水泥生产及余热发电工艺流程共57页
水泥生产及余热发电工艺流程PPT课件

凡以适当成分的生料,烧至部分熔融所得的 以硅酸钙为主要成分的矿物质,称为硅酸盐水 泥熟料。 其主要成分的矿物指:C2S、C3S、C3A、 C4AF
1.3、混合材
混合材是指在粉磨水泥时与熟料、石膏一起 加入磨机内用以改善水泥性能和调节水泥强度 等级的矿物质材料。根据其活性大小分为活性 混合材料和非活性混合材料两大类。 活性混合材料是指具有火山灰性或潜在水硬性, 以及兼有火山灰性或水硬性的矿物质材料。主 要包括粒化高炉矿渣、火山灰质混合材料和粉 煤灰等。 非活性混合材料是在水泥中主要起填充作用而 又不损害水泥性能的矿物质材料。主要包括不 符合标准要求的潜在水硬性或火山灰性的水泥 混合材料以及砂岩和石灰石等。
降低能耗具有重大意义。
立磨又叫辊式磨,是水泥化工、煤炭、电力等部门广泛使用的
一种粉磨机械。具有占地面积小、能耗低、噪音小,流程简单、产 量高、布置紧凑,集中碎、烘干、粉磨、选粉为一体等优点,成为 现代化水泥厂生料粉磨的首选方案。我公司所用的立磨为FLS(史 密斯)电工艺基础知识
编制:冯浩波
1
目录
1、水泥相关名词解释 2、生产水泥所用原料 3、新型干法水泥生产工艺流程
3.1、原材料准备 3.2、生料制备 3.3、煤粉制备 3.4、熟料煅烧 3.5、水泥粉磨制成 4、余热发电工艺流程
1、水泥相关名词解释
1.1、水泥
凡细磨成粉末状,加入适量水后成为塑性 浆体,既能在空气中硬化,双能在水中硬化, 并能将砂、石等散粒或纤维材料牢固地胶结在 一起的水硬胶凝材料,通称为水泥。
3.1、原材料准备
3.2、生料制备及窑尾废气处理
水泥生产过程中,每生产1t硅酸盐水泥至少要 粉磨3t物料(包括各种原料、燃料、熟料、混合材、 石膏),据统计,干法水泥生产线粉磨作业需要消 耗的动力约占全厂动力的60%以上,其中生料粉 磨占30%以上、煤磨占约3%,水泥粉磨约占40%。 因此,合理选择粉磨设备和工艺流程,优化工艺参 数,正确操作、控制作业制度,对保证产品质量、
水泥生产工艺流程图

