a_rpcLab
MPLAB Code Configurator X2C Scope 库版本 2.0.0 发布说明书

Release Notes for MPLAB® Code ConfiguratorX2Cscope Library v2.0.01What is MPLAB Code Configurator X2C Scope LibraryX2CScope is a lightweight firmware-based debugging tool, and it is running on the target MCU parallelto the application. It is a runtime online debugging tool that works in RUN and DEBUGGING mode. X2CScopeis for generic use in any application and perfectly fits motor control applications.For more information, please visit https://x2cscope.github.io/2System Requirements1.MPLAB X 6.00 (or higher)2.XC16 1.50 (or higher)3.XC32 2.10 (or higher)4.MCC5.1.0 (or higher)5.MCC X2C Library v2.0.03Installing MPLAB® Code Configurator X2Cscope LibraryBasic steps for installing MPLAB® Code Configurator needs to be installed as below.To install the MPLAB® Code Configurator v5.1.0 or later Plugin1.In the MPLAB® X IDE, select Plugins from the Tools menu2.Select the Available Plugins tab3.Check the box for the MPLAB® Code Configurator v4, and click on InstallTo install and load different library version when connected to internet1.Open MPLAB® Code Configurator2.In the Versions tab under PIC24\dsPIC33\PIC32MM MCUs or X2Cscope will find the multiplelibrary version (loaded version is indicated by the green dot)3.Right Click on the required version of the library as specified in System Requirements and select Markfor load4.Click on Load Selected Libraries button to load the libraryTo install the X2Cscope Library when not connected to internet1.In the MPLAB® X IDE, select Options from the Tools menu2.Select Plugins tab3.Click on Install Library4.Add the required version(s) of the library as specified in the System Requirements.4What’s New•Migrated X2C Scope library to MCC version 5.1.0•X2C Scope library support in MCC melody.5Supported DevicesThe X2Cscope library supports the following device families.1.dsPIC33EP512GP506 (/dsPIC33EP512GP506)2.dsPIC33EV256GM106(/dsPIC33EV256GM106)3.dsPIC33EV256GM006(/dsPIC33EV256GM006)4.dsPIC33EP128GS806 (/dsPIC33EP128GS806)5.dsPIC33EP64GS506 (/dsPIC33EP64GS506)6.dsPIC33EP512GM710(/dsPIC33EP512GM710)7.dsPIC33CH128MP508 anddsPIC33CH128MP508S1(/dsPIC33CH128MP508)8.dsPIC33CK256MP508 (/dsPIC33CK256MP508)9.dsPIC33CH512MP508 anddsPIC33CH512MP508S1(https:///dsPIC33CH512MP508)10.dsPIC33CK64MP105(https:///dsPIC33CK64MP105)6 Device Support List☑ : The X2Cscope is supported for the device.7 Customer Support7.1 Microchip Web SiteMicrochip provides online support via our web site at . This web site is used to make files and information easily available to customers. Accessible by using your favorite Internet browser, the web site contains the following information:•Product Support – Data sheets and errata, application notes and sample programs, design resources, user’s guides and hardware support documents, latest software releases and archived software •General Technical Support – Frequently Asked Questions (FAQs), technical support requests, online discussion groups/forums (), Microchip consultant program member listing •Business of Microchip – Product selector and ordering guides, latest Microchip press releases, listing of seminars and events, listings of Microchip sales offices, distributors, and factory representatives8.2Additional SupportUsers of Microchip products can receive assistance through several channels:•Distributor or Representative•Local Sales Office•Field Application Engineering (FAE)•Technical SupportCustomers should contact their distributor, representative or field application engineer (FAE) for support. Local sales offices are also available to help customers. A listing of sales offices and locations is available on our web site.Technical support is available through the web site at: 。
pnetlab使用

pnetlab使用Pnetlab是一种网络实验室模拟软件,它可以模拟各种网络设备和拓扑,帮助网络工程师和学生进行网络实验和学习。
本文将介绍Pnetlab的基本用法以及如何进行网络实验和学习。
首先,Pnetlab是一种用于模拟网络环境的软件,它可以模拟各种网络设备,如路由器、交换机、防火墙等,还可以创建复杂的网络拓扑。
Pnetlab可以在单机上运行,并提供了一个图形化界面,使用户可以轻松地创建和管理网络设备。
Pnetlab的使用非常简单,首先需要下载并安装软件。
安装完成后,打开Pnetlab,并创建一个新的项目。
在项目中,可以创建网络拓扑并添加所需的设备。
使用Pnetlab的图形化界面,可以方便地将设备连接起来,并进行不同的配置。
一旦网络拓扑创建完成,用户可以开始进行实验和学习。
Pnetlab提供了模拟设备的功能,用户可以登录到设备上,配置各种网络参数,进行实际的网络操作。
此外,Pnetlab还提供了虚拟机功能,可以在模拟网络中运行虚拟机,并模拟实际网络环境中的各种场景。
Pnetlab还提供了丰富的实验和学习资源。
用户可以使用Pnetlab提供的实验模板进行学习,学习各种网络配置和故障排除的方法。
此外,用户还可以根据自己的需求创建自己的实验,进行自主学习和探索。
Pnetlab的优点不仅在于其易用性和功能丰富性,还在于它的实时性和灵活性。
Pnetlab可以提供实时的网络模拟和监控功能,帮助用户更好地了解网络中的各种问题。
同时,Pnetlab还支持多种网络协议和模式,例如RIP、OSPF、BGP等,用户可以根据需要选择合适的网络协议进行实验和学习。
除此之外,Pnetlab还支持多种网络拓扑和部署方式。
用户可以创建简单的局域网,也可以模拟复杂的广域网拓扑。
此外,Pnetlab还支持使用不同的硬件设备进行实验和学习,如交换机、路由器和防火墙等。
用户可以根据自己的需求选择合适的拓扑和设备。
总之,Pnetlab是一种功能丰富、易用性强的网络实验室模拟软件。
amplab原理
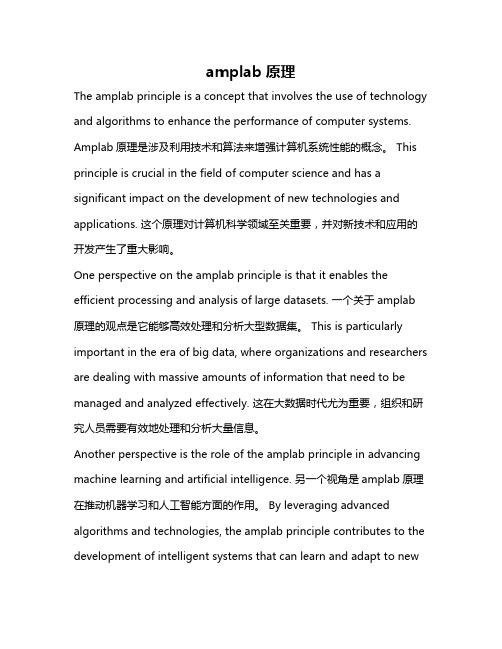
amplab原理The amplab principle is a concept that involves the use of technology and algorithms to enhance the performance of computer systems. Amplab原理是涉及利用技术和算法来增强计算机系统性能的概念。
This principle is crucial in the field of computer science and has a significant impact on the development of new technologies and applications. 这个原理对计算机科学领域至关重要,并对新技术和应用的开发产生了重大影响。
One perspective on the amplab principle is that it enables the efficient processing and analysis of large datasets. 一个关于amplab 原理的观点是它能够高效处理和分析大型数据集。
This is particularly important in the era of big data, where organizations and researchers are dealing with massive amounts of information that need to be managed and analyzed effectively. 这在大数据时代尤为重要,组织和研究人员需要有效地处理和分析大量信息。
Another perspective is the role of the amplab principle in advancing machine learning and artificial intelligence. 另一个视角是amplab原理在推动机器学习和人工智能方面的作用。
企业级应用开发技术考核试卷

B. SOAP
C. CORBA
D. JSON-RPC
15.以下哪个技术主要用于实现分布式系统的服务注册与发现?()
A. Eureka
B. Consul
C. ZooKeeper
D. Etcd
16.企业级应用中,以下哪个组件主要用于实时通信?()
A. WebSocket
B. HTTP
3. Hadoop适合批处理,Spark适合实时处理。Hadoop基于磁盘,Spark基于内存。Hadoop稳定,Spark性能高。
4.容器化技术简化部署,保证环境一致性,促进CI/CD流程自动化。通过容器编排(如Kubernetes)实现滚动更新、蓝绿部署,提高部署效率和稳定性。
3.分布式系统中,CAP定理包含的三个基本特性是______、______和______。()
4.在微服务架构中,服务之间进行通信的常用协议是______。()
5.数据库事务隔离的四个级别分别是______、______、______和______。()
6.下列哪种编程语言被称为“函数式编程语言”:______。()
1.请简述企业级应用开发中,如何实现一个高并发的用户登录系统,并说明需要考虑的技术要点。
2.描述微服务架构的优势和可能面临的挑战,以及如何解决这些挑战。
3.在大数据处理领域,请比较Hadoop和Spark的异同点,并说明它们各自适合解决哪类问题。
4.请阐述容器化技术在企业级应用部署中的作用,以及它如何影响持续集成和持续部署(CI/CD)流程。
7. √
8. √
9. ×
10. √
五、主观题(参考)
1.实现高并发用户登录系统,需要采用分布式缓存、数据库分库分表、使用高效的加密算法和限流措施。技术要点包括缓存一致性、数据库事务、安全性、系统容量规划和性能监控。
RTLAB系统仿真培训知识课件资料
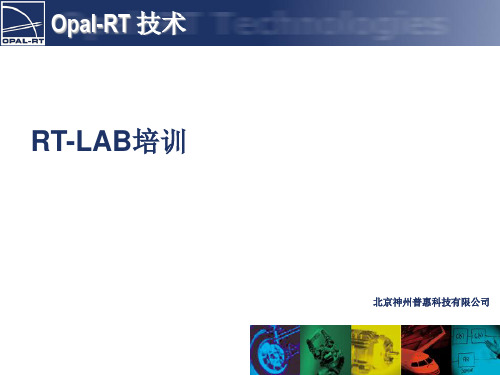
稳定表观抖动
记住,因为SC(控制台)子系统相对于主计算(SM和SS)是异 步运行的:
• 控制台子系统不包括实时模型依赖的计算
• 只有来自于同一个获取组(OpComm)的信号才能互相比较,来 自不同OpComm模块的信号不是一起同步的。
这包括命令区域和计算节点间的通信,以及分布式仿 真假定下计算节点间的通信。
所有到顶层子系统的输入,在使用前都必须首先通过OpComm模 块
OpComm 布局规则
在计算子系统中 (SM or SS):
– 一个OpComm接收来自其他计算子系统的实时同步信号 – 一个OpComm同步接收来自控制台子系统的信号
1 distance s
Integrator
acceleration
velocity
distance
在 Simulink中进行模型开发
依次传递:
– 如果你不熟悉Simulink,请进入下一个幻灯片所展示的实例控制系统 模型模块图表
– 如果你已经熟悉Simulink,通过从文件\\models\x1_cntrl_sys_theoretical.mdl 加载模型保存几分钟
1 s
Integrator
velocity
1 distance s
Integrator1
x
(
F m
dt
c1)dt
c2
带数据示波器仿真…
force
Signal Generator
10 mass
Constant
acceleration Product
1 s
Integrator
velocity
航空航天 •航空电子设备测试工作台 •可重构工程飞行模拟器 •飞行器试验台
PC3k

1. PC-3000 complex1.1. PurposeThe hardware and software complex “PC-3000” version 10.10 is designed for diagnostics and repair of any HDD with IDE interface of all modifications (ATA, ATA-2, ATA-3, ATA-4, UltraATA, E-IDE, UDMA66) and advanced factory mode repairs and restoration of widely used HDDs: Conner, Daeyoung, Fujitsu, Hitachi, IBM, Kalok, Maxtor, NEC, Quantum, Samsung, Seagate, Teac, Western Digital, Xebec, with the help of specialized technological utilities (see utilities list).1.2. PC-3000 Software, version 10.10Universal softwareTechnological utilities1.3. PC-3000 complex suite, version 10.101. Electronic protection key – 1 piece.2. PC-3000AT tester – 1 piece.3. PC-KALOK adapter – 1 piece.4. PC-CONNER adapter – 1 piece.5. PC-SEAGATE adapter – 1 piece.6. PC-TEAC adapter – 1 piece.7. IDE interface cable (40 pin) – 1 piece.8. “COM” cable (9pin) for the connection of PC-KALOK and PC-CONNER adapters to serial RS232 portof the controlling computer – 1 piece.9. “HDD” cable for the connection of PC-KALOK and PC-CONNER adapters to the drives’ technologicalconnectors or PC-SEAGATE / PC-TEAC adapters -1 piece.10. PC-3000 software – 1 CD.11. Technical manuals – 2 books (Russian version).1.4. WarrantyResearch and Production Company “ACE” LLC guarantees normal work of the PC-3000 complex for 12 months since the date of purchase. RPC “ACE” LLC takes the obligation to repair a malfunction or replace defective complex components, if the failure was not caused by t he user’s actions. The transportation fees for warranty repair are paid by the customer.RPC “ACE” LLC – the developer and manufacturer of the PC-3000 complexACE Laboratory –trademark of RPC “ACE” LLC.Mail address: Russia, 344010, Rostov-on-Don, Lermotovskaya Str. 197, of. 412.E-mail: ace@acelab.ruWeb: http://www.acelab.ru1.5. Users registrationIn order to obtain the official user status after purchase of PC-3000, send the following information to ACE Laboratory via fax (863-2) 64-17-10 or e-mail: ace@acelab.ru:1. Date of purchase for PC-3000 or PC-3000 Upgrade2. Version of PC-30003. Number of electronic protection key4. The enterprise that sold the complex5. The enterprise that purchased the complex6. Phone number7. Fax8. E-mail9. Regular mail addressThe registration can also be performed at our web-server at http://www.acelab.ru by filling the “Users registration” form.1.6. Registered PC-3000 users support1. Technical support of PC-3000 users concerning the complex operation and HDD repairs over the phone +7-8632-64-17-10(Russian Users) and e-mail: pc-3000support@acelab.ru; (fax / e-mail for English-speaking users);2. Free upgrade of new versions of complex utilities (PC-3000 Upgrade) via e-mail and federal mail;3. 50% discount during purchase of new complex versions (PC-3000 Update);4. Access to Web conference of PC-3000 complex users –pc-3000user@acelab.ru;5. Technical support at the web site www.acelab.ru/ts.htm.1.7. PC-3000 complex installation1. Insert the PC-3000AT tester board into an empty ISA slot of the controlling computer;2. Connect the electronic protection key to LPT1;3. Create PC3000 directory on the hard drive of the controlling computer. Copy into the directory allfiles from the PC-3000.xxx directory on the supplied CD, where “xxx” is the number of your protection key.4. Remove the “read only” and “archive” attributes from the copied files.5. Connect the HDD to be tested to a free power supply plug of the computer and, via the IDEinterface cable, to the tester board.6. Load the SHELL.EXE file. The complex is ready for work.7. The sequence for drives connection with the help of additional adapters is described in the usermanuals for corresponding utilities.PC-3000 complex usageYou have purchased a wonderful tool for repair of hard disk drives – PC-3000 complex. If you used to repair hard drives before, most likely you can skip this chapter, however, if your experience isn’t very la rge, the authors recommend to read the chapter “IDE (ATA) HDD technical description. Basics of IDE (ATA) HDD repair” before you start.This chapter contains a brief “guide” for the complex.So, you repair a disk drive. Do not hurry to start special technological utilities at once. First of all any drive should be checked with the PC-3000AT universal tester, included in the complex. That may help localize defects and determine the sequence for further actions. In order to achieve that, connect the drive to the tester board PC-3000AT, switch its power supply on and start the PC3000AT.EXE program. After switching on the power supply the disk drive should spin up the spindle motor and perform recalibration (zero track search). During that procedure a typical sound of the positioning device is heard. When the initialization process is complete the drive sends out the readiness signal. If this doesn’t happen (the spindle motor stops or does not spin up at all or you hear a head hit sound) then you should use the method described in part 2.2 of technical appendix.After drive readiness check (DRDY = DSC = 1, BUSY = 0), the program attempts to read the data from drive description area. If the readiness signal was not returned to the program a corresponding message ab out that appears. In such case use the methods described in paragraph 2.2.1 of the “IDE (ATA) HDD technical description. Basics of IDE (ATA) HDD repair” chapter. If, although the readiness signal was received, the drive description data cannot be read (the program returns “Drive parameters are not determined”) or the parameters are read incorrectly, it may mean either a reading channel defect or a corruption of disk firmware. (The firmware data can be restored with the help of corresponding technological utility.) However, it is possible, that the disk drive does not have a drive description area (this refers mostly