SMT产品常见不良及其原因分析
SMT不良产生原因及其对策

SMT不良产生原因及对策零件反向产生的原因:1:人工手贴贴反2:来料有个别反向3;机器FEEDER坏或FEEDER振动过大(导致物料反向)振动飞达4:PCB板上标示不清楚(导致作业员难以判断)5:机器程式角度错6:作业员上料反向(IC之类)7:核对首件人员粗心,不能及时发现问题8:炉后QC也未能及时发现问题对策:1:对作业员进行培训,使其可以正确的辨别元器件方向2:对来料加强检测3:维修FEEDER及调整振动FEEDER的振动力度(并要求作业员对此物料进行方向检查)4:在生产当中要是遇到难以判断元器件方向的。
一定要等工程部确定之后才可以批量生产,也可以SKIP5:工程人员要认真核对生产程式,并要求对首件进行全检(特别要注意有极性的元件)6:作业员每次换料之后要求IPQC核对物料(包括元件的方向)并要求作业员每2小时必须核对一次物料7:核对首件人员一定要细心,最好是2个或以上的人员进行核对。
(如果有专门的IPQC的话也可以要求每2小时再做一次首件)8:QC检查时一定要用放大镜认真检查(对元件数量多的板尽量使用套版)少件(缺件)产生的原因:1:印刷机印刷偏位2:钢网孔被杂物或其它东西给堵塞(焊盘没锡而导致飞件)3:锡膏放置时间太久(元器件不上锡而导致元件飞件)4:机器Z轴高度异常5:机器NOZZLE上有残留的锡膏或胶水(此时机器每次都可以识别但物料放不下来导致少件)6:机器气压过低(机器在识别元件之后气压低导致物料掉下)7:置件后零件被NOZZLE吹气吹开8:机器NOZZLE型号用错9:PCB板的弯曲度已超标(贴片后元件弹掉)10:元件厚度差异过大11:机器零件参数设置错误12:FEEDER中心位置偏移13:机器贴装时未顶顶针14:炉前总检碰撞掉落对策:1:调整印刷机(要求印刷员对每一PCS印刷好的进行检查)2:要及时的清洗钢网(一般5-10PCS清洗一次)3:按照(锡膏储存作业指导书)作业,锡膏在常温下放置一定不能超过24小时4:校正机器Z轴(不能使机器NOZZLE放置零件时Z轴离PCB板过高。
SMT不良产生原因及对策

SMT不良产生原因及对策SMT(Super Multi-vision Test)不良产生原因及对策是电子制造行业中一个重要的话题。
在电子制造过程中,SMT是一种常用的组装技术,它涉及到大量的元件的高速表面安装。
然而,在实践中,SMT不良很常见,它可能会导致产品质量下降、生产效率降低以及成本增加。
因此,了解不良产生的原因,并采取相应的对策,对于提高SMT生产的质量和效率至关重要。
1.材料问题:SMT使用的元件和焊料可能存在质量问题。
元件可能存在焊盘偏移、引脚损坏、尺寸不一致等问题。
焊料可能存在含波点、气孔等质量问题。
2.设备问题:SMT设备的故障或不当使用也可能引起不良。
设备的加热、输送、贴装等环节可能存在问题,导致元件无法准确地安装在PCB上。
3.操作问题:操作人员操作不当、技术不到位也是不良产生的原因之一、操作人员可能存在操作失误、程序设置错误、参数调整不当等问题。
为了解决SMT不良的问题,可以采取以下对策:1.强化质量管理:确保元件和焊料的质量。
从可靠的供应商购买元件和焊料,并对其进行严格的质量检查。
对于质量问题严重的供应商,需要采取相应的措施,如更换供应商。
2.维护和保养设备:定期对SMT设备进行维护和保养,以确保其正常运行。
培训操作人员,让他们掌握设备的正确使用方法,并确保操作人员具备相关的技术能力。
3.检查和修正操作问题:建立操作规程,并进行培训,确保操作人员按照规程操作。
同时,建立检查机制,及时发现和纠正操作问题。
定期举行会议,分享操作问题和经验,以便全员学习和提高。
4.强化数据分析和改进活动:建立良好的数据收集和分析体系,及时发现生产过程中的问题,并采取改进措施。
定期评估数据,评估改进措施的效果,及时调整和完善。
5.推行持续改进:将持续改进的理念贯穿于整个SMT生产过程中。
不断寻找不良产生的原因,通过改进工艺流程、优化设备和培训操作人员等方式,降低不良的发生率。
总结起来,SMT不良产生的原因有材料问题、设备问题和操作问题等。
SMT不良原因及对策

3、上料员上料方向上反;
3、上料前对材料方向进行确认;
4、FEEDER 压盖变开导致,元件供给时方向; 4、维修或更换 FEEDER 压盖;
5、机器归正件时反向;
5、修理机器归正器;
6、来料方向变更,盘装方向变更后程序未变 6、发现问题时及时修改程序;
更方向;
7、Q、V 轴马达皮带或轴有问题。
7、检查马达皮带和马达轴。
11、检查 783 或驱动箱风扇;
12、MPA3 吸咀定位锁磨损导致吸咀晃动造成 12、更换 MAP3 吸咀定位锁。
贴装偏移。
1、PCB 焊盘上有惯穿孔; 2、钢网开孔过小或钢网厚度太薄; 3、锡膏印刷时少锡(脱膜不良); 4、钢网堵孔导致锡膏漏刷。
1、原材料不良; 2、规正器不顺导致元件夹坏; 3、吸着高度或贴装高度过低导致; 4、回焊炉温度设置过高; 5、料架顶针过长导致; 6、炉后撞件。
3、回焊炉升温过快导致;
3、调整回流焊升温速度 90-120sec;
4、元件贴装偏移导致;
4、调整机器贴装座标;
5、钢网开孔不佳(厚度过厚,引脚开孔过长, 5、重开精密钢网,厚度一般为 0.12mm-0.15mm;
开孔过大);
6、锡膏无法承受元件重量;
6、选用粘性好的锡膏;
7、钢网或刮刀变形造成锡膏印刷过厚;
4、锡膏中有异物;
4、印刷过程避免异物掉过去;
5、炉温设置过高或反面元件过重;
5、调整炉温或用纸皮垫着过炉;
6、机器贴装高度过高。
6、调整贴装高度。
错件
1、机器贴装时无吹气抛料无吹气,抛料盒毛 1、检查机器贴片吹气气压抛料吹气气压抛料盒毛刷;
刷不良;
2、贴装高度设置过高元件未贴装到位;
SMT产品常见不良及其原因分析_产品不良的分类

