Operations Management lecture 3
OPERATIONSMANAGEMENT运营管理英文版

O PERATIONS M ANAGEMENTOperations management goes by many names: Production, Production Management, or s imply Operations. For our purposes we will define it as the production and delivery of goods and services. It encompasses d esigning the product and its accompanying production process, acquiring and organizing the necessary resources, and planning and executing production. With such a broad scope, the operations function plays an integral role in the ability of an organization to achieve its goals. A well-trained manager m ust be familiar and conversant with the many issues and concepts that arise within this functional area.In this course we study the management of the operations function. We focus on both understanding how the provision of goods is organized and managed as well as recognizing potential areas of improvement. The course has several objectives:Introducing the functional area of operations management and demonstrating how it interfaces with an organization’s other functional areas.Highlighting the various issues and problems that traditionally arise in the management o f operations within both manufacturing and service organizations.Building a familiarity with the terminology, modeling, and methodology often employed in the operations function.Training students to think critically and use analytical tools in making business decisions and problem solving.R EQUIRED M ATERIALMatching Supply With Demand by Cachon and TerwieschCourse PackThe Goal (2nd Edition) by Eliyahu M. Goldratt and Jeff CoxS UPPLEMENTAL M ATERIALOperations Management For Competitive Advantage by Chase, Jacobs, and Acquiano Virtually all readings or cases listed on the course outline are included in the text or the course pack. Additional materials will be passed out in class.G RADINGEvaluations will be based upon the following components weighted by the given percentages.Class Participation 20%Case Write-up 5%3 Exams (each) 20%Final Project 15%The stated weights will apply for students who perform adequately along each dimension. Thatis, acceptable performance in e ach area is a necessary condition for successfully completing thecourse. Over the term, we will study a large number of cases. A successful case discussionrequires that all students be well prepared. Consequently, class participation will be based onregular attendance, quiz scores, and positive contributions to case and class discussions.Final course grades are determined using the total points accumulated. There will be noadjustments applied to the exams. For final grades, the raw scores will be analyzed to determineif an adjustment is appropriate. If the instructor determines an adjustment is warranted, thenindividual scores will be normalized into the target ranges outlined above.E XAMSAll exams are non-comprehensive closed book, individual efforts. Students may bring one (8? x 11 inches) original hand-written formula sheet (writing allowed on one side only). Tohelp students understand t he material and prepare the exams, homework problems will beassigned. Students are expected to do the homework problems but they will not be collectedand graded. Some problems in the exams and quizzes will very likely be closely related tothe homework assignment. Hence, you should spend time solving them before solutions areprovided. Makeup exams will not be given. Excused absences (for health reasons, etc.)must be documented, and the grade missed will be the average of the other Exam scores. Allother cases will receive a grade of zero for the missed exam. Test review sessions will beoffered before each test. N OTE: Students are expected to have their own calculator foreach exam!!C LASS P ARTICIPATION AND A TTENDANCEClass participation refers to regular class attendance; contributing positively, regularly, andsignificantly to class discussion; and being courteous and professional to both your instructor andyour fellow classmates. Contribution to class discussion will require that you prepare for theclass lesson ahead of time by both reading the material to be covered and working out anyproblems that are suggested in the syllabus. Bring your n ame tent with you to every class. Aswe get into the term, you may find that you have a conflict with attending class. How youresolve that conflict is your choice. Although I will not take attendance in class, you should beaware that missing a session impacts your class participation grade.Practice Problems: The course pack contains some practice problems for many of the topicscovered. These do not have to be handed in and no written requirement exists, but it is stronglysuggested that they be done on a regular basis. Some of the problems may be covered in class,and the learning that takes place will be much greater if you have first tried the problem on yourown. Generally, people who approach the practice problems seriously find both the quizzes andthe exams much easier to prepare for and to successfully complete.Quizzes: Throughout the semester numerous pop quizzes will be assigned. These serve multipleuses. Their primary purpose is to ensure that people are “keeping up” with the course m2。
Operations Management:PPT_03_Link with Finance

Creating ROIC (Value, KPI) Trees
Value
Growth ROIC WACC
Volume
Manufacturing costs per unit
SG&A costs per unit
Invested capital per unit
Labor hours Yield Indirect labor
Number of workers Hours worked per year per worker
Number of workers
Hours worked per year per worker Actual production time (activity time)
Time needed before production time
Drivers of Process Capacity
Process Capacity
Available Hours
÷
Hours per Table
Number of workers
×
Hours worked per year per worker Actual production time (activity time)
Typical value drivers: -If operation currently is capacity constrained (i.e. has high demand), everything
that creates additional capacity is powerful utilization / downtime production yields set-up time / other improvement of overall equipment effectiveness (OEE)
运作管理供应链管理的视角英文版精要版第三版课程设计

Course Design of Operations and Supply Chn Management from a Management Perspective Third Edition IntroductionAs today’s businesses become more complex, it is essential to have an effective operations and supply chn management program in place. This course ms to help students learn how to develop and implement efficient and effective operations and supply chn management strategies in a variety of industry settings, ultimately leading to improved organizational performance and success.Course Objectives•Understand the principles and practices of operations and supply chn management•Analyze supply chn systems and identify potential areas for improvement•Develop and implement operations and supply chn management strategies•Understand the role of technology in operations and supply chn management•Understand the importance of sustnability in operations and supply chn management•Collaborate with team members to undertake supply chn improvement projects•Develop analytical and problem-solving skills specific to operations and supply chn managementCourse OutlineModule 