破解汽车冲压模具技术难题
汽车冲压模具常见问题及解决方法!

汽车冲压模具常见问题及解决方法!汽车冲压模具常见问题及解决方法!一、翻边整形制件变形在翻边和整形过程中往往会出现制件的变形现象,在非表面件中一般不会对制件的质量产生多大影响,但在表面件中,只要有一点变形就会给外观带来很大的质量缺陷,影响整车的质量。
原因:1、由于制件在成形和翻边的过程中,板料发生变形、流动,如果压料不紧就会产生变形;2、在压料力够大的情况下,如果压料面压料不均匀,局部有空隙的话,也会出现以上情况。
解决方法:加大压料力,如果是弹簧压料可采用加弹簧的办法,对上气垫压料通常采用加大气垫力的办法;如果加大压力后,在局部还存在变形的话,可用红丹找出具体问题点,检查是不是压料而局部出现凹陷等情况,此时可采用焊补压料板的办法;压料板焊后与模具的下型而进行研配。
二、刀口崩刃模具在使用中由于各种原因引起的崩刃,都会对制件的质量产生一定的影响。
它是模具修理中最常见的修理内容之一,对刀口的崩刃修理步骤如下:1、根据崩刃的'情况,如果崩刃很小时,通常要将崩刃处用砂轮机磨大些,以保证焊接牢固,不易再次崩刃;2、用相应的焊条进行焊接,目前我们采用的是D332焊条来对刃口进行堆焊。
堆焊之前一定要选好修理的基准面,包括间隙面和非间隙面;3、将刃口的非间隙面修平(参考事先留下的基准);4、对照过渡件进行划线,如果没有过渡件可以用事先留下的基准进行粗磨间隙面;5、上机台对间隙面进行修配,可借助粘土等辅助研配。
在修配过程中一定要小心,开动压力机时尽量慢,必要时用装模高度调整向下开,以避免刀口啃坏的现象发生;6、刀口间隙要合理,对于钢板冲压模,单边刀口间隙取板料厚度的l/20o但在实际操作过程中,可以用板料试冲的办法来检验间隙的大小,只要剪切后制件的毛刺达到要求即可,一般情况下,毛刺大小的判定标准是,毛刺高度不大于板料厚度的1/10;7、检测刀口的间隙面是否与剪切的方向统一;8、间隙配好后,用油石将刀口的间隙面推光滑,以减小生产中板料与刀口的磨擦及废料下落的阻力。
汽车零部件冲压模具若干问题研究
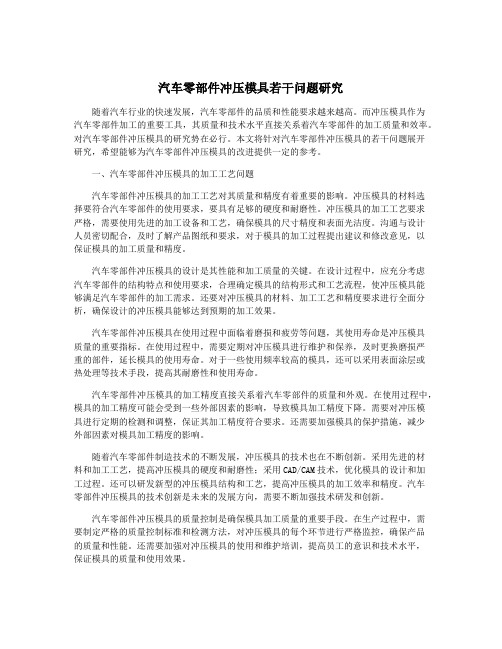
汽车零部件冲压模具若干问题研究随着汽车行业的快速发展,汽车零部件的品质和性能要求越来越高。
而冲压模具作为汽车零部件加工的重要工具,其质量和技术水平直接关系着汽车零部件的加工质量和效率。
对汽车零部件冲压模具的研究势在必行。
本文将针对汽车零部件冲压模具的若干问题展开研究,希望能够为汽车零部件冲压模具的改进提供一定的参考。
一、汽车零部件冲压模具的加工工艺问题汽车零部件冲压模具的加工工艺对其质量和精度有着重要的影响。
冲压模具的材料选择要符合汽车零部件的使用要求,要具有足够的硬度和耐磨性。
冲压模具的加工工艺要求严格,需要使用先进的加工设备和工艺,确保模具的尺寸精度和表面光洁度。
沟通与设计人员密切配合,及时了解产品图纸和要求,对于模具的加工过程提出建议和修改意见,以保证模具的加工质量和精度。
汽车零部件冲压模具的设计是其性能和加工质量的关键。
在设计过程中,应充分考虑汽车零部件的结构特点和使用要求,合理确定模具的结构形式和工艺流程,使冲压模具能够满足汽车零部件的加工需求。
还要对冲压模具的材料、加工工艺和精度要求进行全面分析,确保设计的冲压模具能够达到预期的加工效果。
汽车零部件冲压模具在使用过程中面临着磨损和疲劳等问题,其使用寿命是冲压模具质量的重要指标。
在使用过程中,需要定期对冲压模具进行维护和保养,及时更换磨损严重的部件,延长模具的使用寿命。
对于一些使用频率较高的模具,还可以采用表面涂层或热处理等技术手段,提高其耐磨性和使用寿命。
汽车零部件冲压模具的加工精度直接关系着汽车零部件的质量和外观。
在使用过程中,模具的加工精度可能会受到一些外部因素的影响,导致模具加工精度下降。
需要对冲压模具进行定期的检测和调整,保证其加工精度符合要求。
还需要加强模具的保护措施,减少外部因素对模具加工精度的影响。
随着汽车零部件制造技术的不断发展,冲压模具的技术也在不断创新。
采用先进的材料和加工工艺,提高冲压模具的硬度和耐磨性;采用CAD/CAM技术,优化模具的设计和加工过程。
汽车零部件冲压模具若干问题研究

汽车零部件冲压模具若干问题研究汽车零部件冲压模具的研究是汽车制造工艺的重要组成部分,也是推动汽车工业发展的重要因素。
本文将就汽车零部件冲压模具的若干问题进行深入研究,以便更好地应对当前汽车行业的挑战。
汽车零部件冲压模具的材料选择是研究的关键问题之一。
冲压模具的材料不仅需要具备一定的硬度和强度,还需要具备良好的耐磨性和耐抗拉性能。
在选择材料时,需要考虑到工作条件的要求,选择合适的工程材料,如合金钢、高速钢等。
还需要考虑成本因素,选择经济实用的材料。
汽车零部件冲压模具的设计是研究的另外一个重要问题。
模具设计需要考虑到零部件的形状、尺寸和工艺要求,以及冲压工艺中的力学特性和热学特性等因素。
在设计过程中,需要运用CAD、CAM等辅助设计软件,进行模具的三维建模、零件装配和工艺分析等工作,以确保模具的设计能够满足冲压工艺的要求。
汽车零部件冲压模具的制造是研究的另一个重要问题。
模具制造过程中需要进行材料切割、开槽、钻孔、铣削、磨削等加工工艺。
在制造过程中,需要严格控制模具的尺寸和形状,以保证模具的精度和质量。
还需要对零部件冲压模具进行热处理和表面处理,以提高其硬度和耐磨性能。
汽车零部件冲压模具的使用和维护也是研究的重要问题之一。
模具的使用和维护对于保证冲压工艺的稳定和模具的寿命至关重要。
