Product_Registration_and_Regulatory_Updates
ROG STRIX GO 2.4 无线游戏耳机说明书
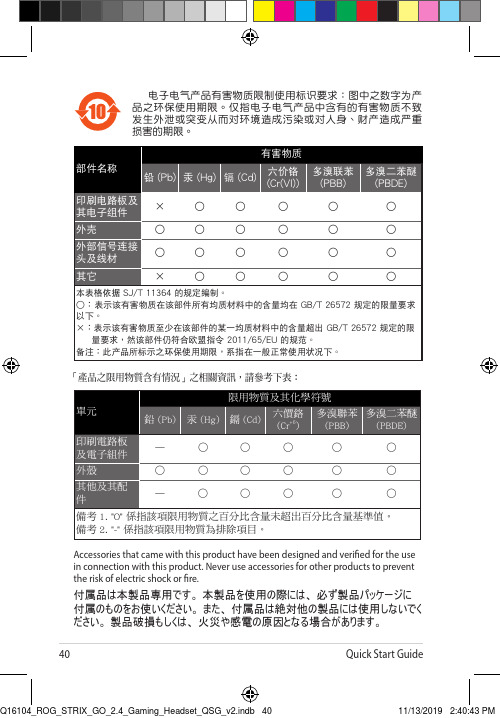
ASUS COMPUTER INTERNATIONAL (America)
Address
48720 Kato Rd., Fremont, CA 94538, USA
Telephone
+1-510-739-3777
Fax
+1-510-608-4555
Web site
/us/
Power output table
Item
ROG STRIX GO 2.4 ROG STRIX GO 2.4 Dongle
Function
2.4GHz RF 2.4GHz RF
Frequency
Maximum Output Power (EIRP)
2409.35-2477.35MHz 4dB
2409.35-2477.35MHz 5.5dB
DO NOT throw this product in fire. DO NOT short circuit the contacts. DO NOT disassemble this product.
ASUS Recycling/Takeback Services ASUS recycling and takeback programs come from our commitment to the highest standards for protecting our environment. We believe in providing solutions for you to be able to responsibly recycle our products, batteries, other components, as well as the packaging materials. Please go to /english/Takeback.htm for the detailed recycling information in different regions.
ICH中英文对照版本

人用药物注册技术要求国际协调会议( I C H :International Conference on Harmonization of Technical Requirements for Registration ofPharmaceuticals for Human Use)ICH三方协调指南原料药的优良制造规范(GMP)指南ICH指导委员会2000年11月10日按ICH规程第4步建议采用本指南根据ICH规程由合适的ICH专家工作组起草并经向法规部门咨询。
在规程的第4步,建议欧洲共同体、日本和美国的药政部门采用其最终的草案。
原料药的优良制造规范(GMP)指南ICH三方协调指南ICH指导委员会2000年11月10日的会议按ICH规程第4步建议ICH的三个药政部门采用本指南目录1 引言INTRODUCTION (6)1.1 目的Objective (6)1.2 法规的适用性Regulatory Applicability (7)1.3 范围Range (7)2 质量管理QUALITY MANAGEMENT (9)2.1 原则Principles (9)2.2 质量部门的职责Responsibilities of the Quality Unit(s) (10)2.3 生产作业的职责Responsibility for Production Activities (12)2.4 内部审计(自检)Internal Audits (Self Inspection) (13)2.5 产品质量审核Product Quality Review (13)3 人员PERSONNEL (14)3.1 员工的资质Personnel qualifications (14)3.2 员工的卫生Personnel Hygiene (14)3.3 顾问Consultants (15)4 建筑和设施BUILDINGS AND FACILITIES (15)4.1 设计和结构Design and Construction (15)4.2 公用设施Utilities (16)4.3 水Water (17)4.4 限制Containment (18)4.5 照明Lighting (18)4.6 排污和垃圾Sewage and Refuse (18)4.7 清洁和保养Sanitation and Maintenance (19)5 工艺设备PROCESS EQUIPMENT (19)5.1 设计和结构Design and Construction (19)5.2 设备保养和清洁Equipment Maintenance and Cleaning (20)5.3 校验Calibration (21)5.4 计算机控制系统Computerized Systems (22)6 文件和记录DOCUMENTATION AND RECORDS (23)6.1 文件系统和规格Documentation System and Specifications (23)6.2 设备的清洁和使用记录Equipment Cleaning and Use Record (24)6.3 原料、中间体、原料药的标签和包装材料的记录Records of Materials , Intermediates, API Labelingand Packaging Materials (25)6.4 生产工艺规程Master Production Instructions (25)6.5 批生产记录Batch Production Records (26)6.6 实验室控制记录Laboratory Control Records (27)6.7 批生产记录审核Batch Production Record Review (28)7 物料管理MATERIALS MANAGEMENT (29)7.1 控制通则General Controls (29)7.2 接收和待验Receipt and Quarantine (30)7.3 进厂物料的取样和测试Sampling and Testing of Incoming Production Materials (30)7.4 储存Storage (32)7.5 重新评估Re-evaluation (32)8 生产和中间控制PRODUCTION AND IN-PROCESS CONTROLS (32)8.1 生产操作Production Operations (32)8.2 时间限制Time Limits (33)8.3 工序间的取样和控制In-process Sampling and Controls (34)8.4 中间体或原料药的混合Blending Batches of Intermediates or APIs (35)8.5 污染的控制Contamination Control (36)9 原料药和中间体的包装和贴签PACKAGING AND IDENTIFICATION LABELING OF APIs AND INTERMEDIATES (36)9.1 总则General (36)9.2 包装材料Packaging Materials (37)9.3 标签的发放和控制Labeling Issuance and Control (37)9.4 包装和贴签操作Packaging and Labeling Operations (38)10 储存和分发STORAGE AND DISTRIBUTION (39)10.1 入库程序Warehousing Procedures (39)10.2 分发程序Distribution Procedures (39)11 实验室控制LABORATORY CONTROLS (40)11.1 控制通则General Controls (40)11.2 中间体和原料药的测试Testing of Intermediates and APIs (41)11.3 分析程序的验证-参见12章Validation of Analytical Procedures - See Section 12. (11.3) (42)11.4 分析报告单Certificates of Analysis (42)11.5 原料药的稳定性监测Stability Monitorint of APIs (43)11.6 有效期和复验日期Expiry and Retest Dating (44)11.7 留样Reserve/Retention Samples (45)12 验证VALIDATION (45)12.1 验证方针Validation Policy (45)12.2 验证文件Validation Documentation (46)12.3 确认Qualification (46)12.4 工艺验证的方法Approaches to Process Validation (47)12.5 工艺验证的程序Process Validation Program (48)12.7 清洗验证Cleaning Validation (49)12.8 分析方法的验证Validation of Analytical Methods (51)13 变更的控制CHANGE CONTROL (51)14 物料的拒收和再用REJECTION AND RE-USE OF MATERIALS (52)14.1 拒收Rejection (52)14.2 返工Reprocessing (53)14.3 重新加工Reworking (53)14.4 物料和溶剂的回收Recovery of Materials and Solvents (54)14.5 退货Returns (54)15 投诉和召回COMPLAINTS AND RECALLS (55)16 协议制造商(包括实验室) CONTRACT MANUFACTURES (INCLUDING LABORATORIES) (56)17 代理商、经纪人、贸易商、经销商、重新包装者和重新贴签者 (57)AGENTS,BROKERS, TRADERS,DISTRIBUTORS,REPACKERS ,AND RELABELLERS (57)17.1 适用性Applicability (57)17.2 已分发原料药的可追溯性Traceability of Distributed APIs and Intermediates (57)17.3 质量管理Quality Management (57)17.4 原料药和中间体的重新包装、重新贴签和待检Repackaging,Relabeling,and Holding of APIs andIntermediates. (58)17.5 稳定性Stability (58)17.6 信息的传达Transfer of Information (58)17.7 投诉和召回的处理Handing of Complaints and Recalls (59)17.8 退货的处理Handing of Returns (59)18 用细胞繁殖/发酵生产的原料药的特殊指南 (59)SPECIFIC GUIDANCE FOR APIs MANUFACTURED BY CELL CULTURE/FERMENTATION (59)18.1 总则General (59)18.2 细胞库的维护和记录的保存Cell Bank Maintenance and Record Keeping (62)18.3 细胞繁殖/发酵Cell Culture/Fermentation (62)18.4 收取、分离和精制Harvesting, Isolation and Purifation (63)18.5 病毒的去除/灭活步骤Viral Removal/Inactivation Steps (64)19 用于临床研究的原料药(APIS FOR USE IN CLINICAL TRIALS) (65)19.1 总则General (65)19.2 质量quality (65)19.3 设备和设施Equipment and Facilities (66)19.4 原料的控制Control of Raw Materials (66)19.5 生产Production (66)19.6 验证Validation (67)19.7 变更Changes (67)19.8 实验室控制Laboratory Controls (67)19.9 文件Documentation (67)20. 术语表(GLOOSSARY) (68)原料药的优良制造规范(GMP) 指南Guidance for IndustryQ7A Good Manufacturing Practice Guidancefor Active Pharmaceutical IngredientsThis guidance represents the Food and Drug Administration's (FDA's) current thinking on this topic. It does not create or confer any rights for or on any person and does not operate to bind FDA or the public. An alternative approach may be used if such approach satisfies the requirements of the applicable statutes and regulations.1 引言INTRODUCTION1.1 目的Objective本文件(指南)旨在为在合适的质量管理体系下制造活性药用成分(原料药以下称原料药)提供有关优良药品生产管理规范(GMP)提供指南。
Autodesk Nastran 2022 用户手册说明书
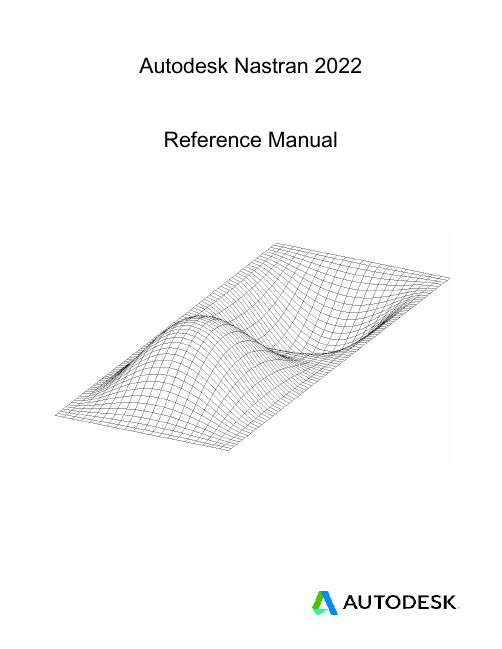
MPA, MPI (design/logo), MPX (design/logo), MPX, Mudbox, Navisworks, ObjectARX, ObjectDBX, Opticore, Pixlr, Pixlr-o-matic, Productstream,
Publisher 360, RasterDWG, RealDWG, ReCap, ReCap 360, Remote, Revit LT, Revit, RiverCAD, Robot, Scaleform, Showcase, Showcase 360,
TrueConvert, DWG TrueView, DWGX, DXF, Ecotect, Ember, ESTmep, Evolver, FABmep, Face Robot, FBX, Fempro, Fire, Flame, Flare, Flint,
ForceEffect, FormIt, Freewheel, Fusion 360, Glue, Green Building Studio, Heidi, Homestyler, HumanIK, i-drop, ImageModeler, Incinerator, Inferno,
Autodesk Nastran 2022
Reference Manual
Nastran Solver Reference Manual
wercs 注册流程

wercs 注册流程英文回答:Wercs registration process can be divided into several steps. First, you need to visit the Wercs website andcreate an account. This involves providing your personal information such as name, email address, and contact details. Once you have successfully created an account, you will receive a confirmation email with a link to activate your account.After activating your account, you can proceed to login to the Wercs platform. This will give you access to various features and functionalities. One important step in the registration process is to provide your company information. This includes details such as the company name, address, and industry.Next, you will need to provide information about the products that your company manufactures or distributes.This includes details such as the product name, ingredients, and safety data sheets. It is important to ensure that all the information provided is accurate and up to date.Once you have provided all the necessary information, you can submit your registration. The Wercs team will then review your application and verify the information provided. This may involve contacting you for additional details or clarifications. It is important to respond promptly to any requests from the Wercs team to avoid delays in the registration process.Once your registration has been approved, you will receive a confirmation email. This will include your Wercs account details and instructions on how to access the platform. You can then start using the Wercs platform to manage your product data, generate safety data sheets, and comply with regulatory requirements.中文回答:Wercs注册流程可以分为几个步骤。
体外诊断试剂注册 中英文对照
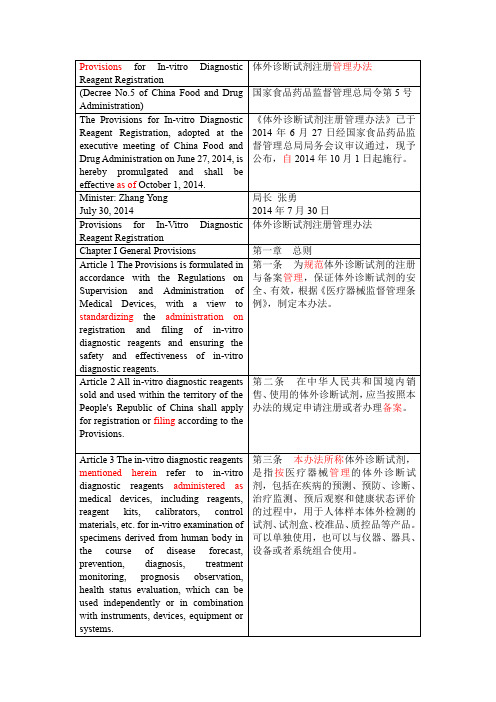
体外诊断试剂注册管理办法
(Decree No.5 of China Food and Drug Administration)
国家食品药品监督管理总局令第5号
The Provisions for In-vitro Diagnostic Reagent Registration, adopted at the executive meeting of China Food and Drug Administration on June 27, 2014, is hereby promulgated and shall be effectiveas ofOctober 1, 2014.
境内第一类体外诊断试剂备案,备案人向设区的市级食品药品监督管理部门提交备案资料。
Class II in-vitro diagnostic reagents shall be reviewed by the food and drug regulatory department of the provinces, autonomous regions and municipalities directly under the central government, and themedical device registration certificateshall be issued after approval.
香港、澳门、台湾地区体外诊断试剂的注册、备案,参照进口体外诊断试剂办理。
Article 7 Where aregistration applicantor filing entityof an in-vitro diagnostic reagent brings the products to the marketin his own name,he shallproduct.
