基于典型齿轮零件的数控工艺分析与加工
数控机床的分类及典型轴类零件的加工
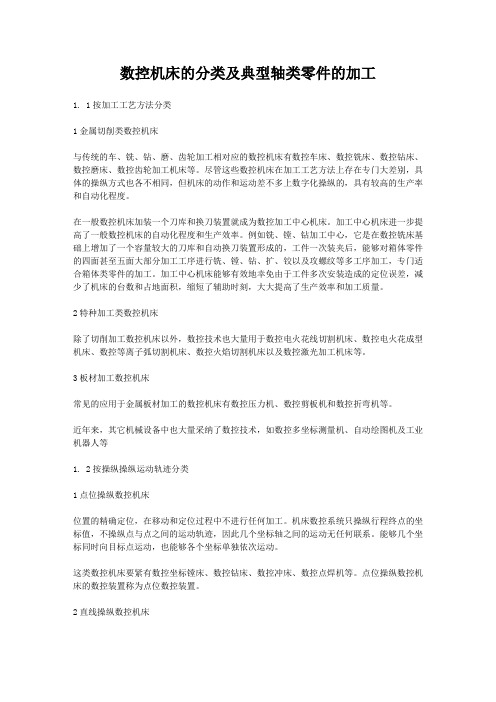
数控机床的分类及典型轴类零件的加工1. 1按加工工艺方法分类1金属切削类数控机床与传统的车、铣、钻、磨、齿轮加工相对应的数控机床有数控车床、数控铣床、数控钻床、数控磨床、数控齿轮加工机床等。
尽管这些数控机床在加工工艺方法上存在专门大差别,具体的操纵方式也各不相同,但机床的动作和运动差不多上数字化操纵的,具有较高的生产率和自动化程度。
在一般数控机床加装一个刀库和换刀装置就成为数控加工中心机床。
加工中心机床进一步提高了一般数控机床的自动化程度和生产效率。
例如铣、镗、钻加工中心,它是在数控铣床基础上增加了一个容量较大的刀库和自动换刀装置形成的,工件一次装夹后,能够对箱体零件的四面甚至五面大部分加工工序进行铣、镗、钻、扩、铰以及攻螺纹等多工序加工,专门适合箱体类零件的加工。
加工中心机床能够有效地幸免由于工件多次安装造成的定位误差,减少了机床的台数和占地面积,缩短了辅助时刻,大大提高了生产效率和加工质量。
2特种加工类数控机床除了切削加工数控机床以外,数控技术也大量用于数控电火花线切割机床、数控电火花成型机床、数控等离子弧切割机床、数控火焰切割机床以及数控激光加工机床等。
3板材加工数控机床常见的应用于金属板材加工的数控机床有数控压力机、数控剪板机和数控折弯机等。
近年来,其它机械设备中也大量采纳了数控技术,如数控多坐标测量机、自动绘图机及工业机器人等1. 2按操纵操纵运动轨迹分类1点位操纵数控机床位置的精确定位,在移动和定位过程中不进行任何加工。
机床数控系统只操纵行程终点的坐标值,不操纵点与点之间的运动轨迹,因此几个坐标轴之间的运动无任何联系。
能够几个坐标同时向目标点运动,也能够各个坐标单独依次运动。
这类数控机床要紧有数控坐标镗床、数控钻床、数控冲床、数控点焊机等。
点位操纵数控机床的数控装置称为点位数控装置。
2直线操纵数控机床直线操纵数控机床可操纵刀具或工作台以适当的进给速度,沿着平行于坐标轴的方向进行直线移动和切削加工,进给速度依照切削条件可在一定范畴内变化。
数控车床零件的工艺分析及编程典型实例

数控车床零件的工艺分析及编程典型实例更新日期:来源:数控工作室根据下图所示的待车削零件,材料为45号钢,其中Ф85圆柱面不加工。
在数控车床上需要进行的工序为:切削Ф80mm 和Ф62mm 外圆;R70mm 弧面、锥面、退刀槽、螺纹及倒角。
要求分析工艺过程与工艺路线,编写加工程序。
图1 车削零件图1.零件加工工艺分析(1)设定工件坐标系按基准重合原则,将工件坐标系的原点设定在零件右端面与回转轴线的交点上,如图中Op点,并通过G50指令设定换刀点相对工件坐标系原点Op的坐标位置(200,100)(2)选择刀具根据零件图的加工要求,需要加工零件的端面、圆柱面、圆锥面、圆弧面、倒角以及切割螺纹退刀槽和螺纹,共需用三把刀具。
1号刀,外圆左偏刀,刀具型号为:CL-MTGNR-2020/R/1608 ISO30。
安装在1号刀位上。
3号刀,螺纹车刀,刀具型号为:TL-LHTR-2020/R/60/1.5 ISO30。
安装在3号刀位上。
5号刀,割槽刀,刀具型号为:ER-SGTFR-2012/R/3.0-0 IS030。
安装在5号刀位上。
(3)加工方案使用1号外圆左偏刀,先粗加工后精加工零件的端面和零件各段的外表面,粗加工时留0.5mm的精车余量;使用5号割槽刀切割螺纹退刀槽;然后使用3号螺纹车刀加工螺纹。
(4)确定切削用量切削深度:粗加工设定切削深度为3mm,精加工为0.5mm。
主轴转速:根据45号钢的切削性能,加工端面和各段外表面时设定切削速度为90m/min;车螺纹时设定主轴转速为250r/min。
进给速度:粗加工时设定进给速度为200mm/min,精加工时设定进给速度为50mm/min。
车削螺纹时设定进给速度为1.5mm/r。
2.编程与操作(1)编制程序(2)程序输入数控系统将程序在数控车床MDI方式下直接输入数控系统,或通过计算机通信接口将程序输入数控机床的数控系统。
然后在CRT 屏幕上模拟切削加工,检验程序的正确性。
齿轮类零件加工工艺分析及夹具设计
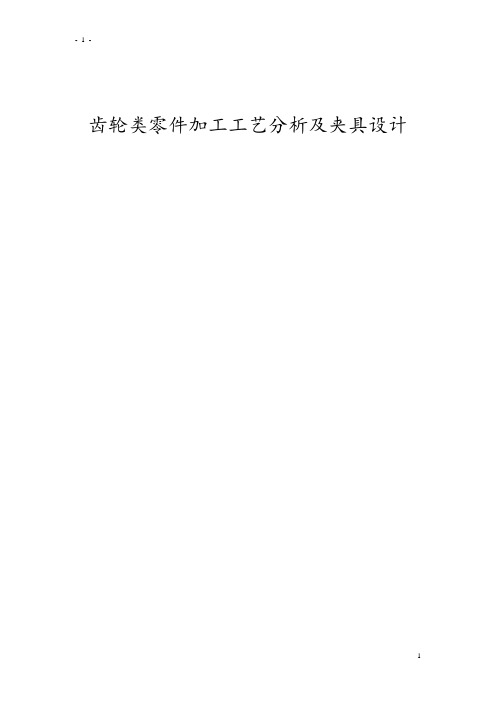
