M44C890-H中文资料
CC4H-4S中文资料
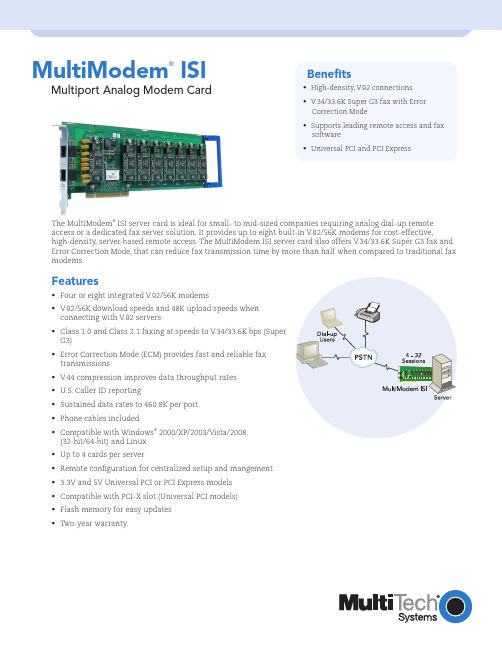
Multiport Analog Modem CardBenefits• High-density , V .92 connections • V .34/33.6K Super G3 fax with Error Correction Mode • Supports leading remote access and fax software • Universal PCI and PCI ExpressThe MultiModem ® ISI server card is ideal for small- to mid-sized companies requiring analog dial-up remote access or a dedicated fax server solution. It provides up to eight built-in V .92/56K modems for cost-effective,high-density , server-based remote access. The MultiModem ISI server card also offers V .34/33.6K Super G3 fax and Error Correction Mode, that can reduce fax transmission time by more than half when compared to traditional fax modems.Features• Four or eight integrated V .92/56K modems• V .92/56K download speeds and 48K upload speeds when connecting with V .92 servers • Class 1.0 and Class 2.1 faxing at speeds to V .34/33.6K bps (Super G3)• Error Correction Mode (ECM) provides fast and reliable fax transmissions • V .44 compression improves data throughput rates • U.S. Caller ID reporting• Sustained data rates to 460.8K per port • Phone cables included• Compatible with Windows ® 2000/XP/2003/Vista/2008 (32-bit/64-bit) and Linux • Up to 4 cards per server• Remote configuration for centralized setup and mangement • 3.3V and 5V Universal PCI or PCI Express models • Compatible with PCI-X slot (Universal PCI models)• Flash memory for easy updates • T wo-year warrantyMultiModem ®ISIWorld Headquarters Tel: (763) 785-3500 (800) EMEA Headquarters Multi-Tech Systems (EMEA)United KingdomTel: +(44) 118-959 7774Multi-Tech Systems (EMEA) FranceTel: +(33) 1 49 19 22 06HighlightsCost-Effective & Scalable. The MultiModem ISI server card provides four or eight dial-up sessions using only one server slot. When demand exceeds one modem card, you can simply add up to three additional cards.V.92 Dial-out Connections. The MultiModem ISI server card supports V .92/56K dial-out and V .34/33.6K dial-inconnections. With V .92 dial-out, you can achieve an upload speed of 48K bps (30% increase over V .90 modems).Enhanced Fax Features. The MultiModem ISI server card supports V .34 fax and Error Correction Mode providingsignificant performance and reliability enhancements over previous fax standards. V .34 sends and receives faxes at speeds up to 33.6K, more than double the speed of the V .17/14.4K fax standard. Error Correction Mode adds reliablility while increasing performance of faxtransmissions. Together these enhancements increase the performance of the MultiModem ISI server card to levels previously only found in more expensive dedicated fax boards and machines.V.44 Compression. V .44 compression standard improves V .42bis data compression anywhere from 20 to 60%, up to as much as 200% for certain types of highly compressible data. This compression technique enables data throughput rates of higher than 300K bps.Simplify Remote Access. The fully-integrated MultiModem ISI server card is easy to set up and manage. You only have to connect the phone lines. There are no external modems and power cords to hassle with; plus it saves back office space since the modems are on the prehensive Service and Support. The Multi-Techcommitment to service means we provide a two-year product warranty and service that includes free telephone technical support, 24-hour web site and ftp support.Ordering InformationProductDescriptionRegion ISI5634UPCI/8 V .92, 8-Modem Card - Universal PCI Global ISI5634UPCI/4 V .92, 4-Modem Card - Universal PCI Global ISI9234PCIE/8 V .92, 8-Modem Card - PCI Express Global ISI9234PCIE/4V .92, 4-Modem Card - PCI ExpressGlobalSpecificationsModemData: V .92, V .90, enhanced V .34, V .32bis, V .22bis Error Correction: V .42, MNP Class 3 & 4Data Compression: V .44, V .42bis, MNP Class 5FaxStandards: V .34, V .17, V .29, V .27ter, V .21, T.30, T.30Annex A, T.30 Annex F , T.31, T.31 Annex B, T.32 Annex C, TR29.2 Class 2 RecommendationRates: 33.6K, 31.2K, 28.8K, 26.4K, 24K, 21.6K, 19.2K, 16.8K, 14.4K, 12K, 9600, 7200, 4800, 2400, 300 bps Error Correction: ECMCompression: MH (T.4), MR (T.4), & MMR (T.6)Conversion: Real time (on-the-fly) compression conversionCommands: Class 1, 2, 1.0, 2.0, 2.1Bus Type3.3V & 5V Universal PCI or PCI Express (x1)Operating System SupportWindows 2000/XP/2003/Vista/2008 (32-bit/64-bit) & LinuxCablingFan out cable with 1 or 2 RJ45 connectors & 4 or 8 RJ11 connectorsPhysical DescriptionUniversal PCI Models:13.87" L × 4.97" W; 8.7 oz (35.2 cm × 12.6 cm; 247 g)PCI Express Models:13.87" L × 4.97" W; 8.5 oz (35.2 cm × 12.6 cm; 241 g)Operating EnvironmentTemperature Range: +23° to +140° F (-5° to +60° C)ApprovalsCE MarkEMC: FCC Part 15 Class B, EN 55022, EN 55024Safety: UL/cUL 60950-1, EN 60950-1, AS/NZS 60950:2000, CCCTelecom: 47CFR Part 68, CS03, TBR21Other countries also includedCopyright © 2008 by Multi-Tech Systems, Inc. All rights reserved.6/08 86000323Made in Mounds View, MN, U.S.A.Features and specifications are subject to change without notice.Trademarks / Registered Trademarks: MultiModem, Multi-Tech, and theMulti-Tech logo: Multi-Tech Systems, Inc. / All other products and technologies are the trademarks or registered trademarks of their respective holders.。
CH412 中文手册说明书

ESD 保护芯片CH412中文手册 版本:1B 1、概述CH412是四路ESD 保护二极管阵列,能够承受IEC 61000-4-2规定的最高±15KV 人体模型、±8KV 接触放电以及±15KV 气隙放电的ESD 脉冲,用于电子产品对外接口中的高速信号和差分信号以及通用信号的ESD 保护。
CH412K 提供4通道低电容二极管保护和TVS 瞬态电压抑制器箝位,适用于高速和中低速信号,可以用于USB 超速、高速和全速以及低速信号保护。
CH412Z 提供4通道TVS 瞬态电压抑制器箝位,适用于中低速信号,可以用于USB 全速和低速信号保护。
CH412K CH412Z2、特点● 支持±15KV 人体模型HBM 。
● 支持±8KV 接触放电。
● 支持±15KV 气隙放电。
● CH412K :内部4路独立箝位二极管,典型值1pF 的低输入电容,适用于高速和中低速信号。
● CH412Z :内部4路TVS 箝位保护,典型值20pF 的输入电容,适用于中低速信号。
● 采用SOT 小体积晶体管级贴片无铅封装,兼容RoHS 。
3、封装封装形式 塑体宽度 引脚间距 封装说明 订货型号 SOT363 1.25mm 49mil 0.65mm 26mil 小型6脚贴片 CH412K SOT353 1.25mm 49mil 0.65mm 26mil 小型5脚贴片 CH412Z 注:1、封装体积较小,正面印字仅有代号而不含全部型号,例如CH412Z 代号是12。
2、盘装,每盘整包装数量为3000只,可以零售,但是零售时不会逐个清点数量。
IO4 IO3 IO3 VCC IO44、型号CH412B已经停产,请换用CH412K,多出的两个通道可以悬空或并联(低速时)。
4、引脚CH412K 引脚号CH412Z引脚号引脚名称类型引脚说明2 2 GND 电源公共接地端,必须直接连接到全局地5 无VCC 电源正电源端,必须靠近引脚对GND连接0.1μF电容,用于USB信号保护时通常为3.3V(或者5V),用于其它信号须同被保护芯片的电源电压(2V~5V)1,3,4,6 1,3,4,5 IO1~IO4 信号ESD保护通道,与被保护芯片的信号引脚并联5、应用说明CH412设计用来与被保护芯片内置的ESD保护一起工作。
XMC4000中文参考手册-第12章 LED和触摸感应(LEDTS)
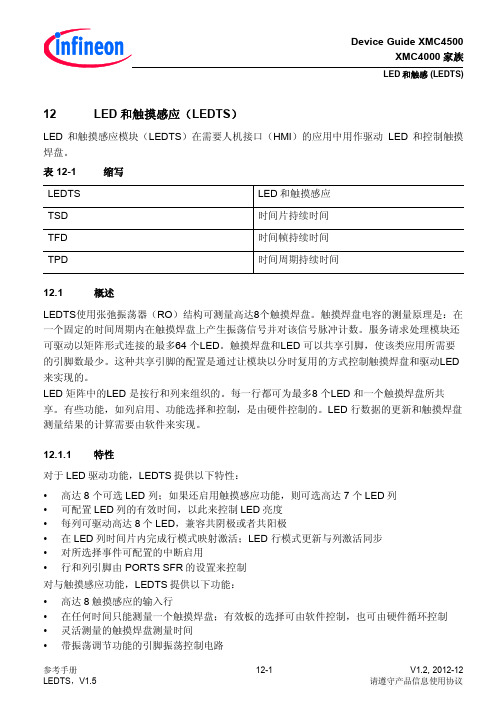
LEDTS 的框图见图 12-1。
参考手册 LEDTS,V1.5
12-2
V1.2, 2012-12 请遵守产品信息使用协议
Device Guide XMC4500 XMC4000 家族
LED 和触感 (LEDTS)
图 12-1
LEDTS 方框图
参考手册 LEDTS,V1.5
12-3
V1.2, 2012-12 请遵守产品信息使用协议
为下一个时间片设置行模式 为下一个时间片设置比较值 评估当前时间片的功能(尤其是分析/调试)
参阅 12.9.1 节得到位段 FNCOL 译码来确定当前有效的时间片的信息。 (已扩展的)时间帧中断指示一个触摸输入行 TSIN[x] 已经被感应到(在连续帧中的一次或几 次),应用层软件可以,例如:
在每个配置的时间片持续时间内,启用一个 LED 列引脚,可以同时间控制最多 8 个 LED。 COL [X]到引脚的分配是可配置的,这可以为具体应用的引脚提供选择。器件引脚的电流能力 也是确定 LED 功能引脚分配的考虑因素。 产品数据表提供与 LED 驱动器相关的所有 I / O 参数的数据。 12.4 触摸感应
注:该章提及 LED 或者触摸感应引脚,比如,‘引脚 COL[x]’,‘引脚 TSIN[x]’。在所有 例子中,它参考选择 LED/触摸感应功能的用户配置引脚(s)。更多详细信息参考 12.9.5 节。
表 12-2 使用分类 非机械开关 LED 反馈 简单 PWM 12.1.2 框图 LEDTS 应用 应用 HMI HMI PWM
参考手册 LEDTS,V1.5
12-8
V1.2, 2012-12 请遵守产品信息使用协议
Device Guide XMC4500 XMC4000 家族
菲尔普斯4100系列50英寸全高清LED电视说明书
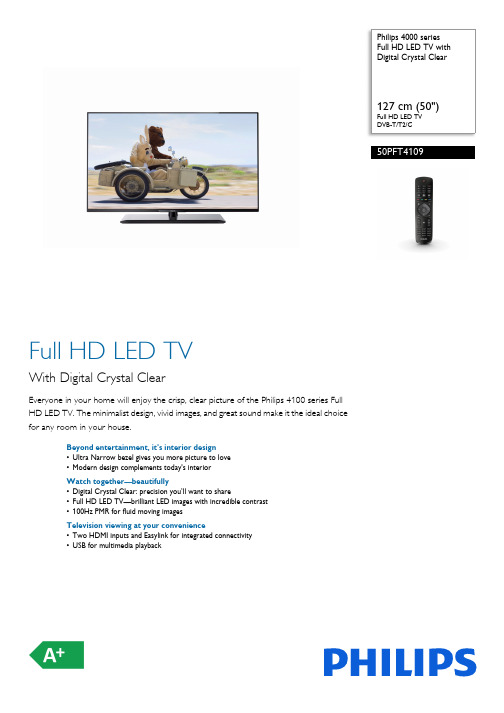
Philips 4000 series Full HD LED TV with Digital Crystal Clear127 cm (50")Full HD LED TV DVB-T/T2/C50PFT4109Full HD LED TVWith Digital Crystal ClearEveryone in your home will enjoy the crisp, clear picture of the Philips 4100 series Full HD LED TV. The minimalist design, vivid images, and great sound make it the ideal choice for any room in your house.Beyond entertainment, it’s interior design •Ultra Narrow bezel gives you more picture to love •Modern design complements today's interiorWatch together—beautifully•Digital Crystal Clear: precision you’ll want to share•Full HD LED TV—brilliant LED images with incredible contrast •100Hz PMR for fluid moving imagesTelevision viewing at your convenience•Two HDMI inputs and Easylink for integrated connectivity •USB for multimedia playbackHighlightsUltra narrow bezelTraditional TVs have a bezel that wraps around the TV like a picture frame. Our Ultra Narrow bezel is modern and thin, so you have more picture to enjoy.Modern DesignDesigned with a contemporary look to blend with your décor. Because your TV should look as beautiful off as it does on.Digital Crystal ClearFor natural pictures from any source, Philips created Digital Crystal Clear. Because whether you indulge in your favorite soap, the news, or have friends over to watch a video—you'llenjoy it all in optimal contrast, color and sharpness.Full HD LED TVPicture Quality matters. Regular HDTVs deliver quality, but you expect more. Imagine crisp detail paired with high brightness, incredible contrast and realistic colors for a true to life picture.100Hz Perfect Motion RateNothing beats the adrenaline rush of gaming, fast paced sporting events or action films. That's why this Philips TV has 100Hz Perfect Motion Rate; so you’ll enjoy fluid moving images. Because even though your pulse may jump, the image you’re watching shouldn’t.Two HDMI inputs with EasylinkAvoid cable clutter with a single HDMI cable to carry both picture and audio signals from your devices to your TV. HDMI uses uncompressed signals, ensuring the highest quality from source to screen. Together with PhilipsEasylink, you’ll need only one remote control to perform most operations on your TV, DVD, Blu-ray, set top box or home theatre system.USB (photos, music, video)Share the fun. Connect your USB memory-stick, digital camera, mp3 player or other multimedia device to the USB port on your TV to enjoy photos, videos and music with theeasy to use onscreen content browser.Issue date 2019-06-28 Version: 5.0.112 NC: 8670 001 11457 EAN: 87 12581 71024 8© 2019 Koninklijke Philips N.V.All Rights reserved.Specifications are subject to change without notice. Trademarks are the property of Koninklijke Philips N.V. or their respective owners.SpecificationsPicture/Display•Display: LED Full HD•Diagonal screen size: 50 inch / 127 cm•Panel resolution: 1920x1080p•Aspect ratio: 4:3/16:9•Brightness: 250 cd/m²•Picture enhancement: Digital Crystal Clear, 100 Hz Perfect Motion RateSmart Interaction•Program: Pause TV, USB Recording*•Ease of Use: One-stop Home button •Firmware upgradeable: Firmware auto upgrade wizard, Firmware upgradeable via USB •Screen Format Adjustments: Advance - Shift, Basic - Fill Screen, Fit to Screen, Stretch, Zoom •Signal strength indication•Teletext: 1000 page Hypertext•Electronic Program Guide*: 8 days Electronic Program GuidSound•Output power (RMS): 20W•Sound Enhancement: Incredible Surround, Clear Sound, Auto Volume Leveller, Bass Enhancement Connectivity•Number of HDMI connections: 3•Number of USBs: 2•Number of scarts(RGB/CVBS):1•Other connections: CI+1.3 certified, Antenna IEC75, Common Interface Plus (CI+), Digital audio out (optical), Audio in (DVI), Headphone out, Service connector•EasyLink (HDMI-CEC): Remote control pass-through, System standby, Auto subtitle shift (Philips)*, Pixel Plus link (Philips)*, One touch play, System audio controlMultimedia Applications•Video Playback Formats: Containers: AVI, MKV, H264/MPEG-4 AVC, MPEG-1, MPEG-2, MPEG-4, WMV9/VC1•Subtitles Formats Support: .AAS, .SMI, .SRT, .SSA,.SUB, .TXT•Music Playback Formats: AAC, AMR, LPCM, M4A,MP3, MPEG1 L1/2, WMA (v2 up to v9.2)•Picture Playback Formats: JPEG, BMP, GIF, JPS,PNG, PNSSupported Display Resolution•Computer inputs: up to 1920x1080 @ 60Hz•Video inputs: 24, 25, 30, 50, 60 Hz, up to1920x1080pTuner/Reception/Transmission•Digital TV: DVB-T/T2/C•MPEG Support: MPEG2, MPEG4•Video Playback: NTSC, PAL, SECAMPower•Mains power: AC 220 - 240 V 50/60Hz•Ambient temperature: 5 °C to 35 °C•Eu Energy Label power: 62 W•Annual energy consumption: 90 kW·h•Energy Label Class: A+•Standby power consumption: < 0.3 W•Off mode power consumption: < 0.3 W•Power Saving Features: Auto switch-off timer, Ecomode, Picture mute (for radio)Dimensions•Box dimensions(W x H x D):1220 x 750 x 160 mm•Set dimensions (W x H x D): 1125 x 656 x 94 mm•Set dimensions with stand (W x H x D):1125 x 709 x 270 mm•Product weight: 10.7 kg•Product weight (+stand): 13.1 kg•Weight incl. Packaging: 15.5 kg•VESA wall mount compatible: 400 x 200 mmAccessories•Included accessories: Remote Control, Table topstand, Power cord, Quick start guide, Legal andsafety brochure, Warranty Leaflet*Software upgrade required for Pause TV and USB recording. Formore details about the software update, please visit/TV and click on support.*The TV supports DVB reception for 'Free to air' broadcast. SpecificDVB operators may not be supported. An up to date list can befound in the FAQ section of the Philips support website. For someoperators Conditional Access and subscripction are required.Contact your operator for more information.*Energy consumption in kWh per year, based on the powerconsumption of the television operating 4 hours per day for 365days. The actual energy consumption will depend on how thetelevision is used.*(Philips) only compatible with specific Philips player device.*EPG and actual visibility (up to 8 days) is country and operatordependent.。
XMC4000中文参考手册-第06章 灵活的CRC引擎(FCE)
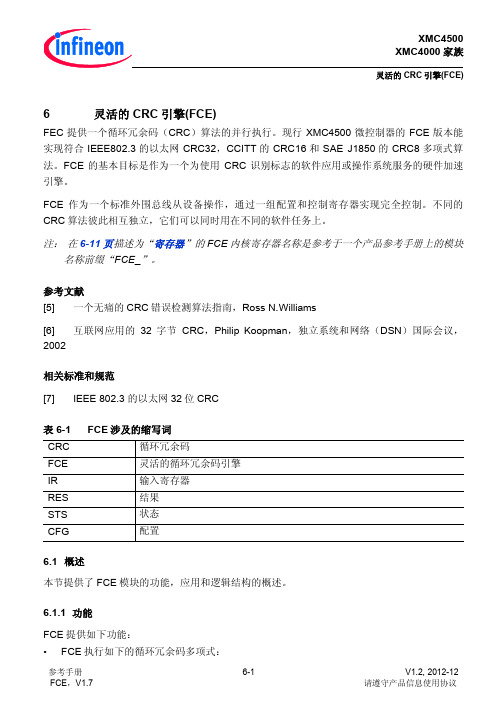
灵活的CRC引擎(FCE)6 灵活的CRC引擎(FCE)FEC提供一个循环冗余码(CRC)算法的并行执行。
现行XMC4500微控制器的FCE版本能实现符合IEEE802.3的以太网CRC32,CCITT的CRC16和SAE J1850的CRC8多项式算法。
FCE的基本目标是作为一个为使用CRC识别标志的软件应用或操作系统服务的硬件加速引擎。
FCE作为一个标准外围总线从设备操作,通过一组配置和控制寄存器实现完全控制。
不同的CRC算法彼此相互独立,它们可以同时用在不同的软件任务上。
注:在6-11页描述为“寄存器”的FCE内核寄存器名称是参考于一个产品参考手册上的模块名称前缀“FCE_”。
参考文献[5] 一个无痛的CRC错误检测算法指南,Ross N.Williams[6] 互联网应用的32字节CRC,Philip Koopman,独立系统和网络(DSN)国际会议,2002相关标准和规范[7] IEEE 802.3 的以太网32位CRC表6-1 FCE涉及的缩写词CRC 循环冗余码FCE 灵活的循环冗余码引擎IR 输入寄存器RES 结果STS 状态CFG 配置6.1 概述本节提供了FCE模块的功能,应用和逻辑结构的概述。
6.1.1 功能FCE提供如下功能:• FCE执行如下的循环冗余码多项式:灵活的CRC引擎(FCE)— CRC内核0和1:IEEE802.3 CRC32以太网多项式:0x04C11DB71) - x32+x26+x23+x22+x16+x12+x11+x10+x8+x7+x5+x4+x2+x+1 —CRC内核2:CCITT CRC16 多项式:0x1021 - x16+x12+x5+1— CRC内核3:SAE J1850 CRC8多项式:0x1D - x8+x4+x3+x2+1• 并行CRC实现—通过FCE计算的数据块会是一个多重二次多项式—通过FCE计算的数据块的开始地址会被排列到二次多项式中• 寄存器接口:— 输入寄存器— CRC寄存器— 配置寄存器启用控制CRC操作和对信息的末端进行自动校验。
兄弟电子A4无线4合一彩色打印机MFC-J890DW说明书
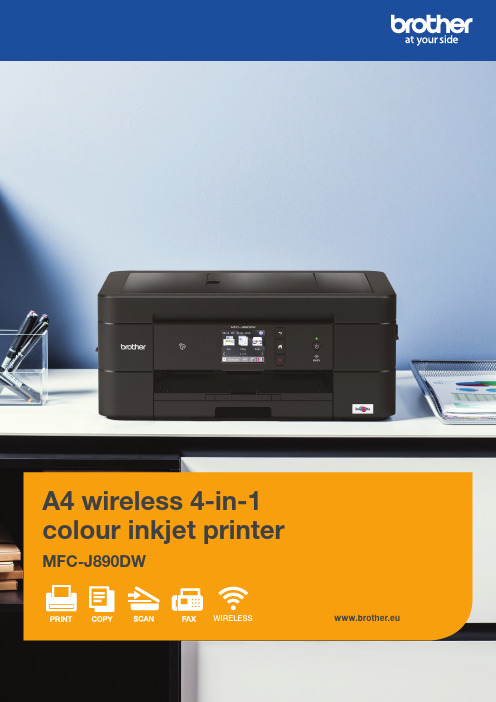
