微型机床变速箱及其结构特点分析
微型变速马达知识点总结
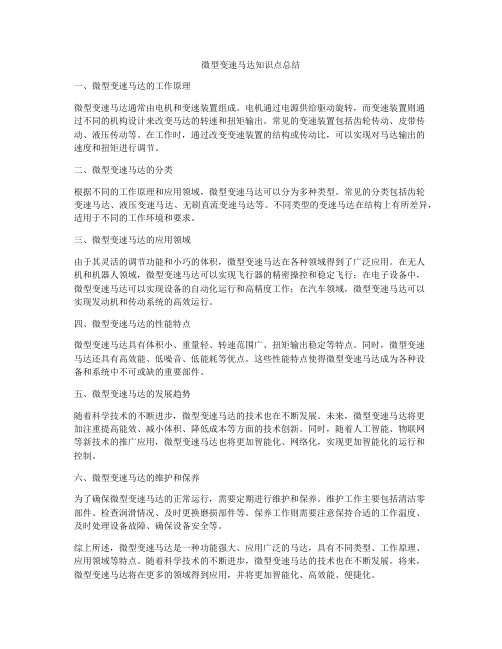
微型变速马达知识点总结一、微型变速马达的工作原理微型变速马达通常由电机和变速装置组成。
电机通过电源供给驱动旋转,而变速装置则通过不同的机构设计来改变马达的转速和扭矩输出。
常见的变速装置包括齿轮传动、皮带传动、液压传动等。
在工作时,通过改变变速装置的结构或传动比,可以实现对马达输出的速度和扭矩进行调节。
二、微型变速马达的分类根据不同的工作原理和应用领域,微型变速马达可以分为多种类型。
常见的分类包括齿轮变速马达、液压变速马达、无刷直流变速马达等。
不同类型的变速马达在结构上有所差异,适用于不同的工作环境和要求。
三、微型变速马达的应用领域由于其灵活的调节功能和小巧的体积,微型变速马达在各种领域得到了广泛应用。
在无人机和机器人领域,微型变速马达可以实现飞行器的精密操控和稳定飞行;在电子设备中,微型变速马达可以实现设备的自动化运行和高精度工作;在汽车领域,微型变速马达可以实现发动机和传动系统的高效运行。
四、微型变速马达的性能特点微型变速马达具有体积小、重量轻、转速范围广、扭矩输出稳定等特点。
同时,微型变速马达还具有高效能、低噪音、低能耗等优点。
这些性能特点使得微型变速马达成为各种设备和系统中不可或缺的重要部件。
五、微型变速马达的发展趋势随着科学技术的不断进步,微型变速马达的技术也在不断发展。
未来,微型变速马达将更加注重提高能效、减小体积、降低成本等方面的技术创新。
同时,随着人工智能、物联网等新技术的推广应用,微型变速马达也将更加智能化、网络化,实现更加智能化的运行和控制。
六、微型变速马达的维护和保养为了确保微型变速马达的正常运行,需要定期进行维护和保养。
维护工作主要包括清洁零部件、检查润滑情况、及时更换磨损部件等。
保养工作则需要注意保持合适的工作温度、及时处理设备故障、确保设备安全等。
综上所述,微型变速马达是一种功能强大、应用广泛的马达,具有不同类型、工作原理、应用领域等特点。
随着科学技术的不断进步,微型变速马达的技术也在不断发展。
数控机床变速箱设计与运行分析
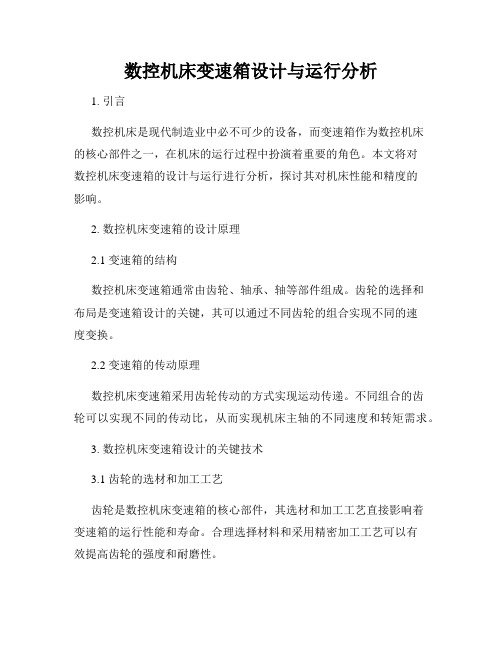
数控机床变速箱设计与运行分析1. 引言数控机床是现代制造业中必不可少的设备,而变速箱作为数控机床的核心部件之一,在机床的运行过程中扮演着重要的角色。
本文将对数控机床变速箱的设计与运行进行分析,探讨其对机床性能和精度的影响。
2. 数控机床变速箱的设计原理2.1 变速箱的结构数控机床变速箱通常由齿轮、轴承、轴等部件组成。
齿轮的选择和布局是变速箱设计的关键,其可以通过不同齿轮的组合实现不同的速度变换。
2.2 变速箱的传动原理数控机床变速箱采用齿轮传动的方式实现运动传递。
不同组合的齿轮可以实现不同的传动比,从而实现机床主轴的不同速度和转矩需求。
3. 数控机床变速箱设计的关键技术3.1 齿轮的选材和加工工艺齿轮是数控机床变速箱的核心部件,其选材和加工工艺直接影响着变速箱的运行性能和寿命。
合理选择材料和采用精密加工工艺可以有效提高齿轮的强度和耐磨性。
3.2 变速箱的布局和优化设计变速箱的布局和设计对机床性能和精度具有重要影响。
通过优化设计齿轮布局、减小齿轮间的传动误差和提高传动效率,可以进一步提高机床的加工精度和稳定性。
4. 数控机床变速箱运行分析4.1 变速箱的工作环境和要求数控机床变速箱在工作过程中面临着高速旋转、大负荷和连续工作等环境要求。
因此,变速箱的设计需要考虑传动效率、噪音和热量等问题,以确保机床的稳定运行和长寿命。
4.2 变速箱运行中的故障分析与处理数控机床变速箱在长时间运行中可能出现齿轮断齿、轴承损坏等故障。
及时发现并处理这些故障是保证机床正常运行的关键。
通过振动监测和润滑状态检测等手段,可以提前发现故障并进行维修。
5. 结论数控机床变速箱设计与运行分析对机床性能和精度具有重要影响。
合理的变速箱设计和优化运行分析可以提高机床的稳定性、加工精度和寿命。
在未来的发展中,需要进一步研究和优化变速箱的设计和运行,以满足不断提高的制造需求。
机床主轴变速箱设计
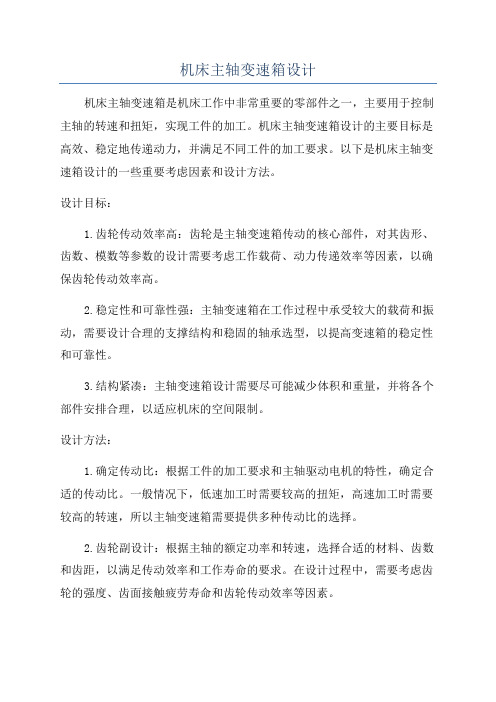
机床主轴变速箱设计机床主轴变速箱是机床工作中非常重要的零部件之一,主要用于控制主轴的转速和扭矩,实现工件的加工。
机床主轴变速箱设计的主要目标是高效、稳定地传递动力,并满足不同工件的加工要求。
以下是机床主轴变速箱设计的一些重要考虑因素和设计方法。
设计目标:1.齿轮传动效率高:齿轮是主轴变速箱传动的核心部件,对其齿形、齿数、模数等参数的设计需要考虑工作载荷、动力传递效率等因素,以确保齿轮传动效率高。
2.稳定性和可靠性强:主轴变速箱在工作过程中承受较大的载荷和振动,需要设计合理的支撑结构和稳固的轴承选型,以提高变速箱的稳定性和可靠性。
3.结构紧凑:主轴变速箱设计需要尽可能减少体积和重量,并将各个部件安排合理,以适应机床的空间限制。
设计方法:1.确定传动比:根据工件的加工要求和主轴驱动电机的特性,确定合适的传动比。
一般情况下,低速加工时需要较高的扭矩,高速加工时需要较高的转速,所以主轴变速箱需要提供多种传动比的选择。
2.齿轮副设计:根据主轴的额定功率和转速,选择合适的材料、齿数和齿距,以满足传动效率和工作寿命的要求。
在设计过程中,需要考虑齿轮的强度、齿面接触疲劳寿命和齿轮传动效率等因素。
3.轴承选型:根据主轴的受力情况和速度要求,选择合适的轴承类型和规格,并进行轴承的定位和支撑结构设计。
轴承的选用应能够承受主轴的径向和轴向载荷,并具有较高的转速限制。
4.润滑系统设计:主轴变速箱需要设计合理的润滑系统,以确保齿轮副和轴承的正常工作。
润滑系统应包括润滑油的供给和循环,以及冷却装置的设计,以控制变速箱的温度。
5.结构支撑设计:主轴变速箱需要设计合理的结构支撑,以保证变速箱的刚性和稳定性。
支撑结构应该能够减少变速箱的振动和变形,提高主轴的工作精度和稳定性。
