不锈钢加工刀具选择
2507 不锈钢 切削参数

2507 不锈钢切削参数(原创实用版)目录1.不锈钢的特性2.切削参数的选择3.切削不锈钢的技巧4.常见问题及其解决方法正文一、不锈钢的特性不锈钢是一种具有良好耐腐蚀性的合金材料,广泛应用于各种工业领域。
然而,其高硬度、高韧性和粘性使得切削加工具有一定的难度。
因此,在切削不锈钢时,需要特别注意切削参数的选择。
二、切削参数的选择1.刀具材料选择:在切削不锈钢时,应选用具有高硬度、高韧性和耐磨性的刀具材料,如高速钢、硬质合金等。
2.刀具几何参数选择:合理的刀具几何参数可以提高切削效率和表面质量。
前角应选取较小的正值,主偏角和副偏角选取较小的正值,以减小切削力和热量。
3.切削速度和进给速度选择:切削速度和进给速度的选择应根据不锈钢的硬度、刀具材料和加工设备来确定。
通常,切削速度较慢,进给速度也较低。
4.切削深度和宽度选择:切削深度和宽度的选择应根据加工工艺和设备性能来确定。
一般情况下,切削深度较浅,切削宽度较窄。
三、切削不锈钢的技巧1.合理选择刀具:针对不同的不锈钢材料和加工工艺,选择合适的刀具,以提高切削效率和表面质量。
2.采用适当的冷却液:在切削过程中,使用适当的冷却液可以降低刀具的温度,减少磨损,提高切削效率。
3.控制切削力:在切削过程中,应尽量减小切削力,以避免刀具的过早磨损和加工精度的下降。
4.合理安排加工工艺:在加工不锈钢时,应根据加工工艺和设备性能,合理安排加工顺序和工艺参数。
四、常见问题及其解决方法1.刀具磨损快:可能是切削参数选择不合理,应重新调整切削参数。
2.切削力过大:可能是刀具几何参数选择不当,应重新选择刀具几何参数。
3.表面粗糙度大:可能是切削速度和进给速度选择不当,应重新调整切削速度和进给速度。
4.不锈钢加工精度低:可能是加工工艺不合理,应重新安排加工工艺和参数。
总之,在切削不锈钢时,应根据不锈钢的特性和加工要求,合理选择切削参数,采用适当的切削技巧,以提高切削效率和加工质量。
加工不锈钢用什么铣刀-加工不锈钢用什么刀具
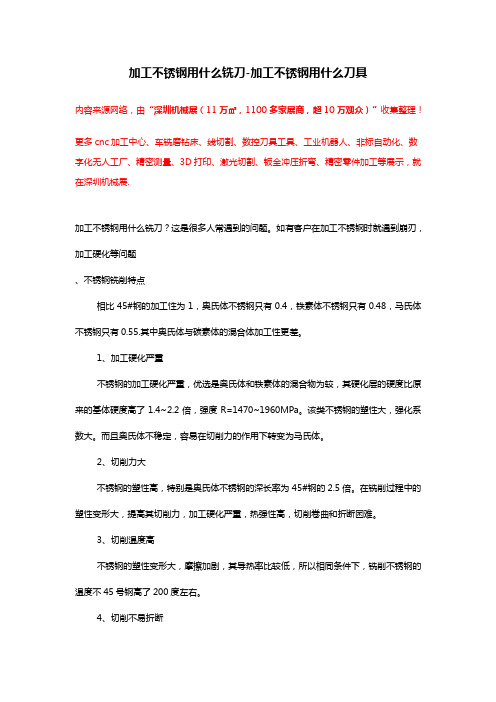
加工不锈钢用什么铣刀-加工不锈钢用什么刀具内容来源网络,由“深圳机械展(11万㎡,1100多家展商,超10万观众)”收集整理!更多cnc加工中心、车铣磨钻床、线切割、数控刀具工具、工业机器人、非标自动化、数字化无人工厂、精密测量、3D打印、激光切割、钣金冲压折弯、精密零件加工等展示,就在深圳机械展.加工不锈钢用什么铣刀?这是很多人常遇到的问题。
如有客户在加工不锈钢时就遇到崩刃,加工硬化等问题、不锈钢铣削特点相比45#钢的加工性为1,奥氏体不锈钢只有0.4,铁素体不锈钢只有0.48,马氏体不锈钢只有0.55.其中奥氏体与碳素体的混合体加工性更差。
1、加工硬化严重不锈钢的加工硬化严重,优选是奥氏体和铁素体的混合物为较,其硬化层的硬度比原来的基体硬度高了1.4~2.2倍,强度R=1470~1960MPa。
该类不锈钢的塑性大,强化系数大。
而且奥氏体不稳定,容易在切削力的作用下转变为马氏体。
2、切削力大不锈钢的塑性高,特别是奥氏体不锈钢的深长率为45#钢的2.5倍。
在铣削过程中的塑性变形大,提高其切削力,加工硬化严重,热强性高,切削卷曲和折断困难。
3、切削温度高不锈钢的塑性变形大,摩擦加剧,其导热率比较低,所以相同条件下,铣削不锈钢的温度不45号钢高了200度左右。
4、切削不易折断加工不锈钢时,易粘结和产生积屑瘤。
不锈钢的塑性和韧性都比较大,铣削时其切削不容易折断。
在高温和高压下,刀具容易产生粘结磨损和积屑瘤。
5、刀具易磨损加工不锈钢当然要用不锈钢铣刀,因为不锈钢的TiC硬质点,容易使刀具产生剧烈的磨练磨损。
在高速高温高压条件下,切削与刀具容易产生粘结,扩散和月牙洼磨损。
二、加工铣不锈钢用什么铣刀?采用硬质合金材质来加工不锈钢,硬选用含TaC或NbC的钨钴类细晶粒或超细晶粒硬质合金。
如YG6x、YG813、YW4、YD15等等。
铣削不锈钢时,应选用极压乳化液或硫化切削油。
硬质合金材质的不锈钢铣刀,其铣削速度应该在40~60m/min,为避免切削刃在硬化层中的切削,加快刀具磨损,进给量应大于0.1mm。
不锈钢加工刀具切削参数

不锈钢加工刀具切削参数一、引言不锈钢是一种常用的材料,应用广泛于各个行业中。
在不锈钢加工中,刀具的选择和切削参数的确定对于加工质量和效率具有重要影响。
本文将从不锈钢加工刀具的选择和切削参数的确定两个方面展开论述。
二、不锈钢加工刀具的选择选择合适的刀具是确保不锈钢加工成功的首要条件。
不锈钢具有较高的硬度和良好的耐磨性,因此在选择刀具时需要考虑以下几个因素:2.1 刀具材料不锈钢加工通常选择硬质合金刀具,因为硬质合金具有较高的硬度和耐磨性,能够在不锈钢的高温和高切削力下保持较好的切削性能。
常见的硬质合金材料有WC-Co、WC-TiC-TaC等。
2.2 刀具形状根据不锈钢加工的具体需求,选择合适的刀具形状是十分重要的。
常见的刀具形状包括平面铣刀、立铣刀、球头铣刀等。
平面铣刀适用于对不锈钢表面进行平整加工,立铣刀适用于进行深度加工,球头铣刀适用于进行轮廓加工等。
2.3 刀具涂层通过刀具涂层可以提高刀具的耐磨性和切削性能,延长刀具的使用寿命。
在不锈钢加工中,常用的刀具涂层有TiN、TiCN、TiAlN等,这些涂层具有良好的耐磨性和热稳定性。
三、不锈钢加工切削参数的确定除了选择合适的刀具外,还需要确定合适的切削参数才能保证加工质量和效率。
切削参数的确定与不锈钢材料的性质、加工要求和刀具特点等因素密切相关。