A4 wireless 4-in-1colour inkjet printerMFC-J890DWwww.brother.euWIRELESSA range of connectivity options for the entire houseSleek and cleverly compact, the MFC-J890DW brings affordable, high-quality printing to your home. With a range of connectivity options to suit, connecting from multiple devices is quick and easy and you don’t even have to be in the same room either thanks to wireless printing.Easy to use with minimal interventionDesigned to make tasks easier, the MFC-J890DW comes with an intuitive 6.8cmcolour touchscreen for easy user control and a 20 sheet Automatic Document Feeder that allows you to scan and copy multi-page documents... perfect for multi-tasking!* Approx declared yield value in accordance with ISO/IEC 19798A4 Print. Copy. Scan.Fax. Cleverly compact.Space saving all-in-one A4 inkjet with touchscreen, 2-sided print, automatic feeding, NFC and wired/wireless connectivity.MFC-J890DW1 Approx declared yield value in accordance with ISO/IEC 247112 Calculated with 80g/m² paper3 Windows ® & Mac ® only4 Windows ® only5 Optional free download from the Brother Solutions Centre 6 Must be web connected7 Vertical x horizontal8 Requires Brother software9 M aximum number of printed pages per month can be used to compare designed durability between like Brother products. Formaximum printer life, it is best to choose a printer with a duty cycle that far exceeds your print requirements10 ESAT (based on ISO/IEC 24735). This spec is for ADF models onlyGeneralEngine InkjetInput Paper Capacity 150 sheets 2 standard tray, single sheet manual feed slot ADF20 sheets 2Max. Flatbed Paper Input Width / Height 215.9/297mmControl Panel6.8cm colour Touchscreen LCD On-Screen Programming YesMemory Capacity 128MBSimultaneous Operation YesLocal Interface Hi-Speed USB 2.0Colour PrinterSpeed12ipm mono & 10ipm colour based on ISO/IEC 24734Speed (Fast Mode)Up to 27 pages per minute mono & up to 23 pages per minute colour First Print Out Time 12 seconds Mono 14 seconds Colour Warm-up Time InstantResolution 7Up to 6,000 x 1,200dpi 2-Sided Print YesPaper Handling Size A4, LTR, EXE, A5, A6, Photo (10x15cm), Indexcard (13x20cm),Photo-2L (13x18cm), Com-10, DL Envelope, Monarch, C5, Photo-L (89x127mm)Media weights: Standard & photo Paper Tray 64-220g/m 2(260g/m 2 with Brother BP71 glossy paper only)Media weights Manual Feed Slot64-300g/m 2Media Weights Auto Duplex 64-105g/m 2 Media Weights ADF 64-90g/m 2Paper OutputFace Up – 50 sheets 2Media TypePlain / Inkjet / GlossyBorderless PrintingBorderless printing is available for A4, LTR, A6, Photo, Indexcard, Photo-2L Droplet SizeMinimum droplet size of 1.5pl Colour EnhancementBrother Image Enhancement allows the user to customise colour outputPrinter DriverCompatible with Windows ® 7/8/8.1/10Server 2008/2008R2/2012/2012 R2/ 2016 (Windows Server ® print only), OS X 10.10.x or laterAll specifications correct at time of printingand are subject to change. Brother is a registered trademark of Brother Industries Ltd. Brand product names are registered trademarks or trademarks of their respective companies.Ink Gauge Indication Ink levels can easily bedisplayed on the LCD using the ink management menu Power Save ButtonThis model has an On/Off button on the control panel Wired Network Interface 10/100BASE-TXWireless Network Interface 802.11b/g/nColour Copier Copy Speed6 mono/6 colour ipm ESAT(based on ISO/IEC 24735)10Resolutionup to 1,200 x 1,200dpi(Colour & Mono)Enlargement/Reduction RatioReduce or enlarge document sizes from 25% to 400% in 1% incrementsColour Scanner TechnologyCIS (Contact Image Sensor)Resolution (Optical)Up to 1,200 x 2,400dpiResolution (Interpolated)Up to 19,200 x 19,200dpi8Speed103.35 seconds Mono/4.38seconds ColourA4 @100 DPIGrey Scale256 shades of grey are availablefor copying or scanningScanner DriverThis model is TWAIN and WIAcompliant for Windows®(WIA is Windows® 7/8/10 only)‘Scan To’Allows the user to scan toE-mail, Image, File, USB FlashDrive and Media Cards,SharePoint8 & Web services6SupportingJPEG, BMP, PDF, TIFF, PNGColour DepthThis model has a 30 bit internaland 24 bit external processingcolour scannerMobile / Web Based Printing & Scanning iPrint&Scan(Android)Print directly from or scandirectly to a smart phone ortablet running the AndroidOperating SystemiPrint&Scan(iPad / iPhone / iPod)Print directly from or scandirectly to an iPad / iPhone /iPodiPrint&Scan(Windows® Phone)Print files directly from or scandirectly to a smart phonerunning the Windows® Phone7/8 Operating SystemGoogle Cloud Print 2.06Print most common file typesfrom any Google Cloud Printenabled application.Brother print service pluginPrint directly from Androiddevices without dedicated appAirPrintPrint most common file typesfrom any Apple AirPrint enabledapplicationMopriaPrint using the Mopriaprint serviceCloud Services6Scan to & print from thefollowing cloud services directfrom the control panelGoogle Drive, Dropbox,Evernote, Box and OneDriveMulti CopyUp to 99 copies of the original1 Approx declared yield value in accordance with ISO/IEC 247112 Calculated with 80g/m² paper3 Windows® & Mac® only4 Windows® only5 Optional free download from the Brother Solutions Centre 6 Must be web connected7 Vertical x horizontal8 Requires Brother software9M aximum number of printed pages per month can be used to compare designed durability between like Brother products. For maximum printer life, it is best to choose a printer with a duty cycle that far exceeds your print requirements10 ESAT (based on ISO/IEC 24735). This spec is for ADF models only All specifications correct at time of printing and are subject to change. Brother is a registered trademark of Brother Industries Ltd. Brand product names are registered trademarks or trademarks of their respective companies.Interface Network functionsPrinting, ScanningNetwork ProtocolsTCP/IP, IPv4(IPv6 turned off as default)IPv4ARP, RARP, BOOTP, DHCP,APIPA(Auto IP), WINS/NetBIOSname resolution,DNS Resolver,mDNS, LLMNR responder,LPR/LPD, Custom Raw Port/Port9100,FTP Server, SNMPv1/v2c, TFTP server, ICMP, WebServices (Print/Scan),SNTP Client IPv6NDP, RA, mDNS,LLMNR Responder, DNS Resolver, LPR/LPD,Custom Raw Port/ Port9100, FTP Server, SNMPv1/v2c, TFTP server, Web Services (Print/Scan), SNTP Client, ICMPv6 Wireless SetupWi-Fi Protected Setup™ (WPS) Wireless SecuritySSID (32 chr), WEP 64/128bit, WPA-PSK(TKIP/AES),WPA2-PSK(AES)Network Management Utilities Embedded Web ServerYesBRAdmin Light4&5Setup and LAN managementsoftwareLocal InterfaceHi-Speed USB 2.0Wired NetworkEthernet 10/100BASE-TX AutoNegotiationWireless Network InterfaceBuilt-in 802.11b/g/n Wirelessnetwork interface(Infrastructure Mode)NFC ConnectivityYes, for printing and scanningby the iPrint&Scan AppWi-Fi Direct TMPrint & scan wirelessly withouthaving to go through a wirelessaccess point or networkBrother Apps6Scan to searchable PDFOCR a document and make asearchable PDF fileWired Network InterfaceEthernet 10/100BASE-TXFax forward to CloudForward your incoming faxes tocloud storage service Enlarge text copy Enlarges only the text in a copied documentEasy Scan to Mobile Easy scan to your mobile devices without being connected to a Wi-Fi networkOffice Doc Creator Converts your scanned document into an editable Microsoft Office document Easy Scan to Email Scan directly to an email address without1 Approx declared yield value in accordance with ISO/IEC 247112 Calculated with 80g/m² paper3 Windows® & Mac® only4 Windows® only5 Optional free download from the Brother Solutions Centre 6 Must be web connected7 Vertical x horizontal8 Requires Brother software9M aximum number of printed pages per month can be used to compare designed durability between like Brother products. For maximum printer life, it is best to choose a printer with a duty cycle that far exceeds your print requirements10 ESAT (based on ISO/IEC 24735). This spec is for ADF models only All specifications correct at time of printing and are subject to change. Brother is a registered trademark of Brother Industries Ltd. Brand product names are registered trademarks or trademarks of their respective companies.Direct Printing Print From USB Flash DiveYes, USB Flash Drives Up to256GB Print From Media CardYes, SD/SDHC/SDXC,Multimedia Card/Plus/MobileDriver Deployment Wizard4Easily create print drivers forhassle free deployment overyour networkImage formatJPEGDimensions and Weights With Carton (WxDxH)477 x 294 x 457mm - 9.9KgWithout Carton (WxDxH)400 x 341 x 172mm - 7.7KgDuty Cycles Recommended Monthly50 to 1,000 pages monthlyprint volume Maximum Monthly9Up to 2,500 pages monthly print volumeEnvironment Power ConsumptionOperating - 17WRead Mode - 3.5WSleep Mode - 1.2WOff Mode - 0.2WSound Pressure Level50 dBA (Maximum)Ink Save ModeThis enables the printer toconsume less energy whennot in useEnergy StarYesBlue AngelBlue Angel expected afterinitial productionNordic SwanNordic Swan expected afterinitial ProductionSupplies Ink Cartridges1Black:LC3211BK 200 pages,LC3213BK 400 pagesCyan:LC-3211C 200 pages,LC3213C 400 pagesMagenta:LC-3211M 200 pages,LC3213M 400 pagesYellow:LC-3211Y 200 pages,LC3213Y 400 pages Carton ContentsInk Cartridges, Power SupplyCord, Driver Software, QuickSet-Up Guide, PC InterfaceCable NOT IncludedThe frequency of replacementconsumables will varydepending on the complexityof the prints, the percentage ofcoverage, paper size, page perjob, and the type of media. Forexample glossy coated paperwill result in a shortened life ofsuch supplies.1 Approx declared yield value in accordance with ISO/IEC 247112 Calculated with 80g/m² paper3 Windows® & Mac® only4 Windows® only5 Optional free download from the Brother Solutions Centre 6 Must be web connected7 Vertical x horizontal8 Requires Brother software9M aximum number of printed pages per month can be used to compare designed durability between like Brother products.For maximum printer life, it is best to choose a printer with a duty cycle that far exceeds your print requirements10 ESAT (based on ISO/IEC 24735). This spec is for ADF models only All specifications correct at time of printing and are subject to change. Brother is a registered trademark of Brother Industries Ltd. Brand product names are registered trademarks or trademarks of their respective companies.Colour FaxFax Modem 14,400bpsPC Fax send & receive 8Sends & receives faxes direct from / to your PC(Receiving is for Windows ® only)Automatic RedialAutomatic redialling if the recipient fax is busyDistinctive Ring Detection A service purchased from a telephone company that allows two or more telephone numbers to share a single fixed line, the function enables the machine to provide a different ring tone for each number(UK and Denmark only)Fax/Tel SwitchAutomatic recognition of fax and telephone reception Super FineEnables quality transmission of very small print and line drawings (B&W only)Enhanced Remote Activate Transfer a fax call, answered on an extension phone, to the fax machineMemory Transmission up to 200 pages(ITU-T Test Chart #1/MMR)Out of Paper Reception up to 200 pages(ITU-T Test Chart #1/MMR)Dual AccessAllows the operator to perform 2 different tasks on the machine at the same time (mono only)BroadcastingSend the same fax message to up to 50 locationsAuto ReductionWhen receiving a single page document more than 297mm long the fax machine will automatically reduce the message to fit onto a single A4 sheetECM(Error Correction Mode)Detects line errors during fax transmission and resends the page(s) of the document that had an error (recipient machines must share this feature for it to work)Remote Set-upAllows the user to set-up the MFC from their PC (Windows ® & Macintosh)Grey Scale256 shades of grey are available for faxing Group DialA combination of up to 6 groups can be stored for broadcasting Caller ID YesDelayed Timer No Polling NoBatch Transmission NoFax Forwarding NoRemote Access NoFax Retrieval NoAddress Book Locations 100 Address Book Locations, each location can store 2 fax numbers1Approx declared yield value in accordance with ISO/IEC 247112 Calculated with 80g/m² paper 3 Windows ® & Mac ® only 4 Windows ® only5 Optional free download from the Brother Solutions Centre 6 Must be web connected7 Vertical x horizontal8 Requires Brother software9 M aximum number of printed pages per month can be used to compare designed durability between like Brother products.For maximum printer life, it is best to choose a printer with a duty cycle that far exceeds your print requirements10 ESAT (based on ISO/IEC 24735). This spec is for ADF models onlyAll specifications correct at time of printingand are subject to change. Brother is a registered trademark of Brother Industries Ltd. Brand product names are registered trademarks or trademarks of theirrespective companies.N ORD IC E C O L AB EL315025Working with you for a better environmentAt Brother, our green initiative is simple. We strive to take responsibility, act respectfully and try to make a positive difference to help build a society where sustainable development can be achieved. We call this approach Brother Earth. All specifications correct at time of printing and are subject to change. Brother is a registered trademark of Brother Industries Ltd. Brand product names are registered trademarks or trademarks of their respective companies.。
EH4使用说明书

美国劳雷工业有限公司
目录
..................... 2 0.0 简介.............................................................................................................. .................... .................... ....................2 1.0 系统配件 .................................................................................................................... . ......................... 3 标准接收机配件................................................................................................................ ...................... 3 可选接收机组件 ................................................................................................................. . ...................3 2 发射机组件(400 统) 安系统) …….......................................................................... …. ……………………………….3. .2 发射机组件(5000安系统)……
AMP04FSZ,AMP04FPZ,AMP04EPZ,AMP04FSZ-RL,AMP04FSZ-R7,AMP04FS-REEL7,AMP04ESZ-R7, 规格书,Datasheet 资料
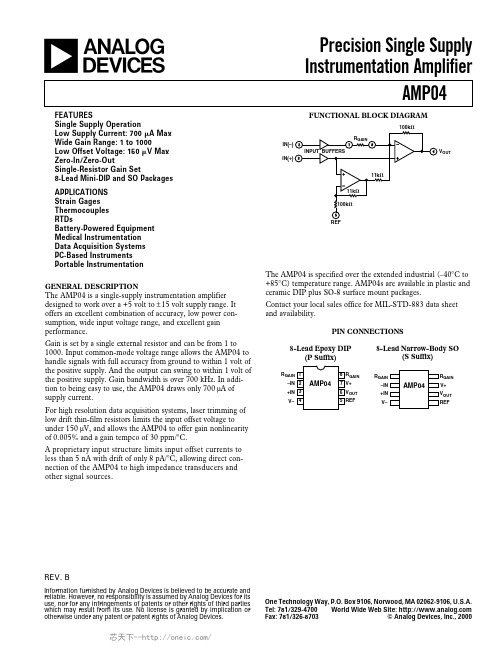
One Technology Way, P.O. Box 9106, Norwood, MA 02062-9106, U.S.A.
Tel: 781/329-4700 World Wide Web Site:
Fax: 781/326-8703
© Analog Devices, Inc., 2000
For high resolution data acquisition systems, laser trimming of low drift thin-film resistors limits the input offset voltage to under 150 µV, and allows the AMP04 to offer gain nonlinearity of 0.005% and a gain tempco of 30 ppm/°C.
1000 1 0.005 0.015 0.025 30
0.75 %
1.0 %
0.75
%
1000 V/V
%
%
%
50
ppm/°C
OUTPUT Output Voltage Swing High
Output Voltage Swing Low Output Current Limit
VOH
RL = 2 kΩ
Contact your local sales office for MIL-STD-883 data sheet and availability.
