机械产品可靠性设计分析案例
机械设计中的产品可靠性分析与评估

机械设计中的产品可靠性分析与评估在当今竞争激烈的市场环境中,机械产品的可靠性已成为企业赢得市场份额和用户信任的关键因素。
可靠性不仅关系到产品的质量和性能,更直接影响着用户的满意度和企业的声誉。
因此,在机械设计过程中,对产品可靠性进行深入的分析与评估具有重要的意义。
一、产品可靠性的概念与重要性产品可靠性,简单来说,是指产品在规定的条件下和规定的时间内,完成规定功能的能力。
这包括了产品在使用过程中的稳定性、耐久性、无故障工作时间等多个方面。
一个可靠的机械产品,能够在各种复杂的工作环境和使用条件下,持续稳定地运行,减少故障和维修的次数,从而为用户提供更好的服务,同时也降低了企业的售后成本。
对于企业而言,产品可靠性的重要性不言而喻。
首先,高可靠性的产品能够提升企业的市场竞争力。
在消费者选择产品时,往往更倾向于那些质量可靠、故障少的品牌。
其次,可靠的产品有助于降低生产成本。
虽然在提高可靠性的过程中可能需要增加前期的研发投入,但由于减少了后期的维修和更换成本,总体成本反而会降低。
再者,良好的可靠性能够增强企业的声誉和品牌形象,促进企业的长期发展。
二、影响产品可靠性的因素在机械设计中,有众多因素会影响产品的可靠性。
设计方面,不合理的结构设计、选用了不合适的材料、零部件之间的匹配度不足等,都可能导致产品在使用过程中出现故障。
制造工艺的优劣也直接关系到产品的质量和可靠性。
例如,加工精度不够、装配不当等都会影响产品的性能和寿命。
此外,使用环境也是一个重要的影响因素。
机械产品在高温、高湿、高压、强腐蚀等恶劣环境下工作,其可靠性会受到极大的挑战。
而用户的操作和维护方式同样不可忽视。
不正确的操作方法、不及时的维护保养,都可能加速产品的损坏。
三、产品可靠性分析方法为了准确评估机械产品的可靠性,需要采用一系列的分析方法。
故障模式与影响分析(FMEA)是一种常用的方法。
它通过对产品可能出现的故障模式进行分析,评估每种故障模式的影响程度和发生概率,从而找出潜在的薄弱环节,并采取相应的改进措施。
机械工程中的可靠性优化设计

机械工程中的可靠性优化设计引言:机械工程是一个广泛应用于各行各业的领域,而在机械工程中,可靠性优化设计是一个至关重要的方面。
可靠性优化设计旨在提高机械系统的可靠性,延长设备的使用寿命,减轻后续的维修成本,提高工业生产效率。
本文将探讨机械工程中的可靠性优化设计的原理和方法,并介绍一些实际应用案例。
一、可靠性的基本概念在机械工程中,可靠性是一个关键的指标,它表示一个系统在给定的时间内正常工作的能力。
可靠性可以通过计算系统的故障率、失效率、平均寿命等指标来评估。
在可靠性优化设计中,目标是降低系统的故障率,提高系统的可靠性。
二、可靠性优化设计的原则1. 考虑系统的可靠性要素可靠性优化设计要考虑系统设计的各个方面,包括材料的选择、结构的设计、工艺的控制等。
系统的可靠性是由多个因素共同作用决定的,因此必须综合考虑各个方面的因素。
2. 运用可靠性工具在可靠性优化设计中,有许多工具和方法可供选择,如故障模式与影响分析(FMEA)、故障树分析(FTA)、可靠性块图(RBD)等。
这些工具能够帮助工程师深入分析系统的故障模式和风险,从而指导设计的改进和优化。
3. 进行系统辨识和优化在可靠性优化设计中,系统辨识是一个重要的步骤。
通过系统辨识,可以找出系统中的关键部件和环节,以及它们之间的相互作用关系。
然后,可以针对这些关键部件和环节进行优化设计,提高系统的可靠性。
三、可靠性优化设计的方法1. 材料的选择材料是机械系统中一个重要的方面,对系统的可靠性起着至关重要的作用。
在选择材料时,需要考虑其物理性质、化学性质、热学性质等因素,并根据系统的工作环境和使用条件选择合适的材料。
2. 结构的设计在机械工程中,结构的设计对系统的可靠性有着重要的影响。
良好的结构设计应该考虑到力学强度、刚度、防振动、冲击和疲劳等因素。
通过优化结构设计,可以提高机械系统的可靠性。
3. 工艺的控制机械系统的制造过程对其可靠性也有重要的影响。
控制好工艺流程、提高工艺的精度和稳定性,可以降低系统的故障率。
机械设计中的可靠性与安全性分析案例验证
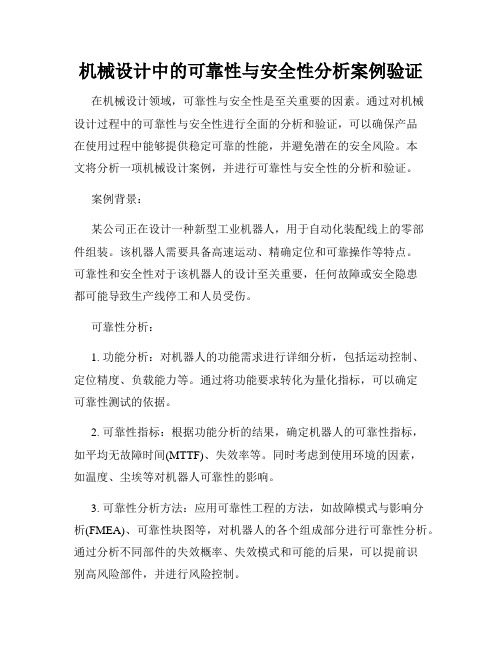
机械设计中的可靠性与安全性分析案例验证在机械设计领域,可靠性与安全性是至关重要的因素。
通过对机械设计过程中的可靠性与安全性进行全面的分析和验证,可以确保产品在使用过程中能够提供稳定可靠的性能,并避免潜在的安全风险。
本文将分析一项机械设计案例,并进行可靠性与安全性的分析和验证。
案例背景:某公司正在设计一种新型工业机器人,用于自动化装配线上的零部件组装。
该机器人需要具备高速运动、精确定位和可靠操作等特点。
可靠性和安全性对于该机器人的设计至关重要,任何故障或安全隐患都可能导致生产线停工和人员受伤。
可靠性分析:1. 功能分析:对机器人的功能需求进行详细分析,包括运动控制、定位精度、负载能力等。
通过将功能要求转化为量化指标,可以确定可靠性测试的依据。
2. 可靠性指标:根据功能分析的结果,确定机器人的可靠性指标,如平均无故障时间(MTTF)、失效率等。
同时考虑到使用环境的因素,如温度、尘埃等对机器人可靠性的影响。
3. 可靠性分析方法:应用可靠性工程的方法,如故障模式与影响分析(FMEA)、可靠性块图等,对机器人的各个组成部分进行可靠性分析。
