铸造残余应力的测定实验报告
实验一(铸造内应力的形成及测量分析)

实验一 铸造内应力的形成及测量分析1、实验目的1)了解坩锅炉熔炼原理及工艺过程。
2)测定应力框产生的铸造热应力。
3)分析应力框产生内应力的原因、应力对铸件质量的影响。
2、实验原理根据“T ”形杆冷却过程中形成“粗杆受拉、细杆受压”的原理,设计如图1所示的应力框。
合金浇铸、冷却后,会在应力框的粗、细杆中形成不同性质的应力。
将粗杆锯断,将使应力约束条件释放,致使应力杆的尺寸发生变化。
测量应力杆的尺寸变化大小,根据虎克定律,便可计算出应力框中应力杆的大小。
应力框尺寸如图1所示,采用潮模砂造型,在电阻坩锅炉中熔炼ZL101合金,浇铸应力框。
3、实验步骤及方法1)手工造型应力框铸型。
2)坩锅电阻炉中熔炼ZL101 合金。
3)浇铸应力框。
4)冷却后清理。
5)将中间的粗杆打两点标志,测量两点距离L 0,然后将中间杆锯断,再测量两点的距离L 1。
6)根据测量结果,计算杆中的铸造应力。
σ= E ε = E (L 1 – L 0)/ L ( N/mm 2)式中: E --- 弹性模量,ZL101 为:72.4×103 N/mm 2;L ---- 中间杆的长度 mm 。
4、实验报告1)画出应力框图,标出细杆和粗杆中存在的铸造应力性质(拉应力为+,压应力为-)。
2)测量、计算铸造应力。
测量结果:L 0、L 1、L ;计算结果:σ3)分析应力框产生的原因和铸造应力对铸件质量的影响。
实测数据:L 0 = 80mm L 1 = 80.5mm L = 300mm图1铸造应力框。
发动机缸体切割法残余应力测试试验
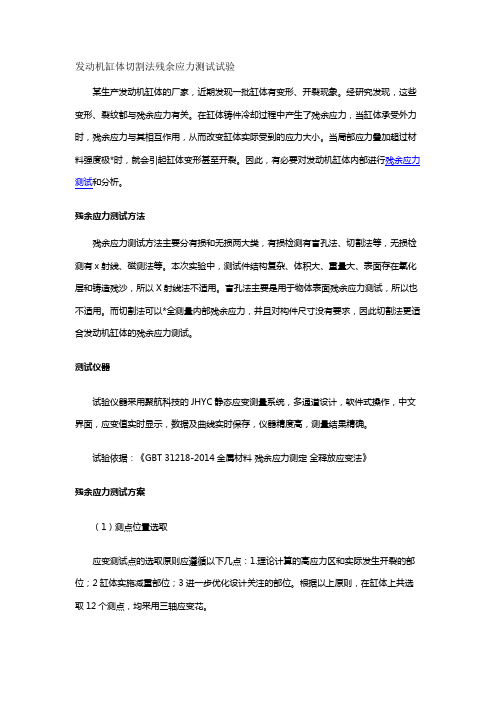
发动机缸体切割法残余应力测试试验某生产发动机缸体的厂家,近期发现一批缸体有变形、开裂现象。
经研究发现,这些变形、裂纹都与残余应力有关。
在缸体铸件冷却过程中产生了残余应力,当缸体承受外力时,残余应力与其相互作用,从而改变缸体实际受到的应力大小。
当局部应力叠加超过材料强度极*时,就会引起缸体变形甚至开裂。
因此,有必要对发动机缸体内部进行残余应力测试和分析。
残余应力测试方法残余应力测试方法主要分有损和无损两大类,有损检测有盲孔法、切割法等,无损检测有x射线、磁测法等。
本次实验中,测试件结构复杂、体积大、重量大、表面存在氧化层和铸造残沙,所以X射线法不适用。
盲孔法主要是用于物体表面残余应力测试,所以也不适用。
而切割法可以*全测量内部残余应力,并且对构件尺寸没有要求,因此切割法更适合发动机缸体的残余应力测试。
测试仪器试验仪器采用聚航科技的JHYC静态应变测量系统,多通道设计,软件式操作,中文界面,应变值实时显示,数据及曲线实时保存,仪器精度高,测量结果精确。
试验依据:《GBT 31218-2014金属材料残余应力测定全释放应变法》残余应力测试方案(1)测点位置选取应变测试点的选取原则应遵循以下几点:1.理论计算的高应力区和实际发生开裂的部位;2缸体实施减重部位;3进一步优化设计关注的部位。
根据以上原则,在缸体上共选取12个测点,均采用三轴应变花。
(2)应变片的粘贴及连接:将各个测点位置进行打磨清洁,粘贴应变片及接线端子。
(3)初始值记录:完成贴片后,将应变片按照1/4桥接入JHYC静态应变仪,查看数据,待数据稳定后记录缸体应变初始值。
(4)测量及缸体切割:拆除测量线缆,依据切割方案将缸体进行切割,沿着各测点位置将应变片尽可能割成小块,切割过程中注意应变片的保护。
(5)终值记录:切割完成后,将切割下来的试块上的应变片按照1/4桥接入应变仪,查看数据,待数据稳定后记录缸体应变终值。
测试结果及计算缸体使用材料是HT250,其弹性模量为120GPa,泊松比为0.3。
实验5 材料表面残余应力的测量

一、实验目的
1.了解金属材料残余应力的种类。
2.掌握 X 射线衍射法测量金属材料表面残余应力的原理和实验方法。
二、实验原理概述
零件或材料内部的应力状态对受力构件的使用寿命有重要影响和直接作用。所谓的残余
应力是,即使构件不受外力作院用,其内部仍然可能存在着不均匀而且在自身范围内平衡的应
中 四、实验步骤
与工
学
1.对样品作 2θ =90°-140°范围的全谱扫描。
料科
2.选择一个峰形较好,衍射强度较高的高角度衍射学峰材,分别取ψ=0°,15°,30°和
45°用慢速度(1°/min)扫描,每次扫描的结果保南存大为不同的文件(设为 A,B,C,D)。
3.用 Jade 打开各个扫描文件,对衍射峰按中抛物线进行拟合,计算峰位。
科学 联动。在 2θ 处附近扫描得出指定的 HKL 衍射线的图谱。当 ψ≠0 时,将衍射仪测角台的 θ-2θ
材料 联动分开。先使样品顺时针转过一个规定的 ψ 角后,而探测器仍处于 0。然后联上 θ-2θ 联
学 动装置在 2θ 处附近进行扫描,得出同一条 HKL 衍射线的图谱。
院
南大 最后,作 2θ-sin2ψ的关系直线,最后按应力表达σ=K·∆2θ/∆sin2ψ= K程·M学求出应力值。
该曲线的斜率就是式 13 的程M学值了。最后,试样表面x方向分量就能按式 14 求出。
三、实验方法
与工
学
在使用衍射科仪测量应力时,试样与探测器 θ-2θ 关系联动,属于固定 ψ 法。通常 ψ 等于
料
院 0°、15°、学3材0°、45°测量数次。 与工程学 处中,南此当大时ψ入=0射时线,及与衍常射规线使相用对衍于射样仪品的表方面法法一线样呈,将对探称测放器射(配记置数。管然)放后在使理试论样算与出探的测衍器射按角θ-22θθ
灰口铸铁件残余应力的测量与消除

处理等)都会产生不同的残余应力。外力或温度变化 引起 的不 均匀 塑性 变形是 产 生残余 应力 的主要原 因圆 。 对于铸铁件 , 残余应力是在铸造冷却过程中,由于受 热应 力 和构 件形 状尺 寸及铸 造 技术等 因素的影 响 而引 起 的结 构应 力 以及 材 料 的组 织 和成分 引起 的组 织应 力
表2 灰 口铸铁试样残余应力测试结果
t - b ! 兰 二 £2 m 日 二 !
