典型轴类零件加工
数控机床的分类及典型轴类零件的加工
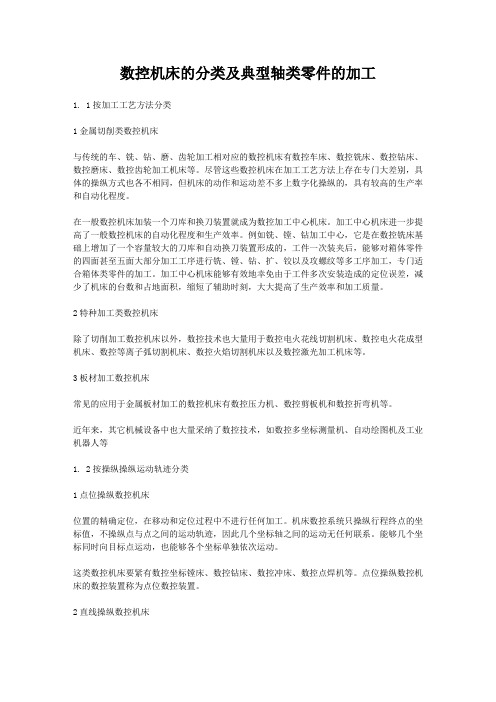
数控机床的分类及典型轴类零件的加工1. 1按加工工艺方法分类1金属切削类数控机床与传统的车、铣、钻、磨、齿轮加工相对应的数控机床有数控车床、数控铣床、数控钻床、数控磨床、数控齿轮加工机床等。
尽管这些数控机床在加工工艺方法上存在专门大差别,具体的操纵方式也各不相同,但机床的动作和运动差不多上数字化操纵的,具有较高的生产率和自动化程度。
在一般数控机床加装一个刀库和换刀装置就成为数控加工中心机床。
加工中心机床进一步提高了一般数控机床的自动化程度和生产效率。
例如铣、镗、钻加工中心,它是在数控铣床基础上增加了一个容量较大的刀库和自动换刀装置形成的,工件一次装夹后,能够对箱体零件的四面甚至五面大部分加工工序进行铣、镗、钻、扩、铰以及攻螺纹等多工序加工,专门适合箱体类零件的加工。
加工中心机床能够有效地幸免由于工件多次安装造成的定位误差,减少了机床的台数和占地面积,缩短了辅助时刻,大大提高了生产效率和加工质量。
2特种加工类数控机床除了切削加工数控机床以外,数控技术也大量用于数控电火花线切割机床、数控电火花成型机床、数控等离子弧切割机床、数控火焰切割机床以及数控激光加工机床等。
3板材加工数控机床常见的应用于金属板材加工的数控机床有数控压力机、数控剪板机和数控折弯机等。
近年来,其它机械设备中也大量采纳了数控技术,如数控多坐标测量机、自动绘图机及工业机器人等1. 2按操纵操纵运动轨迹分类1点位操纵数控机床位置的精确定位,在移动和定位过程中不进行任何加工。
机床数控系统只操纵行程终点的坐标值,不操纵点与点之间的运动轨迹,因此几个坐标轴之间的运动无任何联系。
能够几个坐标同时向目标点运动,也能够各个坐标单独依次运动。
这类数控机床要紧有数控坐标镗床、数控钻床、数控冲床、数控点焊机等。
点位操纵数控机床的数控装置称为点位数控装置。
2直线操纵数控机床直线操纵数控机床可操纵刀具或工作台以适当的进给速度,沿着平行于坐标轴的方向进行直线移动和切削加工,进给速度依照切削条件可在一定范畴内变化。
第三讲典型轴类零件数控车削加工工艺及编程

B
准确定位
B
英制O米制OB:基本功能 0:选购功能 数控车设定—— A功能
2. 进给功能(F功能)
F 功能指令用于在程序中控制切削进给量,有两种指令模式: (1)每转进给模式(G99)
编程格式: G99 F ___; F后面的数字表示主轴每转一转刀具的进给量。 单位:mm/r。
说明:模态指令,一经指定直到被G98取代,一直有效。 系统默认状态,车床上一般常用此种进给量指令方式。
A’ 65,2
B’ 10.01,2
C‘ 18.01,-2
D’ 18.01,-20
E‘ 24,-25
F’ 28,-25 G‘ 48.016,-35 H’ 48.016,-51 I‘ 58.023,-51 J‘ 58.023,-58 K’ 62,-58
符号
含义
编程原点
零件外轮廓走刀路线
工序号 程序段号
工步号 加工内容
粗车左端外轮廓,X轴留0.4、 Z轴留0.1精加工余量
精加工左端面外轮廓,各加工 表面符图示要求
审核
产品名称或代号
零件名称
材料 零件图号
XXX
夹具名称
三爪卡盘
刀具号
刀具规格/ (mm)
主轴转速/ (r/min)
T01
25×25
粗600 精1000
螺纹轴
45钢
XXX
使用设备
车间
CK6132
数控车
进给速度/ 背吃刀量/ 备注 (mm/r) (mm)
恒转速控制 编程格式: S ~
S后面的数字表示主轴转速,单位: r/min。
注意:
在具有恒线速功能的机床上, S 功能指令可限制主轴最高转速
(1)主轴最高转速限制(G50)
典型轴类零件加工

典型表面加工实验(轴类零件加工)一、实验目的1.掌握轴类零件加工的工艺;2.学会用车床车削轴类零件的方法。
二、基本知识概述1. 轴类零件加工的工艺分析(1)轴类零件加工的工艺路线1)基本加工路线外圆加工的方法很多,基本加工路线可归纳为四条。
① 粗车—半精车—精车对于一般常用材料,这是外圆表面加工采用的最主要的工艺路线。
② 粗车—半精车—粗磨—精磨对于黑色金属材料,精度要求高和表面粗糙度值要求较小、零件需要淬硬时,其后续工序只能用磨削而采用的加工路线。
③ 粗车—半精车—精车—金刚石车对于有色金属,用磨削加工通常不易得到所要求的表面粗糙度,因为有色金属一般比较软,容易堵塞沙粒间的空隙,因此其最终工序多用精车和金刚石车。
④ 粗车—半精—粗磨—精磨—光整加工对于黑色金属材料的淬硬零件,精度要求高和表面粗糙度值要求很小,常用此加工路线。
2)典型加工工艺路线轴类零件的主要加工表面是外圆表面,也还有常见的特特形表面,因此针对各种精度等级和表面粗糙度要求,按经济精度选择加工方法。
对普通精度的轴类零件加工,其典型的工艺路线如下:毛坯及其热处理—预加工—车削外圆—铣键槽—(花键槽、沟槽)—热处理—磨削—终检。
(1)轴类零件的预加工轴类零件的预加工是指加工的准备工序,即车削外圆之前的工艺。
校直毛坯在制造、运输和保管过程中,常会发生弯曲变形,为保证加工余量的均匀及装夹可靠,一般冷态下在各种压力机或校值机上进行校值,(2) 轴类零件加工的定位基准和装夹1)以工件的中心孔定位在轴的加工中,零件各外圆表面,锥孔、螺纹表面的同轴度,端面对旋转轴线的垂直度是其相互位置精度的主要项目,这些表面的设计基准一般都是轴的中心线,若用两中心孔定位,符合基准重合的原则。