Motorola T4500 对讲机用户手册说明书

Model T4500@6881043B35@6881043B35-A Two-Way RadioUser's GuideCongratulations on your purchase of a Motorola product!Product registration is an important step. Registering helps us facilitate warranty service and permits us to contact you should your Motorola product require an update or other service.To register your product online, visit:/warranty/radios.Please retain your original dated sales receipt for your records. For warranty service of your Motorola product, you will need to provide a copy of your dated sales receipt to confirm warranty status. Registration is not required for warranty coverage.For a copy of a large-print version of this guide, or for product-related questions, call:1-800-353-2729 in the USA 1-888-390-6456 TTY (Text Telephone)On the Web:/talkaboutFinding the Controls1# - Short press sends call tone.2Push to Talk (PTT)•Push to transmit, release to listen.•In menu mode, push to confirmselection.3$•Long press turns radio on or off.•Short press enters menu mode,where: first press changeschannel, second press turns scanon or off, third press monitorschannel for activity.4%•Increases volume (volume levelflashes and / displays).•In menu mode, increments channel(channel number flashes).•In menu mode, toggles scanselection (h is visible, alongwith flashing Y or–).5&•Decreases volume (volume levelflashes and / displays).•In menu mode, decreases channel(channel number flashes).•In menu mode, toggles scanselection (h is visible, alongwith flashing Y or–).Installing the BatteriesYour radio uses 3 AAA Alkaline batteries, and beeps when the batteries are low.1.Turn the radio off.e a coin to wedge the battery coveropen.3.Insert batteries as shown on inside ofbattery compartment.4.Replace the battery cover.Turning Your Radio On and OffTo turn on, press and hold $ until a channel number appears and the radio beeps.To turn off, press and hold $ until the display goes blank.Adjusting the VolumePress % to increase or & to decrease the volume. The volume level flashes and/displays.Setting the ChannelThe channel is the frequency your radio uses to transmit. Your radio has22channels.1.Briefly press and release $. Thechannel number flashes.2.Press % or & to select a channel.3.Press PTT to confirm.1 462.5625MHz GMRS/FRSMHz GMRS/FRS 2 462.5875MHz GMRS/FRS3 462.61254 462.6375MHz GMRS/FRSMHz GMRS/FRS 5 462.6625MHz GMRS/FRS 6 462.6875MHz GMRS/FRS 7 462.7125MHz FRS8 467.5625MHz FRS9 467.587510 467.6125MHz FRSMHz FRS11 467.6375MHz FRS12 467.6625MHz FRS13 467.6875MHz FRS14 467.7125MHz GMRS 15 462.5500MHz GMRS 16 462.5750MHz GMRS 17 462.6000Talking and ListeningTo talk, press and hold the PTT button.When you are finished talking, release PTT.For maximum clarity, hold the radio2to 3inches away from your mouth and speak directly into the microphone. Do not cover the microphone while talking.Sending a Call ToneA call tone alerts others you want to talk. To send a call tone to other radios in your group, press #.18 462.6250 MHz GMRS19 462.6500 MHz GMRS20 462.6750 MHz GMRS21 462.7000 MHz GMRS22 462.7250 MHzGMRSScanning ChannelsUse scanning to monitor channels and codes for transmissions, or to find someone in your group who has accidentally changed channels.1.Press $ twice until h and flashing Yor – display.2.Press either:% until Y displays to turnscanning on.&until – displays to turnscanning off.3.Press PTT to confirm.When the radio detects channel activity, it stops scanning and you can hear the transmission. To respond, press PTT within 5seconds.Attaching the Belt Clip (Included)Hook the belt clipinto the notch atthe top of theradio and slidedown until it clicksinto place.To remove,squeeze therelease latchtogether and slidethe clip up andaway from theradio.FCC Licensing InformationY our Motorola radio operates on General Mobile Radio Service (GMRS) frequencies and is subject to the Rules and Regulations of the Federal Communications Commission (FCC). The FCC requires that all operators using GMRS frequencies obtain a radio license before operating their equipment. To obtain the FCC forms, please request Forms 605 and 159, which includes all forms and instructions. If you wish to have the document faxed or mailed, or have questions, please use the following contact information. Changes or modifications not expressly approved by Motorola may void the user’s authority granted by the FCC to operate this radio and should not be made. To comply with FCC requirements, transmitter adjustments should be made only by or under the supervision of a person certified as technically qualified to perform transmitter Faxed Contact the Fax-On-Demand system at:1-202-418-0177Mailed Call the FCC forms hotline at:1-800-418-FORM 1-800-418-3676Questions Regarding FCC license Contact the FCC at:1-888-CALL-FCC 1-888-225-5322Or: maintenance and repairs in the private landmobile and fixed services as certified by an organization representative of the user of thoseservices. Replacement of any transmitter component (crystal, semiconductor, etc.) not authorized by the FCC equipment authorizationfor this radio could violate FCC rules.Use of this radio outside the country where it wasintended to be distributed is subject to government regulations and may be prohibited. Safety and General Information Important Information on Safe and EfficientOperation. Read This Information Before Using Your RadioThe information provided in this documentsupersedes the general safety information contained in user guides published prior toJuly2000.Transmit and Receive ProcedureYour two-way radio contains a transmitter and a receiver. To control your exposure and ensure compliance with the general population/ uncontrolled environment exposure limits, always adhere to the following procedure: •Transmit no more than 50% of the time.•To transmit (talk), press the Push to Talk (PTT) button.•To receive calls, release the PTT button.Transmitting 50% of the time, or less, is important because the radio generates measurable RF energy exposure only when transmitting (in terms of measuring standards compliance). Exposure to Radio Frequency EnergyYour Motorola radio is designed to comply with the following national and international standards and guidelines regarding exposure of human beings to radio frequency electromagnetic energy:•United States Federal Communications Commission, Code of Federal Regulations; 47 CFR part 2 sub-part J•American National Standards Institute (ANSI)/ Institute of Electrical and Electronic Engineers (IEEE) C95. 1-1992•Institute of Electrical and Electronic Engineers (IEEE) C95.1-1999 Edition •International Commission on Non-Ionizing Radiation Protection (ICNIRP) 1998•Ministry of Health (Canada) Safety Code 6. Limits of Human Exposure to Radio Frequency Electromagnetic Fields in the Frequency Range from 3 kHz to 300GHz, 1999•Australian Communications Authority Radiocommunications (Electromagnetic Radiation - Human Exposure) Standard 2001 (applicable to wireless phones only)•ANATEL, Brasil Regulatory Authority, Resolution 256 (April 11, 2002) “additional requirements for SMR, cellular, and PCS product certification.”To assure optimal radio performance and make sure human exposure to radio frequency electromagnetic energy is within the guidelines set forth in the above standards, always adhere to the following procedures.Portable Radio Operation and EME Exposure Antenna CareUse only the supplied or an approved replacement antenna. Unauthorized antennas, modifications, or attachments could damage the radio and may violate FCC regulations.DO NOT hold the antenna when the radio is “IN USE.” Holding the antenna affects the effective range.Two-Way Radio OperationWhen using your radio as atraditional two-way radio, hold theradio in a vertical position withthe microphone one to two inches (2.5 to 5cm) away from the lips. Body-Worn OperationTo maintain compliance with FCC/Health Canada RF exposure guidelines, if you wear a radio on your body when transmitting, always place the radio in a Motorola-supplied or approved clip,holder, holster, case, or body harness for this product. Use of non-Motorola-approved accessories may exceed FCC/Health Canada RF exposure guidelines. If you do not use one of the Motorola-supplied or approved body-worn accessories, and are not using the radio held in the normal use position, ensure the radio and its antenna are at least one inch (2.5 cm) from your body when transmitting.Data OperationIf applicable, when using any data feature of the radio with or without an accessory cable, position the radio and its antenna at least one inch (2.5 cm) from the body.Approved AccessoriesFor a list of approved Motorola accessories visit our website at . Electromagnetic Interference/Compatibility Note:Nearly every electronic device is susceptible to electromagnetic interference (EMI) if inadequately shielded, designed, or otherwise configured for electromagnetic compatibility. FacilitiesTo avoid electromagnetic interference and/or compatibility conflicts, turn off your radio in any facility where posted notices instruct you to do so. Hospitals or health care facilities may be using equipment that is sensitive to external RF energy.AircraftWhen instructed to do so, turn off your radio when on board an aircraft. Any use of a radio must be in accordance with applicable regulations per airline crew instructions. Medical Devices - PacemakersThe Advanced Medical Technology Association recommends that a minimum separation of six inches (15 cm) be maintained between a handheld wireless radio and a pacemaker. These recommendations are consistent with the independent research by, and recommendations of the U.S. Food and Drug Administration. Persons with pacemakers should:•ALWAYS keep the radio more than six inches (15 cm) from their pacemaker when the radio is turned ON.•Not carry the radio in the breast pocket.•Use the ear opposite the pacemaker to minimize the potential for interference.•Turn the radio OFF immediately if you have any reason to suspect that interference is taking place.Medical Devices - Hearing AidsSome digital wireless radios may interfere with some hearing aids. In the event of such interference, you may want to consult your hearing aid manufacturer to discuss alternatives.Other Medical DevicesIf you use any other personal medical device, consult the manufacturer of your device to determine if it is adequately shielded from RF energy. Y our physician may be able to assist you in obtaining this information.Safety and General Use While Driving Check the laws and regulations on the use of radios in the area where you drive. Always obey them. When using your radio while driving, please:•Give full attention to driving and to the road.•Use hands-free operation, if available.•Pull off the road and park before making or answering a call if driving conditions so require.Operational WarningsFor Vehicles with an Air BagDo not place a portable radio in the area over an air bag or in the air bag deployment area. Air bags inflate with great force. If a portable radio is placed in the air bag deployment area and the air bag inflates, the radio may be propelled with great force and cause serious injury to occupants of the vehicle.Potentially Explosive AtmospheresTurn off your radio prior to entering any area with a potentially explosive atmosphere, unless it is a radio type especially qualified for use in suchareas as “Intrinsically Safe.” Do not remove, install, or charge batteries in such areas. Sparks in a potentially explosive atmosphere can cause an explosion or fire resulting in bodily injury or even death.Note:The areas with potentially explosive atmospheres referred to above include fueling areas such as below decks on boats, fuel or chemical transfer or storage facilities, areas where the air contains chemicals or particles, such as grain, dust or metal powders, and any other area where you would normally be advised to turn off your vehicle engine. Areas with potentially explosive atmospheres are often but not always posted.Blasting Caps and AreasTo avoid possible interference with blasting operations, turn off your radio when you are near electrical blasting caps, in a blasting area, or in areas posted: “Turn off two-way radio.” Obey all signs and instructions.Operational CautionsAntennasDo not use any portable radio that has a damaged antenna. If a damaged antenna comes into contact with your skin, a minor burn can result.BatteriesAll batteries can cause property damage and/or bodily injury such as burns if a conductive material such as jewelry, keys, or beaded chains touch exposed terminals. The conductive material may complete an electrical circuit (short circuit) and become quite hot. Exercise care in handling any charged battery, particularly when placing it inside a pocket, purse, or other container with metal objects.Battery Charger Safety InstructionsSave these Instructions1.Do not expose the charger to rain or snow.2.Do not operate or disassemble the charger if it has received a sharp blow, or has been dropped or damaged in any way.3.Never alter the AC cord or plug provided with the unit. If the plug will not fit the outlet, have the proper outlet installed by a qualified electri-cian. An improper condition can result in a risk of electric shock.4.To reduce the risk of damage to the cord or plug, pull the plug rather than the cord when disconnecting the charger from the AC recep-tacle.5.To reduce the risk of electric shock, unplug the charger from the outlet before attempting any maintenance or cleaning.e of an attachment not recommended or sold by Motorola may result in a risk of fire, electric shock, or personal injury.7.Make sure the cord is located so it will not be stepped on, tripped over, or subjected to dam-age or stress.8.An extension cord should not be used unless absolutely necessary. Use of an improper extension cord could result in a risk of fire and/ or electric shock. If an extension cord must be used, make sure that:•The pins on the plug of the extension cordare the same number, size, and shape asthose on the plug of the charger.•The extension cord is properly wired andin good electrical condition.•The cord size is 18 AWG for lengths up to100 feet, and 16 AWG for lengths up to150 feet.9.The supply cord of this charger cannot be replaced. If the cord is damaged, call Motorola Product Services at 1-800-353-2729 in the USA or 1-888-390-6456 TTY (Text Telephone).• 22 Channels (8 GMRS + 14 FRS)8 GMRS channels and 14 FRS channels to ensure backward compatibility with FRS two-way radios.• Scan Easily find your group's channel by searching all channels for activity.• Motorola Quality Shock, drop, and temperature tested to meet Motorola's high quality standards.• Talk Confirmation Tone Signals others you are finished talking.• Low Battery Alert Audible tone tells you when your radio's battery is running low.• Weather Resistant Helps protect radios against the elements.• 1 Year Limited Warranty For warranty details, call 1-800-353-2729.• User's Guide IncludedFCC GMRS LICENSE REQUIREDMOTOROLA and the Stylized M Logo are registered in the US Patent & Trademark Office. All other product or service namesare the property of their respective owners.© Motorola, Inc. 2003P WARNING CHOKING HAZARDSMALL PARTS Not for children under 3 years.This product is not intended to be used as a toy or plaything.。
药房食品经营许可证注销流程

药房食品经营许可证注销流程1.申请人需填写《药房食品经营许可证注销申请表》。
The applicant needs to fill out the "Application for Cancellation of Pharmacy Food Business License" form.2.申请人须提供有效的身份证明文件。
The applicant must provide valid identification documents.3.申请人需提交药房食品经营许可证原件。
The applicant needs to submit the original pharmacy food business license.4.申请人需要提供许可证注销的理由和相关证明文件。
The applicant needs to provide reasons for thecancellation of the license and relevant supporting documents.5.提交完整的申请材料到当地食品药品监督管理部门。
Submit the complete application materials to the local food and drug supervision department.6.监管部门对提交的材料进行审核。
The regulatory authority will review the submitted materials.7.审核通过后,发出《药房食品经营许可证注销通知书》。
After the review is approved, the "Notice of Cancellation of Pharmacy Food Business License" will be issued.8.公告取消许可证通知。
Publicize the notice of license cancellation.9.处理实际相关手续并公示。
洗发水备案流程

洗发水备案流程When it comes to the process of registering a shampoo product, there are several steps that need to be followed in order to ensure compliance with regulations and safety standards. 针对洗发水产品的备案流程,需要按照一系列步骤,以确保符合法规和安全标准。
The first step in this process is to gather all the necessary documentation and information required for the registration. 这个过程的第一步是收集所有需要的文件和信息以进行登记。
This may include details about the ingredients used in the shampoo, the manufacturing process, any testing or studies that have been conducted on the product, as well as information about the packaging and labeling of the product. 这可能包括洗发水中使用的成分详细信息、生产工艺、产品的任何测试或研究,以及产品的包装和标签信息。
It is important to ensure that all this information is accurate and upto date in order to avoid any delays or complications in the registration process. 需要确保所有这些信息准确无误,并及时更新,以避免在登记过程中出现任何延迟或问题。
ISO1050中文资料_数据手册_参数
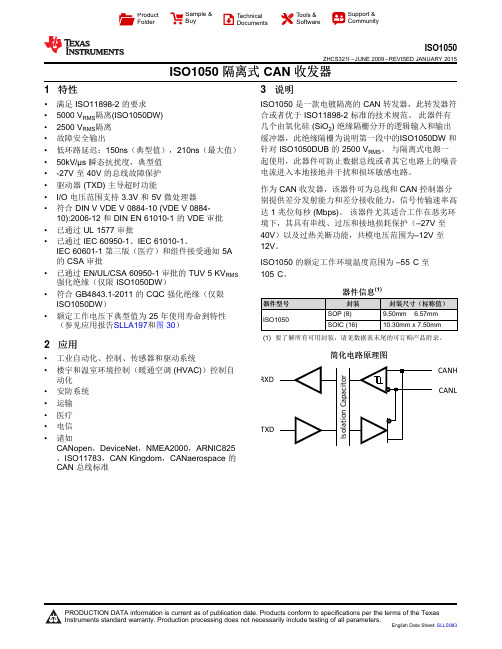
器件型号 ISO1050
器件信息(1)
封装
封装尺寸(标称值)
SOP (8)
9.50mm × 6.57mm
SOIC (16)
10.30mm x 7.50mm
(1) 要了解所有可用封装,请见数据表末尾的可订购产品附录。
简化电路原理图
CANH RXD
CANL
TXD
1பைடு நூலகம்
PRODUCTION DATA information is current as of publication date. Products conform to specifications per the terms of the Texas Instruments standard warranty. Production processing does not necessarily include testing of all parameters.