8 go o-8 o o
() 1
T be2T s rsl fge atr nsmpe eiu l tes a l et eut o ryc s io s a ls rs a rs d s
5 。 0 一 鲁( ) )+(2 4。 0一 9。 一 占 去 一 鲁( ) o一占9。2(2占4口 o一 ) + 。 o)+ 5 o 。 E
o一 9 。 D o
大 程度 的下 降 。这说 明砂 型保 温工 艺 和退 火 处理 一 样 也 能 有效 地 降低 铸 铁 件 的残 余 应力 。需 要 指 出 的是 , H 4 B 试样 的残余 应力 值 (99 a  ̄H 4 3.3MP ) ,T低很 多。 8
察 和力 学性 能试验 ,探 讨退 火 和砂型 保温 工艺 消除 残
( 余应力测试方法 :钻孔应变释放、) 钱 法 )的要求 , 首先
将试 样被 测部 位表 面 打磨 ,使粗 糙度 达 到2 , .l 2a m,然 后在清 理后 的测 点位置贴 上T 101 . . 变花 ( J2—. 1 应 5 5 电 阻 值 15Q,灵 敏 系 数 20),并 把 应 变 花 导 线 和 1 . 8 T 36 恒流 式静 态 电 阻应 变仪 连 接到 一起 调 平 衡后 , S8 1
灰铸铁制动盘铸件残余应力的测定
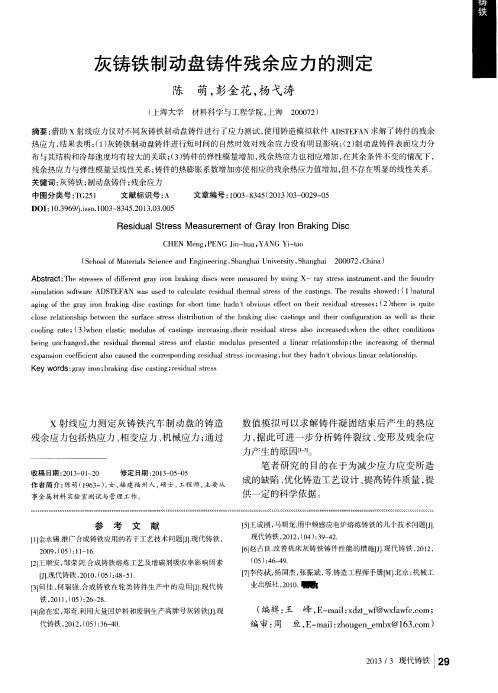
DOI : 1 0 . 3 9 6 9  ̄ . i s s n . 1 0 0 3 — 8 3 4 5 . 2 0 1 3 . 0 3 . 0 0 5 Re s i d u a l St r e s s Me a s u r e me n t o f G r a y l r o n Br a k i n g Di s c
s i mu l a t i o n s o f t w a r e A D S T E F A N w a s u s e d t o c a l c u l a t e r e s i d u a l t h e r ma l s t r e s s o f t h e c a s t i n g s . T h e r e s u l t s s h o w e d : ( 1 ) n a t u r a l
c l o s e r e l a t i o n s h i p b e t we e n t h e s u r f a c e s t r e s s d i s t r i b u t i o n o f t h e b r a k i n g d i s c c a s t i n g s a n d t h e i r c o n f i g u r a t i o n a s we l l a s t h e i r
a g i n g o f t h e g r a y i r o n b r a k i n g d i s c c a s t i n g s f o r s h o r t t i m e h a d n ' t o b v i o u s e f f e c t o n t h e i r r e s i d u a l s t r e s s e s ; ( 2 ) t h e r e i s q u i t e
铸造件切削加工残余应力及变形机理研究

收稿日期 : 2009 - 08 - 05 作者简介 : 刘书群 ( 1963 —) ,男 ,河南南阳人 ,河南职业技术学院机械电子工程系副教授 ,主要从事铸造及计算机辅助设计的研究和教学工作 , ( E - mail) lixia8523@163. com。
・22・
2010 年第 3 期
・ 设计与研究 ・
系是金属切削仿真是否成功的关键技术之一 。 大量实验 证明 , 前刀面上的应力分布是不均匀的 , 在前刀面上可 以分为两个工作区 :滑动区和粘结区 。 在滑动区 , 由于正 应力小所以摩擦较小 , 属于外摩擦 。 而在粘结区 , 由于刀 具前刀面和切屑间的高温高压 , 使得 前刀面和切屑之间变为内摩擦。 内摩 擦实际上就是金属内部的剪切滑移 , 它与材料的流动应力特性以及粘结面 积大小有关 , 所以其变化规律与外摩 擦不同。由式确定 , 第一项是流 动应力受应变硬化影响时的应力增量 , 第二项是流动 应力受温度和应变硬化同时作用而引起的表观应力增 量 , 第三项是流动应力受应变速率和应变硬化同时作 用的影晌而引起的表观应力增量 。
D
ep
金属切削过程虽然是在室温下进行的 , 但局部切 削变形区的温度却远远高于室温 。 因此 ,受切削温度的 影响 ,金属切削加工实际上是在热加工的范畴中进行 的 ,在局部高温下完成了切削层材料向切屑转变 。 故在 进行切削过程数值建模的设计时 , 应考虑切削过程中 工件材料温度一速度效应及物理一化学参量的变化对 切削过程物理现象的影响 。 本文利用 John son 2 Cook 材 料模型 ,该模型是一个能反映应变率强化效应和温升 软化效应的模型 ,能很好的模拟材料的应力流动特性 。
( 10 )
5f 5H 其中 , A = p 5H 5 ε 势面及硬化参数 。
铸钢焊接件残余应力测试
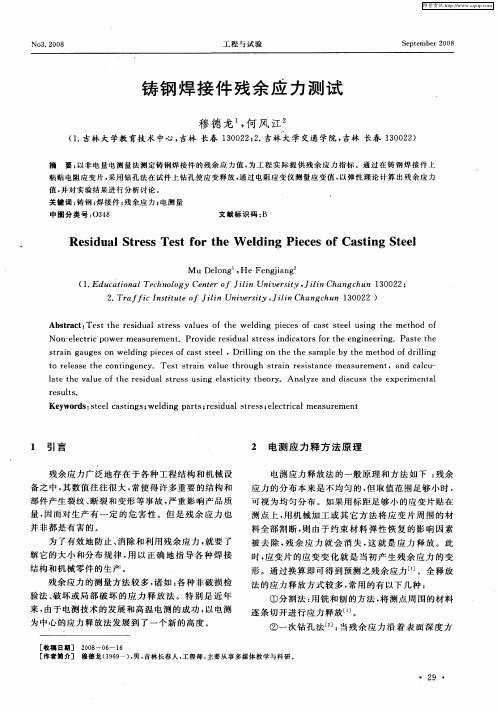
●
关 键 词 : 钢 ; 接件 ; 余 应 力 ; 测 量 铸 焊 残 电