中心孔不仅是车削时的定为基准,也是其它加工工序的定位基准和检验基准,又符合基准统一原则。
当采用两中心孔定位时,还能够最大限度地在一次装夹中加工出多个外圆和端面。
2)以外圆和中心孔作为定位基准(一夹一顶)用两中心孔定位虽然定心精度高,但刚性差,尤其是加工较重的工件时不够稳固,切削用量也不能太大。
轴类零件的加工
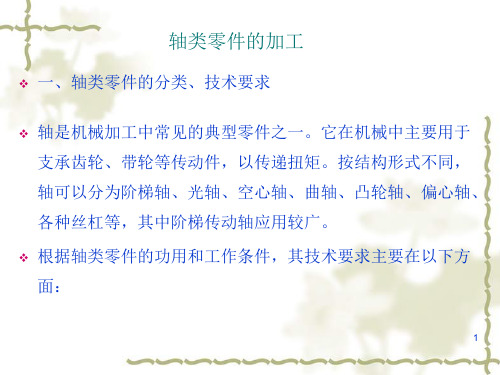
四、典型加工工艺路线
轴类零件的主要加工表面是外圆表面,也还有常见 的特形表面。对普通精度的轴类零件加工,其典型 的工艺路线如下:
毛坯及其热处理→预加工→车削外圆→铣键槽 (花键槽、沟槽)→热处理→磨削→终检
轴类零件的预加工——校直 毛坯在制造、运输 和保管过程中,常会发生弯曲变形,为保证加工余 量的均匀及装夹可靠,一般冷态下在各种压力机或 校直机上进行校直。
图1 锥堵和锥套心轴 a)锥堵 b)锥套心轴
9
锥堵或锥套心轴应具有较高的精度,锥堵和 锥套心轴上的中心孔既是其本身制造的定位 基准,又是空心轴外圆精加工的基准,因此 必须保证锥堵或锥减少重复安装误差。
10
三、外圆面的加工方案
轴类零件的加工
一、轴类零件的分类、技术要求
轴是机械加工中常见的典型零件之一。它在机械中主要用于 支承齿轮、带轮等传动件,以传递扭矩。按结构形式不同, 轴可以分为阶梯轴、光轴、空心轴、曲轴、凸轮轴、偏心轴、 各种丝杠等,其中阶梯传动轴应用较广。
根据轴类零件的功用和工作条件,其技术要求主要在以下方 面:
2
⑶ 相互位置精度 包括内、外表面、重要轴面的同轴度、圆的径向跳
动、重要端面对轴心线的垂直度、端面间的平行度 等。 ⑷ 表面粗糙度 轴的加工表面都有粗糙度的要求,一般根据加工的 可能性和经济性来确定。支承轴颈常为 Ra0.2~1.6um,传动件配合轴颈为Ra0.4~3.2um 。
3
6 磨削 磨蜗杆螺纹到尺寸
两中心孔 两中心孔
两中心孔
16
大批量生产轴类零件的加工---- 1110凸轮轴加工工艺
17
18
19
20
21
22
23
典型轴类零件的加工工艺

典型轴类零件的加工工艺典型轴类零件的加工工艺设计能通过运用机械制造工艺学课程中的基本理论以及在生产实习中学到实践知识,正确的解决一个零件在加工过程中的定位.夹紧以及工艺路线安排.工艺尺寸确定等问题,保证零件的加工质量本文选择了轴的加工工艺设计这一课题,主要阐述了对轴类零件的加工工艺过程,主要表现在从毛坯到成品的的过程它分为零件的热处理,大部分采用的是常见的四把火和调制处理.对典型的轴比如机床主轴、汽车半轴、内燃机曲轴、阶梯轴和CA6140主轴的热处理和加工工艺都有很明确的方案及选材。
对轴的加工工艺流程分为:下料→锻造→正火→机械加工→调质→粗车—半精车—精车—粗磨—精磨—光整加工—终检。
对工件的装夹都采取一次性装夹满足基准重合和基准统一或者互为基准。
对不同的工件采取的加工工艺有所不同。
以上此法操作简便、工效提高、节省材料,能保证加工精度。
对它的工艺性能也有明显的提高和使用寿命长等优点。
关键词:热处理工艺轴加工工艺轴的装夹定位Through the use of machinery manufacturing technology courses in basic theory and practice in the production of learned practical knowledge, the correct solution to a part in the positioning process. Clamping and routing process. Process to determine issues such as size, to ensure that the processing of parts qualityThis article has chosen the design process of the axis of the subject, the main shaft of the machining process, mainly in the finished product from rough to divide it into parts of the process of heat treatment, most commonly used is the four - to deal with fire and modulation. For example, a typical machine tool spindle axis, automotive axle, the internal combustion engine crankshaft, stepped shaft and spindle CA6140 process of heat treatment and processing of the program are very clear and material selection.Processing process of the axis is divided into: forging → → Cutting machining normalizing → → → Rough quenched - semi-refined car - Finish - coarse grinding - Grinding - Finishing - the end of the seizure. Clamping of the work