在使用过程中,需要根据工艺要求进行模具的装配和调试,以确保模具的正常工作。
还需要定期对模具进行清洁和润滑,及时修复和更换损坏的零部件,以延长模具的使用寿命。
汽车零部件冲压模具的研究涉及到材料选择、设计、制造以及使用和维护等多个方面。
只有全面研究和解决这些问题,才能更好地应对当前汽车行业的挑战,推动汽车工业的发展。
冲压磨具结构设计的技术难题解析攻克挑战的秘诀
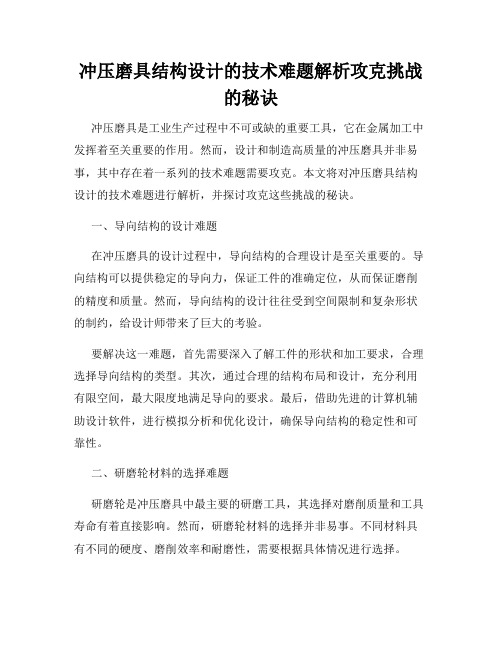
冲压磨具结构设计的技术难题解析攻克挑战的秘诀冲压磨具是工业生产过程中不可或缺的重要工具,它在金属加工中发挥着至关重要的作用。
然而,设计和制造高质量的冲压磨具并非易事,其中存在着一系列的技术难题需要攻克。
本文将对冲压磨具结构设计的技术难题进行解析,并探讨攻克这些挑战的秘诀。
一、导向结构的设计难题在冲压磨具的设计过程中,导向结构的合理设计是至关重要的。
导向结构可以提供稳定的导向力,保证工件的准确定位,从而保证磨削的精度和质量。
然而,导向结构的设计往往受到空间限制和复杂形状的制约,给设计师带来了巨大的考验。
要解决这一难题,首先需要深入了解工件的形状和加工要求,合理选择导向结构的类型。
其次,通过合理的结构布局和设计,充分利用有限空间,最大限度地满足导向的要求。
最后,借助先进的计算机辅助设计软件,进行模拟分析和优化设计,确保导向结构的稳定性和可靠性。
二、研磨轮材料的选择难题研磨轮是冲压磨具中最主要的研磨工具,其选择对磨削质量和工具寿命有着直接影响。
然而,研磨轮材料的选择并非易事。
不同材料具有不同的硬度、磨削效率和耐磨性,需要根据具体情况进行选择。
要攻克这一难题,首先需要充分了解被加工材料的性质和磨削要求,确定研磨轮材料的硬度和颗粒大小。
其次,考虑到研磨轮的寿命和经济性,选择具有较高耐磨性的材料。
最后,通过实验和实际应用的验证,不断优化研磨轮材料的选择,提高磨削效率和质量。
三、磨削参数的优化难题磨削参数的合理选取对于冲压磨具的正常运行和磨削效果的提升至关重要。
然而,由于加工材料、工件形状和磨具结构的不同,磨削参数的优化存在一定的难题。
要解决这一难题,首先需要在实际生产中进行试验和调整,寻找最佳的磨削参数。
其次,借助计算机辅助设计和仿真软件,进行模拟分析和参数优化,提高磨削的效率和精度。
最后,通过长期的实践经验总结和工艺改进,不断优化磨削参数的选择和调整,提高冲压磨具的加工质量和稳定性。
总结:冲压磨具结构设计的技术难题是制约冲压磨具质量和效率提升的主要因素之一。
冲压磨具结构设计的技术难点攻克挑战的秘诀

冲压磨具结构设计的技术难点攻克挑战的秘诀冲压磨具在工业生产中发挥着重要的作用,它们是用来制造各种金属零部件的工具。
然而,冲压磨具的结构设计过程中存在着许多技术难点,攻克这些难点需要设计师面对各种挑战。
本文将探讨冲压磨具结构设计中的技术难点,并分享攻克这些难点的秘诀。
一、冲压磨具的结构设计技术难点1. 材料选择难题冲压磨具的结构设计首先面临的难题是选择材料。
磨具需要具备较高的硬度和耐磨性,同时还要考虑材料的可加工性和成本。
不同工况下的冲压磨具可能需要采用不同的材料,这就对设计师的材料知识和经验提出了更高的要求。
2. 结构强度分析冲压磨具在使用过程中需要承受较大的力和冲击负荷,如果结构设计不合理,就会导致磨具的变形或破裂。
结构强度分析是冲压磨具结构设计中的关键环节,需要通过有限元分析等方法对磨具的应力分布和应变情况进行详细的研究,以确保磨具在工作时具备足够的强度和刚度。
3. 零件排布优化冲压磨具通常由多个零部件组成,如上模、下模、导向柱等。
这些零部件的排布方式对冲压磨具的性能和稳定性有着重要影响。
合理的零件排布可以降低磨具的重量和惯性矩,提高磨具的加工精度和寿命。
二、攻克冲压磨具结构设计技术难点的秘诀1. 深入研究材料特性攻克冲压磨具结构设计技术难点的第一步是深入研究不同材料的特性。
设计师需要了解各种材料的硬度、耐磨性、可加工性等指标,并在实际应用中进行验证。
通过掌握材料的特性,设计师可以更好地选择适用的材料,提高磨具的性能。
2. 结合仿真分析进行结构优化在冲压磨具结构设计过程中,使用仿真分析工具如有限元分析对磨具的结构进行优化是必不可少的。
通过仿真分析,设计师可以准确预测磨具在工作时的应力分布和变形情况,从而针对性地进行结构调整和优化。
3. 引入先进制造技术冲压磨具的制造过程也是攻克技术难点的关键环节。
引入先进的制造技术如数控加工、激光焊接等可以提高磨具的加工精度和一致性。
此外,还可以利用3D打印技术制造出复杂形状的冲压磨具,有助于解决传统加工方法难以实现的结构设计需求。
汽车零部件冲压模具若干问题研究
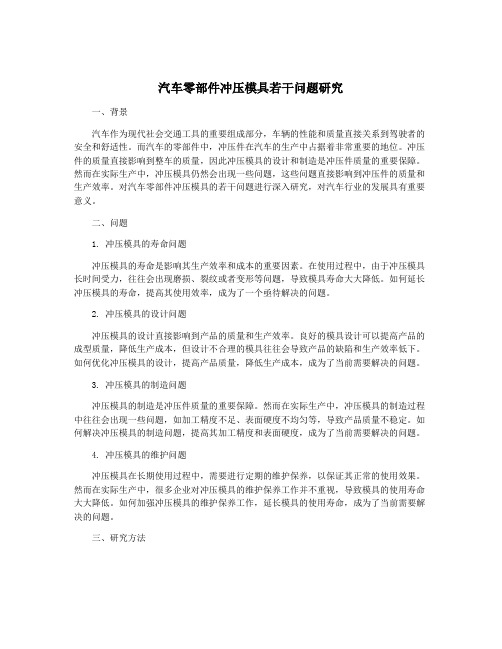
汽车零部件冲压模具若干问题研究一、背景汽车作为现代社会交通工具的重要组成部分,车辆的性能和质量直接关系到驾驶者的安全和舒适性。
而汽车的零部件中,冲压件在汽车的生产中占据着非常重要的地位。
冲压件的质量直接影响到整车的质量,因此冲压模具的设计和制造是冲压件质量的重要保障。
然而在实际生产中,冲压模具仍然会出现一些问题,这些问题直接影响到冲压件的质量和生产效率。
对汽车零部件冲压模具的若干问题进行深入研究,对汽车行业的发展具有重要意义。
二、问题1. 冲压模具的寿命问题冲压模具的寿命是影响其生产效率和成本的重要因素。
在使用过程中,由于冲压模具长时间受力,往往会出现磨损、裂纹或者变形等问题,导致模具寿命大大降低。
如何延长冲压模具的寿命,提高其使用效率,成为了一个亟待解决的问题。
