铝合金切削刀具加工参数分析与选用
6mm铣刀铣铝参数
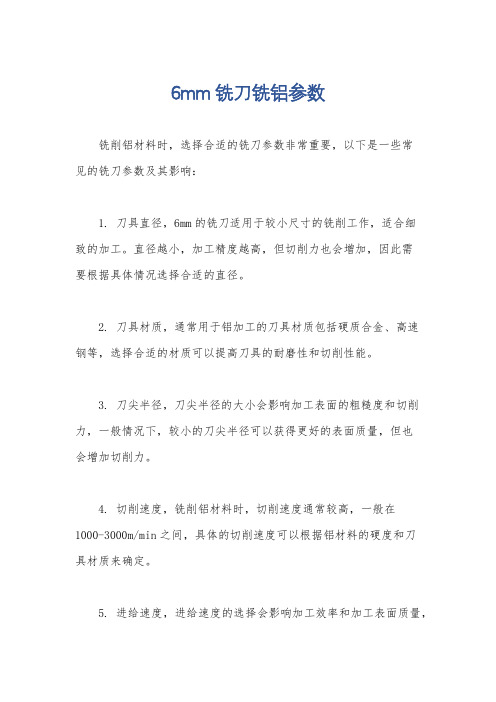
6mm铣刀铣铝参数
铣削铝材料时,选择合适的铣刀参数非常重要,以下是一些常
见的铣刀参数及其影响:
1. 刀具直径,6mm的铣刀适用于较小尺寸的铣削工作,适合细
致的加工。
直径越小,加工精度越高,但切削力也会增加,因此需
要根据具体情况选择合适的直径。
2. 刀具材质,通常用于铝加工的刀具材质包括硬质合金、高速
钢等,选择合适的材质可以提高刀具的耐磨性和切削性能。
3. 刀尖半径,刀尖半径的大小会影响加工表面的粗糙度和切削力,一般情况下,较小的刀尖半径可以获得更好的表面质量,但也
会增加切削力。
4. 切削速度,铣削铝材料时,切削速度通常较高,一般在
1000-3000m/min之间,具体的切削速度可以根据铝材料的硬度和刀
具材质来确定。
5. 进给速度,进给速度的选择会影响加工效率和加工表面质量,
通常情况下,较大的进给速度可以提高加工效率,但较小的进给速度可以获得更好的加工表面质量。
6. 切削深度,切削深度的选择需要考虑刀具的承受能力和加工的要求,一般情况下,较小的切削深度可以减小切削力,获得更好的加工表面质量。
总的来说,铣削铝材料时,6mm的铣刀可以适用于一些细致的加工,但在选择刀具参数时需要综合考虑加工的要求、材料的硬度和刀具的特性,以获得最佳的加工效果。
铝合金的高速切削加工技术研究
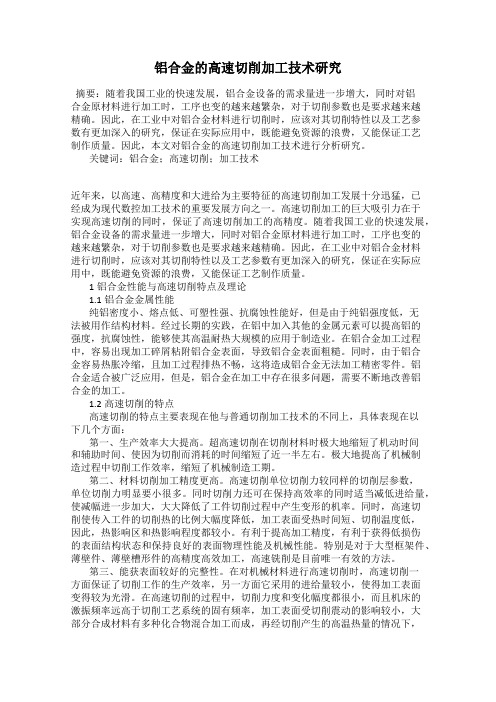
铝合金的高速切削加工技术研究摘要:随着我国工业的快速发展,铝合金设备的需求量进一步增大,同时对铝合金原材料进行加工时,工序也变的越来越繁杂,对于切削参数也是要求越来越精确。
因此,在工业中对铝合金材料进行切削时,应该对其切削特性以及工艺参数有更加深入的研究,保证在实际应用中,既能避免资源的浪费,又能保证工艺制作质量。
因此,本文对铝合金的高速切削加工技术进行分析研究。
关键词:铝合金;高速切削;加工技术近年来,以高速、高精度和大进给为主要特征的高速切削加工发展十分迅猛,已经成为现代数控加工技术的重要发展方向之一。
高速切削加工的巨大吸引力在于实现高速切削的同时,保证了高速切削加工的高精度。
随着我国工业的快速发展,铝合金设备的需求量进一步增大,同时对铝合金原材料进行加工时,工序也变的越来越繁杂,对于切削参数也是要求越来越精确。
因此,在工业中对铝合金材料进行切削时,应该对其切削特性以及工艺参数有更加深入的研究,保证在实际应用中,既能避免资源的浪费,又能保证工艺制作质量。
1铝合金性能与高速切削特点及理论1.1铝合金金属性能纯铝密度小、熔点低、可塑性强、抗腐蚀性能好,但是由于纯铝强度低,无法被用作结构材料。
经过长期的实践,在铝中加入其他的金属元素可以提高铝的强度,抗腐蚀性,能够使其高温耐热大规模的应用于制造业。
在铝合金加工过程中,容易出现加工碎屑粘附铝合金表面,导致铝合金表面粗糙。
同时,由于铝合金容易热胀冷缩,且加工过程排热不畅,这将造成铝合金无法加工精密零件。
铝合金适合被广泛应用,但是,铝合金在加工中存在很多问题,需要不断地改善铝合金的加工。
1.2高速切削的特点高速切削的特点主要表现在他与普通切削加工技术的不同上,具体表现在以下几个方面:第一、生产效率大大提高。
超高速切削在切削材料时极大地缩短了机动时间和辅助时间、使因为切削而消耗的时间缩短了近一半左右。
极大地提高了机械制造过程中切削工作效率,缩短了机械制造工期。
铝合金加工参数

铝合金加工参数
由于在加工过程中发现工件刀纹不致影响表面质量,查找了一些资料,作了一些摘要:
1.由于铝合金强度和硬度相对较低,塑性较小,对刀具磨损小,且热导率较高,使切削温度较低,所以铝合金的切削加工性较好,属于易加工材料,切削速度较高,适于高速切削.但铝合金熔点较低,温度升高后塑性增大,在高温高压作用下,切削界面摩擦力很大。
容易粘刀;特别是退火状态的铝合金,不易获得低的表面粗糙度。
2.与钢材和黄铜相比,铝合金的特点,一是材质软,刚性差,二是弹性模量低,这两个因素显著影响了铝合金的切削加工性。
因此,在加工铝合金工件时,必须充分地夹紧和支撑工件,并保持刀具锋利;否则,工件往往会有离开切削刀具的倾向。
有时工件的表面出现不规则的槽痕和光亮的挤压斑,一种可能是由于刀具对工件的压力不正常引发的,还有一种可能是由于夹持不牢固而引起振颤时,刀具在工件的表面作间隙式的磨蹭,发生挤压现象和粉状切削;然后,当间隙或弹性消失时,刀具就咬人工件的表面,啃出槽痕。
3.为了获得光洁的工件表面,尽可能采用粗切削和精切削的组合,因为各种合格的工件毛坯总会有一些氧化层,致使刀具受到相当程度的磨损。
如果最后切削工序采用抛光过的锋利刀具进行精细切削,就能达到以上要求。
4.通常把铝合金的切削性分为两类:1类是指工业纯铝和硬度小于80HB的退火状态铝合金;2类是指淬火时效状态的变形铝合金。
而铝合金的切削加工工艺参数与此类别有关。
金钢石刀具的典型切削参数
铝合金的典型铣削参数
铝合金攻螺纹前的钻孔的典型参数
铝合金的典型铰孔参数