齿轮类零件加工工艺分析及夹具设计目录摘要 (4)第一章齿轮类零件加工工艺规程编制概述 (5)1.1工艺编制的总体步骤 (5)第二章对齿轮类零件的加工工艺编制及分析 (6)2.1分析齿轮类零件的技术要求 (6)2.2明确毛坯尺寸 (8)2.3拟定工艺路线 (8)2.4设计工序内容 (10)2.5填写工艺文件 (10)第三章对齿轮类零件加工工艺进行合理性分析 (11)第四章夹具设计的要求 (11)4.1 了解夹具设计的总体要求 (11)第五章夹具设计的特点 (12)5.1确定夹具的类型 (12)5.2钻模的主要类型 (12)第六章工件夹紧计算及选择 (13)6.1工件的夹紧 (13)6.2 夹紧力的选择 (13)6.3夹紧力的计算及精度分析 (14)第七章夹具的结构分析及设计 (16)7.1夹具的夹紧和定位 (16)7.2夹具的导向 (17)第八章夹具的总体分析 (17)第九章致谢 (18)摘要齿轮类零件是典型零件之一,它在机械主要用于传动,齿轮类零件主要有齿轮.齿轮轴,涡轮涡杆,在机械领域运用很广泛。
按传动形式分圆柱类齿轮、锥齿轮、齿条等。
按齿形状分:齿轮、齿、字齿等。
按制作方法分:铸造齿轮、烧结齿轮、轧制齿轮等。
我以齿轮加工工艺编制分析齿轮的加工要求,在生产实际中阐述齿轮的工艺过程,及工艺的合理性。
夹具在机械加工中有举足轻重的作用,好的夹具才是保障零件加工的方法。
我从夹具的分析、设计、计算、使用方面概述夹具的用途。
按专业化程度可分为通用夹具、专用夹具、可调夹具、组合夹具、成组夹具、标准夹具、随行夹具、组合机床夹具等。
我这次设计的是盖板式钻夹具。
这是一种专用夹具,专为一工件的一道工序而设计的夹具。
关键词:齿轮、夹具、工艺、设计1.1工艺编制的总体步骤1.分析零件的结构和技术要求(1)分析图样资料①加工工艺表面的尺寸精度和形状精度②各加工表面之间以及加工表面和不加工表面之间的位置精度③加工表面的粗糙度及表面的其他要求④热处理及其他要求(2)零件的结构工艺分析。
典型零件数控加工工艺分析及编程
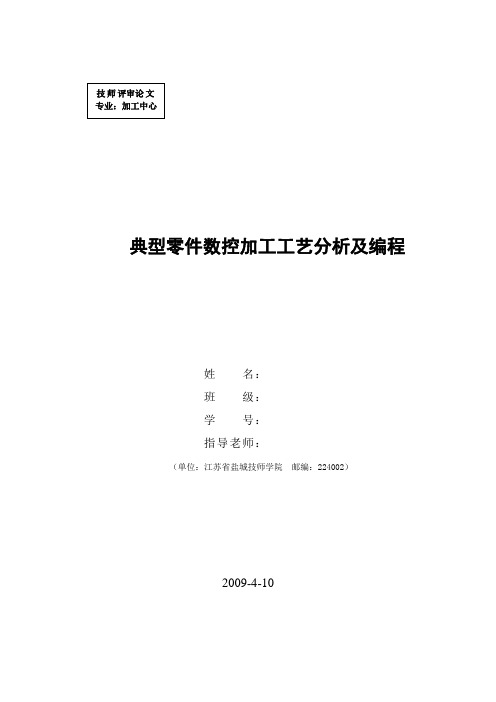
典型零件数控加工工艺分析及编程姓名:班级:学号:指导老师:(单位:江苏省盐城技师学院邮编:224002)2009-4-10典型零件数控加工工艺分析及编程【摘要】针对典型零件选择机床、夹具、刀具及量具,拟定加工工艺路线、切削用量等,编写数控加工的程序。
【关键词】工艺编程一、数控加工工艺路线的设计工艺路线是指零件加工所经过的整个路线,也就是列出工序名称的简略工艺过程。
工艺路线的拟定是制订工艺规程的重要内容,其主要任务是选择各个表面的加工方法,确定各个表面的加工顺序及整个工艺过程的工序数目和工序内容。
数控加工工艺路线的设计与通用机床加工工艺路线的设计的主要区别在于它往往不是只从毛坯到成品的整个过程,而仅是几道数控加工工序工艺过程的具体描述。
因此在工艺路线设计中一定要注意到,由于数控加工工序一般都穿插于零件加工的整个工艺过程中,因而要与其它加工工艺衔接好。
⒈工序的划分根据数控加工的特点,数控加工工序的划分一般可按下列方法进行:⑴以一次安装、加工作为一道工序。
这种方法适合于加工内容较少的零件,加工完后就能达到待检状态。
⑵以同一把刀具加工的内容划分工序。
有些零件虽然能再一次安装加工中加工很多代加工表面,但考虑到程序太长,会受到某些限制(主要是内存容量),机床连续工作时间的限制(如一道工序在一个工作班内不能结束)等,此外,程序太长会增加出错与检索的困难。
因此程序不能太长,一道工序内容不能太多。
⑶以加工部位划分工序。
对于加工内容很多的工件,可按其结构特点将加工部位分成几个部分,如内腔、外形、曲面或平面,并将每一部分的加工作为一道工序。
⑷以粗、精加工划分工序。
对于加工后易发生变形的工件,由于对粗加工后可能发生的变形需要进行校形,故一般来说,凡要进行粗、精加工的过程,都要将工序分开。
⒉顺序的安排顺序的安排应根据零件的结构和毛坯,以及定位、安装与夹紧的需要来考虑。
顺序安排一般应按以下原则进行:⑴上道工序的加工不能影响下道工序的定位与夹紧,中间穿插于通用机床加工工序的也应综合考虑;⑵先进性内腔加工,后进行外形加工;⑶以相同定位、夹紧方式或用同一把刀具加工的工序,最好连续加工,以减少重负定位次数和换刀次数。
数控加工零件的工艺分析与数控铣削加工工艺

数控加工零件的工艺分析与数控铣削加工工艺数控加工是指利用计算机数控系统,通过编写程序控制机床工作来加工零件的一种加工方式。
在工业生产中,数控加工因其高精度、高效率、高灵活性等优点而被广泛应用。
其中数控铣削是一种常见的数控加工方式,本文将从工艺分析、数控铣削加工工艺等方面进行探讨。
一、数控加工零件的工艺分析工艺分析是数控加工的一项前置工作,它的目的是确定加工工艺,选择合适的加工设备和刀具,制定加工程序等,从而保证加工质量和效率。
