Part 07 - Submittals
cofecha输出文件翻译
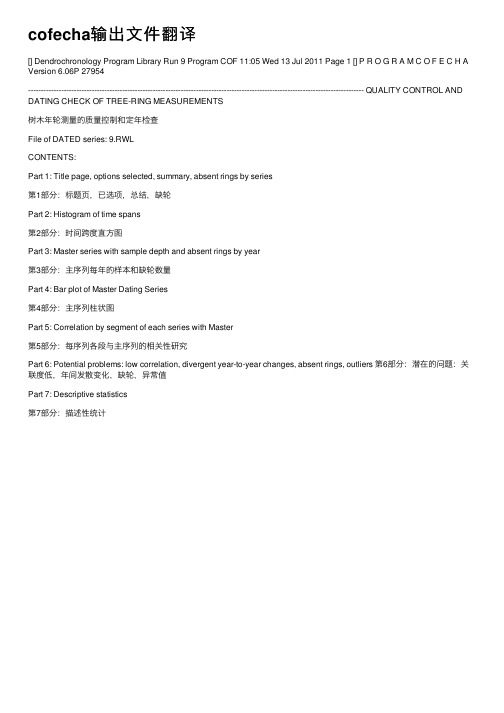
cofecha输出⽂件翻译[] Dendrochronology Program Library Run 9 Program COF 11:05 Wed 13 Jul 2011 Page 1 [] P R O G R A M C O F E C H A Version 6.06P 27954------------------------------------------------------------------------------------------------------------------------------------ QUALITY CONTROL AND DATING CHECK OF TREE-RING MEASUREMENTS树⽊年轮测量的质量控制和定年检查File of DATED series: 9.RWLCONTENTS:Part 1: Title page, options selected, summary, absent rings by series第1部分:标题页,已选项,总结,缺轮Part 2: Histogram of time spans第2部分:时间跨度直⽅图Part 3: Master series with sample depth and absent rings by year第3部分:主序列每年的样本和缺轮数量Part 4: Bar plot of Master Dating Series第4部分:主序列柱状图Part 5: Correlation by segment of each series with Master第5部分:每序列各段与主序列的相关性研究Part 6: Potential problems: low correlation, divergent year-to-year changes, absent rings, outliers 第6部分:潜在的问题:关联度低,年间发散变化,缺轮,异常值Part 7: Descriptive statistics第7部分:描述性统计Time span of Master dating series is 1815 to 2009 195 yearsContinuous time span is 1815 to 2009 195 yearsPortion with two or more series is 1816 to 2009 194 years*****************************************C* Number of dated series4 *C* 定年的样芯数量*O* Master series 1815 2009 195 yrs *O* 主序列*F* Total rings in all series 768 *F* 所有轮数*E* Total dated rings checked 767 *E* 被定年的轮数*C* Series intercorrelation .299 *C* 序列相关系数*H* Average mean sensitivity .195 *H* 平均敏感度*A* Segments, possible problems 26 *A* 可能有问题的部分数*** Mean length of series 192.0 *** 序列平均长度****************************************ABSENT RINGS listed by SERIES: (See Master Dating Series for absent rings listed by year) No ring measurements of zero value------------------------------------------------------------------------------------------------------------------------------------PART 6: POTENTIAL PROBLEMS: 第6部分:潜在的问题:关联度低,年间发散变化,缺轮,异常值08:08 Thu 14 Jul 2011 Page 5------------------------------------------------------------------------------------------------------------------------------------For each series with potential problems the following diagnostics may appear:检测出来的每个序列可能存在的潜在问题。
SCI投稿过程经验分享-投稿状态

SCI投稿过程经验分享-稿件状态投稿结束之后,要是文章格式没有问题且编辑觉得文章符合期刊范围,接下来就进入了漫长的等待。
急需文章的人不免会经常登录系统查看当前稿件状态,有些系统会把每一个状态更改都记录下来,非常详细,而有的期刊则长时间只显示一个“正在审稿”(under review)的状态。
下面放了一个期刊的审稿状态,并且翻译了一下。
Stage(状态)Start Date Manuscript Sent to Production(文章送去出版)21-Sep-2019 00:21:48 Manuscript Ready for Production(文章完成出版前的准备)20-Sep-2019 20:34:22 Decision Sent to Author(给作者发审稿结果)20-Sep-2019 20:34:22 Decision Letter Being Prepared(起草审稿结果)20-Sep-2019 17:37:50 Associate Editor Decision Completed(责任编辑完成审稿结果)20-Sep-2019 17:37:50 Associate Editor Decision Started(责任编辑起草审稿结果)17-Sep-2019 02:57:31 All Reviews Received(收到所有审稿结果)17-Sep-2019 02:57:31 Review Received(收到审稿结果)10-Sep-2019 06:02:53 All Reviewers Secured(所有审稿人都已确认)07-Sep-2019 02:38:33 Review Started(开始审稿)07-Sep-2019 02:38:33 First Reviewer Secured(确认第一个审稿人)07-Sep-2019 02:38:33 Potential Reviewer Agreed to Review(潜在的审稿人同意审稿)07-Sep-2019 02:38:33 Review Started(开始审稿)07-Sep-2019 01:58:08 Potential Reviewer Agreed to Review(潜在的审稿人同意审稿)07-Sep-2019 01:58:08 Potential Reviewer Invitation(s) Sent(给潜在的审稿人发送审稿邀07-Sep-2019 01:56:30请)Potential Reviewers Selected(确定潜在的审稿人)06-Sep-2019 22:56:42 Reviewer Assignment Started(开始寻找审稿人)02-Sep-2019 14:45:23 Securing Associate Editor(确认责任编辑)02-Sep-2019 14:45:23 Securing Editor(确认编辑)02-Sep-2019 14:45:23Submission Check by Editorial Office Completed(编辑完成检查稿02-Sep-2019 14:45:23件)Submission Check by Editorial Office Started(编辑开始检查稿件)02-Sep-2019 05:18:06 Securing Editor(确认编辑)02-Sep-2019 05:18:06 Manuscript Submitted to Editorial Office(编辑收到稿件)02-Sep-2019 05:18:05 Awaiting Author Adjustment/Approval of Converted Files01-Sep-2019 16:44:28(等待作者修正上次的文件)Submission Check by Editorial Office Failed(稿件发现有错误)01-Sep-2019 16:44:28 Submission Check by Editorial Office Started(编辑开始检查稿件)01-Sep-2019 08:08:51 Securing Editor(确认编辑)01-Sep-2019 08:08:51Manuscript Submitted to Editorial Office(编辑收到稿件)01-Sep-2019 08:08:50 Preliminary Manuscript Data Submitted (稿件完成提交)01-Sep-2019 06:17:55其他期刊的状态显示会有出入,但是大致都差不多。
Operable Partitions Acousti-Seal 931 商品说明书

PART 1 – GENERAL1.1RELATED DOCUMENTSA.Drawings and general provisions of the Contractincluding General and Supplementary Conditions and Division 01 Specification Sections, apply tothis Section.1.2SUMMARYA.This Section includes the following:1.Manually operated, individual panel operablepartitions.B.Related Sections include the following:1.Division 03 Sections for concrete tolerancesrequired.2.Division 05 Sections for primary structuralsupport, including pre-punching of supportmembers by structural steel supplier peroperable partition supplier’s template.3.Division 06 Sections for wood framing andsupports, and all blocking at head and jambsas required.4.Division 09 Sections for wall and ceilingframingat head and jambs.1.3QUALITY ASSURANCEA.Installer Qualifications: An experienced installerwho is certified by the operable partition manu -facturer, as qualified to install the manufacturer’s partition systems for work similar in material,design, and extent to that indicated for this Project.B.Acoustical Performance: Test operable partitions inan independent acoustical laboratory in accordance with ASTM E90 test procedure to attain no lessthan the STC rating specified. Provide a complete and unedited written test report upon request.C.Preparation of the opening shall conform to thecriteria set forth per ASTM E557 Standard Guide for the Installation of Operable Partitions.1.4SUBMITTALSA.Product Data: Material descriptions, constructiondetails, finishes, installation details, and operating instructions for each type of operable partition,component, and accessory specified.B.Shop Drawings: Show location and extent ofoperable partitions. Include plans, elevations,sections, details, attachments to other construction, and accessories. Indicate dimensions, weights,conditions at openings, and at storage areas,and required installation, storage, and operatingclearances. Indicate location and installationrequirements for hardware and track, includingfloor tolerances required and direction of travel.Indicate blocking to be provided by others.C.Setting Drawings: Show imbedded items andcutouts required in other work, including supportbeam punching template.D.Samples: Color samples demonstrating full range offinishes available by architect. Verification samples will be available in same thickness and materialindicated for the work.ACOUSTI-SEAL®900 SERIES TECHNICAL DATA• Highly Flexible Single Panel System• Single Panels Allow Multiple Room Setups, Changes in Pass Door and Work SurfaceLocations, and Remote Panel Storage• Panel Moves Independently into Position • Ideal for Applications Requiring Especially Tall Panels • Suspension System Incorporates the Easy to Operate Smart Track™Technology• Smart Track Technology Makes Panel Storage Virtually Foolproof• Right Angle Turn Layouts Available• Used in Multipurpose Rooms, Exhibition Halls, and Commercial BuidingsModernfold ModelAcoutsti-Seal 931 Flat Panels, Individual OperationThis specification along with product information and model details can be downloaded from SPECIFICATION - SECTION 10 22 26 (10650) OPERABLE PARTITIONS1.5DELIVERY, STORAGE, AND HANDLINGA.Clearly mark packages and panels with numberingsystems used on Shop Drawings. Do not usepermanent markings on panels.B.Protect panels during delivery, storage, andhandling to comply with manufacturer’s directionand as required to prevent damage.1.6 WARRANTYA.Provide written warranty by manufacturer ofoperable partitions agreeing to repair or replaceany components with manufacturing defects.B.Warranty period: Two (2) years.PART 2 – PRODUCTS2.1MANUFACTURERS, PRODUCTS, ANDOPERATIONA.Manufacturers: Subject to compliance withrequirements, provide product by the following:1.Modernfold, Inc.B.Products: Subject to compliance with therequirements, provide the following product:1.Acousti-Seal #931 manually operated individualpanel operable partition.2.2OPERATIONA.Acousti-Seal #931: Series of individual flat panels,manually operated, top supported with operablefloor seals.B.Final Closure:1.Horizontally expanding panel edge withremovable crank.2.Hinged panel closure.3.Angle jamb.4.Pass door closure.2.3PANEL CONSTRUCTIONA.Nominal 3-inch (76 mm) thick panels in manufac-turer’s standard 48-inch (1220 mm) widths. Allpanel horizontal and vertical framing membersfabricated from minimum 18-gage formed steel with overlapped and welded corners for rigidity. Topchannel is reinforced to support suspension system components. Frame is designed so that full vertical edges of panels are of formed steel and provideconcealed protection of the edges of the panel skin.B.Panel Skin Options:1.1/2-inch (13 mm) tackable 100% recycledgypsum board, class "A" rated single materialor composite layers continuously bonded topanel frame. Acoustica ratings of panels withthis construction (select one):a.41 STCb.47 STCc.50 STC2.1/2-inch (13 mm) tackable 100% recycledmoisture resistant gypsum board, class "A" ratedsingle material or composite layers continuouslybonded to panel frame. Acoustical ratings ofpanels with this construction (select one):a.41 STCb.47 STCc.50 STC3.1/2-inch (13 mm) NAUF medium densityfiberboard, single material or composite layerscontinuously bonded to panel frame. Acousticalratings of panels with this construction (select one):a.41 STCb.47 STCc.50 STC4.Roll-formed steel wrapping around the paneledge. Panel skins shall be lock formed andwelded directly to the frame for unitizedconstruction. Acoustical ratings of panelswith this construction (select one):a.45 STCb.50 STCc.52 STCC.Hinges for Closure Panels, Pass Doors, and PocketDoors shall be (select one):1.Full leaf butt hinges, attached directly to panelframe with welded hinge anchor plates withinpanel to further support hinge mounting to frame.Lifetime warranty on hinges. Hinges mounted intopanel edge or vertical astragal are not acceptable.2.SOSS®Invisible laminated hinge with antifrictionsegments mounted between each heat treatedlink. Hinge to be attached directly to panel frame.Welded internal hinge bracket shall support thehinge and allow for adjustment of hinge plates.Concealed hinges mounted into edge or verticalastragal are not acceptable (available on steelskin panel only).ACOUSTI-SEAL®900 SERIES TECHNICAL DATAACOUSTI-SEAL®900 SERIES TECHNICAL DATAD.Panel Trim: No vertical trim required or allowed onedges of panels; minimal groove appearance atpanel joints.E.Panel Weights:Non-Steel Skin1.41 STC - 6.5 lbs./square foot2.47 STC - 7 lbs./square foot3.50 STC - 8 lbs./square footSteel Skin1.45 STC - 8 lbs./square foot2.50 STC - 8 lbs./square foot3.52 STC - 11 lbs./square foot2.4PANEL FINISHESA.Panel face finish shall be (select as required):1.Reinforced vinyl with woven backing weighing notless than 15 ounces per lineal yard.2.Reinforced heavy duty vinyl with woven backingweighing not less than 27 ounces per lineal yard.3.Acoustical, non-woven needle punch carpet, withfused fibers to prevent unraveling or fray of material.4.Wall covering and upholstery fabric with surfacetreatment to resist stains.5.Customer’s own material (subject to factoryapproval).6.Full height tackboard with vinyl or fabric covering.a.1/4-inch natural corkb.1/4-inch fiber board tackbase7.Full height steel work surfaces (chalkboard ormarkerboard).8.High pressure plastic laminate on MDF board.9.Wood veneer on MDF board.10.Uncovered for field finishing.11.Primed for field finishing.B.Panel trim: Exposed panel trim of one consistentcolor from manufacturer’s standard offering.2.5SOUND SEALSA.Vertical Interlocking Sound Seals between panels:Roll-formed steel astragals, with reversible tongue and groove configuration in each panel edge foruniversal panel operation. Rigid plastic astragals or astragals in only one panel edge are not acceptable.B.Horizontal Top Seals: Continuous contact extrudedvinyl bulb shape with pairs of non-contacting vinyl fingers to prevent distortion without the need formechanically operated parts.C.Horizontal Bottom Seals (select one):1.Modernfold IA2 bottom seal: Automatic operableseals providing nominal 2-inch (51 mm) operatingclearance with an operating range of +1/2-inch (13 mm) to –1-1/2 inch (38 mm) whichautomatically drop as panels are positioned,without the need for tools or cranks.2.Modernfold IM2 bottom seal: Manually activatedbottom seals with self contained handle providing nominal 2-inch (51 mm) operating clearance with an operating range of +1/2-inch (13 mm) to–1-1/2 inch (38 mm). Seal shall be operablefrom panel edge or face.3.Modernfold IC2 bottom seal: Manually activatedoperable bottom seals with removable handleproviding nominal 2-inch (51 mm) operatingclearance with an operating range of +1/2-inch(13 mm) to –1-1/2 inch (38 mm). Seal shall beoperable from panel edge or face.4.Modernfold IC4 bottom seal: Manually activatedoperable bottom seals with removable handleproviding nominal 4-inch (102 mm) operatingclearance with an operating range of +1/2-inch(13 mm) to –3-1/2 inch (89 mm). Seal shall beoperable from panel edge or face.5.Modernfold L4 bottom seal: Manually activatedoperable bottom seals with removable handleproviding nominal 4-inch (102 mm) operatingclearance with an operating range of +1/2-inch(13 mm) to –3-1/2 inch (89 mm). Seal shall beoperable from panel edge or face.2.6SUSPENSION SYSTEM (select one)A.#17 Suspension System1.Suspension Tracks: Minimum 11-gage, 0.12-inch(3.04 mm) roll-formed steel track, suitablefor either direct mounting to a wood header orsupported by adjustable steel hanger brackets,supporting the load-bearing surface of the track,connected to structural support by pairs of3/8-inch (9.5 mm) diameter threaded rods.Aluminum track is not acceptable.a.Exposed track soffit: Steel, integral to track,and pre-painted off-white.2.Carriers:a.Smart Track™: Two all-steel trolleys with steeltired ball bearing wheels. Non-steel tires arenot acceptable. Suspension system shall provideautomatic indexing of panels into stack areausing preprogrammed switches and trolleyswithout electrical, pneumatic, or mechanicalactivation.ACOUSTI-SEAL®900 SERIES TECHNICAL DATA- OR -b.Right Angle Turn: Two carriers of low-frictionpolymer, reinforced with steel, that permit panels to traverse L, T, and X intersections withoutmechanical switching, on all panels excepthinged closure panels.B.#14 Suspension System: Smart Track1.Suspension Tracks: Minimum 7-gage, 0.18-inch(4.57 mm) roll formed steel. Static loading oftrack with brackets at 48-inch (1220 mm)centers shall show no failure of track or bracketsat 5,000 pounds (2550 kg) point loading atmid-span. Track shall be supported by adjustablesteel hanger brackets connected to structuralsupport pairs of 1/2-inch (13 mm) diameterthreaded rods. Brackets must support the loadbearing surface of the track.a.Exposed track soffit: Steel, removable forservice and maintenance, attached to trackbracket without exposed fasteners, andpre-painted off-white.2.Carriers: Two all-steel trolleys with steel tired ballbearing wheels. Non-steel tires are not acceptable.Suspension system shall provide automaticindexing of panels into stack area usingpreprogrammed switches and trolleys withoutelectrical, pneumatic, or mechanical activation. - OR -C.RT100 Suspension System: Multi-Directional1.Suspension Tracks: Precision heat-treatedextruded aluminum. Track to be supportedby pairs of 3/8-inch (9.5 mm) diameterthreaded rods.2. Exposed track soffit: Aluminum, integral to track,pre-painted white.3.Carriers: Shall have horizontal counter-rotatingwheels with heavy duty thrust steel bearings.Carriers permit panels to traverse L, T, or Xintersections without mechanical switching.- OR -D.RT200 Suspension System: Multi-Directional1.Suspension Tracks: Precision heat-treatedextruded aluminum. Track to be supported bypairs of 3/8-inch (9.5 mm) diameter threaded rods.2.Exposed track soffit: Aluminum, integral to track,pre-painted white.3.Carriers: Shall have horizontal counter-rotatingwheels with oversized, steel reinforced, heavyduty thrust steel bearings. Carriers permit panelsto traverse L,T, or X intersections withoutmechanical switching.2.7OPTIONSA.Pass Doors:1.Single Pass Doors (select one):a.Standard hollow metal door hung in a steelframe. ADA compliant pass door to be equippedwith friction latch and flush pulls for panicoperation. No threshold will be permitted.i. Pass door to be prime painted for fieldfinishing.ii. Pass door to be painted dark bronze, smoke gray, or natural choice.b.Matching pass door same thickness andappearance as the panels. ADA compliant passdoor equipped with friction latch and flushpulls for panic operation. No threshold will bepermitted.2.Double Pass Doors (select one):a.Standard hollow metal doors hung in a steelframe. No center post is permitted. Active leafto be equipped with friction latch and flushpulls for panic operation. No threshold will bepermitted.i. Pass door to be prime painted for fieldfinishing.ii. Pass door to be painted dark bronze, smoke gray, or natural choice.b.Matching pass door same thickness andappearance as the panels. No center post ispermitted. Active leaf to be trimless andequipped with friction latch and flush pulls forpanic operation. No threshold will be permitted.3.Hardware:a.Automatic door closures.b.Self-Illuminated exit signs.c.Panic hardware.B.Work Surfaces:1.Markerboard: White enamel on steel, bonded tothe face of the panel with horizontal trim withoutexposed fasteners. Trim is not acceptable onvertical edges to provide uninterrupted worksurface.2.Chalkboard: Porcelain enamel on steel, bonded tothe face of the panel with horizontal trim withoutexposed fasteners. Trim is not acceptable onvertical edges to provide uninterrupted worksurface.3.Tackboard: Minimum 1/4-inch (6.35 mm)natural cork, covered with vinyl or fabric, withhorizontal trim without exposed fasteners. Trimis not acceptable on vertical edges.C.Available Accessories/Options:1.Pocket Doors: Acousti-Seal Pocket Doors byModernfold, Inc., with same finish andappearance as the adjacent panels.2.Finished end caps at 90°/135°.3.Intersecting partition interface.4.Inset window options: glazed or unglazed. PART 3 – EXECUTION3.1INSTALLATIONA.General: Comply with ASTM E557, operablepartition manufacturer’s written installationinstructions, Drawings and approved Shop Drawings.B.Install operable partitions and accessories afterother finishing operations, including painting have been completed.C.Match operable partitions by installing panels frommarked packages in numbered sequence indicated on Shop Drawings.D.Broken, cracked, chipped, deformed or unmatchedpanels are not acceptable.3.2CLEANING AND PROTECTIONA.Clean partition surfaces upon completinginstallation of operable partitions to remove dust, dirt, adhesives, and other foreign materialsaccording to manufacturer’s written instructions. B.Provide final protection and maintain conditionsin a manner acceptable to the manufacturer andInstaller that insure operable partitions are without damage or deterioration at time of SubstantialCompletion.3.3ADJUSTINGA.Adjust operable partitions to operate smoothly,easily, and quietly, free from binding, warp,excessive deflection, distortion, nonalignment,misplacement, disruption, or malfunction,throughout entire operational range. Lubricatehardware and other moving parts.3.4EXAMINATIONA.Examine fooring, strructural support, and opening,with Installer present, for compliance with require-ments for installation tolerances and other conditions affecting performance of operable partitions.Proceed with installation only after unsatisfactory conditions have been corrected.3.5DEMONSTRATIONA.Demonstrate proper operation and maintenanceprocedures to Owner’s representative.B.Provide Operation and Maintenance Manual toOwner’s representative.STC CONSTRUCTION AND TRACK SYSTEM HEIGHT LIMITATIONSACOUSTI-SEAL ®900 SERIES TECHNICAL DATA STEEL SKIN PANEL CONSTRUCTIONAcousti-Seal 931Standard Panel JointAcousti-Seal 931Panel Section Frame DetailsRoll-formed skin wraps completely around the edge of vertical 16-gage steel channel and is locked in place, eliminating any sharp edges and creating a unitized panel. The finish material is secured under the steel astragal to prevent peeling.PANEL DETAILS ARE NOT TO SCALEACOUSTI-SEAL ®900 SERIES TECHNICAL DATA NON-STEEL SKIN PANEL CONSTRUCTIONAcousti-Seal 931Standard Panel JointAcousti-Seal 931Panel Section Frame DetailsRoll-formed vertical frame channel provides added strength while eliminating any sharp edges. The outer covering is secured under the steel astragal to prevent peeling. The complete vertical edge of the panel is steel for maximum durability.PANEL DETAILS ARE NOT TO SCALEACOUSTI-SEAL ®900 SERIES TECHNICAL DATASUSPENSION SYSTEM OPTIONS#17 Track System Bracket Mount(Smart Track Shown)#17 Track System Direct Mount(Right Angle Shown)#14 Track System Bracket Mount (Smart Track Shown)ACOUSTI-SEAL®900 SERIES TECHNICAL DATA SUSPENSION SYSTEM OPTIONSRT100 Multi-Directional Suspension SystemRT200 Multi-Directional Suspension SystemACOUSTI-SEAL ®900 SERIES TECHNICAL DATAPANEL, WORK SURFACE, AND PASS DOOR OPTIONS2-inch Automatic SealFLOOR SEAL OPTIONS2-inch Manual Seal4-inch Manual SealACOUSTI-SEAL ®900 SERIES TECHNICAL DATA POCKET ENCLOSURE AND STACKING OPTIONSRemote Expandable Closure –Parallel Stack(Angle Stack) Smart TrackBi-Fold Hinged Panel Closure –(Flat Stack) Smart Track Bi-Fold Expandable Closure –(Flat Stack) Smart TrackACOUSTI-SEAL ®900 SERIES TECHNICAL DATA POCKET ENCLOSURE AND STACKING OPTIONSRemote Expandable Closure –90° Side Stack (Flat Stack) Smart TrackBi-Fold Expandable Closure –(Angle Stack) Smart TrackExpandable Closure –90° Side Stack Right Angle Remote Expandable Closure –90° Side Stack Right AngleACOUSTI-SEAL ®900 SERIES TECHNICAL DATA POCKET ENCLOSURE AND STACKING OPTIONSRemote Expandable Closure –Parallel Stack Right AngleRemote Expandable Closure –Offset Stack Right AnglePANEL CROSS SECTIONSHinged JambExpandable Panel w/JambACOUSTI-SEAL ®900 SERIES TECHNICAL DATA PANEL CROSS SECTIONSExpandable Panel w/Bulb SealAngle JambHinged Panel Meeting w/Bulb Seal Hinged Panel Meeting w/Pass Door AstragalACOUSTI-SEAL ®900 SERIES TECHNICAL DATA PANEL CROSS SECTIONSNominal Fixed JambVariable Fixed JambBulb Seal and Intersection 135 Degree Angle AttachmentModernfold, Inc.215 West New RoadGreenfield, IN 46140Toll Free: 800.869.9685email:*******************A DORMA Group CompanyForm No. 2501 11/08 - EREV 9/09。
Nixalite 钢质鸟扑绊网产品说明书

