MAX6318MHUK29BY-T中文资料
车削刀具 - 工具系统

-
J
-
-
18 (.71) 21 (.83)
27 (1.06) 23 (.91) -
-
-
-
20 (.79) 24 (.94)
35 (1.38) 32 (1.26) -
-
-
-
24 (.94) 29 (1.14)
G 11
TURN - CHI
A
工具系统
可乐满 Capto®—— 夹紧单元
手动夹紧单元
圆柄
涨爪夹紧
C
G58
G59
G61
I1
H1
G
用于旋转刀具的工具系统
参见主样本中有关铣削、钻削和镗削刀具的章节。
H
I
工具系统 目录
J
G3
TURN - CHI
A
工具系统
B
可乐满 Capto®
可乐满 Capto®
工具系统
车削中心应用
Coromant Capto 工具系统在车削中心上被广泛应用,通过凸轮轴机构驱动拉刀机构实现手动拉紧刀具。 刀具的快换极大地提高 了机床效率,平均可多出 25 %的切削时间。
不过随着可乐满capto在该应用领域的普及无论是采用液压夹紧自动换刀atc或是专用的手动夹紧单元该挑战已经得到很好的解工具系统可乐满capto非旋转刀具概述手动夹紧单元方形柄圆形柄方形柄圆形柄特殊应用vdi角度型vdivdi燕尾din69880din69880din69881cxrlc2085cxnc2000cxrlc2080cxrlc2045cxrlc2090cxrlc2030cxrlc2030cxrlci115cxnc300020552065204020502060204020502060cxrlci140第g13g12g14g15g16g18g18g25加长cx39101cx39102页码g54g55用于圆柱柄刀具的接杆用于方刀杆刀具的接杆用于corocut和tmaxqcut径向安装轴向安装轴向安装角度安装径向安装轴向安装切断刀板和方刀柄cx131cx131cxashacxashrlcxashrl3cxashrl45cxapbacxapbrl392419ashaashrlabprl第g52h37h28h29h31h30h32h32h38圆柱柄刀具请参见车削切断和切槽以及螺纹切削部分方刀杆刀具请参见车削切断和切槽以及螺纹切削部分切断刀板请参见切断和切槽部分对于圆柱镗杆可使用easyfix夹套请参见第a320用于方刀杆圆柄刀具和切断刀板的cdicxrlci80cxrlce80ashtneabbtneabptne第g20g22g24可乐满capto非旋转刀具概述工具系统自动夹紧单元cdi动力头刀座多任务机床机床适配夹紧单元动力头刀座和用于切断刀板的cbicxnc5010cxnc5110cxnc5210cxdne80cxdni80mazakmoriseikidoosannakamuratomeokumajetbreakg23g23第g35coroturnslcxa570cx570cxa570cx570页码i57i58coroturnsl70cxsl70第i100切削单元请参见普通车削切断和切槽螺纹车削和多任务加工部分
MAX6318MHUK50BW-T中文资料
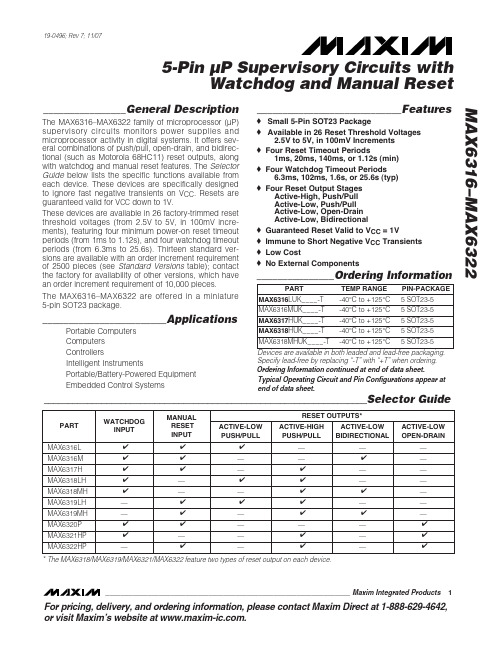
___________________________________________________________________Selector Guide________________General DescriptionThe MAX6316–MAX6322 family of microprocessor (µP)supervisory circuits monitors power supplies and microprocessor activity in digital systems. It offers sev-eral combinations of push/pull, open-drain, and bidirec-tional (such as Motorola 68HC11) reset outputs, along with watchdog and manual reset features. The Selector Guide below lists the specific functions available from each device. These devices are specifically designed to ignore fast negative transients on V CC . Resets are guaranteed valid for V CC down to 1V.These devices are available in 26 factory-trimmed reset threshold voltages (from 2.5V to 5V, in 100mV incre-ments), featuring four minimum power-on reset timeout periods (from 1ms to 1.12s), and four watchdog timeout periods (from 6.3ms to 25.6s). Thirteen standard ver-sions are available with an order increment requirement of 2500 pieces (see Standard Versions table); contact the factory for availability of other versions, which have an order increment requirement of 10,000 pieces.The MAX6316–MAX6322 are offered in a miniature 5-pin SOT23 package.________________________ApplicationsPortable Computers Computers ControllersIntelligent InstrumentsPortable/Battery-Powered Equipment Embedded Control Systems____________________________Features♦Small 5-Pin SOT23 Package♦Available in 26 Reset Threshold Voltages2.5V to 5V, in 100mV Increments ♦Four Reset Timeout Periods1ms, 20ms, 140ms, or 1.12s (min)♦Four Watchdog Timeout Periods6.3ms, 102ms, 1.6s, or 25.6s (typ) ♦Four Reset Output StagesActive-High, Push/Pull Active-Low, Push/Pull Active-Low, Open-Drain Active-Low, Bidirectional♦Guaranteed Reset Valid to V CC = 1V♦Immune to Short Negative V CC Transients ♦Low Cost♦No External ComponentsMAX6316–MAX63225-Pin µP Supervisory Circuits withWatchdog and Manual Reset________________________________________________________________Maxim Integrated Products 119-0496; Rev 7; 11/07_______________Ordering InformationOrdering Information continued at end of data sheet.*The MAX6318/MAX6319/MAX6321/MAX6322 feature two types of reset output on each device.Typical Operating Circuit and Pin Configurations appear at end of data sheet.For pricing, delivery, and ordering information, please contact Maxim Direct at 1-888-629-4642,or visit Maxim’s website at .Specify lead-free by replacing “-T” with “+T” when ordering.ELECTRICAL CHARACTERISTICS(V CC = 2.5V to 5.5V, T A = -40°C to +125°C, unless otherwise noted. Typical values are at T A = +25°C.) (Note 1)M A X 6316–M A X 63225-Pin µP Supervisory Circuits with Watchdog and Manual Reset 2_______________________________________________________________________________________ABSOLUTE MAXIMUM RATINGSStresses beyond those listed under “Absolute Maximum Ratings” may cause permanent damage to the device. These are stress ratings only, and functional operation of the device at these or any other conditions beyond those indicated in the operational sections of the specifications is not implied. Exposure to absolute maximum rating conditions for extended periods may affect device reliability.Voltage (with respect to GND)V CC ......................................................................-0.3V to +6V RESET (MAX6320/MAX6321/MAX6322 only)...... -0.3V to +6V All Other Pins.........................................-0.3V to (V CC + 0.3V)Input/Output Current, All Pins.............................................20mAContinuous Power Dissipation (T A = +70°C)SOT23-5 (derate 7.1mW/°C above +70°C)...............571mW Operating Temperature Range..........................-40°C to +125°C Junction Temperature......................................................+150°C Storage Temperature Range..............................-65°C to +160°C Lead Temperature (soldering, 10s).................................+300°CTH available in 100mV increments from 2.5V to 5V (see Table 1 at end of data sheet).Note 3:Guaranteed by design.MAX6316–MAX63225-Pin µP Supervisory Circuits withWatchdog and Manual Reset_______________________________________________________________________________________3Note 5:Measured from RESET V OL to (0.8 x V CC ), R LOAD = ∞.Note 6:WDI is internally serviced within the watchdog period if WDI is left unconnected.Note 7:The WDI input current is specified as the average input current when the WDI input is driven high or low. The WDI input is designed for a three-stated-output device with a 10µA maximum leakage current and capable of driving a maximum capac-itive load of 200pF. The three-state device must be able to source and sink at least 200µA when active.ELECTRICAL CHARACTERISTICS (continued)M A X 6316–M A X 63225-Pin µP Supervisory Circuits with Watchdog and Manual Reset 4_________________________________________________________________________________________________________________________________Typical Operating Characteristics(T A = +25°C, unless otherwise noted.)021*********-4020-20406080100MAX6316/MAX6317/MAX6318/MAX6320/MAX6321SUPPLY CURRENT vs. TEMPERATURETEMPERATURE (°C)S U P P L Y C U R R E N T (μA )302010504090807060100-40-20020406080100V CC FALLING TO RESET PROPAGATIONDELAY vs. TEMPERATURETEMPERATURE (°C)R E S E T P R O P A G A T I O N D E L A Y (μs )140180160240220200300280260320-40020-20406080100MAX6316/MAX6317/MAX6319/MAX6320/MAX6322MANUAL RESET TO RESETPROPAGATION DELAY vs. TEMPERATURETEMPERATURE (°C)P R O P A G A T I O N D E L A Y (n s )0.950.980.970.961.000.991.041.031.021.011.05-40-2020406080100NORMALIZED RESET TIMEOUT PERIOD vs. TEMPERATUREM A X 6316t o c 04TEMPERATURE (°C)N O R M A L I Z E D R E S E T T I M E O U T P E R I O D0.950.980.970.961.000.991.041.031.021.011.05-40-2020406080100MAX6316/MAX6317/MAX6318/MAX6320/MAX6321NORMALIZED WATCHDOG TIMEOUTPERIOD vs. TEMPERATUREM A X 6316t o c 05TEMPERATURE (°C)N O R M A L I Z E D W A T C H D O G T I M E O U T P E R I O D800101001000MAXIMUM V CC TRANSIENT DURATION vs. RESET THRESHOLD OVERDRIVE2010RESET THRESHOLD OVERDRIVE (mV) V RST - V CCT RA N S I E N T D U R A T I O N (μs )3050604070200ns/divMAX6316M/6318MH/6319MHBIDIRECTIONALPULLUP CHARACTERISTICSMAX6316–MAX63225-Pin µP Supervisory Circuits withWatchdog and Manual Reset_______________________________________________________________________________________5______________________________________________________________Pin DescriptionM A X 6316–M A X 63225-Pin µP Supervisory Circuits with Watchdog and Manual Reset 6______________________________________________________________________________________________________Detailed DescriptionA microprocessor’s (µP) reset input starts or restarts the µP in a known state. The reset output of the MAX6316–MAX6322 µP supervisory circuits interfaces with the reset input of the µP, preventing code-execution errors during power-up, power-down, and brownout condi-tions (see the Typical Operating Circuit ). The MAX6316/MAX6317/MAX6318/MAX6320/MAX6321 are also capa-ble of asserting a reset should the µP become stuck in an infinite loop.Reset OutputThe MAX6316L/MAX6318LH/MAX6319LH feature an active-low reset output, while the MAX6317H/MAX6318_H/MAX6319_H/MAX6321HP/MAX6322HP feature an active-high reset output. RESET is guaran-teed to be a logic low and RESET is guaranteed to be a logic high for V CC down to 1V.The MAX6316–MAX6322 assert reset when V CC is below the reset threshold (V RST ), when MR is pulled low (MAX6316_/MAX6317H/MAX6319_H/MAX6320P/MAX6322HP only), or if the WDI pin is not serviced withinthe watchdog timeout period (t WD ). Reset remains assert-ed for the specified reset active timeout period (t RP ) after V CC rises above the reset threshold, after MR transitions low to high, or after the watchdog timer asserts the reset (MAX6316_/MAX6317H/MAX6318_H/MAX6320P/MAX6321HP). After the reset active timeout period (t RP )expires, the reset output deasserts, and the watchdog timer restarts from zero (Figure 2).Figure 1. Functional DiagramFigure 2. Reset Timing DiagramMAX6316–MAX63225-Pin µP Supervisory Circuits withWatchdog and Manual Reset_______________________________________________________________________________________7Bidirectional R E S E T OutputThe MAX6316M/MAX6318MH/MAX6319MH are designed to interface with µPs that have bidirectional reset pins,such as the Motorola 68HC11. Like an open-drain output,these devices allow the µP or other devices to pull the bidirectional reset (RESET ) low and assert a reset condi-tion. However, unlike a standard open-drain output, it includes the commonly specified 4.7k Ωpullup resistor with a P-channel active pullup in parallel.This configuration allows the MAX6316M/MAX6318MH/MAX6319MH to solve a problem associated with µPs that have bidirectional reset pins in systems where sev-eral devices connect to RESET (F igure 3). These µPs can often determine if a reset was asserted by an exter-nal device (i.e., the supervisor IC) or by the µP itself (due to a watchdog fault, clock error, or other source),and then jump to a vector appropriate for the source of the reset. However, if the µP does assert reset, it does not retain the information, but must determine the cause after the reset has occurred.The following procedure describes how this is done in the Motorola 68HC11. In all cases of reset, the µP pulls RESET low for about four external-clock cycles. It then releases RESET , waits for two external-clock cycles,then checks RESET ’s state. If RESET is still low, the µP concludes that the source of the reset was external and, when RESET eventually reaches the high state, it jumps to the normal reset vector. In this case, stored-state information is erased and processing begins fromscratch. If, on the other hand, RESET is high after a delay of two external-clock cycles, the processor knows that it caused the reset itself and can jump to a different vector and use stored-state information to determine what caused the reset.A problem occurs with faster µPs; two external-clock cycles are only 500ns at 4MHz. When there are several devices on the reset line, and only a passive pullup resis-tor is used, the input capacitance and stray capacitance can prevent RESET from reaching the logic high state (0.8✕V CC ) in the time allowed. If this happens, all resets will be interpreted as external. The µP output stage is guaran-teed to sink 1.6mA, so the rise time can not be reduced considerably by decreasing the 4.7k Ωinternal pullup resistance. See Bidirectional Pullup Characteristics in the Typical Operating Characteristics .The MAX6316M/MAX6318MH/MAX6319MH overcome this problem with an active pullup FET in parallel with the 4.7k Ωresistor (F igures 4 and 5). The pullup transistor holds RESET high until the µP reset I/O or the supervisory circuit itself forces the line low. Once RESET goes below V PTH , a comparator sets the transition edge flip-flop, indi-cating that the next transition for RESET will be low to high. When RESET is released, the 4.7k Ωresistor pulls RESET up toward V CC . Once RESET rises above V PTH but is below (0.85 x V CC ), the active P-channel pullup turns on. Once RESET rises above (0.85 x V CC ) or the 2µs one-shot times out, the active pullup turns off. The parallel combination of the 4.7k Ωpullup and theFigure 3. MAX6316M/MAX6318MH/MAX6319MH Supports Additional Devices on the Reset BusM A X 6316–M A X 63225-Pin µP Supervisory Circuits with Watchdog and Manual Reset 8_______________________________________________________________________________________Figure 4. MAX6316/MAX6318MH/MAX6319MH Bidirectional Reset Output Functional DiagramMAX6316–MAX63225-Pin µP Supervisory Circuits withWatchdog and Manual Reset_______________________________________________________________________________________9P-channel transistor on-resistance quickly charges stray capacitance on the reset line, allowing RESET to transition from low to high within the required two elec-tronic-clock cycles, even with several devices on the reset line. This process occurs regardless of whether the reset was caused by V CC dipping below the reset threshold, the watchdog timing out, MR being asserted,or the µP or other device asserting RESET . The parts do not require an external pullup. To minimize supply cur-rent consumption, the internal 4.7k Ωpullup resistor dis-connects from the supply whenever the MAX6316M/MAX6318MH/MAX6319MH assert reset.Open-Drain R E S E T OutputThe MAX6320P/MAX6321HP/MAX6322HP have an active-low, open-drain reset output. This output struc-ture will sink current when RESET is asserted. Connect a pullup resistor from RESET to any supply voltage up to 6V (Figure 6). Select a resistor value large enough toregister a logic low (see Electrical Characteristics ), and small enough to register a logic high while supplying all input current and leakage paths connected to the RESET line. A 10k Ωpullup is sufficient in most applications.Manual-Reset InputThe MAX6316_/MAX6317H/MAX6319_H/MAX6320P/MAX6322HP feature a manual reset input. A logic low on MR asserts a reset. After MR transitions low to high, reset remains asserted for the duration of the reset timeout peri-od (t RP ). The MR input is connected to V CC through an internal 52k Ωpullup resistor and therefore can be left unconnected when not in use. MR can be driven with TTL-logic levels in 5V systems, with CMOS-logic levels in 3V systems, or with open-drain or open-collector output devices. A normally-open momentary switch from MR to ground can also be used; it requires no external debouncing circuitry. MR is designed to reject fast, negative-going transients (typically 100ns pulses). A 0.1µF capacitor from MR to ground provides additional noise immunity.The MR input pin is equipped with internal ESD-protection circuitry that may become forward biased. Should MR be driven by voltages higher than V CC , excessive current would be drawn, which would damage the part. F or example, assume that MR is driven by a +5V supply other than V CC . If V CC drops lower than +4.7V, MR ’s absolute maximum rating is violated [-0.3V to (V CC + 0.3V)], and undesirable current flows through the ESD structure from MR to V CC . To avoid this, use the same supply for MR as the supply monitored by V CC . This guarantees that the voltage at MR will never exceed V CC .Watchdog InputThe MAX6316_/MAX6317H/MAX6318_H/MAX6320P/MAX6321HP feature a watchdog circuit that monitors the µP’s activity. If the µP does not toggle the watchdog input (WDI) within the watchdog timeout period (t WD ),reset asserts. The internal watchdog timer is cleared by reset or by a transition at WDI (which can detect pulses as short as 50ns). The watchdog timer remains cleared while reset is asserted. Once reset is released, the timer begins counting again (Figure 7).The WDI input is designed for a three-stated output device with a 10µA maximum leakage current and the capability of driving a maximum capacitive load of 200pF.The three-state device must be able to source and sink at least 200µA when active. Disable the watchdog function by leaving WDI unconnected or by three-stating the driver connected to WDI. When the watchdog timer is left open circuited, the timer is cleared internally at intervals equal to 7/8 of the watchdog period.Figure 6. MAX6320P/MAX6321HP/MAX6322HP Open-Drain RESET Output Allows Use with Multiple SuppliesFigure 5. Bidirectional RESET Timing DiagramM A X 6316–M A X 63225-Pin µP Supervisory Circuits with Watchdog and Manual Reset 10______________________________________________________________________________________Applications InformationWatchdog Input CurrentThe WDI input is internally driven through a buffer and series resistor from the watchdog counter. For minimum watchdog input current (minimum overall power con-sumption), leave WDI low for the majority of the watch-dog timeout period. When high, WDI can draw as much as 160µA. Pulsing WDI high at a low duty cycle will reduce the effect of the large input current. When WDI is left unconnected, the watchdog timer is serviced within the watchdog timeout period by a low-high-low pulse from the counter chain.Negative-Going V CC TransientsThese supervisors are immune to short-duration, nega-tive-going V CC transients (glitches), which usually do not require the entire system to shut down. Typically,200ns large-amplitude pulses (from ground to V CC ) on the supply will not cause a reset. Lower amplitude puls-es result in greater immunity. Typically, a V CC transient that goes 100mV under the reset threshold and lasts less than 4µs will not trigger a reset. An optional 0.1µF bypass capacitor mounted close to V CC provides addi-tional transient immunity.Ensuring Valid Reset OutputsDown to V CC = 0The MAX6316_/MAX6317H/MAX6318_H/MAX6319_H/MAX6321HP/MAX6322HP are guaranteed to operate properly down to V CC = 1V. In applications that require valid reset levels down to V CC = 0, a pulldown resistor to active-low outputs (push/pull and bidirectional only,F igure 8) and a pullup resistor to active-high outputs(push/pull only, Figure 9) will ensure that the reset line is valid while the reset output can no longer sink orsource current. This scheme does not work with the open-drain outputs of the MAX6320/MAX6321/MAX6322.The resistor value used is not critical, but it must be large enough not to load the reset output when V CC is above the reset threshold. F or most applications,100k Ωis adequate.Watchdog Software Considerations(MAX6316/MAX6317/MAX6318/MAX6320/MAX6321)One way to help the watchdog timer monitor software execution more closely is to set and reset the watchdog input at different points in the program, rather than pulsing the watchdog input high-low-high or low-high-low. This technique avoids a stuck loop, in which the watchdog timer would continue to be reset inside the loop, keeping the watchdog from timing out.Figure 7. Watchdog Timing RelationshipFigure 9. Ensuring RESET Valid to V CC = 0 on Active-High Push/Pull OutputsFigure 8. Ensuring RESET Valid to V CC = 0 on Active-Low Push/Pull and Bidirectional OutputsMAX6316–MAX6322Watchdog and Manual Reset______________________________________________________________________________________11F igure 10 shows an example of a flow diagram where the I/O driving the watchdog input is set high at the beginning of the program, set low at the end of every subroutine or loop, then set high again when the pro-gram returns to the beginning. If the program should hang in any subroutine, the problem would be quickly corrected, since the I/O is continually set low and the watchdog timer is allowed to time out, causing a reset or interrupt to be issued. As described in the Watchdog Input Current section, this scheme results in higher time average WDI current than does leaving WDI low for the majority of the timeout period and periodically pulsing it low-high-low.Figure 10. Watchdog Flow Diagram__________________Pin ConfigurationsTypical Operating CircuitTable 2. Standard VersionsTable 1. Factory-Trimmed Reset ThresholdsM A X 6316–M A X 6322Watchdog and Manual ResetTable 3. Reset/Watchdog Timeout PeriodsMAX6316–MAX6322Watchdog and Manual Reset______________________________________________________________________________________13__Ordering Information (continued)a watchdog feature (see Selector Guide) are factory-trimmed to one of four watchdog timeout periods. Insert the letter corre-sponding to the desired watchdog timeout period (W, X, Y, or Z from Table 3) into the blank following the reset timeout suffix.TRANSISTOR COUNT: 191SUBSTRATE IS INTERNALLY CONNECTED TO V+Chip Informationdard versions only. The required order increment for nonstandard versions is 10,000 pieces. Contact factory for availability.M A X 6316–M A X 6322Watchdog and Manual Reset 14______________________________________________________________________________________Package Information(The package drawing(s) in this data sheet may not reflect the most current specifications. For the latest package outline information,go to /packages .)M axim cannot assume responsibility for use of any circuitry other than circuitry entirely embodied in a M axim product. No circuit patent licenses are implied. Maxim reserves the right to change the circuitry and specifications without notice at any time.Maxim Integrated Products, 120 San Gabriel Drive, Sunnyvale, CA 94086 408-737-7600 ____________________15©2007 Maxim Integrated Productsis a registered trademark of Maxim Integrated Products, Inc.MAX6316–MAX6322 Watchdog and Manual ResetRevision History。
MAX830中文资料

