(第九章)工艺集成
第09章-刻蚀工艺

微观负载效应
• 微观负载效应
– 对于接触窗和金属层间接触孔刻 蚀,较小的窗孔刻蚀速率比较大 窗孔慢 – 由于光刻胶溅镀沉积到侧壁上, 图形隔离区域的刻蚀轮廓比密集 区域宽
微观负载效应刻蚀轮廓
14
过刻蚀效应
主刻蚀和过刻蚀轮廓
过刻蚀中,被刻蚀薄膜和衬底材料之间的选择性要足够高,避免损失过多衬底材料
15
CF4, CHF3 CF4, CHF3 SF6
4835 6156 2535 7037
半导体制造技术导论(第二版)
第九章
刻蚀工艺
白雪飞 中国科学技术大学电子科学与技术系
提纲
• 简介
• 刻蚀工艺基础
• 湿法刻蚀工艺 • 干法刻蚀工艺 • 等离子体刻蚀工艺
• 刻蚀工艺制程趋势
• 刻蚀工艺发展趋势
2
简
介
先进的集成电路工艺流程
先进的集成电路工艺流程
4
刻蚀工艺简介
• 刻蚀工艺
– 移除晶圆表面材料 – 图形化刻蚀:去除指定区域的材料,将图形转移到衬底薄膜上 – 整面全区刻蚀:去除整个表面薄膜达到所需工艺要求
34
离子辅助刻蚀实验
离子辅助刻蚀实验及结果
XeF2:纯化学刻蚀;Ar+:纯物理刻蚀
35
刻蚀工艺的比较
纯化学刻蚀 应用 刻蚀速率 湿法刻蚀,剥除, 光刻胶刻蚀 可以从高到低
反应式离子刻蚀 等离子体图形化刻蚀 高,可控
纯物理刻蚀 氩轰击 低
选择性
刻蚀轮廓 工艺终点
非常好
等向性 计时或目测
可以接受,可控
������ =
������1 − ������
2
+ ������2 − ������
北大集成电路版图设计课件_第9章集成电路版图设计实例
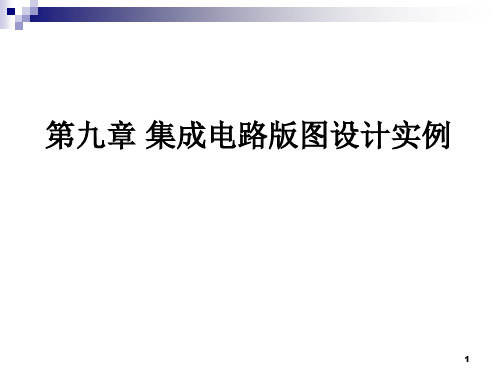
2
1
2
1
2
3
1
3
2
3
1
3
R1和R2的共质心结构版图设计
加入R3后的共质心版图设计
49
9.7带隙基准源版图实例
总体版图实例
比例电阻
运算放大器
1:8 晶体管
50
9.8芯片总体设计
首先,在总体版图的布局上,尽量将数字部分远离模拟部分,如果 总体电路中模拟部分偏多,则在版图设计中将数字部分放在靠边的位 置,而且把模拟部分中最容易被数字干扰的部分放到离数字部分最远 的位置,同时在数字部分和模拟部分中间用接地的衬底接触来进行隔 离,反之亦然。 其次,采用隔离环设计,对每个单元模块都用一层接地的衬底接触, 一层接电源的N阱构成的隔离环来进行隔离。对于整个模拟部分和数 字也分别采用相同的隔离环隔离,数字电路的隔离环可以吸收数字电 路的衬底噪声,从而可以减少通过衬底串扰到模拟电路的衬底噪声。 隔离环包的层数越多,理论上吸收衬底噪声效果越好。但是要避免数 字电路的p隔离环紧靠模拟电路的p型隔离环,因为在这种情况下数字 地的噪声会串扰到模拟地。从而使模拟地受到干扰。
1.反相器-并联反相器的版图
直接并联
共用漏区
7
9.2 数字版图设计实例
2.与非门
VCC A Q1 Q2 OUT B Q3
Q4
按电路图转换
MOS管水平走向设计
8
9.2 数字版图设计实例
3.或非门
VCC A Q1
B
Q2 OUT Q3 Q4
按电路图转换
MOS管水平走向设计
9
9.2 数字版图设计实例
4.传输门
25
9.5静电保护电路设计实例
第九章 ULSI工艺总汇
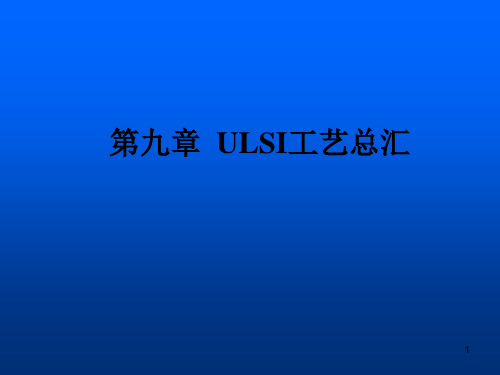
N+区光刻
38
掩膜6 :光刻接触孔
光刻接触孔
39
掩膜7 :光刻铝引线 1、淀积铝 2、光刻铝
AL PSG 场氧 Poly 栅氧 P+ N+ P阱 N 硅衬底
40
光刻铝
三、后部封装 (在另外厂房)
(1)背面减薄 (2)切片 (3)粘片 (4)压焊:金丝球焊 (5)切筋 (6)整形 (7)塑封 (8)沾锡:保证管脚的电学接触 (9)老化 (10)成品测量 (11)打印、包装
一、硅片制备 二、前部工序
Mask 掩膜版
CHIP
31
• 掩膜1: P阱光刻
P-well Si-衬底
具体步骤如下: 1.生长二氧化硅:
SiO2
Si-衬底
32
2.P阱光刻: 涂胶、掩膜对准、曝光、显影、刻蚀 3.去胶 4.掺杂:掺入B元素
涂胶
显影
刻蚀
去胶
掺杂
33
掩膜2 : 光刻有源区
淀积氮化硅 光刻有源区 场区氧化 去除有源区氮化硅及二氧化硅 生长栅氧 淀积多晶硅
第九章 ULSI工艺总汇
1
集成电路制造工艺分类 1. 双极型工艺(bipolar)
2. CMOS工艺 3. BiCMOS工艺
2
§1 双极型(NPN)集成电路工艺
(典型的PN结隔离工艺)
3
思考题
1.与分立器件工艺有什么不同?
