Fatigue behavior of magnesium alloy and application in auto steering wheel frame
考试复习笔记-材料概论(上)

加入铬添加剂可以生产耐腐蚀的不锈钢。
Additions such as tungsten lead to high-hardness alloy used as tool steels .
加入钨之类的添加剂可以生产用做工具刚的高硬度合金。
superalloys include many stainless steels that combine corrosion resistance with high strength at elevated temperatures .
超合金包括多种不锈钢,这些不锈钢在高温下即耐腐蚀同时又具有高强度。
超过90%重量的工程材料是铁基合金,包括刚(含0.05~2.0 wt% C)和铸铁(含2.0~4.5 wt% C)。
Most steels involve a minimum of alloy additions to maintain moderate costs .
大多数的刚只含有少量的合金添加剂使材料的成本适中。
要理解这各种材料的性能需要从微观或亚微观尺度上研究材料的结构。
2、
The relative ductility of certain metal alloys is related to atomic-scale "architecture".
某些金属合金的延展性的相对大小与其原子尺度上的“构造有关。
当我们了解了材料的性能,材料的实际选择就可以在两个层次上进行。
First ,there is competition among the various categories of materials .
镁合金微弧氧化膜在Na2SO4溶液中的腐蚀行为

硅酸盐学报・ 382 ・2013年DOI:10.7521/j.issn.0454–5648.2013.03.18 镁合金微弧氧化膜在Na2SO4溶液中的腐蚀行为郭惠霞1,2,马颖1,张玉福1,董海荣1,郝远1(1. 兰州理工大学,有色金属新材料国家重点实验室培育基地,兰州 730050;2. 西北师范大学化学化工学院,甘肃省生物电化学与环境分析重点实验室,兰州 730070)摘要:在硅酸盐电解液中,采用微弧氧化(micro-arc oxidation,MAO)技术在镁合金AZ91D表面制备了MAO陶瓷膜。
利用电化学方法,结合扫描电子显微镜、X射线衍射等手段研究了该MAO膜层在0.1mol/L Na2SO4溶液及其与不同浓度的NaCl混合液中的腐蚀行为。
结果表明:镁合金AZ91D 表面的MAO膜在Na2SO4溶液中具有较好的耐蚀性;在0.1mol/L Na2SO4+NaCl混合液中,随着添加的Cl–浓度增加,MAO膜层腐蚀速率增加;浸泡初期MAO膜为全面腐蚀,120h后浸泡在0.1mol/L Na2SO4+3.5% NaCl混合液中的试样出现点蚀孔。
腐蚀产物为Mg4(OH)6SO4·8H2O、MgSO4和Mg(OH)2,当有Cl–存在的溶液中,腐蚀产物还有MgCl2·2H2O出现。
关键词:镁合金;微弧氧化膜;硫酸钠溶液;腐蚀行为中图分类号:TG174 文献标志码:A 文章编号:0454–5648(2013)03–0382–06网络出版时间:网络出版地址:Corrosion Behavior of Micro-Arc Oxidation Coating on Magnesium AlloyAZ91D in Na2SO4 SolutionGUO Huixia1,2,MA Ying1,ZHANG Yufu1,DONG Hairong1,HAO Yuan1(1. State Key Laboratory of Gansu Advanced Non-ferrous Metal Materials, Lanzhou University of Technology, Lanzhou 730050,China; 2. Key Laboratory of Bioelectrochemistry & Environmental Analysis of Gansu Province, College of Chemistry &Chemical Engineering, Northwest Normal University, Lanzhou 730070, China)Abstract: Ceramic oxide coatings were prepared on AZ91D magnesium alloys in alkaline silicate electrolyte by a micro-arc oxidation (MAO) technique. The corrosion behavior of MAO coating on AZ91D magnesium alloys in 0.1mol/L Na2SO4 solutions with different NaCl concentrations was investigated by electrochemical analysis, scanning electron microscopy and X-ray diffraction, respectively. The results show that the MAO coating has a superior corrosion resistance in 0.1mol/L Na2SO4 solution. The corrosion rate of the MAO coating increased with increasing chloride ions concentration in 0.1mol/L Na2SO4+NaCl solution. The generalized corrosion was apparent on the MAO coating in the immersion initial stage. The localized corrosion occurred when the samples were immersed in 0.1mol/L Na2SO4+3.5%NaCl solution for >120h. The main corrosion products mainly consisted of Mg4(OH)6SO4·8H2O, MgSO4 and Mg(OH)2 in 0.1mol/L Na2SO4 solution. There was MgCl2·2H2O as a corrosion product when Cl– was in the solution.Key words: magnesium alloys; micro-arc oxidation coating; sodium sulfate aqueous solution; corrosion behavior镁合金是最轻的结构材料,因具有小的密度、高的比刚度和比强度、良好的电磁屏蔽性、易于回收等优点,在航空航天、汽车结构件、3C等领域显示出其独特的优势。
镁合金腐蚀性能研究进展
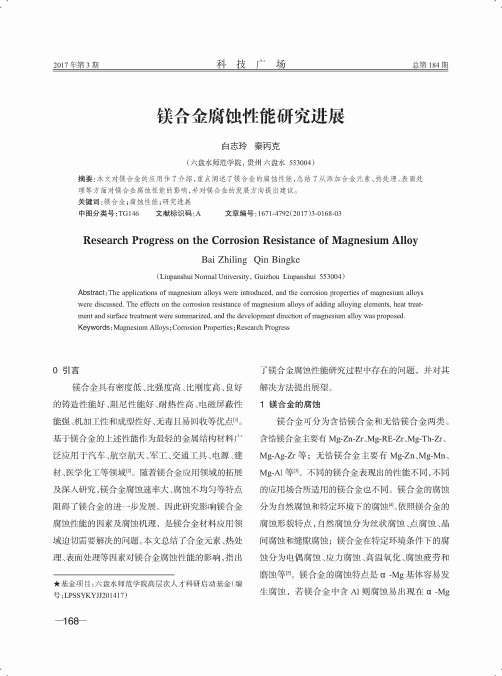
2017年第3期科技广场总第184期镁合金腐蚀性能研究进展白志玲秦丙克(六盘水师范学院,贵州六盘水553004)摘要:本文对镁合金的应用作了介绍,重点阐述了镁合金的腐蚀性能,总结了从添加合金元素、热处理、表面处理等方面对镁合金腐蚀性能的影响,并对镁合金的发展方向提出建议。
关键词:镁合金;腐蚀性能;研究进展中图分类号:TG146 文献标识码:A 文章编号:1671-4792(2017)3-0168-03Research Progress on the Corrosion Resistance of Magnesium AlloyBai Zhiling Qin Bingke(Liupanshui Normal University,Guizhou Liupanshui 553004)Abstract: The applications of magnesium alloys were introduced, and the corrosion properties of magnesium alloyswere discussed. The effects on the corrosion resistance of magnesium alloys of adding alloying elements, heat treatment and surface treatment were summarized, and the development direction of magnesium alloy was proposed.Keywords : Magnesium Alloys ; Corrosion Properties ; Research Progresso引言镁合金具有密度低、比强度高、比刚度高、良好 的铸造性能好、阻尼性能好、耐热性高、电磁屏蔽性 能强、机加工性和成型性好、无毒且易回收等优点[1]。
【机械类文献翻译】铅元素对AZ91镁合金形成过程的影响

Effect of Pb addition on ageing behavior of AZ91magnesium alloyAbstractThe ageing behavior of AZ91alloy containing2wt.%lead is investigated.The results show that addition of Pb suppresses the discontinuous precipitation and thereby slows down the ageing kinetics.Even though the peak hardness obtained for both alloys is almost same,the peak hardness reaches after2400min for Pb added alloy against900min for the base alloy.The presence of Pb in solid solution might have inhibited the diffusion of Al and Mg atoms,which is essential for the formation, and growth of discontinuous precipitation in this alloy.Keywords:AZ91magnesium alloy,Pb addition,Ageing behavior,Microstructure, DTA1.IntroductionMagnesium-based alloys are increasingly used in the auto-mobile industries.The reasons for this lie principally in their improved specific properties compared with aluminum alloys or steels and light weight(30%less than Al,and75%less than steels) [1].Among the most common commercial magnesium alloys,AZ91is endowed with one of the best combinations of castability,mechanical strength and ductility[2]. Presence of aluminum provides mechanical and casting properties as well as corrosion resistance,whereas zinc contributes to solid solution strengthening.The maximum solid solubility of alu-minum in Mg is12.7wt.%at437◦C and decreasing to about2wt.%at room temperature.Hence castings(sand and perma-nent mould castings)of this alloy are heat-treated to obtain better mechanical properties and studies are available in the lit-erature to understand the ageing behavior of this alloy [3–6].During solution treatment at410℃,the Mg17Al12—βphase redissolves in to the Mg matrix and forms a homogenized solid solution.On subsequent ageing at lower temperature,aluminum precipitates out in two forms:i.e.discontinuous and contin-uous precipitates.Discontinuous precipitation is the cellular growth of alternating layers of phase(Mg17Al12)and near equilibrium magnesium matrix at high angle grain boundary[2,7,8].Growth of the discontinuous precipitation regions ceases relatively early in the precipitation process.Continuous pre-cipitation forms in the remaining regions of the matrix that are not already occupied by discontinuous precipitates[7].It is demonstrated that the continuous precipitates are responsi-ble for age hardening,whereas the discontinuous precipitates are detrimental to agehardening[6].Moreover,the discon-tinuous precipitates formed during high temperature exposure(creep)reduce the creep properties considerably[9].Dynamic discontinuous precipitates occur at the grain boundaries from the supersaturated eutectic solid solution lead to the sliding of grain boundaries and weaken the material [9].Hence sup-pressing this dynamic discontinuous precipitation during high temperature exposure is inevitable to improve its high temper-ature properties.It is also reported that addition of some of the trace elements like gold and rare earth suppresses the discontin-uous precipitation during ageing[10,11].But these elements are costlier.The preliminary study on the Pb addition to Mg–7Al has reported that addition of Pb has the tendency to suppress the discontinuous precipitation[12].Besides,Pb is cheaper mate-rial compared to gold and rare earth.So,in this study a detailed investigation on the effect of Pb addition on the ageing behavior of gravity。
基于ProCAST和ANSYS软件分析径向加载的铝合金轮毂应力分布
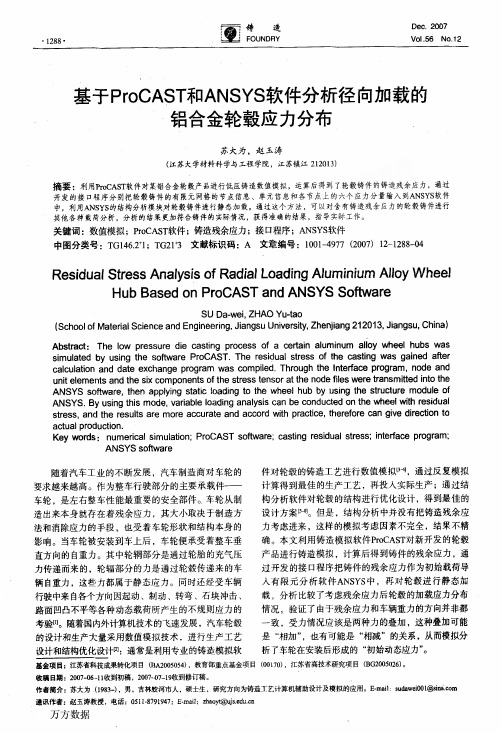
Dec.2007 VOI.56 No.12
图2 ProCAST的网格单元导人到ANSYS中 Fig.2 Mesh elemems ofProCAST transhaitted into ANSYS
3利用ANSYS对轮毂铸件进行结构分析
3.1仅施加径向载荷的分析 在轮毂中间凸台面施加所有自由度约束。在轮毂
时间/s
0
9
23
30
240
240.001
图1计算到1490时间步的等效应力结果 Fig·1 The equivalent s仃css at 1490 time step
2 ProCAST网格单元与ANSYS软件的 连接
压力]X、tlVa
0.1
0.121
0.13
0 17
0.17
01
铸件在ProCAST中划分的单元类型为四节点四面
模具材料为Steel.H13,模具之间的传热系数是 h=500 W/m2K,模具与铸件之间传热系数为h=l 280
礴|积。
1.3初始条件的确定
铸件浇注温度为705℃,模具上模的初始温度为
360℃,侧模为360℃,下模为430℃。充型过程加压
参数见表3。
表3充型过程加压参数
Table 3 Press parameter of filling process
力考虑进来,这样的模拟考虑因素不完全,结果不精 确。本文利用铸造模拟软件ProCAST对新开发的轮毂 产品进行铸造模拟,计算后得到铸件的残余应力,通 过开发的接El程序把铸件的残余应力作为初始载荷导 入有限元分析软件ANSYS中,再对轮毂进行静态加 载,分析比较了考虑残余应力后轮毂的加载应力分布 情况,验证了由于残余应力和车辆重力的方向并非都 一致,受力情况应该是两种力的叠加,这种叠加可能 是“相加”,也有可能是“相减”的关系,从而模拟分 析了车轮在安装后形成的“初始动态应力”。
Corrosion behavior of 2024 AlCuMg alloy 2024合金腐蚀
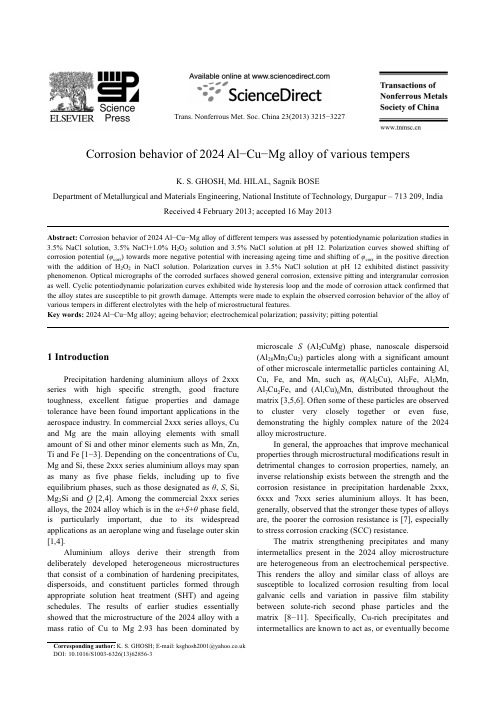
Trans. Nonferrous Met. Soc. China 23(2013) 3215í3227Corrosion behavior of 2024 AlíCuíMg alloy of various tempersK. S. GHOSH, Md. HILAL, Sagnik BOSEDepartment of Metallurgical and Materials Engineering, National Institute of Technology, Durgapur – 713 209, IndiaReceived 4 February 2013; accepted 16 May 2013Abstract: Corrosion behavior of 2024 AlíCuíMg alloy of different tempers was assessed by potentiodynamic polarization studies in 3.5% NaCl solution, 3.5% NaCl+1.0% H 2O 2 solution and 3.5% NaCl solution at pH 12. Polarization curves showed shifting of corrosion potential (ijcorr ) towards more negative potential with increasing ageing time and shifting of ijcorr in the positive direction with the addition of H 2O 2 in NaCl solution. Polarization curves in 3.5% NaCl solution at pH 12 exhibited distinct passivity phenomenon. Optical micrographs of the corroded surfaces showed general corrosion, extensive pitting and intergranular corrosion as well. Cyclic potentiodynamic polarization curves exhibited wide hysteresis loop and the mode of corrosion attack confirmed that the alloy states are susceptible to pit growth damage. Attempts were made to explain the observed corrosion behavior of the alloy of various tempers in different electrolytes with the help of microstructural features.Key words: 2024 AlíCuíMg alloy; ageing behavior; electrochemical polarization; passivity; pitting potential1 IntroductionPrecipitation hardening aluminium alloys of 2xxx series with high specific strength, good fracture toughness, excellent fatigue properties and damage tolerance have been found important applications in the aerospace industry. In commercial 2xxx series alloys, Cu and Mg are the main alloying elements with small amount of Si and other minor elements such as Mn, Zn, Ti and Fe [1í3]. Depending on the concentrations of Cu, Mg and Si, these 2xxx series aluminium alloys may span as many as five phase fields, including up to five equilibrium phases, such as those designated as ș, S , Si, Mg 2Si and Q [2,4]. Among the commercial 2xxx series alloys, the 2024 alloy which is in the Į+S +ș phase field, is particularly important, due to its widespread applications as an aeroplane wing and fuselage outer skin [1,4].Aluminium alloys derive their strength from deliberately developed heterogeneous microstructures that consist of a combination of hardening precipitates, dispersoids, and constituent particles formed through appropriate solution heat treatment (SHT) and ageing schedules. The results of earlier studies essentially showed that the microstructure of the 2024 alloy with a mass ratio of Cu to Mg 2.93 has been dominated bymicroscale S (Al 2CuMg) phase, nanoscale dispersoid (Al 20Mn 3Cu 2) particles along with a significant amount of other microscale intermetallic particles containing Al, Cu, Fe, and Mn, such as, ș(Al 2Cu), Al 3Fe, Al 3Mn, Al 7Cu 2Fe, and (Al,Cu)6Mn, distributed throughout the matrix [3,5,6]. Often some of these particles are observed to cluster very closely together or even fuse, demonstrating the highly complex nature of the 2024 alloy microstructure.In general, the approaches that improve mechanical properties through microstructural modifications result in detrimental changes to corrosion properties, namely, an inverse relationship exists between the strength and the corrosion resistance in precipitation hardenable 2xxx, 6xxx and 7xxx series aluminium alloys. It has been, generally, observed that the stronger these types of alloys are, the poorer the corrosion resistance is [7], especially to stress corrosion cracking (SCC) resistance.The matrix strengthening precipitates and many intermetallics present in the 2024 alloy microstructure are heterogeneous from an electrochemical perspective. This renders the alloy and similar class of alloys are susceptible to localized corrosion resulting from local galvanic cells and variation in passive film stability between solute-rich second phase particles and the matrix [8í11]. Specifically, Cu-rich precipitates and intermetallics are known to act as, or eventually becomeCorresponding author: K. S. GHOSH; E-mail: ksghosh2001@ DOI: 10.1016/S1003-6326(13)62856-3K. S. GHOSH, et al/Trans. Nonferrous Met. Soc. China 23(2013) 3215í3227 3216local cathodes, which facilitate oxygen reduction reactions and ultimately drive anodic dissolution of the surrounding matrix material [12].Thus, in view of the maintenance of aircrafts and their long-term use, it is important to characterize the corrosion behavior (micro- and nano-scale level) and mechanism of corrosion attack influenced by the alloy microstructure. Further, for a longer service life and resistance to sudden catastrophic failure, it is essentially required that the aircraft structures would resist to undergo localized corrosion and environmental assisted cracking (EAC), e.g. stress corrosion cracking (SCC), hydrogen embrittlement (HE) and corrosion fatigue (CF) [13,14] .Localized corrosion behavior of 2024 alloy with varying Cu and Mg content has been studied in details [6,15í23]. The localized corrosion susceptibility is affected in the presence of S (Al2CuMg) and inhomogeneous second phase particles. The localized corrosion studied by micropolarization showed that the Al 2024 alloy with lower Mg content (Cu to Mg mass ratio of 3.7) is significantly different from the 2024 alloy with a more common composition (Cu to Mg mass ratio of 2.9). The localized corrosion (microscale and nanoscale level) initiation behavior of the Al 2024 alloy with a more common composition showed a clear separation of the distribution of the measured pitting potentials for S phase and intermetallic AlCuFeMn particles with variable stoichiometry, and matrix areas. Characterization of the microstructure and its relation to the localized corrosion initiation properties of the 2024-T351 alloy have been done to provide both qualitative and quantitative input data (microstructural geometry and microscale electrochemical measurement data) for development of microscale and macroscale numerical models and simulations of corrosion.Further, a lot of research work and literatures [24í28] are available on corrosion protection of Al alloys by chromate based conversion coating, application of primer and other means. But, the chromate compounds are highly toxic and carcinogenic, so there is an urgent need of development of alternative corrosion inhibitors for protecting aluminium alloy. Among these new inhibitors, rare earth salts were tested to be effective and environmental benign inhibitors. The inhibiting effect of cerium cation on corrosion of aluminium alloy was reported to be due to the shifting of cathodic oxygen reduction reaction by the formation of oxides and hydroxides of Ce(III), La(III) and Al2O3 [28í34].There are many investigations [15í23] on the influence of matrix strengthening phases and intermetallic particles on the localized (nano- and micr-oscale level) corrosion of 2024 alloy with different Cu to Mg ratios, and the critical particle size below which localized corrosion is not affected, but there is a scanty literature on systematic study of corrosion behavior of the 2024 alloy with ageing time and different tempers, i.e. as-quenched, under-, peak- and over-aged tempers. Since the 2024-T3 alloy is being used in structural components of aircraft, it is appropriate to assess the corrosion behavior with ageing time of the alloy in different tempers. Hence, in the present investigation, attempts are made to correlate the ageing and corrosion behavior of a 2024 alloy of various tempers, such as as-quenched, under-, peak- and over-aged in the electrolytes of 3.5% NaCl solution, 3.5% NaCl+1.0% H2O2 solution near neutral pH and 3.5% NaCl solution at pH 12.2 Experimental2.1 Materials2024 AlíCuíMg alloy in square bar shape with dimensions of 15 mm×6.35 mm×6.35 mm was procured from Alfa Aesar(A Johnson Matthey Company)Ward Hill, MA 01835, USA. The chemical compositions of the 2024 alloy are given in Table 1. The grains of the alloy are polygonal with an average size of 25í30 ȝm. Specimens with dimensions of 6.35 mm×6.35 mm× 3 mm (approximately) were cut from the square alloy rod for heat treatment and subsequent other studies.Table 1 Chemical compositions of 2024 alloy (mass fraction, %)Cu Mg Mn Fe Si Cr Al 4.40 1.500.60< 0.50 < 0.50 < 0.10Bal.2.2 Ageing treatment to produce various tempersA large number of specimens cut from the as-received 2024 alloy square bar were subjected to solution heat treatment (SHT) at temperature of 490 °C for 30 min, water quenched at room temperature followed by artificial ageing at temperature of 190 °C for varying time up to 154 h corresponding to over-aged state, and a sample was also naturally aged for prolonged time. The details of various ageing schedules and designated alloy tempers produced for the present investigation are stated in Table 2.2.3 Hardness testingVicker’s hardness tester, Model BV250(S), was used for measuring the hardness of the alloys of various tempers in order to assess the natural and artificial ageingK. S. GHOSH, et al/Trans. Nonferrous Met. Soc. China 23(2013) 3215í3227 3217Table 2 Heat treatment, ageing schedules and designatedtempers of 2024 alloyTemperdesignationAgeing schedule2024-AQ 2024 alloy is solutionised at 490 °C for 30 min followed by water quenching2024-NA-720h 2024-AQ state alloy is naturally aged at room temperature for 30 d, i.e. 720 h2024-190-x h2024-AQ state alloy is artificially aged at temperature of 190 °C for x h. For example: 2024-190-1 h stands for 2024-AQ state alloy is artificially aged attemperature 190 °C for 1 hbehavior of the alloy. The load applied for measuring hardness was 98 N and the reported value of hardness was an average of at least three readings.2.4 X-ray diffractionX-ray diffraction (XRD) was carried out to acquaint with the various phases present in the alloy of different tempers. XRD study was carried out using a PANlytical XPert Pro basic X-ray diffractometer unit with Cu KĮradiation.2.5 SEM, EDAX analysis and elemental mappingX-ray elemental mapping of the 2024 alloy was studied by using a scanning electron microscope (SEM), Model Hitachi Sí3000 N, with an EDAX attachment.2.6 Electrochemical polarisationPotentiodynamic polarizations were carried out on the samples of alloy with various tempers, e.g. 2024-AQ, 2024-190-1 h, and 2024-190-154 h, as stated in Table 2, using a computer controlled V oltaLab potentiostat/ galvanostat (Model P G P201) with an inbuilt V oltamaster4 software. Experiments were carried out by constructing a local electrochemical cell using the standard three electrodes configuration: saturated calomel electrode (SCE) as a reference, a platinum plate as a counter electrode and the sample as the working electrode. Polarization scan was carried out towards more noble value at a scan rate of 0.50 mV/s, after allowing a steady state potential to develop. The electrolytes used for the polarization studies were 3.5% NaCl solution and 3.5% NaCl+1.0%(volume fraction) H2O2 solution at near neutral pH and 3.5% NaCl solution at pH 12 as well. The pH 12 was obtained by adding a small amount of NaOH to 3.5% NaCl solution.In order to assess the pit protection potential (ijprot), cyclic potentiodynamic polarization studies were carried out on a few alloy tempers in 3.5% NaCl solution at pH 12. Samples were polarized below the ijprot potential and the microscopic study revealed no pitting. In order to confirm whether pitting damage or pit repassivation has occurred below the ijprot, further potentiodynamic polarization study on a few alloy tempers was also run below the pit protection potential, and the corroded surfaces were observed.2.7 Observation of corroded surfacesIn order to assess the type and morphology of corrosion attack upon electrochemical polarization studies of these alloy tempers in different environments, an optical microscope (model LEICA DM 2500M) with an inbuilt QWin3 software was used to observe the corroded surfaces. The corroded surface were observed in as-such situation or often gently disk polished to remove the covered oxide/corroded layer.3 Results and discussion3.1 Ageing behavior of 2024 alloyFigure 1 shows the age hardening behavior of the 2024 alloy solution heat treated, water quenched followed by artificial ageing at temperature of 190 °C, and natural ageing as well. The variation of hardness with ageing time displayed the characteristic age hardening behavior of precipitation hardenable aluminium alloys, namely with increasing ageing time, there is a progressive increase of hardness, reaching a maximum value (peak aged temper) and subsequent decrease of hardness with further ageing leading to over-aged state.Fig. 1 Variation of hardness with ageing time of 2024 alloy solution heat treated, water quenched followed by artificial and natural ageingIn the AlíCu system, the most explained precipitation sequence is G P zones, coherent ș'', semi-coherent ș', and finally equilibrium ș(Al2Cu) phase. Small addition of magnesium affects the formation of coherent phase and facilitates the precipitation ofK. S. GHOSH, et al/Trans. Nonferrous Met. Soc. China 23(2013) 3215í3227 3218semi-coherent ș' phase, and generally increases the hardening effect [1,35,36]. Further, the increase of magnesium concentration results in the formation of S (Al2CuMg) phase; and the precipitation sequence is similar to that of the Al2Cu phase: G uinier-Preston- Bagaryatsky zones, coherent S'', semi-coherent S', and equilibrium S. The structure of all S-phases are very close, and literatures suggested them as a structure differently distorted due to coherent or semi-coherent junctions with the matrix [1,35í41].It was proposed that in AlíCuíMg alloys, two stages of hardening occur. An early rapid rise in hardness is due to the formation of fine scale (average 24 atoms) solute clusters of Mg and Cu; MgíMg aggregates were the first to appear, followed by CuíCu aggregates and CuíMg clusters due to the higher binding energy between Mg atoms and vacancies. The second stage of hardening (peak aged state) is dominated by S phase in the form of laths with the {120}Al habit plane elongated along ¢100²Al direction [35,42í43]. Recent work has shown that a semi-coherent phase designated by S'' or GPB2 with orthogonal structure occurs well before peak hardness is reached and remains in the matrix in peak aged state [35,43]. In over aged state, the microstructure comprises coarse S phase with a range of morphologies, including rods with an aspect ratio (the ratio of width to thickness) 3:1 and irregular cross-sections (i.e. agglomeration of rods) [40,44,45], and no presence of GPB zones or solute clusters. All these justify the drop of hardness in the over aged state.3.2 XRD patternFigure 2 shows the XRD pattern of 2024 alloy in three artificially aged states, using Cu KĮ radiation. The patterns of all the tempers indicate the peaks of all the probable phases such as Į(Al), intermetallic S' (Al2CuMg), Al7Cu2Fe and ș' (Al2Cu) phases that wouldFig. 