piece clamping has been taken to meet the benchmark one-time overlap and complement each other or to benchmark thebenchmark reunification. Different parts of the process taken to be different. Above this method is simple, to improve work efficiency, saving materials, can guarantee the processing precision. The performance of its technology has improved and the advantages of long life.Key words: heat treatment process processing shaft axis positioning of the clamping目录第一章前言 (1)第二章轴类零件的分类和技术要求 (2)第一节轴类零件的功用与结构特点 (2)第二节主要技术要求 (3)第三节轴类零件的材料和毛坯 (3)第四节轴类零件的预加工 (4)第三章典型主轴类零件加工工艺分析 (5)第一节轴类零件加工的工艺路线 (5)第二节轴类零件加工的定位基准和装夹 (5)第四章轴类零件选材及工艺设计 (7)第一节机床主轴 (7)第二节汽车半轴 (9)第三节内燃机曲轴 (10)第四节阶梯轴的加工工艺过程 (10)第五节CA6140主轴加工工艺过程 (11)第五章检验 (17)第一节加工中的检验 (17)第二节加工后的检验 (17)结束语 (18)谢辞 (19)参考文献 (20)[1]邱宣怀.机械设计[M].北京:高等教育出版社,1997.. (20)[2]范文慧谭建荣.基于图形单元技术的轴类零件的设计[J].机械设计2001 (20)[3]西北工业大学机械原理及机械零件教研室.机械原理[M].北京:高等教育出版社,1987. 20 [4]机械设计手册编委会.机械设计册[M].北京:接写工业出版社2004 (20)第一章前言在机床、汽车、拖拉机等制造工业中,轴类零件是另一类用量很大,且占有相当重要地位的结构件。
典型轴类零件加工工艺与编程

典型轴类零件加工工艺与编程一、引言轴类零件是机械加工中非常常见的零件类型,其具有复杂的外形和高精度的加工要求。
为了满足零件加工的需求,制定适当的加工工艺和编程方案是非常关键的。
本文将介绍典型轴类零件的加工工艺和编程方法,帮助读者更好地理解和应用于实际的加工过程中。
二、典型轴类零件加工工艺2.1 零件材料选择在选择轴类零件的加工工艺之前,首先要考虑的是零件的材料选择。
常见的轴类零件材料包括铝合金、不锈钢和钢等。
根据零件的具体应用和要求,选择适当的材料能够提高加工效率和产品品质。
2.2 加工工艺流程典型轴类零件的加工工艺流程一般包括以下几个步骤:1.零件装夹:根据零件的形状和要求,选择合适的夹具进行装夹,确保零件的稳定和准确性。
2.设计刀具:根据零件的形状和要求,选择适当的刀具进行加工。
常见的刀具有立铣刀、刨刀和车刀等。
3.粗加工:使用合适的刀具进行粗加工,根据零件的形状和要求,进行适当的切削操作,以去除多余的材料。
4.精加工:在粗加工的基础上,使用更小的切削量进行精细加工,以达到所需的精度和表面质量。
5.修整工序:根据零件的要求,使用刮刀或砂纸等工具进行修整操作,以改善零件的表面质量。
6.检测与测量:对加工完成的零件进行检测和测量,确保零件的尺寸和形状符合要求。
7.表面处理:根据需要,对零件进行表面处理,如喷漆、阳极氧化或镀铬等。
2.3 加工工艺参数在进行轴类零件加工时,需要确定适当的加工工艺参数,以保证加工质量和效率。
常见的加工工艺参数包括:•进给速度:切削刀具在加工过程中每单位时间内移动的距离,通常以毫米/分钟(mm/min)表示。
•切削速度:切削刀具相对于工件表面移动的速度,通常以米/分钟(m/min)表示。
•切削深度:每次切削过程中刀具与工件之间的距离,通常以毫米(mm)表示。
•刀具压力:刀具与工件之间的压力,通常以牛顿(N)表示。
•加工冷却液:加工中使用的冷却液,可降低加工温度,减少刀具磨损和工件变形。
3.2 轴类零件加工

一夹 一顶
车床
3
热处理
调质处理 修研两端中心孔
硬度24~28HRC
4
钳工
中心孔
车床
(续)
工序 号 工序 名称 工序内容 双顶尖装夹半精车三个台阶,长 度达到尺寸要求,螺纹大径车到 0.1 24 0.2 mm,其余两个台阶直径上留 0.5mm余量,切槽三个,倒角三个 工序简图 定位 基准 设备
这样既可避免基准不重合误差,也能保证各表 面之间的位置精度。
2:粗基准 毛坯外圆。 (二) 加工方法的选择 1:主要表面,尺寸精度IT6,Ra0.8µ m,应 选:“车—磨”的加工方法。
2、平键槽:普通铣床铣削; 3、其它表面:均可采用车床车削; (三) 划分加工阶段 对传动轴,中等精度,批量不大,可划 分为粗加工阶段:包括,中心孔,各外圆的 粗车;半精加工阶段:包括各外圆的半精 车,切槽,螺纹加工,铣键槽等 ;精加工 阶段:包括各支承轴颈的磨削,
(四) 安排加工顺序 1、机械加工顺序的安排 1)基准先行 作为定位精基准的表面应首先安排加工;由 于传动轴毛坯为型材,毛坯精度较高,加工余量 不大。粗加工时先车端面钻中心孔,作为粗车各 外圆的定位精基准.
