顶出系统设计手册
顶出缸

一序言液压设计综合运用了我们大学里的基础课程及专业课程,技术基础和大部分专业课程的知识,是对我们大学所学的知识进行一次综合性的贯通和考验。
这次设计是大学学习生活中重要地位,也是我们步入社会的一次适应性的训练。
从中锻炼自己的发现问题、分析问题、解决问题的能力,为今后从事的工作打下了一个良好的基础。
二液压机系统的设计思想液压机是锻压、冲压、冷挤、校直、弯曲、塑料制品的压制成型等工艺广泛应用的压力加工机械。
首先它要满足主机动作和性能方面的规定要求(液压系统的动作:快进---快退---停止和性能要求回程、卸压、换向平衡、保压限时自动快退、到位自动停止、活动横梁停车后不下滑)还需符合体积小、重量轻、成本低、效率高、结构简单、工作可靠、使用和维修方面等设计原则,于是简单、使用变成本次设计的理念,是我们设计开展的一个关键因素和设计目标。
在设计过程中努力朝这个方向发展。
七喜M 集团和中兴通信公司(移动通信实习三液压系统的设计参数和工况分析1、顶出缸设计参数如下:公称压力 1250KN工作压力 25MPa快进速度 30mm∕s回程速度 42mm∕s工作行程 150mm2、中心缸设计参数如下:公称压力 125KN工作压力 25MPa快进速度 75mm∕s回程速度 130mm∕s工作行程 150mm3、工况分析从设计任务书中,系统的运动速度,公称压力和工作压力都可知,在对液压系统元件设计过程中,流量成为了解决问题的关键。
通过液压执行元件的的运动速度和结构尺寸可得出流量,又通过流量和工作压力选用所需的其他元件,诸如液压马达、电动机等。
四液压缸的设计一、设计依据1、液压缸是液压系统中常用的执行元件,是吧液体的压力能转变为机械能的装置,主要用于实现机构的直线往复运动,也可以实现摆动。
它与主机和主机上的机构有着直接的联系,对于不同的机种和机构,液压缸具有不同的机构和工作要求。
因此在设计前要作好调查研究;备齐必要的原始资料和设计依据,其中只要包括:(1)主机的用途和工作条件(2)工作机构的结构特点、负载情况、行程大小和动作要求(3)液压系统所选定的工作压力和流量(4)有关国家标准和技术规范液压缸的额定工作压力,往复运动速比,以及缸体内径、外径、活塞直径和进出口连接的尺寸等基本参数,在JB2183-77现行的标准有规定2、液压缸的设计步骤如下:(1)液压缸类型和各部件的选择(2)基本参数的确定---基本参数主要包括液压缸的工作负载,工作速度和速比,工作行程和导向长度,缸筒内径及活塞杆直径等。
塑胶模具设计原理:顶出系统

尺寸規格及材質
顶针布置 1、 在产品图上,首先在四边打顶针,然后在肋板两边打。 如肋深,则最好拆入子,在边上打肩销,宽度在1.2mm以上。 2、 在大平面上不用小顶针。直径不宜过细,需要足够刚度如不可加大,则做成台阶形。 Boss处用顶出套筒,如不,则必须在其附近打两枝顶针。 3、 顶出套筒尺寸确认,套筒厚度要有1mm以上内外径尺寸抓整数。 4、 顶针不宜设在产品最薄处,应在产品强度最大处布置,效果最好,不易顶白顶伤。 5、 顶针不可布置在滑块下面,必须时要加早回机构配合。顶针尽可能避免在高低面过渡的地方
四.顶板顶出: 如果塑件的沿周都要顶出的话,那就考虑用顶板顶出,另,一些特殊的产品表面不允许
有顶针的痕迹,也可以用顶板顶出的方式,顶板顶出制品受力 比较均匀,不易变形,一般适 用于盒盖类制品.推板内侧和胶位一般需留0.3mm的距离,在胶位不足的情况下,最小可 留到0.05mm,防止刮伤模仁,如图:
顶针的定位 当顶针的顶面为非平面或顶针面有成型胶位时,顶针的沉头部位就需要设计定位装置, 顶针转动或被装错.常用的定位装置有以下几种:
在较深的圆桶形胶位比较适用顶管顶出,司筒的固定方式于普通圆顶针一样,如成型的表面 为非平面,则司筒需加定位装置,方式参照原顶针的定位方式,司筒针定位于公模固定板,司筒 和司筒针前端前端采用精密配合防止制品毛边,后端应逃料0.1-0.2MM.以减少摩擦.具体参 数可参照顶针于模仁的配合.
塑胶模具设计原理 顶出系统
顶出系统
其中机械顶出为最 常用,分为顶针顶出,顶管顶出,顶块顶出及顶板顶出等.而顶针顶又为最常见,分为圆顶针 和扁顶针及异型顶针,此外根据顶出机构的不同还可分为 延时顶出,母模顶出,及二次顶 出等
塑料模具顶出系统设计
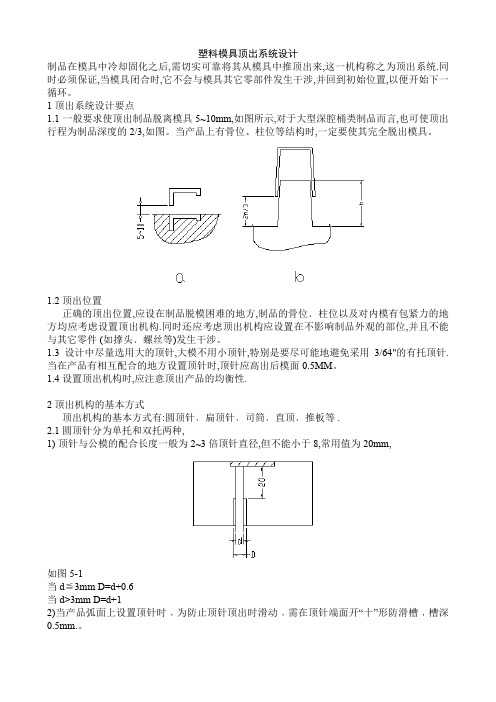
塑料模具顶出系统设计制品在模具中冷却固化之后,需切实可靠将其从模具中推顶出来,这一机构称之为顶出系统.同时必须保证,当模具闭合时,它不会与模具其它零部件发生干涉,并回到初始位置,以便开始下一循环。
1 顶出系统设计要点1.1一般要求使顶出制品脱离模具5~10mm,如图所示,对于大型深腔桶类制品而言,也可使顶出行程为制品深度的2/3,如图。
当产品上有骨位、柱位等结构时,一定要使其完全脱出模具。
1.2 顶出位置正确的顶出位置,应设在制品脱模困难的地方,制品的骨位﹑柱位以及对内模有包紧力的地方均应考虑设置顶出机构.同时还应考虑顶出机构应设置在不影响制品外观的部位,并且不能与其它零件 (如撑头﹑螺丝等)发生干涉。
