内孔的加工讲解
内孔壁直槽加工方法

内孔壁直槽加工方法内孔壁直槽加工是机械制造中的一项重要技术,广泛应用于各种零件的加工过程。
本文将详细介绍内孔壁直槽的加工方法,帮助读者更好地了解并掌握这一技术。
一、内孔壁直槽加工概述内孔壁直槽加工是在零件的内孔壁上加工出一定形状和尺寸的槽,以满足特定的使用要求。
这类加工方法具有较高的精度和表面质量要求,常见的内孔壁直槽加工方式有:机械加工、数控加工、电加工等。
二、内孔壁直槽加工方法详细介绍1.机械加工(1)钻孔:首先在孔壁上钻出所需直径的孔,为后续的直槽加工做好准备。
(2)铰孔:使用铰刀对孔进行加工,提高孔的加工精度和表面质量。
(3)镗孔:使用镗刀对孔进行加工,可加工出精度较高的内孔壁直槽。
(4)拉孔:通过拉刀对孔进行加工,适用于大批量生产,加工效率较高。
2.数控加工(1)数控车削:利用数控车床对内孔壁直槽进行加工,具有加工精度高、表面质量好的特点。
(2)数控铣削:利用数控铣床或加工中心对内孔壁直槽进行加工,适用于复杂形状的直槽加工。
3.电加工(1)电火花加工:通过电火花腐蚀作用,对内孔壁直槽进行加工,适用于高硬度、高精度要求的直槽加工。
(2)电解加工:利用电解液对金属进行腐蚀,实现内孔壁直槽的加工,适用于大批量生产。
三、内孔壁直槽加工注意事项1.选择合适的加工方法和加工设备,根据直槽的形状、尺寸和加工要求进行合理配置。
2.选用合适的刀具和工艺参数,确保加工质量和效率。
3.严格控制加工过程中的温度和切削液使用,降低刀具磨损,提高加工精度。
4.定期对设备进行维护和保养,确保设备正常运行。
总结:内孔壁直槽加工方法多种多样,根据不同的加工要求和生产条件,选择合适的加工方法至关重要。
通过掌握各种加工方法的特点和注意事项,可以提高内孔壁直槽的加工质量和效率。
孔的加工PPT课件
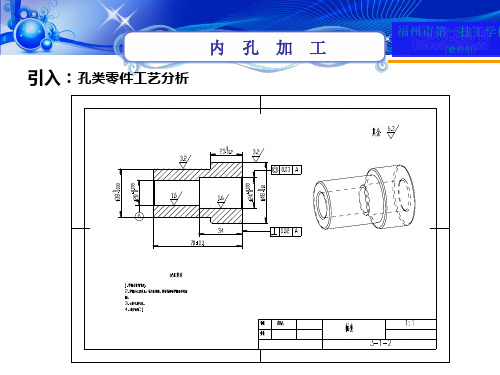
钻孔时,钻头与工件之间的相对运动称为钻削运动。钻削运动由 如下两种运动构成: (1)主运动
钻孔时,钻头装在钻床主轴(或其他机械)上所做的旋转运动称 为主运动。 (2)进给运动 钻头沿轴线方向的移动称为进给运动。
内孔加工
福州市第一技工学校
(数控组)
2、钻削特点
➢ 钻削时,钻头是在半封闭的状态下进行切削的,转速高,切削用量大, 排屑又很困难,因此钻削具有如下特点:
(3)手动进给 通孔将要钻穿时,必须减小进给量,如果采用自动进给,则应改为 手动进给。
内孔加工
福州市第一技工学校
(数控组)
➢ 钻孔时,由于加工零件的材料和加工要求不同,所用切削液的种类和 作用就不同。钻孔一般属于粗加工,又是半封闭状态加工,摩擦严重, 散热困难,加切削液的目的应以冷却为主。
一般用煤油;钻削铸铁、黄铜、青铜时,一般不用切削液;钻削 镁合金时,切忌用切削液。
内孔加工
福州市第一技工学校
(数控组)
➢ ②进给量 孔的精度要求较高且表面粗糙度值较小时,应选择较小的进给量;
钻较深孔、钻头较长以及钻头刚性、强度较差时,也应选择较小的进 给量。
福州市第一技工学校
(数控组)
内孔加工
(2)修磨主切削刃 修磨主切削刃,主要
是磨出二重顶角。延长钻头 寿命,减少孔壁的残留面积, 降低孔的表面粗糙度值。
福州市第一技工学校
(数控组)
内孔加工
(3)修磨前刀面 修磨主切削刃和副切
削刃交角处的前刀面, 磨去一块,如图中阴影 部位所示,这样可提高 钻头强度。钻削黄铜时, 还可避免切削刃过分锋 利而引起扎刀现象。
➢ 硬质合金钻头有整体式和镶嵌式。直径较小的常做成整体式;直径较大 的常做成镶嵌式,它是在钻头切削部分嵌焊硬质合金刀片 硬质合金刀片的材 料是YG8或YT2。
第七课 数车内孔、内腔和套类零件加工(理论讲解)
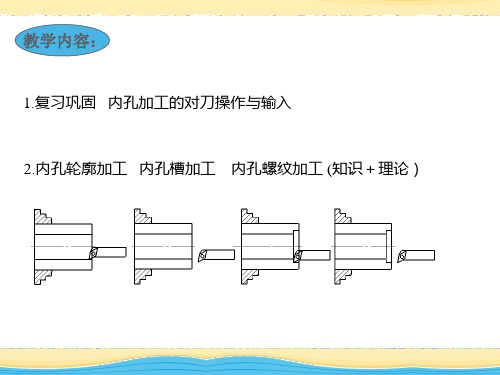
7.孔的精度 套类零件的精度有下列几个项目。
(1)孔的位置精度。 同轴度(孔之间或孔与某些表面间的尺寸精度)、平 行度、垂直度、径向圆跳动和端面圆跳动等。
铰孔是对较小和未淬火孔的精加工方法之一,在成批生
产中已被广泛采用。铰孔之前,一般先镗孔,镗孔后留些 余量,一般粗铰为0.15mm~0.3mm,精铰为0.04mm~ 0.15mm,余量大小直接影响铰孔的质量。
4.孔加工方法的选择 在车床中,孔的加工方法与孔的精度要求、孔径以及
孔的深度有很大的关系。一般来 讲,在精度等级为IT12、 IT13时,一次钻孔就可以实现。在精度等级为IT11,孔径 ≤10mm时,采用一次钻孔方式;当孔径>10~30mm时, 采用钻孔和扩孔方式;孔径>30~80mm时,采用钻孔、扩 钻、扩孔刀或车刀镗孔方式。在精度等级为ITl0、IT9,孔 径≤10mm时,采用钻孔以及铰孔方式;当孔径 >10~30mm时,采用钻孔、扩孔和铰孔方式;孔径 >30~80mm时,采用钻孔、扩孔、铰孔、或者用扩孔刀镗 孔方式。在精度等级为IT8、IT7,孔径≤10mm时,采用钻 孔及一次或二次铰孔方式;当孔径>10~30mm时,采用钻 孔、扩孔、一次或二次铰孔方式;当孔径>30~80mm时, 采用钻孔、扩钻(或者用扩孔刀镗孔)以及一次或二次铰孔 方式。