具体而言,工艺分析主要包括以下几个方面:1. 零件的材质和形状:不同材质的加工性能不同,加工时需要选择相应的切削参数和刀具;而零件的形状和结构也会影响加工难度和精度,需要对其进行全面分析和评估。
2. 加工精度和表面质量要求:根据零件的要求,确定加工精度和表面质量目标,制定相应的切削参数和工艺措施。
3. 工序分析:对零件进行逐个工序分析,确定加工顺序、加工方向、加工路径和刀具选择等重要内容,同时把握好每个工序的加工质量和效率。
4. 刀具选择:根据加工材料、零件形状和要求,选择合适的刀具和刀具尺寸,保证零件的加工质量和加工效率。
5. 加工程序制定:通过数控编程软件,编写机床加工程序,包括各种切削参数、刀具路径、指令参数等信息,为数控加工提供参考。
二、数控铣削加工工艺数控铣削是一种高速旋转的刀具在工件表面上进行切削的加工方式,它广泛应用于金属、塑料等材料制件的加工中。
数控铣削在工件制作中具有大量价值和应用,且数控铣削加工工艺也是半自动化和自动化制造中的重要工艺之一。
要把好铣削的关,需要具备以下几点:1. 刀具选择:刀具的选择是影响加工效率和加工质量的重要因素之一。
首先需要考虑切削材料,选择高速钢、硬质合金、陶瓷等材质的刀具;其次要考虑刀具尺寸和形状,根据零件的要求选择合适的刀具。
2. 切削参数:切削参数包括切削速度、进给量和切削深度等,这些参数的选定与零件材料、刀具材料、刀具尺寸和表面质量等因素密切相关。
齿轮加工工艺过程和分析

齿轮的生产过程一.齿轮的主要加工面1.齿轮的主要加工表面有齿面和齿轮基准表面,后者包括带孔齿轮的基准孔、切齿加工时的安装端面,以及用以找正齿坯位置或测量齿厚时用作测量基准的齿顶圆柱面。
2.齿轮的材料和毛坯常用的齿轮材料有15钢、45钢等碳素结构钢;速度高、受力大、精度高的齿轮常用合金结构钢,如20Cr,40Cr,38CrMoAl,20CrMnTiA等。
齿轮的毛坯决定于齿轮的材料、结构形状、尺寸规格、使用条件及生产批量等因素,常用的有棒料、锻造毛坯、铸钢或铸铁毛坯等。
二、直齿圆柱齿轮的主要技术要求,1.齿轮精度和齿侧间隙GBl0095《渐开线圆柱齿轮精度》对齿轮及齿轮副规定了12个精度等级。
其中,1~2级为超精密等级;3—5级为高精度等级;6~8级为中等精度等级;9~12级为低精度等级。
用切齿工艺方法加工、机械中普遍应用的等级为7级。
按照齿轮各项误差的特性及它们对传动性能的主要影响,齿轮的各项公差和极限偏差分为三个公差组(表13—4)。
根据齿轮使用要求不同,各公差组可以选用不同的精度等级。
齿轮副的侧隙是指齿轮副啮合时,两非工作齿面沿法线方向的距离(即法向侧隙),侧隙用以保证齿轮副的正常工作。
加工齿轮时,用齿厚的极限偏差来控制和保证齿轮副侧隙的大小。
2.齿轮基准表面的精度齿轮基准表面的尺寸误差和形状位置误差直接影响齿轮与齿轮副的精度。
因此GBl0095附录中对齿坯公差作了相应规定。
对于精度等级为6~8级的齿轮,带孔齿轮基准孔的尺寸公差和形状公差为IT6-IT7,用作测量基准的齿顶圆直径公差为IT8;基准面的径向和端面圆跳动公差,在11-22μm之间(分度圆直径不大于400mm的中小齿轮)。
3.表面粗糙度齿轮齿面及齿坯基准面的表面粗糙度,对齿轮的寿命、传动中的噪声有一定的影响。
6~8级精度的齿轮,齿面表面粗糙度Ra值一般为0.8—3.2μm,基准孔为0.8—1.6 μm,基准轴颈为0.4—1.6μm,基准端面为1.6~3.2μm,齿顶圆柱面为3.2μm。
基于数控机床的大型锥齿轮加工工艺研究与误差分析

基于数控机床的大型锥齿轮加工工艺研究与误差分析【摘要】本文基于数控机床对单位内部大型锥齿轮进行加工,在加工过程中结合实际情况,提出改进的加工工艺方法,并对可能产生的误差进行详细分析,结论表明此种方法不仅能完成本次加工也为下一阶段的其他产品加工提供了基础。
【关键词】数控机床大型锥齿轮工艺误差1 绪论随着经济的快速发展,人们对物质的要求越来越多、越来越细,提高加工精度已经成为必然的趁势。
而且快速发展的科学技术和机械制造技术,也为提高加工精度提供了基础。
数控机床己成为柔性制造系统、计算机集成制造系统、智能化制造系统及工厂自动化的基本组成单元。
所以提高数控机床的加工精度是提高加工产品质量的必要路径。
而控制数控机床加工精度在一定的范围内是一个需要不断研究的重要课题。
仅就中国航天、航空制造业来讲,要在10年内完成登月之旅,中国的数控机床将要发挥巨大的作用,这就为机床行业提供了商机。