2 XRD patterns of 2024 alloy of various tempers: (a) 2024-190-1h; (b) 2024-190-5h; (c) 2024-190-150h be present in the alloy system. However, there may be presence of other intermetallic phases, being reflected with smaller peaks, but difficult to confirm from the XRD patterns.3.3 SEM and elemental mappingFigure 3 exhibits a SEM image and X-ray elemental mapping of alloy 2024-190-8h. Figure 3(a) shows grains of Į(Al) matrix and the presence of a large number of intermetallics. The X-ray elemental mapping shows that aluminium is uniformly and densely distributed over the entire matrix. Further, the uniform distribution of Cu and Mg indicates the presence of equilibrium S (Al2CuMg) phase within the matrix, as the observed microstructure in the order of micron. However, Figures 3(d) and (e) exhibit the distribution of Fe and Mn mostly in the intermetallics regions of the microstructure. Also there is a lean distribution of Fe and Mn preferably and probably along the sub- and grain boundaries.3.4 Potentiodynamic polarizationFigure 4 shows the potentiodynamic polarization curves of 2024 alloy of various tempers in 3.5% NaCl, 3.5% NaCl+1.0% H2O2 at near neutral pH and in 3.5% NaCl at pH 12 solutions, respectively.The shape of the polarization curves in Figs. 4(a) and (b) is similar for all the tempers. In all the cases, the cathodic and anodic branches of the curves show typical potentialícurrent density characteristics of aluminium alloy system in 3.5% NaCl solution at near neutral pH. However, the polarization curves in Fig. 4(c) in 3.5% NaCl solution at pH 12 show clearly the acitveípassiveí transpassive phenomenon.The cathodic branches of the polarization curves showing the typical Tafel behavior enable to evaluate cathodic slope or Tafel constant (ȕc) as well as corrosion current density (J corr) by Tafel extrapolation method. The anodic branches of the polarization curves in 3.5% NaCl and 3.5% NaCl+1.0% H2O2 solutions exhibit typical active metal dissolution behavior with an initial sharp increase of corrosion current density under applied anodic overvoltage, and then further increase of current density under higher anodic overvoltage.In 3.5% NaCl solution at pH 12, the anodic branches of the polarization curves for all the alloy tempers exhibit active, spontaneous passive, passive and transpassive regions. In the active region, metal dissolution occurs increasingly with the increase of applied anodic overvoltage, reaching maximum current density, which is called critical current density (J crit). But, beyond the critical current density, the decrease of current density with increasing overvoltage is due to the beginning of formation of passive oxide layer (state of spontaneous passivation), attaining a stable passive stateK. S. GHOSH, et al/Trans. Nonferrous Met. Soc. China 23(2013) 3215í3227 3219Fig. 3 SEM image (a) and X-ray mappings (bíf) of 2024-190-8h alloywith a constant low current density (passive current density, J p ) over a passive potential range (ijpp ). With the further increase of applied potential, the current density increases sharply, and this potential is considered oxide break-down (ijbd ) or pitting potential (ijp ), leading to localized corrosion, i.e. pits formation with rapid metal dissolution.Tables 3 and 4 give the electrochemical data, such as corrosion potential (ijcorr ), corrosion current density (J corr ), critical current density (J crit ), passive potential range (ijpp ), passive current density (J p ) etc, obtained from these polarization curves of the 2024 alloy of various tempers.The electrochemical behavior of the 2024 alloy with heterogeneous microstructure, in general, depends on the degree of segregation, clustering, the morphology and distribution of precipitates and intermetallics, the relative areas of exposed phases, the electrode kinetics of each phase, and the development of electrochemical local cells among them, etc. Therefore, the complexity (in terms of number of phases and intermetallics present) in the alloy microstructure and the problem of judicious selection of cathodic Tafel’s region impose limitations and errors in finding out the corrosion current density, J corr [2,8,21,35,36,39í41,44]. However, these reported electrochemical data give an idea of electrochemical performance of the alloy tempers, although the reported J corr values (Tables 3 and 4) determined by Tafel extrapolation technique may vary by ±15%.A close look of the corrosion current density (J corr ) of various alloy tempers in a given environment seems to be more or less same within an order of variation and or within the error limits of Tafel extrapolation method. But, certainly there must be a definite effect of variation of corrosion behavior of various alloy tempers having different ageing time. This is because in different alloy tempers (from as-quenched (AQ) state to under- to peak- to over-aged tempers), there are variations of solute contents in Į(Al) matrix, differences of size, distribution of GPB zones and S '/S (Al 2CuMg) phase and theirK. S. GHOSH, et al/Trans. Nonferrous Met. Soc. China 23(2013) 3215í3227 3220Fig. 4 Potentiodynamic polarization curves of 2024 alloy of different tempers: (a) In 3.5% NaCl solution; (b) In 3.5% NaCl+10% H2O solution; (c) In 3.5% NaCl solution at pH 12variant as well. In the as-quenched state, the Į(Al) solid solution is supersaturated with solutes of Cu, Mg and Mn, but, as ageing progresses, the Į solid solution gets solute depleted and there is precipitation of GPB zones and S'/S phase (as discussed in section 3.1) in the presence of other intermetallics as well. In the context, it is to state that copper is electrochemically cathodic and the S'/S phase is more anodic (more negative potential) with respect to the matrix Į solid solution [46,47].The expected variation of corrosion behavior of the alloy with different ageing time has been explained by Table 3 Electrochemical data of 2024 alloy of various tempersin 3.5% NaCl solution and 3.5% NaCl+1.0% H2O2 solution AlloytemperSolutionijcorr (vsSCE)/mVJ corr/(mA·cmí2)J anodic (atijcorr of AQ state)/(mA·cmí2)2024-AQí593 0.022 í190-1h í6400.0390.105190-5h í6780.06917.76 190-12hí696 0.041 16.70190-72hí695 0.05 17.30190-154h3.5% NaClí706 0.055 24.362024-AQí579 0.21 í190-1h í6370.30510.66190-5h í6510.07822.40 190-12hí677 0.124 9.40190-72hí691 0.066 24.72190-154h3.5% NaCl+1.0% H2O2í696 0.086 16.80Table 4 Electrochemical data of 2024 alloy in 3.5% NaCl solution at pH 12AlloytemperJ crit/(mA·cmí2)ijcorr(vsSCE)/mVJ p/(mA·cmí2)ijp(vsSCE)/mVijprot(vsSCE)/mV2024-AQ 2.61 1304 1.12í1005 íí511190-1h 3.36 1358 1.35í1040 íí561190-5h 6.82 1320 2.27í1006 íí618190-12h 4.68 1338 1.65í1039 íí663190-72h 3.98 1342 1.36í1012 íí661190-154h 4.62 1337 1.46í1020 íí671Cyclic polarisation190-1h 4.32 1350 1.851039 í553 852 190-5h 3.95 1318 1.481008 í593 842 Polarisation below ijprot190-5h 3.61 1331 1.53190-12h 3.88 1324 1.02190-72h 4.51 1315 1.79comparing the corrosion current density of the polarization curves of various tempers with respect toJ corr at ijcorr of the as-quenched state. The polarization curves show that the current densities of the alloys with higher ageing time have been found to be anodic (denoted in this paper as J anodic) and much higher with respect to J corr of the as-quenched (AQ) state. The way ofK. S. GHOSH, et al/Trans. Nonferrous Met. Soc. China 23(2013) 3215í3227 3221finding out J anodic of the 2024-190-152h alloy with respect to the J corr (at ijcorr) of the 2024-AQ is shown in inset of Fig. 4(a). Similarly, J anodic values have been calculated for other tempers and mentioned in Tables 3 and 4. Thus, it is appropriate to infer that the current density and thereby the corrosion rate increase with ageing time. Polarization curves of intermetallics and phases present in aluminium alloys have also been shown and compared in similar way [17].3.4.1 Electrolyte and its conditionIn 3.5% NaCl solution at near neutral pH, the anodic current density is low (uniform corrosion is repressed by natural oxide layer) and the cathodic current density arising from the number of precipitates and intermetallics acting as local cathodes and the volume of oxidants, e.g. dissolved oxygen in the electrolyte, is dominating; and the summary current density (anodic plus cathodic current density) is negative and low. The corrosion potential (ijcorr) is in the pitting potential (ijbr) range (Tables 3 and 4), and this implies that the alloy will corrode under free corrosion potential.Comparison (for a given alloy temper) of the potentiodynamic polarization curves in 3.5% NaCl and in 3.5% NaCl + 1.0% H2O2 solutions (Figs. 4(a) and (b) and Tables 3 and 4) shows thatijcorr values have shifted towards positive direction with the addition of small amount of H2O2 in 3.5% NaCl solution. This is clearly seen from Figs. 5(a)í(f), the polarization curves for aFig. 5 Potentiodynamic polarisation curves of 2024 alloy in different temper states in 3.5% NaCl and 3.5% NaCl+1.0% H2O2 solutions: (a) 2024-AQ; (b) 2024-190-1h; (c) 2024-190-5h; (d) 2024-190-12h; (e) 2024-190-72h; (f) 2024-190-154hK. S. GHOSH, et al/Trans. Nonferrous Met. Soc. China 23(2013) 3215í32273222given temper in 3.5% NaCl and 3.5% NaCl+1.0% H 2O 2 solutions. The aggressive depassivating nature of the 3.5% NaCl solution makes the alloy bare, but the addition of 1.0% H 2O 2 (volume fraction) shifts the corrosion potential to slightly more positive values due to more oxygen availability in solution, causing to increase the thickness of the oxide layer, to maintain the passive oxide layer and to heal the destroyed oxide layer as well. The difference between ijp (pitting potential) and ijcorr value of the environment containing H 2O 2 is less compared to that in only 3.5% NaCl solution (Table 5). Thus, the environment containing small amounts of H 2O 2 will be more aggressive for localized attack, intergranular corrosion (observed in the present study and discussed in section 3.4.3) and susceptible to environmental assisted cracking (EAC) [13,14], compared to that in only 3.5% NaCl solution. Further, in 3.5% NaCl + 1.0% H 2O 2 solution, the cathodic corrosion reaction (and so the cathodic current density) is increased (as more oxygen available to be reduced) and has to be compensated with a higher anodic current density (dissolution of aluminium). This also accounts for an increase of corrosion current density (J corr ) in 3.5% NaCl solution having a small amount of H 2O 2. In the anodic region of the polarization curves, although the current density is initially higher, the curves tend to converge at higher applied anodic potential corresponding to high value of current density.The dissolution of aluminium, the effect of chloride accelerating attack, and the state for precipitation of Al(OH)3 etc have been stated in Refs. [48,49].In the alkaline solution, the anodic current density (dissolution of aluminium) is dominating and the summary current density is positive, resulting in shifting the corrosion potential (ijcorr ) to negative values (negative threshold of passive area) than the pitting potential. In Al alloys, pH of solution has limited effect on the pitting potential but does affect the open circuit potential [50,51]. Potentiodynamic polarizations curves (Figs. 4(c)) of the various alloy tempers in 3.5% NaCl solution at pH 12 showing the distinct passive region which is associated with the formation of thin passive film on the surface. The main factors controlling the passivation process are the potential of the alloys, the concentration of metallic ion and the interfacial pH. Figure 4(c) also displays that at very negative potential, the current density is higher (approximately 100í400 times) compared to that at near neutral pH solution (Figs. 4(a) and (b)). This is attributed to the fact that at very negative potential, there is higher uniform corrosion; as water splits into H + and OH í, the OH í causes an pH increase on the aluminium surface. Under this situation, aluminium is dissolved due to missing stability of the natural oxide layer resulting in an increase of current density in negative direction. In the positive potential direction beyond the passive range, the passive area is limited by the pitting potential (ijp or ijbr ), localized pitting corrosion occurs. The more the applied potential exceeds in the transpassive region, and the higher the current density is.The pitting potential (ijp ) may be confounded by the density of precipitate phases (S and ș) serving as pit initiation sites, presence of Cu depletion zones, the oxide film thickness and defects in the oxides at risk surface areas, etc. Since repassivation potential (ijrp ) is associated with the repassivation of large pits which seem to be over a hundred times larger than any likely Cu-depleted zones. It is believed that they reflect the corrosion properties of the matrix. 3.4.2 Alloy tempersFigures 4(a) and (b) and Tables 3 and 4 show that the corrosion potential values, ijcorr , shift towards more negative direction with the increase of ageing time. The ijcorr value of the over-aged temper is found to be the most negative and for the as-quenched state it is the least negative. In 2024 alloy, the observed shifting of ijcorr towards more negative direction with increasing ageing time is due to the reduction of copper content in solid solution and the formation of S (Al 2CuMg) precipitate as well [47]. It is well known that the preferred sites for pitting corrosion initiation in 2024 Al alloy are the S phase precipitates. But, the ș and second intermetallic phases (e.g. AlCuFeMnSi) have better resistance to localized corrosion [5,10,15,16,21].Therefore, to elucidate the effect of alloy tempersTable 5 Values of ǻ(ijp –ijcorr ) and passive potential range of various 2024 alloy tempers in different media3.5% NaCl solution at pH 12 3.5% NaCl solution 3.5% NaCl+1.0% H 2O 2 solution Alloy temper ijp (vs SCE)/mVijpp (vs SCE)/mV(ǂijp –ijcorr ) (vs SCE)/mVijcorr (vs SCE)/mV(ijp –ijcorr ) (vs SCE)/mVijcorr (vs SCE)/mV(ijp –ijcorr ) (vs SCE)/mV2024-AQ 511 494 793 593 82 í57968190-1h 561 479 797 640 79 637 76 190-5h 618 388 702 678 60 651 33 190-12h 663 376 675 696 33 677 14 190-72h 661 351 681 695 34 691 30 190-154h671 349 666 706 35 696 25。
Effect of Aging Treatment on Fatigue Behavior of an Al-Cu-Mg-Ag Alloy
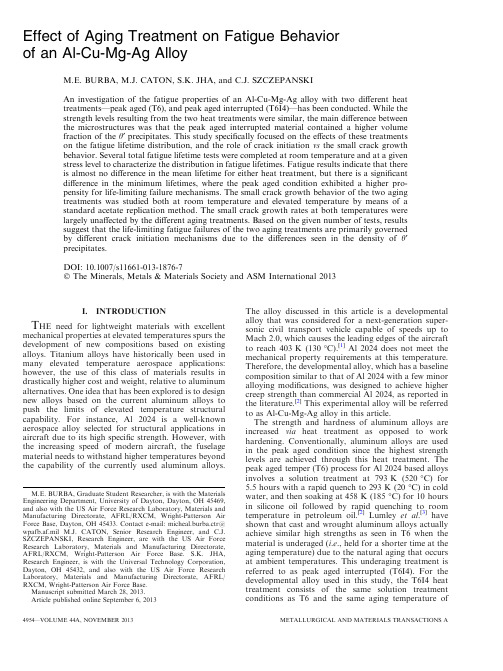
Effect of Aging Treatment on Fatigue Behaviorof an Al-Cu-Mg-Ag AlloyM.E.BURBA,M.J.CATON,S.K.JHA,and C.J.SZCZEPANSKIAn investigation of the fatigue properties of an Al-Cu-Mg-Ag alloy with two different heattreatments—peak aged(T6),and peak aged interrupted(T6I4)—has been conducted.While thestrength levels resulting from the two heat treatments were similar,the main difference betweenthe microstructures was that the peak aged interrupted material contained a higher volumefraction of the h¢precipitates.This study specifically focused on the effects of these treatmentson the fatigue lifetime distribution,and the role of crack initiation vs the small crack growthbehavior.Several total fatigue lifetime tests were completed at room temperature and at a givenstress level to characterize the distribution in fatigue lifetimes.Fatigue results indicate that thereis almost no difference in the mean lifetime for either heat treatment,but there is a significantdifference in the minimum lifetimes,where the peak aged condition exhibited a higher pro-pensity for life-limiting failure mechanisms.The small crack growth behavior of the two agingtreatments was studied both at room temperature and elevated temperature by means of astandard acetate replication method.The small crack growth rates at both temperatures werelargely unaffected by the different aging treatments.Based on the given number of tests,resultssuggest that the life-limiting fatigue failures of the two aging treatments are primarily governedby different crack initiation mechanisms due to the differences seen in the density of h¢precipitates.DOI:10.1007/s11661-013-1876-7ÓThe Minerals,Metals&Materials Society and ASM International2013I.INTRODUCTIONT HE need for lightweight materials with excellent mechanical properties at elevated temperatures spurs the development of new compositions based on existing alloys.Titanium alloys have historically been used in many elevated temperature aerospace applications: however,the use of this class of materials results in drastically higher cost and weight,relative to aluminum alternatives.One idea that has been explored is to design new alloys based on the current aluminum alloys to push the limits of elevated temperature structural capability.For instance,Al2024is a well-known aerospace alloy selected for structural applications in aircraft due to its high specific strength.However,with the increasing speed of modern aircraft,the fuselage material needs to withstand higher temperatures beyond the capability of the currently used aluminum alloys.The alloy discussed in this article is a developmental alloy that was considered for a next-generation super-sonic civil transport vehicle capable of speeds up to Mach2.0,which causes the leading edges of the aircraft to reach403K(130°C).[1]Al2024does not meet the mechanical property requirements at this temperature. Therefore,the developmental alloy,which has a baseline composition similar to that of Al2024with a few minor alloying modifications,was designed to achieve higher creep strength than commercial Al2024,as reported in the literature.