BCS技术在广西柳钢集团二棒生产线加热炉上的应用
探究钢厂热轧加热炉智能烧钢技术应用实践

探究钢厂热轧加热炉智能烧钢技术应用实践钢厂热轧加热炉是一种主要用来对钢材进行加热处理的设备,其负责将钢坯加热至合适的温度,以便进行下一步的轧制工序。
由于热轧加热炉需要消耗大量的能源,而且钢材的加热过程需要精确控制温度和时间,传统的烧钢方式在能源消耗和生产效率方面存在一定的问题。
为了解决这些问题,钢厂热轧加热炉智能烧钢技术应运而生。
智能烧钢技术是一种基于先进的控制系统和传感器技术的烧钢方法,通过实时监测和分析钢材的温度、压力和湿度等参数,以及根据钢材的性质和要求进行智能控制,从而提高烧钢过程的能源利用率和生产效率。
智能烧钢技术的应用实践主要包括以下几个方面:智能烧钢技术可以实现烧钢过程的自动化控制。
通过将传感器安装在热轧加热炉的关键位置,实时监测和采集钢材的温度、压力和湿度等参数,并将数据传输给控制系统进行分析和处理,可以实现对炉内温度和加热时间的准确控制,从而保证钢材加热的精度和一致性。
智能烧钢技术可以提高热能利用效率。
传统的烧钢方法中,由于无法准确控制钢材的温度和热传导速度,常常会导致能源的浪费。
而智能烧钢技术可以根据炉内温度的变化和钢材的特性,通过调整加热功率和时间,最大限度地利用热能资源,提高能源利用效率,降低生产成本。
智能烧钢技术可以提高生产效率和产品质量。
智能烧钢技术不仅可以实现烧钢过程的自动化控制,还可以通过对数据的分析和挖掘,及时发现生产过程中的异常情况和问题,并进行相应的调整和优化。
这样可以提高生产效率,缩短加热时间,降低生产成本的还可以保证钢材的质量和一致性,提高产品的竞争力。
智能烧钢技术还可以提高生产安全和环境保护。
由于热轧加热炉在工作过程中需要消耗大量的能源,若燃烧不完全或发生其他异常情况,很容易引发火灾和爆炸等事故。
而智能烧钢技术可以通过实时监测和报警系统,及时发现和处理异常情况,保障生产安全。
智能烧钢技术还可以减少燃烧产物的排放,降低对环境的污染。
钢厂热轧加热炉智能烧钢技术的应用实践对于提高生产效率、产品质量、能源利用效率、安全性和环境保护等方面具有重要意义。
BCS技术在信钢4~#高炉热风炉自动烧炉中的应用
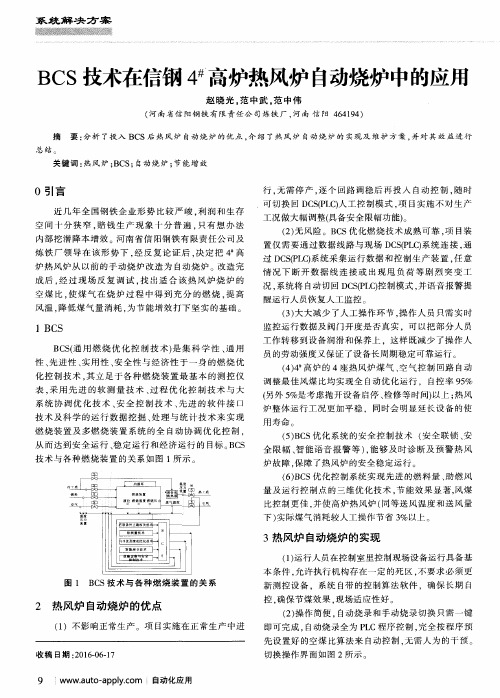
比控制更佳 , 并使高炉热风炉 ( 同等送风温度和送风量
下) 实 际 煤气 消耗 较 人工 操 作 节 省 3 %以上 。
3热 风炉 自动 烧 炉 的 实 现
( 1 ) 运 行人 员 在 控制 室 里控 制 现 场设 备 运行 具 备 基 本条件 , 允 许 执 行 机 构存 在 一 定 的死 区 , 不 要 求 必 须 更
行, 无需停产 , 逐 个 回路 调 稳 后 再 投 入 自动 控 制 , 随 时 可切换 回 D C S ( P L C ) 人工控制模式 , 项 目实 施 不 对 生 产 工 况做 大 幅调 整 ( 具 备 安 全 限 幅功 能) 。 ( 2 ) 无 风 险 。B C S 优 化 燃 烧 技 术 成 熟 可靠 , 项 目装
( 5 ) B C S优 化 系 统 的 安 全 控 制 技 术 ( 安全联锁 、 安
技 术 及 科 学 的运 行 数 据 挖 掘 、 处 理 与 统 计 技 术 来 实 现 燃 烧 装 置 及 多燃 烧 装 置 系 统 的全 自动 协 调 优 化 控 制 , 从 而达到安全运行 、 稳 定 运 行 和 经 济 运 行 的 目标 。 B C S
系 统 解 决 方 案 ◆∥ ≯000
B C S 技术在信钢 4 群 高炉热风炉 自动烧炉中的应用
赵 晓光 , 范 中武 , 范 中伟
( 河 南省 信 阳钢铁 有 限责任 公 司炼铁 厂 , 河南 信阳 4 6 4 1 9 4 )
摘 要 : 分 析 了投 入 BC S后 热 风 炉 自动 烧 炉 的 优 点 , 介 绍 了 热 风 炉 自动 烧 炉 的 实现 及 维 护 方 案 , 并对 其 效益 进行
切 换操 作 界 面 如 图 2所 示 。
DCS在柳钢2号高炉上的应用
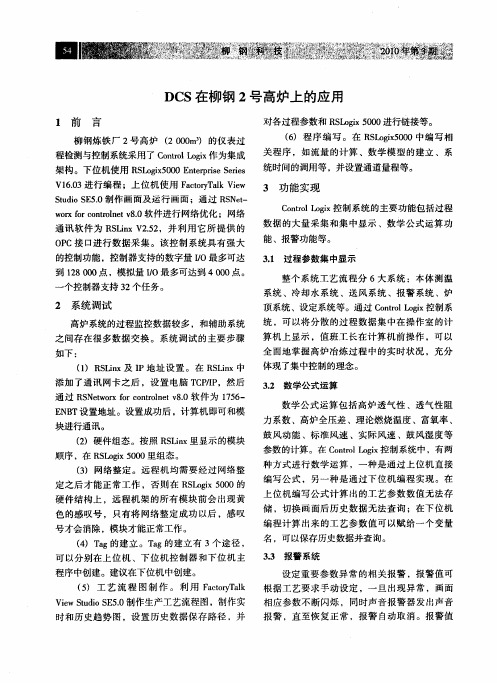
( 3 )气密箱温度高于 7c。 0= 【 ( 4 )炉顶温度高于50 。 0 ̄ C
()炉 顶压力 高 于 2 0 P 。 5 2 K a
3 历史 数据查 询 . 4
4结
语
()过 程参 数 的集 中显示 为 高炉全 局控 制和 1
分析 炉况 、指导 冶炼 提供 了有利 条件 。 () 控制 系统利 用梯 型 图编程 简 单清晰 ;同 2 可 以制作 数 据 趋 势 图 ,通 过 趋 势 图 可 以 观 察 炉况 ,一 旦 出现 异 常 极 易 发 现 ,而 且 可 以 调
定之后才能正常工作 ,否则在 R Lg 0 0 Soi 50 的 x
硬 件 结 构上 ,远 程 机 架 的所 有 模 块 前 会 出现 黄
上位机编写公式计算出的_艺参数数值无法存 丁 储 ,切换画面后历史数据无法查询 ;在下位机 编程计算 出来的工艺参数值 可以赋给一个变量
名 ,可 以保 存历史 数据 并查 询 。
力系数 、高炉全压差 、理论燃烧温度 、富氧率 、