SMT产品常见不良及其原因分析_产品不良的分类SMT 产品常见不良及其原因分析_产品不良的分类SMT 常见不良及其原因分析一. 主要不良分析主要不良分析.锡珠(Solder Balls):1. 丝印孔与焊盘不对位,印刷不精确,使锡膏弄脏PCB 。
2. 锡膏在氧化环境中暴露过多、吸空气中水份太多。
3. 加热不精确,太慢并不均匀.4. 加热速率太快并预热区间太长。
5. 锡膏干得太快。
6. 助焊剂活性不够。
7. 太多颗粒小的锡粉。
8. 回流过程中助焊剂挥发性不适当。
锡球的工艺认可标准是:当焊盘或印制导线的之间距离为0.13mm 时,锡珠直径不能超过0.13mm ,或者在600mm平方范围内不能出现超过五个锡珠。
锡桥(Bridge solder):1. 锡膏太稀, 包括锡膏内金属或固体含量低、摇溶性低、锡膏容易榨开.2. 锡膏颗粒太大、助焊剂表面张力太小.3. 焊盘上太多锡膏.4. 回流温度峰值太高等.开路(Open):1. 锡膏量不够.2. 组件引脚的共面性不够.3. 锡湿不够(不够熔化、流动性不好) ,锡膏太稀引起锡流失.4. 引脚吸锡(象灯芯草一样) 或附近有联机孔. 引脚吸锡可以通过放慢加热速度和底面加热多、上面加热少来防止.5. 焊锡对引脚不熔湿, 干燥时间过长引起助焊剂失效、回流温度过高/时间过长引起氧化.6. 焊盘氧化, 焊锡没熔焊盘.墓碑(Tombstoning/Part shift):墓碑通常是不相等的熔湿力的结果,使得回流后组件在一端上站起来, 一般加热越慢,板越平稳,越少发生。
降低装配通过183° C 的温升速率将有助于校正这个缺陷。
空洞:是锡点的X 光或截面检查通常所发现的缺陷。
空洞是锡点内的微小“气泡”, 可能是被夹住的空气或助焊剂。
空洞一般由三个曲线错误所引起:不够峰值温度;回流时间不够;升温阶段温度过高。
造成没挥发的助焊剂被夹住在锡点内。
这种情况下,为了避免空洞的产生,应在空洞发生的点测量温度曲线,适当调整直到问题解决。
SMT常见障碍及原因分析

SMT常见障碍及原因分析引言本文档旨在分析SMT(表面贴装技术)常见障碍及其原因,帮助读者了解和解决可能出现的问题。
SMT是一种常用的电子元件安装技术,但在实践中常常遇到一些挑战和障碍。
通过深入分析这些障碍及其产生的原因,我们可以更好地发展解决方案,以提高SMT的效率和可靠性。
常见障碍及原因分析1. 部件丢失或错位原因分析:- 复印件问题:复印件质量不佳或被污染。
- 供应链问题:供应商错误地发送错误的零件,导致部件丢失或错位。
- 操作错误:操作人员在组装过程中未注意到部件的正确位置或固定不当。
2. 焊接不良或不完整原因分析:- 材料问题:使用低质量或劣质的焊接材料,导致焊接不牢固或不完整。
- 设备问题:焊接设备故障或操作不当,导致焊接不良。
- 操作问题:操作人员没有按照正确的焊接方法进行操作,导致焊接不完整。
3. 焊盘损坏原因分析:- 设计问题:焊盘设计质量不佳,容易受到外力或温度变化的影响而损坏。
- 加工问题:焊盘加工过程中出现错误或质量控制不当,导致焊盘损坏。
- 使用问题:操作人员在焊盘使用过程中未按照正确的操作方法,导致焊盘损坏。
4. 流量控制问题原因分析:- 设备问题:流量控制设备故障或操作不当,导致流量控制失效。
- 程序设计问题:流量控制程序设计不合理或存在错误,导致无法正确控制流量。
- 材料问题:使用不合适的流量控制材料,导致流量控制不稳定或无法满足要求。
结论本文对SMT常见障碍进行了分析并列举了可能产生这些障碍的原因。
在实践中,了解和解决这些问题是提高SMT效率和可靠性的关键。
为确保SMT工艺的成功应用,建议定期检查并维护设备,选择高质量的材料和零件,并对操作人员进行培训,以保证正确操作。
SMT常见不良鱼骨图分析

对PCB板进行烘烤,去除潮气。 选用优质的焊锡材料,减少杂质含量。
错件
01
错件产生原因
02 贴片程序中未正确设置器件参数,导致机器无法 识别器件。
03 操作员未按照作业指导书操作,导致器件贴错。
错件
器件包装不良,导致取料时出现错误 。
PCB板放置位置不正确,导致取料时 出现错误。
错件
改善措施
1
smt常见不良鱼骨图分 析
目录 CONTENT
• SMT常见不良现象 • 原因分析 • 解决方案 • 预防措施
01
SMT常见不良现象
锡珠
总结词
锡珠是指在焊接过程中,多余的焊锡 在PCB板上形成的小球状焊锡。
详细描述
锡珠可能是由于焊锡量过多、焊剂过 量、加热不足或加热时间过长等原因 造成的。锡珠可能导致电路短路、元 器件短路、降低产品可靠性等问题。
错件
总结词
错件是指在SMT贴片过程中,将元器件贴错位置或贴错型号 的现象。
详细描述
错件可能是由于操作员疏忽、程序错误、标签错误等原因造 成的。错件可能导致电路功能异常、产品性能
偏位是指元器件在PCB板上的位置与设计要求存在偏差的现象。
详细描述
偏位可能是由于贴片程序错误、操作员操作失误、焊锡量不足等原因造成的。 偏位可能导致电路性能不稳定、产品可靠性降低等问题。
立碑
总结词
立碑是指SMT贴片元件的一端或两端翘起,形成类似碑文的效果。
详细描述
立碑可能是由于元件吸嘴选择不当、元件本身翘曲、焊膏量不足等因素引起的。 为了预防立碑问题,可以选用适合的元件吸嘴,确保吸力适中;加强元件存储和 使用管理,避免元件翘曲;控制焊膏的量,确保焊点饱满等。
SMT不良产生原因及解决办法