English Data Sheet: SLLS983
ISO1050
ZHCS321I – JUNE 2009 – REVISED JANUARY 2015
目录
1 特性.......................................................................... 1 2 应用.......................................................................... 1 3 说明.......................................................................... 1 4 修订历史记录 ........................................................... 2 5 Pin Configuration and Functions ......................... 5 6 Specifications......................................................... 6
医疗器械注册管理办法英文(四号令)

Provisions for Medical Device RegistrationChapter I General ProvisionsArticle1The Provisions are formulated in accordance with the Regulations for the Supervision and Administration of Medical Devices with a view to standardizing the registration and filing administration of medical device and guarantee the safety and effectiveness of medical devices.Article2All medical devices sold and used within the territory of the People's Republic of China shall comply with the Provisions to apply for registration or conduct filing. Article3Medical device registration refers to approval process conducted by the food and drug regulatory authority upon an application submitted by the registration applicant, follows the legal procedure to decide whether the medical device to be marked can be approved or not based on a comprehensive assessment on research and its result of medical device’s safety and effectiveness.Medical device filing refers to the food and drug regulatory authority files filing materials submitted by the filing applicant for future reference.Article4Registration and filing shall follow the principle of publicity,justice,and equity. Article5Filing administration shall be implemented for Class I medical devices.Registration administration shall be implemented for Class II and Class III medical devices.Filing for Class I domestic medical device,the filing applicant shall submit the filing to the food and drug regulatory authority of the municipality consisting of districts. Class II domestic medical devices shall be inspected by the food and drug regulatory authority of the provinces,autonomous regions,municipalities directly under the central government,and the Registration Certificate for Medical Device will be granted after approval.Class III domestic medical devices shall be inspected by the China Food and Drug Administration(hereinafter referred to as CFDA),and the Registration Certificate for Medical Device will be granted after approval.Filing for Class I imported medical device,the filing applicant shall submit the filing toCFDA.Class II and Class III imported medical devices shall be inspected by the CFDA,and the Registration Certificate for Medical Device will be granted after approval.The medical devices from Hong Kong,Macau and Taiwan shall be registered or filed refer to the imported medical devices.Article6The registration applicant and filing applicant shall launch product to the market in its own name and hold legal liability for the product.Article7The food and drug regulatory authority shall publicize information of medical device registration and filing according to the regulations.The applicant can inquiry the approval process and results,the public can look up approval results.Article8China encourages research and development and innovation of medical devices, conducts special approval procedures for innovative medical devices,contributes to promotion and application for new technology of medical devices and boosts the development of medical device industry.Chapter II Basic RequirementArticle9The applicant or the filing applicant shall establish quality management system related to R&D and manufacture of product,implement it and keep it operates effectively.For domestic products approved by the special approval procedures for innovative medical device apply for the registration application and samples entrusted other manufacturers to produce,the entrusted manufacturers shall have corresponding manufacturing scope;for domestic products not approved by the special approval procedures for innovative medical device apply for registration application,their samples cannot entrust other manufacturers to produce.Article10The person that apply for registration or conduct filing for medical device shall have the corresponding professional knowledge and be familiar with laws,regulations, normative documents and technical requirements regarding to medical deviceregistration or filing administration.Article11The applicants or the filing applicants shall follow the basic requirement for safety and effectiveness of medical device,ensure R&D process are being truthful and standardized,and all the data is true,complete and traceable when they conduct filing or apply for registration.Article12The materials for registration application shall use Chinese.When the application documents are translated from a foreign language,the original documents shall also be provided at the same time.When referring to unpublished literature,the applicant shall provide evidence of owner’s permission to use the information.The applicant shall take fully responsibility for the authenticity of the registration application documents.Article13For imported medical device intended to apply for registration or conduct filing,the applicant or the filing applicant shall get market clearance of the country or region where their registration or manufacturing place located for the medical device.If country or region where the applicant’s or the filing applicant’s registration or manufacturing places located does not administer the products as medical device, the applicant or the filing applicant shall provide relevant supporting documents, including the approval of legal sales issued by the country or region where their registration or manufacturing place located.Article14The overseas applicant or the filing applicant shall conduct relevant business through their representative office located within the territory of China or designate an enterprise located within the territory of China as agent.Besides conduct registration and filing related work,the agent shall be liable for: (1)Contact with corresponding food and drug regulatory authority and the overseas applicant or the filing applicant;(2)Deliver related laws,regulations and technical requirement to the applicant or the filing applicant truly and faithfully;(3)Collect post-market adverse event information of medical devices and feed back to the overseas applicant or the filing applicant,meanwhile,report to relevant food and drug regulatory authority;(4)Collaborate the recall for post-market medical devices,and report to relevant food and drug regulatory authority;(5)Undertake other joint liabilities related to product quality and after-sales service. Chapter III Product technical requirement and Registration TestingArticle15The applicant or the filing applicant shall prepare the product technical requirement of the medical device to be registered or filed.The product technical requirement of Class I medical device shall be submitted to the food and drug authorities during the applicant conducts filing.The product technical requirement of Class II or Class III medical devices shall be checked and approved by the food and drug authorities at the time of registration approval.The product technical requirement mainly includes the performance indices and testing method of the completed medical device,and the performance indices refer to the objective determination of product functionality,security index and other indicators of quality control.The medical device launched in China shall comply with its product technical requirement which was checked and approved for registration or filed already. Article16The registration testing shall be conducted to apply registration for Class II and Class III medical device.The testing institutes of medical device shall conduct registration testing according to product technical requirement.The manufacture of samples for registration testing shall comply with related requirements of quality management system;products tested to be qualified in registration testing can be used for clinical trial or registration application.The filing applicant can submit self-testing report of the product to conduct filing. Article17To apply for registration testing,the applicant shall provide samples,product technical requirement and other technical materials required by the registration testing to the testing institutes.Article18Testing institutes of medical device shall have certain qualifications,perform testing within their specified testing scope and conduct pre-evaluation on the product technical requirement.The testing institutes shall issue the pre-evaluation opinions and the registration testing report of medical device together to the applicant.For the medical devices that have not been included in testing scope of any medical device testing institutes,the related registration authority shall designate a capable testing institute to conduct the testing.Article19The testing products in a same registration unit shall represent the safety and effectiveness of the rest products in this registration unit.Chapter IV Clinical EvaluationArticle20Clinical evaluation of medical device refers to the process that the applicant or the filing applicant validates whether a product can meet the operating requirements or scope of application or not through clinical literature,clinical practice data,clinical trial and other information.Article21Clinical evaluation materials refer to the documents formed by the applicant or the filing applicant during the clinical evaluation.For those required clinical trial,the clinical evaluation materials to be submitted shall include the protocol and the report of clinical trial.Article22It is not necessary to conduct clinical trial for filing Class I medical devices.It is necessary to conduct clinical trial for registration application of Class II and Class III medical devices;however,in any of the following circumstances,the clinical trial could be exempted.(1)With definite operating principle,established design,mature manufacture process;no record for serious adverse event of substantially equivalent medical devices which have been marketed and clinically applied for years;and without changing the conventional purpose of use;(2)The safety and effectiveness of the medical devices can be proven throughnon-clinical evaluation;(3)The safety and effectiveness of the medical devices can be demonstrated through analyzing and evaluating the data obtained from clinical trial or clinical application of the substantially equivalent medical devices.The clinical trial exemption list of medical device shall be formulated,adjusted and published by the CFDA.For products that not listed in the clinical trial exemption listof medical device and can prove themselves to be safe and effective through analyzing and evaluating the data obtained from clinical trial or clinical application of the substantially equivalent medical devices,the applicant can made an explanation at the time of registration application and provide relevant supporting materials. Article23The clinical trial of medical device shall be conducted in a qualified clinical trial institutes according to the requirements of the Good Clinical Practice(GCP)for medical devices.The manufacture of samples for clinical trial shall comply with the quality management system of medical device.Article24The clinical trial of Class III medical devices with higher risk to human body shall be approved by CFDA before execution.The list for Class III medical devices which required getting an approval for conducting clinical trial shall be formulated,adjusted, and published by CFDA.Article25The approval of clinical trial refer to the process that CFDA decides whether the clinical trial can be conducted by making comprehensive analysis on risk level,clinical trial protocol,clinical benefits,risk analysis report and others of medical device to be conducted clinical trial according to the applicant’s application.Article26For applicants need to process the approval of medical device clinical trial, application materials shall be submitted to the CFDA by following the relevant requirements.Article27CFDA shall pass the application materials to the technical evaluation department for medical device in3workdays after they accepted the application for the approval of medical device clinical trial.The technical evaluation department shall complete technical evaluation in40 workdays and CFDA shall make decision in20days afterwards.For those approved to conduct clinical trial,the Permission for Medical Device Clinical Trial shall be issued; for those not approved to conduct clinical trial,the reason shall be stated in written.Article28If supplementary documents are required during the technical evaluation,the applicant shall be informed once of all the supplements and amendments to be made.The applicant shall submit all necessary supplementary materials once within 1year according to the notice of supplements and amendments.The technical evaluation department shall complete the technical evaluation within40workdays from the date of receiving the materials supplemented or amended.Time required by the applicant for supplementing such materials shall not be calculated in the overall evaluation timeline.The technical evaluation department shall terminate evaluation and come up with disapproval suggestion to the food and drug regulatory authority if the applicant fails to submit the supplementary materials within the specified time,and the decision for disapproval shall be made by the food and drug regulatory authority after checked.Article29Under any of the following circumstances,the food and drug regulatory authorities shall revoke the acquired Permission for Medical Device Clinical Trial:(1)There is false content in clinical trial applications;(2)The original approved clinical trial is verified by the latest research for ethical and scientific problems;(3)Other circumstances shall be revoked.Article30The medical device clinical trial shall be implemented within3year after its approval. For those overdue,the original approved document shall be invalidated automatically.For those that are still need to conduct clinical trial,they shallre-submit the application.Chapter V Product RegistrationArticle31To apply for medical device registration,the applicant shall submit and deliver application documents to the food and drug regulatory authority based on relevant requirements.Article32The food and drug regulatory authority shall conduct administrative review onapplication materials after they received applications for medical device registration, and shall take actions respectively according to the following circumstances:(1)Accept registration applications when the application item is within their function and the application materials are complete and comply with the requirements of administrative review;(2)Allow the applicant to correct the application documents on site if possible;(3)Inform the applicants all the content correction to be made for once within five workdays when found the application materials are incomplete or do not meet the requirement of administrative review;if no information are given by5workdays,the application shall be deemed as being accepted since the acceptance date of application materials;(4)Reject the application and notify the applicant immediately if the application is not within their functions;The food and drug regulatory authority shall grant the dated acceptance ornon-acceptance notice affixed with its special seal to indicate them accepting or rejecting to accept the medical device registration application.Article33The administrative department of the food and drug regulatory authority shall forward the registration application to the technical evaluation department within3 workdays from the date of document acceptance.The technical evaluation department of the food and drug regulatory authority shall complete the technical evaluation within60workdays for Class II medical device registration and complete the technical evaluation within90workdays for Class III medical device registration.For those technical evaluations need to hire outside experts,hold joint technical evaluation with drug evaluation department for drug-device combination products, the extra time shall not be calculated in the overall review timeline,and the technical evaluation department shall give a written notice to applicant for needed extra time. Article34The food and drug regulatory authority can retrieve original research materials,and organize inspection for quality management system regarding to product R&D and manufacture during the technical evaluation.The food and drug regulatory authority of the province,autonomous region,and municipality directly under the central government shall conduct the inspection for quality management system of Class II and Class III domestic medical device registration;for Class III domestic medical device,CFDA shall inform thecorresponding food and drug regulatory authority of the province,autonomous region,and municipality directly under the central government to conduct the inspection,and get itself involved if necessary.The food and drug regulatory authority of the province,autonomous region,and municipality directly under the central government shall complete the inspection within30workdays according to relevant requirement.During the technical evaluation for Class II and Class III imported medical device registration,the technical evaluation department of CFDA can inform technical institute of quality management system of CFDA to conduct the inspection when they deem it is necessary,and the technical evaluation department will also participate in the inspection if necessary.The inspection time for quality management system shall not be calculated in technical evaluation time.Article35If supplementary materials are required during the technical evaluation,the applicant shall be informed once of all the supplementary contents to be made by the technical evaluation department.The applicant shall submit supplementary materials once within1year according to the requirements of supplement notice; the technical evaluation department shall complete the technical evaluation within 60workdays from the date of receiving the supplementary materials.Time required by applicant for supplementing such materials shall not be calculated in overall evaluation timeline.If the applicant has any objection to the content of supplement notice,they can propose written suggestion to the technical evaluation department,explain the reason and provide corresponding technical supporting materials.The technical evaluation department shall terminate evaluation and come up with disapproval suggestion if the applicant failed to supplement materials within the specified timeframe,and the disapproval decision shall be made by the food and drug regulatory authority.Article36The food and drug regulatory authority accepting the registration application shall make decisions within20workdays after technical evaluation.Where requirements concerning safety and effectiveness are met,registration shall be approved and the Registration Certificate for Medical Device shall be granted within10workdays after the date in which approval decision has been made,and the checked and approved product technical requirement shall be provided to the applicant as attachment.Forthose registration are not approved,the authorities shall state the reasons in written and