经验总结四轴
四轴飞行控制原理
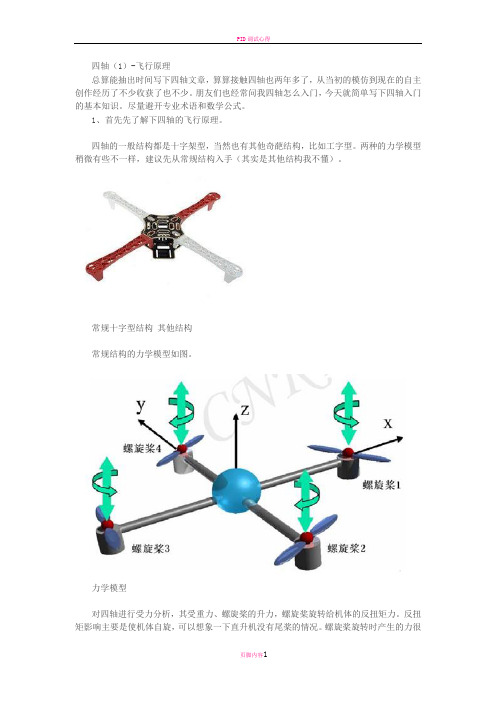
四轴(1)-飞行原理总算能抽出时间写下四轴文章,算算接触四轴也两年多了,从当初的模仿到现在的自主创作经历了不少收获了也不少。
朋友们也经常问我四轴怎么入门,今天就简单写下四轴入门的基本知识。
尽量避开专业术语和数学公式。
1、首先先了解下四轴的飞行原理。
四轴的一般结构都是十字架型,当然也有其他奇葩结构,比如工字型。
两种的力学模型稍微有些不一样,建议先从常规结构入手(其实是其他结构我不懂)。
常规十字型结构其他结构常规结构的力学模型如图。
力学模型对四轴进行受力分析,其受重力、螺旋桨的升力,螺旋桨旋转给机体的反扭矩力。
反扭矩影响主要是使机体自旋,可以想象一下直升机没有尾桨的情况。
螺旋桨旋转时产生的力很复杂,这里将其简化成只受一个升力和反扭矩力。
其它力暂时先不管,对于目前建模精度还不需要分析其他力,顶多在需要时将其他力设为干扰就可以了。
如需对螺旋桨受力进行详细研究可以看些空气动力学的书,推荐两本,空气螺旋桨理论及其应用(刘沛清,北航出版社)空气动力学基础上下册(徐华舫,国防科技大学)网易公开课:这个比麻省理工的那个飞行器构造更对口一些。
荷兰代尔夫特理工大学公开课:空气动力学概论以上这些我是没看下去,太难太多了,如想刨根问底可以看看。
解释下反扭矩的产生:电机带动螺旋桨旋转,比如使螺旋桨顺时针旋转,那么电机就要给螺旋桨一个顺时针方向的扭矩(数学上扭矩的方向不是这样定义的,可以根据右手定则来确定方向)。
根据作用力与反作用力关系,螺旋桨必然会给电机一个反扭矩。
在转速恒定,真空,无能量损耗时,螺旋桨不需要外力也能保持恒定转速,这样也就不存在扭矩了,当然没有空气也飞不起来了。
反扭矩的大小主要与介质密度有关,同样转速在水中的反扭矩肯定比空气中大。
因为存在反扭矩,所以四轴设计成正反桨模式,两个正桨顺时针旋转,两个反桨逆时针旋转,对角桨类型一样,产生的反扭矩刚好相互抵消。
并且还能保持升力向上。
六轴、八轴…类似。
我们控制四轴就是通过控制4个升力和4个反扭矩来控制四轴姿态。
四轴加工理论讲解
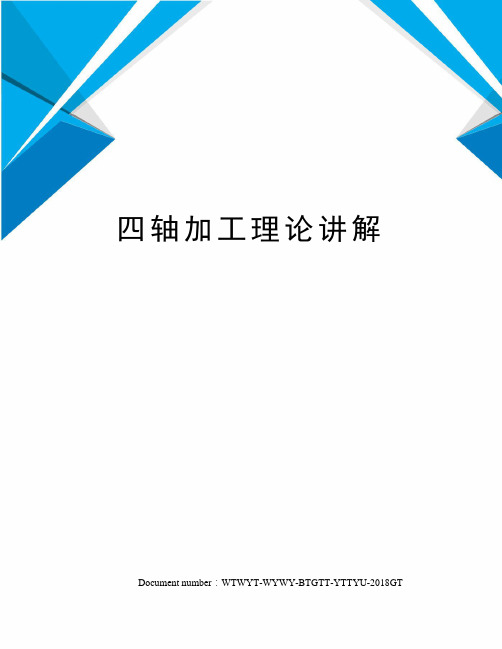
四轴加工理论讲解 Document number:WTWYT-WYWY-BTGTT-YTTYU-2018GT四轴加工典型案例教程第1节四轴机床结构特点与工作原理1.四轴的定义:一台机床上至少有4个坐标,分别为3个直线坐标和1个旋转坐标2.四轴加工特点:(1).三轴加工机床无法加工到的或需要装夹过长(2).提高自由空间曲面的精度、质量和效率(3).四轴与三轴的区别;四轴区别与三轴多一个旋转轴,四轴坐标的确立及其代码的表示Z轴的确定:机床主轴轴线方向或者装夹工件的工作台垂直方向为Z轴X轴的确定:与工件安装面平行的水平面或者在水平面内选择垂直与工件的旋转轴线的方向为X轴,远离主轴轴线的方向为正方向3.直线坐标X轴Y轴Z轴旋转坐标A轴、B轴A轴:绕X轴旋转为A轴(G代码)B轴:绕Y轴旋转为B轴(G代码)XYZ+A、XYZ+B、两种形式四轴XYZ+A适合加工旋转类工件、车铣复合加工XYZ+B工作台相对较小、主轴刚性差、适合加工小产品四轴可以实现产品除底面外5个面都可以做加工,加工前我们必须对产品进行分析,确定四轴机床。
第2节四轴加工优点应运典型零件的工艺方案实际生产加工常发生的问题及其解决方案1.三轴加工的缺点:1.刀具长度过长,刀具成本过高2.刀具振动引发表粗糙度问题3.工序增加,多次装夹4.刀具易破损5.刀具数量增加6.易过切引起不合格工件7.重复对刀产生累积公差2.四轴优点:1.刀具得到很大改善2.加工工序缩短装夹时间3.无需夹具4.提高表面质量5.延长刀具寿命6.生产集中化7.有效提高加工效率和生产效率3.四轴加工主要应运的领域:航空、造船、医学、汽车工业、模具4.四轴应运的典型零件:凸轮、涡轮、蜗杆、螺旋桨、鞋模、人体模型、汽车配件、其他精密零件加工5.四轴加工工工艺及其实际生产加工常发生的问题及其解决方案:(1).四轴工件坐标系的确立、四轴G代码NC程序表示(2).各种不同机台复杂零件的装夹(3).加工辅助线、辅助面的制作(4).四轴加工刀具与工件点接触,非刀轴中心的补偿(5).加工过程中刀具碰撞问题(6).刀轨的校验及其仿真加工(7).不同四轴机器,不同刀轨和后处理第3节结合案例讲解软件的综合使用技巧和新增功能的使用麻花钻四轴加工及其多轴驱动的讲解多轴驱动的应用,四轴加工的基本流程曲面驱动四轴开粗流线加工曲线、点加工2.多轴加工的装夹及其UG5多轴驱动的讲解多轴等高加工多轴外形轮廓加工多轴顺序铣加工第4节几何体9种驱动方法的详细讲解和各参数设置曲线/点驱动方法加工3D刻字、3D流道螺旋式、边界加工曲面加工(重点)曲面必须连续曲面UV方向一致辅助面驱动流线加工(常用)刀轨、径向切削、外形轮廓加工、用户自定义第5节多轴加工18种刀轴方向的控制和复杂零件轴向的判定刀轴:远离直线、朝向直线、远离点、朝向点、相对于矢量、(前倾角、后倾角)垂直于部件、相对于部件插补矢量、插补角度至部件、插补矢量至驱动、(前倾角、后倾角)优化后驱动、垂直于驱动体、侧刃驱动体、相对于驱动体(前倾角、后倾角)前倾角:沿着刀具加工方向来设定倾斜角度侧倾角:刀具加工方向两侧位置夹角的控制如果前倾角控制的是X方向,那么后倾角控制是Y方向,4轴垂直于部件、4轴垂直于驱动当切削方向发生变化后,旋转角度也相对应的发生变化旋转角度:沿着刀具加工方向来设定倾斜角度,加工方向为正角,反方向为负角4轴相对于部件、4轴相对驱动双4轴在部件上、双4轴在驱动上。
(完整word)四轴加工理论讲解

UG8。
5四轴加工典型案例教程第1节四轴机床结构特点与工作原理1。
四轴的定义:一台机床上至少有4个坐标,分别为3个直线坐标和1个旋转坐标2.四轴加工特点:(1).三轴加工机床无法加工到的或需要装夹过长(2).提高自由空间曲面的精度、质量和效率(3)。
四轴与三轴的区别;四轴区别与三轴多一个旋转轴,四轴坐标的确立及其代码的表示Z轴的确定:机床主轴轴线方向或者装夹工件的工作台垂直方向为Z轴X轴的确定:与工件安装面平行的水平面或者在水平面内选择垂直与工件的旋转轴线的方向为X轴,远离主轴轴线的方向为正方向3。