to old KALOK/XEBEC models) or it contains parameters, which cannot be used for drive operation (for example, Conner CP-3000). In such case the parameters should be entered manually or from a PC-3000AT database in order to perform the testing procedure.After drive testing with PC-3000AT and making a preliminary conclusion about its defects (the methods are described in part 2.1 of the chapter “IDE (ATA) HDD technical description. Basics of IDE (ATA) HDD repair”) you can start a technological utility for more advanced diagnostics or restoration of drive firmware. Detailed description of corresponding methods for drive restoration in factory mode is in the utility description part.The PC-3000 complex development team wishes you success.2. Universal tester for diagnostics and repair of HDD of any type2.1. PurposeThe tester software PC-3000AT is the basic program of the PC-3000 complex for IDE (ATA) HDD repairs and restoration and it is designed for:1. Diagnostics of defects and repairs of IDE drive in usual mode;2. Correct restoration of low-level format in drives using 50H command1;3. Hiding of bad sectors in HDDs that support the assign mode;4. Automatic drive testing of input/output control type (complex testing).The tester software PC-3000AT functions together with the tester board PC-3000AT.2.2. Preparation for work1. Connect the PC-3000AT tester board cable to the IDE connector of the drive.2. Connect the power cable to the drive.3. Load the complex shell PC-SHELL and launch PC-3000AT program.2.3. Information output during work with PC-3000ATFor convenient perception of information the tester appears on PC screen in the form of the front panel of the instrument, consisting of the following parts:Display– displays the information concerning the testing procedure. In the upper part of the display you can see the MODEL line, containing information about the type and parameters of the drive being tested: number of cylinders (CYL), heads (HEAD), sectors (SEC).“LBA mode” In LBA mode instead of the CYL, HEAD, SEC parameters the total number of available sectors is displayed in the MODEL line.In the lower part of the display you can see the STATE line, containing the information concerning the drive state: Ready/Busy, duration of current test execution in % (DONE) appears when long tests are performed, current cylinder (CYL), head (HEAD), sector (SEC), number of drive errors (ERRS) detected during the test.“LBA mode” In LBA mode just one current sector number is displayed instead of CYL, HEAD, and SEC parameters of current sector.Two rows of LED-s–display the information about the state register1and errors register1of the HDD being tested, which allows to monitor the drive state while testing and determine the cause of malfunctions. The passive LED state is blue, active – yellow or red, red LED being the ones that inform about errors. The state register shows current state of IDE AT HDD. The register value is updated after execution of every command. The errors re gister shows the HDD state after command execution, if the “Error” bit is set in the state register.Keypad– corresponds to the right numeric keypad of the keyboard. The purpose of the keys changes 1See ATA specification.depending upon the current state of the tester. The purpose of the following keys remains constant: [Enter] – Parameter input, start of various tests.[Cancel] – used to cancel the execution of current test or of the parameter being set (can be substituted with the ESC key).[Exit] – used to cancel the execution of current test or of the parameter being set with subsequent exit to the “MODE SELECTION” menu.2.4. Parameter input for the HDD being testedAt the beginning of the test, when the controlling program is started, the tester determines the tested drive type and parameters in CHS mode. After the said determination procedure the drive type and parameters appear in the MODEL line, and the controller program of the tester goes on to the main “MODE SELECTION” menu. Press the [LBA] key in order to enter the LBA mode. If the drive does not support LBA mode, the [LBA] key does not appear on the screen.If the drive type and parameters cannot be determined because of drive malfunction, the following message will appear:Drive parameters are not determinedPressing any key will change the tester mode to:DRIVE TYPE SELECTIONIdentify DRVUser TypeConnerFujitsuMaxtorQuantumUsing [Up], [Down] and [Enter] keys you can:-attempt to determine the HDD parameters again by selecting Identify DRV;-enter the drive parameters manually by selecting User Type;-select the drive type and parameters from the existing database.“LBA mode” During parameter input or drive type selection from the database the number of available LBA sectors is calculated by multiplication of CYL, HEAD, SEC parameters.When the drive parameters are determined, the controlling program goes on to the main “MODE SELECTION” menu.2.5. PC-3000AT operation modes2.5.1. Operation mode selectionThe operation mode selection is performed from the main menu with the help of [Up], [Down], and [Enter] keys. You can leave the selected operating mode by pressing [Cancel] and [Exit] keys.The main menu:MODE SELECTIONDrive type selectionDrive testController testComplex testDefects relocationFormattingExitDrive type selection – the mode for the determination of parameters or their input for the drive being tested.Drive test – test mode for testing and repair of:-read/write channel;-positioning system;-spindle motor and its controller chip.Controller test – test mode for testing and repair of:-interface controller;-MPU;-Read/write channel;-buffer RAM.Complex test – test mode for input/output control of the drive.Defects relocation – in this mode the tester relocates defective BAD sectors in drives that support assign mode.Formatting – in this mode the tester performs correct restoration of low-level format in HDDs that support the 50H command1.Exit – exit from the program to PC-SHELL interface or to DOS.The keys [SMART] and [Passp] allow to view the S.M.A.R.T. parameters of the drive and the drive description area of HDD, which are read with the Identify DRV command and decrypted in accordance with the ATA-4 specification.2.5.2. Viewing S.M.A.R.T. parameters of the drivePressing the [SMART] key brings the following S.M.A.R.T. parameters of the drive on-screen:ID – the controlled parameter identifierFor Western Digital drives the identifier numbers correspond to the following parameters:ID Controlled parameter1 Read Error Rate4 Start/Stop Count5 Relocated Sector Count10 Spin up Retry Count11 Drive Calibration Retry Count199 ULTRA DMA CRC Error Rate200 Multi-zone Error RateFor Fujitsu drives the identifier numbers correspond to the following parameters:ID Controlled parameter1 Read Error Rate2 Throughput performance3 Spin up time1See ATA specification.4 Number of times the spindle motor is activated5 Number of alternative sectors7 Seek error rate8 Seek time performance9 Power-on time10 Number of retries made to activate the spindle motor12 Number of power-on-power-off times199 Ultra ATA CRC Error Rate200 Write error rateAttribute value – the attribute values may range from 1 to 253. Initially the attributes have maximum values. With subsequent wear or in case of pre-failure situations the values of reliability attributes decrease. Therefore, large values of the attributes mean low probability of drive malfunction while low attribute values mean low reliability of the drive and high probability of its malfunctions. The top values of reliability attributes are usually equal to 100 (IBM, Quantum, Fujitsu) or 253 (Samsung). However, there are exceptions, for example the first reliability attribute of WDAC34000, WDAC33100, and WDAC31600 models manufactured by Western Digital has the maximum value of 200, while the maximum value of the rest is 100.Threshold value – the HDD developers determine thresholds for every reliability attribute. If at least one of the attribute values is lower than the corresponding threshold value, it means that the data kept in the drive is endangered. The composition and number of reliability attributes are determined by the manufacturers individually for each HDD type.“P re-failure/advisory” BIT – apart from the threshold value an additional parameter is determined for each attribute, and it also indicates the pre-failure drive status. Three states are possible for the drive, characterized by the Pre-failure/advisory BIT:“Pre-failure/advisory” BIT = 0, the reliability attribute value is above the corresponding threshold value indicating good reliability resource of the drive;“Pre-failure/advisory” BIT = 0, the reliability attribute value being less than the corresponding threshold value indicating low reliability resource of the drive;“Pre-failure/advisory” BIT = 1, the reliability attribute value is less than the corresponding threshold value indicating pre-failure drive state.Result – generalized result for each of the controlled parameters. It may have the following values:OK – attribute value is higher than the corresponding threshold value;! – attribute value is less than the corresponding threshold value. Pre-failure/advisory BIT = 0;!!! – attribute value is less than the corresponding threshold value. Pre-failure/advisory BIT = 1.If the drive does not support S.M.A.R.T. diagnostics, pressing the [SMART] key causes the drive to initiate the ABRT error and the following message appears on screen:This drive does not support S.M.A.R.T.2.5.3. Drive testDrive test (HDA, PCB)– test mode for testing and repair of:-read/write channel;-positioning system;-spindle motor and its controller chip.The test information is displayed in the STATE line:Ready/Busy – determines the drive state using the BSY bit of the state register;CYL – the value of current (active) cylinder;HEAD – the value of current (active) head;ERRS – number of detected errors.Keys purpose.Pressing the keys of the right tester keypad (right keyboard keypad) causes execution of the following functions:[Tran.] - drive translator test[Step-] – positioning the magnetic heads one step further decreasing the current cylinder value;[Step+] – positioning the magnetic heads one step further decreasing the current cylinder value;[X->0] - drive recalibration, i.e. location of the heads over the zero cylinder;[A<->B] - cyclic positioning between two given cylinders;[RND] - random positioning between two given cylinders;[Eras] – writing code 0000 to all sectors of the HDD;[View] – viewing the contents of the drive sectors on screen;[Wrt] – writing the selected code to current track;[Hd] – switching (selection) of magnetic heads;[T] – measuring the magnetic disk rotation period (ms) and the rotation speed (rev/s) of the disks.Positioning over given cylinder – positioning over a small number of cylinders can be conveniently performed with the help of [Step+] and [Step-] keys. When positioning over large number of cylinders is required, it is necessary to press the [X->A] key – a screen prompt will appear asking you for the number of cylinder A, over which the heads will be positioned. When the value input is complete, press the [Enter] key. If a symbol has been entered incorrectly, you can delete it by pressing backspace key.Positioning between two given cylinders – for cyclic positioning between two given cylinders the [A<->B] key should be pressed. A screen prompt will appear inviting you to enter the numbers of cylinders A and B, between which the heads will be positioned. After inputting the values and pressing the [Enter] key the drive will start positioning the heads between two selected cylinders non-stop. The positioning procedure can be interrupted by pressing the [Cancel] key or the [Exit] key with subsequent exit from the test mode. For heads positioning between two random cylinders the [RND] key should be pressed. The value input for the first and the last cylinders is performed similarly to cyclic positioning mode.Write – pressing the [Wrt] key brings the write code selection menu:Write code:0000FFFF5555AAAA6DB69999After selection of the code for writing press the [Enter] key. Write operation will be performed on all sectors of the current track in the drive.Viewing the sector contents–after pressing [View] key you’ll have to enter the number of the starting cylinder, head and sector. Than the dump of that sector will appear on screen, the [Up] and [Down] keys will allow you to see previous or the following sectors. You can leave the sector view mode be pressing the [Cancel] or [Exit] keys with subsequent exit to the main menu.Erase – pressing the [Eras] key will cause the following message to appear:ARE YOU SURE?Press [Enter] or [Cancel]After pressing [Enter] the drive will be recalibrated and writing the null value will be started beginning with the zero cylinder and the zero head. The erasure procedure can be interrupted by pressing [Cancel] or [Exit] key with subsequent exit to the main menu.Drive translator test –after pressing the [Tran] key you’ll have to enter the starting and ending cylinders of the tested zone. The test is performed in two passes: the first pass writes to each of the sector its corresponding number while the second reads the written number and compares it with the calculated number. If the numbers do not match, an error is reported.Measuring the rotation period and rotation speed for magnetic disks– when [T] key is pressed, the following message appears:Index xx,xx msRotations yyyy RPMwhere xx,xx is the rotation period of the magnetic disks in milliseconds and yyyy is the rotation speed in rev/min. The testing mode can be interrupted by pressing the [Cancel] or [Exit] keys with subsequent exit to the main menu. Several IDE drives do not form the INDEX signal. It is impossible to measure the rotation period and disks rotation speed in such drives and the tester display remains empty after pressing the [T] key.