inform the applicant that they have right to apply for re-evaluation and administrative reconsideration,or bring up to administrative litigation in accordance with laws and regulations.The validity term of the Registration Certificate for Medical Device is five years. Article37Registered matters of medical device include approval matters and administrative matters.Approval matters include product name,model,specifications,structure and composition,scope of application,product technical requirement, manufacturing address of imported medical device and so on;administrative matters include name and resident of the applicant,name and resident of the agent, manufacturing address of domestic medical device and so on.Article38When the food and drug regulatory authority approves registration for much-needed medical devices which are intended to treat rare disease or deal with unexpected public health emergencies,they can require the applicant to do further completion work after the product launch and specify those requirements in the Registration Certificate for Medical Device.Article39If the accepted registration application has one of the following circumstances,the food and drug regulatory authority shall decide to disapprove application and inform the applicant:(1)The research and its result conducted by the applicant cannot approve the safety and effectiveness of medical device to be sold;(2)The registration application documents are false;(3)The registration application documents have confused or inconsistent contents;(4)The registration application documents have clearly inconsistent contents with those of application items;(5)Other circumstances that the registration application shall be refused.Article40For the accepted registration application,the applicant may,prior to the administrative decision is made,withdrawal the registration application and relevant materials,and give reason to the food and drug regulatory authority who accept the application.Article41For those accepted registration application,if there are evidences providing that the registration application documents is false,the food and drug regulatory authority can suspend the approval.After verification,the food and drug regulatory authority shall determine to continue the evaluation or disapprove registration according to the verification conclusion.Article42If the applicant has any objection to the disapproval decision made by the food and drug regulatory authority,the applicant may put forth re-evaluation application to the food and drug regulatory authority that makes the decision within20workdays after the receipt of the notice of disapproval for registration application.The contents applied for re-evaluation shall be limited to original application and original application documents.Article43The food and drug regulatory authority shall make decision for re-evaluation within 30workdays after accepting the application for re-evaluation and inform the applicant the decision in written.In case the original judgment is affirmed,the food and drug regulatory authority will not accept the secondary application forre-evaluation by the applicant.Article44If the applicant has any objection to the disapproval decision made by the food and drug regulatory authority and has applied for administrative reconsideration or administrative litigation,the food and drug regulatory authority will not accept the re-evaluation application raised by the applicant.Article45In case of loss of the Registration Certificate for Medical Device,the applicant shall publish lost declaration at the media specified by original certificate-granting authority,and apply to original certificate-granting authority for re-granting such certificate after1month of declaration.Original certificate-granting authority shall re-grant the Registration Certificate for Medical Device within20workdays. Article46Where major interest relationship between the applicant and others is directly involved in the application for medical device registration,the food and drugregulatory authority shall inform the applicant and interested party of right to apply for hearing in accordance with laws,regulations and other provisions of CFDA;during the process of evaluating the application for medical device registration,the food and drug regulatory authority shall publicize major approval matters that are deemed to have been involved in public interests and hold a hearing.Article47For medical devices newly invented and not yet listed in the classification catalogue, the applicant can directly apply for Class III medical device registration,or estimate the device classification according to the classification principles and apply for confirmation to CFDA,then apply for registration or conduct filing.For those directly apply for the Class III medical device registration,CFDA shall determine the classification based on its risk level.For domestic medical device confirmed to be Class II medical devices,CFDA shall forward application material to the food and drug regulatory authority of the provinces,autonomous regions, municipalities directly under the central government where the applicant is located and to review and approve.For domestic medical device confirmed to be Class I medical devices,the CFDA shall forward application material to the food and drug regulatory authority of the municipality consisting of districts where the applicant is located to conduct filing.Article48If there is patent dispute happened during the technical evaluation for registration,it shall be disposed regarding to the laws and regulations.Chapter VI Change RegistrationArticle49To change the content for registered Class II or Class III medical device in its Registration Certificate for Medical Device and appendixes,the applicant shall apply change registration to the original registration authority and submit the application materials according to the relevant requirements.If the product name,model,specifications,structure and composition,scope of application,product technical requirement,or manufacturing address of imported medical device changes,the applicant shall apply Change of Approval Matters with original registration department.If the name and resident of the applicant,or the name and resident of the agent changes,the applicant shall apply Change of Administrative Matters with originalregistration department;if the manufacturing address of domestic medical device changes,the applicant shall apply for Change of Administrative Matters after it applied corresponding approvals for manufacture changes.Article50The food and drug regulatory authority shall grant the change documents of medical device registration within10workdays if the materials for the Change of Administrative Matters can meet the requirements.The food and drug regulatory authorities shall inform the applicants all the materials need to be supplemented at once if the materials for the Change of Administrative Matters are not complete or cannot meet the requirements through the administrative review.Article51For the Change of Approval Matters,the technical evaluation department shall focus on evaluating the changed parts and evaluate the product safety and effectiveness after the change.The food and drug regulatory authority accepting the application for the Change of Approval Matters shall organize technical evaluation within the period specified in Chapter V of the Provision.Article52The change documents of medical device registration shall be used in conjunction with its Registration Certificate for Medical Device and their validity period shall be the same.After get the change documents of medical device registration,the applicant can revise product technical requirement,IFU and labels by itself. Article53Where provisions concerning application acceptance and approval procedures for the Change of Approval Matters are not available in this chapter,Chapter V of the Provision shall prevail.Chapter VII Registration ExtensionArticle54Where it is required to extent validity period of the Registration Certificate for Medical Device,the applicant shall apply registration extension to corresponding food and drug regulatory authority6months before the expiration date and submit application documents according to relevant requirements.。
ICHQ7(中英文)
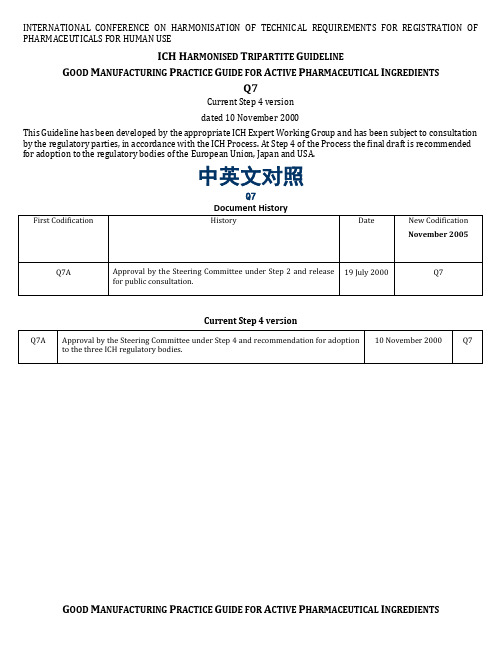
INTERNATIONAL CONFERENCE ON HARMONISATION OF TECHNICAL REQUIREMENTS FOR REGISTRATION OF PHARMACEUTICALS FOR HUMAN USEICH H ARMONISED T RIPARTITE G UIDELINEG OOD M ANUFACTURING P RACTICE G UIDE FOR A CTIVE P HARMACEUTICAL I NGREDIENTSQ7Current Step 4 versiondated 10 November 2000This Guideline has been developed by the appropriate ICH Expert Working Group and has been subject to consultation by the regulatory parties, in accordance with the ICH Process. At Step 4 of the Process the final draft is recommended for adoption to the regulatory bodies of the European Union, Japan and USA.中英文对照Q7Current Step 4 versionG OOD M ANUFACTURING P RACTICE G UIDE FOR A CTIVE P HARMACEUTICAL I NGREDIENTSICH Harmonised Tripartite GuidelineHaving reached Step 4 of the ICH Process at the ICH Steering Committee meeting on 10 November 2000, this guideline is recommended for adoption to the three regulatory parties to ICHTable of Contents 目录1. INTRODUCTION 1. 前言1.1 Objective 1.1 目的1.2 Regulatory Applicability 1.2 法规的适用性1.3 Scope 1.3 范围2. QUALITY MANAGEMENT 2.质量管理2.1 Principles 2.1 总则2.2 Responsibilities of the Quality Unit(s) 2.2 质量部门的责任2.3 Responsibility for Production Activities 2.3 生产的职责2.4 Internal Audits (Self Inspection) 2.4 内部审计(自检)2.5 Product Quality Review 2.5 产品质量回顾3. PERSONNEL 3. 人员3.1 Personnel Qualifications 3.1人员资格3.2 Personnel Hygiene 3.2 个人卫生3.3 Consultants 3.3 顾问4. BUILDINGS AND FACILITIES 4. 建筑和设施4.1 Design and Construction 4.1 设计和建造4.2 Utilities 4.2 公用设施4.3 Water 4.3 水4.4 Containment 4.4 特殊限制4.5 Lighting 4.5 照明4.6 Sewage and Refuse 4.6 污物和废弃物4.7 Sanitation and Maintenance 4.7 卫生和维护5. PROCESS EQUIPMENT 5. 工艺设备5.1 Design and Construction 5.1 设计和建造5.2 Equipment Maintenance and Cleaning 5.2 设备维护和清洁5.3 Calibration 5.3 校验5.4 Computerized Systems 5.4 计算机控制系统6. DOCUMENTATION AND RECORDS 6. 文件和记录6.1 Documentation System and Specifications 6.1 文件系统和质量标准6.2 Equipment cleaning and Use Record 6.2 设备的清洁和使用记录6.3 Records of Raw Materials,Intermediates, 6.3 原料、中间体、原料药的标签和包装材料的记录API Labeling and Packaging Materials6.4 Master Production Instructions 6.4 主生产指令(主生产和控制记录)(Master Production and Control Records)6.5 Batch Production Records 6.5 批生产记录(批生产和控制记录)(BatchProduction and Control Records)6.6 Laboratory Control Records 6.6 实验室控制记录6.7 Batch Production Record Review 6.7 批生产记录审核7. MATERIALS MANAGEMENT 7. 物料管理7.1 General Controls 7.1 一般要求7.2 Receipt and Quarantine 7.2 接收和待验7.3 Sampling and Testing of Incoming Production Materials 7.3 来料的取样与检测7.4 Storage 7.4 储存7.5 Re-evaluation 7.5 再评价8. PRODUCTION AND IN-PROCESS CONTROLS 8. 生产管理和生产过程控制8.1 Production Operations 8.1 生产管理8.2 Time Limits 8.2 时限8.3 In-process Sampling and Controls 8.3 生产过程中的取样和控制8.4 Blending Batches of Intermediates or APIs 8.4 中间体或原料药的混批8.5 Contamination Control 8.5 污染控制9. PACKAGING AND IDENTIFICATION 9. 原料药和中间体的包装和贴签LABELING OF APIs AND INTERMEDIATES9.1 General 9.1 通则9.2 Packaging Materials 9.2 包装材料9.3 Label Issuance and Control 9.3 标签发放与管理9.4 Packaging and Labeling Operations 9.4 包装和贴签管理10. STORAGE AND DISTRIBUTION 10.储存和分发10.1 Warehousing Procedures 10.1 入库程序10.2 Distribution Procedures 10.2 分发程序11. LABORATORY CONTROLS 11.实验室管理11.1 General Controls 11.1通则11.2 Testing of Intermediates and APIs 11.2 中间体和原料药的检测11.3 Validation of Analytical Procedures 11.3 分析方法的验证11.4 Certificates of Analysis 11.4 检验报告11.5 Stability Monitoring of APIs 11.5 原料药的稳定性考察11.6 Expiry and Retest Dating 11.6 有效期和复验期11.7 Reserve/Retention Samples 11.7 留样12. VALIDATION 12.验证12.1 Validation Policy 12.1 验证方针12.2 Validation Documentation 12.2 验证文件12.3 Qualification 12.3 确认12.4 Approaches to Process Validation 12.4 工艺验证的方法12.5 Process Validation Program 12.5 工艺验证的程序12.6 Periodic Review of Validated Systems 12.6 对已验证的系统的定期回顾12.7 Cleaning Validation 12.7 清洗验证12.8 Validation of Analytical Methods 12.8 分析方法的验证13. CHANGE CONTROL 13.变更控制14. REJECTION AND RE-USE OF MATERIALS 14.物料的拒收和再利用14.1 Rejection 14.1 拒收14.2 Reprocessing 14.2 返工14.3 Reworking 14.3 重新加工14.4 Recovery of Materials and Solvents 14.4 物料与溶剂的回收14.5 Returns 14.5 退货15. COMPLAINTS AND RECALLS 15.投诉与召回16. CONTRACT MANUFACTURERS 16.协议生产商(包括实验室)(INCLUDING LABORATORIES)17. AGENTS, BROKERS, TRADERS, DISTRIBUTORS, 17.代理商、经纪人、贸易商、经销商、重新包装者REPACKERS, AND RELABELLERS 和重新贴签者17.1 Applicability 17.1 适用性17.2 Traceability of Distributed APIs and Intermediates 17.2 已分发的原料药和中间体的可追溯性17.3 Quality Management 17.3 质量管理17.4 Repackaging, Relabeling, and Holding of APIs and Intermediates 17.4 原料药和中间体的重新包装、重新贴签和待检17.5 Stability 17.5 稳定性17.6 Transfer of Information 17.6 信息的传达17.7 Handling of Complaints and Recalls 17.7 投诉和召回的处理17.8 Handling of Returns 17.8 退货的处理18. Specific Guidance for APIs Manufactured by Cell 18. 用细胞繁殖/发酵生产的原料药的特殊指南Culture/Fermentation18.1 General 18.1 总则18.2 Cell Bank Maintenance and Record Keeping 18.2 细胞库的维护和记录的保存18.3 Cell Culture/Fermentation 18.3 细胞繁殖/发酵18.4 Harvesting, Isolation and Purification 18.4 收取、分离和精制18.5 Viral Removal/Inactivation steps 18.5 病毒的去除/灭活步骤19. APIs for Use in Clinical Trials 19. 用于临床研究的原料药19.1 General 19.1 总则19.2 Quality 19.2 质量19.3 Equipment and Facilities 19.3 设备和设施19.4 Control of Raw Materials 19.4 原料的控制19.5 Production 19.5 生产19.6 Validation 19.6 验证19.7 Changes 19.7 变更19.8 Laboratory Controls 19.8 实验室控制19.9 Documentation 19.9 文件20. Glossary 20. 术语1. INTRODUCTION 1. 简介1.1 Objective 1.1 目的This document is intended to provide guidance regarding good manufacturing practice (GMP) for the manufacturing of activepharmaceutical ingredients (APIs) under an appropriate system for managing quality. It is also intended to help ensure that APIs meet the quality and purity characteristics that they purport, or are represented, to possess.本文件旨在提供在适当的体系下为了控制生产原料药的质量而实施的药品生产质量管理规范(GMP)的指南。
ARTISAN TECHNOLOGY GROUP 用户指南.pdf_1703278955.63762
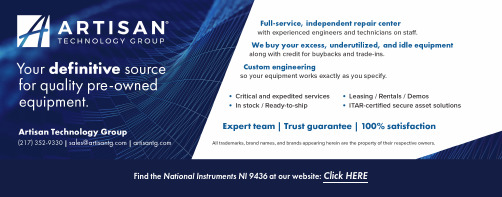
GETTING STARTED GUIDENI 94368 DI, ±100 VDC to ±250 VDC/100 VAC to 250 VAC, Sinking/Sourcing, 20 msThis document explains how to connect to the NI 9436.Note Before you begin, complete the software andhardware installation procedures in your chassisdocumentation.Note The guidelines in this document are specific tothe NI 9436. The other components in the system mightnot meet the same safety ratings. Refer to thedocumentation for each component in the system todetermine the safety and EMC ratings for the entiresystem.Safety GuidelinesOperate the NI 9436 only as described in this document.Caution Do not operate the NI 9436 in a manner notspecified in this document. Product misuse can result ina hazard. You can compromise the safety protectionbuilt into the product if the product is damaged in anyway. If the product is damaged, return it to NI forrepair.2| | NI 9436 Getting Started Guidehnology Group - Quality Instrumentation ... Guaranteed | (888) 88-SOURCE | wwwSafety VoltagesConnect only voltages that are within the following limits:DIa-to-DIb250 Vrms maximum,Measurement Category IIIsolationChannel-to-channelContinuous250 Vrms, MeasurementCategory IIWithstand1,500 Vrms, verified by a 5 sdielectric withstand testChannel-to-earth groundContinuous250 Vrms, MeasurementCategory IIWithstand3,000 Vrms, verified by a 5 sdielectric withstand testMeasurement Category II is for measurements performed oncircuits directly connected to the electrical distribution system.This category refers to local-level electrical distribution, such asNI 9436 Getting Started Guide| © National Instruments| 3 hnology Group - Quality Instrumentation ... Guaranteed | (888) 88-SOURCE | wwwthat provided by a standard wall outlet, for example, 115 V forU.S. or 230 V for Europe.Caution Do not connect the NI 9436 to signals or usefor measurements within Measurement Categories IIIor IV.Safety Guidelines for Hazardous VoltagesIf hazardous voltages are connected to the device, take thefollowing precautions. A hazardous voltage is a voltage greaterthan 42.4 Vpk voltage or 60 VDC to earth ground.Hazardous Voltage This icon denotes a warningadvising you to take precautions to avoid electricalshock.Caution Ensure that hazardous voltage wiring isperformed only by qualified personnel adhering to localelectrical standards.Caution Do not mix hazardous voltage circuits andhuman-accessible circuits on the same module.Caution Ensure that devices and circuits connected tothe module are properly insulated from human contact.4| | NI 9436 Getting Started Guidehnology Group - Quality Instrumentation ... Guaranteed | (888) 88-SOURCE | wwwElectromagnetic Compatibility GuidelinesThis product was tested and complies with the regulatoryrequirements and limits for electromagnetic compatibility (EMC)stated in the product specifications. These requirements andlimits provide reasonable protection against harmful interferencewhen the product is operated in the intended operationalelectromagnetic environment.This product is intended for use in industrial locations. However,harmful interference may occur in some installations, when theproduct is connected to a peripheral device or test object, or if theproduct is used in residential or commercial areas. To minimizeinterference with radio and television reception and preventunacceptable performance degradation, install and use thisproduct in strict accordance with the instructions in the productdocumentation.Furthermore, any changes or modifications to the product notexpressly approved by National Instruments could void yourauthority to operate it under your local regulatory rules.NI 9436 Getting Started Guide| © National Instruments| 5 hnology Group - Quality Instrumentation ... Guaranteed | (888) 88-SOURCE | wwwSpecial Conditions for Marine ApplicationsSome products are Lloyd’s Register (LR) Type Approved formarine (shipboard) applications. To verify Lloyd’s Registercertification for a product, visit /certification and searchfor the LR certificate, or look for the Lloyd’s Register mark onthe product.Caution In order to meet the EMC requirements formarine applications, install the product in a shieldedenclosure with shielded and/or filtered power andinput/output ports. In addition, take precautions whendesigning, selecting, and installing measurement probesand cables to ensure that the desired EMC performanceis attained.6| | NI 9436 Getting Started Guidehnology Group - Quality Instrumentation ... Guaranteed | (888) 88-SOURCE | wwwPreparing the EnvironmentEnsure that the environment in which you are using the NI 9436 meets the following specifications.Operating temperature(IEC 60068-2-1, IEC 60068-2-2)-40 °C to 70 °COperating humidity (IEC 60068-2-78)10% RH to 90% RH, noncondensingPollution Degree2Maximum altitude5,000 mIndoor use only.Note Refer to the device datasheet on /manualsfor complete specifications.NI 9436 Getting Started Guide| © National Instruments| 7 hnology Group - Quality Instrumentation ... Guaranteed | (888) 88-SOURCE | wwwNI 9436 Pinout8| | NI 9436 Getting Started Guidehnology Group - Quality Instrumentation ... Guaranteed | (888) 88-SOURCE | wwwSinking-Output ConnectionsorACThe NI 9436 channel registers as ON when the sinking-outputdevice drives the input within the input ON range. If no device isconnected to DI, the channel registers as OFF.NI 9436 Getting Started Guide| © National Instruments| 9 hnology Group - Quality Instrumentation ... Guaranteed | (888) 88-SOURCE | wwwSourcing-Output ConnectionsSourcing-OutputorAC The NI 9436 channel registers as ON when the sourcing-output device drives enough current or applies enough voltage to DI. If no device is connected to DI, the channel registers as OFF.Switch ConnectionsorACLoad ConnectionsorACNI 9436 Connection GuidelinesMake sure that devices you connect to the NI 9436 are compatible with the module specifications.You must use 2-wire ferrules to create a secure connection when connecting more than one wire to a single terminal on theNI 9436.Wiring the NI 9436Caution For safe operation with hazardous voltages,you must use the NI 9939 Connector Backshell withthe 16-position screw terminal connector on theNI 9436.When connecting all 16 terminals, the total maximum wire diameter including insulation must not exceed 2.3 mm (0.09 in.) per wire in order to fit through the 11.0 mm (0.43 in.) opening on the NI 9939.When connecting all 16 terminals using the cable retainer, the total maximum wire diameter including insulation must notexceed 1.6 mm (0.06 in.) per wire in order to fit under the7.6 mm (0.30 in.) clearance of the NI 9939 cable retainer.Figure 1. NI 9939 Wire Clearance DimensionsComplete the appropriate procedure based on the total maximum wire diameter used.Installing the NI 9939What to Use•NI 9939 kit•0.05 mm2 to 1.5 mm2 (30 AWG to 14 AWG) wire with 6 mm(0.24 in.) of the insulation stripped•Slotted screwdriverWhat to Do1.Insert the stripped end of the wire fully into the appropriateterminal on the 16-Position Screw Terminal Connector (2) and tighten the screw. Make sure no exposed wire extends past the screw terminal.2.Route the wire through the NI 9939 opening and removeslack from the wiring.3.Install the Backshell Top Enclosure (1) to the BackshellBottom Enclosure (3).4.Place the Label (5) in the Label Carrier (4) and attach ontothe backshell.Installing the NI 9939 Using the Cable Retainer What to Use•NI 9939 kit•0.05 mm2 to 1.5 mm2 (30 AWG to 14 AWG) wire with 6 mm(0.24 in.) of the insulation stripped•Slotted screwdriverWhat to Do1.Insert the stripped end of the wire fully into the appropriateterminal on the 16-Position Screw Terminal Connector (2)and tighten the screw. Make sure no exposed wire extends past the screw terminal.2.Route the wire through the NI 9939 opening, remove slackfrom the wiring, and secure wires using the Cable Retainer(6) and tighten the Screws (7).3.Install the Backshell Top Enclosure (1) to the BackshellBottom Enclosure (3).4.Place the Label (5) in the Label Carrier (4) and attach ontothe backshell.High-Vibration Application ConnectionsIf your application is subject to high vibration, NI recommends that you follow these guidelines to protect connections to the NI 9436:•Use ferrules to terminate wires to the detachable connector.