2. 冲压模具的设计问题冲压模具的设计直接影响到产品的质量和生产效率。
良好的模具设计可以提高产品的成型质量,降低生产成本,但设计不合理的模具往往会导致产品的缺陷和生产效率低下。
如何优化冲压模具的设计,提高产品质量,降低生产成本,成为了当前需要解决的问题。
3. 冲压模具的制造问题冲压模具的制造是冲压件质量的重要保障。
然而在实际生产中,冲压模具的制造过程中往往会出现一些问题,如加工精度不足、表面硬度不均匀等,导致产品质量不稳定。
如何解决冲压模具的制造问题,提高其加工精度和表面硬度,成为了当前需要解决的问题。
4. 冲压模具的维护问题冲压模具在长期使用过程中,需要进行定期的维护保养,以保证其正常的使用效果。
然而在实际生产中,很多企业对冲压模具的维护保养工作并不重视,导致模具的使用寿命大大降低。
如何加强冲压模具的维护保养工作,延长模具的使用寿命,成为了当前需要解决的问题。
三、研究方法为了解决上述问题,本研究将采用综合性研究方法,包括实地调研、文献综述、数值模拟、实验验证等多种手段,对汽车零部件冲压模具的若干问题进行深入研究。
具体研究步骤如下:1. 实地调研:通过走访相关汽车制造企业,了解其冲压模具的设计、制造、使用和维护情况,为后续研究提供实际案例和数据支持。
汽车冲压模具常见缺陷及解决方案

本文总结了冲压模具常见的问题,并列出了一些解决方案,供大家参考。
1. 废料跳穴1)冲头长度不够,按冲头刃口切入凹模一个料厚加1mm更换冲头2)凹模间隙过大,割入子减少间隙或用披覆机减小间隙3)冲头或模板未去磁,将冲头或模板用去磁器去磁2. 废料堵穴1)落料孔小或落料孔偏位加大落料孔,使落料顺畅2)落料孔有倒角,加大落料孔去除倒角3)刀口未放锥度,线割锥度或反面扩充孔减小直壁位长度4)刀口直壁位过长,反面钻孔,使刀口直壁位缩短5)刃口崩,造成披锋大,堵料重新研磨刃口3. 披锋不良1)刃口崩,造成披锋过大重新研磨刃口2)冲头与凹模间隙过大,线割入块,重新配间隙3)凹模刀口光洁度差,抛光刀口直壁位4)冲头与凹模间隙过小,重新省模,配间隙5)顶料力过大,反向拉出披锋换弹簧,减小顶料力4. 切边不齐1)定位偏移调整定位2)有单边成型,拉料加大压料力,调整定位3)设计错误,造成接刀不平重新线割切边刀口镶块4)送料不准调整送料器5)送料步距计算有误重新计算步距,重定接刀位5. 冲头易断1)闭合高度过低,冲头切入刀口部位过长调整闭合高度2)材料定位不当,造成冲孔冲头切单边,调整定位或送料装置因受力不均断裂3)下模废料堵死刀口,造成冲头断重新钻大落料孔,使落料顺畅4)冲头的固定部位(夹板)与导向部位修配或重新线割入块使冲头上下顺畅(打板)偏移5)打板导向不良,造成冲头单边受力重新修配打板间隙6)冲头刀口太短,与打板干涉重换冲头,增长刀口部分长度7)冲头固定不好,上下窜动重新固定冲头使之不能上下窜动8)冲头刃口不锋利重新研磨刃口9)冲头表面拉伤,脱料时受力不均重新换冲头10)冲头过细,过长,强度不够重新换冲头类型11)冲头硬度过高,冲头材质不对更换冲头材质,调整热处理硬度6. 铁屑1)压筋错位重新计算压筋位置或折弯位置2)折弯间隙过小,挤出铁屑重新调整间隙,或研磨成型块,或研磨成型冲头3)折弯凸模太锋利修R角4)接刀口材料太少重新接刀口5)压筋太窄重新研磨压筋7. 抽芽不良1)抽芽底孔中心与抽芽冲子中心不重合造确定正确中心位置,或移动抽芽冲子位置,或移成抽芽-边高-边低甚至破裂动预冲孔位置,或调整定位2)凹模间隙不均匀,造成抽芽-边高-边修配抽芽间隙低甚至破裂3)抽芽底孔不符合要求,造成抽芽高度及重新计算底孔孔径,预冲孔增大或减少直径偏差,甚至破裂8. 成型不良1)成型模凸模太锋利,造成材料拉裂成型凸模修R角,刀口处适当修R角2)成型冲头长度不够,造成未能成型计算冲头正确长度调整冲头实际长度以达成型要求3)成型冲头过长,成型处材料压变形,甚确定冲头正确长度,调整冲头实际长度以达到要求至冲头断裂4)成型处材料不够造成拉裂计算展开材料,或修R角,或降低成型高度5)定位不良,造成成型不良调整定位或送料装置6)成型间隙太小造成拉裂或变形调配间隙9. 折弯尺寸1)模具没调到位造成角度误差导致尺寸偏调整闭合高度不良或角度差不良2)弹力不够造成角度不良导致尺寸偏差换弹簧3)材质不符合要求造成角度不良导致尺寸换材料或重新调整间隙偏差4)材料厚度偏差引起角度不良导致尺寸偏确定料厚,换材料或重新调整间隙差5)定位不当导致尺寸偏差调整定位使尺寸OK6)设计或加工错误造成折弯公拼块间有间補焊研磨,消除拼块间的间隙,导致折弯尺寸小7)成型公无R角,在角度及其他正常情况成型公修R角下折弯高度偏小8)两边折弯尺寸偏大加压筋9)单边折弯拉料造成尺寸不稳定加大弹簧力,调整定位10)间隙不合理,引起角度不良和尺寸偏差修配间隙11)折刀高度不够,折弯冲头合入折刀太短增加折刀高度,使折弯冲头尽可能合入折刀部队位造成角度不良多一些12)折弯时速度太快,造成折弯根部变形调整速比控,选择合理转速13)结构不合理,折刀未镶入固定模板,重新铣槽,将折刀镶入模板冲压时,造成间隙变大14)成型公热处理硬度不够,造成压线崩或重制成型公压线打平10. 不卸料1)定位不当或送料不当调整定位或送料装置2)避位不够修磨避位3)内导柱拉伤,造成打板活动不畅更换内导柱4)冲头拉伤或表面不光滑更换冲头5)顶料销摆布不合理重新摆布顶料销位置6)顶料力不够,或脱料力不够更换顶料弹簧或脱料弹簧7)冲头与夹板打板配合不顺畅修配打板和夹板使冲头配合顺畅8)成型滑块配合不畅修整滑块与导向槽使之配合顺畅9)打板热处理不适,冲压一段时间后变形重新研磨打板,矫正变形10)冲头过长或顶料销长度不够增加顶料销长度或换用长度合适之冲头11)冲头断更换冲头12)模板未云磁,工件往上带给模板去磁11. 