直线坐标X轴Y轴Z轴旋转坐标A轴、B轴A轴:绕X轴旋转为A轴(G代码)B轴:绕Y轴旋转为B轴(G代码)XYZ+A、 XYZ+B、两种形式四轴XYZ+A 适合加工旋转类工件、车铣复合加工XYZ+B 工作台相对较小、主轴刚性差、适合加工小产品四轴可以实现产品除底面外5个面都可以做加工,加工前我们必须对产品进行分析,确定四轴机床。
第2节四轴加工优点应运典型零件的工艺方案实际生产加工常发生的问题及其解决方案1。
三轴加工的缺点:1。
刀具长度过长,刀具成本过高2。
刀具振动引发表粗糙度问题3.工序增加,多次装夹4.刀具易破损5。
刀具数量增加6。
易过切引起不合格工件7.重复对刀产生累积公差2。
四轴优点:1.刀具得到很大改善2.加工工序缩短装夹时间3。
无需夹具4.提高表面质量5。
延长刀具寿命6.生产集中化7。
有效提高加工效率和生产效率3.四轴加工主要应运的领域: 航空、造船、医学、汽车工业、模具4。
四轴应运的典型零件:凸轮、涡轮、蜗杆、螺旋桨、鞋模、人体模型、汽车配件、其他精密零件加工5.四轴加工工工艺及其实际生产加工常发生的问题及其解决方案:(1).四轴工件坐标系的确立、四轴G代码NC程序表示(2).各种不同机台复杂零件的装夹(3)。
加工辅助线、辅助面的制作(4)。
四轴加工刀具与工件点接触,非刀轴中心的补偿(5).加工过程中刀具碰撞问题(6)。
四轴总结范文

四轴总结1. 什么是四轴飞行器?四轴飞行器是一种无人机,由四个电动马达驱动四个螺旋桨提供升力,实现飞行控制。
它是最简单、最常见的多旋翼飞行器类型之一。
2. 四轴结构四轴飞行器主要由以下几个组件构成:•机身框架(Frame):通常是由轻质材料如碳纤维或铝合金制成,提供了安装电子元件和电动马达的支撑框架。
•电动马达(Motor):四个电动马达分别安装在飞行器的四个角落,用来驱动螺旋桨提供升力。
通常使用无刷电机,具有高功率输出和高效能的特点。
•螺旋桨(Propeller):四个螺旋桨与电动马达相连接,通过旋转提供升力。
螺旋桨的旋转速度和推力控制着飞行器的姿态和高度。
•飞行控制器(Flight Controller):飞行控制器是四轴飞行器的大脑,负责接收来自传感器的数据,并通过对电动马达的控制来实现飞行器的稳定飞行。
•电子速调(ESC):电子速调连接电动马达和飞行控制器,将控制信号传输给电动马达并调节电动马达的转速。
•电池(Battery):提供飞行器所需的电能。
电池的容量和电压决定了飞行器的续航时间和飞行能力。
•无线遥控器(RC Transmitter):通过无线信号与飞行器进行通信,控制飞行器的起飞、降落、姿态控制等操作。
3. 四轴飞行原理四轴飞行器借助传感器和飞行控制器实现飞行。
基本的飞行原理如下:1.姿态感知:飞行控制器通过加速度计和陀螺仪感知飞行器的姿态。
加速度计测量飞行器的加速度,以及地心引力在飞行器上的分量,从而确定飞行器的姿态。
陀螺仪测量飞行器在各个轴上的旋转速度。
2.姿态控制:飞行控制器根据姿态感知的数据,计算并调整电动马达的转速,使得飞行器保持平衡。
通过调整转速,飞行控制器可以控制飞行器的俯仰、横滚和偏航。
3.高度控制:飞行控制器使用气压计或超声波等传感器感知飞行器的高度,并通过调节电动马达的转速来控制飞行器的升降。
通过增加或减少升力,飞行器可以上升或下降。
4.遥控操作:无线遥控器发送无线信号给飞行器,控制其飞行。
数控加工中心(四轴)大赛感悟

大赛总结
本次大赛集训主攻方向可归纳为三个字“稳”、“准”、“快”。
“稳”就是心态平和,处事不乱;“准”就是加工零件精度高;“快”就是在前两者的基础上加快加工速度。
提高加工速度和产品质量意识,强化操作速度,强化基本功。
出去比赛后,发现自己的“稳”做到了,但是“准”、“快”没有达到一定层次。
在家里训练用的是游标卡尺测量工件,尺寸全部到位,也在规定的时间内完成所有零件的加工。
出去比赛,工件的测量考核全部是三坐标测量仪,不知道工件尺寸在三坐标测量仪的情况下是否合格,自己的工件也从来没有在三坐标测量仪测过,没有这方面的经验和基础。
比赛机床控制面板上的按钮位置与家中机床控制面板上的按钮位置不一样,操作起来不是很顺手。
导致在比赛中工件没有全部加工出来。
我们在热身赛时暴露出的问题,对刀具、量具及工具的包装进行了改进,我们家的工具箱虽然灵活、轻巧、便于运输,却用在比赛现场,是不能满足的,因为现场提供的工具台,电脑桌狭小,对我们的工具、量具的放置以及图纸的展开等均造成影响。
所以我们自带的工具箱希望大点。
通过本次大赛让我看到了无锡、苏州选手用的刀具箱、量具箱、工具箱的规范性、实用性、专业性。
刀具箱外侧安装有安装装置,顶端放置各种刀柄;量具箱顶端安装有检测平板,高度仪,块规等精密测量量具,所有箱子的下层全部为推拉式抽屉,且选手均养成了使用工具后将其放回原位的良好习惯。
在今后的训练我认为,工件精度的测量要通过三坐标测量仪。
训练方案不能保守,要多与周围学校互相取经。
加大数控兴趣小组成员的培训。
多与其他学校比赛选手沟通与联系,时刻关注、追踪大赛发展的最新动态。
数控加工中心四轴加工技术的应用技巧分析
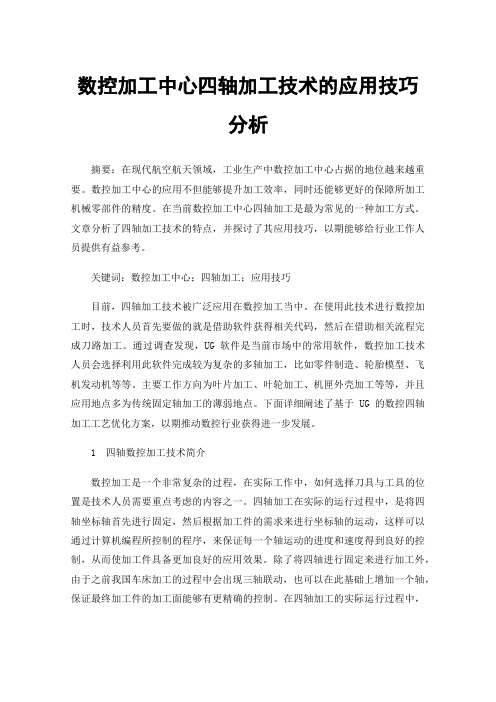
数控加工中心四轴加工技术的应用技巧分析摘要:在现代航空航天领域,工业生产中数控加工中心占据的地位越来越重要。
数控加工中心的应用不但能够提升加工效率,同时还能够更好的保障所加工机械零部件的精度。
在当前数控加工中心四轴加工是最为常见的一种加工方式。
文章分析了四轴加工技术的特点,并探讨了其应用技巧,以期能够给行业工作人员提供有益参考。
关键词:数控加工中心;四轴加工;应用技巧目前,四轴加工技术被广泛应用在数控加工当中。
在使用此技术进行数控加工时,技术人员首先要做的就是借助软件获得相关代码,然后在借助相关流程完成刀路加工。
通过调查发现,UG 软件是当前市场中的常用软件,数控加工技术人员会选择利用此软件完成较为复杂的多轴加工,比如零件制造、轮胎模型、飞机发动机等等。
主要工作方向为叶片加工、叶轮加工、机匣外壳加工等等,并且应用地点多为传统固定轴加工的薄弱地点。
下面详细阐述了基于UG 的数控四轴加工工艺优化方案,以期推动数控行业获得进一步发展。
