Technical Support Document for Compliance with the MS4 Permit & Post-Construction Standards
EM63 MID商品说明书
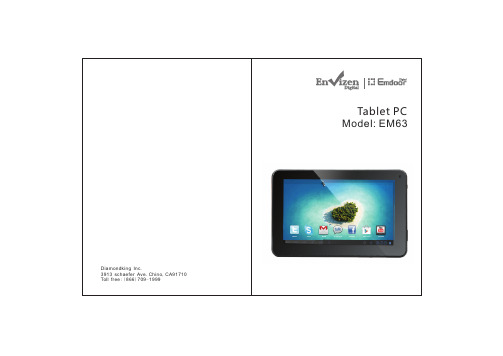
Disclaimer1Thanks very much for purchasing our MID product! Before using this product, please read the manual carefully.We will consider that you have read this manual when you use this product.2. The functions information of this manual is subject to the product itself; we will keep developing new functions. The information in this manual is subject to change without any prior notice.3. The Company will not be responsible for any loss of personal data and damage caused by incorrect operation of software/h ardware, artificial damages, replacement of batteries or any other accident. To avoid loss of your data, please backup your data to your computer at any time.4. We can not control any dispute from users misunderstanding orincorrect operation against the manual, the c ompany will not take any relevant responsibility for any accidental loss potentially occurring in the process of using this manual.5. Please do not repair it by yourself, otherwise, we will not provide you with aftersale service.6.Our c ompany reserves the final explanation right to this manual and other relevant informationPrefaceDear Customers,Thanks very much for purchasing our product! This device is built-in high performance Wifi receiver module, supporting external 3G USB DONGLE wireless network card, turning on the broadband wireless networks, breaking through the restraint of network cable; it will bring you into the portable media player world and fulfill your entertainment needs. It also support picture browsing, E-book Reader, games, online chat and other functions, various settings will fully show your individuality.Safety noticesThis manual contains important information, in order to avoid accidents, please read this manual carefully before you use this product.● Please do not let the player fall or rub or compact with hard objects during using, or it may cause surface scratch of the player,battery loose, data lose or damages of other hardware.. 1 Overview1.1 Appearance and Keys 1.2 Basic Operation 1.2.1 Switch ON 1.2.2 Unlock the Screen 1.2.3 Lock the screen 1.2.4 Switch OFF 1111222Contents1.2.5 Battery charging 1.2.6 Switch input methods 1.2.7 Use T-Flash card1.2.8 Connected to the computer 1.2.9 Browse the file in the device 1.2.10 Startup programs 1.2.11 Close programs 1.2.12 Screen operation 1.2.13 Home screen 1.2.14 Screen gestures 1.2.15 Security setting 1.2.16 Display setting233445555678101.2.17 Wireless And Network Settings 1.3 Technical specifications Warranty811indicating lamp of the device is in high light blue color, the desktop icon of the battery keep rolling which shows it is connected to the device.Press , then it will pop Input Method switch interface.Select the input method you want here.[Noted] After newly install input method, you should choose Settings>Language & input>K e yboard & I n put m ethods then you can use.Please press and drag the icon to the , then the LCD will 1.2.3 Lock the screenWhen the device is in the ON mode, press the POWE R k ey shortly, the system will lock the screen and enter the save power mode. Then the screen is OFF but the system will still un.1.2.4 Switch OFFWhen the device is in the ON mode, press and hold thePOWE R k ey for 3 seconds, the screen will display the power off interface, choose the power off item to confirm, the system will shut automatically.51.2.10 Startup programsClick all the application icon you want to start and it canswitch on.1.2.11Close programsPress the icon continuously or the ESC key, the device willclose the active program. You can also use the correspondingfunction in the management currently running applicationsto close the program.1.2.12 Screen operation● Zoom in and zoom out : In applications which support zoom gestures, such as photo , IE browser, mail and map etc. you can zoom in or out the screen contents by opening or closing your two fingers.● Rolling: In applications which support rolling gestures, such as photo , IE browser, mail and map etc. you can scroll the screen contents by sliding your fingers on the screen. If you want to stop the rolling screen, you just need to touch it.1.2.13 Home screen● Switch home screenIn the home state, you can change the home interface byapplied in one direction.2. Do not remove the TF card before Un i nstalling it, or the card may be damaged.3. If the memory card is write-protected, data will not be formatted and written, please remove the write protection before such operations4. Major brands memory card is recommended to avoid the card is not compatible to this device.5. please well note that the APK (such as application software and games) is default installed to the device. (not the memory card)1.2.8 Connected to the computerOne end of the USB line connect to the computer, the other end connect the MID device, select Settings>Developer options>USB debugging, the device will connect with computer, and you can copy files to the device.41.2.9 Browse the file in the device7If use the pattern, as below:1. You must ensure the four-point connection when you draw the unlock pattern.6s liding your fingers on the screen quickly.● Custom Home ScreenPress the blank area on the home screen interface for a few seconds, it will appear Choose wallpaper from menu, then you can set the home screen.● Move application icons o n screenPress the icons of applications you need to move for several seconds, it will enter the moving model (the icon ofapplication will be turn big), then drag the icon to e xpected position directly.● Move application icons screen to screenPress the icons of applications you need to move for several seconds, and you can drag the icon to the left side or right side.● Delete applicationsPress the icon of application you need to remove for several seconds, drag the icon to × (when the icon turn s big, the bottom of screen will appear ×, then you can delete the application.1.2.14 Screen gestures● ClickWhen you need to input by the on-screen keyboard, you just need to select applications or press the button on the screen, then click the items.● PressWhen you want to start the available options of a project(such as web page link), you only need to press the project.● SlideSliding on the interface with your fingers to make vertical or horizontal dragging action.● DragBefore you start dragging, you must press the items with your fingers, and can not let fingers leave the screen before dragging to the e xpected position.● RotationChanging the screen orientation by rotating the devicelaterally .1.2.15 Security SettingYou can set the unlock pattern , each time you openorwakeyour MID device,you must draw pattern to unlock the screen.in Settings>Security>Screenlock,it support many unlock ways.1.2.16 Display settingClick Settings>Display, you can set the brightness/wallpaper/Auto rotate screen/sleep/font size of the screen.1.2.17 Wireless And Network Settingsa) WIFIClick Settings>Wi-Fi, turn on the wifi, the device will findavailable wireless network n the right interface.o 982. Click Continue and draw again to confirm it3. Cilck confirm to complete unlock pattern designing.4. Each time you open or waking your MID device, you must draw pattern to unlock the screen.Select the expected wireless network, the system will directly connect the network or popup the password input window according to network access security settings. Please consult your wireless network administrator for the password.。
Artisan Technology Group设备维修与售卖手册说明书

Serie PSS SB 3006-3Units with two SafetyBUS p InterfacesAll rights to this documentation are reserved by Pilz GmbH & Co. KG. Copies may be made for internal purposes.Suggestions and comments for improving this documentation will be gratefully received.The names of products, goods and technologies used in this documentation are registered trademarks of the respective companies. Automation Workbench®, Pilz®, PIT®, PMI®, PNOZ®, Primo®, PSS®, SafetyBUS p® are registered trademarks of Pilz GmbH & Co. KG.ContentsContentsIntroductionThis operating manual explains the function and operation of theprogrammable safety system, describes the installation and providesguidelines on how to connect the inputs and test pulse outputs onprogrammable safety systems from the PSS SB 3006-3 series. A PSSfrom the PSS SB 3006-3 series is a 3rd generation programmable safetysystem.For connection to SafetyBUS p, units are available with one SafetyBUS pinterface as well as two SafetyBUS p interfaces.This operating manual describes the programmable safety systems fromthe PSS SB 3006-3 series with two SafetyBUS p interfaces.Different interfaces are available for connection to various non-safety-related standard bus systems, depending on the unit type. Theseinterfaces are described in separate operating manuals. The necessaryoperating manuals are supplied with the relevant unit types.Please refer to the PSS-range manuals, in particular the information andrequirements stated in the “PSS-Range Safety Manual”, “FS SystemDescription”, “ST System Description” and also the “SafetyBUS pInstallation Manual” from the SafetyBUS p manual package.Y ou will need to be conversant with the information in these manuals inorder to fully understand this manual.This documentation is intended for instruction and should be retained forfuture reference.IntroductionValidity of documentationThis documentation is valid for the following programmable safety systemsfrom the PSS SB2 3006-3 series:•PSS SB2 3006-3 DP-S from Version 1.0•PSS SB2 3006-3 IBS-S from Version 1.0•PSS SB2 3006-3 CN-A from Version 1.0•PSS SB2 3006-3 DN-S from Version 1.0•PSS SB2 3006-3 ETH-2 from Version 1.0•PSS SB2 3006-3 ETH-2 DP-S from Version 1.0•PSS SB2 3006-3 ETH-2 IBS-S from Version 1.0It is valid until new documentation is published. The latest documentationis always enclosed with the unit.Overview of documentation1IntroductionThe introduction is designed to familiarise you with the contents,structure and specific order of this manual.2OverviewThis chapter provides information on the most important features ofthe programmable safety systems.3SafetyThis chapter must be read as it contains important information onsafety regulations and intended use.4Function DescriptionThis chapter describes the individual components of theprogrammable safety systems: CPU, inputs and test pulse outputs.5InstallationThis chapter explains how to install the programmable safetysystems.6Supply VoltageThis chapter explains what you need to consider when connecting thesupply voltage.7Wiring the Inputs and Test Pulse OutputsThis chapter describes the safety-related wiring of the inputs and testpulse outputs.8InterfacesThis chapter describes the configuration of the available interfaces.9Operation and MaintenanceThis chapter explains how to commission the safety systems andadvises on what to do if a fault occurs.10Technical Details11AppendixIntroductionOverviewOverviewAUTO PGSTFSPSS SB2 3006-3 DP-S4F-StackOverviewAUTO PGSTFSPSS SB2 3006-3 IBS-S4F-StackOverviewAUTO PGSTFSPSS SB2 3006-3 CN-A 4F-StackOverviewAUTO PGSTFSPSS SB2 3006-3 DN-S 4F-StackOverviewAUTO PGSTFSPSS SB2 3006-3 ETH-24F-StackOverviewAUTO PGSTFSPSS SB2 3006-3 ETH-2 DP-S 4F-StackOverviewAUTO PGSTFSPSS SB2 3006-3 ETH-2 IBS-S 4F-StackPG 6OverviewSafetySafetyDigital inputs (DI2)Depending on the application area and its respective regulations, the PSSmay be used without test pulses for applications up to category 3in accordance with EN 954-1 (03/97). The possibility of a short circuitoccurring in the external wiring between different inputs or to L+ must beeliminated through appropriate wiring.T est pulses must be used for category 4 applications (for connectionexamples please see Chapter 7, “Wiring the Inputs and T est PulseOutputs”).Safety guidelinesFailure to keep to these guidelines will render all warranty and liabilityclaims invalid:•All health and safety / accident prevention regulations for the particulararea of application must be observed.•Before using the unit it is necessary to perform a safety assessment inaccordance with the Machinery Directive 98/37/EC.Use of qualified personnelThe safety system may only be assembled, installed, programmed,commissioned, operated, maintained and decomissioned by qualifiedpersonnel. Qualified personnel are people who, because they are:•Qualified electrical engineers and• Have received training from qualified electrical engineers,are suitably experienced to operate devices, systems, plant and machineryin accordance with the general standards and guidelines for safetytechnology.SafetyEMCDThe safety system is designed for use in an industrial environment.Interference may occur if used within a domestic environment. Warranty and liabilityAll claims to warranty and liability will be rendered invalid if:•The safety system was used contrary to the purpose for which it wasintended•Damage can be attributed to not having followed the guidelines in themanual•Operating personnel are not suitably qualified.