1: Introduction to Operations and Supply Chn Management •Understanding the importance of operations and supply chn management•Overview of supply chn management and its elements•The role of operations and supply chn management in organizational successModule 2: Supply Chn Design and Planning•Designing and planning a supply chn•Demand forecasting and inventory management•Sales and operations planningModule 3: Supply Chn Sourcing•Sourcing strategies•Supplier selection and evaluation•Collaborative relationshipsModule 4: Supply Chn Operations•Production and service processes•Lean manufacturing and just-in-time (JIT) systems•Quality managementModule 5: Supply Chn Logistics•Transportation and warehousing•Distribution planning and management•International logisticsModule 6: Supply Chn Integration•Information technology in supply chn management•Collaboration and communication within supply chns•Sustnable supply chn managementModule 7: Project Management in Supply Chns•Project management fundamentals•Project management tools and techniques•Managing supply chn improvement projectsAssessmentGrading Policy•Class attendance and participation: 20%•Assignments and quizzes: 30%•Midterm exam: 25%•Final project: 25%Final ProjectFor the final project, students will work in teams to identify anarea for improvement within a real-world supply chn and develop and present a comprehensive improvement plan. Students will be evaluated based on the quality of their written plan and their presentation skills.ConclusionThis course is designed to provide students with a thorough understanding of operations and supply chn management concepts and practices. By the end of this course, students will have developed the analytical, problem-solving, and collaboration skills needed to initiate,implement, and manage effective operations and supply chn management programs.。
第三章 战略选择-生产运营战略(OperationManagement)
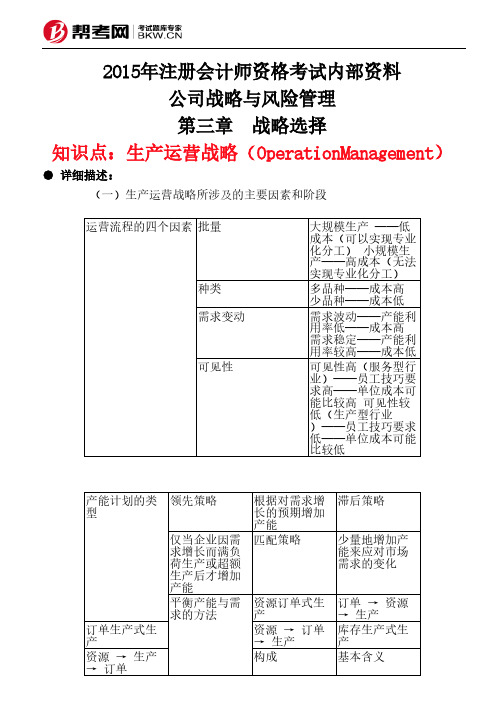
需求波动——产能利 用率低——成本高 需求稳定——产能利 用率较高——成本低
可见性高(服务型行 业)——员工技巧要 求高——单位成本可 能比较高 可见性较 低(生产型行业 )——员工技巧要求 低——单位成本可能 比较低
产能计划的类 型
订单生产式生 产 资源 → 生产 → 订单
B.鉴定成本 C.内部损失成本 D.外部损失成本 正确答案:C 解析:内部损失成本,又称内部故障成本,是指产品出厂前因不满足规定的 质量要求而支付的费用。 16.运营流程中为客户所见的程度是指()。 A.批量 B.种类 C.需求变动 D.可见性 正确答案:D 解析:可见性是指运营流程为客户所见的程度。许多服务都对客户高度可见 。运营流程的高可见性需要员工具备良好的沟通技巧和人际关系技巧。 17.下列各项关于全面质量管理理论的表述,不正确的是()。 A.内部供应商为内部客户做的工作,最终影响提供给外部客户的产品或服务 的质量 B.后台支持人员和行政人员不会对质量产生影响 C.内部损失成本和外部损失成本与预防成本和鉴定成本是有关的 D.鉴定成本、内部损失成本和外部损失成本与预防成本成反比 正确答案:B 解析:全面质量管理提升了内部客户和内部供应商的概念。内部供应商为内 部客户所做的工作,最终会影响提供给外部客户的产品或服务的质量。所以 ,选项A正确;全面质量管理是全员参加的质量管理,全员参加的质量管理 要求全部员工,无论高层管理者还是普通办公职员或一线工人,都要参与质 量改进活动。所以,选项B错误;全面质量管理质量成本模式是基于两个观 点:一是预防成本和鉴定成本都服从管理层的影响或控制。在失败发生之前 花钱预防比在失败发生之后再去检查产品或服务要好得多。二是内部损失成 本和外部损失成本是预防和鉴定方面花费努力的结果。额外的预防努力将会 减少内部损失成本,也可以减少外部损失成本。所以,选项C、D正确。 18.以下属于影响企业运营的企业方式和管理方式因素的有()。
香港大学研究生课程课件 Operation management Lecture 2-2015

2.11
2.12
External and internal benefits f conformance quality
Irrespective of a product or service’s specification quality, producing it so it conforms to its specification consistently brings benefits to any operation.
(p. 48)
2.16
2.17
What does speed mean in…
…a supermarket?
The time for the total transaction of going to the supermarket, making the purchases and returning minimized. The immediate availability of goods.
Flexibility
Cost
(p. 46)
2.5
2.6
Internal / External Effects of Operations Performance
Low price / High margin or both
Short delivery lead time Speed
Cost Low cost high productivity
(p. 48)
2.17
2.18
External and internal benefits of speed
运营管理_第3章_运营系统战略决策PPT资料30页

运营战略内容
一、纵向一体化(Vertical Integration)
纵向扩大自身规模或参股上下游企业
原料生产
原 料 加 零 部 件 制 总装
工
造
用户
零售商
批发 商
生产—营销链图
纵向一体化的决策的内容
A、方向决策(Direction Decision)
后向:朝原材料方向延伸,被看作降低成本或提 高保证供应程度的防御战略
1980年 85%的收入来自产品 品导向的战略不易提高
2000年 70%的收入来自服务 企业的整体竞争力。
客户忠诚度高 价值提升、增加附加价值 业务空间进一步扩展
HP 20亿元 产品70%
服务使其业务扩展100亿元 产品占3%
案例(Case)
背景:上汽公司,开始只有整车厂。
87年时只有整车厂。零部件厂的国产化率2.7%,4种零件 。当时国家政策:国产化率40%以上,自由进口;60%以 上,税减半。
自制、自己销售,其效率往往低于专业制造、 专业经营的企业
(2)加强控制
A、避免前、后向的变动造成生产大幅度波动; B、减少前、后向的竞争压力; C、信息畅通; D、相互之间合作、协调; E、对内部供应产品的质量、交货期、价格等能加强控制
纵向一体化的优势
(3)有利于企业的发展
企业间的竞争变成企业所在供应链之间的竞争。
在有些情况下,供应链上下游企业或是由于技术原 因,或是由于管理原因,不能满足企业的要求,但 短时间内又无法改变现状,这时企业采用纵向一体 化策略,使上、下游的业务满足企业要求,有利于 企业迅速发展。
纵向一体化的缺陷
纵向一体化在相对稳定的市场环境下是比较有效 的,但在顾客要求不断变化的背景下暴露出种 种缺陷:
运营管理原理培训课件(PPT 52页)
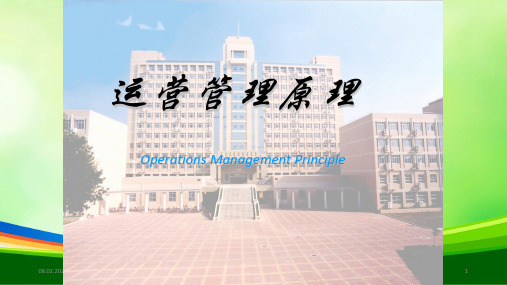
4、运营系统的概念: 运营系统是由人和机器构成的,能将一定输入转化为特定输出的有机整体。
08.02.2020
8
第一节 运营系统及其管理
二、生产/运营系统
4、运营系统的概念:
表1-1 典型组织的输入、转化和输出
组织
主要输入 转化的内容
主要输出
工厂
原材料
加工制造
产品
运输公司 产地的物资
控制-进度 质量 成本 库存
组织-集中程度 转包
指挥-激励 颁布工作秩序 工作分派
08.02.2020
14
第一节、运营系统及其管理
三、运营管理
4、运营系统组织结构
1)目标、功能与结构的关系 2)运营系统的目标:
市场对运营系统的要求:Time、Quality、Cost、Service 高质、高效、低耗、灵活、准时的生产合格产品或提供满意服务。 3)运营系统的功能(6+1) : 创新、质量、柔性、成本、继承性、按期交货+ 特色
控制:如何保证按计划完成任务。 进度、质量、成本、库存
08.02.2020
13
第一节、运营系统及其管理
三、运营管理
3、职能 2)运营职能
· 运营主管/部门经理职能: 通过计划、组织、人事、指挥和控制职能协调资源的使用。
计划-运营能力 产品或服务 自制或外购 布置 进度安排
人事-雇佣/解雇 额外时间利用
离散性生产——指物料离散地按一定工艺顺序运动,在运动中不断
改变形态与性能,最后形成产品的生产。
备货型生产——指在没有接到用户订单时,按已有的标准产品或产
2、
品系列进行的生产。
订货型生产——指按用户订单进行的生产。
operation management概述

Session 1运营管理就是对运营过程的计划、组织、实施和控制,是与产品生产和服务创造密切相关的各项管理工作的总称。
从另一个角度来讲,运营管理也可以指为对生产和提供公司主要的产品和服务的系统进行设计、运行、评价和改进。
现代管理理论认为,企业管理按职能分工,其中最基本的也是最主要的职能是财务会计、技术、生产运营、市场营销和人力资源管理。
这五项职能既是独立的又是相互依赖的,正是这种相互依赖和配合才能实现企业的经营目标。
企业的经营活动是这五大职能有机联系的一个循环往复的过程,企业为了达到自身的经营目的,上述五大职能缺一不可。
运营管理的对象是运营过程和运营系统。
运营过程是一个投入、转换、产出的过程,是一个劳动过程或价值增值的过程,它是运营的第一大对象,运营必须考虑如何对这样的生产运营活动进行计划、组织和控制。
运营系统是指上述变换过程得以实现的手段。
它的构成与变换过程中的物质转换过程和管理过程相对应,包括一个物质系统和一个管理系统。
企业运营管理要控制的主要目标是质量,成本,时间和柔性,它们是企业竞争力的根本源泉。
因此,运营管理在企业经营中具有重要的作用。
特别是近二三十年来,现代企业的生产经营规模不断扩大,产品本身的技术和知识密集程度不断提高,产品的生产和服务过程日趋复杂,市场需求日益多样化、多变化,世界范围内的竞争日益激烈,这些因素使运营管理本身也在不断发生变化。
尤其是近十几年来,随着信息技术突飞猛进的发展,为运营增添了新的有力手段,也使运营学的研究进入了一个新阶段,使其内容更加丰富,范围更加扩大,体系更加完整。
现代运营管理涵盖的范围越来越大。
现代运营的范围已从传统的制造业企业扩大到非制造业。
其研究内容也已不局限于生产过程的计划、组织与控制,而是扩大到包括运营战略的制定、运营系统设计以及运营系统运行等多个层次的内容。
把运营战略、新产品开发、产品设计、采购供应、生产制造、产品配送直至售后服务看作一个完整的“价值链”,对其进行集成管理。
OPERATIONS MANAGEMENT 运营管理英文版

O PERATIONS M ANAGEMENTOperations management goes by many names: Production, Production Management, or simply Operations. For our purposes we will define it as the production and delivery of goods and services. It encompasses designing the product and its accompanying production process, acquiring and organizing the necessary resources, and planning and executing production. With such a broad scope, the operations function plays an integral role in the ability of an organization to achieve its goals. A well-trained manager must be familiar and conversant with the many issues and concepts that arise within this functional area.In this course we study the management of the operations function. We focus on both understanding how the provision of goods is organized and managed as well as recognizing potential areas of improvement. The course has several objectives:∙Introducing the functional area of operations management and demonstrating how it interfaces with an organization’s other functional areas.∙Highlighting the various issues and problems that traditionally arise in the management of operations within both manufacturing and service organizations.∙Building a familiarity with the terminology, modeling, and methodology often employed in the operations function.