通过分析不同部件的失效概率、失效模式和可能的后果,可以提前识别高风险部件,并进行风险控制。
4. 可靠性测试:制定可靠性测试方案,通过模拟实际工作环境和负载条件,对机器人进行可靠性测试。
测试数据可以用于验证设计的可靠性指标是否满足要求,并对异常情况进行改进和修复。
安全性分析:1. 安全需求分析:根据机器人的使用场景和操作要求,确定安全需求和标准。
考虑机器人在高速运动、与人员接触等情况下的安全性要求,并制定相应的安全措施。
2. 风险评估:使用风险评估方法,如风险矩阵、风险优先级指数等,对机器人使用过程中可能出现的安全风险进行评估。
重点评估与人员接触、运动控制等相关的风险,并确定高风险区域和关键控制点。
3. 安全设计:基于风险评估的结果,进行安全设计,包括采用安全传感器、应急停机装置、防护罩等安全防护设施。
机械设备可靠性分析
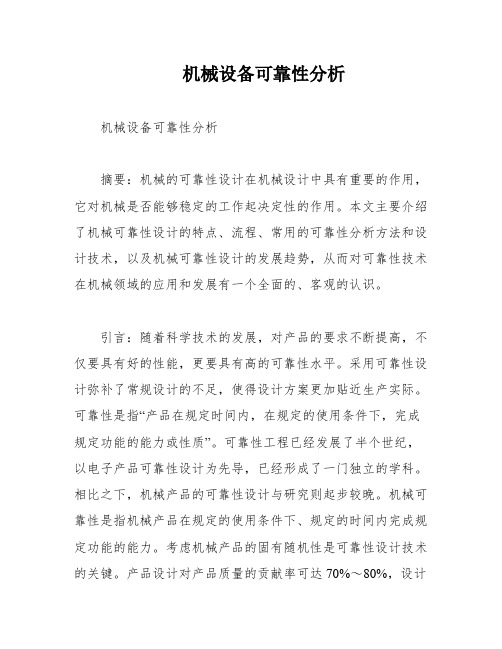
机械设备可靠性分析机械设备可靠性分析摘要:机械的可靠性设计在机械设计中具有重要的作用,它对机械是否能够稳定的工作起决定性的作用。
本文主要介绍了机械可靠性设计的特点、流程、常用的可靠性分析方法和设计技术,以及机械可靠性设计的发展趋势,从而对可靠性技术在机械领域的应用和发展有一个全面的、客观的认识。
引言:随着科学技术的发展,对产品的要求不断提高,不仅要具有好的性能,更要具有高的可靠性水平。
采用可靠性设计弥补了常规设计的不足,使得设计方案更加贴近生产实际。
可靠性是指“产品在规定时间内,在规定的使用条件下,完成规定功能的能力或性质”。
可靠性工程已经发展了半个世纪,以电子产品可靠性设计为先导,已经形成了一门独立的学科。
相比之下,机械产品的可靠性设计与研究则起步较晚。
机械可靠性是指机械产品在规定的使用条件下、规定的时间内完成规定功能的能力。
考虑机械产品的固有随机性是可靠性设计技术的关键。
产品设计对产品质量的贡献率可达70%~80%,设计决定了产品的固有质量特性,赋予了产品“先天优劣”的本质特性。
上世纪60年代,对机械可靠性问题引起了广泛的重视并开始对其进行了系统研究。
虽然国内外都投入了研究力量,但由于机械产品可靠性涉及的领域太多、可靠性研究的范围大、基础性数据缺乏等原因,机械可靠性设计在工程实际中应用得并不广泛。
本文介绍了可靠性技术在机械领域中的应用,主要介绍了一些在机械产品设计中应用的较为成熟的可靠性技术和可靠性设计方法。
常用的可靠性分析方法包括失效模式与影响分析(FMEA)、失效树分析(FTA)和事件树分析(ETA)等。
可靠性设计方法包括可靠性指标的确定、可靠性目标的制定、可靠性设计的方案选择和可靠性设计的验证等。
结合当今可靠性工程学科的发展,本文还指出了可靠性技术在机械领域中的发展和趋势。
综上所述,机械可靠性设计是机械设计中不可或缺的一部分。
通过可靠性设计方法和技术,可以提高机械产品的可靠性和质量,降低生产成本和维护费用,提高产品的市场竞争力。
机械设计中的案例分析与实例讲解

机械设计中的案例分析与实例讲解在机械设计领域中,案例分析和实例讲解是非常重要的学习方法和实践工具。
通过案例分析和实例讲解,可以加深对机械设计原理和应用的理解,掌握解决实际问题的能力。
本文将通过几个案例来分析和讲解机械设计中的关键问题和解决方法。
案例一:轴承选择与设计在机械设计过程中,轴承是不可或缺的重要组件。
选择和设计合适的轴承对于确保机械设备的正常运行至关重要。
在某公司的一个机械设计项目中,设计师面临着选择和设计轴承的问题。
首先,设计师需要根据机械设备的工作条件和要求来确定所需承载能力、转速范围等参数。
然后,根据这些参数和轴承的性能指标表,筛选出合适的轴承型号。
在选择轴承型号后,设计师还需要对轴承进行设计,确定轴承的几何尺寸和安装方式,以确保其在特定工作条件下的可靠性和寿命。
通过这个案例,我们可以看到,在机械设计中,轴承的选择和设计是一个复杂而关键的环节。
合适的轴承选择和设计可以提高机械设备的性能和可靠性。
案例二:零件强度分析与优化在机械设计中,零件的强度是一个重要的设计指标。
在某公司的一个机械结构设计项目中,设计师需要对一个零件进行强度分析和优化。
首先,设计师需要根据零件的工作条件和受力情况,确定零件的受力分析模型,并据此计算零件的应力和变形。
然后,根据零件的材料特性和载荷条件,对零件的强度进行评估。
如果发现零件的强度不满足要求,设计师需要通过调整材料选择、几何尺寸等参数来优化零件的强度。
通过这个案例,我们可以看到,在机械设计中,零件的强度分析和优化是关键的设计环节。
通过对零件的强度进行分析和优化,可以确保零件在工作条件下的安全可靠性,提高机械设备的性能。
案例三:机构设计与运动模拟在机械设计中,机构的设计和运动模拟是一项重要任务。
在某公司的一个机械运动机构设计项目中,设计师面临着设计和优化运动机构的问题。
首先,设计师需要根据机械设备的功能和要求,确定机构的类型和布置方式。
然后,设计师需要进行机构的几何设计,确定机构的连杆比例、驱动方式等参数。
第八章可靠性试验案例

n f (t ) ns (t ) n
其它参数可按如下相应公式计算 可靠度
ns (t ) R (t ) n
《机械可靠性设计》
20
第八章 累积失效概率(不可靠度)
可靠性试验
F (t )
失效概率密度
n f (t ) n
n f (t ) n t
f (t )
其中