•Any type of modification has been made (e.g. exchanging componentson the PCB boards, soldering work etc.).DisposalThe programmable safety system must be disposed of properly when itreaches the end of its service life.Function DescriptionCPUThe CPU controls the test pulse outputs, reads the inputs and processes /stores the user program and variable data. The failsafe section is designedto be multi-channel, i.e. different CPUs process the user programindependently.A four-digit display and several LEDs provide information on the status ofthe safety system and indicate any errors.Function DescriptionInterfacesCPU interfacesThe CPU of each programmable safety system in the PSS SB2 3006-3series provides the following interfaces:•Programming device interfaceCombined RS 232 interface (minimum configuration: TxD, RxD, GND)/RS 485•User interfaceCombined RS 232/RS 485 interfaceFor further information please refer to the “System Manual for thePSS-Range”.SafetyBUS p interfaceEach programmable safety system in the PSS SB2 3006-3 series has twoSafetyBUS p interfaces.The second SafetyBUS p interface can be used to divide up large plants.This can help to optimise the reaction time.For further information on SafetyBUS p, please refer to the “SystemManual for SafetyBUS p”.Interfaces for standard bus systemsDifferent interfaces are available for connection to various standard bussystems, depending on the unit type. The standard bus interfaces aredescribed in separate operating manuals. The necessary operatingmanuals are supplied with the relevant unit types.Digital inputs (DI2)All programmable safety systems in the PSS SB2 3006-3 series have sixintegral on-board inputs, which are suitable for connecting single and dual-channel input devices, with or without test pulses. Input signals must showa “High” (“1” signal) of 24 VDC (+15 ... +30 VDC) and a “Low” (“0” signal)of 0 VDC (-3 ... +5 VDC).LEDs are used as status indicators. An LED lights up as soon as a “1”signal is present at the input. All inputs have input filters.Internal diagnostic circuitry checks the function of the inputs, including theinput filter. If an error occurs, the PSS will switch to a STOP condition andoutput a message to the CPU display. In addition, all the decentralisedoutputs in the I/O-Groups assigned to the PSS Logic Device will beswitched off (see also “SafetyBUS p System Description”).Where test pulses are not used, inputs with single-channel input devicescan be used in applications up to and including Category 2 in accordancewith EN 954-1; in the case of dual-channel input devices, this extends toCategory 3 applications. The device should be suitably wired to eliminatethe risk of a short circuit in the external wiring between the different inputsand also between the PSS supply and any bus interface.Test pulses must be used for applications with single-channel inputdevices above Category 2 and for applications with dual-channel inputdevices above Category 3. Connection examples can be found in Chapter 7of this manual, “Wiring the Inputs and Test Pulse Outputs”.Function DescriptionInstallationInstallationAUTO PG STFS PSS SB 3006-3 DP-S F-StackST FSST FSInstallationSupply VoltageSupply VoltageSupply VoltageSupply VoltageNotes on wiring•Minimum range for cable cross sections on field connection terminals inmm2, in accordance with EN 61131-2, 07/00:-Power supply: 1.5 (AWG16) ... 2.5 (AWG12)-Functional earth: 1.5 (AWG16) ... 2.5 (AWG12)•Use copper wiring.•The torque setting on the terminals should be 0.5 … 0.6 Nm.Wiring the Inputs and Test Pulse Outputs AUTO PG ST FS PSS SB2 3006-3 IBS-S F-StackWiring the Inputs and Test Pulse Outputs•Connecting and laying the cables-Screened cables are not required for digital I/Os. However, if theconnection cables have screening, it should be connected at one end. -Minimum range for cable cross sections on field connection terminals in mm2, in accordance with EN 61131-2, 07/00:¤Digital inputs:0.5 (AWG20) ... 1.5 (AWG16)¤Test pulse outputs:0.5 (AWG20) ... 1.5 (AWG16)¤Power supply: 1.5 (AWG16) ... 2.5 (AWG12)¤Functional earth: 1.5 (AWG16) ... 2.5 (AWG12)-If you use a multi-strand cable with a cross section of 1.5 mm2 toconnect the inputs and test pulse outputs, you will need to use ferrules conforming to DIN 46228, Part 1 and Part 2 0.5 ... 1.5 mm2, Form A orC. To crimp the ferrules you can use crimp pliers (crimp form A or C)conforming to EN 60947-1, such as the PZ 1.5 or PZ 6.5 fromWeidmüller, for example.-Use copper wiring.-The torque setting on the terminals should be 0.5 … 0.6 Nm.The terms “signal inputs with frequent operation” and “single-channel safe input devices” are used in the wiring examples. These terms are defined as follows:•Signal inputs with frequent operationThese are signals which change status on several occasions within a period of time.•Single-channel safe input devicesThese are positively-driven, normally-closed contacts which open on actuation (failsafe principle).Wiring the Inputs and Test Pulse Outputs。
HP 32f 模型 L63916 维护和服务指南说明书

ARTISAN TECHNOLOGY GROUP 设备购买、贮备、租赁和维修服务说明说明书

RACAL INSTRUMENTS™1261B/BLVXI MAINFRAMEPublication No. 980800 Rev. AAstronics Test Systems Inc.4 Goodyear, Irvine, CA 92618Tel: (800) 722-2528, (949) 859-8999; Fax: (949) 859-7139*****************************@*****************************://Copyright 1998 by Astronics Test Systems Inc. Printed in the United States of America. All rights reserved. This book or parts thereof may not be reproduced in any form without written permission of the publisher.THANK YOU FOR PURCHASING THISFor this product, or any other Astronics Test Systems product that incorporates software drivers, you may access our web site to verify and/or download the latest driver versions. The web address for driver downloads is:/support/downloadsIf you have any questions about software driver downloads or our privacy policy, please contact us at:*********************All Astronics Test Systems products are designed to exacting standards and manufactured in full compliance to our AS9100 Quality Management System processes.This warranty does not apply to defects resulting from any modification(s) of any product or part without Astronics Test Systems express written consent, or misuse of any product or part. The warranty also does not apply to fuses, software, non-rechargeable batteries, damage from battery leakage, or problems arising from normal wear, such as mechanical relay life, or failure to follow instructions.This warranty is in lieu of all other warranties, expressed or implied, including any implied warranty of merchantability or fitness for a particular use. The remedies provided herein are buyer’s sole and exclusive remedies.For the specific terms of your standard warranty, contact Customer Support. Please have the following information available to facilitate service.1. Product serial number2. Product model number3. Your company and contact informationYou may contact Customer Support by:E-Mail: *************************Telephone: +1 800 722 3262 (USA)Fax: +1 949 859 7139 (USA)Authorization is required from Astronics Test Systems before you send us your product or sub-assembly for service or calibration. Call or contact Customer Support at 1-800-722-3262 or 1-949-859-8999 or via fax at 1-949-859-7139. We can also be reached at: *************************.If the original packing material is unavailable, ship the product or sub-assembly in an ESD shielding bag and use appropriate packing materials to surround and protect the product.This document and the technical data herein disclosed, are proprietary to Astronics Test Systems, and shall not, without express written permission of Astronics Test Systems, be used in whole or in part to solicit quotations from a competitive source or used for manufacture by anyone other than Astronics Test Systems. The information herein has been developed at private expense, and may only be used for operation and maintenance reference purposes or for purposes of engineering evaluation and incorporation into technical specifications and other documents which specify procurement of products from Astronics Test Systems.TRADEMARKS AND SERVICE MARKSAll trademarks and service marks used in this document are the property of their respective owners.•Racal Instruments, Talon Instruments, Trig-Tek, ActivATE, Adapt-A-Switch, N-GEN, and PAWS are trademarks of Astronics Test Systems in the United States.DISCLAIMERBuyer acknowledges and agrees that it is responsible for the operation of the goods purchased and should ensure that they are used properly and in accordance with this document and any other instructions provided by Seller. Astronics Test Systems products are not specifically designed, manufactured or intended to be used as parts, assemblies or components in planning, construction, maintenance or operation of a nuclear facility, or in life support or safety critical applications in which the failure of the Astronics Test Systems product could create a situation where personal injury or death could occur. Should Buyer purchase Astronics Test Systems product for such unintended application, Buyer shall indemnify and hold Astronics Test Systems, its officers, employees, subsidiaries, affiliates and distributors harmless against all claims arising out of a claim for personal injury or death associated with such unintended use.FOR YOUR SAFETYBefore undertaking any troubleshooting, maintenance or exploratory procedure, read carefully theWARNINGS and CAUTION notices.This equipment contains voltage hazardous tohuman life and safety, and is capable of inflictingpersonal injury. If this instrument is to be powered from the AC line (mains) through an autotransformer, ensure the common connector is connected to the neutral (earth pole) of the powersupply.Before operating the unit, ensure the conductor (green wire) is connected to the ground(earth) conductor of the power outlet. Do not use a two-conductor extension cord or athree-prong/two-prong adapter. This will defeat the protective feature of the thirdconductor in the power cord.Maintenance and calibration procedures sometimes call for operation of the unit withpower applied and protective covers removed. Read the procedures and heed warningsto avoid “live” circuit points.Before operating this instrument:1. Ensure the proper fuse is in place for the power source to operate.2. Ensure all other devices connected to or in proximity to this instrument are properly grounded orconnected to the protective third-wire earth ground.If the instrument:- fails to operate satisfactorily- shows visible damage- has been stored under unfavorable conditions - has sustained stressDo not operate until performance is checked by qualified personnel.This page was left intentionally blank.Publication No. 980800 Rev. A 1261B/BL User Manual Astronics Test Systems vDOCUMENT CHANGE HISTORY Revision Date Description of ChangeA 10/07/10 Revised per EO 30291UL Regulations require UL data removal on pageA-5.Revised and replaced first 4 pages. Manual nowrev. letter controlled. Added document changehistory page v in front of chapter 1.Removed Chap 6 and 7 the information needed isincluded in the first 4 pages starting at the cover.1261B/BL User Manual Publication No. 980800 Rev. AThis page was left intentionally blank.vi Astronics Test Systems。
常用的一些测试英语缩写
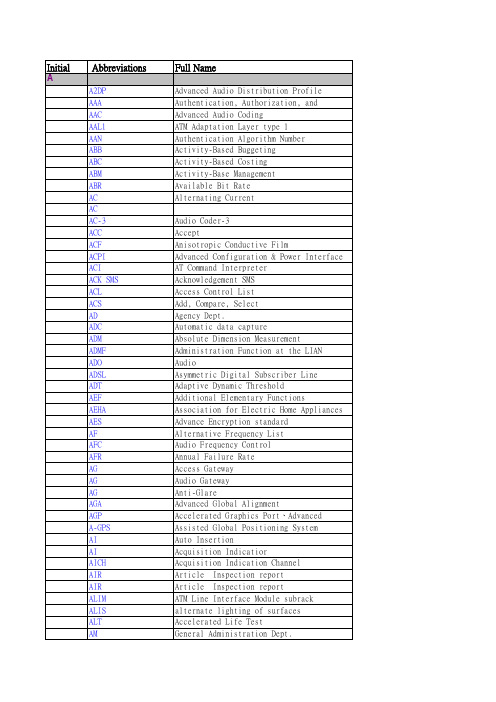
Full Name
Advanced Audio Distribution Profile Authentication, Authorization, and Accounting Advanced Audio Coding ATM Adaptation Layer type 1 Authentication Algorithm Number Activity-Based Buggeting Activity-Based Costing Activity-Base Management Available Bit Rate Alternating Current Audio Coder-3 Accept Anisotropic Conductive Film Advanced Configuration & Power Interface AT Command Interpreter Acknowledgement SMS Access Control List Add, Compare, Select Agency Dept. Automatic data capture Absolute Dimension Measurement Administration Function at the LIAN Audio Asymmetric Digital Subscriber Line Adaptive Dynamic Threshold Additional Elementary Functions Association for Electric Home Appliances Advance Encryption standard Alternative Frequency List Audio Frequency Control Annual Failure Rate Access Gateway Audio Gateway Anti-Glare Advanced Global Alignment Accelerated Graphics Port、Advanced Graphics Port Assisted Global Positioning System Auto Insertion Acquisition Indicatior Acquisition Indication Channel Article Inspection report Article Inspection report ATM Line Interface Module subrack alternate lighting of surfaces Accelerated Life Test General Administration Dept.
