高精度深长孔的精密加工方法
关于用普通车床加工细长孔的工艺技术探究
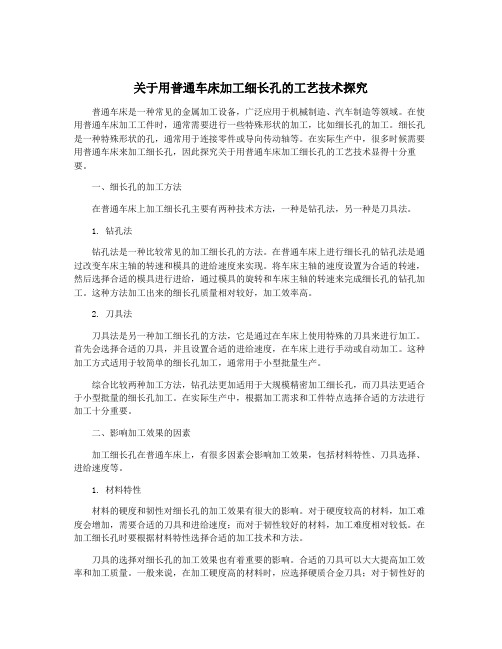
关于用普通车床加工细长孔的工艺技术探究普通车床是一种常见的金属加工设备,广泛应用于机械制造、汽车制造等领域。
在使用普通车床加工工件时,通常需要进行一些特殊形状的加工,比如细长孔的加工。
细长孔是一种特殊形状的孔,通常用于连接零件或导向传动轴等。
在实际生产中,很多时候需要用普通车床来加工细长孔,因此探究关于用普通车床加工细长孔的工艺技术显得十分重要。
一、细长孔的加工方法在普通车床上加工细长孔主要有两种技术方法,一种是钻孔法,另一种是刀具法。
1. 钻孔法钻孔法是一种比较常见的加工细长孔的方法。
在普通车床上进行细长孔的钻孔法是通过改变车床主轴的转速和模具的进给速度来实现。
将车床主轴的速度设置为合适的转速,然后选择合适的模具进行进给,通过模具的旋转和车床主轴的转速来完成细长孔的钻孔加工。
这种方法加工出来的细长孔质量相对较好,加工效率高。
2. 刀具法刀具法是另一种加工细长孔的方法,它是通过在车床上使用特殊的刀具来进行加工。
首先会选择合适的刀具,并且设置合适的进给速度,在车床上进行手动或自动加工。
这种加工方式适用于较简单的细长孔加工,通常用于小型批量生产。
综合比较两种加工方法,钻孔法更加适用于大规模精密加工细长孔,而刀具法更适合于小型批量的细长孔加工。
在实际生产中,根据加工需求和工件特点选择合适的方法进行加工十分重要。
二、影响加工效果的因素加工细长孔在普通车床上,有很多因素会影响加工效果,包括材料特性、刀具选择、进给速度等。
1. 材料特性材料的硬度和韧性对细长孔的加工效果有很大的影响。
对于硬度较高的材料,加工难度会增加,需要合适的刀具和进给速度;而对于韧性较好的材料,加工难度相对较低。
在加工细长孔时要根据材料特性选择合适的加工技术和方法。
刀具的选择对细长孔的加工效果也有着重要的影响。
合适的刀具可以大大提高加工效率和加工质量。
一般来说,在加工硬度高的材料时,应选择硬质合金刀具;对于韧性好的材料,可以选择HSS刀具。
内孔表面加工常用方法大汇总

内孔表面加工方法较多,常用的有钻孔、扩孔、铰孔、镗孔、磨孔、拉孔、研磨孔、珩磨孔、滚压孔等。
一、钻孔用钻头在工件实体部位加工孔称为钻孔。
钻孔属粗加工,可达到的尺寸公差等级为IT13~IT11,表面粗糙度值为Ra50~12.5μm。
钻孔有以下工艺特点:1.钻头容易偏斜。
在钻床上钻孔时,容易引起孔的轴线偏移和不直,但孔径无显著变化;在车床上钻孔时,容易引起孔径的变化,但孔的轴线仍然是直的。
因此,在钻孔前应先加工端面,并用钻头或中心钻预钻一个锥坑,以便钻头定心。
钻小孔和深孔时,为了避免孔的轴线偏移和不直,应尽可能采用工件回转方式进行钻孔。
2.孔径容易扩大。
钻削时钻头两切削刃径向力不等将引起孔径扩大;卧式车床钻孔时的切入引偏也是孔径扩大的重要原因;此外钻头的径向跳动等也是造成孔径扩大的原因。
3.孔的表面质量较差。
钻削切屑较宽,在孔内被迫卷为螺旋状,流出时与孔壁发生摩擦而刮伤已加工表面。
4.钻削时轴向力大。
这主要是由钻头的横刃引起的。
因此,当钻孔直径d﹥30mm时,一般分两次进行钻削。
第一次钻出(0.5~0.7)d,第二次钻到所需的孔径。
由于横刃第二次不参加切削,故可采用较大的进给量,使孔的表面质量和生产率均得到提高。
二、扩孔扩孔是用扩孔钻对已钻出的孔做进一步加工,以扩大孔径并提高精度和降低表面粗糙度值。
扩孔可达到的尺寸公差等级为IT11~IT10, 表面粗糙度值为Ra12.5~6.3μm,属于孔的半精加工方法,常作铰削前的预加工,也可作为精度不高的孔的终加工。
扩孔方法如图7-4所示,扩孔余量(D-d),可由表查阅。
扩孔钻的形式随直径不同而不同。
直径为Φ10~Φ32的为锥柄扩孔钻,如图7-5a所示。
直径Φ25~Φ80的为套式扩孔钻,如图7-5b所示。
扩孔钻的结构与麻花钻相比有以下特点:1.刚性较好。
由于扩孔的背吃刀量小,切屑少,扩孔钻的容屑槽浅而窄,钻芯直径较大,增加了扩孔钻工作部分的刚性。
2.导向性好。
深孔加工的几种方法

深孔加工的几种方法深孔加工是一种用于加工深孔孔径大、长径比高的工件的专业加工方法。
在工业制造中,深孔加工广泛应用于航空航天、汽车、模具、电子等领域。
下面是关于深孔加工的十种常见方法,并对每种方法进行详细描述。
1. 长钻杆深孔加工(Gun drilling)长钻杆深孔加工是最常见的深孔加工方法之一。
它使用带有镶有硬质合金刀片的长钻杆进行加工。
钻杆被安装在特殊的深孔钻床上,通过旋转和进给,将刀片带动至工件内部进行加工。
该方法适用于孔径较小、长径比较高的工件。
2. 刀具旋转切削深孔加工(Boring)刀具旋转切削深孔加工是使用铰孔刀或车刀进行加工的方法。
刀具通过旋转,将材料从工件中间逐渐取出,形成深孔。
由于切削力较大,工件需要具备较好的稳定性,并配备适当的刀具冷却和切屑排出系统。
3. 杆料直插深孔加工(Trepanning)杆料直插深孔加工是一种适用于大孔径深孔加工的方法。
在该方法中,一个圆柱形工具的中心用于插入工件,通过旋转工件和工具,将材料从工件中间逐渐取出,形成深孔。
该方法适用于孔径较大、长径比较高的工件。
4. 进给滚压深孔加工(Skiving)进给滚压深孔加工是一种高效的深孔加工方法。
在该方法中,刀具会逐渐滚动进入工件,并通过旋转和进给来形成深孔。
与切削加工相比,滚压加工具有更高的切削速度和更少的切削力,可以减少加工产生的热量和变形。
5. 穿切切削深孔加工(Reaming)穿切切削深孔加工是一种通过旋转和进给来加工深孔的方法。
与其他深孔加工方法相比,穿切切削深孔加工具有更高的切削速度和更少的切削力。
该方法适用于孔径较小、长径比较高的工件。
6. 穿孔切削深孔加工(Counterboring)穿孔切削深孔加工是一种在工件的底部形成平坦的底座的方法。
通过旋转和进给,切削刀具穿过工件,形成孔径较大的底孔。
该方法广泛应用于需要准确定位或加工底孔的工件。
7. 表面喷涂深孔加工(DLC Coating)表面喷涂深孔加工是一种在工件表面喷涂高硬度的钻石碳涂层的方法。