如出现Z方向的误差,则其修整办法相同。
二、内孔、内腔和套类零件(知识+理论)
课题一 盲孔零件的加工
本课题要求编程并加工如图6.1所示盲孔零件,毛 坯为φ53mm×100mm的棒料,材料为45钢。
a)零件图 b)实体图 图6.1 盲孔零件
一、基础知识 1.孔加工特点 (1)孔加工是在工件内部进行的,观察切削情况比较困 难,尤其是小孔、深孔更为突出。
内孔表面加工常用方法大汇总

内孔表面加工方法较多,常用的有钻孔、扩孔、铰孔、镗孔、磨孔、拉孔、研磨孔、珩磨孔、滚压孔等。
一、钻孔用钻头在工件实体部位加工孔称为钻孔。
钻孔属粗加工,可达到的尺寸公差等级为IT13~IT11,表面粗糙度值为Ra50~12.5μm。
钻孔有以下工艺特点:1.钻头容易偏斜。
在钻床上钻孔时,容易引起孔的轴线偏移和不直,但孔径无显著变化;在车床上钻孔时,容易引起孔径的变化,但孔的轴线仍然是直的。
因此,在钻孔前应先加工端面,并用钻头或中心钻预钻一个锥坑,以便钻头定心。
钻小孔和深孔时,为了避免孔的轴线偏移和不直,应尽可能采用工件回转方式进行钻孔。
2.孔径容易扩大。
钻削时钻头两切削刃径向力不等将引起孔径扩大;卧式车床钻孔时的切入引偏也是孔径扩大的重要原因;此外钻头的径向跳动等也是造成孔径扩大的原因。
3.孔的表面质量较差。
钻削切屑较宽,在孔内被迫卷为螺旋状,流出时与孔壁发生摩擦而刮伤已加工表面。
4.钻削时轴向力大。
这主要是由钻头的横刃引起的。
因此,当钻孔直径d﹥30mm时,一般分两次进行钻削。
第一次钻出(0.5~0.7)d,第二次钻到所需的孔径。
由于横刃第二次不参加切削,故可采用较大的进给量,使孔的表面质量和生产率均得到提高。
二、扩孔扩孔是用扩孔钻对已钻出的孔做进一步加工,以扩大孔径并提高精度和降低表面粗糙度值。
扩孔可达到的尺寸公差等级为IT11~IT10, 表面粗糙度值为Ra12.5~6.3μm,属于孔的半精加工方法,常作铰削前的预加工,也可作为精度不高的孔的终加工。
扩孔方法如图7-4所示,扩孔余量(D-d),可由表查阅。
扩孔钻的形式随直径不同而不同。
直径为Φ10~Φ32的为锥柄扩孔钻,如图7-5a所示。
直径Φ25~Φ80的为套式扩孔钻,如图7-5b所示。
扩孔钻的结构与麻花钻相比有以下特点:1.刚性较好。
由于扩孔的背吃刀量小,切屑少,扩孔钻的容屑槽浅而窄,钻芯直径较大,增加了扩孔钻工作部分的刚性。
2.导向性好。
内孔倒角加工方法

内孔倒角加工方法《嘿,咱来唠唠内孔倒角加工方法》嘿呀,朋友!今天咱来唠唠内孔倒角加工方法,这可是个好玩又实用的本事哦!首先呢,你得把要加工的东西准备好呀,就像上战场得先把枪擦亮一样。
然后嘞,找到那个要倒角的内孔,这就好比是找到你要攻克的小山头。
接下来,就是关键步骤啦!把倒角刀具拿出来,这刀具就像是你的秘密武器。
想象一下,它就是那个能把内孔变得乖乖听话的神奇小魔杖。
你得小心地把它伸进内孔里,就像给内孔挠痒痒一样,可别太粗鲁哦,不然内孔会不高兴的。
然后呢,开始慢慢地转动刀具,让它在内孔边缘轻轻地蹭啊蹭。
这时候你得有耐心,不能着急,就跟哄小孩似的,得慢慢来。
你要是太着急,一下子用力过猛,那可就完蛋啦,说不定会把内孔给弄哭咯!在这个过程中啊,你得时刻注意着角度。
就像你走路得看路一样,不能走歪了。
要是角度不对,那倒角出来可就不漂亮啦,就像一个人长歪了脸一样,多难看呀!我跟你说,我有一次就不小心弄歪了,哎呀妈呀,那可把我给愁坏了。
后来我是费了好大的劲才给弄好的,从那以后我就长记性啦,做这个可得小心小心再小心。
还有哦,在加工的时候,你得注意安全。
这可不是闹着玩的,刀具可不长眼,别一不小心把手给弄伤了。
那就不是好玩的事情啦,搞不好还得去医院呢!另外啊,刀具的选择也很重要。
就像你去挑鞋子一样,得挑合脚的。
不同的内孔可能需要不同的刀具,你可不能随便拿一个就用,不然效果可能会大打折扣哦。
总之呢,内孔倒角加工方法就是这么个事儿。
只要你按照我说的步骤来,有耐心,小心操作,肯定能把内孔倒角加工得漂漂亮亮的。
就像给内孔化了个美美的妆一样,让它变得更加迷人啦!哈哈,朋友,快去试试吧!。
内孔的加工讲解
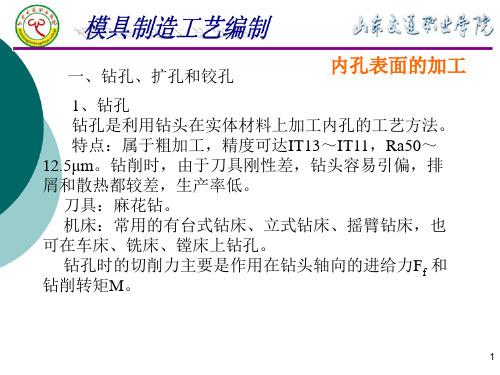
15
11
四、磨孔与孔的精密加工 1 磨孔工艺特点:属于孔的精加方法。精度可达IT7, Ra1.6~0.4 μm。 磨孔不仅能获得较高的尺寸精度和表面质量,而且 还可以提高孔的位置精度和孔的轴线的直线度。与外圆 磨削相比,工作条件较差:砂轮直径小,刚性差,排屑 和散热困难,生产率低。对于淬硬零件中的孔加工,磨 孔是主要的加工方法。 内孔为断续圆周表面(如有键槽或花键的孔)、阶 梯孔及盲孔时,常采用磨孔作为精加工。