术语解释

It's a company that offers individuals or enterprises access over the Internet to applications and related services that would otherwise have to be located in their own personal or enterprise computers. 一种为个人或企业级用户提供通过Internet访问应用程序或相关服务的公司。从而,上述应用程序或相关服务就不必存在 于用户自己的个人电脑或企业服务器上。
资本公积,包括股本溢价,资本重估增值,处理资产溢价等。
A device that supports the seat frame assembly ,provides attachment to the floor pan of the vehicle and provides adjustments to be made to the seated position. 一个支承座椅骨架总成的机构,它提供到汽车地板的连接和使座椅调节定位。 Convert an ideal, want, technology into a feasible product concept. 将主意、需要和技术转化为可行的产品概念。 Inclusion of prevention measures to eliminate product defects during the design and development period. 包含预防性措施来消除在设计和开发期间的产品缺陷。
2TP
2W/4W/6 W/8W
3rd Seat 第三排座椅 4th Seat 第四排座椅 5S/Visual Management 5S和可视化管理
jstd035声学扫描
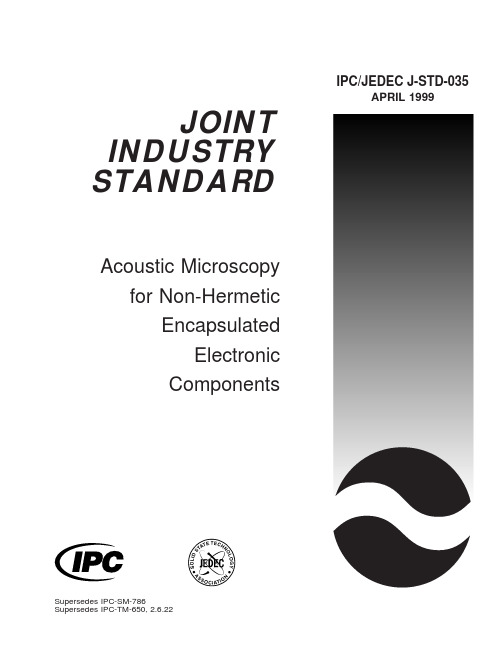
JOINT INDUSTRY STANDARDAcoustic Microscopy for Non-HermeticEncapsulatedElectronicComponents IPC/JEDEC J-STD-035APRIL1999Supersedes IPC-SM-786 Supersedes IPC-TM-650,2.6.22Notice EIA/JEDEC and IPC Standards and Publications are designed to serve thepublic interest through eliminating misunderstandings between manufacturersand purchasers,facilitating interchangeability and improvement of products,and assisting the purchaser in selecting and obtaining with minimum delaythe proper product for his particular need.Existence of such Standards andPublications shall not in any respect preclude any member or nonmember ofEIA/JEDEC or IPC from manufacturing or selling products not conformingto such Standards and Publications,nor shall the existence of such Standardsand Publications preclude their voluntary use by those other than EIA/JEDECand IPC members,whether the standard is to be used either domestically orinternationally.Recommended Standards and Publications are adopted by EIA/JEDEC andIPC without regard to whether their adoption may involve patents on articles,materials,or processes.By such action,EIA/JEDEC and IPC do not assumeany liability to any patent owner,nor do they assume any obligation whateverto parties adopting the Recommended Standard or ers are alsowholly responsible for protecting themselves against all claims of liabilities forpatent infringement.The material in this joint standard was developed by the EIA/JEDEC JC-14.1Committee on Reliability Test Methods for Packaged Devices and the IPCPlastic Chip Carrier Cracking Task Group(B-10a)The J-STD-035supersedes IPC-TM-650,Test Method2.6.22.For Technical Information Contact:Electronic Industries Alliance/ JEDEC(Joint Electron Device Engineering Council)2500Wilson Boulevard Arlington,V A22201Phone(703)907-7560Fax(703)907-7501IPC2215Sanders Road Northbrook,IL60062-6135 Phone(847)509-9700Fax(847)509-9798Please use the Standard Improvement Form shown at the end of thisdocument.©Copyright1999.The Electronic Industries Alliance,Arlington,Virginia,and IPC,Northbrook,Illinois.All rights reserved under both international and Pan-American copyright conventions.Any copying,scanning or other reproduction of these materials without the prior written consent of the copyright holder is strictly prohibited and constitutes infringement under the Copyright Law of the United States.IPC/JEDEC J-STD-035Acoustic Microscopyfor Non-Hermetic EncapsulatedElectronicComponentsA joint standard developed by the EIA/JEDEC JC-14.1Committee on Reliability Test Methods for Packaged Devices and the B-10a Plastic Chip Carrier Cracking Task Group of IPCUsers of this standard are encouraged to participate in the development of future revisions.Contact:EIA/JEDEC Engineering Department 2500Wilson Boulevard Arlington,V A22201 Phone(703)907-7500 Fax(703)907-7501IPC2215Sanders Road Northbrook,IL60062-6135 Phone(847)509-9700Fax(847)509-9798ASSOCIATION CONNECTINGELECTRONICS INDUSTRIESAcknowledgmentMembers of the Joint IPC-EIA/JEDEC Moisture Classification Task Group have worked to develop this document.We would like to thank them for their dedication to this effort.Any Standard involving a complex technology draws material from a vast number of sources.While the principal members of the Joint Moisture Classification Working Group are shown below,it is not possible to include all of those who assisted in the evolution of this Standard.To each of them,the mem-bers of the EIA/JEDEC and IPC extend their gratitude.IPC Packaged Electronic Components Committee ChairmanMartin FreedmanAMP,Inc.IPC Plastic Chip Carrier Cracking Task Group,B-10a ChairmanSteven MartellSonoscan,Inc.EIA/JEDEC JC14.1CommitteeChairmanJack McCullenIntel Corp.EIA/JEDEC JC14ChairmanNick LycoudesMotorolaJoint Working Group MembersCharlie Baker,TIChristopher Brigham,Hi/FnRalph Carbone,Hewlett Packard Co. Don Denton,TIMatt Dotty,AmkorMichele J.DiFranza,The Mitre Corp. Leo Feinstein,Allegro Microsystems Inc.Barry Fernelius,Hewlett Packard Co. Chris Fortunko,National Institute of StandardsRobert J.Gregory,CAE Electronics, Inc.Curtis Grosskopf,IBM Corp.Bill Guthrie,IBM Corp.Phil Johnson,Philips Semiconductors Nick Lycoudes,MotorolaSteven R.Martell,Sonoscan Inc. Jack McCullen,Intel Corp.Tom Moore,TIDavid Nicol,Lucent Technologies Inc.Pramod Patel,Advanced Micro Devices Inc.Ramon R.Reglos,XilinxCorazon Reglos,AdaptecGerald Servais,Delphi Delco Electronics SystemsRichard Shook,Lucent Technologies Inc.E.Lon Smith,Lucent Technologies Inc.Randy Walberg,NationalSemiconductor Corp.Charlie Wu,AdaptecEdward Masami Aoki,HewlettPackard LaboratoriesFonda B.Wu,Raytheon Systems Co.Richard W.Boerdner,EJE ResearchVictor J.Brzozowski,NorthropGrumman ES&SDMacushla Chen,Wus Printed CircuitCo.Ltd.Jeffrey C.Colish,Northrop GrummanCorp.Samuel J.Croce,Litton AeroProducts DivisionDerek D-Andrade,Surface MountTechnology CentreRao B.Dayaneni,Hewlett PackardLaboratoriesRodney Dehne,OEM WorldwideJames F.Maguire,Boeing Defense&Space GroupKim Finch,Boeing Defense&SpaceGroupAlelie Funcell,Xilinx Inc.Constantino J.Gonzalez,ACMEMunir Haq,Advanced Micro DevicesInc.Larry A.Hargreaves,DC.ScientificInc.John T.Hoback,Amoco ChemicalCo.Terence Kern,Axiom Electronics Inc.Connie M.Korth,K-Byte/HibbingManufacturingGabriele Marcantonio,NORTELCharles Martin,Hewlett PackardLaboratoriesRichard W.Max,Alcatel NetworkSystems Inc.Patrick McCluskey,University ofMarylandJames H.Moffitt,Moffitt ConsultingServicesRobert Mulligan,Motorola Inc.James E.Mumby,CibaJohn Northrup,Lockheed MartinCorp.Dominique K.Numakura,LitchfieldPrecision ComponentsNitin B.Parekh,Unisys Corp.Bella Poborets,Lucent TechnologiesInc.D.Elaine Pope,Intel Corp.Ray Prasad,Ray Prasad ConsultancyGroupAlbert Puah,Adaptec Inc.William Sepp,Technic Inc.Ralph W.Taylor,Lockheed MartinCorp.Ed R.Tidwell,DSC CommunicationsCorp.Nick Virmani,Naval Research LabKen Warren,Corlund ElectronicsCorp.Yulia B.Zaks,Lucent TechnologiesInc.IPC/JEDEC J-STD-035April1999 iiTable of Contents1SCOPE (1)2DEFINITIONS (1)2.1A-mode (1)2.2B-mode (1)2.3Back-Side Substrate View Area (1)2.4C-mode (1)2.5Through Transmission Mode (2)2.6Die Attach View Area (2)2.7Die Surface View Area (2)2.8Focal Length(FL) (2)2.9Focus Plane (2)2.10Leadframe(L/F)View Area (2)2.11Reflective Acoustic Microscope (2)2.12Through Transmission Acoustic Microscope (2)2.13Time-of-Flight(TOF) (3)2.14Top-Side Die Attach Substrate View Area (3)3APPARATUS (3)3.1Reflective Acoustic Microscope System (3)3.2Through Transmission AcousticMicroscope System (4)4PROCEDURE (4)4.1Equipment Setup (4)4.2Perform Acoustic Scans..........................................4Appendix A Acoustic Microscopy Defect CheckSheet (6)Appendix B Potential Image Pitfalls (9)Appendix C Some Limitations of AcousticMicroscopy (10)Appendix D Reference Procedure for PresentingApplicable Scanned Data (11)FiguresFigure1Example of A-mode Display (1)Figure2Example of B-mode Display (1)Figure3Example of C-mode Display (2)Figure4Example of Through Transmission Display (2)Figure5Diagram of a Reflective Acoustic MicroscopeSystem (3)Figure6Diagram of a Through Transmission AcousticMicroscope System (3)April1999IPC/JEDEC J-STD-035iiiIPC/JEDEC J-STD-035April1999This Page Intentionally Left BlankivApril1999IPC/JEDEC J-STD-035 Acoustic Microscopy for Non-Hermetic EncapsulatedElectronic Components1SCOPEThis test method defines the procedures for performing acoustic microscopy on non-hermetic encapsulated electronic com-ponents.This method provides users with an acoustic microscopy processflow for detecting defects non-destructively in plastic packages while achieving reproducibility.2DEFINITIONS2.1A-mode Acoustic data collected at the smallest X-Y-Z region defined by the limitations of the given acoustic micro-scope.An A-mode display contains amplitude and phase/polarity information as a function of time offlight at a single point in the X-Y plane.See Figure1-Example of A-mode Display.IPC-035-1 Figure1Example of A-mode Display2.2B-mode Acoustic data collected along an X-Z or Y-Z plane versus depth using a reflective acoustic microscope.A B-mode scan contains amplitude and phase/polarity information as a function of time offlight at each point along the scan line.A B-mode scan furnishes a two-dimensional(cross-sectional)description along a scan line(X or Y).See Figure2-Example of B-mode Display.IPC-035-2 Figure2Example of B-mode Display(bottom half of picture on left)2.3Back-Side Substrate View Area(Refer to Appendix A,Type IV)The interface between the encapsulant and the back of the substrate within the outer edges of the substrate surface.2.4C-mode Acoustic data collected in an X-Y plane at depth(Z)using a reflective acoustic microscope.A C-mode scan contains amplitude and phase/polarity information at each point in the scan plane.A C-mode scan furnishes a two-dimensional(area)image of echoes arising from reflections at a particular depth(Z).See Figure3-Example of C-mode Display.1IPC/JEDEC J-STD-035April1999IPC-035-3 Figure3Example of C-mode Display2.5Through Transmission Mode Acoustic data collected in an X-Y plane throughout the depth(Z)using a through trans-mission acoustic microscope.A Through Transmission mode scan contains only amplitude information at each point in the scan plane.A Through Transmission scan furnishes a two-dimensional(area)image of transmitted ultrasound through the complete thickness/depth(Z)of the sample/component.See Figure4-Example of Through Transmission Display.IPC-035-4 Figure4Example of Through Transmission Display2.6Die Attach View Area(Refer to Appendix A,Type II)The interface between the die and the die attach adhesive and/or the die attach adhesive and the die attach substrate.2.7Die Surface View Area(Refer to Appendix A,Type I)The interface between the encapsulant and the active side of the die.2.8Focal Length(FL)The distance in water at which a transducer’s spot size is at a minimum.2.9Focus Plane The X-Y plane at a depth(Z),which the amplitude of the acoustic signal is maximized.2.10Leadframe(L/F)View Area(Refer to Appendix A,Type V)The imaged area which extends from the outer L/F edges of the package to the L/F‘‘tips’’(wedge bond/stitch bond region of the innermost portion of the L/F.)2.11Reflective Acoustic Microscope An acoustic microscope that uses one transducer as both the pulser and receiver. (This is also known as a pulse/echo system.)See Figure5-Diagram of a Reflective Acoustic Microscope System.2.12Through Transmission Acoustic Microscope An acoustic microscope that transmits ultrasound completely through the sample from a sending transducer to a receiver on the opposite side.See Figure6-Diagram of a Through Transmis-sion Acoustic Microscope System.2April1999IPC/JEDEC J-STD-0353IPC/JEDEC J-STD-035April1999 3.1.6A broad band acoustic transducer with a center frequency in the range of10to200MHz for subsurface imaging.3.2Through Transmission Acoustic Microscope System(see Figure6)comprised of:3.2.1Items3.1.1to3.1.6above3.2.2Ultrasonic pulser(can be a pulser/receiver as in3.1.1)3.2.3Separate receiving transducer or ultrasonic detection system3.3Reference packages or standards,including packages with delamination and packages without delamination,for use during equipment setup.3.4Sample holder for pre-positioning samples.The holder should keep the samples from moving during the scan and maintain planarity.4PROCEDUREThis procedure is generic to all acoustic microscopes.For operational details related to this procedure that apply to a spe-cific model of acoustic microscope,consult the manufacturer’s operational manual.4.1Equipment Setup4.1.1Select the transducer with the highest useable ultrasonic frequency,subject to the limitations imposed by the media thickness and acoustic characteristics,package configuration,and transducer availability,to analyze the interfaces of inter-est.The transducer selected should have a low enough frequency to provide a clear signal from the interface of interest.The transducer should have a high enough frequency to delineate the interface of interest.Note:Through transmission mode may require a lower frequency and/or longer focal length than reflective mode.Through transmission is effective for the initial inspection of components to determine if defects are present.4.1.2Verify setup with the reference packages or standards(see3.3above)and settings that are appropriate for the trans-ducer chosen in4.1.1to ensure that the critical parameters at the interface of interest correlate to the reference standard uti-lized.4.1.3Place units in the sample holder in the coupling medium such that the upper surface of each unit is parallel with the scanning plane of the acoustic transducer.Sweep air bubbles away from the unit surface and from the bottom of the trans-ducer head.4.1.4At afixed distance(Z),align the transducer and/or stage for the maximum reflected amplitude from the top surface of the sample.The transducer must be perpendicular to the sample surface.4.1.5Focus by maximizing the amplitude,in the A-mode display,of the reflection from the interface designated for imag-ing.This is done by adjusting the Z-axis distance between the transducer and the sample.4.2Perform Acoustic Scans4.2.1Inspect the acoustic image(s)for any anomalies,verify that the anomaly is a package defect or an artifact of the imaging process,and record the results.(See Appendix A for an example of a check sheet that may be used.)To determine if an anomaly is a package defect or an artifact of the imaging process it is recommended to analyze the A-mode display at the location of the anomaly.4.2.2Consider potential pitfalls in image interpretation listed in,but not limited to,Appendix B and some of the limita-tions of acoustic microscopy listed in,but not limited to,Appendix C.If necessary,make adjustments to the equipment setup to optimize the results and rescan.4April1999IPC/JEDEC J-STD-035 4.2.3Evaluate the acoustic images using the failure criteria specified in other appropriate documents,such as J-STD-020.4.2.4Record the images and thefinal instrument setup parameters for documentation purposes.An example checklist is shown in Appendix D.5IPC/JEDEC J-STD-035April19996April1999IPC/JEDEC J-STD-035Appendix AAcoustic Microscopy Defect Check Sheet(continued)CIRCUIT SIDE SCANImage File Name/PathDelamination(Type I)Die Circuit Surface/Encapsulant Number Affected:Average%Location:Corner Edge Center (Type II)Die/Die Attach Number Affected:Average%Location:Corner Edge Center (Type III)Encapsulant/Substrate Number Affected:Average%Location:Corner Edge Center (Type V)Interconnect tip Number Affected:Average%Interconnect Number Affected:Max.