•Use the NI 9939 backshell kit.Where to Go NextWorldwide Support and ServicesThe NI website is your complete resource for technical support. At /support, you have access to everything from troubleshooting and application development self-help resources to email and phone assistance from NI Application Engineers. Visit /services for NI Factory Installation Services, repairs, extended warranty, and other services.Visit /register to register your NI product. Product registration facilitates technical support and ensures that you receive important information updates from NI.A Declaration of Conformity (DoC) is our claim of compliance with the Council of the European Communities using the manufacturer’s declaration of conformity. This system affords the user protection for electromagnetic compatibility (EMC) and product safety. You can obtain the DoC for your product by visiting /certification. If your product supports calibration, you can obtain the calibration certificate for your product at /calibration.NI corporate headquarters is located at11500 North Mopac Expressway, Austin, Texas, 78759-3504. NIalso has offices located around the world. For telephone supportin the United States, create your service request at /supportor dial 1 866 ASK MYNI (275 6964). For telephone supportoutside the United States, visit the Worldwide Offices section of/niglobal to access the branch office websites, whichprovide up-to-date contact information, support phone numbers,email addresses, and current events.Refer to the NI Trademarks and Logo Guidelines at /trademarks for information on NItrademarks. Other product and company names mentioned herein are trademarks or trade namesof their respective companies. For patents covering NI products/technology, refer to theappropriate location: Help»Patents in your software, the patents.txt file on your media, or theNational Instruments Patent Notice at /patents. Y ou can find information about end-userlicense agreements (EULAs) and third-party legal notices in the readme file for your NI product.Refer to the Export Compliance Information at /legal/export-compliance for the NIglobal trade compliance policy and how to obtain relevant HTS codes, ECCNs, and other import/export data. NI MAKES NO EXPRESS OR IMPLIED WARRANTIES AS TO THE ACCURACY OFTHE INFORMATION CONTAINED HEREIN AND SHALL NOT BE LIABLE FOR ANY ERRORS.U.S. Government Customers: The data contained in this manual was developed at privateexpense and is subject to the applicable limited rights and restricted data rights as set forth in FAR52.227-14, DFAR 252.227-7014, and DFAR 252.227-7015.© 2016 National Instruments. All rights reserved.376511A-01Sep16hnology Group - Quality Instrumentation ... Guaranteed | (888) 88-SOURCE | www。
Surflan Pro 商品说明书
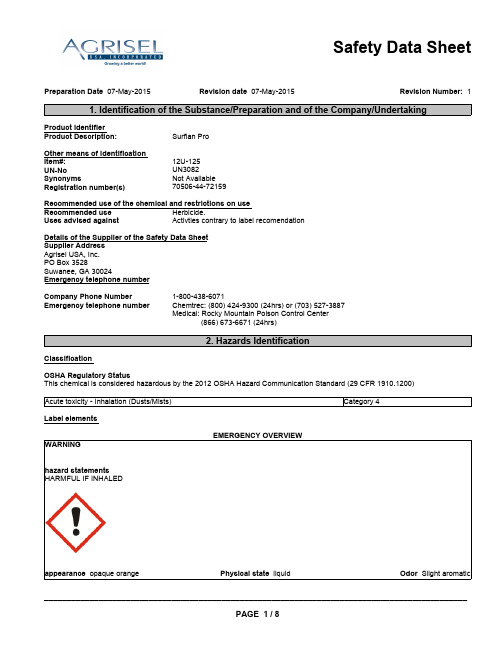
Preparation Date 07-May-2015Revision date 07-May-2015Revision Number: 11.Identification of the Substance/Preparation and of the Company/UndertakingProduct identifierProduct Description:Surflan ProOther means of identificationItem#:12U-125UN-No UN3082Synonyms Not AvailableRegistration number(s)70506-44-72159Recommended use of the chemical and restrictions on useRecommended use Herbicide.Uses advised against Activties contrary to label recomendationDetails of the Supplier of the Safety Data SheetSupplier AddressAgrisel USA, Inc.PO Box 3528Suwanee, GA 30024Emergency telephone numberCompany Phone Number1-800-438-6071Emergency telephone number Chemtrec: (800) 424-9300 (24hrs) or (703) 527-3887Medical: Rocky Mountain Poison Control Center(866) 673-6671 (24hrs)2.Hazards IdentificationClassificationOSHA Regulatory StatusThis chemical is considered hazardous by the 2012 OSHA Hazard Communication Standard (29 CFR 1910.1200)Acute toxicity - Inhalation (Dusts/Mists)Category 4Label elementsEMERGENCY OVERVIEWWARNINGhazard statementsHARMFUL IF INHALEDappearance opaque orange Physical state liquid Odor Slight aromaticPrecautionary Statements - PreventionDo not get in eyes, on skin, or on clothingUse only outdoors or in a well-ventilated areaIF INHALED: Remove victim to fresh air and keep at rest in a position comfortable for breathingCall a POISON CENTER or doctor if you feel unwellHazards Not Otherwise Classified (HNOC)OTHER INFORMATION•M a y b e h a r m f u l i n c o n t a c t w i t h s k i nposition/information on IngredientsChemical name CAS-No Weight %Trade secret Oryzalin19044-88-340.4Glycerin56-81-5<30If CAS number is "proprietary", the specific chemical identity and percentage of composition has been withheld as a trade secret.4.First aid measuresFIRST AID MEASURESEye contact Hold eye open and rinse slowly and gently with water for 15 - 20 minutes. Remove contactlenses, if present, after 5 minutes, then continue rinsing eye. Call a poison control center ordoctor for treatment advice.Skin contact Take off contaminated clothing. Wash off immediately with plenty of water for at least 15minutes. Call poison control center or doctor for treatment advice. Wash face, hands andany exposed skin thoroughly after handling.Inhalation Move person to fresh air. If person is not breathing, call 911 or an ambulance, then giveartificial respiration, preferably mouth-to-mouth if possible. Call a physician or poisoncontrol center immediately.Ingestion Call a physician or poison control center immediately. Never give anything by mouth to anunconscious person. Do not induce vomiting without medical advice.Most Important Symptoms and Effects, Both Acute and DelayedNo information available.Most Important Symptoms andEffectsIndication of Any Immediate Medical Attention and Special Treatment NeededNotes to physician No information available.5.Fire-fighting measuresSuitable extinguishing mediaUse extinguishing measures that are appropriate to local circumstances and the surrounding environment.Unsuitable extinguishing media No information available.Specific hazards arising from the chemicalNo information available.Hazardous combustion products Oxides of nitrogen. Can emit toxic fumes under fire conditions.Explosion dataProtective equipment and precautions for firefightersUse personal protective equipment. As in any fire, wear self-contained breathing apparatus pressure-demand, MSHA/NIOSH (approved or equivalent) and full protective gear.6.Accidental release measuresPersonal precautions, protective equipment and emergency proceduresPersonal Precautions Avoid contact with the skin and the eyes. Use personal protective equipment. Wearprotective gloves/clothing and eye/face protection. Wash thoroughly after handling. Environmental PrecautionsEnvironmental precautions Consult a regulatory specialist to determine appropriate state or local reportingrequirements, for assistance in waste characterization and/or hazardous waste disposaland other requirements listed in pertinenet environmental permits.Methods and material for containment and cleaning upMethods for Clean-Up Soak up with inert absorbent material (e.g. sand, silica gel, acid binder, universal binder,sawdust). Sweep up and shovel into suitable containers for disposal.7.Handling and StoragePrecautions for safe handlingHandling Keep out of reach of children. Do not eat, drink or smoke when using this product. Avoidcontact with skin and eyes. Wear personal protective equipment. Remove and washcontaminated clothing before re-use. Wash thoroughly after handling.Conditions for safe storage, including any incompatibilitiesStorage Keep out of the reach of children. Keep containers tightly closed in a cool, well-ventilatedplace.incompatible materials No materials to be especially mentioned.8.Exposure Controls/Personal ProtectionExposure guidelinesChemical name ACGIH TLV OSHA PELGlycerin TWA: 15 mg/m3 mist, total particulate TWA: 5 mg/m3 mist, respirablefraction(vacated) TWA: 10 mg/m3 mist, total particulate (vacated) TWA: 5 mg/m3mist, respirable fractionEngineering controls Investigate engineering techniques to reduce exposures. Local mechanical exhaustventilation is preferred. Consult ACGIH ventilation manual or NFPA Standard 91 for designof exhaust systems. PESTICIDE APPLICATORS & WORKERS. THESE WORKERS MUSTREFER TO PRODUCT LABELING AND DIRECTIONS FOR USE IN ACCORDANCE WITHEPA WORKER PROTECTION STANDARD 40 CFR PART 170.Personal protective equipmentEye/Face Protection Where there is potential for eye contact have eye flushing equipment available. Use eyeprotection to avoid eye contact.Skin protection Long sleeved clothing. Long pants. Socks and footwear.Respiratory protection Where airborne exposure is likely, use NIOSH approved respiratory protection equipmentappropriate to the material and/or its components. Full facepiece equipment isrecommended and, if used, replaces need for face shield and/or chemical goggles. Ifexposures cannot be kept at a minimum with engineering controls, consult respiratormanufacturer to determine appropriate type equipment for given application. Observerespirator use limitations specified by NIOSH or the manufacturer. For emergency andother conditions where there may be a potential for significant exposure, use an approvedfull face positive-pressure, self-contained breathing apparatus. Respiratory protectionprograms must comply with 29 CFR 1910.134.General hygiene considerationsDo not eat, drink or smoke when using this product. Wear suitable gloves and eye/face protection. Wash hands before breaks and immediately after handling the product. Remove and wash contaminated clothing before re-use.9.Physical and Chemical PropertiesInformation on basic physical and chemical propertiesPhysical state liquidappearance opaque orange Odor Slight aromaticcolor No information availableProperty VALUES R e ma r k s/•M e t h o dpH 5.9Melting point/freezing point 6.9 °C / 44 °FBoiling Point/Range No information availableFlash Point>93 C >200 FEvaporation Rate No information availableflammability (solid, gas)No information availableFlammability limit in airUpper Flammability Limit No information availableLower Flammability Limit No information availablevapor pressure No information availableVapor Density No information availableSpecific gravity 1.138 to 1.239 @ 25 CWater solubility No information availableSolubility in Other Solvents No information availablePartition coefficient: n-octanol/water No information availableAutoignition temperature No information availabledecomposition temperature No information availableViscosity, kinematic No information availableDynamic viscosity No information availableExplosive properties No information availableOxidizing properties No information availableOTHER INFORMATIONSoftening point No information availablemolecular weight No information availableVOC Content No information availabledensity No information availableBulk density No information available10.Stability and ReactivityReactivityno data availableChemical stabilityStable under recommended storage conditions.Possibility of hazardous reactionsNone under normal processing.Conditions to avoidKeep away from open flames, hot surfaces and sources of ignition.incompatible materialsNo materials to be especially mentioned.Hazardous decomposition productsToxic gases and fumes may be formed if product is involved in fire. Oxides of nitrogen.11.Toxicological InformationInformation on Likely Routes of ExposureInhalation May cause irritation of respiratory tract.Eye contact Moderately irritating to the eyes.Skin contact Repeated or prolonged skin contact may cause allergic reactions with susceptible persons.Ingestion MAY BE HARMFUL IF SWALLOWED.Component Information Oryzalin -In animals has been shown to cause liver, kidney, bladder, spleen, and/or blood effects.Repeated excessive exposure to crystalline silica may affect lung function and causesilicosis, a progressive and disabling disease of the lungs. Some evidence suggests thatkidney effects may also result from excessive exposure. Glycerin:No skin allergy was observed in guinea pigs or humans following repeated exposure. Oraladministration in clinical use has caused nausea and vomiting. Repeated or long-term oralexposure produced no adverse effects in rats. No adverse effects on fertility or birth defectswere observed in rats or their offspring following oral exposure before and duringpregnancy. Generally, no genetic changes were observed in tests using bacteria or animalcells.Single exposure studies indicate that this material is practically non-toxic if swallowed (ratLD50 12,600- 27,200 mg/kg) or absrobed through skin (rabbit LD50 >10,000 mg/kg), nomore than slightly toxic if inhaled (rat 1 hr LC50 >0.57 mg/l), and slightly irritating to rabbiteyes and skin.Chemical name LD50 Oral LD50 Dermal LC50 Inhalation> 5000 mg/kg ( Rat )> 2000 mg/kg ( Rabbit )> 4.79 mg/LOryzalin19044-88-3-> 10 g/kg ( Rabbit )570 mg/m3 ( Rat ) 1 h Glycerin56-81-5Information on Toxicological EffectsSymptoms No information available.Delayed and immediate effects as well as chronic effects from short and long-term exposuresensitization No information available.Mutagenic effects No information available.Carcinogenicity The information below indicates whether any agency has listed any ingredient as acarcinogen.Reproductive effects Not Available.STOT - Single Exposure No information available.STOT - repeated exposure No information available.Target organ effects kidney, Respiratory System, EYES, skin.Aspiration hazard No information available.Numerical Measures of Toxicity - Product informationThe following values are calculated based on chapter 3.1 of the GHS document . 5290 mg/kg (rat) 1697.9 mg/kg (rat) 0 mg/l (mist) (dust) mg/m3 0 ml/m3 (Vapor)12.Ecological InformationMarine Pollutant.ecotoxicityOryzalin:Highly toxic to aquatic organisms LC50/EC50 between 0.1 and 1 mg/L in the most sensitive species. Slightly toxic to birds on an acute basis LD50 between 501 and 2000 mg/kg.Bobwhite quail acute oral LD50 1046 mg/kgHoneybee acute oral LD50 >100 ug/beePersistence/DegradabilityNo information available.Bioaccumulation/ AccumulationBioaccumulative potential.Chemical name Log Pow> 2Oryzalin19044-88-3-1.76Glycerin56-81-5Other Adverse EffectsNo information available13.Disposal ConsiderationsWaste Treatment MethodsWaste Disposal Method Pesticide wastes are acutely hazardous. Improper disposal of excess pesticide or rinsate isa violation of Federal law. If the wastes cannot be disposed of by use or according to labelinstructions, contact your State Pesticide or Environmental Control Agency, or theHazardous Waste representative at the nearest EPA Regional Office for guidance. Do notdischarge effluent containing this product into lakes, streams, ponds, estuaries, oceans, orother waters unless in accordance with the requirements of a National Pollutant DischargeElimination System (NPDES) permit. Do not discharge effluent containing this product tosewer systems without previously notifying the local sewage treatment plant authority. Donot apply directly to wetlands or water.Contaminated packaging Refer to product label.14.Transport InformationDOT When shipped domestically by highway in non-bulk containers this product can be shippedas not regulated.UN-No UN3082Proper shipping name Environmentally hazardous substance, liquid, n.o.s (Oryzalin)Hazard class9Packing group PG IIIMarine Pollutant Marine Pollutant.ICAOUN-No UN3082Proper shipping name Environmentally hazardous substance, liquid, n.o.s (Oryzalin)Hazard class9Packing group PG IIIDescription Marine PollutantIATAProper shipping name Environmentally hazardous substances, liquid, n.o.s (Oryzalin)Hazard class9Packing group PG IIIDescription Marine PollutantIMDG/IMOUN-No UN3082Proper shipping name Environmentally hazardous substances, liquid, n.o.s (Oryzalin)Hazard class9Packing group PG IIIMarine Pollutant Yes15.Regulatory InformationThis chemical is a pesticide product registered by the Environmental Protection Agency and is subject to certain labeling requirements under federal pesticide law. These requirements differ from the classification criteria and hazard information required for safety data sheets, and for workplace labels of non-pesticide chemicals. Following is the hazard information as required on the pesticide label:signal word CAUTIONVentilation Control PESTICIDE APPLICATORS & WORKERS THESE WORKERS MUST REFER TOPRODUCT LABELING AND DIRECTIONS FOR USE IN ACCORDANCE WITH EPAWORKER PROTECTION STANDARD 40 CFR PART 170.Keep out of Reach of Children. Causes moderate eye irritation. Prolonged or frequent repeated skin contact may cause allergic reaction in some individuals. Toxic to fish.International InventoriesUSINV Not determinedDSL/NDSL Not determinedDoes not complyEINECS/ELINCSENCS Does not complyChina Does not complyKECL Does not complyPICCS Does not complyAICS Does not complyTSCA Does not complyTSCA - United States Toxic Substances Control Act Section 8(b) InventoryDSL/NDSL - Canadian Domestic Substances List/Non-Domestic Substances ListEINECS/ELINCS - European Inventory of Existing Commercial Chemical Substances/EU List of Notified Chemical SubstancesENCS - Japan Existing and New Chemical SubstancesIECSC - China Inventory of Existing Chemical SubstancesKECL - Korean Existing and Evaluated Chemical SubstancesPICCS - Philippines Inventory of Chemicals and Chemical SubstancesAICS - Australian Inventory of Chemical SubstancesFederal RegulationsSARA 313Section 313 of Title III of the Superfund Amendments and Reauthorization Act of 1986 (SARA). This product contains a chemical or chemicals which are subject to the reporting requirements of the Act and and Title 40n of the Code of Federal Regulations, Part 372:Chemical name SARA 313 - Threshold ValuesOryzalin - 19044-88-3 1.0SARA 311/312 HazardousCategorizationAcute health hazard yes Chronic health hazard NO Fire hazard No Sudden release of pressure hazard No Reactive Hazard No CERCLASARA Product RQ0RCRAPesticide InformationComponent FIFRA - Restricted Use FIFRA - PesticideProduct OtherIngredientsFIFRA - Listing ofPesticide ChemicalsCalifornia Pesticides -Restricted MaterialsOryzalin19044-88-3 ( 40.4 )XGlycerin56-81-5 ( <30 )XState RegulationsComponent CAS-No CATEGORY California Prop. 65Non-additive, corrosivechemical type Oryzalin19044-88-3 ( 40.4 )19044-88-3Carcinogen CarcinogenState Right-to-KnowChemical name Massachusetts New Jersey Pennsylvania Illinois Rhode Island Oryzalin XGlycerin X X XInternational regulationsU.S. EPA Label informationEPA Pesticide registration number70506-4416.Other InformationPreparation Date07-May-2015Revision date07-May-2015Revision SummaryUpdate to GHS formatEnd of MSDSNFPA HEALTH 0flammability 1Instability 0Physical hazard -。
