湿型铸造小件产品缺陷产生的原因与防止措施
铸造铸件常见缺陷原因与解决方法分析

铸造铸件常见缺陷原因与解决方法分析前言铸造工艺过程复杂,影响铸件质量的因素很多,往往由于原材料控制不严,工艺方案不合理,生产操作不当,管理制度不完善等原因,会使铸件产生各种铸造缺陷。
常见的铸件缺陷名称、特征和产生的原因,详见下表。
★ 常见铸件缺陷及产生原因★缺陷名称特征产生的主要原因气孔在铸件内部或表面有大小不等的光滑孔洞①炉料不干或含氧化物、杂质多;②浇注工具或炉前添加剂未烘干;③型砂含水过多或起模和修型时刷水过多;④型芯烘干不充分或型芯通气孔被堵塞;⑤春砂过紧,型砂透气性差;⑥浇注温度过低或浇注速度太快等缩孔与缩松缩孔多分布在铸件厚断面处,形状不规则,孔内粗糙①铸件结构设计不合理,如壁厚相差过大,厚壁处未放冒口或冷铁;②浇注系统和冒口的位置不对;③浇注温度太高;④合金化学成分不合格,收缩率过大,冒口太小或太少砂眼在铸件内部或表面有型砂充塞的孔眼①型砂强度太低或砂型和型芯的紧实度不够,故型砂被金属液冲入型腔;②合箱时砂型局部损坏;③浇注系统不合理,内浇口方向不对,金属液冲坏了砂型;④合箱时型腔或浇口内散砂未清理干净粘砂铸件表面粗糙,粘有一层砂粒①原砂耐火度低或颗粒度太大;②型砂含泥量过高,耐火度下降;③浇注温度太高;④湿型铸造时型砂中煤粉含量太少;⑤干型铸造时铸型未刷涂斜或涂料太薄夹砂铸件表面产生的金属片状突起物,在金属片状突起物与铸件之间夹有一层型砂①型砂热湿拉强度低,型腔表面受热烘烤而膨胀开裂;②砂型局部紧实度过高,水分过多,水分烘干后型腔表面开裂;③浇注位置选择不当,型腔表面长时间受高温铁水烘烤而膨胀开裂;④浇注温度过高,浇注速度太慢铸件沿分型面有相对位置错移①模样的上半模和下半模未对准;②合箱时,上下砂箱错位;③上下砂箱错型未夹紧或上箱未加足够压铁,浇注时产生错箱冷隔铸件上有未完全融合的缝隙或洼坑,其交接处是圆滑的①浇注温度太低,合金流动性差;②浇注速度太慢或浇注中有断流;③浇注系统位置开设不当或内浇道横截面积太小;④铸件壁太薄;⑤直浇道(含浇口杯)高度不够;⑥浇注时金属量不够,型腔未充满浇不足铸件未被浇满裂纹铸件开裂,开裂处金属表面有氧化膜①铸件结构设计不合理,壁厚相差太大,冷却不均匀;②砂型和型芯的退让性差,或春砂过紧;③落砂过早;④浇口位置不当,致使铸件各部分收缩不均匀★ 常见铸件缺陷及预防措施★序缺陷名称缺陷特征预防措施1 气孔在铸件内部、表面或近于表面处,有大小不等的光滑孔眼,形状有圆的、长的及不规则的,有单个的,也有聚集成片的。
铸造缺陷原因及其解决方法

铸造缺陷原因及其解决方法
铸造缺陷是铸造行业经常出现的一类问题,对铸件的功能和使用寿命有负面影响。
在近年来,随着材料科学领域的进步,铸铁、钢、金属等的性能越来越高,越来越多的新型铸造形式和新型工艺方法被开发出来,但是铸造缺陷依然存在,需要及时解决。
铸造缺陷的原因很复杂,主要有以下几类:一是铸件的铸造工艺参数不当,包括铸件尺寸参数不合理,成型材料未能满足要求,流体特性、温度、压力等参数不足;二是模具设计过程中出现问题,包括模具结构设计不当、表面材质不满足要求等;三是原料误差,原料中病害比例高,导致铸件组织结构不稳定,抗拉强度低。
解决铸造缺陷的方法:一是针对工艺参数不当,应采取有效的治理措施,进行工艺参数的优化及控制,在模具设计中加强细部处理或使用更高性能的材料;二是对原材料误差,应采取措施分离优良料和劣料,保证原料质量,增加试验对原料力学和化学性质检测,改善铸件质量;三是在成型前,应做出正确的实验,要求较高,确保模具尺寸精度,应用胶粉注射成型增加工艺性能。
通过科学的铸造工艺参数设计,优质的原材料配置,模具精细设计,合理的实验控制,减少不合格品,增加铸件质量,都可以有效地解决铸造缺陷的问题。
只有把解决这些铸造缺陷的解决方案扎实,从技术、过程、品质等角度进行多方面开展,才能保证铸件的功能以及使用寿命,有助于企业提升铸件的整体质量水平,建立良好的企业形象。
常见铸造缺陷的产生原因及其预防措施
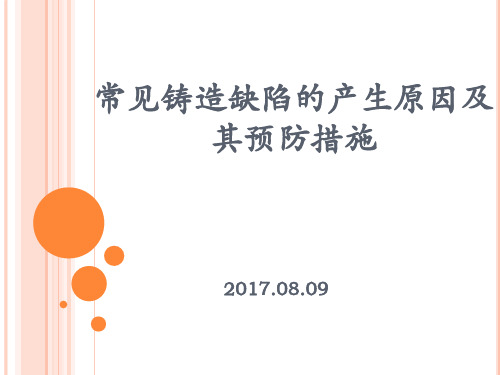
多肉产生的原因:
1、模具原因。 2、砂(芯)型起破。 3、砂(芯)型损坏 4、砂芯和砂型相接 表面不吻合
5、冷铁和模具不吻 合。
6、砂(芯)局部部 位未充满。
冷铁和模具不吻 合引起的铸件多
肉
多肉类缺陷的预防措施
(1) 提高铸型紧实度(下箱型砂的紧实度应高于 上箱的紧实度),避免局部过松;
(2)调整混砂工艺、控制水分,提高型砂强度; (3) 降低浇包的位置、降低浇注速度; (4) 铸型的分型面多压坭条或石棉绳; (5) 坭芯间的可见披缝尽量补死; (6) 需放置直接外冷铁时,外冷铁与铸件的接
根据GB/T 5611-1988《铸造术语》规定,将铸造缺陷 分为八大类。
① 多肉类缺陷 ② 孔洞类缺陷 ③ 裂纹、冷隔类缺陷 ④ 表面缺陷 ⑤ 残缺类缺陷 ⑥ 形状及重量差错类缺陷 ⑦ 夹杂类缺陷 ⑧ 性能、成分、组织不合格
分类(1)
大 类
序 号
缺陷名称
特征
1
飞翅(飞边、 产生在铸件分型面、坭芯间隙处、坭芯与
裂处金属表皮不氧化。
在铸件表面有未完全融合的缝隙或 洼坑,其交接边缘是光滑的。
热裂和冷裂(1) 热裂
图6-1 铸钢件的外热裂
冷裂
热裂和冷裂(2)
冷隔(1)
局 部 放 大
叶片机座 冷隔缺陷
冷隔(2)
典型的冷隔特 征
裂纹冷隔类缺陷的预防措施
(1) 严格按照化学成分的要求,控制钢水中的 S、 P含量;
触面一定要打磨平整; (7) 合箱后,注意保证上、下箱连接位置的紧固,
需放置压铁时上、下箱之间要用冷铁尖死。
分类(2-1)
大 类
序 号
缺陷名称
特征
孔 洞
常见铸造缺陷产生的原因及防止方法