∙Training students to think critically and use analytical tools in making business decisions and problem solving.R EQUIRED M ATERIAL∙Matching Supply With Demand by Cachon and Terwiesch∙Course Pack∙The Goal (2nd Edition) by Eliyahu M. Goldratt and Jeff CoxS UPPLEMENTAL M ATERIAL∙Operations Management For Competitive Advantage by Chase, Jacobs, and Acquiano Virtually all readings or cases listed on the course outline are included in the text or the course pack. Additional materials will be passed out in class.G RADINGEvaluations will be based upon the following components weighted by the given percentages.∙Class Participation 20%∙Case Write-up 5%∙ 3 Exams (each) 20%Final Project 15%The stated weights will apply for students who perform adequately along each dimension. That is, acceptable performance in each area is a necessary condition for successfully completing the course. Over the term, we will study a large number of cases. A successful case discussion requires that all students be well prepared. Consequently, class participation will be based on regular attendance, quiz scores, and positive contributions to case and class discussions.Final course grades are determined using the total points accumulated. There will be no adjustments applied to the exams. For final grades, the raw scores will be analyzed to determine if an adjustment is appropriate. If the instructor determines an adjustment is warranted, then individual scores will be normalized into the target ranges outlined above.E XAMSAll exams are non-comprehensive closed book, individual efforts. Students may bring one (8½ x 11 inches) original hand-written formula sheet (writing allowed on one side only). To help students understand the material and prepare the exams, homework problems will be assigned. Students are expected to do the homework problems but they will not be collected and graded. Some problems in the exams and quizzes will very likely be closely related to the homework assignment. Hence, you should spend time solving them before solutions are provided. Makeup exams will not be given. Excused absences (for health reasons, etc.) must be documented, and the grade missed will be the average of the other Exam scores. All other cases will receive a grade of zero for the missed exam. Test review sessions will be offered before each test. NOTE: Students are expected to have their own calculator for each exam!!C LASS P ARTICIPATION AND A TTENDANCEClass participation refers to regular class attendance; contributing positively, regularly, and significantly to class discussion; and being courteous and professional to both your instructor and your fellow classmates. Contribution to class discussion will require that you prepare for the class lesson ahead of time by both reading the material to be covered and working out any problems that are suggested in the syllabus. Bring your name tent with you to every class. As we get into the term, you may find that you have a conflict with attending class. How you resolve that conflict is your choice. Although I will not take attendance in class, you should be aware that missing a session impacts your class participation grade.Practice Problems: The course pack contains some practice problems for many of the topics covered. These do not have to be handed in and no written requirement exists, but it is strongly suggested that they be done on a regular basis. Some of the problems may be covered in class, and the learning that takes place will be much greater if you have first tried the problem on your own. Generally, people who approach the practice problems seriously find both the quizzes and the exams much easier to prepare for and to successfully complete.Quizzes: Throughout the semester numerous pop quizzes will be assigned. These serve multiple uses. Their primary purpose is to ensure that people are “keeping up” with the course materialand to give a preliminary look at what exam questions are like. Grades are only a secondary purpose. If you are having trouble with the quizzes, it should serve as a major indication that you are not properly learning the material. There will be NO makeup quizzes. A missed quiz will result in a zero for that quiz. Quiz grades will be one of the factors used in determining class participation scores.Classroom Behavior: The following outlines the basic rules of respectful behavior that must be followed to permit the classroom to be a positive learning experience for all who have chosen to attend. Please turn off cell phones, do not talk to your neighbors, or do not read anything other than the class material currently being discussed. Students should make every effort to be at class on time and, if late, find a seat quickly and disturb the class as little as possible. Part of eac h student’s class participation grade is made up from evaluations of the other students at the end of the term.C ASE W RITE-U PSYou will be required to write up (as a group) one of seven cases covered in class (marked with an *). A sign-up sheet will be due by the second session. Case write-ups are limited to four (4) pages (double-spaced, 1-inch margins, 12-point font) and four (4) pages of exhibits. For style considerations, a review of the case is unnecessary, but it is important to cite case facts to justify conclusions. Use the case discussion questions to guide case write-ups. Arriving at satisfactory answers to the questions asked will receive an average grade. The main objective of requiring written case assignments is to provoke thoughtful, reasoned arguments that enhance the educational process for the entire class. For that reason, arguments must be raised in class discussion to count for grading in a case write-up. You may also be asked to participate in a short presentation of the case. All case write-ups should be done in groups of four to five members—to strike a balance between benefits derived from teamwork and cost due to increased logistical complexity.F INAL P ROJECTYou are to form groups to undertake a semester-long exercise involving the application of the main concepts introduced in class. The report should be written from the perspective of an operations management consultant, who is writing for an audience that is familiar with the principles, concepts, problem areas, systems, and techniques of operations management (at the level of MGT 6350). Specific details of the project will be passed out during the first few weeks of class. As with the case write-ups, final projects should be done in groups of four to five members. This group need not be the same as the case write-up group.H ONOR C ODEThe Georgia Tech Honor Code will be strictly enforced in this class. It is each student’s responsibility to understand and abide by the Honor Code, found at / , as it applies to each class activity. In regard to exams, all work is to be done on an individual basis. You may not discuss or exchange information on exam questions or answers with others either in or outside of this class. Asking anyone other than theinstructor to interpret an exam question, its response, or the material covered in the question is a violation of the Honor