零件反向产生的原因:1:人工手贴贴反2:来料有个别反向3;机器FEEDER 坏或FEEDER 振动过大(导致物料反向)振动飞达4:PCB 板上标示不清楚(导致作业员难以判断)5:机器程式角度错6:作业员上料反向(IC 之类)7:核对首件人员粗心,不能及时发现问题8:炉后QC 也未能及时发现问题对策:1:对作业员进行培训,使其可以正确的辨别元器件方向2:对来料加强检测3:维修FEEDER 及调整振动FEEDER 的振动力度(并要求作业员对此物料进行方向检查)4:在生产当中要是遇到难以判断元器件方向的。
一定要等工程部确定之后才可以批量生产,也可以SKIP5:工程人员要认真核对生产程式,并要求对首件进行全检(特别要注意有极性的元件)6:作业员每次换料之后要求IPQC 核对物料(包括元件的方向)并要求作业员每2 小时必须核对一次物料7:核对首件人员一定要细心,最好是2 个或以上的人员进行核对。
(如果有专门的IPQC 的话也可以要求每2 小时再做一次首件)8:QC 检查时一定要用放大镜认真检查(对元件数量多的板尽量使用套版)少件(缺件)产生的原因:1:印刷机印刷偏位2:钢网孔被杂物或其它东西给堵塞(焊盘没锡而导致飞件)3:锡膏放置时间太久(元器件不上锡而导致元件飞件)4:机器Z 轴高度异常5:机器NOZZLE 上有残留的锡膏或胶水(此时机器每次都可以识别但物料放不下来导致少件)6:机器气压过低(机器在识别元件之后气压低导致物料掉下)7:置件后零件被NOZZLE 吹气吹开8:机器NOZZLE 型号用错9:PCB 板的弯曲度已超标(贴片后元件弹掉)10:元件厚度差异过大11:机器零件参数设置错误12:FEEDER 中心位置偏移13:机器贴装时未顶顶针14:炉前总检碰撞掉落对策:1:调整印刷机(要求印刷员对每一PCS 印刷好的进行检查)2:要及时的清洗钢网(一般5-10PCS 清洗一次)3:按照(锡膏储存作业指导书)作业,锡膏在常温下放置一定不能超过24 小时4:校正机器Z 轴(不能使机器NOZZLE 放置零件时Z 轴离PCB 板过高。
SMT制程不良原因及改善对策

SMT制程不良原因及改善对策SMT制程(Surface Mount Technology)是一种常用的电子组装技术,广泛应用于电子产品的制造过程中。
然而,由于各种原因所引起的不良现象在SMT制程中时有发生。
本文将讨论SMT制程不良原因以及改善对策。
1.焊接不良:焊接不良可以导致焊点虚焊、焊接断裂等问题。
常见的原因包括焊接温度不够、焊接时间不足、焊接设备不稳定等。
改善对策包括提高焊接设备的质量和稳定性、增加焊接温度和时间的控制精度等。
2.贴装不良:贴装不良可以导致元件偏移、元件漏贴等问题。
常见的原因包括贴装位置错误、贴装头磨损、胶垫损坏等。
改善对策包括提高贴装机的精度和稳定性、定期更换贴装头和胶垫等。
3.元件损坏:元件在SMT制程中容易受到机械损伤、电静电等因素的影响而受损。
改善对策包括提供合适的防护措施,如使用防静电设备、增加元件存储和运输的保护等。
4.焊盘不良:焊盘不良可以导致焊点接触不良、导致电路连通性问题。
常见的原因包括锡膏质量不佳、焊盘形状不准确等。
改善对策包括使用高质量的锡膏、提高焊盘生产过程的精度等。
5.引脚弯曲:引脚弯曲会导致元件无法正确插入或连接。
常见的原因包括元件存储和运输过程中引脚受到碰撞、搬运过程中的不当操作等。
改善对策包括提供合适的存储和运输保护措施、培训操作人员正确操作等。
改善SMT制程不良有很多对策,下面列举了其中一些常见的:1.提高设备的质量和稳定性:定期对设备进行维护和保养,确保其正常运行和精度稳定。
采用高质量的设备和工具,可大大降低不良率。
2.优化工艺参数:根据产品要求和设备特性,合理的调整焊接温度、焊接时间等工艺参数,以确保焊接效果和质量。
3.加强员工培训:提供必要的培训和指导,使操作人员熟悉SMT制程的原理和操作技巧,减少人为失误和操作不当导致的不良。
4.严格品质管理:建立完善的品质管理体系,包括设备校验、材料检测、过程控制等环节,确保产品质量稳定。
5.提供合适的存储和运输保护:对元件进行正确的存储和运输保护,避免机械损伤、静电损伤等因素导致的元件损坏。
SMT不良产生原因及解决办法

Surface mount technology(SMT)不良产生原因及对策零件反向产生的原因:1:人工手贴贴反2:来料有个别反向3;机器FEEDER坏或FEEDER振动过大(导致物料反向)振动飞达4:PCB板上标示不清楚(导致作业员难以判断)5:机器程式角度错6:作业员上料反向(IC之类)7:核对首件人员粗心,不能及时发现问题8:炉后QC也未能及时发现问题对策:1:对作业员进行培训,使其可以正确的辨别元器件方向2:对来料加强检测3:维修FEEDER及调整振动FEEDER的振动力度(并要求作业员对此物料进行方向检查)4:在生产当中要是遇到难以判断元器件方向的。
一定要等工程部确定之后才可以批量生产,也可以SKIP5:工程人员要认真核对生产程式,并要求对首件进行全检(特别要注意有极性的元件)6:作业员每次换料之后要求IPQC核对物料(包括元件的方向)并要求作业员每2小时必须核对一次物料7:核对首件人员一定要细心,最好是2个或以上的人员进行核对。
(如果有专门的IPQC的话也可以要求每2小时再做一次首件)8:QC检查时一定要用放大镜认真检查(对元件数量多的板尽量使用套版)少件(缺件)产生的原因:1:印刷机印刷偏位2:钢网孔被杂物或其它东西给堵塞(焊盘没锡而导致飞件)3:锡膏放置时间太久(元器件不上锡而导致元件飞件)4:机器Z轴高度异常5:机器NOZZLE上有残留的锡膏或胶水(此时机器每次都可以识别但物料放不下来导致少件)6:机器气压过低(机器在识别元件之后气压低导致物料掉下)7:置件后零件被NOZZLE吹气吹开8:机器NOZZLE型号用错9:PCB板的弯曲度已超标(贴片后元件弹掉)10:元件厚度差异过大11:机器零件参数设置错误12:FEEDER中心位置偏移13:机器贴装时未顶顶针14:炉前总检碰撞掉落对策:1:调整印刷机(要求印刷员对每一PCS印刷好的进行检查)2:要及时的清洗钢网(一般5-10PCS清洗一次)3:按照(锡膏储存作业指导书)作业,锡膏在常温下放置一定不能超过24小时4:校正机器Z轴(不能使机器NOZZLE放置零件时Z轴离PCB板过高。
SMT不良分析报告

