精益生产(福特)p19
福特生产体系(FPS)衡量指标PPT课件讲义

增加生产
提高工数
时数
降低库存
降低原材 料库存
减少在制品
降低安全 存量
提高进 流程稳定化 料频率
降低成品库存
降低安 全存量
提高交 货频率
提高综合 设备有效率
加速推进设备 缩短换模换线 预防性维护 时间并降低批量 FTPM
改善 首检合格率
防差错措施
依计划生产 (包括根据顾客
需求而定的 “拉动式”系统)
► 如果某站的设备实际生产速率 大于顾客需求速率,既表明此 站为瓶颈站。
► 如有多个工作站的设备实际生 产速率均大于顾客需求速率, 则选择实际生产速率最大的工 作站为瓶颈站,优先分析解决 其设备问题,然后再依此方法 继续寻找瓶颈站,依次解决问 题。直至所有工作站设备的实 际生产速率均小于顾客需求速 率。
• 附加价值的工时百分率% • 厂内精实布置程度 • 前置时间 • 批量大小 • 换模换线时间
• 拉动式供料的零部件数 (SMART) • 活性化交货窗口的比率% • 存货周转率 • IM工业材料供料频率
• 依计划生产的比率(BTS) • 总成本 (产量变化的机制) • 整体评价
目标
我们的安 全信条
安排适用的 设备与流程
生产能力与市场需求联系
目标
► 100% 计 划 完 成 率
► 95% 市 场 需 求 完 成率
► < 10 天 控 制 货 物
►从 订 货 到 运 输 < 15 天
衡量指标 ► Build to Schedule
BTS计 划 完 成 率
Build to Schedule (BTS) 计 划 完 成 率(BTS)
目标 ►总 成 本 可 承 受 ►业 务 结 构
通用汽车精益生产主要指标

通用汽车精益生产主要指标摘要精益生产是一种通过优化生产流程,减少浪费并提高效率的方法。
在汽车制造行业,通用汽车(General Motors)凭借着精益生产实践获得了很大的成功。
本文将介绍通用汽车在精益生产方面的主要指标。
1. 生产效率指标1.1 OEE(Overall Equipment Efficiency)OEE是衡量设备综合效率的指标,它考虑了设备的开机时间、生产速度和质量合格率。
OEE的计算公式为:OEE = 设备运行时间 * 生产速度 * 质量合格率1.2 Takt Time(节拍时间)Takt Time指的是完成一个产品所需的时间,它是根据客户需求和生产能力来计算的。
通用汽车使用Takt Time来衡量生产线的效率,并进行生产节奏的调整,以保持生产的平稳和流畅。
1.3 制造周期时间制造周期时间是从订单接收到产品交付的时间。
通用汽车通过减少非价值增加的活动和提高生产流程的效率来缩短制造周期时间。
2. 质量指标2.1 不良品率不良品率是指在生产过程中产生的不合格产品的比例。
通用汽车通过实施严格的质量管理措施来降低不良品率,例如进行充分的员工培训、使用先进的质检设备等。
2.2 返工率返工率是指产品在生产过程中需要重复加工的比例。
通用汽车通过优化生产工艺和改进设备来降低返工率,以提高生产效率和降低成本。
2.3 零缺陷目标通用汽车致力于实现零缺陷的目标,即在生产过程中不产生任何缺陷和质量问题的产品。
为了达到这个目标,通用汽车实施了严格的品质管理和持续改进的措施。
3. 库存指标3.1 WIP(Work in Progress)WIP是指在生产过程中正在进行中的产品数量。
通用汽车通过实施精益生产的原则,尽量减少WIP的数量,以减少库存和降低生产成本。
3.2 周转率周转率是指货物从进入仓库到离开仓库的平均周期。
通用汽车通过优化供应链和生产流程来提高周转率,以实现及时交付和降低库存成本的目标。
4. 成本指标4.1 生产成本生产成本是指生产一个产品所需的所有费用,包括人力资源、原材料、设备维护等。
福特APQP资料
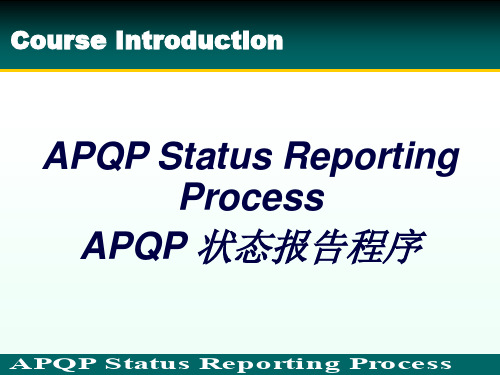
解释在产品/过程设计中 APQP 各要素的要求. 4. Explain the APQP elements required in preparation for
APQP Status Reporting Process
APQP Purpose
The purpose if the APQP process is to establish: APQP的目的是建立:
Common expectations for internal and external suppliers 对内外部供应商共同的要求
把APQP过程与产品开发和制造过程相联系。 Defines roles and responsibilities for the APQP
process 定义APQP过程的角色和职责 Develops a common APQP process for both
internal and external manufacturing and assembly suppliers 为内部制造和外部供应商提供一个通用的开发过程
manufacturing. 解释在准备生产过程中APQP各要素的要求. 5. Explain the APQP Status Reporting Process. 理解APQP 状态报告过程.
