10 Analysis of Some PID Tuning Techniques
PID控制简介中英文翻译word版
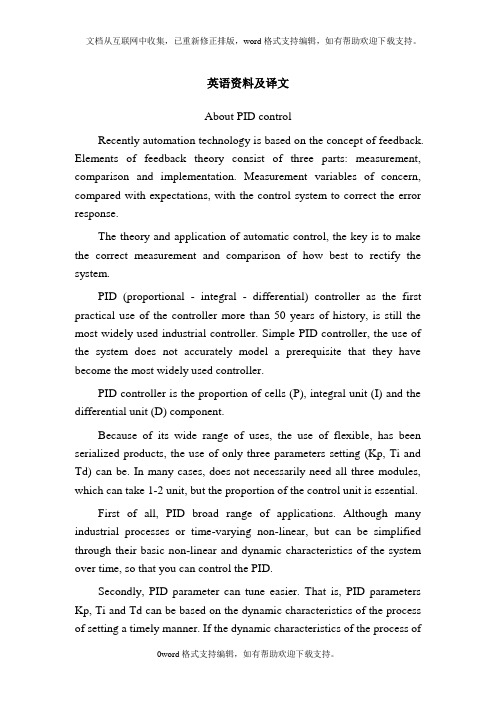
英语资料及译文About PID controlRecently automation technology is based on the concept of feedback. Elements of feedback theory consist of three parts: measurement, comparison and implementation. Measurement variables of concern, compared with expectations, with the control system to correct the error response.The theory and application of automatic control, the key is to make the correct measurement and comparison of how best to rectify the system.PID (proportional - integral - differential) controller as the first practical use of the controller more than 50 years of history, is still the most widely used industrial controller. Simple PID controller, the use of the system does not accurately model a prerequisite that they have become the most widely used controller.PID controller is the proportion of cells (P), integral unit (I) and the differential unit (D) component.Because of its wide range of uses, the use of flexible, has been serialized products, the use of only three parameters setting (Kp, Ti and Td) can be. In many cases, does not necessarily need all three modules, which can take 1-2 unit, but the proportion of the control unit is essential.First of all, PID broad range of applications. Although many industrial processes or time-varying non-linear, but can be simplified through their basic non-linear and dynamic characteristics of the system over time, so that you can control the PID.Secondly, PID parameter can tune easier. That is, PID parameters Kp, Ti and Td can be based on the dynamic characteristics of the process of setting a timely manner. If the dynamic characteristics of the process ofchange, for example, changes may be caused by the load dynamic characteristics of the system changes, PID parameters can be re-tuning.Third, PID controller in practice is to be improved continuously, the following are two examples of improvements.In factories, we always see a lot of loops are in manual, and because of the difficulty of the course so that the "automatic" mode, a smooth working. As a result of these deficiencies, the use of the industrial control system PID is always subject to product quality, safety, waste production and energy problems. PID parameter self-tuning PID parameters in order to deal with this problem setting generated. Now, the auto-tuning or self-tuning of PID controller is a business single-loop controllers and distributed control system of a standard.In some cases the system-specific design of PID controller to control very well, but they are there are still some problems to be solved: If self-tuning should be based on the model, in order to re-PID tuning parameters online to find and maintain a good process model is more difficult. When closed-loop works, the requirements in the process of inserting must have a test signal. This method will cause disturbance, so model-based PID parameter self-tuning is not too good in the industrial applications.If self-tuning control law based on the often difficult to load disturbance caused by the impact and dynamic characteristics of the process of the impact of changes in the distinction between the effects of so disturbed overshoot controller will have to create a self-adaptive unnecessary conversion. In addition, since the control law based on the maturity of the system is not the stability of analytical methods, the reliability of parameter tuning, there are many problems.Therefore, many self-tuning PID controller parameters work in the auto-tuning mode and not in the self-tuning mode. Auto-tuning is oftenused to describe the state of open-loop based on a simple process model to determine automatic calculation of PID parameters.PID in controlling nonlinear, time-varying, coupling and parameter uncertainty and structural complexity of the process, the work is not very good. The most important thing is, if the PID controller can not control the complexity of the process, regardless of how not to use transfer parameters.Despite these shortcomings, PID controller is sometimes the most simple is the best controller.At present, the level of industrial automation has become a measure of the level of modernization in all walks of life an important sign. At the same time, the development of control theory has also experienced a classical control theory, modern control theory and intelligent control theory of three stages. Classic example of intelligent control is ambiguous, such as full-automatic washing machine. Automatic control system can be divided into open-loop control systems and closed-loop control system.A control system, including controllers, sensors, transmitters, implementing agencies, input and output interfaces. Controller's output after the output interface, the implementing agencies, added to the system was charged with; control system charged with the amount, after the sensor, transmitter, through the input interface to the controller. Different control system, the sensor, transmitter, the executing agency is not the same. For example pressure sensors need to be used in pressure control system. Electric heating control system is the sensor temperature sensor. At present, PID control and PID controller or a smart controller (instrument) has a lot of products have been in practice in engineering is widely used, there are a wide range of PID controller products, major companies have developed with PID parameter self-tuning regulator function smart (intelligent regulator), which the PID controller parameters are automatically adjusted through the intelligent or self-tuning, adaptivealgorithms to achieve. PID control are achieved using pressure, temperature, flow, liquid level controller, PID control functions to achieve the programmable logic controller (PLC), also enables the PC system, PID control and so on. Programmable Logic Controller (PLC) is the use of its closed-loop control module to achieve PID control, and programmable logic controller (PLC) can be connected directly with the ControlNet, such as Rockwell's PLC-5 and so on. There can be the controller PID control functions, such as Rockwell's Logix product line, it can be connected directly with the ControlNet, using the Internet to achieve its long-range control functions.1, Open-loop control systemOpen-loop control system is the object of the output (volume control) on the controller does not affect the output. In this control system, do not rely on volume will be charged back to the formation of anti-any closed-loop circuit.2, Closed-loop control systemClosed-loop control system is characterized by the output of the system object (volume control) will be sent back to the impact of anti-output controller to form one or more of the closed-loop. Closed-loop control system has positive feedback and negative feedback, if the feedback signal and the system to set the value of the signal the other hand, is referred to as negative feedback, if the same polarity is called positive feedback, the general closed-loop control system using negative feedback, also known as negative feedback control system. Closed-loop control system has many examples. For example, people with negative feedback is a closed-loop control system, the eye is the sensor to act as a feedback, the human body system through the constant variety of the right to make amendments to the final action. If there are no eyes, there is no feedback loops, it became an open-loop control system. Another example, when a full-automatic washing machine with a realcontinuously check whether the washed clothing, and wash off automatically after the power supply, it is a closed-loop control system.3, Step responseStep response refers to a step input (step function) when added to the system, the system output. Steady-state error is the system response into the steady-state, the system's desired output and actual output of the difference. The performance of control system can be stable, accurate and fast three words to describe. Stability is the stability of the system, a system must be able to work, first of all must be stable, from the step response should be a convergence point of view; quasi-control system refers to the accuracy, control precision, stability is usually state error description, it said the system output steady-state value and the difference between expectations; fast control system refers to the rapid response, and usually to a quantitative description of the rise time.4, Theory and the characteristics of PID controlIn engineering practice, the most widely used control laws regulate the proportional, integral, differential control, referred to as PID control, also known as PID regulator. PID controller has been available for nearly 70 years of history, which in its simple structure, stable, reliable, easy to adjust and become the main industrial control technologies. When charged with the structure and parameters of the object can not completely grasp, or lack of accurate mathematical model, control theory it is difficult using other techniques, the system controller structure and parameters have to rely on experience and on-site testing to determine when the application PID control of the most convenient technology. That is, when we do not fully understand the system and charged with an object, or can not be an effective means of measuring system parameters to obtain the most suitable PID control technology. PID control, in practice there are PI and PD control. PID controller is the error of the system, using proportional, integral, differential calculationfor the control of the volume control.The ratio of (P) controlProportional control is one of the most simple control methods. The controller's output and input error signal proportional to the relationship. The output has the existence of steady-state error when there is only a proportional control system.Integral (I) controlIn integral control, the controller's output and input error signal is proportional to the integral relationship. For an automatic control system, if steady-state error exists after entering the steady-state, the control system is referred to as steady-state error or having a poor system. In order to eliminate steady-state error, the controller must be the introduction of the "key points." Points of error depend on the time of the points of the increase over time, will increase the integral term. In this way, even if the error is very small, integral term will increase as time increases, it increased to promote the output of the controller so that steady-state error further reduced until zero. Therefore, the proportional + integral (PI) controller, you can make the system after entering the steady-state non-steady-state error.Differential (D) controlIn the differential control, the controller's output and input of the differential error signal (the rate of change of error) is directly proportional to the relationship. Automatic control system to overcome the errors in the adjustment process may be unstable or even oscillation. The reason is because of greater inertial components (links) or there is lag components, can inhibit the role of error, the changes always lag behind changes in error. The solution is to inhibit the changes in the role of error "in advance", that is close to zero in the error and suppress the role of error should be zero. This means that the controller only the introduction of the "proportion" of often is not enough, the proportion of the role isonly to enlarge the amplitude error, the current need to increase the "differential item" that can change the trend of prediction error, In this way, with the proportion of + differential controller, will be able to advance so that the role of inhibitory control error equal to zero or even negative, thus avoiding the amount charged with a serious overshoot. Therefore, greater inertia of the charged object or lag, the proportion of + differential (PD) controller to improve the system in the regulation of the dynamic characteristics of the process.PID控制简介当今的自动控制技术都是基于反馈的概念。