1.3设计中尽量选用大的顶针,大模不用小顶针,特别是要尽可能地避免采用3/64"的有托顶针.当在产品有相互配合的地方设置顶针时,顶针应高出后模面0.5MM。
1.4设置顶出机构时,应注意顶出产品的均衡性.2 顶出机构的基本方式顶出机构的基本方式有:圆顶针﹑扁顶针﹑司筒﹑直顶﹑推板等 .2.1圆顶针分为单托和双托两种,1) 顶针与公模的配合长度一般为2~3倍顶针直径,但不能小于8,常用值为20mm,如图5-1当d≦3mm D=d+0.6当d>3mm D=d+12)当产品弧面上设置顶针时﹐为防止顶针顶出时滑动﹐需在顶针端面开“十”形防滑槽﹐槽深0.5mm.。
3)顶针与周边零件的位置关系。
顶针边与骨位﹑镶件的最小距离为2.0mm,与产品边﹑水道最小距离为3.0mm。
.4)当产品中柱位孔为前模碰穿方式,其下放置顶针时,处理方式如图:5)顶针的管位.当顶针位于圆弧面或者当顶针和司筒受胶位方向限制时,往往要设置管位装置,管位方式有下列三种:见图,其中图a为设置管位钉,较常用;图b为加一管位块;图c为将顶针头部加工为直边,此方式较常用于大顶针的场合。
6)镜类产品不允许产品上有顶出痕迹,常采用垃圾钉顶出,产品有扣时,顶针边距产品边2mm,无扣时为3mm,如图:7)有时,将顶针顶端加工成”z”形头,达到制品留后模的目的,此时应保证,使”z”形头方向一致。
塑胶模具设计顶出系统
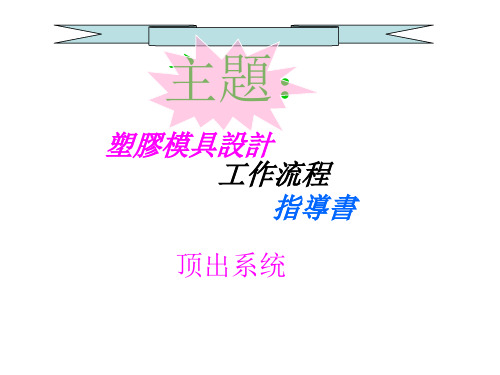
頂出系統
在设计顶出系统时应遵守下列原则: (1). 为使制品不致因顶出产生变形﹐破裂,穿孔等,推力点应作用在制品能 承受力最大的部位,即刚性好的部位,如筋部,突缘,壳体形制品的壁缘等处. (2). 为避免顶出痕迹影响制品外观,顶出装置应设在制品的隐蔽面或非装饰 表面.对于透明制品尤其要注意顶出位置及顶出形式的选择. (3)﹑頂出行程一般在制品脫離模具5~~10mm﹐對于簡單﹑大型的制品可 頂出行程是制品深度的2/3。 (4)﹑回位杆(RP) ﹕在頂杆頂出制品后﹐其頂端會高出模穴許多﹐避免在 下次合模前撞壞模仁﹐必須有保護機構﹐所以設置回位杆(RP)﹐也可設置 拉回機構和彈簧助其復位。 (5)﹑頂杆端面一般會高于模穴面0.05~~0.1mm,以免塑胶上留有顶杆突起 痕迹,但也要依产品情况而定。 (6)﹑有内模镶件的模具,顶杆离镶件边缘不得小于0.80MM.顶杆离运水的 边缘不得小于3MM. (7)﹑顶杆在模仁里的配合长度应小于2D(D<6MM.D为顶杆直径),对于大型 模具不大于1.5D. (8)﹑顶杆的大小根据成品的大小来确定,原则上宁多勿少,直径宁大勿小.
脫料板
頂出系統
6.斜銷 當成品中使用斜銷較多且其它地方不易排頂針時就 可直接用斜銷來頂出成品。用斜销顶出时(特别是较 大的斜销)应考虑产品是否会沾斜顶.并采取相应的措 施预防.
斜銷
頂出系統
7.氣頂 。 氣頂出方式不論是在公模部份或母模部分,其頂出都很方便,不 需要安裝推板.在頂出過程中整個制品的部均受同樣地的壓力,所 以即便是軟的塑料,也可以在不發生變形的條件下脫離模具,通常 氣頂出要求脫模斜度最小大於2∘,所以對於形狀復雜需要較大脫 模力的制品,則無法滿足其要求。
模具设计规范
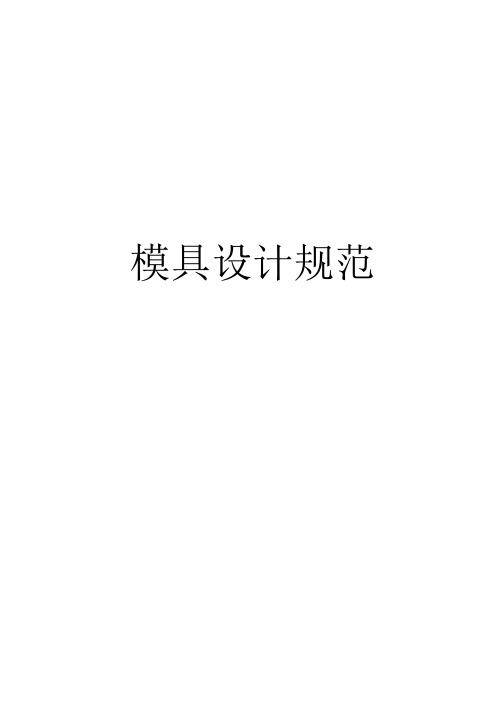
3
5 5
3.5
5 6
φ 3、φ 2.5、φ 2
φ 4、φ 5、φ 6、φ 7 φ 8 、 φ 9 、 φ 10 、 φ 12 、 φ 16 、 φ 20
d
d1+0.5
h
2.方式二:对于非DMG客户的模具顶杆止转及定位采用以下方式:
2.2
为了减少顶杆的加工量,并防止顶杆安装方向错误,特修订我公司顶杆 的杯头止转形式。改为杯头单面止转。设计尺寸见图2。 对于外单模具,若客户另有要求,按客户标准执行。无要求,则按新标 准执行。
模具设计规范
前言
• 为了满足设计及制造的要求, 指导设计工作,现将设计及制 造中应注意的问题加以整理。 待设计标准系统化后再行纳入。
•
海尔模具标准化办公室
一、冷却系统设计
1.1、模板冷却设计要求
* 三板模:要求水口板加冷却水路。 * 热流道模具:要求热流道板加冷却水 路。每个热嘴必须单独冷却。 * 对于模具长度超过1000MM的情况下, 底针板,底板必须加单独的冷却回路, 以保证针板与后模板温度一致。
*三板模倒锥形拉料杆:
三板模倒锥形拉料杆的作用主要是通过倒 扣力拉断点浇口.其设计参照:《标准件库》
*分流道拉料杆:
图5 分流道拉料杆设计
设计要点: (1)对于较长的分流道系统,应设计分流道拉 料杆.其主要作用是顶出分流道. (2) 分流道拉料杆的头部设有冷料井 , 深度 3MM 左右 , 目的为了分流道料把顶出过 程中起到导向作用,使料把顶出平衡.
以上两种形式在没有海尔模具的标准,对于没有特殊设计标准的模具均采用上述方式加工。
3.2、搭接流道设计
对于锥形流道加工在模具的两个零件上的情况,应考虑脱模, 将流道设计成如图3.1形式。一般C>0.2MM.
