高精度细长孔的数控加工研究
关于用普通车床加工细长孔的工艺技术探究
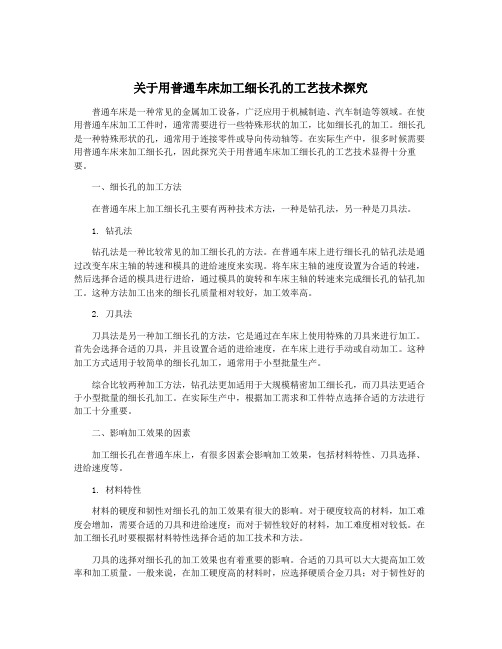
关于用普通车床加工细长孔的工艺技术探究普通车床是一种常见的金属加工设备,广泛应用于机械制造、汽车制造等领域。
在使用普通车床加工工件时,通常需要进行一些特殊形状的加工,比如细长孔的加工。
细长孔是一种特殊形状的孔,通常用于连接零件或导向传动轴等。
在实际生产中,很多时候需要用普通车床来加工细长孔,因此探究关于用普通车床加工细长孔的工艺技术显得十分重要。
一、细长孔的加工方法在普通车床上加工细长孔主要有两种技术方法,一种是钻孔法,另一种是刀具法。
1. 钻孔法钻孔法是一种比较常见的加工细长孔的方法。
在普通车床上进行细长孔的钻孔法是通过改变车床主轴的转速和模具的进给速度来实现。
将车床主轴的速度设置为合适的转速,然后选择合适的模具进行进给,通过模具的旋转和车床主轴的转速来完成细长孔的钻孔加工。
这种方法加工出来的细长孔质量相对较好,加工效率高。
2. 刀具法刀具法是另一种加工细长孔的方法,它是通过在车床上使用特殊的刀具来进行加工。
首先会选择合适的刀具,并且设置合适的进给速度,在车床上进行手动或自动加工。
这种加工方式适用于较简单的细长孔加工,通常用于小型批量生产。
综合比较两种加工方法,钻孔法更加适用于大规模精密加工细长孔,而刀具法更适合于小型批量的细长孔加工。
在实际生产中,根据加工需求和工件特点选择合适的方法进行加工十分重要。
二、影响加工效果的因素加工细长孔在普通车床上,有很多因素会影响加工效果,包括材料特性、刀具选择、进给速度等。
1. 材料特性材料的硬度和韧性对细长孔的加工效果有很大的影响。
对于硬度较高的材料,加工难度会增加,需要合适的刀具和进给速度;而对于韧性较好的材料,加工难度相对较低。
在加工细长孔时要根据材料特性选择合适的加工技术和方法。
刀具的选择对细长孔的加工效果也有着重要的影响。
合适的刀具可以大大提高加工效率和加工质量。
一般来说,在加工硬度高的材料时,应选择硬质合金刀具;对于韧性好的材料,可以选择HSS刀具。
高精度细长轴类零件加工工艺研究
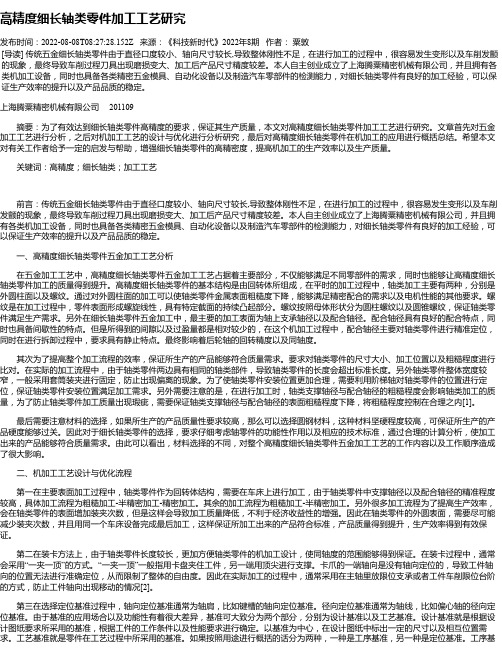
高精度细长轴类零件加工工艺研究发布时间:2022-08-08T08:27:28.152Z 来源:《科技新时代》2022年8期作者:粟敦[导读] 传统五金细长轴类零件由于直径口度较小、轴向尺寸较长,导致整体刚性不足,在进行加工的过程中,很容易发生变形以及车削发颤的现象,最终导致车削过程刀具出现磨损变大、加工后产品尺寸精度较差。
本人自主创业成立了上海腾粟精密机械有限公司,并且拥有各类机加工设备,同时也具备各类精密五金模具、自动化设备以及制造汽车零部件的检测能力,对细长轴类零件有良好的加工经验,可以保证生产效率的提升以及产品品质的稳定。
上海腾粟精密机械有限公司 201109摘要:为了有效达到细长轴类零件高精度的要求,保证其生产质量,本文对高精度细长轴类零件加工工艺进行研究。
文章首先对五金加工工艺进行分析,之后对机加工工艺的设计与优化进行分析研究,最后对高精度细长轴类零件在机加工的应用进行概括总结。
希望本文对有关工作者给予一定的启发与帮助,增强细长轴类零件的高精密度,提高机加工的生产效率以及生产质量。
关键词:高精度;细长轴类;加工工艺前言:传统五金细长轴类零件由于直径口度较小、轴向尺寸较长,导致整体刚性不足,在进行加工的过程中,很容易发生变形以及车削发颤的现象,最终导致车削过程刀具出现磨损变大、加工后产品尺寸精度较差。
本人自主创业成立了上海腾粟精密机械有限公司,并且拥有各类机加工设备,同时也具备各类精密五金模具、自动化设备以及制造汽车零部件的检测能力,对细长轴类零件有良好的加工经验,可以保证生产效率的提升以及产品品质的稳定。
一、高精度细长轴类零件五金加工工艺分析在五金加工工艺中,高精度细长轴类零件五金加工工艺占据着主要部分,不仅能够满足不同零部件的需求,同时也能够让高精度细长轴类零件加工的质量得到提升。
高精度细长轴类零件的基本结构是由回转体所组成,在平时的加工过程中,轴类加工主要有两种,分别是外圆柱面以及螺纹。
提高细长轴数控车削精度工艺方法的研究的开题报告
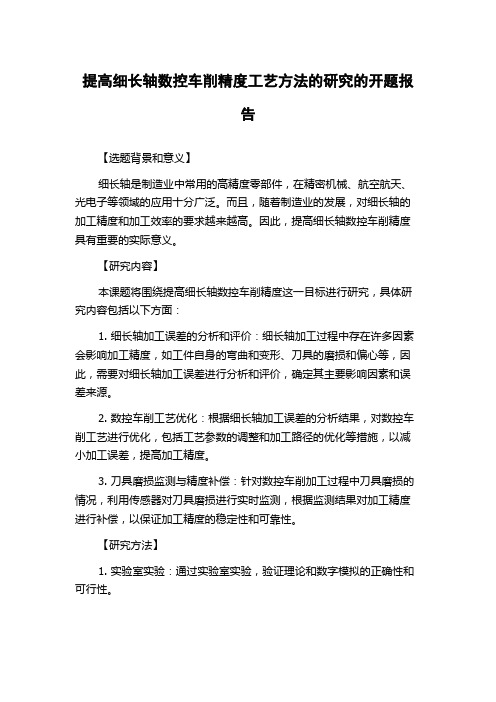
提高细长轴数控车削精度工艺方法的研究的开题报告【选题背景和意义】细长轴是制造业中常用的高精度零部件,在精密机械、航空航天、光电子等领域的应用十分广泛。
而且,随着制造业的发展,对细长轴的加工精度和加工效率的要求越来越高。
因此,提高细长轴数控车削精度具有重要的实际意义。
【研究内容】本课题将围绕提高细长轴数控车削精度这一目标进行研究,具体研究内容包括以下方面:1. 细长轴加工误差的分析和评价:细长轴加工过程中存在许多因素会影响加工精度,如工件自身的弯曲和变形、刀具的磨损和偏心等,因此,需要对细长轴加工误差进行分析和评价,确定其主要影响因素和误差来源。
2. 数控车削工艺优化:根据细长轴加工误差的分析结果,对数控车削工艺进行优化,包括工艺参数的调整和加工路径的优化等措施,以减小加工误差,提高加工精度。
3. 刀具磨损监测与精度补偿:针对数控车削加工过程中刀具磨损的情况,利用传感器对刀具磨损进行实时监测,根据监测结果对加工精度进行补偿,以保证加工精度的稳定性和可靠性。
【研究方法】1. 实验室实验:通过实验室实验,验证理论和数字模拟的正确性和可行性。
2. 数字模拟:利用数学模型对细长轴加工过程进行模拟分析,验证模型的有效性和科学性。
3. 实际加工测试:对实际工作中的细长轴进行试验和测试,验证提出的加工方法和工艺能否达到预期的效果。
【预期成果】完成本研究后,预期可以得到以下成果:1. 分析了细长轴加工误差的主要来源和影响因素;2. 提出了能够有效减小加工误差、提高加工精度的数控车削工艺方法;3. 提出了一种可靠的刀具磨损监测及精度补偿方法。
【研究难点】本研究中的难点主要包括以下方面:1. 细长轴加工误差的分析方法和评价标准的制定,需要充分考虑细长轴加工的特点和现实生产中的具体问题。
2. 数控车削工艺优化,需要根据具体的加工情况和工艺需求进行调整,同时考虑各种因素的影响和相互作用。