研磨孔是一种光整加工方法。精度可达IT7~IT6, Ra0.4~0.025μm,形状精度也有相应的提高,但不能提 高位置精度。
16
珩磨头对孔施加一定压力,结构如图;切除极小的 加工余量。
17
②研磨孔是一种光整加工方法。精度可达IT7~IT6, Ra0.4~0.025μm,形状精度也有相应的提高,但不能提 高位置精度。需要在精镗、精铰或精磨之后进行。
18
固定式研磨棒多用于单件生产。带槽研磨棒便于存 贮研磨剂,用于粗研,光滑研磨棒,一般用于精研。如 图所示 。所有研具采用比工件软的材料制成,这些材料 为铸铁、铜、青铜、巴氏合金及硬木等。有时也可用钢 做研具。研磨时,部分磨粒悬浮于工件与研具之间,部 分磨粒则嵌入研具的表面层,工件与研具作相对运动, 磨料就在工件表面上切除很薄的一层金属 ( 主要是上工 序在工件表面上留下的凸峰 ) 。
12
磨孔时砂轮的尺寸受被加工孔径尺寸的限制,一般 砂轮直径为工件孔径的 0.5—0.9 倍,磨头轴的直径和 长度也取决于被加工孔的直径和深度。故磨削速度低, 磨头的刚度差,磨削质量和生产率均受到影响。
轴类零部件内孔加工方法

轴类零部件内孔加工是机械加工中常见的一项工艺,确保内孔的精度和表面质量对零部件的功能和性能至关重要。
以下是一些常见的轴类零部件内孔加工方法:
1. 钻削:
- 钻削是最基本的内孔加工方法之一。
通过使用钻头,可在工件上创建孔。
对于较小直径和较短深度的内孔,钻削是一种经济有效的方法。
2. 铰削:
- 铰削是通过使用铰刀,将内孔表面进行切削,以提高其精度和表面质量。
铰刀可以调整,使内孔具有所需的直径和形状。
3. 车削:
- 车削是通过使用车刀在工件上旋转的情况下,切削内孔的一种方法。
车削通常用于制作较大直径和较深的内孔,可以实现较高的加工效率。
4. 镗削:
- 镗削是通过使用镗刀,以旋转或振动的方式切削内孔。
这种方法可以实现较高的精度和表面质量,特别适用于对内孔直径和圆度有严格要求的情况。
5. 滚压:
- 滚压是通过使用滚轮或滚动刀具,将内孔材料进行塑性变形,从而形成所需的内孔形状。
这种方法可以提高内孔的表面质量和硬度。
6. 磨削:
- 磨削是通过使用磨石或磨削刀具,对内孔进行精细磨削,以获得高精度和高表面质量。
磨削通常用于对内孔直径和形状有极高要求的情况。
7. 激光加工:
- 激光加工是通过激光束将内孔材料切割或蒸发,以实现对内孔进行精确加工的方法。
这种方法适用于一些特殊材料或需要非常高精度的内孔加工。
在选择合适的轴类零部件内孔加工方法时,需要考虑材料特性、加工精度、生产效率和成本等因素。
通常,工程师会根据具体的要求和工件特点选择最合适的加工方法。
钢套内孔油槽加工方法
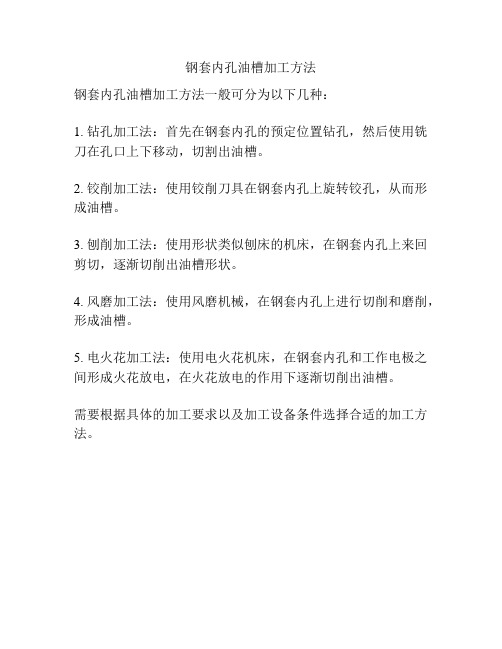
钢套内孔油槽加工方法
钢套内孔油槽加工方法一般可分为以下几种:
1. 钻孔加工法:首先在钢套内孔的预定位置钻孔,然后使用铣刀在孔口上下移动,切割出油槽。
2. 铰削加工法:使用铰削刀具在钢套内孔上旋转铰孔,从而形成油槽。
3. 刨削加工法:使用形状类似刨床的机床,在钢套内孔上来回剪切,逐渐切削出油槽形状。
4. 风磨加工法:使用风磨机械,在钢套内孔上进行切削和磨削,形成油槽。
5. 电火花加工法:使用电火花机床,在钢套内孔和工作电极之间形成火花放电,在火花放电的作用下逐渐切削出油槽。
需要根据具体的加工要求以及加工设备条件选择合适的加工方法。
内孔镜面加工工艺

内孔镜面加工工艺
内孔镜面加工工艺可以采用磨粒流抛光技术。
磨粒流抛光是一种纯物理抛光方式,利用弹性软磨料进行挤压研磨,提升内壁光洁度。
具体来说,弹性软磨料经过增压系统后,挤压进入工件孔内,进行精细研磨。
这种工艺可以兼顾效率与成本,比如一些拉拔模具内孔抛光非常费时,而采用磨粒流抛光可以在5分钟内将拉拔模具内孔研磨至镜面状态,公差损失小(1-2个μ),抛光效果均匀,且可现场试样。
如需更多与内孔镜面加工工艺相关的信息,建议咨询专业技术人员或查阅相关论坛。
铸钢定子架内孔的加工
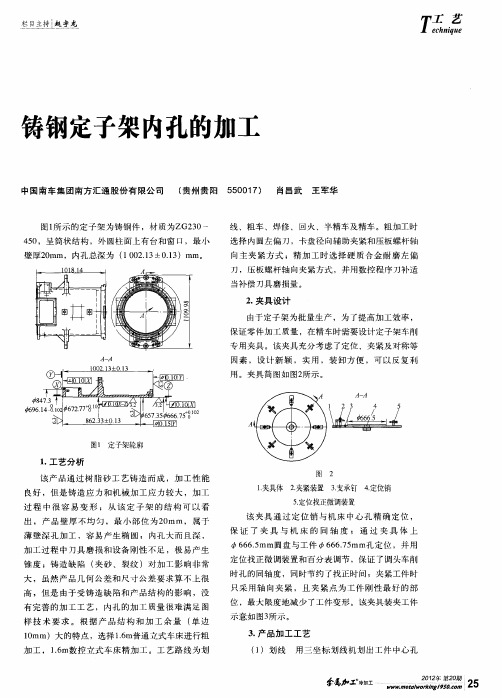
综合上述 因素 ,选择的刀具为硬质合金左偏刀 ,前
角2 。,后角l。 O 1 ,主偏角4 。,刃倾角4 。 5 。
数控程序 补偿 :在精 车削 6 27 im段 7 .7 n
时 ,由于 此段 有近 8 0 7 mm,加 工 至下 端 时 ,由于数 控 车床 滑 枕 伸 出过 长 ,刚 性 相对 较 差 ,同时 刀具 也
广 价值 。MW ( 收稿 日期 :2 10 2 ) 0 2 6 5
道 工 序 ,加 工 工艺 不 完 善或 控 制不 好 都会 直 接导 致 工 件 报废 ,造 成 巨大 的 经济 损 失 。半 精加 工完 的 工
2 6
, 晓
参磊
…
散 夹砂用 5 m的麻花 钻配手工 电钻清理干 净缺 a r 陷。②补焊缺陷部位。采用直流焊机、J2 焊条 , 42 对缺 陷清理后的部位进行补焊 。③打磨焊瘤。先用
