Mountingbrackethavingflexiblelockingarm.
高精度数字压力开关ISE70G ISE75G ISE76G ISE77G产品说明书

Instruction ManualHigh Precision Digital Pressure Switch ISE70G / ISE75G / ISE76G / ISE77GThe intended use of the pressure switch is to measure the pressure of fluid and to provide an output signal.These safety instructions are intended to prevent hazardous situations and/or equipment damage. These instructions indicate the level of potential hazard with the labels of “Caution,” “Warning” or “Danger.”They are all important notes for safety and must be followed in addition to International Standards (ISO/IEC) *1), and other safety regulations. *1)ISO 4414: Pneumatic fluid power - General rules relating to systems. ISO 4413: Hydraulic fluid power - General rules relating to systems.IEC 60204-1: Safety of machinery - Electrical equipment of machines. (Part 1: General requirements)ISO 10218-1: Manipulating industrial robots -Safety. etc.∙ Refer to product catalogue, Operation Manual and Handling Precautions for SMC Products for additional information. ∙ Keep this manual in a safe place for future reference.CautionCaution indicates a hazard with a low level of risk which, ifnot avoided, could result in minor or moderate injury.WarningWarning indicates a hazard with a medium level of riskwhich, if not avoided, could result in death or serious injury.DangerDanger indicates a hazard with a high level of risk which, ifnot avoided, will result in death or serious injury.Warning∙ Always ensure compliance with relevant safety laws and standards.∙ All work must be carried out in a safe manner by a qualified person in compliance with applicable national regulations.∙ This product is class A equipment intended for use in an industrial environment. There may be potential difficulties in ensuring electromagnetic compatibility in other environments due to conducted or radiated disturbances.∙ Do not disassemble, modify (including changing the printed circuit board) or repair. An injury or failure can result.∙ Do not operate the product outside of the specifications. Do not use for flammable or harmful fluids.Fire, malfunction or damage to the product can result.∙ Do not operate in an atmosphere containing flammable or explosive gases.Fire or an explosion can result.This product is not designed to be explosion proof. ∙ If using the product in an interlocking circuit:Provide a double interlocking system, for example a mechanical system.∙ Check the product for correct operation.Otherwise malfunction can result, causing an accident.∙ Do not touch terminals and connectors while the power is on. Otherwise electric shock, malfunction or product damage can result. ∙ Refer to the operation manual on the SMC website (URL: https:// ) for more safety instructions.2 Specifications2.1 General specifications2.2 IO-Link specifications IO-Link type Device IO-Link versionV1.1Communication speed COM2 (38.4 kbps) Min. cycle time2.3 msProcess data lengthInput Data: 2 byte, Output Data: 0 byte On request data comms. Available Data storage function Available Event function Available Vendor ID 131 (0x0083)Device IDISE70G-*-L2-* : 309 (0x0135) ISE75G-*-L2-* : 320 (0x0140) ISE76G-*-L2-* : 321 (0x0141) ISE77G-*-L2-* : 322 (0x0142)Special products (-X) might have specifications different from those shown in this section. Contact SMC for specific drawings.3.13.2 Display4 Installation4.1 InstallationWarning∙ Do not install the product unless the safety instructions have been read and understood. 4.2 EnvironmentWarning∙ Do not install in a location subject to vibration or impact in excess of the product’s specifications.∙ Do not mount in a location exposed to radiant heat that would result in temperatures in excess of the product specification.4.3 Mounting with BracketMount the bracket to the product using mounting screws supplied (M4x6 L (2 pcs)) then set the product in the required position.Tighten the bracket mounting screws to a torque of 0.76 ±0.1 N•m. Bracket A (Part No. ZS-50-A) Bracket B (Part No. ZS-50-B)4.44.5 PipingCaution∙ Before connecting piping make sure to clean up chips, cutting oil, dust etc.∙ After hand tightening, tighten the fitting using a spanner on the flat surfaces of the fitting (24 mm A/F).∙ When tightening, do not hold the upper part of the product (display) with the spanner.∙ For Rc1/4 and NPT1/4 threads the tightening torque must be 8 to 12 N•m. For G1/4 thread the tightening torque must be 4 to 5 N•m.4.6 Display Rotation∙ During installation, the upper part (display) of the product can be rotated by 336°. Take care as rotating the display with excessive force will damage the end stopper.4.7 Wiring∙ Connections should be made with the power supply turned off.∙ Use a separate route for the product wiring and any power or high voltage wiring. Otherwise, malfunction may result due to noise.∙ If a commercially available switching power supply is used, be sure to ground the frame ground (FG) terminal. If a switching power supply is connected, noise will be superimposed and will not meet the product specifications.Insert a noise filter such as a line noise filter/ferrite between the switching power supplies or change the switching power supply to the series power supply.ORIGINAL INSTRUCTIONSSpanneUpper part of productProduct No. ISE70G ISE75GISE76GISE77GApplicable fluid Fluids and Gases (non corrosive)P r e s s u r eRated pressure range 0 to 1.00 MPa 0 to 2.00 MPa 0 to 5.00 MPa 0 to 10.0 MPa Display / set pressurerange-0.105 to 1.050MPa-0.105 to 2.100 MPa -0.25 to 5.25 MPa -0.50 to10.50 MPa Minimum setting unit 0.001 MPa 0.01 MPa Proof pressure 3.0 MPa 5.0 MPa 12.5 MPa 30 MPaE l e c t r i c a lPower supply as switch output device 12 to 24 VDC ±10% with 10% Voltage ripple or less (p-p) Power supply as IO-Link device 18 to 30 VDC, including 10%voltage ripple (p-p)Current consumption 35 mA or less Protection Polarity protectionA c c u r a c yDisplay accuracy ±2% F.S.±1 digit (at ambient 25±3 o C)Repeatability±0.5% F.S.Temp. characteristics(25 o C standard) ±3% F.S.±5% F.S.S w i t c h o u t p u tOutput type NPN or PNP open collector output. Output mode Hysteresis mode, window comparator mode, error or switch output OFF.Switch operation Normal or reversed output.Max. Load current 80 mA Max. Applied voltage 30 V (NPN output)Internal voltage drop (Residual voltage) 1.5 V or less (Load current 80 mA) Delay time2.0 ms or less (for anti-chatter function:variable at 0 to 60 s / 0.01 step)Hysteresis or Window comparator mode Variable from 0 Short circuit protection ProvidedD i s p l a yUnits MPa, kPa, kgf/cm 2, bar, psiDisplay type LCDNumber of displays 3-screen display (Main display,sub display x 2)Display colour Main display: Red/Green, Sub display: OrangeNumber of display digitsMain display: 4 digits (7-segments) Sub display: 4 digits (Upper 1 digit 11-segments, 7-segments for other) Operation lightLED is ON when switch output is ON(OUT1, OUT2: Orange) Digital filterVariable from 0 to 30 s / 0.01 stepOrifice(Part no. ZS-48-A)Tighten the orifice to a torque of 1.5 ±0.1 N•m.Power supply / Output connector (M12 plug)Fitting(24 mm across flats)Part DescriptionOperation Light Displays the switch operating condition Main display Displays pressure measurement values and error codes (2 colour display). Sub display (left) Displays items (Orange)Sub display (right) Displays set values, peak and bottom values. (Orange)UP button Increases mode and ON/OFF set values. DOWN button Decreases mode and ON/OFF set values. SET button Changes the mode and confirms the settings. IO-Link status indicator light Displays OUT1 output communication status (SIO mode, start-up mode, operation mode) and the presence of communication data.Product code is displayed for 3 seconds∙ How to use connectorAlign the cable connector key groove with the product connector key to insert and rotate the knurled part of the connector.Connect the wires of the lead wire to the M12 connector as shown below. M12 Connector (code A)1) When used as a switch output device No. Name Colour Function 1 DC(+) Brown 12 to 24 VDC 2 OUT2 White Switch output 2 3 DC(-) Blue 0 V 4 OUT1 Black Switch output 12) When used as an IO-Link device No. Name Colour Function 1 L+ Brown 18 to 30 VDC 2 DO White Switch output 2 3 L- Blue 0 V4C/QBlackCommunication data (IO-Link) / Switch output 1 (SIO)Power is suppliedDefault settingsWhen the pressure exceeds the set value, the switch will be turned ON. When the pressure falls below the set value by the amount of hysteresis or more, the switch will be turned OFF.The default setting is to turn ON the pressure switch when the pressure reaches the centre of the atmospheric pressure and upper limit of the rated pressure range. If this condition is acceptable, then keep these settings.∙ 3 step setting mode (hysteresis mode)In 3 step setting mode, the set value (P_1 or n_1) and hysteresis (H_1) can be changed. Set the items on the sub display (set value or hysteresis) using the UP and DOWN button. When changing the set value, follow the operation below. The hysteresis setting can be changed in the same way.(1) Press the SET button once whenthe item to be changed is shown on the sub display. The set value on the sub display will start flashing.(2) Press the UP or DOWN button tochange the set value.When the UP and DOWN buttons are pressed and held simultaneously for 1 second or longer, the set value is displayed as [- - -], and the set value will be the same as the current pressure value automatically (snap shot function).Afterwards, it is possible to adjust the value by pressing the UP or DOWN button.(3) Press the SET button to complete the setting.The Pressure switch turns on within a set pressure range (from P1L to P1H) during window comparator mode. Set P1L, the lower limit of the switch operation, and P1H, the upper limit of the switch operation and WH1 (hysteresis) following the instructions given above.(When reversed output is selected, the sub display (left) will indicate [n1L] and [n1H].)∙ Set OUT2 in the same way.∙ Setting of the normal/reverse output switching and hysteresis/window comparator mode switching are performed using the function selection mode [F 1] OUT1 setting and [F 2] OUT2 setting.8 Simple Setting mode(1) Press and hold the SET button between 1 and 3 seconds inmeasurement mode. [SEt] is displayed on the main display. When the button is released while in the [SEt] display, the current pressure value is displayed on the main display, [P_1] or [n_1] is displayed on the sub display (left), and the set value is displayed on the sub display (right) (Flashing).(2) Change the set value using the UP and DOWN button,and press the SET button to set the value. Then, the setting moves to hysteresis setting. (The snap shot function can be used).(3) Change the set value with the UP or DOWN button,to the delay time of the switch output. (The snap shot function can be used).(4) The delay time of the switch output can be selected by pressing theUP or DOWN button at the ON and OFF point of the switch output. Delay time setting can prevent the output from chattering.The delay time can be set in the range 0.00 to 60.00 sec. in 0.01 sec. increments.(5) Press the SET button for less than 2 seconds to complete the OUT1setting. [P_2] or [n_2] is displayed on the sub screen (left). Continue with setting OUT2.Press and hold the SET button for 2 seconds or longer to complete the setting. The product will return to measurement mode. ∙ In window comparator mode, set P1L, the lower limit of the switch operation, and P1H, the upper limit of the switch operation, WH1 (hysteresis) and dtH / dtL (delay time) following the instructions given above. (when reversed output is selected, the sub display (left) will indicate [n1L] and [n1H]). ∙ Set OUT2 in the same way.9 Function Selection modeIn measurement mode, press the SET button between 3 and 5 seconds to display [F 0]. Select to display the function to be changed [F□□].Press and hold the SET button for 2 seconds or longer in function selection mode to return to measurement mode.*: Some products do not have all of the functions. If a function is not available or selected due to configuration of other functions, [- - -] is displayed on the sub display.10 Other Settings∙ Peak / Bottom value displayThe max. (min.) pressure from when power is supplied is detected and monitored. The value can be displayed on the sub display by pressing the UP or DOWN button in measurement mode. ∙ Snap Shot functionThe current pressure value can be stored to the switch output ON/OFF set point. When the set value and hysteresis are set, press the UP and DOWN button for 1 s or longer simultaneously. Then the set value of the sub display (right) shows [---], and the values corresponding to the current pressure values are automatically displayed. ∙ Zero-clear functionIn measurement mode, when the UP and DOWN buttons are pressed for 1 s or longer simultaneously, the main display shows [---] and then will reset to zero. The display will return to measurement mode automatically. ∙ Refer to the operation manual on the SMC website (URL: https// ) for further details of how to set these and other functions.11 Maintenance11.1 General MaintenanceCaution∙ Not following proper maintenance procedures could cause the product to malfunction and lead to equipment damage.∙ If handled improperly, compressed air can be dangerous.∙ Maintenance of pneumatic systems should be performed only by qualified personnel.∙ Before performing maintenance, turn off the power supply and be sure to cut off the supply pressure. Confirm that the air is released to atmosphere.∙ After installation and maintenance, apply operating pressure and power to the equipment and perform appropriate functional and leakage tests to make sure the equipment is installed correctly.How to reset the product after power cut or forcible de-energizing The setting of the product will be retained as it was before a power cut or de-energizing. The output condition is also basically recovered to that before a power cut or de-energizing, but may change depending on the operating environment.Therefore, check the safety of the whole installation before operating the product. If the installation is using accurate control, wait until the product has warmed up (approximately 10 to 15 minutes).12 Troubleshooting12.1 Error Indication If the error cannot be reset after the above measures are taken, or errorsother than the above are displayed, please contact SMC.13 Limitations of Use13.1 Limited warranty and Disclaimer/Compliance Requirements Refer to Handling Precautions for SMC Products.14 Product DisposalThis product shall not be disposed of as municipal waste. Check your local regulations and guidelines to dispose this product correctly, in order to reduce the impact on human health and the environment.15 ContactsRefer to or www.smc.eu for your local distributor/importer.URL : https:// (Global) https://www.smc.eu (Europe) SMC Corporation, 4-14-1, Sotokanda, Chiyoda-ku, Tokyo 101-0021, JapanSpecifications are subject to change without prior notice from the manufacturer. © 2021 SMC Corporation All Rights Reserved. Template DKP50047-F-085MPress the SET button once Press the SET button for 1 to 3 s Press the SET button for 3 to 5 s [3 step setting mode]Set value orhysteresis[Simple setting mode]Set value, hysteresis and delay time[Function selection mode]Change the function settings[Other settings]∙Zero clear ∙Snap lock ∙Key Lock。
ZB-TFQ12 迪欧空调吸尘器维护手册说明书

Installation and Maintenance ManualCompact Vacuum UnitSeries ZBThis manual contains essential information for the protection of users andothers from possible injury and/or equipment damage.∙Read this manual before using the product, to ensure correct handling,and read the manuals of related apparatus before use.∙Keep this manual in a safe place for future reference.∙ These instructions indicate the level of potential hazard by label of“Caution”, “Warning” or “Danger”, followed by important safety informationwhich must be carefully followed.∙To ensure safety of personnel and equipment the safety instructions inthis manual and the product catalogue must be observed, along with otherrelevant safety practices.CautionIndicates a hazard with a low level of risk, which ifnot avoided, could result in minor or moderateinjury.WarningIndicates a hazard with a medium level of risk,which if not avoided, could result in death orserious injury.DangerIndicates a hazard with a high level of risk, whichif not avoided, will result in death or seriousinjury.∙ The compatibility of pneumatic equipment is the responsibility of theperson who designs the pneumatic system or decides its specifications.Since the products specified here can be used in various operatingconditions, their compatibility with the specific pneumatic system must bebased on specifications or after analysis and/or tests to meet specificrequirements.∙Only trained personnel should operate pneumatically operatedmachinery and equipment.Compressed air can be dangerous if an operator is unfamiliar with it.Assembly, handling or repair of pneumatic systems should be performedby trained and experienced personnel.∙Do not service machinery/equipment or attempt to removecomponents until safety is confirmed.1) Inspection and maintenance of machinery/equipment should only beperformed after confirmation of safe locked-out control positions.2) When equipment is to be removed, confirm the safety process asmentioned above. Switch off air and electrical supplies and exhaust allresidual compressed air in the system.3) Before machinery/equipment is re-started, ensure all safety measuresto prevent sudden movement of cylinders etc. (Supply air into the systemgradually to create back pressure, i.e. incorporate a soft-start valve).∙Do not use this product outside of the specifications. Contact SMCif it is to be used in any of the following conditions:1) Conditions and environments beyond the given specifications, or if theproduct is to be used outdoors.2) Installations in conjunction with atomic energy, railway, air navigation,vehicles, medical equipment, food and beverage, recreation equipment,emergency stop circuits, press applications, or safety equipment.3) An application which has the possibility of having negative effects onpeople, property, or animals, requiring special safety analysis.∙Ensure that the air supply system is filtered to 5 microns.2 SpecificationsRefer to the operation manual for this product.3 Installation3.1 Installation∙Do not install the product unless the safety instructions have been readand understood.Note the following points when mounting and installing the product.■ Common Precautions for Mounting and Installation1) It is necessary to perform maintenance and replacement of the suctionfilter regularly to maintain the proper operation of the ejector and vacuumpump system. Ensure sufficient space for maintenance work wheninstalling the product.2) The filter case of this product is integrated with the vacuum piping.Secure sufficient space and some length of the tube with the piping(tubes) on the vacuum side so that the case can be removed.3) Do not fix the piping on the vacuum side such that a load is alwaysapplied to the filter case in a bending or pulling direction. This candamage the body and/or the filter case.4) If the ejector (silencer exhaust specification) is operated in a dustyenvironment or if there is dust on the surface of the workpieces, it cancause clogging of the silencing material as well as the suction filter dueto dust being sucked in. Secure space necessary for the maintenancecheck and replacement of the silencer when the ejector performancedecreases.5) Keep the ambient temperature of the product between -5 and 50o C. Inenvironments such as inside a panel where heat radiation efficiency ispoor, the ambient temperature will rise due to the heat generation of thecoil of the solenoid valve, causing malfunction.6) When handling the product, do not lift it by the lead wires or cables ofthe solenoid valve, pressure sensor or pressure switch for vacuum.Otherwise, it can cause vacuum leakage or broken wire or damage tothe product.■Mounting and Installation of Single Unit Ejectors1) The tightening torque for mounting the product to the wall should bebetween 0.075 and 0.096Nm. Using excessive torque may causedamage to the body. (The width of the product is 10mm.)2) Do not block the exhaust port of the ejector. The ejector of the singleunit specification has only one exhaust port on one side. If the ejector ismounted with the exhaust port facing a wall, secure a space of at least1mm between the product and the wall using a spacer, shim orequivalent.(3) Secure the space for connecting piping on the supply side wheninstalling the product.Mounting with a bracket for single unit (Width of the bracket: 1mm)3 Installation (cont.)Mounting on the wall and the port released to the atmosphere at the bottomPart No. of the bracket for single unit: ZB1-BK1-A (Provided with 2mounting screws M2x14 with washer and 2 hexagon nuts M2.)Recommended tube fittings for the set-up shown above: KQ2H04-M5N,KQ2L04-M5N, KQ2W04-M5N.■Mounting and Installation of an Ejector of Manifold SpecificationWhen mounting the manifold base, it is recommended to mount a spaceron the filter case side in order to make it easier to perform maintenanceservice of the filter element. (Width of the manifold base mounting hole:11.6mm)3.2 Environment∙Do not use in an environment where corrosive gases, chemicals, saltwater or steam are present.∙Do not use in an explosive atmosphere.∙Do not expose to direct sunlight. Use a suitable protective cover.∙Do not install in a location subject to vibration or impact. Check the productspecifications.