Three-Part Specifications - Copyright 2014 - Nixalite of America Inc Premium Nixalite All Stainless Steel Bird Barrier Spikes Includes specifications for: Premium Nixalite Models S, H and W and Mounting Hardware.Nixalite of America Inc designs and manufactures the Premium Nixalite All Stainless Steel Bird Barrier Spikes in the USA with materials processed in the USA. These flexible spike strips repel all bird species, in all levels of infestation, on all types of architectural surfaces. They eliminate costly cleaning and structural maintenance caused by pest birds and their filthy habits. They protect people from the health hazards associated with pest bird waste.There are three (3) separate Premium Nixalite Bird Spike Models; the Model S, Model H and Model W. Each model is designed to fulfill a specific bird control need or application. Nixalite has manufactured these unrivaled bird spike strips since 1950 - there are no approved equals and there are no substitutions allowed. The following specification outline is presented in a modular format making it simple to include or exclude any combination of the Nixalite Premium Bird Control system as needed for each project.List Nixalite Premium Bird Barrier specifications in the following locations;Master Format 1995 – 10290 – Bird & Pest ControlMaster Format 2004 – 10 81 00 - Pest Control DevicesMaster Format 2004 – 10 81 13 – Bird Control DevicesPART 1 - GENERAL1.1 - SYSTEM DESCRIPTION:A.Nixalite Premium All Stainless Steel Bird Barrier Spike Models: Physical surfacebarriers designed to prevent all types of pest birds and climbing animals fromlanding, roosting, nesting or climbing on architectural surfaces, in all infestationlevels. There are three (3) Premium Nixalite Bird Spike models available; Model S,Model H and Model W. There is no equal to Nixalite’s Premium All Stainless SteelBird Barrier Spikes. No substitutions are allowed.B.Nixalite Bird Spike Mounting Hardware: Nixalite designed, stainless steel mountingclips combined with mechanical fasteners to hold the Nixalite Premium Bird Spikesto all types of architectural surfaces. All Premium Nixalite mounting hardware ismade of stainless steel or non-corrosive materials.C.Surface Cleaning System: Surface disinfectants, deodorizers and personal protectionequipment (PPE) that help keep installers safe when neutralizing the potentiallyhazardous bird or animal wastes that may be present. The cleaning system thensanitizes and deodorizes the surface in preparation of the Premium Nixalite BirdSpike installation.1.2 - QUALITY ASSURANCEA.Installer to obtain, review and understand Nixalite of America Inc.’s planning guides,estimating worksheets and installation instructions.B.Installer must be completely familiar with the proper installation procedures for theNixalite Premium All Stainless Steel Bird Spike model or models specified forinstallation.C.Installer must be completely familiar with the specified mounting hardware andmounting hardware installation procedures.D. Installer must obtain and record accurate and complete dimensions for each surfacespecified for Premium Nixalite Bird Spike installation. Surface dimensions are whatdrive Premium Nixalite Bird Spike quantities. Accurate dimensions ensure accuratequotations and material orders.E.All specified bird spikes must be MADE IN THE USA from materials PRODUCEDIN THE USA.F.Installed bird spikes must be Nixalite’s Premium All Stainless Steel Bird BarrierSpikes. There are no equals - no substitutions are allowed.1.3 - SUBMITTALSA.Manufacturers literature including: Nixalite Planning Guide, completed Nixalite EstimateWorksheet(s) and installation instructions for the specified Premium Nixalite Bird Spike Model and specified mounting hardware.B.Sample of specified Premium Nixalite Bird Spike Model - not less than 2” (5.1cm) in length.C.(If ColorCoat finish) Sample of Premium Nixalite Bird Spike Model in the specified color.D.Sample of specified Nixalite Bird Spike Mounting Hardware.E.Premium Nixalite Model S installation instructions and drawings from manufacturer (if specified).F.Premium Nixalite Model H installation instructions and drawings from manufacturer (if specified).G.Premium Nixalite Model W installation instructions and drawings from manufacturer (if specified)1.4 – STORAGE & HANDLINGA.Provide storage and/or protection to keep Premium Nixalite Bird Barrier Spikeshipping boxes dry, clean and undamaged. Do not stack or place other packaging orobjects on the Premium Nixalite Bird Barrier Spike shipping boxes.B.Keep Premium Nixalite All Stainless Steel Bird Barrier Spikes and MountingHardware in original packaging until needed for installation.PART 2 - PRODUCTS2.1 – ACCEPTABLE MANUFACTURERA.Nixalite of America Inc1025 16th Avenue, PO Box 727, Dept. NI, East Moline, Illinois 61244; U.S.A.P: 800.624.1189 or 309.755.8771 - F: 800.624.1196 or 309.755.0077E: ************************ or *********************B.ABC Advanced Bird Control – A division of Nixalite of America Inc.PO Box 727, Dept. NI, East Moline, Illinois 61244, U.S.A.P: 888.212.8682 or 309.755.4708 - F: 309.755.1865E: ***********************2.2 – NIXALITE PREMIUM BIRD BARRIER STRIPSA.ALL Premium Nixalite Models are all stainless steel wire and base strip spikes thatare made in the USA from materials produced in the USA.Wires: Stainless steel, 0.041” (1 mm) diameter, full-hard spring temper.Base Strip: Stainless steel, 0.25” wide x 0.02” thick (6.3 mm x 0.5 mm), full annealfor flexibility, easy strip cutting and surface shape memory.B.Premium Nixalite Spike Strip Lengths: All Premium Nixalite spike strip models areavailable in 24” (61.0 cm) and 48” (122.0 cm) strip lengths.C.Premium Nixalite Model S: Full row spike, 4” high (10.2 cm), 4” wide (10.2 cm) NOLESS THAN 120 wire points per foot. Full 180-degree wire coverage. For all birdspecies on all types of surfaces. Use in conjunction with Premium Nixalite ModelW for climbing animal barrier and mud-nest building bird control applications.D.Premium Nixalite Model H: Half row spike. 4” high (10.2 cm), 2” wide (5.1 cm), NOLESS THAN 60 wire points per foot, 90 degree wire coverage. For flat surfaces lessthan 2” in depth (5.1 cm) or in conjunction with Premium Nixalite Model S onspecific surface widths to achieve proper surface protection.E.Premium Nixalite Model W: Wall mount spike. 5-1/2” high (14.0 cm), 3” wide (7.6cm), NO LESS THAN 120 wires per foot, 180-degree wire coverage. Designed forvertical surfaces only. Use above surfaces less than 2” in depth (5.1 cm) or overother Nixalite Models when specified. Use in conjunction with Premium NixaliteModel S for climbing animal barrier and mud-nest building bird control applications.F.Nixalite Soft Tip Option: Available for Premium Nixalite Models S and H (notavailable on Model W). This replaces the pointed wire tips with flattened wire tips.Otherwise the spike is the same as the regular pointed wire spikes. Use only wherefrequent human contact is possible (or expected) and bird pressure is low.G. Finish: Natural stainless steel finish or manufacturers ColorCoat finish.H.ColorCoat: standard colors are black, white, gray, tan, brown and bronze. Choosestandard color that best suits application. Custom colors available. For custom color: installer must contact manufacturer for color matching procedures.2.3 – NIXALITE BIRD SPIKE MOUNTING HARDWAREA.To be made of stainless steel or non-corrosive materials. Standard mounting hardwareis supplied with Premium Nixalite Bird Barrier Spike Models in set quantities.Mounting Hardware must allow for bird spike strip installation, removal andreinstallation without damaging the installation surface, the spike strips or themounting system.e the Nixalite Bird Spike Mounting Hardware that best suits the installation surface.All hardware is made of either stainless steel or non-corrosive materials.Installation Surface Nixalite Bird Spike Mounting HardwareMasonry, stone, concrete; Mounting clip, sheet metal screw, masonry anchor Wood, plywood, shingles; Mounting clip, sheet metal screw, washerSheet metal, plastic, PVC; Mounting clip, sheet metal screw, washerSteel, cast iron, brass, bronze; Mounting clip, drive screw, washerPipes, cables, conduit, grates; Wire tie, wire tying tool, adhesiveC.Apply adhesive or sealant in all holes that penetrate the installation surface. Aftermounting hardware is installed, apply additional adhesive or sealant over the headsof the sheet metal screws and/or the drive screws. Do not get adhesive or sealant inthe hook end of the mounting clips.D.Optional Fastening:Glue Clips & Adhesive:If surface conditions do not allow for the use of the supplied Bird Spike MountingHardware, use the Glue Clip and Adhesive installation method. Follow the Glue Clip installation instructions available from the manufacturer.Custom Forms:Nixalite offers custom made stainless steel mounting brackets, straps or clamps tohold the Premium Nixalite Bird Spikes to installation surfaces with limited or zerosurface penetration requirements. Contact manufacturer for details on custom formdesign and/or manufacture.2.4 – SURFACE CLEANING SYSTEMA.Steri-Fab: Surface disinfectant and bactericide designed to neutralize bird waste,making it safe for removal. Steri-Fab quickly kills disease causing bacteria, parasites, fungi, insects, etc. This is a non-residual product. It becomes completely inert after it dries. Do not use with Microcide-SQ on the same surface at the same time.B.Microcide-SQ: A broad spectrum disinfectant, cleaner and deodorizer used to sanitizehard surfaces as well as fabrics and clothing. Use to kill a wide spectrum oforganisms and disease causing bacteria. Do not use with Steri-Fab on the samesurface at the same time.C.Microsan: Anti-microbial personal protection products to help prevent diseasetransmittal before, during and after working on and around surfaces contaminatedwith bird and animal wastes. Use to compliment personal protection equipmentstandards (PPE).D.Safety Equipment: Nixalite offers personal protection equipment (PPE) to protectpersonnel from the hazards related to pest bird and animal waste materials.PART 3 - EXECUTION3.1 - INSPECTIONA.Visually inspect all installation surfaces. Make sure all surfaces are clean, dry and freefrom debris or other conditions that could impede the workflow of this section. Allsurfaces must be sanitized and deodorized before Premium Nixalite Bird Spikeinstallation.B.Notify architect of detrimental conditions. Do not proceed until these conditions havebeen corrected.3.2 - PREPARATIONA.Field Measurements: Verify the dimensions for each surface specified for PremiumNixalite Bird Spike installation. Use manufacturers Planning Guides and EstimateWorksheets to verify that sufficient quantities of bird spike strips will be installed on EACH surface specified for bird control.B.Make sure all installation surface finishing requirements have been accomplishedbefore installing Premium Nixalite Bird Spike Models. They are to be the last itemsinstalled on each specified surface. DO NOT apply any surface coating or treatment(paint, sealer, etc.) over the installed Premium Nixalite Bird Spike Models or themounting hardware.C.Remove or relocate all plants, foliage or foreign objects that overhang the installationsurfaces. Note all conditions that could adversely affect the installation andperformance of the Premium Nixalite Bird Spike installation.3.3 – SURFACE CLEANINGA.All surfaces to be clean, dry and free of obstructions before the Premium Nixalite BirdSpikes are installed.B.If Bird Waste Is Present:Treat, neutralize and safely remove all bird waste from installation surfaces. Installer must follow all municipal, state and federal regulations regarding the proper removal and disposal of bird droppings and waste materials such as nests and dead birds.e Nixalite’s surface cleaning products to neutralize any bird droppings, nests andrelated waste materials that may be present. Allow all surfaces to air dry completely, and then reapply to sanitize and deodorize the surface before proceeding. Strictlyfollow treatment instructions provided with Nixalite’s surface cleaning products.e Nixalite anti-microbial and anti-bacterial personal protection products to helpprevent disease transmittal when working around surfaces contaminated with birddroppings.3.4 - INSTALLATIONA.Make sure the installation surfaces are clean, dry and free of any debris orobstructions.B.Install specified Premium Nixalite Bird Spike Models in strict accordance withmanufacturer’s spike strip spacing and installation guidelines. Protect all surfaceswhere pest birds can land, roost and nest.C.Install Nixalite’s bird spike strips so they will protect the entire surface, not just theoutside edges. No gaps are allowed in the bird spike strip coverage. Cut the birdspike strips where necessary to fit the surface properly.D.Wires of Premium Nixalite Bird Spike Models must extend over outside edges of eachsurface by at least 1/4” (0.6cm). The bird spike base strip must extend over the endsof each surface by at least 1/2” (1.2cm).E.Fasten Premium Nixalite Bird Spike Models to the surface with the mountinghardware recommended by the manufacturer. Follow the hardware spacingguidelines and installation procedures supplied by manufacturer.F.Premium Nixalite Model S; A full row spike strip model that repels all bird specieson all types of surfaces. Use in conjunction with Premium Nixalite Model W forclimbing animal barrier and mud-nest building bird control applications.G.Premium Nixalite Model H; A half row spike strip used on flat horizontal surfacesless than 2” in depth (5.1 cm). Use in conjunction with Premium Nixalite Model Son specific surface widths to achieve proper coverage and protection.H.Premium Nixalite Model W; A wall-mount spike strip used on vertical surfaces only.Do not install horizontally (down flat). Install above surfaces less than 2” in depth(5.1 cm) or over other Nixalite Models when specified by manufacturer. Use inconjunction with Premium Nixalite Model S for climbing animal barrier and mud-nest building bird control applications.I.Climbing Animal Barrier Installations;All climbing animal barrier installations use the standard pointed wire PremiumNixalite Model S and Model W bird spike strips. DO NOT use Soft Tip option forspikes installed as a climbing barrier. Installed in multiple rows, the PremiumNixalite spikes can repel the most determined climbing animals. Contact themanufacturer for installation guidelines for climbing animal barrier applications.J.Physical Security System Enhancements;Premium Nixalite All Stainless Steel Barrier Spikes can be used to enhance existingphysical perimeter security systems. Install barrier spikes on key surfaces to denyentry or egress by unauthorized personnel. For best results, install Premium barrierspikes with other physical security barriers. Use the mounting systems recommended by the manufacturer.3.5 – ADJUSTMENTS / CLEANINGA.Remove debris and waste materials from project site. Inspect finished installation.Make any adjustments needed to conform to Nixalite’s spacing and installationguidelines.B.Premium Nixalite All Stainless Steel Bird Barrier Spikes are a physical and passivebarrier. They rely on the system of pointed stainless steel wires to deny pest birdsand nuisance animals access to the surfaces on which they are installed. Periodicinspections are recommended to keep the bird spike strips in good condition.C.Occasionally, debris may fall onto the wires or birds may drop materials into the wiresin an attempt to build a nest. If this happens, begin a monthly inspection of thesystem to remove any debris and to check the condition of the installed bird spikestrips.Nixalite® of America Inc – 1025 16th Avenue – East Moline, IL. 61244 Ph:800.624.1189Fax:800.624.1196Email:************************Website: Copyright 2014 – Nixalite of America Inc Nixalite is a registered trademark of Nixalite of America IncPrinted with pride in the USA。
建筑环境与能源应用工程专业英语

销售工作通用科 技风格模板
Unit Fifteen Commissioning of Variable Air Volume Systems
• Definition: What is Commissioning (Cx) ?
“A quality-focused process for enhancing the delivery of a project. The process focuses on verifying and documenting that the facility and all of its systems and assemblies are planned, designed, installed, tested, operated, and maintained to meet the Owner’s Project Requirements.”
• Provide a facility that can be efficiently operated and maintained
• Provide complete orientation and training to facility staff and occupants
• Provide improved documentation of system characteristics
Planning
Design Construction Acceptance Occupancy
Prepare, Design Intent,
CX Plan, and
Specifications
Review Submittals,
Prepare Checklists
JST 电子连接器产品参考手册说明书
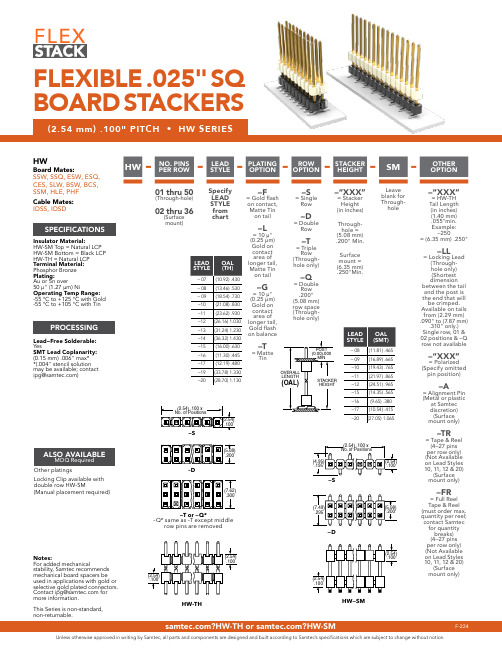
---PLATING OPTION-ROW OPTION-STACKER HEIGHT-SM-OTHER OPTION01 thru 50(Through-hole)02 thru 36(Surface mount)Specify LEAD STYLE from chart–F= Gold flash on contact,Matte Tin on tail –L= 10 µ" (0.25 µm) Gold on contact area of longer tail, Matte Tin on tail –G= 10 µ" (0.25 µm) Gold on contact area of longer tail, Gold flash on balance –T= Matte Tin–S = Single Row –D = Double Row –T= Triple Row (Through-hole only)–Q= Double Row .200" (5.08 mm) row space (Through-hole only)–“XXX”= Stacker Height (in inches)Through-hole =(5.08 mm) .200" Min.Surface mount =(6.35 mm) .250"Min.Leave blank for Through-hole–“XXX”= HW-TH Tail Length (in inches) (1.40 mm) .055"min.Example: –250= (6.35 mm) .250"–LL= Locking Lead (Through-hole only) (Shortest dimension between the tail and the post is the end that will be crimped. Available on tails from (2.29 mm) .090" to (7.87 mm).310" only.)Single row, 01 & 02 positions & –Q row not available –“XXX”= Polarized (Specify omitted pin position)–A= Alignment Pin (Metal or plastic at Samtec discretion)(Surface mount only)–TR= Tape & Reel (4–27 pins per row only)(Not Available on Lead Styles 10, 11, 12 & 20)(Surface mount only)–FR= Full Reel Tape & Reel (must order max. quantity per reel; contact Samtec for quantity breaks) (4–27 pins per row only)(Not Available on Lead Styles 10, 11, 12 & 20)(Surface mount only)Insulator Material:HW-SM Top = Natural LCP HW-SM Bottom = Black LCP HW-TH = Natural LCP Terminal Material: Phosphor Bronze Plating:Au or Sn over50 µ" (1.27 µm) NiOperating Temp Range:-55 °C to +125 °C with Gold -55 °C to +105 °C with TinLead–Free Solderable: YesSMT Lead Coplanarity:(0.15 mm) .006" max**(.004" stencil solution may be available; contact **************)Notes:For added mechanicalstability, Samtec recommends mechanical board spacers be used in applications with gold or selective gold plated connectors. ************************more information.This Series is non-standard,non-returnable.HWBoard Mates:SSW, SSQ, ESW, ESQ, CES, SLW, BSW, BCS, SSM, HLE, PHF Cable Mates:IDSS, IDSDHW-THHW—SM–Q* same as –T except middlerow pins are removedOther platingsLocking Clip available with double row HW-SM(Manual placement required)FLEXIBLE .025" SQ BOARD STACKERSUnless otherwise approved in writing by Samtec, all parts and components are designed and built according to Samtec’s specifications which are subject to change without notice.F-224。
waters质谱masslynx软件使用说明

Copyright Notice
Micromass UK Limited believes that the information in this publication is accurate. However the information is subject to change without notice and should not be construed as a contractual undertaking by Micromass UK Limited. Despite the care that has been given to the preparation of this publication, Micromass UK Limited accepts no responsibility for any loss or any other matter that may arise from any error or inaccuracy that may inadvertently have been included. Copyright 1993-2002 Micromass Ltd. All Rights Reserved. No part of this publication may be copied without the express written permission of Micromass UK Limited.
Page ii
MassLynx NT Users Guide
Contents
MassLynx NT User’s Guide............................................................................
北美电力可靠性公司(NERC)标准授权请求(SAR)说明书

Standard Authorization Request (SAR)The North American Electric Reliability Corporation (NERC) welcomes suggestions to improve the reliability of the bulk power system through improved Reliability Standards.Complete and submit this form, with attachment(s) to the NERC Help Desk . Upon entering the Captcha, please type in your contact information, and attach the SAR to your ticket. Once submitted, you will receive a confirmation number which you can use to track your request.Requested informationOther benefits of this standards project to address issues with MOD-025-2 include, but are not limited to, the following:•Preventing over- or under-estimation of generating facility active and reactive power, which could lead to potential reliability risks or unnecessary and expensive solutions to mitigate •Identifying limitations within a generating facility that could constrain the resource from reaching the expected active/reactive capability at any given time•More clearly communicating the necessary data to be used for modeling the respective resources in steady-state power flow models•Ensure that the data users are part of the verification process to ensure that the necessary and usable data is provided and utilized appropriately•Ensure that raw test data alone is not used for resource modeling, but is analyzed, adjusted, and contextualized to account for measured system conditions•Coordinating with PRC-019 activities to develop a composite capability curve, inclusive of equipment capabilities, limiters, and other plant limitations to develop an appropriate capability curve•Ensuring that other means of verification (other than testing) can be more effectively leveraged to gather necessary and suitable data for verifying plant/machine capabilityPurpose or Goal (How does this proposed project provide the reliability-related benefit described above?):The intent of this standard revision project is to address the issues that exist with MOD-025-2 regarding verification and data reporting of generator active and reactive power capability (and any other relevant equipment capability). Currently, implementation of the standard rarely produces data that is suitable for planning models (i.e., the stated purpose of the standard). The vast majority of testing cases are limited by limits within the plant or system operating conditions that prohibit the generating resource from reaching its “composite capability curve” – the equipment capability or associated limiters. The goal of the proposed project is to:•Ensure that testing and other verification activities produce useful data for verification of plant active and reactive power capability•Ensure that the data is used by Transmission Planners and Planning Coordinators in an appropriate manner, with a sufficient degree of analysis prior to use•Ensure that the data is applicable and usable by the Transmission Planner and Planning Coordinator for reliability studies•Ensure Generator Owners appropriately identify limits within their generating resources (and synchronous condensers), and effectively communicate those limits to Transmission Plannersand Planning Coordinators for the purposes of modeling these resources in reliability studiesRequested informationProject Scope (Define the parameters of the proposed project):The scope of this project is to modify MOD-025-2 to ensure that data provided through verification activities performed by applicable Generator Owner or Transmission Owners produce suitable data for the purposes of developing accurate planning models in Transmission Planner and Planning Coordinator reliability studies. The project should consider, at a minimum, the following:1.Revisions to MOD-025-2 to ensure that verification activities produce data and information thatcan be used by Transmission Planners and Planning Coordinators for the purposes of developing accurate and reasonable plant active and reactive capability data (including possiblyrepresentation of the “composite capability curve” inclusive of capability and limiters, whereapplicable).2.Ensure that each Planning Coordinator and the area Transmission Planners developrequirements for the Planning Coordinator area real and reactive capability data verification3.Ensure that Generator Owners provide the data specified by the Planning Coordinator andTransmission Planners for the Planning Coordinator area4.Ensure that verification activities can apply other methods beyond only testing (or real-timedata) that allow plant capability information, protection settings, PRC-019 reports, and otherdocumentation to also complement the verification activities5.Ensure that data provided by the applicable Generator Owners and Transmission Owners isanalyzed and used appropriately by Transmission Planners and Planning Coordinators6.Ensure that the data provided by Generator Owners, if different from tested values, isacceptable to the Planning Coordinator and Transmission Planners with the standard providing guidance on acceptable reactive capability reporting if system conditions prevent reaching actual capability.7.Ensure alignment of the MOD-025 standard with MOD-032-1 regarding data submittals forannual case creation and PRC-019-2 regarding collection of information that can be effectivelyused for verification purposes. Ensure activities across standards can be applied to effectivelymeet the purpose of these standards, and avoid any potential overlap or duplication of activities.This is dependent on the success of bullet number 1.8.Ensure that equipment limitations are documented and classified as expected (e.g., systemvoltage limit reached) or unexpected (e.g., plant tripped or excitation limiter reachedunexpectedly). In cases of unexpected limitations reached, ensure that the equipment ownerdevelops and implements a corrective action plan to address this unexpected limitation.Requested informationDetailed Description (Describe the proposed deliverable(s) with sufficient detail for a drafting team to execute the project. If you propose a new or substantially revised Reliability