风 砂轮 打 磨 平焊 瘤 ( 磨 后 不能 低 于 工件 表面 ) , 打 再 用 抛光 片 进行 抛 光 。 ( ) 回火 工件 焊 修后 ,局部 产 生硬 点和 焊接 4 应 力 ,车 削时 ,刀尖 极 易磨 损 ;同时 粗加 工 时 采用 大 余 量切 削 ,产生 较 大 的加 工 应 力 ,容 易使 工 件 变
除或减小加工产生的应 力,从而减小工件 由于加工
①工 件
( )粗 车 2
应力而产生 的变形。具体步骤 :①工件的装夹、找
正 方式 同半 精 车 ① ,先车 削 内孔 6 62 . 6. 0 5 2 mm至 6 67 .m m , 再 车 削 6 . 5 m m 至 6 .5 o2 1 o 5 6 6 6 73 rm ,最 后 在 距 离 另一 端面 10 5. a 5 0 mm左 右 的
数控加工内孔加工实训报告

一、实训目的本次实训旨在使学生掌握数控加工内孔加工的基本原理、工艺方法、操作技能及质量检测方法,提高学生的实际操作能力和工程应用能力。
二、实训内容1. 内孔加工的基本原理内孔加工是指利用钻头、扩孔刀、铰刀等工具,对工件内部进行加工,以达到所需尺寸、形状和表面质量的过程。
内孔加工在机械制造、汽车制造、航空航天等领域具有广泛的应用。
2. 内孔加工工艺方法(1)钻孔:钻孔是内孔加工的第一步,通常采用钻头进行加工。
钻孔分为粗加工和精加工,粗加工用于去除材料,精加工用于提高孔的尺寸精度和表面质量。
(2)扩孔:扩孔是在钻孔的基础上,对孔进行扩大,以满足更大的尺寸要求。
扩孔可以使用扩孔刀或扩孔钻头进行加工。
(3)铰孔:铰孔是内孔加工中精度要求较高的加工方法,通常使用铰刀进行加工。
铰孔可以保证孔的尺寸精度、形状精度和表面质量。
(4)镗孔:镗孔是利用镗刀对孔进行加工,以提高孔的尺寸精度和表面质量。
镗孔可以分为粗镗、半精镗和精镗。
(5)磨孔:磨孔是利用磨头对孔进行加工,以提高孔的尺寸精度、形状精度和表面质量。
磨孔适用于高精度、高表面质量要求的内孔加工。
3. 内孔加工操作技能(1)数控机床操作:熟练掌握数控机床的操作,包括开机、关机、调整机床参数、设置加工参数等。
(2)刀具选择:根据加工要求选择合适的刀具,包括钻头、扩孔刀、铰刀、镗刀、磨头等。
(3)加工参数设置:根据加工要求设置切削速度、进给量、切削深度等参数。
(4)加工顺序:按照加工工艺流程进行加工,包括钻孔、扩孔、铰孔、镗孔、磨孔等。
4. 内孔加工质量检测(1)尺寸检测:使用游标卡尺、千分尺等工具对孔的尺寸进行检测。
(2)形状检测:使用形状检测仪、投影仪等工具对孔的形状进行检测。
(3)表面质量检测:使用表面粗糙度仪、光泽度仪等工具对孔的表面质量进行检测。
三、实训过程1. 理论学习:了解内孔加工的基本原理、工艺方法、操作技能及质量检测方法。
2. 实操练习:在数控机床上进行内孔加工操作,包括钻孔、扩孔、铰孔、镗孔、磨孔等。
内孔研磨方法

内孔研磨方法一、前言内孔研磨是机械加工中常见的一种工艺,它可以用于加工精密的内孔,比如气缸套、轴承座等。
而内孔研磨的质量直接影响到零件的精度和寿命,因此需要采取一系列措施来保证其质量。
本文将介绍内孔研磨的方法及注意事项。
二、内孔研磨前的准备工作1. 确定内孔尺寸和形状在进行内孔研磨之前,首先需要明确待加工零件的内孔尺寸和形状。
这需要通过测量或图纸来确定。
2. 选择合适的工装夹具根据待加工零件的形态和尺寸,选择合适的工装夹具。
通常情况下,可以使用弹性夹紧器或真空吸盘等夹具来固定待加工零件。
3. 选择合适的切削液切削液对于内孔研磨来说非常重要,它能够提高切削效率、延长刀具寿命,并且能够有效地降低摩擦热。
因此,需要根据待加工材料的性质和切削液的特性来选择合适的切削液。
4. 选择合适的研磨头内孔研磨头的选择需要根据待加工零件的材料、尺寸和形态来确定。
常见的内孔研磨头有钻杆式、弹性轮式、针式等。
三、内孔研磨方法1. 确定加工顺序在进行内孔研磨之前,需要先确定加工顺序。
通常情况下,应该先进行粗加工,然后再进行精加工。
2. 粗加工粗加工时需要使用较大直径的内孔研磨头,通过旋转和进给运动来去除待加工零件内部较大的毛刺和凸起部分。
在粗加工时,切削液要保持充足,并且要注意控制进给速度和转速。
3. 清洁在完成粗加工之后,需要对待加工零件进行清洁。
这样可以清除掉切削液中残留下来的金属屑和其他杂质。
4. 精加工在进行精加工时,需要使用较小直径的内孔研磨头。
此时,切削液要充分润滑,并且要控制好进给速度和转速。
在精加工过程中,可以通过切削液的流动来清除研磨头上的金属屑和其他杂质。
5. 检查在完成内孔研磨之后,需要对待加工零件进行检查。
这样可以确保内孔的尺寸和形态符合要求。
四、注意事项1. 切削液应该选择合适的类型,并且要保持充足。
2. 内孔研磨头应该选择合适的规格和型号,并且要定期更换。