失效率
n f (t ) n f (t t ) n f (t )
无替换定时截尾试验,记作[n,无,t0];
有替换定时截尾试验,记作[n,有,t0]; 无替换定数截尾试验,记作[n,无,r];
有替换定数截尾试验,记作[n,有,r];
《机械可靠性设计》
11
第八章
可靠性试验
三、寿命试验设计
可靠性寿命试验应根据被试验产品的性质和试验目的 来设计试验方案。但无论试验是否加速,有无替换,定数 还是定时截尾,一般均应包括下列基本内容: 1)明确试验对象 2)确定试验条件 3)拟定失效标准 4)选定测试周期 当产品寿命为指数分布时,累计失效分布函数为:
r 10 n 35.27, 取n 36 F (t ) 0.2835
从上面的计算结果可以看出,要在规定的时间t内观察
到较多的失效数r,则应增加投试样品数n。若要求观测到的 失效数r不变,如能增加投试样品数n,则可以缩短时间。
16
《机械可靠性设计》
第八章
可靠性试验
6)确定试验截止时间
n t0 ln nr
《机械可靠性设计》
第八章
可靠性试验
§8-3
寿命试验结果的统计分析及参数估计
一、一般分布完全寿命试验的数据处理
对n个随机抽取的样品进行寿命试验,直到全部样品 失效为止,这样的试验称为完全寿命试验。 n个随机样品的寿命是n个独立同分布的随机变量。一 次完整试验可以测得n个样品的失效时间。将全部样品失 效时间从小到大顺序排列,其顺序统计量为
机械工程中的可靠性与可行性分析
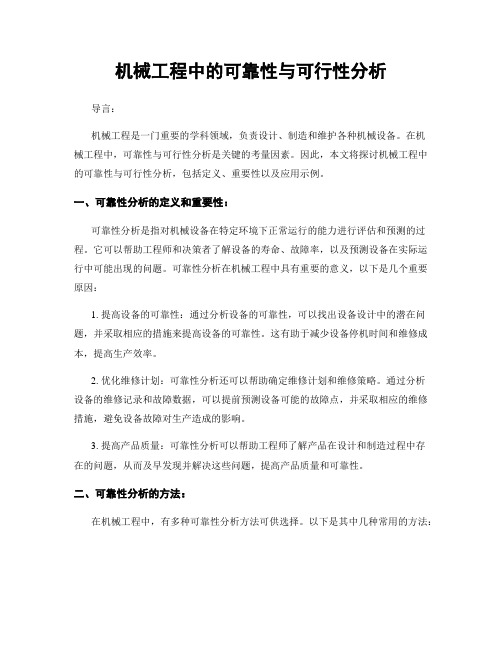
机械工程中的可靠性与可行性分析导言:机械工程是一门重要的学科领域,负责设计、制造和维护各种机械设备。
在机械工程中,可靠性与可行性分析是关键的考量因素。
因此,本文将探讨机械工程中的可靠性与可行性分析,包括定义、重要性以及应用示例。
一、可靠性分析的定义和重要性:可靠性分析是指对机械设备在特定环境下正常运行的能力进行评估和预测的过程。
它可以帮助工程师和决策者了解设备的寿命、故障率,以及预测设备在实际运行中可能出现的问题。
可靠性分析在机械工程中具有重要的意义,以下是几个重要原因:1. 提高设备的可靠性:通过分析设备的可靠性,可以找出设备设计中的潜在问题,并采取相应的措施来提高设备的可靠性。
这有助于减少设备停机时间和维修成本,提高生产效率。
2. 优化维修计划:可靠性分析还可以帮助确定维修计划和维修策略。
通过分析设备的维修记录和故障数据,可以提前预测设备可能的故障点,并采取相应的维修措施,避免设备故障对生产造成的影响。
3. 提高产品质量:可靠性分析可以帮助工程师了解产品在设计和制造过程中存在的问题,从而及早发现并解决这些问题,提高产品质量和可靠性。
二、可靠性分析的方法:在机械工程中,有多种可靠性分析方法可供选择。
以下是其中几种常用的方法:1. 故障模式与影响分析(FMEA):FMEA是一种常用的可靠性分析方法,旨在识别设备可能出现的故障模式以及这些故障对设备正常运行和工作环境的影响。
通过对故障模式进行评估,可以优化设备的设计和维护计划,提高设备的可靠性。
2. 可靠性块图(RBD):可靠性块图是一种图形化的分析方法,用于表示系统中各个组件的可靠性和相互之间的关系。
通过绘制可靠性块图,可以清晰地了解系统的功能和结构,识别潜在的故障点,并对系统进行可靠性分析。
3. 故障树分析(FTA):故障树分析是一种基于逻辑关系的可靠性分析方法,用于识别导致系统故障的关键事件和因素。
通过构建故障树,可以分析设备故障的概率和可能的原因,并采取相应的措施来提高系统的可靠性。
机械工程师机械设计与可靠性分析

机械工程师机械设计与可靠性分析机械工程师是负责设计、开发和制造机械设备及系统的专业人员。
机械设计是机械工程师工作的核心内容之一,而可靠性分析则是确保设计的机械系统在使用过程中能够稳定可靠运行的重要环节。
本文将从机械设计和可靠性分析两个方面进行探讨。
一、机械设计机械设计是指根据使用需求和技术要求,将机械原理、材料科学、运动学等知识应用于机械设备及系统的构思、计划、设计和制造的过程。
良好的机械设计能够确保产品在性能、质量、经济和可制造性等方面达到最佳状态。
1.1 设计概念与需求分析在机械设计的初期阶段,机械工程师需要与客户或需求方充分沟通,了解产品的使用需求和技术要求,明确设计目标和约束条件。
根据这些信息,进行设计概念的产生和需求分析,确定设计的基本框架。
1.2 机械设计过程机械设计过程涉及到理论分析、计算机辅助设计、实验验证等多个环节。
机械工程师需要运用机械学、热力学、流体力学等理论知识进行系统设计,利用CAD、CAE等软件工具进行详细设计,通过实验验证和优化,得出最佳产品方案。
1.3 性能与质量控制在机械设计中,性能和质量是衡量产品优劣的重要标准。
机械工程师需要通过合理的设计和制造工艺,确保产品具备所需的性能指标,并进行相关测试和验证,以保证产品质量符合要求。
二、可靠性分析可靠性分析是指对机械系统进行可靠性评估和预测,找出可能导致系统失效的关键部件与故障机理,并提出相应的改进措施,从而提高机械系统的可靠性和稳定性。
2.1 可靠性评估方法常用的可靠性评估方法包括故障模式与影响分析(FMEA)、故障树分析(FTA)、可靠性增长分析(RGA)等。
机械工程师可以根据具体情况选择合适的方法,对机械系统进行潜在故障分析和风险评估,以确定改进和优化的重点。