送料不顺1)模具没架正,导致料带与送料器及模具重架模具或调整送料器不在同一条直线上2)料带不平调整校平机或更换材料3)不卸料造成送料不顺参照不卸料解决对策4)定位太紧调整定位5)导正销太紧或直壁位太长调整导正销6)冲头固定不好或太长与料带干涉换长度合适之冲头重新固定7)顶料销太短,料带与成型入块相干涉调整顶料销长度,避免干涉8)浮升块位置排配不当调整浮升块位置12. 铆合不良1)模具闭合高度不当铆合不到位调整闭合高度2)工件未放到位,定位偏差调整定位3)铆合前工件不良确认抽芽孔,参考抽芽孔不良解决对策处理确认铆合孔是否倒角,如无倒角则增加倒角4)铆合冲头长度不够换用长度合适之冲头5)铆合冲头不符合要求确认并用符合要求之铆合冲头13. 漏装或装1)不小心组立时细心错冲子2)冲子无方向标记有方向性的冲子做上记号14. 装错螺丝1)不知道模板的厚度了解模板的厚度太长或太短2)不够细心,经验不足选用适当的螺丝15. 拆装模具1)销钉孔没有擦干净将销孔,销钉擦干净,拆模时应先拆定位销时容易损坏装模时,应先用螺丝导正,后打定位销钉孔2)装拆模具程序不对打落销钉时不要碰伤销钉孔16. 定位销1)孔壁拉毛,刮伤致使太紧组模时,细心检查销钉孔是否拉毛,否则应将打不出来销孔重新铰孔2)销孔偏位或下面没有逃孔追加定位销逃孔17. 弹簧太长1)没有注意弹簧孔深度量好弹簧孔深度,算好弹簧的压缩量,重新选择无法下压到2)不够细心,经验不足合适的弹簧下死点。
汽车冲压模具调试存在的问题及解决措施
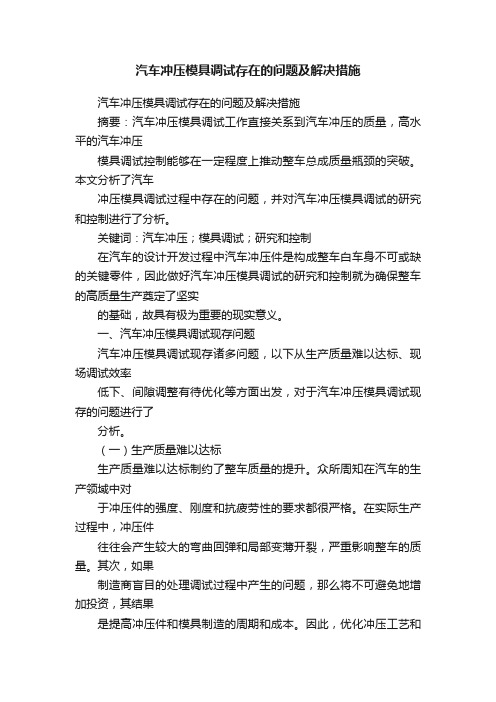
汽车冲压模具调试存在的问题及解决措施汽车冲压模具调试存在的问题及解决措施摘要:汽车冲压模具调试工作直接关系到汽车冲压的质量,高水平的汽车冲压模具调试控制能够在一定程度上推动整车总成质量瓶颈的突破。
本文分析了汽车冲压模具调试过程中存在的问题,并对汽车冲压模具调试的研究和控制进行了分析。
关键词:汽车冲压;模具调试;研究和控制在汽车的设计开发过程中汽车冲压件是构成整车白车身不可或缺的关键零件,因此做好汽车冲压模具调试的研究和控制就为确保整车的高质量生产奠定了坚实的基础,故具有极为重要的现实意义。
一、汽车冲压模具调试现存问题汽车冲压模具调试现存诸多问题,以下从生产质量难以达标、现场调试效率低下、间隙调整有待优化等方面出发,对于汽车冲压模具调试现存的问题进行了分析。
(一)生产质量难以达标生产质量难以达标制约了整车质量的提升。
众所周知在汽车的生产领域中对于冲压件的强度、刚度和抗疲劳性的要求都很严格。
在实际生产过程中,冲压件往往会产生较大的弯曲回弹和局部变薄开裂,严重影响整车的质量。
其次,如果制造商盲目的处理调试过程中产生的问题,那么将不可避免地增加投资,其结果是提高冲压件和模具制造的周期和成本。
因此,优化冲压工艺和调试是解决上述问题的关键,以便最终达到良好的生产质量目标。
(二)现场调试效率低下现场调试效率低下带来的影响是全局性的。
通常来说现场调试效率低下主要是因为拉伸模在调试过程中,工作人员没有解决开裂与起皱之间的矛盾,导致调试过程中出现问题。
其次,工作人员在拉伸调试过程中需要分析制件是否处于良好的受力状态,并且还应当在此基础上根据制件的具体状态来正确地使用塑性变形理论,但是因为许多工作人员达不到这一工作要求,故针对这一问题工作人员应具体问题具体分析,并找到解决方案,最终达到良好的模具调试效果。
(三)间隙调整有待优化汽车冲压模具调试现存问题还体现在间隙调整有待优化。
一般而言间隙调整有待优化主要是指,在第一次调试过程中无法将间隙控制为均匀的状态,故在这一前提下工作人员只有做好上下模间隙的研配,并且根据应力状态来进行整改,否则则无法做好模具的调试工作。
冲压磨具生产中的常见问题及解决方案经验分享解决难题

冲压磨具生产中的常见问题及解决方案经验分享解决难题在冲压磨具生产的过程中,经常会遇到一些问题,这些问题可能会影响到产品的质量和产量。
本文将分享一些常见问题以及解决方案的经验,希望对解决冲压磨具生产中的难题有所帮助。
1. 问题一:磨具磨损严重导致产品质量下降在冲压磨具的使用过程中,由于材料的摩擦和冲击,磨具会不可避免地磨损,导致产品的质量下降。
这是一个非常常见的问题。
解决方案:首先,选择合适的材料来制作磨具,确保其硬度和耐磨性能。
其次,进行定期的磨具维护和更换,及时发现并修复磨损的部位。
最后,优化冲压加工工艺,减少磨具的摩擦和冲击,延长使用寿命。
2. 问题二:磨具尺寸不准确导致产品尺寸偏差在冲压磨具生产过程中,由于各种因素的影响,如材料热胀冷缩、机械变形等,磨具尺寸可能会存在偏差,从而导致产品的尺寸不准确。
解决方案:首先,合理设计和选择磨具结构,考虑到材料的热胀冷缩和机械变形因素,尽量减小磨具尺寸的变化范围。
其次,进行精确的磨具尺寸测量和校正,确保磨具尺寸的准确性。
最后,严格控制冲压工艺参数,减少尺寸偏差的产生。
3. 问题三:磨具生产周期长导致生产效率低下在冲压磨具生产过程中,由于一些技术难题和工艺要求,磨具的制作周期可能会比较长,从而导致生产效率低下。
解决方案:首先,综合考虑磨具制作周期和产品生产周期,提前预留足够的时间进行磨具制作。
其次,优化磨具制作工艺,采用高效的机械加工设备和工艺流程,缩短制作周期。
最后,加强团队协作,合理分配人力资源,提高磨具制造的效率。