“LBA mode” The current LBA sector is displayed in the STATE line in LBA mode instead of the CYL and HEAD parameters. Instead of [Hd] key for switching the magnetic heads, the [Ver.] key appears –which means the current LBA sector verification. All the positioning modes are used for positioning not between the cylinders but between LBA sectors.2.5.4. Controller testController test (PCB)– test mode for test and repair of:-ATA interface controller;-MCU;-Read/write channel;-buffer RAM.Test mode menu:CONTROLLER TESTCyclic reading state registerSector buffer testCyclic writing to a sectorCyclic reading of a sectorIRQ testDrive self-diagnosticsDrive resetExitCyclic reading state register – this test is meant for checking the HOST – the HDD microcontroller bus in cases when the drive does not respond to the incoming commands, erroneously interprets the commands or if the HDD is “busy” all the time – the BSY bit of the state register is active all the time. During testing a short reading cycle is performed over the state register, the malfunction search is performed with the help of an oscilloscope. The cycle is interrupted by the keyboard press.When the test is started, the following message appears on the tester display:The state register read cycleis performedDuring the test execution the state register and error register LEDs are inactive. You can interrupt the test by pressing any key on the tester keyboard or the [Exit] key with subsequent exit to the main menu.IRQ test – the test is meant for checking the interrupt request via the 31 pin of IDE connector of the drive.Sector buffer test–the test is meant for checking the inner HDD data bus, all the bus drivers located on that bus, inner bus of a ATA interface controller and the sector buffer area – buffer RAM MC (limited access). The test program executes the commands1“write buffer” and “read buffer”. First the codes FF, FE, FD, FB, and F7…. (streaming zero) and the codes 00, 01, 02, 04, 08, 10… (streaming one) are written to the sector buffer, with subsequent reading the sector buffer and comparison with the written data.When the test is started the following message appears:Sector buffer test is being performedIf no errors were detected during the test, the testing procedure ends with the following message:Sector buffer testNo errorsTest completeIf an error was detected during testing, the test will end with a message of the following type:Sector buffer testERRORCode written:0000000000000000Code read: 0000000011111111Test completeCyclic writing to a sector –the test is meant for checking the HDD write channel, and write pre-compensation circuit. A short 0000H code write cycle is performed on an HDD sector during testing. The malfunction search is performed with the help of an oscilloscope.When the test is started the following message appears on the tester display:Cyclic writing to a sectorIn response you should enter the cylinder number, head number and sector number, where the data should be written. The said cylinder, head and sector numbers are entered according to the formula: Cylinder: 0 – (N – 1)Head: 0 – (M – 1)Sector: 1- KWhere N, M, and K stand for the number of cylinders, heads and HDD sectors respectively.“LBA mode” In LBA mode in response you should enter the number of LBA sector, to which the data 1See ATA specification.should be written.When the input is complete, press the [Enter] key – the test will start.Cyclic writing to a sectorCylinder: XXXXHead: XSector: XXRunningCyclic reading of a sector –the test is meant for checking the reading HDD channel, data separator and idle clock pulse. A short HDD sector read cycle is performed during the test. The malfunction search is performed with the help of an oscilloscope. When the test is started the following message appears on the tester display:Cyclic reading of a sectorIn response you should enter the cylinder number, head number and number of the sector, the data from which will be read. The said cylinder, head and sector numbers are entered according to the formula:Cylinder: 0 – (N – 1)Head: 0 – (M – 1)Sector: 1- KWhere N, M, and K stand for the number of cylinders, heads and HDD sectors respectively. “LBA mode” In LBA mode in response you should enter the number of LBA sector, from which the data should be read.When the input is complete, press the [Enter] key – the test will start.Cyclic reading of a sectorCylinder: XXXXHead: XSector: XXRunningHDD self-diagnostics –when this test is started, the 90H command1“HDD self-diagnostics” is executed, checking:-MPU;-CRC driver circuit;-Buffer RAM (full access);-ATA interface controller.When the test is started the following message appears on the tester display:HDD self-diagnosticsRunningIf no errors were detected during testing the test completes with the message of the following type:HDD self-diagnosticsCompletion code: 01No errors detectedIf an error was detected during testing, the test will end with a message of the following type:1HDD self-diagnosticsCompletion code: 03Buffer RAM errorHDD self-diagnostics completion codes:01 – no errors detected;02 – microcontroller error;03 – buffer RAM error;04 – CRC driver circuit error;05 – controlling microprocessor error;8X – the drive is defective.HDD reset - meant for resetting the “hanging” drives, during the initiation of which the following is performed:-hardware HDD reset;-initialization;-recalibration.During resetting procedure the RESET interface signal with the 500 mcs duration is sent , after which the initialization and recalibration command is executed. Execution of an HDD reset procedure is followed with the messages about the reset, initialization and recalibration:HDD resetHDD resetHDD initializationHDD recalibrationReset complete2.5.5. Complex testComplex test – test mode for input/output type control of the drive.The following tests are sequentially performed during complex testing:-controller test-IRQ test-Sector buffer test-Recalibration test-Format check;-Random reading;-Surface scanning.The testing information appears on the tester display, in the STATUS line and the state register and error register LED-s. The STATUS line contains:Ready/Busy – determines the drive status using the BSY bit of the state register;DONE – the current test execution duration in % (appears when long tests are performed)CYL – current (active) cylinder value;HEAD – current (active) head value;ERRS – current number of drive errors detected during each test.“LBA mode” The current LBA sector is displayed in the STATE line in LBA mode instead of the CYL and HEAD parameters.The tests are selected from the main “TESTING MODE SELECTION” menu, with the following message appearing on the tester display:ATTENTION!Testing will destroyyour datastart cylinder: Xend cylinder: XXXXdo write test: Yespress [Enter] or [Cancel]By default the starting and ending test cylinders correspond to the zero and the maximum HDD cylinders.“LBA mode” You have to enter the starting and ending LBA sectors for testing in LBA mode. By default the starting and ending test LBA sectors correspond to the zero and the maximum LBA sectors of the drive.As the testing procedures from the “COMPLEX TEST” go on, the evaluation of their results – PASS or FAIL - appears on the tester display near the name of each test. The mark “running” appears near the name of the test, which is executed at the moment. The COMPLEX TEST can be interrupted by pressing the [Enter], [Cancel] or [Exit] keys, which bring the “OPERATOR INTERRUPT” menu on-screen. The menu allows you to:-continue testing from the place where it was stopped;-skip current test;-skip all tests and finish testing.When the testing is complete a sound signal is heard and the message appears on the tester screen:Test complete, press [Enter]Simultaneously with the test completion an XXXXXXX.DAT text file is created in the DAT sub-directory, where XXXXXXX is the number read from the drive. The file contains test results, this information also appears on the computer screen after pressing the [Enter] key. The results listing contains the information about the type and parameters of the drive being tested, test date and time. It also includes the results of all tests with the PASS or FAIL evaluation and the number of detected errors during each test (ERRS). Each detected error is followed with the value of the state register and the error register at the moment of its detection. Total evaluation of the test results is given in the end of the listing: test interrupted, PASS, FAIL. The FAIL evaluation is given if at least one error was detected during the test process. This is caused by the fact that IDE HDDs have a defects relocation capacity and a completely functioning drive should contain no defects. The listing can be viewed with the help of [Up] and [Down] keys.If errors were d etected during the “Surface scanning” test, the following menu will appear after viewing the test results:SELECT ACTIONDo not relocate defectsRelocate detected defects[ESC] – exitIf “Relocate detected defects” is selected – the procedure assign for defects relocation is performed for all defective sectors. If [ESC] is pressed or other menu item selected, the defects are not relocated.“LBA mode” LBA mode allows to hide not only the defects detected during the “Surface scanning” test, but also during th e “Format check” and “Random read”.。
MPLAB Code Configurator v2.25 1 产品说明书
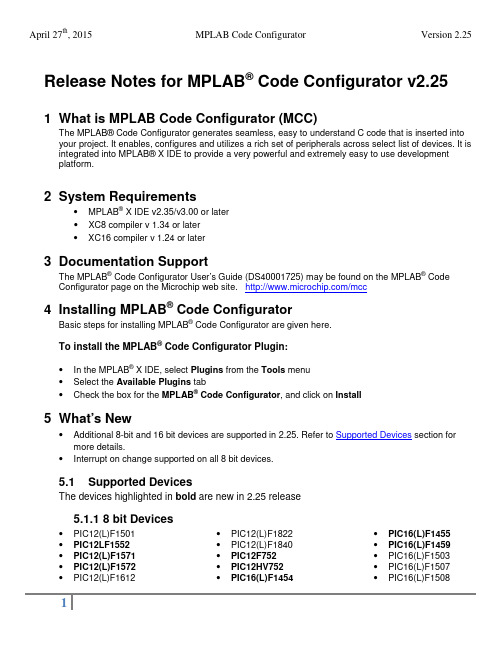
Release Notes for MPLAB® Code Configurator v2.251 What is MPLAB Code Configurator (MCC)The MPLAB®Code Configurator generates seamless, easy to understand C code that is inserted into your project. It enables, configures and utilizes a rich set of peripherals across select list of devices. It is integrated into MPLAB®X IDE to provide a very powerful and extremely easy to use development platform.2 System Requirements•MPLAB® X IDE v2.35/v3.00 or later•XC8 compiler v 1.34 or later•XC16 compiler v 1.24 or later3 Documentation SupportThe MPLAB® Code Configurator User’s Guide (DS40001725) may be found on the MPLAB® Code Configurator page on the Microchip web site. /mcc4 Installing MPLAB® Code ConfiguratorBasic steps for installing MPLAB® Code Configurator are given here.To install the MPLAB® Code Configurator Plugin:•In the MPLAB® X IDE, select Plugins from the Tools menu•Select the Available Plugins tab•Check the box for the MPLAB® Code Configurator, and click on Install5 What’s New•Additional 8-bit and 16 bit devices are supported in 2.25. Refer to Supported Devices section for more details.