2.2 MTBF与RAM分析平均无故障时间(MTBF)是对系统可靠性的一种常用指标,它表示系统在正常使用条件下连续运行的平均时间。
可靠性、可用性和维修率(RAM)分析是评估系统整体性能和可维护性的重要手段。
机械设计中的机械设计案例分析
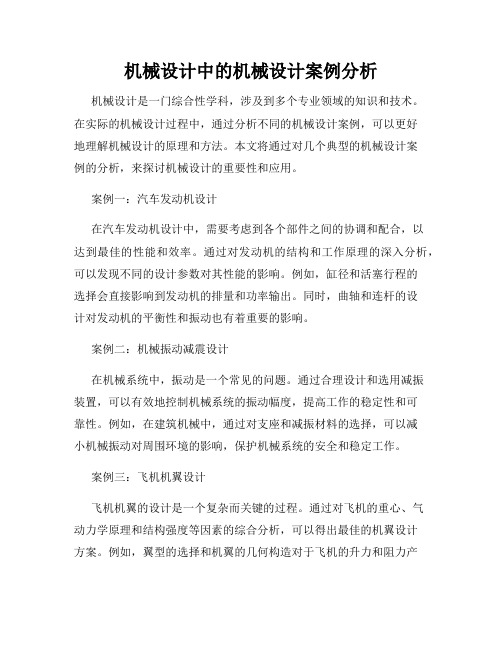
机械设计中的机械设计案例分析机械设计是一门综合性学科,涉及到多个专业领域的知识和技术。
在实际的机械设计过程中,通过分析不同的机械设计案例,可以更好地理解机械设计的原理和方法。
本文将通过对几个典型的机械设计案例的分析,来探讨机械设计的重要性和应用。
案例一:汽车发动机设计在汽车发动机设计中,需要考虑到各个部件之间的协调和配合,以达到最佳的性能和效率。
通过对发动机的结构和工作原理的深入分析,可以发现不同的设计参数对其性能的影响。
例如,缸径和活塞行程的选择会直接影响到发动机的排量和功率输出。
同时,曲轴和连杆的设计对发动机的平衡性和振动也有着重要的影响。
案例二:机械振动减震设计在机械系统中,振动是一个常见的问题。
通过合理设计和选用减振装置,可以有效地控制机械系统的振动幅度,提高工作的稳定性和可靠性。
例如,在建筑机械中,通过对支座和减振材料的选择,可以减小机械振动对周围环境的影响,保护机械系统的安全和稳定工作。
案例三:飞机机翼设计飞机机翼的设计是一个复杂而关键的过程。
通过对飞机的重心、气动力学原理和结构强度等因素的综合分析,可以得出最佳的机翼设计方案。
例如,翼型的选择和机翼的几何构造对于飞机的升力和阻力产生巨大的影响。
同时,机翼材料和结构设计也需要考虑到飞机在不同工况下的安全性和可靠性。
结语通过对上述机械设计案例的分析,我们可以看到机械设计在实际工程中的重要性和应用。
合理的机械设计可以提高机械系统的性能和效率,减少能源消耗和环境影响。
因此,在机械设计过程中,需要综合考虑各个因素,运用科学的方法和技术,以实现最佳的设计效果。
注意:此文章为机械设计案例分析,为了使篇幅符合要求,只涵盖了三个典型案例。
实际上,机械设计领域涉及的案例和内容非常丰富多样。
不同类型的机械设备和系统都有各自的设计要求和特点。
因此,在实际的机械设计工作中,需要根据具体情况进行综合分析和设计方案的制定。
可靠性设计

可靠性设计可靠性设计的概述:可靠性设计(reliability design):为了满足产品的可靠性要求而进行的设计;对系统和结构进行可靠性分析和预测,采用简化系统和结构、余度设计和可维修设计等措施以提高系统和结构可靠度的设计。
可靠性问题是一种综合性的系统工程。
机电产品(零件、部件、设备或系统)的可靠性也和其他产品的可靠性一样,是与其设计、制造、运输、储存、使用、维修等各个环节紧密相关的。
设计只是其中的一个环节,但却是保证产品可靠性最重要的环节,它为产品的可靠性水平奠定了先天性的基础。
因为机械产品的可靠性取决于其零部件的结构形式与尺寸、选用的材料及热处理制造工艺、检验标准、润滑条件、维修方便性以及各种安全保护措施等,而这些都是在设计阶段决定的。
可靠性问题的研究是因处理电子产品不可靠问题于第二次世界大战期间发展起来的。
可靠性设计用在机械方面的研究始于20世纪60年代,首先应用于军事和航天等工业部门,随后逐渐扩展到民用工业。
随着现代科学技术的发展和对产品质量要求的日益提高,可靠性逐步成为科学和工程中一个非常重要的概念。
机械结构的可靠性及其设计直接决定了机械结构的可靠度,因此,对机械可靠性设计的研究具有十分重要的意义。
所谓可靠性,则是指产品在规定的时间内和给定的条件下,完成规定功能的能力。
它不但直接反映产品各组成部件的质量,而且还影响到整个产品质量性能的优劣。
可靠性分为固有可靠性、使用可靠性和环境适应性。
可靠性的度量指标一般有可靠度、无故障率、失效率3种。
对于一个复杂的产品来说,为了提高整体系统的性能,都是采用提高组成产品的每个零部件的制造精度来达到;这样就使得产品的造价昂贵,有时甚至难以实现(例如对于由几万甚至几十万个零部件组成的很复杂的产品)。
事实上可靠性设计所要解决的问题就是如何从设计中入手来解决产品的可靠性,以改善对各个零部件可靠度(表示可靠性的概率)的要求。
可靠度的分配是可靠性设计的核心。
其分配原则为①按重要程度分配可靠度。
某型机械装备的可靠性与维修性分析

某型机械装备的可靠性与维修性分析在现代工业生产中,机械装备是生产力的重要组成部分。
然而,机械装备的可靠性和维修性是影响生产效率和成本的关键因素。
本文将对某型机械装备的可靠性和维修性进行分析,并提出相应的解决方案。
一、可靠性分析可靠性是指机械装备在一定时间内能够正常工作的能力。
对于某型机械装备来说,可靠性分析应该从以下几个方面进行考虑:1. 设计可靠性:机械装备的设计是否符合工程要求,是否考虑到了各项工作条件和环境因素。
设计可靠性不仅仅包括技术可行性,还包括物料的选择、加工工艺等因素。
2. 零部件的可靠性:机械装备的可靠性与其零部件的可靠性密切相关。
因此,对机械装备的关键零部件进行可靠性分析至关重要。
例如,对某型机械装备的发动机进行故障模式与效果分析,确定常见故障点,并采取相应的措施进行预防。
3. 运行环境的可靠性:机械装备通常在复杂的工作环境中运行,如高温、低温、湿度、振动等。
因此,对机械装备在不同环境下的可靠性进行评估和分析,并对可能出现的故障进行预测。
通过对行业数据的统计和分析,我们可以得出某型机械装备的可靠性指标,并根据这些指标进行改进和优化。