1 四轴数控加工技术简介数控加工是一个非常复杂的过程,在实际工作中,如何选择刀具与工具的位置是技术人员需要重点考虑的内容之一。
四轴加工在实际的运行过程中,是将四轴坐标轴首先进行固定,然后根据加工件的需求来进行坐标轴的运动,这样可以通过计算机编程所控制的程序,来保证每一个轴运动的进度和速度得到良好的控制,从而使加工件具备更加良好的应用效果。
除了将四轴进行固定来进行加工外,由于之前我国车床加工的过程中会出现三轴联动,也可以在此基础上增加一个轴,保证最终加工件的加工面能够有更精确的控制。
在四轴加工的实际运行过程中,主要有平面坐标轴以及旋转坐标轴,在平面坐标轴中,由于可以利用空间坐标轴来代替整个空间。
立式主轴回转机床与回转轴机床最大的不同在于它的顶部装有回转装置,可以以Z 轴为中心轴进行360°旋转。
通常情况下,技术人员将运动部分称为C轴,而且在回转装置中,A 轴可以在X 轴±90°内进行旋转。
四轴雕刻机加工实习报告

一、实习背景随着我国制造业的快速发展,数控雕刻技术在雕刻行业中的应用越来越广泛。
四轴雕刻机作为数控雕刻设备的一种,因其灵活的加工方式、高效的加工速度以及广泛的适用范围,受到了广泛关注。
为了提高自身的实践能力,更好地适应社会需求,我在学校的安排下,参加了为期四周的四轴雕刻机加工实习。
二、实习目的1. 了解四轴雕刻机的基本结构、工作原理和操作方法;2. 掌握四轴雕刻机的编程与加工技术;3. 培养实际操作能力,提高加工效率;4. 深入了解雕刻行业的发展趋势,为今后的职业发展奠定基础。
三、实习内容1. 四轴雕刻机的基本结构及工作原理四轴雕刻机主要由主机、控制系统、雕刻刀具、夹具等组成。
主机采用精密伺服电机驱动,实现X、Y、Z三个方向的精密运动。
控制系统负责接收加工指令,控制雕刻机运动。
雕刻刀具用于加工材料,夹具用于固定工件。
2. 四轴雕刻机的编程与加工技术四轴雕刻机的编程主要采用CAD/CAM软件进行。
首先,在CAD软件中绘制出所需加工的图形;然后,将图形导入CAM软件,进行刀具路径规划;最后,生成加工代码,导入控制系统。
加工过程中,根据加工材料、刀具、工件尺寸等因素,调整加工参数,如刀具转速、进给速度等。
此外,还需注意雕刻机的加工顺序、夹具的安装等。
3. 实际操作训练在实习过程中,我参与了以下实际操作训练:(1)熟悉四轴雕刻机的操作界面,掌握基本的操作方法;(2)学习CAD/CAM软件,绘制简单图形,生成加工代码;(3)根据加工要求,调整加工参数,进行实际加工;(4)处理加工过程中出现的问题,如刀具磨损、工件变形等;(5)总结经验,提高加工效率。
四、实习体会1. 四轴雕刻机加工具有高效、精确、灵活等优点,适用于各种材料的雕刻加工;2. 编程与加工技术是四轴雕刻机操作的核心,需要熟练掌握;3. 实际操作过程中,要注意安全,避免发生意外;4. 培养良好的团队合作精神,共同完成加工任务;5. 深入了解雕刻行业的发展趋势,为今后的职业发展做好准备。
四轴无人机项目个人总结

3.如果使用游戏手柄或飞机手柄、键盘等控制飞行器。在这一步中要点击上位机上的“飞行控制”模块,在此过程中应确保上位机的“飞行控制”开关处于“off”的状态。
检查各控制通道的行程是否合理,更为重要的是,检查遥控器的中点是否为1500。如果不为1500,在程序中将中点改为你实际看到的值。(目前匿名四轴的上位机还没出现“中点校准”设置,其实可以将这个值也放到EEPROM里)因为匿名四轴的程序里严格规定了遥控器的中点为1500。(个人觉得在飞控程序里可以加一个死区,增强系统的鲁棒性,对传感器的波动误差不那么敏感。当然了,有很多学术狗为了发论文,把死区也改成模糊控制方法,无非就是换了个名词)
P.S.建议设置为115200,而不是更高的波特率,蓝牙里更高波特率容易引起通信误码。
③AT+NAMEANOTC\n\r(注意要有回车) 这句话的字符串可以分为“AT+NAME”和“ANOTC”两个部分,第一部分是指令,第二部分是自定义的模块名称,也就是主机和从机配对的关键,可以自行更改名字,但要保证主从机名称一致。
4.装上桨叶,将上位机的“飞行控制”开关拨至“on”的状态。
按照上面的硬件装置图装配好,将A桨和B桨设置正确以后,推动油门(thr),每个桨叶产生的风力都应该是向下的,如果不是说明桨叶装配错了。
在这里要提一下,根据本人的经验,桨叶对飞行控制系统的影响是非常巨大的,建议新手测试时使用完好的桨叶来做。我平常在装配飞行器时,为了保障桨叶的重量,会用桨平衡器检测一下桨叶的两轴是否质量对称,如果不对称就给相应的地方贴胶带,这样才能保障飞行过程很平稳。另外,桨叶边缘有缺口或桨叶破损,都会对飞机有一定的影响。当你调节PID或飞控程序时,如果查不到问题可以从这方面想想。
在匿名四轴中,机身上的是蓝牙从机,每次上电后均重新配置了蓝牙从机。
四轴实验报告2
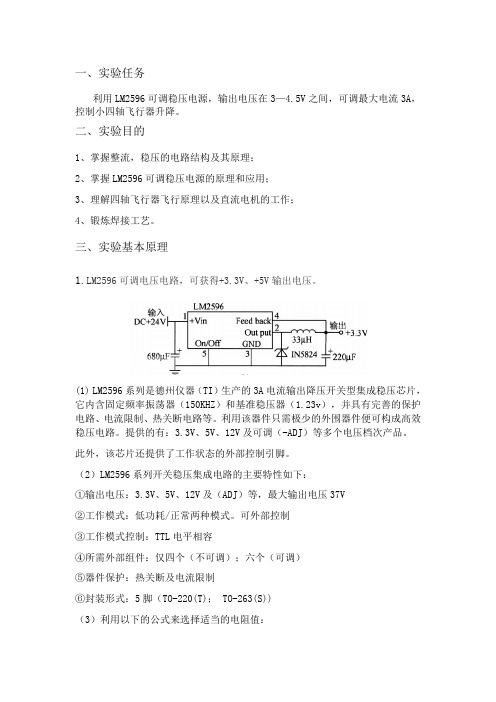
一、实验任务利用LM2596可调稳压电源,输出电压在3—4.5V之间,可调最大电流3A,控制小四轴飞行器升降。
二、实验目的1、掌握整流,稳压的电路结构及其原理;2、掌握LM2596可调稳压电源的原理和应用;3、理解四轴飞行器飞行原理以及直流电机的工作;4、锻炼焊接工艺。
三、实验基本原理1.LM2596可调电压电路,可获得+3.3V、+5V输出电压。
(1) LM2596系列是德州仪器(TI)生产的3A电流输出降压开关型集成稳压芯片,它内含固定频率振荡器(150KHZ)和基准稳压器(1.23v),并具有完善的保护电路、电流限制、热关断电路等。
利用该器件只需极少的外围器件便可构成高效稳压电路。
提供的有:3.3V、5V、12V及可调(-ADJ)等多个电压档次产品。
此外,该芯片还提供了工作状态的外部控制引脚。
(2)LM2596系列开关稳压集成电路的主要特性如下:①输出电压:3.3V、5V、12V及(ADJ)等,最大输出电压37V②工作模式:低功耗/正常两种模式。
可外部控制③工作模式控制:TTL电平相容④所需外部组件:仅四个(不可调);六个(可调)⑤器件保护:热关断及电流限制⑥封装形式:5脚(TO-220(T); TO-263(S))(3)利用以下的公式来选择适当的电阻值:这里的VREF=1.23V R1选择1KΩ。
