耐冲击吸能车体
新型吸能装置的耐撞性分析
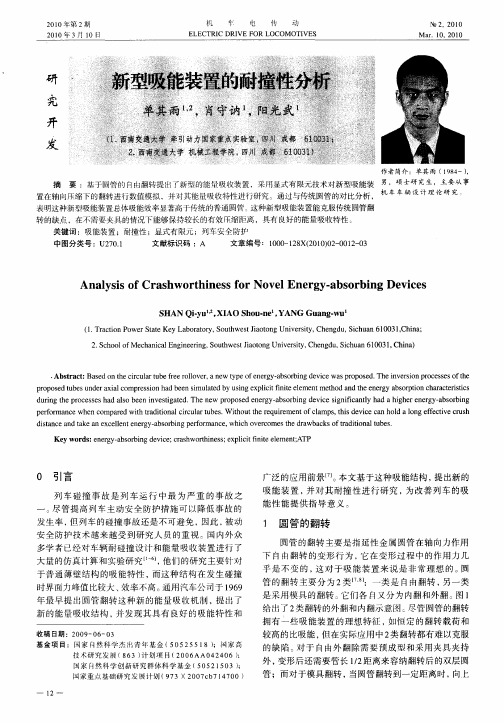
( . a t nP we tt yLa oaoy S uh s Ja tn iest, e g u Sc u n6 0 Chn ; 1 Trci o r aeKe b rtr , o twet ioo gUnv ri Ch n d , ih a 31 ia o S y 1 0 ,
Ke y wor :e e g a o b n e c ; r h ds n r y— bs r i g d vie c as wOrhi s : x i t n t l me ; t ne s e pl iee e ntATP cif i
0 引言
列 车 碰撞 事 故 是 列 车运 行 中最 为 严重 的事 故 之
一
广 泛的应用前景 。 文基于这种 吸能结构 , ]本 提出新 的 吸能装 置 , 对其 耐撞 性进 行研 究 , 并 为改善 列 车的 吸
能 性 能提供 指导 意义 。
。
尽 管提高列 车主动 安全 防护措施 可 以降低事 故 的
发 生率 , 但列 车的碰撞 事故还是不 可避免 , 因此 , 被动
21 0 0年第 2期
21 0 0年 3月 1 0日
机
午
电
传
动
№ 2.2 0 0l
ELECTRI DRI C VE OR F LOCOM OTI VES
M a .1 r 0.2 O 01
研 究 开 发
作 者 简介 :单 其 雨 ( 9 4 ) 18一 ,
摘 要 :基于圆管的 自由翻转提出了新 型的能最吸收装置 ,采用显式有限元技术对新型吸能装 男,硕士研 究生,主要从事 置在轴 向压缩下的翻转进行数值模拟 ,并对其能量吸收特性进行研究。通过 与传统 圆管的对 比分析 , 机 车车辆设计理论研究
地铁车辆吸能结构撞击试验研究
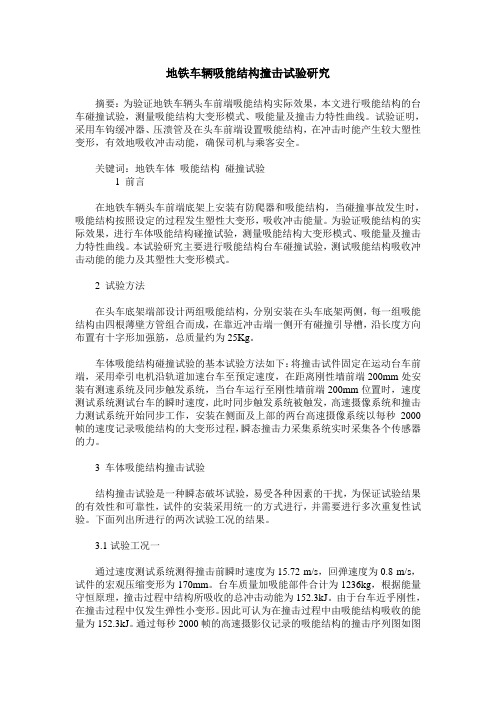
地铁车辆吸能结构撞击试验研究摘要:为验证地铁车辆头车前端吸能结构实际效果,本文进行吸能结构的台车碰撞试验,测量吸能结构大变形模式、吸能量及撞击力特性曲线。
试验证明,采用车钩缓冲器、压溃管及在头车前端设置吸能结构,在冲击时能产生较大塑性变形,有效地吸收冲击动能,确保司机与乘客安全。
关键词:地铁车体吸能结构碰撞试验1 前言在地铁车辆头车前端底架上安装有防爬器和吸能结构,当碰撞事故发生时,吸能结构按照设定的过程发生塑性大变形,吸收冲击能量。
为验证吸能结构的实际效果,进行车体吸能结构碰撞试验,测量吸能结构大变形模式、吸能量及撞击力特性曲线。
本试验研究主要进行吸能结构台车碰撞试验,测试吸能结构吸收冲击动能的能力及其塑性大变形模式。
2 试验方法在头车底架端部设计两组吸能结构,分别安装在头车底架两侧,每一组吸能结构由四根薄壁方管组合而成,在靠近冲击端一侧开有碰撞引导槽,沿长度方向布置有十字形加强筋,总质量约为25Kg。
车体吸能结构碰撞试验的基本试验方法如下:将撞击试件固定在运动台车前端,采用牵引电机沿轨道加速台车至预定速度,在距离刚性墙前端200mm处安装有测速系统及同步触发系统,当台车运行至刚性墙前端200mm位置时,速度测试系统测试台车的瞬时速度,此时同步触发系统被触发,高速摄像系统和撞击力测试系统开始同步工作,安装在侧面及上部的两台高速摄像系统以每秒2000帧的速度记录吸能结构的大变形过程,瞬态撞击力采集系统实时采集各个传感器的力。
3 车体吸能结构撞击试验结构撞击试验是一种瞬态破坏试验,易受各种因素的干扰,为保证试验结果的有效性和可靠性,试件的安装采用统一的方式进行,并需要进行多次重复性试验。
下面列出所进行的两次试验工况的结果。
3.1试验工况一通过速度测试系统测得撞击前瞬时速度为15.72 m/s,回弹速度为0.8 m/s,试件的宏观压缩变形为170mm。
台车质量加吸能部件合计为1236kg,根据能量守恒原理,撞击过程中结构所吸收的总冲击动能为152.3kJ。
机车车体非正面碰撞吸能装置仿真研究
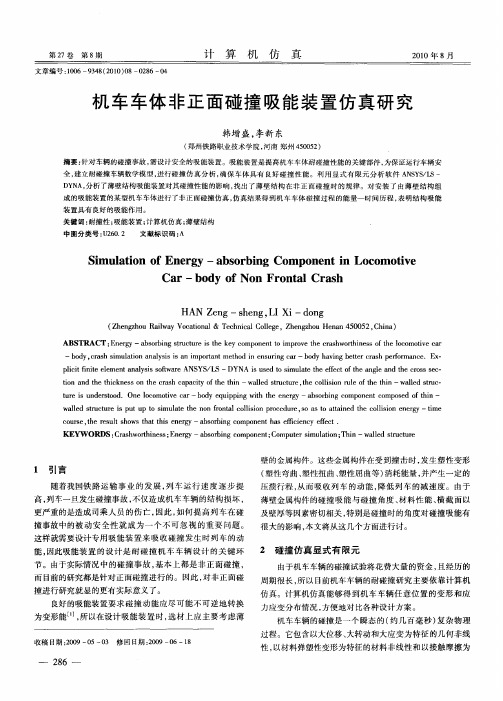
HAN e g—s e g, IXi Zn h n L —d n og
( h nzo aw yV ct nl T cnc ol e Z egh uH n n 50 2 C ia Z eghuR i a oao a & eh i C l g , hnzo e a 0 5 , h ) l i l a e 4 n
tr su d rt o .On o o t e c r o y e u p ig wi h n r —a s r ig c mp n n o o e f hn— u e i n e so d e l c moi a —b d q ip n t t e e e g v h y b ob n o o e tc mp s d o i t
壁 的金 属 构 件 。这 些 金属 构件 在受 到撞 击 时 , 生 塑 性 变形 发
1 引言 Байду номын сангаас
随 着 我 国铁 路 运 输 事 业 的 发 展 , 车 运 行 速 度 逐 步 提 列