鼓 风动 能 、标 准 风速 、实 际 风 速 、鼓 风 湿度 等 参数 的计 算 。在 C nrl oi控 制 系统 中 ,有两 ot g oL x 种 方式 进 行 数 学 运 算 ,一 种 是 通 过 上 位 机 直接
编 写公 式 ,另 一 种 是 通过 下 位 机 编 程 实 现 。在
■l
D S在 柳钢 2号 高炉上 的应 用 C
l 前 言
麓
对各过程参数和 R Lg 0 0 S oi 50 进行链接等。 x
() 程 序 编 写 。在 R Lg 50 6 Soi 00中编 写相 x
柳 钢 炼铁 厂 2号 高 炉 ( 0 m) 的仪 表 过 200
柳钢麦尔兹气烧双膛石灰竖窑自动控制系统应用
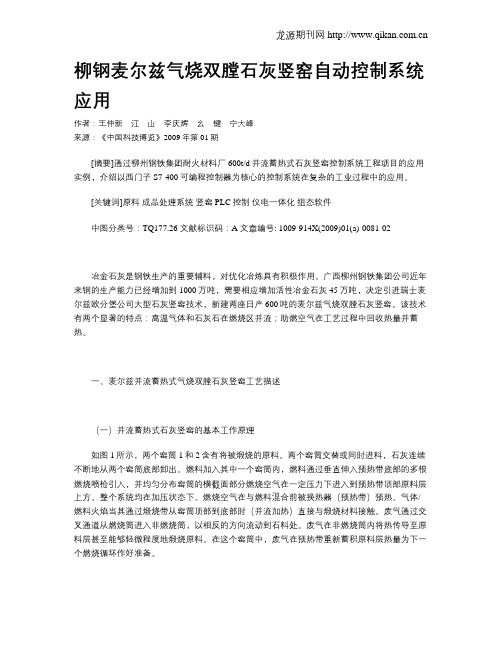
柳钢麦尔兹气烧双膛石灰竖窑自动控制系统应用作者:王仲新江山李庆辉幺键宁大峰来源:《中国科技博览》2009年第01期[摘要]通过柳州钢铁集团耐火材料厂600t/d并流蓄热式石灰竖窑控制系统工程项目的应用实例,介绍以西门子S7-400可编程控制器为核心的控制系统在复杂的工业过程中的应用。
[关键词]原料成品处理系统竖窑PLC控制仪电一体化组态软件中图分类号:TQ177.26 文献标识码:A 文章编号: 1009-914X(2009)01(a)-0081-02冶金石灰是钢铁生产的重要辅料,对优化冶炼具有积极作用。
广西柳州钢铁集团公司近年来钢的生产能力已经增加到1000万吨,需要相应增加活性冶金石灰45万吨,决定引进瑞士麦尔兹欧分堡公司大型石灰竖窑技术,新建两座日产600吨的麦尔兹气烧双膛石灰竖窑。
该技术有两个显著的特点:高温气体和石灰石在燃烧区并流;助燃空气在工艺过程中回收热量并蓄热。
一、麦尔兹并流蓄热式气烧双膛石灰竖窑工艺描述(一)并流蓄热式石灰竖窑的基本工作原理如图1所示,两个窑筒1和2含有将被煅烧的原料。
两个窑筒交替或同时进料,石灰连续不断地从两个窑筒底部卸出。
燃料加入其中一个窑筒内,燃料通过垂直伸入预热带底部的多根燃烧喷枪引入,并均匀分布窑筒的横截面部分燃烧空气在一定压力下进入到预热带顶部原料层上方。
整个系统均在加压状态下。
燃烧空气在与燃料混合前被换热器(预热带)预热。
气体/燃料火焰当其通过煅烧带从窑筒顶部到底部时(并流加热)直接与煅烧材料接触。
废气通过交叉通道从燃烧筒进入非燃烧筒,以相反的方向流动到石料处。
废气在非燃烧筒内将热传导至原料层甚至能够轻微程度地煅烧原料。
在这个窑筒中,废气在预热带重新蓄积原料层热量为下一个燃烧循环作好准备。
每一个窑筒从燃烧模式到非燃烧模式的循环大约间隔12 分钟。
烧产品在整个燃烧循环期间不断地从两个筒内卸出,通过卸料台进入压力料斗。
冷却空气不断的从两窑筒底部引入,使石灰在被排至石灰储存料斗前温度降低。
2号高炉高效护炉生产实践

2 号高炉高效护炉生产实践发布时间:2022-06-22T00:58:19.866Z 来源:《中国科技信息》2022年2月第4期作者:全建邱未名陈元洪李大明李宏玉[导读] 柳钢2号高炉在2021年9月计划检修时发现炉缸温度超高全建邱未名陈元洪李大明李宏玉广西柳州钢铁集团有限公司炼铁厂广西柳州摘要:柳钢2号高炉在2021年9月计划检修时发现炉缸温度超高,在铁口正下方2m处打孔安插热电偶时发现在距离炉壳450mm深度的位置温度高达736℃,经过专家及领导现场勘测分析后决定复风立即进行护炉生产,截止12月,该点温度成功从826℃降低至232℃,护炉效果十分显著。
关键词:高炉炼铁;炉缸监测;护炉技术;操作制度1概述柳钢2号高炉始建于2011年,有效容积2650m3,炉缸直径11200mm,炉喉直径8300mm,设置有3个出铁口,30个风口,于2012年9月3日开炉投产,截止目前已经连续生产了超过9年时间,2021年9月12日进行为期4天的计划检修更换气密箱及热风阀水冷法兰,借此机会在炉缸3个铁口正下方安装热电偶以便监测炉缸侵蚀情况,在进行打孔时,1号铁口正下方标高7700mm打孔深度位置进入环碳100mm便发红,内部温度经过现场实际测量达到736℃,2号、3号铁铁口正下方标高7700mm打孔深度仅与环碳接触也出现发红,其内部温度也高达650℃和550℃,据此推测3个出铁口象脚区侵蚀都较为严重,决定复风后立即进行加钒钛球及调整制度护炉生产。
2炉缸侵蚀情况分析及对策制定2.1 2号高炉炉缸进入炉役后期炉缸寿命往往决定了高炉寿命,根据2021年8月柳钢6号高炉拆除后炉缸侵蚀程度,再结合2号高炉炉缸设计的特点,截至2021年12月,2号高炉炉龄已经达到9年3个月,截止2021年10月累计生产铁水达到2084.5万t,单位容积产铁量7869 t,从该数据来说,2号高炉已经进入炉役后期,而且2021年以来,砌筑炉缸所埋入的热电偶温度监测也呈现出上升趋势,尤其是位于3个铁口象脚区位置;由于铁口区域冷却壁热电偶基本损坏,无法准确判断铁口区域温度情况,2021年9月检修开孔安装插入式热电偶时在开孔过程中发现3个铁口侧壁温度超高后更是证实了此前该区域侵蚀较为严重的猜想。
柳钢中金2号高炉本体烘炉实践
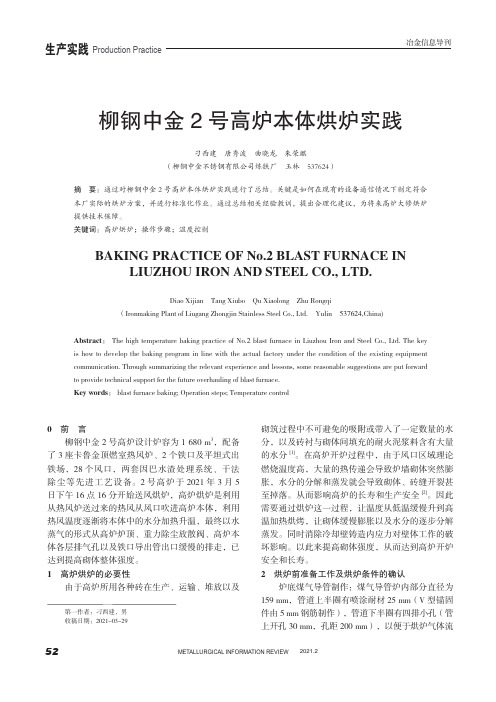