3. 在进行内孔研磨时,需要控制好进给速度和转速,避免过快或过慢导致质量问题。
内孔零件的加工
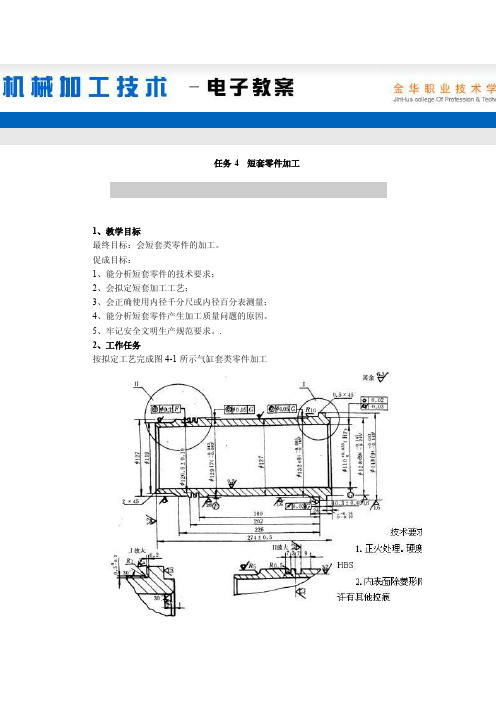
任务4短套零件加工1、教学目标最终目标:会短套类零件的加工。
促成目标:1、能分析短套零件的技术要求;2、会拟定短套加工工艺;3、会正确使用内径千分尺或内径百分表测量;4、能分析短套零件产生加工质量问题的原因。
5、牢记安全文明生产规范要求。
.2、工作任务按拟定工艺完成图4-1所示气缸套类零件加工图4-1A110型柴油机气缸套3、相关实践知识套筒类零件在机械加工中经常碰到,它在机器中主要起支承或导向作用。
气缸套的结构特点:零件的主要表面为内孔与外圆;且两者的同轴度要求较高;零件壁厚较薄;加工中易变形;零件的长度一般大于直径。
主要加工方法是车削和钻削。
3.1选择孔加工刀具,钻床、镗床和工件安装方式3.1.1孔加工刀具类型与选用孔加工刀具主要有麻花钻,扩孔钻,镗刀与铰刀。
(1)麻花钻1)麻花钻的组成标准麻花钻由工作部分、柄部、颈部三部分组成工作部分工作部分是钻头的主要组成部分。
它位于钻头的前半部分,也就是具有螺旋槽的部分,工作部分包括切削部分和导向部分。
切削部分主要起切削的作用,导向部分主要起导向、排屑、切削部分后备的作用,如图4-1a、b所示。
为了提高钻头的强度和刚性,其工作部分的钻心厚度(用一个假设圆直径——称为钻心直径d表示)一般为0.125~0.15 d(d为钻头直径),并且钻心成正锥形,如图4-1d所示,即从切削部分朝后,钻心直径逐渐增大,增大量在每100mm长度上为1.4~2mm。
为了减少导向部分和已加工孔孔壁之间的摩擦,对直径大于lmm的钻头,钻头外径从切削部分朝后制造出倒锥,形成副偏角,如图4-1c所示。
倒锥量在每100mm长度上为0.03~0.12mm。
柄部柄部位于钻头的后半部分,起夹持钻头、传递转矩的作用,如图4-1a、b所示。
柄部有直柄(圆柱形)和莫氏锥柄(圆锥形)之分,钻头直径在13mm以下做成直柄,利用钻夹头夹持住钻头;直径在12mm 以上做成莫氏锥柄,利用莫氏锥套与机床锥孔连接,莫氏锥柄后端有一个扁尾榫,其作用是供楔铁把钻头从莫氏锥套中卸下,在钻削时,扁尾榫可防止钻头与莫氏锥套打滑。
陶瓷内孔磨加工方法

陶瓷内孔磨加工方法摘要:一、陶瓷内孔磨加工方法简介二、陶瓷内孔磨加工工艺流程1.预加工2.粗磨3.精磨4.抛光三、陶瓷内孔磨加工注意事项1.选择合适的磨料和磨具2.控制加工过程中的温度和湿度3.保持设备良好状态四、陶瓷内孔磨加工的应用领域1.电子行业2.光学行业3.医疗器械行业正文:陶瓷内孔磨加工方法是一种在陶瓷材料内部进行精密磨削的技术,广泛应用于电子、光学和医疗器械等领域。
陶瓷材料具有高硬度、高熔点、低热导率等特点,因此陶瓷内孔磨加工具有一定的难度。
为了获得高质量的陶瓷内孔,我们需要掌握合适的加工方法和工艺流程。
陶瓷内孔磨加工的工艺流程主要包括预加工、粗磨、精磨和抛光四个步骤。
1.预加工:在进行内孔磨削前,首先要对陶瓷工件进行预加工,去除工件表面的毛刺和污垢,为后续磨削做好准备。
预加工方法包括磨削、铣削、钻孔等。
2.粗磨:粗磨是将陶瓷工件的内孔尺寸加工到接近最终尺寸的阶段。
在这一阶段,需要选用合适的磨料和磨具,根据工件的材质和加工要求进行磨削。
粗磨过程中,要注意控制磨削速度、进给量和磨削液的流量,以保证磨削效果和磨具的寿命。
3.精磨:精磨是将陶瓷工件的内孔尺寸精确到设计要求的阶段。
精磨时,要选用更高精度的磨具和更细的磨料,同时调整加工参数,以提高内孔的加工精度。
4.抛光:抛光是将陶瓷工件内孔表面抛光至光滑、平整的阶段。
抛光过程中,要选用合适的抛光剂和抛光液,并根据工件的表面状况调整抛光参数。
在进行陶瓷内孔磨加工时,还需注意以下事项:1.选择合适的磨料和磨具:根据工件的材质、加工要求和内孔尺寸,选用合适的磨料和磨具,以提高加工效果和效率。
2.控制加工过程中的温度和湿度:陶瓷材料对温度和湿度的敏感性较高,加工过程中要严格控制温度和湿度,以防止工件变形和裂纹。
3.保持设备良好状态:定期检查和维护加工设备,确保设备在良好的工作状态下进行加工。
陶瓷内孔磨加工在电子、光学和医疗器械等行业具有广泛的应用前景。
各种机床加工内孔的特点

各种机床加工内孔的特点机床是用于金属材料加工的设备,包括铣床、车床、钻床、镗床等。
加工内孔是机床的重要应用之一,下面将针对各种机床加工内孔的特点进行介绍。
1.车床加工内孔特点:车床是用来加工旋转对称零件的机床,它通过旋转工件,同时将刀具沿轴向移动来进行切削。
在车床上加工内孔主要有以下特点:-切削速度高:车床具有高速切削的特点,能够在较短的时间内完成内孔的加工。
-切削精度高:车床具有较高的切削精度,能够满足对内孔直径和精度的要求。
-对于较长内孔,需要使用横切车刀具来进行切削,并进行多次进给和回退来完成加工。
2.铣床加工内孔特点:铣床是用来加工平面、曲面和复杂形状工件的机床,通过旋转刀具将工件上的材料切削除去来进行加工。