过程工业装备成套技术的工程应用实例——水泥生产工艺流程1、破碎及预均化(1)破碎水泥生产过程中,大部分原料要进行破碎,如石灰石、黏土、铁矿石及煤等。
石灰石是生产水泥用量最大的原料,开采后的粒度较大,硬度较高,因此石灰石的破碎在水泥机械的物料破碎中占有比较重要的地位。
(2)原料预均化预均化技术就是在原料的存、取过程中,运用科学的堆取料技术,实现原料的初步均化,使原料堆场同时具备贮存与均化的功能。
2、生料制备水泥生产过程中,每生产1吨硅酸盐水泥设备至少要粉磨3吨物料(包括各种原料、燃料、熟料、混合料、石膏),据统计,干法水泥生产线粉磨作业需要消耗的动力约占全厂动力的60%以上,其中生料粉磨占30%以上,煤磨占约3%,水泥粉磨约占40%。
因此,合理选择粉磨设备和工艺流程,优化工艺参数,正确操作,控制作业制度,对保证产品质量、降低能耗具有重大意义。
3、生料均化新型干法水泥生产过程中,稳定入窖生料成分是稳定熟料烧成热工制度的前提,生料均化系统起着稳定入窖生料成分的最后一道把关作用。
4、预热分解水泥机械把生料的预热和部分分解由预热器来完成,代替回转窑部分功能,达到缩短回窑长度,同时使窑内以堆积状态进行气料换热过程,移到预热器内在悬浮状态下进行,使生料能够同窑内排出的炽热气体充分混合,增大了气料接触面积,传热速度快,热交换效率高,达到提高窑系统生产效率、降低熟料烧成热耗的目的。
(1)物料分散换热80%在入口管道内进行的。
喂入预热器管道中的生料,在与高速上升气流的冲击下,物料折转向上随气流运动,同时被分散。
(2)气固分离当气流携带料粉进入旋风筒后,被迫在旋风筒筒体与内筒(排气管)之间的环状空间内做旋转流动,并且一边旋转一边向下运动,由筒体到锥体,一直可以延伸到锥体的端部,然后转而向上旋转上升,由排气管排出。
(3)预分解预分解技术的出现是水泥设备煅烧工艺的一次技术飞跃。
它是在预热器和回转窑之间增设分解炉和利用窑尾上升烟道,设燃料喷入装置,使燃料燃烧的放热过程与生料的碳酸盐分解的吸热过程,在分解炉内以悬浮态或流化态下迅速进行,使入窑生料的分解率提高到90%以上。
水泥厂余热发电余热发电系统现场操作规程试用版
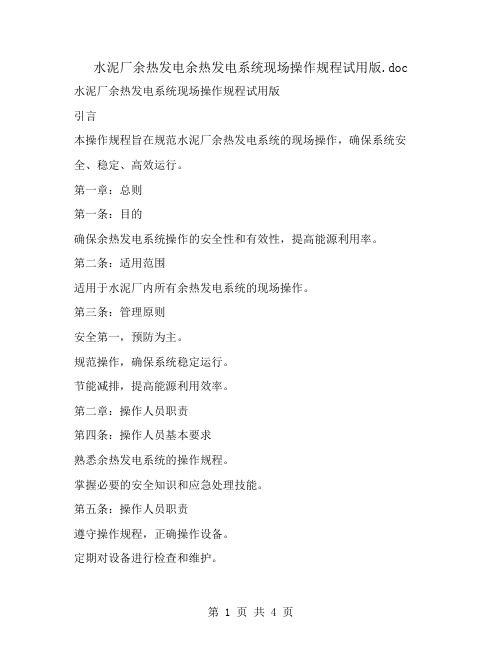
水泥厂余热发电余热发电系统现场操作规程试用版.doc 水泥厂余热发电系统现场操作规程试用版引言本操作规程旨在规范水泥厂余热发电系统的现场操作,确保系统安全、稳定、高效运行。
第一章:总则第一条:目的确保余热发电系统操作的安全性和有效性,提高能源利用率。
第二条:适用范围适用于水泥厂内所有余热发电系统的现场操作。
第三条:管理原则安全第一,预防为主。
规范操作,确保系统稳定运行。
节能减排,提高能源利用效率。
第二章:操作人员职责第四条:操作人员基本要求熟悉余热发电系统的操作规程。
掌握必要的安全知识和应急处理技能。
第五条:操作人员职责遵守操作规程,正确操作设备。
定期对设备进行检查和维护。
发现问题及时上报并采取相应措施。
第三章:设备启动与运行第六条:启动前检查检查系统设备是否处于良好状态。
确认所有安全装置和保护装置正常工作。
第七条:启动程序按照操作手册启动系统。
逐步增加负荷,直至达到额定功率。
第八条:运行监控定时检查系统运行参数。
记录运行数据,分析系统性能。
第四章:设备维护与保养第九条:日常维护每日对系统进行清洁和检查。
定期对设备进行润滑和紧固。
第十条:定期维护制定设备维护计划。
按计划进行设备的大修、中修和小修。
第五章:故障处理与应急措施第十一条:故障报告发现故障,立即停机并报告。
记录故障现象和处理过程。
第十二条:故障处理根据故障类型,采取相应的处理措施。
必要时,联系专业维修团队进行抢修。
第十三条:应急措施制定应急预案,定期进行演练。
发生紧急情况时,立即启动应急预案。
第六章:设备停用与保养第十四条:停用程序按照操作手册停止系统运行。
确保系统设备处于安全状态。
第十五条:停用后保养对系统设备进行清洁和保养。
检查设备是否有损坏,及时维修。
第七章:安全与环保第十六条:安全操作严格遵守安全操作规程。
定期进行安全培训和考核。
第十七条:环保要求遵守环保法规,控制污染物排放。
采取有效措施,减少噪音和粉尘。
第八章:考核与奖惩第十八条:考核标准设备完好率、故障率等作为考核指标。
水泥生产工艺流程

水泥生产工艺流程
《水泥生产工艺流程》
水泥生产是通过多个步骤来实现的复杂过程。
首先,从石灰石、粘土和铁矿石中提取原材料。
然后,将这些原材料送到破碎机进行粉碎。
接下来,将原材料送入煅烧炉中进行加热处理。
在高温下,原材料会燃烧并变成粉末状。
这一步骤被称为煅烧。
接着,将煅烧后的原材料送入水泥磨中进行研磨,使其变成细粉末。
最后,将细粉末送入旋窑进行煅烧,形成水泥熟料。
水泥熟料是水泥的主要成分,可以在加入适量石膏的情况下制成水泥。
在整个生产过程中,需要耗费大量的能源,并且会排放出大量的废气和废水。
因此,为了降低对环境的影响,水泥厂通常会采取一系列的环保措施,如安装废气处理设备、回收废水等。
综上所述,《水泥生产工艺流程》是一个复杂而又重要的工业过程,它不仅对于建筑行业有着重要的意义,也需要在生产过程中注重环保和节能,以减少对环境的影响。
余热发电工艺流程