2、主次分开 零件是由多个不同类型的表面组成的,在安排 这些表面的加工先后顺序时,必须把主要表面和 次要表面的加工分开,先安排主要表面的加工, 再视具体情况安排次要表面的加工。
5
车
调头,双顶尖装夹半精车余下的五个 台阶。 44 mm及 52mm 台阶车到 图样规定的尺寸。螺纹大径车到 24 0.1 0.2 mm,其余两个台阶直径上留0.5mm 余量,切槽三个,倒角四个
中心孔
双顶尖装夹,车一端螺纹M24×1.6-6g 调头,车另一端M24×1.6-6g 6 车 中心孔
典型零件加工工艺(轴和套筒)

25
1)主要表面及其精度要求 ①支承轴颈
是两个锥度为1:12的圆锥面,分别与两个双列 短圆锥轴承相配合。
支承轴颈是主轴部件的装配基准,其精度直接 影响主轴部件的回转精度,尺寸精度一般为IT5。
主轴两支承轴颈的圆度允差和对其公共轴线的 斜向圆跳动允差均为0.005 mm,表面粗糙度Ra值不 大于0.63µm。
21
热处理工序的安排
结构尺寸不大的中碳钢普通轴类锻件,一般在切削加工 前进行调质热处理。
对于重要的轴类零件(如机床主轴),则:
一般在毛坯锻造后安排正火处理,达到消除锻造应 力,改善切削性能的目的;
粗加工后安排调质处理,以提高零件的综合力学性 能,并作为需要表面淬火或氮化处理的零件的预备热处 理;
5
二、轴类零件的材料和毛坯
1、轴类零件的常用毛坯:
①光轴、直径相差不大的阶梯轴常采用热轧或 冷拉的圆棒料;
②直径相差较大的阶梯轴和比较重要的轴大都 采用锻件。
③当轴的结构形状复杂或尺寸较大时,也有采
用铸件的。
自由锻
中小批
毛坯锻造
模锻
大批大量
6
2、轴类零件的材料:
1)一般轴类零件:45钢应用最多,一般须经调
轴上有相对运动的轴颈和经常拆卸的表面,需要进
行表面淬火处理,安排在磨削前。或在粗磨后、精磨前
渗氮处理
22
四、 机床主轴加工工艺及其分析
23
24
(1)零件分析 对机床主轴的共同要求是必须满足机床
的工作性能:即回转精度、刚度、热变形、 抗振性、使用寿命等多方面的要求。
车床主轴是带有通孔的多阶台轴,普通 精度等级,材料为45钢。
9
顶尖的实施
轴类零件加工工艺介绍
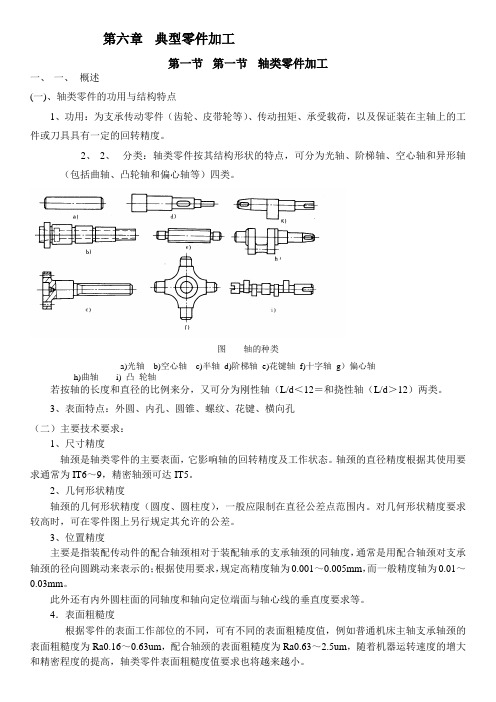
第六章典型零件加工第一节第一节轴类零件加工一、一、概述(一)、轴类零件的功用与结构特点1、功用:为支承传动零件(齿轮、皮带轮等)、传动扭矩、承受载荷,以及保证装在主轴上的工件或刀具具有一定的回转精度。
2、2、分类:轴类零件按其结构形状的特点,可分为光轴、阶梯轴、空心轴和异形轴(包括曲轴、凸轮轴和偏心轴等)四类。
图轴的种类a)光轴b)空心轴c)半轴d)阶梯轴e)花键轴f)十字轴g)偏心轴h)曲轴i) 凸轮轴若按轴的长度和直径的比例来分,又可分为刚性轴(L/d<12=和挠性轴(L/d>12)两类。
3、表面特点:外圆、内孔、圆锥、螺纹、花键、横向孔(二)主要技术要求:1、尺寸精度轴颈是轴类零件的主要表面,它影响轴的回转精度及工作状态。
轴颈的直径精度根据其使用要求通常为IT6~9,精密轴颈可达IT5。
2、几何形状精度轴颈的几何形状精度(圆度、圆柱度),一般应限制在直径公差点范围内。
对几何形状精度要求较高时,可在零件图上另行规定其允许的公差。
3、位置精度主要是指装配传动件的配合轴颈相对于装配轴承的支承轴颈的同轴度,通常是用配合轴颈对支承轴颈的径向圆跳动来表示的;根据使用要求,规定高精度轴为0.001~0.005mm,而一般精度轴为0.01~0.03mm。
此外还有内外圆柱面的同轴度和轴向定位端面与轴心线的垂直度要求等。
4.表面粗糙度根据零件的表面工作部位的不同,可有不同的表面粗糙度值,例如普通机床主轴支承轴颈的表面粗糙度为Ra0.16~0.63um,配合轴颈的表面粗糙度为Ra0.63~2.5um,随着机器运转速度的增大和精密程度的提高,轴类零件表面粗糙度值要求也将越来越小。