低阻值使敏感的反馈脚的噪声容限降到最小(选用精度为1%金属膜电阻,可以使温度系数降低,随时间的稳定度最好)。
因为输出调节范围的要求为3.3V—4.5V,且变位器阻值10KΩ,带入公式计算可知,需并联和串联3.3KΩ的电阻。
2.四轴飞行原理(1)垂直运动图(a)中,因有两对电机转向相反,可以平衡其对机身的反扭矩,当同时增加四个电机的输出功率,旋翼转速增加使得总的拉力增大,当总拉力足以克服整机的重量时,四旋翼飞行器便离地垂直上升;反之,同时减小四个电机的输出功率,四旋翼飞行器则垂直下降,直至平衡落地,实现了沿z轴的垂直运动。
四轴DIY小结

四轴DIY小结徐江 cnmusic@一、概述四轴可以说是机械结构最简单的飞行器了,而且自己做起来也不是很难。
维护起来成本也比一般航模要低不少,所以我就花了差不多6个月的时间摸索着做了2个来玩。
这篇文章就是一个大概的记录,希望对后来人能有些帮助。
由于不少都是自己摸索的,难免有不少错误,所以“仅供参考”!☺在这里要感谢网友feng_matrix对我的帮助,通过和他的交流让我少走了不少弯路。
二、马达、电调、桨的选则在我第一次选择马达的时候,我选择的是有刷马达。
原因很简单,不需要复杂的电调,直接用MOS管就可以驱动了,而且响应速度又快,价格又便宜。
可惜没有买到合适的有刷马达,只好用减速组配高转速马达。
这样一来成本反而高了,而且实际的测试结果是马达里面火化直冒也无法将四轴自身拉离地面。
原因就是马达转速和减速组搭配不合理,转速过快但拉力不够。
经历过失败后,决定不在冒险,于是选择了大众配置:新西达2212,1000KV外转子无刷马达,新西达30A电调(好赢兼容的程序),在解决了如何安装的问题后,终于可以将四轴自身拉离地面了。
对于桨,由于条件所限,只能在淘宝上买到GWS三叶正反桨。
我测试的结果是10英寸桨最结实,因为它最大,最重,带来的结果就是低转速。
优点就是抗撞击。
一般的9英寸桨稍微碰到一点东西就断了,而10英寸桨一点事没有。
以前担心10英寸桨可能引起响应时间过长造成四轴无法稳定,后来发现真正影响响应时间的是电调,桨的关系倒不是很大。
当然这不是说10英寸桨就是金刚不坏之躯,只是比9英寸桨要结实一些罢了。
用商品化电调还是I2C电调?我一开始的四轴采用的就是商品电调,原因很简单,自己焊I2C电调多麻烦啊,还是用买的现成的省事。
但随着后面深入做下去,发现这2种电调的差异还是很大的。
对于我开始的商品电调,由于里面自带的PID控制器。
严重影响了转速的快速反应。
这就造成了对于四轴稳定性之一的“自动悬停”基本无法做到了。
由于自动悬停的首要要求就是在这就要求马达转速在四轴有倾斜时需要加快,而到快回到平衡位置时需要降下来。
数控加工中心四轴加工应用技巧探讨

海峡科技与产业88Technology and Industry Across the Straits数控加工中心四轴加工应用技巧探讨摘要:随着工业4.0和智能制造的发展推广,多轴加工设备的应用成为机械加工行业的必然趋势。
以四轴、五轴加工中心、车铣复合为代表的先进制造技术一直是企业生产技术改革的方向,多轴加工工艺、加工质量、加工效率成为行业追逐的焦点。
针对四轴加工制造及运用进行简单的分析探讨,以平行于X 轴的四轴加工中心为例,详述圆柱面插补加工的方法。
关键词:多轴加工中心;四轴加工;圆柱插补中图分类号:TH137.5 文献标识码:A陈晓燕上海汽车集团股份有限公司培训中心,上海 200086制造业是国民经济和综合国力的重要支柱,其生产总值一般占一个国家国内生产总值的20%~55%。
在一个国家企业生产力构成中,制造技术的作用一般占60%左右。
世界上各个国家经济的竞争,实际上是先进制造技术的竞争,其竞争能力最终体现在所生产的产品的市场占有率。
随着经济技术的高速发展以及顾客的需求和市场环境的不断变化,这种竞争日趋激烈,因而各国政府都非常重视对先进制造技术的研究。
现今,随着工业4.0的深入和智能制造的全面推广,多轴加工中心作为先进生产力的代表在制造企业中的运用越来越广泛。
以航空航天、汽车等制造业龙头企业为代表,由于其产品结构的复杂化、部件的多样化,以及对零件曲面曲片的大量运用,故而对制造加工提出了很高的要求。
传统机床已经满足不了这样的生产要求,四轴、五轴以及多附加轴的机床正是解决这类问题的关键所在。
现代制造企业中,四轴、五轴加工编程多利用CAD/CAM 技术来完成。
利用数据模型、自动编程、仿真加工、后处理技术可以完整处理复杂零件从图纸到成品件的虚拟加工,即工业4.0中提到的“数字双胞胎”。
因此,掌握多轴加工的基本原理和基本编程方式,对于零件的制造、生产效率的提高都起着重要的作用[1]。
1 四轴加工的概述四轴加工准确地说应该是四坐标轴联动加工。
水平加料四轴振动维修经验总结

水平加料四轴振动维修经验总结经过一段时间的实践和总结,我对水平加料四轴振动维修工作有了一些经验,下面是我的经验总结:一、维修前的准备工作1.了解振动维修的基本原理和步骤,熟悉维修所需的工具和设备。
2.对振动维修的常见故障进行分类和归纳,建立起一套完整的故障诊断和排除方法。
3.做好安全防护工作,佩戴好防护用品,确保人身安全。
二、故障诊断1.对振动维修前的机器进行仔细检查,查找可能存在的故障点。
2.根据振动的特点和表现,初步判断可能的故障原因。
3.运用专业的仪器和工具,对机器进行全面的故障检测和分析,确定故障点。
三、维修方法1.根据故障点的不同,采取不同的维修方法。
常见的维修方法包括更换零部件、修复损坏的部件、调整机器的平衡等。
2.在维修过程中,要注意操作的规范和细节,确保维修的质量和效果。
3.在维修过程中,及时记录下维修的步骤和结果,以备日后参考和总结。
四、维修后的测试和调整1.维修完成后,对机器进行全面的测试,确保故障已经完全排除。
2.如果测试结果不理想,需要进一步调整和修正,直到机器的振动达到要求。
五、经验总结1.维修过程中要注重细节,特别是在拆装零部件和调整平衡时要仔细,避免引入新的故障。
2.在维修过程中要注意安全,佩戴好安全帽、手套等防护用品,避免意外事故的发生。
3.维修人员要不断学习和积累经验,通过实践不断提高自己的维修水平。