PIN CONNECTIONS
8-Lead Epoxy DIP (P Suffix)
8-Lead Narrow-Body SO (S Suffix)
25
C4400中文资料

Vectron International · v.2005-11-21 · page 1 of 5Vectron International Vectron international GmbH & Co. KG Vectron Asia Pacific Sales OfficeTypical ApplicationsFeaturesBase Stations 4-Pin Dip Test Equipment Surface Mount Package OptionalSynthesizers Fast Warm-up Digital Switching TCXO Replacement for better short termstabilityPrevious Vectron Model Numbers4887, TQDILOC, OC-400Frequency range10 MHz – 160 MHzStandard frequencies10; 12, 12.8, 16.384, 19.44, 20, 38.88, 51.84, 133MhzFrequency stabilities 1 [AT-Cut Crystal – Standard – 10 to 160MHz]ParameterMin Typ Max. Units Operating temp range Ordering Code vs. operating temperature range -100 +100 ppb -20 … +70°C D107(Referenced to +25°C) -250+250 ppb -20 … +70°C D257-250+250 ppb -40… +85°C F257 Parameter Min Typ Max. Units Condition Initial tolerancevs. supply voltage change vs. load change vs. aging / day vs aging / year vs. aging / year -0.5 -10 -10 -10 -300 -500 +0.5 +10 +10 +10 +300 +500 ppm ppb ppbppbppbppbat time of shipment, nominal EFC V S ± 5%Load ± 5% after 30 days of operation ≤ 60MHz; after 30 days of operation >60MHz; after 30 days of operation Warm-up Time2 minutes to ± 100ppb of final frequency (1 hour reading)@ +25°CFrequency stabilities 1 [SC Cut Crystal – Option – 10 to 52MHz]ParameterMin Typ Max. Units Operating temp range Ordering Code vs. operating temperature range -10 +10 ppb -20 … +70°C D108(Referenced to +25°C) -25+25 ppb -20 … +70°C D258-50+50 ppb -40… +85°C F508 Parameter Min Typ Max. Units Condition Initial tolerancevs. supply voltage change vs. load change vs. aging / day vs aging / year vs. aging / year -0.2 -10 -10 -5 -100 -500 +0.2 +10 +10 +5 +100 +500 ppm ppb ppbppbppbppbat time of shipment, nominal EFC V S ± 5%Load ± 5% after 30 days of operation ≤ 60MHz; after 30 days of operation >60MHz; after 30 days of operation Warm-up Time2 minutes to ± 100ppb of final frequency (1 hour reading)@ +25°CSupply voltage (Vs)ParameterMin Typ Max. Units Condition Ordering CodeSupply voltage [Standard] 4.75 5 5.25 VDC SV050Supply voltage [Option] 11.4 12.0 12.6 VDC SV120 Supply voltage [Option] 3.135 3.3 3.465 VDCSV033Power consumption 2.5 Watts during warm-up1.0Wattssteady state @ +25°CVectron International · v.2005-11-21 · page 2 of 5Vectron International Vectron international GmbH & Co. KG Vectron Asia Pacific Sales Office RF outputParameterMin Typ Max. Units Condition Ordering CodeSignal [Standard] HCMOS RFHLoad 15 pF Signal Level (Vol) 0.5 VDC with Vs=12.0V or 5.0V and 15pF load0.3 VDC with Vs=3.3V and 15pF load Signal Level (Voh) 3.7 VDC with Vs=12.0V or 5.0V and 15pF load2.4 VDC with Vs=3.3V and 15pF load Duty cycle45 55 % @ (Voh-Vol)/2Frequency Tuning (EFC) 10 to 80MHzParameterMin Typ Max. Units Condition Tuning Range ±5.0 ±12ppm with AT cut Crystal Tuning Range ±1.0 ±3ppm with SC cut Crystal Linearity 5 %Tuning SlopePositiveControl Voltage Range 0 2 4 VDC with Vs=12.0V or 5.0VControl Voltage Range0.01.42.8VDCwith Vs=3.3VAdditional parametersParameter Min Typ Max. Units ConditionPhase Noise 3-65 dBc/Hz 1 Hz @ 10 MHz -95 dBc/Hz 10 Hz -120 dBc/Hz 100 Hz -140 dBc/Hz 1 kHz -145 dBc/Hz 10 kHz Weight 8.0 g Processing & Packing Handling & processing noteAbsolute Maximum RatingsParameter Min Typ Max. Units Condition Supply voltage (Vs) 7.0 V with Vs=5.0VDC 28 V with Vs =12VDC 7.0 V with Vs =3.3VDC Output Load 50 pF Operable temperature range -55 +85 °C Storage temperature range -55 +125 °CVectron International · v.2005-11-21 · page 3 of 5Vectron InternationalVectron international GmbH & Co. KG Vectron Asia Pacific Sales OfficeDimensions: mmPin Connections1 Electrical Frequency Adjust Input (EFC) 7 Ground (Case) 8 RF Output14Supply Voltage InputStandard Shipping Method (For Type B Enclosures)AXVectron International · v.2005-11-21 · page 4 of 5 Vectron International Vectron international GmbH & Co. KGVectron Asia Pacific Sales OfficeVectron International · v.2005-11-21 · page 5 of 5Vectron International Vectron international GmbH & Co. KG Vectron Asia Pacific Sales Office How to Order this Product:Step 1Use this worksheet to forward the following information to your factory representative: Model Stability Code Supply Voltage Code RF Output CodePackage CodeFrequencyC4400RFHExample:C4400D207SV050RFHA110.000 MhzStep 2 The factory representative will then respond with a Vectron Model Number in the following configuration: Model Package CodeDash Dash NumberC4400[Customer Specified Package Code]-[Factory Generated 4 digit number]Typical P/N = C4400A1-0001Notes:1 Contact factory for improved stabilities or additional product options. Not all options and codes are available at all frequencies.2 Unless otherwise stated all values are valid after warm-up time and refer to typical conditions for supply voltage, frequency control voltage, load, temperature (25°C)3 Phase noise degrades with increasing output frequency.4 Subject to technical modification.5 Contact factory for availability.。
S04xxxH中文资料

o
1.5 1
I T(AV)(A)
-120
0.5
Tamb ( C)
o
1.5
2
2.5
3
3.5
4
0 0
20
40
60
80
100
120
-125 140
Fig.3 : Average on-state current versus case temperature.
I T(AV) (A)
Fig.4 : Relative variation of thermal impedance versus pulse duration.
Zth/Rth 1
5
DC
4 3
0Байду номын сангаас1
Zt h( j-c)
Zt h( j-a)
2 1
= 180
o
Tcase ( C)
o
tp (s)
0
0
10
20
30
40
50
60
70
80
90 100 110 120 130
0.01 1E-3
1E-2
1E-1
1E +0
1 E +1
1E +2 5 E+2
Fig.5 : Relative variation of gate trigger current and holding current versus junction temperature.
tq
ORDERING INFORMATION
S
SCR MESA GLASS CURRENT
2/5
04
10
C44H中文资料
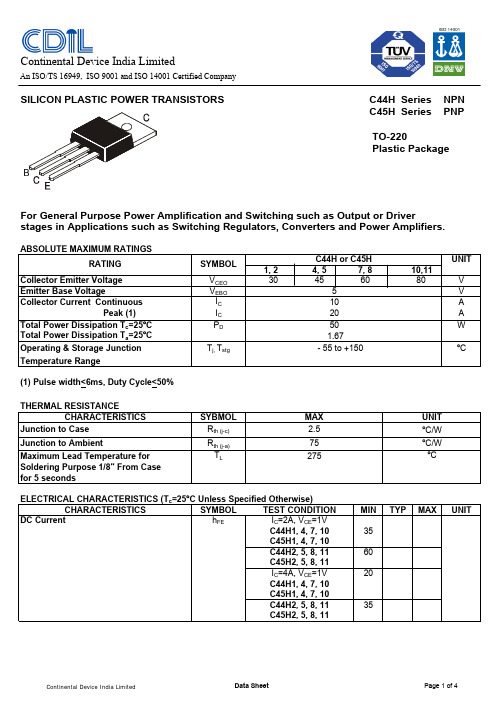
SILICON PLASTIC POWER TRANSISTORSC44H Series NPN C45H Series PNPTO-220Plastic PackageFor General Purpose Power Amplification and Switching such as Output or Driverstages in Applications such as Switching Regulators, Converters and Power Amplifiers.(1) Pulse width<6ms, Duty Cycle<50%THERMAL RESISTANCECHARACTERISTICSSYBMOL Junction to Case R th (j-c)Junction to AmbientR th (j-a)Maximum Lead Temperature for T LSoldering Purpose 1/8" From Case for 5 secondsELECTRICAL CHARACTERISTICS (T c =25ºC Unless Specified Otherwise)CHARACTERISTICS SYMBOL TEST CONDITIONMIN TYP MAX UNITDC Currenth FE I C =2A, V CE =1V C44H1, 4, 7, 1035C45H1, 4, 7, 10C44H2, 5, 8, 1160C45H2, 5, 8, 11I C =4A, V CE =1V 20C44H1, 4, 7, 10C45H1, 4, 7, 10C44H2, 5, 8, 1135C45H2, 5, 8, 11ºCUNIT ºC/W ºC/W 2.5MAX 75275Continental Device India LimitedAn ISO/TS 16949, ISO 9001 and ISO 14001 Certified CompanySILICON PLASTIC POWER TRANSISTORS C44H Series NPNC45H Series PNPTO-220Plastic PackageELECTRICAL CHARACTERISTICS (T c=25ºC Unless Specified Otherwise)CHARACTERISTICS SYMBOL TEST CONDITION MIN TYP MAX UNIT Collector Cut Off Current I CES V BE=0, V CE=Rated V CEO10µA Emitter Cut Off Current I EBO V EB=5V, I C=0100µA Collector Emitter Saturation Voltage V CE(sat)I C=8A, I B=0.4AC44H/C45H2, 5, 8, 11 1.85VI C=8A, I B=0.8A 1.0C44H/C45H1, 4, 7, 10Base Emitter Saturation Voltage V BE(sat)I C=8A, I B=0.8A 1.5VDYNAMIC CHARACTERISTICSCollector Capacitance C Cb V CB=10V, f=1MHzC44H Series130pFC45H Series230Current Gain Product f T I C=0.5A,V CE=10V,f=20MHzC44H Series50MHzC45H Series40SWITCHING TIMESDelay And Rise Time t d+t r I C=5A, I B1=0.5AC44H Series300nsC45H Series135Storage Time t s I C=5A, I B1= I B2= 0.5A500nsC44H Series500C45H SeriesFall Time t f I C=5A, I B1= I B2= 0.5AC44H Series140nsC45H Series100C44H Series NPN C45H SeriesPNPTO-220Plastic PackageTO-220 Plastic PackageTO-220 Tube PackingTO-220 / FP200 pcs/polybag 50 pcs/t u b e 396 g m /200 pcs 120 g m /50 pcs3"x 7.5" x 7.5"3.5" x 3.7" x 21.5"1.0K 1.0K17" x 15" x 13.5"19" x 19" x 19"16.0K 10.0K36k g s 29 k g sPACKAGEN e t W e ight/Q t yDetailsSTANDARD PACKINNER CARTON BOXQ t y OUTER CARTON BOXQ t y G r W t SizeSizePacking DetailPin Configuration 1. Base 2. Collector 3. Emitter 4. CollectorNotes C44H Series NPNC45H Series PNPTO-220Plastic PackageC44H_C45HRev040202E DisclaimerThe product information and the selection guides facilitate selection of the CDIL's Discrete Semiconductor Device(s)best suited for application in your product(s)as per your requirement.It is recommended that you completely review our Data Sheet(s)so as to confirm that the Device(s)meet functionality parameters for your application.The information furnished in the Data Sheet and on the CDIL Web Site/CD is believed to be accurate and reliable.CDIL however,does not assume responsibility for inaccuracies or incomplete information.Furthermore,CDIL does not assume liability whatsoever,arising out of the application or use of any CDIL product;neither does it convey any license under its patent rights nor rights of others.These products are not designed for use in life saving/support appliances or systems.CDIL customers selling these products(either as individual Discrete Semiconductor Devices or incorporated in their end products),in any life saving/support appliances or systems or applications do so at their own risk and CDIL will not be responsible for any damages resulting from such sale(s).CDIL strives for continuous improvement and reserves the right to change the specifications of its products without prior notice.CDIL is a registered Trademark ofContinental Device India LimitedC-120 Naraina Industrial Area, New Delhi 110 028, India.Telephone + 91-11-2579 6150, 5141 1112 Fax + 91-11-2579 5290, 5141 1119email@ 。
PT3C-0494 隔爆型热量计 OHC-800 使用说明书
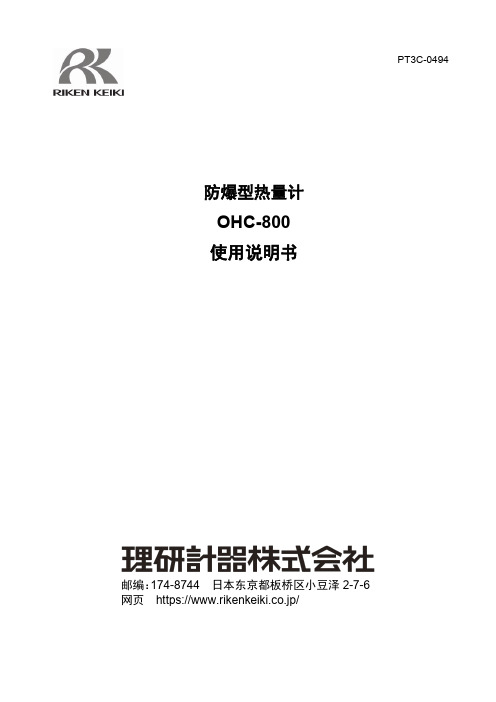
PT3C-0494防爆型热量计OHC-800使用说明书邮编:174-8744 日本东京都板桥区小豆泽2-7-6网页 https://www.rikenkeiki.co.jp/=====目录 ==================================页码1. 安全重要事项1.1 危险事项 ...................................................................................................................... 1-1 1.2 警告事项 ...................................................................................................................... 1-2 1.3 注意事项 ...................................................................................................................... 1-3 1.4 标准及防爆规格的确认方法 .......................................................................................... 1-3 1.5 防爆性能相关的信息(日本国内防爆规格).................................................................. 1-41.5.1 关于OHC-800 .............................................................................................. 1-41.5.2 技术数据....................................................................................................... 1-41.5.3 在危险场所使用时的系统构成 ....................................................................... 1-5 1.6 防爆性能相关的信息(海外防爆规格)......................................................................... 1-61.6.1 关于OHC-800 .............................................................................................. 1-61.6.2 技术数据....................................................................................................... 1-61.6.3 在危险场所使用时的系统构成 ....................................................................... 1-71.6.4 关于安全相关的通知 ..................................................................................... 1-82. 产品的构成2.1 产品的使用目的和特点 ................................................................................................. 2-1 2.2 测定器及标准附件 ........................................................................................................ 2-2 2.3 产品内部的名称............................................................................................................ 2-3 2.4 显示部的名称和功能..................................................................................................... 2-43. 设置方法3.1 设置场所的注意事项..................................................................................................... 3-1 3.2 设置方法和必要的维护空间 .......................................................................................... 3-2 3.3 接线方法 ...................................................................................................................... 3-33.3.1 端子台的说明................................................................................................ 3-33.3.2 推荐电缆....................................................................................................... 3-53.3.3 电缆的拉入/连接方法.................................................................................. 3-63.3.4 保护接地....................................................................................................... 3-83.3.5 电气施工的注意事项 ..................................................................................... 3-9 3.4 配管方法 .................................................................................................................... 3-123.4.1 采样装置..................................................................................................... 3-123.4.2 推荐外部配管系统....................................................................................... 3-133.4.3 配管施工的注意事项 ................................................................................... 3-144. 测定模式时的操作方法4.1 接通电源后从显示到开始测定....................................................................................... 4-1 4.2 显示画面的切换方法..................................................................................................... 4-2 4.3 切换到其他模式............................................................................................................ 4-3 4.4 自我诊断监视功能 ........................................................................................................ 4-4 4.5 关于正常恢复时的接点/显示/信号输出的动作................................................................ 4-55. 检查模式时的操作方法5.1 检查模式的菜单项目..................................................................................................... 5-1 5.2 各项目和详情 ............................................................................................................... 5-25.2.1 光学传感器单元状态的确认"OPTICAL SENSOR UNIT CONDITION" .......... 5-25.2.2 音速传感器单元状态的确认"SONIC SENSOR UNIT CONDITION” .............. 5-35.2.3 主控制器状态的确认"MAIN CONTROLLER CONDITION" .......................... 5-35.2.4 热量测量条件的确认"CALORIFIC VALUE PARAMETER" ........................... 5-45.2.5 密度测量条件的确认"DENSITY PARAMETER" ........................................... 5-45.2.6 4-20mA设定的确认"4-20mA PARAMETER" ............................................... 5-55.2.7 压力传感器输出的确认"PRESSURE SENSOR READINGS" ....................... 5-55.2.8 温度传感器输出的确认"TEMPERATURE SENSOR READINGS" ................ 5-55.2.9 热量计算设定的确认"CALCULATION FACTOR (CALORIFIC VALUE)" ........ 5-65.2.10 密度计算设定的确认"CALCULATION FACTOR (DENSITY) " ..................... 5-65.2.11 声光计算过程的确认"OPT-SONIC READINGS" .......................................... 5-75.2.12 显示/接点设定的确认"DISP. & CONTACT PARAMETER" ........................... 5-85.2.13 显示/接点的保持解除"LATCHING RESET (DISP. & CONTACT)" ................ 5-96. 设置模式时的操作方法6.1 设置模式的项目............................................................................................................ 6-2 6.2 各项目和详情 ............................................................................................................... 6-36.2.1 热量计算的条件设定"CALCULATION FACTOR (CALORIFIC VALUE)" .......... 6-36.2.2 密度计算的条件设定"CALCULATION FACTOR (DENSITY)" ...................... 6-46.2.3 4-20mA的条件设定"4-20mA SETTINGS" ................................................... 6-56.2.4 4-20mA 输出调整"4-20mA ADJUSTMENT" ................................................ 6-66.2.5 4-20mA 输出测试"4-20mA TEST" .............................................................. 6-76.2.6 基准校准"REF. CALIBLATION" ................................................................... 6-86.2.7 补偿调整"OFFSET ADJUSTMENT" ............................................................ 6-96.2.8 显示/接点动作设定"DISP. & CONTACT SETTINGS" ................................ 6-106.2.9 LCD显示的设定"LCD DISPLAY SETTINGS" ............................................ 6-116.2.10 RS-485(MODBUS)通信的设定"RS-485(MODBUS)SETTINGS" ....... 6-126.2.11 接点的励磁设定变更"CONTACT SETTINGS" ........................................... 6-136.2.12 接点动作确认"CONTACT TEST" ............................................................... 6-136.2.13 密码的变更"PASSWORD SETUP (SETUP MODE)" ................................. 6-146.2.14 日志数据下载"IrDA COMMUNICATION" ................................................... 6-157. 保养点检7.1 点检的频度和点检项目 ................................................................................................. 7-17.1.1 日常点检....................................................................................................... 7-17.1.2 每月定期点检................................................................................................ 7-27.1.3 6个月定期点检............................................................................................. 7-3 7.2 推荐定期更换部件 ........................................................................................................ 7-48. 关于储存、移设及废弃8.1 储存或长期不使用时的处理 .......................................................................................... 8-1 8.2 移设或重新使用时的处理.............................................................................................. 8-1 8.3 产品的废弃................................................................................................................... 8-19. 故障检修9.1 异常状态<FAILURE>............................................................................................... 9-1 9.2 规格范围外<OUT OF SPECIFICATION>................................................................. 9-4 9.3 维护要求<MAINTE. REQUIRED>............................................................................ 9-6 9.4 功能确认<FUNCTION CHECK>.............................................................................. 9-7 9.5 注意显示<CAUTION!>............................................................................................. 9-8 9.6 其他 ............................................................................................................................. 9-9 9.7 不符合画面显示内容时 ................................................................................................. 9-910. 产品规格10.1 产品规格 .................................................................................................................... 10-1 10.2 产品原理 .................................................................................................................... 10-210.2.1 声光计算(热量)....................................................................................... 10-210.2.2 声光计算(比重)....................................................................................... 10-410.2.3 光学传感器的原理....................................................................................... 10-610.2.4 音速传感器的原理....................................................................................... 10-711. 术语的定义11.1 使用说明书中使用的术语的定义 ................................................................................. 11-1 11.2 “测定气体规格书”中使用的术语的定义 ..................................................................... 11-2===== 1. 安全重要事项============================= 1.1 危险事项危险<关于防爆>・请遵照设置要件进行设置。
PT4144C中文资料
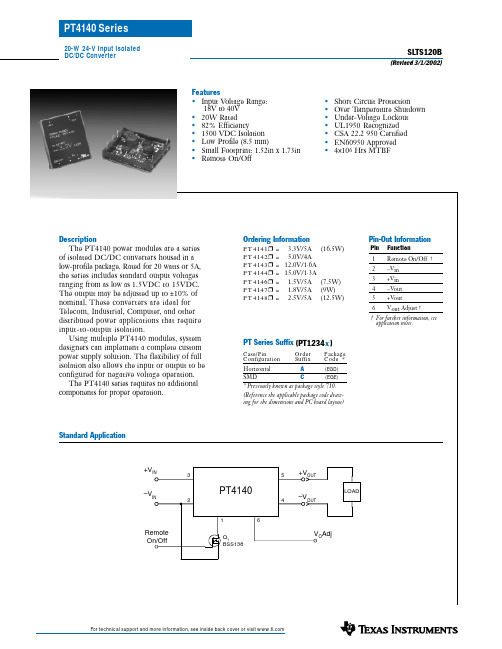
+VIN
3
–VIN
2
Remote On/Off
PT4140
1
6
Q1 BSS138
5
+VOUT
4
–VOUT
LOAD
VOAdj
For technical support and more information, see inside back cover or visit
元器件交易网 PT4140 Series
(2) The Remote On/Off (pin 1) has an internal pull-up, and if it is left open circuit the module will operate when input power is applied. Refer to the application notes for interface considerations.