机械制造基础(第二版)第6章z钻、铰、镗和拉削加工

6.3 铰削加工
三、铰孔时应注意事项
1. 铰刀的选择 铰刀是定尺寸刀具,铰孔的精度在很大程度上决定于铰刀的 精度。故在使用铰刀前,应仔细测量铰刀的直径是否与被铰 孔相符,刃口有无磨损、裂纹、缺口等缺陷,经试铰合格后 方能使用。
2. 铰刀的安装 铰孔作为精加工,切削余量很小。若安装后铰刀轴线与原工 件孔中心线发生偏斜,将会使孔径铰削后尺寸扩大超差和产 生形状误差。因此,铰刀与机床应采用浮动联接。
6.2 钻削加工
三、钻削要素
1.钻削用量
切削速度c 钻削时的切削速度指钻头外缘处的线速度
c
d o n
1000
进给量f、每齿进给量fz及进给速度f
f nf2nfz
背吃刀量ap 对钻头而言,它就是钻头直径的一半
ap d0 2
6.2 钻削加工
2.切削层截面尺寸
钻削时切削层尺寸平面为过 基点D的基面PD
6.3 铰削加工
3. 铰削用量的选择 合理选择铰削用量,可以提高铰孔精度。 精铰时,一般半径上铰削余量为0.03~0.15mm,其值取决
于工件材料及对孔要求的精度和表面粗糙度。一般铰削钢体
时,切削速度c=1.5~5m/min;铰铸铁件时c=8~l0m/min,
进给量不能取得过小,否则切削厚度hd过薄,铰刀的挤压作 用会明显加大,加速铰刀后刀面的磨损。—般铰制钢件时f= 0.3~2mm/r,铰削铸铁件时f=0.5~3mm/r。
铰刀齿槽方向有直槽和螺旋槽两种。直槽铰刀刃磨、检验方 便,生产中常用;螺旋槽铰刀切削过程平稳。加工铸铁等取 β=7~8;加工钢件取β=12~20;加工铝等轻金属取 β=35~45。
6.3 铰削加工
铰刀的几何角度
前角γo和后角o 一般取γo=0。粗铰塑性材料时,为
如何高速高精度孔加工

1.如何高速高精度孔加工?答:除采用CNC切削方式对孔进行精密加工外,还可采用镗削和铰削等方式对孔进行高精度加工。
随着加工中心主轴的高速化,已可采用镗削工具对孔进行高速精密加工。
据报道,目前在铝合金材料上进行φ40mm左右的镗削加工时,切削速度已可提高到1500m/min以上。
在用CBN烧结体作切削刃加工钢材、铸铁及高硬度钢时,也可采用这样的切削速度。
预计,今后镗削加工的高速化将会迅速普及推广。
为了实现镗削加工的高速化和高精度化,必须注意刀齿振动对加工表面粗糙度和工具寿命的影响。
为了防止加工精度和工具寿命下降,所选用的加工中心必须配备动平衡性能优异的主轴,所选镗削刀具也必须具有很高的动平衡特性。
尤其是镗削工具的刀齿部分,应选择适用于高速切削的几何形状、刀具材料及装卡方式。
切削刃端部的R应较大,以利于提高加工效率;在保证获得同等加工表面粗糙度的前提下,应加大进给量。
但加大进给量应适可而止,否则将增大切削阻力,不利于提高加工效率。
切削刃带应设置以下的负倒棱,这样可有效保持刀具寿命的稳定。
至于刀具材料,则视被加工材料性质而有所不同。
如加工40HRC以下的钢等材料时,可选用金属陶瓷刀具,这种刀具在v=300m/min以上的高速切削条件下,可获得良好的加工表面粗糙度与较长的刀具寿命。
涂层硬质合金刀具则适用于对60HRC以下的钢材等进行高速切削,刀具寿命非常稳定,但切削速度稍低于金属陶瓷刀具。
CBN烧结体刀具适用于加工高硬度钢、铸铁等材料,切削速度可达1000m/min以上,而且刀具寿命非常稳定。
CBN刀齿的刃带部分应进行适当的倒棱处理,这种处理对进行稳定的高速切削和延长刀具寿命极为有利。
在对铝合金等有色金属及非金属材料进行超高速切削时,可选用金刚石烧结体刀具,这种刀具切削稳定,刀具寿命也很长。
应注意的是,使用金刚石刀具时,刀齿刃带必须进行倒棱处理,这是保证切削稳定的重要条件。
在铰削加工方面,目前尚未见到高速、高精度的新型刀具问世,该领域的研究开发工作似乎处于停滞不前的状态。
精密加工技术
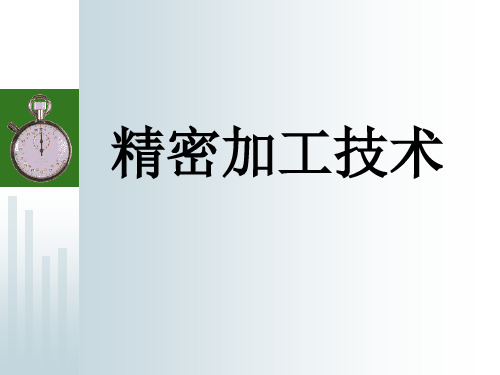
b.混粉加工方法
在放电加工液内混入粉末添加剂 ,以高速获得光泽面的加工方法称 之为混粉加工。该方法主要应用于 复杂模具型腔,尤其是不便于进行 抛光作业的复杂曲面的精密加工。 可降低零件表面粗糙度值,省去手 工抛光工序,提高零件的使用性能 (如寿命、耐磨性、耐腐蚀性、脱 模性等)。混粉加工技术的发展, 使精密型腔模具镜面加工成为现实 。
真空热处理炉已广泛采用了计算机 控制,目前已发展到真空化学热处理 和真空气淬热处理,包括高压真空 气淬、高流率真空气淬和高压高流 率真空气淬技术等。另外,激光热 处理技术在国外已广泛用于航空、 航天、电子、仪表等领域,如各种 复杂表面件、微型构件、需局部强 化处理构件、微型电子器件、大规 模集成电路的生产和修补、精密光 学元件、精密测量元件等。
4.数控电火花加工新工艺的应用
a.标准化夹具
数控电火花加工为保证极高的重 复定位精度且不降低加工效率,采用 快速装夹的标准化夹具。标准化夹具 ,是一种快速精密定位的工艺方法, 它的使用大大减少了数控电火花加工 过程中的装夹定位时间,有效地提升 了企业的竞争力。目前有瑞士的 EROWA和瑞典的3R装置可实现快速精 密定位。
5、抛光 是利用机械、化学、电 化学的方法对工件表面进行的一种微 细加工,主要用来降低工件表面粗糙 度,常用的方法有:手工或机械抛光 、超声波抛光、化学抛光、电化学抛 光及电化学机械复合加工等。手工或 机械抛光加工后工件表面粗糙度 Ra≤0.05µm,可用于平面、柱面、曲 面及模具型腔的抛光加工。超声波抛 光加工精度 0.01~0.02µm,表面粗糙 度Ra0.1µm。化学抛光加工的表面粗糙 度一般为Ra≤0.2µm。电化学抛光可提 高到Ra0.1~0.08µm。
模糊控制技术是由计算机监测来 判定电火花加工间隙的状态,在保持 稳定电弧的范围内自动选择使加工效 率达到最高的加工条件;自动监控加
机械振动-精密深孔镗削中镗杆振动问题

北方工业大学科目机械振动-精密深孔镗削中镗杆振动问题学院机电工程学院专业班级机研-12学生姓名指导教师撰写日期:2012年12月12日摘要在机械制造业中,一般规定孔深L 与孔径d 之比大于5,即L/d>5 的孔称为深孔。