并且为贯彻国家“振兴东北老工业基地”的战略方针,促进辽宁省装备制造业进一步的提高与发展。
2 数控机床大型锥齿轮加工总体框架依据数控机床系统在通信、数控机床数据采集与处理和数控机床远程监视与管理方面的需求,利用关键技术对传统方案进行改进,分步设计出数控机床加工大型锥齿轮总体框架。
整体思路是首先确定系统的主要组成模块,然后解决数控机床与上位机通信问题,最后解决数控机床加工精度与误差分析问题。
在确定系统主要组成模块之前,简要介绍一下嵌入式系统。
嵌入式系统是对设备、机器或车间的运作,进行控制、监视或辅助的装置。
另外,国内有一个更通俗,而且被普遍认同的定义:以应用为中心、以计算机技术为基础,软件硬件可剪裁,能满足应用系统对功能、可靠性、成本、体积、功耗严格要求的专用计算机系统。
首先确定系统的主要组成模块,传统的系统由上位机,下位机,串口服务器和数控机床组成,上位机和下位机均基于通用pc机。
然而通用pc 机体积大、功耗高且灵活性差,在此,利用嵌入式适配器将下位机与串口服务器的功能集成起来,嵌入式适配器是一个典型的嵌入式系统,可依据需求进行定制,灵活性高。
齿形轴零件机械加工工艺过程及加工用夹具设计
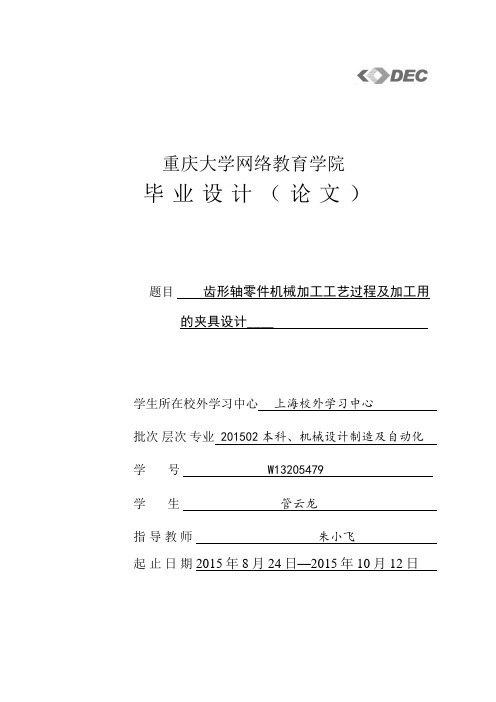
重庆大学网络教育学院毕业设计(论文)题目齿形轴零件机械加工工艺过程及加工用的夹具设计____学生所在校外学习中心上海校外学习中心批次层次专业201502本科、机械设计制造及自动化学号W13205479学生管云龙指导教师朱小飞起止日期 2015年8月24日—2015年10月12日摘要齿轮轴零件的主要作用是支撑回转零件、实现回转运动并传递转矩和动力。
齿轮轴具备传动效率高、结构紧凑和使用寿命长等一系列优点,是通用机械特别是工程机械传动中的重要零件之一。
齿轮轴加工材料、热处理方式、机械加工工艺过程的优化,将对提高齿轮轴的加工质量及寿命有着重要借鉴意义。
本文对某设备中“齿轮轴”零件进行了机械制造工艺规程设计和加工用的夹具设计。
对于工艺规程设计和夹具设计制订了两套不同的方案,从中甄选出最佳方案。
本设计首先分析了齿轮轴零件的作用和加工工艺性,然后进行工艺规程设计,最后是加工用夹具设计。
齿轮轴零件的机械综合性能要求较高,一般选择锻件作为毛坯。
合理安排工艺路线,划分加工阶段对保证零件加工质量至关重要。
使用夹具可以缩短辅助时间,提高劳动生产率,保证加工精度,稳定加工质量,降低对工人的技术要求,扩大机床工艺范围。
本文对所设计的专用夹具进行了精度校核和定位误差分析,对夹具的设计质量也进行了评估。
关键词:齿轮轴;工艺分析;工艺规程设计;夹具设计目录摘要 (2)1 设计背景及目的 (4)2生产纲领及生产类型的确定 (4)3 零件的分析 (5)4 选择毛坯 (5)5 工艺规程设计 (6)5.1 定位基准选择 (6)5.2 零件的加工方法的选择 (6)5.3 定制工艺路线 (6)5.4 确定机械加工的余量及毛坯尺寸,设计毛坯-零件综合图 (7)6 工序设计 (9)6.1 选择加工设备工艺装备 (9)6.2 工序尺寸的确定及计算 (10)6.3 选择切削用量,确定时间定额 (11)7 滚齿用夹具设计 (13)7.1 拟定滚齿夹具的结构方案 (13)7.2 确定刀具的导向方式或对刀装置 (14)7.3 夹具精度的计算 (14)7.4 夹具总图(图4) (15)7.5 夹具零件图(图5、图6) (16)8 课题小结 (17)1 设计背景及目的在我们学完了大学的全部基础课程、技术课程及全部专业课程之后进行的。
数控车典型机械零件的数控工艺设计与编程加工
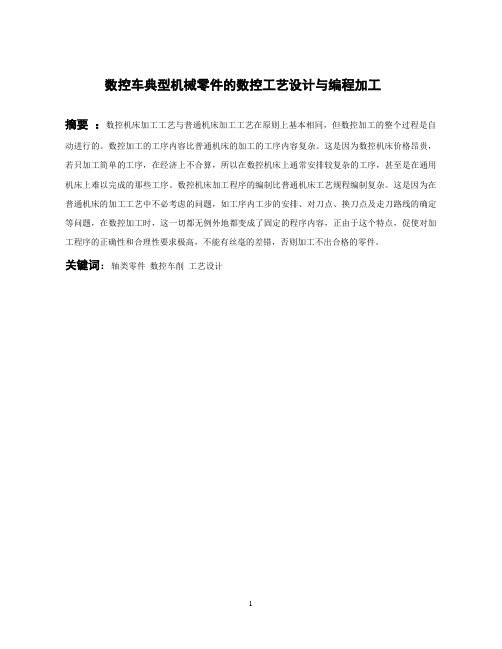
数控车典型机械零件的数控工艺设计与编程加工摘要:数控机床加工工艺与普通机床加工工艺在原则上基本相同,但数控加工的整个过程是自动进行的。
数控加工的工序内容比普通机床的加工的工序内容复杂。
这是因为数控机床价格昂贵,若只加工简单的工序,在经济上不合算,所以在数控机床上通常安排较复杂的工序,甚至是在通用机床上难以完成的那些工序。
数控机床加工程序的编制比普通机床工艺规程编制复杂。
这是因为在普通机床的加工工艺中不必考虑的问题,如工序内工步的安排、对刀点、换刀点及走刀路线的确定等问题,在数控加工时,这一切都无例外地都变成了固定的程序内容,正由于这个特点,促使对加工程序的正确性和合理性要求极高,不能有丝毫的差错,否则加工不出合格的零件。