Between +Vo and –Vo Input to output
Over Vin range — Per Bellcore TR-332 50% stress, Ta =40°C, ground benign Per Mil-Std-883D, method 2002.3, 1mS, half-sine, mounted to a fixture Per Mil-Std-883D, method 2007.2, 20-2000Hz, soldered in a PC board — Materials meet UL 94V-0
(3) See Safe Operating Area curves or contact the factory for the appropriate derating.
AC 890 模块化系统驱动器商品介绍说明书

AC 890 Modular Systems Drive AC Drives 0.55 – 1200kW (0.75 – 1500 HP)AC 890 Modular Systems DrivesAC Drives 0.55 – 1200kW (0.75 – 1500 HP)Product OverviewThe AC890 is a compact, modular systems drive engineered to control speed and position of open-loop and closed-loop AC motors or servo motors.The AC890 meets the requirements of all variable speed applications, from simple motor speed control to the most sophisticated integrated multi-drive systems.One Drive Fits AllThe AC890 is compatible with any AC motor and virtually any speed/position feedback option. With this flexibility you may not even need to replace your existing AC motor to achieve high performance, saving you time and money.Feedback Options • Incremental encoder • EnDat 21 (SinCos) encoder • ResolverInduction motorsTorque motorsBrushless motorsThe AC890 can be user configured for 5 different operating modesOpen-Loop (volts/frequency) ControlThis mode is ideal for basic motor speed control. Sensorless Vector ControlWith its ultra highperformance sensorless vector algorithm, it delivers a combination of both high torque and close speedregulation without the need for any speed measuring transducer.Closed-Loop Vector Control Full closed-loop flux vector performance can be achieved with the AC890 by simply adding an encoder feedback ‘technology box’. This provides 100% continuous full load standstill torque, plus a highly dynamic speed loop more than sufficient for the most demanding applications.Servo ControlDesigned for the mostdemanding servo systems. The ultra fast control loops and process bus make the AC890 ideal for single or multi axis applications.4 Quadrant Active front-end power supply module With this configuration, the energy is fed back into the mains supply with sinusoïdal currents and unity power factor; a very low currentharmonic content is achieved.Modular DesignAvailable in two stylesPerformance Level OptionsAdvanced PerformanceMotion control firmware with added position loop, motion control function blocks, move incremental, move absolute, move home, line drive master ramp and section control, winder blocks (speed winder, current winder), full function PID, machine state, and others.High PerformanceAll Advanced features plus: Library of pre-engineered application specific LINK VM function blocks such as: Shaftless Printing, cut-to-length, advanced winding, advanced traversing and others.Stand Alone VersionCommon Bus VersionCommon Bus DriveThe AC890 is also available in a common bus platform, where individual motor output drives are easily connected to a common bus supply.Common Bus Drive (CD) Features:Power output to 900 kW(1200 HP) in 9 frame sizes access to all feedback and networking options24 VDC control board supply for programming without power USB programming port torque and speed analogue outputsCommon Bus Supply Module (CS) Features:built-in dynamic braking unit diagnostic operator panel 208-500 VAC power supply up to 162A output per module•••••••••The Complete DriveThe AC890 Series Stand Alone Drive provides a complete AC input to AC motor output, with power input and output terminals. Other features of the Stand Alone Drive include:Power output to 900 kW (1200 HP) in 9 frame sizes access to all feedback and networking optionsbuilt-in dynamic brake switch –provisions to add external braking resistor24 VDC control board supply for programming without power USB programming port torque and speed analogue outputs208-500 VAC input supply•••••••FeaturesHigh Speed feedbackResolverProcess Port 125µs cycle timebetween drives•••••BenefitsMinimal delay between the fieldbus setpoints and the control loops Designed to integrate in existing automation systems, the AC890 features high performance portslinked directly to the fast controlloops of the drive.Minimum delay exists between yourdigital setpoint sent through a fieldbus and the control loops.Replacement of analogue solutionsYour existing analogue setpoint-based solutions can be replaced by a digital fieldbus-based solution with minimal bandwidth loss. Flexible feedbackThe AC890 offers system designers complete flexibility in their choice of feedback technology.Open standards for protection of investmentThe AC890 has been deliberately designed to integrate seamlessly into your automation network.To connect to your PLC or fieldbus network you can simply choose from the wide range of communication technology boxes.O pen Communica fast 150Mhz microprocessor, the AC890 drive can achieve very high-bandwidth control loops.This allows you to use the drive for the most demanding industrial applications e.g. printing, cut-to-length, rotary shear, converting and slitting.A High Performance DesignCompact space savingWe have designed the AC890 with your panel space in mind:The AC890 benefits from the latest advances in semiconductor cooling technology which make it extremely compact.The control terminal connectors are removable for easy mon bus configuration can help you achieve a smaller systems design footprint.Common Bus Version*Stand alone version shownModular function blocks for fastand easy project creationDSE, the development environmentfor AC890 drives, has been designedto assist you in the creation andmanagement of your project.At the project creation stage,the project tree contains all thesections or axis of the machine.Function blocks reusabilityDSE offers user-defined macros thatcan be reused. The LINKprogramming environment, withPLC-like function blocks, makesapplication programming simpleand reduces the training needs ofthe technical staff.Built-in library of function blocksfor advanced applicationsDSE comes with a library ofbuilt-in function blocks foradvanced applications at noextra cost:Shaftless printingWinderRegistrationSection controlThe configuration of the mostcomplex machines is fast anderror-free.Parameters setting and projectcreationHigh bandwidth digitaloscilloscopeMonitoring and online tuning••••••Drive System Explorer Configuration and Programming SoftwareChart Variables on lineMonitoringand on linetuningTotally FlexibleLINK Block DiagramAC890 Application ExamplesCorrugated CuttingLaminatingOverload RatingsVector: 150% for 60 secs / 180% for 0.5 secs Servo: 200% for 4 secs Output Frequency0 -1000 Hz; V/Hz mode0 - 350 Hz; closed loop vector mode 0 - 120 Hz; sensorless vector mode 0 - 350 Hz; Servo Switching FrequencyFrame size B - D: 3,6 or 9 KHz (Vector), 4 KHz (Servo) Frame size E: 3 or 6 KHz (Vector) 4KHz (Servo) Frame size F - K: 3 KHz (Vector) 4KHz (Servo) Frame size G - H: 2.5KHz (Vector) 4KHz (Servo) Frame size J: 2KHz (Vector) 4KHz (Servo)Some exceptions apply. All with audibly silent switching frequency Dynamic BrakingAll drive modules have either regenerative braking or dynamic resistor options Operating Temperature0°C to 45°C (32°F to 113°F) for frames B-F 0°C to 40°C (32°F to 104°F) for frames G-KProduct Enclosure Rating - IP21Frame size B-E Open or Enclosed (Type1), frame size F-K Open type suitable for cubicle mount only.Cubicle RatingCubicle to provide 10dB attenuation to radiated emissions between 30-100MHz. Cubicle may also require tool for opening or removing any door or panel.HumidityMaximum 85% relative humidity at 40°C non-condensing AtmosphereNon flammable, non corrosive and dust free Climatic ConditionsClass 3k3, as defined by EN50178 (1998)VibrationTest Fc of EN60068-2-6StandardsPollution DegreePollution Degree ll (non-conductive pollution, except for temporary condensation)EuropeWhen installed in accordance with the manual, this product conforms to the Low Voltage Directive 2006/95/EC.North AmericaComplies with US requirements (UL508C) and Canadian requirements (C22.2 No. 14). (1) Not tested.Globally CertifiedEMC Directive 2004/108/EC Low Voltage Directive 2006/95/ECGlobally certified and compliant with themost stringent international regulations, the AC890 can be used anywhere in the world.Dimensions are in millimeters (inches)Horsepower ratings correspond to appropriate motor ratings.K-frame dimensions include NEMA 12 ventilated enclosures with flange disconnect option *6-pulse input (12-pulse optional)**6-pulse input (18-pulse optional)Please refer to your local regional office for dimensionaldrawings for each Frame.AustraliaParker Hannifin Pty Ltd9 Carrington RoadPrivate Bag 4, Castle Hill NSW 1765Tel: +61 2 9634 7777 Fax: +61 2 9899 6184BelgiumParker Hannifin SA NVParc Industriel Sud Zone 11 23, Rue du BosquetNivelles B -1400 Belgium Tel: +32 67 280 900 Fax: +32 67 280 999BrasilParker Hannifin Ind. e Com. Ltda. Av. Lucas Nogueira Garcez, 2181 Esperança - Caixa Postal 148 Tel: +55 0800 7275374 Fax: +55 12 3954 5262CanadaParker Motion and Control 160 Chisolm Drive MiltonOntario L9T 3G9Tel: +1(905)693 3000 Fax: +1(905)876 1958ChinaParker Hannifin Motion & Control (Shanghai) Co. Ltd. SSD DrivesSuite B2109 21st Floor Hanwei Plaza7 Guanghua Road Chaoyang District Beijing 100004 P.R.ChinaTel: +86(10)6561 0520/1/2/3/4/5 Fax: +86(10)6561 1070FranceParker SSD Parvex 8 Avenue du Lac B.P. 249F-21007 Dijon Cedex Tel: +33 (0)3 80 42 41 40 Fax: +33 (0)3 80 42 41 23GermanyParker Hannifin GmbH Von-Humboldt-Strasse 10 64646 Heppenheim GermanyTel: +49(0)6252 798200 Fax: +49(0)6252 798205IndiaSSD Drives India Pvt Ltd 151 Developed Plots Estate Perungudi,Chennai, 600 O96, India Tel: +91 44 43910700 Fax: +91 44 43910700ItalyParker Hannifin SPA Via Gounod 120092 Cinisello Balsamo Milano ItalyTel: +39 02 66012459 Fax: +39 02 66012808SingaporeParker Hannifin Singapore Pte Ltd 11, Fourth Chin Bee Rd Singapore 619702 Tel: +65 6887 6300 Fax: +65 6265 5125Sales OfficesCatalogue HA50-0346 (Issue 1 Oct. 2007)Your local authorized Parker distributorH Y G E E d . 2007-08-16SpainParker Hannifin (Espana) S.A. Parque Industrial Las Monjas Calle de las Estaciones 8 28850 Torrejonde Ardoz Madrid SpainTel: +34 91 6757300 Fax: +34 91 6757711SwedenParker Hannifin AB Montörgatan 7SE-302 60 Halmstad SwedenTel: +46(35)177300 Fax: +46(35)108407UKParker Hannifin Ltd. Tachbrook Park Drive Tachbrook Park Warwick CV34 6TUTel: +44(0)1926 317970 Fax: +44(0)1926 317980USAParker Hannifin Corp. SSD Drives Division 9225 Forsyth Park Drive CharlotteNorth Carolina 28273-3884 Tel: +1(704)588 3246 Fax: +1(704) 588-3249© 2007 Parker Hannifin Corporation. All rights reserved.Parker Hannifin Ltd SSD Drives DivisionNew Courtwick Lane, Littlehampton,West Sussex BN17 7RZ United KingdomTel: +44 (0) 1903 737 000 Fax: +44 (0) 1903 737 100*********************** 。
Omega HH804系列产品说明书
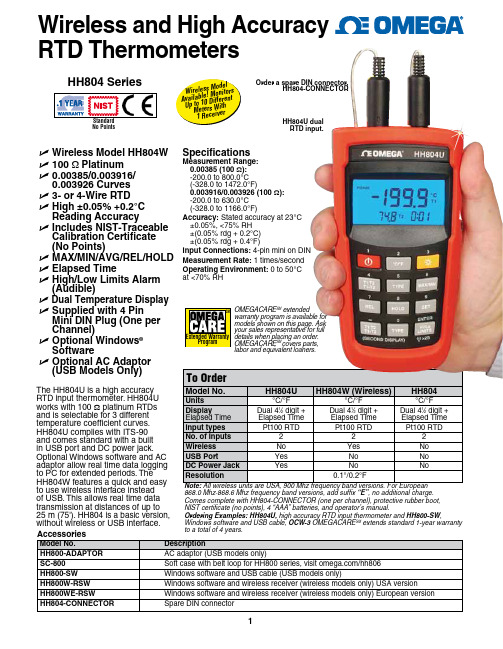
1HH804 SeriesThe HH804U is a high accuracy RTD input thermometer. HH804U works with 100 Ω platinum RTDs and is selectable for 3 different temperature coefficient curves. HH804U complies with ITS-90 and comes standard with a built in USB port and DC power jack. Optional Windows software and AC adaptor allow real time data logging to PC for extended periods. The HH804W features a quick and easy to use wireless interface instead of USB. This allows real time data transmission at distances of up to 25 m (75'). HH804 is a basic version, without wireless or USB interface.U W ireless Model HH804W U 100 Ω Platinum U 0.00385/0.003916/ 0.003926 Curves U 3- or 4-Wire RTD U H igh ±0.05% +0.2°C Reading Accuracy U I ncludes NIST-Traceable Calibration Certificate (No Points)U M AX/MIN/AVG/REL/HO LD U E lapsed Time U H igh/Low Limits Alarm (Audible)U D ual Temperature DisplayU S upplied with 4 Pin Mini DIN Plug (One per Channel)U O ptional Windows ® SoftwareU O ptional AC Adaptor (USB Models Only)No Points868.0 Mhz ˜ 868.6 Mhz frequency band versions, add suffix “E”, no additional es complete with HH804-CONNECTOR (one per channel), protective rubber boot, NIST certificate (no points), 4 “AAA” batteries, and operator’s manual.Ordering Examples: HH804U, high accuracy RTD input thermometer and HH800-SW , Windows software and USB cable, OCW-3 OMEGACARE SM extends standard 1-year warranty to a total of 4 years.W i r e l e s s M o d el A v a i l a b l e ! M o n i t o r s U p t o 10 D i f f e r e n tM e t e r s W i t h 1 R e c e i v e r Order a spare DIN connector, HH804-CONNECTOR HH804U dual RTD input.Wireless and High Accuracy RTD Thermometers OMEGACARE SM extended warranty program is available for models shown on this page. Ask your sales representative for full details when placing an order. OMEGACARE SM covers parts, labor and equivalent loaners.Specifications Measurement Range: 0.00385 (100 Ω): -200.0 to 800.0°C (-328.0 to 1472.0°F) 0.003916/0.003926 (100 Ω): -200.0 to 630.0°C (-328.0 to 1166.0°F)Accuracy: Stated accuracy at 23°C ±0.05%, <75% RH ±(0.05% rdg + 0.2°C) ±(0.05% rdg + 0.4°F) Input Connections: 4-pin mini on DIN Measurement Rate: 1 times/second Operating Environment: 0 to 50°C at <70% RH。
8904资料
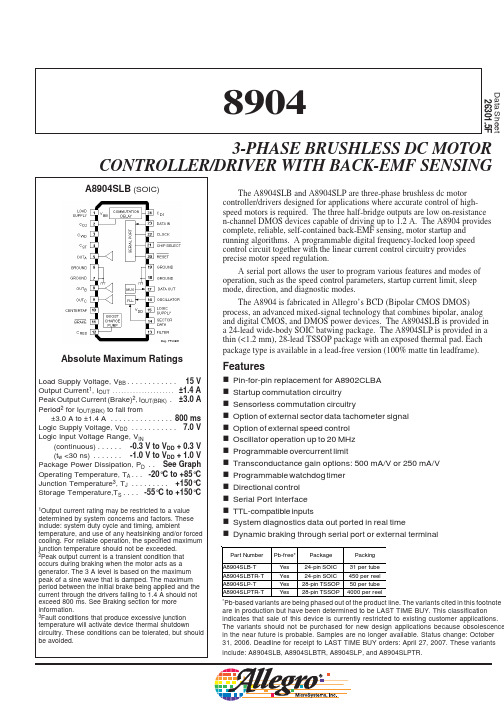
Absolute Maximum RatingsLoad Supply Voltage, V BB . . . . . . . . . . . . 15 V Output Current 1, I OUT . . . . . . . . . . . . . . . . . . . . . ±1.4 A Peak Output Current (Brake)2, I OUT(BRK). ±3.0 A Period 2 for I OUT(BRK) to fall from±3.0 A to ±1.4 A . . . . . . . . . . . . . . . 800 ms Logic Supply Voltage, V DD . . . . . . . . . . . 7.0 V Logic Input Voltage Range, V IN(continuous). . . . . . -0.3 V to V DD + 0.3 V (t w <30 ns). . . . . . . -1.0 V to V DD + 1.0 V Package Power Dissipation, P D . . See Graph Operating Temperature, T A . . . -20°C to +85°C Junction Temperature 3, T J . . . . . . . . . +150°C Storage Temperature,T S . . . . -55°C to +150°C1Output current rating may be restricted to a valuedetermined by system concerns and factors. These include: system duty cycle and timing, ambienttemperature, and use of any heatsinking and/or forced cooling. For reliable operation, the specified maximum junction temperature should not be exceeded.2Peak output current is a transient condition that occurs during braking when the motor acts as a generator. The 3 A level is based on the maximum peak of a sine wave that is damped. The maximum period between the initial brake being applied and the current through the drivers falling to 1.4 A should not exceed 800 ms. See Braking section for more information.3Fault conditions that produce excessive junction temperature will activate device thermal shutdowncircuitry. These conditions can be tolerated, but should be avoided.Data Sheet 26301.5FThe A8904SLB and A8904SLP are three-phase brushless dc motor controller/drivers designed for applications where accurate control of high-speed motors is required. The three half-bridge outputs are low on-resistance n-channel DMOS devices capable of driving up to 1.2 A. The A8904 provides complete, reliable, self-contained back-EMF sensing, motor startup and running algorithms. A programmable digital frequency-locked loop speed control circuit together with the linear current control circuitry provides precise motor speed regulation.A serial port allows the user to program various features and modes of operation, such as the speed control parameters, startup current limit, sleep mode, direction, and diagnostic modes.The A8904 is fabricated in Allegro’s BCD (Bipolar CMOS DMOS)process, an advanced mixed-signal technology that combines bipolar, analog and digital CMOS, and DMOS power devices. The A8904SLB is provided in a 24-lead wide-body SOIC batwing package. The A8904SLP is provided in a thin (<1.2 mm), 28-lead TSSOP package with an exposed thermal pad. Each package type is available in a lead-free version (100% matte tin leadframe).FeaturesPin-for-pin replacement for A8902CLBA Startup commutation circuitry Sensorless commutation circuitryOption of external sector data tachometer signal Option of external speed control Oscillator operation up to 20 MHz Programmable overcurrent limitTransconductance gain options: 500 mA/V or 250 mA/V Programmable watchdog timer Directional control Serial Port Interface TTL-compatible inputsSystem diagnostics data out ported in real timeDynamic braking through serial port or external terminal3-PHASE BRUSHLESS DC MOTORCONTROLLER/DRIVER WITH BACK-EMF SENSING8904A8904SLB (SOIC)*Pb-based variants are being phased out of the product line. The variants cited in this footnoteare in production but have been determined to be LAST TIME BUY. This classification indicates that sale of this device is currently restricted to existing customer applications.The variants should not be purchased for new design applications because obsolescence in the near future is probable. Samples are no longer available. Status change: October 31, 2006. Deadline for receipt fo LAST TIME BUY orders: April 27, 2007. These variants include: A8904SLB, A8904SLBTR, A8904SLP, and A8904SLPTR.Part Number Pb-free*Package Packing A8904SLB-T Yes 24-pin SOIC 31 per tube A8904SLBTR-T Yes 24-pin SOIC 450 per reel A8904SLP-T Yes 28-pin TSSOP 50 per tube A8904SLPTR-TYes28-pin TSSOP4000 per reel89043-PHASE BRUSHLESS DC MOTOR CONTROLLER/DRIVER89043-PHASE BRUSHLESS DC MOTOR CONTROLLER/DRIVER3A8904SLP (TSSOP)* Measured on “High-K” multi-layer PWB per JEDEC StandardJESD51-7.† Measured on typical two-sided PWB with power tabs (LB package) or thermal pad (LP package) connected to copper foil with an area of three square inches (1935 mm 2). See Applica-tion Note 29501.5, Improving Batwing Power Dissipation , for additional information.LB (SOIC) PackageLP (TSSOP) Package89043-PHASE BRUSHLESS DCMOTOR CONTROLLER/DRIVERELECTRICAL CHARACTERISTICS at T A = +25°C, V DD = 5.0 VLimitsCharacteristicSymbol Test ConditionsMin.Typ.Max.Units Logic Supply Voltage V DDOperating 4.5 5.0 5.5V Logic Supply Current I DD Operating —7.510mA Sleep mode —250500µA Undervoltage Threshold UVLO Decreasing V DD — 3.6—V Increasing V DD — 3.9—V Load Supply Voltage V BB Operating 4.0—14V Load Supply Current I BB Operating — 4.08.0mA Sleep mode—2030µA Thermal ShutdownT J —165—°C Thermal Shutdown Hysteresis ∆T J —20—°C Output Drivers Output Leakage Current I DSX V BB = 14 V, V OUT = 14 V, sleep mode —200300µA V BB = 14 V, V OUT = 0 V —-2.0-15µA Total Output ON Resistance r DS(on)I OUT = 600 mA— 1.0 1.4Ω(source + sink + R S )Output Sustaining Voltage V DS(sus)V BB = 14 V, I OUT = I OUT (MAX), L = 3 mH 14——V Clamp Diode Forward Voltage V F I F = 1.0 A— 1.25 1.5V Control LogicLogic Input Voltage V IN(0)SECTOR DATA, RESET, CLK,——0.8V V IN(1)CHIP SELECT, OSC 2.0——V Logic Input Current I IN(0)V IN = 0 V ——-0.5µA I IN(1)V IN = 5.0 V——±1.0µA BRAKE Threshold V BRK 1.5 1.75 2.0V BRAKE Hysteresis Current I BRKL V BRK = 750 mV— 4.0—µA BRAKE Current I BRK Brake set, D2 = 1, I BRK = 750 mV —20—µA DATA Output Voltage V OUT(0)I OUT = 500 µA —— 1.5V V OUT(1)I OUT = -500 µA3.5——V C ST Current I CST Charging-9.0-10-11µA Discharging, V CST = 2.5 V —500—µA C ST Threshold V CSTH High 2.25 2.5 2.75V V CSTL Low 0.85 1.0 1.15V Filter CurrentI FILTERCharging -9.0-10-11µA Discharging9.01011µA Leakage, V FILTER = 2.5 V——±5.0nA Filter Threshold V FILTERTH1.57 1.852.13V C D Current I CD Charging -18-20-22µA (C D1 or C D2)Discharging 324048µA C D Current Matching —I CD(DISCHRG)/I CD(CHRG)1.82.0 2.2—C D Threshold V CDTH 2.25 2.5 2.75V C D Input LeakageI CDIL——1.0µAContinued next page …89043-PHASE BRUSHLESS DC MOTOR CONTROLLER/DRIVER5LimitsCharacteristic Symbol Test ConditionsMin.Typ.Max.Units C WD CurrentI CWDCharging, D26 = 0, D27 = 0-9.0-10-11µA Charging, D26 = 0, D27 =1-18-20-22µA Charging, D26 = 1 D27 = 0-27-30-33µA Charging, D26 = 1, D27 =1-36-40-44µA C WD Threshold Voltage V TL 0.220.250.28V V TH 2.25 2.5 2.75V Max. FLL Oscillator Frequency f OSC 20*——MHz Oscillator High Duration ton 20——ns Oscillator Low Duration toff 20——ns Maximum Output CurrentI OUT (MAX)D3 = 0, D4 = 0, D28 = 0 1.0 1.2 1.4A D3 = 0, D4 = 1, D28 = 00.9 1.0 1.1A D3 = 1, D4 = 0, D28 = 0500600700mA D3 = 1, D4 = 1, D28 = 0—250—mA D3 = 0, D4 = 0, D28 = 1500600700mA D3 = 0, D4 = 1, D28 = 1415500585mA D3 = 1, D4 = 0, D28 = 1—300—mA D3 = 1, D4 = 1, D28 = 1—125—mA Transconductance Gain g m D28 = 1210250290mA/V D28 = 0420500580mA/V Centertap ResistorsR CT 5.01013k ΩBack-EMF Threshold with respect —5.02037mV to V CTAP at FCOM transition-5.0-20-37mVELECTRICAL CHARACTERISTICS continuedNegative current is defined as coming out of (sourcing) the specified device terminal.