常见铸造缺陷产生的原因及防止方法铸件缺陷种类繁多,产生缺陷的原因也十分复杂.它不仅与铸型工艺有关,而且还与铸造合金的性制、合金的熔炼、造型材料的性能等一系列因素有关.因此,分析铸件缺陷产生的原因时,要从具体情况出发,根据缺陷的特征、位置、采用的工艺和所用型砂等因素,进行综合分析,然后采取相应的技术措施,防止和消除缺陷.一、浇不到1、特征铸件局部有残缺、常出现在薄壁部位、离浇道最远部位或铸件上部.残缺的边角圆滑光亮不粘砂.2、产生原因1 浇注温度低、浇注速度太慢或断续浇注;2 横浇道、内浇道截面积小;3 铁水成分中碳、硅含量过低;4 型砂中水分、煤粉含量过多,发气量大,或含泥量太高,透气性不良;5 上砂型高度不够,铁水压力不足.3、防止方法1 提高浇注温度、加快浇注速度,防止断续浇注;2 加大横浇道和内浇道的截面积;3 调整炉后配料,适当提高碳、硅含量;4 铸型中加强排气,减少型砂中的煤粉,有机物加入量;5 增加上砂箱高度.二、未浇满1、特征铸件上部残缺,直浇道中铁水的水平面与铸件的铁水水平面相平,边部略呈圆形.2、产生原因1 浇包中铁水量不够;2 浇道狭小,浇注速度又过快,当铁水从浇口杯外溢时,操作者误认为铸型已经充满,停浇过早.3、防止方法1 正确估计浇包中的铁水量;2 对浇道狭小的铸型,适当放慢浇注速度,保证铸型充满.三、损伤1、特征铸件损伤断缺.2、产生原因1 铸件落砂过于剧烈,或在搬运过程中铸件受到冲撞而损坏;2 滚筒清理时,铸件装料不当,铸件的薄弱部分在翻滚时被碰断;3 冒口、冒口颈截面尺寸过大;冒口颈没有做出敲断面凹槽.或敲除浇冒口的方法不正确,使铸件本体损伤缺肉.3、防止方法1 铸件在落砂清理和搬运时,注意避免各种形式的过度冲撞、振击,避免不合理的丢放;2 滚筒清理时严格按工艺规程和要求进行操作;3 修改冒口和冒口颈尺寸,做出冒口颈敲断面,正确掌握打浇冒口的方向.四、粘砂和表面粗糙1、特征粘砂是一种铸件表面缺陷,表现为铸件表面粘附着难以清除的砂粒;如铸件经清除砂粒后出现凹凸不平的不光滑表面,称表面粗糙.2、产生原因1 砂粒太粗、砂型紧实度不够;2 型砂中水分太高,使型砂不易紧实;3 浇注速度太快、压力过大、温度过高;4 型砂中煤粉太少;5 模板烘温过高,导致表面型砂干枯;或模板烘温过低,型砂粘附在模板上.3、防止方法1 在透气性足够的情况下,使用较细原砂,并适当提高型砂紧实度;2 保证型砂中稳定的有效煤粉含量;3 严格控制砂水分;4 改进浇注系统,改进浇注操作、降低浇注温度;5 控制模板烘烤温度,一般与型砂温度相等或略高.五、砂眼1、特征在铸件内部或表面充塞有型砂的孔眼.2、产生原因1 型砂表面强度不够;2 模样上无圆角或拔模斜度小导致钩砂、铸型损坏后没修理或没修理好就合箱;3 砂型在浇注前放置时间过长,风干后表面强度降低;4 铸型在合箱时或搬运过程中损坏;5 合箱时型内浮砂未清除干净,合箱后浇口杯没盖好,碎砂掉进铸型.3、防止方法1 提高型砂中粘士含量、及时补加新砂,提高型砂表面强度;2 模样光洁度要高,并合理做出拔模斜度和铸造圆角.损坏的铸型要修好后再合箱;3 缩短浇注前砂型的放置时间;4 合箱或搬运铸型时要小心,避免损坏或掉入砂型腔砂粒;5 合箱前清除型内浮砂,并盖好浇口.六、披缝和胀砂1、特征披缝常出现在铸件分型面处,是垂直于铸件表面,且厚薄不均匀的薄片状金属突起物. 胀砂是铸件内、外表面局部胀大,形成不规则的瘤状金属突起物.2、产生原因1 紧实度不够或不匀;2 面砂强度不够、或型砂水分过高;3 液态金属压头过大、浇注速度太快.3、防止方法1 提高铸型紧实度、避免局部过松;2 调整混砂工艺、控制水分,提高型砂强度;3 降低液态金属的压头、降低浇注速度.七、抬箱1、特征铸件在分型面处有大面积的披缝,使铸型外形尺寸发生变化.抬箱过大,造成跑火——铁水自分型面外溢,严重时造成浇不足缺陷.2、产生原因1 砂箱未紧固、压铁质量不够或去除压铁过早;2 浇注过快,冲击力过大;3 模板翅曲.3、防止方法1 增加压铁重量,特铁水凝固后再去除压铁;2 降低浇包位置,降低浇注速度;3 修正模板.八、掉砂1、特征铸件表面上出现的块状金属突起物,其外形与掉落的砂块很相似.在铸件其它部位,则往往出现砂眼或残缺.2、产生原因1 模样上有深而小的凹槽,同于结构特征或拔模斜度小,起模时将砂型带坏或震裂;2 紧实度不匀,铸型局部强度不足;3 合箱、搬运铸型时,不小心使铸型局部砂块掉落.3、防止方法1 模样拔模斜度要合适、表面光洁;2 铸型紧实度高且均匀;3 合箱、搬运过程中,操作小心.九、错型错箱1、特征铸件的一部分与另一部分在分型面的接缝处错开,发生相对位移,使铸件外形与图纸不相符合.2、产生原因1 模样制作不良,上下模没有对准或模样变形;2 砂箱或模板定位不准确,或定位销松动;3 挤压造型机上零件磨损,例如正压板下衬板、反压板轴承的磨损等;4 浇注时用的套箱变形,搬运、围箱时不注意,使上下铸型发生位移.3、防止方法1 加强模板的检查和修理;定2 经常检查砂箱、模板的定位销及销孔、并合理地安装;3 检查挤压造型机的有关零件,及时调整,磨损大的要更换;4 定期对套箱整形.脱箱后的铸型在搬运时要小心.在面浇注的砂型,应该做一排砂型围一排.十、灰口和麻点1、特征铸件断口呈灰黑色或出现黑色小点,中心部位较多,边部较少,金相观察可见到片状石墨.2、产生原因1 铁水化学成分不合要求,碳、硅含量过高;2 炉前孕育的铋加入浇包内过早或过迟,或是铋量不足.3、防止方法1 正确选择化学成分,合理配料,使铁水中碳、硅量在规定范围内;2 增加铋的加入量并严格炉前孕育工艺.十一、裂纹热裂、冷裂1、特征铸件外部或内部有穿透或不穿透的裂纹.热裂时带有暗色或黑色的氧化表面断口外形曲折.