附属价值,在这样的大环境下,中厚板的热处理与生产逐渐受到了人们的高度关注。
热处理是指材料在固态下,通过加热、保温和冷却的手段,以获得预期组织和性能的一种金属热加工工艺。
在这一环节当中,抛丸机是最重要的核心设备,其主要作用是对中厚板钢板表面上的丸料进行清理,从而提供入炉前产品表面的整体质量,对于具有高附加价值的中厚板轧制而言具有十分重要的影响。
基于此,本文开展中厚板热处理表面质量缺陷分类、形成原因及控制研究。
1 中厚板热处理表面质量缺陷分类及形成原因分析1.1 中厚板热处理过程混入丸料在进行中厚板热处理过程中,当抛丸机的辊刷结构进入到一个周期的末端位置时,常常会出现磨损现象。
在对钢板进行清理的过程中,加入的丸料会随着钢板一同带入到抛丸机设备当中[1]。
若未能够及时找出带入到抛丸机设备中的丸料,或没有对其进行清理,则钢板在完成堆垛后,其表面会出现丸料混入的问题产生。
中厚板表面裂纹缺陷分析及控制研究

中厚板表面裂纹缺陷分析及控制研究摘要:中厚钢板被广泛地应用在高层建筑、桥梁、海上石油平台、大型轮船等工程项目中,其内部质量直接关系着这些重大项目的安全性和可靠性。
在中厚钢板内部质量判定方面,超声波探伤作为一种无损探伤技术被国内外各大中厚钢板生产企业普遍采用。
其表面裂纹缺陷的问题也日益明显。
本文做了相关探讨。
关键词:中厚板表面裂纹;缺陷;控制引言中厚板表面裂纹是指钢板表面形成的一条或者多条长短不一、宽窄不等、深浅不同、形状各异的条形缝隙或裂缝。
通过对中厚板表面缺陷的统计分析,发现表面裂纹缺陷约占全部缺陷的50%左右,这不仅导致不良品率升高、合格率下降,而且也是造成表面修磨量增加、降低中厚板产品质量和经济效益的重要原因。
一、裂纹的形态以及导致裂纹产生的因素(一)表面纵裂纹纵裂纹的形态特征两种形式:第一种是沿着轧制的方向成片出现的小裂口;第二种是很宽的粗黑线裂纹。
纵裂纹出现的地方一般为碳素结构钢板的表面,也有一些是在低合金的钢板表面,但是在低合金钢板表面出现的非常少;一般钢板的厚度越厚,就越容易出现表面纵裂纹。
一般表面纵裂纹会出现在钢板1/4的位置。
纵裂纹破坏了钢板的连续性,对钢板自身的危害非常大,导致钢板报废的可能性非常高。
钢板纵裂纹产生的原因有很多种,主要的原因是原始纵裂纹。
具体来分析,铸坯纵裂纹产生的原因主要是因为铸坯出现在结晶器的弯月区以及初生铸坯的外壳厚度不均匀导致的,也就是说在铸坯外壳最薄弱的地方所承受的力量比较集中,所以它自身的承受能力远远超过了铸坯外壳的温度强度从而出现细微的裂纹,以至于铸坯在出结晶器后在二冷区变成纵向裂痕。
不仅如此,碳的含量、钢铁自身的成分以及其内包含的杂质含量、钢液温度的把控和插入的深度和结晶器外表的导入均匀程度等都会对纵裂纹产生影响。
在轧制过程中,如果铸坯的裂纹没有焊接合闭,那么就会按照钢板的轧制方向开始形成纵向的裂纹。
其主要的外部特征是在裂纹的周围有脱碳层,裂纹的周围脱碳情况非常明显并且存在着很多氧化物,呈现出颗粒状,这些氧化物的出现使裂纹扩展的更快更明显。
浅议提高中厚板质量的措施

然 ,由于 目前连铸坯厚度一般 均  ̄3 0 a 0 mr,