3. 刀具磨损监测和精度补偿,在实际应用中需要充分考虑监测设备的精度和稳定性,确保监测数据的准确性和可靠性。
对数控铣加工细长杆工件工艺的研究
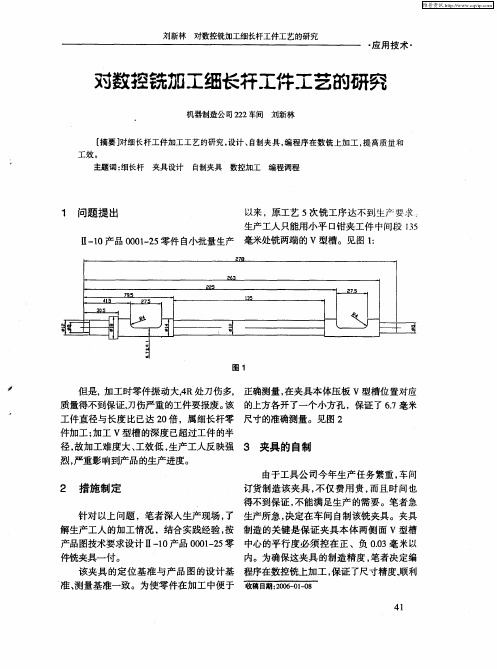
() 1设计 、 自制成功 Ⅱ一0产品 0 0— 5 1 0 12
零件 5 次工序铣夹具 , 比原生产工人加工方
法提高工效一倍 , 优化 了原工艺 , 受到 了生 产工 人 的欢迎 。 () 2 利用 自制夹具 , 将该零件加 工部分
4 数控加工
优 Ⅱ 1 产 品 00 — 5 一0 0 12 零件 5 次铣 工序夹 编程序 ,在数控铣上加工出的实物质 量, 杜绝 了该零 具制成后 , 彻底解决了原用平 口钳加 工振动 于工艺资料的技术要求 。同时, 大的问题 , 质量和工效有较大提高 ; 但在铣 V 件 5次铣工序 的报废。 型槽 2 4 R 时稍不注意, 也容易出现挖刀, 造成 () 3采用数控加工工艺提高了质量和工 刀伤影响工件的加工实物质量 和工效。为确 效 ,取得 了较 好的经 济效益和设 备 的利用 使广大职工看到了数字加工是今后机械 保细长杆零件加工工艺 的最佳方案 , 笔者将 率 , 增强 了职工学习数控加工 该零件 V型槽传统工艺加工改为数控工艺 加工的发展方 向, 加工。经过编程序 , 利用设计 自制的夹具 , 技术 的自觉性 。 在
锯生产工人的加工情况 ,结合实践经验 , 按 制造 的关键是保证夹具本体两侧 面 V型槽 产品图技术要求设计 Ⅱ一 0 1 产品 00 — 5 0 1 2 零 中心 的平行度必 须控在正 、负 0 3 米以 . 毫 0 件铣夹具一付。 准、 测量基准一致。为使零件在加工中便于 内。为确保这夹具 的制造精 度 , 笔者决定编
径, 故加工难度大 、 工效低 , 生产工人反映强 3 夹具的 自制 烈, 严重影响到产品的生产进度。
由于工具公 司今年生产任务 繁重 , 车间
2 措 施制定
订货制造该夹具 , 不仅 费用贵 , 而且时 间也
关于用普通车床加工细长孔的工艺技术探究

关于用普通车床加工细长孔的工艺技术探究车床加工细长孔是机械加工中一项重要的工艺技术。
在制造精密零部件和机械零件中,经常需要进行孔的加工。
而对于长孔或细长孔,则需要用特定的加工方法来处理。
本文将从普通车床加工细长孔的原理、工艺技术及加工技巧三个方面进行探究。
普通车床是一种可以旋转加工工件的机床,它可以通过一些附加的装置来进行不同类型的加工。
加工孔的普通车床也称为孔加工车床。
其原理是通过根据孔的形状和尺寸选择不同的刀具,将刀具沿孔内部的测量线逐渐切削并去除孔壁多余的材料,从而形成所需的细长孔。
在加工细长孔时,常常需要借助附加的工具,如钻头、扩钻头、镗刀等。
钻头用于在工件上钻孔,扩钻头用于对已有孔进行修整,将其拓宽到所需的大小,而镗刀通常用于加工直径较大、长度较长的孔,以免由于加工重量和液压系统的运行产生的振动而使孔出现偏差。
二、加工工艺技术1. 定位工件:在加工细长孔前,必须首先切断工件的其他部分,并将工件端面打磨平整,以确保工件的稳定性和加工质量。
2. 挑选刀具:刀具的选择必须根据所需的孔形状和尺寸而定。
必须确保刀具的质量和正确配置,以达到最佳的加工效果。
3. 加工孔口:开始加工细长孔之前,应先用钻头或其他加工工具对孔口进行钻孔或精加工。
4. 编程和操作:在普通车床上进行细长孔的加工需要进行编程和操作。
编程需要选择合适的参数和切削参数,在操作中要注意孔壁的平整和加工质量。
5. 加工结束:加工结束后,必须对细长孔的质量进行检查。
如果发现有缺陷,应立即进行补救。
三、加工技巧1. 提高加工精度:对于细长孔的加工,加工精度的要求比较高。
在加工过程中,必须尽量减少振动和切削力的干扰,选择合适的切削速度,以确保加工精度。
2. 选择合适的刀具:在加工时,应选择合适的刀具,以便更好地保持孔的精度和平整度。
必要时,应采用多次加工和补偿的方式来保证孔壁的平整度和精度。
3. 润滑剂的使用:使用润滑剂可以减少加工时的摩擦和热量,保护刀具和工件,提高精度,并且能够排出加工过程中产生的金属渣。
关于用普通车床加工细长孔的工艺技术探究

关于用普通车床加工细长孔的工艺技术探究普通车床是一种常见的机械加工设备,广泛应用于汽车、机械、航空航天等领域。
在加工过程中,有时需要对工件进行细长孔的加工,以满足特定的设计要求。
细长孔的加工并不是一件容易的事情,需要掌握一定的工艺技术和操作方法。
本文将对用普通车床加工细长孔的工艺技术进行探究,讨论其加工方法、工艺参数的选择以及注意事项,以期对相关领域的工程技术人员提供一定的参考。
一、加工方法在普通车床上加工细长孔,通常可以采用以下几种方法:1. 镗削法:使用刀具进行旋转切削,镗出所需的细长孔。
这种方法需要较高精度的设备以及刀具,适合加工深度较大,直径较小的细长孔。
以上方法各有优缺点,具体选择应根据工件的要求以及设备条件来确定。
二、工艺参数选择在加工细长孔时,需要合理选择工艺参数,以确保加工效果和工件质量。
1. 切削速度:选择合适的切削速度可以确保刀具在加工过程中不产生过热,同时可以提高加工效率。
一般来说,对于不同材质的工件,其切削速度是不同的,需要根据具体情况进行调整。
2. 进给速度:合理选择进给速度可以确保切削过程中产生的切削力不会过大,同时可以保证加工表面的光洁度。
进给速度与主轴转速的匹配也是需要注意的问题。
3. 切削深度:根据工件的要求和刀具的性能,选择合适的切削深度,以确保加工过程中不会损伤刀具和工件。
以上工艺参数的选择需要结合具体情况,进行一定的试验和调整,以获得最佳的加工效果。
三、注意事项在加工细长孔时,还需要注意以下几点:1. 刀具选择:根据工件材质和要求,选择合适的刀具进行加工。
刀具的质量和性能对加工效果有重要影响,需要引起重视。
2. 刀具冷却:在加工过程中需要对刀具进行冷却,以防止刀具产生过热,同时可以延长刀具的使用寿命。
3. 定位稳定:加工细长孔时,工件的定位应保持稳定,以避免加工过程中产生偏差,影响加工质量。
4. 质量检验:加工完成后需要对细长孔的尺寸和形状进行质量检验,确保加工的符合要求,同时可以及时发现问题,进行调整和改进。
