薄壁深孔高精度套筒的加工与测量
深孔薄壁缸筒的加工

机械制造4 卷 第 59 5 1 期
21 7 / 11 U 1
回I
维普资讯
精 加 工刀 上 的润 滑油 孔 联接 , 将 内孔 精加 工 刀 的导 并
1过盈 量 的选择 原则 上 是 尽量 使 滚 压力 较小 , ) 保
向 套 部 分 提 前 装 入 定 位 导 向 套 的 内 孔 中 ; 孔 精 加 工 内 刀 的 刀 体 长 度 应 根 据 工 件 长 度 来 确 定 , 保 刀 尾 的 联 确 接 部 分 能 从 被 加 工 工 件 的 内 孔 中露 出 。 2 车 床 的 刀 架 上 安 装 刀 杆 , 调 整 好 刀 杆 中 心 高 ) 并
开 口卡 套 ( 止 装 夹 变 形 ) 专 用 工 装 — — 定 位 导 向套 防 和 ( 图 4 示 ) 工 装 可 以反 复 使 用 , 卸 方 便 。 如 所 , 装
2 2 半 精 车 .
半 精 车 内 孔 为 西 93 , 度 车 成 ( 细 工 艺 4 . 8 长 详
维普资讯
深 孔 壁 缸 筒 的 加 工 薄
口 祖 春 丰 口 张聚 海
00 3 5 0 1 石家庄煤矿机械有限责任公 司 河北
摘
要:介绍深孔薄壁缸 筒 内孔 的精加工方法 , 以及采取相应 的工 艺措施。 合理选择/ x  ̄法和工 艺, z - , 是提 高产品质
滚 压 器 ( 图3 示 ) 行 滚 压 至 图 纸 要 求 。 提 高 加 工 如 所 进 为 效 率 、 证 零 件 加 工 质 量 , 精 加 工 内 孔 时 设 计 专 用 的 保 在
2 粗 车 内 孔 为 西4 8 , 外 圆 为 西6 详 细 工 艺 ) 8— 车 s 8(
略 )。
CFRP薄壁圆筒零件的精密加工与测量技术

CFRP薄壁圆筒零件的精密加工与测量技术刘阳;陈军;蒋晓麟;钱志强【摘要】介绍了用于精密加工、测量CFRP薄壁圆筒工件的技术.通过合理的工艺规划、夹具设计,克服了工件的加工难点,实现了工件的精密测量.根据实际加工情况改进了工艺流程与夹具设计,进一步提高了工件加工质量,基本满足设计要求.【期刊名称】《制造技术与机床》【年(卷),期】2016(000)003【总页数】4页(P116-119)【关键词】碳纤维复合材料;薄壁圆筒工件;精密加工【作者】刘阳;陈军;蒋晓麟;钱志强【作者单位】中国工程物理研究院机械制造工艺研究所,四川绵阳621900;中国工程物理研究院机械制造工艺研究所,四川绵阳621900;中国工程物理研究院机械制造工艺研究所,四川绵阳621900;中国工程物理研究院机械制造工艺研究所,四川绵阳621900【正文语种】中文【中图分类】TH162碳纤维复合材料(carbon fiber reinforced plastic,CFRP)由于具有高的比强度、比模量、比刚度以及热膨胀系数小、抗疲劳性能好、耐腐蚀等优点,被广泛应用于航空航天、国防、工业、体育等领域[1]。
然而由于其塑性好、各向异性,加工中易脱丝、分层等特点,碳纤维复合材料的可加工性并不理想。