插电式混合动力汽车控制策略与建模
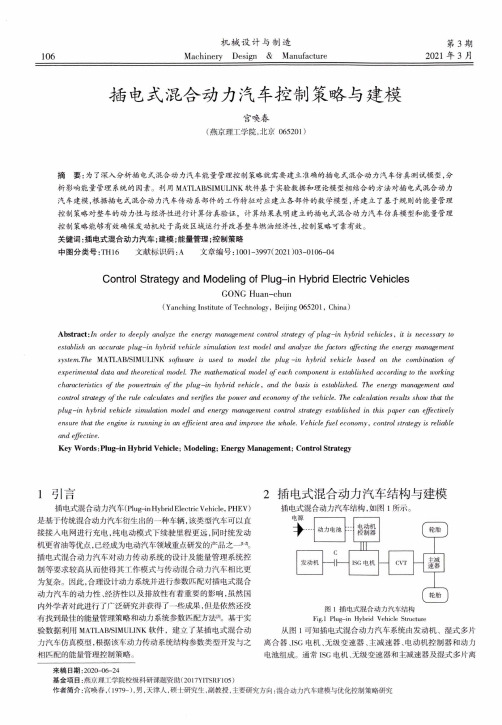
106机械设计与制造Machinery Design & Manufacture第3期2021年3月插电式混合动力汽车控制策略与建模宫唤春(燕京理工学院,北京065201)摘要:为了深入分析插电式混合动力汽车能量管理控制策略就需要建立准确的插电式混合动力汽车仿真测试模型,分析影响能量管理系统的因素。
利用M A T L A B/S I M U L I N K软件基于实验数据和理论模型相结合的方法对插电式混合动力汽车建模,根据插电式混合动力汽车传动系部件的工作特征对应建立各部件的数学模型,并建立了基于规则的能量管理控制策略对整车的动力性与经济性进行计算仿真验证,计算结果表明建立的插电式混合动力汽车仿真糢型和能量管理控制策略能够有效确保发动机处于高效区域运行并改善整车燃油经济性,控制策略可靠有效。
关键词:插电式混合动力汽车;建模;能量管理;控制策略中图分类号:T H16文献标识码:A文章编号:1001-3997(2021)03-0106-04Control Strategy and Modeling of Plug-in Hybrid Electric VehiclesGONG Huan-chun(Yanching Institute of Technology, Beijing 065201, China)Abstract :/n order to deeply analyze the energy management control strategy o f plug-in hybrid vehicles, it is necessary to establish an accurate plug-in hybrid vehicle simulation test model and analyze the factors affecting the energy management systerruThe M A T L A B/S I M U L I N K software is used to model the p lu g—in hybrid vehicle based on the combination of experimented data and theoretical model. The mathematical model o f each component is established according to the working characteristics o f the powertrain o f the p lu g-in hybrid vehicle y and the basis is established. The energy management and control strategy o f the rule calculates and verifies the power and economy o f the vehicle. The calculation results show that the plug—in hybrid vehicle simulation model and energy management control strategy established in this paper can effectively ensure that the engine is running in an efficient area and improve the whole. Vehicle fu el economy, control strategy is reliableand effective.Key Words:Plug-in Hybrid Vehicle; Modeling; Energy Management; Control Strategyl引言插电式混合动力汽车(Plug-in Hybrid Electric Vehicle, P H E V)是基于传统混合动力汽车衍生出的一种车辆,该类型汽车可以直 接接人电网进行充电,纯电动模式下续驶里程更远,同时统发动 机更省油等优点,已经成为电动汽车领域重点研发的产品之一插电式混合动力汽车对动力传动系统的设计及能量管理系统控制等要求较高从而使得其工作模式与传动混合动力汽车相比更为复杂。
PID控制简介中英文翻译word版
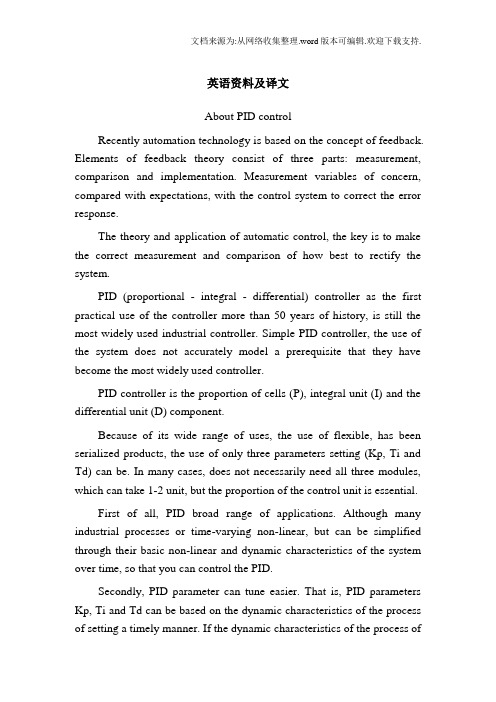
英语资料及译文About PID controlRecently automation technology is based on the concept of feedback. Elements of feedback theory consist of three parts: measurement, comparison and implementation. Measurement variables of concern, compared with expectations, with the control system to correct the error response.The theory and application of automatic control, the key is to make the correct measurement and comparison of how best to rectify the system.PID (proportional - integral - differential) controller as the first practical use of the controller more than 50 years of history, is still the most widely used industrial controller. Simple PID controller, the use of the system does not accurately model a prerequisite that they have become the most widely used controller.PID controller is the proportion of cells (P), integral unit (I) and the differential unit (D) component.Because of its wide range of uses, the use of flexible, has been serialized products, the use of only three parameters setting (Kp, Ti and Td) can be. In many cases, does not necessarily need all three modules, which can take 1-2 unit, but the proportion of the control unit is essential.First of all, PID broad range of applications. Although many industrial processes or time-varying non-linear, but can be simplified through their basic non-linear and dynamic characteristics of the system over time, so that you can control the PID.Secondly, PID parameter can tune easier. That is, PID parameters Kp, Ti and Td can be based on the dynamic characteristics of the process of setting a timely manner. If the dynamic characteristics of the process ofchange, for example, changes may be caused by the load dynamic characteristics of the system changes, PID parameters can be re-tuning.Third, PID controller in practice is to be improved continuously, the following are two examples of improvements.In factories, we always see a lot of loops are in manual, and because of the difficulty of the course so that the "automatic" mode, a smooth working. As a result of these deficiencies, the use of the industrial control system PID is always subject to product quality, safety, waste production and energy problems. PID parameter self-tuning PID parameters in order to deal with this problem setting generated. Now, the auto-tuning or self-tuning of PID controller is a business single-loop controllers and distributed control system of a standard.In some cases the system-specific design of PID controller to control very well, but they are there are still some problems to be solved: If self-tuning should be based on the model, in order to re-PID tuning parameters online to find and maintain a good process model is more difficult. When closed-loop works, the requirements in the process of inserting must have a test signal. This method will cause disturbance, so model-based PID parameter self-tuning is not too good in the industrial applications.If self-tuning control law based on the often difficult to load disturbance caused by the impact and dynamic characteristics of the process of the impact of changes in the distinction between the effects of so disturbed overshoot controller will have to create a self-adaptive unnecessary conversion. In addition, since the control law based on the maturity of the system is not the stability of analytical methods, the reliability of parameter tuning, there are many problems.Therefore, many self-tuning PID controller parameters work in the auto-tuning mode and not in the self-tuning mode. Auto-tuning is oftenused to describe the state of open-loop based on a simple process model to determine automatic calculation of PID parameters.PID in controlling nonlinear, time-varying, coupling and parameter uncertainty and structural complexity of the process, the work is not very good. The most important thing is, if the PID controller can not control the complexity of the process, regardless of how not to use transfer parameters.Despite these shortcomings, PID controller is sometimes the most simple is the best controller.At present, the level of industrial automation has become a measure of the level of modernization in all walks of life an important sign. At the same time, the development of control theory has also experienced a classical control theory, modern control theory and intelligent control theory of three stages. Classic example of intelligent control is ambiguous, such as full-automatic washing machine. Automatic control system can be divided into open-loop control systems and closed-loop control system.A control system, including controllers, sensors, transmitters, implementing agencies, input and output interfaces. Controller's output after the output interface, the implementing agencies, added to the system was charged with; control system charged with the amount, after the sensor, transmitter, through the input interface to the controller. Different control system, the sensor, transmitter, the executing agency is not the same. For example pressure sensors need to be used in pressure control system. Electric heating control system is the sensor temperature sensor. At present, PID control and PID controller or a smart controller (instrument) has a lot of products have been in practice in engineering is widely used, there are a wide range of PID controller products, major companies have developed with PID parameter self-tuning regulator function smart (intelligent regulator), which the PID controller parameters are automatically adjusted through the intelligent or self-tuning, adaptivealgorithms to achieve. PID control are achieved using pressure, temperature, flow, liquid level controller, PID control functions to achieve the programmable logic controller (PLC), also enables the PC system, PID control and so on. Programmable Logic Controller (PLC) is the use of its closed-loop control module to achieve PID control, and programmable logic controller (PLC) can be connected directly with the ControlNet, such as Rockwell's PLC-5 and so on. There can be the controller PID control functions, such as Rockwell's Logix product line, it can be connected directly with the ControlNet, using the Internet to achieve its long-range control functions.1, Open-loop control systemOpen-loop control system is the object of the output (volume control) on the controller does not affect the output. In this control system, do not rely on volume will be charged back to the formation of anti-any closed-loop circuit.2, Closed-loop control systemClosed-loop control system is characterized by the output of the system object (volume control) will be sent back to the impact of anti-output controller to form one or more of the closed-loop. Closed-loop control system has positive feedback and negative feedback, if the feedback signal and the system to set the value of the signal the other hand, is referred to as negative feedback, if the same polarity is called positive feedback, the general closed-loop control system using negative feedback, also known as negative feedback control system. Closed-loop control system has many examples. For example, people with negative feedback is a closed-loop control system, the eye is the sensor to act as a feedback, the human body system through the constant variety of the right to make amendments to the final action. If there are no eyes, there is no feedback loops, it became an open-loop control system. Another example, when a full-automatic washing machine with a realcontinuously check whether the washed clothing, and wash off automatically after the power supply, it is a closed-loop control system.3, Step responseStep response refers to a step input (step function) when added to the