关于用普通车床加工细长孔的工艺技术探究

关于用普通车床加工细长孔的工艺技术探究
普通车床加工细长孔是一项比较常见的工艺技术,在生产加工中也经常会用到。
这种加工工艺技术的主要目的是为了加工出精度要求高、大小比例长输出的孔洞,其加工精度相对较高,是一种非常重要的工艺技术。
下面,我们就来探究一下用普通车床加工细长孔的工艺技术。
普通车床加工细长孔的步骤主要有以下几步:
1、搭设夹具:在加工细长孔前需要先搭设好夹具,选用合适的床架、点钻,固定好工件后再进行加工。
夹具是起着固定工件作用的,固定好之后可以保证加工出来的孔洞精度比较高,而且大小比例也比较长。
2、定好中心线:细长孔的刀轨是需要在车床上边缘上进行加工的,所以在加工之前需要先定好中心线。
确定好中心线可以保证孔洞大小长输出,并保证加工出来的孔洞直,使孔洞表面更加光滑,达到更高的加工精度。
3、加工孔洞:加工时需要选择合适的切削量,刀具的直径要比加工出的孔洞略小,这样才能保证工件切削后形状不会变形。
在加工时,需要控制力度,逐渐进行加工,慢慢地切削出细长孔。
加工过程中还需要注意冷却液的使用,以免过热导致工件烧损。
4、完成加工:加工完成后需要进行检查,检查一下加工出来的孔洞是否符合设计要求,检查孔洞两端是否对称平齐,孔洞表面是否有裂缝、毛刺、齿状物等瑕疵。
综上所述,普通车床加工细长孔是一种比较常见的工艺技术,其加工方法比较简单易行,但需要注意的是在加工时不仅要保持配合度,还要注意冷却液的使用和刀具的选择。
只有加工出精度符合要求的孔洞,才能得到工件的良好加工效果,确保加工的产品有着较好的质量。
孔的数控加工技术性研究及应用
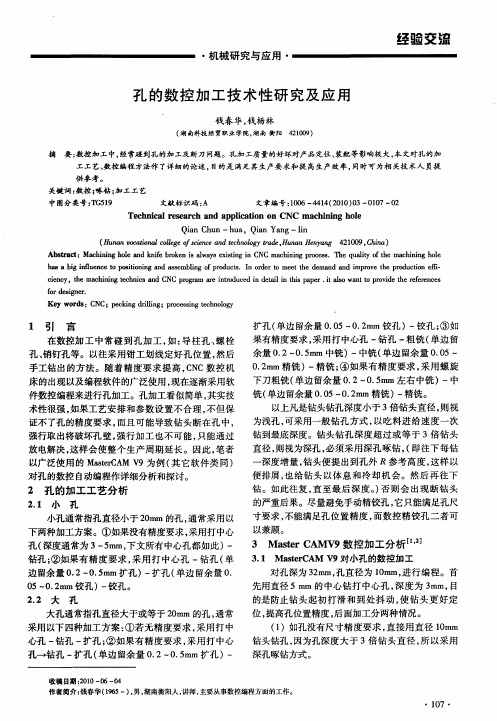
f rd sg e . o ein r Ke r s y wo d :CN C;p e i g d l n ;p o e sn c n l g e kn r l g rc s i g t h oo y i i e
1 引 言
在数控加工 中常碰 到孔加工 , 导柱孔 、 如: 螺栓 孔、 销钉孔等。以往采用钳工划线定好孔位置, 然后 手工钻 出的方法。随着 精度要求 提高 ,N C C数控机
直径, 则视 为深 孔 , 必须 采 用 深孔 啄 钻 , 即往 下 每 钻 (
一
放电解决 , 这样会使整个生产周期延长。因此 , 笔者 以广泛使用 的 M s rA 9为例( ae M V tC 其它软件类 同) 对孑 的数控 自动编程作详细分析和探讨。 L
深度增量 , 钻头便提出到孔外 R参考高度, 这样 以
e e e ,t e ma h n n e h i sa d CN r ga ae it d c d i e al n ti a e i as n t o p vd er fr n e i n y h c i g t c n c n C p o rm r n r u e n d ti i s p p r. t l owa r i e t e e e s i o h t o h o
强行 取 出将破 坏孔 壁 , 行 加 工 也 不 可 能 , 强 只能 通 过
02 m精铣 ) .m 一精铣 ; ④如果有精度要求 , 采用 螺旋 下刀粗铣( 单边 留余量 02— .m . 05 m左右中铣 ) 一中
铣( 单边 留余量 00 — .m .5 0 2 m精铣 ) 精铣。 一 以上凡是钻头钻孔深度小于 3 倍钻头直径 , 则视 为浅孔 , 可采用一般钻孑 方式 , L 以吃料进给速度一次 钻 到最底 深度 。钻 头钻 孔 深 度 超 过 或 等 机械研究与应用 ・
关于用普通车床加工细长孔的工艺技术探究

关于用普通车床加工细长孔的工艺技术探究在机械加工领域中,用普通车床加工细长孔是一项常见的工艺技术。
本文将探究使用普通车床加工细长孔的具体方法和注意事项。
普通车床加工细长孔前需要制定详细的加工方案。
根据加工孔的要求,确定加工过程中的各个参数,例如孔的直径、孔的深度、孔的位置等。
在制定加工方案时,还需要考虑到车床的技术性能和加工刀具的选择,以确保能够在车床上顺利加工细长孔。
在加工细长孔的过程中,有两种常见的方法:钻孔法和镗孔法。
钻孔法适用于孔直径较小的情况,通过不断重复进给和提拉车刀的方式,逐渐将孔镗深。
而镗孔法适用于孔直径较大的情况,通过使用刀具的旋转和车床的进给,将孔逐渐加工成细长形状。
无论是使用钻孔法还是镗孔法,在加工细长孔之前,需要将工件进行上工,以保证工件在车床上的稳定性。
上工时,需要根据实际情况选择适当的夹具,并正确夹紧工件,避免因夹具松动而影响加工质量。
在加工细长孔过程中,还需要注意刀具的选择和切削参数的调节。
刀具的选择应根据加工材料和加工要求来确定,并在加工过程中要定期检查刀具的磨损情况,做好必要的更换。
根据刀具的选择和工件的材料,确定适当的切削速度和切削深度,以达到高效而精确的加工效果。
在加工细长孔中,还需要使用适当的冷却液来降低摩擦热,减少切屑堵塞,并防止工件和刀具过热造成损坏。
冷却液的使用可以通过配备冷却系统来实现,确保在加工过程中工件和刀具保持在适当的温度范围内。
加工细长孔后需要进行必要的检验和整理。
检验可以通过使用测量工具,如千分尺和测量卡尺来进行。
检查孔的直径、深度和形状是否符合要求,并进行合理的修整和整理工作。
使用普通车床加工细长孔需要制定详细的加工方案,选择适当的方法和切削参数,注意刀具的选择和冷却液的使用,最后进行必要的检验和整理。
只有在正确操作和细心管理下,才能够顺利加工出满足要求的细长孔。
高精度孔加工方法初探(1)
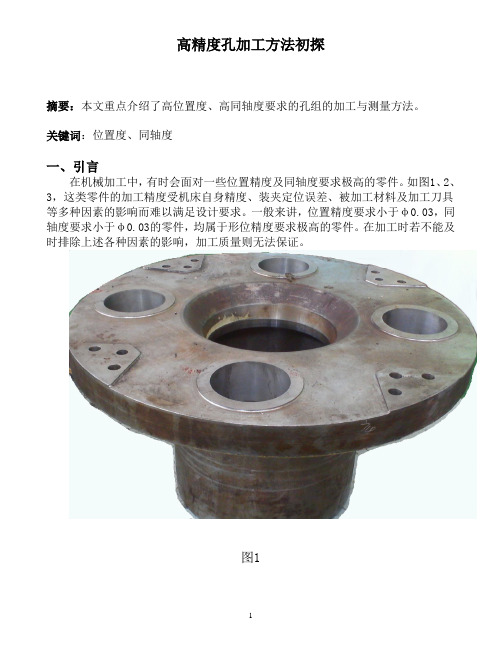
高精度孔加工方法初探摘要:本文重点介绍了高位置度、高同轴度要求的孔组的加工与测量方法。
关键词:位置度、同轴度一、引言在机械加工中,有时会面对一些位置精度及同轴度要求极高的零件。
如图1、2、3,这类零件的加工精度受机床自身精度、装夹定位误差、被加工材料及加工刀具等多种因素的影响而难以满足设计要求。
一般来讲,位置精度要求小于φ0.03,同轴度要求小于φ0.03的零件,均属于形位精度要求极高的零件。