Standard or definition, provide: (1) a technical justification1 which includes a discussion of the reliability-related benefits of developing a new or revised Reliability Standard or definition, and (2) a technical foundation document (e.g., research paper) to guide development of the Standard or definition):The NERC PPMVTF developed White Paper: Implementation of NERC Standard MOD-025-22 that recommends NERC initiate a standards project to address these issues with MOD-025-2. The white paper provides a detailed description and technical justification of the gaps that exist in MOD-025-2 and how the current standard may be leading to inaccurate data being used in BPS reliability studies. Further, the NERC PPMVTF Reliability Guideline: Power Plant Model Verification and Testing for Synchronous Machines3also describes in detail how testing activities per MOD-025-2 can lead to unusable data, and provides further guidance that a SDT could use to develop solutions to these issues.Cost Impact Assessment, if known (Provide a paragraph describing the potential cost impacts associated with the proposed project):The aforementioned NERC PPMVTF White Paper: Implementation of NERC Standard MOD-025-2 includes an example of one Registered Entity’s MOD-025 implementation costs (excluding cost of shifting the optimization of generation fleet assets due to minimum load testing requirements). The entity’s average test cost was $1,259 (897 tests) and $4,326 per generator (261 generators). The verification testing of units generally results in transferring energy to a higher cost resource during the test period. Further, the data produced is often NOT suitable for planning studies, which does not serve the intended purpose of the standard and makes the added cost unjustified.Please describe any unique characteristics of the BES facilities that may be impacted by this proposed standard development project (e.g., Dispersed Generation Resources):The current MOD-025-2 was written around synchronous generation, although it is not specifically applicable only to synchronous generators. Therefore, the project should ensure the language is clear and concise regarding how to handle BES dispersed generating resources (e.g., wind, solar photovoltaic, and battery energy storage systems).To assist the NERC Standards Committee in appointing a drafting team with the appropriate members, please indicate to which Functional Entities the proposed standard(s) should apply (e.g., Transmission Operator, Reliability Coordinator, etc. See the most recent version of the NERC Functional Model for definitions):•Generator Owner and Transmission Owner of synchronous condensers (asset owner that is in the best position to ascertain resource capability)1 The NERC Rules of Procedure require a technical justification for new or substantially revised Reliability Standards. Please attach pertinent information to this form before submittal to NERC.2https:///comm/PC/Power%20Plant%20Modeling%20and%20Verification%20Task%20Force/PPMVTF_White_Paper_MOD-025_Testing.pdf3https:///comm/PC_Reliability_Guidelines_DL/Reliability_Guideline_-_PPMV_for_Synchronous_Machines_-_2018-06-29.pdfRequested information•Transmission Planner and Planning Coordinator (user of the information provided by the Generator Owner; currently has no responsibility of ensuring accurate data per current MOD-025-2 standard)Do you know of any consensus building activities4 in connection with this SAR? If so, please provide any recommendations or findings resulting from the consensus building activity.The NERC PPMVTF White Paper, approved by NERC RSTC, details the challenges with MOD-025-2. The team deliberated this subject for a significant amount of time, and have identified major issues with the standard that need to be addressed by an SDT. The PPMVTF believes that a significant revision to MOD-025-2 is needed, that testing activities are useful and should be retained, but that the activities can focus on more effective means of collecting useful data for planning models. One dissenting opinion of PPMVTF membership believed the standard should be retired completely and not replaced with an alternative.Are there any related standards or SARs that should be assessed for impact as a result of this proposed project? If so, which standard(s) or project number(s)?The NERC standards development Project 2020-02 (Transmission-connected Dynamic Reactive Resources) SAR includes MOD-025-2, specifically addressing the applicability of transmission connected reactive devices in addition to generators and synchronous condensers.The SAR on PRC-019-2 submitted to NERC by the System Protection and Control Subcommittee is also related in that there is significant overlap of activities in PRC-019-2 and the development of planning models of machine capability.This SAR could be combined with those portions of those SARs to address this problem effectively. Are there alternatives (e.g., guidelines, white paper, alerts, etc.) that have been considered or could meet the objectives? If so, please list the alternatives.There are two key industry reference documents on this subject:1.NERC Reliability Guideline: Power Plant Model Verification and Testing for SynchronousMachines5 (July 2018) that provides recommended practices for synchronous machine capability testing. An appendix is devoted to MOD-025-2 testing, and highlights the challenges andinherent errors in MOD-025-2 to obtain useful data that can be applied for planning models.2.NATF Modeling Reference Document Reporting and Verification of Generating Unit ReactivePower Capability for Synchronous Machines6(April 2015) that describes testing activities perMOD-025-2 and means of ensuring data is sufficient for planning studies.4 Consensus building activities are occasionally conducted by NERC and/or project review teams. They typically are conducted to obtain industry inputs prior to proposing any standard development project to revise, or develop a standard or definition.5https:///comm/PC_Reliability_Guidelines_DL/Reliability_Guideline_-_PPMV_for_Synchronous_Machines_-_2018-06-29.pdf 6https:///docs/natf/documents/resources/planning-and-modeling/natf-reference-document-reporting-and-verification-of-generating-unit-reactive-power-capability-for-synchronous-machines.pdfRequested informationNeither industry reference document addresses the identified shortcomings of the standard described above and in NERC PPMVTF White Paper: Implementation of NERC Standard MOD-025-2.7 These reference materials help industry understand how to implement the standards using best practices, but do not address the reliability gaps created by the standard requirements themselves which is leading to inaccurate data being used in planning assessments.Market Interface PrinciplesDoes the proposed standard development project comply with all of the following Market Interface Principles?Enter (yes/no)1. A reliability standard shall not give any market participant an unfair competitiveadvantage. Yes2. A reliability standard shall neither mandate nor prohibit any specific marketstructure. Yes3. A reliability standard shall not preclude market solutions to achieving compliancewith that standard. Yes7https:///comm/PC/Power%20Plant%20Modeling%20and%20Verification%20Task%20Force/PPMVTF_White_Paper_MOD-025_Testing.pdfMarket Interface Principles 4. A reliability standard shall not require the public disclosure of commercially sensitive information. All market participants shall have equal opportunity to access commercially non-sensitive information that is required for compliance with reliability standards. Yes Identified Existing or Potential Regional or Interconnection Variances Region(s)/ Interconnection Explanation N/A None identified.For Use by NERC Only Version History Version Date Owner Change Tracking1June 3, 2013 Revised 1August 29, 2014 Standards Information Staff Updated template 2January 18, 2017 Standards Information Staff Revised 2June 28, 2017 Standards Information Staff Updated template 3February 22, 2019 Standards Information Staff Added instructions to submit via Help Desk 4February 25, 2020 Standards Information Staff Updated template footer。
电子计划审查指南说明书

Customer Electronic Plan Review (ePlans) GuideVersion 2020_0821IntroductionTo help streamline the submittal process, the Building Development Division has established an electronic plan review program (ePlans). Please use the following guide to prepare and submit documents for electronic plan review.Please note:Electronic plan review will not start until fees are paid, and the submittal meets the requirements of this guide. Failure to pay fees or meet requirements of this guide will delay the plan review process.ProjectsProjects listed in Table 1 and 2 must be submitted electronically; paper plan submissions will not be accepted. For all other projects that do not meet the requirements of Table 1 or 2, a paper plan is required. The County reserves the right to require electronic or paper plan submission for any project. Paper plans currently in review shall remain paper submissions until final inspection approval.Submittal ChecklistSubmittals for electronic plan review must meet the minimum requirements below. For assistance, please contact Plan Intake at 703-792-4040 or *********************.Building Development Division (BDD) Forms available here☐ Forms are submitted as individual PDF filesDocuments(GIS Address Validation, Zoning Approval, Site Plans, Plats, Energy Calculations, Structural Calculations, Geotechnical Reports, Truss Submittals, other)☐ Documents meet Credentialing requirements for seal, signature, and date☐ Documents are submitted each as separate PDF filesPlans - General Requirements☐ File names meet the File Naming Convention requirements☐ Plans meet Credentialing requirements☐ Plans include all disciplines in a single PDF file (architectural, mechanical, electrical, plumbing, and structural)☐ PDF files are not password protected☐ PDF does not contain layers or comments☐ Plans with more than 10 sheets have bookmarks listing sheet number and title. For example: A1 First Floor Plan ☐ Plans are in landscape orientation☐ Plans are monochrome, not in color☐ P rovide a 3” x 3” box in the same location each sheet for county review stampCommercial Plans☐ Minimum sheet size is 24” x 30” maximum sheet size is 36” x 48”☐ Plans are to minimum scale 1/8” = 1’-0”. It is preferred that plans are in vector format to allow for measuring☐ Resubmissions include all sheets (complete new set) and Resubmission - Revision Checklist☐ Revisions include only revised sheets and Resubmission - Revision ChecklistResidential Plans(group R-5 single family, townhouse, additions, alterations, repairs, accessory structures, etc.)☐ Minimum sheet size is 8-1/2” x 11” maximum sheet size is 36” x 48”☐ Plans are to minimum scale 1/8” = 1’-0”☐ Plans may be scanned with sheets aligned in landscape orientation☐ Resubmissions include all sheets (complete new set)☐ Revisions include only revised sheets and have changes cloudedCredentialingPlans and documents shall be electronically signed, dated, and sealed in accordance with 18VAC10-20-760 Part C and Policy 1.11. Every sheet in the plan set is required to be sealed, signed, and dated. Any revised sheet should reflect the revision date. SubmittingTo submit Commercial Building Plans, Residential Building Plans, or Residential Stand-alone Trade permits please use the ePortal application found at /eportal. For ePortal user guides, videos, and frequently asked questions click here. To submit via ePortal, you must have an ePortal account.To submit for Commercial Stand-alone Trade permits please email plans and documents up to 30 MB to Plan Intake at*********************. For plans and documents over 30 MB please email Plan Intake at ********************* to request a file sharing link.For assistance, please contact Plan Intake at 703-792-4040 or *********************.File Naming ConventionsFiles for the first submission, resubmissions, and revisions shall be named in accordance with Table 4 below.PaymentsPayments can be made via ePortal (preferred), over the phone by calling 703-792-6930, in person at the county office, or by mailing a check. Payments by mailing a check will delay the plan review process.To pay via ePortal, you must have an ePortal account. To create an ePortal account click here.For assistance, please contact Plan Intake at 703-792-4040 or *********************.Reviewed Documents (Approvals)A copy of the reviewed submittal (BDD Forms, Plans, Documents) with digital County review stamps will be provided electronically to the applicant.Reviewed Documents Required On-site for InspectionsThe applicant shall print the submittal (BDD Forms, Plans, Documents) with digital County review stamps to remain on site for inspection field use. The permit(s) shall be printed and posted at the construction site where it is visible from the public way. For assistance with obtaining the submittal or permit, please contact the Permitting Services at 703-792-6924 or*********************.For assistance with inspections, please contact the Inspections Branch at 703-792-7006.。
流量计说明书

SECTION 40 71 49VORTEX – Shedding Flow MeterPART 1- GENERAL1.01SUMMARYA.Provide a loop powered vortex flow meter consisting of flanged full body orwafer design for the measurement of liquid, gas, or steam media. The system shall utilize the vortex measurement principle by monitoring the shedding frequency ofvortices in fluids which are created by a bluff body.1.02 SUBMITTALSA.Furnish complete Product Data, Test Reports, Operating Manuals, RecordDrawings, Manufacturer’s Certifications, Manufacturer’s Field ReportsB.Product Data:1.Dimensional Drawings.2.Materials of Construction:a. Metering Tube.b. Flanges.3.Measurement accuracy.4.Range and range ability.5.Enclosure Rating.6.Classification Rating.7.Calibration certificates.8.Power:a. Voltage.b. Wattage.9.Output options.1.03 QUALITY ASSURANCEA.Manufacture instruments facilities certified to the quality standards of ISOStandard 9001 - Quality Systems - Model for Quality Assurance inDesign/Development, Production, Installation, and Servicing.B.Factory Calibration – Vortex flowmeters shall be factory calibrated on anapproved test stand with certified accuracy traceable to National Institute ofStandards and Technology (NIST), compliant with ISO 17025 laboratory standardaccredited by a national verification agency such as A2LA.1.04 DELIVERY, STORAGE, AND HANDLINGA.Store all instruments in a dedicated structure with space conditioning tomeet the recommended storage requirements provided by the Manufacturer.B.Any instruments that are not stored in strict conformance with theManufacturer’s recommendation shall be replaced.1.05 PROJECT OR SITE CONDITIONSA.Provide instruments suitable for the installed site conditions including, butnot limited to, material compatibility, process and ambient temperature, andhumidity conditions.1.06 WARRANTYA. The vortex flowmeter shall have a standard one year warranty from dateof shipment; if the meter is commissioned by a factory certified technician, the warranty is extended to three years from the date of shipment.1.07 MAINTENANCEA. Provide all parts and materials necessary for maintenance and calibrationpurposes throughout the warranty period. Deliver all of these supplies before project substantial completion.1.08 LIFECYCLE MANAGEMENTA. Instrument documentation, like original calibration certificates, manuals andproduct status information shall be accessed via a web enabled system with alicense. The instrument-specific information shall be accessed via its serial number.When services are provided by an authorized service provider the servicesinformation like subsequent field calibrations shall be archived and accessible viathis web enabled system.PART 2- PRODUCTS2.01MANUFACTURERA.Endress+Hauser- Prowirl 2002.02 MANUFACTURED UNITSA.The vortex flowmeter system shall consist be a flanged or wafer design (byapplication and instrument schedule) and transmitter which may be mountedintegral (compact) to the sensor or remote with interconnecting cables up to 98 feet in length1.The system shall have an easy, safe and menu guided procedure toensure precise measuring results.2.The system shall support remote configuration.3.The system shall require no regular maintenance, contain no movingparts, and must possess a lifetime calibration with no zero-pointdrift.4.The system shall have the capability of measuring steam qualityor detecting the presence of wet steam as specified.5.The system shall have SIL 2 in accordance with IEC 61508.6.The system shall also have an optional dualsens version forredundant measurements with two sensors and transmittersdesigned for SIL 3 in accordance to IEC 61508.7.The system shall include a method to verify both the sensor andtransmitter to confirm the flowmeter performance to the originalmanufacturer specifications.i.The verification method shall be traceable to factory calibration usinga third party attested onboard system pursuant to ISO standards.ii.The verification technique shall not require but will support externalhandhelds, interfaces, special tooling or electrical access for averification to be performed.iii.The transmitter shall store up to eight verifications in its non-volatilememoryiv. A verification of the system shall be possible at any time, locally orremotely, on demand, and under process conditions and shall notinterrupt the signal to the control system.v.The verification report shall be compliant to common quality systemssuch as ISO 9000 section 7.6a to prove reliability of the meterspecified accuracy.B.The vortex sensing system shall consist of:1.The flow metering system shall possess a non-volatile memory tostore the sensor calibration and transmitter setup information. Theelectronics shall be interchangeable for meter sizes ½” – 12”.2.The sensor shall be the proper size to measure the design flow rateof the piping.3.Wetted materials of 316L stainless steel, CF3M SS, and graphite sealas standard.4.Wetted materials of Alloy C22 and seals of Viton, Kalrez, and Gylonas options5. A sensor body with standard connections such as ASME B16.5flanges (C, F, O, R sensors) or wafer mounted (D sensor) as specifiedby the customer data sheet.6.The sensor shall be rated for NEMA 4X service as standard.7.The sensor to count the vortices shall be of the differential switchedcapacitance (DSC) type and shall be capable of withstandingtemperatures ranging from -40o to 500 o F (or -328o to 752 o F wherespecified).8.The DSC sensor shall be identical for all meter sizes.9.The DSC sensor shall have an option to include a Pt 1000 element forintegral temperature measurement.10.The meter shall be rated for pressures up to Class 300 for vortexsensor bodies with proper process connections.11.The reducer version (R) shall have an optional meter with integratedline size reduction.12.Resistant to mechanical shock such as water hammer and vibrationresistant design up to 2g at 10 to 150 Hz as specified.13.Temperature shock resistant up to 270 o F/s.C.The integral or remote transmitter shall integrate, control and allow setup of the measurement system. The output and source power shall be noted in the drawings in one of the following formats:1.4–20 mA HART2.4-20mA HART, pulse/frequency/switch3.4-20mA HART, 4–20 mA output4.4-20 mA HART, pulse/frequency/switch, 4-20 mA input5. PROFIBUS PA, pulse/frequency/switch6. FOUNDATION Fieldbus, pulse/frequency/switch7. 12 to 35 VDC (1, 2, 4 above); 12 to 30 VDC (3 above); 9 to 32 VDC(5, 6 above)D.The transmitter shall:1.Include a powder coated cast aluminum housing with a NEMA 4Xrating.2.Allow local programming that can be operated through theenclosure window without opening the electrical enclosure asspecified.3.Be capable of displaying instantaneous flow rate and total flow withuser-selectable engineering units, readout of diagnostic events andremedies, and support 16 standard languages.4.Include a low flow cutoff control through the display pushbuttonfunction or via a digital bus (if used).5.Allow no limitation of transmitter operational capability or diagnosticdependency between integral and remote mounting orientation.6.Be supported by device drivers (DD), general station description(GSD) files, instructions and pre-engineered code based on selectedoutput variant.7.Retain all setup parameters and accumulated measurementsinternally in non-volatile memory in the event of power failure. Thememory unit shall be transferrable from a damaged unit or used for aduplicate device with no loss of device parameters or data stored viathe use of the display.8.Include an integral flow computer with calculations for natural gas,industrial gases, or steam as specified.9.Display notification and history of process or system events.2.03SOURCE QUALITY CONTROLA.Vortex flowmeters shall be factory calibrated on an approved test stand withcertified accuracy traceable to NIST, compliant with ISO 17025 laboratory standardaccredited by a national verification agency such as A2LA.B.Each meter shall ship with a certificate of a 3-point calibration reportexceeding stated standard accuracy of 0.75% of rate.C. A real-time computer generated printout of the actual calibration data pointsshall indicate apparent and actual flows. The flow calibration data shall beconfirmed by the manufacturer and shipped with the meters to the project site.D.The manufacturer shall provide complete documentation covering thetraceability of all calibration instruments.E.The manufacturer shall provide ISA data sheet ISA-TR20.00.01 as latestrevision of form 20F2321. The manufacturer shall complete the form with allknown data and model codes and dash out the inapplicable fields. Incomplete datasheets submitted will result in a rejected submittal.2.04 ACCESSORIESA. Stainless steel tag - labeled to match the Contract Documents.B. Optionally, provide a remote transmitter mounting set suitable for postmounting.C. Optionally, the vortex flowmeter will be installed with a flow conditioner dueto inadequate straight run requirements.D. Optionally, provide sun shield for outdoor installations.2.04SAFETYA. All electrical equipment shall meet the requirements of ANSI/NFPA 70,NATIONAL ELECTRIC CODE, latest edition.B. All devices shall be certified for use in hazardous areas as: CSA C/US non-incendive for Class I, Division 2, Group A-D or Class I, II, III, Division 1 XP or IS, Group A-DG services.C. All devices shall be suitable for use as non-incendive devices when used withappropriate non-incendive associated equipment.D. Electrical equipment housing shall conform to NEMA 4X classification.E. Non-intrinsically safe electrical equipment shall be approved by a NationallyRecognized Testing Laboratory (NRTL) such as FM, UL, ETL, CSA, etc. for thespecified electrical area classification.F. Electrical equipment specified as intrinsically safe shall qualify as “simpleapparatus” or NTRL approved intrinsically safe equipment per ANSI/ISA-RP12.6“Installation of Intrinsically Safe Systems for Hazardous (Classified) Locations”, latest edition.PART 3- EXECUTION3.01 EXAMINATIONA.Examine the complete set of plans, the process fluids, pressures, andtemperatures and furnish instruments that are compatible with installed processcondition.B.Examine the installation location for the instrument and verify that theinstrument will work properly when installed.3.02 INSTALLATIONA.As shown on installation details and mechanical Drawings.B.As recommended by the manufacturer’s installation and operation manual.C.Specific attention should be given to the following technical requirements:1.Verify the sensor is installed according to the Manufacturer’srecommendations per TI00069D and ISO 14511 as to the required inlet andoutlet run diameters distance from flow disturbances.3.03 FIELD QUALITY CONTROLA.Demonstrate the performance of all instruments to the ENGINEER beforecommissioning.B.ENGINEER to witness all instrument calibration verifications in the field.C.Each instrument shall be tested before commissioning and the ENGINEERshall witness the response in the PLC control system and associated registers.D.Manufacturer’s Field Services:1.Manufacturer’s representative shall verify installation of all installedflow sensors and transmitters.2.Notify the ENGINEER in writing of any problems or discrepancies andproposed solutions.3.04 ADJUSTINGA.Verify factory calibration of all instruments in accordance with theManufacturer’s instructions.3.05 PROTECTIONA.All instruments shall be fully protected after installation and beforecommissioning. Replace any instruments damaged before commissioning:1. The ENGINEER shall be the sole party responsible for determiningthe corrective measures.。