STEP-DOWN CONVERTER
* CoilCraft DO3316-104
________________________________________________________________ Maxim Integrated Products
1
Call toll free 1-800-998-8800 for free samples or literature.
* THIS THERMAL RESISTANCE NUMBER IS WITH THE DEVICE WELL MOUNTED ON 1 oz. COPPER WITH THERMAL PASTE BETWEEN THE IC AND THE UNDERLYING GROUND PLANE. LOWER THERMAL RESISTANCE IS POSSIBLE (SEE APPLICATIONS SECTION).
NUAL KIT MA ATION U EET L H A S V A E T WS DA FOLLO
___________________________Features
o Input Range: Up to 30V o 1A On-Chip Power Switch o Adjustable Output (MAX830) Fixed Outputs: 5V (MAX831) 3.3V (MAX832) 3V (MAX833) o 100kHz Switching Frequency o Excellent Dynamic Characteristics o Few External Components o 8mA Quiescent Current o 16-Pin SO Package o Evaluation Kit Available
MAX6398中文资料

General DescriptionThe MAX6397/MAX6398 are small, high-voltage overvolt-age protection circuits. These devices disconnect the output load or limit the output voltage during an input overvoltage condition. These devices are ideal for appli-cations that must survive high-voltage transients such as those found in automotive and industrial applications.The MAX6397/MAX6398 monitor the input or output voltages and control an external n-channel MOSFET to isolate or limit the load from overvoltage transient energy.When the monitored input voltage is below the user-adjustable overvoltage threshold, the external n-channel MOSFET is turned on by the GATE output. In this mode,the internal charge pump fully enhances the n-channel MOSFET with a 10V gate-to-source voltage.When the input voltage exceeds the overvoltage thresh-old, the protection can disconnect the load from the input by quickly forcing the GATE output low. In some applications, disconnecting the output from the load is not desirable. In these cases, the protection circuit can be configured to act as a voltage limiter where the GATE output sawtooths to limit the voltage to the load.The MAX6397 also offers an always-on linear regulator that is capable of delivering up to 100mA of output current. This high-voltage linear regulator consumes only 37µA of quiescent current.The regulator is offered with output options of 5V, 3.3V,2.5V, or 1.8V. An open-drain, power-good output (POK)asserts when the regulator output falls below 92.5% or 87.5% of its nominal voltage.The MAX6397/MAX6398 include internal thermal-shut-down protection, disabling the external MOSF ET and linear regulator if the chip reaches overtemperature conditions. The devices operate over a wide 5.5V to 72V supply voltage range, are available in small TDFN packages, and are fully specified from -40°C to +125°C.ApplicationsAutomotive Industrial FireWire ®Notebook Computers Wall Cube Power DevicesFeatures♦5.5V to 72V Wide Supply Voltage Range♦Overvoltage Protection Controllers Allow User to Size External n-Channel MOSFETs ♦Internal Charge-Pump Circuit Ensures MOSFET Gate-to-Source Enhancement for Low R DS(ON)Performance ♦Disconnect or Limit Output from Input During Overvoltage Conditions ♦Adjustable Overvoltage Threshold ♦Thermal-Shutdown Protection♦Always-On, Low-Current (37µA) Linear Regulator Sources Up to 100mA (MAX6397)♦Fully Specified from -40°C to +125°C (T J )♦Small, Thermally Enhanced 3mm x 3mm TDFN PackageMAX6397/MAX6398Overvoltage Protection Switch/LimiterControllers Operate Up to 72V________________________________________________________________Maxim Integrated Products1Pin ConfigurationsOrdering Information19-3668; Rev 3; 1/07For pricing, delivery, and ordering information,please contact Maxim/Dallas Direct!at 1-888-629-4642, or visit Maxim’s website at .Selector Guide and Typical Operating Circuit appear at end of data sheet.FireWire is a registered trademark of Apple Computer, Inc.M A X 6397/M A X 6398Overvoltage Protection Switch/Limiter Controllers Operate Up to 72V 2_______________________________________________________________________________________ABSOLUTE MAXIMUM RATINGSELECTRICAL CHARACTERISTICS(V= 14V; C = 6000pF, C = 4.7µF, T = T = -40°C to +125°C, unless otherwise noted. Typical values are at T = T = +25°C.)(Note 1)Stresses beyond those listed under “Absolute Maximum Ratings” may cause permanent damage to the device. These are stress ratings only, and functional oper-ation of the device at these or any other conditions beyond those indicated in the operational sections of the specifications is not implied. Exposure to absolute maximum rating conditions for extended periods may affect device reliability.(All pins referenced to GND, unless otherwise noted.)IN, GATE, OUT............................................................-0.3V to +80V SHDN ..................................................................-0.3V to (IN + 0.3V)GATE to OUT.................................................................-0.3 to +20V SET, REG, POK...........................................................-0.3V to +12V Maximum Current:IN, REG...............................................................................350mA All Remaining Pins...................................................................50mAContinuous Power Dissipation (T A = +70°C)6-Pin TDFN (derate 18.2mW/°C above +70°C).............1455mW 8-Pin TDFN (derate 18.2mW/°C above +70°C).............1455mW Operating Temperature Range (T A )......................-40°C to +125°C Junction Temperature...........................................................+150°C Storage Temperature Range.................................-65°C to +150°C Lead Temperature................................................................+300°CMAX6397/MAX6398Overvoltage Protection Switch/LimiterControllers Operate Up to 72V_______________________________________________________________________________________3ELECTRICAL CHARACTERISTICS (continued)(V IN = 14V; C GATE = 6000pF, C REG = 4.7µF, T A = T J = -40°C to +125°C, unless otherwise noted. Typical values are at T A = T J = +25°C.)(Note 1)Note 1:Specifications to -40°C are guaranteed by design and not production tested.Note 2:The MAX6397/MAX6398 power up with the external FET in off mode (V GATE = GND). The external FET turns on t START after thedevice is powered up and all input conditions are valid.Note 3:For accurate overtemperature shutdown performance, place the device in close thermal contact with the external MOSFET.Note 4:Dropout voltage is defined as V IN - V REG when V REG is 2% below the value of V REG for V IN = V REG (nominal) + 2V.Note 5:Operations beyond the thermal dissipation limit may permanently damage the device.M A X 6397/M A X 6398Overvoltage Protection Switch/Limiter Controllers Operate Up to 72V 4_______________________________________________________________________________________Typical Operating Characteristics(V IN = 14V, C REG = 4.7µF, I REG = 0, unless otherwise noted.)40608010012014016002010304050607080SUPPLY CURRENT vs. INPUT VOLTAGEINPUT VOLTAGE (V)S U P P L Y C U R R E N T (µA )SUPPLY CURRENT vs. TEMPERATURETEMPERATURE (°C)S U P P L Y C U R R E N T (µA )1007525500-259010011012013014015016017018080-50125405060708090100110120020406080SUPPLY CURRENT vs. INPUT VOLTAGEINPUT VOLTAGE (V)S U P P L Y CU R R E N T (µA )8010090120110130140-502550-25075100125SUPPLY CURRENT vs. TEMPERATURETEMPERATURE (°C)S U P P L YC U R R E N T (µA )20302540354550040206080SHUTDOWN SUPPLY CURRENT vs. INPUT VOLTAGE (MAX6397)INPUT VOLTAGE (V)S U P P L YC U R R E N T (µA )103050700642810121416182020406080SHUTDOWN SUPPLY CURRENTvs. INPUT VOLTAGEINPUT VOLTAGE (V)S U P PL Y C U R R E N T (µA )0642810124121068141618202224GATE-DRIVE VOLTAGE vs. INPUT VOLTAGEINPUT VOLTAGE (V)V G A T E - V O U T (V )4.04.64.44.25.04.85.85.65.45.26.0-50-250255075100125UVLO THRESHOLD vs. TEMPERATUREM A X 6397-98 t o c 08TEMPERATURE (°C)V U V L O (V )SET THRESHOLD vs. TEMPERATUREM A X 6397-98 t o c 09TEMPERATURE (°C)S E T T H R E S H O L D (V )1007525500-251.2041.2081.2121.2161.2201.2241.2281.2321.2361.2401.200-50125MAX6397/MAX6398Overvoltage Protection Switch/LimiterControllers Operate Up to 72V_______________________________________________________________________________________516.016.316.216.116.516.416.916.816.716.617.0-50-25255075100125GATE-TO-OUT CLAMP VOLTAGEvs. TEMPERATUREM A X 6397-98 t o c 10TEMPERATURE (°C)G A T E -T O -O U T C L A M P V O L T A G E (V )00.40.20.80.61.21.01.41.81.62.0040608020100120140160180DROPOUT VOLTAGE vs. REG LOAD CURRENTREG LOAD CURRENT (mA)D R O P O U T V O L T A GE (V )4.905.004.955.105.055.155.20-40-10520-253550658095110125REG OUTPUT VOLTAGEvs. LOAD CURRENT AND TEMPERATURETEMPERATURE (°C)R E G O U T P U T V O L T A G E (V )4.04.64.44.24.85.05.21601204080200240280320360400MAXIMUM REG OUTPUT VOLTAGE vs. LOAD CURRENT AND TEMPERATURELOAD CURRENT (mA)R E G O U T P U T V O L T A G E (V )POWER-SUPPLY REJECTION RATIOvs. FREQUENCYFREQUENCY (Hz)P S R R (d B )1M 100k 10k 1k 100-60-50-40-30-20-100-701010M4ms/divSTARTUP WAVEFORM(R LOAD = 100Ω, C IN = 10µF, C OUT = 10µF)V IN 10V/divMAX6397-98 toc16V GATE 10V/div V OUT 10V/div I OUT200mA/div400µs/divSTARTUP WAVEFORM FROM SHUTDOWN(C IN = 10µF, C OUT = 10µF)V 2V/divV GATE 10V/divV OUT 10V/div I OUT200mA/divR LOAD = 100ΩTypical Operating Characteristics (continued)(V IN = 14V, C REG = 4.7µF, I REG = 0, unless otherwise noted.)GATE-DRIVE VOLTAGE vs. TEMPERATUREM A X 6397-98 t o c 14TEMPERATURE (°C)G A T E -D R I V E V O L T A G E (V )1007525500-2510.45510.46010.46510.47010.47510.48010.48510.49010.49510.50010.450-50125M A X 6397/M A X 6398Overvoltage Protection Switch/Limiter Controllers Operate Up to 72V 6_______________________________________________________________________________________Typical Operating Characteristics (continued)(V IN = 14V, C REG = 4.7µF, I REG = 0, unless otherwise noted.)200µs/divOVERVOLTAGE SWITCH FAULTV IN 20V/divV GATE 20V/div V OUT 20V/div V REG 5V/divV OV = 30V1ms/divVOLTAGE LIMIT FAULTV IN 20V/divV GATE 20V/divV OUT 20V/div V REG 5V/divV OV = 30V400µs/divTRANSIENT RESPONSEV IN 10V/divV REG100mV/divC REG = 10µF I REG = 10mA1ms/divREG LOAD-TRANSIENT RESPONSEV REGAC-COUPLED 500mV/divI REG100mA/divC REG = 10µF1ms/divREGULATOR STARTUP WAVEFORMV IN 10V/divV POK 2V/divV REG 2V/divI REG = 10mA100µs/divREGULATOR POK ASSERTIONV REG 2V/divI REG200mA/div V POK 2V/divI REG = 00V0V0ADetailed Description The MAX6397/MAX6398 are ultra-small, low-current, high-voltage protection circuits for automotive applica-tions that must survive load dump and high-voltage transient conditions. These devices monitor the input/ output voltages and control an external n-channel MOSF ET to isolate the load or to regulate the output voltage from overvoltage transient energy. The con-troller allows system designers to size the external MOSFET to their load current and board size.The MAX6397/MAX6398 drive the MOSF ET’s gate high when the monitored input voltage is below the adjustable overvoltage threshold. An internal charge-pump circuit provides a 5V to 10V gate-to-source drive (see the Typical Operating Characteristics) to ensure low input-to-load voltage drops in normal operating modes. When the input voltage rises above the user-adjusted overvoltage threshold, GATE pulls to OUT, turning off the MOSFET.The MAX6397/MAX6398 are configurable to operate as overvoltage protection switches or as closed-looped volt-age limiters. In overvoltage protection switch mode, theinput voltage is monitored. When an overvoltage condi-tion occurs at IN, GATE pulls low, disconnecting the loadfrom the power source, and then slowly enhances upon removal of the overvoltage condition. In overvoltagelimit mode, the output voltage is monitored and theMAX6397/MAX6398 regulate the source of the external MOSFET at the adjusted overvoltage threshold, allowing devices within the system to continue operating during an overvoltage condition.The MAX6397/MAX6398 undervoltage lockout (UVLO) function disables the devices as long as the input remains below the 5V (typ) UVLO turn-on threshold. TheMAX6397/MAX6398 have an active-low SHDN input toturn off the external MOSFET, disconnecting the load and reducing power consumption. After power is applied and SHDN is driven above its logic-high voltage, there is a100µs delay before GATE enhancement commences.MAX6397/MAX6398Overvoltage Protection Switch/LimiterControllers Operate Up to 72V _______________________________________________________________________________________7M A X 6397/M A X 6398The MAX6397 integrates a high-input-voltage, low-qui-escent-current linear regulator in addition to an over-voltage protector circuit. The linear regulator remains enabled at all times to power low-current “always-on”applications (independent of the state of the external MOSF ET). The regulator is offered with several stan-dard output voltage options (5V, 3.3V, 2.5V, or 1.8V).An open-drain power-good output notifies the system if the regulator output falls to 92.5% or 87.5% of its nomi-nal voltage. The MAX6397’s REG output operates inde-pendently of the SHDN logic input.The MAX6397/MAX6398 include internal thermal-shut-down protection, disabling the external MOSF ET and linear regulator if the chip reaches overtemperature conditions.Linear Regulator (MAX6397 Only)The MAX6397 is available with 5.0V, 3.3V, 2.5V, and 1.8V factory-set output voltages. Each regulator sources up to 100mA and includes a current limit of 230mA. The linear regulator operates in an always-on condition regardless of the SHDN logic. For fully specified operation, V IN must be greater than 6.5V for the MAX6397L/M (5V regulator output). The actual output current may be limited by the operating condition and package power dissipation.Power-OK OutputPOK is an open-drain output that goes low when REG falls to 92.5% or 87.5% (see the Selector Guide ) of its nominal output voltage. To obtain a logic-level output,connect a pullup resistor from POK to REG or another system voltage. Use a resistor in the 100k Ωrange to minimize current consumption. POK provides a valid logic-output level down to V IN = 1.5V.GATE VoltageThe MAX6397/MAX6398 use a high-efficiency charge pump to generate the GATE voltage. Upon V IN exceed-ing the 5V (typ) UVLO threshold, GATE enhances 10V above IN (for V IN ≥14V) with a 75µA pullup current. An overvoltage condition occurs when the voltage at SET pulls above its 1.215V threshold. When the threshold is crossed, GATE falls to OUT within 100ns with a 100mA (typ) pulldown current. The MAX6397/MAX6398 include an internal clamp to OUT that ensures GATE is limited to 18V (max) above OUT to prevent gate-to-source damage to the external FET.The GATE cycle during overvoltage limit and overvolt-age switch modes are quite similar but have distinct characteristics. In overvoltage switch mode (Figure 2a),GATE is enhanced to V IN + 10V while the monitored IN voltage remains below the overvoltage fault threshold (SET < 1.215V). When an