冷裂是较干净的脆性裂纹,断口较平,具有金属光泽或轻微的氧化色泽.2、产生原因1 铁水中碳、硅含苞欲放量过低,含硫量过高;2 浇注温度过高;3 冒口颈过大、过短,造成局部过热严重,或重口太小,补缩不好;4 铸件在清理、运输过程中,受冲击过大.3、防止方法1 控制铁水化学成分在规定的范围内;2 降低浇注温度;3 合理设计冒口系统;4 铸件在清理、运输过程中避免过度冲击.十二、气孔1、特征气孔的孔壁光滑明亮,形状有圆形、梨形和针状,孔的尺寸有大有小,产生在铸件表面或内部.铸件内部的气孔在敲碎后或机械加工时才能被发现.2、产生原因1 小炉料潮湿、锈蚀严重或带有油污,使铁水含气量太多、氧化严重;2 出铁孔、出铁槽、炉衬、浇包衬未洪干;3 浇注温度较低,使气体来不及上浮和逸出;4 炉料中含铝量较高,易造成氢气孔;5 砂型透气性不好、型砂水分高、含煤粉或有机物较多,使浇注时产生大量气体且不易排出.3、防止方法1 炉料要妥善管理,表面要清洁;2 炉缸、前炉、出铁口、出铁槽、浇包必须烘干;3 提高浇注温度;4 不使用铝量过高的废钢;5 适当降低型砂的水分、控制煤粉加入量,扎通气孔等.十三、缩松、疏松1、特征分散、细小的缩孔,带有树枝关结晶的称缩松,比缩松更细小的称疏松.常出现在热世部位.2、产生原因1 铁水中碳、硅含量过低,收缩大;2 浇注速度太快、浇注温度过高,使得液态收缩大;3 浇注系统、冒口设计不当,无法实现顺序凝固;4 冒口太小,补缩不充分.3、防止方法1 控制铁水的化学成分在规定范围内;2 降低浇注速度和浇注温度;3 改进浇冒口系统,利用顺序凝固;4 加大冒口体积,保证充分补缩.十四、反白口1、特征铸件断口内部出现白口组织,边缘部分出现灰口.2、产生原因1 碳、硅含量较高的铁水,含氢量过高;2 炉料中带入的铬等白口形成元素过多;3 元素偏析严重;3、防止方法1 控制化学成分、碳、硅含量不宜过高;2 炉衬、包衬要烘干;型砂水分不宜过高;3 加强炉料管理,减少带入白口化元素.。
湿型铸造小件产品缺陷类型

湿型铸造小件产品缺陷主要是气孔、砂眼、夹砂和粘砂等。
一、缺陷产生的原因1.气孔在湿型铸件废品中,气孔占的比例最大。
在液态金属凝固过程中,侵入金属中的气泡在铸件中形成的孔洞,称之为气孔。
因为潮模砂,型砂中含有水分,水分是产生气体的主要根源之一,如果型腔排气不好;砂芯通气不畅;砂型紧实度过高等,在浇注过程中产生的气体排不出去,就会侵入到铸件中,形成气孔。
在浇注时,浇注系统开设不当,浇注速度不当,金属液都会裹携气泡进入型腔,当气泡不能从型腔中排除时,也会使铸件产生气孔。
另外如果炉料没有烘干,铁水中含气过高,也会形成析出气孔。
2.砂眼主要是在型腔中有脱落或散落的型砂,浇注成铸件后在铸件中形成砂眼。
这主要是由于型砂或砂芯强度低,或水分及发气物过多,在浇注时使型砂脱落,或造型时紧实度不均,修型不当,以及在下芯、合箱时注意不够,发生磕碰造成砂粒脱落,从而造成砂眼。
砂眼是潮模造型操作中特别要注意的缺陷。
3.夹砂浇注过程中,铸型上表面受热膨胀,形成夹层,造成夹砂缺陷。
夹砂是湿型铸造最常见的缺陷。
型砂导热率低,砂型型壁各层间膨胀不均匀,都会产生内应力,形成夹层,造成夹砂。
4.粘砂粘砂对铸件外观质量影响很大,特别是化学粘砂,清除很困难。
这在当今铸件外观质量要求越来越高的情况下,防止粘砂就显得更重要了。
型砂中石英含量低,使型砂耐火度低。
高温合金与石英等形成低熔点氧化铁、其他氧化物和低熔点的化合物等,粘附在铸件表面,形成化学粘砂。
二、防止铸件产生缺陷的措施1.防止气孔产生潮模中砂型和砂芯都没有烘干,型砂中含有一定量的水分,浇注受热后,容易产生气体,造成气孔。
所以控制型砂中的含水量,是防止气孔产生的关键环节。
型砂中除了水分以外,还有煤粉等发气物质,也要严格控制,加入量不能过多。
另外型砂硬度不能过高,过高会使砂型透气性下降,影响型腔中气体的排除,也容易形成气孔。
透气性要控制在55~80之间。
在工艺上要在容易集气的位置设置排气冒口,让气体顺利排除。
常见铸件缺陷及其预防措施

铸件缺陷常见铸件缺陷及其预防措施1).冷紋:原因:熔汤前端的温度太低,相叠时有痕迹.改善方法:1.检查壁厚是否太薄(設計或制造) ,较薄的区域应直接充填.2.检查形狀是否不易充填;距离太远、封閉区域(如鳍片(fin) 、凸起) 、被阻挡区域、圆角太小等均不易充填.並注意是否有肋点或冷点.3.缩短充填时间.缩短充填时间的方法:…4.改变充填模式.5.提高模温的方法:…6.提高熔汤温度.7.检查合金成分.8.加大逃气道可能有用.9.加真空裝置可能有用.2).裂痕:原因:1.收缩应力.2.頂出或整缘时受力裂开.改善方式:1.加大圆角.2.检查是否有热点.3.增压时间改变(冷室机).4.增加或缩短合模时间.5.增加拔模角.6.增加頂出銷.7.检查模具是否有錯位、变形.8.检查合金成分.3).气孔:原因:1.空气夾杂在熔汤中.2.气体的来源:熔解时、在料管中、在模具中、离型剂.改善方法:1.适当的慢速.2.检查流道转弯是否圆滑,截面积是否渐減.3.检查逃气道面积是否够大,是否有被阻塞,位置是否位於最后充填的地方.4.检查离型剂是否噴太多,模温是否太低.5.使用真空.4).空蚀:原因:因压力突然減小,使熔汤中的气体忽然膨胀,冲击模具,造成模具損伤.改善方法:流道截面积勿急遽变化.5).缩孔:原因:当金属由液态凝固为固态时所占的空间变小,若无金属补充便会形成缩孔.通常发生在较慢凝固处.改善方法:1.增加压力.2.改变模具温度.局部冷却、噴离型剂、降低模温、.有时只是改变缩孔位置,而非消缩孔.6).脫皮:原因:1.充填模式不良,造成熔汤重叠.2.模具变形,造成熔汤重叠.3.夾杂氧化层.改善方法:1.提早切換为高速.2.