( 塑性弯 曲、 塑性扭曲、 塑性屈曲等) 消耗能量 , 并产生一定的 压溃行程 , 而吸 收列 车 的动能 , 从 降低列 车的减速 度。由于 薄壁金 属构件 的碰撞 吸能 与碰撞 角度 、 料性能 、 材 横截 面以 及壁厚等 因素密切相关 , 特别是碰撞时的角度对碰撞 吸能有
装置具有 良好 的吸能作用。
关 键 词 : 性 ; 能 装 置 ; 算机 仿 真 ; 壁结 构 耐撞 吸 计 薄
中图 分 类 号 : 2 02 U 6 . 文 献标 识 码 : A
S mu a i n o e g — b o b n mp n n c mo ie i l t fEn r y—a s r i g Co o o e ti Lo o tv n
基于汽车正面碰撞的吸能盒设计及优化_雷刚
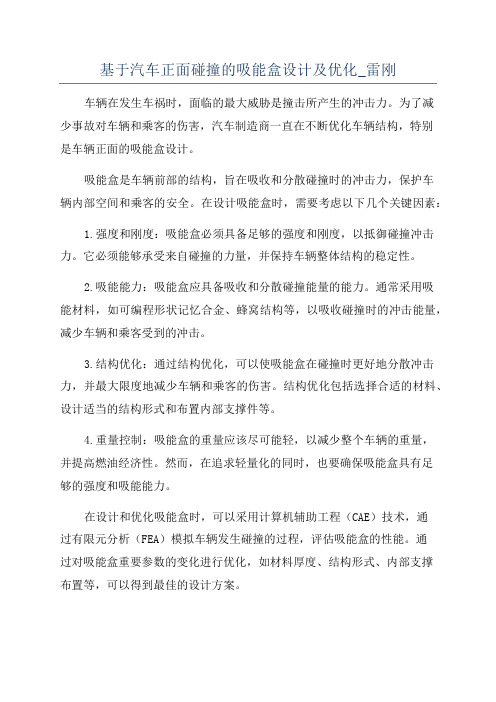
基于汽车正面碰撞的吸能盒设计及优化_雷刚车辆在发生车祸时,面临的最大威胁是撞击所产生的冲击力。
为了减少事故对车辆和乘客的伤害,汽车制造商一直在不断优化车辆结构,特别是车辆正面的吸能盒设计。
吸能盒是车辆前部的结构,旨在吸收和分散碰撞时的冲击力,保护车辆内部空间和乘客的安全。
在设计吸能盒时,需要考虑以下几个关键因素:1.强度和刚度:吸能盒必须具备足够的强度和刚度,以抵御碰撞冲击力。
它必须能够承受来自碰撞的力量,并保持车辆整体结构的稳定性。
2.吸能能力:吸能盒应具备吸收和分散碰撞能量的能力。
通常采用吸能材料,如可编程形状记忆合金、蜂窝结构等,以吸收碰撞时的冲击能量,减少车辆和乘客受到的冲击。
3.结构优化:通过结构优化,可以使吸能盒在碰撞时更好地分散冲击力,并最大限度地减少车辆和乘客的伤害。
结构优化包括选择合适的材料、设计适当的结构形式和布置内部支撑件等。
4.重量控制:吸能盒的重量应该尽可能轻,以减少整个车辆的重量,并提高燃油经济性。
然而,在追求轻量化的同时,也要确保吸能盒具有足够的强度和吸能能力。
在设计和优化吸能盒时,可以采用计算机辅助工程(CAE)技术,通过有限元分析(FEA)模拟车辆发生碰撞的过程,评估吸能盒的性能。
通过对吸能盒重要参数的变化进行优化,如材料厚度、结构形式、内部支撑布置等,可以得到最佳的设计方案。
另外,还可以利用仿生学原理进行吸能盒的设计和优化。
仿生学是一门研究生物体结构、形态和功能的学科,通过借鉴自然界的智慧,可以设计出更有效的吸能盒。
例如,可以通过仿生学原理设计出具有类似骨骼结构的吸能盒,以提高其强度和吸能能力。
总之,基于汽车正面碰撞的吸能盒设计及优化需要考虑多个关键因素,如强度、刚度、吸能能力、结构优化和重量控制。
通过采用CAE技术和仿生学原理,可以得到最佳的设计方案,提高车辆和乘客在碰撞事故中的安全性。
机车吸能装置结构设计及其耐撞性研究
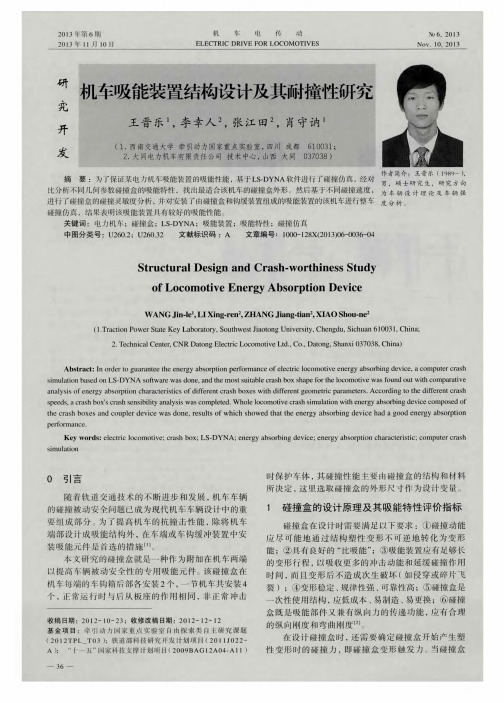
长度/ am r
长度/ am r
程s 为5 0 m m作 为参考尺寸 。
2 . 3 . 1 碰撞盒 吸能壁 厚度对碰撞 盒碰 撞性能 的影 响
1 0 碰 撞 盒 吸 能 容 量 一吸 能
罔 ll 碰 撞 盒 变 形 触 发 力 一吸
容量与吸能壁厚度 近乎线性关 系 , 吸能壁厚度对碰撞盒 吸能能力 的影响非常明显 。 此外 , 在吸能壁厚度为2 1 mm 时, 碰撞盒 吸能容量达 1 4 1 k J , 且此时其变形触发力最 小, 所 以, 碰撞 盒吸能壁厚度的最佳尺寸选择为2 1 mm。 2 . 3 . 2 碰撞 盒吸能壁宽度对 碰撞盒碰撞性 能的影响 选用吸能壁宽度分 别为 1 0 0 mm、 1 1 0 mm、 1 2 0 mm、 1 3 0 mm、 1 4 0 mm, 碰撞盒其他几何参数选用参考 尺寸 。 碰撞 盒 的吸能容量 和变形 触发力 随吸 能壁宽度 的变化 曲线 分别如 图 8 和图 9 所示 。
厚度/ mm 6 碰撞 盒 吸能 答 量 一吸 能 壁 J 刳7 碰 撞 盒 变 彤 触 发 力 一吸
为
m 、
u 4 u 0
2 O — O 0 —
厚 度 曲 线
能 壁 厚 度 曲线
惨
盒
箍: o n
2 4 0
由计算结果 ( 图6 、 图7) 对 比可以看 出, 碰撞 盒吸能
机
车
电
传
动
际, 这 种建模 方 法是 可行 的 。 2 . 3 碰撞盒几何参数对碰撞盒碰撞性能影响分析
是很大 , 且 随着 碰撞 盒吸能壁宽度 的变大 , 其变 形触发
力也在逐渐上升 。 注意到在吸能壁宽 度变化到 1 3 0 mm
泡沫铝冲击吸能器应用设计
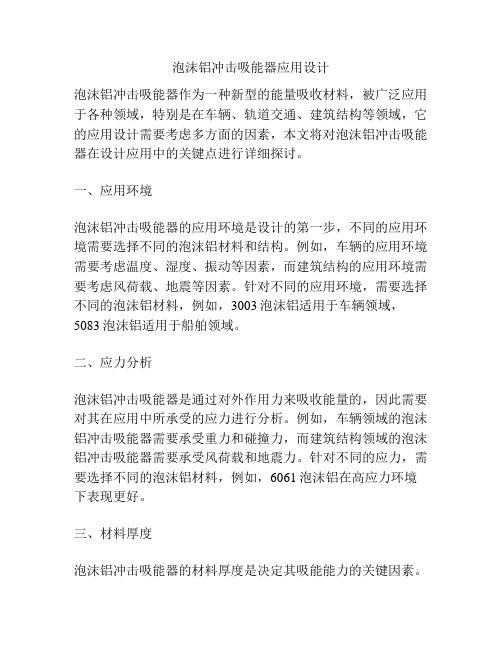
泡沫铝冲击吸能器应用设计泡沫铝冲击吸能器作为一种新型的能量吸收材料,被广泛应用于各种领域,特别是在车辆、轨道交通、建筑结构等领域,它的应用设计需要考虑多方面的因素,本文将对泡沫铝冲击吸能器在设计应用中的关键点进行详细探讨。
一、应用环境泡沫铝冲击吸能器的应用环境是设计的第一步,不同的应用环境需要选择不同的泡沫铝材料和结构。
