830 Appendix P - TS Section 05_Rev A0 (10Dec10)a
ATE Corporation AS-05 Antenna Set 30 MHz to 18 GHz
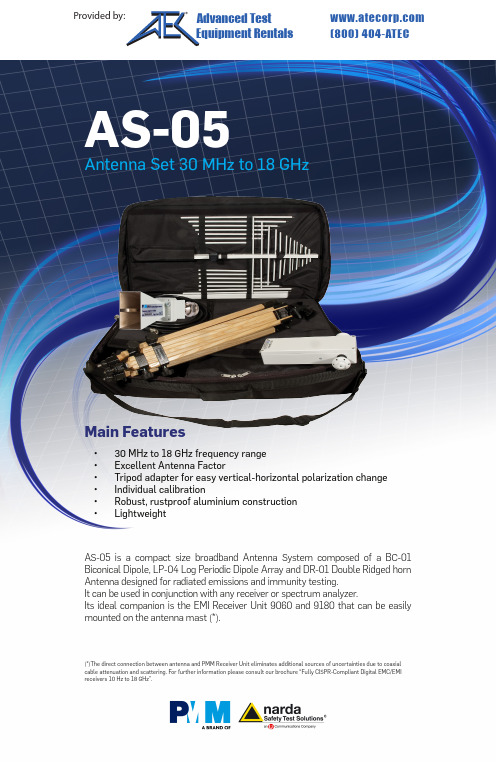
Main Features•30 MHz to 18 GHz frequency range •Excellent Antenna Factor•Tripod adapter for easy vertical-horizontal polarization change •Individual calibration•Robust, rustproof aluminium construction •LightweightAS-05 is a compact size broadband Antenna System composed of a BC-01 Biconical Dipole, LP-04 Log Periodic Dipole Array and DR-01 Double Ridged horn Antenna designed for radiated emissions and immunity testing. It can be used in conjunction with any receiver or spectrum analyzer.Its ideal companion is the EMI Receiver Unit 9060 and 9180 that can be easily mounted on the antenna mast (*).(*)The direct connection between antenna and PMM Receiver Unit eliminates additional sources of uncertainties due to coaxial cable attenuation and scattering. For further information please consult our brochure “Fully CISPR-Compliant Digital EMC/EMI receivers 10 Hz to 18 GHz”.Antenna Set 30 MHz to 18 GHzProvided by: (800)404-ATECAdvanced Test Equipment Rentals®Ordering Information:AS-05 antenna set 30 MHz to 18 GHz with individual calibration reports.AS-05/TC antenna set 30 MHz to 18 GHz with typical calibration reports.Includes: BC-01 biconical antenna; LP-04 Log-periodic antenna; DR-01Double-rideged antenna; TR-01 wooden tripod; RF cable, 6 GHz, N(m)-N(m), 5 m; Soft carrying case; Rigid carrying case (for DR-01), Operating manual; Calibration reports*.* Individual calibration reports are provided with AS-05.AS-05/TC does not include individual calibration but typical antenna factor.Optional accessories:Additional TR-01 Wooden tripod extensible 60 - 180 cm with antenna mounting adapter for fast horizontal to vertical polaritazion changing. Additional RF cable, 3 GHz, N(m)-N(m), 5 m.Sales Office:Via Leonardo da Vinci, 21/2320090 Segrate (Milano) - ITALY Phone: +39 02 2699871Fax: +39 02 26998700Headquarter:Via Benessea, 29/B17035 Cisano sul Neva (SV) - ITALY Phone: +39 0182 58641Fax: +39 0182 586400E-Mail:**************************Internet: www.narda-sts.itRelated ProductsReceiversAntennasCalibrations service• 7010/00: EMI receiver 150 kHz to 1 GHz • 7010/01: EMI receiver 9 kHz to 1 GHz • 7010/03: EMI receiver 9 kHz to 3 GHz • 9010: EMI receiver 10 Hz to 30 MHz • 9010F: EMI receiver 10 Hz to 30 MHz• 9010/03P: EMI receiver 10 Hz to 300 MHz • 9010/30P: EMI receiver 10 Hz to 3 GHz • 9010/60P: EMI receiver 10 Hz to 6 GHz • 9030: EMI Receiver 30 MHz to 3 GHz • 9060: EMI Receiver 30 MHz to 6 GHz •FR-4003: Field Receiver 9 kHz to 30 MHz• LP-02: Log Periodic Antenna 200 MHz to 3 GHz • LP-03: Log Periodic Antenna 800 MHz to 6 GHz • TR-01: Antenna Tripod• VDH-01: Van der Hoofden test-head 20 kHz to 10 MHz • Antenna Set AS-02 (BC01+LP02+TR01)• Antenna Set AS-03 (BC01+LP02+LP03+TR01) • Antenna Set AS-04 (BC01+LP04+TR01)• RA01: Rod Antenna 9 kHz to 30 MHz• RA01-HV: Rod Antenna 150 kHz to 30 MHz •RA01-MIL: Rod Antenna 9 kHz to 30 MHz• Ansi 63,5 Antenna Factor • SAE ARP 958-D• Free-Space Antenna FactorSPECIFICATIONSFrequency range GainAntenna factor Max input power Connector Dimensions (L x H x W)Weight Colour Impedance ConstructionBC-0130 to 200 MHz -15 +2 dBi typical 8 to 14 dB/m typical 100 W N-female 65 x 65 x 137 cm1,8 kg RAL 703550 Ω nominal AluminiumA S 05-F E N -60801 - S p e c i fi c a t i o n s s u b j e c t t o c h a n g e s w i t h o u t p r i o r n o t i c eAS-05Antenna set 30 MHz to 18 GHzLP-04200 MHz to 6 GHz 6 dBi typical 12 to 40 dB/m typical100 W N-female 78 x 10 x 75 cm 1,1 kg RAL 703550 Ω nominal AluminiumDR-016 to 18 GHz 9 to 16 dBi typical 36 to 41 dB/m typical 150 W N-female 55 x 44 x 177 mm 0,25 kg RAL 703550 Ω nominal AluminiumBC-01 - Antenna Factor 106141822A F (d B /m )3090150210MHz MHz MHz MHz LP-04 - Antenna Factor 155253545A F (d B /m )1356GHzGHz GHz GHz DR-01 - Antenna Factor3634384042A F (d B /m )6101418GHzGHz GHz GHz。
ASC88xx_Kilrogg_Reference_Application_UG

User Guide
Rev 3.0 — 24 Aug 2011
5 of 61
NXP Semiconductors
ASC88xx_Kilrogg_Reference_Application_UG
2.3 Hardware installation
Refer Figure 6 to check the ports available on the back-panel of RDK.
User Guide
Rev 3.0 — 24 Aug 2011
2 of 61
NXP Semiconductors
ASC88xx_Kilrogg_Reference_Application_UG
1. Overview
1.1 Introduction
This user manual describes the execution of reference Kilrogg application on ASC88xx (where xx=48/49/50/51) target. The purpose of Kilrogg is to demonstrate capability of ASC88xx SoC encoder and to provide a multi-channel and multi-stream reference design of feature products of IP and Video server box (VS) at professional security and surveillance market. This user manual will explain • Running of Pre-build application • Generating of reference application image • Downloading image to Target
HMC830 PLL+VCO产品手册说明书

HMC830* Product Page Quick Links Last Content Update: 11/01/2016Comparable PartsView a parametric search of comparable partsEvaluation Kits•HMC830LP6GE Evaluation BoardDocumentationApplication Notes•Frequency Hopping with Hittite PLLVCOs Application Note•PLL & PLLVCO Serial Programming Interface ModeSelection Application Note•Power-Up & Brown-Out Design Considerations for RF PLL+VCO Products Application Note•Wideband RF PLL+VCO and Clock Generation Products FAQsData Sheet•HMC830 Data SheetUser Guides•PLLs with Integrated VCO - RF Applications Product & Operating GuideTools and Simulations•ADIsimFrequency Planner Tool•ADIsimPLL™•HMC830 IBIS ModelReference MaterialsQuality Documentation•HMC Legacy PCN: LP6CE and LP6GE QFN - Alternate assembly source•Package/Assembly Qualification Test Report: LP6, LP6C, LP6G (QTR: 2014-00368)•Semiconductor Qualification Test Report: BiCMOS-A(QTR: 2013-00235)Technical Articles•Low Cost PLL with Integrated VCO Enables Compact LO Solutions•Wideband Phase-Locked Loops with Integrated Voltage Controlled OscillatorsDesign Resources•HMC830 Material Declaration•PCN-PDN Information•Quality And Reliability•Symbols and FootprintsDiscussionsView all HMC830 EngineerZone DiscussionsSample and BuyVisit the product page to see pricing optionsTechnical SupportSubmit a technical question or find your regional support numberTHIS PAGE INTENTIONALLY LEFT BLANKHMC830LP6GEv03.0512Fractional-n Pll with integrated Vco25 - 3000 MhzFunctional diagramFeatures• rF Bandwidth:25 - 3000 Mhz• Maximum Phase detector rate100 Mhz• Ultra Low Phase noise-110 dBc/hz in Band typ.• Figure of Merit (FOM) -227 dBc/hz• <180 fs rMs Jitter• 24-bit step size, resolution 3 hz typ• exact Frequency Mode• Built in digital self test• 40 Lead 6x6 mm sMt Package: 36 mm2typical applications• Cellular/4g infrastructure• repeaters and Femtocells• Communications test equipment• CatV equipment• Phased array applications• dds replacement• Very high data rate radios• tunable reference source for spurious-Free PerformanceP L L s w i t h i n t e g r a t e d V C O - s M t25 - 3000 Mhzgeneral descriptionthe hMC830LP6ge is a low noise, wide band, Fractional-n Phase-Locked-Loop (PLL) that features an integrated Voltage Controlled Oscillator (VCO) with a fundamental frequency of 1500 Mhz - 3000 Mhz, and an integrated VCO Output divider (divide by 1/2/4/6.../60/62), that together allow the h MC830LP6ge to generate frequencies from 25 Mhz to 3000 Mhz. the integrated Phase detector (Pd) and delta-sigma modulator, capable of operating at up to 100 Mhz, permit wider loop-bandwidths with excellent spectral performance.the hMC830LP6ge features industry leading phase noise and spurious performance, across all frequencies, that enable it to minimize blocker effects, and improve receiver sensitivity and transmitter spectral purity. the superior noise floor (< -170 dBc/hz) makes the hMC830LP6ge an ideal source for a variety of applications - such as; LO for rF mixers, a clock source for high-frequency data-converters, or a tunable reference source for ultra-low spurious applications.additional features of the hMC830LP6ge include rF output power control from 0 to 9 dB (3 dB steps), output Mute function, and a delta-sigma modulator exact Frequency Mode which enables users to generate output frequencies with 0 hz frequency error.For theory of operation and register map refer to the “PLLs with integrated VCOs - rF VCOs Operating guide ”. To view the Operating Guide, please visit and choose HMC830LP6GE from the “Search by PartNumber” pull down menu.electrical SpecificationsVPPcP, VddlS, Vcc1, Vcc2 = 5 V; rVdd, aVdd, dVdd3V, VccPd, VcchF, VccPS = 3.3 V [1] Measured single-ended. additional 3 dB possible with differential outputs.[2] Measured with 100 Ω external termination. see hittite PLL w/ integraged VCOs Operating guide reference input stage section for more details.25 - 3000 Mhzelectrical Specifications (Continued)[3] slew rate of greater or equal to 0.5 ns/V is recommended, see PLL with integrated rF VCOs Operating guide for more details. Frequency is guaranteed across process voltage and temperature from -40 °C to 85 °C.[4] this maximum phase detector frequency can only be achieved if the minimum n value is respected. eg. in the case of fractional feedback mode, the maximum PFd rate = fvco/20 or 100 Mhz, whichever is less.P L L s w i t h i n t e g r a t e d V C O - s M t25 - 3000 Mhzelectrical Specifications(Continued)25 - 3000 MhzFigure 1. typical closed loop integer Phase noise [“loop Filter configuration table”]Figure 5. typical Vco Sensitivity-200-180-160-140-120-100110100100010000100000fout 875 MHz, Loop BW 74 kHz, rms jitter 147 fs fout 875 MHz, Loop BW 90 kHz, rms jitter 116 fs fout 1600 MHz, Loop BW 74 kHz, rms jitter 127 fs fout 1600 MHz, Loop BW 90 kHz, rms jitter 97 fs fout 2500 MHz, Loop BW 74 kHz, rms jitter 153 fs fout 2500 MHz, Loop BW 90 kHz, rms jitter 104 fsOFFSET (kHz)P H A S E N O I S E (d B c )-180-160-140-120-100-80-60-401101001000100001000002817 MHz 2418 MHz 1996 MHz 1575 MHzOFFSET (kHz)P H A S E N O I S E (d B c /H z )-180-170-160-150-140-130-120-110-1001010010001000027 C -40 C 85 CP H A S E N O I S E (d B c /H z )FREQUENCY (MHz)100 MHz Offset1 MHz Offset100 kHz OffsetFigure 2. typical closed loop Fractional Phase noise [“loop Filter configuration table”]Figure 3. Free running Phase noiseFigure 4. Free running Vco Phase noise vs. temperature12345VCO FREQUENCYT U N E V O L T A G E A F T E R C A L I B R A T I O N (V )1531fminfmax-200-180-160-140-120-100110100100010000100000fout 880 MHz, Loop BW 74 kHz, rms jitter 149 fs fout 880 MHz, Loop BW 90 kHz, rms jitter 142 fsfout 1605 MHz, Loop BW 74 kHz, rms jitter 130 fs fout 1605 MHz, Loop BW 90 kHz, rms jitter 123 fs fout 2505 MHz, Loop BW 74 kHz, rms jitter 157 fs fout 2505 MHz, Loop BW 90 kHz, rms jitter 131 fsOFFSET (kHz)P H A S E N O I S E (d B c )1020304050600123452817 MHz at 2.5V, Tuning Cap 152418 MHz at 2.5V, Tuning Cap 151996 MHz at 2.5V, Tuning Cap 151575 MHz at 2.5V, Tuning Cap 15TUNING VOLTAGE (V)k V C O (M H z /V )Figure 6. typical tuning Voltage after calibrationP L L s w i t h i n t e g r a t e d V C O - s M t25 - 3000 MhzFigure 7. integrated rMS Jitter [1][1] rMs Jitter data is measured in fractional mode with 100 khz Loop bandwidth using 50 Mhz reference frequency from 1 khz to 20 Mhz integration bandwidth. [2] Measured from a 50 Ω source with a 100 Ω external resistor termination. see PLL with integrated rF VCOs Operating guide reference input stage section for more details. Full FOM performance up to maximum 3.3 Vpp input voltage.5010015020025030010100100010000-40C 27C 85CJ I T T E R (f s )OUTPUT FREQUENCY (MHz)-10-551010100100010000O U T P U T P O W E R (d B m )OUTPUT FREQUENCY (MHz)-240-230-220-210-2001010101010N O R M A L I Z E D P H A S E N O I S E (d B c /H z )FREQUENCY OFFSET (Hz)Figure 8. Figure of MeritFigure 9. typical output PowerFigure 10. typical output Power vs. temperature, Maximum gain-30-25-20-15-10-5010100100010000OUTPUT FREQUENCY (MHz)R E T U R N L O S S (d B )Figure 11. rF output return loss220222224226228230232234-15-12-9-6-30314 MHz Square Wave 25 MHz Square Wave 50 MHz Square Wave 100 MHz Square WaveF O M (d B c /H z )REFERENCE POWER (dBm)Figure 12. reference input Sensitivity, Square wave, 50 Ω[2]024681010100100010000O U T P U T P O W E R (d B m )OUTPUT FREQUENCY (MHz)25 - 3000 MhzFigure 14. integer Boundary Spur at 2500.2 Mhz [4]-180-160-140-120-100-80-60110100100010000100000P H A S E N O I S E (d B c /H z )OFFSET (kHz)Figure 13. reference input Sensitivity Sinusoid wave, 50 Ω[3]200205210215220225230235-20-15-10-5514 MHz sin 25 MHz sin 50 MHz sq 100 MHz sqREFERENCE POWER (dBm)F O M (d B c /H z )-180-160-140-120-100-80-60-40-200110100100010000100000P H A S E N O I S E (d B c /H z )OFFSET (kHz)[3] Measured from a 50 Ω source with a 100 Ω external resistor termination. see PLL with integrated rF VCOs Operating guide reference input stage section for more details. Full FOM performance up to maximum 3.3 Vpp input voltage. [4] Fractional Mode in Mode B, integer Boundary at 2500 Mhz[5] reF in = 100 Mhz, Pd = 800 khz, Output divider 4 selected, Loop Filter bandwidth = 16 khz, Channel spacing 200 khz[6] exact Frequency Mode, reF in = 100 Mhz, Pd = 50 Mhz, Output divider 1 selected, Loop Filter bandwidth = 100 khz, Channel spacing = 100 khz [7] exact Frequency Mode, Channel spacing = 100 khz, Fractional Mode B rF out = 2591 Mhz, reF in = 100 Mhz, Pd frequency = 50 Mhz, Output divider 1 selected, Loop Filter bandwidth = 120 khz,[8] Fractional Mode B rF out = 2591 Mhz, reF in = 100 Mhz, Pd frequency = 50 Mhz, Output divider 1 selected, Loop Filter bandwidth = 120 khz.-180-160-140-120-100-80-60-40-200110100100010000100000P H A S E N O I S E (d B c /H z )OFFSET (kHz)-180-160-140-120-100-80-60-40-200110100100010000100000P H A S E N O I S E (d B c /H z )OFFSET (kHz)Figure 15. integer-n exact Frequency Mode on Performance at 704 Mhz [5]-180-160-140-120-100-80-60-40-200110100100010000100000P H A S E N O I S E (d B c /H z )OFFSET (kHz)Figure 16. Fractional-n exact Frequency Mode on Performance at 2113.5 Mhz [6]Figure 17. Fractional-n exact Frequency Mode on Performance at 2591 Mhz [7]Figure 18. Fractional-n exact Frequency Mode oFF Performance at 2591 Mhz [8]P L L s w i t h i n t e g r a t e d V C O - s M t25 - 3000 Mhzloop Filter configuration tableFigure 19. worst Spur, Fixed 50 Mhz reference, output Freq. = 2000.1 Mhz [9]-180-160-140-120-100-80-60-40-2000.1110100100010000100000P H A S E N O I S E (d B c /H z )OFFSET (kHz)Figure 20. worst Spur, tunable reference, output Frequency = 2000.1 Mhz [9]-180-160-140-120-100-80-60-40-200.1110100100010000100000P H A S E N O I S E (d B c /H z )OFFSET (kHz)Figure 21. worst Spur, Fixed vs. tunable reference [10]-120-110-100-90-80-70-60-502GHz +1kHz2GHz +10kHz2GHz +100kHz2GHz +1000kHz2GHz +10000kHzFixed 50 MHz Reference Tunable ReferenceW O R S T S P U R (d B c )OUTPUT FREQUENCY[9] Capability of hMC830LP6ge to generate low frequencies (as low as 25 Mhz), enables the hMC830LP6ge to be used as a tunable reference source into another hMC830LP6ge, which maximizes spur performance of the second hMC830LP6ge. Please see “hMC830LP6ge application information” for more information.[10] the graph is generated by observing, and plotting, the magnitude of only the worst spur (largest magnitude), at any offset, at each output frequency, while using a fixed 50 Mhz reference and a tunable reference tuned to 47.5 Mhz. see “hMC830LP6ge application information” for more details.[11] Phase noise performance of the hMC830LP6ge when used as a tunable reference source. hMC830LP6ge is operating at 3 ghz/30, 3ghz/54, and 1.55 ghz/62 for the 100 Mhz, 55.55 Mhz, and 25 Mhz curves respectively. 25 Mhz output is 50 Mhz low pass filtered prior to input to second PLL. 100 Mhz and 55.55 Mhz curves were not filtered.Figure 22. low Frequency Performance [11]-170-160-150-140-130-1200.1110100100010000100000Carrier Frequency = 25 MHz Carrier Frequency = 55.55 MHz Carrier Frequency = 100 MHzP H A S E N O I S E (d B c /H z )OFFSET (kHz)25 - 3000 MhzPin descriptionsP L L s w i t h i n t e g r a t e d V C O - s M t25 - 3000 Mhzstresses above those listed under absolute Maximum ratings may cause permanent damage to the device. this is a stress rating only; functional operation of the device at these or any other conditions above those indicated in the operational section of this specification is not implied. exposure to absolute maximum rating conditions for extended periods may affect devicereliability.[1] Layout design guidelines set out in Qualification test report are strongly recommended.25 - 3000 Mhzoutline drawing[1] 4-digit lot number XXXXPackage information3. Lead and grOUnd PaddLe PLating: 100% Matte tin.4. diMensiOns are in inChes [MiLLiMeters].5. Lead sPaCing tOLeranCe is nOn-CUMULatiVe.6. Pad BUrr Length shaLL Be 0.15mm MaX. Pad BUrr height shaLL Be 0.25mm MaX.7. PaCKage warP shaLL nOt eXCeed 0.05mm.8. aLL grOUnd Leads and grOUnd PaddLe MUst Be sOLdered tO PCB rF grOUnd.9. reFer tO hittite aPPLiCatiOn nOte FOr sUggested PCB Land Pattern.P L L s w i t h i n t e g r a t e d V C O - s M t25 - 3000 Mhzevaluation PcB Schematicthe circuit board used in the application should use rF circuit design techniques. signal lines should have 50 Ohm impedance while the package ground leads and exposed paddle should be connected directly to the ground plane similar to that shown. a sufficient number of via holes should be used to connect the top and bottom ground planes. the evaluation circuit board shown is available from hittite upon request.To view this evaluation PCB schematicplease visit and choose HMC830LP6GE from the“Search by Part Number” pull down menu to view the product splash page.evaluation PcBevaluation order information25 - 3000 MhzhMc830lP6ge application informationLarge bandwidth (25 Mhz to 3000 Mhz), industry leading phase noise and spurious performance, excellent noise floor (<-170 dBc/hz), coupled with a high level of integration make the hMC830LP6ge ideal for a variety of applications; as an rF or iF stage LO, a clock source for high-frequency data-converters, or a tunable reference source for extremely low spurious applications (< -100 dBc/hz spurs).Figure 23. HMC830LP6GE in a typical transmit chainFigure 24. HMC830LP6GE in a typical receive chainFigure 25. HMC830LP6GE used as a tunable reference for second HMC830LP6GEUsing the hMC830LP6ge with a tunable reference as shown in Figure 25, it is possible to drastically improve spurious emissions performance across all frequencies. example shown in Figure 21 graph shows that it is possible to have spurious emissions < -100 dBc/hz across all frequencies. For more information about spurious emissions, how they are related to the reference frequency, and how to tune the reference frequency for optimal spurious performance please see the “spurious Performance” section of hittite PLL w/ integraged VCOs Operating guide. note that at very low output frequencies < 100 Mhz, harmonics increase due to small internal aC coupling. applications which are sensitive to harmonics may require external low pass filtering.P L L s w i t h i n t e g r a t e d V C O - s M t25 - 3000 Mhznotes:。
ECM_830_Manual BTX公司电转染细胞手册
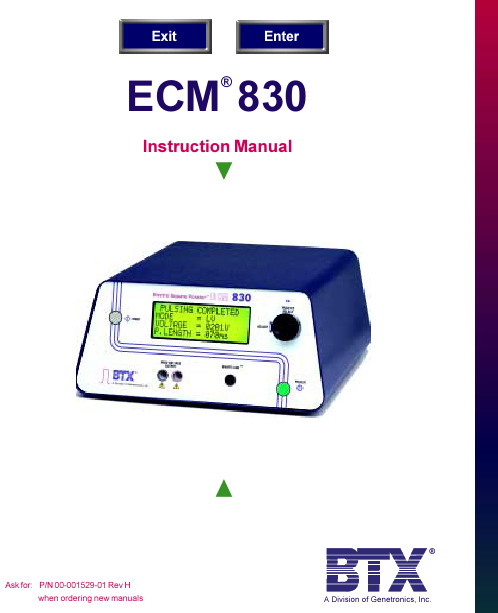
ECM ® 830Instruction ManualWarrantyThe BTX Instrument Division of Genetronics, Inc. (Genetronics) warrants that the ECM 830 is free of defects for a period of two (2) years from time of delivery from an authorized Genetronics Distributor. If any defects covered by this warranty appear within the above period, Genetronics shall have the option of repairing or replac-ing the equipment at its expense. Such repair or replace-ment shall be the customer’s exclusive remedy for breach of warranty or for negligence. This warranty does not extend to any instrumentation which has been (a) sub-jected to misuse, neglect, accident or abuse, (b) repaired or altered by anyone other than Genetronics without Genetronics’ express and prior approval, (c) used in violation of instructions furnished by the BTX Instrument Division of Genetronics, Inc. Manufacturer shall not be liable for any special or consequential damages or for loss, damage or expense (whether or not caused by orresulting from Manufacturer’s negligence) directly or indirectly arising from use of the instrumentation sold hereunder either separately or in combination with any other equipment or from any other cause.The above warranty shall be in lieu of and excludes all other expressed or implied warranties of merchantability, or fitness for any purpose, or otherwise. Without limiting the generality of the foregoing, Manufacturer shall not be liable for any claims of any kind whatsoever, as to the equipment delivered or for non-delivery of equipment and whether or not based on negligence.Manufacturer will correct any malfunction not caused by operator abuse at no charge for parts and labor. All service under the warranty will be made at the Genetronics, Inc. San Diego, CA facilities or at another location approved by Genetronics, Inc. Owner will ship instrument prepaid to San Diego, CA. Manufacturer will return the instrument after servicing, freight prepaid to owner’s address.Warranty is VOID if the instrument is changed in any way from its original factory design or if repairs are attempted without written authorization by Manufacturer.Warranty is VOID if parts or connections not manufac-tured by Manufacturer are used with a BTX instrument.Note: under no conditions should the instrument or accesso-Table of ContentsWarranty Information (i)Customer and Technical Service Information (2)Safety Guidelines (3)Safety Terms and Symbols (4)Electrical and Technical Specifications (4)Getting Started (7)Features (7)Quick Start (7)Connecting (7)Initializing (8)Instrument Controls (9)Operating Basics (16)Advanced Operation (17)Electroporation/Electrofusion Theory (19)Electroporation (19)Electrofusion (20)Applications (21)Electroporation (21)Bacteria and Yeast (21)Mammalian Cells (21)Plant (22)Other (22)Electrofusion (23)Embryo Manipulation (23)Hybridoma Formation (23)Plant Protoplast (23)Other (23)AppendicesAppendix A:ECM 830 Electrode Operation Ranges (24)Appendix B:Optimization Strategies (28)Appendix C:Electrical Troubleshooting (30)Appendix D:Experimental Troubleshooting (30)Appendix E:Glossary of Electrical Terms (32)Appendix F:Glossary of Biological and Technical Terms (33)Appendix G:Electroporation and Electrofusion Pulse GeneratorCompatibility (36)Appendix H:Recommended Reading (37)Appendix I:Product Information and Ordering (37)Appendix J:General Care and Cleaning (38)Appendix K:BTX Generator Footswitch Instructions (39)NotesPage 2Customer and Technical ServiceInformationCustomer ServiceFor any inquiry or request for repair service, contact the BTX Instrument Division of Genetronics, Inc. Customer Service group in writing or by the following:Phone: 1-800-289-2465 1-858-597-6006Fax: 1-858-597-9594E-mail: cust@If outside the United States and Canada, call: 1-858-597-6006or contact your nearest BTX Distributor.Technical ServiceBTX is the ultimate resource for technical information on the use of high voltage electric fields for performing highefficiency cell fusion, embryo manipulation, gene transfer,bacterial transformation and general electroporation ofmolecules and drugs into cells. We constantly track andmonitor all scientific publications in this area. Our Technical Service group extracts and enters pertinent information, such as results and parameters from these papers into a Database Management System. The resultant Electronic Genetics®Database can be accessed and searched on any combination of the field identifiers.For technical assistance or information, contact the BTX Instrument Division of Genetronics, Inc. Technical Service group:Phone: 1-800-289-2465 1-858-597-6006Fax: 1-858-597-9594E-mail: tech@If outside the United States and Canada, call: 1-858-597-6006or contact your nearest BTX Distributor.BTX ®A Division of Genetronics, Inc.11199 Sorrento Valley RoadSan Diego, CA 92121-1334U.S.A.Page 3830 ManualSafety GuidelinesReview the following safety precautions to avoid injury and prevent damage to this product or any products connected to it. To avoid potential hazards, use this product only asspecified.Only qualified personnel should perform service procedures.To Avoid Fire or Personal InjuryUse Proper Power Cord. Use only the power cordspecified for this product and certified for the country of use.Connect and Disconnect Properly. Do not connect ordisconnect probes or test leads while they are connected to a power source.Ground the Product. This product is grounded through the grounding conductor of the power cord. To avoidelectric shock, the grounding conductor must be connected to earth ground. Before making connections to the input or output terminals of the product, ensure that the product is properly grounded.Observe All Terminal Ratings. To avoid fire or shock hazard, observe all ratings and markings on the product.Consult the product manual for further ratings information before making connections to the product.Do Not Operate Without Covers. Do not operate this product with covers or panels removed.Use Proper Fuse. Use only the fuse type and ratingspecified for this product.Avoid Exposure to Circuitry. Do not touch exposedconnections and components when power is present.Do Not Operate With Suspected Failures. If you suspect there is damage to this product, have it inspected byqualified service personnel.Provide Proper Ventilation. Refer to installation instruc-tions for details on installing the product to ensure proper ventilation.Do Not Operate in Wet/Damp Conditions.Do Not Operate in an Explosive Atmosphere.Keep Product Surfaces Clean and Dry.Safety Terms and SymbolsThese terms may appear in this manual:WARNING – Warning statements identify conditionsor practices that could result in injury orloss of life.CAUTION – Caution statements identify conditions orpractices that could result in damage tothis product or other property.These terms may appear on the product:DANGER – Danger indicates an injury hazardimmediately accessible as you read themarking.WARNING – Warning indicates an injury hazard notimmediately accessible as you read themarking.CAUTION – Caution indicates a hazard to propertyincluding the product.Electrical and Technical SpecificationsElectrical and Technical Specifications DisplayType: 20-character by 4-line liquid crystal LED backlitPower SourceV oltage: 100 – 240 Vac, 50 - 60 Hz, CAT IIPower: Pulse: 500WIdle:150WFusing: T2.5250VEnvironmentalFor Indoor Use OnlyOperating Temperature: 10º C to + 40º CCooling: Convection through metal caseHumidity: ≤ 90% relative humidity830 ManualMechanicalFootprint: 12.5” x 12.25” x 5.5” (31.75 x 31.12 x 13.97 cm) (W-D-H)Weight: 15 lbs (6.8 kg)Controls: Single rotary encoder with integrated push buttonElectricalVoltage5-500 V olts (LV mode) @ 1 V olt resolution30-3000 V olts (HV mode) @ 5 V olts resolution(Voltage Delivery @ 5% accuracy and Voltage Monitoring @ 5.0% accuracy)Pulse Length10µs - 999µs (LV mode) @ 1µs resolution1ms – 999ms (LV mode) @ 1ms resolution1s - 10s (LV Mode) @ 0.1 s resolution10µs - 600µs (HV mode) @ 1µs resolutionPulse Interval100ms – 999ms @ 1 ms resolution1.0s – 10.0s @ 0.1s resolution (upper limit is power limited)Multiple Pulsing1 – 99 pulsesCurrent Limit500A limit at 100µsPollution Degree 2Not to be operated in conductive pollutants atmosphere* Note: See Side BarGeneral SpecificationsCertifications and Compliance’sOver voltage Category:CA T III Products in this Category: Distribution-level mains, fixed installationCA T II: Local-level mains, applications and portableequipmentCA T I: Signal levels in special equipment or parts ofequipment, telecommunications and electronicsMeets requirements of Directive 89/336/EEC for Electromag-netic Compatibility (EC) and Low-V oltage Directive73/23/EEC for Product Safety.Compliance was demonstrated to the following specifications as listed in the Official Journal of the European Communities: EN 50081-1 EmissionsEN 55011 Class B Radiated and Conducted EmissionsEN 55082-1 ImmunityIEC 10004-2 Electrostatic Discharge ImmunityIEC 10004-3 RF Electromagnetic Field ImmunityIEC 10004-4 Electrical Fast Transient/Burst ImmunityLow V oltage Directive 73/23/EECEN 61010-1 Safety requirements for electrical equip-ment for measurement, control and laboratory use.830 ManualGetting StartedCarefully open the box containing the ECM 830 Electropora-tion system. Verify receipt of the following items:ECM 830 Pulse Generator (1)Power Cord (1)BTX Electroporation Systems may be customized with the addition of various electrodes and accessories. Thefollowing items complete a typical system order:Model 630 B Electroporation Safety Stand(1)Model 660 Cuvette Rack(1)Model 610 BTX Cuvettes Plus(10)Model 620 BTX Cuvettes Plus (10)Model 640 BTX Cuvettes Plus (10)If you have ordered alternative or different items, pleaseverify their receipt.FeaturesThe ECM 830 is a Square Wave Electroporation Systemdesigned for all in vitro and in vivo electroporation applica-tions. The generator utilizes the new BTX Power Platform Technology and an all-new digital user interface.Quick StartConnectingInsert female end of power cord into male power interface on the back panel of the ECM 830. Plug male end of power cord into appropriate electrical outlet. Insert male banana plugs of the 630 B Safety Stand or alternative electrode device into High V oltage output located on front panel of the ECM 830.InitializingPush the power switch located on the front panel of the ECM 830. The display will flash:ECM 830ElectroporatorOS=v1.08, App =v0.00Genetronics, Inc.Following this initialization screen, the first time the instru-ment is initialized, the factory default display will then read:Set ParametersMode: LVV oltage: 0050VP. Length: 020 msThe first page of the Set Parameter Screen from the last time the ECM 830 was used will be displayed each time the ECM 830 is powered up after this initial startup.830 Manual ParameterControlPowerSwitchParameter Control KnobThe Parameter Control Knob is a rotary encoder controlling both the parameter (i.e. voltage) and the value of the param-eter under control (i.e. 50 volts). The display will indicate which parameter is under control by the presence of an arrow to the left of the parameter. To select a parameter to adjust, rotate the knob until the arrow is to the left of the desired parameter, then push to select. The