冶金信息导刊生产实践Production Practice柳钢中金2号高炉本体烘炉实践刁西建 唐秀波 曲晓龙 朱荣麒(柳钢中金不锈钢有限公司炼铁厂 玉林 537624)摘 要:通过对柳钢中金2号高炉本体烘炉实践进行了总结。
关键是如何在现有的设备通信情况下制定符合本厂实际的烘炉方案,并进行标准化作业。
通过总结相关经验教训,提出合理化建议,为将来高炉大修烘炉提供技术保障。
关键词:高炉烘炉;操作步骤;温度控制BAKING PRACTICE OF No.2 BLAST FURNACE INLIUZHOU IRON AND STEEL CO., LTD.Diao Xijian Tang Xiubo Qu Xiaolong Zhu Rongqi(Ironmaking Plant of Liugang Zhongjin Stainless Steel Co., Ltd. Yulin 537624,China) Abstract: The high temperature baking practice of No.2 blast furnace in Liuzhou Iron and Steel Co., Ltd. The keyis how to develop the baking program in line with the actual factory under the condition of the existing equipmentcommunication. Through summarizing the relevant experience and lessons, some reasonable suggestions are put forwardto provide technical support for the future overhauling of blast furnace.Key words: blast furnace baking; Operation steps; Temperature control第一作者:刁西建,男收稿日期:2021-03-29砌筑过程中不可避免的吸附或带入了一定数量的水分,以及砖衬与砌体间填充的耐火泥浆料含有大量的水分[1]。
轧钢加热炉在生产中的温度控制研究

轧钢加热炉在生产中的温度控制研究轧钢加热炉是轧钢生产线中关键的设备之一,它能够将冷却的钢坯加热至一定温度,使其具备可塑性,以便进一步进行轧制、锻造等工艺。
温度控制是轧钢加热炉生产中的一个关键问题,它直接影响到炉内温度的均匀性和加热效果,进而影响到产品的质量和生产效率。
研究轧钢加热炉在生产中的温度控制具有重要的理论和实际意义。
一般而言,轧钢加热炉的温度控制主要包括两个方面的内容:一是炉内温度的均匀性控制,二是炉内温度的精确控制。
炉内温度的均匀性控制是指炉内不同位置的温度分布要尽可能均匀,以确保钢坯被均匀加热。
在实际生产中,由于炉内不同位置的加热方式和受热程度不同,会导致温度分布不均匀的问题。
为了解决这个问题,可以采取以下措施:1. 设计合理的炉膛结构:合理的炉膛结构设计可以改善炉内的温度分布。
设计适当的加热火焰形状,使炉内的火焰能够均匀覆盖钢坯,避免温度局部上升;在炉膛内设置隔板或屏等装置,引导和控制炉内气流的流动,使炉内气流分布均匀。
2. 优化加热工艺参数:合理的加热工艺参数设置可以改变加热炉的温度分布。
调整加热炉的加热功率、加热速度和加热时间等参数,使钢坯在加热过程中温度分布均匀。
炉内温度的精确控制是指确保钢坯被加热到预定温度,并且能够稳定在预定温度上。
在实际生产中,由于炉内温度受到多种因素的影响,导致温度控制变得复杂。
为了精确控制炉内温度,可以采取以下措施:1. 选择合适的温度传感器:合适的温度传感器能够准确感知炉内温度。
常用的温度传感器有红外线传感器、热电偶、红外测温仪等。
根据不同的场景和要求,选择合适的温度传感器进行温度检测。
2. 采用闭环控制策略:闭环控制是一种常用的温度控制方法,它通过不断监测温度信号并根据信号调整控制器输出,使温度稳定在预定值上。
常见的闭环控制方法有PID控制、模糊控制等。
选择合适的闭环控制策略,并通过对控制参数的调整,提高温度控制的精确性。
轧钢加热炉在生产中的温度控制是一个复杂而又关键的问题。
高炉冷却壁热负荷及水温差监测系统研究
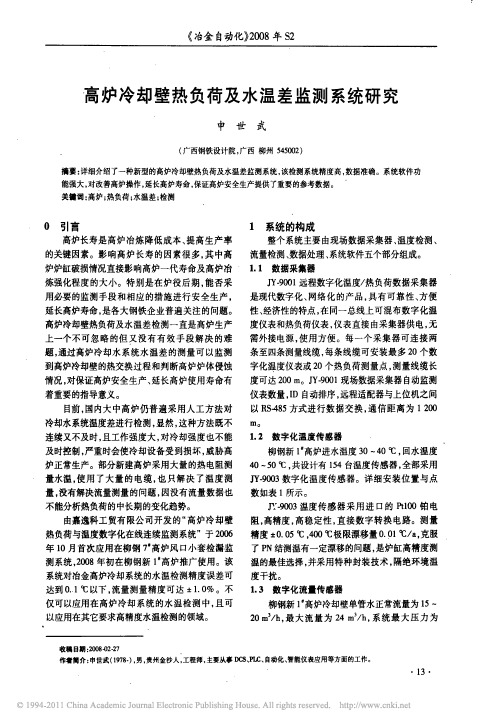
系统对 冶金高炉冷却系统 的水温 检测精度误差 可
达到 +二 ( ℃ 以下 , 流量 测 量 精度可 达 ( 士 , − 。 不
仅可 以应用 在高炉 冷却 系统 的水温 检测 中, 且 可
以应 用在其它要求高精度水 温 检测 的领 域 。
( 系统的构成
整 个系统主 要 由现 场数据采集器 、 温 度检测 、 流量检测 、 数据处理 、 系统软件五 个部分组 成。 ( , ( 数据 采集器
护具有重要作用 , 通 过历 史数据能够准确反 映炉 墙实时温度 、 流量变化。
系统主要功能及 技术参数 数字化 热负荷传感器 集成 了高精度温度测
量 、 抗恶劣水质的流量测量系统 , 可 在线实 时测量