[2]This experimental alloy will be referred to as Al-Cu-Mg-Ag alloy in this article.The strength and hardness of aluminum alloys are increased via heat treatment as opposed to work hardening.Conventionally,aluminum alloys are used in the peak aged condition since the highest strength levels are achieved through this heat treatment.The peak aged temper(T6)process for Al2024based alloys involves a solution treatment at793K(520°C)for 5.5hours with a rapid quench to293K(20°C)in cold water,and then soaking at458K(185°C)for10hours in silicone oil followed by rapid quenching to room temperature in petroleum oil.[2]Lumley et al.[3]have shown that cast and wrought aluminum alloys actually achieve similar high strengths as seen in T6when the material is underaged(i.e.,held for a shorter time at the aging temperature)due to the natural aging that occurs at ambient temperatures.This underaging treatment is referred to as peak aged interrupted(T6I4).For the developmental alloy used in this study,the T6I4heat treatment consists of the same solution treatment conditions as T6and the same aging temperature ofM.E.BURBA,Graduate Student Researcher,is with the Materials Engineering Department,University of Dayton,Dayton,OH45469, and also with the US Air Force Research Laboratory,Materials and Manufacturing Directorate,AFRL/RXCM,Wright-Patterson Air Force Base,Dayton,OH45433.Contact e-mail:micheal.burba.ctr@ M.J.CATON,Senior Research Engineer,and C.J. SZCZEPANSKI,Research Engineer,are with the US Air Force Research Laboratory,Materials and Manufacturing Directorate, AFRL/RXCM,Wright-Patterson Air Force Base.S.K.JHA, Research Engineer,is with the Universal Technology Corporation, Dayton,OH45432,and also with the US Air Force Research Laboratory,Materials and Manufacturing Directorate,AFRL/ RXCM,Wright-Patterson Air Force Base.Manuscript submitted March28,2013.Article published online September6,2013458K(185°C),but is only held at458K(185°C)for 2hours,and then it is rapidly quenched to room temperature.The material remains unstable and con-tinues to naturally age at298K(25°C)until peak aged strengths have been attained.Depending on the alumi-num alloy,natural aging to peak aged strengths is achieved within tens to thousands of hours.[3]Although both aging treatments,T6and T6I4,have the same mechanical properties,their microstructures remain different.There have been several studies evaluating the effect of aging treatment(underaged,peak aged,or overaged)on the fatigue properties of aluminum aerospace alloys.[4–10] All these studies have shown that the overaged condition exhibits the lowest fatigue properties,whereas underaging was shown to result in equivalent or better fatigue properties when compared with the peak aged condition, depending on the alloy composition.These results led Lumley et al.[11]to study the effects of aging on fatigue properties of the Al-Cu-Mg-Ag alloy mentioned previ-ously.Lumley et al.concluded from early test results that there was an increase in lifetimes for the underaged(UA) condition when compared with the T6condition.Yan et al.[12]studied the effect of aging treatment,T3vs T6,on a2E12aluminum alloy with respect to room temperature fatigue.The results showed that there was a significant increase in crack initiation life in the T3aging treatment compared to the T6aging treatment.It was also shown that the T3aging treatment exhibits much slower fatigue crack growth rates than the T6aging treatment.Research conducted on AA2024and an experimental Al-Cu-Mg-Li alloy with aging times varying from0to48hours, indicated that fatigue crack propagation resistance initially improved,reached a maximum,and subsequently decreased with increasing aging times.[13]Changes in precipitation structure are cited as being responsible for this trend.A similar study was conducted by Yanbin et al.[14]on a2524alloy including the comparison of the fatigue properties of a naturally aged T351temper with an artificial aging temper at443K(170°C)/30min.The results demonstrated a decreasing fatigue crack propaga-tion resistance in the following order:artificial aging at 443K(170°C)/30min,T351,T351with additional exposure to373K(100°C)/2000h,and artificial aging 443K(170°C)/30min with an additional exposure to 373K(100°C)/2000h.The higher fatigue crack propa-gation resistance of the443K(170°C)/30min aging temper,both before and after thermal exposures at373K (100°C),was attributed to the larger Cu-Mg co-clusters in the matrix that do not re-dissolve during cycling defor-mation,which suppress the formation of S precipitates during thermal exposure.In terms of the creep properties,the experimental Al-Cu-Mg-Ag alloy has shown enhanced creep resistance when compared with the industrial Al2024.[2]The two aging treatments in this study are fairly similar,with the T6I4being subjected to a shorter aging time of2hours compared with T6which was aged for10hours at the same aging temperature.However,the T6I4material naturally ages at298K(25°C),and eventually both treatments attain the same mechanical properties.The shorter aging time of the T6I4condition,which results in similar mechanical properties as the T6condition, provides the potential for cost savings during production. The question addressed in this study is whether the differences in aging treatment and microstructure have an effect on the fatigue properties of this experimental alloy. Furthermore,in terms of life prediction,recent studies have shown that fatigue lifetime distributions often exhibit a bimodal behavior where the population of specimens dominating the mean lifetime separates from the short-lifetime(or the life-limiting)population.[15–18] These studies have focused on a mechanism-based understanding and prediction of the life-limiting distri-bution,which is the distribution driving fatigue design of fracture critical components.Therefore,the current study also,investigates whether a bimodal distribution in lifetime is revealed for a given microstructure and test condition.Furthermore,it is useful to assess how the two aging treatments affect the mean and minimum fatigue lifetime stly,it would be useful to attribute the effect of aging treatment to either fatigue crack initiation or fatigue crack growth behavior.Since the experimental alloy was developed for enhanced creep properties targeting elevated temperature applica-tions,the current study also investigates the fatigue crack growth rates at room and elevated temperature in the T6and T6I4aging conditions.II.EXPERIMENTAL DETAILSA.Microstructural CharacterizationThe composition of the experimental alloy investi-gated in this study is shown in Table I.The material was received in the form of two extruded bars (70.6927.6mm)which were heat treated in a circulat-ing air furnace for5.5hours at798K(525°C),cold water quenched,and aged in oil.The two aging treatments were(i)the peak aging treatment designated as T6,and(ii)a peak aged interrupted treatment designated as T6I4.The process parameters for the T6 treatment were10hours at458K(185°C)followed by a rapid quench to room temperature.For the T6I4 temper,the parameters were2hours at458K(185°C) followed by a rapid quench to room temperature whereupon natural aging,greater than1200hours,Table I.Experimental Alloy CompositionAlloy Composition(Wt Pct)Cu Mg Ag Mn Zr Fe Si Al 5.600.450.450.300.180.100.07bal.continues until the mechanical properties reach those of T6.[2]The microhardness and tensile values for the two aging treatments are presented in Table II.The strength levels of the two treatments were similar,which suggests that sufficient time was allowed for the natural aging process to complete.Lumley et al.[2]reported the grain size away from the surface region for a similarly processed bar of the current alloy to be245972961l m in the longitudinal, transverse,and short-transverse direction.The micro-structures in the current study were analyzed using a FEI Company(Hillsboro,OR)field emission gun(FEG) scanning electron microscope(SEM)equipped with a4Pi image acquisition system and an EDAX TSL orientation imaging microscopy(OIM)system.The OIM data were collected at an electron accelerating voltage of20kV with a beam current of about10nA,and a step size of 5l m.The inverse polefigure(IPF)map obtained by OIM analysis of the transverse section of the T6I4bar is given in Figure1.As illustrated by thisfigure,the outer edge of the extruded bars exhibited much larger grains (size in excess of those reported for the same alloy that was processed similarly)[2]than those in the interior.The large grain region extends~6.5mm into the material from the extrusion surface.Besides the surface layer, large grains are also intermittently seen in the interior fine-grained region and are referred to as rogue grains, similar to‘‘as large as’’or ALA grains seen in superal-loys,throughout this report.The T6condition had a similar microstructural morphology to that observed in the T6I4condition.The larger grains observed on the outer edge of the extruded bar are attributed to the rapid grain growth induced by the high amount of stored energy in the surface region during the deformation process and is commonly seen in extruded materi-als.[19,20]The extrusion process used for the current alloy was on the laboratory scale,and the presence of large grains at the surface may be minimized in a more optimized industrial scale processing of the alloy.In order to examine the precipitate structures due to the two aging treatments,samples were prepared for transmission electron microscopy(TEM).A Philips CM 200LaB6TEM operated at an accelerating voltage of 200kV was employed for this purpose.Specimens from both aging treatments were prepared using standard metallurgical techniques,followed by thinning the specimen foils to~100l m using600grit silicon carbide paper.The foils were then electropolished using a twin jet electropolishing system that employed a HNO3based electrolyte at253K(À20°C)with a voltage of10V and a current of12mA.For both aging treatments,TEM brightfield images were recorded with respect to two different diffracting conditions,and the results are presented in Figure2. The T6aging treatment is represented by Figures2(a) and(c),whereas the T6I4condition is shown in Figures2(b)and(d).The diffraction condition dis-played in Figures2(a)and(b)corresponds to the incident electron beam direction being parallel to a h001i grain orientation.In Figures2(c)and(d),the crystal orientation is~5deg from a h110i zone axis, toward a two beam diffracting condition with g={111}.The diffraction patterns associated witheach brightfield micrograph are shown in the top inset. The bottom inset represents the precipitate variants and their orientations.The precipitates seen in the current microstructures have been reported by other researchers.[2,3,11,21]The X-phase precipitates have a composition of Al2Cu(with Ag/Mg surface layer),an orthorhombic crystal structure,and exist as plates with the habit plane being{111}a.[21]The h0-phase precipi-tates also have a composition of Al2Cu but a tetrag-onal crystal structure,and plate-like morphology with the habit plane being{001}a.[21]The difference in precipitate microstructures between the two aging treatments is described as follows. Figure2(a)is a representative micrograph of the T6 aging treatment,which shows two variants of the X-phase and one variant of the h0-phase.Figure2(b)is a representative micrograph of the T6I4aging treatment with respect to the same diffraction condition as in Figure2(a)that also shows the same variants of precipitates with an addition of an ellipsoidal precipitate scattered throughout the matrix which is not seen in Figure2(a).The literature on the experimental alloy has reported the existence of a r-phase precipitate with a composition of Al5Cu6Mg2and having a cubic crystal structure in some TEM images.However,the ellipsoidalTable II.Experimental Alloy Mechanical Properties Mechanical Properties T6I4T6 UTS(MPa)489484 Yield Strength(MPa)454457 VHNCoarse Grain177173 Fine Grain155162Fig.1—IPF map of half of the width of the T6I4extruded bar source material used for the fatigue test specimens.A surface layer of coarse grains is observed,while the interior has afine-grained microstructure.The core of the extruded material also has large grains scattered throughout,referred to as rogue grains.The fatigue specimen grip diameter(solid circles)and gage cross section(dotted circles)are overlaid on thefigure to indicate the general microstruc-ture contained within the gage sections.precipitates seen in Figure 2(b)do not appear to have the same morphology as the r -phase and thus are considered to be another variant of the X -phase.[21]The key difference between the T6and T6I4microstructures is revealed while comparing Figure 2(c)with (d).As shown,it appears that T6I4has a higher amount of h 0-phase precipitates than T6,which presumably pre-cipitated during natural aging at room temperature.The differences between the two microstructures are signif-icant in that,as discussed before,similar strength levels are achieved via different microstructural constituents.It appears that the h 0precipitates that form in the T6I4condition at room temperature compensate for the loss of the precipitate-strengthening contribution due to the relative lack of X -phase particles.B.Fatigue Lifetime TestingThe fatigue lifetime specimens were machined from the extruded bars of the T6and T6I4condition according to the layout depicted in Figure 3.The specimens were machined so that the gage section incorporated both the coarse-grain and fine-grain microstructures depicted in Figure 1.Due to the heterogeneity of the microstructure in the gage section,extensive efforts were made to study the role of the differing microstructures on the fatigue initiation response with results being shown in later sections.As shown,the fatigue loading axis was aligned with the longitudinal direction.As illustrated in Figure 4(a),the specimens had a round-bar geometry with auniformFig.2—TEM bright field micrographs of the T6and T6I4microstructures with diffraction pattern insets in the top right of each image and pre-cipitate variant positions insets in the bottom right.(a )and (b )T6and T6I4,respectively,in the [101]a orientation showing two variants of the X -phase and one variant of the h ¢-phase.(c )and (d )T6and T6I4,respectively,in the [001]a orientation showing two variants of the h ¢-phase.gage length of about 12.7mm and a diameter of about 6.1mm,and received a low stress ground surface finish.The fatigue tests were conducted in a uniaxial servohydraulic MTS test frame under load control using MTS MultiPurpose Testware and FlexTest 40Digital Controller.The stress–strain hysteresis loops were periodically recorded using a MTS extensometer,and all the tests were run under nominally elastic loads.The elastic modulus for the material was calculated from the stress–strain data to insure proper alignment before each test.Fatigue test stress levels were selected to provide large fatigue lifetime variability yet produce no run-outs at roughly 107cycles.After some initial exploratory tests,the stress level ðr max Þof 275MPa was selected for all specimens.A total of 18specimens were tested for both aging conditions.The tests were run at room temperature in laboratory air at a frequency of 30Hz and the stress ratio,R ,was 0.1.C.Small Fatigue Crack Growth TestingThe dimensions of the small crack growth specimens,shown in Figure 4(b),were kept similar to those of thefatigue lifetime specimens with the exception that a square gage section was employed for these tests.Also,the small crack specimens were hand polished down to a surface finish of about 1l m to enable detection and accurate measurement of small cracks.Micronotches,~40l m in surface length (2c)and 20l m in depth (a)were machined using a focused ion beam (FIB)to serve as crack initiation sites and enable the collection of more small fatigue crack growth data from fewer tests.A total of 10micronotches were machined in each specimen,with each side containing either two or three notches.To ensure that the cracks did not interact,the notches were staggered along the specimen’s length such that only one notch was located on any given crack growth plane.The test parameters for the small crack growth experiments were the same as the fatigue lifetime tests with the only difference being that they were run at a frequency of 20Hz as opposed to 30Hz.The small cracks were monitored using the acetate replication method where cycling was periodically interrupted to take acetate replicas of the specimen surface with a static hold load of 60pct r max .The crack length was then measured from the replicas using an optical microscope.Fatigue crack growth data were reduced using a method presented by Larsen et al.[22]whereby a crack extension increment,D c inc or D a inc ,is used as a criterion for determining the selection of data that will be regressed.This method takes into consideration the error due to measurement resolution and averages out the error over the full range of crack measurements.D.Elevated Temperature TestingFatigue crack growth rate tests were conducted at elevated temperature to determine the effect of aging treatment in a regime where creep–fatigue mechanisms were active.The specimens had the same dimensions as the room temperature fatigue crack growth tests (Figure 4(b)).There were a total of eight 40l m micronotches machined on the surface of the specimens with two sides consisting of three micronotches each and the third side had a total of two micronotches.The fourth side had three thermocouples spot welded to the surface,spaced evenly along the gage to encompass all of the micronotches to monitor and control the temper-ature throughout the tests.The elevated temperature tests were conducted at 130°C with a r max of 275MPa,stress ratio of 0.1,frequency of 0.33Hz,and 6seconds hold time at r max .The imposed hold time of 6seconds at the maximum stress level of each cycle was an attempt to enhance the creep contributions to crack extension.AtestFig.3—Schematic showing the location and orientation of the specimens extracted from the extrudedbars.Fig.4—(a )Schematic of the cylindrical dogbone specimens that had a low stress ground surface finish which was used for fatigue lifetime tests for both aging conditions.(b )Schematic of the square gage sec-tion dogbone specimens with the 40l m notches micromachined in the gage section for the small fatigue crack growth tests conducted at room temperature and 403K (130°C).temperature of403K(130°C)was selected since creep data are available in the literature[2,11]at this temperature for the experimental alloy,while this is also a practically experienced temperature on the leading edges of wings and skins on aerospace materials at supersonic speeds.[1] All the same protocols were employed in elevated temperature testing as with room temperature testing. The specimen was heated by six quartz lamps(three on each side)wired in parallel to maintain high power output to all lamps.Due to the high thermal conduc-tivity of the aluminum alloy,the specimen grips required modification to maintain a uniform temperature profile of403K(130°C)in the specimen gage.Most elevated temperature tests require that the hydraulic grips be water chilled during testing so as to not damage the grips.In this case,it was necessary to run heated distilled water in a closed loop through the grips to maintain a uniform temperature profile in the specimen gage.The distilled water was kept at a temperature of 305.2K(32.2°C)(90°F)or higher during testing to alleviate the power needed by the quartz lamps to heat the specimen.III.RESULTS AND DISCUSSIONA.Fatigue Lifetime DataThe fatigue lifetimes at the r max of275MPa with respect to the two heat treatments,T6and T6I4,are plotted on a cumulative distribution function(CDF)plot in Figure5.As shown,the18T6I4specimens resulted with a lifetime range of~29106to29107whereas the T6specimens had a much larger range of lifetimes in the same number of tests,~89104to89107.Further examination of the distributions for the two heat treatments indicates that while the mean fatigue lifetime (i.e.,the lifetime corresponding to the probability of failure of50pct)was almost unaffected by aging treatment,there was a greater likelihood of minimum lifetimes in the T6aging treatment than the T6I4 treatment(22pct in T6vs none in T6I4in18tests of each microstructure).The minimum lifetime specimens refer to those specimens that belong to the short lifetime population.The separation of lifetimes into a short lifetime population and a long lifetime population is clearly seen for the T6data,which appears to have a bimodal shape in the CDF plot.The bimodal distribu-tion of lifetimes,where the longer-lifetime failures are separated from the short-lifetime population,has been reported in previous studies on other materials.