在铣床上加工内孔主要有以下特点:-加工效率高:铣床能够进行连续的切削操作,因此加工效率较高。
-切削稳定性差:由于铣削过程中工具接触面积较小,因此切削稳定性较差,容易产生振动和切削力变化。
-内孔形状复杂:铣床可以通过刀具的移动轨迹来实现内孔的各种复杂形状。
3.钻床加工内孔特点:钻床是用来加工圆孔的机床,主要通过具有多个切削刃的钻头进行孔加工。
在钻床上加工内孔主要有以下特点:-加工精度高:钻床具有较高的加工精度,能够满足对内孔直径和精度的要求。
-内孔深度有限:由于钻头的长度限制,钻床加工内孔时需要对孔深度进行限制。
-切削速度低:钻床的切削速度较低,切削效率较低,适合对孔加工要求较高的工件进行加工。
4.镗床加工内孔特点:镗床是用于加工定位精度要求较高的内孔的机床,通过刀具的直线运动将孔加工到所需尺寸和精度。
-加工精度高:镗床具有较高的加工精度,能够满足对内孔直径和轴向精度的要求。
-内孔形状可调节:镗床可以通过刀具的调节来实现内孔的形状和尺寸的调整。
-加工速度较慢:由于镗床需要进行多次进给和回退来完成加工,因此加工速度较慢。
综上所述,不同机床加工内孔的特点各有不同,根据工件的要求和加工工艺的需要,选择合适的机床来进行内孔加工是非常重要的。
内孔高精度加工方法

内孔高精度加工方法嘿,咱今儿就来讲讲内孔高精度加工方法。
你说这内孔加工啊,就好比是给一件宝贝雕琢出最完美的内心。
要想做到高精度,那可不能马虎。
就像咱做饭一样,得讲究火候和调料搭配,一个环节不对,这道菜可能就不美味啦。
首先呢,得选对工具,就跟战士上战场得挑趁手的兵器一个道理。
合适的刀具、钻头,那是关键的第一步。
然后说说加工的过程,那得小心翼翼,轻拿轻放。
不能像个糙汉子似的不管不顾。
你想啊,这内孔就那么点地方,稍微一个不小心,可不就前功尽弃啦?这时候就得有耐心,像绣花一样,一针一线都得精细。
还有啊,加工的参数也得设置得恰到好处。
转速啦、进给量啦,这些都得根据实际情况来调整。
这就好比开车,速度太快容易出事,速度太慢又耽误时间,得找到那个最合适的平衡点。
咱再想想,要是加工的时候不注意冷却,那会咋样?那不就跟人跑了半天不喝水一样,得热晕乎啦!所以冷却也很重要,得让它时刻保持清醒的状态。
而且啊,在加工之前,一定要把准备工作做好。
就跟出门旅行前得收拾好行李一样,别到时候缺这少那的。
检查一下设备,看看有没有啥毛病,可别在关键时刻掉链子。
你说这内孔高精度加工是不是挺不容易的?但只要咱用心去做,就没有办不到的事儿。
就像爬山一样,虽然过程辛苦,但当你爬到山顶,看到那美丽的风景时,一切都值啦!你想想看,那些精密的仪器、设备,里面的内孔加工得多精细啊。
如果没有高精度的加工,这些东西能好用吗?能发挥出它们应有的作用吗?所以说啊,这内孔高精度加工可真是个技术活,也是个精细活。
咱可不能小瞧了它,它可是在很多领域都起着至关重要的作用呢!汽车制造、航空航天、医疗器械等等,哪一个离得开内孔高精度加工?这不就像是大楼的基石一样嘛,虽然不起眼,但没了它可不行。
总之呢,内孔高精度加工是个很有挑战性但又非常有意义的事儿。
咱得认真对待,用心钻研,让咱们加工出来的内孔都能达到高精度的标准。
这样咱们的制造业才能更上一层楼,咱们的国家才能更加强大呀!你说是不是这个理儿?。
《数控车床实训》课件——项目8:内孔零件的加工

项目8:内孔零件的加工
❖ 【导入课题】: ❖ 在前面我们都对外圆零件的编程与加工,那么关于内孔
零件又是应该怎样编程与加工,它们的程序和外圆类零件 的编程是否一样。 ❖ 【讲授新课】: ❖ 一、相关工艺知识 ❖ 1、刀具要求 ❖ (1)合理选用切削刀具。 (2)正确安装所选刀具。 ❖ 2、编程要求 ❖ 熟练掌握各指令的格式、走刀线路及运用。 ❖ 3、粗、精加工 ❖ (1)、了解粗精加工意义。 (2)、合理选配切削用量。
二、编程加工(对下图进行编程、加工)
❖三 2、在自动加工过程中必须关好安全门
❖ 3、加工出来的铁屑必须用铁扣扣出来,不能使用 手来拉。
❖
❖四、学生分组进行实训,教师来回巡察并指导。
❖【课堂小结】:
❖
在本次实训过程中,同学们都做得比较好,
都基本上掌握数控车的对刀操作,其中第一组速度
是最快的,第三组比较慢,说明第一组的配合比较
好,希望其他组向他们学习。
内孔大螺纹加工新技术-概述说明以及解释

内孔大螺纹加工新技术-概述说明以及解释1.引言1.1 概述概述部分是文章的开篇,需要对内孔大螺纹加工新技术进行简要介绍和概括。
以下是可能的概述内容:概述内孔大螺纹加工是制造业中非常重要的一项工艺,广泛应用于各种机械设备和工件的制造过程中。
随着工业化进程的不断推进和技术水平的不断提升,内孔大螺纹加工技术也在不断发展和创新。
本文将介绍一种新的内孔大螺纹加工技术,旨在解决传统加工方法中存在的一些挑战和问题。
传统的内孔大螺纹加工方法通常采用切削工具进行,然而这种方法在加工过程中存在一些困难和不足之处。