冷却壁热流密度变化 , 仪表采用 国际先进技术将 所有检测信号 、 控制信号以数字量 的形式传输 , 速 度更快、 抗干扰能力更强 。
系统最快巡 检周期为 ( 点. 。, 可根据需用
,
设定时间, 系统速度已远超过通 用 8Μ? 或 3 ?! 系 统。
系统可通 过 +8? 标准数据 库接 口 、 快速以 太 网总线与高炉计算机 数据库连接 , 实现 数据共享 , 成为高炉 控制系统的一部分。
系统可移植性强 , 安装简便 、 快速 。 系统 可 在
,
∀Δ % & #) 一> ,
Ο 编样& 夏 宁Ν
引言 高炉长寿是 高炉冶炼降低成本 、 提高生产 率
的关键因素。 影 响高炉 长寿 的因素很多 , 其 中高
炉炉缸破损情况直接影响高炉一 代寿命及高炉冶 炼强化程 度 的大小 。 特别是 在炉 役 后 期 , 能否 采
用必 要 的监 测 手段 和 相 应 的措施进行安全 生 产 , 延长高炉寿命 , 是各大钢铁企 业普遍关注 的问题 。
探究钢厂热轧加热炉智能烧钢技术应用实践
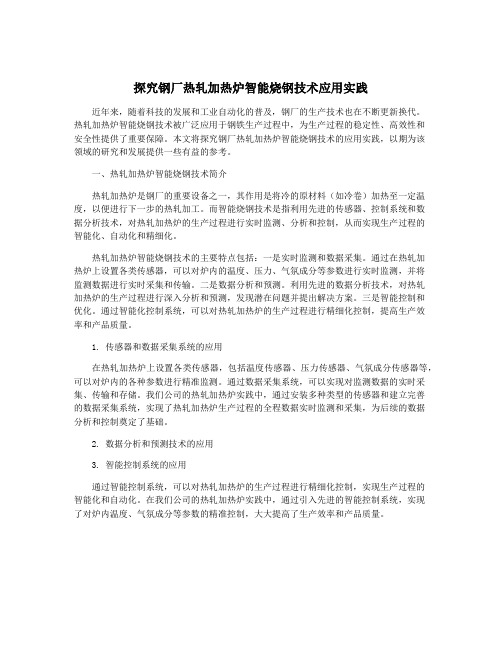
探究钢厂热轧加热炉智能烧钢技术应用实践近年来,随着科技的发展和工业自动化的普及,钢厂的生产技术也在不断更新换代。
热轧加热炉智能烧钢技术被广泛应用于钢铁生产过程中,为生产过程的稳定性、高效性和安全性提供了重要保障。
本文将探究钢厂热轧加热炉智能烧钢技术的应用实践,以期为该领域的研究和发展提供一些有益的参考。
一、热轧加热炉智能烧钢技术简介热轧加热炉是钢厂的重要设备之一,其作用是将冷的原材料(如冷卷)加热至一定温度,以便进行下一步的热轧加工。
而智能烧钢技术是指利用先进的传感器、控制系统和数据分析技术,对热轧加热炉的生产过程进行实时监测、分析和控制,从而实现生产过程的智能化、自动化和精细化。
热轧加热炉智能烧钢技术的主要特点包括:一是实时监测和数据采集。
通过在热轧加热炉上设置各类传感器,可以对炉内的温度、压力、气氛成分等参数进行实时监测,并将监测数据进行实时采集和传输。
二是数据分析和预测。
利用先进的数据分析技术,对热轧加热炉的生产过程进行深入分析和预测,发现潜在问题并提出解决方案。
三是智能控制和优化。
通过智能化控制系统,可以对热轧加热炉的生产过程进行精细化控制,提高生产效率和产品质量。
1. 传感器和数据采集系统的应用在热轧加热炉上设置各类传感器,包括温度传感器、压力传感器、气氛成分传感器等,可以对炉内的各种参数进行精准监测。
通过数据采集系统,可以实现对监测数据的实时采集、传输和存储。
我们公司的热轧加热炉实践中,通过安装多种类型的传感器和建立完善的数据采集系统,实现了热轧加热炉生产过程的全程数据实时监测和采集,为后续的数据分析和控制奠定了基础。
2. 数据分析和预测技术的应用3. 智能控制系统的应用通过智能控制系统,可以对热轧加热炉的生产过程进行精细化控制,实现生产过程的智能化和自动化。
在我们公司的热轧加热炉实践中,通过引入先进的智能控制系统,实现了对炉内温度、气氛成分等参数的精准控制,大大提高了生产效率和产品质量。
蓄热式加热炉在柳钢热轧厂的应用
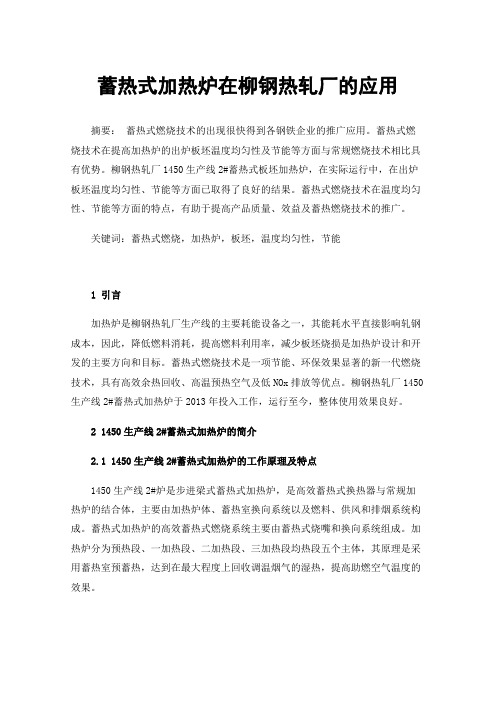
蓄热式加热炉在柳钢热轧厂的应用摘要:蓄热式燃烧技术的出现很快得到各钢铁企业的推广应用。
蓄热式燃烧技术在提高加热炉的出炉板坯温度均匀性及节能等方面与常规燃烧技术相比具有优势。
柳钢热轧厂1450生产线2#蓄热式板坯加热炉,在实际运行中,在出炉板坯温度均匀性、节能等方面已取得了良好的结果。
蓄热式燃烧技术在温度均匀性、节能等方面的特点,有助于提高产品质量、效益及蓄热燃烧技术的推广。
关键词:蓄热式燃烧,加热炉,板坯,温度均匀性,节能1引言加热炉是柳钢热轧厂生产线的主要耗能设备之一,其能耗水平直接影响轧钢成本,因此,降低燃料消耗,提高燃料利用率,减少板坯烧损是加热炉设计和开发的主要方向和目标。
蓄热式燃烧技术是一项节能、环保效果显著的新一代燃烧技术,具有高效余热回收、高温预热空气及低NOx排放等优点。
柳钢热轧厂1450生产线2#蓄热式加热炉于2013年投入工作,运行至今,整体使用效果良好。
2 1450生产线2#蓄热式加热炉的简介2.1 1450生产线2#蓄热式加热炉的工作原理及特点1450生产线2#炉是步进梁式蓄热式加热炉,是高效蓄热式换热器与常规加热炉的结合体,主要由加热炉体、蓄热室换向系统以及燃料、供风和排烟系统构成。
蓄热式加热炉的高效蓄热式燃烧系统主要由蓄热式烧嘴和换向系统组成。
加热炉分为预热段、一加热段、二加热段、三加热段均热段五个主体,其原理是采用蓄热室预蓄热,达到在最大程度上回收调温烟气的湿热,提高助燃空气温度的效果。
加热炉的蓄热室采用陶瓷小球为蓄热体,其表面积大,极大地提高了传热系统,使蓄热室内的体积大大缩小。
再加上可靠的自动控制技术及预热介质预热温度高废气预热到接近极限的回收,是一种高效、节能的加热炉。
2.2 1450生产线2#蓄热式加热炉控制系统1450生产线2#蓄热式加热炉燃控和顺控的操作和监控主要在操作室的操作站上进行。
操作站通过以太网与基础自动化级的SIEMENS公司的S7-400PLC进行通讯。