2.埋层的作用是什么?
3.需要几块光刻掩膜版(mask)? 4.每块掩膜版的作用是什么?
SiO2
SiO2
N–-epi
P+ N+埋层
E B N+ P
C
硅集成电路工艺基础9
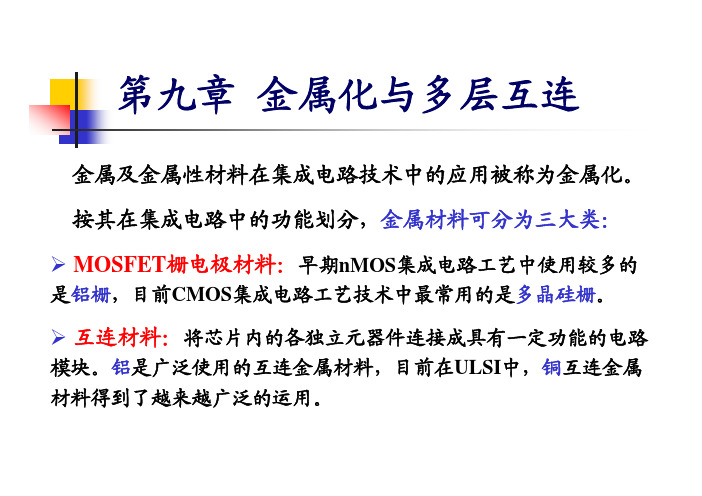
第九章金属化与多层互连金属及金属性材料在集成电路技术中的应用被称为金属化。
按其在集成电路中的功能划分,金属材料可分为三大类:¾MOSFET栅电极材料:早期nMOS集成电路工艺中使用较多的是铝栅,目前CMOS集成电路工艺技术中最常用的是多晶硅栅。
¾互连材料:将芯片内的各独立元器件连接成具有一定功能的电路模块。
铝是广泛使用的互连金属材料,目前在ULSI中,铜互连金属材料得到了越来越广泛的运用。
¾接触材料:直接与半导体接触,并提供与外部相连的连接点。
铝是一种常用的接触材料,但目前应用较广泛的接触材料是硅化)等。
物,如铂硅(PtSi)和钴硅(CoSi2集成电路中使用的金属材料,除了常用的金属如Al,Cu,Pt,W 等以外,还包括重掺杂多晶硅、金属硅化物、金属合金等金属性材料。
9.1、集成电路对金属化材料特性的要求¾与n+,p+硅或多晶硅能够形成欧姆接触,接触电阻小;¾长时期在较高电流密度负荷下,抗电迁移性能要好;¾与绝缘体(如SiO)有良好的附着性;2¾耐腐蚀;¾易于淀积和刻蚀;¾易于键合,而且键合点能经受长期工作;¾多层互连要求层与层之间绝缘性好,不互相渗透和扩散。
9.1.1、晶格结构和外延生长特性的要求金属材料特性与其晶格结构有关,集成电路中金属薄膜:¾外延生长¾单晶膜具有最理想的特性。
采用外延生长可以消除缺陷,晶体结构好,提高金属薄膜的性能,降低电阻率和电迁移率,得到良好的金属/半导体接触或金属/绝缘体接触界面。
9.1.2、电学特性金属材料在集成电路中应用时,须考虑的电学性能主要包括电阻率、电阻率的温度系数(TCR)、功函数、与半导体接触的肖特基势垒高度。
对于接触材料和栅电极材料,其功函数、与半导体材料的肖特基势垒高度和接触电阻是非常重要的参数。
9.1.3,通过优化生长过程可以减小。
集成电路版图设计习题答案第九章集成电路版图设计实例

第9章集成电路版图设计实例【习题答案】1.版图设计关于数字地和模拟地的考虑事项是什么?答:一般的模拟集成电路中,通常既有数字信号又有模拟信号,数字信号和模拟信号之间容易发生干扰。
在版图设计过程中,还要考虑地噪声对电路的影响。
即在整体版图的设计中,需着重考虑电路噪声问题,按照尽量降低噪声的原则进行电路的整体布局。
首先,在总体版图的布局上,尽量将数字部分远离模拟部分,如果总体电路中模拟部分偏多,则在版图设计中将数字部分放在靠边的位置,而且把模拟部分中最容易被数字干扰的部分放到离数字部分最远的位置,同时在数字部分和模拟部分中间用接地的衬底接触来进行隔离,反之亦然。
其次,采用隔离环设计,对每个单元模块都用一层接地的衬底接触,一层接电源的N阱构成的隔离环来进行隔离。
对于整个模拟部分和数字也分别采用相同的隔离环隔离,数字电路的隔离环可以吸收数字电路的衬底噪声,从而可以减少通过衬底串扰到模拟电路的衬底噪声。
隔离环包的层数越多,理论上吸收衬底噪声效果越好。
但是要避免数字电路的p隔离环紧靠模拟电路的p型隔离环,因为在这种情况下数字地的噪声会串扰到模拟地。
从而使模拟地受到干扰。
最后,除了数字模块之外的其它单元模块尽量将距离缩短,这样一方面能尽量地减少互连线经过别的区域引入噪声,同时也能降低引线过长引起电压信号的衰减。
2.总结自己的版图设计技巧和经验。
3. 共质心MOS管设计时的注意事项是什么?答:低精度要求可采用一维共质心,高精度要求必须采用二维共质心。
共质心设计时需保证MO管的对称性和电流通路的对称性。
4. 静电保护的种类以及版图设计注意事项。
答:常用的二极管式的静电保护分为两种方式,一种是用MOS晶体管连接成二极管形式的静电保护,一种利用CMOS工艺中二极管的静电保护。
在MOS型静电保护版图设计中,主要考虑以下几点:●MOS管要分成多个管,叉指结构,以便形成多支路共同放电。