•Interrupt on change supported on all 8 bit devices.5.1 Supported DevicesThe devices highlighted in bold are new in 2.25 release5.1.1 8 bit Devices•PIC12(L)F1501 •PIC12LF1552 •PIC12(L)F1571 •PIC12(L)F1572 •PIC12(L)F1612 •PIC12(L)F1822•PIC12(L)F1840•PIC12F752•PIC12HV752•PIC16(L)F1454•PIC16(L)F1455•PIC16(L)F1459•PIC16(L)F1503•PIC16(L)F1507•PIC16(L)F1508•PIC16(L)F1509 •PIC16(L)F1512 •PIC16(L)F1513 •PIC16(L)F1516 •PIC16(L)F1517 •PIC16(L)F1518 •PIC16(L)F1519 •PIC16(L)F1526 •PIC16(L)F1527 •PIC16(L)F1574 •PIC16(L)F1575 •PIC16(L)F1578 •PIC16(L)F1579 •PIC16(L)F1613 •PIC16(L)F1614 •PIC16(L)F1615 •PIC16(L)F1618 •PIC16(L)F1619 •PIC16(L)F1703 •PIC16(L)F1704 •PIC16(L)F1705 •PIC16(L)F1707 •PIC16(L)F1708 •PIC16(L)F1709 •PIC16(L)F1713 •PIC16(L)F1716 •PIC16(L)F1717 •PIC16(L)F1718 •PIC16(L)F1719 •PIC16(L)F1764•PIC16(L)F1765•PIC16(L)F1768•PIC16(L)F1769•PIC16(L)F1782•PIC16(L)F1783•PIC16(L)F1784•PIC16(L)F1786•PIC16(L)F1787•PIC16(L)F1788•PIC16(L)F1789•PIC16(L)F1823•PIC16(L)F1824•PIC16(L)F1825•PIC16(L)F1826•PIC16(L)F1827•PIC16(L)F1828•PIC16(L)F1829•PIC16(L)F1847•PIC16(L)F1933•PIC16(L)F1934•PIC16(L)F1936•PIC16(L)F1937•PIC16(L)F1938•PIC16(L)F1939•PIC16(L)F1946•PIC16(L)F1947•PIC16F753•PIC16HV753•PIC16LF1554•PIC16LF1559•PIC18(L)F13K22•PIC18(L)F14K22•PIC18(L)F23K22•PIC18(L)F24K22•PIC18(L)F24K50•PIC18(L)F25K22•PIC18(L)F25K50•PIC18(L)F26K22•PIC18(L)F23K20•PIC18(L)F43K22•PIC18(L)F44K22•PIC18(L)F45K22•PIC18(L)F45K50•PIC18(L)F46K22•PIC18(L)F23K20•PIC18(L)F23K20•PIC18(L)F24K20•PIC18(L)F25K20•PIC18(L)F26K20•PIC18(L)F23K20•PIC18(L)F43K20•PIC18(L)F44K20•PIC18(L)F45K20•PIC18(L)F46K20April 27th, 2015 MPLAB Code Configurator Version 2.255.1.2 16 bit Devices•PIC24F08KA101 •PIC24FJ128GB202 •PIC24FJ64GA006•PIC24F08KA102 •PIC24FJ128GB204 •PIC24FJ64GA008•PIC24F(V)08KM101 •PIC24FJ128GB206 •PIC24FJ64GA010•PIC24F(V)08KM102 •PIC24FJ128GB210 •PIC24FJ64GA102•PIC24F(V)08KM202 •PIC24FJ128GC006 •PIC24FJ64GA104•PIC24F(V)08KM204 •PIC24FJ128GC010 •PIC24FJ64GA106•PIC24F(V)16KM102 •PIC24FJ16GA002 •PIC24FJ64GA108•PIC24F(V)16KM104 •PIC24FJ16GA004 •PIC24FJ64GA110•PIC24F(V)16KM202 •PIC24FJ192GA106 •PIC24FJ64GA202•PIC24F(V)16KM204 •PIC24FJ192GA108 •PIC24FJ64GA204•PIC24F16KA101 •PIC24FJ192GA110 •PIC24FJ64GA306•PIC24F16KA102 •PIC24FJ192GB106 •PIC24FJ64GA308•PIC24F(V)16KA301 •PIC24FJ192GB108 •PIC24FJ64GA310•PIC24F(V)16KA302 •PIC24FJ192GB110 •PIC24FJ64GB002•PIC24F(V)16KA304 •PIC24FJ256DA106 •PIC24FJ64GB004•PIC24F(V)32KA301 •PIC24FJ256DA110 •PIC24FJ64GB106•PIC24F(V)32KA302 •PIC24FJ256DA206 •PIC24FJ64GB108•PIC24F(V)32KA304 •PIC24FJ256DA210 •PIC24FJ64GB110•PIC24FJ128DA106 •PIC24FJ256GA106 •PIC24FJ64GB202•PIC24FJ128DA110 •PIC24FJ256GA108 •PIC24FJ64GB204•PIC24FJ128DA206 •PIC24FJ256GA110 •PIC24FJ64GC006•PIC24FJ128DA210 •PIC24FJ256GB106 •PIC24FJ64GC010•PIC24FJ128GA006 •PIC24FJ256GB108 •PIC24FJ96GA006•PIC24FJ128GA008 •PIC24FJ256GB110 •PIC24FJ96GA008•PIC24FJ128GA010 •PIC24FJ256GB206 •PIC24FJ96GA010•PIC24FJ128GA106 •PIC24FJ256GB210•PIC24FJ128GA108 •PIC24FJ32GA002•PIC24FJ128GA110 •PIC24FJ32GA004•PIC24FJ128GA202 •PIC24FJ32GA102•PIC24FJ128GA204 •PIC24FJ32GA104•PIC24FJ128GA306 •PIC24FJ32GB002•PIC24FJ128GA308 •PIC24FJ32GB004•PIC24FJ128GA310 •PIC24FJ48GA002•PIC24FJ128GB106 •PIC24FJ48GA004•PIC24FJ128GB108 •PIC24FJ64GA002•PIC24FJ128GB110 •PIC24FJ64GA0046 Repairs and Enhancements# ID Description Device(s)1. MCC-1456 Pin Names with special characters give warnings ingenerated code All devices2. MCC-1457 System Module EC Value does not reload All 16 bit devices3. MCC-1458 When ADC enabled and uses VREF+ and VREF- pinsmcc generates a source code where TRISA0 and TRISA1bits are cleared so it overwrites the connected referencevoltagePIC24FJ128GA204 andPIC24FJ128GB204 family4. MCC-1459 Pin 44 is not available as a PPS pin for SPI1 PIC24FJ128GC006April 27th, 2015 MPLAB Code Configurator Version 2.25 # ID Description Device(s)5. MCC-1460 Primary Oscillator range is incorrect PIC24FJ128GA204 and PIC24FJ128GB204 family6. MCC-1461 At SPI1 module SPI1_ExchangeBuffer() function uses theenhanced buffer mode of SPI but SPI1CON1L.ENHBUFbit is cleared.PIC24FJ128GA204 andPIC24FJ128GB204 family7. MCC-1284 Interrupt on change (IOC) not available All 8 bit devices8. MCC-910 Timer 0 – Incorrect Variables declared K20\K22 devices9. MCC-1290 Seed Value not getting loaded in the initializer function PIC16F161910. MCC-1470 RTCC module is missing PIC24FJ64GB004 family 7 Known IssuesThe following are enumerated issues for the MPLAB® Code Configurator.# ID Description Device(s)1. MCC-1419 Does not support both commas and periods entered in atextbox as decimal separator. Currently MCC accepts inputsonly with a period as decimal separator.All devices2. MCC-1190 Configuration setting ZCD compatible with XC8 v1.33 only PIC16(L)F161x devices3. MCC-1250MCC-1253 I2C driver errors when multiple initializer are used All 8 bit devices4. MCC-1259 Timer 2/4/6 input pins not configured as digital PIC16(L)F161x devices5. MCC-1295 I2C slave driver does not fit in RAM PIC12(L)F18226. MCC-1466 I2C PPS register value incorrect for RC3 PIC16(L)F161x devices7. MCC-1321 PPS register configuration is wrong. PIC16F17078. MCC-1102 CN\IOC functionality not supported All 16 bit devices9. MCC-1462 MCCP Compare Alert does not go away on selecting outputpin(s) All PIC24F KM devices 10. MCC-1455 Cannot set PWM2 on RA5 through APFCON PIC16(L)F1454/911. MCC-1434 Changing oscillator selection from INTOSC oscillator toexternal clock in Config1 bits does not show up 'ExternalClock' text box (in 'Clock' label) to input external clockfrequency values.PIC12LF1552,PIC16(L)F176xPIC16(L)F157x,PIC16(L)F161xApril 27th, 2015 MPLAB Code Configurator Version 2.25 8 Customer Support8.1 The Microchip Web SiteMicrochip provides online support via our web site at . This web site is used as a means to make files and information easily available to customers. Accessible by using yourfavorite Internet browser, the web site contains the following information:•Product Support – Data sheets and errata, application notes and sample programs, design resources, user’s guides and hardware support documents, latest software releases and archivedsoftware• General Technical Support – Frequently Asked Questions (FAQs), technical support requests, online discussion groups/forums (), Microchip consultant programmember listing• Business of Microchip – Product selector and ordering guides, latest Microchip press releases, listing of seminars and events, listings of Microchip sales offices, distributors and factoryrepresentatives8.2 Additional SupportUsers of Microchip products can receive assistance through several channels:•Distributor or Representative•Local Sales Office•Field Application Engineering (FAE)•Technical SupportCustomers should contact their distributor, representative or field application engineer (FAE) forsupport. Local sales offices are also available to help customers. A listing of sales offices andlocations is available on our web site.Technical support is available through the web site at: 。
Devops技术练习(习题卷1)

Devops技术练习(习题卷1)第1部分:单项选择题,共86题,每题只有一个正确答案,多选或少选均不得分。
1.[单选题]哪一种精益工具描述了跨功能的信息流、原料流和工作流,并且注重量化并消除浪费?A)改善形B)持续交付C)看板D)价值流图答案:D解析:2.[单选题]黄金圈法则中的的核心项“为什么”代表一家公司的A)目的、原因和信念B)产品和服务C)竞争优势D)盈利能力答案:A解析:3.[单选题]使用Kubernetes带来的好处有哪些A)横向扩展B)其他都是C)自动回滚D)自动调度答案:B解析:4.[单选题]下面的内容不是 DevOps 工具链中的典型元素的是?A)监控工具B)自动化测试C)版本控制D)服务台事件管理系统答案:D解析:5.[单选题]以下哪个角色是 DevOps 的利益相关者?A)QA 测试人员B)支持人员C)供应商D)以上全部答案:D解析:6.[单选题]哪项 DevOps 实践依赖于部署流水线?该部署流水线可以按需一键部署。
D)持续交付答案:D解析:7.[单选题]在试图实施重大变革时,谁应参与规划活动并发挥变革推动者的作用?A)早期采用者B)怀疑论者C)管理层D)需要得到证明的人答案:A解析:8.[单选题]一个组织正对于敏捷团队完成一个“冲刺”后,安全检查需要额外时间而头痛。
其间的延迟已经影响了他们的发布能力。
他们希望将更多的安全性测试作为“左移”测试方法的一部分。
他们需要以下哪种DevOps 实践?A)ChatOpsB)持续测试C)DevSecOpsD)漏洞预警答案:C解析:9.[单选题]一个组织正在希望提高团队之间的实时协作。
以下 DevOps 实践他们应该考虑哪种?A)看板B)ChatOpsC)逐步升级D)警报答案:A解析:10.[单选题]除Spring Boot之外,主流的微服务开发框架还有什么?A)DjangoB)MyBaitsC)KubernetesD)Apache Dubbo答案:D解析:11.[单选题]一个组织正在实施 DevOps。
PNETLab模拟器部署及使用配置
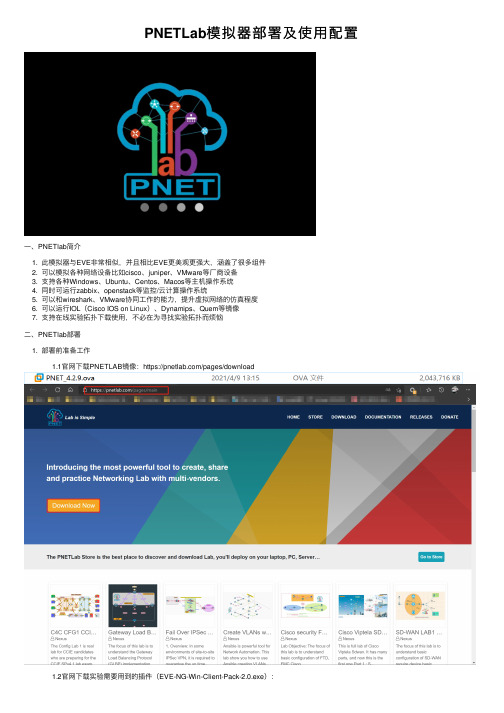
PNETLab模拟器部署及使⽤配置⼀、PNETlab简介1. 此模拟器与EVE⾮常相似,并且相⽐EVE更美观更强⼤,涵盖了很多组件2. 可以模拟各种⽹络设备⽐如cisco、juniper、VMware等⼚商设备3. ⽀持各种Windows、Ubuntu、Centos、Macos等主机操作系统4. 同时可运⾏zabbix、openstack等监控/云计算操作系统5. 可以和wireshark、VMware协同⼯作的能⼒,提升虚拟⽹络的仿真程度6. 可以运⾏IOL(Cisco IOS on Linux)、Dynamips、Quem等镜像7. ⽀持在线实验拓扑下载使⽤,不必在为寻找实验拓扑⽽烦恼⼆、PNETlab部署1. 部署前准备⼯作 1.1官⽹下载PNETLAB镜像:https:///pages/download1.2官⽹下载实验需要⽤到的插件(EVE-NG-Win-Client-Pack-2.0.exe):https:///#!V50gUCQY!ysvjljJrulRT0De96BhIXCEnP2uDkE-zWr7Kyyml3ds * 这个插件必须安装,否则将不能使⽤Wireshark、CRT等⼯具* 该插件同eve所使⽤的插件⼀致 1.3Vmware Workstation 16安装PNETlab使⽤OVA导⼊Vmware Workstation中使⽤ 2.开始部署 2.1导⼊刚刚下载好的OVA虚拟机⽂件 2.2导⼊完成后修改虚机配置 2.3由于Vmware Workstation版本较⾼,以防运⾏的时候出现问题,我们升级刚刚导⼊的虚拟机 2.4升级完成后开启虚拟机 2.5登录PNETlab(默认⽤户名:root 密码:pnet) 2.5.1成功登陆后需要进⾏⼀些设置 2.5.1.1修改root密码 2.5.1.2NTP设置(这边可以回车跳过) 2.5.1.3⽹络连接设置(可以选择DHCP或者⼿⼯静态IP地址) 2.6设置完成后我们使⽤SSH登录对系统进⾏升级apt-get update //更新列表apt-get upgrade //更新系统浏览器打开:http://192.168.109.112/(建议浏览器⽤新版微软EDGE、Google Chome、⽕狐)PNETlab登录⽅式有本地登录及在线登录两种,两者区别在于:本地登录只能使⽤Open标识的实验模板,⽽在线登录则可以使⽤所有实验模板1:本地登录默认账号:admin 密码:pnet2:在线登录账号密码需要注册⾸次登录以本地⽅式登录的话需要设置开启在线登录退出重新以在线⽅式登录或注册四、IOL、Dynamips、QEUM镜像导⼊***上传完镜像打开SSH登录到PNETlab修正镜像权限***每次上传完镜像都需要修正镜像权限/opt/unetlab/wrappers/unl_wrapper -a fixpermissions 4.1导⼊IOL(使⽤WinSCP将IOL镜像上传⾄:/opt/unetlab/addons/iol/bin) 4.2导⼊Dynamips(使⽤WinSCP将IOL镜像上传⾄:/opt/unetlab/addons/dynamips) 4.3导⼊Qeum(使⽤WinSCP将IOL镜像上传⾄:/opt/unetlab/addons/dynamips) 4.4镜像上传、修正权限全部完成就可以使⽤刚刚上传的镜像了五、客户端插件安装配置 5.1安装EVE-NG-Win-Client-Pack-2.0.exe 5.2关联SecureCRT 修改完成后双击添加⾄注册表 5.3关联Wireshark抓包软件**********打开WindowsPowerShell运⾏如下命令:cd 'C:\Program Files\EVE-NG'echo y | .\plink.exe -ssh -l root -pw pnet 192.168.109.112教程制作不易,转发请注明出处,此教程同样适⽤于EVE-NG设置 。
MPLAB Code Configurator SMPS Library说明书
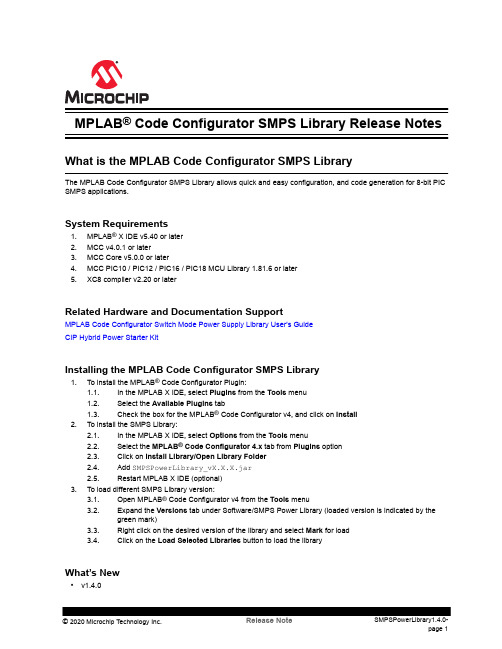
MPLAB® Code Configurator SMPS Library Release NotesWhat is the MPLAB Code Configurator SMPS LibraryThe MPLAB Code Configurator SMPS Library allows quick and easy configuration, and code generation for 8-bit PIC SMPS applications.System Requirements1.MPLAB® X IDE v5.40 or later2.MCC v4.0.1 or later3.MCC Core v5.0.0 or later4.MCC PIC10 / PIC12 / PIC16 / PIC18 MCU Library 1.81.6 or later5.XC8 compiler v2.20 or laterRelated Hardware and Documentation SupportMPLAB Code Configurator Switch Mode Power Supply Library User's GuideCIP Hybrid Power Starter KitInstalling the MPLAB Code Configurator SMPS Library1.To install the MPLAB® Code Configurator Plugin:1.1.In the MPLAB X IDE, select Plugins from the Tools menu1.2.Select the Available Plugins tab1.3.Check the box for the MPLAB® Code Configurator v4, and click on Install2.To install the SMPS Library:2.1.In the MPLAB X IDE, select Options from the Tools menu2.2.Select the MPLAB® Code Configurator 4.x tab from Plugins option2.3.Click on Install Library/Open Library Folder2.4.Add SMPSPowerLibrary_vX.X.X.jar2.5.Restart MPLAB X IDE (optional)3.To load different SMPS Library version:3.1.Open MPLAB® Code Configurator v4 from the Tools menu3.2.Expand the Versions tab under Software/SMPS Power Library (loaded version is indicated by thegreen mark)3.3.Right click on the desired version of the library and select Mark for load3.4.Click on the Load Selected Libraries button to load the libraryWhat’s New•v1.4.0–Compatibility update with MCC Plugin v4.0.1 and MCC Core v5.0.0–Various output pin fixes•v1.3.0–Added CIP Hybrid Starter Kit (PCMC/VMC) Demo modules–Added a CIP SEPIC LED Driver Demo module•v1.2.1–Removed local peripheral modules–Added dependency to the MCC 8bit PIC Library•v1.2.0–Added support for PIC16(L)F176x devices–Updated the Compensator Block module with an override setting–Updated the Fault Block module with CIN- pin options–Updated the PCMC Control Mode module with LED dimming options –Added the Pulse Modulator Block module–Added the SEPIC_LED Topology module–Added up to four instances of each SMPS Library module•v1.0.0–Initial release with support for a Synchronous Buck Topology moduleSupported Families•8-bit Families–PIC16(L)F177x–PIC16(L)F176xTable of ContentsWhat is the MPLAB Code Configurator SMPS Library (1)1.System Requirements (1)2.Related Hardware and Documentation Support (1)3.Installing the MPLAB Code Configurator SMPS Library (1)4.What’s New (1)5.Supported Families (2)The Microchip Website (4)Product Change Notification Service (4)Customer Support (4)Microchip Devices Code Protection Feature (4)Legal Notice (5)Trademarks (5)Quality Management System (6)Worldwide Sales and Service (7)The Microchip WebsiteMicrochip provides online support via our website at /. This website is used to make files and information easily available to customers. Some of the content available includes:•Product Support – Data sheets and errata, application notes and sample programs, design resources, user’s guides and hardware support documents, latest software releases and archived software•General Technical Support – Frequently Asked Questions (FAQs), technical support requests, online discussion groups, Microchip design partner program member listing•Business of Microchip – Product selector and ordering guides, latest Microchip press releases, listing of seminars and events, listings of Microchip sales offices, distributors and factory representativesProduct Change Notification ServiceMicrochip’s product change notification service helps keep customers current on Microchip products. Subscribers will receive email notification whenever there are changes, updates, revisions or errata related to a specified product family or development tool of interest.To register, go to /pcn and follow the registration instructions.Customer SupportUsers of Microchip products can receive assistance through several channels:•Distributor or Representative•Local Sales Office•Embedded Solutions Engineer (ESE)•Technical SupportCustomers should contact their distributor, representative or ESE for support. Local sales offices are also available to help customers. A listing of sales offices and locations is included in this document.Technical support is available through the website at: /supportMicrochip Devices Code Protection FeatureNote the following details of the code protection feature on Microchip devices:•Microchip products meet the specifications contained in their particular Microchip Data Sheet.