例如,车辆的应用环境需要考虑温度、湿度、振动等因素,而建筑结构的应用环境需要考虑风荷载、地震等因素。
针对不同的应用环境,需要选择不同的泡沫铝材料,例如,3003泡沫铝适用于车辆领域,5083泡沫铝适用于船舶领域。
二、应力分析泡沫铝冲击吸能器是通过对外作用力来吸收能量的,因此需要对其在应用中所承受的应力进行分析。
例如,车辆领域的泡沫铝冲击吸能器需要承受重力和碰撞力,而建筑结构领域的泡沫铝冲击吸能器需要承受风荷载和地震力。
针对不同的应力,需要选择不同的泡沫铝材料,例如,6061泡沫铝在高应力环境下表现更好。
三、材料厚度泡沫铝冲击吸能器的材料厚度是决定其吸能能力的关键因素。
厚度越大,吸能能力越强。
但是,过于厚的泡沫铝材料会增加整个结构的重量,从而影响其应用效果。
因此,在设计中需要平衡吸能能力和结构重量,确定适当的材料厚度。
四、结构设计泡沫铝冲击吸能器的结构设计需要考虑力学原理和应用环境。
常见的结构形式有圆柱形、方形、矩形等,并且可以根据具体应用场景添加支撑结构或变形机构。
例如,车辆领域的泡沫铝冲击吸能器通常呈圆柱形状,并且在其周围设置支撑结构,以增强其承载能力。
五、应用检测泡沫铝冲击吸能器的应用检测需要结合实际场景进行。
通过模拟不同的应力场景,对其吸能性能、畸变情况、疲劳寿命等参数进行测试和评估,以确保其安全性和稳定性。
综上所述,泡沫铝冲击吸能器的应用设计需要考虑多方面的因素,包括应用环境、应力分析、材料厚度、结构设计和应用检测等。
只有全面考虑各种因素和多方面的需求,才能设计出安全、稳定、高效的泡沫铝冲击吸能器。
汽车防撞梁和吸能盒原理
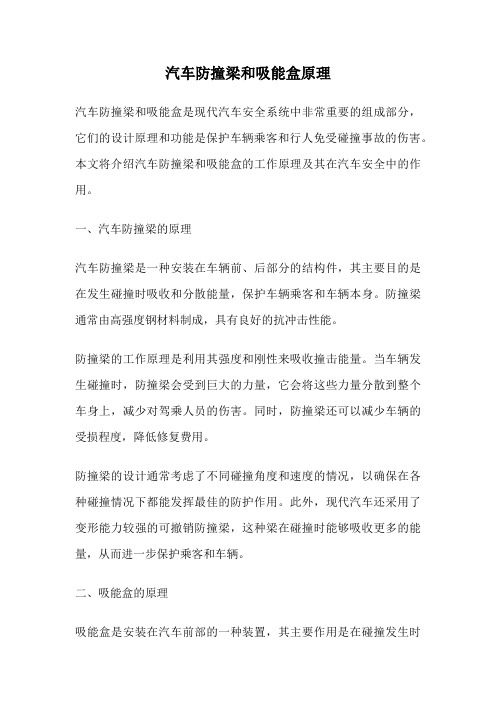
汽车防撞梁和吸能盒原理汽车防撞梁和吸能盒是现代汽车安全系统中非常重要的组成部分,它们的设计原理和功能是保护车辆乘客和行人免受碰撞事故的伤害。
本文将介绍汽车防撞梁和吸能盒的工作原理及其在汽车安全中的作用。
一、汽车防撞梁的原理汽车防撞梁是一种安装在车辆前、后部分的结构件,其主要目的是在发生碰撞时吸收和分散能量,保护车辆乘客和车辆本身。
防撞梁通常由高强度钢材料制成,具有良好的抗冲击性能。
防撞梁的工作原理是利用其强度和刚性来吸收撞击能量。
当车辆发生碰撞时,防撞梁会受到巨大的力量,它会将这些力量分散到整个车身上,减少对驾乘人员的伤害。
同时,防撞梁还可以减少车辆的受损程度,降低修复费用。
防撞梁的设计通常考虑了不同碰撞角度和速度的情况,以确保在各种碰撞情况下都能发挥最佳的防护作用。
此外,现代汽车还采用了变形能力较强的可撤销防撞梁,这种梁在碰撞时能够吸收更多的能量,从而进一步保护乘客和车辆。
二、吸能盒的原理吸能盒是安装在汽车前部的一种装置,其主要作用是在碰撞发生时吸收和分散能量,以保护车辆乘客。
吸能盒通常由塑料或金属材料制成,其设计考虑了不同碰撞情况下的能量吸收需求。
吸能盒的工作原理是通过其结构和材料的特性来吸收和分散碰撞能量。
当车辆发生碰撞时,吸能盒会在瞬间发生变形,将撞击能量转化为热能和机械能,从而减轻对乘客和车辆的伤害。
吸能盒通常由多个层次的结构组成,每个层次的材料和设计都有特定的功能。
例如,吸能盒的外层通常由刚性材料制成,用于分散撞击力和保护内部结构。
而内部层次则通常使用可变形的材料,如泡沫塑料或可压缩材料,用于吸收撞击能量。
吸能盒的设计还考虑了车辆乘客的安全性。
例如,在前部碰撞中,吸能盒可以减少乘客面部和胸部的伤害风险,同时减少颈部和脊柱的受伤风险。
此外,吸能盒还可以减少车辆的受损程度,降低修复费用。
总结:汽车防撞梁和吸能盒是现代汽车安全系统中至关重要的组成部分。
汽车防撞梁利用材料的强度和刚性,通过分散和吸收碰撞能量来保护车辆乘客和车辆本身。
高速列车吸能结构设计和耐撞性分析_李松晏
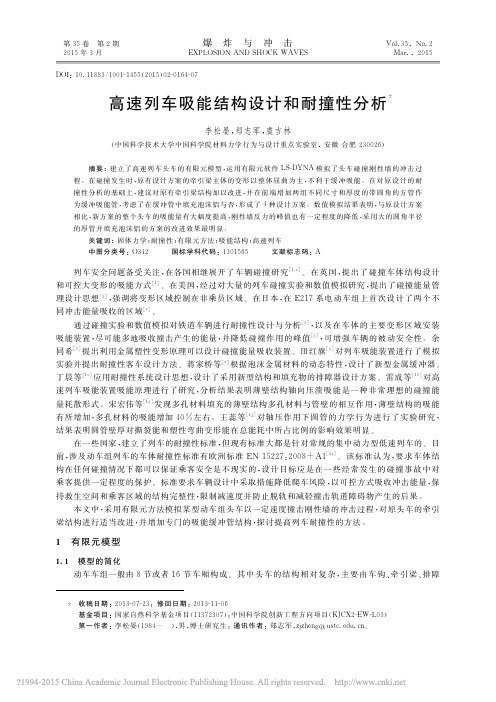
第35卷 第2期爆炸与冲击Vol.35,No.2 2015年3月EXPLOSION AND SHOCK WAVES Mar.,2015 DOI:10.11883/1001-1455(2015)02-0164-07高速列车吸能结构设计和耐撞性分析*李松晏,郑志军,虞吉林(中国科学技术大学中国科学院材料力学行为与设计重点实验室,安徽合肥230026) 摘要:建立了高速列车头车的有限元模型,运用有限元软件LS-DYNA模拟了头车碰撞刚性墙的冲击过程。
在碰撞发生时,原有设计方案的牵引梁主体的变形以整体屈曲为主,不利于缓冲吸能。
在对原设计的耐撞性分析的基础上,建议对原有牵引梁结构加以改进,并在前端增加两组不同尺寸和厚度的带圆角的方管作为缓冲吸能管,考虑了在缓冲管中填充泡沫铝与否,形成了4种设计方案。
数值模拟结果表明,与原设计方案相比,新方案的整个头车的吸能量有大幅度提高,刚性墙反力的峰值也有一定程度的降低,采用大的圆角半径的厚管并填充泡沫铝的方案的改进效果最明显。
关键词:固体力学;耐撞性;有限元方法;吸能结构;高速列车 中图分类号:O342 国标学科代码:1301565 文献标志码:A 列车安全问题备受关注,在各国相继展开了车辆碰撞研究[1-4]。