注:冷却剂为煤油-松节油(5:4)混合物;或用约33°E的矿物油, 或优质油.干铰孔的质量不高。
pcd加工铝合金参数

pcd加工铝合金参数
PCD(聚晶金刚石)是一种高性能切削工具材料,常用于加工硬
质材料,包括铝合金。
在PCD加工铝合金时,需要考虑一些参数,以确保高效、精确的加工过程。
1. 切削速度
切削速度是指刀具切削材料的速度,通常用米/分钟(m/min)表示。
对于铝合金,建议切削速度为200-400 m/min。
当切削速度过高时,可能会导致切削工具损坏或铝合金表面产生热裂纹,而过低的切削速度则会导致加工效率低下。
2. 进给速度
进给速度是指刀具在切削中移动的速度,通常用毫米/转(mm/rev)表示。
对于铝合金,建议进给速度为0.05-0.15 mm/rev。
进给速度
过高可能导致刀具寿命缩短,而进给速度过低则会导致加工效率低下。
3. 切削深度
切削深度是指刀具在每个工作循环中切削材料的深度,通常用毫米(mm)表示。
对于铝合金,建议切削深度为1-3 mm。
切削深度过
大可能导致切削力和热量增加,从而影响刀具寿命和加工质量。
4. 刀具半径
刀具半径是指刀具切削部分的半径大小,通常用毫米(mm)表示。
对于铝合金,建议使用较小的刀具半径,以便更好地控制切削质量和表面光洁度。
5. 刀具材料
PCD刀具是PCD加工铝合金的最佳选择,因为它具有高硬度、高热稳定性和良好的耐磨性。
此外,还可以选择具有涂层的PCD刀具,以提高刀具寿命和加工效率。
总之,PCD加工铝合金需要仔细考虑各个参数,以确保高效、高质量的加工过程。
铝合金7系列和6系列加工参数
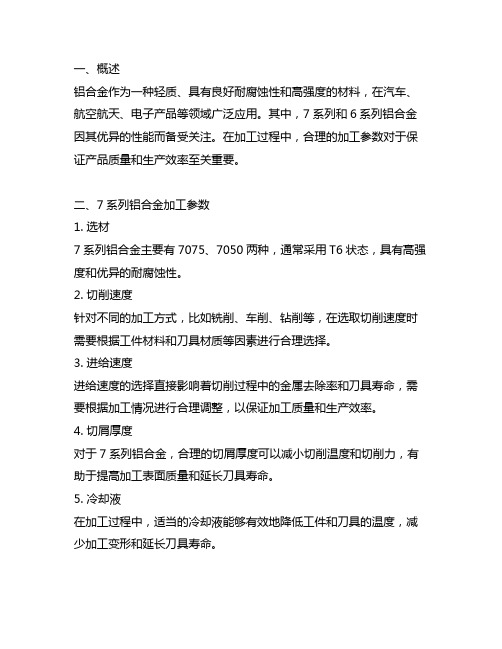
一、概述铝合金作为一种轻质、具有良好耐腐蚀性和高强度的材料,在汽车、航空航天、电子产品等领域广泛应用。
其中,7系列和6系列铝合金因其优异的性能而备受关注。
在加工过程中,合理的加工参数对于保证产品质量和生产效率至关重要。
二、7系列铝合金加工参数1. 选材7系列铝合金主要有7075、7050两种,通常采用T6状态,具有高强度和优异的耐腐蚀性。
2. 切削速度针对不同的加工方式,比如铣削、车削、钻削等,在选取切削速度时需要根据工件材料和刀具材质等因素进行合理选择。
3. 进给速度进给速度的选择直接影响着切削过程中的金属去除率和刀具寿命,需要根据加工情况进行合理调整,以保证加工质量和生产效率。
4. 切屑厚度对于7系列铝合金,合理的切屑厚度可以减小切削温度和切削力,有助于提高加工表面质量和延长刀具寿命。
5. 冷却液在加工过程中,适当的冷却液能够有效地降低工件和刀具的温度,减少加工变形和延长刀具寿命。
三、6系列铝合金加工参数1. 选材6系列铝合金主要有6061、6063两种,广泛应用于航空航天和轨道交通领域。
同样需要根据实际加工情况选择不同的状态和硬度。
2. 切削速度由于6系列铝合金具有较高的塑性,因此在选择切削速度时需要根据工件材料和刀具材质等因素进行合理调整,以避免刀具损坏和加工表面质量下降。
3. 进给速度进给速度的选择需要兼顾加工质量和生产效率,在实际加工中需要根据不同的工件和刀具情况进行合理调整。
4. 刀具材质对于6系列铝合金,选择合适的刀具材质能够有效地提高加工效率和保证加工质量。
5. 切削温度6系列铝合金的切削温度控制尤为重要,合理的切削温度能够避免刀具损坏和工件表面质量下降的问题。
四、结论7系列和6系列铝合金在实际加工中需要根据具体情况选择合适的加工参数,以保证产品质量和生产效率。
合理的切削速度、进给速度、切屑厚度等加工参数对于提高加工效率和延长刀具寿命都具有重要作用。
加工过程中的冷却液和刀具材质选择也同样重要。
数控车床加工铝件技巧

数控车床加工铝件技巧数控车床加工铝件是一种常见且重要的加工工艺,在很多行业中都得到了广泛的应用。
铝合金具有良好的可塑性和加工性能,但由于其热导率高、切削削具极易磨损,所以在加工过程中需要注意一些技巧,以保证加工质量和效率。
以下是一些数控车床加工铝件的技巧:1.选择合适的切削参数:铝合金的切削应力和热导率较高,加工过程中容易产生较大的热量。
因此,应降低切削速度和进给量,以避免过高的切削温度。
同时,要注意选择合适的刀具和切削液,以提高刀具寿命和加工质量。
2.使用合适的刀具:在数控车床加工铝件时,应选择合适的刀具。
通常情况下,采用硬质合金刀具效果较好。
硬质合金刀具具有较高的硬度和耐磨性,能够较好地抵抗铝合金的切削热和磨损。
3.控制刀具磨损:铝合金的磨损对刀具寿命和加工质量影响较大。
因此,要及时检查和更换磨损的刀具,以保持加工质量和效率。
此外,应注意刀具的冷却条件,避免切削温度过高引起刀具磨损。
4.优化切削路径和进给方向:在数控车床加工铝件时,应优化切削路径和进给方向,以减小切削阻力和提高切削效率。
通常情况下,采用螺旋切削和斜切削技术,能够有效地减小切削阻力和热量。
5.控制加工精度:在数控车床加工铝件时,要注意控制加工精度。
铝合金具有较大的热膨胀系数,加工时易出现变形,从而影响加工精度。
因此,要采取合适的工艺措施,如加工温度控制、合理的夹紧方式和切削力控制,以保证加工精度。