∙Do not mount in a location exposed to radiant heat.3.3 Piping■Piping for Air Pressure Supply and Vacuum Pressure Supply1) Preparation before pipingBefore piping, perform air blow (flushing) or cleaning to remove anycutting chips, cutting oil, dust, etc. from the piping.2) Wrapping of pipe tapeWhen installing piping or a tube fitting into a port, prevent cuttingchips and sealant material from getting inside the product.If a sealant tape is used,leave 1 thread exposedat the end of threads.3) When connecting tubing, consider factors such as changes in thetubing length due to pressure, and allow a sufficient margin.Otherwise, it can damage the fitting and cause the tube to come off.Refer to Fittings & Tubing Precautions from 1 to 4 shown in BestPneumatics 6 on SMC’s website (URL ) forthe recommended piping conditions.3 Installation (cont.)■Piping to the Manifold Base1) For the PV port of the manifold base, use a tube fitting whose maximumbore size of the outside dimension is smaller than 12mm.Otherwise, the exterior of the fitting will interfere with the manifold baseinstallation face.Recommended tube fittings:KQ2S06-01□S, KQ2S04-01□S2) Follow the tightening instructions shown below for each thread.1/8 (PV port) : 7 to 9NmTightening torque is 3 to 5N as a guide.M5 (PV, PD port): After tightening by hand, increase the tightening byabout 1/6 turn with a tightening tool.Tightening torque is 1 to 1.5N as a guide.3) When mounting or removing the tube fitting,etc. to the manifold base,hold the manifold base hold the manifold base with a spanner.If the ejector/vacuum pump system is held, it may cause air leakage ordamage to the product.■Piping to the Vacuum (V) Port1) Allow a sufficient margin of tube length when piping, in order to preventtwisting, tensile, moment loads, vibration or impact being applied to thetubes and fittings.This can cause damage to the tube fittings and crushing, bursting ordisconnection of tubing.2) Piping to the product is assumed to be static piping.If the tube moves, it may become worn, elongated or torn due to tensileforces, or disconnected from the fitting. Ensure the tube is in a staticcondition at all times before using.3) Prevent the connected tube from being rotated.If the fittings are used in this way, the fitting may be broken.4) Do not lift the product by holding the piping after the tube is connected tothe vacuum (V) port.Otherwise, the filter case and/or the One-touch tube fitting will bedamaged.4 Settings■Manual OverrideVacuum for the ejector or the vacuum pump system is generated orreleased by manual operation.Use the manual override after confirming that there is no danger.When operating the locking type with a screwdriver, turn it gently using awatchmaker’s screwdriver. (Torque: Less than 0.1Nm)Sealant tapeLeave 1 threadexposed.Wrap this way.Non-locking push type (Tool required)It is turned ON by pressing the manual override allthe way in the direction indicated by the arrow (↓),and it is turned OFF by releasing it.11.65 Maintenance■Construction of ZB seriesManifold / With pressure sensorSingle unit / With vacuum pressure switch■ComponentsThe components from (7) to (15) are available as service parts.■Implement the maintenance and check shown below in order to use the ejector and the vacuum system safely and in an appropriate way for a long period of time.1) Maintenance should be performed according to the procedure indicated in the Operation Manual.Improper handling can cause damage and malfunction of equipment and machinery.2) Maintenance workCompressed air can be dangerous when handled incorrectly. Therefore, in addition to observing the product specifications, replacement of elements and other maintenance activities should be performed by personnel with sufficient knowledge and experience pertaining to pneumatic equipment. 3) DrainingRemove condensate from air filters and mist separators regularly. If the collected drainage is drained to the downstream side, it can stick inside of the product, causing operation failure and failure to reach the specified vacuum pressure.4) Replace the filter element built into the ejector and the vacuum pump system and the silencer regularly. (Refer to the replacement procedure below.)It is recommended to replace the filter element and the silencer when the pressure drop reaches 5kPa as a guideline. The replacement cycle varies depending on the operating conditions, operating environment and supply air quality.However, if there is a vacuum pressure drop and/or delay in the vacuum (adsorption) response time which causes problem with the settings during operation, stop the operation of the product and replace the element regardless of the above mentioned replacement guideline. 5) Operation in an environment where there is a lot of dust in the airThe processing capacity of the filter element built into the product may be insufficient. It is recommended to use SMC's air suction filter (ZFA, ZFB, ZFC series) in order to avoid problems beforehand. 6) Check before and after the maintenance workWhen the product is to be removed, turn off the power supply, and be sure to cut off the supply pressure and exhaust the compressed air. Confirm that the air is released to atmosphere.When mounting the product after the maintenance work, supplycompressed air, connect to the power, check if it functions properly and have a leakage inspection. Especially for the latching type supply valve, be sure to check that the supply valve is OFF in the initial condition because it is possible that it is ON due to vibration.7) Do not disassemble or modify the product, other than the replacement parts specified in this manual.■Spare parts listNo. Description [Application]ModelRemarks (7) Supply valve[Generates vacuum.] ZB1-VQ110U-□□□ N.C. ZB1-VQ110L-□□□ Latching ZB1-VQ120U-□□□ N.C. (8) Release valve [Releases vacuum] ZB1-VQ110-□□□ N.C. (9) V-port Assembly [For vacuum port]ZB1-VPN3-□-A (10)Exchange the One-touch tube fittings with the port plugs KJ □□-C1(11)Filter element[For suction filter]ZB1-FE3-A(12) Silencer [For silencer] ZB1-SE1-A (13) Pressure sensor assemblyZB1-PS □-A (14)Pressure switch assembly forvacuumZB1-ZS □□□□-A(15) Manifold base assemblyZZB □-□□□ ■Replacement Procedure for Filter Element- Hold the V port assembly with your fingers, and turn it45 degrees in the counter-clockwise direction and pull it out.For the straight type One-touch tube fitting, it can be removed by using a hexagon wrench (width across flats: 2).- Remove the filter element from the removed filter case, and mount a new filter element securely to the back of the case. (See Fig. to the right) - Confirm that the filter case gasket is not displaced and that it has no foreign matter stuck to it.- Insert the V port assembly into the ejector/vacuum pump system (Fig. to the right), press it slightly and turn it for approximately 45 degrees in the clockwise direction until it stops. (See Fig. to the right)(Mount the V port assembly in the direction specified in the figure. If the convex side is mounted downward, it will interfere with the floor when the element is mounted on its bottom surface, causing breakage of the filter case and the element.)■Replacement procedure for silencer*- Turn the body upside down. Apply a watchmaker’s screw driver or your finger to the notch, and slide the silencer cover in the direction indicated by the △ mark.- When it clicks, the hook is disconnected. Put your Pry up and remove part A, cover.- Remove the silencer by using a watchmaker’s screw driver.- Insert a new silencer, and mount the cover by the reverse procedure of the disassembly procedure for reassembly.(When replacing the silencer, the metal diffuser can be seen. This part is important to the function. Do not touch or apply force to the metal diffuser when replacing the silencer.)* For vacuum pump system, the silencer is not built in.■Replacement Procedure for Solenoid Valves (supply valve, release valve)-This product has a “supply valve” for generating vacuum and a “release valve” for breaking vacuum. Follow the procedure below to replace the solenoid valves after the product has been used for a long period of time or malfunctions.1) Remove the mounting screw of the solenoid valve. 2) Remove the solenoid valve.3) Before mounting the replacement solenoid valve, check that it has no dust or scratches on the mounting surface. Be certain that the gasket and filter element R of the supply valve are properly mounted as well. (Filter element R is installed in the release valve only.)4) Tighten the mounting screw of the solenoid valve to the specified torque below.Appropriate tightening torque (Nm) 0.054 to 0.08- When replacing the solenoid valves, the valve body will come off if boththe supply valve and the release valve are removed at the same time.Removal and mounting of the solenoid valves should be done one at atime to prevent parts from dropping and foreign matter from entering.* Function of the filter element R: When the supply valve is switched OFF from ON, atmospheric pressure flows from the vent port into the spaceinside the valve where there is “vacuum pressure”. Filter element R is afilter mounted in the flow path. It prevents the dust in the operating environment from entering inside the solenoid valve.Manifold Products■Increasing and Decreasing the Number of Manifold Stations- When decreasing the number of manifold stations, order the manifoldbase (a) exclusive for the required number of stations. When increasing the number of stations, order the required number of single units of the body type 3 valve (b). Refer to Model Indication and How to Order for the part numbers for placing an order. The part number for the manifold base is different depending on whether pressure sensor/ vacuum pressure switch are mountable or not.- When mounting each station, check that all the gaskets are in place and tighten the screws to the specified torque. If the tightening torque is exceeded, the body can be broken.- For the manifold with pressure sensor/vacuum pressure switch, order themanifold base (a) for the required number of stations. When increasing the number of stations, order the required number of single unit of the body type 3 valve (b) and the required number of either the pressure sensor assembly (c) or the vacuum pressures switch assembly (d).- In this case, the pressure sensor (c) /vacuum pressure switch (d) is tightened together with the single unit of the product (b). (Refer to the figure on the right.)- When mounting the pressure sensor/ vacuum pressure switch, be sure to check that the O-ring on the mounting surface of the manifold base is mounted properly and that the O-ring is not displaced from the mounting groove. If the O-ring is not mounted properly, it can cause vacuum pressure leakage.Locking push type (Tool required) <Latching type> - Turn the manual override to the left and line up the arrow () with 0 to return it to the RESET state (flow from A toP). (It is set to RESET state when shipped.)SET RESETNo. Item Main partsmaterial Remarks(1) Valve bodyassembly Resin/HNBR Solenoid valve mounting part(2) Needle assembly Resin/ Brass/ NBR For adjusting release flow, with lock nut retaining mechanism(3) Body ResinBodies for ejector and for pump system both available. (4)Nozzle Aluminum For vacuum pump system: Spacer (5) Diffuser AluminumFor vacuum pump system: No diffuser(6) Silencer cover Resin △ markSilencer coverConcave Part A SilencerMounting screw Valve bodySupply valve Filter element R *)Gasket Gasket(a)Appropriate tighteningtorque (Nm) 0.075 to 0.096(b)(a) (b)(d) (c) Vacuum pressure release port (Pressure sensor/vacuum pressureswitch can be mounted)Locking type (Tool required) <Semi-standard>- Turn the manual override to the left and line up () manual override.Note) For the locking type manual override, be sure to release the lock before starting the normal operation.Filter case■Special transparent filter case made of nylonDo not use in an environment where chemicals such as alcohol are present and where they could stick to the filter case.Vacuum Break Flow Adjusting Needle ■Vacuum break flow characteristicsThe graph on the right shows the flow characteristics with various supply pressures when the vacuum break flow adjustment needle is opened from the fully close state “n” turns.However, the flow characteristics shown in this graph are represent values of the single unit of the product.The flow at the absorption part may vary depending on the piping conditions to the vacuum (V) port, circuit etc.The flow characteristics and the number of rotations of the needle vary due to the range of the specifications of the product.■ This product has a needle retaining mechanism.The needle stops rotating when it reaches the rotation stop position. It may damage the product if the needle is rotated past its stop position. ■Do not tighten the needle any more after it reaches the fully closed position (fully Clockwise).The fully closed position is when the end of the needle touches the resin hole. If it is tightened any more after the needle reaches the position where it stops, the resin part will be deformed, causing breakage. ■Do not tighten the handle with tools such as pliers. This can result in breakage due to idle turning.Exhaust from Ejector■Avoid back pressure being applied to the exhaust air of the ejector. The exhaust resistance should be as small as possible to obtain the full ejector performance.There should be no shield around the exhaust port for the silencer exhaust specification. For the port exhaust specification, the back pressureincrease should be 0.005MPa (5kPa) at maximum, as exhaust resistance is generated with some piping bore sizes and piping lengths. For tube ID 4, as a guideline, it is recommended to make the piping length 1000mm at maximum, although it varies depending on the condition of the equipment at the end.For the silencer exhaust specification, the silencer will gradually getclogged if dust in the operating environment is sucked in or if the supply air is not clean enough. If the silencer is clogged, back pressure is applied to the ejector exhaust which results in a reduction in the vacuum pressure and the adsorption flow rate.7 ContactsAUSTRIA (43) 2262 62280-0 LATVIA(371) 781 77 00 BELGIUM (32) 3 355 1464 LITHUANIA(370) 5 264 8126 BULGARIA (359) 2 974 4492 NETHERLANDS (31) 20 531 8888 CZECH REP. (420) 541 424 611 NORWAY (47) 67 12 90 20 DENMARK (45) 7025 2900 POLAND (48) 22 211 9600 ESTONIA (372) 651 0370 PORTUGAL (351) 21 471 1880 FINLAND (358) 207 513513 ROMANIA (40) 21 320 5111 FRANCE (33) 1 6476 1000 SLOVAKIA (421) 2 444 56725 GERMANY (49) 6103 4020 SLOVENIA (386) 73 885 412 GREECE (30) 210 271 7265 SPAIN (34) 945 184 100 HUNGARY (36) 23 511 390 SWEDEN(46) 8 603 1200 IRELAND (353) 1 403 9000 SWITZERLAND (41) 52 396 3131 ITALY(39) 02 92711UNITED KINGDOM(44) 1908 563888URL : http// (Global) http// (Europe) Specifications are subject to change without prior notice from the manufacturer. © 2012 SMC Corporation All Rights Reserved.。
带进带出

BF, BG and G-SeriesA Wholly Owned Subsidiary of Flanders CorporationOperation andMaintenance ManualPB-1311-0207Bag-In/Bag-Out Manual Operation & Maintenance ManualImportant Message.....................................................................Inside Front Cover Quality Assurance Program.. (4)Introduction (5)BF Gel Seal Design Concept (8)BG Gasket Seal Design Concept (9)G-Series Design Concept (10)Handling and Storage of Filter Elements Prior to Installation (11)Installation of New Filter Housings (12)Filter Housing Start-up Procedures (14)Installation of New Filter Elements (15)Filter Change-Out (Replacing Dirty Filters) (26)System Maintenance (39)Replacement of Access Door Gasket (40)Replacement of BF-Series Gel Seal Locking Mechanism (43)Replacement of BG-Series Gasket Seal Locking Mechanism(Optional Clamping Mechanism) (47)Spare Parts (51)4Flanders/CSC’s Quality Assurance Program was established to address the eighteen criteria structure of ASME NQA-1 (formally N45.2), “Quality Assurance Requirements for Nuclear Facility Applications”. As suppliers of High Efficiency Air Filtration products and services, there are three standards that govern the majority of Flanders/CSC’s activities.1. ASME N509-1989 (reaffirmed 1996)“Nuclear Power Plant Air-cleaning Units and Components”2.ASME N510-1989 (reaffirmed 1995)“Testing of Nuclear Air Treatment Systems”3.ASME AG-1- 1997“Code on Nuclear Air and Gas Treatment”These standards and our customer’s specifications invoke many other standards and codes the Flanders/CSC’s Quality Assurance Program incorporates as standard practice.There are a variety of Quality Assurance Programs that manufacturer’s implement to ensure product and service quality, two such systems are ISO-9001and ASME NQA-1.Abstracts of these programs include:ISO 9001:2000 specifies requirements for a Quality Management System where an organization 1.Needs to demonstrate its ability to consistently provide product that meets customer and applicable regulatory requirements, and 2.Aims to enhance customer satisfaction through the effective application of the sys-tem, including processes for continual im-provement of the system and the assurance of conformity to customer and applicable regu-latory requirements.All requirements of this international standard are generic and are intended to be applicable to all organizations, regardless of type, size and product provided.1ASME NQA-1: This Standard sets forth requirements for the establishment and execution of quality assurance programs for the siting, design,construction, operation, and decommissioning of nuclear facilities. Nonmandatory guidance is provided in the Appendices. NQA-1 establishes 18criteria covering all aspects of quality, from purchase of raw materials, to design and testing. 2Because ASME NQA-1 applies to the Nuclear Industry where containment and safety are of paramount concern, it is generally seen to establish more checks and balances.Containment air filtration started out as a critical requirement in the Nuclear industry to protect workers, the public and the environment. Today,containment air filtration is a critical issue in a variety of industries and applications; from pharmaceutical,health care, military, and the original nuclear applications among others. Because of the critical safety requirements of the nuclear industry, ASME N509, ASME N510, and ASME AG-1 are recognized as the standards for design and testing of containment air filtration systems. Each of these standards requires a Quality Assurance Program that meets the requirements of ASME NQA-1.Flanders/CSC maintains a full scope Quality Assurance Program that meets the requirements of ASME NQA-1, 10 CFR 50 Appendix B, and DOE O 414 1A. Customers that require the stringent application of quality principles that only a mature and developed program can offer routinely audit this Quality Assurance program.Flanders/CSC has evaluated the possibility of certification to ISO-9001 and determined that an ASME NQA-1 program better meets the critical needs of our customers. Although the two programs are comparable, an ASME study indicates that a ISO-9001 Quality Assurance Program will not meet the requirements of ASME NQA-1 without substantial modification. 3parison NQA 1 and ISO 9001 Technical Report,available from 5IntroductionTypical 1 high 1 wide filter housing module for a single primary filter.Five (5) 2 high 2 wide filter housing modules welded together to create a 2 high 2 wide, 5 stage filter train.Flanders/CSC’s line of bag-In/bag-out filter housings for gel or gasket seal primary filters are side-loading filter housings which have been designed to meet the air filtration needs of industries and research facilities that handle dangerous or toxic biological, radiological, or carcinogenic material. To minimize exposure to this harmful contamination while replacing and handling dirty filters, the housing incorporates a ribbed bag-in/bag-out ring, over which a heavy duty plastic bag is attached.Once the initial filters are installed and the first bag attached, all filters ¾ both dirty and new ¾ are handled through the bag using the procedures described in detail throughout this manual, hence the name Bag-In/Bag-Out.Depending upon the user’s requirements, the housing may have an assortment of filter arrangements, including the prefilters, HEPA filters,and/or carbon adsorbers. No matter what type of filters are contained within the housing, the filter change-out procedure is the same.Remember: A filter change-out is not complete until the new filters have been sealed to the housing frame and an in-place leak test has been performed.6Access DoorPrefilter Flanges for Duct ConnectionRibbed Bagging RingHEPA (or Adsorber) FilterSecurity StrapBag Stub Removal Glove SleeveFilter (or Adsorber)Locking MechanismPrimary Filter Removal RodChange-Out Bag (Plastic)Cinching StrapAccess Door KnobIllustration of Bag-In/Bag-Out ComponentsFilter HandlingGlove SleeveThe plan view illustrations below are the basic steps involved in changing contaminated filters in a Bag-In/Bag-Out containment housing. A complete step-by-step change-out instruction manual is furnished with each housing or system.•Extend bag and place arms in filter handlingglove sleeves of bag.