4. 问题四:磨具脱落或损坏导致安全隐患在冲压磨具的生产和使用过程中,由于各种原因,磨具可能会脱落或损坏,给生产带来安全隐患。
解决方案:首先,加强磨具的安装和固定,确保其牢固可靠。
其次,进行定期的磨具检测和维护,及时发现并修复磨具的脱落或损坏问题。
最后,加强人员的安全教育和培训,提高员工对磨具安全的意识和认识。
5. 问题五:磨具生产成本高导致产品成本增加在冲压磨具的生产过程中,由于材料、设备和人力成本的提高,磨具的生产成本可能会不断增加,从而导致产品的成本增加。
汽车零部件冲压模具若干问题研究

汽车零部件冲压模具若干问题研究汽车零部件冲压模具是在汽车生产过程中起着关键作用的工具,它的质量和性能直接影响着汽车的生产效率和品质。
在实际生产中,冲压模具所面临的问题也不容小觑,它们可能会导致生产效率低下或者产品质量不稳定。
对汽车零部件冲压模具若干问题进行研究,有助于提高生产效率、降低成本、提升产品质量。
一、冲压模具的设计问题二、材料选择问题冲压模具的材料选择直接关系到模具的使用寿命和稳定性。
一些模具可能会因为材料选择不当而导致使用寿命过短或者出现断裂等问题。
材料的疲劳性能和抗磨损性能也是影响冲压模具使用寿命的关键因素,选择合适的材料能够有效地提高模具的使用寿命和稳定性。
三、模具加工精度问题冲压模具的加工精度直接影响着产品的成型精度和表面质量。
而在实际生产中,一些模具可能会因为加工精度不足而导致产品的尺寸偏差、表面瑕疵等问题。
提高冲压模具的加工精度是提高产品质量和稳定性的重要途径。
四、模具保养与维护问题冲压模具的保养和维护对于延长模具的使用寿命和稳定性具有重要意义。
在一些企业中,由于对模具的保养和维护不够重视,导致模具的使用寿命较短,甚至出现断裂等问题。
加强对冲压模具的保养和维护是提高模具使用寿命和稳定性的必要手段。
五、模具使用中的技术问题在实际生产中,操作人员的技术水平直接影响着冲压模具的使用效果。
一些操作技术不规范或者不熟练可能会导致模具的损坏、产品的质量不稳定等问题。
加强操作人员的技术培训和指导,提高他们的操作技术水平是提高模具使用效果的重要途径。
汽车零部件冲压模具在实际生产中所面临的问题不容忽视。
只有加强对冲压模具设计、材料选择、加工精度、保养与维护以及操作技术的研究和改进,才能够提高模具的使用寿命和稳定性,降低成本,提高产品质量和生产效率。
希望在未来的研究中,能够深入探讨这些问题,为汽车零部件冲压模具的高效使用提供更多的理论和实践支持。
冲压磨具结构设计的八大难题解决方案

冲压磨具结构设计的八大难题解决方案在冲压工艺中,磨具起着至关重要的作用。
磨具的设计和结构直接影响着冲压品质和生产效率等方面。
然而,在磨具设计过程中,常常会遇到一些难题,给冲压加工带来困扰。
本文将介绍冲压磨具结构设计中的八大难题,并提出相应的解决方案。
一、磨损与寿命短冲压磨具在长时间运行中,往往会出现磨损现象,导致寿命变短。
为解决这一问题,可以采用表面硬化或涂层技术增加磨具的硬度和耐磨性。
此外,优化冲压工艺参数,减少磨具的使用次数,也可以延长其寿命。
二、变形与尺寸误差在冲压过程中,磨具容易发生变形,导致冲压件存在尺寸误差。
解决这一问题的方法是在磨具的结构设计中考虑加强刚度和稳定性,采用适当的支撑和导向机构,避免变形影响冲压精度。
三、噪音与振动问题磨具在运行过程中会产生噪音和振动,给操作人员带来不便,并可能影响冲压品质。
为解决这一问题,可以采用减振材料,对磨具进行减振处理。
同时,合理设计磨具的结构,降低振动和噪音传播。
四、换模与调试耗时长传统的磨具设计需要经过多次调试和验证才能达到理想的冲压效果,导致换模和调试的时间成本高。
为解决这一问题,可采用仿真软件进行磨具设计和优化,减少实际试制的次数,提高换模和调试的效率。
五、锻造与切削难度大部分冲压件需要通过锻造或切削等工艺进行成型,然而现有磨具结构难以满足这些复杂工艺要求。
解决这一问题的方法是采用多工位和分模设计,分阶段完成锻造和切削工艺,提高磨具的适应性和灵活性。
六、冲压件测量与质检困难冲压件的测量和质检一直是冲压行业的难题,尤其是对形状复杂的零件。
为解决这一问题,可以借助先进的三维扫描和检测技术,对冲压件进行全面而快速的测量和质检,提高产品的合格率和一致性。
七、磨具设计与优化手段有限目前,磨具设计和优化主要依靠工程师的经验和试验验证,缺乏系统化和科学化的手段。
为解决这一问题,可以借助计算机辅助设计软件和优化算法,进行磨具设计和结构优化,提高设计的准确性和效率。
冲压磨具结构设计的七大难题解决方案

冲压磨具结构设计的七大难题解决方案冲压磨具在现代制造业中扮演着至关重要的角色,它们在金属成型加工过程中起着关键的作用。
然而,随着制造业的快速发展和产品要求的不断提高,冲压磨具结构设计也面临着一系列的挑战和困难。
本文将介绍冲压磨具结构设计的七大难题,并提供解决方案以应对这些挑战。
一、刚度不足冲压磨具在工作过程中需要承受较大的载荷,因此其刚度是至关重要的。
刚度不足可能导致磨具在加工过程中产生变形或振动,从而影响产品质量。
为了解决这个问题,设计师可以采用以下措施:1.增加磨具的壁厚或采用更坚固的材料;2.在关键部位加入加强结构或支撑;3.优化磨具的几何形状,提高整体刚度。
二、尺寸精度要求高冲压磨具的结构设计中,尺寸精度是一个重要的考量因素。
在高精度加工中,小尺寸误差可能导致产品不合格。
为了满足尺寸精度要求,应注意以下几点:1.采用高精度的制造工艺和加工设备;2.优化磨具的结构,减小尺寸误差的传递;3.加强对磨具制造过程的控制,确保每个环节都符合要求。