APQP Status Reporting Process
FPDS
Months before Job 1 for S1 to S6 programs S1-S6项目在Job 1之前的时间节点
精益生产理念及体系简介word版本

Process Engineer:Edison Chen Amphenol AHSI XM 2012-07-17
第一部分
精益生产理念介绍
第二部分
精益生产工具及手法介绍
第一部分
第三部分
七大浪费与对策
第一部分
第四部分
精益生产交流讨论
精益生产 Lean Production,简称LP
精益生产 Lean Production,简称LP
丰田英二和他的伙伴大野耐一进行了一系列的探索和实验,根据日本的国情,提出了解决问题方案。 经过30多年的努力,终于形成了完整的丰田生产方式,使日本的汽车工业超过了美国,产量达到了1300万辆,占世界汽车总量的30%以上。
精益生产核心
其核心是消除一切无效劳动和浪费,它把目标确定在尽善尽美上 通过不断地降低成本、提高质量、增强生产灵活性、实现无废品和零库存等手段确保企业在市场竞争中的优势 同时,精益生产把责任下放到组织结构的各个层次,采用小组工作法,充分调动全体职工的积极性和聪明才智,把缺陷和浪费及时地消灭在每一个岗位。
防呆法的基本原理
排除化:剔除会造成错误的要因。 替代化:利用更确实的方法来代替。 容易化:使作业变得更容易、更合适、更独特,或共同性以减低失败。适合化、共同化、集中化、特殊、个别化。 异常检出:虽然已经有不良或错误现象,但在下一制程中,能将之检出,以减少或剔除其危害性。 缓和影响:作业失败的影响在其波及的过程中,用方法使其缓和或吸收。
将5S进行到底!!!
5S管理---素养
每个零件都有指定的存放位置,什么东西不在位置上,一目了然.
因为有很好的标记, 需要时很快就能找到所要东西.
现场组织管理- 可视管理
福特-精益生产PPT课件

Ford Motor China Sourcing Office 福特汽车中国采购中心
First Time ThroughCalculation (FTT)
Definition: First Time Through is the percentage of units that complete a process and meet quality guidelines the first time without being scraped, rerun, retested, diverted for off-line repair, or returned. It is a measure of the quality of the manufacturing process. 定义: 首次通过率是指一次性完成一个生产过程并且满足质量要求的零件的百分率, 不包括报废,返工,再测试,下线修理或返回。FTT 用于衡量制造过程的质量。 FTT= Units entering process-(scrap+reruns+retests+repaired offline+returns)
=4.93小时 =2.98小时 =0.05小时 =0.05小时 =3.29小时
Total DTD= 4.93+ 2.98+ 0.05+ 0.05+ 3.29
=11.3小时
Overall Equipment Effectiveness (OEE)
Definition: OEE is a combination of three different calculations. It is a measure of the availability, performance efficiency, and quality rate of a given piece of equipment. OEE data will help identify several wastes caused by machine/process inefficiencies. Stretch objective: 85% 定义:OEE是三个不同计算值的乘积,用于测量指定设备的利用率,性能效率和 质量率。OEE 数据可以帮助识别由设备/过程不足引起的不同的浪费。 接受标准: 85%
精 益 生 产 小 知 识

精益生产小知识精益生产(Lean Production,简称LP)是美国麻省理工学院数位国际汽车计划组织(IMVP)的专家对日本丰田准时化生产JIT(Just In Time)生产方式的赞誉称呼。