Code. In regard to case preparation, analyzing an operations problem in a relatively unstructured case environment is frustrating for some students, especially early in the term. Consequently, you may (but by no means are required to) form study groups in which to prepare for case discussions. Students may not reference notes from, or exchange information with, students from previous years. Looking up case write-ups from other universities on the internet is strictly prohibited. Failure to adhere to any of these requirements constitutes a violation of the Honor Code and the student will be referred to the Dean of Student Affairs for disciplinary action.T HE F IRST C LASSA detailed outline of class topics and readings is given below. In the first class, we provide a general introduction to what operations management is and to how it fits within the firm. We then discuss some typical operations strategies.T ENTATIVE S CHEDULEThe following is a tentative schedule. In general, even if the specific date of coverage may change slightly, the order of coverage should remain as presented below. Modifications may be made as the semester progresses and the appropriate changes will be announced in class. It is highly recommended that all readings and practice problems be prepared prior to the class during which they may be discussed.D ATE R EADINGS AND C ASES1 1/06 Introduction and Course OutlineReadings: MSWD Chapter 1Start reading “The Goal”2 1/08 Operations StrategyCase: Wal-Mart Stores, Inc., HBSP 9-794-024Readings: MSWD Chapter 2“Competing on Capabilities: The New Rules of Corporate Strategy,”HBR, March-April, 1992.“Operations-Based Strategy,” California Management Review,Summer 1998.For additional information on crossdocking, see chapt 13 in:/~jjb/wh/book/wh-sci.pdf3 1/13 Process AnalysisReadings: MSWD Chapters 3 and 5Prepare: Process Analysis Practice Problems 14 1/15 Process AnalysisCase: *Executive Shirt Company, Inc., HBSP 9-696-071Readings: “Infighting Rises, Producti vity Falls, Employees Miss PieceworkSystem,” WSJ, May 20, 1998.5 1/20 Process AnalysisBook: The Goal, Eliyahu M. Goldratt and Jeff Cox, North River Press, 1992.Prepare: Process Analysis Practice Problems 26 1/22 Stochastic Process AnalysisReadings: MSWD Chapters 6, and 7Prepare: Stochastic Process Analysis Practice Problems7 1/27 Stochastic Process AnalysisCase: *Manzana Insurance – Fruitvale Branch, Stanford Bus. School S-DS-87Additional Readings: /jeb/or/queue.html/jeb/or/sim.html8 1/29 Example Problems9 2/3 F IRST E XAM10 2/5 Recap and Introduction to Inventory Management11 2/10 ForecastingReadings: /div898/handbook/pmc/section4/pmc42.htm/div898/handbook/pmc/section4/pmc431.htmPrepare: Forecasting Practice Problems12 2/12 ForecastingCase: *LL Bean, Inc. Item Forecasting and Inventory Management HBSP 9-893-003Readings: “Behind Cisco's Woes are Some Wounds of Its Own Making”,WSJ, April 18, 2001.Additional Readings: /~rnau/411out00.html13 2/17 Inventory Management: NewsvendorReadings: MSWD Chapter 9Prepare: Inventory Practice Problems 114 2/19 Inventory Management: Make-to-OrderCase: *Matching Dell, HBSP 9-799-158Readings: MSWD Chapter 1015 2/24 Inventory Management: Order Up-to ModelReadings: MSWD Chapter 11Prepare: Inventory Practice Problems 216 2/26 Inventory Management: Postponement and Risk PoolingCase: *Hewlett-Packard: Deskjet Printer Supply Chain, HBSP GS3AReadings: MSWD Chapter 12“Facing Up to the New Computer World,” Finc Times, Feb 16, 2001.17 3/2 Example Problems18 3/4 S ECOND E XAM19 3/16 Dependent Demand: Production PlanningReadings: /jeb/or/mrp.html“Quanta's Quantum Leap”, Business Week, Nov 5 2001.Prepare: Production Planning Practice Problems20 3/18 Dependent Demand: Production PlanningPrepare: Production Planning Practice Problems 221 3/23 Lean ManufacturingCase: *Toyota Motor Manufacturing, USA, HBSP 9-693-019Readings: MSWD Chapter 8.3 and 8.4“Getting Control of Just-in-Ti me”, HBR, Sept-Oct 1989.“To the Rescue: Toyota’s Fast Rebound after Fire at Supplier ShowsWhy It Is Tough”, WSJ, May 8, 1997.Additional Reading: /jeb/or/jit.html22 3/25 Quality ManagementReadings: /div898/handbook/pmc/section1/pmc1.htm“Kentucky Plant Workers Are Cranking Out Good Ideas,” WSJ, Aug.13, 1996.“Six Sigma, What Is It and How to Use It” Harvard ManagementUpdate, June, 1999.Prepare: Quality Management Practice Problems23 3/30 Quality ManagementReadings: /div898/handbook/pmc/section4/pmc4.htmCase: *Deutsche Allgemeinversicherung, HBSP 9-696-08424 4/1 Supply Chain ManagementCase: *ZaraReadings: MSWD Chapter 14, “The Bullwhip Effect in Supply Chains,” SloanManagement Review, Spring 1997.25 4/6 Revenue ManagementReadings: MSWD Chapter 1326 4/8 Sustainable OperationsCase: *Interfaces Evergreen Service Agreement, HBSP 9-603-112Readings: “Tree Huggers, Soy Lovers, and Profits”, Fortune, June 23, 2003.27 4/13 T HIRD E XAM28 4/15 Pricing and Revenue Management Workshop29 4/20 Recap30 4/22 Project PresentationsFinals。
operation management 书

一、介绍1.1 Operation Management 的定义 1.2 Operation Management 的重要性 1.3 这本书的主题和内容简介二、 Operation Management 的理论基础2.1 大生产原理2.2 优化理论2.3 运作管理模型三、 Operation Management 的关键概念3.1 生产计划和控制3.2 添加值3.3 质量管理3.4 供应链管理四、 Operation Management 的实践应用4.1 生产流程优化4.2 资源配置4.3 成本控制4.4 在全球化环境中的运作管理五、 Operation Management 的案例研究5.1 著名企业的运作管理案例5.2 成功的运作管理实践经验共享5.3 失败的案例分析和教训六、 Operation Management 的挑战与未来发展6.1 技术变革对运作管理的影响6.2 全球化挑战6.3 环境可持续性与运作管理6.4 数据驱动的运作管理七、结语7.1 总结7.2 对未来运作管理的展望---Operation Management 是企业管理中非常重要的一环。
它涵盖了企业生产计划和控制、优化流程、成本控制、质量管理、供应链管理等方面。
通过合理的运作管理,企业可以提高效益,加强竞争力,取得长期发展。
理论基础部分主要介绍了大生产原理、优化理论和运作管理模型。
这些理论为企业提供了运作管理的思想基础和方法论。
Operation Management 的关键概念包括生产计划和控制、添加值、质量管理和供应链管理。
这些概念是企业运作管理的核心内容,对企业的经营管理起着至关重要的作用。
Operation Management 在实践中的应用涉及生产流程优化、资源配置、成本控制以及在全球化环境中的运作管理。
通过这些实践应用,企业可以提升运作效率,降低成本,满足市场需求。
Operation Management 的案例研究部分介绍了一些著名企业的运作管理案例,共享了成功的实践经验,分析了失败案例并总结了教训。
新版运营管理-Operations-Management课件.ppt
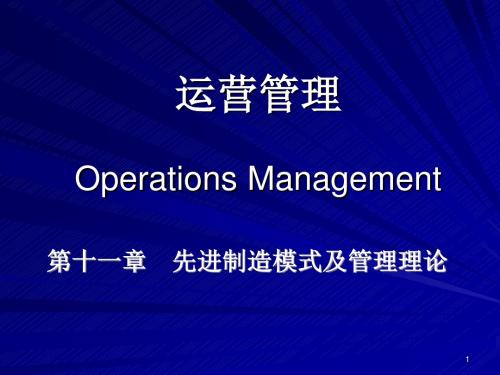
制造模式的分类研究
(2)设计技术
针对于生产系统的工程设计技术,有:计算机辅 助设计(Computer Aided Design, 简称CAD),计 算机辅助工程 (Computer Aided Engineering, 简 称CAE),计算机辅助工艺设计(Computer Aided Process Planning, 简 称 CAPP) , 面 向 X 设 计 (Design For “X”, 简称DFx), 可靠性设计,健壮设 计,优化设计,精度设计,反求工程技术,快速 原型设计,疲劳设计等等。
先进制造技术和先进制造模式是两个不同 的概念。但在实际中它们经常被混淆。在 这里我们列出典型的先进制造技术并对它 们进行了分类。在研究对象上,先进制造 技术主要包括如下三类:
18
制造模式的分类研究
(1)制造技术
先进加工工序中的物流技术。包括工业智能技术、 数字化制造技术和产品、精密制造技术、绿色制 造技术、虚拟制造与网络制造技术、快速响应制 造技术。 各种先进制造技术。加工自动化及设备,材料加 工工艺技术,少无切削加工技术,超精密加工技 术,超高速加工技术,特种加工技术,可装配性 工艺及装配自动化,检测自动化及在线质量控制, 物流系统及辅助过程自动化。
21
制造模式的分类研究
组织管理中技术有: 小组工作(Teamwork),授权(Empowerment)。 在企业集成与建模上有:GRAI/GIM方法、KADS方法、
IFIP方法、CIMOSA方法、IDEF方法、ARIS体系结构、 PERA方法与TOVE方法、工作流建模技术、面向对象 的建模方法。 在 质 量 管 理 上 有 : 质 量 功 能 环 ( Quality Circle ) , ISO9000系列,统计质量控制等。 在信息交流上,各种计算机通讯技术,电子资料交换技 术(Electronic Data Interchange, 简称EDI),产品代码识 别技术等。
运营管理基础 4E-戴维斯英文IMChap003