nVent 13 21 26 H58843 Rev. 03 2019 湿暖系统说明书

SECTION 03 06 00SCHEDULES FOR CONCRETERAYSOL FLOOR HEATING – HEAT LOSS REPLACEMENT SYSTEMThis specification is dated 03/01/2019 and supersedes all previous versions.Any text in RED indicates a choice the user needs to decide upon to suit project requirements and deleted prior to incorporating into final contract documents. For detailed design information, please contact your local representative, our website or nVent Thermal Technical Support 800-545-6258.PART 1 GENERAL1.1. SUMMARYA. Section includes UL Listed and CSA Certified floor heating and heat loss replacement systemthat consists of a self-regulating trace heater, connection kits, and electronic controller.B. Related Requirements1. Section 03 30 00 – Cast-In Place Concrete2. Section 07 24 00 – Exterior Insulation and Finish Systems3. Section 25 12 16 – Direct-Protocol Integration Network Gateways4. Section 25 51 00 – Integrated Automation Control of Facility Equipment1.2. REFERENCESA. Reference Standards1. UL515 – Electrical Resistance Heat Tracing for Commercial Applications2. IEEE 515.1-2012 Standard for the Testing, Design, Installation & Maintenance of ElectricResistance Trace Heating for Commercial Applications.3. CSA Standard C22.2 No. 130-03 Requirements for Electrical Resistance Heating Cables& Heating Device Sets4. NFPA 70 - National Electrical Code5. CSA Standard C22.1 – Canadian Electrical Code1.3. SYSTEM DESCRIPTIONA. System for floor heating and heat lost through floors over non-heated areas such as garagesand loading docks; includes temperature control, monitoring, integrated ground-fault circuitprotection and BMS communication capabilities.1. nVent RAYCHEM RaySol Heating Cablea. 120 and 208 - 277 V, RAYCHEM RaySol self-regulating heating cable with afluoropolymer outer jacket. The heating cable shall be part of a UL Listed and CSACertified system.2. nVent RAYCHEM FTC connection kits and accessories3. nVent RAYCHEM C910-485 multi-circuit group control panel or nVent RAYCHEM ACS-30 multi-circuit distributed group controller [Select one]1.4. ACTION SUBMITTALS / INFORMATIONAL SUBMITTALSA. Product Data1. Heating cable data sheet2. UL Listed and CSA Certified certificates for floor heating and heat loss replacement3. floor heating and heat loss replacement design sheet4. System installation and operation instructions5. System installation details6. Controller/power panel data sheet7. Controller/power wiring diagramB. Shop Drawings1. Provide detailed engineered isometric drawings showing layouts for floor, indicatingpower connections, splice, end terminations, and circuit cable length.1.5. QUALITY ASSURANCEA. Source Limitations: All system components [heating cable, connection kits, and controller]shall be sourced from a single manufacturer, under no circumstances shall any componentsbe installed other than those supplied by the cable manufacturer, to ensure system integrityand meet warranty requirements.B. Qualifications1. Manufacturersa. Manufacturer to show minimum of forty (40) years of experience in manufacturingelectric self-regulating heating cables.b. Manufacturer will be ISO-9001 registered.c. Manufacturer to provide heating cable consistent with IEEE 515.1 and CSA 22.2 No130-03 requirements.d. Self-regulating heating cable shall be qualified and tested to demonstrate a usefullifetime in excess of 20 years.e. The manufacturer shall provide an extensive global reference list for this application,including installations that have been in operation for over 15 years.2. Installersa. System installer shall have complete understanding of product and product literaturefrom manufacturer or authorized representative prior to installation. Electricalconnections shall be performed by a licensed electrician.3. Electrical Components, Devices, and Accessories: Listed and labelled as defined in NFPA70, Article 100, by a Nationally Recognized Testing Laboratory (NRTL), and marked forintended use.C. Certifications1. The system (heating cable, connection kits, and controller) shall be UL Listed and CSACertified for floor heating and heat loss replacement.1.6. DELIVERY, STORAGE, AND HANDLINGA. Delivery And Acceptance Requirements1. Deliver, store and handle products to prevent their deterioration or damage due tomoisture, temperature changes, contaminates or other causes.2. Deliver products to site in original, unopened containers or packages with intact andlegible manufacturers’ labels identifying the following:a. Product and Manufacturerb. Length/Quantityc. Lot Numberd. Installation and Operation Manuale. MSDS (if applicable)B. Storage And Handling Requirements1. Store the heating cable in a clean, dry location with a temperature range not below -40°F(-40°C) or exceeding 140°F (60°C).2. Protect the heating cable from mechanical damage.1.7. WARRANTYA. Manufacturer Warranty1. nVent warrants all goods listed below for two (2) years from date of purchase againstfaulty workmanship and use of defective materials when such goods are properlyinstalled, operated, and maintained according to product documentation. See LimitedProduct Warranty (H57396) at .a. Heating cables, connection kits and accessoriesb. Thermostats, controllers, panels contactors, sensors and accessoriesB. Special Warranty –1. Contractor shall provide the owner an extended product warranty for the heat tracingproducts listed below. The contractor must complete and forward to owner theInstallation, Inspection or Commissioning Record(s), and complete the online warrantyregistration form within thirty (30) days from the date of installation, otherwise onlystandard limited warranty applies. See Limited Product Warranty Extension details(H57397) at a. Heating Cable and Components warranty shall be Ten (10) Years from Date ofPurchaseC. Heating cables, connection kits and accessories not automatically offered with a 10 yearmanufacturer’s warranty, as a standard matter of course, will not be allowed. Warrantyinformation must be published on the manufacturer's website.PART 2 PRODUCTS2.1. HEAT TRACING SYSTEMA. Manufacturers1. Basis of Design Manufacturer: Subject to the compliance with requirements, providenVent RAYCHEM heat tracing products of nVent Thermal Management, LLCRedwood City 94063, 800-545-6258;Email: ********************** Website: Specifier: Retain one of the two paragraphs below based upon Project requirements.2. Submit comparable products of one of the following for approval by the specifier:a. [Specifier: Insert name of manufacturer with comparable products]b. Submit request for substitutions in accordance with Instructions to Bidders andDivision 01 General Requirements.3. Provide specified product; Owner will not consider substitution requests.B. Materials1. Heating Cablea. Heating cable shall be RAYCHEM RaySol self-regulating heating cablemanufactured by nVent. [Select one] RaySol-1 (120 V) or RaySol-2 (208 – 277 V)b. The heating cable shall consist of a continuous core of conductive polymer that isradiation cross-linked, extruded between two (2) 16 AWG nickel-plated copper buswires, that varies its power output in response to temperature changes.c. The heating cable shall have a FLUOROPOLYMER outer jacket for dielectricintegrity and long life expectancy.d. The heating cable shall operate on line voltages of 120, 208, 240, or 277 volts[Select one] without the use of transformers.e. The heating cable shall be part of a UL Listed and CSA Certified system.f. The outer jacket of the heating cable shall have the following markingsa) Heating cable model numberb) Agency listingsc) Meter markd) Lot/Batch ID2. Heating Cable Connection Kitsa. Heating cable connection kits shall be Raychem FTC connection kits.b. Manufacturer shall provide power connection and end seal kits compatible withselected heating cable.c. Connection kits shall be UL Listed and CSA Certified.3. Energy Efficient Control System [Select One Option]a. [Option 1] Single Circuit Local Digital Control System1. Local digital controller shall be C910-485.2. Heating cable manufacturer shall provide a local digital controller with built-inGFPD compatible with selected heating cable3. Digital controller shall be capable of supporting up to two (2) RTDtemperature sensors per control point. Leads can be extended using 18AWG, 3-wire, shielded cable.4. Enclosure type shall be Type 4X fiberglass reinforced plastic (FRP).5. Digital controller shall have an integrated adjustable GFPD (10 – 200 mA).[Date] [Project Location]6. Digital control system can be configured for line-sensing, ambient sensingand PASC modes. PASC control proportionally energizes the power to theheating cable to minimize energy based on ambient sensed conditions.7. Digital controller shall be capable of operating with supply voltages from 100V to 277 V.8. Digital controller will have a built-in self-test feature to verify properfunctionality of heating cable system.9. Digital controller will also be able to communicate with BMS by one of thefollowing protocols. [Select one]a. Modbusb. BACnet® or Metasys® N2 [Select RAYCHEM ProtoNode-RERmulti-protocol gateway as accessory]10. Digital controller will also supply an isolated triac alarm relay and a drycontact relay for alarm annunciation back to the BMS.11. The following variables will be monitored by the digital controller and reportedback to the BMS:a. Temperatureb. Ground-faultc. Current drawd. Power consumptione. Associated alarms12. Digital controller shall have c-CSA-us approvalsb. [Option 2] Multi-Circuit, Distributed Digital Control System1. All floor heating and heat loss replacement circuits shall be controlled andmonitored using a distributed digital control system, known as ACS-30,manufactured by nVent.2. Multi-application: Distributed digital control system shall have pre-programmed parameters to provide concurrent control for heating cablesused for pipe freeze protection, flow maintenance, hot water temperaturemaintenance, surface snow melting, roof and gutter de-icing, freezer frostheave prevention and floor heating applications.3. All programming shall be done through the central User Interface Terminal(ACS-UIT2).4. The ACS-UIT2 shall be a color LCD touch-screen display with passwordprotection to prevent unauthorized access to the system.5. The ACS-UIT2 shall communicate with up to fifty-two (52) ACS PowerControl Panels (ACS-PCM2-5) where each panel can control up to five (5)circuits and accept up to five (5) temperature inputs. C910-485 controllersmay also be added to the ACS-30 system for single circuit extensions.6. Digital control system shall be capable of assigning up to four (4) RTDtemperature inputs per heat-tracing circuit.7. The ACS-UIT2 shall communicate with up to sixteen (16) Remote MonitoringModules (RMM2), where each module can accept up to eight (8) temperatureinputs.8. The ACS-UIT2 shall have a USB port to allow for quick and easy softwareupdate.9. The ACS-UIT2 shall have three (3) programmable alarm contacts includingan alarm light on the enclosure cover.10. A separate offline software tool shall be made available to allow users to pre-program the digital control system and transfer program via a USB drive orEthernet.11. The ACS-UIT2 enclosure shall be NEMA 4 for indoor or outdoor locations.12. The ACS-PCM2-5 panel shall be in a NEMA 4/12 enclosure approved fornonhazardous indoor and outdoor locations.13. The ACS-PCM2-5 panel shall provide ground-fault and line current sensingalarming, switching and temperature inputs for five (5) heat tracing circuits.14. Each ACS-PCM2-5 panel shall have five (5) 3-pole, 30 A contactors (EMRtype).15. The ACS-PCM2-5 panel shall be capable of operating at 120 V to 277 V.[Custom ACS-PCM2-5 panel designs are available if standardconfigurations are not suitable. Please contact your nVent salesrepresentative for more information and pricing].16. The ACS-PCM2-5 shall have an alarm contact including an alarm light on thepanel cover.17. Digital controller shall have an integrated adjustable GFPD (10 – 200 mA).18. Digital control system will have a built-in self-test feature to verify properfunctionality of heating cable system.19. Digital control system will also be able to communicate with BMS by one ofthe following protocols. [Select one]a. Modbus®b. BACnet® or Metasys® N2 [Select RAYCHEM ProtoNode-RERmulti-protocol gateway as accessory]20. The following variables will be monitored by the digital controller and reportedback to the BMS.c. Temperatured. Ground-faulte. Current drawf. Power consumptiong. Associated alarms21. The ACS-UIT2 shall be c-CSA-us Certified. The ACS-PCM2-5 panel shall bec-UL-us Listed.4. Approvala. The system (heating cable and controller) shall be UL Listed and CSA Certified forfloor heating and heat loss replacement.b. The floor heating and heat loss replacement system shall have a design, installationand operating manual.PART 3 EXECUTION3.1. EXAMINATIONA. Preinstalling Testing1. Prior to installing heating cable, an insulation resistance test shall be performed by theinstalling contractor to ensure integrity of heating cable as described in the installationand maintenance manual.3.2. PREPARATIONA. Protection Of In-Place Conditions1. All heating cable ends shall be protected from moisture ingress until cable is terminated.3.3. INSTALLERSA. Acceptable Installers1. Subject to compliance with requirements of Contract Documents, installer shall befamiliar with installing heat-trace cable and equipment3.4. INSTALLATIONA. Comply with manufacturer’s recommendations in the RaySol Floor Heating and Freezer FrostHeave Prevention Installation and Operation Manual (H58138).B. Install and secure the heating cable in accordance with the RaySol Floor Heating and FreezerFrost Heave Prevention Installation and Operation Manual (H58138).C. Install electric heating cable according to the drawings and the manufacturer’s instructions.The installer shall be responsible for providing a complete functional system, installed inaccordance with applicable national and local requirements.D. Grounding of controller shall be performed according to Section 26 05 26 "Grounding andBonding for Electrical Systems."E. Connection of all electrical wiring shall be according to Section 26 05 19 "Low-VoltageElectrical Power Conductors and Cables”.3.5. FIELD QUALITY CONTROLA. Initial start‐up and field testing (commissioning) of the system shall be performed by factorytechnician or factory representative per the owner’s requirements.B. Field Tests And Inspections1. The system shall be commissioned in accordance to the RaySol Floor Heating andFreezer Frost Heave Prevention Installation and Operation Manual.2. The heating cable circuit integrity shall be tested using a 2500 Vdc megohmmeter at thefollowing intervals below. Minimum acceptable insulation resistance shall be 1000megohms.a. Before installing the heating cableb. After heating cable has been installedc. After installing accessoriesd. Prior to initial start-up (commissioning)e. As part of the regular system maintenance3. The technician shall verify that the controller parameters are set to the applicationrequirements.4. The technician shall verify that the ACS-30 and ProtoNode device server (if applicable)are configured correctly with the BMS.5. All commissioning results will be recorded and presented to the owner.C. Non-Conforming Work1. Any heat tracing circuit which fails the any of the above tests must be corrected prior tocommissioning or startup of the system.D. Retain the services of nVent RAYCHEM Management to provide factory design build andinspection services to prepare submittals for complete design layouts, wiring diagrams,installation details for all heat trace equipment including heating cable, connection kits,controllers and sensors. nVent shall supply 11”x17” isometric drawings for every circuit for acomplete heat tracing system.E. Provide factory inspection report as part of a complete manufacturer approved installation thatis compliant to Code.F. Start-up – Start-up of system shall be performed by factory technician or factory representativeper the owner’s requirements.3.6. SYSTEM STARTUP1. Provide a factory-certified technician or manufacturer’s representative for startup andcommissioning of the heat tracing system and controller.2. Coordinate all controller settings with engineer prior to programming the controller.3. Provide commissioning report in submittals package to owner.3.7. MAINTENANCEA. Maintenance Service1. Comply with manufacturer’s recommendations in RaySol Floor Heating and FreezerFrost Heave Prevention Installation and Operation Manual (H58138).END OF SECTION。
工程施工设计英文缩写

工程施工设计英文缩写Construction design is a crucial part of any engineering project, as it lays the foundation for the entire construction process. It involves the planning, analysis, and detailing of all aspects of a construction project, from the structural components to the finishing touches. In order to streamline the construction process and ensure the successful completion of a project, it is essential to have a well-thought-out design that takes into account all relevant factors.This article will cover the key aspects of construction design, including the various stages of the design process, the importance of each stage, and the tools and techniques used in the design process. By understanding these key aspects, engineers and project managers can ensure that their construction projects are executed efficiently and effectively.Stages of Construction DesignThe construction design process typically consists of several key stages, each of which plays a crucial role in the overall success of the project. These stages may vary depending on the complexity of the project and the specific requirements of the client, but generally follow a similar pattern. The following are the most common stages of construction design:1. Preliminary Design: This stage involves the initial planning and conceptualization of the project. It includes determining the project scope, setting goals and objectives, and identifying any potential challenges or constraints. During this stage, the project team may conduct site visits, research local building codes and regulations, and gather information on the client's needs and preferences.2. Schematic Design: In this stage, the project team creates schematic drawings and models that illustrate the overall layout and design of the project. These drawings may include floor plans, elevations, and sections, as well as conceptual designs for key elements such as structural systems, plumbing, and electrical systems. The goal of this stage is to develop a clear and cohesive design concept that meets the client's requirements and complies with all relevant regulations.3. Design Development: Once the schematic design has been approved, the project team moves on to the design development stage. This stage involves further refining the design concept and developing detailed drawings and specifications. The team may work closely with consultants and specialists to determine the specific materials, finishes, and systems that will be used in the project. The design development stage is critical for ensuring that the project meets the client's budget and schedule requirements.4. Construction Documents: The construction documents stage involves preparing detailed drawings, specifications, and other documents that provide a comprehensive set of instructions for the construction of the project. These documents typically include plans for all building components, such as foundations, walls, roofs, and mechanical systems, as well as details on finishes, fixtures, and equipment. The construction documents serve as thebasis for obtaining permits, bidding the project to contractors, and ultimately constructing the project.5. Bidding and Negotiation: Once the construction documents are complete, the project team may solicit bids from contractors and subcontractors to determine the cost of construction. This stage involves reviewing bids, negotiating contracts, and selecting a contractor to build the project. The bidding and negotiation stage is critical for ensuring that the project is constructed within the client's budget and schedule constraints.6. Construction Administration: The final stage of the construction design process is construction administration, which involves overseeing the construction of the project to ensure that it is built according to the design documents. This stage may involve conducting site visits, reviewing shop drawings and submittals, and coordinating with contractors and subcontractors to address any issues that arise during construction. The construction administration stage is essential for ensuring that the project is delivered on time, within budget, and to the highest quality standards.Importance of Construction DesignConstruction design plays a critical role in the success of any engineering project, as it establishes the framework for the entire construction process. A well-designed project is more likely to be completed on time and within budget, with fewer errors and delays. The following are some of the key reasons why construction design is important:1. Ensures Project Feasibility: The design process helps to identify potential challenges, constraints, and risks that may affect the feasibility of a project. By carefully planning and analyzing all aspects of the project, engineers can identify and address potential issues before they arise, ensuring that the project is completed successfully.2. Enhances Communication: A well-designed project provides a clear and cohesive vision for all stakeholders involved in the project, including clients, contractors, and regulatory agencies. By creating detailed drawings, specifications, and other documents, engineers can effectively communicate the design intent and requirements to ensure that everyone is on the same page.3. Improves Efficiency: A well-thought-out design helps to streamline the construction process by providing a roadmap for how the project will be executed. By establishing clear goals, objectives, and specifications, engineers can ensure that the construction team can work efficiently and effectively to complete the project on time and within budget.4. Ensures Compliance: The design process involves research, analysis, and consultation with regulatory agencies to ensure that the project complies with all relevant building codes, regulations, and standards. By working closely with regulators and experts in the field, engineers can ensure that the project meets all necessary requirements and is safe and sustainable.5. Minimizes Risks: By considering all aspects of the project during the design process, engineers can identify potential risks and develop strategies to mitigate them. This may include incorporating redundancy into structural systems, selecting durable materials, and designing systems that are resilient to natural disasters. By carefully planning and analyzing all aspects of the project, engineers can minimize the likelihood of errors, delays, and cost overruns during construction.Tools and Techniques in Construction DesignThere are a variety of tools and techniques that engineers use in construction design to ensure that a project is planned, analyzed, and detailed effectively. These tools and techniques may vary depending on the complexity of the project and the specific requirements of the client, but generally involve a combination of computer software, physical models, and collaborative processes. The following are some of the key tools and techniques used in construction design:1. Building Information Modeling (BIM): BIM is a powerful software tool that allows engineers to create detailed 3D models of a building or structure. These models can be used to visualize the project, analyze structural systems, coordinate building components, and identify clashes. BIM also enables engineers to generate quantities, costs, and schedules, and facilitate collaboration between all stakeholders involved in the project.2. Computer-Aided Design (CAD): CAD software allows engineers to create detailed drawings and plans for a construction project. These drawings may include floor plans, elevations, sections, and details of building components. CAD software also enables engineers to make changes to the design quickly and efficiently, and generate accurate measurements and quantities for construction.3. Virtual Reality (VR) and Augmented Reality (AR): VR and AR technology are increasingly being used in construction design to provide immersive experiences of a project. These technologies allow engineers to visualize the project in 3D, simulate construction processes, and identify potential issues before construction begins. VR and AR technology also enable clients and stakeholders to experience the project and provide feedback on the design.4. Physical Models: Physical models are often used in construction design to help visualize the project and communicate the design intent. These models may be built at various scales, from small study models to large-scale mockups, and may include physical building components, materials, and finishes. Physical models can be used to assess spatial relationships, lighting conditions, and other factors that may impact the design of the project.5. Collaborative Processes: Collaboration is essential in construction design, as it involves working closely with clients, consultants, contractors, and regulatory agencies to ensure that the project is completed successfully. Engineers may use tools such as online project management software, virtual meetings, and shared documents to facilitate communicationand collaboration throughout the design process. By engaging all stakeholders in the design process, engineers can ensure that the project meets all requirements and expectations. ConclusionConstruction design is a complex and iterative process that involves planning, analysis, and detailing of all aspects of a construction project. By following a systematic approach and using the right tools and techniques, engineers and project managers can ensure that their projects are completed successfully. By understanding the key aspects of construction design, including the various stages of the design process, the importance of each stage, and the tools and techniques used in the design process, engineers can deliver projects that meet all requirements and exceed client expectations.。