深孔加工是处于封闭或半封闭状态下进行的,不能直接观察到刀具的切削情况;且受孔径尺寸限制,刀具直径小,悬伸长,刚性差;切屑不易排出,切削热不易传散,因此深孔加工一直是金属切削领域内公认的技术难题。
而对于两端孔径小,中间孔径大的瓶腔深孔加工则难度更大,除了存在上述一般深孔加工的问题外,还要求实现镗刀块的伸出、夹紧、松开、缩回等动作,且受入口直径的限制,镗杆的刚性问题及振动问题变得更加尖锐。
因此精密小深孔加工技术的研究在理论和实践上都具有重要意义。
经过深孔镗削过程中的自激振动分析、深孔镗杆进行了静力学和动力学理论分析、对深孔镗杆进行ANSYS分析、深孔镗杆的模态分析,有一些减小振动的方法可以利用,如合理选择刀具几何形状、提高工艺系统的抗振性、采用减振装置、合理调整振型的刚度比、超声波方法、镗杆结构优化、智能镗杆颤振监测实验系统、镗削振动主动控制、设计辅助结构等方法等等。
关键词:深孔;镗削;减振目录目录 (3)1机械振动概况 (4)1.1机械振动对机械加工的影响 (4)1.2深孔加工的振动问题 (4)2精密振动切削工艺中的振动问题 (4)2.1项目简介 (4)2.1.1项目中的振动 (4)2.1.2项目镗削工序的振动分析 (4)3深孔镗削过程中的振动分析 (6)3.1深孔镗削过程中的自激振动 (6)3.2深孔镗杆进行了静力学和动力学理论分析 (7)3.3对深孔镗杆进行ANSYS分析 (9)3.4深孔镗杆的模态分析 (10)4减小深孔镗削中振动的方法 (11)4.1概述 (11)4.2超声波方法 (11)4.3镗杆结构优化 (13)4.4智能镗杆颤振监测实验系统 (13)4.5镗削振动主动控制 (14)4.6深孔镗削加减振措施后效果 (15)5.总结 (15)参考文献 (16)1机械振动概况1.1机械振动对机械加工的影响在机械加工过程中,工艺系统的振动会破坏刀具与工件之间正常的运动轨迹,给机械加工带来较大的危害,具体表现在以下几个方面:①影响加工表面质量,频率低时产生波纹,频率高时产生微观不平度;②降低生产效率,加工中的振动制约了切削用量的提高,严重时甚至使切削不能正常进行;③缩短刀具、机床等的使用寿命;④振动产生的噪声污染了环境。
精密和超精密加工技术

本章内容
I. 特种加工技术概述 II. 电火花加工 III.电解加工 IV. 高能束加工
特种加工技术概述
➢ 非传统加工又称特种加工,通常被理解为别于传统切 削与磨削加工方法的总称。
➢非传统加工方法 产生于二次大战后。两方面问题传统 机械加工方法难于解决:
1)难加工材料的加工问题。宇航工业等对材料高强度、 高硬度、高韧性、耐高温、耐高压、耐低温等的要求,使 新材料不断涌现。
电火花加工工作要素
➢脉冲宽度与间隔——影响加工速度、表面粗糙 度、电极消耗和表面组织等。脉冲频率高、持 续时间短,则每个脉冲去除金属量少,表面粗 糙度值小,但加工速度低。通常放电持续时间 在2μs至2ms范围内,各个脉冲的能量2mJ到20J (电流为400A时)之间。
电火花加工类型
➢电火花成形加工:主要指孔加工,型腔加工等 ➢电火花线切割
➢ 拓宽现有非传统加工方法的应用领域。
➢ 探索新的加工方法,研究和开发新的元器件。
➢ 优化工艺参数,完善现有的加工工艺。
➢ 向微型化、精密化发展。 ➢ 采用数控、自适应控 2084 制、CAD/CAM、专家系统
等 技 术 , 提 高 加 工 过 程1104
70年代 80年代 90年代
自动化、柔性化程度。
232
424 244 142
441 321 214
353 252 316
激光加工 电火花加工 超声加工 电化学加工 EI 收录文章数比较
几种代表性特种加 工方法
电火花加工的原理示意 图
电火花加工
原理:利用工具电极与工件电极之间脉冲性火花放电, 产生瞬时高温,工件材料被熔化和气化。同时,该处绝 缘液体也被局部加热,急速气化,体积发生膨胀,随之 产生很高的压力。在这种高压作用下,已经熔化、气化 的材料就从工件的表面迅速被除去
高精度孔的加工方法

高精度孔的加工方法
高精度孔的加工方法是指对于精度要求较高的孔进行加工的方法,例如在精密机械、航空航天、高速列车等领域中需要使用的孔。
高精度孔的加工需要保证孔的直径、圆度、表面质量等指标都达到一定的要求。
目前常见的高精度孔加工方法有以下几种:
1. 珩磨加工:珩磨是一种高速旋转的研磨工艺,通过磨头在被加工物表面的摩擦作用中去除材料,从而达到加工目的。
珩磨加工可以在孔内进行,可以加工出高精度圆度的孔。
2. 钻孔加工:钻孔是最常见的孔加工方法之一,可以使用林格曼钻头等工具进行。
钻孔加工可以达到较高的精度要求,但是对于深孔加工会出现偏差的问题。
3. 放电加工:放电加工是一种特殊的非机械加工方法,通过电火花放电来将被加工物表面的材料溶解或脱落,从而达到加工的目的。
放电加工可以加工出高精度的孔,但是加工速度较慢。
4. 激光加工:激光加工是一种高精度的非机械加工方法,通过激光束直接照射被加工物表面,将材料蒸发或熔化,从而达到加工目的。
激光加工可以加工出极高精度的孔,但是设备价格高昂,适用范围有限。
- 1 -。
高精度深长孔的精密加工方法
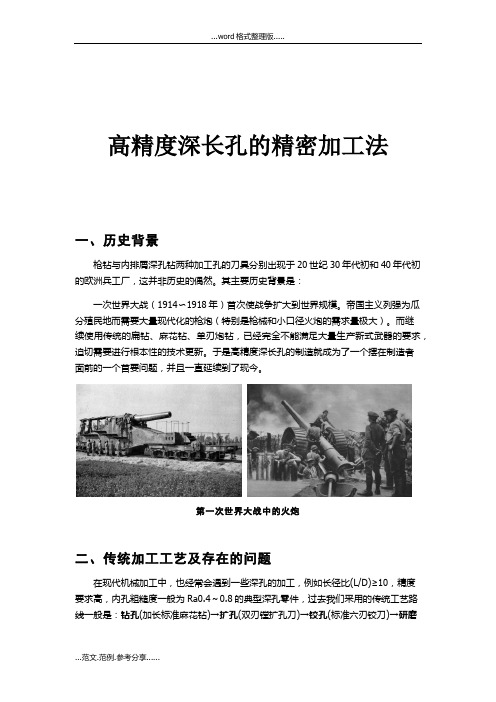
高精度深长孔的精密加工法一、历史背景枪钻与内排屑深孔钻两种加工孔的刀具分别出现于20世纪30年代初和40年代初的欧洲兵工厂,这并非历史的偶然。
其主要历史背景是:一次世界大战(1914〜1918年)首次使战争扩大到世界规模。
帝国主义列强为瓜分殖民地而需要大量现代化的枪炮(特别是枪械和小口径火炮的需求量极大)。
而继续使用传统的扁钻、麻花钻、单刃炮钻,已经完全不能满足大量生产新式武器的要求,迫切需要进行根本性的技术更新。
于是高精度深长孔的制造就成为了一个摆在制造者面前的一个首要问题,并且一直延续到了现今。
第一次世界大战中的火炮二、传统加工工艺及存在的问题在现代机械加工中,也经常会遇到一些深孔的加工,例如长径比(L/D)≥10,精度要求高,内孔粗糙度一般为Ra0.4~0.8的典型深孔零件,过去我们采用的传统工艺路线一般是:钻孔(加长标准麻花钻)→扩孔(双刃镗扩孔刀)→铰孔(标准六刃铰刀)→研磨此工艺虽可达到精度要求,但也存在诸多缺点,特别是在最初工序采用加长麻花钻钻孔时,切削刃越靠近中心,前脚就越大。