* Operation at an oscillator frequency greater than the specified minimum value is possible but not waranteed.89043-PHASE BRUSHLESS DCMOTOR CONTROLLER/DRIVERSerial Port Timing ConditionsA. Minimum CHIP SELECT setup time before CLOCK rising edge ......... 100 nsB. Minimum CHIP SELECT hold time after CLOCK rising edge .............. 150 nsC. Minimum DATA setup time before CLOCK rising edge ....................... 150 nsD. Minimum DATA hold time after CLOCK rising edge ............................ 150 nsE. Minimum CLOCK low time before CHIP SELECT.................................. 50 nsF. Maximum CLOCK frequency .............................................................. 3.3 MHzG. Minimum CHIP SELECT high time ...................................................... 500 ns Note: the A8904 can be directly used in an existing A8902–A application, as the five most significant bits are reset to zero, which is the default condition for A8902–A operation. The only consideration when using the A8904 in an A8902-A application, is to ensure theminimum CHIP SELECT high time is at least 500 ns.89043-PHASE BRUSHLESS DC MOTOR CONTROLLER/DRIVER7Terminal FunctionsA8904SLB A8904SLPTerminal Name Function (SOIC) (TSSOP)LOAD SUPPLYV BB ; the 5 V or 12 V motor supply.115C D2One of two capacitors used to generate the ideal commutation points from216the back-EMF zero crossing points.C WDTiming capacitor used by the watchdog circuit to blank out the back-EMF 317comparators during commutation transients, and to detect incorrect motor position.C ST Startup oscillator timing capacitor.418NC No( internal) connection.–19OUT A Power amplifier A output to motor.520NC No (internal) connection.–21GROUND Power and logic ground and thermal heat sink.6-7–POWER GROUNDPower ground.–22*NC No (internal) connection.–23OUT B Power amplifier B output to motor.824OUT C Power amplifier C output to motor.925CENTERTAP Motor centertap connection for back-EMF detection circuitry.1026BRAKEActive low turns ON all three sink drivers shorting the motor windings to 1127ground. External capacitor and resistor at B RAKE provide brake delay.The brake function can also be controlled via the serial port.C RESExternal reservoir capacitor used to hold charge to drive the source drivers’1228gates. Also provides power for brake circuit.ANALOG GROUNDAnalog ground.–1*FILTER Analog voltage input/output to control motor current. Also, compensation node for internal speed control loop.132SECTOR DATA External tachometer input. Can use sector or index pulses from disk to 143provide precise motor speed feedback to internal frequency-locked loop.LOGIC SUPPLY V DD ; the 5 V logic supply.154OSCILLATOR Clock input for the speed reference counter.165DATA OUTThermal shutdown indicator, FCOM, TACH, or SYNC signals available in 176real time, controlled by 2-bit multiplexer via serial port.NC No (internal) connection.–7GROUND Power and logic ground and thermal heat sink.18-19–DIGITAL GROUNDLogic ground.–8*RESET When pulled low forces the chip into sleep mode; clears all serial port bits.209NC No (internal) connection.–10CHIP SELECTStrobe input (active low) for data word.2111CLOCK Clock input for serial port.2212DATA IN Sequential data input for the serial port.2313C D1One of two capacitors used to generate the ideal commutation points from 2414the back-EMF zero crossing points.* For the A8904SLP, ground terminals 1, 8, and 22 must be connected together externally.89043-PHASE BRUSHLESS DCMOTOR CONTROLLER/DRIVERFunctional DescriptionOverview of operation. Each electrical revolution contains six states that control the three half-bridge outputs.Optimized switching from state to state is achieved through the adaptive commutation circuitry. During any state, one output is high, one is low and the other is high impedance. The back-EMF at the high-impedance output is sensed and compared to the voltage of the centertap and when the two signals areequivalent, the FCOM signal toggles. A controlled delay is then introduced before the sequencer commutates into the next state.Linear current-mode control is employed to provide precision control of the motor speed while maintaining ex-tremely low electrical noise emissions. The speed control is realized through a frequency-locked loop that processes the sensed back-EMF signals from the stator phases to eventually produce a TACH signal. The TACH signal is then compared to the desired programmed speed, to produce an error. The error signal is then used to linearly control the current through the low-side DMOS power devices to obtain the correct speed.Alternative control schemes can be introduced, giving the user maximum flexibility and optimization for each application.An external tachometer signal applied to the SECTOR DATA input, along with the internal speed reference can be used for high-precision speed control. As another alternative, the user can introduce external speed control by driving the FILTER terminal directly.Start-up routines are inherent in the solution to guarantee reliable start-up. During start-up, a YANK feature allows rapid transition to the nominal operating condition on the FILTER terminal. This feature is also available when the external speed control is used.Dynamic braking can be introduced by either the external BRAKE terminal or through the brake bit in the serial port.A serial port allows the user to program various features and modes of operation, such as motor speed, internal or external speed control, internal or external speed reference, current limit,sleep mode, direction, charge current (for blanking pulse), motor poles, transconductance gain, and various diagnostic outputs.Full device protection is incorporated, including program-mable overcurrent limit, thermal shutdown, and undervoltage shutdown on the logic supply.Power outputs. The power outputs of the A8904 are n-channel DMOS transistors with a total source plus sink r DS(on) of typically 1 Ω. An internal charge pump provides a voltage rail above the load supply for driving the high-side DMOS gates.Intrinsic ground clamp and flyback diodes provide protection when switching inductive loads. These diodes will also rectify the motor back-EMF during power-down conditions. If neces-sary, a transient voltage supply can be provided, by connecting an external Schottky power diode or pass FET in series, between the power source and the load supply (V BB ). This FET or diode effectively isolates the low impedance path through the power source. A filter capacitor is also required to ‘hold up’ the rectified signal, and is connected between the load supply and ground.Back-EMF sensing motor startup and running algorithm. The A8904 provides a complete self-contained back-EMF sensing, startup and running commutation scheme. A state machine with six states, (shown in the tables below for both forward and reverse direction) controls the three half-bridge outputs. In each state, one output is high (sourcing current), one low (sinking current), and one is OFF (highimpedance or ‘Z’). Motor back-EMF is sensed at the output that is OFF.Sequencer State (forward direction)OUT A OUT B OUT C1High Z Low 2High Low Z 3Z Low High 4Low Z High 5Low High Z 6Z High Low Sequencer State(reverse direction)OUT A OUT B OUT C 1High Z Low 6Z High Low 5Low High Z 4Low Z High 3Z Low High 2HighLowZAt start-up, the outputs are always enabled in state 1. The back-EMF is examined at the OFF output by comparing the output voltage to the motor centertap voltage at CENTERTAP.The motor will then either step forward, step backward or remain stationary (if in a null-torque position).If the motor does not move during the initial start-up state,the outputs are commutated automatically by the start-up oscillator. When suitable back-EMF signals are detected, the start-up oscillator is overridden and the corresponding timing clock is generated, providing synchronous back-EMF commuta-tion. The start-up oscillator period is determined byt CST = (V CSTH - V CSTL ) x C ST / I ST(charge)where C ST is the start-up capacitor.89043-PHASE BRUSHLESS DC MOTOR CONTROLLER/DRIVER9If the motor moves, the back-EMF detection and direction circuit waits for the correct polarity of back-EMF zero crossing (output crossing through centertap). If the correct polarity of back-EMF is not detected, a watchdog circuit commutates the output until the correct back-EMF is detected. Correct back-EMF sensing is indicated by the FCOM signal, which toggles every time the back-EMF completes a zero crossing (see waveforms below). FCOM is available at the DATA OUTterminal.True back-EMF zero crossings are used by the adaptive commutation delay circuit to advance the state sequencer(commutate) at the proper time to synchronously run the motor.See next section.Adaptive commutation delay. The adaptive commuta-tion delay circuit uses the back-EMF zero-crossing indicator signal (FCOM) to determine an optimal commutation time for efficient synchronous switching of the output drivers. When the FCOM signal changes state, one of the delay capacitors (C D1 or C D2) is discharged at approximately twice the rate of thecharging current. When the capacitor reaches the 2.5 V thresh-old, a commutation occurs. During this discharge period, the other delay capacitor is being charged in anticipation of the next FCOM state change. In addition, there is an interruption to the charging, which is set by the blanking duration (see waveform below, V CWD, and next section). This additional charging delay causes the commutation to occur at slightly less than 50% of the FCOM on or off duration, to compensate for delays caused by winding inductance.Functional Description (cont’d)The typical delta voltage change during normal operation in the commutation capacitors (C D1 & C D2), will range between 1.5 V and 2.0 V. The commutation capacitor values can be determined from:C DX = I CD x t / V CD where V CD = 1.5 V, I CD = 20 µA, and t = (60/rpm)/(#motor poles x 3), duration of each state.To avoid the capacitors charging to the supply rail, the value selected should provide adequate margin, taking into account the effects of capacitor tolerance, charging current, etc.Blanking and watchdog timing functions. The blanking and watchdog timing functions are derived from one timing capacitor C WD .During normal commutation, at the beginning of each new sequencer state, a blanking signal is created until the watchdog capacitor C WD is charged to the threshold V TL (see waveforms below). This blanking signal prohibits the back-EMF compara-tors from tripping due to the discharging of inductive energy and voltage settling transients during sequence state transitions. The duration of this blanking signal depends on the size of the C WD capacitor and the programmed charge current, I CWD (via D26-27). This blanking pulse also interrupts the commutation delay capacitors C D1 and C D2 from charging (see previous section).The ability to select the minimum charge current for C WD is particularly useful during start-up, where the duration of the diode recirculation current is highest. In applications where high motor speeds are experienced, the charge current can be increased so that the blanking period does not encroach signifi-cantly into the period of each sequencer state and does not cause89043-PHASE BRUSHLESS DCMOTOR CONTROLLER/DRIVERunbalance in the commutation points.It is recommended to select the value of C WDin the actual application circuit with the A8904 put into step mode. C ST should be reselected (only for this test), to be between 4.7 µF and 10 µF, so that the motor comes to rest between steps and the maximum diode conduction time can be measured. The value of C WD can be determined as:C WD = I CWD x t d / V TLwhere t d = measured diode conduction, I CWD = charge current at start-up, and V = 250 mV.After the watchdog capacitor C WD charges to the V TL threshold,and if the correct polarity of back-EMF signal is detected, the back-EMF detection circuit discharges C WD to zero volts (see waveform above) and the circuit is ready to detect the next back-EMF zero crossing.If the correct polarity of back-EMF is not detected between the blanking period, t BLANK, and the watchdog period, t WD , then the back-EMF detection circuit does not allow the watchdog capacitor C WD to be discharged and the watchdog circuitcommutates the outputs to the next sequencer state (see wave-form above). This mode of operation continues until a suitable back-EMF signal is detected. This function is useful in prevent-ing excessive reverse rotation, and helps in resynchronising (or starting) with a moving spindle.The duration of the watchdog-triggered commutation is determined by:t WD = V TH x C WD / I CWDwhere I CWD = normal charge current.Speed control . The actual speed of the motor is mea-sured by either internally sensing the back-EMFs or by an external scheme via the SECTOR DATA terminal. A TACH signal is produced from these signals, which is then compared against the desired speed, which is programmed into a 14-bit counter (see diagram and waveforms below - assumes internal scheme used). The resulting error signal, ERROR, is then used to charge or discharge the FILTER terminal capacitor depending on whether the motor is running too slow or too fast. The FILTER terminal voltage is used to linearly drive the low-side MOSFETs to match the desired speed.Each back-EMF signal detected causes the state of the FCOM signal to change. The number of FCOM transitions per mechanical revolution is equal to the number of poles times 3.For example, with a 4-pole motor (as shown on next page), the number of FCOM transitions will equal 12 per mechanicalrevolution. The number of poles are programmed via serial port bits D20 and D21. There are six electrical states per electrical revolution, therefore, for this example, there are 12 commuta-tions or two electrical revolutions per mechanical revolution.The TACH signal changes state once per mechanical revolution and as well as providing information on the actual motor speed is also used to trigger the REF counter which contains the information on the desired motor speed. Alterna-tively an external TACH signal can be used, an explanation of which is presented in the Sector Mode Section.The duration of REF is set by programming the counter to count the desired number of OSCILLATOR cycles, according to the following:total count = 60 x f OSC / desired motor speed (rpm)where the total count (number of oscillator cycles) is equal to the sum of the count numbers selected through bits D5 to D18 in the serial port and f OSC corresponds to the OSCILLATOR fre-quency.Functional Description (cont’d)Watchdog-triggered commutation8904 3-PHASE BRUSHLESS DC MOTOR CONTROLLER/DRIVERA speed error signal is created by integrating the differences between the TACH and REF signal. If the TACH signal goes low before the REF signal then an ERROR FAST is produced and if the TACH signal goes low after the REF signal then an ERROR SLOW is produced. The error signal generated enables the appropriate current source (see diagram next page) to either charge or discharge the filter components on the FILTER terminal.The FILTER voltage is then used to provide linear current control in the windings via the transconductance stage (see diagram next page). The output current is sensed through an internal sense resistor, RS. The voltage across the sense resistor is compared to the lowest of either one-tenth of the voltage at the FILTER terminal, minus the filter threshold voltage, or to the maximum current limit reference.Alternatively, external control of the FILTER terminal can be introduced by disabling the frequency-lock loop circuitry (D24 = 1).The transconductance function is defined as:IOUT= (VFILTER– VFILTERTH) / (10 x RSx G)where RSis nominally 200 mΩ,VFILTERTHis approximately 1.85 V,G = 1, when D28 = 0 and gain = 500 mA/V orG = 2, when D28 = 1 and gain = 250 mA/V.The closed loop control response of the overall system is shaped via the filter components that are introduced at the FILTER terminal.Clamping the current to a level defined by the serial port (D3 & D4) provides output current limit protection. This feature is particularly useful where high transient currents are experi-enced, e.g., during start-up. Once normal running conditions are reached, the current limit can be appropriately reduced. Notethat the current limit is scaled according to the gmvalue selected.Functional Description (cont’d)Speed error detectionSpeed error signals89043-PHASE BRUSHLESS DCMOTOR CONTROLLER/DRIVERSector mode. An external tachometer signal, such as sector or index pulses, can be used to create the TACH signal,rather than the internally generated once-around scheme. The external signal is applied to the SECTOR DATA terminal and the serial port bit (D19 = 1) must be programmed to enable this feature.In applications where both internal and external TACH signals are used, it is important to only switch between modes when the SYNC signal on DATA OUT is low. This ensures the speed control information that is being processed during the transition, is not corrupted. SYNC is accessed through the DATA OUT multiplexer, which is controlled by D22 & D23.DATA OUT. The DATA OUT terminal is the output of a 2-bit input multiplexer controlled by D22 & D23 of the serial port. Data available are TACH signal (internally or externally generated), SYNC signal, FCOM signal, and thermal shutdown (LOW = A8904 operating within thermal limits, HIGH =thermal shutdown has occurred).Speed loop initialization (YANK). To ensure rapid transition from start-up to the normal operating condition, the FILTER terminal is pulled up to the filter threshold voltage,Functional Description (cont’d)V FILTERTH , by the internal YANK command and the initialoutput current will be set to the maximum selected current limit.This condition is maintained until the motor reaches the correct speed and the first ERROR FAST signal is produced which removes the YANK and allows linear current control.The YANK feature is also activated when an external speed control scheme is used (D24 = 1). To ensure the YANK is released at start-up by the internal speed control, it is important to ensure the speed reference is set at a lower speed than what the motor is designed to run at. Note that when the serial port is programmed to run initially, the default condition for the speed is set for the slowest condition so this will guarantee the YANK to be released. It