3.1 切削速度切削速度是切削参数中最重要的一个参数,它决定着切削时刀具与工件之间的相对运动速度。
在不锈钢加工中,切削速度不宜过高,一般建议控制在60-100 m/min之间。
3.2 进给量进给量是指单位切削时间内切削刀具在切削方向上的移动距离。
对于不锈钢加工,进给量要适中,过小会导致加工效率低下,过大则容易导致切削刃磨损过快。
因此,根据具体情况选择合适的进给量十分重要。
3.3 主轴转速主轴转速是指切削时主轴单位时间内旋转的圈数。
选择合适的主轴转速可以保证切削进给率和表面质量。
在不锈钢加工中,一般建议选择较低的主轴转速,以提高刀具寿命和加工质量。
不锈钢螺纹加工技巧
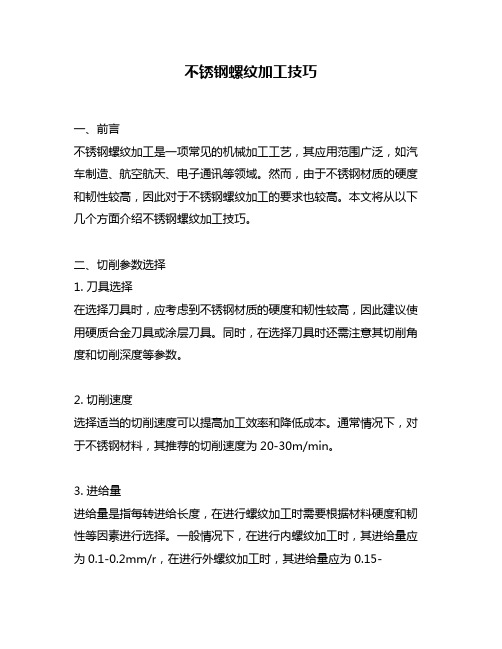
不锈钢螺纹加工技巧一、前言不锈钢螺纹加工是一项常见的机械加工工艺,其应用范围广泛,如汽车制造、航空航天、电子通讯等领域。
然而,由于不锈钢材质的硬度和韧性较高,因此对于不锈钢螺纹加工的要求也较高。
本文将从以下几个方面介绍不锈钢螺纹加工技巧。
二、切削参数选择1. 刀具选择在选择刀具时,应考虑到不锈钢材质的硬度和韧性较高,因此建议使用硬质合金刀具或涂层刀具。
同时,在选择刀具时还需注意其切削角度和切削深度等参数。
2. 切削速度选择适当的切削速度可以提高加工效率和降低成本。
通常情况下,对于不锈钢材料,其推荐的切削速度为20-30m/min。
3. 进给量进给量是指每转进给长度,在进行螺纹加工时需要根据材料硬度和韧性等因素进行选择。
一般情况下,在进行内螺纹加工时,其进给量应为0.1-0.2mm/r,在进行外螺纹加工时,其进给量应为0.15-0.3mm/r。
4. 切削深度切削深度是指每次切削的深度,其选择需要考虑到材料硬度和韧性等因素。
一般情况下,在进行内螺纹加工时,其切削深度应为1-2mm,在进行外螺纹加工时,其切削深度应为1.5-3mm。
三、螺纹加工方法1. 内螺纹加工内螺纹加工通常采用攻丝的方式进行。
在进行攻丝前需要先在孔口处预钻孔,并选择适当的攻丝刀具和攻丝规格。
在进行攻丝时,需注意控制进给量和转速等参数,并及时清理孔口处的铁屑和油渣等杂质。
2. 外螺纹加工外螺纹加工通常采用车床或数控机床进行。
在进行外螺纹加工前需要先确定好刀具的位置和角度,并选择适当的车刀或铣刀。
在进行外螺纹加工时,需注意控制进给量和转速等参数,并及时清理切屑和油渣等杂质。
四、加工注意事项1. 切削液的选择切削液可以起到冷却、润滑和清洗等作用,因此在进行不锈钢螺纹加工时需要选择适当的切削液。
一般情况下,建议使用硫化极压切削油或硫化碱性切削油。
2. 清洗和保养在进行不锈钢螺纹加工后,需要及时对机床和刀具进行清洗和保养。
特别是对于硬质合金刀具或涂层刀具,需要定期进行磨损检查和更换。
常用制刀不锈钢材料的性能及其适用范围
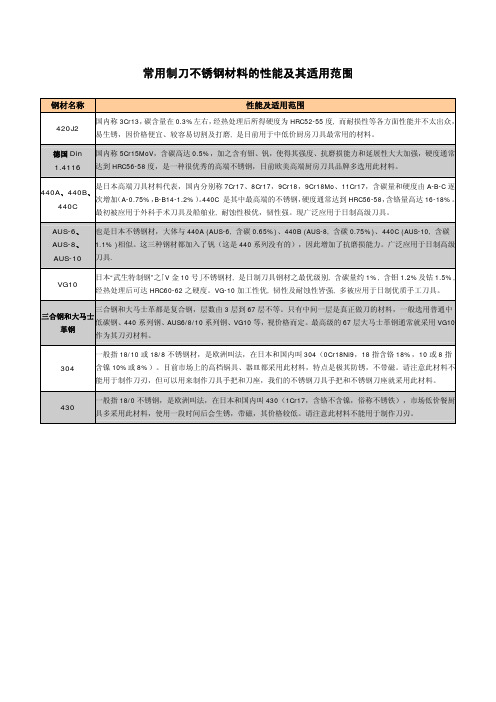
常用制刀不锈钢材料的性能及其适用范围 钢材名称性能及适用范围420J2 国内称3Cr13,碳含量在0.3%左右,经热处理后所得硬度为HRC52-55度, 而耐损性等各方面性能并不太出众,易生锈,因价格便宜、较容易切割及打磨, 是目前用于中低价厨房刀具最常用的材料。
德国Din 1.4116 国内称5Cr15MoV,含碳高达0.5%,加之含有钼、钒,使得其强度、抗磨损能力和延展性大大加强,硬度通常达到HRC56-58度,是一种很优秀的高端不锈钢,目前欧美高端厨房刀具品牌多选用此材料。
440A、440B、440C 是日本高端刀具材料代表,国内分别称7Cr17、8Cr17,9Cr18,9Cr18Mo、11Cr17,含碳量和硬度由A-B-C逐次增加(A-0.75%,B-B14-1.2%)。
440C 是其中最高端的不锈钢,硬度通常达到HRC56-58,含铬量高达16-18%。
最初被应用于外科手术刀具及船舶业, 耐蚀性极优,韧性强。
现广泛应用于日制高级刀具。
AUS-6、AUS-8、AUS-10 也是日本不锈钢材,大体与440A (AUS-6, 含碳0.65%)、440B (AUS-8, 含碳0.75%)、440C (AUS-10, 含碳1.1% )相似。
这三种钢材都加入了钒(这是440系列没有的),因此增加了抗磨损能力。
广泛应用于日制高级刀具.VG10 日本“武生特制钢”之「V金10号」不锈钢材, 是日制刀具钢材之最优级别, 含碳量约1%, 含钼1.2%及钴1.5%, 经热处理后可达HRC60-62之硬度。
VG-10加工性优, 韧性及耐蚀性皆强, 多被应用于日制优质手工刀具。
三合钢和大马士革钢三合钢和大马士革都是复合钢,层数由3层到67层不等。
只有中间一层是真正做刀的材料,一般选用普通中低碳钢、440系列钢、AUS6/8/10系列钢、VG10等,视价格而定。
最高级的67层大马士革钢通常就采用VG10作为其刀刃材料。
不锈钢材料的车削加工

不锈钢材料的车削加工摘要:随着现代工业的日益发达,不锈钢材质也在生产加工中被广泛应用,因此合理选用不锈钢材质加工刀具,是确保正确高效切割不锈钢的关键条件。
针对不锈钢切削特点,一般要求刀具材质应具备耐热性好、耐磨性高、与不锈钢材质的亲和性影响小等优点。
关键词:不锈钢材料车削加工不锈钢,是在空气中或化学腐蚀介质中都可以抗侵蚀的一类高温合金钢,不锈钢是指拥有漂亮的表层和耐腐蚀性能良好,而且无须经过镀色等表层处理过程,而发挥了不锈钢所存在的表层特点,应用在多种多样的钢材的一类,也常简称为不锈耐酸钢材。
一:不锈钢车削加工的弊端1、加工硬化严重。