碳纤维复合材料的机械加工技术一直是制约其产业发展的一个重要因素[2]。
碳纤维复合材料薄壁圆筒工件的加工较少见诸于报道。
由于薄壁工件固有的加工难点,再加上碳纤维复合材料的特点,使得这类工件很难获得较高的加工精度。
为实现此类工件的精密加工,有必要研究一套具有针对性的加工与测量方法。
需要加工的较大的一种碳纤维复合材料薄壁圆筒工件如图1所示。
该工件外径与壁厚之比D/δ≈45,属典型薄壁圆筒工件。
而该工件的尺寸、形位公差要求却很高。
3个主要尺寸,内孔、外圆圆柱度、外圆相对内孔的同轴度均有较高要求。
此外,两端面的平面度、对内孔垂直度也有要求。
加工该工件所用的毛坯为沿圆周缠绕而成的碳纤维筒,各方向均留有少量余量。
深孔薄壁缸筒的加工
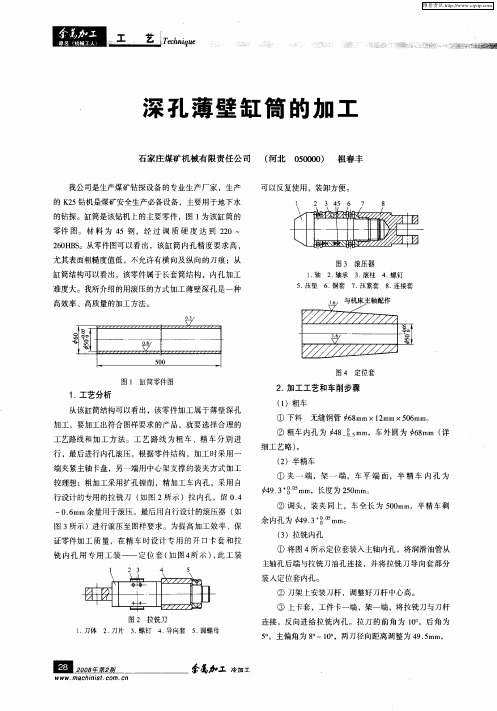
较理想 ;粗加工采用扩孔镗削 ,精加工车 内孔 ,采用 自
行设计 的专用的拉铣刀 ( 图 2所示 )拉 内孔 ,留 0 4 如 . 06 .mm余量用于滚压 ,最后用 自行设计 的滚压器 ( 如
② 调头 ,装 夹 同上 ,车全长 为 5 0 m,半 精车 剩 0m 余 Wf为 4 9 3 O 5 L 4 . . mm。 o 0 ()拉铣 内孔 3 ① 将图 4所示定位套装入 主轴 内孔 ,将润滑油管从 主轴孔后端与拉铣刀油孔连接 ,并将拉铣 刀导 向套部分 装入定位套内孔 。
维普资讯
圜
三
鼙 ≯ 曩 。曩 誊
深 孔 薄 壁 缸 筒 的加 工
石家庄煤矿机械有限责 任公 司 ( 河北 0 00 ) 祖春丰 50 0
我公 司是生产煤矿钻探设备 的专 业生产厂家 ,生产 的K5 2 钻机是煤矿安全生产必备设备 ,主要用于地下水 的钻探。缸筒是该钻机 上的主要零件 ,图 1为该缸筒 的 零件 图。材 料 为 4 5钢 ,经 过 调 质 硬 度 达 到 20 2
解决的问题 。
1 技术要求 .
图 1 6 1C 是 10 K发动机 连杆 ,技术 要求是 :两孑 的 L
扭曲平行为 10 00 、10 00 ,保证尺寸 44 83 0 :. 4 0 :. 3 7 — o o
m m
与 4:: m两孑 中 28 m L 心距 (9 ± . )m , L 柱 1 00 m 孑 圆 5 3
ቤተ መጻሕፍቲ ባይዱ
对称度小于 00 m .1 m,刀片材料为 W1C4 。因拉铣切削速 8 rV
工件与滚珠之间的温升 ,加快滚压器轴 与滚珠的磨损 ,影 响工件尺寸和表面粗糙度。经过多次试验 ,确定缸筒滚压
薄壁套筒零件加工工艺
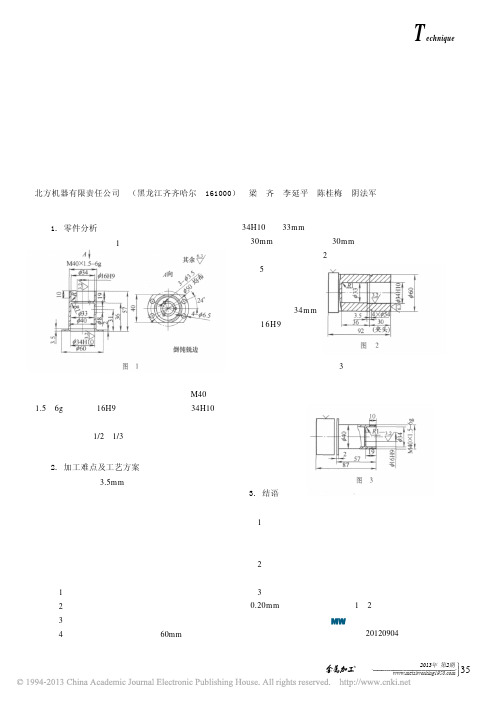
35echniqueT工 艺1. 零件分析典型薄壁套筒如图1所示。
图 1此零件属于薄壁套筒类零件,从图样上看,工艺没有难点。
但是从装配图面上看,外螺纹M40×1.5-6g 与内孔φ16H9及另一端面内止口φ34H10都有同轴度要求,在图样上不给出同轴度要求,加工中可取公差的1/2或1/3。
按正常加工方法很难保证产品图样要求。
