内浇道工艺参数对压铸模具的适应性
压铸工艺参数分析

压铸工艺参数分析1.注射压力:注射压力是指在铸造过程中,金属熔液被压入型腔的压力大小。
注射压力的大小对于铸件的排气、充盈、凝固过程以及零部件的尺寸稳定性有着重要的影响。
过高的注射压力会导致铸件内部气泡的形成、表面粗糙度增大等问题,而过低的注射压力则会导致型腔内充盈不充分。
2.注射速度:注射速度是指熔融金属进入模具腔体的速度。
适当的注射速度可以使熔融金属在型腔内充盈均匀,防止铸件出现疏松、夹杂等缺陷。
过高的注射速度会导致金属熔液的剪切力增加,容易产生气泡和金属破碎现象,而过低的注射速度则会导致金属熔液在充盈过程中受到阻力,形成冷障。
3.注射温度:注射温度是指金属熔液注入型腔时的温度。
注射温度的高低会直接影响到铸件的凝固形态和组织结构。
过高的注射温度会导致铸件的表面质量较差,因为金属熔液的冷却速度过快,易产生冷障和贝氏体组织。
而过低的注射温度则会导致金属熔液黏度增大,充盈性变差。
4.金属液温度:金属液温度是指金属熔体在注射之前的温度。
金属液温度的高低会直接影响到铸件的凝固过程和性能。
过高的金属液温度会导致铸件的组织粗大,出现热裂纹等问题。
而过低的金属液温度则会导致铸件的毛细孔增多,降低铸件的密实性。
5.压射机的闭模力:压射机的闭模力是指用于关闭型腔的力大小。
闭模力的大小会直接影响到铸件的尺寸稳定性和机械性能。
过高的闭模力会导致铸件的尺寸过大,形成表面凸起和冷障等问题。
而过低的闭模力则会导致铸件尺寸的不稳定性和机械性能的下降。
6.模具温度:模具温度是指模具在铸造过程中的温度。
模具温度的高低会直接影响到铸件的组织结构和表面质量。
适当的模具温度可以提高铸件的表面光洁度,减少气孔和缩松等问题。
过高的模具温度会导致铸件的热组织粗大,而过低的模具温度则会导致铸件充盈性差。
总结起来,压铸工艺参数对于铸件质量和性能有着直接的影响。
合理的控制和选择工艺参数可以有效地改善铸件的表面质量、减少缺陷率,提高铸件的力学性能和尺寸稳定性。
压铸模具浇道设计理论与实践

压铸模具浇道设计理论与实践(一)浇口技术不仅指浇口的造型和布置,如今已延伸至浇道,溢流及排气通道的造型与布置。
从压铸工艺方面考虑,对从浇道至浇口通道内液态金属的流动进行控制,使其在进入模具型腔时达到一个最佳的流动状态,是决定铸件质量的一个重要前提。
浇道的主要任务是,将液态金属量以最小的涡流,压力损失和温度损失送至浇口处。
设计良好的浇道系统应保证浇道、浇口及型腔有一个良好的填充、增压作用有效,且金属熔化物流动过程中对型腔冲击力小,因此,最佳的浇道系统与充模过程有着紧密的联系。
压铸模具浇道系统千变万化,体现了压铸工艺的复杂程度。
由于浇道造型展示的是一个金属液压通道,在这样的通道内液态金属以一定的速度流动,其速度要比油压体系内要高,属于流体力学的范畴,故浇道的造型应尽可能按满足流动特性进行设计。
浇道的横断面积通常是从压室出口至浇口持续减小,在到达浇口之前必须大于浇口的横断面积。
另一方面,金属液在浇道内的流动速度要尽可能地高,横断面尽可能小些,以便减小热耗损及材料循环,也要通过计算防止可能出现的压力损失,以及在高流速体进入浇道时形成的空蚀(负压区)。
当浇道几何造型不好,就会出现严重的金属液流动脱离浇道壁,增加形成气泡的危险,考虑到这些原因,浇道的流动速度就要保持尽可能的低。
当浇道形状有加宽部分时,此处将形成负压区,分型面空气会在充型过程被吸入型腔。
为了能对压铸模具进行必要的计算,正确评价压铸机的功率以及确保浇口处所希望的流动速度,就需要进一步考虑浇道各个部分及整个浇道体系的几何造型和阻力系数。