纯低温余热发电工艺流程、主机设备工作原理简介纯低温水泥窑余热发电技术是直接利用水泥窑窑头窑尾排放的中低温废气进行余热回收发电,无需消耗燃料,发电过程不产生任何污染,是一种经济效益可观、清洁环保、符合国家清洁节能产业政策的绿色发电技术,具有十分广阔的发展空间与前景。
工艺流程(见附图): 凝汽器热水井内的凝结水经凝结水泵泵入No.2闪蒸器出水集箱,与出水汇合,然后通过锅炉给水泵升压泵入AQC锅炉省煤器进行加热,经省煤器加热后的水(223℃)分三路分别送到AQC炉汽包,PH炉汽包和No.1闪蒸器内。
进入两炉汽包内的水在锅炉内循环受热,最终产生一定压力下的过热蒸汽作为主蒸汽送入汽轮机做功.进入No.1闪蒸器内的高温水通过闪蒸技术产生一定压力下的饱和蒸汽送入汽轮机第三级后做功,而№.1闪蒸器的出水作为№.2闪蒸器闪蒸饱和蒸汽的热源,№.2闪蒸器闪蒸出的饱和蒸汽送入汽轮机第五级后做功,做过功后的乏汽经过凝汽器冷凝后形成凝结水重新参与热力循环。
生产过程中消耗掉的水由纯水装置制取出的纯水经补给水泵打入热水井。
主机设备性能特点:一、余热锅炉: AQC炉和PH炉AQC锅炉的设计特点如下: 锅炉型式为立式,锅炉由省煤器、蒸发器、过热器、汽包及热力管道等构成。
锅炉前设置一预除尘器(沉降室),降低入炉粉尘。
废气流动方向为自上而下,换热管采用螺旋翅片管,以增大换热面积、减少粉尘磨损的作用。
锅炉内不易积灰,由烟气带走,故未设置除灰装置,工质循环方式为自然循环方式。
过热器作用:将饱和蒸汽变成过热蒸汽的加热设备,通过对蒸汽的再加热,提高其过热度(温度之差),提高其单位工质的做功能力。
蒸发器作用:通过与烟气的热交换,产生饱和蒸汽。
省煤器作用:设置这样一组受热面,对锅炉给水进行预热,提高给水温度,避免给水进入汽包,冷热温差过大,产生过大热应力对汽包安全形成威胁,同时也避免汽包水位波动过大,造成自动控制困难。
一方面最大限度地利用余热,降低排烟温度,另一方面,给水预热后形成高温高压水,作为闪蒸器产生饱和蒸汽的热源。
水泥生产工艺与水泥余热发电

闪蒸余热发电
对于水泥窑余热利用,尽可能地用较高温度段的废气生 产做功能力强的主蒸汽,剩下的较低温度的废气,尽可能 生产较多的热水,用来一级闪蒸,生产低压蒸汽用来增加 余热发电量。
对于一级闪蒸系统,余热锅炉生产的用于闪蒸的热水越 多,低压蒸汽发生器排水量增多,导致余热锅炉给水温度 越高,排烟温度越高,采用多级闪蒸系统可降低末级闪蒸 器出水温度。
额定补汽量:12.8 t/h额定
排汽压力:0.0075MPa
额定排汽温度:40 ℃
汽轮机效率:83%
第二代余热发电技术
指标名称 \ 数值
1300t/d级水泥生 2500t/d级水泥生 3200t/d级水泥生 5000 t/d级水泥生
产线纯低温余热 产线纯低温余热 产线纯低温余热 产线纯低温余热
电站
立窑的日产量已达250~300t/d。立窑又分普通立窑和机 械立窑,普通立窑采用间歇式生产,能耗热耗较高,产生的废气 量约3900立米/吨熟料,相当于2.5万Nm3/h ,粉尘浓度15g/m3。
新型干法旋窑煅烧
它是在旋窑煅烧增加预分解窑与悬浮预热工艺。
预热分解:把生料的预热和部分分解由预热器来完成,代替 回转窑部分功能。
315 不限
0.03 76.2 20.3 3.47 30
窑尾余热锅炉PH型(卧式)
窑
烟气量: 380000Nm3/h 入口烟温:325℃
尾
入口烟气负压:~5800Pa
Hale Waihona Puke 余含尘浓度:80g/m3
热
计算排烟温度:~ 200℃
锅 炉
锅炉烟气阻力:≤ 1700Pa 给水温度:165℃ 锅炉漏风系数:≤ 2%
目台 热泥 气水 条泥 件公
司
水泥生产工艺与水泥余热发电讲解
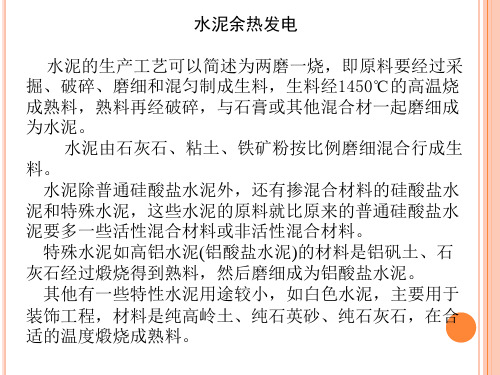
日产量
窑尾
窑头
5000t/h
322000-354000Nm3/h 300-350℃
500t/h中环 保水务
426000Nm3/h 330℃
3200t/h
206000-226000Nm3/h 300-350℃
2500t/h
161000-176000Nm3/h 320-350℃
1300t/d
84000-93000Nm3/h 320-350℃
炉
余热锅炉AQC炉(立式)
及
处理烟气量:380000Nm3/h 入口烟温:315℃
预
最高温度:450℃
除
含尘浓度:8~10g/m3
尘
锅炉漏风系数:≤2% 锅炉烟气阻力:≤1000Pa
装
蒸汽压力:0.8MPa(a)
置
蒸汽温度:291℃
产汽量:25400kg/h
给水温度:60~75℃
热水循环泵2台
汽 轮 机
立窑的日产量已达250~300t/d。立窑又分普通立窑和机 械立窑,普通立窑采用间歇式生产,能耗热耗较高,产生的废气 量约3900立米/吨熟料,相当于2.5万Nm3/h ,粉尘浓度15g/m3。
新型干法旋窑煅烧
它是在旋窑煅烧增加预分解窑与悬浮预热工艺。
预热分解:把生料的预热和部分分解由预热器来完成,代替 回转窑部分功能。
从窟尾预热器引来的320℃左右的高温废气,分成二路:一 路经多管冷却器、混合室至窑尾袋收尘器;一路进出料磨作为烘 干介质,出生料磨的废气由磨房主排风机引入混合室与从高温风 机过来的废气混合后进入窑尾收尘器,净化后排入大气。
据有关专家统计,每生产1t 水泥就要向环境排放1t 有害气 体。我国水泥工业的CO2排放量约为7亿t左右,S02在80万t左右 ,NOx在100万t左右。
水泥生产工艺流程图