●因为放电瞬间流经MOS管的电流特别大,构成整个放电通路的任何导线的宽度一定要有足够保证,而且CMOS工艺对于每个接触孔能通过的电流密度还有要求,因此还要保证放电通路导线上孔的数目应尽量多。
第9章-集成电路设计与制造讲义
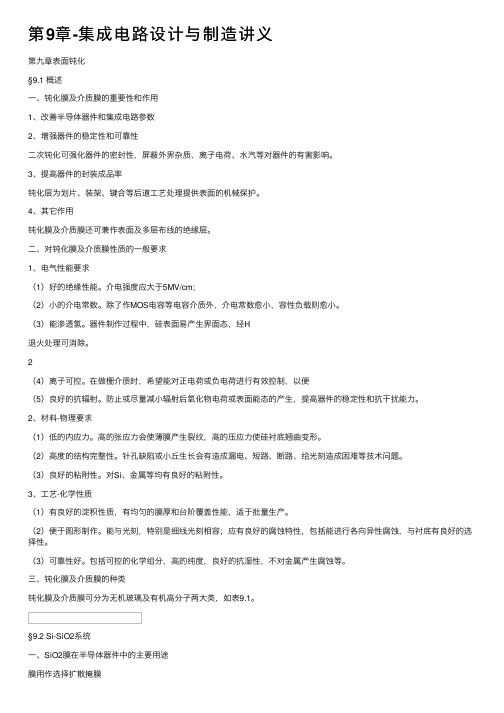
第9章-集成电路设计与制造讲义第九章表⾯钝化§9.1 概述⼀、钝化膜及介质膜的重要性和作⽤1、改善半导体器件和集成电路参数2、增强器件的稳定性和可靠性⼆次钝化可强化器件的密封性,屏蔽外界杂质、离⼦电荷、⽔汽等对器件的有害影响。
3、提⾼器件的封装成品率钝化层为划⽚、装架、键合等后道⼯艺处理提供表⾯的机械保护。
4、其它作⽤钝化膜及介质膜还可兼作表⾯及多层布线的绝缘层。
⼆、对钝化膜及介质膜性质的⼀般要求1、电⽓性能要求(1)好的绝缘性能。
介电强度应⼤于5MV/cm;(2)⼩的介电常数。
除了作MOS电容等电容介质外,介电常数愈⼩,容性负载则愈⼩。
(3)能渗透氢。
器件制作过程中,硅表⾯易产⽣界⾯态,经H退⽕处理可消除。
2(4)离⼦可控。
在做栅介质时,希望能对正电荷或负电荷进⾏有效控制,以便(5)良好的抗辐射。
防⽌或尽量减⼩辐射后氧化物电荷或表⾯能态的产⽣,提⾼器件的稳定性和抗⼲扰能⼒。
2、材料-物理要求(1)低的内应⼒。
⾼的张应⼒会使薄膜产⽣裂纹,⾼的压应⼒使硅衬底翘曲变形。
(2)⾼度的结构完整性。
针孔缺陷或⼩丘⽣长会有造成漏电、短路、断路、给光刻造成困难等技术问题。
(3)良好的粘附性。
对Si、⾦属等均有良好的粘附性。
3、⼯艺-化学性质(1)有良好的淀积性质,有均匀的膜厚和台阶覆盖性能,适于批量⽣产。
(2)便于图形制作。
能与光刻,特别是细线光刻相容;应有良好的腐蚀特性,包括能进⾏各向异性腐蚀,与衬底有良好的选择性。
(3)可靠性好。
包括可控的化学组分,⾼的纯度,良好的抗湿性,不对⾦属产⽣腐蚀等。
三、钝化膜及介质膜的种类钝化膜及介质膜可分为⽆机玻璃及有机⾼分⼦两⼤类,如表9.1。
§9.2 Si-SiO2系统⼀、SiO2膜在半导体器件中的主要⽤途膜⽤作选择扩散掩膜1、SiO2对磷、硼、砷等杂质较强的掩蔽能⼒,在硅上的⼆氧化硅层上刻蚀出选利⽤SiO2择扩散区窗⼝,则在窗⼝区可以向硅中扩散杂质,形成PN结。
chap9-10解析
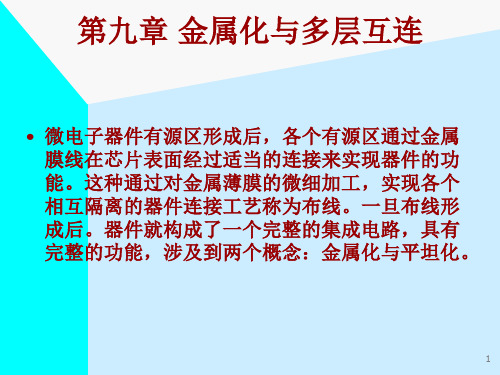
14
• (1)了解电迁移现象的物理机制
• (2)中值失效时间概念
• (3)改进电迁移的方法
•
结构的影响和“竹状”结构的选择;
•
AL-Cu合金(在Al中加入0.5~4%的Cu可
以降低铝原子在晶间的扩散系数。但同时电阻
率会增加!)和AL-Si-Cu合金;
•
三层夹心结构。
15
9.3 铜及低K介质
• 降低互连线延迟时间重要方法之一:使用
➢可以通过掺杂改变MS。如n-poly可以使VT下降1.1 V,
既工业界常用的双多晶栅dual-poly(n & p)工艺。 ➢多晶栅自对准技术,可以进一步提高集成度。
22
多晶硅栅自对准技术
23
LDD(Lightly Doped Drain)+spacer 多晶硅自对准技术
LDD工艺是CMOS集成电路进入亚微米后应用最广泛的技术, LDD结构是 用来降低MOS管源端和漏端在沟道的电场分布,以克服热载流子效应所造成的 I-V特性因长时间作用而漂移的问题。但是LDD结构在导电沟道两段的深度只有 20nm,这等于在源极和漏极 的两端形成了两个尖端,尖端放电现象即静电放电 (ESD) 便容易发生在LDD结构上,从而造成这种结构的抗静电能力较低。
接成为具有一定功能的电路模块。 • 接触材料:直接与半导体材料接触的材料,以及
提供与外部相连的连接点。 • 金属材料:除了常见AL、CU、Pt、W等以外,
还包括重掺杂多晶硅、金属硅化金属合金等金属 性材料。
3
9.1 集成电路对金属化材料特性的要求
对IC金属化系统的主要要求
电学、机械、热学、热力学及化学