模具设计-顶出系统
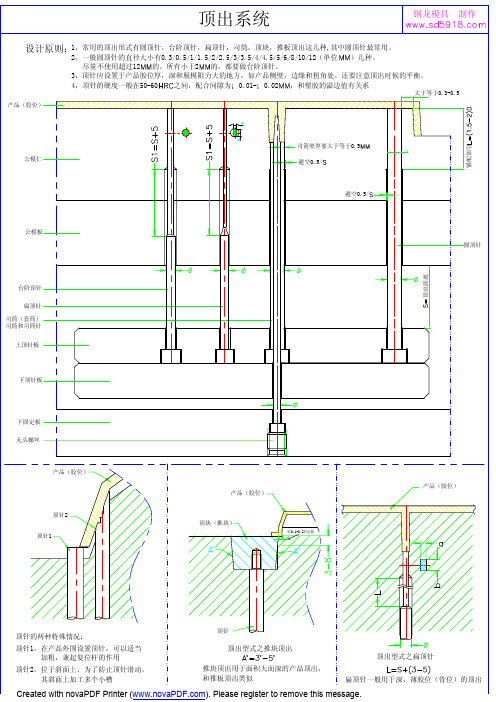
顶针
顶出型式之推块顶出 顶出型式之扁顶针 推块顶出用于面积大而深的产品顶出, 和推板顶出类似 扁顶针一般用于深,薄胶位(骨位)的顶出
Created with novaPDF Printer (). Please register to remove this message.
顶出距离
紧配部分
司筒壁厚要大于等于0.5
大于等于0.3-0.5 产品(胶位)
公模仁
避空0.5/
避空0.5/
公模板 圆顶针
台阶顶针 扁顶针 司筒(套筒) 司筒和司筒针 上顶针板
下顶针板
下固定板 无头螺丝
产品(胶位) 产品(胶位) 产品(胶位)
顶针2 顶块(推块) 顶针1
留0.1-0.2的间隙
顶针的两种特殊情况: 顶针1,在产品外围设置顶针,可以适当 加粗,兼起复位杆的作用 顶针2,位于斜面上,为了防止顶针滑动, 其斜面上加工多个小槽
顶出系统
设计原则:1,常用的顶出形式有圆顶针,台阶顶针,扁顶针,司筒,顶块,推板顶出这几种,其中圆顶针最常用。
钢龙模具
制作
2,一般圆顶针的直径大小有0.3/0.5/1/1.5/2/2.5/3/3.5/4/4.5/5/6/8/10/12(单位 )几种。 尽量不使用超过12 的。所有小于2 的,都要做台阶顶针。 3,顶针应设置于产品胶位厚,深和脱模阻力大的地方,如产品侧壁,边缘和拐角处。还要注意顶出时候的平衡。 4,顶针的硬度一般在50-60 之间,配合间隙为¡ 0.01-¡ 0.02 ,和塑胶的溢边值有关系
没有顶针顶出的模具是如何设计的呢?

没有顶针顶出的模具是如何设计的呢?
没有顶针顶出的模具是如何设计的
题主的问题应该是涉足于塑胶模具,塑胶产品在注塑时从模具中脱落,离不开脱模装置,没有顶针,那么还应该有其它的产品脱模装置。
1例如:纯净水瓶盖产品内部是看不到顶针的,内部是螺纹,这种带螺纹的产品,脱模的方式一般有两种:
1-1 二级缩呵标准件装置,这是一种比较特殊的标准件,螺纹产品在一边顶出时,标准件会一边向内缩呵而脱离内螺纹;
1-2 是利用齿轮齿条的带动,旋转内模件而使产品脱离模具;
2例如:生活中用到的水桶,洗脸盆之类的这类产品也是不需要顶针顶出的,而它一般需要气顶,因为产品的内模在注塑后形成的真空状,这时需要气顶使产品和内模脱离,再用手动取出产品,或者利用机械手取出产品。
3 有些产品为了美观,会用到推块、推板类的顶出,需要具体产品具体对待。
4 还有更加特殊的产品,比如产品在滑块上,将整个滑块系统顶出模具后,利用滑块抽出后,产品自动脱模。
当然,还有其它的很多顶出方式,整个模具设计过程中,需要不断的去积累知识,相信你也会设计出这类不需要顶针顶出的模具的。
ug模具设计三大系统设计方案
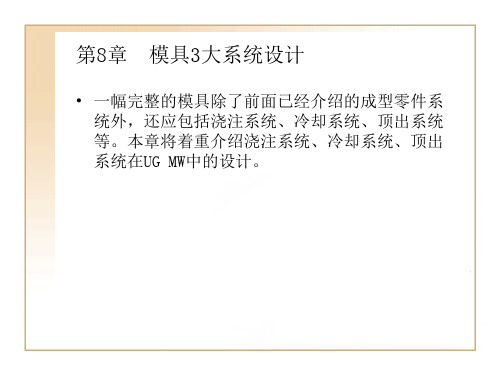
8.4.3 腔体
• “腔体”工具即是用来创建模具标准组件在模架和模腔中 的空腔(有形状但无特征的空间),或者合并标准组件和 模架、模腔以创建新的特征。
• 在“注塑模向导”对话框中单击“腔体”按钮,弹出“腔 体”对话框,如图8-56所示。
8.5 实例:模具3大系统设计
• 本章前面主要介绍了模具的3大系统组件的结构以及在设计中应注 意的问题,并在MW模块中对3大系统组件标准件做了简要介绍,下 面以一个实例来说明3大系统组件标准件在模具设计过程中的应用。 实例模型为已加载完成模架及主流道标准件的初始化项目模型。
8.2.1 冷却系统的设计要点
• 冷却系统在设计过程中的须注意以下设计要点。 • 1. 冷却水路设置要使冷却效果均匀 • 2. 水管的尺寸与排放位置 • 3. 冷却水管的长度 • 4. 冷却水路类型
8.2.2 冷却管道设计
• 在பைடு நூலகம்W模块中,冷却水管的创建仅适用于已项目初始化的模具总装配部件。 假如是一般模型部件,则只能以冷却标准件的加载方式来设计冷却水路。
8.4.1 推杆后处理
• “推杆后处理”工具是用来修剪顶杆标准件的专用工具。 • 在“注塑模向导”工具条上单击“推杆后处理”按钮,弹出“推
杆后处理”对话框,对话框中包括了两个功能标签:“修剪过程” 标签(如图8-46所示)和“修剪组件”标签(如图8-47所示)。
8.4.2 Trim Mold Components(模具修剪)
• 单击“注塑模向导”工具条中的“流道”按钮,弹出“流道设计”对话框, 如图8-2所示。
8.1.3 浇口设计
• 浇口是连接流道与模腔之间的通道。MW中创建浇口所使用的工具 仅针对项目初始化的模具总装配体部件。
• 在“注塑模向导”工具条上单击“浇口”按钮,弹出“浇口设计” 对话框,如图8-8所示。对话框中包括有“平衡”、“位置”、 “方法”、“浇口点表示”、“类型”、“重定位浇口”、“删 除浇口”、“编辑注册文件”和“编辑数据库”功能选项和按钮 命令。