4.维修后要认真做好记录和总结,记录每次维修的具体情况和结果,以备日后参考和总结。
总之,水平加料四轴振动维修是一项技术含量较高的工作,需要维修人员具备扎实的专业知识和丰富的实践经验。
只有不断学习和总结,不断提高自己的技术水平,才能更好地完成振动维修工作。
四轴飞行器的串级PID参数整定经验
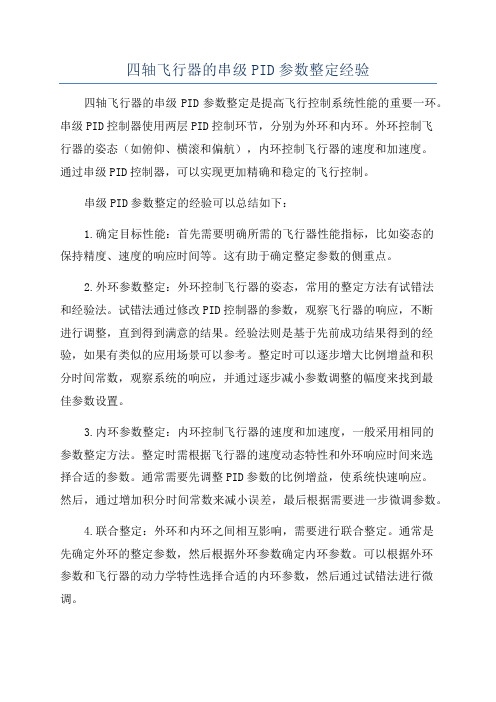
四轴飞行器的串级PID参数整定经验四轴飞行器的串级PID参数整定是提高飞行控制系统性能的重要一环。
串级PID控制器使用两层PID控制环节,分别为外环和内环。
外环控制飞行器的姿态(如俯仰、横滚和偏航),内环控制飞行器的速度和加速度。
通过串级PID控制器,可以实现更加精确和稳定的飞行控制。
串级PID参数整定的经验可以总结如下:1.确定目标性能:首先需要明确所需的飞行器性能指标,比如姿态的保持精度、速度的响应时间等。
这有助于确定整定参数的侧重点。
2.外环参数整定:外环控制飞行器的姿态,常用的整定方法有试错法和经验法。
试错法通过修改PID控制器的参数,观察飞行器的响应,不断进行调整,直到得到满意的结果。
经验法则是基于先前成功结果得到的经验,如果有类似的应用场景可以参考。
整定时可以逐步增大比例增益和积分时间常数,观察系统的响应,并通过逐步减小参数调整的幅度来找到最佳参数设置。
3.内环参数整定:内环控制飞行器的速度和加速度,一般采用相同的参数整定方法。
整定时需根据飞行器的速度动态特性和外环响应时间来选择合适的参数。
通常需要先调整PID参数的比例增益,使系统快速响应。
然后,通过增加积分时间常数来减小误差,最后根据需要进一步微调参数。
4.联合整定:外环和内环之间相互影响,需要进行联合整定。
通常是先确定外环的整定参数,然后根据外环参数确定内环参数。
可以根据外环参数和飞行器的动力学特性选择合适的内环参数,然后通过试错法进行微调。
5.飞行试验和调整:进行参数整定后,进行实际飞行试验来验证系统的性能是否满足要求。
根据飞行试验结果,对参数进行进一步微调,直到达到满意的飞行控制性能。
总的来说,串级PID参数整定是一个迭代的过程,需要根据实际情况进行调整。
经验是根据先前成功的整定结果总结得出的,但是不同的控制系统可能存在不同的参数整定方法和经验。
因此,在实际应用中,需要根据飞行器的具体情况和要求进行参数整定,并进行实时监控和调整,以达到最佳的飞行控制性能。
水平加料四轴振动维修经验总结

水平加料四轴振动维修经验总结
通过观察和检测,确定振动源的位置和性质,例如是否是由不平衡引起的,或者其他机械故障导致的。
确保准确识别问题是解决振动的第一步。
检查螺栓和紧固件:经常检查和紧固机械设备上的螺栓和紧固件。
由于振动会导致它们松动,导致进一步的振动问题。
使用适当的工具,确保螺栓和紧固件牢固固定,以减少振动。
平衡旋转部件:如果振动是由不平衡引起的,必须进行平衡校正。
使用平衡设备,确定哪个旋转部件不平衡,并采取相应措施进行校正。
这可能包括添加或移除配重物,直到旋转部件平衡为止。
平衡旋转部件可以显著减少振动问题。
检查轴承和密封件:振动问题可能与轴承或密封件的损坏有关。
定期检查这些部件的磨损程度,必要时进行更换。
确保轴承润滑良好,并检查密封件是否完好,以防止振动通过它们传递。
调整传动装置:传动装置的问题可能导致振动。
检查传动装置的对齐情况,确保轴线正确对齐,并根据需要调整传动皮带或链条的张力。
正确的传动装置调整可以降低振动并提高设备的运行效率。
检查基础和支撑结构:振动问题可能与设备的基础或支撑结构有关。
确保设备正确安装在坚固的基础上,并检查支撑结构的稳定性。
必要时,加固基础或支撑结构以减少振动传递。
定期维护:定期进行设备的维护保养是防止振动问题的关键。
包括清洁、润滑、紧固部件等。
加工中心加第四轴总结ZHAO1
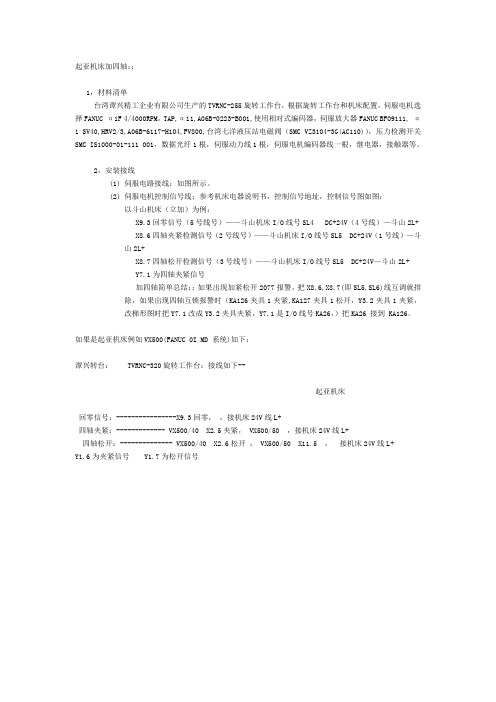
起亚机床加四轴::1,材料清单台湾谭兴精工企业有限公司生产的TVRNC-255旋转工作台,根据旋转工作台和机床配置,伺服电机选择FANUC αiF 4/4000RPM,TAP,αi1,A06B-0223-B001,使用相对式编码器,伺服放大器FANUC BF09111, αi SV40,HRV2/3,A06B-6117-H104,FV800,台湾七洋液压站电磁阀(SMC VZ3104-3G(AC110)),压力检测开关SMC IS1000-01-111 001,数据光纤1根,伺服动力线1根,伺服电机编码器线一根,继电器,接触器等。
2,安装接线(1)伺服电路接线:如图所示。
(2)伺服电机控制信号线;参考机床电器说明书,控制信号地址,控制信号图如图:以斗山机床(立加)为例:X9.3回零信号(5号线号)——斗山机床I/O线号SL4 DC+24V(4号线)—斗山2L+X8.6四轴夹紧检测信号(2号线号)——斗山机床I/O线号SL5 DC+24V(1号线)—斗山2L+X8.7四轴松开检测信号(3号线号)——斗山机床I/O线号SL5 DC+24V—斗山2L+Y7.1为四轴夹紧信号加四轴简单总结::如果出现加紧松开2077报警,把X8,6,X8.7(即SL5,SL6)线互调就排除,如果出现四轴互锁报警时(KA126夹具1夹紧,KA127夹具1松开,Y3.2夹具1夹紧,改梯形图时把Y7.1改成Y3.2夹具夹紧,Y7.1是I/O线号KA26,)把KA26 接到 KA126。