wercs 注册流程
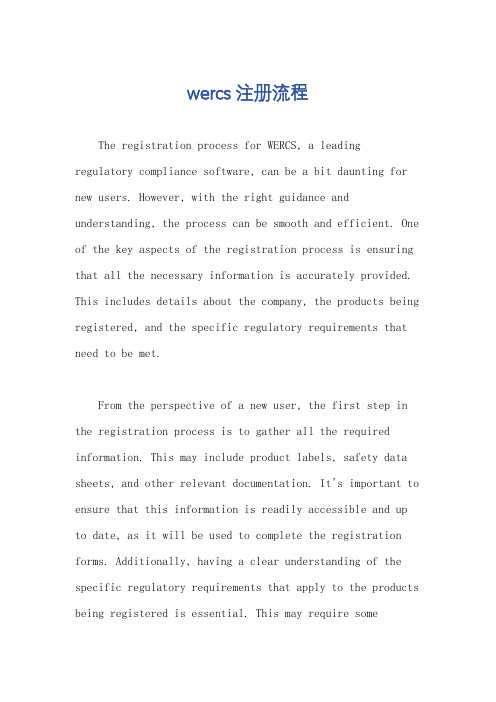
wercs 注册流程The registration process for WERCS, a leading regulatory compliance software, can be a bit daunting for new users. However, with the right guidance and understanding, the process can be smooth and efficient. One of the key aspects of the registration process is ensuring that all the necessary information is accurately provided. This includes details about the company, the products being registered, and the specific regulatory requirements that need to be met.From the perspective of a new user, the first step in the registration process is to gather all the required information. This may include product labels, safety data sheets, and other relevant documentation. It's important to ensure that this information is readily accessible and up to date, as it will be used to complete the registration forms. Additionally, having a clear understanding of the specific regulatory requirements that apply to the products being registered is essential. This may require someresearch or consultation with regulatory experts to ensure that all necessary information is included in the registration.Once all the required information has been gathered, the next step is to navigate the WERCS registration portal. For new users, this may require some familiarization with the platform and its various features. It's important to take the time to carefully read through the instructions and prompts provided to ensure that the registration process is completed accurately. This may also involve creating a new account or logging in with existing credentials, depending on the user's prior experience with the platform.As the registration process progresses, it's important to pay close attention to detail and ensure that all the required fields are completed accurately. This may involve entering product details, ingredient information, and other relevant data. It's essential to double-check all entries to avoid any errors or omissions that could potentially delay the registration process. Additionally, it'simportant to be mindful of any specific formatting or data entry requirements specified by the WERCS platform to ensure that the information is submitted correctly.Throughout the registration process, new users may encounter various challenges or questions that require assistance. It's important to be proactive in seeking help or clarification as needed. This may involve reaching out to the WERCS support team for guidance, consulting online resources or user guides, or seeking assistance from colleagues or industry peers who have experience with the platform. By being proactive and seeking assistance when needed, new users can navigate the registration process with greater confidence and efficiency.Finally, once the registration forms have been completed and submitted, new users should be prepared to follow up as needed. This may involve responding to any requests for additional information or clarification from the WERCS team, addressing any issues or errors that may arise during the review process, and ultimately ensuring that the registration is successfully completed. By stayingengaged and responsive throughout the process, new userscan help to ensure a smooth and successful registration experience with WERCS.In conclusion, the registration process for WERCS may initially seem complex and overwhelming for new users. However, by taking a proactive and detail-oriented approach, gathering all the necessary information, navigating the registration portal with care, seeking assistance when needed, and following up as necessary, new users can successfully complete the registration process and ensure compliance with regulatory requirements. With patience, attention to detail, and a willingness to seek guidance as needed, new users can navigate the WERCS registration process with confidence and efficiency.。
梅特勒-托利多天平使用说明书

To ensure the future success of late -stage product development processes, itcontinuously strengthens its capabilities, and seeks to maximize the time it spendson the science through investment in emerging and state -of -the -art technologiesthat can reduce otherwise trivial manual labor. This mindset drove the productdevelopment team ’s search for an automated solutions preparation system that iscompliant with regulatory requirements in a GMP setting. For example, for themeasuring devices in the system the team needed to follow the requirementsstated in pharmacopeias (USP and Ph.Eur.). They recognized that the balances, pHprobes, conductivity probes, temperature sensors and volumetric glassware mustmeet the stringent requirements set by these pharmacopeias. In addition, it wasalso essential to comply with data integrity requirements set by the FDA ’s 21 CFRPart 11 and EU ’s Annex 11. The selected system needed to capture and log criticalaspects of record keeping such as audit trails, reports, recipe composition, userpermissions and dosing records.THE CHALLENGEA top 20 global pharmaceutical company with headquarters in Europe, has been inoperation for a century. With a mission of developing medicines and treatmentsfor endocrine diseases, this company helps people live better every day. In orderto speed the development of medicines and treatments to market, it has adopteda culture of innovation where implementing cutting edge technology isencouraged, embraced and expected. It was this innovation culture that spurredthe concept of moving a research automation system into the GMP environmentand improve the efficiency of laboratory personnel and operations there.ABOUT OUR CUSTOMER"The flexibility the solution has provided for just -in -time preparation is a major benefit."AUTOMATED PREPARATION OFREAGENT SOLUTIONS FOR GMP LABS Case StudyAT A GLANCEC. SchwartzProject ManagerLabMinds collaborated with aTop 20 Global Pharmaceutical company and madeenhancements to Revo thatevolved the research productinto a GMP compliant solution.C. Schwartz, Project ManagerTHE SOLUTIONAfter an extensive review of available solutions,they selected LabMinds® Revo®,the benchtop automated solution preparation system that enables companies to automate the reagent preparation bMinds,upon the customer’s request,decided to collaborate and make enhancements to Revo that would evolve the research product into a GMP compliant solution.The project was launched in May of2019and they set out to find a dedicated and innovative technical Project Manager to drive this project.Schwartz was assigned as Project Manager.Schwartz is a specialist in laboratory automation and has a strong track record of leading teams and driving transformation.He accepted the challenge in a large part due to the fact that he had previous exposure to the Revo system from the2016SLAS conference when Revo won the innovation award.He recognized the potential to transform Revo into a GMP compliant system and accepted the challenge.REAGENT SUPPLY SCENARIOSThe above graphic demonstrates the need and the options available for reagents in a lab.By using the Revo, just in time reagent solutions are achieved without using lab personnel time.FORMING A TEAMSchwartz formed a dedicated team comprised of subject matter experts including a chemistry specialist and cross functional experts from other departments.This team combined forces with LabMinds and worked to deliver an automated solution preparation system that complied with GMP requirements.They knew that it needed to deliver a solution that provided the consistent quality,traceability and documentation required in the regulated pharmaceutical industry.The team also sought to solve three main challenges: reducing the time lab technicians spent on preparing reagents to allow them to focus on the science; limiting solution overproduction; and eliminating risk associated with manual documentation processes.After 18 months of intense dedication, the team achieved a huge milestone and Revo was approved internally for use in its GMP laboratory. The system approval was earned through a series of rigorous data integrity process reviews and hardware upgrades. They were then able to tackle the challenges they set out to solve. Just a few months after the launch, the team on -boarded many of its recipes and is already seeing positive impact.SYSTEM APPROVAL“I appreciate the opportunity to work for a company that iswilling to implement cutting edge technology. We willreap many benefits moving forward,” commentedSchwartz, the Project Manager. “The flexibility the solutionhas provided for just -in -time preparation is a majorbenefit. We have already reduced solution overproduction costs and leveraged the Revo system toreallocate our reagent prep team from redundant tasks towork that helps increase the speed of productdevelopment.”"I appreciate the opportunity to work for a company that is willing to implement cutting edge technology that will reap many benefits moving forward."C. Schwartz Project ManagerPrior to the implementation of GMP Revo, three laboratory technicians spent an entire daypreparing reagents for the week. Upon review of recipes required, many were found tohave an organic component. To overcome a current system limitation, LabMindsdeveloped a workflow process where the Revo produces the aqueous portion of thesolution with instructions for the organic component addition printed on the label. Eventhough organic components are still added manually it was decided that the newfoundflexibility of automating the manual weighing, pH verification and data registration madethe process worthwhile. The system now allows the team to order the reagents via theWeb or mobile interface, and reduces the FTE time needed to fulfill monotonous,procedural laboratory tasks by 66%. This allows these key team members to focus on thedata analysis and scientific work needed to produce results from sample analysis.POSITIVE RESULTSThis lab technician team also used to ensure that they did not run out of reagents during the week by creating an extra supply. At expiry, extra solutions were thrown away. Now the team has implemented just -in -time inventory best practices and produce the exact quantities of the solutions they need. They know that they have increased flexibility, and if they need more solutions they do not have to stop analysis to create them. They can simply reorder via the easy Web interface, and the solution will be ready within an hour. This flexibility allows the team to reduce the amount of inventory needed each week.Prior to the implementation, the team manually tracked preparation data on paper to ensure they could obtain the necessary information for upcoming audits. Now, the team utilizes a QR code printed on the bottle label that contains all information describing the preparation and scans this data directly into the LIMS system where a record is created for each bottle.C. Schwartz and the Revo systemhttps:///labmindsinchttps:///labmindsinchttps:///company/labminds/“After 6 months in operation I get continued feedback from the users on how happy they are to be relieved from the tight planning of manual preparation they used to have. Even though organic components are still added manually it is by far overshadowed by the newfound flexibility in the fact that all manual weighing, pH verification and data registration are completely removed from the process.”C. SchwartzProject Manager© 2021 LabMinds. . All Rights Reserved. LabMinds and Revo are registered trademarks and the property of LabMinds.Unauthorized use is strictly prohibited.Scanning of QR code imports solutions data into LIMSCHALLENGESBENEFITS Reduce FTE time spent on preparing reagents Reagent prep FTE time decreased by 66%Limit solution waste Just -in -time inventory best practices reduced solutionoverproduction costsEliminate risk with manual documentationprocessesDocumentation completed with full transparency andregulatory compliance provides peace of mind All samples, solutions and controls are registered in the LIMS, and thisdata aligns with existing records to populate the documentation ofthe analysis and ensures audit readiness. This process not onlyreduces the chance of human error, but also frees up time for the labtechnicians to focus on other tasks. Our customer now has peace ofmind knowing that documentation is completed with fulltransparency and regulatory compliance.。
克洛克斯商业解毒湿巾-新鲜香气说明书

SAFETY DATA SHEETIssuing Date 05-Jan-2015 Revision Date 02-Jun-2020 Revision Number 2NGHS - English _____________________________________________________________________________________________Product identifierProduct Name Clorox Commercial Solutions® Clorox® Disinfecting Wipes - Fresh ScentOther means of identificationE PA Pesticide registration number 67619-31Recommended use of the chemical and restrictions on useRecommended Use Wipes, DisinfectingUses advised against No information availableDetails of the supplier of the safety data sheetSupplier Identification Clorox P rofessional P roducts CompanyAddress 1221 Broadw ayOakland, CA 94612USATelephone 1-510-271-7000E mergency telephone numberE mergency Telephone Number For Medical E mergencies call: 1-800-446-1014. Transportation E mergencies, callChemtrec: 1-800-424-9300Not a dangerous substance or mixture according to the Globally Harmonized System (GHS).Odor Fruity Apple Floral Appearance Clear White Physical state P re-Moistened Tow elette(no free liquids)GHS Label elements, including precautionary statementsHazard statementsNot a dangerous substance or mixture according to the Globally Harmonized System (GHS).Precautionary Statements - PreventionNot applicablePrecautionary Statements - ResponseNot applicablePrecautionary Statements - StorageNot applicablePrecautionary Statements - DisposalNot applicableOther informationNot applicable.The product contains no substances w hich at their given concentration, are considered to be hazardous to health.First aid measuresInhalation Remove to fresh air.E ye contact Rinse thoroughly w ith plenty of w ater for at least 15 minutes, lifting low er and upper eyelids.Consult a physician.Skin contact Wash skin w ith soap and w ater.Ingestion Clean mouth w ith w ater and drink afterw ards plenty of w ater.Most important symptoms and effects, both acute and delayedSymptoms No information available.Indication of any immediate medical attention and special treatment neededNote to physicians Treat symptomatically.Suitable E xtinguishing Media Use extinguishing measures that are appropriate to local circumstances and thesurrounding environment.Large Fire CAUTION: Use of w ater spray w hen fighting fire may be inefficient.Unsuitable extinguishing media Do not scatter spilled material w ith high pressure w ater streams.Specific hazards arising from thechemicalNo information available.Hazardous Combustion Products Carbon oxides.E xplosion DataSensitivity to Mechanical Impact None.Sensitivity to Static Discharge None.Special protective equipment for fire-fighters Firefighters should w ear self-contained breathing apparatus and full firefighting turnout gear. Use personal protection equipment.__________________________________________________________________________________________________________________________________________________________________________________________ Personal precautions, protective equipment and emergency proceduresPersonal precautionsE nsure adequate ventilation.E nvironmental precautionsE nvironmental precautionsSee Section 12 for additional E cological Information.Methods and material for containment and cleaning upMethods for containmentP revent further leakage or spillage if safe to do so.Prevention of secondary hazards Clean contaminated objects and areas thoroughly observing environmental regulations.Precautions for safe handlingAdvice on safe handlingHandle in accordance w ith good industrial hygiene and safety practice.Conditions for safe storage, including any incompatibilitiesStorage ConditionsKeep containers tightly closed in a dry, cool and w ell-ventilatedplace.Incompatible productsNone know n based on information supplied.Control parametersE xposure LimitsThis product, as supplied, does not contain any hazardous materials w ith occupational exposure limits established by the region specific regulatory bodies.Appropriate engineering controlsE ngineering controlsNone under normal use conditions.Individual protection measures, such as personal protective equipmentE ye/face protectionNo special protective equipment required.Skin and body protectionNo special protective equipment required.Respiratory protectionNo protective equipment is needed under normal use conditions. If exposure limits are exceeded or irritation is experienced, ventilation and evacuation may be required.General hygiene considerationsHandle in accordance w ith good industrial hygiene and safety practice._____________________________________________________________________________________________ Information on basic physical and chemical properties Physical state P re-Moistened Tow elette (no free liquids) Appearance Clear White Odor Fruity Apple Floral Color No information available Odor Threshold No information available Property ValuesRemarks MethodpH 6 - 7.5 (liquid)None know nMelting / freezing point No data availableNone know nBoiling point / boiling range No data availableNone know nFlash Point No data availableNone know nE vaporation Rate No data availableNone know nFlammability (solid, gas) No data availableNone know nFlammability Limit in AirUpper flammability limit No data availableLow er flammability limit No data availableVapor pressure No data availableNone know nVapor density No data availableNone know nRelative density ~1.0 (liquid)None know nWater Solubility Completely solubleNone know nSolubility(ies) No data availableNone know nPartition coefficient: n-octanol/w ater 0None know nAutoignition temperature No data availableNone know nDecomposition temperature No data availableNone know nKinematic viscosity No data availableNone know nDynamic viscosity No data availableNone know nOther Information E xplosive properties No information available Oxidizing properties No information available Softening Point No information available Molecular Weight No