•Remove access door.Figure 2Figure 1HEPA FilterPlastic BagPlastic BagHandling Glove SleeveHEPA FilterBag Stub Removal Glove SleeveAccess DoorBag-In/Bag-Out Operation & Maintenance Manual8The standard locking mechanism is manufactured ofType 300 Series stainless steel.3W BF-Series Housing Showing Locking Mechanism and Filter Removal RodHousing Knife Edge Front and BottomHousing Knife Edge Front and TopDescription of the BF-Series Filter Locking SystemThe BF-Series housing has a filter locking arm in each tier to operate the replaceable filter locking mechanism. By operating the internal filter locking arm inside the PVC bag and access door, the filter is engaged on, or disengaged from, the housing knife edge (internal sealing frame). The filter locking arm and the access door interface in such a manner that minimizes the possibility of the door being closed until the filters are correctly sealed in the housing and sealed to the mounting frame.Gel Seal Design ConceptThe filter-to-housing gel seal is effected by means of a continu-ous knife edge on the interior of the housing, which mates into the gel-filled perimeter channel on the face of the filter. T o effect the seal, the locking mechanism forces the filter against the knife edge. The knife edge penetrates the gel and a uniform seal is pro-duced on the filter face.Blu-Jel SealKnife EdgeHousingLockingArmFilterGel-Filled ChannelAir Flow®9The filter to housing gasket seal is effected by means of a con-tinuous flat mounting surface on the interior of the housing,which mates to a perimeter gasket on the filter.To effect the seal, the locking mechanism forces the filter against the mounting surface.BG-Series Gasket Seal Housing inside view showing the filter locking mechanism. Note the exterior drive bolts and spring-loaded mechanism.The BG-Series Gasket Seal Design ConceptThe BG-Series Gasket Seal DescriptionBy turning a drive bolt located at the front exte-rior of the BG-Series housing, the independent pressure bars with pre-loaded springs, located in the filter locking mechanism, force the filter against the interior mounting frame. Pre-loaded springs on each pressure bar, for each filter element, ap-ply consistent pressure to maintain filter seal.The applied force has a minimum clamping load of 1,400 pounds per full width filter or 1,050 pounds per half width filter. This force is applied as an even, uniform load along the top and bottom of each filter frame. The standard locking mechanism is manufactured of Type 300 Series stainless steel with brass pivot blocks.Air FlowHousingHousingFilterFilter Locking MechanismGasketThe standard locking mechanism is manufactured ofType 300 Series stainless steel and brass10The G-Series Housing Design ConceptI n addition to the BF-Series side load Bag-In/Bag-Out housing, Flanders/CSC offers round filter housing for in-line applications. The G-Series hous-ing is designed for single filter replacement from the top of the unit. The housing can be installed for side access, but Flanders/CSC does not rec-ommend that the unit be supported by the inlet and outlet connections. Instead, a mounting stand or some other means of support should be used.There is no specific diameter for inlet and outlet connections for the G-Series housing, sincerequirements vary. The purchaser must specify the required pipe sizes and lengths.The G-Series inlet and outlet connection can be a standard rolled stainless steel sheet metal nipple or optional stainless steel piping or tubing.Gel seal filters used in the round housing do not require filter clips.The G-Series housings have a different locking mechanism from the standard BF or BG Series housing.G-Series Round Housing for in-line applicationsFilter Clamping Arm Pressure BarsFilter clamping arm pressure bars secure the filter during operation. Filter elements that are 12 inch x 12 inch require two clamps and filter elements that are 24 inch x 24 inch require four clamps.The clamps are spring loaded and have a “T” handle that is turned 90° by the operator to lock the filter in the sealed position.Gel Seal Clamping Arms for a G1F Housing In a G-Series round housing, the filter is held in place by with spring loaded clamps for the G1F gel seal or pressure bars, for the G1G gasket seal one (1), two(2) or four(4) compression points are used; depending upon the filter size.Gasket Seal Locking Mechanism for a G1G HousingCompression SpringClamping Arm PressureBarPressure Bar StopsClamping Arm HandleFilter Sealing SurfaceCrank and brass port block, optional 300 series staniless steel designKnife Edge Sealing SurfaceFilter Clamping Arms11Handling and Storage of Filter Elements Prior to InstallationParticulate FiltersParticulate filters include a wide range of filter types, sizes, and performance capabilities.Particulate filters are designed to remove airborne particulates from an airstream while carbon adsorbers (see below) remove contaminate gas molecules from an airstream. Particulate filters can be small, disposable, 30% efficient by ASHRAE “Prefilters” or expensive HEPA (High Efficiency Particulate Air) filters with an efficiency of 99.97% by DOP or better.Generally, all types of particulate filters are very fragile and should be handled with a great deal of care. The following precautions should be observed:•Store in a clean, dry environment.•Store filters in correct orientation.(Check marking arrows on cartons.)•Store filters with tagging information easily visible.•Store away from heavy traffic areas.•Do not stack HEPA filters more than three filters high during storage and handling.•Store filters in factory-packed carton and do not remove from carton until just prio to installation into the filter housing.•Do not move stored filters from place to place. Moving filters can cause damage to the filters.Carbon AdsorbersAdequate care should be provided for packaged adsorber cells to assure optimum initial performance. It is important to minimize the exposure of the adsorbers to moisture, since moisture adversely affects the carbon and the special impregnates (if carbon is impregnated).It is important to store adsorbers in a temperature-controlled environment (0° — 120°F). The following precautions should be observed:•Store in a clean, dry environment.•Store adsorbers in correct orientation.(Check marking arrows on cartons.)•Store filters with tagging information easily visible.•Store away from heavy traffic areas.•Store filters in factory-packed carton and do not remove from carton until just prior to installation into the filter housing.•Immediately prior to installation of the adsorbers into the filter housing, insure that filter housing and ductwork is free of loose construction debris. Flanders/CSC recommends operating the system for approximately two (2) hours with prefilters (and HEPA filters, if used) in place before installing adsorbers.•If the adsorbers are exposed to paint fumes or other solvents, the carbon in the adsorbers will be poisoned and the life of the carbon is shortened. Make sure adequate paint drying time is allowed (usually 24-48 hours) before exposing the adsorbers to the paint fumes.Shelf Life InformationFlanders/CSC recommends that every filter be stored in its original shipping carton to prevent it from being exposed to ultraviolet rays, moisture,and possible damage to the filter media. The filter should be stored in a controlled area (0° — 120°F),and it should not be exposed to ozone depleting sources. If these parameters are satisfied and storage requirements as detailed are maintained,the filter shelf life should be three (3) years from gasket cure date or three (3) years from manufacturing date for gel seal filters.121.Be sure position of housing accessdoor(s) and direction of air flow is correct prior to connecting ductwork.2.The housing should be permanentlyconnected to the ductwork by welding or gasketing and bolting before installation of the filters.Installation of New BF-Series and BG-Series HousingsCaution: RTV caulking compounds may deteriorate in service. They are not recommended for permanent installations. (Check your site specifications.)3.Following installation of the housing(s),the system should be cleaned toremove construction dust, etc. before installing any of the filters.DUCT CONNECTION:Welded or bolted; if bolted, use gasket material to insure leak tightness. (Flanders/CSC provides gasket material with factory drilled flanges.)ACCESS DOOR:Face housing so air flow would strike your back. If door is on your right. Then, housing is right-hand access and vice versa to make it left hand access.Allow minimum of 4 ft. clearance for filter changeoutWall, Support Column,or Other ObstructionsPREFILTER:Normally located on upstream side ofhousingPLAN VIEWPRIMARY FILTER:Normally seals on downstream side of housing when prefilter is behind the same door (shown); seals on up-stream side of housing when prefilter has a separate door or if there is no prefilterDOWNSTREAM DUCT :(by others)UPSTREAM DUCT :(by others)131.Be sure the position of housing accessdoor(s) and direction of air flow is correct prior to connecting ductwork.2.The housing should be permanentlyconnected to the ductwork before the filters are installed. G-Series housings are frequently supplied without flanges for butt welding of piping in the field,but may be supplied with separate flanges for installation in the field.Installation of New G-Series Filter HousingsIf flanges are supplied, they are usually bolted when the housing is properly aligned to mating flanges in the field.(Construction plans should be consulted for details.)3.Following installation of the housing(s),the system should be cleaned toremove construction dust, etc. before installing the filters.Allow a minimum of 4 ft. clearance to remove filters from the housing.PROVIDE STAND OR BAG-OUT SHELFProvide a suitable stand or support shelf for filter change. The shelf should be strong enough to support a fully-loaded HEPA filter or carbon adsorber. If the access door is on the side of the housing, locate the stand just outside of and a few inches beneath the bottom of the door. If the ac-cess door is located on the top of the housing, place the stand alongside and level with the top of the door.Note: A filter removal tray is available fromFlanders/CSC for convenient filter change-out.4 Ft.ClearanceRecommendedBag-In/Bag-Out Manual: Start-Up Procedures15Installation of New Filters in New (Uncontaminated) HousingsMaterials and Tools Required:Rest filter on floor whileremoving carton.Remove packing materials.Turn filter over.BF-Series and G-Series Gel Seal Housings •No tools are requiredBG-Series, Gasket Seal Housings •Standard ratchet with short extension and 3/4 inch socket •Filter release agent (silicone grease)All bag-in/bag-out housings•New filters or adsorbers (Check for correct quantity, type, size and model number.)•New plastic change-out bags(Check for correct quantity, type, size and model number.)•One (1) security strap per access door16STEP 1: BF-Series,BG-Series, and G-Series Remove the housing access door by the following method:•Remove the four (4)aluminum knobs.•Grasp handles on thefront of the door.•Pull the door straightforward, toward yourself.Remove aluminum knobs.Note: The access door on the G-Series is round; however, it is removed in the same manner.Pull door forward.Door Latches on BF-Series and BG-Series Standard latches are threaded studs with removable knobs.The studs align with the retainers provided at each corner of the door and are secured with hand knobs, as shown.Swivel Door Latch (Standard on G-Series; optional on BF-Series and BG-Series)Swivel latches swing away from the door to facilitate its removal during the bag-in/bag-out procedure. The hand knobs are held captive on the swivel latch assembly as a precaution against dropping or losing them.Swivel Latch in Closed PositionSwivel Latch in Swing-Away PositionCaution: Avoid contacting door gasket with door bolts as door is removed to prevent damage to gasket material. Also, the door must be positioned in a way to prevent the gasket frombeing damaged.17STEP 2: BF-Series•Release primary filter locking mechanism handle from handle latch.•Swing handle to full open position.Release filter locking arm from handle latch.Filter Locking Arm in Full Open PositionSTEP 3: BF-Series•Insure that filter clips are alignedproperly on the mechanism angle.(Refer to the filter manufacturer’s instructions if clips have not been factory installed.)•Filter clips must interface with filter locking mechanism angle at top and bottom of filter, as shown:Filter Clip to Mechanism Angle DetailFilter ClipFilter Locking Mechanism AngleFilter Frame (Wood or Metal)18STEP 4: BF-Series•Load filter(s) into housing insuring the filter(s) is installed in the correct position.•When air flow is horizontal,separators — or pleats — of prefilter(s) and HEPA filter(s) must run vertical and carbon beds of carbon ad-sorbers must run horizontal .•When sliding the filter(s) in the hous-ing, use the locking mechanism angles as guides by aligning filter clips over mechanism angles and gently but firmly pushing the filter(s) until ittouches the back of the housing or as far as can be reached.•On multi-wide filter housings, repeat procedure for each filter until all filters are installed.•On three-wide filter housings, it may be necessary to use the second filter to push the filter all the way to the back of the housing.Install HEPA filters with pleatsin vertical position.Install adsorbers with beds in horizontal position.STEP 5: BF-Series•Lock filter(s) in place to the housing’sfilter sealing knife-edge by swinging the locking mechanism handle to theclosed position (towards handle latch).Locking Mechanism Latched with Filters InstalledNote: Air flow arrows on filters normally indicate thedirection of air flow during the manufacturer’s factory testing. When installed in a system (filter housing),air may flow through a HEPA filter or adsorber from both directions. It is important that the filter sealing gel filled channel is in contact with the filter housing’s knife edge sealing surface.Note: The locking mechanism handle isdesigned to provide tension against the handle latch with filters installed. Apply the required pressure to the handle with one hand and swing the handle latchover the handle with the other hand.19STEP 6: BG-Series •Be sure the filter locking mechanism is completely open by turning each mechanism counterclockwise with the standard ratchet until you feel it bottom out .Operator Cranking Top Locking Mechanism← Operator Cranking Bottom Locking MechanismATTENTION:Recommended Step for BG and G1GTo prevent filter gasket from sticking to the housing sealing surface after being compressed for an extended period, the entire face of each new filter gasket must be coated with a silicone grease (Flanders/CSC’s Part Number 03-009)before being installed. A 1/8 - 3/16 inch diameter bead of silicone grease should be applied to the middle of the entire 3/4 inch wide filter gasket.The grease should then be spread evenly across the entire gasket face. This thin coating of sili-cone grease acts as a release agent and will also help achieve and maintain a good filter-to-housing seal.Caution: Do not use RTV (Room TemperatureVulcanizing). RTV would stick filter to housing, thereby compounding potential problems of filter removal.Apply bead of grease on center of gasket strips.Evenly spread grease over entire gasket.20STEP 7: BG-Series•Load filter(s) into housing insuring the filter(s)is installed in the correct position.•When air flow is horizontal, separators —or pleats — of prefilter(s) and HEPAfilter(s) must run vertical and carbon beds of carbon adsorbers must run horizontal .•When sliding the filter(s) in the housing, it is helpful to use the pressure bars on the locking mechanism as guides by butting the non-gasket side of the filter(s) to the bars and gently but firmly pushing the filter(s) until it touches the back of the housing, or as far as can be reached.•On multi-wide filter housings, repeatprocedure for each filter until all filters are installed.•On three-wide filter housings, it may be necessary to use the second filter to push the filter all the way to the back of the housing.Note: Air flow arrows on filters normally indicate the direction of air flow during the manufacturer’s factory testing. When installed in a system (filter housing), air may flow through a HEPA filter or adsorber from either direction. It is important that the filter sealing gasket is in contact with the filter housing’s sealing surface.One of the features unique to some of Flanders/CSC’s generic seismic qualified filter housing designs is the filter retaining clips. These clips are required on housings with specific seismic loads. The retaining clips are required to keep the filters stable and functioning during a seismic event.During installation or change-out of filters, care should be taken to avoid contact between clips and filters.Caution for Seismic BF and BG-Series Housing Designs OnlyInstall HEPA filters with pleatsin vertical position.Install adsorbers with bedsin horizontal position.FilterRetaining Clip(Typical Top and Bottom of Filter)Bagging Ring Filter Seal SurfaceHousingTop of FilterSTEP 8: BG-Series•Lock filter(s) in place to the housingsealing surface by alternating from top locking mechanism to bottom locking mechanism.•First, turn top locking mechanismclockwise with ratchet until filter(s)is snug, not completely tightened.•Second, turn bottom lockingmechanism until filter is completely tightened. There are factory-installed stops to determine when the filter is sealed.•Third, completely tighten the top locking mechanism. There arefactory-installed stops to determine when the filter is sealed.•The filter(s) is now sealed.Note: Refer to chart below for maximum recommended torque for locking mechanism of various size housings.STEP 10: G1F and G1G Series•Pick up the filter by the frame, taking care not totouch the filter element. If the door is on the side of the housing, turn the filter so that the pleats in the medium are vertical. The filter seal-ing surface must face toward the housing seal surface. Take care not to hit the clamp arm handles with the filter. The clamp arms will help guide the filter onto the knife edge. When the filter in G1F housings meets the knife edge, there will be some resistance; however, push the fil-ter frame firmly until it will go no further. This mates the knife edge into the gel-filled channel.For G1G housing see step 6 to help prevent fil-ter gasket from sticking to the housing.STEP 9: G1F and G1G Series•If the clamp arm handles are pointing towardthe center of the housing, they will not permit filter installation.Pull the handles and turn 90° to one side.(Stops will permit turning in one direction only.)Filter Clamping Mechanism for G-Series*Exceeding these limits could damage mechanismFilter Seal SurfacePressure BarGel-Filled Channel orGasketFilter Locking Mechanism Torque Requirements Maximum Torque* LimitHousing FilterWidth Normal Torque Required to SealFilter(s)(3)Three filters wide(2)Two filters wide (1)One filter wide 11-13 ft. lbs.22-23 ft. lbs.32-38 ft. lbs.18 ft. lbs.28 ft. lbs.43 ft. lbs.STEP 11: G1F and G1G SeriesFilter Locked into Place on G-Series HousingSTEP 12: BF-Series, BG-Series, andG-Series•Place plastic bag over bag-in/bag-out ring.Shock cord of plastic bag is to be located between second rib of bag-in/bag-out ring and the housing frame.It is easier to work bag from bottom to topof bag-in/bag-out ring. Locate seam of bag at top of ring, so gloves in bag are inthe correct position.•Turn the clamp arm handles 90° toward the filter.Each handle will snap into place, indicating thatthe clamping mechanism is locked, holding thefilter onto the knife edge of the G1F housing.•Turn the “T” handles on the clamping arm untilthe clamping arm pressure bar bottoms out onthe preesure bar stops for the G1G housing.HousingShock CordSecurityStrapSecond RibBagging RingFirst RibBag•Locate security strap between first and second ribs of the bag-in/bag-out ring.•Loop the end of the security strap through the D-ring.•Tighten security strap and secure any excess strap so it won’t interfere with the door seal when it is replaced.STEP 13:BF-Series, BG-Series, andG-Series Locate D-Ring on strap at top of bag-in/bag-out ring before tightening.Pull strap until it is tight around the bag-in/bag-out ring. Press Velcro together. Secure excess strapso it will not interfere with the door seal.STEP 14: BF-Series, BG-Series, andG-Series•Gather bag at a point near the lip ofthe bag-in/bag-out ring, drawing the bag taut (being careful not to pull the bag off the bag-in/bag-out ring); allow the slack to fall off to the side.•Place the cinching strap aroundbag and pull taut.The nylon cinching strap helps minimize the possibility of the bag being drawn into the housing during operation.。
SMC 压力开关说明书