关键词:轴类零件数控车削工艺设计目录一、零件工艺分析 (1)(一)零件工艺分析 (1)1.零件图分析 (1)2.工艺分析 (1)(二)选择零件毛坯 (1)二加工方法的选择 (2)(一)数控车削加工方法拟订 (2)1. 数控车削加工外圆回转体零件与端面加工方法的选择 (2)2. 数控车削加工内圆回转体加工方法的确定 (2)3 .数控车削加工螺纹加工方法的确定 (3)三机床与刀具的选择 (3)(一)机床的选择 (3)1.SSCK20/500数控车床布局 (3)(二)刀具的选择 (6)四定位与夹紧方式的确定 (4)(一)定位与夹紧方式 (4)五加工顺序的安排 (5)六确定走刀路线和工步顺序 (5)(一)确定加工顺序和走刀路线 (5)1.工步顺序的确定 (5)2.走刀路线的确定 (6)(一)切削用量的选择 (7)(二)数控加工工艺卡片拟订 (9)八对刀点与换刀点的确定 (10)(一)对刀点 (10)(二)换刀点 (11)九高速切削技术 (12)十程序的编制 (13)(一)零件各结点尺寸计算就 (12)(二)程序的编制 (13)致谢 (18)参考文献 (18)(一)零件工艺分析图1-11.零件图分析图1-1零件从结构图来看该零件包括内﹑外的加工。
典型零件数控加工工艺分析实例

说明:表格中刀尖半径和备注栏可以不要;25×25 指车刀刀柄的截面尺寸。
(5)切削用量选择
一般情况下,粗车:恒转速 n=800r/min 恒线速 v=100m/min
进给量 f=0.2mm/r 以下
vf=120m/min
背吃刀量 ap=2mm 以下
精车:恒转速 n=1100r/min 恒线速 v=150m/min
以零件右端面和中心轴作为 坐标原点建立工件坐标系。
根据零件尺寸精度及技术要 求,零件从右向左加工,将粗、 精加工分开来考虑。
加工工艺顺序为:车削右端面→复合型车削固定循环粗、精加工右端需要加工的所有轮 廓(粗车Φ44、Φ40.5、Φ34.5、Φ28.5、Φ22.5、Φ16.5 外圆柱面→粗车圆弧面 R14.25→ 精车外圆柱面Φ40.5→粗车外圆锥面→粗车外圆弧面 R4.75→精车圆弧面 R14→精车外圆锥 面→精车外圆柱面Φ40→精车外圆弧面 R5)。 (4)选择刀具
所选定刀具参数如表 1-2 所示。 说明:铣削内、外轮廓时,铣刀直径受槽宽限制,可选择φ6 的立铣刀;精铰的量通常 小于 0.2mm;刀刃和长度通常要比切削的深度大。 5.切削用量选择 一般情况下,粗铣:恒转速 n=600r/min
进给量 f=180mm/min 以下 背吃刀量 ap=5mm 以下 精车:恒转速 n=800r/min 进给量 f=120mm/min 以下
零件的底面和外部轮廓已经加工,本工序是在铣床上加工槽与孔。 1.零件图分析
凸轮内外轮廓由直线和圆弧组成。凸轮槽侧面和
20
0.021 0
、
12
0.018 0
两个内孔尺寸精
度要求较高,表面粗糙度要求也较高,Ra1.6;内孔
20
数控加工工艺大作业典型轴类零件的数控加工工艺设计.doc

目录1.零件图工艺分析2设备选择3确定零件的定位基准和装夹方式4确定加工顺序及进给路线5刀具的选择6确定切削用量7填写数控加工工艺文件轴类零件的数控加工工艺的编制及加工图1.零件图工艺分析零件车削工艺分析如图1-1所示,零件材料处理为:45钢,下面对该零件进行数控车削工艺分析。
零件如图:图1-1 零件图1.1数控加工工艺基本特点数控机床加工工艺与普通机床加工原则上基本相同,但数控机床是自动进行加工,因而有如下特点:①数控加工的工序内容比普通机床的加工内容复杂,加工的精度高,加工的表面质量高,加工的内容较丰富。
②数控机床加工程序的编制比普通机床工艺编制要复杂些。
这是因为数控机床加工存在对刀、换刀以及退刀等特点,这都无一例外的变成程序内容,正是由于这个特点,促使对加工程序正确性和合理性要求极高,不能有丝毫的差错。
否则加工不出合格的零件。
在编程前我们一定要对零件进行工艺分析,这是必不可少的一步,如图1-1我要对该零件进行精度分析,选择加工方法、拟定加工方案、选择合理的刀具、确定切削用量。
该零件由螺纹、圆柱、圆锥、圆弧等表面组成。
可控制球面形状精度、30°的锥度等要求。
经上面的分析,我可以采用以下工艺措施:(1)为便于装夹,为了保证工件的定位准确、稳定,夹紧方面可靠,支撑面积较大,零件的左端是最大直径圆柱ф85mm,中段的圆柱ф80mm。
右端是螺纹,应先装夹毛坯加工出左端圆弧及圆柱ф85mm、ф80mm调头装夹ф80mm的圆柱加工右端螺纹、圆柱及锥面,毛坯选ф85×350mm。
1.2设备选择根据该零件的外形是轴类零件,只有在数控车床上加工才能保证其加工的尺寸精度和表面质量。