JIT源于丰田生产方式,是由美国麻省理工学院组织世界上14个国家的专家、学者,花费5年时间,耗资500万美元,以汽车工业这一开创大批量生产方式和精益生产方式JIT的典型工业为例,经理论化后总结出来的。
它是当前工业界最佳的一种生产组织体系和方式。
精,即少而精,不投入多余的生产要素,只是在适当的时间生产必要数量的市场急需产品(或下道工序急需的产品);益,即所有经营活动都要有益有效,具有经济效益。
精益生产的理念最早起源于日本丰田汽车公司的TPS,是一种以客户需求为拉动,以消灭浪费和不断改善为核心,以最大限度地减少企业生产所占用的资源和降低企业管理和运营成本为主要目标的生产方式,使企业以最少的投入获取成本和运作效益显著改善的一种全新的生产管理模式。
它的特点是强调客户对时间和价值的要求,以科学合理的制造体系来组织为客户带来增值的生产活动,缩短生产周期,从而显著提高企业适应市场万变的能力。
实施精益生产会给企业带来巨大的收益,因而被誉为第二次生产方式革命。
精益生产管理方法的特点(1)拉动式(pull)准时化生产(JIT) 。
以最终用户的需求为生产起点,强调物流平衡,追求零库存,要求上一道工序加工完的零件立即可以进入下一道工序。
组织生产运作依照看板(Kanban)进行,即由看板传递工序间需求信息(看板的形式不限,关键在于能够传递信息)。
生产中的节拍可由人工干预、控制,保证生产中的物流平衡(对于每一道工序来说,即为保证对后工序供应的准时化)。
由于采用拉动式生产,生产中的计划与调度实质上是由各个生产单元自己完成,在形式上不采用集中计划,但操作过程中生产单元之间的协调则极为必要。
(2)全面质量管理强调质量是生产出来而非检验出来的,由过程质量管理来保证最终质量。
精益生产基础知识概述
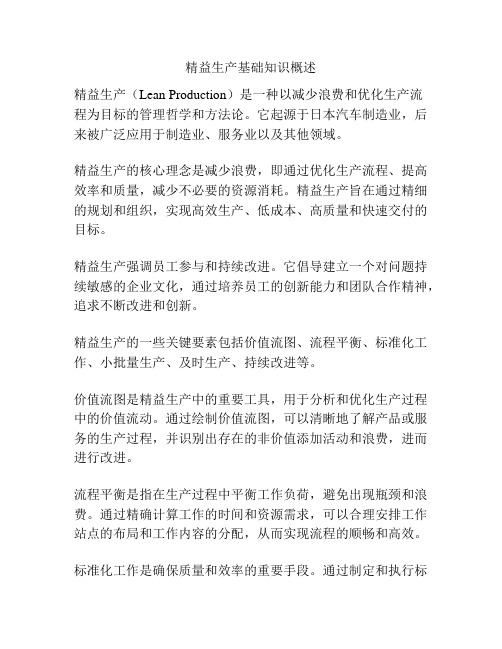
精益生产基础知识概述精益生产(Lean Production)是一种以减少浪费和优化生产流程为目标的管理哲学和方法论。
它起源于日本汽车制造业,后来被广泛应用于制造业、服务业以及其他领域。
精益生产的核心理念是减少浪费,即通过优化生产流程、提高效率和质量,减少不必要的资源消耗。
精益生产旨在通过精细的规划和组织,实现高效生产、低成本、高质量和快速交付的目标。
精益生产强调员工参与和持续改进。
它倡导建立一个对问题持续敏感的企业文化,通过培养员工的创新能力和团队合作精神,追求不断改进和创新。
精益生产的一些关键要素包括价值流图、流程平衡、标准化工作、小批量生产、及时生产、持续改进等。
价值流图是精益生产中的重要工具,用于分析和优化生产过程中的价值流动。
通过绘制价值流图,可以清晰地了解产品或服务的生产过程,并识别出存在的非价值添加活动和浪费,进而进行改进。
流程平衡是指在生产过程中平衡工作负荷,避免出现瓶颈和浪费。
通过精确计算工作的时间和资源需求,可以合理安排工作站点的布局和工作内容的分配,从而实现流程的顺畅和高效。
标准化工作是确保质量和效率的重要手段。
通过制定和执行标准化工作程序,可以减少变异和错误,提高产品和服务的一致性和可靠性。
小批量生产和及时生产是精益生产中的两个重要原则。
小批量生产可以减少库存和等待时间,降低成本和资源消耗。
及时生产则强调按需生产和按时交付,避免过产和库存积压。
持续改进是精益生产的核心精神。
它强调通过持续地观察、分析和改进,不断优化生产过程和提升绩效。
持续改进需要建立一个鼓励员工提出问题和改进建议的文化,同时提供必要的培训和支持。
总之,精益生产是一种在全球范围内被广泛应用的管理方法,它通过减少浪费和优化生产流程,实现高效生产、低成本、高质量和快速交付的目标。
它不断追求改进和创新,强调员工参与和持续学习,是现代企业管理中的重要理念和工具。
精益生产(Lean Production)是一种在制造业和服务业等领域中被广泛应用的管理哲学和方法论。
精益生产案例分享ppt课件
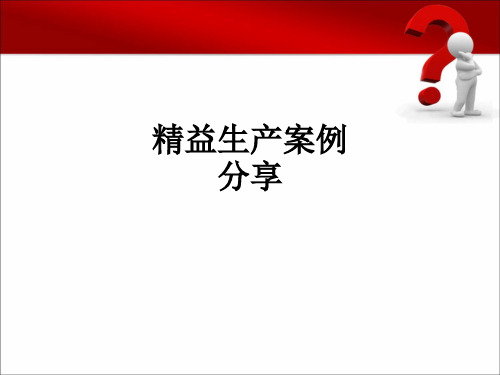
value
to a product or service 对最终产品或服务 不增加价值的 过程
Waste of Inventory 库存浪费
Any supply
in excess of process requirements necessary to produce goods 任何超过加工必须的 物料供应