(三)、轴类零件的材料和毛坯合理选用材料和规定热处理的技术要求,对提高轴类零件的强度和使用寿命有重要意义,同时,对轴的加工过程有极大的影响。
1、轴类零件的材料一般轴类零件常用45钢,根据不同的工作条件采用不同的热处理规范(如正火、调质、淬火等),以获得一定的强度、韧性和耐磨性。
轴类零件的加工(任务一)
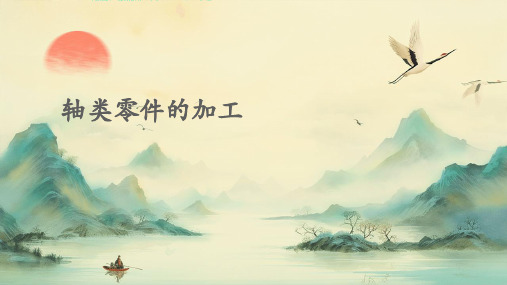
通过比较样块或仪器检测,对轴类零件的表面粗糙度进行评估,确保其表面质量 符合设计要求。
表面缺陷检查
检查轴类零件表面是否存在裂纹、划痕、碰伤等缺陷,这些缺陷会影响零件的强 度和使用寿命。
轴类零件的形位公差检测
直线度检测
通过使用直线度测量仪或样板等工具,对轴类零件的直线度 进行测量,确保其直线度误差在允许范围内。
为了确保轴类零件的质量符合要求,需要建立严格的质量控制体系。这包括对原材料的检验、加工过 程的监控、成品检验等环节。通过持续改进质量控制措施,可以提高生产效率和产品质量。
05
轴类零件加工实例分析
实例一:阶梯轴的加工工艺流程
总结词
阶梯轴是轴类零件中常见的一种,其加工工艺 流程包括下料、粗车、精车、钻孔、磨削等步
总结词
1. 刀具选择
针对复杂轴的加工工艺改进,可从刀具选 择、切削参数优化、加工流程调整等方面 入手。
根据复杂轴的结构和材料特性,选择合适 的刀具材料和刀具几何参数,以提高切削 效率和加工质量。
2. 切削参数优化
3. 加工流程调整
通过试验和仿真等方法,优化切削速度、 进给速度、切削深度等切削参数,以减小 切削力和切削热,降低表面粗糙度。
为了确保加工过程的稳定性和效率,需要对刀具寿命进行管理。通过对刀具磨损的监测和预测,可以及时更换刀 具,避免因刀具过度磨损而导致的加工误差。
加工精度与质量控制
加工精度题
轴类零件的加工精度直接影响其性能和使用寿命。误差来源包括机床误差、刀具误差、夹具误差等。 提高加工精度是保证零件质量的关键。
质量控制
3. 设备精度维护
定期对机床进行精度检测和维护, 确保设备处于良好的工作状态。
总结词
轴类零件加工

3)先外后内与先大后小
先加工外圆,再以外圆定位加工内孔。 加工阶梯外圆时,先加工直径较大的,后加工直径较小的,这样可避免过早地削弱工件的刚度。 加工阶梯深孔时,先加工直径较大的,后加工直径较小的,这样便于使用刚度较大的孔加工工具。
次要表面加工的安排。 轴上的花键、键槽、螺纹等次要表面加工,通常均安排在外圆精车或粗磨之后、精磨外圆之前进行。 如果精车前就铣出键槽,精车时因断续切削而易产生振动,既影响加工质量,又容易损坏刀具,也难控制键槽的深度。 次要表面加工也不能放到主要表面精磨之后,否则会破坏主要表面已获得的精度。
2、轴类零件的毛坯
一般轴——棒料 重要轴——锻件 大型、结构复杂轴——铸件 单件小批生产——自由锻; 成批大量生产——模锻
1
轴类零件在机械中起着突出的作用,工作中受弯曲、扭转和交变载荷,有时还得承受一定冲击性载荷。支承轴颈处还要承受磨擦,产生摩擦热。为了保证轴件的正常工作,轴件的加工质量至关重要。这就需要解决好轴件加工的工艺问题。
3、超精加工
油石—加压力—振动—纵向进给,工件低速回转——不重复轨迹。
强烈切削阶段——压强大,油膜被破坏,切削作用强烈
正常切削阶段——压强降低,切削作用减弱
微弱切削阶段——压强更低,摩擦抛光作用
添加标题
自动停止切削阶段——压强很小,形成油膜,切削作用停止
8.1 轴类零件加工概述(了解)

①机械靠模仿形 机械靠模仿形是利用靠模进 行直接仿形,也就是说刀架的切削力直接作 用于靠模,它易于在卧式车床上使用。
② 液压仿形 刀架的切削力由液压传动装置承 受。 液压传动装置利用油液作介质,通过执 行机构来传递动力 。