热轧板带线加热炉智能燃烧模型的应用

栅镟轉銨0技术论坛戀爾廳能鶴1_驗用丨i f i i r蒙治祥黉W梁-一柳钢2 032热轧板带生产线有3座常规式加 热炉,自2005-10投产以来,燃烧控制模型均 为手动操作,以多年的经验值和理论计算值为 基础,设定空燃比,手动调节加热炉各个加热 段的煤气流量和空气流量,使加热炉内各段炉 气温度达到轧制计划坯料的工艺要求温度。
由于班组对生产工艺的理解和对设备的操作习惯 均有不同,导致在基本满足工艺要求的前提下,每个班组的加热质量均有不同。
且由于2 032生 产线生产品种较多,增加了人工操作的难度,煤气量和空气量的调整次数多,造成炉温波动 频繁,无法保证炉内温度场的稳定性,不但浪 费能源,加热质量也有待优化,还加大了员工 的工作量。
为此,柳钢热轧板带厂与北京科技 大学合作开发加热炉智能燃烧模型。
本文总结 新模型的应用情况。
智能燃烧模型设计与原过程控制系统的各段炉温和最小在炉 时间要求不同,在改造加热炉一级和二级系统 后,智能燃烧模型以坯料升温曲线为基础,以每块坯料出炉目标温度为加热控制最终目标,以每块坯料的加热段段末计算温度为加热控制过程目标。
在坯料进入加热炉的预热段时,智能燃烧 模型开始标记该坯料位置、入炉温度、牌号钢 种和坯料规格等信息,以每个炉子不同的热效 率,按当前坯料出炉节奏推算出一个动态的在 炉时间,使用最合适该坯料的升温曲线,通过 采集该坯料实时的炉温,设定动态目标炉温,操控煤气阀门和空气阀门进行全过程的加热控 制,直至该坯料的计算温度达到出炉目标温度。
整个过程操作工人基本只需进行出钢节奏控制 以及极少的人工温度干预。
应用及优化一二级数据链接在模型离线状态下,进行生产过程的U-L2 的数据通讯模式、电文格式确认,并进行电文 数据组织和通讯测试,实现了双系统数据的异 构同步运行。
制定L2-L3数据接口调试方案,搭建一套调试数据结构并实时同步实际数据,完成L2、L3之间收发数据以及功能测试。
BCS技术在大型圆环形竖炉上的应用

摘
要 : 绍 “ 用 燃烧 优化 控 制技 术 ( C )”在 大型 圆环 形 竖 炉上 的应 用 。由 于煤 气压 力和 热值 的波 动 介 通 B S
维普资讯
解 决 方案
BS C 技术在大型圆环形竖炉上的应用
Ap l a i n o h pi t f e BCS T c n lg c o t e h oo y
_ L re l a q iq p :h f I r a e n n I e ^‘ ・ - n c y = a 一 ; t u
作 的仪 表 和 电气 系 统 , 温 度 、 力 和变 频 器或 特 殊 如 压 智 能软 伺 服 模 块 , 用先 进 的软 测 量技 术 及可 靠 的 测 采 控 信 号 获 得 能 反 映 燃 烧状 态 的 中 间变 量 , 即燃 烧 效
果变量:
=
比, 一 步 影 响竖 炉 燃 烧 室 的温 度 。 作 工往 往 采 用 进 操 最大煤气量燃烧 , 不仅 浪 费 大 量 煤气 ,由于 配 比不 合
的系 统 输 出 变 量 ; 烧 器 可 测 的 过 程 内部 变 量 ; 烧 燃 燃
、v . i. ^ wc mc n n 51
阂俄鬓 儇表2 8 第8 0年 期 0
目标 。
形竖炉之一。 CS 88 T 1 1竖炉工艺流程 图如图1 示。 所 该
竖 炉 工 艺先 进 , 要 与 之 配 套 的 燃 烧 控 制 也 先 进 实 需
用 。 着 高 炉 煤气 利 用水 平 的 上 升 , 炉煤 气 压 力 和 随 高 热 值 波 动较 大 。 方 面 , 一 由于 煤 气 热 值 降 低 , 炉 所 竖
棒材生产线2#收集成捆前辊道电气改造
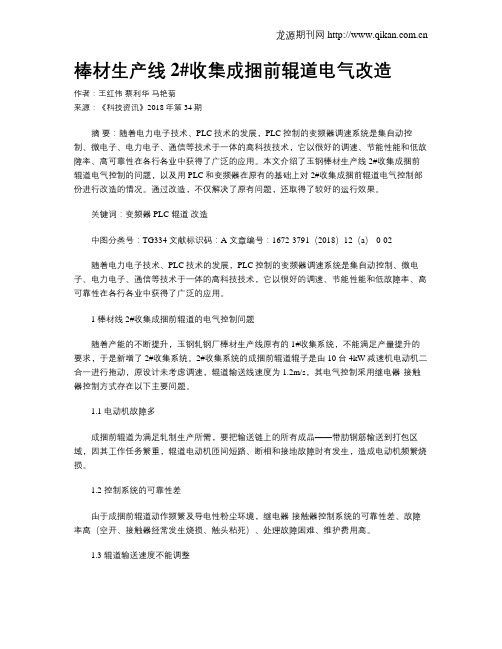
棒材生产线2#收集成捆前辊道电气改造作者:王红伟蔡利华马艳菊来源:《科技资讯》2018年第34期摘要:随着电力电子技术、PLC技术的发展,PLC控制的变频器调速系统是集自动控制、微电子、电力电子、通信等技术于一体的高科技技术,它以很好的调速、节能性能和低故障率、高可靠性在各行各业中获得了广泛的应用。
本文介绍了玉钢棒材生产线2#收集成捆前辊道电气控制的问题,以及用PLC和变频器在原有的基础上对2#收集成捆前辊道电气控制部份进行改造的情况。
通过改造,不仅解决了原有问题,还取得了较好的运行效果。
关键词:变频器 PLC 辊道改造中图分类号:TG334 文献标识码:A 文章编号:1672-3791(2018)12(a)-0-02随着电力电子技术、PLC技术的发展,PLC控制的变频器调速系统是集自动控制、微电子、电力电子、通信等技术于一体的高科技技术,它以很好的调速、节能性能和低故障率、高可靠性在各行各业中获得了广泛的应用。
1 棒材线2#收集成捆前辊道的电气控制问题随着产能的不断提升,玉钢轧钢厂棒材生产线原有的1#收集系统,不能满足产量提升的要求,于是新增了2#收集系统。
2#收集系统的成捆前辊道辊子是由10台4kW减速机电动机二合一进行拖动,原设计未考虑调速,辊道输送线速度为1.2m/s,其电气控制采用继电器-接触器控制方式存在以下主要问题。