[15–18] Those researchers have shown that the minimum lifetime population is controlled by the small and long crack growth regimes(i.e.,crack initiation lifetime,N i=0) whereas the long lifetime population has a non-zero crack initiation lifetime.In powder-processed Ni-based alloys,these lifetime distributions are typically affected by the presence of nonmetallic particles,voids,or other process controlled microstructural features.In the case of titanium alloys,certain combinations of microstructural orientations or clusters appear to drive the separation of lifetime distributions.The bimodal lifetime distribution displayed by the T6microstructure can be viewed in the context of these earlier studies.The shaded region in Figure6corresponds to the calculated crack growth lifetime range assuming immediate crack initiation, which encompasses all of the minimum lifetime failures observed in the T6condition.Since both the T6and the T6I4specimens had the same composition and grain structure,and nominally similar strength levels,the absence of minimum lifetime failures in the T6I4condi-tion(in the given number of tests)can only be attributed to the differences in the precipitate microstructure between the two aging treatments.It is useful to determine whether the bimodal distri-bution in lifetime,which was seen in the T6specimens but absent in the T6I4specimens,can be attributed to surface vs subsurface crack initiation.The crack initia-tion location was determined from fractographic exam-ination,and the data points have been identified accordingly in the CDF plot shown in Figure6.As depicted in thefigure,while all minimum lifetime points with respect to the T6condition were caused by surface crack initiation,the long lifetime population was also marked by a few surface initiated failures.In addition, the lifetime distribution for the T6I4treatment had a mix of both surface and subsurface initiated failures although a bimodal distribution was not seen in that case.Therefore,while surface initiation may be a necessary condition for the minimum lifetime failure, the separation of lifetimes into two populations is not entirely based on the location of crack initiation. Further investigation into the mechanisms behind the bimodal distribution seen for the peak aged condition will be discussed in subsequent sections.B.Crack-Initiation MechanismsFractography was performed on all failed specimens from both aging treatments.Fatigue crack initiationcan Fig.5—Cumulative distribution function(CDF)plot of the18fati-gue lifetime tests for each aging treatment.Mean lifetimes are similar for both treatments,but the minimum lifetimes are only seen in the T6aging treatment producing a bimodal distribution.be attributed to four different types of microstructural features:(1)nonmetallic particles(NMPs),(2)large grains(either rogue or otherwise occurring at the surface of the extrusion),(3)pores,and(4)a combination of two of the mechanisms.As noted before,cracks initiated from both surface and subsurface features.However, neither the feature associated with initiation nor the location of initiation site(i.e.,surface vs subsurface) correlated with lifetime.For example,Figures7(a)and (c)are fractographs of initiation sites in which the crack initiated from NMPs.Both fractographs are taken from the T6condition with Figure7(a)being one of the shortest lifetimes observed in the T6condition.The failure occurred from a NMP near the specimen surface, which was~60l m in diameter.The fractograph in Figure7(c)is another example of a failure in a T6 specimen,which also failed from a NMP at the specimen surface.However,the lifetime of this specimen was in excess of39106cycles over that of the specimen shown in Figure7(a)while the NMP was nearly twice the diameter of the NMP observed at the initiation site for the shorter lifetime specimen.This observation indicates that the lifetime of the specimen is not solely determined by the microstructural feature at the location of the initiation site but that the microstructure surrounding the initiation site must also affect crack initiation and early crack growth.This point can be further illustrated by examining the neighborhood of the crack initiating NMP in Figures7(a)and(c).It appears that the NMPin Figure7(c)was in afine-grained region near the specimen surface while in Figure7(a)the crack initiating NMP was surrounded by large grains near the specimen surface.In addition to the size,the crystallographic orientations of the neighboring grains are also antici-pated to play an important role in crack initiation and early crack growth.Figure7(b)exhibits an initiation site from a large grain on the surface of a specimen in the T6condition. However,specimens with much longer lifetimes than the one shown in Figure7(b)also failed from large grains near the surface which,once again,indicates that more than just the initiation feature or location must be considered in predicting fatigue lifetimes;that is,the local neighborhood must affect crack initiation and small fatigue crack growth.Thisfinding is contrary to the accepted convention where the largest defect equates to the shortest lifetime.In particular,studies of the effect of porosity on the fatigue behavior of cast Al alloys report a negative correlation between pore size and lifetime,for example,the cast Al Alloy E319.[23]It was mentioned that crack initiation can result from a combination of two fatigue critical features,and this is shown in Figure7(d).The crack initiation site in a T6 specimen is shown in thisfigure.This crack initiated in the specimen interior from a combination of a rogue grain and an adjacent pore,which led to a significantly longer fatigue life in this case.The specimens subjected to the T6I4aging treatment exhibited similar crack initiation features as seen in the T6 condition.Some representative fractographs are presented in Figure8.Figures8(a)and(b)are typical of crack initiation sites associated with the specimen surface.The initiation site in Figure8(a)corresponds to a large grain on the surface paired with a pore.Figure8(b)is an example of crack initiation from a large rogue grain located near the surface of the specimen.Figure8(c) displays a subsurface crack initiation site from a NMP that is surrounded by several large grains.Notably,in T6I4specimens,crack initiation from a NMP was found to always occur in association with a surrounding large grain region,which is signified by the large facets around the NMP in the example in Figure8(c).An example of subsurface crack initiation from a large grain paired with a pore is given in Figure8(d).C.Crack Initiation Location with Respect to Large vs Small Grain RegionAs the above discussion indicates,initiation mecha-nisms are likely activated through a complex interaction of microstructure features(pores,NMPs,etc.)with their neighborhood(large grain vs small grain),and the specimen surface.As described previously,the extruded bars from which the current specimens were extracted exhibited a large grain layer along the edge(Figure1). Although the interior of the extruded bars also contained occasional large grains,the presence of large vsfine-grained microstructural neighborhoods at the crack initiation sites makes it imperative to characterize the location of crack initiation with respect to the large grain regions in the specimen cross section.Therefore,a cross-section within the gage of each failed specimen was characterized and the crack initiation site was mapped on to the cross-sectioned microstructure.For this purpose, metallographic samples were extracted from thegage Fig.6—CDF plot of the same data as in Figure5but the points are differentiated in terms of surface vs subsurface crack initiation.The shaded region represents the range of predicted crack growth life-times computed using the largest and smallest failure initiation sizes measured from the fractographs in combination with the fastest and the slowest small crack growth rates,respectively.The predicted crack growth lifetime range fully encapsulates the4minimum life-time points seen in the T6aging condition indicating that those4 specimens likely initiated fatigue cracks almost immediately and therefore,were dominated by fatigue crack growth,whereas the other specimens havefinite fatigue crack initiation lifetimes.。
210984048_镁合金微弧氧化膜层性能优化研究进展
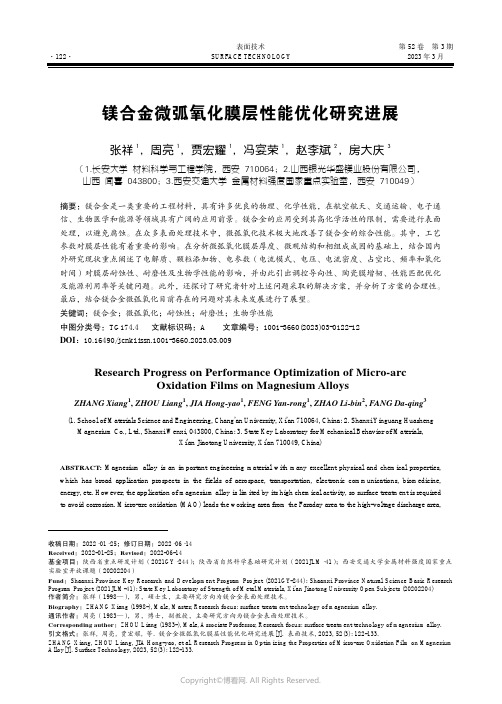
表面技术第52卷第3期镁合金微弧氧化膜层性能优化研究进展张祥1,周亮1,贾宏耀1,冯宴荣1,赵李斌2,房大庆3(1.长安大学 材料科学与工程学院,西安 710064;2.山西银光华盛镁业股份有限公司,山西 闻喜 043800;3.西安交通大学 金属材料强度国家重点实验室,西安 710049)摘要:镁合金是一类重要的工程材料,具有许多优良的物理、化学性能,在航空航天、交通运输、电子通信、生物医学和能源等领域具有广阔的应用前景。
镁合金的应用受到其高化学活性的限制,需要进行表面处理,以避免腐蚀。
在众多表面处理技术中,微弧氧化技术极大地改善了镁合金的综合性能。
其中,工艺参数对膜层性能有着重要的影响。
在分析微弧氧化膜层厚度、微观结构和相组成成因的基础上,结合国内外研究现状重点阐述了电解质、颗粒添加物、电参数(电流模式、电压、电流密度、占空比、频率和氧化时间)对膜层耐蚀性、耐磨性及生物学性能的影响,并由此引出调控导向性、陶瓷膜增韧、性能匹配优化及能源利用率等关键问题。
此外,还探讨了研究者针对上述问题采取的解决方案,并分析了方案的合理性。
最后,结合镁合金微弧氧化目前存在的问题对其未来发展进行了展望。
关键词:镁合金;微弧氧化;耐蚀性;耐磨性;生物学性能中图分类号:TG174.4 文献标识码:A 文章编号:1001-3660(2023)03-0122-12DOI:10.16490/ki.issn.1001-3660.2023.03.009Research Progress on Performance Optimization of Micro-arcOxidation Films on Magnesium AlloysZHANG Xiang1, ZHOU Liang1, JIA Hong-yao1, FENG Yan-rong1, ZHAO Li-bin2, FANG Da-qing3(1. School of Materials Science and Engineering, Chang'an University, Xi'an 710064, China; 2. Shanxi Yinguang HuashengMagnesium Co., Ltd., Shanxi Wenxi, 043800, China; 3. State Key Laboratory for Mechanical Behavior of Materials,Xi'an Jiaotong University, Xi'an 710049, China)ABSTRACT: Magnesium alloy is an important engineering material with many excellent physical and chemical properties, which has broad application prospects in the fields of aerospace, transportation, electronic communications, biomedicine, energy, etc. However, the application of magnesium alloy is limited by its high chemical activity, so surface treatment is required to avoid corrosion. Micro-arc oxidation (MAO) leads the working area from the Faraday area to the high-voltage discharge area,收稿日期:2022–01–25;修订日期:2022–06–14Received:2022-01-25;Revised:2022-06-14基金项目:陕西省重点研发计划(2021GY–244);陕西省自然科学基础研究计划(2021JLM–41);西安交通大学金属材料强度国家重点实验室开放课题(20202204)Fund:Shaanxi Province Key Research and Development Program Project (2021GY-244); Shaanxi Province Natural Science Basic Research Program Project (2021JLM-41); State Key Laboratory of Strength of Metal Materials, Xi'an Jiaotong University Open Subjects (20202204)作者简介:张祥(1998—),男,硕士生,主要研究方向为镁合金表面处理技术。
管道表面蚀坑-裂纹的应力强度因子分析
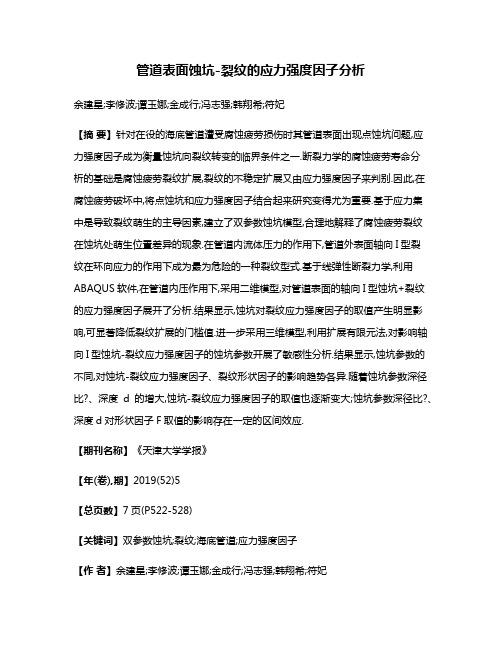
管道表面蚀坑-裂纹的应力强度因子分析余建星;李修波;谭玉娜;金成行;冯志强;韩翔希;符妃【摘要】针对在役的海底管道遭受腐蚀疲劳损伤时其管道表面出现点蚀坑问题,应力强度因子成为衡量蚀坑向裂纹转变的临界条件之一.断裂力学的腐蚀疲劳寿命分析的基础是腐蚀疲劳裂纹扩展,裂纹的不稳定扩展又由应力强度因子来判别.因此,在腐蚀疲劳破坏中,将点蚀坑和应力强度因子结合起来研究变得尤为重要.基于应力集中是导致裂纹萌生的主导因素,建立了双参数蚀坑模型,合理地解释了腐蚀疲劳裂纹在蚀坑处萌生位置差异的现象.在管道内流体压力的作用下,管道外表面轴向I型裂纹在环向应力的作用下成为最为危险的一种裂纹型式.基于线弹性断裂力学,利用ABAQUS软件,在管道内压作用下,采用二维模型,对管道表面的轴向I型蚀坑+裂纹的应力强度因子展开了分析.结果显示,蚀坑对裂纹应力强度因子的取值产生明显影响,可显著降低裂纹扩展的门槛值.进一步采用三维模型,利用扩展有限元法,对影响轴向I型蚀坑-裂纹应力强度因子的蚀坑参数开展了敏感性分析.结果显示,蚀坑参数的不同,对蚀坑-裂纹应力强度因子、裂纹形状因子的影响趋势各异.随着蚀坑参数深径比?、深度d的增大,蚀坑-裂纹应力强度因子的取值也逐渐变大;蚀坑参数深径比?、深度d对形状因子F取值的影响存在一定的区间效应.【期刊名称】《天津大学学报》【年(卷),期】2019(52)5【总页数】7页(P522-528)【关键词】双参数蚀坑;裂纹;海底管道;应力强度因子【作者】余建星;李修波;谭玉娜;金成行;冯志强;韩翔希;符妃【作者单位】天津大学水利工程仿真与安全国家重点实验室;高新船舶与深海开发装备协同创新中心;钦州学院机械与船舶海洋工程学院【正文语种】中文【中图分类】O346.2处于腐蚀海水和疲劳载荷的作用下,海底管道发生腐蚀疲劳破坏.海底管道的腐蚀疲劳过程可简要地概括为:服役于腐蚀疲劳环境体系下的海底管道,其表面产生点蚀,点蚀进一步扩展;临界状态下,点蚀坑转变成裂纹[1-2](以下简称蚀坑-裂纹);裂纹进一步扩展,直至海底管道断裂失效.众所周知,腐蚀疲劳的起点为点蚀[3-5];腐蚀疲劳损伤的主要过程为裂纹扩展(裂纹扩展寿命约占腐蚀疲劳总寿命的90%[6]).基于断裂力学的腐蚀疲劳寿命分析的基础是腐蚀疲劳裂纹扩展,裂纹的不稳定扩展又由应力强度因子来判别.因此,在腐蚀疲劳破坏中,将点蚀坑和应力强度因子结合起来研究变得尤为重要.对于蚀坑和应力强度因子问题,学者们开展了诸多研究[7-12].Pidaparti等[7]对蚀坑处的应力集中情况展开了系统分析;Zhang等[10]对含裂纹构件的裂纹应力强度因子展开了细致分析;Kondo[5]基于腐蚀疲劳现象学建立了蚀坑向裂纹转变的应力强度因子准则;Rokhlin等[13]考查了裂纹在蚀坑处的萌生位置;赵乾坤[14]考查了蚀坑对表面裂纹应力强度因子的影响.目前,国内外学者主要是将存在于结构表面的蚀坑处理为表面椭球形凹坑[5, 7-9],采用单一参数深径比(α=d/c)来描述.采用单参数描述的蚀坑,其应力集中的最大值始终位于蚀坑底部[15],其无法解释由应力集中导致的裂纹萌生[16]于蚀坑不同位置[13](蚀坑底部或肩部)的现象.同时,对于蚀坑参数对蚀坑-裂纹应力强度因子的相关研究很少涉及.在管道内流体压力的作用下,管道外表面轴向I型裂纹在环向应力的作用下成为最为危险的一种裂纹型式.本文拟建立双参数蚀坑模型,基于线弹性断裂力学,利用ABAQUS软件中的扩展有限元法,在管道内压作用下,对存在于管道外表面的I 型蚀坑-裂纹的应力强度因子开展相应的研究;并分析了蚀坑参数对蚀坑-裂纹应力强度因子的影响趋势.服役于腐蚀疲劳体系下的海底管道,点蚀在其表面形核、扩展.目前主要是采用单参数深径比(a=d/c),将点蚀坑描述成存在于结构表面的椭球形凹坑.前文提到,采用单参数椭球形模型的点蚀坑,其应力集中的最大值始终位于蚀坑的底部[15].本文拟采用双参数(深径比(a=d/c)和蚀坑位置(β=b/d)),将点蚀坑依旧处理为表面椭球形凹坑,如图1所示,图中d为蚀坑深度,c为蚀坑半径.改变位置参数β,即通过改变b的值,改变椭球中心垂直位置;通过改变深径比a,改变蚀坑底部(A点)曲率大小;两个参数配合调整,当β取0、a 取1时,点蚀坑为中心位于结构表面的半球形蚀坑.采用双参数蚀坑模型,可以有效模拟出蚀坑处出现最大应力集中的位置随着参数不同将分别出现在蚀坑肩部和底部,如图2所示,与光弹性试验的结果相吻合[15];有效地解释了由应力集中导致的蚀坑-裂纹萌生于蚀坑肩部或底部的差异性.目前学者认为,导致蚀坑向裂纹转变的条件之一为应力强度因子大于裂纹扩展的阈值[5].应力集中导致的蚀坑-裂纹在蚀坑的底部或肩部萌生;换句话说,裂纹首先在蚀坑肩部或底部转变成蚀坑-裂纹,之后再进一步扩展成全局性的裂纹,如图3所示.基于应力集中是导致裂纹萌生主导因素[16]的前提,由图2可知,在位置参数b<0.2的条件下,裂纹在蚀坑处的萌生位置将始终位于蚀坑底部.本文旨在探究位置参数β=0的情形下蚀坑参数a、蚀坑深度d对I型蚀坑-裂纹应力强度因子值的影响规律.为了探究在管道内压作用下蚀坑参数a 和蚀坑深度d对I型蚀坑-裂纹的影响,分别建立如图4所示的蚀坑-裂纹模型.在研究蚀坑参数a、蚀坑深度d对I型蚀坑-裂纹应力强度因子值的影响时,首先要排除管厚对裂纹应力强度因子取值的影响.对于二维I型裂纹受管道内压作用下的应力强度因子表达式[17]为式中:p为管道内压;R0为管道外径;t为管厚;a为裂纹长度;F为形状因子,F为(t,a)的函数,当a/t→0时,F取固定值1.12.利用ABAQUS对二维I型裂纹的应力强度因子进行仿真,相关尺寸见表1,所得结果与《应力强度因子手册》[17]中结果对比,如表2和图5所示.由对比结果可以看出,计算误差都在可接受的范围以内;同时,在a/t0.100的前提下,F的取值为定值1.本文假设在蚀坑-裂纹应力强度因子计算中管厚取定值t=20mm,在裂纹取值a/t 或a/(t-d)0.1条件下,即可认为管厚或剩余管厚对应力强度因子的取值不产生影响.采用二维模型,分别求解出不同初始值的初始裂纹、初始蚀坑+裂纹(蚀坑深度d=1mm)的应力强度因子值,结果见表3及图6.蚀坑的存在明显改变了裂纹应力强度因子的取值,如图7所示.蚀坑+裂纹应力强度因子取值的变化趋势与纯裂纹的变化趋势明显不同;纯裂纹下,裂纹应力强度因子K的取值与裂纹长度存在线性的变化关系;在蚀坑的影响下,应力强度因子K的值随初始裂纹长度的变化趋势为先快速增大,后趋于定值.蚀坑深径比a 影响蚀坑+裂纹应力强度因子的取值;不同的蚀坑参数a 下,变化趋势趋于一致;同一初始裂纹长度下,随着a 变大,即蚀坑越窄深,蚀坑+裂纹应力强度因子的取值越大.在蚀坑向裂纹转变的临界状态下,研究I型蚀坑-裂纹的应力强度因子问题,蚀坑-裂纹初始值选取需要满足以下两个条件:(1)蚀坑-裂纹的初始尺寸要远远小于蚀坑的尺寸,即蚀坑向裂纹转变的前一状态为蚀坑,后一状态为蚀坑-裂纹;(2)蚀坑-裂纹的应力强度因子值要达到或超过裂纹扩展的阈值.综合以上两个因素,本文拟取初始蚀坑-裂纹的长度取为=0.10mm.初始裂纹的形状为圆心与蚀坑中心重合,半径为d+的圆弧,如图3(a)所示. 为了研究蚀坑参数a 和蚀坑深度d对蚀坑-裂纹应力强度因子的影响规律,采用如图4(b)所示的三维模型,采用扩展有限元法,利用ABAQUS对其进行仿真,图8为其网格划分的示意.通过控制变量的方法,对影响I型蚀坑-裂纹应力强度因子的因素展开有限元仿真研究.本文对蚀坑参数a0.89、蚀坑深度d1.5mm的蚀坑-裂纹开展了相关研究,计算结果见表4和图9.从应力云图上可知,应力集中的最大值出现在蚀坑-裂纹处,从侧面说明了,与蚀坑其他位置相比,蚀坑-裂纹萌生位置处的应力集中程度是最大的.深径比a是表征点蚀坑形貌的一个重要参数.由图10可知,对于一定深度d的点蚀坑来说,随着深径比a的增大,蚀坑-裂纹应力强度因子的取值不断增大;各深度值d下,深径比a 对蚀坑-裂纹应力强度因子K取值的影响趋势趋于一致.蚀坑深度d也是表征点蚀坑形貌的一个重要参数.由图11可知,对于一定的深径比a 而言,随着蚀坑深度的增大,蚀坑-裂纹应力强度因子值的变化趋势为先增大后趋于定值;各深径比a下,蚀坑深度d对蚀坑-裂纹应力强度因子取值的影响趋势趋于一致.对于裂纹应力强度因子的表达式,一般采用以下简化形式:式中:σ为应力;a为裂纹长度.对于管道而言,腐蚀疲劳破坏主要是指管道剩余壁厚不足,导致管道失效,也就是说,裂纹沿管道径向的扩展为有效扩展.基于这一思路,直接将蚀坑-裂纹的有效裂纹长度取值a等效为蚀坑深度d与初始裂纹=0.10mm的和.这样就可以进一步的探究形状因子F与蚀坑深径比a 和深度d的关系,进一步可以将F表示为f(a,d)的函数.由图12可知,蚀坑深径比a对F取值的影响存在区间效应,换句话说,当深径比a>0.60时,深径比a对F取值的影响有限.由图13可知,蚀坑深度d对F取值的影响同样存在区间效应,当蚀坑深度d取值较小时,各深径比a 下的形状因子F值趋于定值;随着蚀坑深度的增大,形状因子F的取值不断变大,但变化速率为先快后慢.同时,随着蚀坑深度d的增大,不同深径比a 下F的取值各不相同.通过ABAQUS有限元中的扩展有限元方法,对处于内压作用下的管道外表面的I 型蚀坑-裂纹开展了分析,可得到以下结论:(1)蚀坑对裂纹应力强度因子的取值产生很大的影响,可明显的降低裂纹扩展的门槛值;(2) 随着蚀坑参数深径比α、深度d的增大,蚀坑-裂纹应力强度因子的取值也逐渐变大;(3)蚀坑参数深径比α、深度d对形状因子F值的影响存在一定的区间效应.【相关文献】[1] Muller M. Theoretical considerations on corrosion fatigue crack initiation[J]. Metallurgical Transactions A-Physical Metallurgy and Materials Science,1982(13):649-655.[2] Chlistovsky R M,Heffernan P J,DuQuesnay D L. Corrosion-fatigue behavior of 7075-T651 aluminum alloy subjected to periodic overloads[J]. International Journal of Fatigue,2007(29):1941-1949.[3] Li Shuxin,Akid R. Corrosion fatigue life prediction of a steel shaft material in seawater[J]. Engineering Failure Analysis,2013,34:324-334.[4] Nan Z Y,Ishihara S,Goshima T. Corrosion fatigue behavior of extruded magnesium alloy AZ31 in sodium chloride solution[J]. International Journal of Fatigue,2008,30:1181-1188.[5] Kondo Y. Prediction of fatigue crack initiation life based on pit growth[J]. Corrosion Science,1989,45(1):7-11.[6]蒋祖国. 飞机结构腐蚀疲劳[M]. 北京:航空工业出版社,1991.Jiang Zuguo. Aircraft Structure Corrosion Fatigue[M]. Beijing:Aviation Industry Press,1991(in Chinese).[7] Pidaparti R M,Patel R R. Correlation between corrosion pits and stresses in Al alloys[J]. Mater Lett,2008,21(3):57-62.[8]梁瑞,张新燕,李淑欣,等. 半椭球蚀坑对圆棒应力集中的影响[J]. 中国腐蚀与防护学报,2013,6:532-536.Liang Rui,Zhang Xinyan,Li Shuxin,et al. Influence of semi-ellipsoidal pit on stress concentration of round bar[J]. Journal of Chinese Society for Corrosion and Protection,2013,6:532-536(in Chinese).[9] Cerit M,Genel K,Eksi S. Numerical investigation on stress concentration of corrosion pit[J]. Engineering Failure Analysis,2009,16:2467-2472.[10] Zhang Y M,Fan M,Xiao Z M,et al.Fatigue analysis on offshore pipelines with embedded cracks[J]. Ocean Engineering,2016,117:45-56.[11]李成,铁瑛,郑艳萍. 不同的裂纹尺寸对椭圆形裂纹应力强度因子影响的研究[J]. 船舶力学,2011,15(10):1161-1165.Li Cheng,Tie Ying,Zheng Yanping. Influence of different crack size on stress intensity factor of elliptical crack[J]. Journal of Ship Mechanics,2011,15(10):1161-1165(in Chinese).[12] Newman J C,Raju I S. Stress-intensity factor for circumferencial surface crack in pipes and roads under tension and loads[J]. ASTM,STP905,1986:789-805.[13] Rokhlin S I,Kim J Y,Nagy H,et al. Effect of pitting corrosion on fatigue crack initiation and fatigue life[J]. Engineering Fracture Mechanics,1999,62:425-444. [14]赵乾坤. 含内腐蚀缺陷-裂纹管道的应力强度因子与承压能力研究[D]. 重庆:西南石油大学,2017.Zhao Qiankun. Study on stress intensity factor and bearing capacity of pipeline with internal corrosion defect-crack[D]. Chongqing:Southwest Petroleum Univer-sity,2017(in Chinese).[15]西田正孝. 应力集中[M]. 北京:机械工业出版社,1986.Nishida Masako. Stress Concentration[M]. Beijing:Machinery Industry Press,1986(in Chinese).[16]周向阳,柯伟. 点蚀坑的形貌与腐蚀疲劳裂纹萌生[J]. 金属学报,1992,28(8):356-360.Zhou Xiangyang,Ke Wei. Pit morphology and corrosion fatigue crack initiation[J]. Chinese Journal of Metals,1992,28(8):356-360(in Chinese).[17]中国航空研究院. 应力强度因子手册[M]. 北京:科学出版社,1981.China Aviation Research Institute. Stress Intensity Factor Handbook[M]. Beijing:Science Press,1981(in Chinese).。
教育部推荐2016年度国家科学技术奖励项目公示奖励类别
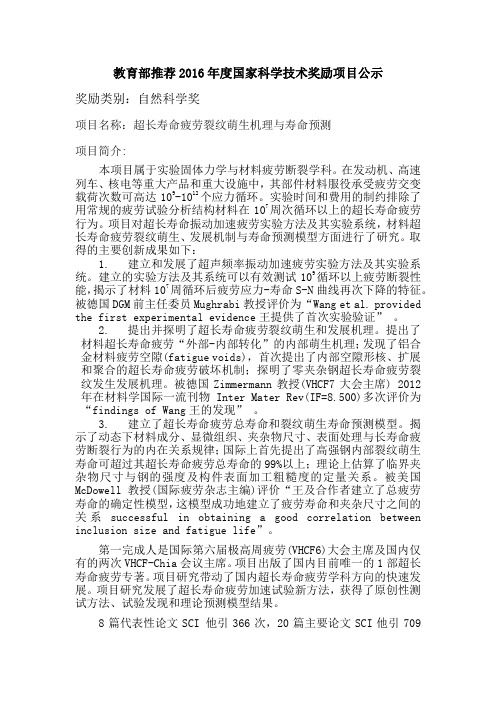
教育部推荐2016年度国家科学技术奖励项目公示奖励类别:自然科学奖项目名称:超长寿命疲劳裂纹萌生机理与寿命预测项目简介:本项目属于实验固体力学与材料疲劳断裂学科。
在发动机、高速列车、核电等重大产品和重大设施中,其部件材料服役承受疲劳交变载荷次数可高达109-1012个应力循环。
实验时间和费用的制约排除了用常规的疲劳试验分析结构材料在107周次循环以上的超长寿命疲劳行为。
项目对超长寿命振动加速疲劳实验方法及其实验系统,材料超长寿命疲劳裂纹萌生、发展机制与寿命预测模型方面进行了研究。
取得的主要创新成果如下:1.建立和发展了超声频率振动加速疲劳实验方法及其实验系统。
建立的实验方法及其系统可以有效测试109循环以上疲劳断裂性能,揭示了材料107周循环后疲劳应力-寿命S-N曲线再次下降的特征。
被德国DGM前主任委员Mughrabi教授评价为“Wang et al. provided the first experimental evidence王提供了首次实验验证” 。
2.提出并探明了超长寿命疲劳裂纹萌生和发展机理。
提出了材料超长寿命疲劳“外部-内部转化”的内部萌生机理;发现了铝合金材料疲劳空隙(fatigue voids),首次提出了内部空隙形核、扩展和聚合的超长寿命疲劳破坏机制;探明了零夹杂钢超长寿命疲劳裂纹发生发展机理。
被德国Zimmermann教授(VHCF7大会主席) 2012年在材料学国际一流刊物Inter Mater Rev(IF=8.500)多次评价为“findings of Wang王的发现” 。
3.建立了超长寿命疲劳总寿命和裂纹萌生寿命预测模型。
揭示了动态下材料成分、显微组织、夹杂物尺寸、表面处理与长寿命疲劳断裂行为的内在关系规律;国际上首先提出了高强钢内部裂纹萌生寿命可超过其超长寿命疲劳总寿命的99%以上;理论上估算了临界夹杂物尺寸与钢的强度及构件表面加工粗糙度的定量关系。
被美国McDowell 教授(国际疲劳杂志主编)评价“王及合作者建立了总疲劳寿命的确定性模型,这模型成功地建立了疲劳寿命和夹杂尺寸之间的关系successful in obtaining a good correlation between inclusion size and fatigue life”。
尿酸对AZ31B 镁合金超声滚压表面在模
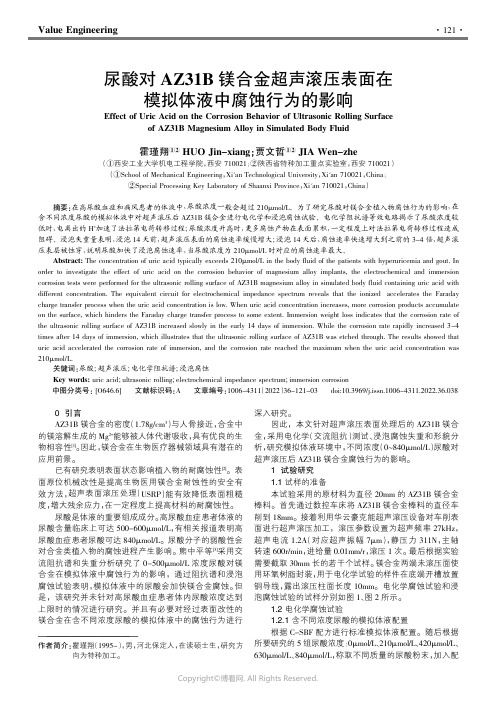
Value Engineering———————————————————————作者简介:霍瑾翔(1995-),男,河北保定人,在读硕士生,研究方向为特种加工。
0引言AZ31B 镁合金的密度(1.78g/cm 3)与人骨接近,合金中的镁溶解生成的Mg 2+能够被人体代谢吸收,具有优良的生物相容性[1]。
因此,镁合金在生物医疗器械领域具有潜在的应用前景。
已有研究表明表面状态影响植入物的耐腐蚀性[2]。
表面原位机械改性是提高生物医用镁合金耐蚀性的安全有效方法,超声表面滚压处理(USRP )能有效降低表面粗糙度,增大残余应力,在一定程度上提高材料的耐腐蚀性。
尿酸是体液的重要组成成分。
高尿酸血症患者体液的尿酸含量临床上可达500-600μmol/L ,有相关报道表明高尿酸血症患者尿酸可达840μmol/L 。
尿酸分子的弱酸性会对合金类植入物的腐蚀进程产生影响。
熊中平等[3]采用交流阻抗谱和失重分析研究了0-500μmol/L 浓度尿酸对镁合金在模拟体液中腐蚀行为的影响,通过阻抗谱和浸泡腐蚀试验表明,模拟体液中的尿酸会加快镁合金腐蚀。
但是,该研究并未针对高尿酸血症患者体内尿酸浓度达到上限时的情况进行研究。
并且有必要对经过表面改性的镁合金在含不同浓度尿酸的模拟体液中的腐蚀行为进行深入研究。
因此,本文针对超声滚压表面处理后的AZ31B 镁合金,采用电化学(交流阻抗)测试、浸泡腐蚀失重和形貌分析,研究模拟体液环境中,不同浓度(0~840μmol/L )尿酸对超声滚压后AZ31B 镁合金腐蚀行为的影响。
1试验研究1.1试样的准备本试验采用的原材料为直径20mm 的AZ31B 镁合金棒料。
首先通过数控车床将AZ31B 镁合金棒料的直径车削到18mm 。
接着利用华云豪克能超声滚压设备对车削表面进行超声滚压加工,滚压参数设置为超声频率27kHz ,超声电流1.2A(对应超声振幅7μm ),静压力311N ,主轴转速600r/min ,进给量0.01mm/r ,滚压1次。
Fatigue behavior of Al0.5CoCrCuFeNi high entropy alloys
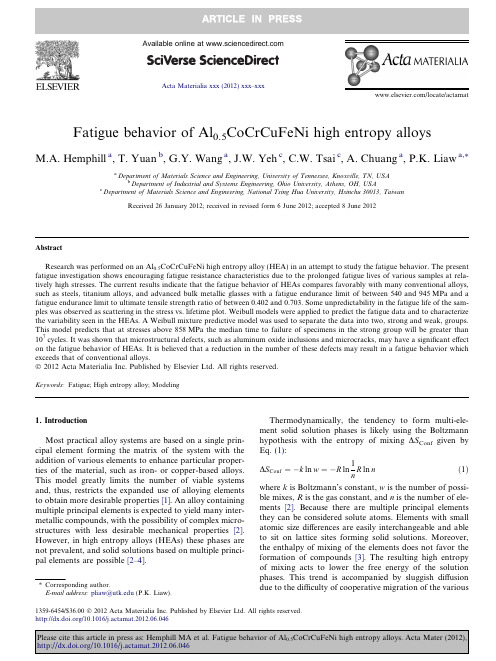
