耐热橡胶的配方设计选材原则
橡胶配方大全
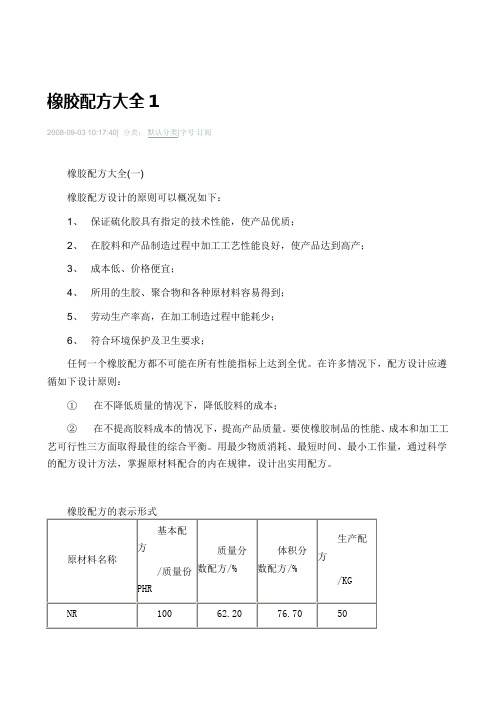
70
25
0.5
0.7
0.5
100
40
2
0.4
0.4
5
5
30
0.6
3.5
100
10
5
60
10
5
1
1
0.5
1
1.5
合计
175.4
183.25
196.5
202.7
186.9
195.0
子午线轮胎胎面胶配方
原材料
载重子午线轮胎胎面胶
轿车子午线轮胎胎面胶
NR
NR/SBR
NR/BR
NR/BR/SBR
NR
NR/BR/SBR
—
—
—
10
0.3
0.1
注:硫化时间为150℃×30min,40min,50min
丙烯酸酯橡胶(ACM)基础配方
原材料名称
质量份
原材料名称
质量份
ACM
快压出炭黑FEF
硬脂酸钾
100
60
0.75
防老剂RD
硬脂酸纳
硫磺
1
1.75
0.25
注:硫化条件为一段166℃×10min;二段硫化180℃×8h。
混炼型聚氨酯橡胶(PUR)基础配方
氯磺化聚乙烯(CSM)基础配方
原材料名称
黑色配方
白色配方
CSM
SRF
一氧化铅
活性氧化锌
促进剂DM
促进剂DPTT
二氧化钛
碳酸钙
季戊四醇
100
40
25
—
0.5
2
—
—
—
100
—
—
丁腈橡胶耐高温配方设计

丁腈橡胶耐高温配方设计丁腈橡胶是一种优异的橡胶材料,具有优良的耐油性、耐化学性和耐磨性,因此在工业领域得到了广泛的应用。
然而,在一些特殊环境下,丁腈橡胶需要具有更高的耐高温性能,以满足特定的工业需求。
为了开发出耐高温的丁腈橡胶配方,需要进行一系列的配方设计和试验验证。
首先,我们需要了解丁腈橡胶的基本性能和特点。
丁腈橡胶是一种合成橡胶,通常具有良好的耐热性,但在高温下仍然会发生硫化交联断裂和变形。
因此,我们需要通过添加耐高温填料和增塑剂来提高丁腈橡胶的耐高温性能。
常用的耐高温填料包括氧化铝、二氧化硅等,而增塑剂则可以提高橡胶的柔韧性和耐热性。
其次,我们需要设计实验方案,根据丁腈橡胶的基本成分和需要的耐高温性能,选择合适的耐高温填料和增塑剂,并确定它们的添加比例。
然后进行实验验证,通过混炼、硫化等工艺,制备出不同配方的丁腈橡胶样品,并进行性能测试,包括耐热性、耐张强度、耐撕裂性等指标的测试。
在实验过程中,需要注意控制不同配方样品的制备工艺和测试条件,保证实验结果的准确性和可靠性。
根据测试结果,选择性能优异的丁腈橡胶配方,并进行大量的批量生产验证,以确保其稳定性和可靠性。
最后,我们需要对耐高温丁腈橡胶的应用领域进行深入研究,了解工业需求和市场趋势,针对不同的应用场景,优化丁腈橡胶的配方设计,推动其在高温领域的应用拓展。
总之,丁腈橡胶耐高温配方设计是一个复杂且系统的工程,需要充分考虑材料的各项性能指标、工艺条件和应用需求,通过理论分析、实验验证和市场导向相结合的方式,开发出性能优异的耐高温丁腈橡胶材料,为工业生产提供更加可靠和耐高温的橡胶制品。
橡胶制品的配方设计原理
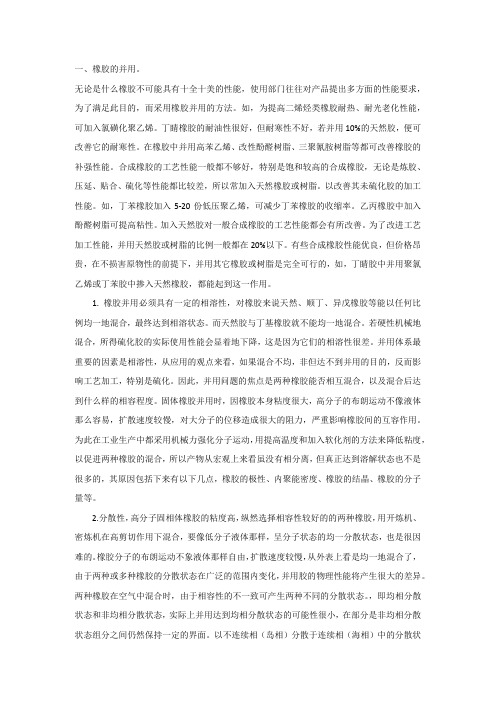
一、橡胶的并用。
无论是什么橡胶不可能具有十全十美的性能,使用部门往往对产品提出多方面的性能要求,为了满足此目的,而采用橡胶并用的方法。
如,为提高二烯烃类橡胶耐热、耐光老化性能,可加入氯磺化聚乙烯。
丁睛橡胶的耐油性很好,但耐寒性不好,若并用10%的天然胶,便可改善它的耐寒性。
在橡胶中并用高苯乙烯、改性酚醛树脂、三聚氰胺树脂等都可改善橡胶的补强性能。
合成橡胶的工艺性能一般都不够好,特别是饱和较高的合成橡胶,无论是炼胶、压延、贴合、硫化等性能都比较差,所以常加入天然橡胶或树脂。
以改善其未硫化胶的加工性能。
如,丁苯橡胶加入5-20份低压聚乙烯,可减少丁苯橡胶的收缩率。
乙丙橡胶中加入酚醛树脂可提高粘性。
加入天然胶对一般合成橡胶的工艺性能都会有所改善。
为了改进工艺加工性能,并用天然胶或树脂的比例一般都在20%以下。
有些合成橡胶性能优良,但价格昂贵,在不损害原物性的前提下,并用其它橡胶或树脂是完全可行的,如,丁睛胶中并用聚氯乙烯或丁苯胶中掺入天然橡胶,都能起到这一作用。
1. 橡胶并用必须具有一定的相溶性,对橡胶来说天然、顺丁、异戊橡胶等能以任何比例均一地混合,最终达到相溶状态。
而天然胶与丁基橡胶就不能均一地混合。
若硬性机械地混合,所得硫化胶的实际使用性能会显着地下降,这是因为它们的相溶性很差。
并用体系最重要的因素是相溶性,从应用的观点来看,如果混合不均,非但达不到并用的目的,反而影响工艺加工,特别是硫化。
因此,并用问题的焦点是两种橡胶能否相互混合,以及混合后达到什么样的相容程度。
固体橡胶并用时,因橡胶本身粘度很大,高分子的布朗运动不像液体那么容易,扩散速度较慢,对大分子的位移造成很大的阻力,严重影响橡胶间的互容作用。
为此在工业生产中都采用机械力强化分子运动,用提高温度和加入软化剂的方法来降低粘度,以促进两种橡胶的混合,所以产物从宏观上来看虽没有相分离,但真正达到溶解状态也不是很多的,其原因包括下来有以下几点,橡胶的极性、内聚能密度、橡胶的结晶、橡胶的分子量等。
第八章 特性橡胶配
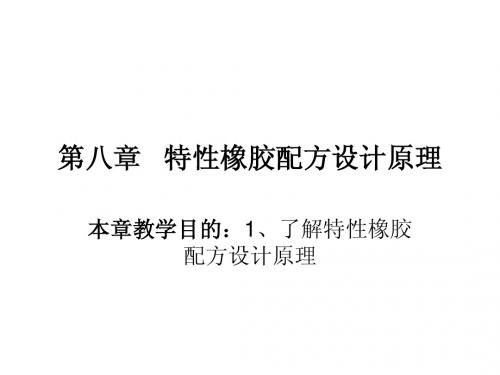
第八节 海绵橡胶
• • • • • 海绵橡胶可用干胶、胶乳来制造 ; 一、生胶 要进行充分塑炼,以获得较大的可塑性。 二、发泡剂 有机发泡剂其优点是:(1)在胶料中分散性较好; (2)分解温度范围较窄,且能控制;(3)分解 产生的气体以氮气为主,不会燃烧和爆炸。且扩 散速度小,不容易逸出,因而发泡率高。 • 在发泡工艺上,为了调节发泡剂的分解温度和分 解速度,或稳定泡沫结构和提高发泡体的质量, 通常还可加入发泡助剂
• • • • • •
(3)硫化体系的选择 —C—C— 过氧化物交联; —C—S—C— 低硫+高促+金属氧化物 —C—S—S—C— 低硫+高促+金属氧化物 —C—Sn—C— 高硫+促进剂+金属氧化物 含单硫键的比多硫键的耐热性较高。因此应尽可 能采用高促低硫的配合,或用有效硫化体系。 • 用过氧化物硫化或树脂硫化的硫化胶耐热性一般 优于硫磺硫化体系,如Q橡胶,EPDM、CSM、 EVA(乙烯醋酸乙烯酯)、NBR, 但过氧化物用 于二烯类橡胶硫化时,NR、SBR、BR有引起分 解的倾向,而IIR非但不能硫化,反会引起断链反 应
第五节 耐气透和真空橡胶
• 一、配方设计原则 • 含极性的橡胶如氯丁、丁腈、聚硫、氟橡胶以及氯乙醇橡 胶等有很高的耐气透性。如丁基、聚异丁烯、乙丙等含大 量甲基的橡胶其耐气透性也很优越。 • (1)呈片形结构粒子的无机矿物质,如滑石粉、云母、 石墨等,比粒子规则的填充剂,能有效地降低透气性,因 此应选用这类材料作填充剂。但使用这类填充剂时将会对 其他性能(特别是撕裂性)有不利影响。 • (2)增加填充剂的用量,降低硫化胶中橡胶的体积含量 都有助于提高耐气透性。 • (3)提高硫化程度,能提高耐气透性。 • (4)无论是生胶或配合剂都不能含有机械杂质所有粒状 的填充剂在胶料中要分散均匀,不能有结团的现象。
耐热橡胶制品设计要点

本文摘自再生资源回收-变宝网()耐热橡胶制品设计要点橡胶作为高分子材料,其主链的化学成分是烃类,易燃而不耐热,所以橡胶的耐热仅仅是相对而言的,不能和真正的耐热材料(如石棉)相提并论。
但出于实际应用的需要,对耐热性提出了越来越多的要求。
而经过材料选择、配方设计,橡胶的耐热等级的上限也在逐步提升。
耐热橡胶制品的品种和应用则与日俱增。
关于耐热橡胶的温度范围,迄今缺乏统一的认识。
比较为业界认同的是“在80°C以上能长期使用后仍能保持原有性能和使用价值的橡胶”。
过去几十年来,耐热橡胶制品的范围在不断扩大,原因在于:第一,若干传统制品过去并不要求耐热,而随着使用条件的变化,也相继提出耐热要求。
典型例子是轮胎。
由于车速的加快,滚动生热大幅上升,提高耐热性是必须跨越的门槛。
其他橡胶制品也有类似情况。
第二,橡胶制品与各种热介质(如各种润滑油、制动油、工作介质及液压油)等的接触机会增加,温度也大大超过常温。
第三,为了顺应橡胶工业自身在加工中的耐热需要,例如轮胎硫化所用的水胎、胶囊都需在170°C~180°C的温度下长期使用,挤出制品的连续硫化更得在200°C以上的高温下进行,它们都必须具备耐热和抗返原的特性。
耐热性是指在一定的高温使用条件下,在较长的时间内保持原有基本物理机械性能的能力。
耐热性决定制品的最高使用温度和寿命,一般物理机械性能在高温下保持稳定,即具有在高温下能够抵抗氧、臭氧、高能辐射、机械疲劳等因素的作用。
硫化橡胶的耐热性表现在橡胶分子、交联键及其配合剂(主要是填充剂和增塑剂)有较高的粘流温度、热分解温度和化学稳定性。
橡胶的粘流温度取决于橡胶分子结构的极性和刚性、橡胶分子之间的作用力、填料与橡胶之间的相互作用和交联键的键能。
橡胶的热分解温度取决橡胶分子结构的化学键性质,化学键能越高,耐热性越好。
橡胶的化学稳定性也是影响耐热性能的一个重要因素。
因为在高温条件下,橡胶与氧、臭氧、其它介质的接触,都会促进橡胶的老化与被腐蚀。
橡胶配方设计基础资料
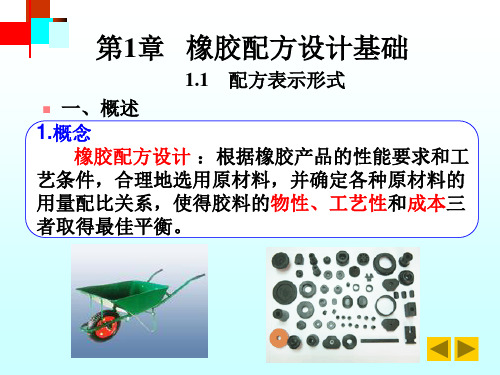
实际用量表示。
表1-1 橡胶配方的表示形式
原材料名称, 基本配方, 质量分数 体积分数 生产配
(g/cm3)
质量份 配方/% 配方/% 方,kg
NR 0.92
100 62.20① 76.70② 50.0③
1.4 橡胶配方设计方法
橡胶配方设计主要依赖于人们在生产当中积累的 经验规律,通过大量而繁复的试验来优化配方,造 成大量人力、物力的浪费。
随着科学技术在各个领域的进步和发展,尤其是 计算机技术的迅速发展,橡胶行业已经开始采用计 算机进行配方设计。
1.单因素设计方法
因素:需要考察的影响试验胶料性能指标的因素, 如橡胶配方组分中的硫化剂、补强剂、防老剂等; 水平:每个试验因素可能取值的状态
确定性能 试验项目
➢加工性能 ➢ 物机性能 ➢ 使用性能
➢其他性能:视产品而定
(4)进行试验并选取最佳配方(试验室进行)
塑炼 混炼 制成硫化胶试样 性能测试 数据整理 对比,取舍 初选最佳配方
(5)复试并扩大中试(车间中进行)
试验配方 复试3-5次
车间规模 试验
检验胶料的工艺性能、 硫化胶的物机性能 和成品的机床性能
单因素配方试验设计主要就是研究某单一试验因 素,如促进剂、炭黑、防老剂或某一新型原材料, 在某一变量区间内,确定哪一个值的性能最优。
这样的设计方法主要包括:黄金分割法(0.618 法)、平分法(对分法)、分批试验法、抛物线法、 爬山法。
2020/9/25
黄金分割法
黄金分割点在线段L的0.618处,故此法又称0.618 法。
(3)原材料价廉易得; (4)重点设计主要性能
橡胶配方设计
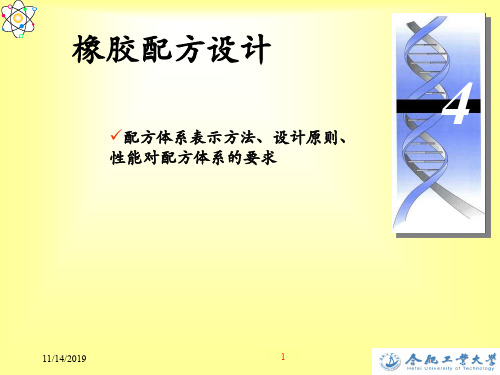
11/14/2019
20
4.2.2 配合体系与撕裂强度的关系
指将带有切口的试片撕裂时所需的最大力,其单位为N/m。 ⑴ 橡胶品种
天然橡胶、氯丁橡胶等结晶性橡胶的撕裂性较好。几种橡胶的抗 撕裂性强弱顺序是:NR>CR>SBR>NBR ⑵ 硫化体系 多硫键具有较高的撕裂强度。 ⑶ 填充体系 粒子细、活性大的炭黑、白炭黑补强时,撕裂强度明显改善;炭 黑用量一般在50~60phr时可获得最高撕裂强度。但用量过大时撕 裂强度反而下降。 ⑷ 增塑体系 适当加入增塑剂有助于撕裂强度的提高,主要是一些树脂类如古 马隆树脂、酚醛树脂等。
炼性主要取决于配合剂与橡胶之间的浸润性。 疏水性填充剂,如炭黑容易被橡胶所浸润,混炼性能较好;亲水
性填充剂,如碳酸钙、陶土、白炭黑等,不易被橡胶浸润,混炼 性能较差。可通过化学改性,或加入表面活性剂加以改进。 增塑剂与橡胶的相容性一般较好,易于分散。
11/14/2019
31
3 配合体系对包辊性能的影响 胶料的包辊性能主要取决于生胶的强度和粘着性能。 影响生胶强度的因素包括生胶的分子量及其拉伸结晶性能。天
所谓配方设计就是如何确定这种比例关系,是橡胶制品生产 过程中的关键环节。
11/14/2019
2
4. 1.1 橡胶配方设计的原则
橡胶配方设计的任务是力求使橡胶制品在性能、成本和工艺可行 性三个方面取得最佳的综合平衡。通常,要遵循以下几条原则:
⑴ 充分了解制品的性能要求、使用条件;半成品的性能一般应 高于成品指标的15%。
然橡胶具有最好的包辊性能,乳聚合成橡胶次之,溶聚的,特别 是分子量分布较宽的橡胶包辊性能较差。改善的途径有以下几种 ⑴ 通过加入活性、结构性高的填充剂,如炭黑、白炭黑等增加生 胶的强度,进而提高胶料地包辊性能。 ⑵ 加入增粘性增塑剂 如高芳烃操作油、松焦油、古马隆树脂、 酚醛树脂等。 ⑶ 与少量天然橡胶并用。
橡胶配方设计第三章
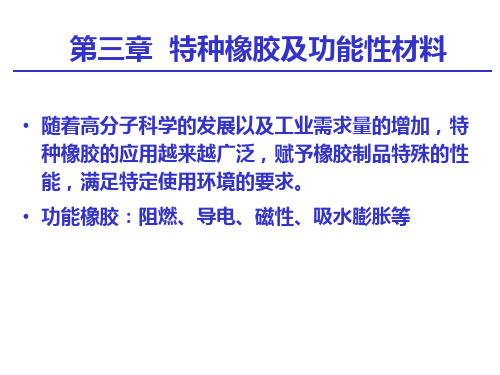
Heat Resistance oC
H 250 G 225
FPM FMVQ
MVQ
F 200 E 175 D 150 C 125 B 100 A 70
ACM
44%ACN HNBR
80%VA 34%ACN
40%VA EVM
CO/ECO 48%ACN
NBR
PU
CM/CSM 18%ACN
CR
SBR
EPDM IIR
四、填料少用或不用,选用软质或球形填料
各种增塑剂对NBR耐寒性的影响
增塑剂
空白 邻苯二甲酸二辛酯 邻苯二甲酸二丁酯 邻苯二甲酸丁基·月桂
酯 邻苯二甲酸丁基·苄酯
磷酸三苯甲酯
脆性温度Tb /℃
增塑剂
脆性温度Tb /℃
-29.5
磷酸三苯酯
-30
-37.5
己二酸二辛酯
-43
-37.5
壬二酸二辛酯
-44.7
-42
癸二酸二辛酯
-49
-37
癸二酸丙二醇酯
-36.5
-29.5
液体古马隆
-27.5
• 橡胶的耐寒系数采用室温(25℃)下的形变值 ε25与指定温度下的形变值εi之比来表示,耐寒 系数K为: K = εi / ε25
• 显然,当温度接近Tg 时,与室温下形变值相比, 接近Tg 的形变值很小,K值接近于零。加入增 塑剂可使高弹态的范围向低温方向扩展。
A
耐热输送带覆盖胶
SBR1500 100
ZnO 10
SA
2
防D 1.5
HAF 30
SRF 50
10#机油 8
古马隆树脂 6
松焦油 5
促TMTM 1
橡胶选材设计方案

橡胶选材设计方案
橡胶是一种具有优良的弹性和耐磨性能的材料,广泛应用于汽车、电子、医疗、建筑等领域。
在进行橡胶选材设计时,需要考虑材料的物理、化学、机械性能以及成本等因素,以满足具体应用的要求。
首先,根据使用环境和要求确定橡胶材料的硬度。
硬度是橡胶的重要物理性能之一,通常用硬度测试仪进行测试。
硬度越大,橡胶材料的弹性越小,耐磨性越好。
根据具体应用需求,可以选择硬度范围在30-90之间的不同橡胶材料。
其次,考虑橡胶材料的耐热性和耐寒性。
不同的橡胶材料对温度的敏感性不同,需要根据具体使用环境选择合适的橡胶材料。
对于高温环境,可以选择硅橡胶或氟橡胶等耐热橡胶材料;对于低温环境,可以选择丁腈橡胶或氟橡胶等耐寒橡胶材料。
第三,考虑橡胶材料的耐化学性能。
不同的橡胶材料对化学品的耐受性有所差异。
在与化学品接触的环境中,需要选择具有良好耐化学性的橡胶材料,以避免材料的老化、膨胀或变形等问题。
常见的耐化学性较好的橡胶材料有丁腈橡胶、氟橡胶和聚四氟乙烯等。
最后,考虑橡胶材料的成本和可加工性。
不同的橡胶材料的价格和可加工性也有所不同。
需要根据项目的预算和生产工艺选择合适的橡胶材料。
同时,还需要考虑橡胶材料的可加工性,以确保材料能够满足生产过程的要求。
综上所述,橡胶选材设计方案需要根据具体应用需求,综合考虑橡胶材料的硬度、耐热性、耐寒性、耐化学性、成本和可加工性等因素。
通过选用合适的橡胶材料,可以满足项目的要求,提高产品的性能和可靠性。
NBR橡胶的配方设计

NBR橡胶的配方设计NBR橡胶是一种合成橡胶,其主要成分是丁腈橡胶。
它具有很高的耐油性、耐燃油性、耐溶剂性以及低温性能等特点,因此广泛应用于汽车零部件、轮胎、密封件等领域。
在进行NBR橡胶的配方设计时,需要考虑以下几个方面的因素。
首先,需要考虑橡胶的硬度。
硬度是衡量橡胶材料硬软程度的指标,通常使用硬度计来进行测量。
硬度的选择应根据具体的应用环境和要求来确定。
例如,在汽车轮胎中使用的NBR橡胶一般具有较高的硬度,以提高轮胎的耐磨性和耐压缩性。
其次,还需要考虑橡胶的耐油性和耐溶剂性。
NBR橡胶具有良好的耐油性,但在不同的油品和溶剂下的耐受性可能会有所不同。
因此,在配方设计中需要选择合适的抗油剂和抗溶剂剂量,以提高橡胶的耐油性和耐溶剂性。
此外,还需要考虑橡胶的耐热性。
NBR橡胶在高温环境下可能会发生老化和失效。
为了提高橡胶的耐热性,可以在配方中加入耐热剂和抗氧剂,以延缓橡胶的老化过程。
另外,还需要考虑橡胶的加工性能。
加工性能包括橡胶的流动性、分散性和可塑性等指标。
在进行配方设计时,可以使用可塑剂和改性剂来改善橡胶的加工性能,以使得橡胶能够更好地进行挤出、压延等加工工艺。
最后,还需要考虑橡胶的物理力学性能。
物理力学性能包括橡胶的拉伸强度、断裂延伸率、硬度变化率等指标。
在配方设计时,可以通过调整不同的添加剂和填料来改变橡胶的物理力学性能,以满足具体的应用要求。
综上所述,NBR橡胶的配方设计需要综合考虑硬度、耐油性、耐溶剂性、耐热性、加工性能和物理力学性能等因素。
通过合理选择不同的添加剂和填料,可以获得满足不同应用要求的NBR橡胶配方。
EPDM的种类及配方设计

EPDM的种类及配方设计
一、EPDM介绍
EPDM (乙丙二烯橡胶,全部称为Ethylene Propylene Diene Monomer)是一种由乙烯,丙烯,二烯组成的一种特殊的橡胶类型。
它由抗氧化剂,硫化剂,活性剂,助剂,一定的金属粉末以及其它特殊添加剂组成。
它的特点是机械性能优异,耐水,耐微生物,耐植物一抗,耐油品,耐酸,耐碱,耐抗老化,UV和太阳,耐臭氧,耐老化等优点。
二、EPDM配方设计
EPDM橡胶的特殊性能使其在橡胶配方中具有最大的应用范围,以下是对EPDM橡胶的配方设计:
1、配方设计原则:在EPDM橡胶的配方设计时要满足以下原则。
(1)考虑橡胶原料的性能,并加以合理选择。
(2)考虑橡胶原料的性价比,合理配比,以降低成本。
(3)考虑橡胶成型后的性能,使产品达到所需要的性能要求。
2、EPDM橡胶的成分
(1)主要成分:乙丙二烯丙烯橡胶;
(2)辅助成分:多种添加剂,抗氧剂,硫化剂,活性剂,助剂,增塑剂,抗老化剂,环保护剂等。
3、EPDM橡胶的配方设计
(1)配方设计:乙丙二烯橡胶+抗氧化剂+硫化剂+活性剂+助剂+一定的金属粉末+其他特殊添加剂
(2)配方计算:一般情况下,抗氧化剂量为1-3%,硫化剂量为1-3%。
橡胶配方设计原理
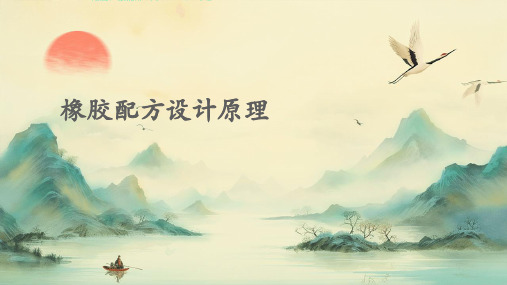
橡胶密封圈在受到外力作用后需要具有良好的弹性恢复性能,以保证密封效果。通常通过 调整配方中的硫化剂比例来实现。
06
橡胶配方设计的发展趋势和挑战
高性能橡胶材料的研发
高强度、高耐磨性
通过添加增强填料和改性剂,提高橡胶材料的强度和耐磨性,以 满足各种高负荷和高摩擦工况的要求。
高温性能和耐老化性能
通过选用耐高温和抗氧化的橡胶品种,以及添加抗老化剂,提高橡 胶材料在高温和老化条件下的性能表现。
电绝缘性和阻燃性
通过选用具有电绝缘性能和阻燃性能的橡胶品种,以及添加相应的 填料和助剂,提高橡胶材料的电绝缘性和阻燃性。
环保和可持续发展的要求
1 2 3
降低VOC排放
通过优化配方和生产工艺,降低橡胶制品在生产 和使用过程中产生的VOC排放,以减少对环境的 污染。
输送带覆盖胶配方设计
01
耐油性
输送带覆盖胶需要能够耐受各种油类物质的侵蚀,以保证输送带的正常
运行。通常通过添加适量的耐油剂来提高覆盖胶的耐油性。
02
抗磨损性
输送带在运行过程中会不断与物料和托辊摩擦,因此覆盖胶需要具备良
好的抗磨损性能。通常通过添加炭黑等填料来提高覆盖胶的抗磨损性能。
03
耐高温能
输送带在运行过程中会受到高温的影响,因此覆盖胶需要具备较好的耐
橡胶的化学性质
可塑性
耐热性和耐寒性
通过添加塑化剂来改变橡胶的可塑性, 使其更易于加工。
不同种类的橡胶具有不同的耐热和耐 寒性能。
耐油性
橡胶能够抵抗某些油类、溶剂和化学 品的侵蚀。
03
橡胶配方设计原则
橡胶的硫化体系
硫化剂
选择合适的硫化剂,如硫磺、多 硫化物等,以实现橡胶的交联反 应,提高橡胶的力学性能和耐热
耐热橡胶的选择

耐热橡胶的选择(技术支持来自)胶种选择:·乙丙橡胶随丙烯含量增加,耐热下降·丁基橡胶一般丁基橡胶使用温度不超过150度。
只有树脂硫化的丁基橡胶才能在150-180度下长期工作。
在一般丁基橡胶中并用10-20份的氯丁橡胶或氯磺化聚乙烯可以提高耐热性。
氯化丁基橡胶的耐热性与硫化体系有关,一般氯化丁基橡胶,长时间使用最高温度为130-150,无空气时为160-170度。
·卤化丁基橡胶·氯磺化聚乙烯橡胶。
氯磺化聚乙烯长期(1000H)最高使用温度为130度。
短时间可以允许升高到160度。
·氯醇橡胶。
耐热性比丁晴橡胶好。
均聚CHR比共聚CHR耐热性好。
·丙烯酸酯耐热性高于丁晴橡胶,低于氟橡胶。
长期(1000H)使用温度为170度,短时间(70H)使用温度可以提高到200度,·硅橡胶。
按照化学结构分类:1.二甲基硅橡胶(MQ)2.甲基乙烯基硅橡胶(MVQ)3.甲基苯基硅橡胶(MPQ)4.甲基苯基乙烯基硅橡胶(MPVQ)5.亚苯基硅橡胶6.亚苯醚基硅橡胶7.氟硅橡胶8.晴硅橡胶9.硼硅橡胶==》耐热性最好。
可以在400度下长期工作,在420-480度下可以连续工作几个小时。
硅橡胶是所有橡胶中耐热等级最高的一种橡胶。
但不耐湿热老化。
-50到+100度:无限期长/120度:10-20年/150度:5-10年/205度:2-5年/260度:3个月-2年/315度:7天-2个月/370度:6H-7天/420度:10分钟-2H。
·氟橡胶。
按照化学组成分类如下:·含氟烯氢氟橡胶类:1.偏氟乙烯与三氟氯乙烯共聚物.国外品牌KEL-F。
国产品牌FPM2301/23022.偏氟乙烯与六氟丙烯共聚物。
国外品牌:VITONA;国产品牌:FPM2601/2602;3.偏氟乙烯,四氟乙烯,与六氟丙烯三元共聚物。
国外品牌:VITONB;国产品牌:FPM2464.四氟乙烯与丙烯共聚物。
橡胶配方设计的原则与表示形式

目录一、橡胶配方设计的原则1二、橡胶配方的表示形式1三、常见基础配方21、天然橡胶(NR)基础配方22、丁苯橡胶(SBR)基础配方23、氯丁橡胶(CR)基础配方24、丁基橡胶(IIR)基础配方25、丁腈橡胶(NBR)基础配方36、顺丁橡胶(BR)基础配方37、异戊橡胶(IR)基础配方38、三元乙丙橡胶(EPDM)基础配方39、氯磺化聚乙烯(CSM)基础配方410、氯化丁基橡胶(CIIR)基础配方411、聚硫橡胶(PSR)基础配方412、丙烯酸酯橡胶(ACM)基础配方513、混炼型聚氨酯橡胶(PUR)基础配方514、氯醇橡胶(CO)基础配方515、氟橡胶(FKM)基础配方516、硅橡胶(Q)基础配方5四、汽车轮胎配方61、国外载重汽车轮胎胎面胶配方62、国内载重汽车轮胎胎面胶配方63、载重汽车轮胎胎体胶配方74、胎圈胶胶料配方75、内胎和气门嘴垫胶的配方86、子午线轮胎胎面胶配方97、载重和轿车子午线轮胎胎侧胶配方98、带束层胶配方109、子午线轮胎胎体胶料配方1010、钢丝圈各部胶料配方11五、橡胶胶管配方111、普通胶管各部件胶料配方112、耐油胶管各部件胶料配方123、耐酸胶管配方13六、输送带配方131、普通输送带胶料配方132、特种性能输送带覆盖胶配方143、普通V带胶料配方154、汽车V带各部件胶料配方155、同步带胶料配方166、胶布制品胶料配方16七、密封与减震配方171、耐油O型圈胶料配方172、油封胶料配方183、制动皮碗胶料配方194、橡胶密封条胶料配方195、汽车橡胶减震器胶料配方206、橡胶空气弹簧胶料配方207、各种胶板胶料配方218、防水卷材胶料配方229、不同防腐橡胶衬里胶料配方2210、各种橡胶衬里与金属黏合用胶浆胶料配方23八、其它用途配方241、造纸胶辊胶料配方242、印染、砻谷、印刷胶辊胶料配方253、纺纱皮圈橡胶配方254、各种纺织皮辊胶料配方265、几种食品用橡胶制品胶料配方26橡胶配方大全一、橡胶配方设计的原则1、保证硫化胶具有指定的技术性能,使产品优质;2、在胶料和产品制造过程中加工工艺性能良好,使产品达到高产;3、成本低、价格便宜;4、所用的生胶、聚合物和各种原材料容易得到;5、劳动生产率高,在加工制造过程中能耗少;6、符合环境保护及卫生要求;任何一个橡胶配方都不可能在所有性能指标上达到全优。
耐热橡胶的配方设计

耐热橡胶的配方设计耐热性是指橡胶及其制品在经受长时间热老化后保持物理机械性能或使用性能的能力,耐温性表示橡胶物理机械性能对温度的敏感性,即在高温条件下,橡胶的力学性能基本不下降的这种性质。
高温时物理机械性能与室温时的差别小,即耐温性好。
表明橡胶物理机械性能随(测试)温度的变化。
高温使用的(耐热)橡胶制品,既要耐热性好,也要耐温性好。
评价耐热性的方法多种多样,如用马丁耐热与维卡耐热评定耐热程度,也可通过热失重仪找出分解温度作为材料的使用温度的上限,或者用真空加热40~45min时,质量减少50%的温度(Tn)———半寿命温度来评估耐热性耐热橡胶是指在高温条件下长时间使用时仍能保持原有力学性能和使用价值的硫化橡胶,常用热老化后性能变化量(如硬度)、性能变化率(如拉伸强度、伸长率)、性能保持率、老化系数表示其力学性能的变化情况。
在橡胶密封制品中,硫化橡胶在压缩状态下的耐热性能称耐热压缩性能,它常由压缩永久变形系数或压缩应力松弛系数评价。
在80℃以上长期使用后仍能基本保持原有性能和使用价值的橡胶都归于“耐热橡胶”的范畴,橡胶制品的耐热和高温性能是橡胶特殊性能中最常见的一种性能。
橡胶在这种情况下性能稳定的本质原因是在高温下能够抵抗氧、臭氧、腐蚀性化学物质、高能辐射以及机械疲劳等因素的影响,橡胶分子结构不发生显著变化和损坏,且能够保持较好的使用性能。
使用温度范围/℃适用的橡胶<70各种橡胶70~100天然橡胶、丁苯橡胶100~130氯丁橡胶、丁腈橡胶、氯醚橡胶130~150丁基橡胶、乙丙橡胶、氯磺化聚乙烯橡胶150~180丙烯酸酯橡胶、氢化丁腈橡胶180~200乙烯基硅橡胶、氟橡胶200~250二甲基硅橡胶、氟橡胶>250全氟醚橡胶、氟硅橡胶、硼硅橡胶国标橡胶的耐温性能可分为以下两档五类普通橡胶A-70~-30℃/90~120℃,例如NR、IR、BR、237SBR、CR。
普通橡胶B-40~-20℃/120~150℃,例如NBR、IIR、EPDM、CSM。
橡胶配方设计
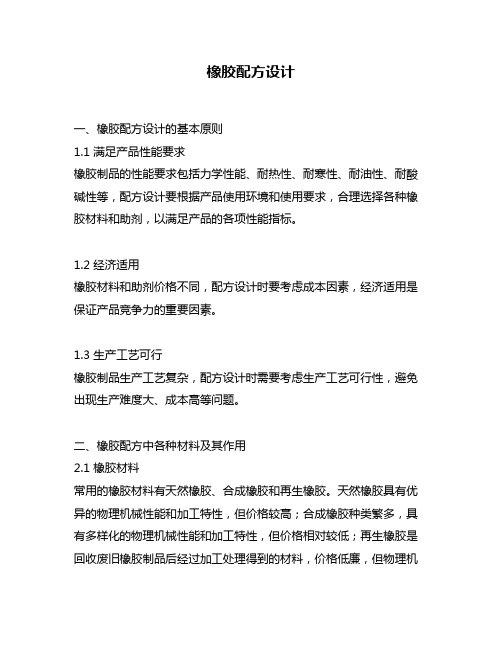
橡胶配方设计一、橡胶配方设计的基本原则1.1 满足产品性能要求橡胶制品的性能要求包括力学性能、耐热性、耐寒性、耐油性、耐酸碱性等,配方设计要根据产品使用环境和使用要求,合理选择各种橡胶材料和助剂,以满足产品的各项性能指标。
1.2 经济适用橡胶材料和助剂价格不同,配方设计时要考虑成本因素,经济适用是保证产品竞争力的重要因素。
1.3 生产工艺可行橡胶制品生产工艺复杂,配方设计时需要考虑生产工艺可行性,避免出现生产难度大、成本高等问题。
二、橡胶配方中各种材料及其作用2.1 橡胶材料常用的橡胶材料有天然橡胶、合成橡胶和再生橡胶。
天然橡胶具有优异的物理机械性能和加工特性,但价格较高;合成橡胶种类繁多,具有多样化的物理机械性能和加工特性,但价格相对较低;再生橡胶是回收废旧橡胶制品后经过加工处理得到的材料,价格低廉,但物理机械性能和加工特性相对较差。
2.2 填料填料是橡胶配方中的重要组成部分,可以改善橡胶制品的力学性能、耐热性、耐寒性等特性。
常用的填料有碳黑、白炭黑、滑石粉、硅灰等。
2.3 功能助剂功能助剂可以改善橡胶制品的物理机械性能、加工特性和使用寿命。
常用的功能助剂有增塑剂、硫化剂、促进剂等。
2.4 加工助剂加工助剂可以提高橡胶混炼和成型的效率和质量。
常用的加工助剂有防老化剂、润滑剂等。
三、橡胶配方设计流程3.1 确定产品要求根据产品使用环境和使用要求,确定产品各项指标要求,如强度、硬度、耐磨损性等。
3.2 选择合适数量级的材料根据产品要求和经济适用原则,选择合适数量级的橡胶材料、填料和助剂。
3.3 设计初步配方根据所选材料的特性和配比原则,设计初步配方,并进行小批量试制,测试各项性能指标。
3.4 优化配方根据试制结果,对配方进行优化调整,再次试制并测试各项性能指标,直至达到产品要求。
3.5 稳定生产确定最终配方后,进行大批量生产,并对生产过程中的各项参数进行控制和调整,保证产品稳定性能。
四、橡胶配方设计常见问题及解决方法4.1 配方中填料过多或过少导致产品性能不稳定。
橡胶的配方设计
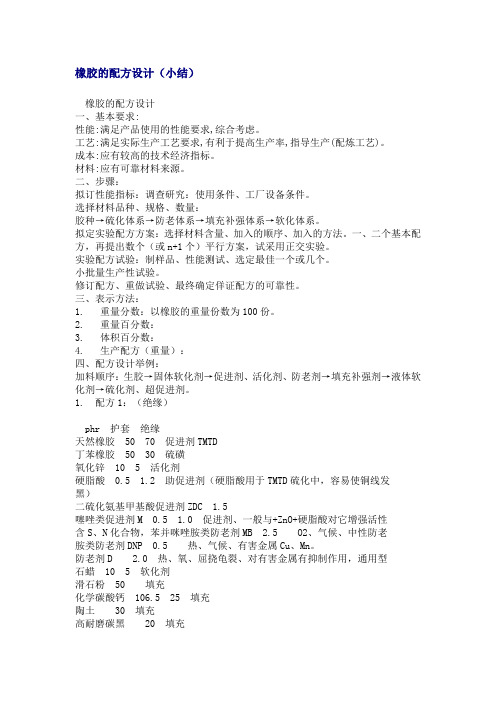
橡胶的配方设计(小结)橡胶的配方设计一、基本要求:性能:满足产品使用的性能要求,综合考虑。
工艺:满足实际生产工艺要求,有利于提高生产率,指导生产(配炼工艺)。
成本:应有较高的技术经济指标。
材料:应有可靠材料来源。
二、步骤:拟订性能指标:调查研究:使用条件、工厂设备条件。
选择材料品种、规格、数量:胶种→硫化体系→防老体系→填充补强体系→软化体系。
拟定实验配方方案:选择材料含量、加入的顺序、加入的方法。
一、二个基本配方,再提出数个(或n+1个)平行方案,试采用正交实验。
实验配方试验:制样品、性能测试、选定最佳一个或几个。
小批量生产性试验。
修订配方、重做试验、最终确定佯证配方的可靠性。
三、表示方法:1. 重量分数:以橡胶的重量份数为100份。
2. 重量百分数:3. 体积百分数:4. 生产配方(重量):四、配方设计举例:加料顺序:生胶→固体软化剂→促进剂、活化剂、防老剂→填充补强剂→液体软化剂→硫化剂、超促进剂。
1. 配方1:(绝缘)phr 护套绝缘天然橡胶 50 70 促进剂TMTD丁苯橡胶 50 30 硫磺氧化锌 10 5 活化剂硬脂酸 0.5 1.2 助促进剂(硬脂酸用于TMTD硫化中,容易使铜线发黑)二硫化氨基甲基酸促进剂ZDC 1.5噻唑类促进剂M 0.5 1.0 促进剂、一般与+ZnO+硬脂酸对它增强活性含S、N化合物,苯并咪唑胺类防老剂MB 2.5 O2、气候、中性防老胺类防老剂DNP 0.5 热、气候、有害金属Cu、Mn。
防老剂D 2.0 热、氧、屈挠龟裂、对有害金属有抑制作用,通用型石蜡 10 5 软化剂滑石粉 50 填充化学碳酸钙 106.5 25 填充陶土 30 填充高耐磨碳黑 20 填充配方2:材料配比/phrCR232 100 氯丁橡胶氧化镁(特级) 4 硫化剂FEF碳黑 25 快压出炉黑SRF碳黑 15 半补强炉黑陶土 50 填充剂氢氧化铝 30 阻然剂氧化锌 5 硫化剂NA—22 1.2 硫脲类促进剂DM 0.5 硫化延迟剂、促进剂DM石蜡 3 软化剂硬脂酸 0.5 软化剂DOP 10 增塑剂、临苯二甲酸二辛脂防老剂ODA 4 防老剂OD、胺类防老剂、P396手册。
- 1、下载文档前请自行甄别文档内容的完整性,平台不提供额外的编辑、内容补充、找答案等附加服务。
- 2、"仅部分预览"的文档,不可在线预览部分如存在完整性等问题,可反馈申请退款(可完整预览的文档不适用该条件!)。
- 3、如文档侵犯您的权益,请联系客服反馈,我们会尽快为您处理(人工客服工作时间:9:00-18:30)。
善贞课堂—耐热橡胶的配方设计选材原则,学习一下
耐热橡胶是指在高温条件下长时间使用后,仍能保持原有力学性能和使用价值的硫化橡胶。
耐热橡胶常用橡胶热老化前后性能变化量(如硬度)、性能变化率(如拉伸强度、伸长率)、性能保持率等表示其力学性能的变化情况。
过去几十年来,耐热橡胶制品的范围在不断扩大,原因在于:第一,若干传统制品过去并不要求耐热,而随着使用条件的变化,也相继提出耐热要求。
典型例子如轮胎。
由于车速的加快,滚动生热大幅上升,提高耐热性是必须跨越的门槛。
其他橡胶制品也有类似情况。
第二,橡胶制品与各种热介质(如各种润滑油、制动油、液压油)等的接触机会增加,温度也大大超过常温。
第三,为了顺应橡胶工业自身在加工中的耐热需要,例如轮胎硫化所用的水胎、胶囊都需在170°C~180°C 的温度下长期使用,挤出制品的连续硫化更得在200°C 以上的高温下进行,它们都必须具备耐热和抗返原的特性。
橡胶在高温即热氧作用下,橡胶大分子会发生降解、交联、环化、异构化,活性填料会与橡胶分子发生进一步的作用,交联键产生断裂、环化或重新交联,橡胶内低分子物质产生挥发、分解。
橡胶的耐热性与橡胶分子结构和组分、温度、机械作用和介质有密切关系。
从配方设计的角度考虑,要提高橡胶制品的耐热性,主要通过如下三种途径:
第一是选择对热和氧稳定性好,其化学结构具有高耐热性的橡胶,选用合成新型橡胶,使其化学结构具有高的耐热性;
第二是在选用橡胶品种的基础上,选择耐热的硫化体系来改善硫化胶的耐热性;
第三是发展优良的稳定剂系统,以提高橡胶制品对热和氧的防护能力。
所以总的说来,主要通过生胶的牌号、硫化体系、防护体系、填料、增塑体系来综合考虑。
关于耐热橡胶的温度范围,迄今缺乏统一的认识,但在选择耐热橡胶时一般考虑以下几个方面:
耐热性条件:短时耐热温度、连续使用温度、介质
耐热老化性的表征:性能保持率/变化率、外观变化情况
耐热橡胶配方设计涉及到主体材料、硫化体系、防护体系和抗返原剂的正确选用,以及它们之间的协调配合。
一、橡胶品种的选择
各胶种的耐热等级不等,但并非说设计时非得局限于几种高耐热生胶不可,还得考虑所要求的耐热上限和配方设计上的协调配合,寻找出最佳的使用效果/成本平衡点,首先要掌握好主体材料的选用,为此应透彻了解产品的实际使用温度及持续时间。
这种选择对配方人员来说往往因人而异,但大体上有如下共识。
由此可见,生胶的耐温等级很大程度上取决于分子结构,主链为杂链的耐温性优于碳链的;主链上不饱和度低的优于高的,饱和结构则更好;侧链含卤族原子或极性基团的也都有较好的耐热性。
主体材料一般可单用或并用,当遇到一种胶不足以满足要求时,就得借助于两种耐热胶种的并用来达到互补。
并用对象也可选用合成树脂,往往能产生协同效应。
如丁腈/聚氯乙烯。
有时,产品除了耐热之外还有其他要求,单一胶种往往难以兼顾,也须借助于并用。
橡胶的分子结构对制品的耐热性起决定性的作用,在耐热橡胶配方中,一般选用高温下不易软化、热稳定性和化学稳定性高的品种。
某些橡胶在高温下变软的程度取决于大分子的极性,因此,所有提高橡胶的极性,例如在橡胶分子中引入腈基、酯基、羟基、氯原子、氟原子等极性基团都有助于提高耐热性。
例如NBR、ACM、CO/ECO等。
橡胶的热稳定性取决于化学键的性质。
聚合物热反应程度与聚合物的结构及化学键的强度有关。
在橡胶中减少弱键的数量,提高其键能,可以提高耐热性。
例如用耐热的无机元素取代主链上的碳原子,如VMQ等,或使用那些具有高键能的聚合物,如FPM等,将获得优异的耐热性。
橡胶的化学稳定性是耐热的重要因素之一。
橡胶的热老化主要起因于持续的自动氧化作用。
自动氧化是以橡胶大分子中特别弱的键产生的自由基为引发点,派生出许多自由基,持续反复生成和分解过氧化物的链锁反应。
具有较高的化学稳定性的橡胶在结构上应避免不饱和结构和支链结构。
二、硫化体系的选择
硫化体系在硫化过程中的任务是在橡胶大分子之间进行交联、架挢。
由于不同交联剂提供的交联键的键能不等而使硫化胶的耐热程度也不等,即使同样是硫键,单硫键、双硫键和多硫键,因键能不等而导致硫化胶的耐热性大相径庭。
几种不同硫化体系所提供的交联结构和耐热程度都不同,如下表所示:
各种交联键的键能和吸氧速度不同。
键能越大则硫化胶的耐热性越好,吸氧速度越慢,硫化胶的耐热氧化性能越好。
为了获得耐热的交联键,应使用低硫高促系统、有效硫化体系、过氧化物硫化体系或其他无硫硫化系统,其中过氧化物硫化体系的耐热性最好。
一般来说,EPDM、CSM、EVA、CPE 都可以用过氧化物硫化,最好是用某些共交联剂或活性剂并用。
过氧化物也可以使NBR达
到满意的硫化,或选用镉镁硫化体系;但NR、SBR和BR使用过氧化物硫化时则效果不是很好,而IIR不能用过氧化物硫化,而树脂硫化的IIR耐热性最好。
FPM用二元酚/苄基三苯基氯化磷或二元酚/四丁基氢氧化铵硫化时,其耐热性优于多胺交联的FPM。
采用过氧化物硫化时,必须并用共交联剂。
三、防护体系的选择
为防止合成橡胶在储存过程中氧化,许多合成橡胶在合成过程中加入少量的抗氧剂,但对高温下长期使用的耐热橡胶而言这是远远不够的,因此在耐热橡胶配方中必须选择高效耐热防老剂。
但由于防老剂的最大用量通常受到其在胶料中的溶解度所限制,所以一般采用具有协同效应的几种防老剂并用。
相对而言,一般防老剂是一些相对分子量较低的物质,橡胶制品在高温下使用过程中,防老剂在高温过程中容易挥发、迁移而迅速消耗,从而减小或丧失对橡胶的防老化功能,引起制品损坏。
例如,在120℃下放置1h,防老剂D、BLE、4010NA、264分别挥发了45%、45%、88%、96%。
可见,在耐热橡胶配方中,必须选择挥发性小、分子量大、熔点较高的防老剂。
最好是使用能与橡胶进行化学结合的聚合型或反应型防老剂,这样可以降低防老剂的损耗。
四、填充体系的影响
一般无机填料比炭黑有更好的耐热性,在无机填料中对耐热配方比较适用的有白炭黑、活性氧化锌、氧化镁、氧化铝和硅酸盐。
炭黑的粒径越小,硫化胶的耐热性越低;白炭黑则可以提高其耐热性;氧化镁和氧化铝对提高橡胶的耐热性有一定的效果。
五、增塑体系的影响
一般软化剂的分子量较低,在高温下容易挥发或迁移渗出,导致硫化胶硬度增加、伸长率降低。
所以耐热橡胶配方中应选用高温下热稳定性好,不易挥发的品种,例如高闪点的石油系油类,分子量大、软化点高的聚酯类增塑剂,以及某些低分子量的齐聚物(如液体橡胶等),且用量不宜过大。
例如,耐热的NBR最好使用古马隆树脂、苯乙烯-茚树脂、聚酯和LNBR 作软化剂。
EPDM采用高闪点的环烷油和石蜡油作软化剂。
善贞实业为客户提供合适的产品和完善服务,以下多种原材料可供客户做耐热橡胶
的参考选择,另外我们的工厂,安徽立信有着多年的混炼胶经验,生产全系列混炼
胶,为客户生产高品质产品保驾护航,我们期待为您服务!汪生139
7582。