2. 加工难点及工艺方案此零件壁厚为3.5mm ,按正常加工方法一次装夹中完成外圆及内孔并切断,设计夹具装夹,车另一端面及内孔。
但是外圆要求不严,壁又薄,用夹具装夹必须提高外圆精度,才能保证产品要求。
这样无形中增加工艺成本,所以说,此零件加工难点就是装夹加工方面。
为避免加工中的变形,特制定加工工艺方案如下:(1)毛坯选择单件下料,包括夹头尺寸。
(2)粗加工内孔,单边留量。
(3)调质处理。
(4)车端面,车外圆到尺寸φ60mm ,车内孔φ34H10及φ33mm 到尺寸,保持深度尺寸(加上夹头30mm ),距端面尺寸30mm 内车外空刀(空刀为夹头切断处),如图2所示。
(5)按外圆找正,装夹(夹头)零件,车端面,保持全长尺寸,车内孔φ34m m 及孔φ16H9定寸,保持深度尺寸,车外圆及外螺纹定寸,按空刀槽切断保证产品质量要求,如图3所示。
此方法加工套筒,增加夹头,可以保证产品质量,加工中没有变形,但是此方法适用于小批量生产零件,不适用大批量生产。
大批量生产最好设计车用夹具,零件定寸基准必须加严才能适用于夹具定位。
3. 结语加工薄壁套筒应注意以下几点:(1)多次装夹完成的套筒,如内孔精度高,可设计车用心轴,定心精度高,可保证较高的形位公差要求。
(2)多次装夹完成的套筒,如外圆精度高,可设计弹性夹具,零件装夹可靠。
(3)如果套筒壁薄,精度高还可以精加工后再留0.20mm ,卸下零件自然时效1~2天后,再从新装夹加工防止加工变形。
(收稿日期:20120904)北方机器有限责任公司 (黑龙江齐齐哈尔 161000) 梁 齐 李延平 陈桂梅 阴法军薄壁套筒零件加工工艺图 2图 3。
长套筒深孔的精密加工
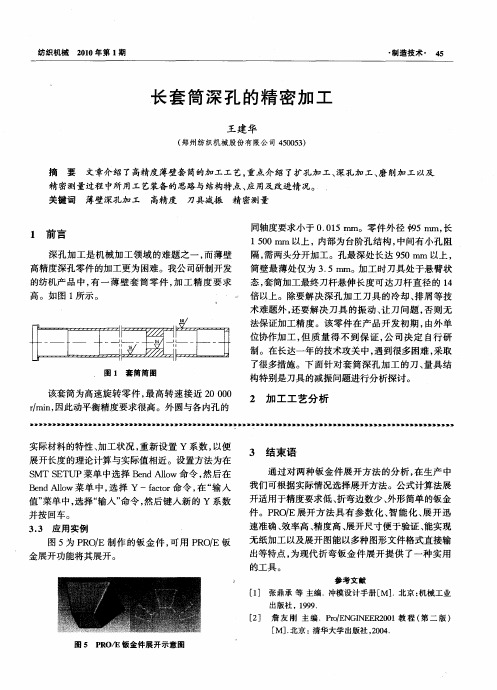
时要合理 、 科学的确定加工顺序及加工余量。内外 圆粗精加工交替进行, 即粗车外圆、 粗加工 内孑 、 L 粗 磨外圆、 半精加工内孔 、 精磨外圆、 精车内孔 、 精磨 内 孔等。中间要进行多次热处理, 消除加工应力。 在套筒深孔加工过程 中, 我们先后进行 了钻、 扩、 铰、 车、 磨等多道工序, 设计 了一系列刀具及其他 工装。下面主要介绍扩孔和粗精车孔等工序的加工
实际材料的特性 、 加工状况 , 重新设置 Y系数 , 以便 展开长度的理论计算与实际值相近。设置方法为在 S E U MT S T P菜单 中选择 B n l w命令 , edAl o 然后在 B n lw菜单 中, ed l Ao 选择 Y—f tr a o 命令 , 输入 c 在“ 值” 菜单 中, 选择“ 输入” 命令 , 然后键 人新 的 Y系数 并按回车。
同轴度 要求 小 于 0 0 5nI。零 件 外径 5Il, .1 l n l 长 Yn 15 0rl 以上 ,内部为 台阶孑 结 构 , 间有 小孔 阻 0 T nl L 中 隔 , 两 头分开 加 工 。孔 最 深处 长达 9011 以上 , 需 5 II TT
l 前 言