CHAPTER 3 NEW PRODUCT AND SERVICES DEVELOPMENT, ANDPROCESS SELECTIONChapter OverviewThis chapter looks at the issues related to new product and service development and the selection of the processes to deliver them. New products and services are being emphasized today because of increased competition and advances in technology. Organizations are constantly looking to reduce the time from idea generation to the market and to improve the ability of the design to meet the customers' requirements for new products. This is being accomplished in several ways including concurrent engineering, quality function deployment, and design for manufacturability. The new service development process varies slightly from products in that in many cases you design the service and the service delivery process simultaneously. Also customer contact plays a very substantial role in the design of the service process.Major Points of Chapter1.Emphasis is being placed on new goods and services because of increased competition andadvances in technology.2.The ability to introduce new products faster than competitors can lead to greater market share,price premiums, quick response to competition, and setting industry standards.3.Categories of new products include incremental or derivative products, next generation orplatform products, breakthrough or radical products.4.Concurrent engineering is being used to shorten the new product development process. Itinvolves a coordinated effort of all functional area.5.Type of manufacturing processes range from project to intermittent to line flow.6.New service offerings include window dressing, breadth of offerings, revolutionary, andchannel development.7.The service-system design matrix is a framework for relating sales opportunities with ways aservice can interact with a customer.8.Service processes include the production line approach, the customer involvement approach,and the personal attention approach.14New Product and Service Development, And Process SelectionReview and Discussion Questions1.Why is it important for a firm to have an effective new product (or service) developmentprocess?Two major causes for the increased emphasis on developing new products are increased competition and advances in technology. Additionally, introduce new products faster than competitors can lead to greater market share, price premiums, quick response to competition, and setting industry standards.2.What are the benefits available to the firm that can develop new products faster than itscompetition?The benefits to developing new products faster than the competition are greater market share, price premiums, quick reaction to competition, and setting industry standards.3.Describe the three different categories of new products. Discuss how each category differsfrom the others in terms of resources expended and the impact on the firm's manufacturing processes.The three categories of new products are incremental or derivative products, next generation or platform products, and breakthrough or radical products. Incremental products or derivative products are hybrids of existing products. Such new products require minimal changes in both product design and the manufacturing process. The resource requirements are significantly less than other types of new products.Next generation or platform products represent new "system" solutions for the customer. They require more resources than incremental new products.Breakthrough or radical products require the most in terms of resources and manufacturing processes. When introduced, this type of product creates an entirely new product category. They require substantial product design and process change.15Chapter 34.Discuss the four different categories of new services that are categorized by the amount ofchange in content and delivery method with respect to a firm's existing services.The four categories of new services are window dressing, breadth of offerings, revolutionary and channel development. Window dressing services define those services that have a small incremental change in terms of content and delivery. These usually have very little impact on the firm's service operations and can be brought to market rapidly.Breadth of offerings represents a significant design change in terms of content. However, it is delivered to the customer in much the same manner. The key to success is to deliver all of the different types of content to each of the corresponding market segments in an effective and efficient manner. This is somewhere in the middle in terms of resources.Revolutionary services represent new services that provide both new content and new delivery method. These types of services typically take longer to bring to market, and require more resources than the other categories.Channel development services provide the same content, but deliver them differently, often through a new channel. When developing these new channels, managers need to recognize that process development is critical. Customers expect to receive the same level of service that they received from previous channels in the new channel.5.What is the difference between incremental and radical service innovations?Incremental new services include service line extensions, service improvements, and style changes. Service line extensions are viewed as new services that augment current services. Service improvements are new services that change the features relative to existing services. Style changes are viewed as modest forms of visible change with respect to how they impact customer perceptions, emotions, and attitudes.Radical service innovations are new service offering that were not previously available, or new service delivery systems for existing services. The three subcategories for radical service innovation are major innovations, start-up services, and new services for current markets. Major innovations consist of new services that address markets that are not fully defined and are often driven by information and computer-based technologies. Start-up services provide new services to established markets that are already served by existing services. New services for current market are defined as new service offerings that are provided to existing customers of an organization.6.Describe what is meant by the "voice of the customer."Voice of the customer refers to customer feedback. It is used in the quality function deployment process to determine product specifications.7.Identify the two methods used by firms to generate new product ideas.Two methods are market pull and technology push. Market pull refers to the primary force being the voice of the customer through marketing. Technology push is where the customer may not even be aware of the new product, but the R&D function is pushing the new product through the company to the customer.16New Product and Service Development, And Process Selection 8.Identify and describe the four major phases of the new product development process.The phases are idea generation, concept development, product development, and production design. Idea generation involves developing the idea for the product, which can come from market pull or technology push.Concept development involves the initial design along with a detailed analysis of the market and customer requirements.Product development involves translating the needs of the customer into design specifications. Many times quality function deployment is used at this stage to perform this