综上所述,机床主轴变速箱的设计需要考虑齿轮传动效率、稳定性和可靠性、结构紧凑等因素,并根据工件的加工要求和主轴驱动电机的特性,确定合适的传动比、齿轮副设计、轴承选型、润滑系统设计和结构支撑设计等。
变速器箱体的结构特点和技术要求
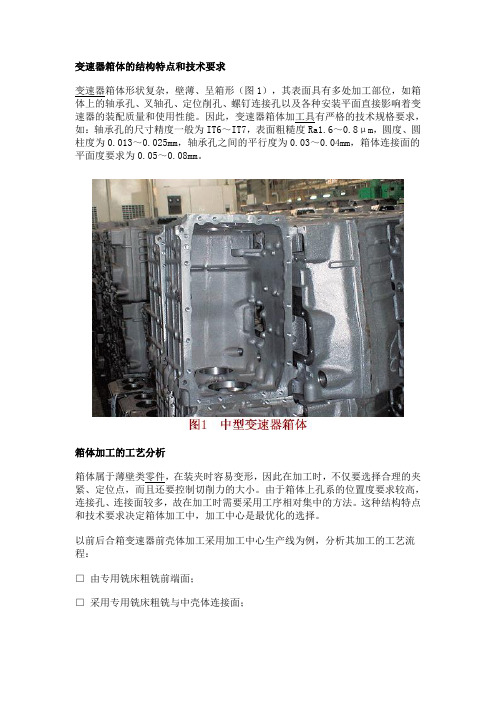
变速器箱体的结构特点和技术要求变速器箱体形状复杂,壁薄、呈箱形(图1),其表面具有多处加工部位,如箱体上的轴承孔、叉轴孔、定位削孔、螺钉连接孔以及各种安装平面直接影响着变速器的装配质量和使用性能。
因此,变速器箱体加工具有严格的技术规格要求,如:轴承孔的尺寸精度一般为IT6~IT7,表面粗糙度Ra1.6~0.8μm,圆度、圆柱度为0.013~0.025mm,轴承孔之间的平行度为0.03~0.04mm,箱体连接面的平面度要求为0.05~0.08mm。
箱体加工的工艺分析箱体属于薄壁类零件,在装夹时容易变形,因此在加工时,不仅要选择合理的夹紧、定位点,而且还要控制切削力的大小。
由于箱体上孔系的位置度要求较高,连接孔、连接面较多,故在加工时需要采用工序相对集中的方法。
这种结构特点和技术要求决定箱体加工中,加工中心是最优化的选择。
以前后合箱变速器前壳体加工采用加工中心生产线为例,分析其加工的工艺流程:□由专用铣床粗铣前端面;□ 采用专用铣床粗铣与中壳体连接面;□ 如图2所示,在立式加工中心上,完成半精铣、精铣前端面,钻、攻前端面与离合器壳体各连接孔,钻、铰叉轴孔和各种油孔;□ 如图3所示,在卧式加工中心上,完成与中壳连接面及连接孔、叉轴孔的加工,粗、精镗轴承孔、叉轴孔;□ 如图4所示,采用卧式加工中心粗精铣顶盖连接面、标牌平面、侧取力面及各面连接螺纹孔;□ 采用摇臂钻床钻斜油孔。
上述工艺过程的安排,具有如下特点:1、粗加工与精加工分开进行,可以消除零件加工时的内应力变形、提高加工效率。
2、用作精基准的部位(前端面及两个工艺孔)优先加工,这样使后序部位的加工具有了一个统一的工艺基准,简化了后序的设备工装,减少了工件的定位误差。
3、与传统的组合机床加工线比较,工艺路线大幅缩减,由原来的30多道工序缩减为6道工序,减少了机床的占地面积,减少了零件搬运过程中的磕碰伤。
4、柔性化程度更高,可以在一条生产线上加工多个品种,满足市场多样化的需求。
变速器箱体的结构特点和技术要求
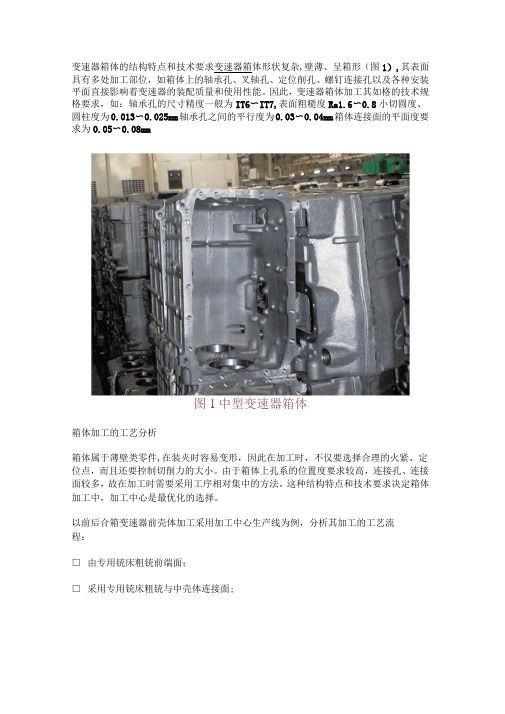
变速器箱体的结构特点和技术要求变速器箱体形状复杂,壁薄、呈箱形(图1),其表面具有多处加工部位,如箱体上的轴承孔、叉轴孔、定位削孔、螺钉连接孔以及各种安装平面直接影响着变速器的装配质量和使用性能。
因此,变速器箱体加工其如格的技术规格要求,如:轴承孔的尺寸精度一般为IT6〜IT7,表面粗糙度Ra1.6〜0.8小切圆度、圆柱度为0.013〜0.025mm轴承孔之间的平行度为0.03〜0.04mm箱体连接面的平面度要求为0.05〜0.08mm图1中型变速器箱体箱体加工的工艺分析箱体属于薄壁类零件,在装夹时容易变形,因此在加工时,不仅要选择合理的火紧、定位点,而且还要控制切削力的大小。
由于箱体上孔系的位置度要求较高,连接孔、连接面较多,故在加工时需要采用工序相对集中的方法。
这种结构特点和技术要求决定箱体加工中,加工中心是最优化的选择。
以前后合箱变速器前壳体加工采用加工中心生产线为例,分析其加工的工艺流程:□由专用铳床粗铳前端面;□采用专用铳床粗铳与中壳体连接面;□如图2所示,在立式加工中心上,完成半精铳、精铳前端面,钻、攻前端面与离合器壳体各连接孔,钻、较叉轴孔和各种油孔;前端面及与离合器连接孔的加工、其他孔的加工□如图3所示,在卧式加工中心上,完成与中壳连接面及连接孔、叉轴孔的加工,粗、精键轴承孔、叉轴孔;图3与中壳连接面及连接孔、叉轴孔的加工口如图4所示,采用卧式加工中心粗精铳顶盖连接面、标牌平面、侧取力面及各面连接螺纹孔;面、侧取力面及各面连接螺纹孔口采用摇臂钻床钻斜油孔。
上述工艺过程的安排,具有如下特点:1、粗加工与精加工分开进行,可以消除零件加工时的内应力变形、提高加工效率。
2、用作精基准的部位(前端面及两个工艺孔)优先加工,这样使后序部位的加工具有了一个统一的工艺基准,简化了后序的设备工装,减少了工件的定位误差。
3、与传统的组合机床加工线比较,工艺路线大幅缩减,由原来的30多道工序缩减为6道工序,减少了机床的占地面积,减少了零件搬运过程中的磕碰伤。
ZF变速箱结构特点解析

ZF变速箱结构特点解析1.多相离器设计:ZF变速箱采用多相离器设计,即每一组动力传输装置(多片式湿离合器或液体离合器)都对应一个离合器壳体,并能够独立控制。
这样的设计使得ZF变速箱能够在换挡过程中实现更快的换挡时间和更平顺的动力传递,同时提高了传动效率。
2.湿式润滑:ZF变速箱采用了湿式润滑系统,即在变速箱中加入润滑油来冷却和润滑传动部件。
相比于干式润滑系统,湿式润滑能够有效降低传动部件的磨损和噪音,延长变速箱的使用寿命。
3.扭矩转换器:ZF变速箱使用扭矩转换器来传递动力。
扭矩转换器是由泵轮、涡轮和液力偶合器组成的离合器装置,它能够将发动机的扭矩通过涡轮的转动传递给传动装置。
扭矩转换器的优点是能够提供较高的启动扭矩和传动效率,同时具有较好的减震和平顺性能。
4.换挡机构:ZF变速箱的换挡机构采用齿轮传动和湿式离合器组成。
在ZF变速箱中,通过控制湿式离合器的开合来实现换挡操作。
换挡机构结构简单可靠,换挡顺畅快速。
5.电子控制系统:ZF变速箱配备了先进的电子控制系统,通过精确的传感器和电脑控制单元对变速箱进行监测和控制。
电子控制系统能够根据行驶条件和驾驶者的需求,智能地选择合适的挡位和换挡时机,提高驾驶的舒适性和燃油经济性。
6.多挡位设计:ZF变速箱具有多挡位设计,通常包括6挡、8挡和9挡等。
多挡位设计能够在不同的行驶条件下选择合适的档位,提供更宽广的速比范围和更好的动力输出。
此外,多挡位设计还可以提高燃油经济性和降低噪音。
总体来说,ZF变速箱具有多相离器设计、湿式润滑、扭矩转换器、换挡机构、电子控制系统和多挡位设计等结构特点。
这些特点使得ZF变速箱具有换挡平顺快速、燃油经济性好、动力输出稳定等优点,被广泛应用于各种汽车和工程机械中。