system, the system output. Steady-state error is the system response into the steady-state, the system's desired output and actual output of the difference. The performance of control system can be stable, accurate and fast three words to describe. Stability is the stability of the system, a system must be able to work, first of all must be stable, from the step response should be a convergence point of view; quasi-control system refers to the accuracy, control precision, stability is usually state error description, it said the system output steady-state value and the difference between expectations; fast control system refers to the rapid response, and usually to a quantitative description of the rise time.4, Theory and the characteristics of PID controlIn engineering practice, the most widely used control laws regulate the proportional, integral, differential control, referred to as PID control, also known as PID regulator. PID controller has been available for nearly 70 years of history, which in its simple structure, stable, reliable, easy to adjust and become the main industrial control technologies. When charged with the structure and parameters of the object can not completely grasp, or lack of accurate mathematical model, control theory it is difficult using other techniques, the system controller structure and parameters have to rely on experience and on-site testing to determine when the application PID control of the most convenient technology. That is, when we do not fully understand the system and charged with an object, or can not be an effective means of measuring system parameters to obtain the most suitable PID control technology. PID control, in practice there are PI and PD control. PID controller is the error of the system, using proportional, integral, differential calculationfor the control of the volume control.The ratio of (P) controlProportional control is one of the most simple control methods. The controller's output and input error signal proportional to the relationship. The output has the existence of steady-state error when there is only a proportional control system.Integral (I) controlIn integral control, the controller's output and input error signal is proportional to the integral relationship. For an automatic control system, if steady-state error exists after entering the steady-state, the control system is referred to as steady-state error or having a poor system. In order to eliminate steady-state error, the controller must be the introduction of the "key points." Points of error depend on the time of the points of the increase over time, will increase the integral term. In this way, even if the error is very small, integral term will increase as time increases, it increased to promote the output of the controller so that steady-state error further reduced until zero. Therefore, the proportional + integral (PI) controller, you can make the system after entering the steady-state non-steady-state error.Differential (D) controlIn the differential control, the controller's output and input of the differential error signal (the rate of change of error) is directly proportional to the relationship. Automatic control system to overcome the errors in the adjustment process may be unstable or even oscillation. The reason is because of greater inertial components (links) or there is lag components, can inhibit the role of error, the changes always lag behind changes in error. The solution is to inhibit the changes in the role of error "in advance", that is close to zero in the error and suppress the role of error should be zero. This means that the controller only the introduction of the "proportion" of often is not enough, the proportion of the role isonly to enlarge the amplitude error, the current need to increase the "differential item" that can change the trend of prediction error, In this way, with the proportion of + differential controller, will be able to advance so that the role of inhibitory control error equal to zero or even negative, thus avoiding the amount charged with a serious overshoot. Therefore, greater inertia of the charged object or lag, the proportion of + differential (PD) controller to improve the system in the regulation of the dynamic characteristics of the process.PID控制简介当今的自动控制技术都是基于反馈的概念。
毕业论文外文翻译-基于智能PID调节的连续烧结炉温度控

毕业设计/论文外文文献翻译系别机电与自动化学院专业班级电气0703姓名评分指导教师教授华中科技大学武昌分校2011 年1 月20日毕业设计/论文外文文献翻译要求:1.外文文献翻译的内容应与毕业设计/论文课题相关。
2.外文文献翻译的字数:非英语专业学生应完成与毕业设计/论文课题内容相关的不少于2000汉字的外文文献翻译任务(其中,汉语言文学专业、艺术类专业不作要求),英语专业学生应完成不少于2000汉字的二外文献翻译任务。
格式按《华中科技大学武昌分校本科毕业设计/论文撰写规范》的要求撰写。
3.外文文献翻译附于开题报告之后:第一部分为译文,第二部分为外文文献原文,译文与原文均需单独编制页码(底端居中)并注明出处。
本附件为封面,封面上不得出现页码。
4.外文文献翻译原文由指导教师指定,同一指导教师指导的学生不得选用相同的外文原文。
2008年国际计算机、电子工程会议基于智能PID调节的连续烧结炉温度控制系统曹树坤,张亚兰,张亨(济南大学机械工程学院·中国济南)摘要:为满足在多个炉床的连续烧结炉精确温度控制精度的要求,该系统是由电脑XMT624和对温度场控制的固态继电器组成。
根据烧结炉加热过程中的温度惯性、时滞的特点,采用智能PID算法来实现大范围温度调节,克服了传统PID控制的局限。
通过在线实时设置智能指令单元, 该系统可以达到2‰的温度控制精度目标。
关键词:1 引言连续烧结炉是一种常用的为金属粉末注射塑料件加热设备,它包含了脱脂和调试的过程。
在粗糙的部分通过脱脂炉后,然后通过一个封闭的输送带进入水平连续烧结炉。
脱脂炉和烧结炉由两台炉子门分隔。
其主要部分被分为加热、烧结、冷却三部分。
连续烧结炉的烧结质量取决于温度的均匀性和烧结过程的稳定性,连续烧结炉的温度控制系统是一个大时滞、非稳定、非线性复杂系统,烧结温度也受到外部因素的影响,如炉门开关、燃气流量。
因此,使用传统的控制方法不能满足连续烧结炉温度控制要求[1-2]。
26421252_变论域模糊PID在无头轧制模拟实验台上的研究
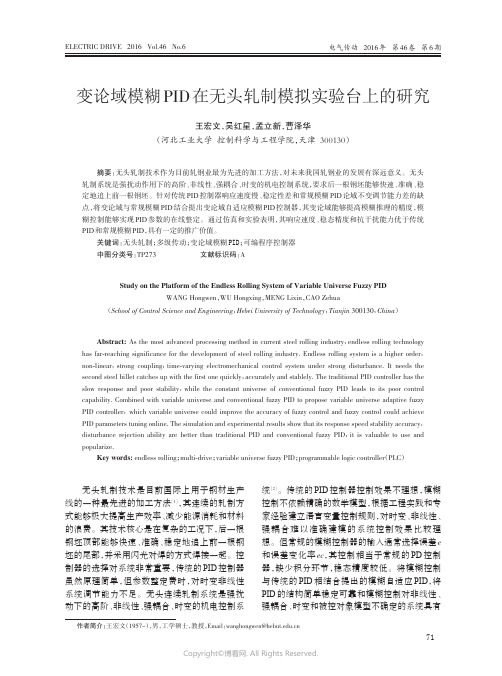
电气传动2016年第46卷第6期变论域模糊PID 在无头轧制模拟实验台上的研究王宏文,吴红星,孟立新,曹泽华(河北工业大学控制科学与工程学院,天津300130)摘要:无头轧制技术作为目前轧钢业最为先进的加工方法,对未来我国轧钢业的发展有深远意义。
无头轧制系统是强扰动作用下的高阶、非线性、强耦合、时变的机电控制系统,要求后一根钢坯能够快速、准确、稳定地追上前一根钢坯。
针对传统PID 控制器响应速度慢、稳定性差和常规模糊PID 论域不变调节能力差的缺点,将变论域与常规模糊PID 结合提出变论域自适应模糊PID 控制器,其变论域能够提高模糊推理的精度,模糊控制能够实现PID 参数的在线整定。
通过仿真和实验表明,其响应速度、稳态精度和抗干扰能力优于传统PID 和常规模糊PID ,具有一定的推广价值。
关键词:无头轧制;多级传动;变论域模糊PID ;可编程序控制器中图分类号:TP273文献标识码:AStudy on the Platform of the Endless Rolling System of Variable Universe Fuzzy PID WANG Hongwen ,WU Hongxing ,MENG Lixin ,CAO Zehua(School of Control Science and Engineering ,Hebei University of Technology ,Tianjin 300130,China )Abstract:As the most advanced processing method in current steel rolling industry ,endless rolling technologyhas far -reaching significance for the development of steel rolling industry.Endless rolling system is a higher order ,non -linear ,strong coupling ,time -varying electromechanical control system under strong disturbance.It needs the second steel billet catches up with the first one quickly ,accurately and stablely.The traditional PID controller has the slow response and poor stability ,while the constant universe of conventional fuzzy PID leads to its poor control bined with variable universe and conventional fuzzy PID to propose variable universe adaptive fuzzy PID controller ,which variable universe could improve the accuracy of fuzzy control and fuzzy control could achievePID parameters tuning online.The simulation and experimental results show that its response speed stability accuracy ,disturbance rejection ability are better than traditional PID and conventional fuzzy PID ,it is valuable to use and popularize.Key words:endless rolling ;multi -drive ;variable universe fuzzy PID ;programmable logic controller (PLC )作者简介:王宏文(1957-),男,工学硕士,教授,Email :*********************.cnELECTRIC DRIVE 2016Vol.46No.6无头轧制技术是目前国际上用于钢材生产线的一种最先进的加工方法[1],其连续的轧制方式能够极大提高生产效率、减少能源消耗和材料的浪费。
PID文献翻译-自动化讲解

PID控制器比例积分微分控制器(PID调节器)是一个控制环,广泛地应用于工业控制系统里的反馈机制。
PID控制器通过调节给定值与测量值之间的偏差,给出正确的调整,从而有规律地纠正控制过程。
PID控制器算法涉及到三个部分:比例,积分,微分。
比例控制是对当前偏差的反应,积分控制是基于新近错误总数的反应,而微分控制则是基于错误变化率的反应。
这三种控制的结合可用来调节过程系统,例如调节阀的位置,或者加热系统的电源调节。
根据具体的工艺要求,通过PID控制器的参数整定,从而提供调节作用。
控制器的响应可以被认为是对系统偏差的响应。
注意一点的是,PID算法不一定就是系统或系统稳定性的最佳控制。
一些应用可能只需要运用一到两种方法来提供适当的系统控制。
这是通过把不想要的控制输出置零取得。
在控制系统中存在P,PI,PD,PID调节器。
PI调节器很普遍,因为微分控制对测量噪音非常敏感。
积分作用的缺乏可以防止系统根据控制目标而达到它的目标值。
注释:由于控制理论和应用领域的差异,很多相关变量的命名约定是常用的。
控制环基础一个关于控制环类似的例子就是保持水在理想温度,涉及到两个过程,冷、热水的混合。
人可以凭触觉估测水的温度。
基于此他们设计一个控制行为:用冷水龙头调整过程。
重复这个过程,调节热水流直到温度处于期望的稳定值。
感觉水温就是对过程值或变量的测量。
期望得到的温度称为给定值。
控制器的输出对象和过程的输入对象称为控制参数。
测量值与给定值之间的差就是偏差值,太高、太低或正常。
作为一个控制器,在确定温度给定值后,就可以粗略决定改变阀门位置多少,以及怎样改变偏差值。
首次估计即是PID 控制器的比例度的确定。
当它几乎正确时,PID控制器的积分作用就是起着逐渐调整温度的作用。
微分作用就是根据水温变得更热、更冷,以及变化速率来决定什么时候、怎样调整那些阀门。
当偏差小时而做了一个大变动,相当于一个大的调整控制器,会导致超调。
如果控制器反复进行大的变动并且反复越过给定值的改变,控制环将会不稳定。
MATLAB的PID控制算法的研究报告
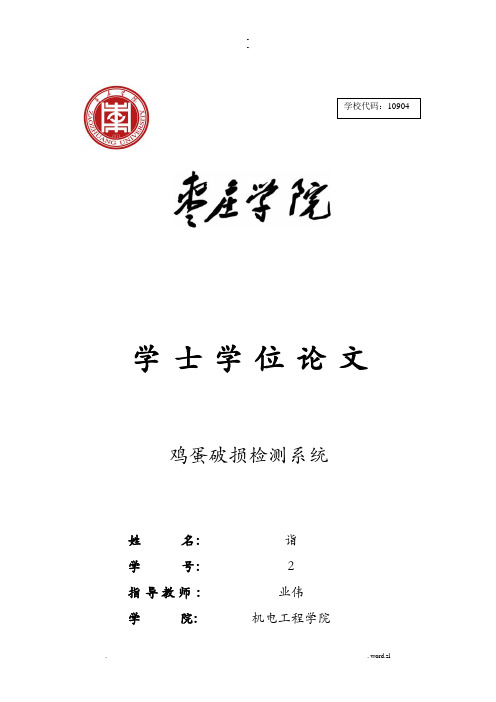
学校代码:10904学士学位论文鸡蛋破损检测系统姓名:诣学号: 2指导教师:业伟学院:机电工程学院专业:机械设计制造及其自动化完成日期:2021 年4月26日学士学位论文基于MATLAB的PID控制算法的研究姓名:学号:指导教师:学院:专业:完成日期:. - -摘要PID控制是一种便捷、稳定、直观的控制方式,它因为原理简单、控制效果好、应用对象广、并且易于实现而被广泛地应用于工程控制以及工业实践当中,也是迄今为止应用最为理想的一种控制方式。
当被控对象的构造和参数不能完全掌握,或得不到准确的数学模型时,控制理论的其他技术难以采用时,系统控制器的构造和参数必须依靠经历和现场调试来确定,这时应用PID控制技术最为方便。
即当我们不完全了解一个系统和被控对象,或不能通过有效的测量手段来获得系统参数时,最适合用PID控制技术。
本文在详尽阐述PID控制的根本原理和开展现状的根底上,对PID控制算法进展了深入的分析和研究,对几种PID控制算法的优缺点进展了比拟,改良了传统的PID控制算法,进展了PID控制参数整定,通过MATLAB/Simulink仿真直观的显示控制效果,进一步比拟分析,针对具体对象选择更加适宜的控制算法,为PID控制在实际工程中的广泛应用提供了行之有效的计算方法,大大节约了物资人力,提高了系统的工作效率。
关键词:PID;控制算法;MATLAB/Simulink;仿真;参数整定ABSTRACTThe control of PID is a kind of convenient, stable and intuitive control mode, it is because of simple principle, good control effect, wide application object, and is easy to implement and widely used in engineering control and industrial practice, It is the most ideal one way to control by far. When the structure and parameters of the controlled object is not be fully grasped, or not be a precise mathematical model, the control theory of other technology is difficult to use, the structure and parameters of system controller must depend on experience and on-site missioning to determine, then the application of PID control technology is the most convenient. When we don't fully understand a system and the controlled object, or cannot obtain system parameters through effective measures, It is most suitable for PID control technology.Detailed in this paper, the PID control is presented on the basis of the basic principle and development present situation, the PID control algorithm is carried on the thorough analysis and research, pares the advantages and disadvantages of several kinds of PID control algorithm, and improved the traditional PID control algorithm, through the MATLAB/Simulink intuitive display control effect, and further parative analysis, in view of the concrete object to choose more appropriate control algorithm, for PID control is widely used in practical engineering provides a effective calculation method, greatly saves materials for human, improve the work efficiency of the system.Key words: PID; Control algorithm; MATLAB/Simulink; The simulation;Parameter setting目录第1章绪论 (1)1.1 PID控制研究的开展和现状 (1)1.2设计目的和意义 (2)1.3设计的主要任务 (3)第2章PID控制算法32.1 PID控制原理 (3)2.2数字PID控制算法 (5)2.2.1 PID控制离散化52.2.2位置式PID控制算法 (6)2.2.3增量式PID控制算法 (7)2.2.4 位置式与增量式PID控制算法优缺点比拟 (8)2.3 改良型PID控制算法 (8)2.3.1积分项的改良 (8)2.3.2微分项的改良 (9)第3章PID参数整定及仿真 (12)3.1 PID参数整定的定义 (12)3.2 PID参数整定方法 (12)3.3 PID参数对控制系统的影响 (15)总结与展望 (23)致 (24)参考文献 (25)第1章绪论1.1 PID控制研究的开展和现状PID控制器起源并开展于二十世纪初,经过50多年的努力取得了颇为丰硕的成果。
PID控制中英文对照翻译