%Length(Type VI)Intra-Laminate Number Affected:Average%Location:Corner Edge Center Comments:CracksAre cracks present:Yes NoIf yes:Do any cracks intersect:bond wire ball bond wedge bond tab bump tab leadDoes crack extend from leadfinger to any other internal feature:Yes NoDoes crack extend more than two-thirds the distance from any internal feature to the external surfaceof the package:Yes NoAdditional verification required:Yes NoComments:Mold Compound VoidsAre voids present:Yes NoIf yes:Approx.size Location(if multiple voids,use comment section)Do any voids intersect:bond wire ball bond wedge bond tab bump tab lead Additional verification required:Yes NoComments:7IPC/JEDEC J-STD-035April1999Appendix AAcoustic Microscopy Defect Check Sheet(continued)NON-CIRCUIT SIDE SCANImage File Name/PathDelamination(Type IV)Encapsulant/Substrate Number Affected:Average%Location:Corner Edge Center (Type II)Substrate/Die Attach Number Affected:Average%Location:Corner Edge Center (Type V)Interconnect Number Affected:Max.%LengthLocation:Corner Edge Center (Type VI)Intra-Laminate Number Affected:Average%Location:Corner Edge Center (Type VII)Heat Spreader Number Affected:Average%Location:Corner Edge Center Additional verification required:Yes NoComments:CracksAre cracks present:Yes NoIf yes:Does crack extend more than two-thirds the distance from any internal feature to the external surfaceof the package:Yes NoAdditional verification required:Yes NoComments:Mold Compound VoidsAre voids present:Yes NoIf yes:Approx.size Location(if multiple voids,use comment section)Additional verification required:Yes NoComments:8Appendix BPotential Image PitfallsOBSERV ATIONS CAUSES/COMMENTSUnexplained loss of front surface signal Gain setting too lowSymbolization on package surfaceEjector pin knockoutsPin1and other mold marksDust,air bubbles,fingerprints,residueScratches,scribe marks,pencil marksCambered package edgeUnexplained loss of subsurface signal Gain setting too lowTransducer frequency too highAcoustically absorbent(rubbery)fillerLarge mold compound voidsPorosity/high concentration of small voidsAngled cracks in package‘‘Dark line boundary’’(phase cancellation)Burned molding compound(ESD/EOS damage)False or spotty indication of delamination Low acoustic impedance coating(polyimide,gel)Focus errorIncorrect delamination gate setupMultilayer interference effectsFalse indication of adhesion Gain set too high(saturation)Incorrect delamination gate setupFocus errorOverlap of front surface and subsurface echoes(transducerfrequency too low)Fluidfilling delamination areasApparent voiding around die edge Reflection from wire loopsIncorrect setting of void gateGraded intensity Die tilt or lead frame deformation Sample tiltApril1999IPC/JEDEC J-STD-0359Appendix CSome Limitations of Acoustic MicroscopyAcoustic microscopy is an analytical technique that provides a non-destructive method for examining plastic encapsulated components for the existence of delaminations,cracks,and voids.This technique has limitations that include the following: LIMITATION REASONAcoustic microscopy has difficulty infinding small defects if the package is too thick.The ultrasonic signal becomes more attenuated as a function of two factors:the depth into the package and the transducer fre-quency.The greater the depth,the greater the attenuation.Simi-larly,the higher the transducer frequency,the greater the attenu-ation as a function of depth.There are limitations on the Z-axis(axial)resolu-tion.This is a function of the transducer frequency.The higher the transducer frequency,the better the resolution.However,the higher frequency signal becomes attenuated more quickly as a function of depth.There are limitations on the X-Y(lateral)resolu-tion.The X-Y(lateral)resolution is a function of a number of differ-ent variables including:•Transducer characteristics,including frequency,element diam-eter,and focal length•Absorption and scattering of acoustic waves as a function of the sample material•Electromechanical properties of the X-Y stageIrregularly shaped packages are difficult to analyze.The technique requires some kind offlat reference surface.Typically,the upper surface of the package or the die surfacecan be used as references.In some packages,cambered packageedges can cause difficulty in analyzing defects near the edgesand below their surfaces.Edge Effect The edges cause difficulty in analyzing defects near the edge ofany internal features.IPC/JEDEC J-STD-035April1999 10April1999IPC/JEDEC J-STD-035Appendix DReference Procedure for Presenting Applicable Scanned DataMost of the settings described may be captured as a default for the particular supplier/product with specific changes recorded on a sample or lot basis.Setup Configuration(Digital Setup File Name and Contents)Calibration Procedure and Calibration/Reference Standards usedTransducerManufacturerModelCenter frequencySerial numberElement diameterFocal length in waterScan SetupScan area(X-Y dimensions)Scan step sizeHorizontalVerticalDisplayed resolutionHorizontalVerticalScan speedPulser/Receiver SettingsGainBandwidthPulseEnergyRepetition rateReceiver attenuationDampingFilterEcho amplitudePulse Analyzer SettingsFront surface gate delay relative to trigger pulseSubsurface gate(if used)High passfilterDetection threshold for positive oscillation,negative oscillationA/D settingsSampling rateOffset settingPer Sample SettingsSample orientation(top or bottom(flipped)view and location of pin1or some other distinguishing characteristic) Focus(point,depth,interface)Reference planeNon-default parametersSample identification information to uniquely distinguish it from others in the same group11IPC/JEDEC J-STD-035April1999Appendix DReference Procedure for Presenting Applicable Scanned Data(continued) Reference Procedure for Presenting Scanned DataImagefile types and namesGray scale and color image legend definitionsSignificance of colorsIndications or definition of delaminationImage dimensionsDepth scale of TOFDeviation from true aspect ratioImage type:A-mode,B-mode,C-mode,TOF,Through TransmissionA-mode waveforms should be provided for points of interest,such as delaminated areas.In addition,an A-mode image should be provided for a bonded area as a control.12Standard Improvement FormIPC/JEDEC J-STD-035The purpose of this form is to provide the Technical Committee of IPC with input from the industry regarding usage of the subject standard.Individuals or companies are invited to submit comments to IPC.All comments will be collected and dispersed to the appropriate committee(s).If you can provide input,please complete this form and return to:IPC2215Sanders RoadNorthbrook,IL 60062-6135Fax 847509.97981.I recommend changes to the following:Requirement,paragraph number Test Method number,paragraph numberThe referenced paragraph number has proven to be:Unclear Too RigidInErrorOther2.Recommendations forcorrection:3.Other suggestions for document improvement:Submitted by:Name Telephone Company E-mailAddress City/State/ZipDate ASSOCIATION CONNECTING ELECTRONICS INDUSTRIESASSOCIATION CONNECTINGELECTRONICS INDUSTRIESISBN#1-580982-28-X2215 Sanders Road, Northbrook, IL 60062-6135Tel. 847.509.9700 Fax 847.509.9798。
惠普词霸大全

其他
英文全名 Admin Assistant Account Operation Management Asia Pacific and Japan Business Support Team Business Unit Corporate Account Representative China Design Center China Hewlett Packard Customer Information Center Customer Information Specialist Closed Leads Management /Close Loop Management City Mobile Sales/Channel Mobile Sales China Personal Computer Manufacturing Operation City Partner Rep. Chong Qing Contract Center City Sales Rep. Channel Telesales Customer Volumn sales Direct Business Consultant Direct Order Management Desktop Solution Organization Desktop System Unit Desktop Organization Engineer Europe Middle East and Africa Global Business Unit HP Asia Pacific Hong Kong SAR Limited HP Financing Service HP Service Imaging and Printing Group Inside Sales Representative Industry Standard Server (NT server) Marketing Communication Manager Mid market representative Operation Support Outside Sales Representative Product Manager/Project Manager Purchase Order Personal Systems Group Personal Systems Group Quality Assurance Regional Business Unit Regional marketing development manager Regional Product Manager Shanghai Trading Limited
微软全球技术支持中心-香港 澳门说明书

Incident Support Services Overview and Ordering GuideIncident Support Services OverviewMicrosoft®Global Technical Support Center – HK/Macau top priority is to help every business, organization, and individual to be more successful with Microsoft products. Fast, accurate issue resolution and comprehensive support services mean you can focus on core business and personal goals rather than on technology. The result: Increased productivity and a higher return on your investments.This guide is designed to help you determine the incident support offering best suited to your business needs and provide you with the information, forms, or phone numbers necessary to obtain the support you need.There are two types of incident support services available, a brief summary of which is listed below with more detailed information online at /default.aspx?ln=en-hk. Support offering follows the product support lifecycle, please refer to /lifecycle/Professional Incident Support - Targeted at technical communities of individuals, including resellers and consultants, OEMs/SBs, Developers, IT Pros, and Microsoft Certified Partners. Support hours Monday – Friday 9:00am -6:00pm, except public holidaysPersonal Incident Support – Targeted for home users and SOHO (small office, home office) users using Microsoft desktop or consumer products in stand-alone or small network environments. Support hours Monday – Friday 9:00am -9:00pm, except public holidaysSeverity A English Product 24X7 business critical support in English - The delivery of Professional incidents on a 24x7 basis will consist of local support during business hours (Monday – Friday, 9:00am – 6:00pm, except public holidays) for all severities, and delivery of out of business hours support for Severity A incidents in English for English product only at a special rate.“Severity A” incidents means the following situations that you may be in: Critical business impact; Customer’sbusiness has significant loss or degradation of services; Need response within 2 hourOrdering Instructions:Credit card purchases can be made by calling our services hotline (852) 2388-9600; by faxing or mailing the Incident Support Services Order Form to the fax number or address below.Microsoft Hong Kong13/F, Cyberport 2100 Cyberport RoadHong KongAttention: Global Technical Support Center – HK/MacauFax: (852) 2967-1679©2011 Microsoft Corporation. All rights reserved. Other product and company names mentioned herein may be the trademarks of their respective owners.Incident Support Services Order FormBoth Personal and Professional Incident Support package allow you to submit an incident over the phone or online. All annual Incident Support Services accounts are valid for one year from the date of purchase.Credit Card Number: Expiration Date ___ / ____Microsoft Global Technical Support Center - HK will send you an official invoice that contains your account information when accepted your purchase.TERMS AND CONDITIONS OF PERSONAL/PROFESSIONAL INCIDENT SUPPORTIMPORTANT - READ CAREFULLY: This Agreement is a legal agreement between you (either an individual or a single entity) and Microsoft Hong Kong Limited (for customers in Hong Kong SAR) or Microsoft Macau Limited (for customers in Macau SAR), as the case may be (“Microsoft”) for the number of support services (“Services”) incidents indicated on the Personal/Professional incident support order form for software products licensed by Microsoft Corporation (“Software”). This P ersonal and Professional incident support service may also include updates and supplements to Software released by Microsoft Corporation. Any software provided along with the Personal and Professional incident support is licensed to you under the terms of a separate end-user license agreement by Microsoft Corporation. By using the Personal/Professional incident support, you agree to be bound by the terms of this Agreement. If you do not agree to the terms of this Agreement, do not use the Services; you may, however, contact Microsoft support hotline for a full refund within 14 days from the date of purchase with the full receipt. If you do not seek a refund within 14 days after your purchase of this service, you will be deemed to have accepted the terms of this Agreement.NOTE : THE SERVICES UNDER THE PERSONAL AND PROFESSIONAL INCIDENT SUPPORT ARE ONLY VALID FOR USE IN HONG KONG SAR AND MACAU SAR AND MUST BE USED ON OR BEFORE THE EXPIRY DATE. IF YOU DO NOT USE THE SERVICES BEFORE THE EXPIRY DATE, IT WILL EXPIRE AND YOU WILL NOT BE ENTITLED TO USE THE SERVICES AFTER SUCH DATE. IN SUCH AN EVENT, YOU EXPRESSLY AGREE THAT MICROSOFT WILL NOT BE LIABLE FOR ANY REFUND OR ANY OTHER DAMAGES WHATSOEVER.1.Definitions :“Incident” means a single use or functionality prob lem and the commercial reasonable effort needed to resolve it regardless of the number of contacts with you concerning the problem. A “Single” use or functionality problem is a problem that cannot be broken down int o subordinate problems. If a problem consists of subordinate problems, each shall be considered a separate incident. Microsoft shall reasonably determine what a single incident is and when it has ended. “Online Support”, “Professional Support” and “Personal Support” shall have t he meaning as desc ribed in the relevant Services Description. “Services Description” means detail description of Services provided for Professi onal Support or Personal Support issued by Microsoft from time to time.2.Microsoft will provide the Services specified in this Agreement and the relevant Service Description (which may be amended by Microsoft fromtime to time). An appropriate number of Incidents will be deducted from the total number of Incidents covered by the Personal/Professional incident support for the services provided. The Services involve telephone and limited web support. You (on behalf of yourself and all employees and representatives (if any)) agree to use the Services on the terms and conditions set out in this Agreement.3.This Agreement applies only to those Services Microsoft has expressly agreed to provide. Provision of any product or services not so specifiedwill be the subject of separate agreement. References to this Agreement include a reference to the relevant Service Description and any annexes or appendices all of which constitute the entire agreement in relation to the Services.4.The Services are for the sole benefit of you as the named user (if you acquired this Personal/Professional incident support in your personalcapacity) or the named contact (if you acquired this Personal/Professional incident support as a corporate customer) provided that for Professional incident support of 5 incidents, corporate customers may register up to two (2) named contacts for receiving the Services.Microsoft reserves the right to immediately terminate any Services and this Agreement on reasonable suspicion that you have allowed someone else to use the Services in your name.5.You will take adequate precaution to ensure that no one will abuse the Services by wrongfully using your contract number to receive theServices. You are responsible for all use (including misuse) of any number provided to you as a prerequisite for the provision of the Services until such time as you advise Microsoft in writing that the relevant contract number or password has been lost or stolen, at which time a replacement number will be issued by Microsoft.6.Only Software which is validly licensed by Microsoft Corporation, purchased within Hong Kong SAR and Macau SAR from a MicrosoftAuthorised reseller or Retailer, properly registered and unaltered is eligible for the Services. Only those Software described in the relevant Services Description from time to time will be supported. Where language versions other than English and Traditional Chinese are validly licensed, Microsoft will use commercially reasonable efforts to provide support for such language versions.7.Services will be provided to assist you in resolving problems you encounter with the use or functionality of the Software and may include advice,recommendations and information concerning your use of the Software with various hardware and software configurations. Microsoft warrants that it will use all commercially reasonable care and skill in trying to resolve problems but is unable to, and does not warrant that every problem will be resolved. To the extent permitted by law, this limited warranty is in lieu of all other warranties and conditions, express, or implied, including all implied warranties of merchantability and fitness for a particular purpose and of all other obligations, conditions, or liabilities on the part of Microsoft.8.Services will not be provided where the Software is be used with less than the minimum system configuration recommended by Microsoft. Onlycurrent versions of the Software at the time the request for Services is made, and the next to current version of the Software, will be supported.