26
金属硅化物作为接触材料
特点:类金属,低电阻率(<0.01多晶硅),高温
集成电路工艺第九章化学机械抛光
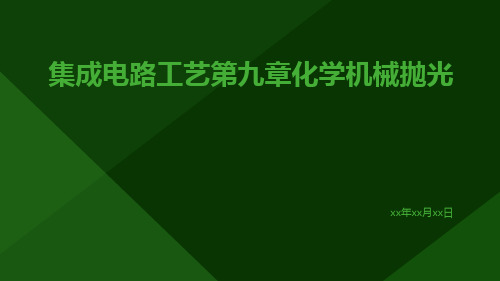
CMP工艺可用于制造高精度光学元件和掩膜板,提高光刻工艺的精度和效率。
高精度表面处理
CMP技术可有效去除芯片制造过程中的结构材料,提高芯片制造效率和成品率。
结构材料去除
化学机械抛光在芯片制造中的应用
化学机械抛光在封装测试中的应用
封装基板处理
CMP工艺可用于封装基板表面的处理,提高封装质量和可靠性。
发布时间
《化学机械抛光液》标准发布时间为2010年,《化学机械抛光设备》标准发布时间为2012年,《化学机械抛光工艺质量要求》标准发布时间为2015年。
适用范围
《化学机械抛光液》标准适用于集成电路制造、光学元件加工等领域用化学机械抛光液的质量要求
化学机械抛光相关标准推荐
03
04
05
THANKS
感谢观看
在介质平坦化中,CMP可以去除介质层表面的凸起,实现介质层的高度平滑。
1
化学机械抛光历史
2
3
CMP技术自20世纪80年代问世以来,经历了从发明到商业化应用的发展过程。
最初的CMP技术主要应用于磁盘驱动器的制造中,后来被引入到集成电路制造中,成为后道工艺中的关键技术之一。
随着CMP技术的不断改进和应用领域的扩大,它已经成为微电子制造中的重要支柱之一。
应用领域
化学机械抛光技术被广泛应用于集成电路制造、光学元件加工、医疗器械制造等领域。在集成电路制造领域,化学机械抛光技术已成为制备高质量表面的关键技术之一。
展望
未来,化学机械抛光技术将继续发挥重要作用,同时,随着新型材料的不断涌现,该技术将不断得到改进和完善,应用领域也将越来越广泛。
化学机械抛光相关论文推荐
xx年xx月xx日
集成电路工艺第九章化学机械抛光
第九章集成电路制造工艺概况
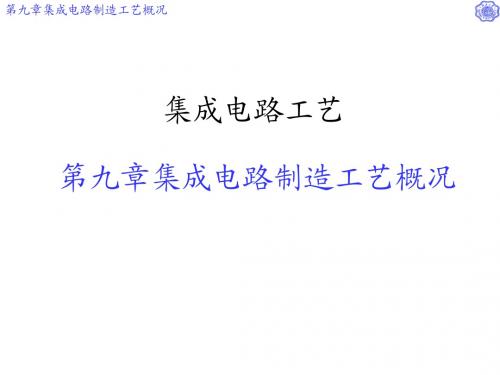
2014-10-14
集成电路工艺
43
第九章集成电路制造工艺概况
2014-10-14
集成电路工艺
44
第九章集成电路制造工艺概况
2014-10-14
集成电路工艺
45
第九章集成电路制造工艺概况
2014-10-14
集成电路工艺
46
第九章集成电路制造工艺概况
2014-10-14
集成电路工艺
47
第九章集成电路制造工艺概况
集成电路工艺
6
第九章集成电路制造工艺概况
扩散
• 扩散区是进行高温工艺及薄膜淀积的区域
• 高温扩散炉和湿法清洗设备 • 高温扩散炉 1200℃,可完成氧化、扩散、 淀积、退火以及合金
2014-10-14
集成电路工艺
7
第九章集成电路制造工艺概况
光刻
• 黄光区
• 光刻的目的 将电路图形转移到覆盖硅片表面的光刻胶上
集成电路工艺
33
第九章集成电路制造工艺概况
2014-10-14
集成电路工艺
34
第九章集成电路制造工艺概况
2014-10-14
集成电路工艺
35
第九章集成电路制造工艺概况
2014-10-14
集成电路工艺
36
第九章集成电路制造工艺概况
2014-10-14
集成电路工艺
37
第九章集成电路制造工艺概况
2014-10-14
集成电路工艺
12
第九章集成电路制造工艺概况
9.2 CMOS制作步骤
• • • • • • • 1、双阱工艺 2、浅槽隔离工艺 3、多晶硅栅结构工艺 4、轻掺杂漏(LDD)注入工艺 5、侧墙的形成 6、源/漏(S/D)注入工艺 7、接触孔的形成
微电子工艺技术-复习要点答案(完整版)

第四章晶圆制造1.CZ法提单晶的工艺流程。
说明CZ法和FZ法。
比较单晶硅锭CZ、MCZ和FZ三种生长方法的优缺点.答:1、溶硅2、引晶3、收颈4、放肩5、等径生长6、收晶。
CZ法:使用射频或电阻加热线圈,置于慢速转动的石英坩埚内的高纯度电子级硅在1415度融化(需要注意的是熔硅的时间不宜过长)。
将一个慢速转动的夹具的单晶硅籽晶棒逐渐降低到熔融的硅中,籽晶表面得就浸在熔融的硅中并开始融化,籽晶的温度略低于硅的熔点。