我们可以应用对液态金属及普通液体流动分析形成的理论基础,通过油压浇道的试验结果,进行设计浇注系统的几何形状。
一、浇口的定位及造型1.1 浇口的定位压铸件表面缺陷及孔隙度,对压铸人员来说是比较难处理。
浇口的位置和形状对压铸件的表面特征和强度,以及压铸模具的结构和工作寿命都有影响。
浇口的作用是将液态金属引入压铸模具型腔内,其在模具型腔内引导的金属射流的方向影响着整个充模过程。
压铸模内浇口的结构设计及工艺分析
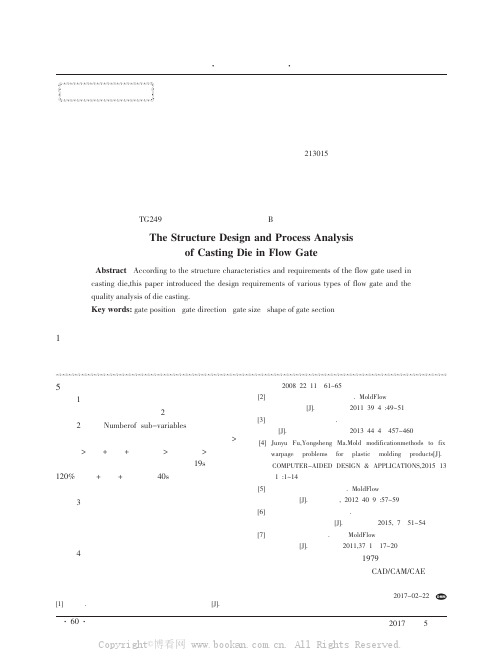
而实现理想充盈。
如图 5A-A、B-B 剖面所示。A-A 剖面是利用动
模上的横浇道与内浇口斜面的导向作用使金属液流
图 6 内浇口的局部特殊导入型腔方向
向上注入左上水平面的型腔;在 B-B 剖面部分,横浇
4
右下水平面的型腔,此时的分型面是位于左上右下两
式,如金属液流经内浇口时的喷射减轻而使铸件裹气
(3)通过分析得到了翘曲变形量的最优工艺参数
组合,有效减小了翘曲变形问题,避免了反复的调整
和试模。希望为平板类薄壁件的工艺参数优化提供
一些有益的借鉴。
(4)模拟结果与实际结果相差稍大,还有待进一
步改善。
考
文
献
赵建. 基于翘曲分析的注塑模工艺参数的优化[J]. 中国塑
· 60 ·
化中的应用[J]. 塑料工业,
柱状体的端部,成型后的铸件气孔多而形成废品。为
此,在扁平的内浇口所对应的异形盲型型腔处开设了
一深浇道,金属液顺这一深浇道流至端部后折转向上
进入异形盲型型腔,排出了该型腔内的气体,从而使
该处的气孔大为减少。
仅对准左上部型腔,或把内浇口仅对准右下部型腔
时,总有一半内浇口导入的金属流无法直接进入另一
把内浇口的导入方向和内浇口的位置综合起来
关键词:浇口位置;浇口方向;浇口尺寸;浇口截面的形状
中图分类号:TG249
文献标识码:B
The Structure Design and Process Analysis
of Casting Die in Flow Gate
【Abstract】According to the structure characteristics and requirements of the flow gate used in
压铸模内浇口的设计分析
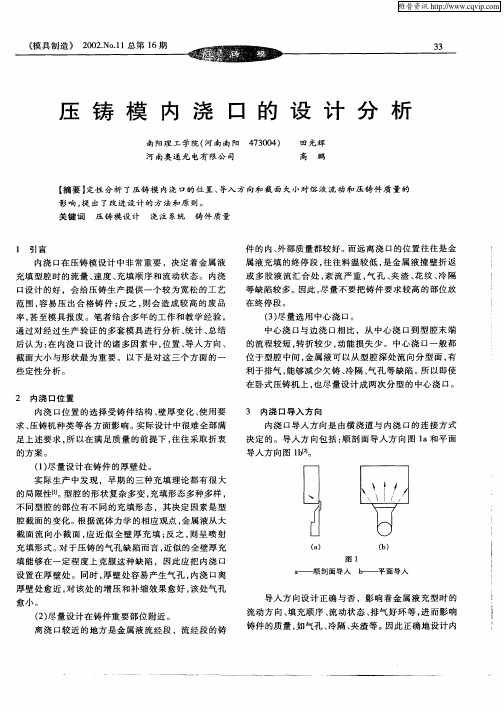
内浇 口位 置 的选 择 受 铸 件 结构 、 厚 变 化 、 用 要 壁 使 求 、 铸机 种 类 等各 方 面影 响 。 际设 计 中很 难 全部 满 压 实
足 上 述要 求 , 以在 满 足 质 量 的前 提 下 , 往 采取 折 衷 所 往
的方 案 。
3 内浇 口导入 方 向
b — 平 面 导 人 r _
厚 壁 处 愈 近 , 该 处 的增 压 和 补缩 效 果 愈好 , 处气 孔 对 该
愈小。
导 人 方 向设 计 正 确 与 否 ,影 响着 金 属 液 充 型 时 的
() 2 尽量 设 计 在铸 件 重要 部 位 附 近 。 离 浇 口较 近 的 地方 是金 属 液 流 经段 ,流 经 段 的铸
【 要 】 性 分析 了压 铸模 内浇 口的位 置 、 摘 定 导入 方 向和 截 面大 小对 熔 液 流动 和 压 铸件 质量 的
影 响 , 出了改进 设 计 的方 法 和原 则 。 提
关键 词 压铸 模 设 计 浇注 系统
铸 件 质量
1 引 言
件 的 内、 外部 质 量都 较 好 。而远 离 浇 口的位 置 往往 是 金 属 液 充填 的终 停 段 , 往往 料 温 较 低 , 是金 属 液 撞 壁 折 返 或 多股 液 流 汇 合 处 , 流 严 重 , 孔 、 渣 、 纹 、 隔 紊 气 夹 花 冷 等 缺 陷较 多 。因此 , 量 不要 把 铸 件要 求 较 高 的部 位 放 尽