Inventory Covers All Problem 库存掩盖所有问题
库存水平
维修问题
效率问题
质量问题
交货问题
Low Down Inventory To Expose Problem 通过降库存暴露问题
库存水平
维修问题
效率问题
质量问题
交货问题
Waste of Waiting 等待
Idle Time That Is Produced When Two Dependent Variables Are Not Fully Synchronized
改进后
1.改进后2人,充分发挥个人效益 2.改进后实现单件流 3.交付周期缩短50% 4.采取防错,当场发现 5.员工收入5800-6200
生产效率的提升大家自己算
12
JIT与TPS
Just In Time
适品 · 适量 · 适时
JIT的基本思想是:只在需要的时候、按需要 的量、 生产所需的产品,故又被称为准时制生产、适时生产方式、 看板生产方式。 JIT的核心是:零库存和快速应对市场变化。 JIT的概念最早由日本丰田汽车提出,在大野耐一带领 下创造出一套具竞争优势的运作方式,人们习惯称之为JIT 模式,又称丰田生产方式(TPS)。
等待浪费
精益的福特生产体系概述(NEW)

15
工作小组要素
工作小组的构成 工作小组的有效性 对工作小组的支持 培训 信息交流
2020/7/16
Michelle Gao
16
FPS模式
可靠性和可维护性小齿轮
世界一流的可靠性和可维护性,
可靠性和 可维护性
FTPM 福特全员生产维护 ISPC 工位过程控制 ME 制造工程
2020/7/16
Michelle Gao
2020/7/16
Michelle Gao
21
SMF要素
人员、计划与支持 零件供料计划 外部物流(出货/收货) 容器管理 物料配送方式
2020/7/16
Michelle Gao
22
精益制造在CFMA的运用
Kitting area
Kitting box
Parts kitted
Empty rack back to Kitting area
2020/7/16
人
Michelle Gao
SHARP 健康与安全 Environment环境 Leadership 领导 Work Group工作小组 Training 培训
14
领导要素
方针展开 时间和数据管理 参与、承诺与支持 变更管理 价值流 最佳实务 问题解决与持续改善
2020/7/16
Michelle Gao
2020/7/16
Kitting boxes in rack
To line side
Michelle Gao
23
精益制造在CFMA的运用
Before: Hardware scattered at each POF
After: Hardware gathered at one or two racks
精益生产体系
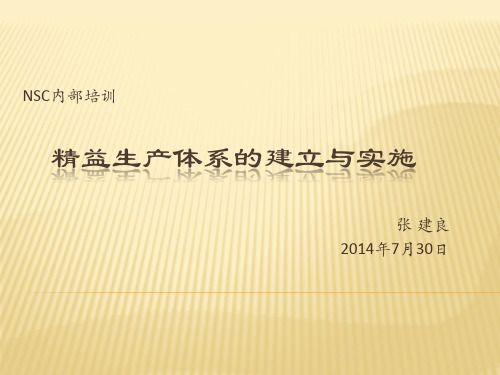
精益生产体系的建立与实施
张 建良 2014年7月30日
目录
NSC内部培训
第一部分:精益生产方式概要 第二部分:精益生产第一步:认识生产中的价值与浪费 第三部分:精益生产之方式与要求 第四部分:精益生产之管理手段活用 第五部分:减少库存 第六部分:精益生产之关键点突破 第七部分:精益思想与文化建立 第八部分:精益生产之推行
非增值过程
并未改变产品或提供服 务的非必要步骤。客户不愿 意付钱,比如返工。
对过程的认识
NSC内部培训
过程的增值与否
•必要 不需要但能使必要工
序顺利完成的工作,比如 机器调校。
•不必要 在流程的设计中加入
的纯粹的不需要的过程, 是通过改善可以消除掉的。
关于过程中的资源
•必要 在过程中投入的资源,
恰好够过程运行使用,既 不多也不少。
精益生产方式简介
NSC内部培训
美国学者的认识:
Lean Production
精益 ·生产
简称LP
上世纪80年代,美国麻省理工学院数位国际汽车计划组 (IMVP)的专家对以日本丰田公司为代表的汽车制造商进行了为 期十年的调查,发现日本汽车企业在生产管理方面有许多独到的 生产方式,正是这些生产方式的实施,使日本汽车企业能通过低 成本、高品质占领国际汽车市场,将这些生产方式进行总结,并 称之为“Lean Production ,简称LP”。
与产品价值核心的功能 不相关的加工与作业都 是浪费
作业浪费
生产制造中的浪费
NSC内部培训
更大的看不见的浪费(第八大浪费): 忽视人的智慧潜力!