6.加工后处理:在加工完铝件后,应注意进行适当的后处理。
例如,进行热处理、表面处理或抛光等,以提高铝件的表面质量和性能。
总之,数控车床加工铝件需要注意切削参数、选择合适的刀具、控制刀具磨损、优化切削路径和进给方向、控制加工精度和进行适当的后处理。
这些技巧可以帮助提高加工效率和质量,确保铝件的精度和表面质量。
数控机床加工铝合金的最佳切削参数选择方法
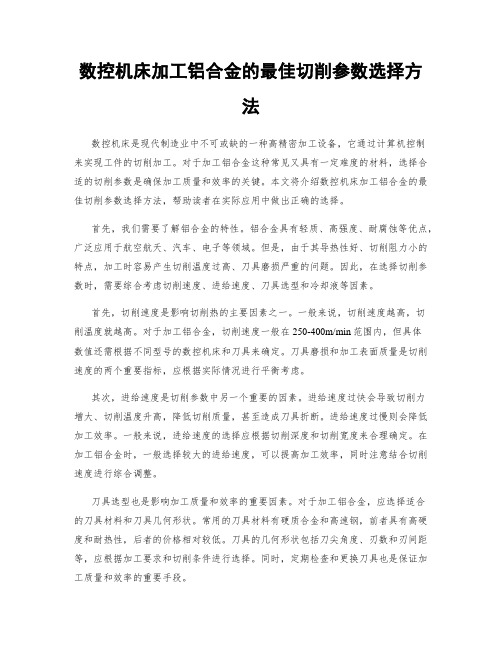
数控机床加工铝合金的最佳切削参数选择方法数控机床是现代制造业中不可或缺的一种高精密加工设备,它通过计算机控制来实现工件的切削加工。
对于加工铝合金这种常见又具有一定难度的材料,选择合适的切削参数是确保加工质量和效率的关键。
本文将介绍数控机床加工铝合金的最佳切削参数选择方法,帮助读者在实际应用中做出正确的选择。
首先,我们需要了解铝合金的特性。
铝合金具有轻质、高强度、耐腐蚀等优点,广泛应用于航空航天、汽车、电子等领域。
但是,由于其导热性好、切削阻力小的特点,加工时容易产生切削温度过高、刀具磨损严重的问题。
因此,在选择切削参数时,需要综合考虑切削速度、进给速度、刀具选型和冷却液等因素。
首先,切削速度是影响切削热的主要因素之一。
一般来说,切削速度越高,切削温度就越高。
对于加工铝合金,切削速度一般在250-400m/min范围内,但具体数值还需根据不同型号的数控机床和刀具来确定。
刀具磨损和加工表面质量是切削速度的两个重要指标,应根据实际情况进行平衡考虑。
其次,进给速度是切削参数中另一个重要的因素。
进给速度过快会导致切削力增大、切削温度升高,降低切削质量,甚至造成刀具折断。
进给速度过慢则会降低加工效率。
一般来说,进给速度的选择应根据切削深度和切削宽度来合理确定。
在加工铝合金时,一般选择较大的进给速度,可以提高加工效率,同时注意结合切削速度进行综合调整。
刀具选型也是影响加工质量和效率的重要因素。
对于加工铝合金,应选择适合的刀具材料和刀具几何形状。
常用的刀具材料有硬质合金和高速钢,前者具有高硬度和耐热性,后者的价格相对较低。
刀具的几何形状包括刀尖角度、刃数和刃间距等,应根据加工要求和切削条件进行选择。
同时,定期检查和更换刀具也是保证加工质量和效率的重要手段。
最后,冷却液的使用在加工铝合金时尤为重要。
冷却液不仅可以降低切削温度,还可以减少切削力和刀具磨损,提高加工质量和效率。
选择冷却液时应考虑其导热性、润滑性和抗腐蚀性等性能,同时要控制冷却液的喷射方式和压力,确保切削过程中刀具和工件始终处于良好的润滑和冷却状态。
关于铝合金材料PCD刀具加工应用的研究

关于铝合金材料PCD刀具加工应用的研究作者:刘源来源:《科教导刊·电子版》2017年第12期摘要铝合金材料被广泛运用于汽车、飞机等装备制造领域,有利于减轻机械动力负荷,实现机械设备的轻型化、小型化发展。
在铝合金材料的运用过程中,PCD切割工具以其硬度高、热膨胀系数低、与铝合金亲合小的特点被广泛运用于铝合金的切削加工领域。
本文对PCD刀具加工应用方法进行了研究,探索了PCD刀具钝化处理的技术,以及钝化处理后对于切削铝合金材料的影响。
关键词 PCD刀具钝化处理铝合金材料目前,PCD(金刚石)刀具已经大规模的运用铝合金等有色金属的切削加工中。
为提高PCD刀具的使用寿命和加工质量,笔者在工作实践的基础上,结合现有的研究成果,进行了PCD刀具钝化和铝合金材料切削实验,对PCD刀具钝化技术和要求,有针对性地进行了优化。
1 PCD刀具的钝化技术的原理PCD刀具的钝化技术是对PCD刀具进行深加工,提高刀具运用水平的重要方法。
笔者在实践中发现,PCD刀具在切削加工铝合金的过程中,使用初期会表现出加工质量不高、磨损较快等问题。
随着使用时间的延长,其加工的质量越来越高。
其实现的原理主要是:PCD刀具在刃磨后会出现一些毛刺和微缺口,但是在车削铝合金材料长时间磨损中,刀具刃口出现钝化,毛刺和微缺口被去除,切削刃变得光滑,提高刀具的使用寿命和加工质量。
2 PCD刀具的钝化和铝合金材料车削实验本文进行的实验主要由两个部分组成:一是PCD刀具的钝化实验;一是钝化PCD刀具对铝合金材料的切削实验。
2.1关于的PCD刀具的钝化实验在实验中,笔者采用了小型可转位刀片刃口钝化机,通过刀具与钝化机磨刷之间的磨损运动,对PCD刀具进行刃口钝化观察。
为了观察不同的磨刷与PCD刀具钝化的关系,笔者在试验中分别选用含400目、800目、1000目、1200目金刚石磨料的磨料刷,转速800r/min,切削刃和磨料刷接触长度为2mm进行实验。
铝用铣刀参数

铝用铣刀参数一、铝用铣刀的作用和应用领域铣刀是一种常用的切削工具,广泛应用于铝合金等金属材料的加工工艺中。
铝合金因其优异的性能,广泛用于航空航天、汽车制造、建筑工程等领域。
铣刀作为铝合金加工中的重要工具,其参数的选择对加工结果有着重要的影响。
二、铝用铣刀参数的选择在选择铝用铣刀参数时,需要考虑以下几个方面:1. 刀具材质铣刀的材质对其切削性能和寿命有着重要影响。
常见的铝用铣刀材质有高速钢、硬质合金和立方氮化硅等。
对于常规的铝合金加工,高速钢铣刀已经可以满足需求。