变速箱的结构及工作原理
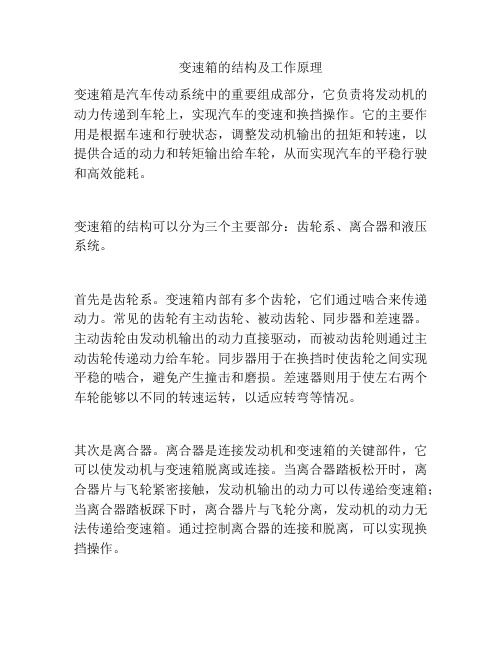
变速箱的结构及工作原理变速箱是汽车传动系统中的重要组成部分,它负责将发动机的动力传递到车轮上,实现汽车的变速和换挡操作。
它的主要作用是根据车速和行驶状态,调整发动机输出的扭矩和转速,以提供合适的动力和转矩输出给车轮,从而实现汽车的平稳行驶和高效能耗。
变速箱的结构可以分为三个主要部分:齿轮系、离合器和液压系统。
首先是齿轮系。
变速箱内部有多个齿轮,它们通过啮合来传递动力。
常见的齿轮有主动齿轮、被动齿轮、同步器和差速器。
主动齿轮由发动机输出的动力直接驱动,而被动齿轮则通过主动齿轮传递动力给车轮。
同步器用于在换挡时使齿轮之间实现平稳的啮合,避免产生撞击和磨损。
差速器则用于使左右两个车轮能够以不同的转速运转,以适应转弯等情况。
其次是离合器。
离合器是连接发动机和变速箱的关键部件,它可以使发动机与变速箱脱离或连接。
当离合器踏板松开时,离合器片与飞轮紧密接触,发动机输出的动力可以传递给变速箱;当离合器踏板踩下时,离合器片与飞轮分离,发动机的动力无法传递给变速箱。
通过控制离合器的连接和脱离,可以实现换挡操作。
最后是液压系统。
液压系统主要由油泵、液压控制阀和液压执行器组成。
油泵负责将液压油送到液压控制阀,液压控制阀根据驾驶员的操作信号控制液压油的流向和压力,从而控制齿轮的换挡。
液压执行器根据液压控制阀的信号,将液压油送到相应的离合器或制动器上,实现换挡和换挡过程中的平稳过渡。
变速箱的工作原理可以简单概括为:根据车速和行驶状态,通过控制离合器和液压系统,实现齿轮之间的换挡操作。
当车辆启动时,离合器踏板踩下,发动机输出的动力通过离合器传递给变速箱。
根据车速和行驶状态,液压系统控制相应的齿轮组合,并通过离合器的连接和脱离实现换挡操作。
当车辆需要加速时,液压系统会使高转速的齿轮组合与发动机连接,提供更大的扭矩输出;当车辆需要减速或停车时,液压系统会使低转速的齿轮组合与发动机连接,提供更低的扭矩输出。
总结起来,变速箱作为汽车传动系统中的重要组成部分,通过调整发动机输出的扭矩和转速,实现汽车的变速和换挡操作。
微型精密车床的设计

摘要微型精密车床的设计,它主要包括以下几个主要部分:床身、主轴箱组件、尾架组件、变速齿轮箱、丝杠等。
床身主要起支撑的作用,所有其他主要部件都安装在床身上,通常在床身上面有内外两组平行的导轨。
主轴箱组件是机床实现旋转运动的执行件,是机床上的一个关键组件。
主轴组件由主轴,主轴支撑和安装在主轴上的传动件,密封件组成。
尾座组件主要由三部分组成。
底座与床身的内侧导轨配合,并可以在导轨上做纵向移动,底座上有一个可以使整个尾座组件夹紧在任意位置上的装置。
变速箱主要通过齿轮的变速最终使刀具按主轴的转数纵向地或横向地精确移动。
采用滚珠丝杠,减小摩擦,提高了运动精度。
本设计主要设计进给部分,包括溜板箱的设计,丝杆的设计,步进电动机的选型和校核计算,刀架的设计。
由于微型精密车床体积小,质量轻,便于运输。
所以微型精密车床得到了广泛的应用关键词微型精密滚珠丝杠溜板箱组件刀架步进电动机AbstractMicro precision lathes design, it mainly includes the following main parts: lathe bed, headstock assembly, tailstock assembly, quick-change gear box ,leadscrew, etc. The bed`s main effect is supporting, all other major components are installed in bed, usually in bed with internal and external two groups of parallel ways. headstock assembly is the realization of rotating machine tools, implementation is a key component. headstock assembly is made up of spindle, spindle support and installed in the transmission shaft and seals. tailstock assembly mainly consists of three parts. Pedestal and the inside of the bed, and can guide ways longitudinal move in on a pedestal, can make whole tailstock assembly clamping device in any position. The quick-change box mainly though changegears eventually made by cutting the number of vertical shaft by turning horizontally o r precise movement. Using the leadscrew, reducing friction, improve the motion precision. This design mainly design the feed part, including the carriage design, leadscrew design, the design of stepping motor selection and design of the check calculation, the tool post design. Because the micro precision lathe, small size, light quality, easy to transport. So the micro precision lathes are widely applied. Keywords micro precision leadscrew carriage assembly tool post stepping motor目录前言 (5)1.