若钻头刚性差,则震动更大,表面形状误差难以控制,加工后孔的直线度误差,钻头易产生不均匀的磨损等现象,生产效率和产品合格率低,而且研磨抛光时,工作环境比较脏,由于钻孔工序的缺点,而带来的影响难以在后面的工序中克服,形状误差不能得以修正,因此加工质量差。
传统深孔的加工流程三、工艺路线与刀具的改进本着提高生产效率提高产品合格率的原则,结合深孔加工的一些特性,对加工工艺及刀具进行了改进,改进后的工艺路线是:钻孔(BTA钻)→扩孔(BTA扩)→铰孔(单刃铰刀)→研磨1、钻孔与扩孔刀具及工艺的改进单管内排屑深孔钻的由来单管内排屑深孔钻产生于枪钻之后。
其历史背景是:枪钻的发明,使小深孔加工中自动冷却润滑排屑和自导向问题获得了满意的解决,但由于存在钻头与钻杆难于快速拆装更换和钻杆刚性不足、进给量受到严格限制等先天缺陷,而不适用于较大直径深孔的加工。
长套筒深孔的精密加工
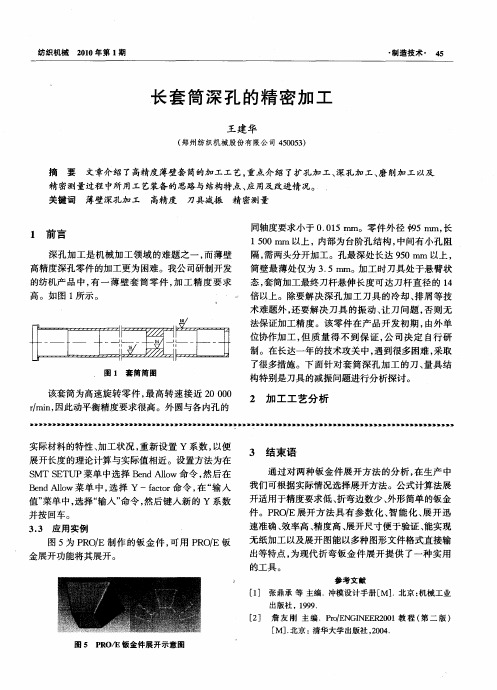
时要合理 、 科学的确定加工顺序及加工余量。内外 圆粗精加工交替进行, 即粗车外圆、 粗加工 内孑 、 L 粗 磨外圆、 半精加工内孔 、 精磨外圆、 精车内孔 、 精磨 内 孔等。中间要进行多次热处理, 消除加工应力。 在套筒深孔加工过程 中, 我们先后进行 了钻、 扩、 铰、 车、 磨等多道工序, 设计 了一系列刀具及其他 工装。下面主要介绍扩孔和粗精车孔等工序的加工
实际材料的特性 、 加工状况 , 重新设置 Y系数 , 以便 展开长度的理论计算与实际值相近。设置方法为在 S E U MT S T P菜单 中选择 B n l w命令 , edAl o 然后在 B n lw菜单 中, ed l Ao 选择 Y—f tr a o 命令 , 输入 c 在“ 值” 菜单 中, 选择“ 输入” 命令 , 然后键 人新 的 Y系数 并按回车。
同轴度 要求 小 于 0 0 5nI。零 件 外径 5Il, .1 l n l 长 Yn 15 0rl 以上 ,内部为 台阶孑 结 构 , 间有 小孔 阻 0 T nl L 中 隔 , 两 头分开 加 工 。孔 最 深处 长达 9011 以上 , 需 5 II TT
l 前 言
深孔 加 工是 机 械 加 工 领域 的难 题 之一 , 薄壁 而 高精度 深孔 零件 的加 工更 为 困难 。我公 司研 制 开发 的纺 机产 品 中 , 一 薄 壁 套 筒 零 件 , 工 精 度 要 求 有 加 高 。如 图 1所示 。
纺织机械
21 年 第 1 00 期
・ 制造技术 ・ 4 5
长套 筒 深 孔 的精 密 加 工
王建华
( 郑州纺织机械股份有 限公 司 4 0 5 ) 5 0 3
解决镗床深孔加工的疑难问题

科技论坛解决镗床深孔加工的疑难问题丁建平(齐二机床(集团)有限责任公司,黑龙江齐齐哈尔161005)在镗床工序中,深孔精密加工一直是孔加工中的难题,加工周期长,钻头、绞刀等工具损耗严重,而本单位产品的深孔工件又比较多,为此、设计新结构的刀具和工艺系统是改善深孔精密加工效果的有效方法。
针对材料为40Cr (调质)钢、长度为2800mm 、孔经为Φ60+0.08mm 、表面粗糙度为Ra0.8μm 、直线度为0.12mm 的缸体内孔精密加工,研制整套自导向镗铰刀及其工艺系统,经实际生产验证,加工效果较好,具体方法如下:1自制导向镗铰刀自制导向镗铰刀,所用刀片材料为YW1,用楔块压紧在刀体上;导向体材料为T15(经淬硬处理),其外圆比刀片部位略小0.04-0.06mm 。
刀片和导向套的外圆表面均需研磨,使其表面粗糙度比工件加工后的孔壁粗糙度要求至少高一级以上。
导向体内孔两端有材料为ZQSn10-1的衬套,衬套内孔与刀体为间隙配合。
刀体、导向套、单向推力球轴承和锁紧螺母组装后,要求导向体及单向推力球轴承转动灵活,无轴向窜动;将镗铰刀顶装在偏摆仪上,用百分表检查,其刀片部位和径向全跳动应不大于0.01mm ,导向体绕刀体转动时的径向跳动应不大于0.02mm 。
镗刀刀片的主要参数为:刃倾角λ=3°,前角γ=0°~3°,后角α=5°~8°,切削刃棱宽f1=0.05~0.08mm,导向刃棱宽f2=0.2~0.25mm ,镗铰内孔时,刀具的断屑性能至关重要。
如果切屑经常缠绕在镗杆或刀具上,就可能损坏刀片,损失已加工表面,且易堵塞出油管。
因此,进行深孔镗铰加工时一定要保证断屑稳定可靠,即加工时切屑应定向流出,先卷曲后折断。
为此需在刀片前处磨出一月牙洼状的断屑槽,使切屑卷成小卷,并越卷越大,直至受刀具前面和切屑表面的挤推而弯曲折断。
月牙洼槽可在工具磨床上磨制,然后用20%白泥加80%碳化硅粉用水调成糊状作为研磨剂,用圆弧半径为1~1.5mm 的铸铁研磨轮研磨15~30秒钟,即可达到要求。
台式钻床加工高精度孔距方法

台式钻床加工高精度孔距方法作者:陈博范来源:《职业·下旬》2019年第05期在国家职业技能鉴定和职业技能大赛中,装配钳工、机修钳工及工具钳工等钳工类工种高级工、技师甚至高级技师技能操作考核试题中,大部分为组合件锉配试题。
该组合件锉配试件中都有精密孔和高精度孔距加工,也是考核的一项重要内容。
在钳工技师操作技能考核试题中有这么一组精孔加工内容,用10mm厚板进行锉配,板上有两个精孔10H7需钻孔加工,板侧面到两孔的距離(边孔距)为30±0.04mm,两孔中心距50±0.04mm。
往往在技能操作考核中,考场一般只准备台式钻床和普通平口钳,在其他准备通知单中不允许准备靠模及钻模等二类加工工具,并要求在规定时间内手工操作完成精孔加工。
这将给操作者带来很大难度,因此大部分操作者很难保证加工精度。
笔者曾多次参加技能大赛,并训练学生参加技能大赛及各类技能鉴定,本文总结出几种提高钻孔精度的方法,与大家共同分享探讨。
一、精密划线找正加工法一般情况下,钻孔划线是用高度尺划出孔位置线,冲眼规圆,然后通过规圆找正钻孔。
由于冲眼规圆误差较大很难保证孔距精度,现在笔者介绍一种精密划线找正加工法。