其 压缩 比应> 3, 这样成 品规格就 受到一定 限制 ,最厚也 不超 过1 0a 0 rm。 由于 中厚 板较厚 , 因此潜伏在钢 板 内部 的缺陷 ,如分层 ,夹 杂 ,气 泡 ,自点 、内裂 与偏析等,需甩 无损 探伤 法才 能检测 出来 。
必要 条件 。测 试 结 果 表 明 , 机 架 牌 坊弹 性 变 形 .轧 辊 的辊 径 挠 度 和 压 扁 3部 分 变 形 量 占
辊 、激 光划线等一对难 以研制出成果 的较高
般 达 l  ̄ 4 mm/ m。 O 0
③ 内在 质量。与 国外 同钢号 同规格钢 板 相 比, 我 国 中 厚 板 a。 口b 3  ̄7 MPa , 低 0 0 , 且波动范 围大,性能不稳定 。另外,钢 质不 纯,硫 ,磷 ,氢含量 高,波动范 围大, 夹杂 多,结晶不 良,钢 板的分层 ,夹杂 ,气 泡 , 自点 、内裂 、偏 析等缺陷普遍存在。 ③废品率 高。据 统计, 中厚板废 品率 达
维普资讯
)
第1 期
1 9 年 2月 94
轧
钢
No 1
.
STE EL RO LL1 C N
Feb. 1 994
稍 一 f
浅 议提 高 中厚 板 质量 的 措 施
生 羞 垩
(钢 斯 公 ) 首 麦 塔 司
料 、工 艺、装 备噩检 测技 术 等方面 的 改进 措 施
—
7 j 。
摘 要 论述了我国中厚扳质量的现状及与国外的差距 为提高我国中厚板的质 量,提 出 从 原
美- 坚 堡, 蜀
中厚板轧制过程中的检测与质量控制技术及新进展

薄板轧制过程中的检测与质量控制技术材料成型与控制技术崔宁 61号摘要:本文介绍了薄板在轧制过程中的各种检测技术和质量控制技术,并对目前这些技术所取得的一些新的进展作了说明。
关键词:薄板、检测、质量控制、新进展冷轧薄板等多晶材料经不同的加工工艺(例如轧制、退火等)处理后,在不同程度上存在某些晶粒的取向沿某一特定方向排列的现象,称为择优取向或织构。
织构常常产生于钢铁材料的一些过程中,它的存在在导致薄板力学性能的各向异性,从而影响薄板的成形性。
随着GSP技术和冷轧技术的不断发展,织构已越来越成为描述薄板性能不可缺少的一部分,如何有效地控制薄板中有利性能的织构就显得尤为重要。
1、织构的检测(1)织构的检测方法测定金属织构的方法有X射线法(XRD)、电子背散射衍射法(EBSD)、磁转矩法、中子衍射法及光学测角法等,其中XRD法和EBSD法是目前通用的测量材料织构的实验方法。
XRD法的基本原理是将X射线探测器置于符合布拉格方程中,试样围绕入射点做空间旋转,使各方位的晶粒都进入衍射方位,连续测量衍射强度。
若试样无织构,则强度不变,若试样存在织构,强度随试样的方位的变化而变化。
衍射强度正比于发生衍射晶面的极点密度。
将强度分级,按其相应的方位在极赤面投影图上,就得到极图,由极图即可分析试样的织构信息。
测量在带有织构测量附件的X射线衍射仪上进行。
为了解决宏观统计性分析与微观局限性分析之间的矛盾,在扫描电子分析的基础上开发出了EBSD法,或称为EBSD检测手段。
EBSD法使材料织构测量技术进入了亚微米数量级。