在英国,提出了碰撞车体结构设计和可控大变形的吸能方式[1]。
在美国,经过对大量的列车碰撞实验和数值模拟研究,提出了碰撞能量管理设计思想[3],强调将变形区域控制在非乘员区域。
在日本,在E217系电动车组上首次设计了两个不同冲击能量吸收的区域[4]。
通过碰撞实验和数值模拟对铁道车辆进行耐撞性设计与分析[5],以及在车体的主要变形区域安装吸能装置,尽可能多地吸收撞击产生的能量,并降低碰撞作用的峰值[6],可增强车辆的被动安全性。
余同希[7]提出利用金属塑性变形原理可以设计碰撞能量吸收装置。
田红旗[8]对列车吸能装置进行了模拟实验并提出耐撞性客车设计方法。
蒋家桥等[9]根据泡沫金属材料的动态特性,设计了新型金属缓冲器。
铝合金车体抗冲击能力的动态有限元仿真

2
兵 工 学 报
第 30 卷
两个问题需要简化处理 :1) 气囊问题 。空投系统的 气囊和车体先后着陆相互作用的问题属于复杂的固 体流体耦合问题[2 ] 。伞降系统的气囊是一组在降
装甲板本体强度的 70 %. 建立车体有限元模型 :1) 定义材料属性 :铝合金
车体材料属性定义为各向同性 、线性 、与温度无关 。
型的少数模态提取 。
3 动态载荷边界条件
板 、炮塔座圈 、动力舱隔板以及承力支座和加强筋板 311 车体承受初始静态载荷
组成 。在 ANS YS 中建立铝焊缝模型及焊缝的实体
着地时 , 铝合金车体受到的冲击载荷还包括车
形状 。考虑的焊缝结构有 :装甲板之间 ,发动机支座 体上安装的主要总成部件对车体产生的动态载荷 :
图 1 车体的有限元模型 Fig. 1 The finite element model for t he hull
车体受到动态加速度冲击最大值为 11176 g , 作用
利用 Block Lanczos 方法进行模态分析
时间 200 ms;3) 极限工况 :铺面路 , 8 m/ s 着速 , 部分
落过程自然充气膨胀的口袋 ,着地时 ,靠气囊底板与 地面间的接合使气囊密闭 , 其作用效果受地面不平 度影响较大 。实车试验中 ,部分气囊失效时 ,着地冲 击加速度会增加 150 %以上 ; 2) 土壤问题 。土壤是 具有弹塑性的 ,使用土壤的弹性模型 ,将使问题过于 简化 。广泛应用的土壤的弹塑性本构模型 , 普遍采 用的办法是通过试验手段测取本构参数来建立土壤 的本构关系[3 ] 。由于空投场地的多变性 , 获得土壤 的弹塑性本构关系在具体研究中的普遍意义不大 。
F/ N
P8/ MPa
车身安全解析碰撞能量吸收结构的材料选择
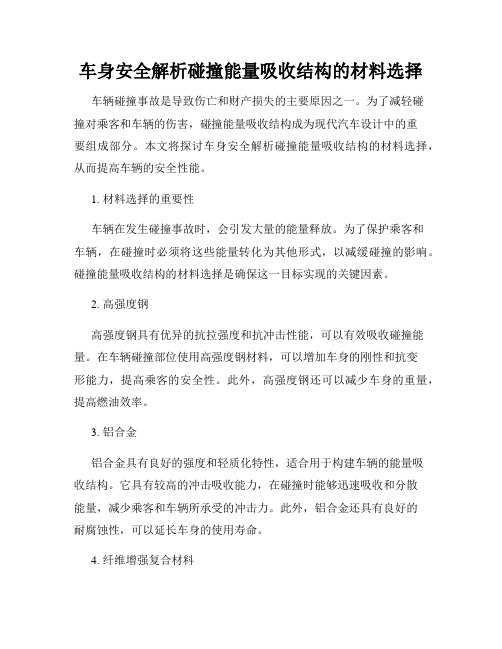
车身安全解析碰撞能量吸收结构的材料选择车辆碰撞事故是导致伤亡和财产损失的主要原因之一。
为了减轻碰撞对乘客和车辆的伤害,碰撞能量吸收结构成为现代汽车设计中的重要组成部分。
本文将探讨车身安全解析碰撞能量吸收结构的材料选择,从而提高车辆的安全性能。
1. 材料选择的重要性车辆在发生碰撞事故时,会引发大量的能量释放。
为了保护乘客和车辆,在碰撞时必须将这些能量转化为其他形式,以减缓碰撞的影响。
碰撞能量吸收结构的材料选择是确保这一目标实现的关键因素。
2. 高强度钢高强度钢具有优异的抗拉强度和抗冲击性能,可以有效吸收碰撞能量。
在车辆碰撞部位使用高强度钢材料,可以增加车身的刚性和抗变形能力,提高乘客的安全性。
此外,高强度钢还可以减少车身的重量,提高燃油效率。
3. 铝合金铝合金具有良好的强度和轻质化特性,适合用于构建车辆的能量吸收结构。
它具有较高的冲击吸收能力,在碰撞时能够迅速吸收和分散能量,减少乘客和车辆所承受的冲击力。
此外,铝合金还具有良好的耐腐蚀性,可以延长车身的使用寿命。
4. 纤维增强复合材料纤维增强复合材料由纤维和树脂基体组成,具有高强度和轻质化的特点。
它们可以在碰撞时吸收和分散能量,减轻碰撞对车辆和乘客的影响。
纤维增强复合材料还具有优异的抗疲劳性和抗腐蚀性能,可以提高车身的耐久性。
5. 聚合物材料聚合物材料具有良好的能量吸收和缓冲性能,适合用于构建车辆的保险杠和车门等部位。
聚合物材料可以在碰撞时迅速变形,吸收和分散能量,减少对乘客和车辆的伤害。
此外,聚合物材料还具有较低的密度和良好的成型性,有利于实现轻量化设计。
6. 混凝土材料混凝土材料具有良好的压缩强度和耐久性,适合用于碰撞能量吸收结构的构建。
它们可以在碰撞时承受较大的压力,将能量转化为其他形式,减缓碰撞的影响。
混凝土材料还具有良好的阻燃性能,可以提高车辆的安全性。
综上所述,车身安全解析碰撞能量吸收结构的材料选择是确保车辆安全性能的关键因素。
高强度钢、铝合金、纤维增强复合材料、聚合物材料和混凝土材料都具有各自的优势和适用范围,可以根据不同部位的需求进行选择和组合,以提高车辆的整体安全性能。
车辆薄壁结构撞击吸能特性研究
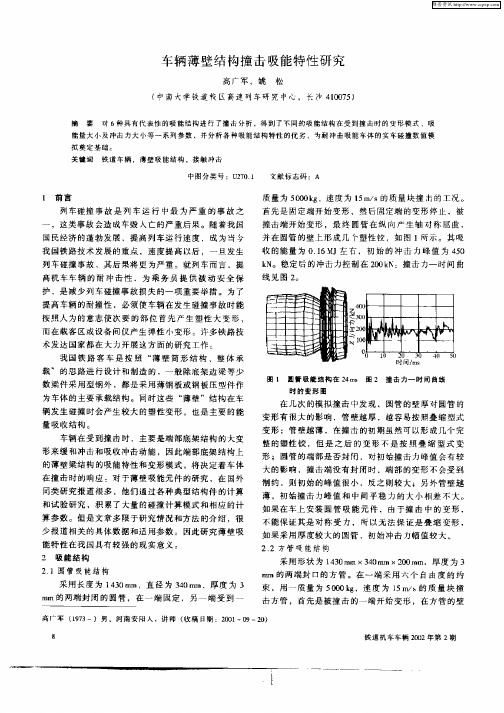
维普资讯
能特 性在 我国具 有较强 的现实 意义 。
2 吸 能 结 构
田 1 圆管 吸能 结 掏 在 2 m 图 2 撞 击 力一 时 间 曲线 4 s