1.1 电动机故障多成捆前辊道为满足轧制生产所需,要把输送链上的所有成品——带肋钢筋输送到打包区域,因其工作任务繁重,辊道电动机匝间短路、断相和接地故障时有发生,造成电动机频繁烧损。
1.2 控制系统的可靠性差由于成捆前辊道动作频繁及导电性粉尘环境,继电器-接触器控制系统的可靠性差、故障率高(空开、接触器经常发生烧损、触头粘死)、处理故障困难、维护费用高。
1.3 辊道输送速度不能调整电动机不能调速,导致轧制品种、负载变化时,启动、运行不平稳,容易造成乱钢或阻钢,同时对堵头的挡板或底座螺栓造成损坏。
探究钢厂热轧加热炉智能烧钢技术应用实践
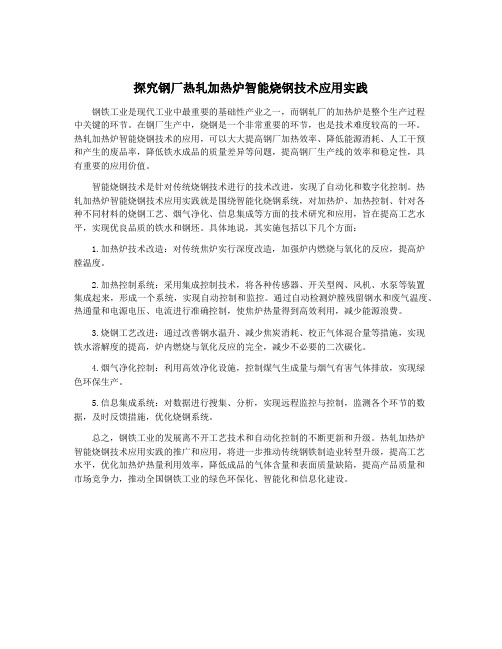
探究钢厂热轧加热炉智能烧钢技术应用实践钢铁工业是现代工业中最重要的基础性产业之一,而钢轧厂的加热炉是整个生产过程中关键的环节。
在钢厂生产中,烧钢是一个非常重要的环节,也是技术难度较高的一环。
热轧加热炉智能烧钢技术的应用,可以大大提高钢厂加热效率、降低能源消耗、人工干预和产生的废品率,降低铁水成品的质量差异等问题,提高钢厂生产线的效率和稳定性,具有重要的应用价值。
智能烧钢技术是针对传统烧钢技术进行的技术改进,实现了自动化和数字化控制。
热轧加热炉智能烧钢技术应用实践就是围绕智能化烧钢系统,对加热炉、加热控制、针对各种不同材料的烧钢工艺、烟气净化、信息集成等方面的技术研究和应用,旨在提高工艺水平,实现优良品质的铁水和钢坯。
具体地说,其实施包括以下几个方面:1.加热炉技术改造:对传统焦炉实行深度改造,加强炉内燃烧与氧化的反应,提高炉膛温度。
2.加热控制系统:采用集成控制技术,将各种传感器、开关型阀、风机、水泵等装置集成起来,形成一个系统,实现自动控制和监控。
通过自动检测炉膛残留钢水和废气温度、热通量和电源电压、电流进行准确控制,使焦炉热量得到高效利用,减少能源浪费。
3.烧钢工艺改进:通过改善钢水温升、减少焦炭消耗、校正气体混合量等措施,实现铁水溶解度的提高,炉内燃烧与氧化反应的完全,减少不必要的二次碳化。
4.烟气净化控制:利用高效净化设施,控制煤气生成量与烟气有害气体排放,实现绿色环保生产。
5.信息集成系统:对数据进行搜集、分析,实现远程监控与控制,监测各个环节的数据,及时反馈措施,优化烧钢系统。
总之,钢铁工业的发展离不开工艺技术和自动化控制的不断更新和升级。
热轧加热炉智能烧钢技术应用实践的推广和应用,将进一步推动传统钢铁制造业转型升级,提高工艺水平,优化加热炉热量利用效率,降低成品的气体含量和表面质量缺陷,提高产品质量和市场竞争力,推动全国钢铁工业的绿色环保化、智能化和信息化建设。
211065582_步进式加热炉防止钢坯剐蹭炉墙技术应用

步进式加热炉防止钢坯剐蹭炉墙技术应用刘健杨军章霞刚(江西省新余钢铁股份公司轧钢厂江西新余338001)摘 要:本文介绍一种防止钢坯刮炉墙技术的应用。
轧钢厂用于方坯加热的加热炉为步进式加热炉,通常加热炉为单根钢坯辊道侧进方式输送进炉,钢坯进炉的过程中会出现输送没有到位的情况,操作人员若未及时发现,钢坯就会对加热炉侧壁炉墙产生剐蹭,造成炉墙损坏,炉壁就会发生穿火故障,对加热炉的运行造成危险,而应用此项技术可以防止钢坯剐蹭炉墙。
关键词:步进式加热炉方坯定位激光测距仪炉墙保护技术中图分类号:T G307文献标识码:A文章编号:1674-098X(2022)08(c)-0032-04 Application of Technology to Prevent Billet from Scratching Furnace Wall in Walking Beam Heating FurnaceLIU Jian YANG Jun ZHANG Xiagang(Steel Rolling Plant of Xinsteel Group Co., Ltd., Xinyu, Jiangxi Province, 338001 China) Abstract: This paper introduces the application of wall protection technology. The heating furnace used for billet heating in a steel rolling plant is a walking-beam heating furnace, and usually the heating furnace is loaded by a single billet roll table in a side-feed manner. During the process of billet entering the furnace, there will be a situa‐tion where the transportation is not in place, if the operator doesn't find it in time, the billet will scratch the side wall of the heating furnace, which will damage the