中 图 分 类 号 : 4 03 8 文 献 标 识 码 : B
Re i u lSt e s Te t f r t e W e di e e f Ca tn t e s d a r s s o h l ng Pi c s o s i g S e l
Ab t a t Te tt e i a t e s v l s o he we d ng i c s of c s s e l usn he me h d of s r c : s he r sdu ls r s a ue f t l i p e e a t t e i g t t o Non ee t i owe e s e e t — lc rc p rm a ur m n .Pr vi e i ua te si i a or o he e ne rng.Pa t h o de r sd ls r s nd c t sf rt ngi e i set e s r i a e n wedi g p e e fc s t e t an g ug s o l n i c s o a ts e l,Drli g on t he s m p e by t e me ho fdrli g iln he t a l h t d o iln t e e s h on i e c . Te t s r i a ue t ou t a n r s s a e me s e e t nd c l u o r la e t e c tng n y s t an v l hr gh s r i e it nc a ur m n ,a a c —
l t he v l e oft e r s d ls r s i g ea tc t he r a e t a u h e i ua t e s usn l s iiy t o y. A n l z n ic s t xp rm e ta a y e a d d s us he e e i r l t
铸造应力

TSINGHUA UNIVERSITY
⑴ 热应力 Thermal Stress
1杆:拉应力 Tensile Stress
2杆:压应力: Compression Stress
⑵ 机械应力 Contraction Stress
TSINGHUA UNIVERSITY
• 将上述2个应力框铸件的粗杆小凸台上成锐角相交的四个 棱柱面锉平;
• 用卡尺测量小凸台长度L0;在小凸台A-A截面处从1、2、 3三面依次锯开粗杆(见图14-1),注意各锯口应在垂直 于杆轴线的同一平面内。
• 锯至粗杆断裂后,再测量小凸台长度L1,测量结果填入 表14-1;
铸件的凝固原则 Solidification Principle
顺序凝固原则 Directional Solidification:
在铸件上从远离冒口或浇 口到冒口或浇口之间建 立一个递增的温度梯度
TSINGHUA UNIVERSITY
• 同时凝固原则:
Simultaneously Solidification :
– 减小铸件冷却过程中的温度差
• 同时凝固 Simultaneously Solidifying
– 减小机械阻碍:Reduction of Restraint
• 改善铸型和砂芯的溃散性
– 去应力退火:Relief Annealing
– 改进铸件结构,避免形成较大应力和应力集 中
TSINGHUA UNIVERSITY
铸件结构上各部分之间没 有温差或温差尽量小
TSINGHUA UNIVERSITY
铸件凝固过程的类型
Solidification Style
残余应力检测
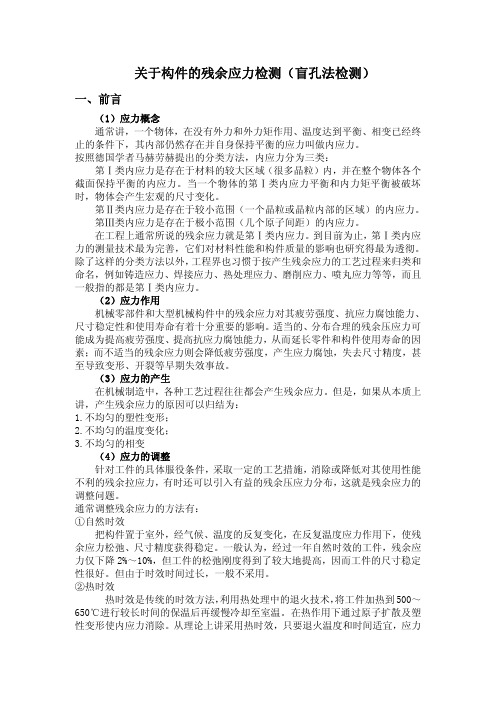
关于构件的残余应力检测(盲孔法检测)一、前言(1)应力概念通常讲,一个物体,在没有外力和外力矩作用、温度达到平衡、相变已经终止的条件下,其内部仍然存在并自身保持平衡的应力叫做内应力。
按照德国学者马赫劳赫提出的分类方法,内应力分为三类:第Ⅰ类内应力是存在于材料的较大区域(很多晶粒)内,并在整个物体各个截面保持平衡的内应力。
当一个物体的第Ⅰ类内应力平衡和内力矩平衡被破坏时,物体会产生宏观的尺寸变化。
第Ⅱ类内应力是存在于较小范围(一个晶粒或晶粒内部的区域)的内应力。
第Ⅲ类内应力是存在于极小范围(几个原子间距)的内应力。
在工程上通常所说的残余应力就是第Ⅰ类内应力。
到目前为止,第Ⅰ类内应力的测量技术最为完善,它们对材料性能和构件质量的影响也研究得最为透彻。
除了这样的分类方法以外,工程界也习惯于按产生残余应力的工艺过程来归类和命名,例如铸造应力、焊接应力、热处理应力、磨削应力、喷丸应力等等,而且一般指的都是第Ⅰ类内应力。
(2)应力作用机械零部件和大型机械构件中的残余应力对其疲劳强度、抗应力腐蚀能力、尺寸稳定性和使用寿命有着十分重要的影响。
适当的、分布合理的残余压应力可能成为提高疲劳强度、提高抗应力腐蚀能力,从而延长零件和构件使用寿命的因素;而不适当的残余应力则会降低疲劳强度,产生应力腐蚀,失去尺寸精度,甚至导致变形、开裂等早期失效事故。
(3)应力的产生在机械制造中,各种工艺过程往往都会产生残余应力。
但是,如果从本质上讲,产生残余应力的原因可以归结为:1.不均匀的塑性变形;2.不均匀的温度变化;3.不均匀的相变(4)应力的调整针对工件的具体服役条件,采取一定的工艺措施,消除或降低对其使用性能不利的残余拉应力,有时还可以引入有益的残余压应力分布,这就是残余应力的调整问题。