如果是起亚机床例如VX500(FANUC 0I MD 系统)如下:潭兴转台:TVRNC-320旋转工作台:接线如下--起亚机床回零信号;----------------X9.3回零,,接机床24V线L+四轴夹紧:------------- VX500/40 X2.5夹紧, VX500/50 ,接机床24V线L+四轴松开:-------------- VX500/40 X2.6松开, VX500/50 X11.5 ,接机床24V线L+Y1.6为夹紧信号 Y1.7为松开信号200刹车电阻图为;伺服电路接线(1)启动四轴功能:参数#9900=4,#1010=4 CNC受控轴数#8130=4,#8130=4总控制轴数, #9943.3=1 控制扩张;;需重启系统参数设定才有效(2)参数设定:FANUC 0IMB/MC系列如果是0I MD系统需改#8130=4总控制轴数参数内容设定值1006 该参数0位定义旋转轴 000000011008 该参数0位设定旋转轴的循环显示是否有效 000000001260 设定工作台每转的移动量 360000如果是0I MD系统1260需改为3601818 参考计数器容量及检出倍率设定值 000100011820 指令倍率 21020 轴名称 651022 基本坐标系中各轴的顺序 X1 Y2 Z3 A41023 各轴的伺服轴号 X1 Y2 Z3 A41827 各轴切削进给到位宽度 201828 各轴移动中的最大允许位置偏差量 40001850 各轴的栅格偏移量1420 各轴快速运行速度 40001620 各轴加减速时间常数 1501851 背隙设定量 13(参考)1423 手动进给速度 3601422 切削最高速度1424 各轴手动快速运行速度 10001421 快速移动调整率最低速度 2001425 原点复归时最低进给率 2001821 点击旋转一周2度 20001825 各轴的伺服环增益 50001826 各轴的到位宽度 201829 停止中的最大允许位置偏差量 5002001 位参数 02020 电机号 2732021 负载惯量比 1282022 电机旋转方向 -1112023 速度脉冲数 81922024 位置脉冲数 125002084 齿轮比(分子) 12085 齿轮比(分母) 500(3)FSSB自动设定:如果是0iMD系统在进行FSSB设定时需改以下参数:1902.0=0 FSSB设定方式;0,自动。
四轴雕刻机加工实习报告

实习报告:四轴雕刻机加工实习一、实习背景与目的近年来,随着我国制造业的快速发展,数控技术在加工领域得到了广泛应用。
作为一种高精度、高效率的加工设备,四轴雕刻机在模具制造、艺术品雕刻、广告制作等领域具有广泛的应用前景。
为了提高自己的实践能力和理论联系实际的能力,我参加了为期一周的四轴雕刻机加工实习。
本次实习的主要目的是了解四轴雕刻机的基本结构、工作原理和操作方法,掌握数控编程的基本技巧,提高动手操作能力。
二、实习内容与过程1. 实习前的准备在实习开始前,指导老师为我们讲解了四轴雕刻机的基本结构、工作原理和操作方法。
我们学习了数控编程的基本知识,了解了常用的G代码和M代码的含义及作用。
此外,我们还学习了安全操作规程,以确保实习过程中的安全。
2. 实习过程实习过程中,我们分组进行了操作练习。
首先,我们在老师的指导下,学会了如何开机、关机、检查设备状态以及日常维护。
接着,我们学习了如何使用数控编程软件进行编程,掌握了从刀具补偿、坐标系设定到程序运行的一系列操作。
在实际操作过程中,我们注意观察设备运行情况,及时记录操作过程中的问题,并与老师和同学进行交流讨论。
3. 实习任务在实习期间,我们完成了多个实习任务,包括平面加工、曲面加工、模具制造等。
通过这些任务的完成,我们不仅提高了自己的动手操作能力,还加深了对数控编程的理解。
三、实习收获与反思1. 实习收获通过本次实习,我掌握了四轴雕刻机的基本结构、工作原理和操作方法,提高了自己的动手操作能力。
同时,我对数控编程有了更深入的了解,学会如何运用编程软件进行程序编写和调试。
此外,实习过程中的团队协作和交流也使我受益匪浅。
2. 实习反思回顾实习过程,我认为自己在以下方面还有待提高:(1)理论知识不够扎实。
在实习过程中,我发现自己在某些理论知识方面存在盲点,如刀具补偿的计算方法等。
今后,我将继续加强理论知识的学习,为实践操作打下坚实基础。
(2)动手操作能力有待提高。
四轴加工中心参数

四轴加工中心参数概述四轴加工中心是一种用于进行金属加工的机床,具有四个坐标轴,可进行多轴数控加工。
为了达到最佳加工效果,四轴加工中心需要根据具体的加工需求进行参数调整。
本文将深入探讨四轴加工中心的参数设置,包括加工速度、加工深度、加工精度、半径补偿等方面内容。
加工速度加工速度是指加工中心在进行加工过程中,工具移动的速度。
加工速度直接影响加工效率和加工质量。
一般而言,加工速度越快,加工效率越高,但也容易导致加工质量不稳定。
因此,在设置加工速度时需要考虑多个因素,如材料硬度、工具刃口磨损等。
在参数设置过程中,通常会选择一个合适的加工速度范围,并根据具体情况进行微调。
加工深度加工深度是指工具在加工过程中进入材料的深度。
加工深度的设置主要受材料性质、工具强度和加工精度要求等因素影响。
一般而言,加工深度越大,加工时间越长,但也可以提高加工效率。
然而,加工深度过大可能导致工具折断或产生加工质量问题。
因此,在设置加工深度时需要综合考虑多个因素,为了实现更好的加工效果,常常需要通过实验和经验总结来确定最佳加工深度。
加工精度加工精度是指加工中心在进行加工过程中的精确度和稳定性。
加工精度对于一些精密零部件的加工尤为重要。
在四轴加工中心中,加工精度的设置涉及到多个参数,如进给速度、回转速度、切削速度等。
为了实现更高的加工精度,需要根据加工材料、加工形状和加工要求等因素,逐步调整不同参数,使其在一个合适的范围内。
半径补偿半径补偿是指在进行切削操作时,考虑到刀具半径的大小,通过适当调整刀具路径,保证最终加工出的尺寸与设计尺寸一致。
四轴加工中心通常会有半径补偿功能,可以根据实际情况进行设置。
半径补偿的参数设置与材料硬度、刀具半径、切削速度等有关,需要通过试验和实践来确定最佳参数。
总结四轴加工中心参数的设置对于加工效果和加工质量具有重要影响。
加工速度、加工深度、加工精度和半径补偿等参数需要根据具体情况进行合理的调整,以满足加工要求。
四轴铣削加工实训报告

四轴铣削加工实训报告一、实训概述本次实训旨在掌握四轴铣削加工的基本原理和操作技巧,通过实践了解设备、工具、材料和编程软件的综合应用,以及优化铣削参数提高加工效率的方法。
同时,通过对实际加工过程的记录和加工结果的评估,总结经验教训,提出改进建议,为今后的工作和学习奠定基础。
二、设备和工具介绍本次实训所使用的设备和工具包括:数控铣床、工具刀具、量具、夹具等。
其中,数控铣床是实现四轴铣削加工的核心设备,具有高精度、高速度和高效率等特点。