外文资料与翻译PID Contro l6.1 IntroductionThe PID controller is the most common form of feedback. It was an essential element of early governors and it became the standard tool when process control emerged in the 1940s. In process control today, more than 95% of the control loops are of PID type, most loops are actually PI control. PID controllers are today found in all areas where control is used. The controllers come in many different forms. There are standalone systems in boxes for one or a few loops, which are manufactured by the hundred thousands yearly. PID control is an important ingredient of a distributed control system. The controllers are also embedded in many special purpose control systems. PID control is often combined with logic, sequential functions, selectors, and simple function blocks to build the complicated automation systems used for energy production, transportation, and manufacturing. Many sophisticated control strategies, such as model predictive control, are also organized hierarchically. PID control is used at the lowest level; the multivariable controller gives the set points to the controllers at the lower level. The PID controller can thus be said to be the “bread and butter of control engineering. It is an important component in every control engineer’s tool box.PID controllers have survived many changes in technology, from mechanics and pneumatics to microprocessors via electronic tubes, transistors, integrated circuits. The microprocessor has had a dramatic influence the PID controller. Practically all PID controllers made today are based on microprocessors. This has given opportunities to provide additional features like automatic tuning, gain scheduling, and continuous adaptation.6.2 AlgorithmWe will start by summarizing the key features of the PID controller. The “textbook” version of the PID algorithm is described by:()()()()⎪⎪⎭⎫ ⎝⎛++=⎰dt t de d e t e K t u T T d t i 01ττ 6.1 where y is the measured process variable, r the reference variable, u is the control signal and e is the control error (e =sp y − y ). The reference variable is often calledthe set point. The control signal is thus a sum of three terms: the P-term (which is proportional to the error), the I-term (which is proportional to the integral of the error), and the D-term (which is proportional to the derivative of the error). The controller parameters are proportional gain K, integral time T i, and derivative time T d. The integral, proportional and derivative part can be interpreted as control actions based on the past, the present and the future as is illustrated in Figure 2.2. The derivative part can also be interpreted as prediction by linear extrapolation as is illustrated in Figure 2.2. The action of the different terms can be illustrated by the following figures which show the response to step changes in the reference value in a typical case.Effects of Proportional, Integral and Derivative ActionProportional control is illustrated in Figure 6.1. The controller is given by D6.1E with T i= and T d=0. The figure shows that there is always a steady state error in proportional control. The error will decrease with increasing gain, but the tendency towards oscillation will also increase.Figure 6.2 illustrates the effects of adding integral. It follows from D6.1E that the strength of integral action increases with decreasing integral time T i. The figure shows that the steady state error disappears when integral action is used. Compare with the discussion of the “magic of integral action” in Section 2.2. The tendency for oscillation also increases with decreasing T i. The properties of derivative action are illustrated in Figure 6.3.Figure 6.3 illustrates the effects of adding derivative action. The parameters K and T i are chosen so that the closed loop system is oscillatory. Damping increases with increasing derivative time, but decreases again when derivative time becomes too large. Recall that derivative action can be interpreted as providing prediction by linear extrapolation over the time T d. Using this interpretation it is easy to understand that derivative action does not help if the prediction time T d is too large. In Figure 6.3 the period of oscillation is about 6 s for the system without derivative Chapter 6. PID ControlFigure 6.1Figure 6.2Derivative actions cease to be effective when T d is larger than a 1 s (one sixth of the period). Also notice that the period of oscillation increases when derivative time is increased.A PerspectiveThere is much more to PID than is revealed by (6.1). A faithful implementation of the equation will actually not result in a good controller. To obtain a good PID controller it is also necessary to consider。
0PID Control

Control Engineering Practice 9(2001)1159–1161PrefacePID ControlAt the beginning of the new millennium the PID controller continuesto be a key component of indus trial control.During the last century many different struc-turesof control have been propos ed to overcome the limitations of PID controllers.Due to their simplicity and usefulness they constitute a powerful solution to the control of a large number of industrial processes.The present-day structure of PID controllers is quite different from the original analogue PID controllers.Now,the implementation of the PID isbas ed on a digital design.These digital PID include many algo-rithmsto improve their performances ,s uch asanti-wind-up,auto-tuning,adaptive,fuzzy fine-tuning.How-ever,the basic actions remain the same.There has been a strong resurgence in the interest towards the PID control over the last few years.Many publicationshave appeared (s ee Fig.1)(Bennett,2000).Many of the new capabilitieshave been introduced by the research community.The industrial control users easily,and sometimes enthusiastically,apply these innovations.The PID control has become one of the most important ways,for the scientific and the industrial control users to work together.In 2000an IFAC Workshop on Digital Control was held in Terrassa (Barcelona,Spain)to analyse the PID history,the evolution of PID,the benefits and draw-backsof PID control applications .New tuning rulesand auto-tuning techniques were presented in the Workshop.The PID was also presented as a building block within more complex controllers,such as non-linear or DMC controllers.Software packages for optimal PID control design were the subject of some papers.The scientific and technical level of more than 100paperspres ented in thisWorks hop wasin general high.The number of attendees,around 150from 30countries,was unusually high for an IFAC Workshop.This Special Issue of Control Engineering Practice on PID control was initially based on 16pre-selected papers of those presented in the Workshop.After a process of revision and improvement 10papers were chosen:*1paper presents the state of the art of PID control and discusses about its future.*4papersinclude s ome contributionson PID tuning of industrial processes:SISO,MIMO,non-linear and/or with dominant dead-time features.*3papersdeal with new s tructure for ratio control,fault-tolerant control and PID controllersus ing smart actuator and fieldbus technologies.*2papersreported PID control applicationsof power hydraulic turbines,AC-motor drives or Optical disc drives.The paper ‘‘The future of PID control’’by K.J.Astr .o m and T.Ha gglund,Department of Automatic Control,Lund University,Sweden,presents the state of the art of PID control and some reflections about its future.Particular issues discussed include specifications,stability regions,design,and performance assessment.An evaluation of competing strategies,general linear controllers,model predictive control and controllers based on state feedback and observers,gives the basis for discussing the future of PID control.Deciding issues are performance,tuning,maintenance and particularly ease of use.The first paper on new procedures for PID tuning is ‘‘PID-deadtime control of distributed processes’’by F.G.Shinskey,Process Control Consultant,USA.The performancesof PID controllershaving time-delay compensation are compared with respect to other structures,such as the internal model control or conventional PID control for distributed lag processes.The author givesthree controller s ettingsfor optimum load regulation (Integral Absolute Error)of distributed processes.The PID-Deadtime controller is then success-fully applied to the temperature control of superheaters in a 500MW power boiler in Ontario.The paper entitled ‘‘Optimal-tuning PID control for industrial systems’’by G.P.Liu and S.Daley,from the Mechanical School of the University of Nottingham and ALSTOM Power Technology Centre,Great Britain,presents the design of three optimal-tuning PID controllers for industrial processes.These schemes are based on time-domain,frequency-domain and multi-objective optimal-tuning design goals.They have been successfully applied to three industrial processes:an hydraulic position control system,a rotary hydraulic speed control system and a MIMO gasifier of an IGCC power plant.The experimental results show good performancesof thes e optimal-tuning PID controllers even though there are changes in the process dynamics.0967-0661/01/$-see front matter r 2001Elsevier Science Ltd.All rights reserved.PII:S 0967-0661(01)00061-2‘‘Robust tuning procedures of dead-time compensat-ing controllers’’by A.Ingimundarson and T.H .agglund from the Automatic Control Department of the Lund Institute of Technology,Sweden,describes new tuning procedures for dead-time controllers for real processes which are described by first-order plus dominant dead-time modelsand by two-parameter integrating models .An identification method based on experimental results in open and closed loop is used.The dead-time controllers presented in this paper are based on some extension of the well-known Smith Predictor.This study dealswith the des ign of automatic tuning proceduresfor these dead-time controllers applied to stable and unstable processes.An analysis of the sensitivity to dead-time errorsisals o included.Finally,the methodol-ogy has been successfully applied to a tank laboratory process.The paper ‘‘Mobile robot path tracking using a robust PID controller’’by J.E.Normey-Rico from the Dept.de Automac ao e Sistemes of Federal University of SantaCatarina,Brazil,I.Alcal !a,J.G !o mez-Ortega and E.F.Camacho from the Dep.Ingenier !