SikaQuick

Section 03 01 00Maintenance of concrete***SIKA SPECIFICATION NOTE:This guide specification includes test methods, materials and installation procedures for SikaQuick®-1000, a fast-setting, one-component, self-consolidating mortar with fiber and an integral corrosion inhibitor for form and pour/pump applications. SikaQuick®-1000is a one-component, rapid hardening, early strength gaining, cementitious, patching material for concrete. This guide specification should be adapted to suit the needs and conditions of individual projects. It is prepared in CSI Master Format and should be included as a separate section under Division 3 - Concrete. ***Part 1 - General1.01SummaryThis Specification shall be read as a whole by all parties concerned. Each Section may contain moreor less the complete Work of any trade. The Contractor is solely responsible to make clear to theSubcontractors the extent of their Work and coordinate overlapping Work.1.02System descriptionThis specification describes the patching or overlay of interior and exterior horizontal surfaces andformed vertical and overhead surfaces with Portland Cement Mortar/Concrete.1.03Related sectionsA.Maintenance of Cast-in-Place Concrete: Section 03 01 30B.Maintenance of Precast Concrete: Section 03 01 40C.Maintenance of Cast Decks and Underlayment: Section 03 01 50D.Maintenance of Mass Concrete: Section 03 01 70E.Structural Concrete: Section 03 33 001.04ReferencesThe following standards are applicable to this section:▪ASTM C-109 - Compressive Strength▪ASTM C-1583 – Direct Pull-Off Bond Strength▪ASTM C-469 - Modulus of Elasticity▪ASTM C-806 – Volume Change▪ASTM C-293 - Flexural Strength▪ASTM C-666 – Freeze-Thaw Resistance1.05Quality AssuranceA.Manufacturing qualifications: The manufacturer of the specified product shall be ISO 9001 certifiedand have in existence a recognized ongoing quality assurance program independently audited on aregular basis.B.Contractor qualifications: Contractor shall be qualified in the field of concrete repair and protectionwith a successful track record of 5 years or more. Contractor shall maintain qualified personnel whohave receivced product training by a manufacturer's representative.C.Store and apply materials in accordance with all safety and weather conditions required bymanufacturer or as modified by applicable rules and regulations of local, state and federalauthorities having jurisdiction. Consult Safety Data Sheets (SDS) for complete handlingrecommendations.1.06Delivery, Storage, and HandlingA.All materials must be delivered in original, unopened containers with the manufacturer's name,labels, product identification, and batch numbers. Damaged material must be removed from thesite immediately.B.Store all materials off the ground and protect from rain, freezing or excessive heat until ready foruse.C.Condition the specified product as recommended by the manufacturer.1.07Job ConditionsA.Environmental Conditions: Do not apply material if it is raining or snowing or if such conditionsappear to be imminent. Minimum application temperature 45o F (7o C) and rising.B.Protection: Precautions should be taken to avoid damage to any surface near the work zone due tomixing and handling of the specified material.1.08SubmittalsA.Submit two copies of manufacturer's literature, to include: Product Data Sheets (PDS), andappropriate Safety Data Sheets (SDS).B.Submit copy of Certificate of Approved Contractor status by manufacturer.1.09WarrantyProvide a written warranty from the manufacturer against defects of materials for a period of one(1) year, beginning with date of substantial completion of the project.Part 2 - Products2.01ManufacturerSikaQuick®-1000, as manufactured by Sika® Corporation, is considered to conform to therequirements of this specification.2.02 MaterialsA.General1)The repair concrete shall be a blend of selected Portland cements, specially gradedaggregates, admixtures for controlling setting time, and water reducers for workability andan organic accelerator.2)The materials shall be non-combustible, both before and after cure.3)The material shall be supplied as a factory-blended unit.4)The Portland cement mortar must be placeable from 1/4” to 1” in depth per lift forhorizontal applications.B.To prepare a rapid-setting portland cement concrete: aggregate shall conform to ASTM C-33. Thematerial shall be extended with 30-lb. of a 3/8” ( No.8 distribution per ASTM C-33, Table II) clean,well-graded, saturated surface dry aggregate, having low absorption, high density and non-reactive(reference ASTM C-1260, C-227, C-289). Aggregate must be approved for use by the Engineer.2.03Performance CriteriaTypical Properties of the mixed polymer-modified, portland cement mortar:1. Yield 0.42 ft3 per bag2. Color Concrete gray3. Mixing Ratio4.5-5 pts per bag4. Density 136 lbs/ft3 (2.18 kg/l)5. Application Thickness Neat: Min 1/4” (7 mm); Max 2 ” (50 mm)Extended: Min 1” (25 mm); Max 6 ” (152 mm)6. Application Temp Min 50o F (10o C) ; Max 86o F (30o C)7. Working Time 30 min.8. Compressive Strength (ASTM C-109) 3 hours – 1,250 psi (8.6 MPa)1 day – 4,000 psi (27.6 MPa)7 day - 5,000 psi (34.5 MPa)28 days - 7,000 psi (48.2 MPa)9. Flexural Strength (ASTM C-293) 28 day – 1,000 psi (6.9 MPa)10. Splitting Tensile Strength (ASTM C-496) 28 days - 500 psi (3.4 MPa)11. Slant Shear (ASTM C-882 Modified) 28 days - 2,500 psi (17.2 MPa)12. Permeability (ASTM C-1202) 28 days < 1,000 C13. Shrinkage (157 Modified per ASTM C-928)28 days - 0.06%14. Modulus of Elasticity (ASTM C-469) 28 days - 4.6 x 106 psi14. Freeze-Thaw Resistance (ASTM C-666) 98%Note: Tests above were performed with the material and curing conditions @ 71o F – 75o F and 45 - 55% relative humidity.Part 3 – Execution3.01Surface PreparationA.Areas to be repaired must be clean, sound, and free of contaminants. All loose and deterioratedconcrete shall be removed by mechanical means. Mechanically prepare concrete substrate to obtaina surface profile of ± 1/8” (CSP 6 or greater as per ICRI Guidelines) with a new exposed aggregatesurface. Area to be patched shall not be less than 1” in depth.B.Where reinforcing steel with active corrosion is encountered, sandblast the steel to a white metalfinish to remove all contaminants and rust. Where corrosion has occurred due to the presence ofchlorides, the steel shall be high pressure washed after mechanical cleaning. Prime steel with 2coats of Sika® Armatec® 110 EpoCem as per the Product Data Sheet (PDS).3.02 Mixing and ApplicationA.Neat: Mechanically mix in appropriate sized mortar mixer or with a Sika jiffy paddle and low speed(400-600 rpm) drill. Pour approximately 4-1/2 pints of water into the mixing container. Add thepowder while continuing to mix. Mix to a uniform consistency for a maximum of three minutes. Addup to another ½ pint of water to mix if a greater flow is desired. Should smaller quantities beneeded, be sure the proper water/powder ratio is maintained and that the dry material is uniformlyblended before mixing the components together. Mix only that amount of material that can beplaced in 30 minutes. Do not retemper material.B.Extended: Pour 4-1/2 to 5 pints of water into the mixing container. Add the powder whilecontinuing to mix. Add correct amount of the pre-approved coarse aggregate, and continue mixingto a uniform consistency. Mixing time should be 3 minutes maximum.e of SikaLatex R: For latex modified polymer overlay, Sika® Latex R can be substituted for water.Consult Sika® Latex R Product Data Sheet for full product usage guidelines.D.Placement Procedure: At the time of application, the substrate should be Saturated Surface Dry(SSD) with no standing water. Mortar and/or concrete must be scrubbed into substrate filling allpores and voids. While the scrub coat is still plastic, force material against edge of repair, workingtoward center. After filling, consolidate, then screed. Allow mortar or concrete to set to desiredstiffness, then finish with a trowel for a smooth surface. Broom or burlap drag for rough surface.Areas where the depth of the repair is less than 1” shall be repaired with the neat rapid settingPortland cement mortar. In areas where the depth of the repair is greater than 1”, the repair shallbe made with the extended rapid-setting Portland cement concrete.E.As per ACI recommendations for portland cement concrete, curing is required. Moist cure with wetburlap and polyethylene, a fine mist of water or a water-based* compatible curing compound.Moist curing should commence immediately after finishing and continue for 48 hours. Protect newlyapplied material from rain, sun, and wind until compressive strength is 70% of the 28 daycompressive strength. To prevent from freezing cover with insulating material. Setting time isdependent on temperature and humidity.*Pretesting of curing compound is recommended.F.Adhere to all procedures, limitations and cautions for the polymer-modified portland cementmortar in the manufacturers current printed Product Data Sheet (PDS) and literature.3.02CleaningA.The uncured portland cement mortar can be cleaned from tools with water. The cured polymermodified portland cement mortar can only be removed mechanically.B.Leave finished work and work area in a neat, clean condition without evidence of spillovers ontoadjacent areas.SikaQuick 1000SikaQuick®-1000 1/26/20186The preceding specifications are provided by Sika Corporation as a guide for informational purposes only and are not intended to replace sound engineering practice and judgment and should not be relied upon for that purpose. Sika Corporation makes no warranty of any kind, either express or implied, as to the accuracy, completeness or the contents of these guide specifications. Sika Corporation assumes no liability with respect to the provision or use of these guide specifications, nor shall any legal relationship be created by, or arise from, the provision of such specifications SIKA SHALL NOT BE RESPONSIBLE UNDER ANY LEGAL THEORY TO ANY THIRD PARTY FOR ANY DIRECT OR CONSEQUENTIAL DAMAGES OF ANY KIND ARISING FROM THE USE OF THESE GUIDE SPECIFICATIONS. The specifier, architect, engineer or design professional or contractor for a particular project bears the sole responsibility for the preparation and approval of the specifications and determining their suitability for a particular project or application.Prior to each use of any Sika product, the user must always read and follow the warnings and instructions on the product’s most current Product Data Sheet, product label and Safety Data Sheet which are available online at / or by calling Sika's Technical Service Department at 800-933-7452. Nothing contained in any Sika materials relieves the user of the obligation to read and follow the warnings and instruction for each Sika product as set forth in the current Product Data Sheet, product label and Safety Data Sheet prior to product use.。
卡塔尔建筑细则
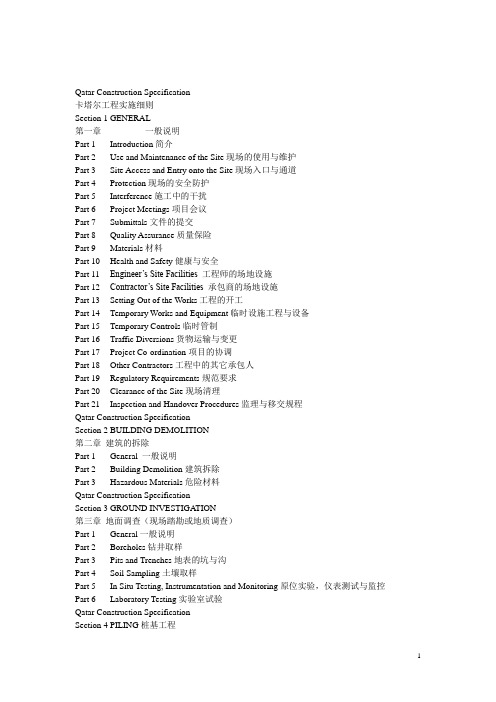
Qatar Construction Specification卡塔尔工程实施细则Section 1 GENERAL第一章一般说明Part 1 Introduction简介Part 2 Use and Maintenance of the Site现场的使用与维护Part 3 Site Access and Entry onto the Site现场入口与通道Part 4 Protection现场的安全防护Part 5 Interference施工中的干扰Part 6 Project Meetings项目会议Part 7 Submittals文件的提交Part 8 Quality Assurance质量保险Part 9 Materials材料Part 10 Health and Safety健康与安全Part 11 Engineer’s Site Facilities 工程师的场地设施Part 12 Contractor’s Site Facilities 承包商的场地设施Part 13 Setting Out of the Works工程的开工Part 14 Temporary Works and Equipment临时设施工程与设备Part 15 Temporary Controls临时管制Part 16 Traffic Diversions货物运输与变更Part 17 Project Co-ordination项目的协调Part 18 Other Contractors工程中的其它承包人Part 19 Regulatory Requirements规范要求Part 20 Clearance of the Site现场清理Part 21 Inspection and Handover Procedures监理与移交规程Qatar Construction SpecificationSection 2 BUILDING DEMOLITION第二章建筑的拆除Part 1 General 一般说明Part 2 Building Demolition建筑拆除Part 3 Hazardous Materials危险材料Qatar Construction SpecificationSection 3 GROUND INVESTIGATION第三章地面调查(现场踏勘或地质调查)Part 1 General一般说明Part 2 Boreholes钻井取样Part 3 Pits and Trenches地表的坑与沟Part 4 Soil Sampling土壤取样Part 5 In Situ Testing, Instrumentation and Monitoring原位实验,仪表测试与监控Part 6 Laboratory Testing实验室试验Qatar Construction SpecificationSection 4 PILING桩基工程Part 1 General Requirements for Piling Work桩基工程的一般要求Part 2 General Requirements for Concrete Piles混凝土桩的一般要求Part 3 Precast Reinforced and Prestressed Concrete Piles预制钢筋砼桩与预应力钢筋砼桩Part 4 Precast Reinforced Concrete Segmental Piles预制钢筋砼部分的桩Part 5 Bored Cast-In-Place Piles现场浇筑螺旋钻孔桩Part 6 Bored Piles Constructed Using Continuous Flight Augers and Concrete or Grout Injection through Hollow Auger Stems用连续不断钻动的螺旋钻通过中空的螺旋钻杆来注水泥浆或者砼的工艺来浇筑螺旋钻孔桩。
高阻地线系统(HRG)-中等电压部分说明书
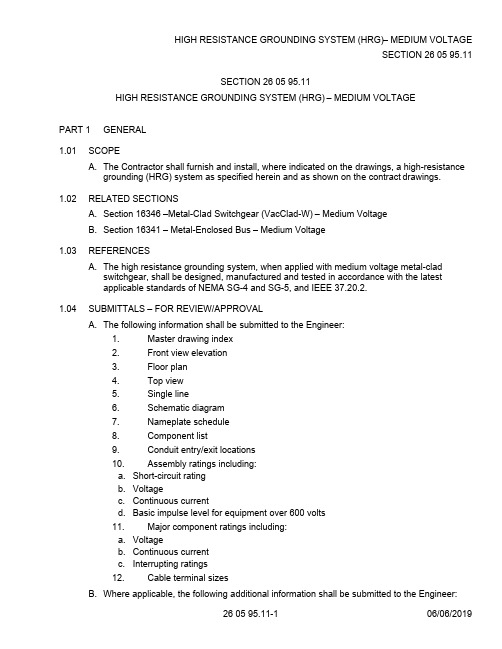
SECTION 26 05 95.11HIGH RESISTANCE GROUNDING SYSTEM (HRG) – MEDIUM VOLTAGEPART 1GENERAL1.01SCOPEA.The Contractor shall furnish and install, where indicated on the drawings, a high-resistancegrounding (HRG) system as specified herein and as shown on the contract drawings.1.02RELATED SECTIONSA.Section 16346 –Metal-Clad Switchgear (VacClad-W) – Medium VoltageSection 16341 – Metal-Enclosed Bus – Medium VoltageB.1.03REFERENCESA.The high resistance grounding system, when applied with medium voltage metal-cladswitchgear, shall be designed, manufactured and tested in accordance with the latestapplicable standards of NEMA SG-4 and SG-5, and IEEE 37.20.2.1.04SUBMITTALS – FOR REVIEW/APPROVALA.The following information shall be submitted to the Engineer:1.Master drawing index2.Front view elevationFloor plan3.4.Top viewSingle line5.6.Schematic diagram7.Nameplate schedule8.Component list9.Conduit entry/exit locations10.Assembly ratings including:Short-circuit ratinga.b.Voltagec.Continuous currentd.Basic impulse level for equipment over 600 volts11.Major component ratings including:a.VoltageContinuous currentb.c.Interrupting ratings12.Cable terminal sizesBus Run connection1.2.Connection details between close-coupled assemblies3.Composite floor plan of close-coupled assemblies4.Key interlock scheme drawing and sequence of operations5.Descriptive bulletins6.Product data sheetsSUBMITTALS – FOR CONSTRUCTION1.05A.The following information shall be submitted for record purposes:1.Final as-built drawings and information for items listed in Paragraph 1.04, and shall incorporate all changes made during the manufacturing process2.Wiring diagrams3.Certified production test reports4.Installation information including equipment anchorage provisions5.Seismic certification as specified1.06QUALIFICATIONSA.The manufacturer of the assembly shall be the manufacturer of the major components withinthe assembly.B.For the equipment specified herein, the manufacturer shall be ISO 9001 or 9002 certified.C.The manufacturer of this equipment shall have produced similar electrical equipment for aminimum period of five (5) years. When requested by the Engineer, an acceptable list ofinstallations with similar equipment shall be provided demonstrating compliance with thisrequirement.D.*Provide Seismic tested equipment as follows:1.The equipment and major components shall be suitable for and certified by actual seismic testing to meet all applicable seismic requirements of the [latest InternationalBuilding Code (IBC)] [latest California Building Code (CBC) with OSHPD Amendments].[The equipment shall have OSHPD Special Seismic Certification (OSP) Pre-Approval.] The Project Structural Engineer will provide site specific ground motion criteria for 2.use by the manufacturer to establish SDS values required.3.The IP rating of the equipment shall be 1.54.The Structural Engineer for the Site will evaluate the SDS values published on the [Manufacturer’s] [OSHPD] website to ascertain that they are "equal to" or "greaterthan" those required for the Project Site.5.The following minimum mounting and installation guidelines shall be met, unless specifically modified by the above referenced standards.The Contractor shall provide equipment anchorage details, coordinated with the a.equipment mounting provision, prepared and stamped by a licensed civil engineer inthe state. Mounting recommendations shall be provided by the manufacturer basedupon the above criteria to verify the seismic design of the equipment.b.The equipment manufacturer shall certify that the equipment can withstand, that is,function following the seismic event, including both vertical and lateral requiredresponse spectra as specified in above codes.c.The equipment manufacturer shall document the requirements necessary for properseismic mounting of the equipment. Seismic qualification shall be consideredachieved when the capability of the equipment, meets or exceeds the specifiedresponse spectra.1.07REGULATORY REQUIREMENTSDELIVERY, STORAGE AND HANDLING1.08A.Equipment shall be handled and stored in accordance with manufacturer’s instructions. One(1) copy of these instructions shall be included with the equipment at time of shipment.B.HRG system assembly shall be designed to be shipped by truck, rail, or ship. Indoor groupsshall be bolted to skids. HRG system assembly shall be equipped to be handled by crane.Where cranes are not available, it shall be suitable for skidding in place on rollers usingjacks to raise and lower the groups.C.Equipment being stored prior to installation shall be stored so as to maintain the equipmentin a clean and dry condition. If stored outdoors indoor equipment shall be covered andheated, and outdoor equipment shall be heated.1.09OPERATION AND MAINTENANCE MANUALSA.Equipment operation and maintenance manuals shall be provided with each assemblyshipped, and shall include instruction leaflets and instruction bulletins for the completeassembly and each major component.PART 2PRODUCTS2.01MANUFACTURERSA.EatonB.*__________C.*__________The listing of specific manufacturers above does not imply acceptance of their products that do not meet the specified ratings, features and functions. Manufacturers listed above are notrelieved from meeting these specifications in their entirety. Products in compliance with thespecification and manufactured by others not named will be considered only if pre-approved by the Engineer ten (10) days prior to bid date.* Note to Spec. Writer – Insert data in blanksRATINGS2.02 The assembly shall be suitable for maximum service voltage and the type of power systemA.as indicated on the drawings.The assembly shall be rated to withstand mechanical forces exerted during short-circuitB.conditions when connected directly to a power source having available fault current of *______amperes.The assembly shall be UL approved and supplied with the UL label.C.CONSTRUCTION2.03The assembly shall consist of a free standing NEMA 1 enclosure. The sides and rear shallA.be covered with removable bolt-on covers. Front and rear access are required. All edges of front covers or hinged front panels shall be formed. Provide adequate ventilation within the enclosure.The assembly shall be provided with adequate lifting means and shall be capable of beingB.moved into installation position and bolted directly to *[contractor supplied floor sills to be set level in concrete per manufacturer's recommendations] [the floor without the use of floor sills provided the floor is level to 1/8-inch per 3-foot distance in any direction]. Base of assembly shall be suitable for rolling directly on pipes without skidsThe assembly shall be equal to Eaton type C-HRG high-resistance grounding equipmentC.utilizing grounding transformers and resistors as herein specified or as required.Each vertical steel unit forming part of the assembly shall be a self-contained housing havingD.an instrument compartment and a resistor compartment. The control compartment shall be segregated from the resistor compartment by means of steel barriers or, if indicated on the drawings, the resistor assembly shall be a separately mounted component furnished in its own ventilated.BUS2.04 A 1/4-inch x 2-inch copper ground bus shall be firmly secured to the assembly. ProvideA.terminals for connection of the system grounding conductor, suitable for #8 AWG to 500 kcmil, copper or aluminum.WIRING/TERMINATIONS2.05The switchgear manufacturer shall provide suitable terminal blocks for secondary wireA.terminations and a minimum of 10% spare terminals shall be provided. One control circuit cutout device shall be provided in each control circuit. Switchgear secondary wire shall be #14 AWG, type SIS rated 600 volt, 90 degrees C, furnished with wire markers at each termination. Wires shall terminate on terminal blocks with marker strips numbered inagreement with detailed connection diagrams.*[Phase terminals for delta connected system] [Neutral terminal for wye connected system]B.shall be suitable for #4 AWG to 500 kcmil power cables. The power cable (supplied by owner) shall enter HRG enclosure from *[top] [bottom].