缩短充填时间.3.改变充填模式,浇口位置,浇口速度.4.检查模具強度是否足夠.5.检查銷模裝置是否良好.6.检查是否夾杂氧化层.7).波紋:原因:第一层熔汤在表面急遽冷却,第二层熔汤流過未能将第一层熔解,却又有足夠的融合,造成組织不同. 改善方法:1.改善充填模式.2.缩短充填时间.8).流动不良产生的孔:原因:熔汤流动太慢、或是太冷、或是充填模式不良,因此在凝固的金属接合处有孔.改善方法:1.同改善冷紋方法.2.检查熔汤温度是否稳定.3.检查模具温充是否稳定.9).在分模面的孔:原因:可能是缩孔或是气孔.改善方法:1.若是缩孔,減小浇口厚度或是溢流井进口厚度.2.冷却浇口.3.若是气孔,注意排气或捲气問题.10).毛边:原因:1.鎖模力不足.2.模具合模不良.3.模具強度不足.4.熔汤温度太高.11).缩陷:原因:缩孔发生在压件表面下面.改善方法:1.同改善缩孔的方法.2.局部冷却.3.加热另一边.12).积碳:原因:离型剂或其他杂质积附在模具上.改善方法:1.减小离型剂喷洒量.2.升高模温.3.选择适合的离型剂.4.使用软水稀釋离型剂.13).冒泡:原因:气体捲在铸件的表面下面.改善方式:1.減少捲气(同气孔).2.冷却或防低模温.14).粘模:原因:1.鋅积附在模具表面.2.熔汤冲击模具,造成模面损坏.改善方法:1.降低模具温度.2.降低划面粗糙度.3.加大拔模角.4.镀膜.5.改变充填模式.6.降低浇口速度序缺陷名称缺陷特征预防措施1气孔在铸件内部、表面或近于表面处,有大小不等的光滑孔眼,形状有圆的、长的及不规则的,有单个的,也有聚集成片的。
铸件生产时的缺陷介绍以及预防措施
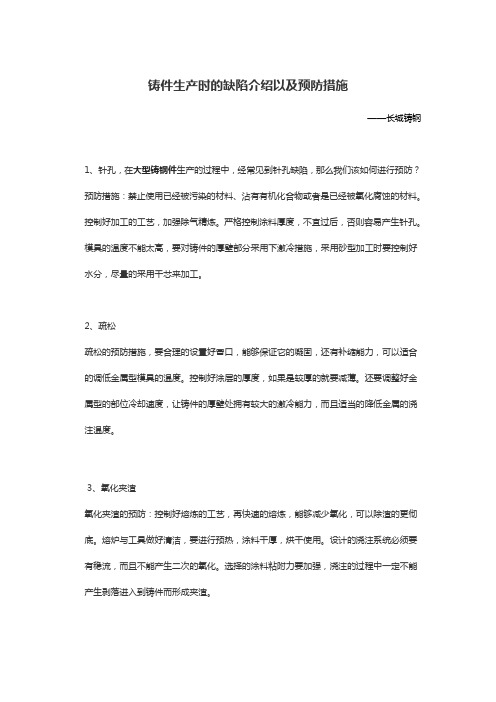
铸件生产时的缺陷介绍以及预防措施
——长城铸钢
1、针孔,在大型铸钢件生产的过程中,经常见到针孔缺陷,那么我们该如何进行预防?预防措施:禁止使用已经被污染的材料、沾有有机化合物或者是已经被氧化腐蚀的材料。
控制好加工的工艺,加强除气精炼。
严格控制涂料厚度,不宜过后,否则容易产生针孔。
模具的温度不能太高,要对铸件的厚壁部分采用下激冷措施,采用砂型加工时要控制好水分,尽量的采用干芯来加工。
2、疏松
疏松的预防措施,要合理的设置好冒口,能够保证它的凝固,还有补缩能力,可以适合的调低金属型模具的温度。
控制好涂层的厚度,如果是较厚的就要减薄。
还要调整好金属型的部位冷却速度,让铸件的厚壁处拥有较大的激冷能力,而且适当的降低金属的浇注温度。
3、氧化夹渣
氧化夹渣的预防:控制好熔炼的工艺,再快速的熔炼,能够减少氧化,可以除渣的更彻底。
熔炉与工具做好清洁,要进行预热,涂料干厚,烘干使用。
设计的浇注系统必须要有稳流,而且不能产生二次的氧化。
选择的涂料粘附力要加强,浇注的过程中一定不能产生剥落进入到铸件而形成夹渣。
湿型铸造铸件缺陷产生的原因与控制

湿型铸造铸件缺陷产生的原因与控制一.产品报废的原因及分析由湿型小件车间灰铸铁小件废品统计情况可以看出,砂眼、粘砂、气孔类缺陷是产品报废的主要原因。
根据统计,加工后因气眼类缺陷报废的湿型灰铁小件,其中最常见的是气孔,铁豆气孔,缩孔,气缩孔等铸造类缺陷,此外,粘砂,夹层,表面质量差也是影响产品质量的一个重要原因。
分析产生废品的原因及防止措施,主要有以下几点:1.夹砂:因砂型表层受热膨胀而造成的铸件缺陷以夹砂形态最为典型,在湿型铸造生产条件下铸件产生夹砂极为常见,但干型铸件就很少产生这种缺陷。
它常见于铸件上表面,并且上表面越大越容易产生夹砂。
产生这种缺陷主要由以下三个方面:1)型砂的导热率差,甚或有砂粒晶型转变而增大膨胀率,使砂型型壁各层间造成大的温度梯度,从而使各层膨胀不均而产生压应力。
2)提高干砂层后背的高湿度弱砂带的阻力,可以通过提高高湿度弱砂带的热湿拉强度以使型壁表面的干砂层难以鼓出,翘起。
将钙膨胀土用碳酸钠进行活化处理,变成钠膨润土,可以增加高湿度弱砂带的热湿拉强度,要使用优质粘土,还应增加型砂中粘土含量,以保证有高热湿拉强度。
可以在湿型型砂中添加淀粉来增加型砂的热湿拉强度。
在手工造型时,造型完毕,常在上箱型腔顶面插入钉子,并使钉子头与型腔表面齐平,钉子的作用是浇注时,将型壁表层的干砂层牢牢地钉住在后背的砂层中,使干砂层不能突出,翘起,防止夹砂产生。
3)砂型紧实均匀,有利于减少夹砂缺陷。
另外在造型操作中砂型扎出通气孔对防止夹砂缺陷是有效的。
防止夹砂有以下三方面对策:(1)减少砂型(芯)的宏观膨胀量。
(2)增加干砂层与砂型本体之间的水份凝聚区的热湿拉强度(3)增加干砂层的热变形量,使热变形量值超过它的受热膨胀值。
2.砂眼生成原因主要来自于造型材料,型砂和芯砂灰分高,强度低或水分及发气物质过多,则浇注时由于砂型或砂芯的强度不足或甚至金属液发生沸腾而使型砂掉落。
造型时紧实不匀,修型不当,以及在下芯,合箱时因不注意而发生碰撞都会造成砂粒的掉落,从而造成砂眼。
铸造的主要缺陷及防止

铸造的主要缺陷及防止1、缺肉缺肉将导致铸件局部加工不起来,造成零件壁厚不均,甚至影响配合或密封。
造成缺肉的原因有许多因素,如工人在清理过程中,打磨量过大;组芯时型芯下偏;模具尺寸超差等。
2、砂眼砂眼是在铸件内部或表面冲塞着型砂的孔洞类缺陷。
主要由于型砂或芯砂强度低;型腔内散砂未吹尽;铸型被破坏;铸件结构不合理等原因产生的。
防止砂眼的方法是:提高型砂强度;合理设计铸件结构;增加紧实度。
3、气孔气孔是气体在金属液结壳之前未及时逸,在铸件内生成的孔洞类缺陷。
气孔的内壁光滑,明亮或带有轻微的氧化色。
铸件中产生气孔后,将会减少其有效承载面积,且在气孔周围会引起应力集中而降低铸件地抗冲击性和抗疲劳性。
气孔还会降低铸件的致密性,致使某些要求承受水压试验的铸件报废。
