第五章金属疲劳
第05章 金属的疲劳1

(1)基本特征: 呈现贝壳花样或海滩花样,它是以疲
劳源区为中心,与裂纹扩展方向相垂直的 呈半圆形或扇形的弧形线,又称疲劳弧线。
疲劳弧线是裂纹扩展过程中,其顶端 的应力大小或状态发生变化时,在断裂面 上留下的塑性变形的痕迹。
47
(2)贝纹花样的形成: 是由载荷变动引起的,因为机器运转时
不可避免地常有启动、停歇、偶然过载等, 均可留下塑性变形的痕迹——贝纹线(疲 劳弧线)。
r=-1称为对称循环应力;
r=0(或r=-∽)这种非对称循环又称为 脉动循环。这种载荷是一种最危险的载荷。
r偏离-1越远,应力对称性越差,疲劳 极限越高。
29
(2)循环应力的种类
(交变当)r应=-力1,;即σmin=-σmax时,称为对称循环
当r=0,即σmin=0时,称为脉动循环应力。
2
1、金属疲劳破坏的形成过程 在正常使用机械时,重复的推、拉、扭
或其他的外力情况都会造成机械部件中金 属的疲劳。
这是因为机械受压时,金属中原子的排 列会大大改变,从而使金属原子间的化学 键断裂,导致金属裂开。
3
构件承受交变应力的大小超过一定限 度,并经历了多次的循环重复后,在构件 内部应力最大处或材质薄弱处将产生细微 裂纹(称为疲劳源),这种裂纹随着应力 交变次数增加而不断向四周扩展。
53
(5)不同情况下贝纹线的形状
① 当轴类机件拉压疲劳时, 轴向应力包括拉-拉或拉-压疲劳。它的疲劳
源一般也在表面形成,只有内部有缺陷时才在缺 陷处形成。
54
若表面无应力集中(无缺口),则裂纹因截 面上应力均等而沿截面等速扩展,贝纹线呈一簇 平行的圆弧线;
55
若机件表面存在应力集中(环形缺口), 则因截面表层的应力比中间的高,裂纹沿表层 的扩展快于中间区;高应力时,瞬断区面积相 对较大,疲劳裂纹扩展区面积小,裂纹沿两边 及中间扩展差别不大。
金属疲劳

劳断裂前所经历的应力循环周次越低,反之越高。根据循环
应力σmax和应力循环周次N建立S-N曲线。 由于疲劳断裂时周次很多,所以S-N曲线的横坐标取对数坐 标。
能力知识点2 疲劳极限
当应力低于某值时,材料经受无限次循环应 力也不发生疲劳断裂,此应力称为材料的疲 劳极限,记作σR(R为应力比),就是S-N曲 线中的平台位置对应的应力。 通常,材料的疲劳极限是在对称弯曲疲劳条 件下(R=-1)测定的,对称弯曲疲劳极限 记作σ-1。
第5单元 金属的疲劳
想一想
人工作久了就会感 到疲劳,难道金属 工作久了也会疲劳 吗? 金属的疲劳能得到 恢复吗?
金属材料在受到交变应力或重复循环应力时,经一定循环
次数后,往往在工作应力小于屈服强度的情况下突然断裂,
这种现象称为疲劳。
金属“疲劳”一词,最早是由法国学者J-V彭赛(Panelet) 于1839年提出来的。 1850年德国工程师沃勒(A.Woler)设计了第一台用于机 车车轴的疲劳试验机,用来进行全尺寸机车车轴的疲劳试 验。 1871年沃勒系统论述了疲劳寿命和循环应力的关系,提 出了S-N曲线和疲劳极限的概念,确立了应力幅是疲劳破 坏的决定因素,奠定了金属疲劳的基础。
四、疲劳极限的测定
常规试验法
升降法
1.常规试验法
在疲劳试验中,当试样个数有限,工程急需,或 者为了节省费用,不宜进行大量试验时,常常采 用常规试验法。 这种试验方法除了直接为工程设计部门提供疲劳 性能数据外,还可作为一些特殊疲劳试验的预备 性试验。 由于常规试验方法耗费少,周期短,因此得到广 泛采用,其中最简单的是单点法。
疲劳极限与抗拉强度的关系
试验表明,金属材料的抗拉强度越大,其疲劳极 限也越大。
Chapter 5 金属的疲劳
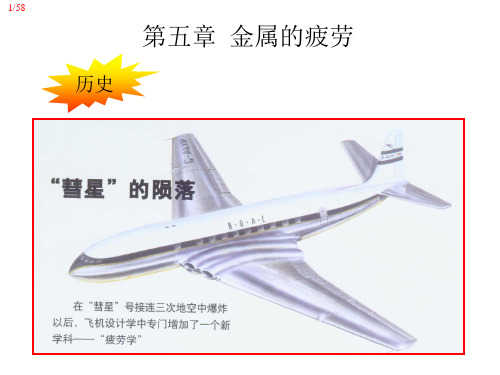
25/58
1、过载损伤和过载持久值 过载损伤: 过载损伤 : 在高于疲劳极限的应力水平 下运转一定周次后,其疲劳极限或疲劳寿命 减小的现象。 过载持久值: 过载持久值 : 金属材料在高于疲劳极限 的应力下运行时,发生疲劳断裂的应力循环 周次。
26/58
2、过载损伤界和过载损伤区 金属材料抵抗疲劳过载的能力,用过载 损伤界或过载损伤区表示。
4/58
5/58
6/58
最大与最小应力 平均应力 应力幅 应力比
σ max、σ min
1 σ m = (σ max + σ min ) 2 1 σ a = (σ max − σ min ) 2
σ min γ= σ max
应力幅:循环应力中应力变动部分的幅 应力幅: 值。 应力比: 应力比:应力循环对称系数,指应力循 环的不对称程度。
20/58