overvoltage fault occurs (SET ≥1.215V), GATE is pulled one diode below OUT, turn-ing off the external F ET and disconnecting the load from the input. GATE remains low (FET off) as long as V IN is above the overvoltage fault threshold. As V IN falls back below the overvoltage fault threshold (-5% hys-teresis) GATE is again enhanced to V IN + 10V.In overvoltage limit mode (Figure 2b), GATE is enhanced to V IN + 10V. While the monitored OUT voltage remains below the overvoltage fault threshold (SET < 1.215V).When an overvoltage fault occurs (SET ≥1.215V),GATE is pulled low one diode drop below OUT until OUT drops 5% below the overvoltage fault threshold.GATE is then turned back on until OUT again reaches the overvoltage fault threshold and GATE is again turned off.Overvoltage Protection Switch/Limiter Controllers Operate Up to 72V 8_______________________________________________________________________________________GATE cycles on-off-on-off-on in a sawtooth waveform until OUT remains below the overvoltage fault threshold and GATE remains constantly on (V IN + 10V). The over-voltage limiter’s sawtooth GATE output operates the MOSFET in a switched-linear mode while the input volt-age remains above the overvoltage fault threshold. The sawtooth frequency depends on the load capacitance,load current, and MOSFET turn-on time (GATE charge current and GATE capacitance).GATE goes high when the following startup conditions are met: V IN is above the UVLO threshold, SHDN is high, an overvoltage fault is not present and the device is not in thermal shutdown.Overvoltage MonitoringWhen operating in overvoltage mode, the MAX6397/MAX6398 feedback path (F igure 3) consists of IN,SET’s internal comparator, the internal gate charge pump, and the external n-channel MOSFET resulting in a switch-on/off function. When the programmed over-voltage threshold is tripped, the internal fast compara-tor turns off the external MOSFET, pulling GATE to OUT within t OV and disconnecting the power source from the load. When IN decreases below the adjusted over-voltage threshold, the MAX6397/MAX6398 slowly enhance GATE above OUT, reconnecting the load to the power source.Overvoltage LimiterWhen operating in overvoltage limiter mode, the MAX6397/MAX6398 feedback path (F igure 4) consists of OUT, SET’s internal comparator, the internal gate charge pump and the external n-channel MOSF ET,which results in the external MOSF ET operating as a voltage regulator.During normal operation, GATE is enhanced 10V above OUT. The external MOSFET source voltage is monitored through a resistor-divider between OUT and SET. When OUT rises above the adjusted overvoltage threshold, an internal comparator sinks the charge-pump current, dis-charging the external GATE, regulating OUT at the set overvoltage threshold. OUT remains active during the overvoltage transients and the MOSFET continues to con-duct during the overvoltage event, operating in switched-linear mode.MAX6397/MAX6398Overvoltage Protection Switch/LimiterControllers Operate Up to 72V_______________________________________________________________________________________9V GATE 10V/divV OUT 10V/divV IN 10V/div10ms/divV GATE 10V/divV OUT 10V/divV IN 10V/div4ms/divM A X 6397/M A X 6398As the transient begins decreasing, OUT fall time will depend on the MOSF ET’s GATE charge, the internal charge-pump current, the output load, and the tank capacitor at OUT.For fast-rising transients and very large-sized MOSFETs,add an additional external bypass capacitor from GATE to GND to reduce the effect of the fast-rising voltages at IN. The external capacitor acts as a voltage-divider working against the MOSF ETs’ drain-to-gate capaci-tance. For a 6000pF C gd , a 0.1µF capacitor at GATE will reduce the impact of the fast-rising V IN input.Caution must be exercised when operating the MAX6397/MAX6398 in voltage-limiting mode for long durations. If the V IN is a DC voltage greater than the MOSFET’s maximum gate voltage, the FET will dissipate power continuously. To prevent damage to the external MOSFET, proper heatsinking should be implemented.Applications InformationLoad DumpMost automotive applications run off a multicell, 12V lead-acid battery with a nominal voltage that swings between 9V and 16V (depending on load current,charging status, temperature, battery age, etc.). The battery voltage is distributed throughout the automobile and is locally regulated down to voltages required by the different system modules. Load dump occurs when the alternator is charging the battery and the battery becomes disconnected. Power in the alternator (essen-tially an inductor) flows into the distributed power sys-tem and elevates the voltage seen at each module. The voltage spikes have rise times typically greater than 5ms and decays within several hundred milliseconds but can extend out to 1s or more depending on thecharacteristics of the charging system (F igure 5).These transients are capable of destroying semicon-ductors on the first ‘fault event.’Setting Overvoltage ThresholdsSET provides an accurate means to set the overvoltage level for the MAX6397/MAX6398. Use a resistor-divider to set the desired overvoltage condition (Figure 6). SET has a rising 1.215V threshold with a 5% falling hysteresis.Begin by selecting the total end-to-end resistance,R TOTAL = R1 + R2. Choose R TOTAL to yield a total cur-rent equivalent to a minimum 100 x I SET (SET’s input bias current) at the desired overvoltage threshold.For example:With an overvoltage threshold set to 20V:R TOTAL < 20V/(100 x I SET )where I SET is SET’s 50nA input bias current.R TOTAL < 4M ΩUse the following formula to calculate R2:where V TH is the 1.215V SET rising threshold and V OV is the overvoltage threshold.R2 = 243k Ω, use a 240k Ωstandard resistor.R TOTAL = R2 + R1, where R1 = 3.76M Ω.Use a 3.79M Ωstandard resistor.A lower value for total resistance dissipates morepower but provides slightly better accuracy.Overvoltage Protection Switch/Limiter Controllers Operate Up to 72V 10______________________________________________________________________________________Reverse-Battery ProtectionUse a diode or p-channel MOSF ET to protect the MAX6397/MAX6398 during a reverse-battery insertion (Figures 7a, 7b). Low p-channel MOSFET on-resistance of 30m Ωor less yields a forward-voltage drop of only a few millivolts (versus hundreds of millivolts for a diode,Figure 7a) thus improving efficiency.Connecting a positive battery voltage to the drain of Q1(F igure 7b) produces forward bias in its body diode,which clamps the source voltage one diode drop below the drain voltage. When the source voltage exceeds Q1’s threshold voltage, Q1 turns on. Once the F ET is on, the battery is fully connected to the system and can deliver power to the device and the load.An incorrectly inserted battery reverse-biases the F ET’s body diode. The gate remains at the ground potential.The FET remains off and disconnects the reversed bat-tery from the system. The zener diode and resistor com-bination prevent damage to the p-channel MOSF ET during an overvoltage condition.MAX6397/MAX6398Overvoltage Protection Switch/LimiterControllers Operate Up to 72V______________________________________________________________________________________11M A X 6397/M A X 6398REG Capacitor Selection for StabilityFor stable operation over the full temperature range and with load currents up to 100mA, use ceramic capacitor values greater than 4.7µF. Large output capacitors help reduce noise, improve load-transient response, and power-supply rejection at REG. Note that some ceramic dielectrics exhibit large capacitance and ESR variation with temperature. At lower temperatures, it may be nec-essary to increase capacitance.Under normal conditions, use a 10µF capacitor at rger input capacitor values and lower ESR provide bet-ter supply-noise rejection and line-transient response.Inrush/Slew-Rate ControlInrush current control can be implemented by placing a capacitor at GATE (F igure 8) to slowly ramp up the GATE, thus limiting the inrush current and controlling GATE’s slew rate during initial turn-on. The inrush cur-rent can be approximated using the following formula:where I GATE is GATE’s 75µA sourcing current, I LOAD is the load current at startup, and C OUT is the output capacitor.Input Transients ClampingWhen the external MOSFET is turned off during an over-voltage occurrence, stray inductance in the power path may cause voltage ringing exceeding the MAX6397/MAX6398 absolute maximum input (IN) supply rating.The following techniques are recommended to reduce the effect of transients:•Minimize stray inductance in the power path usingwide traces, and minimize loop area including the power traces and the return ground path.•Add a zener diode or transient voltage suppressor(TVS) rated below the IN absolute maximum rating (Figure 9).Add a resistor in series with IN to limit transient currentgoing into the input for the MAX6398 only.Overvoltage Protection Switch/Limiter Controllers Operate Up to 72V 12______________________________________________________________________________________Figure 8. MAX6397/MAX6398 Controlling GATE Inrush CurrentFigure 9. Protecting the MAX6397/MAX6398 Input from High-Voltage TransientsMOSFET SelectionSelect external MOSF ETs according to the application current level. The MOSF ET’s on-resistance (R DS(ON))should be chosen low enough to have minimum voltage drop at full load to limit the MOSFET power dissipation.Determine the device power rating to accommodate an overvoltage fault when operating the MAX6397/MAX6398 in overvoltage limit mode.During normal operation, the external MOSFETs dissipate little power. The power dissipated in normal operation is:P Q1 = I LOAD 2x R DS(ON).The most power dissipation will occur during a pro-longed overvoltage event when operating the MAX6397/MAX6398 in voltage limiter mode, resulting in high power dissipated in Q1 (F igure 10) where the power dissipated across Q1 is:P Q1= V Q1x I LOADwhere V Q1is the voltage across the MOSF ET’s drain and source.Thermal ShutdownThe MAX6397/MAX6398 thermal-shutdown feature shuts off the linear regulator output, REG, and GATE if it exceeds the maximum allowable thermal dissipation.Thermal shutdown also monitors the PC board tempera-ture of the external nF ET when the devices sit on thesame thermal island. Good thermal contact between the MAX6397/MAX6398 and the external nF ET is essential for the thermal-shutdown feature to operate effectively.Place the nFET as close as possible to OUT.When the junction temperature exceeds T J = +150°C,the thermal sensor signals the shutdown logic, turning off REG’s internal pass transistor and the GATE output,allowing the device to cool. The thermal sensor turns the pass transistor and GATE on again after the IC’s junction temperature cools by 20°C. Thermal-overload protection is designed to protect the MAX6397/MAX6398 and the external MOSFET in the event of cur-rent-limit fault conditions. For continuous operation, do not exceed the absolute maximum junction-tempera-ture rating of T J = +150°C.Thermal ShutdownOvervoltage Limiter ModeWhen operating the MAX6397/MAX6398 in overvoltage limit mode for a prolonged period of time, a thermal shutdown is possible due to device self-heating. The thermal shutdown is dependent on a number of differ-ent factors:•The device’s ambient temperature (T A )•The output capacitor (C OUT )•The output load current (I OUT )•The overvoltage threshold limit (V OV )•The overvoltage waveform period (t OVP )•The power dissipated across the package (P DISS )MAX6397/MAX6398Overvoltage Protection Switch/LimiterControllers Operate Up to 72V______________________________________________________________________________________13M A X 6397/M A X 6398When OUT exceeds the adjusted overvoltage threshold,an internal GATE pulldown current is enabled until OUT drops by 5%. The capacitance at OUT is discharged by the internal current sink and the external OUT load cur-rent. The discharge time (∆t1) is approximately:where V OV is the adjusted overvoltage threshold, I OUT is the external load current and I GATEPD is the GATE’s internal 100mA (typ) pulldown current.When OUT falls 5% below the overvoltage threshold point, the internal current sink is disabled and the MAX6397/MAX6398’s internal charge pump begins recharging the external GATE voltage. The OUT volt-age continues to drop due to the external OUT load current until the MOSF ET gate is recharged. The time needed to recharge GATE and re-enhance the external nFET is approximately:where C ISS is the MOSFET’s input capacitance, V GS(TH)is the MOSFET’s gate-to-source threshold voltage, V F is the internal clamp diode forward voltage (V F = 1.5V typ),and I GATE is the MAX6397/MAX6398 charge-pump cur-rent (75µA typ).During ∆t2, C OUT loses charge through the output load.The voltage across C OUT (∆V2) decreases until the MOSF ET reaches its V GS(TH) threshold and can be approximated using the following formula:Once the MOSFET V GS (TH ) is obtained, the slope of the output voltage rise is determined by the MOSF ET Q G charge through the internal charge pump with respect to the drain potential. The time for the OUT voltage to rise again to the overvoltage threshold can be approxi-mated using the following formula:where ∆V OUT = ( V OV x 0.05) + ∆V2.The total period of the overvoltage waveform can be summed up as follows:t OVP = ∆t1 + ∆t2 + ∆t3The MAX6397/MAX6398 dissipate the most power dur-ing an overvoltage event when I OUT = 0 (C OUT is dis-charged only by the internal current sink). The maximum power dissipation can be approximated using the follow-ing equation:The die temperature (T J ) increase is related to θJC (8.3°C/W and 8.5°C/W for the MAX6397 and MAX6398,respectively) of the package when mounted correctly with a strong thermal contact to the circuit board. The MAX6397/MAX6398 thermal shutdown is governed by the equation:T J = T A + P DISS x (θJC + θCA) < 170°C (typical thermal-shutdown temperature)For the MAX6397, the power dissipation of the internal linear regulator must be added to the overvoltage pro-tection circuit power dissipation to calculate the die temperature. The linear regulator power dissipation is calculated using the following equation:P REG = (V IN – V REG ) (I REG )F or example, using an IRF R3410 100V n-channel MOSF ET, F igure 12 illustrates the junction temperature vs. output capacitor with I OUT = 0, T A = +125°C, V OV < 16V,V F = 1.5V, I GATE = 75mA, and I GATEPD =100mA. Figure 12 shows the relationship between output capacitance versus die temperature for the conditionslisted above.Overvoltage Protection Switch/Limiter Controllers Operate Up to 72V 14______________________________________________________________________________________。
科尔摩根AKM 同步伺服电机 选型指南说明书