通常调整残余应力的方法有:①自然时效把构件置于室外,经气候、温度的反复变化,在反复温度应力作用下,使残余应力松弛、尺寸精度获得稳定。
一般认为,经过一年自然时效的工件,残余应力仅下降2%~10%,但工件的松弛刚度得到了较大地提高,因而工件的尺寸稳定性很好。
残余应力分析报告
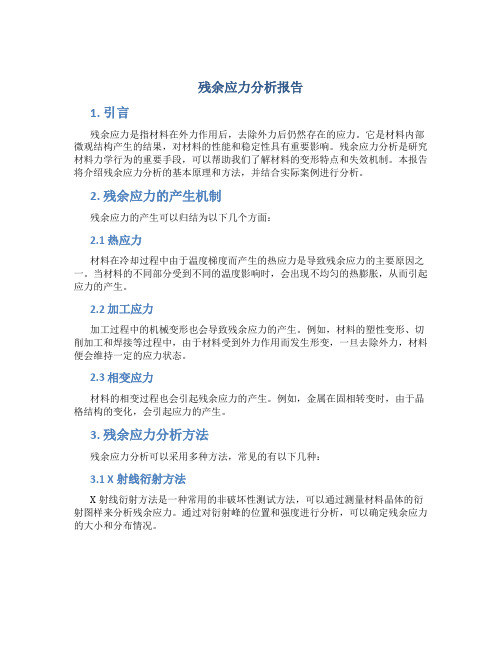
残余应力分析报告1. 引言残余应力是指材料在外力作用后,去除外力后仍然存在的应力。
它是材料内部微观结构产生的结果,对材料的性能和稳定性具有重要影响。
残余应力分析是研究材料力学行为的重要手段,可以帮助我们了解材料的变形特点和失效机制。
本报告将介绍残余应力分析的基本原理和方法,并结合实际案例进行分析。
2. 残余应力的产生机制残余应力的产生可以归结为以下几个方面:2.1 热应力材料在冷却过程中由于温度梯度而产生的热应力是导致残余应力的主要原因之一。
当材料的不同部分受到不同的温度影响时,会出现不均匀的热膨胀,从而引起应力的产生。
2.2 加工应力加工过程中的机械变形也会导致残余应力的产生。
例如,材料的塑性变形、切削加工和焊接等过程中,由于材料受到外力作用而发生形变,一旦去除外力,材料便会维持一定的应力状态。
2.3 相变应力材料的相变过程也会引起残余应力的产生。
例如,金属在固相转变时,由于晶格结构的变化,会引起应力的产生。
3. 残余应力分析方法残余应力分析可以采用多种方法,常见的有以下几种:3.1 X射线衍射方法X射线衍射方法是一种常用的非破坏性测试方法,可以通过测量材料晶体的衍射图样来分析残余应力。
通过对衍射峰的位置和强度进行分析,可以确定残余应力的大小和分布情况。
3.2 高能同步辐射方法高能同步辐射方法是一种精密的残余应力分析方法,可以提供更高的分辨率和更精确的测量结果。
该方法利用高能同步辐射源产生的高强度辐射束,通过测量辐射束的散射特性来分析残余应力。
3.3 数值模拟方法数值模拟方法是一种基于数学建模和计算机仿真的分析方法,可以通过建立材料的力学模型和边界条件来计算残余应力。
该方法可以通过调整模型参数和边界条件来模拟不同情况下的残余应力分布。
4. 残余应力分析案例分析以某航空发动机叶片为例,进行残余应力分析。
通过X射线衍射方法对叶片进行测试,得到了残余应力的分布情况。
结果显示,叶片的根部和尖部存在较大的残余应力,而中部相对较小。
残余应力的相关检验

残余应力测试经验
1被测位置打磨不平整,产品的实际位置与技术条件要求的位置有所偏差。
在确定好被测试的位置要先进行表面粗磨、再表面抛光。
对于经过粗磨的、不够清洁光滑的表面,采用抛光布轮进行表面抛光处理,在抛光过表面作进一步打磨处理,打磨时可在两个相互垂直的方向上来回进行,便于粘贴应力片并能减小由于表面粗磨可能造成的附加应力影响。
2在打磨的位置贴片操作规范。
再贴应力片前拿酒精再次擦洗,从选定测试中心部位开始,向两头粘贴应力片,两个应力片的间距不小于10mm.应力片两个相互垂直,宽度一致。
3在锯的同时速度快慢,力度大小、震动,等因素都会导致应力变化。
在锯的同时要掌握好力度,来保证数据的合理性。
残余应力测试是一个需要每一步都要仔细操作的实验,某个步骤粗心大意都可能导致测不到真实的数据或者误差特别大。
残余应力测试实验报告

一、实验目的本实验旨在通过残余应力测试,了解材料在制造过程中的残余应力分布情况,为优化加工工艺、提高产品质量提供依据。
通过本次实验,我们希望能够掌握以下内容:1. 残余应力的概念及其对材料性能的影响。
2. 残余应力测试方法及原理。
3. 残余应力测试设备的使用与操作。
4. 残余应力测试数据的处理与分析。
二、实验原理残余应力是指材料在加工过程中由于各种因素(如热处理、机械加工等)引起的内应力,在加工完成后仍然存在。
残余应力对材料的性能、使用寿命和可靠性具有重要影响。
因此,对残余应力进行测试和分析,对于优化加工工艺、提高产品质量具有重要意义。
残余应力测试方法主要有机械检测法和无损检测法。
本实验采用机械检测法中的盲孔法进行残余应力测试。
三、实验材料与设备1. 实验材料:20CrMnMo钢棒。
2. 实验设备:应变花、应变片、INV3062T智能信号采集仪、INV1861A应变调理仪、DASP-V10工程版数据采集和信号处理软件、导线及工具。
四、实验步骤1. 将20CrMnMo钢棒加工成所需形状和尺寸。
2. 在钢棒上选择测试部位,用砂纸打磨去除氧化层,并清洗干净。
3. 将应变花粘贴在测试部位,用导线连接应变片和信号采集仪。
4. 启动信号采集仪,进行初始平衡,记录应变片初始应变值。
5. 使用专用刀具在应变花中心位置钻孔,形成盲孔,释放残余应力。
6. 等待残余应力释放完全后,停止采样,记录应变片应变值。
7. 使用DASP-V10工程版数据采集和信号处理软件对测试数据进行处理和分析。
五、实验结果与分析1. 残余应力分布情况:通过实验,我们得到了钢棒测试部位的残余应力分布情况。
结果表明,钢棒内部存在一定的残余应力,且分布不均匀。
在加工过程中,由于热处理和机械加工等因素的影响,钢棒内部产生了一定的拉应力和压应力。
2. 残余应力对材料性能的影响:残余应力对材料的性能具有重要影响。