二、疲劳图和不对称循环疲劳极限 疲劳图是各种循环疲劳极限的集合图, 疲劳图 是疲劳曲线的另一种表达形式。主要用于求 解不对称循环疲劳极限。 疲劳图的建立是建立在以下事实上的: 疲劳图的建立是建立在以下事实上的: (1) 不 对 称 循 环 应 力 可 分 解 为 : σr=σm+σaf(t)。 (2) 当σm增加时,允许的σa降低。 (3) 由最大循环应力σmax表示的疲劳极限σr是
随应力比r(或平均应力σm)的增大而升高的。
21/58
那么, 那么 , 如何根据对称应力循环求不对称 应力循环的疲劳极限呢? 应力循环的疲劳极限呢? (1) 极限循环振幅图(σa-σm疲劳图)。 (2) 极限循环应力图(σmax(σmin)-σm 疲劳 图)。
22/58
疲劳图) 1、极限循环振幅图(σa-σm疲劳图) 极限循环振幅图(σ
第05章金属的疲劳

第05章金属的疲劳1.解释下列名词(1) 应力范围△σ;(2) 应变范围△ε;(3) 应力幅σa;(4) 应变幅(△εt/2,△εe/2,△εp/2);(5) 平均应力σm;(6) 应力比r;(7) 疲劳源;(8) 疲劳贝纹线;(9) 疲劳条带;(10) 驻留滑移带;(11) 挤出脊和侵入沟;(12)ΔK;(13) da/dN;(14) 疲劳寿命;(15) 过渡寿命;(16) 热疲劳;(17) 过载损伤。
2.解释下列疲劳性能指标的意义(1)疲劳强度σ-1、σ-1p、τ-1、σ-1N;(2) 疲劳缺口敏感度qf;(3) 过载损伤界;(4) 疲劳门槛值△Kth。
3.试述金属疲劳断裂的特点。
4.试述疲劳宏观断口的特征及其形成过程。
5.试述疲劳曲线(S—N)及疲劳极限的测试方法。
6.试述疲劳图的意义、建立及用途。
7.试述疲劳裂纹的形成机理及阻止疲劳裂纹萌生的一般方法。
8.试述影响疲劳裂纹扩展速率的主要因素,并和疲劳裂纹萌生的影响因素进行对比分析。
9.试述疲劳微观断口的主要特征及其形成模型。
10.试述疲劳裂纹扩展寿命和剩余寿命的估算方法及步骤。
11.试述σ-1与ΔKth的异同及各种强化方法影响的异同。
12.试述金属表面强化对疲劳强度的影响。
13.试述金属循环硬化和循环软化现象及产生条件。
14.试述低周疲劳的规律及曼森一柯芬关系。
15.试述多冲疲劳规律及提高多冲疲劳强度的方法。
16.)试述热疲劳和热机械疲劳的特征及规律;欲提高热锻模具的使用寿命,应该如何处理热疲劳与其它性能的相互关系?17.正火45钢的σb=610MPa,σ-l=300MPa,试用Goodman公式绘制靠σmax(σmin)一σm疲劳图,并确定σ-0.5、σ0和σ0.5等疲劳极限。
18.有一板件在脉动载荷下工作,σmax=200MPa,σmin =0,其材料的σb=70MPa、σ0.2=600MPa、KIC=104MPa·m1/2,Paris公式中c=6.9×10-12,n=3.0,使用中发现有0.1mm 和1mm的单边横向穿透裂纹,试估算它们的疲劳剩余寿命。
金属疲劳

5 非对称循环应力下的疲劳
• 大多数机械和工程结构的零件,是在非 对称循环应力下服役的。 • 实质是研究平均应力或应力比对疲劳寿 命的影响。 • 如齿轮,滚珠轴承,内燃机连杆,汽缸 盖螺栓工作时的应力循环
• 对于任一个不对称循环应力,我们总是可以把它 分解为一个平均应力分量 和在的基础上叠加一 个应力半幅 。它们之间的关系为 应力范围 应力半幅 平均应力 也可以用应力比 对完全对称循环 R=-1。对于脉动疲劳 R=0。对于静 载 R = +1。 •
• 1 疲劳源:是疲劳裂纹萌生的策源地。一般在机件 表面,常和缺口、裂纹、刀痕、腐蚀坑等缺陷相连。 • 断口形貌:疲劳源区光亮度最大。 • 2 疲劳区:是疲劳裂纹亚稳扩展形成的断口区,是 疲劳断裂的重要特征证据。 • 宏观特征:断口光滑并分布有贝纹线。贝纹线是疲 劳区的最大特征。 • 3 瞬断区:裂纹最后失稳快速扩展所形成的断口区 域。断口比疲劳区粗糙。瞬断区位置一般应在疲劳 源的对侧。 • 宏观特征:同静载的裂纹件断口试样
2 金属在对称循环应力下的疲劳
• 2.1 循环加载的特征参数 循环应力是指应力随时间呈 周期性的变化,变化波形通 常是正弦波,如图8-1所示
图8-1 各种循环加载 方式的应力-时间图。
循环应力的特征参数:
① 应力幅σa或应力范围Δσ
σa=Δσ/2=(σmax-σmin)/2, σmax和σmin分别为循环最大应力和循环最小应力;
• 通常的S-N 曲线是仿照 火车轮轴的失效,用旋 转弯曲疲劳试验方法测 得的。
4.3 疲劳寿命曲线的数学表达式
在高循环疲劳区,当R=-1时,疲劳寿命与 应力幅间的关系可表示为: Nf=A'(σa-σac)-2 (8-2)