工具刀具包括铣刀、钻头、铰刀等,用于实现不同的切削加工。
量具用于检测工件的尺寸和形状精度,夹具用于装夹工件,保证加工过程的稳定性和精度。
三、材料和编程软件选用本次实训所使用的材料为铝材,具有密度小、加工容易、散热性好等优点。
编程软件选用CATIA,是一款功能强大的三维建模软件,可用于数控加工的编程和仿真。
四、铣削参数选择及优化铣削参数的选择直接影响到加工效率和加工质量。
在本次实训中,我们通过实验和理论分析,选择了最佳的铣削参数组合。
同时,通过调整切削深度、进给速度和主轴转速等参数,实现了对加工效率和加工质量的优化。
五、实际加工过程记录在实训过程中,我们详细记录了实际加工过程,包括工件的装夹、刀具的选用和调整、切削条件的设定和调整、加工过程的监控等。
这些记录为今后的学习和工作提供了宝贵的参考。
六、加工结果评估及分析通过对加工结果的评估和分析,我们发现本次实训的加工效率和加工质量均得到了较好的实现。
同时,我们也发现了一些问题,如刀具磨损、加工表面质量不均匀等。
这些问题需要我们在今后的工作中进一步研究和改进。
七、经验总结与改进建议通过本次实训,我们总结了以下经验:1)正确选择和调整铣削参数对提高加工效率和加工质量至关重要;2)合理的装夹方案和刀具路径规划可以减少加工时间和提高加工精度;3)在加工过程中要密切关注刀具磨损和加工表面质量,及时更换刀具和调整参数;4)编程软件的合理使用可以实现高效准确的数控加工编程。
- 1、下载文档前请自行甄别文档内容的完整性,平台不提供额外的编辑、内容补充、找答案等附加服务。
- 2、"仅部分预览"的文档,不可在线预览部分如存在完整性等问题,可反馈申请退款(可完整预览的文档不适用该条件!)。
- 3、如文档侵犯您的权益,请联系客服反馈,我们会尽快为您处理(人工客服工作时间:9:00-18:30)。
四轴DIY小结徐江 cnmusic@一、概述四轴可以说是机械结构最简单的飞行器了,而且自己做起来也不是很难。
维护起来成本也比一般航模要低不少,所以我就花了差不多6个月的时间摸索着做了2个来玩。
这篇文章就是一个大概的记录,希望对后来人能有些帮助。
由于不少都是自己摸索的,难免有不少错误,所以“仅供参考”!☺在这里要感谢网友feng_matrix对我的帮助,通过和他的交流让我少走了不少弯路。
二、马达、电调、桨的选则在我第一次选择马达的时候,我选择的是有刷马达。
原因很简单,不需要复杂的电调,直接用MOS管就可以驱动了,而且响应速度又快,价格又便宜。
可惜没有买到合适的有刷马达,只好用减速组配高转速马达。
这样一来成本反而高了,而且实际的测试结果是马达里面火化直冒也无法将四轴自身拉离地面。
原因就是马达转速和减速组搭配不合理,转速过快但拉力不够。
经历过失败后,决定不在冒险,于是选择了大众配置:新西达2212,1000KV外转子无刷马达,新西达30A电调(好赢兼容的程序),在解决了如何安装的问题后,终于可以将四轴自身拉离地面了。
对于桨,由于条件所限,只能在淘宝上买到GWS三叶正反桨。
我测试的结果是10英寸桨最结实,因为它最大,最重,带来的结果就是低转速。
优点就是抗撞击。
一般的9英寸桨稍微碰到一点东西就断了,而10英寸桨一点事没有。
以前担心10英寸桨可能引起响应时间过长造成四轴无法稳定,后来发现真正影响响应时间的是电调,桨的关系倒不是很大。
当然这不是说10英寸桨就是金刚不坏之躯,只是比9英寸桨要结实一些罢了。
用商品化电调还是I2C电调?我一开始的四轴采用的就是商品电调,原因很简单,自己焊I2C电调多麻烦啊,还是用买的现成的省事。
但随着后面深入做下去,发现这2种电调的差异还是很大的。
对于我开始的商品电调,由于里面自带的PID控制器。
严重影响了转速的快速反应。
这就造成了对于四轴稳定性之一的“自动悬停”基本无法做到了。
由于自动悬停的首要要求就是在这就要求马达转速在四轴有倾斜时需要加快,而到快回到平衡位置时需要降下来。
商品电调里的PID恰好阻止了这个的发生。
转速上去可以,想要马上降下来?没门!我试验的结果就是一旦转速上去了,想要降下来,等0.2秒吧。
即使这段时间里通知电调降低转速也没效果。
带来的后果就是四轴一旦倾斜后就会不可控地晃来晃去,好像抬轿子。
这并不是说不能用商品电调飞四轴。
完全可以飞,而且也可以飞的很稳。
从旁观者眼里看这2者区别并不是很大,而对操作者来说,差别是相当大的。
商品电调的四轴基本好像是当年赖特兄弟发明的飞机,所有操作都要操作者来处理,包括方向飞行后的机身偏转修正。
而用I2C电调的四轴就好像F22,相当智能,操作起来很容易。
对PI参数来说,商品电调和I2C电调主要差别在I参数上。
商品电调的I参数不能大,否则就会变成一个“飞行轿子”,而I2C电调就没有这个问题,它的高响应速度可以适应大转速变化。
三、机架设计对于像我这种没有机械加工条件,本身又没有任何机械加工经验的人来说,最小加工程度是我对机架的基本要求之一。
我的第一架四轴就是按照这个目的设计的。
利用450电直的尾管做四轴的轴,用450尾管固定座来固定,包括马达的固定。
然后利用波纤板将四个轴整合到一起就完成了。
最后就是这个样子中间的大板就是玻纤板,说更简单一点就是我送去加工的一块电路板。
这就是原始的设计稿,只有KeepOutLayer上的打孔和开槽。
拿回来后所需要我做的就是拧螺丝。
对于马达部分的固定,我也采用了电路板+尾管固定座的方法。
同样用电路板做了一个马达座,这样比单纯用铝的马达固定座强度大了不止一点。
这是原始设计图,照例还是电路板。
对于脚架的固定,我也用了这种板。
通常的塑料450脚架虽然看起来漂亮、重量轻,但强度不够。
但水平速度很大的情况下滑翔着地时,基本都会断掉。
所以我用塑料柱加马达座来当脚架,到目前为止还一个都没坏掉呢。
整合到一起就是这个样子不过这种机架的问题不少,最最严重的问题就是那个450碳纤尾杆非常容易断掉。
用铝杆的话长时间冲击又会弯掉。
为了修理这个也花了我好多钱呢。
另外一个问题就是重量,整个四轴加上电池已经1.2公斤了,带来的问题就是续航时间太短,很快就飞不动了。
于是下一个机架又开始设计了,这会依旧用电路板来做。
整个机架分为2部分。
和2片上面的大“衬衣”组成中间的机架,下面的2片小的组成一个轴,一共需要8片小的才能组成完整的一架。