\
、
\ /
() b
充 填 形式 。 于 压铸 的气 孔缺 陷而 言 , 对 近似 的全 壁厚 充
填 能 够在 一 定 程 度上 克服 这 种 缺 陷 ,因此 应 把 内浇 口 设 置 在厚 壁 处 。同 时 , 壁 处容 易 产 生气 孔 , 厚 内浇 口离
压铸工艺参数的设定和调节

压铸工艺参数的设定和调节压铸工艺参数的设定和调节是在铸造过程中对机器设备的参数进行调整,以达到铸件质量要求的过程。
这些参数包括压力、速度、温度、冷却时间等,正确的设定和调节能够改善铸件的成型质量,提高生产效率和降低生产成本。
首先,压铸工艺参数的设定和调节应考虑到铸件的形状、尺寸、材料等因素。
根据铸件的设计要求,选择合适的压力和速度来满足铸件的成型需求。
一般情况下,增加压力可以提高铸件的致密度、强度和表面质量,但过高的压力可能导致铸件断裂或变形;增加速度可以减少热损失,提高铸件的凝固速度和成型质量,但过高的速度可能导致冷隔离缺陷等问题。
其次,压铸工艺参数的设定和调节还需要考虑到机器设备的性能和工作状态。
例如,如果机器设备的液压系统压力低于要求,就需要调整液压泵的工作压力,保证其在一定范围内稳定工作;如果机器设备的液压缸行程不足,就需要增加液压泵的行程或调整行程限位开关。
第三,压铸工艺参数的设定和调节还需要根据铸件的材料和成型温度来决定。
铸件的成型温度对铸件的凝固速度、收缩率、热裂纹倾向等有着重要影响。
一般情况下,增加成型温度可以加快铸件的凝固速度,提高铸件的致密度和强度,但过高的成型温度可能导致材料的氧化或烧损、铸件变形等问题。
此外,压铸工艺参数的设定和调节还需要考虑到铸件的冷却时间。
冷却时间是指在铸件成型后,需要经过一定时间的冷却才能取出铸件。
合理的冷却时间可以保证铸件的成型质量和尺寸稳定性,但过长的冷却时间可能导致生产效率低下。
在设定和调节压铸工艺参数时,需要根据实际工艺经验和试制铸件的质量情况进行有针对性的调整。
如果发现铸件存在不良缺陷,例如气孔、疏松、缩孔、冷隔离等,就需要重新评估和调整工艺参数,以减少或消除这些缺陷。
总之,压铸工艺参数的设定和调节是一个复杂而严谨的过程,在实践中需要不断摸索和总结经验。
合理设定和调节这些参数,可以提高铸件的成型质量、降低缺陷率,并最终提高生产效率和降低生产成本。
压铸模内浇口的结构设计及工艺分析

使浇 【 1 优 化 没
汁… .太 f { I I 人 学 报 , 2 ( ) 1 3 . 4 4 ( 4) : 4 5 7 ~ 4 6 0
1 4 1. I L I I I V L I I ; l 1 . Y t l i l g s h l  ̄ I l g Ma . M ̄ , I I I I n l l d i [ i ‘ 。 a t i o l i i I 1 ( I l 1 . 1 l s f l l f i x
‘ -
的肜 状 h接 影 响 铸 f , t - f i  ̄ 质 , 以f 』 l 累的 践 经 验 依{ J l , j 1 通 过 ^合 、 乍 f 』 他 彤 弋的浇 l ; 1 刈比. 埘} 』 、 】
_ - ● , - ● ●
-
『 』 、 J 浇f 1 进 料的J t  ̄ . , - L , 1 人 】 浇} J n , J f
Ke y wor ds :g ai t p o s i t i o n:g a t e di i ’ P ( ‘ I i o n;g a t e b i t ;s h a p e o t a I l s P ( ‘ l i o n