在加工时若不能及时排除上述各种因素的影响,加工质量则无法保证。
图1图2图3二、高精度位置孔的加工方法1、影响高精度位置孔加工的因素材料的性能及内部应力的消除情况,基准面的加工精度,如圆度、粗糙度、圆柱度,数控机床的定位精度和重复定位精度,主轴的刚性及旋转圆度,刀具的锋利程度、工件材料刚性、机床几何精度、零件装夹方法、切削速度、润滑冷却方式等有关。
2、具备有大型三坐标机测量方法的厂家,采用如下方法,如图4。
图4例如某个公司,采用如图将零件装夹在龙门五面加工中心上面,工件找正方法是采用将千分表把2个φ196孔打正,将千分表从4处φ196孔穿进去,以相同直径大小打表检测基准φ660h7的4处外圆弧面,X、Y方向分中设定程序坐标原点。
首先将φ195孔加工到φ194h6,送三坐标机检测,数据如下:位置度为0.0022、0.0556、0.0223、0.0556;半径为434.9403、434.9788、435.0190、434.9656;弦长为615.1653、615.1444、615.1656、615.1363。
分析半径和弦长与理论值偏小,将加工程序多加大0.01,第二次将φ196孔加工到φ195h6,送三坐标机检测,数据如下:位置度为0.0647、0.0564、0.0917、0.0859;半径为434.9677、435.0045、434.9671、434.9760;弦长为615.1682、615.1435、615.1599、615.1400。
高精度细长孔的数控加工研究

高精度细长孔的数控加工研究高精度细长孔的数控加工研究在15世纪时,人们很难想象,有一天可以将金属精细地切割成所需要的形状,更难想象的是,通过数控技术可以实现对器件的高精度加工。
如今,我们已经进入了高速发展的数控加工时代,随之而来的是对于高精度细长孔加工的需求的增大。
本文将就高精度细长孔数控加工的一些研究内容进行讨论。
首先,我们需要了解什么是高精度细长孔。
高精度细长孔可以理解为,其长度相对于直径非常大,一般是直径的十倍以上。
在传统机械加工中,加工这类细长孔是一项技术难点,并且存在量大、质量易变等问题。
同时,细长孔的加工难度随着直径的减小而增加。
但是,在现代数控加工技术的发展下,加工难度已大大降低,能够满足高精度细长孔的加工需要。
因此,高精度细长孔的数控加工成为了研究的热点。
对于高精度细长孔的数控加工,其工艺流程大致如下:首先进行CAD/CAM程序设计,然后确定加工参数,例如刀具直径、进给率等,并确定合适的工件加工定位,然后就是数控加工设备的操作,最后进行检验。
其中,参数的确定直接影响到加工质量和加工效率。
因此,要在确保加工精度的前提下,尽可能地提高加工效率,从而达到生产成本最小化。
数控机床的进步使得高精度细长孔的加工工艺更加优化。
在前人研究的基础上,现在已经有了更多的加工方法。
例如,如果要使用铣刀进行加工,就需要使用长刀具,这种方法就能够较好地解决细长孔加工时碰撞和折断问题。
同时,目前还有毛细管放电加工技术,这种新型数控加工技术具有精度高、适应性强等特点,能够加工出高质量的细长孔,不仅是加工光学模组类组件必要的技术手段,也是制造微型流道和微流器件的重要手段之一。
除了这些加工方法外,采用钻孔、磨削等加工方式,同样也能够实现高精度细长孔的加工。
另外,为了保证加工质量,选择合适的工件加工定位也是非常重要的。
原则上,硬质合金、铸铁、铸钢等等材料可以用于细长孔的加工。
但在实际中,有些材料显性地表现出一些较为特殊的加工特性,加工中需要进行相应的工艺安排。
关于用普通车床加工细长孔的工艺技术探究

关于用普通车床加工细长孔的工艺技术探究普通车床是一种大型机械加工设备,既可以加工直径较大的轴类零件,也可以进行各种形状大体积的成型加工。
在车床加工中,常常需要进行细长孔的加工,而这涉及到一定的工艺技术。
一般而言,细长孔的加工需要使用特殊的工具,如小直钻、刃子(砂轮)等。
而由于细长孔的加工形态独特,具有长、细、难加工等难度高的特点,所以在加工时需要特别注意以下几点:1. 刀具的选择:由于细长孔的加工对刀具的要求很高,所以在选择刀具时需要考虑诸多因素,如刀具的材料、硬度、长度、截面形状等。
通常选择刀具应具备高硬度、耐磨性好、切削性好的特点。
2. 切削参数的控制:切削参数对细长孔加工的效果至关重要。
合理的切削速度、进给速度、切削深度能够有效避免切削过程中产生的振动、毛边、切屑等不良现象,同时还能够保证加工效率和加工精度。
3. 支撑和固定:细长孔加工过程中需要对工件进行支撑和固定。
由于细长孔具有长而细的特点,所以在加工的过程中容易产生工件晃动、变形等现象,影响加工效率和加工精度。
为此需要采取合适的支撑和固定措施,如可用PMMA、气垫、气浮技术等。
4. 冷却液和冷却系统:加工过程中往往会产生大量的热量和毛屑,如果不能及时清理,不仅会影响加工质量,还会损坏刀具和工件。
因此,在加工细长孔时需要采用专用的冷却液和冷却系统,使其能够快速而有效地将热量和毛屑清理掉,从而保障加工的质量和安全性。
总之,细长孔的加工需要选用合适的刀具,采用正确的切削参数,做好支撑和固定工作,配备适当的冷却液和冷却系统,从而保证加工质量和安全性。
此外,操作人员还需要掌握一定的经验和技能,在实际加工中遵循先进的工艺流程和操作标准,从而更好地完成加工任务。
细长筒零件内孔的精加工方法

细长筒零件内孔的精加工方法细长筒零件内孔的精加工是一种高精度、高难度的工艺操作,它的加工难度主要在于两个方面:一是加工孔径小、深度大的精密孔,需要具有高精度的加工设备和技术;二是受到材料易变形、加工误差等多种因素的影响,需要进行加工过程的严格控制,以保证加工质量。
1.齿轮磨床加工齿轮磨床在内孔加工中有着广泛的应用。
它的优点在于能够加工出高精度、光洁度好的孔壁,同时还能够进行大量的自动化加工,提高了生产效率。
但它的缺点也很明显,那就是需要具备高精度的加工设备和技术,并且加工难度较大,需要进行精密的加工控制。
2.钻床加工钻床是一种常用的孔加工设备,特别适用于加工深度较小、直径较大的孔。
钻床与齿轮磨床相比,操作简单、容易掌握,而且成本也较低。
然而,由于钻床通常只能进行简单的一次切削,所以它不能满足加工深度大、精度高的加工要求。