K O L L M O R G E N | A K o l l m o r g e n C O M PA N Y欢迎来到科尔摩根官方微信科尔摩根3目录u AKM ™ 同步伺服电机4u AKD ™ 伺服驱动器8u AKM ™ 各种选件12u AKM ™ 防水型和食品级防水型电机13u AKM ™ 系统综述14u AKM ™ 图纸和性能数据AKM1x 16AKM2x 20AKM3x24AKM4x 28AKM5x 34AKM6x 40AKM7x 44AKM8x48u L 10 轴承疲劳寿命和轴负载53u 反馈选件56u 抱闸选件60u 伺服电机连接器选件61u 型号命名67u MOTIONEERING ® Online71科尔摩根A K M 同步伺服电机选型指南克服设计、采购和时间障碍科尔摩根明白:帮助原始设备制造商的工程师克服障碍,可以显著提高其工作成效。
因而,我们主要通过如下三种方式来提供帮助:集成标准和定制产品在很多情况下,理想方案都不是一成不变的。
我们拥有专业应用知识,可以根据全面的产品组合来修改标准产品或开发全定制解决方案,从而为设计奠定良好的基础。
提供运动控制解决方案而不仅仅是部件在各公司减少供应商数量和工程人力的过程中,他们需要一家能够提供多种集成解决方案的全系统供应商。
科尔摩根就采用了全面响应模式,为客户提供全套解决方案,这些方案将编程软件、工程服务以及同类优秀的运动控制部件结合起来。
覆盖全球我们在美洲、欧洲、中东和亚洲拥有众多直销、工程支持单位、生产工厂以及分销商,临近全球各地的原始设备制造商。
这种便利优势可以加速我们的供货过程,根据客户需要随时随地供货。
财务和运营稳定性科尔摩根隶属于Fortive 公司。
Fortive 业务系统是推动Fortive 各部门发展的一个关键力量。
该系统采用“不断改善”(Kaizen )原理。
由高素质人才构成的多学科团队使用世界级的工具对过程进行评估,并制定相关计划以达到卓越的性能。
日立水冷螺杆机资料

运行画面,按下“机组启动”按钮,启动主机。
——如出现紧急情况,可按下机组面板上的紧急按
钮停止机组。
指示灯: 1. 红灯指示正常运转状态。 2. 当红灯闪烁或橙灯亮时,表示有保护装置可能动
作。如发觉此情况,请联络您的维修人员。 ☆当液晶显示屏上出现红色报警闪烁信号时,表示 有保护装置可能动作,请根据液晶显示屏提示的排除 方法检查机组故障位置,排除报警。
日立牌水冷式冷水机组
—螺杆式—
注 意:
在使用此冷水机组之前, 请仔细阅读该手册,并请 保存完好,供以后参考。
重要通知
日立对产品的设计和性能将不断进行改良,规格如有更改,恕不另行通知。
日立对每一个可能的情况可引致有潜在的危险不作预测。
没有书面允许,此说明书不得翻印。
信号字句(危险、警告和小心)用于鉴定危险性的级别,有关各信号字句所提示的
主机运行参数设定正确后,按主板上电按钮,进入机组 ——机组运行画面中的“停止”灯闪烁
运行画面,按下“机组启动”按钮,启动主机。
——如出现紧急情况,可按下机组面板上的紧急按
钮停止机组。
指示灯: 1.红灯指示正常运转状态。 2.当红灯闪烁或橙灯亮时,表示有保护装置可能动作。 如发觉此情况,请联络您的维修人员。
初步检查 …………………………………………………………………………………1 机组安装…………………………………………………………………………………… 1
2.安装工作………………………………… …………………………………………… 6
电线连接…………………………………………………………………………………… 7 工作范围…………………………………………………………………………………… 9 水管接驳…………………………………………………………………………………… 10 水质控制…………………………………………………………………………………… 11 标准管路和接线…………………………………………………………………………… 12
日本光电MEK-6318K操作注意事项和故障排除

日本光电MEK-6318K操作注意事项和故障排除MEK-6318K操作注意事项和故障排除日本光电MEK-6318是精密检测仪器,为更好地使用和维护仪器提高其检测结果的准确度,使结果对临床诊断疾病更有价值。
为此要注意按正规操作使用此仪器,下面提出操作中要注意的故障的排除方法:一、操作注意事项:1. 仪器中的各种参数和设置请不要随意去更改,否则,不但可能得不到正确的结果,反得到相反的结果。
2. 请各位操作人员要特别注意,在仪器进行运行测试(屏幕显示COUNTING)或仪器进行清洗和冲洗(屏幕显示CIEANING或PRIMING)或屏幕显示Please wait、一直到吸样针头完全伸出和测试结果在屏幕上显示并打印出来这段时间内,请千万不要再按任何按键,否则,会产生死机不再执行测试无法发报告。
3. 要求在“READY”或“显示上一次测试结果”两种状态下,才能进行样本测试。
若在其它显示状态下,请连续按“OK”键返回到这两个状态下,再进行下一次测试。
不然就直接进行样本测试属不正规操作,仪器极易出现故障。
4. 测试一定要注意,样本是未梢血时,一定要按“”键使指示灯亮的状态下,才能测试样本,而抗凝静脉血时,“”键指示灯不亮就直接测样本。
如果偶然不注意把抗凝静脉血当作未梢血测试,这会造成仪器严重的堵塞,处理方法是按清洗键“”进行清洗仪器,直至做空白测试符合要为止。
5. 未经厂商或主管人员同意,请最好不要私自打开仪器外壳,调整仪器内部部件,以免人为造成不属保修范围内的损坏,厂家不包修理。
二、常见故障及排除方法:1. 当屏幕显示“CLOE或LEVEL3”时,表示堵孔,请按清洗键()进行洗(约3—5分钟),若依然有警报提示,得清洗管道和换泵。
2. 在RBC、WBC的结果中显示BUBBE1、BUBBE2、BUBBE3、BUBBE4(缩写为BBL1 、BBL2、BBL3、BBL4)表示有气泡存在或缺试剂,请按清洗键清洗仪器或换试剂。
SANYO电器制造有限公司 AHX0952型号空调商品说明书

FILE NO. PAC-0479N O T I C EPLEASE ADD THIS NOTICE TO THE MANUALS LISTED BELOW. CATEGORY : Air Conditioner DATE : November.2006 MODEL: AHX0952REF.No. : PL 833828 DESTINATION : USA ISSUE No.: 1THE REASON OF CHANGE.. A : MisprintB : Quality ReliabilityC : StandardizationD : Design ChangeE : Addition of Missing PartsF : Parts CompatibilityParts ListAir Conditioner INDOOR UNITA HX0952Made in JapanR EFERENCE No.PL 833828-01KeyNo.Part No.Description Q'ty Reference No.* 1 623 189 4968 Heat Exch Ass'y 1 854-0-4124-559002 623 175 2213 Strainer Ass'y 1 854-0-4522-29100 * 3 623 175 2251 Solenoid Control Valve UKV-18D31 1 854-2-4548-202004 623 178 3767 Strainer Ass'y 1 854-0-4522-302005 623 189 4951 Capillary Tube 1 854-2-4237-485006 623 189 4944 Capillary Tube 1 854-2-4237-486007 623 189 4937 Capillary Tube 1 854-2-4237-487008 623 189 4920 Capillary Tube 1 854-2-4237-488009 623 201 6352 Cabinet Plate 1 854-2-1105-431H210 623 189 5026 Cabinet Plate 1 854-2-1105-4310111 623 201 6345 Insulation 1 854-2-1413-406H212 623 189 5002 Plate Partition Blower 1 854-2-2505-2690113 623 189 4999 Side Cover Ass'y, Left 1 854-2-1107-761H114 623 189 4982 Side Cover Ass'y, Right 1 854-2-1108-479H115 623 178 3958 Support Fan Motor 2 854-2-2516-3840116 623 189 4975 Support Fan Motor 1 854-2-2516-4060117 623 201 1791 Joint Drain 1 854-2-2334-2021018 623 189 5040 Mounting Plate 2 854-2-1136-2300119 623 000 0735 Eyelet 1 3-9041-0150020 623 171 4891 Hook Plate 4 854-2-1130-2610121 623 201 6369 Packing 4 854-2-1362-32110 * 22 623 175 2206 Magnetic Coil(PMV) UKV-U030E 1 1FA-4-L8A0-30500 * 23 623 171 4877 Thermistor Ass'y(E1) PBC-41E-AS4 1 854-0-5259-64600 * 24 623 176 0157 Thermistor Ass'y(E3) PBC-41E-AS12-1 1 854-0-5259-74100 * 25 623 178 5624 Thermistor(BL) KTEC-35-S103-2 1 1FA-4-V2E0-2700026 623 054 6073 Insulation Tube 1 852-2-4514-2860027 623 081 5254 Insulation, Thermostat 1 854-2-4312-1200028 623 160 8206 Insulation Special 1 854-2-2411-2411029 623 201 6376 Insulation Special 1 854-2-2411-5681030 623 090 0172 Mounting Rubber, Tube 1 854-2-4315-1610031 623 192 9929 Spacer SPRF-10 2 854-2-2349-2170032 623 132 0078 Mounting Thermostat 1 852-2-5303-1920133 623 201 1777 Elec. Wiring Diagram 1 8FA-2-5250-0560034 638 020 7220 Vibration Insulation 1 854-2-2475-1720035 623 189 5095 Mounting Plate,Evaporator 1 854-2-2303-39101 * 36 623 189 5088 Switch Ass'y FS-0218-103 1 8FA-0-5152-02000 * 37 623 201 6390 Motor Pump Ass'y 1 8FA-0-5264-0420038 638 004 9523 Cushion Rubber 3 854-2-2318-1380039 623 171 4778 Clip 1 854-2-2315-1070040 623 201 6383 Cover Plate 1 854-2-2342-857H2 NOTE:Metal and plastic parts will be supplied basicallywith necessary heat insulation pads or packing.Each key number with an asterisk (*) means therecommended service parts.KeyNo.Part No.Description Q'ty Reference No.41 623 189 5118 Elec Component Box Ass'y 1 854-0-5311-04401* 42 623 311 6990 Controller Ass'y CR-UMHX0762 1 854-9-9536-05711 * 43 623 179 0444 Fuse BET5A 1 1FJ-4-S3A0-00500 * 44 623 171 4884 Thermistor Ass'y(TA) KTEC-35-S98 1 854-0-5259-64500 * 45 623 177 7124 Terminal Base HP-T3041-C3E4-S 1 1FA-4-J3A0-2390046 623 192 9912 Spacer SPRH-10 4 854-2-2349-2160047 623 027 4990 Bushing 1 800-2-5337-1790048 623 160 1450 Blower Casing 1 854-2-2506-19210* 49 623 201 6413 Fan Motor DK8-63E280HB 1 1FA-4-M4A0-13400 * 50 623 160 1351 Fan Ass'y 1 854-0-2501-2273051 623 160 1474 Blower Casing 1 854-2-2506-1931052 623 189 5149 Cover Plate 1 854-2-2342-8560153 623 178 3880 Cover,ponent Box 1 854-0-5304-58401* 54 623 201 6406 Drain Pan Ass'y 1 854-0-2301-647H155 623 189 5125 Drain Hose 1 854-2-4297-2090056 623 171 4839 Clip 1 854-2-2315-1080157 623 171 4907 Packing 1 854-2-1362-19500* 58 623 179 1502 P.C.B. Ass'y FIL-XDR94GXH56 1 8FA-0-5178-1940059 623 097 1677 Spacer SPLSN-6 4 851-2-5366-0380060 623 201 6444 Mounting Plate 1 854-2-2362-1680161 623 201 6437 Packing 1 854-2-2370-0110062 623 201 6420 Cover Terminal 1 854-2-5305-21801* 63 638 010 7827 Fuse BET6.3A 1 1FJ-4-S3A0-00600 623 201 1050 Operation Manual 1 854-6-4189-83700 NOTE:Metal and plastic parts will be supplied basicallywith necessary heat insulation pads or packing.Each key number with an asterisk (*) means therecommended service parts.For Parts or Service Assistance please contact your local Sanyo HVAC Contractor or DistributorUnited States: SCS, HVAC Solutions Canada: Sanyo Canada Inc.Web: Web: Parts:********************.comParts/Service:**************.comService:**********************.comJan / '10 Printed in Japan。
MAX3183EEUK-T中文资料