一般主轴颈的圆度和素线平行度误差, 卧式车床为5-8 µm,精密外圆磨床不超过1 µm。 各主轴颈的同轴度误差将会造成主轴 径向圆跳动,故规定了同轴度公差,普通机床 为0.005-0.01 mm,精密机床为1-5 µm 。
主轴轴肩和轴承端面对主轴回转轴线的
垂直度误差将会使主轴产生端面跳动 。 从
三、 轴类零件的技术要求
轴类零件是同轴线的回转体零件,在机械 加工中经常遇到外圆柱面、圆锥面、内孔 和螺纹等的加工 。 轴类零件与其他所有零 件一样,其主要技术要求有:
(1) 尺寸公差、几何形状公差和相互位置公差。 (2)表面粗糙度及其他表面质量要求。 (3) 材料、热处理及其他方面的要求。
此外,根据用途和结构的不同,轴类零件 还规定有不同的技术要求,因此,应采取各种 相应的加工方法来加工。 下面以车床主轴的结构特点 轴类零件是机械加工中最典型、最常见
的零件之一 ,一般由圆柱面、阶台、端面、 沟槽等结构组成 。 轴类零件大都是回转体 零件,其长度远大于直径,它的主要表面是同 轴线的若干外圆柱面、圆锥面、孔和螺纹 等。
二、軸类零件的功用
机床主轴是一种典型的轴类零件,是机 床的关键零件之一 ,它把回转运动和转矩通 过主轴端部的夹具传递给工件或刀具。 因 此,主轴在工作中要承受转矩和弯矩,而且还 要求有很高的回转精度 。 所以,主轴的制造 质量将直接影响到整台机床的工作精度和 使用寿命。 C6140型车床主轴的结构如图81所示。
例如当用调整螺母调整轴承间隙时,其端面 会使被压紧的轴承套圈倾斜,从而使主轴径 向圆跳动增大 。这不但会影响工件的加工
典型轴类零件加工工艺
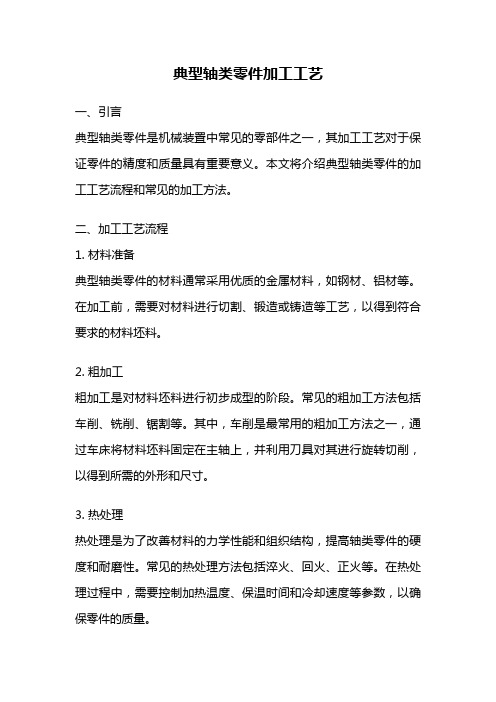
典型轴类零件加工工艺一、引言典型轴类零件是机械装置中常见的零部件之一,其加工工艺对于保证零件的精度和质量具有重要意义。
本文将介绍典型轴类零件的加工工艺流程和常见的加工方法。
二、加工工艺流程1. 材料准备典型轴类零件的材料通常采用优质的金属材料,如钢材、铝材等。
在加工前,需要对材料进行切割、锻造或铸造等工艺,以得到符合要求的材料坯料。
2. 粗加工粗加工是对材料坯料进行初步成型的阶段。
常见的粗加工方法包括车削、铣削、锯割等。
其中,车削是最常用的粗加工方法之一,通过车床将材料坯料固定在主轴上,并利用刀具对其进行旋转切削,以得到所需的外形和尺寸。
3. 热处理热处理是为了改善材料的力学性能和组织结构,提高轴类零件的硬度和耐磨性。
常见的热处理方法包括淬火、回火、正火等。
在热处理过程中,需要控制加热温度、保温时间和冷却速度等参数,以确保零件的质量。
4. 精加工精加工是在粗加工的基础上对零件进行精细加工的阶段。
常见的精加工方法包括磨削、镗削、拉削等。
其中,磨削是最常用的精加工方法之一,通过磨床将零件与磨削工具接触,以去除表面的凸起部分,提高零件的精度和表面质量。
5. 表面处理表面处理是为了提高零件的耐腐蚀性和美观度。
常见的表面处理方法包括镀层、喷涂、抛光等。
其中,镀层是最常用的表面处理方法之一,通过将零件浸泡在镀液中,使其表面形成一层保护性的金属膜,以提高零件的耐腐蚀性。
6. 检测和检验检测和检验是为了保证零件的质量和精度。
常见的检测和检验方法包括尺寸测量、外观检查、硬度测试等。
其中,尺寸测量是最常用的检测和检验方法之一,通过测量零件的尺寸和形状,以判断其是否符合设计要求。
7. 组装和调试组装和调试是将已加工好的轴类零件按照设计要求进行组装,并进行必要的调试和试运行。
通过组装和调试,可以确保零件的相互配合和工作正常,以保证整个机械装置的正常运行。
三、常见加工方法1. 车削车削是通过车床将材料坯料固定在主轴上,并利用刀具对其进行旋转切削的方法。
轴类零件的加工方法
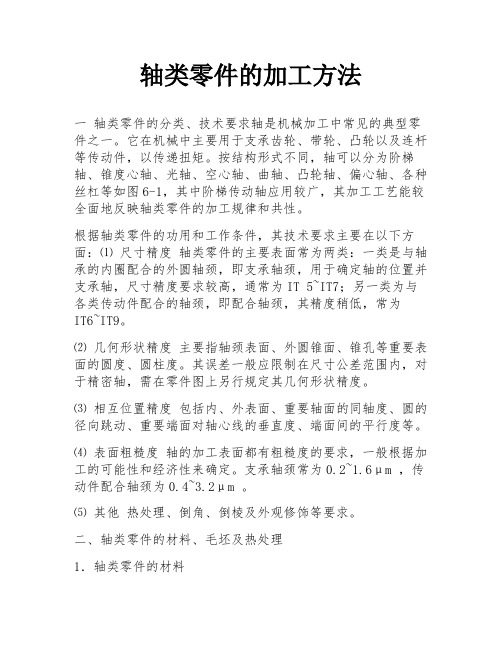
轴类零件的加工方法一轴类零件的分类、技术要求轴是机械加工中常见的典型零件之一。
它在机械中主要用于支承齿轮、带轮、凸轮以及连杆等传动件,以传递扭矩。