式中A'是与材料拉伸性能有关的常数。 当σa≤σac,Nf→∞,从而表明了疲劳极 限的存在。 疲劳极限与静强度之间的关系
金属疲劳
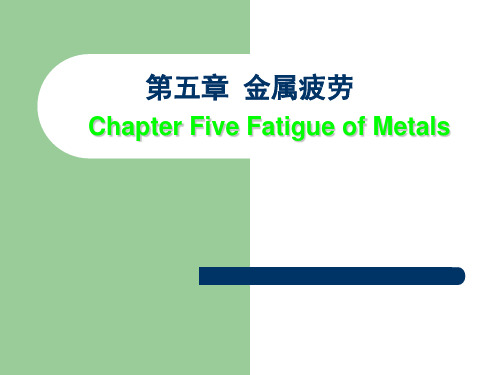
当n=2时,则有: 具体例子见P.127。
Nc
1 [ln ac ln ao ] 2 c(Y )
5.5 疲劳过程及机理 (Fatigue process and mechanism)
疲劳破坏包括裂纹萌生,亚稳扩展及失稳扩展 等三个阶段,每阶段扩展过程及其机理如下:
一、疲劳裂纹萌生过程及其机理
(一) 疲劳裂纹扩展曲线 (Propagation curve of fatigue crack)
典型的疲劳裂纹扩展曲线如图5-8所示。
从图可见: 疲劳裂纹扩展速率(da/dN)随裂纹a 的增加而不断增加; 当循环加载次数达到某一临界值Npc时, 裂纹a趋于临界值ac,此时疲劳裂纹扩展 速率(da/dN)趋于∞, 则裂纹失稳扩展而 导致断裂; 当σ增加,da/dN也增大,则ac 和Npc 减少。
图5-10 低碳钢在交变应力(=200MPa)下滑移带 的形成过程 a) N=1105次;b) 5105次;c)15105次
图5-12 金属表面“挤出”、“侵入”,并形成裂纹
(二)疲劳裂纹扩展过程及其机理
(Process and mechanism of fatigue crack Propagation)
5.2 疲劳曲线及疲劳抗力 (Fatigue curves and resistance)
(一) 疲劳曲线(Fatigue curves)
试验表明:金属疲劳曲线有两大类(如图5-5所 示)。一类是有水平线段(即有疲劳极限)的曲 线。如一般结构钢及球墨铸铁的疲劳曲线即为该 类型。另一类是无水平线段(即无疲劳极限)的 曲线,如有色金属,不锈钢,高强度钢的疲劳曲 线则为该类型。
具体特征:
1、 疲劳源 该区最光亮(因该断面经多次摩擦挤压之故); 疲劳源位于疲劳区的贝纹弧线凹向一侧的焦点位 置; 疲劳源可以一个或多个(与应力状态有关); 对于有数个疲劳源,可根据疲劳源的光亮度,疲 劳区的大小及贝纹线的密蔬程度可以确定多个源产 生的先后次序,一般源区越亮,疲劳区越大,贝纹 线越密,则该源越早产生。
第5章_金属的疲劳

与静载荷断裂或一次冲击载断裂相比: (1)疲劳断裂是低应力循环延时断裂,即具有寿 命的断裂。 断裂应力水平往往低于材料抗拉强度,甚至低于 屈服强度。 断裂寿命随应力不同而变化,应力高寿命短,应 力低寿命长。 当应力低于某一临界值时,寿命可达无限长。
5.1 金属疲劳现象及特点
(2)疲劳断裂是突然断裂,即脆性断裂。断裂前 没有明显的征兆。 由于一般疲劳的应力水平比屈服强度低,所以不 论是韧性材料还是脆性材料,在疲劳断裂前不会发 生塑性变形及有形变预兆。 它是在长期积累损伤过程中,经裂纹萌生和缓慢 亚稳扩展到临界尺寸ac时才突然发生的。 因此,疲劳是一种潜在的突发性断裂。
按循环周期、断裂寿命或应力高低不同可分为:
高周疲劳:循环次数>105,因断裂应力 低(< σs ),所以又称低应力疲劳。 低周疲劳:循环次数102~105,由于断裂 应力水平高,≧σs ,往往伴有塑性变形, 故称为高应力疲劳(或应变疲劳)。
按破坏原因可分为:机械疲劳、腐蚀疲劳、热疲 劳。
5.1 金属疲劳现象及特点
随机变动应力:载荷大小、方向呈无规则 随机变化。
5.1 金属疲劳现象及特点
3、循环应力的表示方法:
最大应力: σmax 最小应力:σmin 平均应力: σm σm= (σmax+ σmin)/2 应力幅: σa σa= (σmax- σmin)/2 应力循环对称系数(应力比):r= σmin/ σmax
第5章 金属的疲劳
1、实际工作中的许多机件均是在变动载荷下工作的。 2、失效形式:主要为疲劳断裂,占80%以上。 3、表现为突然断裂,危害极大。无论材料为韧材还是 脆材均表现为突然断裂。 4、本章从材料学的角度研究金属疲劳的一般规律、疲 劳破坏过程及机理、疲劳力学性能及其影响因素,以便 为疲劳强度设计、选用材料、改进工艺、提高寿命、估 计寿命提供基础知识。
工程材料力学性能第五章 金属的疲劳
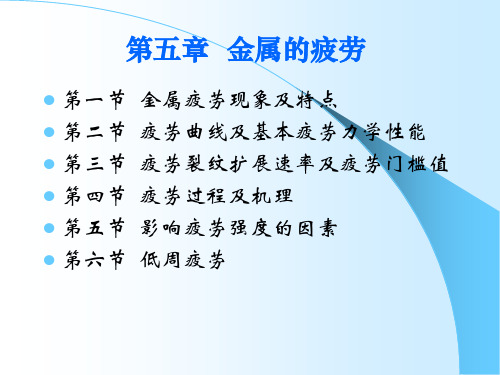
第一节 第二节 第三节 第四节 第五节 第六节
金属疲劳现象及特点 疲劳曲线及基本疲劳力学性能 疲劳裂纹扩展速率及疲劳门槛值 疲劳过程及机理 影响疲劳强度的因素 低周疲劳
第一节 金属疲劳现象及特点