水泥生产工艺流程水泥的生产工艺可以简述为两磨一烧,即原料要经过采掘、破碎、磨细和混匀制成生料,生料经1450℃的高温烧成熟料,熟料再经破碎,与石膏或其他混合材一起磨细成为水泥。
一、水泥生产的生料制备1 破碎工艺水泥生产过程中,很大一部分原料要进行破碎,如石灰石、黏土、铁矿石及煤等。
2生料的预均化工艺原料预均化,实现原料的初步均化,。
3 生料的烘干工艺烘干工艺是将生料通过烘干机加热干燥。
烘干设备有回转式和悬浮式烘干机、烘干塔等,回转式烘干机内温度约700℃,排放废气量约1300m3/t料。
4 生料的粉磨工艺二、水泥生产的煅烧目前大中型水泥厂多使用回转窑,小型水泥厂多使用立窑,我国还有50﹪以上的水泥仍使用立窑生产。
1 立窑煅烧立窑工艺的设备是静止的竖窑,分为普通立窑和机械化立窑,属于半干法生产。
立窑的日产量已达250~300t/d。
立窑又分普通立窑和机立窑,普通立窑采用间歇式生产,能耗热耗较高,产生的废气量约3900立米/吨熟料,粉尘浓度15g/m3。
2 新型干法旋窑煅烧它是在旋窑煅烧增加预分解窑与悬浮预热工艺。
生料在预热器以内悬浮状态或沸腾状态下与热气流进行热交换,又在分解炉中加入占总燃料用量50~60%的燃料,使生料在入窑前的碳酸钙分解率达80%以上。
预热分解把生料的预热和部分分解由预热器来完成,代替回转窑部分功能。
(1)物料分散换热80%在入口管道内进行的。
喂入预热器管道中的生料,在与高速上升气流的冲击下,物料折转向上随气流运动,同时被分散。
(2)气固分离当气流携带料粉进入旋风筒后,被迫在旋风筒筒体与内筒(排气管)之间的环状空间内做旋转流动,并且一边旋转一边向下运动,由筒体到锥体,一直可以延伸到锥体的端部,然后转而向上旋转上升,由排气管排出。
(3)预分解预分解技术是在预热器和回转窑之间增设分解炉和利用窑尾上升烟道,设燃料喷入装置,使燃料燃烧的放热过程与生料的碳酸盐分解的吸热过程,在分解炉内以悬浮态或流化态下迅速进行,使入窑生料的分解率提高到90%以上。
水泥企业余热发电技术介绍

根据汽轮机进汽参数,考虑利用废气 余热生产水蒸气所需传热温差的要求, 水泥窑余热品位应当确定为:
高温废气余热:废气温度大于650℃ 中温废气余热:废气温度350~650℃ 低温废气余热:废气温度小于350℃
3国内余热发电系统简介
3.1熟料生产线余热分布 2500t/d水泥生产线
窑尾废气:169000Nm3/h--340℃----200℃ 窑头废气:142000Nm3/h--230℃----104℃
朗肯循环过程图(T-S图)
汽轮机排汽2(一般为绝对压力0.007-0.01MPa并含有10-5%的水分的3945℃饱和蒸汽及水的混合物)经凝汽器凝结成水3后(水温不变)在经凝结 水泵升压至锅炉给水压力(由于泵做功,使水温升高1-2℃),在锅炉内通 过吸收热量,使水变成给水压力下的饱和温度5,继续加热变成饱和蒸汽6 ,再继续加热为给水压力下的过热蒸汽1,过热蒸汽进入汽轮机推动汽轮 机做功后自汽轮机排汽排出2,完成一个热力循环。
17.61 535
0.82 0.007
39 2229.65
0.8579 12457.07
3.28 403.69
临界 22.01
590 100000
1000 2087.94
2068.9
1601.14
14.75
100
150.33
4648.99 6264.88
21.62 575
0.82 0.007
39 2244.07
0.8639 13439.83
3.12 374.17
2.3水泥窑低温余热电站汽轮机汽耗率
蒸汽参数采用0.69~0.98MPa—300~340℃时,汽 轮机汽耗率为:每KWh发电量消耗蒸汽6.1~ 5.5Kg—汽机叶片为全三维叶片;
水泥厂余热发电窑尾工作流程