绪论 (6)1.1 设计的目的和意义 (6)1.2 微型机械加工技术发展现状趋势分析 (6)1.3 微型精密车床的现状 (7)2.微型精密车床总体方案拟定 (9)2.1 进给部分电动机的选用 (9)2.1.1 步进电动机及其发展 (9)2.1.2步进电动机的特点 (10)2.1.3 步进电动机的类型 (10)2.1.4 步进电机的工作原理 (11)2.1.5 步进电机的常用参数 (12)2.1.6 步进电机具有如下优点 : (13)2.2 丝杆螺母的选用 (14)2.3机床导轨及尾座的设计 (14)2.4 机床床身的设计 (14)3.纵向进给机构设计 (17)3.1 进给系统的概述和总体方案设计 (17)3.2 滚珠丝杠螺母的概述 (17)3.2.1 滚珠丝杠螺母工作原理及其特点 (17)3.2.2 滚珠丝杠螺母的结构循环方式 (18)3.3 丝杆螺母副的选择 (21)3.3.1内循环与外循环的选用说明 (21)3.3.2 滚珠丝杠的轴向间隙调整和预紧方法 (21)3.3.3.滚珠丝杠的安装 (21)3.4 滚珠丝杠螺母副的计算 (22)3.5 滚珠丝杠螺母副的验算 (24)3.5.1 刚度计算 (24)3.5.2 稳定性验算: (25)3.5.3丝杠系统的刚度计算: (26)3.5.4 反向死区的验算: (26)3.6 滚珠丝杠的设计与计算 (27)3.6.1 切削力的计算 (28)3.6.2 滚珠丝杠设计计算 (29)3.7 纵向步进电动机的验算 (30)3.8 消隙齿轮的计算 (34)3.9 消隙轴的设计 (39)3.10 动力计算 (44)3.10.1 小齿轮的转动惯量 (44)3.10.3 计算工作台的转动惯量JW (45)3.10.4 计算丝杠的转动惯量Js (45)4.横向进给机构的设计 (46)4.1 横向滚珠丝杠螺母副的型号选择与校核步骤 (46)4.1.1型号选择 (46)4.1.2 横向滚珠丝杠的校核 (46)4.2 横向进给系统的设计和计算 (47)4.2.1 横向进给系统的设计 (47)4.2.2 横向进给系统的设计和计算 (47)4.2.3 滚珠丝杠设计计算 (48)4.2.4 动载强度计算 (49)4.2.5 静强度计算 (51)4.2.6 临界转速校核 (51)4.2.7 额定寿命的校核 (52)4.3 横向进给步进电机的计算 (52)5. 刀架的设计 (54)5.1 减速传动机构的设计 (54)5.2 自动回转刀架的工作原理 (55)结论 (60)致谢 (61)参考文献 (62)前言大学的学习生活即将结束,大学学习生活中的最后一个环节也是最重要一个环节——毕业设计,它是对所学知识和技能的综合运用和检验。
微型机床变速箱及其结构特点分析
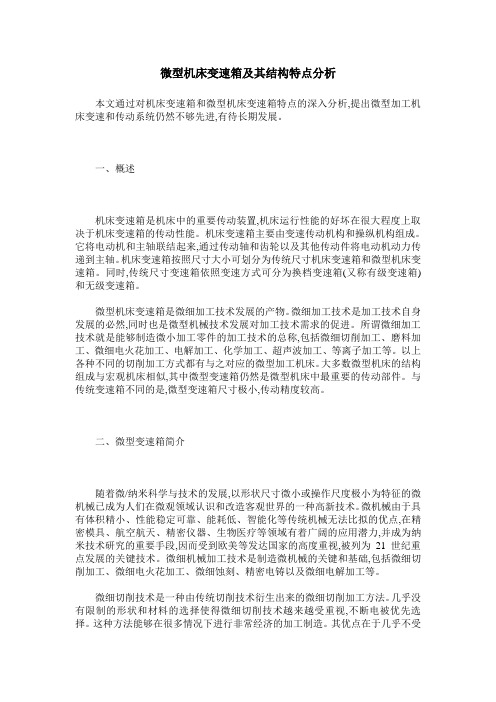
微型机床变速箱及其结构特点分析本文通过对机床变速箱和微型机床变速箱特点的深入分析,提出微型加工机床变速和传动系统仍然不够先进,有待长期发展。
一、概述机床变速箱是机床中的重要传动装置,机床运行性能的好坏在很大程度上取决于机床变速箱的传动性能。
机床变速箱主要由变速传动机构和操纵机构组成。
它将电动机和主轴联结起来,通过传动轴和齿轮以及其他传动件将电动机动力传递到主轴。
机床变速箱按照尺寸大小可划分为传统尺寸机床变速箱和微型机床变速箱。
同时,传统尺寸变速箱依照变速方式可分为换档变速箱(又称有级变速箱)和无级变速箱。
微型机床变速箱是微细加工技术发展的产物。
微细加工技术是加工技术自身发展的必然,同时也是微型机械技术发展对加工技术需求的促进。
所谓微细加工技术就是能够制造微小加工零件的加工技术的总称,包括微细切削加工、磨料加工、微细电火花加工、电解加工、化学加工、超声波加工、等离子加工等。
以上各种不同的切削加工方式都有与之对应的微型加工机床。
大多数微型机床的结构组成与宏观机床相似,其中微型变速箱仍然是微型机床中最重要的传动部件。
与传统变速箱不同的是,微型变速箱尺寸极小,传动精度较高。
二、微型变速箱简介随着微/纳米科学与技术的发展,以形状尺寸微小或操作尺度极小为特征的微机械已成为人们在微观领域认识和改造客观世界的一种高新技术。
微机械由于具有体积精小、性能稳定可靠、能耗低、智能化等传统机械无法比拟的优点,在精密模具、航空航天、精密仪器、生物医疗等领域有着广阔的应用潜力,并成为纳米技术研究的重要手段,因而受到欧美等发达国家的高度重视,被列为21世纪重点发展的关键技术。
微细机械加工技术是制造微机械的关键和基础,包括微细切削加工、微细电火花加工、微细蚀刻、精密电铸以及微细电解加工等。
微细切削技术是一种由传统切削技术衍生出来的微细切削加工方法。
几乎没有限制的形状和材料的选择使得微细切削技术越来越受重视,不断电被优先选择。
这种方法能够在很多情况下进行非常经济的加工制造。
变速箱结构与原理

变速箱结构与原理在汽车工程中,变速箱被认为是车辆传动系统的核心部件之一。
它的作用是将发动机的输出转矩通过不同齿轮比例的调整,提供适合不同行驶状态和路况的扭矩输出,以达到更高的速度或更大的爬坡能力。
本文将详细介绍变速箱的结构与工作原理。
一、变速箱结构1. 齿轮系统:变速箱的核心部分是齿轮系统。
它由主轴、从轴和齿轮组成。
主轴连着发动机,从轴则连接传动轴。
通过主轴和从轴上的齿轮之间的啮合,扭矩被传送到传动轴,从而推动车辆行驶。
2. 离合器:变速箱中的离合器主要用于断开发动机和变速箱之间的连接。
当车辆停止或换挡时,离合器可以使发动机与变速箱脱离,避免熄火或者损坏其他传动部件。
3. 轴承:变速箱中的轴承主要用于支撑和固定齿轮。
它们减少了齿轮与壳体之间的摩擦,并保持齿轮的稳定运行。
4. 润滑系统:变速箱的润滑系统用于提供润滑油,降低齿轮和轴承的摩擦,并帮助散热。
润滑油还可以冲洗齿轮系统的沉积物,保证变速箱长期稳定运行。
5. 操作装置:变速箱的操作装置包括换挡杆和换挡机构。