铣床也是一种常用的内孔加工设备,通过铣头的回转来实现加工。
铣床的优点在于能够进行多次切削,同时还能够进行多种不同的加工方式。
但由于铣床在加工过程中会对加工材料造成大量的切削力,所以需要在加工过程中进行严格的控制以避免变形。
4.研磨加工研磨加工是一种重要的细长筒零件内孔加工方式,特别适用于加工高精度、光洁度要求高的精密部件。
研磨加工具有较高的加工精度和加工效率,可以实现高度自动化加工。
但由于研磨加工容易产生温度和热应力,所以在加工过程中需要进行严格的温度和热应力控制,以确保加工质量。
在进行细长筒零件内孔加工时,需要注意以下几点:1.选用合适的加工方式和设备。
细长筒零件内孔加工需要选用符合要求的加工方式和设备,以确保加工质量。
在考虑加工方式和设备时,需要考虑加工要求、工件特点、材料条件等多方面因素,并根据实际情况进行选择。
2.严格控制加工精度。
细长筒零件内孔加工需要进行高精度的加工控制,要确保加工精度符合要求。
在进行精度控制时,需要考虑加工中的误差来源,如机床误差、工件变形、材料变化等因素,并采用相应的措施进行补偿和控制。
高精度细长孔的数控加工研究

高精度细长孔的数控加工研究高精度细长孔加工技术是数控加工领域中的一个重要领域,也是目前工业制造领域中一个快速发展的技术。
随着现代高科技的不断发展,对细小孔洞的要求越来越高,因此,高精度细长孔加工技术的发展有着广泛而深远的意义。
一、高精度细长孔加工的背景现代工业生产中,高精度细长孔扮演着至关重要的角色。
例如在航空航天、汽车、电子、医疗设备等行业制造中,都需要进行细小孔洞的加工。
以航空制造为例,飞机发动机的缸体内需要加工出数百个细小孔洞,以保证发动机正常工作。
而在医疗设备领域,医学导管、内镜、骨钉等医疗器械的制造也需要进行高精度细小孔洞的加工。
因此,高精度细长孔加工技术的研究和发展对于现代工业制造具有重要的战略意义。
二、高精度细长孔加工技术的研究内容高精度细长孔加工技术的研究包含着多个方面,其中最主要的是细小孔径和长孔的加工。
1. 细小孔径的加工目前,传统的钻床加工细小孔洞已经无法满足工业制造对高精度细长孔加工的要求。
因此,需要对传统加工方法进行改进和优化,以适应工业现代化对细小孔径加工的需要。
现代高精度细长孔加工技术最常用的方法是电火花加工和激光加工。
电火花加工是高精度细小孔洞加工技术中的一种常用方法。
该技术主要采用电极和工件之间的电火花放电的方式对工件进行加工,可以高效地加工出高精度的细小孔洞。
这种加工方法可以加工各种不锈钢、塑料、玻璃等材料的细小孔洞。
但是,由于电极磨损等问题的存在,加工稳定性有待提高。
激光加工技术也是一种高效、高精度的细小孔洞加工方法。
它采用激光束对工件材料进行熔化并蒸发的方式进行加工。
相比于传统的机械加工方法,激光加工方法可以通过激光照射来实现对细小孔洞的加工。
同时,激光加工可以加工各种材料的孔洞,并且由于激光加工具有高能量密度和能量集中等特点,可以达到高精度、高速度、高质量的加工效果。
2. 长孔的加工高精度细小孔洞加工不仅涉及到孔径的大小,也与孔洞长度有关,因为现代制造工业生产中,很多机械零部件都需要有一定长度的孔洞,以实现该部件特定的功能。
轴类零件高精度孔的制造工艺技术探讨和分析
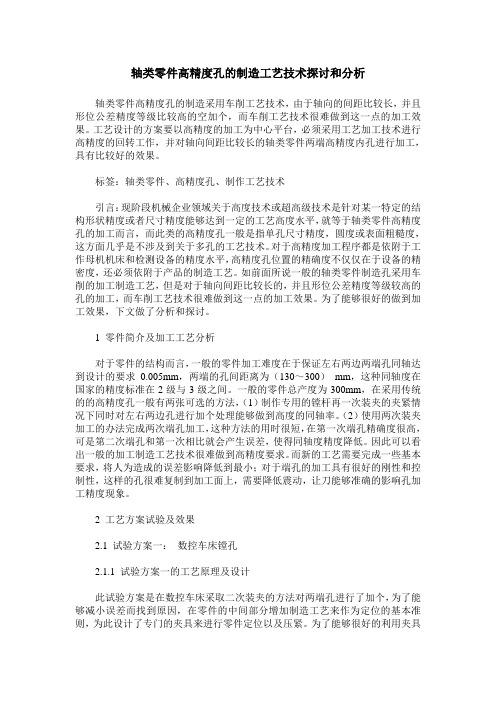
轴类零件高精度孔的制造工艺技术探讨和分析轴类零件高精度孔的制造采用车削工艺技术,由于轴向的间距比较长,并且形位公差精度等级比较高的空加个,而车削工艺技术很难做到这一点的加工效果。
工艺设计的方案要以高精度的加工为中心平台,必须采用工艺加工技术进行高精度的回转工作,并对轴向间距比较长的轴类零件两端高精度内孔进行加工,具有比较好的效果。
标签:轴类零件、高精度孔、制作工艺技术引言:现阶段机械企业领域关于高度技术或超高级技术是针对某一特定的结构形状精度或者尺寸精度能够达到一定的工艺高度水平,就等于轴类零件高精度孔的加工而言,而此类的高精度孔一般是指单孔尺寸精度,圆度或表面粗糙度,这方面几乎是不涉及到关于多孔的工艺技术。
对于高精度加工程序都是依附于工作母机机床和检测设备的精度水平,高精度孔位置的精确度不仅仅在于设备的精密度,还必须依附于产品的制造工艺。
如前面所说一般的轴类零件制造孔采用车削的加工制造工艺,但是对于轴向间距比较长的,并且形位公差精度等级较高的孔的加工,而车削工艺技术很难做到这一点的加工效果。
为了能够很好的做到加工效果,下文做了分析和探讨。
1 零件简介及加工工艺分析对于零件的结构而言,一般的零件加工难度在于保证左右两边两端孔同轴达到设计的要求0.005mm,两端的孔间距离为(130~300)mm,这种同轴度在国家的精度标准在2级与3级之间。
一般的零件总产度为300mm,在采用传统的的高精度孔一般有两张可选的方法,(1)制作专用的镗杆再一次装夹的夹紧情况下同时对左右两边孔进行加个处理能够做到高度的同轴率。
(2)使用两次装夹加工的办法完成两次端孔加工,这种方法的用时很短,在第一次端孔精确度很高,可是第二次端孔和第一次相比就会产生误差,使得同轴度精度降低。
因此可以看出一般的加工制造工艺技术很难做到高精度要求。
而新的工艺需要完成一些基本要求,将人为造成的误差影响降低到最小;对于端孔的加工具有很好的刚性和控制性,这样的孔很难复制到加工面上,需要降低震动,让刀能够准确的影响孔加工精度现象。
超精密数控加工技术研究进展

超精密数控加工技术研究进展摘要:文章介绍了超精密数控加工的概念,综述了超精密数控加工技术特别是超精密磨削、超精密切削和超精密抛光的发展。
探讨了数控超精密度控制改进方案。
关键词:超精密磨削;超精密切削;超精密抛光引言目前我国数控技术日益成熟,精度逐渐提高,可以说,超精密加工能力是一个出国家发展实力的综合体现。
目前来看,超精密加工技术属于科技发展的尖端技术,更是数控技术发展过程中的难点。
由此可见,探讨数控超精密加工十分必要。
1数控超精密加工概述数控超精密加工是现代工业发展的重点,更是技术的核心,综合体现了国家综合实力。
尤其在信息技术发展时代,机械工程与信息技术深度结合,推动了机械工程的自动化发展,为超精密加工进一步发展提供了新的技术支持。