一、变动载荷和循环应力 1、变动载荷和变动应力 变动载荷:载荷大小、甚至方向均随时间变化的载荷。 变动应力:变动载荷在单位面积上的平均值。分规则周 期变动应力和无规则随机变动应力两种。 2、循环应力 规则周期性变化的应力称循环应力,表征应力循环特征的几个 参量: 最大应力 σmax 最小应力 σmin 平均应力 σm=(σmax+σmin)/2 应力幅 σa=(σmax-σmin)/2
三、疲劳宏观断口特征
典型的疲劳断口按照断裂过程可分为三个 区域,疲劳源、疲劳区和瞬断区。
1、疲劳源
疲劳源(或称疲劳核心),疲劳裂纹萌生的策源地,一 般总是产生在构件表面层的局部应力集中处,但如果构件 内部存在冶金缺陷或内裂纹,也可在构件内部或皮下产生 疲劳源。 疲劳源区光亮度最大,在断口上常能看到一个明显的亮斑。 疲劳源有时不止一个,尤其在低周疲劳下,其应力幅值较 大,断口上常有几个不同位臵的疲劳源。可以根据源区的 光亮度、相邻疲劳区的大小,贝纹线的密度去确定各个疲 劳源的产生顺序。 源区光亮度↑;相邻疲劳区越大;贝纹线越多越密者→疲 劳源越先产生。
如认为疲劳裂纹扩展的每一微小过程类似 是裂纹体小区域的断裂过程,ΔK就是裂纹 尖端控制疲劳裂纹扩展的复合力学参量。
3、da/dN--Δk ( lgda/dN-- lgΔk)曲线 将a-N曲线可转化为由Δk控制 的疲劳裂纹扩展速率曲线: da/dN -Δk 或 lgda/dNlgΔk 由曲线可知,可分为三个区: I区:疲劳裂纹初始扩展阶段 da/dN很小。 随Δk↑→da/dN快速提高,但 Δk变化范围很小, da/dN提 高有限,所占扩展寿命不长。
第五章 材料的疲劳性能

(2)晶界处开裂
晶界就是面缺陷; 位错运动易发生塞积,出现应力集中,晶界开裂。
(3)相界面开裂
两相(包括第二相、夹杂)间的结合力差,各相的形变速率不同,易在 相结合处或弱相内出现开裂。
只有首先达到临界尺寸的裂纹核,才能继续长大。
材料科学与工程学院
4
(2)循环应力的种类
(1)对称循环,σm=0,r =-1,大多数旋转轴类 零件承受此类应力。
(2)不对称循环: σm≠0, -1<r<1。发动机连杆或 结构中某些支撑杆、螺栓 承受此类应力, σa>σm>0,-1<r<0。
(3)脉动循环: σm=σa>0,r=0,齿轮的齿根及某些压力容 器承受此类应力; σm=σa<0, r=∞ ,轴承承受脉动循环压 应力。 (4)波动循环: σm>σa,0<r<1。发动机气缸盖、螺栓承受这 种应力。
材料科学与工程学院
18
材料科学与工程学院
19
疲劳条带(疲劳辉纹)定义:是略呈弯曲并相互平行的沟槽状 花样,与裂纹扩展方向垂直,是裂纹扩展时留下的微观痕 迹,为疲劳断口最典型的微观特征。
材料科学与工程学院
20
在失效分析中,常利用疲劳微观断口中疲劳条带间宽和 裂纹尖端的应力强度因子幅KI间关系分析破坏原因。
分子的微结构损伤。
材料科学与工程学院
25
2.高分子聚合物的疲劳破坏机理
3)聚合物疲劳断口上可有两种特征的条纹:疲劳辉纹 (fitigue striation)和疲劳斑纹(marking)。
A:前者是每周期变动应力作用时引起的裂纹扩展,间距为 10um左右;后者是不连续的、跳跃式的变动应力引起的 裂纹扩展,间距为50um左右。
材料性能---金属的疲劳
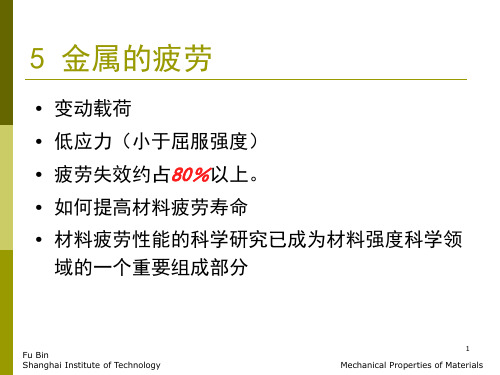
Fu Bin Shanghai Institute of Technology
9
Mechanical Properties of Materials
高周疲劳和低周疲劳
按应力高低和断裂寿命分,最基本的分类方法。
表 高周疲劳和低周疲劳对比
类别 疲劳类型 高周疲劳 (低应力疲劳) 低周疲劳 (高应力疲劳)
7
Mechanical Properties of Materials
5.1.2 疲劳现象及特点
金属机件在变动应力和应变长期作用下,由 于积累损伤而引起的断裂现象称为疲劳。 疲劳的破坏过程是材料内部薄弱区域的组织 在变动应力作用下,逐渐发生变化和损伤累 积、开裂,当裂纹扩展达到一定程度后发生 突然断裂的过程,是一个从局部区域开始的 损伤累积,最终引起整体破坏的过程。
Fu Bin Shanghai Institute of Technology
21
Mechanical Properties of Materials
各类疲劳断口形貌
Fu Bin Shanghai Institute of Technology
22
Mechanical Properties of Materials
Fu Bin Shanghai Institute of Technology
12
Mechanical Properties of Materials
ቤተ መጻሕፍቲ ባይዱ
疲劳宏观断口