process.Finally, manufacturing must translate the product design into a manufacturable product. Design for manufacturability (DFM) is commonly used for this process.9.What is concurrent engineering and why is it critical for a successful new productdevelopment effort? Describe the concept of design for manufacturability and indicate why it is closely connected to concurrent engineering.Concurrent engineering is the simultaneous and coordinated efforts of all functional areas that it accelerates the time to market for new products. Its real advantage is the reduction to time to market that provides for a competitive advantage to the firm.Design for manufacturability (DFM) provides guidance as an organization translates the functional product design into a manufacturable product. For example, one aspect of DFM is to reduce the number of parts. One basic rule is "Be obvious.” Design a product so that a user can look at it, understand it, and figure out how to use it--quickly, and without an instruction manual.DFM is part of concurrent engineering. Concurrent engineering takes the product from idea to manufacturable product. Therefore DFM is part of this process.10.Identify and describe the four stages of the new service development (NSD) process.The four stages are design, analysis, development, and full launch. Design consists of the formulation of the objectives and strategies of the new service. The analysis stage considers the financial implications of the new service and examines the supply chain issues relevant to its delivery. In the development stage, the service design is completed and tested, and a pilot run of the service is conducted. Finally, the full launch stage begins when the service is released to the marketplace.11.What are the three major categories of manufacturing processes, and how do they differ interms of operational characteristics?The three major types of processes operate on a continuum from project to intermittent to line-flow. The extremes of the continuum are project and line-flow. Production volumes are higher at the line flow end versus flexibility in product offerings at the project end. Line-flow typically has higher fixed cost, but low variable cost compared to project. Additionally, skill level of workers is generally higher for project processes than for line-flow processes. There has been some discussion that this categorization of processes might be outmoded with the advent of new processes such as FMS. However, alternative categorizations have not been terribly convincing or widely adopted.17Chapter 312.Why is it important that managers understand the relationship between the various stages of aproduct’s life cycle and the different types of processes that are available for manufacturing that product?Changes occurring during the product life cycle have implications for process choice. During the early stages of the product life, a project orientation is utilized to produce prototypes and small numbers of product for testing. As time passes, the product is accepted by the customer and demand increases. This increasing demand drives the choices in process technologies, as higher volume, standardized production is required. Eventually, when the product becomes a commodity, very efficient mass processes may be required to maintain competitiveness.13.Identify the high-contact and low-contact operations of the following services:a. A dental office.Dental office high contact includes waiting rooms, receptionists, dentist(s), hygienist(s), x-ray, etc., while labs would be low contact.b.An airline.Airline high contact includes reservations desk, loading concourse, plane with crew and attendants, etc. Low contact includes maintenance, baggage handling, tower operations, etc.c.An accounting office.In an accounting office, high contact includes reception and CPAs, while low contact includes records, computer, library, etc.d.An automobile agencyAutomobile agency high contact includes showroom and offices. Low contact includes maintenance, and preparation.14.Where would you place a drive-in church, a campus food vending machine, and a bar’sautomatic mixed drink machine on the service-system design matrix?Referring to the exhibit, the most logical placement would appear to be on-site technology.18New Product and Service Development, And Process Selection15.a. List specific products that you especially like. What do you like most about them?b. Create a list of products that your dislike or are unhappy with. What don't you like aboutthem?c. Are there common reasons for your lists? For example, is it more important for productsthat you don't see or see very little to be functional rather than attractive (e.g., the furnace or air conditioning in the house, the transmission or engine in the car)? Is it more important for things to be well designed that other people see and relate to you such as your car, your clothes, or your apartment based on your answers?The lists and reasons will tend to group by performance, quality, function, beauty, user friendliness, simplicity, reliability, etc. It is interesting to note that the conflict in reasons-even similar products--will be chosen for very different reasons. Because of this, designers and manufacturers typically have a very difficult time evaluating markets.16.Pick a product and make a list of issues that need to be considered in its design andmanufacture. The product can be something such as a stereo, a telephone, a desk, a kitchen appliance, and so on. Consider the functional and aesthetic aspects of design as well as the important concerns for manufacturing.Answers will vary based upon the product selected and the student. Issues that should be considered in the design and manufacture of a product include design process (traditional vs. concurrent engineering), customer needs and expectations, legal considerations (EPA, OSHA, etc.), service life, reliability, appearance, standardization, any industry standards that should be considered (e.g., television set and the type of signal received from stations), method of shipment, material cost and availability, stage of the product life cycle, design for manufacturability, design for assembly, packaging, environmental, unit cost, pricing, availability of purchased material, availability of capacity, availability of subcontractors, setup cost, manufacturing time, volume, and expected product life.19Chapter 317.Place the flowing functions of a department store on the service-system design matrix: Mail-order (i.e., catalog), phone order, hardware, stationery, apparel, cosmetics, customer service(i.e., complaints).20New Product and Service Development, And Process Selection 18.Place the following functions of a hospital on the service-system design matrix:Physician/patient, nurse/patient, billing, medical records, lab tests, admissions, diagnostic tests (e.g., X-rays).19.The first step in studying a production process is to develop a description of that process.Once the process is described, we are better able to determine why it works well or poorly and to recommend production-related improvements. Since we are