水泥厂余热发电窑尾工作流程英文回答:Cement Plant Waste Heat Power Generation Kiln Tail Working Process.The kiln tail of a cement plant is the section of the kiln where the clinker is cooled and the waste heat is recovered. The waste heat is used to generate electricity by a waste heat boiler and a steam turbine. The working process of the kiln tail can be divided into the following steps:1. Clinker cooling: The clinker is discharged from the kiln at a temperature of about 1250°C. It is then cooled by air in a clinker cooler. The air is blown through the clinker bed, and the heat is transferred from the clinker to the air. The cooled clinker is then discharged from the cooler.2. Waste heat recovery: The hot air from the clinker cooler is used to heat water in a waste heat boiler. The water is converted into steam, which is then used to drivea steam turbine. The steam turbine is connected to a generator, which generates electricity.3. Dust removal: The flue gas from the waste heatboiler contains dust particles. These particles must be removed before the flue gas is discharged to the atmosphere. The dust is removed by a dust collector.The kiln tail working process is an important part ofthe cement production process. It allows the recovery of waste heat and the generation of electricity. This helps to improve the energy efficiency of the cement plant andreduce its environmental impact.中文回答:水泥厂余热发电窑尾工作流程。
余热发电工艺流程
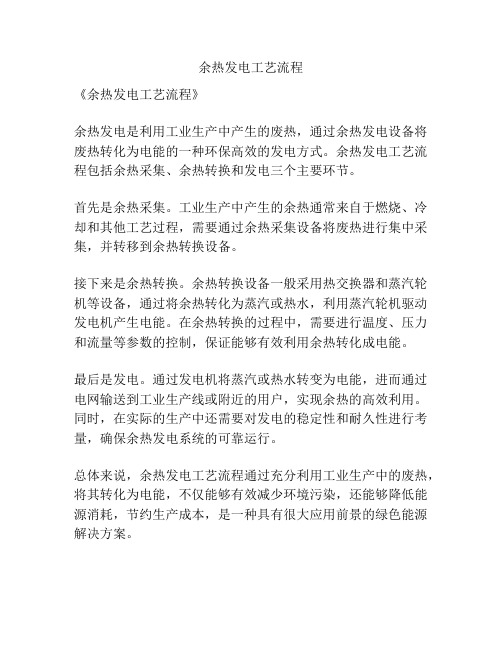
余热发电工艺流程
《余热发电工艺流程》
余热发电是利用工业生产中产生的废热,通过余热发电设备将废热转化为电能的一种环保高效的发电方式。
余热发电工艺流程包括余热采集、余热转换和发电三个主要环节。
首先是余热采集。
工业生产中产生的余热通常来自于燃烧、冷却和其他工艺过程,需要通过余热采集设备将废热进行集中采集,并转移到余热转换设备。
接下来是余热转换。
余热转换设备一般采用热交换器和蒸汽轮机等设备,通过将余热转化为蒸汽或热水,利用蒸汽轮机驱动发电机产生电能。
在余热转换的过程中,需要进行温度、压力和流量等参数的控制,保证能够有效利用余热转化成电能。
最后是发电。
通过发电机将蒸汽或热水转变为电能,进而通过电网输送到工业生产线或附近的用户,实现余热的高效利用。
同时,在实际的生产中还需要对发电的稳定性和耐久性进行考量,确保余热发电系统的可靠运行。
总体来说,余热发电工艺流程通过充分利用工业生产中的废热,将其转化为电能,不仅能够有效减少环境污染,还能够降低能源消耗,节约生产成本,是一种具有很大应用前景的绿色能源解决方案。
水泥生产工艺流程图