图 带键的轴旋转弯曲疲劳断口,40钢
Fu Bin Shanghai Institute of Technology
13
Mechanical Properties of Materials
材料力学性能金属的疲劳课件
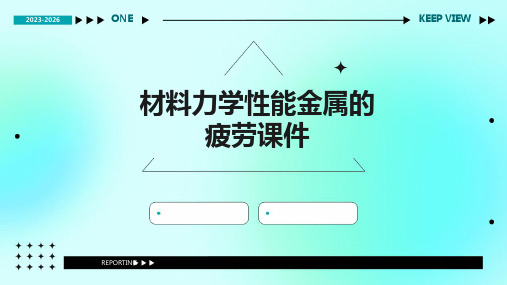
由于温度变化引起的热应力导致的疲劳。
疲劳的机理
01
02
03
滑移与位错
在循环应力作用下,金属 内部的滑移面和位错发生 移动,逐渐形成微裂纹。
微裂纹扩展
微裂纹在应力作用下逐渐 扩展,最终导致宏观断裂 。
疲劳断口形貌
疲劳断口通常呈现脆性断 裂的特征,如光滑表面和 放射区。
PART 02
金属的疲劳性能
随机疲劳测试
模拟实际工况中的随机载荷对金属进行疲劳测 试。
断裂力学测试
通过测量裂纹扩展速率来评估金属的疲劳性能。
疲劳数据的处理与评估
1 2
数据整理
对实验数据进行整理,绘制疲劳曲线,分析金属 的S-N曲线。
疲劳极限确定
根据实验结果确定金属的疲劳极限,即金属在一 定循环次数下不发生疲劳断裂的最大应力。
环境因素的影响
•·
在高温环境下,金属材料容易发生蠕变和松弛,导致疲劳强度下降;在腐蚀介质中,金属表面容易发 生腐蚀,产生腐蚀疲劳。因此,在高温或腐蚀环境下工作的金属结构需要进行特殊处理或选择耐腐蚀 材料。
温度的影响
显著影响
温度对金属的疲劳性能有显著影响。在低温环境下,金属材料的脆性增加,可能导致疲劳强度下降;而在高温环境下,金属 材料的抗蠕变性能降低,也会影响疲劳性能。
高速列车车轮的疲劳分析
总结词
高速列车车轮在频繁的制动和加速过程中承受着交变 载荷,对其疲劳性能的分析是保证列车安全运行的关 键。
详细描述
高速列车车轮在运行过程中,由于频繁的制动和加速 ,承受着周期性的交变载荷。这种循环载荷会导致车 轮产生疲劳裂纹,甚至发生断裂。为了确保列车的安 全运行,需要对车轮进行疲劳分析,评估其疲劳寿命 和可靠性。这需要考虑车轮的材料、几何形状、表面 处理、工作环境以及制动和加速模式等因素,采用适 当的疲劳分析方法和实验手段进行验证。
金属疲劳

8)开动试验机检查机器运转情况,若噪声较大,应即停机检查;当运转正常时,抽去主轴套下垫 板,然后将加载手轮逆时针旋转到极点,进行加载,并随即记下计数器上的读数。
六.实验方法简介
在疲劳实验中,当不宜进行大量实验时,常常采用常规实验法。这种实验方法除了直接为工程
疲劳破坏是机械零部件早期失效的主要形式。据统计,约有 80%以上的零部件失效是由疲劳引 起的,无论是脆性或韧性的材料,在疲劳断裂时都不产生明显的塑性变形,断裂是突然发生的,这 种特点是由疲劳破坏的机理决定的。实践证明,疲劳断裂是由裂纹的萌生、扩展、直至最终断裂 3 个阶段。当工作应力超过疲劳极限 σR 时,由于循环应力的反复交变,构件上的应力最大处往往是应 力集中,首先形成微裂纹,随着循环次数的增加,裂纹逐渐扩展,构件的承载面积也随之逐渐减少, 当裂纹面上的应力达到材料的断裂强度时,构件就突然断裂。
作为备品,其余 7~8 个试件用于疲劳实验。
应力比 R 的大小应根据设计要求和试验机条件来确定,材料的 S-N 曲线是在给定应力比的条件
下实验得到的,旋转弯曲疲劳实验,其应力比 R=-1。
6
实验时,应力水平至少取 7
7
级,相邻两极应力水平差的相对值不超过
5%。疲劳实验都是从高应
力向低应力进行的,第一级的应力水平取 0.6 ������������������������������������������������������������������������������������������������������������������������������������������������������������������������
第05章 金属的疲劳
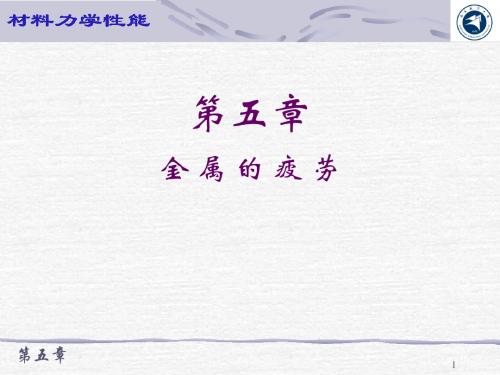
三、疲劳宏观断口的特征
断口有三个形貌不同区域: 疲劳源、疲劳区、瞬断区,随 材质、应力状态的不同,三个 区大小和位臵不同。见下页表格
疲劳区 断裂区 疲劳源 宏观贝纹线
旋转弯曲试样疲劳断口形貌
8
第五章
第五章
9
1、疲劳源
裂纹的萌生地;裂纹处在亚稳扩展过程中。 由于应力交变,断面摩擦而光亮。 加工硬化 随应力状态及其大小的不同,可有一个或几个疲劳源。
低 (<σs),所以也叫低应力疲劳。 低周疲劳( Nf {102105} 周次),由于断裂应力水平高(≥σs),往往伴有塑性变形, 故称为高应力疲劳(或应变疲劳)。 (4)按破坏原因:机械疲劳、腐蚀疲劳、热疲劳。
第五章
7
2、特点
(不一定是低应力脆断!)