通过操作换挡杆,驾驶员可以选择前进、倒退、停车等不同的驾驶模式。
二、变速箱的工作原理变速箱的工作原理基于齿轮的不同啮合比例,以调整发动机输出的扭矩。
下面将介绍自动变速箱和手动变速箱的工作原理。
1. 自动变速箱工作原理:自动变速箱通过液压系统和离合器控制来实现换挡过程。
当车辆行驶时,变速箱内的液压泵会将液压油传输至液压控制单元。
该单元通过控制离合器的开闭程度,调整齿轮的输入和输出比例,从而实现平稳的换挡过程。
2. 手动变速箱工作原理:手动变速箱的工作原理相对简单。
驾驶员通过踩离合器,将发动机与变速箱分离。
然后利用换挡杆选择不同的齿轮比例,再通过松开离合器使发动机重新连接到变速箱,实现换挡过程。
三、变速箱的优势和应用变速箱作为汽车传动系统的重要组成部分,具有以下优势和应用:1. 提供多种行驶模式选择:变速箱可以根据行驶状态和路况,提供不同的变速比例,以满足驾驶员的需求。
铣床变速原理

铣床变速原理
铣床变速原理即是通过变速机构来实现铣床主轴的转速调节。
铣床通常会配备一个变速箱,在变速箱内部设置了不同的齿轮组合,以改变传动比例来达到变速的目的。
变速箱通常由输入轴、输出轴和多个齿轮组成。
输入轴通过电机或液压系统驱动,将动力传递给变速箱。
输出轴与铣床的主轴连接,将动力传输到铣刀。
齿轮组则根据不同的传动比例来控制主轴的转速。
当需要调节主轴转速时,可以通过改变输入轴的转速来实现。
通过选择不同的齿轮组合,变速箱可以将输入轴的转速按照一定比例传递到输出轴。
较大的齿轮组会降低转速,而较小的齿轮组则会提高转速。
通过不同齿轮组的组合,可以得到多种不同的转速选择。
变速箱内的齿轮组通常由电机或操作杆来控制。
通过调节齿轮组的位置或使用不同的齿轮组,可以实现不同的速度选择。
有些铣床还可以配备变频器,通过改变电机输入的频率来实现主轴转速的调节。
铣床变速原理的主要目的是为了适应不同的加工需求。
不同的工件和加工材料对于铣刀的转速有不同的要求。
通过变速机构的调节,可以使铣床在加工过程中达到最佳的效果。
机床变速箱拆装实训报告

一、实训目的1. 熟悉机床变速箱的结构、原理和拆装方法;2. 培养动手操作能力,提高实际操作技能;3. 增强团队协作意识,提高沟通能力;4. 深入了解机床变速箱的工作原理,为今后的学习和工作打下基础。
二、实训内容1. 机床变速箱的结构及工作原理;2. 机床变速箱的拆装步骤;3. 机床变速箱的故障诊断与排除。
三、实训过程1. 机床变速箱的结构及工作原理机床变速箱是机床的动力传输装置,主要作用是将电动机的旋转运动转换为机床所需的旋转或直线运动,以满足机床加工的需求。
机床变速箱主要由输入轴、输出轴、齿轮、轴承、离合器、制动器等部件组成。
机床变速箱的工作原理:电动机通过输入轴将动力传递给离合器,离合器将动力传递给制动器,制动器使齿轮啮合,齿轮转动带动输出轴旋转,实现机床的运动。
2. 机床变速箱的拆装步骤(1)拆卸前准备1)检查机床变速箱的防护罩,确保安全;2)将机床变速箱与机床分离,断开电源;3)准备拆装工具,如扳手、螺丝刀、钳子等。
(2)拆卸步骤1)拆卸输入轴:拧下输入轴轴承盖螺丝,取下轴承盖,拆卸输入轴;2)拆卸输出轴:拧下输出轴轴承盖螺丝,取下轴承盖,拆卸输出轴;3)拆卸齿轮:拆卸齿轮前,先检查齿轮啮合情况,如有异常,应先进行修复;4)拆卸轴承:拧下轴承座螺丝,取下轴承座,拆卸轴承;5)拆卸离合器、制动器:拆卸离合器、制动器时,注意检查其磨损情况,如有异常,应进行更换;6)清理机床变速箱内部,检查各部件磨损情况。
(3)组装步骤1)组装轴承:将轴承安装在轴承座上,拧紧轴承座螺丝;2)组装齿轮:将齿轮安装在输出轴上,检查齿轮啮合情况,确保啮合正常;3)组装离合器、制动器:将离合器、制动器安装在变速箱内部,确保其工作正常;4)组装输出轴:将输出轴安装在轴承座上,拧紧轴承座螺丝;5)组装输入轴:将输入轴安装在轴承盖内,拧紧轴承盖螺丝;6)组装机床变速箱:将机床变速箱与机床连接,确保连接牢固。
3. 机床变速箱的故障诊断与排除(1)故障现象:机床变速箱齿轮啮合异常,发出噪音;(2)故障原因:齿轮磨损、齿轮间隙过大;(3)排除方法:更换齿轮、调整齿轮间隙。
车床变速箱拆装实习报告

一、实习目的本次实习旨在通过实际操作,使学生掌握车床变速箱的拆装方法、步骤和注意事项,加深对车床变速箱结构和工作原理的理解,提高动手能力和实际操作技能。
二、实习内容1. 车床变速箱的结构与工作原理- 了解车床变速箱的整体结构,包括输入轴、输出轴、齿轮、轴承、离合器等主要部件。
- 研究变速箱的工作原理,了解各部件之间的配合关系和动力传递过程。
2. 变速箱的拆装步骤- 拆卸变速箱:按照拆卸顺序,依次拆除输入轴、输出轴、齿轮、轴承、离合器等部件。
- 检查各部件:检查各部件的磨损情况、损坏情况,并进行必要的维修或更换。
- 组装变速箱:按照组装顺序,依次安装各部件,确保各部件之间的配合关系正确。
3. 拆装过程中的注意事项- 操作安全:穿戴好防护用品,如安全帽、手套、眼镜等。
- 严格按照拆装步骤进行操作,避免损坏部件。
- 注意各部件的标记和位置,确保组装时能够正确放置。
三、实习步骤1. 准备工作- 确保车床变速箱处于停止状态,切断电源。
- 检查工具和设备是否齐全,如扳手、螺丝刀、拉力器等。
2. 拆卸变速箱- 首先拆除输入轴,拆卸时注意不要损坏轴上的齿轮和轴承。
- 然后拆除输出轴,拆卸时注意不要损坏轴上的齿轮和轴承。
- 接下来拆除齿轮、轴承、离合器等部件,拆卸过程中注意记录各部件的标记和位置。
3. 检查与维修- 检查各部件的磨损情况、损坏情况,并进行必要的维修或更换。
- 检查齿轮、轴承、离合器等部件的配合关系,确保无松动或卡滞现象。
4. 组装变速箱- 按照拆卸时的记录,依次组装各部件。
- 注意各部件的标记和位置,确保组装时能够正确放置。
- 组装完成后,进行试运转,检查变速箱是否正常工作。
四、实习体会通过本次实习,我深刻体会到以下几方面:1. 理论与实践相结合的重要性:通过实际操作,加深了对车床变速箱结构和工作原理的理解,将课堂所学知识应用于实践。
2. 动手能力的提高:在实习过程中,我学会了使用各种工具和设备,提高了自己的动手能力。