information available VOC Content (%) No information available Liquid Density No information available Bulk Density No information available Particle SizeNoinformation availableParticle Size DistributionNo data availableReactivityNo information available.Chemical stabilityStable under normal conditions.Possibility of Hazardous Reactions None under normal processing.Conditions to avoidNone know n based on information supplied.Incompatible materialsNone know n based on information supplied.Hazardous Decomposition Products None know n._____________________________________________________________________________________________ Information on likely routes of exposureProduct InformationInhalationInhalation of vapors in high concentration may cause irritation of respiratory system.E ye contactMay cause slight irritation.Skin contactNone know n.IngestionIngestion may cause irritation to mucous membranes.Information on toxicological effectsSymptomsNo information available.Numerical measures of toxicityAcute ToxicityNo information availableUnknow n acute toxicityNo information availableDelayed and immediate effects as w ell as chronic effects from short and long -term exposureSkin corrosion/irritationNo information available.Serious eye damage/eye irritation No information available.Respiratory or skin sensitizationNo information available.Germ cell mutagenicityNo information available.CarcinogenicityNo information available.Reproductive toxicityNo information available.STOT - single exposureNo information available.STOT - repeated exposureNo information available.Aspiration hazardNoinformation available.E cotoxicityThe environmental impact of this product has not been fully investigated.Persistence and DegradabilityNo information available.BioaccumulationNo information available. MobilityNo information available.Other adverse effectsNo information available.Waste treatment methodsWaste from residues/unused products Dispose of in accordance w ith local regulations. Dispose of w aste in accordance w ith environmental legislation.Contaminated packaging Do not reuse empty containers.DOT Not regulatedTDG Not regulatedICAO Not regulatedIATA Not regulatedIMDG Not regulatedSafety, health and environmental regulations/legislation specific for the substance or mixtureInternational RegulationsOzone-depleting substances (ODS) Not applicablePersistent Organic Pollutants Not applicableE xport Notification requirements Not applicableInternational InventoriesTSCA Contact supplier for inventory compliance statusDSL/NDSL Contact supplier for inventory compliance statusE INE CS/ELINCS Contact supplier for inventory compliance status.E NCS Contact supplier for inventory compliance status.KE CL Contact supplier for inventory compliance status.PICCS Contact supplier for inventory compliance status.AICS Contact supplier for inventory compliance status.LegendTSCA - United States Toxic Substances Control Act Section 8(b) InventoryDSL/NDSL - Canadian Domestic Substances List/Non-Domestic Substances ListE INE CS/ELINCS - E uropean Inventory of E xisting Chemical Substances/E uropean List of Notified Chemical SubstancesE NCS - Japan E xisting and New Chemical SubstancesKE CL - Korean E xisting and E valuated Chemical SubstancesPICCS - P hilippines Inventory of Chemicals and Chemical SubstancesAICS - Australian Inventory of Chemical Substances_____________________________________________________________________________________________US Federal RegulationsSARA 313Section 313 of Title III of the Superfund Amendments and Reauthorization Act of 1986 (SARA). This product may contain a chemical or chemicals w hich are subject to the reporting requirements of the Act and Title 40 of the Code of Federal Regulations,P art 372Acute Health Hazard NoChronic Health Hazard NoFire Hazard NoSudden release of pressure hazard NoReactive Hazard NoCWA (Clean Water Act)This product does not contain any substances regulated as pollutants pursuant to the Clean Water Act (40 CFR 122.21 and 40 CFR 122.42)CE RCLAThis material, as supplied, does not contain any substances regulated as hazardous substances under the ComprehensiveE nvironmental Response Compensation and Liability Act (CE RCLA) (40 CFR 302) or the Superfund Amendments and Reauthorization Act (SARA) (40 CFR 355). There may be specific reporting requirements at the local, regional, or state level pertaining to releases of this materialUS State RegulationsCalifornia Proposition 65This product does not contain any P roposition 65 chemicals.U.S. State Right-to-Know RegulationsThis product does not contain any substances above threshold limits that are regulated by state right-to-know.US E PA Label InformationE PA Pesticide Registration No. 67619-31E PA StatementThis chemical is a pesticide product registered by the E nvironmental P rotection Agency and is subject to certain labeling requirements under federal pesticide law. These requirements differ from the classification criteria and hazard information r equired for safety data sheets, and for w orkplace labels of non-pesticide chemicals. Follow ing is the hazard information as required on the pesticide label:E PA Pesticide labelCAUTION: Causes moderate eye irritation. Avoid contact w ith eyes or clothing. Wash thoroughly w ith soap and w ater after handling. Wear gloves for prolonged or frequent use._____________________________________________________________________________________________NFPA Health hazards 0 Flammability 0 Instability 0 Physical and ChemicalProperties -HMIS Health hazards 0 Flammability 0 Physical hazards 0 Personal Protection X Prepared By P roduct Stew ardship23 British American Blvd.Latham, NY 121101-800-572-6501Issuing Date 05-Jan-2015Revision Date 02-Jun-2020Revision Note No information availableDisclaimerThe information provided in this Safety Data Sheet is correct to the best of our know ledge, information and belief at the date of its publication. The information given is designed only as a guidance for safe handling, use, processing, storage, transportation, disposal and release and is not to be considered a w arranty or quality specification. The information relates only to the specific material designated and may not be valid for such material used in combination w ith any other materials or in any process, unless specified in the textEnd of Safety Data Sheet_____________________________________________________________________________________________。
华为系统文件系统转换指南说明书

123IMPORTANT:When the computer starts,the systemautomatically converts the file system on your harddrive.The conversion may take several minutes.Do notstop the process.When the conversion is completed thecomputer will restart.When prompted,begin your product registrationprocess.Online instructions will guide you through theregistration and preinstalled software setup process.The setup time varies by computer configuration.Start UpPower orNOTE:Your model may not include a voltageselection switch.If a switch is available,thevoltage is factory set to the correct rating.If in doubt,contact your local power utility.The rating label on the device shows which FCC class (A or B) the equipment falls into.Class B devices have an FCC logo or FCC ID on the label.Class A devices do not have an FCC ID or logo on the label.Once the class of the device is determined,refer to the corresponding statement.For complete details,read the Safety and Regulatory Information guide contained on the Documentation LibraryCD.©2002 Compaq Information Technologies Group,L.P paq,the Compaq logo and Presario are trademarks of Compaq Information Technologies Group,L.P .inthe United States and other countries.All other product names mentioned herein may be trademarks of their respective companies.Nothing herein should be construed as constituting an additional warranty.Second Edition May Presario 6000 Series Quick Setupand ContentsConnectors may vary by model.Printers,network connectivity,and other accessories should be connected only after computer setup and registration are complete.Keyboard and Mouse Audigy or Phone Optional Connecting Speakers Monitor 132NOTE:To install other types of speakers that were purchased with your computer,follow the instructions provided with the speakers.An AC adaptermay be included with some speaker sets.Powered speakers (included in Compaq FS and MV series monitors) are required.Attaching Speakers。
研制与生产注册现场核查指南

研制与生产注册现场核查指南英文回答:Development and Production On-Site Inspection Guidance for Registration.Introduction:On-site inspections are a critical aspect of the registration process for clinical trials, pharmaceutical products, and medical devices. They provide regulatory authorities with an opportunity to assess the research facilities, manufacturing sites, and quality control systems of trial sponsors and manufacturers to ensure compliance with regulatory standards.Purpose:The purpose of this guidance is to establish comprehensive guidelines for conducting on-site inspectionsin the context of registration. It covers the planning, preparation, execution, and reporting of inspections to ensure consistency, objectivity, and adherence to regulatory requirements.Planning and Preparation:Prior to conducting an on-site inspection, the regulatory authority should:Define the scope and objectives of the inspection.Gather relevant documentation, including study protocols, manufacturing records, and quality assurance reports.Identify key personnel to be interviewed and areas to be inspected.Develop inspection checklists and data collection forms.Secure necessary resources, such as translators and safety equipment.Inspection Execution:During the inspection, the regulatory authority should:Verify compliance with regulatory requirements, including Good Clinical Practice (GCP) and Good Manufacturing Practice (GMP) guidelines.Assess the adequacy of research facilities, manufacturing processes, and quality control systems.Interview relevant personnel to obtain information about study conduct, product manufacturing, and safety measures.Inspect records and documentation to verify accuracy and completeness.Observe operations to assess adherence to establishedprocedures.Take photographs or videos to document observations.Reporting:After the inspection, the regulatory authority should prepare a comprehensive inspection report that includes:A summary of the inspection activities and findings.Observations and recommendations for corrective actions, if any.An assessment of the compliance status of the research facility or manufacturing site.A recommendation on whether to approve or grant conditional approval for registration.Follow-Up:The regulatory authority may conduct follow-up inspections to verify that corrective actions have been taken and that the research facility or manufacturing site remains compliant with regulatory standards.Quality Assurance:To ensure the quality of on-site inspections, regulatory authorities should:Train inspectors on relevant regulatory requirements and inspection techniques.Develop and implement standardized inspection protocols.Conduct internal audits to assess the effectiveness of the inspection program.Seek external accreditation or certification to demonstrate adherence to best practices.中文回答:注册现场核查指南的研制与生产。
productid翻译
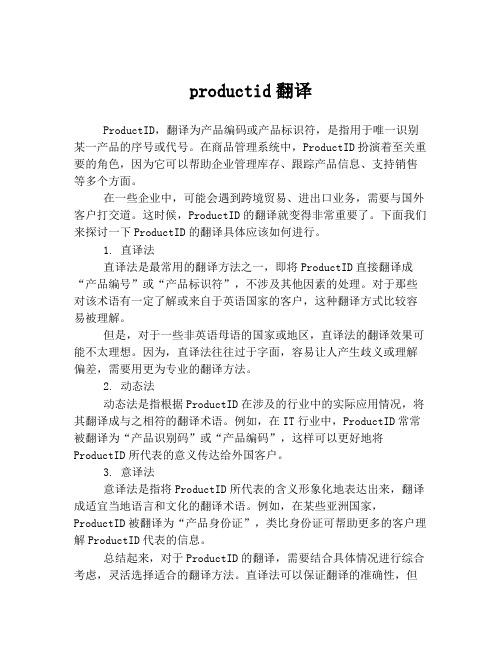
productid翻译ProductID,翻译为产品编码或产品标识符,是指用于唯一识别某一产品的序号或代号。
在商品管理系统中,ProductID扮演着至关重要的角色,因为它可以帮助企业管理库存、跟踪产品信息、支持销售等多个方面。
在一些企业中,可能会遇到跨境贸易、进出口业务,需要与国外客户打交道。
这时候,ProductID的翻译就变得非常重要了。
下面我们来探讨一下ProductID的翻译具体应该如何进行。
1. 直译法直译法是最常用的翻译方法之一,即将ProductID直接翻译成“产品编号”或“产品标识符”,不涉及其他因素的处理。
对于那些对该术语有一定了解或来自于英语国家的客户,这种翻译方式比较容易被理解。
但是,对于一些非英语母语的国家或地区,直译法的翻译效果可能不太理想。
因为,直译法往往过于字面,容易让人产生歧义或理解偏差,需要用更为专业的翻译方法。
2. 动态法动态法是指根据ProductID在涉及的行业中的实际应用情况,将其翻译成与之相符的翻译术语。
例如,在IT行业中,ProductID常常被翻译为“产品识别码”或“产品编码”,这样可以更好地将ProductID所代表的意义传达给外国客户。
3. 意译法意译法是指将ProductID所代表的含义形象化地表达出来,翻译成适宜当地语言和文化的翻译术语。
例如,在某些亚洲国家,ProductID被翻译为“产品身份证”,类比身份证可帮助更多的客户理解ProductID代表的信息。
总结起来,对于ProductID的翻译,需要结合具体情况进行综合考虑,灵活选择适合的翻译方法。
直译法可以保证翻译的准确性,但在跨文化交流时,动态法和意译法的应用更能起到有效沟通和信息传达的作用。
哈罗德音乐设备用户指南说明书

L1® model 1S system with ToneMatch® portOwner’s GuideGuía de usuarioNotice d’utilisation2S AFETY I NFORMATIONPlease read this owner’s guidePlease take the time to follow the instructions in this owner’s guide carefully. It will help you set up and operate yoursystem properly and enjoy its advanced features. Please save this owner’s guide for future reference.WARNING: To reduce the risk of fire or electrical shock, do not expose the system to rain or moisture.WARNING: To reduce the risk of electric shock, do not disassemble this system unless you are qualified.Refer servicing to qualified service personnel.The lightning flash with arrowhead symbol within an equilateral triangle alerts the user to the presence of uninsulated, dangerous voltage within the system enclosure that may be of sufficient magnitude to constitute a risk of electrical shock.The exclamation point within an equilateral triangle, as marked on the system, is intended to alert the user to the presence of important operating and maintenance instructions in this owner’s guide.CAUTION: This product shall be connected to a mains socket outlet with a protective earthing connection.CAUTION: Make no modifications to the system or accessories. Unauthorized alterations may compromise safety, regulatory compliance, and system performance.CAUTION: Do not place any naked flame sources, such as lighted candles, on or near the apparatus.CAUTION: Where the mains plug or appliance coupler is used as the disconnect device, such disconnect device shallremain readily operable.Note: The product must be used indoors. It is neither designed nor tested for use outdoors, in recreation vehicles, or on boats.This product conforms to all applicable EU requirements.The complete Declaration of Conformity can be found at: /compliance.Please complete for your recordsNow is a good time to record the serial numbers of your system here and on your product registration card. You can register your product online at /register or call (800) 905-1044. Failure to do so will not affect your warranty rights.L1® model 1S power stand: _____________________________________________________________________Top array and bottom extension:_________________________________________________________________B1 or B2 bass module: _________________________________________________________________________©2012 Bose Corporation. No part of this work may be reproduced, modified, distributed, or otherwise used without prior written permission.3I MPORTANT S AFETY I NSTRUCTIONS1.Read these instructions.2.Keep these instructions.3.Heed all warnings.4.Follow all instructions.5.Do not use this apparatus near water.6.Clean only with a dry cloth.7.Do not block any ventilation openings. Install inaccordance with the manufacturer’s instruc-tions.8.Do not install near any heat sources, such asradiators, heat registers, stoves, or other appa-ratus (including amplifiers) that produce heat. 9.Do not defeat the safety purpose of the polar-ized or grounding-type plug. A polarized plug has two blades with one wider than the other. A grounding-type plug has two blades and a third grounding prong. The wider blade or third prong is provided for your safety. If the provided plug does not fit into your outlet, consult an electri-cian for replacement of the obsolete outlet.10.Protect the power cord from being walked on orpinched, particularly at plugs, conveniencereceptacles, and the point where they exit from the apparatus. 11.Only use attachments/accessories specified bythe manufacturer.12.Use only with the cart, stand, tripod,bracket, or table specified by the man-ufacturer or sold with the apparatus. When a cart is used, use caution whenmoving the cart/apparatus combination to avoid injury from tip-over.13.Unplug this apparatus during lightning stormsor when unused for long periods of time.14.Refer all servicing to qualified service personnel.Servicing is required when the apparatus has been damaged in any way, such as power-supply cord or plug is damaged, liquid has been spilled or objects have fallen into the apparatus, the apparatus has been exposed to rain or moisture, does not operate normally, or has been dropped.15.To prevent risk of fire or electric shock, avoidoverloading wall outlets, extension cords, or integral convenience receptacles.16.Do not let objects or liquids enter the product –as they may touch dangerous voltage points or short-circuit parts that could result in a fire or electric shock.17.See product enclosure bottom for safety-relatedmarkings. e proper power sources – Plug the product intoa proper power source, as described in the operating instructions or as marked on the product.19.Apparatus shall not be exposed to dripping orsplashing, and no objects filled with liquids, such as vases, shall be placed on the apparatus.Information about products that generate electrical noiseNOTE: This equipment has been tested and found to comply with the limits for a Class A digital device, pursuant to part 15 of the FCC Rules.These limits are designed to provide reasonable protection against harmful interference when the equipment is operated in a commercial environment. This equipment generates, uses, and can radiate radio frequency energy and, if not installed and used in accordance with theinstruction manual, may cause harmful interference to radio communications. Operation of this equipment in a residential area is likely to cause harmful interference in which case the user will be required to correct the interference at their own expense.Changes or modifications not expressly approved by Bose Corporation could void the user's authority to operate this equipment.This Class A digital apparatus complies with Canadian ICES-003.Initial turn on inrush current: 32 AmpsInrush current after AC mains interruption of 5 seconds: 32 AmpsThis product meets all EN55103-2 immunityrequirements for E2 electromagnetic environment.I NTRODUCTION5Welcome . . . . . . . . . . . . . . . . . . . . . . . . . . . . . . . . . . . . . . . . . . . . . . . . . . . . . . . . . . . . . . . . . . . . . . . . . . . . . . . . . . . 5 Features and benefits . . . . . . . . . . . . . . . . . . . . . . . . . . . . . . . . . . . . . . . . . . . . . . . . . . . . . . . . . . . . . . . . . . . . . . . . . 5 Product overview . . . . . . . . . . . . . . . . . . . . . . . . . . . . . . . . . . . . . . . . . . . . . . . . . . . . . . . . . . . . . . . . . . . . . . . . . . . . . 6 Connections and controls . . . . . . . . . . . . . . . . . . . . . . . . . . . . . . . . . . . . . . . . . . . . . . . . . . . . . . . . . . . . . . . . . . . . . . 7S YSTEM S ETUP8 Parts list . . . . . . . . . . . . . . . . . . . . . . . . . . . . . . . . . . . . . . . . . . . . . . . . . . . . . . . . . . . . . . . . . . . . . . . . . . . . . . . . . . . . 8 Positioning your system . . . . . . . . . . . . . . . . . . . . . . . . . . . . . . . . . . . . . . . . . . . . . . . . . . . . . . . . . . . . . . . . . . . . . . . . 9 Setting up the power stand . . . . . . . . . . . . . . . . . . . . . . . . . . . . . . . . . . . . . . . . . . . . . . . . . . . . . . . . . . . . . . . . . . . . . 10 Assembling the L1® model 1S system . . . . . . . . . . . . . . . . . . . . . . . . . . . . . . . . . . . . . . . . . . . . . . . . . . . . . . . . . . . . . 10 Connecting to AC power . . . . . . . . . . . . . . . . . . . . . . . . . . . . . . . . . . . . . . . . . . . . . . . . . . . . . . . . . . . . . . . . . . . . . . . 11 Connecting the B1 or B2 bass module . . . . . . . . . . . . . . . . . . . . . . . . . . . . . . . . . . . . . . . . . . . . . . . . . . . . . . . . . . . . 