* Note to Spec. Writer – Select oneMETERING AND CONTROLS2.06Provide a separate control compartment with front hinged door that includes the following:A. A switchboard type ground current ammeter, 1% accuracy, 250 degree scale, 0 1.to 10 A ACSystem control selector switch with PULSE/NORMAL/TEST positions. Switch 2.shall spring-return to NORMAL from the TEST positionReset control selector switch with AUTO/MANUAL/RESET positions. Switch shall 3.spring-return to MANUAL from RESET position. The AUTO position shall cause theground fault relay to automatically reset when a ground is no longer detected. TheMANUAL position shall cause the ground alarm relay to latch and remain latched until the selector is moved to the RESET position by the operatorA green lamp to indicate that the system is in normal condition, a red lamp to 4.indicate that a ground fault has been detected and a white lamp that flashes at the same time as the pulsing contactor, at an adjustable rate of 3 to 60 pulses per minuteAn instruction nameplate that provides the operator with a step-by-step5.procedure for operating the controlsA rating nameplate that states the maximum ground current, maximum pulse 6.current and duty rating of the equipment at maximum current levels*[A single set point ground voltage meter relay, with two pointers, one for voltage7.indication and an adjustable pointer for ground voltage pickup level. [Set pointadjustment shall be front mounted knob on the meter] [A dual set point ground voltage meter relay, with one set point output contact set shall be wired to terminal blocks forfield connection as shown on the drawings. Set point adjustments shall be via front-mounted knobs]*An alarm horn with an alarm silence pushbutton and re-alarm timer. The horn shall be a 8.heavy-duty, high-decibel type, adjustable from 78 to 103 db. Alarm silence control shall reset when ground relay is reset. Alarm shall automatically re-sound at the end of a 2- to 48-hour field-settable time interval if alarm has been silenced but ground fault still exists. Re-alarm timer shall not be defeated via any control deviceProvide the following control devices and features:B.One normally open and one normally closed ground fault alarm contact each 1.rated 10 amps at 240 volts ACA test circuit shall be included to functionally test all controls of the fault indication 2.and pulsing circuitry. The test shall be inhibited if the system is sensing a faultA pulsing contactor, controlled by an adjustable recycle timer, allowing a3.momentary increase of approximately 4 amperes above ground currentTerminal shall be supplied to accommodate owner furnished 120 V 60 Hz control 4.power supplyDead-front pull-out type fuse block with fuses for control power disconnect5.Tapped resistors with taps wired out to a convenient front accessible terminal6.block. Taps shall provide 3 to 6 amperes of ground current in 1 ampere increments.Resistors shall be heavy-duty industrial type, *[edgewound] [wirewound] design. Eachresistor tube shall have a stamped steel rating nameplate. The resistor assembly shallbe interconnected with suitable wire size as required for the circuit current7.All control wiring shall be #14 AWG type SIS minimum8.A detailed schematic shall be furnished that accurately and completely describesthe control and grounding circuits. All wire designations, terminal points, control device,and selector switch contact developments shall be shown. The schematic and theaccompanying wiring diagrams shall be amended as required after final testing at thefactory. An as-built copy of the schematic, wiring diagrams and material list shall bepacked with the unit prior to shipment. Provide a drawing pocket secured by screws orweldment for drawing storage within the assembly9.When the power system source has a neutral terminal, as indicated on the contract drawings, a single phase distribution type transformer of proper kVA and voltagerating shall be connected from power system neutral to ground, with the required resistorassembly inserted in the secondary circuit of that transformer. When the power systemsource has no neutral point, WYE-broken DELTA distribution transformers shall befurnished in the assembly to provide a neutral point, and required resistor assembly shallbe inserted across the broken DELTA secondary of those transformers2.07ENCLOSURESA.The HRG system described in these specifications shall be indoor construction, with devicesarranged as shown on contract drawings.2.08NAMEPLATESA.Engraved nameplates, mounted on the face of the assembly, shall be furnished for allcontrol devices as indicated on the drawings. Nameplates shall be laminated plastic, blackcharacters on white background, and secured with screws. Characters shall be 3/16-inchhigh, minimum. Furnish master nameplate giving HRG system designation, voltage andampere ratings, manufacturer’s name, catalog number, and general order number.Control components mounted within the assembly, such as fuse blocks, relays, pushbuttons, B.switches, etc., shall be suitably marked for identification corresponding to appropriatedesignations on manufacturer’s wiring diagrams.2.09FINISHA.The finish shall consist of a coat of gray (ANSI-61), thermosetting, polyester powder paintapplied electrostatically to pre-cleaned and phosphatized steel and aluminum for internaland external parts. The coating shall have corrosion resistance of 600 hours to 5% saltspray.EXECUTIONPART 33.01FACTORY TESTINGA.The following standard factory tests shall be performed on the equipment provided underthis section. All tests shall be in accordance with latest version of ANSI and NEMAstandards.1.Completely test the high-resistance grounding system for operation under simulated service conditions to assure the accuracy of the wiring and the functioning ofall equipment2.The wiring and control circuits shall be given a dielectric test of 1500 volts for one(1) minute between live parts and ground in accordance with ANSI C37.20.2B.A certified test report of all standard production tests shall be available to the Engineer onrequest.3.02FIELD QUALITY CONTROLA.Provide the services of a qualified factory-trained manufacturer’s representative to assist theContractor in installation and startup of the equipment specified under this section for aperiod of *_____ working days. The manufacturer’s representative shall provide technicaldirection and assistance to the contractor in general assembly of the equipment, connectionsand adjustments, and testing of the assembly and components contained therein.B.The Contractor shall provide three (3) copies of the manufacturer’s field startup report.3.03MANUFACTURER’S CERTIFICATIONA.A qualified factory-trained manufacturer’s representative shall certify in writing that theequipment has been installed, adjusted and tested in accordance with the manufacturer’srecommendations.B.The Contractor shall provide three (3) copies of the manufacturer’s representative’scertification.TRAINING3.04The Contractor shall provide a training session for up to five (5) owner’s representatives for ***_______ normal workdays at a job site location determined by the owner.B.The training session shall be conducted by a manufacturer’s qualified representative.Training program shall include instructions on the assembly, protective devices, and othermajor components.3.05INSTALLATIONA.The Contractor shall install all equipment per the manufacturer’s recommendations andcontract drawings.All necessary hardware to secure the assembly in place shall be provided by the Contractor.B.3.06FIELD ADJUSTMENTSThe relays shall be set in the field by:A.1.The Contractor in accordance with settings designated by the engineer-- *OR --1.The Contractor in accordance with settings designated in a coordination study of the system as required elsewhere in the contract documents-- *OR --1.A qualified representative of the manufacturer, retained by the Contractor, inaccordance with settings designated in a coordinated study of the system as requiredelsewhere in the contract documents。
湿热保护(中英文版)
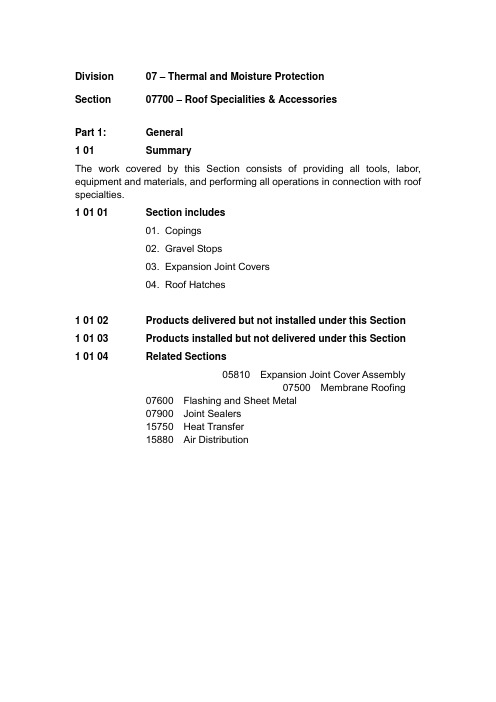
Division 07 – Thermal and Moisture ProtectionSection 07700 – Roof Specialities & AccessoriesPart 1: General1 01 SummaryThe work covered by this Section consists of providing all tools, labor, equipment and materials, and performing all operations in connection with roof specialties.1 01 01 Section includes01. Copings02. Gravel Stops03. Expansion Joint Covers04. Roof Hatches1 01 02 Products delivered but not installed under this Section1 01 03 Products installed but not delivered under this Section1 01 04 Related Sections05810 Expansion Joint Cover Assembly07500 Membrane Roofing 07600 Flashing and Sheet Metal07900 Joint Sealers15750 Heat Transfer15880 Air Distribution1 02 References1 02 01 Applicable Standards1 02 01 01 Saudi Arabian Standards1 02 01 02 Gulf Standards1 02 01 03 International Standards1 02 01 04 USA Standards1 02 01 04 01 American Society for Testing and Materials (ASTM)ASTM A167 : 99 Standard Specification for Stainless andHeat-ResistingChromium-Nickel Steel Plate, Sheet andStripASTM B209 : 01 Standard Specification for Aluminum andAluminum-Alloy Sheet and Plate.ASTM B221 : 00 Standard Specification for Aluminum andAluminum-Alloy Extruded Bars, Rods, Wire,Profiles, and Tubes.ASTM B370 : 98 Standard Specification for Copper Sheet andStrip for Building ConstructionASTM B749 : 97 Standard Specification for Lead andLead-Alloy Strip, Sheet and Plate Products.ASTM D2178 : 97Standard Specification for Asphalt Glass Feltused in Roofing and Waterproofing.ASTM D2822 : 97 Specification for Asphalt Roof Cement1 02 01 04 14Sheet Metal & Air Conditioning Contractors National Association Inc (SMACNA)Architectural Sheet Metal Manual1 02 01 05 European Standards1 02 01 06 British Standards1 02 01 07 German Standards1 02 02 CodesUBCUniform Building Code1 02 03 Other References1 02 03 01 American Architectural Manufacturers Association (AAMA)AAMA 603 : 98 Voluntary Performance Requirements andTest Procedures for Pigmented OrganicCoatings on Extruded Aluminum.AAMA 605 : 98 Voluntary Specifications for HighPerformance Organic Coatings onArchitectural Extrusions and Panels.AAMA 606.1 : 76 Voluntary Guide Specifications andInspection Methods for Integral Color AnodicFinishes for Architectural Aluminum.AAMA 607.1 : 77 Voluntary Guide Specification andInspection Methods for Clear AnodicFinishes for Architectural Aluminum.1 03 Definitions1 03 01 Technical TermsEPDM –elastomer - propylene diene rubber1 03 02 AbbreviationsB.o.Q. Bill of Quantitydeg. C degree CelsiuskPa kilo Pascalmax. maximummin. minimumo.c. off centerUL Underwriters Laboratories (US)µm Micrometer = 1/10 mm1 04 System Description1 05 SubmittalsSubmit the following in accordance with Conditions of Contract and specification Section 01300.1 05 01 Product DataProvide product data for each type of prefabricated components and their accessories.1 05 02 Shop Drawings施工图纸Provide shop drawings indicating material profile, jointing details, fastening methods, and installation details. Do not proceed with fabrication and / or installation until approval from the Engineer.1 05 03 SamplesSamples of typical prefabricated components with required finish, shall be submitted to the Engineer prior to application for approval.1 05 04 Quality Control SubmittalsDocumented experience of Contractor’s site supervisor(s) (see ref. 1 06 01 02) Certificates for all elements indicated showing compliance with referenced Standards and requirements of local authorities.Records and reports of Contractor’s Internal Q.C.. Records and reports of Contractor’s External Q.C..1 05 05 Handing-Over Submittals1 05 05 01 Project Records1 05 05 02 Operation and Maintenance Data1 05 06 Other Submittals1 06 Quality Assurance1 06 01 Qualifications1 06 01 01 Qualifications of Manufacturers Products used in the work of this Section shall be produced by manufacturers regularly engaged in this work, with a history of successful production acceptable to the Engineer, or preferably a certification according to ISO 9000 series.1 06 01 02 Qualifications of Installers Use adequate number of skilled workmen who are thoroughly trained and experienced in the necessary crafts and who are completely familiar with the specified requirements and the methods needed for proper performance of work .Contractor’s site supervisor(s) shall have knowledge of referenced Standards and at least five (5) years of documented experience.1 06 03 CertificationsProvide 'Third Party' certificates issued by an authorized and independent agency or laboratory where indicated.1 06 04 Quality Control1 06 04 01 Internal Quality ControlContractor’s internal Quality Cont rol shall include but not be limited to: Checking supplier’s certificates of compliance with specification and referenced Standards prior to application or installation.Checking supplier’s delivery tickets for compliance with supply order and specification.1 06 04 02 External Quality Controlsee 1 06 03 “Certifications”1 06 04 03 Source Quality Control1 07 Delivery, Storage and Handling1 07 01 Packing and ShippingDeliver materials to site originally packed by manufacturer. Protect materials duri ng delivery to comply with manufacturer’s directions. Damaged materials shall be replaced at Contractor's cost.1 07 02 Storage and ProtectionStore materials and prefabricated components at site in an adequate manner to prevent twisting, bending and abrasion, and make sure that the storage stays dry and is properly ventilated.1 08 Project and Site Conditions1 08 01 Existing ConditionsNote: Should include references to documents whereinformation may be found pertaining to such items as existingstructures, public utility lines, geophysical reports etc.!1 08 02 Environmental RequirementsRefer to Section 01060 Regulatory Requirements, 1 01 02 .1 09 Schedules and ProgramsNote: Specify requirements for coordinating certain workswhich must be done in special sequence with, or at the time aswork in other Sections.1 10 Special WarrantyNote: Describe special or extended warranty only (e.g. inlandscaping when warranty depends on growing, periods maybe exceeding the normal warranty period).1 11 Maintenance1 11 01 Maintenance Service1 11 02 Operation Services1 11 03 Extra MaterialNote: Specify products to be supplied by the Contractor forfuture maintenance and repair and state to whom, when andwhere the items are to be delivered!Part 2: Products2 01 Basic Materials2 01 01 Galvanized SteelGalvanized sheet steel shall comply with ASTM A361, Grade A or ASTM A526 – G90 (275 g/m2) zinc-coating. Minimum thickness shall be 0,6 mm.2 01 01 01 Coating to Galvanized SteelCoating to galvanized sheet steel shall be as follows:01.0 Modified Silicone, baked enamelsystem, complying with AAMA 603.02.0 Acrylic, baked enamel system,complying with AAMA 603.03.0 Polyester, baked enamel system,complying with AAMA 603.04.0 PVDF (polyvinylidene fluoride), multiplecoat, thermally cured, complying withAAMA 605.2 01 02 Aluminium01.0 Aluminium sheet shall comply withASTM B209 or an equivalent Standard;minimum thickness shall be 0,8 mm.02.0 Extruded aluminium shall comply withASTM B221 or an equivalent Standard;min. thickness shall be 0,8 mm.2 01 02 01 Finish and Coating for Aluminium01.0 mill finish02.0 Anodized finish of min. 15 µm thickness,complying with AAMA 607.1- Class I(clear) or AAMA 606.1- Class I (color)03.0 Shop coated with modified silicone,baked enamel system, complying withAAMA 603.04.0 Shop coated with acrylic, baked enamelsystem, complying with AAMA 603.05.0 Shop coated with polyester, bakedenamel system, complying with AAMA603.06.0 Shop coated with PVDF (polyvinylidenefluoride), multiple coat, thermally cured,complying with AAMA 605.07.0 Color as indicated or to be selected bythe Engineer from manufacturer’s colorchart.2 01 03 Stainless SteelStainless Steel sheet shall comply with ASTM A167, type 304; minimum thickness 0,4 mm. Provide pattern and finish as indicated.2 01 04 CopperCopper sheet shall comply with ASTM B370, cold rolled, minimum thickness 0,5 mm, natural or lacquered finish as indicated.2 01 05 Titan ZincTitan Zinc sheets shall comply with the relevant Standards2 02 Manufactured Items2 02 01 Copings and Gravel StopsNote: Select the required material from one of the optionsmarked with asterisk (*) and indicate the finish in B.o.Q..Copings and gravel stops shall be made of material as follows:* 01.0 Extruded aluminum, of min. 0,8 mmthickness.* 02.0 Aluminum sheet, of min. 0,8 mmthickness.* 03.0 Stainless Steel sheet, of min. 0,4 mmthickness.* 04.0 Galvanized steel sheet of min. 0,6 mmthickness.* 05.0 Copper sheet of min. 0,5 mm thickness.* 06.0 Titan zinc sheet of min. 0,7 mmthickness.Copings and gravel stops shall be shaped as indicated or selected by the Engineer from manufacturer’s production range. It shall include special supports and cover plates to conceal and weather seal joints and attachment flanges.Finish shall be as indicated.2 02 02 Expansion Joint CoversExpansion joint covers shall be of composite construction with flexible EPDMor neoprene flashing with closed-cell polyurethane foam backing. Each edge shall be seamed to aluminum or stainless steel sheet flanges, designed for indicated joint width, inclusive special formed corners, tees, intersections, each sealed watertight.Expansion joint covers shall comply with requirements established in Section 05810.2 02 03 Roof Hatches01.0 Provide roof hatches of size, material,curb, leaf-type and model indicated.02.0 Integral steel curb shall be of min. 2 mmgalvanized steel (G90), min. 25 mm rigidglassfiber or foam insulation and shallhave integral cap flashing and extendedflange for mounting.03.0 Integral aluminum curb shall be of min. 3mm aluminum, anodized, min. 25 mmrigid glassfiber or foam insulation andshall have integral cap flashing andappropriate extended flange formounting.04.0 Flush steel cover shall be of min. 2 mmgalvanized steel (G90), min. 25 mm rigidglassfiber or foam insulation, steelinterior liner of min. 0,6 mm galvanizedsheet steel and continuous neoprene orvinyl gasket to provide a weatherproofseal.05.0 Flush aluminum cover shall be of min. 3mm aluminum, anodized, min. 25 mmrigid glassfiber or foam insulation,aluminum interior liner of min. 1 mmmill-finish aluminum and continuousneoprene or vinyl gasket to provide aweatherproof seal.06.0 Skylight cover shall be single or doublelined as indicated. Double lined onesshall have a min. 12 mm airspacebetween the two panes.Skylights shall be fabricated frompolycarbonate according to shape, colorand pattern indicated; designshall be for a min. live load of 1,5 kPa; acontinuous neoprene or vinyl gasketshall provide a weatherproof seal.The external face shall have anUV-protection of min. 50 micron.Live load of min. 1,5 kPa shall be testedby an authorized and independentlaboratory.07.0 Hardware:- Compression spring operator withshock absorber- Steel manual pull handle for interiorand exterior operation- Steel hold open arm with grip handle foreasy release- Heavy duty type hinges08.0 Fire rating: Roof hatches which are to beused as heat or smoke vents shall becertified by an authorized laboratory forthe required fire rating and automaticopening system as indicated.2 03 Accessories01.0 Sealant shall be acrylic, silicon,polyurethane or polysulfide based,unless otherwise indicated. Sealant andexecution shall comply withrequirements in Section 07900 – JointSealers.02.0 Roofing Cement shall comply with ASTMD2822, Type I or II.Part 3: Execution3 01 General ExaminationExamine structure where work of this Section will be installed. Verify that deck, curbs, roof membrane and base flashing are in place and positioned correctly. Correct conditions detrimental to the proper and timely completion of the work. Verify that materials and prefabricated items to be used for the work comply with requirements in specifications and schedules. Do not proceed with installation until unsatisfactory conditions have been corrected.3 02 General Preparation3 03 InstallationInstall components in accordance with manufacturer’s instructions.Conform to SMACNA and NRCA manuals or/and drawing details. Coordinate installation of components with installation of roofing membrane and base flashings.Apply sealant indicated and follow requirements in Section 07900 –Joint Sealers.Apply bituminous paint on surfaces of units in contact with cementitious materials or dissimilar metals.Automatic operated hatches shall be tested after installation and report submitted to the Engineer for approval.3 04 Field Quality Control3 05 Adjusting and CleaningAdjust hinges of hatches for smooth operation. Clean flashings from any on-site soldering and soiling. Special care shall be taken not to soil adjacent finished construction.3 06 Demonstration3 07 ProtectionProtect completed work from damage until handing over.3 08 SchedulesContractor shall provide schedules of his works, coordinated with other trades, prior to commencing with installation.Part 4: Method of Measurement4 01 GeneralThe quantities to be paid for will be measured in place or determined from drawings.Where work is measured by area, no deductions will be made for voids not exceeding 1,0 m2.4 02 Units of MeasurementCopings, gravel stops and expansion joint covers etc. will be measured by m length according to different material, coating and size.Roof hatches will be enumerated according to different size, type, material and finish.Part 5: Basis of Payment5 01 GeneralPayment will be made for complete work including furnishing all material, equipment, tools, scaffolding, storage facilities, water, power, for all labor, samples, coordinating work with other trades, checking, examination, testing, quality assurance, cleaning and protecting.5 02 Ancillary Works to be included in the Unit Price Rates The following ancillary works shall be included in the unit price rates and will not be measured separately:- Painting of concealed surfaces- Brackets, cleats and any other holding devices- Sealing of joints第七章–湿热保护07700节–屋顶及附件第一部分总述1 01 概要此部分的施工范围包括:提供所有的工具,人力,设备,材料和所有房屋连接所需的操作。
05120 STRUCTURAL STEEL结构钢