“Current” means that the relevant version of the Software is available for purchase by the public at the time of the d ate of the request for service. Microsoft may, at its sole discretion agree to provide services to support non-current software, in which case the appropriate number of Incidents to deal with such request for services will be deducted. The following are excluded from the Services: (a) failure, difficulty or inability in operation (“failure”) caused by equipment, product or services not supplied by Microsoft; (b) failure resulting from modifica tion of a Software; (c) misuse of a Software or operator error; and (d) unlicensed software.9.You must provide Microsoft with up to date, accurate and complete configuration and topology information concerning your computer system(s)and network(s) if asked to do so. Microsoft reserves the right to refuse to provide Services to you at any time if in its sole discretion Microsoft determines that your computer and network configuration(s) and topology(ies) are not supportable by Microsoft, you fail to provide the requested information or you have provided insufficient information for Microsoft to progress the issue. If Microsoft makes such a determination it may terminate this Agreement forthwith and you will be refunded an amount representing any unused Incidents on a pro-rata basis, except where you fail to provide or provide insufficient information on request from Microsoft and Microsoft has already spent more than 30 minutes working on the relevant problem.10.If Microsoft determines that the problem experienced by you is caused by hardware or software not provided by Microsoft the support will beregarded as a single Incident request, but support provided for that Incident will end upon such determination.11.Microsoft may amend the terms of this Agreement and/or the relevant Service Description on giving 30 days* written notice. If Microsoftprovides such notice and you do not accept the changes, then you may terminate this Agreement by notice in writing to Microsoft pursuant to Clause 13 below.12.Each fully paid Personal/Professional incident support shall be valid for a period of twelve (12) months from the date you register and use theServices unless terminated earlier in accordance with the conditions of this Agreement. ANY INCIDENTS OF PERSONAL/PROFESSIONAL INCIDENT SUPPORT WHICH HAVE NOT BEEN USED WITHIN THE SAID TWELVE (12) MONTHS WILL AUTOMATICALLY EXPIRE AT THE END OF THE SAID PERIOD. THE SERVICES UNDER PERSONAL/PROFESSIONAL INCIDENT SUPPORT ARE ONLY VALID FOR USE IN HONG KONG SAR AND MACAU SAR AND MUST BE USED ON OR BEFORE THE EXPIRY DATE. IF YOU DO NOT USE THE SERVICES BEFORE THE EXPIRY DATE, THE PERSONAL/PROFESSIONAL INCIDENT SUPPORT WILL EXPIRE AND YOU WILL NOT BE ENTITLED TO USE THE SERVICES AFTER SUCH DATE. IN SUCH AN EVENT, YOU EXPRESSLY AGREE THAT MICROSOFT WILL NOT BE LIABLE FOR ANY REFUND OR ANY OTHER DAMAGES WHATSOEVER.13.Either party may terminate this Agreement immediately by notice in writing if the other party has breached any term of this Agreement and hasfailed to remedy that breach within 14 days of being requested to do so or, alternatively, if the other party is no longer able to meet its debts as and when they fall due. Microsoft may terminate this Agreement by giving you 30 days* written notice. You may terminate this Agreement by giving Microsoft 90 days* written notice. Where this Agreement is terminated without fault on your side, you will be refunded an amount representing the number of unused Incidents on a pro-rata basis. At its discretion Microsoft may suspend provision of the Services if at any time your conduct is such that, in its reasonab le view, Microsoft’s ability to provide the Services is detrimentally affected by that conduct.14.You acknowledge that you have relied on your own skill and judgment in deciding to acquire the Services. You assume ALL RISKS for the useyou may make of the information, software and other materials and media made available to you under the Personal/Professional Incident Support or through access to the Services.15.You are not entitled to rely on, and Microsoft makes no warranties in respect of, the Services being uninterrupted or error-free. Microsoft doesnot warrant, and you must not rely on Microsoft providing, error-free or continuous availability communications links as the provision of Services via telephone or data links is dependent on the continued availability of communications facilities provided by third parties. You agree to take adequate precautions against damage to your operation that could be caused by such interruption or errors, including making appropriate data backups, and that Microsoft will not be held responsible for any loss of your data. You must ensure that means to access the Services are available and you must also ensure proper and lawful use of the same.16.If the relevant Services Description specifies response times then all reasonable efforts will be made by Microsoft to resolve service requests inaccordance with those response times, provided always that such requests can ultimately be resolved by Microsoft. If no specific response times are indicated, the Services will be provided within a reasonable time.17.Microsoft’s sole obligation and your exclusive remedy in the event of breach of any terms of this Agreement or any the warran ties by Microsoftshall be to use commercially reasonable efforts to correct the breach if the same results in the material impairment of the operation of the Services as warranted. If Microsoft cannot correct the breach within fourteen (14) days, Microsoft or you may terminate this Agreement immediately whereupon Microsoft shall have no obligation or liability to you except to refund an amount representing the unused Incidents, if any, on a pro-rata basis.18.Subject to, and to the extent permitted by applicable law, neither Microsoft, its Contractor (as defined below) nor anyone else who has beeninvolved in the creation, production, or delivery of the Services shall be liable for any direct, indirect, consequential or incidental damages (including damages for loss of business profits, business interruption, loss of business information, and the like or any other pecuniary loss) arising out of the use or inability to use Microsoft products or provision of, or failure to provide, the Services even if Microsoft, its Contractor orsuch third party has been advised of the possibility of such damages. In any event, the liability of Microsoft, its Contractor or such third party, whether for negligence, breach of contract, breach of warranty, or otherwise shall, in the aggregate, not exceed the total amount you paid for the Personal/Professional incident support. No action, whether in contract, tort, or otherwise, arising out of the performance of the Services or these Terms and Conditions may be brought by either party more than two (2) years after the cause of action arises.19.If Microsoft’s performance of any obligat ion under this Agreement is prevented or delayed by causes beyond its reasonable control including,but not limited to, Acts of God, fire, explosion, vandalism, storm, strikes, labour disputes, wars, national emergencies, lockout, work stoppages or other labour difficulties, supplier failures, breaches or delays, failures and down times of utilities and/or telecommunications equipment or computer down times then Microsoft shall be excused from such performance for the duration of the period during which such cause continues to bring about such prevention or delay.20.You may not assign this Agreement, or the right to receive the Services to any person or company without Microsoft’s prior wr itten permission.21.Notwithstanding any other provision of this Agreement, Microsoft may engage, hire, license or sub-contract such persons as it considersnecessary to provide the Services (“Contractor”). Where a Contractor is engaged by Microsoft to perform the Services or any p art thereof then the references to Microsoft in this Agreement shall be deemed to include Microsoft’s Contractors.22.Microsoft treats the personal information provided by you during registration as confidential. The information may be disclosed or transferred ona confidential basis to our parent company, Microsoft Corporation, in the United States and/or other associated companies, partners andagents. Your personal data will only be used for the purpose for which it was originally collected and for general marketing purposes of products or services of Microsoft, Microsoft Corporation and affiliated companies and/or our selected partners. For details, please visit our web site at /hk/privacy.23.You may cancel any annual support incident within 90 days from time of purchase and receive a pro-rata refund provided that all requests forrefund are made in writing within the said 90 days period. All such requests should be directed to Customer Service hotline at (852) 2388-9600.24.This Agreement shall be construed in accordance with the laws of in Hong Kong SAR of the People’s Republic of China.。
惠普工具文档说明书
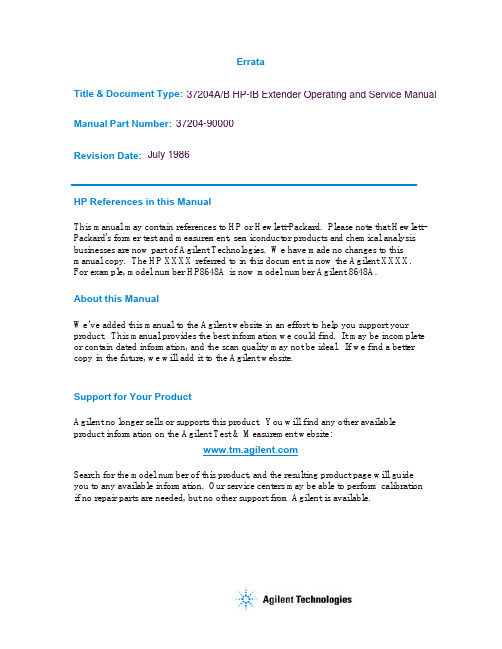
ErrataTitle & Document Type:Manual Part Number:Revision Date:HP References in this ManualThis manual may contain references to HP or Hewlett-Packard. Please note that Hewlett-Packard's former test and measurement, semiconductor products an d chemical analysis businesses are now part of Agilent Technologies. We have made no changes to this manual copy. The HP XXXX referred to in this document is now the Agilent XXXX. For example, model number HP8648A is now model number Agilent 8648A.About this ManualWe’ve added this manual to the Agilent website in an effort to help you support your product. This manual provides the best information we could find. It may be incomplete or contain dated information, and the scan quality may not be ideal. If we find a better copy in the future, we will add it to the Agilent website.Support for Your ProductAgilent no longer sells or supports this product. You will find any other available product information on the Agilent Test & Measurement website:Search for the model number of this product, and the resulting product page will guide you to any available information. Our service centers may be able to perform calibration if no repair parts are needed, but no other support from Agilent is available.37204A/B HP-IB Extender Operating and Service Manual 37204-90000July 1986。
Oracle Retail Place Release Notes Release 12.3.3 A

Oracle® Retail PlaceRelease NotesRelease 12.3.3April 2011Welcome to Oracle® Retail Place Release 12.3.3.This document highlights the enhancements and fixed defect included in this release.It includes the following sections:■Hardware and Software Requirements■Upgrading to Place Release 12.3.3■Technical Enhancements■Noteworthy Fixed Issue■Known Issue■Customer Support■Review Patch Documentation■Oracle Retail Documentation on the Oracle Technology Network■Documentation AccessibilityHardware and Software RequirementsFor more information on the hardware and software requirements for Place Release12.3.3, refer to the section Supported Configurations in the chapter Planning YourInstallation of the Oracle Retail Place Installation Guide.Upgrading to Place Release 12.3.3For more information on upgrading to Place Release 12.3.3, refer to the sectionUpgrading to the Latest Release of Place in the chapter Installing Place of the Oracle RetailPlace Installation Guide.Technical EnhancementsThe following technical enhancements are included in this release:Noteworthy Fixed IssueThe following functional issue is fixed in this release:Known IssueThe following known issue is identified in this release:Table 1Technical Enhancements in this ReleaseReference Number Description11800754 The P lace application is now also supported on Microsoft Internet Explorer 8 Web browser. It continues to be supported on Microsoft Internet Explorer 7.Using Microsoft Internet Explorer 7, you can log in to the Plan or Place applications in multiple windows. Each time you will be presented with the Login screen, and you may even login with different user accounts.Using Microsoft Internet Explorer 8, when you access the applications from multiple tabs or windows, the login information is cached by the Web browser. While logged into the Plan or Place application, when you access a second application, you will be logged in automatically. You will be directed to the home screen of the second application without needing to log in again.18180The Place application is now supported to work with BEA WebLogic Server 10.0 MP1 running on Oracle Linux 5 Update 5 (64-bit).Table 2Issues Fixed in this ReleaseReference Number Description10380167The color IDs displayed in the Like Items tab of the Item Properties screen were inconsistent with those displayed for the same like item in the Plan application. This occurred because internal IDs were being displayed, which can sometimes be different from the IDs displayed to users.The application has been updated to display the correct IDs and this will now be consistent with Plan.Table 3Known Issue in this ReleaseReference Number Description18322While you are logged into the Plan application, when you try accessing the application in a second instance (window or tab) a system error will occur. You must close the new window or tab.Although this issue does not occur when you try opening multiple instances of the Place application, opening multiple instances is not supported by both the applications.Customer SupportTo contact Oracle Customer Support, access My Oracle Support at the following URL:■https://When contacting Customer Support, please provide the following:■Product