l 引 言
竹 l , I 勺 总装 设汁 I 1 . 浇铸进料流道 果川
料. 2 0 0 8 , 2 2 ( I 1 ) : 6 1 ~ 6 5
l 2 l I , J 、 i l l j , 1 I J ] { f i 】 , l 场 t 奶: 尊.M t , I t l 1 一 I t m f i _ : 州 ) J J J
5 结 论
( 1 ) 过 分析 允上 r 川‘ 、 流动 } Y { L …  ̄ f : 1 1 、 熔 接 痕 及 … I 肜/ - 4 - r 。 J 力 ‘ 案2 优 浇 系统 案 ( 2 ) 川N L I I I l i / r n ) 1 ’ S L l i ) 一 V { I I — i a l l l c s 实验力 ‘ 法, 符 l
压铸工艺参数分析

压铸工艺参数分析压铸是一种常见的金属制造工艺,通过将熔化的金属填充到金属模具中,然后施加高压使其凝固成型。
在压铸过程中,工艺参数的选择对成品的质量和性能起着关键作用。
本文将对压铸工艺参数进行详细分析。
首先,压铸的工艺参数包括模具温度、熔融温度、注射速度和压力等。
模具温度是指模具的加热温度,通常使用电加热或液体循环来加热模具。
模具温度的选择取决于金属材料的熔点和凝固温度,以及成品的要求。
较高的模具温度可以提高熔融金属的流动性,有利于填充模具腔体,但过高的温度可能导致熔融金属的挥发和氧化,影响成品的质量。
因此,选择适当的模具温度非常重要。
熔融温度是指金属材料的熔化点,选择适当的熔融温度可以确保金属完全熔化,保证充分填充模具腔体。
熔融温度的选择需要考虑到金属的熔点、凝固温度和成品要求等因素。
较高的熔融温度可以提高金属的流动性,但可能导致金属的挥发和氧化,对模具寿命和成品质量有不利影响。
因此,熔融温度的选择应当在保证金属材料完全熔化的基础上考虑到其他方面的因素。
注射速度是指金属材料由喷嘴注入模具腔体的速度,是影响成品质量的重要参数之一、较高的注射速度可以提高金属的流动性,有利于填充模具腔体,减少缺陷的产生。
然而,过高的注射速度可能导致金属的喷溅和气泡的产生,影响成品的质量。
因此,注射速度的选择需要通过试验确定,以获得最佳的成品质量。
压力是指施加在金属材料上的压力大小,可以有效地提高金属的密度和减少气孔的产生。
较高的压力可以提高金属材料的填充性和成品的致密性,但过高的压力可能导致模具磨损和应力集中,降低模具的寿命。
因此,选择适当的压力非常重要,需要结合金属材料的性质和成品的要求来确定。
此外,还有一些其他的工艺参数需要考虑,如金属的成分和含气量等。
金属的成分可以影响其熔点、流动性和机械性能等,需要根据成品的要求来确定。
含气量是指金属中气体的含量,过高的含气量可能导致成品中气孔的产生,影响成品的质量。
因此,需要通过适当的气体处理措施来减少含气量。
压铸模具设计浇道流道设计精讲教程

压铸模具设计浇道流道设计精讲教程压铸模具是压铸工艺中的一种重要工具,其设计的好坏直接影响到产品的质量和生产效率。
而浇道流道设计则是压铸模具设计中的关键环节之一,它决定了熔化金属流动的路径和方式,直接影响到铸件的充型性能和凝固过程。
在压铸模具设计中,浇道是指从熔化金属进入模腔的通道,流道是指熔化金属在模具中流动的路径。
浇道流道的设计合理与否直接关系到铸件的充型质量和凝固性能。
因此,设计师在进行浇道流道设计时需要考虑以下几个方面:1. 浇道流道的位置:浇道流道的位置应尽量选择在铸件较厚的部位,以便熔化金属在流动过程中能够充分填充铸件细节,避免铸件出现空隙和缺陷。
2. 浇道流道的长度:浇道流道的长度应尽量短,以减小熔化金属的流动阻力,提高充型速度。