注塑模具设计:第三章:顶出系统
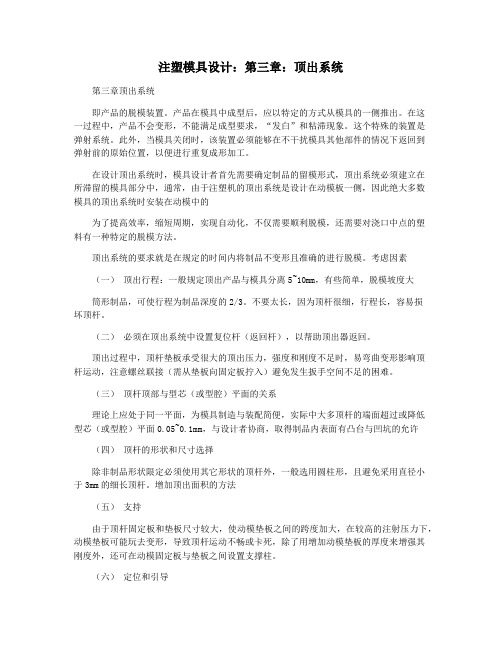
注塑模具设计:第三章:顶出系统第三章顶出系统即产品的脱模装置。
产品在模具中成型后,应以特定的方式从模具的一侧推出。
在这一过程中,产品不会变形,不能满足成型要求,“发白”和粘滞现象。
这个特殊的装置是弹射系统。
此外,当模具关闭时,该装置必须能够在不干扰模具其他部件的情况下返回到弹射前的原始位置,以便进行重复成形加工。
在设计顶出系统时,模具设计者首先需要确定制品的留模形式,顶出系统必须建立在所滞留的模具部分中,通常,由于注塑机的顶出系统是设计在动模板一侧,因此绝大多数模具的顶出系统时安装在动模中的为了提高效率,缩短周期,实现自动化,不仅需要顺利脱模,还需要对浇口中点的塑料有一种特定的脱模方法。
顶出系统的要求就是在规定的时间内将制品不变形且准确的进行脱模。
考虑因素(一)顶出行程:一般规定顶出产品与模具分离5~10mm,有些简单,脱模坡度大筒形制品,可使行程为制品深度的2/3。
不要太长,因为顶杆很细,行程长,容易损坏顶杆。
(二)必须在顶出系统中设置复位杆(返回杆),以帮助顶出器返回。
顶出过程中,顶杆垫板承受很大的顶出压力,强度和刚度不足时,易弯曲变形影响顶杆运动,注意螺丝联接(需从垫板向固定板拧入)避免发生扳手空间不足的困难。
(三)顶杆顶部与型芯(或型腔)平面的关系理论上应处于同一平面,为模具制造与装配简便,实际中大多顶杆的端面超过或降低型芯(或型腔)平面0.05~0.1mm,与设计者协商,取得制品内表面有凸台与凹坑的允许(四)顶杆的形状和尺寸选择除非制品形状限定必须使用其它形状的顶杆外,一般选用圆柱形,且避免采用直径小于3mm的细长顶杆。
增加顶出面积的方法(五)支持由于顶杆固定板和垫板尺寸较大,使动模垫板之间的跨度加大,在较高的注射压力下,动模垫板可能玩去变形,导致顶杆运动不畅或卡死,除了用增加动模垫板的厚度来增强其刚度外,还可在动模固定板与垫板之间设置支撑柱。
(六)定位和引导在制品产量大,或顶出行程长,同时使用较细的顶杆,以及使用顶管顶出并在动模固定板装有细长芯子时,为保护顶杆(或长芯子)使其运动平稳,顶出系统需要设置导向装置,并且在动模板与垫条以及动模固定板之间装有定位销钉,以保证位置精度(七)弹射位置制品凡是有塑料包围钢件的地方,脱模都会困难,这是因为塑料熔体冷却后的收缩应力而产生对钢件的“抱紧”现象所导致的,故这些地方(筋、柱)都应重点考虑喷射器的分类一、圆顶杆,易加工,最普通,最简单的标准件,顶杆需淬火处理,获得足够的轻度和耐磨性。
注塑模具设计第10讲 实例1-2D-09 顶出系统的设计
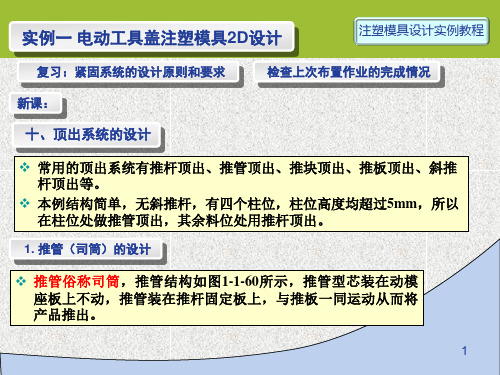
推管插入第1点
图1-1-62 侧剖视图中的推管
2. 推杆排布及规格选用 (1)推杆排布要点: ①为防止产品变形,受力点应尽量靠近型芯或难以脱模的部位,如细 小的加强筋、柱位、台阶、金属嵌件、局部厚壁等结构复杂部位。相 邻两推杆的排布边距一般为20mm左右,视产品的结构情况而定。 ②受力点应作用在制品能承受最大力的部位,即刚性好的部位。 4
IN2 OUT2
推杆与型芯的配合 段为20mm左右
流道推杆
拉料杆
图1-1-67 推杆在正剖视图中的表达
3. 冷料井及拉料杆的设计 在主流道的末端通常要设计冷料井及拉料杆。 拉料杆结构形式有Z字形拉料杆、锥形拉料杆和圆头形拉料杆等几 种,如图1-1-68所示。图1-1-68 (a)所示为点浇口拉料杆,图1-168 (b)、(c)、(d)所示为侧浇口拉料杆,其中图1-1-68 (b)为常 见的Z字形拉料杆。本例采用较常见的Z字形拉料杆。
注塑模具设计实例教程
型芯
动模板
顶出空间
推杆 固定板
推板
动模座板
推管 C角
推管
推管型芯
无头螺钉
图1-1-60 推管结构
确定推管型芯和推管的大小:本例柱位的内孔直径为Φ2.41mm,外径为 Φ5.02mm,故选用推管型芯直径为Φ2.4mm,推管外径为Φ5.0mm的标准 推管,柱位的C角一般在推管上磨出,以保证推管壁厚的强度。 推管型芯的固定:推管型芯固定于模具的动模座板上。 根据推管型芯直径的大小不同,有不同的固定方式。推管型芯较 小时,采用无头螺钉固定;当推管型芯直径d>8mm或多个推管型 芯相距较近时,采用压板方式固定。 本例的推管型芯较小,故采用无头螺钉固定。
2
顶出系统的设计
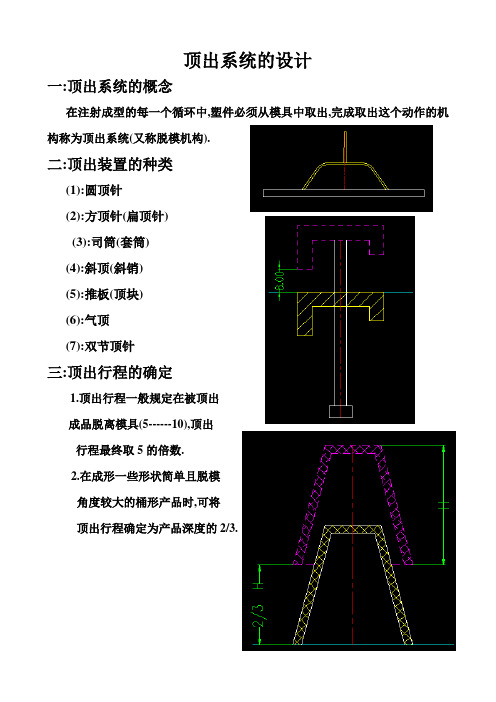
顶出系统的设计
一:顶出系统的概念
在注射成型的每一个循环中,塑件必须从模具中取出,完成取出这个动作的机
构称为顶出系统(又称脱模机构).