wall, and the wall will break down, which will bring danger to the operation of the heating furnace. This technology can prevent the billet from scratching the wall.Key Words: Walking beam furnace; Billet orientation; Laser rangefinder; Furnace wall protection technology随着钢铁市场的竞争越来越激烈,资源控制力强、原料和能源采购成本低、工艺结构优化、产品附加值高的企业具备较强的市场竞争力。
转炉钢渣热焖渣自动控制及热焖作业介绍
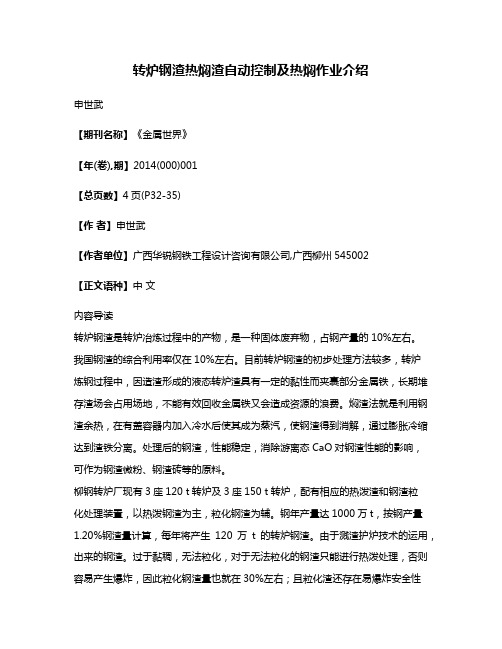
转炉钢渣热焖渣自动控制及热焖作业介绍申世武【期刊名称】《金属世界》【年(卷),期】2014(000)001【总页数】4页(P32-35)【作者】申世武【作者单位】广西华锐钢铁工程设计咨询有限公司,广西柳州545002【正文语种】中文内容导读转炉钢渣是转炉冶炼过程中的产物,是一种固体废弃物,占钢产量的10%左右。
我国钢渣的综合利用率仅在10%左右。
目前转炉钢渣的初步处理方法较多,转炉炼钢过程中,因造渣形成的液态转炉渣具有一定的黏性而夹裹部分金属铁,长期堆存渣场会占用场地,不能有效回收金属铁又会造成资源的浪费。
焖渣法就是利用钢渣余热,在有盖容器内加入冷水后使其成为蒸汽,使钢渣得到消解,通过膨胀冷缩达到渣铁分离。
处理后的钢渣,性能稳定,消除游离态CaO对钢渣性能的影响,可作为钢渣微粉、钢渣砖等的原料。
柳钢转炉厂现有3座120 t转炉及3座150 t转炉,配有相应的热泼渣和钢渣粒化处理装置,以热泼钢渣为主,粒化钢渣为辅。
钢年产量达1000万t,按钢产量1.20%钢渣量计算,每年将产生120万t的转炉钢渣。
由于溅渣护炉技术的运用,出来的钢渣。
过于黏稠,无法粒化,对于无法粒化的钢渣只能进行热泼处理,否则容易产生爆炸,因此粒化钢渣量也就在30%左右;且粒化渣还存在易爆炸安全性差、设备磨损严重、胶凝性差难以在建材行业使用的缺点。
为了实现钢渣“零”排放,对于不能进行渣粒化的70%左右的转炉钢渣,采用目前最先进、渣利用率最高的钢渣热焖工艺,可以有效减少炼钢厂现场污染,实现转炉渣处理跨的干净整洁,实现国家节能减排目标及可持续发展,也符合企业的当前实际情况,还可以充分回收钢渣中的含铁物料,降低炼钢成本,后续产品开发及综合利用价值较高,在回收铁钢的同时,更重要是尾渣的综合利用,尾渣粉可用来生产钢渣超细粉、钢渣砖,也可用于水泥厂配料,不存在钢渣膨胀开裂及稳定性的问题,不仅提高了企业的效益,更重要的是保护了环境和生态。
渣热焖是近年发展起来的一种新型的钢渣处理技术。
加热炉二级优化控制系统的应用
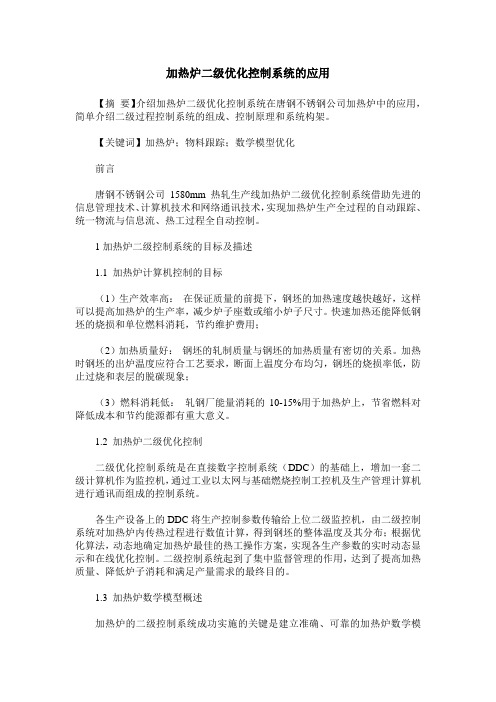
加热炉二级优化控制系统的应用【摘要】介绍加热炉二级优化控制系统在唐钢不锈钢公司加热炉中的应用,简单介绍二级过程控制系统的组成、控制原理和系统构架。
【关键词】加热炉;物料跟踪;数学模型优化前言唐钢不锈钢公司1580mm热轧生产线加热炉二级优化控制系统借助先进的信息管理技术、计算机技术和网络通讯技术,实现加热炉生产全过程的自动跟踪、统一物流与信息流、热工过程全自动控制。
1加热炉二级控制系统的目标及描述1.1 加热炉计算机控制的目标(1)生产效率高:在保证质量的前提下,钢坯的加热速度越快越好,这样可以提高加热炉的生产率,减少炉子座数或缩小炉子尺寸。
快速加热还能降低钢坯的烧损和单位燃料消耗,节约维护费用;(2)加热质量好:钢坯的轧制质量与钢坯的加热质量有密切的关系。
加热时钢坯的出炉温度应符合工艺要求,断面上温度分布均匀,钢坯的烧损率低,防止过烧和表层的脱碳现象;(3)燃料消耗低:轧钢厂能量消耗的10-15%用于加热炉上,节省燃料对降低成本和节约能源都有重大意义。
1.2 加热炉二级优化控制二级优化控制系统是在直接数字控制系统(DDC)的基础上,增加一套二级计算机作为监控机,通过工业以太网与基础燃烧控制工控机及生产管理计算机进行通讯而组成的控制系统。
各生产设备上的DDC将生产控制参数传输给上位二级监控机,由二级控制系统对加热炉内传热过程进行数值计算,得到钢坯的整体温度及其分布;根据优化算法,动态地确定加热炉最佳的热工操作方案,实现各生产参数的实时动态显示和在线优化控制。
二级控制系统起到了集中监督管理的作用,达到了提高加热质量、降低炉子消耗和满足产量需求的最终目的。
1.3 加热炉数学模型概述加热炉的二级控制系统成功实施的关键是建立准确、可靠的加热炉数学模型。
加热炉内的热过程包括流体流动、传热传质、燃料燃烧等复杂的物理化学过程,建立的模型包括加热炉内炉膛的辐射传热模型、钢坯的导热模型、钢坯的氧化模型以及黑印模型等。
热轧2级计算机燃烧控制系统的应用研究
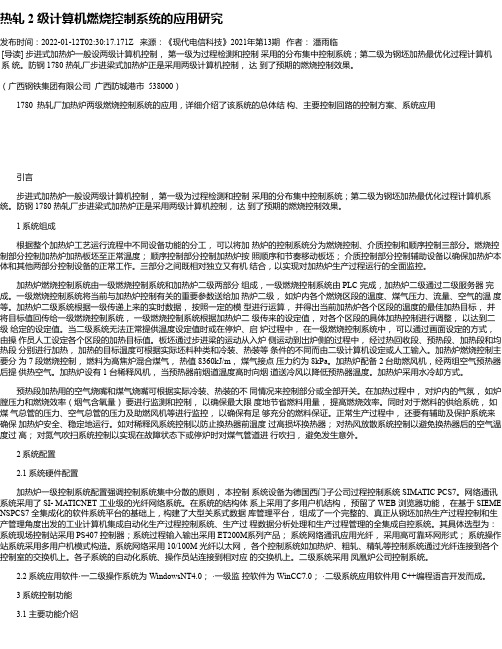