但对于一些高硬度或高速加工的情况,可选择硬质合金或立方氮化硅等更耐磨的材质。
2. 铣刀涂层铣刀涂层可以提高切削刃的硬度和润滑性,提高刀具的耐磨性和寿命。
常见的涂层有TiN、TiCN、TiAlN等。
TiAlN涂层具有较高的硬度和耐高温性能,在铝合金加工中表现出较好的切削性能。
3. 刀具几何参数刀具几何参数包括刀尖半径、主切削角、切削刃长度等。
这些参数的选择会直接影响切削过程中的切削力、切削温度等因素。
一般来说,铝合金的切削温度较低,选择较小的刀尖半径和切削角可以获得更好的切削效果。
4. 刀具转速和进给速度刀具转速和进给速度是加工过程中需要调整的参数。
较高的刀具转速可以提高加工效率,而适当的进给速度可以控制切削力和切削温度。
在铝合金加工中,一般可以选择较高的刀具转速和进给速度,以提高加工效率。
三、铝用铣刀参数的优化为了获得更好的加工效果,铝用铣刀参数的优化是必要的。
以下是一些常见的优化策略:1. 切削液的选择切削液的选择对切削过程中的润滑和冷却都有着重要的作用。
合适的切削液可以有效地降低切削温度、减少刀具磨损。
在铝合金加工中,常用的切削液有水溶性切削油和合成切削液等。
2. 切削参数的调整通过调整刀具转速和进给速度等参数,可以更好地适应不同的加工需求。
在实际操作中,可以通过试切和观察切削情况,逐步调整切削参数,找到最佳的加工参数。
3. 定期刀具检修和更换刀具在使用过程中会出现磨损和刃口破损等情况,影响切削质量和加工效率。
如何选择刀具和切削参数
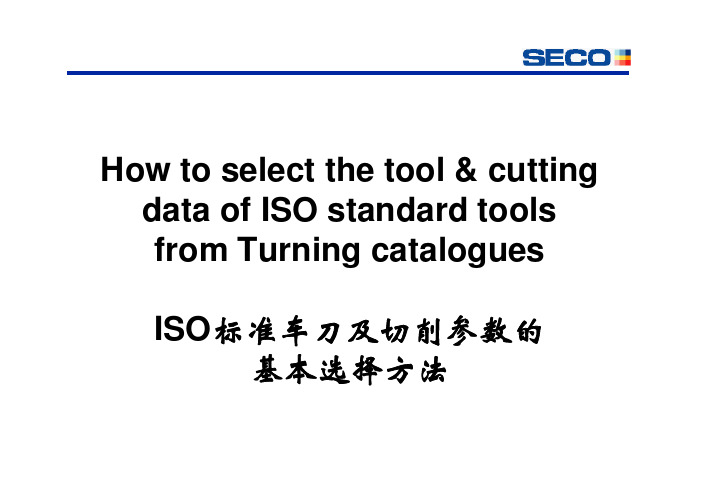
205
6:依切削参数的优化 • 根据刚才选择的刀片,您可以很方便地选得适用的切削参数推荐值。 线速度Vc=200m/min,每齿进给fz=0.25mm/z,因为刀盘直径我们已 经知道是D=100mm,所以转速N=636rpm,刀盘齿数为Z=7,所以实 际的工作进给量F=636*7*0.25=1110mm/min。 实际每转的进给量为Fr=7*0.25=1.75mm>1.5mm的修光刃实际有效 宽度,所以可以预计加工的光洁度不是很好,要提高光洁度您认为应 该采用什么措施? 正确的办法应该是加用修光刃刀片而不是简单地降低每齿进给量。
Plunging Plunging 插铣 插铣
3:确定最适合的首选刀片 • 如我们以加工45钢为例,即山高第4组材料,根据被加工材料在样本的 相应组别中您可以非常容易地找到首选刀片的推荐。 XOMX090308TR-ME06 T350M
4:您也可以在样本中了解 到有关刀盘的其它信息
• 这些信息包括: 刀盘的有效工作直径、杆式 刀的柄直径、刀盘高度、齿 数、重量、盘式刀盘安装孔 径、备用板手、适用的刀柄 规格、安全最大切深等等。
1:确定被加工工件的材料组别 • 依据国际ISO标准的规定,常见的 工件材料被分为六类: 钢件类(P类)--山高组别1-6 不锈钢类(M类)--山高组别7-11 铸铁类(K类)--山高组别12-15 有色金属类(N类)--山高组别16-17 耐热合金类(S类)--山高组别20-22 淬硬钢类(H类)--山高组别7 我们最常用的45号钢为第3 组材料,不 锈钢( 316 )属于第9组材料,铸铁HT25 ( GG25 )属于第12组, 铝合金属于第 16组,钛合金( Ti6Al4V )属于20组,镍 基合金( 718 )属于第22组。
铝合金加工刀具使用注意要求

铝合金加工刀具使用注意要求刀具在铝合金加工中起着至关重要的作用,正确的使用和维护可以保证加工质量和效率。
以下是关于铝合金加工刀具使用的注意要求。
1. 选择合适的刀具在铝合金加工中,需要选择适合加工对象和加工方式的刀具。
不同的铝合金材料和加工方式需要不同类型的刀具,如铣刀、钻头、车刀等。
根据加工要求选择合适的刀具,可以提高加工效率和质量。
2. 定期检查刀具状态刀具是加工过程中最易磨损的部件,定期检查刀具状态可以及早发现问题并采取相应措施。
检查刀具的磨损情况、刃口是否钝化、是否有损伤等。
如果发现刀具有问题,及时更换或修复,以保证加工质量。
3. 注意切削速度和进给量切削速度和进给量是影响加工效果的重要因素。
切削速度过高会导致刀具过早磨损,切削速度过低则会降低加工效率。
进给量过大会增加切削力,影响刀具寿命,进给量过小则会降低加工效率。
根据加工材料和刀具类型选择合适的切削速度和进给量,以保证加工效果和刀具寿命的平衡。
4. 使用合适的冷却润滑剂铝合金加工过程中产生的高温会对刀具造成损伤,使用冷却润滑剂可以有效降低温度并减少刀具磨损。
选择合适的冷却润滑剂,根据加工方式进行适当的喷洒或浸润,以保证刀具和加工质量。
5. 定期刀具磨砺刀具磨损会影响加工效果和切削质量,定期进行刀具磨砺可以恢复刀具的切削能力。
根据刀具类型和磨损情况选择合适的磨砺方法,保持刀具的锋利度和精度。
6. 注意安全操作在使用刀具时,要注意安全操作,避免发生事故。
使用刀具时要戴好防护眼镜和手套,确保加工过程中不会受伤。
在切削过程中要注意切削方向,避免刀具脱离工件或产生剧烈振动。
以上是关于铝合金加工刀具使用的注意要求,正确的使用和维护可以提高加工效率和质量,延长刀具寿命,保证安全生产。