另外,气孔对铸件的耐腐蚀性和耐热性也有不良的影响。
产生原因一般是金属液除气不良;另一方面是铸型或型芯发气侵入金属液造成的。
防止气孔产生的有效方法是:降低金属液中的含气量,增大砂型的透气性,以及在型腔的最高处增设出气冒口;对铸型或型芯进行烘烤,减少其发气量。
4、粘砂铸件表面上粘附有一层难以清除的砂粒称为粘砂。
粘砂既影响铸件外观,又增加铸件清理和切削加工的工作量,甚至会影响机器的寿命。
(例如铸齿表面有粘砂时容易损坏,泵或发动机等机器零件中若有粘砂,则影响燃料油、气体、润滑油和冷却水等流体的流动,并会沾污和磨损整个机器。
)防止粘砂的方法是:在型砂中加入煤粉,以及在铸型表面涂刷防粘砂涂料等。
5、夹砂夹砂是在铸件表面形成的沟槽和疤痕缺陷,在用湿型铸造厚大平板类铸件时极易产生。
铸件中产生夹砂的部位大多是与砂型上表面相接触的地方,型腔上表面受金属液辐射热的作用,容易拱起和翘曲,当翘起的砂层受金属液流不断冲刷时可能断裂破碎,留在原处或被带入其它部位。
铸件的上表面越大,型砂体积膨胀越大,形成夹砂的倾向性也越大。
防止夹砂的方法是:避免大的平面结构。
6、胀砂浇注时在金属液的压力作用下,铸型型壁移动,铸件局部胀大形成的缺陷。
铸造缺陷及其解决方法
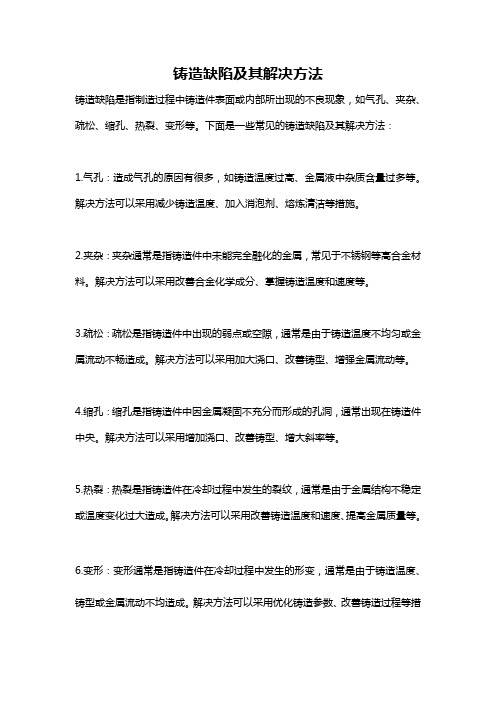
铸造缺陷及其解决方法
铸造缺陷是指制造过程中铸造件表面或内部所出现的不良现象,如气孔、夹杂、疏松、缩孔、热裂、变形等。
下面是一些常见的铸造缺陷及其解决方法:
1.气孔:造成气孔的原因有很多,如铸造温度过高、金属液中杂质含量过多等。
解决方法可以采用减少铸造温度、加入消泡剂、熔炼清洁等措施。
2.夹杂:夹杂通常是指铸造件中未能完全融化的金属,常见于不锈钢等高合金材料。
解决方法可以采用改善合金化学成分、掌握铸造温度和速度等。
3.疏松:疏松是指铸造件中出现的弱点或空隙,通常是由于铸造温度不均匀或金属流动不畅造成。
解决方法可以采用加大浇口、改善铸型、增强金属流动等。
4.缩孔:缩孔是指铸造件中因金属凝固不充分而形成的孔洞,通常出现在铸造件中央。
解决方法可以采用增加浇口、改善铸型、增大斜率等。
5.热裂:热裂是指铸造件在冷却过程中发生的裂纹,通常是由于金属结构不稳定或温度变化过大造成。
解决方法可以采用改善铸造温度和速度、提高金属质量等。
6.变形:变形通常是指铸造件在冷却过程中发生的形变,通常是由于铸造温度、铸型或金属流动不均造成。
解决方法可以采用优化铸造参数、改善铸造过程等措
施。
铸造缺陷特征、原因及预防措施(图文并茂)

缺陷名称特征产生的主要原因预防措施实例照片气孔在铸件内部或表面有大小不等的光滑孔洞①炉料不干或含氧化物、杂质多;②浇注工具或炉前添加剂未烘干;③型砂含水过多或起模和修型时刷水过多;④型芯烘干不充分或型芯通气孔被堵塞;⑤春砂过紧,型砂透气性差;⑥浇注温度过低或浇注速度太快等①降低熔炼时金属的吸气量,减少砂型在浇注过程中的发气量②改进铸件结构,提高砂型和型芯的透气性,使型内气体能顺利排出缩孔与缩松缩孔多分布在铸件厚断面处,形状不规则,孔内粗糙①铸件结构设计不合理,如壁厚相差过大,厚壁处未放冒口或冷铁;②浇注系统和冒口的位置不对;③浇注温度太高;④合金化学成分不合格,收缩率过大,冒口太小或太少①壁厚小且均匀的铸件要采用同时凝固②壁厚大且不均匀的铸件采用由薄向厚的顺序凝固③合理放置冒口的冷铁砂眼在铸件内部或表面有型砂充塞的孔眼①型砂强度太低或砂型和型芯的紧实度不够,故型砂被金属液冲入型腔;②合箱时砂型局部损坏;③浇注系统不合理,内浇口方向不对,金属液冲坏了砂型;④合箱时型腔或浇口内散砂未清理干净①严格控制型砂性能和造型操作②合型前注意打扫型腔③改进浇注系统粘砂铸件表面粗糙,粘有一层砂粒①原砂耐火度低或颗粒度太大;②型砂含泥量过高,耐火度下降;③浇注温度太高;④湿型铸造时型砂中煤粉含量太少;⑤干型铸造时铸型未刷涂斜或涂料太薄①适当降低金属的浇注温度②提高型砂、芯砂的耐火度夹砂铸件表面产生的金属片状突起物,在金属片状突起物与铸件之间夹有一层型砂①型砂热湿拉强度低,型腔表面受热烘烤而膨胀开裂;②砂型局部紧实度过高,水分过多,水分烘干后型腔表面开裂;③浇注位置选择不当,型腔表面长时间受高温铁水烘烤而膨胀开裂;④浇注温度过高,浇注速度太慢①严格控制型砂、芯砂性能②改善浇注系统,使金属液流动平稳③大平面铸件要倾斜浇注④适当调整浇注温度和浇注速度错型铸件沿分型面有相对位置错移①模样的上半模和下半模未对准;②合箱时,上下砂箱错位;③上下砂箱未夹紧或上箱未加足够压铁,浇注时产生错箱④砂箱或模板定位不准确,或定位销松动①定期检查砂箱、模板的定位销及销孔、并合理地安装;②定期对套箱整形,脱箱后的铸型在搬运时要小心。
铸造缺陷及其对策书

铸造缺陷及其对策书(实用版)目录一、铸造缺陷的概述二、铸造缺陷的种类三、铸造缺陷产生的原因四、铸造缺陷的对策五、结论正文一、铸造缺陷的概述铸造缺陷是指在铸造过程中,由于各种原因导致的铸件不符合设计要求的缺陷。
铸造缺陷不仅会影响铸件的性能和质量,还会增加生产成本,甚至可能导致设备损坏和安全事故。
因此,研究铸造缺陷及其对策对于提高铸件质量具有重要意义。
二、铸造缺陷的种类铸造缺陷种类繁多,根据缺陷的性质和形态,可以分为以下几类:1.表面缺陷:如砂眼、气孔、麻点、裂纹等。
2.内部缺陷:如缩孔、缩松、夹杂、偏析等。
3.形状缺陷:如变形、歪曲、尺寸偏差等。
4.成分缺陷:如碳、硅、锰等元素含量偏离设计要求。
5.组织缺陷:如晶粒粗大、组织不均匀、白口组织等。
三、铸造缺陷产生的原因1.原材料方面:如铸造砂质量差、石英砂含泥量过高、熔炼过程中元素烧损等。
2.工艺方面:如熔炼温度过高或过低、浇注速度过快或过慢、浇注过程中气泡产生等。