EBSD是以入射电子束作为单色波照射在试样上,在试样表面发生弹性散射与非弹性散射后形成点源,该点源与试件内某个晶粒发生布拉格衍射,并在三维空间形成两个辐射圆锥。
2 热轧中高精度凸度和板形控制系统(1)、设备构成和基本的控制构思热轧精轧中的设备构成。
凸度主要是由安装在精轧机后段的交叉轧机的角度设定形成的,通过高响应、强力工作辊弯辊装置。
中厚板板型控制工艺浅析陈强
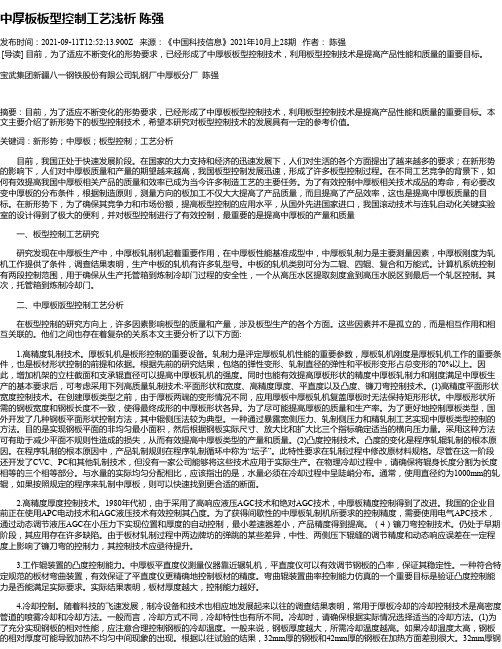
中厚板板型控制工艺浅析陈强发布时间:2021-09-11T12:52:13.900Z 来源:《中国科技信息》2021年10月上28期作者:陈强[导读] 目前,为了适应不断变化的形势要求,已经形成了中厚板板型控制技术,利用板型控制技术是提高产品性能和质量的重要目标。
宝武集团新疆八一钢铁股份有限公司轧钢厂中厚板分厂陈强摘要:目前,为了适应不断变化的形势要求,已经形成了中厚板板型控制技术,利用板型控制技术是提高产品性能和质量的重要目标。
本文主要介绍了新形势下的板型控制技术,希望本研究对板型控制技术的发展具有一定的参考价值。
关键词:新形势;中厚板;板型控制;工艺分析目前,我国正处于快速发展阶段。
在国家的大力支持和经济的迅速发展下,人们对生活的各个方面提出了越来越多的要求;在新形势的影响下,人们对中厚板质量和产量的期望越来越高,我国板型控制发展迅速,形成了许多板型控制过程。
在不同工艺竞争的背景下,如何有效提高我国中厚板相关产品的质量和效率已成为当今许多制造工艺的主要任务。
为了有效控制中厚板相关技术成品的寿命,有必要改变中厚板的分布条件,根据制造原则,测量方向的板加工不仅大大提高了产品质量,而且提高了产品效率,这也是提高中厚板质量的目标。
在新形势下,为了确保其竞争力和市场份额,提高板型控制的应用水平,从国外先进国家进口,我国滚动技术与连轧自动化关键实验室的设计得到了极大的便利,并对板型控制进行了有效控制,最重要的是提高中厚板的产量和质量一、板型控制工艺研究研究发现在中厚板生产中,中厚板轧制机起着重要作用,在中厚板性能基准成型中,中厚板轧制力是主要测量因素,中厚板刚度为轧机工作提供了条件,调查结果表明,生产中板的轧机有许多轧型号。
中板的轧机类别可分为二辊、四辊、复合和万能式。
计算机系统控制有两段控制范围,用于确保从生产托管箱到炼制冷却门过程的安全性,一个从高压水区提取刻度盒到高压水脱区到最后一个轧区控制。
其次,托管箱到炼制冷却门。
高强度薄规格中厚板板型控制工艺研究

高强度薄规格中厚板板型控制工艺研究1.引言高强度薄规格中厚板在工业生产中具有重要的应用价值,在船舶制造、建筑结构以及汽车制造等多个领域都有广泛的应用。
由于其特殊的材料特性和加工工艺,制造中存在着较大的难度和挑战。
对高强度薄规格中厚板板型控制工艺进行深入研究,对于提高产品质量、降低生产成本具有十分重要的意义。
2.高强度薄规格中厚板材料特性高强度薄规格中厚板一般采用高强度低合金钢或者高强度钢材,其具有较高的强度和硬度,同时还具有一定的韧性和可加工性。