加工人员应严格按照要求进行操作,确保加工过程顺利进行。
金刚石刀具切削铝合金时刀具材料和切削用量的选择
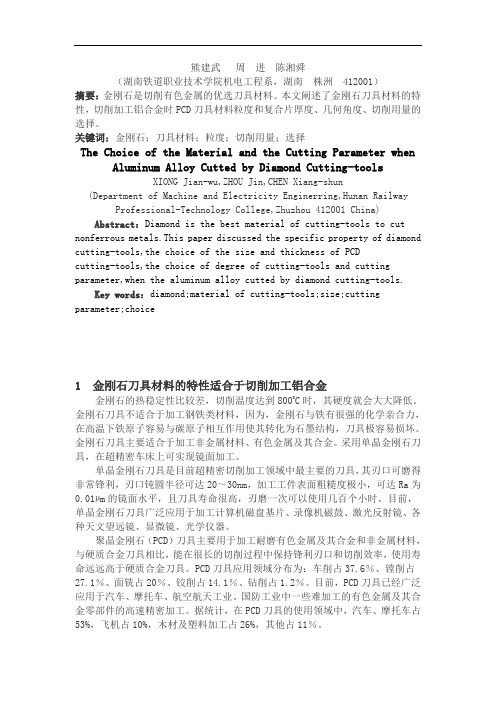
熊建武周进陈湘舜(湖南铁道职业技术学院机电工程系,湖南株洲 412001)摘要:金刚石是切削有色金属的优选刀具材料。
本文阐述了金刚石刀具材料的特性,切削加工铝合金时PCD刀具材料粒度和复合片厚度、几何角度、切削用量的选择。
关键词:金刚石;刀具材料;粒度;切削用量;选择The Choice of the Material and the Cutting Parameter when Aluminum Alloy Cutted by Diamond Cutting-toolsXIONG Jian-wu,ZHOU Jin,CHEN Xiang-shun (Department of Machine and Electricity Enginerring,Hunan Railway Professional-Technology College,Zhuzhou 412001 China) Abstract:Diamond is the best material of cutting-tools to cut nonferrous metals.This paper discussed the specific property of diamond cutting-tools,the choice of the size and thickness of PCDcutting-tools,the choice of degree of cutting-tools and cutting parameter,when the aluminum alloy cutted by diamond cutting-tools.Key words:diamond;material of cutting-tools;size;cutting parameter;choice1 金刚石刀具材料的特性适合于切削加工铝合金金刚石的热稳定性比较差,切削温度达到8000C时,其硬度就会大大降低。
铝合金切削参数
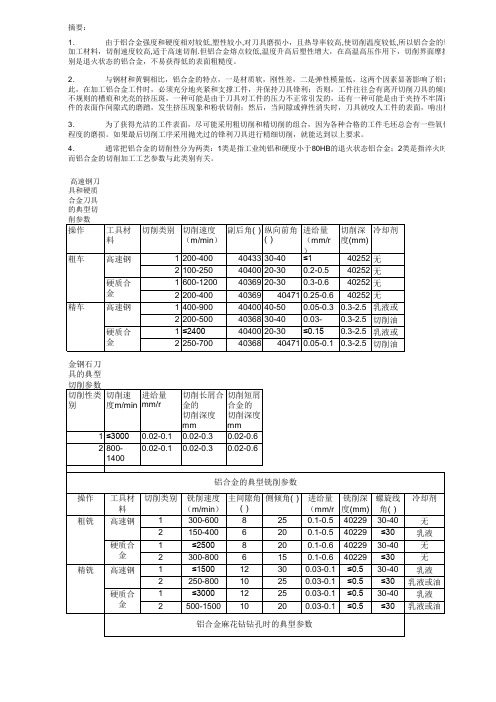
摘要:1.由于铝合金强度和硬度相对较低,塑性较小,对刀具磨损小,且热导率较高,使切削温度较低,所以铝合金的切削加工性较好,加工材料,切削速度较高,适于高速切削.但铝合金熔点较低,温度升高后塑性增大,在高温高压作用下,切削界面摩擦力很大。
容易粘别是退火状态的铝合金,不易获得低的表面粗糙度。
2.与钢材和黄铜相比,铝合金的特点,一是材质软,刚性差,二是弹性模量低,这两个因素显著影响了铝合金的切削加工性此,在加工铝合金工件时,必须充分地夹紧和支撑工件,并保持刀具锋利;否则,工件往往会有离开切削刀具的倾向。
有时工件的表不规则的槽痕和光亮的挤压斑,一种可能是由于刀具对工件的压力不正常引发的,还有一种可能是由于夹持不牢固而引起振颤时,刀件的表面作间隙式的磨蹭,发生挤压现象和粉状切削;然后,当间隙或弹性消失时,刀具就咬人工件的表面,啃出槽痕。
3.为了获得光洁的工件表面,尽可能采用粗切削和精切削的组合,因为各种合格的工件毛坯总会有一些氧化层,致使刀具受程度的磨损。
如果最后切削工序采用抛光过的锋利刀具进行精细切削,就能达到以上要求。
4.通常把铝合金的切削性分为两类:1类是指工业纯铝和硬度小于80HB的退火状态铝合金;2类是指淬火时效状态的变形铝而铝合金的切削加工工艺参数与此类别有关。
高速钢刀具和硬质合金刀具的典型切金钢石刀具的典型铝合金攻螺纹前的钻孔的典铝合金的典型镗孔铝合金的典型铰孔注:冷却剂为煤油-松节油(5:4)混合物;或用约33°E 的矿物油,或优质油.干铰孔的质量不高合金的切削加工性较好,属于易界面摩擦力很大。
容易粘刀;特响了铝合金的切削加工性。
因具的倾向。
有时工件的表面出现不牢固而引起振颤时,刀具在工,啃出槽痕。
一些氧化层,致使刀具受到相当指淬火时效状态的变形铝合金。
m/r)5-40。
铝合金加工全参数

铝合金加工参数由于在加工过程中发现工件刀纹不致影响表面质量,查找了一些资料,作了一些摘要:1.由于铝合金强度和硬度相对较低,塑性较小,对刀具磨损小,且热导率较高,使切削温度较低,所以铝合金的切削加工性较好,属于易加工材料,切削速度较高,适于高速切削.但铝合金熔点较低,温度升高后塑性增大,在高温高压作用下,切削界面摩擦力很大。
容易粘刀;特别是退火状态的铝合金,不易获得低的表面粗糙度。
2.与钢材和黄铜相比,铝合金的特点,一是材质软,刚性差,二是弹性模量低,这两个因素显著影响了铝合金的切削加工性。
因此,在加工铝合金工件时,必须充分地夹紧和支撑工件,并保持刀具锋利;否则,工件往往会有离开切削刀具的倾向。
有时工件的表面出现不规则的槽痕和光亮的挤压斑,一种可能是由于刀具对工件的压力不正常引发的,还有一种可能是由于夹持不牢固而引起振颤时,刀具在工件的表面作间隙式的磨蹭,发生挤压现象和粉状切削;然后,当间隙或弹性消失时,刀具就咬人工件的表面,啃出槽痕。