arrow will move to the left of the value displayed for that parameter. To adjust the value of a parameter under control, rotate the knob clockwise to increase the value and counter clockwise to decrease it. In order to move between screens, move the cursor to the bottom of the screen and rotate the knob clockwise to move to the next screen. In order to move to the previous screen, move the cursor to the top of the screen and rotate the knob counterclockwise.DisplayThe ECM 830 Display will show two possible screens, the Set Parameter Screen and the Pulsing Completed Screen as well as various Status Messages.Set Parameter ScreenThe Set Parameter Screen is indicated by a display showing “Set Parameters” on the first line of each of three screen pages. The Mode, V oltage and Pulse Length are shown on the first page; the Number of Pulses, Pulsing Interval and Polarity are shown on the second page and the Advanced Features including Save, View and Load are shown on the third and final page of the Set Parameter Screen. The ECM 830 will beep when toggling from one page to another. ModeThe Mode indicates “LV” for low voltage mode or “HV” for high voltage mode. Adjusting the voltage as appropriate automatically controls the mode. There is no manual mode control.VoltageThe V oltage indicates the set voltage in volts. The low voltage mode range is 5V– 500V in 1V increments and the high voltage mode range is 30V-3000V in 5V increments. A beep is heard when transitioning between LV and HV modes.830 ManualTable 1P . LengthPulse Length indicates the set pulse length in m s or ms. The pulse length minimum is 10 m s in both HV and LV modes. In the LV mode, the maximum pulse length is 10 seconds. The pulse length units change from m s to ms at 1ms and from ms to s at 1s. Refer to Table 1 for HV pulse length maximum limits. To estimate approximate pulse lengths at various voltages in the high voltage mode, refer to Table 1 below.Please note that the voltage determines the maximum pulse length in the HV mode. If the voltage is increased and the pre-set pulse length is longer than the maximum pulse length allowed, the pulse length will automatically adjust to that level.Page 12Interval protocols!Programability protocols # Pulses The # Pulses indicates the number of set pulses from 1-99.Interval The Interval indicates the time duration between pulses. The interval range is 100 ms to 10.0 seconds, switching from units of ms to seconds after 999 ms, with 0.1 sec resolution.Advanced Features The final Set Parameters page enables the user to save, view, and load up to three programs. Please note that parameters can be changed inadvertently once a program is loaded. A default program is used to initialize the system. Program 1 is used to automatically store changes in parameters set each time the system is pulsed. Programs #2 and #3 can be used to set and save experimental parameters for instant use.Save To save the current set parameters as a program, push the parameter control knob to move the arrow to the left of the program number. Rotate the knob to designate the appropriate program number, then push and hold the knob in, releasing after a new screen is displayed. The new screen will read Saved Current Parameters to Set N . Push the parameter control knob again to return to the setup screen.View To view the appropriate program parameters, push the parameter control knob to move the arrow to the left of the program number. Select the appropriate program number by rotating the parameter control knob, then hold the knob in, releasing after a new screen is displayed. The new screen will outline the parameters currently stored under that program number. Push the parameter control knob again to return to the setup screen.Load To load a saved program, push the parameter control knob to move the arrow to the left of the program number. Please note that in addition to three available programs, there is also the default program as outlined in the Initializing section. Rotate the knob to change the program number. Push and hold the knob in, releasing after a new screen is displayed. The new screen will read Loaded Set N to Current Parameters . Push the parameter control knob again to return to the setup screen.On-Line Help In the Set Parameter Mode, an On-Line Help function is enabled. On-Line Help provides a definition for all setparameters and advanced functions. To use On-Line Help,830 Manual rotate the parameter control knob so that the arrow is to the left of the parameter or feature of interest (not the value of the parameter). Push the parameter control knob in and hold until the definition is displayed. Push a second time to return to the Set Parameter Screen.ModeLow voltage or high voltage range modeVoltageThe amplitude of the output pulseP LengthThe time duration or length of the pulse# PulsesThe number of output pulsesIntervalThe time interval between pulsesSaveSave current setup parameters to nonvolatile memoryViewShow the setup parameters stored in nonvolatile memoryLoadLoad setup parameters from memory to useStatus MessagesFollowing the initiation of a pulsing sequence, various status messages are displayed. The following status messages may be observed: Charging, Pulsing, Pulse Aborted, and Tem-perature Failure.ChargingAs soon as the start switch is pressed, the Charging status message is displayed. The capacitors in the ECM 830 are overcharged during the duration of this message.PulsingOnce the capacitors have reached the preset voltage level, they are discharged and the Pulsing status message is displayed for the duration of the pulse or preset number of pulses. A click or a beep will be heard upon the delivery of each pulse. The sound that is heard is a function of the pulse length. At pulse lengths less than 1-2 ms, clicks will likely be heard. At pulse lengths at or above 1-2 ms beeps should be heard. A final, more extended beep will be heard upon completion of the pulsing sequence. Following the pulsing status message, the Pulsing Completed Screen is displayed.Pulsing Aborted During ChargingIf the start switch is activated a second time prior to delivery of a pulse, the pulsing sequence is aborted and the Pulsing Aborted During Charging status message is displayed.Temperature FailureIf unit is rapidly pulsed at the high end of the two voltage modes, it is possible for a high temperature warning to occur. In this event, the status message observed is Unit Cooling Please Wait . When the unit has cooled down to a safe level, two beeps will sound and the message will change to Ready . Pushing the start button, or rotating the parameter control knob will shift user back to Parameter Set Screen.Pulsing Completed ScreenThe Pulsing Completed Screen is displayed following the delivery of a pulse or train of pulses and is indicated by the display Pulsing Completed on the top line of each of two screen pages. Page 1 comes up automatically; rotate the parameter control knob clockwise to view page 2 and counterclockwise to go back to page 1. Press the knob to return to the Set Parameters Screen or press the start switch to deliver another pulse. The pulsing completed screen displays monitored parameters including Mode, V oltage, Pulse Length, Number of Pulses, Pulse Interval and Polarity. Please note that parameters will be displayed, even if Safety Stand or other output is not connected. Always verify that your sample is connected with the HV output.ModeMode indicates the voltage mode used in the delivery of the last pulse: LV or HV.830 Manual VoltageV oltage indicates the output voltage of the last pulse, in volts. For pulses of 10 255 µs, the voltage is measured at the end of the pulse, and for pulses longer than 255 µs, the voltage is measured at the beginning, or peak.P LengthP Length indicates the duration of the pulse in m s from10-999 µs, ms from 001 to 999 ms, or in seconds from 1.0 to 10.0 s.# Pulses# Pulses delivered in the last pulsing sequence is displayed, from 1-99.IntervalThe Interval between the next-to-last and the last pulse is monitored and displayed in ms from 100-999 ms and in seconds from 1.0 to 10.0 seconds. If only one pulse is delivered, none is displayed.PolarityThe Polarity used in the last sequence of pulses is monitored and displayed as Unipolar.High Voltage OutputThe High V oltage Output is located in the lower center portion of the front panel. Plug the high voltage cables into this output following the color-coded polarity.SmartLinkThe Smartlink port on v1.08 ECM 830 and beyond is equipped with footswitch connection capabilities. If your instrument falls in this category and you wish to use the footswitch, please see appendix K on page 39. If your instrument does not fall into this category, contact BTX customer service at (800) 289-2465 orcust@ for assistance.630B & 630 RB-1Simple, single dial operation with parameter control knobOperating BasicsUse with Safety Stand 630B and BTX Disposable Electroporation Cuvettes Plus1.Insert the safety stand banana plugs into the HV Output on the front panel of the ECM 830.2.Press the power switch to initialize the ECM 830.3.Rotate parameter control knob to move arrow to voltage and push to select. Rotate knob to adjust voltage. Push again to select that voltage.4.Rotate parameter control knob to move arrow to P Length and push to select. Rotate knob to adjust pulse length. Push again to select that pulse length.5.Rotate parameter control knob to move arrow to #Pulses (Page 2) and push to select. Rotate knob to adjust the number of pulses. Push again to select that number of pulses.6.Rotate parameter control knob to move arrow to Interval if you have designated more than one pulse in 5 and push to select. Rotate knob to adjust the pulse interval. Push again to select that pulse interval.7.Prepare sample, pipette into the appropriate BTX Disposable Cuvettes Plus, place the cuvette in the 630B Safety Stand and secure the safety cover.8.Press the Start button. The ECM 830 will charge and then deliver the electroporation pulse or train of pulses selected, beeping with the delivery of each pulse.9.Process sample. Do not forget to recordappropriate parameters as displayed on thePulsing Completed Screens, for documentationpurposes.10.To return to ready mode, press the Start button.11.To abort a pulse before delivery, press the Startbutton during the charging mode.Use with Alternative Electrode Chambers and ApplicatorsThe ECM 830 may be used to power all BTX electroporation and electrofusion chambers and applicators. Follow the above instructions in conjunction with instructions provided for the specific electrode. Refer to Appendix A for graphical representation of operating ranges of various chambers and applicators with the ECM 830.Use with FootswitchPlease see Appendix K on page 39 Advanced Operation: Programming1.Set parameters as outlined in Operating Basics.2.Once presetting of parameters has been completed, rotatethe parameter control knob until the save function has been reached.3.Press knob in and release. Now rotate to select whichprogram number the chosen settings (see Preset Param-eters above) should be saved under. Program #1 isreserved for current parameters in active use and cannotbe used for pre-set storage.4.Push and hold knob in, releasing only after a new screenreading Saved Current Parameters to Set N is displayed.(N refers to program number designated in step 2)5.Push the parameter control knob again to return to the SetParameter Screen.6.From the Set Parameter Screen, use the parametercontrol knob to rotate until the load function has beenreached.7.Push the knob in and release. Now rotate to select theappropriate program number.8.Push and hold knob in, releasing only after a new screenreading Loaded Set N to Current Parameters isdisplayed.9.Push the parameter control knob again to return to theSet Parameter Screen.Pore FormationElectroporation ProcessElectroporation/Electrofusion TheoryElectroporationElectroporation is the application of controlled, pulsed electric fields to biological systems. If the biological system contains a lipid bilayer, such as is the case if the system is a suspension of cells or liposomes, the pulsed electric field may overcome the field potential of the lipid bilayer, resulting in a reversible breakdown of the bilayer and a resulting formation of temporal pores in the mem-brane. The pores formed are of the order of 40-120 nm.Most pores reseal within a few seconds, after allowing the transfer of materials into and out of the cells.During a typical electroporation process, target cells and molecules are mixed together. When an electroporation pulse is delivered, the result is the formation of temporal pores. Before the pores reseal, the target molecules are observed to enter the cells. Upon resealing of the pores,the molecules become incorporated within the cell. The eventual target site depends on the application; forexample, molecules can remain in the cytoplasm, interact with the membrane and move into the nucleus.Applications for electroporation include permeabilization of virtually all cells to a wide variety of molecules and ions. The most common applications for electroporation are the transformation or transfection of cells with DNA or RNA. Other applications for electroporation include electroactivation, electroinsertion of proteins into cell membranes and electroextraction of molecules from cells.Although electroporation has mainly been used as aresearch tool, recent work has demonstrated its potential for clinical applications. Some areas being exploredinclude: electrochemotherapy which involves electropora-tion for delivering chemotherapeutic agents directly to tumor cells, encapsulation of drugs/genes into cells for their use as carrier systems, transdermal delivery of drugs/genes, gene therapy and delivery of drugs/genes with an electroporation catheter.Electrofusiontransgenic plant production. characterized by waveform.Voltage may be directly set on the instrument. gentler to cells which yields higher viability.Alternating CurrentMammalian Cells Expressing GFP Following EPAlternating current generators, such as the BTX ECM 2001and radio frequency (RF) generators deliver a sinusoidal wave. These are used to cause dielectrophoresis, in which cells may be brought together for fusion. Parameters, which typically may be set, include amplitude, duration and frequency.ApplicationsElectroporationBacteria and Yeast ElectroporationThe most common application is transformation. Fieldstrength and pulse length are critical parameters for reporting,optimization and troubleshooting bacterial and yeast applica-tions.Mammalian Cell ElectroporationElectroporation has been used successfully to introduce many different molecule types into cells. Most commonly, elec-troporation is used for the processes of transfection, in which nucleic acid (DNA and RNA), is introduced into cells.Electroporation can be used to deliver oligonucleotides into cells for anti-sense applications. It can be used to deliver proteins into cells, even large enzymes such as restriction enzymes and antibodies, for various purposes. Peptides have also been electroincorporated. Smaller molecules have been incorporated into cells and liposomes, such as dyes, sugars and dNTP S.Electroporation has been used to study cellular activation processes, by electropermeabilizing cells to Ca 2+, Mg 2+ and Na +. Electroporation is also used to electroinsert proteins into the cell membrane. Finally, electroporation has been used to introduce drugs, such as the chemotherapeutic agent bleomy-cin, into cancer cells, in vitro and in vivo .The use of low impedance buffers such as PBS may result in a voltage drop so that the actual peak voltage delivered to samples may be less than the set voltage.With exponential decay generators, monitoring is necessary to identify the pulse length, or time constant, since this param-eter may be very much dependent on the impedance of the sample (sample load).。
AppendixA-IEEE

Transformers Collection2002 Special Edition ContentsIEEE Std 62-1995, Guide for Diagnostic Field Testing of Electric Power Apparatus —Part 1: Oil Filled Power Transformers, Regulators, and Reactors (ANSI)IEEE Std 259-1999, Standard Test Procedure for Evaluation of Systems of Insulation for Specialty Transformers (ANSI)IEEE Std 637-1985 (Reaff 1992), Guide for the Reclamation of Insulating Oil and Criteria for Its Use (ANSI)IEEE Std 638-1992 (Reaff 1999), Standard for Qualification of Class 1E Transform ers for Nuclear Power Generating StationsIEEE 1276-2000 Edition, Guide for the Application of High Temperature Insulation Materials in Liquid-Immersed Power TransformersIEEE Std 1277-2000, General Requirements and Test Code for Dry-Type and Oil-Immersed Smoothing Reactors for DC Power TransmissionIEEE Std 1388-2000, IEEE Standard for the Electric Reporting of Transformer Test Data (ANSI)IEEE Std 1538-2000, IEEE Guide for Determining of Maximum Winding Temperature Rise in Liquid-Filled Transformers (ANSI)IEEE Std C57.12.00-2000, Standard General Requirements for Liquid-Immersed Distribution, Power, and Regulating TransformersIEEE Std C57.12.01-1998, Standard General Requirements for Dry-Type Distribution and Power Transformer Including Those with Solid-Cast and/or Resin-Encapsulated WindingsANSI C57.12.10-1997, Standard for Transformers—230 Kv and Below 833/958 Through 8333/10 417 kVA, Single-Phase, and 750/862 Through 60 000/80 000/100 000 kVA, Three-Phase Without Load Tap Changing; and 3750/4687 Through 60 000/80 000/100 000 kVA with Load Tap Changing—Safety RequirementsANSI C57.12.20-1997, Standard for Overhead-Type Distribution Transformers, 500 kVA and Smaller: High Voltage, 34 500 Volts and Below; Low Voltage, 7970/13 800 Y Volts and BelowANSI C57.12.21-1992, Standard for Transformers—Pad-Mounted, Compartmental-Type, Self-Cooled, Three-Phase Distribution Transformers with High Voltage Bushings; High-Voltage, 34500 GRYD/19920 Volts and Below; Low-Voltage, 240/120 volts; 167 kVA and SmallerANSI C57.12.22-1993 (Reaff 1998), Standard for Transformers—Pad-Mounted, Compartmental-Type, Self-Cooled, Three-Phase Distribution Transformers with High-Voltage Bushings, 2500 kVA and Smaller: High-Voltage, 34 500 GrdY/19 920 Volts and Below; Low Voltage, 480 Volts and BelowIEEE C57.12.23-1992 (Reaff 1999), Standard for Transformers—Underground-Type, Self-Cooled, Single-Phase Distribution Transformers With Separable, Insulated, High-Voltage Connectors; High Voltage (24 940 GrdY/14 400 V and Below) and Low Voltage (240/120 V, 167 kVA and Smaller) (ANSI)ANSI C57.12.24-2000, Requirements for—Underground-Type Three-Phase Distribution Transformers, 2500 kVA and Smaller; High Voltage, 34 500 GrdY/19 920 Volts and Below; Low Voltage, 480 Volts and Below—RequirementsANSI C57.12.25-1990, Standard for Transformers—Pad-Mounted, Compartmental-Type, Self-Cooled, Single-Phase Distribution Transformers with Separable Insulated High-Voltage Connectors: High-Voltage, 34 500 GrdY/19 920 Volts and Below; Low-Voltage, 240/120 Volts; 167 kVA and Smaller—RequirementsANSI C57.12.26-1992, Pad-Mounted, Compartmental-Type, Self-Cooled, Three-Phase Distribution Transformers for Use with Separable Insulated High-Voltage Connectors (34 500 GrdY/19 920 Volts and Below; 2500 kVA and Smaller)ANSI C57.12.28-1999, Standard for Pad-Mounted Equipment—Enclosure IntegrityANSI C57.12.29-1991, Standard for Pad-Mounted Equipment—Enclosure Integrity for Coastal EnvironmentsANSI C57.12.31-1996, Standard for Pole-Mounted Equipment—Enclosure IntegrityANSI C57.12.32-1994, Standard for Submersible Equipment—Enclosure IntegrityIEEE C57.12.35-1996, Standard for Bar Coding for Distribution TransformersANSI C57.12.40-2000, Standard for Secondary Network Transformers—Subway and Vault Types (Liquid Immersed)—RequirementsIEEE C57.12.44-2000, Requirements for Secondary Network Protectors (ANSI)ANSI C57.12.50-1981 (Reaff 1998), Requirements for Ventilated Dry-Type Distribution Transformers, 1 to 500 kVA, Single-Phase, and 15 to 500 kVA, Three-Phase, with High-Voltage 601 to 34 500 Volts, Low-Voltage 120 to 600 VoltsANSI C57.12.51-1981 (Reaff 1998), Requirements for Ventilated Dry-Type Power Transformers, 501 kVA and Larger, Three Phase, with High-Voltage 601 to 34 500 Volts, Low-Voltage 208Y/120 to 4160 VoltsANSI C57.12.52-1981 (Reaff 1998), Requirements for Sealed Dry Type Power Transformers, 50a kVA and Larger, Three Phase and High Voltage 601 to 34500 Volts, Low Voltage208Y/120 to 4160 VoltsANSI C57.12.55-1987 (Reaff 1998), Standard for Dry Type Transformers in Unit Installations, Including Unit Substations—Conformance StandardIEEE C57.12.56-1986 (Reaff 1998), Standard Test Procedure for Thermal Evaluation of Insulation Systems for Ventilated Dry-Type Power and Distribution Transformers (ANSI) IEEE C57.12.58-1991 (Reaff 1996), Guide for Conducting a Transient Voltage Analysis of a Dry-Type Transformer Coil (ANSI)IEEE Std C57.12.59-2001, Guide for Dry-Type Transformer Through-Fault Current DurationIEEE C57.12.60-1998, Guide for Thermal Evaluation of Insulation Systems for Solid-Cast and Resin-Encapsulated Power and Distribution Transformers (ANSI)IEEE C57.12.70-2000, Standard for Terminal Markings and Connections for Distribution and Power TransformersIEEE C57.12.80-1978 (Reaff 1992), Standard Terminology for Power and Distribution Transformers (ANSI)IEEE C57.12.90-1999, Standard Test Code for Liquid-Immersed Distribution, Power, and Regulating Transformers and Guide for Short-Circuit Testing of Distribution and Power Transformers (ANSI)IEEE C57.12.91-2001, Test Code for Dry-Type Distribution and Power Transformers (ANSI)IEEE C57.13-1993, Standard Requirements for Instrument TransformersIEEE C57.13.1-1981 (Reaff 1999), Guide for Field Testing of Relaying Current Transformers (ANSI)IEEE C57.13.3-1983 (Reaff 1990), Guide for the Grounding of Instrument Transformer Secondary Circuits and Cases (ANSI)IEEE C57.15-1999, Standard Requirements, Terminology, and Test Code for Step-Voltage and Induction-Voltage Regulators (ANSI)IEEE C57.16-1996 (Reaff 2001), Standard Requirements, Terminology, and Test Code for Dry-Type Air-Core Series-Connected Reactors (ANSI)IEEE C57.18.10-1998, Standard Practices and Requirements for Semiconductor Power Rectifier Transformers (Revision and redesignation of ANSI/IEEE C57.18-1964) (ANSI) IEEE C57.19.00-1991 (Reaff 1997), Standard General Requirements and Test Procedure for Outdoor Power Apparatus Bushings (ANSI)IEEE C57.19.01-2000, Standard Performance Characteristics and Dimensions for Outdoor Apparatus Bushings (ANSI)IEEE C57.19.03-1996, Standard Requirements, Terminology, and Test Bar Coding for Bushings for DC Applications (ANSI)IEEE C57.19.100-1995, Guide for Application of Power Apparatus Bushings (ANSI) IEEE C57.21-1990 (Reaff 1995), Standard Requirements, Terminology, and Test Code for Shunt Reactors Over 500 kVA (ANSI)IEEE C57.91-1995, Guide for Loading Mineral-Oil-Immersed Overhead and Pad-Mounted Distribution Transformers Rated 500 kVA and Less with 65° C or 55° C Average Winding RiseIEEE C57.93-1995 (Reaff 2001), Guide for Installation of Liquid-Immersed Power Transformers (ANSI)IEEE C57.94-1982 (Reaff 2000), Recommended Practice for Installation, Application, Operation, and Maintenance of Dry-Type General Purpose Distribution and Power TransformersIEEE C57.96-1999, Guide for Loading Dry-Type Distribution and Power Transformers IEEE C57.98-1993 (Reaff 1999), Guide for Transformer Impulse Tests (ANSI)IEEE C57.100-1999, Standard Test Procedure for Thermal Evaluation of Oil-Immersed Distribution Transformers (ANSI)IEEE C57.104-1991, Guide for the Interpretation of Gases Generated in Oil-Immersed Transformers (ANSI)IEEE C57.105-1978 (Reaff 1999), Guide for Application of Transformer Connections in Three-Phase Distribution Systems (ANSI)IEEE C57.106-1991 (Reaff 1998), IEEE Guide for Acceptance and Maintenance of Insulating Oil in Equipment (ANSI)IEEE C57.109-1993 (Reaff 2000), Guide for Liquid-Immersed Transformer Through-Fault-Current Duration (ANSI)IEEE C57.110-1998, Recommended Practice for Establishing Transformer Capability When Supplying Nonsinusoidal Load CurrentsIEEE C57.111-1989 (Reaff 1995), Guide for Acceptance of Silicone Insulating Fluid and Its Maintenance in Transformers (ANSI)IEEE C57.113-1991, Guide for Partial Discharge Measurement in Liquid-Filled Power Transformers and Shunt ReactorsIEEE C57.116-1989 (Reaff 2000), Guide for Transformers Directly Connected to Generators (ANSI)IEEE C57.117-1986 (Reaff 1998), Guide for Reporting Failure Data for Power Transformers and Shunt Reactors on Electric Utility Power Systems (ANSI)IEEE C57.119-2001, Performing Temperature Rise Tests on Oil-Immersed Power Transformers at Loads Beyond Nameplate Ratings (ANSI)IEEE C57.121-1998, Guide for Acceptance and Maintenance of Less Flammable Hydrocarbon Fluid in Transformers (ANSI)IEEE C57.124-1991 (Reaff 1996), Recommended Practice for the Detection of Partial Discharges and the Measurement of Apparent Charge in Dry -Type Transformers (ANSI) IEEE C57.125-1991 (Reaff 1998), Guide for Failure Investigation, Documentation, and Analysis for Power Transformers and Shunt ReactorsIEEE C57.127-2000, Trial-Use Guide for the Detection of Acoustic Emissions from Partial Discharges in Oil-Immersed Power TransformersIEEE C57.129-1999, General Requirements and Test Code for Oil-Immersed HVDC Converter TransformersIEEE C57.131-1995, Guide for the Application of Metal Oxide Sure Arresters for AC Systems (ANSI)IEEE Std C57.134-2000, Guide for Determination of Hottest Spot Temperature in Dry Type Transformers (ANSI)IEEE C57.138-1998, Recommended Practice for Routine Impulse Test for Distribution Transformers (ANSI)。
CG1777_Wire_Crimp_Process_Audit_rev001_2009-10-24

Appendix X-1(CG-1777)Statement of Requirements forSolder-less Crimp ConnectionsRevision: 001Issue Date: 2009-10-24This document contains Component and Manufacturing Description of Requirements for PSDS Vehicle Wiring Systems under sourcing. This document is used in conjunction with the PSDS SOR document package, GMN11012 - Summary Document for All Product Commodities and GMN 11039 - Statement of Requirements for All Electrical and Electronic Systems and Components.Revision Level: 001CHANGE LOG for SOR Appendix "X-1"Beginning with Initial ReleaseRevision Level: 001Table of Contents1Scope of Document (4)2Solder-Less Crimp Requirement Overview (4)2.1Description of Crimp System Applications (4)2.2Overview of Deliverables (4)3Crimp Validation and Process Requirements (4)3.1Crimp Validation (4)3.2Manufacturing Process Control (5)3.3Visual aids and Operator Training (6)3.4Self Process Audits (6)3.5Records Retention (6)4Resolution of Nonconformance of Crimp Validation (6)Revision Level: 0011Scope of DocumentThis appendix provides solder-less crimp requirements for PSDS components which are in addition to those specified in other PSDS sourcing documents or not covered elsewhere in SOR product documents. Included are additional requirements and deviations to GMN-11012 and/or GMN-11039, additional requirements and deviations to Connector SOR Appendix C, and other program specific requirements.Questions regarding this document can be directed to the GM Connection System or PSDS BOM Family Owner (BFO).2Solder-Less Crimp Requirement Overview2.1Description of Crimp System ApplicationsThis specification provides the validation test method and manufacturing process requirements for solder-less crimped connections (crimp) using stranded automotive copper wire. Wire types using compressed, compacted, or solid core construction or other core materials (clad, steel core, etc) or non-mechanical type wire to terminal applications will require additional requirements to be developed and agreed to by the GM PSDS DRE and the wiring harness supplier. Deviations to this document must be approved by the GM PSDS Lead Wiring Engineer.2.2Overview of DeliverablesThe awarded PSDS wiring harness supplier will be responsible for establishing and providing the following:1. Crimp validation for all wire to terminal applications used in wiring harnesses.2. Manufacturing process controls to ensure crimp conformance adherence on a regular basis.3. Various manufacturing plant and operator training.4. Validation and process control record retention.3Crimp Validation and Process Requirements3.1Crimp ValidationAll cable to terminal crimp applications must be validated to SAE/USCAR-21, Performance Specification for Cable to Terminal Electrical Crimps. The SAE/USCAR-21 document is available through SAE at .1. Every terminal to cable type, cable size, cable strand configuration and cable manufacturer(non-SAE cable type only) combination must be validated accordingly.2. To claim conformance to this specification, the tooling and process settings used to crimp aterminal/wire application must be traceable to a passed USCAR-21 test using the samesettings. The tooling and process used to meet USCAR-21 are very likely to be different than what is listed on a terminal drawing or process sheet developed per anotherspecification. Therefore, the settings traceable to USCAR-21 must supersede allRevision Level: 001Revision Level: 001documentation to the contrary (including crimp information on the part drawings) in order to claim compliance.3. All data compiled to validate each crimp shall be documented and stored for production use andaudit retrieval. This data shall include but not be limited to the following:a. Conductor crimp height (CCH)b. Conductor crimp width (CCW)c. Insulation crimp height (ICH)d. Insulation crimp width (ICW)e. Core compaction ratiof. Cross section visual inspection photographg. Cable pull test valuesh. Insulation strip length valuesi. Any and all values established in USCAR-21 documents.Crimp settings and data shall be documented in a form similar to that found in the document “Sample Report and Inspection.xls” shown in Section 3.2.3.2 Manufacturing Process ControlThe PSDS harness and/or lead prep supplier shall institute a manufacturing process control plan that ensures that crimp settings established to meet the validation criteria for each terminal to cable application are maintained throughout the build life cycle of the harness assembly. Each lead prep processing manufacturing plant shall have access to equipment capable of inspecting and logging the crimp performance validation data (a thru i) in Section 3.1. The process control plan must include at a minimum the following:1. Regular monitoring of production crimps. The beginning setup, during regular intervals andat the end of the production run for any cable to terminal configuration, the physical inspection and measurement of the crimp parameters shall be performed and compared against data compiled and documented in the validation process to verify that crimp settings are inconformance. Unless SPC data can prove otherwise, the minimum regular interval shall be set at no more than 40K crimp applications. Crimp monitoring data shall be documented for the purpose of inspection audits. Documentation information shall be similar to that shown in the document “Sample Report and Inspection.xls ”.2. Tool maintenance schedule. The Lead prep manufacturing plant shall perform a SPC studyto establish the maintenance schedule for crimp dies and tool adjustments. Tool maintenance shall be documented for inspection audits.3. Crimp force monitoring. Crimp force monitoring equipment capable of identifying crimpanomalies such as missing core strands, cable insulation under core crimp wings and damaged/worn crimp dies and tooling shall be utilized.4. Post crimp material handling, storage and handling. Processes and procedures shall beestablished for post production storage, protection and identification of terminated leads.Revision Level: 0013.3 Visual aids and Operator TrainingThe lead prep manufacturing plant shall utilize visual aids and provide operator training such that all aspects of the crimp process are clearly defined and that the expected quality of the terminated lead can be confirmed.3.4 Self Process AuditsThe lead prep manufacturing plant shall on a regular basis, perform self audits of the crimp process perthe wire crimp process audit form.3.5 Records RetentionThe supplier shall maintain a central file for the storage of laboratory reports and calibration records. Such record storage must be in accordance with established ISO and AIAG policies and practices.4Resolution of Nonconformance of Crimp ValidationThe GM DRE shall approve root cause and corrective actions (including any re-validation testing) of any Validation Plan failures, functional, mechanical, or failing to meet the requirements. Discrepancies, variations, and deviations shall be resolved by irreversible corrective action and retest to complete first article component design validation requirements. Resolution by waiver may be granted at thediscretion of the platform as a last resort if justified by circumstance but not to the extent of failure to meet performance requirements.In summary, no changes to this SOR and its subsequently developed components will be made without the written consent of the GM Lead Wiring Engineer.End of documentOnce printed, this document is uncontrolled。