当系统稳定后,将籽晶缓慢拉出,同时熔融的硅也被拉出。
使其沿着籽晶晶体的方向凝固。
籽晶晶体的旋转和熔化可以改善整个硅锭掺杂物的均匀性.FZ法:即悬浮区融法.将一条长度50-100cm 的多晶硅棒垂直放在高温炉反应室。
加热将多晶硅棒的低端熔化,然后把籽晶溶入已经熔化的区域。
熔体将通过熔融硅的表面张力悬浮在籽晶和多晶硅棒之间,然后加热线圈缓慢升高温度将熔融硅的上方部分多晶硅棒开始熔化。
此时靠近籽晶晶体一端的熔融的硅开始凝固,形成与籽晶相同的晶体结构。
当加热线圈扫描整个多晶硅棒后,便将整个多晶硅棒转变成单晶硅棒。
CZ法优点:①所生长的单晶的直径较大,成本相对较低;②通过热场调整及晶转,坩埚等工艺参数的优化,可以较好的控制电阻率径向均匀性。
缺点:石英坩埚内壁被熔融的硅侵蚀及石墨保温加热元件的影响,易引入氧、碳杂质,不易生长高电阻率单晶.FZ法优点:①可重复生长,提纯单晶,单晶纯度较CZ法高.②无需坩埚、石墨托,污染少③高纯度、高电阻率、低氧、低碳④悬浮区熔法主要用于制造分离式功率元器件所需要的晶圆。
缺点:直径不如CZ法,熔体与晶体界面复杂,很难得到无位错晶体,需要高纯度多晶硅棒作为原料,成本高。
MCZ:改进直拉法优点:较少温度波动,减轻溶硅与坩埚作用,降低了缺陷密度,氧含量,提高了电阻分布的均匀性2.晶圆的制造步骤【填空】答:1、整形处理:去掉两端,检查电阻确定单晶硅达到合适的掺杂均匀度。
2、切片3、磨片和倒角4、刻蚀5、化学机械抛光3. 列出单晶硅最常使用的两种晶向。
半导体制造技术复习总结
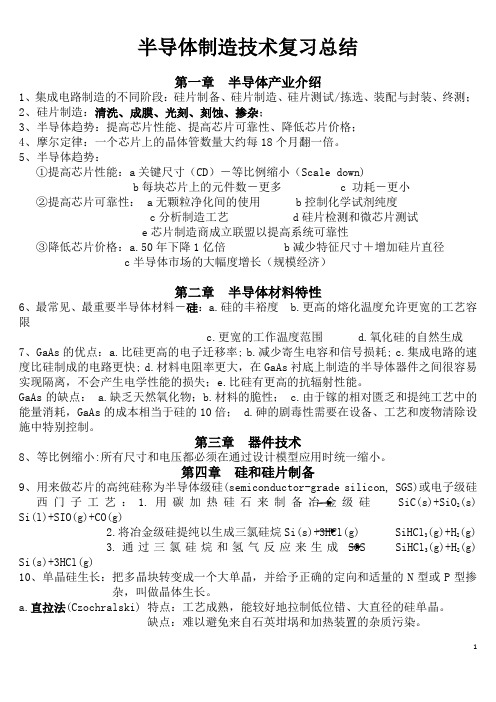
半导体制造技术复习总结第一章半导体产业介绍1、集成电路制造的不同阶段:硅片制备、硅片制造、硅片测试/拣选、装配与封装、终测;2、硅片制造:清洗、成膜、光刻、刻蚀、掺杂;3、半导体趋势:提高芯片性能、提高芯片可靠性、降低芯片价格;4、摩尔定律:一个芯片上的晶体管数量大约每18个月翻一倍。
5、半导体趋势:①提高芯片性能:a关键尺寸(CD)-等比例缩小(Scale down)b每块芯片上的元件数-更多 c 功耗-更小②提高芯片可靠性: a无颗粒净化间的使用 b控制化学试剂纯度c分析制造工艺 d硅片检测和微芯片测试e芯片制造商成立联盟以提高系统可靠性③降低芯片价格:a.50年下降1亿倍 b减少特征尺寸+增加硅片直径c半导体市场的大幅度增长(规模经济)第二章半导体材料特性6、最常见、最重要半导体材料-硅:a.硅的丰裕度 b.更高的熔化温度允许更宽的工艺容限c.更宽的工作温度范围d.氧化硅的自然生成7、GaAs的优点:a.比硅更高的电子迁移率; b.减少寄生电容和信号损耗; c.集成电路的速度比硅制成的电路更快; d.材料电阻率更大,在GaAs衬底上制造的半导体器件之间很容易实现隔离,不会产生电学性能的损失;e.比硅有更高的抗辐射性能。
GaAs的缺点: a.缺乏天然氧化物;b.材料的脆性; c.由于镓的相对匮乏和提纯工艺中的能量消耗,GaAs的成本相当于硅的10倍; d.砷的剧毒性需要在设备、工艺和废物清除设施中特别控制。
第三章器件技术8、等比例缩小:所有尺寸和电压都必须在通过设计模型应用时统一缩小。
第四章硅和硅片制备9、用来做芯片的高纯硅称为半导体级硅(semiconductor-grade silicon, SGS)或电子级硅西门子工艺:1.用碳加热硅石来制备冶金级硅SiC(s)+SiO2(s) Si(l)+SIO(g)+CO(g)2.将冶金级硅提纯以生成三氯硅烷Si(s)+3HCl(g) SiHCl3(g)+H2(g)3.通过三氯硅烷和氢气反应来生成SGS SiHCl3(g)+H2(g) Si(s)+3HCl(g)10、单晶硅生长:把多晶块转变成一个大单晶,并给予正确的定向和适量的N型或P型掺杂,叫做晶体生长。
集成电路制造习题

《集成电路制造工艺》习题集第一章序言1.简述集成电路制造工艺发展的大致状况。
2.描述圆片和芯片的关系和区别。