1、管理者管理上的浪费 2、员工潜力未挖掘的浪费
案例: 设计一条新生产线,管理人员未对原来的流程中存在 的问题进行总结和未收集员工原来操作过程中的意见 就进行设计、安装、生产,大量生产后发现生产线和 作业台都过长和过大,并且还增加了很多搬运时间。
精益生产在福特生产车间中的应用

精益生产在福特生产车间中的应用作者:赵曜铭来源:《速读·下旬》2016年第04期摘要:介绍了福特公司在工业工程的应用上取得的成果,重点阐述了精益生产以及5s管理方法在福特生产车间的应用,并对此提出了进一步的认识。
关键词:工业工程;精益生产;5S;福特;生产车间1.前言随着中国工业的不断发展,工业工程这一在发达国家得到了广泛使用的应用性工程专业技术逐步进入中国。
而中国工业工程的发展,也促进了精益生产这一重要生产组织体系和方式的产生。
5s作为一个精益生产的基础管理方法,有着举足轻重的地位,5s也是表现企业正在走向精益生产模式的标志之一。
我利用在重庆福特生产车间参观学习的机会,仔细观察了福特的5s管理方法,了解了福特的精益生产道路,并对其中依然存在的问题提出了自己的建议。
2.工业工程与精益生产2.1工业工程在中国工业工程(IE-Industrial Engineering)是对人、材料、设备所集成的系统进行设计、改善和实施一门科学。
它直接面向企业的生产运作过程,在利用数学、自然科学、社会科学中的专门知识和技术的同时,工业工程还采用工程上的分析和设计的原理和方法。
它与人因学、经济管理学、各种工程技术有着密切的关系,同时辅以系统工程,运筹学等数学方法、现代信息技术等工具,用工程量化的分析方法对各种企业或实际工程与管理问题进行定量、系统的分析、设计与优化,从而获得最大的效率和效益。
从世界范围来看,工业工程在企业的生产管理中具有不可替代的作用。
因此,工业工程有着极其广大的市场。
虽然目前国内大多数企业对工业工程还没有足够的认识,不过放眼未来,工业工程仍然存在着极大发展空间。
工业工程也是完成精益生产方式的工程基础,它是精益生产的重要组成部分及生产结果的评价方法。
2.2精艺生产与5S精益生产(Lean Production)是当今世界最佳的一种生产组织体系和方式。
精益生产管理,是一种以客户需求为拉动,以消除浪费和不断改善为核心,使企业以最少的投入获取成本并显著改善运作效益的一种全新的生产管理模式。
精益生产五大原则参考PPT

2021/5/9
1
精益生产方式是继单件生产方式和大量生 产方式之后在日本丰田汽车公司诞生的全 新生产方式。这种生产方式与传统的生产 方式相比,具有非常卓越的模式,是具有 几千年历史的工业生产方式的巨大变革。 同时精益生产的思想又被广泛的应用于传 统制造业之外的行业,如服务业、物流运 输业、饮食业等,并且推行十分成功。
2021/5/9
12
福特将轿车总装生产转变为连续流动 生产,使福特的T型车的总装工作量减少了 90%,同样,将产品从接到订单到发货中 的活动按照流水线的原理设计也将大大提 高效率,保证按期向顾客交货。
精益生产方式的价值流动原则要求企业 重新定义职能、部门和企业的作用,使他 们能对创造价值做出积极的贡献;说明价 值流上每一点的员工的真正需要,因此, 使价值流动起来才真正符合员工的利益。 这不仅要求为每种产品建立精益企业,还 应该重新思考传统的企业、职能、职业, 重新考虑精益战略的发展。
2021/5/9
10
识别是否增值的活动
活动可以分为又可分为三种类型:ຫໍສະໝຸດ 第一种:明确的创造价值的活动;
第二类:不创造价值但是在现阶段不可避 免的活动,通常称之为一型浪费;
第三种:不创造价值,可立即去除的活动, 通常称之为二型浪费。
如果按照是否增值的角度来考察企业的产
品过程,我们不难发现,原来我们习以为
5
2021/5/9
6
一、精确的确定产品的价值
• 产品的价值通常由功效和价格等组成。功 效又可分为功能和质量,功能可进一步细 分为主要功能和辅助功能。产品的价值构 成如下图所示:
产 品 价 值
2021/5/9
7
1、产品的价值是由顾客定义 产品的价值构成中,如果产品的价格过高,超过
精益生产五大原则
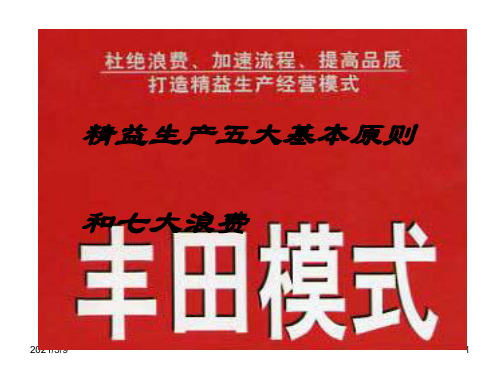
2021/5/9
15
精益生产的此种做法能从库存量下降和资金周 转速度加快中一下子节省巨量资金。从下图传统 生产方式和精益生产方式中产品生产过程中资金 占用对比情况可得出此结论。