3.为了获得光洁的工件表面,尽可能采用粗切削和精切削的组合,因为各种合格的工件毛坯总会有一些氧化层,致使刀具受到相当程度的磨损。
如果最后切削工序采用抛光过的锋利刀具进行精细切削,就能达到以上要求。
4.通常把铝合金的切削性分为两类:1类是指工业纯铝和硬度小于80HB的退火状态铝合金;2类是指淬火时效状态的变形铝合金。
而铝合金的切削加工工艺参数与此类别有关。
高速钢刀具和硬质合金刀具的典型切削参数操作工具材料切削类别切削速度(m/min)副后角(°)纵向前角(°)进给量(mm/r)切削深度(mm)冷却剂粗车高速钢12200-400100-2509-128-1030-4020-30≤10.2-0.53-153-15无无硬质合金12600-1200200-4007-107-1020-3010-200.3-0.60.25-0.63-153-15无无精车高速钢12400-900200-5008-107-940-5030-400.05-0.30.03-0.250.3-2.50.3-2.5乳液或切削油硬质合金12≤2400250-7008-107-920-3010-20≤0.150.05-0.10.3-2.50.3-2.5乳液或切削油金钢石刀具的典型切削参数切削性类别切削速度m/min进给量mm/r 切削长屑合金的切削深度mm切削短屑合金的切削深度mm1 2 ≤3000800-14000.02-0.10.02-0.10.02-0.30.02-0.30.02-0.60.02-0.6铝合金的典型铣削参数操作工具材料切削类别铣削速度(m/min)主间隙角(°)侧倾角(°)进给量(mm/r)铣削深度(mm)螺旋线角(°)冷却剂粗铣高速钢12300-600150-4008625200.1-0.50.1-0.52-202-2030-40≤30无乳液硬质合金12≤2500300-8008620150.1-0.60.1-0.62-202-2030-40≤30无无精铣高速钢12≤1500250-800121030250.03-0.10.03-0.1≤0.5≤0.530-40≤30乳液乳液或油硬质合金12≤3000500-1500121025200.03-0.10.03-0.1≤0.5≤0.530-40≤30乳液乳液或油铝合金麻花钻钻孔时的典型参数工具材料切削类别铣削速度(m/min)项角(°) 螺旋角(°)进给量(mm/r)副后角(°) 冷却剂高速钢12100-12080-10014012045-3035-200.02-0.50.02-0.517-1515乳液乳液硬质合金12200-300100-20013012025-1515-100.06-0.30.06-0.31212无无或乳液备注钻小孔宜用低速在薄板上钻孔,宜增大角度或用正项角钻钻小孔宜用小螺旋角钻小孔进刀量宜小在磨副后角时,应注意选择角度最好用乳液铝合金攻螺纹前的钻孔的典型参数标准螺纹M3 M3.5 M4 M4.5 M5 M6 M8 M10 M12 M14 M16 孔的直径/mm2.73.75 3.64.1 4.65.5 7.3 9.1 11 12.8 14.8 铝合金的典型镗孔参数工具工具材料铣削速度(m/min)进给量(mm/r)项角(°) 螺旋角(°) 副后角(°)冷却剂可换的镗刀高速钢硬质合金25-4060-1000.2-0.30.1-0.314012030-2020-1586乳液乳液试镗镗刀高速钢硬质合金25-4060-1000.2-0.30.1-0.3-------------------30-2020-1586乳液乳液扩孔镗刀高速钢硬质合金20-3050-700.3-0.60.2-0.560-12060-120-------------------66乳液乳液镗杆高速钢硬质合金25-4060-1000.05-0.60.05-0.6-------------------30-2020-151210无或乳液无或乳液铝合金的典型铰孔参数工具工具材料倒角(°) 导角铰速铰孔直径(mm)如下的进给量(mm/r)(°) (m/min)≤10 >10-25 >25-4>4手铰刀高速钢硬质合金45453-43-4----------------------------------------------------------------------------------------------------机绞刀高速钢硬质合金303010-2020-500.1-0.20.2-0.30.2-0.40.3-0.50.3-0.50.4-0.7.4-.8.5-1.0 偏差铰孔直径(mm)如下的允许偏差(mm/r)预钻孔直径尺寸不足高速钢硬质合金≤10 >10-25>25-40 >40≤0.20.06-0.10.1-0.30.1-0.20.1-0.30.1-0.30.2-0.50.2-0.4注:冷却剂为煤油-松节油(5:4)混合物;或用约33°E的矿物油, 或优质油.干铰孔的质量不高。
铝合金切削刀具加工参数分析与选用

冷加工
! ! !
!"##$%& ’(()*
刀! ! 具
! ! ! ! ! ! !