在材料的使用过程中,残余应力可能导致以下问题:(1)降低材料的疲劳性能:残余应力会加速裂纹的产生和扩展,降低材料的疲劳性能。
残余应力测试报告

残余应力测试报告1. 引言残余应力是物体在经历了外力作用后,消除外力作用后仍然存在的内部应力状态。
残余应力测试是一种评估材料或构件内部应力状况的方法,对于判断材料的工艺性能以及结构的可靠性具有重要意义。
本报告旨在对进行残余应力测试的方法、测试结果以及结论进行详细的描述。
2. 测试方法在本次残余应力测试中,我们使用了非破坏性测试方法进行测试,具体测试方法如下:1.X射线衍射法:X射线衍射法是一种常用的测试方法,可通过测量材料中的晶体结构来估计残余应力的大小和分布。
在测试中,我们使用了X射线衍射仪对待测试材料进行扫描,并分析衍射图谱来获得残余应力的信息。
2.中子衍射法:中子衍射法与X射线衍射法相似,但使用的是中子束而不是X射线束。
中子具有与材料发生相互作用时不同于X射线的特性,因此中子衍射法可以提供不同的测试结果。
我们在本次测试中也使用了中子衍射法来对测试样品进行分析。
3.光栅法:光栅法是一种基于光学原理的残余应力测试方法。
通过测量材料表面反射光的偏移来获得残余应力的信息。
在测试中,我们使用了专用的光栅仪器来对测试样品进行测试。
3. 测试结果经过以上测试方法的应用,我们获得了如下的测试结果:1.X射线衍射法:通过X射线衍射仪对样品进行测试后,我们得到了样品不同区域的衍射图谱。
进一步分析衍射图谱,我们获得了样品中的残余应力分布情况。
测试结果显示,在样品的表面以及深入一定厚度的地方都存在着不同程度的残余应力。
2.中子衍射法:使用中子衍射仪器对样品进行测试后,我们得到了样品的中子衍射图谱。
通过分析图谱,我们发现样品的不同位置存在着不同的残余应力大小。
尤其是在样品的焊接处以及表面附近的区域,残余应力较高。
3.光栅法:通过光栅仪器对样品进行测试,我们观察到样品表面的光栅条纹发生了偏移。
根据光栅条纹的偏移情况,我们可以推测样品的残余应力分布情况。
测试结果显示,在样品的边缘处以及焊接部位都存在着较大的残余应力。
4. 结论根据以上测试结果,我们得出了以下的结论:1.测试样品在进行加工和焊接过程中产生了残余应力,并且这些残余应力在不同区域存在着差异。
铸造合金应力框实验指导书[3]
![铸造合金应力框实验指导书[3]](https://img.taocdn.com/s3/m/0efb87d926fff705cc170ae4.png)
铸造合金应力框实验指导书
一、实验目的
本实验通过测量具有较大残余铸造应力的框形铸件在应力消失后的应变值,来计算框形铸件中的残余应力的大小。
并据此分析、了解铸件中不同壁厚部分内应力是如何产生的。
二、试样简介
实验所用的试样如下图所示,该试样有三根不同厚度的杆件组成,中间杆件横截面积大,两端杆件横截面积相同且比中间杆件小。
三根杆件的两端均横向连接在一起。
具体尺寸如图所示。
应力框图
三、实验所需仪器设备
实验所需仪器设备如下:钳工工作台、台钳、手锯、游标卡尺、砂轮机等。
四、实验步骤
1、 观察所用试样,并准备有关实验工具;
2、 在中间厚壁杆件上,找沿长度方向上距离100mm 左右的两点,将该位置用砂轮机各打磨出一光滑平面。
3、 用铁錾子在两个平面上各打出一个圆点,然后用游标卡尺测量两点之间的距离。
并记录,计为 L 2。
4、 有手锯将中间杆件在中间部位锯断。
5、 用游标卡尺重新测量前述两点之间的距离,并记录数据,计为 L 3。
6、 计算残余应力
按照胡克定律计算杆件中的残余应力
1E /L σε=⨯
其中 σ 应力; L 1 中间杆的总长; E 弹性模量; 实验所用的试样的材料为灰铸铁,其弹性模量一般为:70~110kN/mm 2, ε 应变; ε=L 3-L 2
五、实验报告要求
1、 根据应力框铸件的形状和结构,分析各部分内残余应力的方向和形成原因。
2、 计算出应力框内应力的大小;
3、 思考题:铸件中的铸造应力有那些类型,如何减少和消除?。
金属铸造中残余应力的数值模拟研究

金属铸造中残余应力的数值模拟研究一、引言金属铸造是一项基础性工艺,它在现代工业生产中占有不可替代的重要地位。
然而,由于金属铸造过程中金属被快速加热和冷却,导致金属铸件内部产生残余应力。
如果残余应力得不到有效控制,将会导致铸件的变形、裂纹、失效等问题,从而影响铸件的功能和质量。
因此,准确地研究金属铸造中残余应力的产生和分布规律,对于提高铸造质量和生产效率具有非常重要的意义。
二、金属铸造中残余应力的产生机制在金属铸造中,铸件内部的残余应力主要有热应力和冷却应力两种。
其中,热应力是由于金属在铸造过程中受到高温冲击而引起的,而冷却应力则是因为金属在冷却过程中收缩而产生的。
具体来说,金属在熔化和注入模具时受到热冲击,温度梯度造成铸件的局部收缩和膨胀,进而形成热应力。
当铸件从高温状态快速冷却到室温时,金属在与模具的接触面上发生冷却收缩,并通过连通的铸造结构传递,最终导致整个铸件内部出现冷却应力。
这些残余应力可以持续存在并在使用中不断积累,对铸件的性能和寿命产生严重影响。
因此,了解金属铸造中残余应力的产生机制和规律,对于减少铸件失效和提高其使用寿命至关重要。
三、金属铸造中残余应力的数值模拟研究为了准确地研究金属铸造中的残余应力和控制其产生,数值模拟已经成为一种有效的方法。