SPC560P34x SPC560P40x串行引导自动波特率自动扫描参考手册补充说明说明书

TN0837Technical note SPC560P34x/SPC560P40x Serial Boot with Autobaud Autoscanreference manual addendumIntroductionThe aim of this document is to give a supplementary description for serial boot modes inaddition to the description in RM0046, rev. 3 (see Section Appendix A). It is described thehardware configuration to allow the right selection of the serial boot mode with autobaud bymeans of autoscan and the RX pins configuration of serial communication peripherals(FlexCAN and LINFlex).September 2013Doc ID 022359 Rev 21/11Contents SPC560P34x, SPC560P40x Contents1Hardware configuration to select boot mode . . . . . . . . . . . . . . . . . . . . . 51.1SPC560P34x/SPC560P40x boot pins . . . . . . . . . . . . . . . . . . . . . . . . . . . . 51.2Autobaud feature . . . . . . . . . . . . . . . . . . . . . . . . . . . . . . . . . . . . . . . . . . . . 6 Appendix A Reference document. . . . . . . . . . . . . . . . . . . . . . . . . . . . . . . . . . . . . . 9 Revision history . . . . . . . . . . . . . . . . . . . . . . . . . . . . . . . . . . . . . . . . . . . . . . . . . . . . 102/11Doc ID 022359 Rev 2SPC560P34x, SPC560P40x List of tables List of tablesTable 1.Hardware configuration to select boot mode . . . . . . . . . . . . . . . . . . . . . . . . . . . . . . . . . . . . 5 Table 2.SPC560P34x/SPC560P40x boot pins . . . . . . . . . . . . . . . . . . . . . . . . . . . . . . . . . . . . . . . . . 5 Table 3.Document revision history . . . . . . . . . . . . . . . . . . . . . . . . . . . . . . . . . . . . . . . . . . . . . . . . . 10Doc ID 022359 Rev 23/11List of figures SPC560P34x, SPC560P40x List of figuresFigure 1.BAM Autoscan code flow . . . . . . . . . . . . . . . . . . . . . . . . . . . . . . . . . . . . . . . . . . . . . . . . . . . 8 4/11Doc ID 022359 Rev 2SPC560P34x, SPC560P40x Hardware configuration to select boot modeDoc ID 022359 Rev 25/111 Hardware configuration to select boot modeThe SPC560P34x/SPC560P40x devices detect the serial boot mode based on external pins.To enter boot mode via FlexCAN or LINFlex, the device must be forced into an Alternate Boot Loader Mode via the FAB (Force Alternate Boot Mode), which must be asserted before initiating the reset sequence. The type of alternate boot mode is selected according to the ABS (Alternate Boot Selector) pins (see Table 1).Boot configuration pins are:●PAD A[2] - ABS[0],●PAD A[3] - ABS[1],●PAD A[4] - FABNote:PAD A[2] - ABS[0] is not bonded on SPC560P34x/SPC560P40x LQFP64 so for thispackage the option 'FlexCAN without Autobaud ' is not available and the internal pull-down on PAD A[2] assures that it is at low logical value at reset."1.1 SPC560P34x/SPC560P40x boot pinsThe TX/RX pin (LINFlex_0 and FlexCAN_0) used for serial boot and configuration boot pins to select the serial boot mode are described in the Table 2 for LQFP64 and LQFP100 packages.Table 1.Hardware configuration to select boot modeFAB (1)1.During reset the boot configuration pins are weak pull down.ABS[1,0]Standby-RAM boot flagBoot IDBoot mode1000-Serial Boot via LINFlex without autobaud 1010-Serial Boot via FlexCAN without autobaud 110-Scan of both serial interfaces (FlexCAN and LINFlex) for Serial Boot with autobaudTable 2.SPC560P34x/SPC560P40x boot pinsPort pinFunctionPin64-pin100-pin A[2](1)ABS[0]-57A[3](1)ABS[1]4164A[4](1)FAB 4875B[0]CAN_0 TX 4976B[1]CAN_0 RX 5077B[2]LIN_0 TX5179Hardware configuration to select boot modeSPC560P34x, SPC560P40x6/11Doc ID 022359 Rev 21.2 Autobaud featureSPC560P34x/SPC560P40x devices implement the autobaud feature via FlexCAN orLINFlex selecting the active serial communication peripheral by means of an autoscan routine.When autobaud configuration is selected by ABS and FAB pins, the autoscan routine starts and listens to the active bus protocol. Initially the LinFlex_0 RX pin and FlexCAN_0 RX pin are configured as GPIO inputs:●for LQFP100 internal weak pull-up enabled for both RX pins,●for LQFP64 internal weak pull-up enabled only for FlexCAN_0 RX pin.The autoscan routine waits in polling for the first LOW level to select which routine will be executed:●FlexCAN Autobaud routine ●LinFlex Autobaud routineThen the measurement baud rate is computed to configure the serial communication at the right rate. In the end of baud rate measurement, LinFlex_0 RX pin and FlexCAN_0 RX pin switches to work as dedicated pin.Baud rate measurement is using the System Timer Module (STM) which is driven by the system clock. Measurement itself is performed by software polling the related inputs as general purpose IO’s, resulting in a detection granularity that is directly related to the execution speed of the software.One main difference of the autobaud feature is that the system clock is not driven directly by the external oscillator, but it is driven by the FMPLL output. The reason is that to have an optimum resolution for baud rate measurement, the system clock needs to be nearer to the maximum allowed device’s frequency.This is achieved with the following two steps:ing the Clock Monitor Unit (CMU) and the internal RC oscillator (IRC), the external frequency is measured using the IRC as reference to determine this frequency.2.Based on the result of this measurement, the FMPLL is programmed to generate a system clock that is configured to be near, but lower, to the maximum allowed frequency.After setting up the system clock, the BAM autoscan code configures the FlexCAN RX pin (B[1] on all packages) and LINFlex RX pin (B[3] on LQFP100 or B[7] on LQFP64) as GPIO inputs and searches for FlexCAN RX pin level to verify if CAN is connected or not.B[3](2)LIN_0 RX -80(2)B[7](3)LIN_0 RX20(3)291.Weak pull down during reset.2.SPC560P34x/SPC560P40x LQFP100 package uses only PAD B[3] - pin 80 for boot via LINFLEX3.SPC560P34x/SPC560P40x LQFP64 package uses only PAD B[7] - pin 20 for boot via LINFLEXTable 2.SPC560P34x/SPC560P40x boot pins (continued)Port pinFunctionPin64-pin100-pinSPC560P34x, SPC560P40x Hardware configuration to select boot mode Then continuously waits in polling on change of RX pins level.The FlexCAN RX pin leveltakes precedence. First signal found at low level selects the serial boot routine that will beexecuted.In case a low level is detected on any input, the corresponding autobaud measurementfunctionality is started:●when FlexCAN RX (corresponds to pin B[1]) level is low, the CAN autobaudmeasurement starts and then sets up the FlexCAN baud rate accordingly;●when UART RX (corresponds to pin B[3] on LQFP100 or B[7] on LQFP64) level is low,the UART autobaud measurement starts and then sets up the LINFlex baud rateaccordingly.After performing the autobaud measurement and setting up the baud rate, thecorresponding RX input is reconfigured and the related standard download process isstarted; in case of a detected CAN transmission a download using the CAN protocol asdescribed in section “Bootstrap with FlexCAN— autobaud disabled”of RM0046, rev. 3 (seeSection Appendix A), and in case of a detected UART transmission a download using theUART protocol as described in Section” Boot from UART— autobaud disabled” of RM0046,rev.3 (see Section Appendix A).The following Figure1 identifies the corresponding flow and steps.Note:When autobaud scan is selected, initially both LINFlex_0 RX pin and FlexCAN_0 RX pin should be at high level. No external circuity should pull-down them to allow right autoscan.Doc ID 022359 Rev 27/11Hardware configuration to select boot modeSPC560P34x, SPC560P40x8/11Doc ID 022359 Rev 2Figure 1.BAM Autoscan code flowFlexCAN RX and LINFlex RX configured as GPIO inputsFlexCAN RX== 1FlexCAN RX== 0LINFlex RX== 0C A N A u t o b a u dSet matching baud rate for FlexCANAutobaud measurement Continue with FlexCANL I N F l e x A u t o b a u dSet matching baud rate for LINFlexAutobaud measurement downloadContinue with LINFlexdownloadNOYESdetecteddetectedLINFlex RX== 0detectedBoth RDX pins have to be at high level.Avoid to connect them to external pull-down resistor.If CAN is connected, after reset CAN_RX has to be at high levelSPC560P34x, SPC560P40x Reference document Appendix A Reference document1.SPC560P34/SPC560P40 32-bit MCU family built on the embedded PowerArchitecture® (RM0046, rev.3 - Doc ID 16912)Doc ID 022359 Rev 29/11Revision history SPC560P34x, SPC560P40x Revision historyTable 3.Document revision historyDate Revision Changes12-Oct-20111Initial release.18-Sep-20132Updated disclaimer.10/11Doc ID 022359 Rev 2SPC560P34x, SPC560P40xPlease Read Carefully:Information in this document is provided solely in connection with ST products. STMicroelectronics NV and its subsidiaries (“ST”) reserve the right to make changes, corrections, modifications or improvements, to this document, and the products and services described herein at any time, without notice.All ST products are sold pursuant to ST’s terms and conditions of sale.Purchasers are solely responsible for the choice, selection and use of the ST products and services described herein, and ST assumes no liability whatsoever relating to the choice, selection or use of the ST products and services described herein.No license, express or implied, by estoppel or otherwise, to any intellectual property rights is granted under this document. If any part of this document refers to any third party products or services it shall not be deemed a license grant by ST for the use of such third party products or services, or any intellectual property contained therein or considered as a warranty covering the use in any manner whatsoever of such third party products or services or any intellectual property contained therein.UNLESS OTHERWISE SET FORTH IN ST’S TERMS AND CONDITIONS OF SALE ST DISCLAIMS ANY EXPRESS OR IMPLIED WARRANTY WITH RESPECT TO THE USE AND/OR SALE OF ST PRODUCTS INCLUDING WITHOUT LIMITATION IMPLIED WARRANTIES OF MERCHANTABILITY, FITNESS FOR A PARTICULAR PURPOSE (AND THEIR EQUIVALENTS UNDER THE LAWS OF ANY JURISDICTION), OR INFRINGEMENT OF ANY PATENT, COPYRIGHT OR OTHER INTELLECTUAL PROPERTY RIGHT.ST PRODUCTS ARE NOT DESIGNED OR AUTHORIZED FOR USE IN: (A) SAFETY CRITICAL APPLICATIONS SUCH AS LIFE SUPPORTING, ACTIVE IMPLANTED DEVICES OR SYSTEMS WITH PRODUCT FUNCTIONAL SAFETY REQUIREMENTS; (B) AERONAUTIC APPLICATIONS; (C) AUTOMOTIVE APPLICATIONS OR ENVIRONMENTS, AND/OR (D) AEROSPACE APPLICATIONS OR ENVIRONMENTS. WHERE ST PRODUCTS ARE NOT DESIGNED FOR SUCH USE, THE PURCHASER SHALL USE PRODUCTS AT PURCHASER’S SOLE RISK, EVEN IF ST HAS BEEN INFORMED IN WRITING OF SUCH USAGE, UNLESS A PRODUCT IS EXPRESSLY DESIGNATED BY ST AS BEING INTENDED FOR “AUTOMOTIVE, AUTOMOTIVE SAFETY OR MEDICAL” INDUSTRY DOMAINS ACCORDING TO ST PRODUCT DESIGN SPECIFICATIONS. PRODUCTS FORMALLY ESCC, QML OR JAN QUALIFIED ARE DEEMED SUITABLE FOR USE IN AEROSPACE BY THE CORRESPONDING GOVERNMENTAL AGENCY.Resale of ST products with provisions different from the statements and/or technical features set forth in this document shall immediately void any warranty granted by ST for the ST product or service described herein and shall not create or extend in any manner whatsoever, any liability of ST.ST and the ST logo are trademarks or registered trademarks of ST in various countries.Information in this document supersedes and replaces all information previously supplied.The ST logo is a registered trademark of STMicroelectronics. All other names are the property of their respective owners.© 2013 STMicroelectronics - All rights reservedSTMicroelectronics group of companiesAustralia - Belgium - Brazil - Canada - China - Czech Republic - Finland - France - Germany - Hong Kong - India - Israel - Italy - Japan - Malaysia - Malta - Morocco - Philippines - Singapore - Spain - Sweden - Switzerland - United Kingdom - United States of AmericaDoc ID 022359 Rev 211/11。
DS2278 Digital Scanner Product Reference Guide

Digital Scanner Product Reference GuideDS2278DS2278 DIGITAL SCANNER PRODUCT REFERENCE GUIDEMN-002915-13ENRevision AJanuary 2023ii DS2278 Digital Scanner Product Reference GuideNo part of this publication may be reproduced or used in any form, or by any electrical or mechanical means, without permission in writing from Zebra. This includes electronic or mechanical means, such as photocopying, recording, or information storage and retrieval systems. The material in this manual is subject to changewithout notice.The software is provided strictly on an “as is” basis. All software, including firmware, furnished to the user is ona licensed basis. Zebra grants to the user a non-transferable and non-exclusive license to use each softwareor firmware program delivered hereunder (licensed program). Except as noted below, such license may not be assigned, sub-licensed, or otherwise transferred by the user without prior written consent of Zebra. No right to copy a licensed program in whole or in part is granted, except as permitted under copyright law. The user shall not modify, merge, or incorporate any form or portion of a licensed program with other program material, createa derivative work from a licensed program, or use a licensed program in a network without written permissionfrom Zebra. The user agrees to maintain Zebra’s copyright notice on the licensed programs deliveredhereunder, and to include the same on any authorized copies it makes, in whole or in part. The user agrees not to decompile, disassemble, decode, or reverse engineer any licensed program delivered to the user or any portion thereof.Zebra reserves the right to make changes to any software or product to improve reliability, function, or design.Zebra does not assume any product liability arising out of, or in connection with, the application or use of any product, circuit, or application described herein.No license is granted, either expressly or by implication, estoppel, or otherwise under any Zebra Technologies Corporation, intellectual property rights. An implied license only exists for equipment, circuits, and subsystems contained in Zebra products.WarrantyFor the complete Zebra hardware product warranty statement, go to: /warranty.PatentsiiiRevision HistoryChanges to the original guide are listed below:Change Date DescriptionMN-002915-01 Rev. A7/2017Initial Release.MN-002915-02 Rev. A8/2017Removed "Microsoft UWP Bluetooth" information.MN-002915-03 Rev. A04/2018Rev. B software and miscellaneous updates.Added:-Battery Preservation Timeout Value.-Re-pair on Double Trigger Press.-Note to Out of Range Batch Mode about Auto-Reconnect.-Added note below Bluetooth Security.Updated:-Pairing bar code format with STC info.-Values under bar codes for SSI baud rates: 230,400, 460,800,921,600.-Pairing Using the Scan-To-Connect (STC) Utility.-Max time value in Hands-Free Decode Session Timeout.-Deleted Bluetooth HID - Wait for Connection (not supported).-Added note to MSI Reduced Quiet Zone (Level 3 not supported byMSI).-Changed Microsoft UWP USB to USB HID POS.-Second paragraph under "Connection Maintenance Interval".-123Scan chapter-Picklist Mode description.-Trigger Mode, Presentation (Blink) description.MN-002915-04 Rev. A7/2018Added:-LED on Good Decode.-Pairing Bar Code Format for Serial Port Connections.-USB certification.-Setting Up a Windows Product To Work With The Digital Scanner.-New Appendix N - U pgrading Over Bluetooth Without a Cradle.Updated:-One instance of Class 1 to Class 2.-Firmware download option (not supported with Micro USB cable).-Configurations.-"Connecting the Cradle" and "Changing the Host Interface".MN-002915-05 Rev. A10/2018-Added Grid Matrix sample bar code.-Moved 123Scan chapter.MN-002915-06 Rev. A01/2020-Added ARINC param.-Updated URLs.-Updated Zebra copyright statement.MN-002915-07EN Rev. A04/2020-Split 123Scan chapter to Chapter 2 123Scan and Software Tools andChapter 14 Data Formatting: ADF.-Updated Chapter 2 123Scan Requirements.-Updated Chapter 3 introduction section.-Updated Environmental Sealing in Table 4-2.-Added the USB Cert information in Table 4-2.MN-002915-08EN Rev. A12/2020Replaced offending terms.iv DS2278 Digital Scanner Product Reference GuideChange Date DescriptionMN-002915-09EN Rev. A02/2021Updated LED on Good Decode.MN-002915-10EN Rev. A04/2021Removed Bluetooth Classic Bluetooth and/or Low Energy (CradleParameter Only/ Cradle Host Only).MN-002915-11EN Rev. A07/2021Added Standard Bluetooth Version 4.0 with BLE.MN-002915-12EN Rev. A09/2021Added DotCode, DotCode Inverse, DotCode Mirrored, DotCodePrioritize, DotCode Erasure Limit, Codabar Mod 16 Check Digit,Transmit Codabar Check Digit, Transmit Ean-8 Check Digit, TransmitEan-13 Check Digit, Weblink QR, and Linked QR Mode.MN-002915-13EN Rev. A01/2023Add Virtual Tether parameters. Update Bluetooth State Note.TABLE OF CONTENTSWarranty (ii)Patents (ii)Revision History (iii)About This GuideIntroduction (xix)Configurations (xix)Related Product Line Configurations (xx)Cables (xx)Chapter Descriptions (xx)Notational Conventions (xxi)Related Documents (xxii)Service Information (xxii)Provide Documentation Feedback (xxii)Chapter 1: Getting StartedIntroduction .................................................................................................................................... 1-1 Interfaces ....................................................................................................................................... 1-2 Unpacking ...................................................................................................................................... 1-2 DS2278 Features ........................................................................................................................... 1-3 Cradle Features ............................................................................................................................. 1-3 Presentation Cradle ................................................................................................................. 1-4 Connecting the Cradle ............................................................................................................. 1-4 Changing the Host Interface .................................................................................................... 1-4 Using a DC Power Supply ........................................................................................................ 1-5 Charging the DS2278 Battery ........................................................................................................ 1-5 Charging Using the Cradle ....................................................................................................... 1-5 Charging Using the Micro USB Cable ...................................................................................... 1-6 Shutting Off the Digital Scanner Battery ........................................................................................ 1-7 Inserting the Battery ....................................................................................................................... 1-7 Removing the Battery .................................................................................................................... 1-8 Inserting the Digital Scanner in the Cradle .................................................................................... 1-9vi DS2278 Digital Scanner Product Reference GuidePairing ...................................................................................................................................... 1-9Lost Connection to Host ......................................................................................................... 1-10 Configuring the Digital Scanner ................................................................................................... 1-10 Radio Communications ................................................................................................................ 1-10 Accessories .................................................................................................................................. 1-10Chapter 2: 123Scan and Software ToolsIntroduction .................................................................................................................................... 2-1 123Scan ......................................................................................................................................... 2-1 Communication with 123Scan .................................................................................................. 2-2123Scan Requirements ............................................................................................................ 2-2123Scan Information ................................................................................................................ 2-2 Scanner SDK, Other Software Tools, and Videos ......................................................................... 2-3 Scanner Control App ...................................................................................................................... 2-4 Scan-To-Connect (STC) Utility ...................................................................................................... 2-4Chapter 3: Data CaptureIntroduction .................................................................................................................................... 3-1 Beeper and LED Indications .......................................................................................................... 3-1 Digital Scanner Indications ....................................................................................................... 3-1Cradle LED Indications ............................................................................................................ 3-5 Scanning ........................................................................................................................................ 3-6 Hand-Held Scanning ................................................................................................................ 3-6Hands-Free Scanning .............................................................................................................. 3-7Aiming with Digital Scanner ..................................................................................................... 3-8Aiming ...................................................................................................................................... 3-8 Decode Ranges ............................................................................................................................. 3-8Chapter 4: Maintenance, Troubleshooting, & Technical SpecificationsIntroduction .................................................................................................................................... 4-1 Maintenance .................................................................................................................................. 4-1 Known Harmful Ingredients ...................................................................................................... 4-1Approved Cleaners for the Digital Scanner and Cradle ........................................................... 4-2Cleaning the Digital Scanner .................................................................................................... 4-2 Troubleshooting ............................................................................................................................. 4-3 Report Software Version Bar Code .......................................................................................... 4-7 Technical Specifications ................................................................................................................ 4-8 Cradle Signal Descriptions ........................................................................................................... 4-11Chapter 5: User Preferences & Miscellaneous OptionsIntroduction .................................................................................................................................... 5-1 Setting Parameters ....................................................................................................................... 5-1 Scanning Sequence Examples ................................................................................................ 5-2Errors While Scanning ............................................................................................................. 5-2 User Preferences/Miscellaneous Options Parameter Defaults ...................................................... 5-2 User Preferences ........................................................................................................................... 5-5 Default Parameters .................................................................................................................. 5-5Parameter Bar Code Scanning ................................................................................................ 5-6Table of Contents viiBeep After Good Decode ......................................................................................................... 5-6 Beeper Volume ........................................................................................................................ 5-7 Beeper Tone ............................................................................................................................ 5-8 Beeper Duration ....................................................................................................................... 5-9 Suppress Power Up Beeps ...................................................................................................... 5-9 LED on Good Decode ............................................................................................................ 5-10 Direct Decode Indicator .......................................................................................................... 5-10 Low Power Mode ................................................................................................................... 5-11 Time Delay to Low Power Mode ............................................................................................ 5-12 Timeout to Low Power Mode from Auto Aim .......................................................................... 5-14 Battery Preservation Mode ..................................................................................................... 5-15 Trigger Mode .......................................................................................................................... 5-16 Hands-Free Mode .................................................................................................................. 5-17 Hand-Held Decode Aiming Pattern ........................................................................................ 5-18 Hands-Free (Presentation) Decode Aiming Pattern ............................................................... 5-19 Picklist Mode .......................................................................................................................... 5-20 Continuous Bar Code Read ................................................................................................... 5-21 Unique Bar Code Reporting ................................................................................................... 5-21 Decode Session Timeout ....................................................................................................... 