2、塑性变形大,热硬度高,切削抗力大,刀具卷曲折断难。
3、由于切屑和工作物之间的磨擦大,所形成的剪切热较多。
4、切削刀具表面容易粘附,易生成积屑瘤,使切削刀具表面出现粘附、扩大损坏,造成前刃面出现月牙洼,切削后刃生成较小的剥落和缺陷;不锈耐酸钢的碳化物微粒硬度很高,在切割时会直接和菜刀接触,从而损坏菜刀,使菜刀的磨损程度加大。
不锈耐酸钢材质的加热强度高、加工韧性大对数控车高速切削并不适用,相较而言,不锈钢材质在高温下的加工硬度下降较小,但实践已证明,在相同切削高温的作用下,不锈钢车削用量远较于一般的碳素钢更难以加工,其中加热强度高是个至关重要的原因。
加工质量硬化趋势强,对数控车削用量影响大在数字控制高速切削的过程中,由于刃刃对工件材料挤出的效果使车削用量区的金属材料形成了变化,晶内出现滑移,晶体畸变,组织致密,加工力学性能也随之改变,而一般的车削用量硬度也可提高2~3倍。
数控切割后的机械加工生硬层深入可能从数十微米至数百微米之间,所以前一次性走刀所形成的机械加工生硬状态,也阻碍了下一次性走刀时的切割,同时加工生硬层的高硬度也使得刀具非常易于损坏,而且岩屑的粘着性强、导热差对数控技术切割也有一定危害。
此外,刀由于受剥肋断面宽度形状的影响,再加上本身硬度不够,加工中易形成振动,刃刃也易在切削过程中因为内部温度过高而烧坏或由于其震动太大而崩裂。
不锈钢加工方法

不锈钢加工方法一、前言不锈钢是一种具有耐腐蚀性和抗氧化性的材料,广泛应用于制造业中。
在不锈钢加工过程中,需要掌握一些技巧和方法,以确保加工质量和安全。
本文将介绍不锈钢加工的方法和注意事项。
二、材料准备1. 选择合适的不锈钢材料在选择不锈钢材料时,需要考虑其用途、环境条件、耐腐蚀性等因素。
常用的不锈钢材料有304、316、321等。
2. 准备切割工具切割不锈钢需要使用专门的切割工具,如电动剪切机、气割机等。
在使用时需要注意安全,避免发生意外事故。
3. 准备焊接设备焊接不锈钢需要使用专门的焊接设备,如TIG焊机、MIG焊机等。
在使用时需要注意安全,并根据实际情况选择合适的焊接方式。
三、切割方法1. 电动剪切机切割法电动剪切机是一种常用的切割工具,可以快速而准确地将不锈钢材料切割成所需的形状和尺寸。
在使用电动剪切机时,需要注意以下事项:(1)选择合适的刀具不同的不锈钢材料需要使用不同的刀具,选择合适的刀具可以提高切割效率和质量。
(2)调整剪切角度根据不锈钢材料的厚度和硬度,需要调整剪切角度以确保切口光滑、无毛边。
(3)定期检查机器定期检查电动剪切机的电源线、开关、保险丝等部件是否正常工作,避免发生故障。
2. 气割法气割法是一种常用的不锈钢切割方法,在氧化性环境下可以快速而准确地将不锈钢材料分离。
在使用气割法时,需要注意以下事项:(1)选择合适的气体气体对于气割效果有很大影响,需要根据不锈钢材料的特性选择合适的气体。
(2)掌握正确操作方法正确操作气割设备可以提高工作效率和安全性,避免发生意外事故。
(3)定期维护设备定期维护气割设备可以延长其使用寿命,提高切割效果。
需要注意清洗气管、更换切割嘴等部件。
四、焊接方法1. TIG焊接法TIG焊接法是一种常用的不锈钢焊接方法,具有高强度、美观的特点。
在使用TIG焊机时,需要注意以下事项:(1)选择合适的电极和气体根据不锈钢材料的特性选择合适的电极和气体可以提高焊接效果和质量。
不锈钢加工参数表

不锈钢加工参数表1. 引言不锈钢是一种具有耐腐蚀性能的合金材料,广泛应用于制造业中。
在不锈钢加工过程中,为了保证产品质量和生产效率,需要确定适当的加工参数。
本文将详细介绍不锈钢加工参数表的编写方法和相关注意事项。
2. 不锈钢材料特性不锈钢具有以下特性:•高强度:不锈钢具有较高的强度,能够承受较大的载荷。
•耐腐蚀性:不锈钢能够抵抗大多数化学物质的侵蚀。
•良好的机械性能:不锈钢具有良好的塑性和可焊接性。
•耐高温性:不锈钢在高温下仍然保持较好的力学性能。
3. 不锈钢加工参数3.1 切削速度(Cutting Speed)切削速度是指切削刀具在单位时间内通过工件表面的线速度。
在不同材料和切削过程中,切削速度会有所变化。
下表列出了常见类型的不锈钢材料的推荐切削速度范围(单位:m/min):不锈钢材料范围304不锈钢50-100316不锈钢40-80430不锈钢60-1203.2 进给量(Feed Rate)进给量是指切削工具在单位时间内与工件接触的长度。
进给量的选择需要考虑切削力和表面粗糙度等因素。
下表列出了常见类型的不锈钢材料的推荐进给量范围(单位:mm/rev):不锈钢材料范围304不锈钢0.1-0.2316不锈钢0.08-0.15430不锈钢0.15-0.253.3 刀具半径(Tool Radius)刀具半径是指切削工具刀尖到刀具轴线的距离。
合适的刀具半径能够减小加工过程中产生的振动和应力集中。
下表列出了常见类型的不锈钢材料的推荐刀具半径范围(单位:mm):不锈钢材料范围304不锈钢0.5-1.0316不锈钢0.4-0.8430不锈钢0.6-1.23.4 冷却液(Coolant)冷却液在不锈钢加工过程中起到冷却切削区域、润滑切削面和清洁切屑的作用。
选择适当的冷却液可以提高加工效率和延长刀具寿命。
常用的冷却液有水溶性切削油和合成切削油。
3.5 加工方式(Machining Method)根据不同的加工要求,可以选择旋转铣削、车削、线切割等加工方式。
不锈钢的车削参数

不锈钢的车削参数不锈钢是一种耐腐蚀、耐高温的金属材料,常用于制造机械零件、压力容器、航空航天器械等领域。