3.和分立器件相比,集成电路有何特有的工艺?4.你如何理解集成电路制造工艺课程的性质和任务。
第二章 薄膜制备2.二氧化硅在半导体生产中有何作用?3.二氧化硅要阻挡杂质要满足什么条件?4.组成二氧化硅基本单元是什么?它有哪两种主要的结构?5.氧在二氧化硅中起何作用?它有哪两种基本形态?5.二氧化硅中的杂质主要有哪几种形式?它们对二氧化硅的结构有何影响?6.什么是热氧化生长法?热氧化后硅的体积如何变化?7.如果要行长20000A的二氧化硅膜,要消耗多少厚度的硅?8.写出三种的热氧化生长法的原理及各自的特点。
9.写出热氧化生长法的主要规律。
10.影响氧化生长速率的因素有哪些?11.在半导体生产中为何常采用干—湿—干的氧化方法。
如果要生长5000纳米的膜,需要多长的氧化时间?(已知在T=1200℃,B湿=117.5um2/min)12.描述二氧化硅-硅系统电荷的种类、产生原因及改进措施。
13.如何测试二氧化硅的厚度?14.二氧化硅的缺陷包括哪几个方面?15.叙述氢氧合成氧化的原理及特点。
16.叙述高压氧化的原理及特点。
17.什么叫掺氯氧化?它有何优点?掺氯氧化时要注意哪些问题?18.热分解氧化和热氧化有何区别?它有何特点?19.简述外延在半导体生产中的主要作用有哪些?20.叙述最常用的外延生长的化学原理?21.外延生长系统包括哪几个主要部份?加热炉的形状有哪几种,各有什么特点?22.画出四氯化硅汽化器的结构框图并说明其工作原理。
23.说明在外延生长过程中如何适当的选择四氯化硅的浓度和外延生长温度?24.外延生长中的热扩散效应对外延质量有何影响?如何减小热扩散现象?25.什么是外延中的自掺杂效应?自掺杂的原因是什么?如何减小自掺杂现象?26.什么是层错?产生的原因是什么?以(111)晶向为例说明如何用层错法测外延层的厚度?测量时要注意些什么问题?27.说明外延厚度的检测方法?28.说明用三探针法测外延层电阻率的原理和方法?29.简述硅烷热分解外延法的原理及特点?30.简述SOS外延的作用及方法。
9、CMOS工艺--现代CMOS工艺基本流程

工艺集成
工艺目的:
① 形成薄膜:化学反应,PVD,CVD,旋涂,电镀; ② 光刻:实现图形的过渡转移; ④ 刻蚀:最后图形的转移; ③ 改变薄膜:注入,扩散,退火;
器件的制备:各种工艺的集成
MOS,CMOS,
4
工艺的选择
器件参数:
阈值电压, 击穿电压, 漏电流, 增益,…
工艺参数:
厚度, 介电常数, 应力, 浓度, 速度,…
淀积铝薄膜之前,先淀积一层重磷或重砷掺杂的多晶硅薄膜,构成 Al-重磷(砷)掺杂多晶硅双层金属化结构。
Al - 掺杂多晶硅双层金属化结构已成功地应用于nMOS工艺中。
3、铝-阻挡层结构
在铝与硅之间淀积一个薄金属层,替代重磷掺杂多晶硅层,阻止铝与 硅之间的作用,从而抑制Al尖楔现象。这层金属称为阻挡层。
宽度为w,厚度为d的铝引线,与硅接触的接触孔 面积为A,如图所示。
Al/Si接触中的改进
1、 Al-Si合金 金属化引线 为了解决Al的尖楔问题,在纯Al中加入硅至饱和,形成Al-Si合金
,代替纯Al作为接触和互连材料。但是,在较高合金退火温度时溶解 在Al中的硅,冷却过程中又从Al中析出。硅从Al-Si合金薄膜中析出是 Al-Si合金在集成电路中应用的主要限制: 2、铝- 掺杂多晶硅双层金属化结构
在400-500℃退火温度范围内,Si在Al薄膜中的扩散系数比在晶 体Al中大40倍。这是因为Al薄膜通常为多晶,杂质在晶界的扩散 系数远大于在晶粒内的扩散系数。
(2) Al与SiO2的反应
3SiO2 4Al 3Si 2Al2O3
Al与SiO2反应对于Al在集成电路中的应用十分重要: ➢Al与Si接触时,可以“吃”掉Si表面的自然氧化层,使
– CMP除去表面的氧化层 – 到Si3N4层为止
第九章 后端工艺
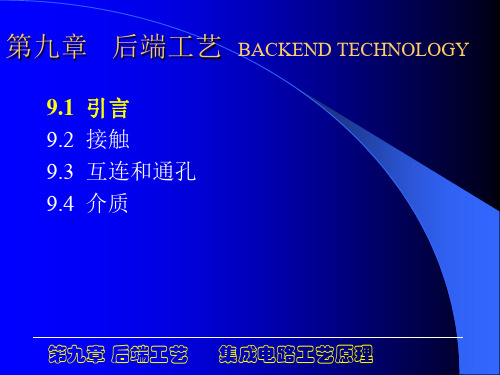
集成电路工艺原理
• Backend processing is becoming more important.