5-22 Hands-Free Decode Session Timeout ................................................................................... 5-22 Timeout Between Decodes, Same Symbol ............................................................................ 5-23 Timeout Between Decodes, Different Symbols ...................................................................... 5-23 Decode Mirror Images (Data Matrix Only) ............................................................................. 5-24 Mobile Phone/Display Mode .................................................................................................. 5-24 PDF Prioritization ................................................................................................................... 5-25 PDF Prioritization Timeout ..................................................................................................... 5-25 Decoding Illumination ............................................................................................................. 5-26 Illumination Brightness ........................................................................................................... 5-26 Low Light Scene Detection .................................................................................................... 5-27 Motion Tolerance (Hand-Held Trigger Modes Only) .............................................................. 5-28 Product ID (PID) Type ............................................................................................................ 5-29 Product ID (PID) Value ........................................................................................................... 5-29 ECLevel .................................................................................................................................. 5-30 Miscellaneous Scanner Parameters ............................................................................................ 5-31 Enter Key ............................................................................................................................... 5-31 Tab Key .................................................................................................................................. 5-31 Transmit Code ID Character .................................................................................................. 5-32 Prefix/Suffix Values ................................................................................................................ 5-33 Scan Data Transmission Format ............................................................................................ 5-34 FN1 Substitution Values ......................................................................................................... 5-36 Transmit “No Read” Message ................................................................................................ 5-37 Unsolicited Heartbeat Interval ................................................................................................ 5-38 Send Versions .............................................................................................................................. 5-39 Software Version .................................................................................................................... 5-39 Serial Number ........................................................................................................................ 5-39 Manufacturing Information ..................................................................................................... 5-39Chapter 6: Radio CommunicationsIntroduction .................................................................................................................................... 6-1viii DS2278 Digital Scanner Product Reference GuideScanning Sequence Examples ................................................................................................ 6-2Errors While Scanning ............................................................................................................. 6-2 Radio Communications Parameter Defaults .................................................................................. 6-2 Wireless Beeper Definitions ........................................................................................................... 6-5 Radio Communication Host Types ................................................................................................ 6-5 Bluetooth Classic vs. Low Energy Bluetooth ............................................................................ 6-5Cradle ....................................................................................................................................... 6-5Human Interface Device (HID) Keyboard Emulation ................................................................ 6-6Simple Serial Interface (SSI) .................................................................................................... 6-7Serial Port Profile (SPP) ........................................................................................................... 6-9Bluetooth Technology Profile Support ...................................................................................... 6-9Central/Peripheral Set Up ...................................................................................................... 6-10 Bluetooth Friendly Name ............................................................................................................. 6-10 Discoverable Mode ................................................................................................................ 6-11 Wi-Fi Friendly Mode ..................................................................................................................... 6-12 Notes ...................................................................................................................................... 6-12Wi-Fi Friendly Channel Exclusion .......................................................................................... 6-12 Radio Output Power ..................................................................................................................... 6-14 Link Supervision Timeout ....................................................................................................... 6-15 Bluetooth Radio State .................................................................................................................. 6-16 HID Host Parameters ................................................................................................................... 6-16 Apple iOS Virtual Keyboard Toggle ....................................................................................... 6-16HID Keyboard Keystroke Delay ............................................................................................. 6-18HID CAPS Lock Override ....................................................................................................... 6-18HID Ignore Unknown Characters ........................................................................................... 6-19Emulate Keypad ..................................................................................................................... 6-19Fast HID Keyboard ................................................................................................................. 6-20Quick Keypad Emulation ........................................................................................................ 6-20HID Keyboard FN1 Substitution ............................................................................................. 6-21HID Function Key Mapping .................................................................................................... 6-21Simulated Caps Lock ............................................................................................................. 6-22Convert Case ......................................................................................................................... 6-22 Auto-Reconnect Feature .............................................................................................................. 6-23 Reconnect Attempt Beep Feedback ...................................................................................... 6-23Reconnect Attempt Interval .................................................................................................... 6-24Auto-Reconnect ..................................................................................................................... 6-25 Out of Range Indicator ................................................................................................................. 6-25 Beep on Insertion ......................................................................................................................... 6-26 Beep on <BEL> ............................................................................................................................ 6-26 Digital Scanner To Cradle Support .............................................................................................. 6-27 Pairing .................................................................................................................................... 6-27Pairing Methods ..................................................................................................................... 6-28Connection Maintenance Interval ........................................................................................... 6-29 Pairing Using the Scan-To-Connect (STC) Utility ........................................................................ 6-31 Pairing Bar Code Format for Serial Port Connections ................................................................. 6-31 Pairing Bar Code Example ..................................................................................................... 6-31 Batch Mode .................................................................................................................................. 6-32 Modes of Operation ................................................................................................................ 6-32 Persistent Batch Storage ............................................................................................................. 6-34Table of Contents ixPIN Code ................................................................................................................................ 6-35 Bluetooth Security Levels ....................................................................................................... 6-37 Bluetooth Radio, Linking, and Batch Operation ........................................................................... 6-38 Setting Up an iOS or Android Product To Work With The Digital Scanner ............................ 6-38 Setting Up a Windows Product To Work With The Digital Scanner ....................................... 6-39 Save Bluetooth Connection Information ...................................................................................... 6-40 Virtual Tether ............................................................................................................................... 6-41 Virtual Tether Alarm on the Scanner ...................................................................................... 6-41 Virtual Tether Alarm on the Cradle ......................................................................................... 6-44 Delay Before Virtual Alarm Activates ..................................................................................... 6-44 Virtual Tether Alarm Duration ................................................................................................. 6-45 Defeat Virtual Tether Alarm .................................................................................................... 6-46 Pause Virtual Tether Alarm Duration ..................................................................................... 6-46Chapter 7: Signature Capture PreferencesIntroduction .................................................................................................................................... 7-1 Setting Parameters ........................................................................................................................ 7-1 Scanning Sequence Examples ................................................................................................ 7-2 Errors While Scanning ............................................................................................................. 7-2 Signature Capture Preferences Parameter Defaults ..................................................................... 7-2 Signature Capture Preferences ..................................................................................................... 7-3 Signature Capture .................................................................................................................... 7-3 Signature Capture File Format Selector ................................................................................... 7-4 Signature Capture Bits Per Pixel .............................................................................................. 7-5 Signature Capture Width .......................................................................................................... 7-6 Signature Capture Height ......................................................................................................... 7-6 Signature Capture JPEG Quality ............................................................................................. 7-6Chapter 8: USB InterfaceIntroduction .................................................................................................................................... 8-1 Setting Parameters ....................................................................................................................... 8-1 Scanning Sequence Examples ................................................................................................ 8-1 Errors While Scanning ............................................................................................................. 8-1 Connecting a USB Interface .......................................................................................................... 8-2 USB Parameter Defaults ................................................................................................................ 8-3 USB Host Parameters .................................................................................................................... 8-5 USB Device Type ..................................................................................................................... 8-5 Symbol Native API (SNAPI) Status Handshaking .................................................................... 8-7 Native Firmware Update .......................................................................................................... 8-7 USB Keystroke Delay ............................................................................................................... 8-8 USB CAPS Lock Override ........................................................................................................ 8-8 Bar Codes with Unknown Characters ...................................................................................... 8-9 USB Convert Unknown to Code 39 .......................................................................................... 8-9 USB Fast HID ......................................................................................................................... 8-10 USB Polling Interval ............................................................................................................... 8-11 Keypad Emulation .................................................................................................................. 8-13 Quick Keypad Emulation ........................................................................................................ 8-13。
Freescale 半导体用户指南:Proximity Sensing软件快速参考用户指南说明书

KITPROXIMITYEVM© Freescale Semiconductor, Inc., 2008. All rights reserved.PROXQRUG Rev 2, 05/2008Freescale Semiconductor User’s Guide Proximity Sensing Software Quick Reference User’s GuideDevices Supported: HCs08, RS08 and V1 MCUProximity Sensing SoftwareOverviewAny MCU can be enabled for touch sensing capabilities with a properly designed layout and a simple software module. This document explains how to use the Proximity Sensing Software in different MCU’s boards. This application can be used in conjunction with the Proximity daughter board PROXIMITYDBOARD0 for a complete evaluation set.NOTEThe Proximity Software is compatible with all S08, RS08 and V1 microcontrollers but hardware is necessary to test it. This document explains how to setup up the Proximity Software with a DEMO board and the PROXIMITYDBOARD0 board, which are included in the KITPROXIMITYEVM. The kit can be purchased at /proximity.System RequirementsThe requirements needed for the system are listed below.Proximity Software Requirements:•Freescale MCU (A demo board such as DEMOQE128 is recommended)•CodeWarrior 5.1 or later•Properly designed hardware for electrodes (PROXIMITYDBOARD0 recommended)Proximity GUI Requirements:•Freemaster 1.3 software for BDM connection. •.Net Framework 2.0•MCU loaded with the Proximity Software•BDM connection to MCU (included in most Demo boards, currently only P&E modules are supported)•Certified USB cable to avoid noise •15Mb of hard drive spacePROXQRUG SensorsApplication SetupOverviewThis section explains how to program your MCU and how to connect the MCU evaluation board with the PROXIMITYBOARD0 board to test the Software.NOTEThis application is configured by default for the DEMOQE128 board. Keep in mind the electrode pins can be configured by the user. The intention of this software is for the users to create their own applications.Hardware SetupBoard DescriptionThe next figure shows the board PROXIMITYDBOARD0. This board has three different electrode arrangements, a jumper, a pin header and a buzzer.NOTEThe three different electrode arrangements of the PROXIMITYDBOARD0 are connected in parallel. Electrode1 (E1) from the Key pad is connected to E1 from the Slider and E1 from the Rotary.Figure 1. PROXIMITYDBOARD0 Board 1. Buzzer 4. Key pad 2. Jumper5. Slider 3. 30 pin header6. RotaryPROXQRUGSensorsFigure 2 shows the possible connections depending of the jumper position.Figure 2. Jumper ConnectionsTable 1 shows the header pins that are connected to the electrodes in the PROXIMITYDBOARD0 board. For detailed information about connections, please refer to Appendix A of this document.CompatibilityThe PROXIMITYDBOARD0 board is only compatible with the following MCU boards.•DEMO9S08QG8•DEMO9S08QD4•DEMOQE128•DEMO9S08AW60•DEMO9S08DZ60•DEMO9S08LC60•DEMOJMSKT •DEMO9S08RG60Table 1. PROXIMITYDBOARD0 30 Pin HeaderSignal PinPin Signal Vcc 12NC GND 34NC NC 56NC NC 78Buzzer Electrode 1910NC Electrode 21112NC Electrode 31314NC Electrode 41516NC Electrode 51718NC Electrode 61920NC Electrode 72122NC Electrode 82324Buzzer NC 2526NC NC 2728NC NC2930NCPROXQRUG SensorsHow to Connect the PROXIMITYDBOARD0 with an MCU Demo Board1.Remove the jumpers that share functions in the Demo board. For example, in DEMOQE128 remove the jumpers associated to PTC0, PTC1 and PTB5 pins. For detailed information regarding jumper removal, see Appendix B .2.Find pin 1 in the male header of the PROXIMITYDBOARD0.3.Locate the female header slot number 1 in the supported Demo board as shown in Figure 3. The back side of the DEMOQE128 board is shown inFigure 4.Figure 3. MCU Port Socket HeaderPROXQRUGSensors4.Plug PROXIMITYDBOARD0 socket into the MCU port header. Remember that pins 1 and 3 from both headers must be connected. The two boards must look like the example below.Figure 4. The Two Boards Connected5.Connect the USB cable to your PC, and the other side of the cable to the DEMO board.6.The boards are connected as shown in Figure 5.Figure 5. System SetupFirmware SetupThis section explains how to program any supported Freescale MCU with the Proximity Software. Also described is how to change from one demo board to another one and how to configure the software for a custom application.How to Program the MCU1.It is necessary to have installed CodeWarrior 5.1 or later to program the required MCU. If it is not installed,please install it.2.You can find the Proximity project in: C:/Program Files/Freescale/Freescale Proximity SensingSoftware/proximity Source Code. There are two folders, just select the desired one.3.Open CodeWarrior and open the Proximity.mcp project file.4.Click on the Make button as shown in Figure 6Make button Debug buttonFigure 6. CodeWarrior Buttons5.Click on the Debug button.6.A new window appears, then click Connect and the debugger window will pop up. If this action fails, verify thehardware connections.PROXQRUGSensors7.In the debugger window click on the Run buttonRun buttonFigure 7. Run Button8.Now the microcontroller is running the Proximity Sensing Software.PROXQRUG SensorsPROXQRUG SensorsPower Demo BoardThe Proximity Software uses the MC9S08QE128 microcontroller by default. If the user wants to change the board, for example to the DEMO9S08DZ60, follow the next steps:1.Change the target in CodeWarrior as shown in the steps in the figure below.Figure 8. Changing the Targetpile the Proximity Project.3.Load the Proximity Software in the DZ60 microcontroller4.Plug the DEMO9S08DZ60 board with the PROXIMITYDBOARD0 board.5.The Demo board has been changed.PROXQRUGSensorsBuilding an ApplicationIf a user builds their own application and wants to use the Proximity Software as a guide, some considerations must be taken:•Change the required GPIOs (this will be explained further in the document). The pins used to connect the electrodes must be I/O.•Change the Timer interrupt vector number in the Timer.h file, as the timer overflow vector number is different in the S08 families.•Change the DD_OFFSET, within the GPIO.h file, as some MCUs have the data direction register in a different memory address.The next steps explain how to correctly use the pins that will be connected to the electrodes. 1.Open the GPIO.c file that contains all the MCU definitions.2.Search at the end of the file the line “User defined” (Figure 9). There are two definitions that might be used to write the pin number to be connected to the electrodes. vpPort1 is used to define the port pins that will be connected to the electrodes. vpPort2 is used to define the pin that will drive the buzzer. Remember that Proximity Software uses only eight electrodes, and if it is desired to change the number of electrodes, other steps will be necessary to do. Please refer to AN3579 for detailed information.Figure 9. GPIO.c File3.The next figure shows the GPIO.c file configured to work with the DEMOQE128 board and the PROXIMITYDBOARD0.Figure 10. GPIO.c File for DEMOQE128Table 2 shows the pins from the DEMOQE128 MCU port that will be connected to PROXIMITYDBOARD0 board and were previously configured in Figure 10.Table 2. DEMOQE128 MCU PortSignal Pin Pin SignalVDD12PTA5/RESETVSS34PTA5/RESETPTB156PTA4PTB078PTE7PTA2910VREFHPTA31112VREFLPTC01314PTA0PTC11516PTA1PTB31718PTF0PTB41920PTF1PTB22122PTA6PTB52324PTA7PTD12526PTH6PTD22728PTH7PTD02930PTD4PTD33132PTD5PTC23334PTD6PTC33536PTD7PTC43738PTC7PTC53940PTC6PTF23738PTB7PTF33940PTB6PTF43940PTG0PTF53738PTG1PTF63940PTH0PTF73940PTH1PTG23738NCPTG33940NCConclusionThis users guide explains the Proximity Sensing Software and the porting to different Freescale microcontroller platforms.The software is provided to speed up the design of new applications and to test the Proximity Sensing Technology.This document describes the required changes for the system to work properly. The example application demonstrates how to use the PROXIMITYDBOARD0 and the supported MCU tools. Any new design for a particular application with the required electrodes arrangement should consider this document and reference material below:•AN3579 - Enabling an MCU for Touch Sensing with Proximity Sensor SoftwarePROXQRUGSensorsPROXQRUGSensorsAppendix A: Electrode Configuration for Commonly Used Demo BoardsTable 3. Configuration Table for the Demo BoardsSignals Demo QE128Demo 9S08QG8Demo 9S08QD4Demo 9S08AW60Demo JM Demo 9S08RG60Demo 9S08LC60Demo 9S08DZ60Electrode 1PTA2PTA2PTA2PTG0PTG0PTC0PTC4PTG2Electrode 2PTA3PTA3PTA3PTG1PTG1PTC1PTC5PTG3Electrode 3PTC0PTA5(1)NOTES:1. This pin is the RESET pin. This pin must not be connected to an electrode, because it operates only as input.PTA5(2)2. This pin is the RESET pin. This pin must not be connected to an electrode, because it operates only as input.PTE2PTE2PTD6PTC2PTD2Electrode 4PTC1PTA0PTA0PTE3PTE3PTB7PTC3PTD3Electrode 5PTB3PTB3NC PTE6PTE5PTC4PTB5PTE4Electrode 6PTB4PTB4NC PTE5PTE4PTC5PTB4PTE5Electrode 7PTB2PTB2NC PTE7PTE6PTC6PTB6PTE3Electrode 8PTB5PTB5NC PTE4PTE7PTC7PTB7PTE2Time Vector Number 77711156711BuzzerPTE7/PTA7PTB7/NCPTB7/NCPTG4/PTB7NC/PTB7PTB2/PTA1NC/PTA7PTF7/PTB0Appendix B: Jumper Configurations for Demo BoardsThe following figures show the jumpers that need to be removed from the supported demo boards.PTB4, PTB5, PTB6, PTB7 PTC3, PTC4, PTC5PTC2Figure 11. DEMO9S08LC60 BoardPROXQRUGSensorsPTC0 andPTC1PTB5Figure 12. DEMOQE BoardPTE2 and PTE3Figure 13. DEMOJM BoardPROXQRUG SensorsRV1Figure 14. DEMO9S08QG8 BoardRV1Figure 15. DEMO9S08QD4 BoardPROXQRUGSensorsIn the following boards, the jumpers do not need to be removed.Jumper does not need to be removedFigure 16. DEMO9S08DZ60 BoardJumper does not need to be removedFigure 17. DEMO09S08AW60 BoardPROXQRUG SensorsAppendix C: Proximity PROXIMITYDBOARD0 Board SchematicsFigure 18. PROXIMITYDBOARD0 Board SchematicsPROXQRUGSensorsPROXQRUGSensorsFigure 19. PROXIMITYDBOARD0 Board Top ViewFigure 20. PROXIMITYDBOARD0 Board Bottom ViewPROXQRUG SensorsFigure 21. PROXIMITYDBOARD0 Board Top Etch ViewFigure 22. PROXIMITYDBOARD0 Board Bottom Etch ViewHow to Reach Us:Home Page:Web Support:/supportUSA/Europe or Locations Not Listed: Freescale Semiconductor, Inc. Technical Information Center, EL516 2100 East Elliot RoadTempe, Arizona 852841-800-521-6274 or +1-480-768-2130 /supportEurope, Middle East, and Africa:Freescale Halbleiter Deutschland GmbHTechnical Information CenterSchatzbogen 781829 Muenchen, Germany+44 1296 380 456 (English)+46 8 52200080 (English)+49 89 92103 559 (German)+33 1 69 35 48 48 (French)/supportJapan:Freescale Semiconductor Japan Ltd.HeadquartersARCO Tower 15F1-8-1, Shimo-Meguro, Meguro-ku,Tokyo 153-0064Japan0120 191014 or +81 3 5437 9125***************************Asia/Pacific:Freescale Semiconductor China Ltd.Exchange Building 23FNo. 118 Jianguo RoadChaoyang DistrictBeijing 100022China+86 010 5879 8000**************************For Literature Requests Only:Freescale Semiconductor Literature Distribution Center P.O. Box 5405Denver, Colorado 802171-800-441-2447 or +1-303-675-2140Fax: +1-303-675-2150*********************************************Information in this document is provided solely to enable system and software implementers to use Freescale Semiconductor products. There are no express or implied copyright licenses granted hereunder to design or fabricate any integrated circuits or integrated circuits based on the information in this document.Freescale Semiconductor reserves the right to make changes without further notice to any products herein. Freescale Semiconductor makes no warranty, representation or guarantee regarding the suitability of its products for any particular purpose, nor does Freescale Semiconductor assume any liability arising out of the application or use of any product or circuit, and specifically disclaims any and all liability, including without limitation consequential or incidental damages. “Typical” parameters that may be provided in Freescale Semiconductor data sheets and/or specifications can and do vary in different applications and actual performance may vary over time. All operating parameters, including “Typicals”, must be validated for each customer application by customer’s technical experts. Freescale Semiconductor does not convey any license under its patent rights nor the rights of others. Freescale Semiconductor products are not designed, intended, or authorized for use as components in systems intended for surgical implant into the body, or other applications intended to support or sustain life, or for any other application in which the failure of the Freescale Semiconductor product could create a situation where personal injury or death may occur. Should Buyer purchase or use Freescale Semiconductor products for any such unintended or unauthorized application, Buyer shall indemnify and hold Freescale Semiconductor and its officers, employees, subsidiaries, affiliates, and distributors harmless against all claims, costs, damages, and expenses, and reasonable attorney fees arising out of, directly or indirectly, any claim of personal injury or death associated with such unintended or unauthorized use, even if such claim alleges that Freescale Semiconductor was negligent regarding the design or manufacture of the part. Freescale™ and the Freescale logo are trademarks of Freescale Semiconductor, Inc. All other product or service names are the property of their respective owners.© Freescale Semiconductor, Inc., 2008. All rights reserved.PPROXQRUG Rev. 2KITPROXIMITYEVM。
LM201U05-SLA2_CAS_1230_DELL_Rev1[1].0_Final
![LM201U05-SLA2_CAS_1230_DELL_Rev1[1].0_Final](https://img.taocdn.com/s3/m/adf21b6e58fafab069dc02e9.png)
Table 2. ELECTRICAL CHARACTERISTICS
Parameter
Values
Symbol
Units
Notes
: Power Supply Input Voltage Power Supply Input Current Power Consumption Differential Impedance Rush Current
/
/
Please return 1 copy for your confirmation with your signature and comments.
Ver 1.0
Dec. 30. 2005
1 /27
Product Specification
LM201U05 Liquid Crystal Display
The LM201U05-SLA1requires two power inputs. One is employed to power the LCD electronics and to drive the TFT array and liquid crystal. The second input which powers the CCFL, is typically generated by an inverter. The inverter is an external unit to the LCD.