机床变速箱的结构特性分析
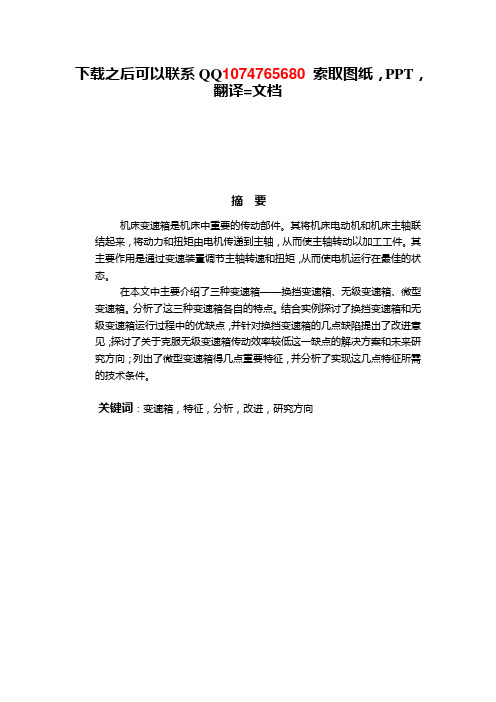
下载之后可以联系QQ1074765680索取图纸,PPT,翻译=文档摘要机床变速箱是机床中重要的传动部件。
其将机床电动机和机床主轴联结起来,将动力和扭矩由电机传递到主轴,从而使主轴转动以加工工件。
其主要作用是通过变速装臵调节主轴转速和扭矩,从而使电机运行在最佳的状态。
在本文中主要介绍了三种变速箱——换挡变速箱、无级变速箱、微型变速箱。
分析了这三种变速箱各自的特点。
结合实例探讨了换挡变速箱和无级变速箱运行过程中的优缺点,并针对换挡变速箱的几点缺陷提出了改进意见;探讨了关于克服无级变速箱传动效率较低这一缺点的解决方案和未来研究方向;列出了微型变速箱得几点重要特征,并分析了实现这几点特征所需的技术条件。
关键词:变速箱,特征,分析,改进,研究方向Analysis of the structural characteristics of gear-box of machine toolAbstractThe gearbox of machine is the most important transmission part of machine tool. The machine motor and the machine tool spindle are linked by it, and it deliveries power and torque from machine motor to machine tool spindle, so the machine tool spindle can rotate to process the work piece. The main role of the gearbox machine is to regulate the speed and torque of the spindle with the variable-speed device ,so the motor can run in a best state.In this article three kinds of gearboxes are introduced (Shift Gearbox; Continuously Variable Trans-mission; Micro Gearbox); The features of each kind of three gearboxes are analysized ; The advantages and disadvantages of Shift Gearbox and Continuously Variable Trans-mission are discussied with examples ,and some improvements are made for some defects of Shift Gearbox .The solutions and the direction of future research arediscussied to overcome the disadvantages of the CVT ,which is inefficient ;Some important features of Micro Gearbox are stated ,and The technical conditions ,using to achieve the features ,are considered.Key words: Gearbox,Feature, Analysis,Improvements,Direction of research目录1.绪论 (27)1.1概述 (27)1.2 变速箱的发展状况 (28)1.3 研究目的、意义和内容 (29)2.换挡变速箱 (29)2.1换挡变速箱的特点 (29)2.2 CA6140车床换挡变速箱结构分析 (29)2.3 关于换挡变速箱的部分改进意见 (33)3. 无级变速箱 (36)3.1无级变速箱的简介和发展 (36)3.2 两种无级变速箱工作原理 (38)3.2.1 液压无级变速器 (38)3.2.2摩擦盘式无级变速器 (39)3.3 关于提高无级变速箱效率的方法探究 (41)4.微型机床变速箱 (41)4.1微型变速箱简介 (41)4.2 微型变速箱的特点 (42)4.3 微型变速箱特点的深入分析 (42)5. 结论 (44)谢辞 (45)参考文献 (46)1.绪论1.1概述机床变速箱是机床中的重要的传动装臵,机床运行性能的好坏很大程度上决定于机床变速箱的传动性能。
微型无级变速车床
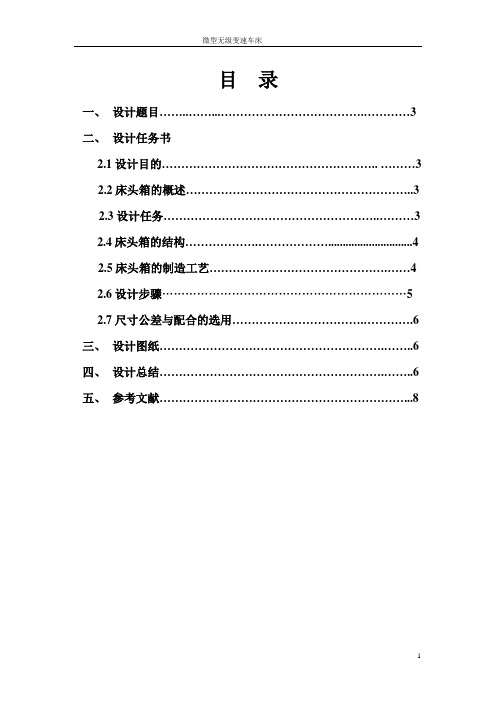
目录一、设计题目 (3)二、设计任务书2.1设计目的........................................................ (3)2.2床头箱的概述 (3)2.3设计任务 (3)2.4床头箱的结构 (4)2.5床头箱的制造工艺 (4)2.6设计步骤 (5)2.7尺寸公差与配合的选用 (6)三、设计图纸 (6)四、设计总结 (6)五、参考文献 (8)一、设计题目设计题目:微型无级变速车床设计零件:床头箱二、设计任务书2.1设计目的(1)了解微型无级变速车床床头箱的结构及工作方式。
(2)灵活运用所学知识,熟练掌握制图工具,学会查阅专业资料,在构思及分析方面得到综合训练。
(3)培养我们建立正确的设计思路,掌握基本的设计方法,提升我们初步的结构设计能力。
2.2床头箱的概述床头箱,又称主轴箱,采用多级齿轮传动,主要任务是通过一定的传动系统,经主轴箱内各个位置上的传动齿轮和传动轴,最后把运动传到主轴上,使主轴获得规定的转速和方向。
床头箱对主轴起着支承作用,使主轴在轴承上平稳运转,主轴运转的平稳性直接影响工件的加工质量。
2.3设计任务为了满足机器的各项要求,必须以组成机器的机械零件的正确设计和制造为前提。