例如,可以通过改进机械装备的设计和关键零部件的选择,提高机械装备的可靠性。
二、维修性分析维修性是指机械装备在发生故障后能够快速修复和恢复正常工作的能力。
对于某型机械装备来说,维修性分析应该从以下几个方面进行考虑:1. 维修过程的复杂度:机械装备维修过程中涉及到的步骤、工具、人力等因素都会影响维修的时间和成本。
因此,对机械装备的维修过程进行分析,并评估其复杂度。
可以通过减少维修步骤、优化维修工具和设备等方式降低维修的难度。
2. 维修资源的可获得性:机械装备维修所需的零部件、人力、技术等资源是否能够及时获得也是维修性的一项重要指标。
因此,建立起完善的备件管理系统和培训体系,确保维修所需的资源能够及时到位。
3. 维修数据的积累和分析:通过对维修记录和统计数据的积累和分析,可以找出机械装备常见的故障模式,并采取相应的措施进行预防。
APQP经典机械案例

注:上述表格的填表说明为
1.产品要求:阐述产品的名称、型号、规格、图号等,将 顾客的产品要求列入。
2.进度要求:需要首先将经确认的顾客进度要求阐述,并 包括根据顾客要求展开的进度预计。
3.产品构成分解:将产品向下分解成各零部件组成,如可 能的采购件和自己加工件。
4. 风险评估:描述可能的风险、可能性、影响和危害。
生产部
品质部 品质部
品质部
技术部
标识
任务名称
1 试生产
工期
开始时间
完成时间
7个工作日 2001年9月24日 2001年10月2日
前置 任务
资源名称
生产部
2 测量系统分析
10个工作日 2001年10月3日 2001年10月16日 1
品质部
3 初始过程能力研究 19个工作日 2001年9月24日 2001年10月18日 1SS 品质部
a ) 将其他厂家的类似产品和自己的以前类似产品的失效 模式分析结果进行汇总:
b ) 开发出如下清单
希望设计做什么?
希望设计不做什么?
……
……
……
……
c ) 顾客需求,包括QFD(质量功能展开)输入和其他的需求 文件,包括已知的产品要求和制造/装配要求;
d ) 产品分解方框图(略,可参见FMEA手册的附录A)。
XXX DER公司 2001年3月13日
APQP第一步:计划和确定项目
一、这个阶段公司根据顾客要求,定义项目并 确定项目范围,将顾客的要求和样品确认后转化为 公司的内部文件,并通过项目任务书立项。
项目任务书如下:
项目定义(例):
产品定义:两极同轴式斜齿轮圆柱齿轮减速器; 产品要求: 1.外观要求:XX 2.技术要求:齿轮装置的传递功率P1=40kW,齿轮转速nl=1 450r/min,
机械产品设计案例

机械产品设计案例在工业和制造业的领域中,机械产品设计起着至关重要的作用。
机械产品设计的目标是创建和开发能够满足用户需求的高效、可靠且实用的机械设备。
本文将通过一个机械产品设计案例来深入探讨机械产品设计的过程、关键考虑因素以及成功设计的要素。
案例:汽车发动机设计汽车发动机是一种复杂的机械设备,它有着严格的工程要求和性能需求。
一个成功的汽车发动机设计案例包括以下几个关键考虑因素:1. 功能需求:汽车发动机的主要功能是提供动力和驱动力。
设计师需要考虑车辆的使用环境、驾驶需求以及所需的性能参数,如扭矩和马力输出等。
通过仔细分析这些需求,设计师可以确定发动机的结构、排气系统和燃油供应等方面的设计要素。
2. 可靠性和耐久性:汽车发动机需要具备高可靠性和耐久性,以确保长期可靠运行和降低维护成本。
设计师需要考虑材料的选择、零部件的强度和耐用性以及结构设计的合理性。
此外,考虑到不同条件下的使用情况,如高温、湿度或脏污环境等,还需要进行充分的测试和验证。
3. 燃油效率:随着能源的稀缺性和环境问题的日益严重,汽车发动机的燃油效率也成为重要的设计考虑因素。
设计师需要通过优化发动机结构、减少摩擦和提高燃烧效率等方式来提高燃油经济性。
此外,使用先进的燃油喷射系统和智能控制技术也可以提高发动机的燃油效率。
4. 排放要求:为了减少对环境的影响和符合政府的排放标准,汽车发动机设计必须考虑到排放的控制和净化。
设计师需要关注废气处理系统的设计、选择有效的排放控制技术,如催化转化器和颗粒捕捉器,并确保发动机能够实现低排放。
5. 制造和装配要求:汽车发动机的设计还必须考虑到制造和装配的可实现性。
设计师需要选择适用的制造工艺和材料,并优化结构设计以简化生产流程并降低制造成本。
此外,考虑到装配过程中的易用性和效率,设计师还需注重设计的可装配性和易维护性。
通过对上述关键考虑因素的分析,设计师可以制定出一个综合的设计方案,以满足汽车发动机的功能需求、性能要求和制造可行性。
机械工程中的工程实例与工程案例分析
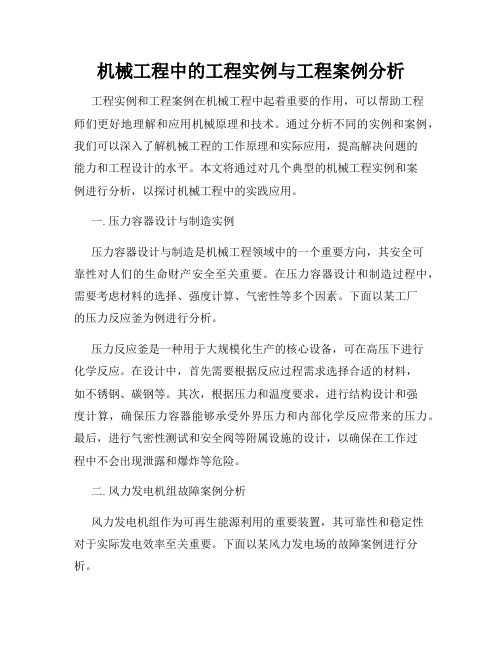
机械工程中的工程实例与工程案例分析工程实例和工程案例在机械工程中起着重要的作用,可以帮助工程师们更好地理解和应用机械原理和技术。
通过分析不同的实例和案例,我们可以深入了解机械工程的工作原理和实际应用,提高解决问题的能力和工程设计的水平。
本文将通过对几个典型的机械工程实例和案例进行分析,以探讨机械工程中的实践应用。
一. 压力容器设计与制造实例压力容器设计与制造是机械工程领域中的一个重要方向,其安全可靠性对人们的生命财产安全至关重要。
在压力容器设计和制造过程中,需要考虑材料的选择、强度计算、气密性等多个因素。
下面以某工厂的压力反应釜为例进行分析。