同时,短浇道流道还能减少熔化金属在流动过程中的冷却损失,提高铸件的凝固性能。
3. 浇道流道的截面积:浇道流道的截面积应根据铸件的充型需求和熔化金属的流动特性进行合理选择。
截面积过小会增加金属的流动阻力,导致充型不良;截面积过大则会增加金属的冷却损失,影响铸件的凝固性能。
4. 浇道流道的形状:浇道流道的形状应尽量简洁,避免出现过多的转弯和分支,以减小金属流动的阻力和能量损失。
同时,浇道流道的形状也要考虑到铸件的结构特点和充型需求,以保证熔化金属能够充分填充铸件细节。
在进行浇道流道设计时,还需要考虑到以下几个问题:1. 浇道流道的位置和长度如何确定:浇道流道的位置和长度的确定需要考虑到铸件的结构特点、充型需求和凝固性能。
一般来说,浇道流道的位置应选择在铸件较厚的部位,长度应尽量短,以提高充型速度和凝固性能。
2. 浇道流道的截面积如何确定:浇道流道的截面积的确定需要考虑到铸件的充型需求和熔化金属的流动特性。
一般来说,截面积应根据铸件的充型速度和凝固性能进行合理选择,过小会增加金属的流动阻力,过大则会增加金属的冷却损失。
3. 浇道流道的形状如何确定:浇道流道的形状的确定需要考虑到金属流动的阻力和能量损失。
压铸模具的重要参数与原重要参数与原理

压铸模具的重要参数与原重要参数与原理上海压铸技术咨询一、压铸模具重要参数定义:1,决定着铸件的形状和尺寸公差等级;2,其浇注系统特别是浇口位置决定了熔融金属的填充状况;3,溢流排气系统影响着熔融金属的溢渣排气条件‘4,控制和调节压铸过程的热平衡;5,决定了铸件的表面质量及变形程度;6,模具的强度限期制了压射比压的最大限度;7,影响着生产操作的效率。
二、压铸模具基本要求定义:1,所生产的压铸件,应保持铸件图纸所规定的尺寸和各项技术要求,减少机械加工部位和加工余量,2,模具应适应压铸生产的工艺要求,在设计、审图、制作时要核实铸件脱模结构,冷却,模具结构等;3,应采用先进的结构,减少操作程序,动作准确可靠,构件钢性良好,具有足够的硬度,便于拆卸和维修;4,模具的各种零件应具备良好的机械加工工艺和热处理工艺和热处理工艺条件,选材适当,分差配合等级合理;5,符合压铸机的技术规范,准确选定安装尺寸,能充分发挥压铸机的生产能力;6,尽可能实现标准化,通用化以缩短设计和制造周期,便于管理;7,具备加执和冷却的条件,有利于使模具各部位达到理想的热平衡状态,提高模具的使用寿命。
三、压铸模具的主要组成部分及作用:序号各部分名称作用1定模定模是压铸模的主要组成部分,它与机器压射部分相连接,并固定在压铸机的定模板上,浇注系统与压室相通,是铸件型腔镶块的一个重要部分。
2动模动模是压铸模的另一个主要组成部分,它与定模组成压铸模成型部分的一个整体,它一般固定在模架上,模架又固定在压铸机动模板上,随动模板作开合运动,与定模部分分开,合拢,一般抽芯机构和顶出机构全部在这个部分。
3成型部分(又称型腔及型芯部分)成型部分由镶块及型芯组成装在动定模上,模具在合拢后,构成铸件的形成空腔,通常驻称型腔,是决定铸件几何形状和尺寸公差等级的部位。
4浇注系统浇注系统是熔融金属进入型腔的通道,它是沟通模具型腔与机器压室的部分,对压铸工艺因素、速度、以及排气、排渣、填充条件起着主要作用。
压铸工艺-影响压铸件质量的主要工艺参数

②冲头按调定的最大速度移动,金属液突破 内浇口阻力,在较短时间内填满型腔。
③冲头继续移动,压实金属,使金属组织致 密。
Ⅱ 影响冲头速度的因素 ①压力变化 ②冲头与鹅颈的配合状态 ③活塞与压射缸的配合状态 ④蓄能器内气体与液体体积比的变化
(2)内浇口速度
金属液通过内浇口导入型腔时的线速度称 为金属液的内浇口速度,也称填充速度。