空焊现象的产生可能是由于焊盘与焊料之间的润湿性差、焊点尺寸过小、焊接 温度过低等原因所致。空焊可能导致电气连接不良、机械连接不稳定等问题, 影响电子产品的性能和可靠性。
短路现象
总结词
短路是指SMT加工过程中,两个原本 不应该连接的焊点意外地形成了连接 的现象。
详细描述
短路现象的产生可能是由于焊料飞溅 、元器件贴装位置偏差、焊盘重叠等 原因所致。短路可能导致电路功能异 常、安全风险等问题,影响电子产品 的性能和可靠性。
提高焊接温度和时间
适当提高焊接温度和时间,确 保焊点充分熔融、浸润,减少 空焊现象的产生。
控制焊膏量
根据焊接需求,合理调整焊膏 量,确保焊点表面光滑、饱满 。
加强工艺控制
定期对设备和工艺进行检查和 校准,确保工艺稳定、可靠。
短路现象的预防措施
短路现象
在SMT工艺中,由于焊点之间存在杂质 或气泡等原因,可能导致焊接后出现短
锡珠
在焊接过程中,锡 膏熔化后形成的小 珠状突起。
冷焊
焊接点表面不光滑 ,呈现凹凸不平的 状态。
元件移位
元件在焊接过程中 位置发生偏移。
CHAPTER 02
SMT不良现象分析
锡珠现象
总结词
锡珠是指在SMT加工过程中,焊料在经过回流焊后形成的球状物,通常出现在焊 点周围。
详细描述
锡珠现象的产生通常是由于焊料在熔融状态下受到重力、表面张力以及温度梯度 的影响,导致焊料在冷却过程中无法完全回流,从而形成球状物。锡珠可能导致 电气连接不良、机械卡滞等问题,影响电子产品的性能和可靠性。
选用低残留焊膏
选择低残留、低松香含量的焊 膏,减少锡珠形成。
锡珠现象
在SMT工艺中,由于焊膏过多 或温度过高,导致焊膏在回流 过程中形成锡珠状残留物。
SMT不良分析及改善措施

板 模 2、开口不当
3、开口偏移
重新制作模板
4、模板太厚
5、
.
7
锡珠的产生原因与解决办法(二)
接焊
产生原因 1、预热区升温太急 2、保温区时间太短
3、焊接区温度太高
装 贴 1、贴片压力太大
2、 1、压力太小,使锡膏偏厚
刷 印 2、未对好位就开始印刷
3、未及时清洁模板
产生原因 1、板面氧化 2、有水份或污物
3、 1、焊端氧化 2、焊端有水份或污物 1、开口偏小
解决办法 PCB来料控制 清除PCB上的水份或污物
元件来料控制
板 模 2、毛刺过多
3、厚度太薄
重新制作模板 使用电抛光工艺
4、未及时清洗
及时清洗模板
5、
.
10
空焊的产生原因与解决办法(二)
刷印
产生原因 1、印刷压力太大 2、印刷速度太快
2、焊端有水份
3、焊端有污物
膏 锡 1、品质不好或变质
2、粘度太高 1、焊盘氧化
板 基 2、焊盘有水份或污物
3、焊盘上有过孔
4、焊盘大小不一
解决办法 元件来料控制 更换锡膏
清除PCB上的水份或污物 修改PCB Layout
5、小元件设计太靠近大颗黑色元件
.
12
墓碑的产生原因与解决办法(二)
产生原因 1、开口过大
焊
接 装贴
产生原因 1、焊接区升温太剧烈 2、回流炉内温度不均
3、履带运行时振动 1、贴件偏位
2、 1、印刷偏移
刷 印 2、印刷压力偏小
3、刮刀有磨损(缺口)
4、印刷机工作台不水平
解决办法 调整Reflow炉温 降低Reflow履带速度 检修Reflow
smt不良分析及改善措施
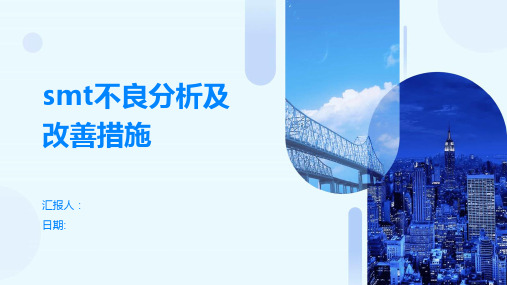
清洁保养
02
定期对设备表面进行清洁保养,保持设备整洁,防止灰尘、异
物等对设备造成损害。
润滑保养
03
按照设备制造商的推荐,定期对设备的运动部件进行润滑保养
,以减少磨损工艺文件,确保每个生产步骤都符合规范和标 准。
人员培训
对操作人员进行专业培训,确保他们熟悉设备的操作和维护,能 够及时发现并解决潜在问题。
总结词
PCB板的设计不合理可能会导致元件脱落、短路等问题。
详细描述
如果PCB板的线路设计不合理,可能会导致元件无法准确吸附在指定位置;如果 PCB板的焊盘设计不合理,则可能会导致短路或虚焊。因此,需要对PCB板的设 计进行严格审核和测试。
案例四:温度和湿度控制不当
总结词
温度和湿度控制不当可能会导致元件引脚氧化、焊接不良等问题。
工艺不良
温度异常
SMT生产线温度异常波动 ,导致零件贴装偏差、焊 接不良等
湿度异常
SMT生产线湿度异常波动 ,导致零件受潮、焊接不 良等
大气污染
SMT生产线大气污染严重 ,导致零件表面污染、焊 接不良等
管理不良
计划管理不良
生产计划不合理、生产安排不科 学等导致生产效率低下、产品质
量不稳定等不良现象
零件材质不良
零件材质不达标,如PCB 板材质不均、零件镀层不 均匀等
零件质量不良
零件本身存在质量问题, 如气泡、划痕等
设备不良
贴片机不良
贴片机精度下降、机械故障等导 致贴装位置偏差、零件损坏等不
良现象
印刷机不良
印刷机精度下降、机械故障等导致 印刷不均匀、印刷错误等不良现象
检测设备不良
检测设备精度下降、机械故障等导 致检测不准确、误判等不良现象
SMT制程常见异常分析