这种方法是用高度游标卡尺或量块校准划出孔位置加工线及不同孔径的方格线,以试件孔10H7为例,分别划出6、8、9.8mm孔径边框方格线,也可多划几个不同孔径边框方格线。
钻孔时采用9.8mm、顶角为90°~100°麻花钻头,钻锪窝边线依次与孔径边框线同时相切,若没有相切,应及时找正试件位置直至9.8mm孔窝相切(若没有相切可反面再试一次)。
钻孔时注意要不同方位观察相切情况,也可用精密游标卡尺测量孔窝边线到孔径边框线位置尺寸,位置确定后钻通9.8mm孔,孔口倒角后,机铰或手铰10H7至精度要求。
这里需要注意的是划线钻孔前,用样冲冲眼也非常关键。
冲眼是一项技术工作,如果冲眼小了钻孔时定心不好,开始钻孔时钻头钻尖就会偏移,有时无法定心,有时刚定心就得开始找正,费时费劲。
超大深径比深小孔电火花加工工艺探索

超大深径比深小孔电火花加工工艺探索电火花加工是现代机械加工领域中一种常见的工艺方法。
其利用电热作用原理,将电能转化为热能,在工件表面产生高温电火花,从而实现对工件材料的加工和雕刻。
在电火花加工中,深径比是一个重要的参数,深度与直径的比值越大,说明电极能够加工更深的孔和更细小的孔,因而也能产生更高的加工效率。
而对于超大深径比深小孔电火花加工,则需要更深入的探索和技术创新。
超大深径比深小孔电火花加工能够广泛应用于微机械制造、晶体管制造、精密仪器制造等领域。
传统的电火花加工一般只能加工小孔,而加工大孔则需要使用其他的机械加工方法,如钻孔、铰孔或摇床等。
但是由于部分材料的硬度特别高,而且孔径较小,所以上述传统的机械加工方式很难达到理想的加工效果。
因此,超大深径比深小孔电火花加工成为此类工件加工的主要手段。
在超大深径比深小孔电火花加工过程中,需要对电极材料、电极尺寸、电极距离等因素进行适当地选择和调整。
首先,电极材料应选择高导电率、低膨胀系数、高熔点和与加工材料有一定成分的材料。
同时,电极材料还应具有非常好的耐腐蚀性和强度。
常用的电极材料有金属钨、铜、钼等。
其次,电极尺寸的选择要适合孔径的大小,并应选择具有更高机械强度和稳定性的电极。
此外,为了在超大深度的加工中维持稳定的电极放电状态,电极距离的控制也非常重要。
因此,应根据具体的加工要求对电极距离进行调整和控制。
在超大深径比深小孔电火花加工中,由于电极材料的限制以及加工过程中产生的高能量放电,容易导致电极的损坏和烧蚀,从而影响加工质量。
因此,在工艺设计时应采取一些控制措施,如增强放电控制技术、优化加工参数、采用先进的降热措施等,以实现工艺的优化和稳定性的提高。
总的来说,超大深径比深小孔电火花加工是一种技术含量较高的精密加工方法,需要对其优化设计和控制技术进行更深入的探索和创新。
通过不断的技术更新和改进,将为实现更加高效、精密和经济的工件制造提供更好的选择和解决方案。
利用摇臂钻床加工高位置精度孔的方法

、
时要求位 置精度 ≤ 0 . 2 5 mm才能保证装配时螺栓
轻 松 装 入 ,且 满 足 零 件 之 间 的 互换 性 要 求 ,如 图 1
所示 。
B 基 准和 定 位 销 l 定位。
l
皇
/一。 。 —\
度 ≤0 . 0 2 mm。 图1 中框图
( 2 )在 安装 中框 ,内框 轴系时 ,根据 分别测
量 的 中框 、内 框 以 及 u 形 支 架 两 安 装 定 位 面 之 间 尺 寸 以 及安 装 关 系 分 别计 算 中框 轴 系 和 内框 轴 系 固 定
( 1 )加工转 台的中框两组轴 系孔 时 ,在精密 a 床上加工 ,同时通过采用坐标镗和光学转台实现
调 头 镗 加 工 工 艺 。加 工 过 程 中 度 ,修磨该垫片厚度
尺 寸 ,先 安 装 中框 轴 系 ,使 内框 轴 线 与U形 支 架 两 定 位 面 对 称 中心 重 合 ;重 合 度 误 差 ≤0 . 0 5 mm ;再
工作台回转中心位置 ,通过检测工装和千分表来确
加 工 大锥 齿 轮 和 后桥 轴 螺 栓 孔 均需 三 套 钻 模 ,
其不仅在后桥轴轴 肩与大锥齿轮止 口处采用小间隙 配合 ,而且用于紧固的螺栓也采用 了铰制孔与铰制
孔 螺栓 小 间隙 配合 的 联接 方 式 ,因此 在加 工 螺栓 孔
分别进行 钻孔 、扩 孔和铰孔 ,其中大锥 齿轮钻模 ( 以下简称钻模一 )如图2 所示 ,后桥 轴钻模 ( 以 下简称钻模二)如图3 所示 ,使用时钻模一 ,钻模
图3 后桥轴铰孔钻模
1 完 位销 2 . 钻套 3 . 钻模 体
钻、扩、铰、研的特点

钻、扩、铰、研的特点用标准麻花钻钻削的特点1)切削刃上各点的切屑流出方向不同;主切削刃上各点的切屑流出方向和切屑速度均不相同,这造成切削刃上各点切屑卷曲的差异,增加了切屑上各点间的相互牵制和切屑的附加变形。
2)切削刃上各点前角不同,标准麻花钻切削刃上各点静态前角均不同,而且相差悬殊,造成切削条件上的差别。
工作时,因为各点切屑流出方向的不同,实际工作前角也发生了不同的变化。
实际工作前角不仅与半径有关,而且与钻头转速有关。
3)横刃切削条件极差,因横刃前角为极大的负值,切屑变形十分剧烈,形成很大的轴向力,使钻头工作不稳定。
4)切削刃上各点切屑变形不同,标准麻花钻钻削碳钢时切削刃上各点的变形系数切点半径及钻深有关。
5)为半封闭式切削,钻削时,切屑和切削液只能沿钻头螺旋沟进出,是半封闭式切削。
切削热不易传出,主切削刃与棱带交界转角处磨损严重。
6)多刃切削,麻花钻有两个主切削刃、一个横刃。
如果刃磨的不好,切削刃不对称,就会造成孔的偏斜、振动,使加工孔呈多角形(不圆),并使钻头磨损加剧。
深孔钻削的特点1)由于孔的深度与直径的比较大,钻杆细长,刚性差,工作时容易偏斜及产生振动,因此,孔的精度及表面粗糙度较难保证,2)切屑多而排屑通道长,若不采取必要措施,随时可能由于切屑堵塞耐导致个头损坏。
3)钻头在近似封闭的状态下工作,热量不易散出,钻头损严重。
扩孔钻加工的特点1)扩孔钻与麻花钻相比,由于没有横刃,刀体强度及刚性都较好,齿数多,切削平稳;2)加工精度及加工效率均较高。
铰削的特点1)铰削的精度.高。
用于孔的半精加工和精加工,由于加工余量小,齿数多,又有较长的修光刃等原因,铰孔精度可达it6-it11,表面粗糙度可达Ra1.6-0.2。
2)浮动铰孔时不能提高孔的位置精度。