调整导柱和导套的配合使动定模完全贴合,如果配合不好, 则修理相抵的部分
压
压铸机合型力不够,造成铸件飞边过大,则要调节合型力
射
模具锁紧不完
清理分型面,去掉飞边毛刺 检查并修整型芯和型腔分型面的表面,使平面度、表面粗糙
跑全
水
度、凹凸部分的嵌合呈良好状态,以不产生飞边为准 调整滑块和导轨的间隙 检查滑块和缩紧块的磨损情况,并进行修理
力等)
调整铸造条件:提高模具温度和浇注温度,减少脱模剂喷涂量
流
●铸件形状不合适 (壁厚、形状等)
研讨模具设计,提供足够的排气道和溢渣包,改进模具表面附近的金属液 流向
痕
●模具设计不合理 (分形线、内浇口、
通过喷丸等方法改善便面粗糙,改变模具表面附近的金属液流向 调整压铸机的工艺参数:提高压射速度和压铸压力
多 2)型芯断裂
2)更换型芯
3)型腔冲蚀
肉 4)型腔腐蚀
3)修模 4)修模
5)顶针过短
5)更换并调整顶针的长度
浇
在浇口、渣包和型腔连接处倒角
口
1)浇口、渣包和铸 件结合部位设计不合
改变浇口的位置和设计
部理
改变去掉浇口的方向
2)去浇口方向不当 分析并改进去浇口的方法
破 3)去浇口方法不当
裂
压铸工艺参数(一)解读
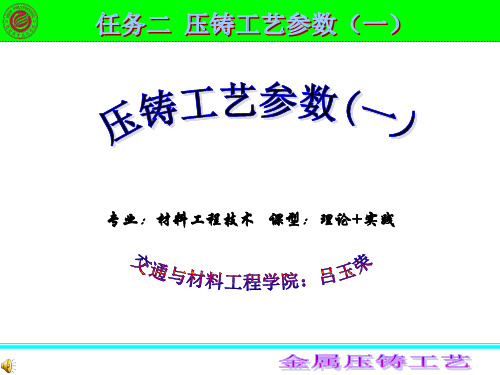
Ⅰ级压射速度又称为慢压射速度,是指冲头起始动作直至冲头将室内的金属液送 入内浇口之前的运动速度。在这一阶段中,要求将压室中的金属液充满压室,在 既不过多降低合金液温度,又有利于排除压室中的气体的原则下,该阶段的速度 应尽量的低,一般应低于0.3 m/s。
表3-7 铸件的平均壁厚与内浇口速度的关系
3、压射速度与内浇口速度的关系
根据连续性原理,金属流以速度vc流过压室截面为AS的体积应等于 以速度vn流过内浇口截面积为An的体积。
于是
Asvc==Anvn
即
vc
An
vn As
4、速度与压力的关系
因为金属液是黏性液体, 它在流经浇注系统时, 会因摩擦而引起动能损失, 所以内浇口速度vn与比压Pb的关系式为:
压力表示形式:压射力和比压两种。
1、压射力
压力传递方向示意图
压铸机压射缸内的工作液作用于压射冲头,使其推动金属液充填模具
型腔的力称为压射力。
D 压射力计算:
P P 4 y
g
2 式中:Py——压射力,N
Pg——压射缸内工作液的压力,MPa; D——压射缸直径,mm。
2、比压
压射过程中,压室内单位面积上金属液所受到的静压力即压射力与
图3-12 压射速度对力学性能的影响
b、压射速度对填充特性的影响
提高压射速度,使合金熔液在填 充型腔时的温度上升,如图3-13所示。
内浇道流速有利于改善填充条
件,可压铸出质量优良的复杂薄 壁铸件。但压射速度过高时,填 充条件恶化,在厚壁铸件中尤为 显著。内浇道流速与填充流程长 度的关系如图3-14所示,图中s为 铸件厚度。
压铸工艺是把压铸合金、压铸模和压铸机这三大生产要素有机组合 和运用的过程。
压铸模流道与浇口设计
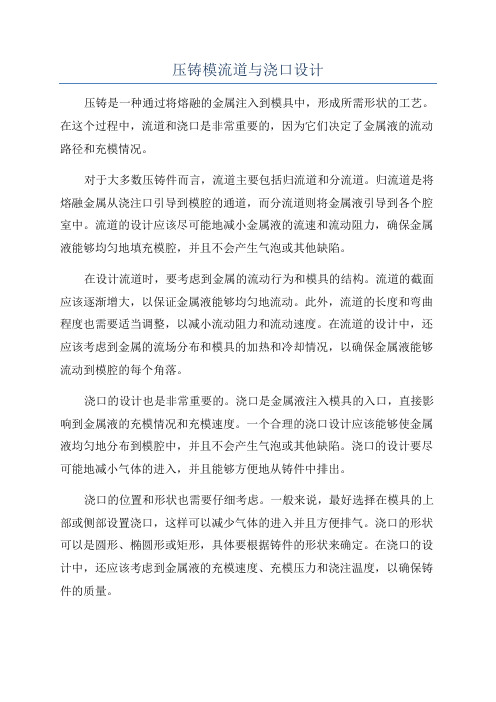
压铸模流道与浇口设计压铸是一种通过将熔融的金属注入到模具中,形成所需形状的工艺。
在这个过程中,流道和浇口是非常重要的,因为它们决定了金属液的流动路径和充模情况。
对于大多数压铸件而言,流道主要包括归流道和分流道。
归流道是将熔融金属从浇注口引导到模腔的通道,而分流道则将金属液引导到各个腔室中。
流道的设计应该尽可能地减小金属液的流速和流动阻力,确保金属液能够均匀地填充模腔,并且不会产生气泡或其他缺陷。
在设计流道时,要考虑到金属的流动行为和模具的结构。
流道的截面应该逐渐增大,以保证金属液能够均匀地流动。