三、液压系统的设计液压系统在冲压磨具中起着关键的作用,它提供了所需的压力和力量。
然而,液压系统的设计也面临着一些难题。
为了解决这些问题,我们可以考虑以下方案:1.优化系统的工作流程,降低能耗和噪音;2.选择合适的液压元件,确保其性能和质量;3.设计合理的控制策略,提高系统的响应速度和稳定性。
四、磨具寿命短磨具的寿命是制造企业关注的一项重要指标,寿命短可能导致频繁更换和维修,增加成本和生产周期。
为了延长磨具的寿命,我们可以采取以下措施:1.选择高品质的材料,提高抗磨损和抗腐蚀能力;2.合理设置磨具的工作参数,降低磨具的磨损;3.定期对磨具进行保养和维修,延长使用寿命。
五、设计效率低冲压磨具结构设计的效率直接影响到产品的制造周期和成本。
为了提高设计效率,可以考虑以下几点:1.采用CAD(计算机辅助设计)系统进行设计,提高设计速度和精度;2.充分利用现有的设计资源和经验,避免重复设计;3.与制造部门和工艺工程师紧密合作,加快设计验证和改进的速度。
冲压磨具生产的技术难点与解决方案

冲压磨具生产的技术难点与解决方案冲压工艺在工业生产中起着重要的作用,而冲压磨具则是冲压工艺实施的关键工具。
冲压磨具的质量和性能直接决定了冲压产品的精度和质量。
然而,冲压磨具的生产过程中存在着许多技术难点,需要采取一系列的解决方案来保证磨具的生产质量。
本文将对冲压磨具生产中的技术难点进行探讨,并提出相应的解决方案。
一、冲压磨具生产的技术难点1. 材料选择难题冲压磨具的材料选择直接影响到其使用寿命和工作效果。
对于不同类型的冲压磨具,需要选择适合的材料,以满足不同的工艺要求和使用环境。
然而,材料的选择并不是一件简单的事情,需要综合考虑磨具的强度、硬度、韧性等因素,并与工艺要求相匹配。
2. 磨具制造精度要求高冲压磨具的制造精度要求非常高,特别是工作面的加工精度和表面粗糙度。
冲压磨具的工作面需要具备较高的平整度和精度,以保证冲压件的加工精度和表面质量。
然而,由于加工难度大、工艺复杂等原因,磨具制造时容易出现误差,影响到磨具的使用效果。
3. 磨具寿命短在实际应用中,冲压磨具的寿命普遍偏短。
这是因为磨具在使用过程中受到了较大的冲击力和磨损,导致磨具使用寿命的降低。
尤其对于高强度材料的冲压工艺,更容易导致磨具寿命的缩短。
二、冲压磨具生产的解决方案1. 优化材料选择针对冲压磨具的材料选择难题,可以采用精细的材料评估和筛选方法。
通过实验研究、模拟仿真等手段,选择合适的材料,以满足冲压磨具在不同工艺条件下的使用要求。
此外,还可以利用表面处理技术,对磨具进行强化处理,提高其使用寿命。
2. 加强制造工艺控制为了确保冲压磨具的制造精度,需要加强制造工艺的控制。
通过制定合理的生产工艺流程、选用适合的设备和工具,保证磨具的加工精度和表面质量。
同时,采用精密的检测方法,对磨具进行全面的检测和测试,及时发现和修复潜在的缺陷和问题。
3. 提高磨具的耐磨性能为了解决冲压磨具寿命短的问题,可以在材料选择和加工工艺上进行优化。
选用高强度、高硬度的材料,提高磨具的耐磨性能。
冲压磨具设计中的关键技术与难点分析

冲压磨具设计中的关键技术与难点分析冲压磨具设计在工业制造领域中扮演着重要的角色,为零件的生产提供了关键的工艺支持。
然而,在冲压磨具设计的过程中,会面临一些技术和难点问题。
本文将就冲压磨具设计中的关键技术与难点进行分析,并提出解决方法。
一、材料选择与设计参数确定在冲压磨具设计中,材料的选择及设计参数的确定是首要的任务。
材料的选择直接影响着磨具的使用寿命和性能。
常见的磨具材料包括高速钢、硬质合金等。
设计参数的确定包括磨具的尺寸、结构、刃口形状等。
这些参数的选择需要充分考虑零件的形状、尺寸、材料等因素,以确保磨具在工作中能够达到预期的效果。
二、冲压磨具的结构设计冲压磨具的结构设计是冲压磨具设计过程中的关键环节。
合理的结构设计可以提高工作效率和加工精度,减少能耗和材料浪费。
在设计过程中,需要综合考虑磨具的强度、刚度和稳定性,避免出现过度振动、变形等问题。
此外,还需要考虑冲压磨具的可拆卸性,以便于更换磨损部件或进行维修。
三、冲压磨具的表面处理与热处理冲压磨具在使用过程中容易受到磨损和腐蚀的影响,因此需要进行表面处理和热处理,提高磨具的表面硬度和耐磨性。
常用的表面处理方法包括镀铬、氮化和涂覆等。
而热处理则可以通过改变磨具的晶体结构和组织状态来提高其力学性能和耐磨性。
在进行表面处理和热处理时,需要注意处理工艺的选择和参数的控制,以确保处理效果的稳定性和一致性。
四、磨具的精度控制与检测冲压磨具的精度控制和检测是设计过程中需要重视的难点。
磨具的精度直接影响着零件的加工精度和质量。
在设计过程中,需要充分考虑磨具加工和装配的误差,采取有效的措施控制磨具的精度。
同时,还需要设计合适的检测装置和方法,对磨具的精度进行检测和验证,以确保磨具在工作中能够稳定地达到要求的加工精度。
五、冲压磨具的寿命预测与维护冲压磨具的寿命预测与维护是冲压磨具设计中的关键问题。
寿命预测可以通过模拟和实验的方法进行,以确定磨具的使用寿命和更换周期。
冲压磨具制造的四大挑战及应对之道

冲压磨具制造的四大挑战及应对之道冲压磨具制造在现代工业生产中发挥着重要的作用。
然而,随着市场需求的不断变化和技术的不断更新,冲压磨具制造面临着一些挑战。
本文将探讨冲压磨具制造的四大挑战,并给出相应的解决方案。
挑战一:精度要求越来越高随着产品精度要求的提高,冲压磨具制造面临更高的技术要求。
精度问题可能导致产品质量不稳定,导致浪费和延误。
为了解决这个挑战,冲压磨具制造商可以采取以下措施:1.优化设备和工艺流程。