For free samples & the latest literature: , or phone 1-800-998-8800.For small orders, phone 1-800-835-8769.General DescriptionThe MAX3180E–MAX3183E single RS -232 receivers in a SOT23-5 package are designed for space- and cost-constrained applications requiring minimal RS -232communications. The receiver inputs are protected to ±15kV using IEC 1000-4-2 Air-Gap Discharge, to ±8kV using IEC 1000-4-2 Contact Discharge, and to ±15kV per the Human Body Model, ensuring compliance with international standards.The devices minimize power and heat dissipation by consuming only 0.5µA supply current from a +3.0V to +5.5V supply, and they guarantee true RS -232 perfor-mance up to a 1.5Mbps data rate. The MAX3180E/MAX3182E feature a three-state TTL/CMOS receiver output that is controlled by an EN logic input. The MAX3181E/MAX3183E feature an INVALID output that indicates valid RS-232 signals at the receiver input for applications requiring automatic system wake-up. The MAX3182E/MAX3183E have a noninverting output,while the MAX3180E/MAX3181E have a standard inverting output.ApplicationsFeatureso Tiny SOT23-5 Packageo ESD-Protected RS-232 Input±15kV—Human Body Model±8kV—IEC 1000-4-2, Contact Discharge ±15kV—IEC 1000-4-2, Air-Gap Discharge o 0.5µA Supply Currento 1.5Mbps Guaranteed Data Rateo Meets EIA/TIA-232 and V.28/V.24 Specifications Down to V CC = +3.0V o INVALID Output Indicates Valid RS-232 Signal at Receiver Input (MAX3181E/MAX3183E)o Three-State TTL/CMOS Receiver Output (MAX3180E/MAX3182E)o Noninverting RS-232 Output (MAX3182E/MAX3183E)MAX3180E–MAX3183E±15kV ESD-Protected, 0.5µA, +3V to +5.5V ,1.5Mbps RS-232 Receivers in SOT23-5________________________________________________________________Maxim Integrated Products 119-1479; Rev 1; 7/99Ordering InformationM A X 3180E –M A X 3183E±15kV ESD-Protected, 0.5µA, +3V to +5.5V ,1.5Mbps RS-232 Receivers in SOT23-52_______________________________________________________________________________________ABSOLUTE MAXIMUM RATINGSELECTRICAL CHARACTERISTICS(V CC = +3.0V to +5.5V, T A = T MIN to T MAX , unless otherwise noted. Typical values are at V CC = +5.0V, T A = +25°C.) (Note 1)Stresses beyond those listed under “Absolute Maximum Ratings” may cause permanent damage to the device. These are stress ratings only, and functional operation of the device at these or any other conditions beyond those indicated in the operational sections of the specifications is not implied. Exposure to absolute maximum rating conditions for extended periods may affect device reliability.V CC to GND..............................................................-0.3V to +6V RIN to GND..........................................................................±25V EN , ROUT, INVALID to GND......................-0.3V to (V CC + 0.3V)Continuous Power Dissipation (T A = +70°C)SOT23-5 (derate 7.1mW/°C above +70°C)...................571mWOperating Temperature Range ...........................-40°C to +85°C Storage Temperature Range.............................-65°C to +150°C Lead Temperature (soldering, 10sec).............................+300°CMAX3180E–MAX3183E±15kV ESD-Protected, 0.5µA, +3V to +5.5V ,1.5Mbps RS-232 Receivers in SOT23-5_______________________________________________________________________________________3ELECTRICAL CHARACTERISTICS (continued)(V CC = +3.0V to +5.5V, T A = T MIN to T MAX , unless otherwise noted. Typical values are at V CC = +5.0V, T A = +25°C.) (Note 1)Typical Operating Characteristics(V CC = +5V, T A = +25°C, unless otherwise noted.)00.20.10.40.30.60.50.700.51.0 1.5SUPPLY CURRENT vs. DATA RATEDATA RATE (Mbps)S U P P L Y C U R R E N T (m A )2302702502903303103503.0 3.5 5.04.54.0 5.5RIN TO INVALID HIGH vs. SUPPLY VOLTAGEM A X 3180E -02V CC (V)t I N V H (n s )Note 1:Specifications are 100% tested at T A = +25°C. Limits over temperature are guaranteed by design.Detailed DescriptionThe MAX3180E–MAX3183E are EIA/TIA-232 and V.28/V.24communications receivers that convert RS -232signals to CMOS logic levels. They operate on a +3V to +5.5V supply, have 1.5Mbps data rate capability, and feature enhanced electrostatic discharge (ESD) protec-tion (see ESD Protection ). All of these devices achieve a typical supply current of 0.5µA. The MAX3180E/MAX3182E have a receiver enable control (EN ). The MAX3181E/MAX3183E contain a signal invalid output (INVALID ). The MAX3180E/MAX3181E invert the ROUT signal relative to RIN (standard RS -232). The MAX3182E/MAX3183E outputs are not inverted. The devices come in tiny SOT23-5 packages.M A X 3180E –M A X 3183E±15kV ESD-Protected, 0.5µA, +3V to +5.5V ,1.5Mbps RS-232 Receivers in SOT23-54_______________________________________________________________________________________25353045405550603.03.54.04.55.05.5RIN TO INVALID LOW vs. V CCM A X 3180E -03V CC (V)t I N V L (µs )Typical Operating Characteristics (continued)(V CC = +5V, T A = +25°C, unless otherwise noted.)5V010V 0-10V RINROUTENABLE5V 0500ns/divMAX3180EENABLE ASSERTION TO ROUT RESPONSEV CC = 5.0V R L = 50k ΩC L = 100pFReceiver Output EnablePin DescriptionFUNCTIONOutput of the Valid Input Detector Inverting Receiver Output Figure 1. Receiver Propagation-Delay Timing Noninverting Receiver OutputSignal Invalid DetectorIf no valid signal levels appear on RIN for 30µs (typ),INVALID goes low. This event typically occurs if the RS -232 cable is disconnected, or if the connected peripheral transmitter is turned off. INVALID goes high when a valid level is applied to the RS -232 receiver input. Figure 2 shows the input levels and timing dia-gram for INVALID operation.Enable InputThe MAX3180E/MAX3182E feature an enable input (EN ). Drive EN high to force ROUT into a high-imped-ance state. In this state, the devices ignore incoming RS-232 signals. Pull EN low for normal operation.ESD ProtectionAs with all Maxim devices, ES D protection structures are incorporated on all pins to protect against ES D encountered during handling and assembly. The receiver inputs of the MAX3180E–MAX3183E have extra protection against static electricity. Maxim’s engineers have developed state-of-the-art structures enabling these pins to withstand ESD up to ±15kV without dam-age or latchup. The receiver inputs of the MAX3180E–MAX3183E are characterized for protection to the fol-lowing limits:•±15kV using the Human Body Model•±8kV using the Contact Discharge method specified in IEC 1000-4-2•±15kV using the Air-Gap Discharge method speci-fied in IEC 1000-4-2Human Body ModelFigure 3 shows the Human Body Model, and Figure 4shows the current waveform it generates when dis-charged into a low impedance. This model consists ofa 100pF capacitor charged to the ESD voltage of inter-est, and then discharged into the test device through a 1.5k Ωresistor.MAX3180E–MAX3183E±15kV ESD-Protected, 0.5µA, +3V to +5.5V ,1.5Mbps RS-232 Receivers in SOT23-5_______________________________________________________________________________________5Figure 3. Human Body ESD Test ModelFigure 4. Human Body Model Current WaveformFigure 2. Input Levels and INVALID TimingM A X 3180E –M A X 3183EIEC 1000-4-2The IEC 1000-4-2 standard covers ES D testing and performance of finished equipment; it does not specifi-cally refer to ICs. The MAX3180E–MAX3183E enable the design of equipment that meets the highest level (Level 4) of IEC 1000-4-2 without the need for additional ESD-protection components.The major difference between tests done using the Human Body Model and IEC 1000-4-2 is higher peak current in IEC 1000-4-2. Because series resistance is lower in the IEC 1000-4-2 model, the ES D withstand voltage measured to this standard is generally lower than that measured using the Human Body. Figure 5shows the IEC 1000-4-2 model, and Figure 6 shows thecurrent waveform for the ±8kV IEC 1000-4-2 Level 4ESD Contact Discharge test.The Air-Gap test involves approaching the device with a charged probe. The Contact Discharge method con-nects the probe to the device before the probe is ener-gized.Power-Supply DecouplingIn most circumstances, a 0.1µF V CC bypass capacitor is adequate. Connect the bypass capacitor as close to the IC as possible.±15kV ESD-Protected, 0.5µA, +3V to +5.5V ,1.5Mbps RS-232 Receivers in SOT23-56_______________________________________________________________________________________Figure 5. IEC 1000-4-2 ESD Test ModelFigure 6. IEC 1000-4-2 ESD Generator Current WaveformMAX3180E–MAX3183E±15kV ESD-Protected, 0.5µA, +3V to +5.5V ,1.5Mbps RS-232 Receivers in SOT23-5_______________________________________________________________________________________7Pin Configurations/Functional Diagrams___________________Chip InformationTRANSISTOR COUNT: 41M A X 3180E –M A X 3183E±15kV ESD-Protected, 0.5µA, +3V to +5.5V ,1.5Mbps RS-232 Receivers in SOT23-5Maxim cannot assume responsibility for use of any circuitry other than circuitry entirely embodied in a Maxim product. No circuit patent licenses are implied. Maxim reserves the right to change the circuitry and specifications without notice at any time.8_____________________Maxim Integrated Products, 120 San Gabriel Drive, Sunnyvale, CA 94086 408-737-7600©1999 Maxim Integrated ProductsPrinted USAis a registered trademark of Maxim Integrated Products.Package Information。
Ultimax和Max控制台NC部件编程704-0111-302用户手册说明书

The following table lists the G codes, identifies the defaults (in the shaded areas), lists Modal (M) or Non-modal (N) types, identifies groups, and describes the G codes’ functions.Some G codes are strictly BNC or strictly ISNC, and are identified as such in this manual. Otherwise, the G codes apply to either dialect.G Code Type Group FunctionG00M01Positioning (Rapid Traverse)G01M Linear Interpolation (Cutting Feed)G02M Circular Interpolation/Helical CWG02.4M3D Circular Interpolation CWG03M Circular Interpolation/Helical CCWG03.4M3D Circular Interpolation CCWG04N00Dwell, Exact StopG05.1M19Surface Finish ParametersG05.2M19Data SmoothingG09N00Decelerate Axis to ZeroG10N Data SettingG11N Data Setting Mode CancelG15M17Polar Coordinates CancelG16M Polar CoordinatesG17M02XY Plane SelectionG18M ZX Plane SelectionG19M YZ Plane SelectionISNC G20M06Input in InchISNC G21M Input in mmG28N00Return to Reference PointG29N Return from Reference PointG31N Skip FunctionContinuedNC Part Programming Ultimax and Max Consoles704-0111-302NC Part Programming — 37G40M07Cutter Compensation CancelG41M Cutter Compensation LeftG42M Cutter Compensation RightG43M08Tool Length Compensation + DirectionG44M Tool Length Compensation - DirectionG45N00Tool Offset IncreaseG46N Tool Offset DecreaseG47N Tool Offset Double IncreaseG48N Tool Offset Double DecreaseG49M08Tool Length Offset Compensation CancelG50M11Scaling CancelG51M ScalingG50.1M18Mirroring CancelG51.1M MirroringG52N00Local Coordinate System SettingG53N Machine Coordinate System SelectionG54M14Work Coordinate System 1 SelectionG55M Work Coordinate System 2 SelectionG56M Work Coordinate System 3 SelectionG57M Work Coordinate System 4 SelectionG58M Work Coordinate System 5 SelectionG59M Work Coordinate System 6 SelectionG61M15Decelerates to Zero–Precision CorneringG64M Cancels Precision CorneringG65N12Macro Command, Subprogram CallG66M Modal Subprogram CallG67M Modal Subprogram Call CancelG68M16Coordinate RotationG69M Coordinate Rotation CancelBNC G70M06Input in InchBNC G71M Input in mmG73M09Peck Drilling CycleISNC G74M Left-handed Tapping CycleISNC G74M Rigid Tappingwith M2938 - NC Part Programming704-0111-302NC Part Programming Ultimax and Max ConsolesBNC G74M01Single-quadrant Circular InterpolationBNC G75M Multi-quadrant Circular InterpolationG76M09Bore Orient CycleG80M Canned Cycle CancelG81M Drilling Cycle, Spot BoringG82M Drilling Cycle, Counter BoringG83M Peck Drilling CycleG84M Tapping CycleISNC G84.2M Rigid Tapping CycleISNC G84.3M Rigid Tapping CycleM Rigid Tapping CycleISNC G84with M29G85M Boring CycleBNC G86M Bore Orient CycleISNC G86M Bore Rapid Out CycleBNC G87M Chip Breaker CycleISNC G87M Back Boring CycleBNC G88M Rigid Tapping CycleISNC G88M Boring Cycle Manual Feed Out, DwellG89M Boring Cycle Bore and DwellG90M03Absolute CommandG91M Incremental CommandG92N00Programming of Absolute Zero PointG93M05Inverse TimeG94M Feed per MinuteG98M10Return to Initial Point in Canned CycleG99M Return to R Point in Canned CycleTable 3.G Codes in order of CodesNC Part Programming Ultimax and Max Consoles704-0111-302NC Part Programming — 39。
ADM6316AY29ARJZ-R7中文资料

Push-pull active low Open-drain active low Push-pull active high Low power consumption: 5 μA Guaranteed reset output valid to VCC = 1 V Power supply glitch immunity Specified over industrial temperature range 5-lead SOT-23 package
RESET
Push-pull No Push-pull Push-pull Open-drain Open-drain Open-drain
Output Stage
RESET No Push-pull Push-pull Push-pull No Push-pull Push-pull
Rev. D
Information furnished by Analog Devices is believed to be accurate and reliable. However, no responsibility is assumed by Analog Devices for its use, nor for any infringements of patents or other rights of third parties that may result from its use. Specifications subject to change without notice. No license is granted by implication or otherwise under any patent or patent rights of Analog Devices. Trademarks and registered trademarks are the property of their respective owners.
SIM SAM 6 8Pin 机械插槽卡插座说明书