二:顶出装置的种类
(1):圆顶针
(2):方顶针(扁顶针)
(3):司筒(套筒)
(4):斜顶(斜销)
(5):推板(顶块)
(6):气顶
(7):双节顶针
三:顶出行程的确定
1.顶出行程一般规定在被顶出
成品脱离模具(5------10),顶出
行程最终取5的倍数.
2.在成形一些形状简单且脱模
角度较大的桶形产品时,可将
顶出行程确定为产品深度的2/3.
三:顶出系统的设计原则
1.顶出机构的运动要准确,可靠灵活,无卡死现象,机构本身要有足够的强度与刚度,足以克服脱模阻力.
2.保证塑件在顶出过程中不变形.顶出要平衡.
3.冷却后由于塑件会对模仁产生收缩应力,而有抱紧现象,在靠破孔的两边成品肉厚强度最弱,应设置顶针.
4.在成品垂直的壁厚正下方就设置顶针,便于脱模.
5.在”十字肋”下方应设置顶针,即可排气也可顶出.
6.在公模侧顶针时,需要注意模仁强度,顶针距模仁边最小距离为0.8
7.选择顶针时,在允许的范围内直径尽可能大,且是标准品.同一产品上的顶针不宜多类,为加工节约成本与时间.
8.小于3mm以下的顶针一定要做成双节顶针.。
塑胶模具设计规范

模具设计规范(此规范主要应用于手机模具)一、模具排位1、根据产品大小、结构、产量、精密程度、材料或客户要求等因素确定模穴,如1X1、1X2等。
2、当几个产品出在同一套模具中时,考虑进胶的均匀性,应将大的产品排在中间位置,小的产品置于两边。
确保冲胶平衡,保证产品尺寸的精确性。
3、当几个分型面不规则的产品在同一模具中时,排位必须充分考虑其分型面连接的顺畅,且容易加工。
4、一模多穴模具中,当有镶拼,行位等结构时,不得使其发生干涉。
5、排位多时应综合模具每一方面,对流道,是否镶拼,行位,顶出,运水等结构要有一个全局性思考。
6、排位时产品在模上的定位基准要和产品图的基准一致,当一模出一件时,可以考虑以产品对称方向处分中。
7、内模钢料和模胚的大小尺寸如下图所示。
8.产品大小和胶位厚度有较大相差时尽量不要出在同一套模具中。
9.模具方铁高度尽量订做标准高度。
10.模胚型号和中托司使用情况一定要写清楚(细水口需注明SP长度)11.必要时需注明模胚吊模孔移位情况12.考虑需不需开精框及内模料材料和规格(确定后模要不要镶大呵,如需要则一起订料,此为粗料.)二、模具系统设计一)、行位系统当塑胶产品确定前后模开模方向后,有下列情况时一般会采用行位或斜顶等结构:1)、相对出模方向塑胶产品上有倒扣或零度面;2)、产品的出模斜度不够蚀纹的角度;3)、保证特殊的外观面不能有夹线。
1、后模行位:1)、后模行位统一做镶件压块,行位压块用螺丝固定,行位压块材料为油钢淬火至HRC48-52°.2)、所有与行位相对运动的零部件的滑动面(包括行位底耐磨片,压条,铲基斜面)须锣(磨)油坑,油坑可为平行四边行、V形或圆环形。
3)、行位铲机钢材整体采用738H,在铲机斜面上镶耐磨片,耐磨片可突出斜面0.5mm,耐磨片厚度为6mm(如下图),材料为油钢,淬硬至HRC48—52°。
康铨公司的铲基采用国产S136淬硬至HRC46—50°.4)、行位沉深B板25mm以上,行位压块沉深B板15mm以上.5)、行位开模采用斜导柱。
塑胶模具设计指引
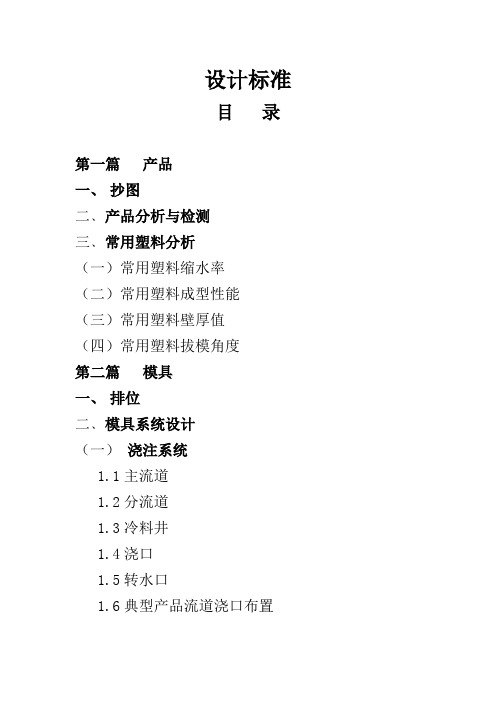
设计标准目录第一篇产品一、抄图二﹑产品分析与检测三﹑常用塑料分析(一)常用塑料缩水率(二)常用塑料成型性能(三)常用塑料壁厚值(四)常用塑料拔模角度第二篇模具一、排位二﹑模具系统设计(一)浇注系统1.1主流道1.2分流道1.3冷料井1.4浇口1.5转水口1.6典型产品流道浇口布置(二)成形系统2.1行位系统行位斜顶2.2镶件(三)顶出系统4.1顶出系统设计要点4.2顶出机构的基本方式 4.2.1顶针4.2.2司筒4.2.3扁顶针4.2.4直顶4.2.5推板4.3先复位机构(四) 冷却系统5.1.运水位置5.2.水路大小5.3.水路与模胚位置关系5.4.水井(五) 导向定位系统(六) 排气系统7.1产品排气7.2导套排气槽7.3尼龙螺丝排气孔(七)模胚结构件(支撑)及周边辅助件 7.1撑头7.2垃圾钉7.3锁模机构7.4温控箱、水管、紧固件三﹑细水口模设计四、模具零部件材料选择六、分模(一)模具档分模(二)组立档分模七、注射机选择第三篇图档一、出图要求1.排位图2.装配图3.顶针图4.线割图5.零件图6.分模图7.爆炸图二、图纸管理与进度控制(一)图纸管理(二)审图(三)进度三、电脑图档管理第四篇附录一、标准件二、工程表格产品篇抄图一.抄图前,先要看懂,看透产品线图,然后班顺思路,特别是外形面的画法。
抄好产品图要转为2D线图与设计部提供的平面线图套。
要保证主要的视图和边界线完全重合一致。
若有不重合、不一致的情况,首先分析是2D线图本身表达有问题,还是抄图时造成的。
若为2D线图表达问题则应及时标明,并与设计部沟通、反映;若为抄图问题,及时修改。