SMT制程常见异常分析SMT制程(表面贴装技术)是一种在电子元件制造中常用的制程技术,用于将电子元件贴装在印刷电路板(PCB)上。
然而,在SMT制程中,常会出现一些异常情况,如焊接不良、元件丢失等问题。
本文将针对SMT制程常见的异常进行分析。
1.焊接不良:焊接不良是SMT制程中常见的问题之一、焊接不良可能由于锡膏的质量问题、焊垫的尺寸偏差、焊接设备的操作不当等原因引起。
常见的焊接不良有焊接剪切、焊锡球、云母等问题。
焊接不良会导致元件与PCB之间的电连接不良,影响产品的性能和可靠性。
2.元件丢失:元件丢失是SMT制程常见的问题之一、元件丢失可能由于操作不当、元件自身缺陷、供应链问题等原因引起。
元件丢失会导致产品的功能性能下降,严重的情况下可能导致产品不能正常工作。
3.印刷问题:印刷问题是SMT制程中常见的问题之一、印刷问题可能由于锡膏的质量问题、印刷设备的操作不当、PCB的表面不平整等原因引起。
常见的印刷问题有锡膏剪切、印刷偏移、印刷污染等问题。
印刷问题会导致焊接质量不良,影响产品的性能和可靠性。
4.质量控制问题:质量控制问题是SMT制程中常见的问题之一、质量控制问题可能由于生产过程中缺乏足够的质量控制措施、操作工人技术水平不足、设备维护不良等原因引起。
质量控制问题会导致产品的性能和可靠性不稳定,严重的情况下可能导致产品不合格。
针对SMT制程常见的异常,可以采取以下措施进行分析和解决:1.异常分析:对于出现的异常情况,首先要进行详细的分析,排查出具体的原因。
可以通过观察异常的形态特征、分析生产过程中的操作记录、检查原材料的质量等方式进行分析。
2.数据收集:在SMT制程中可以采集相关的数据,如焊接温度、湿度、气压等参数,以及生产过程中的记录。
这些数据可以用于分析异常情况的原因,帮助找出潜在的问题。
3.过程优化:针对分析结果,可以进行制程的优化。
例如,对于焊接不良问题,可以优化焊接设备的参数,选择质量更好的焊接材料,加强操作工人的培训等。
SMT常见不良及原因分析

SMT常见不良及原因分析1、立碑产生原因:通常由于回流焊时元件两端的湿润力不平衡,引发元件两端的力矩也不平衡,导致“立碑”。
成因分析因素A:焊盘设计与布局不合理①元件的两边焊盘之一与地线相连接或有一侧焊盘面积过大,焊盘两端热容量不均匀;②PCB表面各处的温差过大以致元件焊盘两边吸热不均匀;③大型器件QFP、BGA、散热器周围的小型片式元件焊盘两端会出现温度不均匀。
解决方法:工程师调整焊盘设计和布局因素B:焊锡膏与焊锡膏印刷存在问题①焊锡膏的活性不高或元件的可焊性差,焊锡膏熔化后,表面张力不一样,将引起焊盘湿润力不平衡。
②两焊盘的焊锡膏印刷量不均匀,一侧锡厚,拉力大,另一侧锡薄拉力小,致使元件一端被拉向一侧形成空焊,一端被拉起就形成立碑。
解决办法:需工厂选用活性较高的焊锡膏,改善焊锡膏印刷参数,特别是钢网的窗口尺寸因素C:贴片移位Z轴方向受力不均匀该情况会导致元件浸入到焊锡膏中的深度不均匀,熔化时会因时间差而导致两边的湿润力不平衡,如果元件贴片移位会直接导致立碑。
解决办法:调节贴片机工艺参数因素D:炉温曲线不正确如果回流焊炉炉体过短和温区太少就会造成对PCB加热的工作曲线不正确,以致板面上湿差过大,从而造成湿润力不平衡。
解决办法:需要工厂根据每种不同产品调节好适当的温度曲线2、“锡珠”现象产生原因:它不仅影响外观而且会引起桥接(下文会讲)。
锡珠可分两类:一类出现在片式元器件一侧,常为一个独立的大球状(如下图1);另一类出现在IC 引脚四周,呈分散的小珠状。
因素A:温度曲线不正确回流焊曲线可以分为预热、保温、回流和冷却4个区段。
预热、保温的目的是为了使PCB表面温度在60~90s内升到150℃,并保温约90s,这不仅可以降低PCB 及元件的热冲击,更主要是确保焊锡膏的溶剂能部分挥发,避免回流焊时因溶剂太多引起飞溅,造成焊锡膏冲出焊盘而形成锡珠。
解决办法:工厂需注意升温速率,并采取适中的预热,使溶剂充分挥发因素B:焊锡膏的质量①焊锡膏中金属含量通常在(90±0.5)℅,金属含量过低会导致助焊剂成分过多,因此过多的助焊剂会因预热阶段不易挥发而引起飞珠;②焊锡膏中水蒸气和氧含量增加也会引起飞珠。
smt常见品质问题及解决方案

smt常见品质问题及解决方案
《SMT常见品质问题及解决方案》
SMT(表面贴装技术)在电子制造和组装中扮演着重要的角色,然而在生产过程中常常会遇到一些品质问题。
了解这些问题并找到相应的解决方案是至关重要的,下面我们就来探讨一些常见的SMT品质问题及解决方案。
1. 焊接不良
焊接不良是SMT中最常见的问题之一。
这可能是由于焊锡量
不足、焊接温度不合适或焊接时间过短等原因造成的。
解决这个问题的方法包括调整焊接参数、使用适当的焊接设备和材料,以及加强工艺控制。
2. 组件偏移
在SMT过程中,组件偏移可能会导致焊接不良或装配错误,
从而影响产品的品质。
要解决这个问题,可以通过优化贴装设备的校准和调整,以及加强工艺控制来避免组件偏移。
3. 焊漆缺陷
在SMT过程中,焊漆缺陷可能会导致短路、断路或其它问题。
要解决这个问题,可以通过使用高质量的焊漆材料、优化焊接工艺和检验工艺以及加强工艺控制来避免焊漆缺陷。
4. 焊盘氧化
焊盘氧化可能会导致焊接不良和器件失效。
要避免这个问题,可以通过优化存储和处理焊盘的方法,保持焊盘的表面清洁和
干燥,以及加强工艺控制来减少焊盘氧化的发生。
总的来说,要解决SMT中的品质问题,关键在于优化工艺、加强质量控制和培训员工等方面。
只有通过不断改进和完善SMT生产过程,才能提高产品的品质和可靠性。
SMT制程不良原因及改善对策