3)铰孔的生产率较高,费用较低,既可铰圆柱孔,亦可铰圆锥孔,因此在孔的精加工中应用广泛。
研磨加工的特点与经济精度1)尺寸精度高。
磨料采用极细的微粉,在低速、低压下,磨除一层极薄的金属。
精密加工_第二讲__精密超精密加工

精密与特种加工
HIGH EDUCATION PRESS
2.精密和镜面磨削 磨削时尺寸精度和几何精度主要靠精密磨床保
证,可达亚微米级精度(指精度为1~10-2μm)。在 某些超精密磨床上可磨出十纳米精度的工件。在精
密磨床上使用细粒度磨粒砂轮可磨削出Ra=0.1~ 0.05μm的表面。使用金属结合剂砂轮的在线电解修 整砂轮的镜面磨削技术可得到 Ra0.01~0.002μm的 镜面。
精密与特种加工
加工4.5mm陶瓷球
HIGH EDUCATION PRESS
金刚石车床主要性能指标
最大车削直径和长度 /mm 最高转速 r/min
400×200 5000~10000
最大进给速度mm /min
5000
数控系统分辩率 /μm
0. 1~0.01
重复精度(±2σ) / μ m
≤0. 2/100
精密与特种加工
HIGH EDUCATION PRESS
性质
用途
自然界中存在的最硬物
经仔细琢磨后,成为
质,熔点高。
装饰品——钻石。
无色透明、正八面体形
划玻璃、切割大理石、
状的固体,加工后有夺目光 泽。
加工坚硬的金属,装在钻探 机的钻头钻凿坚硬的岩层。
精密与特种加工
HIGH EDUCATION PRESS
精密与特种加工
HIGH EDUCATION PRESS
精密加工机床 研究方向:提高机床主轴的回转精度、工作台
的直线运动精度以及刀具的微量进给精度。(主轴 轴承和导轨)
超精密级滚动轴承——液体静压或空气静压轴承。
金刚石刀具 金刚石晶面选择、金刚石刀具刃口的圆弧半径。
先进国家达到纳米级,我国0.1~0.3um。
不锈钢精密零件深孔数控车加工的方法
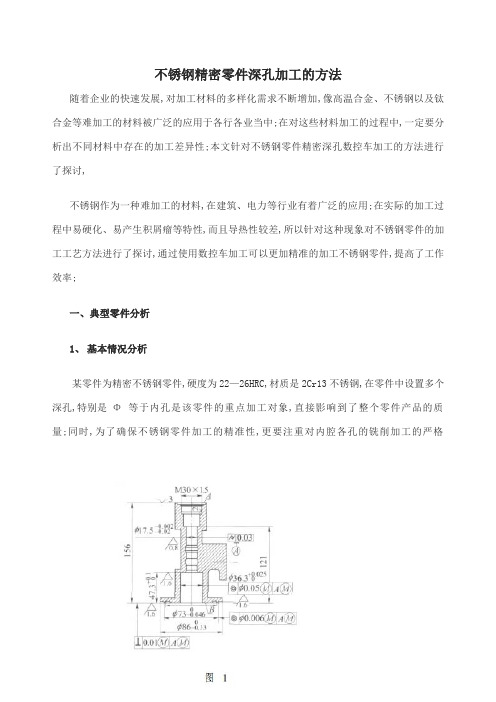
不锈钢精密零件深孔加工的方法随着企业的快速发展,对加工材料的多样化需求不断增加,像高温合金、不锈钢以及钛合金等难加工的材料被广泛的应用于各行各业当中;在对这些材料加工的过程中,一定要分析出不同材料中存在的加工差异性;本文针对不锈钢零件精密深孔数控车加工的方法进行了探讨,不锈钢作为一种难加工的材料,在建筑、电力等行业有着广泛的应用;在实际的加工过程中易硬化、易产生积屑瘤等特性,而且导热性较差,所以针对这种现象对不锈钢零件的加工工艺方法进行了探讨,通过使用数控车加工可以更加精准的加工不锈钢零件,提高了工作效率;一、典型零件分析1、基本情况分析某零件为精密不锈钢零件,硬度为22—26HRC,材质是2Cr13不锈钢,在零件中设置多个深孔,特别是Φ等于内孔是该零件的重点加工对象,直接影响到了整个零件产品的质量;同时,为了确保不锈钢零件加工的精准性,更要注重对内腔各孔的铣削加工的严格把控,才能满足尺寸、位置以及精度的要求;2、加工难点分析通过上图可以看出,由于零件结构的特殊构成,在内腔车削时只能采用螺纹胎具的定位方式进行装夹,图中工作断面与轴向定位面的距离为156mm,由于工件加工的特殊要求,而且重心不规则,所以在装夹系统中就很容易失衡;在深孔数控车加工时,Φ的内控深度达到了121mm,是高的七倍之多,镗削刀具的长径比超过了十倍,所以就增加了刀具的装夹的难度;同时对于尺寸精度、同轴度、垂直度都有很高的要求,如果在加工的过程中出现一点误差,都可能会对零件的实用性能造成严重的影响;所以对于不锈钢精密深孔的数控车加工要对刀具的选择、切削参数以及工艺路线的设置等都要有严格的要求,这些因素都会影响到该零件加工之后是否合格;二、工艺路线的设计及加工刀具的选择根据该零件的特点以及加工的难点,可以制定出以下数控车削工艺路线:粗车内外形—半精车内外形—精车内外形—精车Φ内孔—精车内孔环形槽—车端面槽;1、刀具的选择要根据不锈钢自身的特性,从各方面综合考虑选择合适的刀具;包括以下四点:①为了避免出现工件脱落的现象发生,所以就要选择与螺纹胎具螺纹反向的右手刀具;②要尽量选择刀具的形状及切削槽形中切削力最小的,这样就可以减少对零件刚性的影响;③刀尖的圆弧要适中;圆弧过大,会产生颤纹;圆弧过小,刀尖容易损坏,影响了刀具的使用寿命;④在刀杆的选择上要选择内冷却的形式,这样在加工的过程中就会使零件得到充分的冷却,同时还要对排屑方向做好相应的控制;所以根据以上情况选择以下的刀具:2、工件的装夹由于不锈钢零件的结构特征,只能通过采用螺纹胎具对轴向定位面进行定位;在安装螺纹胎具的时候要保证精准性和严密性,确保螺纹和主轴同轴;在螺纹胎具材料的选择上也要有一定的要求,要使用40Cr材料作为基体材料,然后经过热处理式硬度发生变化,达到28—32HRC才能满足加工的需求;同时还要保证在螺纹胎具上的导向面的粗糙程度Ra不能大于m,圆柱定位面的长度不能大于,这样就能够保证在加工的过程中不会出现错位的状况;3、切削参数及内孔测量方式根据零件的各参数以及精度,通过在表面粗糙程度的计算公式基础上Ra=50f2/r;其中r代表刀尖圆弧的半径,f代表刀具的进给量;然后通过在刀具手册上找到对应的切削参数,就可以得到对应的数值,所以不锈钢精密深孔的刀具切削参数为下图所示:在对零件加工的过程中要时刻的关注刀片的磨损程度,要及时的更换刀片,减小对零件产生的不良影响,避免出现螺纹胎具与工件的“研死”状况;对于内孔的测量,在内孔Φ上存在的公差,如果是采用内径三爪千分尺对内孔进行测量,会存在更大的误差,而且在测量的过程中还可能会对内孔造成划痕,所以应该使用气动测量仪进行测量,因为它的测量精度能够精准到,而且使用氮气作为主要能源,在测量的过程中一般不会对内孔造成影响,而且精度很高;4、冷却方式及排屑问题在切削方式上要选择刀杆内冷却与刀座外冷却相结合的方式,使用的切削液要使用水溶剂极压切削液,这样更能保证冷却的效果达到最佳效果;在进行外冷却的过程中要将切削液与刀尖的部位一致,就能够将刀尖与零件接触的部位快速的冷却,避免了在加工切削的过程中切削热对零件产生的不良影响;由于该不锈钢零件的内孔长径比较大,所以在进行镗孔的过程中,在半精车、精车的每个加工环节都要暂停检查,将切屑及时的