时 的 变 形 图
在 几次 的模 拟撞击 中发 现 ,圆管的壁 厚对 圆管 的 变形有 很大 的影 响 ,管 壁越厚 ,越 容易按 照叠缩 型 式 变形 ;管壁 越薄 ,在撞击 的初 期虽 然可 以形 成几 个 完
维普资讯
车辆 薄壁结 构 撞 击 吸能特 性 研究
高广 军 ,姚 松
( 中南大学铁 道校 区高速 列 车研 究中心 ,长沙 40 7 ) 10 5
摘 要 对 6 具 有 代 表 性 的吸 能结 构 进 行 了撞 击 分 析 ,得 到 了 不 同 的 吸能 结 构 在 受 到 撞 击 时 的 变 形 模 式 、 吸 种 能量 大 小 及 冲 击 力 大 小 等 一 系 列 参 数 ,井分 析各 种 吸能 结 构 特 性 的 优 劣 .为 耐 冲 击 吸能 车体 的宴 车碰 撞 数 值 模
而 在 载 客 区 或 设 备 问 仅 产 生 弹 性 小 变 形 : 许 多 铁 路 技 术发 达 国家都在 大力 开展这方 面 的研究 工作 。
并在 圆管 的壁上 形成几 个塑性 铰 ,如图 1 示 。其 吸 所
收的能 量 为 0 1 M 左 右 ,初 始 的 冲击 力 峰 值 为 4 0 6 J 5
拟奠定基础。
关键词
铁 道 车 辆 .薄 壁 吸 能 结 构 ,接 触 冲击 中图 分 类 号 :U 7 20 1 文 献标 志 码 :A
l 前 言
质 量 为 5 0 、速 度 为 1 m s 质 量 块 撞 击 的 工 况 。 00 g k 5 / 的 首 先 是 固定 端 开 始 变 形 ,然 后 固定 端 的变 形 停 止 , 被 撞 击 端 开 始 变 形 .最 终 圆 管 在 纵 向 产 生 轴 对 称 屈 曲
轨道车辆新型组合结构吸能装置耐碰撞性分析

关键词 : 道 车辆 ; 轨 耐碰 撞性 ;组合 结构 ; 能装 置 ;非 线性有 限元 ; 真 ; N Y ;L — Y A 吸 仿 A S S SD N
中图分 类号 : 2 0 1 T 15 2 U 7 . ;B 1 . 文献 标志 码 : B
Cr s wo t i e s a l s O。 e c m .o ie sr c ur r h a r h n s na  ̄ i In w o p st t u t e y" s
■ 1 ● 一 ‘ ● ‘ l - ● ’
e r y- ne g abS r ng de i e n a l y ve c e 0 bl v c s i r iwa hi l
员伤 亡 . 出组 合 结构吸 能装 置的设 计 思想 . 据 耐撞 性 车体 吸 能 装 置设 计 原理 , 计 出不 同截 面 提 根 设 形状 管 的组合 结构 吸能装 置 .,用 A S S L . Y A 对其 分 别进 行 动 态仿 真 , 究其 吸 能特 性 , f i 1 N Y / SD N 研 并
a s r i g d v c s i p o o e . T e c mp s e sr cu e e e g — b o b n e ie t i e e t c o s b o b n e ie s rp s d h o o i t t r n r a s r i g d v c s wi d f r n r s ・ t u y h f
第2 1卷 第 5期
21 0 2年 1 0月
计 算 机 辅 助 工 程
Co u e d d En i e rn mp t rAi e 0c . 2 2 t O1
吸能式车身简介-2011118

谢谢
吸能式车身简介
保险杠:带气腔式
当碰撞发生时,气腔被压缩, 进而影响其外面包裹部件的 变形方式,从而改善吸能效 果。这是一种专门为了保护 行人而设计的保险杠。
车身数模阶段 前纵梁
1、前纵梁设计要求从前向后强度逐渐增大 2、 前纵梁后部是前碰撞(特别是偏置碰撞)中 最敏感区域,在碰撞中极容易折弯使前挡板入侵 量增大,因此要求其截面尽可能做大。 3、前纵梁前部吸能区设计诱导槽,并可设计成 截面前小后大的梯形结构,使形成手风琴式的折 叠变形 4、前纵梁中部纵向方向设计强大的加强筋,以 支掌前部吸能区充分变形,同时也可防止纵梁折 弯。
吸能式车身简介
保险杠:普通式(自身吸能式)
这种类型保险杠结构比较简单,由横杠、 横杠内侧加强件和树脂类填料等组成。 它是在保险杠 U形横杠内部装入氨基甲 酸乙酯泡沫或树脂块,使其充满横杠 U 形面和加强件之间,碰撞时利用泡沫或 树脂块变形吸收能量。
吸能式车身简介
保险杠:液压缓冲型
利用液压油通过节流孔时的黏性 阻力吸收撞击的能量,吸收能量 的效率可以高达 80%。这类油 气弹簧式的缓冲减振器有效利用 了气体缓冲、液体节流减振的工 作方式,工作特性比较稳定。撞 击后靠氮气产生复原动力,使保 险杠复位。这种保险杠由于造价 较高,通常使用在高档轿车上。
吸能式车身简介
技术规划部 徐亮亮 2011年11月18日
吸能式车身简介
前 汽车安全
言
(设计及制造理念)
基本理念:在碰撞发生时有效吸 收碰撞能量,并将其分散至车身 各部位骨架,能有效的减少驾驶 舱的变形程度,确保座舱空间。!