version and program/module name■Functional and technical description of the problem (include business impact)■Detailed step-by-step instructions to recreate■Exact error message received■Screen shots of each step you takeReview Patch DocumentationIf you are installing the application for the first time, you install either a base release (for example, 12.3) or a later patch release (for example, 12.3.2). If you are installing a software version other than the base release, be sure to read the documentation for each patch release (since the base release) before you begin installation. Patch documentation can contain critical information related to the base release and code changes that have been made since the base release.Oracle Retail Documentation on the Oracle Technology Network In addition to being packaged with each product release (on the base or patch level), all Oracle Retail documentation is available on the following Web site (with the exception of the Data Model which is only available with the release packaged code): /technology/documentation/oracle_retail.htmlDocumentation should be available on this Web site within a month after a product release. Note that documentation is always available with the packaged code on the release date.Documentation AccessibilityOur goal is to make Oracle products, services, and supporting documentation accessible to all users, including users that are disabled. To that end, our documentation includes features that make information available to users of assistive technology. This documentation is available in HTML format, and contains markup to facilitate access by the disabled community. Accessibility standards will continue to evolve over time, and Oracle is actively engaged with other market-leading technology vendors to address technical obstacles so that our documentation can be accessible to all of our customers. For more information, visit the Oracle Accessibility Program Web site at /accessibility/.Accessibility of Code Examples in DocumentationScreen readers may not always correctly read the code examples in this document. The conventions for writing code require that closing braces should appear on an otherwise empty line; however, some screen readers may not always read a line of text that consists solely of a bracket or brace.Accessibility of Links to External Web Sites in DocumentationThis documentation may contain links to Web sites of other companies or organizations that Oracle does not own or control. Oracle neither evaluates nor makes any representations regarding the accessibility of these Web sites.Access to Oracle SupportOracle customers have access to electronic support through My Oracle Support. For information, visit /support/contact.html or visit /accessibility/support.html if you are hearing impaired.Oracle® Retail Place Release Notes, Release 12.3.3Copyright © 2011, Oracle and/or its affiliates. All rights reserved.This software and related documentation are provided under a license agreement containing restrictions on use and disclosure and are protected by intellectual property laws. Except as expressly permitted in your license agreement or allowed by law, you may not use, copy, reproduce, translate, broadcast, modify, license, transmit, distribute, exhibit, perform, publish, or display any part, in any form, or by any means. Reverse engineering, disassembly, or decompilation of this software, unless required by law for interoperability, is prohibited.The information contained herein is subject to change without notice and is not warranted to be error-free. If you find any errors, please report them to us in writing.If this software or related documentation is delivered to the U.S. Government or anyone licensing it on behalf of the U.S. Government, the following notice is applicable:U.S. GOVERNMENT RIGHTS Programs, software, databases, and related documentation and technical data delivered to U.S. Government customers are "commercial computer software" or "commercial technical data" pursuant to the applicable Federal Acquisition Regulation and agency-specific supplemental regulations. As such, the use, duplication, disclosure, modification, and adaptation shall be subject to the restrictions and license terms set forth in the applicable Government contract, and, to the extent applicable by the terms of the Government contract, the additional rights set forth in FAR 52.227-19, Commercial Computer Software License (December 2007). Oracle USA, Inc., 500 Oracle Parkway, Redwood City, CA 94065.This software is developed for general use in a variety of information management applications. It is not developed or intended for use in any inherently dangerous applications, including applications which may create a risk of personal injury. If you use this software in dangerous applications, then you shall be responsible to take all appropriate fail-safe, backup, redundancy, and other measures to ensure the safe use of this software. Oracle Corporation and its affiliates disclaim any liability for any damages caused by use of this software in dangerous applications.Oracle is a registered trademark of Oracle Corporation and/or its affiliates. Other names may be trademarks of their respective owners.This software and documentation may provide access to or information on content, products, and services from third parties. Oracle Corporation and its affiliates are not responsible for and expressly disclaim all warranties of any kind with respect to third-party content, products, and services. Oracle Corporation and its affiliates will not be responsible for any loss, costs, or damages incurred due to your access to or use of third-party content, products, or services.Value-Added Reseller (VAR) LanguageOracle Retail VAR ApplicationsThe following restrictions and provisions only apply to the programs referred to in this section and licensed to you. You acknowledge that the programs may contain third party software (VAR applications) licensed to Oracle. Depending upon your product and its version number, the VAR applications may include:(i) the MicroStrategy Components developed and licensed by MicroStrategy Services Corporation (MicroStrategy) of McLean, Virginia to Oracle and imbedded in the MicroStrategy for Oracle Retail Data Warehouse and MicroStrategy for Oracle Retail Planning & Optimization applications.(ii) the Wavelink component developed and licensed by Wavelink Corporation (Wavelink) of Kirkland, Washington, to Oracle and imbedded in Oracle Retail Mobile Store Inventory Management.(iii) the software component known as Access Via™ licensed by Access Via of Seattle, Washington, and imbedded in Oracle Retail Signs and Oracle Retail Labels and Tags.(iv) the software component known as Adobe Flex™ licensed by Adobe Systems Incorporated of San Jose, California, and imbedded in Oracle Retail Promotion Planning & Optimization application.You acknowledge and confirm that Oracle grants you use of only the object code of the VAR Applications. Oracle will not deliver source code to the VAR Applications to you. Notwithstanding any other term or condition of the agreement and this ordering document, you shall not cause or permit alteration of any VAR Applications. For purposes of this section, "alteration" refers to all alterations, translations, upgrades, enhancements, customizations or modifications of all or any portion of the VAR Applications including all reconfigurations, reassembly or reverse assembly,re-engineering or reverse engineering and recompilations or reverse compilations of the VAR Applications or any derivatives of the VAR Applications. You acknowledge that it shall be a breach of the agreement to utilize the relationship, and/or confidential information of the VAR Applications for purposes of competitive discovery.The VAR Applications contain trade secrets of Oracle and Oracle's licensors and Customer shall not attempt, cause, or permit the alteration, decompilation, reverse engineering, disassembly or other reduction of the VAR Applications to a human perceivable form. Oracle reserves the right to replace, with functional equivalent software, any of the VAR Applications in future releases of the applicable program.。
CURT 接收器牵引爪说明书

LEVEL OF DIFFICULTY: HARD
EASY
MODERATE
HARD
REMOVE (2) RUBBER ISOLATORS
TORQUE WRENCH
SAFETY GLASSES
FISHWIRE HARDWARE
VEHICLE PHOTO:
REPRESENTATIVE PHOTO HITCH ILLUSTRATION:
8. (2010 models only) On the passenger side frame rail fishwire (1) 3/8 x 2" carriage bolt and (1) SP-18 spacer into the upper hole on the inside of frame rail. Place (1) SP-52 and exhaust hanger onto bolt and secure with 3/8" flange nut. (See EXHAUST HANGER HARDWARE ORIENTATION on page 2)
For more information log onto , & for helpful towing tips log onto
8/11/2010
INSTALLATION WALKTHROUGH:
ITEM QTY PART NUMBER 1 2 7/16-14 x 1
JOINT TO UNFASTEN EXHAUST PIPES (BOTH SIDES)
ACCESS HOLE (BOTH SIDES)
2 3
PASSENGER SIDE FRAME RAIL
EXHAUST HANGER RELOCATION
技术协议-Technicalagreement--中英

Recycle Hydrogen Compressor(UK-202)循环氢压缩机(UK-202)Procurement Technical Agreement订货技术协议单元名称:Unit name:业主:Owner:总承包方:Contractor:设计单位:Designer:供货商:Supplier:June, 2014Content1、概述General (1)2、离心压缩机技术要求及说明Technical requirements & descriptions for centrifugal compressor (2)3、现场及公用工程条件(根据终版MR文件填写)Site & utility conditions(Fill in based on MR documents) (4)4、供货清单supply list (5)5、备品、备件和专用工具清单List for spare parts & special devices (5)6、设计制造中执行的标准及规范Executive standard & specs in design & manufacturing (6)7、检验和试验项目Items for check & test (6)8、设计分工及图纸和资料交付Division of design & delivery of drawings & documents (8)9、主要配套部件分供货商名单及联系方式Supplier lists for main parts & contact (9)10、机组的性能保证和寿命保证Performance & lifespan guarantee for units 1011、协调会及设备验收Coordination meeting & equipment acceptance (10)12、压缩机主要零部件材质清单material list for main parts of compressor .. 1013、离心式压缩机预期性能曲线Expected performance curve for centrifugal compressor (11)14、离心式压缩机组数据表Data table for centrifugal compressor (11)15、压缩机组流程图(包括油、水、气等)Flow chart of compressor units (including oil, water & gas, etc.) (11)16、压缩机剖面图Section plan of compressor (11)17、齿轮箱剖面图Section plan of gear box (11)18、润滑油/脂清单List for lubricating oil/grease (11)19、灌浆原材料的推荐Recommended raw materials for grouting (11)20、现场服务On-site service (11)21、交货期Delivery time (11)22、质量保证期Quality warranty period (11)23、其它要求及说明Other requirements & descriptions (12)24、偏离表Deviation table (12)25、联系方式Contact (13)1、概述General1.1原则 Principles1.1.1本技术协议是对XXXXXXXXX炼油厂现代化改造工程XXXXXXX设计和制造的最一般要求,包括设计、制造、检验、验收、包装、运输、安装指导和售后服务。
1-1410353-9 板级指导硬件指南栏指导模块,板到板,1位,印刷电路板,1A接触电流等级(最大

1-1410353-9Backplane Guide Hardware, Guide Socket Module, Board-to-Board, 1 Position,Printed Circuit Board, 1A Contact Current Rating (Max), Board MountConnectors>PCB Connectors>Backplane Connectors>Backplane Guide HardwareContact Current Rating (Max): 1 AConnector & Contact Terminates To:Printed Circuit BoardNumber of Positions:1Connector System:Board-to-BoardBackplane Guide Hardware Type:Guide Socket ModuleFeaturesProduct Type FeaturesBackplane Guide Hardware Type Guide Socket ModuleConnector System Board-to-BoardConnector & Contact Terminates To Printed Circuit BoardConfiguration FeaturesPCB Mount Orientation Right AngleNumber of Positions1Contact FeaturesContact Current Rating (Max) 1 AMechanical AttachmentGuide Hardware WithConnector Mounting Type Board MountUsage ConditionsOperating Temperature Range-55 – 105 °C[-67 – 221 °F]Product ComplianceFor compliance documentation, visit the product page on >EU RoHS Directive 2011/65/EU CompliantEU ELV Directive 2000/53/EC Compliant1-1410353-9 ACTIVEMULTIGIG RTTE Internal #:1-1410353-9Backplane Guide Hardware, Guide Socket Module, Board-to-Board, 1 Position, Printed Circuit Board, 1A Contact Current Rating(Max), Board MountView on >EU ELV Directive 2000/53/ECCompliantChina RoHS 2 Directive MIIT Order No 32, 2016No Restricted Materials Above Threshold EU REACH Regulation (EC) No. 1907/2006Current ECHA Candidate List: JUN 2020 (209)Candidate List Declared Against: JAN 2020 (205)Does not contain REACH SVHCHalogen ContentLow Halogen - Br, Cl, F, I < 900 ppm per homogenous material. Also BFR/CFR/PVC FreeSolder Process Capability Not reviewed for solder process capabilityProduct Compliance DisclaimerThis information is provided based on reasonable inquiry of our suppliers and represents our current actual knowledge based on the information they provided. This information is subject to change. The part numbers that TE has identified as EU RoHS compliant have a maximum concentration of 0.1% by weight in homogenous materials for lead, hexavalent chromium, mercury, PBB, PBDE, DBP, BBP, DEHP, DIBP, and 0.01% for cadmium, or qualify for an exemption to these limits as defined in the Annexes of Directive 2011/65/EU (RoHS2). Finished electrical and electronic equipment products will be CE marked as required by Directive 2011/65/EU. Components may not be CE marked. Additionally, the part numbers that TE has identified as EU ELV compliant have a maximum concentration of 0.1% by weight in homogenous materials for lead, hexavalent chromium, and mercury, and 0.01% for cadmium, or qualify for an exemption to these limits as defined in the Annexes of Directive 2000/53/EC (ELV). Regarding the REACH Regulation, the information TE provides on SVHC in articles for this part number is based on the latest European Chemicals Agency (ECHA) ‘Guidance onrequirements for substances in articles’ posted at this URL: https://echa.europa.eu/guidance-documents/guidance-on-reachTE Model / Part #4-1617352-4JMGAP-5L=M39016/17-025LTE Model / Part #1-5120529-11FHR,64,50A/S,N,C,S11,12TE Model / Part #1-1410353-2MULTIGIG RT 9MM GUIDE/ESD 45 DTE Model / Part #5-1542000-6HTS191-P=25MM HS ASSY PPA CLIPTE Model / Part #1410354-7MULTI-GIG GUIDEPIN, 9MM 2.60TE Model / Part #1410477-2MULTI-GIG GD PIN KEY/ESD NI PLCompatible PartsCustomers Also BoughtTE Model / Part #546353-000D-704-0042TE Model / Part #YCFX24F1108GAN0000RECP ASSYTE Model / Part #2085200-3Assy 2x6 MINIPAK HDE seq3, RoHTE Model / Part #1757256-1SMPM FEMALE BULLET ADAPTERTE Model / Part #1-1410354-2MULTIGIG RT GUIDEPIN, 9MM 2.60TE Model / Part #1-1410353-1MULTIGIG RT 9MM GUIDE/ESD 0 DEDocumentsProduct DrawingsMULTIGIG RT 9MM GUIDE/ESD UNKEEnglish CAD Files3D PDF3DCustomer View ModelENG_CVM_CVM_1-1410353-9_A.2d_dxf.zipEnglishCustomer View ModelENG_CVM_CVM_1-1410353-9_A.3d_igs.zipEnglishCustomer View ModelENG_CVM_CVM_1-1410353-9_A.3d_stp.zipEnglishBy downloading the CAD file I accept and agree to the of use.Terms and Conditions Product SpecificationsApplication SpecificationEnglishProduct Environmental ComplianceTE Material DeclarationEnglish。
HP StorageWorks Fibre Channel Disk Drive Replaceme