按结构形式不同,轴可以分为阶梯轴、锥度心轴、光轴、空心轴、曲轴、凸轮轴、偏心轴、各种丝杠等如图6-1,其中阶梯传动轴应用较广,其加工工艺能较全面地反映轴类零件的加工规律和共性。
根据轴类零件的功用和工作条件,其技术要求主要在以下方面:⑴ 尺寸精度轴类零件的主要表面常为两类:一类是与轴承的内圈配合的外圆轴颈,即支承轴颈,用于确定轴的位置并支承轴,尺寸精度要求较高,通常为IT 5~IT7;另一类为与各类传动件配合的轴颈,即配合轴颈,其精度稍低,常为IT6~IT9。
⑵ 几何形状精度主要指轴颈表面、外圆锥面、锥孔等重要表面的圆度、圆柱度。
其误差一般应限制在尺寸公差范围内,对于精密轴,需在零件图上另行规定其几何形状精度。
⑶ 相互位置精度包括内、外表面、重要轴面的同轴度、圆的径向跳动、重要端面对轴心线的垂直度、端面间的平行度等。
⑷ 表面粗糙度轴的加工表面都有粗糙度的要求,一般根据加工的可能性和经济性来确定。
支承轴颈常为0.2~1.6μm ,传动件配合轴颈为0.4~3.2μm 。
⑸ 其他热处理、倒角、倒棱及外观修饰等要求。
二、轴类零件的材料、毛坯及热处理1.轴类零件的材料⑴ 轴类零件材料常用45钢,精度较高的轴可选用40Cr 、轴承钢GCr15、弹簧钢65M n ,也可选用球墨铸铁;对高速、重载的轴,选用20CrMnTi 、20Mn2B 、20Cr 等低碳合金钢或38CrMoAl 氮化钢。
⑵ 轴类毛坯常用圆棒料和锻件;大型轴或结构复杂的轴采用铸件。
毛坯经过加热锻造后,可使金属内部纤维组织沿表面均匀分布,获得较高的抗拉、抗弯及抗扭强度。
2.轴类零件的热处理锻造毛坯在加工前,均需安排正火或退火处理,使钢材内部晶粒细化,消除锻造应力,降低材料硬度,改善切削加工性能。
调质一般安排在粗车之后、半精车之前,以获得良好的物理力学性能。
典型零件的加工工艺

图4-1
二、轴类零件的材料、毛坯和热处理
• 轴类零件的毛坯常用棒料和锻件。光滑轴、直径相差不大 的非重要阶梯轴宜选用棒料,一般比较重要的轴大都采用 锻件作为毛坯,只有某些大型的、结构复杂的轴采用铸件。 • 根据生产规模的不同,毛坯的锻造方式有自由锻和模锻两 种。中小批生产多采用自由锻,大批大量生产时通常采用 模锻。 • 45钢是轴类零件的常用材料,它价格便宜,经过调质(或 正火)后,可得到较好的切削性能,而且能够获得较高的 强度和韧性,淬火后表面硬度可达45~52HRC。 • 40Cr等合金结构钢适用于中等精度而转速较高的轴类零 件。这类钢经调质和淬火,具有较好的综合力学性能。
3.主轴的检验
• 主轴的最终检验要按一定顺序进 行,先检验各个外圆的尺寸精度、 素线平行度和圆度,再用外观比 较法检验各表面的粗糙度和表面 缺陷,最后再用专用检具检验各 表面之间的位置精度,这样可以 判明和排除不同性质误差之间对 测量精度的干扰。 • 检验前、后支承轴径对公共基准 的同轴度误差,通常采用如图4-6 所示的方法。 • C6150型车床主轴上其他各表面 相对于支承轴径位置精度的检验 常在图4-7所示的专用检具上进行。
6加工方法和加工设备的选择
More to learn
定位基准选择
(1)精基准的选择 精基准选择时应尽量符合“基准重合” 和“基准统一”原则,保证主要加工表面(主要轴径的支 承孔)的加工余量均匀,同时定位基面应形状简单、加工 方便,以保证定位质量和夹紧可靠。此外,精基准的选择 还与生产批量的大小有关。箱体零件典型的定位方案有两 种:
图4-11
(2)粗基准的选择 箱体零件加工面较多,粗基准选择时 主要考虑各加工面能否分配到合理的加工余量,以及加工 面与非加工面之间是否具有准确的相互位置关系。箱体零 件上一般有一个(或几个)主要的大孔,为了保证孔加工 的余量均匀,应以该毛坯孔作为粗基准。箱体零件上的不 加工面以内腔为主,它和加工面之间有一定的相互位置关 系。箱体中往往装有齿轮等传动件,它们与不加工的内壁 之间只有不大的间隙,如果加工出的轴承孔与内腔壁之间 的误差太大,就有可能使齿轮安装时与箱体壁相碰。从这 一要求出发,应选内壁为粗基准,但这将使夹具结构十分 复杂。考虑到铸造时内壁与主要孔都是由同一个泥芯浇铸 的,因此实际生产中常以孔为主要粗基准,限制4个自由 度,而辅之以内腔或其他毛坯孔为次要基准面,以实现完 全定位。