吸发动机的车体前部空 间很小,在高速碰撞的情况下会 由于驾驶舱发生变形从而不能确 保乘员的生存空间。 2、车身过分坚实,会产生较大 减速度,超过伤害指数HIC值, 使乘员无法承受
地铁车辆耐撞性分析及多级能量吸收系统的验证

地铁车辆耐撞性分析及多级能量吸收系统的验证牛超;邵微;陈秉智【摘要】为研究地铁头车的耐撞性及其多级能量吸收系统设计的合理性,建立能够反映真实情况的头车用半自动车钩及其剪切装置模型.利用PAMCRASH软件,参考EN 15227标准,设定模拟运营工况,计算头车与刚性墙撞击工况,得到该车吸能结构的变形模式和最大吸能量;然后计算两头车对撞工况,从逃生空间、撞击力和加速度等方面评价车体的耐撞击性.计算结果表明该地铁头车耐撞击性能良好,多级能量吸收系统设计合理.【期刊名称】《计算机辅助工程》【年(卷),期】2014(023)002【总页数】5页(P85-89)【关键词】地铁;多级能量吸收系统;车钩;剪切装置;碰撞仿真;变形模式【作者】牛超;邵微;陈秉智【作者单位】大连交通大学交通运输工程学院,辽宁大连116028;大连交通大学交通运输工程学院,辽宁大连116028;大连交通大学交通运输工程学院,辽宁大连116028【正文语种】中文【中图分类】U270.2;TB115.10 引言随着城市化进程的加快和人口的急剧增加,交通拥堵已经成为各大城市亟待解决的问题.修建地铁是减轻地面交通压力、缓解拥堵的好方法之一,因此许多城市都在大力发展地铁.尽管地铁有许多的优点,但由于其运量大、运行速度快,一旦发生碰撞和追尾等事故,将会造成大量的人员伤亡和经济损失,后果非常严重,因此其安全性显得尤为重要.[1]地铁车辆主要依靠主动控制的方式避免行车事故的发生,但是仅依靠主动控制并不能完全避免碰撞事故的发生,因此需要对车身进行防撞设计,使其结构以可控的方式发生变形,吸收碰撞中的能量,以保护司机和乘客的安全.目前,计算机仿真已经成为研究大变形碰撞的主要方法,这给本文研究提供思想和平台,即:通过计算机仿真分析,评价车辆的耐撞击性能.以某地铁车为研究对象,参考欧洲标准委员会颁布的EN 15227标准,对其进行碰撞仿真分析,评价其碰撞安全性是否符合标准的要求,并验证其多级能量吸收系统设计的合理性.1 评价标准有学者指出,车体的耐撞性设计应采用多级能量吸收系统[2].仔细分析现有的车辆吸能装置(见图1)可知,碰撞时车钩缓冲器首先发生变形,当车钩压馈管压溃后,车钩剪切装置达到触发力被破坏,车钩与底架分离;然后两车前端防爬器相互啮合,防爬器后面的吸能元件开始吸收能量;若碰撞速度较大,前两部分吸收的能量达到极限,剩余的能量就会被车体易变形区域吸收.这3部分构成列车的多级能量吸收系统,车体按顺序依次发生变形,能够有效降低最大撞击力峰值,延长碰撞作用时间,降低平均加速度,起到保护乘客安全的作用.要设计出合理的能量吸收系统,合理分配各部分的刚度是关键.图1 多级能量吸收系统Fig.1 Multistage energy absorption system目前,国内尚无轨道车辆耐撞性的评价标准和方法,本文采用2008年欧洲标准委员会颁布的EN 15227标准作为评价标准.该标准规定:对于地铁车辆,假设一列满载列车与一列同类型编组列车在25 km/h速度下发生对撞,构成逃生空间的结构应保持完整无损并可以承受在吸能元件完全被撞毁期间作用到其上的最大力;以受控的方式吸收撞击能量;在逃生空间的平均纵向减速度应限制到5g.由于该标准没有对列车的吸能要求进行量化,因此通过查阅相关文献,对标准进行补充:列车首端的设计能量计算公式[3]为式中:m1为车辆质量;v为列车速度.因此,本文在评估地铁头车及车前结构耐撞性时考虑的计算工况和评估条件[4]为:(1)满载头车以25 km/h的初速度撞击刚性墙,根据头车变形和吸能情况验证该车多级能量吸收系统设计的合理性;(2)根据EN 15227标准,一节乘客满员的地铁头车以25 km/h的初速度与另一节同类型保持静止状态的头车相撞时,从吸能、撞击力、加速度和逃生空间等方面评估车体的耐撞击性能.2 碰撞仿真模型和算法原理2.1 模型建立选取的地铁车辆模型的满载质量为55.03 t,材料为钢.工厂提供的头车用半自动车钩数据为:长度1670 mm,压馈管长度260 mm,稳态力700 kN,过载保护螺栓触发力1400 kN.已知压馈管吸能185 kJ,建立车钩的有限元模型.车钩结构复杂,无法建立其真实模型,因此简化处理:根据等效吸能原则,车钩的主体用实体单元模拟,缓冲器和压馈管用壳单元模拟,用壳单元压溃变形吸收的能量等效车钩缓冲装置的压溃吸能;经过验证可知,压馈管厚度取6 mm时刚好满足吸能要求.车钩剪切装置用于底架的过载保护[5],在碰撞过程中起着重要作用.本文建立剪切装置的完整模型:模套和环状柱体之间采用间隙配合,定义两者间的接触类型为33号主从接触,通过设置两者间的接触厚度和摩擦因数,控制摩擦力的大小.经多次调节,使得过载保护螺栓触发力达到1400 kN.车钩模型见图 2.将车钩安装在头车前端,导入到PAMCRASH中设置参数,得到完整计算模型见图3.2.1 碰撞原理车辆碰撞是一个集几何非线性、材料非线性和边界非线性等于一体的复杂的瞬态物理过程.在碰撞过程中,车体的运动和变形必须满足动量守恒方程、质量守恒定律、能量守恒定律和边界条件等的约束.图2 车钩模型及其压溃过程Fig.2 Coupler model and its crushing progress图3 整车碰撞模型Fig.3 Whole vehicle collision models2.1.1 质量守恒方程在碰撞过程中,车体内任何部件都满足质量守恒定律,且有质量守恒方程:任意体积内的质量在撞击过程中保持不变,则式中:V为相对体积;ρ为当前质量密度;ρ0为初始质量密度.由形变梯度的定义知:dV=·dV0,其中,Jx为形变梯度,则2.1.2 运动方程假设某质点在初始时刻的位置为Xj(j=1,2,3);在任意时刻t,该质点的坐标定义为xi(i=1,2,3),速度定义为 Vi(i=1,2,3),那么其运动方程可以表示为在初始时刻t=0时,该质点的运动方程为2.1.3 能量守恒方程根据能量守恒定律,得到在车辆大变形碰撞仿真分析时的能量方程为式中:E为当前时刻构件的能量;V为现时构件的体积;Sij为偏应力,为应变率;q为体积黏性阻力;p为当前构件的压力,p=-σkk/3-q.2.1.4 动量守恒方程在碰撞过程中,车体内任意部件都满足动量守恒定律,其动量方程为3 车体性能分析3.1 地铁头车撞击刚性墙结果分析由于车体变形只发生在车头部分,为方便观察,此处只截取车头变形(见图4);能量-时间曲线见图5.可知:碰撞初始阶段(0~150 ms)主要是车体前端吸能结构发生变形,之后的阶段(150~234 ms)车体易变形区发生变形,司机室地板变形,威胁司机安全;车体的吸能结构在不影响司机安全的情况下(即0~150 ms)共吸收能量755 kJ,而由公式计算,列车首端设计吸能至少为可见,该车吸能结构的设计能够满足吸能要求.图4 头车撞击刚性墙时车体变形Fig.4 Deformations of vehicle body during collision between head vehicle and rigid wall图5 头车撞击刚性墙时的能量-时间曲线Fig.5 Energy-time curves during collision between head vehicle and rigid wall3.2 两头车对撞结果分析两车对撞时车体变形见图6,T表示顶部视图,B表示底部视图.可知,在碰撞过程中,只有车体前端吸能结构发生变形,为司机和乘客保留足够的逃生空间;吸能结构有序地发生变形,能量逐级吸收,其刚度分配合理.由图7可知,在碰撞过程中系统能量守恒,动能逐渐减小,内能逐渐增加,动能转化为内能,最终两车以共同速度运行,能量不再转化;两车最终吸能560 kJ,平均每车吸能280 kJ,可见在此速度下碰撞,该车还有很大的安全裕量,能经受更大速度的碰撞.