is important when using external speed control that, as a minimum, the number of poles, speed control mode,and speed reference are programmed in the serial port.Forward/reverse. Directional control is managed through D25 in the serial port.Serial port. Control features and diagnostic data selection are communicated to the A8904 through the 29-bit serial port.See serial port timing diagrams on page 6. When CHIP SE-LECT is low, data is written to the serial port on the positive edge of the clock with the MSB (D28) fed in first. At the end ofSpeed and current control8904 3-PHASE BRUSHLESS DC MOTOR CONTROLLER/DRIVERthe write cycle, the CHIP SELECT goes high, the serial port is disabled and no more data can be transferred. In addition, the data written to the serial port is latched and becomes active.If a word of less than 29 bits is sent, the unused most significant bits that are not programmed, are reset to zero. There are no compatibility issues when using the A8904 in an existing A8902-A application as the five MSBs are reset to zero, which is the default condition for A8902-A operation. The only consideration when using the A8904 in an A8902-A application is to ensure the minimum CHIP SELECT high time is at least 500 ns.D0 - Sleep/Run Mode; LOW = Sleep, HIGH = Run. This bit allows the device to be powered down when not in use.D1 - Step Mode; LOW = Normal Operation, HIGH = Step Only. When in the step-only mode the back-EMF commutation circuitry is disabled and the start-up oscillator commutates the power outputs. This mode is intended for device and system testing.D2 - Brake; LOW = Run, HIGH = Brake.D3, D4, and D28 - The output current limit is set by D3 & D4; D28 sets the transconductance gain.Current limit Transconductance D3D4D28(typical)gain000 1.2 A500 mA/V010 1.0 A500 mA/V100600 mA500 mA/V110250 mA500 mA/V001600 mA250 mA/V011500 mA250 mA/V101300 mA250 mA/V111125 mA250 mA/VD5 to D18 - 14-bit word, active low. Programs the count number to produce the corresponding REF signal, which indicates the desired motor speed.Bit number Count numberD516D632D764D8128D9256D10512D111,024D122,048D134,096D148,192D1516,384D1632,768D1765,536D18131,072D19 - Speed control mode; LOW = internal, once-around speed signal, HIGH = external sector data.D20 and D21 - Programs the number of motor poles for the once-around FCOM counter.D20D21Motor poles00801410161112D22 and D23 - Controls the multiplexer for DATA OUT. See DATA OUT Section for status definitions.D22D23DATA OUT00TACH (once around or sector) signal01Thermal shutdown10SYNC signal11FCOM signalD24 - Speed Reference. LOW = Internal, using back-EMF technique, HIGH = External (internal control disabled).D25 - Direction. LOW = Forward, HIGH = Reverse.D26 and D27 - Programs the charging current for the watchdog capacitor. This function is used for adjusting the blanking duration and also the watchdog commutation period.D26D27Watchdog charge current (typical)00-10 µA01-20 µA10-30 µA11-40 µAFunctional Description (cont’d)。
HT47C10L资料

HT47C10L8-Bit R-F Type Low Voltage Mask MCUBlock DiagramRev.1.101October 2,2002Features·Operating voltage:1.2V~2.2V ·Eight bidirectional I/O lines·On-chip 32kHz/128kHz built-in RC oscillator(Mask option;128kHz is selected especially for EL driving)·Watchdog timer·1K ´16program memory ROM ·32´8data memory RAM ·One time base (TB)·One buzzer output ·One EL output·One externally adjustable low voltage detector·HALT function and wake-up feature reduce powerconsumption·One LCD driver with 9´4segments,1/4duty,1/2bias ·RC type A/D converter ·Two-level subroutine nesting ·Bit manipulation instruction ·16-bit table read instruction·Up to 122m s instruction cycle with 32768Hz systemclock·All instructions in one or two machine cycles ·63powerful instructions ·44-pin QFP packageGeneral DescriptionThe HT47C10L is an 8-bit high performance RISC-like microcontroller.Its single cycle instruction and two-stage pipeline architecture make it suitable for highspeed applications.The device is suited for clinical ther-mometers.Pin AssignmentPad Assignment*The IC substrate should be connected to VSS in the PCB layout artwork.Rev.1.102October2,2002Pad DescriptionPad Name I/O Function RES I Schmitt trigger reset input.Active lowPA0/BZ PA1/BZ I/OI/OBidirectional2-bit input/output port.Each bit can be a wake-up input.The PA0and PA1 are pin-shared with the BZ and BZ,respectively.Once the PA0and PA1are selected as buzzer driving outputs,the output signals come from an internal buzzer clock generator.Software instructions determine the CMOS output or Schmitt trigger input with pull-high resistorPA2/EL1 PA3/EL2I/OI/OBidirectional2-bit input/output port.Each bit can be a wake-up input.The PA2and PA3 are pin-shared with the EL1and EL2,respectively.Once the PA2and PA3are selected as EL driving outputs,the output signals come from an internal EL clock generator.Software instructions determine the CMOS output or Schmitt trigger input with pull-high resistorPA4~PA7I/O Bidirectional4-bit input/output port.Each bit can be a wake-up input.Software instructions determine the CMOS output or Schmitt trigger input with pull-high resistorVSS¾Negative power supply,groundVCC,C1,C2¾For double voltage.VCC=2´VDDVCC:LCD power supply voltage,a capacitor has to be connected between VCC and VSS.C1,C2:Switching pins for VCC,a capacitor has to be connected between C1and C2SEG8~SEG0COM3~COM0O LCD driver outputs for LCD panel segments and commons.VDD¾Positive power supplyLVD B Low voltage detector.A resistor has to be connected between VSS and LVD RCIN I RC type A/D converter input pin for RC oscillation.RREF O RC type A/D converter output pin for reference resistor oscillation.RSEN O RC type A/D converter output pin for sensor resistor oscillationTEST1 TEST2ITEST mode input pin with pull-high resistor.Let open in normal modeTRIM1~TRIM6I TEST mode input pin.Let open in normal modeAbsolute Maximum RatingsSupply Voltage.........................................-0.3V to2.5V Storage Temperature............................-50°C to125°C Input Voltage..............................V SS-0.3V to V DD+0.3V Operating Temperature...........................-40°C to85°CNote:These are stress ratings only.Stresses exceeding the range specified under²Absolute Maximum Ratings²may cause substantial damage to the device.Functional operation of this device at other conditions beyond those listed in the specification is not implied and prolonged exposure to extreme conditions may affect device reliabil-ity.Rev.1.103October2,2002Symbol ParameterTest ConditionsMin.Typ.Max.Unit V DD ConditionsV DD Operating Voltage¾¾ 1.2 1.5 2.2V V CC LCD Voltage¾VCC=2´VDD 2.43 4.4V V LVD Low Voltage Detector Voltage¾*R LVD=30k W 1.25 1.3 1.35VI DD1Operating Current 1.5V No load,f OSC=128kHzf SYS=32kHz,A/D Off,LVD disable¾920m AI DD2Operating Current 1.5V No load,f OSC=128kHzf SYS=32kHz,A/D On,LVD disable*R=30k W,*C=2200pF¾2650m AI DD3Operating Current 1.5V No load,f OSC=32kHzf SYS=32kHz,A/D Off,LVD disable¾510m AI DD4Operating Current 1.5V No load,f OSC=32kHzf SYS=32kHz,A/D On,LVD disable*R=30k W,*C=2200pF¾2340m AI LVD LVD Current 1.5V LVD enable¾50100m A I STB1Standby Current(LVD Disable,LCD Off) 1.5V No load,system HALTA/D Off,LVD Off¾¾1m AI STB2Standby Current(LCD On) 1.5V No load,f OSC=128kHzf SYS=32kHz,A/D Off,LVD disable¾715m AI STB3Standby Current(LCD On) 1.5V No load,f OSC=32kHzf SYS=32kHz,A/D Off,LVD disable¾ 2.55m AV IL1Input Low Voltage for I/O Ports 1.5V¾0¾0.3V DD V V IH1Input High Voltage for I/O Ports 1.5V¾0.7V DD¾ 1.5V V IL2Input Low Voltage(RES) 1.5V¾0¾0.4V DD V V IH2Input High Voltage(RES) 1.5V¾0.9V DD¾V DD VI OL1Sink CurrentPA0(BZ),PA1(BZ),PA2(EL1),PA3(EL2),PA4~PA71.5V V OL=0.15V0.50.8¾mAI OH1Source CurrentPA0(BZ),PA1(BZ),PA2(EL1),PA3(EL2),PA4~PA71.5V V OH=1.35V-0.3-0.6¾mAI OL2Common Output Sink Current 1.5V V OL=0.3V(1/2bias)50100¾m AI OH2Common Output Source Current 1.5V V OH=2.7V(1/2bias)-50-100¾m A I OL3Segment Output Sink Current 1.5V V OL=0.3V(1/2bias)50100¾m AI OH3Segment Output Source Current 1.5V V OH=2.7V(1/2bias)-50-100¾m A R PH1Pull-high Resistance of I/O Ports 1.5V V IL=0V75150300k WR PH2Pull-high Resistance of TEST 1.5V V IL=0V75150300k W Note:*R means the resistance of RC type A/D converter*C means the capacitance of RC type A/D converter*R LVD value may be different for different lotRev.1.104October2,2002Symbol ParameterTest ConditionsMin.Typ.Max.Unit V DD Conditionsf32K Oscillator Clock(32kHz option) 1.5V¾283236kHz f128K Oscillator Clock(128kHz option) 1.5V¾112128144kHz t RES External Reset Low Pulse Width 1.5V¾100¾¾m sf AD A/D Converter Frequency 1.5V¾¾¾50kHz Rev.1.105October2,2002Rev.1.106October 2,2002Execution flowFunctional DescriptionExecution flowThe HT47C10L system clock is derived from an about 32kHz built-in RC oscillator.The system clock is inter-nally divided into four non-overlapping clocks (T1,T2,T3and T4).One instruction cycle consists of four sys-tem clock cycles.Instruction fetching and execution are pipelined in such a way that a fetch takes one instruction cycle while de-coding and execution takes the next instruction cycle.However,the pipelining scheme causes each instruction to effectively execute in one cycle.If an instruction changes the program counter,two cycles are required to complete the instruction.Program counter -PCThe 10-bit program counter (PC)controls the sequence in which the instructions stored in the program ROM are executed and its contents specify a maximum of 1024addresses.After accessing a program memory word to fetch an in-struction code,the contents of the program counter are incremented by one.The program counter then points to the memory word containing the next instruction code.When executing a jump instruction,conditional skip ex-ecution,loading PCL register,subroutine call,initial re-set,internal interrupt,external interrupt or return from subroutine,the PC manipulates the program transfer by loading the address corresponding to each instruction.The conditional skip is activated by instruction.Once the condition is met,the next instruction,fetched during the current instruction execution,is discarded and a dummy cycle replaces it to get the proper instruction.Otherwise proceed with the next instruction.The lower byte of the program counter (PCL)is a read-able and writeable register (06H).Moving data into the PCL performs a short jump.The destination will be within 256locations.When a control transfer takes place,an additional dummy cycle is required.ModeProgram Counter*9*8*7*6*5*4*3*2*1*0Initial Reset0000000000Timer/event Counter Interrupt 0000000100Time Base Interrupt 0000001Skip PC+2Loading PCL *9*8@7@6@5@4@3@2@1@0Jump,Call Branch #9#8#7#6#5#4#3#2#1#0Return from SubroutineS9S8S7S6S5S4S3S2S1S0Program counterNote:*9~*0:Program counter bits#9~#0:Instruction code bits S9~S0:Stack register bits@7~@0:PCL bitsProgram memory-ROMThe program memory is used to store the program in-structions,which are to be executed.It also contains data,table,and interrupt entries,and is organized into 1024´16bits,addressed by the program counter and table pointer.Certain locations in the program memory are reserved for special usage:·Location000HThis area is reserved for the initialization program.Af-ter chip reset,the program always begins execution at location000H.·Location004HThis area is reserved for the timer/event counter inter-rupt service program.If timer interrupt results from a timer/event counter A or B overflow,and if the inter-rupt is enabled and the stack is not full,the program begins execution at location004H.·Location008HThis area is reserved for the time base interrupt ser-vice program.If a time base interrupt occurs,and if the interrupt is enabled and the stack is not full,the pro-gram begins execution at location008H.·Table locationAny location in the ROM space can be used as look-up tables.The instructions TABRDC[m](the cur-rent page,1page=256words)and TABRDL[m](the last page)transfer the contents of the lower-order byte to the specified data memory,and the higher-order byte to TBLH(08H).Only the destination of the lower-order byte in the table is well-defined,the higher-order byte of the table word are transferred to the TBLH.The table higher-order byte register(TBLH) is read only.The table pointer(TBLP)is a read/write register(07H),which indicates the table location.Be-fore accessing the table,the location must be placed in TBLP.The TBLH is read only and cannot be re-stored.If the main routine and the ISR(interrupt ser-vice routine)both employ the table read instruction, the contents of the TBLH in the main routine are likely to be changed by the table read instruction used in the ISR.Errors can occur.In other words using the table read instruction in the main routine and the ISR simul-taneously should be avoided.However,if the tableread instruction has to be applied in both the main rou-tine and the ISR,the interrupt is supposed to be dis-abled prior to the table read instruction.It will not be enabled until the TBLH has been backed up.All table related instructions need two cycles to complete the operation.These areas may function as normal pro-gram memory depending upon the requirements.Stack register-STACKThis is a special part of the memory which is used to save the contents of the program counter(PC)only.The stack is organized into two levels and is neither part of the data nor part of the program space,and is neither readable nor writeable.The activated level is indexed by the stack pointer(SP)and is neither readable nor writeable.At a subroutine call or interrupt acknowledg-ment,the contents of the program counter are pushed onto the stack.At the end of a subroutine or an interrupt routine,signaled by a return instruction(RET or RETI), the program counter is restored to its previous value from the stack.After a chip reset,the SP will point to the top of the stack.If the stack is full and a non-masked interrupt takes place,the interrupt request flag will be recorded but the acknowledgment will be inhibited.When the stackProgram memoryInstruction(s)Table Location*9*8*7*6*5*4*3*2*1*0TABRDC[m]P9P8@7@6@5@4@3@2@1@0 TABRDL[m]11@7@6@5@4@3@2@1@0Table locationNote:*9~*0:Bits of table location@7~@0:Bits of table pointerP9~P8:Bits of current program counterRev.1.107October2,2002pointer is decremented(by RET or RETI),the interrupt will be serviced.This feature prevents stack overflow al-lowing the programmer to use the structure more easily. In a similar case,if the stack is full and a²CALL²is sub-sequently executed,stack overflow occurs and the first entry will be lost(only the most recent two return ad-dresses is stored).Data memory-RAMThe data memory is designed with54´8bits.The data memory is divided into two functional groups:special function registers and general-purpose data memory(32´8). Most are read/write,but some are read only.The special function registers include the indirect address-ing register0(00H),the memory pointer register0(MP0; 01H),the indirect addressing register1(02H),the memory pointer register1(MP1;03H),the bank pointer(BP;04H), the accumulator(ACC;05H),the program counter lower-order byte register(PCL;06H),the table pointer (TBLP;07H),the table higher-order byte register (TBLH;08H),the time base control register(TBC;09H),the status register(STATUS;0AH),the interrupt control regis-ter0(INTC;0BH),the I/O registers(PA;12H),I/O port con-trol register(PAC;13H),the timer/event counter A higher-order byte register(TMRAH;20H),the timer/event counter A lower-order byte register(TMRAL;21H),the timer/event counter control register(TMRC;22H),the timer/event counter B higher-order byte register(TMRBH; 23H),the timer/event counter B lower-order byte register (TMRBL;24H),the RC oscillator type A/D converter con-trol register(ADCR;25H)and the option register(OPT1; 26H,OPT2;27H).The remaining space before the60H are reserved for fu-ture expanded usage and reading these location will re-turn the result00H.The general-purpose data memory, addressed from60H to7FH,is used for data and control information under instruction command.All data memory areas can handle arithmetic,logic,in-crement,decrement and rotate operations.Except for some dedicated bits,each bit in the data memory can be set and reset by the SET[m].i and CLR[m].i instruction, respectively.They are also indirectly accessible through memory pointer registers(MP0;01H,MP1;03H).Indirect addressing registerLocation00H and02H are indirect addressing registers that are not physically implemented.Any read/write op-eration of[00H]and[02H]access data memory pointed to by MP0(01H)and MP1(03H)respectively.Reading location00H or02H indirectly will return the result00H. Writing indirectly results in no operation.The function of data movement between two indirect ad-dressing registers are not supported.The memory pointer registers,MP0and MP1,are both8-bit registers which can be used to access the data memory by com-bining corresponding indirect addressing registers.MP0only can be applied to data memory,while MP1 can be applied to data memory and LCD display mem-ory.AccumulatorThe accumulator is closely related to ALU operations.It is also mapped to location05H of the data memory and is capable of carrying out immediate data operations.The data movement between two data memory locations must pass through the accumulator.RAM mapping(bank0)Rev.1.108October2,2002Rev.1.109October 2,2002Labels Bits FunctionC 0C is set if an operation results in a carry during an addition operation or if a borrow does not take place during a subtraction operation;otherwise C is cleared.C is also affected by a rotate through carry instruction.AC 1AC is set if an operation results in a carry out of the low nibbles in addition or no borrow from the high nibble into the low nibble in subtraction;otherwise AC is cleared.Z 2Z is set if the result of an arithmetic or logical operation is zero;otherwise Z is cleared.OV 3OV is set if an operation results in a carry into the highest-order bit but not a carry out of the highest-order bit,or vice versa;otherwise OV is cleared.PD 4PD is cleared by either a system power-up or executing the CLR WDT instruction.PD is set by executing the HALT instruction.TO 5TO is cleared by a system power-up or executing the CLR WDT or HALT instruction.TO is set by a WDT time-out.