CCM03-3003LFT R102 Sim card connector 8 inlay contacts with hinged cover
CCM03-3004LFT R102 Sim card connector 8 inlay conatcts with hinged cover with plastic peg
Fixed cover: 3N max
Card extraction force
Hinged cover: 1N max Fixed cover: 0,80N min / 3N max
Contact force
0,25N min / 0,50N max
Slide locking force
Soldering Process
Compatible with lead free SMT soldering process
SIM/SAM
How To Order Part number list is shown below. For individual part details, please refer to the following pages.
5,08 3,7 9,65
10,16 20,32
6x
1,3
0,7 25˚
S 3,5
Slider locked
29,65 13,8
2,45 R 1,9
1,25 0,7
ø1±0,05 DETAIL A Scale 5
1,25
11,25 17,2
Normally open 100 mΩ max 250 Vrms min 1 mA min / 10m A max 0.2 VA
Environment Data
Maxi-Air 185 产品说明书
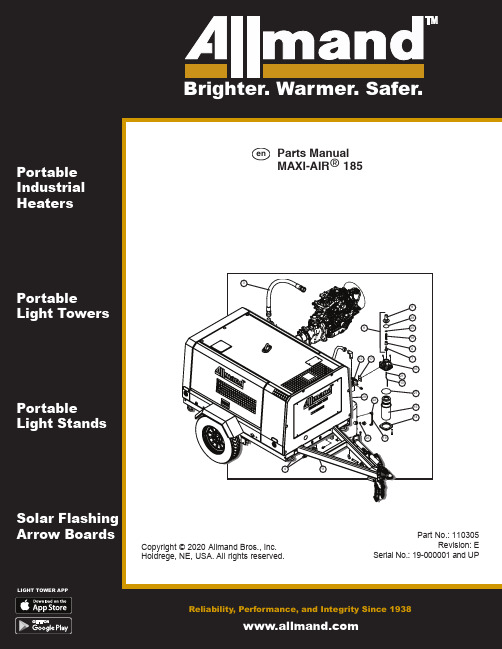
205323411242102922261912179828251867162113271514Parts ManualMAXI-AIR 185®Copyright © 2020 Allmand Bros., Inc. Holdrege, NE, USA. All rights reserved.enPart No.: 110305Revision: ESerial No.: 19-000001 and UPPortable Industrial HeatersPortableLight TowersPortableLight StandsSolar Flashing Arrow BoardsBrighter. Warmer. Safer.TABLE OF CONTENTS1.0 TRAILER PARTS GROUPAxle and Wheel Group ...................................................................................(1.1) Tongue Group .................................................................................................(1.2) Tongue Coupler Options ................................................................................(1.3) Trailer Base Parts .........................................................................................(1.4) 2.0 ENGINE AND COMPRESSOR GROUPEngine Exhaust and Fuel Line Group ...........................................................(2.1) Engine Air Filter Group ..................................................................................(2.2) Cooling Group .................................................................................................(2.3) Oil Lines ..........................................................................................................(2.4) Separator and Receiver Group .....................................................................(2.5) Air End Assembly Group ................................................................................(2.6) Air Lines ..........................................................................................................(2.7) 3.0 ELECTRICAL GROUPElectrical Controller Group ..............................................................................(3.1) Trailer Lighting Group (Old Style Harness) ....................................................(3.2) Trailer Lighting Group (New Style Harness) ..................................................(3.3) Trailer Lighting Hole Covers ...........................................................................(3.4) Battery Charger Option ...................................................................................(3.5) Battery Disconnect Option ..............................................................................(3.6) 4.0 DECALSLeft Side Decals .............................................................................................(4.1) Right Side Decals ...........................................................................................(4.2) Front Side Decals ...........................................................................................(4.3) Rear Side Decals ...........................................................................................(4.4)Maxi-Air 185 PAGE LEFT BLANKINTENTIONALLY1.1 - Axle and Wheel GroupSN 19-000001 and UPMaxi-Air 1851.1 - Axle and Wheel GroupSN 19-000001 and UP1.2 - Tongue GroupSN 19-000001 and UPMaxi-Air 1851.2 - Tongue GroupSN 19-000001 and UP1.3 - Tongue Coupler OptionsSN 19-000001 and UPMaxi-Air 1851.3 - Tongue Coupler OptionsSN 19-000001 and UP1.4 - Trailer Base PartsSN 19-000001 and UPMaxi-Air 1851.4 - Trailer Base PartsSN 19-000001 and UP2.1 - Engine Exhaust and Fuel Line GroupSN 19-000001 and UPMaxi-Air 1852.1 - Engine Exhaust and Fuel Line GroupSN 19-000001 and UP2.2 - Engine Air Filter GroupSN 19-000001 and UPMaxi-Air 1852.2 - Engine Air Filter GroupSN 19-000001 and UP2.3 - Cooling GroupSN 19-000001 and UPMaxi-Air 1852.3 - Cooling GroupSN 19-000001 and UP2.4 - Oil Lines and Block HeaterSN 19-000001 and UPMaxi-Air 1852.4 - Oil Lines and Block HeaterSN 19-000001 and UP2.5 - Separator and Receiver GroupSN 19-000001 and UPMaxi-Air 1852.5 - Separator and Receiver GroupSN 19-000001 and UP2.6 - Air End Assembly GroupSN 19-000001 and UPMaxi-Air 1852.6 - Air End Assembly GroupSN 19-000001 and UP2.7 - Air LinesSN 19-000001 and UPMaxi-Air 1852.7 - Air LinesSN 19-000001 and UP2.8 - Hose Reel GroupSN 19-000001 and UPMaxi-Air 1852.8 - Hose Reel GroupSN 19-000001 and UP3.1 - Electrical Controller GroupSN 19-000001 and UPMaxi-Air 1853.1 - Electrical Controller GroupSN 19-000001 and UP3.2 - Trailer Lighting Group (Old Style Harness)SN 19-000001 and UPMaxi-Air 1853.2 - Trailer Lighting Group (Old Style Harness)SN 19-000001 and UP3.3 - Trailer Lighting Group (New Style Harness)SN 19-000001 and UPMaxi-Air 1853.3 - Trailer Lighting Group (New Style Harness)SN 19-000001 and UPMaxi-Air 1853.4 - Trailer Lighting Hole CoversSN 19-000001 and UP3.5 - Battery Charger OptionSN 19-000001 and UPMaxi-Air 1853.5 - Battery Charger OptionSN 19-000001 and UP3.6 - Battery Disconnect OptionSN 19-000001 and UP5Maxi-Air 1853.6 - Battery Disconnect OptionSN 19-000001 and UP4.1 - Left Side Decals15 2Maxi-Air 1854.1 - Left Side DecalsSN 19-000001 and UP4.2 - Right Side Decals1Maxi-Air 1854.2 - Right Side DecalsSN 19-000001 and UP4.3 - Front Side DecalsSN 19-000001 and UPMaxi-Air 1854.3 - Front Side DecalsSN 19-000001 and UP4.4 - Rear Side DecalsSN 19-000001 and UPMaxi-Air 1854.4 - Rear Side DecalsSN 19-000001 and UPTM BRIGHTER. WARMER. SAFER.。
MAX9813HEKA-T中文资料

Applications
Notebook Computers PDAs Smart Phones Car Kit Adapters Digital Cameras Video Tape Recorders
Pin Configurations, Selector Guide, and Typical Operating Circuits appear at end of data sheet. Rail-to-Rail is a trademark of Nippon Motorola Ltd.
元器件交易网
Tiny, Low-Cost, Single/Dual-Input, Fixed-Gain Microphone Amplifiers with Integrated Bias MAX9812/MAX9813
ABSOLUTE MAXIMUM RATINGS
(All voltages referenced to GND) VCC ........................................................................-0.3V to +6.0V All Other Pins..............................................-0.3V to (VCC + 0.3V) Continuous Current (IN, SHDN, IN1, IN2, IN1/IN2)...........±20mA OUT, BIAS Short-Circuit Duration (to GND or VCC) ...Continuous Continuous Power Dissipation (TA = +70°C) 6-Pin SC70 (derate 3.1mW/°C above +70°C) ..............245mW 8-Pin SOT23 (derate 8.9mw/°C above +70°C) ............714mW Operating Temperature Range ...........................-40°C to +85°C Storage Temperature Range .............................-65°C to +150°C Junction Temperature ......................................................+150°C Lead Temperature (soldering, 10s) .................................+300°C
广日MAX调试介绍材料

端子 FL2-24、FL2-25
≥0.5
4 照明回路 36V
端子 FL2-22、FL2-23
≥0.5
5 抱闸回路
端子 FL2-9、FL2-10
≥0.5
6* 安全回路
端子 FL1-2 和 FL1-8、FL1-11、 FL1-12、FL1-13
≥0.25
7*
空气开关 K2、K3、K4、K5、 K6、K7、K15
空气开关 K2 一次侧—YC 接触器的 A1
表 3-2 各回路的混杂电压检查顺序
合上
测量电压 K2
测量各回路的混杂电压(V)
K3
K15
K4
K7
K6
K5
DC15
0
0
0
0
0
0
K6
DC24
0
0
0
0
0
K7
DC24
0
0
0
0
.-
K4
DC48
0
0
0
K15
AC100
0
0
K3
AC110
0
K2
AC200
注:1、混杂电压应从低电压回路开始测定。 2、混杂电压是指当有回路电源开关置 ON 后,未置 ON 电源开关的二次侧电压。正常时未置 ON
隔磁板未插入感应器时 ON
轿内照明 DL1-2(6)、DL1-3(4)
10 AC220V
轿顶插座
D10-6、D10-7
至日光灯 至轿顶照明箱
11
停电照明
DL2-1、DL2-2
至停电明灯
12
AC36V
13
风扇
D10-8、D10-9 DL1-5、DL1-6
LED升压、升降压的驱动恒流IC推荐二

LED升压、升降压的驱动恒流IC推荐宝剑锋从磨砺出,梅花香自苦寒来;此句是中国流传下来的一句古训,喻为如果想要取得成绩,获取成就,就要能吃苦,勤于锻炼,这样才能靠自己的努力赢得胜利。
各个行业皆是如此。
在电源网论坛里,就存在这样一些人,他们时常能DIY出被网友们称之为的经典设计,出于大家能够共同学习的目的,小编抓住了难得的机会,整理了这些经典帖,供分享学习。
本文续接上一篇LED升压、升降压的驱动恒流IC推荐一。
--------小编语。
美国美信集成产品公司MAX16831 可配置升降压型高功率LED驱动ICMAX16831是一款电流型、高亮LED (HBLED)驱动器,设计为通过控制2个外部n沟道MOSFET来调节单串LED的电流。
MAX16831集成了宽范围亮度控制、固定频率HBLED驱动器所需的全部组件。
MAX16831可配置为降压型(buck)、升压型(boost)或升/降压型(buck-boost)电流调节器。
带有前沿消隐的电流模式简化了控制回路的设计。
内部斜率补偿可在占空比超过50%时保持电流环路的稳定。
MAX16831工作于较宽的输入电压范围,并可承受汽车抛负载事件。
多个MAX16831可相互同步或同步至外部时钟。
MAX16831包含一个浮动亮度驱动器,驱动串联在LED串的n沟道MOSFET实现亮度控制。
使用MAX16831架构的HBLED驱动器可在汽车应用中实现超过90%的效率。
MAX16831还包括一个可源出1.4A、吸收2.5A电流(sink)的栅极驱动器,用于在高功率LED驱动器应用中驱动开关MOSFET,如车灯总成等。
亮度控制允许宽范围的PWM调光,其频率可高达2kHz。
在较低的调光频率下可实现高达1000:1的调光比。
MAX16831提供带裸焊盘的32引脚薄型QFN封装,工作于-40°C至+125°C汽车级温基本参数:宽输入范围:6V至76V;集成LED电流检测差分放大器;可驱动n沟道MOSFET;具有浮动亮度驱动能力;LED电流精度:5%;200Hz片上斜坡发生器,可同步至外部PWM亮度信号;可编程开关频率(125kHz至600kHz),可被同步;输出过压、负载开路、LED短路、过热保护;低至107mV LED电流检测可提高效率;使能/关断输入,关断电流低于45µA。
MAX3181EEUK-T中文资料

For free samples & the latest literature: , or phone 1-800-998-8800.For small orders, phone 1-800-835-8769.General DescriptionThe MAX3180E–MAX3183E single RS -232 receivers in a SOT23-5 package are designed for space- and cost-constrained applications requiring minimal RS -232communications. The receiver inputs are protected to ±15kV using IEC 1000-4-2 Air-Gap Discharge, to ±8kV using IEC 1000-4-2 Contact Discharge, and to ±15kV per the Human Body Model, ensuring compliance with international standards.The devices minimize power and heat dissipation by consuming only 0.5µA supply current from a +3.0V to +5.5V supply, and they guarantee true RS -232 perfor-mance up to a 1.5Mbps data rate. The MAX3180E/MAX3182E feature a three-state TTL/CMOS receiver output that is controlled by an EN logic input. The MAX3181E/MAX3183E feature an INVALID output that indicates valid RS-232 signals at the receiver input for applications requiring automatic system wake-up. The MAX3182E/MAX3183E have a noninverting output,while the MAX3180E/MAX3181E have a standard inverting output.ApplicationsFeatureso Tiny SOT23-5 Packageo ESD-Protected RS-232 Input±15kV—Human Body Model±8kV—IEC 1000-4-2, Contact Discharge ±15kV—IEC 1000-4-2, Air-Gap Discharge o 0.5µA Supply Currento 1.5Mbps Guaranteed Data Rateo Meets EIA/TIA-232 and V.28/V.24 Specifications Down to V CC = +3.0V o INVALID Output Indicates Valid RS-232 Signal at Receiver Input (MAX3181E/MAX3183E)o Three-State TTL/CMOS Receiver Output (MAX3180E/MAX3182E)o Noninverting RS-232 Output (MAX3182E/MAX3183E)MAX3180E–MAX3183E±15kV ESD-Protected, 0.5µA, +3V to +5.5V ,1.5Mbps RS-232 Receivers in SOT23-5________________________________________________________________Maxim Integrated Products 119-1479; Rev 1; 7/99Ordering InformationM A X 3180E –M A X 3183E±15kV ESD-Protected, 0.5µA, +3V to +5.5V ,1.5Mbps RS-232 Receivers in SOT23-52_______________________________________________________________________________________ABSOLUTE MAXIMUM RATINGSELECTRICAL CHARACTERISTICS(V CC = +3.0V to +5.5V, T A = T MIN to T MAX , unless otherwise noted. Typical values are at V CC = +5.0V, T A = +25°C.) (Note 1)Stresses beyond those listed under “Absolute Maximum Ratings” may cause permanent damage to the device. These are stress ratings only, and functional operation of the device at these or any other conditions beyond those indicated in the operational sections of the specifications is not implied. Exposure to absolute maximum rating conditions for extended periods may affect device reliability.V CC to GND..............................................................-0.3V to +6V RIN to GND..........................................................................±25V EN , ROUT, INVALID to GND......................-0.3V to (V CC + 0.3V)Continuous Power Dissipation (T A = +70°C)SOT23-5 (derate 7.1mW/°C above +70°C)...................571mWOperating Temperature Range ...........................-40°C to +85°C Storage Temperature Range.............................-65°C to +150°C Lead Temperature (soldering, 10sec).............................+300°CMAX3180E–MAX3183E±15kV ESD-Protected, 0.5µA, +3V to +5.5V ,1.5Mbps RS-232 Receivers in SOT23-5_______________________________________________________________________________________3ELECTRICAL CHARACTERISTICS (continued)(V CC = +3.0V to +5.5V, T A = T MIN to T MAX , unless otherwise noted. Typical values are at V CC = +5.0V, T A = +25°C.) (Note 1)Typical Operating Characteristics(V CC = +5V, T A = +25°C, unless otherwise noted.)00.20.10.40.30.60.50.700.51.0 1.5SUPPLY CURRENT vs. DATA RATEDATA RATE (Mbps)S U P P L Y C U R R E N T (m A )2302702502903303103503.0 3.5 5.04.54.0 5.5RIN TO INVALID HIGH vs. SUPPLY VOLTAGEM A X 3180E -02V CC (V)t I N V H (n s )Note 1:Specifications are 100% tested at T A = +25°C. Limits over temperature are guaranteed by design.Detailed DescriptionThe MAX3180E–MAX3183E are EIA/TIA-232 and V.28/V.24communications receivers that convert RS -232signals to CMOS logic levels. They operate on a +3V to +5.5V supply, have 1.5Mbps data rate capability, and feature enhanced electrostatic discharge (ESD) protec-tion (see ESD Protection ). All of these devices achieve a typical supply current of 0.5µA. The MAX3180E/MAX3182E have a receiver enable control (EN ). The MAX3181E/MAX3183E contain a signal invalid output (INVALID ). The MAX3180E/MAX3181E invert the ROUT signal relative to RIN (standard RS -232). The MAX3182E/MAX3183E outputs are not inverted. The devices come in tiny SOT23-5 packages.M A X 3180E –M A X 3183E±15kV ESD-Protected, 0.5µA, +3V to +5.5V ,1.5Mbps RS-232 Receivers in SOT23-54_______________________________________________________________________________________25353045405550603.03.54.04.55.05.5RIN TO INVALID LOW vs. V CCM A X 3180E -03V CC (V)t I N V L (µs )Typical Operating Characteristics (continued)(V CC = +5V, T A = +25°C, unless otherwise noted.)5V010V 0-10V RINROUTENABLE5V 0500ns/divMAX3180EENABLE ASSERTION TO ROUT RESPONSEV CC = 5.0V R L = 50k ΩC L = 100pFReceiver Output EnablePin DescriptionFUNCTIONOutput of the Valid Input Detector Inverting Receiver Output Figure 1. Receiver Propagation-Delay Timing Noninverting Receiver OutputSignal Invalid DetectorIf no valid signal levels appear on RIN for 30µs (typ),INVALID goes low. This event typically occurs if the RS -232 cable is disconnected, or if the connected peripheral transmitter is turned off. INVALID goes high when a valid level is applied to the RS -232 receiver input. Figure 2 shows the input levels and timing dia-gram for INVALID operation.Enable InputThe MAX3180E/MAX3182E feature an enable input (EN ). Drive EN high to force ROUT into a high-imped-ance state. In this state, the devices ignore incoming RS-232 signals. Pull EN low for normal operation.ESD ProtectionAs with all Maxim devices, ES D protection structures are incorporated on all pins to protect against ES D encountered during handling and assembly. The receiver inputs of the MAX3180E–MAX3183E have extra protection against static electricity. Maxim’s engineers have developed state-of-the-art structures enabling these pins to withstand ESD up to ±15kV without dam-age or latchup. The receiver inputs of the MAX3180E–MAX3183E are characterized for protection to the fol-lowing limits:•±15kV using the Human Body Model•±8kV using the Contact Discharge method specified in IEC 1000-4-2•±15kV using the Air-Gap Discharge method speci-fied in IEC 1000-4-2Human Body ModelFigure 3 shows the Human Body Model, and Figure 4shows the current waveform it generates when dis-charged into a low impedance. This model consists ofa 100pF capacitor charged to the ESD voltage of inter-est, and then discharged into the test device through a 1.5k Ωresistor.MAX3180E–MAX3183E±15kV ESD-Protected, 0.5µA, +3V to +5.5V ,1.5Mbps RS-232 Receivers in SOT23-5_______________________________________________________________________________________5Figure 3. Human Body ESD Test ModelFigure 4. Human Body Model Current WaveformFigure 2. Input Levels and INVALID TimingM A X 3180E –M A X 3183EIEC 1000-4-2The IEC 1000-4-2 standard covers ES D testing and performance of finished equipment; it does not specifi-cally refer to ICs. The MAX3180E–MAX3183E enable the design of equipment that meets the highest level (Level 4) of IEC 1000-4-2 without the need for additional ESD-protection components.The major difference between tests done using the Human Body Model and IEC 1000-4-2 is higher peak current in IEC 1000-4-2. Because series resistance is lower in the IEC 1000-4-2 model, the ES D withstand voltage measured to this standard is generally lower than that measured using the Human Body. Figure 5shows the IEC 1000-4-2 model, and Figure 6 shows thecurrent waveform for the ±8kV IEC 1000-4-2 Level 4ESD Contact Discharge test.The Air-Gap test involves approaching the device with a charged probe. The Contact Discharge method con-nects the probe to the device before the probe is ener-gized.Power-Supply DecouplingIn most circumstances, a 0.1µF V CC bypass capacitor is adequate. Connect the bypass capacitor as close to the IC as possible.±15kV ESD-Protected, 0.5µA, +3V to +5.5V ,1.5Mbps RS-232 Receivers in SOT23-56_______________________________________________________________________________________Figure 5. IEC 1000-4-2 ESD Test ModelFigure 6. IEC 1000-4-2 ESD Generator Current WaveformMAX3180E–MAX3183E±15kV ESD-Protected, 0.5µA, +3V to +5.5V ,1.5Mbps RS-232 Receivers in SOT23-5_______________________________________________________________________________________7Pin Configurations/Functional Diagrams___________________Chip InformationTRANSISTOR COUNT: 41M A X 3180E –M A X 3183E±15kV ESD-Protected, 0.5µA, +3V to +5.5V ,1.5Mbps RS-232 Receivers in SOT23-5Maxim cannot assume responsibility for use of any circuitry other than circuitry entirely embodied in a Maxim product. No circuit patent licenses are implied. Maxim reserves the right to change the circuitry and specifications without notice at any time.8_____________________Maxim Integrated Products, 120 San Gabriel Drive, Sunnyvale, CA 94086 408-737-7600©1999 Maxim Integrated ProductsPrinted USAis a registered trademark of Maxim Integrated Products.Package Information。
MAXXHAUL Dual Pull Trailer Dolly Model 70881 说明书