•Microchip believes that its family of products is secure when used in the intended manner and under normal conditions.•There are dishonest and possibly illegal methods being used in attempts to breach the code protection features of the Microchip devices. We believe that these methods require using the Microchip products in a manner outside the operating specifications contained in Microchip’s Data Sheets. Attempts to breach these codeprotection features, most likely, cannot be accomplished without violating Microchip’s intellectual property rights.•Microchip is willing to work with any customer who is concerned about the integrity of its code.•Neither Microchip nor any other semiconductor manufacturer can guarantee the security of its code. Code protection does not mean that we are guaranteeing the product is “unbreakable.” Code protection is constantly evolving. We at Microchip are committed to continuously improving the code protection features of our products.Attempts to break Microchip’s code protection feature may be a violation of the Digital Millennium Copyright Act.If such acts allow unauthorized access to your software or other copyrighted work, you may have a right to sue for relief under that Act.Legal NoticeInformation contained in this publication is provided for the sole purpose of designing with and using Microchip products. Information regarding device applications and the like is provided only for your convenience and may be superseded by updates. It is your responsibility to ensure that your application meets with your specifications.THIS INFORMATION IS PROVIDED BY MICROCHIP “AS IS”. MICROCHIP MAKES NO REPRESENTATIONS OR WARRANTIES OF ANY KIND WHETHER EXPRESS OR IMPLIED, WRITTEN OR ORAL, STATUTORY OR OTHERWISE, RELATED TO THE INFORMATION INCLUDING BUT NOT LIMITED TO ANY IMPLIED WARRANTIES OF NON-INFRINGEMENT, MERCHANTABILITY, AND FITNESS FOR A PARTICULAR PURPOSE OR WARRANTIES RELATED TO ITS CONDITION, QUALITY, OR PERFORMANCE.IN NO EVENT WILL MICROCHIP BE LIABLE FOR ANY INDIRECT, SPECIAL, PUNITIVE, INCIDENTAL OR CONSEQUENTIAL LOSS, DAMAGE, COST OR EXPENSE OF ANY KIND WHATSOEVER RELATED TO THE INFORMATION OR ITS USE, HOWEVER CAUSED, EVEN IF MICROCHIP HAS BEEN ADVISED OF THE POSSIBILITY OR THE DAMAGES ARE FORESEEABLE. TO THE FULLEST EXTENT ALLOWED BY LAW, MICROCHIP'S TOTAL LIABILITY ON ALL CLAIMS IN ANY WAY RELATED TO THE INFORMATION OR ITS USE WILL NOT EXCEED THE AMOUNT OF FEES, IF ANY, THAT YOU HAVE PAID DIRECTLY TO MICROCHIP FOR THE INFORMATION. Use of Microchip devices in life support and/or safety applications is entirely at the buyer’s risk, and the buyer agrees to defend, indemnify and hold harmless Microchip from any and all damages, claims, suits, or expenses resulting from such use. No licenses are conveyed, implicitly or otherwise, under any Microchip intellectual property rights unless otherwise stated.TrademarksThe Microchip name and logo, the Microchip logo, Adaptec, AnyRate, AVR, AVR logo, AVR Freaks, BesTime, BitCloud, chipKIT, chipKIT logo, CryptoMemory, CryptoRF, dsPIC, FlashFlex, flexPWR, HELDO, IGLOO, JukeBlox, KeeLoq, Kleer, LANCheck, LinkMD, maXStylus, maXTouch, MediaLB, megaAVR, Microsemi, Microsemi logo, MOST, MOST logo, MPLAB, OptoLyzer, PackeTime, PIC, picoPower, PICSTART, PIC32 logo, PolarFire, Prochip Designer, QTouch, SAM-BA, SenGenuity, SpyNIC, SST, SST Logo, SuperFlash, Symmetricom, SyncServer, Tachyon, TempTrackr, TimeSource, tinyAVR, UNI/O, Vectron, and XMEGA are registered trademarks of Microchip Technology Incorporated in the U.S.A. and other countries.APT, ClockWorks, The Embedded Control Solutions Company, EtherSynch, FlashTec, Hyper Speed Control, HyperLight Load, IntelliMOS, Libero, motorBench, mTouch, Powermite 3, Precision Edge, ProASIC, ProASIC Plus, ProASIC Plus logo, Quiet-Wire, SmartFusion, SyncWorld, Temux, TimeCesium, TimeHub, TimePictra, TimeProvider, Vite, WinPath, and ZL are registered trademarks of Microchip Technology Incorporated in the U.S.A.Adjacent Key Suppression, AKS, Analog-for-the-Digital Age, Any Capacitor, AnyIn, AnyOut, BlueSky, BodyCom, CodeGuard, CryptoAuthentication, CryptoAutomotive, CryptoCompanion, CryptoController, dsPICDEM, , Dynamic Average Matching, DAM, ECAN, EtherGREEN, In-Circuit Serial Programming, ICSP, INICnet, Inter-Chip Connectivity, JitterBlocker, KleerNet, KleerNet logo, memBrain, Mindi, MiWi, MPASM, MPF, MPLAB Certified logo, MPLIB, MPLINK, MultiTRAK, NetDetach, Omniscient Code Generation, PICDEM, , PICkit, PICtail, PowerSmart, PureSilicon, QMatrix, REAL ICE, Ripple Blocker, SAM-ICE, Serial QuadI/O, SMART-I.S., SQI, SuperSwitcher, SuperSwitcher II, Total Endurance, TSHARC, USBCheck, VariSense, ViewSpan, WiperLock, Wireless DNA, and ZENA are trademarks of Microchip Technology Incorporated in the U.S.A. and other countries.SQTP is a service mark of Microchip Technology Incorporated in the U.S.A.The Adaptec logo, Frequency on Demand, Silicon Storage Technology, and Symmcom are registered trademarks of Microchip Technology Inc. in other countries.GestIC is a registered trademark of Microchip Technology Germany II GmbH & Co. KG, a subsidiary of Microchip Technology Inc., in other countries.All other trademarks mentioned herein are property of their respective companies.© 2020, Microchip Technology Incorporated, Printed in the U.S.A., All Rights Reserved.ISBN:Quality Management SystemFor information regarding Microchip’s Quality Management Systems, please visit /quality.Worldwide Sales and Service。
Windows进程详解

Ver.exeewidoguard.exe!e5d141.tmp00THotkey.exe17lele.exe3.exe3cdminic.exe3cmlnkw.exe3dfxman.exe3DMark2000.exe3DMark2001.exe3DMark2003.exe3DMark2005.exe3DMark99.exeA~NSISu_.exe aboutagirl.exeabsr.exeacad.exeacbtnmgr_x73.exe acbtnmgr_x83.exe accstat.exeaccwiz.exeACDSee.exeAchelp.exeaclayer.exeacrobat.exeAcroRd32.exe AcroTray.exeACS.exeAcsd.exeacsetups.exe ActionAgent.exe activation.exe actmovie.exeadam.exeAd-Aware.exe addrbook.exeaddreg.exeadgjdet.exeAdobe Gamma Loader.exe AdskCleanup.0001 AdskScSrv.exeADSlx2.EXE adusermon.exe Advchk.exeAD-Watch.exe agentsvr.exe AGSatellite.exe AHQInit.exeAHQtb.exeAHQTbU.exeahquinit.exeaim.exeaiw2.exe AlarmApp.exe Alcohol.exe alertsvc.exe ALG.EXE alogserv.exe alunotify.exe Annclist.exe aolfix.exe aoltray.exe Aornum.exe Aornumsp.exe apache.exe APASServ.exe aplica32.exe apntex.exe apoint.exe append.exe AppLoc.exe AppServices.exe Apropos.exe Aptezbp.exe apwheel.exe Armon32.exe Armon32a.exe arp.exe Artworld.exe ARUpld32.exe Asd.exe ASDSCSVC.exe asiadial.exe aspnet_state.exe aspnet_wp.exe assistse.exe at.exeATDialler1.exe ATDialler2.exe ATDialler3.exe ATI2cwxx.exeATI2evxx.exeATI2mdxx.exeATI2plab.exeATI2plxx.exe ATIcwd32.exe ATIevxx.exe ATIKey32.exe ATIptaab.exe ATIPtaxx.exe ATIQIPcl.exe ATISched.exe ATITask.exe ATIX10.exe atmadm.exe ATnotes.exeattrib.exeAttune_ce.exe AUPD1ATE.EXE AUpdate.exe autochk.exe autoconv.exe autofmt.exe autolfn.exe AutoUpdate.exeAv1synmgr.exeAvc1onsol.exe avconsol.exeavf.exeavg23emc.exeavgc3c.exeAVGCC32.exe AVGNT.EXE AVGUARD.EXEavp.exeavp32.exeavpcc.exeavpm.exeavserve.exe avsynmgr.exe AVWUPSRV.EXE awadpr32.exe AWHOST32.EXEax.exeBackRav.exe backWeb.exe BaiduDiskSearch.exe BaiduX.exe Bartshel.exe BBCTicker.exe bbeagle.exebcb.exeBCDetect.exe Bcmdmmsg.exe BCMSMMsg.exe BCUP.EXEbdmcon.exe bdnagent.exe bdoesrv.exe BitComet.exe BitSpirit.exe BLUEDON.EXE BlueSoleil.exe BMate.exe BNUpdate.exe bootok.exe bootvrfy.exe BootWarn.exe botzor.exebrdiag.exebtengine.exe BTNtService.exe BugReport.exe C1CSETMGR.EXE c6a5fix.exe ca.execacls.exe CAExp.exe calc.exe CalCheck.exe CalSprite.exe CapFax.exeCC1EVTMGR.EXE ccA1pp.exe ccapp.exe CCD.exe CCenter.exe ccevtmgr.exe CCProxy.exe ccPwdSvc.exe ccSetMgr.exe cdac11ba.exe cdantsrv.exe cdnup.exe CDPlay.exe CDPlayer.exe cfgwiz32.exe CfgWzSvc.exe cfiadmin.exe cfiavdit.exe cfinet32.exe change.exe charmap.exe ChatRoom.exe checkdll.exe CheckWP.exe chglogon.exe chgport.exe chgusr.exe chkdsk.exe chkntfs.exe cidaemon.exe cipher.exe cisvc.exe ckcnv.exe CLCL.EXE cleanmgr.exe Cleanup.exe cliconfg.exe clipbrd.exe clipmate.exe clipsrv.exe ClipTray.exe clspack.exeCM1Grdian.exe cmd.exe CmdAgent.exe cmdl32.exe cmesys.exe CMGrdian.exe cmmgr32.exe cmmon32.exe cmstp.exe cnxdsltb.exe comclust.exe comime.exe comp.exe compact.exe CONIME.EXE control.exe convert.exe convlog.exe coolbot.exe coolpro2.exe CoreCenter.exe CPD.exe CPDClnt.exe cprofile.exe cps.execps_config.exe cps_net.exe cpuz.exe Crypserv.exe cscript.exe csetup.exe csm.exe CSRSS.EXE csscan.exe csvde.exe CTFMON.EXE cthelper.exe ctrlpan.exe ctsvccda.exe CursorXP.exe cuteftp32.exe cuteftppro.exe cutftp.execvt1.exe CyberArticle.exe daemon.exe DavCData.exe dbgtrace.exe dcomcnfg.exe dcphelp.exe dcpromo.exe ddeshare.exe ddhelp.exe debug.exedefwatch.exe delttoul.exe DeviceManager.exe devldr32.exe dfrgfat.exedfs_cmd_.exe dfsinit.exe dfssvc.exe dhcore.exe diagcfg.exe dialer.exe dialmon.exe diantz.exe directcc.exe Directcd.exe diskperf.exe disrr.exe DkService.exe dllhost.exe Dlview32.exeDM2005.exe dmadmin.exe dmconfig.exe dns.exedoskey.exedosx.exe dplaysvr.exe dramweaver.exe DreamMail.exe Dreamweaver.exe drvspace.exe Drwatson.exe Drwtsn32.exe DS.EXEdtcsetup.exe DuDuAcc.exe DuDuPros.exe DuDuProsvc.exe dumprep.exe DVDPLAY.EXEdvldr32.exe dxdiag.exeedlin.exe ehRecvr.exe ehSched.exeem_exec.exe emeditor.exe Emm386.exe eMule.exe EnterNet.exe entvutil.exe eph.exeesafe.exe esentutl.exeet.exeeudcedit.exe eventvwr.exe everest.exe evntwin.exe ewidoctrl.exe EXCEL.EXEexe2bin.exe expand.exe EXPLORER.EXE explorer32.exe External.exeExtrac32.exe EyeCare.exeEyeElf.exeFastAIT.exe fastopen.exe faxqueue.exe faxsend.exefaxsvc.exefc.exeFDFReader.exe feweb.exefilexfer.exefind.exefindfast.exe findstr.exefinger.exefirefox.exe fixdemo.exe fixmapi.exe flashfxp.exe flashget.exe flattemp.exeflcss.exeflyODBG.eXe fmgrsrv.exefont16.exe Fontview.exefoobar2000.exe forcedos.exe formatsys.exe foutline.exe Foxitreader.exe foxmail.exeFpdisp4.exeFpdisp4a.exeFpdisp5a.exeFppdis1.exeFppdis1a.exeFppdis2a.exe Framework.exe Frameworkservice.exe Freecell.exeFRONTPAGE.EXEfrw.exeFtp.exeftpte.exefwr.exeGameClient.exe gcasDtServ.exe gcasServ.exegdi.exeGearNT.exe GetCDInfo.exe GhostStartService.exe GhostStartService2.exe GhostStartTrayApp.exe gmt.exe GoogleDesktop.exe GreenBrowser.exe grovel.exegrpconv.exegsfbwsr.exeGSpot.exehdp.exeHDTune.exehh.exeHIDEIT.EXEhidserv.exeHijackThis1991zww.exe HKCMD.EXEHNMainUI.exe HomeShare.exe hostname.exehotkey.exehplj600.exeHprSnap5.exeHTime.exehw51.exehxdef.exehxgame-update.exe hzkbd.exehzvio95.exeI_VIEW32.exeICalClk.exe IceSword.exeicload95.exeicloadnt.exeicmon.exe IconWorkshop.exeicq.exeicsupp95.exe idaemon.exeIDMan.exeie4uinit.exeiecplore.exeiedw.exeieshwiz.exe iexplore.exe iexpress.exe IGamesinaddt.exe igfxtray.exe iisreset.exe imapi.exe imetool.exe imgst_tr.exe imgstart.exe InBuild.exe INETINFO.EXE InfoMgr.exe internat.exe intrenat.exe Iparmor.exe ipconfig.exe iPodService.exe ipsecmon.exe ipxroute.exe irftp.exe irmon.exeis5a6fe.exe Isass.exe ismserv.exe ISSUE.exe ISSVC.exe iTouch.exe java.exejavaw.exe jdbgmgr.exe jetconv.exe JetTB.exe JJSvr.EXE jusched.exe jview.exeK2A2V.exe Kamun.exe KATMain.exe kav.exekav12mm.exekav32.exe kavmm.exe KAVPF.EXE Kavpfw.exe KAVPlus.exe KAVRun.exe KAVStart.exe KAVSvc.exe kavsvc9x.exe kavsvcUI.exe KConvert.exe kernel32.dll KingTrans.exekktProView.exeKlog.exeKMailMon.EXE KMPlayer.exe kodakccs.exe kodakimage.exe kodakimg.exe kodakprv.exe KPfwSvc.EXEkpopmon.exeeKRegEx.exekrnl386.exeKuGoo.exeKULANSyn.EXE KVCenter.kxpkvfw.exeKVMonXp.kxpKVMonXP_1.kxp KVMonXP-1.kxpkvolself.exe KVSrvXP.exeKVSrvXP_1.exe KVWSC.exeKvXP.kxpKWatch.EXEKWatchUI.exelabel.exeLangSet.exeLCC.exelcwiz.exeldifde.exelexbces.exelexmark.exelexpps.exelicmgr.exeLien Van de Kelderrr.ex lights.exellsmgr.exellssrv.exelmscript.exelntrenat.exeloadqm.exeloadwc.exelocator.exelockdown2000.exe lodctr.exe LogitechDesktopMessenge logo1_.exelogoff.exelogonuit.exe logparser.exe looknstop.exelpq.exelpr.exelsas32.exe LSASS.EXE Lsasss.exe lserver.exe LsFlashPlayer.exe LUAL1L.EXELuup1date.exe lxdevclient.exeM3.EXEmacfile.exemad.exe MagicICO.exe MagicSet.exe magnify.exe MailMon.exe main.exe Makeboot.exe MakeDisk.exe mantispm.exe Mathchk.exe Maxthon.exe MaxUpdate.exe MazeSvr.exe McAgent.exe mcconsol.exe McScript.exe McScript_InUse.exe Mcsh1ield.exe mcshield.exe mcupdate.exe MCVSEscn.exe MCVSFTSN.exe MCVSRTE.exe McVSShld.exe MDM.EXEmem.exeMemDef.exe Memory Booster.exe mgabg.exe microsoft.exe migpwd.exemixer.exe mkcompat.exe mmc.exeMmm.exemmtask.tsk mnmsrvc.exe mobmeter.exe mobsync.exe Monitor.exe MPFAgent.exe MPFTray.exe mplayer.exe mplayer2.exemprexe.exe MRT.exemrtstub.exe msaccess.exe msbb.exe msblast.exe Mscifapp.exe msconfig.exe msdtc.exe MsgPlus.exe msgsrv32.exe msgsvc.exe mshearts.exe msiexec.exe msimn.exe msmbw.exe msmsgs.exe msnexch.exe msnmsgr.exe MSNShell.exe msoobe.exe