¾6Unused bit,read as ²0²¾7Unused bit,read as ²0²STATUS registerArithmetic and logic unit -ALUThis circuit performs 8-bit arithmetic and logic operation.The ALU provides the following functions:·Arithmetic operations (ADD,ADC,SUB,SBC,DAA)·Logic operations (AND,OR,XOR,CPL)·Rotation (RL,RR,RLC,RRC)·Increment and Decrement (INC,DEC)·Branch decision (SZ,SNZ,SIZ,SDZ ....)The ALU not only saves the results of a data operation but can change the status register.Status register -STATUSThis 8-bit register (0AH)contains the zero flag (Z),carry flag (C),auxiliary carry flag (AC),overflow flag (OV),power down flag (PD)and watchdog time-out flag (TO).It also records the status information and controls the operation sequence.With the exception of the TO and PD flags,bits in the status register can be altered by instructions like most other registers.Any data written into the status register will not change the TO or PD flags.In addi-tion it should be noted that operations related to the status register may give different results from those intended.The TO and PD flags can only be changed by the watchdog timer overflow,system power-up,clearing the watchdog timer and executing the HALT instruction.The Z,OV,AC and C flags generally reflect the status of the latest operations.In addition,on entering the interrupt sequence or exe-cuting the subroutine call,the status register will not be automatically pushed onto the stack.If the contents of status are important and if the subroutine can corrupt the status register,precautions must be taken to save it properly.InterruptsThe HT47C10L provides an internal timer/event counter interrupt and an internal time base interrupt.The inter-rupt control register (INTC;0BH)contains the interrupt control bits to set the enable/disable and interrupt re-quest flags.Once an interrupt subroutine is serviced,all other inter-rupts will be blocked (by clearing the EMI bit).This scheme may prevent any further interrupt nesting.Other interrupt requests may happen during this interval,but only the interrupt request flag is recorded.If a certain in-terrupt needs servicing within the service routine,the programmer may set the EMI bit and the corresponding bit of INTC allow interrupt nesting.If the stack is full,the in-terrupt request will not be acknowledged,even if the re-lated interrupt is enabled,until the SP is decremented.If immediate service is desired,the stack must be prevented from becoming full.As an interrupt is serviced,a control transfer occurs by pushing the program counter onto the stack,followed by a branch to a subroutine at specified locations in the pro-gram memory.Only the program counter is pushed onto the stack.If the contents of the register and status regis-ter (STATUS)is altered by the interrupt service program which corrupts the desired control sequence,the con-tents must be saved first.The internal timer/event counter interrupt is initialized by setting the timer/event counter interrupt request flag (TF;bit 4of INTC),caused by a timer A or timer B over-flow.When the interrupt is enabled,and the stack is not full and the TF bit is set,a subroutine call to location 04H will occur.The related interrupt request flag (TF)will be reset and the EMI bit cleared to disable further inter-rupts.The time base interrupt is initialized by setting the time base interrupt request flag(TBF;bit5of INTC),caused by a regular time base signal.When the interrupt is en-abled,and the stack is not full and the TBF bit is set,a subroutine call to location08H will occur.The related in-terrupt request flag(TBF)will be reset and the EMI bit cleared to disable further interrupts.During the execution of an interrupt subroutine,other in-terrupt acknowledgments are held until the RETI instruc-tion is executed or the EMI bit and the related interrupt control bit are set to1(if the stack is not full).T o return from the interrupt subroutine,RET or RETI instruction may be invoked.RETI will set the EMI bit to enable an in-terrupt service,but RET does not.Interrupts occurring in the interval between the rising edges of two consecutive T2pulses,will be serviced on the latter of the two T2pulses,if the corresponding inter-rupts are enabled.In the case of simultaneous requests the following table shows the priority that is applied. These can be masked by resetting the EMI bit.No.Interrupt Source Priority Vectora Timer/event counter interrupt104Hb Time base interrupt208HOscillator configurationThe HT47C10L provides one built-in RC oscillator which frequency(f OSC)is32kHz or128kHz decided by mask option.However,the CPU system clock(f SYS)is always 32kHz.The HALT mode may stop the oscillator decided by software er should select128kHz mask op-tion for EL driving mode.Watchdog timer-WDTThe clock source of the WDT(f s)is f SYS.The timer is designed to prevent a software malfunction or sequence jumping to an unknown location with unpredictable re-sults.The Watchdog timer can be disabled by software option.If the Watchdog timer is disabled,all the execu-tions related to the WDT result in no operation.The²HALT²instruction is executed,WDT still counts if f OSC is on and can wake-up from HALT mode due to the WDT time-out.The WDT overflow under normal operation will initialize ²chip reset²and set the status bit TO.Whereas in the HALT mode,the overflow will initialize a²warm reset²only the PC and SP are reset to zero.To clear the con-tents of WDT,three methods are adopted,external reset (a low level to software instruction,or a HALT in-struction.The software instruction is CLR WDT.Any ex-ecution of the CLR WDT instruction will clear the WDT. The WDT may reset the chip because of the time-out.The WDT time-out period ranges from f S/215~f S/216.The ²CLR WDT²instruction only clear the last two-stage of the WDT.Multi-function timerThe HT47C10L provides a multi-function timer for the WDT and time base but with different time-out periods. The multi-function timer consists of an8-stage divider and a7-bit prescaler,with the clock source coming from f SYS.The multi-function timer also provides a fixed fre-quency signal(f S/8)for the LCD driver circuits,and buzzer output.Register Bit bel FunctionINTC (0BH)0EMI Control the master or global interrupt(1=enabled;0=disabled)1ETI Control the timer/event counter interrupt(1=enabled;0=disabled) 2ETBI Control the time base interrupt(1=enabled;0=disabled)3¾Unused bit,read as²0²4TF Timer/event counter interrupt request flag(1=active;0=inactive) 5TBF Time base interrupt request flag(1=active;0=inactive)6¾Unused bit,read as²0²7¾Unused bit,read as²0²INTC RegisterMulti-function timerRev.1.1010October2,2002Time base-TBThe time base is used to supply a regular internal inter-rupt.Its time-out period ranges from f s/28to f s/215by software programming.Writing data to RT2,RT1and RT0(bits2,1,0of TBC;09H)yields various time-out periods.If a time base time-out occurs,the related inter-rupt request flag(TBF;bit5of INTC)is set.But if the in-terrupt is enabled,and the stack is not full,a subroutine call to location08H occurs.When the HALT instruction is executed,the time base still works and can wake-up from HALT mode if f OSC is on.If the TBF is set1before entering the HALT mode,the wake-up function will be disabled.RT2RT1RT0Time Base Divided Factor0002800129010210011211100212101213110214111215Power down operation-HALTThe HALT mode is initialized by the HALT instruction and results in the following.·The f OSC and f SYS will still work or stop depend on STANDBY option(Option register bit5),but T1will turn off.·The contents of the on-chip RAM and registers remain unchanged.·The WDT will be cleared and recount again.·All I/O ports maintain their original status.·The PD flag is set and the TO flag is cleared.·LCD driver can be off or on depend on STANDBY op-tion(Option register bit5)·The time base will stop or run depends on STANDBY option(Option register bit5).The port A wake-up and interrupt methods can be con-sidered as a continuation of normal execution.Awaken-ing from an I/O port stimulus,the program will resume execution of the next instruction.If awakening from an interrupt,two sequences may happen.If the related in-terrupt is disabled or the interrupt is enabled but the stack is full,the program will resume execution at the next instruction.If the interrupt is enabled and the stack is not full,a regular interrupt response takes place.If an interrupt request flag is set to²1²before entering the HALT mode the wake-up function of the related in-terrupt will be disabled.If the wake-up results from an interrupt acknowledg-ment,the actual interrupt subroutine execution will be delayed by more than one cycle.However,if the wake-up results in the next instruction execution,the ex-ecution will be performed immediately.To minimize power consumption,all the I/O pins should be carefully managed before entering the HALT mode.ResetThere are three ways in which a reset may occur.·RES reset during normal operation·RES reset during HALT mode·WDT time-out reset during normal operationThe WDT time-out during HALT mode is different from other chip reset conditions,since it can perform a warm reset that just resets the PC and SP leaving the other circuits in their original state.Some registers remain un-changed during other reset conditions.Most registers are reset to the²initial condition²when the reset condi-tions are met.By examining the PD and TO flags,the program can distinguish between different²chip resets².TO PD RESET Conditions00System power-upu uRES reset or LVR reset during normaloperation01RES reset or LVR reset wake-up fromHALT mode1u WDT time-out during normal operation 11WDT wake-up from HALT modeNote:²u²means²unchanged²The chip-reset status of the functional units are shown be-low.PC000HInterrupt DisabledPrescaler,Divider ClearedWDT,Time BaseClear.After master reset,begin countingTimer/event Counter OffInput/output Ports Input modeSP Points to the top of the stackRev.1.1011October2,2002Rev.1.1012October 2,2002The states of the registers are summarized in the following table:Register Reset (Power On)WDT time-out (Norma Operation)RES reset(Normal Operation)RES reset (HALT)WDT time-out(HALT)TMRAH xxxx xxxx uuuu uuuu uuuu uuuu uuuu uuuuuuuu uuuu TMRAL xxxx xxxx uuuu uuuu uuuu uuuuuuuu uuuu uuuu uuuu TMRC -0001----0001----0001----0001----uuu u---TMRBH xxxx xxxx uuuu uuuu uuuu uuuu uuuu uuuu uuuu uuuu TMRBL xxxx xxxx uuuu uuuu uuuu uuuu uuuu uuuu uuuu uuuu ADCR 000x 0000000x 0000000x 0000000x 0000uuuu ---u Program Counter 000H 000H 000H 000H 000H*MP0xxxx xxxx uuuu uuuu uuuu uuuu uuuu uuuu uuuu uuuu MP1xxxx xxxx uuuu uuuu uuuu uuuu uuuu uuuu uuuu uuuu ACC xxxx xxxx uuuu uuuu uuuu uuuu uuuu uuuu uuuu uuuu TBLP xxxx xxxx uuuu uuuu uuu uuuu uuuu uuuu uuuu uuuu TBLH xxxx xxxx uuuu uuuu uuuu uuuu uuuu uuuu uuuu uuuu STATUS --00xxxx --1u uuuu --uu uuuu --01uuuu --11uuuu INTC --00-000--00-000--00-000--00-000--uu -uuu TBC --x-0111--x-0111--x-0111--x-0111--u-uuuu PA 11111111111111111111111111111111uuuu uuuu PAC 11111111111111111111111111111111uuuu uuuu OPT100000010000000100000001000000010uuuu uuuu OPT200000000000000000000000000000000uuuu uuuuNote:²*²refers to ²warm reset ²²u ²means ²unchanged ²²x ²means ²unknown ²Reset。
- 1、下载文档前请自行甄别文档内容的完整性,平台不提供额外的编辑、内容补充、找答案等附加服务。
- 2、"仅部分预览"的文档,不可在线预览部分如存在完整性等问题,可反馈申请退款(可完整预览的文档不适用该条件!)。
- 3、如文档侵犯您的权益,请联系客服反馈,我们会尽快为您处理(人工客服工作时间:9:00-18:30)。
M44C890-HM44C090-H Rev.A3, 14-Dec-013 (63)Table of Contents1Introduction 5. . . . . . . . . . . . . . . . . . . . . . . . . . . . . . . . . . . . . . . . . . . . . . . . . . . . . . . . . . . . . . . . . . . . . . 2MARC4 Architecture 5. . . . . . . . . . . . . . . . . . . . . . . . . . . . . . . . . . . . . . . . . . . . . . . . . . . . . . . . . . . . . . 2.1General Description 5. . . . . . . . . . . . . . . . . . . . . . . . . . . . . . . . . . . . . . . . . . . . . . . . . . . . . . . . . 2.2Components of MARC4 Core 6. . . . . . . . . . . . . . . . . . . . . . . . . . . . . . . . . . . . . . . . . . . . . . . . .2.2.1ROM 6. . . . . . . . . . . . . . . . . . . . . . . . . . . . . . . . . . . . . . . . . . . . . . . . . . . . . . . . . . . . 2.2.2RAM 6. . . . . . . . . . . . . . . . . . . . . . . . . . . . . . . . . . . . . . . . . . . . . . . . . . . . . . . . . . . . 2.2.3Registers 7. . . . . . . . . . . . . . . . . . . . . . . . . . . . . . . . . . . . . . . . . . . . . . . . . . . . . . . . . 2.2.4ALU 9. . . . . . . . . . . . . . . . . . . . . . . . . . . . . . . . . . . . . . . . . . . . . . . . . . . . . . . . . . . . . 2.2.5I/O Bus 9. . . . . . . . . . . . . . . . . . . . . . . . . . . . . . . . . . . . . . . . . . . . . . . . . . . . . . . . . . 2.2.6Instruction Set 9. . . . . . . . . . . . . . . . . . . . . . . . . . . . . . . . . . . . . . . . . . . . . . . . . . . . . 2.2.7Interrupt Structure 9. . . . . . . . . . . . . . . . . . . . . . . . . . . . . . . . . . . . . . . . . . . . . . . . . .Software Interrupts 11. . . . . . . . . . . . . . . . . . . . . . . . . . . . . . . . . . . . . . . . . . . . . . . . . Hardware Interrupts 11. . . . . . . . . . . . . . . . . . . . . . . . . . . . . . . . . . . . . . . . . . . . . . . .2.3Master Reset 11. . . . . . . . . . . . . . . . . . . . . . . . . . . . . . . . . . . . . . . . . . . . . . . . . . . . . . . . . . . . . . .2.3.1Power-on Reset and Brown-out Detection 12. . . . . . . . . . . . . . . . . . . . . . . . . . . . . . . 2.3.2Watchdog Reset 13. . . . . . . . . . . . . . . . . . . . . . . . . . . . . . . . . . . . . . . . . . . . . . . . . . . 2.3.3External Clock Supervisor 13. . . . . . . . . . . . . . . . . . . . . . . . . . . . . . . . . . . . . . . . . . .2.4V oltage Monitor 13. . . . . . . . . . . . . . . . . . . . . . . . . . . . . . . . . . . . . . . . . . . . . . . . . . . . . . . . . . . .2.4.1V oltage Monitor Control / Status Register 14. . . . . . . . . . . . . . . . . . . . . . . . . . . . . . .2.5Clock Generation 15. . . . . . . . . . . . . . . . . . . . . . . . . . . . . . . . . . . . . . . . . . . . . . . . . . . . . . . . . . .2.5.1Clock Module 15. . . . . . . . . . . . . . . . . . . . . . . . . . . . . . . . . . . . . . . . . . . . . . . . . . . . . 2.5.2Oscillator Circuits and External Clock Input Stage 16. . . . . . . . . . . . . . . . . . . . . . . .RC-Oscillator 1 Fully Integrated 16. . . . . . . . . . . . . . . . . . . . . . . . . . . . . . . . . . . . . . External Input Clock 16. . . . . . . . . . . . . . . . . . . . . . . . . . . . . . . . . . . . . . . . . . . . . . . . RC-Oscillator 2 with External Trimming Resistor 16. . . . . . . . . . . . . . . . . . . . . . . . . 4-MHz Oscillator 16. . . . . . . . . . . . . . . . . . . . . . . . . . . . . . . . . . . . . . . . . . . . . . . . . . 32-kHz Oscillator 17. . . . . . . . . . . . . . . . . . . . . . . . . . . . . . . . . . . . . . . . . . . . . . . . . .2.5.3Clock Management 17. . . . . . . . . . . . . . . . . . . . . . . . . . . . . . . . . . . . . . . . . . . . . . . . .Clock Management Register (CM)17. . . . . . . . . . . . . . . . . . . . . . . . . . . . . . . . . . . . . System Configuration Register (SC)18. . . . . . . . . . . . . . . . . . . . . . . . . . . . . . . . . . .2.6Power-down Modes 18. . . . . . . . . . . . . . . . . . . . . . . . . . . . . . . . . . . . . . . . . . . . . . . . . . . . . . . . . . 3Peripheral Modules 19. . . . . . . . . . . . . . . . . . . . . . . . . . . . . . . . . . . . . . . . . . . . . . . . . . . . . . . . . . . . . . . 3.1Addressing Peripherals 19. . . . . . . . . . . . . . . . . . . . . . . . . . . . . . . . . . . . . . . . . . . . . . . . . . . . . . . 3.2Bidirectional Ports 20. . . . . . . . . . . . . . . . . . . . . . . . . . . . . . . . . . . . . . . . . . . . . . . . . . . . . . . . . .3.2.1Bidirectional Port 221. . . . . . . . . . . . . . . . . . . . . . . . . . . . . . . . . . . . . . . . . . . . . . . . .Port 2 Data Register (P2DAT)21. . . . . . . . . . . . . . . . . . . . . . . . . . . . . . . . . . . . . . . . Port 2 Control Register (P2CR)21. . . . . . . . . . . . . . . . . . . . . . . . . . . . . . . . . . . . . . .3.2.2Bidirectional Port 522. . . . . . . . . . . . . . . . . . . . . . . . . . . . . . . . . . . . . . . . . . . . . . . . . 3.2.3Bidirectional Port 424. . . . . . . . . . . . . . . . . . . . . . . . . . . . . . . . . . . . . . . . . . . . . . . . .3.3Universal Timer/Counter / Communication Module (UTCM)25. . . . . . . . . . . . . . . . . . . . . . . .3.3.1Timer 126. . . . . . . . . . . . . . . . . . . . . . . . . . . . . . . . . . . . . . . . . . . . . . . . . . . . . . . . . .Timer 1 Control Register 1 (T1C1)27. . . . . . . . . . . . . . . . . . . . . . . . . . . . . . . . . . . . Timer 1 Control Register 2 (T1C2)27. . . . . . . . . . . . . . . . . . . . . . . . . . . . . . . . . . . .元器件交易网M44C890-HM44C090-H Rev.A3, 14-Dec-014 (63)Table of Contents (continued)Watchdog Control Register (WDC)28. . . . . . . . . . . . . . . . . . . . . . . . . . . . . . . . . . . .3.3.2Timer 228. . . . . . . . . . . . . . . . . . . . . . . . . . . . . . . . . . . . . . . . . . . . . . . . . . . . . . . . . .Timer 2 Modes 29. . . . . . . . . . . . . . . . . . . . . . . . . . . . . . . . . . . . . . . . . . . . . . . . . . . . Timer 2 Output Modes 30. . . . . . . . . . . . . . . . . . . . . . . . . . . . . . . . . . . . . . . . . . . . . . Timer 2 Output Signals 31. . . . . . . . . . . . . . . . . . . . . . . . . . . . . . . . . . . . . . . . . . . . . . Timer 2 Registers 34. . . . . . . . . . . . . . . . . . . . . . . . . . . . . . . . . . . . . . . . . . . . . . . . . . Timer 2 Control Register (T2C)34. . . . . . . . . . . . . . . . . . . . . . . . . . . . . . . . . . . . . . . Timer 2 Mode Register 1 (T2M1)35. . . . . . . . . . . . . . . . . . . . . . . . . . . . . . . . . . . . . Timer 2 Mode Register 2 (T2M2)36. . . . . . . . . . . . . . . . . . . . . . . . . . . . . . . . . . . . . Timer 2 Compare and Compare Mode Registers 37. . . . . . . . . . . . . . . . . . . . . . . . . . Timer 2 Compare Mode Register (T2CM)37. . . . . . . . . . . . . . . . . . . . . . . . . . . . . . . Timer 2 COmpare Register 1 (T2CO1)37. . . . . . . . . . . . . . . . . . . . . . . . . . . . . . . . . Timer 2 COmpare Register 2 (T2CO2) Byte Write 37. . . . . . . . . . . . . . . . . . . . . . . .3.3.3Synchronous Serial Interface (SSI)38. . . . . . . . . . . . . . . . . . . . . . . . . . . . . . . . . . . . .SSI Peripheral Configuration 38. . . . . . . . . . . . . . . . . . . . . . . . . . . . . . . . . . . . . . . . . General SSI Operation 38. . . . . . . . . . . . . . . . . . . . . . . . . . . . . . . . . . . . . . . . . . . . . . 8-bit Synchronous Mode 39. . . . . . . . . . . . . . . . . . . . . . . . . . . . . . . . . . . . . . . . . . . . . 9-bit Shift Mode (I2C compatible)41. . . . . . . . . . . . . . . . . . . . . . . . . . . . . . . . . . . . . 8-bit Pseudo I2C Mode 42. . . . . . . . . . . . . . . . . . . . . . . . . . . . . . . . . . . . . . . . . . . . . . I2C Bus Protocol 42. . . . . . . . . . . . . . . . . . . . . . . . . . . . . . . . . . . . . . . . . . . . . . . . . . . SSI Interrupt 43. . . . . . . . . . . . . . . . . . . . . . . . . . . . . . . . . . . . . . . . . . . . . . . . . . . . . . Modulation 43. . . . . . . . . . . . . . . . . . . . . . . . . . . . . . . . . . . . . . . . . . . . . . . . . . . . . . . Internal 2-Wire Multi-Chip Link 44. . . . . . . . . . . . . . . . . . . . . . . . . . . . . . . . . . . . . . Serial Interface Registers 45. . . . . . . . . . . . . . . . . . . . . . . . . . . . . . . . . . . . . . . . . . . . Serial Interface Control Register 1 (SIC1)45. . . . . . . . . . . . . . . . . . . . . . . . . . . . . . . Serial Interface Control Register 2 (SIC2)45. . . . . . . . . . . . . . . . . . . . . . . . . . . . . . . Serial Interface Status and Control Register (SISC)46. . . . . . . . . . . . . . . . . . . . . . . Serial Transmit Buffer (STB) – Byte Write 46. . . . . . . . . . . . . . . . . . . . . . . . . . . . . . Serial Receive Buffer (SRB) – Byte Read 47. . . . . . . . . . . . . . . . . . . . . . . . . . . . . . .3.3.4Combination Modes 47. . . . . . . . . . . . . . . . . . . . . . . . . . . . . . . . . . . . . . . . . . . . . . . .Combination Mode Timer 2 and SSI 47. . . . . . . . . . . . . . . . . . . . . . . . . . . . . . . . . . .4M44C89050. . . . . . . . . . . . . . . . . . . . . . . . . . . . . . . . . . . . . . . . . . . . . . . . . . . . . . . . . . . . . . . . . . . . . . . . 