过程工业装备成套技术的工程应用实例——水泥生产工艺流程1、破碎及预均化(1)破碎水泥生产过程中,大部分原料要进行破碎,如石灰石、黏土、铁矿石及煤等。
石灰石是生产水泥用量最大的原料,开采后的粒度较大,硬度较高,因此石灰石的破碎在水泥机械的物料破碎中占有比较重要的地位。
(2)原料预均化预均化技术就是在原料的存、取过程中,运用科学的堆取料技术,实现原料的初步均化,使原料堆场同时具备贮存与均化的功能。
2、生料制备水泥生产过程中,每生产1吨硅酸盐水泥设备至少要粉磨3吨物料(包括各种原料、燃料、熟料、混合料、石膏),据统计,干法水泥生产线粉磨作业需要消耗的动力约占全厂动力的60%以上,其中生料粉磨占30%以上,煤磨占约3%,水泥粉磨约占40%。
因此,合理选择粉磨设备和工艺流程,优化工艺参数,正确操作,控制作业制度,对保证产品质量、降低能耗具有重大意义。
3、生料均化新型干法水泥生产过程中,稳定入窖生料成分是稳定熟料烧成热工制度的前提,生料均化系统起着稳定入窖生料成分的最后一道把关作用。
4、预热分解水泥机械把生料的预热和部分分解由预热器来完成,代替回转窑部分功能,达到缩短回窑长度,同时使窑内以堆积状态进行气料换热过程,移到预热器内在悬浮状态下进行,使生料能够同窑内排出的炽热气体充分混合,增大了气料接触面积,传热速度快,热交换效率高,达到提高窑系统生产效率、降低熟料烧成热耗的目的。
(1)物料分散换热80%在入口管道内进行的。
喂入预热器管道中的生料,在与高速上升气流的冲击下,物料折转向上随气流运动,同时被分散。
(2)气固分离当气流携带料粉进入旋风筒后,被迫在旋风筒筒体与内筒(排气管)之间的环状空间内做旋转流动,并且一边旋转一边向下运动,由筒体到锥体,一直可以延伸到锥体的端部,然后转而向上旋转上升,由排气管排出。
(3)预分解预分解技术的出现是水泥设备煅烧工艺的一次技术飞跃。
它是在预热器和回转窑之间增设分解炉和利用窑尾上升烟道,设燃料喷入装置,使燃料燃烧的放热过程与生料的碳酸盐分解的吸热过程,在分解炉内以悬浮态或流化态下迅速进行,使入窑生料的分解率提高到90%以上。
余热发电工艺

•
㈡炉内水处理
•
为了防止锅炉内腐蚀结垢,主要采用化学方法处理。
•
通过加药泵向锅炉内加磷酸三钠Na3PO4药品,使进入
炉水中的钙离子、镁离子等形成不粘附的水渣,通过连续、
定期排污排掉.
给水加药装置所加药品为吗啉和联氨。 吗啉作用是
调节给水的PH值.联氨作用是除去水中溶解的氧气.
系统开启步骤
• 1、确认辅机电源是否配送。 • 2、确认各挡板开闭情况,(特别注意AQC
胁,同时也避免汽包水位波动过大,造成自动控制困难。一方面最大限度地
利用余热,降低排烟温度,另一方面,给水预热后形成高温高压水,作为闪
蒸器产生饱和蒸汽的热源。
•
沉降室作用:利用重力除尘的原理将烟气中的大颗粒熟料粉尘收集,避
免粉尘对锅炉受热面的冲刷、磨损。
•
PH 锅炉的设计特点如下: 锅炉型式为卧式,锅炉由蒸发器、过热器、汽
• 组成主要有冷却水泵、冷却风扇、集水槽、散水嘴、散水管、填料、 分离器和相应的连接管道等。
• 冷却风扇:对冷却塔内进行强制通风,对冷却水进行强制换热。 • 散水嘴与散水管:将循环冷却水呈水滴状均匀地洒向填料层。 • 填料:将散水嘴喷射出的水滴在填料的表面形成水膜,增大冷却面积。 • 分离器:防止散水嘴喷射出的水滴因强制通风造成飞沫损失,从而降
• 冲转
• 1、油系统运行正常,盘车正常。
• 2、真空系统启动。
• 3、复位危机遮断器。挂闸,确认前轴承座 显示挂闸位置上(正常/遮断)
升速前的检查与条件
• ①汽轮机振动值在规定范围内; • ②凝汽器真空度在-80kPa以上; • ③控制油压0.65-1.3MPa之间,润滑油压在
0.08-0.15MPa之间; • ④冷凝水温度不大于50℃; • ⑤凝汽器水位不高于380mm; • ⑥倾听内部有无异常声音,检查轴承回油油
余热发电工艺流程

余热发电工艺流程
余热发电是指将工业生产过程中产生的热能通过发电装置转化为电能利用的一种方法。
它能够有效地利用工业过程中产生的废热,实现资源的再利用,提高能源利用效率,减少能源浪费。
下面是一种典型的余热发电工艺流程。
首先,在工业生产过程中产生的废热通过烟囱、排气口等通道收集起来,然后通过热交换器将废热传导给工作介质,提高工作介质的温度。
然后,高温的工作介质通过管道输送到热能转化装置,该装置可以是蒸汽轮机、燃气轮机等。
在这个装置中,工作介质的热能被转化为机械能。
接下来,转化为机械能的工作介质驱动涡轮旋转,进而将旋转的动能传给发电机。
发电机通过利用磁场感应的原理,将机械能转化为电能。
然后,发电机产生的交流电通过变压器进行变压、变流处理后输送到电网中,供给社会各个领域使用。
最后,经过发电机的电能供应到电网后,余热发电装置的工作介质已经失去了大部分的热能,温度降低后通过冷却装置进行冷却,然后重新进入热能转化装置。
整个余热发电工艺流程中,废热被充分利用,使得能源资源得到了充分利用,节省了能源开支。
同时,也减少了温室气体的
排放,对保护环境起到了积极的作用。
总的来说,余热发电工艺流程是通过收集工业生产过程中产生的废热,将废热转化为工作介质的热能,然后通过热能转化装置将热能转化为机械能,最终通过发电机将机械能转化为电能,进而供给社会使用。
这种工艺流程可以有效地提高能源利用效率,减少能源浪费,同时也对环境保护起到了一定的作用。
水泥生产与余热发电工艺流程