数值模拟可以针对特定材料和工艺,模拟铸件的生产过程,预测铸件内部残余应力、变形等情况,从而为工程师和设计师提供重要的参考依据。
在金属铸造中,一般采用有限元法进行数值模拟,该方法可以将铸造过程分割成许多小区域,精细地描述局部温度、应力、变形等情况,并对铸件的结构以及加工工艺进行优化设计。
(一)数值模拟流程金属铸造中残余应力数值模拟的流程如下:1、建立三维数值模型,并进行网格划分;2、设定边界条件,包括温度、热流、材料物性等参数;3、对模型进行数值计算,模拟铸件的加热、注模、冷却等过程;4、计算铸件内部应力和变形,并分析残余应力的大小和分布情况;5、根据分析结果,优化设计金属铸造的结构和工艺,减少残余应力的产生。
铸造合金中的残余应力分析与控制

铸造合金中的残余应力分析与控制在铸造工艺中,残余应力是一种不可忽视的因素,它对铸件的性能和稳定性有着重要的影响。
合理分析和控制铸造合金中的残余应力,对于提高铸件的质量和寿命具有重要意义。
本文将重点探讨铸造合金中残余应力的产生机制和控制方法。
一、残余应力的产生机制1. 温度差异引起的热塑性残余应力在铸造过程中,液态合金在凝固过程中由于温度变化会出现体积收缩,而模具和模型由于热胀冷缩的原因产生应变。
这种温度差异引起的应变在冷却过程中将会形成残余应力。
2. 金属液态及凝固过程引起的组织和晶体排列的不均匀性金属在凝固过程中由于晶体的生成以及晶界的形成,其组织和晶体排列的不均匀性将导致残余应力的产生。
3. 熔化金属与模型之间的溶解反应在铸造合金中,金属与模型之间会发生溶解反应,而金属的表面会因此产生变化,导致应力的积累。
二、残余应力的分析方法1. 数值模拟分析法利用有限元分析等数值模拟方法,可以对铸造合金中的残余应力进行准确的预测和分析。
通过建立合适的模型和输入相关的工艺参数,可以模拟和分析金属在凝固过程中的应变和应力变化。
2. 试验测量法通过引入适当的试验装置和传感器,可以对铸造合金中的残余应力进行直接测量。
利用应力测量仪器,如应变计和拉压计等设备,可以准确测量不同位置和方向上的残余应力,为分析和改善铸造工艺提供依据。
三、残余应力的控制方法1. 优化铸造工艺参数通过调整铸造过程中的工艺参数,如浇注温度、冷却速率和模具的材料等,可以有效控制残余应力的产生。
选择合适的工艺参数对于减少金属体积收缩和模具热胀冷缩之间的差异是十分重要的。
2. 合理设计铸件结构合理设计铸件的结构,减少应力的集中和应变的局部堆积。
通过合理的几何尺寸和结构设计,可以改善金属的流动性和凝固过程,从而降低残余应力的产生。
3. 采用热处理工艺对于一些易产生残余应力的铸件,在铸造过程结束后,采用适当的热处理工艺可以有效减少残余应力的存在。
热处理过程中的固溶、时效等工艺手段,可以通过改变金属的组织和晶体排列状态,从而减缓和消除残余应力。
铸造残余应力的测定实验报告

铸造残余应力的测定实验报告1. 实验目的(1) 了解铸造残余应力的产生原因。
(2) 了解用应力框测定铸造残余应力的方法。
(3) 了解退火对消除残余应力的效果。
2. 实验原理2.1 铸造应力铸件在凝固和冷却过程中由于各部分体积变化不一致导致彼此制约而引起的应力称为铸造应力。
铸造应力可分为三种,即热应力、相变应力和收缩应力。
铸造应力可能是暂时性的,当引起应力的原因消除以后,应力随之消失,称为临时应力;否则为残余应力。
铸造应力对铸件质量有重要影响,如果铸造应力超过材料的屈服强度,铸件则产生变形;如果铸造应力超过材料的强度极限时,铸件则产生裂纹。
残余应力还会降低铸件的使用性能,如失去精度、在使用过程中造成断裂或产生应力腐蚀等。
2.2 铸造应力的测定方法——应力框试验法图1为测定铸造残余应力的框形铸件,由于I 杆和II 杆截面尺寸差别大,因而铸造后细杆I 中形成压应力,粗杆II 中形成拉应力。
若在A-A 截面处将粗杆锯开,锯至一定程度时,由于截面变小,粗杆被拉断。
受弹性拉长的粗杆长度较自由收缩条件下的长度缩短,其缩短量∆L 和铸造残留应力成正比,其值可根据锯断前、后粗杆上小凸台的长度(L 0 ,L 1)差求出,即∆L =L 1一L 0。
铸造残留应力σ1和σ2的计算公式为:细杆残留应力σ1=-E)21(211F F L L L +- ,粗杆残留应力σ2=-E )21(1201F F L L L +-图 1 应力框铸件图式中:σ1,σ2——细杆、粗杆中的铸造应力(MPa ); L 0,L 1——锯断前、后小凸台的长度(mm ); F 1,F 2——细杆、粗杆的横截面积(mm 2);L——杆的长度,L=130mm;E——弹性模量,普通灰铸铁取9×104MPa,球墨铸铁取1.8×105MPa。
2.3减小及消除残余应力的方法铸造应力导致铸件翘曲变形甚至开裂,特别是铸件中的残余应力,如不消除,将降低零件的加工精度,在使用中会继续变形,降低机械性能和使用性能。
金属铸件应力测定实验报告

金属铸件应力测定实验报告一、实验目的本实验旨在通过对金属铸件应力测定实验的进行,了解金属铸件加工过程中的应力分布情况,并掌握应力测定的方法和步骤。
二、实验原理在金属铸件加工过程中,由于化学成分、凝固过程、热处理等因素的影响,铸件内部会产生应力。
应力的大小和分布对铸件的性能和寿命有着重要的影响。
因此,了解铸件内部应力的大小和分布情况就显得尤为重要。