1.0
Dec. 30. 2005
LM201U05 Liquid Crystal Display
Product Specification
RECORD OF REVISIONS
Page
Description
APPENDIX COVER SHEETS

APPENDIX-1 ADMINISTRATION INSTRUCTONS TO VENDORS(Doc no: JS1034-XX-G01-0001)APPENDIX-2QUALITY REQUIRMENTS – INSTRUCTIONS TO VENDORS (Doc no: JS1034-XX-G01-0002)APPENDIX-3 TECHNICAL SPECIFICATION(Doc no: JS1034-XX-J01-0001)APPENDIX-4 MECHANICAL DATA SHEETS(Doc no: JS1034-XX-J02-0001)APPENDIX-5TABLE OF COMPLAINCE (Doc no: JS1034-XX-G01-0003)APPENDIX-6COMPANY SPECIFICATONS AND DRAWINGSCompany SpecificationJS1006-X-G02-0003 Rev C1 General Specification for PaintingJS1006-X-G02-0001 Rev C1 General Specification for Packing and Marking JS1006-X-G02-0002 Rev C1 General Specification for Spare PartsJS1006-X-G02-0004 Rev C1 General Specification for Hot insulationI-14-4004 Rev 0 General Instrument SpecificationI-14-4008 Rev 0 Instrument Cables General SpecificationI-14-4010 Rev 0 Specification for Isolation Block valvesP-07-1002 Rev A General Specification for Piping Stress Analysis P-09-1001 Rev 0 General Specification for ValvesP-08-1000 Rev 0 Specification for Piping Material Classes Company Data SheetsJS1006-X-I02-4150 Rev A1 D.S. for Control ValvesJS1006-X-I02-4151 Rev A1 D.S. for Pneumatic On / Off valvesJS1006-X-I02-4153 Rev A2 D.S. for Safety ValvesJS1006-X-I02-4157 Rev A1 D.S. for Level transmitter (Guided wave radartype)JS1006-X-I02-4159 Rev A1 D.S. for Vortex Flow MeterJS1006-X-I02-4160 Rev A1 D.S. for Magnetic Flow MeterCompany As-built Drawings of Train-1 Production SeparatorJS1006-F02-0624 Sh1,2,3 Rev C2 P&ID Symbols for P&ID and PFDJS1006-S-F02-0642-001 Rev B1 P&ID -SAIWAN Production SeparatorJS1006-S-TOE-H802 Rev B1 Vessel data sheet for Production Separator –Saiwan (200-VS-001A)JS1006-S-TOE-F104 Rev B1 P&ID- Production Separator – Saiwan (200-XY-003A)JS1006-S-TOE-H102 Rev B1 Vessel GAD for Production Separator –Saiwan (200-VS-001A)JS1006-S-TOE-J104 Rev B1 GAD for Production Separator Skid –Saiwan (200-XY-003A)JS1006-S-TOE-H202 Rev B1 Vessel construction drawings for ProductionSeparator– Saiwan (200-VS-001A) JS1006-F-F02-0681-001 Rev B1 P&ID -FARHA Production SeparatorJS1006-F-TOE-H802 Rev B1 Vessel data sheet for Production Separator –Farha (201-VS-001A)JS1006-F-TOE-F105 Rev B1 P&ID- Production Separator –Farha (201-XY-003A)JS1006-F-TOE-H102 Rev B1 Vessel GAD for Production Separator –Farha (201-VS-001A)JS1006-F-TOE-J104 Rev B1 GAD for Production Separator Skid – Farha(201-XY-003A)JS1006-F-TOE-H202 Rev B1 Vessel construction drawings for ProductionSeparator– Farha (201-VS-001A)。
AD830 设置维修手册SETUP&MAINTENANCE
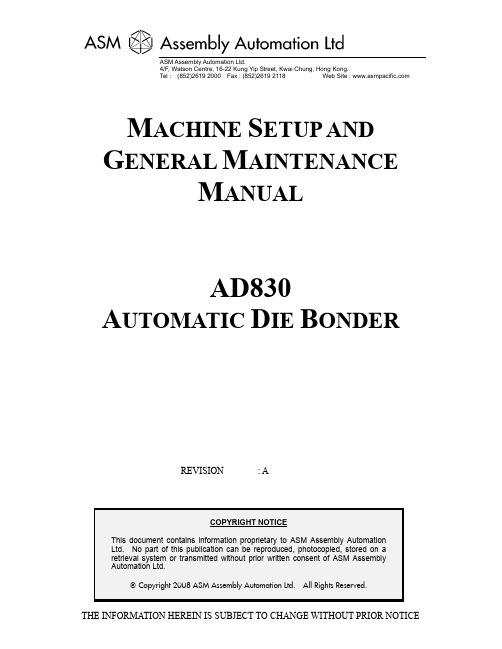
MACHINE SETUP AND GENERAL MAINTENANCE
MANUAL
AD830 AUTOMATIC DIE BONDER
REVISION
:A
COPYRIGHT NOTICE
This document contains information proprietary to ASM Assembly Automation Ltd. No part of this publication can be reproduced, photocopied, stored on a retrieval system or transmitted without prior written consent of ASM Assembly Automation Ltd.
No. 4-2, East 3 Road Street N.E.P.Z. Kaohsiung Taiwan, R.O.C. 高雄分公司 高雄市 811 楠梓加工出口區 東三街 4-2 號 Tel : 886-7-367 6300 Fax : 886-7-367 6399
2/F, No. 9, Lane 379, Sec 1 Ching Kuo Road Hsin-Chu, Taiwan, R.O.C. 新竹分公司 新竹市 300 經國路 一段 379 巷 9 號 2 樓 Tel : 886-3-543 1500 Fax : 886-3-543 1555
0250-20000 Rev 11
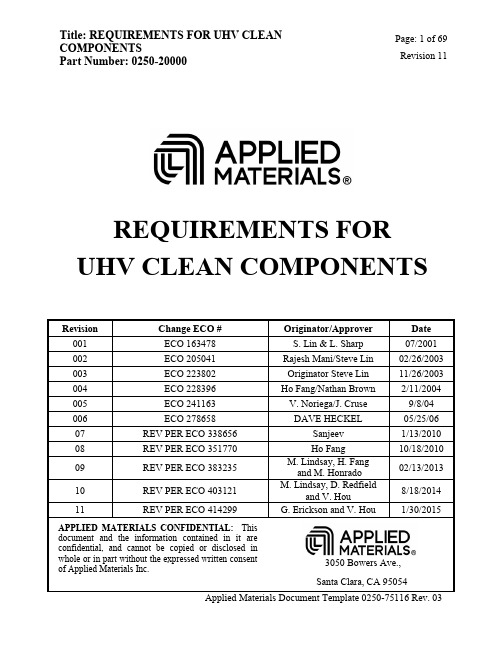
Page: 2 of 69 01/30/2015
SAFETY PRECAUTIONS
Applied Materials does not assume responsibility for the safety of activities at its vendors and suppliers. Consult your supervisor and/or safety department regarding precautions, including, without limitation, proper Personal Protective Equipment (PPE) and potential exhaust ventilation system requirements. FOR INFORMATION ONLY: Chemicals used in these procedures may cause damage to the skin, eyes, and respiratory tract. In addition, some of these procedures require chemicals used at elevated temperatures (above room temperature). Hydrogen gas may be generated from these or other processes; therefore, appropriate controls are required. Extreme care must be taken when handling these substances. Always read the chemical supplier precautions and the Material Safety Data Sheets (MSDS) before using. Personal Protective Equipment (PPE) may be necessary, as well as an adequate exhaust ventilation system capable of removing harmful fumes and by products.
Pyxis Lab ST-588 PTSA Fluorescent Polymer Dual Inl
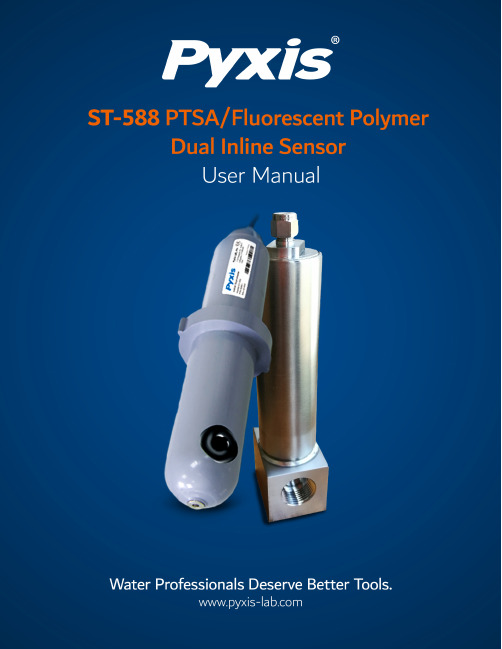
ST-588PTSA/Fluorescent Polymer DualInline SensorUser ManualOctober12,2020Rev.2.00Pyxis Lab,Inc.1729Majestic Dr.Suite5Lafayette,CO80026USA©2017Pyxis Lab,Inc.Pyxis Lab Proprietary and ConfidentialTable of Contents1Introduction21.1Main Features (2)2Specifications3 3Unpacking Instrument43.1Standard Accessories (4)3.2Optional Accessories (5)4Installation64.1ST-588Piping (6)4.2ST-588SS Piping (6)4.3Wiring (7)4.4Connecting via Bluetooth (8)4.5Connecting via USB (8)5Setup and Calibration with uPyxis®Mobile App95.1Download uPyxis®Mobile App (9)5.2Connecting to uPyxis®Mobile App (9)5.3Calibration Screen and Reading (10)5.4Diagnosis Screen (11)5.5Device Info Screen (12)6Setup and Calibration with uPyxis®Desktop App126.1Install uPyxis®Desktop App (12)6.2Connecting to uPyxis®Desktop App (13)6.3Information Screen (13)6.4Calibration Screen (14)6.5Diagnosis Screen (14)7Outputs157.14–20mA Output Setup (15)7.2Communication using Modbus RTU (15)8Sensor Maintenance and Precaution158.1Methods to Cleaning the ST-588 (16)8.2Storage (16)9Troubleshooting17 10Contact Us18Warranty InformationConfidentialityThe information contained in this manual may be confidential and proprietary and is the property of Pyxis Lab,rmation disclosed herein shall not be used to manufacture,construct,or otherwise reproduce the goods rmation disclosed herein shall not be disclosed to others or made public in any manner without the express written consent of Pyxis Lab,Inc.Standard Limited WarrantyPyxis Lab warrants its products for defects in materials and workmanship.Pyxis Lab will,at its option,repair or replace instrument components that prove to be defective with new or remanufactured components (i.e.,equivalent to new).The warranty set forth is exclusive and no other warranty,whether written or oral, is expressed or implied.Warranty TermThe Pyxis warranty term is thirteen(13)months ex-works.In no event shall the standard limited warranty coverage extend beyond thirteen(13)months from original shipment date.Warranty ServiceDamaged or dysfunctional instruments may be returned to Pyxis for repair or replacement.In some in-stances,replacement instruments may be available for short duration loan or lease.Pyxis warrants that any labor services provided shall conform to the reasonable standards of technical com-petency and performance effective at the time of delivery.All service interventions are to be reviewed and authorized as correct and complete at the completion of the service by a customer representative,or des-ignate.Pyxis warrants these services for30days after the authorization and will correct any qualifying deficiency in labor provided that the labor service deficiency is exactly related to the originating event.No other remedy,other than the provision of labor services,may be applicable.Repair components(parts and materials),but not consumables,provided during a repair,or purchased individually,are warranted for90days ex-works for materials and workmanship.In no event will the in-corporation of a warranted repair component into an instrument extend the whole instrument’s warranty beyond its original term.Warranty ShippingA Repair Authorization(RA)Number must be obtained from Pyxis Technical Support before any product can be returned to the factory.Pyxis will pay freight charges to ship replacement or repaired products to the customer.The customer shall pay freight charges for returning products to Pyxis.Any product returned to the factory without an RA number will be returned to the customer.To receive an RMA you can generate a request on our website at https:///request-tech-support/.Pyxis Technical SupportContact Pyxis Technical Support at+1(866)203-8397,*********************,or by filling out a request for support at https:///request-tech-support/.1IntroductionThe Pyxis ST-588inline fluorometer probe simultaneously measures the concentration of PTSA and Fluores-cent Polymer in water.It can be simply inserted to the compression fitting port of a custom-made tee.The standard ST-001installation tee provided with each ST-588sensor,has two¾inch female NPT ports and can be placed to an existing¾inch sample water line.Pyxis Lab also offers2”and3”Tee formats for larger flow installations.The4–20mA current output of the ST-588probe can be connected to any controller that accepts an isolated or non-isolated4–20mA input.The ST-588probe is a smart device.In addition to mea-suring PTSA and Fluorescent Polymer,the ST-588probe has extra photo-electric components that monitor the color and turbidity of the sample water.This extra feature allows automatic color and turbidity com-pensation to eliminate interference commonly associated with real-world waters.The Pyxis ST-588probe has a short fluidic channel and can be easily cleaned.The fluidic and optical ar-rangement of the ST-588probe is designed to overcome shortcomings associated with other fluorometers that have a distal sensor surface or a long,narrow fluidic cell.Traditional inline fluorometers are susceptible to color and turbidity interference and fouling and are difficult to properly clean.1.1Main FeaturesThe ST-588measures PTSA and Fluorescent Polymer in a water sample and includes the following features:•Easy calibration with using uPyxis®Mobile or Desktop App.•Automatic compensation for turbidity up to150NTU and color created by up to10ppm iron or equivalent to10ppm humic acid.•Diagnostic information(probe fouling,color or turbidity over range,failure modes)are available in uPyxis®App or via Modbus RTU.•Easy to remove from the system for cleaning and calibration without the need for any tools.2SpecificationsTable1.ST-588Specifications*With Pyxis’s continuous improvement policy,these specifications are subject to change without notice.†The fluorescent polymer concentration scale is based on the polymer containing0.25mole%fluorescent monomer.Typical polymer specifications are attached below but may vary by producer.‡See Figure4for ST-588SS dimensions.3Unpacking InstrumentRemove the instrument and accessories from the shipping container and inspect each item for any damage that may have occurred during shipping.Verify that all accessory items are included.If any item is missing or damaged,please contact Pyxis Lab Customer Service at*********************.3.1Standard Accessories•Tee Assembly3/4”NPT(1x Tee,O-ring,and Nut)P/N:ST-001*NOTE*ST-001is not included for ST-588SS•8-Pin Female Adapter/Flying Leads Cable(1.5ft)•User Manual available online at https:///support/3.2Optional AccessoriesFigure1.4Installation4.1ST-588PipingThe provided ST-001Tee Assembly can be connected to a pipe system through the3/4”female ports,either socket or NPT threaded.To properly install the ST-588probe into the ST-001Tee Assembly,follow the steps below:1.Insert the provided O-ring into the O-ring groove on the tee.2.Insert the ST-588probe into the tee.3.Tighten the tee nut onto the tee to form a water-tight,compression seal.Figure2.Dimension of the ST-588and the ST-001Tee Assembly(mm)4.2ST-588SS PipingThe ST-588SS probe has3/4”female NPT threaded ports on the probe itself and therefore does not require a custom tee assembly.It is recommended that two3/4”NPT to1/4”tubing adapters are used to connect the probe to the sampling system.Sample water entering the probe must be cooled down to below104°F (40°C).The probe can be held by a1.75-inch pipe clamp or mounted to a panel with four1/4-28bolts.See Figure4for ST-588SS dimensions.Figure3.Dimension of the ST-588SS(inch)4.3WiringIf the power ground terminal and the negative4–20mA terminal in the controller are internally connected (non-isolated4–20mA input),it is unnecessary to connect the4–20mA negative wire(gray)to the4–20mA negative terminal in the controller.If a separate DC power supply other than that from the controller is used,make sure that the output from the power supply is rated for22–26VDC@85mA.*NOTE*The negative24V power terminal(power ground)and the negative4–20mA ter-minal on the ST-588probe are internally connected.Follow the wiring table below to connect the ST-588probe to a controller:Table2.*Internally connected to the power ground4.4Connecting via BluetoothA Bluetooth adapter(P/N:MA-WB)can be used to connect a ST-588probe to a smart phone with the uPyxis®Mobile App or a computer with the uPyxis®Desktop App.Figure4.Bluetooth connection to ST-588probe4.5Connecting via USBA USB-RS485adapter(P/N:MA-485)can be used to connect a ST-588probe to a computer with the uPyxis®Desktop App.*NOTE*Using non-Pyxis USB-RS485adapters may result in permanent damage of the ST-588probe communication hardware.B connection to ST-588probe5Setup and Calibration with uPyxis®Mobile App5.1Download uPyxis®Mobile AppDownload uPyxis®Mobile App from Apple App Store or Google Play.Figure6.5.2Connecting to uPyxis®Mobile AppTurn on Bluetooth on your mobile phone(Do not pair the phone Bluetooth to the ST-588probe).Open uPyxis®Mobile App.Once the app is open the app will start to search for the sensor.Once the uPyxis®Mobile App connects to the sensor,press the ST-588probe.Figure7.5.3Calibration Screen and ReadingWhen connected,the uPyxis®Mobile App will default to the Calibration screen.From the Calibration screen,you can perform calibrations by pressing on Zero Calibration,Slope Calibration,and4–20mA Span for either Fluorescent Polymer or PTSA,independently.Follow the screen instructions for each calibration step.Figure8.5.4Diagnosis ScreenFrom the Diagnosis screen,you can check the diagnosis condition.This feature may be used for technical support when communicating with*********************.To preform a probe cleaniness check,first select the Diagnosis Condition which defines the fluid type that the ST-588probe in currently measuring,then press Cleanliness Check.If the probe is clean,a Clean mes-sage will be shown.If the probe is severely fouled,a Dirty message will be shown.In this case,follow the procedure in the Methods to Cleaning the ST-588section of this manual.Figure9.5.5Device Info ScreenFrom the Device Info screen.You can name the Device or Product as well as set the Modbus address.Figure10.6Setup and Calibration with uPyxis®Desktop App6.1Install uPyxis®Desktop AppDownload the latest version of uPyxis®Desktop software package from:https:///upyxis/this setup package will download and install the Framework4.5(if not previously installed on the PC),the USB driver for the USB-Bluetooth adapter(MA-NEB),the USB-RS485adapter(MA-485),and the main uPyxis®Desktop application.Double click the uPyxis.Setup.exe file to install.Figure11.Click Install to start the installation process.Follow the screen instructions to complete the USB driver and uPyxis®installation.6.2Connecting to uPyxis®Desktop AppWhen the uPyxis®Desktop App opens,click on Device,then click either Connect via USB-Bluetooth or Connect via USB-RS485depending on the connection type.Figure12.6.3Information ScreenOnce connected to the device,a picture of the device will appear on the top left corner of the window and the uPyxis®Desktop App will default to the Information screen.On the Information screen you can set the information description for Device Name,Product Name,and Modbus Address,then click Apply Settings to save.Figure13.6.4Calibration ScreenTo calibrate the device,click on Calibration.On the Calibration screen there are six calibration options:•Fluorescent Polymer:Zero Calibration,Slope Calibration,and4-20mA Span•PTSA:Zero Calibration,Slope Calibration,and4-20mA SpanThe screen also displays the reading of the device.The reading refresh rate is every4seconds.Figure14.6.5Diagnosis ScreenAfter the device has been calibrated and installation has been completed,to check diagnosis,click on Di-agnosis.When in the Diagnosis screen you can view the Diagnosis Condition of the device.This feature may be used for technical support when communicating with*********************.To preform a probe Cleaniness Check,first select the Diagnosis Condition which defines the fluid type that the ST-588probe inCheck.If the probe is clean,a Clean message will be shown.message will be shown.In this case,follow the procedure in theof this manual.Figure15.7Outputs7.14–20mA Output SetupThe4–20mA output of the ST-588sensor is scaled as:•Fluorescent Polymer:–4mA=0ppm–20mA=20ppm•PTSA:–4mA=0ppb–20mA=200ppb7.2Communication using Modbus RTUThe ST-588probe is configured as a Modbus slave device.In addition to the ppm Fluorescent Polymer and ppb PTSA values,many operational parameters,including warning and error messages,are available via a Modbus RTU connection.Contact Pyxis Lab Customer Service(*********************)for more informa-tion.8Sensor Maintenance and PrecautionThe ST-588probe is designed to provide reliable and continuous Fluorescent Polymer and PTSA readings even when installed in moderately contaminated industrial cooling waters.Although the optics are com-pensated for the effects of moderate fouling,heavy fouling will prevent the light from reaching the sensor, resulting in low readings and the potential for product overfeed if the ST-588probe is used as part of an au-tomated control system.When used to control product dosing,it is suggested that the automation system be configured to provide backup to limit potential product overfeed,for example by limiting pump size or duration,or by alarming if the pumping rate exceeds a desired maximum limit.The ST-588probe is designed to be easily removed,inspected,and cleaned if required.It is suggested that the ST-588probe be checked for fouling and cleaned/calibrated on a monthly basis.Heavily contam-inated waters may require more frequent cleanings.Cleaner water sources with less contamination may not require cleaning for several months.The need to clean the ST-588probe can be determined by the Cleanliness Check using either the uPyxis®Mobile App(see the Mobile Diagnosis Screen section)or the uPyxis®Desktop App(see the Desktop Diagnosis Screen section).8.1Methods to Cleaning the ST-588Any equipment in contact with industrial cooling systems is subject to many potential foulants and con-taminants.Our inline probe cleaning solutions below have been shown to remove most common foulants and contaminants.A small,soft bristle brush,Q-Tips cotton swab,or soft cloth may be used to safely clean the probe housing and the quartz optical sensor channel.These components and more come with a Pyxis Lab Inline Probe Cleaning Solution Kit(P/N:SER-01)which can be purchased at our online Estore/Catalog https:///product/probe-cleaning-kit/Figure16.Inline Probe Cleaning Solution KitTo clean the ST-588probe,soak the lower half of the probe in100mL inline probe cleaning solution for 10minutes.Rinse the ST-588probe with distilled water and then check for the flashing blue light inside the ST-588probe quartz tube.If the surface is not entirely clean,continue to soak the ST-588probe for an e the small,soft bristle brush and Q-Tips cotton swabs as necessary to remove any remaining contaminants in the ST-588probe quartz tube.8.2StorageAvoid long term storage at temperature over100°F.In an outdoor installation,properly shield the ST-588 probe from direct sunlight and precipitation.9TroubleshootingIf the ST-588probe output signal is not stable and fluctuates significantly,make an additional ground con-nection––connect the clear(shield,earth ground)wire to a conductor that contacts the sample water electrically such as a metal pipe adjacent to the ST-588tee.Carry out routine calibration verification against a qualified Fluorescent Polymer and PTSA combined stan-dard.After properly cleaning the ST-588sensor,carry out the zero point calibration with distilled water and slope calibration using the qualified Fluorescent Polymer and PTSA combined standard.10Contact UsPyxis Lab,Inc1729Majestic Dr.Suite5Lafayette,CO80026USAPhone:+1(866)203-8397Email:*********************。
ECM_830_Manual(操作说明书)
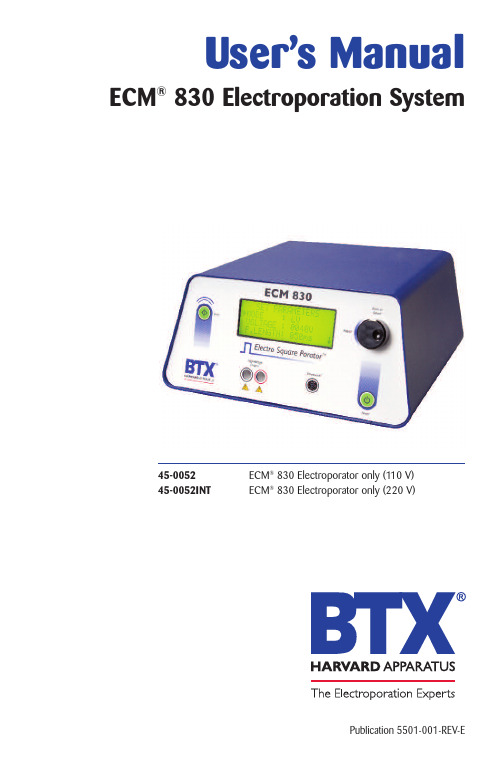
Publication 5501-001-REV-E45-0052ECM ®830Electroporator only (110V)45-0052INT ECM ®830Electroporator only (220V)User’s Manual ECM ®830ElectroporationSystemTable of ContentsGeneral Information:Serial Number (2)Calibration (2)Warranty....................................................................2-3 Service.. (4)Repair Facilities and Parts (5)General Safety Summary..............................................6-7 Electrical&Technical Specifications............................8-9 General Specifications. (10)Introduction:Features (11)Operation:Getting Started (12)Quick Start:Installation (13)Connecting (13)Initializing (13)Instrument Controls..............................................14-21 Operating Basics (22)Advanced Operation:Programming (23)Electroporation/Electrofusion Theory:Electroporation (24)Electrofusion..........................................................24-25 Applications:Electroporation......................................................26-27 Electrofusion. (27)Appendix A:ECM®830ElectrodeOperation Ranges................................28-29 Appendix B:Optimization Strategies......................30-31 Appendix C:Electrical Troubleshooting (32)Appendix D:Experimental Troubleshooting (33)Appendix E:Glossary of Electrical Terms..............34-35 Appendix F:Glossary of Biological&Technical Terms..............................36-38 Appendix G:Electroporation and ElectrofusionPulse Generator Compatibility (39)Appendix H:Recommended Reading (39)Appendix I:Accessories and Replacement Parts..40-41 Appendix J:General Care and Cleaning (42)Appendix K:Footswitch Connection........................43-44 Appendix L:Connecting Electrodes........................45-50Table of Contents(continued)Appendix M:Plate Handlers....................................51-52 ECM®830Generator TroubleshootingGuidelines............................................53-54General InformationSerial NumberThe serial number for the ECM®830is located on the rear of the instrument case.All inquiries concerning these products should refer to the serial numbers on the units.CalibrationThere is no calibration required for the ECM®830.WarrantyBTX-Harvard Apparatus warranties the ECM®830for a period of two years from the date of purchase.At its option,BTX–Harvard Apparatus will repair or replace the unit if it is found to be defective as to workmanship or materials.This warranty does not extend to any instrumentation which has been(a)subjected to misuse,neglect, accident or abuse,(b)repaired or altered by anyone other thanBTX-HARVARD APPARATUS without BTX-HARVARD APPARATUS’express and prior approval,(c)used in violation of instructions furnished by BTX-HARVARD APPARATUS.This warranty extends only to the original customer purchaser.Failure to use the Enhancer3000High Voltage probe to connect a BTX Generator to an external digital oscilloscope for monitoring will result in voiding your warranty;connecting directly to the external monitoring equipment or modified monitoring setup will damage the Generator.IN NO EVENT SHALL BTX-HARVARD APPARATUS BE LIABLE FOR INCIDENTAL OR CONSEQUENTIAL DAMAGES.Some states do not allow exclusion or limitation of incidental or consequential damages so the above limitation or exclusion may not apply to you.THERE ARE NO IMPLIED WARRANTIES OF MERCHANTABILITY,OR FITNESS FOR A PARTICULAR USE,OR OF ANY OTHER NATURE.Some states do not allow this limitation on an implied warranty,so the above limitation may not apply to you.Without limiting the generality of the foregoing,BTX-HARVARD APPARATUS shall not be liable for any claims of any kind whatsoever, as to the equipment delivered or for non-delivery of equipment,and whether or not based on negligence.Warranty is void if the ECM®830is changed in any way from its original factory design or if repairs are attempted without written authorization by BTX-HARVARD APPARATUS.Warranty is void if parts,connections or cell fusion chambers not manufactured by BTX-HARVARD APPARATUS are used with the ECM®830.General Information(Continued)If a defect arises within the warranty period,promptly contactBTX–Harvard Apparatus,84October Hill Road,Building7,Holliston, Massachusetts,USA01746-1388using our toll free number1-800-272-2775(US Only)or508-893-8999(E-mail:techsupport.btx@).Goods will not be accepted for return unless an RMA(Returned Materials Authorization) number has been issued by our customer service department.The customer is responsible for shipping charges.Please allow a reason-able period of time for completion of repairs,replacement and return. If the unit is replaced,the replacement unit is covered only for the remainder of the original warranty period dating from the purchase of the original device.This warranty gives you specific rights,and you may also have other rights,which vary from state to state.ServiceAll service under the warranty will be made at the BTX-HARVARD APPARATUS,Holliston,Massachusetts facilities or an authorized service site.Owner will ship instrument prepaid to Holliston, Massachusetts,USA or the service site.BTX-HARVARD APPARATUS will return the instrument after servicing,freight prepaid to owner’s address.Obtaining Service:Service During Warranty1.Write or call the BTX-HARVARD APPARATUS CustomerSupport Group and describe the nature of the problem.2.Carry out minor adjustments or tests as suggested byBTX-HARVARD APPARATUS.3.If proper performance is not obtained,BTX-HARVARDAPPARATUS will notify you to ship the instrument,prepaid,to its Service Department.The instrument will be repairedand returned at no charge for all customers in thecontinental United States.Customers outside of the continental United States who have purchased our equipment from distributors should contact the distributor.If you have purchased your equipment from us,you should contact us directly.We will repair at no charge,but will not pay for shipment,documentation,etc.These charges will be billed at cost.Note:Under no condition should the instrument or accessories be returned without prior approval from BTX-HARVARD APPARATUS.An RMA(Returned Materials Authorization)number must be obtained.General Information(continued)Out-Of-Warranty ServiceProceed exactly as for Warranty Service,above.If our Service Department can assist you by phone or correspondence,we will be glad to,at no charge.Repair service will be billed on the basis of labor and materials.A complete statement of time spent and materials used will be supplied.Shipment to BTX-HARVARD APPARATUS should be prepaid.Your bill will include return shipment freight charges. Disassembly by the user is prohibited.Service should only be carried out by experienced BTX-HARVARD APPARATUS technicians. Repair Facilities and PartsBTX-Harvard Apparatus stocks replacement and repair parts. When ordering,please describe parts as completely as possible, preferably using our part numbers.If practical,enclose a sample or drawing.We offer complete reconditioning service.General Safety SummaryReview the following safety precautions to avoid injury and prevent damage to this product or any products connected to it. To avoid potential hazards,use this product only as specified. Only qualified personnel should perform service procedures. To Avoid Fire or Personal InjuryUSE PROPER POWER CORDUse only the power cord specified for this product and certified for the country of use.CONNECT AND DISCONNECT PROPERLYDo not connect or disconnect probes or test leads while they are connected to a power source.GROUND THE PRODUCTThis product is grounded through the grounding conductor of the power cord.To avoid electric shock,the grounding conductor must be connected to earth ground.Before making connections to the output terminals of the product,ensure that the product is properly grounded.OBSERVE ALL TERMINAL RATINGSTo avoid fire or shock hazard,observe all ratings and markings on the product.Consult the product manual for further ratings information before making connections to the product.DO NOT OPERATE WITHOUT COVERSDo not operate this product with covers or panels removed.Use Proper e only the fuse type and rating specified for this product.AVOID EXPOSURE TO CIRCUITRYDo not touch exposed connections and components when power is present.DO NOT OPERATE IN LOW IMPEDANCESample:Load or SampleIf the electroporation samples have an impedance of less than20Ωin L V and40Ωin HV,the samples may arc and result in sam-ple loss and potential damage to unit.DO NOT OPERATE WITH SUSPECTED FAILURESIf you suspect there is damage to this product,have it inspected by qualified BTX service personnel.PROVIDE PROPER VENTILATIONRefer to installation instructions for details on installing the product to ensure proper ventilation.General Safety Summary(Continued)DO NOT OPERATE IN WET/DAMP