ıa de Sistemas yAutom !atica,University of Sevilla,Spain,deals with a methodology for tuning PID controllers.The structure of the PID controllersincludesa reference filter for stable processes and a cascade loop with a proportional gain for integrating processes.The parameters of the controllersare tuned us ing the root locusmethod,looking for quick response without oscillations.The robust performances of this methodology are also analysed.Finally,it has been applied to a mobile robot path tracking problem and the experimental results show good performance in spite of delay estimation uncertainties.The next paper proposes a new structure for ratio control to overcome the poor performancesof the classical ratio control structure during transients caused by setpoint changes.The title of this paper is ‘‘The blendstation.a new ratio control structure’’by T.H .agglund from the Automatic Control Department,Lund In-stitute of Technology.The suggested Blend station demonstrates the improved performances during tran-sients through simulations as well as applied to a pulpbleaching process.Constant-gain and adaptive version of the proposed blend station are described in the paper.The paper ‘‘Fault-tolerant PID controllersus ing a passive robust fault diagnosis approach’’by V.Puig and J.Quevedo from the Automatic Control Department of Polytechnical University of Catalonia,Spain,presents a complete scheme of fault-tolerant control.The paper describes an analytical redundancy method to detect faultsin the proces son real time.When a fault occursa robust fault diagnosis module,named DMP,is used for residual generation and decision making in order to find out the location of the faultsand finally,from the analysis of the system recoverability,a supervisor system activatesaccommodation actionsto get a fault-tolerant system.The proposed methodology has been success-fully applied to two interconnected tankswhere a level sensor fault has been simulated.The fault-tolerant PID detects a fault,isolates the fault in the level sensor and,in order to close the loop,changes the measure of the sensor by an estimator.The paper,‘‘PID control for a distributed system with a smart actuator’’by D.Lee,J.Allan,A.Thompson and S.Bennett from Rolls-Royce University Technol-ogy Centre and Automatic Control Department of Sheffield University,Great Britain,describes how a smart actuator technology can improve the PID control performances in the presence of undesirable actuator characteristics.The proposed smart actuator is imple-mented using an add-on intelligence,CAN bus and an actuator rig.The smart actuator is applied to on-line PID controller retuning using a distributed architecture demonstrator to counteract degraded actuator perfor-mances.The first paper of PID control applications is ‘‘Digital servo IC for optical disc drives’’by T.H.Akkermans and S.G.Stan from PhilipsOptical Storage,The Netherlands.This paper deals with several control problemsin high and very high-s peed optical dis c drives.The conventional PID controllers are not only useful in the disc standards for reference purposes but also to properly control the laser spot in focus and on track.The paper presents a fully programmable servo integrated circuit implementation to perform the men-tioned control task and it describes the functionality and the advantages of using the proposed control architec-ture for optical disc drives.Finally,the paper entitled,‘‘Dynamic model reference PI control of permanent magnet AC motor drives’’by P.Stewart and V.Kadirkamanathan from the Auto-matic Control and System Engineering Department of Sheffield University,describes the application of PI current controllersto permanent magnet AC motor drives.A non-linear model reference scheme including the constraints of the system has been used in this application.Two PI current regulatorsallow to track the non-linear model reference command valuesinorderFig.1.PID publications historical evolution in the last 30yr.Preface /Control Engineering Practice 9(2001)1159–11611160to achieve an optimal torque speed trajectory.The proposed algorithm has been implemented on an experimental dynamometer test rig.The results maintain proper control of the current vector at all times throughout the operating range of the AC motor.We hope that the readerswillfind the papers presented in this special issue of interest for them.This selection of PID control papers shows that nowadays it is possible to contribute to the improvement of control science using PID control structures.It is also very important to know that any improvement on PID control performancescan have a huge impact in the industrial society due to the high degree of its use in industrial processes.We would like to thank all the contributing authors and many reviewers.In fact we had a very difficult task to select only10papers out of over100preliminary papers presented in PID’00IFAC Workshop.Finally, we would also like to thank Prof.George Irwin,CEP Editor-in chief and hiss tafffor their encouragement and assistance on this PID special issue.ReferencesBennett,S.,(2000).The past of PID controllers.Proceedin g s Volume of Di g ital Control:Past,Pr s nt and Futur of PID Control IFAC Workshop,Pergamon Elsevier Science,Great Britain,pp.1–11.ISBN0-08-0436242.Karl J.A str.o mDepartment of Automatic Control,Lund University,Lund,SwedenPedro AlbertosDepartment of Automatic Control,Polytechnical University of Valencia,Valencia,SpainJoseba QuevedoDepartment of Automatic Control, Polytechnical University of Catalonia UPC,Campus de Terrassa,C/Colom.1108222,Terrassa,Barcelona,SpainE-mail address:joseba@esaii.upc.esPreface/Control Engineering Practice9(2001)1159–11611161。
中英文翻译--常规PID和模糊PID算法的分析比较

中英文翻译--常规PID和模糊PID算法的分析比较毕业设计(论文) 中英文资料信电系工业电气自动化专业 03 级 1 班课题名称:基于单片机的模糊PID温度控制系统设计毕业设计(论文)起止时间:2006 年 2月15日,6月8日(共17周)学生姓名: 学号: 20指导教师:报告日期: 2006年6月8日信息与电子工程系毕业设计(中英文资料)常规PID和模糊PID算法的分析比较摘要:模糊PID控制器实际上跟传统的PID控制器有很大联系。
区别在于传统的控制器的控制前提必须是熟悉控制对象的模型结构,而模糊控制器因为它的非线性特性,所以控制性能优于传统PID控制器。
对于时变系统,如果能够很好地采用模糊控制器进行调节,其控制结果的稳定性和活力性都会有改善。
但是,如果调节效果不好,执行器会因为周期振荡影响使用寿命,特别是调节器是阀门的场合,就必须考虑这个问题。
为了解决这个问题,出现了很多模糊控制的分析方法。
本文提出的方法采用一个固定的初始域,这样相当程度上简化了模糊控制的设定问题以及实现。
文中分析了振荡的原因并分析如何抑制这种振荡的各种方法,最后,还给出一种方案,通过减少隶属函数的数量以及改善解模糊化的方法缩短控制信号计算时间,有效的改善了控制的实时性。
1 引言模糊控制器的一个主要缺陷就是调整的参数太多。
特别是参数设定的时候,因为没有相关的书参考,所以它的给定非常困难。
众所周知,优化方法的收敛性跟它的初始化设定有很大关联,如果模糊控制器的初始域是固定的,那么它的控制就明显的简化了。
而且我们要控制的参数大多有其实际的物理意义,所以模糊控制器完全可以利用PID算法的控制规律进行近似的调整。
也就是说最简单的模糊PID控制器就是同时采用几种基本模糊控制算法(P+I+D或者PI+D),控制过程中它会根据控制要求,做出适当的选择,保证在处理跟踪以抗阶跃干扰问题上,其控制性能接近于任何一种PID控制。
假设模糊集的初始域是对称的,两个调节器的参数采用Ziegler-Nichols方法。
实验反应堆功率调节系统PID控制器的解析设计方法
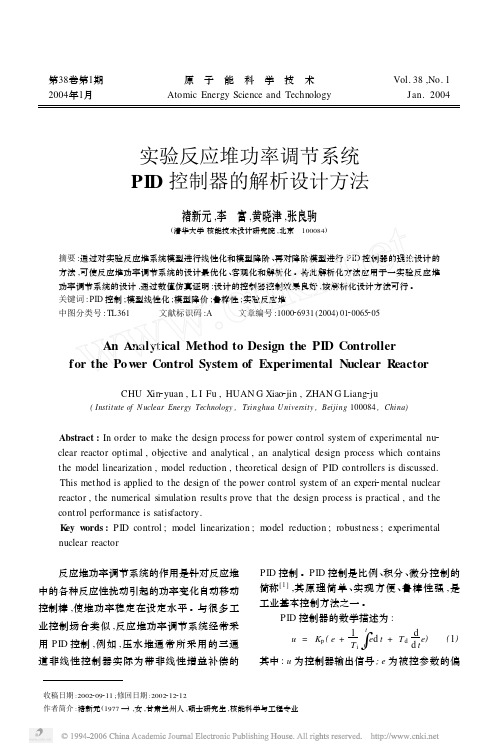
第38卷第1期原子能科学技术Vol.38,No.1 2004年1月Atomic Energy Science and TechnologyJan.2004实验反应堆功率调节系统PID 控制器的解析设计方法褚新元,李 富,黄晓津,张良驹(清华大学核能技术设计研究院,北京 100084)摘要:通过对实验反应堆系统模型进行线性化和模型降阶、再对降阶模型进行PID 控制器的理论设计的方法,可使反应堆功率调节系统的设计最优化、客观化和解析化。
将此解析化方法应用于一实验反应堆功率调节系统的设计,通过数值仿真证明:设计的控制器控制效果良好,该解析化设计方法可行。
关键词:PID 控制;模型线性化;模型降价;鲁棒性;实验反应堆中图分类号:TL361 文献标识码:A 文章编号:100026931(2004)0120065205An Analytical Method to Design the PID Controllerfor the Pow er Control System of Experimental Nuclear R eactorCHU Xin 2yuan ,L I Fu ,HUAN G Xiao 2jin ,ZHAN G Liang 2ju(Institute of N uclear Energy Technology ,Tsinghua U niversity ,Beijing 100084,China )Abstract :In order to make the design process for power control system of experimental nu 2clear reactor optimal ,objective and analytical ,an analytical design process which contains the model linearization ,model reduction ,theoretical design of PID controllers is discussed.This method is applied to the design of the power control system of an experi 2mental nuclear reactor ,the numerical simulation results prove that the design process is practical ,and the control performance is satisfactory.K ey w ords :PID control ;model linearization ;model reduction ;robustness ;experimental nuclear reactor收稿日期:2002209211;修回日期:2002212212作者简介:褚新元(1977—),女,甘肃兰州人,硕士研究生,核能科学与工程专业 反应堆功率调节系统的作用是针对反应堆中的各种反应性扰动引起的功率变化自动移动控制棒,使堆功率稳定在设定水平。
基于正交试验法整定主动悬架PID控制器参数

第35卷第1期2021年1月山东理工大学学报(自然科学版)Journal of Shandong University of Technology(Natural Science Edition)Vol.35No.1Jan.2021文章编号:1672-6197(2021)01-0063-06基于正交试验法整定主动悬架PID控制器参数张裕晨1,高坤明1,路艳玲2,郭宗和1,马驰骋1(1.山东理工大学交通与车辆工程学院,山东淄博255049;2.莱芜职业技术学院机械与汽车工程系,山东莱芜271100)摘要:针对主动悬架PID控制器参数整定问题,运用Matlab/Simulink软件搭建基于PID控制策略的汽车1/4主动悬架模型以及路面时域模型,以整定PID控制器的P参数为例,通过设计寻取轮胎动载荷最小极差值的正交试验与结果分析,得到了单一评价指标下的P参数相对最优值与相对最优区间,达到了提升汽车平顺性能的目的。
关键词:主动悬架;Matlab/Simulink;正交试验法;极差分析;参数整定中图分类号:U467.4+99文献标志码:ASetting active PID controller parameters based on orthogonal test methodZHANG Yuchen1,GAO Kunming1,LU Yanling2,GUO Zonghe1,MA Chicheng1(1.School of Transportation and Vehicle Engineering,Shandong University of Technology,Zibo255049,China;2.Department of Machinery and Automotive,Laiwu Vocational and Technical College,Laiwu271100,China)Abstract:Aiming at the problem of parameter setting of active suspension PID controller,this paper uses Matlab/Simulink software to build a1/4active suspension model and pavement time domain model based on PID control strategy.Taking the P parameter of the PID controller as an example,the orthogonal test seeking the minimum differential value of the dynamic load of the tire is designed and anglyzed.The relative optimal value and relative optimal interval of the P parameter under the single evaluation index are obtained,achieving the purpose of improving the smoothness of the car.Keywords:active suspension;Matlab/Simulink;range analysis;orthogonal test;parameter tuningPID算法凭借其结构简单易实现、良好稳定性、工作可靠等优点在过程控制应用领域有广泛的应用[1],但基于PID控制策略设计的控制器,其控制品质很大程度上受控制参数的影响,因而优化控制参数对于提升PID控制器的控制品质尤为重要。
模糊PID控制器的鲁棒性研究外文文献翻译
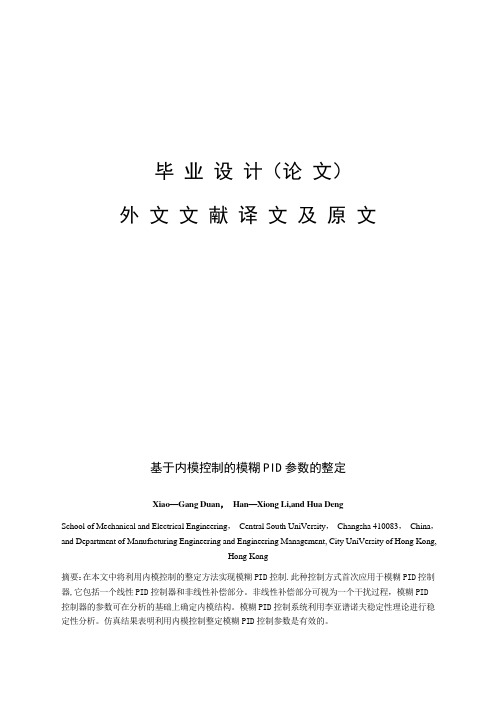
毕业设计(论文)外文文献译文及原文基于内模控制的模糊PID参数的整定Xiao—Gang Duan,Han—Xiong Li,and Hua DengSchool of Mechanical and Electrical Engineering,Central South UniVersity,Changsha 410083,China,and Department of Manufacturing Engineering and Engineering Management, City UniVersity of Hong Kong,Hong Kong摘要:在本文中将利用内模控制的整定方法实现模糊PID控制.此种控制方式首次应用于模糊PID控制器,它包括一个线性PID控制器和非线性补偿部分。
非线性补偿部分可视为一个干扰过程,模糊PID控制器的参数可在分析的基础上确定内模结构。
模糊PID控制系统利用李亚谱诺夫稳定性理论进行稳定性分析。
仿真结果表明利用内模控制整定模糊PID控制参数是有效的。
1 引言一般而言,传统的PID 控制器对于十分复杂的被控对象控制效果不太理想, 如高阶时滞系统。
在这种复杂的环境下, 众所周知,模糊控制器由于其固有的鲁棒性可以有更好的表现,因此,在过去30年中,模糊控制器,特别是,模糊PID 控制器因其对于线性系统和非线性系统都能进行简单和有效的控制,已被广泛用于工业生产过程[1—4]。
模糊PID 控制器有多种形式[5],如单输入模糊PID 控制器,双输入模糊PID 控制器和三个输入的模糊PID 控制器。
一般情况下,没有统一的标准。
单输入可能会丢失派生信息, 三输入模糊PID 控制器会产生按指数增长的规则.在本文中所采用的双输入模糊PID 控制器有一个适当的结构并且实用性强,因此在各种研究和应用中,是最流行的模糊PID 类型。
尽管业界对于应用模糊PID 有越来越大的兴趣,但从控制工程的主流社会的角度来看,它仍然是一个极具争议的话题。
PID Controllers - Theory Design and Tuning 翻译
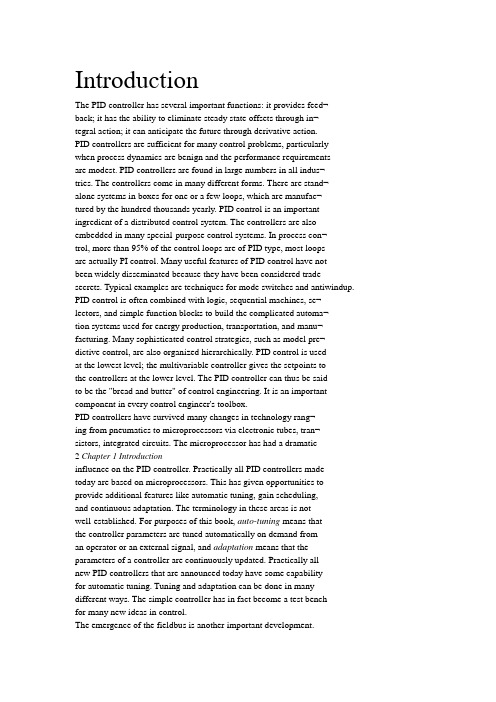