数控超精密加工主要体现在两方面,分别是软件与硬件,目前我国精密加工硬件与软件发展水平都得到了持续提升,尤其在数控机床编程方面,借助自动化信息技术,其精确度大幅度提升,实现了编程合理化、精确化与自动化。
2超精密数控加工基础研究的发展超精密数控加工是指每个局部加工点的微变形或材料去除效果的结合。
当硬脆性材料(如陶瓷、单晶硅)表面用硬切削头开槽时,会出现脆性损伤和大量微裂纹。
将材料去除量控制到一定程度,就可以实现仅由塑料开槽造成延性损伤的材料去除过程。
虽然在数控加工过程中可以在韧性区域获得光滑的表面,但不能忽视位错、滑移等亚表面损伤。
如果材料去除率可以在分子上进一步控制,当材料去除过程在纳米级时,会出现细观物理现象,如小尺度效应和量子尺寸效应。
宏观切削理论不足以描述数控加工过程和细观现象,难以解释表面生成机理。
要进一步研究机械加工过程,必须运用分子动力学、量子力学和原子物理学等现代基础理论。
然后,建立纳米级材料去除模型,指导实际超精密车削过程。
分子动力学仿真可以设置不同的加工参数、材料属性和刀具几何形状,而不受加工设备和条件的限制。
因此,基于分子动力学模拟的切削机理研究近年来受到越来越多的关注。
细长零件数控纵切的加工探讨

细长零件数控纵切的加工探讨摘要:通过对细长轴类零件加工时弯曲变形的原因分析,阐述了保证细长轴加工质量的工艺方法、切削用量与数控纵切零件的具体运用。
关键词:细长轴;加工特点;加工工艺;数控纵切1 细长轴工件的常用加工工艺细长类工件的长度和直径之比在25倍以上,该种工件加工时刚度不足在切削力、自重和顶尖压力的联合作用下,极易产生过度弯曲或者失去稳定。
因此,车削细长轴时应对轴的受力状态进行改善。
2 细长轴类零件物理性分析2.1 切削力分析径向切削力Px是使细长类工件在径向产生弯曲的主要根源,这个切削分力始终存在于整个加工过程中,降低径向切削力Px可明显改善细长类工件的加工质量,实践中有好多降低降低径向切削力Px的有效措施,应认真分析并针对性地应用。
对于非细长类工件,因工件刚度富足,轴向切削力Py不致于使工件轴向受压失稳,不必过多分析。
对于细长类工件,因工件刚度极弱,如果对轴向切削力Py不进行仔细研究,在切削过程中,因轴向切削力Py的作用,使细长类工件受压失稳的现象发生比比皆是。
2.2 切削热对细长类工件加工的作用:在细长类工件加工过程中,因切削刀具与细长类工件的回转摩擦,在工件上引起大量切削热,是不可避免的正常现象。
因细长类工件在加工过程中被牢靠地加持在机床工艺系统中阻碍了其受热变形,细长类工件必将在水平面内发生横向弯曲。
因此,对于细长类工件加工,要提高加工质量,除了采用合适的加工工艺外,还要在工艺系统参数选用和加工过程冷却措施等方面采取相应可行手段,才能达到理想结果。
3 数控纵切设备3.1 数控纵切机床加工原理采用数控纵切机床加工零件,零件的加工长度对加工的影响很大。
并且对于不同长度的零件加工原理有所不同,又相互统一。
在零件开始加工时按照数控纵切机床加工原理图1进行。
这时虽然加工零件较细,但在根部切削,刀具切削点的切削力Px几乎对零件弯曲无影响,零件受到的重力影响也不大,零件几乎不会发生弯曲变形;刀具切削点不变,所以径向切削力Px在后续加工下几乎仍无影响。
细长轴加工
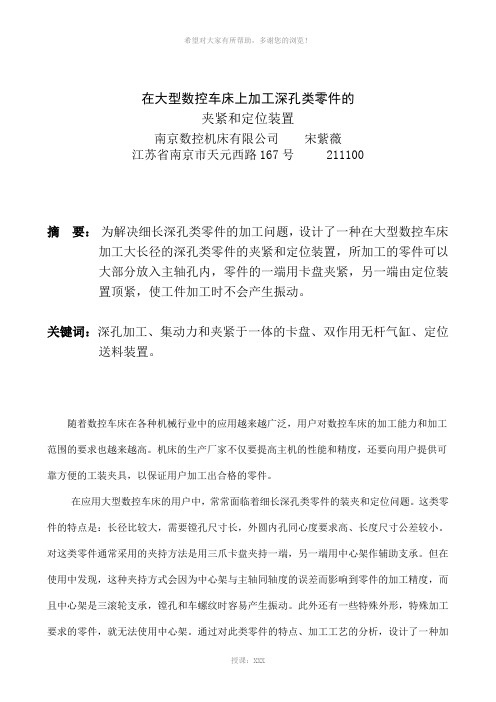
夹紧和定位装置
南京数控机床有限公司 宋紫薇
江苏省南京市天元西路167号211100
摘 要:为解决细长深孔类零件的加工问题,设计了一种在大型数控车床加工大长径的深孔类零件的夹紧和定位装置,所加工的零件可以大部分放入主轴孔内,零件的一端用卡盘夹紧,另一端由定位装置顶紧,使工件加工时不会产生振动。
关键词:深孔加工、集动力和夹紧于一体的的应用越来越广泛,用户对数控车床的加工能力和加工范围的要求也越来越高。机床的生产厂家不仅要提高主机的性能和精度,还要向用户提供可靠方便的工装夹具,以保证用户加工出合格的零件。
在应用大型数控车床的用户中,常常面临着细长深孔类零件的装夹和定位问题。这类零件的特点是:长径比较大,需要镗孔尺寸长,外圆内孔同心度要求高、长度尺寸公差较小。对这类零件通常采用的夹持方法是用三爪卡盘夹持一端,另一端用中心架作辅助支承。但在使用中发现,这种夹持方式会因为中心架与主轴同轴度的误差而影响到零件的加工精度,而且中心架是三滚轮支承,镗孔和车螺纹时容易产生振动。此外还有一些特殊外形,特殊加工要求的零件,就无法使用中心架。通过对此类零件的特点、加工工艺的分析,设计了一种加工细长深孔类零件的夹紧定位装置。
(1)夹紧部分。夹持工件的部分没有选用常用的液压卡盘,而是设计了一种大行程的动力卡盘。这种卡盘集动力和夹紧为一体,用气源作动力。它的通孔直径较大。为定位送料装置提供了较大的空间。这种卡盘的卡爪行程大,能够夹持有特殊形状的零件。如外形呈弧形零件,切削时需将大端放入主轴孔内夹持小端。
(2)定位碗、定位杆组件。这套组件分为内外二层。外层的定位碗组件由定位碗8、定心套6、气缸2等组成。需加工的工件放入机床主轴5孔内后(如图2),工件后端与定位碗8接触,切削时卡盘夹紧工件前端,气缸2向前用定位碗顶紧工件后端(定心套6、定位碗8、长套4、定位块11与工件同步旋转)。在镗深孔、车孔口螺纹及切削负荷较大的情况下,因零件被顶紧而不会产生振动。起缸套作用的长套4在卡盘前端和主轴孔内都有高精度的配合面,而定心套6与长套4之间用耐磨复合材料的导向带12定心,因此定心套与主轴的同轴度很好,保证了工件的夹持精度高,支承刚度好。
细长深孔锐棱数控车削技术
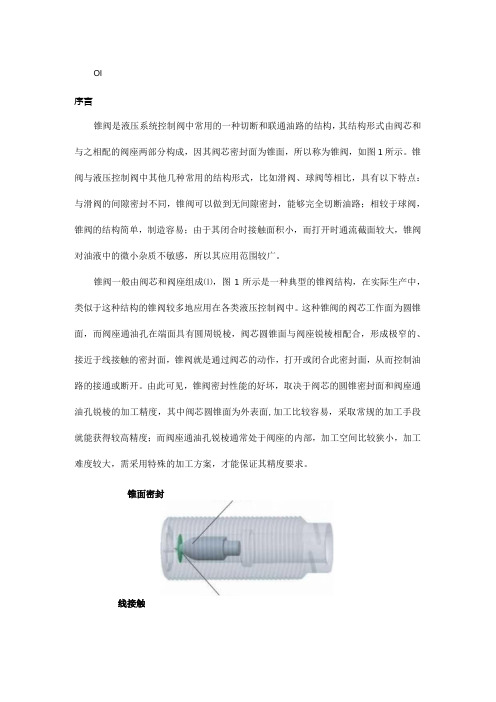
Ol序言锥阀是液压系统控制阀中常用的一种切断和联通油路的结构,其结构形式由阀芯和与之相配的阀座两部分构成,因其阀芯密封面为锥面,所以称为锥阀,如图1所示。
锥阀与液压控制阀中其他几种常用的结构形式,比如滑阀、球阀等相比,具有以下特点:与滑阀的间隙密封不同,锥阀可以做到无间隙密封,能够完全切断油路;相较于球阀,锥阀的结构简单,制造容易;由于其闭合时接触面积小,而打开时通流截面较大,锥阀对油液中的微小杂质不敏感,所以其应用范围较广。