精益生产方式是一个革命性的成就。因为,一 旦有了在客户需要的时候就能设计、排产和制造 出用户真正需要的产品的能力,就意味着企业可 以抛开销售预测,直接按用户告诉企业的实际要 求生产就行了,在电脑制造业中,DELL公司就是 典型的此种模式。这就是说,企业可以让用户从 企业那里按照需求拉动产品,而不是把用户不想 要的产品硬推给用户。
21
2021/5/9
22
2021/5/9
23
2021/5/9
24
2021/5/9
25
2021/5/9
26
不合格品干扰了生产活动,也耗费昂
贵的重修费用。不合格品通常被丢掉,是
资源及设备的最大浪费。在今日大量生产
的环境中,一部出差错的高速度性能自动
机器在问题被发现之前,就已吐出了巨量
的不合格品了。不合格品有时也可能伤害
2021/5/9
18
以上是精益生 产方式的五大基本 原则,此五项原则 是环环相扣的关系, 即后一原则必须依 存于前一原则;企 业没有全面深入掌 握此五项原则,对 精益生产方式的追 求和推行只能是形 式上的貌合,至于 精神,早已经离开 了。
2021/5/9
19
2021/5/9
20
2021/5/9
在许多实例中,加工浪费也是由于流程无
法同步所造成的。作业员经常把工作分得太精
细,超越了需要的程度,这也是加工浪费的另
一个例子。
2021/5/9
35
2021/5/9
羸家大讲堂-精益生产培训学习心得

羸家大讲堂-精益生产培训学习心得主讲:巩怿一、精益生产的概念精益生产(Lean Production,简称LP)是美国麻省理工学院数位国际汽车计划组织(IMVP)的专家对日本“丰田JIT(Just In Time)生产方式”的赞誉之称,精,即少而精,不投入多余的生产要素,只是在适当的时间生产必要数量的市场急需产品(或下道工序急需的产品);益,即所有经营活动都要有益有效,具有经济性。
精益生产是当前工业界最佳的一种生产组织体系和方式。
精益生产是21世纪几乎所有产业的主要生产制造模式,所以美国把它定为其国家2006年必须达到的目标。
在最小化经济批量的同时,提高品质、效率和应变能力,提高收益就是它的精髓。
二、精益生产的起源精益生产是战后日本汽车工业遭到的“资源稀缺”和“多品种、少批量”的市场制约的产物,它是从丰田相佐诘开始,经丰田喜一郎及大野耐一等人的共同努力直到60年代才逐步完善而形成的。
丰田生产方式的诞生:因石油危机而觉醒。
1973年秋石油危机爆发以后,社会上对丰田生产方式开始表现密切的关注。
应该说,石油危机对政府、企业以及个人生活等各方面的影响都是很大。
第二年,日本经济一落千丈,增长率降到零,当时整个产业界都有万劫不复之感。
由于经济萧条,各家公司一筹莫展。
这时,丰田盈利虽然有所减少,却仍较其他公司为多,所以颇引人注意。
人们说,丰田这家企业的结构是经得起冲击的……远在石油危机之前,就推出了什么叫做丰田式的制造技术和丰田生产方式,但当时却没有引起人们多大兴趣。
石油危机之后,1975年至1977年,丰田的盈利逐年增加,逐渐拉大了同其他公司的差距。
于是,丰田生产方式便开始引起了注意。
在1973年之前,日本处于经济持续高速增长时代。
当时企业的生产采用美国方式还是可行的。
但是,到了高速增长停顿下来、增长率下降的时期,美国的有计划大批量生产方式便行不通了。
二战后1950年至1951年,对于现在这么大的汽车产量真是不敢想象。
精益生产方式的历史发展过程

精益生产方式的历史发展过程20世纪初,从美国福特汽车公司创立第一条汽车生产流水线开始,大规模的生产流水线一直是现代工业生产的主要特征,改变了效率低下的单件生产方式,被称为生产方式的第2个里程碑。
大规模生产方式是以标准化、大批量生产来降低生产成本,提高生产效率的。
这种方式适应了美国当时的国情,汽车生产流水线的产生,一举把汽车从少数富翁的奢侈品变成了大众化的交通工具,美国汽车工业也由此迅速成长为美国的一大支柱产业,并带动和促进了包括钢铁、玻璃、橡胶、机电以至交通服务业等在内的一大批产业的发展。
大规模流水生产在生产技术以及生产管理史上具有极为重要的意义。
但是第二次世界大战以后,社会进入了一个市场需求向多样化发展的新阶段,相应地要求工业生产向多品种、小批量的方向发展,单品种、大批量的流水生产方式的弱点就日渐明显了。
为了顺应这样的时代要求,由日本丰田汽车公司首创的精益生产,作为多品种、小批量混合生产条件下的高质量、低消耗进行生产的方式在实践中摸索、创造出来了。
精益生产方式在实践应用中根据丰田实际生产的要求而被创造、总结出来的一种革命性的生产方式,被人称为“改变世界的机器”,是继大量生产方式之后人类现代生产方式的第3个里程碑。