CONDITIONSDO NOT OPERATE IN AN EXPLOSIVE ATMOSPHERE KEEP PRODUCT SURFACES CLEAN AND DRYShould you have any safety concerns,immediately contact BTX Technical Support(1-800-272-2775)Safety Terms and Symbols:Terms that appear in this manual:WARNING.Warning statements identifyconditions or practices that could result in injuryor loss of life.CAUTION.Caution statements identifyconditions or practices that could result indamage to these products or other property. Symbols that may appear on the products:Danger Attention Protective FunctionalHigh Refer to(Earth)GroundVoltage Manual TerminalElectrical&Technical Specifications Standard Capabilities:Display Type:20-character by4-line liquid crystal LEDbacklitPower SourceVoltage100to240Vac,50to60Hz,CAT IIPower Pulse:500W Idle:150WFusing T2.5250VEnvironmental Characteristics:Intended Use Indoor use onlyOperating Temperature10°C to+40°CCooling Convection through metalcaseRelative Humidity90%relative humidity Altitude2,000m(operating) Mechanical Characteristics:Footprint12.5”x12.25”x5.5”(31.75x3.12x13.97cm)(W x D x H)Weight15lbs(6.8kg)Controls Single rotary encoder withintegrated push button Electrical Characteristics:Voltage5to500Volts(LV mode)@1Volt resolution30to3000Volts(HV mode)@5Volts resolution(Voltage Delivery@5%accuracy and VoltageMonitoring@5.0%accuracy) Pulse Length10µs to999µs(LV mode)@1µs resolution1ms to999ms(LV mode)@1ms resolution1s to10s(LV Mode)@0.1sresolution10µs to600µs(HV mode)@1µs resolutionElectrical&Technical Specifications(Continued)Pulse Interval100ms to10sec@1msresolutionMultiple Pulsing1to99pulsesCurrent Limit500A limit at100µsPollution Degree2Not to be operated inconductive pollutantsatmosphereNote:L V ModeLess than a20%V drop at the end of the pulse with the following constraints:PL≤25ms,load320ΩPL≤1sec,load31kΩPL≤10sec,load310kΩHV ModeLess than a10%V drop at the end of the pulse with the following constraints:PL≤600µs,load340ΩBTX instruments are designed for in vitro and in vivo animal and plant applications only and are not for human Clinic.General SpecificationsCertifications and CompliancesOvervoltage Category:CAT III Products in this Category:Distribution-level mains,fixed installationCAT II:Local-level mains,applications and portableequipmentCAT I:Signal levels in special equipment or parts ofequipment,telecommunications and electronicsMeets requirements of Directive89/336/EEC for Electromagnetic Compatibility(EC)and Low-Voltage Directive73/23/EEC for Product Safety.Compliance was demonstrated to the following specifications as listed in the Official Journal of the European Communities: EN50081-1EmissionsEN55011Class B Radiated and Conducted EmissionsEN55082-1ImmunityIEC10004-2Electrostatic Discharge ImmunityIEC10004-3RF Electromagnetic Field ImmunityIEC10004-4Electrical Fast Transient/Burst ImmunityLow Voltage Directive73/23/EECEN61010-1Safety requirements for electricalequipment for measurement,control and laboratory use.IntroductionThe ECM®830is a square wave electroporation system designed for in vitro and in vivo electroporation applications.BTX square wave technology offers researchers the ability to transfect cells efficiently and with higher cell viabilites.ECM®830features include:•A wide range of voltages from5to3000V•Finer voltage discrimination•Pulse durations from10µsec to10sec•Arc Quenching•Digital display of actual voltage and pulse length deliveredOperation:Getting StartedCarefully open the box containing the ECM®830Electroporation System.Verify receipt of the following items:ECM®830Pulse Generator(1)Power Cord(1)Model830E Electronic Manual(1)BTX Electroporation Systems may be customized with the addition of various electrodes and accessories.The following items com-plete a typical system order:Model630B Electroporation Safety Stand(1)Model660Cuvette Rack(1)Model610BTX Cuvettes Plus(10)Model620BTX Cuvettes Plus(10)Model640BTX Cuvettes Plus(10)If you have ordered alternative or different items,please verify their receiptQuick StartInstallation1.Install on a bench or work table.2.Allow a 1to 2inch clearance for proper cooling.It is normalfor the instrument to be slightly warmer than its’operating environment.3.Choose an outlet that is readily accessible.Connecting1.Insert female end of power cord into male powerinterface on the back panel of the ECM ®830.2.Plug male end of power cord into appropriate electricaloutlet.3.Insert male banana plugs of the 630B Safety Stand oralternative electrode device into HV output located onfront panel of the ECM ®830.Initializing1.Push the power switch located on the front panel of theECM ®830.2.Push the power switch located on the front panel of theECM ®830.The display will flash:3.Following this initialization screen,the first time theinstrument is initialized,the factory default display willthen read:4.The first page of the Set Parameter Screen from the lasttime the ECM ®830was used will be displayed each time the ECM ®830is powered up after this initial start up.#! ! # !" % %!% ! ! #$" # # # ! # !"%µ"Quick Start (Continued)Instrument ControlsPower Switch1.Switch located on the lower right front panel.2.Press once to initialize the ECM ®830and once more toturn off.Note:A stabilization period of 3seconds is required after connecting to an outlet.Start Switch1.The electronic Start Switch on the upper left front panelis activated in the “ready”mode when the parameter set screen is displayed.2.Once the start switch is activated,the generator willcharge the capacitor bank,then “settle”by bleeding off the capacitors to the preset voltage,prior to deliveringthe pulse.3.The maximum setting time is 3seconds.A pulsesequence may be aborted by pressing the start switch a second time before the delivery of the pulse.4.Following the delivery of a pulse,press the start switchonce to deliver another pulse,or press the parametercontrol knob to return to “ready”mode.Power Switch ParameterControl KnobStart SwitchDisplayHigh VoltageOutput Smart Link ™Quick Start(Continued)Parameter Control KnobThe Parameter Control Knob is a rotary encoder controlling both the parameter(i.e.voltage)and the value of the parameter under control(i.e.50volts).The display will indicate which parameter is under control by the presence of an arrow to the left of the parameter.1.To select a parameter to adjust,rotate the knob until thearrow is to the left of the desired parameter,then pushto select.The arrow will move to the right of the valuedisplayed for that parameter.2.To adjust the value of a parameter under control,rotatethe knob clockwise to increase the value and counterclockwise to decrease it.After the values are set undercontrol,push the knob to lock set value and arrowwill return to left of parameter under control.3.In order to move between screens,move the cursor tothe bottom of the screen and rotate the knob clockwiseto move to the next screen.4.In order to move to the previous screen,move thecursor to the top of the screen and rotate the knobcounterclockwise.DisplayThe ECM®830Display will show two possible screens,the Set Parameter Screen and the Pulsing Completed Screen as well as various Status Messages.Set Parameter Screen1.The Set Parameter Screen is indicated by a displayshowing“Set Parameters”on the first line of each ofthree screen pages.2.The Mode,Voltage and Pulse Length are shown on thefirst page;the Number of Pulses,Pulsing Interval andPolarity are shown on the second page and theAdvanced Features including Save,View and Load areshown on the third and final page of the Set ParameterScreen.3.The ECM®830will beep when toggling from one pageto another.ModeThe Mode indicates“L V”for low voltage mode or“HV”for high voltage mode.Adjusting the voltage as appropriate automatically controls the mode.There is no manual mode control.Quick Start(Continued)VoltageThe Voltage indicates the set voltage in volts.The low voltage mode range is5V to500V in1V increments and the high voltage mode range is505V to3000V in5V increments.A beep is heard when transitioning between LV and HV modes. P.Length1.Pulse Length indicates the set pulse length inµs or ms.The pulse length minimum is10µs in both HV and L Vmodes.2.In the L V mode,the maximum pulse length is10seconds.The pulse length units change fromµs to ms at1ms andfrom ms to s at1s.3.Refer to Table1for HV pulse length maximum limits.Toestimate approximate pulse lengths at various voltagesin the high voltage mode,refer to Table1below.4.Please note that the voltage determines the maximumpulse length in the HV mode.5.If the voltage is increased and the pre-set pulse length islonger than the maximum pulse length allowed,thepulse length will automatically adjust to that level.Table1HV ModeVoltage Maximum Pulse Length(µs)50559475040010003001500200200015025001203000100Quick Start (Continued)#PulsesThe #Pulses indicates the number of set pulses from 1-99.IntervalThe Interval indicates the time duration between pulses.Theinterval range is 100ms to 10.0seconds,switching from units of ms to seconds after 999ms,with 0.1sec resolution.Advanced FeaturesThe final Set Parameters page enables the user to save,view,and load up to three programs.Please note that parameters can be changed inadvertently once a program is loaded.A default program is used to initialize the system.Program 1is used to automatically store changes in parameters set each time the system is pulsed.Programs #2and #3can be used to set and save experimental parameters for instant use.Save1.To save the current set parameters as a program,pushthe parameter control knob to move the arrow to theleft of the program number.2.Rotate the knob to designate the appropriate programnumber,then push and hold the knob in,releasing after a new screen is displayed.3.The new screen will read “Saved Current Parameters toSet N”.Push the parameter control knob again to return to the setupscreen.Figure 2Quick Start(Continued)View1.To view the appropriate program parameters,push theparameter control knob to move the arrow to the left ofthe program number.2.Select the appropriate program number by rotating theparameter control knob,then hold the knob in,releasingafter a new screen is displayed.3.The new screen will outline the parameters currentlystored under that program number.Push the parametercontrol knob again to return to the setup screen.Load1.To load a saved program,push the parameter controlknob to move the arrow to the left of the programnumber.Please note that in addition to three availableprograms,there is also the default program as outlinedin the“Initializing”section.2.Rotate the knob to change the program number.3.Push and hold the knob in,releasing after a new screenis displayed.The new screen will read“Loaded Set N toCurrent Parameters”.4.Push the parameter control knob again to return to thesetup screen.On-Line HelpIn the Set Parameter Mode,an On-Line Help function is enabled. On-Line Help provides a definition for all set parameters and advanced functions.1.To use On-Line Help,rotate the parameter control knobso that the arrow is to the left of the parameter or featureof interest(not the value of the parameter).2.Push the parameter control knob in and hold until thedefinition is displayed.3.Push a second time to return to the Set Parameter Screen.ModeLow voltage or high voltage range modeVoltageThe amplitude of the output pulseP LengthThe time duration or length of the pulseQuick Start(Continued)#PulsesThe number of output pulsesIntervalThe time interval between pulsesSaveSave current setup parameters to nonvolatile memoryViewShow the setup parameters stored in nonvolatile memoryLoadLoad setup parameters from memory to useStatus MessagesFollowing the initiation of a pulsing sequence,various status messages are displayed.The following status messages may be observed:Charging,Pulsing,Pulse Aborted,and Temperature Failure.ChargingAs soon as the start switch is pressed,the“Charging”status message is displayed.The capacitors in the ECM®830are overcharged during the duration of this message.PulsingOnce the capacitors have reached the preset voltage level,they are discharged and the“Pulsing”status message is displayed for the duration of the pulse or preset number of pulses.A click or a beep will be heard upon the delivery of each pulse.The sound that is heard is a function of the pulse length.At pulse lengths less than1to2ms,clicks will likely be heard.At pulse lengths at or above1to2ms beeps should be heard.A final,more extend-ed beep will be heard upon completion of the pulsing sequence. Following the pulsing status message,the Pulsing Completed Screen is displayed.Pulsing Aborted During ChargingIf the start switch is activated a second time prior to delivery of a pulse,the pulsing sequence is aborted and the“Pulsing Aborted During Charging”status message is displayed.Quick Start(Continued)Temperature FailureIf unit is rapidly pulsed at the high end of the two voltage modes, it is possible for a high temperature warning to occur.In this event,the status message observed is“Unit Cooling”“Please Wait”.When the unit has cooled down to a safe level,two beeps will sound and the message will change to“Ready”.Pushing the start button,or rotating the parameter control knob will shift user back to Parameter Set Screen.Pulsing Completed ScreenThe Pulsing Completed Screen is displayed following the delivery of a pulse or train of pulses and is indicated by the display “Pulsing Completed”on the top line of each of two screen pages.1.Page1comes up automatically;rotate the parametercontrol knob clockwise to view page2and counterclockwise to go back to page1.2.Press the knob to return to the Set Parameters Screenor press the start switch to deliver another pulse.Thepulsing completed screen displays monitoredparameters including Mode,Voltage,Pulse Length,Number of Pulses,Pulse Interval and Polarity.Pleasenote that parameters will be displayed,even if SafetyStand or other output is not connected.Always verifythat your sample is connected with the HV output.ModeMode indicates the voltage mode used in the delivery of the last pulse:L V or HV.VoltageVoltage indicates the output voltage of the last pulse,in volts.For pulses of10to255µs,the voltage is measured at the end of the pulse,and for pulses longer than255µs,the voltage is measured at the beginning,or peak.P LengthP Length indicates the duration of the pulse inµseconds from10to 999µs,mseconds from001to999ms,or in seconds from1.0to 10.0s.#Pulses#Pulses delivered in the last pulsing sequence is displayed,from 1to99.Quick Start(Continued)IntervalThe Interval between the next-to-last and the last pulse is monitored and displayed in ms from100to999ms and in seconds from1.0to10.0seconds.If only one pulse is delivered,“none”is displayed.PolarityThe Polarity used in the last sequence of pulses is monitored and displayed as Unipolar.To reverse the polarity manually,simply switch the+(positive)and-(negative)leads from the safety stand.High Voltage OutputThe High Voltage Output is located in the lower center portion of the front panel.Plug the high voltage cables into this output following the color-coded polarity.SmartLink™The Smartlink™port on v1.08ECM®830and beyond is equipped with footswitch connection capabilities.If your instrument falls in this category and you wish to use the footswitch,please see appendix K on page44.If you are using an older modelECM®830,you may not have the ability to use a footswitch or your unit may be upgraded for this accessory,contact BTX Technical Support at1-800-272-2775ortechsupport.btx@ for assistance.630B 45-0207Operating BasicsUSE WITH SAFETY STAND AND BTX DISPOSABLE ELECTROPORATION CUVETTES PLUS1.Insert the safety stand banana plugs into the HV Outputon the front panel of the ECM ®830.2.Press the power switch to initialize the ECM ®830.3.Rotate parameter control knob to move arrow to voltageand push to select.Rotate knob to adjust voltage.Push again to select that voltage.4.Rotate parameter control knob to move arrow to PLength and push to select.Rotate knob to adjust pulselength.Push again to select that pulse length.5.Rotate parameter control knob to move arrow to #Pulses (Page 2)and push to select.Rotate knob to adjust the number of pulses.Push again to select that number of pulses.6.Rotate parameter control knob to move arrow to Intervalif you have designated more than one pulse in 5andpush to select.Rotate knob to adjust the pulse interval.Push again to select that pulse interval.7.Prepare sample,pipette into the appropriate BTXDisposable Cuvettes Plus,place the cuvette in the 630B Safety Stand and secure the safety cover.8.Press the Start button.The ECM ®830will charge andthen deliver the electroporation pulse or train of pulses selected,beeping with the delivery of each pulse.9.Process sample.Do not forget to record appropriateparameters as displayed on the Pulsing CompletedScreens,for documentation purposes.10.To return to “ready”mode,press the Start button.11.To abort a pulse before delivery,press the Startbutton during the “charging”mode.Use with Alternative Electrode Chambers and Applicators The ECM ®830may be used to power all BTX electroporation and electrofusion chambers and applicators.Follow the above instructions in conjunction with instructions provided for the specific electrode.Refer to Appendix A for graphicalrepresentation of operating ranges of various chambers and applicators with the ECM ®830.Use with Footswitch.Please see Appendix K on page 44.。
ME830_Circuit

6
7
S9
S10
S11
S12
8
9
A
B
S13
S14
S15
S16
C
D
E
F
ME830/ME850单片机实验仪 Push Button
P14 JP8 K1
P15
K2
P16
K3
P17
K4
P32
K5
P33
K6
P34
K7
P35
K8
K1 K1
P14
K2 K2
P15
K3 K3
P16
K4 K4
P17
COL1 JP7
P10
USB电源
SW1
PIN1
板载 ICE52 编程器/仿真器
烧写控制线 复位控制线
STA 状态指示
JP1 51/AVR选择
K9 复位按钮
11.0592
Y1
晶振
VCC
P1.0 P1.1 P1.2 P1.3 P1.4 P1.5 P1.6 P1.7 RST P3.0/RXD P3.1/TXD P3.2/INT0 P3.3/INT1 P3.4/T0 P3.5/T1 P3.6/WR P3.7/RD XTAL2 XTAL1 GND
dp
dp
dp g f e d c b a
4
7
11
DIG0 a
gb
dc dp
VCC
1 2 3 P20 4 P21 5 P22 6 P00 7 P01 8 P02 9 P03 10 P04 11 P05 12 P06 13 P07 14 15 16
VSS VDD VL RS R/W EN D0 D1 D2 D3 D4 D5 D6 D7 BL+ BL-
AEC_Q200_Rev_D_Base_Document
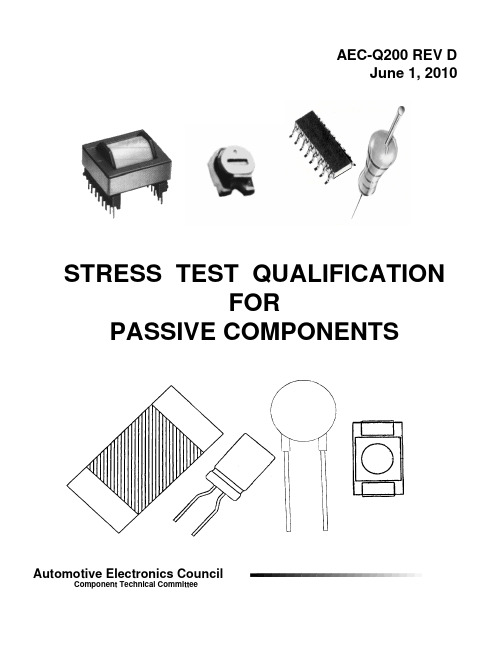
AEC-Q200 REV DJune 1, 2010STRESS TEST QUALIFICATIONFORPASSIVE COMPONENTSAutomotive Electronics CouncilComponent Technical CommitteeComponent Technical CommitteeAcknowledgementAny Document involving a complex technology brings together experience and skills from many sources. The Automotive Electronics Council would especially like to thank the technical committee members that provided input for this document and recognize the following co-authors:Sustaining MembersRobert Hulka, Jr. Delphi (765)451-8079 robert.s.hulka.jr@Bob Knoell Visteon (734)710-7687 rknoell@Ken Kirby Jr. Visteon (734)710-7689 kkirby10@Ron Haberl Visteon (734)710-7691 rhaberl@Hadi Mehrooz Continental (256)464-1481 hadi.mehrooz@Jason Larson ContinentalTom Mitchell Autoliv (248)223-8165 thomas.mitchell@Gary Fisher JCI (616)394-6356 gary.b.fisher@Technical MembersSteve Maloy TDK (770)487-1460 steve.maloy@Patrick Neyman Tyco pneyman@Andy Mahard Vishay (847)862-0223 andy.mahard@Dave Richardson Vishay (770)887-2021 david.richardson@Ted Krueger Vishay +(886) 2-2914-2601 ted.krueger@Roger Roberts VishayMary Carter-Berrios Kemet (650)361-2256 marycarterberrios@Daniel Vanderstraeten AMIS +32 (/55) .33.23.30 daniel.vanderstraeten@Nick Lycoudes Freescale (480)413-3343 nick.lycoudes@Jeff Jarvis AMRDEC (256)842-0160 jeff.jarvis@Lanney McHargue Murata (770)319-5159 lmchargue@Chris Reynolds AVX (843)444-2868 creynolds@Component Technical CommitteeNOTICEAEC documents contain material that has been prepared, reviewed, and approved through the AEC Technical Committee.AEC documents are designed to serve the automotive electronics industry through eliminating misunderstandings between manufacturers and purchasers, facilitating interchangeability and improvement of products, and assisting the purchaser in selecting and obtaining with minimum delay the proper product for use by those other than AEC members, whether the standard is to be used either domestically or internationally.AEC documents are adopted without regard to whether or not their adoption may involve patents or articles, materials, or processes. By such action AEC does not assume any liability to any patent owner, nor does it assume any obligation whatever to parties adopting the AEC documents. The information included in AEC documents represents a sound approach to product specification and application, principally from the automotive electronics system manufacturer viewpoint. No claims to be in conformance with this document shall be made unless all requirements stated in the document are met.Inquiries, comments, and suggestions relative to the content of this AEC document should be addressed to the AEC Technical Committee on the link .Published by the Automotive Electronics Council.This document may be downloaded free of charge, however AEC retains the copyright on this material. By downloading this file, the individual agrees not to charge for or resell the resulting material.Printed in the U.S.A.All rights reservedCopyright © 2010 by the Automotive Electronics Council. This document may be freely reprinted with this copyright notice. This document cannot be changed without approval from the AEC Component Technical Committee.Component Technical CommitteeTable of ContentsSection Title Page(s) 1.0 Scope 61.1 Description 61.2 Reference Documents 72.0 General Requirements 8-103.0 Qualification and Requalification 11-124.0 Qualification Tests 12-13Table 1 - Qualification Sample Size Requirements 14-15Table 2 - Table of Methods Referenced Tantalum and Ceramic Capacitors 16-17Table 2A - Ceramic/Tantalum Process Change Qualification guidelines for the Selected Test 18Table 2B - Acceptance Criteria for Ceramic COG SMD Capacitors 19Table 2C - Acceptance Criteria for Ceramic X7R and X5R SMD Capacitors 20Table 2D - Acceptance Criteria for Ceramic Tantalum and Niobium Oxide Capacitors 21Table 3 - Table of Methods Referenced Aluminum Electrolytic Capacitors 22-23Table 3A - Electrolytic Capacitor Process Change Qualification Guidelines for the Selected Test 24Table 4 - Table Methods Referenced Film Capacitors 25-26Table 4A - Film Capacitor Process Change Qualification Guidelines for the Selection of Test 27Table 5 - Table of Methods Referenced Magnetics (Inductors/Transformers) 28-29Table 5A - Inductive Products Process Change Qualification Guidelines for the selection of Test 30Table 6 - Table of Methods Referenced Networks (R-C/C/R) 31-32Table 6A/7A - Networks and Resistors Process Change Qualification Guidelines for Selection of Test 33Table 7 - Table of Methods Reference Resistors 34-35Table 7B - Acceptance Criteria for Carbon Film Leaded Fixed Resistors 36Table 7C - Acceptance Criteria for Metal Film Leaded Fixed Resistors 37Table 7D - Acceptance Criteria for Metal Oxide Leaded Fixed Resistors 38Table 7E - Acceptance Criteria for Wire Wound Leaded Fixed Resistors 39Table 7F - Acceptance Criteria for SMD Chip Resistors 40Table 8 - Table of Methods Referenced Thermistors 41-42Table 8A - Thermistor Process Change Qualification Guideline for the Selection of Test 43Table 9 - Table of Methods Referenced Trimmer Capacitors/Resistors 44-45Table 9A - Trimmers Capacitors/Resistors Process Change Qualification Guidelines for the 46Selection of TestTable 10 - Table of Methods Referenced Varistors 47-48Table 10A - Varistors Process Change Qualification Guidelines for the Selection of Test 49Table 11 - Table of Methods Referenced Quartz Crystals 50-51Table 11A - Quartz Crystal Process change Qualification guidelines for the Selection of Test 52Table 11B - Acceptance Criteria for Quartz Crystals 53Table 12 - Table of Methods Referenced Ceramic Resonators 54-55Table 12A - Ceramic Resonator Process Change Qualification Guidelines for the Selection of Test 56Table 12B - Acceptance Criteria for Ceramic Resonators 57Table 13 - Table of Methods Referenced Ferrite EMI Suppressors/Filters 58-59Table 13A - Ferrite EMI Suppressors/Filters Process Change Qualification /Guideline for the Selection of Test 60Table 14 - Table of Methods Referenced Polymeric Resettable Fuses 61-62Table 14A - Polymeric Resettable Fuses Process Change Qualification /Guideline for the Selection of Test 63Component Technical CommitteeTable of Contents - ContinuedSection Title Page(s) Appendix 1 - Definition of a Qualification Family 64-66Appendix 2 - Certificate of Design, Construction and Qualification (CDCQ) 67Appendix 3 - Qualification Test Plan Format - Example 68-69Appendix 4 - Data Presentation Format and Content - Example 70Production Part Approval – Parametric Verification Summary – Example 71Revision History 71-74Attachment 1 - AEC – Q200-001 - Flame Retardance -Attachment 2 - AEC – Q200-002 - Human Body Model Electrostatic Discharge Test -Attachment 3 - AEC – Q200-003 - Beam Load (Break Strength) Test -Attachment 4 - AEC – Q200-004 - Resettable Fuse Test -Attachment 5 - AEC – Q200-005 - Board Flex / Terminal Bond Strength Test -Attachment 6 - AEC – Q200-006 - Terminal Strength Surface Mount / Shear Stress Test -Attachment 7 - AEC – Q200-007 - Voltage Surge Test -AEC-Q005 Pb-Free Requirements -STRESS TEST QUALIFICATIONFOR PASSIVE ELECTRICAL DEVICES1.0 SCOPE1.1 DescriptionThis specification defines the minimum stress test driven qualification requirements and references test conditions for qualification of passive electrical devices. This document does not relieve the supplier of their responsibility to meet their own company's internal qualification program or meeting any additional requirements needed by their customers. In this document, "user" is defined as all companies that adhere to this document. The user is responsible to confirm and validate all qualification and assessment data that substantiates conformance to this document.1.1.1 Definition of Stress-Test QualificationStress-Test “Qualification” is defined as successful completion of test requirements outlined in this document. The minimum temperature range required for each passive electrical component type is listed below (maximum capability) as well as example applications typical of each grade (application specific):TEMPERATURERANGE GRADEMINIMUM MAXIMUMPASSIVE COMPONENT TYPEMaximum capability unless otherwisespecified and qualifiedTYPICAL/EXAMPLEAPPLICATION0 -50°C +150°C Flat chip ceramic resistors, X8Rceramic capacitorsAll automotive1 -40°C +125°C Capacitor Networks, Resistors,Inductors, Transformers, Thermistors,Resonators, Crystals and Varistors, allother ceramic and tantalum capacitorsMost underhood2 -40°C +105°C Aluminum Electrolytic capacitors Passengercompartment hot spots3 -40°C +85°C Film capacitors, Ferrites, R/R-CNetworks and Trimmer capacitors Most passenger compartment4 0°C +70°C Non-automotiveQualification of the noted device type to its minimum temperature grade allows the supplier to claim the part as "AEC qualified" to that grade and all lesser grades. Qualification to temperatures less than the minimum specified above would allow the supplier to claim the part as "AEC qualified" at the lower grade only.Determining the temperature grade of a passive component type or an application not mentioned above should be agreed to between the supplier and user.1.1.2 Approval for Use in an Application“Approval” is defined as user approval for use of the part being qualified in the intended application along with any applicable supplements and compliance to any applicable user packaging specification. The user’s method of approval is beyond the scope of this document.1.2 Reference DocumentsCurrent revision of the referenced documents will be in effect at the date of agreement to the qualification plan. Subsequent qualification plans will automatically use updated revisions of these referenced documents.1.2.1 Military/EIA1. EIA-469 Destructive Physical Analysis (DPA)2. MIL-STD-202 Test Methods for Electronic and Electrical Parts3. EIA-198 Ceramic Dielectric Capacitors Classes I,II,III,IV4. EIA-535 Tantalum Capacitors5. J-STD-002 Solderability Spec6. JESD22 JEDEC Standard7. MIL-PRF-27 Test Methods for Inductors/Transformers8. JESD201 Environmental Requirements for Tin Whisker Susceptibility of Tin andTin Alloy Surface Finishes9. JESD22-A121 Test Method for Measuring Whisker Growth on Tin and Tin AlloySurface Finishes1.2.2 Industrial1. UL-STD-94 Test for Flammability of Plastic Materials2. ISO-7637-1 Road Vehicle Electrical Disturbance3. IEC ISO/DIS10605 ESD Human Body Model (modify Q200-002)4. iNEMI Recommendations for Pb-free Termination Plating1.2.3 AEC1. AEC-Q200-001 Flame Retardance Test2. AEC-Q200-002 ESD (Human Body Model) Test3. AEC-Q200-003 Beam Load (Break Strength) Test4. AEC-Q200-004 Polymeric Resettable Fuse Test5. AEC-Q200-005 Flame Retardance Test6. AEC-Q200-006 Measurement Methods for Resettable Fuses7. AEC-Q200-007 Voltage Surge Test8. AEC-Q005 Pb-Free Test Requirements1.3 Glossary of Terms/Abbreviations1. AEC AUTOMOTIVE ELECTRONIC COUNCIL2. ESD ELECTROSTATIC DISCHARGE3. FIT FAILURE IN TIME4. DWV DIELECTRIC WITHSTANDING VOLTAGE5. 