此外,流道的长度和弯曲程度也需要适当调整,以减小流动阻力和流动速度。
在流道的设计中,还应该考虑到金属的流场分布和模具的加热和冷却情况,以确保金属液能够流动到模腔的每个角落。
浇口的设计也是非常重要的。
浇口是金属液注入模具的入口,直接影响到金属液的充模情况和充模速度。
一个合理的浇口设计应该能够使金属液均匀地分布到模腔中,并且不会产生气泡或其他缺陷。
浇口的设计要尽可能地减小气体的进入,并且能够方便地从铸件中排出。
浇口的位置和形状也需要仔细考虑。
一般来说,最好选择在模具的上部或侧部设置浇口,这样可以减少气体的进入并且方便排气。
浇口的形状可以是圆形、椭圆形或矩形,具体要根据铸件的形状来确定。
在浇口的设计中,还应该考虑到金属液的充模速度、充模压力和浇注温度,以确保铸件的质量。
在流道和浇口的设计中,还需要考虑到模具的制造成本和生产效率。
流道和浇口的设计应该尽可能地简单和经济,同时也要能够满足产品的质量要求。
此外,在模具的制造过程中,还需要考虑到流道和浇口的冷却和加热情况,以确保模具的寿命和稳定性。
总之,流道和浇口的设计是压铸工艺中非常重要的环节。
一个合理的流道和浇口设计可以确保金属液能够均匀地填充到模腔中,并且不会产生气泡或其他缺陷。
同时,流道和浇口的设计还需要考虑到模具的制造成本和生产效率。
通过合理的流道和浇口设计,可以提高压铸件的质量和性能。
- 1、下载文档前请自行甄别文档内容的完整性,平台不提供额外的编辑、内容补充、找答案等附加服务。
- 2、"仅部分预览"的文档,不可在线预览部分如存在完整性等问题,可反馈申请退款(可完整预览的文档不适用该条件!)。
- 3、如文档侵犯您的权益,请联系客服反馈,我们会尽快为您处理(人工客服工作时间:9:00-18:30)。
洛阳高新欣华 福利加 工有限公 司 ( 河南 4 10 ) 崔爱军 7 0 0
道截面积相 差悬殊 ,在实践 中就会 出现 模具 “ 适应性”
【 摘要】 本文主要通过实例,从内浇道的面 积、导 向角 等 方 面,论 述 了内 浇道 与模 具 “ 应 适
4 0 3 0 2 0 1 O
铸工艺的调 整留下 了充分的余地 ,这 样的模具 基本可以
适应在各种不 同性 能的压铸设备上生产 。 用修 改后 的模具 试 生产 ,操 作人 员普 遍 反映 模具
“ 好用 了”,废 品率也下降到 了3 左右 。 %
流量Q( S1 / L・-)
1 O109 0 7 3 1 08 0 6 0 5 O
性 ”之 间 的 关 系 .为今 后 的模 具 设 计及压 铸 生 产
中类似 问题 的 解 决提 供 了思路 。
差的现象 。
生 产 实践 中 ,模具 内浇 道截 面 积与压 铸件 不 匹配 的情况 屡见不鲜 ,当这种不 匹配 差距不大时 ,其表现 并不是很 明显。在模具使用 中,操 作人员常会感到模具
填 充 时 间 rms /
()修 模 前 1 f
。
●
根 据计算 ,当内浇道面 积达 ̄ 7 0 ] I0 mm ,系统所 时 能达到的最小 充型时 间为6 . ,这 个值 与压铸件需要 49 ms
:
的最长填 充时 间相比 ,留有较大 的调 整空间 ,这就为压
要5 董 0 :
度 2 0℃ ;快 压 射 行 程 3
22 0 mm ;快 压射手轮开 度
7圈 。 在 生 产过 程 中发 现 压 铸件填充不满 ,表面 质量差 ,废品率高达5 %以上 。 0 图1 壳体零件示意
填充速 度过低 ,金属过早凝 固 ,甚至导致充填 不足 ;而
过小 的内浇道面积 ,会使喷射加 剧 ,增加热量损 失 ,产 生涡流并 卷入过多的 气体 ,对模具 冲刷加剧 ,导致 模具 早期报废。
2 内浇道形状对压铸件质量的影 响 .