(1)断裂应力σb,甚至σs; (2)出现脆性断裂; (3)对材料的缺陷十分敏感; (4)疲劳破坏能清楚显示裂纹的 萌生、扩展、断裂。
第五章
32
2、循环软化的危害 使材料的形变抗力下降,导致工件产生过量 的塑性变形而失效。 3、原因 决定于材料的初始状态,工件结构特性;应 变幅,温度等。 σb/σs>1.4循环硬化 σb/σs<1.2循环软化 微观原因:位错的循环运动;相变强化;应 力松驰。
第五章
33
三、低周疲劳的应变—寿命曲线
第五章
12
3、疲劳极限与静强度之间的关系
钢:σ-1p=0.23(σs+σb) σ-1=0.27(σs+σb) 铸铁:σ-1p=0.4σb σ-1=0.45σb 铝合金:σ-1p=σb/6 +7.5(MPa) σ-1p=σb/6 -7.5(MPa)
4、疲劳断裂判据
第五章
1, r
金属疲劳学
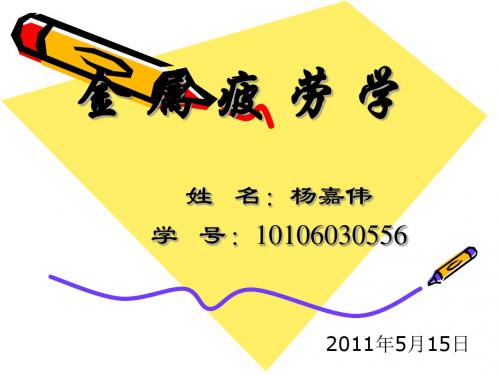
在工程上测定疲劳极限常使用升降法。
升降法也称高低法。用这种方法测定疲劳极限时,先根据以往 的经验,对疲劳极限作一粗略的估计。在此应力水平上试验第一个试 样。若该试样在达到所规定的循环次数之前就破坏了,则将应力降低 一级进行第二级试验;反之,则增加一级进行试验。对以后的试样, 也按这个方法一个接一个地相继试验下去。试验中应合理地选取应力 增量,使得整个试验在四到五级的应力水平上进行。
加
载
di
前
的
形
状
do
Lo Li
L Li Lo P
轴向加载试样
在不断加大负荷
的情况下,材料的
形变行为如右图所 示,虚线表示塑性 材料的工程应力— —应变曲线,实线
真是应力——应变 B
工程应力——应变
。A
表示同一种材料的
真实应力——应变
曲线。A点之后出现 0
塑性流变
单次拉伸应力——应变Biblioteka 第二节 循环加载的滞后回线
1850一1860年德国工程师WőhLer提出了应力-寿命图和疲 劳极限的概念。
1870一1890年间,Gerber研究了平均应力对疲劳寿命的影 响。Goodman提出了考虑平均应力影响的简单理论。
1920年Griffith发表了关于脆性材料断裂的理论和试验结果。 发现玻璃的强度取决于所包含的微裂纹长度,Griffith理论 的出现标志着断裂力学的开端。
t 0
(b)
0
t
(c) 恒应变幅下材料的循环特性
53 1
0
13 5
0
24
恒应力下循环硬化时的回线形状
5 3
0
材料力学性能金属的疲劳课件

金属疲劳的宏观机理
金属疲劳的宏观机理主要涉及宏观尺度的物理过程。在循 环应力作用下,金属会发生塑性变形,导致应力集中和微 裂纹的形成。随着时间的推移,这些微裂纹会扩展并连接 起来,最终导致金属断裂。
断口分析
对金属材料的断口进行微观分析,了解其疲 劳断裂机理。
X射线检测
通过X射线检测金属内部的疲劳损伤和裂纹 。
金属疲劳的预测模型
线性累积损伤模型
基于线性累积损伤理论,预测金属的 疲劳寿命和断裂行为。
非线性累积损伤模型
考虑非线性因素,更准确地预测金属 在复杂应力状态下的疲劳寿命。
断裂力学模型
基于断裂力学理论,预测金属的疲劳 裂纹扩展行为和寿命。
钢的疲劳性能和断裂机制。
THANKS
感谢观看
金属材料的晶体结构和相组成
金属材料的晶体结构和相组成对其疲劳性能也有重要影响,例如多相合金的疲劳性能受各相比例和相界面的影响 。
应力状态和应力集缺陷引起的应力集中现象,会 显著降低金属的疲劳性能。
应力状态
金属在复杂应力状态下的疲劳行 为与单轴应力状态下存在差异, 例如在多轴应力状态下,金属的 疲劳强度可能会降低。
压力容器接管的低周疲劳失效分析
压力容器接管在循环载荷下容易发生低周疲劳失效,这种失效通常与接管的几何形 状、材料特性、应力水平和循环特性等因素有关。
低周疲劳失效通常表现为接管局部区域的塑性变形和裂纹萌生,这些裂纹会随着循 环次数的增加而逐渐扩展,最终导致接管断裂。
分析压力容器接管的低周疲劳失效问题,需要综合考虑接管的应力分布、应变状态 、循环次数和温度等因素,以评估接管的疲劳寿命和安全性。
- 1、下载文档前请自行甄别文档内容的完整性,平台不提供额外的编辑、内容补充、找答案等附加服务。
- 2、"仅部分预览"的文档,不可在线预览部分如存在完整性等问题,可反馈申请退款(可完整预览的文档不适用该条件!)。
- 3、如文档侵犯您的权益,请联系客服反馈,我们会尽快为您处理(人工客服工作时间:9:00-18:30)。
da/dN=c (△K)n
式中,n、c为材料常数,n在2-4之间变化。
具体有:
铁素体+珠光体:da/dN=6.910-12△K3.0 奥氏体不锈钢: da/dN=5.610-12△K3.25 马氏体不锈钢: da/dN=1.3510-10△K2.25
注:Paris公式一般适用于多周疲劳(即低应 力疲劳)
2、 Forman 公式
Forman考虑了应力比γ和断裂韧度KIC(或KC) 对da/dN的影响,具体如下:
da/dN=c(ΔK)n/[(1-γ) KC-ΔK]
3、综合式 根据以上的讨论,可以得到以下的综合公式:
da/dN=c(ΔK-ΔKth)n/[(1-γ) KC-ΔK] 从上式可见:当ΔKΔKth,da/dN=0,即疲劳 裂纹不扩展。
裂纹扩展曲线的测量常用有三种方法: 1、 三点弯曲试样(TPB) 2、 中心裂纹试样(CCT) 3、 紧凑拉伸试样(CT)
(二)疲劳裂纹扩展门槛值 (Threshold of fatigue crack propagation)
应用断裂力学理论可得,应力强度因子范围ΔK为: △K =Kmax —Kmin =Yσmax (a)1/2 —Yσmin (a)1/2
σ-1p=0.4σb
σ-1=0.45σb
铝合金: σ-1p=1/6σb+7.5MPa
σ-1=1/6σb—7.5MPa
青铜: σ-1 = 0.21σb
5.3 疲劳裂纹扩展及疲劳门槛值
(Propagation of fatigue crack and fatigue threshold)
疲劳的三个过程中(裂纹萌生、亚稳扩展、失稳 扩展)以亚稳扩展最重要,对于构件中本身含有 裂纹,则其亚稳扩展就更重要,同时疲劳裂纹扩展 的规律,对于预测疲劳寿命以及提高寿命都有重 大意义。
2、疲劳区:
断口宏观特征。断口比较光滑并分布有纹线(或 海滩花样),有时还有裂纹扩展台阶; 贝纹线是载荷变动引起的,如机器的开停,而在 实验室由于载荷变动较小,所以贝纹较浅而细小; 贝纹线是一簇以疲劳源为圆心的平行弧线,近源 处则贝纹线距越密,远离源处则贝纹线距越疏。
3、 瞬断区
该断口区比疲劳区粗糙,与静载的断口相似; ➢ 如脆性材料,则为结晶状断口; ➢ 如韧性材料,则中间平面应变区为放射状或人 字纹断口,边缘平面应力区为剪切唇; ➢ 一般在疲劳源的对侧; ➢ 瞬断区大小。若名义应力较高或材料韧性较差, 则瞬断区较大,反之,则瞬断区较小。
2
2)c(Y )n
1 [ (n2) / 2 ao
1 ] (n2) / 2 ac
当n=2时,则有:
1
Nc c(Y )2 [ln ac ln ao ]
具体例子见P.127。
5.5 疲劳过程及机理 (Fatigue process and mechanism)
疲劳破坏包括裂纹萌生,亚稳扩展及失稳扩展 等三个阶段,每阶段扩展过程及其机理如下:
第五章 金属疲劳
Chapter Five Fatigue of Metals
5.1 概述(Brief Introduction)
㈠ 定义(Definition)
疲劳破坏——指材料在低于抗拉强度 的交变应力作用下,经过一定循环后所发生 的突然断裂,即在断裂前没有明显的宏观塑 性变形。
疲劳破坏过程虽然有突然性,但仍然是一个逐渐发
(五) 疲劳裂纹扩展寿命的估算(Evaluation of fatigue crack propagation life)
当已知构件中的裂纹长度(可用无损探伤法测定)以及构
件所承受的应力状态。
则可从下式:
da/dN=c(Yσa1/2)n
来计算疲劳寿命N。
dN=da/[c(Yσa1/2)n] 当n2时,有: Nc (n
展的过程。它是由疲劳裂纹核心的萌生、扩展及断 裂三个阶段组成的,因而相应的研究领域包括:
1 . 疲劳微观机理(包括疲劳断裂的成因、裂纹 核心的萌生、扩展、断口形貌及组织的变化); 2. 疲劳宏观理论(包括疲劳累计损失理论、裂 纹扩展理论、疲劳强度理论及疲劳设计理论); 3. 疲劳实验(包括机器的设计、载荷的测定、 数据的统计与分析以及疲劳寿命的计算) 。
(一) 疲劳裂纹扩展曲线 (Propagation curve of fatigue crack)
典型的疲劳裂纹扩展曲线如图5-8所示。
从图可见:
✓ 疲劳裂纹扩展速率(da/dN)随裂纹a 的增加而不断增加; ✓ 当循环加载次数达到某一临界值Npc时, 裂纹a趋于临界值ac,此时疲劳裂纹扩展 速率(da/dN)趋于∞, 则裂纹失稳扩展而 导致断裂; ✓ 当σ增加,da/dN也增大,则ac 和Npc 减少。
(三) 疲劳裂纹扩展的影响因素(Factors of affecting fatigue crack propagation)
影响疲劳裂纹扩展因素有如下几种: 1. △K(应力强度因子范围)的影响
△K↑则da/dN↑ 2. 应力比γ(或平均应力σm)的影响