我选择在本校的数控机床HNC-CK6140加工该零件。
1.3确定零件的定位基准和装夹方式1.3.1粗基准选择原则(1)为了保证不加工表面与加工表面之间的位置要求,应选不加工表面作粗基准。
(2)合理分配各加工表面的余量,应选择毛坯外圆作粗基准。
数控车床车削典型零件工艺分析

数控车床车削典型零件工艺分析数控车床是一种利用数控技术进行自动化车削加工的机床,广泛应用于制造业的各个领域。
下面将以数控车床车削典型零件为例进行工艺分析。
以加工一台螺杆为例,工艺分析如下:1.零件材质选择:根据螺杆的使用要求,选择适当的材料,常见的有碳钢、不锈钢等。
2.设计图纸:根据产品需求,在CAD软件中绘制螺杆的设计图纸,包括尺寸、形状等。
3.工艺规程编制:根据零件的设计要求,编制螺杆的工艺规程,包括车削工序、工艺参数、刀具选择等。
4.刀具选择:根据工艺规程选择适合的刀具,考虑切削力、刀具寿命等因素。
5.数控编程:根据工艺规程,利用CAM软件编写数控程序,确定刀具路径、切削深度、进给速度等参数。
6.夹紧装夹:将材料切割到合适的长度后,将工件固定在数控车床的主轴上,使用合适的夹具夹紧。
7.车削加工:根据数控程序进行车削加工,包括外径车削、内径车削、螺纹加工等工序。
8.检测与修正:每一道工序完成后,需要进行质量检测,确保零件尺寸、表面粗糙度等符合要求。
若发现问题,及时进行修正。
9.表面处理:根据产品要求,对螺杆表面进行处理,如抛光、镀层等。
10.质量检验:经过表面处理后,对零件进行再次质量检验,确保各项指标符合要求。
11.包装运输:将加工好的螺杆进行包装和标识,便于运输和使用。
以上是加工一台螺杆的工艺流程,数控车床的精度高、重复性好,能够高效、精确地进行复杂零件的加工。
在实际应用中,根据不同的零部件要求,工艺流程可能会有所不同,但总的来说,工艺分析包括材料选择、工艺规程编制、刀具选择、数控编程、夹紧装夹、车削加工、检测与修正、表面处理、质量检验、包装运输等环节。
通过合理的工艺分析和流程设计,可以实现零件的高效、精确加工,提高生产效率和产品质量。
齿轮加工工艺过程与分析

齿轮加工工艺过程与分析齿轮是一种常见的零件,广泛建筑、机械、汽车、数控机床、船舶等领域都有广泛的应用。
在生产中,齿轮加工的工艺是非常重要的一步。
齿轮加工工艺的好坏,直接影响着齿轮质量的稳定性和耐久性。
齿轮加工工艺主要分为以下几个环节:齿轮零件规划、零件加工准备、齿轮加工方法选择、齿轮加工技术和齿轮加工后处理。
一、齿轮零件规划齿轮加工工艺的第一步就是齿轮零件规划。
根据齿轮使用条件、所需制品、制造费用等因素,选定合适的齿轮零件结构和材料。
一般来说,齿轮材料可选择铸钢、锻钢或热处理钢等。
钢材经过合理的热处理后,可以提高齿轮的硬度、强度、耐磨性和韧性。
二、零件加工准备齿轮加工的准备是齿轮加工工艺过程中最重要的步骤之一。
而零件加工准备的关键在于保证零件加工的精度和质量。
零件加工准备包括如下几个方面:1. 零件加工线路零件加工必须具有严密的加工线路,包括工具选择、加工顺序、加工设备选择等,以保证零件加工有序进行。
2. 技术资料制定必要的齿轮加工工艺方案,如齿轮数、模数、齿轮位移、等值距、齿宽等技术资料,以便工匠们操作。
3. 加工设备准备根据工艺方案,选择适当的机器和工具,以满足零件加工所需的精度、表面质量等。
三、齿轮加工方法选择根据齿轮零件的结构和使用要求,选择合适的齿轮加工方法。
现阶段,常用的齿轮加工方法主要有:铣削法、齿轮滚爬法、齿轮锻造法、齿轮打磨法等。
四、齿轮加工技术齿轮加工技术使上面的工艺方案具体操作起来,它包含了齿轮加工的每一个具体的步骤。
1. 齿轮倒角齿轮加工后角度的处理要非常规范,能够防止异形齿轮的出现。
同时还可避免轴瓦因夹在齿形上而引起的磨损。
2. 齿轮校正齿轮加工时,有时会出现不同工序的误差,导致齿轮非常难以拼合。
因此,需要进行校准,以提高加工精度。
3. 齿轮热处理齿轮加工工艺的最后一步是进行热处理,以获得良好的综合性能。
常见的热处理方法有淬火、正火、渗碳等。
五、齿轮加工后处理齿轮加工后处理是为了检查齿轮是否符合相关的性能要求。
典型轴类零件的数控车削工艺与加工实验报告
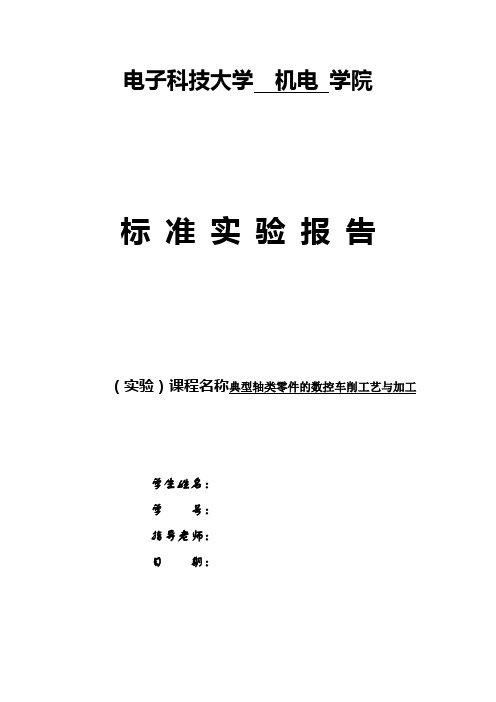
电子科技大学机电学院标准实验报告(实验)课程名称典型轴类零件的数控车削工艺与加工学生姓名:学号:指导老师:日期:电子科技大学教务处制表电子科技大学实验报告学生姓名:学号:指导教师:实验地点:工程训练中心114 实验时间:一、实验室名称:工程训练中心二、实验项目名称:典型轴类零件的数控车削工艺与加工实验学时:32三、实验原理:在软件中进行设计绘图,运用G代码,将工艺文件编制成数控加工程序,输入数控车床,加工出零件。