IntroductionThe PID controller has several important functions: it provides feed¬back; it has the ability to eliminate steady state offsets through in¬tegral action; it can anticipate the future through derivative action.PID controllers are sufficient for many control problems, particularly when process dynamics are benign and the performance requirementsare modest. PID controllers are found in large numbers in all indus¬tries. The controllers come in many different forms. There are stand¬alone systems in boxes for one or a few loops, which are manufac¬tured by the hundred thousands yearly. PID control is an important ingredient of a distributed control system. The controllers are also embedded in many special-purpose control systems. In process con¬trol, more than 95% of the control loops are of PID type, most loopsare actually PI control. Many useful features of PID control have notbeen widely disseminated because they have been considered trade secrets. Typical examples are techniques for mode switches and antiwindup. PID control is often combined with logic, sequential machines, se¬lectors, and simple function blocks to build the complicated automa¬tion systems used for energy production, transportation, and manu¬facturing. Many sophisticated control strategies, such as model pre¬dictive control, are also organized hierarchically. PID control is usedat the lowest level; the multivariable controller gives the setpoints tothe controllers at the lower level. The PID controller can thus be saidto be the "bread and butter" of control engineering. It is an important component in every control engineer's toolbox.PID controllers have survived many changes in technology rang¬ing from pneumatics to microprocessors via electronic tubes, tran¬sistors, integrated circuits. The microprocessor has had a dramatic2 Chapter 1 Introductioninfluence on the PID controller. Practically all PID controllers madetoday are based on microprocessors. This has given opportunities to provide additional features like automatic tuning, gain scheduling,and continuous adaptation. The terminology in these areas is notwell-established. For purposes of this book, auto-tuning means thatthe controller parameters are tuned automatically on demand froman operator or an external signal, and adaptation means that the parameters of a controller are continuously updated. Practically allnew PID controllers that are announced today have some capabilityfor automatic tuning. Tuning and adaptation can be done in many different ways. The simple controller has in fact become a test benchfor many new ideas in control.The emergence of the fieldbus is another important development.This will drastically influence the architecture of future distributed control systems. The PID controller is an important ingredient ofthe fieldbus concept. It may also be standardized as a result of the fieldbus development.A large cadre of instrument and process engineers are familiarwith PID control. There is a well-established practice of installing, tuning, and using the controllers. In spite of this there are substantial potentials for improving PID control. Evidence for this can be found in the control rooms of any industry. Many controllers are put in man¬ual mode, and among those controllers that are in automatic mode, derivative action is frequently switched off for the simple reason that it is difficult to tune properly. The key reasons for poor performance is equipment problems in valves and sensors, and bad tuning practice. The valve problems include wrong sizing, hysteresis, and stiction. The measurement problems include: poor or no anti-aliasing filters; excessive filtering in "smart" sensors, excessive noise and improper calibration. Substantial improvements can be made. The incentive for improvement is emphasized by demands for improved quality, which is manifested by standards such as ISO 9000. Knowledge and un¬derstanding are the key elements for improving performance of the control loop. Specific process knowledge is required as well as knowl¬edge about PID control.Based on our experience, we believe that a new era of PID controlis emerging. This book will take stock of the development, assess its potential, and try to speed up the development by sharing our expe¬riences in this exciting and useful field of automatic control. The goal of the book is to provide the technical background for understanding PID control. Such knowledge can directly contribute to better product quality.Process dynamics is a key for understanding any control problem. Chapter 2 presents different ways to model process dynamics thatare useful for PID control. Methods based on step tests are discussed Chapter 1 Introduction 3together with techniques based on frequency response. It is attempted to provide a good understanding of the relations between the different approaches. Different ways to obtain parameters in simple transfer function models based on the tests are also given. Two dimensionfree parameters are introduced: the normalized dead time and thegain ratio are useful to characterize dynamic properties of systems commonly found in process control. Methods for parameter estimation are also discussed. A brief description of disturbance modeling is also given.An in depth presentation of the PID controller is given in Chap¬ter 3. This includes principles as well as many implementation de¬tails, such as limitation of derivative gain, anti-windup, improvement of set point response, etc. The PID controller can be structured in dif¬ferent ways. Commonly used forms are the series and the parallel forms. The differences between these and the controller parameters used in the different structures are treated in detail. Implementationof PID controllers using digital computers is also discussed. The un¬derlying concepts of sampling, choice of sampling intervals, and anti¬aliasing niters are treated thoroughly. The limitations of PID control are also described. Typical cases where more complex controllers are worthwhile are systems with long dead time and oscillatory systems. Extensions of PID control to deal with such systems are discussed briefly.Chapter 4 describes methods for the design of PID controllers. Specifications are discussed in detail. Particular attention is given to the information required to use the methods. Many different meth¬ods for tuning PID controllers that have been developed over the years are then presented. Their properties are discussed thoroughly.A reasonable design method should consider load disturbances, model uncertainty, measurement noise, and set-point response. A drawback of many of the traditional tuning rules for PID control is that such rules do not consider all these aspects in a balanced way. New tuning techniques that do consider all these criteria are also presented.The authors believe strongly that nothing can replace under¬standing and insight. In view of the large number of controllers used in industry there is a need for simple tuning methods. Such rules will at least be much better than "factory tuning," but they can always be improved by process modeling and control design. In Chapter 5 we present a collection of new tuning rules that give significant improve¬ment over previously used rules.In Chapter 6 we discuss some techniques for adaptation and au¬tomatic tuning of PID controllers. This includes methods based on parametric models and nonparametric techniques. A number of com¬mercial controllers are also described to illustrate the different tech¬niques. The possibilities of incorporating diagnosis and fault detection 4 Chapter 1 Introductionin the primary control loop is also discussed.In Chapter 7 it is shown how complex control problems can be solved by combining simple controllers in different ways. The control paradigms of cascade control, feedforward control, model following, ratio control, split range control, and control with selectors are dis¬cussed. Use of currently popular techniques such as neural networks and fuzzy control are also covered briefly.ReferencesA treatment of PID control with many practical hints is given inShinskey (1988). There is a Japanese text entirely devoted to PID control by Suda et al. (1992). Among the books on tuning of PID controllers, we can mention McMillan (1983) and Corripio (1990), which are published by ISA.There are several studies that indicate the state of the art of in¬dustrial practice of control. The Japan Electric Measuring Instrument Manufacturers'Association conducted a survey of the state of process control systems in 1989, see Yamamoto and Hashimoto (1991). Ac¬cording to the survey more than than 90% of the control loops wereof the PID type.The paper, Bialkowski (1993), which describes audits of papermills in Canada, shows that a typical mill has more than 2000 control loops and that 97% use PI control. Only 20% of the control loops were found to work well and decrease process variability. Reasons for poor performance were poor tuning (30%) and valve problems (30%). The remaining 20% of the controllers functioned poorly for a variety of reasons such as: sensor problems, bad choice of sampling rates, and anti-aliasing filters. Similar observations are given in Ender (1993), where it is claimed that 30% of installed process controllers operatein manual, that 20% of the loops use "factory tuning," i.e., default parameters set by the controller manufacturer, and that 30% of the loops function poorly because of equipment problems in valves and sensors.CHAPTER 2Process Models2.1 IntroductionA block diagram of a simple control loop is shown in Figure 2.1. The system has two major components, the process and the controller, rep¬resented as boxes with arrows denoting the causal relation between inputs and outputs. The process has one input, the manipulated vari¬able, also called the control variable. It is denoted by u. The process output is called process variable (PV) and is denoted by y. This vari¬able is measured by a sensor. The desired value of the process variable is called the setpoint (SP) or the reference value. It is denoted by y sp. The control error e is the difference between the setpoint and the process variable, i.e., e = y sp —y. The controller in Figure 2.1 hasone input, the error, and one output, the control variable. The figure shows that the process and the controller are connected in a closed feedback loop.The purpose of the system is to keep the process variable closeto the desired value in spite of disturbances. This is achieved by thefeedback loop, which works as follows. Assume that the system is in equilibrium and that a disturbance occurs so that the process variable becomes larger than the setpoint. The error is then negative and the controller output decreases which in turn causes the process outputto decrease. This type of feedback is called negative feedback, because the manipulated variable moves in direction opposite to the process variable.The controller has several parameters that can be adjusted. The control loop performs well if the parameters are chosen properly. It performs poorly otherwise, e.g., the system may become unstable. The procedure of finding the controller parameters is called tuning.6 Chapter 2 Process ModelsController! Process- 1 -*Figure 2.1 Block diagram of a simple feedback system.i )This can be done in two different ways. One approach is to choose some controller parameters, to observe the behavior of the feedback system, and to modify the parameters until the desired behavior is obtained. Another approach is to first develop a mathematical model that describes the behavior of the process. The parameters of the controller are then determined using some method for control design. An understanding of techniques for