深孔 加 工是 机 械 加 工 领域 的难 题 之一 , 薄壁 而 高精度 深孔 零件 的加 工更 为 困难 。我公 司研 制 开发 的纺 机产 品 中 , 一 薄 壁 套 筒 零 件 , 工 精 度 要 求 有 加 高 。如 图 1所示 。
纺织机械
21 年 第 1 00 期
・ 制造技术 ・ 4 5
长套 筒 深 孔 的精 密 加 工
王建华
( 郑州纺织机械股份有 限公 司 4 0 5 ) 5 0 3
薄壁套的检测与质量分析概要
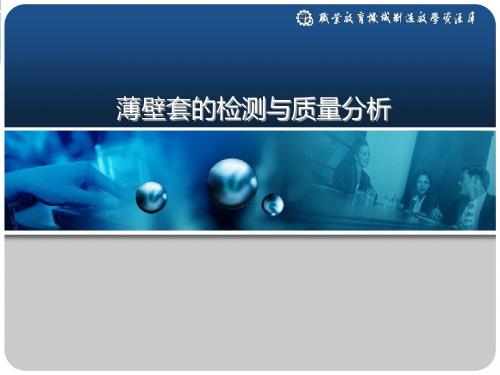
薄壁套的检测与质量分析
2 1 3 2 2 5 3 3
游标卡尺 薄壁工件的检测
工件检测表 百分表 薄壁工件变形质量检测分析 工件在花盘上的装夹
Produced by Мiss Хiè
一、薄壁工件的检测
1、壁厚的检测。
2、圆度误差的检测。
3、圆柱度误差的检测。
Produced by Мiss Хiè
形状为弧形三边或多边
夹紧力或弹性 力
表面有振纹、工件不圆 等
切削力
表面热膨胀变形 表面受压变形
切削热
1.合理选择车刀几何参数和切削用量 2.充分加注切削液
1.测量力适当 测量力(极薄 的工件) 2.增加测量接触面积 Produced by Мiss Хiè
尺寸
5
超差不得分
6
长度
86mm
尺寸
5
超差不得分
7
4mm
尺寸
5
超差不得分
8
圆跳动
0.04mm
10
超差不得分
9
平行度
0.03mm
10
超差不得分
10
垂直度
0.01mm
Produced by Мiss Хiè
10
超差不得分
三、薄壁工件变形质量检测分析
问题 产生原因 预防和解决方法 1.增大装夹接触面积,使工件表面受背向 力均匀 2.采用轴向夹紧 3.装夹部位增加工艺肋,使夹紧力作用在 工艺肋上 1.合理选择车刀几何参数,使切削刃锋利 2.合理选择切削用量 3.分粗、精加工 4.充分加注切削液,以减小摩擦,降低切 削温度
一、薄壁工件的检测
1、壁厚的检测 薄壁工件的壁厚可用壁厚千分尺(如 图1a 所示 )进行测量。如果工作现场没有壁厚千分尺, 可以用外径千分尺配合钢球进行检测,如图1b所示。
薄壁零件的加工精度及注意事项

薄壁零件的加工精度及注意事项影响薄壁零件加工精度的因素1.易受力变形:由于工件壁薄,在夹紧力作用下容易变形,影响工件的尺寸精度和形状精度;2易受热变形:因工件较薄,切削热会引起工件热变形,使工件尺寸难于控制;3易振动和变形:在切削力尤其是径向切削力的作用下,容易产生振动和变形,影响工件的尺寸精度、形状、位置精度和表面粗糙度。
如何提高薄壁零件的加工精度为了提高产品的合格率,我们综合考虑工件的夹紧、刀具的几何参数和编程。
实践证明,零件精度得到有效提高,产品质量得到保证。
1、利用零件的整体刚性加工薄壁零件随着零件壁厚的减小,其刚度降低,加工变形增大。
因此,在切割过程中,应尽可能使用零件的原始零件作为切割零件的支撑,以使切割过程处于更好的刚性状态。