如车削、镗削加工小型铝合金零件时,可采用小尺 寸的钎焊硬质合金刀具,经整体刃磨后使用。主切削刃 参数应选择:前角 ! " # $% 左右,后角 " " # &&% ’ ()% ,刃 倾角 # * # )% ’ &)% ,主偏角 $ + # ,-% ’ .)% ,刀尖角 % + / .)% ,刀尖圆弧半径 + ! # )0 1 ’ &22。 如采用硬质合金铣刀进行铣削时,切削刃应保持锋 利,前刀面应抗粘接,排屑应流畅。有关切削刃参数选 择为:圆周刃径向前角 ! " %,% ,后角 " " %&)% 。立铣刀 螺旋角 &%1)% ,大的螺旋角可使圆周刃的实际切削前角 变大。用于粗加工的铣刀,在切削刃上开出分屑槽,或 将切削刃制造成波形刃都能使排屑更好,切削更顺畅, 效率更高。 ( ( ) 345 刀具! 一般而言, 345 刀片只制成单刃, 其结 构 形 式 和 几 何 参 数 符 合 67(),$ —&.8) 的 规 定。 345 刀具的刀尖刃口几何参数有如下几种情形:前角 ! " # )% 、&)% ,后 角 " " # ,% 、 &&% 、 ()% , 主 偏 角 $ + # ,-% 、 .)% , 刀 尖 圆 弧 半 径 + ! # )0 )-22、 )0 &22、 )0 (22、)0 922、)0 822、&0 (22,各 切 削 参 数 可 根 据 加工需求组合应用。 ( 1 ) 天然金刚石刀具! 天然金刚石刀具的切削刃有 四种基本几何形状,即尖刃、直刃、圆弧刃和多棱刃。 尖刃,在主切削刃和副切削刃之间有圆角,刀尖圆 弧半径 + ! 一般为 &0 ) ’ &0 822,主偏角 $ + # 9-% ,副偏角 $ + :# (% ,前角 ! " # 80 -% ,后角 " " # )% 。该形状切削刃的 刃磨和对刀比较方便,故应用最为广泛,但磨损后需要 立即重磨。 直刃即修光刃,长度为 )0 &8 ’ )0 (-22。必须与工 件表面平行或形成极小的副偏角,其刃磨和对刀比较困 难,但加工表面粗糙度值较小,多用于铝合金零件表面 质量要求较高的表面加工。 圆弧刃刃口圆弧半径为 (0 -22,该形状切削刃的对 刀调整比较方便,但刃磨最困难,多用于对刀调整比较 困难的场合。具有这种切削刃的刀具在切削时被切金属 的切削区变形程度较大,因而工件的表面粗糙度值较 大。 多棱刃,具有该刃形的刀具切削时,切削层残留面 高度的实际值和理论值较接近,切削区变形程度较小, 因而工件表面质量较好。但其刃磨工作量较大,故其应 用并不广泛。
加工6061铝合金切削参数

加工6061铝合金切削参数6061铝合金是一种常用的高强度、耐蚀性好的铝合金材料,适用于各种加工领域,如航空航天、汽车制造、建筑等。
在进行切削加工时,合理选择切削参数可以提高加工效率和质量。
本文将从切削速度、进给量、切削深度等方面介绍6061铝合金的切削参数。
首先,切削速度是切削加工中最重要的参数之一、切削速度的选择应根据具体的刀具、切削条件和工件材料来确定。
一般来说,6061铝合金的切削速度范围为100~200 m/min。
较高的切削速度可以提高加工效率,但要注意控制切削温度,避免过高的切削温度导致刀具磨损和工件变形。
其次,进给量也是切削加工中需要关注的参数之一、进给量的选择应考虑到切削力、表面质量和切削效率等因素。
对于6061铝合金来说,一般的进给量范围为0.1~0.3 mm/r。
较大的进给量可以提高加工效率,但要注意避免过大的进给量导致切削力过大和表面质量下降。
此外,切削深度也是切削加工中需要重视的参数之一、切削深度是指每次切削时刀具切入工件的深度。
对于6061铝合金来说,一般的切削深度范围为0.5~5 mm。
切削深度的选择应根据刀具和工件的特性来确定,较大的切削深度可以提高加工效率,但要注意避免过大的切削深度导致切削力过大、刀具磨损和工件变形。
此外,刀具的选择也是影响切削参数的关键因素之一、对于6061铝合金的切削加工,通常可以选择高硬度、高刚性的硬质合金刀具。
硬质合金刀具可以更好地抵抗6061铝合金的磨损和热疲劳。
最后,还要考虑切削润滑液的选择。
切削润滑液可以降低切削温度、减小切削力和延长刀具寿命。
对于6061铝合金的切削加工,可以选择液体切削润滑剂或气体切削润滑剂。
液体切削润滑剂常用的有水溶性切削液和油类切削液,气体切削润滑剂常用的有空气、湿空气和氧气等。
总之,要合理选择6061铝合金的切削参数,需要综合考虑切削速度、进给量、切削深度、刀具选择和切削润滑液等因素。
通过合理选择切削参数,可以提高加工效率和质量,延长刀具寿命,减少切削成本。
加工6061铝合金切削参数
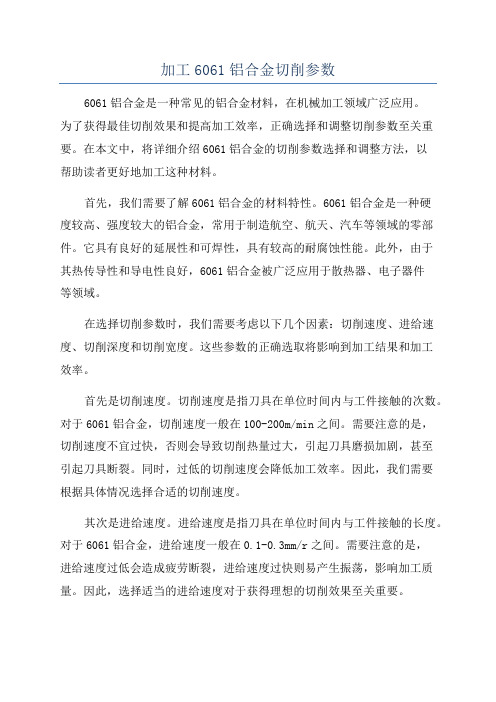
加工6061铝合金切削参数6061铝合金是一种常见的铝合金材料,在机械加工领域广泛应用。
为了获得最佳切削效果和提高加工效率,正确选择和调整切削参数至关重要。
在本文中,将详细介绍6061铝合金的切削参数选择和调整方法,以帮助读者更好地加工这种材料。
首先,我们需要了解6061铝合金的材料特性。