尽 管 压铸 件 内浇道 的形 状 与压铸 件 的外 形有 很大 的关 系,实际设计 中更是千差万 别。但是 ,参照一些模
具设计手册和 一些成功的经验数据 ,一般都能设计 出比
填 充 时间 rms /
()修模后 a
图 2
1 0 1O9 O 7 3 1 08 0 6 O
4 O 3 0
2 O 1 O
餐
件表面产生 各种各样的缺 陷。这样 的模具 如果放到一 台 性能更高 的压 铸机上生产 ,也有 可’, * 地生产 出合格 HJ l  ̄l l J {
的压铸件 ,但 在现 有的压铸机上是很难正 常生产的。
( 图2 如 所示 )。
■ 一型 垫 : 参 加 堕塑 丝 丝 堡 磊 工热工
www m ea wo kn 5 o tl r ig1 0 c m 9
Ra pcn 壅 皇 e & pa 【 皇 里 sc Ali 里 eh io r t
。 ● 验计 算来自 。 由P Q 计 算可知 ,在 内浇道面 积为4 0 _ 6 mm。
主要 工 艺 参 数 为 : 浇 注 温 度 6 0 ;模具 温 5 ℃
实 际生 产过程中 ,影响压铸件 质量的因素较 多,诸如 : 压射 压力、压射速度 、快压 启动位置 、熔炉保温 温度 、 模具温 度及模具 结构等 。在这 些因素中哪些 因素 对压铸
件的 质量 影响较大呢?
。
所谓 模具 的 适应性 ,是指 同一 副模 具 在不 同的 压
“ 不好 用” ;当其差距较大时就会 明显地表现出来— —
压铸件无法成形 、废 品率高 、质量不稳定 等。
铸机 上、由不同的人 员操 作 ,以及在较宽范 围内的工艺
参数 条件下 ,生产 出合格压铸 件的顺利程度 ;而 在压铸
5 0
至 :
1
时 ,该压铸 模具和设备所组成 的压铸系统所能达到的最
小充 型时 间为8 .ms 63 。显然 ,这 个值与压铸件需要的最 长填 充时 间相差无几 ,在这种 条件下 ,生产过程 中就会 对工艺参数要 求很高 ,工艺 的略 微波动 ,就会造成压铸
流 量Q/ ・ ) 【L S ( 1
下面 所述 的产 品生 产实 例是 一 个桶状 的壳 体类 零 件 ,平 均壁 厚45 . mm左右 ,采
铸 件重 量 ( 含 净重 和 渣 包 包 )47 g . ,内浇 道截面 积 k 40 6 mm ( 见图1 )。 使 用 设备 :8 0 压 铸 0t 机 ,压射 头直 径lO lmm。
在 压铸 生产 企业 中 一个 普遍的 观 点是 :模 具对 压 铸件 质量的影响 占了7%,而 内浇 道参数对模具 的 “ 0 适
应性 ”又起着举足轻重的 作用。现略举几例 说明模具 内 浇道对模具 的 “ 适应性” 的影 响及处理方式 。
1 内浇道截面积对压铸 件质 量的影响 .
在一 定 的压射 条 件下 ,内浇道 面积 过大 时 ,会 使
积 ,割 裂了内浇道截面积 与充填速度和充填时 间的密切 联 系,内浇道截面积与充 填速 度和充填时 间之 间存在着 不能有效 匹配的风险 ,设计结 果能在多大的 工艺范围 内 进行修 改,设计者并不清 楚。个人经验不 同得出的内浇
为此 ,我们根据模具 和压铸机的参数 画出TPQ - 图
从图l 可以 看 出 ,这是 一 个形 状 比 较 简单 的 压铸 件 , 浇排 系统的设计基本上是 合理的。一般情况下 , 其
上述压铸 工艺是 能生产 出合格 产品的。针对出现的质量 问题 ,我们 本着先易后难的方针 ,再次 对生产工艺进行
了适 当的调 整 ;但是 基本无效 。
内 浇道 截面 积 的大 小 ,常凭 经验 在 设计绘 图过 程 中来确 定 ,单纯 地 依据 经验 公式 所计 算 内浇道 的截 面