首先,由于内孔空间狭小、形状复杂,刀具进入和操作都比较困难,容易造成刀具断裂和加工精度不高的问题。
其次,传统方法的加工速度较慢,效率不高,需要耗费大量的时间和人力成本。
此外,由于切削工具在内孔加工中的摩擦和振动,还容易导致工件表面质量下降和切削刃易损等问题。
为了解决传统加工方法的这些问题,近年来出现了一种全新的内孔大螺纹加工技术。
该新技术采用了先进的数控加工设备和创新的工艺方法,通过激光或电火花进行加工,可快速、高效地加工各种内孔大螺纹。
这种新技术具有许多优势,如加工精度高、速度快、效率高、操作简便等,大大提高了内孔大螺纹加工的质量和效率。
本文的目的就是介绍这种新技术,并探讨它的优势和未来的发展潜力。
接下来的章节将详细阐述新技术的工作原理和操作方法,并分析内孔大螺纹加工中所面临的挑战和难题。
最后,我们将总结这种新技术的优势和潜在的应用前景,展望内孔大螺纹加工在未来的发展方向和趋势。
通过本文的撰写,我们希望能够进一步推动内孔大螺纹加工技术的发展,为制造业的提升和发展做出一定的贡献。
1.2 文章结构文章结构部分主要介绍了本篇长文的组织结构,目的是为读者提供一个清晰的整体框架,让读者在阅读文章时能够更好地理解每个章节的内容,同时也方便读者找到自己感兴趣的部分进行阅读。
本篇长文的结构可以分为引言、正文和结论三个部分。
常用的内孔加工方法与特点解析

常用的内孔加工方法与特点解析Company Document number:WTUT-WT88Y-W8BBGB-BWYTT-19998一、钻孔在模具零件上用钻头主要有两种方式:一种是钻头回转,零件固定不回转,如在普通台式钻床、摇臂钻、镗床上钻孔;另外一种方式零件回转而钻头不回转,如在车床上钻孔,这两种不同的钻孔方式所产生的误差不一样,在钻床或镗床上钻孔,由于钻头回转,使刚性不强的钻头易引偏,被加工孔的中心线偏移,但孔径不会发生变化。
钻头的直径一般不超过75mm,若钻孔大于30mm以上,通过采用两次钻销,即先用直径较小的钻头(被要求加工孔径尺寸的~倍)先钻孔,再用孔径合适的钻头进行第二次钻孔直到加工到所要求的直径。
以减小进给力。
钻头钻孔的加工精度,一般可以达到IT11~IT13级,表面粗糙度Ra为~。
二、扩孔用扩孔钻扩大零件孔径的加工方法,既可以作为精加工(铰孔、镗孔)前的预加工,也可以作为要求不高的孔径最终加工。
孔径的加工精度,一般可以达到IT10~IT13级,表面粗糙度Ra为~。
三、铰孔是用铰刀对未淬火孔进行精加工的一种孔径的加工方法。
铰孔的加工精度,一般可以达到IT6~IT10级,表面粗糙度Ra为~。
在模具制造加工中,一般用手工铰孔,其优点是切削速度慢,不易升温和产生积屑瘤,切削时无振动,容易控制刀具中心位置,因此当孔的精度要求很高时,主要用手工铰孔,或机床粗铰再用手工精铰。
在铰孔时应主要以下几点:a. 合理选择铰孔销孔余量及切削和规范;b. 铰孔刃口平整,能提高刃磨质量;c. 铰销钢材时,要用乳化液作为切削液。
四、车孔在车床上车孔,主要特征是零件随主轴回转,而刀具做进给运动,其加工后的孔轴心线与零件的回转轴线同轴。
孔的圆度主要取决于机床主轴的回转精度,孔的纵向几何形状误差主要取决于刀具的进给方向。
这种车孔方式适用于加工外圆表面与孔要求有同轴度的零件。
五、镗孔在镗床上镗孔,主要靠刀具回转,而零件做进给运动。
- 1、下载文档前请自行甄别文档内容的完整性,平台不提供额外的编辑、内容补充、找答案等附加服务。
- 2、"仅部分预览"的文档,不可在线预览部分如存在完整性等问题,可反馈申请退款(可完整预览的文档不适用该条件!)。
- 3、如文档侵犯您的权益,请联系客服反馈,我们会尽快为您处理(人工客服工作时间:9:00-18:30)。
研磨孔是一种光整加工方法。精度可达IT7~IT6, Ra0.4~0.025μm,形状精度也有相应的提高,但不能提 高位置精度。
16
珩磨头对孔施加一定压力,结构如图;切除极小的 加工余量。
17
②研磨孔是一种光整加工方法。精度可达IT7~IT6, Ra0.4~0.025μm,形状精度也有相应的提高,但不能提 高位置精度。需要在精镗、精铰或精磨之后进行。
1
钻孔方式: ① 工件旋转,刀具进给(如在车床上钻孔),加工 中如刀具引偏,会造成工件孔径扩大。 ② 工件不动,刀具既旋转又进给(如在钻床上钻 孔),加工中如刀具引偏,会造成工件孔轴线弯曲。
2
麻花钻的组成① 柄部 : ② 颈部 ③ 工作部分:
3
2、扩孔 扩孔是用扩孔钻在已钻出、铸出、锻出或冲出的孔 进行加工的方法。 特点:相当于半精加工,精度可达IT10,Ra 6.3~ 3.2μm。扩孔可以修正孔轴线的歪斜,生产率高。
6
铰刀特点 :刀齿多、刀槽浅、刚度好、定尺寸(一 把刀加工一种孔);精度:H7、H8、H9 。
7