Dual PullTrailer DollyModel 70881Read and understand this entire manual before assembling, installing, operating, or servicing this product.SAVE THIS MANUALCopyright c 2016 by MAXXHAUL. All rights reserved. No portion of this manual or any artwork contained herein may be reproduced in any shape or form without the express written consent of MAXXHAUL. Due to continuing improvements, actual product may differ slightly from the product described herein. Tools required for assembly and maintenance may not be included.Instruction Manual &Parts CatalogIMPORTANT SAFETYINFORMATIONThis is a SAFETY ALERT symbol. It is used to alert you to potential personalinjury hazards. Obey all safety messages that follow this symbol to avoid possible injury or death. DANGER indicates a hazardous situation which, if not avoided, will result in death or injury.WARNING indicates a hazardous situation which, if not avoided, could result in death or serious injury.CAUTION indicates a hazardous situation which, if not avoided, could result in minor or moderate injury. NOTICE indicatesimportant information which, if not followed, may cause damage to equipment.SAVE THIS MANUALKeep this manual for the safety warnings and precautions. The manual offers impor -tant information on how to assemble, useand maintain this product.Write the product’s model number and pur-chase date on the cover page of this man-ual. Keep this manual (and your purchase receipt) in a safe place.UNPACKINGThe shi pment should be thoroughly inspected as soon as it is received. The signed “bill of lad -ing” is acknowledgement by the carrier of receipt in good condition or shipment covered by our invoice. For your own protection, if any of the goods called for on the bill of lading are shorted or damaged, do not accept them until the carrier makes a notation on the freight bill of the shorted or damaged goods.Notify MAXXHAUL immediately if any hidden loss or damage is discovered after receipt.DANGER WARNING CAUTION NOTICE INSTRUCTION MANUALWARNING concerning Risk of EyeInjury. Wear ANSI approved eyeprotection.WARNING concerning Risk of Hearing Loss. Wear hearing pro-tection.Definition of SymbolsIMPORTANT SAFETYINSTRUCTIONS1. Read and understand all safety warnings and in-structions. Failure to follow the warnings and instructions may result in serious injury or death. Save all warnings and instructions for future reference.2. Personal and Work Area Safety A. Always wear ANSI approved safety goggles. B. Always wear hearing protec- tection when working in noisy environments. Prolonged exposure to high intensity noise can cause hearing loss.C. Use safety equipment. Safe- ty shoes, hard hat and work gloves must be used for applicable condi-tions.Model 70881 Page 2D. Dress appropriately. Never wear loose fitting clothing or jewelry when working. Contain long hair, and keep hair, clothing and gloves away from moving parts.E. Use common sense when working. Stay alert and concentrate when setting up and using the Dual Pull Trailer Dolly. Never work while under the influence of alcohol, drugs or medications.Personal and Work Area Safety (continued) F. While assembling and using the Dual Pull Trailer Dolly keep work area clean and well lighted. Keep spectators and children out of the work area.3. Use of the Dual Pull Trailer DollyA. This product can be set up for two differ-ent functions:In manual mode, the product can be usedto move an attached lightweight trailer short distances over a flat, level surface.The Dual Pull Trailer Dolly can also be setup to attach to an ATV (All Terrain Vehicle), UTV (Utility Terrain Vehicle) or lawn tractorto pull a loaded trailer in an off-road situation at a speed not to exceed 10 MPH.B. Do not modify the Dual Pull Trailer Dolly and do not use this product for pur-poses that it was not designed for.C. Never exceed the maximum capacity of 600 Lbs.D. Be aware of the danger of “dynamic loading”. This situation arises when a load is dropped onto the Dual Pull Trailer Dolly, resulting in a short term excessive load. Dynamic loading can result in damage and failure of the Dual Pull Trailer Dolly and/or trailer tongue, and personal injury to the per-son loading the trailer/Dual Pull Trailer Dolly.E. Never load people or animals onto the Dual Pull Trailer Dolly. Keep children and spectators well clear when loading, unload-ing and using this product.F. Adhere to all Department of Transpor-tation (D.O.T.) requirements when using this product. Use ropes and tie downs to securely hold all cargo in place on the at-tached trailer.G. For the trailer that is being attached to the Dual Pull Trailer Dolly, read all pertinent trailer instructions and warnings providedin the owner’s manual. Make sure thatthe trailer is on a flat, level surface, with wheels chocked when attaching the trailer to the Dual Pull Trailer Dolly, and when loading/unloading the trailer.Only use the Dual Pull Trailer Dolly when and where the load can be transferred safely. Be cautious: The pull of gravity on a slightly slopped surface can result in an out of control trailer.H. Hitch Ball (10) is 1-7/8” diameter. Make sure the trailer tongue connection is compat-ible to this Hitch Ball.I. When attaching the Dual Pull Trailer Dolly to an ATV, UTV or lawn tractor, make sure the connection is secure and stable. If using a hitch pin connection, hitch pin should be5/8” diameter steel, with a matching R-Shaped Safety Clip (pin and safety clip not included).J. Never leave the Dual Pull Trailer Dolly unattended while under load.K. Always keep arms, feet and legs away from under the trailer when hitching, unhitch-ing or moving the trailer. Keep spectators away when using this trailer dolly.L. Use an appropriate tongue jack to safely raise and lower the trailer tongue.Keep in mind that the warnings previ-ously discussed cannot cover all pos-sible conditions or situations that could occur. It is important that the person loading/unloading and using this product understand that common sense and cau-tion are factors which cannot be built into this product, and must be supplied by the person(s) using this product.Model 70881 Page 3Model 70881 Page 4Assembling and Setting Up the Dual Pull Trailer Dolly 1. The Dual Pull Trailer Dolly will require complete assembly. If you are not experi-enced in doing this type of assembly work, you should get assistance from qualified service technicians.Refer to photos on this page of an already assembled Dual Pull Trailer Dolly, and to the Assembly Diagram at end of this manu-al.2. Always wearANSI approved safety goggles when set-ting up, using and loading/unloading the Dual Pull Trailer Dolly.It is suggested that a qualified assistant help in the set up and loading of the Dual Pull Trailer Dolly. 3. Join together Adjustable U-Bracket (5) with extended piece in center of AxleAssembly (16). Secure both together with Bolt (4), Washer (9) and Nut (8) - on lower front corner of Adjustable U-Bracket.Secure upper portion of Adjustable U-Bracket to Axle Assembly with Bolt (11), Washer (6) and Nut (7).4. Attach Handle Assembly (1) to Adjust-able U-Bracket (5) using Bolt (2), Washer (6) and Nut (7).Note: Lock Pin (3) can be inserted in any of 3 locations to change the angle of the Handle (1).5. Assemble each Tire (13) to Axle Assem -bly (16) using Flat Washer (14) and R-Pin (15).6. Secure Hitch Ball (10) to top of Axle As-sembly (16) with Nut (12).7. With assembly complete, make sure all hardward is tightly secured in place. LockPin (3) must be fully inserted. Make sure the wire loop of the Lock Pin fully engag-es the tip of the Lock Pin to keep the pin in place.Before each use, make sure that Nut (12) securing Hitch Ball (10), is fully engaged and tightened down.8. This product can be set up for two differ -ent functions:In manual mode, the product can be used to move an attached lightweight trailer short distances over a flat, level surface. (See photo below)The Dual Pull Trailer Dolly can also be set up to attach to an ATV (All Terrain Vehi-cle), UTV (Utility Terrain Vehicle) or lawn tractor to pull a loaded trailer in an off-road situation at a speed not to exceed 10 MPH. (See photo below)WARNING Manual ModeExtended Support Stand DownLock Pin (3) in lowest positionHandles RetractedSupport Stand UpLock Pin (3) inhighest positionAttaches to vehicle with 5/8” diameter steel Hitch Pin, with a matching R-Shaped Safety Clip (pin and safety clip not included).Attach to VehicleModel 70881 Page 5WARNING SPECIFICATIONSMaximum Capacity 600 Lbs.Construction Heavy Duty, All Steel Hitch Ball1-7/8” Diameter Hitch Ball Shank Diam-eter 3/4”ApplicationWhen attached to avehicle, OFF-ROAD-USE ONLY. Speed not to ex-ceed 10 MPHUsing the Dual Pull Trailer Dolly1. Once the desired mode of use is deter-mined and set-up complete, check all hard-ware, check Lock Pin and hitch pin with R-shaped safety clip to make sure everything is secured in place.2. Never exceed the600 Lb. maximum capacity.3. Chock the wheels of the loaded trailer. Trailer must be on a level, flat surface.4. Carefully move the Dual Pull Trailer Dolly in place and connect the trailer tongue to the Trailer Dolly. Use an appropriate tongue jack to safely raise and lower the trailer tongue.5. Once Dual Pull Trailer Dolly is securely connected to the trailer, remove trailer’s wheel chocks.6. If in manual mode, with hands on the extended Handles, slowly roll and maneuver the trailer to the desired location.7. If Trailer Dolly is attached to an ATV,UTV or lawn tractor, carefully pull the loaded trailer (only in an off-road situation and at a speed not to exceed 10 MPH) to the desired location.8. Once trailer is in the new location, chock wheels again. Never leave the Trailer Dolly unattended while it is under load.9. With job complete, unhitch the Dual Pull Trailer Dolly and move it away from the trailer.10. Frequently check the condition of the Dual Pull Trailer Dolly, the Lock Pin (3), the Hitch Ball (10), the hardware, and the hitch pin and safety R-Pin. Make sure all compo -Limited WarrantyMAXXHAUL warrants to the original retail purchaser that the product is free of defects in material and workmanship at the time of shipment. This Dual Pull Trailer Dolly is warranteed for 90 days from the date of purchase. This warranty is expressly in lieu of all other warranties, express or implied.Proof of purchase is required for warranty transactions; a copy of the original invoice or sales receipt is required.of this product is critical and beyond the control of MAXHAUL. It neither guaran-tees, nor will it be liable for any damage resulting from the attachment or improp-er use of the Dual Pull Trailer Dolly.nents are in good condition. Make sure tires are properly inflated. If the Dual Pull Trailer Dolly becomes damaged through accident, or if any weld damage is noted, the product should be replaced. Check to make sure that all hardware is tightly secured in place.Model 70881 Page 61 Handle Assembly 12 Bolt M10x60 13 Lock Pin 14 Bolt M12x60 15 Adjustable U-Bracket 16 Washer M10 27 Nut M10 28 Nut M12 19 Washer M12 110 1-7/8" Hitch Ball 111 Bolt M10 x 25 112 Nut 113 12" Tire 214 Flat Washer 215 R-pin 216 Axle Assembly 116Assembly DrawingPart # DescriptionQtyParts ListNote: The Parts List and Assembly Diagram is provided as a reference tool only. Some parts are listed and shown for illustration purposes only, and are not available as replacement parts. All repairs to this tool (including replacing parts) should only be done by a qualified service technician.Manufactured and Distributed by:Maxx Group, LLC, 1500 E. Wooley Rd., Unit C, Oxnard, CA USA 93030Telephone: 1-855-6299869。
- 1、下载文档前请自行甄别文档内容的完整性,平台不提供额外的编辑、内容补充、找答案等附加服务。
- 2、"仅部分预览"的文档,不可在线预览部分如存在完整性等问题,可反馈申请退款(可完整预览的文档不适用该条件!)。
- 3、如文档侵犯您的权益,请联系客服反馈,我们会尽快为您处理(人工客服工作时间:9:00-18:30)。
___________________________________________________________________Selector Guide________________General DescriptionThe MAX6316–MAX6322 family of microprocessor (µP)supervisory circuits monitors power supplies and microprocessor activity in digital systems. It offers sev-eral combinations of push/pull, open-drain, and bidirec-tional (such as Motorola 68HC11) reset outputs, along with watchdog and manual reset features. The Selector Guide below lists the specific functions available from each device. These devices are specifically designed to ignore fast negative transients on V CC . Resets are guaranteed valid for V CC down to 1V.These devices are available in 26 factory-trimmed reset threshold voltages (from 2.5V to 5V, in 100mV incre-ments), featuring four minimum power-on reset timeout periods (from 1ms to 1.12s), and four watchdog timeout periods (from 6.3ms to 25.6s). Thirteen standard ver-sions are available with an order increment requirement of 2500 pieces (see Standard Versions table); contact the factory for availability of other versions, which have an order increment requirement of 10,000 pieces.The MAX6316–MAX6322 are offered in a miniature 5-pin SOT23 package.________________________ApplicationsPortable Computers Computers ControllersIntelligent InstrumentsPortable/Battery-Powered Equipment Embedded Control Systems____________________________Features♦Small 5-Pin SOT23 Package♦Available in 26 Reset Threshold Voltages2.5V to 5V, in 100mV Increments ♦Four Reset Timeout Periods1ms, 20ms, 140ms, or 1.12s (min)♦Four Watchdog Timeout Periods6.3ms, 102ms, 1.6s, or 25.6s (typ) ♦Four Reset Output StagesActive-High, Push/Pull Active-Low, Push/Pull Active-Low, Open-Drain Active-Low, Bidirectional♦Guaranteed Reset Valid to V CC = 1V♦Immune to Short Negative V CC Transients ♦Low Cost♦No External ComponentsMAX6316–MAX63225-Pin µP Supervisory Circuits withWatchdog and Manual Reset________________________________________________________________Maxim Integrated Products 119-0496; Rev 7; 11/07_______________Ordering InformationOrdering Information continued at end of data sheet.*The MAX6318/MAX6319/MAX6321/MAX6322 feature two types of reset output on each device.Typical Operating Circuit and Pin Configurations appear at end of data sheet.For pricing, delivery, and ordering information, please contact Maxim Direct at 1-888-629-4642,or visit Maxim’s website at .Specify lead-free by replacing “-T” with “+T” when ordering.ELECTRICAL CHARACTERISTICS(V CC = 2.5V to 5.5V, T A = -40°C to +125°C, unless otherwise noted. Typical values are at T A = +25°C.) (Note 1)M A X 6316–M A X 63225-Pin µP Supervisory Circuits with Watchdog and Manual Reset 2_______________________________________________________________________________________ABSOLUTE MAXIMUM RATINGSStresses beyond those listed under “Absolute Maximum Ratings” may cause permanent damage to the device. These are stress ratings only, and functional operation of the device at these or any other conditions beyond those indicated in the operational sections of the specifications is not implied. Exposure to absolute maximum rating conditions for extended periods may affect device reliability.Voltage (with respect to GND)V CC ......................................................................-0.3V to +6V RESET (MAX6320/MAX6321/MAX6322 only)...... -0.3V to +6V All Other Pins.........................................-0.3V to (V CC + 0.3V)Input/Output Current, All Pins.............................................20mAContinuous Power Dissipation (T A = +70°C)SOT23-5 (derate 7.1mW/°C above +70°C)...............571mW Operating Temperature Range..........................-40°C to +125°C Junction Temperature......................................................+150°C Storage Temperature Range..............................-65°C to +160°C Lead Temperature (soldering, 10s).................................