例如,对于腔体中带有腹板的空腔部件,在加工过程中,铣刀从坯料中部以螺旋方式切割,以减小腹板上的垂直分量的压力,使Milles达到深度方向的尺寸,然后从中间延伸到周围到侧壁。
当内腔深度较大时,应按上述方法进行多层加工。
这种方法可以有效地减少切削变形及其影响,并减少因刚度降低而可能产生的切削振动。
2、采用辅助支撑对于薄壁型腔零件的加工,关键问题是解决夹紧力引起的变形。
因此,可以通过在空腔中添加薄膜轮胎、橡胶薄膜轮胎或硬质薄膜轮胎来提高零件的刚度,抑制零件的加工变形;或采用石蜡、低熔点合金填充法等工艺方法加强支撑,以减少变形,提高精度。
3、设计工艺加强筋,提高刚性对于薄壁零件,增加工艺筋条,以加强刚性,是工艺设计常用的手段之一。
4.对称分层铣削允许均匀应力释放毛坯初始残余应力对称释放,可以有效减小零件的加工变形。
对厚度两面需进行加工的板类零件,采用上下两面去除余量均等的原则,进行轮流加工,即在上平面去除δ余量,然向后转,去掉另一侧的边缘。
在加工过程中,采用依次减小余量的原则。
旋转次数越多,应力释放越彻底,加工后工件的变形越小。
5、刀具下刀方式的优化切削方法直接影响零件的加工变形。
高精度筒类零件的加工及测量方法

高精度筒类零件的加工及测量方法张金生;苟罗成;廖世超;谭万斌【摘要】通过设计专用工装,满足了高精度筒类零件的形位公差及尺寸公差;通过对外径千分尺进行改进,利用尺弓的外形特点,解决了测量止口的难题.【期刊名称】《中国重型装备》【年(卷),期】2018(000)003【总页数】2页(P47-48)【关键词】筒类零件;专用工装;千分尺;测量头【作者】张金生;苟罗成;廖世超;谭万斌【作者单位】二重(德阳)重型装备有限公司,四川618013;二重(德阳)重型装备有限公司,四川618013;二重(德阳)重型装备有限公司,四川618013;二重(德阳)重型装备有限公司,四川618013【正文语种】中文【中图分类】TG806大型筒类零件(如水电轴)图纸要求外圆及止口全跳动0.02 mm,见图1,要求两总长端面全跳动0.02 mm,要求两端止口尺寸公差等级为H6,必须一次装夹完成加工才能保证设计要求。
由于其长径比大,尺寸公差小,形位公差严,选用立式车床根本无法达到图纸要求。
在卧式车床上采用一夹一架的装夹方式,虽然能够加工床尾一端的止口及外圆,但不能加工床头一端的止口及端面,在工件调头装夹后,根本无法保证止口全跳动0.02 mm的要求。
在工件空心的情况下,要保证一次装夹完成两端止口及外圆的加工,只有在工件芯部安装芯轴,让两端止口、端面及外圆同时处于可加工状态。
图1 大型筒类零件示意图Figure 1 Sketch of heavy cylinder part在筒类零件的芯部安装芯轴后,给止口的测量带来难题,特别是止口尺寸公差等级为H6,必须精确测量止口尺寸。
如果能够在芯部有芯轴的情况下完成两端止口尺寸的测量,将明显提高加工效率。
1 芯轴结构根据筒类零件内孔直径及支撑爪的尺寸,选用合适直径的芯轴,为了减小芯轴挠度,在芯轴中心加工适当直径的通孔,同时起到一定的减重作用;在芯轴两端设计有顶尖孔,可实现两顶装夹工件,或一夹一架装夹工件。