采用先进的数控设备和自动化生产线,提高生产效率和精度。
2.严格质量控制。
建立完善的质量管理体系,制定严格的工艺规范,确保产品达到要求的精度。
挑战二:材料选择和加工难度增加随着材料技术的发展,更多种类的材料被应用于冲压磨具制造中。
这些新材料具有较高的硬度、强度和耐磨性,给加工带来了新的挑战。
针对这一问题,制造商可以采取以下方法:1.合理选择材料。
根据具体产品的要求和工艺特点,选择适合的材料,确保加工性能和产品质量。
2.引进新技术和设备。
如高速铣削、激光切割等先进技术,提高加工效率和精度。
挑战三:生产周期压力增大随着市场竞争的日益激烈,产品的交付时间越来越紧迫,冲压磨具制造商面临着加快生产周期的压力。
为了应对这一挑战,制造商可以采取以下措施:1.合理优化生产计划。
根据市场需求和设备利用率,合理安排生产任务,提高生产效率。
2.提高生产线的自动化水平。
采用自动化设备和智能化管理系统,减少人工干预,提高生产速度和精度。
挑战四:技术更新和人员培训难题随着技术的不断进步,冲压磨具制造技术也在不断更新。
制造商需要不断学习新技术,培训员工,以适应市场的变化。
为了解决这一挑战,制造商可以采取以下措施:1.加强研发和创新能力。
为了跟上市场需求的变化,制造商应不断投入研发和创新,引进新的技术和工艺。
2.加强员工培训。
制定培训计划,提高员工的技术水平和专业素养,以适应技术更新的需求。
总结冲压磨具制造面临着精度要求高、材料选择和加工难度增加、生产周期压力增大以及技术更新和人员培训难题等四大挑战。
冲压模具提速出现的问题及解决措施
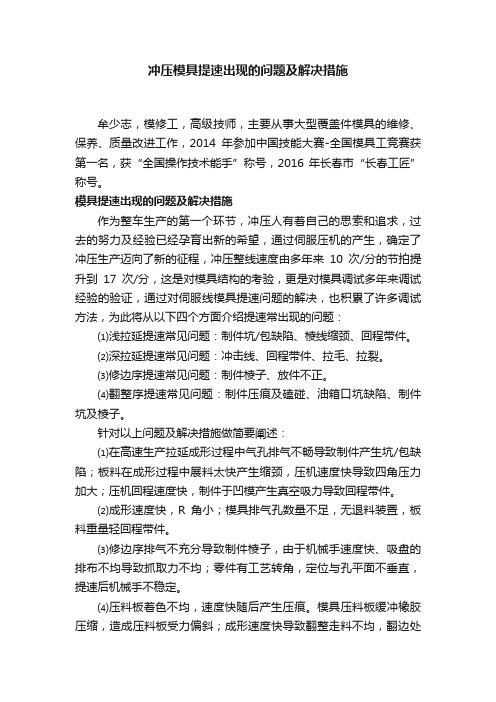
冲压模具提速出现的问题及解决措施牟少志,模修工,高级技师,主要从事大型覆盖件模具的维修、保养、质量改进工作,2014年参加中国技能大赛-全国模具工竞赛获第一名,获“全国操作技术能手”称号,2016年长春市“长春工匠”称号。
模具提速出现的问题及解决措施作为整车生产的第一个环节,冲压人有着自己的思索和追求,过去的努力及经验已经孕育出新的希望,通过伺服压机的产生,确定了冲压生产迈向了新的征程,冲压整线速度由多年来10次/分的节拍提升到17次/分,这是对模具结构的考验,更是对模具调试多年来调试经验的验证,通过对伺服线模具提速问题的解决,也积累了许多调试方法,为此将从以下四个方面介绍提速常出现的问题:⑴浅拉延提速常见问题:制件坑/包缺陷、棱线缩颈、回程带件。
⑵深拉延提速常见问题:冲击线、回程带件、拉毛、拉裂。
⑶修边序提速常见问题:制件棱子、放件不正。
⑷翻整序提速常见问题:制件压痕及磕碰、油箱口坑缺陷、制件坑及棱子。
针对以上问题及解决措施做简要阐述:⑴在高速生产拉延成形过程中气孔排气不畅导致制件产生坑/包缺陷;板料在成形过程中展料太快产生缩颈,压机速度快导致四角压力加大;压机回程速度快,制件于凹模产生真空吸力导致回程带件。
⑵成形速度快,R角小;模具排气孔数量不足,无退料装置,板料重量轻回程带件。
⑶修边序排气不充分导致制件棱子,由于机械手速度快、吸盘的排布不均导致抓取力不均;零件有工艺转角,定位与孔平面不垂直,提速后机械手不稳定。
⑷压料板着色不均,速度快随后产生压痕。
模具压料板缓冲橡胶压缩,造成压料板受力偏斜;成形速度快导致翻整走料不均,翻边处压料板压料不实;填充斜器速度快,制件在凸模结合处产生磕碰形成棱子。
在高产能、高负荷生产中应根据模具结构进行综合分析,可以参考以上现阶段总结经验进行缺陷排查。
案例分析⑴门外板作为整车的一部分,其工艺要求更为严格,其属于浅拉延胀形模具。
现以某车型后门外板为例进行具体阐述。
在门外板的生产节拍由7次提升到15次的过程中,制件出现多处坑缺陷,如图1所示。
冲压磨具制造技术突破创新的新途径

冲压磨具制造技术突破创新的新途径随着制造业的不断发展,冲压加工作为一种常见的金属材料成形方法得到了广泛应用。
而冲压磨具作为冲压加工过程中的重要设备之一,在保证产品质量和生产效率方面扮演着至关重要的角色。
本文将介绍冲压磨具制造技术的发展现状,分析现有技术的局限性,并提出了新的突破创新的途径。
一、冲压磨具制造技术的发展现状冲压磨具制造技术是制造高质量、高效率冲压产品的关键步骤。
随着制造技术的不断进步,冲压磨具制造技术也在不断发展。
目前主要应用的冲压磨具制造技术包括传统的数控加工、电火花加工、线切割加工等。
1. 传统的数控加工技术传统的数控加工技术通过编程控制数控机床进行材料加工,具有成本低、加工精度高的特点。
然而,在实际应用中,该技术存在着生产周期长、效率低等问题,无法满足现代制造业对高效、精确生产的要求。
2. 电火花加工技术电火花加工技术通过放电腐蚀工艺进行材料加工,具有能够加工硬度高的材料、加工精度高等优点。
但是,该技术也存在着加工效率低、电极磨损快等问题,制约了其在冲压磨具制造中的应用广度。
3. 线切割加工技术线切割加工技术通过利用金属丝切割原理进行材料加工,具有加工速度快、切割精度高等特点。
然而,该技术仍然存在着切割粗糙度高、切割面不平等等问题,无法满足高要求的冲压磨具制造需要。
二、现有技术的局限性尽管现有的冲压磨具制造技术在一定程度上满足了生产需求,但还存在许多局限性。
首先,现有技术在材料选择方面存在一定的限制。
不同的材料对冲压磨具的制造具有不同的要求,传统的数控加工技术难以满足对材料有着更高要求的应用场景。
其次,现有技术在加工精度和加工效率方面存在矛盾。
传统的数控加工技术虽然能够保证加工精度,但生产周期长、效率低。
相反,电火花加工和线切割加工技术虽然提高了加工效率,但加工精度和表面质量有所下降。