Fatigue behavior of Al 0.5CoCrCuFeNi high entropy alloysM.A.Hemphill a ,T.Yuan b ,G.Y.Wang a ,J.W.Yeh c ,C.W.Tsai c ,A.Chuang a ,P.K.Liaw a ,⇑aDepartment of Materials Science and Engineering,University of Tennessee,Knoxville,TN,USA bDepartment of Industrial and Systems Engineering,Ohio University,Athens,OH,USAcDepartment of Materials Science and Engineering,National Tsing Hua University,Hsinchu 30013,TaiwanReceived 26January 2012;received in revised form 6June 2012;accepted 8June 2012AbstractResearch was performed on an Al 0.5CoCrCuFeNi high entropy alloy (HEA)in an attempt to study the fatigue behavior.The present fatigue investigation shows encouraging fatigue resistance characteristics due to the prolonged fatigue lives of various samples at rela-tively high stresses.The current results indicate that the fatigue behavior of HEAs compares favorably with many conventional alloys,such as steels,titanium alloys,and advanced bulk metallic glasses with a fatigue endurance limit of between 540and 945MPa and a fatigue endurance limit to ultimate tensile strength ratio of between 0.402and 0.703.Some unpredictability in the fatigue life of the sam-ples was observed as scattering in the stress vs.lifetime plot.Weibull models were applied to predict the fatigue data and to characterize the variability seen in the HEAs.A Weibull mixture predictive model was used to separate the data into two,strong and weak,groups.This model predicts that at stresses above 858MPa the median time to failure of specimens in the strong group will be greater than 107cycles.It was shown that microstructural defects,such as aluminum oxide inclusions and microcracks,may have a significant effect on the fatigue behavior of HEAs.It is believed that a reduction in the number of these defects may result in a fatigue behavior which exceeds that of conventional alloys.Ó2012Acta Materialia Inc.Published by Elsevier Ltd.All rights reserved.Keywords:Fatigue;High entropy alloy;Modeling1.IntroductionMost practical alloy systems are based on a single prin-cipal element forming the matrix of the system with the addition of various elements to enhance particular proper-ties of the material,such as iron-or copper-based alloys.This model greatly limits the number of viable systems and,thus,restricts the expanded use of alloying elements to obtain more desirable properties [1].An alloy containing multiple principal elements is expected to yield many inter-metallic compounds,with the possibility of complex micro-structures with less desirable mechanical properties [2].However,in high entropy alloys (HEAs)these phases are not prevalent,and solid solutions based on multiple princi-pal elements are possible [2–4].Thermodynamically,the tendency to form multi-ele-ment solid solution phases is likely using the Boltzmann hypothesis with the entropy of mixing D S Conf given by Eq.(1):D S Conf ¼Àk ln w ¼ÀR ln 1nR ln nð1Þwhere k is Boltzmann’s constant,w is the number of possi-ble mixes,R is the gas constant,and n is the number of ele-ments [2].Because there are multiple principal elements they can be considered solute atoms.Elements with small atomic size differences are easily interchangeable and able to sit on lattice sites forming solid solutions.Moreover,the enthalpy of mixing of the elements does not favor the formation of compounds [3].The resulting high entropy of mixing acts to lower the free energy of the solution phases.This trend is accompanied by sluggish diffusion due to the difficulty of cooperative migration of the various1359-6454/$36.00Ó2012Acta Materialia Inc.Published by Elsevier Ltd.All rights reserved./10.1016/j.actamat.2012.06.046⇑Corresponding author.E-mail address:pliaw@ (P.K.Liaw)./locate/actamatActa Materialia xxx (2012)xxx–xxxelements.Thus,simple solid solutions and nanostructures that avoid the problems of difficult analyses and processing are formed [2,3].Furthermore,it has been shown that the valence elec-tron concentration (VEC)of the constituent elements has an effect on the phase stability [5].Guo et al.have deter-mined the face-centered cubic (fcc)and body-centered cubic (bcc)phase stabilities of solid solutions,such as HEAs,when the atomic size ratios are nearly identical [5].This raises the possibility of thousands of alloy compo-sitions [2]in addition to bulk metallic glass (BMG)HEA derivatives [6],an exciting development for future alloy design.HEAs can be defined as being composed of five or more elements in equimolar ratios or near equimolar ratios and can be extended to those compositions in which each principal element concentration is between 5and 35at.%[2].These alloys could be used for a wide range of applications,such as those requiring high temperature strength,high tensile strength,increased wear resistance,and corrosion resistance [2,6–10].This investigation will study the fatigue behavior of an Al 0.5CoCrCuFeNi (molar ratio)HEA.Structural charac-terization of this alloy showed two distinct phases,a major a -fcc phase and a copper-rich b -fcc phase [11,12].Bothshowed similar lattice constants of about 3.6A˚[12].In the homogenized and water-quenched condition both phases are in a supersaturated state and exhibit aging hard-ening between 300°C and 700°C due to the precipitation of Al-and Ni-rich bcc phases [13].This precipitation hard-ening increases the strength but is accompanied by a loss of ductility.In the as-rolled and as-annealed (at 900°C)con-dition the Al 0.5CoCrCuFeNi HEA displayed a better com-bination of strength and ductility compared with conventional alloys,such as 304stainless steel and Ti–6Al–4V titanium alloys [13].The mechanical properties of the as-cast Al x CoCrCuFeNi (x =0–3)alloys are readily available [14].However,essentially no research has been conducted on investigating the fatigue behavior of this and other promising HEA systems [2–16].The present research will examine and study the fatigue behavior of a Al 0.5CoCrCuFeNi HEA.Moreover,statistical modeling will be conducted to further investigate the fatigue charac-teristics of the HEA.2.Experimental procedures2.1.Materials and sample preparationThe samples of Al 0.5CoCrCuFeNi (molar ratio)were prepared by arc melting the constituent elements at a cur-rent of 500A in a water-cooled copper hearth.The ele-ments were all at least 99wt.%pure,and melting was accomplished in a vacuum of at least 0.01T.The melting and solidification processes were repeated at least five times to improve the chemical homogeneity of the sample.The cast samples were annealed at 1000°C for 6h,water quenched,and cold rolled.The rolling reduction was84%,with a final thickness of 3mm.The rolled sheets were subsequently machined to fatigue samples with dimensions of 25Â3Â3mm for four point bending fatigue experi-ments,as described below.Samples were machined parallel to the rolling direction,i.e.the 25mm length of the samples ran parallel to the rolling direction.Thus the applied stress on the tensile edge was parallel to the rolling direction.Two distinct microstructures were observed in this region (and in the samples as a whole)depending on the sample position in the mold during casting,as discussed below.Hence,the fatigue behavior as a function of the character-istic microstructure was also determined.To remove as many surface imperfections as possible,the samples were polished on a Buehler rotating grinder and polisher.240,400,600,and 1200grits were used in that order.The sample was turned through 90°after each pol-ishing step,finishing with the 1200grit running parallel along the length direction of the sample.2.2.Tensile testTensile experiments were performed on samples of the as-rolled HEAs to characterize the mechanical behavior of the alloys,and their results were used for comparison with other conventional alloys.The gage section of the specimens was machined to a size of 3Â12mm and tested in an Instron 4505at a strain rate of 1Â10À3s À1.The specimens were tested to failure to determine the yield strength,ultimate tensile strength (UTS),and percent elongation.2.3.Four point bending fatigue experimentsTo study the fatigue behavior of the HEA samples four point bending tests were conducted at various applied loads and run until failure of the specimen or 107cycles had been reached.The results of the fatigue tests were plot-ted as a typical stress range vs.number of cycles to failure (S –N )curve.The maximum stress r on the tensile surface within the span of the two outer pins in the four point bending fatigue experiment was calculated,using the beam theory relationship [17]r ¼3P ðS o ÀS i Þ2BW 2ð2Þwhere P is the applied load,S o is the outer span length 20mm,S i is the inner span length 10mm,B is the thick-ness,and W is the height.In this investigation,B =W =3mm.The samples were tested at 10Hz with a loading ratio of R =r min./r max.=0.1[17],where r min.and r max.are the minimum and maximum applied stresses,respectively.2.4.Microstructural characterizationHigh energy X-ray diffraction (XRD)was performed at the Advanced Photon Source (APS)using the 11-ID beam-2M.A.Hemphill et al./Acta Materialia xxx (2012)xxx–xxx3.Experimental results3.1.Tension propertiesTension tests were initially performed on the samples to characterize the mechanical behavior of the rolled material. The results are shown in Fig.1.The specimens exhibited a high yield stress of1284MPa and a UTS of,generally, 1344MPa,exceeding that of conventional alloys,such as steels,titanium,aluminum,and nickel alloys[19–22]. Advanced alloys,such as BMGs,usually have higher strengths and lack tensile ductility.However,the present HEAs show the degree of plastic deformation necessary in structural applications with a tensile elongation of 7.6%for the as-rolled material(Fig.1).3.2.Microstructural characterization observed previously by transmission electron microscopy (TEM)[12,23].The low peak intensity can be partially attributed to the high lattice strain present in the alloy [12].The lower heights of the(111)and(220)peaks rel-ative to the(200),(311),and(400)peaks are due to the texture in the sample,introduced by rolling deformation. The detection limits of XRD,approximately1vol.%, masked the detection of any minor phases,such as oxide particles,later shown to be present by EDS analysis.Only one set of fcc peaks is seen in the XRD pattern.Previous studies have shown that the lattice constants of these two phases are very similar,approximately 3.6A˚[12].This trend will cause an overlap of the characteristic diffraction peaks,if the resolution of the experimental set-up is not high enough.It is important to note that because no bcc characteristic peaks were observed the structure is indeed a two-phase fcc structure.BSE and EDS analyses of the specimens were performed to observe and determine the elemental compositions of the specimens.Fig.3shows an SEM micrograph of a typical sample.The microstructure consists of two phases:the a fcc matrix phase,formed from the fcc dendrite phase(theFig.1.Tension testflow curve for the Al0.5CoCrCuFeNi HEA.Fig.2.Diffraction pattern of the Al0.5CoCrCuFeNi HEA specimen using synchrotron high energy X-rays.Fig.3.SEM micrograph showing the a-fcc matrix dendrite phase and b Cu-rich fcc interdendritic phase elongated along the rolling direction, indicated by the arrow.noticeable amount of scatter at various stress levels.The results display the typical fatigue behavior for crystallinematerials of an increase in the number of cycles to failure as the stress level decreases.At a maximum stress of 1250MPa,near the yield stress of1284MPa,most failures were within an order of magnitude of35,000–450,000cycles,although there was still a wide range of scatter.As the stress level decreased the spread in the data became even more pronounced,which is generally charac-teristic of fatigue behavior[24].Estimations of the endur-ance limits based on the stress ranges were within a lower bound of540MPa and an upper bound of945MPa.Val-ues were chosen because the specimens reached107cycles without failure.The microstructural morphology was taken into account to try to determine whether this feature had an effect on the fatigue life.Although the fatigue specimens were machined parallel to the rolling direction,the morphologies of the matrix phase(a)and the Cu-rich phase(b)in the tensile region of the sample might be different from sample to sample.This trend could be tracked to their position and different heatflow directions in the copper mold during solidification.Therefore,the orientation of the loading direction in relation to the different morphologies was investigated.The SEM micrographs presented in Fig.5 show two typical morphologies observed in the tensile region of the samples.Fig.5a displays a parallel morphol-ogy,which features a lamellarflow pattern of alternating a and b phases.Fig.5b presents a vertical type characterized by a random orientation of the a and b phases.After microstructure identification for all tested samples by SEM,Fig.4was replotted as Fig.6,showing the fatigue behavior of the parallel and vertical types of samples.It appears that there is no correlation between the scatter in the fatigue life and the orientation of the loading direction with respect to the different morphologies,and later statis-tical modeling efforts confirmed this trend.Thus the orien-tation and morphology of the phases do not appear to have a significant effect on the fatigue life.A likely cause of the variable fatigue life is the number of defects in the sample,introduced during the casting and rolling processes,in particular aluminum oxide-rich particles formed during the melting and solidification pro-cess.EDS analyses were performed on these particles to examine their approximate compositions(Fig.7).This fea-ture shows the presence of approximately50%oxygen, consistent with aluminum oxide particles.These particles provide nucleation sites for microcracks,due to stress con-centration at the particles.Fig.8presents the number of cycles to failure vs.the number of defects per240Â165l m unit area observed at500Âmagnification in specimens at various stress levels. It can be observed that a decrease in the number of defects generally correlates with an increase in the fatigue life at various stress levels.In reality the air-cooled andfinal solidification sides of the casting contain greater segrega-tion,more inclusions,and more shrinkage pores,which could induce microcracks during cold rolling.If high den-sities of these microcracks are located on the tensile side during four point fatigue loading then the fatigue resistance will be reduced,and failure would occur after fewer cycles.3.4.FractographyFracture surfaces were analyzed to determine the unique fatigue characteristics of the samples,such as crack initia-tion sites,crack propagation,andfinal fracture.Fig.9a shows the fracture surface of a sample that failed at a stress of900MPa after555,235cycles.Fig.9b presents the crackTable1EDS analyses of the matrix and Cu-rich phases in the Al0.5CoCrCuFeNi HEA microstructures.Al0.5CoCrCuFeNi phase compositions(at.%)Region Al Co Cr Cu Fe Ni Matrix phase72021112218 Cu-rich phase1054596154.S–N curve for the Al0.5CoCrCuFeNi HEA plotted as the stress range vs.the number of cycles to failure.initiation behavior from microcracks that formed from defects on the surface of the sample.The samples exhibited similar fracture patterns,with crack initiation within the tensile region of the sample surface.Cracks usually initiated at defects present on the surface,as discussed below,or at the corner of the samples.These areas repre-high stress concentration regions favorable for crack nucleation.Numerous cracks nucleated and grew perpen-dicular to the stress in the specimen(parallel to the applied load)through the tensile region.Crack propagation gener-occurred through approximately one-third of cross-section beforefinal failure,depending on the applied The phenomenon of fatigue shows a stochastic nature [25].Statistical models and data analysis methods are, therefore,necessary tools in studying fatigue behavior.In this investigation statistical fatigue–lifespan models were developed to predict the fatigue life of the HEAs.Thefirstmicrographs showing two different types of morphology:(a)the parallel type with a lamellarflow pattern of alternatinga random orientation of a andb phases.Fig.7.SEM micrograph with EDS analyses of the aluminum oxide particles.The compositions of the regions labeled A and B are given in the corresponding tables,indicating the presence of aluminum oxide particles.8.The cycles to failure compared with the number of surface defects various stress levels showing that as the number of defects decreases generally increases at a particular maximum stress level.6.S–N curves for the Al0.5CoCrCuFeNi HEAs showing scatteringcycles to failure for the parallel and vertical type morphologies, respectively,in the samples.predictive model assumes a Weibull distribution to describe the fatigue–lifespan distribution in eachfixed stress range, based on a commonly used analytical representation of the S–N curve given by Eq.(3)[26]NðSÞ¼cSÀd;ð3Þwhere S denotes the applied stress range,N(S)is the ex-pected number of fatigue life cycles at stress level S,and c and d are positive material parameters.Taking the natu-ral logarithm on the S–N relation(Eq.(3))results inlogðNðSÞÞ¼c0þc1logðSÞ;ð4Þwhere c0¼logðcÞand c1¼Àd:The S–N relation given by Eqs.(3)and(4)provides a simple way to relate the effect of a stress applied to the test item to the number of cycles to fatigue failure[26].However,it does not capture the vari-ability in the observed fatigue–lifespan data.To account for such variability we introduced an error term e into Eq.(4),i.e.logðNðSÞÞ¼c0þc1logðSÞþe:ð5ÞWe assume that the error term e follows the standard-ized smallest extreme value distribution.The fatigue–life-span model given by Eq.(5)then becomes a Weibull regression model[27].The Weibull regression model given by Eq.(5)can be written as an equivalent Weibull-acceler-ated life testing model that is widely used in reliability engi-neering and lifetime data analyses[27].The fatigue life at a given stress level S follows the Weibull distribution.The probability density function(pdf)and the cumulative dis-tribution function of the Weibull distribution are described by Eqs.(6)and(7),respectively:fðNðSÞj aðSÞ;bÞ¼baðSÞNðSÞaðSÞbÀ1expÀNðSÞaðSÞb!ð6ÞFðNðSÞj aðSÞ;bÞ¼1ÀexpÀNðSÞaðSÞb!ð7Þwhere b is the Weibull shape parameter,and the Weibull scale parameter a(S)depends on the stress S according to, logðaðSÞÞ¼c0þc1logðSÞ:ð8ÞIn this experiment four samples had not failed when the bending fatigue test was terminated at107cycles,and they became censored observations.The probability of obtaining a censored observation at stress level S is given by Eq.(9): PðNðSÞP N cÞ¼1ÀFðN c j aðSÞ;bÞ¼expÀN caðSÞb!;ð9Þwhere N c equals107cycles,denoting the censor time of the experiment.Thefirst fatigue–lifespan model,hereafter termed the Weibull predictive model,consists of two components:micrograph of the fracture surface of a sample that failed at a stress value of900MPa after555,235cycles.(b)Crack sample,with microcracks forming before the fatigue test.Note that the loading direction comes out of the micrographs showing(a)fatigue striations in the crack propagation region with the crack growth direction indicated fracture region,indicating ductile fracture of the sample.the Weibull distribution describing the fatigue–lifespan variability at a fixed stress range,and the relation describ-ing the stress dependence of the fatigue life,given by Eq.(8).Note that lifetime distributions other than the Weibull distribution may be used.For example,if the error term e in Eq.(5)is assumed to be a standardized normal random variable,then the fatigue life N (S )at a given stress level S follows a log–normal distribution.This study assumes a Weibull distribution,because it is the most widely used life-time distribution in reliability engineering and lifetime data analyses,and has been applied to model the fatigue behav-ior of a variety of materials,such as steels [28,29],alumi-num alloys [30],and metallic glasses [31,32].The Weibull predictive model has three unknown model parameters,b ,c 0,and c 1,which can be estimated by the maximum likelihood method [27].We denote the observed fatigue–lifespan data by {(N i ,S i ,d i ),i =1,2,...,m },where m is the total number of samples tested,and N i and S i are,respectively,the fatigue–lifespan cycles and the applied stress to the i th sample.The binary indicator variable d i equals 1if N i is a failure observation,and d i =0if N i is a censored observation.Given the observed fatigue–lifespan data the maximum likelihood method esti-mates the model parameters by maximizing the likelihood function given in Eq.(10)L ðb ;c 0;c 1Þ¼Y m i ¼1b ec 0þc 1log ðS i ÞN ie c 0þc 1log ðS i Þ b À1"#d i Âexp ÀN ie c 0þc 1log ðS i Þ b "#:ð10ÞOnce the model parameters are estimated the fatigue–lifespan behavior at a given stress S can be predicted by estimating the p quantile life,which is given by (Eq.