在进行车削加工时,需要根据不锈钢的特性和要求选择合适的车削参数,以达到理想的加工效果。
一、切削速度(vc)切削速度是车刀在工件表面移动的速度,也是车削过程中最基本的参数。
不锈钢的切削速度较低,一般在30-60m/min之间。
过高的切削速度会导致刀具过热、磨损加剧,影响切削质量和加工效率;过低的切削速度则会造成切削力增大,刀具负荷过大,甚至造成刀具断裂。
二、进给速度(f)进给速度是指车刀在单位时间内向工件进给的量。
在车削不锈钢时,进给速度一般在0.05-0.15mm/r之间。
进给速度过高会造成刀具磨损加剧、表面质量下降;进给速度过低则会导致车削效率低下。
需要根据具体材料硬度和刀具的质量要求来确定合适的进给速度。
三、切削深度(ap)切削深度是指车刀在一次切削过程中,刀尖与工件表面的距离。
不锈钢的切削深度一般在0.5-4mm之间,具体取决于工件的硬度和刀具的强度。
切削深度过大会增加切削力,容易造成刀具断裂;切削深度过小则会导致车削效率低下。
四、切削角度(γ)切削角度是指车刀主切削刃与工件表面的切削角。
在车削不锈钢时,一般选择切削角较小的刀具,如30度左右。
切削角较小的刀具可以减小切削力,提高刀具的切削性能和寿命。
五、冷却液由于不锈钢的切削过程会产生较高的温度,因此在车削不锈钢时需要使用冷却液进行冷却和润滑。
冷却液的选择应根据不锈钢的材质和车削过程的具体要求来确定,以保证切削效果和刀具的使用寿命。
六、切削工具选择不锈钢的切削难度较大,对切削工具的要求也比较高。
一般采用硬质合金或散热钨钢制成的切削工具。
此外,还可以通过涂覆刀具和刀具几何形状的优化来提高不锈钢的切削效果。
总结起来,车削不锈钢需要根据不锈钢的特性和要求选择适当的车削参数,包括切削速度、进给速度、切削深度、切削角度等。
同时还需要选择合适的切削工具和冷却液,以保证切削效果和刀具的使用寿命。
不锈钢nc加工参数
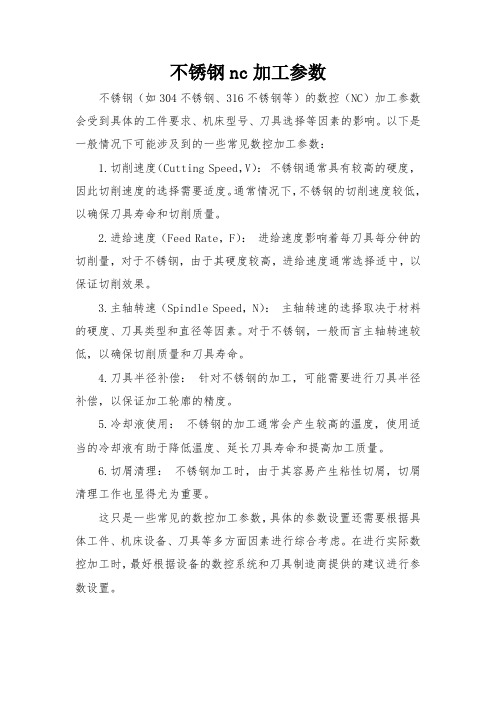
不锈钢nc加工参数
不锈钢(如304不锈钢、316不锈钢等)的数控(NC)加工参数会受到具体的工件要求、机床型号、刀具选择等因素的影响。
以下是一般情况下可能涉及到的一些常见数控加工参数:
1.切削速度(Cutting Speed,V):不锈钢通常具有较高的硬度,因此切削速度的选择需要适度。
通常情况下,不锈钢的切削速度较低,以确保刀具寿命和切削质量。
2.进给速度(Feed Rate,F):进给速度影响着每刀具每分钟的切削量,对于不锈钢,由于其硬度较高,进给速度通常选择适中,以保证切削效果。
3.主轴转速(Spindle Speed,N):主轴转速的选择取决于材料的硬度、刀具类型和直径等因素。
对于不锈钢,一般而言主轴转速较低,以确保切削质量和刀具寿命。
4.刀具半径补偿:针对不锈钢的加工,可能需要进行刀具半径补偿,以保证加工轮廓的精度。
5.冷却液使用:不锈钢的加工通常会产生较高的温度,使用适当的冷却液有助于降低温度、延长刀具寿命和提高加工质量。
6.切屑清理:不锈钢加工时,由于其容易产生粘性切屑,切屑清理工作也显得尤为重要。
这只是一些常见的数控加工参数,具体的参数设置还需要根据具体工件、机床设备、刀具等多方面因素进行综合考虑。
在进行实际数控加工时,最好根据设备的数控系统和刀具制造商提供的建议进行参数设置。
合金铣刀加工不锈钢参数
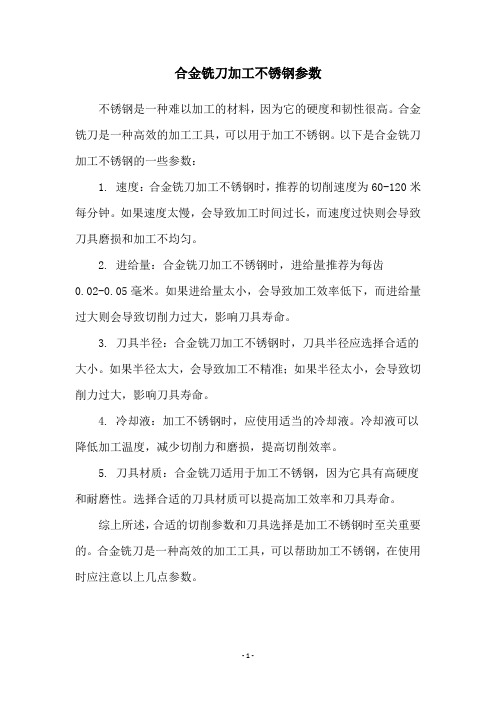
合金铣刀加工不锈钢参数
不锈钢是一种难以加工的材料,因为它的硬度和韧性很高。
合金铣刀是一种高效的加工工具,可以用于加工不锈钢。
以下是合金铣刀加工不锈钢的一些参数:
1. 速度:合金铣刀加工不锈钢时,推荐的切削速度为60-120米每分钟。
如果速度太慢,会导致加工时间过长,而速度过快则会导致刀具磨损和加工不均匀。
2. 进给量:合金铣刀加工不锈钢时,进给量推荐为每齿
0.02-0.05毫米。
如果进给量太小,会导致加工效率低下,而进给量过大则会导致切削力过大,影响刀具寿命。
3. 刀具半径:合金铣刀加工不锈钢时,刀具半径应选择合适的大小。
如果半径太大,会导致加工不精准;如果半径太小,会导致切削力过大,影响刀具寿命。
4. 冷却液:加工不锈钢时,应使用适当的冷却液。
冷却液可以降低加工温度,减少切削力和磨损,提高切削效率。
5. 刀具材质:合金铣刀适用于加工不锈钢,因为它具有高硬度和耐磨性。
选择合适的刀具材质可以提高加工效率和刀具寿命。
综上所述,合适的切削参数和刀具选择是加工不锈钢时至关重要的。
合金铣刀是一种高效的加工工具,可以帮助加工不锈钢,在使用时应注意以上几点参数。
- 1 -。
不锈钢材料的车削技巧
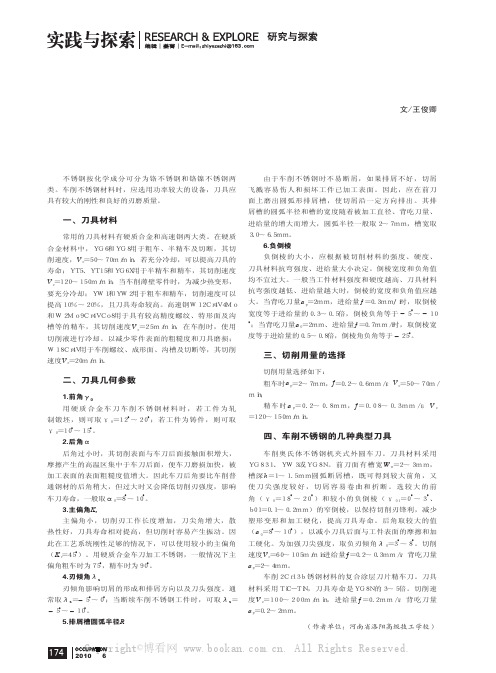
OCCUPATION1742010 6不锈钢按化学成分可分为铬不锈钢和铬镍不锈钢两类。
车削不锈钢材料时,应选用功率较大的设备,刀具应具有较大的刚性和良好的刃磨质量。
一、刀具材料常用的刀具材料有硬质合金和高速钢两大类。
在硬质合金材料中,YG6和YG8用于粗车、半精车及切断,其切削速度,V c=50~70m/min,若充分冷却,可以提高刀具的寿命;YT5、YT15和YG6X用于半精车和精车,其切削速度V c=120~150m/min,当车削薄壁零件时,为减少热变形,要充分冷却;YW1和YW2用于粗车和精车,切削速度可以提高10%~20%,且刀具寿命较高。
高速钢W12Cr4V4Mo和W2Mo9Cr4VCo8用于具有较高精度螺纹、特形面及沟槽等的精车,其切削速度V c=25m/min,在车削时,使用切削液进行冷却。