最后,现有技术在加工成本和设备投入方面存在较高的限制。
冲压磨具制造工艺繁琐,设备成本高,制约了该领域技术的进一步发展。
冲压模具设计过程中的工程管理问题及解决方案
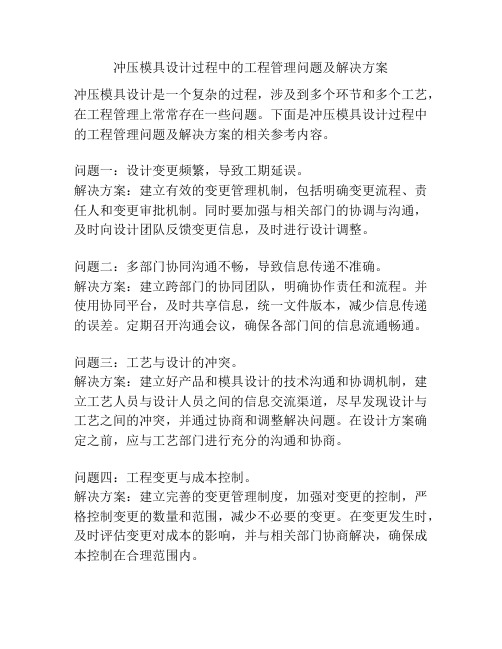
冲压模具设计过程中的工程管理问题及解决方案冲压模具设计是一个复杂的过程,涉及到多个环节和多个工艺,在工程管理上常常存在一些问题。
下面是冲压模具设计过程中的工程管理问题及解决方案的相关参考内容。
问题一:设计变更频繁,导致工期延误。
解决方案:建立有效的变更管理机制,包括明确变更流程、责任人和变更审批机制。
同时要加强与相关部门的协调与沟通,及时向设计团队反馈变更信息,及时进行设计调整。
问题二:多部门协同沟通不畅,导致信息传递不准确。
解决方案:建立跨部门的协同团队,明确协作责任和流程。
并使用协同平台,及时共享信息,统一文件版本,减少信息传递的误差。
定期召开沟通会议,确保各部门间的信息流通畅通。
问题三:工艺与设计的冲突。
解决方案:建立好产品和模具设计的技术沟通和协调机制,建立工艺人员与设计人员之间的信息交流渠道,尽早发现设计与工艺之间的冲突,并通过协商和调整解决问题。
在设计方案确定之前,应与工艺部门进行充分的沟通和协商。
问题四:工程变更与成本控制。
解决方案:建立完善的变更管理制度,加强对变更的控制,严格控制变更的数量和范围,减少不必要的变更。
在变更发生时,及时评估变更对成本的影响,并与相关部门协商解决,确保成本控制在合理范围内。
问题五:设计与试产之间的协调。
解决方案:设计团队要与试产工程师进行密切配合与沟通,及时了解试产情况和问题,并根据试产结果及时进行设计调整和改进。
同时要建立试产数据与设计数据的对接机制,确保设计方案的准确性和可行性。
问题六:质量控制与验收问题。
解决方案:建立完善的质量控制制度,明确质量控制点和责任人,进行全过程的质量控制。
制定质量验收标准和流程,建立验收文件和记录,确保模具设计的质量和稳定性。
严格按照验收标准进行验收,并制定相应的改进措施。
总之,冲压模具设计过程中的工程管理问题有很多,解决这些问题需要建立完善的管理机制和流程,加强部门间的协调与沟通,确保设计的准确性和质量,提高工程管理的效率和效果。
- 1、下载文档前请自行甄别文档内容的完整性,平台不提供额外的编辑、内容补充、找答案等附加服务。
- 2、"仅部分预览"的文档,不可在线预览部分如存在完整性等问题,可反馈申请退款(可完整预览的文档不适用该条件!)。
- 3、如文档侵犯您的权益,请联系客服反馈,我们会尽快为您处理(人工客服工作时间:9:00-18:30)。
破解汽車衝壓模具技術難題
2005-3-9 11:04:00 添加到生意宝
中科院知識創新工程重大專案“集成化鐳射智慧製造及柔性加工系統”已成功研製, 由中國科學院力學研究所主持的第一批中國科學院知識創新工程重大專案“集成化鐳射智慧製造及柔性加工研究”,經虞鋼研究員為首席科學家的專案組三年刻苦攻關,研製出國內首套“集成化鐳射智慧製造及柔性加工系統”,並針對制約我國汽車產業進一步發展的衝壓模具使用壽命短、維護費用高這一難題,利用鐳射與材料相互作用原理並結合智慧測量等技術對其表面進行強化處理,從而大幅度提高了大型汽車衝壓模具的使用壽命。
該技術已提供給上海大型汽車有限公司,並將為企業帶來巨大的經濟效益。
5月18日,以許祖彥院士、關橋院士、周壽桓院士眾組長的專家組以及上海大?汽車有限公司相關負責人在力學研究所聽取了該專案的鑒定、驗收報告會,並參觀了該鐳射智慧製造系統,觀看了模具強化過程的現場演示。
專家一致認為:該專案研究成果整體達到了國際先進水平。
鑒於“集成化鐳射智慧製造及柔性加工系統”具有重大的應用前景,專家提出專案成果應繼續以汽車模具鐳射表面強化等領域為突破口,並迅速推廣到其他廠家,解決長期困擾我國汽車廠家的大型衝壓模具使用壽命問題,進而實現產業化。
專案研製出一套“集成化鐳射智慧製造及柔性加工系統”,集成了數控千瓦級工業固體雷射器,大範圍高精度5軸框架式機器人,模具表面快速智慧測量和曲面重構,模具成型工藝參數的數值和物理類比軟體,高功率雷射光束的空間變換和柔性傳輸技術,汽車模具鐳射表面強化技術和物理數學模型,底層控制和CAx過程資料庫等。
專案具有基礎研究與技術發展相結合、鐳射加工機器人技術與鐳射製造工藝力學相結合的特色,取得了多項重要進展和創新。
該系統可滿足3D鐳射加工和快速成型的需求,實現鐳射機器人製造與加工過程的智慧化、柔性化和模組化,以及資訊過程的數位元元元化和控制過程的集成化;可提供具有自主知識產權的技術和裝備系統,為汽車車身快速開發提供了關鍵技術支援。
專案研製過程中,充分發揮了中國科學院多學科交叉的綜合優勢,廣泛吸收社會資源,與國內外同行進行了廣泛深入的合作與交流,聯合攻克了一系列難關。
專案組與瑞典勒呂奧科技大學、瀋陽自動化所、本所LNM、LHD開放實驗室等單位建立了密切合作,在相關國際前沿領域開展了基礎和關鍵技術研究。
同時,為了滿足衝壓模具表面強化這一實際工程需要,專案組與上海大眾汽車有限公司隨時溝通、密切配合,保證了終端用戶對專案研製各階段的認同。
力學研究所作為國家級研究機構,瞄準國際科學技術發展的前沿,開展我國先進製造及相關力學科學技術領域前瞻性、基礎性和戰略性研究,發現新的力學現象並積累創新技術,?國家急需的鐳射智慧製造工藝力學的探索研究奠定基礎,為實現製造業的跨越式發展提供了必備的研究平臺。
* 本信息来源于网上,真实性未经中国塑料模具网证实,仅供您参考!。