3.设备方面:如砂箱振动不均匀、浇注器设计不合理、炉子温度控制不准确等。
4.操作方面:如砂型制作不规范、合箱时压实不均匀、浇注高度不够等。
四、铸造缺陷的对策1.选择优质的原材料,提高铸型的质量。
2.优化熔炼工艺,控制熔炼温度、元素烧损和气体含量。
3.改进浇注工艺,合理控制浇注速度、压注压力和浇注高度。
4.完善设备设施,提高设备的精度和稳定性。
5.加强操作培训,提高工人的操作技能和质量意识。
五、结论通过对铸造缺陷及其对策的研究,可以降低铸件的缺陷率,提高铸件的质量和性能。
铸造缺陷特征、原因及预防措施(图文并茂)

缺陷名称特征产生的主要原因预防措施实例照片气孔在铸件内部或表面有大小不等的光滑孔洞①炉料不干或含氧化物、杂质多;②浇注工具或炉前添加剂未烘干;③型砂含水过多或起模和修型时刷水过多;④型芯烘干不充分或型芯通气孔被堵塞;⑤春砂过紧,型砂透气性差;⑥浇注温度过低或浇注速度太快等①降低熔炼时金属的吸气量,减少砂型在浇注过程中的发气量②改进铸件结构,提高砂型和型芯的透气性,使型内气体能顺利排出缩孔与缩松缩孔多分布在铸件厚断面处,形状不规则,孔内粗糙①铸件结构设计不合理,如壁厚相差过大,厚壁处未放冒口或冷铁;②浇注系统和冒口的位置不对;③浇注温度太高;④合金化学成分不合格,收缩率过大,冒口太小或太少①壁厚小且均匀的铸件要采用同时凝固②壁厚大且不均匀的铸件采用由薄向厚的顺序凝固③合理放置冒口的冷铁编辑版word砂眼在铸件内部或表面有型砂充塞的孔眼①型砂强度太低或砂型和型芯的紧实度不够,故型砂被金属液冲入型腔;②合箱时砂型局部损坏;③浇注系统不合理,内浇口方向不对,金属液冲坏了砂型;④合箱时型腔或浇口内散砂未清理干净①严格控制型砂性能和造型操作②合型前注意打扫型腔③改进浇注系统粘砂铸件表面粗糙,粘有一层砂粒①原砂耐火度低或颗粒度太大;②型砂含泥量过高,耐火度下降;③浇注温度太高;④湿型铸造时型砂中煤粉含量太少;⑤干型铸造时铸型未刷涂斜或涂料太薄①适当降低金属的浇注温度②提高型砂、芯砂的耐火度夹砂铸件表面产生的金属片状突起物,在金属片状突起物与铸件之间夹有一层型砂①型砂热湿拉强度低,型腔表面受热烘烤而膨胀开裂;②砂型局部紧实度过高,水分过多,水分烘干后型腔表面开裂;③浇注位置选择不当,型腔表面长时间受高温铁水烘烤而膨胀开裂;④浇注温度过高,浇注速度太慢①严格控制型砂、芯砂性能②改善浇注系统,使金属液流动平稳③大平面铸件要倾斜浇注④适当调整浇注温度和浇注速度编辑版word错型铸件沿分型面有相对位置错移①模样的上半模和下半模未对准;②合箱时,上下砂箱错位;③上下砂箱未夹紧或上箱未加足够压铁,浇注时产生错箱④砂箱或模板定位不准确,或定位销松动①定期检查砂箱、模板的定位销及销孔、并合理地安装;②定期对套箱整形,脱箱后的铸型在搬运时要小心。
铸钢件常见铸造缺陷及预防措施
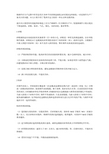
铸钢件在生产过程中经常会发生各种不同的铸造缺陷,如何预防这些缺陷,一直是铸件生产厂家关注的问题。
本文主要介绍了笔者在这方面的一些认识和实践经验。
我车间主要采用传统湿型砂铸造工艺生产铸钢件,在长期的生产中,发现铸钢件主要出现以下铸造缺陷,砂眼,粘砂,气孔,缩孔,夹砂结疤,胀砂等等。
1砂眼砂眼缺陷处内部或表面有充塞着型(芯)砂的小孔,砂眼是一种常见的铸造缺陷,往往导致铸件报废。
砂眼是由于金属液从砂型型腔表面冲下来的砂粒(块),或者在造型,合箱操作中落人型腔中的砂粒(块)来不及浮入浇冒系统,留在铸件内部或表面而造成的。
砂眼的预防措施:(1)严格控制型砂性能,提高砂型芯的表面强度和紧实度,减少毛刺和锐角,减少冲砂。
(2)合箱前把型腔和砂芯表面的浮砂处理干净,平稳合箱,如果是明冒口或贯通出气眼,应避免散砂从中掉人型腔,合箱后要尽快浇注。
(3)设置正确合理的浇冒系统,避免金属液对型壁和砂芯的冲刷力过大。
(4)浇口杯表面要光滑,不能有浮砂。
2粘砂在铸件表面上,全部或部分覆盖着一层金属(或金属氧化物)与砂(或涂料)的混(化)合物或一层烧结构的型砂,致使铸件表面粗糙,难于清理。
粘砂多发生在型、芯表面受热作用强烈的部位,分机械粘砂和化学粘砂两种。
机械粘砂是由金属液渗入铸型表面的微孔中形成的,当渗入深度小于砂粒半径时,铸件不形成粘砂,只是表面粗糙,当渗入深度大于砂粒半径时,就形成机械粘砂,化学粘砂是金属氧化物和造型材料相互进行化学作用的产物,与铸件牢固地结合在一起而形成的。
粘砂的预防措施:(1)选用耐火度高的砂,以提高型砂,芯砂的耐火度,原砂的SiO2含量在96%(质量分数)以上,而且砂粒应对粗些。
铸钢件的浇注温度越高,壁厚越厚,对原砂中SiO2含量的要求越高。
(2)适当降低浇注温度和提高浇注速度,减轻金属液对砂型的热力学和物理化学作用。
(3)砂型紧实度要高(通常大于85)且均匀,减少砂粒间隙;型、芯修补到位,不能有局部疏松。
铸造缺陷与防止(精选五篇)
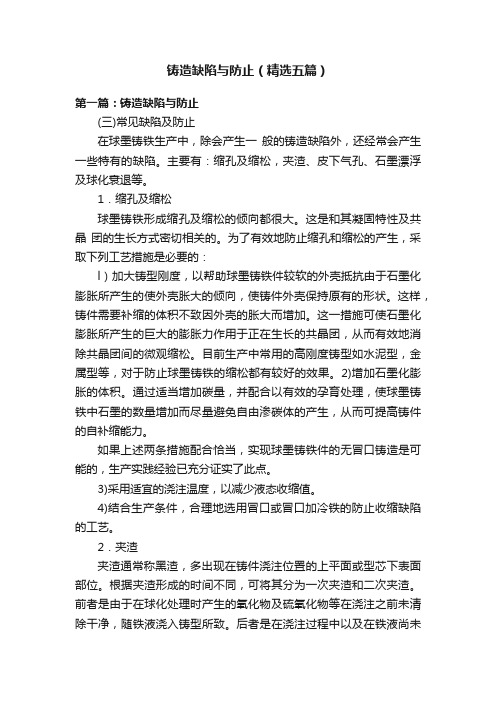
铸造缺陷与防止(精选五篇)第一篇:铸造缺陷与防止(三)常见缺陷及防止在球墨铸铁生产中,除会产生一般的铸造缺陷外,还经常会产生一些特有的缺陷。
主要有:缩孔及缩松,夹渣、皮下气孔、石墨漂浮及球化衰退等。
1.缩孔及缩松球墨铸铁形成缩孔及缩松的倾向都很大。
这是和其凝固特性及共晶团的生长方式密切相关的。
为了有效地防止缩孔和缩松的产生,采取下列工艺措施是必要的:l)加大铸型刚度,以帮助球墨铸铁件较软的外壳抵抗由于石墨化膨胀所产生的使外壳胀大的倾向,使铸件外壳保持原有的形状。
这样,铸件需要补缩的体积不致因外壳的胀大而增加。