HP StorageWorksFibre Channel Disk Drive Replacement InstructionsThese instructions apply to the EVA4000/6000/8000product family.The partmay also be used in other HP products.Please refer to documentation for your specific product for detailed replacement instructions.20052005*5697-5248*Warranty InformationIf the product in which this part is being replaced is still underHP warranty,then the replacement part(s)referred to in these Replacement Instructions is provided under the terms and conditionsof the Hewlett-Packard Company Limited Warranty for that product.A copy of this Limited Warranty may be viewed at:/products/storageworks/warranty.html If this is a trade sale part(product out of warranty),then the replacement part(s)referred to in these Replacement Instructions is provided under HP's express limited warranty statement,which may be viewed at: /1sw/pdm_om/warranty_support/ policies/2330100.docThe replacement part takes on either the Limited Warranty Period of the part being replaced or a ninety-day period that begins upon installation of the replacement part,whichever is greater.The only warranty for this replacement product is as noted above. Nothing in these replacement instructions should be construed as constituting an additional warranty.The information provided in these replacement instructions is provided"AS IS"and HP is not liable for technical or editorial errors or omissions contained herein.1About This DocumentThis document describes the procedure for replacing the Fibre Channel disk drive used in the EVA4000/6000/8000products.2Before you beginObserve the following precautions when replacing the diskdrive.CAUTION:Make sure you have a replacement part available beforeremoving the failed component.Removing a componentimpacts cooling within the enclosure.Do not remove more than one disk drive at a time from theenclosure.Doing so will impact cooling of the enclosureand may cause data loss.Parts can be damaged by electrostatic eproper anti-static protection.Refer to the documentation thatshipped with your system for additional information.Have a copy of the product User Guide available forreference.You can download a copy of the User Guidefrom the product support page on the HP web site.3Verifying component failureBefore replacing a disk drive,use the following methods to verify the componentfailure:CAUTION:If Command View EVA does not present a status consistentwith that of the disk drive status indicators,or if CommandView or the System Event Analyzer indicates multiplehardware failures,contact HP support for assistance.The HPsupport web site is located at /support•Analyze any failure messages you may have received from systemmonitoring (System Event Analyzer).•Check the disk drive status indicators.See Figure 1.The Faultindicator should be On.•Check status using Command View EVA:1.In the Navigation pane,select Storage system >Hardware >Rack >Disk enclosure >Bay2.In the Content pane,select the Disk Drive tab.The Operational state shouldbeFailed .3.Verify the following status conditions are met before proceeding:•Migration state -Not migrating •Requested usage -Ungrouped •Actual usage -Ungrouped4.Click Remove to prepare the disk for removal.The status indicators on the disk drive will begin flashing to help you locate the disk.Figure 1Disk drive status indicators 1.Activity2.Online3.Fault4Removing a diskCAUTION:Rotating media can make the disk drive dif ficult to handle.To avoid dropping and damaging the disk drive,wait approximately 30seconds for the media to stop rotating before removing the drive from the enclosure.1.Push in the wine-colored ejector button (1)and pull the release lever (2)down to the full open position.2.Pull the disk drive part way out of the enclosure (3)and wait for the media to stop spinning.3.When the media has stopped spinning,remove the disk drive from the enclosure.0115aFigure 2Removing a disk drive5Installing a disk drive1.Push in the ejector button on the disk drive and pull the release lever down to the full open position.2.Insert the drive into the enclosure as far as it will go (1).3.Close the release lever until it engages the ejector button,and the disk drive seats in the backplane (2).4.Press in firmly on the disk drive to ensure it is seatedproperly.0116aFigure 3Installing a disk drive6Verifying proper operationAfter replacing the disk drive,check the following to verify that the disk drive is operatingnormally:NOTE:It may take up to 10minutes for the component to display good status.•Check the disk drive status indicators.See Figure 1.•Activity indicator (1)should be on or flashing •Online indicator (2)should be on or flashing •Fault indicator (3)should be off•Check the following using Command View EVA.•Navigate back to the component and check the operationalstate.It shouldbe•Ensure the disk drive is using the correct firmware.Check theFirmware Version against the supported disk firmware in the HP StorageWorks Enterprise Virtual Array Release Notes .The most current edition of the release notes can be downloaded from the following web site:/go/eva8000If the disk drive is using an unsupported version of firmware,contact HP support for assistance.Do not add the disk drive to a disk group if it using an unsupported firmware version.7Adding the disk to a disk groupAfter replacing the disk,it should be added to a disk group.The disk is typically added back into its original disk group.1.In the Navigation pane,select Storage system >Hardware >Rack >Disk enclosure >Bay2.In the Content pane,select the Disk Drive tab.3.Click Group to initiate the process for adding the disk to a diskgroup.NOTE:If the Device Addition Policy is set to automatic,the disk will automatically be added to a disk group.In this case the Group option will not be available.8Returning the failed componentPlease follow the return instructions provided with the new component.。
LAOWA CF 4mm F2.8 210° Circular Fisheye 全手动圆周鱼眼镜头使

使用手册Instruction Manual400-066-1316Email:********************************合肥市庐阳区天水路与太和路交口庐阳中科大校友创新园5号楼Building 5, USTC Alumni Innovation Park, Crossing of Tianshui and Taihe Road, Luyang District, Hefei City, Anhui Province, China安徽长庚光学科技有限公司FACEBOOKCIRCULAR FISHEYEF2.8 210° Circular Fisheye 全手动圆周鱼眼镜头。
此镜头是无反半画幅系统镜头,拥有约210°圆周视角,主打摄影创意与乐趣,助您拍摄更富创意的作品。
为了操作上的安全,使用本产品前请务必详细阅读使用手册与注意事项,并将手册放在需要时容易取得的地方。
如遇到不能解决的问题请通过售后电话获取技术支持。
4mm F2.8拥有无反半画幅系统的210°圆周视野,可以拍摄具有创意性的圆周广角照片。
两张照片即可拍摄出360°全景照片,带给你不一样的拍摄体验。
为了使用更加方便,镜头在对焦环上增加了拇指拨杆,可以帮助您在拍摄时更方便单手操作。
4mm F2.8镜头体积小巧,重量仅约135g,省出了背包空间同时减轻了使用者的负担。
镜头每块镜片均采用低反射多层镀膜,尽可能的消除了鬼影和炫光,且前端镜片采用蛙眼仿生镀膜,使水滴、灰尘不易附着。
切勿自行拆解、修改或改装。
当产品由于外力原因破损,切勿触碰外露部分或破损边缘处。
切勿放置于直射阳光下、封闭车辆中或其余高温处,否则过高的温度会使镜片和其他部件产生伸缩变形。
不使用镜头时,请将镜头前盖盖上或置于没有阳光照射处。
凸透镜反射出的光线可能会聚集在附近物体上,导致发生火灾。
在逆光拍摄时,切勿将太阳置于画面中心,应该使太阳充分偏离画角,否则阳光会在相机内部聚集并导致火灾或灼伤眼睛。
【外贸英语】给客户提供技术支持和协助时常用的外贸英语口语
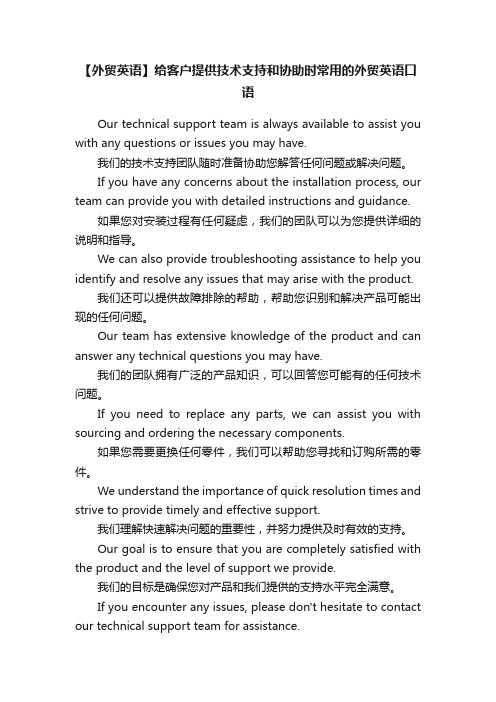
【外贸英语】给客户提供技术支持和协助时常用的外贸英语口语Our technical support team is always available to assist you with any questions or issues you may have.我们的技术支持团队随时准备协助您解答任何问题或解决问题。
If you have any concerns about the installation process, our team can provide you with detailed instructions and guidance.如果您对安装过程有任何疑虑,我们的团队可以为您提供详细的说明和指导。
We can also provide troubleshooting assistance to help you identify and resolve any issues that may arise with the product.我们还可以提供故障排除的帮助,帮助您识别和解决产品可能出现的任何问题。
Our team has extensive knowledge of the product and can answer any technical questions you may have.我们的团队拥有广泛的产品知识,可以回答您可能有的任何技术问题。
If you need to replace any parts, we can assist you with sourcing and ordering the necessary components.如果您需要更换任何零件,我们可以帮助您寻找和订购所需的零件。
We understand the importance of quick resolution times and strive to provide timely and effective support.我们理解快速解决问题的重要性,并努力提供及时有效的支持。
专利产品手册英文
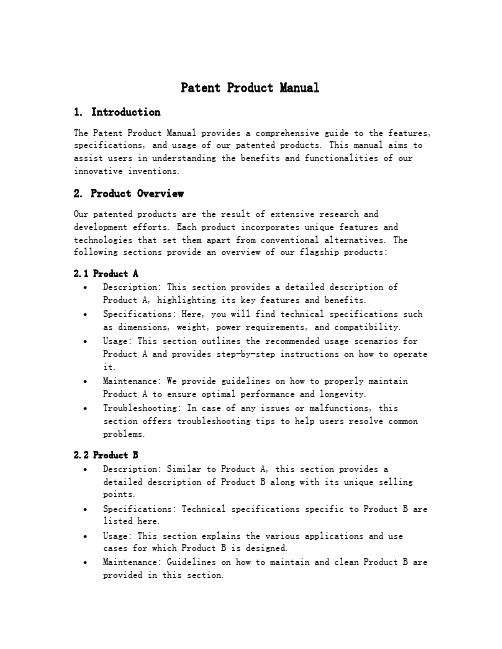
Patent Product Manual1. IntroductionThe Patent Product Manual provides a comprehensive guide to the features, specifications, and usage of our patented products. This manual aims to assist users in understanding the benefits and functionalities of our innovative inventions.2. Product OverviewOur patented products are the result of extensive research and development efforts. Each product incorporates unique features and technologies that set them apart from conventional alternatives. The following sections provide an overview of our flagship products:2.1 Product A•Description: This section provides a detailed description of Product A, highlighting its key features and benefits.•Specifications: Here, you will find technical specifications such as dimensions, weight, power requirements, and compatibility.•Usage: This section outlines the recommended usage scenarios for Product A and provides step-by-step instructions on how to operate it.•Maintenance: We provide guidelines on how to properly maintain Product A to ensure optimal performance and longevity.•Troubleshooting: In case of any issues or malfunctions, this section offers troubleshooting tips to help users resolve commonproblems.2.2 Product B•Description: Similar to Product A, this section provides a detailed description of Product B along with its unique sellingpoints.•Specifications: Technical specifications specific to Product B are listed here.•Usage: This section explains the various applications and use cases for which Product B is designed.•Maintenance: Guidelines on how to maintain and clean Product B are provided in this section.•Troubleshooting: Users can refer to this section fortroubleshooting assistance related to common issues with Product B.3. Features and BenefitsIn this section, we delve deeper into the features and benefits offered by our patented products:3.1 Advanced Technology IntegrationOur products incorporate cutting-edge technologies that enhance their performance and functionality. These technologies include [Technology X], [Technology Y], and [Technology Z]. The integration of thesetechnologies results in superior performance, increased efficiency, and enhanced user experience.3.2 Unique DesignThe patented designs of our products not only make them visually appealing but also contribute to their functionality. Our design teamhas focused on ergonomics, aesthetics, and user-friendliness to ensure a seamless user experience.3.3 Enhanced Safety MeasuresUser safety is of utmost importance to us. Therefore, our patented products incorporate advanced safety features that minimize the risk of accidents or injuries during usage.3.4 Environmental SustainabilityWe are committed to reducing our environmental footprint. Our patented products are designed with sustainability in mind, utilizing eco-friendly materials and energy-efficient technologies.4. Product CustomizationWe understand that different users may have unique requirements or preferences. Therefore, we offer customization options for our patented products based on specific needs. Whether it’s color variations, additional functionality, or branding opportunities, our team is dedicated to meeting individual customer demands.5. Warranty and SupportTo ensure customer satisfaction and confidence in our products, we offer a comprehensive warranty program. This program covers any manufacturing defects or malfunctions during the specified warranty period.Additionally, we provide ongoing support through various channels such as phone support, email assistance, and an online knowledge base. Our dedicated support team is available to address any queries or concerns promptly.ConclusionThe Patent Product Manual serves as a comprehensive guide for users interested in understanding the features, specifications, and usage of our patented products. By providing detailed information and support resources, we aim to enhance the overall user experience andsatisfaction with our innovative inventions.For further assistance or inquiries regarding our patented products, please refer to the contact information provided in this manual or visit our website at [website URL].。
- 1、下载文档前请自行甄别文档内容的完整性,平台不提供额外的编辑、内容补充、找答案等附加服务。
- 2、"仅部分预览"的文档,不可在线预览部分如存在完整性等问题,可反馈申请退款(可完整预览的文档不适用该条件!)。
- 3、如文档侵犯您的权益,请联系客服反馈,我们会尽快为您处理(人工客服工作时间:9:00-18:30)。
Technical Support Document for the Post-Construction Stormwater Management Conditions in the General Stormwater Permit (MNR040000) for Small Municipal Separate Storm Sewer SystemsIntroductionThis guidance document is intended to describe the post construction stormwater management permit conditions (Minimum Control Measure 5) as required by the General Stormwater Small Municipal Separate Storm Sewer Systems (MS4) Permit issued by the Minnesota Pollution Control Agency (MPCA). MS4 permittees are required to develop a regulatory mechanism (ordinance, policy, etc.) for construction activity within their jurisdiction such that a permanent stormwater treatment system is in place once the construction activity is complete. Construction activity is defined as any activity (i.e. clearing, grading, excavating) that will result in the disturbance of one or more acres of land or that is part of a larger common plan of development that will ultimately disturb one or more acres of land. The requirements for post construction stormwater treatment set forth in the Permit are narrative in nature and do not contain specific numeric standards, in order to allow MS4 permittees maximum flexibility in determining how their community will meet the treatment conditions. The MPCA expects MS4 permittees to adopt treatment requirements in their regulatory mechanism that are reflective of the narrative requirements found within the Permit. There are already a number of different post construction treatment approaches currently in effect around the state of Minnesota that meet the intention of the post-construction treatment conditions as stated in Part III.D.5.a(2)(a) and (b) of the Permit. This guidance document refers to several of these stormwater treatment approaches in addition to others that communities may adopt.In order to meet the post-construction stormwater management conditions, existing permittees have 12 months from the date the MS4 Permittee is extended Permit coverage to revise their regulatory mechanism (e.g., contract language, an ordinance, permits, standards, etc.) as well as develop a municipal review and approval process. Any new MS4 permittees designated during this permit cycle will need to develop post-construction requirements within 24 months after permit coverage is granted. Post construction stormwater treatment requirementsPart III.D.5 of the MS4 Permit – “Post-Construction Stormwater Management”:The MS4 permittee shall develop and implement a Post-Construction Stormwater Management program that requires the use of any combination of BMPs, with highest preference given to Green Infrastructure techniques and practices (e.g., infiltration, evapotranspiration, reuse/harvesting, conservation design, urban forestry, green roofs, etc.), necessary to meet the following conditions on the site of a construction activity to the Maximum Extent Practicable (MEP).For new development projects – no net increase from pre-project conditions (on an annual average basis) of:1.Stormwater discharge Volume, unless precluded by the stormwater management limitationsoutlined in Part III.D.5.a.(3)(a)2.Stormwater discharges of Total Suspended Solids (TSS)3.Stormwater discharges of Total Phosphorus (TP)For redevelopment projects – a net reduction from pre-project conditions (on an annual average basis) of:1.Stormwater discharge Volume, unless precluded by the stormwater management limitationsoutlined in Part III.D.5.a.