PART 1 - GENERAL1.1 DESCRIPTIONA Section includes but not limited to the following: structural steel framingmembers, support members, suspension cables, and struts; base or bearingplates, shear stud connectors; anchor bolts for structural steel; beams, girders,purlins, and girts; bearing of steel for girders, trusses or bridges; bracing;columns, posts; connecting materials for framing structural steel to structuralsteel; splices, stops, bolts, and clamps; expansion joints connected to thestructural steel frame; fasteners for connecting structural steel items;permanent shop bolts; shop bolts for shipment; field bolts for permanentconnections; permanent pins; grillage beams and girders; hangers essential tothe structural steel frame; leveling plates, wedges, shims, and leveling screws;trusses; and grouting under base plates all as shown on the drawings and whereapplicable and required.B Related Sections:1. Section 05500 - Metal Fabrications: Steel fabrications affecting structuralsteel work.1.2 REFERENCESA AISC (American Institute of Steel Construction) - Load and Resistance Factor(LRFD) Specification for Structural Steel Buildings.B AISC (American Institute of Steel Construction) - Code of Standard Practicefor Structural Steel Buildings and Bridges.C AISC (American Institute of Steel Construction) - Seismic Provisions forStructural Steel Buildings.D ASTM A36/A36M - Carbon Structural Steel.E ASTM A53 - Pipe, Steel, Black and Hot-Dipped, Zinc-Coated, Welded andSeamless.F ASTM A123 - Zinc (Hot Dipped Galvanized) Coatings on Iron and SteelProducts.G ASTM A153 - Zinc Coating (Hot Dip) on Iron and Steel Hardware.H ASTM A242/A242M - High-Strength Low-Alloy Structural Steel.I ASTM A307 - Carbon Steel Bolts and Studs, 60 ksi Tensile Strength.J ASTM A325 - Structural Bolts, Steel, Heat-Treated, 120/105 ksi Minimum Tensile Strength.K ASTM A449 - Tempered Steel Bolts and Studs.L ASTM A490 - Heat-Treated Steel Structural Bolts, 150 ksi Minimum Tensile Strength.M ASTM A500 - Cold-Formed Welded and Seamless Carbon Steel Structural Tubing in Rounds and Shapes.N ASTM A501 - Hot-Formed Welded and Seamless Carbon Steel Structural Tubing.O ASTM A514/A514M - High-Yield Strength, Quenched and Tempered Alloy Steel Plate, Suitable for Welding.P ASTM A529/A529M - High-Strength Carbon-Manganese Steel of Structural Quality.Q ASTM A563 - Carbon and Alloy Steel Nuts.R ASTM A568/A568M - Steel, Sheet, Carbon and High-Strength, Low-Alloy, Hot-Rolled and Cold-Rolled Sheet, General Requirements for.S ASTM A572/A572M - High-Strength, Low-Alloy Columbium-Vanadium Structural Steel.T AWS A2.4 (American Welding Society) - Standard Symbols for Welding, Brazing, and Nondestructive Examination.U AWS D1.1 (American Welding Society) - Structural Welding Code - Steel.V FM (Factory Mutual) - Roof Assembly Classifications.W RCSC (Research Council on Structural Connections) - Specification for Structural Joints Using ASTM A325 or A490 Bolts, LRFD or ASD.X SSPC (Steel Structures Painting Council) - Steel Structures Painting Manual, V olumes 1 and 2.Y UL (Underwriters Laboratory, Inc.) - Fire Resistance Directory.Z WH (Warnock Hersey) - Certification Listings.1.3 SUBMITTALSA Section 01300 - Submittals Procedures: Submittal procedures.B Shop Drawings:1.Indicate profiles, sizes, spacing, locations of structural members,openings, attachments, and fasteners.2.Connections.3.Cambers and loads.4.Indicate welded connections with AWS A2.4 welding symbols.Indicate net weld lengths.C Mill Test Reports: Submit indicating structural strength and destructive andnon-destructive test analysis.D Manufacturer's Mill Certificate: Certify that products meet or exceed specifiedrequirements.E Welders Certificates: Certify welders employed on the Work, verifying AWSqualification within the previous 12 months.1.4 QUALITY ASSURANCEA Fabricate structural steel members in accordance with AISC Code of StandardPractice.B Perform Work in accordance with AISC Code of Standard Practice, Section 10.C Maintain one copy of each document on site.D Fabricator: Company specializing in performing the Work of this section withminimum five years documented experience and holding current AISCCertification.E Erector: Company specializing in performing the Work of this section withminimum five years documented experience.PART 2 - PRODUCTS2.1 MATERIALSA Structural Steel Members: ASTM A36/A36M or ASTM A572/A572M,Grade 50.B Structural Tubing: ASTM A500, Grade B.C Pipe: ASTM A53, Grade B.D Shear Stud Connectors: ASTM A449.E Suspension Cable: wire rope.F Bolts, Nuts, and Washers:1.Unfinished bolts shall be used only for non-structural connections suchas handrails, etc.. Conform to ASTM A307 grade A, nuts to ASTMA563 with hardened washer.2.High Strength Bolts shall be used for all primary bolted connections.Conform to ASTM A325 type, Nuts to ASTM A563m Grade DH3. Forbolted connections exposed to weather, use type 3 bolts, nuts andwashers.G Anchor Bolts: ASTM A307.H Welding Materials: AWS D1.1; type required for materials being welded.I Sliding Bearing Plates: Teflon coated.J Grout: Non-shrink type, pre-mixed compound consisting of non-metallic aggregate, cement, water reducing and plasticizing additives, capable ofdeveloping a minimum compressive strength of 7,000 psi (48MPa) at 28 days.K Shop and Touch-Up Primer: SSPC 15, Type 1, red oxide.L Finish: Hot dipped galvanized coating to ASTM A123 or painted for corrosion to SSPC.2.2 FABRICATIONA Space shear stud connectors as indicated on the Drawings.B Continuously seal joined members by intermittent welds and plastic fillercontinuous welds. Grind exposed welds smooth.C Fabricate connections for bolt, nut, and washer connectors.D Develop required camber for members.2.3 FINISHA Shop prime structural steel members. Do not prime surfaces that will be field welded,in contact with concrete, and high strength bolted.B. Finish coating shall be in compliance with the requirements as specified in Section09900 – PAINTING.2.4 SOURCE QUALITY CONTROL AND TESTSA Provide shop testing and analysis of structural steel sections.PART 3 - EXECUTION3.1 EXAMINATIONSection 01300 - Submittal.3.2 ERECTIONA Allow for erection loads, and for sufficient temporary bracing to maintainstructure safe, plumb, and in true alignment until completion of erection andinstallation of permanent bracing.B Field weld components and shear studs indicated on Drawings.C Field connect members with threaded fasteners; torque to required resistance.D Do not field cut or alter structural members without approval of Engineer.E After erection, prime welds, abrasions, and surfaces not shop primed orgalvanized, except surfaces to be in contact with concrete.F Grout under base plates: After being plumbed and properly positioned, columnbase plates, bearing plates for beams and similar structural members, andmachinery and equipment base plates shall be grouted according tomanufacturer’s written recommendations. Plates shall be set and anchored tothe proper line and elevation. Metal wedges, shims, and/or setting nuts shall beused for leveling and plumbing structural members. Concrete and metalsurfaces in contact with grout shall be clean and free of oil and grease. Concretesurfaces shall be free of laitance and shall be dampened but not puddled.Trowel grouted surface smooth, splay neatly to 45 degrees.3.3 ERECTION TOLERANCESA Section 01400 – Quality Control.B Maximum Variation From Plumb: 6mm per story, non-cumulative.C Maximum Offset From True Alignment: 6mm3.4 FIELD QUALITY CONTROLA Section 01400 – Quality Control.END OF SECTION。
SECTION220700PLUMBINGINSULATIONPART1…

Stanford University – Facilities Design GuidelinesSECTION 22 07 00PLUMBING INSULATIONPART 1 -GENERAL1.1SUMMARYA.Section includes equipment insulation, covering, and thermal insulation for pipingsystems including vapor retarders, jackets and accessories.B.Related Sections:1.Section 09 05 00 – Common Work Results for Finishes: Execution requirementsfor painting insulation jackets and covering specified by this section.1.2REFERENCESA.ASTM A167 - Standard Specification for Stainless and Heat-Resisting Chromium-Nickel Steel Plate, Sheet, and Strip.B.ASTM B209 - Standard Specification for Aluminum and Aluminum-Alloy Sheet andPlate.C.ASTM C177 - Standard Test Method for Steady-State Heat Flux Measurements andThermal Transmission Properties by Means of the Guarded Hot Plate Apparatus.D.ASTM C195 - Standard Specification for Mineral Fiber Thermal Insulating Cement.E.ASTM C449/C449M - Standard Specification for Mineral Fiber Hydraulic-SettingThermal Insulating and Finishing Cement.F.ASTM C518 - Standard Test Method for Steady-State Heat Flux Measurements andThermal Transmission Properties by Means of the Heat Flow Meter Apparatus.Stanford University – Facilities Design GuidelinesG.ASTM C533 - Standard Specification for Calcium Silicate Block and Pipe ThermalInsulation.H.ASTM C534 - Standard Specification for Preformed Flexible Elastomeric CellularThermal Insulation in Sheet and Tubular Form.I.ASTM C547 - Standard Specification for Mineral Fiber Preformed Pipe Insulation. J.ASTM C552 - Standard Specification for Cellular Glass Thermal Insulation.K.ASTM C553 - Standard Specification for Mineral Fiber Blanket Thermal Insulation for Commercial and Industrial Applications.L.ASTM C591 - Standard Specification for Unfaced Preformed Rigid Cellular Polyurethane Thermal Insulation.M.ASTM C592 - Standard Specification for Mineral Fiber Blanket Insulation and Blanket-Type Pipe Insulation (Metal-Mesh Covered) (Industrial Type).N.ASTM C610 - Standard Specification for Expanded Perlite Block and Pipe Thermal Insulation.O.ASTM C612 - Standard Specification for Mineral Fiber Block and Board Thermal Insulation.P.ASTM C795 - Standard Specification for Thermal Insulation for Use in Contact with Austenitic Stainless Steel.Q.ASTM C1126- Standard Specification for Preformed Closed Cell Phenolic Foam Pipe and Board Insulation.R.ASTM C1136 – Standard Specification for Flexible, Low Permeance Vapor Retarders for Thermal Insulation.S.ASTM D1784 - Standard Specification for Rigid Poly (Vinyl Chloride) (PVC) Compounds and Chlorinated Poly (Vinyl Chloride) (CPVC) Compounds.T.ASTM E84 - Standard Test Method for Surface Burning Characteristics of Building Materials.U.ASTM E96 - Standard Test Methods for Water Vapor Transmission of Materials.V.ASTM E162 - Standard Test Method for Surface Flammability of Materials Using a Radiant Heat Energy Source.W.ASTM G21 - Standard Practice for Determining Resistance of Synthetic Polymeric Materials to Fungi.X.NAIMA (North American Insulation Manufacturers Association) - National Insulation Standards.Y.SMACNA (Sheet Metal and Air Conditioning Contractors’ National Association) - HVAC Duct Construction Standards - Metal and Flexible.1.3SUBMITTALSA.Section 01 33 00 - Submittal Procedures: Submittal procedures.B.Product Data: Provide product description, thermal characteristics and list of materialsand thickness for each service, and locations.C.Manufacturer's Installation Instructions: Indicate installation procedures that ensureacceptable workmanship and installation standards will be achieved.D.Manufacturer's Certificate: Certify that products meet or exceed specified requirements.1.4QUALIFICATIONSA.Manufacturer: Company specializing in manufacturing products specified in thissection with minimum three years experience.B.Applicator: Company specializing in performing work of this section with minimumthree years experience.1.5DELIVERY, STORAGE, AND HANDLINGA.Accept materials on site in original factory packaging, labeled with manufacturer'sidentification, including product density and thickness.B.Protect insulation from weather and construction traffic, dirt, water, chemical, andmechanical damage, by storing in original wrapping.1.6ENVIRONMENTAL REQUIREMENTSA.Do not install insulation outside ambient conditions required by manufacturer of eachproduct.B.Maintain temperature during and after installation for minimum period of 24 hours.1.7FIELD MEASUREMENTSA.Verify field measurements prior to fabrication.1.8WARRANTYA.Section 01 77 00 – Closeout Procedures: Execution Requirements: Product warrantiesand product bonds.B.Provide five year manufacturer warranty for man made fiber.PART 2 -PRODUCTS2.1MANUFACTURERSA.Insulation1.Owens Corning2.Certainteed3.Schuller4.Armstrong5.or equal.B.PVC Jackets1.Schuller2.Speedline3.or equal2.2MAN MADE MINERAL FIBERA.Insulation: ASTM C547 Mineral Fiber Pipe Insulation, Type I 850(454), Type II1200(650), Type III 1200(650). Conform to ASTM C795 for application on Austeniticstainless steel.B.Insulation: ASTM C795; semi-rigid, noncombustible, end grain adhered to jacket.1.‘K’ ('ksi') factor: ASTM C177, 0.24 at 75 degrees F.2.Maximum service temperature: 650 degrees F.3.Maximum moisture absorption: 0.2 percent by volume.C.Vapor Retarder Jacket:1.ASTM C921, White Kraft paper with glass fiber yarn, bonded to aluminizedfilm.2.Moisture vapor transmission: ASTM E96; 0.02 perm-inches.D.Tie Wire: 0.048 inch stainless steel with twisted ends on maximum 12 inch centers.E.Vapor Retarder Lap Adhesive: Compatible with insulation.F.Insulating Cement/Mastic:1.ASTM C195; hydraulic setting on mineral wool.G.Fibrous Glass Fabric:1.Cloth: Untreated; 9 oz/sq yd weight.2.Blanket: 1.0 lb/cu ft density.3.Weave: 5x5.H.Indoor Vapor Retarder Finish:1.Cloth: Untreated; 9-oz/sq yd weight.2.Vinyl emulsion type acrylic, compatible with insulation, color TBD.I.Outdoor Vapor Retarder Mastic: Compatible with insulation.J.Vinyl emulsion type acrylic or mastic, compatible with insulation, black color.K.Outdoor Breather Mastic: Compatible with insulation.L.Vinyl emulsion type, black acrylic or mastic, compatible with insulation.M.Insulating Cement: ASTM C449/C449M.2.3MAN MADE MINERAL FIBER, FLEXIBLE BLANKET OR BATTSA.Insulation: ASTM C553; Mineral Fiber Blanket Thermal Insulation for Commercialand Industrial Applications. Type I, Type II, or Type III, depending on design.B.Vapor Retarder Jacket: ASTM 1136, Type II Flexible and Low Permeance VaporRetarders for Thermal Insulation.1.For systems operating at temperatures below ambient, close and secure seamsand joints. If outward clinching staples are used, then the staple penetrationsmust also be sealed.C.Tie Wire: 0.048 inch stainless steel with twisted ends on maximum 12 inch centers.D.Vapor Retarder Lap Adhesive: Compatible with insulation.E.Insulating Cement/Mastic:1.ASTM C195; hydraulic setting on mineral wool.2.4CELLULAR GLASSA.Insulation: ASTM C552, Type II – pipe and tubing insulation, Class 2 - Jacketed.1.‘K’ factor: ASTM C177 or ASTM C518, 0.29 at 75 degrees F. GLASS FIBER,RIGIDB.Insulation: ASTM C612 [or ASTM C592]; rigid, noncombustible.1.‘K’factor: ASTM C177 or ASTM C518, 0.24 at 75 degreesF.2.Maximum Service Temperature: 450 F degrees.3.Maximum Moisture Absorption: 0.1 percent by volume.4.Density: 3.0lb/cu ft.C.Vapor Retarder Jacket: ASTM C1136 Flexible, Low Permeance Vapor Retarders forThermal Insulation, Type II.D.Facing: 1 inch stainless steel hexagonal wire mesh stitched on one face of insulation.E.Vapor Retarder Lap Adhesive: Compatible with insulation.F.Insulating Cement/Mastic: ASTM C195; hydraulic setting on mineral wool.2.5EXPANDED PERLITEA.Molded Expanded Perlite Block and Pipe Insulation: ASTM C610, Pipe Insulation.2.6HYDROUS CALCIUM SILICATEA.Calcium Silicate Block and Pipe Thermal Insulation: ASTM C533, Type II – for useon surfaces up to 1200 F.B.Tie Wire: 0.048 inch stainless steel with twisted ends on maximum 12 inch centers.C.Mineral Fiber Hydraulic-Setting Thermal Insulating and Finishing Cement:1.ASTM C449/C449M.2.7CELLULAR POLYISOCYANURATE THERMAL INSULATIONA.Unfaced Preformed Rigid Cellular Polyisocyanurate Thermal Insulation: ASTM C591,Type III, compressive strength 50 psi(345 kPa)2.8CELLULAR PHENOLIC FOAMA.Faced or Unfaced Rigid Cellular Phenolic Pipe and Board Thermal Insulation, ASTMC1126, Type II and Type III.2.9ELASTOMERIC CELLULAR FOAMA.Preformed Flexible Elastomeric Cellular Thermal Insulation in Sheet and Tubular form:ASTM C534; Type I, Tubular formB.Elastomeric Foam Adhesive:1.Air dried, contact adhesive, compatible with insulation.2.10PVC PLASTICA.Pipe Jacket: ASTM D1784, One piece molded type fitting covers and sheet material,off-white color.1.Thickness: 30 mil2.Connections: Brush on welding adhesive, Tacks or Pressure sensitive colormatching vinyl tape.B.Equipment Jacket: Sheet material, off-white color.1.Minimum Service Temperature: -40 degrees F.2.Maximum Service Temperature: 150 degrees F.3.Moisture Vapor Transmission: ASTM E96; 0.002 perm-inches.4.Thickness: 30 mil.5.Connections: Brush on welding adhesive, Tacks or Pressure sensitive colormatching vinyl tape.C.Covering Adhesive Mastic: Compatible with insulation.D.ABS Plastic:1.Jacket: One piece molded type fitting covers and sheet material, off-white color.a.Minimum service temperature: -40 degrees F.b.Maximum service temperature of 180 degrees F.c.Moisture vapor transmission: ASTM E96; 0.012 perm-inches.d.Thickness: 30 mil.e.Connections: Brush on welding adhesive.E.Canvas Jacket: UL listed.1.Fabric: 6 oz/sq yd, plain weave cotton.2.Fire retardant lagging adhesive. Composite of insulation, jacket and laggingadhesive shall have a flame spread index not greater than 25 and a smokedeveloped index not greater than 50 per ASTM E84.gging Adhesive: Compatible with insulation.G.Aluminum Jacket: ASTM B209.1.Thickness: 0.016 inch thick sheet.2.Finish: Smooth or Embossed.3.Joining: Longitudinal slip joints and 2 inch laps.4.Fittings: 0.016 inch thick die shaped fitting covers with factory attachedprotective liner.5.Metal Jacket Bands: 3/8 inch wide; 0.015 inch thick aluminum.H.Stainless Steel Jacket: ASTM A167 316 stainless steel.1.Thickness: 0.018inch thick.2.Finish: Smooth or Corrugated.3.Metal Jacket Bands: 3/8 inch wide; 0.010 inch thick stainless steel.I.Mineral Fiber (Outdoor Duct) Jacket: Asphalt impregnated and coated sheet, 50lb/square.PART 3 -EXECUTION3.1EXAMINATIONA.Section 01330 - Administrative Requirements: Coordination and project conditions.B.Verify that piping and equipment has been tested before applying insulation materials.C.Verify that surfaces are clean and dry, with foreign material removed.3.2INSTALLATIONA.Install in accordance with NAIMA National Insulation Standards.B.Exposed Piping: Locate insulation and cover seams in least visible locations.C.Insulated pipes conveying fluids below ambient temperature: Insulate entire systemincluding fittings, valves, unions, flanges, strainers, flexible connections, and expansionjoints.D.Man made mineral fiber insulated pipes conveying fluids below ambient temperature:1.Provide factory-applied or field-applied vapor retarder jackets. Secure factory-applied jackets with pressure sensitive adhesive self-sealing longitudinal lapsand butt strips. Secure field-applied jackets with outward clinch expandingstaples and seal all staple penetrations with vapor retarder mastic.2.Insulate fittings, joints, and valves with molded insulation of like material andthickness as adjacent pipe. Finish with glass cloth and vapor retarder adhesiveor PVC fitting covers.E.For hot piping conveying fluids over 140 degrees F insulate flanges and unions atequipment with removable sections and jackets.F.Man made mineral fiber insulated pipes conveying fluids above ambient temperature:1.Provide factory-applied or field-applied standard jackets. Secure with outwardclinch expanding staples or the pressure sensitive adhesive system on standardfactory-applied jacket and butt strips or both.2.Insulate fittings, joints, and valves with insulation of like material and thicknessas adjoining pipe. Finish with glass cloth and adhesive or PVC fitting covers.G.Inserts and Shields:1.Application: Piping or Equipment all piping2.Shields: Galvanized steel between pipe hangers or pipe hanger rolls and inserts.3.Insert location: Between support shield and piping and under the finish jacket.4.Insert configuration: Minimum 6 inches long, of same thickness and contour asadjoining insulation; may be factory fabricated.5.Insert material: Compression resistant insulating material suitable for theplanned temperature range and service.H.Continue insulation through penetrations of building assemblies or portions ofassemblies having a fire resistance rating of one hour or less. Provide intumescentfirestopping when continuing insulation through assembly. Finish at supports,protrusions, and interruptions.I.Pipe Exposed in Mechanical Equipment Rooms or Finished Spaces (less than 10 feetabove finished floor): Finish with PVC jacket and fitting covers.J.Exterior Applications: Provide vapor retarder jacket. Insulate fittings, joints, and valves with insulation of like material and thickness as adjoining pipe, and finish with glassmesh reinforced vapor retarder cement. Cover with aluminum jacket with seamslocated at the 3 or 9 o’clock position on the side of horizontal piping with the overlapfacing down to shed water or on the bottom side of horizontal equipment.K.Buried Piping: Insulate only where the manufacturer of a specific insulation recommends that their product may be installed either in a trench, tunnel or directburied. Provide factory fabricated assembly with inner all-purpose service jacket withself-sealing lap, and asphalt impregnated open mesh glass fabric, with 1 mil thickaluminum foil sandwiched between three layers of bituminous compound; outer surface faced with a polyester film.L.Heat Traced Piping: Insulate fittings, joints, and valves with insulation of like material, thickness, and finish as adjoining pipe. Provide a size large enough to enclose pipe and heat tracer. Cover with aluminum jacket with seams located at the 3 or 9 o’clockposition on the side of horizontal piping with the overlap facing down to shed water. M.Factory Insulated Equipment: Do not insulate.N.Exposed Equipment: Locate insulation and cover seams in least visible locations.O.Apply insulation close to equipment by grooving, scoring, and beveling insulation.Fasten insulation to equipment with studs, pins, clips, adhesive, wires, or bands.P.Fill joints, cracks, seams, and depressions with bedding compound to form smooth surface. On cold equipment, use vapor retarder cement.Q.Factory-applied or field-applied. Finish with glass cloth and adhesive.R.Finish insulation at supports, protrusions, and interruptions.S.Equipment in Mechanical Equipment Rooms or Finished Spaces: Finish with PVC jacket and fitting covers.plates and ASME Stamps: Bevel and seal insulation around; do not insulate over. U.Equipment Requiring Access for Maintenance, Repair, or Cleaning: Install insulation so it can be easily removed and replaced without damage.3.3THICKNESSA.Provide insulation thicknesses per California Energy Commission (CEC) Title-24.END OF SECTION。
CORE商业炖锅系统消火保护系统说明书
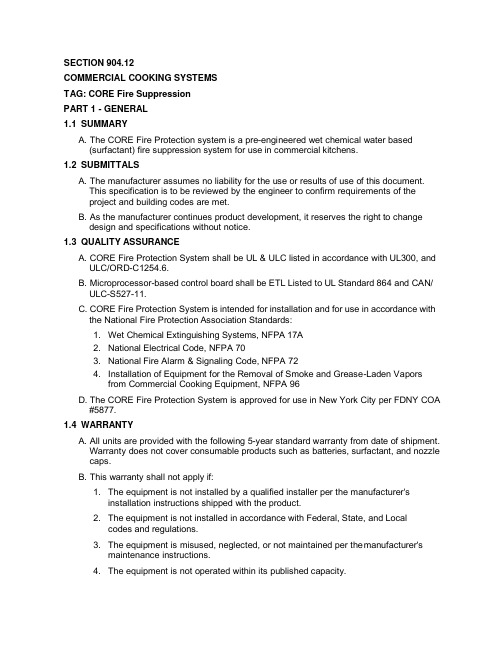
SECTION 904.12COMMERCIAL COOKING SYSTEMSTAG: CORE Fire SuppressionPART 1 - GENERAL1.1 SUMMARYA. The CORE Fire Protection system is a pre-engineered wet chemical water based(surfactant) fire suppression system for use in commercial kitchens.1.2 SUBMITTALSA. The manufacturer assumes no liability for the use or results of use of this document.This specification is to be reviewed by the engineer to confirm requirements of theproject and building codes are met.B. As the manufacturer continues product development, it reserves the right to changedesign and specifications without notice.1.3 QUALITY ASSURANCEA. CORE Fire Protection System shall be UL & ULC listed in accordance with UL300, andULC/ORD-C1254.6.B. Microprocessor-based control board shall be ETL Listed to UL Standard 864 and CAN/ULC-S527-11.C. CORE Fire Protection System is intended for installation and for use in accordance withthe National Fire Protection Association Standards:1. Wet Chemical Extinguishing Systems, NFPA 17A2. National Electrical Code, NFPA 703. National Fire Alarm & Signaling Code, NFPA 724. Installation of Equipment for the Removal of Smoke and Grease-Laden Vaporsfrom Commercial Cooking Equipment, NFPA 96D. The CORE Fire Protection System is approved for use in New York City per FDNY COA#5877.1.4 WARRANTYA. All units are provided with the following 5-year standard warranty from date of shipment.Warranty does not cover consumable products such as batteries, surfactant, and nozzle caps.B. This warranty shall not apply if:1. The equipment is not installed by a qualified installer per the manufacturer'sinstallation instructions shipped with the product.2. The equipment is not installed in accordance with Federal, State, and Localcodes and regulations.3. The equipment is misused, neglected, or not maintained per the m anufacturer'smaintenance instructions.4. The equipment is not operated within its published capacity.5. The invoice is not paid within the terms of the sales agreement.C. The manufacturer shall not be liable for incidental and consequential losses anddamages potentially attributable to malfunctioning equipment. Should any part of theequipment prove to be defective in material or workmanship within the 5-year warranty period, upon examination by the manufacturer, such part will be repaired or replaced by the manufacturer at no charge. The buyer shall pay all labor costs incurred in connection with such repair or replacement. Equipment shall not be returned withoutmanufacturer's prior authorization. All returned equipment shall be shipped by the buyer, freight prepaid to a destination determined by the manufacturer.PART 2 - PRODUCTS2.1 GENERAL ASSEMBLYA. A pre-engineered, fixed pipe, automatic wet chemical (surfactant) fire suppressionsystem for protection of all hazard areas associated with cooking operations, including exhaust hoods, plenums, ductwork, and cooking appliances.B. The fire system shall be factory assembled, tested, and shipped as a complete unit.C. The following specifications, delivering all capacities scheduled and conforming to thedesign indicated herein. Alternate layouts or dimensional changes will not be accepted.2.2 COMPONENTSA. Exhaust hood fire system components to be factory installed.B. Distribution Nozzles1. Nozzles shall be located to protect the exhaust ducts, plenums, and all cookingappliances requiring protection.2. All nozzles shall be equipped with a metal blow off cap. The cap preventscontamination from entering the pipe network and is designed to pop-off uponsystem discharge, allowing agent to flow to the protected hazard area.3. All nozzles shall incorporate a stamped part number to quickly identify nozzle type.C. Distribution System1. The distribution system shall consist of Copper, Schedule 40 black iron, chrome-plated or stainless-steel pipe and fittings. All exposed piping and fittings must bechrome-plated or stainless-steel.2. Fittings shall be minimum class 150. Galvanized fittings shall not be used.3. Flow rate for the hood, when in a fire condition, would be 1.5 gallons per minute perfoot of hood.4. Operating pressure for water lines, both hot water and dedicated line, is 30 to 70psi, depending on the system configuration.5. The maximum static pressure cannot exceed 125 psi; pressure reducing valves canbe utilized to meet the correct operating water pressureD. Suppression System1. The system control equipment shall be capable of all functions associated withautomatically and manually discharging surfactant from surfactant tank, includingautomatic shutdown of the heat source or fuel and electrical power to all protectedareas upon system discharge.2. For automatic activation, the system will be activated by a Firestat (heat) detector.3. For manual activation, an electrically operated manual release shall be used toactuate the system manually.E. Firestat1. Normally Open, Close on Rise 360°F or 600°F.2. Additional firestats may be required based on hood temperature rating and length ofductwork. Refer to Installation, Operation, and Maintenance Manual for information.F. Electrical1. Electrical Division to provide shunt trip breakers at main power panel, ordisconnects, as designated by the Electrical Engineer; interconnection provided athood control panel for the signal to shut down all electricity in and under theexhaust hood. Shunt trips/disconnects to accomplish shut off of electricity in theevent of fire system activation by others.2. Printed circuit board with microprocessor-based controller that provides all thenecessary monitoring, timing, and supervision functions required for the reliableoperation of the fire system.3. Independent supervised loops incorporate redundancy and fault detection.4. Real-time cloud-based monitoring connection provided with system by ownership.5. All wiring must be in accordance to NFPA 70 and the Authority Having Jurisdiction(AHJ).6. Electric gas valve provided for equipment below exhaust hood. Coordinate size andinstallation with Plumbing Division.7. All wiring is to be in accordance with the applicable manufacturer’s instruct ions forthe fire alarm control panel, gas shut-off valve, manual reset relay, and contractorsupplied shut-off devices.PART 3 - EXECUTION3.1 EXAMINATIONA. Examine all areas and conditions under which package(s) are to be installed. Do notproceed with work until unsatisfactory conditions have been corrected in a manneracceptable to Installer.3.2 INSTALLATIONA. Install the package in accordance with manufacturer's instructions, drawings, writtenspecifications, manufacturer's installation manual, and all applicable building codes.3.3 CONNECTIONSA. Electrical connections conform to applicable requirements in Division 26 Sections.3.4 SYSTEM START-UPA. System start-up is performed by a factory-trained Service Technician.。