8D DISCIPLINED APPROACH FOR PROBLEM SOLVING PROCESS2.0 GENERAL REQUIREMENTS2.1 ObjectiveThe objective of this document is to ensure the device to be qualified meet the qualification requirements detailed in Tables 2 - 14.2.2 Precedence of RequirementsIn the event of conflict in the requirements of this specification and those of any other documents, the following order of precedence applies:1. The purchase order2. The user’s individual device specification3. This document4. The reference documents in Section 1.2 of this document5. The supplier's data sheetFor the device to be considered a qualified part, the purchase order and/or individual device specification cannot waive or detract from the requirements of this document.2.3The Use of Generic Data to Satisfy Qualification and Requalification RequirementsGeneric data is relevant data that the supplier can use as a substitute for part-specific data per the family rules outlined in Appendix 1.Appendix 1 defines the criteria by which components are grouped into a qualification family for the purpose of considering the data from all family members to be equal and generically acceptable to the qualification of the device in question.With proper attention to these qualification family guidelines, information applicable to other devices in the family can be accumulated. This information can be used to demonstrate generic reliability of a device family and minimize the need for device-specific qualification test programs. This can be achieved through qualification of a range of devices representing the “four corners” of the qualification family (e.g. maximum value / temperature extremes / rated voltage). The supplier needs to define what constitutes four corners for a given device family(e.g., mid/low/hi C value, hi/low V for capacitors, case size for resistors and other large partfamilies and communicate that to the user as part of the qualification reporting. These corners need to account for different materials (e.g., X7R capacitors with several different dielectrics, thicknesses, number of layers, K of powder). This determination can be complicated by the number of relevant variables that may need to be considered for a given part family (e.g., the worst case board flex may not necessarily be the highest CV value).Sources of generic data can come from certified test labs, internal supplier's qualifications, user-specific qualifications and supplier's in-process monitors. The generic data to be submitted must meet or exceed the test conditions specified in Tables 2-14. End-point test temperature must address worst case temperature extremes and designed product life for the applications.The user(s) will be the final authority on the acceptance of generic data in lieu of specific device test data (to include temperature ranges of the devices.)2.3.1 Wearout Reliability Tests (End of Life Testing)Testing for the failure mechanisms specific to each component technology should be available to the user whenever a new technology or material relevant to the appropriate wearout failure mechanism is to be qualified. The data, test method, calculations, and internal criteria need not be demonstrated or performed on the qualification of every new device, but should be available to the user upon request.Note: This information may be subject to a confidentiality agreement, since it contains proprietary information of the supplier.2.4 Test Samples2.4.1 Lot RequirementsLot requirements are designated in Table 1, herein.2.4.2 Production RequirementsAll qualification parts shall be produced on tooling and processes at the manufacturing site that will be used to support part deliveries at projected production volumes.2.4.3 Reusability of Test SamplesDevices used for nondestructive qualification tests may be used to populate other qualification tests. Devices that have been used for destructive qualification tests may not be used any further except for engineering analysis.2.4.4 Sample Size RequirementsSample sizes used for qualification testing and/or generic data submission must be consistent with the specified minimum sample sizes and acceptance criteria in Table 1. If the supplier elects to submit generic data for qualification, the specific test conditions and results must be reported. Existing applicable generic data shall first be used to satisfy these requirements and those of Section 2.3 for each test required in Table 1. Such generic data shall not be more than2 years old. Part specific qualification testing shall be performed if the generic data does notsatisfy these requirements. Dip-fixturing of parts during reliability testing is prohibited when stress-testing a large number of components.2.4.5 Pre and Post Stress Test RequirementsPre- and post-stress electrical tests are performed at nominal (room) temperature only unlessotherwise stated in the additional requirements section of the applicable test. Any extremeendpoint test temperatures (e.g., minimum and maximum designed operational per section1.1.1 or the device datasheet) are specified in the "Additional Requirements" column Tables 2-13 for each test.For qualifications to applications in higher grade environments, the specific value of temperature must address the temperature extremes and designed product life for the application for at least one lot of data (generic or part specific) submitted per test. For example, if the supplier designsa device intended solely for use in a Grade 3 environment (e.g. -40°C to +85°C), his endpointtest temperature extremes need only address those application limits for the applicable stress tests requiring electrical testing to the designed operational temperature extremes. Qualification to applications in higher grade environments (e.g. -40°C to +125°C for Grade 1) will require testing of at least one lot using these additional endpoint test temperature extremes. All endpoint test conditions must include all user specifications for any given family.2.5 Definition of Test Failure After StressingTest failures are defined as those devices not meeting the user’s individual device specification, post-test criteria specific to the test or the supplier's data sheet, in order of significance as defined in Section 2.2. Any device that shows external physical damage attributable to the environmental test is also considered a failed device. If the cause of failure is agreed (by the manufacturer and the user) to be due to mishandling or ESD, the failure shall be discounted, but reported as part of the data submission. Suppliers must describe their parametric fail criteria for each stress test as part of the qualification data submission to the user for approval. A listing of suggested parameters for each component type is included after each component type test table. The specific listing of failure criteria for each component type and parameter in this document is beyond its scope.2.6Criteria for Passing QualificationPassing all appropriate qualification tests specified in Tables 1 and 2-14, either by performing the test (acceptance of zero failures using the specified minimum sample size) on the specific part or demonstrating acceptable family generic data (using the family definition guidelines defined in Appendix 1 and the total required lot and sample sizes), qualifies the device per this document.Passing the acceptance criteria of all the tests in Table 1 and the conditions in Tables 2-14 qualify the device per this document. When the number of failures for any given test in Table 1 exceeds the acceptance criteria using the procedure herein, the device shall not be qualified until the root cause of the failure(s) is (are) determined and the corrective and preventive actions are implemented and confirmed to be effective in an 8D or other acceptable user format. New samples or data may be requested to verify the corrective and prevented action.Any unique reliability test or conditions requested by the user and not specified in this document shall be agreed upon between the supplier and user requesting the test, and will not preclude a device from passing stress-test qualification as defined by this document.2.7 Alternative Testing RequirementsAny deviation from the test requirements, listed in Table 1 and the test conditions listed in Tables 2-14, must be approved by the users through supporting data presented by the supplier demonstrating equivalency. These deviations will be clearly reported when the results of the qualification are submitted to the user for approval.3.0 QUALIFICATION AND REQUALIFICATION3.1 Qualification of a New DeviceRequirements for qualification of a new device are listed in Table 1, with the corresponding testconditions listed in Tables 2-14. For each qualification, the supplier must present data for ALL ofthese tests, whether it is stress test results on the device to be qualified or acceptable genericfamily data. A review is to be made of other parts in the same generic family to ensure thatthere are no common failure mechanisms in that family. Justification for the use of generic data,whenever it is used, must be demonstrated by the supplier and approved by the user.For each part qualification, the supplier must present a Certificate of Design, Construction andQualification data see Appendix 2.3.2 Qualification of a Lead (Pb) – Free DeviceAdded requirements needed to address the special quality and reliability issues that arise whenlead (Pb) free processing is utilized is specified in AEC-Q005 Pb-Free Requirements. Materialsused in lead-free processing include the termination plating and the board attachment (solder).These new materials usually require higher board attach temperatures to yield acceptablesolder joint quality and reliability. These higher temperatures will likely adversely affect themoisture sensitivity level of plastic packaged semiconductors. As a result, new, more robustmold compounds may be required. If an encapsulation material change is required to provideadequate robustness for Pb-free processing of the device, the supplier should refer to theprocess change qualification requirements in this specification. Preconditioning should be runat the Pb-free reflow temperatures described in AEC-Q005 Pb-Free Requirements beforeenvironmental stress tests.3.3 Requalification of a DeviceRequalification of a device shall be required when the supplier makes a change to the productand/or process that impact the form, fit, function, quality and reliability of the device.3.3.1 Process Change NotificationThe supplier shall submit a projection to the users of all forecasted process changes. Thisprojection of implemented changes shall be submitted at least 6 months in advance.Information required for submission to the user will include the following as a minimum:1. Benefit to the user (value, time and quality).2. For each user part numbers involved in the change, the following information is required:a) Supplier part numberb) An estimated date of the last production lot of unchanged parts.c) An estimated final order date and final ship date of unchanged parts.d) The first projected shipment date and date code of changed parts.3. A detailed description of the change in terms of the materials, processes,visual/electrical/mechanical characteristics, rating, circuit design, internal element layoutand size, as applicable.4. Technical data and rationale to support the proposed changes.5. An electrical characterization comparison (between the new and original product) ofall significant electrical parameters over temperature extremes which could be affectedby the change. Changes in median and dispersion performances shall be noted eventhough conformance to specification limits is still guaranteed. This is needed to evaluateany adverse impact on specific end customer applications.6. The supplier shall submit an updated Certificate of Design, Construction and Qualificationalong with information required by this section (section 3.2.1) plus any changes impactingAppendix 2 information as originally submitted.7. The results of completed supplier Requalification tests of the changed device(s).Items 1 through 5 are background information needed up front to evaluate the impact of the change on supply and reliability and to come to agreement on a qualification plan acceptable to the supplier and user. Items 5, 6 and 7 must be submitted prior to any final approval to implement any change on the user's product. No change shall be implemented without prior approval of the users.3.3.2 Changes Requiring RequalificationAs a minimum, any change to the product, as defined in Appendix 1, requires performing the applicable tests listed in Tables 1 and 2-14. Table 2A-14A will be used as a guide for determining which tests need to be performed or whether equivalent generic data can be submitted for that test. This table is a superset of tests that the supplier and user should use asa baseline for discussion of tests that are required for the qualification in question. It is thesupplier's responsibility to present rationale for why any of these tests need not be performed or whether any of the tests can be supplemented with generic data. Original test data from the old process (if it exists and is applicable) can be used as a baseline for comparative data analysis.At a minimum, electrical characterization test #19 should be performed on a comparative basis.An agreement between the supplier and the user(s) with justification for performing or not performing any recommended test shall occur before the implementation of a Requalification plan.3.3.3 Criteria for Passing RequalificationIt is the responsibility of each user to review the data, change notices, and supporting documentation to either qualify or not qualify the change based on the results of the tests performed. All criteria requirements described in 2.6 apply.3.3.4 User ApprovalA change may not affect a part's qualification status, but may affect it's performance in anapplication. Individual user authorization of a process change will be required for that user's particular application(s), and this method of authorization is outside the scope of this document.4.0 QUALIFICATION TESTS4.1 General TestsTest details are given in Tables 1-14. Not all tests apply to all devices. For example, certain tests apply only to hermetically packaged devices, others apply only to SMD large can devices, and so on. The applicable tests for the particular device type are indicated in the "Note" column of Table 1 and the "Additional Requirements" in Tables 2-14. The "Additional Requirements"column of Tables 2-14 also serves to highlight test requirements that supersede those described in the referenced test.4.2 Device Specific TestsThe following tests must be performed on the specific device to be qualified for all devices.Generic data is not allowed for these tests. Device specific data, if it exists, is acceptable.1. Electrostatic Discharge (ESD) - All product.2. Electrical Characterization - The supplier must demonstrate that the part is capable ofmeeting parametric limits detailed in the individual user device specification. This data mustbe taken from at least three lots of the required sample size over the specified temperaturerange.3. Additional Environmental Testing may be required because of the user's experience withthe supplier.4.3 Data Submission FormatData summary shall be submitted as defined in Appendix 4. Raw data and histograms shall besubmitted upon request by the individual user. All data and documents (e.g justification fornon-performed test, etc.) shall be maintained by the supplier in accordance with QS-9000 requirements.。
XPOWER 专业级多功能空气扇说明书
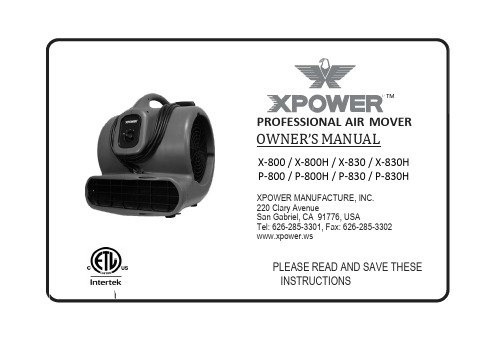
TMX-800 / X-800H / X-830 / X-830HP-800 / P-800H / P-830 / P-830HXPOWER MANUFACTURE, INC.PLEASE READ AND SAVE THESEIndexIntroduction (2)Operation / Instructions (3)Safety Instructions (4)Maintenance Instructions / Troubleshooting (5)Specifications (6)Warranty / Service (7)Parts List (8)Accessories (9)Warranty Registration Form (10)- 1 -IntroductionXPOWER Air Movers are Certified Professional Level Multifunctional Air Movers with the most efficient engineering design.Features:•Low power draw with high velocity air flow from 3,300 to 3600 CFM•Super quiet motor and super lightweight•Easy carrying handle and stackable up to 4 units high.•Easy and quick to disassemble for thorough cleaning and service.•Power cords lengths a re 20’ for P models and 25’ for X models.•Easy cord wrap on handle.•Luggage handle and wheels for "T" series models•3-speed switch.•Durable and rugged housing with 5 years warranty.• 4 air flow positions (0°, 20° Kickstand, 45° and 90°).0° 20° 45° 90°- 2 -Operation / InstructionsXPOWER Air Movers are intended to move air and to dry floors, walls, furniture, etc. Durable and easy to operate withan effective balance of static pressure and airflow, the units are suitable for a variety of applications.1. XPOWER Air Movers are shipped ready-to-use.Prior to plugging the unit into the power source,inspect completely for any shipping damage.2. Plug the electrical cord into the power outlet.3. Carefully place the Air Mover unit on a stable, flat dry surface.4. The unit is capable to be used at 4 different angles to directair flow.5. Turn the switch to desired speed and make sure unitoperates normally.6. All Air Movers in operation must be supervised at all times.AIR MOVER STORAGE:Air Movers can be stacked(up to 4) ontheir sides for storage.NOTICE: Stacking feature is not secure for transportation.- 3 -Safety Instructions1. To prevent electric shock, do not operate the unit in standing water. Never plug in or unplugthe unit with wet hands or while standing in water.2. To avoid risk of injury, do not direct air flow at face or body.3. To reduce the risk of fire or electric shock, do not use the Air Mover with any solid-state speedcontrol device.4. Use only with GFCI protected receptacles. Please contact a qualified electrician for verificationand / or installation of a GFCI receptacle if necessary.5. Do not operate any Air Mover with a damaged cord or plug. Discard the unit or return it to anauthorized service facility for examination and/or repair.6. Unplug the Air Mover from the power supply before servicing or cleaning.7. Do not run the power cord under carpeting. Do not cover the power cord with throw rugs,runners, or similar coverings. Place the power cord away from traffic area to prevent tripping.8. Do not allow children to play with or around an Air Mover at any time.9. Do not move or carry an Air Mover while unit is operating.10.All Air Movers in operation must be supervised at all times.- 4 -Maintenance Instructions1. To keep the Air Mover clean, use a damp cloth to wipe the surface of the housing.2. Never clean the Air Mover with water.3.When not in use, unplug and store the Air Mover in a dry indoor place out of reach of children.4. Always disconnect the Air Mover from its power source before performing any maintenance or cleaning.TroubleshootingFor any problems not listed below, call your local distributor or contact our Service Department.- 5 -Specifications- 6 -XPOWER LIMITED WARRANTYXPOWER Warranty covers the unit from defects in materials and craftsmanship. The Warranty covers normal use for a term of one year from the original date of purchase including parts, labor and one way shipping. The XPOWER Air Mover Housing is covered for a term of five years from the date of original purchase.Important !This Warranty does not cover signs of misuse including, but not limited to, a unit that has been dropped, subjected to water damage, tampered with, improper voltage use and unauthorized maintenance and repairs. The POWER CORD is not covered by the warranty.ServiceIn order to receive service or replacement parts under warranty, you must:A. Must Call for a Return Merchandise Authorization (RMA) number through ServiceDepartment and obtain ship back instructions.B. Must have original proof of purchase.C. Must use original none damaged packaging or Industrial certified packaging method.The end user will be responsible to ship the unit (with the RMA number showing on the shipping label) to the XPOWER Service Department. Upon inspection, we will advise you of the repairs needed and the cost (if applicable). XPOWER will provide repair or replacement parts depending on warranty.- 7 -800 Series Parts List- 8 -.Luggage Handle & Wheels (for 800T and 830T models)XPOWER Air Mover Model Nos. P-800T, P-830T, X-800T & X-830T comes with built-in adjustable luggage handle and wheels for easy transport and mobility.Accessories- 9 -WARRANTY REGISTRATIONPlease complete and mail or fax for your product warranty. For a multiple of please list serial numbers on a separate sheet paper Address: MANUFACTURE, INC. 220 Clary Avenue, San Gabriel, CA 91776,Tel: (626) 285-3301; Fax: 626)Company Name / Contact Person / Title _______________________________________ Address _________________________________________ City ____________________ State / Province ___________________ Zip ____________ Country _________________ Phone __________________ Fax _________________ E-mail ______________________ Model # _______________________ Serial # ___________________________________ Date of Purchase _____/_____/_____ Purchased From ___________________________ Additional Comments / Suggestions ___________________________________________- 10 -TO:XPOWER MANUFACTURE, INC.220 Clary AvenueSan Gabriel, CA 91776, USATel: (626) 285-3301; Fax: (626) 285-3302From: ________________________ ________________________ ________________________。
Arcalyst(rilonacept)(浴室沐浴)说明书

Arcalyst® (rilonacept)(Subcutaneous)Document Number: IC-0182 Last Review Date: 04/06/2021Date of Origin: 11/07/2013Dates Reviewed: 11/2013, 08/2014, 07/2015, 04/2016, 04/2017, 04/2018, 08/2018, 08/2019, 08/2020, 01/2021, 04/2021I.Length of AuthorizationCoverage will be provided for 6 months and may be renewed.II.Dosing LimitsA.Quantity Limit (max daily dose) [NDC Unit]:-Arcalyst 220 mg injection: 8 vials every 28 daysB.Max Units (per dose and over time) [HCPCS Unit]:Cryopyrin-Associated Periodic Syndromes (CAPS)/Recurrent Pericarditis (RP)-Loading Dose given on Day 1: 320 billable units-Maintenance Dose:160 billable units every 7 daysDeficiency of Interleukin-1 Receptor Antagonist (DIRA)∙320 billable units every 7 daysIII.Initial Approval Criteria 1Coverage is provided in the following conditions:∙Patient is up to date with all vaccinations, in accordance with current vaccination guidelines, prior to initiating therapy; ANDUniversal Criteria 1•Patient has been evaluated and screened for the presence of latent tuberculosis (TB) infection prior to initiating treatment and will receive ongoing monitoring for the presenceof TB during treatment; AND•Patient does not have an active infection, including clinically important localized infections;AND•Must not be administered concurrently with live vaccines; AND•Patient is not on concurrent therapy with other IL-1 blocking agents (e.g., canakinumab, anakinra*, etc.) [*Note: For DIRA, anakinra must be discontinued 24 hours prior tostarting Arcalyst]; AND•Patient is not on concurrent treatment with another TNF inhibitor, biologic response modifier or other non-biologic immunomodulating agent (i.e., apremilast, tofacitinib,baricitinib); ANDCryopyrin-Associated Periodic Syndromes (CAPS) †Ф1-4∙Patient is at least 12 years of age; AND∙Used as a single agent; AND∙Patient has documented baseline serum levels of inflammatory proteins (C-Reactive Protein [CRP] and/or Serum Amyloid A [SAA], etc.); AND∙Patient has documented laboratory evidence of a genetic mutation in the Cold-Induced Auto-inflammatory Syndrome 1 (CIAS1), also known as NLRP3; ANDo Documented diagnosis of Familial Cold Autoinflammatory Syndrome (FCAS); ORo Documented diagnosis of Muckle-Wells Syndrome (MWS); AND∙Patient has two or more of any of the CAPS-typical symptoms:-urticaria-like rash-cold-triggered episodes-sensorineural hearing loss-musculoskeletal symptoms-chronic aseptic meningitis-skeletal abnormalitiesDeficiency of Interleukin-1 Receptor Antagonist (DIRA) †1,5∙Patient weighs at least 10 kg; AND∙Patient has a confirmed diagnosis of DIRA as evidenced by a mutation in the IL1RN gene;AND∙Used as maintenance of remission in patients who have previously experienced clinical benefit from anakinra therapy for the treatment of DIRARecurrent Pericarditis (R P) † 6,7∙Patient is at least 12 years of age; AND∙Used for the treatment of recurrent pericarditis and/or reducing the recurrence of disease;AND∙Patient has documented baseline serum levels of inflammatory proteins (C-Reactive Protein [CRP], etc.); AND∙Patient has failed standard therapy (e.g., NSAID, colchicine, corticosteroids, etc.)†FDA Approved Indication(s);‡ Compendia recommended indication(s);Ф Orphan DrugIV.Renewal Criteria 1-7Coverage can be renewed based upon the following criteria:∙Patient continues to meet universal and other indication-specific relevant criteria identified in section III; AND∙Absence of unacceptable toxicity from the drug. Examples of unacceptable toxicity include: severe hypersensitivity reactions, serious infections (including but not limited totuberculosis), lipid profile changes, etc.; ANDCryopyrin-Associated Periodic Syndromes∙Disease response as indicated by improvement in patient’s symptoms from baseline AND improvement in serum levels of inflammatory proteins (e.g. CRP and/or SAA, etc.) frombaselineDeficiency of Interleukin-1 Receptor Antagonist (DIRA)∙Disease response as indicated by improvement in patient’s symptoms (e.g., fever, skin rash, bone pain), inflammatory markers (e.g., CRP, ESR), and/or radiological evidence of activebone lesions compared to baselineRecurrent Pericarditis (RP)∙Disease response as indicated by improvement in patient’s symptoms (e.g., pericarditis pain, etc.), inflammatory markers (e.g., CRP, etc.), and/or decreased rate of recurrence of diseasecompared to baselineV.Dosage/Administration 1VI. Billing Code/Availability InformationHCPCS Code:∙ J2793 – Injection, rilonacept, 1 mg : 1 billable unit = 1 mg NDC:∙ Arcalyst 220 mg injection: 61755-0001-xxVII. References1. Arcalyst [package insert]. Tarrytown, NY; Regeneron Pharmaceuticals, Inc; March 2021.Accessed March 2021. 2. Hoffman HM, Throne ML, Amar NJ, et al. Efficacy and safety of rilonacept (interleukin-1Trap) in patients with cryopyrin-associated periodic syndromes: results from two sequential placebo-controlled studies. Arthritis Rheum. 2008 Aug;58(8):2443-52. 3. Kuemmerle-Deschner JB, Ozen S, Tyrrell PN, et al. Diagnostic criteria for cryopyrin-associated periodic syndrome (CAPS). Ann Rheum Dis. 2017 Jun;76(6):942-947. doi: 10.1136/annrheumdis-2016-209686. 4. Terreri MT, Bernardo WM, Len CA, et al. Guidelines for the management and treatment ofperiodic fever syndromes: Cryopyrin-associated periodic syndromes (cryopyrinopathies - CAPS). Rev Bras Reumatol Engl Ed. 2016 Jan-Feb;56(1):44-51. doi: 10.1016/j.rbre.2015.08.020. 5. Garg M, de Jesus AA, Chapelle D, et al. Rilonacept maintains long-term inflammatoryremission in patients with deficiency of the IL-1 receptor antagonist. JCI Insight. 2017 Aug 17;2(16):e94838. doi: 10.1172/jci.insight.94838. 6. Klein AL, Imazio M, Cremer P, et al; RHAPSODY Investigators. Phase 3 Trial ofInterleukin-1 Trap Rilonacept in Recurrent Pericarditis. N Engl J Med. 2021 Jan 7;384(1):31-41. doi: 10.1056/NEJMoa2027892. Epub 2020 Nov 16. 7. Klein AL, Imazio M, Brucato A, et al. RHAPSODY: Rationale for and design of a pivotalPhase 3 trial to assess efficacy and safety of rilonacept, an interleukin-1α and interleukin -1β trap, in patients with recurrent pericarditis. Am Heart J. 2020 Oct;228:81-90. doi: 10.1016/j.ahj.2020.07.004. Epub 2020 Jul 14.Appendix 1 – Covered Diagnosis CodesAppendix 2 – Centers for Medicare and Medicaid Services (CMS)Medicare coverage for outpatient (Part B) drugs is outlined in the Medicare Benefit Policy Manual (Pub. 100-2), Chapter 15, §50 Drugs and Biologicals. In addition, National Coverage Determination (NCD), Local Coverage Determinations (LCDs), and Local Coverage Articles (LCAs) may exist and compliance with these policies is required where applicable. They can be found at: /medicare-coverage-database/search/advanced-search.aspx. Additional indications may be covered at the discretion of the health plan.Medicare Part B Covered Diagnosis Codes (applicable to existing NCD/LCD/LCA: N/A。
TEKTRONIX 数据通信分析仪 830系列产品说明书
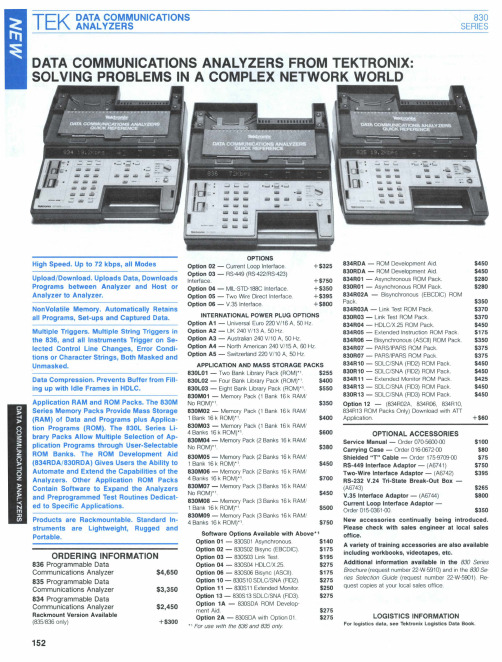
$4,650
835 Programmable Data Communications Analyzer
$3,350
834 Programmable Data Communications Analyzer
$2,450
Rackmount Version Available (835/836 only)
+ $60
OPTIONAL ACCESSORIES Service Manual - Order 070-5600-00 Carrying Case - Order 016-0672·00 Shielded "T" Cable - Order 175-9709-00 RS-449 Interface Adaptor - (A6741) Two-Wire Interface Adaptor - (A6742) RS-232 V.24 Tri-State Break-Out Box -
APPLICATION AND MASS STORAGE PACKS
830L01 - Two Bank Library Pack (ROM).