Other SettingsSummary of Product partsSimple Setting ModeTroubleshootingNote: Specifications are subject to change without prior notice and any obligation on the part of the manufacturer.© 2017 SMC Corporation All Rights ReservedAkihabara UDX 15F, 4-14-1, Sotokanda, Chiyoda-ku, Tokyo 101-0021, JAPANPhone: +81 3-5207-8249 Fax: +81 3-5298-5362URL Specifications/Outline with Dimensions (in mm)Refer to the product catalog or SMC website (URL ) for moreinformation about the product specifications and outline dimensions.PS※※-OMU0004 InstallationMountingMount the optional bracket and panel mount adapter to the pressure switch.When the pressure switch is to be mounted in a place where water and dustsplashes occur, insert a tube into the air-relieving port of the pressure switch.(Refer to "Tube attachment")Mounting with bracketMount the bracket to the body with mounting screws (Self tapping screws:Nominal size 3 x 8L (2 pcs)), then set the body to the specified position.∗: Tighten the bracket mounting screws to a torque of 0.5±0.05 Nm.Self tapping screws are used, and should not be re-used several times.∗: The panel mount adaptercan be rotated through 90degrees for mounting.•Bracket A (Part No.: ZS-46-A1)•Bracket B (Part No.: ZS-46-A2)Mounting with panel mount adapterMount part (a) to the front of the body and fix it. Then insert the body with (a) intothe panel until (a) comes into contact with the panel front surface. Next, mountpanel for fixing.•Panel mount adapter(Part No.: ZS-46-B)Panel mount adapter +Front protective cover(Part No.: ZS-46-D)WiringWiring connectionsUse a separate route for the product wiring and any power or high voltage wiring.Otherwise, malfunction may result due to noise.If a commercially available switching power supply is used, be sure to ground theframe ground (FG) terminal. If the switching power supply is connected for use,switching noise will be superimposed and it will not be able to meet the productspecifications. In that case, insert a noise filter such as a line noise filter/ferritebetween the switching power supplies or change the switching power supply tothe series power supply.How to use connectorConnector attachment/detachmentWhen connecting the connector, insert itstraight onto the pins, holding the lever andconnector body, and lock the connector bypushing the lever hook into the concavegroove on the housing.To detach the connector, remove the hookfrom the groove by pressing the leverdownward, and pull the connector straight out.DC(+)OUT1OUT2FUNCDC(-)BrownBlackWhiteGrayBluePipingTightening the connection threadFor connecting to the body (piping specification: -M5)After hand tightening, apply a spanner of the correct size tothe spanner flats of the piping body, and tighten with a 1/6 to1/4 rotation.As a reference, the tightening torque is 1 to 1.5 Nm.(When replacing the piping adapter ZS-46-N∗, tighten it usingthe same method.)Piping specification: -01, -N01After hand tightening, hold the hexagonal spanner flats of thepressure port with a spanner, and tighten with 2 to 3 rotations.As a reference, the tightening torque is 3 to 5 Nm.When tightening, do not hold the pressure switch body with aDefault settingsWhen the pressure exceeds the setvalue, the switch will be turned on.When the pressure falls below theset value by the amount ofhysteresis or more, the switch willbe turned off. The default setting isto turn on the pressure switch whenthe pressure reaches the centre ofthe atmospheric pressure and upper limit of the rated pressure range. If this condition,shown to the right, is acceptable, then keep these settings.Error indication functionThis function is to display error location and content when a problem or error has occurred.above are displayed, please contact SMC.Refer to the SMC website (URL ) for more information abouttroubleshooting.Power is supplied.button between1 and 3 sec.∗:The outputs will continue to operate during setting.∗:If a button operation is not performed for 3 seconds during the setting, the display will flash.(This is to prevent the setting from remaining incomplete if, for instance, an operator were to leave duringsetting.)∗:3 step setting mode, simple setting mode and function selection mode settings are reflected each other.[3 step setting mode (hysteresis mode)]orcan be changed in the same way.button once when the item to beThe set value on the sub display (right) will startflashing.orbutton.buttons are pressed and held simultaneously for 1 second orlonger, the set value is displayed as [- - -], and the set value will be the same as thecurrent pressure value automatically (snap shot function).Afterwards, it is possible to adjust the value by pressing button.button to complete the setting.The pressure switch turns on within a set pressure range (from P1L to P1H) duringwindow comparator mode.Set P1L, the lower limit of the switch operation, and P1H, the upper limit of the switchoperation and WH1 (hysteresis) following the instructions given above.(When reversed output is selected, the sub display (left) shows [n1L] and [n1H].)∗:Set OUT2 in the same way. (ex. P_2, H_2)∗:Setting of the normal/reverse output switching and hysteresis/window comparator mode switchingare performed with the function selection mode [F 1] OUT1 setting and [F 2] OUT2 setting.value[F 0] Units selection functionPeak/bottom value indicationbutton inmeasurement mode.Snap shot functionbuttons for 1 secondor longer simultaneously. Then, the set value of the sub display (right) shows [- - -], andthe values corresponding to the current pressure values are automatically displayed.Zero-clear functionbuttons are pressed for 1 second orlonger simultaneously, the main display shows [- - -], and the reset to zero.The display returns to measurement mode automatically.Key-lock functionTo set each of these functions, refer to the SMC website(URL ) for more detailed information, or contact SMC.button between 1 and 3 seconds in measurementmode. [SEt] is displayed on the main display. When the button is releasedwhile in the [SEt] display, the current pressure value is displayed on themain display, [P_1] or [n_1] is displayed on the sub display (left), and theset value is displayed on the sub display (right) (Flashing).or button to(The snap shot function can be used.)or button to set the(The snap shot function can be used.)or button, the delay time of the switch output can be selected.button for 2 seconds or longer to complete the setting.∗:If the button is pressed for less than 2 seconds, the setting will moves to the OUT2 setting.In the window comparator mode, set P1L, the lower limit of the switch operation, andP1H, the upper limit of the switch operation, WH1 (hysteresis) and dt1 (delay time)following the instructions given above.(When reversed output is selected, the sub display (left) shows [n1L] and [n1H].)∗:Set OUT2 in the same way.Function selection modebuttonbetween 3 and 5 seconds, to display [F 0].Select to display the function to be changed[F button for 2seconds or longer in function selection modeto return to measurement mode.∗:Some products do not have all the functions. If no functionis available or selected due to configuration of otherfunctions, [- - -] is displayed on the sub display (right).Names of individual partsRefer to the product catalog or SMC website (URL ) for moreinformation about panel cut-out and mounting hole dimensions.Pressure Setting3 Step Setting Mode(URL ) for more detailed information, or contact SMC.MaintenanceHow to reset the product after a power cut or forcible de-energizingThe setting of the product will be retained as it was before a power cut or de-energizing.The output condition is also basically recovered to that before a power cut or de-energizing, but may change depending on the operating environment. Therefore, checkthe safety of the whole installation before operating the product. If the installation is usingaccurate control, wait until the product has warmed up (approximately 10 to 15 minutes). Safety InstructionsBefore UseDigital Pressure SwitchZSE20B(F)/ISE20BThank you for purchasing an SMC ZSE20B(F)/ISE20B Series Digital Pressure Switch.Please read this manual carefully before operating the product and make sure youunderstand its capabilities and limitations. Please keep this manual handy for futurereference.Safety InstructionsThese safety instructions are intended to prevent hazardous situations and/orequipment damage.These instructions indicate the level of potential hazard with the labels of "Caution","Warning" or "Danger". They are all important notes for safety and must be followed inaddition to International standards (ISO/IEC) and other safety regulations.OperatorSwitch ONAt normal output Switch OFFSet valueP_1HysteresisH_1TimePressureDefault settingThe default setting is as follows.If no problem is caused by this setting,keep these settings.Connector pin numbers[F 2] Setting of OUT2Same setting as [F 1] OUT1.NOTE•The direct current power supply to be used should be UL approved as follows:Circuit (of Class 2) which is of maximum 30 Vrms (42.4 V peak), with UL1310 Class2 power supply unit or UL1585 Class 2 transformer.•The product is a UL approved product only if it has a mark on the body.Tube attachmentWhen this pressure switch is used in a place wherewater and dust splashes may occur, insert a tube in theair-relieving port, and bring piping of the opposite sideup to the safe position to keep it from water and dust.(See the right figure.)∗: The tube should be inserted to the end of the air-relieving port.∗: SMC TU0425 (polyurethane, O.D ø4, I.D ø2.5) is a suitable tubing.。
MOUNTING BRACKET
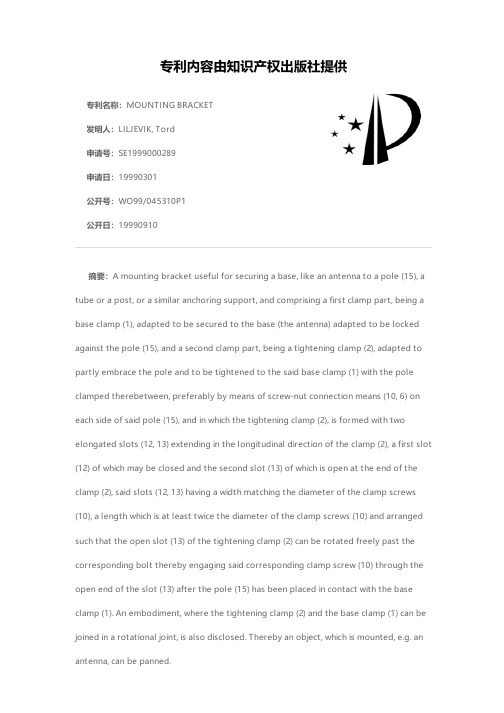
专利名称:MOUNTING BRACKET 发明人:LILJEVIK, Tord申请号:SE1999000289申请日:19990301公开号:WO99/045310P1公开日:19990910专利内容由知识产权出版社提供摘要:A mounting bracket useful for securing a base, like an antenna to a pole (15), a tube or a post, or a similar anchoring support, and comprising a first clamp part, being a base clamp (1), adapted to be secured to the base (the antenna) adapted to be locked against the pole (15), and a second clamp part, being a tightening clamp (2), adapted to partly embrace the pole and to be tightened to the said base clamp (1) with the pole clamped therebetween, preferably by means of screw-nut connection means (10, 6) on each side of said pole (15), and in which the tightening clamp (2), is formed with two elongated slots (12, 13) extending in the longitudinal direction of the clamp (2), a first slot (12) of which may be closed and the second slot (13) of which is open at the end of the clamp (2), said slots (12, 13) having a width matching the diameter of the clamp screws (10), a length which is at least twice the diameter of the clamp screws (10) and arranged such that the open slot (13) of the tightening clamp (2) can be rotated freely past the corresponding bolt thereby engaging said corresponding clamp screw (10) through the open end of the slot (13) after the pole (15) has been placed in contact with the base clamp (1). An embodiment, where the tightening clamp (2) and the base clamp (1) can be joined in a rotational joint, is also disclosed. Thereby an object, which is mounted, e.g. an antenna, can be panned.申请人:LILJEVIK, Tord地址:SE,SE国籍:SE,SE代理机构:EHRNER & DELMAR PATENTBYRÅ AB 更多信息请下载全文后查看。
Mounting bracket and mounting assembly for photovo
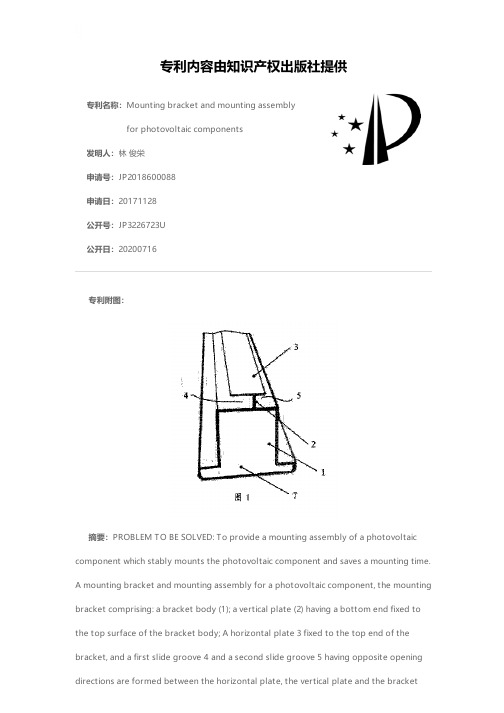
专利名称:Mounting bracket and mounting assemblyfor photovoltaic components发明人:林 俊栄申请号:JP2018600088申请日:20171128公开号:JP3226723U公开日:20200716专利内容由知识产权出版社提供专利附图:摘要:PROBLEM TO BE SOLVED: To provide a mounting assembly of a photovoltaic component which stably mounts the photovoltaic component and saves a mounting time.A mounting bracket and mounting assembly for a photovoltaic component, the mounting bracket comprising: a bracket body (1); a vertical plate (2) having a bottom end fixed to the top surface of the bracket body; A horizontal plate 3 fixed to the top end of the bracket, and a first slide groove 4 and a second slide groove 5 having opposite opening directions are formed between the horizontal plate, the vertical plate and the bracketbody. The depth of the first slide groove is larger than the depth of the second slide groove. By forming the first slide groove and the second slide groove by the horizontal plate and the vertical plate in the bracket body, engagement of the first slide groove and the second slide groove with the photovoltaic component causes a photovoltaic effect. It is possible to directly mount the electronic components. [Selection diagram] Figure 1申请人:北京▲ぼ▼陽頂栄光伏科技有限公司代理人:TRY国際特許業務法人更多信息请下载全文后查看。
Sonance Mariner天气防护音箱说明书
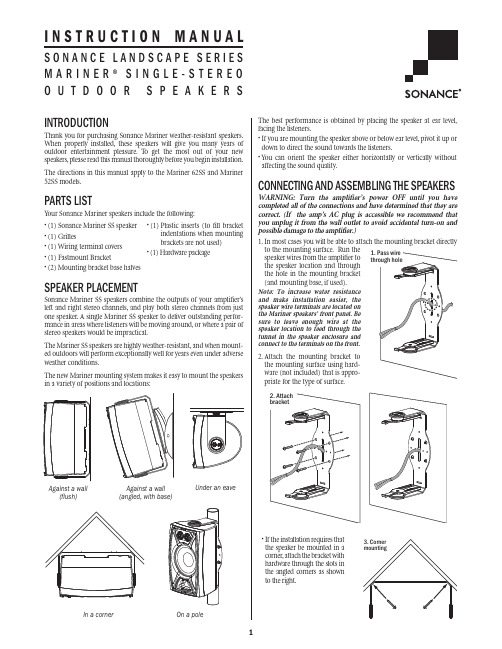
INTRODUCTIONThank you for purchasing Sonance Mariner weather-resistant speakers.When properly installed,these speakers will give you many years of outdoor entertainment pleasure.T o get the most out of your new speakers,please read this manual thoroughly before you begin installation.The directions in this manual apply to the Mariner 62SS and Mariner 52SS models.PARTS LISTY our Sonance Mariner speakers include the following:SPEAKER PLACEMENTSonance Mariner SS speakers combine the outputs of your amplifier’s left and right stereo channels,and play both stereo channels from just one speaker.A single Mariner SS speaker to deliver outstanding perfor-mance in areas where listeners will be moving around,or where a pair of stereo speakers would be impractical.The Mariner SS speakers are highly weather-resistant,and when mount-ed outdoors will perform exceptionally well for years even under adverse weather conditions.The new Mariner mounting system makes it easy to mount the speakers in a variety of positions and locations:The best performance is obtained by placing the speaker at ear level,facing the listeners.• If you are mounting the speaker above or below ear level,pivot it up or down to direct the sound towards the listeners.• Y ou can orient the speaker either horizontally or vertically without affecting the sound quality.CONNECTING AND ASSEMBLING THE SPEAKERSWARNING: Turn the amplifie r’s powe r OFF until you have completed all of the connections and have determined that they are corre ct. (If the amp’s AC plug is acce ssible we re comme nd that you unplug it from the wall outlet to avoid accidental turn-on and possible damage to the amplifier.)1.In most cases you will be able to attach the mounting bracket directly to the mounting surface.Run the speaker wires from the amplifier to the speaker location and through the hole in the mounting bracket (and mounting base,if used).Note : To incre ase wate r re sistance and make installation e asie r, the speaker wire terminals are located on the Mariner speakers’ front panel. Be sure to le ave e nough wire at the spe ake r location to fe e d through the tunne l in the spe ake r e nclosure and connect to the terminals on the front.2.Attach the mounting bracket to the mounting surface using hard-ware (not included) that is appro-priate for the type of surface.• If the installation requires that the speaker be mounted in a corner,attach the bracket with hardware through the slots in the angled corners as shown to the right.• (1) Sonance Mariner SS speaker • (1) Grilles• (1) Wiring terminal covers• (1) Fastmount Bracket• (2) Mounting bracket base halves• (1) Plastic inserts (to fill bracketindentations when mounting brackets are not used)• (1) Hardware packageAgainst a wall(angled, with base)Under an eaveOn a poleIn a corner Against a wall (flush)M A R I N E R ®S I N G L E -S T E R E O O U T D O O R S P E A K E R S3.If the installation requires that the speaker be mounted vertically and that it pivot in the vertical dimension (or be mounted horizontally and pivot in the horizontal dimension),you must use the included mounting base in addition to the bracket:3a.Run the speaker wire through the hole in the wall half of the base.3b.Attach the wall half of the base to the mounting surface using hardware (not included) that is appropriate for the type of surface.3c.Pass the speaker wire through the slot in the bracket half of the e the included hardware and allen wrench to assemble the basee the included 4 self-tapping screws to attach the bracket to the mounting base.• Before attaching the bracket to the base,pass the speaker wire through the hole in the center of the bracket.• T o adjust the speaker,loosen the hex screw with the sup-plied allen wrench,pivot the bracket/base and tighten the hex screw.4.If the installation requires that the speaker be mounted on a pole you can attach the brackets to the pole using 2½”U-bolts (not included).5.Feed the speaker wires from the bracket into the wire entry grommet on the back of the speaker,through the wire tun-nel and out the opening on the speaker’s front panel.• The grommet forms a water-resistant seal around the speaker wire.• Make sure there is enough slack in the wire to allow the speaker to pivot on the bracket.6.Slide the speaker onto the bracket until the locks snap into place.• Pull enough wire through the front of the speaker to allow connec-• The binding post connectors can accept wire up to 14 gauge.• Double-check that you connected all of the wires properly (amplifier ‘+’to speaker ‘+’;amplifier ‘–’to speaker ‘–’) at all connections.IMPORTANT: Be sure not to let any stray ‘+’ and ‘–’ wires touch each othe r. Touching wire s can cause a short-circuit that could damageyour amplifier.(Bracket Half)(Wall Half)washer 3e: Pass wire through bracket and attach M A R I N E R ®S I N G L E -S T E R E O O U T D O O R S P E A K E R S8.Fit the wiring connector cover into the recess in the speaker’s front panel.The cover should fit tightly,but can be removed and replaced if the speaker needs to be disconnected.9.Fit the grille onto the speaker.• The Sonance logo can be removed,rotated 90° and replaced in its centering dimple.This maintains the correct logo orientation on a speaker that is mounted vertically.10.If you’re placing the speaker on a shelf without using the bracket,attach the 2 plastic inserts to the speaker’s top and bottom ends so they snap into place.• If you wish to mount the speaker on its bracket at a later time you can remove the inserts by pulling-down the tabs behind the grille.Note: All Sonance Mariner speakers are compatible with Omnimount 20.5Series speaker brackets. The 20.5 series includes several different mounts that accommodate a wide range of different mounting requirements. For more information contact your Sonance Authorize d de ale r or go to .WIRE GAUGEExtra resistance in the speaker wire can make a speaker sound less dynamic and reduce definition of the bass frequencies.In extreme cases,it can even attenuate high frequencies.Also,amplifier power is wasted in wire with extra resistance,reducing your system’s maximum output level.T o prevent degrading sound quality,the total wire resistance should be less than 10% of the speaker’s impedance.This means that for an 8-ohm speaker,the total resistance of the wire should be less than 0.8 ohms.Refer to the following table when selecting the proper wire gauge for your system:PAINTING THE SPEAKER AND GRILLEAll Mariner speakers feature a tough polypropylene enclosure that can be painted.Sonance recommends using a weather-resistant outdoor paint and a spray gun to paint the Mariner speakers.1.If it has already been installed,remove the grille from the speaker.2.T o protect the speaker driver units during painting,place the grille on a piece of cardboard and trace around its outline.Then cut the card-board just inside of the trace line and fit this “paint plug”into the speaker’s baffle.(Be careful not to damage the driver components while fitting the paint plug.)3.Paint the speaker the desired color according to the paint manufacturer’s instructions.Remove the paint plug after the paint has thoroughly dried.4.Remove the Sonance logo before painting the grille.Paint the grille separately from the speaker using very thin paint (5:1 thinner:paint ratio).Avoid plugging the grille holes with excess paint.5.After the paint has thoroughly dried,re-attach the Sonance logo to the grille and attach the grille to the speaker.PIVOTING THE SPEAKERY ou can rotate the speaker in the bracket to direct the sound towards the listeners.1.Unlock the slide locks on the speaker pivots by moving them towards the rear of the speaker.2.Rotate the speakers to the desired position.3.Lock the slide locks by moving them towards the front of the speaker.SPECIFICATIONSMariner 62SSTweeter:Two 1”(25mm) Polyurethane domeWoofer:6½”(165mm) One-piece black Polypropylene cone with a rubber surround,dual voice coil Frequency Response:55Hz – 20kHz ±3dBImpedance:8 ohms nominal;6 ohms minimum Power Handling: 5 watts minimum;80 watts maximum Sensitivity:89dB SPL (2.83V/1 meter)Grille Material:Perforated aluminum;Dimensions (H x W x D):12”x 7½”x 71/8”(305mm x 191mm x 181mm)Shipping Weight:7 lbs (3.2 KG) per eachMariner 52SSTweeter:Two 1”(25mm) Polyurethane domeWoofer:5¼”(133mm) One-piece black Polypropylene cone with a rubber surround,dual voice coil Frequency Response:65Hz – 20kHz ±3dBImpedance:8 ohms nominal;6 ohms minimum Power Handling: 5 watts minimum;70 watts maximum Sensitivity:88dB SPL (2.83V/1 meter)Grille Material:Perforated aluminumDimensions (H x W x D):10¼”x 6½”x 6”(260mm x 165mm x 153mm)Shipping Weight:6 lbs (2.75 KG) per eachUNLOCK(towards rear of speaker)LOCK(towards front of speaker)M A R I N E R ®S I N G L E -S T E R E O O U T D O O R S P E A K E R SLIMITED FIVE (5) YEAR WARRANTYSonance warrants to the first end-user purchaser that this Sonance-brand product (“Product”),when purchased from an authorized Sonance Dealer/Distributor,will be free from defective workmanship and materials for the period stated below.Sonance will at its option and expense during the warranty period,either repair the defect or replace the Product with a new or remanufactured Product or a reasonable equivalent. EXCLUSIONSTO THE EXTENT PERMITTED BY LA W,THE W ARRANTY SET FORTH ABOVE IS IN LIEU OF,AND EXCLUSIVE OF,ALL OTHER W ARRANTIES,EXPRESS OR IMPLIED,AND IS THE SOLE AND EXCLUSIVE W ARRANTY PROVIDED BY SONANCE.ALL OTHER EXPRESS AND IMPLIED W ARRANTIES,INCLUDING THE IMPLIED W ARRANTIES OF MERCHANTABILITY,IMPLIED W ARRANTY OF FITNESS FOR USE,AND IMPLIED W ARRANTY OF FITNESS FOR A PARTICULAR PURPOSE ARE SPECIFICALLY EXCLUDED.No one is authorized to make or modify any warranties on behalf of Sonance.The warranty stated above is the sole and exclusive remedy and Sonance’s performance shall constitute full and final satisfaction of all obligations, liabilities and claims with respect to the Product.IN ANY EVENT,SONANCE SHALL NOT BE LIABLE FOR CONSEQUENTIAL,INCIDENTAL, ECONOMIC,PROPERTY,BODILY INJURY,OR PERSONAL INJURY DAMAGES ARISING FROM THE PRODUCT,ANY BREACH OF THIS W ARRANTY OR OTHERWISE.This warranty statement gives you specific legal rights,and you may have other rights which vary from state to state.Some states do not allow the exclusion of implied warranties or limitations of remedies,so the above exclusions and limitations may not apply.If your state does not allow disclaimer of implied warranties,the duration of such implied warranties is limited to period of Sonance’s express warranty.Y our Product Model and Description:Landscape Series Mariner SpeakersWarranty Period for this Product:Five (5) years from the date on the original sales receipt or invoice or other satisfactory proof of purchase.Additional Limitations and Exclusions from Warranty Coverage:The warranty described above is non-transferable,applies only to the initial installation of the Product,does not include installation of any repaired or replaced Product,does not include damage to allied or associated equipment which may result for any reason from use with this Product,and does not include labor or parts caused by accident,disaster,negligence, improper installation,misuse (e.g.overdriving the amplifier or speaker,excessive heat or cold or humidity),or from service or repair which has not been authorized by Sonance.Obtaining Authorized Service:T o qualify for the warranty,you must contact your authorized Sonance Dealer/Installer or call Sonance Customer Service at (800) 582-0772 within the warranty period,must obtain a return merchandise number (RMA),and must deliver the Product to Sonance shipping prepaid during the warranty period,together with the original sales receipt,or invoice or other satisfactory proof of purchase.©2008 Sonance.All rights reserved.Sonance and Sonance Mariner are registered trademarks of Dana Innovations.Sonance • 212 Avenida Fabricante • San Clemente,CA 92672-7531,USA • (800)582-7777 or(949)492-7777 • FAX:(949)361-5151 • T echnical Support:(800)582-0772w w w.s o n a n c e.c o m。