这一措施可使石墨化膨胀所产生的巨大的膨胀力作用于正在生长的共晶团,从而有效地消除共晶团间的微观缩松。
目前生产中常用的高刚度铸型如水泥型,金属型等,对于防止球墨铸铁的缩松都有较好的效果。
2)增加石墨化膨胀的体积。
通过适当增加碳量,并配合以有效的孕育处理,使球墨铸铁中石墨的数量增加而尽量避免自由渗碳体的产生,从而可提高铸件的自补缩能力。
如果上述两条措施配合恰当,实现球墨铸铁件的无冒口铸造是可能的,生产实践经验已充分证实了此点。
3)采用适宜的浇注温度,以减少液态收缩值。
4)结合生产条件,合理地选用冒口或冒口加冷铁的防止收缩缺陷的工艺。
2.夹渣夹渣通常称黑渣,多出现在铸件浇注位置的上平面或型芯下表面部位。
根据夹渣形成的时间不同,可将其分为一次夹渣和二次夹渣。
前者是由于在球化处理时产生的氧化物及硫氧化物等在浇注之前未清除干净,随铁液浇入铸型所致。
后者是在浇注过程中以及在铁液尚未在铸型中凝固以前的一段时间内产生的渣。
一次渣的尺寸较大,二次渣一般很细小,在铸件的加工表面上表现为暗灰色无光泽的斑纹或云片状。
夹渣缺陷严重影响铸件的力学性能,特别是硬度、韧性及耐磨性,并能导致耐压铸件发生渗漏。
防止措施主要有:1)尽量降低原铁液的含硫量。
2)在保证石墨球化条件下,降低铁液的残留镁量和残留稀土量。
3)提高浇注温度,应不低于1350℃。
湿砂型铸铁件的表面缺陷

湿型铸铁件的表面缺陷比起其它铸造方法而言,湿砂型铸造固有的缺点是砂型强度、硬度低,含水分多,发气量大,型砂的韧性不高,流动性有限,造型起模时容易掉砂,浇铸时又易被冲蚀和与金属液起反应,因而最易产生铸件缺陷。
湿砂型铸铁最容易形成的铸件表面缺陷主要为粘砂、夹砂、砂孔和渣孔、气孔、胀砂等多种。
轻微的缺陷可以通过修补、打磨和机械加工后仍然可用,而明显的和严重的表面缺陷则只能作为废品重新回炉熔炼。
国外技术先进的湿砂型铸造工厂废品率只有1%~3%左右。
而我国当前有很多铸造工厂的技术水平不高,原材料品质不善,缺乏有效的生产过程检测控制,造成铸件废品率居高不下。
我国铸造行业总的来说废品率一般都在6%~16%之间,有的甚至到20%以上。
其中由于型砂引起的废品率大约占一半。
因此有必要研究铸件缺陷的生成原因和防止措施。
铸造工厂的技术人员经常感到对铸件的缺陷“捉摸不定”,“神出鬼没”。
很多情况下不知缺陷是怎么来的,后来又不知缺陷是怎样自已跑掉的。
其主要原因为缺陷是个复杂的多因素系统工程。
一种缺陷的形成因素有多种,而且通常是多种因素同时起作用形成的。
这些因素都控制在安全限度之内就不会产生缺陷。
即使其中某一种因素稍微超出安全限度,也不一定会出现缺陷。
但是,如果多种因素超出限度,或者又有某一因素严重超出限度,缺陷的生成就会经常化,废品连续不断。
要想消除缺陷,虽然在具体条件下,某一特定因素可能是属于主要因素之一,也要尽一切可能使每一影响因素全处于安全范围内。
否则仍然不能彻底消除铸件缺陷。
这与日本等国在铸造行业推行TQC (Total Quality Control 全面品质管理)时采用魚骨图的做法是类似的。
以一家铸铁工厂的铸件表面出现机械粘砂查找原因所用鱼骨图为例。
列举出所有影响因素后,通过分析忽略一些不可改变的因素(如铸件壁厚、粗芯砂混入)。
又通过检测排除一些不重要的因素,突出几种关键性因素,用方框显示。
然后即可有针对性地采取措施重点解决这些影响因素。
铸造缺陷及其对策书

铸造缺陷及其对策书一、铸造缺陷的类型与影响1.缺陷类型概述铸造过程中,铸件可能出现的缺陷种类繁多,主要包括裂纹、气孔、夹渣、变形、缩孔等。
这些缺陷不仅影响铸件的外观质量,还会对其性能产生不良影响。
2.缺陷对铸件性能的影响铸造缺陷会对铸件的强度、韧性、耐磨性等性能造成负面影响。
例如,裂纹会导致铸件在使用过程中出现断裂;气孔会使铸件的强度降低;夹渣会使铸件的内部性能不均匀。
二、铸造缺陷的成因与分析1.原材料问题原材料的质量对铸件的缺陷产生具有重要影响。
金属原材料中的有害物质、非金属杂质、气体含量等都会导致铸件出现缺陷。
2.铸造工艺问题铸造工艺参数设置不合理、充型速度过快或过慢、冷却速度不适等都会导致铸件产生缺陷。
3.模具与设备问题模具质量不佳、磨损严重、设备精度不足等都会对铸件的质量产生不良影响。
4.操作问题操作过程中,工人技术水平低、操作不当、责任心不强等也是导致铸件缺陷的重要原因。
三、对策与改进措施1.选用优质原材料为确保铸件质量,应选用优质金属原材料,并对原材料进行严格检测,控制有害物质和杂质的含量。
2.优化铸造工艺根据铸件的结构和性能要求,合理设置铸造工艺参数,提高充型速度和冷却速度,以减少缺陷产生。
3.提高模具与设备质量定期检查和维修模具与设备,确保其精度和可靠性。
同时,加强工人的技术培训,提高操作水平。
4.加强操作培训与管理加强操作人员的培训与管理,提高其技术水平和责任心,降低人为因素导致的缺陷。
四、缺陷预防与控制方法1.完善质量管理体系建立健全质量管理体系,确保铸件生产过程中的质量控制。
2.强化过程控制加强对生产过程的监控,及时发现和处理问题。
3.检测与评估技术采用先进的检测与评估技术,对铸件进行全面的质量检测,确保铸件质量达到要求。
4.故障排查与处理针对出现的铸件缺陷,进行故障排查,找出原因并采取相应措施进行处理。
五、案例分析与总结1.案例一:铸件裂纹缺陷分析与改进通过对裂纹缺陷的成因分析,发现原材料中有害物质含量过高、铸造工艺参数设置不合理等问题。
(整理)铸件常见缺陷产生原因及防治措施汇总

铸件常见缺陷产生原因及防治措施汇总一、压铸件表面有花纹,并有金属流痕迹产生原因: 1、通往铸件进口处流道太浅。
2、压射比压太大,致使金属流速过高,引起金属液的飞溅。
调整方法:1、加深浇口流道。
2、减少压射比压。