- 1、下载文档前请自行甄别文档内容的完整性,平台不提供额外的编辑、内容补充、找答案等附加服务。
- 2、"仅部分预览"的文档,不可在线预览部分如存在完整性等问题,可反馈申请退款(可完整预览的文档不适用该条件!)。
- 3、如文档侵犯您的权益,请联系客服反馈,我们会尽快为您处理(人工客服工作时间:9:00-18:30)。
4&6 6HFWLRQ 3DUW 6XEPLWWDOV3DJH 68%0,77$/6 *(1(5$/ 6FRSH 0LVWDNHV LQ ,QIRUPDWLRQ '(),1,7,216 3URGXFW 'DWD DQG 6KRS 'UDZLQJV $V %XLOW 6XUYH\ 'UDZLQJV $V %XLOW 5HFRUG 'UDZLQJV 0DQXIDFWXUHU¶V 5HSUHVHQWDWLYH 7HPSRUDU\ :RUNV 'UDZLQJV 6DPSOHV 0DQXDOV 68%0,77$/ 352&('85(6 *HQHUDO 6FKHGXOH RI 6XEPLWWDOV 0HWKRG RI 6XEPLWWDO &RQWUDFWRU V 5HYLHZ DQG $SSURYDO &RUUHFWLRQV DQG 5HVXEPLWWDOV &KHFN RI 5HWXUQHG 6XEPLWWDOV 5HYLHZ DQG $SSURYDO ,QFRPSOHWH 6XEPLWWDOV &RQIRUPDQFH ,QWHUUHODWHG 6XEPLWWDOV 352*5$00( 3URJUDPPH RI :RUNV 25*$1,=$7,21 &+$576 6WDII 2UJDQLVDWLRQ &KDUW +HDOWK DQG 6DIHW\ 2UJDQLVDWLRQ &KDUW 4XDOLW\ $VVXUDQFH 2UJDQLVDWLRQ &KDUW 3/$16 +HDOWK DQG 6DIHW\ 3ODQ 4XDOLW\ $VVXUDQFH 3ODQ 6,7( ',$5< *HQHUDO 5(32576 *HQHUDO 3URFXUHPHQW 6WDWXV 5HSRUWV 3URJUHVV 5HSRUW 3+272*5$3+6 *HQHUDO 3UH &RQVWUXFWLRQ 3KRWRJUDSKV 0RQWKO\ 3KRWRJUDSKV4&6 6HFWLRQ 3DUW 6XEPLWWDOV3DJH '5$:,1*6 :RUNLQJ 'UDZLQJV DQG 6KRS 'UDZLQJV $V %XLOW 5HFRUG 'UDZLQJV $V %XLOW 6XUYH\ 'UDZLQJV 0$7(5,$/6 $33529$/6 *HQHUDO /LVW RI 0DWHULDOV 6DPSOHV &HUWLILFDWHV 0DQXIDFWXUHU¶V *XDUDQWHHV DQG :DUUDQWLHV ,16758&7,21 0$18$/6 2SHUDWLRQ DQG 0DLQWHQDQFH 0DQXDOV 6859(< $1' /$<287 '(7$,/6 6HWWLQJ RXW RI WKH :RUNV 0(7+2' 67$7(0(176 *HQHUDO $33/,&$7,216 $1' ,192,&(6 )25 &203/(7(' :25.6 *HQHUDO68%0,77$/6*(1(5$/6FRSH7KLV 3DUW VSHFLILHV WKH JHQHUDO SURFHGXUHV DQG UHTXLUHPHQWV IRU VXEPLWWDOV5HODWHG 3DUWV DQG 6HFWLRQV DUH DV IROORZV7KLV 6HFWLRQ3DUW 4XDOLW\ $VVXUDQFH3DUW 0DWHULDOV3DUW +HDOWK DQG6DIHW\3DUW 6HWWLQJ RXW RI WKH :RUNV0LVWDNHV LQ ,QIRUPDWLRQ7KH &RQWUDFWRU VKDOO EH UHVSRQVLEOH IRU DQG VKDOO SD\ WKH H[WUD FRVW LI DQ\ RFFDVLRQHG E\ DQ\ GLVFUHSDQFLHV HUURUV RU RPLVVLRQV LQ VXEPLWWDOV VXSSOLHG E\ KLP ZKHWKHU WKH\ KDYHEHHQ DSSURYHG E\ WKH (QJLQHHU RU QRW'(),1,7,2163URGXFW 'DWD DQG 6KRS 'UDZLQJV3URGXFW 'DWD DQG 6KRS 'UDZLQJV LQFOXGH GUDZLQJV GLDJUDPV LOOXVWUDWLRQV EURFKXUHV VFKHGXOHV ELOOV RI PDWHULDOV DQG RWKHU GDWD SUHSDUHG VSHFLILFDOO\ IRU WKH :RUNV7KH LQIRUPDWLRQ P D\ EH SUHSDUHG E\ WKH &RQWUDFWRU KLV VXE FRQWUDFWRUV VXSSOLHUV RU GLVWULEXWRUV PDQXIDFWXUHUV RU IDEULFDWRUV7KH LQIRUPDWLRQ PXVW LOOXVWUDWH RU GHVFULEH WKH PDQXIDFWXUH IDEULFDWLRQ FRQVWUXFWLRQ DQG LQVWDOODWLRQ RI WKH :RUNV RU D SRUWLRQ WKHUHRI$V %XLOW 6XUYH\ 'UDZLQJV$V %XLOW 6XUYH\V DUH WRSRJUDSKLFDO VXUYH\V WKDW VKRZ FKDQJHV WR WRSRJUDSK\ DV D UHVXOW RI WKH FRQVWUXFWLRQ RI WKH :RUNV &KDQJHV WR WRSRJUDSK\ LQFOXGH WKH FRQVWUXFWLRQ RI QHZVWUXFWXUHV DQG URDGV GHPROLWLRQ RI H[LVWLQJ VWUXFWXUHV DQG URDGV DQG WKH OLNH 7KH $V %XLOW 6XUYH\ 'UDZLQJV VKDOO IRUP D FRPSUHKHQVLYH UHFRUG RI WKH WRSRJUDSKLFDO FKDQJHV UHVXOWLQJIURP WKH FRQVWUXFWLRQ RI WKH :RUNV LQ DOO UHVSHFWV$V %XLOW 6XUYH\V VKDOO DOVR VKRZ DOO VXE VXUIDFH HOHPHQWV RI WKH :RUNV 6XE VXUIDFH HOHPHQWV LQFOXGH SLSHOLQHV GXFWV FDEOHV FKDPEHUV PDQKROHV DQG WKH OLNH 7KH $V %XLOW 6XUYH\ 'UDZLQJV VKDOO IRUP D FRPSUHKHQVLYH UHFRUG RI WKH VXE VXUIDFH HOHPHQWV RI WKH :RUNV DV FRQVWUXFWHG LQ DOO UHVSHFWV$V %XLOW 5HFRUG 'UDZLQJV$V %XLOW 5HFRUG 'UDZLQJV DUH GUDZLQJV WKDW VKRZ WKH :RUNV DV FRQVWUXFWHG LQ DOO UHVSHFWV 7KH\ DUH LQ DGGLWLRQ WR WKH HOHPHQWV RI WKH :RUNV VKRZQ RQ WKH $V %XLOW 6XUYH\ 'UDZLQJV0DQXIDFWXUHU¶V 5HSUHVHQWDWLYH0DQXIDFWXUHU¶V UHSUHVHQWDWLYHV DUH SHUVRQV DFWLYHO\ ZRUNLQJ D W WKH PDQXIDFWXUHU¶V IDFWRU\ ZLWK D PLQLPXP RI \HDUV H[SHULHQFH 7KH\ VKRXOG EH IDPLOLDU ZLWK WKH DFWXDO SURFHVV RIPDQXIDFWXULQJ LQVWDOOLQJ DQG RSHUDWLQJ WKH SURGXFW WKH\ UHSUHVHQW6DOHV UHSUHVHQWDWLYHV RU DJHQWV DUH QRW DQ DFFHSWDEOH DOWHUQDWLYH WR PDQXIDFWXUHU¶V UHSUHVHQWDWLYHV7HPSRUDU\ :RUNV 'UDZLQJV7HPSRUDU\ :RUNV 'UDZLQJV DUH SODQV IRU WHPSRUDU\ VWUXFWXUHV DQG IDFLOLWLHV SUHSDUHG E\ WKH &RQWUDFWRU VSHFLILFDOO\ IRU WKH :RUNV(OHPHQWV RI ZRUN WKDW PD\ DIIHFW WKH VDIHW\ RI SHUVRQV RU SURSHUW\ V KDOO EH FKHFNHG DQG FHUWLILHG E\ DQ DSSURYHG VDIHW\ LQVSHFWRU&DOFXODWLRQV GHPRQVWUDWLQJ DGHTXDF\ RI &RQWUDFWRU¶V GHVLJQ VKDOO EH VXEPLWWHG ZLWK WKH 7HPSRUDU\ :RUNV 'UDZLQJV6DPSOHV6DPSOHV DUH SK\VLFDO H[DPSOHV LOOXVWUDWLQJ PDWHULDOV HTXLSPHQW RU ZRUN PDQVKLS DQG VKDOO EH XVHG WR HVWDEOLVK VWDQGDUGV E\ ZKLFK WKH ZRUN ZLOO EH MXGJHG0DQXDOV0DQXDOV DUH PDQXIDFWXUHU¶V ZULWWHQ LQVWDOODWLRQ VWDUW XS RSHUDWLQJ PDLQWHQDQFH DQG UHSDLU LQVWUXFWLRQV 7KH\ VKDOO LQFOXGH SDUWV OLVWV SLFWXUHV VNHWFKHV DQG GL DJUDPV VSHFLILF WR WKH HTXLSPHQW VXSSOLHG68%0,77$/ 352&('85(6*HQHUDO7KH &RQWUDFWRU VKDOO VXEPLW WR WKH (QJLQHHU IRU KLV UHYLHZ DQG DSSURYDO DOO GUDZLQJV DQG GDWD DV FDOOHG IRU LQ WKH 3URMHFW 'RFXPHQWDWLRQ RU VXEVHTXHQWO\ DV FRYHUHG E\ YDULDWLRQV6XEPLWWDOV DQG WKHLU FRQWHQWV VKDOO EH SURSHUO\ SUHSDUHG LGHQWLILHG DQG WUDQVPLWWHG LQ DFFRUGDQFH ZLWK WKH 3URMHFW 'RFXPHQWDWLRQ RU DV WKH (QJLQHHU PD\ RWKHUZLVH GLUHFW :KHUHSRVVLEOH DQG SUDFWLFDEOH WKH &RQWUDFWRU VKDOO SUHVHQW VXEPLWWDOV RQ $ VL]H SDSHU$OO VXEPLWWDOV VKDOO EH LQ WULSOLFDWH XQOHVV RWKHUZLVH VSHFLILHG LQ WKH 3URMHFW 'RFXPHQWDWLRQ 6FKHGXOH RI 6XEPLWWDOV7KH &RQWUDFWRU VKDOO SUHSDUH DQG VXEPLW D OLVW RI DOO VXEPLWWDOV UHTXLUHG E\ WKH &RQWUDFW RU RWKHUZLVH VKRZLQJ WKH IRUHFDVW GDWH IRU V XEPLVVLRQ RI HDFK LWHP ZLWKLQ WKLUW\ GD\V RI WKH VWDUW RI WKH &RQWUDFW'UDZLQJV DQG GDWD VKDOO EH VXEPLWWHG WR PHHW WKH WLPH VFKHGXOHV VWLSXODWHG LQ WKH 3URMHFW 'RFXPHQWDWLRQ DQG ZKHUH VXFK WLPH VFKHGXOHV DUH QRW VSHFLILHG WR PHHW WKH UHTXLUHPHQWVRI WKH DSSURYHG SURJUDPPH 8QOHVV VSHFLILHG RWKHUZLVH WKH &RQWUDFWRU VKDOO DOORZ QRW OHVVWKDQ WKLUW\ GD\V IRU WKH UHYLHZ RI VXEPLWWDOV E\ WKH (QJLQHHU H[FOXGLQJ WKH WLPHQHFHVVDU\ IRU GHOLYHU\ RU SRVWDJH DQG VKDOO FDXVH QR GHOD\ LQ WKH ZRUN RU WKH ZRUN RI DQ\ RWKHU &RQWUDFWRU([WHQVLRQ RI WLPH ZLOO QRW EH JUDQWHG EHFDXVH RI WKH &RQWUDFWRU V IDLOXUH WR PDNH WLPHO\ DQG FRUUHFWO\ SUHSDUHG DQG SUHVHQWHG VXEPLWWDOV ZLWK DOORZDQFH IRU WKH FKHFNLQJ DQG UHYLHZSHULRGV0HWKRG RI 6XEPLWWDO7KH &RQWUDFWRU VKDOO GHOLYHU VXEPLWWDOV E\ PHDQV RI GDWHG VLJQHG DQG VHTXHQFH QXPEHUHG WUDQVPLWWDOV 7KH WUDQVPLWWDO VKDOO EH RQ WKH &RQWUDFWRU V OHWWHUKHDG DQG VKDOO IXOO\ GHVFULEHWKH VXEPLWWDO FRQWHQWV 6XEPLWWDOV DUH QRW DFFHSWDEOH GLUHFWO\ IURP VXE FRQWUDFWRUV VXSSOLHUV RU PDQXIDFWXUHUV,Q HDFK WUDQVPLWWDO WKH &RQWUDFWRU VKDOO VWDWH WKH 'UDZLQJ QXPEHUV DQG 6SHFLILFDWLRQ 6HFWLRQV 3DUWV DQG 3DUDJUDSKV WR ZKLFK WKH VXEPLWWDO SHUWDLQV $FFRPSDQ\LQJ GDWD VKHHWVFDWDORJXHV DQG EURFKXUHV VKDOO EH LGHQWLILHG LQ WKH VDPH PDQQHU :KHUH VHYHUDO W\SHV RU PRGHOV DUH LQFOXGHG LQ D VLQJOH GDWD VKHHW FDWDORJXH RU EURFKXUH WKH &RQWUDFWRU VKDOO GHOHWHQRQ DSSOLFDEOH SRUWLRQV RU VSHFLILFDOO\ LQGLFDWH ZKLFK SRUWLRQV DUH LQWHQGHG DQG DSSOLFDEOH &RQWUDFWRU V 5HYLHZ DQG $SSURYDO(YHU\ VXEPLWWDO VKDOO EHDU WKH &RQWUDFWRU V UHYLHZ DQG DSSURYDO VWDPS FHUWLI\LQJ WKDW WKH &RQWUDFWRU KDVD UHYLHZHG FKHFNHG DQG DSSURYHG WKH VXEPLWWDOE FR RUGLQDWHG WKH FRQWHQWV ZLWK WKH UHTXLUHPHQWV RI WKH :RUNV WKH 3URMHFW'RFXPHQWDWLRQ DQG DQ\ UHODWHG ZRUNF GHWHUPLQHG DQG YHULILHG DOO TXDQWLWLHV ILHOG PHDVXUHPHQWV ILHOG FRQVWUXFWLRQ FULWHULDPDWHULDOV HTXLSPHQW FDWDORJXH QXPEHUV DQG VLPLODU GDWD&RUUHFWLRQV DQG 5HVXEPLWWDOV7KH &RQWUDFWRU VKDOO PDNH DOO UHTXLUHG FRUUHFWLRQV DQG VKDOO U HVXEPLW FRUUHFWHG VXEPLWWDOV XQWLO DSSURYHG7KH &RQWUDFWRU VKDOO GLUHFW VSHFLILF DWWHQWLRQ LQ ZULWLQJ WR UHYLVLRQV RWKHU WKDQ WKH FRUUHFWLRQV FDOOHG IRU RQ SUHYLRXV VXEPLWWDOV7KH &RQWUDFWRU VKDOO LGHQWLI\ HDFK UHVXEPLWWDO ZLWK WKH VHTXHO QXPEHU RI WKH R ULJLQDO VXEPLWWDO IROORZHG E\ FRQVHFXWLYH OHWWHUV VWDUWLQJ ZLWK $ IRU ILUVW UHVXEPLWWDO % IRU VHFRQGUHVXEPLWWDO HWF&KHFN RI 5HWXUQHG 6XEPLWWDOV7KH &RQWUDFWRU VKDOO FKHFN VXEPLWWDOV UHWXUQHG WR KLP IRU FRUUHFWLRQ DQG DVFHUWDLQ LI WKH FRUUHFWLRQV UHVXOW LQ H[WUD FRVW WR KLP DERYH WKDW LQFOXGHG DQG DOORZHG IRU XQGHU WKH 3URMHFW'RFXPHQWDWLRQ 7KH &RQWUDFWRU VKDOO JLYH ZULWWHQ QRWLFH WR WKH (QJLQHHU ZLWKLQ ILYH GD\VLI LQ KLV RSLQLRQ VXFK H[WUD FRVW UHVXOWV IURP FRUUHFWLRQV%\ IDLOLQJ WR VR QRWLI\ WKH (QJLQHHU RU E\ VWDUWLQJ DQ\ :RUN FRYHUHG E\ D VXEPLWWDO WKH &RQWUDFWRU ZDLYHV DOO FODLPV IRU H[WUD FRVWV UHVXOWLQJ IURP UHTXLUHG FRUUHFWLRQV5HYLHZ DQG $SSURYDO6XEPLWWDOV ZLOO EH UHYLHZHG RQO\ IRU FRQIRUPDQFH ZLWK WKH GHVLJQ FRQFHSW RI WKH 3URM HFW DQG ZLWK LQIRUPDWLRQ JLYHQ LQ WKH 3URMHFW 'RFXPHQWDWLRQ 7KH DSSURYDO RI D VHSDUDWH LWHP DVVXFK VKDOO QRW LQGLFDWH DSSURYDO RI WKH DVVHPEO\ LQ ZKLFK WKH LWHP IXQFWLRQV7KH DSSURYDO RI VXEPLWWDOV VKDOO QRW UHOLHYH WKH &RQWUDFWRU RI UHVSRQVLELOLW\ IRU DQ\ GHYLDWLRQ IURP WKH UHTXLUHPHQWV RI WKH 3URMHFW 'RFXPHQWDWLRQ XQOHVV RWKHUZLVH DJUHHG ZLWK DQGFRQILUPHG LQ ZULWLQJ E\ WKH (QJLQHHU$Q\ DSSURYDO IURP WKH (QJLQHHU VKDOO QRW UHOLHYH WKH &RQWUDFWRU RI UHVSRQVLELOLW\ IRU HUURUV RU RPLVVLRQV LQ WKH VXEP LWWDOV,QFRPSOHWH 6XEPLWWDOV6XEPLWWDOV ZKLFK DUH LQFRPSOHWH LQFOXGLQJ WKRVH QRW FRUUHFWO\ WUDQVPLWWHG QRW FRUUHFWO\ WLWOHG DQG LGHQWLILHG RU QRW EHDULQJ WKH &RQWUDFWRU V UHYLHZ DQG DSSURYDO VWDPS PD\ EH UHWXUQHG WRWKH &RQWUDFWRU ZLWKRXW UHYLHZ&RQIRUPDQFH:RUN VKDOO FRQIRUP WR WKH DSSURYHG VXEPLWWDOV DQG DOO RWKHU UHTXLUHPHQWV RI WKH 3URMHFW 'RFXPHQWDWLRQ XQOHVV VXEVHTXHQWO\ UHYLVHG E\ DQ DSSURSULDWH YDULDWLRQ RUGHU LQ ZKLFK FDVHWKH &RQWUDFWRU VKDOO SUHSDUH DQG VXEPLW UHYLVHG VXEPLWWDOV DV PD\ EH UHTXLUHG,QWHUUHODWHG 6XEPLWWDOV([FHSW ZKHUH WKH SUHSDUDWLRQ RI D VXEPLWWDO LV GHSHQGHQW XSRQ WKH DSSURYDO RI D SULRU VXEPLWWDO DOO VXEPLWWDOV SHUWDLQLQJ WR WKH VDPH SRUWLRQ RI WKH :RUNV VKDOO EH VXEPLWWHGVLPXOWDQHRXVO\7KH &RQWUDFWRU VKDOO QRW SURFHH G ZLWK DQ\ UHODWHG ZRUN ZKLFK PD\ EH DIIHFWHG E\ WKH ZRUN FRYHUHG XQGHU VXEPLWWDOV XQWLO WKH DSSOLFDEOH VXEPLWWDOV KDYH EHHQ DSSURYHG352*5$00(3URJUDPPH RI :RUNV7KH &RQWUDFWRU VKDOO SUHSDUH DQG VXEPLW WR WKH (QJLQHHU D 3URJUDPPH RI :RUNV LQ DFFRUGDQFH ZLWK &ODXVH RI WKH *HQHUDO &RQGLWLRQV RI &RQWUDFW7KH &RQWUDFWRU VKDOO XSGDWH WKH 3URJUDPPH RI :RUNV DV UHTXLUHG GXULQJ WKH FRQVWUXFWLRQ RI WKH :RUNV:KHQ LQVWUXFWHG E\ WKH (QJLQHHU WKH &RQWUDFWRU VKDOO SUHSDUH DQG VXEPLW D GHWDLOHG SURJUDPPH IRU D SD UWLFXODU VHFWLRQ RI WKH :RUNV 7KH GHWDLOHG SURJUDPPH VKDOO EH DQHODERUDWLRQ RI WKH RYHUDOO SURJUDPPH DQG VKDOO EH LQ DQ DSSURSULDWH IRUP7KH &RQWUDFWRU VKDOO LQFRUSRUDWH WKH WLPHV RI RFFXSDWLRQ RI DOO VXE FRQWUDFWRUV LQ WKH SURJUDPPH DQG VKDOO PDNH SU RYLVLRQV IRU WKH DFFHVV RI RWKHU &RQWUDFWRUV DV UHTXLUHG E\ WKH(QJLQHHU25*$1,=$7,21 &+$5766WDII 2UJDQLVDWLRQ &KDUW7KH &RQWUDFWRU VKDOO VXEPLW D 6WDII 2UJDQLVDWLRQ &KDUW IRU WKH (QJLQHHU¶V DSSURYDO ZLWKLQ WHQ GD\V RI WKH VWDUW RI WKH &RQWUDFW7KH FKDUW VKDOO VKRZ WKH RUJDQLVDWLRQ RI H[HFXWLYH DGPLQLVWUDWLYH DQG VXSHUYLVRU\ SHUVRQQHO DVVRFLDWHG ZLWK WKH 3URMHFW DQG LQGLFDWH WKH UHODWLRQVKLS EHWZHHQ WKHP ZKHUH DSSURSULDWH ,WVKDOO LQFOXGH DOO SHUVRQQHO IURP 3URMHFW 0DQDJHU GRZQ WR IRUHPDQ OHYHO D QG JLYH D IXOO GHVFULSWLRQ RI WKHLU GXWLHV 7KH TXDOLILFDWLRQV DQG H[SHULHQFH RI DOO SHUVRQQHO VKRZQ RQ WKHFKDUW VKDOO EH SURYLGHG7KH (QJLQHHU PD\ LQWHUYLHZ DQ\ RI WKH SHUVRQQHO SURSRVHG E\ WKH &RQWUDFWRU SULRU WR DSSURYDO7KH &RQWUDFWRU VKDOO XSGDWH WKH FKDUW ZKHQHYHU NH\ SHUVRQQHO DUH UHDVVLJQHG+HDOWK DQG 6DIHW\ 2UJDQLVDWLRQ &KDUW7KH &RQWUDFWRU VKDOO VXEPLW D +HDOWK DQG 6DIHW\ 2UJDQLVDWLRQ &KDUW IRU (QJLQHHU¶V DSSURYDO ZLWKLQ WHQ GD\V RI WKH VWDUW RI WKH &RQWUDFW7KH FKDUW VKDOO EH DV GHWDLO HG LQ 3DUW RI WKLV 6HFWLRQ +HDOWK DQG 6DIHW\4XDOLW\ $VVXUDQFH 2UJDQLVDWLRQ &KDUW7KH &RQWUDFWRU VKDOO VXEPLW D 4XDOLW\ $VVXUDQFH 2UJDQLVDWLRQ &KDUW IRU (QJLQHHU¶V DSSURYDO ZLWKLQ WHQ GD\V RI WKH VWDUW RI WKH &RQWUDFW7KH FKDUW VKDOO EH DV GHWDL OHG LQ 3DUW RI WKLV 6HFWLRQ 4XDOLW\ $VVXUDQFH3/$16+HDOWK DQG 6DIHW\ 3ODQ7KH &RQWUDFWRU VKDOO VXEPLW KLV +HDOWK DQG 6DIHW\ 3ODQ WR WKH (QJLQHHU QR ODWHU WKDQ WKLUW\ GD\V RI WKH VWDUW RI WKH &RQWUDFW7KH FKDUW VKDOO EH DV GHWDLOHG LQ 3DUW RI WKLV 6HFWLRQ +HDOWK DQG 6DIHW\4XDOLW\ $VVXUDQFH 3ODQ7KH &RQWUDFWRU VKDOO VXEPLW KLV 4XDOLW\ $VVXUDQFH 3ODQ WR WKH (QJLQHHU QR ODWHU WKDQ WKLUW\ GD\V RI WKH VWDUW RI WKH &RQWUDFW7KH FKDUW VKDOO EH DV GHWDLOHG LQ 3DUW RI WKLV 6HFWLRQ 4XDOLW\ $V VXUDQFH6,7( ',$5<*HQHUDO$ 6LWH 'LDU\ VKDOO EH NHSW RQ VLWH E\ WKH &RQWUDFWRU DQG HQWHUHG GDLO\ IRU WKH GXUDWLRQ RI WKH &RQWUDFW 7KH GLDU\ PXVW EH HQWHUHG QHDWO\ DQG OHJLEO\ LQ (QJOLVK DQG VKRXOG LQGLFDWH DOOYLVLWRUV WR WKH 6LWH DQG WKH UHDVRQ IRU WK H YLVLW 7KH GLDU\ VKDOO DOVR UHFRUG WKH IROORZLQJD ODERXU RQ VLWH E\ WUDGH DQG LWV DOORFDWLRQE VXE FRQWUDFWRUV ZRUNLQJ RQ VLWHF PDWHULDO DQG HTXLSPHQW GHOLYHUHG WR VLWHG PDWHULDO DQG HTXLSPHQW XWLOLVHGH SODQW HTXLSPHQW DQG WRROV EURXJKW RQ WR RU UHPRYHG IUR P VLWH LQFOXGLQJ KLUHG SODQWI ZRUN SURJUHVV GXULQJ WKH GD\J YHUEDO LQVWUXFWLRQV UHTXLULQJ ZULWWHQ FRQILUPDWLRQK WHPSHUDWXUH DQG ZHDWKHU FRQGLWLRQVL GHWDLOV RI DQ\ RFFXUUHQFH ZKLFK PD\ DIIHFW WKH SURJUHVV RI WKH :RUNV7KH GLDU\ VKDOO EHFRPH WKH SURSHUW\ RI WKH(QJLQHHU RQ FRPSOHWLRQ RI WKH :RUNV5(32576*HQHUDO:KHUH UHOHYDQW UHSRUWV VKRXOG EH UHIHUHQFHG WR WKH 3URJUDPPH RI :RUNV7KH &RQWUDFWRU VKDOO VXEPLW WKUHH FRSLHV RI HDFK UHSRUW XQOHVV RWKHUZLVH VSHFLILHG3URFXUHPHQW 6WDWXV 5HSRUWV7KH &RQWUDFWRU VKDOO SUHSDUH DQG VXEPLW D 3URFXUHPHQW 6WDWXV 5HSRUW RQ D ZHHNO\ EDVLV IRU WKH GXUDWLRQ RI WKH &RQWUDFW 7KH UHSRUW VKDOO LQFOXGH WKH IROORZLQJD D OLVW RI PDWHULDOV DQG LWHPV SURFXUHGE D OLVW RI LWHPV GHOLYHUHG WR WKH VLWHF UHIHUHQFHV WR DOO FRUUHVSRQGHQFH DQG W UDQVPLWWDOV EHWZHHQ WKH &RQWUDFWRU DQG WKH(QJLQHHU UHJDUGLQJ DSSURYDO RI VXFK PDWHULDOV DQG LWHPV3URJUHVV 5HSRUW7KH &RQWUDFWRU VKDOO SUHSDUH DQG VXEPLW D 3URJUHVV 5HSRUW RQ D PRQWKO\ EDVLV IRU WKH GXUDWLRQ RI WKH &RQWUDFW 7KH UHSRUW VKDOO EH VXEPLWWH G WR WKH (QJLQHHU EHIRUH WKH VHYHQWK GD\ RI HDFK PRQWK 7KH UHSRUW VKDOO LQFOXGH WKH IROORZLQJD ODERXU HPSOR\HG RQ WKH 6LWH GLYLGHG LQWR VXSHUYLVRU\ VWDII WUDGHVPHQ DQG RWKHUV JLYLQJGDLO\ WRWDOVE ODERXU HPSOR\HG RQ WKH 6LWH E\ VXE FRQWUDFWRUV GLYLGHG LQW R VXSHUYLVRU\ VWDIIWUDGHVPHQ DQG RWKHUV JLYLQJ GDLO\ WRWDOVF SODQW WRROV DQG HTXLSPHQW LQ ZRUNLQJ RUGHU RQ WKH 6LWH RQ HDFK GD\G DFFLGHQWV WR DQ\RQH ZRUNLQJ RQ WKH 6LWH ZKLFK UHTXLUHG PHGLFDO DWWHQWLRQH GHWDLOV RI PRQWKO\ SURJUHVV DQG VWDWXV RI WKH :RUNV LQ JHQHUDO WHUPVI WKH GDWH RI FRPPHQFHPHQW DQG FRPSOHWLRQ RI DOO FULWLFDO DFWLYLWLHVJ GHWDLOV RI SUREOHP DUHDVK GHWDLOV RI FXUUHQW RU DQWLFLSDWHG FDXVHV RI GHOD\ DORQJ ZLWK WKHLU HVWLPDWHG LPSDFW RQ SURJUHVV DQG WKH FRUUHFWLYH PHDVXUHV WDNHQ RU SURSRVHGL SURJUHVV SKRWRJUDSKV3+272*5$3+6*HQHUDO7KH &RQWUDFWRU VKDOO REWDLQ D SKRWRJUDSKLF UHFRUG RI WKH H[HFXWLRQ RI WKH :RUNV E\ WDNLQJ SKRWRJUDSKV IURP YDULRXV SRLQWV DV WKH (QJLQHHU VKDOO VSHFLI\ IURP WLPH WR WLPH $Q\SKRWRJUDSK ZKLFK LV QRW FOHDU DQG GLVWLQFW GRXEOH H[SRVHG RYHU H[SRVHG HWF VKDOO EH UHWDNHQ XQWLO DSSURYHG E\ WKH (QJLQHHU DW WKH &RQWUDFWRU V H[SHQVH3KRWRJUDSKV WDNHQ LQ FRQQHFWLRQ ZLWK WKH 3URMHFW VKDOO QRW EH XWLOLVHG E\ WKH &RQWUDFWRU IRU FRPPHUFLDO DGYHUWLVHPHQW HLWKHU RI KLV RUJDQLVDWLRQ RU RI DQ\ PDWHULDOV RU HTXLSPHQW XVHG RQ WKH :RUNV ZLWKRXW WKH ZULWWHQ DSSURYDO RI WKH (QJLQHHU3UH &RQVWUXFWLRQ 3KRWRJUDSKV7KH &RQWUDFWRU VKDOO WDNH D VHW RI SKRWRJUDSKV SULRU WR FRPPHQFHPHQW RI ZRUN LQ RUGHU WR IXOO\ UHFRUG GHWDLOV RI H[LVWLQJ FRQGLW LRQV7KH QXPEHU RI SKRWRJUDSKV WDNHQ VKDOO EH VXIILFLHQW WR FOHDUO\ LQGLFDWH WKH FRQGLWLRQ RI H[LVWLQJ FRQGLWLRQV$IWHU DSSURYDO WKH &RQWUDFWRU VKDOO VXSSO\ WZR SULQWV ZKLFK VKDOO EH PRXQWHG DQG ODEHOOHG E\ WKH &RQWUDFWRU DQG WKHVH VKDOO WKHQ EH V LJQHG DQG GDWHG E\ WKH &RQWUDFWRU DQG WKH (QJLQHHU 2QH VHW RI SULQWV VKDOO EH UHWXUQHG WR WKH &RQWUDFWRU0RQWKO\ 3KRWRJUDSKV7KH &RQWUDFWRU VKDOO WDNH SKRWRJUDSKV GXULQJ WKH FRXUVH RI WKH :RUNV LQ RUGHU WR SURYLGH D YLVXDO UHFRUG RI WKH :RUNV DQG WKHLU FRQVWUXFWLRQ7KHVH SKRWRJUDSKV VKDOO EH LQFOXGHG LQ WKH 3URJUHVV 5HSRUW DV GHVFULEHG LQ &ODXVH RI WKLV 3DUW FRPSOHWH ZLWK ODEHOV DQG DQ\ SHUWLQHQW VXSSRUWLQJ WH[W'5$:,1*6:RUNLQJ 'UDZLQJV DQG 6KRS 'UDZLQJV(DFK VXEPLWWHG GUDZLQJ VKDOO EH FRPSOHW H ZLWK UHVSHFW WR GLPHQVLRQV GHVLJQ FULWHULD PDWHULDOV FRQQHFWLRQV EDVHV IRXQGDWLRQV DQFKRUV DQG WKH OLNH DQG VKDOO EH DFFRPSDQLHGE\ WHFKQLFDO DQG SHUIRUPDQFH GDWD DQG E\ FDOFXODWLRQV DV QHFHVVDU\ WR VXSSRUW WKHLQIRUPDWLRQ VKRZQ RQ WKH GUDZLQJV8QOHVV RWKHUZLVH VSHFLILHG HDFK VXEPLWWDO VKDOO LQFOXGH VL[ VHWV RI FRSLHV DQG VKDOO EH VXEPLWWHG DW OHDVW WKLUW\ GD\V SULRU WR EHJLQQLQJ WKH ZRUN WR ZKLFK WKH GUDZLQJV DUHUHODWHG 7KUHH VHWV RI FRSLHV ZLOO EH UHWXUQHG WR WKH &RQWUDFWRU PDUNHG WR VKRZ WKH UHTXLUHG FRUUHFWLRQV RU DSSURYDO$V %XLOW 5HFRUG 'UDZLQJV7KH &RQWUDFWRU VKDOO SUHSDUH $V %XLOW UHFRUG 'UDZLQJV DQG VXEPLW WKHP WR WKH (QJLQHHU IRU DSSURYDO 8SRQ DSSURYDO WKH &RQWUDFWRU VKDOO VXEPLW D IXUWKHU IRXU FRSLHV RI HDFK $V %XLOW 5HFRUG 'UDZLQJ WR WKH (QJLQHHU $OO $V %XLOW UHFRUG 'UDZLQJV VKDOO EH SUHSDUHG RQ FOHDU ZKLWH SRO\HVWHU ILOP RU RWKHU GXUDEOH DQG HDVLO\ UHSURGXFLEOH PHGLXP DSSURYHG E\ WKH(QJLQHHU1R ILQDO SD\PHQW VKDOO EH PDGH XQWLO WKH $V EXLOW 5HFRUG 'UDZLQJV DUH FRPSOHWH LQ DOO UHVSHFWV 7KH &RQWUDFWRU VKDOO QRW EH HQWLWOHG WR DQ\ H[WUD SD\PHQW RU H[WHQVLRQ RI WLPH IRUWKH SUHSDUDWLRQ RI WKH $V EXLOW 5HFRUG 'UDZLQJV$V %XLOW 6XUYH\ 'UDZLQJV7KH &RQWUDFWRU VKDOO DUUDQJH IRU $V %XLOW 6XUYH\ 'UDZLQJV WR EH SUHSDUH G 7KH VXUYH\ VKDOO EH WR WKH VSHFLILFDWLRQ RI WKH 0LQLVWU\ RI 0XQLFLSDO $IIDLUV DQG $JULFXOWXUH DQG VKDOO EHXQGHUWDNHQ E\ D VXUYH\ FRPSDQ\ RQ WKH 0LQLVWU\ RI 0XQLFLSDO $IIDLUV DQG $JULFXOWXUH¶V OLVW RIDSSURYHG VXUYH\ FRPSDQLHV7KH &RQWUDFWRU VKDOO VXE PLW RQH VHW RI $V %XLOW VXUYH\ 'UDZLQJV WR WKH (QJLQHHU IRU DSSURYDO 8SRQ DSSURYDO WKH &RQWUDFWRU VKDOO VXEPLW D IXUWKHU IRXU VHWV WR WKH (QJLQHHU$OO $V %XLOW 6XUYH\ 'UDZLQJV VKDOO EH SUHSDUHG RQ FOHDU ZKLWH SRO\HVWHU ILOP RU RWKHU GXUDEOHDQG HDVLO\ UHSURGXFLEOH PHGLXP DSSURYHG E\ WKH (QJLQHHU8QOHVV RWKHUZLVH VWDWHG LQ WKH &RQWUDFW 'RFXPHQWDWLRQ WKH &RQWUDFWRU VKDOO DUUDQJH IRU WKH $V %XLOW 6XUYH\ 'UDZLQJV WR EH SUHSDUHG LQ GLJLWDO HOHFWURQLF IRUPDW 7KH GLJLWDO IRUPDW VKDOOEH LQ DFFRUGDQFH ZLWK UHTXLUHPHQWV RI WKH &HQWUH IRU *HRJUDSKLF ,QIRUPDWLRQ 6\VWHPV&*,61R ILQDO SD\PHQW VKDOO EH PDGH XQWLO WKH $V EXLOW 6XUYH\ 'UDZLQJV DUH FRPSOHWH LQ DOO UHVSHFWV 7KH &RQWUDFWRU VKDOO QRW EH HQWLWOHG WR DQ\ H[WUD SD\PHQW RU H[WHQVLRQ RI WLPH IRU WKH SUHSDUDWLRQ RI WKH $V EXLOW 6XUYH\ 'UDZLQJV0$7(5,$/6 $33529$/6*HQHUDO6XEPLWWDOV VKDOO EH DSSURYHG EHIRUH WKH PDWHULDOV RU HTXLSPHQW FRYHUHG E\ WKH VXEPLWWDOV DUH VKLSSHG RXW LQ WKH FDVH RI IRUHLJQ VXSSOLHV DQG GHOLYHUHG WR WKH 6LWH LQ WKH FDV H RI ORFDO VXSSOLHV/LVW RI 0DWHULDOV7KH &RQWUDFWRU VKDOO SUHSDUH DQG VXEPLW D OLVW RI WKH PDWHULDOV WR EH XVHG LQ WKH &RQVWUXFWLRQ RI WKH :RUNV ZLWKLQ WKLUW\ GD\V RI WKH VWDUW RI WKH &RQWUDFW 7KH PDWHULDOV OLVW VKDOO EHQHDWO\ ERXQG DQG VKDOO KDY H DQ LQGH[ OLVWLQJ WKH FRQWHQWV7KH GDWD IRU HDFK LWHP OLVWHG VKDOO EH H[SOLFLW ZLWK UHJDUG WR GHWDLOV RI WKH DFWXDO LWHPV EHLQJ IXUQLVKHG DQG VKDOO LQFOXGH VXIILFLHQW LQIRUPDWLRQ IRU WKH (QJLQHHU WR GHWHUPLQH WKDW WKHSURGXFWV VXEPLWWHG FRQIRUP WR WKH UH TXLUHPHQWV RI WKH 3URMHFW 'RFXPHQWDWLRQ 6XFKLQIRUPDWLRQ VKDOO LQFOXGH EXW QRW EH OLPLWHG WRD PDQXIDFWXUHU V QDPH DQG DGGUHVVE WUDGH RU EUDQG QDPHF ORFDO VXSSOLHU V QDPH DQG DGGUHVVG FDWDORJXHV EURFKXUHV DQG FXWV PDUNHG WR LQGLFDWH WKH LWHPV SURSRVHG WKH LQWHQGHGXVHH WHUPV DQG FRQGLWLRQV RI WKH PDQXIDFWXUHU V JXDUDQWHH DQG ZDUUDQW\I PDWHULDO LQVSHFWLRQ DQG WHVWLQJ DJHQF\J DQ\ RWKHU LQIRUPDWLRQ WR IXOO\ GHVFULEH WKH LWHPK VXSSOHPHQWDU\ LQIRUPDWLRQ DV PD\ EH UHTXLUHG IRU DSSURYDO8QOHVV RWKHUZLVH VSHFLILHG I LYH ERXQG FRSLHV RI WKH PDWHULDOV OLVW VKDOO EH VXEPLWWHG WZR RI ZKLFK ZLOO EH UHWXUQHG WR WKH &RQWUDFWRU PDUNHG WR VKRZ WKH UHTXLUHG FRUUHFWLRQV RUDSSURYDO6DPSOHV8QOHVV RWKHUZLVH VSHFLILHG HDFK VXEPLWWDO VKDOO LQFOXGH WZR VHWV RI VDPSOHV 2QH VHW RI DSSURYHG VDPSOHV DQG DOO GLVDSSURYHG VDPSOHV ZLOO EH UHWXUQHG WR WKH &RQWUDFWRU6DPSOHV VKDOO EH WDNHQ LQ DFFRUGDQFH ZLWK WKH SURYLVLRQV RI UHOHYDQW VWDQGDUGV ZKHUH DSSURSULDWH8QOHVV RWKHUZLVH VSHFLILHG VDPSOHV VKDOO EH ODEHOOHG DQG SURSHUO\ LGHQWLILHG ZLWK WKH IROORZLQJD GDWHE SDUW V RI WKH :RUNV IRU ZKLFK RIIHUHGF 6SHFLILFDWLRQ 6HFWLRQ 3DUW DQG DSSOLFDEOH 3DUDJUDSK QXPEHUVG VXSSOLHU PDQXIDFWXUHUH SURGXFW LGHQWLILFDWLRQ WUDGH QDPH6DPSOHV VKDOO EH DFFRPSDQLHG E\ DQ DSSURYHG WUDQVPLWWDO IRUP DORQJ ZLWK VSHFLILFDWLRQV DQG RWKHU SHUWLQHQW GDWD UHTXLUHG IRU WKH (QJLQHHU WR GHWHUPLQH WKDW WKH PDWHULDO FRQIRUPV WR WKHUHTXLUHPHQWV RI WKH 3URMHFW 'RFXPHQWDWLRQ,I UHTXHVWHG LQ ZULWLQJ E\ WKH &RQWUDFWRU VDPSOHV RI YDOXH ZLOO EH UHWXUQHG WR WKH &RQWUDFWRU DIWHU FRPSOHWLRQ RI WKH :RUN$SSURYHG VDPSOHV UHWXUQHG WR WKH &RQWUDFWRU PD\ RQO\ EH LQFRUSRUDWHG LQWR WKH :RUNV XSRQ ZULWWHQ DSSURYDO RI WKH (QJLQHHU&HUWLILFDWHV:KHQ VWDWHG LQ WKH 3URMHFW 'RFXPHQWDWLRQ RU UHTXHVWHG E\ WKH (QJLQHHU LQ ZULWLQJ WKH &RQWUDFWRU VKDOO VXEPLW PDQXIDFWXUHU¶V FHUWLILFDWHV LQGLFDWLQJ WKDW WHVW UHVXOWV FRPSRQHQWPDQXIDFWXUH RU LQVWDOODWLRQ FRPSOLHV ZLWK WKH UHTXLUHPHQWV RI WKH 3URMHFW 'RFXPHQWDWLRQ$ VWDWHPHQW IURP WKH &RQWUDFWRU VXE FRQWUDFWRU HTXLSPHQW VXSSOLHU RU DJHQW LQGLFDWLQJ WKH SURGXFW LQVWDOODWLRQ FRPSOLHV ZLWK WKH UHTXLUHPHQWV RI WKH 3URMHFW 'RFXPHQWDWLRQ VKDOO QRW EHFRQVLGHUHG DV D FHUWLILFDWH0DQXIDFWXUHU¶V *XDUDQWHHV DQG :DUUDQWLHV0DQXIDFWXUHU¶V *XDUDQWHHV DQG :DUUDQWHHV VKDOO EH VXEPLWWHG SULRU WR K DQGRYHU DQG ILQDO DFFHSWDQFH4&6 6HFWLRQ 3DUW 6XEPLWWDOV3DJH ,16758&7,21 0$18$/62SHUDWLRQ DQG 0DLQWHQDQFH 0DQXDOV7KH &RQWUDFWRU VKDOO VXEPLW LQVWUXFWLRQ PDQXDOV FRYHULQJ DOO PHFKDQLFDO DQG HOHFWULFDO HTXLSPHQW DQG PDFKLQHU\ LQVWDOOHG LQ WKH :RUNV DV VSHFLILHG XQGHU VHFWLRQV GHDOLQJ ZL WK PHFKDQLFDO DQG HOHFWULFDO ZRUN7KH &RQWUDFWRU VKDOO SUHSDUH DQG VXEPLW WZR FRSLHV RI 2SHUDWLRQ DQG 0DLQWHQDQFH 0DQXDOV WR WKH (QJLQHHU IRU UHYLHZ 7KH (QJLQHHU ZLOO PDUN XS RQH FRS\ DQG UHWXUQ LW WR WKH&RQWUDFWRU IRU FRUUHFWLRQ LI QHFHVVDU\7KH &RQWUDFWRU VKDOO VXEPLW VL[ FRSLHV RI DSSURYHG PDQXDOV LQFRUSRUDWLQJ DOO RI (QJLQHHU¶V FRPPHQWV DQG FRUUHFWLRQV6859(< $1' /$<287 '(7$,/66HWWLQJ RXW RI WKH :RUNV6XEPLWWDOV DVVRFLDWHG ZLWK VHWWLQJ RXW RI WKH :RUNV VKDOO FRPSO\ ZLWK WKH UHOHYDQW SURYL VLRQV RI 3DUW RI WKLV 6HFWLRQ 6HWWLQJ RXW RI WKH :RUNV0(7+2' 67$7(0(176*HQHUDO7KH &RQWUDFWRU VKDOO SUHSDUH DQG VXEPLW PHWKRG VWDWHPHQWV IRU DOO PDMRU ZRUN DFWLYLWLHV +H VKDOO DOVR SUHSDUH DQG VXEPLW PHWKRG VWDWHPHQW IRU VSHFLILF ZRUN DFWLYLWLHV LI LW LV D UHTXLUHPHQW RI WKH 3URMHFW 'RFXPHQWDWLRQ RU LI LQVWUXFWHG WR GR VR E\ WKH (QJLQHHU7KH PHWKRG VWDWHPHQWV VKDOO LQFRUSRUDWH DQ\ VXSSRUWLQJ FDOFXODWLRQV GUDZLQJV DQG PDQXIDFWXUHU¶V JXLGHOLQHV$33/,&$7,216 $1' ,192,&(6 )25 &203/(7(' :25.6*HQHUDO$SSOLFDWLRQV DQG LQYRLFHV IRU FRPSOHWHG :RUNV VKDOO EH VXEPLWWHG LQ DFFRUGDQFH ZLWK WKH &RQGLWLRQV RI &RQWUDFW(1' 2) 3$57。