清理干净,避免切屑缠绕在刀杆上对零件产生划痕,严重的可能使刀尖断刃;三、不锈钢零件精密深孔数控车加工过程及注意事项将螺纹车胎旋入到机床中,然后利用扳手将其固定好,通过在百分表的测量下,使工件的径向圆跳动与端面圆跳动不能超过,为了防止在加工的过程中刀具的切削力太大,切削不稳定的状况,就要在没加工十件就要用百分表测量一次,这样就可以避免螺纹胎具产生位移,对加工的零件精度产生影响;同时还要保证在加工的外圆、端面槽时,要控制切削的速度、进给量不能太大,避免对端面槽和外圆上产生振纹;在加工内孔时,由于镗孔道与内孔直径距离很近,所以就要用百分表测量出道具的垂直位置;在精加工的过程中要排屑干净,避免切屑对零件刀杆产生影响,对深孔精加工的过程中要加工余量要控制在—之间;在以上所有的加工环节中都要对切屑形状、内孔表面粗糙度以及刀尖的使用情况进行及时的检查,保证机床的所有设备处于正常的运行状态,还要及时的更换刀片,确保零件加工的质量;通过以上的方法进行实际的验证,对上百多件的零件加工后,测量不锈钢内孔的粗糙度值为09 m,圆柱度为、垂直度为,其他各参数都符合加工的要求,所以该方法的加工合格率达到98%以上,在很大程度上提升了加工的效率;这种数控车加工的方法对不锈钢零件、精密深孔以及端面槽零件车削加工的工艺提供了良好的技术支撑,提高了零件加工的精准度,同时也节省了材料的使用;。
- 1、下载文档前请自行甄别文档内容的完整性,平台不提供额外的编辑、内容补充、找答案等附加服务。
- 2、"仅部分预览"的文档,不可在线预览部分如存在完整性等问题,可反馈申请退款(可完整预览的文档不适用该条件!)。
- 3、如文档侵犯您的权益,请联系客服反馈,我们会尽快为您处理(人工客服工作时间:9:00-18:30)。
高精度深长孔的精密加工法一、历史背景枪钻与内排屑深孔钻两种加工孔的刀具分别出现于20世纪30年代初和40 年代初的欧洲兵工厂,这并非历史的偶然。
其主要历史背景是:一次世界大战(1914? 1918 年)首次使战争扩大到世界规模。
帝国主义列强为瓜分殖民地而需要大量现代化的枪炮(特别是枪械和小口径火炮的需求量极大)。
而继续使用传统的扁钻、麻花钻、单刃炮钻,已经完全不能满足大量生产新式武器的要求,迫切需要进行根本性的技术更新。
于是高精度深长孔的制造就成为了一个摆在制造者面前的一个首要问题,并且一直延续到了现今。
第一次世界大战中的火炮二、传统加工工艺及存在的问题在现代机械加工中,也经常会遇到一些深孔的加工,例如长径比(L/D)≥10,精度要求高,内孔粗糙度一般为Ra0.4 ~0.8 的典型深孔零件,过去我们采用的传统工艺路线一般是:钻孔(加长标准麻花钻)→扩孔(双刃镗扩孔刀)→铰孔(标准六刃铰刀)→研磨此工艺虽可达到精度要求,但也存在诸多缺点,特别是在最初工序采用加长麻花钻钻孔时,切削刃越靠近中心,前脚就越大。
若钻头刚性差,则震动更大,表面形状误差难以控制,加工后孔的直线度误差,钻头易产生不均匀的磨损等现象,生产效率和产品合格率低,而且研磨抛光时,工作环境比较脏,由于钻孔工序的缺点,而带来的影响难以在后面的工序中克服,形状误差不能得以修正,因此加工质量差。
传统深孔的加工流程三、工艺路线与刀具的改进本着提高生产效率提高产品合格率的原则,结合深孔加工的一些特性,对加工工艺及刀具进行了改进,改进后的工艺路线是:钻孔(BTA 钻)→扩孔(BTA 扩)→铰孔(单刃铰刀)→研磨1、钻孔与扩孔刀具及工艺的改进单管内排屑深孔钻的由来单管内排屑深孔钻产生于枪钻之后。
其历史背景是:枪钻的发明,使小深孔加工中自动冷却润滑排屑和自导向问题获得了满意的解决,但由于存在钻头与钻杆难于快速拆装更换和钻杆刚性不足、进给量受到严格限制等先天缺陷,而不适用于较大直径深孔的加工。
如能改为内排屑,则可以保持钻头和枪杆为中空圆柱体,使钻头快速拆装和提高刀具刚性问题同时得到解决。
20 世纪内排屑深孔钻的发展,可概括出以下6 项里程碑式的成果:①单出屑口单管内排肩深孔钻基本结构的形成。
②用硬质合金取代工具钢和高速钢做切削刃及导向条,使加工效率大幅度提髙。
...word 格式整理版③由单出屑口单切削刃发展成双出屑口的错齿结构。
④错齿焊接式结构进一步发展为硬质合金刀片机夹结构,最后发展为机夹可转位涂层刀片结构并实现了专业化制造。
⑤双管喷吸钻和DF 系统喷吸钻的问世。
⑥SIED 抽屑器和SIED 刀具系列的发明。
最初的内排屑深孔钻结构有三种模式。
图2.1 是由双刃麻花钻演变而成的内排屑莫尔斯钻头。
为了易于排屑,在麻花钻的对称切削刃后刀面上磨出间隔有序的分屑刃。
这种钻头的柄部由于和刀杆同属圆柱体,可以很方便地实现可快速拆装的方牙螺纹连接。
为了保持钻头与钻杆的同轴度,同时在受力情况下有足够的结合刚度,在连接螺纹的前后方各设一个互相同轴的短圆柱面(俗称“制口”)。
这种可拆卸的钻柄结构,一举克服了枪钻与钻杆不可拆卸的弊端,成为内排屑深孔刀具柄部的通用模式。
图2.2 为一种比莫尔斯钻更加完善的内排屑深孔钻头(又名“维列梅丘克整体深孔钻”)。
钻头由整体的合金工具钢或高速钢制成,其切削刃部继承了枪钻的单边刃自导向结构,柄部则借鉴了莫尔斯钻头和枪钻:当钻头直径大于22mm时采用方牙螺纹连接;钻头直径小于等于22mm时采用钻柄与钻杆对焊。
这种钻头曾采用两种分屑方法以克服排屑故障:图2.2(a)为在后刀面磨出纪末,我国和国外一些兵工厂都仍有其应用,可认为它是现代内排屑深孔钻的原创结构。
这分屑刃(二三个);图 2.2(b)_ 为在前刀面磨出分削刃,其中前者应用最多。
直到20 世种内排屑深孔钻的最大缺点是制造成本高,而且工效低(平均切削速度不超过20m/min),不易重磨。
到二战后期的1942 年,德国人Beisner 设计出一种带3 片硬质合金镶片(一片为切削刃,其余2片为导向条)组成的单出屑口内排屑深孔钻(图2.3)。
其外刃后刀面上磨出一二个分屑刃,外刃前刀面磨有断屑台。
钻头有一个封闭的空腔,后部有制口和方牙螺纹,与钻杆相应的外制口和外方牙螺纹构成快速连接副。
直到Beisnei 钻头的出现,内排屑深孔钻都是单出屑口的结构。
这种内排屑钻头的明显优点在于钻头和枪杆的快速拆卸功能和远大于枪钻的刚度,因而可以采用更大的进给量,工效高于枪钻。