图6 两头车对撞时车体变形Fig.6 Deformations of vehicle body during collision of two head vehicles图7 两头车对撞时的能量-时间曲线Fig.7 Energy-time curves during collision between head vehicle and rigid wall由图8可知,在碰撞开始后,撞击力迅速增加,第一个峰值对应于压馈管变形的触发力;随后曲线发生波动,对应于压馈管的屈曲变形,其每出现一个褶皱,表示撞击力出现一次峰值;在压馈管完全压溃后,撞击力达到1400 kN,此时剪切装置被破坏,车钩与底架分离;经过100 mm左右,防爬器开始啮合,之后吸能元件和车体易变形区域开始变形,直至碰撞结束;压馈管触发力为1230 kN,其稳态力在700 kN左右,剪切装置触发力为1400 kN,可见该简化车钩的性能完全符合实际情况,模拟很精确.图8 两头车对撞时的撞击力-变形曲线Fig.8 Curve of impact force vs deformation during collision between head vehicle and rigid wall在逃生空间的前、中、后部关键位置选取3个观察点,其速度-时间和加速度-时间曲线分别见图9和10.图9 速度-时间曲线Fig.9 Velocity-time curves图10 加速度-时间曲线Fig.10 Acceleration-time curves车体在碰撞过程中的激烈程度可以从速度衰减的快慢反映出来.由图9可知,逃生空间前、中、后3个位置的速度变化趋势基本相同,速度在小范围内发生振荡,碰撞过程相对平稳;加速度的大小直接关系到乘客的安全.由图10可知,3个观察点的平均纵向加速度分别为-8.3,-10.4 和-9.7 m/s2,满足标准中对加速度的要求.4 结论通过以上分析,可以得出如下结论:(1)基于建立的头车用半自动车钩及剪切装置模型进行碰撞分析,结果表明,其撞击性能与工厂提供的数据符合得很好,验证模拟的精确性.此模型可以在今后研究头车碰撞问题时广泛应用.(2)对车体的多级能量吸收系统进行验证,其变形顺序和能量吸收都能满足要求,可见该车多级能量吸收系统设计合理.(3)对车体的碰撞安全性进行评价,逃生空间没有发生变形,吸能结构逐级吸收撞击能量,最大撞击力只有1400 kN,逃生空间平均纵向加速度满足标准要求.因此,该车耐撞击性能良好,能够保证司机和乘客的安全,也为工厂设计人员提供参考. 参考文献:【相关文献】[1]杨慧芳.CRH3动车组被动安全性和耐撞性优化研究[D].大连:大连交通大学,2009.[2]李兰,刘金朝,王成国,等.城轨车辆耐碰撞结构的数字设计研究[J].铁道机车车辆,2008,28(2):28-32.LI Lan,LIU Jinzhao,WANG Chengguo,et al.Numerical study on crashworthy structure for urban rail vehicle[J].Railway Locomotive & Car,2008,28(2):28-32.[3]LU G.耐碰撞车辆的能量吸收要求[J].国外铁道车辆,2006,43(3):8-13.LU G.Energy absorption requirement for crashworthy vehicles[J].Foreign Rolling Stock,2006,43(3):8-13.[4]张乐乐,张啸雨,崔进,等.地铁头车车体耐撞性仿真分析[J].铁道学报,2012,34(3):22-27.ZHANG Lele,ZHANG Xiaoyu,CUI Jin,et al.Numerical analysis on crashworthiness of subway head car body[J].J China Railway Soc,2012,34(3):22-27.[5]LU G.耐碰撞车辆的撞击性能[J].国外铁道车辆,2005,42(5):26-34.LU G.Collision behaviour of crashworthy vehicles[J].Foreign Rolling Stock,2005,42(5):26-34.。
车身吸能区分布
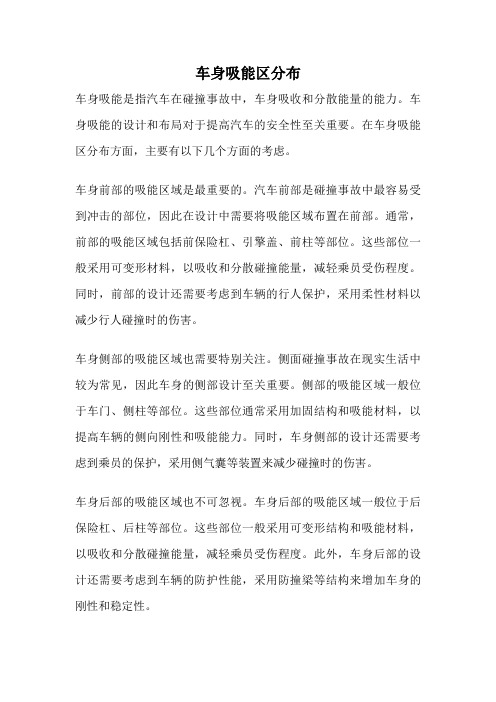
车身吸能区分布车身吸能是指汽车在碰撞事故中,车身吸收和分散能量的能力。
车身吸能的设计和布局对于提高汽车的安全性至关重要。
在车身吸能区分布方面,主要有以下几个方面的考虑。
车身前部的吸能区域是最重要的。
汽车前部是碰撞事故中最容易受到冲击的部位,因此在设计中需要将吸能区域布置在前部。
通常,前部的吸能区域包括前保险杠、引擎盖、前柱等部位。
这些部位一般采用可变形材料,以吸收和分散碰撞能量,减轻乘员受伤程度。
同时,前部的设计还需要考虑到车辆的行人保护,采用柔性材料以减少行人碰撞时的伤害。
车身侧部的吸能区域也需要特别关注。
侧面碰撞事故在现实生活中较为常见,因此车身的侧部设计至关重要。
侧部的吸能区域一般位于车门、侧柱等部位。
这些部位通常采用加固结构和吸能材料,以提高车辆的侧向刚性和吸能能力。
同时,车身侧部的设计还需要考虑到乘员的保护,采用侧气囊等装置来减少碰撞时的伤害。
车身后部的吸能区域也不可忽视。
车身后部的吸能区域一般位于后保险杠、后柱等部位。
这些部位一般采用可变形结构和吸能材料,以吸收和分散碰撞能量,减轻乘员受伤程度。
此外,车身后部的设计还需要考虑到车辆的防护性能,采用防撞梁等结构来增加车身的刚性和稳定性。
除了以上几个方面的吸能区域,车身底部的吸能区域也需要特别关注。
车辆在碰撞事故中,往往会发生悬挂系统的损坏和车身底部的撞击。
因此,在车身底部的设计中需要考虑到底盘的保护和吸能能力。
一般来说,车身底部的吸能区域采用可变形材料,以吸收和分散来自底部的碰撞能量。
车身吸能区的布局对于提高汽车的安全性至关重要。
在设计中,需要将吸能区域布置在前部、侧部、后部和底部等关键部位。
这些区域一般采用可变形结构和吸能材料,以吸收和分散碰撞能量,减轻乘员受伤程度。
同时,吸能区域的设计还需要考虑到车辆的行人保护和底盘保护等方面。
通过合理的吸能区域布局,可以提高汽车的碰撞安全性,保护乘员的生命安全。
- 1、下载文档前请自行甄别文档内容的完整性,平台不提供额外的编辑、内容补充、找答案等附加服务。
- 2、"仅部分预览"的文档,不可在线预览部分如存在完整性等问题,可反馈申请退款(可完整预览的文档不适用该条件!)。
- 3、如文档侵犯您的权益,请联系客服反馈,我们会尽快为您处理(人工客服工作时间:9:00-18:30)。
第3卷 第3期2003年9月交通运输工程学报Journal of T raffic and T ranspo rtation EngineeringV o l 13 N o 13Sep.2003收稿日期:2002203203作者简介:高广军(19732),男,河南林州人,讲师,博士生,从事结构撞击动力学研究.文章编号:167121637(2003)0320050204耐冲击吸能车体高广军,田红旗,姚 松(中南大学高速列车研究中心,湖南长沙 410075)摘 要:借鉴两个美国标准提出了列车端部吸能区和中部载人区的评价指标,采用数值模拟方法,对25型车体与刚性墙进行了撞击计算。
结果表明,耐冲击车体在吸收规定的5M J 的塑性变形能的情况下,仅车体的端部发生了塑性变形,车体的中间部位仅发生弹性小变形;塑性变形位移量较改进前有较大提高,且撞击力明显减小,加速度指标明显改善。