总体来说,根据精益生产方式的形成过程可以将其划分为三个阶段:丰田生产方式形成与完善阶段,丰田生产方式的系统化阶段(即精益生产方式的提出),精益生产方式的革新阶段(对以前的方法理论进行再思考,提出新的见解)。
1丰田生产方式的形成与完善阶段1950年一个年轻的日本工程师丰田英二到底特律对福特的鲁奇厂进行了三个月的参观,当时鲁奇厂是世界上最大而且效率最高的制造厂.但是丰田英二对这个庞大企业的每一个细微之处都作了审慎的考察,回到名古屋后和生产制造方面富有才华的大野耐一一起很快得出了结论:大量生产方式不适合于日本。
因为第一,当时日本国内市场狭小,所需汽车的品种又很多,多品种、小批量并不适合大量生产方式的要求;第二战后的日本缺乏大量外汇来大量购买西方的技术和设备,不能单纯地仿效鲁奇厂并在此基础上改进;第三缺乏大量廉价劳动力。
- 1、下载文档前请自行甄别文档内容的完整性,平台不提供额外的编辑、内容补充、找答案等附加服务。
- 2、"仅部分预览"的文档,不可在线预览部分如存在完整性等问题,可反馈申请退款(可完整预览的文档不适用该条件!)。
- 3、如文档侵犯您的权益,请联系客服反馈,我们会尽快为您处理(人工客服工作时间:9:00-18:30)。
精益生产
Ford Motor China Sourcing Office
福特汽车中国采购中心
First Time Through Calculation (FTT)
Definition: First Time Through is the percentage of units that complete a process and meet quality guidelines the first time without being scraped, rerun, retested, diverted for off-line repair, or returned. It is a measure of the quality of the manufacturing process. 定义: 首次通过率是指一次性完成一个生产过程并且满足质量要求的零件的百分率, 不包括报废,返工,再测试,下线修理或返回。FTT 用于衡量制造过程的质量。 FTT= Units entering process-(scrap+reruns+retests+repaired off-line+returns) Units entering process
Process with a sequenced ‘batch of many’ schedule
--中国现场改善网--企业管理资料免费分享平台
Build to Schedule (BTS)
Build to Schedule (BTS-1)
FOCUS/COUGAR/JAGUAR CONDENSER
Process with a sequenced ‘batch of many’ schedule --中国现场改善网--企业管理资料免费分享平台
定义: BTS是指在指点的生产日按照正确的生产顺序完成生产计划的比例情况。BTS 反映了工厂能够按照客户的要求完成生产的能力,客户需何种产品,何时需要和客 户使用产品的顺序。 BTS% = Volume% X Mix% X Sequence% Volume Performance: 产量性能用于监控生产计划完成情况。 Mix Performance: BTS的混线性能用于测量在厂内制造的产品系/型号/类型等在适当的生产日的完 成比率。 Sequence Performance: BTS的顺序性能用于测量在适当的生产日按照正确的生产顺序完成生产任务的比 率。
理想循环时间 总零件数 作业时间
性能效率
= 0.33分钟/件 = 1440 = 570分钟
= 0.33 X 1料免费分享平台
Overall Equipment Effectiveness (OEE)
质量率: 总零件数 返工数 报废数 质量率 总设备利用率: 利用率 性能效率 质量率 总设备利用率 OEE = = = = 86.3% 83.4% 93.8% 86.3% X 83.4% X 93.8% = 1440 = 50 = 40 = 1440 – (50+ 40) = 93.8%
Sequence Performance: The sequence component of BTS measures the percentage of those products built on the right day that were also built in the right sequence.