determining process dynamics is a necessary background for both methods for controller tuning. This chapter will present such techniques.Static models are discussed in the next section. Dynamic modelsare discussed in Section 2.3. Transient response methods, which are useful for determining simple dynamic models of the process, are pre¬sented in Section 2.4. Section 2.5 treats methods based on moments. These methods are less sensitive to measurement noise and, further¬more, are not restricted to any specific input signal. The frequency response methods, described in Section 2.6, can be used to obtain both simple models and more detailed descriptions. Methods basedon estimation of parametric models are more complex methods that require more computations but less restrictions on the experiments. These methods are presented in Section 2.7. The models discussed so far describe the relation between the process input and output. It is also important to model the disturbances acting on the system. Thisis discussed in Section 2.8. Section 2.9 treats methods to simplify a complex model and the problem of unmodeled dynamics and mod¬eling errors. Conclusions and references are given in Sections 2.10 and 2.11.2.2 Static ModelsThe static process characteristic is a curve that gives the steady state relation between process input signal u and process output y. See Figure 2.2. Notice that the curve has a physical interpretation onlyfor a stable process.2.2 Static ModelsFigure 2.2 Static process characteristic. Shows process output yas a function of process input u under static conditions.All process investigations should start by a determination of thestatic process model. It can be used to determine the range of control signals required to change the process output over the desired range,to size actuators, and to select sensor resolution. It can also be usedto assess whether static gain variations are so large that they haveto be accounted for in the control design.The static model can be obtained in several ways. It can be de¬termined by an open-loop experiment where the input signal is setto a constant value and the process output is measured when it has reached steady state. This gives one point on the process characteris¬tics. The experiment is then repeated to cover the full range of inputs. An alternative procedure is to make a closed-loop experiment.The setpoint is then given a constant value and the corresponding control variable is measured in steady state. The experiment is then repeated to cover the full range of setpoints.The experiments required to determine the static process modeloften give a good intuitive feel for how easy it is to control the process, if it is stable, and if there are many disturbances.Sometimes process operations do not permit the experiments to be done as described above. Small perturbations are normally permitted, but it may not be possible to move the process over the full operating range. In such a case the experiment must be done over a long period of time.Process NoiseProcess disturbances are easily determined by logging the process output when the control signal is constant. Such a measurement8 Chapter 2 Process Modelswill give a combination of measurement and load disturbances. There are many sophisticated techniques such as time-series analysis and spectral analysis that can be used to determine the characteristicsof the process noise. Crude estimates of the noise characteristicsare obtained simply by measuring the peak-to-peak value and by determining the average time between zero crossings of the error signal. This is discussed further in Section 2.8.2.3 Dynamic ModelsA static process model like the one discussed in the previous sectiontells the steady state relation between the input and the output sig¬nal. A dynamic model should give the relation between the input andthe output signal during transients. It is naturally much more diffi¬cult to capture dynamic behavior. This is, however, very significantwhen discussing control problems.Fortunately there is a restricted class of models that can often beused. This applies to linear time-invariant systems. Such models canoften be used to describe the behavior of control systems when thereare small deviations from an equilibrium. The fact that a system islinear implies that the superposition principle holds. This means thatif the input u\ gives the output yi and the input ui gives the outputj2 it then follows that the input au\ + bui gives the output ay\ + by 2-A system is time-invariant if its behavior does not change with time.A very nice property of linear time-invariant systems is that theirresponse to an arbitrary input can be completely characterized interms of the response to a simple signal. Many different signals can beused to characterize a system. Broadly speaking we can differentiatebetween transient and frequency responses.In a control system we typically have to deal with two signalsonly, the control signal and the measured variable. Process dynamicsas we have discussed here only deals with the relation between thosesignals. The measured variable should ideally be closely related to thephysical process variable that we are interested in. Since it is difficultto construct sensors it happens that there is considerable dynamicsin the relation between the true process variable and the sensor. Forexample, it is very common that there are substantial time constantsin temperature sensors. There may also be measurement noise andother imperfections. There may also be significant dynamics in theactuators. To do a good job of control, it is necessary to be aware ofthe physical origin the process dynamics to judge if a good r绪论PID控制器有几个重要的功能: 它能提供反馈; 它有能力通过积分作用消除稳态补偿; 它通过微分作用可以有预见性。
PID控制中英文对照翻译

外文资料与翻译PID Contro l6.1 IntroductionThe PID controller is the most common form of feedback. It was an essential element of early governors and it became the standard tool when process control emerged in the 1940s. In process control today, more than 95% of the control loops are of PID type, most loops are actually PI control. PID controllers are today found in all areas where control is used. The controllers come in many different forms. There are standalone systems in boxes for one or a few loops, which are manufactured by the hundred thousands yearly. PID control is an important ingredient of a distributed control system. The controllers are also embedded in many special purpose control systems. PID control is often combined with logic, sequential functions, selectors, and simple function blocks to build the complicated automation systems used for energy production, transportation, and manufacturing. Many sophisticated control strategies, such as model predictive control, are also organized hierarchically. PID control is used at the lowest level; the multivariable controller gives the set points to the controllers at the lower level. The PID controller can thus be said to be the “bread and butter of control engineering. It is an important component in every control engineer’s tool box.PID controllers have survived many changes in technology, from mechanics and pneumatics to microprocessors via electronic tubes, transistors, integrated circuits. The microprocessor has had a dramatic influence the PID controller. Practically all PID controllers made today are based on microprocessors. This has given opportunities to provide additional features like automatic tuning, gain scheduling, and continuous adaptation.6.2 AlgorithmWe will start by summarizing the key features of the PID controller. The “textbook” version of the PID algorithm is described by:()()()()⎪⎪⎭⎫ ⎝⎛++=⎰dt t de d e t e K t u T T d t i 01ττ 6.1 where y is the measured process variable, r the reference variable, u is the control signal and e is the control error (e =sp y − y ). The reference variable is often calledthe set point. The control signal is thus a sum of three terms: the P-term (which is proportional to the error), the I-term (which is proportional to the integral of the error), and the D-term (which is proportional to the derivative of the error). The controller parameters are proportional gain K, integral time T i, and derivative time T d. The integral, proportional and derivative part can be interpreted as control actions based on the past, the present and the future as is illustrated in Figure 2.2. The derivative part can also be interpreted as prediction by linear extrapolation as is illustrated in Figure 2.2. The action of the different terms can be illustrated by the following figures which show the response to step changes in the reference value in a typical case.Effects of Proportional, Integral and Derivative ActionProportional control is illustrated in Figure 6.1. The controller is given by D6.1E with T i= and T d=0. The figure shows that there is always a steady state error in proportional control. The error will decrease with increasing gain, but the tendency towards oscillation will also increase.Figure 6.2 illustrates the effects of adding integral. It follows from D6.1E that the strength of integral action increases with decreasing integral time T i. The figure shows that the steady state error disappears when integral action is used. Compare with the discussion of the “magic of integral action” in Section 2.2. The tendency for oscillation also increases with decreasing T i. The properties of derivative action are illustrated in Figure 6.3.Figure 6.3 illustrates the effects of adding derivative action. The parameters K and T i are chosen so that the closed loop system is oscillatory. Damping increases with increasing derivative time, but decreases again when derivative time becomes too large. Recall that derivative action can be interpreted as providing prediction by linear extrapolation over the time T d. Using this interpretation it is easy to understand that derivative action does not help if the prediction time T d is too large. In Figure 6.3 the period of oscillation is about 6 s for the system without derivative Chapter 6. PID ControlFigure 6.1Figure 6.2Derivative actions cease to be effective when T d is larger than a 1 s (one sixth of the period). Also notice that the period of oscillation increases when derivative time is increased.A PerspectiveThere is much more to PID than is revealed by (6.1). A faithful implementation of the equation will actually not result in a good controller. To obtain a good PID controller it is also necessary to consider。
PID控制器中英文对照外文翻译文献
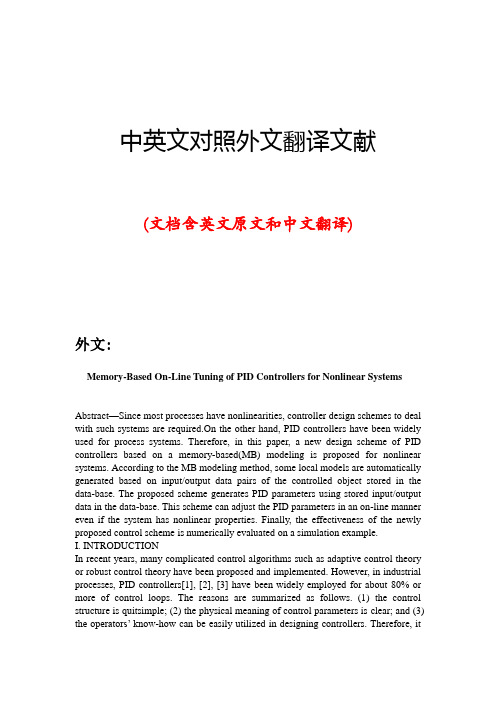