压力反应釜是一种用于大规模化生产的核心设备,可在高压下进行化学反应。
在设计中,首先需要根据反应过程需求选择合适的材料,如不锈钢、碳钢等。
其次,根据压力和温度要求,进行结构设计和强度计算,确保压力容器能够承受外界压力和内部化学反应带来的压力。
最后,进行气密性测试和安全阀等附属设施的设计,以确保在工作过程中不会出现泄露和爆炸等危险。
二. 风力发电机组故障案例分析风力发电机组作为可再生能源利用的重要装置,其可靠性和稳定性对于实际发电效率至关重要。
下面以某风力发电场的故障案例进行分析。
在某风力发电场中,一台风力发电机组突然停止工作,导致发电量减少。
经过检测和分析,发现故障原因为叶片损坏。
进一步分析发现,叶片因长期运行而引起疲劳断裂,导致发电机组无法继续正常转动。
根据此案例,工程师们需要加强对风力发电机组的定期检测和维护,及时更换老化叶片,确保其正常运行和发电效率。
三. 工业机器人应用实例工业机器人在机械工程领域中具有广泛的应用和发展前景。
下面以某汽车制造厂的焊接机器人实例进行分析。
在某汽车制造厂的生产线上,焊接机器人用于对汽车车身进行焊接工作。
通过精确的运动控制和独特的焊接工艺,在高速生产线上完成焊接任务,提高生产效率和焊接质量。
该机器人采用先进的传感器和控制系统,可以根据不同形状和材料的汽车零部件进行灵活的焊接操作。
机械设计中的可靠性分析与评估
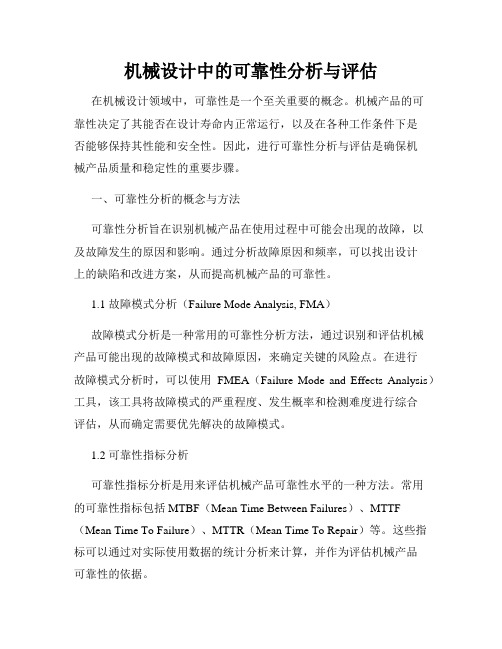
机械设计中的可靠性分析与评估在机械设计领域中,可靠性是一个至关重要的概念。
机械产品的可靠性决定了其能否在设计寿命内正常运行,以及在各种工作条件下是否能够保持其性能和安全性。
因此,进行可靠性分析与评估是确保机械产品质量和稳定性的重要步骤。
一、可靠性分析的概念与方法可靠性分析旨在识别机械产品在使用过程中可能会出现的故障,以及故障发生的原因和影响。
通过分析故障原因和频率,可以找出设计上的缺陷和改进方案,从而提高机械产品的可靠性。
1.1 故障模式分析(Failure Mode Analysis, FMA)故障模式分析是一种常用的可靠性分析方法,通过识别和评估机械产品可能出现的故障模式和故障原因,来确定关键的风险点。
在进行故障模式分析时,可以使用FMEA(Failure Mode and Effects Analysis)工具,该工具将故障模式的严重程度、发生概率和检测难度进行综合评估,从而确定需要优先解决的故障模式。
1.2 可靠性指标分析可靠性指标分析是用来评估机械产品可靠性水平的一种方法。
常用的可靠性指标包括MTBF(Mean Time Between Failures)、MTTF (Mean Time To Failure)、MTTR(Mean Time To Repair)等。
这些指标可以通过对实际使用数据的统计分析来计算,并作为评估机械产品可靠性的依据。
二、可靠性评估的方法与工具可靠性评估是对机械产品进行综合评估,包括从设计、生产到维修等多个环节。
通过进行可靠性评估,可以评估机械产品在不同使用条件下的可靠性,找出潜在的问题和改进的方向。
2.1 故障树分析(Fault Tree Analysis, FTA)故障树分析是一种常用的可靠性评估方法,通过根据故障原因和结果之间的逻辑关系绘制故障树图,来评估故障事件的概率和可能性。
故障树分析可以帮助设计人员找出导致机械产品故障的主要原因,进而采取相应的措施来提高产品的可靠性。
机械设计基础了解机械系统的可靠性设计

机械设计基础了解机械系统的可靠性设计机械设计基础:了解机械系统的可靠性设计机械系统的可靠性设计是指在机械产品的设计过程中,通过合理的设计措施和技术手段,确保机械系统能够在规定的使用寿命内,以安全可靠、高效运行的方式满足用户的需求。
本文将介绍机械设计基础中与可靠性设计相关的几个重要概念和技术。
一、可靠性概念及评估方法1. 可靠性概念可靠性是指产品在规定的使用条件下,在一定时间内无故障运行的能力。
在机械设计中,可靠性设计是提高产品质量和性能的重要手段,也是保证机械产品寿命的重要因素。
2. 可靠性评估方法(1)失效率:失效率是指在一段时间内,系统出现故障的频率。
通过失效率的分析,可以评估系统的可靠性水平,并确定失效率的变化规律,从而采取相应的措施提高系统的可靠性。
(2)失效模式与影响分析(FMEA):FMEA是一种通过识别失效模式、分析失效影响以及制定控制措施的方法,用于评估系统的可靠性。
通过FMEA的分析,可以确定优先解决的部件或环节,并采取相应的改进措施,提高系统的可靠性。
(3)可用性分析:可用性是指系统在规定时间内能够正常运行的概率。
通过对系统的可用性进行分析,可以评估系统的可靠性,找出存在的问题并进行改进。
二、机械系统的可靠性设计原则1. 设计可靠性原则(1)可靠性分级原则:根据机械产品使用的重要性,确定不同的可靠性目标和设计要求。
对于一些关键性机械系统,需要提高其可靠性水平,确保其在任何工况下都能正常运行。
(2)防御层次原则:采取多层次的防御措施,以防止发生单一失效导致系统停止工作。
例如,通过设计双路冗余系统、使用多重保护装置等方式提高系统的可靠性。
(3)维修便捷性原则:合理设计机械系统的结构,便于维修和检修。
对于易损件和关键部件,应提供便捷的拆卸和更换方式,减少维修时间,降低维修成本。