1、生产前先对材料进行检查,有NG品修好后再贴装; 2、清洁归正座; 3、修改程序; 4、拆下规正器进行调整。
浮高
产生原因
1、PCB 板上有异物; 2、胶量过多; 3、红胶使用时间过久; 4、锡膏中有异物; 5、炉温设置过高或反面元件过重; 6、机器贴装高度过高。
15、在网网下垫胶纸或调整钢网与PCB
16、锡膏印刷脱膜不良。
间距;
17、锡膏使用时间过长,活性剂挥发掉; 16、开精密的激光钢钢,调整印刷
18、机器反光板孔过大误识别造成;
机;
19、原材料设计不良;
17、用新锡膏与旧锡膏混合使用;
20、料架中心偏移;
18、更换合适的反光板;
5、加过量稀释剂;
5、避免在锡膏内加稀释剂;
6、钢网开孔设计不当;
6、重新开设密钢网;
7、锡粉颗粒不均。
7、更换适用的锡膏,按照规定的时间对锡膏
进行搅拌:回温4H搅拌3-5MIN。
翘脚
产生原因
改善对策
1、原材料翘脚; 2、规正座内有异物; 3、程序设置有误; 4、MK规正器不灵活;
产生原因
1、原材料不良; 2、规正器不顺导致元件夹坏; 3、吸着高度或贴装高度过低导致; 4、回焊炉温度设置过高; 5、料架顶针过长导致; 6、炉后撞件。
改善对策
1、检查原材料并反馈IQC处理; 2、维修调整规正座; 3、调整机器贴装高度; 4、调整回焊炉温度; 5、调整料架顶针; 6、人员作业时注意撞件。
2、原材料反向;
2、上料前对材料方向进行检验;
3、上料员上料方向上反;
SMT常见不良分析

SMT常见不良原因分析一.锡球:1.印刷前,锡膏未充分回温解冻并搅拌均匀。
2.印刷后太久未回流,溶剂挥发,膏体变成干粉后掉到油墨上。
3.印刷太厚,元件下压后多余锡膏溢流。
时升温过快(SLOPE>3),引起爆沸。
5.贴片压力太大,下压使锡膏塌陷到油墨上。
6.环境影响:湿度过大,正常温度25+/-5,湿度40-60%,下雨时可达95%,需要抽湿。
7.焊盘开口外形不好,未做防锡珠处理。
8.锡膏活性不好,干的太快,或有太多颗粒小的锡粉。
9.锡膏在氧化环境中暴露过久,吸收空气中的水分。
10.预热不充分,加热太慢不均匀。
11.印刷偏移,使部分锡膏沾到PCB上。
12.刮刀速度过快,引起塌边不良,回流后导致产生锡球。
:锡球直径要求小于0.13MM,或600平方毫米小于5个.二、立碑:1.印刷不均匀或偏移太多,一侧锡厚,拉力大,另一侧锡薄拉力小,致使元件一端被拉向一侧形成空焊,一端被拉起就形成立碑。
2.贴片偏移,引起两侧受力不均。
3.一端电极氧化,或电极尺寸差异太大,上锡性差,引起两端受力不均。
4.两端焊盘宽窄不同,导致亲和力不同。
5.锡膏印刷后放置过久,FLUX挥发过多而活性下降。
预热不足或不均,元件少的地方温度高,元件多的地方温度低,温度高的地方先熔融,焊锡形成的拉力大于锡膏对元件的粘接力,受力不均匀引起立碑。
三、短路太厚、变形严重,或STENCIL开孔有偏差,与PCB焊盘位置不符。
2.钢板未及时清洗。
3.刮刀压力设置不当或刮刀变形。
4.印刷压力过大,使印刷图形模糊。
5.回流183度时间过长,(标准为40-90S),或峰值温度过高。
6.来料不良,如IC引脚共面性不佳。
7.锡膏太稀,包括锡膏内金属或固体含量低,摇溶性低,锡膏容易榨开。
8.锡膏颗粒太大,助焊剂表面张力太小。
四、偏移:一).在REFLOW之前已经偏移:1.贴片精度不精确。
2.锡膏粘接性不够。
在进炉口有震动。
二).REFLOW过程中偏移:升温曲线和预热时间是否适当。
smt不良分析及改善措施

材料问题
原材料缺陷:如PCB板、电子元器件等原材料存 在缺陷,将直接影响SMT产品的品质。
使用过期材料:使用过期的原材料进行生产,可 能导致产品性能不稳定,产生不良品。
储存不当:原材料在储存过程中未按照要求进行 保管,可能导致性能受损,进而影响SMT产品质 量。
针对以上原因,可以采取相应的改善措施,如加 强员工培训、规范操作流程、定期维护设备、严 格把控原材料质量等,以降低SMT不良品率,提 高产品质量和生产效率。
03
SMT不良改善措施
人员培训和管理
提高技能水平
定期举办技术培训课程,提升员工在SMT操作、维护、质检等方面 的技能水平,确保员工熟悉并掌握设备操作规程和质量标准。
严格考核与奖惩制度
建立员工绩效考核体系,对操作规范、良品率等方面进行考核,奖 励优秀员工,对操作不规范、产品质量差的员工进行惩罚和再培训 。
强化质量意识
通过定期的质量教育活动,增强员工的质量意识,使其充分认识到产 品质量对企业和个人的重要性。
设备维护和管理
制定维护计划
根据设备使用情况和维护要求,制定合理的设备维护计划,确保 设备按时进行保养、检修,减少设备故障。
监控设备运行状况
通过设备自带的监测系统或额外安装传感器等方式,实时监测设备 运行状况,及时发现异常,避免故障扩大。
• 焊接不良:包括冷焊、虚焊、 焊盘脱落等问题,主要由于焊 接温度、时间等参数设置不当 或焊接材料质量差引起。
• 基板不良:包括基板变形、裂 纹、污染等,可能由基板材料 、设计或生产工艺导致。
SMT不良现象对生产的影响
01
02
03
生产效率下降
SMT不良现象会增加检修 、返工等工作量,降低生 产效率。
SMT 产品常见不良及其原因分析