all familiar with fast-food restaurants, try your hand at describing the production process employed at say, a McDonald's. In doing so, answer the following questions:a.What are the important aspects of the service package?The important aspects of the service package are rapid delivery of a uniform, high-quality mix of prepared foods in an environment of obvious cleanliness, order, and cheerful courtesy.b.Which skills and attitudes are needed by the service personnel?Most of the skills needed by employees are easily obtained through training. Probably one of the most important aspects i s the employee’s attitude. They should be willing to provide efficient service with cheerful courtesy.c.How can customer demand be altered?Customer demand can be altered through promotions, such as discount for off-peak period.Also, extra services could be offered during off-peak periods to encourage customers. These could include having an employee walk through the facility offering free refills on drinks21Chapter 3d.Can the customer/provider interface be changed to include more technology? More self-service?The customer/provider interface could be changed to include more technology by having the customer place the order himself on a display screen (this would also be more self-service).Many fast food restaurants have the customers get their own drinks.e.How does it measure up on the seven characteristics of a well-designed service?1. Yes, each element of the system is consistent with the operation focus.2.Somewhat. The sign are understandable, although because of their increased offeringin recent years, it is harder to order. They have implemented “value meals” to makeit easier to order.3.No, they rely on their equipment substantially.4.Yes, consistency is one of their trademarks.5.Yes, they have effective links between the front and back office.6.Yes, evidence of quality is easy for the customer to see.7.Yes, they pride themselves on being cost-effective.Case: The Best Engineered Part is No PartNCR has achieved or overcome the following:1.less components2.less suppliers3.less assembly time4.eliminating screws and fasteners5.faster speed of concept to market6.lower cost7.better on-time delivery8.no “over the wall” syndrome22New Product and Service Development, And Process SelectionCase: Kinko’s Copier Stores1.Yes. The technology is the same for all shops and the types of jobs performed by thecustomers. Differences in culture exist in different areas causing a need to handle the behavioral problems differently.2.At Kinko’s this functional layout is useful in that it allows customers to perform differentjobs simultaneously.3.First, there is the problem of capacity (e.g., how much is allotted to what?). This makeslayout decisions more challenging as there is a need for different machinery for each task.This provides a need for front room and back room operations (even though at Kinko’s the back room is clearly visible to the customer). The problem is not unlike a manufacturer with high volume and low volume production lines in the same facility. Pricing is different for each type of service.4.As anyone in academia knows, it is getting more difficult to procure the needed copyrightreleases in a timely fashion. Professors might procrastinate until the last minute to provide materials to Kinko’s making it difficult to obtain releases on time. This program creates a capacity problem in that there is a huge demand on resources during the beginning of every semester. However, this service is still available at most Kinko’s.23。
运作管理供应链管理的视角英文版精要版第三版教学设计

Teaching Design for the Third Edition of Operations and Supply Chn Management from a Managerial Perspective IntroductionOperations and supply chn management (OSCM) plays a critical role in an organization’s success. Efficiently managing the supply chn can lead to cost savings, improved quality, and better customer satisfaction. This teaching design ms to provide a comprehensive overview of OSCM from a managerial perspective, emphasizing its importance in the contemporary business environment.Course GoalsBy the end of this course, students are expected to: - Understand the fundamental concepts of OSCM and its role in the overall business strategy - Analyze different supply chn models and design an effective one for a given context - Evaluate the external factors that impact supply chn decisions - Develop strategies for minimizing costs without compromising quality - Implement techniques for quality control and continuous improvement in operationsCourse OutlineModule 1: Introduction to OSCM•Definition and scope of OSCM•Evolution of OSCM and its current significance•OSCM in the context of the overall business strategyModule 2: Supply Chn Management•The structure of a supply chn•Different types of supply chn models•Evaluation criteria for choosing the appropriate model•Supply chn designModule 3: Supply Chn Coordination and Collaboration •Coordination and collaboration in the supply chn•The bullwhip effect and ways to mitigate its effects•The role of information technology in coordination and collaborationModule 4: Supply Chn Partnerships•Building and mntning supply chn partnerships•Supplier selection and evaluation•Supplier development and performance measurement Module 5: Supply Chn Risk Management•Risks in the supply chn•Assessment and prioritization of risks•Risk mitigation strategiesModule 6: Operations Management•Operations strategy and competitiveness•Techniques for improving operations efficiency•Process analysis and improvementModule 7: Total Quality Management•The principles of total quality management•Techniques for achieving and mntning high quality•Continuous improvement in operationsModule 8: OSCM and Sustnability•The concept of sustnability and its relevance to OSCM•Green operations and reverse logistics•Corporate social responsibility in OSCM Teaching MethodsThe teaching methods for this course include: - Lectures to introduce the fundamental concepts and theories of OSCM -Case studies and problem-solving exercises to apply the theories to real-world examples - Group activities and discussions to enhance collaboration and critical thinking - Guest speakers to share their practical experiences in OSCM - Site visits to observe and learn from supply chn operationsin actionAssessment MethodsThe assessment methods for this course include: - Mid-term and final exams to test students’ understanding of the theories and concepts - Case study reports and problem-solving exercises to evaluate students’ ability to apply the theories to real-world situations - Group project presentations to asses s students’ collaboration, communication, and critical thinking skills - Class participation and attendance to encourage active engagementin the courseConclusionThis teaching design ms to provide students with a comprehensive understanding of OSCM from a managerial perspective. By the end of this course, students should be equipped with the knowledge, skills, and tools necessary toapply OSCM theories in practice and contribute to their organization’s success.。
介绍operationmanagement项目管理3

the forecast.