四、实验目的:1.了解典型零件的特点、生产过程与应用;2.学习工程制造工艺,学习工程手册的使用,掌握典型零件的毛坯制造、热处理、机加工方法;3.将传统加工与现代制造技术有机结合,合理制定数控加工工艺,正确使用数控设备及刀夹量具;4.培养和提高综合分析轴类零件的问题和解决问题的能力,以及培养科学的研究和创造能力。
五、实验内容1.轴类零件的功用、结构特点及技术要求;2.轴类零件的毛坯和材料及热处理;3.运用Mastercam9.0进行轴的设计以及程序的生成;4.轴类零件的安装方式;5.数控车削工艺;6.编制数控车削程序加工出所设计的零件;7.数控车床的操作。
六、实验器材(设备、元器件):计算机、数控车床、90°外圆车刀、93°偏头仿形车刀、60°螺纹刀、切槽刀、量具及金属材料。
七、实验步骤:1.设计零件,绘制图形。
2.轴类零件的功用,结构特点及技术要求。
3.轴类零件的毛坯材料及热处理。
4.结构设计、工艺分析。
5.轴类零件的数控工艺、编程。
6.上机操作加工。
7.检验。
八、实验数据及结果分析:1.被加工零件的零件图。
(见附件)2.数控加工工艺文件。
(见附件)3.数控加工程序(见附件)。
4.结果分析:在整个加工过程中,存在加工误差,原由是:1)对刀引起的加工误差,尽管加工时,对刀点尽量选在工件的设计基准或工艺基准上;2)进给线对零件的加工精度和表面粗糙度的直接影响,在实验中尽量保证了进给线长短的合理设计;3)加工时刀具的磨损导致零件尺寸不合格;4)加工工艺上刀具的选着以及工艺安排上努力做到最优化。
齿轮范成加工实验报告
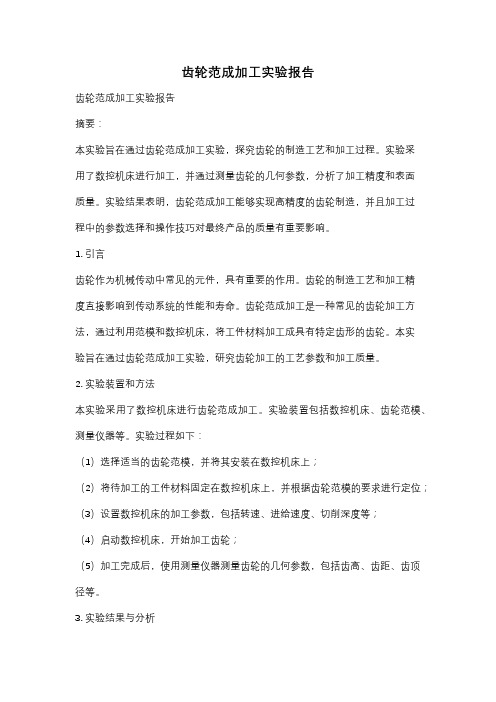
齿轮范成加工实验报告齿轮范成加工实验报告摘要:本实验旨在通过齿轮范成加工实验,探究齿轮的制造工艺和加工过程。
实验采用了数控机床进行加工,并通过测量齿轮的几何参数,分析了加工精度和表面质量。
实验结果表明,齿轮范成加工能够实现高精度的齿轮制造,并且加工过程中的参数选择和操作技巧对最终产品的质量有重要影响。
1. 引言齿轮作为机械传动中常见的元件,具有重要的作用。
齿轮的制造工艺和加工精度直接影响到传动系统的性能和寿命。
齿轮范成加工是一种常见的齿轮加工方法,通过利用范模和数控机床,将工件材料加工成具有特定齿形的齿轮。
本实验旨在通过齿轮范成加工实验,研究齿轮加工的工艺参数和加工质量。
2. 实验装置和方法本实验采用了数控机床进行齿轮范成加工。
实验装置包括数控机床、齿轮范模、测量仪器等。
实验过程如下:(1)选择适当的齿轮范模,并将其安装在数控机床上;(2)将待加工的工件材料固定在数控机床上,并根据齿轮范模的要求进行定位;(3)设置数控机床的加工参数,包括转速、进给速度、切削深度等;(4)启动数控机床,开始加工齿轮;(5)加工完成后,使用测量仪器测量齿轮的几何参数,包括齿高、齿距、齿顶径等。
3. 实验结果与分析通过实验得到的齿轮样品,进行了几何参数的测量和分析。
结果显示,齿轮的几何参数符合设计要求,并且加工精度较高。
通过测量结果可以得出以下结论:(1)齿高和齿距的测量结果与设计值相近,表明齿轮的加工精度较高;(2)齿顶径的测量结果与设计值存在一定的偏差,这可能是由于加工过程中的刀具磨损和数控机床的误差所导致;(3)齿轮的表面质量较好,没有明显的划痕和毛刺。
4. 影响加工精度和表面质量的因素在齿轮范成加工过程中,加工精度和表面质量受到多种因素的影响。
以下是一些重要因素的讨论:(1)切削参数的选择:切削速度、进给速度和切削深度等参数的选择对齿轮加工的精度和表面质量有重要影响。
合理的切削参数能够提高加工效率和加工质量。
- 1、下载文档前请自行甄别文档内容的完整性,平台不提供额外的编辑、内容补充、找答案等附加服务。
- 2、"仅部分预览"的文档,不可在线预览部分如存在完整性等问题,可反馈申请退款(可完整预览的文档不适用该条件!)。
- 3、如文档侵犯您的权益,请联系客服反馈,我们会尽快为您处理(人工客服工作时间:9:00-18:30)。
Ab s t r a c t :A r t i c l e s a c c o r d i n g t o t h e g e a r p a ts r d r a wi n g s a n d t e c h n i c a l r e q u i r e me n t s ,t h e p a r t s c a r r i e d o u t a d e t a i l e d