锥阀一般由阀芯和阀座组成⑴,图1所示是一种典型的锥阀结构,在实际生产中,类似于这种结构的锥阀较多地应用在各类液压控制阀中。
这种锥阀的阀芯工作面为圆锥面,而阀座通油孔在端面具有圆周锐棱,阀芯圆锥面与阀座锐棱相配合,形成极窄的、接近于线接触的密封面,锥阀就是通过阀芯的动作,打开或闭合此密封面,从而控制油路的接通或断开。
由此可见,锥阀密封性能的好坏,取决于阀芯的圆锥密封面和阀座通油孔锐棱的加工精度,其中阀芯圆锥面为外表面,加工比较容易,采取常规的加工手段就能获得较高精度;而阀座通油孔锐棱通常处于阀座的内部,加工空间比较狭小,加工难度较大,需采用特殊的加工方案,才能保证其精度要求。
锥面密封线接触02加工难点分析图2所示为实际生产中典型的锥阀阀座结构。
锥阀阀芯通过与阀座内部)2.9mm 和)1Omm端面的锐棱棱线来实现锥面线接触密封,该零件在数控车削加工时存在以下难点。
M22×15-6h图2典型阀座结构1))10H8孔加上与其同轴的M12螺纹孔,两者的长径比达5.2左右,为典型的细长深孔结构。
由于其直径较小,限定了车削加工中刀具刀杆直径,较细的刀杆刚性差,切削过程中易产生振动,使孔的直线度、表面粗糙度差,零件尺寸精度难以保证,同时因刀杆进入深孔加工,在切削力作用下会产生弹性变形,致使该深孔口部尺寸合适,而往深度方向加工时,则孔径逐渐缩小,出现孔径线性减小的情况,导致孔径超差。
- 1、下载文档前请自行甄别文档内容的完整性,平台不提供额外的编辑、内容补充、找答案等附加服务。
- 2、"仅部分预览"的文档,不可在线预览部分如存在完整性等问题,可反馈申请退款(可完整预览的文档不适用该条件!)。
- 3、如文档侵犯您的权益,请联系客服反馈,我们会尽快为您处理(人工客服工作时间:9:00-18:30)。
高精度细长孔的数控加工研究摘要:目前世界上利用外排屑(如枪钻)深孔钻削技术,可钻削的孔径小到f2mm。
而内排屑深孔钻削的孔径很少有小于f16mm的,且多数仍采用传统的BTA钻削系统。
由于枪钻结构为不对称形状,质心偏离中轴,这给制造、重磨都带来一定的困难,也使造价增高。
另外,其结构刚度和扭转强度低(同直径的圆形钻杆扭转刚度是枪钻的2.3倍),使其使用的钻削速度降低,进给量小。
采用单管内排屑喷吸钻(SED)钻削系统,钻削小深孔直径可小到f3.7mm。
我工艺所采用SED技术,进行了孔径(mm)f16、f12、f10、f8、f7.62、f5.7、f3.7的小深孔钻削加工,钻削过程平稳,排屑流畅,孔的尺寸形状精度和孔壁表面粗糙度均能满意,在上述孔径范围内,完全可以替代枪钻对小深孔进行钻削加工。
由于其刚度好,可加大进给量和钻削速度,使生产效率、钻孔质量和经济效益均有所提高,显示了一定的技术优势。
关键词:高精度细长孔数控加工一、孔的定义与分类根据国家标准GB1800—1979的规定:孔主要指圆柱形的内表面。
由此可知,广义的孔泛指包容面。
孔通常可按如下方法分类:(1)按形状来分。
有圆柱孔、圆锥孔、鼓形孔、多边形孔、花键孔和其它异形孔以及特形孔(如弯曲孔)等。
其中,以圆柱孔使用最为广泛。
(2)按形态来分。
有通孔及盲孔(不通孔);深孔(指孔的深度L与孔径D之比超过5的孔,L/D简称深径比或长径比;L/D=5~20属一般深孔,L/D﹥20~30属中等深孔,L/D ﹥30~100称为特殊深孔)及浅孔。
(3)按孔径的大小来分。
有大孔(D﹥100mm)、普通孔(D=10~100mm)、小孔(D=1~10mm)和微孔(D<1mm的孔)。
(4)按加工机理来分。
有机械加工、特种加工(见表1)、机电复合加工等。
尽管特种加工方法较多,但目前由于设备比较昂贵和加工效率不高等原因,所以无论是现在还是可预见的未来,传统的机械加工仍将是孔加工的主要手段。
表1 孔加工的方法(5)按加工精度分。
有粗孔(如钻孔和粗镗后的孔)、半精孔(如扩孔、粗铰、半精镗的孔)和精密孔(如精铰、精拉、精磨、珩磨、研磨后的孔)等。
精密孔通常是指公差等级在IT7~IT6级以上,表面粗糙度Ra﹤ 0.8~0.4m的孔,它的几何形状精度(如圆度、圆柱度、轴线直线度等)一般规定在其尺寸公差带的1/2~1/3范围内。
随着航空航天、汽车、高速列车、风电、电子、家电、能源、模具、液压、机床及精密机械等装备制造业的迅速发展和产品的更新换代,精密孔的应用日益增多。
例如液压系统中广泛使用的各种阀孔、高压油缸筒都是一些典型的精密孔。
孔加工由于其自身的特点,加工难度较大,而精密孔加工的难度更大。
二、孔加工的特点孔加工是一种比较复杂的工艺过程,加工时必须妥善解决排屑、冷却润滑和导向等问题。
孔加工的主要特点是:(一)由于受被加工工件孔径尺寸、长度和形状的制约,故切削刀具相应较细长,刚性差,并且大多呈悬臂装夹的方式,加工容易引起刀具的偏斜和震动。
1、切屑排除比较困难。
要改善容屑与排屑条件,势必要增大容屑槽,但这样将会使刀具的强度和刚度降低。
2、切削液难以引入到切削区,切屑、刀具与工件孔壁之间的摩擦很大,切削温度很高,尤其是在加工深孔时。
所以,切削液在孔加工中具有特殊的重要作用。
切削液的合理选择和正确使用,对孔的加工质量、刀具寿命和切削效率等有极大的影响。
3.孔加工常用的切削液供液方法有浇注法和高压内冷却法两种。
前者最为简单,但供液效果差,且切削液消耗量大。
内冷却法多用于油孔钻、深孔钻、喷吸钻、套料刀和单刃镗铰刀等孔加工刀具上,需在刀具上作出高压内冷却的供液(油)通道孔,油气混合物通过此通道被输送到切削区,此法消耗的切削液用量少,但刀具结构较复杂。
目前,随着刀具制造技术的进步,国内外各刀具公司已推出了各种带高压内冷却供液(油)通道孔刀具的新品,为采用内冷却法创造了条件。
例如,ISCAR公司推出的包括DR、DZ和DS系列的机夹硬质合金可转位刀片浅孔钻,德国MAPAL公司的涂层硬质合金单刃铰刀(切削速度高达150-400m/min),日本三菱公司的硬质合金小钻头等,它们都有提供通向射流应用区域的高压切削液通道孔,并且规格越来越小。
据报道,国外一家公司生产的硬质合金小钻头,其直径可小到3-4.5mm,油孔直径为0.4-0.6mm。
(二)切削液采用近乎干式切削的“汽束”喷雾冷却法的特点1、“汽束”喷雾冷却是以一定压力(0.3~1MPa)的空气使切削液雾化,并以很高的速度喷向切削区域,使在该区域高温下呈雾化状的切削液滴很快汽化。