二.一个产品通常要多次转图与标题栏对上几次逐步确认(看版本),避免最后的问题堆积。
三.在抄图的整个过程中,最为重要的是基体外形面的控制和核对。
四.抄好的UG尽可能保证可以再生,以实现UG的参数设计功能。
五.通常抄图应先抄好影响模具结构之处,如外形面、行位处倒勾、前后模基面加减胶。
顶出系统的设计
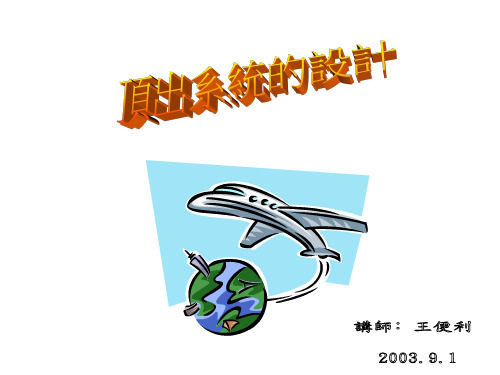
圖7-08
(6)﹑透明件﹕需視其用途及外觀考慮頂針的排布及頂出方式。
A﹑頂針排在LENS柱旁邊(LENS柱下方不便排頂針)﹐見圖7-09﹔ B﹑頂針排在LENS柱下方(依其形狀)﹐見圖7-10﹔
C﹑頂針排在LENS柱下方(頂針大于LENS柱)﹐見圖7D﹑利用假流道頂出(外觀11件﹔不能有頂針印)﹐見圖7E﹑整塊頂出﹐見圖7-13﹔12﹔
備料時需附圖﹐總長須往正向取整數。
4.套筒
材質 硬度(熱處理)
表7-04
套筒 標准參數
備注:套筒尺寸需依照模具實際情況而定﹔ 沉頭部分參照標准頂針﹐套筒壁厚一般為0.75~~1.5MM﹔ 備料時需附圖﹐總長須往正向取整數。
5.雙節套筒
材質 硬度(熱處理)
表7-05
雙節套筒 標准寸法
備注:雙節套筒作用為增加強度﹐尺寸需依實際情況而 定﹔
2.雙節頂針
材質 硬度(熱處理)
表7-02
備注:表格內參數為一廠商標准﹐僅供參考,N值確定可參照圖7-03﹔ 當Φd<1.5且L>100 or Φd<=3且L>200時﹐采用雙節頂針﹔ 備料時需附圖﹐總長須往正向取整數。
3.扁梢
材質 硬度(熱處理)
表7-03
扁梢 標准參數
備注﹕設計扁梢時先確定A﹑B值﹐再依(Φd>a)選用標准頂針﹐ N值確定可參照圖7-03;
脫模步驟﹕
見圖7-18﹐公母模分開;
頂出時﹐因開閉器(13)的作用力保持四塊頂板一出﹔
當頂出L時﹐限位柱(12)碰到公模板﹐阻止頂板(6﹑7)繼 續頂出,此時成品已完全脫離模仁﹐只有倒勾部(17)﹔
頂板(4﹑5)繼續頂出﹐頂針(16)使成品脫離(17),完成頂 出。
顶出系统的设计
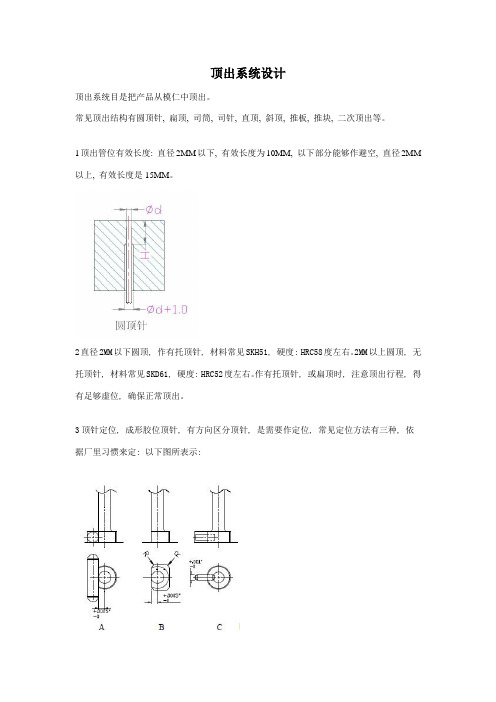
顶出系统设计顶出系统目是把产品从模仁中顶出。
常见顶出结构有圆顶针, 扁顶, 司筒, 司针, 直顶, 斜顶, 推板, 推块, 二次顶出等。
1顶出管位有效长度: 直径2MM以下, 有效长度为10MM, 以下部分能够作避空, 直径2MM 以上, 有效长度是15MM。
2直径2MM以下圆顶, 作有托顶针, 材料常见SKH51, 硬度: HRC58度左右。
2MM以上圆顶, 无托顶针, 材料常见SKD61, 硬度: HRC52度左右。
作有托顶针, 或扁顶时, 注意顶出行程, 得有足够虚位, 确保正常顶出。
3顶针定位, 成形胶位顶针, 有方向区分顶针, 是需要作定位, 常见定位方法有三种, 依据厂里习惯来定: 以下图所表示:当采取第三种方法时, 顶针托高为4MM时。
销针直径为1.5MM, 当托高大于4时, 销钉直径为2.5MM。
4顶针位置: 标准: 顶针尽可能大, 型号尽可能小。
4.1顶针应该离开后模边最少0.5MM, 尽可能不得超出3.0MM。
4.2顶针尽可能放在成品底部, 如A针, 尽可能离模芯0.3, 避免放在顶部, 如B针。
4.3斜面上尽可能不要下顶针, 如一定要, 应在斜面上顶针加防滑位。
4.4碰穿面上顶针, 为了预防她撞坏前模, 通常装顶针磨低0.02MM, 相当于加了个排气, 同时, 回针底下加弹簧, 起保护作用。
4.5胶柱顶出, 有二种方法, 一是胶柱下直接加顶针, 起顶出和排气二种作用。
二是胶柱旁边下顶针, 胶柱底部能够选择是否加一支排气镶针。
4.6司筒柱顶出; 有二种方法: 高度在6MM以下, 能够选择中间镶针, 二侧加顶针方法。
高度在6MM以上, 直接用司筒顶出。
4.7深骨位顶出: 优先选择扁顶, 最终才选择底部加圆顶。
5用司筒顶出时注意:5.1中间孔位有没有导向C角, C角成形有二种方法, 理是成形在司针上, 一是成形在司筒上。
成形在司针上时, 用磨床加工, 成形在司筒上时, 用EDM加工。
顶出系统的设计

5.顶出系统5.1概述:塑件顶出方法受塑件材料及形状等所左右。
常用的顶出方法有:顶针类、推板类、空气压出类等。
5.2顶针类:最常用的顶出元件,包括圆顶针、有托顶针、扁顶针、司筒。
5.2.1顶针的设计和选用5.2.2顶针选用的注意事项:1)防止塑件变形或损坏,正确分析塑件对模腔的粘附力的大小及其所在部位,有针对性地选择合适的脱模装置,使顶出力施于塑件刚性及强度最大的部位,即尽可能顶在壁边,骨位、柱位下面,作用面积也尽可能大一些(即尽可能选直径大的顶针),以防塑件变形或损坏。
2)结构合理可靠,顶出机构应工作可靠,运动灵活,制造方便,更换容易且具有足够的强度和刚度。