mspaint.exe mspmspsv.exe mssearch.exe MSSTART.EXE mstask.exe Mstray.exe MyIM.exe MyIMLite.exe mysqld-nt.exe naiavfin.exe naPrdMgr.exeNAV1APSVC.EXE navapsvc.exe navapw32.exe nbtstat.exe ncdaemon.exe ndetect.exe ndsntsvr.exe neogeo.exe neogeo_config.exe neogeo_net.exe net.exenetants.exe netdde.exe nethell.exe netscape.exe netspy.exe netstat.exe NetTransport.exe netwatch.exe NewRmtService.exe NJCOM32.exe NMWizardA14.exenod32krn.exenod32kui.exe notepad .exe NOTEPAD.EXE notepads.exe NPFM1NTOR.EXE NSMdtr.exe Nspm.exe Nspmon.exe Nsum.exe nSvcAppFlt.exe ntbackup.exe NTdhcp.exentfrs.exe nTrayFw.exe ntvdm.exenvchip4.exe NvMixerTray.exe NVSVC32.EXE nwiz.exe nwlsproc.exe odbcad32.exe Ollydbg.exe omtsreco.exe ONENOTEM.EXE oodag.exeorder.exe Ornum.exeosa.exe OSAKey.exeOSE.EXEoutlook.exeoutp1ost.exe outpost.exep2psvr.exe packager.exe Patch.exepbios.exe pbrush.exe pcboost.exe PCCGuide.exe PCCIomon.exe PCClient.exe PCCPFW.exe pctspk.exe PDEngine.exe pds.exe PDSched.exe PDVDServ.exe PetKeeper.exe PFW.exe PFWLiveUpdate.exe PhMain.exe photo.gif.exe photoshop.exeping.exepintlphr.exe pintsetp.exe pireg.exePoco2004.exepoint32.exePop3trap.exe popo.exe POWERPNT.EXE PPLive.exe PrcMgr.exe ProcessMonitor.exe procexp.exe progman.exe prtmon.exe pstores.exe pstrip.exe pyintau.exe qfecheck.exeQQ.exe QQexternal.exe QQGame.exe QQLiveUpdate.exe QQMail.exe QQMusic.exe QQPet.exe QQPetProxy.exe qttask.exequit.exer_server.exeRa2.exeracer.exe RacerKp.exeram.exeRAM_XP.exe ramcleaner.exe Rav.exe RavCopy.exe RAVDOS.EXE RavHDBak.exe RavMon.exe RavMonD.exe RAVMOND.exee RavPatch.exe RavStore.exe RavStub.exe RavTimer.exe RavXp.exe ReadBook.exe realplay.exe REALPROD.EXE realsched.exe reboot.exe RegClean.exe regedit.exeRegGuide.exe regsvc.exe regsvr32.exe regwiz.exe rfw.exe rfwcfg.exe rfwcopy.exe rfwmain.exe rfwsrv.exe rnaapp.exe route.exe rpcclient.exe rpcsrv.exe rpcss.exe RsAgent.exe RsEng.exe RsFsa.exe RsMsg.exe rsrcmtk.exe RsSub.exe rsvp.exe rtvscan.exe RuLa1unch.exe rundll.exe RUNDLL32.EXE runouce.exes1ymlcsvc.exe SavRoam.exe SAVScan.exe scan.exescan32.exe ScanBD.exe scandskw.exe scanrew.exe SCardSvr.exe SchSvr.exe scncfg32.exe sdemm.exe Search.exe serbw.exe SERVICES.EXE servudaemon.exe ServUTray.exe sessmgr.exe setup.exesfc.exe sfmprint.exe Sgser.exe sgserv.exe shcfg32.exe shstat.exe sigverif.exe SinaProc327.exe skdaemon.exe slserv.exesmartdrv.exe SmartUp.exe smlogsvc.exe SMSS.EXESnagIt32.exeSND1Srvc.exe SNDMon.exesndrec32.exe SNDSrvc.exesndvol32.exe snmp.exe snmptrap.exesol.exe soundman.exeSP1BBCSvc.exe SPBBCSvc.exespfw.exespool32.exe SPOOLSS.EXE SPOOLSV.EXE SpybotSD.exe sqlagent.exe sqlmangr.exe sqlservr.exe SRIECLI.EXEsrms.exeSRRest.exe SRSearch.exe srshut.exeSRSI.exeSrvany.exesrvd.exeSrvroam.exe srvset.exesrw.exeS-Spline.exe ssreader.exeSt6unst.exe starter.exe StarWindService.exe STHSDVD.exe stimon.exestisvc.exe StormDownloader.exe StormSet.exe StyleXP.exe StyleXPService.exe SUPER_PI.EXE SVCHOST.EXE SVOHOST.exesws32.exesygate.exe symlcsvc.exe SymWSC.exesysedit.exe SysHotKey.exe sysmon.exe sysocmgr.exe SystemSystem Idle Process System Process systray.exe tapisrv.exe taskgmr.exe taskman.exe taskmgr.exe taskmon.exe TaskSwitch.exe tbmon.exe tcmsetup.exe TCPsvcs.exetds2-nt.exe TDUpdate.exe TeaTimer.exe telnet.exe termsrv.exetftp.exetftpd.exe TGEMon.exe TheWorld.exe Thunder.exe Thunderbird.exe ThunderMiNi.exe Timer.exe TIMPlatform.exe TkBellExe.exe tlntsvr.exeTM.exeTmntsrv.exe TMOAgent.exe TMProxy.exe TotalCmd.exetour98.exe TPSBattM.exe TPSMain.exe tracert.exetray.exetrojdie.kxpTrojDie_1.kxp tshoot.exe TTPlayer.exe TTraveler.exe TTVMaster.exetu.exetuneup.exe TurboLaunch.exe TWCU.exeTweakUI.exeUAService7.exe uc.exeUedit32.exe uGuru.exe UIInfo.exe ULCDRSvr.exe UltraISO.exe UltraSnap.exe UMSD.exe UnInst.exe UnPatch.exeUp222Date.exe Upd.exe Update.exe Update_OB.exe UpdaterUI.exe UPEngine.exe Upgrade.exe uphclean.exe ups.exe Usbmonit.exe USBTD.exe USDM.EXEuser.exe userinit.exe UsrPrmpt.exe UtilMan.exeVB6.exeVchm.exevcmui.exeve6tre5dir.dll VIPClient.exe visio.exeVM_STI.EXE vmnat.exe vmnetdhcp.exe vmware.exe vmware-authd.exe vmware-vmx.exe VnetClient.exe vptray.exe vrvnet.exeVs1Stat.exevs6va5ult.dll Vshw1in32.exe vshwin32.exe vsmon.exe vsserv.exe vsstat.exe vssvc.exe VStart.exe Vstskmgr.exe VTPreset.exevw32.exew3wp.exewab.exewalign.exewangimg.exe WangWang.exe WBLOAD.EXEwcmdmgr.exe WDFMGR.EXEwebscanx.exewelcome.exewinalign.exeWinAMP.exe WinCinemaMgr.exe windcheck2.exewindll.exeWindows-KB890830-V1.6-C Windows-KB890830-V1.7-C Windows优化大师.exe windrg32.exewinfile.exeWinGate.exewinhelp.exewinhlp32.exewinhost.exeWinIme.exewininit.exewinipcfg.exe WinKawaks.exe WinKawaks1.52.exe WINLOGON.EXEWinMem.exewinmgmt.exewinmine.exewinoa386.mod winpopup.exe WinProcess.exe winproj.exeWinRAR.exewinrep.exewinroute.exewins.exewinser.exewinsex.exewinshost.exe winspeed.exewint2k.exewintbp.exeWinup.exewinver.exe WINWORD.EXEWinXP Manager.exe WinZip32.exewisptis.exewiwshost.exe wkcalrem.exewkqkpick.exe wmiapsrv.exe WMIEXE.EXE wmimgr.exe wmiprvse.exe wmplayer.exe wnb.exewnwb.exe Womcc.exe WomEncrypt.exe WomUpdate.exe WomWipe.exe WORDPAD.EXE wowexec.exe wpp.exewps.exeWrite.exe wrkgadm.exews32.exe wscenfy.exe wscntfy.exe WSCommCntr1.exe wscript.exe wuauc.exe wuauclt.exe wupdmgr.exe xcommsvr.exe XDeskWeather.exe XDICT.EXE xfilter.exe Xplus.exe xTools.exe YDownloader.exe YDTMain.exe yisou_sc.exe yminisvr.exe ypager.exezatu6tor.exezl5avscan.dll zlclient.exezo3nealarm.exe ZSTATUS.EXE屏录专家.exe优化大师.exeDescription2005-09-10QQ白骨精病毒的进程。
pnetlab使用 -回复
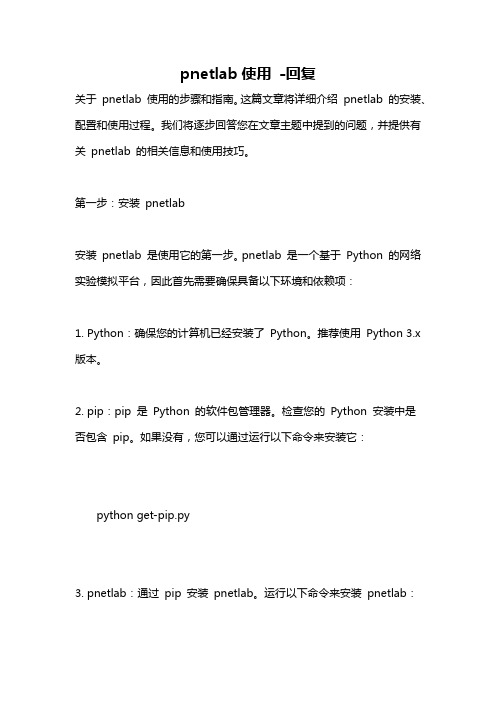
pnetlab使用-回复关于pnetlab 使用的步骤和指南。
这篇文章将详细介绍pnetlab 的安装、配置和使用过程。
我们将逐步回答您在文章主题中提到的问题,并提供有关pnetlab 的相关信息和使用技巧。
第一步:安装pnetlab安装pnetlab 是使用它的第一步。
pnetlab 是一个基于Python 的网络实验模拟平台,因此首先需要确保具备以下环境和依赖项:1. Python:确保您的计算机已经安装了Python。
推荐使用Python 3.x 版本。
2. pip:pip 是Python 的软件包管理器。
检查您的Python 安装中是否包含pip。
如果没有,您可以通过运行以下命令来安装它:python get-pip.py3. pnetlab:通过pip 安装pnetlab。
运行以下命令来安装pnetlab:pip install pnetlab这将自动安装pnetlab 并其所需的依赖项。
第二步:配置pnetlab安装完pnetlab 后,需要进行一些必要的配置,以确保其顺利运行。
1. 网络设备镜像:为了模拟网络设备的行为,pnetlab 需要相应的网络设备镜像文件。
您可以从官方供应商处获取这些镜像文件(如Cisco IOS 镜像),并将它们放置在一个单独的文件夹中。
确保该文件夹的路径易于访问,以便将来在配置中引用。
2. 网络拓扑:在使用pnetlab 前,您需要根据您的需求创建网络拓扑。
可以使用pnetlab 提供的图形界面工具或编程API 来创建和修改网络拓扑。
pnetlab topology create mytopology这会创建一个名为"mytopology" 的新拓扑。
3. 设备导入:为了使pnetlab 能够管理网络设备实例,您需要将网络设备导入到拓扑中。
您可以使用pnetlab 提供的设备库或导入自定义设备。
以下是一个示例命令,用于将一个Cisco 设备导入到拓扑中:pnetlab topology import_device mytopology device cisco_ios name router1这将在名为"mytopology" 的拓扑中导入一个名为"router1" 的Cisco 设备。
计算机机箱主板EMC 测试报告

Report on theEMC EmissionsTesting of theL440GX+ Server Board in theAMC RPC-500 Rack Mount ChassisLab. Ref. PVCS1117Power Line Conduction(as per BS EN55022 (1995)) Radiated Emissions (E-Field)(as per BS EN55022 (1995))In making any use of this test report you are expressly agreeing to the disclaimers and notices below:THIS TEST REPORT IS PROVIDED "AS IS" WITH NO WARRANTY WHATSOEVER, WHETHER EXPRESS, IMPLIED OR STATUTORY, INCLUDING BUT NOT LIMITED TO THOSE FOR NON-INFRINGEMENT OF INTELLECTUAL PROPERTY, MERCHANTABILITY OR SATISFACTIRY QUALITY, FITNESS FOR ANY PARTICULAR PURPOSE, OR ANY WARRANTY OTHERWISE ARISING OUT OF ANY PROPOSAL, SPECIFICATION OR SAMPLE.INTEL ASSUMES NO RESPONSIBILITY FOR ANY ERRORS WHICH MAY APPEAR IN THIS DOCUMENT.THIS INFORMATION IS FOR REFERENCE USE BY PC INTEGRATORS ONLY. PC INTEGRATORS ARE NOT AUTHORISED TO REFER TO INTEL’S TESTING OR REPORTING ACTIVITIES IN ADVERTISING OR ANY OTHER MANNER.Information in this document is provided solely in connection with and to enable the use of Intel products. Intel assumes no liability whatsoever, including infringement of any patent or copyright, for sale and use of Intel products except as provided in Intel's Terms and Conditions of Sale for such products. Intel retains the right to make changes to its test specifications and Intel Products at any time, without notice nor does Intel make a commitment to update the information contained herein. The hardware vendor remains solely responsible for the design, sale and functionality of its product, including any liability arising from product infringement or product warranty. Intel accepts no liability for the quality of third party suppliers, and cannot guarantee that third party products are compatible with Intel products or that third party suppliers will not change parts so that they are no longer compliant.No license, express or implied, by estoppel or otherwise, to any intellectual property rights is granted by this document or by the sale of Intel products.Intel products are not intended for use in medical, life saving, or life sustaining applications.IN NO EVENT WILL INTEL BE LIABLE FOR ANY LOSS OF PROFITS, LOSS OF USE, BUSINESS INTERRUPTIONS, INCIDENTAL, INDIRECT, SPECULATIVE CONSEQUENTIAL OR SPECIAL DAMAGES, IRRESPECTIVE OF WHETHER INTEL HAS ADVANCE NOTICE OF THE POSSIBILITY OF SUCH DAMAGES.IN NO EVENT WILL INTEL’S TOTAL LIABILITY TO BUYER UNDER THIS AGREEMENT EXCEED THE VALUE OF THE INTEL PRODUCT THAT CAUSES SUCH LOSS OR DAMAGE.IN NO EVENT WILL INTEL BE LIABLE IN INDEMNITY.THE LIMITATIONS AND DISCLAIMERS SET OUT IN THIS AGREEMENT WERE AN ESSENTIAL ELEMENT IN INTEL AGREEING TO SUPPLY THIS TEST REPORT FREE OF CHARGE.© 1997, 1998, 1999 Intel Corporation* Other brands and names are the trademarks of their respective ownersCONDUCTED TEST TESTED BY & DATE SIGNATURE Power Line Conduction(as per BSEN55022 (1995))Ann Nicholas23/02/99 _________________________ Radiated Emissions (E-Field)(as per BSEN55022 (1995))Ann Nicholas24/02/99 _________________________APPROVED BY & DATE SIGNATURESimon Lambden 24/02/99_________________________ _________________________CONTENTS1. INTRODUCTION (5)1.1. Introduction (5)1.2. Summary of Issues (5)1.2.1. Action Items51.2.2. FYI Items52. EQUIPMENT UNDER TEST (EUT) (6)2.1. EUT Configuration (6)2.2. Support Equipment (7)2.2.1. Anechoic Chamber 3 metre72.2.2. Open Area Test Site (OATS 2) 10 metre72.2.3. Screened Chamber72.3. EUT Deviations and Comments (7)2.4. Software (8)3. POWER LINE CONDUCTION (AS PER BS EN55022 (1995)) (9)3.1. Test Setup (9)3.2. Test Equipment (9)3.2.1. Powerline Conduction93.3. EUT (9)3.4. Support Equipment Deviations (9)3.5. Test Method (9)3.6. Test Results (10)4. RADIATED EMISSIONS (E-FIELD) (AS PER BS EN55022 (1995)) (11)4.1. Test Setup (11)4.2. Test Equipment (12)4.2.1. Radiated Emissions (E-FIELD)124.3. EUT (12)4.4. Support Equipment Deviations (12)4.5. Test Method (12)4.6. Test Results (13)4.6.1. Preliminary Scan in 3 meter Anechoic Chamber131. INTRODUCTION1.1. IntroductionThis report presents the results of the EMC Emissions tests on the L440GX+ server board in the AMCRPC-500 Rack Mount Chassis - Lab. Ref. PVCS1117 the following Standards•Power Line Conduction(as per BS EN55022 (1995))•Radiated Emissions (E-Field)(as per BS EN55022 (1995))The testing was carried out by INTEL CORPORATION (UK) LTD at their Engineering test facilitieslocated atIntel Corporation (UK) Ltd Intel Corporation (UK) LtdPipers Way(iSF1)Swindon Sheppards FarmWiltshire and ChiseldonEngland SwindonSN3 1RJ WiltshireEnglandThis report also details the configuration of the equipment under test, the test methods used, and anyrelevant modifications where appropriate.1.2. Summary of IssuesA summary of Action Items for hardware related issues is given below.An Action Item (AI) means that the particular test is not meeting the relevant specification and couldprevent correct operation of the named EUT.Other items in this report may be marked as FYI. These are recommendations or observations that may beof interest to the system designer.1.2.1. Action Items•None.1.2.2. FYI Items•From the results in this report it can be seen that the EUT passed the Class B limit.2. EQUIPMENT UNDER TEST (EUT)2.1. EUT.Figure 2-1AMC RPC-500 Rack Mount Chassis2.2. EUT Configuration.Supplier Description Model/Part Number Serial Number LocationAMC ATX Rack MountChassisRPC-500DOB0528009N/APortwell*ATX Power Supply PW-300ATX5388798R/H back of chassisIntel L440GX+ ServerboardPBA 721242-001INLW90300235N/AIntel Pentium® IIIProcessor 80525PY500512Q818ES48479406-0384 A4CPU Slot 2Intel Pentium® IIIProcessor 80525PY500512Q818ES48479406-0328 A4CPU Slot 1Toshiba*128MB 100MHzECC DIMMTHMY721661EG-10None N/ASony*Floppy Drive MPF920-E53172285Top External 3.5”BaySony32X IDE CDROMDriveCDU7015122189-10Top 5.25” baySeagate*9GB Hard Drive ST39173W LM040217Bottom Internal 3.5”BayTable 2-1NOTE: Four 128MB, 100MHz ECC DIMM were fitted.2.3. Support Equipment2.3.1. Anechoic Chamber 3 metreSupplier Description Model/Part Number Serial Number Cherry*Keyboard PS/2G 027286 G21Logitec*Mouse PS/2NoneNEC*Monitor Multisync* E5007Z05020EAIntel Corporation USB Camera680942-002NoneIntel Corporation Serial Emulator C12573NoneIntel Corporation Parallel Emulator C12574NoneTable 2-22.3.2. Open Area Test Site (OATS 2) 10 metreSupplier Description Model/Part Number Serial Number Cherry Keyboard PS/2023480 I04Logitec Mouse