关键词:机车车辆工程;耐撞击;数值模拟;吸能车体中图分类号:U 271;U 270.2 文献标识码:ACra shworthy ra iway car -body w ith energy absorb i ngGA O Guang 2jun ,T IA N H ong 2qi ,YA O S ong(R esearch Cen ter of H igh 2Speed T rain ,Cen tral Sou th U n iversity ,Changsha 410075,Ch ina )Abstract :Evaluati on system of end and m iddle p art of car w as estab lished acco rding to the Am er 2ican criteri on s .U sing num erical si m u lati on m ethod ,the defo rm ati on of 25typ e o riginal p assenger car crashed w ith rigid w all w as calcu lated .T he resu lts show that the crashw o rthy car’s end p art has p lastic defo rm ati on ,m iddle p art has s m all elastic defo rm ati on ,the disp lacem en t of p lastic de 2fo rm ati on is larger than the fo rm er ,and crash fo rce is s m aller ,the criteri on of accelerati on is i m 2p roved obvi ou sly .14figs ,8refs.Key words :rail veh icle engineering ;crashw o rthy ;num erical si m u lati on ;car 2body w ith ab so rb 2ing energyAuthor resu m e :GAO Guang 2jun (19732),m ale ,docto ral studen t ,86273122655294,ggj 883@ch ina .com . 高速运行的列车一旦发生碰撞事故,将造成生命、财产的重大损失。
尽管世界各国轨道运输行业都在努力杜绝列车碰撞事故的发生,但列车碰撞事故仍不断出现。
采用被动安全保护可以有效减少乘客的生命财产损失。
被动保护的主要方法是采用耐冲击吸能车体,即当发生撞击事故时仅在车体的次要部位发生塑性大变形,吸收冲击动能;在车辆的主要部位仅发生弹性小变形,以保护旅客的安全。
在铁路列车碰撞研究方面,尽管20世纪60年代初英国有文章论述,真正开始研究始于20世纪80年代中期,其后相继有法、德、美等国。
英国在D erby 研究中心(现属A EA 公司)对单节车辆进行了大量的撞击模拟试验研究,制定出新规范:新造客车必须设计成耐冲击吸能车体,且抽样进行实车试验考核;法国根据曾经发生的一起事故,通过对单节车辆进行在线实车撞击试验及列车撞击理论分析,在高速列车设计时,按整列车结构变形吸收20M J 的能量考虑,其中动车吸收8M J 能量,紧靠动车的第一节拖车吸收5M J 能量,其余拖车吸收7M J 能量;德国的高速列车设计完全借鉴这一规定;美国根据上述各国的研究结果于1997年9月23日颁布了“621FR 49727旅客列车设备安全标准”,标准中§2381403为撞击吸能装置条款。
中国铁路机车车辆行业对这一领域的研究起步较晚,从20世纪80年代开始研究货车的低速冲击, 20世纪90年代后开始从事被动安全保护这方面的研究工作。
目前耐冲击吸能车体已应用于伊朗国际招标软卧车和北京地铁(四方机车车辆厂生产)。
对耐冲击吸能车体进行研究的主要方法有实车试验和模拟撞击计算,实车试验成本较高,且为验证性试验,目前进行过这方面试验的国家主要有法国、美国等;而模拟试验成本相对较低,并可进行多方案比选。
本文采用数值模拟方法对耐冲击吸能车体进行研究。
1 耐冲击吸能车体评价由于中国对列车耐撞性的研究起步较晚,尚无列车耐撞性评价标准和方法,因此对耐撞性的评价借鉴了美国的两个标准,分别对列车端部吸能区和中部载人区进行评价。
(1)美国于199729223颁布的“621FR49727旅客列车设备安全标准”中§2381403撞击吸能装置条款规定:列车在低于200km h速度运行发生碰撞时,端车头部吸收5M J能量,尾部吸收3M J能量,相邻拖车的端部吸收5M J的能量。
(2)利用美国交通部(DO T)和国家高速公路安全管理局(N H T SA)制定的联邦汽车安全标准(FM V SS208)关于结构在冲击状态下,人体的耐受性条款来评价客车中部载人区的性能。
这个标准规定了载人碰撞事故中人体耐受程度的两个伤害指数。
①头部伤害指数(H IC):要求头部重心的合成加速度(头部伤害标准H IC)表示如下H IC=1t1-t2∫t21a d t215(t1-t2)≤1000式中:a为头部质心合成减速度与重力加速度g的比值(无因次量);t1和t2是整个客车碰撞时间内的两个任意时间点(m s),且t1和t2时间间隔不大于36m s。
②胸部重心的合成减速度(C R)一般不超过60g(m s2);如果C R超过60g时,则持续作用时间不超过3m s。
根据法国的研究,车辆在碰撞过程中大约只有10◊的冲击动能被结构所产生的塑性大变形吸收,其余90◊的能量以别的形式耗散。
由于数值计算方法的基本控制方程包括能量守恒方程,不能模拟能量的耗散,所以第二个评估指标中的具体数值在本次计算中不考虑,但不同计算工况的计算结果可以作横向比较。
2 普通车模拟撞击计算本次模拟计算采用25型客车(不锈钢车体)为原型车进行计算,见图1。
车辆的阴影部分为通过台、配电室和卫生间等,是车辆的次要部分,中间部图1 原型车体结构F ig.1 O riginal car structure图2 内能2时间曲线F ig.2 Inner energy vs ti m e 分为载客区,是车辆的主要部分。
车体钢结构的重量为8148×103kg,载重为8×103kg。
计算工况为车体与刚性墙的撞击计算,计算速度为35m s,计算时间为100m s,计算结果见图2~8。
在计算时全部采用板壳单元,用更图3 t=50m s时的变形F ig.3 D efo rm ati on at50m s 新的拉格朗日法求解。
从上述曲线来看,在t=50m s,车体一端吸收3M J的能量(图2),此时枕梁内侧发生屈曲,产生局部塑性大变形(图3),导致结构失稳,使撞击力迅图4 撞击力2时间曲线F ig.4 Co llisi on fo rce vs ti m e 速减小(图4),从而导致能量与时间的斜率减小。
当t=100m s时,其吸能量为314M J。
相对与前50m s吸能量相对较小。
从车体的中间客室的前、中、后部选取3点(图6),这3点的加速度2时间图5 t=100m s时的变形F ig.5 D efo rm ati on at100m s 曲线见图7。
从图7可以看出,前端的加速度最大为700m s2,相当于7214g,中间部分最大值为200m s2,相当于2014g。
从图8可以看出,在车辆枕梁开始失稳时,车辆的纵向塑性变形长度为111m。
15第3期 高广军,等:耐冲击吸能车体 图6 选取3点位置F ig .6 T h ree po int’s locations图7 加速度2时间曲线F ig .7 A ccelerati on vs ti m e图8 位移2时间曲线F ig .8 D isp lacem ent vs ti m e上述计算结果表明,在车辆吸收3M J 的能量时,车辆两端的非载客区没有完全产生塑性大变形,而载客区却产生了塑性变形。
3 耐撞击车设计原则从普通车的撞击情况看来,通过台与枕梁之间的结构的刚度较大,所以当变形到50m s 时,这部分结构没有发生塑性变形。
同时在枕梁内侧的顶车位处,由于边梁内侧封口,导致边梁的刚度发生突变,容易在这部分发生塑性变形。
针对这两种情况,需要对原结构进行改进。
由于底架的结构强度远大于侧墙和车顶的强度,要使车辆在受到撞击时能产生合理的变形,只有改进底架的结构。
首先,部分减弱通过台与枕梁之间结构的刚度。
由于这部分的牵引梁刚度较大,所以在不影响车辆正常运营的情况下适当减小枕梁的刚度,会使这部分在受到撞击时产生理想的变形。
本文采用了牵引梁上局部挖孔的办法减小牵引梁的刚度,为了使这部分在受到撞击时能按照人为意志产生稳定的变形,开孔的位置和大小要经过多次的计算得出。
其次,由于中国现在的新型车辆都是薄壁筒形结构,车体底架中部没有中梁,强度比端部底架结构弱,车体在受到撞击时容易在中间部位产生塑性大变形。
适当加强底架中部边梁的结构以增强中间部分的刚度,使车体在受到撞击时不会产生塑性大变形。
在文中,槽钢上焊接了盖板,大幅度提高了边梁的弯曲刚度。
第三,纵向力要合理传递。
在碰撞发生时,在枕梁前端承受的力包括牵引梁的纵向压缩力和边梁的纵向压缩力。
在枕梁的内侧,枕梁上承受的力只有两侧边梁上的反力,所以在牵引梁上会产生较大的弯矩。
在受到较大的冲击时,由于枕梁两端的变形会在边梁上产生较大的附加力矩,导致这部分结构迅速破坏。
所以在新结构中,枕梁和边梁之间安装两根斜向的纵向梁,经过多次撞击计算,效果较为理想。