第 4 0卷 第 1 1期 ・ 学 术
VoI . 40 NO V. 1 1
湖
南
农
机
2 O1 3年 1 1 月
N OV. 201 3
HUNAN AGRI CUL TURAL MACHI NER Y
基于典型齿轮零件 的数控 工艺 分析 与加工
聂 荣臻
( 常 州刘 国钧 高等 职业技 术学 校 , 江苏 常 州 2 1 3 0 0 1 )
Nl E Ron g一 e n
( C h a n g z h o u L i u g u o j u n v o c a t i o n a l a n d t e c h n i c l a s c h o o l s ,C h a n g z h o  ̄J i ng a s u 2 1 3 0 0 1 , C h i n a )
( 3 ) 工序与工步 的划分 : ①为装夹零件左端加工零件右端 面和外型面。 ②掉头装夹零件右端加工零件左端面和外型面。
③卸下零件装夹在加工中心上加工 内腔 。④卸下零件装夹在
滚齿机上 。
工序 1 : 为装夹零件右端 加工零件 左端 内外 型面 数控加 工
工 厂
产 品名称或代号
摘 要: 文章根据该齿轮零件的 图纸及技 术要 求 , 对该零件进行 了详 细的数控加 工工艺分 析 , 依据 分析的结果 , 确 定 了该零件 的装 夹方式、 定位基准 、 使 用刀具 、 加 工顺序安排 、 工步划分 , 走 刀路 线和切 削用量等 , 最后 , 采用手工编程编
制 了该零件 的数控加 工程序。
S K 0 5 5 5 4
零件名称
零件 图号
S N T — J Z Q - O 0 0 5 4
工 序 卡
工序 。④ 以粗 、 精加工划分工序。
2 齿轮 零件 的数控 J j  ̄ - r - r 序 设计
( 1 ) 切削用量 的确定 。 此齿轮零件粗加工选择的转速应该 为: 8 0 0转 /r a i n ,背吃刀量应该选择大 约 1  ̄ 5 m m通常工件 留 出一定的精加工余量 ,通过精加工来实现 图样 上提出的技术
a n d f i n a l l y ,t h e u s e o f t h e p r e p a r a t i o n o f t h e ma n u a l p r o g r a mmi n g CNC ma c h i n i n g p a r t s p r o g r a m. Ke y wo r d s :Ge a r p a t r s ;Ma n u a l p r o g r a mmi n g , ; CNC ma c h i n i n g
关键 词 : 齿轮零件 ; 手工编程 ; 数 控 加 工
中图分类号 : T G 6 1
文献标识码 : A
文章编号 : 1 0 0 7 — 8 3 2 0 ( 2 0 1 3 ) 1 1 - 0 1 3 0 - 0 2
CNC g e a r p a r t s b a s e d o n t y p i c a l p r o c e s s a n a l y s i s a n d p r o c e s s i n g
p o s i t i o n i n g r e f e r e n c e ,t h e u s e o f t o o l s ,ma c h i n i n g s e q u e n c e a r r a n g e me n t ,s t e p i n t o ,t a k e t h e k n i f e a n d t h e c u t t i n g l i n e ,
0 . 3 mm。
( 2 ) 刀具的选择 。根据加工要求需选择刀具如下:1 号刀
机夹车 刀( 硬质合金 可转位 刀片 , 副偏 角 K r 大于 5 0度 ) ; 2 号刀宽 1 6 m m的硬质合金切槽刀 ; 3 号刀 A 4中心钻 ; 4号刀 口
1 0锥柄麻花钻 ; 5号刀 5 0元宝刀 ; 6号刀 R 6 球头刀 。
1 零 件 的结构 工艺性 分析
工艺路线 的拟定 。 根据数控加工 的特点 , 该零件数控工序 的划分可按下列方法进行 :①以一次安装 、加工作为一道工 序。 ② 以同一把刀具加工的内容划分工序 。 ③以加工部位划分
要求 。 一般精加工的背吃 刀量为 O . 1 ~ 0 . 3 m m 。 此齿轮零件精加 工选 择的转速应该 为 : 1 2 0 0转 / m i n ,背吃 刀量 应该选择大约