• Larger fraction of total structure and processing. • Starting to dominate total speed of circuit.
cm2接触电阻rrcs第九章后端工艺集成电路工艺原理金属化层和硅衬底的接触既可以形成整流接触也可以形成欧姆接触主要取决于半导体的掺杂浓度及金半接触的势垒高度heavilydopedsimetalohmiccontactsimetalschottkycontact第九章后端工艺集成电路工艺原理低势垒欧姆接触一般金属和型半导体的接触势垒较低高复合欧姆接触alnsi势垒高度07ev需高掺杂欧姆接触alpsi势垒高度04ev晶体缺陷和杂质在半导体表面耗尽区起复合中心作用第九章后端工艺集成电路工艺原理铝和硅接触的问题spikingproblems硅不均匀溶解到al中并向al中扩散形成孔洞al填充到孔洞微米是不能采用纯铝工艺为了确保铝将si表明的自然氧化层还原和铝和硅良好的物理接触要在450度和氢气中进行退火
第九章Байду номын сангаас后端工艺
集成电路工艺原理
Intel 奔腾 III Merced (1999) 6层金属互连,0.18µ m工艺,集成晶体管数2500万个,连线总长 度达5km
第九章 后端工艺
集成电路工艺原理
电路特征尺寸不断缩小 芯片引线数急剧增加
芯片内部连线长度迅速上升
金属布线层数不断增加
第九章 后端工艺
9.1 9.2 9.3 9.4 引言 接触 互连和通孔 介质
BACKEND TECHNOLOGY
- 1、下载文档前请自行甄别文档内容的完整性,平台不提供额外的编辑、内容补充、找答案等附加服务。
- 2、"仅部分预览"的文档,不可在线预览部分如存在完整性等问题,可反馈申请退款(可完整预览的文档不适用该条件!)。
- 3、如文档侵犯您的权益,请联系客服反馈,我们会尽快为您处理(人工客服工作时间:9:00-18:30)。
钛金属接触的主要步骤 1. 钛淀积:溅射钛 2. 退火:700℃以上形成硅化钛TiSi2,硅化钛的电阻 率比钛低很多 3. 刻蚀金属钛:湿法腐蚀未反应的Ti,所有有源区 上都保留TiSi2 钛Ti的优点: ①使硅和随后淀积的金属紧密地结合 ②Ti的电阻率低,且与硅反应生成TiSi2的电阻率更 低。
制作局部互连金属的步骤 1. 金属钛Ti的淀积:溅射Ti,作用:充当钨与二氧化 硅的粘合剂
2. 氮化钛TiN淀积:与Ti溅射使用一台设备,在溅射 Ti后不出工艺腔直接溅射TiN,氮化钛就是阻挡层 金属 阻挡层金属形成的工艺目的:阻挡后续淀积的金 属钨的扩散,提高器件的可靠性 3. 钨淀积:CVD法,钨的作用①比溅射铝有更好的 孔填充,形成钨塞;②具有良好的磨抛特性
P阱的形成步骤 1. 第二次光刻(用N阱的反版):光刻P阱注入区, 不去胶。 2. P阱硼注入(连续三次) :①倒掺杂注入以减小 CMOS器件的闭锁效应,结深1.0μm左右②中等能量 注入以保证源漏击穿电压③小剂量注入以调整阈值 电压。
3. 退火 作用同“N阱的形成”。 形成N阱和P阱的工艺目的:确定PMOS和NMOS 管的有源区(即源区、栅区和漏区)。
4. 轻掺杂漏(LDD)工艺 轻掺杂漏(LDD)工艺目的:减小源漏间的穿通和 沟道漏电,提高源漏击穿电压。 1. 第五次光刻:光刻N-LDD注入区,不去胶。 2. N-LDD注入:低能量注入As,As的作用①分子量 大利于表面非晶化,②慢扩散杂质在后续的热处理 中利于维持浅结
P-轻掺杂漏注入步骤 1. 第六次光刻:光刻P-LDD注入区,不去胶 2. P-LDD注入:低能量注入BF2, BF2的作用①比硼 的分子量大利于表面非晶化,②比硼的扩散系数 低在后续的热处理中利于维持浅结
习 题
第九章(书中第9章): 13、 16、19、25 、26、 28、35 附加题 1.在基本的CMOS IC技术中,P阱的作用是什么? 2. 在先进的0.18um CMOS工艺中,什么是轻掺杂漏 (LDD)注入?它的作用是什么?
3. 第一次光刻:光刻N阱注入区,不去胶,光刻 胶阻挡注入。 4. N阱磷注入(连续三次):①倒掺杂注入以减 小CMOS器件的闭锁效应,能量高200KEV、结深 1.0μm左右②中等能量注入以保证源漏击穿电压③ 小剂量注入以调整阈值电压。 5. 退火 作用①杂质再分布②修复注入损伤③注 入杂质电激活
8. 局部互连工艺 局部互连LI(Local Interconnect)工艺目的:形成金 属布线与器件之间的连接。该工艺称为大马士革。 形成局部互连氧化硅介质的步骤 1. 淀积氮化硅:PECVD法,作用:保护有源区以防后 续掺杂二氧化硅中的杂质向有源区扩散。
2. 掺杂二氧化硅BPSG的淀积:PECVD或HDCVD法, 快速热退火:使BPSG回流 3. 二氧化硅抛光CMP:抛光后氧化层的厚度约8000Å 4. 第九次光刻:光刻局部互连区(引线孔),局部 互连区刻蚀
多晶硅掺杂:也可以原位掺杂,作用:形成导电 的栅电极 3. 第四次光刻:光刻多晶硅栅,DUV深紫外步进式 光刻机曝光,多晶硅上涂抗反射层(ARC),随 后进行特征尺寸、套刻精度、缺陷等质量检查。 4. 多晶硅栅刻蚀:用最好的RIE刻蚀机,保证垂直的 侧壁
注意:从栅氧生长到多晶硅要连续进行以免硅片 沾污等其它问题
制作金属塞1的主要步骤 金属塞的作用:完成金属线之间的电连接。 1. 金属钛Ti的淀积:溅射Ti 2. 氮化钛TiN淀积:在溅射Ti后不出工艺腔直接溅射 TiN 3. 钨淀积:CVD法 4. 钨磨抛