薄壁套筒零件的加工工艺分析

进行大余量切削, 加工效率较 高, 很好地解决 了加 工质量
与加 工效率 的 问题 。
最初 , 我们 以为芯轴 这样装 入薄壁筒 后 内孔就 可 以胀
紧。但实际操作过程 中发现, 将胀圆芯轴装入薄壁筒拧紧
螺母 后 , 筒两 端胀 紧 了而 中间 还有 间 隙 , 进 行 加 工 薄壁 若 将 由于 刀具接 触该 空 隙处 产生振 动而无 法满足 加工要 求 。 对 上述 问题经 仔细 分析 , 为使芯轴 与简 体 内孔 的 发现
・
【 收稿 日 2o—o—o 期】08 3 4 【 作者简介】 汪小平(96 , 四川渠县人 , 17一) 男, 助理工程师, 主要从事零件加工工艺研究。
1 77
维普资讯
20 08年专辑
汪 小平 : 薄壁 套筒 零件 的加 工工 艺分 析
’
紧力太大时, 薄壁筒就有可能产生塑性变形, 造成 圆柱度
超差 ; 二是 因为筒 壁材 料 壁厚 不均 匀 , 同一 截 面 上 各 点 在
直径约 30 m, 0 r 长度近 50 m, a 0r 而筒壁仅 15 m厚 , a .r a 是典 型 的弱刚 性件。其 内孔 尺 寸公 差为 0 1 , . 3 圆柱 度公 差 000 要求壁厚均匀, .5 , 且还要在薄壁简体外壁上开出沿轴
方案 2 无需在薄壁筒一端焊接法兰。设计一套弹性 :
胀圆芯轴 , 该芯轴两端都是弹性夹头, 拧紧两端螺母 时可 通过端盖斜面将外 圆胀开。在 薄壁筒精加工时先把内孔 镗到尺寸 , 然后 套人芯轴将 内孔撑 圆再车外圆 , 这时加工 外圆即使增加切削量也不怕零件变形, 可提高加工效率 。
() 2 引起圆柱度超差 的原因一是夹 紧方式 , 当采用径
套筒类零件加工——机械工程技术作业
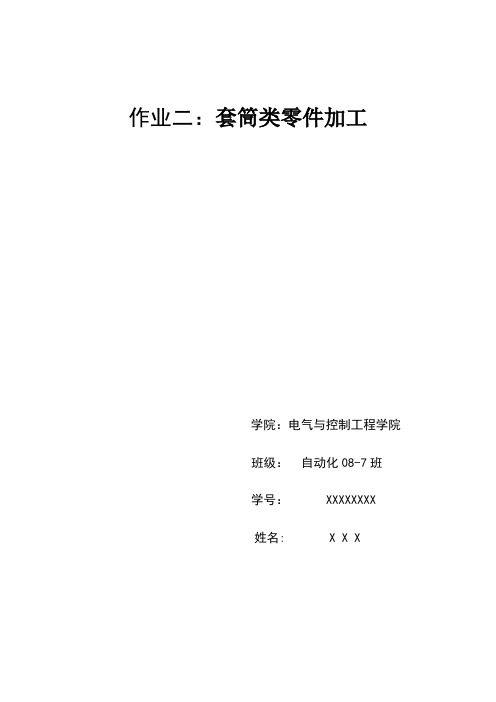
作业二:套筒类零件加工学院:电气与控制工程学院班级:自动化08-7班学号: XXXXXXXX姓名: X X X套筒类零件加工一、工作任务按工艺完成图2-1所示套筒类零件加工。
二、任务分析套筒类零件是指在回转体零件中的空心薄壁件,是机械加工中常见的一种零件,在各类机器中应用很广,主要起支承或导向作用。
套筒类零件的结构与尺寸随其用途不同而异,但其结构一般都具有以下特点:外圆直径 d一般小于其长度L,通常L/d<5;内孔与外圆直径之差较小,故壁薄易变形较小;内外圆回转面的同轴度要求较高。
任务一:孔加工刀具与机床1、钻床(1)应用:钻床是用钻头在工件上加工孔的机床。
通常用于加工尺寸较小,精度要求不太高的孔。
可完成钻孔,扩孔,铰孔及攻螺纹等工作。
(2)运动分析:工件固定,刀具作旋转主运动,同时沿轴向作进给运动。
(3)钻床的主参数:最大钻孔直径(4)分类:a.立式钻床:适用于中小工件的单件,小批量生产b.摇臂钻床:适用于加工一些大而重的工件上的孔(工件不动,移动主轴)c.台式钻床:小型钻床,常安装在台桌上,用来加工直径<12mm 的孔。