以减少零件表面的粗糙度和刀具磨损;W18Cr4V用于车削螺纹、成形面、沟槽及切断等,其切削速度V c=20m/min。
二、刀具几何参数1.前角γ0用硬质合金车刀车削不锈钢材料时,若工件为轧制锻坯,则可取γ0=12˚~20˚;若工件为铸件,则可取γ0=10˚~15˚。
2.后角α后角过小时,其切削表面与车刀后面接触面积增大,摩擦产生的高温区集中于车刀后面,便车刀磨损加快,被加工表面的表面粗糙度值增大。
因此车刀后角要比车削普通钢材的后角稍大,但过大时又会降低切削刃强度,影响车刀寿命,一般取α0=8˚~10˚。
3.主偏角K r主偏角小,切削刃工作长度增加,刀尖角增大,散热性好,刀具寿命相对提高,但切削时容易产生振动。
因此在工艺系统刚性足够的情况下,可以使用较小的主偏角(K r=45˚)。
用硬质合金车刀加工不锈钢,一般情况下主偏角粗车时为75˚,精车时为90˚。
4.刃倾角λs刃倾角影响切屑的形成和排屑方向以及刀头强度。
通常取λs =﹣5˚~0˚;当断续车削不锈钢工件时,可取λs =﹣5˚~﹣10˚。
5.排屑槽圆弧半径R由于车削不锈钢时不易断屑,如果排屑不好,切屑飞溅容易伤人和损坏工件已加工表面。
不锈钢加工刀具的选择

不锈钢加工刀具的选择1、不锈钢加工对刀具的基本要求对刀具几何参数的要求加工不锈钢时,刀具切削部分的几何形状,一般应从前角、后角方面的选择来考虑。
在选择前角时,要考虑卷屑槽型、有无倒棱和刃倾角的正负角度大小等因素。
不论何种刀具,加工不锈钢时都必须采用较大的前角。
增大刀具的前角可减小切屑切离和清出过程中所遇到的阻力。
对后角选择要求不十分严格,但不宜过小,后角过小容易和工件表面产生严重摩擦,使加工表面粗糙度恶化,加速刀具磨损。
并且由于强烈摩擦,增强了不锈钢表面加工硬化的效应;刀具后角也不宜过大,后角过大,使刀具的楔角减小,降低了切削刃的强度,加速了刀具的磨损。
通常,后角应比加工普通碳钢时适当大些。
对刀具切削部分表面粗糙度的要求提高刀具切削部分的表面光洁度可减少切屑形成卷曲时的阻力,提高刀具的耐用度。
与加工普通碳钢相比较,加工不锈钢时应适当降低切削用量以减缓刀具磨损;同时还要选择适当的冷却润滑液,以便降低切削过程中的切削热和切削力,延长刀具的使用寿命。
对刀杆材料的要求加工不锈钢时,由于切削力较大,故刀杆必须具备足够的强度和刚性,以免在切削过程中发生颤振和变形。
这就要求选用适当大的刀杆截面积,同时还应采用强度较高的材料来制造刀杆,如采用调质处理的45号钢或50号钢。
对刀具切削部分材料的要求加工不锈钢时,要求刀具切削部分的材料具有较高的耐磨性,并能在较高的温度下保持其切削性能。
目前常用的材料有:高速钢和硬质合金。
由于高速钢只能在600°C以下保持其切削性能,因此不宜用于高速切削,而只适用于在低速情况下加工不锈钢。
由于硬质合金比高速钢具有更好的耐热性和耐磨性,因此用硬质合金材料制成的刀具更适合不锈钢的切削加工。
硬质合金分钨钴合金(YG)和钨钴钛合金(YT)两大类。
钨钴类合金具有良好的韧性,制成的刀具可以采用较大的前角与刃磨出较为锋利的刃口,在切削过程中切屑易变形,切削轻快,切屑不容易粘刀,所以在一般情况下,用钨钴合金加工不锈钢比较合适。
不锈钢加工刀具的选择技巧
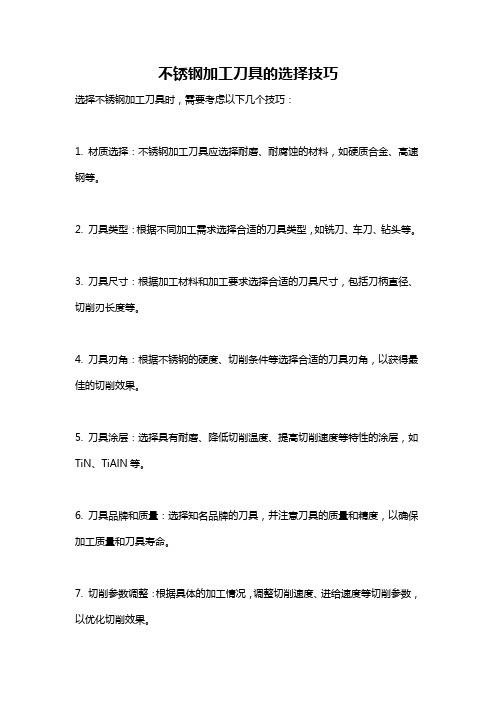
不锈钢加工刀具的选择技巧
选择不锈钢加工刀具时,需要考虑以下几个技巧:
1. 材质选择:不锈钢加工刀具应选择耐磨、耐腐蚀的材料,如硬质合金、高速钢等。
2. 刀具类型:根据不同加工需求选择合适的刀具类型,如铣刀、车刀、钻头等。
3. 刀具尺寸:根据加工材料和加工要求选择合适的刀具尺寸,包括刀柄直径、切削刃长度等。
4. 刀具刃角:根据不锈钢的硬度、切削条件等选择合适的刀具刃角,以获得最佳的切削效果。
5. 刀具涂层:选择具有耐磨、降低切削温度、提高切削速度等特性的涂层,如TiN、TiAlN等。
6. 刀具品牌和质量:选择知名品牌的刀具,并注意刀具的质量和精度,以确保加工质量和刀具寿命。
7. 切削参数调整:根据具体的加工情况,调整切削速度、进给速度等切削参数,以优化切削效果。
总的来说,选择不锈钢加工刀具时需要考虑材质、类型、尺寸、刃角、涂层、品牌和质量等因素,以确保切削效果和工作寿命。
菜刀的硬度最佳对照表

菜刀的硬度最佳对照表
菜刀的硬度与材料、制造工艺和用途有关,不同的菜刀可能需要不同的硬度以达到最佳性能。
以下是一些常见的菜刀材料及其硬度范围:
1.碳钢:硬度范围大约在50-65 HRC。
碳钢菜刀锋利度高,但容易生锈和磨损,
需要定期保养。
2.不锈钢:硬度范围通常在50-60 HRC。
不锈钢菜刀耐腐蚀,易于清洁,但锋
利度可能不如碳钢。
3.高碳不锈钢:硬度范围可以达到60-65 HRC。
高碳不锈钢结合了碳钢和不锈
钢的优点,既耐腐蚀又锋利。
4.陶瓷:硬度范围非常高,可以达到90 HRA以上。
陶瓷菜刀非常锋利,耐腐蚀,
但容易碎裂,不适合切割硬物。
需要注意的是,硬度并不是唯一衡量菜刀性能的标准,还需要考虑韧性、耐磨性、抗腐蚀性等因素。
此外,不同的菜刀用途也需要不同的硬度,例如切片刀需要更高的锋利度,而砍骨刀则需要更高的韧性和抗冲击性。
因此,没有一份通用的菜刀硬度最佳对照表。
在选择菜刀时,需要根据自己的需求和用途选择合适的材料和硬度。
不锈钢316铣削加工参数
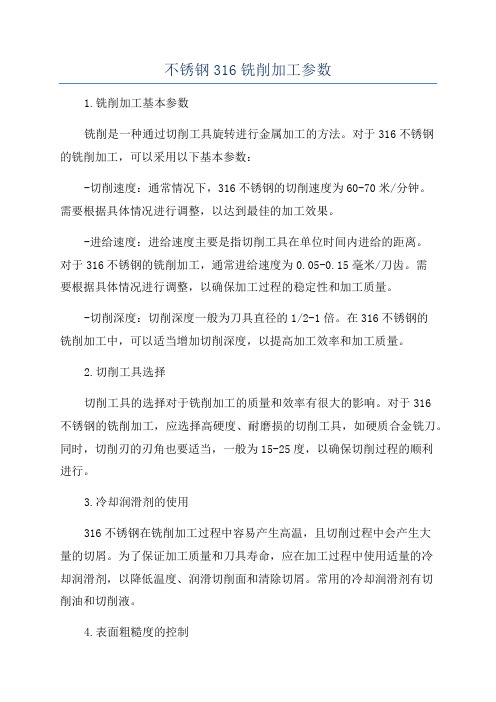
不锈钢316铣削加工参数1.铣削加工基本参数铣削是一种通过切削工具旋转进行金属加工的方法。