工艺流程:
凝汽器热水井内的凝结水经凝结水泵泵入低压闪蒸器出水集箱,与出水汇合,然后 通过锅炉给水泵升压后泵入AQC锅炉省煤器进行加热,经省煤器加热后的水分三路分别送 到AQC炉汽包,PH炉汽包和闪蒸器内。进入两炉汽包内的水在锅炉内循环受热,最终产生 一定压力下的过热蒸汽作为主蒸汽送入汽轮机做功.进入闪蒸器内的高温水通过闪蒸技术 产生一定压力下的饱和蒸汽送入汽轮机第八级后做功,做过功后的乏汽经过凝汽器冷凝后
3、新型干法水泥生产工艺流程
新型干法水泥厂的生产过程,就是以悬浮预热和窑外分 解技术内核心,应用现代科学技术和工业生产最新成就, 以新型的烘干粉磨及原燃料均化工艺及装备,采用以计算 机控制为代表的自动化过程控制手段,实现高效、优质、 低耗的水泥生产过程,使水泥生产具有高效、优质、节约 资源、清洁生产、符合环境保护要求和大型化、自动化、 科学管理特征的现代水泥生产方法。与传统的湿法、干法、 半干法水泥生产相比,其工艺过程比较复杂,系统环节多, 连续性强。许多工序联合操作,相互影响,相互制约。生 产过程本身要求具有高度的稳定性,设备运转的可靠性和 参数调节控制的及时性。这就需要中控室的操作人员及现 场人员必须很好掌握新型干法工艺过程的特点,了解其工 作原理和各种工艺热工过程的特性,更好地服务于生产。
热值 燃料热值高,可以提高发热能力和煅烧温度;热值 低,使煅烧熟料的单位煤耗增加,窑的单位产量降低。一 般要求燃料的低位热值大于21000kJ/kg。 挥发分 挥发分和固定碳是可燃成分;挥发分低,着火温 度高,黑火头长,热力不集中。一般要求煤的挥发分在18 %以上。但随着能源紧张和燃烧器的改进,低挥发分煤在 回转窑上的应用越来越普遍。如福建普遍采用挥发分在3 %~5%的无烟煤,也能正常生产。 煤粉细度 主要取决于燃煤种类和质量。煤种不同,煤粉 质量不同,煤粉的燃烧温度、燃烧所产生的废气量也不同。 对正常运行的回转窑,在燃烧温度和系统通风量基本稳定 的情况下,煤粉的燃烧速度与煤粉的细度、灰分、挥发分
水泥厂余热发电综合讲义.

目录第一章余热发电发展史及基本工艺流程 (3)第一节水泥余热发电发展史 (3)第二节水泥余热发电技术发展史 (5)第三节余热发电基本工艺流程 (6)第二章余热锅炉设备及运行 (9)第一节余热锅炉的分类 (9)第二节余热锅炉设备的构造和功能 (9)第三节余热锅炉的工作原理 (15)第三章余热发电系统常见事故应急操作规程 (17)1、锅炉发生汽水共腾时的具体操作过程 (17)2、锅炉缺水时具体操作 (18)3、锅炉满水时具体操作 (20)4、锅炉承压部件的损坏具体操作过程 (21)5、发电系统全线失电时应急操作 (22)第四章余热发电管理制度 (24)一、总则 (24)二、职责分工 (24)三、运行操作、设备检修与维护 (25)四、锅炉、汽机发电机组、化水系统的管理 (27)五、考核 (28)六、附则 (28)附件一、窑及余热发电系统运行控制指导原则 (28)附件二、发电系统运行规程及制度名录 (31)第一章余热发电发展史及基本工艺流程第一节水泥余热发电发展史我国是世界水泥生产大国,据中国水泥协会统计,2006年,我国水泥产量为12.2亿吨,约占全球水泥产量的40%。
但我国水泥工业却“大而不强”,突出问题是耗能高、污染重。
在工业生产中使用的各种炉窑,都耗用大量的燃料,但它们的热效率都很低,一般只有30%左右,大部分热量都被高温烟气、炉渣和高温产品带走。
随着工业的发展,科学技术水平的不断提高,余热利用对节约能源、改善劳动条件、增加生产、降低生产成本等方面起着越来越重要的作用,已成为工业生产不可分割的组成部分。
在近几十年中,世界各国对余热利用进行了一些研究工作,但发展一直不快,其原因除了对余热利用重视不够之外,更主要的是没有掌握好它的规律。
60年代以来,世界各国余热利用技术发展很快。
我国目前余热利用的现状,与世界先进水平相比还有很大的差距,大部分余热尚未被利用。
在当前能源供应紧张的形势下,大力开展回收余热的工作已显得极为重要。
水泥厂余热发电操作规程完整