wnAt-n + … wn-1At-2 + w1At-1
Ft = WMAn=
n
3-18
Simple Moving Average
Actual
47 45 43 41 39 37 35
1 2 3 4 5 6 7 8 9 10 11 12
MA5 MA3
Ft = MAn=
At-n + … At-2 + At-1 n
3-20
Exponential Smoothing
Ft = Ft-1 + (At-1 - Ft-1)
Weighted averaging method based on preof the forecast error
A-F is the error term, is the % feedback
3-21
Example 3: Exponential Smoothing
Period Actual Alpha = 0.1 Error
Alpha = 0.4 Error
1
42
2
40
42
-2.00
42
-2
3
43
41.8
1.20
41.2
1.8
4
40
41.92
-1.92
41.92
-1.92
5
41
41.73
3-5
Uses of Forecasts
Accounting Finance Human resources Marketing MIS Operations Product/service design
Cost/profit estimates Cash flow and funding Hiring/recruiting/training Pricing, promotion, strategy IT/IS systems, services Schedules, MRP, workloads New products and services
- 1、下载文档前请自行甄别文档内容的完整性,平台不提供额外的编辑、内容补充、找答案等附加服务。
- 2、"仅部分预览"的文档,不可在线预览部分如存在完整性等问题,可反馈申请退款(可完整预览的文档不适用该条件!)。
- 3、如文档侵犯您的权益,请联系客服反馈,我们会尽快为您处理(人工客服工作时间:9:00-18:30)。
Last Year
2,475,738 113,000 $40,831 $33,000
Year Before Last
2,175,447 115,00 — —
Calculate the year-to-date labor productivity:
This Year
factory unit sales employment
Multifactor productivity =
Value of output Labor cost + Materials cost + Overhead cost
=
(400 units)($10/unit) $4,000 = = $400 + $1,000 + $300 $1,700
2.35
Lecture 3
Student tuition:
a. Multifactor productivity is the ratio of the value of output to the value of input resources.
3 credit hours student $150 tuition + $100 state support credit hour
= 360 hours
Output Input = $20,680 360 hours
= $57.44 in sales per hour
Lecture 3
This Year
Factory unit sales Employment (hrs) Sales of manufactured products ($) Total manufacturing cost of sales ($) 2,762,103 112,000 $49,363 $39,000
a. What is the multifactor productivity ratio for this course process? b. If instructors work an average of 14 hours per week for 16 weeks for each 3credit class of 50 students, what is the labor productivity ratio?
Labor productivity = Policies processed Employee hours =
=
600 policies (3 employees)(40 hours/employee)
5 policies/hour
Lecture 3
Calculate the Multifactor Productivity:
Value of output =
50 student class
= $37,500/class Value of inputs = Labor + Materials + Overhead = $4,000 + ($20/student 50 students/class) + $25,000 = $30,000/class Output Multifactor productivity = Input $37,500/class = $30,000/class = 1.25
A team of workers makes 400 units of a product, which is sold in the market for $10 each. The accounting department reports that for this job the actual costs are $400 for labor, $1,000 for materials, and $300 for overhead.
This Year
sales of mfg products total mfg cost
Last Year
=
$49,363 $39,000
= 1.27
$40,831 $33,000
= 1.24
Multifactor Productivity
Lecture 3
Student tuition at Boehring University is $150 per semester credit hour. The state supplements school revenue by $100 per semester credit hour. Average class size for a typical 3-credit course is 50 students. Labor costs are $4,000 per class, material costs are $20 per student per class, and overhead costs are $25,000 per class.
Last Year 2,475,738 113,000 = 21.91/hr
Year Before Last 2,175,447 115,000 = 18.91/hr
Hale Waihona Puke 2,762,103 112,000
= 24.66/hr
Labor Productivity
Calculate the multifactor productivity:
Lecture 3
Natalie Attire:
Value of output= (52 defective 90/defective) + (80 garments 200/garment)
= $20,680
Labor hours of input
Labor productivity =
Output Productivity = Input
Lecture 3
Calculate the Labor Productivity: Three employees process 600 insurance policies in a week. They work 8 hours per day, 5 days per week.
Operations Management
Rongjuan Chen Fall 2015 Wenzhou-Kean University
Lecture 3
Productivity
The value of outputs (services and products) produced divided by the values of input resources (wages, costs of equipment, etc.)
Lecture 3
Student tuition:
b. Labor productivity is the ratio of the value of output to labor hours. 14 hours week 16 weeks class
Labor hours of input =
= 224 hours/class Labor productivity = Output = $37,500/class Input 224 hours/class = $167.41/hour
Lecture 3
Natalie Attire makes fashionable garments. During a particular week employees worked 360 hours to produce a batch of 132 garments, of which 52 were “seconds” (meaning that they were flawed). Seconds are sold for $90 each at Attire’s Factory Outlet Store. The remaining 80 garments are sold to retail distribution at $200 each. What is the labor productivity ratio of this manufacturing process?