热轧 2 级计算机燃烧控制系统的应用研究发布时间:2022-01-12T02:30:17.171Z 来源:《现代电信科技》2021年第13期作者:潘雨临[导读] 步进式加热炉一般设两级计算机控制,第一级为过程检测和控制采用的分布集中控制系统;第二级为钢坯加热最优化过程计算机系统。
防钢 1780 热轧厂步进梁式加热炉正是采用两级计算机控制,达到了预期的燃烧控制效果。
(广西钢铁集团有限公司广西防城港市 538000)1780 热轧厂加热炉两级燃烧控制系统的应用,详细介绍了该系统的总体结构、主要控制回路的控制方案、系统应用引言步进式加热炉一般设两级计算机控制,第一级为过程检测和控制采用的分布集中控制系统;第二级为钢坯加热最优化过程计算机系统。
防钢 1780 热轧厂步进梁式加热炉正是采用两级计算机控制,达到了预期的燃烧控制效果。
1 系统组成根据整个加热炉工艺运行流程中不同设备功能的分工,可以将加热炉的控制系统分为燃烧控制、介质控制和顺序控制三部分。
燃烧控制部分控制加热炉加热板坯至正常温度;顺序控制部分控制加热炉按照顺序和节奏移动板坯;介质控制部分控制辅助设备以确保加热炉本体和其他两部分控制设备的正常工作。
三部分之间既相对独立又有机结合,以实现对加热炉生产过程运行的全面监控。
加热炉燃烧控制系统由一级燃烧控制系统和加热炉二级两部分组成,一级燃烧控制系统由 PLC 完成,加热炉二级通过二级服务器完成。
一级燃烧控制系统将当前与加热炉控制有关的重要参数送给加热炉二级,如炉内各个燃烧区段的温度、煤气压力、流量、空气的温度等。
加热炉二级系统根据一级传递上来的实时数据,按照一定的模型进行运算,并得出当前加热炉各个区段的温度的最佳加热目标,并将目标值回传给一级燃烧控制系统,一级燃烧控制系统根据加热炉二级传来的设定值,对各个区段的具体加热控制进行调整,以达到二级给定的设定值。
当二级系统无法正常提供温度设定值时或在停炉、启炉过程中,在一级燃烧控制系统中,可以通过画面设定的方式,由操作员人工设定各个区段的加热目标值。
- 1、下载文档前请自行甄别文档内容的完整性,平台不提供额外的编辑、内容补充、找答案等附加服务。
- 2、"仅部分预览"的文档,不可在线预览部分如存在完整性等问题,可反馈申请退款(可完整预览的文档不适用该条件!)。
- 3、如文档侵犯您的权益,请联系客服反馈,我们会尽快为您处理(人工客服工作时间:9:00-18:30)。
BCS技术在广西柳钢集团二棒生产线加热炉上的应用
一、生产装置情况概述
柳钢集团二棒生产线加热炉为130t/h步进式加热炉,以燃烧高炉煤气为主。
现场的煤气支管流量几乎都不准确,有的甚至不显示;煤气阀门的控制精度在3~8%左右,性能较差。
煤气总管流量和压力相对准确。
现场所有回路均手动控制。
正因为存在这些问题,对不断变化的工况不能及时调节煤气量和风量,现场测量又不准,手动操作时的大起大落造成加热炉运行不稳定,造成燃料消耗较高。
加热炉采用西门子控制系统,下位为s7-400控制器,上位为wincc6.0监控软件,支持opc通讯。
现场运行画面:
手动操作下的温度控制曲线:
二、项目概述
北京和隆优化控制技术有限公司采用BCS(通用燃烧优化控制技术的简称)系统作为运行平台对柳钢集团第二棒材生产线130t/h加热炉的燃烧系统进行优化控制改造,达到节能减排提高加热炉效率的目的。
如上图所示,BCS通过交换机与加热炉DCS系统中的操作员站连成一个网络。
通过opc通讯协议,BCS与加热炉DCS系统完成数据交换,BCS系统从DCS得到温度、压力、阀位、流量等现场工艺数据,BCS使用这些工艺参数,通过燃烧优化控制模型进行相应计算,BCS将计算结果返回DCS中进行实时控制。
三、项目采用的核心技术及功能
1)燃烧效果软测量技术
2)最佳运行工况的自寻优及滚动优化技术
3)故障诊断与容错控制技术
4)扰动观测器模型和智能控制器模型
5)炉膛温度梯度不平衡处理模型
6)加热炉燃烧制度设定功能
7)加热炉经济运行统计与考核功能
8)基于优化控制云服务系统HeroRTS的远程服务
四、基于BCS技术,加热炉可投入自动控制的回路:
1)上加热段煤气控制回路
2)上加热段空气控制回路
3)上均热段煤气控制回路
4)上均热段空气控制回路
5)下均热段煤气控制回路
6)下均热段空气控制回路
7)煤气总管压力控制回路
8)空气总管压力控制回路
9)炉压控制回路
改造后燃烧主流程画面:包含燃烧装置的全部运行信息和操作功能
五、实现的技术经济指标
1)实现加热炉长期可靠的全自动优化运行,长期自控率大于90%;
2)投入燃烧系统优化控制, 使吨钢煤气消耗平均下降3%以上。
3)使加热炉温度控制精度达到R±10℃, 稳定产品质量;
4)使钢损在原来基础上相对下降5%。
六、现场优化控制运行效果
优化操作与手动操作切换时的出钢温度控制对比曲线:
BCS自动控制与DCS手动控制下的均热段温度控制对比图:
七、验收结论
1.二棒130t/h加热炉的BCS控制系统实现了全自动优化烧炉,长期的自控率达到95%以上。
2.吨钢煤气消耗下降为
3.35%。
3.运行过程中,运行人员普遍反映运行状态良好,操作简单方便,减轻了工人的劳动强度,实现了加热炉自动优化控制,使加热炉的运行更趋安全、稳定和经济。
八、验收报告。