SMT 产品常见不良及其原因分析一、主要不良分析主要不良分析、锡珠(Solder Balls):1、丝印孔与焊盘不对位,印刷不精确,使锡膏弄脏PCB。
2、锡膏在氧化环境中暴露过多、吸空气中水份太多。
3、加热不精确,太慢并不均匀、4、加热速率太快并预热区间太长。
ﻫ5、锡膏干得太快。
ﻫ6、助焊剂活性不够。
7、太多颗粒小得锡粉。
ﻫ8、回流过程中助焊剂挥发性不适当。
ﻫ锡球得工艺认可标准就是:当焊盘或印制导线得之间距离为0、13mm 时,锡珠直径ﻫ不能超过0、13m m,或者在600mm平方范围内不能出现超过五个锡珠。
ﻫ锡桥(Bridge solder):1、锡膏太稀,包括锡膏内金属或固体含量低、摇溶性低、锡膏容易榨开、ﻫ2、锡膏颗粒太大、助焊剂表面张力太小、ﻫ3、焊盘上太多锡膏、ﻫ4、回流温度峰值太高等、ﻫ开路(Open):1、锡膏量不够、2、组件引脚得共面性不够、3、锡湿不够(不够熔化、流动性不好),锡膏太稀引起锡流失、4、引脚吸锡(象灯芯草一样)或附近有联机孔、引脚吸锡可以通过放慢加热速度与底面加热多、上面加热少来防止、ﻫ5、焊锡对引脚不熔湿, 干燥时间过长引起助焊剂失效、回流温度过高/时间过长引起氧化、6、焊盘氧化,焊锡没熔焊盘、墓碑(Tombstoning/Part shift):墓碑通常就是不相等得熔湿力得结果,使得回流后组件在一端上站起来,一般加热越ﻫ慢,板越平稳,越少发生。
降低装配通过183°C得温升速率将有助于校正这个缺陷。
空洞:ﻫ就是锡点得 X 光或截面检查通常所发现得缺陷。
空洞就是锡点内得微小“气泡”,可能就是被夹住得空气或助焊剂。
空洞一般由三个曲线错误所引起:不够峰值温度;回流时间不够;升温阶段温度过高。
造成没挥发得助焊剂被夹住在锡点内。
这种情况下,为了避ﻫ免空洞得产生,应在空洞发生得点测量温度曲线,适当调整直到问题解决。
二、印刷问题印刷问题ﻫ印刷偏位: ﻫ1、机器换线生产前首片印刷偏移2、PCBmark 不好3、PCB 夾持不好ﻫ4、機器Vision系統出故障及機器 XY Table有問題ﻫﻫ錫膏橋1、鋼板刮傷或張力不足ﻫ2、2、鋼板擦拭不好3、3、鋼板背面膠帶就是否脫落ﻫ4、4、鋼板背面粘有錫膏ﻫ5、5、 PCB 零件面有凸出物6、6、印刷機XY Table傾斜﹐導制與鋼板有間隙7、7、印刷機刮刀水平度校正不良,造成印刷錫膏多錫現象ﻫ錫膏塞孔ﻫ1、錫膏太幹ﻫ2、2、Slow Snapoff Speed 設定太快3、3、 Slow Snapoff distance設定太小ﻫ錫膏下塌ﻫ1、錫膏粘度太低或吸入濕氣ﻫ2、刮刀速度太快ﻫ少印漏印錫膏1、鋼板上錫膏量少2、錫膏粘刮刀ﻫ錫膏拉尖1、 Slow Snap-off速度設置太快ﻫ2、2、 PCB与 STENCIL間隙太大ﻫ3、3、刮刀印刷速度設定太高ﻫ4、4、刮刀壓力設定太低ﻫ5、5、板子支承不夠ﻫ錫膏過薄1、鋼板上錫膏量少2、刮刀印刷速度設定太高ﻫ3、錫膏粘刮刀ﻫﻫ錫膏過厚1、 PCB 零件面有凸出物﹒2、PCB 与 STENCIL間隙太大ﻫ3、刮刀Down stop設定太小ﻫ4、刮刀壓力設定太低三、元件贴装不元件贴装不良问题良问题ﻫ元件偏位1、 Program中定義坐標差异ﻫ2、元件置放速度太快ﻫ3、元件尺寸數据設置錯誤4、元件高度設置錯誤元件出現翻件/側件ﻫ1、料架安放不良ﻫ2、料帶安裝不良3、料架送帶不良ﻫ元件漏件ﻫ1、元件高度設置錯誤2、元件置放速度太快ﻫ3、 Nozzle有螢光紙臟或歪斜現象ﻫ元件拋料ﻫ1、 Camera鏡片臟2、 Nozzle 有螢光紙臟或歪斜現象ﻫ3、元件尺寸數据設置錯誤ﻫ絞帶現象ﻫ1、料帶安裝不良2、料架送帶不良ﻫ四、Reflow四、Reflow不良问题不良问题溫度偏高ﻫ1、爐溫設置太高2、鏈條速度設置太慢ﻫ3、測溫點異常4、熱風頻率設置過大、5、測溫方法不正確、溫度偏低1、爐溫設置太低ﻫ2、鏈條速度設置太快3、測溫點異常4、熱風頻率設置過小、5、測溫方法不正確、熔錫時間太短1、溫度設置不佳ﻫ2、鏈條速度設置太快ﻫ3、測溫點異常4、冷卻速度過快、5、測溫方法不正確、ﻫ熔錫時間太長ﻫ1、溫度設置不佳2、鏈條速度設置太慢ﻫ3、測溫點異常ﻫ4、冷卻速度太慢5、測溫方法不正確、6、測溫方法不正確、ﻫ7、鏈條速度設置太快、ﻫ8、測溫方法不正確、ﻫ升溫斜率太快ﻫ1、溫度設置不佳2、測溫點異常ﻫ3、鏈條速度設置太慢4、測溫方法不正確、ﻫ升溫斜率太慢1、溫度設置不佳ﻫ2、測溫點異常ﻫ3、鏈條速度設置太快、ﻫ4、測溫方法不正確、ﻫﻫ預熱時間太長1、溫度設置不佳ﻫ2、測溫點異常3、鏈條速度設置太快、4、測溫方法不正確、ﻫ預熱時間太短1、溫度設置不佳2、測溫點異常3、鏈條速度設置太快、4、測溫方法不正確、。
- 1、下载文档前请自行甄别文档内容的完整性,平台不提供额外的编辑、内容补充、找答案等附加服务。
- 2、"仅部分预览"的文档,不可在线预览部分如存在完整性等问题,可反馈申请退款(可完整预览的文档不适用该条件!)。
- 3、如文档侵犯您的权益,请联系客服反馈,我们会尽快为您处理(人工客服工作时间:9:00-18:30)。
S M T产品常见不良及其