d.深孔钻床及其他钻床(5).钻削特点:刀具刚性差,排屑困难,切削热不易排出。
2、镗床(1)应用:镗床是一种主要用镗刀在工件上加工孔的机床。
通常用于加工尺寸较大,精度要求较高的孔,特别是分布在不同表面上,孔距和位置精度要求较高的孔。
如箱体上的孔,还可以进行铣削,钻孔,扩孔,铰孔等工作。
(2)镗削特点:刀具结构简单,通用性达,可粗加工也可半精加工和精加工,适用批量较小的加工,镗孔质量取决于机床精度.(3)运动分析:主运动为镗刀的旋转运动,进给运动为镗刀或工件的移动。
(4)分类:a.卧式镗床b.坐标镗床:是一种高精度的机床。
主要特点:具有坐标位置的精密测量装置。
c.金刚镗床:一种高速精密镗床。
主要特点:vc很高,ap和f 很小,加工精度可达IT5--IT6.Ra达0.63--0.08μm3、孔加工刀具一类是从实体材料种加工出孔的刀具,如:麻花钻,扁钻,中心钻和深孔钻等。
套筒零件加工工艺分析
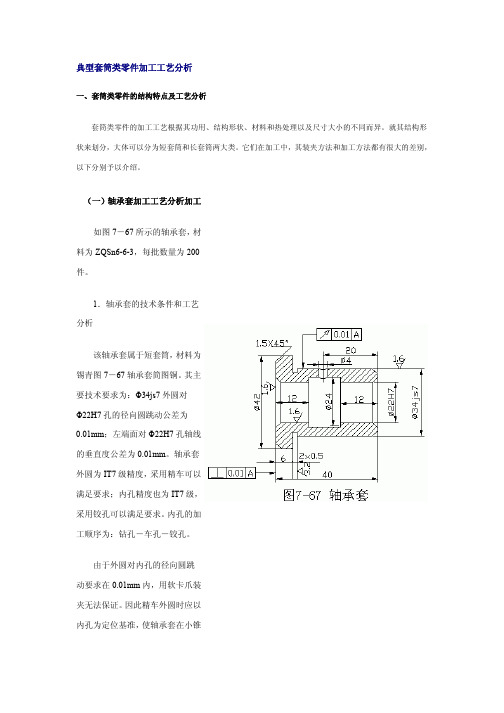
3
粗车 空刀槽 2×0.5mm,取总长 40.5mm,车分割槽 Ф20×3mm, 中心孔
两端倒角 1.5×45°,5 件同加工,尺寸均相同
钻孔 Ф22H7 至 Ф22mm 成单件
4
钻
软爪夹 Ф42mm 外圆
• 车端面,取总长 40mm 至尺寸
5 车、铰
• 车内孔 Ф22H7 为 Ф22 mm • 车内槽 Ф24×16mm 至尺寸 • 铰孔 Ф22H7 至尺寸 • 孔两端倒角
由于外圆对内孔的径向圆跳 动要求在 0.01mm 内,用软卡爪装 夹无法保证。因此精车外圆时应以 内孔为定位基准,使轴承套在小锥
度心轴上定位,用两顶尖装夹。这 样可使加工基准和测量基准一致, 容易达到图纸要求。
车铰内孔时,应与端面在一次 装夹中加工出,以保证端面与内孔 轴线的垂直度在 0.01mm 以内。
3.精铰(浮动镗刀镗孔)到 Ф70±0.02mm,
表面粗糙度值 Ra 为 2.5µm
4
滚压孔 用滚压头滚压孔至 Ф70
mm,表面粗糙 一端用螺纹固定在夹具中, 另一
度值 Ra 为 0.32µm
端搭中心架
1.车去工艺螺纹,车 Ф82h6 到尺寸,割 R7 槽
软爪夹一端,以孔定位顶另一端
2.镗内锥孔 1°30′及车端面
5
车
软爪夹一端,中心架托另一端(百 分表找正孔)
3.调头,车 Ф82h6 到尺寸,割 R7 槽
软爪夹一端,顶另一端
4.镗内锥孔 1°30′及车端面
软爪夹一端,顶另一端
二、套筒类零件加工中的主要工艺问题
一般套筒类零件在机械加工中的主要工艺问题是保证内外圆的相互位置精度(即保证内、外圆表面的 同轴度以及轴线与端面的垂直度要求)和防止变形。
- 1、下载文档前请自行甄别文档内容的完整性,平台不提供额外的编辑、内容补充、找答案等附加服务。
- 2、"仅部分预览"的文档,不可在线预览部分如存在完整性等问题,可反馈申请退款(可完整预览的文档不适用该条件!)。
- 3、如文档侵犯您的权益,请联系客服反馈,我们会尽快为您处理(人工客服工作时间:9:00-18:30)。