(11)),N p ðS Þ¼exp ðc 0þc 1log ðS ÞÞðÀlog ð1Àp ÞÞ1=b :ð11ÞThe median fatigue life (i.e.p =0.5)can be used todescribe the relationship between the applied stress and the average fatigue–lifespan response.The 2.5and 97.5quantiles can be employed to construct a 95%predic-tive interval for the fatigue life,and to quantify the scatter in the fatigue life cycles.4.2.Weibull mixture predictive modelThe Weibull predictive model,however,may not be able to adequately characterize the excessive variability in the observed fatigue data shown in Fig.4.The observed fati-gue lives seem to form two groups,a strong group and a weak group,especially when the applied stress was less than 1000MPa.The fatigue lives in the weak group were much shorter than those in the strong group.This variabil-ity in the fatigue data may be caused by variability in the defect density in the experimental units,as discussed below.A Weibull mixture model (termed the multimodal Weibull model)may be used when the population of units isnon-homogeneous [33].The second predictive model there-fore assumes a mixture of two Weibull distributions for the fatigue lives at each stress range value.The pdf and cdf of the Weibull mixture model are given in Eqs.(12)and (13),respectively,f ðN ðS Þj p ;a w ðS Þ;b w ;a s ðS Þ;b s Þ¼p b w a w ðS ÞN ðS Þa w ðS Þb w À1exp ÀN ðS Þa w ðS Þ b w !þð1Àp Þb s a s ðS ÞN ðS Þa s ðS Þb s À1exp ÀN ðS Þa s ðS Þ b s!;ð12ÞF ðN ðS Þj p ;a w ðS Þ;b w ;a s ðS Þ;b s Þ¼p 1Àexp ÀN ðS Þa w ðS Þb w !"#þð1Àp Þ1Àexp ÀN ðS Þa s ðS Þ b s!"#;ð13Þwhere the subscripts w and s denote the weak and strong groups,respectively,and the parameter p is the fraction of samples belonging to the weak group.The probability of obtaining a censored observation in the Weibull mixture model is then given by Eq.(14).P ðN ðS Þ>N c Þ¼p exp Àta w ðS Þb w "#þð1Àp Þexp Àta s ðS Þb s "#:ð14ÞAgain,the Weibull scale parameters a w (S )and a s (S )are assumed to be dependent on the stress S according to Eqs.(15)and (16)log ða w ðS ÞÞ¼c w ;0þc w ;1log ðS Þ;ð15Þandlog ða s ðS ÞÞ¼c s ;0þc s ;1log ðS Þ;ð16Þrespectively.The second fatigue–lifespan model,termed the Weibull mixture predictive model,has 7unknown param-eters p ,c w ,0,c w ,1,b w ,c s ,0,c s ,1,and b s .The unknown param-eters can again be estimated,using the maximum likelihood method.The likelihood function of the model parameters is given by:L ðp ;b w ;c w ;0;c w ;1;b s ;c s ;0;c s ;1Þ¼Ym i ¼1f ðN i Þd i ð1ÀF ðN i ÞÞ1Àd i ;ð17Þwhere f (N i )and F (N i )are given by Eqs.(12)and (13),respectively.Once the maximum likelihood estimates of the seven model parameters are obtained the observed fa-tigue data can be clustered into the two groups.If N i is a failure observation the likelihoods of the i th sample belonging to the weak group and the strong group are given byM.A.Hemphill et al./Acta Materialia xxx (2012)xxx–xxx7b we c w ;0þc w ;1log ðS i ÞN ie c w ;0þc w ;1log ðS i Þb w À1exp ÀN ie c w ;0þc w ;1log ðS i Þb w !andb se c s ;0þc s ;1log ðS i ÞN ie c s ;0þc s ;1log ðS i Þb s À1exp ÀN ie c s ;0þc s ;1log ðS i Þ b s !;respectively.The i th sample is then assigned to the group with a higher likelihood value.Similarly,if N j is a censored observation the likelihoods of the j th sample belonging to the two groups are given byexp ÀN ie c w ;0þc w ;1log ðS i Þb w !andexp ÀN je c s ;0þc s ;1log ðS j Þ b s !;respectively.The p quantile fatigue lives of the strong group and the weak group are predicted by Eqs.(18)and (19),N p ;w ðS Þ¼exp ðc w ;0þc w ;1log ðS ÞÞðÀlog ð1Àp ÞÞ1=b w;ð18ÞN p ;s ðS Þ¼exp ðc s ;0þc s ;1log ðS ÞÞðÀlog ð1Àp ÞÞ1=b s;ð19Þrespectively.4.3.General log–linear modelThis study also developed a third predictive model to study the correlation between the fatigue of morphology.A binary variable X i indicate the morphology type of the i thi.e.X i =0for the parallel morphology,X i tical morphology.A general log–linear describe the effect of stress and scale parameter,i.e.ln a i ¼c 0þc 1log ðS i Þþc 2X i :To determine whether the morphology life,a test of significance can be sion coefficient c 2.The two hypotheses in icance are H 0:c 2=0vs.H 1:c 2–0.If H 0is evidence that the type of morphology life.If the test of significance fails to evidence against the hypothesis that the not affect the fatigue life.putational results and implications 5.1.Weibull predictive modelThe Weibull predictive model is first the observed fatigue–lifespan data.The hood estimates of the three model b ¼0:492;c 0¼70:869,and c 1¼À8:327:Fig.11shows the predicted median,0.025quantile,and 0.975quantile fatigue lives.The 2.5and 97.5quantiles are used to con-struct the 95%predictive interval for the fatigue life.This 95%predictive interval captures all the failure observa-tions.This predictive interval,however,is very wide,due to the excessive variability in the data and the limited sam-ple size.5.2.Weibull mixture modelNext,the Weibull mixture predictive model is used to analyze the experimental data.The maximum likelihood estimates of the seven model parameters are p ¼0:369;b w ¼3:773;c w ;0¼15:238,c w ;1¼À0:555;b s ¼0:612;c s ;0¼126:454,and c s ;1¼À16:245:Fig.12shows the quantile lives predicted by the Weibull mixture predictive model.The observed data are also clustered into two groups.We are more interested in the strong group,because samples in the strong group contain fewer fabrication defects and can,therefore,reveal the intrinsic fatigue behavior of the HEA,as discussed below.The median life of the strong group exceeded 107cycles when the applied stress was less than 858MPa,which may be used as an estimate of the endurance limit of this HEA.parison of the Weibull predictive model and Weibull mixture predictive modelWhen the applied stresses were 1125,1080,and 1035MPa there were four failure observations at each of the three stress levels.A Kolmogorov–Simirnov goodness Fig.11.Predicted quantile lives using the Weibull predictive model.8M.A.Hemphill et al./Acta Materialia xxx (2012)xxx–xxx。
2.镁合金微弧氧化技术的研究进展_董凯辉
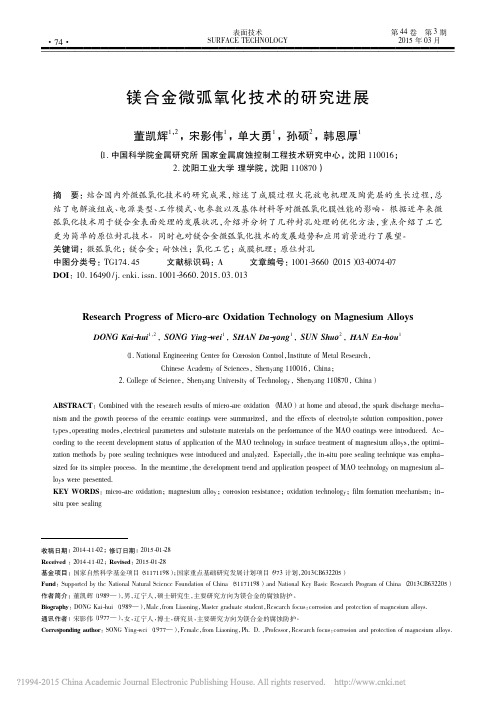
VeysRenaux 等人提出氧化过程中初始形成钝化膜的 成分不同, 就会改变界面层的阻抗值, 进而影响了击 穿电压
[19 ]
。 WANG 等认为击穿电压越低, 微弧氧化
[20 ]
。直到 20 世纪中后期, 随着科学水平
越容易在基体上进行, 同时膜层的厚度与击穿放电的 范围越大, 膜层越厚 电压范围有关, 烧结—再成膜 ” 的多次循环过程 。 “成膜—击穿—熔化— 微弧氧化膜的生长是一个
1102 ; 修订日期: 20150128 收稿日期: 2014Received : 20141102 ; Revised: 20150128 2013CB632205 ) 基金项目: 国家自然科学基金项目( 51171198 ) ; 国家重点基础研究发展计划项目( 973 计划, Fund: Supported by the National Natural Science Foundation of China ( 51171198 ) and National Key Basic Research Program of China ( 2013CB632205 ) 作者简介: 董凯辉( 1989 —) , 男, 辽宁人, 硕士研究生, 主要研究方向为镁合金的腐蚀防护。 Biography: DONG Kaihui ( 1989 —) , Male, from Liaoning, Master graduate student, Research focus: corrosion and protection of magnesium alloys. 通讯作者: 宋影伟( 1977 —) , 女, 辽宁人, 博士, 研究员, 主要研究方向为镁合金的腐蚀防护。 Corresponding author: SONG Yingwei ( 1977 —) , Female, from Liaoning, Ph. D. , Professor, Research focus: corrosion and protection of magnesium alloys.
The behavior of materials under fatigue
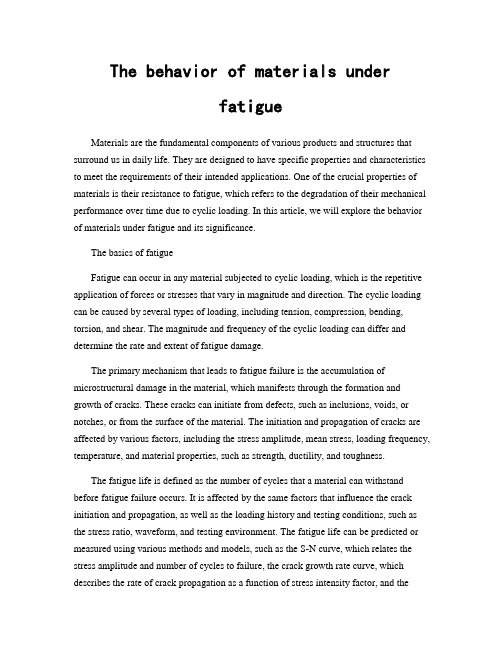
The behavior of materials underfatigueMaterials are the fundamental components of various products and structures that surround us in daily life. They are designed to have specific properties and characteristics to meet the requirements of their intended applications. One of the crucial properties of materials is their resistance to fatigue, which refers to the degradation of their mechanical performance over time due to cyclic loading. In this article, we will explore the behavior of materials under fatigue and its significance.The basics of fatigueFatigue can occur in any material subjected to cyclic loading, which is the repetitive application of forces or stresses that vary in magnitude and direction. The cyclic loading can be caused by several types of loading, including tension, compression, bending, torsion, and shear. The magnitude and frequency of the cyclic loading can differ and determine the rate and extent of fatigue damage.The primary mechanism that leads to fatigue failure is the accumulation of microstructural damage in the material, which manifests through the formation and growth of cracks. These cracks can initiate from defects, such as inclusions, voids, or notches, or from the surface of the material. The initiation and propagation of cracks are affected by various factors, including the stress amplitude, mean stress, loading frequency, temperature, and material properties, such as strength, ductility, and toughness.The fatigue life is defined as the number of cycles that a material can withstand before fatigue failure occurs. It is affected by the same factors that influence the crack initiation and propagation, as well as the loading history and testing conditions, such as the stress ratio, waveform, and testing environment. The fatigue life can be predicted or measured using various methods and models, such as the S-N curve, which relates the stress amplitude and number of cycles to failure, the crack growth rate curve, which describes the rate of crack propagation as a function of stress intensity factor, and thefracture mechanics approach, which considers the interaction of multiple cracks and their effect on the overall strength of the material.The importance of fatigue resistanceFatigue resistance is a critical factor in the design, manufacturing, and maintenance of various products and structures. Examples of applications that require high fatigue resistance include aircraft components, automobile parts, bridges, offshore structures, and medical devices. The consequences of fatigue failure can range from inconvenience, such as a broken zipper or a flat tire, to catastrophic, such as a plane crash, a bridge collapse, or a medical implant failure.The design of a product or structure for fatigue resistance involves several steps, including identifying the potential loading conditions, selecting appropriate materials, designing for safe stress levels and stress concentrations, providing adequate margins of safety, and conducting testing and validation. The design process can be aided by various tools and techniques, such as finite element analysis, computational optimization, and probabilistic approaches. The selection of materials for fatigue resistance is based on their fatigue properties, which can be improved through various means, such as alloying, heat treatment, surface treatment, or structural optimization.The maintenance of products and structures for fatigue resistance involves periodic inspection, testing, and repair to detect and mitigate any signs of fatigue damage. The methods for fatigue inspection and testing can include visual inspection, dye penetrant examination, ultrasonic testing, eddy current testing, and other non-destructive testing methods.ConclusionIn conclusion, the behavior of materials under fatigue is a complex phenomenon that affects the performance and safety of various products and structures. It involves the accumulation of microstructural damage, the formation and propagation of cracks, and the ultimate failure of the material. Fatigue resistance is a critical factor in the design, manufacturing, and maintenance of such products and structures, and requires carefulconsideration and evaluation of the material properties, loading conditions, and testing methods. With proper attention and care, fatigue failure can be minimized or prevented, ensuring the reliability and longevity of materials.。
Fatigue behavior of nanocrystalline metals and alloys

Fatigue behavior of nanocrystalline metals and alloysT.Hanlon a,c,E.D.Tabachnikova b,S.Suresh a,*a Department of Materials Science and Engineering,Massachusetts Institute of Technology,Cambridge,MA02139,USAb B.Verkin Institute for Low Temperature Physics and Engineering,National Academy of Sciences of the Ukraine,Kharkov-103,61103Ukrainec GE,Global Research Center,Niskayuna,NY12309,USAAvailable online2August2005AbstractIn this work,the stress-life fatigue behavior and fatigue crack growth characteristics of pure Ni were studied as a function of grain size spanning a range of tens of nanometer to tens of micrometer.The fatigue response of electrodeposited,fully dense,nanocrystalline pure Ni, with average and total range of grain sizes well below100nm,was compared and contrasted with that of electrodeposited ultrafine-crystalline pure Ni with an average grain size of about300nm and conventional microcrystalline Ni with an average grain size in excess of 10m m.It was found that grain refinement to the nanocrystalline regime generally leads to an increase in total life under stress-controlled fatigue whereas a deleterious effect was seen on the resistance to fatigue crack growth at low and high tensile load ratio levels.To explore the generality of the above trends,systematic experiments were also performed in ultrafine-crystalline pure Ti produced by equal-channel angular pressing where a reduction in grain size was found to cause an increase in fatigue crack growth rates at different tensile load ratios. Grain refinement from the microcrystalline to the ultrafine-crystalline regime by cryomilling of Al alloys also showed a similar response. Possible mechanistic origins of such trends are explored,and some general conclusions are extracted on strategies for improvements in the fatigue resistance of engineering structures by recourse to grain refinement down to the nanocrystalline regime.q2005Elsevier Ltd.All rights reserved.1.IntroductionControl of the resistance of metals and alloys to fracture and fatigue through grain refinement has long been a strategy for improving the structural integrity of engineering components.The vast majority of studies in this area have dealt with microcrystalline(mc)metals and alloys with an average grain size typically larger than1m m(see,for example[1]),although a limited amount of experimental information is also available for ultrafine-crystalline(ufc) metals[2–6].An examination of these studies leads to the following general observations[1,5].Grain refinement, which leads to the strengthening of mc and ufc metals and alloys,is usually accompanied by an increase in fatigue endurance limit.Consequently,stress-life curves,which provide an indication of the dependence of total fatigue life on cyclic stress in nominally smooth fatigue specimens subjected to constant amplitude cyclic load,generally point to an improvement in fatigue resistance with decreasing grain size.Here the beneficial effect on fatigue life is typically considered to arise from the inhibition of cracks that nucleate at nominally smooth surfaces in response to the higher endurance limit.In contrast to this trend,fatigue damage tolerance generally deteriorates with grain refine-ment especially at low stress intensity range,D K,in the near-threshold regime.This apparent increase in resistance to fatigue fracture with increasing grain size is attributed to possible effects of the lowering of effective driving force from microstructurally induced changes in crack path and the attendant possibility of contact between crack face asperities[7].This apparently beneficial effect is typically more pronounced at low D K levels where the cyclic plastic zone size and the cyclic crack tip opening displacement are smaller than the grain size in mc metals.The foregoing general trends pertaining to grain size effects of fatigue crack initiation and crack growth have thus far not been assessed fully for the broad spectrum of grain sizes spanning the microcrystalline to the nanocrystalline regime.Indeed,the recent surge in research interest in nanostructured materials has provided valuable insights into the potential benefits and drawbacks of grain refinement in the nanocrystalline(nc)regime,where the grain size is typically smaller than100nm,on various mechanical properties[8–11].However,the role of nanoscalegrainsInternational Journal of Fatigue27(2005)1147–1158/locate/ijfatigue0142-1123/$-see front matter q2005Elsevier Ltd.All rights reserved.doi:10.1016/j.ijfatigue.2005.06.035*Corresponding author.Tel.:C16172533320;fax:C16172530868.E-mail address:ssuresh@(S.Suresh).in influencing the resistance to fatigue of engineering metals and alloys has not been explored in sufficient detail,despite the fact that the potential use of nanocrystalline materials in load-bearing engineering structures critically depends on their tolerance to the onset and progression of damage from cyclic loading.One factor contributing to this relative lack of information on the fatigue response of nc materials is the difficulty in producing truly nc metals and alloys(whose average as well as extreme grain dimensions are all smaller than about100nm)in sufficiently large quantities to facilitate‘valid’tests that comply with the American Society for Testing and Materials(ASTM)standards for minimum specimen dimensions and small-scale yielding for characterization using linear elastic fracture mechanics (LEFM).In an attempt to circumvent these difficulties, several studies[2–4]have employed ufc metals produced by equal-channel angular pressing(ECAP)to explore grain size effects on cyclic deformation.However,the high initial defect density inherent in these materials significantly biases the fatigue response of the material.Furthermore, such processing methods are not presently amenable to produce truly nc metals in that the microstructure comprises a significantly large fraction of grains whose dimensions exceed100nm;these grains typically dominate the overall mechanical response.The only study available to date on the fatigue response of fully nc metals is a preliminary report from the present work[5].This investigation was initiated with the objective of probing the effects of cyclic loading on the fatigue resistance of fully dense nc metals.The stress-life(S–N) fatigue response and the fatigue crack growth resistance of truly nc electrodeposited pure Ni was assessed,with the crack growth response further examined over a wide range of tensile load ratios.In order to assess the effects of grain size control and grain-boundary engineering on fatigue response,the results obtained for nc Ni are compared with those for ufc and mc metals and alloys,wherever feasible. In order to further assess the broad generality of the conclusions of this study,additional crack growth experiments were also conducted in a cryomilled ufc Al–Mg alloy and an equal channel angular pressed(ECAP) Grade2pure Ti,for which sizeable quantities of bulk specimens were available such that conventional fatigue testing could be employed.From these observations, mechanistic interpretations of the effects of grain size on fatigue response are developed,and possible strategies for grain size engineering in damage-critical applications are suggested.2.Materials and experimental methods2.1.Model material systemThe choice of a model material system,and correspond-ing fabrication technique,was predicated upon the following requirements:(1)the attainability of a true nc grain structure where the average and the largest grain size are both below100nm,(2)the ability to achieve a high level of material purity,with sufficient reproducibility,and (3)the capability to produce a fully dense structure.Such requirements ensure that the material produced can accurately be described as nc.Particular attention was paid to maintaining a range of grain sizes well below 100nm to avoid having any larger‘outlier’grains dominate the fatigue response.While there are many methods currently available to fabricate nc materials[12–22],electrodeposited Ni was chosen as the model system for this investigation.It can be produced over a broad range of grain sizes,from the nc to the mc regime,and is capable of satisfying the above-mentioned requirements.Two notable advantages of the electrodeposition process are the ability to produce relatively large(in-plane)quantities of uniform,fully dense material(e.g.80!80mm),and the capacity to confine the grain size to a narrow distribution(Fig.1). Although the attainable thickness resides in the millimeter range,samples in this investigation were purposely limited to a thickness of approximately100–150m m,to ensure through-thickness grain size uniformity and to avoid processing induced residual stresses.Electrodeposited Ni foils with two different grain sizes(nc Ni with an average grain size of20–40nm and a ufc equi-axed structure with an average grain size of approximately300nm)were procured from Integran Corporation,Toronto,Canada.2.2.Experimental detailsFor the purpose of minimizing processing-induced residual stresses,all fatigue specimens were extracted from the