Festo PK产品类型安装说明说明书
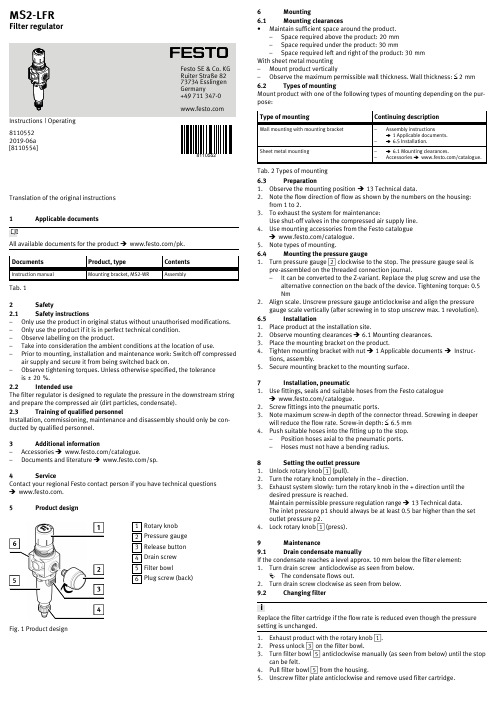
Translation of the original instructions 1Applicable documentsAll available documents for the product è/pk.DocumentsProduct, typeContentsInstruction manualMounting bracket, MS2-WRAssemblyTab. 1 2Safety2.1Safety instructions–Only use the product in original status without unauthorised modifications.–Only use the product if it is in perfect technical condition.–Observe labelling on the product.–Take into consideration the ambient conditions at the location of use.–Prior to mounting, installation and maintenance work: Switch off compressed air supply and secure it from being switched back on.–Observe tightening torques. Unless otherwise specified, the toleranceis ± 20 %.2.2Intended useThe filter regulator is designed to regulate the pressure in the downstream string and prepare the compressed air (dirt particles, condensate).2.3Training of qualified personnelInstallation, commissioning, maintenance and disassembly should only be con-ducted by qualified personnel.3Additional information–Accessories è /catalogue.–Documents and literature è /sp.4ServiceContact your regional Festo contact person if you have technical questions è.5Product design1Rotary knob 2Pressure gauge 3Release button 4Drain screw 5Filter bowl6Plug screw (back)Fig. 1 Product design6Mounting 6.1Mounting clearances•Maintain sufficient space around the product.–Space required above the product: 20 mm –Space required under the product: 30 mm–Space required left and right of the product: 30 mm With sheet metal mounting –Mount product vertically–Observe the maximum permissible wall thickness. Wall thickness: £ 2 mm 6.2Types of mountingMount product with one of the following types of mounting depending on the pur-pose:Type of mountingContinuing descriptionWall mounting with mounting bracket–Assembly instructionsè1 Applicable documents.–è 6.5 Installation.Sheet metal mounting–è 6.1 Mounting clearances.–Accessories è /catalogue.Tab. 2 Types of mounting 6.3Preparation1.Observe the mounting position è 13 Technical data.2.Note the flow direction of flow as shown by the numbers on the housing:from 1 to 2.3.To exhaust the system for maintenance:Use shut-off valves in the compressed air supply line. e mounting accessories from the Festo catalogueè/catalogue.5.Note types of mounting.6.4Mounting the pressure gauge1.Turn pressure gauge 2 clockwise to the stop. The pressure gauge seal ispre-assembled on the threaded connection journal.–It can be converted to the Z-variant. Replace the plug screw and use thealternative connection on the back of the device. Tightening torque: 0.5Nm2.Align scale. Unscrew pressure gauge anticlockwise and align the pressuregauge scale vertically (after screwing in to stop unscrew max. 1 revolution).6.5Installation1.Place product at the installation site.2.Observe mounting clearances è 6.1 Mounting clearances.3.Place the mounting bracket on the product.4.Tighten mounting bracket with nut è 1 Applicable documents è Instruc-tions, assembly.5.Secure mounting bracket to the mounting surface.7Installation, pneumatice fittings, seals and suitable hoses from the Festo catalogueè/catalogue.2.Screw fittings into the pneumatic ports.3.Note maximum screw-in depth of the connector thread. Screwing in deeperwill reduce the flow rate. Screw-in depth: £ 6.5 mm 4.Push suitable hoses into the fitting up to the stop.–Position hoses axial to the pneumatic ports.–Hoses must not have a bending radius.8Setting the outlet pressure1.Unlock rotary knob 1 (pull).2.Turn the rotary knob completely in the z direction.3.Exhaust system slowly: turn the rotary knob in the + direction until thedesired pressure is reached.Maintain permissible pressure regulation range è 13 Technical data.The inlet pressure p1 should always be at least 0.5 bar higher than the set outlet pressure p2.4.Lock rotary knob 1 (press).9Maintenance 9.1Drain condensate manuallyIf the condensate reaches a level approx. 10 mm below the filter element:1.Turn drain screw anticlockwise as seen from below.ÄThe condensate flows out.2.Turn drain screw clockwise as seen from below.9.2Changing filterReplace the filter cartridge if the flow rate is reduced even though the pressure setting is unchanged.1.Exhaust product with the rotary knob 1.2.Press unlock 3 on the filter bowl.3.Turn filter bowl 5 anticlockwise manually (as seen from below) until the stopcan be felt.4.Pull filter bowl 5 from the housing.5.Unscrew filter plate anticlockwise and remove used filter cartridge.8110552MS2-LFRFilter regulator81105522019-06a [8110554]Festo SE & Co. KG Ruiter Straße 82 73734 Esslingen Germany+49 711 6.Install new filter cartridge:–Hold filter cartridge at the bottom and push onto the support.–Position filter plate, screw in and hand-tighten. Tightening torque:0.07 Nm ±20%7.Mount filter bowl 5:–Align lock release of filter bowl on the cutout on the housing and insert it.–Turn filter bowl clockwise until the lock audibly locks at the end stop.9.3Clean product•Clean the outside of the product with a soft cloth as required. Cleaning agents include all non-abrasive media.10Fault clearanceError description Cause RemedyConstriction in the supply line Check supply line.Low flow rate (operating pres-sure breaks down with air con-sumption)Filter cartridge dirty Replace filter cartridgeè 9 Maintenance.Pressure increases above the set working pressure.Valve disc defective at sealingseatReplace product.Audible, continuous blowingnoise at rotary knobValve seat damaged Replace product.Blowing noise can be heard atthe drain screw.Drain screw leaking Replace product.Tab. 3 Fault clearance11Disassembly1.Exhaust the complete system and product.2.Release interlock at the fittings by pressing it and pull out hose assembly.3.Release fittings at the connecting flanges and unscrew.12Disposal•Dispose of the packaging, used filters and product at the end of the produc-tion service life according to the valid provisions for environmentally sound recycling.13Technical data13.1Technical data, mechanicalTab. 413.2Technical data, pneumaticTab. 5。
IDEM不锈钢门螺栓型开关说明书
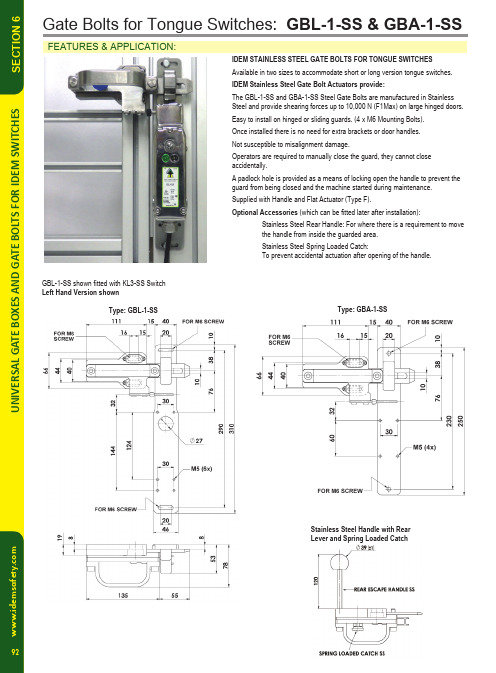
w w w .i d e m s a f e t y .c o mU N I V E R S A L G A T E B O XE SA NDG AT E B O L T S F O R I D E M S W I T C H E S92S E C T I O N 6Available in two sizes to accommodate short or long version tongue switches.IDEM Stainless Steel Gate Bolt Actuators provide:The GBL-1-SS and GBA-1-SS Steel Gate Bolts are manufactured in Stainless Steel and provide shearing forces up to 10,000 N (F1Max) on large hinged doors.Easy to install on hinged or sliding guards. (4 x M6 Mounting Bolts).Once installed there is no need for extra brackets or door handles.Not susceptible to misalignment damage.Operators are required to manually close the guard, they cannot close accidentally.A padlock hole is provided as a means of locking open the handle to prevent the guard from being closed and the machine started during maintenance.Supplied with Handle and Flat Actuator (Type F).Optional Accessories (which can be fitted later after installation): Stainless Steel Rear Handle: For where there is a requirement to move the handle from inside the guarded area. Stainless Steel Spring Loaded Catch: To prevent accidental actuation after opening of the handle.GBL-1-SS shown fitted with KL3-SS SwitchLeft Hand Version shownType: GBL-1-SSType: GBA-1-SSStainless Steel Handle with Rear Lever and Spring Loaded Catchw w w .i d e m s a f e t y .c o mU N I V E R S A L G A T E B O X E S A N D G A T E B O L T S F O R I D E MS W I T C H E S93S E C T I O N 6Gate Bolts for Tongue Switches: GBL-1-SS & GBA-1-SSType: GBA-1-SSShown fitted with KM-SS Stainless Steel 316 Tongue SwitchType: GBL-1-SSShown fitted with KL3-SS Stainless Steel 316 Solenoid Locking Tongue SwitchFlat Actuator supplied with 300mm (12”) chain.Can be used where poor alignment exists and provides manual insertion of actuator by operator.Manufactured in Stainless Steel.2 colour LED (3 wires) Steady Red and Steady Green.Fits to conduit entry of most switches and provides option for LED indication based upon switch contacts.The dome shaped LED is visible from narrow angles.Available voltages 24Vdc, 110Vac or 230Vac and either M20 or 1/2” NPT conduit thread.PVC conductors, fully encapsulated IP67. Maximum temperature: 60C.Maintenance Lock Out Actuator. Fits to IDEM Tongue Switches.Manufactured in Stainless Steel.Fits to switch aperture during maintenance and provides multiple padlock holes.Shown fitted to KM Switch (padlock not included). CONDUIT FITTING LED BEACON:Black is common(0Vdc or negative for ac versions).When power is applied to the RED wire the lamp will illuminate Red.When power is applied to the GREEN wire the lamp will illuminate Green.。
Trailer Valet XL Mounting Bracket Assembly说明书
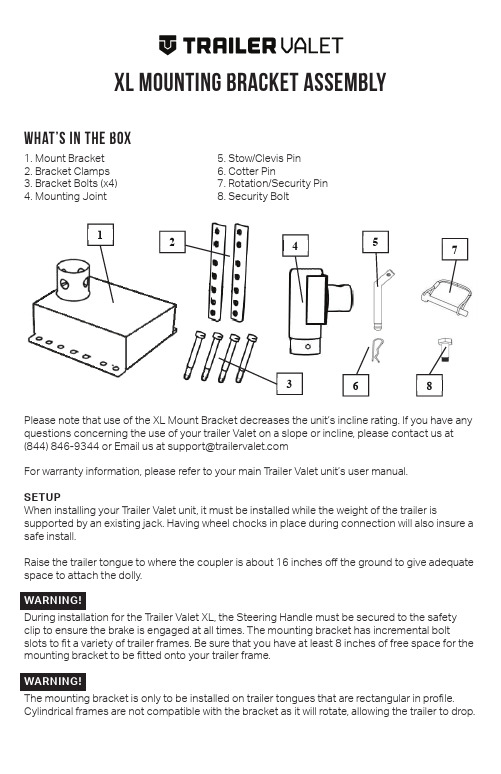
XL Mounting bracket assemblyPlease note that use of the XL Mount Bracket decreases the unit’s incline rating. If you have any questions concerning the use of your trailer Valet on a slope or incline, please contact us at (844)*******************************************For warranty information, please refer to your main Trailer Valet unit’s user manual.SETUP When installing your T railer Valet unit, it must be installed while the weight of the trailer is supported by an existing jack. Having wheel chocks in place during connection will also insure a safe install.Raise the trailer tongue to where the coupler is about 16 inches off the ground to give adequate space to attach the dolly. WARNING!During installation for the T railer Valet XL, the Steering Handle must be secured to the safety clip to ensure the brake is engaged at all times. The mounting bracket has incremental bolt slots to fit a variety of trailer frames. Be sure that you have at least 8 inches of free space for the mounting bracket to be fitted onto your trailer frame.WARNING!The mounting bracket is only to be installed on trailer tongues that are rectangular in profile.Cylindrical frames are not compatible with the bracket as it will rotate, allowing the trailer to drop.123468571. Mount Bracket2. Bracket Clamps3. Bracket Bolts (x4)4. Mounting Joint5. Stow/Clevis Pin6. Cotter Pin7. Rotation/Security Pin8. Security BoltWHat’s in the boxConnectionIt is recommended that you ensure that there is adequate height to install the unit. The trailer should be high enough that, when the frame is level, there is enough space for the unit to be at least one inch off the ground once attached to the bracket. If there is not enough space, adjust the placement of the bracket on your trailer frame.Place the mounting bracket and clamps onto the area of the frame you have designated and secure with the four bolts. NOTE: While it is recommended that the bracket is installed with the attachment point in the low position for stability reasons, the bracket can be flipped prior to install if the space is required.The T railer Valet mounting bracket comes with a security bolt (part 7) that is an option to secure the device. This will add stability if needed, but may slow the process of attaching and detaching the unit from your trailer. If you choose to use it, the bolt slots through the back of the mountingbracket and threads into the mounting joint.Fit the mounting joint into the rotating coupler on your T railer Valet unit and secure with the rotation/security pin. This joint replaces your unit’s ball adapter.Place the connection point of the mounting joint into the mount bracket and fasten with the included stow/clevis pin. Lastly, set the cotter pin through the stow/clevis pin.。
杜谱(Draper)大型电动投影屏操作说明书
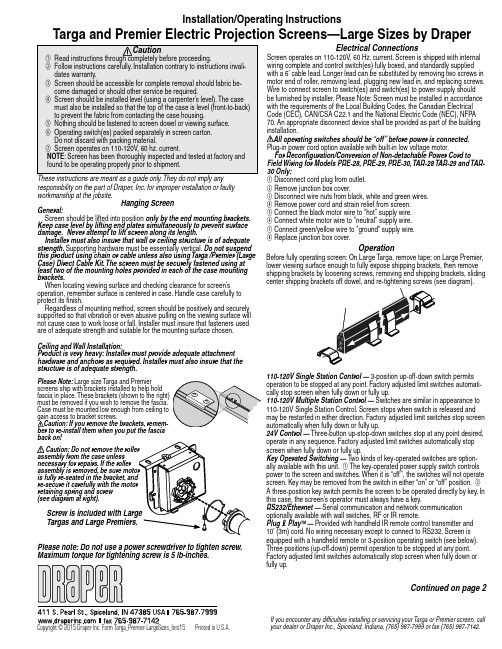
Installation/Operating InstructionsHanging ScreenGeneral:Screen should be lifted into position only by the end mounting brackets.Keep case level by lifting end plates simultaneously to prevent surfacedamage. Never attempt to lift screen along its length.Installer must also insure that wall or ceiling structure is of adequatestrength. Supporting hardware must be essentially vertical. Do not suspendthis product using chain or cable unless also using Targa /Premier (LargeCase) Direct Cable Kit. The screen must be securely fastened using atleast two of the mounting holes provided in each of the case mountingbrackets.When locating viewing surface and checking clearance for screen’soperation, remember surface is centered in case. Handle case carefully toprotect its finish.Regardless of mounting method, screen should be positively and securelysupported so that vibration or even abusive pulling on the viewing surface willnot cause case to work loose or fall. Installer must insure that fasteners usedare of adequate strength and suitable for the mounting surface chosen.Ceiling and Wall Installation:Product is very heavy: Installer must provide adequate attachmenthardware and anchors as required. Installer must also insure that thestructure is of adequate strength.These instructions are meant as a guide only. They do not imply anyresponsibility on the part of Draper, Inc. for improper installation or faultyworkmanship at the jobsite.OperationBefore fully operating screen: On Large Targa, remove tape; on Large Premier,lower viewing surface enough to fully expose shipping brackets, then removeshipping brackets by loosening screws, removing end shipping brackets, sliding110-120V Single Station Control — 3-position up-off-down switch permitsoperation to be stopped at any point. Factory adjusted limit switches automati-cally stop screen when fully down or fully up.110-120V Multiple Station Control — Switches are similar in appearance to110-120V Single Station Control. Screen stops when switch is released andmay be restarted in either direction. Factory adjusted limit switches stop screenautomatically when fully down or fully up.24V Control — Three-button up-stop-down switches stop at any point desired,operate in any sequence. Factory adjusted limit switches automatically stopscreen when fully down or fully up.Key Operated Switching — Two kinds of key-operated switches are option-ally available with this unit. 1 The key-operated power supply switch controlspower to the screen and switches. When it is “off”, the switches will not operatescreen. Key may be removed from the switch in either “on” or “off” position. 2A three-position key switch permits the screen to be operated directly by key. Inthis case, the screen’s operator must always have a key.RS232/Ethernet — Serial communication and network communicationoptionally available with wall switches, RF or IR remote.Plug & Play TM — Provided with handheld IR remote control transmitter and10' (3m) cord. No wiring necessary except to connect to RS232. Screen isequipped with a handheld remote or 3-position operating switch (see below).Three positions (up-off-down) permit operation to be stopped at any point.Factory adjusted limit switches automatically stop screen when fully down orfully up.Electrical ConnectionsScreen operates on 110-120V, 60 Hz. current. Screen is shipped with internalwiring complete and control switch(es) fully boxed, and standardly suppliedwith a 6' cable lead. Longer lead can be substituted by removing two screws inmotor end of roller, removing lead, plugging new lead in, and replacing screws.Wire to connect screen to switch(es) and switch(es) to power supply shouldbe furnished by installer. Please Note: Screen must be installed in accordancewith the requirements of the Local Building Codes, the Canadian ElectricalCode (CEC), CAN/CSA C22.1 and the National Electric Code (NEC), NFPA70. An appropriate disconnect device shall be provided as part of the buildingFor Reconfiguration/Conversion of Non-detachable Power Cord toField Wiring for Models PRE-28, PRE-29, PRE-30, TAR-28 TAR-29 and TAR-30 Only:1 Disconnect cord plug from outlet.2 Remove junction box cover.3 Disconnect wire nuts from black, white and green wires.4 Remove power cord and strain relief from screen.5 Connect the black motor wire to "hot" supply wire.6 Connect white motor wire to "neutral" supply wire.7 Connect green/yellow wire to "ground" supply wire.8 Replace junction box cover.necessary for repairs. If the rollerretaining spring and screw(see diagram at right).Please note: Do not use a power screwdriver to tighten screw.Maximum torque for tightening screw is 5 lb-inches.Continued on page 2 Please Note: Large size Targa and Premierscreens ship with brackets installed to help holdfascia in place. These brackets (shown to the right)must be removed if you wish to remove the fascia.Case must be mounted low enough from ceiling toback on!Targa and Premier—Large Sizes by DraperCase Dimensions* (Premier Tab Tension Surface Shown)Page 2 of 4Wall MountedCeiling MountedTypes of Installation (Targa Dowel Shown)A BProduct is very heavy: Installer must provide adequateattachment hardware and anchors as required. Installer mustPage 3 of 4Targa and Premier—Large Sizes by DraperADJUSTMENTSCREWTENSIONINGCABLEDOWELC L O C K W I SEADJUSTMENTSCREWTENSIONINGCABLEDOWELTab-Tension Adjustment ProcedureDraper’s Tab-Tensioning System is factory-set, and under normal circumstances will not require field adjustment.If, however, you notice wrinkles, waves or other indications that the tensioning cables need to be adjusted, follow the procedure below.1 Determine which side requires adjustment.2 Secure dowel with one hand.3 Using Phillips-head screwdriver, depress spring-loaded adjustment screw and slowly turn CLOCKWISE TO INCREASE tension, or COUNTER-CLOCKWISE TO RELEASE tension. The screw adjusts in ¼ turn increments. Adjust only one increment (¼ turn) at a time4 If problem is not corrected, leave screen in position for 24 hours to allow surface material to stretch into position.5 If problem still is not corrected, repeat steps 2 and 3.Page 4 of 4Targa and Premier—Large Sizes by DraperWiring Diagrams (Standard and Quiet Motors)Single Station ControlMultiple Station ControlDashed wiring by electrician1/8" x 17/8" deep.To110-120 VAC LineInternal Screen WiringNWiring Diagram – External LVC-IVPlease Note: Do not wire motors in parallel.Wiring Diagrams—Plug & Play 110-120V Motor(Low Voltage Control Built Into Motor)Single Low Voltage ControlMultiple Low Voltage ControlsData CablesPlugWiring Diagrams—110-120V Motor and Quiet Motor with Built-in Low Voltage Controller (LVC-IV)Single Low Voltage ControlInternal Screen Wiring White (Neutral)BlackGreen (Ground)Dashed wiring by electrician To 110-120V LineMultiple Low Voltage ControlsInternal Screen Wiring White (Neutral)BlackGreen (Ground)Dashed wiring by electricianTo 110-120V LineWall Switch,RF or IR Receiver,or integrated control systemWall Switch(es),RF or IR Receivers,or integrated control systemsData CableData Cable(s)M otor Type Up Down Standard Black Red Quiet Red Black*Motor DirectionBuilt-in Low Voltage Motor: Switch-to-Motor— Dry Contacts or Data Cable connectionPlease Note: This Splitter/Jack is located inside the motor-end endcap of your screen. To access, remove access panel from endcap.Please Note: Although both Dry Contact and Data Cable connections are shown, you should only use one connection type per motor.Data Cables to switches or to additional motors can be plugged into any of the three open jacks.。
AP-220-MNT-W2 壁挂支架安装指南说明书
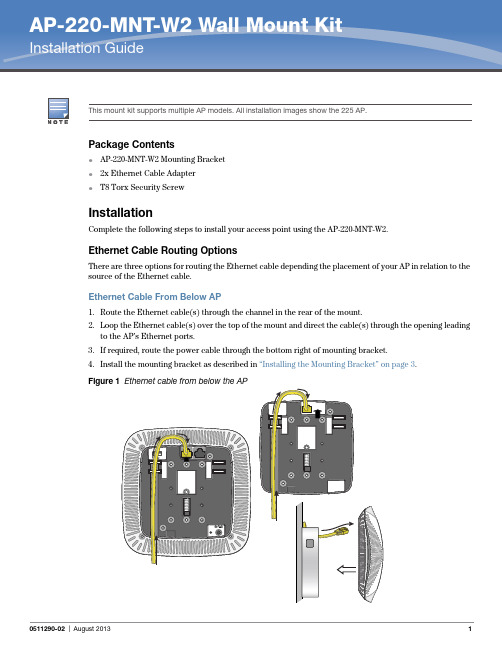