$255
830L02 - Four Bank Library Pack (ROM).
$400
830L03 - Eight Bank Library Pack (ROM)• 1• $550
$600
830M04 - Memory Pack (2 Banks 16 k RAM/
No ROM).
$380
830M05 - Memory Pack (2 Banks 16 k RAM/ 1 Bank 16 k ROM). 830M06 - Memory Pack (2 Banks 16 k RAM/ 4 Banks 16 k ROM). 830M07 - Memory Pack (3 Banks 16 k RAM/ No ROM)• 1•
- 1、下载文档前请自行甄别文档内容的完整性,平台不提供额外的编辑、内容补充、找答案等附加服务。
- 2、"仅部分预览"的文档,不可在线预览部分如存在完整性等问题,可反馈申请退款(可完整预览的文档不适用该条件!)。
- 3、如文档侵犯您的权益,请联系客服反馈,我们会尽快为您处理(人工客服工作时间:9:00-18:30)。
SECTION 5 TESTING AND INSPECTION GENERALLaboratory Testing 5.1 (1)The Contractor shall have all materials, components andassemblies, unless otherwise noted, tested by anApproved certified independent testing facility todemonstrate that they satisfy the requirements of the TSand/or the relevant sections of the Materials andWorkmanship Specification for Civil Engineering WorksVolume 1, 2 and 3, when tested in accordance with theprocedures defined in this Section and/or those of theParticular Specification. Where no procedure is defined,the Contractor shall propose suitable standard or particularprocedures for Approval.(2) All submissions shall be in accordance with Section 1Clause 1.1(7).Quality Assurance 5.2 (1)All materials, components or assemblies shall be testedand inspected by the Contractor to the degree andfrequency stated within the TS.(2) A comprehensive schedule of all material inspection/testsand the required/specified frequency of testing shall beproduced by the Contractor.(3) A sample proforma, with typical examples, for the materialinspections/tests has been included as Appendix 5.1. Thisproforma shall be completed by the Contractor.(4) The Contractor shall complete the material inspection/testschedule and submit for Approval as part of his QualityPlan.(5) On receiving Approval of the material inspection/testschedule, the Contractor shall use the schedule to producethe required individual test and inspection plan.(6) The test requirements referenced 'P' and 'Q' in theschedule shall mean the following:(a) The material inspection schedule shall be marked 'P'or 'Q' as appropriate. Tests referenced 'P' in theschedule test requirements column shall beundertaken by an Approved independent testingfacility on prototype qualification/preproduction unitsfor proving purposes before full scale manufacturecommences.(b) Tests referenced 'Q' shall be production qualitycontrol tests undertaken by the Contractor or anindependent testing facility as specified or Approvedby the Engineer.(7) All tests and inspections shall be carried out by theContractor in the presence of the Engineer to demonstratecompliance with the specification. All test and inspectionresults shall be submitted for Approval.(8) Suitable proforma for the recording and witnessing of alltests and inspections shall be submitted for Approval. Theproforma shall be completed and the material, componentor assemblies compliance assured by the Contractor priorto inviting the Engineer to check or inspect. Confirmationof a test or inspection shall be presented by the Contractoron an Approved proforma, not less than 21 Days prior tothe date for inspection.(9) No material, component or assembly shall be shipped untilit has been inspected by the Engineer and signed asreleased for shipment.(10) Should the items to be tested or inspected fail to meet therequirements of this Specification, necessitating additionalvisits to the laboratories or works for retesting or inspectionthe costs of these additional visits shall be at the expenseof the Contractor.(11) Periodically during the Contract the Engineer shall conductinspections of manufacturing activities at the premises ofthe Contractor and those of his suppliers andsubcontractors. Such inspections shall include qualityprocedure checks, witness inspections, both routine andprototype, and shall also be for the purpose of monitoringprogress. Not less than 7 Days notice shall be given.During each inspection suitably qualified staff shall beprovided by the Contractor to assist the Engineer, inaddition to suitable access and facilities.Acceptance Tests 5.3 (1)The tests and inspections have been divided intocategories as defined in the following clauses. The testslisted are not comprehensive and shall be revised by theContractor to include all identified tests in the TS and anyadditional test as required by suppliers of proprietary trackcomponents.(2) Category 1 - Works Tests as follows:(a) All material/component manufacturing tests asdetailed in the material inspection/test scheduleprepared by the Contractor.(b) The assembly verification tests as detailed inClauses 5.25 to 5.31.(c) The tests and inspections of the switch, crossing,trap point assemblies as detailed in Clauses 5.32 to5.37.(d) The precast prestressed concrete sleeper andbearer tests as detailed in Clauses 5.40 to 5.45.(e) Bi-block concrete block tests as detailed inClauses 5.46 to 5.52.(f) Buffer stop tests as detailed in Clause 5.53.(g) Insulated rail joint tests as detailed in Clause5.12(1)(a) to (c) and 5.12(2)(a) to (n).(h) Welding materials as detailed in Clause 5.21.(i) Weld/welder proving tests of Clauses 5.22 and 5.23.(3) Category 2 - Site Tests as follows:(a) Insulated rail joint tests of Clause 5.12(1)(d) and/or(e).(b) Ballast tests of Clause 5.16.(c) Not Used.(d) Void and compaction tests of Clause 5.39.(e) Running line and depot line turnouts, crossovers,diamond crossings in accordance with Clause 5.38.(f) Rail insulation to earth and ballast resistance tests ofClause 5.56 and 5.57.(g) Holding down assembly tests of Clause 5.58.(h) Site weld quality tests of Clauses 5.22 and 5.23.(4) Tests on Completion(a) All the tests and inspections described in Clauses5.54 to 5.63.(b) The additional tests as described in the ParticularSpecification.(5) The site tests and commissioning tests shall beduplicated/repeated by the Contractor as necessary toensure the commissioning is completed to the satisfactionof the Engineer.Material Tests 5.4(1) In addition to the requirements of the TS, all materials shallbe tested in accordance with the requirements of therelevant sections of the Materials and WorkmanshipSpecification for Civil Engineering Works Volumes 1, 2 or 3as appropriate, Section G9 of the General Specification forTrackwork and Overhead Line System, all specifically listedCodes and Standards and any Code, Standard orprocedure submitted by the Contractor and Approved.(2) A series of approved test and inspection proforma aregiven in Appendices 5.12 and these shall not be revisedwithout Approval. These proforma do not include all itemsof test or inspection, the Contractor shall submit forApproval proforma for any test or inspection omitted.(3) A number of inspection proforma for S&C are available tothe Contractor on request.Additionally test and inspection proforma, hard copy only,are available on request for as-built data recording.MATERIALS AND COMPONENTSRails 5.5(1) Rails shall be tested in accordance with BS EN 13674-1.All the testing and inspection facilities granted under BS EN13674 shall be made available to the Engineer.(2) All rails subject to forging processes and all flash-butt oralumino thermic welds used in the manufacture ofcrossings and combination rails shall be tested for quality ofthe finished product in accordance with Clauses 4.90 or4.94 of the TS and compliant test certificates submitted tothe Engineer for record.Fastener Assembly Creep Resistance 5.6 Static creep resistance of a single assembly shall be undertakenwith two fastening assemblies at 650mm centres. The number oftests and the test procedure shall be in accordance with BS EN13146-1.Fastening Shoulders 5.7 Fastening shoulders shall be tested and inspected in accordancewith the manufacturer test procedure as Approved by the Engineer.Helical Springs 5.8Not Used.Cast Baseplates 5.9(1) Cast baseplates for Running Lines shall be tested andinspected in accordance with BS EN 1562 or BS EN 1563and to the manufacturer‟s test and inspection procedure asApproved by the Engineer.(2) Cast slide baseplates shall be tested in accordance with BSEN1562 or BS EN1563 and to the manufacturer‟s test andinspection procedure as Approved by the Engineer.(3) Cast baseplates for Stabling Lines shall be tested andinspected in accordance with BS EN 1561 and to themanufacturer‟s test and inspection procedure as Approvedby the Engineer.(4) Prior to the commencement of bulk production, one samplecasting of each type shall be submitted to the Engineer,together with the results of the physical tests taken from thesame pre-production batch. Each sample baseplate shallbe examined by NDT to confirm the internal integrity of thecasting and the test result submitted to the Engineer.(5) One sample baseplate of each type shall be provided to thefastening system supplier for dimensional checks on theshoulder and rail seat, and a certificate of acceptancesubmitted to the Engineer.(6) Bulk production will only commence following theEngineer‟s Review wit hout objection of the pre-productionsamples.(7) Baseplates shall be inspected to a Normal Single SamplePlan, Inspection Level I, as specified in British Standard6001, with an Acceptable Quality Level equal to 2.5 percent, with regard to significant dimensions, and for surfacedefects. The approved pre-production samples define thesurface finish required.(8) One percent of spheroidal graphite baseplatesmanufactured shall be Brinell hardness tested to BS EN10003-1:1995 in a central position on the underside of theplate. The hardness shall comply with the relevant materialcode section of BS EN 1563:1997.(9) Each production batch shall be accepted if the samplesmeet all the test requirements. In the case of a failure, thebatch shall be re-inspected to the original sampling plan. Ifa further failure results, the batch shall be rejected. In thecase of dimensional failures, surface defects, or hardness,the batch may be 100% inspected and re-submitted foracceptance.(10) The supplier shall submit with each production batch ofbaseplates a certificate of conformity and associated testresults confirming that the baseplates supplied meet therequirements of the specification.Resilient Baseplate Pads 5.10 (1)Resilient baseplate pads shall be tested and inspected inaccordance with UIC Code 864-5.(2) The resilient baseplate pads shall be tested at 21o C fordeflection after being aged for a minimum of 168 hours at70o C in accordance with DIN53508.(3) The pad shall then be tested and the load/deflectiondiagram produced for a minimum of 10 load cycles with thedeflection being taken up to 5mm.(4) The calculated stiffness from the tenth recording shall notvary from the designed stiffness by more than +/- 10%.(5) The pads shall be fatigue tested by placing a full padbetween two steel plates and applying a changeablesinusoidal load in the range 10kN to 70kN at a frequency of5Hz for a minimum of 2 million cycles. On completion ofthe test there shall be no signs of physical deterioration ofthe pad.(6) On completion of the fatigue test the pad shall be tested forboth static and dynamic stiffness. The dynamic stiffnessshall be obtained at the frequencies 10Hz, 20Hz, and 40Hz.The test methods for obtaining the dynamic stiffnessesshall be submitted by the Contractor for Approval.(7) The static stiffness test result of one pad under anydesigned baseplate area at 21o C shall be 50MN/m inaccordance with Section 2, or to the individual paddesigned value as shown on the Drawings.(8) The calculated static to dynamic stiffness ratio of the springcoefficients of tests results shall not be greater than 1.4 atall frequencies listed in Clause 5.10(6) for ResilientBaseplate Pads.Standard Fishplates and Fishbolts 5.11 (1)Standard fishplates and fishbolts for CHN60 rail sectionfishplates shall be tested and inspected in accordance withBS 3692 and UIC Codes 864-4 and 864-8.(2) Arrangements shall be made for the Engineer to beaccorded access to all the testing and inspecting facilitiesas specified under the relevant British Standard and UICCodes.Insulated Rail Joints 5.12 (1)Tests shall be undertaken on a sample joint as follows andthe result submitted on an Approved proforma:Proving Tests(a) A test joint shall be prepared using short rails andshall be tested dry for electrical resistance whichshall be a minimum of 100 megohms using 500 voltsDC.(b) The test joint shall then be immersed in a bath ofpotable water for a minimum of 24 hours andallowed to drip dry, after the period of immersion, fora maximum of half a minute. The test joint shall thenbe tested for electrical resistance and shall have aminimum electrical resistance of 10kilo-ohms usinga voltage of 500 DC.(c) Should the IRJ fail to meet the minimum electricalresistance after 30 seconds, the test shall berepeated every 30 seconds until the specifiedresistance is achieved. The values taken every 30seconds up until compliance shall be submitted tothe Engineer for comment/Approval.Production Tests(d) Every IRJ after assembly and prior to installation inthe Works shall be tested prior to installation inaccordance with Clause 5.12(1)(a) and inaccordance with Appendix 5.8 for alignment.Insitu Installed IRJ's(e) The test described in Clause 5.12(1)(a) shall berevised as follows for IRJ's in-situ assembled.- the test voltage shall be a minimum of 36Volts DC- the minimum electrical resistance shall be500 ohms(2) (a) The Contractor shall undertake the followingadditional proving tests on his proposed insulatedrail joint.Test Piece(b) The following described tests shall be undertaken bythe Contractor on sample joints, which shall havebeen assembled in accordance with themanufacturer's recommendations, using twominimum 1000mm pieces of the relevant rail section.(c) The test pieces shall have datum points, placed byan Approved means, on the railhead for the purposeof measuring the separation of the two halves of thejoint before and after testing.(d) Before the commencement of any test, and oncompletion, the vertical alignment of the joint, thedistance between the two datum points and thetorque of each bolt shall be measured and recorded.(e) All data that is to be recorded shall be obtained bythe Contractor and be submitted in duplicate, in hardand or electronic copy, within maximum 7 days ofcompletion of the tests.(f) All acceptance tests shall be undertaken by anApproved independent testing facility.(g) All tests shall be carried out in the presence of theEngineer with formal notification of the tests beinggiven to the Engineer in writing a minimum of 7working days prior to the date of the tests.TestsThe following tests shall be undertaken:(h) Test 1: Dynamic Test- The test piece shall be centrally placed between round supports, of nominal radius 100 mm,placed at 1000mm centres. A vertical load shallbe applied to the centre of the test piece by adouble acting applicator placed equally eitherside of the joint. The load applicator shall consistof two nominal 30mm diameter applicators,placed 75mm apart.- A vertical load shall be applied to the joint at maximum 50kN/sec up to 150kN and then slowlyreleased.- The joint shall then be subjected to a dynamic test for up to 2 million cycles at a frequency of2.5Hz.- The pulsating load for the dynamic tests shall bea maximum of 150kN and minimum of 15kN. (i) Test 2 : Tensile load Test- With one end of the sample joint securely anchored a tensile load shall be applied to theother end of the joint at 50kN/sec. The load shallbe applied until a load of 800kN is achieved orthe measured distance between the two datumpoints increases by a maximum of 1mm, atwhich point the load shall be released and theresidual gap noted. The load against thedimension between the two datum points shallbe continually recorded throughout the test. Number of test Samples(j) Two samples for each type of rail section shall be produced as described above and tested to thesequence given below.Acceptance Testing(k) The first sample test sequence shall be undertaken as follows:- The tests as described in Clause 5.12(1)(l) The second sample test sequence shall be undertaken as follows:- The test as described in Clause 5.12(2)(h) followed by the test of Clause 5.12(2)(i) Acceptance Criteria(m) The tests results of Clause 5.12(2)(k) shall comply with Clause 5.12(1)(a) and (b)(n) The tensile load that each joint shall withstand without the two halves of the joint separating bymore than 1mm shall be:- Test 2 of Clause 5.12(2)(i) - 800kNHigh and Low Density Polyethylene Material 5.13 Tests shall be carried out on all HDPE and LDPE moulded itemsto demonstrate compliance with Section 2 requirements forHDPE, and the results shall be submitted for Approval. At leastone sample shall be tested for each 500 items produced.Sub-grade 5.14Not Used.Sub-ballast 5.15Not Used.Ballast 5.16(1) Ballast shall be tested by an Approved HOKLAS certifiedlaboratory to demonstrate that the material satisfies therequirements set out for ballast in Section 2 of thisSpecification.(2) The minimum ballast sample size submitted to thelaboratory shall be 50kg and shall be obtained in thepresence of the Engineer by Approved means.(3) The minimum frequency of sampling and testing duringballast production shall be as given in Table 5.1:Table 5.1 : Minimum Testing Frequency During Ballast Production(4) The minimum frequency of sampling and testing duringplacing of the ballast in the Works shall be as defined inTable 5.2:Table 5.2 : Minimum Testing Frequency During Ballast Placement(5) The minimum frequency of sampling and testing shall beincreased to at least four times the minimum frequencygiven in Tables5.1and5.2during any of the following timeperiods:(a) during trial runs of ballast production.(b) during placement of the first 2½% (by weight) ofballast from each source or stockpile.(c) whenever the rock is quarried from a new face andshall continue until the quality level is consistent andto the satisfaction of the Engineer.(d) when any test result on the ballast fails to complywith the specified requirements. The increasedtesting frequency shall continue until the quality levelis consistent and to the satisfaction of the Engineer.(6) The frequency of sampling and testing shall be increasedto at least twice the minimum frequency during placementof the first 10% (by weight) of ballast from each source orstockpile.(7) At least five particle size distribution tests shall be takenfrom any section laid or production run of ballast,irrespective of the weight laid or produced.Rubber Boots 5.17Not Used.Block ResilientPads5.18 Not Used.Precast Prestressed Concrete Sleepers/Bearers 5.19Precast prestressed concrete sleepers and bearers shall betested and inspected in accordance with Clauses 5.40 to 5.45.PrecastBi-Block Concrete Sleepers/Bearers 5.20Precast bi-block concrete sleepers and bearers shall be tested inaccordance with Clauses 5.46 to 5.52.Welding Materials 5.21Welding materials shall be tested in accordance with theApproved manufacturers recommended procedure, Network RailNR/WI/TRK/00116 and as stated in Clauses 5.22 and 5.23.Flash-Butt Welding Quality Control 5.22 (1)The following tests, in accordance with the relevant Section5 Appendices and in addition to the recorded parameterslisted in Section 4 - Flash-Butt Welding Process, shall beundertaken on flash-butt welds to the frequency stated inClause 5.22(3) to (7).(a) Slow Bend Test (Appendix 5.4)(b) Fatigue Test (Appendix 5.5)(c) Ultra-Sonic Test (Appendix 5.3)(d) Dye Penetrant Test in accordance with BS EN 571 -1/Magnetic Particle Test in accordance with BS EN9934–1(e) Hardness (Appendix 5.6)(f) Alignment (Appendix 5.8)(g) Metallurgical (Appendix 5.7)(h) Visual in accordance with BS EN 970(2) The ultra-sonic test procedure shall be as specified inAppendix 5.3 or as improved by the welding equipmentsupplier and Approved.(3) The results of the Section 4 - Flash-butt Welding Processspecified recording shall be checked against the designparameters for conformity for all welds.(4) The first two production welds after commissioning of themachine shall be tested in accordance with Clause 5.22(1)and (3).(5) On the first production shift after making any adjustmentsto the machine, or on commencement of production afterany non-continuous period in excess of 48 hours, twowelds shall be produced and tested in accordance withClause 5.22 (1) and (3) with the exception of the FatigueTest, Hardness Test, and Metallurgical Test.(6) All welds shall be subjected to ultra-sonic, magnetic particleand alignment tests in addition to a visual inspection.(7) The first weld from each day of production and the firstweld following a change of rail grade shall be subjected to aslow bend test.(8) All test welds shall be undertaken using two minimum raillengths of 5m. This length shall then be cut, in accordancewith Clause 4.21 to a suitable length for testing oncompletion of the weld. Rails to be welded together to formtest pieces shall be from rail with the same cast numbersrolled in the web.(9) Weld tests have been tabulated in Table 5.3.Appendix P : TS for XRL Trackwork D/MTRCL/XRL/830/PS/001/A1 Table 5.3Flash Butt Welding - Summary of Weld TestingNote: 1. Test pieces to be A, B, C, D, etc.5/15December 2010Alumino- Thermic Weld Tests 5.23 (1)The following tests shall be undertaken on alumino-thermicwelds and portions in addition to those tests required onportions specified in Clauses 4.92(4) and 5.21, at thefrequency stated in Clause 5.23(2), and in accordance withthe relevant Section 5 Appendices, to ensure the specifiedquality is maintained.(a) Slow Bend Test (Appendix 5.4)(b) Fatigue Test (Appendix 5.5)(c) Hardness Test (Appendix 5.6)(d) Metallurgical Tests (Appendix 5.7)(e) Ultra-sonic Test (Appendix 5.3)(f) Dye Penetrant Test in accordance with BS EN 571 -1/Magnetic Particle Test in accordance with BS EN9934 -1(g) Alignment (Appendix 5.8)(h) Visual in accordance with BS EN 970(2) Frequency of weld testing shall be as follows:(a) All alumino-thermic welds shall be tested ultra-sonically, visually, by Magnetic Particle Test and foralignment as described in the relevant Appendicesto Section 5.(b) All welds for welder certification shall be fully testedin accordance with Clause 5.23(1) with theexception of the Metallurgical Test, Fatigue Test,and Hardness Test.(c) Three number test welds shall be produced fromeach shipment of weld materials and the welds shallbe tested in accordance with Clause 5.23(1). If anyweld fails the tests a further three welds from thesame batch shall be produced and tested. Furtherfailure shall result in the rejection of that batch ofweld material.(d) The test welds of Clause 5.23(2)(c) shall beundertaken by the Contractor on site or at themanufacturer‟s premises at the Contractorsdiscretion. Wherever the tests are undertaken theyshall be witnessed by the Engineer.(e) Weld tests have been tabulated and presented inTable 5.4.Appendix P : TS for XRL Trackwork D/MTRCL/XRL/830/PS/001/A1 Table 5.4Alumino-Thermic Welding - Summary of Weld TestingNote: 1. Test pieces to be A, B, C, D, etc.5/18December 2010WaterproofingMembrane onStationTrackbase5.24 Not Used.TESTING COMPONENT ASSEMBLIESGeneral 5.25(1) The following components shall be tested at anindependent test facility as described in Clause 5.1. to 5.4as complete assemblies in accordance with the testsdescribed in Clauses 5.26 to 5.31:(a) Baseplate Assembly(b) Bi-Block Concrete Sleepers(c) Concrete Bearers(2) The tests shall be undertaken with the rails set at thespecified inclination and at an ambient air temperature of20 C.Baseplate Assembly 5.26 (1)The baseplate assembly shall be fixed to a precast concretebeam or timber block using the method specified for theWorks and complete with all nuts, bolts, insulators, pads,shims, bushes or ferrules, clips, rail and grout levelling layeras necessary.(2) The bushes or ferrules used in the test assembly shall bemeasured for actual diameter of the holding down boltholes, in a minimum of four equally spaced positions, priorto commencing the test.(3) The baseplates shall be set to gauge i.e. rails at 1435 mmapart.(4) The assembly shall be tested as described in Clauses 5.29to 5.31 for Fastening Repeated Load Test, ElectricalInsulation Test and Fastening Longitudinal Restraint Test.(5) Baseplate assembly verification tests shall be undertakenfor all baseplate assemblies, plus all turnout specialassemblies.Precast Bi-Block Concrete Sleepers 5.27 (1)One bi-block sleeper shall be cast into a beam, in themanner as described for the Works, complete with railfastening, rail, and all accessories.(2) The blocks shall be set to gauge i.e. rail at 1435 mm apart.(3) The assembly shall be tested as described in Clauses 5.29to 5.31 for Fastening Repeated Load Test, ElectricalInsulation Test and Fastening Longitudinal Restraint Test. Concrete Bearers 5.28 (1)One bearer shall be assembled complete with all clips, pads,insulators and rail as per the assembly to be used in theWorks. The assembly shall be tested as described inClauses 5.29 to 5.31 for Fastening Repeated Load Test,Electrical Insulation Test and Longitudinal Restraint Test.(2) For the purposes of the test each type of bearer shall bedescribed as follows:-(a) Type 1Two rail fastening types through the switch slidebaseplate area.(b) Type 2Four rail fastening types through the lead.(c) Type 3Three/four rail fastening types through the checkrail/crossing areas.Fastening Repeated Load Test 5.29 (1)Two short sections of rail shall be fastened to eachassembly using the complete rail fastening assembly. Therepeated load shall be applied by a scissor arm oscillator.The scissor arm oscillator shall be set to apply the load tothe rail head at an angle of 26.5 to the vertical.(2) With the assembly as described in Clauses 5.26, 5.27 and5.28, the repeated load test shall be undertaken atmaximum 5 Hz for a minimum of 3 million cycles.(3) The loads to be applied to the scissor arm oscillator are asfollows:(a) Baseplate assemblies and bi-block concretesleepers - 90kN.(b) Prestressed concrete sleepers - 120kN.(4) The minimum load shall be 10kN and the assemblies shallhave a static preload applied prior to starting the sinusoidaloscillations and an amplitude and range as defined inTable 5.5:(5) Prior to applying the preload and commencing theoscillations the load shall be applied at a rate notexceeding 25 kN/sec up to 150kN and oscillated for 2000cycles to ensure the rail is against the outside fasteners.The load shall be released to 20 kN maximum and allgauges reset to zero before applying the static preload andcommencing the repeated load test. This repeated loadtest may generate heat in the pads and this heat shall notbe allowed to exceed 50 C.(6) Dial gauges shall be set to record gauge; head of railrotation; rail foot slippage; baseplate outside edge lateraland vertical movements and head of rail vertical deflection.(7) The requirements of the test shall have been met onlywhen:(a) there is no sign of failure of any component of thewhole fastening system.(b) the track gauge, when the load has been completelyreleased, shall not, have increased by more than3 mm over standard gauge.(c) the maximum rail head rotation shall not exceed4 mm.(d) the rail foot shall not have slipped by more than+1 mm.(e) The diameter of the holding down bolt hole in thebush/ferrule shall not have increased by more than0.5 mm.。