electrodeposited Ni foils by way of electro-discharge machining.Both low-and high-cyclefatigue Fig.1.Grain size distribution of electrodeposited pure nc Ni,illustrating the relatively narrow range of grain sizes,as well as the confinement of all grains below the100nm range.T.Hanlon et al./International Journal of Fatigue27(2005)1147–1158 1148experiments were carried out in a laboratory air environ-ment(approximately258C and50%relative humidity).Full details of the stress-life set-up and experimental methods are available elsewhere[5,20].High cycle fatigue crack growth experiments for the nc,ufc,and mc Ni foils were conducted using single edge-notched specimens,where fatigue cracks were initiated in cyclic tension at load ratios ranging from 0.1to0.7at a cyclic frequency of10Hz(sinusoidal waveform).The specimens were39mm long,9.9mm wide,and100m m in thickness.Changes in crack length as a function of the number of fatigue cycles were monitored optically with a traveling microscope.The crack growth rate,d a/d N,was monitored as the length of the crack increased under a constant range of imposed cyclic loads.To ensure that small-scale yielding conditions prevailed,all data were collected such that the remaining uncracked ligament length was always at least twenty times greater than the maximum plastic zone size at the crack tip.In order to assess the overall generality of the trends observed in electrodeposited Ni,we studied the fatigue properties of two additional material systems,for which larger bulk specimens could be produced.First,a cryomilled Al-7.5Mg alloy was fabricated in billet form,50mm in diameter,and several inches in length(and was procured from the University of California,Irvine).This choice was motivated by the fact that grain size effects could be assessed in the ufc regime using specimens whose dimensions are sufficiently large(35!35!5mm)to meet the requirements of conventional standards for fatigue testing of bulk materials.A complete review of the Al-7.5Mg powder production and consolidation techniques is given in[23,24].In addition,ufc,ECAP pure Ti was also investigated,with direct comparisons made to its mc counterpart.Compact specimens,5mm in thickness,were extracted from extruded Al–Mg billets in the circumferential–radial (C–R)configuration.The notch tip was machined to a radius of0.09mm and the specimen faces were polished to a mirrorfinish,with afinal0.25m m polishing step.The through-holes,located on either side of the notch to pin-load the specimens,were machined after the fatigue pre-crack was introduced via cyclic compression loading[1,25, 26].Full details of the experimental technique are given in[5].For the study of fatigue of ECAP materials,billets of Grade2commercially pure mc Ti,40mm in diameter and 150mm in length,were subjected to eight ECAP cycles at a temperature of4258C,using a molybdenum disulphide lubricant and a die angle pact specimens,3mm in thickness,were extracted in the radial–longitudinal(R–L) configuration from billets from the same batch exposed to either zero(mc Ti)or eight(ufc Ti)such pressing cycles.In-plane dimensions of the specimens measured33!31.75mm.The notch tip was machined to an initial radius of0.12mm,and subsequently sharpened to a radius of 0.03mm with a razor blade sprayed with a0.25m m diamond polishing suspension.A fatigue pre-crack was introduced in cyclic tension at load ratios of R Z0.1and0.3, at a cyclic frequency of10Hz(sinusoidal waveform)at room temperature.Crack growth was monitored in-situ with a telescopic video camera module,and ex-situ with an optical microscope.2.3.Shape factor considerationsIn order to characterize the variation of the fatigue crack growth rate as a function of D K,a proper evaluation of the shape factor,f(a/W),specific to the present specimen geometry(single-edge-notched tension specimen)and loading configuration was required.For a rectangular plate of width,W,containing a through-thickness edge crack of length,a,it is commonly known that the stress intensity factor can be expressed by:K I Z sffiffiffiapfaW;f aWZ1:99K0:41aWC18:7aW2K38:48aW3C53:85aW4ð1ÞHowever,the above expression is limited to loading configurations capable of producing a uniform stress throughout the specimen.Typically,this can be accom-plished by utilizing proper sample geometry(i.e.height, H O2W).Eq.(1)must be modified when a non-uniform stress is applied.In order to conduct experiments at a sufficiently high frequency,it was necessary to load the edge-notch speci-mens using rigid,as opposed to pin-loaded grips.In the latter,there exists a rotational degree of freedom,which produces an opening moment at the crack tip during tensile loading.Upon loading with such grips,a significant degradation of the imposed sinusoidal waveform occurred at approximately3–5Hz.This was accompanied by machine resonance,which rendered the system unstable. Conversely,when the specimens were loaded with rigid grips(i.e.‘fixed end displacement’loading),where the ends of the specimens were displaced by a constant amount,a clean sinusoidal waveform at the desired frequency of 10Hz was easily achieved.Several authors[27–30]have previously recognized that the application of Eq.(1)to afixed-end displacement loading configuration can substantially overestimate the mode I stress intensity factor.The boundary conditions associated with this type of loading are such that a closing bending moment is imposed on the crack,even during tensile loading,due to the lack of rotational freedom in the grips.This imposed closing moment effectively reduces the stress intensity factor,and therefore the driving force for crack propagation.To account for this relative reduction in D K,the shape factor,f(a/W),was evaluated viafinite element analysis forT.Hanlon et al./International Journal of Fatigue27(2005)1147–11581149the specific loading geometry used in this investigation.In the analysis,the J -integral was calculated for a /W values ranging from 0.1to 0.7,fully encompassing the range investigated experimentally.Assuming that the stress intensity factor,K I ,has the form given in Eq.(1),the shape factor can be expressed as follows:f a W Z ffiffiffiffiffiffiffiffiJE a s r (2)where E is Young’s modulus and the relationship in Eq.(2)pertains to plane stress conditions.By applying a prescribed load,J can be systematically solved for over a range of crack lengths.In this manner,the shape factor can be fully characterized for the loading configuration and specimen geometry of interest.To confirm the accuracy of the analysis,a constant stress loading configuration was modeled,and the resulting shape factor was found to compare well with the standard formula given in Eq.(1).Eq.(3)specifies the shape factor determined from the analysis (detailed descriptions of which can be found in Ref.[20])for the fixed end displacement case,which was employed in all calculations of the stress intensity factor used to interpret the fatigue crack growth results.f a W Z 2:03K 0:43a W C 3:96a W2K 6:04a W 3C 5:68a W4(3)3.Results3.1.Structure and tensile propertiesSpecimens of nc and ufc Ni were fully characterized in their as-received state by recourse to electron microscopy (Fig.2)and/or x-ray diffraction.The electrodeposited nc Ni had a columnar grain structure with an aspect ratio of 7–10,whereas the electrodeposited ufc Ni was nearly equiaxed.The micrographs in Fig.2a,b depict relatively defect-free initial structures,a critical factor in assessing the role ofgrain size on the overall fatigue response.Full details of theelectrodeposition process and resulting Ni structure are reported elsewhere [14,31,32].Tensile testing of nc and ufc Ni specimens revealed 0.2%offset yield strength values of 930and 525MPa,respectively,and strain to failure values of 3and 10%,respectively.The mc Ni had a yield strength of 180MPa,tensile strength of 450MPa and tensile strain to failure of 35%.Transmission electron microscopy (TEM)images show that the Al–Mg alloy investigated has a relatively equiaxed grain structure,with an average grain size of w 300nm [24].Its yield and tensile strengths were measured experimentally to be 540and 551MPa,respectively.The structure of the ufc ECAP Ti was also relatively equiaxed,with an average grain size of approximately 250nm (Fig.3)and a yield strength of 635MPa.Image analysis of the mc Ti revealed an average grain size of w 22m m,while its yield strength was measured at 430MPa.Full processing and property details are reported in [33].3.2.Fatigue response3.2.1.Stress-controlled fatigueThe effect of grain size on the fatigue resistance of initially smooth-surfaced pure Ni is shown in Fig.4in the form of stress-life fatigue curves,from our earlier report [5].It is evident that nc Ni has a slightly (and reproducibly)higher resistance to stress-controlled fatigue loading than ufc Ni.Additionally,the endurance limit of the mc Ni is significantly below that of both the nc and ufcmaterial,Fig.2.Electron and optical micrographs of the (a)nc Ni,(b)ufc Ni,and (c)mc Ni investigated [5].Fig.3.(a)Optical micrograph showing the grain size distribution of the Grade 2pure mc Ti investigated (zero pressing cycles).(b)TEM image of the ufc ECAP Ti,subjected to 8pressing cycles at a temperature of 4258C.T.Hanlon et al./International Journal of Fatigue 27(2005)1147–11581150clearly illustrating the beneficial effects of grain size reduction on the resistance to S–N fatigue.3.2.2.Fatigue crack growthThe variation in fatigue crack growth rate with respect to D K for pure Ni at load ratios of R Z0.1,0.3,and0.7is plotted in Fig.5.In order to enforce the assumptions inherent to LEFM,all data collection was truncated to incorporate only those data points corresponding to an uncracked ligament length of at least20times the plastic zone size at the tip of the crack during fatigue crack growth experiments.Due to the relatively limited strength of mc Ni, valid fatigue crack growth experiments using D K as the characterizing parameter were not possible under the abovementioned requirements.It is evident from Fig.5 that the resistance to fatigue crack growth is substantially lower in nc Ni at all levels of applied loading,over a wide range of load ratios.To circumvent the foregoing issues associated with the extent of crack-tip plasticity,a set of data was also collected relating the change in crack length to the number of fatigue cycles in mc,ufc,and nc Ni(Fig.6).Each material was subjected to identical initial loading conditions of D K Z 9.5MPa m1/2,R Z0.3,and a cyclic frequency of10Hz at room temperature.Fig.6clearly illustrates that the crack growth rate in the nc Ni is significantly higher than that in the ufc and mc Ni.The effects of load ratio R on the fatigue crack growth response in nc and ufc Ni are plotted in Fig.7, where an increase in R leads to faster crack growth in both materials over the entire range of D K examined.These results are replotted in Fig.8where the stress intensity factor range D K required for a growth rate of10K6mmper Fig.5.Variation of the fatigue crack growth rate,d a/d N,as a function of D K for pure electrodeposited ufc,and nc Ni at load ratios(a)R Z0.1,(b)R Z0.3,and (c)R Z0.7,at a fatigue frequency of10Hz at room temperature.101010107StressRange(MPa)No. of Cycles to FailureFig.4.The effects of grain size from the micro to the nano-regime on thecyclic stress vs.total number of cycles to failure plot in pure Ni.(From[5]).T.Hanlon et al./International Journal of Fatigue27(2005)1147–11581151cycle in nc and ufc Ni is plotted as a function of R and maximum stress intensity factor,K max .The deleterious effect of grain refinement on crack growth is evident in this figure.Further,discussion of the trends seen in this figure is taken up in a later section.To further explore the validity and generality of the above fatigue crack growth trends to fine-grained metals and alloys produced by other processing methods,additional ufc materials fabricated via cryomilling (ufc Al-7.5Mg)and equal channel angular pressing (ufc pure Ti),for which larger bulk specimens could be procured,were examined.Since the solid solution Al-7.5Mg alloy234567800.20.40.60.81Load Ratio234567805101520255K max (MPa m 1/2)K (M P a m 1/2)K (M P a m 1/2)Fig.8.Stress intensity factor range D K required to induce a growth rate of 10K 6mm per cycle in nc and ufc Ni is replotted from the information in Fig.7as a function of R (top figure)and maximum stress intensity factorrange,K Ãmax (bottom figure).The solid lines in both figures show actual trend lines whereas the dashed lines denote assumed trends.Here it is assumed that there exists a critical R above which crack growth is unaffected by R .The filled symbols in the latter figure are experimental data and the open symbols are interpolated points extracted from the informationgiven in the upper figure.D K Ãand K Ãmax ,respectively,denote the limiting or threshold values of alternating and maximum values of stress intensity factor required for the particular growth rate of 10K 6mm per cycle.These values increase with increasing crack growth rate.The apparently detrimental effect of grain refinement on crack growth is evident in bothfigures.V a r i a t i o n I n C r a c k L e n g t h (m m )Fatigue Cycles (In Thousands)Fig.6.Variation in crack length as a function of the number of imposed fatigue cycles for mc,ufc,and nc Ni subjected to an initial D K of 9.5MPa m 1/2,load ratio R Z 0.3,and cyclic frequency of 10Hz at roomtemperature.10–710–610–510–4234567891020d a /d N (m m /c y c le )d a /d N (m m /c y c le )K (MPa m 1/2)K (MPa m 1/2)10–710–610–510–4234567891020Fig.7.Fatigue crack growth rate as a function of D K at different load ratios for nc Ni (upper figure)and ufc Ni (lower figure).T.Hanlon et al./International Journal of Fatigue 27(2005)1147–11581152could only be fabricated via cryomilling,which ultimately results in a very fine grain structure,a direct comparison to mc Al-7.5Mg could not be made.However,Al-5083is a close mc counterpart,and is often used for comparison purposes [24].Consistent with the results obtained for electrodeposited Ni,it was found that the ufc Al-7.5Mg fatigue crack growth rates over the entire d a /d N range,from threshold to final failure,were substantially higher than those in the mc Al-5083(Fig.9).The threshold stress intensity factor range was also considerably lower in the ufc material.In addition,the critical value of D K at which catastrophic failure occurred was several times smaller in the cryomilled Al–Mg.Examination of the fracture surface of the ufc material revealed a significant amount of cracking at inclusion particles [5],which were likely introduced during the cryomilling process.Such particles are believed to play a significant role in the lowering of the critical value of D K .Fatigue crack growth response of pure mc and ECAP-processed ufc Ti was also fully characterized from threshold to final failure.Fig.10shows effects of grain size on the variation of d a /d N as a function of D K at load ratios of R Z 0.1and 0.3.Here,grain refinement from the mc to the ufc regime leads to a reduction in D K th by a factor of 2.5.The rate of fatigue crack propagation is more than an order of magnitude higher in the ufc Ti,over a wide range of applied loading,further reflecting the same trends captured in the electrodeposited Ni.4.DiscussionStudies of fatigue crack initiation in microcrystalline metals and alloys have long considered the critical role ofpurity,surface preparation and material strength in influencing the stress-life response.In nominally smooth-surfaced and defect-free fatigue specimens without notches and other stress concentrators,the initiation of cracks is known to occur in high-cycle fatigue at surfaces.An increase in the strength and hardness of the material,especially near the surface regions which serve as crack nucleation sites,is therefore considered to impart a greater resistance to fatigue crack initiation and hence to S–N fatigue.In the present experiments involving pure Ni and smooth laboratory specimens,this trend is seen to extend down to the nanocrystalline regime,where the higher strength and hardness of the nc material serves to provide a greater resistance to high cycle fatigue than the ufc and mc Ni.1Prior work on the fatigue crack growth resistance of conventional mc metals and alloys has shown (see,for example,[1]for a review of the literature)that predominantly crystallographic and stage I crack growth mechanisms arising at low D K levels of fatigue crack growth lead to microstructurally tortuous crack paths in the coarser grained materials.Grain refinement in mc alloys then serves to reduce the extent of such crack path tortuosity,especially in the near-threshold regime where the cyclic plastic zone size is typically smaller than the average grain size and where the maximum crack-tip opening displacement can be markedly smaller than the surface asperity dimension.These seemingly small periodic deflections in the path of the crack can lead to changes in effective D K as a result of the net reduction in the local stress intensity factor range compared to the case of a perfectly straight crack front [7].In addition,when the10–810–710–610–510–410–310–2110d a /d N (m m /c y c le )∆K (MPa m 1/2)Fig.9.Variation of the fatigue crack growth rate,d a /d N ,as a function of the stress intensity factor range,D K ,for ufc cryomilled Al-7.5Mg at R Z 0.1–0.5at a fatigue frequency of 10Hz at room temperature.Also shown are the corresponding crack growth data for a commercial mc 5083aluminum alloy at R Z 0.33[14].10–810–710–610–510–410–311d a /d N (m m /c y c le )K (MPa m 1/2)Fig.10.Variation in fatigue crack growth rate as a function of D K for commercially pure mc Ti and ECAP ufc Ti at a fatigue frequency of 10Hz at room temperature.1Nanocrystalline metals produced by electrodeposition are known to contain hydrogen which is introduced during processing.However,in the present work,the effects of such impurities are not found to play a major role in introducing damage in nc Ni,as corroborated through high-resolution transmission electron microscopy [31].T.Hanlon et al./International Journal of Fatigue 27(2005)1147–11581153。
工艺参数对AZ31B_镁合金单点渐进翻边精度的影响
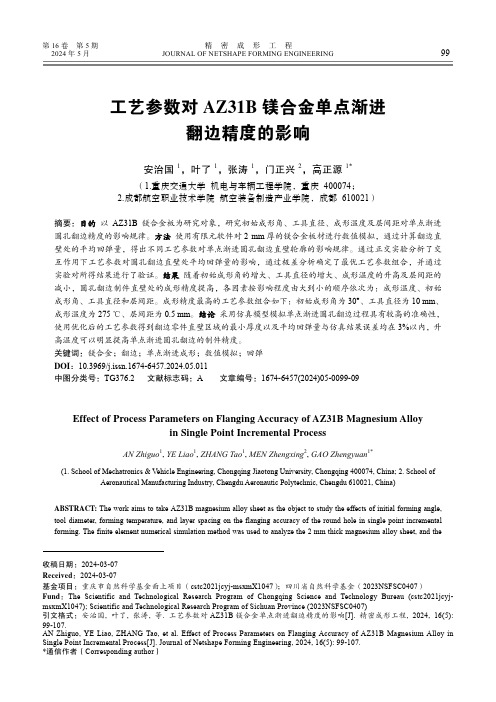
第16卷第5期精密成形工程2024年5月JOURNAL OF NETSHAPE FORMING ENGINEERING99工艺参数对AZ31B镁合金单点渐进翻边精度的影响安治国1,叶了1,张涛1,门正兴2,高正源1*(1.重庆交通大学机电与车辆工程学院,重庆 400074;2.成都航空职业技术学院航空装备制造产业学院,成都 610021)摘要:目的以AZ31B镁合金板为研究对象,研究初始成形角、工具直径、成形温度及层间距对单点渐进圆孔翻边精度的影响规律。
方法使用有限元软件对2 mm厚的镁合金板材进行数值模拟,通过计算翻边直壁处的平均回弹量,得出不同工艺参数对单点渐进圆孔翻边直壁轮廓的影响规律。
通过正交实验分析了交互作用下工艺参数对圆孔翻边直壁处平均回弹量的影响,通过极差分析确定了最优工艺参数组合,并通过实验对所得结果进行了验证。
结果随着初始成形角的增大、工具直径的增大、成形温度的升高及层间距的减小,圆孔翻边制件直壁处的成形精度提高,各因素按影响程度由大到小的顺序依次为:成形温度、初始成形角、工具直径和层间距。
成形精度最高的工艺参数组合如下:初始成形角为30°、工具直径为10 mm、成形温度为275 ℃、层间距为0.5 mm。
结论采用仿真模型模拟单点渐进圆孔翻边过程具有较高的准确性,使用优化后的工艺参数得到翻边零件直壁区域的最小厚度以及平均回弹量与仿真结果误差均在3%以内,升高温度可以明显提高单点渐进圆孔翻边的制件精度。
关键词:镁合金;翻边;单点渐进成形;数值模拟;回弹DOI:10.3969/j.issn.1674-6457.2024.05.011中图分类号:TG376.2 文献标志码:A 文章编号:1674-6457(2024)05-0099-09Effect of Process Parameters on Flanging Accuracy of AZ31B Magnesium Alloyin Single Point Incremental ProcessAN Zhiguo1, YE Liao1, ZHANG Tao1, MEN Zhengxing2, GAO Zhengyuan1*(1. School of Mechatronics & Vehicle Engineering, Chongqing Jiaotong University, Chongqing 400074, China; 2. School ofAeronautical Manufacturing Industry, Chengdu Aeronautic Polytechnic, Chengdu 610021, China)ABSTRACT: The work aims to take AZ31B magnesium alloy sheet as the object to study the effects of initial forming angle, tool diameter, forming temperature, and layer spacing on the flanging accuracy of the round hole in single point incremental forming. The finite element numerical simulation method was used to analyze the 2 mm thick magnesium alloy sheet, and the收稿日期:2024-03-07Received:2024-03-07基金项目:重庆市自然科学基金面上项目(cstc2021jcyj-msxmX1047);四川省自然科学基金(2023NSFSC0407)Fund:The Scientific and Technological Research Program of Chongqing Science and Technology Bureau (cstc2021jcyj- msxmX1047); Scientific and Technological Research Program of Sichuan Province (2023NSFSC0407)引文格式:安治国, 叶了, 张涛, 等. 工艺参数对AZ31B镁合金单点渐进翻边精度的影响[J]. 精密成形工程, 2024, 16(5): 99-107.AN Zhiguo, YE Liao, ZHANG Tao, et al. Effect of Process Parameters on Flanging Accuracy of AZ31B Magnesium Alloy in Single Point Incremental Process[J]. Journal of Netshape Forming Engineering, 2024, 16(5): 99-107.*通信作者(Corresponding author)100精密成形工程 2024年5月effect of different process parameters on the straight wall profile of the round hole flanging was obtained by calculating the av-erage springback value. The effect of process parameters under the interaction on the average springback at the straight wall of the flanging was analyzed by an orthogonal experiment. The optimal combination of process parameters was determined by range analysis, and the results were verified by experiments. With the increase of the initial forming angle, tool diameter and forming temperature and the decrease of the layer spacing, the flanging accuracy increased, and the importance of parameters ina descending order was as follows: forming temperature, initial forming angle, tool diameter, and layer spacing. The combina-tion of process parameters with the highest forming accuracy included the initial forming angle of 30°, tool diameter of 10 mm, forming temperature of 275 ℃, and layer spacing of 0.5 mm. The simulation model has a high accuracy for simulating the single point incremental flanging process. The profile error of the flanging by the optimal combination of process parameters between the physical experiments and the simulation results is less than 3%. The elevated temperature can significantly improve the flanging profile accuracy of the round hole.KEY WORDS: magnesium alloy; flanging; single point incremental forming; numerical simulation; springback翻边是一种将薄板边缘或预制孔边缘的材料沿着曲线或直线向竖直方向翻折的加工工艺[1]。