PS/2NoneNEC Monitor Multisync XV15+6207123TAIntel Corporation USB Camera680942-002NoneIntel Corporation Serial Emulator C12573NoneIntel Corporation Parallel Emulator C12574NoneTable 2-32.3.3. Screened ChamberSupplier Description Model/Part Number Serial Number Cherry Keyboard PS/200007Logitec Mouse PS/2NoneNEC Monitor Multisync XV156Z00287EAIntel Corporation USB Camera680942-002NoneIntel Corporation Serial Emulator C12573NoneIntel Corporation Parallel Emulator C12574NoneTable 2-42.4. EUT Deviations and CommentsEUT tested with two 500MHz modules, Intel Pentium® III Processor with active heatsink and fan.The Intel Independent I/O shield was fitted in the chassis.Two Delta Electronics Inc fans (P/N AFB0812H and WFB1212H) fitted at the front of the chassis.BIOS version L440GX0.86B.0029.P01.9812180939.2.5. SoftwareThe program used to exercise the EUT was the EMC test software version 2.0 which was running underMicrosoft Windows NT* 4.0 Server. Video resolution was set at 800x600.The EMC test software version 2.0 is designed to exercise the various EUT components in a manner similar to typical use. The software was installed on the hard disk drive and starts automatically on EUT power up.Once started the software exercises each of the following EUT components:CDROM drive - reads data from the CD-ROM. The directory tree is scanned and data is read until a given number of bytes (1.5M) have been read.Hard disk drive - writes, read and verifies 64K bytes of data on each drive.Floppy drive - writes, read and verifies one sector for each working drive.Keyboard - performs a keyboard confidence test.Monitor - either inverts the colour of every pixel on the screen or continually outputs ‘H’characters.Mouse uses the driver to do a mouse confidence test.Parallel port - either 256 (with loopback connector) or 54 (without) characters (A-z, a-z) are written (and with loopback connector, also read back).Serial port - the line is configured, if a loopback connector is present a non-blocking read is issued,(baudrate/20, max 6000) characters (streams of 0-9) are written, and the same number of characters must be read back (only if a loopback connector is present).USB - Reads device descriptor from each device attached. On subsequent reads it verifies that the data iscorrect.Network - Writes a file to a specified directory then reads it back.3. Power Line Conduction(as per BS EN55022 (1995))3.1. Test SetupThe EUT was placed on top of a fixed wooden table.3.2. Test Equipment3.2.1. Powerline ConductionSupplier Description Model/Part Number Serial Number Rohde & Schwarz LISN ESH3-Z5839135/022Rohde & Schwarz EMI Test Receiver ESHS 10839698/002Table 3-13.3. EUTSee section 2.13.4. Support Equipment DeviationsNone3.5. Test MethodThe EUT was powered up via the LISN and the EUT exercising software was invoked to exercise all subsystems of the EUT. The RF conducted emissions from the EUT were measured using the R&S ESHS 10via the LISN under computer control. Using R&S ES-K1 version 1.4x software the “Average” and “Peak”levels were measured at the same time for all frequencies in the range 150kHz to 30 MHz. Any frequencyover the Av or QP limit respectively constituted a failure.3.6. Test ResultsEnvironmental Status 24.5°C Temperature, 30% Humidity and 1282mB Barometric Pressure-2020406080Level [dBµV]150k 300k 500k1M 2M3M 4M 6M 10M 30MFrequency [Hz]++ + MES s01117a1_fin AVMES s01117a1_pre PK MES s01117a1_pre AV LIM EN 55022 V QP LIM EN 55022 V AV Figure 3-1Frequency MHz AV Level dBuV AV Limit dBuV AV Delta dB Phase PE16.00540.17509.83L1GND 16.0140.59509.41L1GNDTable 3-2No frequencies were determined to be over the Av or QP limits.4. Radiated Emissions (E-Field)(as per BS EN55022 (1995))4.1. Test SetupFigure 4-1Generic test set-up1. Equipment Under Test2. Monitor3. Peripheral Emulators (Parallel and Serial)4. USB Camera5. PS/2 Mouse6. PS/2 Keyboard4.2. Test Equipment4.2.1. Radiated Emissions (E-FIELD)Serial Number Reference Supplier Description Model/PartNumber1Chase Bilog Antenna CBL6112A22042Chase Bilog Antenna CBL6121A10173Rohde & Schwarz EMI Test Receiver (OATS 2)ESVS 10843744/0134Rohde & Schwarz EMI Test Receiver & Analyser ESMI839049/0145n/a10m OATS SF2n/a Table 4-14.3. EUTSee section 2.14.4. Support Equipment DeviationsNone.4.5. Test MethodEUT is first tested in 3 metre Anechoic Chamber as outlined below and if any frequencies are determined to be over or within 7dB of limit then the EUT is further tested at the Open Area Test Site (OATS) alsooutlined below.Test Method in 3 metre Anechoic ChamberThe EUT was placed on or beside (if floor standing) a table. The top of the table was 0.8 meters above the ground plane and 3 meters from the antenna. The antenna was positioned 1.5 meters up from the ground plane. From 30MHz to 1000MHz a BiLog antenna was used. The receiver was equipment reference 4 and the antenna used was equipment reference 1. The test was run automatically under computer control using R&S ESK1 version 1.4. The algorithm used was as follows:Five scans of the EUT were performed using the peak detector and the resulting graphs superimposed. Up to Thirty frequencies on the resultant graph with amplitude within 10dB of the quasi peak limit detected between 30MHz to 1 GHz were selected. With the receiver set to each of the selected frequencies the EUT was rotated, the antenna raised and lowered from 2 meters to 1 meter and the antenna polarisation was changed from the vertical to the horizontal and the maximum Quasi-Peak (QP) signal strength noted.Test Method in 10 metre Open Area Test Site (OATS)The EUT was tested on OATS equipment reference 5 where it was placed on or beside a table 0.8 meters above the ground plane and 10 meters from the antenna. The EUT was powered on and ran the referenced EUT exercising software (see 2.4). The antenna was mounted on a mast permitting movement from 1.0 meters to 4.0 metres above the ground plane in horizontal or vertical polarisation. From 30MHz to 1000MHz a BiLog antenna equipment reference 2 was used. The receiver was a Rohde and Schwarz ESVS equipment reference 3. All frequencies found to be over or within 7dB of the quasi peak limit when tested in the 3 metre Anechoic Chamber were measured. The EUT was rotated and the antenna raised and lowered from 1 meter to 4 meters and the antenna was also changed from the vertical polarisation to the horizontal polarisation and the maximum Quasi Peak (QP) signal strength noted.4.6. Test Results4.6.1.Preliminary Scan in 3 meter Anechoic ChamberEnvironmental Status 23.5°C Temperature, 33% Humidity and 987mB Barometric Pressure-2020406080Level [dBµV/m]30M 40M 50M 70M 100M200M 300M 400M 600M 1GFrequency [Hz]xxxxxxx xxxx xxx xx xxxx x x xxx x MES s01117aa_fin QPMES s01117aa_pre PK LIM EN 55022B F 3 Meter Figure 4-2Frequency MHzQP Level dBuV/MClass B Limit dBuV/MDelta dBRotation °HeightOrientation49.9231.86408.14261100Vertical 69.9630.02409.98238100Vertical 179.9831.55408.45319100Vertical 19030.73409.286100Vertical 199.9636.3540 3.6536100Vertical 32041.0647 5.947135Vertical 340.0439.43477.5782100Horizontal 694.4843.0147 3.99148119Horizontal 992.240.5347 6.47178100VerticalTable 4-2Results from maximising frequencies in the 3M chamberFour frequencies were determined to be within 7dB of limit so further testing at 10 meter Open Area Test Site was required.Environmental Status 8.5°C Temperature, 77% Humidity and 985mB Barometric PressureFrequency MHzQP LeveldBuV/MClass B Limit dBuV/MDelta dBRotation °HeightOrientation199.96Ambient only - No signal detected from the EUT32024.03713.00150Vertical 694.4834.037 3.0140150Horizontal 992.235.837 1.20150VerticalTable 4-3Results from maximising at the 10M OATSAs can be seen from the results in Table 4-3, no frequencies were determined to be over the limit.。
软件开发中的云原生技术与架构考核试卷

B. JUnit
C. Selenium
D. Kubernetes
19.以下哪些是云原生应用监控工具?()
A. Prometheus
B. Grafana
C. Kibana
D. Docker
20.以下哪些是云原生架构中支持的服务发现工具?()
A. Consul
B. Etcd
C. ZooKeeper
5.服务网格主要用于管理微服务之间的通信。()
6.在云原生架构中,所有的服务都应该是有状态的。()
7. Serverless架构可以显著降低运营成本,因为用户只需为实际代码运行时间付费。()
8.云原生应用不需要考虑容错和灾难恢复。()
9. Prometheus是一种日志管理工具。()
10.云原生技术只适用于新开发的应用程序,不适用于现有的传统应用程序。()
()
标准答案
一、单项选择题
1. D
2. D
3. D
4. D
5. D
6. D
7. B
8. D
9. D
10. D
11. A
12. D
13. D
14. D
15. D
16. D
17. D
18. A
19. A
20. D
二、多选题
1. ABC
2. AB
3. AC
4. ABC
5. ABC
6. ABC
7. ABC
8. ABC
B.微服务
C.不可变基础设施
D.以上都是
2.以下哪个不是云原生计算基金会(CNCF)支持的项目?()
A. Kubernetes
B. Docker
G7125-250 品牌:Belimo,类型:商品说明书
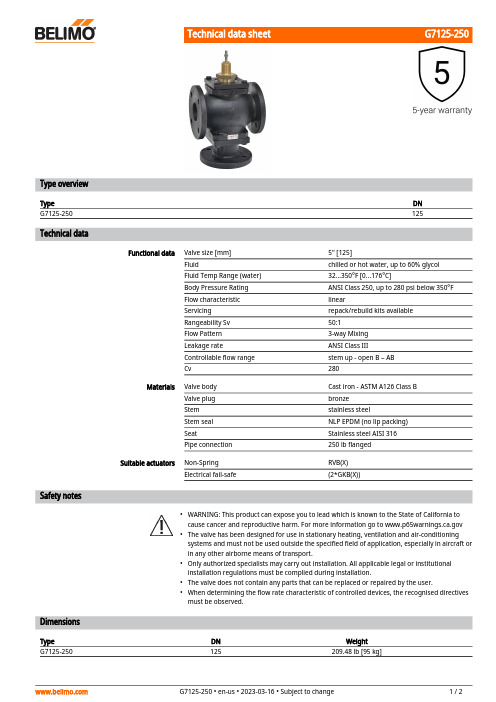
•••••Type overviewTypeDN G7125-250125Technical dataFunctional dataValve size [mm]5" [125]Fluidchilled or hot water, up to 60% glycol Fluid Temp Range (water)32...350°F [0...176°C]Body Pressure Rating ANSI Class 250, up to 280 psi below 350°F Flow characteristic linearServicing repack/rebuild kits available Rangeability Sv 50:1Flow Pattern 3-way Mixing Leakage rateANSI Class III Controllable flow range stem up - open B – AB Cv280MaterialsValve body Cast iron - ASTM A126 Class B Valve plug bronze Stem stainless steelStem seal NLP EPDM (no lip packing)SeatStainless steel AISI 316Pipe connection250 lb flanged Suitable actuatorsNon-Spring RVB(X)Electrical fail-safe(2*GKB(X))Safety notesWARNING: This product can expose you to lead which is known to the State of California to cause cancer and reproductive harm. For more information go to The valve has been designed for use in stationary heating, ventilation and air-conditioning systems and must not be used outside the specified field of application, especially in aircraft or in any other airborne means of transport.Only authorized specialists may carry out installation. All applicable legal or institutional installation regulations must be complied during installation.The valve does not contain any parts that can be replaced or repaired by the user.When determining the flow rate characteristic of controlled devices, the recognised directives must be observed.DimensionsTypeDN WeightG7125-250125209.48 lb [95 kg]EVB, EVX, RVB, RVXA B C D E F Number of Bolt Holes16.6" [422]15.5" [394]28.0" [711]17.5" [445]5.5" [140]5.5" [140]82*GMB, 2*GMX, 2*GKB, 2*GKXA B C D E F Number of Bolt Holes15.1" [383]16.6" [422]30.0" [762]17.5" [445]5.0" [127]6.3" [160]8RVB24-3FootnotesOn/Off, Floating Point, Non-Spring Return, Linear, 24 VTechnical dataElectrical dataNominal voltageAC/DC 24 V Nominal voltage frequency 50/60 HzNominal voltage rangeAC 19.2...28.8 V / DC 21.6...28.8 V Power consumption in operation 6 W Power consumption in rest position 1.5 W Transformer sizing 11 VAElectrical Connection 18 GA plenum cable, 1 m, with 1/2" conduit connector, degree of protection NEMA 2 / IP54Overload Protection electronic throughout full stroke Electrical Protectionactuators are double insulated Functional dataActuating force motor 4500 N [1010 lbf]Position feedback U note No Feedback Direction of motion motor selectable with switchManual override 5 mm hex crank (3/16" Allen), supplied Stroke2" [50 mm]Running Time (Motor)90 s /Running time motor note constant, independent of load Noise level, motor 65 dB(A)Position indicationMechanical, with pointer Safety dataPower source ULClass 2 Supply Degree of protection IEC/EN IP54Degree of protection NEMA/UL NEMA 2Enclosure UL Enclosure Type 2Agency ListingcULus acc. to UL60730-1A/-2-14, CAN/CSA E60730-1:02, CE acc. to 2014/30/EU and 2014/35/EU Quality Standard ISO 9001Ambient humidity Max. 95% RH, non-condensing Ambient temperature -22...122°F [-30...50°C]Storage temperature -40...176°F [-40...80°C]Servicingmaintenance-free Weight Weight9.02 lb [4.1 kg]MaterialsHousing material Die cast aluminium and plastic casing† Use flexible metal conduit. Push the listed conduit fitting device over the actuator’s cable to butt against the enclosure. Screw in conduit connector. Jacket the actuators input wiring with listed flexible conduit. Properly terminate the conduit in a suitable junction box. Rated impulse Voltage 800V. Type of action 1. Control pollution degree 3.RVB24-3 AccessoriesElectrical accessories Description TypeBattery backup system, for non-spring return models NSV24 USBattery, 12 V, 1.2 Ah (two required)NSV-BAT Electrical installationINSTALLATION NOTES ArrayActuators may be connected in parallel. Power consumption and input impedance must beobserved.Actuators may also be powered by DC 24 V.Control signal may be pulsed from either the Hot (Source) or Common (Sink) 24 V line.For triac sink the common connection from the actuator must be connected to the hotconnection of the controller. Contact closures A & B also can be triacs. A & B should both beclosed for the triac source and open for triac sink.Actuators with plenum cable do not have numbers; use color codes instead.Meets cULus requirements without the need of an electrical ground connection.Warning! Live electrical components!During installation, testing, servicing and troubleshooting of this product, it may be necessaryto work with live electrical components. Have a qualified licensed electrician or other individualwho has been properly trained in handling live electrical components perform these tasks.Failure to follow all electrical safety precautions when exposed to live electrical componentscould result in death or serious injury.Wiring diagramsOn/Off Floating Point。