就是这个样子:最后所有东西都装好后,算上电池大约900克,至少比以前的轻了。
而且这些电路板加起来的总成本也比以前用450尾管固定座要便宜不少,大约¥150左右就都搞定了。
电池固定采用了更结实的方法,电池里面还用魔术贴粘到机架上了。
起落架依旧使用经过考验的马达固定座,而且是3个塑料柱组成一个三角形,抗水平冲击强度更大。
这也是现在的固定座的唯一用途了。
四、硬件电路设计在硬件上,我采用了一个单独的Mega8处理器对遥控器的输入舵量进行解析,M8的IO口数量可以做到8路输入和8路输出。
姿态控制我用了一个ARM7核心的AT91SAM7S256,最高55Mhz的主频,有64KB的内存、256KB的Flash可以供我“挥霍”,这样我就可以将注意力集中到算法上而不比担心资源不够用了。
这2个处理器利用I2C总线通讯,在比较关键的诸如舵量数据等都加了CRC16校验。
对于陀螺仪传感器,我采用了下面的滤波电路。
这个电路没有放大,只有滤波。
而加速度计我就直接并上一个高频滤波电容直接接到处理器的AD上了。
为了便于分析,我使用了一个MicroSD卡做飞行数据记录。
利用AT91SAM7S256的SPI口和它进行通讯,同时移植了EFSL文件系统,这样就可以按照文件形式一个文件一个文件地记录下去了。
不过用这个文件系统最麻烦的地方就是断电的时候,由于EFSL的缓存的关系,如果没有在断电前将数据写回SD卡,有可能造成数据丢失。
这里我的方法是在没有起飞前间歇性地将文件关闭,SD卡卸载,然后再重新装载。
在起飞后就不必这么麻烦了,就直接一直写下去就可以了。
这种策略兼顾了方便性同时最大限度避免文件损坏。
由于有了SD卡,对于M8上的程序升级我也转成了I2C方式。
通过一个小巧的I2C BootLoader 直接把SD卡上的BIN文件传输上去,非常方便了。
在第一版四轴上,我采用了分板的设计。
PPM解码/输出一个,陀螺仪一个,加速度计一个,姿态处理器一个,SD卡和电源一个。
分了好多个板,当时为了测试各种安装位置,看到地要怎么装才是最佳组合。
后来被这些板之间的连线搞到头大,经常因为线接触不良引起莫名其妙的故障。
最后又回归单板设计,处理器,SD卡,PPM编码/解码,3轴加速度计/3轴陀螺仪,温度传感器,包括一个电源分线器作为一个板。
GPS、气压传感器、电子罗盘、ZigBee 无线模块等作为另外一块板。
2个板之间用1.27间距的插针连接,如果调试完成后可以直接焊到一起。
这样就避免了多余电缆的接触不良问题,实践检验效果还是很好的。
五、软件设计相比硬件,软件才是四轴当中的最大难点。
对于PPM编码/解码的部分相对简单,我采用了M8的16位定时器,在ICP引脚收到PPM 波形的时候开始计时,一直记录到波形结束,记录下当时的计时器数值,然后切换到下一个通道,没有去管那些前1.5ms的引导波形。
输出也是如此,只是为了加快输出速度,我一下子输出8个通道,利用硬件定时器计数来判断哪个通道的输出可以结束了。
这样整体输出速度最大可以达到200Hz,这个频率一般舵机是受不了的。
不过新西达的商品电调确可以接受这个频率,工作正常不会有任何问题。
这部分的麻烦之处是要兼顾输入舵量的解析速度和I2C的响应。
由于我没有将所有通道都合并到ICP引脚上,所以要想采集完完整8个通道需要至少1.5ms * 8 = 12ms,最多可能有(1.5+2)ms * 8 = 28ms的时间。
而且有些接收机输出的速度达到63Hz,算下来基本上M8都会忙于解析PPM信号而无暇顾及I2C了。
这里我的方法是采集完后只有等到数据被取走后才会再次解析一遍,这样就可以给M8足够的时间来处理别的事情了。
在姿态控制算法里,我只用到了标准的PI和加权移动平均这2种算法,没有采用卡尔曼滤波或别的“高深”算法。
具体流程如下:首先利用处理器的AD功能,将陀螺仪、加速度计的数值读取近来。
由于加速度计对振动非常敏感,所以我这里对加速度计做了一个移动期为10的加权移动平均,用来过滤掉部分振动。
由于我的四轴对这些数据的采集是工作在300Hz的频率下,所以移动期为10对我的四轴来说只相当于延迟33ms,再加上适当的加权,基本可以消除由于加权移动平均带来的响应滞后问题。
对于陀螺仪,由于这个比较重要,所以我没有做多余的处理,就把AD的数据直接拿来用了。
以前也测试过移动期为2的情况下,也没有问题。
下面对每个轴的陀螺仪做PI,就可以得到马达修正量。
将这个量加上油门后输出给马达,就完成姿态调整任务了。
不过这里就有一个“隐患”。
由于陀螺仪有漂移,也就是以恒定速度右转90度,然后再左转90度后,陀螺仪积分不会为0。
如下图所示:可以看到在四轴最后回到平衡位置时,陀螺仪积分并不为0。
这个偏差在所有陀螺仪里都存在,在ENC‐03上更加厉害一些,所以需要对陀螺仪的积分数据进行适当处理后才能使用,否则积分会越积越大。
这就是下面要讨论的。
如何将加速度计的数据融合进陀螺仪积分里根据上面的说明,已经可以大概了解为什么要对陀螺仪积分进行处理了。
但这里的陀螺仪积分还有另一个重要的物理意义,那就是这个积分记录了四轴偏转的绝对角度(虽然不是直接的角度,但是只要乘一个系数就可以变角度了),而不再是角速度。
为了能做到四轴的稳定悬停,这个角度的重要性不可小看。
通常的做法,是利用加速度计一个轴的偏转和陀螺仪积分建立对照关系,通过试验测出一个系数。
然后程序不断通过加速度计的偏转计算得出陀螺仪应该的积分大小,根据这个数值对陀螺仪积分进行修正。
当然这个修正也有讲究,决不能直接替换掉陀螺仪的积分。
通常都是将通过加速度计得出的积分“猜测值”缩小,限幅后加入陀螺仪的积分里。
过大或过小都可能造成问题,须要反复试验才能得出合理值。
在我的四轴里,我测出的陀螺仪和加速度计的对照关系是:当加速度计偏差=94时,陀螺仪积分 = ‐696。
这是100Hz积分频率,加速度计数据放大6倍,3.3V参考电压下得出的。
这个系数决定了加速度计积分猜测值的“斜率”大小。
然后我把这个计算值缩小22倍,然后限制幅度为正负5,最后才将数据加入陀螺仪积分里。
在加入了积分修正代码后,陀螺仪积分就可以正确收敛了。
更高级的做法是利用卡尔曼滤波将加速度计和陀螺仪数据进行融合,得出绝对角度,以次来进行姿态纠正。