NH4F_浓度对镁合金表面微弧氧化制备氟化物膜层结构和性能的影响

表面技术第52卷第6期NH4F浓度对镁合金表面微弧氧化制备氟化物膜层结构和性能的影响罗兰1,2,彭振军3,周健松1,2,梁军3,4(1.中国科学院兰州化学物理研究所 中国科学院材料磨损与防护重点实验室,兰州730000;2.中国科学院大学 材料与光电研究中心,北京 100049;3.中国科学院兰州化学物理研究所 固体润滑国家重点实验室,兰州 730000;4.东莞理工学院 材料科学与工程学院,广东 东莞 523808)摘要:目的考察乙二醇-氟化铵电解液中氟化铵浓度对镁合金表面微弧氧化制备氟化物膜层结构和性能的影响,提高镁合金氟化物膜层的耐腐蚀性能。
方法在含不同浓度NH4F的EG-NH4F电解液中,采用微弧氧化的方法制备氟化物膜层,NH4F质量浓度分别为40、60、80、100、120 g/L。
通过扫描电子显微镜(SEM)、X射线能量色散谱仪(EDS)和X射线衍射仪(XRD),对膜层表面微观形貌和成分组成进行分析,并通过电化学测试表征了膜层的腐蚀防护性能,通过盐雾试验评估了膜层长效防腐蚀行为,通过SEM和EDS表征了腐蚀形貌和腐蚀产物。
结果在EG-NH4F中制备膜层的物相组成主要是MgF2。
随着NH4F浓度的提高,微弧氧化的起弧电压与工作电压均逐渐减小,膜层中氟含量逐渐增加,膜层的孔径减小,孔数量分布更加均匀,膜层表面粗糙度降低。
质量浓度为100 g/L NH4F的膜层自腐蚀电流密度(J corr)为2.226×10‒7 A/cm2,较镁合金基材降低了1个数量级,极化电阻R p增大到90.156 kΩ·cm2,其阻抗模量|Z|f=0.01 Hz=8.55×105 Ω·cm2,与镁合金基材的阻抗模量|Z|f=0.01 Hz=8.86×102 Ω·cm2相比,提高了3个数量级。
结论微弧氧化处理能够显著改善AZ31镁合金的腐蚀防护性能。
NH4F浓度的增加有利于提高膜层的耐腐蚀性能,质量浓度为100 g/L NH4F的膜层耐腐蚀性能最优。
镁合金疲劳性能的研究现状_高洪涛

镁合金疲劳性能的研究现状高洪涛,吴国华,丁文江(上海交通大学材料科学与工程学院,上海200030)摘要:针对近几年镁合金疲劳性能的研究进行总结,从冶金因素、形状因素、加载制度、介质和温度等方面考察对镁合金疲劳性能的影响。
归纳提高镁合金抗疲劳性能的途径:热处理、滚压强化和喷丸处理等。
提出对镁合金疲劳性能研究的展望。
关键词:镁合金;疲劳性能;影响因素;强化途径中图分类号:TG146.2 文献标识码:A 文章编号:1000-8365(2003)04-0266-03Review on the Fatigue Behavior of Magnesiu m AlloysGAO Hong-tao,W U Guo-hua,DI NG W en-jiang(Schoo l of M aterials Science and Engineering,Shang hai Jiaotong U niversity,Shang hai200030,China)A bstract:This report provides some of the results of magnesium alloy s studying,especially about its fatigue behavior, in recent years.The facto rs that influence the fatigue behavior of magnesium alloy s can be given from several aspects of metallurgy,form factor,loading system,medium and tem perature.The strengthening methods can be concluded in three aspects.One is heat treatment;the o ther tw o are roller burnishing and shot blasting.In addition,the prospect of fatigue behavio r observation on mag nesium alloy s is discussed.Key words:M ag nesium alloy;Fatigue behavior;Influencing factors;Strengthening approach 综合性能优良的镁合金已大量应用于航空航天、汽车、电子等领域[1]。
材料表面裂纹的红外热像显微检测
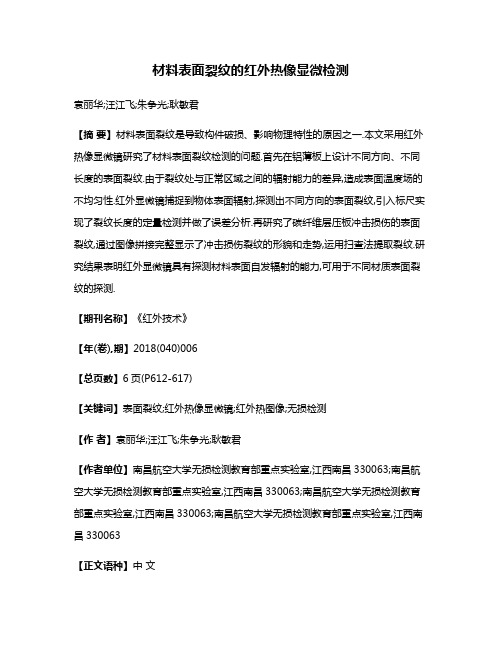
材料表面裂纹的红外热像显微检测袁丽华;汪江飞;朱争光;耿敏君【摘要】材料表面裂纹是导致构件破损、影响物理特性的原因之一.本文采用红外热像显微镜研究了材料表面裂纹检测的问题.首先在铝薄板上设计不同方向、不同长度的表面裂纹.由于裂纹处与正常区域之间的辐射能力的差异,造成表面温度场的不均匀性.红外显微镜捕捉到物体表面辐射,探测出不同方向的表面裂纹,引入标尺实现了裂纹长度的定量检测并做了误差分析.再研究了碳纤维层压板冲击损伤的表面裂纹,通过图像拼接完整显示了冲击损伤裂纹的形貌和走势,运用扫查法提取裂纹.研究结果表明红外显微镜具有探测材料表面自发辐射的能力,可用于不同材质表面裂纹的探测.【期刊名称】《红外技术》【年(卷),期】2018(040)006【总页数】6页(P612-617)【关键词】表面裂纹;红外热像显微镜;红外热图像;无损检测【作者】袁丽华;汪江飞;朱争光;耿敏君【作者单位】南昌航空大学无损检测教育部重点实验室,江西南昌330063;南昌航空大学无损检测教育部重点实验室,江西南昌330063;南昌航空大学无损检测教育部重点实验室,江西南昌330063;南昌航空大学无损检测教育部重点实验室,江西南昌330063【正文语种】中文【中图分类】TH7422002年5月25日中华航空公司一架编号为611的班机由台湾中正国际机场飞往香港国际机场发生了客机解体坠毁,225人罹难。
事故原因是由于该航机于1980年机尾擦地损伤了机尾蒙皮,却没有妥善处理其机尾损伤,长时间的疲劳裂纹导致飞机空中解体。
红外热成像检测技术作为一种新兴的无损检测技术,被学者用于裂纹的探测中,研究了裂纹的检测和评价。
对微裂纹,如腐蚀裂纹,紧贴型裂纹等,一般采用主动式红外热成像检测技术进行探测。
提出了多种激励方法,例如,超声激励[1-2],感应激励[3],震动激励[4],热空气加热[5]等方法。
对裂纹扩展采用被动式方法直接用红外热像仪进行监控。
铸态和挤压态AZ31镁合金在3.5%的NaCl溶液中的腐蚀性能比较

铸态和挤压态AZ31镁合金在3.5%的NaCl溶液中的腐蚀性能比较李捷帆;马莹;惠增哲;徐春杰;张忠明【摘要】The aim of this study was to investigate the corrosion performance of AZ31 alloy in 3.5% sodium chloride water solution.Optical microscopy and X-ray diffraction analysis were performed to examine microstructure of AZ31 alloys before and after hot extrusion. The corrosion behavior of the alloys prepared by as-casting and extrusion were investigated in 3.5%NaCl aqueous solution by immersion and electrochemical tests.The results indicated that the hot extrusion can obviously reduce the grain size of AZ31 alloy.The average grain size of the as-cast alloy was about 111 m,and the average size of the hot extruded alloy was about 9 m.There was no surface passivation at the initial stage during immersion corrosion of the AZ31 alloy in 3.5% sodium chloride water solution. The corrosion potential of the AZ31 alloy at as-cast state was-1.55 V,and increased to-1.52 V at extruded state. When the AZ31 was immersed for 72 h,the average corrosion rates of as-cast and extruded alloys were 4.293 mm/a and 2.957 mm/a,respectively. Hot extrusion can improve the corrosion resistance of AZ31 alloy in 3.5%NaCl solution.%目的:研究铸态和挤压态AZ31镁合金在3.5%NaCl溶液中的腐蚀性能。
- 1、下载文档前请自行甄别文档内容的完整性,平台不提供额外的编辑、内容补充、找答案等附加服务。
- 2、"仅部分预览"的文档,不可在线预览部分如存在完整性等问题,可反馈申请退款(可完整预览的文档不适用该条件!)。
- 3、如文档侵犯您的权益,请联系客服反馈,我们会尽快为您处理(人工客服工作时间:9:00-18:30)。
Fatigue behavior of magnesium alloy and application inauto steering wheel frameM AO Ping-li(毛萍莉), L IU Zheng(刘正), W ANG Chang-yi(王长义),G UO Quan-ying(郭全英), S UN Jin(孙晶), W ANG Feng(王峰), L IN Li(林立)School of Materials Science and Engineering, Shenyang University of Technology,Shenyang 110023, ChinaReceived 12 June 2008; accepted 5 September 2008Abstract: The low-cycle fatigue behaviors of AZ91HP-F, AZ91HP-T6, AZ91HP-T4 and AM50HP-F were investigated, and the potential application of AM50HP-F in steering wheel frame was studied. The steering wheel properties were characterized by bend fatigue and tensile testing, and the fatigue fracture was analyzed by SEM. The results show that the fatigue lives of AZ91HP-F and AZ91HP-T6 have little difference by comparing the low-cycles fatigue properties of different heat treatment states. The crack propagation velocity of AZ91HP-T4 is lower than that of AZ91HP-F and AZ91HP-T6. The die casting technological parameters of the magnesium steering wheel have been optimized with the aid of flow-3D software. The tensile testing results of the different part of magnesium steering wheel show that the ultimate tensile strength and elongation in the wheel arm and wheel rim have no difference and the average value are 220 MPa and 5%, respectively. The fracture is in the brittleness mode and the fatigue crack initiates at the outside of the wheel rim.Key words: magnesium alloy; low cycle fatigue behavior; magnesium steering wheel frame1 IntroductionMagnesium alloy components equal in strength are 40% lighter than steel and 20% lighter than their aluminum counterparts, which enables car manufacturers to meet regulatory requirements for lighter weight vehicles and a corresponding reduction in emissions. Among the magnesium alloys AZ91 and AM50 (or AM60) are the most widely used die-cast magnesium alloys for producing some automobile parts such as steering wheel frame, transmission case, housing, engine cradle, and pedal[1−2]. Since these mechanically loaded automobile components are often subjected to cyclic stresses, it is necessary to investigate the cyclic deformation behavior of those alloys. Previous work concerning fatigue behavior of the die-cast AZ91 and AM50 alloys have been focused on its high-cycle fatigue properties, and some helpful research results have been well documented[3−10]. However, few low-cycle fatigue data are available for these alloys[11−13]. Related investigations have revealed that the ductility of AZ91 can be greatly improved and the fatigue crack propagation rate reduced with a treatment that produces a supersaturated solution (T4)[14]. The S-N curve of AZ91 has shown that precipitation from supersaturated solutions results in little improvement in the fatigue strength although the yield stress may significantly increase (T6)[15]. It is known that the mechanical properties of die-casting alloy AM60 can be improved following a supersaturated solution and artificial aging treatment[15]. This work is concerned with the low-cyclic deformation behavior of the alloy AZ91HP in F, T4 and T6 conditions in comparison with the alloy AM50HP (F).2 ExperimentalThe testing materials are AZ91HP and AM50HP. The ingots were melted and cast into a plate of 150 mm×100 mm×5 mm with a cold chamber die-casting machine GDK200. The specimen was cut from the die-casting plate and its geometry is shown in Fig.1. The thickness of specimen is equal to that of die-casting plate and the surface of specimen was not machined after die casting, but polished with 400 and then 600 grit emery papers. Table 1 lists the parameters of high pressure die casting for AZ91HP and AM50HPFoundation item: Project (2007CB613705) supported by the National Basic Research Program of China Corresponding author: MAO Ping-li; Tel: +86-24-25497131; E-mail: pinglimao@MAO Ping-li, et al/Trans. Nonferrous Met. Soc. China 18(2008)s219Table 1 Parameters of high pressure die casting and heat treatmentDie casting parametersSupersaturated solutionparametersAging parametersCasting temperature/℃ Mouldtemperature/℃ Gate speed/(m·s −1)Crystal pressure/Pa Treatmenttemperature/℃Treatment time/h CoolingmediumTreatment temperature/℃ Treatment time/h Coolingmedium670−690 22080 7.0×107 415 8 Air160 10−56AirFig.1 Dimensions of fatigue specimen (unit: mm)and the subsequent heat treatments for AZ91HP .The fully reversed total strain-controlled low-cycle fatigue tests were performed with a servo hydraulic testing system MTS810 at room temperature in air. A triangular waveform with a strain rate ranging from 7.5×10−3 to 1×10−2and five strain levels ranging from 2.5×10−3−1.5×10−2were used in all tests. Lower strain rates were used for the larger strain amplitude tests and the higher strain rates for the smaller strain amplitude tests. The fatigue failure was defined as specimen fracture or 20% drop in maximum tensile load.3 Low-cycle fatigue behaviorThe fatigue life data of plastic, elastic and total strain amplitude vs. reversals to failure (2N f ) are shown in Figs.2 and 3. The plastic and elastic strain amplitudes and the corresponding stress amplitudes are obtained at a half of the cyclic life. The fatigue life data can be described in the following conventional equation and displayed very well in terms of Basquin and Manson- Coffin laws as a result of lg-lg linear regression of the elastic and plastic strain amplitudes.c b N N E )2()2(222f f f f p e t εσεεε′+′−=Δ+Δ=Δ (1)where E is elastic modulus, which is about 45 GPa for the magnesium alloys; σ′f and ε′f are fatigue strength and ductility coefficients respectively whose values have been expressed in Figs.2 and 3. By comparison of Fig.2 and Fig.3, it can be seen that there are almost no difference in the fatigue life between AZ91HP-F and -T6, but some changes have happened for AZ91HP-T4.The fatigue life for supersaturated solution treatment will be prolonged at high strain amplitude but reduced at low strain amplitude. AM50HP exhibits the similar characteristics to AZ91HP-T4, but the prolongingFig.2 Strain amplitude vs. reversals to failure (2N f ) ofAZ91HP-F and AZ91HP-T6Fig.3 Strain amplitude vs. reversals to failure (2N f ): (a) AZ91HP-T4; (b) AM50HP-FMAO Ping-li, et al/Trans. Nonferrous Met. Soc. China 18(2008) s220fatigue life at high strain amplitude shows in a little smaller degree than that of AZ91HP-T4, as shown in Fig.3. It is obvious that the transition fatigue life (NT) is elongated with solution treatment. Thereby, it will be significant that the attempt of some potential automobile application such as steering wheel would take AZ91HP-T4 as an alternative material of AM50HP for more safety.Fig.4 shows the cyclic stress—strain curves together with the monotonic stress—strain curves of AZ91HP-F and AM50HP-F. The strain amplitude (Δεt/2) and corresponding stress amplitude (Δσ/2) are obtained at half of the cyclic life (N f/2). It was found that the cyclic strength increased in an order of AM50HP, AZ91HP-T4, AZ91HP-F and AZ91HP-T6. By comparing with the monotonic stress—strain curve, all the cyclic configurations exhibit the cyclic strain hardening in different degrees depending on the composition, heat treatment and strain amplitudes. The cyclic strain hardening is accelerated with increasing the strain amplitudes. Solid solution alloy AZ91HP-T4 shows the highest and artificial aging alloy AZ91HP-T6 exhibits the lowest cyclic strain hardening of all the testing materials although AZ91HP-T6 has the highest cyclic strength and AZ91HP-T4 has much lower cyclic strength.Fig.4 Monotonic and cyclic stress—strain curve4 Fatigue crack propagationAt load ratio of 0.5, load frequency of 50 Hz and under constant load amplitude control in air, Δk was measured to be 0.774 MPa⋅m1/2 for artificial aging specimens, 0.997 MPa⋅m1/2 for die-casting specimens and 1.174 MPa⋅m1/2 for supersaturated solution treated specimens. The testing fatigue crack propagation rate of AZ91HP was decreased in the order of artificial aging, die casting and supersaturated solution treatment, as shown in Fig.6. Where the value of crack length a was measured with a microscope and the stress intensity factor range, Δk was calculated with the following formulas (2) and (3) according to ASTM standard E647:2/312.)()(Δα−+=ΔαWBPk(0.886+4.64α-13.32α2+14.72α3−5.6α4)(2)11d/d−−−−=llllnnaana(3)where ΔP =P max−P min represents load range; B is the specimen thickness, and it is equal to 4 mm; W is the specimen width, and it is equal to 20 mm; α=a/W is the normalized crack length; n is the applied cycles and l is the number of cycles.Fig.5 Fatigue crack propagation rate at 50 Hz load frequencyFig.6 Fluid field simulation result5 Application of AM50 magnesium alloy on motor steering wheelWhen magnesium alloy was used in steering wheel frame, it could not only lower the weight, but also lower the vibration of road and control system and absorb more compact energy when there was a accident. More and more magnesium steering wheels were used in auto industry. The investigation and development of magnesium steering wheel for Jinbei coach was conducted in the present study.MAO Ping-li, et al/Trans. Nonferrous Met. Soc. China 18(2008) s221The software of Flow-3D was used to optimize the die-casting parameters such as filling velocity, mould temperature and pouring temperature. According to the simulation results of fluid field, temperature field and probability of the surface defect the three parameters of filling velocity, mould temperature and pouring temperature for the present steering wheel structure and die casting running system are 2.34 m/s, 220 ℃ and 700 ℃ respectively. Figs.6 and 7 show the examples of simulation results of fluid field and the probability of surface defect.Fig.7 Surface defect probability simulation resultAM50 steering wheel frame was manufactured using the parameters according to the simulation results. The tensile tests were conducted on the five locations of the steering wheel, one is in the wheel rim and the others are in the wheel arms. The test results show that the ultimate tensile strength and elongation of five locations have no difference, and the average values were 220 MPa and 5% respectively. It is implied that the magnesium steering wheel manufactured using the current parameters has homogenous microstructure. The fatigue testing of AM50 steering wheel frame was conducted in a universal steering wheel testing machine, when the steering wheel was fixed at centre and the wheel rim was applied with ±250 kN load repeatedly. The average fatigue life of AM50 HP-F steering wheel was 110 000 cycle, and the enterprise standard for AM50 HP-F steering wheel is 100 000 cycle. It was implied that AM50HP-F had the capability of meeting the requirement of fatigue life for steering wheel frame. The fatigue fracture morphology is shown in Fig.8. It can be seen from Fig.8(a) that the crack initiated from the outside of the wheel rim. When the outside of the wheel rim underwent the maximum tension and compression stress repeatedly, it was possible for the stress concentration at outside of the wheel rim, as indicated by arrow in Fig.8(a). The morphology of fatigue crack propagation zone is shown in Fig.8(b), and the instantaneous fracture zone shows the feature of transgranular and cleavage (Fig.8(c)).6 Conclusions1) AM50HP, AZ91HP-T4, AZ91HP-F and AZ91HP- T6 exhibit the cyclic strain hardening in different degrees depending on the heat treatment and strain amplitudes. AZ91HP-T4 shows the highest,AZ91HP-T6 the lowest cyclic strain hardening of all the testing materials.2) No difference of the fatigue life between die casting alloy AZ91HP-F and artificial aging alloy AZ91HP-T6 is observed. Solid solution alloy AZ91HP-T4 and die casting alloy AM50HP-F have longer fatigue life only at very high strain amplitude butFig.8 Fatigue fracture morphologiesof AM50 HP-F steering wheel frame:(a) Full view of fracture; (b) Crackpropagation zone; (c) Instantaneousfracture zoneMAO Ping-li, et al/Trans. Nonferrous Met. Soc. China 18(2008) s222much shorter at low strain amplitude than AZ91HP-F and -T6. Fatigue crack propagation rate is reduced by solution treatment.3) The mechanical and fatigue properties of AM50HP-F were tested and it was found that AM50HP-F was suit for manufacturing magnesium steering wheel frame.References[1] FRIEDRICH H, SCHUMANN S. Research for a “new age ofmagnesium” in the automotive industry [J]. J Mater Proc Technol,2001, 117: 276−281[2] AGHION E, BRONFIN B, ELILEZER D. The role of themagnesium industry in protecting the environment [J]. J Mater ProcTechnol, 2001, 117: 381−385.[3] ZENNER H, RENNER F. Cyclic material behaviour of magnesiumdie castings and extrusions [J]. Int J Fatigue, 2002, 24: 1255−1260. [4] MAYER H, PAPAKYRIACOU M, ZETTL B. Influence of porosityon the fatigue limit of die cast magnesium and aluminium alloys [J].Int J Fatigue, 2003, 25: 245−256.[5] HORSTEMEYER M F, YANG N, GALL K, MCDOWELL D L.High cycle fatigue of a die cast AZ91E-T4 magnesium alloy [J]. ActaMater, 2004, 52: 1327−1336.[6] EISENMEIER G, HOLZWARTH B, HÖPPEL H W, MUGHRABI H.Cyclic deformation and fatigue behaviour of the magnesium alloyAZ91 [J]. Mater Sci Eng, 2001, A319-321: 578−582.[7] YANG Y, LIU Y B, YANG X H. High cycle fatigue properties ofAZ91D die cast magnesium alloy [J]. Special Casting & NonferrousAlloys, 2006, 26(2): 105−108 [8] HORSTERMEYER M F, YANG N, GALL K, MCDOWELL D, FANJ, GULLETT P. High cycle fatigue mechanisms in a cast AM60Bmagnesium alloy [J]. Fatigue Fract Eng Mater Struct, 2002, 25:1045−1052.[9] EISENMEIER G, HOLZWARTH B. Cyclic deformation and fatiguebehavior of the magnesium alloy AZ91 [J]. Materials Science andEngineering, 2001, A319: 578−582.[10] WANG X S, LU X, WANG D H. Investigation of surface fatiguemicrocrack growth behavior of cast Mg-Al alloy [J]. MaterialsScience and Engineering, 2004, A364: 11−16.[11] LAMARK T T, CHEMLIK F, YURI ESTRIN Y. Cyclic deformationof a magnesium alloy investigated by the acoustic emissiontechnique [J]. Journal of Alloys and Compounds, 2004, 378:202−206.[12] LIU Z, WANG Z G, WANG Y. Cyclic deformation behavior andfatigue crack propagation in AZ91HP and AM50HP[J]. MaterialsScience and Technology, 2001, 17(3): 264−268.[13] GALL K, BIALLAS G, MAIER H J, GULLETT I,HORSTEMEYER M F, MCDOWELL D L, FAN J H. In-situobservations of high cycle fatigue mechanism in cast AM60Bmagnesium in vacuum and water vapor environmental [J].International Journal of Fatigue, 2004, 26: 59−70.[14] WOLF B, FLECK C, EIFLER D. Characterization of the fatiguebehavior of the magnesium alloy AZ91D by means of mechanicalhysteresis and temperature measurements [J]. International Journal ofFatigue, 2004, 26: 1357−1363.[15] LEE S G, PATEL G R, GOKHALE A M. Inverse surfacemacro-segregation in high-pressure die-cast AM60 magnesium alloyand its effects on fatigue behavior [J]. Scipta Materialia, 2005, 52:1063−1068.(Edited by YANG You-ping)。