互联网平台技术架构演进考核试卷
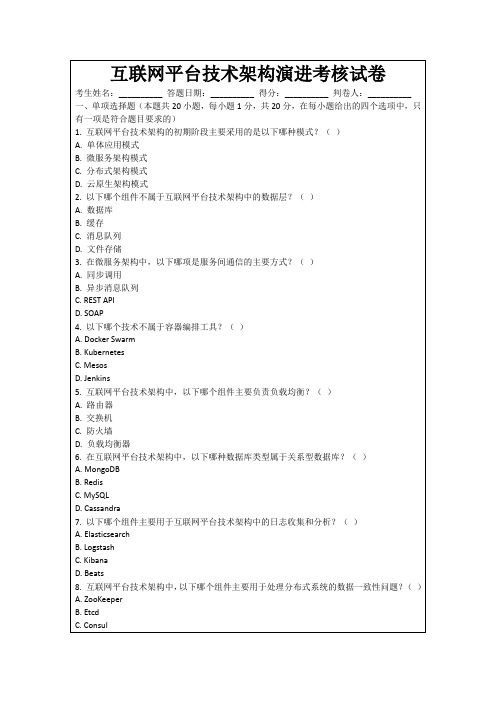
D. Cassandra
7.以下哪个组件主要用于互联网平台技术架构中的日志收集和分析?()
A. Elasticsearch
B. Logstash
C. Kibana
D. Beats
8.互联网平台技术架构中,以下哪个组件主要用于处理分布式系统的数据一致性问题?()
A. ZooKeeper
14.以下哪个组件主要用于互联网平台技术架构中的自动化部署?()
A. Jenkins
B. GitLab CI/CD
C. Docker Swarm
D. Kubernetes
15.在互联网平台技术架构中,以下哪个组件主要用于安全认证?()
A. OAuth2.0
B. OpenID
C. SAML
D. JWT
A. Prometheus
B. Grafana
C. Zipkin
D. Jaeger
20.以下哪些技术可以用于边缘计算?()
A. Kubernetes
B. Apache Kafka
C. IoT Edge
D. AWS Greengrass
三、填空题(本题共10小题,每小题2分,共20分,请将正确答案填到题目空白处)
A. Istio
B. Linkerd
C. Consul
D. Etcd
19.以下哪个技术不属于区块链技术?()
A. Bitcoin
B. Ethereum
C. Hyperledger Fabric
D. Spring Boot
20.在互联网平台技术架构中,以下哪个组件主要用于实现分布式搜索引擎?()
A. Elasticsearch
A. Hadoop
容器技术与微服务架构考核试卷
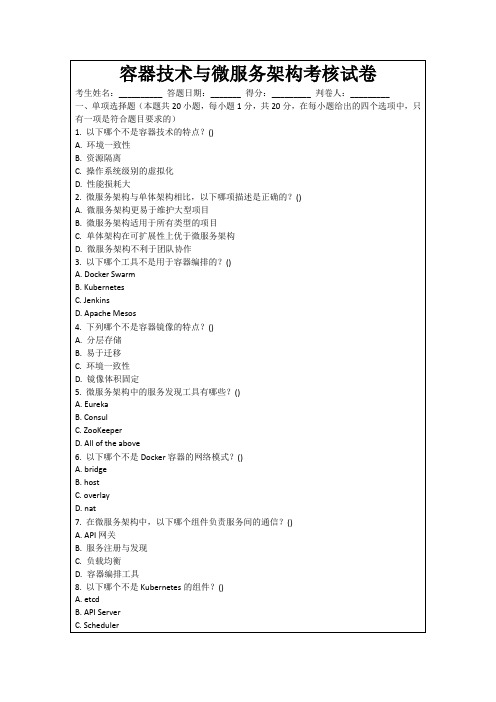
B. host
C. overlay
D. nat
7.在微服务架构中,以下哪个组件负责服务间的通信?()
A. API网关
B.服务注册与发现
C.负载均衡
D.容器编排工具
8.以下哪个不是Kubernetes的组件?()
A. etcd
B. API Server
C. Scheduler
D. Docker
C. Jenkins
D. Apache Mesos
4.下列哪个不是容器镜像的特点?()
A.分层存储
B.易于迁移
C.环境一致性
D.镜像体积固定
5.微服务架构中的服务发现工具有哪些?()
A. Eureka
B. Consul
C. ZooKeeper
D. All of the above
6.以下哪个不是Docker容器的网络模式?()
答案:
6. Prometheus是一个用于容器监控的开源工具,它可以自动发现目标服务。( )
答案:
7. Docker容器在运行时一定会创建一个独立的网络命名空间。( )
答案:
8.微服务的部署通常比单体应用更加简单。( )
答案:
9. Kubernetes中的Pod是一组可以共享网络和存储资源的容器集合。( )
答案:
4.在微服务架构中,如何实现服务熔断和服务降级?请举例说明这些策略在实际应用中的重要性。
答案:
标准答案
一、单项选择题
1. D
2. A
3. C
4. D
5. D
6. C
7. A
8. D
9. B
10. B
11. D
MPLAB Code Configurator V3.25 1 用户指南说明书

Release Notes for MPLAB® Code Configurator V3.251 What is MPLAB Code Configurator (MCC)The MPLAB®Code Configurator generates seamless, easy to understand code that is inserted into your project. It enables, configures and utilizes a rich set of peripherals and libraries across select devices. It is integrated into MPLAB®X IDE to provide a very powerful and extremely easy to use development platform.2 System Requirements∙MPLAB® X IDE 3.40 or later∙XC8 compiler v 1.38 or later∙XC16 compiler v 1.26 or later∙XC32 compiler v1.42 or later3 Documentation SupportThe MPLAB® Code Configurator v3 User’s Guide may be found on the MPLAB® Code Configurator page on the Microchip web site. /mcc4 Installing MPLAB® Code ConfiguratorBasic steps for installing MPLAB® Code Configurator V3 Plugin are given here.To install the MPLAB® Code Configurator V3.25 Plugin:1. In the MPLAB® X IDE, select Plugins from the Tools menu2. Select the Available Plugins tab3. Check the box for the MPLAB® Code Configurator v3, and click on Install5 What’s NewThe following features were added in new in MCC 3.25 release1. Help Framework Suppor t: Now MCC help or a module help is available by right clicking onmodule in Resource or Composer Area or on the icon, to get a help window similar to one listed below:2. Traffic Light Support: MCC adds support to allow libraries to release support early byproviding Red\Yellow\Green level support based on testing performed by the libraries.3. SDK Support: Changes in the software to allow developers to interface with MCC using apublished SDK available at a later date.4. MCC Plugin options and settings moved to Tools/Options/Plugins5. New Devices and peripherals are listed in the each peripheral library release notes.6 Repairs and EnhancementsThis section lists the repairs and enhancements for the plugin, for library specific issues please look at the individual library release notes.6.1 Generic7 Known IssuesThis section lists the known issues for the plugin, for library specific issues please look at the individual library release notes.7.1 WorkaroundMCCV3XX-4650: Migration from v3.0.5 to v3.25 may not work correctly. If you are using v3.0.5, to migrate from MCC 3.0.5 to MCC 3.25, first migrate from MCC 3.0.5 to MCC 3.16 and then migrate MCC 3.16 to MCC 3.25. MCC 3.16 can be obtained from /mcc from“Archive” tab.7.2 Generic8 Frequently Asked QuestionsFor frequently asked questions, please refer to the FAQ post on the MCC Forum(/forums/f293.aspx)9 Supported FamiliesFor the list of supported families, refer to the release notes of respective libraries.10 C ustomer Support10.1 The Microchip Web SiteMicrochip provides online support via our web site at . This web site is used as a means to make files and information easily available to customers. Accessible by using your favorite Internet browser, the web site contains the following information:∙Product Support – Data sheets and errata, application notes and sample programs, design resources, user’s guides and hardware support documents, latest software releases and archived software∙ General Technical Support – Frequently Asked Questions (FAQs), technical support requests, online discussion groups/forums (), Microchip consultant programmember listing∙ Business of Microchip – Product selector and ordering guides, latest Microchip press releases, listing of seminars and events, listings of Microchip sales offices, distributors and factoryrepresentatives10.2 Additional SupportUsers of Microchip products can receive assistance through several channels:∙Distributor or Representative∙Local Sales Office∙Field Application Engineering (FAE)∙Technical SupportCustomers should contact their distributor, representative or field application engineer (FAE) for support. Local sales offices are also available to help customers. A listing of sales offices and locations is available on our web site.Technical support is available through the web site at: 11 Appendix: Supported DevicesFor the list of supported devices, refer to the release notes of respective libraries.。
- 1、下载文档前请自行甄别文档内容的完整性,平台不提供额外的编辑、内容补充、找答案等附加服务。
- 2、"仅部分预览"的文档,不可在线预览部分如存在完整性等问题,可反馈申请退款(可完整预览的文档不适用该条件!)。
- 3、如文档侵犯您的权益,请联系客服反馈,我们会尽快为您处理(人工客服工作时间:9:00-18:30)。
Wind River Systems Tornado Training Workshop © Copyright Wind River Systems F -15RPC AppendixRPC LabThe RPC programming lab is unsupported.Remote Procedure Call (RPC) Objective:To be able to call functions on remote nodes using the RPC protocol.In a X window, change your directory to HomeDir/unsupported/ rpc. In this directory there is a program which runs on UNIX and prints the date.%unixDateFri Dec 27 06:35:31 1991This exercise is to modify this program so that, using RPC, we can execute the code from VxWorks. The steps below provide an overview of what is required. These steps will be discussed in more detail later.1.Remake VxWorks with RPC included.2.Create time.x, a RPC specifications file. To keep everyone’swork separate, use the following RPC program number: Team Program Number10x2000000120x2000000230x20000003......80x200000083.Write unixTimeServer.c (a modification of unixDate.c) to actas a RPC server.4.Write vxTimeClient.c to act as an RPC client.e rpcgen on time.x to generate the time.h, time_svc.c andtime_clnt.c files.6.Modify time.h so that it will compile for VxWorks. You mayuse the script provided:%rpcModify time.h(Note: this step is optional if you compile with -nostdinc.)pile and link unixTimeServer.c and time_svc.c intotimeServer. Since timeServer will run on the host side, use the native compiler for your host (cc in the laboratory). You may want to compile unixTimeServer.c with a native ANSIcompiler, and time_svc.c with a traditional compiler, then link the resulting object modules. Run timeServer in background.pile vxTimeClient.c and time_clnt.c. Since the client runsunder VxWorks, use the appropriate cross-compiler for your target.9.Incrementally link vxTimeClient.o and time_clnt.o to create afile called timeClient.o. Use the cross-linker for yourarchitecture.10.Load timeClient.o on your VxWorks target and test it.You can either stop here and start the lab or you can continue reading for a more detailed description of each of the steps above. Do what you think will make best use of your lab time.1.Modify config.h so that the symbol INCLUDE_RPC is defined, oruse WindConfig. Remake the system image. Then reboot your target.2.Creating time.x, the RPC specification fileThe RPC specification file has the following format:program PROG_NAME {version VERSION_NAME {type routineName (type) = 1;type routineName (type) = 2;...} =versionNumber;} =programNumber;The PROG_NAME and VERSION_NAME are arbitrary names that will be converted by rpcgen into symbolic constants. We’ll call them TIME_PROG and TIME_VERS respectively. Since this is our first version, we’ll assign versionNumber to be 1. The program number must be in the range 0x200000000 to 0x3ffffff. Other numbers are reserved by Sun. Use a program number of0x2000000n where n is your team number (0-8). Now we have: program TIME_PROG {version TIME_VERS {type routineName (type) = 1;type routineName (type) = 2;...} = 1;T eam 1 program number shown } = 0x20000001;The innermost part of the structure is just a list of the routines in your program. We only have one routine, let’s call itprint_time. By convention, the program name is written inupper case. So we have:program TIME_PROG {version TIME_VERS {type PRINT_TIME (type) = 1;} = 1;} = 0x20000001;What are we going to pass as an argument to print_time?Nothing, so it is type void. What does print_time return? A pointer to a character (string). RPC has predefined term,string, for a NULL terminated character string. So, now we have:program TIME_PROG {version TIME_VERS {string PRINT_TIME (void) = 1;} = 1;} = 0x20000001;3.Modify unixDate.cCopy unixDate.c to unixTimeServer.c. We will make ourchanges in unixTimeServer.cRemove the main() routine. The time_svc.c generated byrpcgen has the program’s main().As a local routine print_time returns a pointer to a character (a string). Remote calls always use one more level of indirection than you would locally, i.e. if the local routine passes (orreturns) a long, the remote call uses a pointer to a long. So,print_time must return a pointer to a string, i.e. “char **”.The name of the routine,PRINT_TIME, described in thespecification file is converted to lower case and appended with the version number. That is, if you have a routine name ofBLAH_BLAH in the specifications file and your version number is 2, then you need to define a routine called blah_blah_2. For our purposes, we need to changed the name of the routinefrom print_time to print_time_1. So, the declaration should now read:char ** print_time_1 ()Lastly, we need to modify the return value from:return (pStr);— return a character pointer — to:return (&pStr);returning a pointer to a string.4.Write a routine called printTime in a file called vxTimeClient.c:This routine must call:q rpcTaskInit ()Initializes the VxWorks RPCpackage for this taskq clnt_create ()Creates a client handle to the RPCtask on the remote host. TheCLIENT handle returned fromthis routine should be stored in aglobal variable. By only callingclnt_create if the global variableis NULL, you avoid establishingthis handle every time printTimeis called. Note, however, that theCLIENT handle may not beshared between tasks. If youintend to call printTime() directlyfrom the Wind Shell, you mustrecreate (and later delete, withclnt_destroy) the client handle oneach call, as in this case a newtask is created for each call. Youmight define a macro and useconditional compilation to treatthese two cases differently.Another possible solution isgiven in the lab answers.q print_time_1 ()Gets the time from the server task q printf ()Prints the string received fromprint_time_1q free()Free memory allocated for thestring.5.Call rpcgen.%rpcgen time.xThis should create a time.h,time_clnt.c, and time_svc.c.6.Call rpcModify.%rpcModify time.hThis changes the include line in time.h from#include <rpc/rpc.h>to#ifdef VXWORKS#include “vxWorks.h”#include “rpc/rpc.h”#else#include <rpc/rpc.h>#endifIf VXWORKS is defined,vxWorks.h and rpc/rpc.h will beincluded, otherwise rpc/rpc.h (under/usr/include).pile and link the server program with:%cc unixTimeServer.c time_svc.c-o timeServerStart the server program.%./timeServerpile the main client program and client stub:%ccx -DVXWORKS vxTimeClient.c%ccx -traditional -DVXWORKS time_clnt.cThe “-traditional” flag is required because rpcgen generates non-ANSI code. The “-DVXWORKS” is to define VXWORKS so that the correct header files will be included in time.h. 9.Link the client modules to form a client program:%ld Arch-r vxTimeClient.o time_clnt.o\-o timeClient.o10.From VxWorks, change directory to HomeDir/unsupported/rpc and load the client module:->ld < timeClient.ovalue = 0 = 0x0Call the printTime routine (It was defined in client.o).->printTimeFri Dec 27 14:36:09 1991Output from remote routine value = 0 = 0x0。