二、铸件表面有细小的凸瘤产生原因:1、表面粗糙。
2、型腔内表面有划痕或凹坑、裂纹产生。
调整方法:1、抛光型腔。
2、更换型腔或修补。
三、压铸件表面有推杆印痕,表面不光洁,粗糙产生原因:1、推件杆(顶杆)太长;2、型腔表面粗糙,或有杂物。
调整方法:1、调整推件杆长度。
2、抛光型腔,清除杂物及油污。
四、铸件表面有裂纹或局部变形产生原因:1、顶料杆分布不均或数量不够,受力不均:2、推料杆固定板在工作时偏斜,致使一面受力大,一面受力小,使产品变形及产生裂纹。
3、铸件壁太薄,收缩后变形。
调整方法:1、增加顶料杆数量,调整其分布位置,使铸件顶出受力均衡。
2、调整及重新安装推杆固定板。
五、压铸件表面有气孔产生原因:1、润滑剂太多。
2、排气孔被堵死,气孔排不出来。
调整方法:1、合理使用润滑剂。
2、增设及修复排气孔,使其排气通畅。
六、压铸件表面有缩孔产生原因:压铸件工艺性不合理,壁厚薄变化太大。
金属液温度太高。
调整方法:1、在壁厚的地方,增加工艺孔,使之薄厚均匀。
2、降低金属液温度。
七、压铸件外轮廓不清晰,成不了形,局部欠料产生原因:1、压铸机压力不够,压射比压太低。
2、进料口厚度太大;3、浇口位置不正确,使金属发生正面冲击。
调整方法:1、更换压铸比压大的压铸机; 2、减小进料口流道厚度;3、改变浇口位置,防止对铸件正面冲击。
八、压铸件部分未成形,型腔充不满产生原因:1、压铸模温度太低;2、金属液温度低;3、压机压力太小,4、金属液不足,压射速度太高;5、空气排不出来。
调整方法:1、 2、提高压铸模,金属液温度;3、更换大压力压铸机。
4、加足够的金属液,减小压射速度,加大进料口厚度。
九、压铸件锐角处充填不满产生原因:1、内浇口进口太大;2、压铸机压力过小;3、锐角处通气不好,有空气排不出来。
- 1、下载文档前请自行甄别文档内容的完整性,平台不提供额外的编辑、内容补充、找答案等附加服务。
- 2、"仅部分预览"的文档,不可在线预览部分如存在完整性等问题,可反馈申请退款(可完整预览的文档不适用该条件!)。
- 3、如文档侵犯您的权益,请联系客服反馈,我们会尽快为您处理(人工客服工作时间:9:00-18:30)。
湿型铸造小件产品缺陷产生的原因与防止措施
湿型铸造小件产品缺陷主要是气孔、砂眼、夹砂和粘砂等。
一、缺陷产生的原因
1.气孔:在湿型铸件废品中,气孔占的比例最大。
在液态金属凝固过程中,侵入金属中的气泡在铸件中形成的孔洞,称之为气孔。
因为潮模砂,型砂中含有水分,水分是产生气体的主要根源之一,如果型腔排气不好;砂芯通气不畅;砂型紧实度过高等,在浇注过程中产生的气体排不出去,就会侵入到铸件中,形成气孔。
在浇注时,浇注系统开设不当,浇注速度不当,金属液都会裹携气泡进入型腔,当气泡不能从型腔中排除时,也会使铸件产生气孔。
另外如果炉料没有烘干,铁水中含气过高,也会形成析出气孔。
2.砂眼:主要是在型腔中有脱落或散落的型砂,浇注成铸件后在铸件中形成砂眼。
这主要是由于型砂或砂芯强度低,或水分及发气物过多,在浇注时使型砂脱落,或造型时紧实度不均,修型不当,以及在下芯、合箱时注意不够,发生磕碰造成砂粒脱落,从而造成砂眼。
砂眼是潮模造型操作中特别要注意的缺陷。
3.夹砂:浇注过程中,铸型上表面受热膨胀,形成夹层,造成夹砂缺陷。
夹砂是湿型铸造最常见的缺陷。
型砂导热率低,砂型型壁各层间膨胀不均匀,都会产生内应力,形成夹层,造成夹砂。
4.粘砂:粘砂对铸件外观质量影响很大,特别是化学粘砂,清除很困难。
这在当今铸件外观质量要求越来越高的情况下,防止粘砂就显得更重要了。
型砂中石英含量低,使型砂耐火度低。
高温合金与石英等形成低熔点氧化铁、其他氧化物和低熔点的化合物等,粘附在铸件表面,形成化学粘砂。
二、防止铸件产生缺陷的措施
1.防止气孔产生:潮模中砂型和砂芯都没有烘干,型砂中含有一定量的水分,浇注受热后,容易产生气体,造成气孔。
所以控制型砂中的含水量,是防止气孔产生的关键环节。
型砂中除了水分以外,还有煤粉等发气物质,也要严格控制,加入量不能过多。
另外型砂硬度不能过高,过高会使砂型透气性下降,影响型腔中气体的排除,也容易形成气孔。
透气性要控制在55~80之间。
在工艺上要在容易集气的位置设置排气冒口,让气体顺利排除。
另外在上型适当部位,扎一定数量的出气孔,也是一种防止气孔的办法。
其次为防止金属液中含有气体,炉料要进行烘干处理,浇注前金属液要进行脱气处理,以减少金属液中的含气量。
2.砂眼的防止:为了防止砂眼的形成,最主要的是操作要稳妥,紧实度要均匀,修型操作要仔细,散落的砂块要清除干净。
下芯、合箱要稳当,防止摩擦、磕碰掉砂。
型砂中灰分不能过高,保证型砂有足够的强度和韧性。
同时良好的浇注系统,适当的浇注速度,也能减少金属液对砂型的过分冲击,减少砂眼的形成。
3.夹砂的控制:夹砂是砂型表层受热膨胀而造成的铸件缺陷。
湿型铸造铸件产生夹砂是很常见的。
为防止夹砂,提高型砂的导热率,减少型壁各层间的温度梯度,使各层膨胀均匀,不产生应力。
将钙基膨润土进行活化处理,变成钠基膨润土,以提高型砂的热湿拉强度,避免砂层鼓出、翘起。
在造型操作中,要紧实均匀。
在上箱型腔表面,插入适当的钉子,并使钉子与型腔表面齐平。
钉子的作用是牢牢钉住表层砂,使之不能突起、翘开,防止夹砂的产生。
4.粘砂的防止:为防止粘砂可以采用较细的原砂,提高型砂的流动性和紧实度,以减少砂型表面的孔隙。
在型砂中适当加入抗粘砂附加物,以减少粘砂,如煤粉,是湿型主要的抗粘砂附加物。
煤粉的存在使型砂砂粒间形成碳膜或烧结壳,减少金属液体表面氧化,和对砂型表面的润湿和渗透,避免粘砂。
另外在砂型表面喷涂耐活度较高的涂料,也能减少金属液体对型砂表面的熔和渗透,这也是减少粘砂的有效方法。