to the AP’s Ethernet ports.3.If required, route the power cable through the bottom right of mounting bracket.4.Install the mounting bracket as described in “Installing the Mounting Bracket” on page 3.Ethernet Cable Behind AP1.Route the Ethernet cable(s) through the large opening in the center of the mount.2.If required, route the power cable through the bottom right of mounting bracket.3.Install the mounting bracket as described in “Installing the Mounting Bracket” on page 3.Using The Ethernet Cable Adapter1.Install Ethernet cable adapter(s) by sliding the female end of the adapter into the slot behind the accesson the side of the mounting bracket. The adapter is secured when it clicks into place.2.If required, route the power cable through the bottom right of mounting bracket.3.Install the mounting bracket as described in “Installing the Mounting Bracket” on page 3.Figure 3 Using the Ethernet cable adapterInstalling the Mounting Bracket1.Install any necessary wall anchors. Wall anchors are not included in this kit.2.Align the screw holes in the mounting bracket with the previously installed anchors or demarcatedscrew points.3.Insert the screws to secure the mounting bracket. Screws are not included in this kit. Ensure that noEthernet cable(s) are obstructing the screw holes.4.Attach any necessary cables and/or antennas to the AP.6.Push the metal slider up to allow the AP to connect.7.While still pushing the metal slider, align the mounting posts on the bracket with the mounting holesshown in Figure 5.8.Install the T8 Torx security screw into the screw hole on the bottom of the mounting bracket, next toslider to complete the installation.。
第三代极速柔性磁盘系列用户指南说明书

Handling PrecautionsAllow the drive to reach room temperature before installing it in the computer.Do not open the E S D bag until youÕre ready to install the drive. Handle the drive by its sides. Do not touch the circuit board (electronics). Do not connect/disconnect any drive cables while your computer is turned on.Do not drop, jar, or bump the drive.1PreIn s tallatio nT hank yo u fo r se le c ting a Maxto r hard d rive sto rag e p ro d uc t.Maxto r's g o al is to p ro vid e yo u w ith the m o st up -to -d ate p ro d uc t p o ssib le ,and w e are c o nstantly e nhanc ing o ur so ftw are and d o c um e ntatio n to b e tte r m e e t yo ur ne e d s .Ple ase visit o ur w e b -site at to vie w the late st that Maxto r has to o ffe r!System /OS Requirem ents¥ A full version of your operating system (OS) is required for a new hard drive installation(see kit package for details)Tools for InstallationThe following tools are needed to install your new M axtor hard drive:¥Small Phillips head screw driver ¥Small pair of pliers or tweezers ¥Your computer user manual ¥Operating system softwareBackup Your DataM axtor highly recommends that you make a backup copy of your files before installing the new M axtor hard drive.Please refer to your computer user manual for more information.2D r ive J um p e r S e t u p Configure the Drive J um persIf specific jumper options are needed for your system configuration, refer to the illustrations and definitions provided in this section.SCSI ID J umper SettingsM axtor SCSI drives typically ship from the factory with jumpers set to SCSI ID 6, and termination power jumped.SCSI ID 7 is usually reserved for the SCSI host adapter.3D rive InstallInstalling Drive Inside of Y our Com puter SystemM ake sure your com puter is pow ered dow n before installing the drive.The following illustrations are of typical computer systems and hard drive mounting styles.Your computer may have a different mounting style. Please refer to your computer user manual for more information.B e sure to secure the drive to the device bay with all four screws.The drive should be oriented with its printed circuit board facing down.Installing 5.25-inch Mounting BracketsIf the hard drive will be installed in a 5.25-inch device bay, attach mounting brackets (available separately) to the hard drive as shown in the figure below.Mounting ScrewsMounting ScrewsMounting BracketNote:M axtor LVD SCSI drives do not support on-board termination. M axtor recommends the use of Active LVD terminators and 68-pin twisted pair cabling.S CS I hos t adapter manufacturers us ually s upply proper cabling and termination with the purchase of an LVD S CS I hos t adapter.A ttention:The R ear J umper O ption Connector is an O E M specific con-nector. M ost installations will never use the jumper options on this connector. Always configure the drive using the jumpers at the Front J umper O ption Connector .Other J umper SettingsTP - Termination Pow er (12 Pin O ption Connector)Pins 11-12 T ermination power ensures that there is a sufficient power level along the entire SCSI bus. It is recommended that the final device on the SCSI bus have the Termination Power jumper installed. All devices in between the host and final device typically have no jumper on Termination Power.Note that Termination Power is not the same as on-board termination, which this drive does not support.S S - S tagger S pinPins 13-14 For most configurations this option is not utilized.M ost current SCSI host adapters offer a Start Unit command enable or disable, which supersedes the functionality of the SS jumper setting. W hen the Delay Spin (DS) jumper isenabled on the drive, the Start Unit command from the SCSI host adapter will send Start Unit commands to all devices on the bus at pre-determined intervals. This can help prevent power supply overload when running several devices on the SCSI bus.W P - W rite ProtectionPins 11-12 B y factory default, the drive is shipped with no jumper on these pins, and the drive can be written to unless protected by application software. W ith the pins jumped, the drive can be used as a read-only device. This feature prevents accidental overwrites and is useful for frequently accessed archives and reference files.Force S E Ð Force S ingle Ended O perationPins 17-18 By factory default, the drive is shipped with no jumper on these pins. W ith most system configurations, it is not necessary to use this jumper. LVD drives are multi-mode capable. They will automatically detect the presence of a sin-gle-ended bus and revert to single-ended mode.DS - Delay S pin Disable Delay S pin: No jumper across pins 15-16 (factory default). Disabling Delay Spin allows the drive to spin up when the system is powered up.Enable Delay S pin: J umper across pins 15-16 This setting will prevent the drive from spinning up until it receives a Start Unit command from a SCSI host adapter. M ost SCSI host adapters have the Start Unit command enabled by default in the host adapter BIOS. Enabling Delay Spin is only necessary when you are starting multiple devices at power on.S CS I IDPin numbers 1-8 are typically referred to in pairs as A0 (pins 1and 2), A1 (3,4), A2 (5,6), A3 (7,8). The jumper pairs will allow configuration of SCSI ID's 0 to 15. All SCSI devices must have an individual ID on the SCSI bus (there is no M aster/Slave set-ting). SCSI ID 7 is usually reserved for the SCSI host adapter.Fault LED and B usy O ut J umpersTypical installations do not require the use of the Fault LED and Busy Out jumpers. The Busy Out signal is usually supplied through the PCI bus to the PC motherboard's Busy indicator LED. If connecting the Busy Out jumper for a drive installed in an external case, please refer to the wiring documentation sup-plied by the manufacturer of the case. Connection of the Fault LED is not recommended in internal or external installations.Computer with available 3.5-inch device bayComputer with available 5.25-inch device bayD I e v i r D O t i B D I 1t i B D I 2t i B D t i B D I 0D I F F O F F O F F F O 1D I N O F F O F F F O 2D I F F O N O F F F O 3D I N O N O F F F O 4D I F F O F F O N F O 5D I N O F F O N F O 6D I F F O N O N F O 7D I T SO H I S C S R O F D E V R E S E R 8D I F F O F F O F F O N O 9D I N O F F O F F O N O 01D I F F O N O F F O N O 11D I N O N O F F O N O 21D I F F O F F O N O N O 31D I N O F F O N O N O 41D I F F O N O N O N O 51D I NO NO NO NO Pin 2Pin 1Pin 17Pin 18SCSI ID 3SCSI ID 2SCSI ID 1SCSI ID 0BUSY LED -/+WRT PROTECT STAGGER SPIN DELAY SPINSINGLE ENDEDFAULT LED GROUND GROUND BUSY LED GROUND TERM POWERSCSI ID 3SCSI ID 2SCSI ID 1SCSI ID 0NOT USED+5 VPin 1Pin 2Pin 11Pin 124 Pin PowerConnector12 Pin Option Connector68 Pin SCSIConnectorPin 168-pin Connector68-pin Drive ConnectorDC Power ConnectorUltra LVD/SE CablePower Supply Cable(3-Pin or 4-Pin)Bevel4Cable Hook-up Attach the SCSI and Power CablesIf the M axtor SCSI drive is the only device attached to the SCSI adapter card, attach the drive at the end of the Ultra LV D/SE cable, farthest from the SCSI adapter card. This connector has a beveled edge and will only fit one way. Then attach an external active LVD/SE SCSI terminator.Please refer to the SCSI adapter card user guide for additional recommendations on data cable place-ment and SCSI termination requirements.Attach a power cable to the power connector on the hard drive. This connector is keyed and willonly fit one way. Check all other cable connections before you turn on the computer.Caution:Do not force or rock the connectors into their sockets on the hard drive. Push them in straight until they are seated firmly.5P a r t it io n i n g F o r m a t t i n gMaxtor hard drives can accept nearly all operating systems. Some operating sys-tems have volume size limitations that may require you to partition your drive into multiple volumes. Please refer to your system or SCSI adapter card user guide for information about formatting and partitioning the drive.General Guidelines¥ DOS /W indow s 9X /M E:Use FDISK.EXE to partition and FORM to format the drive.¥ W indow s N T/2000:Boot your system from the installa-tion floppy disks provided with the OS to partition and format the drive.If you do not have the original installa-tion floppies, you can create them using your W indows installation CD.¥ W indow s X P:Boot your system from the W indows XP installation CD to partition and for-mat the drive. If your system is not capable of booting from a CD, you can download bootable W indows XP installation floppies from M icrosoft's website at ¥ Macintosh:Most non-Apple branded hard drives can be formatted using the Drive Setup utility included in Mac OS 8.6 and above. Mac OS versions before 8.6 will require a third-party hard drive utility such as FW B Hard Disk Toolkit () or Intech Hard Disk SpeedTools() to partition and initialize the drive. Please visit the FW B or Intech website for details on these non-Maxtor software products.www.maxtor.c om6P r o d u c t R e g i st r a t io nTake Advantage of the Benefits!By registering your new M axtor prod-uct,youll have the option to receive product updates, special offers, and other valuable information about other data storage solutions from M axtor.S imply point your web browser to:w w go to theproduct registration page, and com-plete the short questionnaire.Changes are periodically made to the information herein Ð which will be incorporated in revised editions of the publication. M axtor may make changes or improvements in the product(s) described in this publication at any time and without notice.Copyright © 2001 M axtor Corporation. All rights reserved. Printed in the U.S.A. 12/01. M axtor ¨is a regis-tered trademark of M axtor Corporation. Other brands or products are trademarks or registered trademarks of their respective holders.Active LVD TerminatorConnect to SCSI Host Adapter CardUltra LVD/SE CableStandard Cabling for Single SCSI Drive in System(Ultra LVD/ SE cable connections)Cable Connections for SCSI Drive。
mounting 完形填空

mounting 完形填空Mounting refers to the process of 1) attaching or fixing something firmly to a support or base. It can be used in various contexts, such as mounting a picture frame on the wall, mounting a TV on a bracket, or mounting a horse for horseback riding.In the context of mounting a picture frame on the wall, you typically need to follow a few steps. First, you need to decide where you want to hang the picture frame and mark the exact spot on the wall. Then, you may need to use a drill to create holes in the wall for the screws or nails that will hold the frame in place. After that, you can position the frame on the wall and secure it by driving the screws or nails into the pre-drilled holes. Finally, you can double-check the stability of the frame and make any necessary adjustments.Mounting a TV on a bracket is a bit more complex. You usually need to locate the studs in the wall to ensure that the bracket is securely attached. Once you have found the studs, you can mark the spots where the screws will go. Then, you need to attach the bracket to the wall by driving the screws through the bracket and into the studs. After that, you can mount the TV onto the bracket, making sure that it is firmly attached and level.Mounting a horse for horseback riding involves getting on the horse's back in a proper and safe manner. You typically need to approach the horse from the side and gently place one foot in the stirrup while holding onto the saddle. Then, you can use your other hand to hold the reins and support yourself as you swing your other leg over the horse's back. Once on the horse, you can adjust yourposition and make sure that you have a secure and balanced seat before starting to ride.Overall, mounting is a common process used to attach or fix objects or oneself in a stable and secure manner.。
Acendo Vibe 会议通话声音条与摄像头的快速启动指南说明书

QUICK START GUIDEACV-5100 Acendo Vibe™ Conferencing Sound Bar with CameraOverviewThe ACV-5100 features a hinged Wall Mount Bracket, which allows easy installation aswell as access to the Connector Bay without having to dismount the unit. The WallMount Bracket features a cutout for cable routing and straps for cable management.Note : Do not lift the ACV-5100 by the camera or rest the unit on the camera.Credenza InstallationNote : To ensure highest possible sound quality, the rubber feet on the bottom panelmust remain in place for surface-mount installations.The ACV-5100 can sit on a hard, flat surface such as a credenza, tabletop or desk.When choosing a surface location, consider a space that will not interfere withworkspaces or other installed devices. Connect cables as necessary - see theConnections section for details.Wall Mount InstallationFor best aesthetic in wall mount installations, remove the rubber feet from the bottompanel: carefully peel each foot off of the bottom surface.Removing the Wall Mount Bracket1.Open the Wall Mount Bracket (held closed by internal magnets).2.Press and hold the Release Button to slide the Bracket out (over the button) todisengage the pins on the Bracket from the hinges on the unit (FIG.2).3.Lift the Wall Mount Bracket off of the hinges to remove (FIG.3):Wall Mount Considerations•Distance between conference table and display:The closer the table is to thewall-mounted display. the lower the display should be mounted. As a generalguide, the display should be mounted between 40” and 48” from the floor.•Avoid obstructing the camera view:If the display protrudes from the wall morethan the ACV-5100, then additional spacing between the display and theACV-5100 may be needed.•Position camera for full visibility: In small rooms, it may be necessary to manuallytilt the camera up to maximize visibility for all participants.Using the Bracket Mounting GuideThe Wall Mount Bracket features instructions etched on the inner surface that describehow to position the ACV-5100 beneath a wall-mounted display to avoid obstructing thecamera view (FIG.5):1.Remove the Bracket from the ACV-5100 (see FIG.7on page9).2.Turn the Bracket vertically and place against the wall, centered directly beneaththe wall-mounted display.3.Align the top of the Bracket (see Bottom of Display) with the bottom surface of thedisplay.e the top edge of the notch in the Bracket (see Top flat surface of Acendo Vibeto determine the closest placement for the ACV-5100 beneath the display. Markthe mounting surface.5.Align the top flat surface of the ACV-5100 with the mark made in step 4.6.Mount the Bracket using mounting screws and optional mounting spacers (seeFIG.6).Mounting the Wall Mount Bracket and Attaching the ACV-5100e the Wall Mount Bracket as a template to mark the locations for the fourmounting screws (not included). Use mounting screws and hardware appropriatefor the surface being utilized to secure the Bracket to the wall.Optionally, if not hiding them behind the drywall, place the four included WallMount Spacers between the Bracket and the wall to create a 5mm gap forrouting flat cables (see FIG.6).2.Attach the ACV-5100 to the Bracket by sliding the pins on the Bracket into thehinges on the rear of the main unit (see FIG.3):a. Position the ACV-5100 with the bottom panel facing the wall and align thehinges on the main unit with the pins on the Bracket.b. Carefully slide the pins into the hinges, until the Bracket snaps into place.Note: Press the Bracket into place so that the last pin depresses the ReleaseButton, allowing the pins to slide into the hinges (see FIG.3)c. With the ACV-5100 attached to the Bracket, rotate the unit up to its seatedposition. Note that the Bracket snaps shut and is held closed via internalmagnets.Note: Ensure that cables do not obstruct the complete closing of the unit. FIG. 1 ACV-5100 (FRONT/REAR VIEWS)MODELS AVAILABLE•ACV-5100GR, Grey (FG4151-00GR)•ACV-5100BL, Black (FG4151-00BL)INCLUDED ACCESSORIES•15V / 4A.Power Supply•Remote Control•6’ USB 2.0 Cable•5mm Wall Mount Spacers (4)•Lock-Down Screws(2)DIMENSIONS (HWD)•5" x 23 1/2" x 3 15/16" (76 mm x 590 mm x 100 mm)•Depth with optional wall mount spacers: 4 1/8” (105 mm)WEIGHT 6.45 lbs (2.93 kg)ACTIVE POWER REQUIREMENTS•~100-240V, 1.3A max•Only use the included power supplyREGULATORY COMPLIANCE FCC 47 CFR Part 15, Subpart C / Subpart B (emissions)EN 55024, EN 60950-1, IEC/EN/UL 60065:2014ENVIRONMENTAL•T emperature (Operating): 32° F to 113° F (0° C to 45° C)•T emperature (Storage): -4° F to 158° F (-20° C to 70° C)•Humidity (Operating): 5% to 85% RH non-condensingOPTIONAL ACCESSORIES•CBL-USB-FL2-16, USB 2.0 16ft Extension Cable (FG10-2220-16)•CBL-USB-FL2-33, USB 2.0 33ft Extension Cable (FG10-2220-33)•ACR-5100, Meeting Collaboration System (FG4051-00)FIG. 2 ACV-5100 BOTTOM VIEW - OPENING THE WALL MOUNT BRACKETFIG. 3 ACV-5100 BOTTOM VIEW - REMOVING THE BRACKETCameraFrontRearRubber feet (removable, x2)mounting holes (x4)Wall Mount BracketSide PanelKeypadCable Pass-ThruWall Mount BracketHinges/PinsRelease ButtonConnector BayWall Mount BracketPins (x4)Hinges (x4)Slide pins in to install Slide pins out to removeRelease ButtonFIG. 4 ACV-5100 WALL MOUNT CONSIDERATIONSFIG. 5 USING THE MOUNTING GUIDEFIG. 6 WALL MOUNTING THE ACV-510040-48” from floorDisplayMounting Bracket Mounting Guide(etched into surface)(top view)ACV-5100DisplayMount the Bracket to thewall via 4 mounting screwsAttach the ACV-5100 to theBracket via hinges & pinsbamounting screws(x4, not included)mounting spacers (x4, optional)Note: Use M4 or #8mounting screwsCable Pass-Thru© 2018 Harman. All rights reserved. Modero, AMX, AV FOR AN IT WORLD, HARMAN, and their respective logos are registered trademarks ofHARMAN. Oracle, Java and any other company or brand name referenced may be trademarks/registered trademarks of their respective companies.AMX does not assume responsibility for errors or omissions. AMX also reserves the right to alter specifications without prior notice at any time.The AMX Warranty and Return Policy and related documents can be viewed/downloaded at .3000 RESEARCH DRIVE, RICHARDSON, TX 75082 | 800.222.0193 | 469.624.8000 | +1.469.624.7400 | fax 469.624.7153AMX (UK) LTD, AMX by HARMAN - Unit C, Auster Road, Clifton Moor, York, YO30 4GD United Kingdom | +44 1904-343-100 | /eu/REV: ALast Revised: 1/19/20183.Connect cables as necessary (inside the Connector Bay - see FIG.2).4.Rotate the ACV-5100 into seated position. The Bracket is secured with magnets (FIG.7).ConnectionsAll connectors are located within the Connector Bay (rear panel).•For surface installations, place the unit face-down and open the Connector BayDoor to manage cables/connectors.•For wall-mounted installations, simply rotate the ACV-5100 unit down and awayfrom the wall to access the Connector Bay.There are two sets of connectors on the inner side panels of the Connector Bay. Each connector is labeled on the elastic cable straps. Run each cable through the cable pass-thru in the bracket/door and under the cable straps.Rotating the ACV-5100 Into the Seated PositionAfter connecting all cables, close the Bracket to return the ACV-5100 to its seated position. The Bracket is secured via internal magnets (FIG.7):Installing Lock-Down ScrewsThe ACV-5100 comes with two (flat-head) Lock-Down Screws that can be added after the ACV-5100 has been installed and connected. The Lock-Down Screws prevent the Bracket from being opened accidentally. With the Bracket/Connector Bay Doorclosed, install the Lock-Down Screws in the bottom panel (FIG.8):Note : The Lock Down screws are not to be used to mount the ACV-5100 unit to the wall.Side Panel KeypadAll controls and LEDs are on the left side panel of the ACV-5100 (FIG.9):Volume and Mute ControlsThe ACV-5100 features Sound by JBL, including a 10W/channel stereo amplifier,speakers, microphones, and DSP algorithms with AEC •Use the Volume Up/Down buttons on either the ACV-5100 side panel or on theremote control to adjust speaker volume.