零件的设计的好坏,将对机器使用性能的优劣起着决定性的作用。
(1)类型选择根据使用条件及载荷性质。
尺寸大小的选择零件的类型。
为此,必须对各种常用的机械零件的类型。
特点及适用范围有明确的了解。
(2)受力分析通过受力分析求出作用在零件上的负荷,以便进行设计计算准则。
(3)选择材料根据零件工作条件及受力情况,选择合适的材料,并确定计算中的许用应力等。
(4)确定计算准则根据失效分析确定出零件的设计计算准则。
(5)理论设计计算由设计准则所得到的设计计算公式,确定出零件的相关参数。
(6)结构设计根据功能要求、加工及装配工艺性的要求等进行零件的结构设计,确定出其结构尺寸。
(7)精确校核零件全部设计完成后,对有些重要的零件应进行详细的校核计算,以判定结构的合理性。
箱体类零件的功用及结构特点
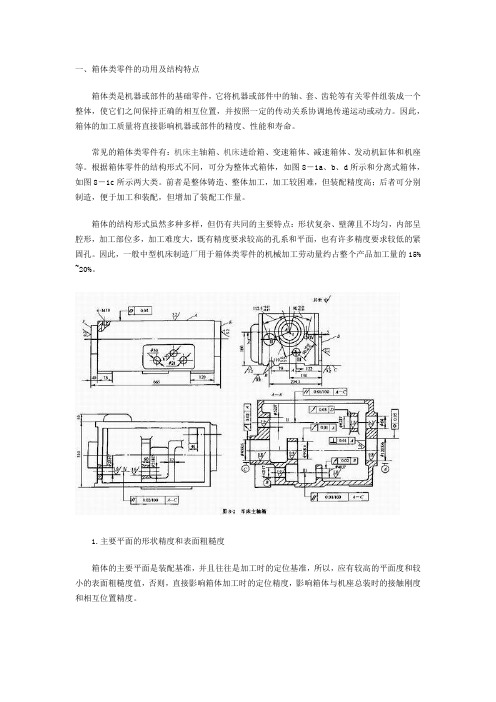
一、箱体类零件的功用及结构特点箱体类是机器或部件的基础零件,它将机器或部件中的轴、套、齿轮等有关零件组装成一个整体,使它们之间保持正确的相互位置,并按照一定的传动关系协调地传递运动或动力。
因此,箱体的加工质量将直接影响机器或部件的精度、性能和寿命。
常见的箱体类零件有:机床主轴箱、机床进给箱、变速箱体、减速箱体、发动机缸体和机座等。
根据箱体零件的结构形式不同,可分为整体式箱体,如图8-1a、b、d所示和分离式箱体,如图8-1c所示两大类。
前者是整体铸造、整体加工,加工较困难,但装配精度高;后者可分别制造,便于加工和装配,但增加了装配工作量。
箱体的结构形式虽然多种多样,但仍有共同的主要特点:形状复杂、壁薄且不均匀,内部呈腔形,加工部位多,加工难度大,既有精度要求较高的孔系和平面,也有许多精度要求较低的紧固孔。
因此,一般中型机床制造厂用于箱体类零件的机械加工劳动量约占整个产品加工量的15% ~20%。
1.主要平面的形状精度和表面粗糙度箱体的主要平面是装配基准,并且往往是加工时的定位基准,所以,应有较高的平面度和较小的表面粗糙度值,否则,直接影响箱体加工时的定位精度,影响箱体与机座总装时的接触刚度和相互位置精度。
一般箱体主要平面的平面度在0.1~0.03mm,表面粗糙度ra2.5~0.63μm,各主要平面对装配基准面垂直度为0.1/300。
2.孔的尺寸精度、几何形状精度和表面粗糙度箱体上的轴承支承孔本身的尺寸精度、形状精度和表面粗糙度都要求较高,否则,将影响轴承与箱体孔的配合精度,使轴的回转精度下降,也易使传动件(如齿轮)产生振动和噪声。
一般机床主轴箱的主轴支承孔的尺寸精度为it6,圆度、圆柱度公差不超过孔径公差的一半,表面粗糙度值为ra0.63~0.32μm。
其余支承孔尺寸精度为it7~it6,表面粗糙度值为ra2.5~0.63μm。
3.主要孔和平面相互位置精度同一轴线的孔应有一定的同轴度要求,各支承孔之间也应有一定的孔距尺寸精度及平行度要求,否则,不仅装配有困难,而且使轴的运转情况恶化,温度升高,轴承磨损加剧,齿轮啮合精度下降,引起振动和噪声,影响齿轮寿命。
微型汽车手动变速器结构原理与型式分析
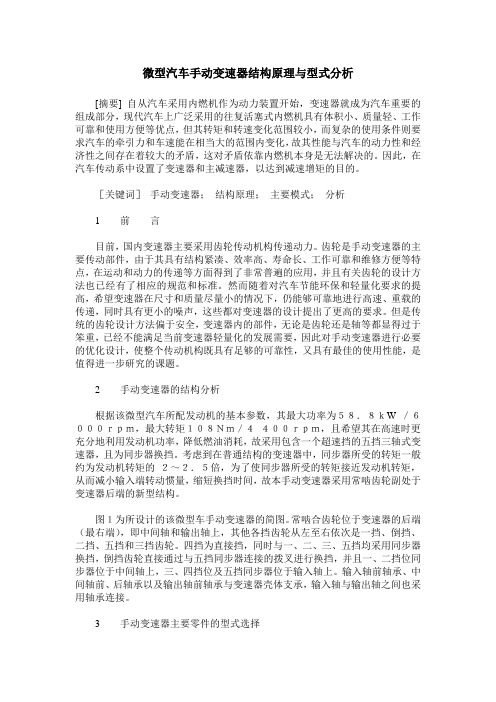
微型汽车手动变速器结构原理与型式分析[摘要] 自从汽车采用内燃机作为动力装置开始,变速器就成为汽车重要的组成部分,现代汽车上广泛采用的往复活塞式内燃机具有体积小、质量轻、工作可靠和使用方便等优点,但其转矩和转速变化范围较小,而复杂的使用条件则要求汽车的牵引力和车速能在相当大的范围内变化,故其性能与汽车的动力性和经济性之间存在着较大的矛盾,这对矛盾依靠内燃机本身是无法解决的。
因此,在汽车传动系中设置了变速器和主减速器,以达到减速增矩的目的。
[关键词]手动变速器;结构原理;主要模式;分析1 前言目前,国内变速器主要采用齿轮传动机构传递动力。
齿轮是手动变速器的主要传动部件,由于其具有结构紧凑、效率高、寿命长、工作可靠和维修方便等特点,在运动和动力的传递等方面得到了非常普遍的应用,并且有关齿轮的设计方法也已经有了相应的规范和标准。
然而随着对汽车节能环保和轻量化要求的提高,希望变速器在尺寸和质量尽量小的情况下,仍能够可靠地进行高速、重载的传递,同时具有更小的噪声,这些都对变速器的设计提出了更高的要求。
但是传统的齿轮设计方法偏于安全,变速器内的部件,无论是齿轮还是轴等都显得过于笨重,已经不能满足当前变速器轻量化的发展需要,因此对手动变速器进行必要的优化设计,使整个传动机构既具有足够的可靠性,又具有最佳的使用性能,是值得进一步研究的课题。
2 手动变速器的结构分析根据该微型汽车所配发动机的基本参数,其最大功率为58.8kW /6000rpm,最大转矩108Nm/4400rpm,且希望其在高速时更充分地利用发动机功率,降低燃油消耗,故采用包含一个超速挡的五挡三轴式变速器,且为同步器换挡。
考虑到在普通结构的变速器中,同步器所受的转矩一般约为发动机转矩的2~2.5倍,为了使同步器所受的转矩接近发动机转矩,从而减小输入端转动惯量,缩短换挡时间,故本手动变速器采用常啮齿轮副处于变速器后端的新型结构。
图1为所设计的该微型车手动变速器的简图。
- 1、下载文档前请自行甄别文档内容的完整性,平台不提供额外的编辑、内容补充、找答案等附加服务。
- 2、"仅部分预览"的文档,不可在线预览部分如存在完整性等问题,可反馈申请退款(可完整预览的文档不适用该条件!)。
- 3、如文档侵犯您的权益,请联系客服反馈,我们会尽快为您处理(人工客服工作时间:9:00-18:30)。
微型机床变速箱及其结构特点分析
作者:刘会明
来源:《职业·下旬》2010年第03期
本文通过对机床变速箱和微型机床变速箱特点的深入分析,提出微型加工机床变速和传动
系统仍然不够先进,有待长期发展。
一、概述
机床变速箱是机床中的重要传动装置,机床运行性能的好坏在很大程度上取决于机床变速
箱的传动性能。
机床变速箱主要由变速传动机构和操纵机构组成。
它将电动机和主轴联结起来,通过传动轴和齿轮以及其他传动件将电动机动力传递到主轴。
机床变速箱按照尺寸大小可划分为传统尺寸机床变速箱和微型机床变速箱。