4.4.努力维护和保养好各辅助设备,以延长发电机组的平安运行周期。
5.SP锅炉升温升压前的准备工作
5.1通知电气人员检查电力室开关柜并给相关辅机设备送电;
5.3检查所有电动和气动阀门并经开关试验正常后处于关闭状态;
5.4通知现场巡检人员对现场手动阀门进展检查并置于相应的开关状态;
5.5通知现场巡检人员检查平安阀是否投入正常运行状态;
5.6通知现场巡检人员将所有仪表投入正常工作状态;
5.7检查PH锅炉入口及旁路挡板动作是否灵活并提前做好“三对应〞工作;
5.8通知现场巡检人员对锅炉本体和灰斗人孔门进展检查是否关闭严密,
5.9检查并核对SP汽包、AQC汽包及闪蒸器、凝汽器液位;
5.10翻开SP锅炉过热器、汽包排汽阀;
6.辅机系统启动
9.3暖管停机12小时后,冷态暖管时间一般不少于2小时;12小时为热态,暖管时间为0.5-1.0小时;
9.4在暖管过程中时刻与现场保持联系,检查管道的热膨胀点是否有泄
漏,管道支架是否有变形、脱落现象,核对汽包水位、压力、主蒸汽温度与中控保持一致;
9.5当汽轮机入口温度到达300℃以上,压力到达0.689Mpa以上,通知现场暖管完毕,对汽轮机进展全面检查;
在升压过程中,通知现场巡检人员检查确认各承压部件的受热膨胀情况,如有异常,应立即查明情况及时处理;
余热发电系统中控操作规程
修改记录
批准人
受控号
版 次
日 期
修改单
修改人
实施日期
第4页共10页
℃通知现场巡检人员全面检查锅炉系统,如发现有不正常情况,应立即停止升压,待故障消除后继续升压;
SP锅炉主蒸汽截止阀,关闭锅炉起动阀;
17.7按照锅炉降温降压曲线,锅炉旁路挡板以20%逐渐开启, 入口挡板以20%逐渐关闭;
余热锅炉发电的详细描述

一、水泥余热发电的工艺流程从余热发电的工艺流程图我们可以看出,整个系统的设置是:一台PH锅炉,一台AQC锅炉,二级闪蒸器及锅炉给水系统,一套汽轮机发电机及其冷却水系统,水泥工艺线的设备不作大的改动。
下面以宁国水泥厂一线的纯低温余热发电为例,分三部分来叙述余热发电的工艺流程。
图1-1 水泥余热发电的工艺流程图1、含中低温余热废气的工艺流程:1.1PH锅炉部分:在预热器的废气出口的总管上开孔,用管道将开口处与PH 锅炉的入口进行连接;管道的入口处设置一台挡板(编号490),在预热器的废气的总管开孔下部设置一台挡板(编号491),PH锅炉废气的出口用管道连接至窑尾风机入口。
当PH锅炉具备升温条件时,打开490挡板,同时关闭491挡板,这样,预热器出口的350℃,258550Nm3/h的废气被引入PH锅炉,先后通过炉内的过热器、蒸发器后,尚有250℃的废气由窑尾风机抽出,一部分用来烘干生料,另一部分经过增湿塔及窑尾电收尘后排入大气之中。
1.2AQC锅炉部分:在熟料冷却机的4~5室处开口,用管道分别将开口处与AQC炉前端的沉降室入口、EP风机入口相联结。
在沉降室入口前设置一台挡板(编号390),在通往EP风机的管道出口处设置一台挡板(编号391);沉降室出口用管道联接至AQC锅炉入口,锅炉出口用管道联结至EP风机。
当AQC锅炉具备升温条件时,打开390挡板,同时关闭391挡板,篦冷机内的360℃,流量为165300Nm3/h的废气被引入AQC锅炉,先后通过炉内的过热器、蒸发器及省煤器,出口废气温度为91℃,由窑头风机抽出排入大气。
2、锅炉水的工艺流程:余热电站的热力循环是基本的蒸汽动力循环,即汽、水之间的往复循环过程。
:蒸汽进入汽轮机做功后,经凝汽器冷却成凝结水,凝结水经凝结水泵(150A/B)泵入No.2闪蒸器出水集箱,与闪蒸器出水汇合,然后通过锅炉给水泵(230A/B)升压泵入AQC锅炉省煤器进行加热,经省煤器加热后的高温水(223℃)分三路分别送到AQC炉汽包,PH炉汽包和No.1闪蒸器内。