(3)(a)2.Stormwater discharges of TSS3.Stormwater discharges of TPNew developmentThe MPCA believes that the objectives of the post-construction stormwater management conditions for new development will be met if any of the following treatment requirements are adopted into the post-construction stormwater management program. The U.S. Environmental Protection Agency (EPA) MS4 Permit Improvement Guide (dated April 2010) suggests a number of recommended treatment requirements that state permitting authorities may incorporate into their MS4 permits. The MPCA has determined that of those options outlined in the improvement guide, three, with slight modifications, will achieve the conditions set forth in the Permit which states; no net increase from pre-project conditions (on an average annual basis) of Volume, TSS or TP. In addition to the three EPA recommended post-construction stormwater management approaches (1-3 below), the MPCA will except other scientifically defensible treatment approaches. The options are:1.Retain a runoff volume equal to one inch times the area of the proposed increase of impervioussurfaces on-site:Design and construct stormwater management practices that manage rainfall on-site, and prevent the off-site discharge of the precipitation from the first one inch of runoff from the new impervious surfaces created by the project. Discharge volume reduction can be achieved by engineeredinfiltration, canopy interception, soil amendments, evaporation, rainfall harvesting, and/orevapotranspiration and any combination of the aforementioned practices. This first one inch of rainfall must be 100% managed with no discharge to surface waters.2.Retain the post-construction runoff volume on site for the 95th percentile storm:Design, construct, and maintain stormwater management practices that manage rainfall on-site, and prevent the off-site discharge of the precipitation from all rainfall events less than or equal to the 95th percentile rainfall event. Discharge volume reduction can be achieved by engineeredinfiltration, canopy interception, soil amendments, evaporation, rainfall harvesting, and/orevapotranspiration and any combination of the aforementioned practices. The 95th percentilerainfall event is an event of which precipitation total is greater than or equal to 95% of all storm events over a given period of record. This approach to stormwater management is further explained in the EPA document titled ”Technical Guidance on Implementing the Stormwater RunoffRequirements for Federal Projects under Section 438 of the Energy Independence and Security Act”./polwaste/nps/upload/eisa-438.pdf3.Match the pre-development runoff conditions:Design and construct stormwater management practices that preserve the pre-development runoff conditions following construction. The post-construction rate, volume and duration of discharges must not exceed the pre-project rates and the pre-project hydrograph for 1 and 2 year storms must be replicated through site design and other appropriate practices. These goals can be achieved by engineered infiltration, canopy interception, soil amendments, evaporation, rainfall harvesting, and/or evapotranspiration and any combination of the aforementioned practices. Defensible and4.Any other stormwater performance standard that achieves the volume, TSS and TP goals listedabove based on modeling, research and acceptable engineering practices.5.Adopting the Minimal Impact Design Standards (MIDS) as developed by the MPCA.Using MIDS to meet stormwater management requirementsThe 2009 Legislature directed the MPCA to “develop performance standards, design standards, or other tools to enable and promote the implementation of low impact development and other storm water management techniques” such that the “rate and volume of predevelopment storm water reaching receiving waters is unchanged compared to the runoff from developed land” (Minn. Stat. § 115.03, subd. 5c.). Upon passage of the legislation, a stakeholder group was created to assist the MPCA in this effort and the results were termed “Minimal Impact Design Standards”.MIDS is a voluntary tool for MS4 permittees to use to reduce impacts from stormwater discharges. If a MS4 permittee adopts MIDS into their Regulatory Mechanism, the MPCA will consider the community to have satisfied the post-construction stormwater management conditions (MCM5). The MIDS performance goal for new development, which was developed considering historic Minnesota specific precipitation events, is to capture and retain on site 1.1 inches of runoff from the impervious surfaces in post-construction conditions. For redevelopment projects, the performance goal is to capture and retain on site 1.1 inches of runoff from the new and/or fully redeveloped impervious surfaces. For linear projects, the performance goal is to capture and retain onsite the larger of the following: ·0.55 inches of runoff from the new and fully reconstructed impervious surfaces·1.1 inches of runoff from the net increase in impervious surfacesThe MIDS performance goals above will not always be possible due to site constraints such as contaminated soils or soils with low infiltration rates. For this reason, the MIDS stakeholder group developed a Design Sequence Flowchart to assist users in determining when a different performance goal is appropriate.The MPCA has developed a new calculator that allows project proposers and regulatory reviewers to easily quantify the volume reduction expected from a specific stormwater management system. The MIDS calculator includes some less traditional systems that often received no volume reduction credit in the past such as a grass swale. The MPCA has also developed a Community Assistance Package (CAP) that contains ordinance development guidance to help communities adopt the MIDS standard. For more information on the MIDS approach to stormwater management, see the Minnesota Stormwater Manual:/index.php/Performance_goals_for_new_development,_re-development_and_linear_projectsTo be viewed by the MPCA as adopting MIDS a community must:1.Incorporate the MIDS performance goals for new development and redevelopment into theirRegulatory Mechanism.2.Incorporate the flexible treatment options as outlined in the MIDS Design Sequence Flowchart intotheir Regulatory Mechanism.3.Incorporate the use of the MIDS calculator.Communities should understand that while MIDS contains many components, they do not all need to be adopted in order to meet the post-construction stormwater management permit conditions. As an example, in order to meet the treatment requirements of the Permit, a community could choose to adopt only the new development and redevelopment performance goals of MIDS. The Permit requires MS4 permittees to develop a Regulatory Mechanism to address the infiltration prohibitions and restrictions outlined in Part III.D.5.a(3). While this permit requirement is addressed in the DesignSequence Flowchart, an MS4 permittee could choose to develop an alternative methodology to address this requirement. It is important to note that MS4 permittees cannot use the Design Sequence Flowchart unless they have adopted MIDS.Post construction stormwater treatment requirements cont.Post-construction stormwater management strategies implemented by a permittee should take into account the variability in hydrologic conditions which may exist in different areas within the permittee’s jurisdiction. Ideally, design requirements should reflect the local naturally-occurring hydrology with respect to runoff, infiltration, evapotranspiration, and storage in order to mimic the water balance that would be present in the absence of development. Key parameters, such as rainfall patterns, soil characteristics, and topography, can be used to establish likely ‘natural’ hydrology. The MPCA recommends that the Regulatory Mechanism developed by the MS4 permittee allow for a combination of techniques that utilize infiltration, capture and re-use evapotranspiration and other types of low impact development techniques as appropriate, rather than relying only on infiltration or some other technique alone to meet performance goals. If infiltration practices are not appropriate for a particular project due to site limitations, other volume reduction techniques must still be considered.If theMS4’s jurisdiction lies within a Watershed District that has developed a volumereduction/treatment management strategy for post-construction that is at least as stringent as one of the management strategies above, the MS4 permittee may choose to implement those requirements across the entire MS4 jurisdiction. Some existing stormwater requirements may be similar to the ones listed above, but might be slightly less restrictive in one area while being more restrictive in another. The MPCA will evaluate these volume reduction strategies on a case by case basis.Where re-use of stormwater is implemented, such as use with an irrigation system, volumes captured shall be given equal credit toward the volume reduction requirement by the permittees Regulatory Mechanism. Such re-use measures must be fully documented in the post-construction stormwater management program.RedevelopmentFor redevelopment projects, the MS4 Permit requires a net reduction in the amount of TP, TSS and stormwater runoff volume (unless precluded by one of the prohibitions or restrictions listed below) leaving the site as compared with pre-project conditions. Most redevelopment projects contain both impervious and pervious land cover. Impervious cover types include pavement, buildings, gravel, stockpiles and other types of highly impacted cover in which the native hydrology has been greatly altered. The MS4 Permit defines any site with less than 15% of existing impervious surfaces prior to the commencement of construction activity as new development and the new development treatment conditions would apply as if the site had no impervious surfaces prior to construction. The percentage of impervious cover is calculated by dividing the area of the existing impervious cover by the limits of disturbance of the construction activities, not by the size of the property itself.For redevelopment projects (those with more than 15% impervious surface prior to construction) where the project proposer intends to add more impervious surfaces, the new development treatment requirements must be applied to the net increase of impervious surfaces. Additional treatment must also be included to reduce the volume (unless precluded by the limits or exceptions listed below), TP and TSS loads from the existing impervious surfaces.Stormwater management prohibitions and restrictionsA key component of maintaining the volume of stormwater leaving a site is practices that allow infiltration to groundwater. For most sites, meeting the volume reduction requirement will require the use of infiltration. However, there can often be physical site constraints that limit the effectiveness of an infiltration system or site conditions in which stormwater infiltration must be prohibited. If construction activity is proposed on a site that meets one of the prohibitions or restrictions listed below, runoff from the limiting areas may be excluded from meeting the full volume reduction component of PartIII.D.5.a(2)(a) or (b) of the MS4 permit. However the full treatment standard for TSS and TP must still be met on-site or mitigated for off-site.Infiltration prohibitionsThe use of infiltration as a stormwater treatment method is prohibited in the following areas(PartIII.D.5.a [3]):1.Where industrial facilities are not authorized to infiltrate industrial stormwater under an NPDES/SDSIndustrial Stormwater Permit issued by the Agency2.Where vehicle fueling and maintenance occur3.With less than three (3) feet of separation distance from the bottom of the infiltration system to theelevation of the seasonally saturated soils or the top of bedrock4.Where high levels of contaminants in soil or groundwater will be mobilized by the infiltratingstormwaterInfiltration restrictionsThe permittees Regulatory Mechanism(s) shall restrict the use of infiltration techniques without a detailed engineering review, to achieve the conditions outlined in Part III.D.5.a(2)(a) or (b) sufficient to prevent adverse impacts to groundwater, when the infiltration device will receive discharges from, or be constructed in:1.Areas of predominately Hydrologic Soil Group D (clay) soils2.Areas within 1,000 feet up-gradient, or within 100 feet down-gradient of active karst features3.Areas within a Drinking Water Supply Management Area (DWSMA) as defined in Minn. R.4720.5100, subp. 134.Areas where soil infiltration rates are more than 8.3 inches per hourThe restrictions above do not preclude proposers of construction activity from infiltrating stormwater. Rather, the restrictions simply require that a higher level of design and review is needed. There may be opportunities to infiltrate in these areas and not impact groundwater or experience a system failure because of one of the site restrictions. For example, in an area known to have karst features, an MS4 permittee may require additional soil borings to ensure that no karst features are present in the immediate area of the infiltration system.Exception for meeting the volume control standardThe MS4 permittee’s Regulatory Mechanism may allow a lesser volume reduction requirement than required in Part III.D.5.a (2) (a) or (b) if the project meets one of the prohibitions or restrictions listed above and if the owner or operator of the construction activity implements to the Maximum Extent Practicable (MEP) other volume reduction techniques such as evapotranspiration, reuse/harvesting, conservation design, green roofs, etc. on site. If other volume reduction techniques are not used, documentation must be provided on why that decision was made.Mitigation provisionsMitigation provisions must be developed by the permittee for circumstances where the permittee or other owners and operators of a construction activity cannot meet the TSS and/or TP reduction requirements on the site of the original construction activity. The mitigation provisions of the Regulatory Mechanism(s) shall ensure that any stormwater discharges of TSS or TP not addressed on the site of the original construction activity are addressed through mitigation and, at a minimum, shall ensure the following mitigation requirements are met:·Mitigation project areas are selected in the following order of preference:1.Locations that yield benefits to the same receiving water that receives runoff from the originalconstruction activity2.Locations within the same Department of Natural Resource (DNR) catchment area as theoriginal construction activity3.Locations in the next adjacent DNR catchment area up-stream4.Locations anywhere within the permittee’s jurisdiction·Mitigation projects must involve the creation of new structural stormwater BMPs or the retrofit of existing structural stormwater BMPs, or the use of a properly designed regional structuralstormwater BMP.·Routine maintenance of structural stormwater BMPs already required by this permit cannot be used to meet mitigation requirements of this Part.·Mitigation projects shall be completed within 24 months after the start of the originalconstruction activity.·The permittee shall determine, and document, who is responsible for long-term maintenance on all mitigation projects of this Part.·If the permittee receives payment from the owner and/or operator of a construction activity for mitigation purposes in lieu of the owner or operator of that construction activity meeting theconditions for post-construction stormwater management in Part III.D.5.a(2), the permittee shall apply any such payment received to a public stormwater project, and all projects must be incompliance with Part III.D.5.a(4)(a)-(e).The MS4 permittee must identify priority areas within the various watersheds of its jurisdiction where mitigation projects could occur. If the owner of a construction activity cannot meet the TSS and TP requirements because of site limitations, they may either perform a mitigation project or make an in-lieu-of payment to the MS4 permittee to apply to a mitigation project at a later time.。