由于液体在汽化时会吸收大量热量,因而可使切削区域内的温度大幅度下降,同时切削液还能带走切削区域和空间的热量和粉末,改善作业环境。
实践证明,在使用等量切削液情况下,“汽束”喷雾冷却在相同时间内所吸收的热量是浇注法的1000倍。
所以,它不但可提高刀具使用寿命,而且可使切削液的消耗大大减少。
据德国格林(Guhring)公司试验证实,在汽车生产线上采用“汽束”喷雾冷却,每班只需耗用半杯油,并且可用廉价的工厂再生油。
“汽束”喷雾冷却既适用于自动生产线上,也适用于一般的金属切削加工中。
图1所示为在普通钻床上利用“汽束”供给切削液的一种装置。
该装置由贮液箱1(包括工作部I和溢流部II)、过滤器2和3、集液盘5、喷嘴6、箱盖8、喷吸器9、气阀11、节气阀12、水管13及管道4、7和10等组成。
工作时,开动气阀11,压缩空气将以Pc=0.4MPa的压力从管路中压出,产生高压气流。
高压气流在水管13的上部通过时会产生负压,而将切削液从贮液箱中吸出,并击成雾滴状。
上述高压气流带着微小液滴的切削液渗透到切削区,在高温下会迅速汽化,吸收大量的热量,从而能有效地降低切削温度。
而在集液盘中收集的废液经过滤后可流回贮液箱继续使用。
节气阀12是用来改变管路中的压力,以便调节切削液的流量。
而气阀11则可利用电信号(通过直流电压U=24V)操纵。
使用表明,该装置结构简单,使用方便。
加工时不能直接观察刀具的切削情况,尤其在加工微孔和深孔时。
所以,自动监测控制较其它加工方式更为重要。
2、孔的尺寸精度、几何形状精度、相互位置精度和表面粗糙度常因孔加工的特殊性而难于控制,但是一旦试验成功,较其它加工方式反而能更有规律性地保持。
三、影响加工精度的因素(一)加工精度包括三个方面内容:●尺寸精度指加工后零件的实际尺寸与零件尺寸的公差带中心的相符合程度。
●形状精度指加工后的零件表面的实际几何形状与理想的几何形状的相符合程度。
●位置精度指加工后零件有关表面之间的实际位置与理想位置相符合程度。
在机械加工中,机床、夹具、工件和刀具构成一个完整的系统,称为工艺系统工艺系统中的各组成部分,包括机床、刀具、夹具的制造误差、安装误差、使用中的磨损都直接影响工件的加工精度。
也就是说,在加工过程中工艺系统会产生各种误差,从而改变刀具和工件在切削运动过程中的相互位置关系而影响零件的加工精度。
这些误差与工艺系统本身的结构状态和切削过程有关,产生加工误差的主要因素有:(二)系统的几何误差1、加工原理误差加工原理误差是由于采用了近似的加工运动方式或者近似的刀具轮廓而产生的误差,因在加工原理上存在误差,故称加工原理误差。
只要原理误差在允许范围内,这种加工方式仍是可行的。
2、机床的几何误差机床的制造误差、安装误差以及使用中的磨损,都直接影响工件的加工精度。
其中主要是机床主轴回转运动、机床导轨直线运动和机床传动链的误差。
3、刀具的制造误差及磨损刀具的制造误差、安装误差以及使用中的磨损,都影响工件的加工精度。
刀具在切削过程中,切削刃、刀面与工件、切屑产生强烈摩擦,使刀具磨损。
当刀具磨损达到一定值时,工件的表面粗糙度值增大,切屑颜色和形状发生变化,并伴有振动。
刀具磨损将直接影响切削生产率、加工质量和成本。
4、夹具误差夹具误差包括定位误差、夹紧误差、夹具安装误差及对刀误差等。
这些误差主要与夹具的制造和装配精度有关。
下面将对夹具的定位误差进行详细的分析。
工件在夹具中的位置是以其定位基面与定位元件相接触(配合)来确定的。
然而,由于定位基面、定位元件工作表面的制造误差,会使各工件在夹具中的实际位置不相一致。
加工后,各工件的加工尺寸必然大小不一,形成误差。
这种由于工件在夹具上定位不准而造成的加工误差称为定位误差。
它包括基准位移误差和基准不重合误差。
在采用调整法加工一批工件时,定位误差的实质是工序基准在加工尺寸方向上的最大变动量。
5、工艺系统的受力变形由机床、夹具、工件、刀具所组成的工艺系统是一个弹性系统,在加工过程中由于切削力、传动力、惯性力、夹紧力以及重力的作用,会产生弹性变形,从而破坏了刀具与工件之间的准确位置,产生加工误差。
例如车削细长轴时(图3-53),在切削力的作用下,工件因弹性变形而出现“让刀”现象。
随着刀具的进给,在工件的全长上切削深度将会由多变少,然后再由少变多,结果使零件产生腰鼓形。
四、小深孔加工技术的难点和对策深孔钻削加工就有相当的难度,内排屑小深孔钻削的难点就更加突出。
(一)排屑难度排屑小深孔钻屑时切屑,要经过钻杆内的排屑通道排出,孔径越小,其排屑就越困难。
例如,要钻削f8mm的深孔,钻杆外径是f5.2 mm,钻杆内径仅有f4~4.2 mm,而钻杆长一般达500~1500 mm。
因此,在钻削过程中,发生堵屑是经常的。
为使排屑流畅,钻头切削刃上设计出合理的断屑和分屑台,保证可靠断屑十分重要。
但小深孔的进给量很小,实现C形断屑对于某些韧性材料是不可能的,钻屑常常是柔软的小带状,钻削过程中作为冷却和冲刷切屑的切削液压力产生波动或压力下降时,切屑瞬时滞流、折叠而堵塞,进而导致钻刃损坏和钻杆扭断。
为彻底解决这一问题,可以从断屑和排屑两方面采取措施。
最有效的断屑方法是采用振动断屑技术,能稳定地得到所需要的切削形状。
增加切削液对钻屑的排屑作用力,是SED钻削系统的特点,高压切削液一路进入授油器,润滑冷却钻削区和刀具,并以3MPa~4.5 MPa的压力迫使切屑进入排屑通道,并将切屑推出;另一路切削液进入可调式负压抽屑装置,形成负压,对切屑产生吸力,吸出切屑。
切屑在推和吸的双重作用下能顺利排出。
实践证明,即使钻屑呈带状,且从钻削开始到加工结束一直保持连绵不断,都能保证排屑流畅顺利。
(二)钻杆刚度不足深孔钻削的钻杆细而长,小深孔钻削的钻杆更是细长,其刚度很低,因此,在设计小深孔刀具时,应当尽可能提高刀具(包括钻头和钻杆)整体的刚度。
在传统设计中,钻杆与钻头采用了方牙螺纹联接方式。
这要在管壁很薄的钻杆上切出方牙螺纹,势必更使细长钻杆的强度和刚度下降。
如;钻削f5.7mm深孔,钻杆外径只能取f4mm,在壁厚不足1mm上再挖去一个方牙螺纹的深度0.25mm,螺纹联接处的强度和刚度大大下降,在钻削中,钻杆常在螺纹联接处扭断。