6061铝合金是一种硬度较高、强度较大的铝合金,常用于制造航空、航天、汽车等领域的零部件。
它具有良好的延展性和可焊性,具有较高的耐腐蚀性能。
此外,由于其热传导性和导电性良好,6061铝合金被广泛应用于散热器、电子器件等领域。
在选择切削参数时,我们需要考虑以下几个因素:切削速度、进给速度、切削深度和切削宽度。
这些参数的正确选取将影响到加工结果和加工效率。
首先是切削速度。
切削速度是指刀具在单位时间内与工件接触的次数。
对于6061铝合金,切削速度一般在100-200m/min之间。
需要注意的是,切削速度不宜过快,否则会导致切削热量过大,引起刀具磨损加剧,甚至引起刀具断裂。
同时,过低的切削速度会降低加工效率。
因此,我们需要根据具体情况选择合适的切削速度。
其次是进给速度。
进给速度是指刀具在单位时间内与工件接触的长度。
对于6061铝合金,进给速度一般在0.1-0.3mm/r之间。
需要注意的是,进给速度过低会造成疲劳断裂,进给速度过快则易产生振荡,影响加工质量。
因此,选择适当的进给速度对于获得理想的切削效果至关重要。
切削深度是指切削刀具在每次进给中切削下来的长度。
对于6061铝合金,切削深度一般在0.5-1.0mm之间。
需要注意的是,切削深度过大容易造成刀具振动,切削深度过小则会降低加工效率。
因此,选择适当的切削深度能够有效提高加工质量及效率。
最后是切削宽度。
切削宽度是指切削刀具与工件外圆或表面之间的距离。
对于6061铝合金,切削宽度一般在0.2-0.5mm之间。
需要注意的是,切削宽度过大会增加切削力,切削宽度过小则会降低加工效率。
压铸铝合金材料加工问题的分析
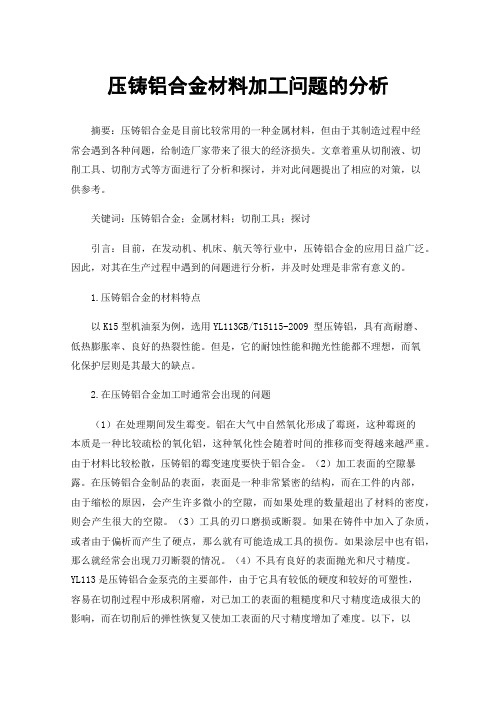
压铸铝合金材料加工问题的分析摘要:压铸铝合金是目前比较常用的一种金属材料,但由于其制造过程中经常会遇到各种问题,给制造厂家带来了很大的经济损失。
文章着重从切削液、切削工具、切削方式等方面进行了分析和探讨,并对此问题提出了相应的对策,以供参考。
关键词:压铸铝合金;金属材料;切削工具;探讨引言:目前,在发动机、机床、航天等行业中,压铸铝合金的应用日益广泛。
因此,对其在生产过程中遇到的问题进行分析,并及时处理是非常有意义的。
1.压铸铝合金的材料特点以K15型机油泵为例,选用YL113GB/T15115-2009 型压铸铝,具有高耐磨、低热膨胀率、良好的热裂性能。
但是,它的耐蚀性能和抛光性能都不理想,而氧化保护层则是其最大的缺点。
2.在压铸铝合金加工时通常会出现的问题(1)在处理期间发生霉变。
铝在大气中自然氧化形成了霉斑,这种霉斑的本质是一种比较疏松的氧化铝,这种氧化性会随着时间的推移而变得越来越严重。
由于材料比较松散,压铸铝的霉变速度要快于铝合金。
(2)加工表面的空隙暴露。
在压铸铝合金制品的表面,表面是一种非常紧密的结构,而在工件的内部,由于缩松的原因,会产生许多微小的空隙,而如果处理的数量超出了材料的密度,则会产生很大的空隙。
(3)工具的刃口磨损或断裂。
如果在铸件中加入了杂质,或者由于偏析而产生了硬点,那么就有可能造成工具的损伤。
如果涂层中也有铝,那么就经常会出现刀刃断裂的情况。
(4)不具有良好的表面抛光和尺寸精度。
YL113是压铸铝合金泵壳的主要部件,由于它具有较低的硬度和较好的可塑性,容易在切削过程中形成积屑瘤,对已加工的表面的粗糙度和尺寸精度造成很大的影响,而在切削后的弹性恢复又使加工表面的尺寸精度增加了难度。
以下,以K15机油泵本体加工工艺中出现的问题为例,阐述了在加工K1、K2的情况下,无论单孔的直径大小,还是两孔的定位度,均存在着较大的难度,因此必须寻找合适的解决方案。
3.压铸铝合金的种类铝锰合金是目前国内应用的主要材料,相对于其它金属而言,铝锰合金制作的刀具寿命更长,更容易被切割,在常温下,铝合金的耐蚀性是最好的。
m2丝锥加工铝合金的加工参数

m2丝锥加工铝合金的加工参数
加工铝合金使用M2丝锥的加工参数如下:
1. 速度:一般情况下,建议使用中速或高速进行加工,以确保加工效率和表面质量。
速度可以根据具体情况进行调整,一般在1000-2000转/分钟之间。
2. 进给量:进给量是指每分钟丝锥进给的距离。
对于铝合金,建议使用较小的进给量,以避免过度切削和过热。
进给量可以根据具体情况进行调整,一般在0.05-0.2毫米/转之间。
3. 冷却润滑剂:在加工铝合金时,应使用适当的冷却润滑剂来降低切削温度和减少切削力。
常用的冷却润滑剂包括切削液和切削蜡。
冷却润滑剂可以提高加工质量和工具寿命。
4. 切削深度:切削深度是指丝锥每次进给切削的深度。
对于铝合金,建议使用较小的切削深度,以避免过度切削和过热。
切削深度可以根据具体情况进行调整,一般在0.1-0.5毫米之间。
5. 切削角度:切削角度是指丝锥切削刃的倾斜角度。
对于铝合金,建议使用较小的切削角度,以减少切削力和切削温度。
一般来说,切削角度为5-10度之间。
需要注意的是,以上的加工参数仅供参考,具体的加工参数还需要根据具体的铝合金材料、丝锥规格和加工要求进行调整。
在实际加
工过程中,应根据试切实验和经验来确定最佳的加工参数。