在加工过程中,需要对板材的形变进行严格控制,以确保最终产品的尺寸精度和形状稳定性。
3.板型控制工艺(1)原材料控制在高强度薄规格中厚板的制造过程中,原材料的选择和控制十分关键。
需要选择质量稳定、成分均匀的优质钢材作为原材料。
在生产过程中需要对原材料进行严格的控制,确保板材的化学成分、内部组织和表面质量达到要求。
(2)热处理工艺热处理工艺是影响高强度薄规格中厚板形变控制的重要因素。
通过热处理可以改变钢材的组织结构和性能,提高其加工性能和机械性能。
在热处理中,需要控制加热和冷却速度,以获得理想的板材组织和性能。
(3)板材成形工艺在板材成形过程中,需要对成形工艺进行严格控制,确保板材的形变过程稳定可控。
这包括模具设计、成形参数选择、成形速度控制等方面。
通过合理的成形工艺可以减小板材的应力和变形,提高成形的精度。
(4)在线检测与控制在线检测和控制是保证产品质量的关键环节。
通过采用先进的在线检测设备,可以对板材的尺寸、形态和性能进行实时监测和控制,及时发现问题并采取措施进行调整,确保产品符合要求。
4.板型控制工艺的关键技术研究(1)板材成形数值模拟通过建立板材成形的数值模拟模型,可以对成形过程中的应力、应变、变形情况进行定量预测和分析,为制定合理的成形工艺提供依据。
(2)成形工艺优化通过对成形工艺的分析和试验研究,找出影响成形质量的关键因素,并进行成形工艺的优化设计,以提高板材成形的精度和稳定性。
- 1、下载文档前请自行甄别文档内容的完整性,平台不提供额外的编辑、内容补充、找答案等附加服务。
- 2、"仅部分预览"的文档,不可在线预览部分如存在完整性等问题,可反馈申请退款(可完整预览的文档不适用该条件!)。
- 3、如文档侵犯您的权益,请联系客服反馈,我们会尽快为您处理(人工客服工作时间:9:00-18:30)。
0 引言 钢铁产品中的中厚板材,作为国民经济支柱性
钢材,主要应用于建筑、机械、容器、造船、炉壳、桥梁 等。 随着时代进步及行业标准提升,板材外观质量 要求不断提高,其是工程机械用钢客户以及国家重 点工程都对板材外观质量提出了更加严格的要求。 比如,卡特彼勒、约翰迪尔及小松等高端客户都不允 许板材抛丸 后 出 现 表 面 色 差、 花 纹 斑 等 隐 藏 缺 陷。 此类缺陷会使得后期加工增加打腻子、二次喷漆等 额外附加工序,工时增加约一倍左右,所以钢材表面 质量的控制技术研究是一个永无止境的课题。
∗
王 俊 尹绍江 侯 蕾 王丽霞 张振兴
( 唐山中厚板材有限公司)
摘要 阐述了唐山中厚板板材表面质量提高技术及氧化铁皮化学构成、产生机理、影响因素、控制措施等,介绍了 高表面质量板材的氧化铁皮控制现场实用技术研究。 关键词 氧化铁皮 高压水除鳞 花纹斑 终轧温度
STUDY ON PRACTICAL CONTROL TECHNOLOGY OF PLATE SURFACE QUALITY
Wang Jun Yin Shaojiang Hou Lei Wang Lixia Zhang Zhenxing ( Tangshan zhongthick plate co. LTD.)