12 Adding a T1 ToneMatch® audio engine (optional) . . . . . . . . . . . . . . . . . . . . . . . . . . . . . . . . . . . . . . . . . . . . . . . . . . . . 13 Adding a second B1 bass module (optional) . . . . . . . . . . . . . . . . . . . . . . . . . . . . . . . . . . . . . . . . . . . . . . . . . . . . . . . . 14O PERATING I NFORMATION 15 Setting the analog input level . . . . . . . . . . . . . . . . . . . . . . . . . . . . . . . . . . . . . . . . . . . . . . . . . . . . . . . . . . . . . . . . . . . . 15 Using a T1 ToneMatch® audio engine and an analog input source . . . . . . . . . . . . . . . . . . . . . . . . . . . . . . . . . . . . . . . 15 User scenarios . . . . . . . . . . . . . . . . . . . . . . . . . . . . . . . . . . . . . . . . . . . . . . . . . . . . . . . . . . . . . . . . . . . . . . . . . . . . . . . 15 Single musician . . . . . . . . . . . . . . . . . . . . . . . . . . . . . . . . . . . . . . . . . . . . . . . . . . . . . . . . . . . . . . . . . . . . . . . . . 15 Multiple musicians . . . . . . . . . . . . . . . . . . . . . . . . . . . . . . . . . . . . . . . . . . . . . . . . . . . . . . . . . . . . . . . . . . . . . . . 16 Full band . . . . . . . . . . . . . . . . . . . . . . . . . . . . . . . . . . . . . . . . . . . . . . . . . . . . . . . . . . . . . . . . . . . . . . . . . . . . . . . 17 DJ events . . . . . . . . . . . . . . . . . . . . . . . . . . . . . . . . . . . . . . . . . . . . . . . . . . . . . . . . . . . . . . . . . . . . . . . . . . . . . . 18C ARE AND M AINTENANCE 19 Caring for your product . . . . . . . . . . . . . . . . . . . . . . . . . . . . . . . . . . . . . . . . . . . . . . . . . . . . . . . . . . . . . . . . . . . . . . . . 19 Cleaning . . . . . . . . . . . . . . . . . . . . . . . . . . . . . . . . . . . . . . . . . . . . . . . . . . . . . . . . . . . . . . . . . . . . . . . . . . . . . . . 19 Getting service . . . . . . . . . . . . . . . . . . . . . . . . . . . . . . . . . . . . . . . . . . . . . . . . . . . . . . . . . . . . . . . . . . . . . . . . . . 19 Troubleshooting . . . . . . . . . . . . . . . . . . . . . . . . . . . . . . . . . . . . . . . . . . . . . . . . . . . . . . . . . . . . . . . . . . . . . . . . . . . . . . 19 Limited Warranty and Registration . . . . . . . . . . . . . . . . . . . . . . . . . . . . . . . . . . . . . . . . . . . . . . . . . . . . . . . . . . . . . . . . 21 Accessories . . . . . . . . . . . . . . . . . . . . . . . . . . . . . . . . . . . . . . . . . . . . . . . . . . . . . . . . . . . . . . . . . . . . . . . . . . . . . . . . . 21 Technical Information . . . . . . . . . . . . . . . . . . . . . . . . . . . . . . . . . . . . . . . . . . . . . . . . . . . . . . . . . . . . . . . . . . . . . . . . . . 21 Mechanical . . . . . . . . . . . . . . . . . . . . . . . . . . . . . . . . . . . . . . . . . . . . . . . . . . . . . . . . . . . . . . . . . . . . . . . . . . . . . 21 Electrical . . . . . . . . . . . . . . . . . . . . . . . . . . . . . . . . . . . . . . . . . . . . . . . . . . . . . . . . . . . . . . . . . . . . . . . . . . . . . . . 21 Audio Input/Output . . . . . . . . . . . . . . . . . . . . . . . . . . . . . . . . . . . . . . . . . . . . . . . . . . . . . . . . . . . . . . . . . . . . . . . 214I NTRODUCTIONWelcomeThank you for purchasing the Bose® L1® model 1S system with ToneMatch® port. Based on arevolutionary new technology, this system brings the benefits of an intimate acoustic concertto amplified performance.This owner’s guide provides detailed setup and operating instructions for your L1 system andexplains how to connect equipment to it.For additional information on using this system, including tips, techniques, and frequentlyasked questions, please visit /livesound on the Internet.Features and benefits•You control the sound – Just as in an unamplified performance, you control the sound.You will no longer wonder how you sound to your fellow musicians or to your audiencebecause you will hear what they hear.•Quick and easy setup – The L1 system is easy to carry and can be set up in minutes, nothours. This frees you from the time-consuming and often frustrating effort required to prop-erly set up conventional sound equipment.•Dramatically improved performance – Compared to using conventional equipment,performance and enjoyment dramatically improve because the struggle to hear yourselfand the other musicians is diminished.•Creates excitement and emotion – Enhanced performance of the musicians creates thekind of excitement and emotion that is valued by music lovers.•You hear what the audience hears – For the first time, musicians hear what theiraudiences hear and thus, are less likely to play at uncomfortable sound levels.•The music is naturally dynamic – The softest to the most intense passages can beheard and enjoyed.•Improves your appearance – There is less equipment on the stage and more room.•Sound reproduction unlike before – Audience members report that the clarity andexcitement that come from hearing the accurate reproduction of sound from eachinstrument, and from hearing the sound of each instrument in its position on stage(as opposed to mono or even stereo mix of all instruments), is unlike anything they haveheard before in an amplified performance.5I NTRODUCTIONProduct overviewThe L1® model 1S system – with ToneMatch® port consists of: the power stand, bottomextension, top array, and a B1 or B2 bass module. The system also comes with a paddedcarrying bag for each of its parts.To expand your system and enhance performance, you can add:•A second B1 bass module for bass guitar, kick drum, or organ. Each power stand canpower up to two B1 bass modules.•A T1 ToneMatch audio engine for digital signal processing, additional inputs and user-inter-face control.For a complete list of optional equipment and accessories, please visit:/livesound.Figure 1optional equipmentL1 model 1S system with ToneMatch port and B1 bass module Optional equipmentB1 bassmoduleB2 bassmodule6I NTRODUCTION® port78S YSTEM S ETUPParts listThe L1® system is shipped in three cartons. Carefully unpack the cartons and check that youhave all the items listed on this page.WARNING:To avoid danger of suffocation, keep the plastic bags out of the reach of children.S YSTEM S ETUPPositioning your systemPlacing the power stand in the right location is an important part of setting up this product.Determining the best location for your performance depends on several things.•Size of staging area•Number of performers•Shared system (adding a T1 ToneMatch® audio engine and multiple instruments)The following guidelines should get you started in setting up for a concert or show.•Set up your system in the rear area of the performance stage.•If possible, position your system behind the performer(s).•If you are part of a group, avoid crowding together on stage. Allow some distance,ideally 7-8 feet (2.1-2.4 m), between you and the L1® system and anotherperformer. This allows the sound to wrap around performers and reflect off adjacentsurfaces of the room, creating a more pleasing room-filling sound.Figure 1 PlacementrecommendationsBest910S YSTEM S ETUPSetting up the power stand1.The legs must be2.Figure 2Putting the power stand on the floorchosen location before assembling the system.Figure 3Setting up the systemCAUTION: Bose recommends using a quality surge suppressor on all electronic equipment. Voltage variations and spikes can damage electronic components in any system. A quality suppressor, which can eliminate the vast majority of failures attributed to surges, may bepurchased at electronics stores.S YSTEM S ETUPFigure 5B1 and B2 bass modulesCAUTIONS:•DO NOT connect any bass module other than the B1 or B2 to the power stand.•DO NOT substitute the supplied cable with a 2-wire speaker cable. Use only the supplied B1 bass module 4-wire cable to connect the B1 bass module to the power stand. The power stand uses the signals on two of the wires to automatically sense how many B1 or B2 bass modules are connected.•DO NOT connect a B1 or B2 bass module to two power stands at the same time.S YSTEM S ETUPAdding a T1 ToneMatch® audio engine (optional)The T1 ToneMatch® audio engine provides additional input/output capabilities to yoursystem, plus digital signal processing to customize the way you sound. The audio enginecomes with hardware for mounting it on the left or right side of the bottom extension.Note: The audio engine mounts on the bottom section of the loudspeaker and requires removalof the top section before starting this procedure.1.Slide the carriage into the channel on the rear of the bottom extension and turn the knobclockwise to lock it in place (Figure 6).2.Insert the mounting bar into the slot in the carriage and push it downward.3.Place the T1 on the mounting bar as shown.4.Plug one end of the ToneMatch cable (supplied with the audio engine) into theToneMatch output port () on the T1.ing the hook and loop strap, secure the cable to the carriage.6.Plug the other end of the cable into the ToneMatch port on the power stand.Figure 6Mounting the T1S YSTEM S ETUPAdding a second B1 bass module (optional)The bass module output of the power stand can adequately drive one or two B1 bass1.2.Figure 7Installation of two B1 bassmodulescableO PERATING I NFORMATIONO PERATING I NFORMATIONSetting the analog input levelWhen connecting an audio source to the Analog Input, follow these steps to adjust the inputTrim control.1.Set the Trim control on the power stand to the 0 (zero) position.2.Connect the audio source to the Analog Input.3.Adjust the volume of the audio source to the desired level.4.While playing the source, increase the Trim level until the Signal/Clip indicator glowsgreen or yellow.5.If the Signal/Clip indicator glows red, decrease the Trim level so that it glows only greenor yellow.®User scenariosFigure 1Single system withkeyboardC ARE AND M AINTENANCEC ARE AND M AINTENANCE Caring for your productCleaning•Clean the product enclosures using only a soft, dry cloth.•Do not use any solvents, chemicals, or cleaning solutions containing alcohol, ammonia,or abrasives.•Do not use any sprays near the product or allow liquids to spill into any openings.•If necessary, you may carefully vacuum the grille of the L1® loudspeaker.Getting serviceFor additional help in solving problems, contact Bose® Live Music Customer Service Productand Technical Support Team at (877) 335-2673 or visit our support area online at/livesound.TroubleshootingIf you experience problems while using this product, try the following solutions. If you stillcan’t solve the problem, please call the Bose Live Music Product and Technical SupportTeam direct at (877) 335-2673 to arrange for service.Recommended troubleshooting tools•Portable voltmeter •XLR and ¼" phone plug cables•Cable tester•B1 bass module 4-wire cable•AC outlet tester•Spare AC power cordProblem What to doSystem is plugged in, power switch is on, but power LED is off •Make sure you have power at the AC outlet. Try operating a lamp or other equipment from the same AC outlet or test the outlet using an AC outlet tester.•Make sure the power stand’s power cord plug is fully inserted into the AC outlet.Power LED is on (green), but no sound •Make sure volume control is turned up on your instrument.•Make sure the Trim level control is turned up on the power stand.•Make sure your instrument is plugged into the Analog Input jack.•Connect your instrument to the power stand using a different cable.•Plug your instrument into a different amplifier to make sure the instrument is working.Power LED is red while thepower stand is on•Please call Bose Live Music Customer Support at (877) 335-2673 for assistance.House circuit breaker keeps tripping •If more than one power stand is plugged into the same AC circuit, stagger the turn-on times. Each power stand has an inrush current of about 32 amps when turned on.•If you have more than three power stands plugged into a single 15 amp circuit, move some systems to another AC circuit. Each power stand can draw 5 amps or more when playing at high volumes for long periods of time.C ARE AND M AINTENANCEWith nothing plugged into the power stand, a slight hum or buzz is heard •Using an AC outlet tester, test the AC outlet that the power stand is plugged into for reversed or open (hot, neutral, and/or ground) contacts.•If using an extension cord, make sure that the cord is also tested as above.B1 or B2 bass module is plugged in, but no bass audio is heard •Make sure you are using the included 4-wire B1/B2 bass module cable.•Make sure the B1 or B2 bass module cable is plugged into the Bass Module Out connector and the cable plug is fully engaged in the connector.•Try a different 4-wire cable.•If available, try a different B1/B2 bass module.B1 bass module sounds out of balance with the system •Make sure you are using the B1/B2 bass module 4-wire cable included with the B1 bass module package.•Make sure that the B1 or B2 bass module grille is facing forward toward the musicians and audience.No mid/high sounds heard from the L1® top array •Make sure the L1 top array and bottom extension are firmly seated in their connectors.•Make sure connections are not bent or broken.•Try cleaning the contacts on the loudspeaker top and bottom with electronic contact spray cleaner.Instrument or audio source sounds distorted •Make sure the Signal/Clip LED is not constantly red. If it is, lower the trim level.•Try a different source or instrument.•Try your source or instrument on another power stand.Microphone is encountering feedback •Orient the microphone so that it is not pointing directly at its respective L1 system.•Try a different microphone.•Try a different position for the loudspeaker and/or vocalist on stage.•Increase the distance from the loudspeaker to the microphone.•If using a vocal effects processor, make sure it is not contributing to the feedback problem.Problem What to doC ARE AND M AINTENANCELimited Warranty and RegistrationYour product is covered by a limited warranty. Details of the warranty are provided with yourproduct. Register your products online at /register or call (800) 905-1044.Failure to do so will not affect your warranty rights.AccessoriesVisit /livesound, or call (800) 905-0886 for accessory information.Technical InformationMechanicalComponent Dimensions WeightPower stand:5''H x 10''W x 27''D(12.8 cm x 26.2 cm x 69.2 cm)23.7 lb (10.7 kg)Top array:43½''H x 3½''W x 4''D(111.0 cm x 9.0 cm x 10.5 cm)16.3 lb (7.4 kg)Bottom extension:39.63''H x 4.15''W x 4.13''D(100.6 cm x 10.6 cm x 10.5 cm)8.5 lb (3.8 kg)B1 bass module:15''H x 10¼''W x 17¾''D(38.0 cm x 26.0 cm x 45.0 cm)25.1 lb (11.4 kg)B2 bass module:23.4''H x 13.31''W x 18.9''D(59.4 cm x 33.8 cm x 48 cm)45 lb (20.41 kg)Electrical•AC power rating:50/60Hz 500W (Europe)•Peak inrush current:50Hz (Europe)Component ImpedanceL1® model 1S loudspeaker:4ΩB1 bass module:8ΩB2 bass module:4ΩAudio Input/Output•T1 ToneMatch® port:DC output/data input Ethercon/RJ45 connector for aT1 ToneMatch audio engine•Analog Input:Line-level input channel for ¼" TRS phone plug•Bass Module Out:Neutrik® NL4 output for one or two B1 bass modulesL1 and ToneMatch are registered trademarks of Bose Corporation in the U.S. and other countries.All trademarks are the property of their respective owners.21©2012 Bose Corporation, The Mountain, Framingham, MA 01701-9168 USAAM356144 Rev.00/livesound。
- 1、下载文档前请自行甄别文档内容的完整性,平台不提供额外的编辑、内容补充、找答案等附加服务。
- 2、"仅部分预览"的文档,不可在线预览部分如存在完整性等问题,可反馈申请退款(可完整预览的文档不适用该条件!)。
- 3、如文档侵犯您的权益,请联系客服反馈,我们会尽快为您处理(人工客服工作时间:9:00-18:30)。
SFDA
All imported medical products must be registered with SFDA prior to selling in China Products made outside China need to go to central SFDA for approval Registration is valid for 4 years Registration cannot be transferred
3 / / 3 / 3 3 3 2 3 3 3 3 3 /
3 3 / 3 / 3 3 3 2 3
Active Device
Passive Device
SFDA Registration, Cont.
Registration timeline
• Class I: 5-6 months • Class II & III without clinical: 7-8 months – Marketed in country of origin – Manufacture is ISO 9000-certified – Product modification does not affect safety and efficiency – Non-implants, no radioactive sources – Would not cause serious injury or death to patient and operator • Class II & III with clinical: 12-14 months
Device for transportation and storage of pharmaceutical liquid Device for alternation of blood and body fluid Device for medical dressing Surgical instrument (inserted) Reusable surgical instrument Disposable aseptic surgical device Implantables Device for contraception and birth control Device for sterilization and cleaning Other contacting passive device Device for Treatment through energy Device for diagnostic monitoring Device for body fluid transportation Device for ionized radiation Other general active device
1 month Yes Clinical Trial Final Approval
Clinical trial not required
Health Food Registration
Health food is defined as food that has specified health functions, suitable to be taken by specified group(s) of people, and for the regulation of the functional states of the human body and is not used for the treatment of diseases. The category includes vitamin and mineral supplements that may not be used for the purpose of disease treatment. All health food sold within China must be approved and registered with the SFDA, which will assess and examine the security, effectiveness, quality control and labeling of products.
General Administration of Quality Supervision, Inspection and Quarantine (AQSIQ)
• Drafts rules and regulations on certification and accreditation, safety and quality licensing, hygiene registration and qualification assessment • Conducts mandatory safety registration, certification and inspection for certain devices (CCC mark)
into the human body, or used for life support or sustenance, or pose potential risk to the human body and thus must be strictly controlled in respect to safety and effectiveness
SFDA Registration, Cont.
Medical device classification
• Class I: low risk, considered safety, general control
safety and effectiveness can be ensured through routine administration
Regulatory Environment
State Food & Drug Administration (SFDA)
• Became part of MOH since Mar 2008 • National regulatory authority of drug and medical device • In charge of comprehensive supervision on food safety management
Health Food Registration
27 categories of health functions claims are approved by the SFDA
• Enhancing immune function, Improving sleep, Improving endurance during anoxia, Assisting protection against irradiation, Increasing bone density Improving tired eyesight, Eliminating acne, Eliminating yellow-brown spot, Improving skin moisture, Improving skin oil content, Improving constipation, Assisting protection against chemical liver injury Assisting blood lipids reduction , Assisting blood sugar reduction, Antioxidation, Assisting memory improvement, Facilitating lead excretion, Moistening and cleaning throat, Assisting blood pressure reduction, Increasing milk secretion, Improving growth and development, Improving nutritional anemia, Regulating intestinal micro flora, Facilitating digestion, Alleviating Physical Fatigue, Controlling obesity
SFDA Registration, Cont.
Required documentation
• • • • Test report issued by SFDA-certified test center Clinical trail report Quality Guarantee letter Letter of authorization to agent undertaking the registration • Post-sales authorization • Self-guarantee declaration
Product Registration and Regulatory Updates
Don Chen, MBA CMDA North American Liaison Office
Agenda
Regulatory Environment SFDA Medical Device Registration SFDA Health Food Registration Regulatory Updates Implications for Manufacturers
2 / 1 1 1 1 / 2 2 1
2 / 2 2 1 2 / 2 2 2 2 2 2 2 2
3 3 2 3 2 3 / 3 2 3
2 / 1 2 / 2 / 2 2 2
2 / 2 2 / 3 / 3 2 2 2 2 3 3 2
3 3 2 3 / 3 / 3 2 3