实验中,常用的应力测定方法有两种:一种是切割法,即在铸件上进行切割,然后测量切口两侧的应力;另一种是钻孔法,即在铸件上钻孔,然后测量钻孔周围的应力。
三、实验步骤1. 准备工作:(1)将需要测定应力的铸件上表面清理干净,去掉表面的氧化物和油污等杂质。
(2)准备好应力测量仪器。
常见的应力测量仪器有应力计、应变计等。
2. 应力测定:(1)切割法:①在需要测定应力的位置上,用锯子或切割机进行切割,切口长度一般为5-10mm。
②用应力计或应变计测量切口两侧的应力,记录数据。
(2)钻孔法:①在需要测定应力的位置上,用钻头在铸件上钻孔,钻孔的深度和直径要足够大。
②将应力计或应变计插入钻孔中,测量钻孔周围的应力,记录数据。
四、实验数据处理将所测得的应力数据进行统计和分析,计算出铸件内部应力的大小和分布情况。
可以建立应力分布图,进一步了解铸件内部应力的分布规律。
五、实验注意事项1. 在进行应力测定实验前,务必保证铸件表面清洁干净,避免杂质的干扰。
2. 在进行钻孔法测定时,要注意钻孔的深度和直径,以免造成铸件的破坏。
3. 在进行数据处理时,要保证数据的准确性和可靠性,避免出现误差。
六、实验结论通过本次实验,我们了解了金属铸件加工过程中应力的产生原因和分布情况,掌握了应力测定的方法和步骤。
实验结果对于进一步提高金属铸件的性能和寿命具有重要的指导意义。
残余应力分析报告
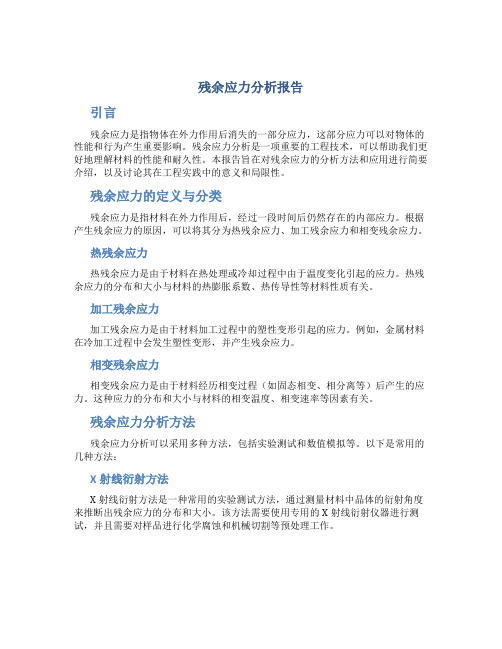
残余应力分析报告引言残余应力是指物体在外力作用后消失的一部分应力,这部分应力可以对物体的性能和行为产生重要影响。
残余应力分析是一项重要的工程技术,可以帮助我们更好地理解材料的性能和耐久性。
本报告旨在对残余应力的分析方法和应用进行简要介绍,以及讨论其在工程实践中的意义和局限性。
残余应力的定义与分类残余应力是指材料在外力作用后,经过一段时间后仍然存在的内部应力。
根据产生残余应力的原因,可以将其分为热残余应力、加工残余应力和相变残余应力。
热残余应力热残余应力是由于材料在热处理或冷却过程中由于温度变化引起的应力。
热残余应力的分布和大小与材料的热膨胀系数、热传导性等材料性质有关。
加工残余应力加工残余应力是由于材料加工过程中的塑性变形引起的应力。
例如,金属材料在冷加工过程中会发生塑性变形,并产生残余应力。
相变残余应力相变残余应力是由于材料经历相变过程(如固态相变、相分离等)后产生的应力。
这种应力的分布和大小与材料的相变温度、相变速率等因素有关。
残余应力分析方法残余应力分析可以采用多种方法,包括实验测试和数值模拟等。
以下是常用的几种方法:X射线衍射方法X射线衍射方法是一种常用的实验测试方法,通过测量材料中晶体的衍射角度来推断出残余应力的分布和大小。
该方法需要使用专用的X射线衍射仪器进行测试,并且需要对样品进行化学腐蚀和机械切割等预处理工作。
中子衍射方法中子衍射方法是一种非常灵敏和准确的实验测试方法,可以用于测量材料中的残余应力。
相比于X射线衍射方法,中子衍射方法对于非晶态材料和大晶粒材料具有更好的适应性。
数值模拟方法数值模拟方法是一种利用计算机模拟材料结构和应力行为的方法。
通过建立材料的几何模型和力学模型,并采用有限元方法进行数值计算,可以得到材料内部的应力分布情况。
这种方法需要对材料的物理和力学性质有较好的了解,并进行合理的参数设定。
残余应力的意义和应用残余应力的存在对材料的性能和行为产生重要影响,对以下方面具有重要意义和应用:材料强度和疲劳性能的评估残余应力会影响材料的强度和疲劳性能。
- 1、下载文档前请自行甄别文档内容的完整性,平台不提供额外的编辑、内容补充、找答案等附加服务。
- 2、"仅部分预览"的文档,不可在线预览部分如存在完整性等问题,可反馈申请退款(可完整预览的文档不适用该条件!)。
- 3、如文档侵犯您的权益,请联系客服反馈,我们会尽快为您处理(人工客服工作时间:9:00-18:30)。
铸造残余应力的测定实验报告
1. 实验目的
(1) 了解铸造残余应力的产生原因。
(2) 了解用应力框测定铸造残余应力的方法。
(3) 了解退火对消除残余应力的效果。
2. 实验原理
2.1 铸造应力
铸件在凝固和冷却过程中由于各部分体积变化不一致导致彼此制约而引起的应力称为铸造应力。
铸造应力可分为三种,即热应力、相变应力和收缩应力。
铸造应力可能是暂时性的,当引起应力的原因消除以后,应力随之消失,称为临时应力;否则为残余应力。
铸造应力对铸件质量有重要影响,如果铸造应力超过材料的屈服强度,铸件则产生变形;如果铸造应力超过材料的强度极限时,铸件则产生裂纹。
残余应力还会降低铸件的使用性能,如失去精度、在使用过程中造成断裂或产生应力腐蚀等。
2.2 铸造应力的测定方法——应力框试验法
图1为测定铸造残余应力的框形铸件,由于I 杆和II 杆截面尺寸差别大,因而铸造后细杆I 中形成压应力,粗杆II 中形成拉应力。
若在A-A 截面处将粗杆锯开,锯至一定程度时,由于截面变小,粗杆被拉断。
受弹性拉长的粗杆长度较自由收缩条件下的长度缩短,其缩短量∆L 和铸造残留应力成正比,其值可根据锯断前、后粗杆上小凸台的长度(L 0 ,L 1)差求出,即∆L =L 1一L 0。
铸造残留应力σ1和σ2的计算公式为:
细杆残留应力σ1=-E
)21(2101F F L L L +-,粗杆残留应力σ2=-E )
21(1
2
1F F L L L +-
图1应力框铸件图
式中:
σ1,σ2——细杆、粗杆中的铸造应力(MPa ); L 0,L 1——锯断前、后小凸台的长度(mm );
F1,F 2——细杆、粗杆的横截面积(mm2);
L——杆的长度,L=130mm;
E——弹性模量,普通灰铸铁取9×104MPa,球墨铸铁取1.8×105MPa。
2.3减小及消除残余应力的方法
铸造应力导致铸件翘曲变形甚至开裂,特别是铸件中的残余应力,如不消除,将降低零件的加工精度,在使用中会继续变形,降低机械性能和使用性能。
因此应设法减小和消除残余应力。
(1)减小铸造应力的措施和途径
①选用弹性模量E和热膨胀系数α小的合金作为铸件材质。
②减小铸件冷却过程中的温差:
(a)在铸件厚实部位放置冷铁或蓄热系数大的型砂,加速厚实部分的冷却。
(b)对铸件厚实部分的铸型或砂芯实行强制冷却。
(c)在铸件壁薄处开内浇道,使铸件各部分温度趋于一致。
(d)提高浇注时铸型的温度。
(e)将铸件于红热状态开箱取出,尽快置于已加热到500~600℃的保温炉中,保持一定时间使铸件各部分温度趋于一致,然后随炉缓冷至200~250℃出炉。
③改善铸型和砂芯的溃散性。
④改进铸件结构,避免形成较大应力和应力集中。
(2)消除铸件中残余应力的方法
消除铸件中残余应力的方法有自然失效、人工时效和共振时效等方法。
①自然失效
将有残余应力的铸件放置在露天场地,经半年乃至一年以上,让残余应力逐渐自然消退,这种方法称为自然时效。
②人工时效
人工时效又称热时效或消除内应力退火。
把铸件加热到合金的弹塑性状态的温度范围内,保持一定时间,使残余应力得以消除,然后缓慢冷却,以免重新产生残余应力。
③共振时效
共振时效的原理是:在激振器的周期性外力即激振力作用下,与铸件发生共振,因而使铸件获得相当大的振动能量。
在共振过程中交变应力与残余应力叠加,产生局部屈服,引起塑性变形,使铸件中的残余应力逐渐松弛甚至消失,达到稳定铸件尺寸的目的。
3.实验内容
本次实验测定应力框铸件(灰口铸铁)铸态及其退火热处理后的残余应力,测定步骤如下:
(1)造型(3个应力框试样);
(2)浇注(铁水温度为1330~1350℃);
(3)用热分析装置测试一个铸型中应力框铸件厚、薄壁的冷却曲线。
(4)浇注后30min打箱,用钢丝刷刷去应力框铸件表面型砂;
(5)将其中1个应力框放入热处理炉中,在550℃保温3小时后炉冷;
(6)将上述2个应力框铸件的粗杆小凸台上成锐角相交的四个棱柱面锉平;
(7)用卡尺测量小凸台长度L0;
(8)在小凸台A-A截面处从1、2、3三面依次锯开粗杆(见图1),注意各锯口应在垂
直于杆轴线的同一平面内。
(9)锯至粗杆断裂后,再测量小凸台长度L1,测量结果填入表1;
(10)计算铸造残余应力σ1和σ2。
4.实验结果与分析
应力框铸件中热应力的形成过程如图21所示。
图2上部表示了杆I和杆II的冷却曲线,T临表示金属弹塑性临界温度。
在T0~T1阶段,杆I和杆II均处于塑性状态,由于杆II较粗,其冷却速度较慢,从而两杆收缩不一致,会产生应力,但铸件可以通过两杆的塑性变形使应力很快自行消失。
在T1~T2间,此时杆I温度较低,已进入弹性状态,但杆II仍处于塑性状态。
杆I由于冷却快,收缩大于杆II,在横杆作用下将对杆II产生压应力,如图2(b)所示。
处于塑性状态的杆II受压力作用产生压缩塑性变形,使杆I、杆II的收缩一致,应力随之消失,如图2(c)所示。
在T2~T3阶段,当铸件进一步冷却至更低温度时,杆I和杆II均进入弹性状态,此时杆II温度较高,冷却时还将产生较大收缩,杆I温度较低,收缩已趋停止,在最后冷却阶段时,杆II的收缩将受杆I强烈影响,因此杆II受拉,杆I受压,并保留到室温,形成了残余应力,如图2(d)所示。
图2热应力的形成(+表示拉应力;-表示压应力)
5.思考题
1翟封祥,尹志华等.材料成形工艺基础.哈尔滨:哈尔滨工业大学出版社,2003
(1)简述铸造应力的危害。
答:在铸件冷却过程中,临时应力与残余应力同时对铸件起作用,开模后,只有残余应力对铸件起作用。
在铸造过程中,铸造应力的存在能引起铸件产生变形和开裂,当铸件中总的铸造应力超过屈服极限时,将产生塑性变形,引起铸件尺寸的改变;当铸造应力超过强度极限时,引起铸件开裂,形成铸造裂纹。
而低于弹性极限的热应力和部分相变应力则会保留在铸件内形成残余应力。
残余应力的存在对铸件的质量有很大影响,有残余应力的铸件在长时间放置或随后的机械加工时,可能引起铸件的变形,失去原来的精度,甚至开裂;为此需要加大加工余量。
在大批量生产时,变形的铸件在机械加工时往往因放不进夹具而报废。
有残余应力的铸件,机械加工后残余应力失衡,可能产生新的变形使精度降低或尺寸超差。
加工后有残余应力的零件在使用过程中如果受力方向和铸造应力的方向一致时,其叠加应力可能超过材料的屈服极限甚至强度极限,使铸件产生变形和开裂以致报废。
若在腐蚀介质中存放或工作,还会因抗腐蚀性降低而产生应力腐蚀而开裂。
(2)铸造残余应力的大小与浇注后落砂时间的早晚是否有关系?
答:有关。
为减小铸造残余应力,应使落砂时间晚些,从而使铸件能够充分冷却,提高铸件温度分布的均匀性。
(3)车床导轨处的残余应力一般是拉应力还是压应力?如何防止和消除?
答:受拉应力。
因为车床导轨部分铸壁很厚,而侧壁、筋板部分壁较薄,根据对应力框铸件的分析可知,厚大部位在铸件冷却到室温后承受拉应力,因此导轨处的残余应力为压应力。