对于316不锈钢的铣削加工,可以采用以下基本参数:-切削速度:通常情况下,316不锈钢的切削速度为60-70米/分钟。
需要根据具体情况进行调整,以达到最佳的加工效果。
-进给速度:进给速度主要是指切削工具在单位时间内进给的距离。
对于316不锈钢的铣削加工,通常进给速度为0.05-0.15毫米/刀齿。
需要根据具体情况进行调整,以确保加工过程的稳定性和加工质量。
-切削深度:切削深度一般为刀具直径的1/2-1倍。
在316不锈钢的铣削加工中,可以适当增加切削深度,以提高加工效率和加工质量。
2.切削工具选择切削工具的选择对于铣削加工的质量和效率有很大的影响。
对于316不锈钢的铣削加工,应选择高硬度、耐磨损的切削工具,如硬质合金铣刀。
同时,切削刃的刃角也要适当,一般为15-25度,以确保切削过程的顺利进行。
3.冷却润滑剂的使用316不锈钢在铣削加工过程中容易产生高温,且切削过程中会产生大量的切屑。
为了保证加工质量和刀具寿命,应在加工过程中使用适量的冷却润滑剂,以降低温度、润滑切削面和清除切屑。
常用的冷却润滑剂有切削油和切削液。
4.表面粗糙度的控制在316不锈钢的铣削加工中,控制表面粗糙度是非常重要的。
表面粗糙度的大小与加工参数有关,切削速度和进给速度的增大会使表面粗糙度增加,而切削深度的增大会使表面粗糙度减小。
因此,需要根据具体要求,调整加工参数,以获得满足要求的表面粗糙度。
总结:316不锈钢的铣削加工需要选择合适的加工参数,如切削速度、进给速度和切削深度等,同时选择合适的切削工具和使用适量的冷却润滑剂。
通过合理设置加工参数和控制加工过程中的温度等因素,可以获得最佳的加工效果和加工质量。
合金铣刀加工不锈钢参数

合金铣刀加工不锈钢参数合金铣刀是一种广泛应用于不锈钢加工中的工具。
在不锈钢加工过程中,选择合适的参数对于加工质量和工具寿命至关重要。
下面将详细介绍合金铣刀加工不锈钢的参数。
1.刀具材料合金铣刀通常由高速钢、硬质合金或立方氮化硼(CBN)等材料制成。
在加工不锈钢中,由于其较高的切削温度和切削压力,一般选择硬质合金刀具。
硬质合金刀具拥有较高的硬度和耐磨性,能够在高温和高切削压力下保持较好的切削性能。
2.速度和进给在加工不锈钢时,由于不锈钢的硬度较高,一般需要比较低的切削速度和进给速度。
过高的切削速度和进给速度会导致切削力增大,不仅加剧刀具磨损,还可能导致不锈钢表面出现粗糙度过大、刀具折断等问题。
需要根据具体的不锈钢材料和加工要求选择合适的速度和进给。
3.切削深度和切削宽度在不锈钢加工中,切削深度和切削宽度的选择也是非常重要的。
过大的切削深度和切削宽度会增加切削力和切削温度,导致刀具过早磨损和加工表面粗糙。
合理选择切削深度和切削宽度可以减少切削力和切削温度,提高加工效率和加工质量。
4.刀具润滑方式在不锈钢加工中,切削液的使用对于工具寿命和加工质量有着重要影响。
切削液可以冷却刀具和工件,减小切削温度,降低刀具磨损。
同时,切削液还可以冲洗加工区域,防止切屑堵塞刀具和切口。
因此,在不锈钢加工中,合理选择切削液,确保充分润滑是非常重要的。
5.刀具几何结构合金铣刀的几何结构也会影响加工效果。
一般来说,刀具的齿数越多,切削时每齿所受的切削压力越小,切削效果越好。
此外,刀具的刃磨角度、后刀角、径向切削角等参数也会影响加工效果。
需要根据不锈钢的硬度和切削要求选择合适的刀具几何结构。
以上是关于合金铣刀加工不锈钢的一些参数介绍。
在实际应用过程中,需要根据具体的不锈钢材料和加工要求进行参数选择和调整,以获得最佳的加工效果。
同时,及时更换磨损的刀具是保证加工质量和工具寿命的关键。
不锈钢菜刀用哪种钢好什么牌子好呢

不锈钢菜刀用哪种钢好什么牌子好呢刀具是每个家庭厨房中必备的设施,主要用来辅助烹饪者完成切菜、切肉的工作。
当然了,一把好的菜刀才不会影响烹饪者的发挥。
如今,许多人都选择不锈钢菜刀,因为其的优点就是不易生锈。
那么下面这篇文章小编就给大家说说不锈钢菜刀什么材质好,感兴趣的朋友一起看看吧!一、不锈钢菜刀用哪种钢好1、三铬钢此钢的含碳量占0.28-0.35%,含铬量占12.8-13.5%。
经过油淬火处理后,其硬度可达到54-56HRC。
该钢质系列产品的特点:锋利、易复磨、不易生锈。
2、四铬钢此钢的含碳量占0.35-0.45%,含铬量占12.8-13.5%,含钼量占0.5%,含钒量占0.3-0.5%。
经加热扩张后加以锻打,其硬度可达到56-58HRC。
该钢质系列产品的特点:锋利、防锈、具韧性、不易断脆、晶粒更细、易复磨。
3、五铬钢此钢的含碳量占0.68-0.75%,含铬量占16.7-17.5%,含钼量占0.5%。
经过油淬火处理后,其硬度可达到58-60HRC。
该钢质系列产品的特点:坚硬、锋利、持久、防锈、韧性高。
4、复合钢此钢是以爆炸产生的高温高压轧合而成的,外层侧面采用耐蚀性优良的低碳不锈钢、中间芯部材料则是高碳合金钢。
虽然经热处理淬火,但由于外层采用的是低碳不锈钢材料,所以硬度值较低,在HRC48以下。
它具有复合层保护,不易崩口与卷口。
二、不锈钢菜刀什么牌子好1、十八子作阳江十八子集团有限公司,刀具十,始创于1983年,广东省商标,广东省产品,其以手工生产碳钢菜刀起家,集科研炼钢、产、销、旅游为一体的高新技术企业。
2、双立人双立人始创于1731年德国,是享誉全球的家用及专业刀具品牌,也是专业厨房用具品牌、美甲及发剪生产商,它旗下的“S”和四星系列刀具广受欢迎。
3、张小泉张小泉始创于1663年,是中华,我国手工业的传统,其传统锻造技艺被国务院认定为非物质文化遗产,国内制剪行业领先企业。