中英文对照外文翻译文献(文档含英文原文和中文翻译)外文:Memory-Based On-Line Tuning of PID Controllers for Nonlinear Systems Abstract—Since most processes have nonlinearities, controller design schemes to deal with such systems are required.On the other hand, PID controllers have been widely used for process systems. Therefore, in this paper, a new design scheme of PID controllers based on a memory-based(MB) modeling is proposed for nonlinear systems. According to the MB modeling method, some local models are automatically generated based on input/output data pairs of the controlled object stored in the data-base. The proposed scheme generates PID parameters using stored input/output data in the data-base. This scheme can adjust the PID parameters in an on-line manner even if the system has nonlinear properties. Finally, the effectiveness of the newly proposed control scheme is numerically evaluated on a simulation example.I. INTRODUCTIONIn recent years, many complicated control algorithms such as adaptive control theory or robust control theory have been proposed and implemented. However, in industrial processes, PID controllers[1], [2], [3] have been widely employed for about 80% or more of control loops. The reasons are summarized as follows. (1) the control structure is quitsimple; (2) the physical meaning of control parameters is clear; and (3) the operators’ know-how can be easily utilized in designing controllers. Therefore, itis still attractive todesign PID controllers. However, since most process systems have nonlinearities, it is difficult to obtain good control performances for such systems simply using the fixed PIDparameters. Therefore, PID parameters tuning methods using neural networks(NN)[4] and genetic algorithms(GA)[5] have been proposed until now. According to these methods, the learning cost is considerably large, and these PID parameters cannot be adequately adjusted due to the nonlinear properties. Therefore, it is quite difficult to obtain good control performances using these conventional schemes.By the way, development of computers enables us to memorize, fast retrieve and read out a large number of data. By these advantages, the following method has been proposed: Whenever new data is obtained, the data is stored.Next, similar neighbors to the informat ion requests, called’queries’, are selected from the stored data. Furthermore,the local model is constructed using these neighbors. Thismemory-based(MB) modeling method, is called Just-In-Time(JIT) method[6], [7] , Lazy Learning method[8] or Model-on-Demand(MoD)[9], and these scheme have lots of attention in last decade.In this paper, a design scheme of PID controllers based onthe MB modeling method is discussed. A few PID controllers have been already proposed based on the JIT method[10] and the MoD method[11] which belong to the MB modeling methods. According to the former method, the JIT method is used as the purpose of supplementing the feedback controller with a PID structure. However, the tracking property is not guaranteed enough due to the nonlinearities in the case where reference signals are changed, because the controller does not includes any integral action in the whole control system. On the other hand, the latter method has a PID control structure.PID parameters are tuned by operators’ skills, and they are stored in the data-base in advance. And also, a suitable set of PID parameters is generated using the stored data. However,the good control performance cannot be necessarily obtained in the case where nonlinearities are included in the controlled object and/or system parameters are changed, because PID parameters are not tuned in an on-line manner corresponding to characteristics of the controlled object. Therefore, in this paper, a design scheme of PID controllers based on the MB modeling method is newly proposed.According to the proposed method, PID parameterswhich are obtained using the MB modeling method areadequately tuned in proportion to control errors, and modifiedPID parameters are stored in the data-base. Therefore, moresuitable PID parameters corresponding to characteristics ofthe controlled object are newly stored. Moreover, an algorithmto avoid the excessive increase of the stored data,is further discussed. This algorithm yields the reduction of memories and computational costs. Finally, the effectiveness of the newly proposed control scheme is examined on asimulation example.II. PID CONTROLLER DESIGN BASED ON MEMORY-BASED MODELING METHODA. MB modeling methodFirst, the following discrete-time nonlinear system is considered:, (1)where y(t) denotes the system output and f(·) denotes the nonlinear function. Moreover, _(t−1) is called ’information vector’, which is defied by the following equation:)](),1(),(,),1([:)(u y n t u t u n t y t y t ----= φ, (2) where u(t) denotes the system input. Also, ny and nure spectively denote the orders of the system output and the system input, respectively. According to the MB modeling method, the data is stored in the form of the information vector _ expressed in Eq.(2). Moreover, _(t) is required in calculating the estimate of the output y(t+1) called ’query’.That is, after some similar neighbors to the query are selected from the data-base, the predictive value of the system can beobtained using these neighbors.B. Controller design based on MB modeling methodIn this paper, the following control law with a PID structure is considered: )()()()(2t y T T k t e T T k t u SD c I s c ∆+∆-=∆ (3))()()(2t y K t y K t e K D P I ∆-∆-= (4)where e(t) denotes the control error signal defined bye(t) := r(t) − y(t). (5) r(t) denotes the reference signal. Also, kc, TI and TD respectively denote the proportional gain, the reset time and the derivative time, and Ts denotes the sampling interval. Here, KP , KI and KD included in Eq.(4) are derived by therelations P K =c k ,I K =c k s T /I T 和D K =c k D T /s T 。
PID控制器的性能监控与评估

l一q 一 1
{1
Ly p
(2)
毛 =S lF k z S k S s,一 k 0 a H
i一 0
其中: k:, 棍, k 3 分别是 P I D 的设定值参数
可 以得到任意输出与干扰之间的关系:
恩 甲
球t )= 0
( 犷 ,) K
,( ,) =艺 ( , +s l +, +;2 * , ) 一 *( 卜 )
(倒园m 叨 m va i a r c ec n o nt r ol ) 基准的性能评估方法 M v C 墓准 的评估方法还被扩展到反馈/前馈控制系统[ ] 非最 8 小相 位 系统 l ] , 以及变 工 作 点系 统 的性 能 评 估[ 9 ] 0 1
2
I D 性能评估与监控原理 P
K 和 E dga l 6 r 1 提出了可 以随即负荷扰动情况下进行 By n g一 u u K s 和 Ed g 护 ]
(9)
图 1 闭环系统结构图
I +S ( l +尺 k 弘2+ F ZS 3 )一 k ,而 矛
设Q = I + S , +只 k 狱2 + F ZS s 则由式 (9 k ) 得到最小方 差下对应的 P I D 参数表达式如下:
设G c , 为从 a ( O 到y ( O 的闭环传递函数 则在 P ID 控
而时变性会影响控制系统的控制效果 , 有时甚至会破坏
是在 1970 年时 , 由 B ox , Jen k i ns[ 3] 还有 ^ st r om I 41 提 出,
系统 的正常运行, 而原来的 P I D 最小方差准则对控制系 统性能评估并不适合时变系统, 也就是说时变系统的控 制系统性 能评估结果是不准确的 本文针对时变系统 , 提 出了 P I D 循环评估优化算法: 利用在线辨识技术对 时 变控制系统进行性能评估, 得到 P I D 参数的优化值, 当 评估性能结果最优方差与输出方差相比小于 8 5 % 时, 对 I D 参数进行更新, 使 P P I D 控制能随着工况 的变化而进 行改变
- 1、下载文档前请自行甄别文档内容的完整性,平台不提供额外的编辑、内容补充、找答案等附加服务。
- 2、"仅部分预览"的文档,不可在线预览部分如存在完整性等问题,可反馈申请退款(可完整预览的文档不适用该条件!)。
- 3、如文档侵犯您的权益,请联系客服反馈,我们会尽快为您处理(人工客服工作时间:9:00-18:30)。
Case 1: r > 1.2. In this case, we have 0 < fcp < ^ Then the stabilizing set is given either by Fig. 8.6(a) or by Fig. 8.6(b). Notice from (10.6) that the parameter kd is always less than j as illustrated in Fig. 10.2. The derivative gain value provided by the Ziegler-Nichols method is robust in the sense that it is not close to the stability boundary j . Following the same principle, we would like to guarantee that the integral gain value is also far away from the stability boundary. __ Let xi be the fc^-coordinate of the point where the line kd = kd intersects the line kd = miki-\-bi. From Fig. 10.2, we now find the conditions under
k
பைடு நூலகம்
-i
- a i sin(Q;i) — cos(ai)
T
(10.4)
where ai is now the solution of the equation tan(a) = ^ ^ a 1+ r
in the interval (0, TT). We now compare kp k and kupp k as functions of the parameter r. As can be seen from Fig. 10.1, the proportional gain value given by the Ziegler-Nichols step response method is always less than the upper bound kupp- Thus_this tuning technique always provides a feasible proportional gain value kp. We now set kp = kp and consider two cases, requiring different treatments according to the results of Chapter 8. Moreover, for clarity of presentation, let us rewrite the parameters ki and kd in (10.2) as h kd = = j -J^ . (10.5) (10-6)
10
Analysis of Some PID Tuning Techniques
In this chapter we present an analysis of some PID tuning techniques that are based on first-order models with time delays. Using the characterization of all stabilizing PID controllers derived in Chapter 8, each tuning rule is analyzed to first determine if the proportional gain value dictated by that rule lies inside the range of admissible proportional gains. Then the integral and derivative gain values are examined to determine conditions under which the tuning rule exhibits robustness with respect to controller parameter perturbations.
1 \ Kp \
_ l T
Kupp •— J
- T Q I s i n ( a i ) — COS(Q;I) JL
where ai is the solution of the equation
tan(a) =
'YTI^
T
in the interval (0,7r). Let us rewrite the upper bound on kp as a function of the parameter r:
5=i-
<'°-^'
10.2 The Ziegler-Nichols Step Response Method
225
Since A > 0 and r > 0 (the plant is open-loop stable), then kp > 0. From : Theorem 8.1, the range of kp values for which a given open-loop stable plant, with transfer function G(s) as in (10.1), can be stabilized using a PID controller is given by 1
where k is the steady-state gain, L is the apparent time delay, and T is the apparent time constant. A simple way to determine the parameters of a PID controller based on step response data was developed by Ziegler and Nichols in 1942. This method first characterizes the plant by the parameters L and a, where the parameter a is defined as a = k— . T Once these parameters are determined, the PID controller parameters are given in terms of L and a by the following formulas:
224
10. Analysis of Some PID Tuning Techniques
troller that is to be practically implemented must necessarily be nonfragile or the system must be controller-robust. Four tuning techniques will be discussed: (1) the classical Ziegler-Nichols step response method, (2) the Chien, Hrones, and Reswick (CHR) method, (3) the Cohen-Coon method, and (4) the internal model controller (IMC) design technique. In each case, we will first study if the proposed proportional gain value lies inside the allowable range determined in Chapter 8. We then analyze for this fixed proportional gain the possible location of the integral and derivative gains inside the stabilizing region. This procedure will allow us to determine conditions under which each tuning technique provides a good parametric stability margin in the space of the controller parameters. In this way, we will avoid undesirable scenarios such as PID controller parameters that are dangerously close to instability.
jr^Li
1.2
_ _ _ 0.6
t;=^ ki ~
—
E = —— . K>d
7^_
0 ^
(10.2)
a aL a This tuning rule was developed by empirical simulations of many different systems and is only applicable to open-loop stable plants. We now define the parameter r as the ratio of the apparent time delay to the apparent time constant of the plant, that is, L First we focus on the proportional gain expression given in (10.2) and rewrite it as a function of r: