10- 热塑性成型工艺
管道热塑成型工艺流程

管道热塑成型工艺流程全文共四篇示例,供读者参考第一篇示例:管道热塑成型工艺是一种常用的管道制造方法,该方法通过将塑料材料加热到一定温度后,塑料具有一定的流动性,然后借助成型机器将其压制成管道形状。
管道热塑成型工艺一般适用于工业领域的管道制造,例如给排水管道、冷热水管道、电气保护管道等。
下面将详细介绍管道热塑成型工艺的流程。
一、原料准备制作管道的第一步就是准备原料。
一般来说,管道热塑成型工艺使用的主要原材料是聚氯乙烯(PVC)、聚丙烯(PP)、聚乙烯(PE)等塑料材料。
这些材料具有良好的耐热性和耐腐蚀性,适合用于管道制造。
在选择原料时,需要根据管道的实际使用环境和要求来进行选择。
二、挤出成型挤出是管道热塑成型工艺的主要步骤之一。
在挤出过程中,将预先准备好的塑料原料加热到一定温度后,通过挤出机器将其压制成圆形或方形橡胶条状,然后将其送入模具中。
模具会给其一个固定的形状,并且冷却后会使其保持形状。
三、热塑成型热塑成型是管道制造的关键步骤。
在热塑过程中,将预先挤出的橡胶条加热到一定温度后,通过成型机器将其压制成管道形状。
成型机器会根据管道的尺寸和形状来调整成型模具。
在成型过程中,尽量避免管道内部和外部产生气泡和瑕疵,以保证管道质量。
四、冷却处理成型完成后的管道需要进行冷却处理。
在冷却处理过程中,管道会通过冷却装置降温,使其固化和保持形状。
对管道进行一定的拉伸和挤压,以消除内部应力和改善管道的物理性能。
五、切割和检验冷却完成后的管道需要进行切割和检验。
切割是将管道按照要求的长度进行切断,以满足不同场合的需要。
检验是对管道的质量进行检测,主要检查管道的尺寸、表面平整度、外观和内部质量等方面,以确保管道符合相关标准和要求。
六、包装和运输最后一步是对管道进行包装和运输。
将成品管道按照一定规格进行包装,并标注产品信息和注意事项。
然后通过合适的运输方式将管道送到用户手中。
管道热塑成型工艺流程包括原料准备、挤出成型、热塑成型、冷却处理、切割和检验、包装和运输等多个步骤。
热成型简介
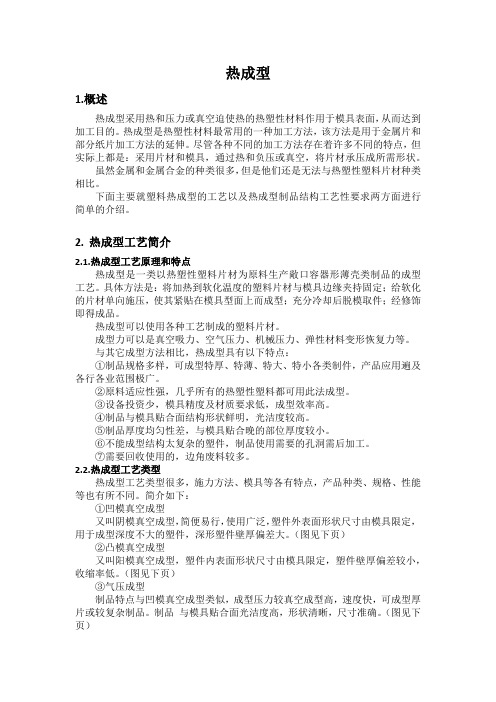
热成型1.概述热成型采用热和压力或真空迫使热的热塑性材料作用于模具表面,从而达到加工目的。
热成型是热塑性材料最常用的一种加工方法,该方法是用于金属片和部分纸片加工方法的延伸。
尽管各种不同的加工方法存在着许多不同的特点,但实际上都是:采用片材和模具,通过热和负压或真空,将片材承压成所需形状。
虽然金属和金属合金的种类很多,但是他们还是无法与热塑性塑料片材种类相比。
下面主要就塑料热成型的工艺以及热成型制品结构工艺性要求两方面进行简单的介绍。
2.热成型工艺简介2.1.热成型工艺原理和特点热成型是一类以热塑性塑料片材为原料生产敞口容器形薄壳类制品的成型工艺。
具体方法是:将加热到软化温度的塑料片材与模具边缘夹持固定;给软化的片材单向施压,使其紧贴在模具型面上而成型;充分冷却后脱模取件;经修饰即得成品。
热成型可以使用各种工艺制成的塑料片材。
成型力可以是真空吸力、空气压力、机械压力、弹性材料变形恢复力等。
与其它成型方法相比,热成型具有以下特点:①制品规格多样,可成型特厚、特薄、特大、特小各类制件,产品应用遍及各行各业范围极广。
②原料适应性强,几乎所有的热塑性塑料都可用此法成型。
③设备投资少,模具精度及材质要求低,成型效率高。
④制品与模具贴合面结构形状鲜明,光洁度较高。
⑤制品厚度均匀性差,与模具贴合晚的部位厚度较小。
⑥不能成型结构太复杂的塑件,制品使用需要的孔洞需后加工。
⑦需要回收使用的,边角废料较多。
2.2.热成型工艺类型热成型工艺类型很多,施力方法、模具等各有特点,产品种类、规格、性能等也有所不同。
简介如下:①凹模真空成型又叫阴模真空成型,简便易行,使用广泛,塑件外表面形状尺寸由模具限定,用于成型深度不大的塑件,深形塑件壁厚偏差大。
(图见下页)②凸模真空成型又叫阳模真空成型,塑件内表面形状尺寸由模具限定,塑件壁厚偏差较小,收缩率低。
(图见下页)③气压成型制品特点与凹模真空成型类似,成型压力较真空成型高,速度快,可成型厚片或较复杂制品。
tpe的成型工艺

tpe的成型工艺
TPE(热塑性弹性体)的成型工艺主要有以下几种:
1. 注射成型(Injection Molding):将加热熔融的TPE材料注入到模具中,然后冷却固化后取出成型件。
这是最常用的TPE成型工艺,适用于各种复杂形状和尺寸的产品。
2. 挤出成型(Extrusion):将加热熔融的TPE材料通过挤出机的螺杆压入模具中,通过不同形状的模口冷却后形成所需截面形状。
挤出成型适用于制作连续长度的产品,如管材、密封条等。
3. 压延成型(Calendering):将加热熔融的TPE材料通过压延机的辊子进行挤压和冷却,形成所需的薄片或薄膜。
压延成型适用于制作薄膜、垫片等产品。
4. 真空热成型(Vacuum Forming):将加热熔融的TPE材料放置在热模具上,然后通过真空将材料吸附在模具上,并冷却固化后取出成型件。
真空热成型适用于制作薄壁产品,如吸塑产品、包装膜等。
此外,TPE还可以通过压缩成型、注压成型、喷涂成型等工艺进行成型,具体选择的成型工艺取决于产品的设计要求和材料特性。
热塑性塑料成型工艺技术
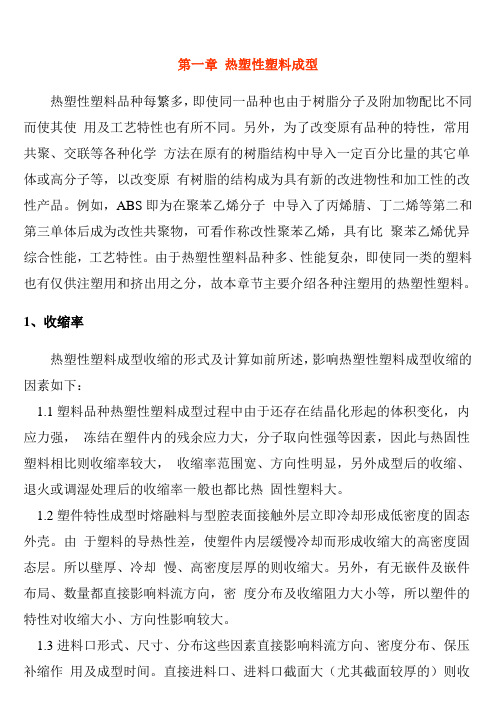
第一章热塑性塑料成型热塑性塑料品种每繁多,即使同一品种也由于树脂分子及附加物配比不同而使其使用及工艺特性也有所不同。
另外,为了改变原有品种的特性,常用共聚、交联等各种化学方法在原有的树脂结构中导入一定百分比量的其它单体或高分子等,以改变原有树脂的结构成为具有新的改进物性和加工性的改性产品。
例如,ABS即为在聚苯乙烯分子中导入了丙烯腈、丁二烯等第二和第三单体后成为改性共聚物,可看作称改性聚苯乙烯,具有比聚苯乙烯优异综合性能,工艺特性。
由于热塑性塑料品种多、性能复杂,即使同一类的塑料也有仅供注塑用和挤出用之分,故本章节主要介绍各种注塑用的热塑性塑料。
1、收缩率热塑性塑料成型收缩的形式及计算如前所述,影响热塑性塑料成型收缩的因素如下:1.1塑料品种热塑性塑料成型过程中由于还存在结晶化形起的体积变化,内应力强,冻结在塑件内的残余应力大,分子取向性强等因素,因此与热固性塑料相比则收缩率较大,收缩率范围宽、方向性明显,另外成型后的收缩、退火或调湿处理后的收缩率一般也都比热固性塑料大。
1.2塑件特性成型时熔融料与型腔表面接触外层立即冷却形成低密度的固态外壳。
由于塑料的导热性差,使塑件内层缓慢冷却而形成收缩大的高密度固态层。
所以壁厚、冷却慢、高密度层厚的则收缩大。
另外,有无嵌件及嵌件布局、数量都直接影响料流方向,密度分布及收缩阻力大小等,所以塑件的特性对收缩大小、方向性影响较大。
1.3进料口形式、尺寸、分布这些因素直接影响料流方向、密度分布、保压补缩作用及成型时间。
直接进料口、进料口截面大(尤其截面较厚的)则收缩小但方向性大,进料口宽及长度短的则方向性小。
距进料口近的或与料流方向平行的则收缩大。
1.4成型条件模具温度高,熔融料冷却慢、密度高、收缩大,尤其对结晶料则因结晶度高,体积变化大,故收缩更大。
模温分布与塑件内外冷却及密度均匀性也有关,直接影响到各部分收缩量大小及方向性。
另外,保持压力及时间对收缩也影响较大,压力大、时间长的则收缩小但方向性大。
塑料成型工艺流程
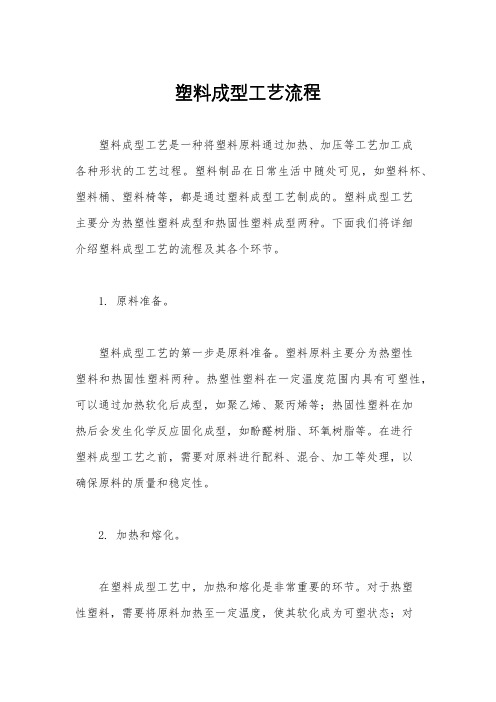
塑料成型工艺流程塑料成型工艺是一种将塑料原料通过加热、加压等工艺加工成各种形状的工艺过程。
塑料制品在日常生活中随处可见,如塑料杯、塑料桶、塑料椅等,都是通过塑料成型工艺制成的。
塑料成型工艺主要分为热塑性塑料成型和热固性塑料成型两种。
下面我们将详细介绍塑料成型工艺的流程及其各个环节。
1. 原料准备。
塑料成型工艺的第一步是原料准备。
塑料原料主要分为热塑性塑料和热固性塑料两种。
热塑性塑料在一定温度范围内具有可塑性,可以通过加热软化后成型,如聚乙烯、聚丙烯等;热固性塑料在加热后会发生化学反应固化成型,如酚醛树脂、环氧树脂等。
在进行塑料成型工艺之前,需要对原料进行配料、混合、加工等处理,以确保原料的质量和稳定性。
2. 加热和熔化。
在塑料成型工艺中,加热和熔化是非常重要的环节。
对于热塑性塑料,需要将原料加热至一定温度,使其软化成为可塑状态;对于热固性塑料,需要将原料加热至一定温度,使其发生化学反应固化成型。
在加热和熔化的过程中,需要控制加热温度、加热时间等参数,以确保原料能够达到适合成型的状态。
3. 成型。
成型是塑料成型工艺的核心环节。
在成型过程中,需要将熔化后的塑料原料注入模具中,并施加一定的压力,使其充分填充模具腔体,并形成所需的产品形状。
成型过程中需要控制注塑压力、注塑速度、注塑时间等参数,以确保成型品质量和生产效率。
4. 冷却。
在成型完成后,需要对产品进行冷却。
冷却过程中,需要控制冷却时间、冷却速度等参数,以确保产品能够充分冷却固化,并保持所需的形状和尺寸稳定。
5. 脱模。
脱模是将成型后的产品从模具中取出的过程。
在脱模过程中,需要注意产品与模具之间的脱模性能,以确保产品能够顺利脱模并保持完整的形状和表面质量。
6. 加工和表面处理。
在脱模后,还需要对产品进行加工和表面处理。
加工包括修整、打磨、去毛刺等工艺,以确保产品的尺寸和表面质量达到要求;表面处理包括喷漆、印刷、镀铬等工艺,以美化产品外观并提高产品的耐磨性和耐腐蚀性。
热塑性复合材料及其工艺
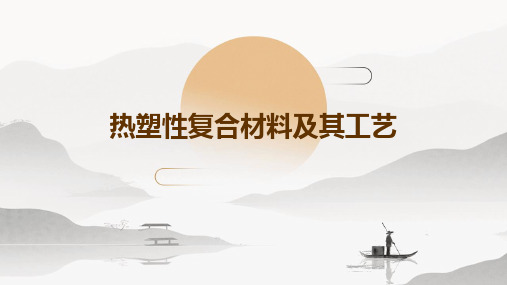
具有优良的力学性能、耐腐蚀性、绝 缘性、重量轻、易加工成型等特性。
分类与组成
分类
根据基体材料的不同,热塑性复合材料可分为聚合物基、无机非金属基和金属 基等。
组成
通常由增强材料、基体材料和各种添加剂组成,其中增强材料提供强度和刚度, 基体材料提供塑性和韧性。
历史与发展
历史
自20世纪50年代以来,热塑性复合材料的研究和应用逐渐受 到重视,随着科技的发展和环保意识的提高,热塑性复合材 料的应用领域不断扩大。
建筑行业
建筑模板
热塑性复合材料可用于建筑模板的制造 ,具有轻便、易加工和可重复使用的特 点。
VS
建筑管道
热塑性复合材料也可用于制造建筑管道, 如雨水管、排水管等,具有耐腐蚀、寿命 长的优点。
其他领域
医疗器械
热塑性复合材料可用于制造医疗器械,如导管、支架等,具有生物相容性好、耐高温和耐腐蚀的优点 。
挤出成型工艺具有生产效率高、制品尺寸精度高、可连续生 产等优点,广泛应用于管材、型材、板材等产品的生产。
注射成型工艺
01
注射成型工艺是一种将热塑性复 合材料加热至熔融状态,然后通 过注射机注入模具,冷却固化后 得到制品的加工方法。
02
注射成型工艺具有生产效率高、 制品尺寸精度高、可生产复杂结 构制品等优点,广泛应用于汽车 、电子、家电等领域。
加工效率高
热塑性复合材料的加工效率较高,能够提高 生产效率,降低生产成本。
市场接受度挑战
认知度低
相对于传统的金属和塑料材料,热塑性复合 材料的认知度较低,需要加强宣传和推广。
价格较高
热塑性复合材料的价格相对较高,可能会影 响其在某些领域的应用和推广。
技术成熟度挑战
热塑性塑料注塑成型的工艺性能热固性塑塑料工艺性能
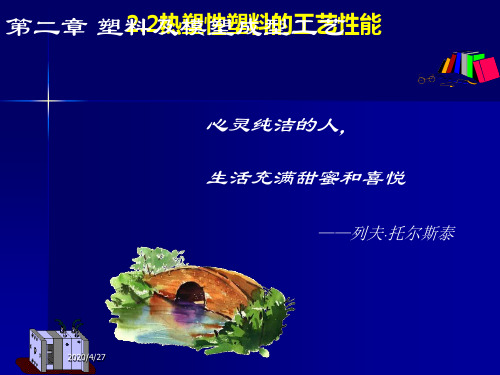
晶的性质称为结晶性。
Tm — 结晶型塑料熔融温度
2020/4/27
图2-2 结晶型聚合物结构示意图 1-晶区 2-非晶区
2.2热塑3性. 塑结料晶的性工艺性能
2)结晶度:
结晶型聚合物的结晶区在聚合物中所占的重量百 分数。(大多数聚合物的结晶度约为10%~60%, 但有些也可能达到很高的数值,如PP的结晶度达到 70%~95%,HDPE和PTFE的也能超过90%)。
时间较长或进料口截面过小,剪切作用大时, 料温增高易出现变色、降解、分解的倾向。
这种性能称为热敏性。
水敏性 —— 有的塑料(如聚碳酸酯)即使
含有少量水分,在高温、高压下也会发生分
解,这种性能称为水敏性。
2020/4/27
25..2热热敏塑性性、塑水料敏的性工、艺降性解能
(1)降解
① 降解概念:
指聚合物在某些特定条件下发生的大分子链 断裂及相对分子质量降低的现象或大分子结构改 变等化学变化的现象叫降解或裂解。 (由于聚合物大分子受热和应力的作用,或由于在高温 下受微量水分、酸、碱等杂质及空气中氧的作用)
.掌握热塑性塑料的成型特性;
2020/4/27
▪注射成型的工艺性能指标.
▪影响注塑成型工艺性能指标的 因素艺.
2.2热塑性塑料的工艺性能
目的和要求: 1.掌握热固性塑料和热塑性塑料的成型特性; 2.掌握常用塑料的牌号,性能。 重点难点: 固化特性 结晶性
2020/4/27
2.2热塑性塑料的工艺性能
塑料在一定温度与压力下填充型腔的能
力称为流动性。
▪常用塑料根据它的流动性可分为三类: 流动性好、流动性中等、流动性差
2020/4/27
塑料热压成型工艺
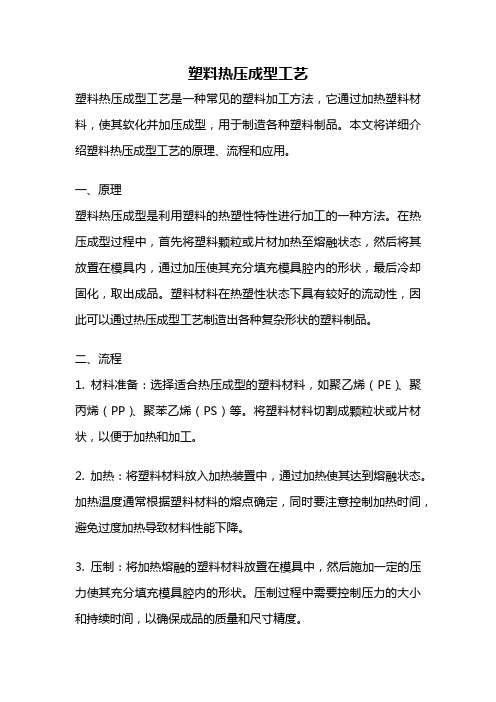
塑料热压成型工艺塑料热压成型工艺是一种常见的塑料加工方法,它通过加热塑料材料,使其软化并加压成型,用于制造各种塑料制品。
本文将详细介绍塑料热压成型工艺的原理、流程和应用。
一、原理塑料热压成型是利用塑料的热塑性特性进行加工的一种方法。
在热压成型过程中,首先将塑料颗粒或片材加热至熔融状态,然后将其放置在模具内,通过加压使其充分填充模具腔内的形状,最后冷却固化,取出成品。
塑料材料在热塑性状态下具有较好的流动性,因此可以通过热压成型工艺制造出各种复杂形状的塑料制品。
二、流程1. 材料准备:选择适合热压成型的塑料材料,如聚乙烯(PE)、聚丙烯(PP)、聚苯乙烯(PS)等。
将塑料材料切割成颗粒状或片材状,以便于加热和加工。
2. 加热:将塑料材料放入加热装置中,通过加热使其达到熔融状态。
加热温度通常根据塑料材料的熔点确定,同时要注意控制加热时间,避免过度加热导致材料性能下降。
3. 压制:将加热熔融的塑料材料放置在模具中,然后施加一定的压力使其充分填充模具腔内的形状。
压制过程中需要控制压力的大小和持续时间,以确保成品的质量和尺寸精度。
4. 冷却:在压制完成后,需要将模具中的塑料制品进行冷却固化。
冷却时间通常根据塑料材料的特性和成型件的厚度来确定,以确保成品具有足够的强度和稳定性。
5. 取出成品:冷却固化后,打开模具,取出成品。
这时,成品已经具备了所需的形状和性能特点。
三、应用塑料热压成型工艺广泛应用于各个领域,包括日常生活用品、工业制品、电子产品等。
例如,塑料热压成型可以用于制造塑料碗、塑料杯等日常生活用品,具有成本低、生产效率高的优点;在工业制品中,塑料热压成型可以用于制造塑料托盘、塑料箱等,具有轻质、坚固、耐用的特点;在电子产品领域,塑料热压成型可以用于制造手机壳、键盘等,具有外观精美、绝缘性能好的特点。
总结:塑料热压成型工艺是一种常见且重要的塑料加工方法,通过加热、压制、冷却等步骤,将塑料材料加工成各种形状的塑料制品。
管道热塑成型工艺流程

管道热塑成型工艺流程
管道热塑成型工艺流程一般包括以下步骤:
1. 原料准备:选择适合的热塑性塑料作为原料,并准备好所需的辅助材料,如添加剂、颜料等。
2. 原料预处理:将原料进行加热、干燥、熔融等处理,以确保原料质量和流动性,并去除其中的水分和杂质。
3. 挤出成型:将经过预处理的原料通过挤出机加热、塑化,然后通过挤压头挤出成型,形成管道的初始形状。
4. 冷却和固化:将挤出成型的管道通过冷却装置,使其迅速冷却并固化,以保持其形状和尺寸的稳定。
5. 切割和修整:将冷却固化后的管道进行切割和修整,以达到所需的长度和形状。
6. 质量检验:对成型的管道进行质量检验,包括尺寸、外观、力学性能等方面的检测,以确保产品符合要求。
7. 包装和存储:对合格的管道进行包装,并按照规定的方式进行存储,以便后续的运输和使用。
需要注意的是,不同的管道热塑成型工艺流程可能会有所不同,具体的流程还需要根据具体的产品和生产要求进行调整。
tpe材料成型工艺

tpe材料成型工艺摘要:1.TPE 材料的概述2.TPE 材料的成型工艺3.TPE 材料的优点4.TPE 材料的应用领域正文:1.TPE 材料的概述TPE,即热塑性弹性体,是一种具有良好弹性和耐磨性的塑料材料。
它具有橡胶的弹性和塑料的可塑性,可以在较广的温度范围内保持其良好的性能。
TPE 材料具有较高的抗拉强度、良好的耐疲劳性能和耐化学品性,因此在各种工业领域得到了广泛应用。
2.TPE 材料的成型工艺TPE 材料的成型工艺主要包括以下几种:(1)压延成型:压延成型是将TPE 材料通过压延机进行连续压延,形成所需厚度和宽度的片状产品。
这种成型方法适用于生产较薄的产品,如薄膜、片材等。
(2)注塑成型:注塑成型是将TPE 材料通过注塑机注入模具中,经过一定的压力和温度作用,形成所需形状的产品。
这种成型方法适用于生产较复杂的结构件,如齿轮、螺丝等。
(3)挤出成型:挤出成型是将TPE 材料通过挤出机进行连续挤出,形成所需形状的产品。
这种成型方法适用于生产线材、管材等长条状产品。
3.TPE 材料的优点TPE 材料具有以下优点:(1)良好的弹性和耐磨性:TPE 材料具有较高的弹性和耐磨性,可以在各种恶劣环境下保持其性能。
(2)耐化学品性:TPE 材料具有较好的耐化学品性,对于大多数酸、碱、盐等化学物质具有良好的耐受性。
(3)良好的耐热性和耐寒性:TPE 材料可以在较广的温度范围内保持其良好的性能。
(4)可回收利用:TPE 材料可回收再利用,降低生产成本,有利于环境保护。
4.TPE 材料的应用领域TPE 材料广泛应用于以下领域:(1)汽车工业:TPE 材料可用于生产汽车密封件、减震器、油箱等部件,提高汽车的性能和安全性。
(2)电子电器:TPE 材料可用于生产电线、电缆、插头等电子电器产品,具有良好的绝缘性和抗干扰性。
(3)医疗卫生:TPE 材料可用于生产医疗器械、注射器等产品,具有良好的生物相容性和耐消毒性。
(4)建筑工程:TPE 材料可用于生产防水材料、密封胶等建筑工程材料,具有良好的耐候性和耐老化性。
热塑性塑料板材制品的压力成型

进一步干燥 , 含水量降低 使 降低加热温度或缩短加热时间 降低模具温度和压制速度 延长脱模时间, 增加冷却 时间或均匀冷却
由于塑料板压力成型的特殊性,其模具结构也不 同于常用的热塑性塑料成型模具。具体要求如下:
() 1 不能因为在连续生产中上下模之 间的压力波 动而使制品的厚度随之变化。对于板材厚度的控制问 题, 可在上下模合拢处设置一个固定扣合点. 即可得到 解决 。
性塑料板 的工艺技术进行了理论研究。在此基础上, 建立了一套具有广泛适用性和实用性的工艺方法 .具 有较好的推广价值。 2 成型工艺原理
5 8
1 2
必须注意的是, 板材在烘箱中应悬挂或支撑放置, 以免损伤板材装饰面或纹路而影响零件的外观质量。 32 成型温度控制 . 板材在烘箱中的加热温度和保温时间是制品成型
燥处理。 耐磨尼龙板材的干燥处理一般在 10 4℃ 2 ~10
鼓风干燥箱中进行、 具体要求见表 1 。
表l 板 材厚度( mm)
l0 2 1 5 .3
2 0 4 3 1 8
干燥时间 ( 小时)
4
零件厚度均匀,但—般不成型大型零件。热塑性塑料 板材压力成型是公司干线机零件生产的需要,麦道公 司不给提供成型工艺标准 ,而且压力成型热塑性塑料 板在我公司属于新工艺。因此.本文对压力成型热塑
5 模胎结构要求
原因分 析及排除
不能太大, 施压速度不能太快, 否则会 使零件表面拉伤
表2
缺
陷
成型缺陷的原 因分析
排
除
零 件表 面鼓包( 气泡 ) 材料含水量过大, 干燥时问不足 零件烧焦 零件表 面起皮、 变色 零 件翘 曲、 变形 材料加温过高 模具温度太高压制速度太快 零件脱模过早, 冷却 不足 零件
热塑性塑料常用的加工工艺
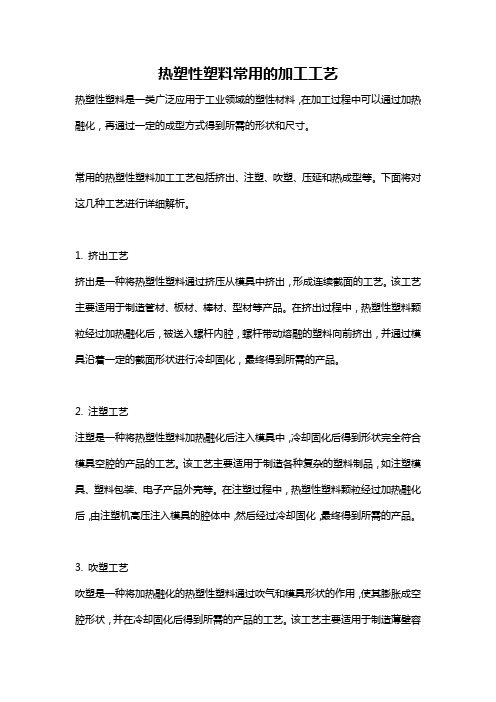
热塑性塑料常用的加工工艺热塑性塑料是一类广泛应用于工业领域的塑性材料,在加工过程中可以通过加热融化,再通过一定的成型方式得到所需的形状和尺寸。
常用的热塑性塑料加工工艺包括挤出、注塑、吹塑、压延和热成型等。
下面将对这几种工艺进行详细解析。
1. 挤出工艺挤出是一种将热塑性塑料通过挤压从模具中挤出,形成连续截面的工艺。
该工艺主要适用于制造管材、板材、棒材、型材等产品。
在挤出过程中,热塑性塑料颗粒经过加热融化后,被送入螺杆内腔,螺杆带动熔融的塑料向前挤出,并通过模具沿着一定的截面形状进行冷却固化,最终得到所需的产品。
2. 注塑工艺注塑是一种将热塑性塑料加热融化后注入模具中,冷却固化后得到形状完全符合模具空腔的产品的工艺。
该工艺主要适用于制造各种复杂的塑料制品,如注塑模具、塑料包装、电子产品外壳等。
在注塑过程中,热塑性塑料颗粒经过加热融化后,由注塑机高压注入模具的腔体中,然后经过冷却固化,最终得到所需的产品。
3. 吹塑工艺吹塑是一种将加热融化的热塑性塑料通过吹气和模具形状的作用,使其膨胀成空腔形状,并在冷却固化后得到所需的产品的工艺。
该工艺主要适用于制造薄壁容器,如瓶子、罐子等。
在吹塑过程中,热塑性塑料颗粒经过加热融化后,通过模具内的吹气,使其膨胀成空腔形状,然后经过冷却固化,最终得到所需的产品。
4. 压延工艺压延是一种将热塑性塑料加热融化后,通过压力作用使其均匀地挤出成一定厚度和宽度的连续膜或板的工艺。
该工艺主要适用于制造塑料膜、塑料板等产品。
在压延过程中,热塑性塑料颗粒经过加热融化后,被挤出成一定厚度和宽度的连续膜或板,然后通过冷却固化,最终得到所需的产品。
5. 热成型工艺热成型是一种将热塑性塑料加热融化后,通过模具形状的作用,将其成型成所需的产品的工艺。
该工艺主要适用于制造各种形状复杂的塑料制品,如塑料容器、塑料包装等。
在热成型过程中,热塑性塑料颗粒经过加热融化后,被加压使其进入模具中,然后通过冷却固化,最终得到所需的产品。
热塑性塑料成型工艺技术

热塑性塑料成型工艺技术热塑性塑料成型工艺技术是一种常见的塑料加工方法,广泛应用于塑料制品的生产过程中。
它基于热塑性塑料的特性,通过加热、塑形、冷却等步骤来实现塑料产品的形成。
首先,在热塑性塑料成型工艺技术中,首要的步骤是选材。
不同的热塑性塑料有不同的熔化温度、流动性和机械性能,选择合适的塑料对于产品质量和性能至关重要。
接下来就是加热过程。
将所选的热塑性塑料加热到其熔化温度以上,使其变得可塑性并具有良好的流动性。
加热的方法包括电加热、气体加热、热风加热等。
其中,温度的控制非常重要,过高会导致热塑性塑料分解,过低则无法达到所需的流动性。
然后是塑形过程。
通过一系列的操作,将热塑性塑料塑造成所需要的形状。
常见的塑形工艺包括注塑、挤出、吹塑、压延等。
在注塑过程中,将熔融的热塑性塑料注入到模具的腔体中,经过冷却后形成所需的产品。
而挤出则是将熔融的塑料通过模头挤出成连续的形状,然后经过后续的切割、冷却等工艺处理。
最后是冷却过程。
将塑形好的热塑性塑料迅速冷却固化,以保持其所需的形状。
冷却可以通过水冷却、风冷却等方式进行。
冷却的速度和方式对于产品的质量和性能也有着重要的影响。
除了以上的基本工艺步骤外,还有一些辅助步骤和技术会被应用到热塑性塑料成型工艺中,如表面处理、模具设计和制造、辅助设备的选择等。
总的来说,热塑性塑料成型工艺技术在塑料制品生产过程中起着至关重要的作用。
通过适当的选材、加热、塑形和冷却等步骤,可以生产出具有良好品质和性能的塑料制品。
在实际应用中,还需要根据不同的产品需求和工艺要求进行相应的调整和改进,以提高生产效率和产品质量。
热塑性塑料成型工艺技术是一种常见、广泛应用于塑料制品生产的工艺方法。
不仅具有灵活性和可塑性,还能够满足各种产品形状和尺寸的需求。
下面将继续介绍与热塑性塑料成型相关的一些工艺和技术。
一、模具设计和制造模具是热塑性塑料成型工艺中非常重要的一环。
通过模具的设计和制造,可以实现对热塑性塑料进行精确塑形。
热塑性复合材料成型工艺

热塑性复合材料成型工艺热塑性复合材料是以玻璃纤维、碳纤维、芳纶纤维等增强各种热塑性树脂的总称,国外称FRTP(Fiber Rinforced Thermo Plastics)。
由于热塑性树脂和增强材料种类不同,其生产工艺和制成的复合材料性能差别很大。
从生产工艺角度分析,塑性复合材料分为短纤维增强复合材料和连续纤维增强复合材料两大类:(1)短纤维增强复合材料①注射成型工艺;②挤出成型工艺;③离心成型工艺。
(2)连续纤维增强及长纤维增强复合材料①预浸料模压成型;②片状模塑料冲压成型;③片状模塑料真空成型;④预浸纱缠绕成型;⑤拉挤成型。
热塑性复合材料的特殊性能如下:(1)密度小、强度高热塑性复合材料的密度为1.1~1.6g/cm3,仅为钢材的1/5~1/7,比热固性玻璃钢轻1/3~1/4。
它能够以较小的单位质量获得更高的机械强度。
一般来讲,不论是通用塑料还是工程塑料,用玻璃纤维增强后,都会获得较高的增强效果,提高强度应用档次。
(2)性能可设计性的自由度大热塑性复合材料的物理性能、化学性能、力学性能,都是通过合理选择原材料种类、配比、加工方法、纤维含量和铺层方式进行设计。
由于热塑性复合材料的基体材料种类比热固性复合材料多很多,因此,其选材设计的自由度也就大得多。
(3)热性能一般塑料的使用温度为50~100℃,用玻璃纤维增强后,可提高到100℃以上。
尼龙6的热变形温度为65℃,用30%玻纤增强后,热形温度可提高到190℃。
聚醚醚酮树脂的耐热性达220℃,用30%玻纤增强后,使用温度可提高到310℃,这样高的耐热性,热固性复合材料是达不到的。
热塑性复合材料的线膨胀系数比未增强的塑料低1/4~1/2,能够降低制品成型过程中的收缩率,提高制品尺寸精度。
其导热系数为0.3~0.36W(㎡·K),与热固性复合材料相似。
(4)耐化学腐蚀性复合材料的耐化学腐蚀性,主要由基体材料的性能决定,热塑性树脂的种类很多,每种树脂都有自己的防腐特点,因此,可以根据复合材料的使用环境和介质条件,对基体树脂进行优选,一般都能满足使用要求。
常用聚合物加工方法及工艺
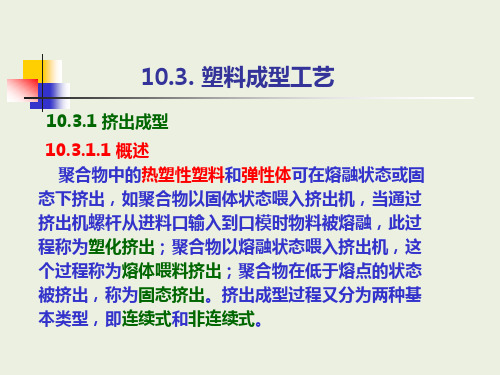
10.5.纤维成型 10.5.纤维成型
10. 10.5.2 熔体纺丝过程
原料 1 2 3 空气
4
熔体纺丝示意图
5
6 7
1-螺杆挤出机 2-喷丝板 3-吹风窗 4-纺丝通道 5-给油盘 6-导丝盘 7-卷绕装置
10.5.纤维成型 10.5.纤维成型
纺丝流程
(a)聚合物熔体 熔体过滤及分配 (b)聚合物切片 熔体制备 纺丝 后加工 纤维
c.调距装置 c.调距装置
10.4.橡胶压延加工 10.4.橡胶压延加工
(C )
(a) )
(b) )
胶片压型工艺示意图
(a)两辊压延机压型 (b)三辊压延机压型 (c)四辊压延 (a)两辊压延机压型 (b)三辊压延机压型 (c)四辊压延 图中带剖面线者为花纹辊筒) 机压型 (图中带剖面线者为花纹辊筒)
10.3. 塑料成型工艺
10. 10.3.1.2 挤出成型的基本过程 聚合物熔融( 挤出机) 成型( 口模) 聚合物熔融 ( 挤出机 ) --- 成型 ( 口模 ) --- 定型 定型装置) 冷却(水或风冷装置) ( 定型装置 ) --- 冷却 ( 水或风冷装置 ) --牵引 牵引机) 切割(切割机) 堆放(堆放装置) (牵引机)--- 切割(切割机)--- 堆放(堆放装置)。 下图为吹塑薄膜示意图: 下图为吹塑薄膜示意图: 吹塑薄膜示意图
10.3.2.4 注射成型工艺过程 (1)成型前的准备 a.粒料预热与干燥 b.料筒清洗 c.嵌件预热 d.脱模剂选用 a.粒料预热与干燥 b.料筒清洗 c.嵌件预热 d.脱模剂选用 (2)注射成型过程 a.加料 b.加热塑化 c.合模 d.加压注射 加压注射、 e.冷却定 a.加料 b.加热塑化 c.合模 d.加压注射、保压 e.冷却定 f.开模 取出制品。 开模、 型 f.开模、取出制品。 (3)制件的后处理
热塑性弹性体成型工艺流程
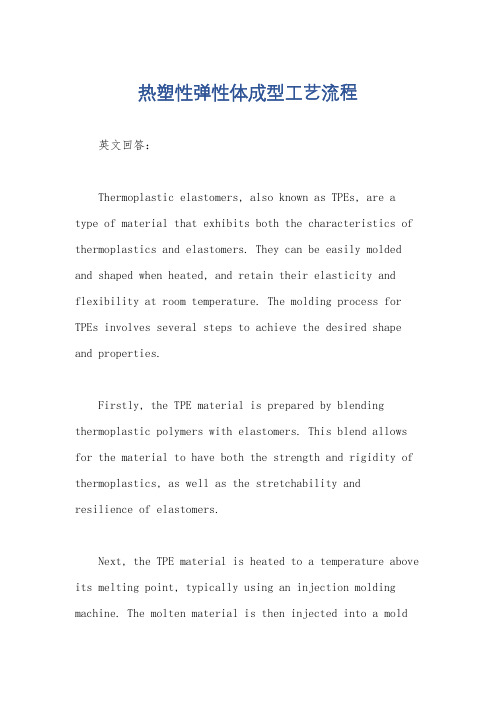
热塑性弹性体成型工艺流程英文回答:Thermoplastic elastomers, also known as TPEs, are a type of material that exhibits both the characteristics of thermoplastics and elastomers. They can be easily molded and shaped when heated, and retain their elasticity and flexibility at room temperature. The molding process for TPEs involves several steps to achieve the desired shape and properties.Firstly, the TPE material is prepared by blending thermoplastic polymers with elastomers. This blend allows for the material to have both the strength and rigidity of thermoplastics, as well as the stretchability andresilience of elastomers.Next, the TPE material is heated to a temperature above its melting point, typically using an injection molding machine. The molten material is then injected into a moldcavity, which is designed to give the desired shape to the final product. The mold cavity is usually made of metal and is precision machined to ensure accuracy and consistency.Once the molten TPE material is injected into the mold cavity, it is allowed to cool and solidify. This process is called cooling and takes place either naturally or with the help of cooling systems such as water or air. The cooling time depends on the thickness and complexity of the molded part.After the TPE material has solidified, the mold is opened and the molded part is ejected. The mold release agents or lubricants are often used to facilitate the easy removal of the part from the mold. The molded part is then inspected for any defects or imperfections, such as air bubbles or warping.Finally, the molded part is trimmed and finished to remove any excess material or rough edges. This can be done by hand or using automated trimming equipment. The finished part is now ready for further processing or assembly.中文回答:热塑性弹性体,也称为TPE,是一种同时具有热塑性和弹性体特性的材料。
tpe注塑成型工艺

tpe注塑成型工艺TPE注塑成型工艺TPE(热塑性弹性体)是一种具有优异弹性和可加工性的材料,广泛应用于各种领域。
TPE注塑成型工艺是一种常用的加工方法,通过注塑机将熔融的TPE材料注入模具中,经冷却固化后得到所需的产品。
本文将详细介绍TPE注塑成型工艺的流程和相关注意事项。
一、TPE注塑成型工艺的流程1. 原料准备:首先需要准备TPE颗粒和其他辅助材料,如增塑剂、阻燃剂等。
确保原料的质量和配比符合要求,以保证成品的性能。
2. 注塑机调试:将注塑机调至适宜的温度和压力,以保证TPE材料能够充分熔融且顺利注入模具中。
同时,通过调整注射速度和压力来控制产品的尺寸和外观。
3. 模具设计和制造:根据产品的形状和尺寸要求,设计和制造适合的模具。
模具的设计应考虑到TPE材料的收缩率和流动性,以确保成品的精度和一致性。
4. 模具安装和调试:将制作好的模具安装到注塑机上,并进行调试,以确保模具的开闭动作和冷却系统的正常工作。
同时,调整模具温度和冷却时间,以控制产品的性能和外观。
5. 注塑成型:将预热好的TPE颗粒放入注塑机的料斗中,通过旋转螺杆将颗粒推入加热筒中熔化。
当TPE完全熔化后,通过注射装置将熔融的TPE材料注入模具中,注射后保持一定的压力,直到TPE 冷却固化。
6. 产品取出和整理:待TPE完全冷却后,打开模具,取出成品。
根据需要进行后续的修整、喷漆或组装等工艺,最终得到符合要求的TPE制品。
二、TPE注塑成型工艺的注意事项1. 温度控制:TPE材料对温度敏感,过高或过低的温度都会影响成型效果和产品性能。
因此,在注塑过程中需要严格控制注塑机的温度,特别是模具的温度,以保证TPE材料的熔融和流动性。
2. 压力控制:适当的注射压力可以保证TPE材料充分填充模具的腔体,避免产生空洞和缺陷。
同时,还要控制保压时间和保压压力,以确保成品的尺寸和外观质量。
3. 模具设计:模具的设计应考虑到TPE材料的特性,如收缩率和流动性。
热压成型工艺流程
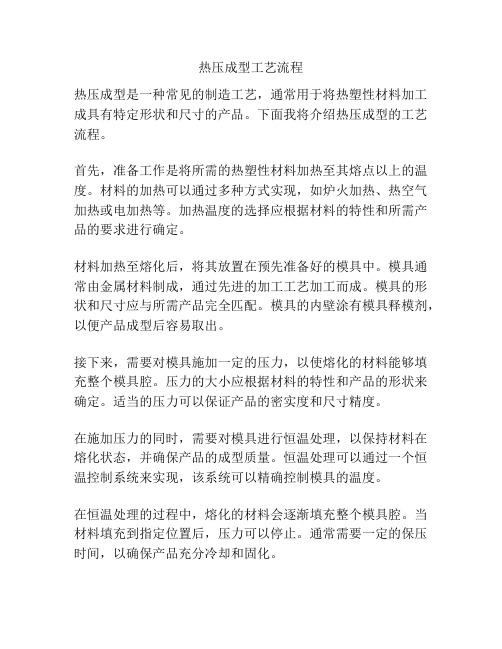
热压成型工艺流程热压成型是一种常见的制造工艺,通常用于将热塑性材料加工成具有特定形状和尺寸的产品。
下面我将介绍热压成型的工艺流程。
首先,准备工作是将所需的热塑性材料加热至其熔点以上的温度。
材料的加热可以通过多种方式实现,如炉火加热、热空气加热或电加热等。
加热温度的选择应根据材料的特性和所需产品的要求进行确定。
材料加热至熔化后,将其放置在预先准备好的模具中。
模具通常由金属材料制成,通过先进的加工工艺加工而成。
模具的形状和尺寸应与所需产品完全匹配。
模具的内壁涂有模具释模剂,以便产品成型后容易取出。
接下来,需要对模具施加一定的压力,以使熔化的材料能够填充整个模具腔。
压力的大小应根据材料的特性和产品的形状来确定。
适当的压力可以保证产品的密实度和尺寸精度。
在施加压力的同时,需要对模具进行恒温处理,以保持材料在熔化状态,并确保产品的成型质量。
恒温处理可以通过一个恒温控制系统来实现,该系统可以精确控制模具的温度。
在恒温处理的过程中,熔化的材料会逐渐填充整个模具腔。
当材料填充到指定位置后,压力可以停止。
通常需要一定的保压时间,以确保产品充分冷却和固化。
固化完成后,产品可以从模具中取出。
这通常需要借助一些辅助工具,如千斤顶或气动系统。
取出时需要注意产品的形状和尺寸,以避免损坏。
最后,对产品进行后续处理,如修整边缘、打磨表面等。
这些工艺可以使产品的外观更加美观,同时也可调整产品的尺寸精度和质量。
总的来说,热压成型是一种常见的制造工艺,通过将热塑性材料熔化并填充到模具中,然后在恒温和加压的条件下固化,最后取出并进行后续处理,可以制造出具有特定形状和尺寸的产品。
这种工艺适用于多种材料和产品类型,广泛应用于汽车、电子、家电等行业。
热塑性成型工艺
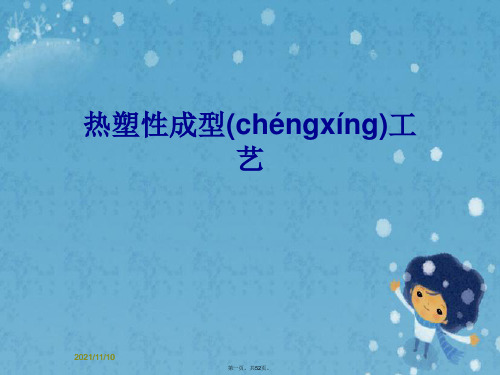
10.4 缠绕(chánrào)成 型工艺
需要在缠绕机上增加预浸纱预热装置和加 热加压辊。
缠绕成型时,先将预浸纱加热到软化 (ruǎnhuà)点,缠绕到芯模上,再加热加压,使 其熔接成一个整体。
第三十六页,共52页。
第三十七页,共52页。
10.5 热塑性复合材料(fùhécái liào)拉 挤成型
次可成型(chéngxíng)形状复杂及带有嵌件的制品,生产 效率高。
第十八页,共52页。
缺点: 不能生产长纤维增强复合材料制品 对模具(mújù)质量要求高
第十九页,共52页。
根据目前的技术发展水平,注射成型 的最大产品为5kg,最小到1g。
主要用来生产(shēngchǎn)各种机械 零件,建筑制品,家电壳体,电器材料, 车辆配件等.
复合材料焊接原理与塑料焊接相似。
第五十一页,共52页。
(3)管件对接(duì jiē)焊
热塑性复合材料管的对接焊方法有直接对接和 补强对接焊两种。 优点是工艺简单,可在现场施工(shī gōng),不 需对管子进行机械加工,连接强度高,不易断 裂。 缺点是成本高,工艺要求严格,要保证尺寸紧密 配合。
第十四页,共52页。
热塑性复合材料(fù hé cái liào)
第十五页,共52页。
10. 2 注射(zhùshè)成型工艺
第十六页,共52页。
10. 2 . 1 概述(ɡài shù)
注射成型是热塑性复合材料的主要生产方法(fāngfǎ), 历史悠久,应用最广。
第十七页,共52页。
优点: 成型(chéngxíng)周期短,能耗小,产品精度高,一
❖ 注射(zhùshè)成型工艺 ❖ 挤出成型工艺 ❖ 离心成型工艺
- 1、下载文档前请自行甄别文档内容的完整性,平台不提供额外的编辑、内容补充、找答案等附加服务。
- 2、"仅部分预览"的文档,不可在线预览部分如存在完整性等问题,可反馈申请退款(可完整预览的文档不适用该条件!)。
- 3、如文档侵犯您的权益,请联系客服反馈,我们会尽快为您处理(人工客服工作时间:9:00-18:30)。
10. 2.2 注射成型工艺
将粒状或粉状的纤维-树脂混合料从 注射机的料斗送入机筒内,加热熔化后 由柱塞或螺杆加压,通过喷嘴注入闭合 模内,经冷却定型后,脱模得制品。
注射成型的主要控制参数是料筒温度、 塑化时间、注射压力、模具温度、锁模力和 保压冷却时间。 料筒温度由树脂种类定,纤维增强比纯 树脂稍高,注射压力一般在 80–200MPa。
(2)焊接
热塑性复合材料的焊接处理,是将被连接 材料的焊接表面加热到熔化状态,然后搭接加 压,使之接成一体。 复合材料焊接原理与塑料焊接相似。
(3)管件对接焊
热塑性复合材料管的对接焊方法有直接对接和 补强对接焊两种。 优点是工艺简单,可在现场施工,不需对管子 进行机械加工,连接强度高,不易断裂。 缺点是成本高,工艺要求严格,要保证尺寸紧 密配合。
第十章
热塑性复合材料 成型工艺
10、1 概述
热塑性复合材料是以玻璃纤维、碳纤维、 芳纶纤维等增强各种热塑性树脂的总称。 国外称 FRTP (Fiber Reinforced Thermo Plastics) 地区性一百万上台阶是不是中医药管理局国产
10、1 概述
国产 由于热塑性树脂和增强材料种类不同, 其生产工艺和制成的复合材料性能差别很大。
10.7 热塑性片状模塑料制品冲压成型 工 艺
热塑性片状模塑料是以连续玻璃纤维毡、 短切玻璃纤维毡、布、无捻粗纱和热塑性树脂 复合而成的一种片状模塑料。
热塑性片状模塑料制品的特性:
①比强度高 ②能重复加工成型:边角余料可回收利用,不污 染环境,减少材料消耗,降低成本。 ③成型周期短:热固性SMC的成型周期一般为 6min~15min,热塑性片状模塑料的成型周期仅 为20s~50s。 ④成型压力低:冲压力只有几兆帕。
注射成型是热塑性复合材料的主要生产方 法,历史悠久,应用最广。
优点: 成型周期短,能耗小,产品精度高,一次 可成型形状复杂及带有嵌件的制品,生产效率 高。
缺点: 不能生产长纤维增强复合材料制品 对模具质量要求高
根据目前的技术发展水平,注射成型 的最大产品为5kg,最小到1g。 主要用来生产各种机械零件,建筑制 品,家电壳体,电器材料,车辆配件 等.
(4)耐化学腐蚀性
复合材料的耐化学腐蚀性,主要由基体材 料的性能决定。 热塑性树脂的种类很多,每种树脂都有自 己的防腐特点。 热塑性复合材料的耐水性优于热固性复合 材料。
(5)电性能
一般热塑性复合材料都具有良好的介电性 能,不反射无线电电波,透过微波性能良好等。 由于热塑性复合材料的吸水率比热固性玻 璃钢小,故其电性能优于后者。
冲压成型工艺分为固态冲压成型和流动态冲压成型 ①固态冲压成型是按样板将片状模塑料剪切成坯料,然后 在加热器内将料片加热到到低于树脂熔点10 ℃ ~ 20 ℃, 装入模内,快速合模加压,冷却脱模,再经修边成制品。 ②流动态冲压成型是先将裁成与制品质量相同的坯料,在 加热器内加热到高于树脂熔点10 ℃ ~ 20 ℃,放入模具 内,快速加压,迫使坯料流动并填满模腔,冷却定型后 脱模成制品。
一般来讲,不论是通用塑料还是工程塑料, 用玻璃纤维增强后,都会获得较高的增强效果, 提高强度应用档次。
(2)性能可设计性大
热塑性复合材料的物理性能、化学性能、 力学性能,都可通过合理选择原材料种类、配 比、加工方法、纤维含量和铺层方式来进行设 计。 由于热塑性复合材料的基体材料种类比 热固性复合材料多很多,因此,其选材设计的 自由度也就大得多。
湿法生产工艺
湿法生产热塑性片状是将玻璃纤维无捻粗 纱切成7mm~50mm(最佳长度为13mm左右)的短纤 维,在搅拌器内与粉末树脂(PP·PVC·HDPE)。 加水搅拌成均匀的悬浮料浆,用泵将其输 送到传送网带上,经减压脱水,形成湿毡,再 经干燥、切断、收卷成中间产品。
热塑性复合材料制品冲压成型工艺及设备
10.4 缠绕成型工艺
需要在缠绕机上增加预浸纱预热装置和加 热加压辊。 缠绕成型时,先将预浸纱加热到软化点, 缠绕到芯模上,再加热加压,使其熔接成一个 整体。
10.5 热塑性复合材料拉挤成型
热塑性复合材料的拉挤成型工艺与热固性 玻璃钢的基本相似。只要把进入模具前的浸胶 方法加以改造,生产热固性玻璃钢的设备便可 使用。
热塑性复合材料分为短纤维增强复合材料和
连续纤维增强复合材料两大类
短纤维增强复合材料
注射成型工艺 挤出成型工艺 离心成型工艺
连续纤维增强及长纤维增强复合材料
预浸料模压成型 片状模塑料冲压成型 片状模塑料真空成型 预浸纱缠绕成型 拉挤成型
热塑性复合材料的特性
(1)密度小、强度高 热塑性复合材料的密度为1.1~1.6g/cm3, 仅为钢材的1/5~1/7,比热固性玻璃钢轻1/3~ 1/4。
(3)热性能好
一般塑料的使用温度为50~100℃,用玻 璃纤维增强后,可提高到100℃以上。
例:尼龙6的热变形温度为65℃,用30%玻纤增 强后,热变形温度可提高到190℃。 聚醚醚酮树脂的耐热性达220℃,用30%玻 纤增强后,使用温度可提高到310℃,这样高 的耐热性,热固性复合材料是达不到的。
⑤贮存期长:热固性预浸料和片状模塑料的贮存期只 有3个月(常温贮存),而热塑性模塑料则可长期贮存 几年以上。 ⑥比热固性玻璃钢具有较高的耐化学腐蚀性、耐水性 的气密性等。 ⑦原料来源充足,价格便宜。 ⑧成本低 ⑨机械化程度高
热塑性片状模塑料的生产工艺及设备
原材料 树脂:尼龙、聚乙烯、聚氯乙烯和聚丙烯等 增强材料:主要是玻璃纤维
冲压成型设备
冲压成型设备由剪切、加热、冲压等设备及模具组成 ①剪切设备:一般选用钢板剪切机 ②加热炉:热源为红外线加热或热风加热 ③压机:液压式或机械传动式 ④模具:冲压成型用的模具材料一般为铸钢。对固态 冲压成型用的模具,因为成型压力小于1MPa,故 可选用轻金属、复合材料。
10.8 热塑性复合材料的连接技术
生产方法可归纳为湿法和干法两大类
干法生产工艺
干法工艺又分为层合法和分散法 (1)层合法生产热塑性片状模塑料工艺 将连续玻璃纤维毡和聚丙烯(或其它热塑性塑料) 薄片叠合后,经过加热、加压、浸渍、冷却定型和切 断等工序制造片状模塑料的方法。 (2)分散法生产热塑性片状模塑料工艺 将短切玻璃与聚丙烯或尼龙等树脂粉末在特殊的 搅拌机内混合均匀,然后按设计厚度铺撒均匀,再经 加热、加压制成此法是用超声波对被连接处进行加热焊接,一 般能够获得较高的连接强度。
10.6 焊接层合法
此法系利用热塑性复合材料的可焊性,生 产复合材料板材。 其方法如下: 先在工作台上压铺一层预浸料(一般宽 500mm),铺第二层预浸料时,开动压辊的焊 接器,使预浸料进入压辊下,焊接器使上下两 层预浸料在几秒钟内同时受热熔化,预浸料在 压辊的压力(0.3MPa)作用下粘合成一体。如 此重复,可生产任意厚度的板材。
卧式注塑机
HTL68 注塑成 型机
立式注塑机
注塑产品
10.3 挤出成型工艺
10.3 挤出成型工艺
挤出成型是热塑性复合材料制品生产中应 用较广的工艺之一。 主要特点: 生产过程连续,生产效率高,设备简单, 技术容易掌握等。
挤出成型
粒料从料斗进入挤出机加热料筒,料筒中螺杆 旋转,物料沿螺槽前移。
热塑性复合材料的连接方法: 铆接 焊接 管件对接焊 缠绕焊接 薄板超声波焊接
(1)铆接
用于热塑性复合材料铆接用的铆钉,一般 都是用连续纤维增强热塑性塑料制造,最好是 用拉挤棒材制造。也可以用金属螺栓。 施工时,铆钉预热到可以加压塑变的温度, 铆钉与孔径应能严密配合,不能大,也不能小。 铆接的优点是耐冲击性好,无电化学腐蚀, 价格便宜。
挤出成型
前移过程中物料受机械剪切作用摩擦热和 料筒的加热逐渐熔融成熔体,熔体受螺杆轴向 推力的作用通过机头和口模,获得与口模形状 相似的连续体。
双螺杆挤出机
单螺杆挤出机
应用
主要应用: 用于生产管、棒、板及异型断面型等 产品。
挤出产品
挤出灯罩
挤出成型吸尘器管
10.4 缠绕成型工艺
热塑性复合材料的缠绕成型工艺原理和 缠绕机设备与热固性玻璃的一样,不同的是热 塑性复合材料缠绕制品的增强材料不是玻纤粗 纱,而是经过浸胶(热塑性树脂)的预浸纱。
(6)加工性能
热塑性复合材料可重复加工成型,废品和 边角余料能回收利用。
由于热塑性复合材料有很多优于热 固性玻璃钢的特殊性能,应用领域十分 广泛,从国外的应用情况分析,热塑性 复合材料主要用于车辆制造工业、机电 工业、化工防腐及建筑工程等方面。
热塑性复合材料
10. 2 注射成型工艺
10. 2 . 1 概述