4、王麻子王麻子始创于1651年,其传统锻制技艺入选非物质文化遗产,是主要从事系列刀具的生产、销售的现代化企业。
sus303和304加工 -回复

sus303和304加工-回复制造业中的机械加工是一项非常重要的工艺过程,其中sus303和sus304不锈钢的加工是常见的一种。
这两种材料具有优秀的耐腐蚀性和机械强度,适用于各种机械零件的制造。
本文将一步一步详细介绍sus303和sus304不锈钢的加工过程。
首先,对于sus303和sus304的加工,我们需要准备相应的材料和工具。
材料方面,我们需要优质的sus303和sus304不锈钢,可以通过购买或者与供应商合作获得。
对于工具方面,我们需要切削加工所需的刀具,如钻头、铣刀和车刀等。
此外,还需要量具来确保加工尺寸的准确性,如千分尺和测微计等。
接下来,我们将开始实际的加工步骤。
首先,我们需要进行设计和规划。
根据零件的要求,我们需要设计出合适的加工方案,并制定详细的步骤和工艺。
这一步骤的目的是确保加工的顺利进行,并最大程度地提高生产效率。
然后,我们需要对sus303和sus304进行预处理。
这包括切割和修边等步骤,以确保材料的尺寸符合要求,并达到加工的需求。
在这一步骤中,我们可以使用切削工具如锯片或磨具来完成。
接下来,我们进入正式的机械加工过程。
首先是钻孔加工。
我们可以使用钻头来钻孔,为以后的加工步骤做准备。
这一步骤需要注意的是选择适当的转速和进给速度,以避免过度加热和切削负荷过大。
接下来是铣削加工。
我们可以使用铣刀进行铣削,将不锈钢材料切削成所需的形状和尺寸。
在这一步骤中,我们需要控制好铣削的速度和深度,以保证加工表面的质量。
此外,还需要注意及时清洁切屑,以免对加工过程产生干扰。
最后是车削加工。
我们可以使用车刀对不锈钢材料进行车削,使得其尺寸和形状更加精确。
这一步骤需要注意的是选择适当的车削刀具,并控制好车削的速度和进给速度,以确保加工的精度和表面光洁度。
完成上述加工步骤后,我们需要进行检查和调整。
通过使用量具,我们可以检查加工零件的尺寸是否满足要求,并进行必要的调整。
如果有必要,我们还可以进行表面处理,如研磨和抛光,以获得更好的表面光洁度。
- 1、下载文档前请自行甄别文档内容的完整性,平台不提供额外的编辑、内容补充、找答案等附加服务。
- 2、"仅部分预览"的文档,不可在线预览部分如存在完整性等问题,可反馈申请退款(可完整预览的文档不适用该条件!)。
- 3、如文档侵犯您的权益,请联系客服反馈,我们会尽快为您处理(人工客服工作时间:9:00-18:30)。
不锈钢加工刀具选择
1.引言
随着航空、航天、石油、化工、冶金和食品等工业的蓬勃发展,不锈钢材料已得到广泛应用,而不锈钢材料由于韧性大、热强度高、导热系数低、切削时塑性变形大、加工硬化严重、切削热多、散热困难等原因,造成刀尖处切削温度高、切屑粘附刃口严重、容易产生积屑瘤,既加剧了刀具的磨损,又影响加工表面粗糙度。
此外,由于切屑不易卷曲和折断,也会损伤已加工表面,影响工件的质量。
为提高加工效率和工件质量,正确选择刀具材料、车刀几何参数和切削用量至关重要。
2.刀具材料的选择
正确选用刀具材料是保证高效率加工不锈钢的决定因素。
根据不锈钢的切削特点,刀具材料应具备足够的强度、韧性、高硬度和高耐磨性且与不锈钢的粘附性要小。
常用的刀具材料有硬质合金和高速钢两大类,形状复杂的刀具主要采用高速钢材料。
由于高速钢切削不锈钢时的切削速度不能太高,因此影响生产效率的提高。
对于较简单的车刀类刀具,刀具材料应选用强度高、导热性好的硬质合金,因其硬度、耐磨性等性能优于高速钢。
常用的硬质合金材料有:钨钴类(YG3、YG6、YG8、YG3X、YG6X),钨钴钛类(YT30、YT15、YT14、YT5),通用类(YW1、YW2)。
YG类硬质合金的韧性和导热性较好,不易与切屑粘结,因此适用于不锈钢粗车加工;而YW类硬质合金的硬度、耐磨性、耐热性和抗氧化性能以及韧性都较好,适合于不锈钢的精车加工。
加工1Cr18Ni9Ti奥氏体不锈钢时,不宜选用YT类硬质合金,由于不锈钢中的Ti和YT类硬质合金中的Ti 产生亲合作用,切屑容易把合金中的Ti带走,促使刀具磨损加剧。
〕
3.刀具几何角度的选择
刀具切削部分的几何角度,对于不锈钢切削加工的生产率、刀具耐用度、被加工表面粗糙度、切削力以及加工硬化等方面都有很大的影响,合理选择和改进刀具几何参数是保证加工质量、提高效率、降低成本的有效途径。
(1)车刀前角γ0的选择
前角的大小决定刀刃的锋利与强度。
增大前角可以减小切屑的变形,从而减小切削力和切削功率,降低切削温度,提高刀具耐用度。
但是增大前角会使楔角减小,降低刀刃强度,造成崩刃,使刀具耐用度下降。
车削不锈钢时,在不降低刀具强度的条件下,应把前角适当取大一些。
在刀具前角大时其塑性变形小,切削力和切削热降低,减轻加工硬化趋势,提高刀具耐用度,一般刀具前角宜取12°~20°。
(2)车刀后角α0的选择
在切削过程中,后角可以减小后刀面与切削表面的摩擦。
若后角过大,则楔角减小,使散热条件恶化,刀具刃口强度下降,降低刀具耐用度;若后角过小,摩擦严重,则会使刃口变钝,增大切削力,增高切削温度,加剧刀具磨损。
在一般情况下,后角变化不大,但必须有一个合理的数值,以利于提高刀具的耐用度。
车削不锈钢时,由于不锈钢的弹性和塑性都比普通碳素钢大,所以刀具后角过小会使切断表面与车刀后角的接触面积增大,摩擦产生的高温区集中于车刀后角,加快车刀磨损,降低被加工表面光洁度,所以车削不锈钢时的车刀后角要比车削普通碳钢时稍大一些,但后角过大又会降低刀刃强度,直接影响车刀的耐用度,因此,一般情况下车刀后角宜取6°~10°。