2. 设计优化原则(1)减少失效源:通过选用优质材料、使用合理的润滑方式、降低工作温度等措施,减少机械系统的失效源并延长其使用寿命。
基于机械结构产品的可靠性设计分析

4 ) 电子 产 品 的 基 本 可 靠 性 可 以用 MT B F参 数 来 表 征 , 而 机
械 产 品 的可 靠 性 表征 参 数 有 自身 的 特 点 和 性 质 ,不 能 完 全 使 用 电子 产 品 的 可靠 性 研 究方 法 。 在实际使用过程中 , 可 以注 意 到 机 械 产 品 的零 部 件 有 突 发 的 故 障 ,也 有 经 历 一 段 时 间 后 的 机 械 疲 劳故 障 , 也称为耗损故障 。 研 究 机 械 产 品 的总 的故 障 应 该 包 括 两
1 2 4
基 于 机 械 结 构 产 品 的 可靠 性 设 计 分 析
基于机械结构产品的可靠性设计分析
卓 红 艳 刘 志 强 金 晓 叶 长春 陈 涛 陈代 兵
( 中 国工程 物理研 究院 应 用 电子 学研 究所 , 四川 绵 阳 6 2 设 计 是 产 品研 制过 程 中的 重 要 环 节 , 也 是 实 现 产 品 工 程 化 的 必 要 途 径 。电子 产 品 的 可 靠 性 设 计 在 国 内外 研 究较
的 工 程 研 制 经 验 开 展 机 械 产 品 的 可 靠 性 设 计 要 求 的应 用 分 析 , 以期为工程设计人员提供一定的设计依据 。
1 机械 产 品 的 可 靠 性 特 点 分 析
机 械 产 品 与 电 子 产 品不 同 , 在 可 靠 性 方 面 有 自 己 的特 点 :
应力环境下 , 其 损 耗 规 律 是 很 难 定 量 的研 究 。 3 ) 环 境 试 验 是 机 械 产 品 和 电子 产 品 的 必 要 试 验 。两 者 的 试 验考核周期 、 试验 项 目、 费 用 以及 试 验 数 据 结 果 应 用 范 围等 都 较 大 的区 别 。 按 照 产 品可 靠 性 工 作 项 目的要 求 , 机 械 产 品结 合 环 境 适应性需要做如温度 、 振动 、 加 速度 、 湿 度 等环 境试 验 , 对 机 械 产 品来说 , 寿命 试 验 也 经 常 是 必 不 可 少 的 。 而 电子 产 品 其 电 磁 兼 容
机械设计中的可行性与可靠性分析
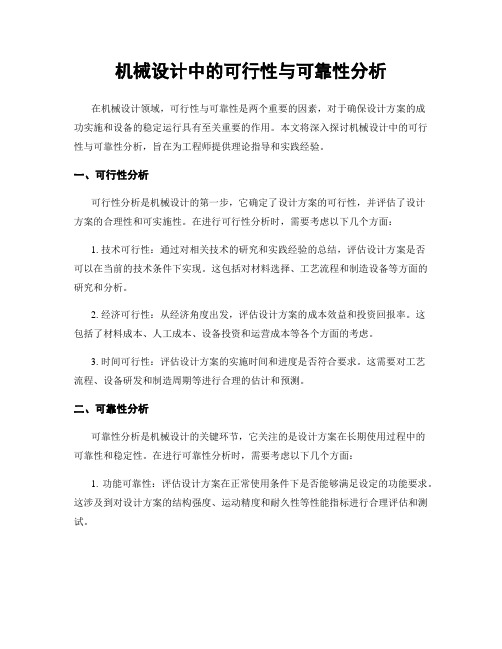
机械设计中的可行性与可靠性分析在机械设计领域,可行性与可靠性是两个重要的因素,对于确保设计方案的成功实施和设备的稳定运行具有至关重要的作用。
本文将深入探讨机械设计中的可行性与可靠性分析,旨在为工程师提供理论指导和实践经验。
一、可行性分析可行性分析是机械设计的第一步,它确定了设计方案的可行性,并评估了设计方案的合理性和可实施性。
在进行可行性分析时,需要考虑以下几个方面:1. 技术可行性:通过对相关技术的研究和实践经验的总结,评估设计方案是否可以在当前的技术条件下实现。
这包括对材料选择、工艺流程和制造设备等方面的研究和分析。
2. 经济可行性:从经济角度出发,评估设计方案的成本效益和投资回报率。
这包括了材料成本、人工成本、设备投资和运营成本等各个方面的考虑。
3. 时间可行性:评估设计方案的实施时间和进度是否符合要求。
这需要对工艺流程、设备研发和制造周期等进行合理的估计和预测。
二、可靠性分析可靠性分析是机械设计的关键环节,它关注的是设计方案在长期使用过程中的可靠性和稳定性。
在进行可靠性分析时,需要考虑以下几个方面:1. 功能可靠性:评估设计方案在正常使用条件下是否能够满足设定的功能要求。
这涉及到对设计方案的结构强度、运动精度和耐久性等性能指标进行合理评估和测试。
2. 环境可靠性:评估设计方案在不同环境条件下的适应性和可靠性。
这包括温度、湿度、振动、腐蚀等环境因素对设备的影响,并通过模拟实验和可靠性试验进行评估。
3. 可维修性与可更换性:评估设计方案的可维修性和可更换性。
这包括设备的拆装维修性和零部件的可更换性能,为日常维护和故障排除提供便利。
三、案例分析为了更好地理解机械设计中的可行性与可靠性分析,我们以一台机床的设计为例进行分析。
在进行机床设计时,工程师需要考虑材料的强度和刚度、导轨的精度和稳定性、动力传动系统的效率和可靠性等因素。
在可行性分析阶段,工程师需要根据机床的使用环境及功能要求,选择合适的材料和工艺,确保设计方案的可实现性和经济可行性。
- 1、下载文档前请自行甄别文档内容的完整性,平台不提供额外的编辑、内容补充、找答案等附加服务。
- 2、"仅部分预览"的文档,不可在线预览部分如存在完整性等问题,可反馈申请退款(可完整预览的文档不适用该条件!)。
- 3、如文档侵犯您的权益,请联系客服反馈,我们会尽快为您处理(人工客服工作时间:9:00-18:30)。
I、II类故障模式(零件)清单 危害性矩阵
•2020/4/21
某锁机构FMEA分析
图1主动钩组件结构功能图
•2020/4/21
某锁机构FMEA分析
某锁机构(正常)对接阶段功能流程图
•2020/4/21
某锁机构FMEA分析
故障判据
在正常的设计、使用、维护和环境条件下,凡是满 足不了对接锁系设计指标及要求的故障,都定为系 统故障。
Ⅳ类(轻度的) 这种故障对航天器的功能及航天员健康无影响,仅轻度影 响产品有效使用和操作。
•2020/4/21
某锁机构FMEA分析
危害性定性分析
对接锁系故障模式发生概率等级定义
故障模式
等级
定义
发生概率 的特征