由于压应力使裂纹闭合而不扩展,所以只研 究γ>0, σm>0对da/dN的影响
(二)疲劳极限及其测量 (Fatigue limit and measurement)
1、定义:
疲劳极限是指材料抵抗无限次应力循环而不断裂的强 度指标(见图5-7)。
条件疲劳极限:是指材料抵抗有限次应力循环而不断 裂的强度指标。
二者统称为疲劳强度。
2、种类
对称循环载荷是一种常规载荷,有对称弯曲、对称 扭转及对称拉压等。其对应的疲劳极限称为σ-1、τ -1、σ-1p. 其中σ-1是最常用的对称循环疲劳极限。
✓ Ⅲ区 疲劳裂纹扩展最后阶段,da/dN 很大,扩 展周次不多,材料便发生断裂。
另外从该图还可见:
当△K≤△Kth时,da/dN=0,表示裂纹不扩展 只有当△K>△Kth时,da/dN>0,表示裂纹才扩展 因此△Kth称为疲劳裂纹扩展门槛值,单位为 Mpa.m1/2 △Kth和疲劳极限σ-1均表示无限寿命的疲劳性能 值。 σ-1指无裂纹的光滑试样,而△Kth则指有裂 纹的试样。
当γ>0,γ↑则da/dN↑,△Kth↓
3. 过载峰影响
当交变应力的振幅不恒定,而有偶然增大及 过载时,则疲劳裂纹扩展缓慢或停滞一段时 间,即发生过载停滞现象(原因是在交变应 力正半周过载,即过载拉应力,则产生较大 塑性区,并阻碍循环负半周时弹性变形的恢 复,从而产生残余压应力,则裂纹尖端闭合, 即△K↓,则da/dN↓)
➢ 疲劳源(疲劳裂纹萌生的源地,一般位于断 口表面,常与缺陷引起的应力集中相关);
➢ 疲劳区(疲劳区是疲劳裂纹亚稳扩展所组成 的断口区域,是测定疲劳断裂重要特征)
➢ 瞬断区(裂纹最后失稳、快速扩展所形成的 断口区域)。
具体特征:
1、 疲劳源 ➢ 该区最光亮(因该断面经多次摩擦挤压之故); ➢ 疲劳源位于疲劳区的贝纹弧线凹向一侧的焦点位 置; ➢ 疲劳源可以一个或多个(与应力状态有关); ➢ 对于有数个疲劳源,可根据疲劳源的光亮度,疲 劳区的大小及贝纹线的密蔬程度可以确定多个源产 生的先后次序,一般源区越亮,疲劳区越大,贝纹 线越密,则该源越早产生。
5.2 金属疲劳的基本现象与规律
(Basic phenomenon and regulation of metal fatigue)
一、交变载荷及循环应力 (Alternative loads and circulative stress)
定义:
交变载荷: 指载荷大小、方向均随时间发生变化的载荷。
对于图5-3的复杂载荷,可以经过傅 立叶变化成几种循环应力,再进行相关 分析,比及特点 (Types and characteristic of fatigue)
1、 分类(Classification)
1)按应力状态分有:
a)弯曲疲劳 b)扭转疲劳 c)拉压疲劳 d)复合疲劳
5.2 疲劳曲线及疲劳抗力 (Fatigue curves and resistance)
(一) 疲劳曲线(Fatigue curves)
试验表明:金属疲劳曲线有两大类(如图5-5所 示)。一类是有水平线段(即有疲劳极限)的曲 线。如一般结构钢及球墨铸铁的疲劳曲线即为该 类型。另一类是无水平线段(即无疲劳极限)的 曲线,如有色金属,不锈钢,高强度钢的疲劳曲 线则为该类型。
一、疲劳裂纹萌生过程及其机理
(Process and mechanism of fatigue crack origin)
宏观疲劳裂纹是由微观裂纹的形成、长大及 连接而成。在确定裂纹萌生期时尚无统一的裂 纹长度标准。常将0.05~0.1mm长的裂纹作为疲 劳裂纹核,对应的时间则作为裂纹萌生期。
研究表明,疲劳微观裂纹都是由不均匀的局 部滑移和显微开裂等引起的,主要方式有:
交变载荷又可分为规则周期变动应力(称为 循环应力)和无规随机变动应力两种(见图 5-1)。
规则变化应力(即循环应力)有:
a)正方形波 b) 矩形波 c)三角形波
循环应力可用几个特征参量来表示,即:
最大应力σmax、最小应力σmin 及平均应力σm、 应力振幅σa。
σa=(σmax-σmin) 2 应力比γ: γ=σmin/σmax 几种常见的循环应力见图5-2。
(Process and mechanism of fatigue crack Propagation)
疲劳微裂纹萌生后,即进入裂纹扩展阶段,根 据裂纹扩展方向,可分为两个阶段(见图5- 13所示)。
图5-13 疲劳裂纹内扩展的几个过程
第一阶段:
从个别侵入沟(或挤出脊)先形成微裂纹, 再沿最大切应力方向向内扩展(45°)。在众多 微裂纹中,只有个别裂纹会扩展到2~5个晶粒。 da/dN很小。断口形貌特征不明显。