原因分析
The Standardization Office was revised on the afternoon of December 13, 2020
SMT 产品常见不良及其原因分析
一. 主要不良分析主要不良分析.
锡珠(Solder Balls):
1. 丝印孔与焊盘不对位,印刷不精确,使锡膏弄脏PCB。
2. 锡膏在氧化环境中暴露过多、吸空气中水份太多。
3. 加热不精确,太慢并不均匀.
4. 加热速率太快并预热区间太长。
5. 锡膏干得太快。
6. 助焊剂活性不够。
7. 太多颗粒小的锡粉。
8. 回流过程中助焊剂挥发性不适当。
锡球的工艺认可标准是:当焊盘或印制导线的之间距离为时,锡珠直径
不能超过,或者在 600mm平方范围内不能出现超过五个锡珠。
锡桥(Bridge solder):
1. 锡膏太稀,包括锡膏内金属或固体含量低、摇溶性低、锡膏容易榨开.
2. 锡膏颗粒太大、助焊剂表面张力太小.
3. 焊盘上太多锡膏.
4. 回流温度峰值太高等.
开路(Open):
1.锡膏量不够.
2. 组件引脚的共面性不够.
3. 锡湿不够(不够熔化、流动性不好),锡膏太稀引起锡流失.
4. 引脚吸锡(象灯芯草一样)或附近有联机孔. 引脚吸锡可以通过放慢加热速度和底面加热多、上面加热少来防止.
5. 焊锡对引脚不熔湿, 干燥时间过长引起助焊剂失效、回流温度过高/时间过长引起氧化.
6. 焊盘氧化,焊锡没熔焊盘.
墓碑(Tombstoning/Part shift):
墓碑通常是不相等的熔湿力的结果,使得回流后组件在一端上站起来,一般加热越慢,板越平稳,越少发生。
降低装配通过183° C的温升速率将有助于校正这个缺陷。
空洞:
是锡点的 X 光或截面检查通常所发现的缺陷。
空洞是锡点内的微小“气泡”,可能是被夹住的空气或助焊剂。
空洞一般由三个曲线错误所引起:不够峰值温度;回流时间
不够;升温阶段温度过高。
造成没挥发的助焊剂被夹住在锡点内。
这种情况下,为了避
免空洞的产生,应在空洞发生的点测量温度曲线,适当调整直到问题解决。
二. 印刷问题印刷问题
印刷偏位:
1. 机器换线生产前首片印刷偏移
2. PCB mark 不好
3. PCB 夾持不好
4. 機器Vision系統出故障及機器 XY Table 有問題
錫膏橋
1. 鋼板刮傷或張力不足
. 鋼板擦拭不好
. 鋼板背面膠帶是否脫落
. 鋼板背面粘有錫膏
. PCB 零件面有凸出物
. 印刷機XY Table傾斜﹐導制與鋼板有間隙
. 印刷機刮刀水平度校正不良,造成印刷錫膏多錫現象
錫膏塞孔
1. 錫膏太幹
. Slow Snapoff Speed 設定太快
. Slow Snapoff distance設定太小
錫膏下塌
1. 錫膏粘度太低或吸入濕氣
2. 刮刀速度太快
少印漏印錫膏
1. 鋼板上錫膏量少
2. 錫膏粘刮刀
錫膏拉尖
1. Slow Snap-off速度設置太快
. PCB 和 STENCIL間隙太大
. 刮刀印刷速度設定太高
. 刮刀壓力設定太低
. 板子支承不夠
錫膏過薄
1. 鋼板上錫膏量少
2. 刮刀印刷速度設定太高
3. 錫膏粘刮刀
錫膏過厚
1. PCB 零件面有凸出物﹒
2. PCB 和 STENCIL間隙太大
3. 刮刀Down stop設定太小
4. 刮刀壓力設定太低
三. 元件贴装不元件贴装不良问题良问题
元件偏位
1. Program中定義坐標差异
2. 元件置放速度太快
3. 元件尺寸數据設置錯誤
4. 元件高度設置錯誤
元件出現翻件/側件
1. 料架安放不良
2. 料帶安裝不良
3. 料架送帶不良
元件漏件
1. 元件高度設置錯誤
2. 元件置放速度太快
3. Nozzle 有螢光紙臟或歪斜現象
元件拋料
1. Camera 鏡片臟
2. Nozzle 有螢光紙臟或歪斜現象
3. 元件尺寸數据設置錯誤
絞帶現象
1. 料帶安裝不良
2. 料架送帶不良
四. Reflow四. Reflow不良问题不良问题
溫度偏高
1. 爐溫設置太高
2. 鏈條速度設置太慢
3. 測溫點異常
4. 熱風頻率設置過大.
5. 測溫方法不正確.
溫度偏低
1. 爐溫設置太低
2. 鏈條速度設置太快
3. 測溫點異常
4. 熱風頻率設置過小.
5. 測溫方法不正確.
熔錫時間太短
1. 溫度設置不佳
2. 鏈條速度設置太快
3. 測溫點異常
4. 冷卻速度過快.
5. 測溫方法不正確.
熔錫時間太長
1. 溫度設置不佳
2. 鏈條速度設置太慢
3. 測溫點異常
4. 冷卻速度太慢
5. 測溫方法不正確.
6. 測溫方法不正確.
7. 鏈條速度設置太快.
8. 測溫方法不正確.
升溫斜率太快
1. 溫度設置不佳
2. 測溫點異常
3. 鏈條速度設置太慢
4. 測溫方法不正確.
升溫斜率太慢
1. 溫度設置不佳
2. 測溫點異常
3. 鏈條速度設置太快.
4. 測溫方法不正確.
預熱時間太長
1. 溫度設置不佳
2. 測溫點異常
3. 鏈條速度設置太快.
4. 測溫方法不正確.
預熱時間太短
1. 溫度設置不佳
2. 測溫點異常
3. 鏈條速度設置太快.
4. 測溫方法不正確.。