但在实际应用中很快就暴露出以下各种缺陷:钻头出屑口通道面积不足,对切屑的宽度和形态要求苛刻,必须根据工件材质的变化刃磨出与之相适应的断屑台(高度、宽度和过渡圆角R,使切屑成为“C”形,并_且屑宽度不大于钻头直径的1/3 。
曾经有不少史料报道过这种单出屑口的内排屑硬质合金深孔钻的极限加工记录(例如,最小钻孔直径达令6mm ,达到的钻孔深度超过孔径的300 倍等)。
但是,这些实验记录与生产实践中的应用效果并不能相提并论。
要求操作人员根据不同的工件材质、钻头直径、进给量大小相应地控制断屑台尺寸参数和分屑刃参数,并且在切削刃重磨时,保持断屑台的参数不变,这在实践中几乎是行不通的。
基于上述原因,当时欧洲的跨国研究机构“钻镗孔与套料协会"对这种内排屑钻头加以总结后,推出了由双出屑口单管内排屑深孔钻和扩孔钻、套料钻三种内排屑深孔刀具组成的BTA 刀具系列。
20 世纪60 年代后,BTA 刀具基本上由瑞典SANDVIK/COROMANT 公司独家生产,单出屑口的实体钻结构一律由双出屑口结构取代,又称为STS(Single-TubeSystem, 单管钻)钻头。
STS 钻采用Φ18.4~ Φ65mm 焊接刀片结构,Φ65~Φ180mm 的大直径钻头采取机夹可转位刀片的组装结构,分别见图2.4(a)、2.4(b)。
焊接刀片型BTA 钻原来为可重磨式,其切削刀片和导向条较长。
但由于断屑台的刃磨涉及工件材质、进给量等复杂因素,加上刀具为错齿结构,中间齿的切削刃与其他齿的切削刃不在一个圆锥面上(关于这方面的论述,详见本章以下各节),因而一般企业用户基本不具备重磨条件,不得不在一次使用后尚可重磨的情况下将钻头报废。
20 世纪80 年代后,这种焊片式钻头一律改为短刀齿的一次性使用(Disposible)产品BTA 扩钻由BTA 实体钻所派生,其排屑方法与实体钻相同。
BTA 扩钻的主要用途是对工件已有的粗孔(无缝管孔、铸孔等)进行加工,也可对已钻出的较小孔进行扩大。
目前,以商品形式提供的BTA 扩钻,一律采用机夹可转位刀片型结构,仅有一片刀齿,见图2.5 。
直径大于100mm 的扩钻,则设计成一种结构更复杂的直径可调式机夹结构。
图2.6 为BTA 套料钻,其直径为Φ120~ Φ250mm, 可套出料心Φ32.5~ Φ142.5mm, 全部为机夹可转位结构。
套料钻用于在大型棒料上钻出Φ120mm 以上的深孔。
2、BTA 刀具的工作原理单管内排屑深孔机床的基本配置见图2.7 。
不论是实体钻、扩钻或套料钻,都采用相同的供油和排屑方式。
钻头的柄部有方牙螺纹与钻杆相连接。
具有一定压力的切削液进人输油器5 后通过钻杆外部的环状空隙流向切削刃部(钻杆与输油器的右端有密封),将切削刃上形成的切屑反向压人钻头的出屑口,经钻杆的中空内腔向后排出,直至积屑盘。
切削液经过滤网回落到油箱中,经过若干层过滤网后,重新被供油泵抽出,反复使用。
20 世纪70 年代以前,内排屑深孔钻床主要用于加工管形工件,绝大多数深孔机床属于主轴(带工件)旋转、刀具进给或刀具与主轴反向旋转工件进给的运动方式。
80 年代以后,在固定工件上钻系列孔、坐标孔的事例越来越多,工件固定、刀具旋转并进给的内排屑深孔机床已经很常见。
图2.8(a)、(b)、(c)分别示出BTA 实体钻、扩孔钻和套料钻的供油和出屑情况。
图中箭头表示切削液进人通道和切屑排出通道的走向。
图2.9 为输油器(或称油压头)的示意图。
输油器是内排屑深孔钻床上一个十分重要的部件(也称辅具),它同时要承担以下三项重要功能。
①将高压切削液输向钻头切削刃,以完成冷却、润滑和排屑三重使命由图可见,切削液从输油器中间的孔口进人空腔后,由于其右方是封闭的,切削液只能向左通过钻套与钻杆之间的环状空隙和切削刃与导向条之间的空隙流向切削刃部,然后将切屑以反方向推入钻头出屑口,进人钻杆内腔并向后排出。
②对工件定心和实行轴向夹紧。
③对钻头进行导向以上②、③两项功能一般都由钻套来完成。
钻套的外部与车床的尾顶尖相似,通常加工成60 °锥面,而内腔为钻头导向孔。
钻套的内外径须高度精确同轴,轴的中心线与主轴中心严格保持一致。
钻套孔与钻头之间的间隙必须严格控制。
这种兼有工件后顶尖作用的导向套,又称空心顶尖,是棒料毛坯钻深孔时常见的一种定位和钻头导向方法。
采用这种定位方法的棒料,在钻深孔之前一般应先切平端面,预钻顶尖孔并粗车外圆,以保证在工件旋转情况下不发生振摆。
推荐采用图所示三种顶尖孔型式之一。
当工件过重、过长或弯曲度较中心架大时,不适于采用带有外锥的空心顶尖。
常见的对策有两种:①工件钻人端支承在中心架上,用带有平头端面和密封环的钻套顶紧工件的端面(图2.102.11) 。
工件旋转时,钻套也随之旋转。
采用本方案时,工件的后端必须切平,与中心②将工件钻人端的外部车出60 °锥面,在输油器前端相应置带有60 °内锥的定位套,见图2.12 。
钻套内径与钻头之间的间隙,对深孔钻切入阶段的正常工作有重大影响,间隙过大还会加大钻头走偏。
根据国内外的实践经验,对于Φ50mm 以下的钻头,新钻头与新钻套之间的直径差应不大于0.01mm; 已磨损的钻套,其直径的最大磨损量应控制在0.005mm 范围内。
Φ50rnm 以上的钻头与新钻套之间的间隙应不大于0.02mm, 钻套的直径磨损量应不大于0.01mm 。
为此,应从钻头直径和钻套内径两方面加以保证。
Φ50mm 以内的钻头,其直径公差不大于0.005mm, Φ50mm 以上的钻头不大于0.01mm 。
钻套内径一般经研磨而成,新钻套的内径应允许尺寸为钻头直径上限的柱塞规刚刚能通过。
钻套的内外径应严格同轴。
—般是先研出钻套孔,再以孔为基准,套在锥度心棒上磨出外圆。
输油器后端与钻杆的密封也很重要。
除了保证切削液不泄露这一基本功能以外,密封件实际上还起到钻杆辅助支承的作用。
密封件因磨损而必须及时调节或更换,当更换不同直径的钻杆时,需相应地换装不同直径的密封件。
因此,换装密封件是否方便快速,将直接影响机床的工作效率。
装配好的输油器,其钻套中心线应与机床主轴的回转中心严格保持一致。
在深孔钻削工序的精度指标中,钻孔偏移量常常是受普遍重视的一项技术指标。