•Mute Speaker and Mute Microphoneenable/disable the speakers andmicrophone. Note that these buttons are lit on the ACV-5100 (and flash on the remote control) to indicate that the sound functions are muted.CameraThe ACV-5100 is equipped with a wide-angle camera for videoconferencing and supports a wide range of web conferencing applications via USB. To configure your USB device, such as a laptop, to work with the ACV-5100:1.Connect the ACV-5100 to a laptop/PC via e Source Select button on the the ACV-5100 (FIG.9) to select USB (if necessary).3.Select AMX Acendo Vibe as the camera.4.Select AMX Acendo Vibe as the microphone.5.Select USB AUDIO CODEC as the speakers.Note : To adjust the camera’s view, simply grasp the camera and rotate to the desired position.Remote ControlThe ACV-5100 includes a wireless remote control (FIG.10):Pairing the Remote Control to the Acendo Vibe1.Press and hold both the Source Select and Bluetooth Pairing buttons on theremote control for 5 seconds (see FIG.10). All LEDS on the remote control should start blinking or remain blinking (once per second).2.Press and hold both the Source Select and Bluetooth Pairing buttons on theACV-5100 (see FIG.9). After 3-5 seconds the LEDS on the remote control should stop flashing to indicate the remote control has paired.Note : If the remote control remains in pairing mode (all LEDS blinking) for longer than 60 seconds the remote control will go to sleep. Press any button on the remote control to wake it up and continue with step 2.Pairing the Acendo Vibe with a Bluetooth Source Device1.Press the Bluetooth Pairing button on the Acendo Vibe or the remote control to initiate pairing (see FIG.9).The Bluetooth button will flash on both the ACV-5100 and the remote control.Note : To exit pairing mode without pairing a device, press either Bluetooth button again for 5 seconds.2.On the source device, verify that Bluetooth pairing is enabled, and look for“Acendo Vibe ” (or custom discoverable name) as a found device. Select the Acendo Vibe device for pairing. The Bluetooth LED on the ACV-5100 side panel lights solid to indicate that the Bluetooth device is paired.If automatic switching is disabled, use the Source Select button on the ACV-5100 to select Bluetooth as the audio source (if necessary). At this point, the Bluetooth LED is lit solid , Bluetooth audio is sent to the ACV-5100 speakers, and microphone audio is sent to the paired Bluetooth device.Note : Once the ACV-5100 has paired to a device, it must either be "removed" or "forgotten" from your device’s Bluetooth pairing list before it can be paired again.Acendo Vibe Configuration ToolThe ACV-5100 is configured via the Acendo Vibe Configuration Tool software (available to download from AMX). In most cases the default settings should not require adjustment. For details, see the Acendo Vibe Instruction Manual , available to view or download from .Setup ModeIn order for the Acendo Vibe Configuration Tool to communicate with the ACV-5100,the unit must be in Setup Mode. To place the ACV-5100 in Setup Mode, press the Audio Source Select and Mic Mute buttons on the ACV-5100 simultaneously (see FIG.9) for 3seconds. All of the LEDs blink to indicate that the unit is in Setup Mode.Note : Press and hold the Audio Source Select and Mic Mute buttons for 3 seconds to exit Setup mode.Additional DocumentationFor instructions on configuring the Acendo Vibe, file transfers, firmware updates,programming and troubleshooting info, see the Acendo Vibe Instruction Manual ,available to view or download from .Refer to AMX University for online videos that demonstrate many of the installation steps described in this Quick Start Guide.DC POWER Connect the included 15V power supply to this barrel connector. Only use the power supply included with the ACV-5100.OPTICAL AUDIO Use this TOSLINK connector to receive Optical Stereo Input from an audio source device.AUX OUT Use this 1/8” mini-stereo connector to send analog stereo sound from the ACV-5100 to an auxiliary device.AUX IN Use this 1/8” mini-stereo connector to receive analog stereo sound from an analog audio source device.HDMI OUT (T ype A) Connect to an HDMI input on a display device.HDMI IN (T ype A) Connect to an HDMI output from a source device, such as a laptop or Acendo Core.USBUse the USB 2.0 Type-B port to connect a PC/laptop to the ACV-5100 as a source device. Acendo Vibe is plug-and-play with PC/laptop using standard UAC/UVC drivers. The USB connection is also used to configure the ACV-5100 via the Acendo Vibe Configuration T ool for settings and firmware updates.RS-2323-pin captive-wire connector provides serial communication with the Acendo Vibe. Refer to the Acendo Vibe Instruction Manual for serial command definitions.MOTION(future firmware update)3-pin captive-wire connector provides connectivity for an (optional) motion sensor (reserved for future implementation).•PWR (+5V 0.1A)•OCC •GroundThe logic of OCC is "High" for occupancy detected, and "Low" for vacancy.FIG. 7 ROTATING THE ACV-5100 INTO ITS SEATED POSITIONFIG. 8 ACV-5100 BOTTOM VIEW - LOCK DOWN SCREW LOCATIONSFIG. 9 ACV-5100 LEFT SIDE PANEL KEYPADRotate the ACV-5100 into seated position (Bracket is secured with magnets)frontopenclosedLock-Down ScrewsActive Audio SourceAudio Source Select (press to cycle throughthe source options)Mute SpeakerMute MicrophoneVolume Up/Down Bluetooth Pairing(indicates the current selection FIG. 10 ACENDO VIBE REMOTE CONTROLMute MicrophoneMute SpeakerEnd CallSource Select pushbutton (on back side)Volume Up/Down +-(rotate ring to adjust)Battery Compartment (bottom panel)Unlock & twist to openBluetooth Pairing(press to pair remote to user device)。
Elkay 1-1 8 英寸无挂缸浴室洗手盆说明书
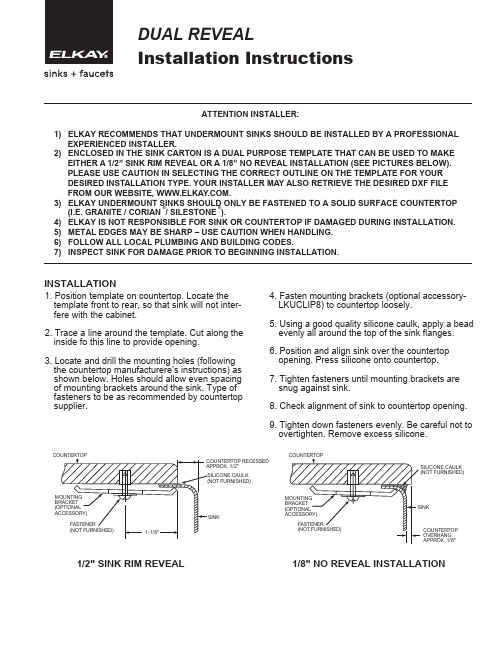
ATTENTION INSTALLER:1) ELKAY RECOMMENDS THAT UNDERMOUNT SINKS SHOULD BE INSTALLED BY A PROFESSIONAL EXPERIENCED INSTALLER.2) ENCLOSED IN THE SINK CARTON IS A DUAL PURPOSE TEMPLATE THAT CAN BE USED TO MAKE EITHER A 1/2” SINK RIM REVEAL OR A 1/8” NO REVEAL INSTALLATION (SEE PICTURES BELOW). PLEASE USE CAUTION IN SELECTING THE CORRECT OUTLINE ON THE TEMPLATE FOR YOUR DESIRED INSTALLATION TYPE. YOUR INSTALLER MAY ALSO RETRIEVE THE DESIRED DXF FILE FROM OUR WEBSITE, .3) ELKAY UNDERMOUNT SINKS SHOULD ONLY BE FASTENED TO A SOLID SURFACE COUNTERTOP (I.E. GRANITE / CORIAN / SILESTONE ).4) ELKAY IS NOT RESPONSIBLE FOR SINK OR COUNTERTOP IF DAMAGED DURING INSTALLATION.5) METAL EDGES MAY BE SHARP – USE CAUTION WHEN HANDLING.6) FOLLOW ALL LOCAL PLUMBING AND BUILDING CODES.7) INSPECT SINK FOR DAMAGE PRIOR TO BEGINNING INSTALLATION.INSTALLATION1. Position template on countertop. Locate the template front to rear, so that sink will not inter-fere with the cabinet.2. Trace a line around the template. Cut along the inside fo this line to provide opening.3. Locate and drill the mounting holes (following the countertop manufacturere’s instructions) as shown below. Holes should allow even spacing of mounting brackets around the sink. Type of fasteners to be as recommended by countertop supplier.4. Fasten mounting brackets (optional accessory-LKUCLIP8) to countertop loosely.5. Using a good quality silicone caulk, apply a bead evenly all around the top of the sink flanges.6. Position and align sink over the countertop opening. Press silicone onto countertop.7. Tighten fasteners until mounting brackets are snug against sink.8. Check alignment of sink to countertop opening.9. Tighten down fasteners evenly. Be careful not to overtighten. Remove excess silicone.Installation InstructionsDUAL REVEAL1/2" SINK RIM REVEAL 1/8" NO REVEAL INSTALLATION®®Suggestions for the Care and Cleaning of your Elkay Stainless Steel SinkRECOMMENDED CLEANSERSElkay has tested general household cleansers to measure their effec-tiveness in cleaning stainless steel sinks. The most aggressivecleansers consist of Bar Keeper’s Friend, Zud and Lawrence Right Work.Other cleansers, which are still effective, but less aggressive include Ajax, Comet, Shiny Sinks Plus, Luneta, Soft Scrub, Mr. Clean, Maas and Flitz. The non-abrasive formula is safe and effective for day to day cleaning. So to help maintain the beautiful finish of your stainless steel sink, use one of the cleansers that Elkay recommends.RECOMMENDATIONSFOR PROPER MAINTENANCEDo ...Rinse thoroughly after each use. “Thorough” rinsing can be done by running water for a few minutes and rubbing the cleaned area with a clean sponge.Do ...Towel dry after each use to prevent mineral deposits from building up on the surface of the sink.Do ... Clean the sink once a week, being sure to rub in the direction of the finish grain lines, using an Elkay recommended cleanser.Do e an Elkay bottom grid or rinsing basket to “protect” the finish. Bottom grids and rinsing baskets can remain in the sink and will not cause rusting or pitting.Do Not .. Rub the sink across the finish lines. Scouring across the finish lines can damage the original sink finish.Do Not ...Allow soap or other household cleansers to dry on the surface of the sink. Most brands contain chemical additives which will affect the original finish.Do Not e solutions of chlorine bleach and water in the sink.Chlorides, which are found in most soaps, detergents, bleaches,and cleansers, are very aggressive to stainless steel. If left on the sink too long they can cause surface pitting.Do Not e a steel wool pad to clean your sink. If a more abra-sive product is needed, use a green Scotch Brite pad being sure to rub in the direction of the finish grain lines. Steel wool pads have a tendency to break apart and small particles of steel canbecome embedded in the surface of the sink. The steel particles will rust and will give the appearance that the sink itself is rusting.Elkay warrants to the original purchaser of an Elkay stainless steel sink that Elkay will, at its option, replace or repair, without charge, such product ifit fails due to a manufacturing defect for a lifetime of normal residential use.Product replacement does not include transportation cost or labor installa-tion cost. This warranty covers only stainless steel self-rimming drop-in sinks installed in a conventional countertop surface and stainless steel under-mount sinks installed in a conventional solid surface countertop and applies to residential installations only. Elkay reserves the right to examine product in question and its installation prior to replacement.This warranty applies to sinks purchased after March 1st 2001 as shown on the purchaser’s dated receipt. For sinks purchased prior to march 1st 2001,the applicable warranty at that time will be in effect. Our warranty does not cover product failure or damage caused by the use of optional Elkay acces-sories, abusive treatment, misuse, evironmental factors, normal wear includ-ing dents and scratches, improper care and cleaning, use of aggressive andabrasive cleaners, damage due to handling or failure to follow the recommended procedures for installation, care and maintenance as detailed in the installation care guide provided with every sink. This warranty is extended only to the original consumer purchaser of the product. This warranty does not cover shipping costs,or any other charges for such items as installation or replacement of the sink, diagnosis or replacement of any faucet or component part, or any other expense or loss.All incidental or consequential damages are specifically excluded. No additional warranties, express or implied are given, including but not limited to, any implied warranty of merchantability or fitness for a part-icular purpose.Some states do not allow the exclusion or limitation of incidental or consequential damages or limitations on how long an implied warranty lasts, so the above limita-tions or exclusions may not apply to you.This warranty gives you specic legal rights, and you may also have other rights which vary from state to state.1. Write to: Elkay Manufacturing CompanyAttention: Consumer Services 2222 Camben Court Oak Brook, IL 605232. Include a letter containing the following information:a. Date of purchase and installationb. Proof of Purchase (copy of original dated voice)c. Description of nature of defectd. Model number or description of model and/or component part if possible.WASTE FITTINGS AND ACCESSORIES ARE NOTE WARRNTED OTHER WARRANTY CONDITIONS ON SINKSTO OBTAIN SERVICE UNDER WARRANTYDo Not e rubber mats or dishpans in the sink. Leaving rubber mats or dishpans in the sink can lead to surface rust or possible pitting. However, if you insist on using mats or dishpans, please remove them after each use and rinse thoroughly.Do Not ...Leave wet sponges, cloths, or cleaning pads on the sink.This can lead to surface rust.Following these recommendations for the care and cleaning of your stainless steel sink will insure that it will provide you with many years of service.CHLORIDESToday, chlroides are found in most all soap, detergents, bleaches and cleansers; chlorides can be aggressive to stainless steel. However,chlorides are very water soluble. Therefore, THOROUGH RINSING of your sink after each use to remove any chloride residue and a weekly cleaning is all that is required to keep your sink looking bright and shiny.SCRATCHESLike many metallic surfaces, your stainless steel sink will scratch.These are merely usage scratches and over time will blend into the overall finish of your sink with proper cleaning.KNIVESYour sink is designed to serve as many things but not as a cutting board or chopping block. This type of use will lead to deep scratches in the sink finish and will dull your knives. Elkay does offer various cutting boards which provide an additional work area.WATER QUALITYThe quality of your water can affect your sink’s appearance. If your water has a high iron content, a brown surace stain can form on the sink giving the appearance of rust. Additionally, in areas with a high concentration of minerals, or with over-softened water, a white film may develop on the sink. To combat these problems, we suggest that the sink be towel dried after use, and again, on a weekly basis, the sink should be cleaned using a recommended cleanser.FOODSHeavy salt concentration or foods containing high levels of salt should not be allowed to dry on the sink surface. Rinse your sink thoroughly after use.••••••••••Installation InstructionsELKAY2222 Camden Court Oak Brook, IL 60523© 2014 Elkay (Rev C 8/18)1000002045ELKAY LIMITED LIFETIME SINK WARRANTY。
JKS 按摩椅 Manufacturing Wrangler JK 车辆 brake 线位移套件说明
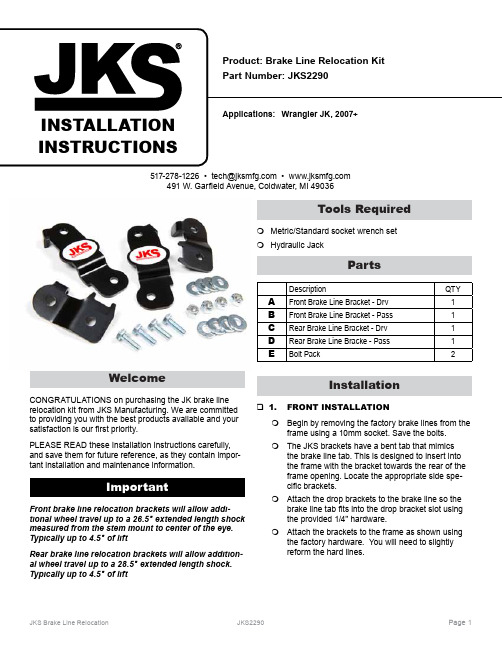
WelcomeCONGRATULATIONS on purchasing the JK brake line relocation kit from JKS Manufacturing. We are committed to providing you with the best products available and your satisfaction is our first priority.PLEASE READ these Installation Instructions carefully, and save them for future reference, as they contain impor-tant installation and maintenance information.ImportantFront brake line relocation brackets will allow addi-tional wheel travel up to a 26.5" extended length shock measured from the stem mount to center of the eye. Typically up to 4.5" of liftRear brake line relocation brackets will allow addition-al wheel travel up to a 28.5" extended length shock. Typically up to 4.5" of liftTools RequiredMetric/Standard socket wrench setHydraulic JackPartsDescription QTYA Front Brake Line Bracket - Drv1B Front Brake Line Bracket - Pass1C Rear Brake Line Bracket - Drv1D Rear Brake Line Bracke - Pass1E Bolt Pack2Installation1. FRONT INSTALLATIONBegin by removing the factory brake lines from the frame using a 10mm socket. Save the bolts.The JKS brackets have a bent tab that mimics the brake line tab. This is designed to insert intothe frame with the bracket towards the rear of theframe opening. Locate the appropriate side spe-cific brackets.Attach the drop brackets to the brake line so the brake line tab fits into the drop bracket slot usingthe provided 1/4" hardware.Attach the brackets to the frame as shown using the factory hardware. You will need to slightlyreform the hard lines.491 W. Garfield Avenue, Coldwater, MI 49036Verify the newly formed hard lines are not rubbingon the frame or shock mount. Cycle the suspension to full droop to ensure thebrake lines have enough slack. If more slack is necessary, reform the bend in the hard line down10-15 degrees.2. REAR INSTALLATIONBegin by removing the factory brake lines from theframe using a 10mm socket. Save the bolts. The JKS brackets have a bent tab that mimics thefactory brake line tab that inserts into the frame with the bracket towards to front. Locate the ap-propriate side specific brackets. Attach the JKS brackets to the inside of factorybrake line brackets using the provided 1/4" hard-ware. Attach the brackets to the frame as shown usingthe factory hardware.Cycle the suspension to full droop to ensure thebrake lines have enough slack and clearance to the sway bar.©2013 JKS Manufacturing, Inc & Aftermarketing, LLC Revision Date 1/30/2014。
Panasonic WX-SA250 无线抗干扰天线说明书

Panasonic WX-SA250 Features & SpecificationsPage 1 of 2 WX-SA250 Wireless AntennaThe WX-SA250 wireless antenna is an integralpart of Panasonic's SR200 1.9 GHz DigitalWireless Microphone system, providing line ofsight communication with Panasonic’s ST200wireless microphones and routes the signalflawlessly back to the WX-SR202 digitalwireless receiver via CAT5 / 6 connection.Multiple antennas can be placed in a room toaccommodate for room size or multiple 2-channel microphone systems. Each antennahas a maximum range of 131 feet (40-meters)and is easily adjustable to 3 lower steps so youcan easily accommodate room size andminimize interference with other Panasonicwireless microphone systems installed inadjacent rooms. The WX-SA250 can easily bemounted on a wall, ceiling, or even on amicrophone stand for mobile installations usingthe bracket included.• Provides in-room line of sight connection with Panasonic’s WX-ST wireless microphones,enabling the Panasonic WX-SR202 digital wireless receiver to be hidden in a cabinet orcloset.• Easy to install and configure.• Connects via a CAT5 / 6 cable to the WX-SR202 digital wireless receiver (up to 8 can beconnected to one receiver).• Selectable range to accommodate room size and minimize interference with multiplesystems installed in adjacent rooms.• Multiple antennas can be installed in one zone for maximum coverage.• Flexible mounting options (on wall, on ceiling, or on a microphone stand).• Mounting plate included.Panasonic WX-SA250 Features & SpecificationsPage 2 of 2 Antenna Field Selection:Three-step switching (set at WX-SR202 receiver) using Panasonic’s Operation Support SoftwareWireless Frequency: 1920 MHz to 1930 MHzOperating Ambient Temp.: 14° F to +122° F (-10° C to +50°C) LED Indicators:Power Power Source:RJ45 from WX-SR202 Receiver Compatible cables: CAT5 / CAT5e / CAT6 straight cable Water Resistance:IPX4 equivalentWarranty (Parts & Labor):3 yearsFinish:Sail White (color approximate to Munsell N9.3)Accessories Included:Mounting PlateDimensions (W x H x D): 7-9/32 in W x 6-19/64 in H x 1-17/64 in D(185mm W x 160mm H x 32mm D)Weight: 0.88 lbs. (400 g)Leveraging Panasonic's 20-year experience in DECT wireless audio communications, the WX-SR200P 1.9 GHz digital wireless microphone system is the best-in-class solution for classroom or corporate presentations providing low latency for hybrid in-room/virtual presentations. Panasonic's digital wireless microphone system is easy to set up, easy to integrate with third-party control systems (such as Crestron, Extron, and Q-SYS) and easy to use. Setup is a breeze - the wireless microphones pair wirelessly with Panasonic's digital wireless mic receiver and assigns channels automatically, eliminating the need for manual channel assignment. Thesystem can be expandable to suit a variety of spaces, fromsmall classrooms, medium sized classrooms / conferencerooms, to large auditoriums. Up to 8 separate antennas(per receiver) can be mounted to the wall or the ceiling inthe room and connected via CAT5 back to the receiverlocked away in a cabinet or closet and multiple digitalwireless microphone receivers can be installed to addwireless microphone channels to the room .。
Series ADPS 差压电子切换器说明书