4.1U505M EEPROM 50. . . . . . . . . . . . . . . . . . . . . . . . . . . . . . . . . . . . . . . . . . . . . . . . . . . . . . . . . . .4.1.1Serial Interface 51. . . . . . . . . . . . . . . . . . . . . . . . . . . . . . . . . . . . . . . . . . . . . . . . . . . .Serial Protocol 51. . . . . . . . . . . . . . . . . . . . . . . . . . . . . . . . . . . . . . . . . . . . . . . . . . . . .4.1.2EEPROM 52. . . . . . . . . . . . . . . . . . . . . . . . . . . . . . . . . . . . . . . . . . . . . . . . . . . . . . . . .EEPROM – Operating Modes 52. . . . . . . . . . . . . . . . . . . . . . . . . . . . . . . . . . . . . . . . Write Operations 52. . . . . . . . . . . . . . . . . . . . . . . . . . . . . . . . . . . . . . . . . . . . . . . . . . . Read Operations 53. . . . . . . . . . . . . . . . . . . . . . . . . . . . . . . . . . . . . . . . . . . . . . . . . . . Initialization after a Reset Condition 53. . . . . . . . . . . . . . . . . . . . . . . . . . . . . . . . . . .5Electrical Characteristics 54. . . . . . . . . . . . . . . . . . . . . . . . . . . . . . . . . . . . . . . . . . . . . . . . . . . . . . . . . . 5.1Absolute Maximum Ratings 54. . . . . . . . . . . . . . . . . . . . . . . . . . . . . . . . . . . . . . . . . . . . . . . . . . . 5.2DC Operating Characteristics 54. . . . . . . . . . . . . . . . . . . . . . . . . . . . . . . . . . . . . . . . . . . . . . . . . . 5.3AC Characteristics 56. . . . . . . . . . . . . . . . . . . . . . . . . . . . . . . . . . . . . . . . . . . . . . . . . . . . . . . . . . 6Package Information 61. . . . . . . . . . . . . . . . . . . . . . . . . . . . . . . . . . . . . . . . . . . . . . . . . . . . . . . . . . . . . . 7Ordering Information 62. . . . . . . . . . . . . . . . . . . . . . . . . . . . . . . . . . . . . . . . . . . . . . . . . . . . . . . . . . . . .元器件交易网M44C890-HM44C090-H Rev.A3, 14-Dec-01 5 (63)1IntroductionThe M44C090-H / M44C890-H are members of Atmelsfamily of 4-bit single-chip microcontrollers. They con-tain ROM, RAM, parallel I/O ports, one 8-bitprogrammable multifunction timer/counter, voltage su-pervisor, interval timer with watchdog function and a sophisticated on-chip clock generation with integrated RC-, 32-kHz crystal- and 4-MHz crystal-oscillators.Table 2 provides an overview of the available variants.2MARC4 Architecture2.1General DescriptionThe MARC4 microcontroller consists of an advanced stack-based, 4-bit CPU core and on-chip peripherals. The CPU is based on the HARV ARD architecture with physically separate program memory (ROM) and data memory (RAM). Three independent buses, the instruction bus, the memory bus and the I/O bus, are used for parallel communication between ROM, RAM andperipherals. This enhances program execution speed by allowing both instruction prefetching, and a simultaneous communication to the on-chip peripheral circuitry. The extremely powerful integrated interrupt controller with associated eight prioritized interrupt levels supports fast and efficient processing of hardware events. The MARC4is designed for the high-level programming language qFORTH. The core includes both, an expression and a return stack. This architecture enables high-level language programming without any loss of efficiency or code density.94 8973Figure 3. MARC4 core元器件交易网M44C890-HM44C090-H Rev.A3, 14-Dec-016 (63)2.2Components of MARC4 Core7FFFh1FFh 000h1F0h 1F8h 010h 018h 000h008h 020h 1E8h 1E0hS C A L L a d d r e s s e s140h 180h 040h0C0h 008h $AUTOSLEEP$RESETINT0INT1INT2INT3INT4INT5INT6INT71E0h 1C0h 100h 080hZ ero page000h13391Figure 4. ROM map of M44C090-HThe core contains ROM, RAM, ALU, program counter,RAM address registers, instruction decoder and interrupt controller. The following sections describe each functional block in more detail:2.2.1ROMThe program memory (ROM) is mask programmed with the customer application program during the fabrication of the microcontroller. The ROM is addressed by a 12–bit wide program counter, thus predefining a maximum program bank size of 2 Kbytes. An additional 1 Kbyte of ROM exists which is reserved for quality control self –test software The lowest user ROM address segment is taken up by a 512 byte zero page which contains predefined start addresses for interrupt service routines and special subroutines accessible with single byte instructions (SCALL).The corresponding memory map is shown in figure 4.Look-up tables of constants can also be held in ROM and are accessed via the MARC4’s built-in TABLE instruction.2.2.2RAMThe M44C090-H / M44C890-H contains 256 x 4-bit wide static random access memory (RAM). It is used for theexpression stack, the return stack and data memory for variables and arrays. The RAM is addressed by any of the four 8-bit wide RAM address registers SP, RP , X and Y .Expression StackThe 4-bit wide expression stack is addressed with the expression stack pointer (SP). All arithmetic, I/O and memory reference operations take their operands from,and return their results to the expression stack. The MARC4 performs the operations with the top of stack items (TOS and TOS –1). The TOS register contains the top element of the expression stack and works in the same way as an accumulator. This stack is also used for passing parameters between subroutines and as a scratch pad area for temporary storage of data.Return StackThe 12-bit wide return stack is addressed by the return stack pointer (RP). It is used for storing return addresses of subroutines, interrupt routines and for keeping loop index counts. The return stack can also be used as a temporary storage area.The MARC4 instruction set supports the exchange of data between the top elements of the expression stack and the return stack. The two stacks within the RAM have a user definable location and maximum depth.元器件交易网M44C890-HM44C090-H Rev.A3, 14-Dec-017 (63)RAMX YR A M a d d r es s r e g i s t e r :(192 x 4-bit)Global variablesExpression stackReturn stackv 13392Figure 5. RAM map2.2.3RegistersThe MARC4 controller has seven programmable registers and one condition code register. They are shown in the following programming model.Program Counter (PC)The program counter (PC) is a 12-bit register which contains the address of the next instruction to be fetched from the ROM. Instructions currently being executed are decoded in the instruction decoder to determine the internal micro-operations. For linear code (no calls or branches) the program counter is incremented with every instruction cycle. If a branch-, call-, return-instruction or an interrupt is executed, the program counter is loaded with a new address. The program counter is also used with the TABLE instruction to fetch 8-bit wide ROM constants.PCProgram counterReturn stack pointer Expression stack pointerRAM address register (X)RAM address register (Y)Top of stack registerCondition code registerCarry / borrowBranch Interrupt enable ReservedFigure 6. Programming model元器件交易网M44C890-HM44C090-H Rev.A3, 14-Dec-018 (63)RAM Address RegistersThe RAM is addressed with the four 8-bit wide RAM address registers: SP, RP, X and Y. These registers allow access to any of the 256 RAM nibbles.Expression Stack Pointer (SP)The stack pointer (SP) contains the address of the next-to-top 4-bit item (TOS –1) of the expression stack. The pointer is automatically pre-incremented if a nibble is moved onto the stack or post-decremented if a nibble is removed from the stack. Every post-decrement operation moves the item (TOS –1) to the TOS register before the SP is decremented. After a reset the stack pointer has to be initialized with ” >SP S0 ” to allocate the start address of the expression stack area.Return Stack Pointer (RP)The return stack pointer points to the top element of the 12-bit wide return stack. The pointer automatically pre-increments if an element is moved onto the stack, or it post-decrements if an element is removed from the stack.The return stack pointer increments and decrements in steps of 4. This means that every time a 12-bit element is stacked, a 4-bit RAM location is left unwritten. This location is used by the qFORTH compiler to allocate 4-bit variables. After a reset the return stack pointer has to be initialized via ”>RP FCh ”.RAM Address Registers (X and Y)The X and Y registers are used to address any 4-bit item in the RAM. A fetch operation moves the addressed nibble onto the TOS. A store operation moves the TOS to the addressed RAM location. By using either the pre –increment or post –decrement addressing mode arrays in the RAM can be compared, filled or moved.Top Of Stack (TOS)The top of stack register is the accumulator of the MARC4. All arithmetic/logic, memory reference and I/O operations use this register. The TOS register receives data from the ALU, ROM, RAM or I/O bus.Condition Code Register (CCR)The 4-bit wide condition code register contains the branch, the carry and the interrupt enable flag. These bits indicate the current state of the CPU. The CCR flags are set or reset by ALU operations. The instructions SET_BCF, TOG_BF, CCR! and DI allow direct manipulation of the condition code register.Carry/Borrow (C)The carry/borrow flag indicates that the borrowing or carrying out of arithmetic logic unit (ALU) occurred during the last arithmetic operation. During shift and rotate operations, this bit is used as a fifth bit. Boolean operations have no affect on the C-flag.Branch (B)The branch flag controls the conditional program branching. Should the branch flag have been set by a previous instruction a conditional branch will cause a jump. This flag is affected by arithmetic, logic, shift, and rotate operations.Interrupt Enable (I)The interrupt enable flag globally enables or disables the triggering of all interrupt routines with the exception of the non-maskable reset. After a reset or on executing the DI instruction, the interrupt enable flag is reset thus disabling all interrupts. The core will not accept any further interrupt requests until the interrupt enable flag has been set again by either executing an EI, RTI or SLEEP instruction.元器件交易网M44C890-HM44C090-H Rev.A3, 14-Dec-019 (63)2.2.4ALU94 8977Figure 7. ALU zero-address operationsThe 4-bit ALU performs all the arithmetic, logical, shiftand rotate operations with the top two elements of the expression stack (TOS and TOS –1) and returns the result to the TOS. The ALU operations affect the carry/borrow and branch flag in the condition code register (CCR).2.2.5I/O BusThe I/O ports and the registers of the peripheral modules are I/O mapped. All communication between the core and the on-chip peripherals takes place via the I/O bus and the associated I/O control. With the MARC4 IN and OUT instructions the I/O bus allows a direct read or write access to one of the 16 primary I/O addresses. More about the I/O access to the on-chip peripherals is described in the section ”Peripheral Modules ”. The I/O bus is internal and is not accessible by the customer on the final micro-controller device, but it is used as the interface for the MARC4 emulation (see also the section ”Emulation ”).2.2.6Instruction SetThe MARC4 instruction set is optimized for the high level programming language qFORTH. Many MARC4instructions are qFORTH words. This enables the compiler to generate a fast and compact program code.The CPU has an instruction pipeline allowing the controller to prefetch an instruction from ROM at the same time as the present instruction is being executed.The MARC4 is a zero address machine, the instructions containing only the operation to be performed and no source or destination address fields. The operations are implicitly performed on the data placed on the stack.There are one and two byte instructions which are executed within 1 to 4 machine cycles. A MARC4machine cycle is made up of two system clock cycles (SYSCL). Most of the instructions are only one byte long and are executed in a single machine cycle. For more information refer to the ”MARC4 Programmer ’s Guide ”.2.2.7Interrupt StructureThe MARC4 can handle interrupts with eight different priority levels. They can be generated from the internal and external interrupt sources or by a software interrupt from the CPU itself. Each interrupt level has a hard-wired priority and an associated vector for the service routine in the ROM (see table 2). The programmer can postpone the processing of interrupts by resetting the interrupt enable flag (I) in the CCR. An interrupt occurrence will still be registered, but the interrupt routine only started after the I flag is set. All interrupts can be masked, and the priority individually software configured by programming the appropriate control register of the interrupting module.(see section ”Peripheral Modules ”).元器件交易网M44C890-HM44C090-H Rev.A3, 14-Dec-0110 (63)76543210P r i o r i t y l e v e lTime94 8978Figure 8. Interrupt handlingInterrupt ProcessingFor processing the eight interrupt levels, the MARC4includes an interrupt controller with two 8-bit wide ”interrupt pending ” and ”interrupt active ” registers. The interrupt controller samples all interrupt requests during every non-I/O instruction cycle and latches these in the interrupt pending register. If no higher priority interrupt is present in the interrupt active register, it signals the CPU to interrupt the current program execution. If the interrupt enable bit is set, the processor enters an interrupt acknowledge cycle. During this cycle a short call (SCALL) instruction to the service routine is executed and the current PC is saved on the return stack. An interrupt service routine is completed with the RTI instruction. This instruction sets the interrupt enable flag,resets the corresponding bits in the interrupt pending/active register and fetches the return address from the return stack to the program counter. When the interrupt enable flag is reset (triggering of interrupt routines are disabled), the execution of new interruptservice routines is inhibited but not the logging of the interrupt requests in the interrupt pending register. The execution of the interrupt is delayed until the interrupt enable flag is set again. Note that interrupts are only lost if an interrupt request occurs while the corresponding bit in the pending register is still set (i.e., the interrupt service routine is not yet finished).It should also be noted that automatic stacking of the RBR is not carried out by the hardware and so if ROM banking is used, the RBR must be stacked on the expression stack by the application program and restored before the RTI.After a master reset (power-on, brown-out or watchdog reset), the interrupt enable flag and the interrupt pending and interrupt active register are all reset.Interrupt LatencyThe interrupt latency is the time from the occurrence of the interrupt to the interrupt service routine being activated. In MARC4 this is extremely short (taking between 3 to 5 machine cycles depending on the state of the core).元器件交易网Rev.A3, 14-Dec-0111 (63)Software InterruptsThe programmer can generate interrupts by using the software interrupt instruction (SWI) which is supported in qFORTH by predefined macros named SWI0...SWI7.The software triggered interrupt operates exactly like any hardware triggered interrupt. The SWI instruction takes the top two elements from the expression stack and writes the corresponding bits via the I/O bus to the interrupt pending register. Therefore, by using the SWI instruction,interrupts can be re-prioritized or lower priority processes scheduled for later execution.Hardware InterruptsIn the M44C090-H, there are eleven hardware interrupt sources with seven different levels. Each source can be masked individually by mask bits in the corresponding control registers. An overview of the possible hardware configurations is shown in table 4.2.3Master ResetThe master reset forces the CPU into a well-defined condition. It is unmaskable and is activated independent of the current program state. It can be triggered by either initial supply power-up, a short collapse of the power sup-ply, brown-out detection circuitry, watchdog time-out, or an external input clock supervisor stage (see figure 9). A master reset activation will reset the interrupt enable flag,the interrupt pending register and the interrupt active register. During the power-on reset phase the I/O bus con-trol signals are set to ’reset mode ’ thereby initializing all on-chip peripherals. All bidirectional ports are set to input mode. Attention: During any reset phase, the BP20/NTE input is driven towards V DD by a strong pull-up transistor.Releasing the reset results in a short call instruction (opcode C1h) to the ROM address 008h. This activates the initialization routine $RESET which in turn has to initialize all necessary RAM variables, stack pointers and peripheral configuration registers (see table 7).Rev.A3, 14-Dec-0112 (63)V resetDD SS DD SS 13752Figure 9. Reset configuration2.3.1Power-on Reset and Brown-out DetectionThe M44C090-H / M44C890-H has a fully integrated power-on reset and brown-out detection circuitry. For re-set generation no external components are needed .These circuits ensure that the core is held in the reset state until the minimum operating supply voltage has beenreached. A reset condition will also be generated should the supply voltage drop momentarily below the minimum operating level except when a power down mode is activated (the core is in SLEEP mode and the peripheral clock is stopped). In this power-down mode the brown-out detection is disabled.Two values for the brown-out voltage threshold areprogrammable via the BOT-bit in the SC-register.V t d = 1.5 ms (typically)13753BOT = 1, low brown-out voltage threshold. (1.7 V) is reset value.BOT = 0, high brown-out voltage threshold (1.9 V).Figure 10. Brown-out detectionRev.A3, 14-Dec-0113 (63)A power-on reset pulse is generated by a V DD rise across the default BOT voltage level (1.7 V). A brown-out reset pulse is generated when V DD falls below the brown-out voltage threshold. Two values for the brown-out voltage threshold are programmable via the BOT-bit in the SC-register. When the controller runs in the upper supply voltage range with a high system clock frequency, the high threshold must be used. When it runs with a lower system clock frequency, the low threshold and a wider supply voltage range may be chosen. For further details,see the electrical specification and the SC-register description for BOT programming.2.3.2Watchdog ResetThe watchdog ’s function can be enabled at the WDC-reg-ister and triggers a reset with every watchdog counter overflow. To supress the watchdog reset, the watchdog counter must be regularly reset by reading the watchdog register address (CWD).The CPU reacts in exactly the same manner as a reset stimulus from any of the above sources.2.3.3External Clock SupervisorThe external input clock supervisor function can be enabled if the external input clock is selected within the CM- and SC-registers of the clock module.The CPU reacts in exactly the same manner as a reset stimulus from any of the above sources.2.4Voltage MonitorThe voltage monitor consists of a comparator with internal voltage reference. It is used to supervise the supply voltage or an external voltage at the VMI-pin. The comparator for the supply voltage has three internal programmable thresholds one lower threshold (2.2 V),one middle threshold (2.6 V). and one higher threshold (3.0 V). For external voltages at the VMI-pin, the comparator threshold is set to V BG = 1.3 V . The VMS-bit indicates if the supervised voltage is below (VMS = 0) or above (VMS = 1) this threshold. An interrupt can be generated when the VMS-bit is set or reset to detect a rising or falling slope. A voltage monitor interrupt (INT7)is enabled when the interrupt mask bit (VIM) is reset in the VMC-register.BP41/VMIFigure 11. V oltage monitor。