+300°CTH available in 100mV increments from 2.5V to 5V (see Table 1 at end of data sheet).Note 3:Guaranteed by design.MAX6316–MAX63225-Pin µP Supervisory Circuits withWatchdog and Manual Reset_______________________________________________________________________________________3Note 5:Measured from RESET V OL to (0.8 x V CC ), R LOAD = ∞.Note 6:WDI is internally serviced within the watchdog period if WDI is left unconnected.Note 7:The WDI input current is specified as the average input current when the WDI input is driven high or low. The WDI input is designed for a three-stated-output device with a 10µA maximum leakage current and capable of driving a maximum capac-itive load of 200pF. The three-state device must be able to source and sink at least 200µA when active.ELECTRICAL CHARACTERISTICS (continued)M A X 6316–M A X 63225-Pin µP Supervisory Circuits with Watchdog and Manual Reset 4_________________________________________________________________________________________________________________________________Typical Operating Characteristics(T A = +25°C, unless otherwise noted.)021*********-4020-20406080100MAX6316/MAX6317/MAX6318/MAX6320/MAX6321SUPPLY CURRENT vs. TEMPERATURETEMPERATURE (°C)S U P P L Y C U R R E N T (μA )302010504090807060100-40-20020406080100V CC FALLING TO RESET PROPAGATIONDELAY vs. TEMPERATURETEMPERATURE (°C)R E S E T P R O P A G A T I O N D E L A Y (μs )140180160240220200300280260320-40020-20406080100MAX6316/MAX6317/MAX6319/MAX6320/MAX6322MANUAL RESET TO RESETPROPAGATION DELAY vs. TEMPERATURETEMPERATURE (°C)P R O P A G A T I O N D E L A Y (n s )0.950.980.970.961.000.991.041.031.021.011.05-40-2020406080100NORMALIZED RESET TIMEOUT PERIOD vs. TEMPERATUREM A X 6316t o c 04TEMPERATURE (°C)N O R M A L I Z E D R E S E T T I M E O U T P E R I O D0.950.980.970.961.000.991.041.031.021.011.05-40-2020406080100MAX6316/MAX6317/MAX6318/MAX6320/MAX6321NORMALIZED WATCHDOG TIMEOUTPERIOD vs. TEMPERATUREM A X 6316t o c 05TEMPERATURE (°C)N O R M A L I Z E D W A T C H D O G T I M E O U T P E R I O D800101001000MAXIMUM V CC TRANSIENT DURATION vs. RESET THRESHOLD OVERDRIVE2010RESET THRESHOLD OVERDRIVE (mV) V RST - V CCT RA N S I E N T D U R A T I O N (μs )3050604070200ns/divMAX6316M/6318MH/6319MHBIDIRECTIONALPULLUP CHARACTERISTICSMAX6316–MAX63225-Pin µP Supervisory Circuits withWatchdog and Manual Reset_______________________________________________________________________________________5______________________________________________________________Pin DescriptionM A X 6316–M A X 63225-Pin µP Supervisory Circuits with Watchdog and Manual Reset 6______________________________________________________________________________________________________Detailed DescriptionA microprocessor’s (µP) reset input starts or restarts the µP in a known state. The reset output of the MAX6316–MAX6322 µP supervisory circuits interfaces with the reset input of the µP, preventing code-execution errors during power-up, power-down, and brownout condi-tions (see the Typical Operating Circuit ). The MAX6316/MAX6317/MAX6318/MAX6320/MAX6321 are also capa-ble of asserting a reset should the µP become stuck in an infinite loop.Reset OutputThe MAX6316L/MAX6318LH/MAX6319LH feature an active-low reset output, while the MAX6317H/MAX6318_H/MAX6319_H/MAX6321HP/MAX6322HP feature an active-high reset output. RESET is guaran-teed to be a logic low and RESET is guaranteed to be a logic high for V CC down to 1V.The MAX6316–MAX6322 assert reset when V CC is below the reset threshold (V RST ), when MR is pulled low (MAX6316_/MAX6317H/MAX6319_H/MAX6320P/MAX6322HP only), or if the WDI pin is not serviced withinthe watchdog timeout period (t WD ). Reset remains assert-ed for the specified reset active timeout period (t RP ) after V CC rises above the reset threshold, after MR transitions low to high, or after the watchdog timer asserts the reset (MAX6316_/MAX6317H/MAX6318_H/MAX6320P/MAX6321HP). After the reset active timeout period (t RP )expires, the reset output deasserts, and the watchdog timer restarts from zero (Figure 2).Figure 1. Functional DiagramFigure 2. Reset Timing DiagramMAX6316–MAX63225-Pin µP Supervisory Circuits withWatchdog and Manual Reset_______________________________________________________________________________________7Bidirectional R E S E T OutputThe MAX6316M/MAX6318MH/MAX6319MH are designed to interface with µPs that have bidirectional reset pins,such as the Motorola 68HC11. Like an open-drain output,these devices allow the µP or other devices to pull the bidirectional reset (RESET ) low and assert a reset condi-tion. However, unlike a standard open-drain output, it includes the commonly specified 4.7k Ωpullup resistor with a P-channel active pullup in parallel.This configuration allows the MAX6316M/MAX6318MH/MAX6319MH to solve a problem associated with µPs that have bidirectional reset pins in systems where sev-eral devices connect to RESET (F igure 3). These µPs can often determine if a reset was asserted by an exter-nal device (i.e., the supervisor IC) or by the µP itself (due to a watchdog fault, clock error, or other source),and then jump to a vector appropriate for the source of the reset. However, if the µP does assert reset, it does not retain the information, but must determine the cause after the reset has occurred.The following procedure describes how this is done in the Motorola 68HC11. In all cases of reset, the µP pulls RESET low for about four external-clock cycles. It then releases RESET , waits for two external-clock cycles,then checks RESET ’s state. If RESET is still low, the µP concludes that the source of the reset was external and, when RESET eventually reaches the high state, it jumps to the normal reset vector. In this case, stored-state information is erased and processing begins fromscratch. If, on the other hand, RESET is high after a delay of two external-clock cycles, the processor knows that it caused the reset itself and can jump to a different vector and use stored-state information to determine what caused the reset.A problem occurs with faster µPs; two external-clock cycles are only 500ns at 4MHz. When there are several devices on the reset line, and only a passive pullup resis-tor is used, the input capacitance and stray capacitance can prevent RESET from reaching the logic high state (0.8✕V CC ) in the time allowed. If this happens, all resets will be interpreted as external. The µP output stage is guaran-teed to sink 1.6mA, so the rise time can not be reduced considerably by decreasing the 4.7k Ωinternal pullup resistance. See Bidirectional Pullup Characteristics in the Typical Operating Characteristics .The MAX6316M/MAX6318MH/MAX6319MH overcome this problem with an active pullup FET in parallel with the 4.7k Ωresistor (F igures 4 and 5). The pullup transistor holds RESET high until the µP reset I/O or the supervisory circuit itself forces the line low. Once RESET goes below V PTH , a comparator sets the transition edge flip-flop, indi-cating that the next transition for RESET will be low to high. When RESET is released, the 4.7k Ωresistor pulls RESET up toward V CC . Once RESET rises above V PTH but is below (0.85 x V CC ), the active P-channel pullup turns on. Once RESET rises above (0.85 x V CC ) or the 2µs one-shot times out, the active pullup turns off. The parallel combination of the 4.7k Ωpullup and theFigure 3. MAX6316M/MAX6318MH/MAX6319MH Supports Additional Devices on the Reset BusM A X 6316–M A X 63225-Pin µP Supervisory Circuits with Watchdog and Manual Reset 8_______________________________________________________________________________________Figure 4. MAX6316/MAX6318MH/MAX6319MH Bidirectional Reset Output Functional DiagramMAX6316–MAX63225-Pin µP Supervisory Circuits withWatchdog and Manual Reset_______________________________________________________________________________________9P-channel transistor on-resistance quickly charges stray capacitance on the reset line, allowing RESET to transition from low to high within the required two elec-tronic-clock cycles, even with several devices on the reset line. This process occurs regardless of whether the reset was caused by V CC dipping below the reset threshold, the watchdog timing out, MR being asserted,or the µP or other device asserting RESET . The parts do not require an external pullup. To minimize supply cur-rent consumption, the internal 4.7k Ωpullup resistor dis-connects from the supply whenever the MAX6316M/MAX6318MH/MAX6319MH assert reset.Open-Drain R E S E T OutputThe MAX6320P/MAX6321HP/MAX6322HP have an active-low, open-drain reset output. This output struc-ture will sink current when RESET is asserted. Connect a pullup resistor from RESET to any supply voltage up to 6V (Figure 6). Select a resistor value large enough toregister a logic low (see Electrical Characteristics ), and small enough to register a logic high while supplying all input current and leakage paths connected to the RESET line. A 10k Ωpullup is sufficient in most applications.Manual-Reset InputThe MAX6316_/MAX6317H/MAX6319_H/MAX6320P/MAX6322HP feature a manual reset input. A logic low on MR asserts a reset. After MR transitions low to high, reset remains asserted for the duration of the reset timeout peri-od (t RP ). The MR input is connected to V CC through an internal 52k Ωpullup resistor and therefore can be left unconnected when not in use. MR can be driven with TTL-logic levels in 5V systems, with CMOS-logic levels in 3V systems, or with open-drain or open-collector output devices. A normally-open momentary switch from MR to ground can also be used; it requires no external debouncing circuitry. MR is designed to reject fast, negative-going transients (typically 100ns pulses). A 0.1µF capacitor from MR to ground provides additional noise immunity.The MR input pin is equipped with internal ESD-protection circuitry that may become forward biased. Should MR be driven by voltages higher than V CC , excessive current would be drawn, which would damage the part. F or example, assume that MR is driven by a +5V supply other than V CC . If V CC drops lower than +4.7V, MR ’s absolute maximum rating is violated [-0.3V to (V CC + 0.3V)], and undesirable current flows through the ESD structure from MR to V CC . To avoid this, use the same supply for MR as the supply monitored by V CC . This guarantees that the voltage at MR will never exceed V CC .Watchdog InputThe MAX6316_/MAX6317H/MAX6318_H/MAX6320P/MAX6321HP feature a watchdog circuit that monitors the µP’s activity. If the µP does not toggle the watchdog input (WDI) within the watchdog timeout period (t WD ),reset asserts. The internal watchdog timer is cleared by reset or by a transition at WDI (which can detect pulses as short as 50ns). The watchdog timer remains cleared while reset is asserted. Once reset is released, the timer begins counting again (Figure 7).The WDI input is designed for a three-stated output device with a 10µA maximum leakage current and the capability of driving a maximum capacitive load of 200pF.The three-state device must be able to source and sink at least 200µA when active. Disable the watchdog function by leaving WDI unconnected or by three-stating the driver connected to WDI. When the watchdog timer is left open circuited, the timer is cleared internally at intervals equal to 7/8 of the watchdog period.Figure 6. MAX6320P/MAX6321HP/MAX6322HP Open-Drain RESET Output Allows Use with Multiple SuppliesFigure 5. Bidirectional RESET Timing DiagramM A X 6316–M A X 63225-Pin µP Supervisory Circuits with Watchdog and Manual Reset 10______________________________________________________________________________________Applications InformationWatchdog Input CurrentThe WDI input is internally driven through a buffer and series resistor from the watchdog counter. For minimum watchdog input current (minimum overall power con-sumption), leave WDI low for the majority of the watch-dog timeout period. When high, WDI can draw as much as 160µA. Pulsing WDI high at a low duty cycle will reduce the effect of the large input current. When WDI is left unconnected, the watchdog timer is serviced within the watchdog timeout period by a low-high-low pulse from the counter chain.Negative-Going V CC TransientsThese supervisors are immune to short-duration, nega-tive-going V CC transients (glitches), which usually do not require the entire system to shut down. Typically,200ns large-amplitude pulses (from ground to V CC ) on the supply will not cause a reset. Lower amplitude puls-es result in greater immunity. Typically, a V CC transient that goes 100mV under the reset threshold and lasts less than 4µs will not trigger a reset. An optional 0.1µF bypass capacitor mounted close to V CC provides addi-tional transient immunity.Ensuring Valid Reset OutputsDown to V CC = 0The MAX6316_/MAX6317H/MAX6318_H/MAX6319_H/MAX6321HP/MAX6322HP are guaranteed to operate properly down to V CC = 1V. In applications that require valid reset levels down to V CC = 0, a pulldown resistor to active-low outputs (push/pull and bidirectional only,F igure 8) and a pullup resistor to active-high outputs(push/pull only, Figure 9) will ensure that the reset line is valid while the reset output can no longer sink orsource current. This scheme does not work with the open-drain outputs of the MAX6320/MAX6321/MAX6322.The resistor value used is not critical, but it must be large enough not to load the reset output when V CC is above the reset threshold. F or most applications,100k Ωis adequate.Watchdog Software Considerations(MAX6316/MAX6317/MAX6318/MAX6320/MAX6321)One way to help the watchdog timer monitor software execution more closely is to set and reset the watchdog input at different points in the program, rather than pulsing the watchdog input high-low-high or low-high-low. This technique avoids a stuck loop, in which the watchdog timer would continue to be reset inside the loop, keeping the watchdog from timing out.Figure 7. Watchdog Timing RelationshipFigure 9. Ensuring RESET Valid to V CC = 0 on Active-High Push/Pull OutputsFigure 8. Ensuring RESET Valid to V CC = 0 on Active-Low Push/Pull and Bidirectional OutputsMAX6316–MAX6322Watchdog and Manual Reset______________________________________________________________________________________11F igure 10 shows an example of a flow diagram where the I/O driving the watchdog input is set high at the beginning of the program, set low at the end of every subroutine or loop, then set high again when the pro-gram returns to the beginning. If the program should hang in any subroutine, the problem would be quickly corrected, since the I/O is continually set low and the watchdog timer is allowed to time out, causing a reset or interrupt to be issued. As described in the Watchdog Input Current section, this scheme results in higher time average WDI current than does leaving WDI low for the majority of the timeout period and periodically pulsing it low-high-low.Figure 10. Watchdog Flow Diagram__________________Pin ConfigurationsTypical Operating CircuitTable 2. Standard VersionsTable 1. Factory-Trimmed Reset ThresholdsM A X 6316–M A X 6322Watchdog and Manual ResetTable 3. Reset/Watchdog Timeout PeriodsMAX6316–MAX6322Watchdog and Manual Reset______________________________________________________________________________________13__Ordering Information (continued)a watchdog feature (see Selector Guide) are factory-trimmed to one of four watchdog timeout periods. Insert the letter corre-sponding to the desired watchdog timeout period (W, X, Y, or Z from Table 3) into the blank following the reset timeout suffix.TRANSISTOR COUNT: 191SUBSTRATE IS INTERNALLY CONNECTED TO V+Chip Informationdard versions only. The required order increment for nonstandard versions is 10,000 pieces. Contact factory for availability.M A X 6316–M A X 6322Watchdog and Manual Reset 14______________________________________________________________________________________Package Information(The package drawing(s) in this data sheet may not reflect the most current specifications. For the latest package outline information,go to /packages .)M axim cannot assume responsibility for use of any circuitry other than circuitry entirely embodied in a M axim product. No circuit patent licenses are implied. Maxim reserves the right to change the circuitry and specifications without notice at any time.Maxim Integrated Products, 120 San Gabriel Drive, Sunnyvale, CA 94086 408-737-7600 ____________________15©2007 Maxim Integrated Productsis a registered trademark of Maxim Integrated Products, Inc.MAX6316–MAX6322 Watchdog and Manual ResetRevision History。