ADPS Adjustable Differential Pressure Switch overpressure, vacuum, and differential pressure applications. The scaled adjustment knob allows changes to the switching pressure to be made without a pressure gage. The ADPS is available with settings from 0.08 in w.c. (20 Pa) to 20 in w.c. (5000 Pa). The silicone diaphragm and PA 6.6 body make the Series ADPS perfect for use with air and other noncombustible gases. The Series ADPS can be used in monitoring air filters, ventilators, and industrial cooling-air circuits along with controlling air and fire-protection flaps and many other applications.Use only with mediums such as air, or other noncombustible or non-aggressive gases. Otherwise operating faults or accidents may occur.horizontally. In this case, however, the switching values are approximately 0.08 in w.c.(20 Pa) higher as indicated on the scale. In the horizontal position, the pressure switch should be mounted ‘lying down’ only (that is to say with the electrical connections pointing upwards). Do not mount the pressure switch in a hanging position (that is to say, not ‘overhead’ with the electrical connections pointing downwards). Otherwise the device will function inaccurately.a) Mounting with screws or brackets1. To mount the pressure switch, L-shaped A-288 and S-shaped A-289mounting brackets can be ordered separately. To secure the device on therear side of the housing, only use the sheet metal screws (3.5 x 8 mm)which are supplied together with the mounting brackets. Under nocircumstances must you use longer screws. Otherwise, the base of thehousing could be punctured resulting in the pressure switch leaking.2. You can also mount the pressure switch directly on a wall. To do this usescrews with a maximum diameter of 0.315˝ (8.0 mm), if you use the outermounting lugs to screw the device in place. Do not tighten the screws somuch that the base of the device is deformed. Otherwise, the pressureswitch can be shifted out of position, or leak.Installing HosesImportant: Pressure tubing cannot be kinked. Pay particular attention to this point if you run hoses over an edge. It is better to form a loop. If the hoses are kinked, the device cannot function accurately.a) For connection to the pressure switch two fittings inherent in the housing areprovided for hoses with an internal diameter of 1/4˝ (6.0 mm).1. Connect a hose with the higher pressure to socket P1 which is located on the lower section of the housing.2. Connect a hose with the lower pressure to socket P2 which is located on the middle section of the housing.After you have installed the hoses, it is absolutely essential to check them for tightness of fit at the connection points and to make sure that they run without any kinks.Printed in U.S.A. 4/20FR# 443602-00 Rev. 3©Copyright 2020 Dwyer Instruments, Inc.Electrical ConnectionWork on electrical installations must only be carried out by electricians who are specifically trained for this purpose.For cable gland models, the seal in the screw cable connection is designed for cables with alternative sheath diameters of 0.275˝ (7 mm) or 0.393˝ (10 mm). Only use these sizes – otherwise the screw cable connection cannot seal adequately.1. If using a 0.275˝ (7 mm) connecting cable, you can line up the press nut, the plain washer and the sealing ring directly on the cable.2. If using a 0.393˝ (10 mm) connecting cable, you must first break the inner rubber ring out of the sealing ring directly on the cable. Then line up the press nut, the plain washer and the sealing ring on the cable.WiringThe switching device in this pressure switch is designed as a change-over contact as can be seen from the wiring diagram (Figure 1). The rest position is shown in Figure 1 (pressure below the activation switch point on dial).1. In the instance where pole 3 (COM) closes to Pole 2, the pressure is increasing (NO).2. In the instance where pole 3 (COM) closes to Pole 1, the pressure is decreasing (NC).Protect the feed line (to pole 3) by fuse, either in control system or along the line, and do so with:1. Max 1.5 A / 250 VAC, if you are loading the contact with an resistive load.2. Max 0.4 A / 250 VAC, if you are loading the contact with an inductive load (such as relay).3. Max 0.1 A / 24 VDC, if you are using the pressure switch in the weak current version with gold-plated contacts.The connections are intended for crimp-type sockets, 0.25 in (6.3 mm).1. Make sure the crimp connection is perfect, and that the cable lugs fit properly on to the connections.2. If you do not have any crimp-type sockets available, you can also use the cable lugs which are supplied with mounted screw terminals. However, these are only intended for rigid copper wire.3. On flex, it is either necessary to crimp on strand end sleeves – and then you can also screw the strands on – or to crimp cable lugs on directly as previously described.Setting the Pressure RangeMake absolutely certain that there is no voltage on the electrical connections before you carry out any setting on the pressure switch. Otherwise, it could be fatal if you accidentally touch the electrical connections or the metal adjusting screw while you are performing the settings.a) Use the adjustment dial to set the pressure which should trip the switch on an increase of pressure.1. The indications on the dial are only correct for the vertical mounting position.2. When the pressure falls, the switch returns to its resting position as soon as the pressure falls below the dead band.Attaching Covera) Insert the screw cable connection into the recess provided for this purpose on the housing.b) Then place the housing cover in position and screw it down evenly on to the pressure switch.Testing the SettingDo not operate the system until the housing is closed. Otherwise there is the possibility of an electric shock if you accidentally touch live parts.Check the trip and reset pressures by slowly increasing the pressure and then allowing it to fall again.Important: Observe the maximum permissible operating pressure of 40 in w.c. (10 kPa) which is indicated in the data sheet. Otherwise the pressure switch may be damaged.MAINTENANCEUpon final installation of the Series ADPS Adjustable Differential Pressure Switch, no routine maintenance is required. A periodic check of system operation is recommended. The Series ADPS is not field serviceable and should be returned if repair is needed (field repair should not be attempted and may void warranty). Be sure to include a brief description of the problem plus any relevant application notes. Contact customer service to receive a return goods authorization number before shipping.Figure 11. Break contact2. Operating contact3. Power supply lineFirst make sure that there is no voltage on the connecting cable while you are working on the electrical connections. Otherwise, apossible electric shock may result and the connected equipment may be damaged. The connecting cable can be run to the pressure switch from three sides, according to choice. The screw cable connection has a plug-in design for this purpose. Rotate protective cover accordingly.1233 COM。
- 1、下载文档前请自行甄别文档内容的完整性,平台不提供额外的编辑、内容补充、找答案等附加服务。
- 2、"仅部分预览"的文档,不可在线预览部分如存在完整性等问题,可反馈申请退款(可完整预览的文档不适用该条件!)。
- 3、如文档侵犯您的权益,请联系客服反馈,我们会尽快为您处理(人工客服工作时间:9:00-18:30)。
Mounting bracket having flexible locking armBACKGROUND OF THE INVENTIONThe present invention pertains to a mounting bracket. More particularly, the present invention pertains to a mounting bracket having a flexible locking arm to enable secure attachment to a mounting base such as a rack vertical beam.Sign display is a vitally important function for the retail industry. The principle function of a sign in a retail trade or store is to notify consumers of particular information about the product. While signs are quite effective in directing the consumers attention to a particular location, item or product, because the signs and the brackets from which the signs hang, can extend into an aisle way,they can be susceptible to damage from collisions with shopping carts, forklifts, or people. Thus, it is important that the sign mounting bracket maintains a secure connection to the base to ensure that the sign remains securely intact for viewing, while being sufficiently sturdy to withstand the weight of the attached sign or display andany inadvertent contact.Typically mounting brackets are made out of relatively rigid heavyweight materials, such as metal. Although a rigid or metal bracket may provide an effective secure connection with the base and have a sturdy frame capable of withstanding the weight of a hanging display, the cost in manufacturing a metal bracket can be relatively expensive. Furthermore, a rigid bracket may not readily absorb the impact of a collision, and to this end, may become damaged, bent or broken upon such a collision.In addition, one requirement of such mounting brackets is ready installation. Many brackets require fastening to the display using mechanical fasteners, such as nuts, bolts, screws and the like. While these fasteners provide acceptable attachment vis-a-vis strength and integrity, they can be quite labor intensive to install. Thus, brackets that use these fasteners may not be acceptable, particularlyin those instances where many such signs are to be installed or mounted.One conventional flexible bracket used in mounting systems has a two prong latching connection for attaching to the mounting system or display. One disadvantage of this type of brackets is that the two prongs are susceptible to bending and thus becoming disengaged in a small-scale collision. Further, because the brackets are flexible, the two-prong connection may not provide a secure locked connection with the mounting system.Accordingly, there exists a need for a display bracket that is easy to manufacture and provides a secure lockable connection to a mounting base. Most desirably, the mounting bracket is flexibly designed and is properly reinforced to enable hanging a display or sign and to withstand inadvertent impact. Such a bracket is cost effective to manufacture and requires minimal or no external hardware for installation.SUMMARY OF THE INVENTIONA bracket for mounting an associated sign to an associated post includes a post mounting portion and a coupling portion for mounting the sign to the bracket. A post to which the bracket is mounted post has at least three linearly arranged slots formed therein and defines wall portions between the slots and a lip at the slot. The post has an exterior surface and an interior surface.The bracket is formed from a flexible, resilient material and includes a main body portion having first and second retaining elements spaced from one another. The retaining elements are configured for engagement with the post by insertion into first and second post slots. The retaining elements engage the interior surface of the post at the slots. Preferably, the retaining elements have a hook shape defining a shoulder that engages the interior surface of the post. The bracket includes a coupling portion for mounting the sign to the bracket.The main body portion is arcuate and extends away from the post intermediate the first and second retaining elements. A flexible locking arm extends from the main body portion intermediate the first and second retaining elements. The locking arm has a portion that extends non-linearly from the main body portion. Preferably, the non-linear portion extends along the arcuate shape of the main body portion.The locking arm includes a latching element for insertion into and engagement with a third post slot intermediate the first and second post slots. The latching element engages the post at the slot to maintain the bracket secured to the post.In a present embodiment, the latching element includes a head portion insertable into the third post slot. The latching element includes a first detent for engaging the slot lip. Preferably, the latching element also includes a second detent for engaging the slot lip, with the first and second detents being adjacent one another.The locking arm can include a flange extending transversely therefrom. The flange extends along a portion of the locking arm and terminates prior to a juncture of the locking arm and the bracket main body. The flange provides a finger or gripping region for bending (e.g., flexing) the arm to install or lock the bracket to the post.The main body portion can include a curved flange extending along an outer portion of the arcuate shape. The flange has a length such that it extends beyond the first and second retaining members and is configured to rest against the post when the bracket is in place thereon.The coupling portion can be formed on the bracket spaced from themain body portion. This provides a mounting for the sign that is spaced from the post to which the bracket is mounted. A beam can extend between the coupling portion and the main body portion. An angled truss can extend between the main body portion and the beam proximal the coupling portion to provide additional support for the sign and rigidity to the bracket.These and other features and advantages of the present invention will be apparent from the following detailed description, the accompanying drawings and appended claims.BRIEF DESCRIPTION OF THE FIGURESThe benefits and advantages of the present invention will become more readily apparent to those of ordinary skill in the relevant art after reviewing the following detailed description and accompanying drawings, wherein:FIG. 1 is a side view of an embodiment of a mounting bracket embodying the principles of the present invention, the bracket being shown in a resting or non-flexed state, FIG. 1A being an enlargedview of the locking arm head and latching member; andFIG. 2 is a side view of a portion of the mounting bracket of FIG. 1, as the bracket is installed on an upright for a display rack.DETAILED DESCRIPTION OF THE INVENTIONWhile the present invention is susceptible of embodiment in various forms, there is shown in the drawings and will hereinafter be described a presently preferred embodiment with the understandingthat the present disclosure is to be considered an exemplification of the invention and is not intended to limit the invention to the specific embodiment illustrated. It should be further understood that the title of this section of this sp ecification, namely, “Detailed Description Of The Invention”, relates to a requirement of theUnited States Patent Office, and does not imply, nor should beinferred to limit the subject matter disclosed herein.Referring now to the figures, and in particular FIG. 1, there is shown a mounting bracket 10 embodying the principles of the present invention. The mounting bracket 10 is mounted to a conventional mounting base 12, which is shown in FIG. 2. An exemplary base 12 isan upright 32 having a plurality of spaced channels or slotted openings 14a-f, enabling the bracket 10 to interlock with the base 12. In a typical application, the upright 12 will be one of a number of vertical posts to, for example, support a pallet rack. In an interlocked state, the mounting bracket 10 extends outwardly from the mounting base 12, as shown in FIG. 2, enabling an associated sign or display (not shown) to hang from the bracket 10.The mounting bracket 10 is formed as an integral member and includesa first portion 16 for mounting to the base 12 that is contiguouswith a second portion 18 from which a sign is mounted. The base mounting portion 16 includes an intermediate main support bar 20 extending between a coupling portion 22 and an adjoined beam 24 and truss 26 combination.The mounting bracket 10 is formed from a molded plastic, polymeric or like resilient material, which enables flexible manipulation of thebracket 10 for connection to the mounting base 12. Notably, it is contemplated that the mounting bracket 10 can be formed from any resilient material without departing from the scope of the present invention.The main support bar 20 has upper and lower edges or flange 28, 30, that extend along the bar 20 to provide stability to the bar against bending or flexing and to provide the bar 20 with additional structural reinforcement.The coupling portion 22 is integrally connected to (e.g., formed as part of) an end of the bar 20. The coupling portion 22 includes a connecting arm 32 and a wedge-like element 34, configured for receipt in and connection to the sign or display (not shown). One exemplary arrangement for securing the coupling portion 22 to the sign is disclosed in Padiak et al., U.S. Pat. No. 5,933,932, which patent is commonly assigned herewith and is incorporated herein by reference.The wedge 34 and connecting arm 32 are configured for receipt in an opening defined in the sign or display support or channel. As disclosed in the aforementioned patent to Padiak et al., the wedge 34 has a head 36 that cooperates with the sign support to prevent it from sliding or disengaging from the bracket 10.The angled truss 26 and extending beam 24 combine in an adjoining manner for integral connection to the support bar 20. The beam 24 projects in a generally horizontal direction from the support bar 20, thus providing connection to the second or sign mount portion 18. The extended beam 24 engages the sign mount portion 18 in a generally upper region of a mounting portion 38.The angled truss 26 extends from the support bar 20 to the sign mount portion 18. Preferably, the truss 26 engages a lower region of the mounting portion 38. The truss 26 has a supporting bottom edge or flange 40, which stabilizes the truss 26 against bending.The mounting portion 38 provides a secure connection to the mounting base 12. Referring now to FIG. 2, the mounting portion 38 has a curved or arcuate configuration, and includes a first spine mount 42, a flexible locking arm 44 and a second spine mount 46. The first and second spine mounts 42, 46, in association with the locking arm 44 securely lock the bracket 10 to the base 12. The first and second spine mounts 42, 46 extend from a curved main support body 48.The support body 48 has a curved flange 50 that enhances stability and structural integrity of the mounting portion 38. As illustratedin FIGS. 1 and 2, the curved flange 50 extends along a portion of the support body 48 at an outer region of the arc. The flange 50facilitates securing the bracket 10 to the base 12. The flange 50 has a length somewhat longer than that of the mounting portion 38, and extends beyond the first and second spine mounts 42, 46.The first spine mount 42 has a hook-like shape and includes a head portion 52 terminating at a shoulder or retaining element 54 at one end and extending to the other end into a rounded region 56. Similarly, the second spine mount 46 has a hook-like shape and includes a head portion 58 terminating at a shoulder or retaining element 60 and rounded region 62. Notably, the head portion rounded regions 56, 62 can take any shape to facilitate insertion into the mounting base slots 14.The flexible locking arm 44 provides for secure locking engagement with the mounting base 12, to fasten the bracket 10 into position on the base 12. The locking arm 44 extends from a generally intermediate region (as indicated at 64) of the support body 48, extending arcuately along the body 48. In a current embodiment, the arm 44 extends in an upward direction, toward the first spine mount 42. A supporting flange 66 extends along a portion of the locking arm 44 to provide a finger hold for installation and removal.The locking arm 44 has a rounded head 68 portion that extends outward from the locking arm 44, and is configured for insertion into an opening 14c, between the openings 14b, 14e, into which the first and second spine mounts 42, 46 insert into the base 12. An upper portion of head 68 terminates at a latching member 70. The latching member 70 has a plurality of graduated steps 72, 74 that define detents 76, 78. As illustrated in FIG. 2, upon insertion into a selected opening (such as 14c), one of the steps 72 or 74 engages an outer surface 80 of the base 12, while a corresponding detent 76 or 78 engages a lip portion 82 of the opening 14c.Referring again to FIG. 2, the base 12 has the openings 14a-f formed therein, spaced apart from one another. As illustrated, each opening 14a-f is configured to receive a spine mount 42, 46 or the locking arm 44. Each opening 14a-f is separated from each adjacent opening by a portion, as indicated at 84, of the base wall W that defines thelip 82. The wall W also defines an interior surface 86 of the base 12 that is engaged by the spine mount shoulder 54, 60 when the bracketis in place.The bracket 10 is locked into the base 12, by inserting the first and second spine mounts 42, 46 into openings 14b, 14e, respectively, and the locking arm 44 into opening 14c. As is readily apparent from FIG. 2, when the bracket is urged downwardly, the shoulders 54 and 60 are positioned against the interior surface 86. The locking arm head 68 inserts into opening 14c between those openings 14b, 14e into which the first and second spine mounts 42, 46 insert.To provide a stabilizing lock, the locking arm 44 is flexed or compressed from a resting position (FIG. 1) into an engaging position FIG. 2). To compress the arm 44, the flange 66 is pulled back (toward the coupling member 22) until one of the detents 76 or 78 engages the opening 14c lip 82. The latching member 70 thus engages opening 14c with a comer of the lip 82 positioned in one of the detents 76 or 78. In this manner, the arm 44 is locked onto the base 12 in both the horizontal and vertical directions.Because the arm 44 is pulled or flexed toward the body 48 to engage the latching member 70 with the opening 14c, the natural tendency of the arm 44 is move back to the resting position (FIG. 1). Thus, the arm 44 exerts a force against and into the base 12. This places a tension in the spine mounts 42, 46thus enhancing the “locking” feature of the bracket 10 to the base 12. That is, the spine mounts 42, 46 are generally aligned with one another (as indicated at L in FIG. 1), and the arm head 68 is out of alignment with the mounts 42, 46. When the head 68 is inserted into opening 14c and the arm 44 is flexed rearward (toward body 48) to lock to the base 12, the head essentially aligns with the mounts 42, 46 (as seen in FIG. 2).In addition, as seen in FIG. 2, the wall W portion 84 is captured between the first mount 42 and the latching portion 70. This provides a more secure engagement of the bracket 10 to the base 12. Moreover, when latching the latching member 70 to the base 12, it is necessary to flex the entirety of the body 48. Thus, the body ends 88, 90 provide an additional tension-like locking feature of the bracket 10 to the base 12.A present embodiment of the bracket 10 is provided with two steps 72,74. As will be appreciated by those skilled in the art, the base 12 can be formed (e.g., manufactured) having a variety of wall W thicknesses, as indicated at t, in FIG. 2. To this end, the number or steps 72, 74 formed in the bracket 10 can vary accordingly to permit use of the bracket 10 with a variety of upright 12 support designs and sizes.To unfasten the mounting bracket 10 from the mounting base 12, the locking arm 44 is moved from the engaging position with opening 14c by urging or pulling the arm 44 (by the flange 66) rearwardly or back toward the body 48. This unlocks the detent 76 or 78 from the lip 82. The first and second mounts 42, 46 are then removed from the base 12 by unhooking or upwardly urging the bracket 10 to disengage the shoulders 54, 60 from the interior surface 86.From the foregoing, it will be observed that numerous modifications and variations can be effectuated without departing from the true spirit and scope of the normal concepts of the present invention. It is to be understood that no limitation with respect to the specific embodiments illustrated is intended should be inferred. The disclosure is intended to cover by the appended clams all such modifications as fall within the scope of the invention.。