故障模式发生概率(在产品使用时间内)
A
经常发 生
高概率
某一故障模式发生概率大于产品总故障概率的 20%
寿命期内某锁系自身引起的故障(不含人为故障) 均计为影响系统基本可靠性的关联故障;
在任务剖面中,凡不能完成某锁系正常功能的故障 计为影响任务的关联故障。
零件级产品故障判据 组件级产品故障判据 部件级产品故障判据
•2020/4/21
某锁机构FMEA分析
严酷度定义
表 14 对接锁系故障严酷度的定义
不同步
是指同一组锁的主动锁钩不能满足 同步性要求
是指在主、被动航天器对接过程中
2
锁紧失败
,锁系正常锁紧失败后,备份锁紧 失败。(这里对控制系统、转换装
置的可靠性不进行展开分析)
3
锁紧保持 失败
是指在主、被动航天器在联合飞行 期间,主、被动锁系结构无法保持 结构完整性。
•2020/4/21
某锁机构FTA分析
机械产品可靠性设计分 析案例
2020年4月21日星期二
某锁机构可靠性设计分析
某锁机构产品说明 某锁机构FMEA分析 某锁机构FTA分析 了解强度分析仿真 了解动力学分析仿真 了解可靠性分析仿真
•2020/4/21
概述
•2020/4/21
锥杆式
概述
•2020/4/21
锥杆式
概述
•2020/4/21
锥杆式
概述
•2020/4/21
周边外翻式
概述
•2020/4/21
周边内翻式
产品说明
某锁结构示意图
•2020/4/21
2020年4月21日星期二
2020年4月21日星期二
某锁机构FMEA分析
某锁机构FMEA实施
对接锁系功能分析 故障判据 对接锁系故障模式分析 严酷度定义 危害性定性分析
故障树的建造
•2020/4/21
锁紧失败故障树
某锁机构FTA分析
故障树定性分析
锁紧失败故障树的最小割集
•2020/4/21
某锁机构FTA分析
故障树定性分析
底事件清单
•2020/4/21
某锁机构FTA分析
故障树分析的结果和建议
•2020/4/21
强度分析仿真
输入条件
功能分析 材料属性 工作环境 载荷分析计算
动力学分析仿真
被动锁碟簧力vs偏心轴转角
•2020/4/21
性能试验数据 低温-50℃
动力学分析仿真
滑轮、绳轮与钢丝绳索之间的空间摩擦特性对 同步性影响较大;
钢丝绳索和碟簧的预紧力对锁系同步性影响较 大;
碟簧的阻尼系数对锁系动力学响应的稳定性影 响较大;
电机驱动力矩曲线对锁系同步性较大; 按照理论模型优化结果,设置递增预紧力,滞
严酷度类别
严重程度定
Ⅰ类(灾难的) 这是一种会导致主动(被动)航天器毁坏或引起航天员伤 亡的故障。
Ⅱ类(致命的) 这种故障会导致航天器部分系统严重损坏,不能完成基本 功能或影响航天员健康的故障。
Ⅲ类(临界的) 这种故障会引起航天器的部分功能无法完成,为了完成这 些功能,需要采取应急措施,对航天员的健康有些影响。
后最严重的不一定是最后一把单锁,锁系各单 锁之间存在一个动态平衡过程,该过程受多种 因素影响,主要有摩擦系数以及刚性阻尼系数 等。
仿真时间:16916.78 cpu seconds(约4.7小时)
•2020/4/21
动力学分析仿真
单组锁动力学模型(含柔性绳索,显示了全部的约束和碰撞关系)
•2020/4/21
动力学分析仿真
•2020/4/21
绳轮驱动力矩vs偏心轴转角
动力学分析仿真
锁系锁紧前期的绳轮转角vs时间
•2020/4/21
(2)硬件环境
处理器:双Xeon P4 2.8G Hz处理器 物理内存:Kingston Ecc Reg奇偶校验工作站专用内存 4×1G 储存介质:双SataII 80G×2 组raid0磁盘阵列
为了充分利用系统资源,采用了多线程处理技术来提高 仿真速度,利用外部单独的adams solver求解模块进行多 线程计算。
输出结果
零件静强度分析计算 组合件整体分析计算 零件、组件对比分析
•2020/4/21
强度分析仿真
材料属性
•2020/4/21
载荷分析计算
•2020/4/21
某锁载荷、约束示意图
传力路线分析
•2020/4/21
主动钩组件传力路线
锁系静强度分析计算
零件的应力变形云图 零件承载能力分析 组件的应力变形云图 零件、组件计算结果对比分析
B
有时发 生
中等概率
某一故障模式发生概率大于产品总故障概率的 10%,小于20%
C
偶然发 生
不常发生
某一故障模式发生概率大于产品总故障概率的 1%,小于10%
D
很少发 不大可能 某一故障模式发生概率大于产品总故障概率的
生
发生
0.1%,小于1%
E
极少发 生
近乎为零
某一故障模式发生概率小于产品总故障概率的 0.1%
•2020/4Leabharlann 21零件计算示例•2020/4/21
主动锁钩常温下的应力变形云图
零件计算结果
•2020/4/21
动力学分析仿真
由于多柔体动力学分析仿真计算量要远远高于刚性体动 力学分析,为了仿真效率,采用了双Xeon核心处理器 的工作站进行计算,仿真计算环境如下:
(1)软件环境
操作系统:windows 2000 server sp4 仿真软件:MSC.adams 2005 r2
•2020/4/21
某锁机构FMEA分析
FMEA输出
I、II类故障模式(零件)清单
•2020/4/21
某锁机构FTA分析
顶事件的选择和描述 故障树的建造 故障树的定性分析 故障树分析的结果和建议
•2020/4/21
某锁机构FTA分析
某锁机构顶事件的选择和描述
序号
顶事件定 义
说明
1