二、镗孔 镗孔是在工件已有的孔上进行扩大孔径的加工方法。 特点:镗孔可分为粗镗(IT13~IT11,Ra50 ~ 12.5μm)、半精镗(IT10~IT9,Ra6.3~3.2 μm)和精 镗(IT8~IT6,Ra1.6~0.8μm)。镗孔除了能提高尺寸 精度和表面质量外,还可以修正孔的轴线的弯曲误差, 且较容易保证各孔的孔距精度和位置精度。 镗孔方式有主轴进给、工作台进给两种,当工件较大、 孔较短时采用主轴进给,反之则采用工作台进给。
11
四、磨孔与孔的精密加工 1 磨孔工艺特点:属于孔的精加方法。精度可达IT7, Ra1.6~0.4 μm。 磨孔不仅能获得较高的尺寸精度和表面质量,而且 还可以提高孔的位置精度和孔的轴线的直线度。与外圆 磨削相比,工作条件较差:砂轮直径小,刚性差,排屑 和散热困难,生产率低。对于淬硬零件中的孔加工,磨 孔是主要的加工方法。 内孔为断续圆周表面(如有键槽或花键的孔)、阶 梯孔及盲孔时,常采用磨孔作为精加工。
珩磨头与工件之间的旋转和往复运动,使砂条的磨 粒在孔表面上的切削轨迹形成交叉而又不相重复的网纹。 珩磨时磨条便从工件上切去极薄的一层材料,并在孔表 面形成交叉而不重复的网纹切痕 ( 如图 ), 这种交叉而不 重复的网纹切痕有利于贮存润滑油,使零件表面之间易 形成—层油膜,从而减少零件间的表面磨损。
15
一、钻孔、扩孔和铰孔
内孔表面的加工
1、钻孔 钻孔是利用钻头在实体材料上加工内孔的工艺方法。 特点:属于粗加工,精度可达IT13~IT11,Ra50~ 12.5μm。钻削时,由于刀具刚性差,钻头容易引偏,排 屑和散热都较差,生产率低。 刀具:麻花钻。 机床:常用的有台式钻床、立式钻床、摇臂钻床,也 可在车床、铣床、镗床上钻孔。 钻孔时的切削力主要是作用在钻头轴向的进给力Ff 和 钻削转矩M。
18
固定式研磨棒多用于单件生产。带槽研磨棒便于存 贮研磨剂,用于粗研,光滑研磨棒,一般用于精研。如 图所示 。所有研具采用比工件软的材料制成,这些材料 为铸铁、铜、青铜、巴氏合金及硬木等。有时也可用钢 做研具。研磨时,部分磨粒悬浮于工件与研具之间,部 分磨粒则嵌入研具的表面层,工件与研具作相对运动, 磨料就在工件表面上切除很薄的一层金属 ( 主要是上工 序在工件表面上留下的凸峰 ) 。
4
① 整体式; ② 镶齿套式 ; ③ 硬质合金可转位式 。
5
3、铰孔 特点:铰孔一般作为未淬硬小孔的精加工方法。精 度可达精度可达IT8~IT6,Ra1.6~0.4μm。手铰和机铰 两种。机铰时,铰刀与机床采用浮动连接。铰孔只能提 高孔本身的尺寸精度及形状精度,但不能校正孔的位置 精度。注意:钻孔、扩孔和铰孔是加工小孔常用的方法。
8
镗刀 (1)单刃镗刀 ① 车床用:即内孔车刀 ② 镗床用:镗杆+刀头(一般——较难调刀;微调镗 刀——有刻度,较易调整)。
9
(2)双刃镗刀 ① 固定镗刀块 ≈ 没有横刃的钻头 ② 浮动镗刀块 ≈ 只有两条刀刃的铰刀——不修正 位置误差。
10
三、拉孔 特点:属于的孔的精加工方法。在拉床上进行。精 度可达 IT8~IT7,Ra0.8~0.4μm。加工时以孔本身定位, 不能修正孔的轴线歪斜。生产率高,但刀具复杂。
在研具与工件加工表面之间加入研磨剂,在一定压 力下 表面作复杂的相对运动,使磨粒在工件表面上滚动 或滑动,起切削、刮擦和挤压作用,从加工表面上切下 极薄的一层材料,得到尺寸精度和表面粗糙度极低的表 面。按研磨方式可分为手工研磨和机械研磨两种。
研磨前,将套上工件的研磨棒安装在车床上,涂上 研磨剂,调整研磨棒直径使其对工件有适当的压力,即 可进行研磨。研磨时,研磨棒旋转,手握工件往复移动。 固定式研磨棒多用于单件生产
12
磨孔时砂轮的尺寸受被加工孔径尺寸的限制,一般 砂轮直径为工件孔径的 0.5—0.9 倍,磨头轴的直径和 长度也取决于被加工孔的直径和深度。故磨削速度低, 磨头的刚度差,磨削质量和生产率均受到影响。
磨孔的方式有中心内圆磨削、无心内圆磨削。 中心内圆磨削是在普通内圆磨床或万能磨床上进行。 无心内圆磨削是在无心内圆磨床上进行的,被加工工件 多为薄壁件,不宜用夹盘夹紧,工件的内外圆同轴度要 求较高。这种磨削方法多用于磨削轴承环类型的零件, 其工艺特点是精度高,要求机床具有高精度、高的自动 化程度和高的生产率,以适应大批大量生产。
13
14
2 孔的精密加工①②③④⑤
①珩பைடு நூலகம் 是磨削加工的一种特殊形式,属于光整加工。 需要在磨削或精镗的基础上进行。
珩磨所用的工具是由若干砂条 ( 油石 ) 组成的珩磨 头,四周砂条能作径向张缩,并以一定的压力与孔表面 接触,珩磨头上的砂条有 3 种运动 ( 如 图 );即旋转运 动、往复运动和加压力的径向运动。
19
③滚压 利用经过淬硬和精细抛光过的、可自由旋转 的滚柱或滚珠,对零件表面进行挤压,以提高加工表面 质量的一种机械强化加上方法。滚压加工可减小表面粗 糙度值 2-3 级,提高硬度 10 % -40 % ,表面层耐疲劳 强度一般提高 30 % ~ 50 % 。滚柱或滚珠材质通常用 高速钢或硬质合金。