(3)车刀主偏角Kr的选择
当切削深度ap和进给量f不变时,减小主偏角Kr可使散热条件得到改善,减少刀具损坏,使刀具切入、切出平稳。
但主偏角减小又会使径向力增大,在切削时容易引起振动。
车削不锈钢的硬化倾向性强,易产生振动,振动又会使加工硬化严重。
因此,主偏角一般宜取45°~90°。
具体角度应根据机床、零件、刀具系统的刚性和切削用量来选择。
(4)车刀刃倾角λs的选择
刃倾角可控制切屑流向,当刃倾角λs为负值时,切屑流向已加工表面;当刃倾角λs为正值时,切屑流向待加工表面。
为了使切屑不划伤已加工表面,在精加工时,刃倾角λs值为正值。
当λs为正值时,刀尖强度低并首先接触工件,易损坏;当λs为负值时,刀尖强度高,耐冲击,可避免崩坏刀尖,切入、切出平稳,车削不锈钢时,一般刀具刃倾角宜取0°~20°。
4.切削用量的选择
切削用量的大小对生产效率和加工质量有很大影响,因此在确定了刀具的几何参数以后,还要选定合理的切削用量。
在选择切削用量时,应注意考虑以下因素:一是要根据不锈钢及各类毛坯的硬度等来选择切削用量;二是要根据刀具材料、焊接质量和车刀的刃磨条件来选择切削用量;三是要根据零件直径、加工余量和车床精度等来选择切削用量。
同时为了抑制积屑瘤和鳞刺的产生,提高表面质量,在采用硬质合金刀具进行加工时,切削用量应比车削一般碳钢类工件稍低些,特别是切削速度不宜过高(vc=50~80m/min);切削深度ap不宜过小,以避免切削刃和刀尖划过硬化层,ap=0.4~4mm;因此进给量f对刀具耐用度影响不如切削速度大,但会影响断屑和排屑,拉伤、擦伤工件表面,影响加工
的表面质量,进给量一般取f=0.1~0.5mm/r。
不锈钢尤其是奥氏体型不锈钢的塑性较好,在切削加工时,产生的切屑难以折断,加大了切屑与刀具前刀面之间的摩擦力,增大了切削力。
同时,因加工硬化会增大被切削材料的硬度和强度,也导致切削力增大。
为此,在合理选择刀具材料、刀具的几何角度和切削用量的基础上,对不锈钢和45钢做了切削力对比试验。
试验结果表明,在相同切削用量的情况下,加工不锈钢时切削力比加工45钢时只增加了8.5%。
5.结语
合理选择刀具材料、刀具几何角度和切削用量,对于提高不锈钢切削加工的生产效率和加工工件质量是完全能够实现的
加工不锈钢刀具及参数的选择
对刀杆材料的要求加工不锈钢时,由于切削力较大,故刀杆必须具备足够的强度和刚性,以免在切削过程中发生颤振和变形。
这就要求选用适当大的刀杆截面积,同时还应采用强度较高的材料来制造刀杆,如采用调质处理的45号钢或50号钢。
对刀具切削部分材料的要求加工不锈钢时,要求刀具切削部分的材料具有较高的耐磨性,并能在较高的温度下保持其切削性能。
目前常用的材料有:高速钢和硬质合金。
由于高速钢只能在600°C以下保持其切削性能,因此不宜用于高速切削,而只适用于在低速情况下加工不锈钢。
由于硬质合金比高速钢具有更好的耐热性和耐磨性,因此用硬质合金材料制成的刀具更适合不锈钢的切削加工。
硬质合金分钨钴合金(YG)和钨钴钛合金(YT)两大类。
钨钴类合金具有良好的韧性,制成的刀具可以采用较大的前角与刃磨出较为锋利的刃口,在切削过程中切屑易变形,切削轻快,切屑不容易粘刀,所以在一般情况下,用钨钴合金加工不锈钢比较合适。
特别是在振动较大的粗加工和断续切削加工情况下更应采用钨钴合金刀片,它不象钨钴钛合金那样硬脆,不易刃磨,易崩刃。
钨钴钛合金的红硬性较好,在高温条件下比钨钴合金耐磨,但它的脆性较大,不耐冲击、振动,一般作不锈钢精车用刀具。
2 刀具材料牌号的选择
刀具材料的切削性能关系着刀具的耐用度和生产率,刀具材料的工艺性影响着刀具本身的制造与刃磨质量。
宜选择硬度高、抗粘结性和韧性好的刀具材料,如YG类硬质合金,最好不要选用YT 类硬质合金,尤其是在加工1Gr18Ni9Ti奥氏体不锈钢应绝对避免选用YT类硬质合金,因为不锈钢中的钛(Ti)和YT类硬质合金中的Ti产生亲合作用,切屑容易把合金中的Ti带走,促使刀具磨损加剧。
生产实践表明,选用YG532、YG813及YW2三种牌号材料加工不锈钢具有较好的加工效果。
3 刀具几何参数的选择
前角的选择从切削热的产生和散热方面说,增大前角可减小切削热的产生,切削温度不致于太高,但前角过大则因刀头散热体积减小,切削温度反而升高。
减小前角可改善刀头散热条件,切削温度有可能降低,但前角过小,则切削变形严重,切削产生的热量不易散掉。
实践表明,取前角go=15°~20°最为合适。
后角的选择粗加工时,对强力切削的刀具则要求切削刃口强度高,则应取较小的后角;精加工时,其刀具磨损主要发生在切削刃区和后刀面上,对于不锈钢这种易出现加工硬化的材料,其后刀面摩擦对加工表面质量及刀具磨损影响较大,合理的后角应为:加工奥氏体不锈钢(185HB以下),其后角可取6°~8°;加工马氏体不锈钢(250HB以上),其后角取6°~8°;加工马氏体不锈钢(250HB以下),其后角为6°~10°为宜。
刃倾角的选择刃倾角的大小和方向,确定了流屑的方向,合理选择刃倾角ls,通常取-10°~20°为宜。
在微量精车外圆、精车孔、精刨平面时,应采用大刃倾角刀具:应取ls45°~75°。
4 切削用量的选择
为了抑制积屑瘤和鳞刺的产生,提高表面质量,用硬质合金刀具进行加工时,切削用量要比车削一般碳钢类工件稍低些,特别是切削速度不宜过高,一般推荐切削速度Vc=60~80m/min,切削深度为ap=4~7mm,进给量f=0.15~0.6mm/r为宜。