3)顶针直径在φ2.5以下而且位置足够时要做有托顶针;司筒壁在1mm以下或司筒壁径比≤0.1的要做有托司筒,托长尽量取大值。
4)顶针的有效配合长度=(2.5~3)D,最小不得小于8mm,5)司筒倒角6)一般场合顶针面应高于呵(CORE)平面0.03 ~ 0.05,对于胶位平面有要求的场合可考虑在顶针周边加沉台,7)顶针尽量不要放在镶件拼接处8)对于10mm以上高的长骨位胶位,建议用扁顶针顶出。
其扁身部分越短强度越好,加工也容易,设计规格中要注明圆柱部分长度;对于10mm以上高的管柱位建议用司筒顶出。
9)对于难下顶针的薄骨要征得客户同意加顶针。
上述场合下顶针后骨位多了胶,要保证:①不影响客户使用功能;②不导致制品表面缩水10)对于有斜顶针的场合,为防止产品跟斜顶滑行,斜顶附近的顶针面要磨“+”槽位11)对于表面不能有顶针印的产品,可在产品周边适当位置加辅助垃圾钉顶出5.3推板类推板类脱模机构适用于大筒形塑件,薄壁容器及各型罩壳形塑件的脱模。
推件板脱模的特点是顶出均匀、力量大、运动平稳、塑件不易变形。
5.3.1推板类脱模机构设计要点:(1)推板应与模呵(CORE)呈锥度配合,推板内孔应比模呵(CORE)成形部分大0.2~0.3,防止两者之间磨伤,卡死等。
顶出系统设计参考
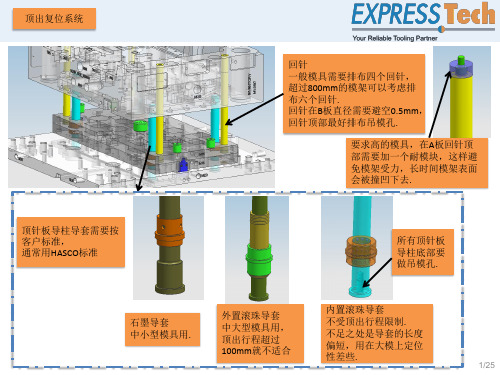
拉杆定位套 因为顶出时拉杆必须保证 垂直,因此需要做个定位 套来导向.
运动原理 拉杆垂直顶出,顶针板在导柱的导向下斜方向运动,顶针板 斜方向运动时A相对B做横向移动,类似斜顶运动.
6/25
顶出复位系统
强制复位 适用于顶针板不能完全复位,同时又不能合模,可以全长度.
12/25
顶出复位系统
回针 一般模具需要排布四个回针, 超过800mm的模架可以考虑排 布六个回针. 回针在B板直径需要避空0.5mm, 回针顶部最好排布吊模孔. 要求高的模具,在A板回针顶 部需要加一个耐模块,这样避 免模架受力,长时间模架表面 会被撞凹下去.
顶针板导柱导套需要按 客户标准, 通常用HASCO标准
3/25
顶出复位系统
油缸顶出 适用于倒灌模,客户ZININI经常使用油缸顶出. 另外超大型模具,由于顶出不平衡,可以考 虑使用多个油缸顶出.
4/25
顶出复位系统 油缸斜顶出
大模顶出方向斜的,我们可以考虑使用油缸顶出.
5/25
顶出复位系统 机械式斜顶出
顶针板T槽 镶件A 拉杆T槽镶 件B
此距离为拉杆的最 大顶出长度.
顶针板限位开关 通常每套模都要有顶针板限位开关,客 户不同开关品牌不同. 小于400mm的模具可以使用一个,超过 的需要使用两个.
2/25
顶出复位系统
拉杆复位 通常每套模都有一个拉杆,拉杆的尺寸和内 部螺纹需要按照客户标准. 超过700mm的模具需要建议客户多根拉杆, 以保证顶出拉回平衡.
弹簧复位 顶针板复位优先考虑拉杆,如果客户机器没有配拉回 机构,就可以考虑使用弹簧复位,通常国内和日本客 户会使用弹簧复位. 另外我们公司小于200吨机器没有配拉回装置,因此也 要使用弹簧复位. 顶针板弹簧通常使用蓝色弹簧,弹簧的压缩量需要按 照弹簧资料计算准确,并留有10~15mm的预压量.
第十一章注塑模顶出系统设计

6 第十一章 注塑模顶出系统设计
2021/12/29
•11-8 脱模力的估算:计算公式见书。以下情况包紧力较大
,要求脱模力也较大: • 塑料模具设计 •1. 收缩率越大塑件; •2. 脱模斜度越小的胶件; •3.深腔塑件; •4.有深骨位的胶件; •5. 透明胶件模。
7
第十一章 注塑模顶出系统设计 2021/12/29
•11-2-2 扁顶针: •
•常用于顶边或深骨部位。
•优点:顶出力大。 •缺点:加工困难,
•易磨损,以及成本高。
塑料模具设计
8
第十一章 注塑模顶出系统设计
2021/12/29
11-3 司筒顶出:(掌握什么情况下用司筒,司筒及司 筒针的装配方法,司筒• 及塑司料模筒具设针计 尺寸的确定)
常用于细长螺丝柱, 圆筒形零件的顶出。 1、优点:顶出力较 大且均匀,不会留下 明显痕迹。 2、缺点:制造和装配 麻烦,易磨损,出披 锋,成本高。
针位置,特殊结构的顶出方法• )塑料模具设计
•11-2-1 圆顶针:
•1、优点: •1)制造加工方便; •2)阻力小; •3)维修方便。 •2、缺点:顶出位置有 •一定的局限性。
4 第十一章 注塑模顶出系统设计
2021/12/29
3、设计要点:
(1)顶针的装配。见图。 • 塑料模具设计 ①顶针与后模镶件的配合长度一般在 12—20mm之间。顶针长度为50的倍 数,最小100mm. ②顶针顶出面如果是斜面或曲面,顶针 沉头要做定位防转,顶面要加阶梯防滑。
复习与思考:
1、注射模的脱模机构分哪几类?
2、如何用圆顶针顶骨,顶边和顶Boss•柱?塑料模具设计
3、司筒顶出因成本贵,制作复杂,故尽量避免使用。但什么情况下必须用司筒顶出?