同时,传统尺寸变速箱依照变速方式可分为换档变
速箱(又称有级变速箱)和无级变速箱。
微型机床变速箱是微细加工技术发展的产物。
微细加工技术是加工技术自身发展的必然,
同时也是微型机械技术发展对加工技术需求的促进。
所谓微细加工技术就是能够制造微小加工零件的加工技术的总称,包括微细切削加工、磨料加工、微细电火花加工、电解加工、化学加工、超声波加工、等离子加工等。
以上各种不同的切削加工方式都有与之对应的微型加工机床。
大多数微型机床的结构组成与宏观机床相似,其中微型变速箱仍然是微型机床中最重要的
传动部件。
与传统变速箱不同的是,微型变速箱尺寸极小,传动精度较高。
二、微型变速箱简介
随着微/纳米科学与技术的发展,以形状尺寸微小或操作尺度极小为特征的微机械已成为人们在微观领域认识和改造客观世界的一种高新技术。
微机械由于具有体积精小、性能稳定可靠、能耗低、智能化等传统机械无法比拟的优点,在精密模具、航空航天、精密仪器、生物医
疗等领域有着广阔的应用潜力,并成为纳米技术研究的重要手段,因而受到欧美等发达国家的高度重视,被列为21世纪重点发展的关键技术。
微细机械加工技术是制造微机械的关键和基础,包括微细切削加工、微细电火花加工、微细蚀刻、精密电铸以及微细电解加工等。
微细切削技术是一种由传统切削技术衍生出来的微细切削加工方法。
几乎没有限制的形状和材料的选择使得微细切削技术越来越受重视,不断电被优先选择。
这种方法能够在很多情况下进行非常经济的加工制造。
其优点在于几乎不受形状的限制,特别是在使用5轴机床时,每一种切削材料哪怕一次只生产几件,也能够很经济系列地进行加工。
但为了保证工艺的安全,必须满足一系列的条件。
必须保证零件的尺寸偏差在几微米以内,且表面粗糙度很低,主要包括微细车削、微细铣削、微细钻削、微细磨削、微冲压等。
与宏观加工类似,也需要微细车床以及相应的控制和传动系统。
我们把微型机床中所应用的变速装置称为微型机床变速箱。
三、微型变速箱的特点
与宏观机床变速箱相比较,微型机床变速箱的传动原理和其内部组件基本相同,但是微型机床变速箱在尺寸上要小得多。
由此使得微型机床变速箱具有许多其自身特点:
第一,由于微型变速箱箱体尺寸的限制,变速箱内部各传动件的尺寸都极小。
同时,其传动链长度也受到了很大的限制。
第二,微型机床变速箱中的主轴直径极小,但是微细切削在加工工件时所需的切削速度较大。
为满足加工条件、保证工件加工质量,主轴的转速应当相当高。
这也意味着箱体内其他传动件的转速同时也很高。
第三,需要精度很高的微细操作和装配技术。
在狭窄的空间内进行微操作要同时具有微动和微型,也就是说,操
作器能够进行微米尺度的微操作,同时还需要兼顾操作本体的微小性。
四、微型变速箱特点分析
下面对以上几点展开进行分析。
微型变速箱箱体体积限制了传动件的尺寸和传动链的长度,但是由于现代微细加工技术的逐步发展和成熟,通过许多现代化的加工方法能够加工出尺寸极小且精度相当高的传动齿轮以及传动轴。
这在技术上保证了微型化的要求。
现代化的微机械加工方法有微细电火花加工、离子束刻蚀、LIGA技术。
除以上几种微细加工方法外,还有多种特种微细加工方法可以加工出尺寸极小的传动件,同时在考虑变速箱的制造成本和精度要求时为我们提供了多重的选择空间。
变速箱的主轴转速的高低主要取决于电动机的性能。
目前电动机主要分为静电式和电磁式两种。
静电式电机结构简单,易于实现电动机的微型化,但是其转速较低,不能满足微型机床的加工要求。
电磁式电机结构中包含产生场的线圈,不易实现电机的微小型化,但是近些年来通过在这一领域的研究实践,已经开发出可以满足尺寸以及转速条件的微型电磁式电机。
另外,为满足高速运转的要求,微型变速箱中传动轴的支承轴承在工作时摩擦阻力应当尽可能小,同时也必须做到微型。
因此,可以选用空气静压轴承,其结构为圆柱面径向、平面止推型,前后径向轴承采用双轴承,同轴套结构,可以很好地保证同轴结构,同时摩擦系数也相当小。
微装配是指毫米以下大于纳米的器件装配,微装配并不是一个新兴的领域,它很早就存在于人们的生活中,如钟表的装配。
只不过随着微机电系统(MEMS)和纳米技术(nanotechnology)的发展,以及人们在生活中对微产品的迫切需要,微装配技术的地位越来越重要。
为了保证微型变速箱的传动精度和性能,在装配时需要采用先进的微型装配技术。
1. 使用微机械手的装配
机械手因具有操作灵活,柔性好, 能适应各种作业的特点,在现代工业中被广泛应用。
在微装配中,由于要求的定位精度高,必须使得微机械手有高的制造精度,零件的公差必须被限制在纳米范围内,装配时必须控制振动、摩擦、热膨胀和计算误差,虽然在“宏” 装配中这些因素可以忽略,但在微装配中它们起着举足轻重的作用,同时这些微机械手在使用中要经常维护和标定。
机械手用压电器件作为微机器人的腿,以蠕动的方式运动,运动速度可达30 mm,机械手具有三个自由度(两个平移,一个旋转)在一个玻璃平台上移动,它具有一个可拆换的三自由度手爪,能达到工作空间的任一点,玻璃平板被固定在桌子上。
一个固定摄像机被用来控制机械手爪的精
确定位,另一个摄像机和激光测距仪被用来控制机械手的粗定位。
2. 微型零件的胶结技术
近年来, 国外许多企业和研究机构致力于开发高质量的胶黏剂和胶滴点样技术。
无论在胶黏剂产品,还是在胶滴点样技术等方面都取得较大的进步,已能满足微小型零件胶结的要求。
该技术具有装配精度高、误差小的特点,通过该技术可以很好地保证微型变速箱内部零件配合精度,达到良好的传动效果。
随着微机械技术的迅速发展,相信会有更多更先进的微细加工和装配方法诞生。
同时,尺寸更小、精度更高、材质更优越的微型变速、传动件的问世将会推动微型变速装置和微型机床的进步。
微型变速箱的发展相对宏观变速箱速度较慢,其原因是多方面的。
目前微型加工技术不够
先进;微型装配工艺虽有突破,但仍处于不成熟阶段。
这使得微型加工机床变速和传动系统仍然不够先进,有待长期发展。
微型变速装置进一步发展的基础是微细加工和装配技术的进一步成熟。
因此,应当把重点放在其基础技术的研发上,制造出尺寸极小、精度极高、传动性能极好的传动零件。
(任意单位:河南省漯河高级技工学校)。