钨互连LI和钨塞的SEM照片
10. 金属1互连的形成
制作金属1互连的步骤
1. 金属钛阻挡层淀积:溅射Ti,此步Ti的作用①在钨 塞与后续铝金属之间有良好的粘合;②提高金属叠 加结构的稳定性
12. 金属2互连的形成
13. 制作金属3直到制作压点及合金
14. 参数测试
1. 双阱工艺
N阱的形成步骤 1. 外延生长:φ8英寸、P-外延/P+衬底、外延层厚 度约5.0μm、片厚约2.0mm 2. 薄氧氧化:厚度150Å 作用 ①表面保护以免沾污 ②减小注入损伤③有助于减轻注入沟道效应
5. 侧墙形成工艺
侧墙工艺目的:侧墙用来环绕多晶硅栅侧壁掩蔽大 剂量的S/D注入以免其接近沟道导致源漏穿通。 1. 淀积二氧化硅:LPCVD法,厚度1000Å 2. 二氧化硅反刻
6. 源/漏(S/D)注入工艺
N+源漏注入步骤 1. 第七次光刻:光刻N+源/漏注入区,不去胶 2. N+源/漏注入: 中等剂量注As
P+源漏注入步骤 1. 第八次光刻:光刻P+源/漏注入区,不去胶 2. P+源/漏注入: 中等剂量注硼 3. 退火:快速热退火RTP,温度1000℃,时间几秒, RTP的作用:①减小注入深度的推进,②其它同 普通的热退火
7. 接触形成工艺
接触形成工艺目的:在硅片所有的有源区上形成金 属接触使硅和随后淀积的导电材料更紧密的结合, 降低欧姆接触电阻。
制作金属塞2的主要步骤 1. 金属钛Ti的淀积:溅射Ti 2. 氮化钛TiN淀积:在溅射Ti后不出工艺腔直接溅射 TiN 3. 钨淀积:CVD法 4. 钨磨抛
12. 金属2互连的形成 1. 金属钛阻挡层淀积:溅射Ti 2. 淀积铝铜合金Al-Cu(1%) 3. 淀积氮化钛TiN:溅射法 4. 第十三次光刻:光刻金属2,刻蚀金属2
第九章
集成电路制造工艺集成
9.1 引 言
工艺集成 前面第二~八章分别介绍了氧化、扩散/离 子注入、淀积、光刻、刻蚀、金属化以及 化学机械抛光,这些都是单项工艺,这些 单项工艺的组合称为工艺集成。 不同的工艺集成形成了不同的集成电路制 造技术。
双极型 MOS型 BiMOS
硅片制造厂的分区 硅片制造厂分成6个独立的生产区:扩散(包括 氧化、热掺杂等高温工艺)、光刻、刻蚀、薄 膜(包括APCVD、 LPCVD、 PECVD、溅射 等)、离子注入和抛光(CMP)。
2. 淀积铝铜合金Al-Cu(1%) 3. 淀积氮化钛TiN:溅射法,作用:充当光刻中的抗 反射层 4. 第十一次光刻:光刻金属1,刻蚀金属1
金属1的SEM照片
11. 通孔2和金属塞2的形成 制作通孔2的主要步骤 1. ILD-2氧化硅的间隙填充:HDCVD法 2. ILD-2氧化硅淀积:PECVD法 3. ILD-2氧化硅抛光 CMP 4. 第十二次光刻:光刻通孔2,通孔2的刻蚀
2. 氮化硅淀积:LPCVD淀积,作用:做CMP的阻挡 层,保护有源区免受CMP的过度抛光
3. 第三次光刻:光刻浅槽隔离区
4. STI槽刻蚀:RIE刻蚀,槽深1.0μm左右
STI氧化物填充步骤 1. 沟槽衬垫氧化硅生长:厚度150Å 作用:改善硅与 沟槽填充氧化物之间的界面特性。 2. 沟槽CVD氧化物填充:LPCVD方法
STI氧化层抛光-氮化物去除步骤 1. 沟槽氧化物抛光CMP 2. 氮化硅去除:热磷酸煮
3. 多晶硅栅结构工艺 该工艺是工艺流程中的最关键工艺!!因为①它包 括最薄、质量最好的栅氧化层的热生长!②多晶硅 栅的线宽是整个硅片上的特征尺寸! 1. 栅氧化层的生长:厚度20~50Å ,形成MOS管的栅 电极介质 2. 多晶硅淀积:LPCVD法,厚度5000Å
13. 制作金属3直到制作压点及合金
多次重复11和12完成金属3至金属4的形成工艺 淀积顶层二氧化硅和顶层氮化硅做为表面钝化复合 介质 第十八次光刻:光刻压焊窗口 合金化
Full 0.18 μm CMOS Cross Section
AMD处理器剖面SEM照片来自14. 参数测试 探针台测试Prober
4. 钨磨抛
局部互连LI 工艺-大马士革
9. 通孔1和金属塞1的形成
层间介质ILD(InterLayer Dielectric)的作用:做为 各层金属之间以及第一层金属与硅之间的绝缘介质 材料以隔离各层金属、多晶硅或硅导电层。 制作通孔1的主要步骤
1. 第一层层间介质氧化物的淀积:APCVD或PECVD 法 2. 第一层层间介质CMP:抛光后氧化层的厚度约 8000Å 3. 第十次光刻:光刻通孔1,通孔1的刻蚀
2. 浅槽隔离工艺
局域氧化LOCOS隔离的缺点 ①LOCOS隔离技术存在鸟嘴,浪费有源区面积影响 集成度 ②横向尺寸不能精确控制。
2. 浅槽隔离工艺 浅槽隔离STI(Shallow Trench Isolation)工艺目的: 把硅片上的各个晶体管进行电隔离。 STI槽刻蚀步骤 1. 薄氧生长:厚度150Å 作用:在去掉上面氮化硅时 保护有源区以防被腐蚀。
CMOS简要工艺流程
CMOS简要工艺流程(续)
CMOS简要工艺流程(续)
9.2 先进的0.18μm CMOS集成电路工艺技术
1. 双阱工艺 2. 浅槽隔离工艺 3. 多晶硅栅结构工艺
4. 轻掺杂漏(LDD)工艺
5. 侧墙形成工艺
6. 源/漏(S/D)注入工艺
7. 接触形成工艺
8. 局部互连工艺 9. 通孔1和金属塞1的形成 10. 金属1互连的形成 11. 通孔2和金属塞2的形成