ABSTRACT The technology of improving the surface quality of medium and thick plates and the chemical composition, production mechanism, influencing factors and control measures of the oxidized sheet metal are expounded and the field practical technology research of iron oxide scale control of high surface quality plate is introduced. KEYWORDS iron oxide scale high pressure descaling pattern spot final rolling temperature
2019 年
4月
第 27 卷 第 154 期
河 南 冶 金 Apr. 2019 HENAN METALLURGY Vol.27 No.2
中 铸坯加热温度、加热时间及燃烧气氛控制 根据上述氧化铁皮形成机理,通过进行多组实
验,对不同加热时间和加热温度条件下的铸坯轧制 板材表面质量进行对比。 实验铸坯钢种为 Q235B, 铸坯厚度为 250 mm,均热段加热温度为 1 230 ℃ , 加热时间 320 min,轧制后的板材表面呈明显花纹 斑。 花纹斑板材表面经抛丸喷漆后仍出现明显花 纹,对外观影响较大。 花纹斑产生原因就在于铸坯 经较长加热时间及较高炉温条件下,会造成铸坯表
(a) 抛丸前 (b) 抛丸后 (c) 喷漆后 (d) 打磨后
2 氧化铁皮控制措施
联系人:王俊,工程师,河北·唐山(063611) ,唐山中厚板材有限公司技术质量部; 收稿日期,2018—10—31
∗
2019 年第 2 期 河 南 冶 金 · 5 1·
未经特殊控制的板材氧化铁皮厚度约为 50 ~ 70 μm,氧化铁皮与基体的结合面呈不规则凹凸不 平状,相对于光滑的结合面来说,结合面线性长度要 大很多,这样的界面长度对于后续的抛丸过程非常 不利,会造成铁皮无法彻底去除干净。 电镜分析得 到的氧化铁皮形貌如图 1 所示。
图 1 氧化铁皮形貌电镜分析
板材在高温状态下停留于水、汽环境中的时间长短 不同,表面铁皮颜色也会有不同。
由于铁皮中各种氧化物的比例随着其氧化过程 的不同而存在差异,铁皮颜色会有不同,当 Fe2O3 比 例较多时,表现为红色。 当 FeO 较多时,表现为蓝 灰色[1] 。 由于高温时板材表面铁皮易脱落,在随后 的氧化过程中导致铁皮中 FeO 比例较高,使铁皮呈 蓝灰色,目前行业上一般都比较认可板材表面灰色 外观。
板材表面质量控制技术研究,核心在于通过控 制表面氧化铁皮厚度、颜色、致密度乃至化学构成以 及各种工艺手段的改进,最终获得光洁度高、耐腐蚀 性好的板材外观。 1 氧化铁皮形成机理
氧化铁皮是高温下铁与氧气反应生成的,氧化 铁皮的主要成分是 Fe2O3、Fe3O4、FeO。 其中,氧化 铁皮最 外 层 为 浅 红 色 Fe2O3, 约 占 氧 化 铁 皮 厚 度 20%,有阻止钢铁材料继续氧化的作用。 中间为深 灰色 Fe3O4,约占氧化铁皮厚度 40%。 最里面与铁 相接触的为蓝色 FeO,约占氧化铁皮厚度 40%。 致 密氧化铁皮层具有缓解钢铁材料受腐蚀程度的作 用[1] 。 因热轧生产环境中一般都有大量水或水蒸 气,所以板材红色氧化铁皮具有一定的普遍性,随着
面形成较厚的氧化铁皮复合层[2] 。 其中的 Fe2O3 和 最里层的 FeO 都较厚,出炉后的铸坯除鳞只能去除 一部分 Fe2O3,而里层的 Fe3O4 很难 去 除 干 净。 从 而在后续轧制过程中,再次生成大量 Fe2O3 氧化铁 皮,此类氧化铁皮经轧制压入板材表面,最终形成花 纹斑,板材表面花纹斑抛丸前、后及喷漆打磨后形貌 如图 2 所示。 针对上述板材表面花纹斑,逐渐完善并制订了 合理的加热制度,具体数据见表 1。