模具设计手册—顶出系统规范-1

模具设计手册标题:顶出系统规范-1章节编号修改次数版本日期2010-4-1 M-01 0 A 页数顶出系统:产品在模具中冷却后,要切实可靠的将产品从模具中顶出,这一机构称之为顶出系统。
同时在合模时,要保证它不会与其它零件干涉,并回复原位,以便进行下一个循环。
顶出系统设计的注意要点:①顶针设置要均衡,要让产品能平衡顶出。
②顶针应设置在产品脱模困难的地方,产品的骨位,柱位以及对模仁有包紧力的地方。
同时应考虑不要影响产品的外观,并且不要与其它零件发生干涉。
③顶出行程一般在产品完全脱离模具5~10MM。
对于大型,较高的产品可顶出产品深度的2/3。
④有内模镶件的模具,顶针离镶件边缘不要小于0.8MM, 对于一些边上胶位较高的产品,顶针离边缘要有1.5~2MM;顶针离运水不得小于3MM。
⑤顶针的配合长度在25MM左右,长于此值时可在模仁底部做避空。
⑥顶针的大小应根据产品的大小而定,大的产品用大顶针。
顶针排布原则是:宁多勿少,宁大勿小。
常用的顶出方式有:圆顶针,扁顶针,司筒,直顶,推板,斜顶,气顶等。
1 圆顶针圆顶针分为单节和双节两种,一般来说小于3MM的顶针要考虑做双节顶针。
圆顶针是最常用的顶出方式,因其孔加工比较方便。
2 扁顶针扁顶针一般放在较深骨位底部,尽量做在镶件旁边,用磨床加工。
扁顶针有一缺点是其四个角易走毛边。
3 司筒针司筒用于出BOSS。
司筒可分为两种:单节司筒和双节司筒。
一般来说司筒壁小的要用双节司筒。
司筒不可正对顶棍孔,如果司筒在顶棍孔上,可做镶针,然后在其两边做顶针(如下图)。
C=A+0.1且取整数D≤B 且取整数。
- 1、下载文档前请自行甄别文档内容的完整性,平台不提供额外的编辑、内容补充、找答案等附加服务。
- 2、"仅部分预览"的文档,不可在线预览部分如存在完整性等问题,可反馈申请退款(可完整预览的文档不适用该条件!)。
- 3、如文档侵犯您的权益,请联系客服反馈,我们会尽快为您处理(人工客服工作时间:9:00-18:30)。
頂出系統設計概要
頂出系統
A--1
1. 回位杆:
頂針在將制品頂出后,其頂端位置會高於公模面許多,在下一次合模時(模具合
聚之前)必須使其退回到頂出前的初始位置,以免頂針碰壞母模面,所以必須有
回位杆幫助頂針回位。
PS:有時我們亦會在回位杆底部鉆圓孔放彈簧或優力膠開模時回位杆先彈出,合模時回位杆早一步先頂住母模PL面,以免頂針碰壞母模成品面。
A---2
設置導向裝置,並且導杆要深入公模板底部至少15mm以確保位置精度。
4. 支撐柱:
當成型較大制品時由於頂板的尺寸較大,使得間隔板之間的跨度隨之增大,當射出壓力較高時公模板可能會變形而導致制品結合線處會溢料,甚至發生頂針動不暢或卡死,為解決此一問題除了增加公模板的厚度外,還可在公模板和下固定板間用支撐柱來防止在成型過程中公模板的變形。
5. 停止銷:
在下頂出板與下固定板間設置停止銷是為防止成型中有異物雜質進入或頂出板翹曲變形而導致回位不確實成型不良,所以使用停止銷來減少接觸面積以確保回位確實。
6. KO孔:
在下固定板間開口使射出機的打擊杆能直接進入下頂出板頂出其位置如(A-1) 當成型較大制品時,由於模具體積大如果以一般的方式如設計會導致射出廠工作人員架模不方便,因此改為如圖(A-3)並改為套筒式由打擊杆強制將頂出板拉回。
C.頂出位置的設定:
1.冷卻后由於塑料會對鋼件產生收縮的應力,而有抱緊的現象所以正確的頂出應設置
在制品脫模有困難(抱緊現象)的地方見圖C-1,C-2 。
2.頂針設計時應儘量排在成品垂直之壁厚之正下方,可獲得較大之頂出力量見圖C-3。
3.當在斜面或曲面上配置頂針時,需考慮沉頭定位問題及頂出時頂針先端會有頂滑現
象見圖C-5。
4.頂針配置時在允許範圍內直徑應儘量加大且為標準規格品,相對也需考慮頂針(異材
質)散熱問題否則將來成品表面會留痕跡。
5.每一套模具頂針直徑尺寸不宜太多種,否則加工時需頻頻換刀既浪費時間及易出錯
6.頂針孔配合公差,模仁孔為(ψXX.XX +0.02,+0.01) ,XY方向位置度±0.1內即可頂管
XY 方向位置度公差需在±0.02內見圖C-3。
7.頂針在配置時需考慮頂出時力量分佈是否平均成品深度是否一致。
C-3 C-4
圓頂針、扁頂針、套筒、頂出塊、斜銷、氣頂
1. 圓頂針:
為最普遍最簡單的頂出裝置圓頂針及頂針孔都易於加工,因此已被作為標準件而廣泛使用,在加工較長的頂針孔時可採用距公模入子表面一段距離后改為擴孔的方式來減少頂針與模具接觸面,避免發生咬蝕以簡化模具製造,頂針需淬火處理,使其具有足夠的強度和耐磨性。
在成品內部有RIB時常需採用扁頂針的方法比較有效。
扁頂針的形狀如圖D-3 ,R角處是為增加頂針強度。
D--3
3. 套筒
在成品中出現boss時采用頂針套筒是非常有效的,這種方式可以將boss的脫模角度減小到0.5°,同時為使頂出順暢平穩應設置頂出導杆。
D—4
在中大型的模具中為使成品易於脫模經常使用頂出塊配合頂針的頂出結構
當頂出塊上有滑塊時為防止干涉,應在頂出塊的端面設有角度,以防止當
頂出塊回位不徹底時影响滑塊的運動。
D--5
PS:若成品在頂針處有頂白現象時,可配合延時頂出裝置來解決。
5. 斜梢:
當制品側壁內表面出現凹凸形狀或制品頂端內表面出現L型倒勾等情況時採用成型斜頂杆是非常有效的。
設計成型斜頂杆時應注意以下幾點:
1. 為避免成型斜頂杆在作動時受翻轉力矩的作用而發生卡死現象,斜頂杆的角度
通常采用(6∘<a<8∘)。
2. 為使斜頂杆在頂出過程中順暢在設計時應使斜頂杆頂端低於公模表面
0.05MM。
3. 為保証成型斜頂杆的強度與耐磨性應進行表面淬火處理(HRC50)以上或表面滲
氮硬化。
6. 氣頂:
氣頂出方式不論是在公模部份或母模部分其頂出都很方便不需要安裝推板。
在頂出過程中整個制品的底部均受同樣地的壓力,所以即便是軟的塑料,也可以在不發生變形的條件下脫離模具,通常氣頂出要求脫模斜度最小大於2∘,所以對於
形狀復雜需要較大脫模力的制品,則無法滿足其要求。
某些模具結構無法避免頂出杆與側滑塊發生干涉時必須裝置急回機構使頂出杆在合模時先回復原位見圖D-7,D-8。
D-8。