薄壁深孔高精度套筒的加工与测量
薄壁深孔零件加工难度大,特别是高精度套筒的加工更困难,我公司有一套筒零件如图1 所示。
设计要求严格,加工精度高,产品开发初期由外协加工,存在问题较多,无法满足产品正常运转需要,公司决定自制。
1 工艺分析
该套筒为高速旋转零件,最高转速近20000r/min,设计要求动平衡极为严格,动平衡等级为G1级。
外圆和各台阶孔同轴度越小越好,最好能控制在0.01之内。
该件号为整体结构,台阶孔为深孔,最深孔近900mm,长径比接近13mm。
深孔切削时,振动、让刀、排屑困难、不易散热等现象使得加工难度较大,并且测量深孔、深孔与外圆的同轴度也很困难。
由于是整体结构,毛坯料采用圆钢,加工前坯料重达127kg,加工后仅剩20kg,不到原重量的六分之一。
大量的金属被切削掉,因此变形严重。
2 工艺措施
针对以上问题,编制加工工艺时,从以下方面采取工艺措施。
采用多次热处理处理,消除加工应力和变形。
针对冷热加工交替,编制工艺时科学计算合理安排工序余量,使每道工序既留有余量,又不能余量太大,防止产生新的应力变形。
深孔粗半精加工,采用我公司比较成熟的后导向扩孔,孔一层层的扩大,层层导向。
导向扩孔克服了深孔加工的振动和孔中心的偏斜。
导向扩孔刀如图2 所示。
图2 导向扩孔刀
图3 刀座
图4 减震刀杆
图5 车床找正外圆测量法
深孔的导向扩孔只解决了孔的粗半精加工,要保证该件号制造成功,还是要解决各台阶孔的精车精磨。
加工深孔的基准是外圆,加工外圆的基准是中心孔。
编制工艺时考虑到孔口较大,不易保证孔口的圆度,因此需要多次镶配闷头。
粗车后两端配闷头,以闷头中心孔为准粗磨外圆,然后半精加工孔,半精加工孔后配闷头,然后半精磨外圆,时效后配闷头精磨外圆,最后精车孔,精磨孔。
深孔车削时最大的问题是振动,防振减振为薄壁深孔套筒加工的关键。
为此编制工艺采取以下几种措施。
专用刀座将深孔刀具的刀柄做成圆柱形,用专用刀座将刀柄固定在车床的中拖板上,可以大大提高刀具的刚性(见图3)。
采用减振刀杆精车孔时专门定做了防震结构的减振刀杆(见图4)。
采用滚动中心架精车孔时为防止工件外圆与中心架的磨擦发热,应采用精密滚动轴承中心架。
精车孔时冷却液要充分,防止工件发热引起新的变形。
合理选用刀具几何参数选用主偏角为90°的小圆弧半径的可转位刀片,尽量减小背吃刀力。
合理选用切削用量根据切削用量可转位刀片选用断屑性能好的槽形,保证深孔切削排屑顺利。
选用高精度数控车床要求数控车床径向轴向跳动小,导轨直线度好,抗震性好。
深孔磨削 d孔是配合孔,不仅精度要求高而且粗糙度低。
我们采用加长磨头的深孔磨床加工,保证了尺寸精度和粗糙度。
深孔测量
无公差要求的深孔尺寸,采用加长测量杆内径百分表测量。
有公差要求的深孔尺寸,采用加长测量杆的气动量仪测量。
外圆与孔的同轴度测量有三种方法:三座标测量法;车床找正外圆测量孔跳动测量法(见图5);V形铁直线导轨测微头测量法。
经过努力多次改进工艺,薄壁深孔高精度套筒加工获得成功。
经过试车达到设计要求。