轴类零件的加工方法

轴类零件的加工方法
轴类零件的加工方法包括以下几种:
1. 车削加工:通过旋转的刀具将工件的材料逐渐削除,形成所需的轴状结构。
车削加工可以分为外圆车削和内圆车削两种形式。
2. 镗削加工:利用旋转刀具进行波纹状运动,将工件内孔的材料逐渐削除,形成所需的内轴孔。
3. 铣削加工:通过刀具在工件表面上进行旋转和直线运动,将工件表面的材料逐渐削除,形成所需的轴状结构。
铣削加工可以分为平铣和立式铣两种形式。
4. 磨削加工:利用磨削工具对工件进行高速磨削,精确地去除工件表面的材料,以达到精密加工的目的。
磨削加工可以分为平面磨削和外圆磨削两种形式。
5. 钻削加工:通过旋转刀具对工件进行钻孔,形成所需的孔状结构。
钻削加工可以使用钻头进行,也可以使用钻床进行。
6. 切削加工:通过使用切削刀具对工件进行切削,将工件材料一部分削除,形成所需的轴形结构。
切削加工可以包括切削、切削、切割等操作。
此外,还可以使用其他加工方法如冲压、锻造、热处理等进行轴类零件的加工。
具体的加工方法选择取决于轴类零件的材料、尺寸、形状等要求。
- 1、下载文档前请自行甄别文档内容的完整性,平台不提供额外的编辑、内容补充、找答案等附加服务。
- 2、"仅部分预览"的文档,不可在线预览部分如存在完整性等问题,可反馈申请退款(可完整预览的文档不适用该条件!)。
- 3、如文档侵犯您的权益,请联系客服反馈,我们会尽快为您处理(人工客服工作时间:9:00-18:30)。
典型轴类零件加工
【任务引入】
轴类零件的两端通常都要加工。
本节任务我来学习如何加工此类零件。
【任务描述】
按照给定的程序和要求完成下图6-1所示工件的加工。
图6-1
【任务实施】
1.分析零件图
该轴类零件成形轮廓的结构为两头加工,而且轨迹精度要求高,零件的总体结构主要包括外圆面、圆弧面、切槽、倒角和螺纹。
零件轴向尺寸以该零件右端面为基准,总长为98mm。
零件材料为45钢,毛坯规格为Ø50mm×105 mm。
2.确定加工方案及加工工艺路线
加工方案:使用三爪自定心卡盘夹持零件的毛坯外圆,并确定零件伸出合适的长度(应将机床的限位距离考虑进去)。
零件需要调头加工,因此需要考虑二次装夹的位置。
从零件图上可以看出Ø4O mm处外圆长度较长,可以用来装夹,因此先加工零件左端,加工至Ø48mm外圆右侧,加工长度为48mm,考虑到刀具与卡盘的安全距离,伸出长度选55mm左右,加工完零件左端后调头夹住Ø40mm处外圆,保证工件总长后加工零件右端。
零件编程原点设在零件端面与主轴轴线的交点处,为防止换刀时刀具与零件或尾座相碰,加工时换刀点可设置在(X100,Z100)的位置。
为提高循环加工的效率,循环的起刀点可以设置在(X52,Z2)的位置。
2.加工工艺路线:
1)夹紧零件毛坯,伸出卡盘55 mm,加工零件左端。
2)粗车零件左端外轮廓。
3)精车零件左端外轮廓,利用外径千分尺保证尺寸精度要求。
4) 切槽4mm×2mm至要求尺寸。
5) 车削零件的M30×1.5三角形螺纹,利用螺纹千分尺或螺纹环规保证精度要求。
6) 调头装夹,垫铜皮夹紧Ø40mm处外圆,校正并加工零件右端。
7) 粗车零件右端外轮廓。
8) 精车零件右端外轮廓,利用外径千分尺保证尺寸精度要求。
9)检测、校核。
3.编制加工工艺卡片
表6-1 刀具表
表6-2 工序表
4.参考程序
表6-3 工件左端加工程序
表6-4 工件右端加工程序
5.运用数控车床,进行实际加工
6.巩固练习
图6-2
【任务评价】。