--中国现场改善网--企业管理资料免费分享平台
= 44.22%
Total Dock To Dock Calculation (DTD)
Definition: Dock to Dock is the elapsed time between the unloading of raw materials and the release of finished goods for shipment. DTD measures how fast raw materials are converted to finished goods and shipped. It is a measure of the speed of material through the plant, not the speed of the processes.
实际批次顺序
实际产量
290 340 60 690
混线批次
混线生产
290 250 0 540
按顺序生产批次
计划批次顺序
1 2 3 4 5
1 2 N/A 4 3
Yes Yes No Yes Yes 4批
Yes Yes N/A Yes No 3批
Process with a sequenced ‘batch of many’ schedule --中国现场改善网--企业管理资料免费分享平台
定义: DTD指从原材料到发运产品之间的总运转时间间隔。DTD用于测量原材料转化 成成品发运的速度。也就是指材料通过工厂的速度,而不是加工工艺的速度。
DTD (Single Operation) = Total Units of Control Part End of line Rate DTD (Multiple Operation)= DTD(OP 1)+DTD(OP 2)+… End of line Rate
BTS% = Volume% X Mix% X Sequence% Volume Performance: Volume Performance, is the traditional measure that manufacturing has used to monitor their performance to schedule. Mix Performance: The Mix component of BTS measures the percentage of product derivatives/models/types that a plant builds on the right day.
--中国现场改善网--企业管理资料免费分享平台
Total Dock To Dock Calculation (DTD)
The End of Line Rate is calculated off the last operation in the manufacturing line for a product: 总产量 = 730 (最终工位) 生产时间 = 12小时 (正常生产时间10小时+加班时间2小时) End of Line Rate 各区域数量 原材料 工序1 工序2 工序3 最终产品 DTD(原材料) DTD (工序1) DTD (工序2) DTD (工序3) DTD (最终产品) = = = = = = = = = = = = 730/12 原材料+半成品+最终产品 300 181 3 3 200 300/60.83 181/60.83 3/60.83 3/60.83 200/60.83 =60.83
=4.93小时 =2.98小时 =0.05小时 =0.05小时 =3.29小时
Total DTD= 4.93+ 2.98+ 0.05+ 0.05+ 3.29 =11.3小时 --中国现场改善网--企业管理资料免费分享平台
Overall Equipment Effectiveness (OEE)
Definition: OEE is a combination of three different calculations. It is a measure of the availability, performance efficiency, and quality rate of a given piece of equipment. OEE data will help identify several wastes caused by machine/process inefficiencies. Stretch objective: 85% 定义:OEE是三个不同计算值的乘积,用于测量指定设备的利用率,性能效率 和质量率。OEE 数据可以帮助识别由设备/过程不足引起的不同的浪费。 接受标准: 85% OEE Availability Performance Efficiency Quality = = = = Availability X Performance Efficiency X Quality Operation Time Net Available Time Ideal cycle time X Total parts run Operating Time Total parts run – Total defects Total parts run
Process with a sequenced ‘batch of many’ schedule --中国现场改善网--企业管理资料免费分享平台
Build to Schedule (BTS-1)
冷凝器类型
Cougar Focus Jaguar
计划产量
560 250 0 810
--中国现场改善网--企业管理资料免费分享平台
First Time Through Calculation (FTT)
单工序: 进入数量 报废 返工 测试 下线修理 FTT% FTT% 多工序: FTT (工序1) FTT (工序2) FTT (工序3) 最终检验(工序4) 总FTT% Total FTT% = = = = = 92.87% 87.65% 82.34% 82.34% 92.87% X 87.65% X 82.34% X 82.34% = 1000 = 10 = 15 = 5 = 0 = 1000 -(10+ 15+ 5+ 0) 1000 = 97.0%